3D-gedruckte Wärmetauscher für die Automobil- und Luftfahrtindustrie
Inhaltsübersicht
Revolutionierung des Wärmemanagements: 3D-gedruckte Wärmetauscher für die Automobil- und Luftfahrtindustrie
Das unablässige Streben nach höherer Leistung, größerer Effizienz und geringerem Gewicht in der Automobil- und Luftfahrtbranche stellt immense Anforderungen an Wärmemanagementsysteme. Wärmetauscher, die unbesungenen Helden, die für die Übertragung von Wärmeenergie zwischen Flüssigkeiten oder zwischen einer festen Oberfläche und einer Flüssigkeit verantwortlich sind, sind entscheidende Komponenten in Motoren, Leistungselektronik, Umweltkontrollsystemen und Hilfstriebwerken. Traditionell war die Herstellung dieser komplizierten Geräte mit komplexen Verfahren wie Löten, Schweißen und dem Zusammenbau mehrerer Teile verbunden, was oft die Designmöglichkeiten einschränkte und das Gewicht erhöhte. Doch das Aufkommen von 3D-Druck von Metallauch bekannt als additive Fertigung (AM), verändert grundlegend die Art und Weise, wie Wärmetauscher entworfen, produziert und optimiert werden. Durch den schichtweisen Aufbau von Teilen direkt aus Metallpulver eröffnet AM eine noch nie dagewesene Designfreiheit und ermöglicht die Herstellung hochkomplexer, leichter und effizienter Wärmetauscher, die bisher nicht hergestellt werden konnten. Dieser technologische Wandel bietet Ingenieuren und Beschaffungsmanagern, die nach innovativen Lösungen für anspruchsvolle thermische Herausforderungen in anspruchsvollen Branchen wie der Automobil- und Luftfahrtindustrie suchen, erhebliche Vorteile und ebnet den Weg für die nächste Generation von Fahrzeug- und Flugzeugdesigns. Unternehmen, die sich auf hochentwickelte Metallpulver und Drucksysteme spezialisiert haben, wie Met3dp, stehen an vorderster Front und bieten die Materialien und das Fachwissen, die erforderlich sind, um das volle Potenzial von AM für Wärmemanagementanwendungen zu nutzen.
Die kritische Rolle von Wärmetauschern in Automobil- und Luftfahrtsystemen
Wärmetauscher sind unverzichtbare Komponenten, die für die Aufrechterhaltung optimaler Betriebstemperaturen in einer Vielzahl von Systemen in Fahrzeugen und Flugzeugen eine entscheidende Rolle spielen. Ihre Hauptfunktion besteht darin, eine effiziente Wärmeübertragung zu ermöglichen, indem sie entweder überschüssige Wärme abführen, um eine Überhitzung zu verhindern, oder die Wärme dorthin leiten, wo sie für eine optimale Leistung benötigt wird. Der Ausfall oder die Ineffizienz eines Wärmetauschers kann zu Leistungseinbußen, Bauteilschäden, Sicherheitsrisiken und sogar zu einem katastrophalen Systemausfall führen. Das Verständnis ihrer spezifischen Rolle unterstreicht ihre Bedeutung:
Automobilanwendungen:
- Motorkühlung (Kühler): Die wohl bekannteste Anwendung: Kühler leiten die Wärme des Kühlmittels an die Umgebungsluft ab und verhindern so eine Überhitzung des Motors.
- Ölkühler: Durch die Kühlung des Öls wird die optimale Viskosität des Motor- oder Getriebeöls aufrechterhalten, was eine ordnungsgemäße Schmierung und Langlebigkeit der Komponenten gewährleistet.
- Ladeluftkühler (Intercooler): Kühlen Sie die komprimierte Luft, die von einem Turbolader oder Kompressor kommt, bevor sie in die Motorzylinder gelangt. Mit kühlerer, dichterer Luft kann mehr Kraftstoff verbrannt werden, was die Leistung und den Wirkungsgrad erhöht.
- Kühler für die Abgasrückführung (EGR): Kühlt die Abgase, bevor sie in die Motorzylinder zurückgeführt werden, um die NOx-Emissionen zu verringern.
- HVAC-Systeme (Verdampfer und Verflüssiger): Erleichterung des für Klimaanlagen (Kühlung der Kabinenluft) und Heizungssysteme erforderlichen Wärmeaustauschs.
- Thermomanagement von Batterien (Elektro- und Hybridfahrzeuge): Entscheidend für die Aufrechterhaltung optimaler Temperaturbereiche für Leistung, Sicherheit und Lebensdauer der Batterien. Dazu gehört die Kühlung von Batterien bei schneller Aufladung oder starker Entladung und die mögliche Erwärmung bei Kälte.
- Kühlung der Leistungselektronik: Ableitung der von Wechselrichtern, Umrichtern und Onboard-Ladegeräten erzeugten Wärme, die für den Betrieb von EV/HEVs entscheidend ist.
Luft- und Raumfahrtanwendungen:
- Entlüftung der Motorkühlung (Vorkühler): Kühle heiße Luft, die aus den Kompressorstufen der Triebwerke entweicht, bevor sie für die Druckbeaufschlagung der Kabine, die Enteisung und andere Systeme an Bord verwendet wird.
- Umweltkontrollsysteme (ECS-Pakete): Komplexe Systeme mit mehreren Wärmetauschern (Kondensatoren, Verdampfer, Zwischenüberhitzer) zur Bereitstellung konditionierter Luft (Temperatur, Druck, Feuchtigkeit) für die Kabine und das Cockpit.
- Kraftstoffgekühlte Ölkühler (FCOC): Verwenden Sie kalten Kraftstoff, um das Motor- oder Getriebeschmieröl zu kühlen, und heizen Sie gleichzeitig den Kraftstoff vor, um eine bessere Verbrennung zu erreichen.
- Kühlung der Hydraulikflüssigkeit: Aufrechterhaltung der optimalen Betriebstemperatur von Hydrauliksystemen, die für die Flugsteuerung, das Fahrwerk und andere Aktuatoren unerlässlich sind.
- Kühlung von Avionik und Elektronik: Ableitung von Wärme, die von empfindlichen elektronischen Geräten (Radar, Kommunikationssysteme, Flugcomputer) erzeugt wird, die oft auf engem Raum untergebracht sind, und Gewährleistung der Zuverlässigkeit.
- Kühlung der Hilfsturbine (Auxiliary Power Unit, APU): Bewältigung der von der APU erzeugten Wärme, die den Strom am Boden und den Notstrom im Flug liefert.
- Thermomanagement für den Hyperschallflug: Extreme Temperaturen erfordern hochentwickelte Wärmetauscher, die in die Fahrzeugstruktur oder das Antriebssystem integriert sind.
Gemeinsame Anforderungen für beide Branchen:
- Hoher thermischer Wirkungsgrad: Maximale Wärmeübertragung innerhalb der vorgegebenen Volumen-/Gewichtsbeschränkungen.
- Geringes Gewicht: Besonders kritisch ist dies in der Luft- und Raumfahrt, aber auch in der Automobilindustrie wird es immer wichtiger, um Kraftstoff zu sparen und Leistung zu erzielen.
- Kompakte Größe: Einbau komplexer thermischer Lösungen in eng gepackte Triebwerksschächte oder Flugzeugstrukturen.
- Langlebigkeit und Verlässlichkeit: Widersteht Vibrationen, Temperaturschwankungen, Druckschwankungen und potenziell korrosiven Flüssigkeiten.
- Auslaufsicherer Betrieb: Unerlässlich für die Aufnahme von Kühlmitteln, Kraftstoffen, Ölen oder Kältemitteln.
Die zunehmende Komplexität und Leistungsdichte moderner Systeme in der Automobil- und Luft- und Raumfahrt stößt immer wieder an die Grenzen der traditionellen Wärmetauscher-Konstruktion und -Herstellung. Genau hier bietet die additive Fertigung von Metallen ein transformatives Potenzial.
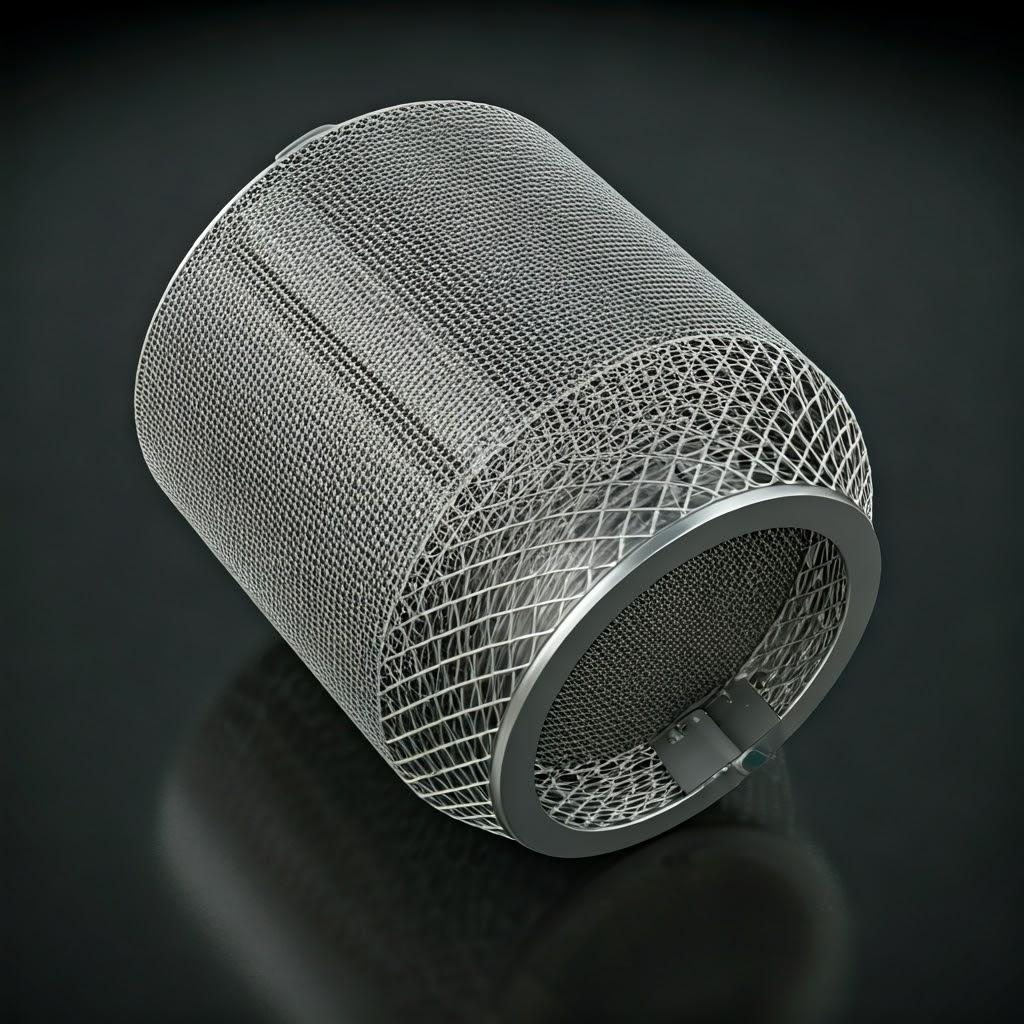
Warum sollte man sich bei der Produktion von Wärmetauschern für die additive Fertigung von Metall entscheiden?
Herkömmliche Fertigungsmethoden wie Umformen, Löten, Gießen und maschinelle Bearbeitung haben sich in der Branche zwar bewährt, begrenzen jedoch die geometrische Komplexität und die Integration, die bei der Konstruktion von Wärmetauschern erreicht werden kann. Die additive Fertigung von Metallen überwindet viele dieser Einschränkungen und bietet überzeugende Vorteile für die Herstellung von Wärmemanagementlösungen der nächsten Generation:
- Unerreichte Gestaltungsfreiheit: AM ermöglicht die Herstellung hochkomplexer innerer und äußerer Geometrien, die auf konventionellem Wege nicht oder nur mit unverhältnismäßig hohen Kosten hergestellt werden können. Dies schließt ein:
- Optimierte Flusspfade: Entwurf komplizierter, nichtlinearer Kanäle, die den Druckabfall minimieren und gleichzeitig die Flüssigkeitsturbulenz und den Oberflächenkontakt für eine verbesserte Wärmeübertragung maximieren.
- Integrierte Funktionen: Kombination mehrerer Komponenten (z. B. Verteiler, Montagehalterungen, Sensoranschlüsse) in einem einzigen gedruckten Teil, wodurch Montageschritte, potenzielle Leckstellen und das Gesamtgewicht reduziert werden.
- Konforme Kühlkanäle: Kanäle, die den Konturen der Wärmequelle genau folgen, um eine effektivere Kühlung zu gewährleisten.
- Fortgeschrittene Oberflächenstrukturen: Interne Merkmale wie dreifach periodische minimale Oberflächen (TPMS), Gitterstrukturen oder komplexe Rippengeometrien werden direkt in das Design integriert, um das Verhältnis von Oberfläche zu Volumen drastisch zu erhöhen und die thermische Leistung bei kompakter Grundfläche zu steigern.
- Gewichtsreduzierung: AM ermöglicht die Schaffung topologisch optimierter Strukturen und die Verwendung interner Gitter, wodurch der Materialverbrauch und das Gewicht der Komponenten erheblich reduziert werden können, ohne die strukturelle Integrität oder die thermische Leistung zu beeinträchtigen. Dies ist ein entscheidender Vorteil in der Luft- und Raumfahrt, wo jedes eingesparte Gramm zur Treibstoffeffizienz oder zur Erhöhung der Nutzlast beiträgt, und wird auch in der Automobilindustrie immer wichtiger, um den Treibstoffverbrauch, die Fahrzeugdynamik und die Reichweite von Elektrofahrzeugen zu verbessern.
- Teil Konsolidierung: Durch das Drucken komplexer Baugruppen als ein einziges monolithisches Teil entfallen bei AM mehrere Fertigungsschritte (Bearbeitung, Löten, Schweißen) und die dazugehörigen Werkzeuge. Dies vereinfacht die Lieferkette, reduziert die Montagezeit und die Arbeitskosten und minimiert potenzielle Fehlerquellen (z. B. Lötstellen).
- Rapid Prototyping und Iteration: Mit AM können Konstrukteure schnell funktionale Prototypen von Wärmetauschern herstellen und testen. Designänderungen können digital umgesetzt und innerhalb von Tagen statt Wochen oder Monaten nachgedruckt werden, was den Entwicklungszyklus beschleunigt und eine schnellere Optimierung ermöglicht.
- Materialvielfalt: AM-Prozesse können mit einer wachsenden Anzahl von Hochleistungsmetalllegierungen arbeiten, die speziell für die anspruchsvollen thermischen und strukturellen Anforderungen in der Automobil- und Luftfahrtindustrie geeignet sind, einschließlich leichter Aluminiumlegierungen, hochleitfähiger Kupferlegierungen und hochfester, temperaturbeständiger Superlegierungen.
- Personalisierung und Kleinserienproduktion: AM ist wirtschaftlich rentabel für die Herstellung kundenspezifischer Wärmetauscher oder kleiner Serien ohne die hohen Werkzeugkosten, die bei herkömmlichen Verfahren anfallen. Dies ist ideal für Spezialfahrzeuge, Motorsportanwendungen, Entwicklungsprogramme in der Luft- und Raumfahrt oder Ersatzteile für ältere Systeme.
Vergleich: Traditionelle vs. Additive Fertigung für Wärmetauscher
Merkmal | Traditionelle Fertigung (z. B. gelötete Platten) | Additive Fertigung von Metallen (z. B. LPBF) |
---|---|---|
Gestaltungsfreiheit | Begrenzt durch Umformung, Stanzen, Löten Beschränkungen | Hoch; komplexe Kanäle, TPMS, integrierte Funktionen |
Geometrie | Hauptsächlich lineare Kanäle, gestapelte Platten/Finnen | Komplexe, konforme, bio-inspirierte Geometrien möglich |
Gewicht | Oft schwerer durch Montage, weniger Optimierung | Potenzial für eine erhebliche Gewichtsreduzierung durch Topologieoptimierung, Gitternetze |
Anzahl der Teile | Hoch (mehrere Platten, Rippen, Krümmer, Tanks) | Gering (oft als ein einziges monolithisches Teil gedruckt) |
Montage | Komplexe Löt-/Schweißarbeiten erforderlich | Minimale oder keine Montage erforderlich |
Mögliche Lecks | Verbindungen (gelötete/geschweißte Nähte) sind Schwachstellen | Reduzierte Leckagepfade (monolithische Struktur) |
Werkzeugkosten | Hoch (Werkzeuge, Vorrichtungen, Halterungen) | Niedrig/Keine (digitale Fertigung) |
Vorlaufzeit (Proto) | Wochen/Monate | Tage/Wochen |
Ideales Volumen | Hohe Produktionsmengen | Prototypen, geringe bis mittlere Stückzahlen, kundenspezifische Anpassung |
Materielle Verwendung | Potenziell weniger effizient | Optimierte Materialverteilung |
In Blätter exportieren
AM bietet zwar erhebliche Vorteile, aber es ist wichtig zu wissen, dass herkömmliche Methoden für die Produktion von sehr hohen Stückzahlen bei einfacheren Designs kosteneffektiv bleiben. Für Anwendungen, die maximale Leistung, minimales Gewicht und kompakte Abmessungen erfordern - Eigenschaften, die in der Automobil- und Luft- und Raumfahrtindustrie sehr gefragt sind -, ist Metall 3D-Druck stellt eine überlegene und oft ermöglichende Technologie dar.
Empfohlene Metallpulver für 3D-gedruckte Wärmetauscher: AlSi10Mg, CuCrZr, IN625
Die Wahl des Materials ist von grundlegender Bedeutung für die Leistung und Zuverlässigkeit eines 3D-gedruckten Wärmetauschers. Die Betriebsumgebung (Temperatur, Druck, Flüssigkeitstyp) und die Leistungsanforderungen (Wärmeleitfähigkeit, Festigkeit, Korrosionsbeständigkeit) bestimmen das optimale Metallpulver. Für Anwendungen in der Automobil- und Luft- und Raumfahrtindustrie bieten sich mehrere Legierungen an, die von spezialisierten Pulverherstellern wie Met3dp in hoher Qualität und Konsistenz angeboten werden und fortschrittliche Zerstäubungstechniken nutzen.
1. Aluminiumlegierung (AlSi10Mg): Das leichte Arbeitspferd
- Wichtige Eigenschaften:
- Hervorragende Wärmeleitfähigkeit (im Verhältnis zu seinem Gewicht)
- Geringe Dichte (leicht)
- Gutes Verhältnis zwischen Stärke und Gewicht
- Gute Korrosionsbeständigkeit
- Hervorragende Bedruckbarkeit durch Laser Powder Bed Fusion (LPBF)
- Warum es für Wärmetauscher wichtig ist: AlSi10Mg ist oft die erste Wahl, wenn es darum geht, Gewicht zu sparen, ohne zu große Kompromisse bei der thermischen Leistung einzugehen. Seine gute Druckbarkeit ermöglicht die Herstellung sehr komplexer und dünnwandiger Strukturen, die in modernen Wärmetauscherkonstruktionen üblich sind.
- Typische Anwendungen: Automobilkühler, Ladeluftkühler, Ölkühler, HVAC-Komponenten, Elektronikkühlung, ECS-Komponenten für die Luft- und Raumfahrt, wo die Betriebstemperaturen moderat sind.
- Erwägungen: Niedrigerer Schmelzpunkt und geringere Festigkeit im Vergleich zu Stahl oder Superlegierungen, was den Einsatz bei sehr hohen Temperaturen einschränkt.
2. Kupferlegierung (CuCrZr): Der Wärmeleitfähigkeits-Champion
- Wichtige Eigenschaften:
- Hervorragende elektrische und thermische Leitfähigkeit (ähnlich wie reines Kupfer)
- Gute Festigkeit und Härte (ausscheidungshärtbar)
- Gute Hochtemperaturbeständigkeit (im Vergleich zu reinem Kupfer)
- Gute Verschleißfestigkeit
- Warum es für Wärmetauscher wichtig ist: Wenn es auf maximale thermische Leistung ankommt, werden Kupferlegierungen aufgrund ihrer überlegenen Fähigkeit zur Wärmeübertragung häufig bevorzugt. CuCrZr bietet ein gutes Gleichgewicht zwischen hoher Leitfähigkeit und verbesserten mechanischen Eigenschaften im Vergleich zu reinem Kupfer und ist daher für anspruchsvolle Anwendungen geeignet.
- Typische Anwendungen: Hochleistungskühlkörper, Elektronikkühlung, die eine maximale Wärmeableitung erfordert, Induktionsspulen, Komponenten für Wärmemanagementsysteme in der Luft- und Raumfahrt, bei denen extreme Wärmeströme auftreten, Hochleistungs-Kühllösungen für die Automobilindustrie.
- Erwägungen: Höhere Dichte als Aluminium, aufgrund der hohen Reflektivität und Leitfähigkeit schwieriger über LPBF zuverlässig zu drucken (erfordert optimierte Prozessparameter), höhere Materialkosten.
3. Nickel-Superlegierung (IN625): Der Hochtemperatur-Hochfestigkeits-Performer
- Wichtige Eigenschaften:
- Ausgezeichnete Hochtemperaturfestigkeit und Kriechfestigkeit
- Hervorragende Korrosions- und Oxidationsbeständigkeit (auch in rauen Umgebungen)
- Hohe Ermüdungsfestigkeit
- Gute Bedruckbarkeit durch LPBF und Electron Beam Melting (EBM)
- Warum es für Wärmetauscher wichtig ist: IN625 ist das Material der Wahl für Wärmetauscher, die bei extremen Temperaturen und/oder in korrosiven Umgebungen eingesetzt werden. Seine Fähigkeit, die strukturelle Integrität bei hohen Temperaturen zu erhalten, macht es ideal für Anwendungen in der Nähe von Motoren oder beim Umgang mit heißen Gasen.
- Typische Anwendungen: Triebwerkskomponenten für die Luft- und Raumfahrt (Zapfluftkühler, Abgaswärmetauscher), Hochleistungsabgassystemkomponenten für Kraftfahrzeuge, Wärmetauscher für die chemische Verarbeitung, Schiffsanwendungen.
- Erwägungen: Geringere Wärmeleitfähigkeit im Vergleich zu Aluminium- und Kupferlegierungen, höhere Dichte, höhere Materialkosten.
Zusammenfassung des Leitfadens zur Materialauswahl:
Material | Primärer Vorteil | Hauptvorteil | Typische maximale Temperatur (°C) | Relative Kosten | Dichte (g/cm³) | Wärmeleitfähigkeit (W/m-K) |
---|---|---|---|---|---|---|
AlSi10Mg | Leichtgewicht | Gutes Gleichgewicht zwischen Eigenschaften, Kosten | ~150-200 | Niedrig | ~2.67 | ~130-150 |
CuCrZr | Wärmeleitfähigkeit | Maximale Wärmeübertragung | ~400-500 | Hoch | ~8.89 | ~300-320 |
IN625 | Hochtemperaturfestigkeit | Langlebigkeit in extremen Umgebungen | ~800-1000+ | Sehr hoch | ~8.44 | ~10-15 |
In Blätter exportieren
Die Rolle von Met3dp: Die Wahl des richtigen Pulvers ist nur ein Teil der Gleichung. Für einen erfolgreichen Druck ist es entscheidend, dass das Pulver strenge Qualitätsstandards erfüllt - Partikelgrößenverteilung, Sphärizität, Fließfähigkeit und chemische Reinheit. Met3dp nutzt die branchenführenden Technologien der Gaszerstäubung und des Plasma-Rotations-Elektroden-Verfahrens (PREP) zur Herstellung hochwertiger Metallpulver, einschließlich Varianten dieser wichtigen Legierungen. Unser Fachwissen gewährleistet, dass die für die Herstellung Ihrer Wärmetauscher verwendeten Pulver die optimalen Eigenschaften aufweisen, um dichte, zuverlässige und leistungsstarke Teile herzustellen, die den anspruchsvollen Spezifikationen der Automobil- und Luftfahrtindustrie entsprechen.
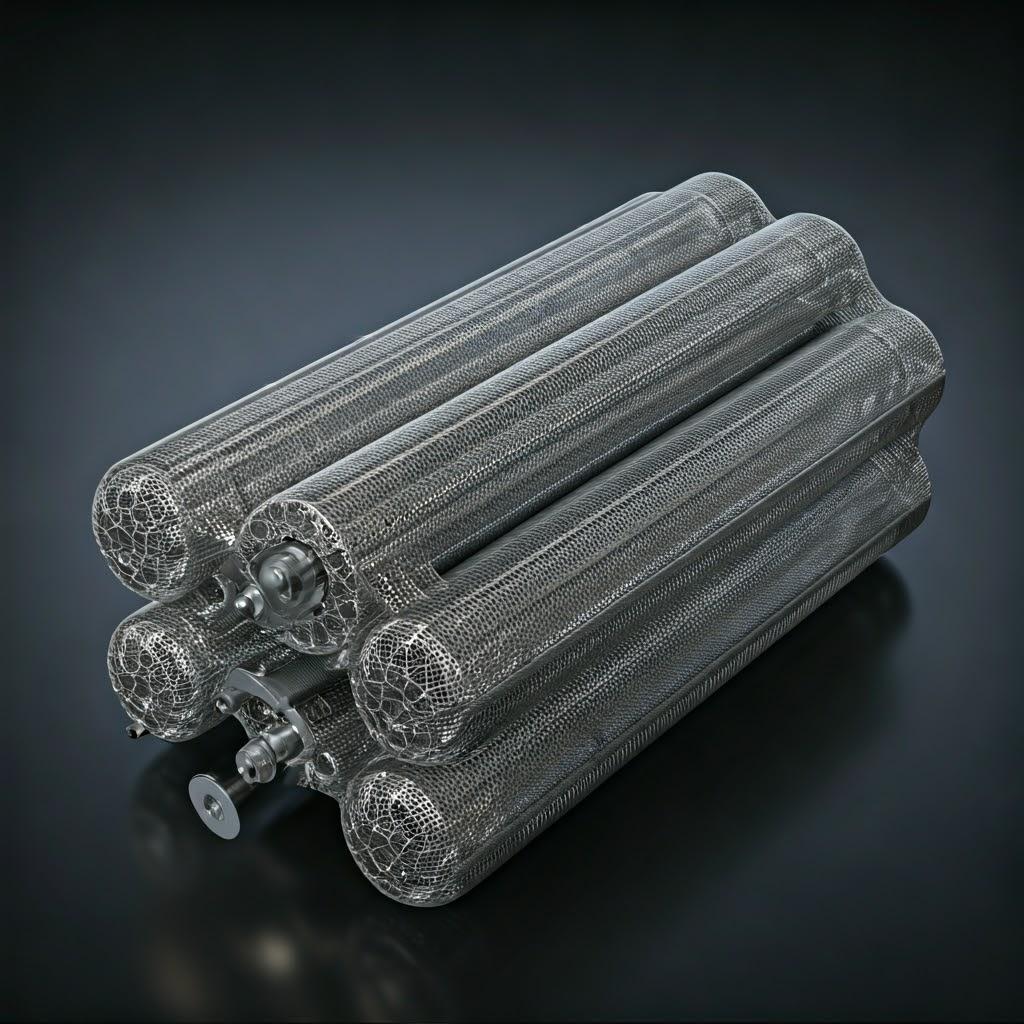
Design for Additive Manufacturing (DfAM) Prinzipien für optimale Wärmetauscherleistung
Die einfache Nachbildung eines konventionell konstruierten Wärmetauschers mit Hilfe der additiven Fertigung schöpft oft nicht das wahre Potenzial der Technologie aus und kann sogar zu suboptimalen Ergebnissen oder Fertigungsproblemen führen. Um die Vorteile des 3D-Drucks von Metallen - Komplexität, Leichtbau, Konsolidierung - voll auszuschöpfen, müssen Ingenieure die Prinzipien des Design for Additive Manufacturing (DfAM) anwenden, die speziell auf Wärmemanagementanwendungen zugeschnitten sind. Bei DfAM geht es nicht nur darum, ein Teil druckbar zu machen, sondern es so zu konstruieren, dass Leistung und Herstellbarkeit maximiert werden. denn es wird gedruckt.
Wichtige DfAM-Überlegungen für 3D-gedruckte Wärmetauscher:
- Geometrische Komplexität für thermische Effizienz nutzen:
- Optimierte Kanalformen: Gehen Sie über einfache kreisförmige oder rechteckige Kanäle hinaus. Entwerfen Sie gekrümmte Kanäle mit variablem Querschnitt oder biologisch inspirierte Kanäle (wie Gefäßnetze), um die Durchmischung von Flüssigkeiten (Turbulenzen) zu verbessern und die Wärmeübertragungskoeffizienten zu maximieren und gleichzeitig den Druckverlust zu kontrollieren.
- Dreifach periodische Minimalflächen (TPMS) und Gitter: Integrieren Sie TPMS-Strukturen (z. B. Gyroid, Schwarz-P) oder komplexe Gittergeometrien in den Wärmetauscherkern. Diese Strukturen bieten ein unglaublich hohes Verhältnis von Oberfläche zu Volumen, was die thermische Leistung innerhalb eines kompakten Designs deutlich erhöht. Sie können auch bis zu einem gewissen Grad selbsttragend sein, was die Herausforderungen beim Druck verringert.
- Konformes Design: Entwerfen Sie Kanäle und Rippen, die sich genau an die Form der zu kühlenden Komponente oder an den verfügbaren Raum anpassen, um den direktesten und effizientesten Wärmepfad zu gewährleisten.
- Dünne Wände und Formate:
- Gleichgewicht zwischen Wärmewiderstand und Druckfähigkeit: Dünnere Wände verringern den Wärmewiderstand und verbessern die Wärmeübertragung. Bei AM-Verfahren gibt es jedoch Mindestgrößen für druckbare Merkmale (abhängig von Maschine, Material und Parametern). Entwerfen Sie die Wände dick genug, um zuverlässig gedruckt zu werden und dem Betriebsdruck standzuhalten, aber so dünn wie für die thermische Leistung möglich. Typische Mindestwandstärken für LPBF können zwischen 0,3 mm und 0,8 mm liegen.
- Aspekt-Verhältnisse: Sehr hohe, dünne Wände können sich während des Drucks aufgrund von thermischen Spannungen verformen. Erwägen Sie die Integration von Rippen oder die Gestaltung von Wänden mit geeigneten Seitenverhältnissen, um Stabilität zu gewährleisten.
- Verwaltung von Stützen und Überhängen:
- Selbsttragende Winkel: Entwerfen Sie Innenkanäle und Außenbauteile mit Auskragungswinkeln von typischerweise mehr als 45 Grad zur horizontalen Bauebene, um den Bedarf an Stützkonstruktionen zu minimieren. Stützen in komplexen internen Kanälen können extrem schwierig oder unmöglich zu entfernen sein.
- Strategie unterstützen: Wo Stützen unvermeidlich sind (z. B. horizontale Flächen, Überhänge mit geringem Winkel), sollten sie strategisch so ausgelegt werden, dass sie leicht entfernt werden können, ohne kritische Oberflächen zu beschädigen. Berücksichtigen Sie die Zugänglichkeit von Werkzeugen oder Nachbearbeitungsschritten wie der elektrochemischen Bearbeitung zur Entfernung von Stützen. Manchmal können problematische Halterungen durch eine geringfügige Änderung der Teileausrichtung oder -geometrie vermieden werden.
- Entfernung von Puder:
- Planung einer Evakuierung: Stellen Sie sicher, dass komplexe interne Kanäle über angemessene Ein- und Auslassöffnungen und glatte interne Übergänge verfügen, um die vollständige Entfernung von ungeschmolzenem Metallpulver nach dem Druck zu erleichtern. Eingeschlossenes Pulver kann den Fluss behindern, die thermische Leistung verringern, zusätzliches Gewicht verursachen und sich während des Betriebs lösen. Sehen Sie bei Bedarf an strategischen Stellen Entwässerungslöcher vor, die später verstopft werden können.
- Teil Konsolidierung:
- Integration der Funktionalität: Suchen Sie nach Möglichkeiten, Verteiler, Einlässe, Auslässe, Montagevorrichtungen und Sensoranschlüsse direkt in das Hauptgehäuse des Wärmetauschers zu integrieren. Dies reduziert die Komplexität der Montage, das Gewicht und mögliche Leckagepfade.
- Überlegungen zur Fluidströmung:
- Reibungslose Übergänge: Vermeiden Sie scharfe Ecken oder abrupte Änderungen im Querschnitt des Fließweges, die zu stagnierenden Zonen oder hohen Druckabfällen führen können. Verwenden Sie Verrundungen und sanfte Übergänge.
- Flussausgleich: Bei Mehrkanalkonstruktionen ist darauf zu achten, dass die Geometrie eine ausgewogene Strömungsverteilung über alle Kanäle fördert, um eine gleichmäßige Wärmeübertragung zu gewährleisten. CFD-Simulationen (Computational Fluid Dynamics) sind hier von unschätzbarem Wert.
- Simulationsgestützter Entwurf:
- Wärme- und Strömungssimulation (CFD): Setzen Sie CFD frühzeitig und häufig im Designprozess ein, um die Strömung und Wärmeübertragung zu simulieren und die Leistung verschiedener Geometrien (Kanäle, TPMS, Rippen) vor dem Druck zu bewerten.
- Strukturelle Simulation (FEA): Analyse des Entwurfs im Hinblick auf mechanische Spannungen (aufgrund von Druck- und Wärmegradienten) und Optimierung der Struktur im Hinblick auf Festigkeit und Haltbarkeit, besonders wichtig beim Leichtbau.
- Simulation des Bauprozesses: Simulieren Sie den Druckprozess selbst, um thermische Spannungen und potenzielle Verformungen vorherzusagen und um die Ausrichtung der Bauteile und die Unterstützungsstrategien zu optimieren und so Druckfehler zu minimieren.
Die Anwendung dieser DfAM-Prinzipien erfordert ein Umdenken und oft eine enge Zusammenarbeit zwischen Konstrukteuren und AM-Spezialisten. Unternehmen wie Met3dp, die über umfassendes Know-how in verschiedenen Druckverfahren wie Selective Electron Beam Melting (SEBM) und Laser Powder Bed Fusion (LPBF), können in der Konstruktionsphase entscheidende Hilfestellung leisten, um sicherzustellen, dass die endgültige Wärmetauscherkonstruktion nicht nur leistungsfähig, sondern auch für eine erfolgreiche und effiziente additive Fertigung optimiert ist.
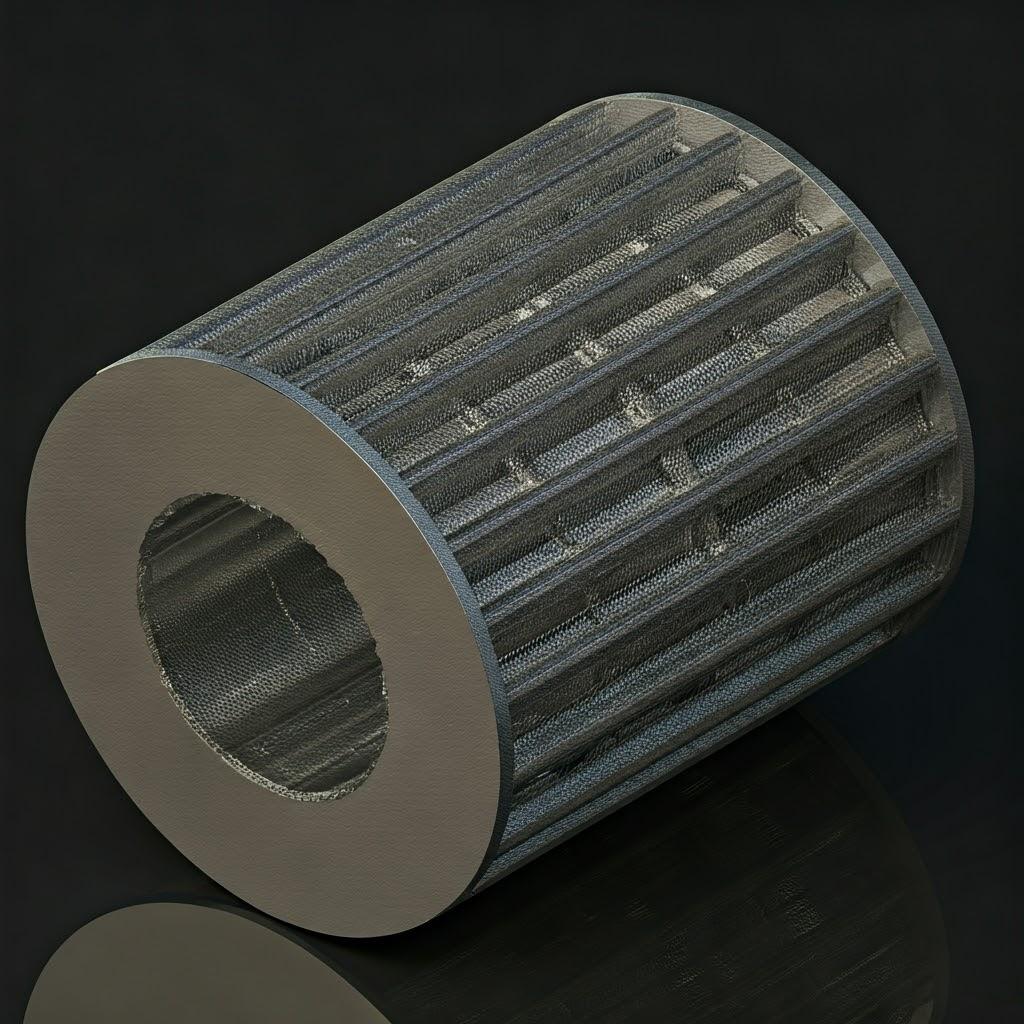
Erreichen von Präzision: Toleranz, Oberflächengüte und Maßgenauigkeit bei 3D-gedruckten Wärmetauschern
Während AM komplexe Geometrien ermöglicht, ist das Verständnis des erreichbaren Präzisionsniveaus entscheidend für die Gewährleistung der Funktionalität und Integration von 3D-gedruckten Wärmetauschern, insbesondere für Dichtungsflächen, Schnittstellen und Flüssigkeitsanschlüsse. Toleranz, Oberflächengüte und allgemeine Maßgenauigkeit werden durch das gewählte AM-Verfahren, das Material, die Komplexität des Designs, die Bauausrichtung und die Nachbearbeitungsschritte beeinflusst.
Typische Toleranzen:
- Laser-Pulver-Bett-Fusion (LPBF): Bietet im Allgemeinen eine höhere Genauigkeit und eine feinere Auflösung der Merkmale. Typische erreichbare Toleranzen für kleinere Teile (<100mm) können im Bereich von ±0,1mm bis ±0,2mm liegen, bei größeren Teilen können die Toleranzen näher bei ±0,1% bis ±0,2% der Abmessung liegen.
- Elektronenstrahlschmelzen (EBM): EBM wird häufig für Werkstoffe wie Titanlegierungen und IN625 verwendet und arbeitet in der Regel bei höheren Temperaturen, was zur Verringerung der Eigenspannung beiträgt, aber im Vergleich zu LPBF zu einer etwas geringeren Maßgenauigkeit führen kann. Die Toleranzen können zwischen ±0,2 mm und ±0,4 mm oder bei großen Bauteilen auch höher liegen.
- Faktoren, die die Verträglichkeit beeinflussen:
- Kalibrierung der Maschine: Die regelmäßige Kalibrierung und Wartung des AM-Systems ist von entscheidender Bedeutung.
- Prozessparameter: Laserleistung, Scangeschwindigkeit, Schichtdicke usw. beeinflussen die Genauigkeit erheblich.
- Materialeigenschaften: Verschiedene Materialien schrumpfen und verziehen sich beim Erhitzen und Abkühlen unterschiedlich.
- Thermische Spannungen: Eine ungleichmäßige Abkühlung kann zu einem Verzug der Teile führen.
- Teilegeometrie und -ausrichtung: Große, flache Oberflächen oder hohe, dünne Elemente sind anfälliger für Verformungen. Die Bauausrichtung wirkt sich auf den Stützbedarf und das thermische Verhalten aus.
- Nachbearbeiten: Spannungsabbau und Bearbeitungsschritte können die Endmaße beeinflussen.
Oberflächengüte (Rauhigkeit):
- Ist-Zustand: AM-Teile aus Metall haben im Vergleich zu maschinell gefertigten Teilen in der Regel eine rauere Oberflächenbeschaffenheit. Die Rauheit (gemessen als Ra - arithmetisches Mittel der Rauheit) hängt von der Schichtdicke, der Größe der Pulverpartikel, dem Auftragswinkel und den Prozessparametern ab.
- LPBF: Ra-Werte liegen oft zwischen 6 µm und 20 µm. Vertikale Wände sind in der Regel glatter als schräge oder horizontale Flächen (insbesondere nach unten gerichtete Flächen, die durch Stützstrukturen beeinflusst werden).
- EBM: Erzeugt im Allgemeinen rauere Oberflächen als LPBF, möglicherweise Ra 20 µm bis 40 µm oder höher.
- Auswirkungen auf Wärmetauscher:
- Fluiddynamik: Raue interne Kanaloberflächen können die Turbulenz erhöhen (was die Wärmeübertragung leicht verbessern kann), aber auch den Druckabfall erheblich steigern.
- Verschmutzung: Rauere Oberflächen können im Laufe der Zeit anfälliger für Ablagerungen (Fouling) sein, die den thermischen Wirkungsgrad verringern.
- Versiegeln: Für kritische Abdichtungen sind die Oberflächen im Ist-Zustand in der Regel ungeeignet; sie müssen nachbearbeitet werden.
- Verbesserung der Oberflächengüte: Nachbearbeitungsschritte wie abrasive Fließbearbeitung (AFM), elektrochemisches Polieren, Mikrobearbeitung oder Standard-CNC-Bearbeitung werden eingesetzt, um bei Bedarf glattere Oberflächen zu erzielen (z. B. Dichtungsflächen, kritische Fließwege).
Maßgenauigkeit und Metrologie:
- Verifizierung: Es ist von entscheidender Bedeutung, dass das endgültige Teil die Maßspezifikationen erfüllt. Dies erfordert robuste Messtechniken.
- Methoden:
- Koordinatenmessmaschinen (KMG): Ermöglicht hochpräzise Punktmessungen für kritische Merkmale.
- 3D-Laser/Strukturiertes Licht-Scanning: Erfassen Sie die vollständige Geometrie des Teils, was einen Vergleich mit dem ursprünglichen CAD-Modell und die Erstellung von Abweichungskarten (Heatmaps) zur Visualisierung von Ungenauigkeiten ermöglicht.
- CT-Scan: Kann insbesondere bei komplexen internen Kanälen zur Überprüfung der Geometrie und zur Erkennung interner Defekte wie Porosität oder eingeschlossenes Pulver verwendet werden.
Um die geforderte Präzision zu erreichen, muss bei der Konstruktion oft die Nachbearbeitung berücksichtigt werden. Kritische Schnittstellen, Dichtungsflächen oder Lagerbohrungen sollten mit zusätzlichem Material (Bearbeitungszugabe) ausgelegt werden, das nach dem Druck und dem Spannungsabbau durch CNC-Bearbeitung fertiggestellt wird. Die Zusammenarbeit mit einem AM-Anbieter wie Met3dp, der mit hochpräzisen Druckern und robusten Qualitätskontrollverfahren einschließlich fortschrittlicher Messtechnik ausgestattet ist, stellt sicher, dass Ihre Wärmetauscher die strengen Maßanforderungen der Automobil- und Luft- und Raumfahrtanwendungen erfüllen.
Wesentliche Nachbearbeitungsschritte für funktionale Wärmetauscher aus Metall
Ein 3D-gedrucktes Metallteil ist, wenn es die Bauplatte verlässt, nur selten bereit für die Endanwendung, insbesondere bei anspruchsvollen Anwendungen wie Wärmetauschern. Die Nachbearbeitung ist eine kritische Phase, in der das endkonturnah gedruckte Teil in eine funktionale, zuverlässige Komponente verwandelt wird, die alle Leistungs- und Qualitätsanforderungen erfüllt.
Gemeinsame Nachbearbeitungsschritte für AM-Wärmetauscher:
- Stressabbau / Wärmebehandlung:
- Zweck: Die schnellen Erwärmungs- und Abkühlungszyklen, die dem Pulverbettschmelzverfahren eigen sind, erzeugen erhebliche innere Spannungen im gedruckten Teil. Diese Spannungen können zu Verformungen, Rissen und verminderter mechanischer Leistung (insbesondere Ermüdungsfestigkeit) führen. Durch eine Wärmebehandlung in einem Ofen mit kontrollierter Atmosphäre werden diese Spannungen abgebaut, das Gefüge stabilisiert und die gewünschten Materialeigenschaften (Härte, Festigkeit, Duktilität) der Legierung erreicht (z. B. Ausscheidungshärtung für CuCrZr, Lösungsglühen/Alterung für IN625).
- Wichtigkeit: Dies ist wohl der kritischste Nachbearbeitungsschritt, um Maßhaltigkeit und langfristige Zuverlässigkeit zu gewährleisten. Er wird in der Regel durchgeführt, bevor das Teil von der Bauplatte genommen wird, um den Verzug zu minimieren.
- Teilentfernung:
- Methode: Schneiden der Teile von der Bauplatte, in der Regel durch Drahterodieren (Electrical Discharge Machining) oder mit einer Bandsäge. Dabei muss darauf geachtet werden, dass das Teil nicht beschädigt wird.
- Entfernung der Stützstruktur:
- Methode: Stützen, die zur Verankerung des Teils während der Herstellung gedruckt wurden, müssen entfernt werden. Dies kann manuelles Brechen/Schneiden für zugängliche Stützen oder CNC-Bearbeitung für stärker integrierte Stützen oder kritische Oberflächen bedeuten. Für komplexe interne Kanalhalterungen können spezielle Techniken wie die elektrochemische Bearbeitung (ECM) in Betracht gezogen werden, auch wenn die Konstruktion für einen unterstützungsfreien Druck vorzuziehen ist.
- Herausforderungen: Kann arbeitsintensiv sein und birgt das Risiko, die Oberfläche des Teils zu beschädigen, wenn nicht sorgfältig gearbeitet wird. Der Zugang zu internen Stützen ist eine große Herausforderung.
- Puderentfernung / Reinigung:
- Zweck: Entfernen des gesamten ungeschmolzenen Metallpulvers, insbesondere aus komplizierten internen Kanälen und komplexen Merkmalen wie TPMS-Strukturen. Eingeschlossenes Pulver beeinträchtigt die Leistung und Sicherheit.
- Methoden: Manuelles Bürsten, Ausblasen mit Druckluft, Ultraschallreinigungsbäder, abrasive Fließbearbeitung (AFM). In der DfAM-Phase ist die Gestaltung der Pulverentfernung (Entwässerungslöcher, glatte Kanäle) entscheidend. Eine Überprüfung (z. B. Wiegen des Teils, visuelle Inspektion mit Endoskopen, CT-Scan) kann erforderlich sein.
- Bearbeitungen:
- Zweck: Erzielung enger Toleranzen, spezifischer Oberflächengüten und kritischer Merkmale, die mit dem AM-Verfahren allein nicht genau hergestellt werden können.
- Anwendungen: Herstellung von ebenen Dichtungsflächen, Bearbeitung von Gewinden für Flüssigkeitsanschlüsse, Endbearbeitung von Lagerbohrungen, Erzielung präziser Schnittstellenmaße für die Montage. Die Teile werden oft mit Bearbeitungsaufmaß (+ Aufmaß) für diese kritischen Merkmale konstruiert.
- Oberflächenveredelung:
- Zweck: Verbesserung der Oberflächenrauheit zur Verbesserung der Fluiddynamik, zur Verringerung der Verschmutzung, zur Verbesserung der Ermüdungslebensdauer oder aus ästhetischen Gründen.
- Methoden:
- Shot Peening/Strahlen: Verbessert die Ermüdungsfestigkeit und kann eine gleichmäßige matte Oberfläche erzeugen.
- Taumeln/Gleitschleifen: Glättet Oberflächen und entgratet Kanten, insbesondere bei kleineren Teilen.
- Polieren (manuell, elektrochemisch, AFM): Erzielt sehr glatte Oberflächen für bestimmte Anwendungen (z. B. Verringerung der Reibung, Verbesserung der Reinigungsfähigkeit).
- Beschichtung: Auftragen spezieller Beschichtungen für verbesserte Korrosionsbeständigkeit, Verschleißfestigkeit oder Wärmedämmungseigenschaften.
- Dichtheitsprüfung:
- Zweck: Unerlässlich für Wärmetauscher, um die Eindämmung von Flüssigkeiten unter Betriebsdruck zu gewährleisten.
- Methoden: Druckprüfung (hydrostatisch oder pneumatisch) unter Eintauchen des Teils oder unter Verwendung von Lecksuchflüssigkeiten/-gasen (z. B. Helium-Lecktests bei hohen Empfindlichkeitsanforderungen). Die Prüfparameter (Druck, Dauer, Flüssigkeit) sollten der Endanwendung entsprechen.
- Inspektion und Qualitätssicherung:
- Zweck: Abschließende Überprüfung, ob das Teil alle Maß-, Material- und Funktionsspezifikationen erfüllt.
- Methoden: Maßprüfung (CMM, Scannen), Prüfung der Materialeigenschaften (falls erforderlich auf neben dem Teil gedruckten Testcoupons), Sichtprüfung, NDT (Non-Destructive Testing) wie CT-Scannen oder FPI (Fluorescent Penetrant Inspection) zur Prüfung auf Risse oder Porosität, falls angegeben.
Die spezifische Abfolge und Kombination dieser Schritte hängt stark vom Material, der Komplexität des Designs und den Anwendungsanforderungen ab. Die Integration von Nachbearbeitungsüberlegungen in die anfängliche Entwurfsphase (DfAM) ist der Schlüssel zum Erreichen eines kostengünstigen und effizienten Gesamtfertigungsprozesses.

Überwindung allgemeiner Herausforderungen beim 3D-Druck von Metall für Wärmetauscher
Metall-AM bietet zwar enorme Vorteile für Wärmetauscher, aber Ingenieure und Beschaffungsmanager sollten sich der potenziellen Herausforderungen bewusst sein, die mit dieser Technologie verbunden sind. Diese Herausforderungen zu verstehen und mit erfahrenen AM-Anbietern zusammenzuarbeiten, die über robuste Prozesse verfügen, ist der Schlüssel zur erfolgreichen Umsetzung.
Zentrale Herausforderungen und Strategien zur Abhilfe:
- Eigenspannung und Verzug:
- Herausforderung: Die schnelle, örtlich begrenzte Erwärmung und Abkühlung während des Drucks führt zu inneren Spannungen. Diese können dazu führen, dass sich das Teil während oder nach der Herstellung verzieht oder sogar Risse entstehen, insbesondere bei großen oder komplexen Geometrien.
- Milderung:
- Simulation: Nutzen Sie die Simulation des Bauprozesses, um Spannungskonzentrationen und Verformungen vorherzusagen.
- Optimierte Build-Strategie: Sorgfältige Auswahl der Bauausrichtung, der Laserscanmuster und möglicherweise Vorheizen der Bauplatte (üblich bei EBM).
- Unterstützende Strukturen: Gut gestaltete Stützen verankern das Teil und tragen zur Wärmeableitung bei.
- Stressabbau: Eine rechtzeitige und angemessene Wärmebehandlung nach dem Druck ist entscheidend.
- Auswahl der Materialien: Einige Legierungen sind anfälliger für Rissbildung als andere.
- Porosität:
- Herausforderung: Im gedruckten Material können sich kleine Hohlräume oder Poren bilden, die durch eingeschlossenes Gas, unvollständige Verschmelzung oder Unregelmäßigkeiten im Pulver entstehen. Poren können die mechanische Festigkeit und Ermüdungslebensdauer verringern und bei Wärmetauschern potenzielle Leckagepfade schaffen.
- Milderung:
- Optimierte Prozessparameter: Entwicklung und strenge Kontrolle der material- und maschinenspezifischen Parameter (Laserleistung, Geschwindigkeit, Schichtdicke, Gasfluss). Met3dp nutzt umfangreiche Forschung, um die optimalen Parameter für seine Produkt einschließlich Druckern und Pulvern.
- Hochwertiges Pulver: Verwendung von Pulver mit gleichmäßiger Kugelform, Partikelgrößenverteilung und geringer innerer Porosität/Gasgehalt. Die fortschrittlichen Zerstäubungstechniken von Met3dp gewährleisten eine hohe Pulverqualität.
- Kontrollierte Bauatmosphäre: Aufrechterhaltung einer hochreinen Inertgasumgebung (Argon oder Stickstoff) zur Minimierung von Oxidation und Gasaufnahme.
- Heiß-Isostatisches Pressen (HIP): Ein Nachbearbeitungsschritt mit hohem Druck und hoher Temperatur zum Schließen der inneren Poren (verursacht zusätzliche Kosten, kann aber die Dichte und die Eigenschaften erheblich verbessern).
- Unterstützung bei der Beseitigung von Komplexität:
- Herausforderung: Das Entfernen von Stützstrukturen, insbesondere von komplizierten internen Kanälen oder empfindlichen Merkmalen, kann zeitaufwändig und kostspielig sein und birgt die Gefahr, das Teil zu beschädigen. Unzugängliche interne Stützen lassen sich unter Umständen nicht vollständig entfernen.
- Milderung:
- DfAM: Planung von selbsttragenden Winkeln (>45°), wo immer möglich.
- Optimierte Ausrichtung: Die Wahl einer Bauausrichtung, die den Bedarf an kritischen Stützen minimiert.
- Barrierefreies Support-Design: Gestaltung von Halterungen, die leichter zugänglich und abnehmbar sind (z. B. Verwendung bestimmter Halterungstypen, Optimierung der Kontaktpunkte).
- Erweiterte Entfernungstechniken: Erwägung von Methoden wie ECM oder AFM für schwierige interne Stützen, obwohl Prävention durch Design besser ist.
- Pulverentfernung aus internen Kanälen:
- Herausforderung: Die Entfernung des gesamten ungeschmolzenen Pulvers aus den komplexen, verschlungenen internen Kanälen ist entscheidend für die Durchfluss- und Wärmeleistung. Teilweise verstopfte Kanäle führen zu geringerer Effizienz und potenzieller Verunreinigung.
- Milderung:
- DfAM: Gestaltung von Kanälen mit sanften Übergängen, ausreichenden Durchmessern und Zugangsöffnungen/Entleerungslöchern. Vermeidung von Sackgassen.
- Gründliche Reinigungsverfahren: Einführung strenger Reinigungsprotokolle unter Verwendung von Druckluft, Vibration, Ultraschallbädern oder Durchflusssystemen.
- Verifizierung: Verwendung von Methoden wie Wiegen, boreskopische Inspektion oder CT-Scannen zur Bestätigung der vollständigen Pulverentfernung.
- Erreichen von Dichtheit:
- Herausforderung: Sicherstellung, dass der fertige Wärmetauscher unter Betriebsdruck völlig dicht ist, da bei dünnwandigen Strukturen die Gefahr von Mikroporosität oder Defekten besteht.
- Milderung:
- Robuste Prozesskontrolle: Minimierung der Porosität beim Druck durch optimierte Parameter und Qualitätspulver.
- Angemessenes Design: Sicherstellung einer ausreichenden Wandstärke für den Druckausgleich.
- Strenge Tests: Einführung strenger Lecktestprotokolle (z. B. Druckabfall, Heliumlecktest) als Teil des Qualitätssicherungsprozesses.
- Potenzielle Imprägnierung: In einigen Fällen kann die Versiegelung von Mikroporen mit speziellen Imprägnierharzen in Betracht gezogen werden (obwohl dies im Allgemeinen vermieden wird, wenn dies durch eine bessere Prozesskontrolle möglich ist).
Um diese Herausforderungen erfolgreich zu meistern, ist umfassendes Fachwissen in den Bereichen Materialwissenschaft, Verfahrenstechnik und Qualitätskontrolle erforderlich. Die Zusammenarbeit mit einem etablierten AM-Anbieter wie Met3dp, der fortschrittliche Anlagen mit strengen Prozessvalidierungs- und Qualitätsmanagementsystemen kombiniert, erleichtert die Einführung der additiven Fertigung für kritische Komponenten wie Wärmetauscher für die Automobil- und Luftfahrtindustrie erheblich.
Auswahl des idealen 3D-Metalldruck-Dienstleisters für Ihren Bedarf an Wärmetauschern
Die Wahl des richtigen Partners für die additive Fertigung ist für den Erfolg Ihres 3D-gedruckten Wärmetauscherprojekts ebenso entscheidend wie das Design und die Materialauswahl. Nicht alle Dienstleister verfügen über die gleichen Fähigkeiten, Fachkenntnisse oder Qualitätsstandards, insbesondere wenn es um die anspruchsvollen Anforderungen der Automobil- und Luftfahrtindustrie geht. Beschaffungsmanager und Ingenieure sollten potenzielle Lieferanten auf der Grundlage einer Reihe von technischen und betrieblichen Kriterien sorgfältig prüfen.
Schlüsselfaktoren für die Bewertung von Anbietern von Metall-AM-Dienstleistungen:
- Technisches Fachwissen und Unterstützung durch das DfAM:
- Verfügt der Anbieter über Ingenieure, die sich speziell mit thermischen Anwendungen und der Konstruktion von Wärmetauschern auskennen?
- Können sie wertvolle DfAM-Beratung anbieten, um Ihre Konstruktion hinsichtlich Leistung, Herstellbarkeit und Kosteneffizienz zu optimieren?
- Verstehen sie die Feinheiten der Strömungsdynamik und der Prinzipien der Wärmeübertragung, wie sie bei AM angewendet werden?
- Ausrüstung und Technologie:
- Welche spezifischen AM-Technologien bieten sie an (z. B. LPBF, EBM)? Entspricht die Technologie den von Ihnen gewählten Material- und Designanforderungen?
- Wie groß ist das Bauvolumen ihrer Maschinen? Können sie die Größe Ihres Wärmetauschers aufnehmen?
- Wie alt sind die Maschinen, in welchem Zustand befinden sie sich und wie oft werden sie kalibriert? Moderne, gut gewartete Maschinen produzieren in der Regel gleichmäßigere und genauere Teile.
- Fähigkeiten und Qualität des Materials:
- Bieten sie die spezifischen Legierungen an, die Sie benötigen (z. B. AlSi10Mg, CuCrZr, IN625)?
- Entscheidend ist, wie sie die Qualität der Metallpulver qualifizieren und kontrollieren? Beziehen sie es von renommierten Lieferanten oder stellen sie im Idealfall ihre eigenen hochwertigen Pulver wie Met3dp her? Einheitliche Pulvereigenschaften (Sphärizität, Partikelgrößenverteilung, Reinheit) sind für die Teilequalität von grundlegender Bedeutung.
- Haben sie Erfahrung im Druck mit dem von Ihnen gewählten Material und kennen sie dessen spezifische Verarbeitungsanforderungen?
- Qualitätsmanagementsysteme und Zertifizierungen:
- Verfügen sie über ein solides Qualitätsmanagementsystem (QMS)? Die Zertifizierung nach ISO 9001 ist eine Grundvoraussetzung.
- Für Anwendungen in der Luft- und Raumfahrt ist die AS9100-Zertifizierung (oder eine gleichwertige Zertifizierung) oft obligatorisch, da sie die Einhaltung strenger Qualitätsstandards in der Luft- und Raumfahrt bescheinigt.
- Für die Automobilindustrie kann die Kenntnis der IATF 16949 oder eine Zertifizierung je nach Anwendungsebene von Bedeutung sein.
- Wie sieht die Rückverfolgbarkeit von Materialien und Prozessen aus?
- Hausinterne Nachbearbeitungsmöglichkeiten:
- Können sie notwendige Nachbearbeitungsschritte wie Spannungsarmglühen/Wärmebehandlung, CNC-Bearbeitung, Oberflächenveredelung und Dichtheitsprüfung selbst durchführen? Die interne Durchführung dieser Prozesse führt oft zu einer besseren Qualitätskontrolle und kürzeren Vorlaufzeiten im Vergleich zur Auslagerung.
- Verfügen sie über die entsprechende Ausrüstung und das Fachwissen für diese kritischen Schritte?
- Inspektion und Metrologie:
- Über welche messtechnischen Einrichtungen verfügen sie (CMM, 3D-Scanner, CT-Scanner)?
- Wie sehen ihre Standardprüfverfahren aus, und können sie spezielle ZfP-Anforderungen erfüllen?
- Erfahrung und Erfolgsbilanz:
- Haben sie erfolgreich Teile hergestellt, die in Bezug auf Komplexität, Material und industrielle Anwendung Ihrem Wärmetauscher ähneln?
- Können sie Fallstudien oder Referenzen vorlegen?
- Kapazität, Vorlaufzeit und Kommunikation:
- Verfügen sie über die Kapazitäten, um Ihre Mengenanforderungen und Lieferfristen zu erfüllen?
- Wie lange sind die typischen Vorlaufzeiten für Angebotserstellung, Produktion und Nachbearbeitung?
- Wie reaktionsschnell und transparent ist ihre Kommunikation während des gesamten Projektzyklus?
Warum eine Partnerschaft mit Met3dp?
Met3dp zeichnet sich als umfassender Lösungsanbieter aus, der einzigartig positioniert ist, um anspruchsvolle Wärmetauscherprojekte zu unterstützen. Wie auf unserer Website weiter ausgeführt Über uns Seite, bieten wir an:
- Integriertes Fachwissen: Wir verfügen über jahrzehntelange Erfahrung in der Herstellung von Metallpulvern (mit branchenführenden Gaszerstäubungs- und PREP-Technologien), in der Entwicklung von Hochleistungsdruckern für SEBM und LPBF sowie in der umfassenden anwendungstechnischen Unterstützung.
- Material Exzellenz: Wir stellen eine breite Palette an hochwertigen sphärischen Metallpulvern her, die für AM optimiert sind, darunter Aluminium-, Kupfer- und Nickellegierungen, die optimale Materialeigenschaften für Ihre Wärmetauscher gewährleisten.
- Erweiterte Ausrüstung: Unsere Drucker bieten ein branchenführendes Druckvolumen, Genauigkeit und Zuverlässigkeit und eignen sich für unternehmenskritische Komponenten in der Automobil- und Luftfahrtindustrie.
- End-to-End-Lösungen: Von der DfAM-Beratung und Materialauswahl über den Druck und die Nachbearbeitung bis hin zur Qualitätssicherung bieten wir einen nahtlosen Weg zu funktionalen Teilen.
- Schwerpunkt Industrie: Wir kennen die strengen Anforderungen der Luft- und Raumfahrt, der Automobilindustrie, der Medizin und der Industrie.
Die Wahl eines Partners wie Met3dp, der sowohl die Materialien als auch die Maschinen kontrolliert, bietet einen erheblichen Vorteil bei der Gewährleistung der Qualität, Zuverlässigkeit und Leistung Ihrer 3D-gedruckten Wärmetauscher.
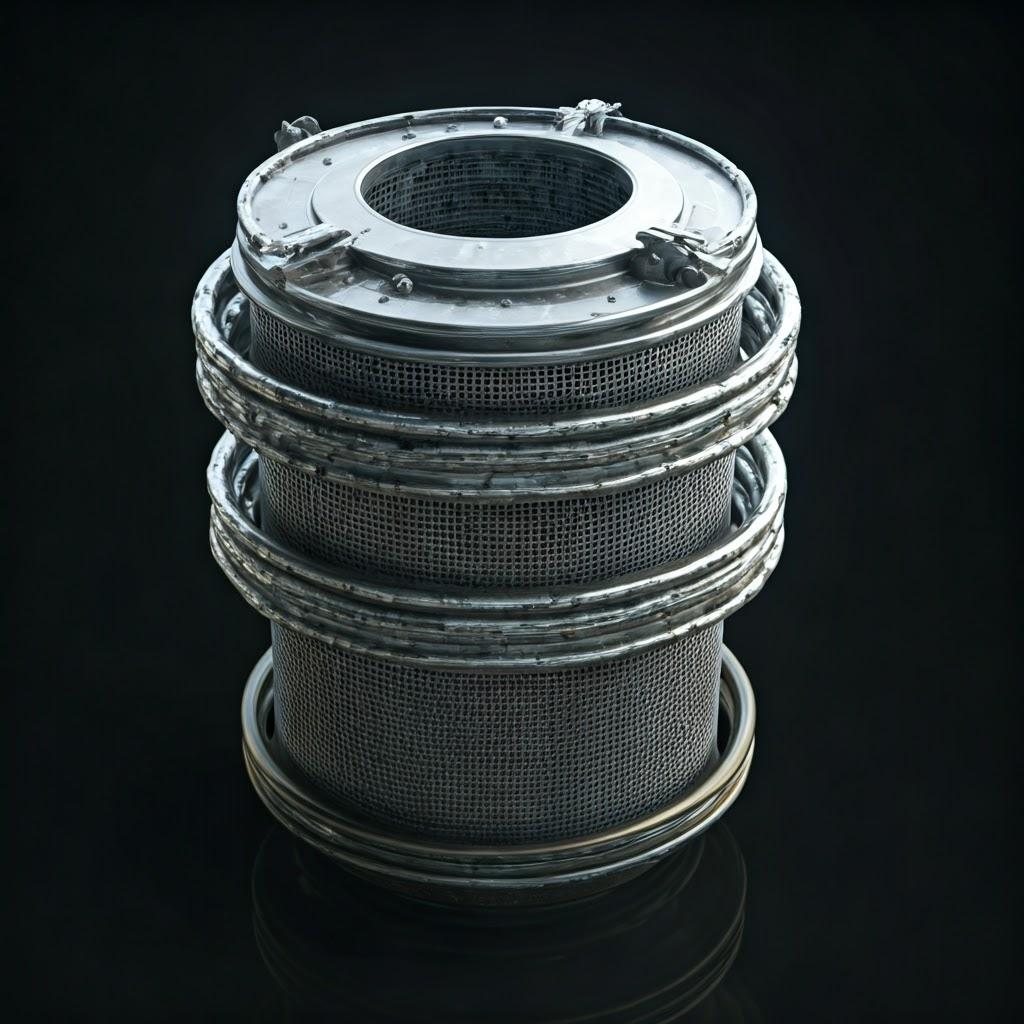
Verständnis der Kostentreiber und Vorlaufzeiten für 3D-gedruckte Wärmetauscher
Obwohl sie erhebliche Leistungsvorteile bietet, ist es wichtig, die Faktoren zu verstehen, die die Kosten und die Produktionszeit für die additive Fertigung von Metallteilen beeinflussen. Anders als bei der traditionellen Massenproduktion, bei der die Werkzeugkosten die Anfangskosten dominieren, sind die AM-Kosten enger mit dem Materialverbrauch und der Maschinenzeit pro Teil verbunden.
Primäre Kostentreiber:
- Materialart und Verbrauch:
- Pulverkosten: Hochleistungslegierungen wie IN625 oder CuCrZr sind wesentlich teurer als AlSi10Mg oder nichtrostende Stähle.
- Teil Volumen & Gewicht: Die Menge des Pulvers, die direkt zur Herstellung des Teils verbraucht wird, ist ein wichtiger Kostenfaktor. Größere oder dichtere Teile kosten mehr.
- Unterstützende Strukturen: Das für die Stützen verwendete Material trägt ebenfalls zu den Kosten bei, was den Vorteil von DfAM zur Minimierung der Stützen unterstreicht.
- Maschinenzeit:
- Bauhöhe: Der wichtigste Faktor für die Druckzeit. Höhere Teile brauchen länger, unabhängig davon, wie viele Teile auf der Bauplatte verschachtelt sind (innerhalb der Grenzen).
- Teil Volumen/Komplexität: Die Höhe ist zwar ausschlaggebend, aber auch das vom Laser-/Elektronenstrahl abgetastete Gesamtvolumen beeinflusst die Zeit. Sehr komplexe Geometrien mit umfangreicher Abtastung verlängern die Zeit.
- Maschine Stundensatz: Abhängig von der AM-Technologie, der Maschinengröße und den Gemeinkosten des Anbieters.
- Arbeit und Einrichtung:
- Vorbereitung der Datei: Vorbereitung der Konstruktionsdatei, Erzeugung von Stützen und Schneiden des Modells.
- Einrichten und Abrüsten der Maschine: Einfüllen des Pulvers, Einrichten des Aufbaus und anschließende Reinigung der Maschine.
- Nachbearbeiten: Dies kann eine erhebliche Kostenkomponente darstellen, da der Arbeitsaufwand für den Spannungsabbau, die Entfernung der Teile, die Entfernung der Halterung, die Pulverabsaugung, die Bearbeitung, die Endbearbeitung und die Inspektion sehr hoch ist. Komplexe Innengeometrien, die eine umfangreiche Reinigung oder die manuelle Entfernung von Halterungen erfordern, erhöhen die Arbeitskosten erheblich.
- Qualitätssicherung und Prüfung:
- Standard-Inspektion: Maßkontrollen, Sichtprüfung.
- Fortgeschrittene ZfP: Anforderungen wie CT-Scans oder FPI verursachen zusätzliche Kosten.
- Dichtheitsprüfung: Unverzichtbar für Wärmetauscher, die zusätzliche Prozesszeit und Kosten verursachen.
- Zertifizierungen: Die Erfüllung bestimmter Branchenzertifizierungen (z. B. AS9100) erfordert eine strengere Prozesskontrolle, Dokumentation und Prüfung, was sich auf die Kosten auswirkt.
- Auftragsvolumen:
- Skalenvorteile: Durch AM werden zwar Werkzeugkosten vermieden, aber es gibt auch einige Größenvorteile. Das Einrichten eines Bauprozesses und die Durchführung von Nachbearbeitungsschritten wird pro Teil oft effizienter, wenn Chargen statt einzelner Prototypen hergestellt werden. Allerdings ist die Kostenreduzierung pro Teil im Allgemeinen weniger dramatisch als bei der traditionellen Massenproduktion.
Typische Vorlaufzeiten:
Die Durchlaufzeit hängt stark von der Komplexität der Teile, der Größe, dem Material, der erforderlichen Nachbearbeitung und der aktuellen Kapazität des Dienstleisters ab.
- Zitieren: 1-3 Arbeitstage (eine druckfertige CAD-Datei vorausgesetzt).
- Drucken:
- Kleine/einfache Prototypen: 2-5 Tage
- Mittlere Komplexität/Größe Teile: 5-10 Tage
- Große/sehr komplexe Teile oder Chargen: 1-3+ Wochen
- Nachbearbeiten: Hochgradig variabel.
- Basic (Stressabbau, Entfernung von Stützen): 2-5 Tage
- Umfangreich (Bearbeitung, Polieren, komplexe Reinigung, Prüfung): 1-3+ Wochen
- Gesamtvorlaufzeit (Tür-zu-Tür):
- Einfache Prototypen: 1-2 Wochen
- Produktionsteile (mäßige Komplexität): 3-6 Wochen
- Komplexe Teile/Lose mit umfangreicher Nachbearbeitung: 6+ Wochen
Es ist von entscheidender Bedeutung, die spezifischen Anforderungen und Zeitpläne mit dem gewählten AM-Anbieter zu einem frühen Zeitpunkt des Projekts zu besprechen. Die Bereitstellung eines klaren technischen Datenpakets (CAD-Modell, Materialspezifikation, Toleranzen, Prüfanforderungen) erleichtert die Erstellung eines genauen Angebots und eine realistische Einschätzung der Vorlaufzeit.
Häufig gestellte Fragen (FAQ) zu 3D-gedruckten Wärmetauschern
Hier finden Sie Antworten auf einige häufig gestellte Fragen von Ingenieuren und Beschaffungsmanagern zur Verwendung von Metall-AM für Wärmetauscher:
- F1: Wie ist der thermische Wirkungsgrad von 3D-gedruckten Wärmetauschern im Vergleich zu herkömmlichen Wärmetauschern (z. B. gelötete Rippenplatten)?
- A: Wenn 3D-gedruckte Wärmetauscher unter Anwendung der DfAM-Prinzipien effektiv entworfen werden, können sie herkömmliche Konstruktionen deutlich übertreffen. AM ermöglicht eine viel höhere Oberflächendichte (unter Verwendung von TPMS oder komplexen Rippen), optimierte Strömungswege zur Verringerung von Stagnation und Verbesserung von Turbulenzen sowie konforme Designs für besseren thermischen Kontakt. Dies führt oft zu einem höheren thermischen Wirkungsgrad bei gleichem Volumen/Gewicht oder zu einem ähnlichen Wirkungsgrad in einem viel kompakteren und leichteren Gehäuse. Das einfache Drucken eines herkömmlichen Designs bringt jedoch möglicherweise keine wesentlichen Vorteile.
- F2: Sind 3D-gedruckte Wärmetauscher aus Metall langlebig und zuverlässig genug für anspruchsvolle Umgebungen in der Automobil- und Luftfahrtindustrie?
- A: Ja, vorausgesetzt, das richtige Material wird ausgewählt, das Teil wird entsprechend konstruiert (unter Berücksichtigung von Druck, Vibration und Temperaturwechsel), mit optimierten Parametern gedruckt, um eine hohe Dichte und geringe Porosität zu gewährleisten, und ordnungsgemäß nachbearbeitet (insbesondere Spannungsabbau). AM-Metallteile aus Legierungen wie IN625, Ti6Al4V oder Spezialstählen können mechanische Eigenschaften aufweisen, die mit denen von Guss- oder Knetwerkstoffen vergleichbar oder ihnen sogar überlegen sind, so dass sie sich nach gründlicher Validierung und Prüfung für raue Betriebsbedingungen eignen. Strenge Qualitätskontrollen und Tests (wie Dichtheitsprüfungen und Ermüdungsanalysen) sind von entscheidender Bedeutung.
- F3: Wie groß ist der typische Kostenunterschied zwischen der Herstellung eines Wärmetauschers mittels AM und herkömmlichen Methoden?
- A: Das hängt stark von der Komplexität, dem Volumen und dem Design ab. Bei einfachen Konstruktionen, die in sehr hohen Stückzahlen (Tausende und mehr) hergestellt werden, sind herkömmliche Verfahren wie das Löten aufgrund von Skaleneffekten oft kostengünstiger. Bei hochkomplexen Konstruktionen, geringen bis mittleren Produktionsmengen, kundenspezifischen Teilen oder Anwendungen, bei denen Leistung, Gewicht und Teilekonsolidierung ausschlaggebend sind, kann AM jedoch wettbewerbsfähig oder sogar billiger sein, wenn man die Gesamtbetriebskosten betrachtet (reduzierte Montage, verbesserte Leistung, vereinfachte Lieferkette). AM zeichnet sich dort aus, wo traditionelle Methoden nur schwer oder gar nicht anwendbar sind.
- F4: Können Sie Wärmetauscher aus anderen Materialien als AlSi10Mg, CuCrZr und IN625 drucken?
- A: Ganz genau. Diese drei sind zwar eine gängige Wahl, um verschiedene Anforderungen (geringes Gewicht, Leitfähigkeit, hohe Temperaturbeständigkeit) auszugleichen, aber bei der Metall-AM können je nach den spezifischen Anforderungen auch andere für Wärmetauscher geeignete Legierungen verwendet werden. Dazu gehören andere Aluminiumlegierungen, verschiedene Edelstahlsorten (z. B. 316L für Korrosionsbeständigkeit), Titanlegierungen (Ti6Al4V für hervorragende Festigkeit im Verhältnis zum Gewicht und Korrosionsbeständigkeit, häufig in der Luft- und Raumfahrt verwendet) und andere Nickelsuperlegierungen (z. B. Hastelloy X). Das Werkstoffportfolio wird ständig erweitert. Die Erörterung Ihrer spezifischen Betriebsumgebung und Anforderungen mit einem fachkundigen Anbieter wie Met3dp wird Ihnen helfen, die optimale Werkstoffauswahl zu treffen.
Schlussfolgerung: Die Zukunft des Wärmemanagements ist additiv
Die Herausforderungen des Wärmemanagements in immer leistungsfähigeren, kompakteren und effizienteren Automobil- und Luftfahrtsystemen erfordern innovative Lösungen. Die additive Fertigung von Metallen hat sich über das Prototyping hinaus zu einer praktikablen und oft überlegenen Produktionsmethode für kritische Komponenten wie Wärmetauscher entwickelt.
Der 3D-Metalldruck befreit die Konstrukteure von den Zwängen der traditionellen Fertigung und ermöglicht so die Herstellung von Wärmetauschern mit:
- Noch nie dagewesene geometrische Komplexität: Dies führt zu einer verbesserten thermischen Leistung durch optimierte Strömungswege und maximierte Oberflächen (TPMS, Gitter).
- Signifikante Gewichtsreduzierung: Reduzierung der Bauteilmasse durch Topologieoptimierung und Materialeffizienz, die für die Fahrzeugdynamik und den Kraftstoffverbrauch entscheidend sind.
- Teil Konsolidierung: Vereinfachung von Baugruppen, Verringerung potenzieller Leckstellen und Straffung der Lieferketten.
- Beschleunigte Entwicklung: Ermöglicht schnelle Iterationen und Funktionstests.
Materialien wie das leichte AlSi10Mg, das hochleitfähige CuCrZr und das robuste IN625 bieten maßgeschneiderte Lösungen für unterschiedliche Betriebsbedingungen. Zwar gibt es Herausforderungen bei Design, Prozesssteuerung und Nachbearbeitung, doch die Zusammenarbeit mit einem erfahrenen und kompetenten AM-Anbieter mindert diese Risiken.
Unternehmen wie Met3dp, die über integriertes Fachwissen in den Bereichen Hochleistungsmetallpulver, fortschrittliche Drucksysteme und Anwendungstechnik verfügen, versetzen die Industrie in die Lage, das volle Potenzial von AM auszuschöpfen. Wir bieten die modernsten Materialien und Technologien, die für die Herstellung der nächsten Generation von Hochleistungs-Wärmemanagementsystemen erforderlich sind.
Die Zukunft eines effizienten, leichten und leistungsstarken Wärmemanagements in der Automobil- und Luftfahrtindustrie liegt in der Nutzung der Designfreiheit und der Fertigungsmöglichkeiten der additiven Fertigung von Metallen.
Sind Sie bereit zu erfahren, wie 3D-gedruckte Wärmetauscher Ihre Herausforderungen im Wärmemanagement revolutionieren können? Kontakt Met3dp heute, um Ihre Anwendung mit unseren Experten für additive Fertigung zu besprechen und zu erfahren, wie unsere umfassenden Lösungen Ihre Innovation vorantreiben können.
Teilen auf
MET3DP Technology Co., LTD ist ein führender Anbieter von additiven Fertigungslösungen mit Hauptsitz in Qingdao, China. Unser Unternehmen ist spezialisiert auf 3D-Druckgeräte und Hochleistungsmetallpulver für industrielle Anwendungen.
Fragen Sie an, um den besten Preis und eine maßgeschneiderte Lösung für Ihr Unternehmen zu erhalten!
Verwandte Artikel
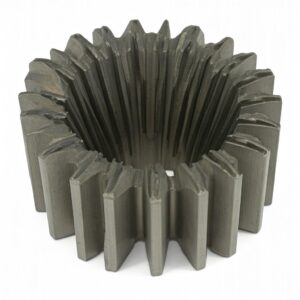
Hochleistungs-Düsenschaufelsegmente: Revolutionierung der Turbineneffizienz mit 3D-Metalldruck
Mehr lesen "Über Met3DP
Aktuelles Update
Unser Produkt
KONTAKT US
Haben Sie Fragen? Senden Sie uns jetzt eine Nachricht! Wir werden Ihre Anfrage mit einem ganzen Team nach Erhalt Ihrer Nachricht bearbeiten.
Holen Sie sich Metal3DP's
Produkt-Broschüre
Erhalten Sie die neuesten Produkte und Preislisten
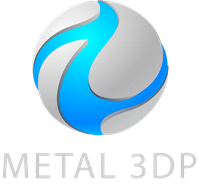
Metallpulver für 3D-Druck und additive Fertigung