Kundenspezifische Werkzeuge mit 3D-Metalldruck für die Fertigung
Inhaltsübersicht
Einführung: Revolutionierung der Fertigung mit 3D-gedruckten kundenspezifischen Werkzeugen
In ihrem unermüdlichen Streben nach Effizienz, Geschwindigkeit und Innovation sind die modernen Fertigungsindustrien - von der Luft- und Raumfahrt über die Automobilindustrie bis hin zur Herstellung medizinischer Geräte und Konsumgüter - ständig auf der Suche nach neuen Technologien. Kundenspezifische Werkzeuge, die Vorrichtungen, Formen, Gesenke und andere Produktionshilfsmittel umfassen, bilden die Grundlage für wiederholbare, hochwertige Fertigungsprozesse. Traditionell war die Herstellung dieser wichtigen Werkzeuge ein erheblicher Engpass, der oft durch lange Vorlaufzeiten, hohe Kosten und konstruktive Einschränkungen bei subtraktiven Methoden wie CNC-Bearbeitung oder Gießen gekennzeichnet war. Mit dem Aufkommen und der Reifung der Additive Fertigung von Metall (AM)gemeinhin als Metall bekannt 3D-Druck, ist dabei, die Landschaft der kundenspezifischen Werkzeuglösungen grundlegend zu verändern. Diese Technologie bietet eine noch nie dagewesene Möglichkeit, hochkomplexe, leistungsoptimierte Werkzeuge mit bemerkenswerter Geschwindigkeit und wachsender Kosteneffizienz zu erstellen, was einen Paradigmenwechsel in der Herangehensweise der Hersteller an die Produktionseinrichtung und -ausführung bewirkt.
Der 3D-Metalldruck überwindet die Einschränkungen herkömmlicher Verfahren, indem er Teile Schicht für Schicht direkt aus digitalen Modellen mit speziellen Metallpulvern aufbaut. Dieser additive Ansatz eröffnet bisher unerreichte geometrische Freiheiten und ermöglicht die Integration komplizierter interner Merkmale, topologieoptimierter Leichtbaustrukturen und, was für viele Werkzeuganwendungen entscheidend ist, konforme Kühlkanäle, die den Konturen der Werkzeugoberfläche genau folgen. Die Auswirkungen auf die Fertigungseffizienz sind tiefgreifend. Schnellere Werkzeug-Iterationszyklen, geringerer Materialabfall, längere Werkzeuglebensdauer durch optimierte Konstruktionen und Materialien und verbesserte Endteilqualität durch besseres Wärmemanagement sind nur einige der Vorteile, die Ingenieure und Beschaffungsmanager dazu veranlassen, die Vorteile zu erforschen und zu übernehmen. additive Fertigung von Werkzeugen.
Stellen Sie sich vor, Sie könnten die Vorlaufzeit für einen komplexen Spritzgusseinsatz von Monaten auf Wochen oder sogar Tage verkürzen. Stellen Sie sich die Herstellung einer leichten, ergonomischen Montagevorrichtung vor, die perfekt an ein bestimmtes Bauteil angepasst ist und die Effizienz der Mitarbeiter verbessert und Ermüdung reduziert. Stellen Sie sich Stanzwerkzeuge mit integrierter Kühlung vor, die Zykluszeiten und Verschleiß drastisch reduzieren. Dies sind keine futuristischen Konzepte, sondern greifbare Realitäten, die durch den 3D-Druck von Metall ermöglicht werden. Diese Technologie ermöglicht es Herstellern, flexibler auf Marktanforderungen zu reagieren, Produktionslinien schnell anzupassen und ein Leistungsniveau zu erreichen, das bisher als unmöglich galt. Als führender Anbieter von fortschrittlichen additiven Fertigungslösungen hat Met3dp das transformative Potenzial dieser Technologie für kundenspezifische Werkzeuge erkannt. Durch den Einsatz von branchenführenden SEBM-Druckern (Selective Electron Beam Melting) und Hochleistungsmetallpulvern, die mit modernsten Gaszerstäubungs- und PREP-Technologien (Plasma Rotating Electrode Process) hergestellt werden, ermöglicht Met3dp Unternehmen die Nutzung des vollen Potenzials von Einführung in den 3D-Metalldruck für ihren kritischen Werkzeugbedarf. Dabei geht es nicht nur darum, Werkzeuge anders herzustellen, sondern die gesamte Wertschöpfungskette in der Fertigung grundlegend zu verbessern.
Der Übergang zur additiven Fertigung für den Werkzeugbau ist nicht nur ein Trend, sondern eine strategische Notwendigkeit für Unternehmen, die sich einen Wettbewerbsvorteil sichern wollen. Damit werden zentrale Herausforderungen in der Fertigung angegangen: Verkürzung der Markteinführungszeit, Senkung der Produktionskosten, Verbesserung der Teilequalität und Ermöglichung größerer Designinnovationen. Für Beschaffungsmanager, die zuverlässige Kundenspezifische Lösungen für den Werkzeugbau Lieferanten ist das Verständnis der Fähigkeiten und Feinheiten der Metall-AM von entscheidender Bedeutung. Für Konstruktions- und Fertigungsingenieure erschließt sich das volle Potenzial der Technologie, wenn sie die Grundsätze des Design for Additive Manufacturing (DfAM) beherzigen. Dieser Artikel dient als umfassender Leitfaden für Fachleute aus Technik und Einkauf, in dem die verschiedenen Anwendungen, überzeugende Vorteile, kritische Materialüberlegungen, bewährte Konstruktionsverfahren, Qualitätserwartungen, Nachbearbeitungsanforderungen, potenzielle Herausforderungen, Kriterien für die Lieferantenauswahl, Kostenfaktoren und häufig gestellte Fragen im Zusammenhang mit dem Einsatz von 3D-Druck aus Metall für kundenspezifische Werkzeuge untersucht werden. Seien Sie dabei, wenn wir uns damit beschäftigen, wie diese revolutionäre Technologie die Zukunft der effizienten, flexiblen und leistungsstarken Fertigung prägt.
Vielfältige Anwendungen: Wo sich 3D-gedruckte Werkzeuge aus Metall auszeichnen
Die Vielseitigkeit der additiven Fertigung von Metallen ermöglicht es, ein breites Spektrum an kundenspezifischen Werkzeuganforderungen in zahlreichen Branchen zu erfüllen. Ihre Fähigkeit, komplexe Geometrien schnell zu erstellen und hochfeste, langlebige Materialien zu verwenden, macht sie zu einer idealen Lösung für Anwendungen, bei denen herkömmliche Methoden in Bezug auf Geschwindigkeit, Kosten oder Leistungsoptimierung versagen. Beschaffungsmanager, die nach B2B-Lieferanten und Großhandelsoptionen für Anwendungsfälle im industriellen Werkzeugbau werden feststellen, dass Metal AM für mehrere Schlüsselkategorien überzeugende Vorteile bietet:
1. Lehren und Vorrichtungen: Diese Geräte sind unerlässlich für die Positionierung, Unterstützung und Führung von Werkstücken oder Werkzeugen bei Fertigungsvorgängen wie Montage, Bearbeitung, Schweißen oder Prüfung.
- Traditionelle Herausforderungen: Sie erfordern oft eine komplexe Bearbeitung, was zu langen Vorlaufzeiten und hohen Kosten führt, insbesondere bei Kleinserien oder stark kundenspezifischen Designs. Auch das Gewicht kann bei manueller Bearbeitung ein Faktor sein.
- AM Vorteil:
- Geschwindigkeit: Schnelles Prototyping und Produktion von kundenspezifischen Vorrichtungen in Tagen, nicht Wochen oder Monaten.
- Komplexität und Konformität: Die Fähigkeit, äußerst ergonomische Formen zu erstellen, die perfekt zu komplexen Teilegeometrien passen, verbessert die Genauigkeit und Benutzerfreundlichkeit. Interne Gitterstrukturen können das Gewicht erheblich reduzieren, ohne die Steifigkeit zu beeinträchtigen, was für Handheld-Geräte entscheidend ist.
- Konsolidierung: Mehrere Komponenten einer Vorrichtungsbaugruppe können oft in einem einzigen 3D-gedruckten Teil zusammengefasst werden, was die Montagezeit und potenzielle Fehlerquellen reduziert.
- Beispiele: Montagevorrichtungen für Luft- und Raumfahrtkomponenten, CMM-Vorrichtungen für die Qualitätskontrolle, Schweißvorrichtungen für Automobilrahmen, chirurgische Führungen (eine Art medizinischer Vorrichtungen). Beschaffung 3D-gedruckte Schablonen und Vorrichtungen ermöglicht ein schnelleres Einrichten und Umrüsten der Linie.
2. Formen (Spritzgießen, Blasformen, Thermoformen): Werkzeugeinsätze, Kerne und Kavitäten, die in verschiedenen Formgebungsverfahren verwendet werden, profitieren in hohem Maße von AM, insbesondere aufgrund der Möglichkeit der konformen Kühlung.
- Traditionelle Herausforderungen: Die Bearbeitung von tiefen, komplexen Kühlkanälen ist schwierig, teuer und oft unmöglich. Dies führt zu suboptimaler Kühlung, längeren Zykluszeiten, Werkstückverzug und einer geringeren Werkzeugstandzeit.
- AM Vorteil:
- Konforme Kühlung: Der entscheidende Vorteil. Der 3D-Druck ermöglicht die Gestaltung von Kühlkanälen, die exakt den Konturen der Formoberfläche folgen, in der Regel 1-2 mm darunter. Dies ermöglicht eine schnelle, gleichmäßige Kühlung, die die Zykluszeiten drastisch reduziert (oft um 20-50%+), die Teilequalität verbessert (weniger Verzug, bessere Dimensionsstabilität) und die Lebensdauer der Form verlängert.
- Komplexität: Ermöglicht komplizierte Formmerkmale, Texturen und Hinterschneidungen, die schwer oder gar nicht zu bearbeiten sind.
- Hybrid-Ansatz: AM-Einsätze können in konventionell bearbeitete Formen integriert werden und bieten eine kostengünstige Möglichkeit, Leistungsvorteile dort zu erzielen, wo sie am meisten benötigt werden.
- Beispiele: Spritzgussformeinsätze für komplexe Automobilinnenteile, Blasformwerkzeuge für komplizierte Flaschendesigns, Thermoformwerkzeuge für Verpackungen. Formen für die additive Fertigung mit konformer Kühlung stellen einen erheblichen Wettbewerbsvorteil dar.
3. Matrizen (Stanzen, Umformen, Druckgießen): Werkzeuge, die zum Schneiden, Formen oder Umformen von Materialien wie Blechen oder geschmolzenen Metalllegierungen verwendet werden, sind extremen Belastungen und Temperaturen ausgesetzt.
- Traditionelle Herausforderungen: Hohe Verschleißraten, lange Vorlaufzeiten für harte Werkzeuge, Schwierigkeiten bei der Integration einer effektiven Kühlung in Hochtemperaturverfahren wie Druckguss.
- AM Vorteil:
- Material-Optionen: Fähigkeit, mit hochfesten, verschleißfesten Werkzeugstählen (wie H13, M300) zu drucken, die anspruchsvollen Operationen standhalten.
- Konforme Kühlung (Druckgießen): Ähnlich wie beim Spritzgießen können integrierte Kühlkanäle die Zykluszeiten erheblich verbessern, die thermische Belastung reduzieren, das Löten der Teile minimieren und die Lebensdauer der Form bei Druckgussanwendungen verlängern.
- Rapid Prototyping/Bridge Tooling: Schnelle Herstellung von Prototypen oder Kleinserien von Stanz- und Umformwerkzeugen zur Validierung von Entwürfen, bevor teure herkömmliche Werkzeuge angeschafft werden.
- Komplexität: Erstellen Sie Umformwerkzeuge mit komplexen Oberflächen für komplizierte Blechteile.
- Beispiele: Blechstanzwerkzeuge für Karosserieteile (insbesondere für Versuche oder Kleinserien), Druckgusseinsätze für komplexe Aluminiumkomponenten, Umformwerkzeuge für Halterungen in der Luftfahrt. Beschaffung Metalldruckstempel kann die Produktentwicklung beschleunigen und die Effizienz von Hochtemperaturprozessen verbessern.
4. End-of-Arm-Tooling (EoAT) / Greifer: Kundenspezifische Greifer für Roboterarme, die in der automatischen Handhabung, Montage und bei Pick-and-Place-Vorgängen eingesetzt werden.
- Traditionelle Herausforderungen: Sie müssen oft aus mehreren Komponenten zusammengesetzt werden, können schwer sein und die Anpassung an bestimmte Teile kann zeitaufwändig sein.
- AM Vorteil:
- Gewichtsreduzierung: Durch Topologieoptimierung und Gitterstrukturen entstehen starke und dennoch leichte Greifer, die es den Robotern ermöglichen, sich schneller zu bewegen oder schwerere Nutzlasten zu handhaben.
- Anpassungsfähigkeit und Komplexität: Einfaches Erstellen von Greifern, die perfekt an die Form des zu handhabenden Objekts angepasst sind und die Sicherheit und Zuverlässigkeit des Greifens verbessern. Interne Kanäle für Vakuum oder Pneumatik können direkt integriert werden.
- Teil Konsolidierung: Reduzieren Sie Komplexität und Montagezeit durch den Druck monolithischer Greiferdesigns.
- Beispiele: Maßgeschneiderte Greifer für die Handhabung empfindlicher elektronischer Komponenten, EoAT für Automobilmontagelinien, Spezialgreifer für die Lebensmittelverarbeitung.
Branchenspezifische Anwendungen:
- Luft- und Raumfahrt: Bohrschablonen, Montagevorrichtungen, Prüflehren, Umformwerkzeuge für Kleinserien.
- Automobilindustrie: Prototypen für Stanzwerkzeuge, Einsätze für Spritzgussformen, Montagevorrichtungen, Robotergreifer.
- Medizinisch: Kundenspezifische chirurgische Führungen, Vorrichtungen für die Montage medizinischer Geräte, Formeinsätze für die Herstellung von Implantaten (bei Bedarf unter Verwendung biokompatibler Werkstoffe wie Ti6Al4V oder CoCrMo, obwohl für die Werkzeuge häufig Werkzeugstähle verwendet werden).
- Industrielle Fertigung: Komponenten für Werkzeugmaschinen, Spannvorrichtungen, Umformwerkzeuge, Spezialwerkzeuge für die Reparatur.
Das Ausmaß dieser Rapid-Tooling-Anwendungen unterstreicht die transformative Wirkung von Metal AM. Der 3D-Metalldruck ermöglicht eine schnellere Produktion, komplexere Designs und eine verbesserte Leistung durch Funktionen wie die konforme Kühlung und versetzt Hersteller in allen Branchen in die Lage, herkömmliche Werkzeugbeschränkungen zu überwinden und neue Ebenen der Produktivität und Innovation zu erschließen. Unternehmen wie Met3dp sind mit ihrem Fachwissen in fortschrittlichen Drucktechnologien und Materialwissenschaften wichtige Partner bei der Realisierung dieser Vorteile für verschiedene Anwendungsfälle im industriellen Werkzeugbau.
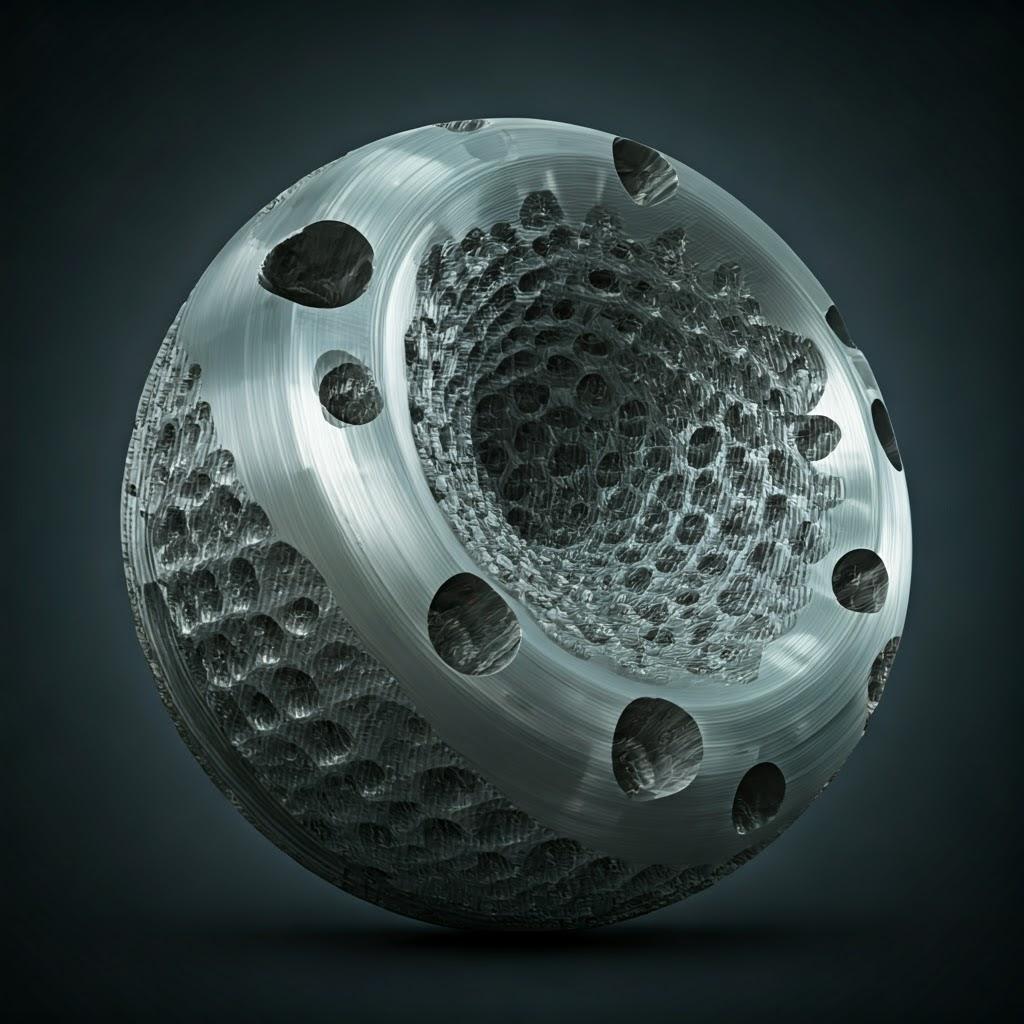
Der Additiv-Vorteil: Warum sollten Sie sich für den 3D-Druck von Metall für kundenspezifische Werkzeuge entscheiden?
Während herkömmliche Fertigungsverfahren für Werkzeuge wie CNC-Bearbeitung, Funkenerosion (EDM) und Guss weiterhin relevant sind, bietet die additive Fertigung von Metallen eine Reihe überzeugender Vorteile, die viele der inhärenten Einschränkungen dieser älteren Verfahren direkt beseitigen. Für Ingenieure, die eine optimale Leistung anstreben, und für Beschaffungsmanager, die sich auf die Gesamtbetriebskosten und die Flexibilität der Lieferkette konzentrieren, ist das Verständnis dieser Vorteile entscheidend für die Bewertung von Kundenspezifische Lösungen für den Werkzeugbau. Die Entscheidung für den 3D-Metalldruck beruht häufig auf seiner Fähigkeit, in mehreren Schlüsselbereichen einen Mehrwert zu bieten: Geschwindigkeit, Komplexität, Leistung und Kosteneffizienz in bestimmten Szenarien.
1. Beispiellose Geschwindigkeit und verkürzte Vorlaufzeiten: Dies ist wohl der wichtigste Grund für die Einführung von AM im Werkzeugbau.
- Traditionell: Die Erstellung komplexer Werkzeuge, insbesondere von Formen und Gesenken, kann aufgrund komplizierter Bearbeitungsprozesse, mehrfacher Einstellungen und der Verfügbarkeit von Fachkräften Wochen oder sogar Monate dauern. Konstruktionswiederholungen sind langsam und kostspielig.
- Zusatzstoff: Metall-3D-Drucker können komplexe Werkzeugkomponenten, wie z. B. Formeinsätze oder kundenspezifische Vorrichtungen, oft innerhalb weniger Tage direkt aus einer CAD-Datei herstellen. Das erleichtert die Arbeit:
- Rapid Prototyping: Schnelles Erstellen und Testen von funktionalen Werkzeugprototypen, was eine schnellere Designvalidierung und Iteration ermöglicht.
- Bridge Tooling: Schnelle Herstellung von Werkzeugen für Kleinserien, um die Produktion zu starten, während konventionelle Werkzeuge für Großserien hergestellt werden, was die Markteinführungszeit verkürzt.
- Produktion auf Abruf: Stellen Sie bei Bedarf schnell Ersatz- oder Spezialwerkzeuge her und reduzieren Sie so den Lagerbedarf und die Ausfallzeiten.
- Auswirkungen: Durch diese Beschleunigung werden die Produktentwicklungszyklen drastisch verkürzt und die Hersteller können viel schneller auf Marktveränderungen oder Kundenwünsche reagieren. Rapid Tooling Prototyping machbar und hochwirksam wird.
2. Geometrische Komplexität und Gestaltungsfreiheit: AM baut Teile Schicht für Schicht auf und befreit die Designer von vielen Einschränkungen, die bei subtraktiven Verfahren bestehen.
- Traditionell: Begrenzungen bei der Bearbeitung schränken interne Merkmale, komplizierte Formen und die Möglichkeit ein, bestimmte Hinterschnitte oder komplexe Kurven wirtschaftlich herzustellen.
- Zusatzstoff: Ermöglicht die Erstellung von:
- Konforme Kühlkanäle: Wie bereits erwähnt, folgen diese komplizierten internen Kanäle der Form der Werkzeugoberfläche und sorgen so für eine äußerst effiziente und gleichmäßige Kühlung. Dies ist auf konventionelle Weise extrem schwierig oder unmöglich zu erreichen, mit AM jedoch relativ einfach. Die Leistungsgewinne bei der Zykluszeit und der Teilequalität beim Formen und Druckgießen sind erheblich.
- Topologie-Optimierung und Gewichtsreduzierung: Algorithmen können Werkzeugdesigns so optimieren, dass das Material nur dort platziert wird, wo es strukturell benötigt wird, und so stabile und dennoch leichte Vorrichtungen, Halterungen und EoAT mit internen Gitterstrukturen oder organischen Formen erstellen.
- Teil Konsolidierung: Komplexe Baugruppen können oft neu entworfen und als ein einziges, monolithisches Teil gedruckt werden, wodurch die Montagezeit, potenzielle Leckagepfade (in gekühlten Werkzeugen) und Fehlerpunkte reduziert werden.
- Auswirkungen: Dies ermöglicht Werkzeuge, die nicht nur schneller zu produzieren sind, sondern auch deutlich mehr leisten, ergonomischer sind oder völlig neue Fertigungsmöglichkeiten bieten. Werkzeuge mit komplexer Geometrie ist kein großes Kosten- oder Zeithindernis mehr.
3. Verbesserte Leistung und Lebensdauer der Werkzeuge: Die Kombination aus Designfreiheit und fortschrittlichen Werkstoffen ermöglicht eine überragende Leistung der Werkzeuge.
- Konforme Kühlung: Dies führt zu schnelleren Zyklen, geringerer thermischer Belastung, weniger Verzug der Teile und oft zu einer längeren Lebensdauer der Werkzeuge aufgrund niedrigerer Spitzentemperaturen und gleichmäßigerer Temperaturverteilung.
- Optimierte Materialien: AM ermöglicht die Verwendung fortschrittlicher Werkzeugstähle (z. B. H13, martensitaushärtende Stähle wie M300/1.2709) und anderer Hochleistungslegierungen, die speziell für die Verschleiß-, Härte- und Temperaturanforderungen der Anwendung ausgewählt werden. Unternehmen wie Met3dp bieten eine Reihe von Spezialpulvern an, die für anspruchsvolle Werkzeuganwendungen optimiert sind.
- Oberflächenmerkmale: Texturen, kleine Gravuren oder spezifische Funktionsflächen können direkt beim Druck in das Werkzeugdesign integriert werden.
- Auswirkungen: Leistungsfähigere Werkzeuge führen direkt zu einer höheren Qualität der Endteile, einem höheren Produktionsdurchsatz und geringeren Betriebskosten.
4. Kosten-Wirksamkeit (kontextabhängig): Während die anfänglichen Kosten pro Teil für AM manchmal höher sein können als bei traditionellen Methoden für einfache GeometrienWenn man den gesamten Lebenszyklus und die spezifischen Anwendungsbedürfnisse berücksichtigt, ist der Gesamtwertvorschlag oft kostengünstiger.
- Geringere Vorlaufzeitkosten: Eine schnellere Markteinführung bedeutet eine schnellere Umsatzgenerierung. Geringere Ausfallzeiten bedeuten geringere Betriebsverluste.
- Reduzierter Arbeitsaufwand: Hochautomatisierte AM-Prozesse verringern den Bedarf an ständiger Aufsicht durch Fachkräfte im Vergleich zur komplexen mehrstufigen Bearbeitung.
- Materialeffizienz: AM ist ein additiver Prozess, bei dem in der Regel weniger Materialabfall anfällt (insbesondere im Vergleich zur maschinellen Bearbeitung eines großen Knüppels), auch wenn die Stützstrukturen einen gewissen Abfall verursachen.
- Leistungssteigerungen: Schnellere Zykluszeiten und geringere Ausschussraten durch konform gekühlte Werkzeuge wirken sich direkt auf die Rentabilität aus.
- Komplexität "umsonst": Im Gegensatz zur maschinellen Bearbeitung, bei der die Komplexität die Kosten drastisch erhöht, verursacht die Komplexität bei der AM nur geringe oder gar keine zusätzlichen Kosten, abgesehen von möglicherweise längeren Druckzeiten oder mehr Trägermaterial.
- Verlängerung der Lebensdauer von Werkzeugen: Langlebigere Werkzeuge verringern die Häufigkeit des Austauschs und die damit verbundenen Kosten.
- Auswirkungen: Bei der Evaluierung Traditionelle vs. additive WerkzeugherstellungEine TCO-Analyse (Total Cost of Ownership) zeigt oft ein erhebliches Einsparungspotenzial für AM auf, insbesondere bei komplexen, leistungsstarken oder zeitkritischen Werkzeuganwendungen.
5. Anpassungsfähigkeit und Agilität: AM eignet sich ideal für die Herstellung hochgradig kundenspezifischer oder einzigartiger Werkzeugkomponenten.
- Lebensfähigkeit bei geringen Mengen: Kostengünstige Herstellung von Einzelstücken oder Kleinserien von kundenspezifischen Werkzeugen ohne die hohen Einrichtungskosten herkömmlicher Verfahren.
- Einfache Design-Updates: Ändern Sie Werkzeugentwürfe digital und drucken Sie sie schnell nach, um sie an Produktänderungen oder Prozessverbesserungen anzupassen.
- Auswirkungen: Hersteller können ihre Produktionslinien flexibler anpassen, neue Konzepte testen und die Anforderungen von Nischenmärkten erfüllen.
Zusammenfassend lässt sich sagen, dass die zwingenden Vorteile von 3D-gedruckten Werkzeugen - Geschwindigkeit, Designfreiheit und Funktionen wie konforme KühlkanäleDie verbesserte Leistung, die potenziellen Kosteneinsparungen und die Flexibilität machen es zu einer leistungsstarken Alternative und Ergänzung zu herkömmlichen Methoden. Durch die Nutzung von Metall-AM können Hersteller kritische Engpässe überwinden, die betriebliche Effizienz verbessern und ein höheres Maß an Produktivität und Innovation in ihren Werkzeugstrategien freisetzen.
Das Material ist entscheidend: Die Auswahl des richtigen Metallpulvers für Hochleistungswerkzeuge
Der Erfolg eines 3D-gedruckten Werkzeugs aus Metall hängt entscheidend von der Auswahl des geeigneten Materials ab. Werkzeuganwendungen sind oft mit anspruchsvollen Bedingungen verbunden: hohe mechanische Beanspruchung, hohe Temperaturen, abrasiver Verschleiß und die Notwendigkeit einer hervorragenden Dimensionsstabilität. Die additive Fertigung bietet ein wachsendes Angebot an Metallpulvern, die speziell für diese Herausforderungen geeignet sind. Die Wahl des richtigen Pulvers erfordert ein Verständnis der spezifischen Anforderungen der Anwendung (z. B. Spritzguss vs. Stanzwerkzeug vs. Vorrichtung) und der Eigenschaften, die die verschiedenen Legierungen bieten. Für Beschaffungsmanager bei der Beschaffung Lieferanten von Materialien für die additive Fertigung und Ingenieure, die Werkzeuge spezifizieren, ist die Kenntnis gängiger Hochleistungs-Werkzeugpulver unerlässlich.
Met3dp nutzt seine fortschrittlichen Pulverproduktionskapazitäten, einschließlich Gaszerstäubung und PREP-Technologien, und stellt eine Reihe hochwertiger sphärischer Metallpulver her, die für AM-Prozesse wie Selective Electron Beam Melting (SEBM) und Laser Powder Bed Fusion (LPBF) optimiert sind. Unser Fokus auf die Pulverqualität - hohe Sphärizität, gute Fließfähigkeit, kontrollierte Partikelgrößenverteilung und geringer Sauerstoff-/Verunreinigungsgehalt - gewährleistet, dass Kunden dichte, hochintegrierte Werkzeugkomponenten mit hervorragenden mechanischen Eigenschaften drucken können. Zu den wichtigsten Materialien für den kundenspezifischen Werkzeugbau gehören spezielle Werkzeugstähle und martensitaushärtende Stähle.
Empfohlene Tooling-Pulver:
1. H13 Werkzeugstahl:
- Beschreibung: Ein vielseitiger Chrom-Molybdän-Vanadium-Warmarbeitsstahl, der in der traditionellen Werkzeugherstellung weit verbreitet ist und sich gut für AM eignet. Bekannt für seine hervorragende Kombination aus hoher Zähigkeit, Verschleißfestigkeit, guter Beständigkeit gegen thermische Ermüdung und Dimensionsstabilität bei erhöhten Temperaturen.
- Wichtige Eigenschaften:
- Hohe Härte (typischerweise bis zu 45-52 HRC nach der Wärmebehandlung).
- Ausgezeichnete Anlassbeständigkeit (behält die Härte bei hohen Temperaturen bei).
- Gute Wärmeleitfähigkeit (vorteilhaft für Kühlanwendungen).
- Hohe Zähigkeit und Duktilität (Widerstandsfähigkeit gegen Rissbildung bei Stößen).
- Gute Bearbeitbarkeit (im Vergleich zu anderen Werkzeugstählen) nach dem Glühen.
- AM Überlegungen: Erfordert eine sorgfältige Kontrolle der Druckparameter und eine obligatorische Wärmebehandlung nach dem Druck (Härten und Anlassen), um die gewünschten Eigenschaften zu erzielen. Häufig sind Spannungsabbauzyklen erforderlich.
- Typische Anwendungen: Spritzgusseinsätze und -kerne (insbesondere mit konformer Kühlung), Druckgusswerkzeuge, Strangpresswerkzeuge, Schmiedewerkzeuge, Umformwerkzeuge, Strukturkomponenten, die hohe Festigkeit und Härte erfordern. H13 Werkzeugstahl 3D-Druck ist eine beliebte Wahl für anspruchsvolle thermische und mechanische Belastungen.
2. Martensitaushärtende Stähle (z. B. M300 / 1.2709 / MS1):
- Beschreibung: Eine Familie von kohlenstoffarmen Stählen mit hohem Nickelgehalt, die durch die Ausscheidung intermetallischer Verbindungen während der Alterung verfestigt werden, und nicht wie herkömmliche Werkzeugstähle durch den Kohlenstoffgehalt. Sie bieten eine extrem hohe Festigkeit, gute Zähigkeit und eine ausgezeichnete Dimensionsstabilität bei der Wärmebehandlung. M300 (oft ähnlich bezeichnet wie 1.2709 oder MS1 in AM) ist eine gängige Sorte.
- Wichtige Eigenschaften:
- Sehr hohe Härte und Festigkeit (in der Regel bis zu 50-55+ HRC nach einfacher Wärmebehandlung).
- Außergewöhnliche Zähigkeit im Vergleich zu herkömmlichen Werkzeugstählen bei ähnlichen Härtegraden.
- Hervorragende Schweißbarkeit (nützlich für Reparaturen oder Hybridfertigung).
- Minimale und vorhersehbare Verformung während der Wärmebehandlung bei niedrigen Temperaturen (typischerweise ~480-500°C), was die Nachbearbeitung im Vergleich zum Hochtemperaturvergüten bei H13 vereinfacht.
- Gute Bearbeitbarkeit im gedruckten oder geglühten Zustand.
- AM Überlegungen: Relativ leicht mit guter Dichte zu drucken. Die einfache Alterungswärmebehandlung ist ein wesentlicher Vorteil, der die Komplexität der Nachbearbeitung und das Risiko von Verformungen reduziert.
- Typische Anwendungen: Hochleistungs-Spritzgussformen (Kerne, Einsätze, Heber), Werkzeuge, die hohe Festigkeit und Zähigkeit erfordern, komplizierte Druckgussteile, hochpräzise Vorrichtungen, Bauteile für die Luft- und Raumfahrt. Die Website M300 martensitaushärtender Stahl AM (oder 1.2709 Pulvereigenschaften) machen es ideal für hochpräzise Werkzeuge, bei denen minimaler Verzug während der Wärmebehandlung entscheidend ist.
Vergleichstabelle: H13 vs. Maraging-Stahl (M300/1.2709) für AM-Werkzeuge
Merkmal | H13 Werkzeugstahl | Martensitaushärtender Stahl (M300 / 1.2709) | Zusammenfassung der Hauptvorteile |
---|---|---|---|
Primärlegierung | Cr, Mo, V, C | Ni, Co, Mo, Ti | Verschiedene Verstärkungsmechanismen |
Typische Härte (HRC) | 45-52 | 50-55+ | Martensitaushärtender Stahl erreicht im Allgemeinen eine höhere Härte/Festigkeit |
Zähigkeit | Gut | Ausgezeichnet (bei hoher Härte) | Martensitaushärtender Stahl bietet bessere Zähigkeit |
Heiße Härte | Sehr gut | Gut (kann aber über der Alterungstemperatur erweichen) | H13 im Allgemeinen besser für sehr hohe Betriebstemperaturen |
Wärmebehandlung | Komplex (Austenitisieren, Abschrecken, Temperieren) | Einfach (Aushärtung ~480°C) | Martensitaushärtender Stahl viel einfacher, geringeres Verformungsrisiko |
Dimensionsstabilität (HT) | Mäßig (Risiko der Verzerrung) | Ausgezeichnet (minimale Verzerrung) | Martensitaushärtender Stahl überlegen für Präzisionsanwendungen |
Schweißeignung | Messe | Ausgezeichnet | Martensitaushärtender Stahl lässt sich leichter reparieren/verändern |
Kosten | Im Allgemeinen niedriger | Im Allgemeinen höher | H13 oft kostengünstigeres Material |
Gemeinsame AM-Verwendung | Warmarbeitswerkzeuge, Formen, Gesenke | Hochpräzise Formen, Hochfeste Werkzeuge | Beide sind weit verbreitet, die Wahl hängt vom jeweiligen Bedarf ab |
In Blätter exportieren
Andere mögliche Materialien: H13 und martensitaushärtender Stahl sind zwar die Arbeitspferde, aber je nach den spezifischen Anforderungen an das Werkzeug können auch andere Materialien in Betracht gezogen werden:
- Rostfreie Stähle (z. B. 17-4PH, 316L): Wird für Werkzeuge verwendet, die korrosionsbeständig sein müssen, wie z. B. bei der Lebensmittelverarbeitung oder einigen medizinischen Anwendungen, oder für weniger anspruchsvolle Vorrichtungen. Oft einfacher zu drucken und nachzubearbeiten.
- Kobalt-Chrom (CoCrMo): Bietet hervorragende Verschleißfestigkeit, hohe Festigkeit bei hohen Temperaturen und Korrosionsbeständigkeit. Wird für hochanspruchsvolle Verschleißteile oder spezielle medizinische Werkzeuge verwendet.
- Titan-Legierungen (z. B. Ti6Al4V): Leicht, stabil und korrosionsbeständig. Sie werden für leichte Vorrichtungen, Robotergreifer oder spezielle Werkzeuge für die Medizin und die Luft- und Raumfahrt verwendet (allerdings weniger häufig für stark beanspruchte Formen und Werkzeuge). Met3dp bietet innovative Titanlegierungen wie TiNi, TiTa, TiAl, TiNbZr an, die für Nischenanwendungen im Werkzeugbau in Frage kommen. Entdecken Sie das vielfältige Angebot von Met3dp Metallpulver-Angebote.
- Nickel-Superlegierungen (z. B. Inconel 718): Für Werkzeuge, die bei extrem hohen Temperaturen oder in korrosiven Umgebungen eingesetzt werden.
Die Wahl des richtigen Materiallieferanten: Auswählen eines Metallpulver für die Werkzeugherstellung umfasst mehr als nur die Auswahl einer Legierung. Die Qualität des Pulvers hat einen direkten Einfluss auf die Qualität des fertigen Werkzeugs. Die Zusammenarbeit mit einem seriösen Lieferanten wie Met3dp gewährleistet dies:
- Konsistente Chemie: Strenge Kontrolle der Legierungszusammensetzung.
- Optimierte Partikeleigenschaften: Hohe Sphärizität, kontrollierte Größenverteilung (PSD) und gute Fließfähigkeit, geeignet für spezifische AM-Prozesse (wie SEBM oder LPBF).
- Geringe Verunreinigungen: Minimierung von Sauerstoff und anderen Verunreinigungen, die die mechanischen Eigenschaften beeinträchtigen können.
- Rückverfolgbarkeit der Chargen: Gewährleistung von Konsistenz und Qualitätskontrolle.
- Technische Unterstützung: Fachwissen bei der Auswahl des besten Materials für die jeweilige Anwendung.
Zusammenfassend lässt sich sagen, dass die Materialauswahl ein Eckpfeiler eines erfolgreichen 3D-gedruckten Metallwerkzeugs ist. Durch die sorgfältige Berücksichtigung der Anwendungsanforderungen und die Nutzung der Eigenschaften fortschrittlicher Materialien wie H13 und M300/1.2709 können Hersteller leistungsstarke, langlebige Werkzeuge herstellen, die erhebliche betriebliche Vorteile bieten. Die Zusammenarbeit mit einem erfahrenen Anbieter von Materialien für die additive Fertigung wie Met3dp bietet Zugang zu hochwertigen Pulvern und das nötige Fachwissen, um eine fundierte Materialauswahl zu treffen.
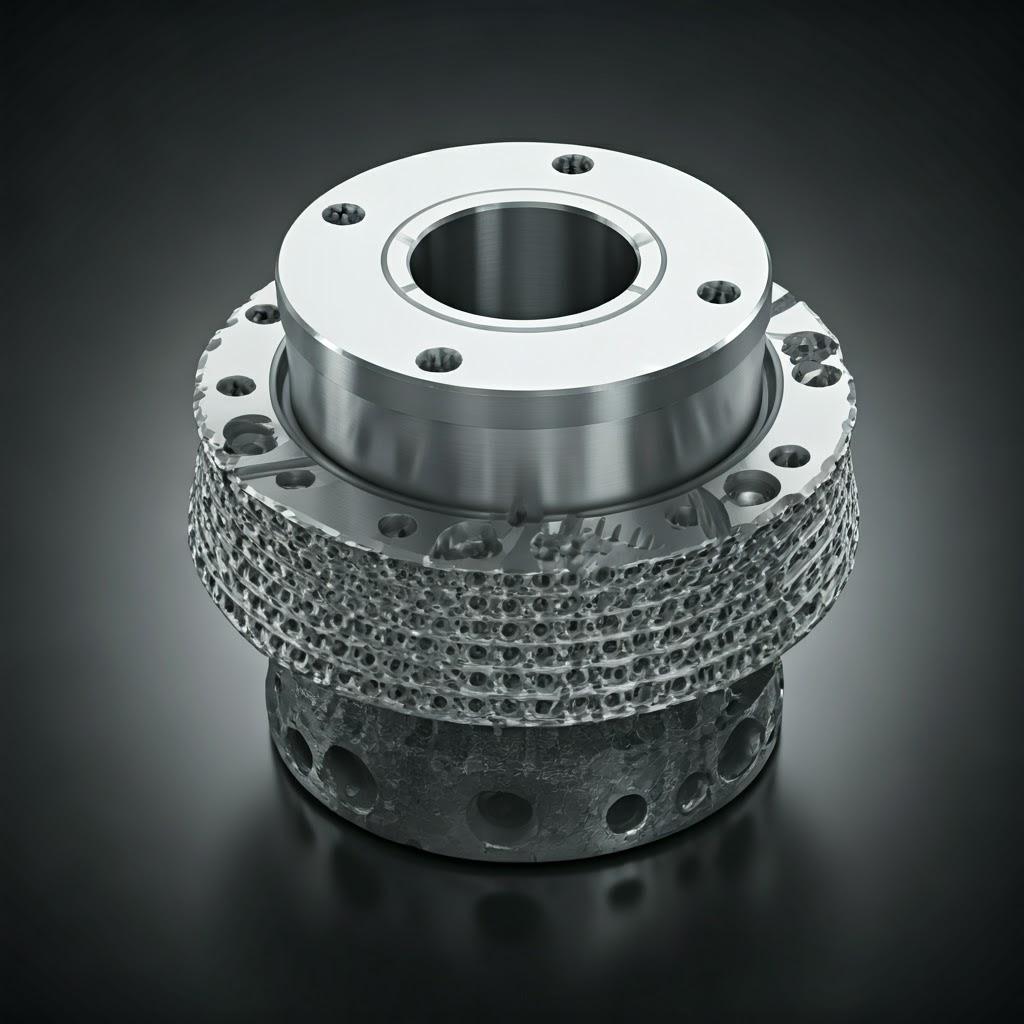
Design für additive Fertigung (DfAM): Optimierung von Werkzeugen für den 3D-Druck von Metall
Die einfache Nachbildung eines herkömmlich konstruierten Werkzeugs mit Hilfe der additiven Fertigung von Metallen schöpft nur selten das volle Potenzial dieser Technologie aus. Um die bereits erwähnten Vorteile in Bezug auf Geschwindigkeit, Komplexität und Leistung wirklich nutzen zu können, müssen die Ingenieure die folgenden Aspekte berücksichtigen Design für additive Fertigung (DfAM). DfAM ist nicht nur ein Regelwerk, sondern ein Umdenken, das die Konstrukteure dazu anregt, von Anfang an additiv zu denken und dabei den schichtweisen Herstellungsprozess, die Materialeigenschaften, die Anforderungen an die Stützstruktur und die Nachbearbeitungsschritte zu berücksichtigen. Die Anwendung der DfAM-Prinzipien speziell auf kundenspezifische Werkzeuge - ob es sich nun um Formen, Gesenke, Vorrichtungen oder Halterungen handelt - ist von entscheidender Bedeutung, um funktionale, kostengünstige und leistungsstarke Ergebnisse zu erzielen. Auch Beschaffungsmanager sollten DfAM kennen, da es sich direkt auf die Machbarkeit, die Kosten und die Qualität der 3D-gedruckten Werkzeuge auswirkt, die sie beschaffen. Die Investition in DfAM-Fachwissen, entweder intern oder durch einen sachkundigen Dienstleister wie Met3dp, ist der Schlüssel zur Maximierung des ROI von Metal AM für Werkzeuge.
Grundlegende DfAM-Prinzipien für den kundenspezifischen Werkzeugbau:
- Orientierungs- und Unterstützungsstrategie:
- Orientierung aufbauen: Wie ein Teil auf der Bauplatte ausgerichtet ist, hat erhebliche Auswirkungen auf die Druckzeit, die Oberflächenbeschaffenheit der verschiedenen Flächen, die Menge und die Position der erforderlichen Stützstrukturen und die potenziellen thermischen Spannungen. Bei Werkzeugen sollten kritische Funktionsflächen (z. B. Flächen im Formhohlraum, Befestigungspunkte) idealerweise so ausgerichtet sein, dass sie möglichst wenig oder gar keine Stützen aufweisen, oft nach oben zeigen oder selbsttragend sind.
- Überhänge und Winkel: Bei Metall-AM-Verfahren gibt es Einschränkungen hinsichtlich des Winkels von Überhängen, die ohne Stützstrukturen gebaut werden können. Winkel, die in der Regel größer als 45 Grad zur Horizontalen sind, sind oft selbsttragend, aber dies variiert je nach Material und Maschine (für SEBM und LPBF können unterschiedliche Überlegungen gelten, da verschiedene Druckverfahren ist hilfreich), und die spezifische Geometrie. Die Entwürfe sollten nach Möglichkeit selbsttragende Elemente enthalten.
- Entwurf der Stützstruktur: Halterungen sind oft notwendig, verursachen aber zusätzliche Materialkosten, Druckzeit und Nachbearbeitungsaufwand (Entfernung). DfAM beinhaltet:
- Minimierung von Unterstützungen: Ausrichtung des Teils und Änderung unkritischer Merkmale (z. B. Verwendung von Fasen anstelle von scharfen Überhängen), um die Abhängigkeit von Stützen zu verringern.
- Entwerfen für die Beseitigung: Sicherstellung der Zugänglichkeit der Halterungen für Entnahmewerkzeuge (manuell oder maschinell). Die Verwendung optimierter Stützenarten (z. B. Gitter- oder Baumstützen) kann den Materialverbrauch und die Kontaktpunkte reduzieren. Erwägen Sie den Einbau von Merkmalen, die die Demontage erleichtern, wie z. B. Zugangsfenster, wenn interne Stützen unvermeidbar sind.
- Überlegungen zum Unterstützungsmaterial: Einige fortschrittliche Systeme bieten lösliche oder leicht zerbrechliche Trägermaterialien, die die Entfernung vereinfachen.
- Feature Design und Auflösung:
- Mindestwanddicke: Bei AM-Verfahren gibt es Grenzen dafür, wie dünn ein Merkmal zuverlässig gedruckt werden kann. Dies ist je nach Maschine und Material unterschiedlich, liegt aber in der Regel im Bereich von 0,4-1,0 mm. Bei der Konstruktion von Werkzeugen müssen diese Grenzen eingehalten werden, um die strukturelle Integrität und die Druckbarkeit zu gewährleisten.
- Minimale Featuregröße: Bei kleinen Löchern, Stiften oder komplizierten Details gibt es ebenfalls Einschränkungen aufgrund der Größe des Laser-/Elektronenstrahls und der Pulverpartikelgröße. Sehr feine Merkmale müssen möglicherweise nach dem Druck bearbeitet werden.
- Ausrichtung der Löcher: Horizontale Löcher werden aufgrund des schichtweisen Aufbaus oft mit besserer Maßhaltigkeit gedruckt als vertikale Löcher. Sehr kleine Löcher, vor allem horizontale, müssen möglicherweise unterstützt oder nach dem Druck besser gebohrt werden.
- Scharfe Ecken: Scharfe Innenecken können Spannungskonzentrationspunkte sein. Die Verwendung von Verrundungen oder Radien kann die Ermüdungslebensdauer verbessern und Spannungen reduzieren, was bei hochbelasteten Werkzeugen entscheidend ist.
- Entwerfen für konforme Kühlung (Formen und Gesenke):
- Dies ist ein hervorragendes Beispiel dafür, dass DfAM eine bessere Leistung ermöglicht. Zu den wichtigsten Überlegungen gehören:
- Kanalpfad: Entwerfen Sie die Kanäle so, dass sie den Konturen der wärmeerzeugenden Oberflächen (Formhohlraum, Formfläche) in einem gleichmäßigen Abstand folgen (normalerweise 1-3 mm unter der Oberfläche). Vermeiden Sie scharfe Biegungen, die den Durchfluss behindern.
- Durchmesser und Form der Rinne: Die Durchmesser liegen in der Regel zwischen 2 und 10 mm. Runde Querschnitte sind üblich, aber AM ermöglicht optimierte Formen (z. B. Teardrop), um die Wärmeübertragung zu verbessern oder den Druckabfall zu verringern. Stellen Sie sicher, dass die Durchmesser groß genug sind, um bedruckbar zu sein und Verstopfungen zu vermeiden.
- Fluss-Optimierung: Entwerfen Sie eine turbulente Strömung (fördert die Wärmeübertragung) und sorgen Sie für eine ausgewogene Strömung in den verschiedenen Kühlkreisläufen. CFD-Simulationen (Computational Fluid Dynamics) werden häufig zur Optimierung der Kanalauslegung eingesetzt.
- Einlässe/Auslässe: Entwerfen Sie robuste Anschlüsse für externe Kühlleitungen, oft mit Standardschnittstellen, die eventuell nachbearbeitet werden müssen.
- Entparzellierung: Stellen Sie sicher, dass die internen Kanäle nach dem Druck effektiv von ungeschmolzenem Pulver befreit werden können. Dies kann die Gestaltung von Zugangsöffnungen oder die Gewährleistung eines ausreichenden Kanaldurchmessers beinhalten.
- Dies ist ein hervorragendes Beispiel dafür, dass DfAM eine bessere Leistung ermöglicht. Zu den wichtigsten Überlegungen gehören:
- Gewichtsreduzierung mit Topologieoptimierung und Gitterstrukturen:
- Besonders relevant für Vorrichtungen und Roboter-EoAT, bei denen eine Gewichtsreduzierung die Ergonomie oder die Roboterleistung verbessert.
- Topologie-Optimierung: Software-Tools analysieren die Belastungsbedingungen und entfernen Material aus unkritischen Bereichen, was zu organisch wirkenden, hocheffizienten Strukturen führt.
- Gitterförmige Strukturen: Das Ersetzen von Volumenkörpern durch interne, sich wiederholende Einheitszellen (Gitter) kann das Gewicht und den Materialverbrauch drastisch reduzieren, während die erforderliche Steifigkeit und Festigkeit erhalten bleibt. Verschiedene Gittertypen (z. B. kubisch, Oktett-Fachwerk) bieten unterschiedliche Eigenschaften.
- Anwendung: Erstellen Sie ergonomische, leichte Montagevorrichtungen; reduzieren Sie die Trägheit von Robotergreifern; minimieren Sie die Materialkosten für große Vorrichtungen. Werkzeuge für Gitterstrukturen bietet erhebliche Vorteile bei der Handhabung und Automatisierung.
- Teil Konsolidierung:
- Nutzen Sie den Komplexitätsvorteil von AM, um mehrteilige Werkzeugbaugruppen zu einer einzigen, monolithisch gedruckten Komponente umzugestalten.
- Vorteile: Reduziert den Arbeits- und Zeitaufwand für die Montage, eliminiert potenzielle Leckagepfade (z. B. an den Verbindungsstellen in den Kühlkanälen), reduziert die Anzahl der Teile und die Lagerverwaltung und verbessert häufig die Gesamtsteifigkeit und Festigkeit durch den Wegfall von Verbindungsstellen.
- Beispiel: Kombination mehrerer Teile einer komplexen Vorrichtung oder Integration von Klemmen direkt in einen Vorrichtungskörper.
- Entwerfen für die Nachbearbeitung:
- AM-Teile, insbesondere Werkzeuge, müssen fast immer nachbearbeitet werden. DfAM umfasst die Planung dieser Schritte:
- Zulagen für die Bearbeitung: Fügen Sie zusätzliches Rohmaterial (z. B. 0,5-1,0 mm) zu Oberflächen hinzu, die hohe Präzision, spezifische Ebenheit oder glatte Oberflächen erfordern, die nur durch CNC-Bearbeitung erreicht werden können (z. B. Formtrennlinien, Fixierungspunkte von Vorrichtungen, Dichtungsflächen).
- Werkstückspannung Merkmale: Integrieren Sie in die Konstruktion Merkmale, die das Halten des Teils während der nachfolgenden Bearbeitungs- oder Endbearbeitungsvorgänge vereinfachen.
- Überlegungen zur Wärmebehandlung: Verstehen Sie, wie das gewählte Material (z. B. H13 vs. M300) auf die Wärmebehandlung reagiert und ob die Konstruktion den thermischen Belastungen ohne übermäßige Verformung standhalten kann. Einfache, robuste Geometrien schneiden im Allgemeinen besser ab.
- AM-Teile, insbesondere Werkzeuge, müssen fast immer nachbearbeitet werden. DfAM umfasst die Planung dieser Schritte:
Durch eine durchdachte Anwendung dieser DfAM für Werkzeugbau Prinzipien können Hersteller über die einfache Substitution traditioneller Methoden hinausgehen und wirklich innovativ sein, indem sie kundenspezifische Werkzeuge entwickeln, die schneller zu produzieren, leichter und langlebiger sind und bessere Leistungen als je zuvor erbringen. Die Zusammenarbeit mit AM-Experten wie Met3dp stellt sicher, dass Entwürfe nicht nur im Hinblick auf die Funktion, sondern auch auf die Herstellbarkeit optimiert werden, indem fortschrittliche Metall-AM-Designrichtlinien.
Präzision und Qualität: Verständnis von Toleranz, Oberflächengüte und Genauigkeit bei 3D-gedruckten Werkzeugen
Bei der Spezifizierung und Beschaffung von kundenspezifischen Werkzeugen ist das Erreichen des erforderlichen Niveaus an Präzision, Oberflächenqualität und allgemeiner Maßgenauigkeit von größter Bedeutung. Die Werkzeuge stehen oft in direktem Zusammenhang mit den endgültigen Teilen oder anderen Fertigungsanlagen und erfordern eine strenge Kontrolle über kritische Abmessungen und Oberflächeneigenschaften. Obwohl die additive Fertigung von Metallen eine bemerkenswerte geometrische Freiheit bietet, ist es für Ingenieure und Beschaffungsmanager wichtig, realistische Erwartungen in Bezug auf die inhärenten Toleranzen und die Oberflächengüte zu haben, die direkt vom Drucker erreicht werden können, und zu verstehen, welche Rolle die Nachbearbeitung bei der Erfüllung strenger Anforderungen spielt. Sicherstellung Qualitätskontrolle 3D-gedruckter Teile die für Werkzeuganwendungen bestimmt sind, erfordern ein sorgfältiges Prozessmanagement, eine angemessene Messtechnik und häufig auch sekundäre Nachbearbeitungsschritte.
Maßgenauigkeit und Toleranzen:
- As-Built-Genauigkeit: Die Genauigkeit eines AM-Metallteils direkt nach dem Druck und der Spannungsentlastung, aber vor der Bearbeitung. Typische erreichbare Toleranzen hängen stark ab von:
- Kalibrierung der Maschine: Gut gewartete und kalibrierte Maschinen (wie die von Met3dp verwendeten branchenführenden Systeme) bieten eine bessere Genauigkeit.
- Prozess (LPBF vs. SEBM): Verschiedene Verfahren können leicht unterschiedliche Genauigkeitsanforderungen haben. SEBM arbeitet oft bei höheren Temperaturen, was zu einem anderen Spannungs-/Verformungsverhalten führen kann als LPBF.
- Material: Verschiedene Metallpulver weisen während des Drucks und der Abkühlung unterschiedliche Schrumpfungs- und Spannungseigenschaften auf.
- Größe und Geometrie der Teile: Größere Teile und komplexe Geometrien sind in der Regel anfälliger für thermische Verformung und Abweichung. Während des Drucks aufgebaute innere Spannungen können zu Verzug führen.
- Orientierung und Unterstützung: Die Ausrichtung des Gebäudes wirkt sich darauf aus, wie sich thermische Gradienten ansammeln, und die Stützstrukturen beeinflussen die Stabilität während des Baus.
- Typische As-Built-Toleranzen: Die allgemeinen Richtlinien für gut kontrollierte Metall-AM-Prozesse sind zwar prozess- und materialspezifisch, liegen aber in der Größenordnung von:
- ±0,1 mm bis ±0,3 mm für kleinere Merkmale (< 50 mm).
- ±0,2% bis ±0,5% des Nennmaßes für größere Merkmale.
- Anmerkung: Dies sind allgemeine Schätzungen; spezifische Fähigkeiten sollten mit dem AM-Dienstanbieter (wie Met3dp, bekannt für Genauigkeit und Zuverlässigkeit). Um engere Toleranzen zu erreichen, ist häufig eine Nachbearbeitung erforderlich.
- Nachbearbeitete Toleranzen: Für kritische Abmessungen, wie z. B. Formtrennlinien, Auswerferstiftlöcher, Befestigungsflächen oder Lagerschnittstellen, wird in der Regel eine CNC-Bearbeitung nach dem Druck eingesetzt. Durch die maschinelle Bearbeitung können wesentlich engere Toleranzen erreicht werden, oft vergleichbar mit der traditionellen Fertigung:
- ±0,01 mm bis ±0,05 mm sind leicht erreichbar, je nach Bearbeitungsprozess und Einrichtung.
- Bedeutung für den Werkzeugbau: Die Kenntnis dieser Toleranzbereiche ist entscheidend. Unkritische Merkmale einer Vorrichtung können mit den vorhandenen Toleranzen akzeptabel sein, während die Arbeitsflächen eines Präzisionsformeinsatzes mit ziemlicher Sicherheit bearbeitet werden müssen.
Oberflächengüte (Rauhigkeit):
- As-Built Oberflächenbeschaffenheit: AM-Teile aus Metall haben von Natur aus eine rauere Oberfläche als maschinell bearbeitete Oberflächen, was auf den schichtweisen Prozess und die teilweise geschmolzenen Pulverpartikel zurückzuführen ist, die an der Oberfläche haften. Die Oberflächenrauheit (üblicherweise gemessen als Ra - Arithmetic Average Roughness) hängt ab von:
- Orientierung: Nach oben gerichtete Flächen und steile Winkel haben im Allgemeinen die beste Oberfläche. Nach unten weisende Flächen, die von Strukturen gestützt werden, sind nach dem Entfernen der Stützen tendenziell rauer. Die Seitenwände weisen Schichtlinien auf.
- Schichtdicke: Dünnere Schichten führen im Allgemeinen zu einem glatteren Ergebnis, verlängern aber die Druckzeit.
- Pulver Partikelgröße: Feinere Puder können zu glatteren Oberflächen beitragen.
- Prozessparameter: Laser-/Strahlleistung, Scangeschwindigkeit usw. beeinflussen die Eigenschaften des Schmelzbades und die resultierende Oberfläche.
- Typische As-Built Ra-Werte:
- LPBF: Häufig im Bereich von 6-15 µm Ra (240-600 µin Ra).
- SEBM: Kann manchmal aufgrund der Prozesseigenschaften etwas rauer sein, möglicherweise 15-35 µm Ra (600-1400 µin Ra).
- Anmerkung: Dies sind typische Werte, die erheblich variieren können.
- Nachbearbeitetes Oberflächenfinish: Zur Verbesserung der Oberflächengüte bei Werkzeuganwendungen werden verschiedene Nachbearbeitungsverfahren eingesetzt:
- Perlstrahlen/Shot Peening: Sorgt für ein gleichmäßiges mattes Finish, entfernt loses Pulver und kann Druckspannungen erzeugen (Verbesserung der Ermüdungsfestigkeit). Die Ra-Werte können sich leicht verbessern oder ähnlich bleiben, aber gleichmäßiger werden.
- Taumeln/Gleitschleifen: Kann Oberflächen und Kanten glätten, insbesondere bei kleineren Teilen. Erreichbare Ra hängt von den Medien und der Zeit ab.
- Schleifen/Polieren: Unerlässlich für Formoberflächen, die glatte Oberflächen für den Teileauswurf oder optische Klarheit erfordern, sowie für Oberflächen mit hohem Verschleiß. Durch manuelles oder automatisiertes Polieren lassen sich sehr glatte Oberflächen erzielen, oft < 0,1 µm Ra (< 4 µin Ra) für Hochglanzoberflächen auf Formen.
- Bearbeitungen: Bietet eine kontrollierte, glatte Oberflächengüte, wie sie für Fräs- oder Dreharbeiten typisch ist (z. B. 0,8-3,2 µm Ra oder besser).
- Bedeutung für den Werkzeugbau: Die Oberflächenbeschaffenheit wirkt sich auf die Reibung, die Verschleißfestigkeit, die Entformung der Teile (in Formen), die Farbhaftung (für Vorrichtungen) und die Ästhetik aus. Die erforderliche Oberfläche bestimmt die notwendigen Nachbearbeitungsschritte. Verstehen Oberflächengüte additive Fertigung Fähigkeiten und Grenzen ist entscheidend.
Qualitätskontrolle und -überprüfung:
- Prozessüberwachung: Fortschrittliche AM-Systeme beinhalten eine In-situ-Überwachung (Schmelzbadüberwachung, Wärmebildtechnik), um die Konsistenz der Fertigung zu verfolgen.
- Kontrolle der Materialqualität: Die Sicherstellung der Pulverqualität (Chemie, Partikelgröße, Fließfähigkeit) ist von entscheidender Bedeutung - ein Hauptaugenmerk für integrierte Anbieter wie Met3dp.
- Zerstörungsfreie Prüfung (NDT):
- CT-Scan (Computertomographie): Zunehmend werden sie eingesetzt, um interne Defekte wie Porosität oder fehlende Verschmelzung zu erkennen und um zu überprüfen, ob komplexe interne Merkmale wie konforme Kühlkanäle eindeutig sind und dem Design entsprechen.
- Farbeindringprüfung / Magnetpartikelprüfung: Dient zur Erkennung von Oberflächenrissen.
- Dimensionelle Metrologie:
- CMM (Koordinatenmessmaschine): Für die hochpräzise Überprüfung kritischer Abmessungen, insbesondere nach der Bearbeitung.
- 3D-Scannen: Optische oder Laserscanner erfassen die gesamte Geometrie des gedruckten Teils und ermöglichen einen Vergleich mit dem ursprünglichen CAD-Modell, um die Gesamtabweichung und Genauigkeit zu bewerten. Nützlich für komplexe Formen, bei denen CMM schwierig ist.
- Härteprüfung: Die Überprüfung, ob das Werkzeug nach der Wärmebehandlung die angegebene Härte erreicht hat, ist entscheidend für die Leistung und die Verschleißfestigkeit.
Zusammenfassend lässt sich sagen, dass der 3D-Metalldruck zwar unglaubliche Designmöglichkeiten für kundenspezifische Werkzeuge bietet, aber das Erreichen der notwendigen Toleranzen beim 3D-Druck von MetallOberflächengüte und Gesamtqualität Werkzeuge für die Maßgenauigkeit erfordert oft eine Kombination aus sorgfältiger DfAM, kontrollierten Druckprozessen und geeigneten Nachbearbeitungs- und Qualitätsprüfungsschritten. Die Zusammenarbeit mit einem erfahrenen Partner, der diese Nuancen versteht und über robuste Qualitätsmanagementsysteme verfügt, ist für die Herstellung von zuverlässigen, leistungsstarken Werkzeugen, die den anspruchsvollen Fertigungsanforderungen entsprechen, von entscheidender Bedeutung.
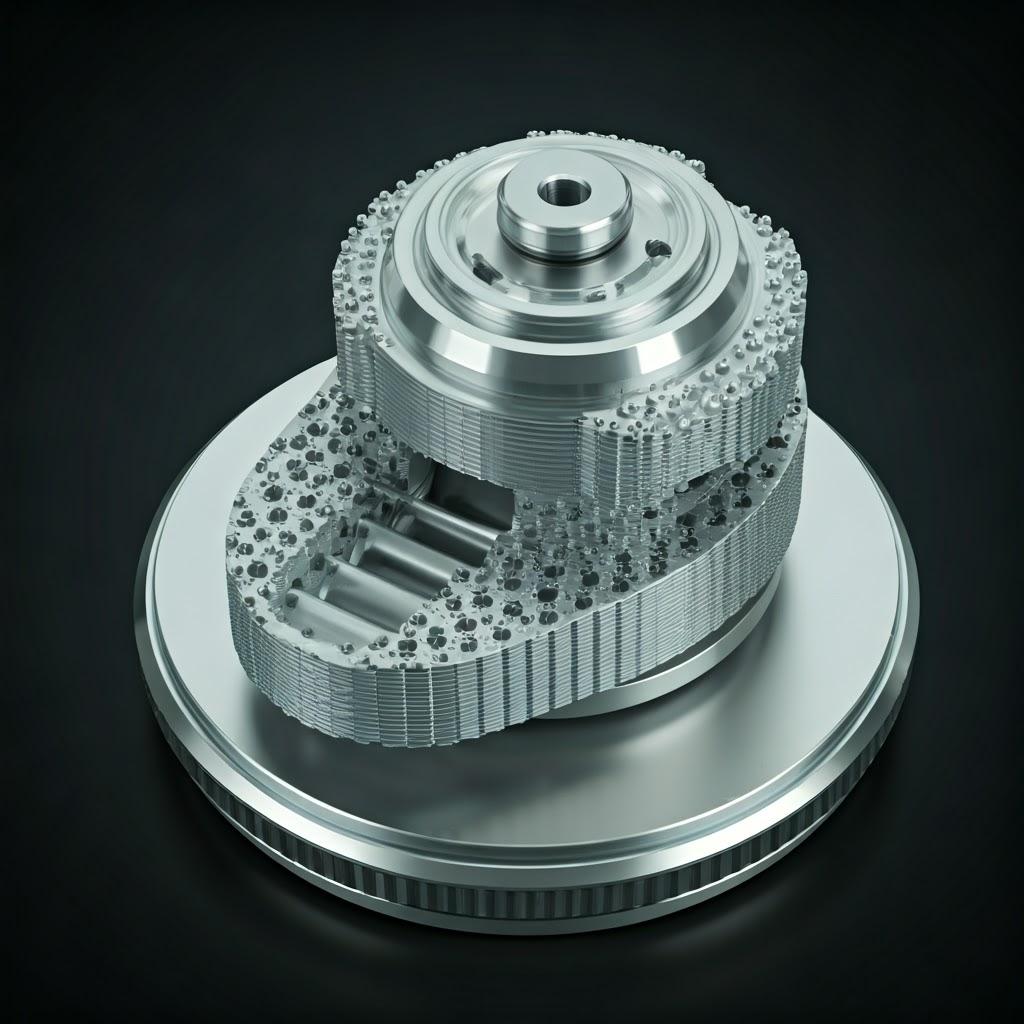
Über den Druck hinaus: Wesentliche Nachbearbeitung für 3D-gedruckte Metallwerkzeuge
Die Herstellung eines kundenspezifischen Werkzeugs endet nicht, wenn der 3D-Metalldrucker seine Arbeit beendet hat. Das "grüne" Teil, das frisch von der Bauplatte kommt, ist selten sofort für den Einsatz in einer anspruchsvollen Fertigungsumgebung bereit. Eine Reihe von kritischen Nachbearbeitung bei der additiven Fertigung sind fast immer Schritte erforderlich, um das fertige Bauteil in ein funktionsfähiges, haltbares und präzises Werkzeug zu verwandeln. Diese Schritte sind notwendig, um innere Spannungen abzubauen, Stützstrukturen zu entfernen, die gewünschten Materialeigenschaften (Härte, Festigkeit, Zähigkeit) zu erreichen, kritische Abmessungen und Oberflächengüten zu erzielen und die Gesamtleistung und Langlebigkeit des Werkzeugs sicherzustellen. Das Verständnis dieser allgemeinen Nachbearbeitungsanforderungen ist für die Ingenieure, die die Werkzeuge konstruieren, und für die Beschaffungsmanager, die die Gesamtkosten und die Vorlaufzeit in die Beschaffungsentscheidungen einbeziehen, entscheidend. Das Ignorieren oder die unsachgemäße Ausführung dieser Schritte kann zu einem vorzeitigen Ausfall des Werkzeugs, schlechter Leistung und beeinträchtigter Qualität des Endprodukts führen.
Gemeinsame Nachbearbeitungsschritte für Metall-AM-Werkzeuge:
- Stressabbau:
- Warum sie gebraucht wird: Die schnellen Erwärmungs- und Abkühlungszyklen bei schichtweisen Metall-AM-Prozessen führen zu erheblichen inneren Spannungen innerhalb des gedruckten Teils. Diese Spannungen können zu Verformungen, Verwerfungen (insbesondere nach dem Entfernen von der Bauplatte) und sogar zu Rissen führen, wenn sie nicht abgebaut werden.
- Prozess: In der Regel der erste Schritt nach dem Druck, der oft durchgeführt wird, während das Teil noch an der Bauplatte befestigt ist, um die Stabilität zu erhalten. Dabei wird das Teil in einem Ofen auf eine bestimmte Temperatur erhitzt (unter der Umwandlungstemperatur des Materials, z. B. ~550-650 °C für H13, oder je nach Zielsetzung ein Glühzyklus), für eine bestimmte Dauer gehalten und dann langsam abgekühlt. Dadurch kann sich das Gefüge des Materials entspannen und die inneren Spannungen werden abgebaut.
- Wichtigkeit: Dies ist von entscheidender Bedeutung für die Dimensionsstabilität und die Vermeidung von Verformungen oder Rissen bei der Entfernung der Auflage, der Bearbeitung oder der Wärmebehandlung.
- Entfernen des Teils von der Bauplatte:
- Prozess: Nach dem Spannungsabbau (sofern dieser auf der Platte erfolgt) muss das Teil von der Metallbauplatte getrennt werden, auf der es gedruckt wurde. Zu den gängigen Methoden gehören:
- Drahterodieren (Electrical Discharge Machining): Bietet präzises Schneiden mit geringer Kraft, ideal für empfindliche Teile oder wenn eine saubere Schnittfläche benötigt wird.
- Sägen (Bandsäge): Eine schnellere und häufigere Methode für robuste Teile, die jedoch eine rauere Oberfläche hinterlässt, die in der Regel nachbearbeitet werden muss.
- Bearbeitungen: In einigen Fällen können auch Fräsen oder Schleifen eingesetzt werden.
- Prozess: Nach dem Spannungsabbau (sofern dieser auf der Platte erfolgt) muss das Teil von der Metallbauplatte getrennt werden, auf der es gedruckt wurde. Zu den gängigen Methoden gehören:
- Entfernung der Stützstruktur:
- Warum sie gebraucht wird: Stützstrukturen, die für den Druck von Überhängen und komplexen Geometrien erforderlich sind, müssen entfernt werden.
- Prozess: Dies kann einer der arbeitsintensivsten Schritte sein, abhängig von der Komplexität und Zugänglichkeit der Träger. Zu den Methoden gehören:
- Manuelle Entfernung: Verwendung von Zangen, Schleifgeräten, Meißeln oder anderen Handwerkzeugen. Erfordert Geschick und Sorgfalt, um die Oberfläche des Teils nicht zu beschädigen. Hinterlässt oft Bearbeitungsspuren, die nachbearbeitet werden müssen.
- CNC-Bearbeitung: Durch Fräsen oder Drehen können Halterungen präzise entfernt werden, insbesondere größere oder integrierte Halterungen. Wird oft in Verbindung mit manuellen Methoden eingesetzt.
- Drahterodieren: Kann verwendet werden, um Stützen in schwer zugänglichen Bereichen zu erreichen und zu schneiden.
- DfAM Auswirkungen: Das Design für den Ausbau der Stützen (Zugänglichkeit, Minimierung der Kontaktpunkte) hat einen erheblichen Einfluss auf die Leichtigkeit und die Kosten dieser Phase.
- Wärmebehandlung (Härtung/Alterung):
- Warum sie gebraucht wird: Ungedruckte Metallteile weisen selbst nach dem Spannungsabbau in der Regel nicht die optimale Härte, Festigkeit oder Verschleißfestigkeit auf, die für Werkzeuganwendungen erforderlich sind. Durch eine Wärmebehandlung werden die gewünschte Mikrostruktur und die mechanischen Eigenschaften erreicht. Die spezifische Behandlung hängt stark vom jeweiligen Material ab.
- Prozess:
- Werkzeugstähle (z. B. H13): Erfordert einen mehrstufigen Prozess:
- Austenitisierung: Erhitzen auf eine hohe Temperatur (z.B. ~1000-1050°C), um Karbide aufzulösen und Austenit zu bilden.
- Abschrecken: Schnelles Abkühlen (in Luft, Öl oder Inertgas), um Austenit in harten Martensit umzuwandeln.
- Anlassen: Wiedererwärmung auf eine niedrigere Temperatur (z. B. ~500-600 °C, oft mehrfach durchgeführt), um die Sprödigkeit zu verringern, die Zähigkeit zu erhöhen und die Zielhärte zu erreichen (z. B. 45-52 HRC). Wärmebehandlung von Werkzeugstahl wie H13 ist entscheidend, erfordert aber eine sorgfältige Kontrolle, um Verzerrungen zu minimieren.
- Martensitaushärtende Stähle (z. B. M300/1.2709): Erfordert einen viel einfacheren Alterungsprozess bei niedrigeren Temperaturen:
- Altershärtung: Erhitzen auf eine moderate Temperatur (typischerweise ~480-500°C) für mehrere Stunden. Dies führt zur Ausscheidung von verfestigenden intermetallischen Verbindungen. Ein Abschrecken ist nicht erforderlich. Der größte Vorteil ist die minimale Verformung während dieses Prozesses.
- Werkzeugstähle (z. B. H13): Erfordert einen mehrstufigen Prozess:
- Atmosphärenkontrolle: Wärmebehandlungen werden in der Regel in Vakuumöfen oder unter kontrollierter Schutzgasatmosphäre durchgeführt, um Oxidation und Entkohlung zu verhindern, insbesondere bei hohen Austenitisierungstemperaturen.
- Spanende Bearbeitung (CNC):
- Warum sie gebraucht wird: Um enge Toleranzen bei kritischen Abmessungen zu erreichen, können Sie flache Dichtungsflächen (z. B. Formtrennlinien) erzeugen, Gewinde oder präzise Bohrungen bearbeiten und bestimmte Oberflächengüten erzielen, die besser sind als der Ist-Zustand.
- Prozess: Standard CNC-Bearbeitung von 3D-Drucken Techniken wie Fräsen, Drehen, Schleifen und Erodieren werden eingesetzt. Zu den Überlegungen gehören:
- Werkstückspannung: Sicheres Befestigen des potenziell komplexen AM-Teils.
- Härte des Materials: Die Bearbeitung von vollständig gehärtetem Werkzeugstahl ist eine Herausforderung und erfordert geeignete Schneidwerkzeuge und Parameter. Die zerspanende Bearbeitung ist vor dem letzten Härtungsschritt oft einfacher (obwohl martensitaushärtende Stähle wegen ihrer Maßhaltigkeit oft nach der Bearbeitung gealtert werden).
- Zulage für Vorräte: Das DfAM sollte ausreichend Material für die Bearbeitung enthalten.
- Oberflächenveredelung:
- Warum sie gebraucht wird: Zur Erzielung der erforderlichen Oberflächenrauheit für die Funktion (z. B. glatte Formoberfläche für die Teileentnahme, strukturierte Oberfläche für die Griffigkeit), Ästhetik oder Verschleißfestigkeit.
- Prozess: Verschiedene Methoden je nach Zielsetzung:
- Perlenstrahlen / Sandstrahlen: Reinigt die Oberfläche, sorgt für ein gleichmäßig mattes Finish, entfernt losen Puder.
- Taumeln / Vibrationsgleitschleifen: Glättet Kanten und Oberflächen, insbesondere bei kleineren Teilen.
- Schleifen: Wird für hochpräzise Ebenheit und glatte Oberflächen an spezifischen Merkmalen verwendet.
- Polieren: Manuelles oder automatisiertes Polieren, unerlässlich für Spritzgussformen, die hohen Glanz oder optische Klarheit erfordern. Kann Hochglanzoberflächen erzielen (<0,1 µm Ra). Polieren von Metallteilen ist oft ein hochqualifizierter, manueller Prozess für komplexe Formen.
- Beschichtung (z. B. PVD, Nitrieren): Das Auftragen spezieller Beschichtungen kann die Verschleißfestigkeit weiter erhöhen, die Reibung verringern oder die Trenneigenschaften für anspruchsvolle Werkzeuganwendungen verbessern.
Die spezifische Abfolge und Kombination dieser Werkzeuge für die Oberflächenbearbeitung und andere Nachbearbeitungsschritte variieren je nach Werkzeugtyp, Material und Anwendungsanforderungen. Für Hersteller ist es entscheidend, mit AM-Dienstleistern wie Met3dp zusammenzuarbeiten, die nicht nur über fortschrittliche Druckfähigkeiten, sondern auch über umfassende Nachbearbeitungskenntnisse und -anlagen verfügen, um einen optimierten Arbeitsablauf von der digitalen Datei bis zum fertigen, funktionalen Werkzeug zu gewährleisten. Die Vernachlässigung dieser Phase "nach dem Druck" untergräbt die erheblichen Investitionen, die in die additive Fertigungstechnologie getätigt wurden.
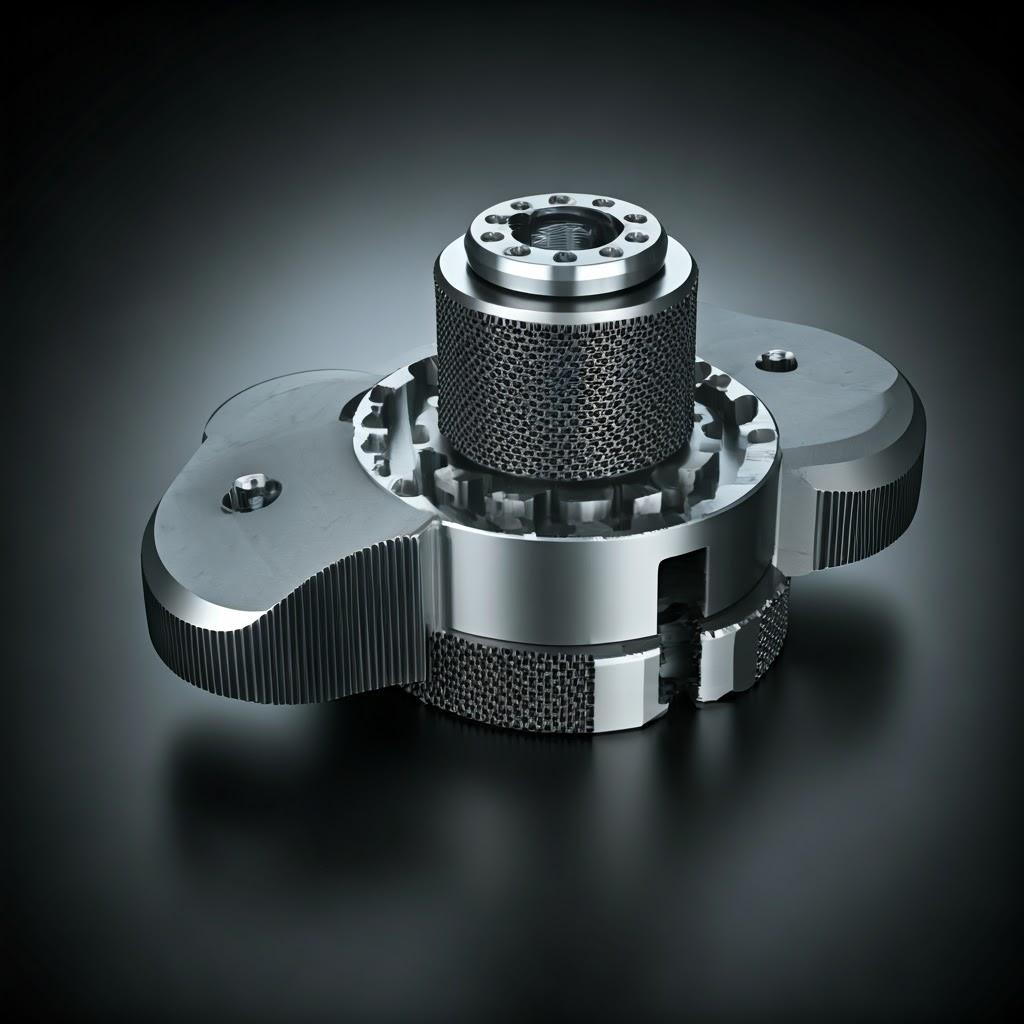
Hürden überwinden: Häufige Herausforderungen bei 3D-gedruckten Metallwerkzeugen und Lösungen
Die additive Fertigung von Metallen bietet ein revolutionäres Potenzial für die Herstellung kundenspezifischer Werkzeuge, ist aber nicht ohne Herausforderungen. Wie bei jedem fortschrittlichen Fertigungsverfahren erfordert die Erzielung konsistenter, qualitativ hochwertiger Ergebnisse eine sorgfältige Kontrolle, Prozessverständnis und Erfahrung bei der Fehlerbehebung. Ingenieure und Beschaffungsmanager sollten sich der potenziellen Hürden bewusst sein, um realistische Erwartungen zu setzen und proaktiv mit ihren AM-Partnern zusammenzuarbeiten, um Risiken zu minimieren. Die Bewältigung dieser Herausforderungen ist der Schlüssel zur erfolgreichen Implementierung von Metall-AM für anspruchsvolle Werkzeuganwendungen. Glücklicherweise bieten die ständigen Fortschritte in den Bereichen Technologie, Materialien, Software und Prozesswissen effektive Lösungen und Strategien zur Risikominderung.
Gemeinsame Herausforderungen und Abhilfestrategien:
- Eigenspannung, Verformung und Verzug:
- Herausforderung: Die schnelle, örtlich begrenzte Erwärmung und Abkühlung beim AM führt zu inneren Spannungen. Wenn diese Spannungen die Streckgrenze des Materials überschreiten oder ungleichmäßig verteilt sind, können sie dazu führen, dass sich das Teil verzieht, seine Form verzerrt (insbesondere nach der Entnahme aus der Bauplatte) oder sogar reißt. Dies ist besonders relevant für große Teile oder komplexe Geometrien, wie sie im Werkzeugbau üblich sind. Verringerung des Verzugs der Werkzeuge ist ein Hauptanliegen.
- Die Ursachen: Hohe thermische Gradienten, schnelle Abkühlungsraten, Schrumpfungseigenschaften des Materials, Teilegeometrie (z. B. große flache Abschnitte, scharfe Übergänge).
- Lösungen und Abhilfemaßnahmen:
- Optimierte Build-Strategie: Eine sorgfältige Auswahl der Bauausrichtung, geeignete Stützstrukturen (die als Wärmesenken und Verankerungen fungieren) und optimierte Scan-Strategien (z. B. Insel-Scanning, rotierende Scan-Vektoren) können dazu beitragen, den Wärmestau und die Wärmeverteilung zu kontrollieren.
- Kontrolle der Prozessparameter: Feinabstimmung von Laser-/Elektronenstrahlleistung, Scangeschwindigkeit und Schichtdicke auf das jeweilige Material und die Geometrie. Vorheizen (üblich bei SEBM- und einigen LPBF-Systemen) zur Verringerung der thermischen Gradienten.
- Thermische Simulation: Die Software kann Spannungsakkumulation und Verformung vorhersagen und ermöglicht so Designanpassungen oder kompensierte Geometrien vor dem Druck.
- Obligatorischer Stressabbau: Die Durchführung eines ordnungsgemäßen Wärmebehandlungszyklus zum Spannungsabbau unmittelbar nach dem Druck, oft noch auf der Bauplatte, ist von entscheidender Bedeutung, um die inneren Spannungen vor der weiteren Verarbeitung abzubauen.
- Robuste Teilekonstruktion (DfAM): Die Vermeidung großer, nicht gestützter, flacher Bereiche, die Verwendung allmählicher Dickenübergänge und eine auf Eigensteifigkeit ausgerichtete Konstruktion können dazu beitragen, Verformungen zu vermeiden.
- Entfernung der Stützstruktur:
- Herausforderung: Das Entfernen von Stützstrukturen, insbesondere von internen oder komplizierten Strukturen, kann zeitaufwändig und kostspielig sein und das Risiko bergen, die Oberfläche des Teils zu beschädigen. Herausforderungen beim Umzug unterstützen sind ein wesentlicher Faktor für die Gesamtkosten und die Vorlaufzeit.
- Die Ursachen: Dichtes Trägermaterial, schlechte Zugänglichkeit, starke Bindung zwischen Träger und Teil, empfindliche Teilemerkmale.
- Lösungen und Abhilfemaßnahmen:
- DfAM für die Minimierung der Unterstützung: Entwerfen Sie Teile mit selbsttragenden Winkeln (>45°), wenn möglich. Richten Sie das Teil so aus, dass der Bedarf an kritischen Oberflächenstützen reduziert wird.
- Optimiertes Support-Design: Verwenden Sie Halterungstypen (z. B. Gitter, Baum, Kegel), die die Kontaktpunkte und den Materialverbrauch minimieren und gleichzeitig die erforderliche Stabilität gewährleisten. Nutzen Sie Softwarefunktionen, die die Platzierung und Art der Stützen optimieren.
- Design für den Zugang: Stellen Sie sicher, dass die Stützen mit Werkzeugen (manuell oder maschinell) erreicht werden können, um sie zu entfernen. Erwägen Sie den Einbau von temporären Zugangslöchern oder Fenstern, wenn interne Stützen unvermeidbar sind.
- Wahl des Materials: Manche Materialien lassen sich von Natur aus leichter oder schwerer von Stützen befreien.
- Nachbearbeitungstechniken: Einsatz von Drahterodier- oder speziellen Bearbeitungstechniken für schwierige Träger.
- Porosität:
- Herausforderung: Das Vorhandensein von kleinen Hohlräumen oder Poren im gedruckten Metall. Porosität kann als Spannungskonzentrator wirken, die Festigkeit und Lebensdauer des Werkzeugs verringern und möglicherweise die Wärmeleitfähigkeit oder die Oberflächengüte nach dem Polieren beeinträchtigen. Erkennung und Kontrolle Porosität im 3D-Druck ist bei kritischen Werkzeugen unerlässlich.
- Die Ursachen: Gaseinschlüsse während der Zerstäubung oder des Drucks, Verdampfung flüchtiger Elemente, unzureichende Energiedichte (fehlende Verschmelzung zwischen Schichten/Spuren), Keyholing (Instabilität durch zu hohe Energiedichte), schlechte Pulverqualität oder Handhabung (Feuchtigkeit, Verschmutzung).
- Lösungen und Abhilfemaßnahmen:
- Optimierte Prozessparameter: Die präzise Steuerung von Laser-/Strahlleistung, Scangeschwindigkeit, Schraffurabstand und Schichtdicke ist der Schlüssel zum Erreichen des vollständigen Schmelzens und Verschmelzens. Die Entwicklung der Parameter ist für jede Material-/Maschinenkombination entscheidend.
- Hochwertiges Pulver: Die Verwendung von Pulvern mit geringem Gasgehalt, kontrollierter Partikelgrößenverteilung und hoher Sphärizität (wie sie bei Met3dp durch fortschrittliche Zerstäubung hergestellt werden) ist von entscheidender Bedeutung. Die richtige Handhabung und Lagerung des Pulvers (z. B. Trocknen, Sieben) verhindert Verunreinigungen und die Aufnahme von Feuchtigkeit.
- Kontrollierte Bauatmosphäre: Die Aufrechterhaltung einer hochreinen Inertgasatmosphäre (Argon oder Stickstoff) in der Baukammer minimiert die Oxidation und Verunreinigung während des Drucks.
- Heiß-Isostatisches Pressen (HIP): Ein Nachbearbeitungsschritt unter hohem Druck und hoher Temperatur. HIP kann die inneren Poren wirksam schließen und so die Dichte und die mechanischen Eigenschaften erheblich verbessern. Wird häufig für kritische Anwendungen wie Komponenten für die Luft- und Raumfahrt verwendet, verursacht aber zusätzliche Kosten und Vorlaufzeiten. Kann bei sehr anspruchsvollen Werkzeugen in Betracht gezogen werden.
- Qualitätskontrolle (CT-Scanning): Einsatz von CT-Scans zur zerstörungsfreien Prüfung von Teilen auf innere Porosität.
- Oberflächenbeschaffenheit und Defekte:
- Herausforderung: Die Oberflächen im eingebauten Zustand können rau sein und Defekte wie teilweise geschmolzene Pulverpartikel ("Balling"), Krätzebildung oder Abdrücke von Trägern aufweisen. Diese beeinträchtigen Reibung, Verschleiß, Ablöseeigenschaften (Formen) und Ästhetik.
- Die Ursachen: Prozessinstabilitäten, suboptimale Parameter, Interaktion mit der Trägerstruktur, Pulverspritzer.
- Lösungen und Abhilfemaßnahmen:
- Optimierung der Parameter: Feinabstimmung der Parameter, um stabile Schmelzbäder und eine gleichmäßige Schichtabscheidung zu gewährleisten.
- Optimierte Orientierung und Stützen: Optimale Positionierung der kritischen Flächen und Verwendung gut gestalteter Stützen.
- Nachbearbeiten: Anwendung geeigneter Nachbearbeitungstechniken (Strahlen, Trowalisieren, Bearbeiten, Polieren), um die gewünschte Oberflächenqualität zu erreichen. Siehe den vorherigen Abschnitt über Nachbearbeitung.
- Knacken:
- Herausforderung: Risse können sich während des Drucks oder der anschließenden Wärmebehandlung bilden, insbesondere bei kohlenstoffreichen oder rissempfindlichen Legierungen, oder aufgrund hoher Eigenspannungen.
- Die Ursachen: Hohe Eigenspannungen, spröde Materialphasen, schnelle Abkühlung, Materialunverträglichkeit (bei Drucken aus mehreren Materialien), vorhandene Defekte, die als Auslöser dienen.
- Lösungen und Abhilfemaßnahmen:
- Auswahl der Materialien: Auswahl von Legierungen mit besserer Druckbarkeit und geringerer Rissanfälligkeit, wo dies möglich ist (z. B. weisen martensitaushärtende Stähle während des Drucks oft ein geringeres Rissrisiko auf als einige Werkzeugstähle).
- Prozesskontrolle: Durch Vorheizen, optimierte Scan-Strategien zur Bewältigung thermischer Gradienten und sorgfältige Parameterauswahl.
- Stressabbau: Ein rechtzeitiger und angemessener Stressabbau ist entscheidend.
- Kontrolle der Wärmebehandlung: Sorgfältige Rampen und Abkühlungsraten bei der Wärmebehandlung nach dem Druck, insbesondere bei empfindlichen Materialien wie H13.
Um diese Herausforderungen erfolgreich zu meistern, ist ein tiefes Verständnis der Materialwissenschaft, der Physik des AM-Prozesses, der DfAM-Prinzipien und robuster Qualitätskontrollverfahren erforderlich. Die Zusammenarbeit mit einem erfahrenen Optimierung des Metall-AM-Prozesses Ein Experte wie Met3dp, der hochwertige Materialien, fortschrittliche Drucktechnologie (einschließlich SEBM) und umfassende Nachbearbeitungsmöglichkeiten kombiniert, mindert diese Risiken erheblich. Eine offene Kommunikation zwischen dem Kunden und dem AM-Anbieter in Bezug auf die Anwendungsanforderungen und potenziellen Herausforderungen ist der Schlüssel zu erfolgreichen Ergebnissen bei 3D-gedruckten Metallwerkzeugen.
Die Wahl Ihres Partners: Auswahl des idealen Metall-3D-Druck-Dienstleisters für den Werkzeugbau
Die erfolgreiche Nutzung der additiven Fertigung von Metall für kundenspezifische Werkzeuge geht über das Verständnis der Technologie hinaus; sie erfordert die Zusammenarbeit mit dem richtigen Fertigungspartner. Die Qualität, Leistung, Kosteneffizienz und rechtzeitige Lieferung Ihrer 3D-gedruckten Werkzeuge hängt stark von den Fähigkeiten, dem Fachwissen und den Prozessen des von Ihnen gewählten Dienstleisters ab. Für Ingenieure und Beschaffungsmanager, die mit der Beschaffung beauftragt sind Metall-3D-Druck-Dienstleistung B2B Lösungen zu finden, erfordert die Bewertung potenzieller Lieferanten eine gründliche Beurteilung in mehreren kritischen Bereichen. Eine fundierte Entscheidung sichert nicht nur den Zugang zu Druckkapazitäten, sondern auch den entscheidenden technischen Support und die Qualitätssicherung, die für anspruchsvolle Werkzeuganwendungen erforderlich sind.
Bei der Bewertung von potenziellen Bewertung der Lieferanten von kundenspezifischen Werkzeugen Kriterien sind die folgenden Faktoren zu berücksichtigen:
1. Technisches Fachwissen und Erfahrung in der Anwendung von Werkzeugen:
- Tiefes AM-Wissen: Verfügt der Anbieter über grundlegende Kenntnisse der Metallurgie, der Physik des AM-Prozesses (LPBF, SEBM usw.) und der für die Werkzeugherstellung relevanten Werkstoffkunde?
- Spezialisierung auf Werkzeuge: Haben sie erfolgreich Werkzeuge hergestellt, die Ihrer Anwendung ähnlich sind (z. B. Spritzgussformen mit konformer Kühlung, hochpräzise Vorrichtungen, Stanzwerkzeuge)? Können sie Fallstudien oder Beispiele vorlegen? Erfahrung ist von großer Bedeutung, wenn es darum geht, Herausforderungen zu antizipieren und die Ergebnisse für bestimmte Werkzeugtypen zu optimieren.
- DfAM-Unterstützung: Bieten sie Beratung zu Design for Additive Manufacturing an? Können sie Ihre Ingenieure bei der Optimierung bestehender oder der Entwicklung neuer Designs speziell für AM unterstützen, um die Vorteile wie konforme Kühlung oder Leichtbau zu maximieren? Diese Fähigkeit zur Zusammenarbeit bringt einen erheblichen Mehrwert.
- Problemlösungskompetenz: Wie gehen sie mit potenziellen Problemen wie Druckfehlern, Verzugskontrolle oder dem Erreichen bestimmter Materialeigenschaften um?
2. Maschinenfähigkeiten und Technologie:
- Angemessene Technologie: Verwenden sie die richtige Art von AM-Technologie (z. B. Laser Powder Bed Fusion - LPBF, Selective Electron Beam Melting - SEBM) für Ihre Material- und Anwendungsanforderungen? SEBM, das häufig von Anbietern wie Met3dp eingesetzt wird, eignet sich beispielsweise hervorragend für reaktive Materialien oder Anwendungen, die aufgrund der Vakuumumgebung und der höheren Verarbeitungstemperaturen eine hohe Produktivität und geringere Eigenspannungen erfordern.
- Bauvolumen: Können die Maschinen die Größe der von Ihnen benötigten Werkzeuge aufnehmen?
- Qualität und Wartung der Maschinen: Sind die Maschinen von renommierten Herstellern? Haben sie strenge Wartungspläne, um eine gleichbleibende Leistung und Genauigkeit zu gewährleisten?
- Prozessüberwachung: Verfügen ihre Maschinen über In-situ-Überwachungsfunktionen, um die Konsistenz des Aufbaus zu verfolgen und potenzielle Fehler während des Drucks zu erkennen?
3. Materialbestand und Qualitätskontrolle:
- Einschlägige Materialien: Bieten sie die spezifischen Werkzeugstähle (H13, M300/1.2709) oder andere Legierungen an, die für Ihre Anwendung erforderlich sind?
- Qualität des Pulvers: Dies ist von größter Bedeutung. Erkundigen Sie sich nach den Verfahren zur Beschaffung und Qualitätskontrolle des Pulvers. Werden die Pulverprüfungen, die Handhabung, die Lagerung und die Rückverfolgbarkeit rigoros gehandhabt? Unternehmen wie Met3dp, die ihre eigenen hochwertigen Pulver mit Hilfe fortschrittlicher Gaszerstäubungs- und PREP-Technologien herstellen, bieten einen deutlichen Vorteil bei der Materialkonsistenz und -optimierung. Sie gewährleisten eine hohe Sphärizität, eine kontrollierte Partikelgrößenverteilung, eine gute Fließfähigkeit und einen geringen Gehalt an Verunreinigungen, die für dichte, leistungsstarke Werkzeuge entscheidend sind.
- Entwicklung neuer Materialien: Beschäftigen sie sich mit der Erforschung oder dem Angebot fortschrittlicher oder spezieller Legierungen (wie TiNi, TiTa, TiAl, TiNbZr, CoCrMo von Met3dp), die einzigartige Vorteile für den künftigen Werkzeugbedarf bieten könnten?
4. Umfassende Post-Processing-Fähigkeiten:
- In-House vs. Outsourced: Übernimmt der Anbieter kritische Nachbearbeitungsschritte wie Spannungsabbau, Wärmebehandlung (mit kalibrierten Öfen und Fachwissen über spezifische Zyklen für Werkzeugstähle), CNC-Bearbeitung und Oberflächenveredelung im eigenen Haus oder verlässt er sich auf externe Anbieter? Inhouse-Kapazitäten bieten im Allgemeinen eine bessere Kontrolle, potenziell schnellere Durchlaufzeiten und eine optimierte Verantwortlichkeit.
- Spezifisches Fachwissen: Verfügen sie nachweislich über Fachkenntnisse in der spezifischen Nachbearbeitung, die für Werkzeuge? Dazu gehören eine präzise Wärmebehandlung, um die Zielhärte ohne übermäßige Verformung zu erreichen, eine hochpräzise Bearbeitung kritischer Merkmale und möglicherweise ein fortschrittliches Polieren von Formen.
- Ausrüstung: Verfügen sie über die notwendige Ausrüstung (Öfen, CNC-Maschinen, Messgeräte), um die erforderlichen Nachbearbeitungsschritte effektiv durchzuführen?
5. Qualitätsmanagementsystem und Zertifizierungen:
- QMS: Verfügen sie über ein solides Qualitätsmanagementsystem (QMS)? Zertifizierungen wie ISO 9001 sind ein grundlegender Indikator für etablierte Qualitätsprozesse. Für Branchen wie die Luft- und Raumfahrt kann die AS9100-Zertifizierung relevant sein.
- Rückverfolgbarkeit: Können sie eine vollständige Rückverfolgbarkeit vom Rohmaterial (Pulvercharge) über den Druck und die Nachbearbeitung bis zum fertigen Teil gewährleisten?
- Metrologie und Inspektion: Über welche Möglichkeiten der Dimensionsprüfung verfügen sie (CMM, 3D-Scannen)? Bieten sie NDT-Optionen wie CT-Scannen an, falls dies für die Überprüfung der internen Integrität erforderlich ist?
6. Vorlaufzeit, Kapazität und Reaktionsfähigkeit:
- Zitiergeschwindigkeit: Wie schnell können sie detaillierte Angebote auf der Grundlage Ihrer Anforderungen vorlegen?
- Angegebene Vorlaufzeiten: Wie lang sind die typischen Vorlaufzeiten für ähnliche Teile wie die Ihren? Verstehen Sie, welche Faktoren dies beeinflussen könnten (z. B. aktueller Auftragsbestand, Komplexität der Nachbearbeitung).
- Produktionskapazität: Verfügen sie über ausreichende Maschinenkapazitäten, um Ihr potenzielles Volumen zu bewältigen oder dringende Anforderungen zu erfüllen?
- Kommunikation: Sind sie reaktionsschnell, transparent und leicht zu erreichen? Gutes Projektmanagement und gute Kommunikation sind unerlässlich.
7. Kostenstruktur und -transparenz:
- Klare Preisgestaltung: Ist ihre Preisstruktur transparent? Werden die Kosten für Druck, Material, Träger und Nachbearbeitung aufgeschlüsselt?
- Wert-Angebot: Bewerten Sie die Kosten nicht nur isoliert, sondern im Zusammenhang mit Qualität, Fachwissen, Vorlaufzeit und dem gebotenen Gesamtwert (z. B. DfAM-Unterstützung, integrierte Nachbearbeitung). Manchmal ist die billigste Option nicht die beste, insbesondere bei kritischen Werkzeugen.
8. Standort und Logistik:
- Versand: Berücksichtigen Sie die Versandkosten und -zeiten, insbesondere bei internationalen Lieferanten. Informieren Sie sich über Zoll- und Import-/Exportbestimmungen, falls zutreffend. Met3dp, mit Hauptsitz in Qingdao, China, bedient einen globalen Markt und nutzt eine effiziente Logistik.
- Besuche vor Ort/Audits: Ist es möglich, den Betrieb zu besuchen oder ein Audit (auch virtuell) durchzuführen, um die Arbeitsabläufe aus erster Hand zu beurteilen?
Met3dp als Ihr Partner: Met3dp zeichnet sich als führender Anbieter durch das Angebot einer umfassenden, integrierten Lösung aus. Mit jahrzehntelanger kollektiver Erfahrung kombinieren wir branchenführende SEBM-Drucker, die bekannt sind für Genauigkeit und ZuverlässigkeitWir verfügen über fortschrittliche Produktionskapazitäten für Metallpulver, die eine hohe Materialqualität gewährleisten, über ein breites Angebot an Standard- und innovativen Legierungen sowie über solide Dienstleistungen zur Anwendungsentwicklung. Unser Engagement reicht von der anfänglichen Beratung und DfAM-Unterstützung bis hin zum sorgfältigen Druck und der Nachbearbeitung, um sicherzustellen, dass Sie Werkzeuge erhalten, die für Leistung und Zuverlässigkeit optimiert sind. Um mehr über unser Unternehmen und unsere Werte zu erfahren, besuchen Sie bitte unsere Über uns Seite.
Die Wahl des richtigen Partners ist eine strategische Entscheidung. Durch eine sorgfältige Bewertung dieser Kriterien können Sie einen Metall-3D-Druck-Dienstleistung B2B Anbieter, der über das technische Know-how, das Qualitätsbewusstsein und die umfassenden Fähigkeiten verfügt, die erforderlich sind, um erfolgreich leistungsstarke kundenspezifische Werkzeuge für Ihre Fertigungsanforderungen zu liefern.
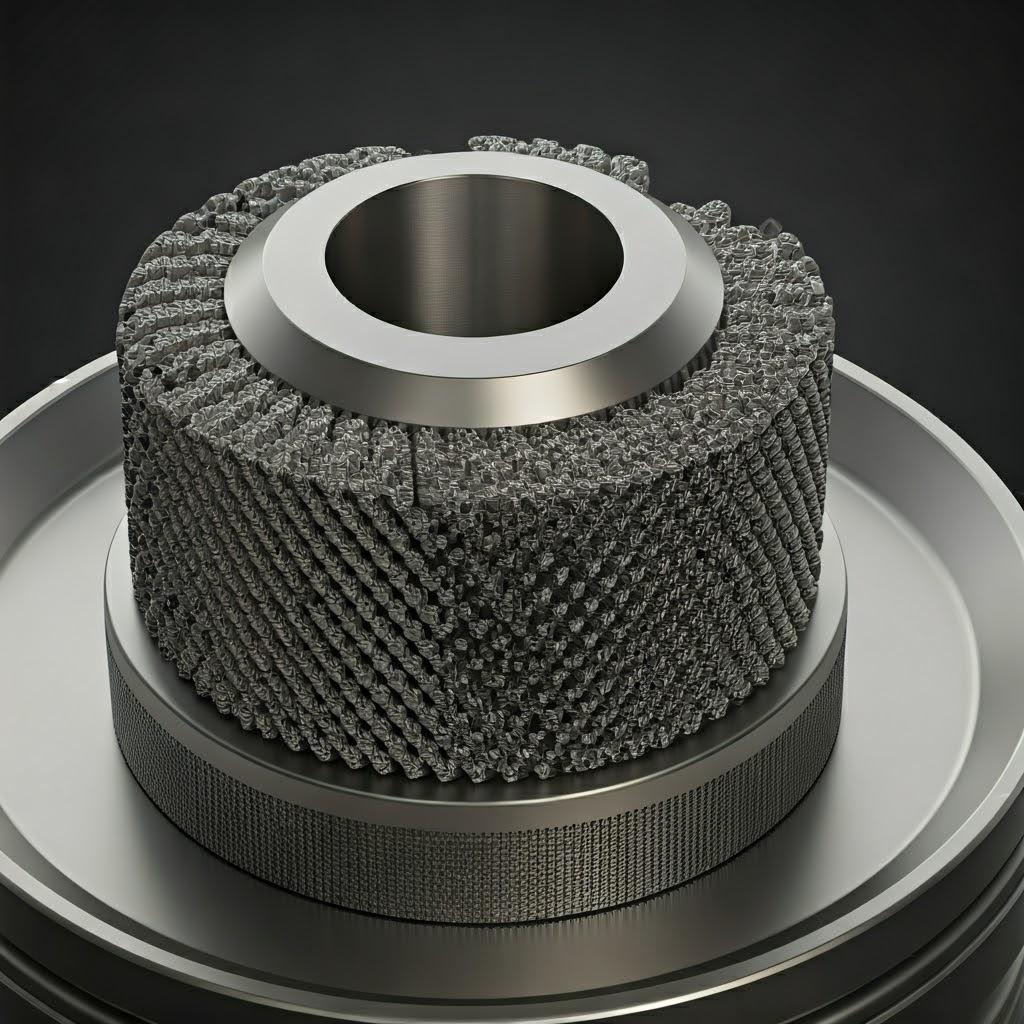
Kostenanalyse und Durchlaufzeit: Faktoren, die den Preis und die Vorlaufzeit für 3D-gedruckte Werkzeuge beeinflussen
Eine der drängendsten Fragen für Ingenieure und Beschaffungsmanager, die Metall-AM für kundenspezifische Werkzeuge in Betracht ziehen, dreht sich um Kosten und Vorlaufzeiten. Obwohl oft für Geschwindigkeit geworben wird, ist es wichtig, die Nuancen dessen zu verstehen, was die 3D-Druck: Kostenvoranschlag für Werkzeuge und Vorlaufzeit der additiven Fertigung ist entscheidend für eine genaue Projektplanung, Budgetierung und den Vergleich von AM mit traditionellen Methoden oder anderen Anbietern. Die Preisgestaltung ist nicht willkürlich, sondern wird durch eine Kombination aus Materialverbrauch, Maschinenzeit, Arbeitsaufwand und der Komplexität von Druck und Nachbearbeitung beeinflusst. In ähnlicher Weise ist die Vorlaufzeit mehr als nur die Druckdauer; sie umfasst den gesamten Arbeitsablauf von der Auftragserteilung bis zur endgültigen Lieferung.
Schlüsselfaktoren, die die Kosten beeinflussen:
- Materialart und Verbrauch:
- Pulverkosten: Die Rohstoffkosten variieren erheblich zwischen den verschiedenen Metallpulvern. Martensitaushärtende Stähle oder Speziallegierungen sind in der Regel teurer als Standardwerkzeugstähle wie H13 oder rostfreie Stähle.
- Teilband: Das tatsächliche Volumen des fertigen Teils wirkt sich direkt auf die Menge des verbrauchten Pulvers aus.
- Unterstützende Strukturen: Auch das für Stützstrukturen verwendete Material trägt zu den Kosten bei. Optimierte Entwürfe (DfAM), die die Anzahl der Stützen minimieren, können zu Einsparungen führen.
- Abfall: Da es sich bei AM um ein additives Verfahren handelt, entsteht bei der Handhabung, dem Druck und dem Recycling ein gewisser Pulverabfall.
- Geometrie, Größe und Komplexität der Teile:
- Bounding Box / Bauhöhe: Größere oder höhere Teile beanspruchen die Maschine für längere Zeit und verbrauchen mehr Material. Die Gesamtgröße im Verhältnis zum Bauvolumen der Maschine wirkt sich darauf aus, wie viele Teile in einem Bauvorgang verschachtelt werden können, was die Effizienz beeinträchtigt.
- Komplexität: Während AM die Komplexität gut handhaben kann, können sehr komplizierte Designs umfangreichere Stützstrukturen erfordern, was die Druckzeit und den Nachbearbeitungsaufwand für die Entfernung erhöhen kann. Merkmale wie komplexe interne konforme Kühlkanäle erhöhen den Zeitaufwand für Design und Überprüfung.
- Wanddicke/Dichte: Dickere Abschnitte benötigen mehr Zeit zum Drucken. Designs mit leichten Gitterstrukturen können den Materialverbrauch und die Druckzeit im Vergleich zu massiven Körpern reduzieren.
- Maschinenzeit (Drucken):
- Stundensatz: AM-Maschinen stellen eine beträchtliche Kapitalinvestition dar, und die Anbieter kalkulieren in der Regel einen Stundensatz ein, der Abschreibung, Energie, Wartung, Inertgas und Verbrauchsmaterial umfasst.
- Drucken Dauer: Bestimmt durch das Volumen des Teils, die Höhe, die Komplexität (Anzahl der zu scannenden Konturen), die gewählte Schichtdicke und die Scanstrategie. Längere Druckzeiten erhöhen direkt die Kosten.
- Nachbearbeitungsanforderungen: Dies ist oft ein Haupt Kostentreiber für die Werkzeugherstellung.
- Stressabbau und Wärmebehandlung: Ofenzeit, Energieverbrauch und Arbeitsaufwand. Komplexe Zyklen für Werkzeugstähle sind aufwendiger als die einfache Alterung von Maraging-Stählen.
- Unterstützung bei der Entfernung: Arbeitsintensiv, insbesondere bei komplexen Teilen oder schwer zugänglichen Halterungen. Der Einsatz spezieller Verfahren wie Drahterodieren verursacht zusätzliche Kosten.
- CNC-Bearbeitung: Erforderlich für kritische Toleranzen und Oberflächengüten. Die Kosten hängen vom Umfang der Bearbeitung, der Komplexität der Aufspannungen und der gewünschten Präzision ab. Die Bearbeitung von gehärtetem Werkzeugstahl ist langsamer und kostspieliger.
- Oberflächenveredelung: Das Strahlen ist relativ kostengünstig, aber das manuelle Polieren für hochwertige Formoberflächen kann sehr zeitaufwendig sein und erfordert qualifizierte Arbeitskräfte, was die Kosten erheblich erhöht. Das Beschichten verursacht weitere Kosten.
- Qualitätssicherung und Inspektion:
- Grundlegende QA: Standardmäßige Maßkontrollen und Sichtprüfungen sind in der Regel inbegriffen.
- Fortgeschrittene ZfP: Anforderungen wie CT-Scans zur Erkennung interner Porosität oder detaillierte CMM-Berichte zur Überprüfung der Abmessungen verursachen aufgrund der erforderlichen Ausrüstung und des Fachwissens erhebliche Kosten.
- Zertifizierungen: Für Projekte, die besondere Bescheinigungen oder umfangreiche Unterlagen erfordern, können zusätzliche Verwaltungskosten anfallen.
- Arbeit und Fachwissen:
- DfAM und technische Unterstützung: Beratungs- und Designoptimierungsdienste können separat oder gebündelt in Rechnung gestellt werden.
- Einrichtung und Betrieb der Maschine: Qualifizierte Techniker sind für die Vorbereitung von Anfertigungen, die Bedienung von Maschinen und die erste Reinigung von Teilen erforderlich.
- Nachbearbeitungsarbeiten: Wie bereits erwähnt, erfordern das Entfernen der Stützen, die Bearbeitung und das Polieren qualifizierte Arbeitskräfte.
- Auftragsvolumen und Dringlichkeit:
- Menge: Während die Einrichtungskosten im Vergleich zu herkömmlichen Werkzeugen relativ gering sind, können bei größeren Chargen (z. B. bei mehreren identischen Formeinsätzen) durch optimierte Verschachtelung und rationelle Nachbearbeitung Größenvorteile erzielt werden. Erkundigen Sie sich nach Großhandel mit 3D-Druckwerkzeugen Optionen, falls zutreffend.
- Eiliger Dienst: Für Eilaufträge, die eine Unterbrechung des Zeitplans oder eine spezielle Maschinenzeit erfordern, fallen in der Regel zusätzliche Kosten an.
Verständnis der Komponenten der Vorlaufzeit:
Die Vorlaufzeit ist die Gesamtdauer von der Auftragsbestätigung bis zur Auslieferung des endgültigen Teils. Sie umfasst:
- Angebotserstellung und Auftragsabwicklung: Überprüfung des Entwurfs, Bestätigung der Anforderungen, Erstellung eines Angebots (Stunden bis Tage).
- Zeit in der Warteschlange: Warten auf die Verfügbarkeit von Maschinen (kann je nach Rückstand des Anbieters erheblich variieren - möglicherweise Tage bis Wochen).
- Vorbereitung des Baus: Schneiden des Modells, Planung der Stützen, Vorbereitung der Maschine (Stunden).
- Druckzeit: Tatsächliche Maschinenlaufzeit (Stunden bis mehrere Tage, je nach Teilegröße/Komplexität).
- Abkühlzeit: Ausreichendes Abkühlen der Baukammer und des Bauteils vor dem Ausbau (Stunden).
- Nachbearbeiten:
- Stressabbau/Wärmebehandlung: Ofenzyklen (Stunden bis Tage, einschließlich Rampe/Weiche/Kühlung).
- Entfernen der Stützen und einfache Nachbearbeitung: (Stunden bis Tage).
- Bearbeitung: (Stunden bis Tage, je nach Komplexität und Werkstattplanung).
- Polieren/Beschichten: (Stunden bis Tage oder sogar Wochen bei komplexen Formen).
- Qualitätsinspektion: (Stunden bis Tage).
- Versand: (Tage, je nach Ort und Methode).
Typischer Turnaround: Für mäßig komplexe Metall-AM-Werkzeuge, die eine Standard-Nachbearbeitung (Spannungsabbau, Wärmebehandlung, Grundbearbeitung) erfordern, liegen die Vorlaufzeiten oft zwischen 1 bis 4 Wochen. Bei hochkomplexen Werkzeugen, Werkzeugen, die eine umfangreiche Politur erfordern (z. B. Spritzgussformen), oder bei Aufträgen, die während der Spitzenauslastungszeiten erteilt werden, können die Fristen jedoch länger sein. Erkundigen Sie sich bei Ihrem Anbieter immer nach den Vorlaufzeiten für Ihr spezifisches Projekt. Erkunden Sie die verschiedenen Anwendungen und Prozesse innerhalb der 3D-Druck von Metall kann weitere Informationen zu den Zeitplänen liefern.
Durch das Verständnis der Faktoren, die die Metall-AM-Preisfaktoren und die verschiedenen Stadien, die zum Gesamtergebnis beitragen Vorlaufzeit der additiven Fertigungkönnen Hersteller Projekte besser planen, Budgets verwalten und realistische Erwartungen festlegen, wenn sie 3D-gedruckte kundenspezifische Werkzeuge in ihre Produktionsabläufe integrieren. Eine transparente Kommunikation mit Ihrem AM-Partner ist der Schlüssel zur erfolgreichen Bewältigung dieser Aspekte.
Häufig gestellte Fragen (FAQ) über 3D-gedruckte kundenspezifische Werkzeuge aus Metall
Da die additive Fertigung von Metallen für Werkzeuganwendungen zunehmend an Bedeutung gewinnt, haben Ingenieure, Konstrukteure und Beschaffungsspezialisten häufig Fragen zu den Möglichkeiten, Grenzen und praktischen Auswirkungen. Hier finden Sie Antworten auf einige häufig gestellte Fragen zu 3D-gedruckte Werkzeuge FAQ:
1. Wie sieht es mit der Haltbarkeit und Lebensdauer von 3D-gedruckten Werkzeugen im Vergleich zu traditionell hergestellten Werkzeugen aus?
Dies ist eine kritische Frage, deren Antwort stark von mehreren Faktoren abhängt: Materialauswahl, Druckqualität (Dichte), Designoptimierung (DfAM) und ordnungsgemäße Nachbearbeitung (insbesondere Wärmebehandlung).
- Materielle Äquivalenz: Bei der Verwendung gleichwertiger Werkstoffe (z. B. gedruckter H13-Werkzeugstahl im Vergleich zu H13-Knetstahl) und dem Erreichen einer hohen Dichte (>99,5%) bei ordnungsgemäßer Wärmebehandlung können die mechanischen Kerneigenschaften (Härte, Festigkeit) des AM-Werkzeugs vergleichbar und manchmal sogar etwas besser sein, da bei AM häufig ein feinkörniges Gefüge erreicht wird.
- Leistungsverbesserungen: Metal AM bietet einzigartige Vorteile, die erweitern. Lebensdauer der Werkzeuge über die traditionellen Möglichkeiten hinaus. Das Wichtigste ist konforme Kühlung in Formen und Gesenken. Durch eine effizientere und gleichmäßigere Wärmeabfuhr reduziert die konforme Kühlung die thermische Belastung, minimiert den mit hohen Temperaturen verbundenen Verschleiß und kann zu einer deutlich längeren Werkzeuglebensdauer bei anspruchsvollen Zyklusanwendungen führen.
- Potenzielle Herausforderungen: Wird der AM-Prozess nicht ordnungsgemäß kontrolliert, können interne Defekte wie Porosität oder fehlende Verschmelzung als Ausgangspunkt für Risse dienen, was die Ermüdungslebensdauer im Vergleich zu fehlerfreiem Knetmaterial verringern kann. Eigenspannungen können sich ebenfalls negativ auf die Haltbarkeit auswirken, wenn sie nicht angemessen abgebaut werden. Auch die Oberflächenbeschaffenheit kann sich auf die Verschleißeigenschaften auswirken, wenn sie nicht entsprechend der Anwendung nachbearbeitet wird.
- Schlussfolgerung: Richtig konstruierte, gedruckte (hohe Dichte) und nachbearbeitete (korrekte Wärmebehandlung und Nachbearbeitung) AM-Werkzeuge aus Metall, insbesondere wenn sie einzigartige AM-Vorteile wie die konforme Kühlung nutzen, können in vielen Anwendungen die Lebensdauer herkömmlicher Werkzeuge erreichen oder sogar übertreffen. Um dies zu erreichen, sind jedoch Fachwissen und eine strenge Prozesskontrolle durch den AM-Anbieter erforderlich. Dabei geht es weniger um den Prozess selbst als vielmehr darum, die erforderliche Materialintegrität und die endgültigen Eigenschaften zu erreichen. Beratung Fragen zum Metall-AM-Werkzeugbau mit erfahrenen Anbietern wie Met3dp wird empfohlen.
2. Ist der 3D-Druck von Metall für die Herstellung von Großserienwerkzeugen kosteneffizient?
Im Allgemeinen findet Metall-AM seinen "Sweet Spot" in Anwendungen, bei denen die einzigartigen Vorteile die potenziell höheren Kosten überwiegen. pro Teil Druckkosten im Vergleich zu hoch optimierten traditionellen Methoden für sehr einfachWerkzeuge mit hohem Durchsatz.
- AM-Stärken: Der 3D-Druck von Metall ist in der Regel am kosteneffektivsten für:
- Prototypen und Brückenkonstruktionen: Schnelle Herstellung von Funktionswerkzeugen für Tests oder erste Kleinserien, während die konventionellen Hartwerkzeuge hergestellt werden.
- Komplexe Geometrien: Werkzeuge mit komplizierten Merkmalen, die auf herkömmliche Weise sehr schwierig oder teuer zu bearbeiten sind. AM-Komplexität ist mit geringen bis keinen zusätzlichen Kosten verbunden.
- Konforme Kühlung: Die Leistungsvorteile (Verkürzung der Zykluszeit, Qualitätsverbesserung) rechtfertigen häufig die Investition in AM für Formen und Werkzeuge, selbst bei moderaten Stückzahlen, wenn man die Gesamtbetriebskosten (TCO) betrachtet.
- Kundenspezifische Werkzeuge/Kleinserienfertigung: Vorrichtungen oder Spezialwerkzeuge, die in kleinen Mengen benötigt werden und bei denen die herkömmlichen Einrichtungskosten unerschwinglich sind.
- Reparatur/Änderung von Werkzeugen: AM kann manchmal dazu verwendet werden, verschlissene oder beschädigte Werkzeuge zu reparieren oder Merkmale hinzuzufügen.
- Traditionelle Stärken: Für einfache Werkzeuggeometrien, die in sehr hohen Stückzahlen benötigt werden (z. B. Tausende von identischen einfachen Einsätzen), können herkömmliche Methoden wie die CNC-Bearbeitung aus Lagermaterial aufgrund der etablierten Infrastruktur und der Größenvorteile immer noch einen niedrigeren Stückpreis bieten.
- Die Landschaft entwickelt sich weiter: Da die AM-Technologie immer ausgereifter wird, die Druckgeschwindigkeiten steigen, die Maschinenkosten sinken und die Automatisierung zunimmt, verbessert sich die Kosteneffizienz von AM kontinuierlich und dehnt sich auf Anwendungen mit höheren Stückzahlen aus.
- Schlussfolgerung: Auch wenn sie normalerweise nicht die erste Wahl für extrem Metall-AM bietet eine überzeugende Kosteneffizienz für Prototypen, komplexe Designs, leistungskritische Werkzeuge (konforme Kühlung) und die Produktion von kleinen bis mittleren Stückzahlen, wenn man die TCO, die Markteinführungszeit und die Designfreiheit berücksichtigt. Bewerten Sie die Kosten für 3D-gedruckte Gussformen oder Vorrichtungen auf der Grundlage der Werttreiber der jeweiligen Anwendung.
3. Welche Angaben muss ich machen, um ein genaues Angebot für ein 3D-gedrucktes Werkzeug zu erhalten?
Um von einem Metall-AM-Dienstleister wie Met3dp ein rechtzeitiges und genaues Angebot zu erhalten, ist die Bereitstellung umfassender Informationen im Vorfeld unerlässlich. Fehlende Details können zu Verzögerungen oder ungenauen Preisen führen. Zu den wichtigsten Informationen gehören:
- CAD-Modell: Ein 3D-CAD-Modell in einem neutralen Standardformat (z. B. STEP (.stp/.step), Parasolid (.x_t)) ist zwingend erforderlich. Vermeiden Sie nach Möglichkeit Netzdateien (z. B. STL) für erste Angebote, es sei denn, dies wird ausdrücklich verlangt, da Volumenmodelle genauere geometrische Informationen enthalten.
- Spezifikation des Materials: Geben Sie eindeutig die gewünschte Metalllegierung an (z. B. H13 Werkzeugstahl, Maraging-Stahl M300/1.2709, Edelstahl 17-4PH). Wenn Sie unsicher sind, beschreiben Sie die Anforderungen der Anwendung (Härte, Temperaturbeständigkeit, Verschleißanforderungen), damit der Anbieter einen geeigneten Werkstoff empfehlen kann.
- Kritische Abmessungen und Toleranzen: Geben Sie eindeutig (z. B. auf einer 2D-Zeichnung, die dem 3D-Modell beigefügt ist) alle kritischen Maße und ihre erforderlichen Toleranzen an. Geben Sie an, ob diese Toleranzen im eingebauten Zustand gelten oder nachbearbeitet werden müssen.
- Anforderungen an die Oberflächenbeschaffenheit: Geben Sie die erforderliche Oberflächenrauhigkeit (z. B. Ra-Wert) für kritische Oberflächen (z. B. Formhohlraum, Kontaktpunkte der Vorrichtung) und unkritische Oberflächen an. Geben Sie an, ob spezielle Endbearbeitungsverfahren wie Polieren oder Strahlen erforderlich sind.
- Nachbearbeitungsanforderungen: Geben Sie alle vorgeschriebenen Wärmebehandlungen (einschließlich des angestrebten Härtebereichs, z. B. HRC 48-52 für H13), Spannungsabbauzyklen oder spezielle Bearbeitungsvorgänge an, die über das Erreichen von Toleranzen hinausgehen (z. B. Gewindeschneiden, Endschleifen).
- Beschreibung der Anwendung: Erläutern Sie kurz die Funktion des Werkzeugs (z. B. Spritzgusseinsatz für ABS-Kunststoff, Montagevorrichtung für Automobilteile, Stanzwerkzeug für Aluminiumblech) und die Betriebsbedingungen (Temperatur, Belastung, erwartete Lebensdauer). Dieser Kontext hilft dem Anbieter, die Anforderungen besser zu verstehen.
- Menge: Geben Sie die Anzahl der benötigten gleichen oder ähnlichen Teile an.
- Anforderungen an die Vorlaufzeit: Geben Sie an, ob es bestimmte Lieferfristen gibt.
- Vertraulichkeit: Wenn es sich um einen sensiblen Entwurf handelt, sollten Sie vor der Weitergabe von Dateien eine Geheimhaltungsvereinbarung (NDA) abschließen.
Die Bereitstellung dieser Details ermöglicht es dem AM-Dienstleister, die Druckbarkeit, die Komplexität, den Materialverbrauch, die erforderliche Nachbearbeitung und die damit verbundenen Kosten und Vorlaufzeiten genau zu beurteilen, was zu einem zuverlässigen Angebot für Ihre Langlebigkeit von kundenspezifischen Werkzeugen und Produktionsanforderungen.
Schlussfolgerung: Die Zukunft der effizienten Fertigung wird mit 3D-gedruckten kundenspezifischen Werkzeugen geschmiedet
Die Landschaft der kundenspezifischen Werkzeugherstellung unterliegt einem bedeutenden Wandel, der durch die Möglichkeiten der additiven Fertigung von Metall vorangetrieben wird. Wie wir erforscht haben, bietet der 3D-Druck von Metallen über die Grenzen der traditionellen subtraktiven Methoden hinaus eine leistungsstarke Kombination aus Geschwindigkeit, geometrische Komplexität und Leistungsverbesserung die direkt auf kritische Herausforderungen in der Fertigung eingehen. Von der schnellen Herstellung komplizierter Vorrichtungen bis hin zur Erstellung von Hochleistungs-Spritzgießformen mit integrierter konforme Kühlkanäledie Vorteile von 3D-gedruckten Werkzeugen sind in verschiedenen Branchen wie der Luft- und Raumfahrt, der Automobilindustrie, der Medizintechnik und der allgemeinen Fertigung greifbar und wirkungsvoll.
Die Möglichkeit, die Vorlaufzeiten von Monaten auf Wochen oder Tage zu verkürzen, beschleunigt die Produktentwicklungszyklen und ermöglicht eine noch nie dagewesene Flexibilität bei der Reaktion auf Marktanforderungen. Die Designfreiheit, die AM mit sich bringt, ermöglicht es den Ingenieuren, funktionsoptimierte Werkzeuge zu entwickeln, die leicht und ergonomisch sind und komplexe interne Strukturen wie eine konforme Kühlung aufweisen, die die Produktivität und die Qualität des Endprodukts drastisch erhöhen. Die Verwendung von Hochleistungswerkstoffen wie H13-Werkzeugstahl und Maraging-Stahl M300/1.2709 stellt sicher, dass diese Vorteile nicht auf Kosten der Haltbarkeit oder Langlebigkeit gehen, vorausgesetzt, die Grundsätze des Design for Additive Manufacturing (DfAM) werden beachtet und strenge Nachbearbeitungsschritte, insbesondere Wärmebehandlung und Endbearbeitung, werden korrekt umgesetzt.
Um das volle Potenzial dieser Technologie auszuschöpfen, muss man sich jedoch mit ihren Feinheiten vertraut machen, z. B. mit Toleranzen, Oberflächenbeschaffenheit, potenziellen Problemen wie Eigenspannungen und der entscheidenden Bedeutung der Nachbearbeitung. Der Erfolg hängt nicht nur von der Technologie selbst ab, sondern auch von der Wahl des richtigen Partners. Ein idealer Metall-3D-Druck-Dienstleistung B2B Anbieter bietet mehr als nur Druckkapazitäten; er verfügt über Fachwissen in der Materialwissenschaft, DfAM-Beratung, robuste Prozesskontrollen, umfassende interne Nachbearbeitungsmöglichkeiten und eine starke Verpflichtung zur Qualitätssicherung.
Met3dp ist ein Beispiel für einen solchen Partner. Als führendes Unternehmen im Bereich Metall-AM mit Hauptsitz in Qingdao, China, bieten wir umfassende Lösungen mit branchenführenden SEBM-Druckern, die bekannt sind für Genauigkeit und ZuverlässigkeitWir bieten hochentwickelte Metallpulver, die im eigenen Haus mit modernsten Zerstäubungstechniken hergestellt werden, und umfassende Erfahrung in der Anwendungsentwicklung. Wir arbeiten mit Unternehmen auf der ganzen Welt zusammen, um Folgendes zu implementieren 3D-Druck von Metall effektiv zu nutzen, die Umstellung auf die digitale Fertigung zu beschleunigen und die Produktion von Werkzeugen der nächsten Generation zu ermöglichen.
Die Zukunft einer effizienten, agilen und leistungsstarken Fertigung ist untrennbar mit den Fortschritten in der additiven Fertigung verbunden. Für den kundenspezifischen Werkzeugbau ist der 3D-Metalldruck nicht länger eine Nischenneuheit, sondern eine strategische Fähigkeit, die es den Herstellern ermöglicht, schneller zu innovieren, Kosten zu senken, die Qualität zu verbessern und einen bedeutenden Wettbewerbsvorteil zu erlangen. Indem sie sich diese Technologie zu eigen machen und mit kompetenten Partnern wie Met3dp zusammenarbeiten, können Unternehmen Werkzeuglösungen entwickeln, die neue Produktivitätsniveaus erschließen und die Fertigung optimieren.
Sind Sie bereit, Ihre Strategie für kundenspezifische Werkzeuge zu revolutionieren? Kontaktieren Sie Met3dp noch heute um zu erfahren, wie unsere hochmodernen Systeme, fortschrittlichen Metallpulver und unser umfassendes Fachwissen die Ziele Ihres Unternehmens im Bereich der additiven Fertigung unterstützen können.
Teilen auf
MET3DP Technology Co., LTD ist ein führender Anbieter von additiven Fertigungslösungen mit Hauptsitz in Qingdao, China. Unser Unternehmen ist spezialisiert auf 3D-Druckgeräte und Hochleistungsmetallpulver für industrielle Anwendungen.
Fragen Sie an, um den besten Preis und eine maßgeschneiderte Lösung für Ihr Unternehmen zu erhalten!
Verwandte Artikel
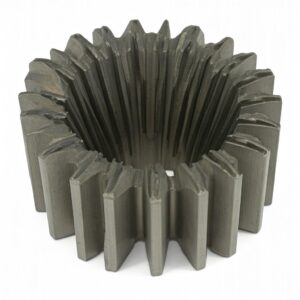
Hochleistungs-Düsenschaufelsegmente: Revolutionierung der Turbineneffizienz mit 3D-Metalldruck
Mehr lesen "Über Met3DP
Aktuelles Update
Unser Produkt
KONTAKT US
Haben Sie Fragen? Senden Sie uns jetzt eine Nachricht! Wir werden Ihre Anfrage mit einem ganzen Team nach Erhalt Ihrer Nachricht bearbeiten.
Holen Sie sich Metal3DP's
Produkt-Broschüre
Erhalten Sie die neuesten Produkte und Preislisten
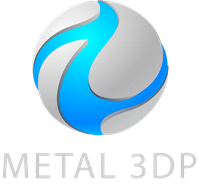
Metallpulver für 3D-Druck und additive Fertigung