AlSi10Mg für Kfz-Halterungen im Metall-3D-Druck
Inhaltsübersicht
Einführung: Revolutionierung von Kfz-Halterungen mit AlSi10Mg-Metall-3D-Druck
Die Automobilindustrie steht bei der Einführung neuer Technologien an vorderster Front und wird ständig von den Erfordernissen der Leistungssteigerung von Fahrzeugen, der Verbesserung der Kraftstoffeffizienz (oder der elektrischen Reichweite), der Gewährleistung der Sicherheit der Fahrgäste und der Beschleunigung der Produktentwicklungszyklen angetrieben. Bei diesem unerbittlichen Streben nach Innovation spielen die Fertigungsmethoden eine zentrale Rolle. Herkömmliche Verfahren wie Gießen, Stanzen und Zerspanen sind zwar für die Massenproduktion ausgereift und zuverlässig, stoßen aber oft an ihre Grenzen, wenn es um Designflexibilität, Gewichtsoptimierung und die für das Rapid Prototyping und die Anpassung von Kleinserien erforderliche Geschwindigkeit geht. Hier kommt die additive Fertigung von Metall (AM) ins Spiel, besser bekannt als Metall 3D-Druck - eine transformative Technologie, die die Art und Weise, wie kritische Automobilkomponenten, wie z. B. Halterungen, konzipiert, entworfen und hergestellt werden, neu definieren wird.
Kfz-Halterungen sind, obwohl sie oft unscheinbar sind, grundlegende Komponenten, die wichtige Funktionen erfüllen. Sie dienen als strukturelle Schnittstelle, Befestigungspunkte und Stützstrukturen für eine Vielzahl von Systemen innerhalb eines Fahrzeugs - von Motor- und Antriebsstrangkomponenten bis hin zu Fahrwerkselementen, Innenausstattungselementen und empfindlichen elektronischen Modulen. Ihre Leistung wirkt sich direkt auf die Fahrzeugintegrität, das Schwingungsverhalten, den Geräuschpegel und die Gesamteffizienz der Montage aus. Traditionell war die Entwicklung und Herstellung dieser Halterungen mit Kompromissen verbunden. Um eine höhere Festigkeit zu erreichen, musste oft Gewicht hinzugefügt werden, komplexe Geometrien erforderten mehrteilige Baugruppen oder komplizierte Werkzeuge, und die Herstellung von Prototypen oder Kleinserien war mit erheblichen Zeit- und Kosteneinbußen bei der Einrichtung der Werkzeuge verbunden.
Hier schafft die Synergie zwischen fortschrittlichen Werkstoffen und hochmodernen Fertigungsverfahren ein bahnbrechendes Potenzial. AlSi10Mg, eine Aluminium-Silizium-Magnesium-Legierung, hat sich zu einem Eckpfeiler in der Metall-AM-Landschaft entwickelt, insbesondere für Pulverbettschmelzverfahren wie Selective Laser Melting (SLM) und Direct Metal Laser Sintering (DMLS). AlSi10Mg ist bekannt für seine ausgezeichneten mechanischen Eigenschaften - einschließlich eines guten Verhältnisses von Festigkeit zu Gewicht, Schweißbarkeit, Korrosionsbeständigkeit und hervorragender Verarbeitbarkeit in AM-Systemen - und bietet eine ideale Lösung für viele Anwendungen im Bereich der Automobilhalterungen. Seine Eigenschaften ähneln denen herkömmlicher Gusslegierungen und bieten Ingenieuren eine vertraute Materialbasis, während sie gleichzeitig die beispiellose Designfreiheit des 3D-Drucks nutzen können.
Die Kombination von AlSi10Mg-Pulver und 3D-Druck von Metall Techniken ermöglicht es Ingenieuren und Beschaffungsmanagern in der gesamten automobilen Wertschöpfungskette - von globalen OEMs und Tier 1/Tier 2-Zulieferern bis hin zu Nischen-Motorsportteams und Aftermarket-Spezialisten -, das Design von Halterungen neu zu gestalten. Es ermöglicht die Entwicklung von leichten, topologieoptimierten Strukturen, die bisher nicht herstellbar waren. Es erleichtert die Konsolidierung mehrerer Komponenten in einem einzigen, komplexen gedruckten Teil, wodurch die Komplexität der Montage und potenzielle Fehlerquellen reduziert werden. Darüber hinaus verkürzt es die Vorlaufzeiten für Funktionsprototypen drastisch und ermöglicht kosteneffiziente Kleinserien, ohne dass teure Spezialwerkzeuge benötigt werden. Diese Agilität ist in der heutigen schnelllebigen Entwicklungsumgebung der Automobilindustrie von größter Bedeutung.
Als führender Anbieter von umfassenden Lösungen für die additive Fertigung steht Met3dp an der Spitze dieses technologischen Wandels. Met3dp mit Hauptsitz in Qingdao, China, ist nicht nur auf hochmoderne 3D-Metalldruckgeräte spezialisiert, die für branchenführende Druckvolumen, Genauigkeit und Zuverlässigkeit bekannt sind, sondern auch auf die Forschung, Entwicklung und Produktion von Hochleistungsmetallpulvern, einschließlich hochwertigem AlSi10Mg, das für AM-Prozesse optimiert ist. Unser umfassendes Know-how, das wir über Jahrzehnte in der additiven Fertigung von Metallen erworben haben, umfasst das gesamte Ökosystem - von der fortschrittlichen Pulverzerstäubung mit einzigartigen Gaszerstäubungs- und PREP-Technologien bis hin zu hochentwickelten Drucksystemen wie Selective Electron Beam Melting (SEBM) und Unterstützung bei der Anwendungsentwicklung. Wir arbeiten mit Automobilherstellern zusammen, um die Leistungsfähigkeit von AM nutzbar zu machen, ihre Fertigungskapazitäten zu verändern und ihre Reise in Richtung Fahrzeugdesign und -produktion der nächsten Generation zu beschleunigen. Dieser Artikel befasst sich mit den Besonderheiten der Verwendung von AlSi10Mg mittels 3D-Metalldruck für Kfz-Halterungen. Er untersucht Anwendungen, Vorteile, Materialüberlegungen und bewährte Verfahren für die Beschaffung und Umsetzung und positioniert Met3dp als Ihren zuverlässigen B2B-Partner für additive Fertigungslösungen in Industriequalität. Für Ingenieurteams, die einen Leistungsdurchbruch anstreben, und Beschaffungsmanager, die nach zuverlässigen, kosteneffizienten B2B-Metalldrucklieferanten suchen, ist das Verständnis der Nuancen von AlSi10Mg in der AM entscheidend.
Vielfältige Anwendungen: Wo werden 3D-gedruckte AlSi10Mg-Automobilhalterungen eingesetzt?
Die Vielseitigkeit von AlSi10Mg in Kombination mit der Designfreiheit des 3D-Metalldrucks eröffnet eine breite Palette von Anwendungsmöglichkeiten für Kfz-Halterungen, die weit über den einfachen Ersatz konventionell gefertigter Teile hinausgehen. Durch die Möglichkeit, komplexe, leichte und kundenspezifische Geometrien zu erstellen, können diese Halterungen spezifische technische Herausforderungen in praktisch jedem System eines modernen Fahrzeugs lösen. Beschaffungsexperten und Ingenieure, die Komponenten für Erstausrüster, Tier-Zulieferer oder spezialisierte Automobilsektoren beschaffen, müssen die Bandbreite dieser Anwendungen erkennen, um das Potenzial der Technologie voll auszuschöpfen.
Kernfunktionen und warum AM sich auszeichnet:
Kfz-Halterungen dienen im Wesentlichen dazu:
- Komponenten verbinden: Verbindung verschiedener Teile oder Subsysteme miteinander (z. B. Motor und Fahrgestell).
- Stützlasten: Aufnahme von statischen oder dynamischen Lasten zur Aufrechterhaltung der strukturellen Integrität (z. B. Aufhängebügel).
- Systeme montieren: Sichere Befestigung von Komponenten wie Sensoren, Aktuatoren, Steuergeräten, Pumpen oder Flüssigkeitsleitungen.
- Vibrationen bewältigen: Manchmal mit speziellen Geometrien zur Dämpfung oder Isolierung von Vibrationen.
Metall-AM, insbesondere mit AlSi10Mg, zeichnet sich in diesen Rollen durch die Möglichkeit aus:
- Optimierte Lastpfade: Topologieoptimierungssoftware kann Halterungsdesigns erstellen, die das Material genau dort platzieren, wo es für bestimmte Lastfälle benötigt wird, um das Gewicht zu minimieren und gleichzeitig die Festigkeit zu erhalten oder zu erhöhen.
- Integrierte Funktionalitäten: Merkmale wie Flüssigkeitskanäle, Kabelkanäle oder Kühlkörper können direkt in das Halterungsdesign integriert werden, wodurch die Anzahl der Teile und die Komplexität der Montage reduziert werden.
- Komplexe Schnittstellen: Die Herstellung von Halterungen mit komplizierten Montageflächen oder Merkmalen zur Anpassung an beengte Platzverhältnisse wird möglich.
Konkrete Anwendungsbeispiele für verschiedene Fahrzeugsysteme:
Sehen wir uns konkrete Beispiele an, bei denen 3D-gedruckte AlSi10Mg-Brackets einen erheblichen Wert darstellen:
- Motor und Antriebsstrang:
- Lichtmaschinen-/Anlassermotorhalterungen: Oftmals sind sie Vibrationen und moderaten Temperaturen ausgesetzt. AM ermöglicht leichte Konstruktionen, die für Steifigkeit und Schwingungsdämpfung optimiert sind.
- Sensorhalterungen (z. B. Klopfsensoren, Temperatursensoren): Komplexe Geometrien können für eine präzise Positionierung in engen Motorräumen erforderlich sein. AM ermöglicht ein schnelles Prototyping und die Produktion von kundenspezifischen Halterungen.
- Auspuffanlagenaufhängungen/-halterungen: Während hohe Temperaturen in der Nähe des Verteilers möglicherweise andere Legierungen erfordern, können Halterungen weiter stromabwärts von der Leichtigkeit und Korrosionsbeständigkeit von AlSi10Mg profitieren. AM ermöglicht Konstruktionen, die die Wärmeausdehnung berücksichtigen.
- Halterungen für Kraftstoffpumpe/Filter: Kann mit integrierten Funktionen für die Schlauchführung oder Schwingungsisolierung entworfen werden.
- Turbolader/Supercharger-Halterungen (untere Temperaturbereiche): Komponenten, die Nebenaggregate von Zwangsinduktionssystemen tragen, können in Leichtbauweise hergestellt werden.
- Fahrwerk und Aufhängung:
- Halterungen für Aufhängungskomponenten (z. B. obere/untere Querlenkerhalterungen - für Prototypen/geringe Stückzahlen): Während für die Großserienproduktion Schmieden/Gießen in Frage kommt, ist AM von unschätzbarem Wert für das Rapid Prototyping komplexer Aufhängungsgeometrien und für Hochleistungsfahrzeuge in Kleinserien, bei denen Leichtbau von größter Bedeutung ist. AlSi10Mg bietet ein gutes Gleichgewicht für Tests, bevor bei Bedarf zu höherfesten Materialien gewechselt werden kann.
- Bremsleitung und Sensorhalterungen (ABS): Komplexes Routing und präzise Sensorpositionierung profitieren von der geometrischen Freiheit des AM. Die Konsolidierung von Teilen kann Montageschritte reduzieren.
- Halterungen für das Lenksystem: Montage von Zahnstangen oder zugehörigen Sensoren.
- Anti-Rollbar-Halterungen: Die Topologie kann hinsichtlich Steifigkeit und Gewicht optimiert werden.
- Karosserie und Exterieur:
- Halterungen für die Stoßstange: Vor allem bei Kleinserien- oder Sonderfahrzeugen ermöglicht AM komplexe Schnittstellen mit dem Fahrgestell und der Stoßfängerstruktur, die für die Energieabsorptionswege optimiert sind (wobei die Materialauswahl im Hinblick auf die Aufprallsicherheit sorgfältig geprüft werden muss).
- Halterungen für Spoiler/Aerodynamikelemente: Häufig sind leichte, komplexe Formen erforderlich, was AM ideal für Hochleistungsanwendungen macht.
- Halterungen für die Beleuchtungsanlage (Scheinwerfer, Rückleuchten): Sie können komplizierte Formen erfordern, um in das moderne Fahrzeugdesign und die engen Verpackungsvorgaben zu passen.
- Spiegelhalterungen: Die internen Strukturen können zur Schwingungsdämpfung und Gewichtsreduzierung optimiert werden.
- Innere Systeme:
- Sitzrahmenhalterungen: Die Gewichtsreduzierung von Innenraumkomponenten trägt erheblich zur Verringerung der Gesamtmasse des Fahrzeugs bei.
- Halterungen für Armaturenbrett/Instrumententafel: Komplexe Geometrien sind oft erforderlich, um HVAC-Kanäle, Kabelbäume und Strukturteile zu steuern. AM ermöglicht Konsolidierung und Gewichtseinsparungen.
- Halterungen für HVAC-Komponenten: Halterungen für Gebläse, Verdampfer oder Heizungsrohre.
- Mittelkonsole Halterungen: Unterstützung von Infotainment-Systemen, Schalthebeln usw.
- Elektrofahrzeuge (EVs) und Hybridfahrzeuge (HEVs):
- Akku-Montagehalterungen/Rahmenkomponenten: Die Halterung von schweren Batteriemodulen erfordert starke und dennoch leichte Strukturen. AlSi10Mg bietet eine gute Ausgangsbasis, und AM ermöglicht integrierte Wärmemanagementfunktionen (z. B. Kanäle für Kühlflüssigkeiten) in den Halterungen.
- Halterungen für Elektromotoren: Ähnliche Anforderungen wie bei ICE-Motorlagern, jedoch mit anderen Schwingungsprofilen.
- On-Board Charger (OBC) und Leistungselektronikhalterungen: Sie erfordern häufig spezielle Befestigungspunkte und möglicherweise integrierte Kühlfunktionen.
- Halterungen für die Ladeanschlüsse: Sichere Befestigung der Ladebuchse des Fahrzeugs.
- Motorsport- und Leistungsanwendungen:
- Hochgradig kundenspezifische Klammern: Praktisch jede Halterung kann schnell entworfen, gedruckt und für Rennwagen oder Hochleistungsfahrzeuge getestet werden, bei denen Iterationsgeschwindigkeit und ultimative Leistung wichtiger sind als Kostenbeschränkungen.
- Maßgeschneiderte Sensorhalterungen: Für zusätzliche Datenerfassungssysteme.
- Leichte Alternativen: Ersetzen von Standard-Brackets durch topologieoptimierte AlSi10Mg-Versionen als Wettbewerbsvorteil.
Kategorisierung von Anwendungsfällen für B2B-Sourcing:
Beschaffungsmanager und Großabnehmer sollten diese Anwendungskategorien berücksichtigen, wenn sie mit AM-Dienstleistern wie Met3dp zusammenarbeiten:
Anwendungsfall Kategorie | Beschreibung | Die wichtigsten Vorteile für B2B-Kunden aus der Automobilindustrie | Typisches Volumen |
---|---|---|---|
Schnelles Prototyping | Schnelle Erstellung funktionaler Halterungen für die Designvalidierung, Passformkontrolle und Leistungsprüfung. | Beschleunigte Entwicklungszyklen, kürzere Iterationszeiten, frühzeitige Erkennung von Designfehlern, geringeres Risiko. | Sehr niedrig (1-10) |
Kleinserienproduktion | Herstellung von Endverbraucher-Halterungen für Nischenfahrzeuge, den Motorsport oder erste Produktionsläufe vor der Erweiterung der Produktion. | Vermeidung hoher Werkzeugkosten, ermöglicht den Markteintritt für Spezialfahrzeuge, Designflexibilität. | Niedrig (10-1000s) |
Personalisierung/Sonderanfertigung | Herstellung einzigartiger Halterungen für kundenspezifische Fahrzeuge, Modifikationen auf dem Nachrüstungsmarkt oder spezielle Leistungsanforderungen. | Große Gestaltungsfreiheit, Bedienung von Nischenmärkten, hochwertige Produktangebote. | Sehr niedrig bis niedrig |
Aftermarket-Teile | Lieferung von Ersatz- oder leistungssteigernden Halterungen für bestehende Fahrzeuge. | Die Fähigkeit, verbesserte Konstruktionen anzubieten (z. B. geringeres Gewicht) und die Veralterung von Teilen zu vermeiden. | Niedrig bis mittel |
Legacy Ersatzteil | Neuanfertigung von Halterungen für ältere Fahrzeuge, für die es keine Originalwerkzeuge mehr gibt (digitaler Bestand). | Löst Veralterungsprobleme, unterstützt die Restaurierung von Oldtimern und vermeidet die kostspielige Neuanfertigung von Werkzeugen. | Sehr niedrig bis niedrig |
Teil Konsolidierung | Neugestaltung von Baugruppen, um mehrere Halterungen/Komponenten in einem einzigen gedruckten Teil zu kombinieren. | Geringere Montagezeit/-kosten, geringeres Gewicht, höhere Zuverlässigkeit, vereinfachte Lieferkette. | Niedrig bis mittel |
In Blätter exportieren
Das Verständnis dieses vielfältigen Anwendungsspektrums ermöglicht es den Unternehmen der Automobilindustrie, den AlSi10Mg-3D-Druck strategisch einzusetzen und auf die Bereiche zu zielen, in denen er die größte Wirkung entfaltet, sei es bei der Beschleunigung von Forschung und Entwicklung, bei der Ermöglichung innovativer Designs oder bei der Bereitstellung kostengünstiger Lösungen für Kleinserien und kundenspezifische Anforderungen. Met3dp, mit seiner robusten Druckverfahren und Materialkenntnis, ist in der Lage, B2B-Kunden in all diesen Anwendungsszenarien zu unterstützen, vom ersten Prototyp bis zum Serienteil.
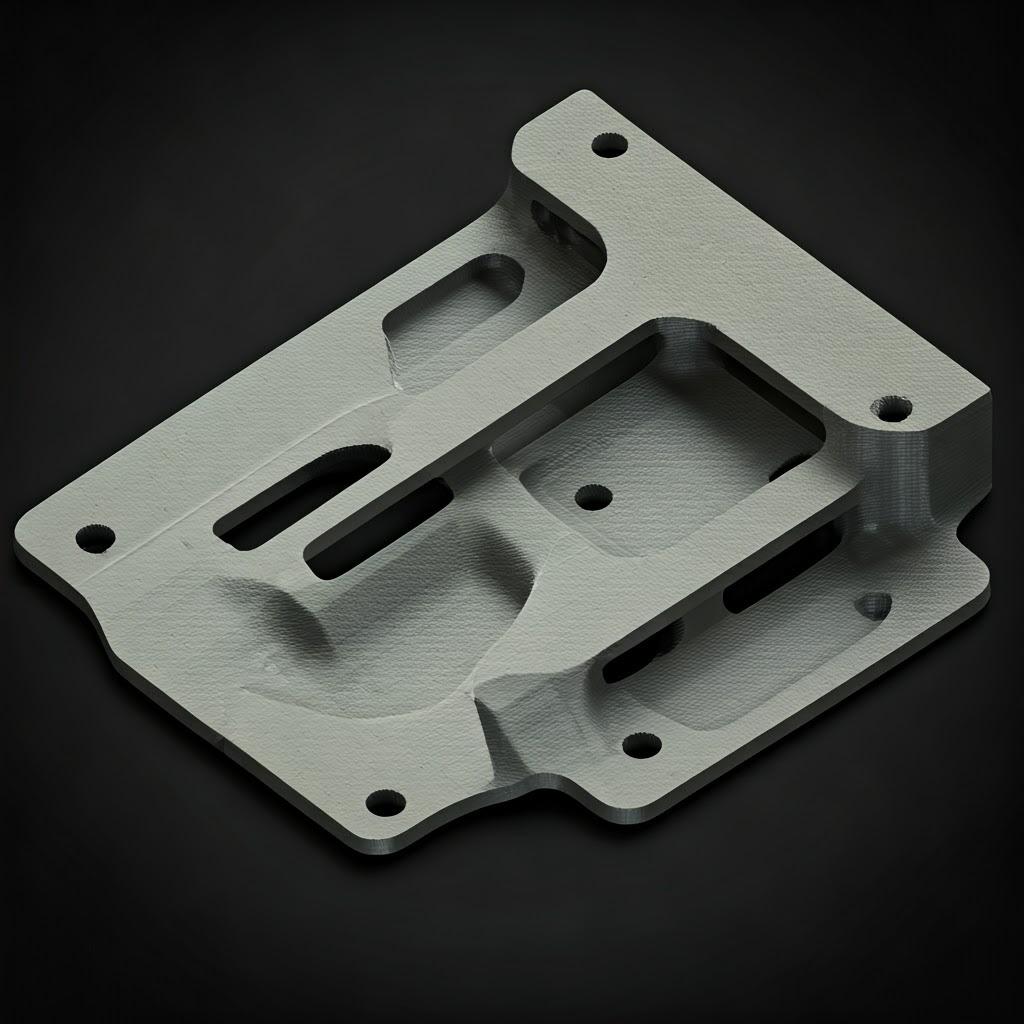
Der Additiv-Vorteil: Warum 3D-Metalldruck für die Produktion von Fahrzeughalterungen?
Während herkömmliche Fertigungsmethoden nach wie vor der Standard für die Produktion von Automobilhalterungen in hohen Stückzahlen sind, bietet die additive Fertigung von Metallen, insbesondere unter Verwendung von Materialien wie AlSi10Mg mittels Pulverbettfusionsverfahren (SLM/DMLS), überzeugende Vorteile, insbesondere in Bereichen, in denen Innovation, Schnelligkeit, individuelle Anpassung und optimierte Leistung gefragt sind. Für Ingenieure, die die Grenzen des Designs verschieben, und für Beschaffungsmanager, die nach effizienten, flexiblen Beschaffungslösungen suchen, ist das Verständnis dieser Vorteile der Schlüssel zur effektiven Nutzung von AM. Bei der Entscheidung für AM geht es nicht nur darum, ein altes Verfahren durch ein neues zu ersetzen, sondern auch darum, bisher unerreichbare Fähigkeiten freizusetzen.
Vergleich: Metall-AM (AlSi10Mg) vs. traditionelle Methoden für Brackets
Merkmal | Metall-AM (SLM/DMLS mit AlSi10Mg) | Traditionelles Gießen (z. B. Druckguss) | Traditionelle Zerspanung (subtraktiv) | Traditionelles Stanzen/Umformen |
---|---|---|---|---|
Entwurfskomplexität | Extrem hoch (interne Kanäle, Gitter, organische Formen) | Mäßig (begrenzt durch Entformungswinkel, Wandstärke) | Hoch (Begrenzt durch Zugang zu Werkzeugen, Funktionen) | Gering bis mäßig (Blechformen, Biegungen, einfache Merkmale) |
Gewichtsreduzierung | Ausgezeichnet (Topologieoptimierung, Material nur dort, wo es benötigt wird) | Gut (kann nahezu eine Netzform erreichen) | Mäßig (Materialentfernung, beginnt jedoch mit einem festen Block) | Mäßig (begrenzt durch die Blechdicke) |
Teil Konsolidierung | Ausgezeichnet (mehrere Funktionen in einem Teil integriert) | Begrenzt (Schwierig, komplexe interne Funktionen zu integrieren) | Begrenzt (komplexe mehrachsige Bearbeitung erforderlich) | Sehr begrenzt (typischerweise Teile mit einer Funktion) |
Werkzeugkosten | Keine (digitale Datei ist die Eingabe) | Sehr hoch (Entwurf und Herstellung von Formen) | Gering bis mäßig (Vorrichtungen, Standardwerkzeuge) | Hoch (Entwurf und Herstellung von Werkzeugen) |
Vorlaufzeit (Proto) | Sehr schnell (Tage) | Sehr langsam (Wochen bis Monate für die Werkzeugherstellung) | Schnell (Tage bis Wochen, je nach Komplexität) | Langsam (Wochen bis Monate für die Werkzeugherstellung) |
Vorlaufzeit (Prod) | Mäßig (Abhängig vom Bauvolumen, Nachbearbeitung) | Schnell (für hohe Stückzahlen, sobald die Werkzeuge vorhanden sind) | Mäßig bis langsam (abhängig von der Komplexität, Materialabtrag) | Sehr schnell (für hohe Stückzahlen, sobald die Werkzeuge vorhanden sind) |
Materialabfälle | Gering (ungebrauchtes Pulver weitgehend recycelbar) | Gering (Effizienter Materialeinsatz in der Form) | Hoch (Erheblicher Materialabtrag als Späne) | Mäßig (Verschnitt vom Blech) |
Stückkosten (Low Vol) | Wettbewerbsfähig bis hoch (abhängig von Maschinenzeit und Material) | Sehr hoch (Amortisation von Werkzeugen dominiert) | Hoch (Bearbeitungszeit pro Teil) | Sehr hoch (Amortisation von Werkzeugen dominiert) |
Stückkosten (hohe Volumina) | Hoch | Sehr niedrig | Mäßig bis hoch | Sehr niedrig |
Material-Optionen | Wachsende Auswahl an schweißbaren/druckbaren Legierungen | Breite Palette an gießbaren Legierungen | Sehr breite Palette an bearbeitbaren Materialien | Angebot an verformbaren Blechen |
In Blätter exportieren
Die wichtigsten Vorteile von Metal AM für Automobilhalterungen:
- Unerreichte Gestaltungsfreiheit und geometrische Komplexität: Dies ist wohl der bedeutendste Vorteil. AM befreit Konstrukteure von den Zwängen, die durch herkömmliche Fertigungswerkzeuge und -verfahren auferlegt werden.
- Topologie-Optimierung: Algorithmen können Halterungen auf der Grundlage von Lastpfaden in optimale Formen bringen, die das Gewicht minimieren und gleichzeitig die Steifigkeitsanforderungen erfüllen. Das Ergebnis sind organisch anmutende, hocheffiziente Strukturen.
- Gitterförmige Strukturen: Interne Gitter- oder Zellstrukturen können eingebaut werden, um das Gewicht weiter zu reduzieren, die Energieabsorption zu steuern oder die Schwingungseigenschaften zu verändern.
- Interne Kanäle: Leitungen für Kühlflüssigkeiten, Kabel oder Hydraulikleitungen können nahtlos in die Halterungsstruktur integriert werden, was die Teile zusammenfasst und die Montage vereinfacht.
- Negative Tiefgangswinkel und Hinterschneidungen: Merkmale, die beim Gießen ohne komplexe Kerne oder mehrteilige Formen nicht möglich sind, können problemlos gedruckt werden.
- Erhebliches Potenzial zur Gewichtsreduzierung: In der Welt des Automobils führt die Verringerung der Masse direkt zu einem geringeren Kraftstoffverbrauch, einer größeren Reichweite, einer besseren Fahrdynamik und einer höheren Leistung. AM ermöglicht Leichtbau durch:
- Topologie-Optimierung: Wie bereits erwähnt, wird das Material nur dort angebracht, wo es strukturell notwendig ist. Gewichtseinsparungen von 20-60% im Vergleich zu traditionell konstruierten Gegenstücken sind oft möglich.
- Wahl des Materials: Während AlSi10Mg bereits leicht ist, ermöglicht AM eine präzise Kontrolle der Wandstärken und inneren Strukturen, die beim Gießen oder bei der Bearbeitung von Massenware nicht möglich ist.
- Beschleunigtes Prototyping und Iteration: Die Möglichkeit, innerhalb von Tagen von einer CAD-Datei zu einem funktionsfähigen Metallprototyp zu gelangen, anstatt Wochen oder Monate auf die Werkzeugherstellung zu warten, revolutioniert den Produktentwicklungszyklus.
- Schnellere Design-Validierung: Ingenieure können schnell mehrere Designvarianten auf Passform, Form und Funktion testen.
- Geringere Entwicklungskosten: Das frühzeitige Erkennen von Konstruktionsfehlern durch kostengünstige Prototypen erspart später teure Nacharbeiten.
- Schnelleres Time-to-Market: Verkürzte Entwicklungszeiträume bieten einen Wettbewerbsvorteil.
- Wegfall der Werkzeugkosten: Die beträchtlichen Investitionen, die für Formen (Gießen) oder Gesenke (Stanzen) erforderlich sind, werden mit AM vollständig umgangen.
- Kosteneffiziente Kleinserienproduktion: Die Herstellung von Dutzend-, Hunderter- oder sogar Tausenderchargen wird dadurch wirtschaftlich rentabel, ideal für Nischenfahrzeuge, den Motorsport oder erste Produktionsanläufe.
- Ermöglicht Anpassungen: Die Herstellung maßgeschneiderter oder kundenspezifischer Halterungen wird möglich, ohne dass für jede Variante hohe Werkzeugkosten anfallen.
- Möglichkeiten der Teilkonsolidierung: AM ermöglicht es Designern, Baugruppen neu zu überdenken. Mehrere einfache Halterungen, Befestigungen und Verbindungselemente können oft neu entworfen und als eine einzige komplexe monolithische Komponente gedruckt werden.
- Reduzierte Montagezeit und -arbeit: Weniger Teile zu handhaben, auszurichten und zu befestigen.
- Niedrigere Kosten für Lagerhaltung und Logistik: Verwaltung einer Teilenummer anstelle von mehreren.
- Verbesserte Verlässlichkeit: Eliminiert potenzielle Fehlerstellen an Verbindungen und Schnittstellen.
- Gewichtsreduzierung: Oft ist das konsolidierte Teil leichter als die Summe seiner ursprünglichen Bestandteile.
- Fertigung auf Abruf und digitale Bestandsaufnahme: Teile können nach Bedarf gedruckt werden, wodurch sich der Bedarf an großen physischen Beständen verringert. Digital gespeicherte Entwürfe können an jedem beliebigen Ort mit der richtigen Ausrüstung hergestellt werden, was eine dezentralisierte Fertigung und eine hohe Widerstandsfähigkeit gegen Unterbrechungen der Lieferkette ermöglicht. Dies ist besonders wertvoll für B2B-Zulieferer, die verschiedene Teileportfolios verwalten, und für die Beschaffung älterer Komponenten.
- Materialeffizienz: Im Vergleich zur subtraktiven Bearbeitung, bei der ein großer Teil des ursprünglichen Materialblocks zu Abfallspänen wird, nutzen PBF-Verfahren das Pulver-Rohmaterial effizienter. Ungeschmolzenes Pulver in der Baukammer kann in der Regel gesiebt und in den Prozess zurückgeführt werden, wodurch der Rohstoffverbrauch minimiert wird.
Das Engagement von Met3dp für die Bereitstellung robuster, industrietauglicher Lösungen für die additive Fertigung ermöglicht es den Kunden der Automobilindustrie, diese Vorteile voll auszuschöpfen. Unsere Drucker, bekannt für ihre Genauigkeit und ZuverlässigkeitSie stellen sicher, dass komplexe, topologieoptimierte AlSi10Mg-Halterungen den strengen Qualitätsstandards der Automobilindustrie entsprechen. Durch eine Partnerschaft mit Met3dp erhalten Unternehmen nicht nur Zugang zu Anlagen und Materialien, sondern auch zu dem Fachwissen, das für eine effektive Umsetzung von AM erforderlich ist, und können so ihre Herangehensweise an die Konstruktion und Produktion von Halterungen mit spürbaren Vorteilen bei Leistung, Kosten und Geschwindigkeit verändern. Beschaffungsteams, die auf der Suche nach agilen und innovativen Fertigungspartnern sind, werden feststellen, dass AM, insbesondere durch erfahrene Anbieter wie Met3dp, für viele Halterungsanwendungen einen überzeugenden Mehrwert gegenüber herkömmlichen Methoden bietet.
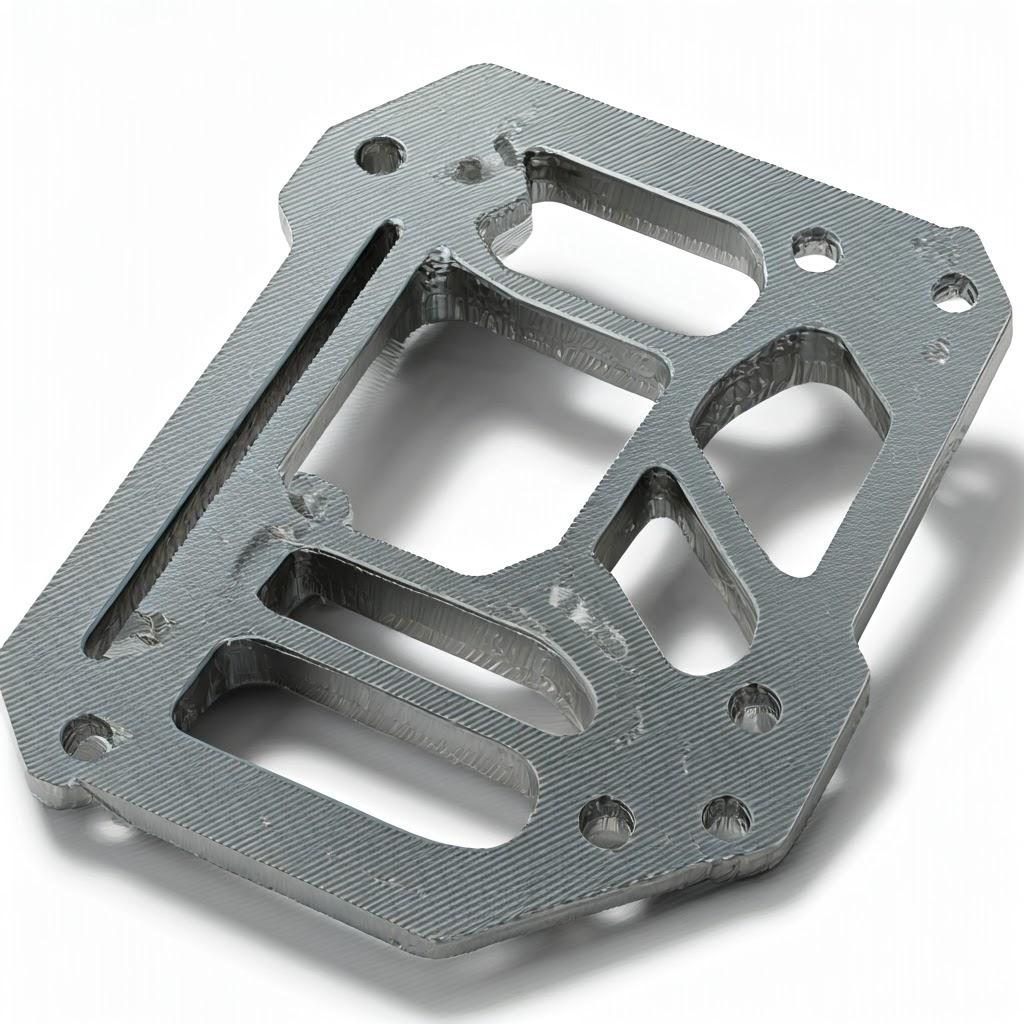
Das Material ist entscheidend: Auswahl von AlSi10Mg- und A7075-Pulvern für optimale Bracket-Leistung
Der Erfolg einer 3D-gedruckten Kfz-Halterung hängt entscheidend von der Wahl des richtigen Materials ab. Während Metall-AM mit einer wachsenden Anzahl von Legierungen kompatibel ist, sind Aluminiumlegierungen aufgrund ihres geringen Gewichts besonders attraktiv für Automobilanwendungen. Innerhalb dieser Kategorie sticht AlSi10Mg als Arbeitspferd hervor, doch ist es für Ingenieure, die Teile entwerfen, und für Beschaffungsspezialisten, die Materialien oder Dienstleistungen einkaufen, von entscheidender Bedeutung, seine Eigenschaften neben potenziellen Alternativen wie A7075 zu verstehen. Die Wahl des Werkstoffs wirkt sich auf die Druckbarkeit, die mechanische Leistung, die Nachbearbeitungsanforderungen und letztlich auf die Kosteneffizienz des Endprodukts aus.
AlSi10Mg: Der vielseitige Standard
- Zusammensetzung: Hauptsächlich Aluminium (Al), mit etwa 9-11% Silizium (Si) und 0,2-0,45% Magnesium (Mg). Spuren von anderen Elementen wie Eisen (Fe), Mangan (Mn) und Titan (Ti) sind ebenfalls vorhanden.
- Wichtige Eigenschaften und Merkmale:
- Ausgezeichnete Druckbarkeit: AlSi10Mg ist eine der am besten verarbeitbaren Aluminiumlegierungen in Laser Powder Bed Fusion (L-PBF) Systemen wie SLM/DMLS. Seine eutektische Beschaffenheit führt zu einer guten Schmelzbadstabilität und einer geringeren Anfälligkeit für Risse während der schnellen Aufheiz- und Abkühlzyklen, die für AM typisch sind.
- Gutes Verhältnis von Stärke zu Gewicht: Obwohl sie nicht die stärkste Aluminiumlegierung ist, bietet sie ein günstiges Gleichgewicht und eignet sich für eine Vielzahl von strukturellen und halbstrukturellen Halterungsanwendungen, bei denen moderate Belastungen zu erwarten sind.
- Hohe Wärmeleitfähigkeit: Vorteilhaft für Halterungen, die Wärme ableiten müssen, z. B. in der Nähe von Motorkomponenten oder Leistungselektronik.
- Gute Korrosionsbeständigkeit: Geeignet für viele Automobilbereiche.
- Schweißeignung: Kann geschweißt werden, obwohl spezielle Verfahren empfohlen werden.
- Wärmebehandelbar: Ungedrucktes AlSi10Mg hat eine mäßige Festigkeit. Eine T6-Wärmebehandlung (Lösungsglühen mit anschließender künstlicher Alterung) erhöht die Zugfestigkeit, die Streckgrenze und die Härte erheblich, so dass sie mit Aluminiumgusslegierungen wie A360 vergleichbar ist.
- Vorteile für Kfz-Halterungen:
- Ideal für komplexe Geometrien, die durch AM ermöglicht werden, da es sich hervorragend drucken lässt.
- Geeignet für Leichtbauprojekte, bei denen es nicht in erster Linie auf extreme Festigkeit ankommt.
- Kostengünstig im Vergleich zu höherfesten Aluminiumlegierungen oder Titan.
- Gut bekanntes Material mit etablierten Druckparametern und Nachbearbeitungsprotokollen.
- Erwägungen:
- Geringere Ermüdungsfestigkeit im Vergleich zu Knetlegierungen wie A7075.
- Die mechanischen Eigenschaften können anisotrop (richtungsabhängig) sein, je nach Ausrichtung des Bauteils.
- Erfordert Druck unter kontrollierter Atmosphäre (normalerweise Argon), um Oxidation zu verhindern.
- Eine T6-Wärmebehandlung ist in der Regel für eine optimale Leistung bei strukturellen Anwendungen erforderlich.
A7075: Der hochbelastbare Konkurrent
- Zusammensetzung: Eine Aluminium-Zink-Legierung (Zn ~5,1-6,1%), die auch Magnesium (Mg ~2,1-2,9%) und Kupfer (Cu ~1,2-2,0%) enthält.
- Wichtige Eigenschaften und Merkmale:
- Sehr hohe Festigkeit: Eine der höchstfesten handelsüblichen Aluminiumlegierungen, die an die Festigkeit einiger Baustähle heranreicht, aber etwa ein Drittel der Dichte aufweist. Ausgezeichnete Zugfestigkeit und Streckgrenze, insbesondere nach Wärmebehandlung (z. B. T6).
- Gute Ermüdungsfestigkeit: Deutlich bessere Ermüdungseigenschaften als AlSi10Mg, wodurch es sich für zyklisch belastete Bauteile eignet.
- Gute Bearbeitbarkeit: Kann bei Bedarf nach dem Druck leicht bearbeitet werden.
- Geringere Druckfähigkeit: Im Vergleich zu AlSi10Mg ist es schwieriger, es zuverlässig mit L-PBF zu bearbeiten. Anfällig für Erstarrungsrisse und Porosität aufgrund des größeren Erstarrungsbereichs und der Verdampfung von Elementen mit niedrigem Siedepunkt wie Zink unter dem Laser. Erfordert sorgfältig optimierte Parameter und möglicherweise eine spezielle Ausrüstung.
- Geringere Korrosionsbeständigkeit: Besonders anfällig für Spannungsrisskorrosion (SCC) im Vergleich zu AlSi10Mg. Kann Schutzbeschichtungen erfordern.
- Schlechte Schweißeignung: Gilt allgemein als schwierig zu schweißen.
- Vorteile für Kfz-Halterungen:
- Geeignet für hochbelastete Strukturhalterungen, bei denen es auf maximale Festigkeit und Ermüdungsbeständigkeit ankommt (z. B. kritische Aufhängungspunkte, Hochleistungsmotorlager).
- Ermöglicht im Vergleich zu AlSi10Mg potenziell größere Gewichtseinsparungen bei festigkeitskritischen Anwendungen, da weniger Material benötigt werden könnte.
- Erwägungen:
- Es ist wesentlich schwieriger und potenziell teurer, zuverlässig zu drucken.
- Erfordert eine genaue Kontrolle der Druckparameter und der Atmosphäre.
- Die Anfälligkeit für Defekte wie Porosität und Rissbildung muss durch eine sorgfältige Prozesskontrolle und möglicherweise durch heißisostatisches Pressen (HIP) gesteuert werden.
- Erfordert eine geeignete Wärmebehandlung (z. B. T6), um sein hohes Festigkeitspotenzial zu erreichen.
- Häufig sind Korrosionsschutzmaßnahmen erforderlich.
Vergleich der Materialeigenschaften (typische Werte nach entsprechender Wärmebehandlung):
Eigentum | AlSi10Mg (Zustand T6) | A7075 (Zustand T6) | Einheiten | Anmerkungen |
---|---|---|---|---|
Dichte | ~2.67 | ~2.81 | g/cm³ | Beide bestehen aus leichten Aluminiumlegierungen. |
Endgültige Zugfestigkeit | 330 – 430 | 510 – 570 | MPa | A7075 deutlich stärker. AM-Werte können variieren. |
Streckgrenze (0.2%) | 230 – 320 | 450 – 500 | MPa | A7075 hat eine viel höhere Streckgrenze. |
Dehnung beim Bruch | 3 – 10 | 5 – 11 | % | Die Duktilität kann bei AM-Teilen geringer sein als bei Knet-/Gussteilen. |
Härte | 90 – 120 | 140 – 150 | HV / HB | A7075 ist härter. |
Ermüdungsfestigkeit (R=-1) | 90 – 130 | 150 – 160 | MPa | A7075 ist im Allgemeinen bei zyklischer Belastung überlegen. Hängt stark von der Oberflächenbeschaffenheit ab. |
Wärmeleitfähigkeit | 130 – 150 | 130 – 150 | W/(m-K) | Ähnliche Wärmeleitfähigkeit. |
Druckbarkeit | Ausgezeichnet | Herausfordernd | – | Wichtige Überlegungen zum Prozess. |
Korrosionsbeständigkeit | Gut | Fair (anfällig für SCC) | – | AlSi10Mg im Allgemeinen besser in korrosiven Umgebungen. |
Relative Kosten (Puder) | Unter | Höher | – | A7075-Pulver ist in der Regel teurer. |
Relative Kosten (Druck) | Unter | Höher | – | Aufgrund der strengeren Parameterkontrolle potenziell geringere Erfolgsquoten. |
In Blätter exportieren
Die Wichtigkeit der Pulverqualität: Der Vorteil von Met3dp
Unabhängig von der gewählten Legierung ist die Qualität des Metallpulver-Ausgangsmaterials für eine erfolgreiche und reproduzierbare additive Fertigung von größter Bedeutung. Die Pulvereigenschaften haben einen direkten Einfluss auf die Fließfähigkeit im Recoatersystem, die Dichte des Pulverbettes, das Verhalten des Schmelzbades und letztendlich auf die mechanischen Eigenschaften und das Fehlerniveau der fertigen gedruckten Halterung.
Met3dp nutzt branchenführende Technologien zur Pulverherstellung:
- Fortschrittliche Gaszerstäubung: Unsere Systeme nutzen firmeneigene Düsen- und Gasströmungsdesigns, um Metallpulver mit hoher Sphärizität (Rundheit) und engen Partikelgrößenverteilungen herzustellen. Die hohe Sphärizität gewährleistet eine hervorragende Fließfähigkeit des Pulvers, was zu gleichmäßigen Pulverschichten während des Drucks führt.
- Plasma-Rotations-Elektroden-Verfahren (PREP): Für bestimmte reaktive oder Hochleistungslegierungen kann PREP außergewöhnlich saubere Pulver mit noch höherer Sphärizität und minimalen Satellitenpartikeln herstellen.
Diese Konzentration auf hochwertige Metallpulvereinschließlich des optimierten AlSi10Mg, stellt sicher, dass die B2B-Kunden von Met3dp - egal ob sie Pulver direkt kaufen oder unsere Druckdienstleistungen in Anspruch nehmen - davon profitieren:
- Konsistente Druckqualität: Ein zuverlässiges Materialverhalten führt zu vorhersehbaren Teileigenschaften und Maßgenauigkeit.
- Weniger Defekte: Hochreine, kugelförmige Pulver minimieren Probleme wie Porosität, die die Integrität des Brackets beeinträchtigen können.
- Optimale mechanische Leistung: Die gleichbleibende Qualität des Pulvers führt dazu, dass die gewünschten mechanischen Eigenschaften der endgültigen wärmebehandelten T6-Komponenten erreicht werden.
Die richtige Wahl für B2B-Bedürfnisse treffen:
Für Beschaffungsmanager und Ingenieurteams, die Materialien für 3D-gedruckte Kfz-Halterungen bewerten:
- AlSi10Mg ist aufgrund seiner hervorragenden Druckbarkeit, seiner guten Allround-Eigenschaften und seiner Kosteneffizienz die erste Wahl für eine Vielzahl von Anwendungen. Es ist ideal für das Prototyping, komplexe Geometrien, leichtgewichtige, unkritische Strukturen und die Produktion kleiner bis mittlerer Mengen, wenn seine Festigkeit ausreichend ist.
- A7075 sollte für sehr anspruchsvolle Anwendungen in Betracht gezogen werden, bei denen es auf maximale Festigkeit und Ermüdungsbeständigkeit ankommt, vorausgesetzt, die Probleme der Bedruckbarkeit und der mögliche Bedarf an Korrosionsschutz werden berücksichtigt. Es eignet sich besser für kleinvolumige, hochleistungsfähige Teile, bei denen seine überlegenen mechanischen Eigenschaften den erhöhten Verarbeitungsaufwand und die Kosten rechtfertigen.
Die Zusammenarbeit mit einem sachkundigen Anbieter wie Met3dp, der über Fachwissen sowohl in der Werkstoffkunde als auch in der AM-Verarbeitung verfügt, ist von entscheidender Bedeutung. Wir können B2B-Kunden bei der Auswahl des optimalen Pulvers unterstützen - ob Standard-AlSi10Mg, hochfeste Alternativen oder sogar kundenspezifische Legierungen aus unserem umfangreichen Portfolio (einschließlich TiNi, TiTa, TiAl, CoCrMo, rostfreie Stähle usw.) - um sicherzustellen, dass das gewählte Material die spezifischen Leistungs-, Kosten- und Produktionsanforderungen für ihre Automobilhalterungsanwendungen erfüllt.
Design für additive Fertigung (DfAM): Optimierung von Kfz-Halterungen für den Erfolg im 3D-Druck
Ein Halterungsdesign, das für das Gießen oder die maschinelle Bearbeitung vorgesehen ist, einfach an einen 3D-Metalldrucker zu schicken, ist selten der optimale Ansatz. Um die Möglichkeiten der additiven Fertigung wirklich zu nutzen und erfolgreiche, kosteneffektive Ergebnisse mit AlSi10Mg-Automobilhalterungen zu erzielen, müssen Ingenieure das Design for Additive Manufacturing (DfAM) anwenden. DfAM ist nicht nur ein Regelwerk, sondern ein Umdenken, das sich darauf konzentriert, die einzigartigen Fähigkeiten der schichtweisen Fertigung zu nutzen und gleichzeitig die ihr innewohnenden Beschränkungen zu verringern. Die Anwendung der DfAM-Prinzipien von Anfang an ist entscheidend für die Maximierung des Leichtbaupotenzials, die Minimierung von Druckzeit und -kosten, die Verringerung des Nachbearbeitungsaufwands und die Gewährleistung der strukturellen Integrität und Funktionalität des fertigen Bauteils. Für B2B-Zulieferer und OEMs in der Automobilindustrie ist die Beherrschung von DfAM der Schlüssel zur Erschließung der Wettbewerbsvorteile, die Metall-AM bietet.
Warum DfAM für Metal AM nicht verhandelbar ist:
Im Gegensatz zur subtraktiven Fertigung (maschinelle Bearbeitung), bei der Material abgetragen wird, oder zu formgebenden Verfahren (Gießen, Schmieden), bei denen das Material mit Hilfe von Formen oder Gesenken geformt wird, werden bei der additiven Fertigung die Teile Schicht für Schicht von Grund auf aufgebaut. Dieser grundlegende Unterschied führt zu besonderen Überlegungen:
- Schwerkraft und Überhänge: Jede neue Schicht muss durch die darunter liegende Schicht gestützt werden. Steile Überhänge oder horizontale Merkmale erfordern Stützstrukturen, die zusätzliches Material verbrauchen, die Druckzeit verlängern und in der Nachbearbeitung entfernt werden müssen.
- Thermische Spannungen: Die starke Hitze des Laser- oder Elektronenstrahls, gefolgt von einer schnellen Abkühlung, erzeugt während des Aufbaus erhebliche Wärmegradienten und innere Spannungen im Bauteil. Schlechte Konstruktionsentscheidungen können diese Spannungen noch verstärken und zu Verzug, Verformung oder sogar Rissbildung führen.
- Anisotropie: Der schichtweise Aufbau kann zu richtungsabhängigen mechanischen Eigenschaften (Anisotropie) führen. Die Festigkeit und Duktilität eines AlSi10Mg-Bauteils kann unterschiedlich sein, je nachdem, ob es parallel oder senkrecht zu den Aufbauschichten belastet wird.
- Oberfläche: Das Verschmelzen von Pulverschichten führt zu einer charakteristischen Oberflächenrauhigkeit, die je nach Ausrichtung der Oberfläche in Bezug auf die Baurichtung variiert.
- Merkmal Auflösung: Die Größe des Laserspots, die Größe der Pulverpartikel und die Schichtdicke begrenzen die Mindestgröße der Merkmale (Wände, Löcher, Stifte), die präzise hergestellt werden können.
Die wichtigsten DfAM-Prinzipien für AlSi10Mg-Kraftfahrzeughalterungen:
Die Anwendung dieser Grundsätze in der Entwurfsphase, oft mit der Unterstützung erfahrener AM-Dienstleister wie Met3dp, ist von entscheidender Bedeutung:
- Strategische Gebäudeausrichtung:
- Auswirkungen: Die Ausrichtung der Halterung auf der Bauplatte hat erhebliche Auswirkungen auf den Stützbedarf, die Oberflächenqualität auf den verschiedenen Flächen, die potenzielle Anisotropie, die Bauzeit (die Höhe hat den größten Einfluss auf die Bauzeit) und die thermische Spannungsverteilung.
- Strategien:
- Minimieren Sie die Z-Höhe (Bauhöhe), um die Druckzeit zu verkürzen.
- Richten Sie kritische Oberflächen vertikal oder als "up-skins" (nach oben gerichtete Oberflächen) aus, um ein besseres Finish zu erzielen. "Nach unten weisende Oberflächen, die durch Pulver oder Stützen gestützt werden, sind in der Regel rauher.
- Richten Sie kritische Merkmale an der X-Y-Ebene aus, um die Maßgenauigkeit zu verbessern.
- Berücksichtigen Sie die Belastungsbedingungen, um die Schichten im Verhältnis zu den primären Spannungsrichtungen günstig auszurichten, obwohl AlSi10Mg nach einer angemessenen Wärmebehandlung im Allgemeinen eine weniger starke Anisotropie aufweist als einige andere AM-Werkstoffe.
- Verwenden Sie Simulationswerkzeuge, um thermische Spannungen und Verformungen für verschiedene Ausrichtungen vorherzusagen.
- Minimierung und Optimierung der Stützstruktur:
- Die Notwendigkeit: Stützen sind entscheidend für die Verankerung des Teils auf der Bauplatte, für die Abstützung von Überhängen, die einen bestimmten Winkel überschreiten (typischerweise >45° aus der Horizontalen für AlSi10Mg), und für die Ableitung von Wärme aus kritischen Bereichen, um Überhitzung und Zusammenbruch zu vermeiden.
- Strategien:
- Selbsttragende Winkel entwerfen: Gestalten Sie, wo immer möglich, Elemente mit einem Winkel von 45° oder weniger zur Bauplatte. Eine gängige Technik ist das Abfasen von Kanten anstelle von scharfen horizontalen Überhängen.
- Optimieren Sie Überhänge: Wenn Überhänge unvermeidlich sind, versuchen Sie, sie kurz zu halten oder verwenden Sie Opferrippen/ -elemente, die leicht zu entfernen sind.
- Unterstützungsarten: Verwenden Sie Software, um geeignete Stützstrukturen (z. B. Block-, Kegel- oder Baumstützen) zu generieren, die eine angemessene Verankerung und Wärmeableitung gewährleisten und gleichzeitig den Materialverbrauch und die Kontaktpunkte mit der Werkstückoberfläche minimieren. Perforierte oder gitterförmige Halterungen können Material sparen und die Entfernung erleichtern.
- Zugänglichkeit: Konstruieren Sie das Teil so, dass die Stützstrukturen für die manuelle oder maschinelle Entfernung leicht zugänglich sind. Vermeiden Sie Abstützungen in tiefen inneren Kanälen, es sei denn, dies ist absolut notwendig und vorgesehen.
- Geeignete Wanddicke:
- Mindestdicke: Bei L-PBF-Verfahren gibt es Einschränkungen hinsichtlich der minimalen bedruckbaren Wandstärke, die bei AlSi10Mg in der Regel bei 0,4-0,5 mm liegt, obwohl aus Gründen der Robustheit häufig 0,8-1,0 mm empfohlen werden.
- Strukturelle Integrität: Stellen Sie sicher, dass die Wände ausreichend dick sind, um den erwarteten Belastungen standzuhalten, und berücksichtigen Sie dabei mögliche Spannungskonzentrationen.
- Wärmemanagement: Vermeiden Sie übermäßig dicke, massive Abschnitte, da diese die Wärme stauen und Eigenspannungen und Verformungen erhöhen können. Erwägen Sie die Verwendung von Innengittern oder Hohlstrukturen für dicke Abschnitte, wenn die Festigkeit dies zulässt.
- Überlegungen zum Lochdesign:
- Vertikale Löcher: Im Allgemeinen ist der Druck präzise und die Oberfläche ist gut.
- Horizontale Löcher: Anfällig für Verformungen (Durchhängen an der Oberseite) aufgrund von Überhängen. Durch die Gestaltung in Tropfen- oder Rautenform ist die Oberseite selbsttragend.
- Mindestdurchmesser: Bei kleinen Löchern (typischerweise < 0,5 mm) kann es schwierig sein, sie präzise und frei von Pulver zu drucken. Oft ist es besser, kleinere Löcher leicht unterdimensioniert zu entwerfen und sie in der Nachbearbeitung auf die endgültige Größe zu bohren oder zu reiben.
- Gewindelöcher: Entwerfen Sie die für das Gewindedrucken vorgesehenen Löcher leicht unterdimensioniert, um ein sauberes Gewindeschneiden bei der Bearbeitung nach dem Druck zu ermöglichen. Das direkte Drucken von Gewinden ist möglich, führt aber oft zu schlechter Qualität und Festigkeit.
- Nutzung von Topologieoptimierung und Gitterstrukturen:
- Topologie-Optimierung: Verwenden Sie spezielle Software (z. B. Altair Inspire, nTopology, Ansys Discovery), um Lastfälle, Einschränkungen und Designbereiche zu definieren. Die Software entfernt dann iterativ Material aus unkritischen Bereichen und erzeugt so hocheffiziente, organisch anmutende Halterungsdesigns, die hinsichtlich des Verhältnisses von Steifigkeit zu Gewicht optimiert sind. Dies ist eine der Hauptstärken von AM.
- Gitterförmige Strukturen: Ersetzen Sie Volumenkörper durch interne Gitterstrukturen (z. B. kubisch, Oktett-Fachwerk), um das Gewicht drastisch zu reduzieren und gleichzeitig eine signifikante strukturelle Unterstützung zu erhalten oder die Schwingungsdämpfungseigenschaften anzupassen. Software-Tools erleichtern die Erstellung komplexer Gitterstrukturen.
- Vorteile für Brackets: Ideal für Leichtbauziele in der Automobilindustrie, um Hochleistungshalterungen zu schaffen, die strenge Gewichtsvorgaben erfüllen, ohne die Festigkeit zu beeinträchtigen.
- Umfassende Teilkonsolidierung:
- Konzept: Suchen Sie aktiv nach Möglichkeiten, Baugruppen, die aus mehreren Halterungen, Befestigungselementen und Verbindungselementen bestehen, in eine einzige, integrierte AM-Komponente umzuwandeln.
- Beispiele: Integration eines Flüssigkeitskanals direkt in eine Halterung, Kombination von zwei ineinander greifenden Halterungen in einem Stück, Integration von Schnappverschlüssen oder Befestigungsdomen direkt in die Struktur.
- Prozess: Erfordert ein Überdenken der Funktion der gesamten Baugruppe, nicht nur einzelner Teile. Die Zusammenarbeit zwischen Konstrukteuren und AM-Spezialisten ist oft von Vorteil.
- Stressbewältigung Konzentrationen:
- Filetieren: Fügen Sie großzügige Verrundungen (abgerundete Kanten) an inneren Ecken und scharfen Übergängen in der Geometrie hinzu. Scharfe Ecken wirken wie Spannungserhöhungen und erhöhen das Risiko von Rissen während des Drucks oder Ermüdungsbrüchen während des Betriebs.
- Reibungslose Übergänge: Vermeiden Sie abrupte Änderungen der Querschnittsfläche, die auch Spannungen konzentrieren und thermische Probleme beim Druck verursachen können.
- Entwerfen für die Wärmeableitung:
- Wärmemanagement: Überlegen Sie, wie sich die Wärme während des Drucks aufbaut und ableitet. Sehr feine, empfindliche Features könnten überhitzen. Das Hinzufügen von kleinen Opferfeatures oder die Optimierung der Ausrichtung kann manchmal dazu beitragen, die Wärme besser abzuführen. Auch Halterungen spielen beim Wärmemanagement eine entscheidende Rolle.
Die Rolle von Met3dp bei DfAM:
Die erfolgreiche Implementierung von DfAM erfordert Fachwissen. Met3dp unterstützt seine B2B-Kunden nicht nur mit fortschrittlichen Druckern und hochwertigen Pulvern, sondern auch mit Dienstleistungen zur Anwendungsentwicklung. Unser Team verfügt über jahrzehntelange Erfahrung und kann entscheidende Hinweise zu den DfAM-Prinzipien geben. Wir helfen bei der Optimierung des Designs von Automobilhalterungen für die additive Fertigung und gewährleisten funktionale Leistung, Kosteneffizienz und Herstellbarkeit. Wir helfen dabei, die Lücke zwischen traditionellem Designdenken und den Möglichkeiten von AM zu schließen.
Durch die Anwendung dieser DfAM-Strategien können Automobilingenieure und Beschaffungsspezialisten sicherstellen, dass sie das Potenzial des 3D-Drucks von AlSi10Mg-Metall voll ausschöpfen, was zu besseren, leichteren und effizienter hergestellten Automobilhalterungen führt.
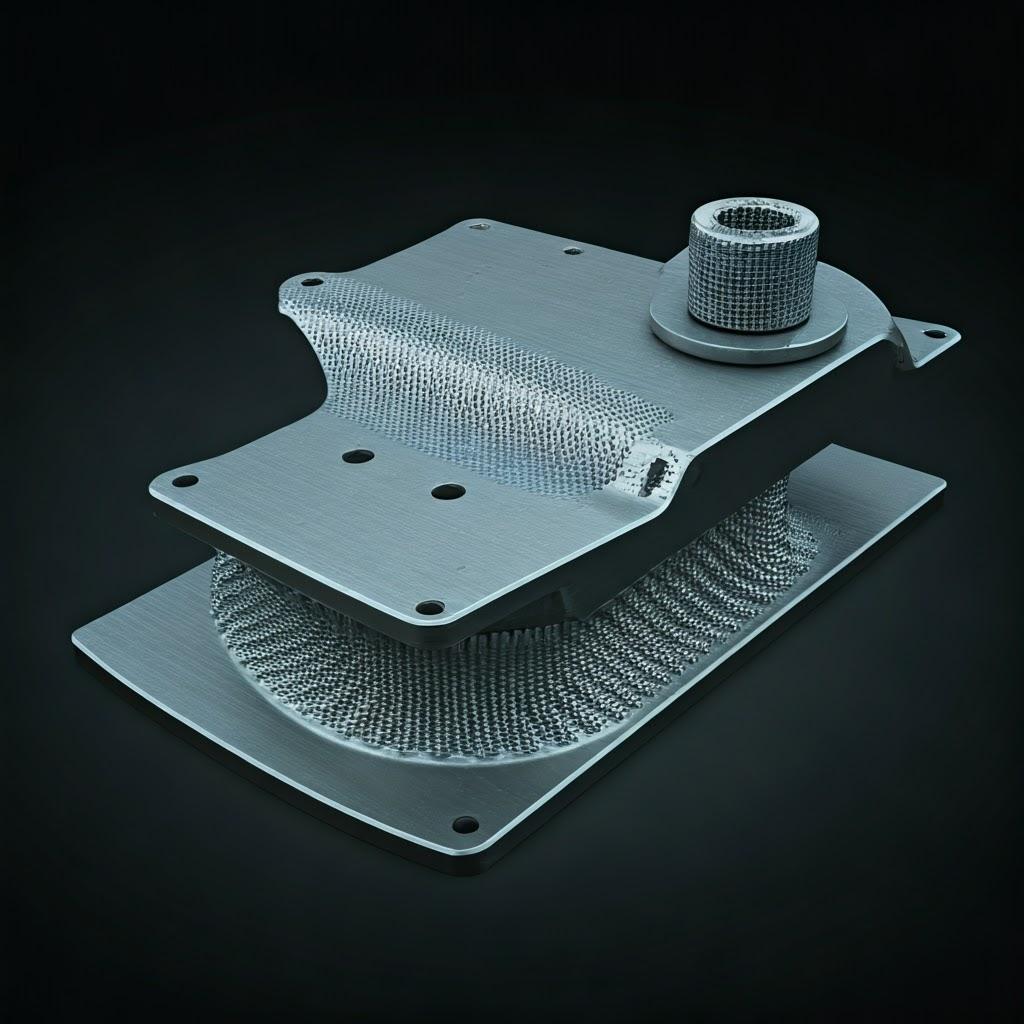
Erreichen von Präzision: Verständnis von Toleranz, Oberflächengüte und Maßgenauigkeit bei gedruckten Halterungen
Während die additive Fertigung von Metallen eine beispiellose Designfreiheit bietet, erfordert das Erreichen des hohen Präzisionsniveaus, das für Automobilkomponenten oft erforderlich ist, ein klares Verständnis der Toleranzen, der Oberflächenbeschaffenheit und der Maßgenauigkeit, die mit dem Verfahren verbunden sind, insbesondere L-PBF für AlSi10Mg. Ingenieure müssen diese Faktoren bei der Konstruktion berücksichtigen, und Beschaffungsmanager brauchen realistische Erwartungen, wenn sie die Anforderungen für 3D-gedruckte Halterungen festlegen. Es ist von entscheidender Bedeutung, sowohl die Fähigkeiten als auch die Grenzen des gedruckten Zustands zu erkennen und eine Nachbearbeitung einzuplanen, wenn strengere Spezifikationen erforderlich sind.
Faktoren, die die Präzision bei L-PBF beeinflussen:
Mehrere Elemente wirken zusammen, um die endgültige Genauigkeit und Ausführung eines gedruckten Teils zu bestimmen:
- Kalibrierung der Maschine: Die regelmäßige Kalibrierung der Laser, Scanner (Galvanometer) und Bewegungssysteme des Druckers ist für die Genauigkeit unerlässlich.
- Laserpunktgröße und Schichtdicke: Feinere Laserspots und dünnere Schichten ermöglichen im Allgemeinen eine höhere Auflösung und eine bessere Oberflächengüte auf abgewinkelten Oberflächen, verlängern jedoch die Fertigungszeit. Typische Schichtdicken für AlSi10Mg liegen zwischen 30 und 60 Mikrometern.
- Scan-Strategie: Das vom Laser zum Schmelzen des Pulvers verwendete Muster (z. B. Schraffuren, Konturen) wirkt sich auf die Oberflächengüte, die Eigenspannung und die Mikrostruktur aus.
- Thermische Effekte: Die Schwindung tritt auf, wenn das geschmolzene Material abkühlt und erstarrt. Eine ungleichmäßige Abkühlung führt zu Eigenspannungen, die Verformungen und Verwerfungen verursachen können, die sich auf die gesamte Maßgenauigkeit auswirken, insbesondere bei größeren Teilen oder solchen mit erheblichen Querschnittsschwankungen. Die Zyklen zum Aufheizen der Bauplatten und zum Spannungsabbau tragen dazu bei, dieses Problem zu mindern.
- Eigenschaften des Pulvers: Partikelgrößenverteilung, Form (Sphärizität) und Fließfähigkeit beeinflussen die Pulverbettdichte und das Schmelzverhalten und wirken sich auf die Oberflächenbeschaffenheit und die innere Porosität aus.
- Geometrie und Größe des Teils: Größere Teile und komplexere Geometrien sind im Allgemeinen anfälliger für thermische Verformungen.
- Orientierung aufbauen: Beeinflusst die Oberflächenbeschaffenheit auf den verschiedenen Flächen unterschiedlich und kann aufgrund der anisotropen Schrumpfung und der Wechselwirkungen mit der Unterlage die Maßhaltigkeit beeinflussen.
Maßgenauigkeit und Toleranzen:
- Allgemeine Toleranzen: Für AlSi10Mg-Teile, die mittels L-PBF auf gut kalibrierten Industriemaschinen, wie sie von Met3dp angeboten werden, hergestellt werden, werden typische erreichbare Maßtoleranzen oft im Bereich von:
- ± 0,1 mm bis ± 0,2 mm für kleinere Merkmale (z. B. bis zu 50-100 mm)
- ± 0,1% bis ± 0,2% des Nennmaßes für größere Merkmale.
- Vergleich: Dieser Genauigkeitsgrad ist im Allgemeinen besser als Sand- oder Feinguss im gegossenen Zustand, aber weniger genau als die CNC-Bearbeitung.
- Wichtige Überlegungen:
- Kritische Dimensionen: Die Toleranzen sind nicht über das gesamte Teil gleich. Um die engsten Toleranzen zu erreichen, ist in der Regel eine Nachbearbeitung kritischer Merkmale erforderlich (z. B. Passflächen, Lagerbohrungen, genaue Lochpositionen).
- Verwerfungswirkung: Die Verformung des gesamten Teils aufgrund thermischer Spannungen ist oft der größte Faktor für Maßabweichungen bei größeren Bauteilen. DfAM-Praktiken und kontrollierte Verarbeitung sind entscheidend, um dies zu minimieren.
- Messung: Eine genaue Überprüfung erfordert hochentwickelte Messgeräte wie Koordinatenmessmaschinen (KMG) oder hochauflösende 3D-Scanner.
Oberflächengüte (Rauhigkeit):
- As-Built Ausführung: L-PBF erzeugt Teile mit einer charakteristischen Oberflächenrauhigkeit, die durch das Anhaften der teilweise aufgeschmolzenen Pulverpartikel an der Oberfläche und den schichtweisen Aufbau entsteht (Treppeneffekt bei schrägen Oberflächen).
- Typische Ra-Werte: Die Oberflächenrauheit (Ra - arithmetisches Mittel der Rauheit) von AlSi10Mg-Bauteilen liegt in der Regel im Bereich von 8 µm bis 20 µm (Mikrometer).
- Orientierungsabhängigkeit:
- Vertikale Wände (parallel zur Gebäuderichtung): Neigen dazu, das beste Finish innerhalb des typischen Bereichs zu haben.
- Up-Skins (nach oben gerichtete Oberflächen): Im Allgemeinen glatter als Daunenhäute, oft am unteren Ende des Ra-Bereichs.
- Down-Skins (nach unten gerichtete Oberflächen): Neigen dazu, aufgrund der Interaktion mit losem Pulver oder Stützstrukturen rauer zu sein, oft am oberen Ende des Ra-Bereichs oder leicht darüber.
- Abgewinkelte Oberflächen: Sie zeigen den "Treppeneffekt", bei dem die Rauheit zunimmt, je mehr sich der Winkel der Horizontalen nähert.
- Unterstützte Bereiche: Oberflächen, an denen Stützstrukturen angebracht waren, weisen nach der Entfernung Spuren oder Narben auf, die eine weitere Bearbeitung erfordern, wenn die Glätte entscheidend ist.
- Vergleich: Die Oberflächenbeschaffenheit im Rohzustand ist wesentlich rauer als bei maschinell bearbeiteten oder polierten Oberflächen, kann aber mit einigen Gussoberflächen vergleichbar oder sogar besser sein als diese.
- Verbesserung der Oberflächengüte: Wenn aus funktionalen Gründen (z. B. Fließverhalten, Ermüdungsfestigkeit, Ästhetik) oder aufgrund von Toleranzanforderungen eine glattere Oberfläche erforderlich ist, sind Nachbearbeitungsmethoden notwendig.
Strengere Spezifikationen erreichen:
Für Kfz-Halterungen, die engere Toleranzen als ±0,1-0,2 mm oder glattere Oberflächen als Ra 8-10 µm bei bestimmten Merkmalen erfordern, ist eine Nachbearbeitung unerlässlich:
- Entwerfen für die maschinelle Bearbeitung: Der gängigste Ansatz ist die Konstruktion des AM-Teils mit zusätzlichem Material (Bearbeitungszugabe, typischerweise 0,5-2 mm) auf kritischen Oberflächen. Diese Oberflächen werden dann CNC-bearbeitet, um die endgültigen erforderlichen Abmessungen, Toleranzen und Oberflächengüte (Ra < 1 µm) zu erreichen.
- Techniken der Oberflächenveredelung: Verfahren wie Perlstrahlen, Trommeln oder Polieren können die Oberflächenbeschaffenheit insgesamt verbessern, führen aber in der Regel nicht zu einer signifikanten Verbesserung der Maßhaltigkeit über große Entfernungen. Sie eignen sich zur Entfernung von losem Pulver, zur Verbesserung der Ästhetik und zur potenziellen Verbesserung der Ermüdungsleistung durch Einbringen von Druckspannungen (Perlstrahlen).
Qualitätskontrolle und Inspektion:
Um sicherzustellen, dass die Halterungen die vorgegebene Präzision erfüllen, ist eine strenge Qualitätskontrolle erforderlich:
- Prüfung der Abmessungen: KMGs bieten hochpräzise Punktmessungen zur Überprüfung kritischer Abmessungen, Bohrungspositionen und geometrischer Bemaßungen und Toleranzen (GD&T). Das 3D-Scannen bietet eine schnelle Erfassung der gesamten Teilegeometrie zum Vergleich mit dem CAD-Modell, was für die Identifizierung von Verformungen oder größeren Abweichungen nützlich ist.
- Messung der Oberflächenrauhigkeit: Profilometer werden eingesetzt, um die Oberflächenrauheit (Ra, Rz usw.) auf bestimmten Flächen zu messen.
- Interne Integrität: Bei hochkritischen Brackets kann die Computertomographie (CT) zerstörungsfrei eingesetzt werden, um interne Defekte wie Porosität zu untersuchen und die Geometrie interner Kanäle oder komplexer Merkmale zu überprüfen.
Das Engagement von Met3dp für Präzision:
Met3dp weiß um die Bedeutung von Präzision bei industriellen Anwendungen. Unsere 3D-Metalldrucker sind auf Genauigkeit und Zuverlässigkeit ausgelegt und verfügen über Funktionen zur Aufrechterhaltung der thermischen Stabilität und präzisen Lasersteuerung. Wir legen Wert auf eine strenge Kalibrierung und Prozesskontrolle. Darüber hinaus umfasst unser umfassender Ansatz die Beratung unserer Kunden zu erreichbaren Toleranzen, notwendigen Nachbearbeitungsschritten und geeigneten Qualitätssicherungsmaßnahmen, um sicherzustellen, dass die fertigen AlSi10Mg-Halterungen den hohen Anforderungen der Automobilindustrie entsprechen. Die Zusammenarbeit mit erfahrenen B2B-Lieferanten, die der Qualitätskontrolle Priorität einräumen, ist für Beschaffungsmanager, die Präzisions-AM-Komponenten beschaffen, von entscheidender Bedeutung.
Tabelle der Präzisionsspezifikationen:
Parameter | L-PBF (AlSi10Mg) im Ist-Zustand | Typische CNC-Bearbeitung | Typischer Feinguss | Typische Druckgussteile |
---|---|---|---|---|
Dimensional Tol. | ±0,1 bis ±0,2 mm / ±0,1-0,2% | ±0,01 bis ±0,05 mm | ±0,1 bis ±0,4 mm | ±0,05 bis ±0,2 mm |
Oberflächengüte (Ra) | 8 - 20 µm | < 0,8 µm (fein) bis 3,2 µm (std) | 1,6 - 6,3 µm | 0,8 - 3,2 µm |
In Blätter exportieren
Hinweis: Die Werte sind typische Werte und können je nach Teilegröße, Geometrie, spezifischen Prozesskontrollen und Nachbearbeitung erheblich variieren.
Wenn die Konstrukteure diese Möglichkeiten und Grenzen kennen, können sie Zeichnungen mit den entsprechenden Toleranzen für gedruckte und bearbeitete Merkmale erstellen, und die Beschaffungsabteilung kann die Teile sicher beschaffen und weiß, wann zusätzliche Nachbearbeitungsschritte erforderlich sind, um die Anwendungsanforderungen zu erfüllen.
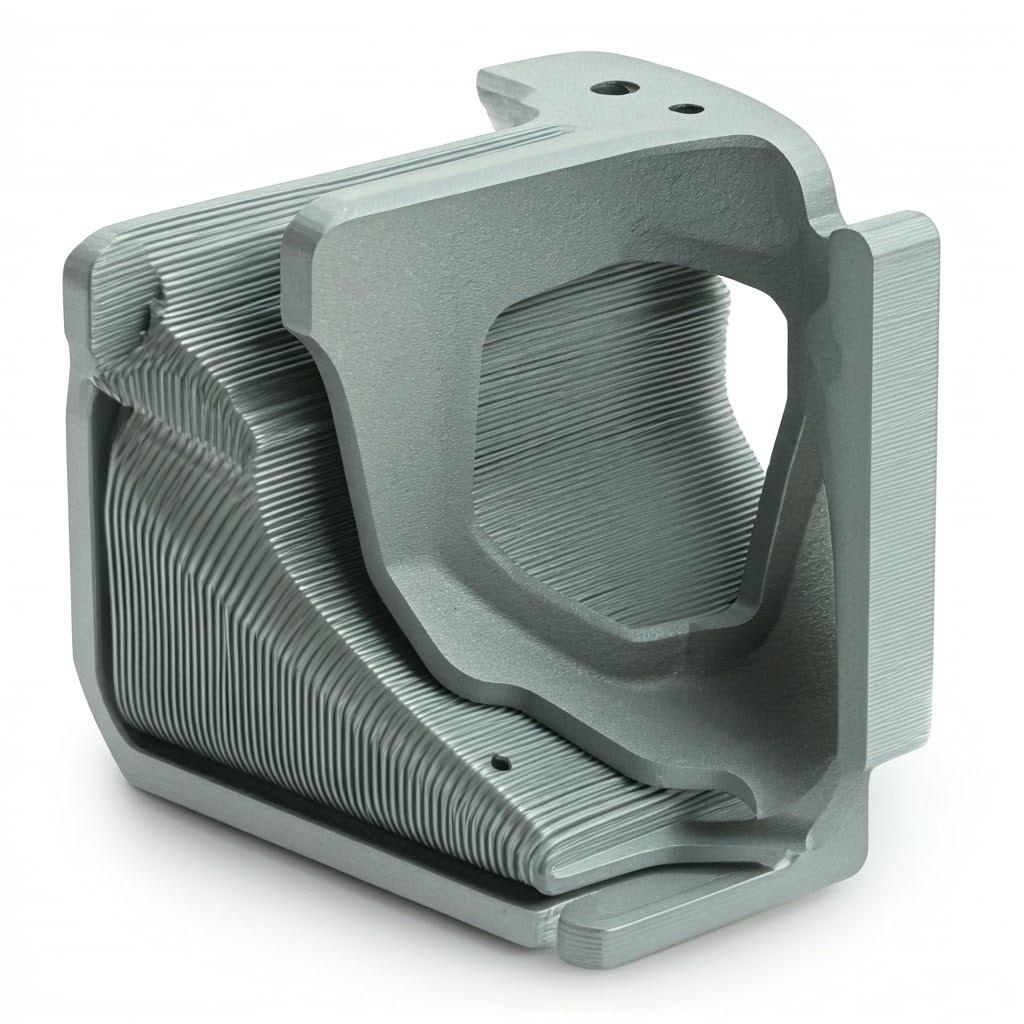
Mehr als der Druck: Wesentliche Nachbearbeitungsschritte für AlSi10Mg-Kfz-Halterungen
Die Herstellung einer AlSi10Mg-Automobilhalterung mittels Laser Powder Bed Fusion (L-PBF) ist ein anspruchsvoller Prozess, aber die Reise von der digitalen Datei zum funktionalen Bauteil endet nicht, wenn der Drucker anhält. In der Regel ist eine Reihe von entscheidenden Nachbearbeitungsschritten erforderlich, um das rohe, gedruckte Teil in ein fertiges Produkt zu verwandeln, das die strengen Automobilstandards für mechanische Leistung, Maßgenauigkeit, Oberflächenqualität und Haltbarkeit erfüllt. Das Verständnis dieses Arbeitsablaufs ist für Ingenieure, die die Produktion planen, und für Beschaffungsmanager, die bei der Beschaffung von 3D-gedruckten Metallteilen die Gesamtvorlaufzeit und die Kosten berücksichtigen, von entscheidender Bedeutung.
Die spezifische Nachbearbeitungskette kann je nach Komplexität der Halterung, ihrer vorgesehenen Anwendung und den erforderlichen Spezifikationen variieren. Ein typischer Ablauf für AlSi10Mg-Strukturteile umfasst jedoch mehrere wichtige Schritte:
Typischer Nachbearbeitungsablauf für L-PBF AlSi10Mg Brackets:
- Stressabbau (optional, aber empfohlen):
- Zweck: Zur Reduzierung der hohen inneren Eigenspannungen, die während der schnellen Aufheiz- und Abkühlzyklen des L-PBF-Prozesses entstehen. Diese Spannungen können zu Verformungen oder Rissen führen, wenn das Teil von der Bauplatte entfernt wird.
- Verfahren: Wird in der Regel durchgeführt, während das Teil noch auf der Bauplatte in einem Ofen mit kontrollierter Atmosphäre (normalerweise Argon, um Oxidation zu verhindern) befestigt ist. Die Baugruppe wird auf eine moderate Temperatur erhitzt (z. B. 200-300 °C für AlSi10Mg), eine Zeit lang gehalten (z. B. 1-2 Stunden) und dann langsam abgekühlt.
- Vorteile: Verbessert die Dimensionsstabilität nach dem Ablösen von der Platte und verringert das Risiko von Rissen.
- Entfernen des Teils von der Bauplatte:
- Zweck: Um die gedruckte(n) Halterung(en) von der Metallbauplatte zu trennen, auf der sie verschmolzen wurden.
- Methoden: In der Regel erfolgt dies durch Drahterodieren oder mit einer Bandsäge. Drahterodieren liefert einen saubereren Schnitt mit minimaler mechanischer Belastung, ist aber langsamer. Das Sägen ist schneller, kann aber eine Nachbearbeitung der Grundfläche erfordern.
- Erwägungen: Erfordert eine vorsichtige Handhabung, um eine Beschädigung der Teile zu vermeiden.
- Pulverentfernung (Depowdering):
- Zweck: Zum Entfernen von ungeschmolzenem Pulver, das in internen Kanälen, Hohlräumen oder dicht gepackten Stützstrukturen eingeschlossen ist.
- Methoden: In der Regel wird mit Druckluft gestrahlt, von Hand gebürstet und manchmal mit Ultraschallbädern gereinigt. Die gründliche Entfernung des Pulvers ist von entscheidender Bedeutung, da eingeschlossenes Pulver die Leistung beeinträchtigen oder nachgeschaltete Prozesse (wie die Wärmebehandlung) verunreinigen kann.
- Herausforderungen: Komplexe Innengeometrien können die vollständige Entfernung des Pulvers erschweren. Die DfAM-Prinzipien (z. B. die Gestaltung von Entwässerungslöchern) können diesen Schritt erleichtern.
- Entfernung der Stützstruktur:
- Zweck: Um die während des Bauprozesses erforderlichen temporären Stützstrukturen zu entfernen.
- Methoden: Je nach Art und Lage der Stützen kann die Entfernung Folgendes beinhalten:
- Manuelles Brechen: Leicht zerbrechliche Halterungen mit Schnittstellen geringer Dichte.
- Handwerkzeuge: Zangen, Schleifer, Feilen für hartnäckigere Halterungen.
- Bearbeitungen: Fräs- oder Schleifarbeiten, insbesondere bei Blockstützen oder großen Kontaktflächen.
- Drahterodieren: Zum präzisen Entfernen von Stützen an empfindlichen Stellen.
- Herausforderungen: Kann arbeitsintensiv und zeitaufwendig sein. Risiko der Beschädigung der Teileoberfläche an den Kontaktpunkten der Stützen. Die während der DfAM geplante Zugänglichkeit ist entscheidend. Oberflächen, an denen Stützen angebracht wurden, müssen oft nachbearbeitet werden.
- Wärmebehandlung (Zustand T6 - ausschlaggebend für AlSi10Mg):
- Zweck: Deutliche Verbesserung der mechanischen Eigenschaften (Festigkeit, Härte, Duktilität) des AlSi10Mg-Bügels. Die unbedruckte Mikrostruktur hat eine mäßige Festigkeit; die T6-Behandlung optimiert sie für strukturelle Anwendungen.
- Verfahren: Ein mehrstufiges Verfahren, das in kalibrierten Öfen mit kontrollierter Atmosphäre durchgeführt wird:
- Lösungsglühen: Erhitzen des Teils auf eine hohe Temperatur (z. B. ~515-540 °C) für eine bestimmte Dauer (z. B. 1-6 Stunden, je nach Dicke des Teils), um die in der Aluminiummatrix vorhandenen Mg₂Si-Ausscheidungen in eine feste Lösung aufzulösen.
- Abschrecken: Schnelles Abkühlen des Teils (in der Regel in Wasser oder einem polymeren Abschreckmittel), um die gelösten Elemente in der übersättigten festen Lösung "einzufrieren". Die Abkühlgeschwindigkeit ist entscheidend.
- Künstliche Alterung (Ausscheidungshärtung): Wiedererwärmen des Teils auf eine niedrigere Temperatur (z. B. ~160-180 °C) und Halten des Teils für mehrere Stunden (z. B. 4-12 Stunden). Dies ermöglicht die kontrollierte Ausscheidung feiner Mg₂Si-Partikel in der gesamten Aluminiummatrix, die die Versetzungsbewegung behindern und die Festigkeit und Härte deutlich erhöhen.
- Vorteile: Verwandelt AlSi10Mg von einem Werkstoff mit mittlerer Festigkeit in einen Werkstoff, der mit herkömmlichen Gusslegierungen vergleichbar ist, und macht ihn damit für anspruchsvolle Belastungen im Automobilbereich geeignet.
- Erwägungen: Erfordert präzise Temperaturkontrolle und Atmosphärenmanagement (Argon oder Vakuum), um Oxidation zu verhindern und gleichmäßige Eigenschaften zu gewährleisten. Die Teile können sich während der Wärmebehandlung leicht verformen, was bei der anschließenden Bearbeitung berücksichtigt werden muss.
- Heiß-Isostatisches Pressen (HIP) (optional):
- Zweck: Schließen der inneren Porosität (Mikroporen), die selbst in gut gedruckten Teilen vorhanden sein kann, und dadurch Verbesserung der Ermüdungsfestigkeit, Duktilität und Bruchzähigkeit.
- Verfahren: Die Teile werden in einer speziellen HIP-Anlage, die in der Regel Argon-Gas als Druckmedium verwendet, einem hohen Druck (z. B. 100-200 MPa) und einer erhöhten Temperatur (unterhalb des Schmelzpunkts, oft integriert mit oder anstelle von Lösungsglühen) ausgesetzt. Durch den Druck kollabieren die inneren Hohlräume.
- Vorteile: Verbessert die Materialintegrität, was für hochkritische Komponenten, die Ermüdung oder hohen Belastungen ausgesetzt sind, entscheidend ist. Kann die Konsistenz der mechanischen Eigenschaften verbessern.
- Erwägungen: Erhöht die Kosten und die Vorlaufzeit erheblich. In der Regel reserviert für Luft- und Raumfahrt, Medizintechnik oder sicherheitskritische Anwendungen in der Automobilindustrie, wo die Leistungsvorteile die Kosten rechtfertigen.
- Oberflächenveredelung:
- Zweck: Zur Erzielung der gewünschten Oberflächenstruktur, zur Beseitigung von Zeugenspuren, zur Verbesserung der Ästhetik oder zur Vorbereitung einer Beschichtung.
- Gemeinsame Methoden für AlSi10Mg:
- Abrasives Strahlen (Perlen-/Sandstrahlen): Sorgt für ein gleichmäßiges, sauberes, mattes Finish. Eignet sich zum Entfernen von losem Pulver und zum Ausgleichen kleinerer Oberflächenfehler. Kann vorteilhafte Druckeigenspannungen hervorrufen. Verschiedene Medien (Glasperlen, Aluminiumoxid) bieten unterschiedliche Oberflächen.
- Taumeln/Gleitschleifen: Verwendet Schleifmittel in einem rotierenden oder vibrierenden Behälter zum Glätten von Oberflächen und Entgraten von Kanten. Geeignet für Chargen von kleineren Teilen.
- Manuelles Schleifen/Polieren: Für spezielle Anforderungen wie Spiegelglanz oder Glätten kritischer Radien. Arbeitsintensiv.
- Auswahl: Abhängig von den funktionalen und ästhetischen Anforderungen und den Kostenzielen des Trägers.
- CNC-Bearbeitung:
- Zweck: Zur Erzielung enger Toleranzen bei bestimmten Merkmalen, zur Herstellung präziser Passflächen, zur Bearbeitung von Gewinden oder zur Erzielung sehr glatter Oberflächen, falls erforderlich.
- Verfahren: Verwendet herkömmliche CNC-Fräs- oder Drehzentren. Die Teile müssen ordnungsgemäß aufgespannt werden. Wie in DfAM besprochen, müssen Bearbeitungszugaben in den Entwurf des gedruckten Teils aufgenommen werden.
- Integration: Kombiniert die geometrische Freiheit der AM mit der Präzision der subtraktiven Fertigung für kritische Schnittstellen.
- Beschichtung oder Oberflächenbehandlung:
- Zweck: Zur Erhöhung der Korrosionsbeständigkeit, zur Verbesserung der Verschleißfestigkeit, zur elektrischen Isolierung oder zur Erzielung eines bestimmten Aussehens (Farbe).
- Gemeinsame Methoden für Aluminium:
- Eloxieren: Ein elektrochemischer Prozess, der eine harte, korrosionsbeständige Oxidschicht erzeugt. Kann in verschiedenen Farben eingefärbt werden. Typ II (dekorativ/korrosionsbeständig) und Typ III (Hartbeschichtung) sind üblich.
- Chromat-Umwandlungsbeschichtung (Alodin/Iridit): Bietet Korrosionsschutz und dient als gute Grundierung für Farbe.
- Anstrich/Pulverbeschichtung: Für spezifische Farben und zusätzlichen Umweltschutz.
- Auswahl: Basierend auf der Betriebsumgebung und den funktionalen Anforderungen der Halterung.
Der umfassende Ansatz von Met3dp:
Met3dp ist sich bewusst, dass zur Herstellung einer funktionalen Fahrzeughalterung mehr gehört als nur das Drucken. Obwohl unsere Kernkompetenzen in fortschrittlichen SEBM- und L-PBF-Druckern und hochwertigen Metallpulvern liegen, bieten wir umfassende Lösungen an. Dazu gehört auch die fachkundige Beratung zu den erforderlichen Nachbearbeitungsschritten und die Zusammenarbeit mit einem Netzwerk von vertrauenswürdigen Partnern für spezielle Dienstleistungen wie Wärmebehandlung, HIP, Präzisionsbearbeitung und Beschichtung. Wir stellen sicher, dass unsere B2B-Kunden eine durchgängige Unterstützung erhalten, von der Designoptimierung bis zur Lieferung der fertigen Teile.
Das Verständnis dieses kompletten Arbeitsablaufs ermöglicht es den Automobilherstellern, ein genaues Budget zu erstellen, Zeitpläne zu planen und sicherzustellen, dass die von ihrem B2B-Metalldrucklieferanten gelieferten AlSi10Mg-Halterungen alle erforderlichen Spezifikationen für eine erfolgreiche Integration in ihre Fahrzeuge erfüllen.
Herausforderungen meistern: Überwindung von Hürden beim 3D-Druck von Kfz-Halterungen
Die additive Fertigung von Metallen, insbesondere das L-PBF-Verfahren von AlSi10Mg, ist eine leistungsstarke Technologie, aber sie ist nicht ohne Komplexität und potenzielle Herausforderungen. Sich dieser Hürden bewusst zu sein und die Strategien zu verstehen, mit denen sie gemildert werden können, ist entscheidend, um konsistente, hochwertige Ergebnisse zu erzielen, die für anspruchsvolle Automobilanwendungen geeignet sind. Erfahrene AM-Anbieter wie Met3dp investieren viel in Prozesskontrolle, Materialwissenschaft und technisches Know-how, um diese Probleme effektiv zu bewältigen und B2B-Kunden zuverlässige Lösungen zu bieten. Beschaffungsmanager sollten mit Lieferanten zusammenarbeiten, die ein tiefes Verständnis für diese Herausforderungen haben und über bewährte Methoden verfügen, um sie zu bewältigen.
Allgemeine Herausforderungen bei L-PBF von AlSi10Mg-Brackets und Strategien zur Abhilfe:
Herausforderung | Häufige Ursachen | Strategien und Lösungen zur Schadensbegrenzung |
---|---|---|
Verziehen und Verzerrung | Hohe thermische Gradienten während des Drucks, die eine unterschiedliche Ausdehnung/Kontraktion verursachen; Aufbau von Eigenspannungen. | DfAM: Optimieren Sie die Teileausrichtung, minimieren Sie große flache Bereiche parallel zur Platte, nutzen Sie die Topologieoptimierung, um das Volumen zu reduzieren. <br> Unterstützt: Robuste Stützstrukturen, um das Teil fest zu verankern. <br> Prozesskontrolle: Optimierte Scan-Strategien, Aufbau der Plattenheizung. <br> Nachbearbeiten: Spannungsarmglühen auf der Platte vor der Entnahme des Teils. <br> Simulation: Thermische Simulation während des Entwurfs zur Vorhersage und Kompensation von Verformungen. |
Unterstützung Entfernung Schwierigkeit/Schaden | Dichte Stützstrukturen; Stützen in unzugänglichen Innenbereichen; starke Bindung zwischen Stützen und Bauteil. | DfAM: Konstruktion für minimalen Stützbedarf (selbsttragende Winkel), Optimierung der Stützart (z. B. baumförmig, perforiert) und der Schnittstellenschichten für leichteres Lösen, Gewährleistung der Zugänglichkeit für Entfernungswerkzeuge. <br> Prozess: Verwenden Sie optimierte Stützparameter in der Software für die Bauvorbereitung. <br> Beseitigung: Verwendung geeigneter Werkzeuge (manuell, maschinell, EDM), sorgfältige Handhabung. |
Porosität (Gas & Schlüsselloch) | Gas Porosität: Gelöstes Gas (z. B. Wasserstoff im Pulver), das während der Verfestigung ausgeschieden wird, eingeschlossenes Gas im Pulvereinsatzmaterial. <br> Schlüsselloch-Porosität: Zu hohe Energiedichte (zu hohe Laserleistung / zu niedrige Scangeschwindigkeit) führt zu Metallverdampfung und Schmelzbadinstabilität/-zusammenbruch. | Materialqualität: Verwenden Sie hochwertiges, gasarm zerstäubtes kugelförmiges Pulver (die Spezialität von Met3dp). Richtige Handhabung und Lagerung des Pulvers, um Feuchtigkeitsaufnahme zu vermeiden. <br> Prozess-Optimierung: Präzise kalibrierte Laserparameter (Leistung, Geschwindigkeit, Lukenabstand), kontrollierte inerte Atmosphäre (Argonreinheit). <br> Nachbearbeiten: Heiß-Isostatisches Pressen (HIP) kann interne Porosität effektiv schließen (zusätzliche Kosten/Zeit). |
Rissbildung (Verfestigung/Verflüssigung) | Erstarrungsrisse: Entsteht in der breiigen Zone während der Erstarrung aufgrund von thermischen Spannungen, die schwache interdritische Bereiche auseinanderreißen. <br> Verflüssigungsspaltung: Wiederaufschmelzen von Phasen mit niedrigerem Schmelzpunkt in der wärmebeeinflussten Zone benachbarter Schienen/Schichten. (AlSi10Mg ist im Allgemeinen weniger anfällig als Legierungen wie A7075). | Prozess-Optimierung: Feinabgestimmte Laserparameter und Scan-Strategien zur Steuerung von Temperaturgradienten und Abkühlungsraten. <br> DfAM: Vermeiden Sie scharfe Innenecken (verwenden Sie Verrundungen), sorgen Sie für weiche Übergänge in der Geometrie. <br> Nachbearbeiten: Eine spannungsreduzierende Wärmebehandlung kann das Risiko der Rissbildung vermindern. |
Schlechte Oberflächenbeschaffenheit/Rauhigkeit | Schichtweiser Aufbau (Treppenstufen); teilweise aufgeschmolzene Pulverpartikel, die an Oberflächen haften; Stützkontaktpunkte. | DfAM: Optimieren Sie die Teileausrichtung (kritische Oberflächen vertikal oder mit der Haut nach oben). <br> Prozess: Verwenden Sie feinere Schichtdicken (erhöht den Zeitaufwand), optimierte Laserparameter und Konturscans. <br> Nachbearbeiten: Strahlen, Trommeln, Polieren oder maschinelle Bearbeitung für kritische Oberflächen, die glatt sein müssen. |
Eigenspannung | Inhärente Folge der schnellen Erwärmungs-/Abkühlungszyklen bei L-PBF. Kann die Dimensionsstabilität und die mechanischen Eigenschaften (insbesondere Ermüdung) beeinträchtigen. | Prozesskontrolle: Aufbau einer Plattenheizung, optimierte Abtaststrategien für eine gleichmäßigere Wärmeverteilung. <br> Nachbearbeiten: Eine spannungsreduzierende Wärmebehandlung (auf oder außerhalb der Platte) ist äußerst wirksam. HIP reduziert auch die Eigenspannung. <br> DfAM: Entwerfen Sie so, dass große thermische Gradienten so weit wie möglich minimiert werden. |
Inkonsistente mechanische Eigenschaften | Schwankungen in der Pulverqualität, Schwankungen der Prozessparameter, ungleichmäßige Abkühlungsraten, Porosität, unvollständige Wärmebehandlung. | Qualitätskontrolle: Strenges Pulverqualitätsmanagement, strenge Maschinenkalibrierung und -wartung, validierte/verriegelte Prozessparameter, präzise Wärmebehandlungskontrolle (kalibrierte Öfen, Atmosphärenkontrolle), zerstörungsfreie Prüfung (z. B. CT-Scanning) für kritische Teile. <br> Kompetenz der Lieferanten: Arbeiten Sie mit erfahrenen Anbietern wie Met3dp zusammen, die über solide Qualitätsmanagementsysteme verfügen. |
Kosten pro Teil | Hohe Investitionskosten, relativ langsame Herstellungsgeschwindigkeiten im Vergleich zu Massenproduktionsverfahren, spezielle Pulverkosten, notwendige Nachbearbeitung. | DfAM: Maximierung von Leichtbau und Teilekonsolidierung zur Wertschöpfung. Optimieren Sie das Baulayout (Verschachtelung mehrerer Teile). <br> Auswahl der Anwendung: Konzentrieren Sie sich auf Teile, bei denen die einzigartigen Vorteile von AM (Komplexität, Geschwindigkeit, individuelle Anpassung) die Kosten überwiegen - Prototypen, Kleinserien, hochoptimierte Designs. <br> Prozess-Effizienz: Rationalisierte Nachbearbeitungsabläufe, Automatisierung wo möglich. |
Herausforderungen bei der Skalierbarkeit | Die Skalierung auf hohe Stückzahlen in der Automobilindustrie (Millionen) mit AM erfordert erhebliche Investitionen in Maschinen und Infrastruktur. | Strategische Umsetzung: Nutzen Sie AM für geeignete Nischen (Prototyping, Aftermarket, Motorsport, Kleinserien, komplexe/konsolidierte Teile). <br> Hybride Ansätze: Kombinieren Sie AM für komplexe Abschnitte mit traditionellen Methoden für einfachere Teile einer Baugruppe. <br> Entwicklung AM-spezifischer Lieferketten: Aufbau von Beziehungen zu zuverlässigen, skalierbaren B2B-AM-Dienstleistern. |
In Blätter exportieren
Met3dp: Risikominimierung durch Fachwissen
Um diese Herausforderungen zu meistern, sind fundierte technische Kenntnisse und Prozessdisziplin erforderlich. Met3dp bringt jahrzehntelange Erfahrung in der additiven Fertigung von Metallen mit sich:
- Materialwissenschaft: Wir konzentrieren uns auf die Herstellung von hochkugelförmigen, hochreinen Pulvern mit fortschrittlicher Zerstäubung, um materialbedingte Fehler wie Porosität zu minimieren.
- Prozess-Optimierung: Wir verfeinern kontinuierlich die Druckparameter für verschiedene Legierungen, einschließlich AlSi10Mg und anspruchsvolle Legierungen wie A7075, auf unseren modernen Anlagen.
- Technische Unterstützung: Unsere Anwendungsingenieure unterstützen unsere Kunden bei der DfAM, indem sie ihnen helfen, Teile robust zu konstruieren und potenzielle Probleme wie Verzug oder Stützprobleme zu minimieren.
- Qualitätsmanagement: Strenge Qualitätskontrollen, von der Pulverinspektion bis zur Validierung der fertigen Teile, gewährleisten Konsistenz und Zuverlässigkeit.
Durch die Zusammenarbeit mit Met3dp erhalten Automobilunternehmen nicht nur Zugang zu Druckkapazitäten, sondern auch einen sachkundigen Partner, der sich der Bewältigung der mit Metall-AM verbundenen Herausforderungen verschrieben hat und hochwertige, zuverlässige AlSi10Mg-Halterungen liefert, die ihre spezifischen Konstruktions- und Beschaffungsanforderungen erfüllen.
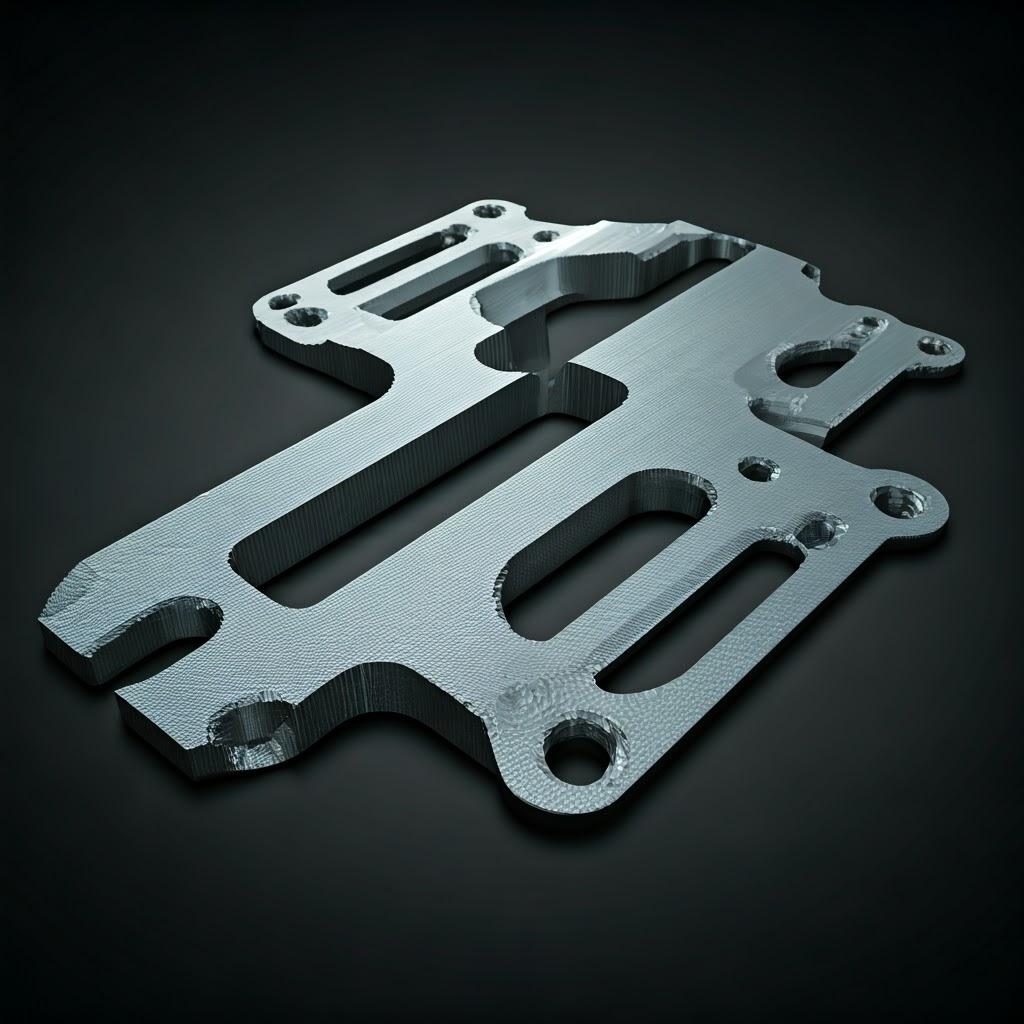
Auswahl der Lieferanten: Die Wahl des richtigen Partners für den 3D-Druck von Metall für Ihre Bedürfnisse in der Automobilindustrie
Die Entscheidung, die additive Fertigung von Metall für Kfz-Halterungen unter Verwendung von AlSi10Mg zu nutzen, ist ein wichtiger Schritt in Richtung Innovation und Effizienz. Die Ausschöpfung des vollen Potenzials dieser Technologie hängt jedoch stark von der Auswahl des richtigen Fertigungspartners ab. Das Angebot an Metall-AM-Dienstleistungen ist vielfältig, und die Anbieter unterscheiden sich erheblich in Bezug auf Fachwissen, technologische Fähigkeiten, Qualitätssysteme und Kapazitäten. Für Automobilingenieure und Beschaffungsmanager ist eine gründliche Due-Diligence-Prüfung von entscheidender Bedeutung, um eine zuverlässige B2B-Beziehung aufzubauen, die qualitativ hochwertige Teile, konsistente Lieferungen und wertvolle technische Unterstützung gewährleistet. Eine kluge Wahl mindert die Risiken und maximiert die Rendite von AM-Investitionen.
Warum die Auswahl von Partnern in der Automobil-AM entscheidend ist:
- Qualität und Verlässlichkeit: Automobilteile haben oft strenge Sicherheits- und Leistungsanforderungen. Ihr Zulieferer muss eine solide Qualitätskontrolle und Prozessstabilität nachweisen, um Teile zu liefern, die die Spezifikationen durchgehend erfüllen.
- Technische Komplexität: Metall-AM beinhaltet komplizierte Wechselwirkungen zwischen Materialien, Maschinen und Prozessparametern. Ein sachkundiger Partner kann entscheidende DfAM-Unterstützung bieten, Probleme beheben und die Produktion optimieren.
- Nachbearbeitungsintegration: Der Druck ist nur ein Teil der Gleichung. Ein Anbieter muss entweder über umfassende interne Nachbearbeitungskapazitäten (Wärmebehandlung, maschinelle Bearbeitung, Endbearbeitung) verfügen oder ein qualifiziertes Netz von Unterauftragnehmern effizient verwalten.
- Skalierbarkeit: Ihr Bedarf kann sich von Prototypen bis hin zur Kleinserienproduktion entwickeln. Ihr Partner sollte über die Kapazitäten und die Infrastruktur verfügen, um entsprechend zu skalieren.
- Risiko in der Lieferkette: Sich auf einen unqualifizierten Lieferanten zu verlassen, birgt das Risiko von Qualitätsmängeln, Lieferverzögerungen und mangelnder technischer Unterstützung.
Schlüsselkriterien für die Bewertung von Metall-AM-Lieferanten für Kfz-Halterungen:
Nutzen Sie diese Checkliste als Leitfaden für die Bewertung potenzieller B2B-Metalldruckdienstleister:
1. Technisches Fachwissen und nachgewiesene Erfahrung: * [] Spezifische Materialerfahrung: Nachgewiesener Erfolg beim Druck von AlSi10Mg und potenziell anderen relevanten Automobillegierungen (z. B. A7075, rostfreie Stähle). Fragen Sie nach Fallstudien oder Beispielen. * [] DfAM-Unterstützung: Bieten sie Konstruktionsberatung oder Überprüfungsdienste zur Optimierung von Teilen für die additive Fertigung an? * [] Automobilanwendungen Verstehen: Vertrautheit mit den Anforderungen der Automobilindustrie in Bezug auf Toleranzen, Oberflächengüte, strukturelle Integrität und allgemeine Halterungsfunktionen. * [] Jahre in Betrieb & Erfolgsbilanz: Etablierte Präsenz und positiver Ruf in der Branche. * [_] Ingenieurteam: Qualifizierte Metallurgen, AM-Verfahrensingenieure und Konstruktionsspezialisten im Unternehmen.
2. Ausrüstung und Technologie: * [] Druckertechnologie: Geeignete L-PBF-Maschinen (SLM/DMLS), die für AlSi10Mg geeignet sind. Handelt es sich um industrietaugliche, gut gewartete Maschinen von namhaften Herstellern? * [] Bauvolumen: Ausreichende Größe der Baukammer, um die Abmessungen Ihrer Halterung zu berücksichtigen und möglicherweise mehrere Teile für mehr Effizienz zu verschachteln. * [] Kalibrierung und Wartung von Maschinen: Regelmäßige dokumentierte Kalibrierungsprotokolle für Laser, Scanner und Bewegungssysteme. Vorbeugende Wartungspläne. * [] Atmosphärenkontrolle: Zuverlässige Inertgas-Managementsysteme (Argon) zur Vermeidung von Oxidation während des Drucks.
3. Materialkapazitäten und Qualitätskontrolle: * [] Material-Portfolio: Bietet zertifiziertes AlSi10Mg-Pulver, das speziell für AM optimiert ist. Welche anderen relevanten Materialien sind verfügbar? * [] Pulverbeschaffung und -handhabung: Stellen sie das Pulver selbst her (wie Met3dp) oder beziehen sie es extern? Wie sehen die Qualifizierungsprozesse der Lieferanten aus? Strenge Verfahren für die Handhabung, Lagerung, Prüfung (z. B. Chemie, Partikelgrößenverteilung, Fließfähigkeit) und Rückverfolgbarkeit von Pulver sind entscheidend. * [_] Pulver-Recycling-Strategie: Dokumentierte Verfahren zum Sieben und Wiederverwenden von ungeschmolzenem Pulver, um Qualität und Konsistenz zu gewährleisten.
4. Nachbearbeitungsmöglichkeiten: * [] In-House vs. Outsourced: Welche Schritte (Spannungsarmglühen, Wärmebehandlung, Entfernen von Stützen, Bearbeitung, Endbearbeitung, HIP) werden im eigenen Haus und welche bei Zulieferern durchgeführt? * [] Ausrüstung und Fachwissen: Zugang zu kalibrierten Öfen für die Wärmebehandlung (mit Atmosphärensteuerung), CNC-Bearbeitungszentren, geeignete Endbearbeitungsgeräte. * [] Verwaltung von Unterauftragnehmern: Falls Outsourcing, wie sieht das Verfahren zur Qualifizierung und Verwaltung dieser Partner aus? * [] Integrierter Arbeitsablauf: Fähigkeit, die gesamte Prozesskette effizient zu verwalten.
5. Qualitätsmanagementsystem (QMS): * [] Zertifizierungen: Die ISO 9001-Zertifizierung ist ein grundlegender Indikator für ein strukturiertes QMS. AS9100 (Luft- und Raumfahrt) zeigt eine höhere Strenge, die für die Automobilindustrie oft von Vorteil ist. Vertrautheit mit oder Schritte in Richtung IATF 16949 (Automobilindustrie) sind ein Plus. * [] Dokumentation und Rückverfolgbarkeit: Robuste Systeme zur Dokumentation von Prozessparametern, Materialchargen, Bedieneraktionen und Prüfergebnissen, die eine vollständige Rückverfolgbarkeit vom Pulver bis zum fertigen Teil gewährleisten. * [] Inspektionskapazitäten: Eigenes Messlabor mit CMMs, 3D-Scannern und Oberflächenprofilometern. Zerstörungsfreie Prüfung (NDT) (z. B. CT-Scannen), falls erforderlich. * [] Prozesskontrolle: Anwendung der statistischen Prozesskontrolle (SPC) oder anderer Methoden zur Überwachung und Gewährleistung der Prozessstabilität.
6. Kapazität und Skalierbarkeit: * [] Anzahl der Maschinen: Ausreichende Maschinenkapazitäten zur Bewältigung der aktuellen und geplanten Mengen ohne übermäßige Vorlaufzeiten. * [] Operative Effizienz: Mehrschichtiger Betrieb, optimierte Bauplanung, effiziente Arbeitsabläufe. * [_] Wachstumspotenzial: Nachgewiesene Fähigkeit oder Pläne, den Betrieb zu skalieren, um der steigenden Nachfrage von B2B-Kunden gerecht zu werden.
7. Vorlaufzeiten und Reaktionsfähigkeit: * [] Zitiergeschwindigkeit: Fähigkeit, zeitnahe und genaue Kostenvoranschläge zu erstellen. * [] Angegebene Vorlaufzeiten: Realistische und zuverlässige Schätzungen für verschiedene Produktionsstufen (Prototyp vs. Serie, verschiedene Nachbearbeitungsstufen). * [_] Kommunikation: Klare, proaktive Kommunikation über den Projektstatus, mögliche Probleme und Liefertermine. Engagierte Projektmanager?
8. Wettbewerbsfähigkeit bei den Kosten: * [] Transparente Preisgestaltung: Klare Aufschlüsselung der Kosten (Material, Maschinenzeit, Arbeit, Nachbearbeitung). * [] Wert-Angebot: Konzentrieren Sie sich auf den Gesamtwert (Qualität, Zuverlässigkeit, Fachwissen, Unterstützung) und nicht nur auf den niedrigsten Einzelpreis. Sind sie für das angebotene Dienstleistungsniveau wettbewerbsfähig?
9. Standort & Logistik: * [] Geografischer Standort: Die Nähe kann ein Faktor für kürzere Lieferzeiten oder eine einfachere Zusammenarbeit sein, aber oft überwiegt das Fachwissen. * [] Erfahrung im Versand: Nachgewiesene Fähigkeit, Teile sicher zu verpacken und den nationalen und internationalen Versand effektiv zu verwalten.
10. Kundenbetreuung und Zusammenarbeit: * [] Technische Unterstützung: Verfügbarkeit von Ingenieuren zur Beantwortung von Fragen und für technische Unterstützung. * [] Kollaborativer Ansatz: Bereitschaft, als Partner zu arbeiten, Verbesserungen vorzuschlagen und Herausforderungen gemeinsam zu lösen. * [_] Langfristige Vision: Interesse am Aufbau einer langfristigen B2B-Beziehung und nicht nur an transaktionalen Aufträgen.
Warum Met3dp sich als Ihr Automotive AM Partner auszeichnet:
Met3dp zeichnet sich als führender B2B-Anbieter im Bereich der additiven Fertigung aus und erfüllt diese entscheidenden Auswahlkriterien in hohem Maße:
- Umfassendes Fachwissen: Jahrzehntelange Erfahrung, die sich speziell auf Metall-AM konzentriert, von der Pulverherstellung bis zur Anwendungstechnik.
- Integrierte Lösungen: Wir bieten ein umfassendes Portfolio an: fortschrittliche SEBM- und L-PBF-Drucker, Hochleistungsmetallpulver (einschließlich AlSi10Mg, Ti-Legierungen, Superlegierungen usw.), die im eigenen Haus unter Verwendung modernster Gaszerstäubungs- und PREP-Technologien hergestellt werden, sowie fachkundige Anwendungsentwicklungsdienste.
- Schwerpunkt Qualität: Unser Engagement für Qualität beginnt beim Pulver und erstreckt sich über eine strenge Prozesskontrolle auf unseren branchenführenden Druckern, die Zuverlässigkeit und Wiederholbarkeit für unternehmenskritische Teile gewährleisten.
- Technologische Führerschaft: Wir investieren kontinuierlich in die Forschung und Entwicklung sowohl von Materialien als auch von Geräten, um modernste Lösungen anzubieten.
- Partnerschaftliche Zusammenarbeit: Wir arbeiten eng mit unseren Kunden aus der Automobilindustrie zusammen, bieten DfAM-Unterstützung und passen unsere Lösungen an die jeweiligen Bedürfnisse an, um die digitale Transformation der Fertigung zu fördern.
Die Wahl eines Lieferanten ist eine strategische Entscheidung. Durch die sorgfältige Bewertung potenzieller Partner anhand dieser Kriterien können sich Automobilunternehmen vertrauensvoll für einen Anbieter wie Met3dp entscheiden, der die technischen Fähigkeiten, die Qualitätssicherung und die Bereitschaft zur Zusammenarbeit bietet, die für eine erfolgreiche Implementierung von 3D-gedruckten AlSi10Mg-Brackets erforderlich sind.
Kostenanalyse und Vorlaufzeit: Faktoren, die die Zeitpläne und Budgets für die Produktion von AlSi10Mg-Brackets beeinflussen
Die Umstellung auf die additive Fertigung von Kfz-Halterungen erfordert ein klares Verständnis der damit verbundenen Kosten und Vorlaufzeiten. Im Gegensatz zu traditionellen Methoden, die von Werkzeuginvestitionen dominiert werden, wird die Preisgestaltung bei Metall-AM in erster Linie vom Materialverbrauch, der Maschinenauslastung und dem Umfang der erforderlichen Nachbearbeitung bestimmt. Für Beschaffungsmanager, die Budgets aufstellen, und Ingenieure, die Projektzeiträume planen, ist das Verständnis dieser Faktoren für eine genaue Schätzung und eine effektive B2B-Beschaffung unerlässlich.
Kostentreiber für 3D-gedruckte AlSi10Mg-Kfz-Halterungen:
Der Endpreis einer gedruckten Klammer setzt sich aus mehreren Faktoren zusammen:
- Materialverbrauch:
- Teilband: Das Nettovolumen der endgültigen Klammerkonstruktion.
- Unterstützungsstruktur Volumen: Für Stützen verwendetes Material, das später wieder entfernt wird. Ein optimiertes DfAM minimiert dies.
- Pulverkosten: Der Preis pro Kilogramm AlSi10Mg-Pulver in AM-Qualität. Obwohl er im Vergleich zu Titan- oder Nickelsuperlegierungen moderat ist, ist er deutlich teurer als ein Gussbarren. Qualität und Konsistenz des Pulvers beeinflussen die Kosten.
- Recycling-Effizienz: Die Fähigkeit des Lieferanten, ungeschmolzenes Pulver effektiv zu recyceln, wirkt sich auf die gesamten Materialkosten des Teils aus.
- Maschinenzeit (Auslastung):
- Bauhöhe (Z-Höhe): Der wichtigste Faktor für die Druckzeit. Höhere Teile brauchen länger, unabhängig von ihrer Grundfläche innerhalb der Grenzen. Die Optimierung der Ausrichtung ist der Schlüssel.
- Teilmenge & Komplexität: Größere Volumina und komplizierte Merkmale erfordern mehr Laserscanzeit pro Schicht.
- Build Chamber Packing: Durch das gleichzeitige Drucken mehrerer Teile (Nesting) wird die Maschinenzeit effizienter genutzt, wodurch die Kosten pro Teil gesenkt werden. Die Zulieferer optimieren die Fertigung oft auf diese Weise.
- Maschinentarif: Ein Stundensatz, der die Amortisation der teuren L-PBF-Maschine, die Wartung, den Energieverbrauch, den Inertgasverbrauch und die Gemeinkosten der Anlage berücksichtigt.
- Arbeitskosten:
- Einrichtung aufbauen: Vorbereitung der Build-Datei (Ausrichtung, Stützen, Schneiden), Laden von Pulver, Einrichten der Maschine.
- Überwachung: Überwachung des Druckprozesses (bei stabilen Prozessen oft minimal).
- Teilentfernung und Entparzellierung: Der Arbeitsaufwand für das Abnehmen des Teils von der Platte und das Entfernen des losen Pulvers.
- Unterstützung bei der Entfernung: Dies kann zu erheblichen Arbeitskosten führen, insbesondere bei komplexen Teilen oder schlecht konstruierten Halterungen.
- Endbearbeitung und Inspektion: Manuelle Arbeit für die Oberflächenbearbeitung, CMM-Bedienung, Sichtprüfung usw.
- Nachbearbeitungskosten:
- Stressabbau/Wärmebehandlung: Kosten für Ofenzeit, Energieverbrauch und kontrollierte Atmosphäre. Die T6-Behandlung für AlSi10Mg ist für die Eigenschaften wichtig, verursacht aber zusätzliche Kosten.
- Heiß-Isostatisches Pressen (HIP): Ein spezielles und relativ teures Verfahren, das erhebliche Kosten verursacht, wenn es zur Beseitigung der Porosität erforderlich ist.
- CNC-Bearbeitung: Die Kosten basieren auf der Maschinenzeit, den Werkzeugen, der Programmierung und dem Arbeitsaufwand, der erforderlich ist, um enge Toleranzen oder spezifische Merkmale zu erreichen.
- Oberflächenveredelung: Kosten im Zusammenhang mit Perlstrahlen, Trommeln, Polieren (Arbeit, Medien, Zeit für Ausrüstung).
- Beschichtung/Eloxierung: Kosten für externe Anbieter, wenn sie nicht intern durchgeführt werden.
- Qualitätssicherung und Inspektion:
- Der Zeitaufwand für Maßkontrollen (CMM, Scannen), Messungen der Oberflächenrauheit, Dokumentation und alle erforderlichen zerstörungsfreien Prüfungen oder Materialtests erhöhen die Kosten.
- Design- und Ingenieurdienstleistungen (falls zutreffend):
- Wenn der Anbieter DfAM-Beratung, Topologieoptimierungsdienste oder umfangreiche technische Unterstützung anbietet, kann dies in die Gesamtprojektkosten einfließen.
- Bestellmenge:
- Bei AM entfallen zwar die Werkzeugkosten, aber es gibt auch einige Größenvorteile. Höhere Stückzahlen ermöglichen eine bessere Auslastung der Baukammer und die Amortisation der Rüstkosten über mehr Teile, was zu einem niedrigeren Stückpreis im Vergleich zu Einzelteilbestellungen führt. Allerdings flacht die Kostensenkungskurve sehr viel schneller ab als bei herkömmlichen Verfahren mit hohen Stückzahlen.
Aufschlüsselung der Vorlaufzeit für AlSi10Mg-Brackets:
Die Vorlaufzeit ist oft ein entscheidender Vorteil von AM, insbesondere bei Prototypen und geringen Stückzahlen, aber es ist wichtig, die einzelnen Phasen zu verstehen:
Bühne | Typische Dauer | Wichtige Einflussfaktoren |
---|---|---|
Zitat | Wenige Stunden - 2 Arbeitstage | Komplexität der Anfrage, Arbeitsbelastung des Lieferanten, Klarheit der bereitgestellten Informationen. |
Auftragsabwicklung & Bauvorbereitung | 0,5 - 2 Arbeitstage | Dateiprüfungen, DfAM-Prüfung (falls erforderlich), Support-Generierung, Planung des Build-Layouts. |
Drucken (L-PBF) | 1 - 5+ Tage | Teilhöhe (Z-Höhe) dominant ist. Teilevolumen, Komplexität, Menge pro Bau. |
Kühlung und Entpuffung | 0,5 - 1 Arbeitstag | Abkühlzeit der Maschine, Komplexität der Teile (interne Kanäle). |
Entspannung | 0,5 - 1 Arbeitstag | Zykluszeit des Ofens (normalerweise mehrere Stunden + Abkühlung). |
Entfernen von Teilen und Stützen | 0,5 - 2+ Arbeitstage | Größe des Teils, Komplexität des Trägers, Entnahmeverfahren (Säge, EDM, manuell). |
Wärmebehandlung (T6) | 1 - 2 Arbeitstage | Zykluszeit des Ofens (Lösung + Abschrecken + Alterung dauert >12-24 Stunden), Chargenplanung. |
HIP (falls erforderlich) | 3 - 10 Arbeitstage | Spezialisierter Prozess, oft ausgelagert, Batch Scheduling. |
CNC-Bearbeitung | 2 - 10+ Geschäftstage | Merkmalskomplexität, Anzahl der Rüstvorgänge, Maschinenverfügbarkeit, Auslagerungszeitpläne. |
Oberflächenveredelung | 1 - 5 Arbeitstage | Verwendete Methode, Chargengröße, geforderter Grad der Endbearbeitung. |
Inspektion und Qualitätssicherung | 0,5 - 2 Arbeitstage | Erforderlicher Inspektionsumfang (visuell, CMM, Scan), erforderliche Dokumentation. |
Verpackung & Versand | 1 - 5+ Geschäftstage | Versandart, Bestimmungsort (Inland/International). |
In Blätter exportieren
Geschätzte Gesamtvorlaufzeit:
- Schnelle Prototypen (wie gedruckt oder einfaches Finish, minimale Nachbearbeitung): Ungefähr 5 - 12 Arbeitstage.
- Funktionsprototypen / Kleinserien (mit Wärmebehandlung, Grundbearbeitung): Ungefähr 2 – 4 Wochen.
- Produktionsteile (vollständige Nachbearbeitung einschließlich Bearbeitung/Beschichtung): Ungefähr 3 - 6+ Wochen.
Das Wichtigste zum Mitnehmen: Durch AM entfallen zwar die wochen- oder monatelangen Vorlaufzeiten für die Herstellung von Werkzeugen, die beim Gießen oder Stanzen anfallen, aber der Druck und die umfangreiche Nachbearbeitung bedeuten, dass die Vorlaufzeiten für fertige AM-Metallteile in Wochen und nicht in Tagen gemessen werden (es sei denn, es handelt sich um sehr einfache, unfertige Teile). Dies ist jedoch immer noch deutlich schneller als die herkömmlichen Verfahren zur Herstellung von Werkzeugen für erste Teile und geringe Stückzahlen.
Met3dp's Ansatz für Kosten und Vorlaufzeit:
Met3dp ist bestrebt, B2B-Kunden klare, wettbewerbsfähige Preise und realistische Vorlaufzeitschätzungen zu bieten. Unsere integrierten Fähigkeiten, von der hochwertigen Pulverproduktion bis hin zum fortschrittlichen Druck und starken Partnerschaften in der Nachbearbeitung, tragen zur Rationalisierung des Arbeitsablaufs bei. Wir arbeiten mit unseren Kunden zusammen, um ihre spezifischen Anforderungen zu verstehen und transparente Angebote zu erstellen, die die notwendigen Schritte zur Erreichung der gewünschten Qualität und Leistung für ihre AlSi10Mg-Kraftfahrzeughalterungen widerspiegeln. Das Verständnis dieser Kosten- und Zeitdynamik ermöglicht es den Beschaffungs- und Konstruktionsteams, Metal AM effektiv in ihre Projektplanung und Beschaffungsstrategien zu integrieren.
Häufig gestellte Fragen (FAQ) zu 3D-gedruckten AlSi10Mg-Kfz-Halterungen
Hier finden Sie Antworten auf einige häufig gestellte Fragen von Ingenieuren und Beschaffungsmanagern, wenn sie den 3D-Druck von Metall mit AlSi10Mg für Fahrzeughalterungen in Betracht ziehen:
1. Ist 3D-gedrucktes AlSi10Mg stark genug für strukturelle Automobilhalterungen?
Ja, in vielen Fällen. Bei ordnungsgemäßer Verarbeitung und Wärmebehandlung bis zu einem T6-Zustand weist L-PBF-gedrucktes AlSi10Mg mechanische Eigenschaften (Zugfestigkeit, Streckgrenze) auf, die mit den üblicherweise verwendeten Aluminiumgusslegierungen wie A360 oder A356 vergleichbar sind. Dadurch eignet es sich für ein breites Spektrum von mäßig belasteten strukturellen und halbstrukturellen Halterungen, bei denen Leichtbau ein wichtiges Ziel ist.
- Wichtige Überlegungen:
- T6 Wärmebehandlung: Dieser Schritt ist entscheidend, um eine optimale Festigkeit zu erreichen. Die Eigenschaften im gedruckten Zustand sind deutlich geringer.
- Gestaltung (DfAM): Der Einsatz von Topologieoptimierung und FEA (Finite-Elemente-Analyse) stellt sicher, dass das Halterungsdesign die Festigkeit und Steifigkeit des Materials dort effizient nutzt, wo sie benötigt wird.
- Vergleich: Es ist im Allgemeinen nicht so stabil wie hochfeste Aluminium-Knetlegierungen (wie A7075) oder Stähle. Für extrem hoch belastete oder ermüdungskritische Anwendungen kann eine andere Legierung oder ein anderes Herstellungsverfahren erforderlich sein. Eine FEA-Validierung wird für kritische Strukturteile immer empfohlen.
- Met3dp Fachwissen: Anbieter wie Met3dp können über die Eignung von Werkstoffen auf der Grundlage von Anwendungsanforderungen beraten und Materialdatenblätter für Teile bereitstellen, die mit ihren validierten Verfahren hergestellt wurden.
2. Wie hoch sind die Kosten für eine 3D-gedruckte AlSi10Mg-Halterung im Vergleich zu einer gegossenen oder maschinell bearbeiteten Halterung?
Der Kostenvergleich hängt stark von den Anforderungen an Volumen, Komplexität und Vorlaufzeit ab:
- Prototypen und sehr geringe Stückzahlen (<50 Einheiten): Der 3D-Druck ist oft kostengünstiger weil die hohen Vorlaufkosten für das Gießen von Gussformen oder Stanzwerkzeugen (die sich auf mehrere zehn- oder hunderttausend Dollar belaufen können) vollständig entfallen. Die Bearbeitung von Prototypen aus Knüppeln kann je nach Komplexität vergleichbar oder teurer als AM sein.
- Geringes bis mittleres Volumen (50 - 1000 Einheiten): Der Vergleich fällt differenziert aus. Die AM-Stückkosten sinken langsam mit dem Volumen, während die Guss-/Stanzkosten deutlich sinken, sobald die Werkzeuge amortisiert sind. Die Bearbeitungskosten bleiben pro Stück relativ hoch. AM kann wettbewerbsfähig sein, wenn die Halterungsgeometrie sehr komplex ist (schwierig/kostspielig zu gießen oder zu bearbeiten) oder wenn die durch AM erreichte Konsolidierung der Teile die Montagekosten reduziert.
- Hohe Stückzahlen (10.000+ Einheiten): Traditionelle Verfahren wie Druckguss oder Stanzen sind fast immer deutlich billiger pro Teil aufgrund von Skaleneffekten, trotz der anfänglichen Investitionen in die Werkzeuge.
- Wert-Faktoren: Der Wert von AM geht oft über den direkten Vergleich der Stückkosten hinaus und berücksichtigt auch die kürzeren Vorlaufzeiten für die Entwicklung, die Ermöglichung komplexer/leichter Konstruktionen, die sonst nicht möglich wären, und die Erleichterung der On-Demand-Produktion oder der kundenspezifischen Anpassung.
3. Welche Angaben muss ich machen, um ein genaues Angebot für eine 3D-gedruckte Halterung zu erhalten?
Um einen rechtzeitigen und genauen Kostenvoranschlag von einem Metall-AM-Dienstleister wie Met3dp zu erhalten, sollten Sie so viele der folgenden Informationen wie möglich angeben:
- 3D-CAD-Modell: Ein hochwertiges 3D-Modell in einem Standardformat (z. B. STEP, STP wird bevorzugt; STL ist ebenfalls üblich). Stellen Sie sicher, dass das Modell wasserdicht ist und die gewünschte Endgeometrie darstellt.
- Spezifikation des Materials: Geben Sie klar und deutlich "AlSi10Mg" an. Geben Sie den gewünschten Endzustand an (z. B. "T6 wärmebehandelt").
- 2D-Zeichnungen (sehr empfehlenswert): Legen Sie technische Zeichnungen vor, aus denen klar hervorgeht:
- Kritische Maße und Toleranzen (unter Verwendung von GD&T-Symbolen).
- Spezifische Anforderungen an die Oberflächengüte (Ra-Werte) für das gesamte Teil oder kritische Flächen.
- Stellen für erforderliche Bearbeitungen, Gewinde oder andere spezifische Merkmale.
- Alle Anforderungen an zerstörungsfreie Prüfungen (NDT) oder spezifische Inspektionen.
- Menge: Anzahl der benötigten Klammern. Geben Sie an, ob es sich um einen einmaligen Prototyp oder eine potenzielle Dauerbestellung handelt.
- Erforderliche Nachbearbeitung: Führen Sie alle erforderlichen Schritte auf, die über den Druck hinausgehen (z. B. Spannungsarmglühen, T6-Wärmebehandlung, Perlstrahlen, spezielle Bearbeitungsvorgänge, Eloxalart/-farbe).
- Gewünschtes Lieferdatum: Ihr Zielzeitplan.
- Anwendungskontext (fakultativ, aber hilfreich): Eine kurze Beschreibung der Funktion und der Betriebsumgebung der Halterung kann dem Lieferanten manchmal helfen, ein besseres DfAM-Feedback oder eine bessere Materialberatung zu geben.
- Kontaktinformationen: Ihr Name, Ihr Unternehmen, Ihre E-Mail-Adresse und Ihre Telefonnummer.
4. Können interne Kanäle oder komplexe interne Merkmale zuverlässig gedruckt und gereinigt werden?
Ja, die Schaffung komplexer interner Merkmale ist ein großer Vorteil der Metall-AM. Die erfolgreiche Ausführung erfordert jedoch eine sorgfältige Konstruktion und Verarbeitung:
- DfAM für interne Merkmale: Die Kanäle müssen einen Mindestdurchmesser haben (in der Regel >1-2 mm), damit das ungeschmolzene Pulver während des Entpuderns entweichen kann. Entwerfen Sie sanfte Kurven und keine scharfen Ecken. Wenn das Kanalnetz sehr komplex ist, sollten Zugangsöffnungen vorgesehen werden. Berücksichtigen Sie nach Möglichkeit selbsttragende Kanalformen.
- Entfernung von Puder: Eine gründliche Entleerung mit Druckluft, Vibration und möglicherweise Ultraschall ist unerlässlich. Der Lieferant muss über solide Verfahren verfügen.
- Verifizierung: Bei kritischen Anwendungen kann durch CT-Scans zerstörungsfrei überprüft werden, ob die internen Kanäle frei sind und der vorgesehenen Geometrie entsprechen.
- Fähigkeit der Lieferanten: Besprechen Sie Ihre spezifischen Anforderungen an interne Merkmale mit potenziellen Lieferanten wie Met3dp, um sicherzustellen, dass diese in der Lage sind, solche Geometrien effektiv zu drucken und zu reinigen.
Klare Antworten auf diese Fragen helfen den Fachleuten in der Automobilindustrie, fundierte Entscheidungen über die Einführung des 3D-Drucks von AlSi10Mg zu treffen und effektiv mit B2B-Lieferanten zusammenzuarbeiten.
Schlussfolgerung: Innovation in der Automobilindustrie mit Met3dp's AlSi10Mg Additive Manufacturing Lösungen
Das Streben der Automobilindustrie nach leichteren, schnelleren und effizienteren Fahrzeugen erfordert kontinuierliche Innovationen sowohl in der Konstruktion als auch in der Fertigung. Die additive Fertigung von Metallen, insbesondere unter Verwendung vielseitiger und zuverlässiger Materialien wie AlSi10Mg, stellt einen bedeutenden Fortschritt dar und bietet leistungsstarke Werkzeuge, um diese Herausforderungen zu meistern. Wie wir erforscht haben, bietet der 3D-Druck von AlSi10Mg-Automobilhalterungen einen überzeugenden Weg zur Realisierung komplexer Geometrien, erheblicher Gewichtsreduzierungen durch Topologieoptimierung und Teilekonsolidierung sowie drastisch beschleunigter Entwicklungszyklen durch die Beseitigung herkömmlicher Werkzeugbeschränkungen für Prototypen und Kleinserien.
Der erfolgreiche Einsatz dieser Technologie erfordert jedoch mehr als nur den Zugang zu einem Drucker. Es bedarf eines ganzheitlichen Ansatzes, der die Prinzipien des Design for Additive Manufacturing (DfAM), ein tiefes Verständnis der Materialeigenschaften und der entscheidenden Rolle der Nachbearbeitung, wie z. B. der T6-Wärmebehandlung, die sorgfältige Beachtung von Präzision und Qualitätskontrolle sowie die strategische Auswahl von Lieferanten umfasst. Die Bewältigung der potenziellen Herausforderungen der Metall-AM, von der Beherrschung thermischer Spannungen bis hin zur Sicherstellung der Pulverqualität, erfordert die Zusammenarbeit mit einem Anbieter, der über umfassendes Know-how und robuste Prozesse verfügt.
Met3dp ist ein führender B2B-Partner für Unternehmen der Automobilindustrie, die die transformative Kraft der additiven Fertigung von Metallen nutzen wollen. Unsere umfassenden Lösungen umfassen das gesamte AM-Ökosystem:
- Erweiterte Ausrüstung: Die branchenführenden L-PBF- und SEBM-Drucker wurden für Genauigkeit, Zuverlässigkeit und industrielle Produktion entwickelt.
- Leistungsstarke Materialien: Eigene Produktion von Metallpulvern höchster Qualität, einschließlich AlSi10Mg, unter Einsatz modernster Gaszerstäubungs- und PREP-Technologien, die Konsistenz und optimale Leistung gewährleisten. Unser Portfolio umfasst auch innovative Legierungen wie TiNi, TiTa, TiAl, CoCrMo, rostfreie Stähle und Superlegierungen.
- Jahrzehntelange Erfahrung: Unser Team verfügt über fundierte Kenntnisse in den Bereichen Materialwissenschaft, Optimierung von AM-Prozessen, Anwendungsentwicklung und Qualitätssicherung, die uns in die Lage versetzen, komplexe Herausforderungen zu meistern und unternehmenskritische Komponenten zu liefern.
- End-to-End-Unterstützung: Wir arbeiten eng mit unseren Kunden zusammen, bieten ihnen DfAM-Anleitungen, verwalten die Nachbearbeitungsanforderungen und stellen sicher, dass die Teile die strengen Spezifikationen erfüllen, und erleichtern ihnen so die Umstellung auf die digitale Fertigung.
Ganz gleich, ob Sie ein Ingenieur sind, der eine kritische Halterung in Leichtbauweise herstellen, eine Baugruppe konsolidieren oder schnell einen Prototyp für ein neues Design entwickeln möchte, oder ob Sie ein Beschaffungsmanager sind, der einen zuverlässigen, qualitativ hochwertigen B2B-Lieferanten für die additive Fertigung von kleinen bis mittleren Stückzahlen sucht - Met3dp verfügt über die Fähigkeiten und die Erfahrung, um Ihnen zum Erfolg zu verhelfen.
Machen Sie den nächsten Schritt in der Automobil-Innovation.
Entdecken Sie das Potenzial des 3D-Drucks von AlSi10Mg-Metall für Ihre Anwendungen im Bereich der Kfz-Halterungen. Kontaktieren Sie Met3dp noch heute:
- Besprechen Sie Ihre spezifischen Projektanforderungen mit unseren Anwendungsingenieuren.
- Fordern Sie einen Kostenvoranschlag für Ihr Klammerdesign an.
- Erfahren Sie mehr über unser umfassendes Angebot an Metallpulvern und additiven Fertigungsdienstleistungen.
Gehen Sie eine Partnerschaft mit Met3dp ein und beschleunigen Sie Ihren Weg zur Fahrzeugherstellung der nächsten Generation.
Teilen auf
MET3DP Technology Co., LTD ist ein führender Anbieter von additiven Fertigungslösungen mit Hauptsitz in Qingdao, China. Unser Unternehmen ist spezialisiert auf 3D-Druckgeräte und Hochleistungsmetallpulver für industrielle Anwendungen.
Fragen Sie an, um den besten Preis und eine maßgeschneiderte Lösung für Ihr Unternehmen zu erhalten!
Verwandte Artikel
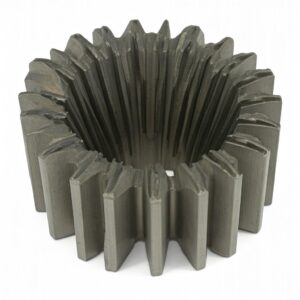
Hochleistungs-Düsenschaufelsegmente: Revolutionierung der Turbineneffizienz mit 3D-Metalldruck
Mehr lesen "Über Met3DP
Aktuelles Update
Unser Produkt
KONTAKT US
Haben Sie Fragen? Senden Sie uns jetzt eine Nachricht! Wir werden Ihre Anfrage mit einem ganzen Team nach Erhalt Ihrer Nachricht bearbeiten.
Holen Sie sich Metal3DP's
Produkt-Broschüre
Erhalten Sie die neuesten Produkte und Preislisten
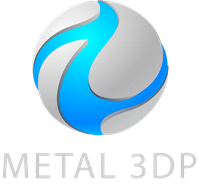
Metallpulver für 3D-Druck und additive Fertigung