Motorgehäuse 3D-Druck mit Aluminium und Titan
Inhaltsübersicht
Einführung: Revolutionierung der Herstellung von Motorgehäusen durch 3D-Druck von Metall
Das Motorgehäuse, das je nach Anwendung und Branchenterminologie oft als Motorblock, Gehäuse oder Kurbelgehäuse bezeichnet wird, ist ein Eckpfeiler in praktisch allen Verbrennungsmotoren und vielen anderen Arten von Stromerzeugungs- und -umwandlungsmaschinen. Es dient als strukturelles Fundament und umschließt kritische bewegliche Teile wie Kolben, Kurbelwellen und Nockenwellen, während es gleichzeitig Befestigungspunkte für Hilfssysteme und das Management lebenswichtiger Flüssigkeiten wie Öl und Kühlmittel bietet. Bei der Herstellung dieser komplexen und robusten Komponenten wurden bisher vor allem etablierte Verfahren wie Gießen (Sand- und Druckguss) und anschließende umfangreiche mechanische Bearbeitung eingesetzt. Diese konventionellen Verfahren sind zwar effektiv, stoßen aber oft an ihre Grenzen, wenn es um Konstruktionsfreiheit, Gewichtsoptimierung, Vorlaufzeiten für die Werkzeugherstellung und die Fähigkeit geht, hochgradig kundenspezifische oder Kleinserien kostengünstig zu produzieren. Das Streben nach höherer Leistung, verbesserter Kraftstoffeffizienz, geringeren Emissionen und rationalisierten Lieferketten in Branchen wie der Luft- und Raumfahrt, der Automobilindustrie und der industriellen Fertigung führt zu einem Paradigmenwechsel hin zu fortschrittlicheren Produktionsverfahren. Der Einstieg in die additive Fertigung von Metallen (AM), allgemein bekannt als Metall 3D-Druck. Diese transformative Technologie bewegt sich schnell über das Prototyping hinaus in den Bereich der Serienproduktion für anspruchsvolle Anwendungen und bietet beispiellose Möglichkeiten, die Art und Weise, wie kritische Komponenten wie Motorgehäuse entworfen, entwickelt und hergestellt werden, neu zu gestalten.
3D-Drucktechnologien für Metall, wie selektives Laserschmelzen (SLM), direktes Metall-Lasersintern (DMLS) und Elektronenstrahlschmelzen (EBM), bauen Teile Schicht für Schicht direkt aus digitalen CAD-Modellen auf und verwenden dabei Hochenergiequellen (Laser oder Elektronenstrahlen), um feine Metallpulver zu verschmelzen. Dieser additive Ansatz unterscheidet sich grundlegend von subtraktiven (maschinelle Bearbeitung) oder formgebenden (Gießen, Schmieden) Verfahren und bietet eine Reihe von Vorteilen, die perfekt auf die Herausforderungen der modernen Motorgehäuseproduktion abgestimmt sind. Stellen Sie sich Motorgehäuse mit komplizierten inneren Kühlkanälen vor, die exakt den Konturen der wärmeerzeugenden Bereiche folgen, was durch Gießen oder Bohren unmöglich zu erreichen ist. Stellen Sie sich deutlich leichtere Strukturen vor, die durch Topologieoptimierung erreicht werden, wobei nur dort Material entfernt wird, wo es strukturell nicht notwendig ist, was zu direkten Kraftstoffeinsparungen in Fahrzeugen und Flugzeugen führt. Stellen Sie sich die Möglichkeit vor, mehrere Komponenten in einem einzigen, integrierten 3D-gedruckten Teil zusammenzufassen und so die Montagezeit, potenzielle Leckagepfade und die Gesamtkomplexität des Systems zu reduzieren. Darüber hinaus macht AM teure und zeitaufwändige Werkzeuge (Gussformen oder Gesenke) überflüssig, was die Herstellung von kundenspezifischen Designs, alten Teilen, für die es keine Werkzeuge mehr gibt, oder kleinen bis mittleren Produktionsserien wirtschaftlich macht. Diese Fähigkeit ist von unschätzbarem Wert für Leistungstuning, Nischenfahrzeugmärkte, schnelle Entwicklungszyklen und Ersatzteilmanagement auf Abruf und entspricht direkt den Bedürfnissen von Beschaffungsmanagern, die nach agilen und effizienten Fertigungslösungen suchen.
Unternehmen, die an der Spitze dieser technologischen Welle stehen, wie Met3dpliefern die wesentlichen Bausteine für diese Fertigungsrevolution. Met3dp mit Hauptsitz in Qingdao, China, ist nicht nur auf die Entwicklung und Lieferung von branchenführenden 3D-Druckgeräten aus Metall spezialisiert, die für ihr Druckvolumen, ihre Genauigkeit und Zuverlässigkeit bekannt sind, sondern auch auf die Herstellung von Hochleistungsmetallpulvern, die für die Herstellung von dichten, hochwertigen Teilen entscheidend sind. Durch den Einsatz fortschrittlicher Pulverherstellungstechniken wie Gaszerstäubung und Plasma-Rotations-Elektroden-Verfahren (PREP) stellt Met3dp sicher, dass seine kugelförmigen Metallpulver eine ausgezeichnete Fließfähigkeit und Konsistenz aufweisen, was zu hervorragenden mechanischen Eigenschaften der endgültigen gedruckten Komponenten führt. Met3dp verfügt über ein breites Spektrum an Materialien, die für Triebwerksgehäuse relevant sind, darunter Aluminiumlegierungen, Titanlegierungen und Superlegierungen auf Nickelbasis. Da Ingenieure und Beschaffungsspezialisten zunehmend das Potenzial von AM erforschen, ist das Verständnis ihrer Anwendung auf Komponenten wie Motorgehäuse entscheidend, um einen Wettbewerbsvorteil zu erhalten und die Vorteile der nächsten Generation der Fertigung voll auszuschöpfen. Dieser Artikel taucht tief in die Welt der 3D-gedruckten Motorgehäuse ein und untersucht ihre Anwendungen, die überzeugenden Vorteile der Metall-AM, empfohlene Materialien wie AlSi10Mg, Ti-6Al-4V und IN718, kritische Designüberlegungen, erreichbare Präzision, Nachbearbeitungsanforderungen, potenzielle Herausforderungen, Kriterien für die Auswahl von Zulieferern, Kostenfaktoren und häufig gestellte Fragen und bietet damit einen umfassenden Leitfaden für Unternehmen, die diesen innovativen Ansatz in Betracht ziehen.
Wozu werden Motorgehäuse verwendet? Schlüsselindustrien und Funktionen
Das Motorgehäuse ist weit mehr als nur eine Schutzhülle; es ist ein multifunktionales, hoch beanspruchtes Bauteil, das das Rückgrat eines Motors oder eines verwandten Antriebsstrang-/Fluidsystems bildet. Seine Konstruktion und sein Material müssen strenge Anforderungen erfüllen, die durch die spezifische Anwendung, die Betriebsumgebung und die Leistungserwartungen vorgegeben sind. Das Verständnis der vielfältigen Aufgaben und industriellen Anwendungen von Motorgehäusen verdeutlicht, warum die Optimierung ihrer Konstruktion und ihres Herstellungsprozesses durch Technologien wie den 3D-Metalldruck für B2B-Lieferanten, -Hersteller und -Endverbraucher ein so großes Potenzial birgt.
Kernfunktionen eines Motorgehäuses:
- Strukturelle Unterstützung: Stellt den Hauptrahmen des Motors dar und trägt die Kurbelwelle, die Zylinder (oder Zylinderlaufbuchsen) und häufig auch den/die Zylinderkopf/Zylinderköpfe. Er muss erheblichen mechanischen Belastungen durch Verbrennungsdruck, rotierende/umlaufende Massen und externe Vibrationen standhalten.
- Eindämmung: Umschließt die beweglichen Teile im Inneren und schützt sie vor Verunreinigungen von außen (Schmutz, Wasser) und enthält Motorflüssigkeiten (Schmieröl, Kühlmittel). Die Aufrechterhaltung der Dichtungsintegrität ist entscheidend.
- Ausrichtung: Gewährleistet die präzise Ausrichtung kritischer Komponenten wie der Hauptlager der Kurbelwelle und der Zylinderbohrungen, was für den effizienten Betrieb, die Minimierung des Verschleißes und die Gewährleistung der Langlebigkeit unerlässlich ist. Die Toleranzen sind oft sehr eng.
- Wärmeableitung: Spielt eine Rolle beim Wärmemanagement des Motors, oft mit Wassermänteln oder Kühlrippen, um die Wärme von den Verbrennungskammern und Zylindern an das Kühlsystem (Flüssigkeit oder Luft) zu übertragen.
- Flüssigkeitsmanagement: Er enthält komplizierte Kanäle für Schmieröl (Kanäle, Zuleitungen zu den Lagern) und Kühlmittel (Wassermäntel). Die Konstruktion muss einen effizienten Durchfluss gewährleisten und Leckagen verhindern.
- Befestigungspunkte: Bietet sichere Stellen für die Befestigung des Motors am Fahrzeug- oder Geräterahmen sowie Befestigungspunkte für Hilfskomponenten wie Anlasser, Lichtmaschine, Wasserpumpe, Ölpumpe, Sensoren und Kraftübertragung/Getriebe.
- Geräusch- und Schwingungsdämpfung: Die Masse und Steifigkeit des Gehäuses tragen dazu bei, Motorgeräusche und Vibrationen zu dämpfen, den Fahrerkomfort zu verbessern und die Ermüdung der umgebenden Strukturen zu verringern.
Schlüsselindustrien und spezifische Anwendungen:
- Automobilindustrie:
- Personenkraftwagen: Motorblöcke (Kurbelgehäuse) für Benzin- und Dieselmotoren, Getriebegehäuse, Differentialgehäuse. Das Streben nach Leichtbau zur Verbesserung des Kraftstoffverbrauchs und der Leistung ist von größter Bedeutung. Aluminiumlegierungen (wie AlSi10Mg) sind weit verbreitet, aber AM eröffnet Möglichkeiten für optimierte Designs und potenziell leistungsfähigere Materialien in Nischenanwendungen. Großhandelslieferketten sind auf gleichbleibende Qualität und kostengünstige Produktion angewiesen.
- Motorsport: Hochleistungsmotorblöcke, Getriebegehäuse, Trockensumpfwannen. Hier sind Individualisierung, schnelle Iteration, Leichtbau und Leistungsmaximierung durch komplexe Innengeometrien (Öl-/Kühlmittelkanäle) entscheidend. Materialien wie hochfestes Aluminium, Titan (Ti-6Al-4V) und manchmal sogar Nickelsuperlegierungen (IN718) für Komponenten in der Nähe des Turboladers werden in Betracht gezogen. AM ermöglicht es den Teams, sich durch maßgeschneiderte Designs einen Wettbewerbsvorteil zu verschaffen.
- Nutzfahrzeuge (Lastkraftwagen, Busse): Größere, robuste Kurbelgehäuse von Dieselmotoren, Getriebegehäuse. Langlebigkeit, Zuverlässigkeit und Kosteneffizienz über eine lange Lebensdauer sind entscheidend. Während der traditionelle Guss dominiert, könnte AM Lösungen für Spezialfahrzeuge oder den Ersatz von Altteilen bieten.
- Luft- und Raumfahrt:
- Flugzeugtriebwerke (Jet & Turboprop): Getriebegehäuse, Nebenantriebsgehäuse, Lagergehäuse, Strukturgehäuse im Motorkern. Extremer Leichtbau (mit Ti-6Al-4V), hohe Betriebstemperaturen (die IN718 oder ähnliche Superlegierungen erfordern) und absolute Zuverlässigkeit sind nicht verhandelbar. AM ermöglicht komplexe, hochgradig optimierte Geometrien und die Konsolidierung von Teilen, wodurch das Gewicht reduziert und das Verhältnis zwischen Anschaffung und Betrieb verbessert wird. Strenge Zertifizierungen (AS9100) sind für Zulieferer obligatorisch.
- Raumfahrt & Trägerraketen: Komponenten von Raketentriebwerken, Turbopumpengehäuse, Gehäuse von Treibstoffmanagementsystemen. Ähnliche Anforderungen wie bei Flugzeugtriebwerken, aber oft mit noch extremeren Temperaturunterschieden und Druckanforderungen. AM erleichtert die schnelle Entwicklung und Produktion komplizierter Komponenten, die für komplexe Strömungsdynamik und strukturelle Integrität benötigt werden.
- Industrielle Fertigung und Stromerzeugung:
- Stationäre Motoren (Generatoren, Pumpen): Kurbelgehäuse, Gehäuse für Industriepumpen, Kompressoren und Turbinen. Zuverlässigkeit, Lebensdauer und oft auch Lärmreduzierung sind wichtige Faktoren. AM kann für kundenspezifische Konfigurationen, Ersatzteile für veraltete Geräte, für die es keine Originalwerkzeuge mehr gibt, oder Komponenten mit verbesserten Kühlungs- oder Haltbarkeitsmerkmalen eingesetzt werden.
- Schiffsmotoren: Motorblöcke, Gehäuse von Getrieben. Die Korrosionsbeständigkeit (insbesondere in Salzwasser) ist neben der Haltbarkeit ein wichtiger Aspekt. Spezielle Legierungen, die für den Einsatz in der Schifffahrt geeignet sind, können mittels AM bearbeitet werden.
- Schwermaschinen (Bauwesen, Landwirtschaft): Motorblöcke, Gehäuse für Hydrauliksysteme, Getriebegehäuse. Robustheit und Kosteneffizienz sind die wichtigsten Faktoren. AM kann für spezielle Geräte oder optimierte Ersatzteile eingesetzt werden.
In diesen unterschiedlichen Branchen stehen Beschaffungsmanager und Ingenieure vor den gleichen Herausforderungen: Beschaffung zuverlässiger Lieferanten, Verwaltung des Lagerbestands für zahlreiche Konfigurationen, Verkürzung der Vorlaufzeiten für Entwicklung und Produktion, Minimierung des Gewichts bei gleichzeitiger Beibehaltung der Festigkeit und Kontrolle der Herstellungskosten. Die Fähigkeit, komplexe Motorgehäuse auf Anfrage zu produzieren, indem man 3D-Druck von Metall bietet eine überzeugende Lösung für viele dieser Herausforderungen und ermöglicht flexiblere, effizientere und potenziell leistungsstärkere Designs, die auf die spezifischen Anforderungen der Branche zugeschnitten sind. Met3dp ist mit seinen robusten Drucksystemen und seinem hochwertigen Pulverportfolio, darunter AlSi10Mg, Ti-6Al-4V und IN718, gut positioniert, um mit Unternehmen in diesen Sektoren zusammenzuarbeiten und die Vorteile der additiven Fertigung für kritische Triebwerkskomponenten zu nutzen.
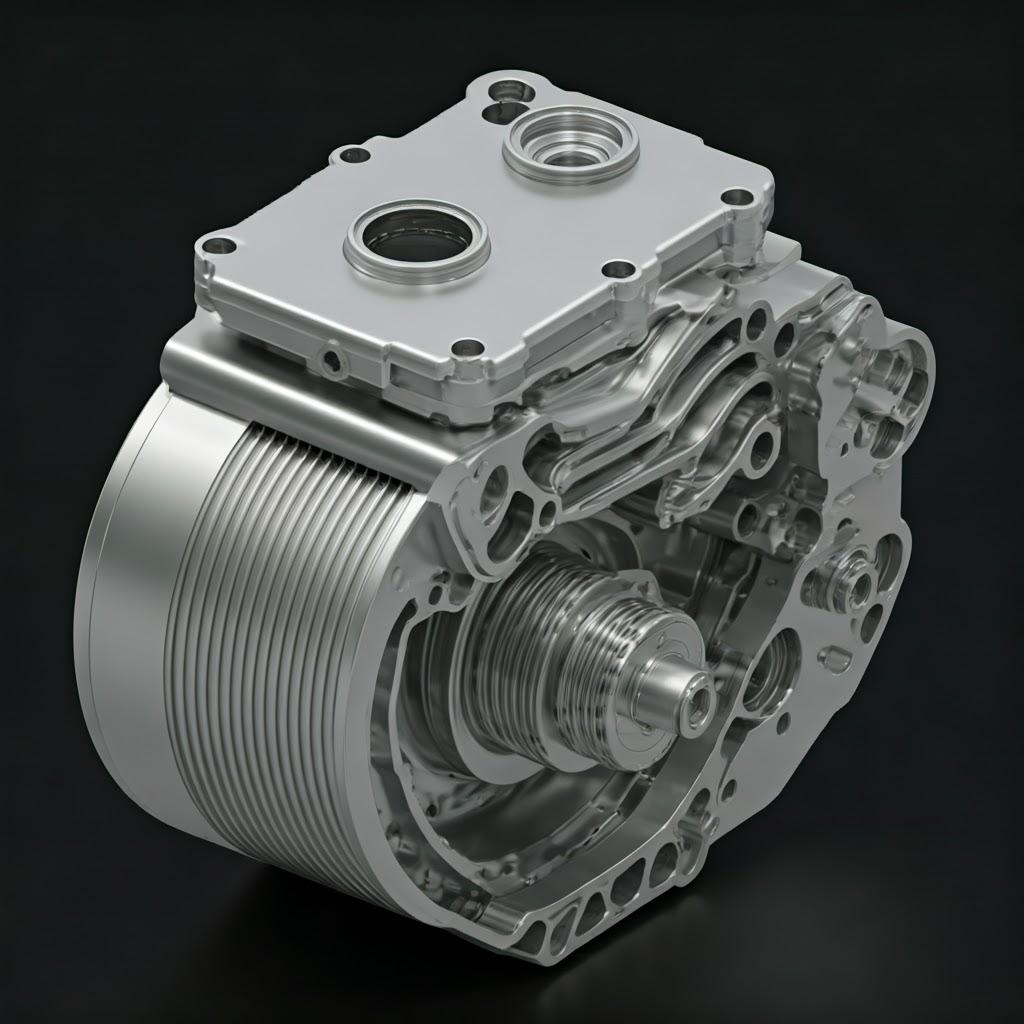
Warum Metalladditive Fertigung für Motorgehäuse? Vorteile gegenüber traditionellen Methoden
Herkömmliche Fertigungsverfahren wie Gießen und maschinelle Bearbeitung haben sich in der Industrie seit Jahrzehnten bei der Herstellung von Motorgehäusen bewährt. Sie weisen jedoch inhärente Beschränkungen auf, die durch die additive Fertigung von Metall (AM) wirksam überwunden werden können. Für Ingenieure, die nach Innovation streben, und für Beschaffungsmanager, die auf Effizienz und Kosteneffizienz achten, ist das Verständnis der eindeutigen Vorteile der Metall-AM der Schlüssel, um fundierte Entscheidungen über zukünftige Fertigungsstrategien zu treffen. Bei der Umstellung auf AM geht es nicht nur um die Einführung einer neuen Technologie, sondern um die Erschließung eines neuen Niveaus an Leistung, Designfreiheit und Flexibilität in der Lieferkette, die auf wettbewerbsintensiven globalen Märkten immer wichtiger werden.
Grenzen der traditionellen Fertigung (Guss und Bearbeitung):
- Design-Zwänge: Das Gießen beruht auf Formen und Kernen, was die Komplexität der inneren Merkmale (z. B. hinterschnittene Kanäle, komplizierte Gitter) einschränkt. Um komplexe Innengeometrien zu erreichen, müssen oft mehrere Gussteile zusammengesetzt oder aufwendig und kostspielig bearbeitet werden.
- Werkzeugkosten und Vorlaufzeiten: Die Herstellung von Gussformen (für den Guss) oder speziellen Vorrichtungen (für die Bearbeitung) ist teuer und zeitaufwändig. Dies macht die Produktion von Kleinserien, Prototypen und Design-Iterationen langsam und kostspielig. Jede Konstruktionsänderung macht eine Änderung oder einen Austausch des Werkzeugs erforderlich.
- Materialabfälle: Bei der subtraktiven Fertigung (spanabhebende Bearbeitung) wird zunächst ein größerer Materialblock abgetragen, was zu erheblichem Ausschuss führt (niedriges Verhältnis zwischen Einkauf und Fertigung), insbesondere bei teuren Materialien wie Titan oder Superlegierungen. Während das Gießen zunächst materialsparender ist, fällt bei der anschließenden Bearbeitung immer noch Abfall an.
- Herausforderungen bei der Gewichtsoptimierung: Optimale Leichtbauweise allein durch Gießen und Bearbeitung zu erreichen, ist schwierig. Material kann nur dort entfernt werden, wo die Werkzeuge hinkommen, und das Gießen erfordert minimale Wandstärken und Entformungswinkel, wobei oft nicht tragendes Material intakt bleibt.
- Teil Konsolidierung Schwierigkeitsgrad: Komplexe Baugruppen erfordern oft, dass mehrere Einzelteile gegossen, bearbeitet und dann zusammengefügt (geschweißt, geschraubt) werden, was die Montagezeit, das Gewicht, potenzielle Leckstellen und Probleme mit der Toleranzüberlagerung erhöht.
- Komplexität der Lieferkette: Die Verwaltung von Gießereien, Maschinenwerkstätten, Montagelinien und der damit verbundenen Logistik für traditionell gefertigte Teile kann sehr komplex sein, insbesondere bei globalen Aktivitäten oder vielfältigen Produktportfolios. Lange Vorlaufzeiten im Zusammenhang mit der Werkzeug- und Produktionsplanung können die Reaktionsfähigkeit behindern.
Vorteile der additiven Fertigung von Motorgehäusen aus Metall:
Metal AM geht viele dieser Einschränkungen direkt an und bietet überzeugende Vorteile für die Produktion von Motorgehäusen:
- Beispiellose Designfreiheit:
- Komplexe Geometrien: AM baut Teile Schicht für Schicht auf und ermöglicht so die Herstellung hochkomplexer innerer und äußerer Merkmale ohne die Einschränkungen von Formen oder Werkzeugzugang. Dies ermöglicht:
- Konforme Kühl-/Schmierkanäle: Die Durchgänge können komplexen Oberflächen oder wärmebeeinflussten Zonen genau folgen, um das Wärmemanagement oder die gezielte Schmierung zu verbessern, was auf herkömmliche Weise nicht möglich ist.
- Interne Netze und optimierte Strukturen: Topologie-Optimierungssoftware kann organische, lastpfadoptimierte Designs erstellen, bei denen Material aus unkritischen Bereichen entfernt und interne Gitterstrukturen für mehr Steifigkeit bei minimalem Gewicht eingebaut werden.
- Nutzen: Leichtere, effizientere Konstruktionen, verbesserte Leistung (bessere Kühlung, Schmierung), Potenzial für verbesserte Geräusch- und Vibrationsdämpfung durch technische Strukturen.
- Komplexe Geometrien: AM baut Teile Schicht für Schicht auf und ermöglicht so die Herstellung hochkomplexer innerer und äußerer Merkmale ohne die Einschränkungen von Formen oder Werkzeugzugang. Dies ermöglicht:
- Teil Konsolidierung:
- Reduzierte Montage: Mehrere Komponenten, die zuvor separat hergestellt und zusammengebaut wurden, können oft neu entworfen und als ein einziges, monolithisches Teil gedruckt werden.
- Nutzen: Geringere Teilezahl, weniger Montageschritte und -kosten, weniger potenzielle Leckagepfade oder Fehlerstellen, verbesserte strukturelle Integrität, vereinfachte Lieferkette für Beschaffungsmanager.
- Signifikante Gewichtsreduzierung:
- Topologie-Optimierung: Wie bereits erwähnt, ermöglicht AM die praktische Umsetzung von Entwürfen, die durch Topologieoptimierung entstanden sind, und führt zu einer erheblichen Gewichtsreduzierung (oft 20-50% oder mehr) bei gleichbleibender oder sogar höherer struktureller Leistung.
- Nutzen: Verbesserte Kraftstoffeffizienz (Automobil, Luft- und Raumfahrt), höhere Nutzlast (Luft- und Raumfahrt), bessere Fahrdynamik (Automobil, Motorsport), geringere Gesamtmasse des Systems.
- Rapid Prototyping und Iteration:
- Werkzeugfreie Produktion: Die Teile werden direkt aus den CAD-Daten gedruckt, so dass keine Gussformen oder Matrizen erforderlich sind. Designänderungen können schnell in das digitale Modell implementiert und innerhalb von Tagen, nicht Wochen oder Monaten, neu gedruckt werden.
- Nutzen: Schnellere Entwicklungszyklen, geringere F&E-Kosten, die Möglichkeit, mehrere Konstruktionsvarianten schnell zu testen, kürzere Markteinführungszeiten für neue Motorkonstruktionen.
- Personalisierung und Kleinserienproduktion:
- Kostengünstige kleine Chargen: Da keine Werkzeugkosten anfallen, ist AM für die Herstellung von kundenspezifischen Motorgehäusen (z. B. für den Motorsport oder Spezialgeräte) oder für Kleinserien, die eine Investition in herkömmliche Werkzeuge nicht rechtfertigen würden, wirtschaftlich sinnvoll.
- Nutzen: Die Fähigkeit, Nischenmärkte zu bedienen, maßgeschneiderte Lösungen anzubieten und ältere Teile auf Anfrage zu produzieren, ohne einen teuren Werkzeugbestand zu unterhalten.
- Materialeffizienz:
- Fast-Netzform: Bei AM-Verfahren wird in der Regel nur das Material verwendet, das für die Herstellung des Teils und seiner Halterungen benötigt wird, was im Vergleich zur subtraktiven Bearbeitung zu deutlich weniger Abfall führt, was insbesondere bei teuren Legierungen für die Luft- und Raumfahrt wie Ti-6Al-4V oder IN718 wichtig ist. Ungeschmolzenes Pulver kann oft recycelt werden.
- Nutzen: Geringere Rohstoffkosten, verbesserte Nachhaltigkeit und ein besseres Verhältnis zwischen Anschaffung und Nutzung sind entscheidend für die Wirtschaftlichkeit der Luft- und Raumfahrt.
- Vereinfachung der Lieferkette und digitale Bestandsaufnahme:
- Fertigung auf Abruf: Teile können bei Bedarf näher am Ort des Bedarfs hergestellt werden, wodurch die Abhängigkeit von komplexen globalen Lieferketten und großen physischen Beständen verringert wird. Entwürfe können digital gespeichert werden.
- Nutzen: Geringere Lagerkosten, Minimierung des Veralterungsrisikos der Bestände, höhere Belastbarkeit der Lieferkette, schnellere Reaktion auf die Nachfrage nach Ersatzteilen oder Sonderbestellungen.
Nutzung der Fähigkeiten von Met3dp:
Durch die Wahl eines Partners wie Met3dp werden diese Vorteile noch verstärkt. Die Konzentration auf fortschrittliche Drucksysteme (wie SEBM, das für die Verarbeitung reaktiver Materialien und die Reduzierung von Eigenspannungen bekannt ist) und hochwertige, sphärische Metallpulver gewährleistet, dass die theoretischen Vorteile von AM in reale, leistungsstarke Motorgehäuse umgesetzt werden. Die branchenführenden Gaszerstäubungs- und PREP-Technologien von Met3dp produzieren Pulver mit der Konsistenz und Reinheit, die für anspruchsvolle Anwendungen in der Luft- und Raumfahrt, im Automobilbau und in der Medizintechnik erforderlich sind, und stellen sicher, dass die fertigen Teile die erforderliche Dichte, die mechanischen Eigenschaften und die Zuverlässigkeit aufweisen. Ihre umfassenden Lösungen, die Anlagen, Materialien und Anwendungsentwicklungsdienste umfassen, ermöglichen es Unternehmen, das Potenzial von AM für Komponenten wie Motorgehäuse voll auszuschöpfen. Während herkömmliche Methoden weiterhin für die standardisierte Großserienproduktion geeignet sind, bietet Metall-AM einen leistungsstarken, ergänzenden und oft überlegenen Ansatz für Komponenten, die hohe Leistung, komplexe Designs, geringes Gewicht und Flexibilität in der Fertigung erfordern.
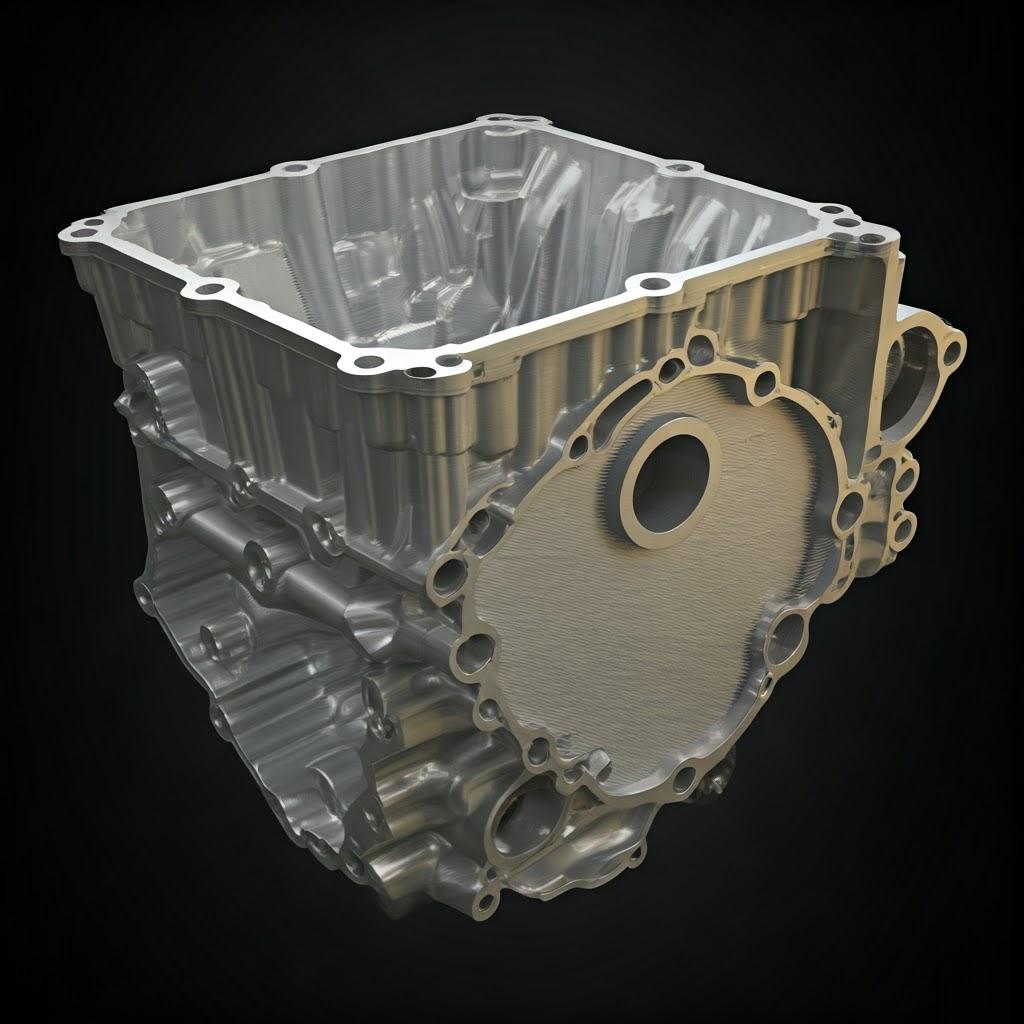
Empfohlene Materialien für 3D-gedruckte Motorgehäuse: AlSi10Mg, Ti-6Al-4V, IN718
Die Wahl des richtigen Materials ist für den Erfolg jeder technischen Komponente von grundlegender Bedeutung, und 3D-gedruckte Motorgehäuse bilden da keine Ausnahme. Die Wahl hängt stark von den spezifischen Anforderungen der Anwendung ab, einschließlich Betriebstemperatur, strukturelle Lasten, Gewichtsziele, Umweltbedingungen (Korrosion) und Kostenbeschränkungen. Die additive Fertigung von Metallen bietet ein wachsendes Portfolio an Werkstoffen, aber für Motorgehäuse stechen drei Legierungen aufgrund ihrer gut bekannten Eigenschaften, ihrer Verarbeitbarkeit und ihrer Bedeutung für Schlüsselindustrien hervor: Aluminium AlSi10Mg, Titan Ti-6Al-4V und die Nickellegierung IN718. Jedes dieser Werkstoffe bietet ein einzigartiges Gleichgewicht an Eigenschaften, die sie für verschiedene Arten von Motorgehäuseanwendungen geeignet machen. Um optimale Ergebnisse zu erzielen, ist die Zusammenarbeit mit einem kompetenten Metallpulverlieferanten und AM-Dienstleister wie Met3dp, der über umfassende Erfahrung in der Verarbeitung dieser spezifischen Materialien verfügt, von entscheidender Bedeutung. Met3dp stellt diese hochwertigen Pulver nicht nur unter Verwendung fortschrittlicher Zerstäubungstechniken her, sondern verfügt auch über umfangreiche Erfahrungen beim Druck auf seinen fortschrittlichen SEBM-Systemen, wodurch sichergestellt wird, dass die Teile strenge Qualitäts- und Leistungsstandards erfüllen.
1. Aluminium-Legierung: AlSi10Mg
- Beschreibung: AlSi10Mg ist eine weit verbreitete Aluminiumlegierung für den Guss und hat sich zu einem der beliebtesten Materialien für die Metall-AM mittels Laser Powder Bed Fusion (LPBF) Verfahren wie SLM/DMLS entwickelt. Sie enthält Silizium (Si) zur Verbesserung der Gießbarkeit (relevant für das Schmelzbadverhalten bei AM) und der Fließfähigkeit sowie Magnesium (Mg) zur Ausscheidungshärtung durch Wärmebehandlung.
- Wichtige Eigenschaften und Vorteile für Motorgehäuse:
- Leichtes Gewicht: Aluminiumlegierungen haben im Vergleich zu Stählen oder Titan eine geringe Dichte (ca. 2,68 g/cm³), was sie ideal für Anwendungen in der Automobil- und Luftfahrtindustrie macht, wo eine Gewichtsreduzierung für die Kraftstoffeffizienz und Leistung entscheidend ist.
- Gutes Verhältnis von Stärke zu Gewicht: AlSi10Mg ist zwar nicht so fest wie Stahl oder Titan, bietet aber ein ausgewogenes Verhältnis von Festigkeit und geringem Gewicht, das für viele Motor- und Getriebegehäuseanwendungen ausreicht, insbesondere nach einer entsprechenden Wärmebehandlung (z. B. T6).
- Ausgezeichnete Wärmeleitfähigkeit: Aluminiumlegierungen leiten Wärme effektiv ab, was für Motorkomponenten, die thermische Belastungen bewältigen müssen, von Vorteil ist.
- Gute Korrosionsbeständigkeit: Bietet ausreichende Korrosionsbeständigkeit in typischen Betriebsumgebungen.
- Bewährte Verarbeitbarkeit: Es ist eine der ausgereiftesten Legierungen für LPBF, mit genau definierten Druckparametern und Nachbearbeitungsprotokollen (wie Spannungsabbau und T6-Wärmebehandlung).
- Kostengünstig (Relativ): Im Vergleich zu Titan- oder Nickelsuperlegierungen ist AlSi10Mg-Pulver deutlich preiswerter, so dass es sich für eine breite Palette von Automobil- und Industrieanwendungen anbietet.
- Typische Anwendungen: Automobil-Motorblöcke (insbesondere für Leistungs-/Nischenfahrzeuge), Getriebegehäuse, Ölwannen, Getriebegehäuse, Abdeckungen, Halterungen, Prototyping-Gehäuse für Form-/Passform-/Funktionsprüfungen.
- Erwägungen: Geringere Hochtemperaturfestigkeit im Vergleich zu Ti oder IN718 (im Allgemeinen bis zu ~150-200°C je nach Belastung geeignet). Erfordert eine sorgfältige Wärmebehandlung, um optimale Eigenschaften zu erzielen. Kann im Vergleich zu anderen Legierungen schwierig zu schweißen oder zu reparieren sein.
Tabelle: Übersicht der AlSi10Mg-Eigenschaften (typische Werte nach T6-Wärmebehandlung)
Eigentum | Typischer Wert (LPBF, T6) | Einheit | Bedeutung für Motorgehäuse |
---|---|---|---|
Dichte | ~2.68 | g/cm³ | Hauptantrieb für Leichtbau |
Endgültige Zugfestigkeit | 430 – 480 | MPa | Zeigt die Bruchfestigkeit unter Spannung an |
Streckgrenze | 280 – 350 | MPa | Spannung, bei der eine dauerhafte Verformung beginnt |
Dehnung beim Bruch | 6 – 10 | % | Maß für die Duktilität vor dem Bruch |
Elastizitätsmodul | ~70 | GPa | Steifigkeit, Widerstand gegen elastische Verformung |
Wärmeleitfähigkeit | 120 – 140 | W/(m-K) | Fähigkeit, Wärme von heißen Stellen wegzuleiten |
Maximale Betriebstemperatur | ~150 – 200 | °C | Ungefährer Grenzwert für die Beibehaltung einer signifikanten Stärke |
In Blätter exportieren
2. Titan-Legierung: Ti-6Al-4V (Grad 5)
- Beschreibung: Ti-6Al-4V (oft Ti64 genannt) ist das Arbeitspferd der Titanindustrie und macht über 50% des gesamten Titanverbrauchs aus. Es handelt sich um eine Alpha-Beta-Legierung, die Aluminium (Al) und Vanadium (V) enthält und für ihre ausgezeichnete Kombination aus hoher Festigkeit, geringer Dichte und hervorragender Korrosionsbeständigkeit bekannt ist. Es wird häufig mittels LPBF und Elektronenstrahlschmelzen (EBM) verarbeitet. Die Erfahrung von Met3dp mit EBM (SEBM - Selective Electron Beam Melting) ist besonders wichtig, da EBM oft Ti-6Al-4V-Teile mit geringeren Eigenspannungen im Vergleich zu LPBF produziert.
- Wichtige Eigenschaften und Vorteile für Motorgehäuse:
- Außergewöhnliches Verhältnis von Stärke zu Gewicht: Ti-6Al-4V bietet eine mit vielen Stählen vergleichbare Festigkeit, jedoch bei einer um etwa 40% geringeren Dichte (~4,43 g/cm³). Dies ist ein großer Vorteil für Triebwerkskomponenten in der Luft- und Raumfahrt sowie für Hochleistungsanwendungen in der Automobilindustrie, bei denen die Minimierung der Masse von größter Bedeutung ist.
- Eignung für hohe Temperaturen: Behält eine gute Festigkeit bei hohen Temperaturen (bis zu ~350-400°C), deutlich höher als Aluminiumlegierungen.
- Ausgezeichnete Korrosionsbeständigkeit: Hochgradig korrosionsbeständig gegenüber Motorflüssigkeiten, Witterungseinflüssen und sogar Salzwasser, wodurch es sich für anspruchsvolle Umgebungen in der Luft- und Raumfahrt sowie auf See eignet.
- Biokompatibilität: Obwohl es für Motorgehäuse normalerweise nicht relevant ist, unterstreicht seine Biokompatibilität seine Inertheit.
- Gute Ermüdungsfestigkeit: Gute Leistung unter zyklischen Belastungsbedingungen, wie sie in Motoren üblich sind.
- Typische Anwendungen: Getriebegehäuse für die Luft- und Raumfahrt, Gehäuse für Nebenaggregate, Lagerträger, kritische Motorbauteile, Hochleistungsmotorenteile für den Motorsport (bei denen die Kosten gegenüber der Leistung/dem Gewicht zweitrangig sind), Bauteile, die eine hohe spezifische Festigkeit erfordern.
- Erwägungen: Erheblich höhere Materialkosten im Vergleich zu Aluminium oder Stahl. Anspruchsvollere und kostspieligere Bearbeitung während der Nachbearbeitung. Die reaktive Natur erfordert eine kontrollierte Atmosphäre (Argon) oder ein Vakuum (EBM) während des Drucks. Geringere Wärmeleitfähigkeit als Aluminium.
Tabelle: Ti-6Al-4V Eigenschaften Übersicht (Typische Werte, geglüht)
Eigentum | Typischer Wert (LPBF/EBM, geglüht) | Einheit | Bedeutung für Motorgehäuse |
---|---|---|---|
Dichte | ~4.43 | g/cm³ | Deutlich leichter als Stahl, schwerer als Aluminium |
Endgültige Zugfestigkeit | 900 – 1100 | MPa | Hohe Festigkeit für anspruchsvolle strukturelle Belastungen |
Streckgrenze | 830 – 1000 | MPa | Hoher Widerstand gegen dauerhafte Verformung |
Dehnung beim Bruch | 10 – 18 | % | Gute Duktilität |
Elastizitätsmodul | ~110 – 115 | GPa | Gute Steifigkeit |
Wärmeleitfähigkeit | ~6.7 – 7.5 | W/(m-K) | Relativ gering, kann bei Nichtbeachtung zu einem Hitzestau führen |
Maximale Betriebstemperatur | ~350 – 400 | °C | Geeignet für Abschnitte mit mäßig hohen Temperaturen |
In Blätter exportieren
3. Superlegierung auf Nickelbasis: IN718 (Inconel 718)
- Beschreibung: Inconel 718 ist eine hochfeste, korrosionsbeständige Nickel-Chrom-Superlegierung, die mit Niob (Nb), Molybdän (Mo), Aluminium (Al) und Titan (Ti) ausscheidungsgehärtet ist. Sie ist bekannt für ihre außergewöhnliche Festigkeit und Kriechbruchbeständigkeit bei sehr hohen Temperaturen. Für anspruchsvolle Anwendungen wird es in der Regel mittels LPBF und EBM verarbeitet.
- Wichtige Eigenschaften und Vorteile für Motorgehäuse:
- Hervorragende Hochtemperaturfestigkeit: Behält hervorragende mechanische Eigenschaften (Zug-, Kriech- und Bruchfestigkeit) bei Temperaturen bis zu 700°C (1300°F) und eine nutzbare Festigkeit bis zu ~980°C (1800°F). Dies ist entscheidend für Komponenten in der Nähe von Verbrennungszonen oder Abgaswegen.
- Ausgezeichnete Korrosions- und Oxidationsbeständigkeit: Widersteht rauen chemischen Umgebungen und Hochtemperaturoxidation, was unter aggressiven Motorbetriebsbedingungen entscheidend ist.
- Hohe Festigkeit: Bietet eine sehr hohe Zug-, Streck- und Ermüdungsfestigkeit selbst bei Raumtemperatur.
- Gute Schweißbarkeit (im Vergleich zu anderen Superlegierungen): IN718 erfordert zwar immer noch Fachwissen, gilt aber im Allgemeinen als eine der schweißbareren Nickelsuperlegierungen, was bei Bedarf für die Nachbearbeitung oder Montage von Bedeutung sein kann.
- Typische Anwendungen: Triebwerkskomponenten in der Luft- und Raumfahrt in heißen Bereichen (z. B. Turbinengehäuse, Abgaskomponenten, Hitzeschilder, Gehäuse in der Nähe von Turboladern), Gasturbinenteile an Land, industrielle Hochtemperaturanwendungen. Aufgrund der Kosten und der Dichte sind sie für typische Motorblöcke in der Automobilindustrie weniger verbreitet, aber für extreme Leistungen oder spezielle Hochtemperaturkomponenten relevant.
- Erwägungen: Höchste Materialkosten unter den drei. Höchste Dichte (~8,19 g/cm³), was es schwer macht, es sei denn, es wird strategisch eingesetzt, wo seine Temperaturbeständigkeit entscheidend ist. Erfordert eine sorgfältige Prozesskontrolle während des Drucks und spezifische, oft komplexe, mehrstufige Wärmebehandlungen (Lösungsglühen und Aushärten), um optimale Eigenschaften zu erzielen. Die maschinelle Bearbeitung ist aufgrund der hohen Festigkeit und der Tendenz zur Kaltverfestigung schwierig und kostspielig.
Tabelle: IN718 Eigenschaften im Überblick (Typische Werte, lösungsgeglüht & gealtert)
Eigentum | Typischer Wert (LPBF/EBM, gealtert) | Einheit | Bedeutung für Motorgehäuse |
---|---|---|---|
Dichte | ~8.19 | g/cm³ | Der schwerste der drei; Verwendung bei extremen Temperaturanforderungen gerechtfertigt |
Endgültige Zugfestigkeit | 1250 – 1450 | MPa | Extrem hohe Festigkeit, die auch bei hohen Temperaturen erhalten bleibt |
Streckgrenze | 1050 – 1250 | MPa | Sehr hohe Nachgiebigkeit, entscheidend für hochbeanspruchte Teile |
Dehnung beim Bruch | 12 – 20 | % | Ausreichende Duktilität für eine hochfeste Superlegierung |
Elastizitätsmodul | ~200 | GPa | Sehr steifes Material |
Wärmeleitfähigkeit | ~11.4 | W/(m-K) | Geringe Wärmeleitfähigkeit |
Maximale Betriebstemperatur | ~700 (bei hoher Belastung) | °C | Hervorragende Leistung in Motorumgebungen mit sehr hohen Temperaturen |
In Blätter exportieren
Die Wahl des richtigen Materials mit Met3dp:
Bei der Auswahl müssen die Leistungsanforderungen gegen Kosten und Gewicht abgewogen werden.
- Für allgemeine Automobil- oder Industriegehäuse, bei denen eine Gewichtsreduzierung wichtig ist, aber die Temperaturen moderat sind, AlSi10Mg ist oft die wirtschaftlichste und praktischste Wahl.
- Für Luft- und Raumfahrt- oder Hochleistungsanwendungen, die eine erhebliche Gewichtseinsparung und eine moderate Temperaturbeständigkeit erfordern, Ti-6Al-4V ist trotz der höheren Kosten die bevorzugte Option.
- Für Bauteile, die extremer Hitze ausgesetzt sind, z. B. in der Nähe von Auspuffanlagen oder in den heißen Bereichen von Triebwerken oder Turbinen, IN718 ist unverzichtbar, trotz seiner hohen Dichte und Kosten.
Die Zusammenarbeit mit einem Partner wie Met3dp zu einem frühen Zeitpunkt im Entwicklungsprozess ist sehr empfehlenswert. Ihr fundiertes Wissen über die Materialwissenschaft, die Pulvereigenschaften, die sich aus ihren fortschrittlichen Herstellungsverfahren (Gasverdüsung, PREP) ergeben, und ihre umfangreiche Erfahrung mit verschiedenen Druckverfahren (einschließlich SEBM, das für Ti-6Al-4V und potenziell IN718 optimiert ist) können sie wertvolle Hilfestellung leisten. Sie können Ingenieuren und Beschaffungsmanagern helfen, Kompromisse zu bewerten, das optimale Pulver aus ihrem Portfolio auszuwählen und sicherzustellen, dass das gewählte Material korrekt verarbeitet wird, um ein Motorgehäuse zu liefern, das alle Leistungsspezifikationen erfüllt oder übertrifft.
Entwurf für additive Fertigung (DfAM): Optimierung von Motorgehäusen für den 3D-Druck
Wenn man einen Entwurf, der für das Gießen oder die maschinelle Bearbeitung vorgesehen ist, direkt an einen 3D-Metalldrucker sendet, wird das Potenzial der additiven Fertigung nur selten voll ausgeschöpft. Um die zuvor beschriebenen Vorteile - Leichtbau, Teilekonsolidierung, verbesserte Leistung und Kosteneffizienz - wirklich nutzen zu können, müssen Ingenieure das Design for Additive Manufacturing (DfAM) anwenden. DfAM ist nicht nur ein Regelwerk, sondern ein Umdenken, bei dem die Konstruktion von Bauteilen von Grund auf neu überdacht wird, wobei insbesondere die einzigartigen Fähigkeiten der schichtweisen Fertigung genutzt und die damit verbundenen Einschränkungen berücksichtigt werden. Bei komplexen Bauteilen wie Motorgehäusen ist die Anwendung der DfAM-Prinzipien entscheidend für die Maximierung der Kapitalrendite und die Erzielung besserer Ergebnisse als mit herkömmlichen Methoden. Die Zusammenarbeit mit erfahrenen AM-Dienstleistern wie Met3dp, deren Anwendungsingenieure die Feinheiten von DfAM für Materialien wie AlSi10Mg, Ti-6Al-4V und IN718 kennen, kann die Lernkurve erheblich beschleunigen und zu erfolgreicheren, optimierten und produktionsreifen Designs führen.
Die wichtigsten DfAM-Prinzipien für Motorgehäuse:
- Topologie-Optimierung:
- Konzept: Dies ist vielleicht die wirkungsvollste DfAM-Technik für Motorgehäuse. Mithilfe spezieller Software (z. B. Altair Inspire, nTopology, Autodesk Generative Design) definieren die Ingenieure Lastfälle, Randbedingungen, Designraum und Leistungsziele (z. B. Minimierung der Masse, Maximierung der Steifigkeit). Die Software entfernt dann iterativ Material aus nicht tragenden Bereichen und erzeugt so eine organische, hocheffiziente Struktur, die den Hauptspannungspfaden folgt.
- Anwendung: Reduzieren Sie das Gewicht von Motorblöcken, Getriebegehäusen, Halterungen und Strukturträgern drastisch, während Sie die Steifigkeit und Festigkeit beibehalten oder sogar erhöhen. Dies führt direkt zu einem geringeren Kraftstoffverbrauch, einer verbesserten Fahrzeugdynamik oder einer höheren Nutzlast.
- Erwägungen: Optimierte Formen können sehr komplex und nicht intuitiv sein und ähneln oft Knochenstrukturen. Sie lassen sich in der Regel nicht auf herkömmliche Weise herstellen oder sind unerschwinglich, eignen sich aber gut für AM. Erfordert eine sorgfältige Validierung durch FEA (Finite-Elemente-Analyse).
- Gitterstrukturen und Ausfachung:
- Konzept: AM ermöglicht die Schaffung interner Gitterstrukturen - komplexer Netze miteinander verbundener Streben oder sich wiederholender Einheitszellen - in festen Körpern. Diese können auf bestimmte Eigenschaften zugeschnitten werden, z. B. ein hohes Verhältnis von Steifigkeit zu Gewicht, Energieabsorption (Schwingungsdämpfung) oder Erleichterung der Wärmeübertragung. Verschiedene Gittertypen (z. B. kubisch, Oktett-Fachwerk, gyroid) bieten unterschiedliche Eigenschaften. Gitter mit variabler Dichte können die Materialverteilung weiter optimieren.
- Anwendung: Ersetzen Sie massive Gehäuseteile durch leichte Gitter, wenn eine hohe Festigkeit nicht im Vordergrund steht, sondern Steifigkeit oder Schwingungsdämpfung gewünscht sind. Sie können auch verwendet werden, um interne Ablenkungen zu schaffen oder die Wärmeaustauschflächen in den Flüssigkeitskanälen zu verbessern.
- Erwägungen: Erfordert spezielle Software für die Erzeugung und Simulation. Die Entfernung des Pulvers aus feinen Gittern kann eine Herausforderung darstellen (siehe unten). Die strukturelle Leistung muss gründlich validiert werden.
- Teil Konsolidierung:
- Konzept: Nutzen Sie die Fähigkeit von AM, komplexe Geometrien zu erzeugen, um mehrere, zuvor getrennte Komponenten zu einem einzigen, monolithisch gedruckten Teil zu kombinieren.
- Anwendung: Integrieren Sie Halterungen, Befestigungsvorsprünge, Flüssigkeitsanschlüsse oder sogar Elemente angrenzender Systeme direkt in die Hauptmotorgehäusestruktur. So könnten zum Beispiel eine Ölwanne, ein Pumpengehäuse und eine Halterung zusammengefasst werden.
- Nutzen: Reduziert die Anzahl der Teile, eliminiert Verbindungselemente und Dichtungen (potenzielle Leckstellen), vereinfacht die Montage, reduziert das Gewicht, verbessert die strukturelle Integrität und rationalisiert die Bestandsverwaltung für Beschaffungsteams.
- Erwägungen: Erfordert eine ganzheitliche Betrachtung des Systems. Kann die Komplexität des einzelnen gedruckten Teils erhöhen. Der Zugang für Inspektionen oder mögliche Reparaturen muss durchdacht werden.
- Integration von Merkmalen (z. B. konforme Kanäle):
- Konzept: Entwerfen Sie interne Kanäle und Durchgänge, die genau den Konturen von Oberflächen oder funktionalen Anforderungen folgen, anstatt sich auf gerade Linien zu beschränken, die durch Bohren oder einfache Kerne im Guss erreicht werden können.
- Anwendung: Erstellen Sie hocheffiziente, konforme Kühlkanäle, die eng an Zylinderlaufbuchsen oder Hochtemperaturzonen anliegen, um ein hervorragendes Wärmemanagement zu gewährleisten. Optimieren Sie die internen Ölkanäle für einen geringeren Druckabfall und eine gezielte Schmiermittelzufuhr. Integrieren Sie Sensorgehäuse oder Verdrahtungskanäle direkt in die Gehäusewände.
- Nutzen: Verbesserte Motorleistung, längere Lebensdauer, geringere thermische Belastung, Möglichkeit der Verkleinerung des Motors aufgrund besserer Kühlleistung.
- Erwägungen: Bei der Gestaltung der internen Kanäle müssen die Anforderungen an die Abstützung und die Zugänglichkeit zur Pulverentfernung berücksichtigt werden. Der minimale Kanaldurchmesser wird durch die Auflösung des AM-Prozesses und die Entpuderungsmöglichkeiten begrenzt.
- Design für minimale Unterstützungsstrukturen:
- Konzept: Pulverbettschmelzverfahren (LPBF, EBM) erfordern Stützstrukturen für überhängende Merkmale (typischerweise unter 45 Grad aus der Horizontalen) und zur Verankerung des Teils auf der Bauplatte, um die thermische Belastung zu bewältigen. Diese Stützen verbrauchen zusätzliches Material, verlängern die Druckzeit und müssen in der Nachbearbeitung entfernt werden, was arbeitsintensiv sein kann und die Oberfläche des Teils möglicherweise beschädigt. DfAM zielt darauf ab, den Bedarf an Stützen so weit wie möglich zu minimieren.
- Anwendung: Richten Sie das Teil strategisch auf der Bauplatte aus. Entwerfen Sie allmähliche Übergänge und Fasen/Flanken anstelle von scharfen Überhängen. Verwenden Sie selbsttragende Winkel (oft >45 Grad). Integrieren Sie Opferrippen oder Merkmale, die leicht weggearbeitet werden können, wenn Stützen in kritischen Bereichen unvermeidbar sind. Entwerfen Sie Innenkanäle mit rautenförmigem oder tropfenförmigem Querschnitt anstelle von kreisförmigen, um sie selbsttragend zu machen.
- Nutzen: Geringere Druckzeit und -kosten, weniger Arbeitsaufwand bei der Nachbearbeitung, minimiertes Risiko von Oberflächenbeschädigungen beim Entfernen des Trägers, leichtere Entfernung des Pulvers aus inneren Hohlräumen.
- Erwägungen: Bei komplexen Gehäusen ist es oft schwierig, völlig stützenfreie Konstruktionen zu erreichen. Erfordert das Verständnis der spezifischen Prozessbeschränkungen (z. B. minimale Featuregröße, erreichbare Überhangswinkel für das gewählte Material und die Maschine).
- Wanddicke und Größe der Merkmale:
- Konzept: Bei AM-Prozessen gibt es Grenzen für die minimal erreichbare Wandstärke und die Auflösung der Merkmale (z. B. kleine Löcher, dünne Rippen). Ein Design unterhalb dieser Grenzen kann zu Druckfehlern oder zu Teilen mit mangelnder struktureller Integrität führen. Umgekehrt können übermäßig dicke Abschnitte die thermische Belastung, die Druckzeit und den Materialverbrauch erhöhen.
- Anwendung: Halten Sie die empfohlenen Mindestwandstärken ein (oft 0,4-1,0 mm, je nach Verfahren und Material, aber für die strukturelle Integrität kann eine größere Stärke erforderlich sein). Vermeiden Sie nach Möglichkeit große, massive Massen; ziehen Sie Schalen und Füllungen (Gitter) in Betracht. Stellen Sie sicher, dass Merkmale wie kleine Löcher oder feine Details innerhalb der Prozessauflösung liegen.
- Erwägungen: Die Richtlinien variieren je nach Maschine, Material und spezifischer Feature-Geometrie. Wenden Sie sich an den AM-Anbieter (z. B. Met3dp), um spezifische Empfehlungen auf der Grundlage seiner Ausrüstung und Erfahrung zu erhalten.
- Berücksichtigung der Nachbearbeitung:
- Konzept: Berücksichtigen Sie bei der Konstruktion nachgelagerte Prozesse. Wenn Oberflächen eine hohe Präzision oder ein spezielles Finish erfordern, stellen Sie sicher, dass sie für die Bearbeitung oder das Polieren zugänglich sind. Wenn interne Kanäle gründlich gereinigt werden müssen, sollten Zugangsöffnungen für die Pulverentfernung und Spülung vorgesehen werden.
- Anwendung: Fügen Sie zusätzliches Rohmaterial (Bearbeitungszugabe) auf Oberflächen hinzu, die bis zur Endtoleranz CNC-gefräst werden sollen. Entwerfen Sie robuste Merkmale zum Einspannen während der Bearbeitung. Stellen Sie sicher, dass die internen Kanäle über angemessene Einlass-/Auslassöffnungen für die Entpuderung verfügen. Vermeiden Sie übermäßig komplexe Innengeometrien, die das Pulver dauerhaft festhalten.
- Nutzen: Rationalisierter Nachbearbeitungsablauf, geringeres Risiko von Beschädigungen, Gewährleistung, dass das Endprodukt alle Spezifikationen erfüllt.
Durch die Integration dieser DfAM-Prinzipien können Ingenieure über die einfache Nachbildung bestehender Konstruktionen hinausgehen und mit der Entwicklung wirklich optimierter Motorgehäuse beginnen, die die einzigartigen Vorteile der Metall-AM nutzen. Dies erfordert einen kooperativen Ansatz zwischen dem Konstruktionsteam und dem Fertigungspartner, um Machbarkeit, Effizienz und Qualität während des gesamten Prozesses zu gewährleisten, vom ersten Konzept bis zur Endfertigung Produkt.
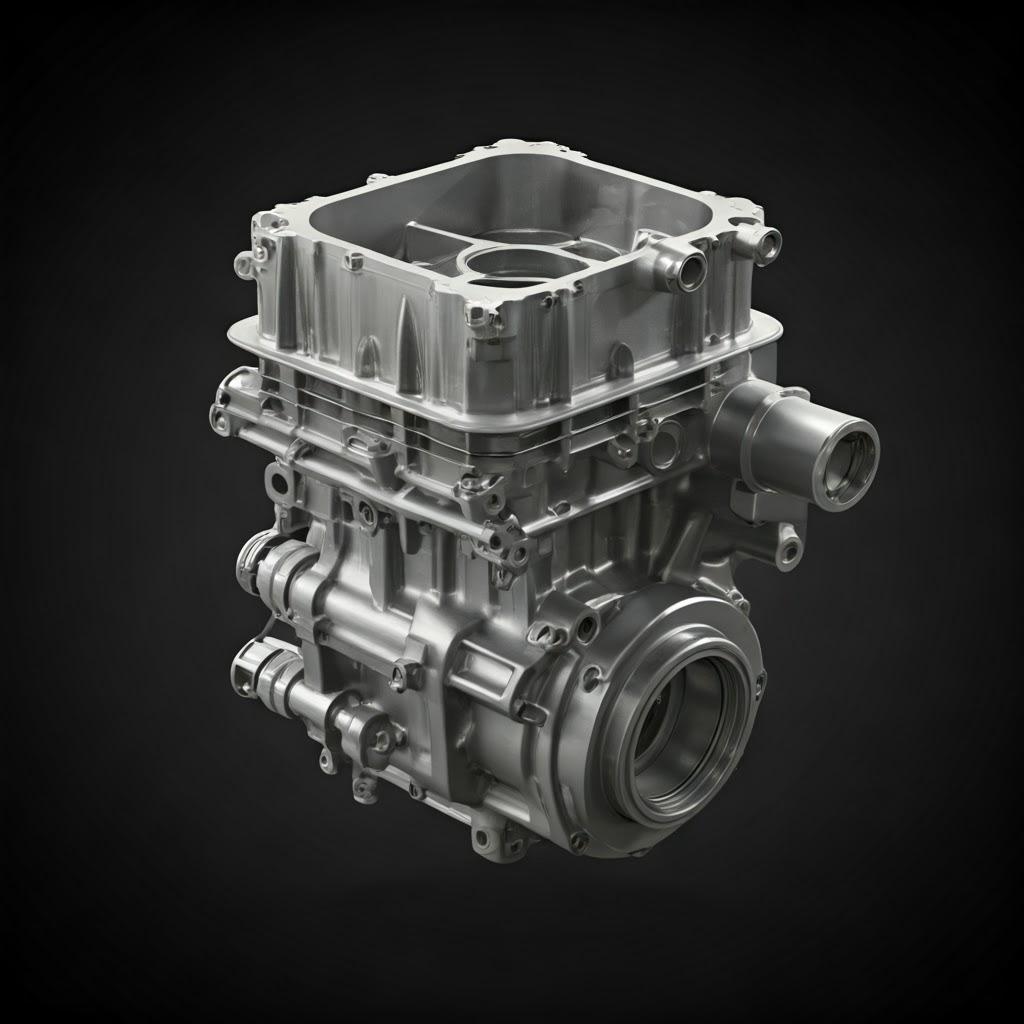
Erreichbare Präzision: Toleranz, Oberflächengüte und Maßgenauigkeit bei Metall-AM
Motorgehäuse weisen häufig kritische Merkmale auf, die enge Toleranzen, spezifische Oberflächengüten und eine hohe Gesamtmaßgenauigkeit erfordern, um eine ordnungsgemäße Montage, Abdichtung und Funktion zu gewährleisten. Beschaffungsmanager und Ingenieure, die die additive Fertigung von Metallbauteilen evaluieren, müssen realistische Erwartungen hinsichtlich der direkt aus dem Drucker erreichbaren Präzision ("as-built") und der typischerweise erforderlichen Nachbearbeitungsschritte wie der maschinellen Bearbeitung haben. Die Metall-AM-Technologie hat sich zwar erheblich weiterentwickelt, ist aber im Allgemeinen kein direkter Ersatz für die Hochpräzisionsbearbeitung, was die erreichbaren Toleranzen und die Oberflächenglätte direkt ab der Bauplatte angeht. Sie bietet jedoch eine hervorragende Ausgangsbasis für eine endkonturnahe Form, wodurch sich der nachfolgende Bearbeitungsaufwand im Vergleich zu einem rohen Gussteil oder Knüppel erheblich verringert. Die erreichbare Präzision hängt von mehreren Faktoren ab, darunter das spezifische AM-Verfahren (LPBF vs. EBM), die Maschinenqualität und -kalibrierung, das verwendete Material (AlSi10Mg, Ti-6Al-4V, IN718 verhalten sich unterschiedlich), die Teilegröße und -geometrie sowie die Bauausrichtung.
Maßgenauigkeit und Toleranzen:
- Allgemeine Erwartungen: Als Faustregel kann man sagen, dass gut kalibrierte industrielle Metall-AM-Systeme (LPBF/EBM) bei Teilen mittlerer Größe oft eine Maßgenauigkeit im Bereich von ±0,1 mm bis ±0,3 mm oder ±0,1% bis ±0,2% des Nennmaßes erreichen, je nachdem, welcher Wert größer ist. Bei kleineren Teilen können lokal engere Toleranzen gelten.
- LPBF (SLM/DMLS): Generell feinere Auflösung der Merkmale und möglicherweise etwas bessere Genauigkeit bei kleineren Details im Vergleich zu EBM aufgrund der kleineren Strahlfleckgröße und der dünneren Schichten.
- EBM (wie Met3dp's SEBM): Arbeitet bei höheren Temperaturen im Vakuum, was den Aufbau von Eigenspannungen während des Drucks erheblich reduziert. Dies kann zu einer besseren Gesamtmaßstabilität und weniger Verzug führen, insbesondere bei größeren oder komplexen Teilen aus rissempfindlichen oder stark beanspruchten Materialien wie Ti-6Al-4V oder bestimmten Nickellegierungen. Allerdings sind die minimale Featuregröße und die Oberflächenrauhigkeit im eingebauten Zustand in der Regel größer als beim LPBF.
- Faktoren, die die Genauigkeit beeinflussen:
- Kalibrierung der Maschine: Die regelmäßige Kalibrierung des Scannersystems, der Laser-/Elektronenstrahlfokussierung und der Bauplattform ist entscheidend. Qualitativ hochwertige Maschinenanbieter gewährleisten solide Kalibrierungsverfahren.
- Thermische Effekte: Die wiederholten Erhitzungs- und Abkühlungszyklen, die dem AM-Verfahren eigen sind, führen zu Ausdehnung und Schrumpfung, was zu Spannungsaufbau und Verformung führen kann, insbesondere bei großen oder geometrisch komplexen Teilen. Das Heißverfahren von EBM mildert dies erheblich. Die Wärmebehandlung zum Spannungsabbau nach der Herstellung ist für LPBF-Teile von entscheidender Bedeutung.
- Materialeigenschaften: Jedes Material (AlSi10Mg, Ti-6Al-4V, IN718) hat eine andere Wärmeleitfähigkeit, einen anderen Ausdehnungskoeffizienten und ein anderes Verhalten im Schmelzbad, was die endgültige Genauigkeit beeinflusst.
- Geometrie und Größe des Teils: Große, flache Flächen sind anfälliger für Verformungen. Hohe, dünne Elemente können weniger stabil sein. Komplexe innere Strukturen können örtlich begrenzte Spannungen verursachen.
- Unterstützende Strukturen: Richtig konstruierte Halterungen helfen, das Teil zu verankern und thermische Spannungen zu bewältigen, was die Genauigkeit verbessert. Eine schlechte Unterstützungsstrategie kann zu Verformungen führen.
- Orientierung aufbauen: Die Ausrichtung des Teils auf der Bauplatte wirkt sich auf den Stützbedarf, die thermischen Gradienten und möglicherweise auf die Genauigkeit bestimmter Merkmale aus, da der schichtweise Aufbau anisotrop ist.
- Erzielung enger Toleranzen: Für kritische Merkmale wie Lagerbohrungen, Zylinderlaufbuchsen, Passflächen oder Gewindebohrungen, die engere Toleranzen als die allgemeine AM-Fähigkeit erfordern (z. B. weniger als ±0,05 mm), ist eine CNC-Nachbearbeitung unumgänglich. Die DfAM-Prinzipien sollten das Hinzufügen von Bearbeitungsmaterial (z. B. 0,5 - 1,5 mm) zu diesen spezifischen Merkmalen im CAD-Modell vorsehen.
Oberflächengüte (Rauhigkeit):
- As-Built Oberfläche: Die Oberflächenbeschaffenheit von AM-Metallteilen ist von Natur aus rauer als die von bearbeiteten Oberflächen. Sie wird durch die Größe der Pulverpartikel, die Schichtdicke, die Strahlparameter und die Oberflächenausrichtung beeinflusst.
- LPBF: Die Oberflächenrauheit (Ra) liegt in der Regel zwischen 6 µm und 20 µm, je nach dem Winkel der Oberfläche im Verhältnis zur Baurichtung (nach oben gerichtete und vertikale Oberflächen sind im Allgemeinen glatter als nach unten gerichtete Oberflächen, die auf Stützen angewiesen sind).
- EBM: Aufgrund der größeren Pulverpartikel und des höheren Energieeintrags führt EBM im Allgemeinen zu raueren Oberflächen, oft mit Ra-Werten von 20 µm bis 40 µm oder höher.
- Bedeutung für Motorgehäuse:
- Fließwege: Raue Innenflächen in Kühlmittel- oder Ölkanälen können den Druckabfall erhöhen und möglicherweise die Durchflussleistung beeinträchtigen.
- Versiegeln von Oberflächen: Vorhandene Oberflächen sind in der Regel für kritische Dichtungen (z. B. Dichtungsschnittstellen) ungeeignet; sie müssen bearbeitet oder speziell beschichtet werden.
- Müdigkeit Leben: Oberflächenrauhigkeiten können als Ansatzpunkte für Ermüdungsrisse dienen. Bei dynamisch belasteten Gehäusen ist es oft notwendig, die Oberflächengüte in kritischen Bereichen durch Polieren oder maschinelle Bearbeitung zu verbessern.
- Verbesserung der Oberflächengüte: Verschiedene Nachbearbeitungstechniken können die Oberflächenbeschaffenheit im eingebauten Zustand erheblich verbessern:
- Abrasives Strahlen (Perlenstrahlen, Sandstrahlen): Sorgt für ein gleichmäßiges, mattes Finish, entfernt loses Pulver und kann Ra leicht verbessern (z. B. bis zu 5-10 µm Ra, je nach Ausgangspunkt und Medium).
- Taumeln/Gleitschleifen: Verwendet Schleifmittel in einer Trommel oder einer Rütteltrommel, um Oberflächen zu glätten und Kanten zu entgraten; effektiv für Chargen kleinerer Teile oder zur Erzielung allgemeiner Glätte.
- CNC-Bearbeitung: Bietet die beste Kontrolle über die Oberflächenbeschaffenheit spezifischer Merkmale, wobei Ra-Werte unter 1,6 µm oder sogar noch niedriger (Hochglanzpolitur) leicht erreicht werden können.
- Polieren (manuell oder automatisiert): Kann sehr glatte, spiegelähnliche Oberflächen erzielen (Ra < 0,1 µm), ist aber oft arbeitsintensiv und in der Regel spezifischen funktionalen oder ästhetischen Anforderungen vorbehalten.
- Elektrochemisches Polieren: Kann komplexe Geometrien glätten, erfordert jedoch spezielle Elektrolyte und eine spezielle Einrichtung.
Die Rolle von Met3dp bei der Präzision:
Das Erreichen der erforderlichen Präzision erfordert eine robuste Prozesssteuerung. Met3dp bietet mit seinem Schwerpunkt auf hochwertigen, sphärischen Metallpulvern, die durch fortschrittliche Zerstäubung hergestellt werden, in Verbindung mit seinen branchenführenden Druckanlagen, die für ihre Genauigkeit und Zuverlässigkeit bekannt sind, eine starke Grundlage. Dank ihres Verständnisses der Wechselwirkungen zwischen Material und Prozess für Legierungen wie AlSi10Mg, Ti-6Al-4V und IN718 können sie die Herstellungsparameter optimieren und geeignete Nachbearbeitungsstrategien empfehlen (einschließlich der Nutzung der einzigartigen Aspekte der verschiedenen Druckverfahren wie SEBM), um die spezifischen Toleranz- und Oberflächenanforderungen zu erfüllen, die in den Konstruktionsplänen für anspruchsvolle Motorgehäuseanwendungen festgelegt sind. Eine frühzeitige Zusammenarbeit mit ihnen ermöglicht eine realistische Einschätzung dessen, was im Ist-Zustand erreicht werden kann, im Gegensatz zu dem, was sekundäre Operationen erfordert, was eine effiziente Planung und Kostenkalkulation für die Beschaffung gewährleistet.
Wesentliche Nachbearbeitungsschritte für 3D-gedruckte Motorgehäuse
Im Gegensatz zu Teilen, die durch Net-Shape-Verfahren wie Druckguss oder Spritzguss hergestellt werden, sind bei additiv gefertigten Metallbauteilen fast immer mehrere Nachbearbeitungsschritte erforderlich, um sie aus dem Rohzustand in ein funktionsfähiges, einbaufertiges Motorgehäuse zu verwandeln. Diese Schritte sind entscheidend für das Erreichen der geforderten mechanischen Eigenschaften, der Maßhaltigkeit, der Oberflächenbeschaffenheit und der allgemeinen Qualität und Zuverlässigkeit. Das Verständnis dieses Arbeitsablaufs ist für Ingenieure, die die Teile konstruieren, und für Beschaffungsmanager, die Zeit und Kosten einplanen, von entscheidender Bedeutung. Die spezifische Abfolge und Notwendigkeit der einzelnen Schritte hängt von der verwendeten AM-Technologie (LPBF vs. EBM), dem Material (AlSi10Mg, Ti-6Al-4V, IN718 haben unterschiedliche Anforderungen), der Komplexität des Teils und den endgültigen Anwendungsanforderungen ab. Oft ist die Zusammenarbeit mit einem Komplettanbieter oder die Koordination mit spezialisierten Unterauftragnehmern erforderlich.
Typischer Post-Processing-Workflow für AM-Motorgehäuse aus Metall:
- Entpudern:
- Zielsetzung: Entfernen Sie so viel ungeschmolzenes Metallpulver wie möglich von dem Teil, insbesondere von inneren Kanälen und komplexen Geometrien.
- Methoden: Manuelles Bürsten, Ausblasen mit Druckluft, Absaugen, automatische Entpuderungsstationen mit Vibration oder Rotation. Bei komplexen internen Kanälen sind ein sorgfältiges Design (Zugangsöffnungen, glatte Wege) und spezielle Verfahren erforderlich. Manchmal wird auch eine Ultraschallreinigung in einem Lösungsmittelbad durchgeführt.
- Wichtigkeit: Pulverrückstände können die Funktionalität beeinträchtigen (Durchgänge blockieren), das Gewicht erhöhen und nachfolgende Schritte wie Wärmebehandlung oder HIP stören. Eine unvollständige Pulverentfernung ist ein erhebliches Qualitätsproblem.
- Stressabbau Wärmebehandlung:
- Zielsetzung: Reduzieren Sie die hohen Eigenspannungen, die während der schnellen Aufheiz- und Abkühlzyklen des Druckprozesses entstehen, was besonders bei LPBF-Teilen kritisch ist. Diese Spannungen können während des Drucks, nach der Entnahme von der Bauplatte oder bei der anschließenden Bearbeitung zu Verformungen oder Rissen führen.
- Methoden: Erhitzen des Teils (oft noch auf der Bauplatte) in einem Ofen mit kontrollierter Atmosphäre (z. B. Argon, Vakuum) auf eine bestimmte Temperatur unterhalb der Alterungs- oder Glühtemperatur des Materials, Halten des Teils für eine bestimmte Zeit und anschließendes langsames Abkühlen. Die Parameter sind je nach Material sehr unterschiedlich (z. B. AlSi10Mg ~300°C, Ti-6Al-4V ~650-800°C, IN718 ~980-1065°C für Homogenisierung/Spannungsabbau, wobei die spezifischen Zyklen variieren).
- Wichtigkeit: Wesentlich für die Dimensionsstabilität, die Vermeidung von Rissen und die sichere Entnahme aus der Bauplatte und die anschließende Bearbeitung. EBM-Teile weisen aufgrund des Warmverfahrens im Allgemeinen viel geringere Eigenspannungen auf, aber je nach Legierung und Geometrie kann ein Spannungsabbauzyklus dennoch von Vorteil sein.
- Entnahme von der Bauplatte:
- Zielsetzung: Trennen Sie das/die gedruckte(n) Motorgehäuse von der Metallbauplatte, mit der sie während des Drucks verschmolzen wurden.
- Methoden: Dies geschieht in der Regel durch Drahterodieren (Electrical Discharge Machining) oder mit einer Bandsäge. Dabei muss darauf geachtet werden, dass die Teile nicht beschädigt werden.
- Wichtigkeit: Ein notwendiger Schritt, um die Teile für die weitere Bearbeitung freizugeben.
- Entfernung der Stützstruktur:
- Zielsetzung: Entfernen Sie die während des Bauprozesses erforderlichen provisorischen Stützkonstruktionen.
- Methoden: Das kann vom einfachen manuellen Brechen (für leicht zugängliche, leichte Stützen) bis zum Schneiden mit Handwerkzeugen, CNC-Bearbeitung oder manchmal Drahterodieren für empfindliche oder schwer zugängliche Stützen reichen.
- Wichtigkeit: Halterungen sind nicht funktionsfähig und müssen entfernt werden. Dieser Schritt kann arbeitsintensiv sein und erfordert Geschick, um die Oberfläche des Teils nicht zu beschädigen, insbesondere bei komplexen Gehäusen mit internen Halterungen. DfAM-Strategien zielen darauf ab, Stützen zu minimieren.
- Heißisostatisches Pressen (HIP) - optional, aber oft empfohlen:
- Zielsetzung: Beseitigung der inneren Porosität (kleine Hohlräume), die manchmal nach dem AM-Prozess verbleiben kann, wodurch mechanische Eigenschaften wie Ermüdungsfestigkeit, Bruchzähigkeit und Duktilität verbessert werden.
- Methoden: Das Teil wird in einem speziellen HIP-Gefäß gleichzeitig einer hohen Temperatur (unter dem Schmelzpunkt) und einem hohen Inertgasdruck (typischerweise Argon, ~100-200 MPa) ausgesetzt. Durch den Druck kollabieren die inneren Hohlräume und das Material wird durch Diffusion an den Grenzflächen der Hohlräume gebunden.
- Wichtigkeit: Entscheidend für kritische, ermüdungsanfällige Komponenten, wie sie in der Luft- und Raumfahrt und in Hochleistungsmotoren für Kraftfahrzeuge verwendet werden. Verbessert die Materialkonsistenz und Zuverlässigkeit erheblich. Wird häufig für Teile aus Ti-6Al-4V und IN718 in anspruchsvollen Anwendungen eingesetzt. Es kann auch die Eigenschaften von AlSi10Mg verbessern.
- Lösungsglühen und Alterungswärmebehandlung (Entwicklung der Eigenschaften):
- Zielsetzung: Entwicklung der endgültigen gewünschten Mikrostruktur und mechanischen Eigenschaften (Festigkeit, Härte, Duktilität) der Legierung. Dies ist ein Unterschied zum Spannungsabbau.
- Methoden: Es handelt sich um spezifische mehrstufige Wärmebehandlungszyklen, die auf die Legierung zugeschnitten sind.
- AlSi10Mg: Typischerweise ein T6-Zyklus (Lösungsbehandlung bei 500-540°C, Abschrecken, dann künstliche Alterung bei 150-170°C), um Ausscheidungshärtung zu erreichen.
- Ti-6Al-4V: Häufig geglüht (z. B. ~700-850 °C, kühl) zur Verbesserung der Duktilität und Stabilität oder möglicherweise lösungsgeglüht und gealtert (STA) für höhere Festigkeit. Spezifische Zyklen hängen davon ab, ob LPBF oder EBM verwendet wurde und von der gewünschten Eigenschaftsbilanz.
- IN718: Erfordert einen komplexen Zyklus, in der Regel eine Lösungsbehandlung (~950-980°C), gefolgt von einem zweistufigen Alterungsprozess (~720°C, dann ~620°C) zur Ausfällung von Verfestigungsphasen (Gamma-Prime und Gamma-Double-Prime).
- Wichtigkeit: Unbedingt erforderlich, um die in den Materialdatenblättern aufgeführten mechanischen Zielwerte zu erreichen. Ohne eine ordnungsgemäße Wärmebehandlung weist das Material im eingebauten Zustand oder nach dem Spannungsabbau keine optimale Festigkeit oder Leistung auf.
- CNC-Bearbeitung:
- Zielsetzung: Erzielen Sie enge Toleranzen, präzise Geometrien und glatte Oberflächen bei kritischen Merkmalen, die mit dem AM-Prozess im Ist-Zustand nicht erreicht werden können.
- Methoden: Einsatz von Standard-CNC-Fräsen, -Drehen, -Bohren, -Gewindebohren und -Schleifen. Erfordert ein sorgfältiges Vorrichtungsdesign, um das komplexe AM-Teil sicher und ohne Verformung zu halten.
- Wichtigkeit: Erforderlich für Passflächen, Lagerbohrungen, Zylinderdeck-Ebenheit, Dichtungsnuten, Gewindebohrungen und alle Merkmale, die eine hohe Präzision für Montage und Funktion erfordern.
- Oberflächenveredelung und Reinigung:
- Zielsetzung: Erzielen Sie die gewünschte endgültige Oberflächenstruktur, reinigen Sie das Teil gründlich und tragen Sie gegebenenfalls Schutz- oder Funktionsschichten auf.
- Methoden: Wie zuvor beschrieben (Strahlen, Trommeln, Polieren). Anschließend gründliche Reinigung und Inspektion, um sicherzustellen, dass keine Verunreinigungen, Bearbeitungsspäne oder Pulverreste zurückbleiben, insbesondere in den inneren Durchgängen. Oberflächenbeschichtungen (z. B. Eloxieren von Aluminium, spezielle Verschleißschutz- oder Wärmedämmschichten) können je nach Anwendung aufgebracht werden.
- Wichtigkeit: Beeinflusst die Ästhetik, die Korrosionsbeständigkeit, die Verschleißfestigkeit, die Ermüdungslebensdauer und die Flüssigkeitsdynamik in den Kanälen. Die Endreinigung ist für Motoreinbauten entscheidend.
Integrierter Ansatz:
Die Verwaltung dieses mehrstufigen Arbeitsablaufs erfordert Fachwissen und Koordination. Unternehmen wie Met3dp sind zwar auf Drucker und Pulver spezialisiert, kennen aber die gesamte Wertschöpfungskette und können oft beraten oder durch Partnerschaften bei der Verwaltung dieser Nachbearbeitungsschritte helfen, um sicherzustellen, dass das endgültige Motorgehäuse alle Spezifikationen erfüllt. Beschaffungsmanager sollten die Kosten und die Vorlaufzeit, die mit diesen wesentlichen Schritten verbunden sind, in ihre Gesamtprojektplanung einbeziehen, wenn sie Metall-AM in Betracht ziehen.
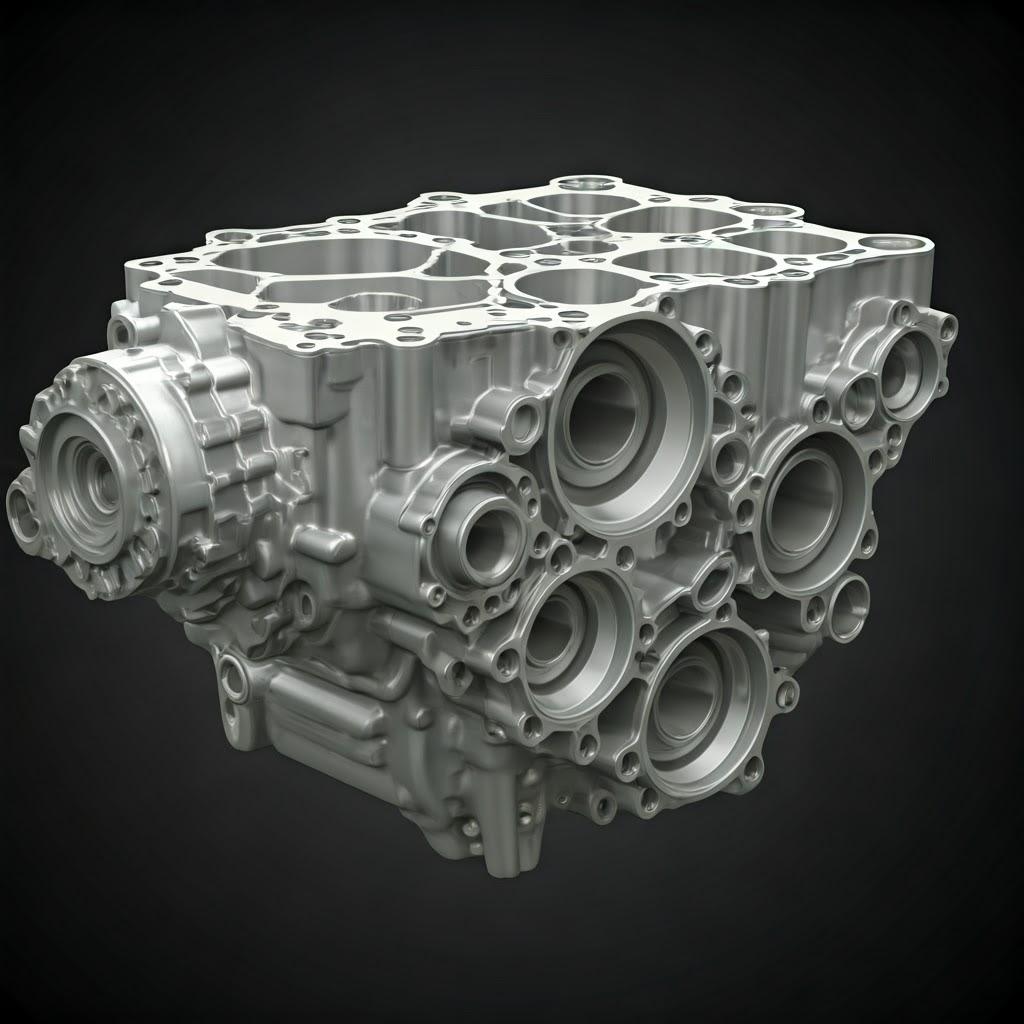
Allgemeine Herausforderungen beim 3D-Druck von Motorgehäusen und Strategien zur Abhilfe
Die additive Fertigung von Metall bietet zwar ein transformatives Potenzial für Motorgehäuse, ist aber nicht ohne Herausforderungen. Ingenieure, Betreiber und Beschaffungsmanager sollten sich der potenziellen Probleme bewusst sein, die während der Druck- und Nachbearbeitungsphasen auftreten können. Das Verständnis dieser Herausforderungen ermöglicht eine proaktive Entschärfung durch sorgfältiges Design (DfAM), strenge Prozesskontrolle, geeignete Materialauswahl und die Nutzung des Fachwissens von erfahrenen AM-Anbietern wie Met3dp. Die erfolgreiche Bewältigung dieser Hürden ist der Schlüssel zur Nutzung der Qualitäts-, Leistungs- und Kostenvorteile der AM-Technologie.
Gemeinsame Herausforderungen und Abhilfestrategien:
- Eigenspannung, Verformung und Rissbildung:
- Herausforderung: Die intensive, örtlich begrenzte Erwärmung und die schnelle Abkühlung bei Pulverbettschmelzverfahren (insbesondere LPBF) erzeugen erhebliche Wärmegradienten, die zu inneren Spannungen im Bauteil führen. Diese Spannungen können zu Verformungen (Abweichung von der beabsichtigten Geometrie), zur Ablösung von der Bauplatte oder sogar zu Rissen führen, insbesondere bei großen Teilen, komplexen Geometrien oder Materialien, die zur Heißrissbildung neigen (wie einige Aluminiumlegierungen oder Nickelsuperlegierungen, wenn sie nicht korrekt verarbeitet werden).
- Strategien zur Schadensbegrenzung:
- Prozessauswahl: Das Elektronenstrahlschmelzen (EBM/SEBM), das bei hohen Temperaturen im Vakuum arbeitet (z.B. >600°C für Ti-6Al-4V), reduziert thermische Gradienten und Eigenspannungen im Vergleich zu LPBF erheblich, was es für große Titan- oder spannungsempfindliche Teile vorteilhaft macht. Der Fokus von Met3dp auf die SEBM-Technologie ist eine direkte Antwort auf diese Herausforderung für relevante Materialien.
- Optimierte Build-Parameter: Die Feinabstimmung von Laser-/Elektronenstrahlleistung, Scan-Geschwindigkeit, Scan-Strategie (z. B. Insel-Scanning, Schichtrotation) und Schichtdicke kann die Spannungsakkumulation minimieren.
- Build Plate Heating (LPBF): Durch das Vorheizen der Bauplatte (auf bis zu 200 °C oder bei bestimmten Materialien auch höher) wird der Temperaturunterschied zwischen dem erstarrten Material und dem umgebenden Pulverbett bzw. der Platte verringert, wodurch die Spannungen sinken.
- Intelligente Unterstützungsstrategie: Gut konzipierte Stützstrukturen wirken als Wärmesenken und Verankerungen und helfen, thermische Spannungen zu bewältigen und Verformungen zu verhindern. Software-Simulationen können helfen, die Platzierung der Stützen zu optimieren.
- DfAM: Die Konstruktion von Teilen mit allmählichen Übergängen, die Vermeidung von großen massiven Blöcken und die Einbeziehung von spannungsentlastenden Merkmalen können helfen.
- Unmittelbare Entlastung nach der Bauphase: Durchführung eines Entspannungswärmebehandlungszyklus vor Die Entnahme des Teils aus der Bauplatte ist für LPBF-Teile von entscheidender Bedeutung, um eine Verformung oder Rissbildung beim Ablösen zu verhindern.
- Schwierigkeiten bei der Beseitigung von Stützstrukturen:
- Herausforderung: Stützstrukturen sind zwar notwendig, verursachen aber zusätzliche Kosten (Material, Zeit) und müssen entfernt werden. Das Entfernen von Stützen aus internen Kanälen, komplizierten Geometrien oder empfindlichen Merkmalen ohne Beschädigung der Teileoberfläche kann sehr schwierig, zeitaufwändig und kostspielig sein. Unzugängliche interne Stützen lassen sich unter Umständen nicht vollständig entfernen.
- Strategien zur Schadensbegrenzung:
- DfAM für die Selbsthilfe: Konstruieren Sie vorrangig Teile mit selbsttragenden Winkeln (im Allgemeinen >45°, aber material- und maschinenspezifisch), verwenden Sie Merkmale wie Fasen und Verrundungen und wählen Sie eine optimale Bauausrichtung. Entwerfen Sie Innenkanäle mit Tropfen- oder Rautenform.
- Optimiertes Support-Design: Verwenden Sie Software zur Erstellung von Stützen, die während der Bauphase stabil genug sind, sich aber leichter entfernen lassen (z. B. kleinere Kontaktpunkte, perforierte Strukturen). Spezielle Stützentypen (z. B. Baumstützen) können die Zugänglichkeit verbessern.
- Planung der Zugänglichkeit: Stellen Sie sicher, dass die Konstruktion einen physischen oder werkzeugtechnischen Zugang zur Entfernung der Stützen ermöglicht. Wenn interne Halterungen unvermeidbar sind, muss bei der Konstruktion sorgfältig geprüft werden, wie sie entfernt werden können (z. B. chemisches Ätzen - selten bei diesen Strukturmetallen, maschineller Zugang).
- Auswahl des Prozesses: Einige Verfahren können für bestimmte Geometrien weniger Halterungen erfordern (z. B. erfordert EBM aufgrund des Pulversinterns manchmal weniger Halterungen als LPBF).
- Pulverentfernung aus internen Kanälen:
- Herausforderung: Motorgehäuse enthalten oft komplexe interne Kanäle für Kühl- oder Schmiermittel. Die Sicherstellung, dass das gesamte ungeschmolzene Metallpulver nach dem Druck aus diesen Kanälen entfernt wird, ist entscheidend für die Funktionalität, kann aber extrem schwierig sein, insbesondere bei langen, engen oder gewundenen Pfaden. Eingeschlossenes Pulver kann den Durchfluss blockieren oder sich während des Betriebs lösen und einen katastrophalen Motorausfall verursachen.
- Strategien zur Schadensbegrenzung:
- DfAM für De-Powdering: Entwerfen Sie interne Kanäle mit sanften Übergängen und vermeiden Sie scharfe Ecken oder tote Enden, in denen sich Pulver ansammeln kann. Achten Sie auf ausreichende Ein- und Auslassöffnungen (möglicherweise größer als funktional erforderlich und später verstopft/bearbeitet), um die Entleerung des Pulvers und den Zugang zur Inspektion zu ermöglichen. Berücksichtigen Sie den minimalen Kanaldurchmesser auf der Grundlage der Pulverpartikelgröße und der Entpuderungsfähigkeiten (oft sind >1-2 mm erforderlich).
- Optimierte Ausrichtung: Richten Sie das Teil auf der Bauplatte so aus, dass die Schwerkraft den Abfluss des Pulvers erleichtert.
- Wirksame De-Powdering-Verfahren: Einsatz von mehrachsigen Rotations-/Vibrationsstationen, gezielten Druckluft-/Inertgasdüsen, eventuell Ultraschallreinigung in geeigneten Flüssigkeiten.
- Inspektion: Verwenden Sie zerstörungsfreie Methoden wie CT-Scanning (Computertomographie) oder boreskopische Inspektion, um die vollständige Entfernung des Pulvers in kritischen Passagen zu überprüfen.
- Porosität und Materialdefekte:
- Herausforderung: Eine unvollständige Verschmelzung zwischen den Schichten oder Gaseinschlüsse beim Schmelzen können zu mikroskopisch kleinen Hohlräumen (Porosität) im gedruckten Material führen. Eine hohe Porosität verschlechtert die mechanischen Eigenschaften, insbesondere die Ermüdungsfestigkeit und Bruchzähigkeit. Auch andere Defekte wie Einschlüsse (aus verunreinigtem Pulver) oder Lücken im Schmelzbereich können auftreten.
- Strategien zur Schadensbegrenzung:
- Hochwertiges Pulver: Die Verwendung hochreiner, kugelförmiger Pulver mit gleichmäßiger Partikelgrößenverteilung und guter Fließfähigkeit ist von größter Bedeutung. Die fortschrittlichen Gaszerstäubungs- und PREP-Prozesse von Met3dp sind auf die Herstellung solcher Pulver ausgelegt und minimieren die im Rohmaterial enthaltene Gasporosität. Sorgfältige Pulverhandhabungs- und Recyclingprotokolle sind ebenfalls entscheidend, um Verunreinigungen zu vermeiden.
- Optimierte Prozessparameter: Die Entwicklung und strenge Kontrolle optimierter Parameter (Strahlleistung, Geschwindigkeit, Fokus, Schichtdicke, Atmosphärensteuerung) für jede spezifische Material- und Maschinenkombination ist der Schlüssel zum Erreichen dichter (>99,5%, oft >99,9%) Teile.
- Heiß-Isostatisches Pressen (HIP): Wie bereits bei der Nachbearbeitung erwähnt, ist HIP äußerst wirksam beim Schließen der internen Gasporosität und bei der Verbesserung der Dichte und der mechanischen Eigenschaften. Es ist häufig eine Standardanforderung für kritische AM-Teile in der Luft- und Raumfahrt sowie in der Medizintechnik.
- Qualitätskontrolle & NDT: Strenge Qualitätskontrollen, einschließlich Pulveranalyse, Schmelzbadüberwachung (sofern vorhanden) und zerstörungsfreie Prüfungen (NDT) wie CT-Scans oder Ultraschallprüfungen an fertigen Teilen, helfen bei der Erkennung und Vermeidung von Fehlern.
- Kosten und Vorlaufzeit:
- Herausforderung: Metall-AM bietet zwar langfristige Vorteile, aber die anfänglichen Kosten pro Teil können aufgrund der teuren Maschinen, Materialien und umfangreichen Nachbearbeitung höher sein als bei herkömmlichen Methoden, insbesondere bei größeren Komponenten oder höheren Stückzahlen. Auch die Vorlaufzeiten können länger sein als erwartet, wenn der gesamte Arbeitsablauf nicht effizient verwaltet wird.
- Strategien zur Schadensbegrenzung:
- Optimierung des Designs (DfAM): Die Maximierung des Gewichtsreduzierung, die Konsolidierung von Teilen und das Design für minimale Stützen/Nachbearbeitung reduzieren direkt den Materialverbrauch, die Druckzeit und die Arbeitskosten.
- Verschachtelung und Optimierung der Erstellung: Das gleichzeitige Drucken mehrerer Teile auf einer einzigen Bauplatte (Nesting) verbessert die Maschinenauslastung und reduziert die Kosten pro Teil.
- Gezielte Anwendungsauswahl: Konzentrieren Sie sich auf Anwendungen, bei denen die einzigartigen Vorteile von AM (Komplexität, Leichtbau, Anpassung, Konsolidierung) den größten Nutzen versprechen, anstatt zu versuchen, kosteneffiziente herkömmliche Methoden für einfache Teile mit hohen Stückzahlen zu ersetzen.
- Partnerschaften mit erfahrenen Anbietern: Die Zusammenarbeit mit effizienten, erfahrenen Dienstleistern wie Met3dp, die über optimierte Arbeitsabläufe verfügen und die Kostentreiber verstehen, kann dazu beitragen, die Ausgaben zu verwalten und realistische Vorlaufzeitschätzungen zu gewährleisten. Eine offene Kommunikation mit den Beschaffungsteams hinsichtlich der Kostenaufschlüsselung ist von entscheidender Bedeutung.
Durch die Anerkennung dieser Herausforderungen und die Umsetzung solider Strategien zur Schadensbegrenzung, die auf soliden DfAM-Prinzipien, einer sorgfältigen Prozesskontrolle und starken Partnerschaften beruhen, können Hersteller die additive Fertigung von Metallen vertrauensvoll nutzen, um hochwertige, leistungsstarke Motorgehäuse für die anspruchsvollen Anforderungen der Luft- und Raumfahrt, der Automobilindustrie und der Industrie herzustellen.
Auswahl eines Partners für den 3D-Druck von Metall: Bewertung von Dienstleistern und Zulieferern
Die erfolgreiche Implementierung der additiven Fertigung von Metall für kritische Komponenten wie Motorgehäuse erfordert mehr als nur den Zugang zu einem Drucker, sondern auch eine strategische Partnerschaft mit einem kompetenten und zuverlässigen Dienstleister oder Lieferanten. Der richtige Partner fungiert als Erweiterung Ihrer Entwicklungs- und Beschaffungsteams und bietet technisches Fachwissen, robuste Prozesse, gleichbleibende Qualität und zuverlässige Lieferung. Für B2B-Einkäufer, Großhändler und Beschaffungsmanager, die sich in der wachsenden Landschaft der AM-Anbieter zurechtfinden müssen, ist die Bewertung potenzieller Partner auf der Grundlage einer Reihe definierter Kriterien unerlässlich, um Risiken zu minimieren und den Projekterfolg sicherzustellen. Eine kluge Wahl bedeutet, dass man nicht nur auf den Angebotspreis schaut, sondern auch die Gesamtkapazitäten des Anbieters, die Qualitätssysteme und die Eignung für Ihre spezifischen Branchen- und Anwendungsanforderungen beurteilt.
Schlüsselkriterien für die Bewertung von Metall-AM-Partnern:
- Technisches Fachwissen und Anwendungsunterstützung:
- Bewertung: Verfügt der Anbieter über fundierte Kenntnisse des spezifischen AM-Prozesses (LPBF, EBM/SEBM), der Werkstoffe (AlSi10Mg, Ti-6Al-4V, IN718) und der damit verbundenen Verhaltensweisen? Bieten sie Unterstützung beim Design for Additive Manufacturing (DfAM) an, um das Design Ihres Motorgehäuses hinsichtlich Druckbarkeit, Leistung und Kosteneffizienz zu optimieren? Können sie Sie bei der Materialauswahl beraten? Verfügen sie über Ingenieure mit Erfahrung in Ihrer Branche (Luft- und Raumfahrt, Automobilindustrie, Industrie)?
- Warum das wichtig ist: Motorgehäuse sind komplexe Bauteile. Ein Partner mit hoher technischer Kompetenz kann helfen, kostspielige Konstruktionsfehler zu vermeiden, die Leistung zu optimieren, Probleme zu beheben und sicherzustellen, dass das Teil die funktionalen Anforderungen erfüllt. Anbieter wie Met3dp mit jahrzehntelanger kollektiver Erfahrung in der Metall-AM, die Werkstoffkunde, Verfahrenstechnik und Anwendungsentwicklung umfasst, bieten hier einen erheblichen Mehrwert.
- Maschinenpark & Technologie:
- Bewertung: Mit welchen Arten und Marken von Metall-AM-Systemen arbeiten sie? Verfügen sie über die richtige Technologie (z. B. LPBF für feine Merkmale, EBM/SEBM für spannungsarme Titanteile) für Ihre spezifischen Gehäuseanforderungen? Wie hoch ist die Maschinenkapazität (Bauvolumen, Anzahl der Maschinen), um Ihre Projektgröße und Ihr potenzielles Produktionsvolumen zu bewältigen? Sind die Maschinen gut gewartet und kalibriert?
- Warum das wichtig ist: Die spezifische Technologie wirkt sich auf die erreichbaren Merkmale, Toleranzen, Oberflächengüte und Materialeigenschaften aus. Ausreichende Kapazitäten gewährleisten angemessene Vorlaufzeiten und Skalierbarkeit. Anbieter, die in branchenführende Ausrüstung investieren, wie Met3dp, die sich auf Systeme mit hohem Druckvolumen, Genauigkeit und Zuverlässigkeit konzentrieren, zeigen ihr Engagement für eine Qualitätsproduktion.
- Materialportfolio und Qualitätskontrolle von Pulver:
- Bewertung: Bietet der Anbieter die spezifischen Legierungen an, die für Ihr Motorgehäuse erforderlich sind (z. B. AlSi10Mg, Ti-6Al-4V, IN718)? Wie sehen die Prozesse für die Beschaffung, Handhabung, Lagerung und das Recycling von Metallpulvern aus? Verfügen sie über eine solide Qualitätskontrolle für das eingehende Pulver (z. B. chemische Analyse, Partikelgrößenverteilung, Morphologie, Fließfähigkeit)? Können sie Materialzertifizierungen und Rückverfolgbarkeit anbieten?
- Warum das wichtig ist: Die Qualität des gedruckten Endprodukts hängt im Wesentlichen von der Qualität des Pulverrohstoffs ab. Inkonsistentes oder verunreinigtes Pulver führt zu Defekten und schlechten mechanischen Eigenschaften. Unternehmen wie Met3dp, die Herstellung Ihre eigenen Hochleistungsmetallpulver, die mit fortschrittlichen Techniken wie Gasverdüsung und PREP hergestellt werden, bieten eine bessere Kontrolle über die Qualität und Konsistenz des Pulvers und damit eine größere Sicherheit für kritische Anwendungen.
- Qualitätsmanagementsystem und Zertifizierungen:
- Bewertung: Verfügt der Anbieter über ein zertifiziertes Qualitätsmanagementsystem (QMS)? Zu den wesentlichen Zertifizierungen gehört ISO 9001 (allgemeines Qualitätsmanagement). Für Anwendungen in der Luft- und Raumfahrt ist in der Regel AS9100 vorgeschrieben. Für medizinische Anwendungen könnte ISO 13485 relevant sein (allerdings weniger für Motorgehäuse). Sind sie offen für Audits? Wie sehen die internen Qualitätskontrollverfahren während und nach der Fertigung aus?
- Warum das wichtig ist: Zertifizierungen belegen die Verpflichtung zu standardisierten Prozessen, Rückverfolgbarkeit und kontinuierlicher Verbesserung und schaffen Vertrauen in die Zuverlässigkeit und Wiederholbarkeit der Herstellungsprozesse. Dies ist für sicherheitskritische Komponenten nicht verhandelbar und für regulierte Branchen unerlässlich.
- Nachbearbeitungsmöglichkeiten:
- Bewertung: Bietet der Anbieter die erforderlichen Nachbearbeitungsschritte im eigenen Haus an (z. B. Wärmebehandlung, Entfernen von Stützen, Grundveredelung) oder wickelt er sie über ein qualifiziertes Netz von Partnern ab (z. B. HIP, CNC-Bearbeitung, NDT, fortschrittliche Beschichtung)? Wie nahtlos ist diese Integration?
- Warum das wichtig ist: Motorgehäuse erfordern mehrere Nachbearbeitungsschritte. Ein Partner, der diesen gesamten Arbeitsablauf verwalten kann, vereinfacht die Lieferkette für das Beschaffungsteam und gewährleistet die Verantwortlichkeit während des gesamten Prozesses. Es ist wichtig zu verstehen, welche Schritte intern und welche extern durchgeführt werden, um die Kontrolle und mögliche Auswirkungen auf die Vorlaufzeit zu beurteilen.
- Erfolgsbilanz und Fallstudien:
- Bewertung: Kann der Anbieter erfolgreiche frühere Projekte vorweisen, insbesondere mit Komponenten, die in Bezug auf Komplexität, Material oder Branche mit Ihrem Motorgehäuse vergleichbar sind? Ist der Anbieter bereit, Fallstudien oder Referenzen zur Verfügung zu stellen (innerhalb der Vertraulichkeitsgrenzen)?
- Warum das wichtig ist: Nachgewiesene Erfahrung verringert das Risiko. Der Nachweis der erfolgreichen Durchführung ähnlicher Projekte schafft Vertrauen in die Fähigkeit des Unternehmens, Ihre Anforderungen zu erfüllen.
- Kommunikation, Unterstützung und Transparenz:
- Bewertung: Wie ansprechbar und kommunikativ ist der Anbieter während der Angebots- und Projektbesprechungsphase? Sind sie transparent in Bezug auf ihre Prozesse, Fähigkeiten und potenziellen Herausforderungen? Bietet er klare Projekt-Updates?
- Warum das wichtig ist: Eine starke Arbeitsbeziehung beruht auf einer klaren, offenen Kommunikation. Dies ist besonders wichtig für komplexe AM-Projekte, die iterative Designanpassungen oder gemeinsame Problemlösungen erfordern können.
- Kosten und Vorlaufzeit:
- Bewertung: Ist die Preisgestaltung wettbewerbsfähig und transparent? Erscheinen die angegebenen Vorlaufzeiten angesichts des Arbeitsumfangs (Druck und Nachbearbeitung) realistisch? Wie schneiden sie im Vergleich zu anderen qualifizierten Anbietern ab?
- Warum das wichtig ist: Die Kosten sind zwar immer ein Faktor, doch sollten sie im Zusammenhang mit Qualität, Fachwissen und Zuverlässigkeit bewertet werden. Das billigste Angebot bietet möglicherweise nicht den besten Wert oder das geringste Risiko. Vergewissern Sie sich, dass in den Angeboten alle enthaltenen Schritte klar aufgeführt sind.
Tabelle: Zusammenfassung der Checkliste zur Partnerbewertung
Kriterien | Zentrale Fragen | Warum es bei Motorgehäusen kritisch ist |
---|---|---|
Technisches Fachwissen | DfAM-Unterstützung? Material-/Prozesskenntnisse? Industrieerfahrung? | Optimiert komplexes Design, gewährleistet Funktionalität und vermeidet kostspielige Fehler. |
Maschinenpark/Technik | Das richtige Verfahren (LPBF/EBM)? Volumen aufbauen? Kapazität? Qualität der Maschine? | Bestimmt Machbarkeit, Qualität, Vorlaufzeit, Skalierbarkeit. |
Material/Pulverqualität | Erforderliche Legierungen verfügbar? Pulver-QC? Rückverfolgbarkeit? Lieferant vs. Hersteller (wie Met3dp)? | Grundlagen der Teilequalität, mechanische Eigenschaften, Fehlervermeidung. |
Qualitätssystem/Zertifikate | ISO 9001? AS9100 (falls Luft- und Raumfahrt)? Interne QC-Verfahren? Auditierbar? | Gewährleistet Prozesskontrolle, Wiederholbarkeit und Konformität für kritische Teile. |
Nachbearbeitung | Eigene Kapazitäten? Verwaltetes Netzwerk? Workflow-Integration? | Strafft komplexe Arbeitsabläufe und gewährleistet ein durchgängiges Qualitätsmanagement. |
Erfolgsbilanz/Fallstudien | Einschlägige Projekterfahrung? Referenzen? | Reduziert das Risiko und schafft Vertrauen in die Ausführungsmöglichkeiten. |
Kommunikation/Unterstützung | Reaktionsfähigkeit? Transparenz? Kooperationspotenzial? | Erleichtert die reibungslose Durchführung von Projekten und die Lösung von Problemen. |
Kosten und Vorlaufzeit | Wettbewerbsfähige und transparente Preise? Realistische Lieferzeiten? Detaillierte Kostenvoranschläge? | Ausgewogenes Verhältnis zwischen Budget und Anforderungen an Qualität, Zuverlässigkeit und Markteinführungszeit. |
In Blätter exportieren
Die Auswahl des richtigen Metall-AM-Partners ist eine wichtige strategische Entscheidung. Durch eine gründliche Bewertung potenzieller Lieferanten anhand dieser Kriterien und die Konzentration auf Anbieter wie Met3dp, die End-to-End-Fähigkeiten von der fortschrittlichen Pulverproduktion bis hin zu zuverlässigen Drucksystemen und Anwendungssupport nachweisen, können Unternehmen die starken Partnerschaften aufbauen, die erforderlich sind, um die additive Fertigung für hochwertige Komponenten wie Motorgehäuse erfolgreich zu nutzen.
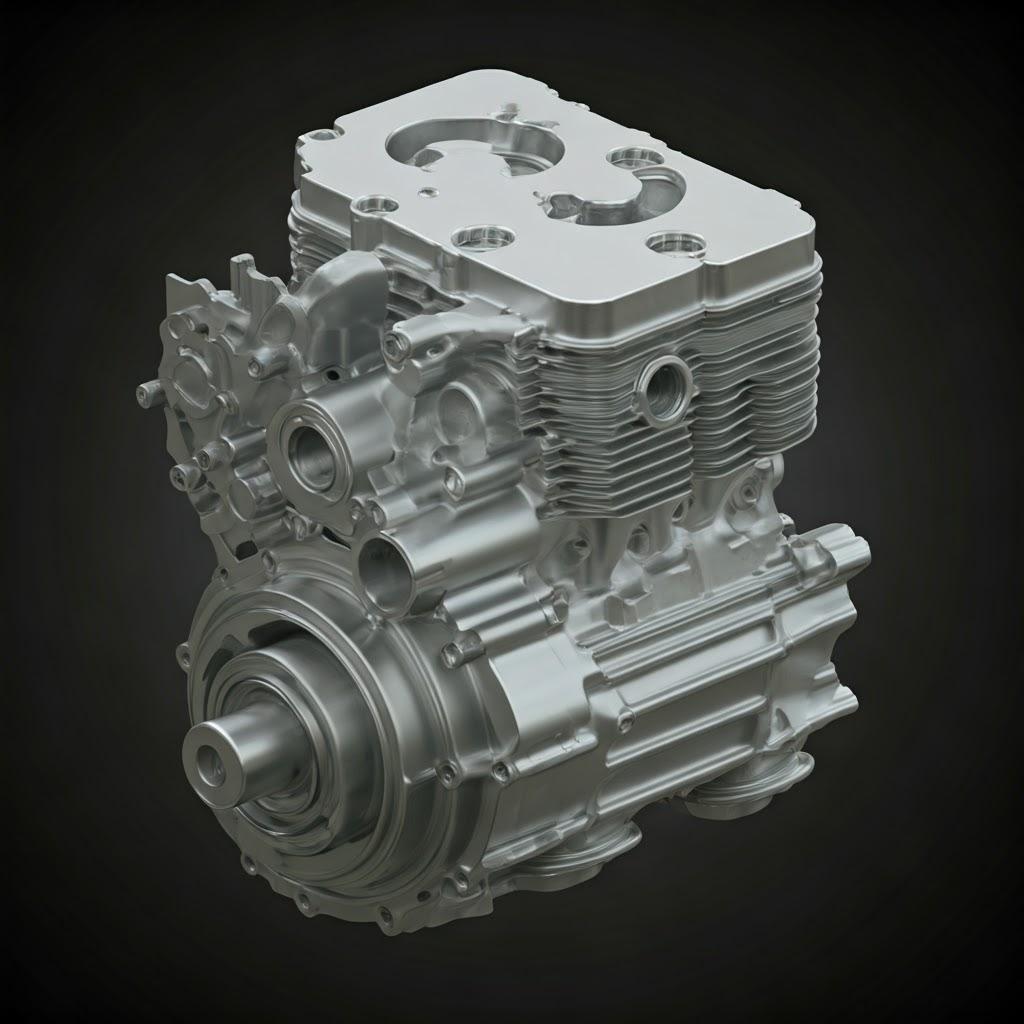
Verständnis der Kostenfaktoren und Vorlaufzeiten für 3D-gedruckte Motorgehäuse
Eine der häufigsten Fragen von Ingenieuren und Beschaffungsmanagern, die eine additive Fertigung von Motorgehäusen aus Metall in Erwägung ziehen, dreht sich um Kosten und Vorlaufzeiten. AM bietet zwar erhebliche Vorteile in Bezug auf die Designfreiheit und den potenziellen langfristigen Wert, aber es ist entscheidend, die Faktoren zu verstehen, die die Preisstruktur und die Produktionszeiten im Vergleich zu herkömmlichen Verfahren bestimmen. Die Kosten basieren nicht einfach auf dem Gewicht, sondern sind eine komplexe Berechnung, die von der Materialauswahl, der Maschinenauslastung, der Komplexität der Teile, dem Arbeitsaufwand und den umfangreichen Nachbearbeitungsanforderungen beeinflusst wird. Auch die Vorlaufzeiten umfassen mehr als nur die Druckdauer.
Hauptkostentreiber für AM-Motorgehäuse aus Metall:
- Materialkosten:
- Pulver Preis: Metallpulver unterscheiden sich erheblich im Preis pro Kilogramm. AlSi10Mg ist relativ preiswert, Ti-6Al-4V ist erheblich teurer, und IN718 ist in der Regel das teuerste der drei.
- Materialverbrauch: Dazu gehört auch das Material im letzten Teil plus das für Stützstrukturen verwendete Material. Die Bemühungen des DfAM, Stützen zu minimieren und das Konstruktionsvolumen zu optimieren, reduzieren direkt den Materialverbrauch.
- Die Dichte: Dichtere Materialien (wie IN718) bedeuten, dass für das gleiche Volumen mehr Kilogramm benötigt werden als bei leichteren Materialien (wie AlSi10Mg).
- Pulver-Recycling: Ein effizientes Recycling von ungeschmolzenem Pulver trägt zur Senkung der Gesamtmaterialkosten bei, erfordert jedoch eine sorgfältige Qualitätskontrolle, um eine Verschlechterung oder Verunreinigung zu verhindern. Erfahrene Anbieter haben ihre Recycling-Protokolle optimiert.
- Maschinenzeit:
- Vorbereitung des Baus: Die Einrichtung der Software, die Vorbereitung der Bauplatten und das Be- und Entladen der Maschine tragen zur Gesamtzeit bei.
- Druckzeit: Dies ist oft der größte Anteil der Maschinenzeit. Sie hängt in erster Linie ab von der Bauteilhöhe (mehr Schichten = mehr Zeit), die Band des pro Schicht zu verschmelzenden Materials, der gewählten Schichtdicke und der Scangeschwindigkeit/-strategie. Komplexe interne Merkmale oder umfangreiche Stützstrukturen erhöhen die Druckzeit.
- Abkühlzeit: Nach dem Druck muss die Baukammer abkühlen, bevor die Teile sicher entnommen werden können, was besonders für das Hochtemperaturverfahren von EBM wichtig ist.
- Maschinenabschreibung und Gemeinkosten: Die hohen Investitionskosten für industrielle Metall-AM-Systeme sind in den von den Dienstleistern berechneten Stundensätzen enthalten.
- Arbeitskosten:
- Techniker Zeit: Für das Einrichten der Maschine, den Betrieb, die Überwachung, das Entpulvern, den Ausbau von Teilen, den Ausbau von Grundträgern und die allgemeine Handhabung sind qualifizierte Techniker erforderlich.
- Technische Unterstützung: Die DfAM-Beratung, die Prozessplanung und das Qualitätssicherungs-Engineering ergänzen den Arbeitsanteil.
- Nachbearbeitungsarbeiten: Die manuelle Entfernung von Halterungen, die Oberflächenbearbeitung (Strahlen, Polieren), die Inspektion und die Koordinierung der ausgelagerten Schritte können einen erheblichen Arbeitsaufwand bedeuten.
- Nachbearbeitungskosten:
- Wärmebehandlung: Die Ofenzeit, der Energieverbrauch und die kontrollierten Atmosphären (Vakuum/Schutzgas) für den Spannungsabbau, das HIP und die abschließende Behandlung der Eigenschaften verursachen zusätzliche Kosten. HIP ist ein besonders spezialisierter und kostspieliger Schritt.
- Bearbeitungen: Die CNC-Bearbeitungszeit für kritische Merkmale hängt von der Menge des abzutragenden Materials, der Komplexität der Merkmale, der Bearbeitbarkeit des Materials (Ti-6Al-4V und IN718 sind viel schwieriger zu bearbeiten als AlSi10Mg) und den Anforderungen an die Spannvorrichtung ab.
- Oberflächenveredelung: Die Kosten variieren je nach Methode (Strahlen ist relativ billig, umfangreiches Polieren ist teuer).
- Inspektion und Qualitätssicherung: Zerstörungsfreie Prüfungen (CT-Scanning, Ultraschall, Farbeindringverfahren), Maßprüfungen (CMM) und Materialprüfungen erhöhen die Gesamtkosten, sind aber für die Qualitätssicherung unerlässlich.
- Teil Komplexität & Größe:
- Komplexität: Auch wenn sich AM durch seine Komplexität auszeichnet, erfordern hochkomplexe Designs oft mehr Stützstrukturen und eine deutlich schwierigere Entpuderung und Entfernung der Stützen, was den Arbeitsaufwand und das Risiko erhöht. Komplexe interne Kanäle können fortschrittliche Prüfmethoden erfordern.
- Größe: Größere Teile verbrauchen mehr Material und erfordern längere Druckzeiten und potenziell größere, teurere Maschinen. Sie stellen auch höhere Anforderungen an das Wärmemanagement und die Nachbearbeitung.
- Produktionsvolumen:
- Amortisation einrichten: Feste Einrichtungskosten (Bauvorbereitung) werden über die Anzahl der Teile in einem einzelnen Bauvorgang amortisiert. Durch das Drucken mehrerer Teile (Verschachtelung) oder größere Losgrößen werden die Kosten pro Teil im Allgemeinen gesenkt.
- Mengenrabatte: Bei laufender Produktion oder größeren Großhandelsbestellungen bieten die Lieferanten möglicherweise Mengenrabatte auf Material und Verarbeitung an.
Tabelle: Zusammenfassung des Kostenfaktors
Kostenkategorie | Wichtige Einflüsse | Auswirkungen auf die Kosten des Motorgehäuses |
---|---|---|
Material | Pulverpreis (Al < Ti < IN718), Teilvolumen, Stützvolumen, Dichte, Recycling | Ein bedeutender Treiber, insbesondere für Ti und IN718. |
Maschinenzeit | Teilehöhe, Volumen/Komplexität pro Schicht, Maschinengeschwindigkeit, Kühlzeit | Hauptkostenkomponente, die direkt mit der Bauzeit zusammenhängt. |
Arbeit | Einrichten, Betrieb, Entpulvern, Entstützen, Nachbearbeitung, QA Engineering | Erheblich, insbesondere bei komplexen Teilen, die eine umfangreiche Handhabung erfordern. |
Nachbearbeitung | Wärmebehandlungsarten (HIP ist kostspielig), Umfang und Schwierigkeit der Bearbeitung, Endbearbeitung | Kann 50% oder mehr der Gesamtkosten ausmachen. |
Komplexität/Größe | Komplexität (Stützen, Reinigung), Gesamtabmessungen | Beeinflusst den Materialverbrauch, die Druckzeit, den Arbeitsaufwand und die Bearbeitungskosten. |
Volumen | Anzahl der Teile pro Build, Gesamtbestellmenge | Amortisation der Einrichtung und mögliche Rabatte reduzieren die Kosten pro Teil. |
In Blätter exportieren
Überlegungen zur Vorlaufzeit:
Die Gesamtvorlaufzeit für ein 3D-gedrucktes Motorgehäuse setzt sich aus mehreren Schritten zusammen:
- Angebotserstellung und Entwurfsprüfung (1-5 Tage): Erstbeurteilung der Unterlagen, Überprüfung/Feedback durch das DfAM, Erstellung von Angeboten.
- Auftragsbestätigung und Terminierung (1-3 Tage): Fertigstellung der Auftragsdetails und Einplanung des Baus in die Maschinenwarteschlange.
- Bauvorbereitung und Druck (2 Tage - 2+ Wochen): Abhängig von der Größe des Teils, der Komplexität, der Anzahl der verschachtelten Teile und der Verfügbarkeit der Maschine. Der Druck selbst kann bei großen/komplexen Gehäusen viele Tage dauern.
- Abkühlung und Entpuderung (1-2 Tage): Erforderliche Abkühlungsphase mit anschließender Pulverentfernung.
- Nachbearbeitung (1 - 4+ Wochen): Dies ist oft die variabelste und möglicherweise längste Phase. Sie umfasst:
- Stressabbau (1-2 Tage)
- Entfernen der Bauplatte / Entfernen der Stütze (1-3 Tage, je nach Komplexität)
- HIP (falls erforderlich, erfordert oft die Versendung von Teilen, was 1-2 Wochen einschließlich Logistik bedeutet)
- Endgültige Wärmebehandlung (2-5 Tage, je nach Komplexität des Zyklus)
- CNC-Bearbeitung (2 Tage - 2+ Wochen, je nach Komplexität und Zeitplanung der Werkstatt)
- Fertigstellung und Inspektion (1-5 Tage)
- Versand (1-5 Tage): Je nach Ort und Methode.
Geschätzte Gesamtvorlaufzeit: Für ein komplexes AM-Motorgehäuse aus Metall, das eine vollständige Nachbearbeitung erfordert, können die typischen Vorlaufzeiten zwischen 4 Wochen bis 10 Wochen oder mehr. Die Herstellung von Prototypen mit minimaler Nachbearbeitung könnte schneller sein (2 bis 4 Wochen), während für die Luft- und Raumfahrt zugelassene Teile, die eine umfangreiche Qualitätskontrolle und spezielle Bearbeitung erfordern, wahrscheinlich länger dauern werden.
Arbeiten mit Met3dp:
Erfahrene Anbieter wie Met3dp kennen diese Kosten- und Vorlaufzeitfaktoren. Sie können detaillierte, transparente Angebote erstellen, in denen alle Schritte aufgeführt sind, und mit den Kunden zusammenarbeiten, um Designs und Prozesse zu optimieren. Ihr integrierter Ansatz, der hochwertige Pulverproduktion, zuverlässige Drucksysteme und Anwendungserfahrung kombiniert, zielt darauf ab, den Arbeitsablauf zu rationalisieren und hochwertige Komponenten innerhalb eines vorhersehbaren Zeitrahmens zu liefern. Eine klare Kommunikation mit dem von Ihnen gewählten AM-Partner über spezifische Anforderungen und Fristen ist für ein effektives Projektmanagement entscheidend.
Häufig gestellte Fragen (FAQ) zu 3D-gedruckten Motorgehäusen
Da die additive Fertigung von Metallen immer häufiger für funktionale Komponenten eingesetzt wird, haben Ingenieure und Beschaffungsmanager oft spezielle Fragen zu ihrer Anwendung bei Motorgehäusen. Hier finden Sie Antworten auf einige häufig gestellte Fragen:
1. Ist 3D-gedrucktes Metall so stabil und zuverlässig wie Metallteile, die durch Gießen oder Schmieden hergestellt werden?
- Antwort: Ja, absolut. Bei der Herstellung mit optimierten Prozessparametern, hochwertigen Metallpulvern (wie denen von Met3dp) und geeigneter Nachbearbeitung (insbesondere Wärmebehandlungen wie Spannungsabbau, HIP und Lösungs-/Alterungszyklen) können AM-Metallteile mechanische Eigenschaften (Zugfestigkeit, Streckgrenze, Ermüdungsfestigkeit, Härte) erreichen, die mit denen von Knet- oder Gusswerkstoffen vergleichbar und manchmal sogar besser sind. So kann zum Beispiel Ti-6Al-4V, das mittels AM hergestellt wird, die ASTM-Normen für Guss- und Knetwerkstoffe erfüllen oder übertreffen. Der Schlüssel dazu ist eine strenge Prozesskontrolle, eine geeignete, auf die Legierung zugeschnittene Wärmebehandlung (z. B. T6 für AlSi10Mg, spezifische Zyklen für Ti-6Al-4V und IN718) sowie Qualitätssicherungsmaßnahmen wie HIP zur Minimierung der Porosität bei kritischen Anwendungen. Es ist von entscheidender Bedeutung, mit erfahrenen Anbietern zusammenzuarbeiten, die sich mit Werkstoffkunde und Prozessoptimierung auskennen, um sicherzustellen, dass das endgültige Teil die erforderlichen Spezifikationen für Zuverlässigkeit und Haltbarkeit in anspruchsvollen Motorumgebungen erfüllt oder übertrifft.
2. Können große Motorkomponenten, wie ein kompletter V8-Motorblock, in 3D gedruckt werden?
- Antwort: Technisch gesehen, ja, das ist zunehmend machbar. Die Hersteller von Metall-AM-Maschinen entwickeln kontinuierlich Systeme mit größeren Bauvolumen, die in der Lage sind, große Bauteile zu drucken. So sind zum Beispiel Bauumfänge von mehr als 500 mm x 500 mm x 500 mm erhältlich, und es gibt sogar noch größere kundenspezifische Systeme. Met3dp bietet Drucker mit branchenführenden Druckvolumina an, die für große Teile geeignet sind. Bei sehr großen Gehäusen müssen jedoch mehrere Faktoren berücksichtigt werden:
- Kosten: Das Drucken sehr großer Stückzahlen verbraucht erhebliche Mengen teuren Pulvers und erfordert viel Maschinenzeit, so dass die Kosten im Vergleich zum herkömmlichen Gießen für die Standardproduktion potenziell unerschwinglich sind, es sei denn, die Vorteile (z. B. extrem geringes Gewicht, integrierte komplexe Merkmale für hohe Leistung) rechtfertigen die Kosten.
- Druckzeit: Die Fertigungszeiten für sehr große, massive oder komplexe Teile können sich über Wochen erstrecken.
- Wärmemanagement: Der Umgang mit Eigenspannungen und potenziellem Verzug wird bei größeren Teilen schwieriger, so dass Verfahren wie EBM/SEBM (mit seiner beheizten Kammer) potenziell vorteilhafter sind oder sehr sorgfältige LPBF-Parameter und Unterstützungsstrategien erfordern.
- Nachbearbeiten: Die Handhabung, Wärmebehandlung und Bearbeitung von sehr großen AM-Teilen erfordert spezielle Ausrüstung.
- Alternativ: Bei einigen sehr großen Strukturen könnte ein alternativer Ansatz darin bestehen, kleinere Abschnitte zu drucken, die optimal für AM ausgelegt sind, und sie dann mit konventionellen Methoden wie Schweißen zusammenzufügen, obwohl dies zusätzliche Montageschritte erfordert. Die Durchführbarkeit und Kosteneffizienz müssen von Fall zu Fall sorgfältig geprüft werden.
3. Wie hoch sind die Kosten eines 3D-gedruckten Motorgehäuses im Vergleich zu einem traditionell gegossenen?
- Antwort: Darauf gibt es keine einheitliche Antwort, da dies stark von mehreren Faktoren abhängt:
- Lautstärke: Bei sehr hohen Produktionsmengen (Tausende oder Zehntausende) bietet das traditionelle Gießen (insbesondere Druckguss) aufgrund von Skaleneffekten in der Regel niedrigere Kosten pro Teil, trotz hoher anfänglicher Werkzeugkosten. Bei geringen Stückzahlen (Prototypen, kundenspezifische Teile, Kleinserien bis zu einigen Hundert Stück) ist Metall-AM oft deutlich kostengünstiger, da keine teuren Werkzeuge (Gussformen) benötigt werden.
- Komplexität: AM eignet sich hervorragend für komplexe Geometrien. Wenn das Design komplizierte interne Kanäle, eine optimierte Topologie oder konsolidierte Merkmale umfasst, die sich nur schwer oder gar nicht gießen lassen, kann AM selbst bei mäßigen Stückzahlen kosteneffizienter sein, da komplexe Kernpakete, mehrere Bearbeitungsvorrichtungen oder Montageschritte, die für das Gussäquivalent erforderlich sind, vermieden werden können.
- Material: Bei teuren Werkstoffen wie Ti-6Al-4V oder IN718 kann das endkonturnahe AM-Verfahren im Vergleich zur Bearbeitung von Knüppeln zu einer besseren Materialausnutzung (weniger Abfall) führen, was trotz höherer anfänglicher Pulverkosten zu Kosteneinsparungen führen kann.
- Vorlaufzeit und Agilität: AM bietet viel kürzere Vorlaufzeiten für die ersten Teile (keine Verzögerung bei der Werkzeugherstellung) und ermöglicht eine schnelle Design-Iteration, was in F&E-Phasen oder bei zeitkritischen Projekten von erheblichem wirtschaftlichen Wert ist.
- Total Cost of Ownership: Wenn man die Vorteile des Leichtbaus (Kraftstoffeinsparungen über die gesamte Lebensdauer), Leistungsverbesserungen (bessere Kühlung) oder die Vereinfachung der Lieferkette (digitales Inventar, reduzierte Montage) in Betracht zieht, ist die Gesamtbetriebskosten für ein AM-Teil niedriger sein kann als für ein traditionell hergestelltes, auch wenn der Anschaffungspreis höher ist.
- Break-Even-Punkt: In der Regel gibt es ein Break-even-Volumen, unterhalb dessen AM billiger ist und oberhalb dessen Gießen billiger wird (für Entwürfe, die sich für beides eignen). Dieser Punkt ist je nach Komplexität und Material sehr unterschiedlich. Eine detaillierte Kostenanalyse, die AM (einschließlich aller Nachbearbeitungsschritte) mit traditionellen Methoden (Werkzeug + Teilekosten + Bearbeitung + Montage) vergleicht, ist für bestimmte Fälle erforderlich.
4. Welche Qualitätszertifizierungen sind bei der Auswahl eines Lieferanten für 3D-gedruckte Triebwerksgehäuse für die Luft- und Raumfahrt am wichtigsten?
- Antwort: Für Luft- und Raumfahrtanwendungen sind Qualität und Rückverfolgbarkeit von größter Bedeutung. Zu den wichtigsten Zertifizierungen, auf die man bei einem Anbieter von Metall-AM achten sollte, gehören:
- AS9100: Dies ist die standardisierte Anforderung an ein Qualitätsmanagementsystem für die Luft- und Raumfahrtindustrie. Sie umfasst die Anforderungen der ISO 9001 und fügt spezifische Kriterien in Bezug auf Sicherheit, Zuverlässigkeit, Lufttüchtigkeit und Rückverfolgbarkeit hinzu, die für Luft- und Raumfahrtkomponenten entscheidend sind. Die Einhaltung ist im Allgemeinen für Zulieferer, die flugkritische oder primäre Strukturteile herstellen, obligatorisch.
- ISO 9001: Während AS9100 für die Luft- und Raumfahrt bevorzugt wird, zeigt die ISO 9001-Zertifizierung ein grundlegendes Engagement für die Prinzipien des Qualitätsmanagements, der Prozesskontrolle und der Dokumentation, was eine wesentliche Grundlage für die Glaubwürdigkeit darstellt.
- NADCAP (National Aerospace and Defense Contractors Accreditation Program): Während AS9100 das gesamte QMS abdeckt, bietet NADCAP eine spezifische Akkreditierung für spezielle Prozesse. Zu den relevanten NADCAP-Akkreditierungen für einen AM-Arbeitsablauf könnten Wärmebehandlung, zerstörungsfreie Prüfung (ZfP), Materialprüflabore und möglicherweise Schweißen (wenn AM-Teile zusammengefügt werden) gehören. Zulieferer benötigen eine Akkreditierung für die spezifischen Prozesse, die sie durchführen oder verwalten.
- Spezifische Kundenzulassungen: Die großen OEMs (Original Equipment Manufacturers) der Luft- und Raumfahrtindustrie haben oft ihre eigenen zusätzlichen Anforderungen an die Lieferantenqualifikation und Listen zugelassener Lieferanten.
Wenn Sie sich vergewissern, dass der von Ihnen gewählte Partner über die erforderlichen Zertifizierungen verfügt, können Sie sicher sein, dass er die strengen Qualitätskontroll-, Prozessvalidierungs- und Rückverfolgbarkeitsstandards einhält, die von der Luft- und Raumfahrtindustrie für Komponenten wie Triebwerksgehäuse gefordert werden.
Schlussfolgerung: Die Zukunft der Motorgehäuseproduktion ist additiv
Die Reise durch die Feinheiten der metallischen additiven Fertigung für Motorgehäuse offenbart eine Technologie, die sich endgültig über das Rapid Prototyping hinaus in den Bereich der fortschrittlichen Fertigung für anspruchsvolle Endanwendungen bewegt hat. Für Ingenieure und Beschaffungsverantwortliche in der Automobilbranche, der Luft- und Raumfahrt und der Industrie bietet Metall-AM unter Verwendung von Werkstoffen wie AlSi10Mg, Ti-6Al-4V und IN718 eine Reihe von Vorteilen, die mit herkömmlichen Methoden einfach nicht zu erreichen sind. Die Möglichkeit, eine noch nie dagewesene Designfreiheit zu erreichen, die eine Topologieoptimierung für radikalen Leichtbau, komplizierte konforme Kühlkanäle für hervorragendes Wärmemanagement und die Konsolidierung mehrerer Teile in einer einzigen, robusten Komponente ermöglicht, stellt einen Paradigmenwechsel in Bezug auf Leistung, Effizienz und Zuverlässigkeit von Motoren dar.
Zwar gibt es Herausforderungen im Zusammenhang mit Eigenspannungen, Stützstrukturen, Pulverentfernung und der Notwendigkeit einer umfassenden Nachbearbeitung, doch werden diese durch Fortschritte bei den DfAM-Prinzipien, eine ausgefeilte Prozesssteuerung (wie bei Technologien wie den SEBM-Systemen von Met3dp), eine hochwertige Materialproduktion und ein integriertes Workflow-Management wirksam angegangen. Der Schlüssel liegt im Verständnis sowohl des immensen Potenzials als auch der praktischen Aspekte der Technologie. Der Erfolg erfordert einen ganzheitlichen Ansatz: Überdenken der Designmöglichkeiten, sorgfältige Auswahl des richtigen Materials für die Anwendung, sorgfältige Planung und Ausführung der Nachbearbeitungsschritte und - vielleicht am wichtigsten - die Wahl des richtigen Fertigungspartners.
Ein Partner wie Met3dp, der sowohl in der Wissenschaft der Hochleistungsmetallpulverproduktion als auch in der Entwicklung von branchenführenden additiven Fertigungsanlagen tief verwurzelt ist, verkörpert das erforderliche integrierte Know-how. Ihr Engagement für Qualität, von der Zerstäubung sphärischer Pulver bis hin zum zuverlässigen Betrieb ihrer Drucker, bildet die Grundlage für die Herstellung von Motorgehäusen, die den strengen Anforderungen der modernen Industrie gerecht werden. Durch die Nutzung solcher Partnerschaften können Unternehmen das Risiko bei der Einführung von AM verringern, Entwicklungszyklen beschleunigen und Leistungsvorteile erschließen, die zuvor unerreichbar waren.
Die Entscheidung für Metall-AM bei Motorgehäusen ist eine strategische Entscheidung. In manchen Szenarien können die Anschaffungskosten pro Teil höher sein als bei Großseriengussteilen, aber das Wertversprechen geht oft weit über den Anschaffungspreis hinaus. Geringere Montagekosten, ein geringerer Kraftstoffverbrauch über die gesamte Lebensdauer aufgrund des geringeren Gewichts, eine längere Lebensdauer der Komponenten durch ein besseres Wärmemanagement und eine beispiellose Flexibilität in der Lieferkette durch bedarfsgerechte Produktion und digitale Bestände tragen zu einer überzeugenden Gesamtbetriebskostenrechnung bei.
Da die Industrie die Grenzen von Leistung und Effizienz immer weiter verschiebt, wird die additive Fertigung von Metallen zweifellos eine immer wichtigere Rolle bei der Produktion von Motorgehäusen der nächsten Generation und anderen wichtigen Komponenten spielen. Die Zukunft der Motorenproduktion besteht nicht nur in der Herstellung von Teilen, sondern in der intelligenten Fertigung integrierter Systeme - leichter, stärker, effizienter und genau auf ihre Funktion zugeschnitten. Metall-AM ist eine Eckpfeilertechnologie, die diese Zukunft ermöglicht.
Sind Sie bereit zu erfahren, wie die additive Fertigung von Metallen die Konstruktion Ihrer Motorgehäuse revolutionieren kann? Besuchen Met3dp um mehr über unsere fortschrittlichen SEBM-Drucker, Hochleistungsmetallpulver und umfassenden Anwendungsentwicklungsdienste zu erfahren. Setzen Sie sich noch heute mit unserem Team in Verbindung, um Ihre Projektanforderungen zu besprechen und zu erfahren, wie unser Fachwissen die Ziele Ihres Unternehmens im Bereich der additiven Fertigung unterstützen kann.
Teilen auf
MET3DP Technology Co., LTD ist ein führender Anbieter von additiven Fertigungslösungen mit Hauptsitz in Qingdao, China. Unser Unternehmen ist spezialisiert auf 3D-Druckgeräte und Hochleistungsmetallpulver für industrielle Anwendungen.
Fragen Sie an, um den besten Preis und eine maßgeschneiderte Lösung für Ihr Unternehmen zu erhalten!
Verwandte Artikel
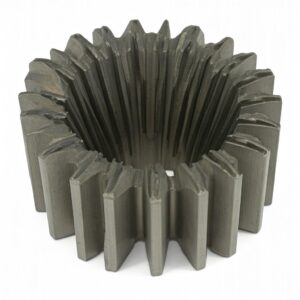
Hochleistungs-Düsenschaufelsegmente: Revolutionierung der Turbineneffizienz mit 3D-Metalldruck
Mehr lesen "Über Met3DP
Aktuelles Update
Unser Produkt
KONTAKT US
Haben Sie Fragen? Senden Sie uns jetzt eine Nachricht! Wir werden Ihre Anfrage mit einem ganzen Team nach Erhalt Ihrer Nachricht bearbeiten.
Holen Sie sich Metal3DP's
Produkt-Broschüre
Erhalten Sie die neuesten Produkte und Preislisten
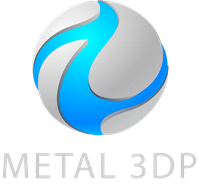
Metallpulver für 3D-Druck und additive Fertigung