3D-gedruckte Greifer für die Robotik mit hoher Festigkeit
Inhaltsübersicht
Einführung: Revolutionierung der Robotik mit hochfesten 3D-gedruckten Greifern
In der unaufhaltsamen Entwicklung der industriellen Automatisierung und Robotik spielen die Komponenten, die für Interaktion und Manipulation verantwortlich sind – die Greifer oder End-of-Arm-Werkzeuge (EOAT) – eine entscheidende Rolle. Dies sind die „Hände“ des Roboters, die mit dem sicheren Greifen, Bewegen und Positionieren von Objekten beauftragt sind, die von empfindlichen elektronischen Bauteilen bis hin zu schweren Automobilteilen reichen. Traditionell waren die Konstruktion und Herstellung dieser kritischen Komponenten mit erheblichen Vorlaufzeiten, hohen Kosten, insbesondere für kundenspezifische oder komplexe Designs, und Einschränkungen verbunden, die durch herkömmliche Methoden wie CNC-Bearbeitung oder Gießen auferlegt wurden. Das Aufkommen von Additive Fertigung von Metall (AM), allgemein bekannt als 3D-Druck von Metall, verändert jedoch grundlegend die Landschaft des Robotergreiferdesigns und der -produktion.
Dieser technologische Wandel ermöglicht es Ingenieuren und Einkaufsmanagern in Sektoren wie der Luft- und Raumfahrt, der Automobilindustrie, der Medizin und der allgemeinen industriellen Fertigung, frühere Einschränkungen zu überwinden. Metall 3D-Druck ermöglicht die Erstellung von hochfeste, leichte und hochgradig kundenspezifische Robotergreifer mit beispielloser Geschwindigkeit und Designfreiheit. Stellen Sie sich Greifer vor, die perfekt konturiert sind, um ein bestimmtes komplexes Teil zu handhaben, mit internen Kühlkanälen für Hochtemperaturanwendungen oder die Integration mehrerer Funktionen in eine einzige, konsolidierte Komponente. Dies ist keine futuristische Vision mehr, sondern eine gegenwärtige Realität, die durch Fortschritte in den Drucktechnologien und der Materialwissenschaft vorangetrieben wird.
Die wichtigsten Vorteile, die diese Revolution antreiben, sind:
- Geometrische Komplexität: AM ermöglicht komplizierte interne Strukturen, konforme Kanäle und organische Formen, die für die Funktion optimiert sind und oft unmöglich oder wirtschaftlich nicht vertretbar mit herkömmlichen Methoden zu bearbeiten sind.
- Gewichtsreduzierung: Durch Techniken wie Topologieoptimierung und Gitterstrukturen können Greifer mit deutlich reduziertem Gewicht konstruiert werden, während gleichzeitig die Festigkeit und Steifigkeit erhalten oder sogar erhöht werden. Leichtere EOAT führen zu schnelleren Roboterbewegungen, geringerem Energieverbrauch und möglicherweise zum Einsatz kleinerer, kostengünstigerer Roboter.
- Leistung des Materials: Der Zugang zu Hochleistungs-Metalllegierungen wie 17-4PH-Edelstahl und Aluminiumlegierung AlSi10Mg stellt sicher, dass 3D-gedruckte Greifer die erforderliche Festigkeit, Haltbarkeit, Verschleißfestigkeit und Umweltbeständigkeit für anspruchsvolle industrielle Aufgaben aufweisen.
- Anpassung & Agilität: AM zeichnet sich durch die Herstellung von Kleinserien, hochgradig kundenspezifischen Teilen ohne teure Werkzeuge aus. Dies ist ideal für Roboteranwendungen, bei denen Greifer oft auf bestimmte Produkte oder Aufgaben zugeschnitten werden müssen, was ein schnelles Prototyping und Iteration ermöglicht.
- Teil Konsolidierung: Mehrere Komponenten einer herkömmlichen Greiferbaugruppe können oft in ein einziges 3D-gedrucktes Teil integriert werden, wodurch die Montagezeit, potenzielle Fehlerquellen und die Gesamtkomplexität des Systems reduziert werden.
Unternehmen wie Met3dp mit Hauptsitz in Qingdao, China, stehen an vorderster Front dieser Transformation und bieten nicht nur fortschrittliche Metall-3D-Druckausrüstung , sondern auch die Hochleistungsmetallpulver , die für die Herstellung dieser Komponenten der nächsten Generation unerlässlich sind. Ihr Fachwissen in Technologien wie Selective Electron Beam Melting (SEBM) und fortschrittlichen Pulverherstellungsverfahren (Gaszerstäubung, PREP) stellt sicher, dass die resultierenden Teile die strengen Anforderungen an Genauigkeit, Dichte und mechanische Leistung erfüllen, die von missionskritischen Anwendungen gefordert werden.
Für Einkaufsmanager, die nach Robotergreifer-Lieferanten oder kundenspezifische EOAT-Herstellersuchen, ist das Verständnis des Potenzials von Metall-AM von entscheidender Bedeutung. Es eröffnet Türen zu Beschaffungslösungen, die nicht nur Ersatz für traditionell hergestellte Teile sind, sondern von Natur aus überlegen in Bezug auf Leistung, Effizienz und Anpassungsfähigkeit sind. Für Ingenieure eröffnet es ein neues Paradigma der Designmöglichkeiten, das es ihnen ermöglicht, Greiferlösungen zu entwickeln, die zuvor als unmöglich galten. Dieser Blogbeitrag wird tief in die Welt der 3D-gedruckten Metall-Robotergreifer eintauchen und ihre Anwendungen, die Vorteile der Verwendung von AM, empfohlene Materialien, Designüberlegungen, erreichbare Präzision, Nachbearbeitungsanforderungen, häufige Herausforderungen und die Auswahl des richtigen Fertigungspartners untersuchen. Unser Ziel ist es, eine umfassende Ressource für Fachleute bereitzustellen, die diese leistungsstarke Technologie für ihre Automatisierungsanforderungen nutzen und hochfeste Komponenten von zuverlässigen Großhandelsdistributoren für industrielle Robotikkomponenten oder Direktleistungsanbietern beziehen möchten.
Wofür werden 3D-gedruckte Robotergreifer verwendet? Anwendungen in verschiedenen Branchen
3D-gedruckte Metall-Robotergreifer sind nicht auf eine einzige Nische beschränkt; ihre Vielseitigkeit, Festigkeit und Anpassungsmöglichkeiten machen sie für eine Vielzahl von Aufgaben in zahlreichen anspruchsvollen Branchen geeignet. Die Fähigkeit, maßgeschneiderte Greifer schnell zu entwerfen und herzustellen, die auf bestimmte Objekte oder Prozesse zugeschnitten sind, eröffnet erhebliche Effizienzsteigerungen und ermöglicht die Automatisierung in zuvor herausfordernden Bereichen. Als Partner für additive Fertigung ihre Prozesse und Materialangebote verfeinern, erweitert sich der Anwendungsbereich ständig.
Hier ist eine Aufschlüsselung der wichtigsten Anwendungsbereiche, in denen 3D-gedruckte Metallgreifer einen erheblichen Einfluss haben:
1. Automobilherstellung: Die Automobilindustrie ist stark auf Robotik für Fließbandarbeiten angewiesen. Metall-AM-Greifer bieten Lösungen für:
- Komponentenhandhabung: Sicheres Greifen und Handhaben von schweren, komplexen oder Hochtemperaturteilen wie Motorblöcken, Getriebekomponenten, Abgasanlagen oder Fahrwerkselementen. Hier werden häufig hochfeste Materialien wie 17-4PH bevorzugt.
- Montageaufgaben: Präzises Platzieren kleinerer Komponenten, Befestigungsvorgänge und Halten von Teilen während des Schweißens oder Klebens. Leichte AlSi10Mg-Greifer können schnellere Roboterbewegungen ermöglichen.
- Kundenspezifische Vorrichtungen: Erstellen von Greifern, die gleichzeitig als Vorrichtungen dienen und Teile präzise für nachfolgende Arbeitsgänge halten.
- Handhabung empfindlicher Teile: Konstruktion von Weichbacken-Greifern oder Nachgiebigen Mechanismen, die direkt in die Metallstruktur integriert sind, um empfindliche Gegenstände wie Elektronik oder lackierte Oberflächen zu handhaben.
- B2B Fokus: Automobilhersteller und Tier-1-Zulieferer, die nach langlebigen Montagegreifern für die Automobilindustrie, kundenspezifischen EOAT-Lösungenund Robotik-Automatisierungsteile-Händlern suchen, sehen einen erheblichen Wert in AM.
2. Luft- und Raumfahrt & Verteidigung: Dieser Sektor erfordert hohe Präzision, Zuverlässigkeit und umfasst häufig komplexe, hochwertige Komponenten.
- Handhabung empfindlicher Materialien: Greifen empfindlicher Verbundstrukturen, Turbinenschaufeln oder Satellitenkomponenten, ohne Schäden zu verursachen. Die Topologieoptimierung ermöglicht minimale Kontaktbelastung.
- Montage komplexer Strukturen: Positionieren und Halten von Komponenten während komplizierter Montageprozesse für Flugzeugtriebwerke, Rumpfsektionen oder Raketensysteme.
- Wartung, Reparatur und Überholung (MRO): Erstellen spezialisierter Werkzeuge und Greifer für spezifische MRO-Aufgaben, die häufig in kleinen Stückzahlen benötigt werden.
- Hochtemperaturanwendungen: Handhabung von Teilen, die aus Wärmebehandlungsprozessen stammen oder in heißen Umgebungen innerhalb von Motoren oder Fertigungszellen betrieben werden.
- B2B Fokus: Luft- und Raumfahrt-OEMs und MRO-Anbieter suchen nach Lösungen für die Luft- und Raumfahrtfertigung, hochpräzisen Roboterkomponentenund zertifizierten Metall-AM-Dienstleister.
3. Herstellung von Medizinprodukten und Gesundheitswesen: Präzision, Sauberkeit und oft Biokompatibilität sind von größter Bedeutung.
- Handhabung chirurgischer Instrumente: Greifen und Handhaben empfindlicher, komplex geformter chirurgischer Werkzeuge während der Herstellung oder Sterilisationsprozesse. Edelstahl (wie 17-4PH) ist aufgrund seiner Sterilisierbarkeit und Korrosionsbeständigkeit oft geeignet.
- Montage von Medizinprodukten: Präzises Handhaben und Platzieren von Miniaturkomponenten für Geräte wie Implantate, Herzschrittmacher oder Diagnosegeräte.
- Laborautomatisierung: Pick-and-Place-Operationen für Fläschchen, Reagenzgläser und Mikrotiterplatten in Hochdurchsatz-Screening- oder Diagnostiklaboren. Die Anpassung gewährleistet die Kompatibilität mit spezifischem Laborzubehör.
- Prothetik & Orthopädie: Während diese oft auf Polymeren basieren, können bestimmte Strukturkomponenten oder Fertigungshilfen von der Festigkeit von Metall-AM profitieren.
- B2B Fokus: Hersteller von Medizinprodukten und Unternehmen für Laborautomatisierung suchen nach Roboterkomponenten für die Medizin, Präzisionshandhabungslösungenund Lieferanten, die in der Lage sind, strenge Qualitäts- und Sauberkeitsstandards zu erfüllen, möglicherweise einschließlich biokompatibler Materialoptionen falls für den direkten Kontakt erforderlich (obwohl Greifer in der Regel Fertigungshilfen sind).
4. Industrielle Fertigung & Automatisierung: Diese breite Kategorie umfasst verschiedene Anwendungen in der Maschinenbedienung, Verpackung und allgemeinen Materialhandhabung.
- Maschinenbedienung: Be- und Entladen von Teilen aus CNC-Maschinen, Spritzgussmaschinen oder Stanzpressen. Haltbarkeit und Verschleißfestigkeit sind entscheidend.
- Pick-and-Place-Operationen: Hochgeschwindigkeits-Sortierung, -Verpackung und -Palettierung von Waren. Leichte Konstruktionen (AlSi10Mg) sind entscheidend für die Maximierung des Durchsatzes.
- Handhabung von abrasiven oder schweren Gegenständen: Greifen von Gussteilen, Schmiedeteilen oder Rohmaterialien in Gießereien oder in der Primärfertigung. 17-4PH bietet eine ausgezeichnete Verschleißfestigkeit.
- Inspektion und Qualitätskontrolle: Integration von Sensoren oder Bildverarbeitungssystemen direkt in das Greiferdesign für Inline-Qualitätskontrollen.
- B2B Fokus: Systemintegratoren, Maschinenbauer und Fabriken suchen nach Greifern für die industrielle Automatisierung, Hochleistungs-EOAT, kundenspezifischen Greiferherstellernund zuverlässigen Großhandelskomponenten-Lieferanten.
5. Logistik & Lagerhaltung: Der Aufstieg des E-Commerce befeuert die Nachfrage nach automatisierten Lagerlösungen.
- Auftragsabwicklung: Kommissionierung verschiedener Artikel (Kartons, Beutel, unregelmäßig geformte Objekte) in Fulfillment-Centern. Kundenspezifische Greiferfinger, die für verschiedene Produkttypen optimiert sind, sind unerlässlich.
- Sortierung & Vereinzelung: Trennen und Ausrichten von Paketen oder Artikeln auf Fördersystemen.
- Entpalettierung/Palettierung: Handhabung von Kisten oder Produktschichten. Festigkeit und Zuverlässigkeit sind für den Dauerbetrieb entscheidend.
- B2B Fokus: Logistikunternehmen und Anbieter von Lagerautomatisierung suchen nach Greifern für die Lagerautomatisierung, Hochgeschwindigkeits-Sortierlösungenund Komponenten für Roboter-Kommissioniersysteme.
Tabelle: Industrieanwendungen und Greiferanforderungen
Industrie | Gemeinsame Anwendungen | Wichtige Greiferanforderungen | Potenzielle Materialien |
---|---|---|---|
Automobilindustrie | Komponentenhandhabung, Montage, Vorrichtung | Hohe Festigkeit, Haltbarkeit, kundenspezifische Formen, Temperaturbeständigkeit | 17-4PH, Werkzeugstähle |
Luft- und Raumfahrt/Verteidigung | Handhabung empfindlicher Teile, komplexe Montage, MRO | Hohe Präzision, geringes Gewicht, Zuverlässigkeit, kundenspezifische Geometrie | AlSi10Mg, Ti6Al4V |
Medizin/Gesundheitswesen | Instrumentenhandhabung, Gerätebaugruppe, Laborautomatisierung | Präzision, Sauberkeit, Sterilisierbarkeit, kundenspezifische Passform | 17-4PH, Ti6Al4V |
Industrielle Fertigung | Maschinenbedienung, Pick & Place, Schwerlasthandhabung | Haltbarkeit, Verschleißfestigkeit, Geschwindigkeit (geringes Gewicht), kundenspezifische Backen | 17-4PH, AlSi10Mg |
Logistik/Lager | Kommissionierung, Sortierung, Palettierung | Geschwindigkeit (geringes Gewicht), Vielseitigkeit, Zuverlässigkeit, kundenspezifische Finger | AlSi10Mg, 17-4PH |
In Blätter exportieren
Die Fähigkeit, zu nutzen, 3D-Metalldruckdienste ermöglicht es Unternehmen in diesen Sektoren, über Standard-Greiferlösungen hinauszugehen und EOAT zu entwickeln, die perfekt auf ihre spezifischen Bedürfnisse zugeschnitten sind, was zu erheblichen Verbesserungen in Bezug auf Produktivität, Zuverlässigkeit und allgemeine Automatisierungseffektivität führt.
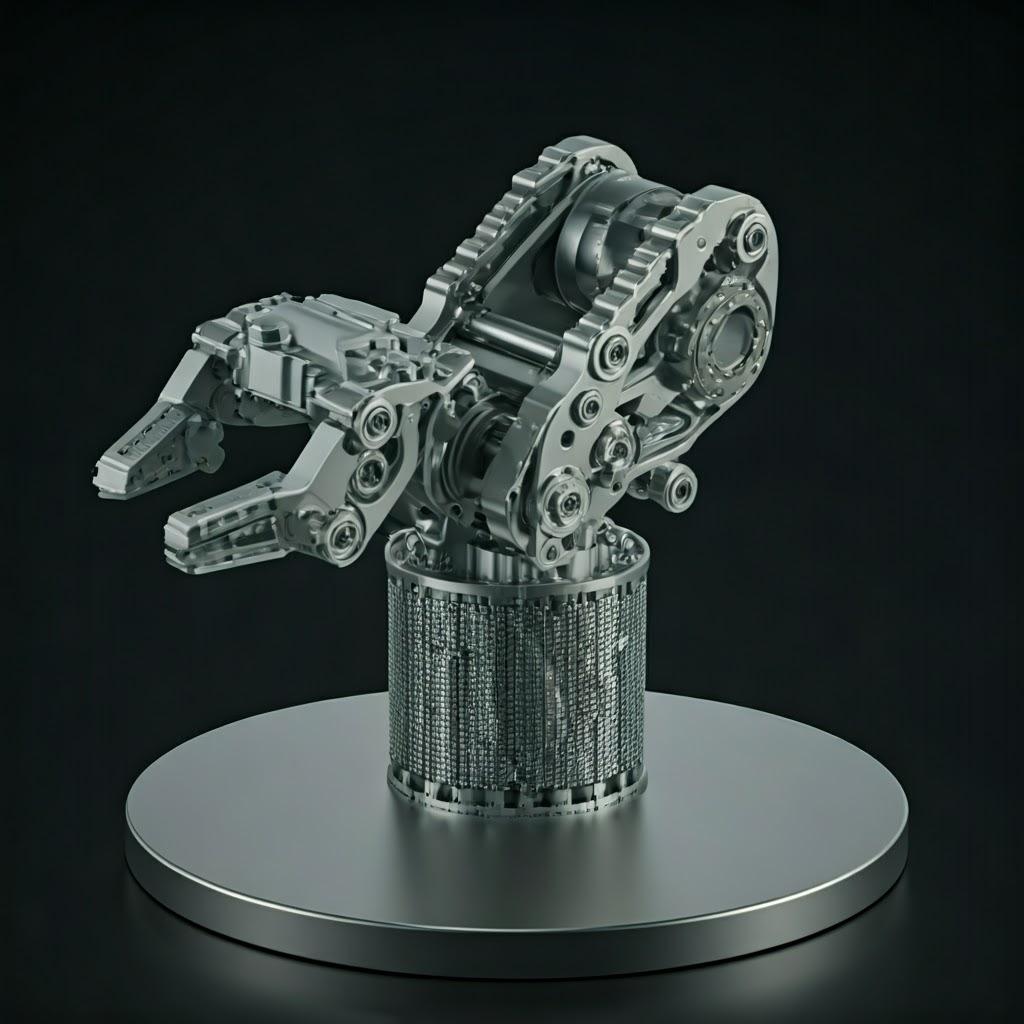
Warum Metall-3D-Druck für Robotergreifer verwenden? Vorteile gegenüber der traditionellen Fertigung
Während traditionelle Fertigungsmethoden wie CNC-Bearbeitung, Gießen und sogar Spritzguss (für Polymergreifer) der Robotikindustrie seit Jahrzehnten dienen, bietet die additive Metallfertigung eine überzeugende Reihe von Vorteilen, die speziell für die Konstruktion und Herstellung von Hochleistungs-Robotergreifern von Vorteil sind. Die Wahl von AM ist nicht nur die Einführung einer neuen Technologie, sondern auch die Erschließung von Fähigkeiten, die die Einschränkungen älterer Methoden direkt angehen und zu überlegenen End-of-Arm-Tooling (EOAT) führen. Ingenieure und Einkaufsmanager, die Greiferfertigungsoptionen evaluieren, müssen diese wesentlichen Vorteile berücksichtigen:
1. Unerreichte Gestaltungsfreiheit und Komplexität:
- Traditionell: Die CNC-Bearbeitung ist subtraktiv und beginnt mit einem Block und entfernt Material. Dies schränkt die erreichbaren Geometrien ein, insbesondere interne Merkmale, Hinterschneidungen und komplexe Kurven. Der Werkzeugzugang ist eine große Einschränkung. Das Gießen erfordert Formen, deren Erstellung und Änderung teuer und zeitaufwändig ist, was die Designiterationen und die Komplexität einschränkt.
- Metall-AM: Baut Teile Schicht für Schicht auf und ermöglicht so nahezu unbegrenzte geometrische Freiheit. Dies ermöglicht:
- Topologie-Optimierung: Algorithmen bestimmen die effizienteste Materialverteilung, um die Lastanforderungen zu erfüllen, was zu organischen, skelettartigen Strukturen führt, die unglaublich stark und dennoch leicht sind.
- Interne Kanäle: Komplexe Kühl-, Pneumatik- oder Vakuumkanäle können ohne sekundäres Bohren oder Montieren direkt in den Greifkörper integriert werden, wodurch die Leistung verbessert und die Teileanzahl reduziert wird. Denken Sie an konforme Kühlung für Hochtemperaturanwendungen oder integrierte Vakuumleitungen für Pick-and-Place.
- Gitterförmige Strukturen: Interne Gitter können das Gewicht weiter reduzieren und gleichzeitig die strukturelle Integrität erhalten oder bestimmte Dämpfungseigenschaften einführen.
- Konsolidierte Designs: Mehrere Teile einer traditionellen Greiferbaugruppe (Finger, Halterungen, Aktuatorhalterungen) können oft als eine einzige, komplexe Komponente neu gestaltet und gedruckt werden, wodurch die Montage vereinfacht und potenzielle Fehlerquellen reduziert werden.
2. Überlegene Leichtbau-Fähigkeiten:
- Traditionell: Das Erreichen einer erheblichen Gewichtsreduzierung erfordert oft eine aufwändige Bearbeitung (was die Kosten und den Abfall erhöht) oder den Wechsel zu schwächeren Materialien wie Kunststoffen oder Standard-Aluminiumqualitäten, wodurch die Festigkeit oder Haltbarkeit beeinträchtigt wird.
- Metall-AM: Ermöglicht aggressiver Leichtbau ohne Leistungseinbußen. Durch die Kombination von Topologieoptimierung mit hochfesten Materialien (wie optimiertem AlSi10Mg oder sogar Titanlegierungen, die von Lieferanten wie Met3dp angeboten werden) können Greifer deutlich leichter als ihre bearbeiteten Stahl- oder Standard-Aluminium-Pendants hergestellt werden.
- Nutzen: Leichtere EOAT ermöglichen es Robotern, sich schneller zu bewegen (was den Durchsatz erhöht), den Verschleiß an den Robotergelenken zu reduzieren, potenziell den Einsatz kleinerer/billigerer Roboter für dieselbe Aufgabe zu ermöglichen und den Energieverbrauch zu senken.
3. Schnelles Prototyping & Anpassung:
- Traditionell: Das Erstellen von Prototypen durch Bearbeitung kann langsam und kostspielig sein, insbesondere für komplexe Designs. Die Anpassung erfordert oft eine erhebliche Neuprogrammierung oder neue Vorrichtungen. Prototypen aus Guss beinhalten die Erstellung teurer Formen, was die Iteration unpraktisch macht.
- Metall-AM: Übertrifft sich bei der wirtschaftlichen Herstellung von Einzelstücken und Kleinserien. Designs können digital modifiziert und schnell neu gedruckt werden, was eine schnelle Iteration und das Testen verschiedener Greiferkonfigurationen ermöglicht. Dies ist ideal für:
- Anwendungsspezifische Greifer: Entwicklung einzigartiger Greifer, die auf die Handhabung eines neu eingeführten Produkts oder einer besonders anspruchsvollen Teilegeometrie zugeschnitten sind.
- Schnelle Entwicklungszyklen: Schnelles Testen von Konzepten und Verfeinern von Designs basierend auf der realen Leistung.
- Produktion von Kleinserien: Wirtschaftliche Herstellung spezialisierter Greifer, die nur in kleinen Mengen benötigt werden.
4. Zugriff auf Hochleistungsmaterialien & Optimierung:
- Traditionell: Die Materialauswahl wird oft durch die Bearbeitbarkeit oder Gießbarkeit bestimmt. Während starke Materialien verfügbar sind, kann es schwierig sein, deren Verwendung innerhalb geometrischer Einschränkungen zu optimieren.
- Metall-AM: Bietet Zugang zu einer wachsenden Palette von Hochleistungs-Metallpulvern, die speziell für AM-Verfahren wie SEBM oder Laser Powder Bed Fusion (LPBF) optimiert wurden. Anbieter wie Met3dp sind auf Materialien wie 17-4PH-Edelstahl für hohe Festigkeit und Härte und AlSi10Mg-Aluminium für ein ausgezeichnetes Verhältnis von Festigkeit zu Gewicht spezialisiert. Darüber hinaus ermöglicht AM die präzise Platzierung dieser Materialien genau dort, wo sie benötigt werden, wodurch die Leistungseffizienz maximiert wird. Erforschen Sie verschiedene Druckverfahren um zu verstehen, wie Materialeigenschaften erreicht werden können.
5. Reduzierte Vorlaufzeiten & Werkzeugkosten:
- Traditionell: Komplexe bearbeitete Teile erfordern umfangreiche Programmierung, Einrichtung und Bearbeitungszeit. Das Gießen beinhaltet erhebliche Vorabinvestitionen und lange Vorlaufzeiten für die Formherstellung.
- Metall-AM: Eliminiert die Notwendigkeit für traditionelle Werkzeuge (Formen, Vorrichtungen, Vorrichtungen). Sobald das Design fertiggestellt ist, kann der Druck oft relativ schnell beginnen. Während die Druckzeiten selbst erheblich sein können, kann die Gesamtvorlaufzeit von der Designfertigstellung bis zum fertigen Teil (einschließlich Nachbearbeitung) erheblich kürzer sein, insbesondere bei komplexen oder Kleinserienkomponenten. Dies beschleunigt den Einsatz und reduziert Ausfallzeiten.
Tabelle
Merkmal | Additive Fertigung von Metall (AM) | CNC-Bearbeitung (Subtraktiv) | Gießen (Formen) |
---|---|---|---|
Entwurfskomplexität | Sehr hoch (Interne Kanäle, Gitterstrukturen, organisch) | Mäßig (begrenzt durch den Zugang zu Werkzeugen) | Mittel (begrenzt durch Formdesign) |
Gewichtsreduzierung | Hervorragend (Topologieoptimierung, Netze) | Gut (Erfordert umfangreiche Bearbeitung) | Ausreichend (Begrenzt durch Gussbeschränkungen) |
Personalisierung | Ausgezeichnet (Wirtschaftlich für Einzelanfertigungen/Kleinserien) | Ausreichend (Erfordert Neuprogrammierung/Vorrichtungen) | Schlecht (Erfordert neue/modifizierte Formen) |
Prototyping-Geschwindigkeit | Schnell (Direkte digitale Fertigung) | Mäßig bis langsam | Sehr langsam (Erfordert Formherstellung) |
Material-Optionen | Wachsendes Angebot an AM-optimierten Pulvern (z. B. 17-4PH, AlSi10Mg) | Große Auswahl an bearbeitbarem Material | Breite Palette an gießbaren Legierungen |
Teil Konsolidierung | Ausgezeichnet (Integrieren Sie mehrere Funktionen) | Begrenzt | Begrenzt |
Werkzeugkosten | Keine (Direkte Fertigung) | Gering (Vorrichtung) | Sehr hoch (Formen) |
Vorlaufzeit (komplex) | Oft schneller (Keine Werkzeugvorlaufzeit) | Kann lang sein (Programmierung, Bearbeitung) | Sehr lang (Formherstellung + Gießen) |
Ideales Volumen | Niedrig bis mittel, hohe Komplexität, kundenspezifisch | Mittel bis hoch, mäßige Komplexität | Hohes Volumen, etablierte Designs |
B2B-Lieferantenfokus | Hersteller kundenspezifischer Greifer, AM-Dienstleister | Maschinenbauunternehmen, Komponentenlieferant | Gießereien, Gießereizulieferer |
In Blätter exportieren
Zusammenfassend lässt sich sagen, dass traditionelle Methoden zwar für die einfache, großvolumige Greiferherstellung geeignet sind, 3D-Druck von Metall bietet transformative Vorteile für Anwendungen, die hohe Leistung, komplexe Geometrien, Leichtbau und Individualisierung erfordern. Für Unternehmen, die einen Wettbewerbsvorteil durch optimierte Roboterautomatisierung suchen, ist die Zusammenarbeit mit einem sachkundigen Metall-AM-Dienstleister zunehmend zur strategischen Wahl.
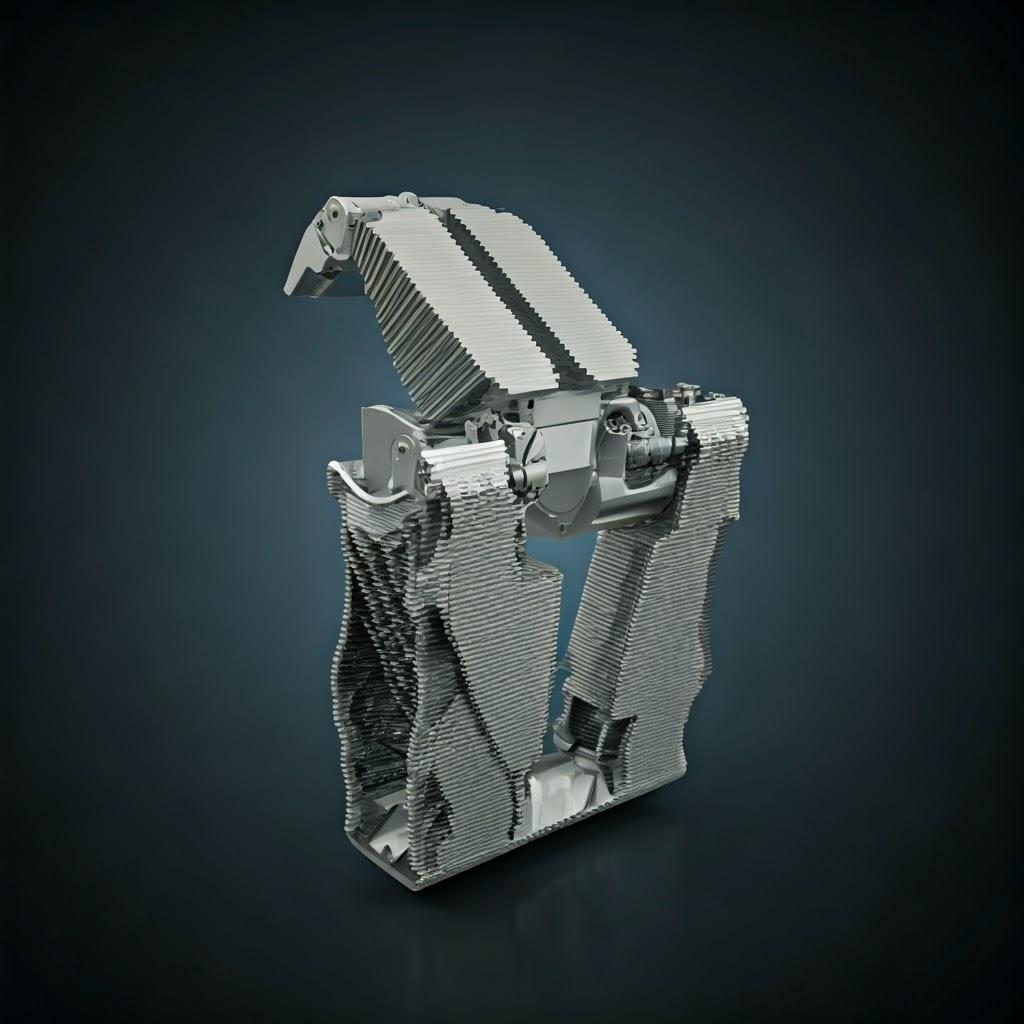
Empfohlene Materialien für 3D-gedruckte Greifer: 17-4PH und AlSi10Mg im Vergleich
Die Auswahl des richtigen Materials ist für den Erfolg jedes 3D-gedruckten Robotergreifers von entscheidender Bedeutung. Das Material bestimmt die Festigkeit, Haltbarkeit, das Gewicht, die Beständigkeit gegen Umwelteinflüsse und letztendlich die Eignung des Greifers für die vorgesehene Anwendung. Während die additive Metallfertigung eine Vielzahl von Legierungen unterstützt, zeichnen sich zwei Materialien als besonders gut geeignet für ein breites Spektrum an Robotergreifaufgaben aus: 17-4PH-Edelstahl und AlSi10Mg-Aluminiumlegierung. Führende Lieferanten von hochwertige Metallpulver, wie z. B. Met3dp, verwenden fortschrittliche Produktionstechniken wie Gasverdüsung und PREP-Technologie, um sicherzustellen, dass diese Pulver die anspruchsvollen Spezifikationen für Sphärizität, Fließfähigkeit und Reinheit erfüllen, die für optimale 3D-Druckergebnisse erforderlich sind.
Lassen Sie uns die Eigenschaften und typischen Anwendungsfälle für diese beiden bewährten Materialien im Zusammenhang mit 3D-gedruckten Greifern untersuchen:
1. 17-4PH-Edelstahl:
- Überblick: 17-4 Precipitation Hardening (PH)-Edelstahl ist eine martensitische Chrom-Nickel-Kupfer-Legierung, die für ihre ausgezeichnete Kombination aus hoher Festigkeit, Härte, guter Korrosionsbeständigkeit und guten mechanischen Eigenschaften bei Temperaturen bis zu 315 °C (600 °F) bekannt ist. Sein Hauptvorteil liegt in seiner Fähigkeit, durch eine einfache, niedertemperaturige Wärmebehandlung (Aushärten durch Ausscheidung oder Alterung) gehärtet zu werden.
- Haupteigenschaften für Greifer:
- Hohe Festigkeit und Härte: Nach der Wärmebehandlung (z. B. Zustand H900) erreicht 17-4PH eine sehr hohe Zug- und Streckgrenze, wodurch es sich für das Heben schwerer Lasten, hohe Klemmkräfte und die Beständigkeit gegen Verformung unter Last eignet. Seine Härte bietet eine ausgezeichnete Verschleißfestigkeit gegen abrasive Materialien oder wiederholten Kontakt.
- Gute Korrosionsbeständigkeit: Im Allgemeinen vergleichbar mit 304-Edelstahl, bietet eine gute Beständigkeit in vielen industriellen Umgebungen, obwohl es in chloridreichen Umgebungen weniger beständig ist als 316L. Ausreichend für die meisten allgemeinen Automatisierungsaufgaben.
- Wärmebehandelbar: Ermöglicht die Anpassung der mechanischen Eigenschaften nach dem Drucken. Verschiedene Alterungsbehandlungen (H900, H1025, H1075, H1150) erzielen unterschiedliche Gleichgewichte zwischen Festigkeit, Zähigkeit und Duktilität.
- Gute Bearbeitbarkeit (im geglühten Zustand): Wenn Nachbearbeitungsvorgänge für kritische Toleranzen oder Merkmale erforderlich sind, ist 17-4PH vor der endgültigen Alterung relativ gut bearbeitbar.
- Schweißeignung: Kann geschweißt werden, obwohl Vorsichtsmaßnahmen und eine Wärmebehandlung nach dem Schweißen oft erforderlich sind.
- Warum 17-4PH für Greifer verwenden?
- Haltbarkeit und Langlebigkeit: Ideal für Greifer, die hohen Belastungen, Stößen oder Abrieb ausgesetzt sind. Geeignet für die Handhabung schwerer Metallteile, Gussteile, Schmiedeteile oder Werkzeuge.
- Raue Umgebungen: Funktioniert gut in mäßig korrosiven oder leicht erhöhten Temperaturumgebungen.
- Hohe Klemmkräfte: Seine Festigkeit stellt sicher, dass die Greiferstruktur unter hohen pneumatischen oder mechanischen Betätigungskräften nicht nachgibt.
- Strukturelle Steifigkeit: Behält die Form und Präzision unter anspruchsvollen Belastungen bei, was für genaue Platzierungsaufgaben entscheidend ist.
- Typische Greiferanwendungen: Schwerlast-Maschinenbedienung, Handhabung von Rohmetallmaterial, Manipulation von Automobilantriebsstrangkomponenten, Vorrichtungsanwendungen, die eine hohe Steifigkeit erfordern, Greifer für abrasive Umgebungen.
- Erwägungen: Es ist relativ dicht (ca. 7,8 g/cm³), was es weniger geeignet für Anwendungen macht, bei denen die Minimierung des EOAT-Gewichts oberste Priorität hat (z. B. ultraschnelles Pick-and-Place).
2. AlSi10Mg-Aluminiumlegierung:
- Überblick: AlSi10Mg ist eine Gussaluminiumlegierung, die für ihr gutes Festigkeits-Gewichts-Verhältnis, ihre ausgezeichnete Wärmeleitfähigkeit, ihre gute Korrosionsbeständigkeit und ihre Eignung zur Herstellung komplexer Geometrien bekannt ist. In der additiven Fertigung entstehen daraus Teile mit mechanischen Eigenschaften, die oft mit ihren Gussteilen vergleichbar oder diesen überlegen sind.
- Haupteigenschaften für Greifer:
- Leichtes Gewicht: Mit einer Dichte von ca. 2,67 g/cm³ ist es fast dreimal leichter als 17-4PH-Stahl. Dies ist sein wichtigster Vorteil für viele Roboteranwendungen.
- Gute Festigkeit und Härte (für Aluminium): Obwohl nicht so stark wie wärmebehandeltes 17-4PH, bietet AM AlSi10Mg eine respektable Festigkeit und Härte, die für viele Handhabungsaufgaben ausreicht, insbesondere in Kombination mit optimierten Designs. Es kann auch wärmebehandelt werden (Zustand T6), um die Festigkeit zu verbessern.
- Ausgezeichnete Wärmeleitfähigkeit: Nützlich, wenn der Greifer Wärme ableiten muss, entweder vom gehandhabten Teil oder von integrierter Elektronik, oder wenn konforme Kühlkanäle integriert sind.
- Gute Korrosionsbeständigkeit: Widersteht atmosphärischer Korrosion gut.
- Komplexe Geometrien: Das Material fließt und verfestigt sich während des Druckens gut und eignet sich für komplizierte Designs, dünne Wände und Gitterstrukturen, die häufig zur Gewichtsreduzierung verwendet werden.
- Warum AlSi10Mg für Greifer verwenden?
- Minimierung des EOAT-Gewichts: Entscheidend für Hochgeschwindigkeitsroboter (Pick-and-Place, Verpackung, Montage), bei denen die Trägheit minimiert werden muss, um schnellere Beschleunigungen/Verzögerungen und kürzere Zykluszeiten zu erzielen. Ermöglicht kleinere, kostengünstigere Roboter.
- Komplexe, leichte Designs: Ideal für die Nutzung von Topologieoptimierung und Gitterstrukturen zur Erstellung hocheffizienter Greifkörper.
- Anwendungen mit moderaten Lasten: Geeignet für die Handhabung von Kunststoffen, Elektronik, Konsumgütern, Lebensmitteln (mit entsprechender Oberflächenbehandlung/Beschichtung) und vielen Automobilkomponenten, bei denen extreme Festigkeit nicht der Haupttreiber ist.
- Wärmemanagement: Anwendungen, die Wärmeableitung erfordern.
- Typische Greiferanwendungen: Hochgeschwindigkeits-Pick-and-Place, Verpackung und Palettierung, Handhabung elektronischer Komponenten, Montage von Leichtbauteilen, Greifer für kollaborative Roboter (Cobots), bei denen das Gewicht für die Sicherheit entscheidend ist, allgemeine Materialhandhabung, bei der keine Stahlfestigkeit erforderlich ist.
- Erwägungen: Geringere absolute Festigkeit, Härte und Verschleißfestigkeit im Vergleich zu 17-4PH. Nicht geeignet für Anwendungen mit sehr hohen Temperaturen oder extrem abrasiven Umgebungen ohne Schutzbeschichtungen.
Tabelle: Vergleich von 17-4PH und AlSi10Mg für 3D-gedruckte Greifer
Eigentum | 17-4PH-Edelstahl (typisch H900) | AlSi10Mg-Aluminiumlegierung (typisch T6) | Bedeutung für Greifer |
---|---|---|---|
Dichte | ~7,8 g/cm³ | ~2,67 g/cm³ | Gewicht: AlSi10Mg ermöglicht viel leichtere EOAT für Geschwindigkeit. |
Endgültige Zugfestigkeit | ~1300-1400 MPa | ~300-350 MPa | Tragfähigkeit: 17-4PH bewältigt deutlich höhere Lasten. |
Streckgrenze | ~1150-1250 MPa | ~230-280 MPa | Beständigkeit gegen dauerhafte Biegung: 17-4PH ist viel höher. |
Härte (HRC/HRB) | ~40-45 HRC | ~60-70 HRB (~100-120 HV) | Abnutzungswiderstand: 17-4PH ist deutlich härter, haltbarer. |
Korrosionsbeständigkeit | Gut | Gut | Beide sind für viele industrielle Umgebungen geeignet. |
Max. Betriebstemperatur | ~315 °C (600 °F) | ~150 °C (300 °F) | Hochtemperatur-Anwendungen: 17-4PH hat eine höhere Temperaturgrenze. |
Wärmeleitfähigkeit | Niedrig (~16 W/m·K) | Hoch (~130-150 W/m·K) | Wärmeableitung: AlSi10Mg ist viel besser. |
Primärer Vorteil | Hohe Festigkeit, Härte, Haltbarkeit | Leichtbau, komplexe Geometrien | Steuert die Eignung für die Anwendung. |
Ideal für | Schwere Lasten, hoher Verschleiß, robuste Aufgaben | Geschwindigkeit, geringe Trägheit, komplizierte Designs | Passen Sie das Material an den primären Leistungsbedarf an. |
In Blätter exportieren
Auswahl zwischen 17-4PH und AlSi10Mg:
Die Auswahl hängt von einem klaren Verständnis der primären Anforderungen der Anwendung ab:
- Wenn maximale Festigkeit, Haltbarkeit und Verschleißfestigkeit entscheidend sind (Handhabung schwerer, abrasiver Teile, hohe Klemmkraft): Wählen Sie 17-4PH.
- Wenn minimales Gewicht und maximale Geschwindigkeit Priorität haben (Hochgeschwindigkeits-Pick-and-Place, Reduzierung der Roboterlast): Wählen Sie AlSi10Mg.
- Wenn ein Gleichgewicht erforderlich ist: Analysieren Sie die spezifischen Lasten und Umgebungsfaktoren. Manchmal kann ein gut konstruierter AlSi10Mg-Greifer unter Verwendung der Topologieoptimierung moderate Festigkeitsanforderungen erfüllen und gleichzeitig erhebliche Gewichtseinsparungen erzielen.
Die Zusammenarbeit mit einem erfahrenen Metall-AM-Dienstleister wie Met3dp, das über fundierte Kenntnisse der Materialwissenschaft und der additiven Fertigungsprozesse verfügt, ist von unschätzbarem Wert. Sie können Hinweise zur Materialauswahl, Designoptimierung und zur geeigneten Nachbearbeitung (wie z. B. Wärmebehandlung) geben, um sicherzustellen, dass der endgültige 3D-gedruckte Greifer eine optimale Leistung und Zuverlässigkeit für Ihre spezifische Roboteranwendung liefert. Ihr Engagement für die Herstellung von branchenführenden Metallpulvern bildet die Grundlage für die Erstellung dieser Hochleistungskomponenten.
Konstruktionsüberlegungen für additiv gefertigte Robotergreifer
Der Übergang von traditionellen Fertigungsmethoden zur additiven Metallfertigung (AM) für Robotergreifer bedeutet nicht nur den Austausch von Produktionstechniken; er erfordert einen grundlegenden Wandel im Design-Denken. Um die Leistungsfähigkeit von AM voll auszuschöpfen und wirklich optimierte, leistungsstarke Greifer zu erstellen, müssen Ingenieure Design für additive Fertigung (DfAM) Prinzipien anwenden. Die bloße Nachbildung eines für die CNC-Bearbeitung vorgesehenen Designs führt häufig dazu, dass die einzigartigen Stärken von AM nicht genutzt werden, und kann sogar zu suboptimalen Ergebnissen oder höheren Kosten führen. Erfolgreiches AM-Greiferdesign konzentriert sich auf Funktion, Effizienz und Herstellbarkeit innerhalb des Schicht-für-Schicht-Paradigmas. Die frühzeitige Zusammenarbeit mit AM-Experten, wie z. B. dem Team von Met3dp, kann unschätzbare Hinweise bei der Berücksichtigung dieser Aspekte und der Maximierung des Potenzials der Technologie liefern.
Hier sind wichtige Konstruktionsüberlegungen für die Erstellung effektiver additiv gefertigter Robotergreifer:
1. Umfassen Sie die Topologie-Optimierung:
- Was es ist: Die Topologieoptimierung ist eine computergestützte Konstruktionstechnik, bei der Softwarealgorithmen die effizienteste Materialanordnung innerhalb eines definierten Konstruktionsraums bestimmen, die bestimmten Lasten, Einschränkungen und Leistungszielen unterliegt (z. B. Gewicht minimieren, Steifigkeit maximieren).
- Warum es für Greifer wichtig ist: Greifer benötigen oft hohe Steifigkeit und Festigkeit, profitieren aber auch immens davon, leichtgewichtig zu sein. Die Topologieoptimierung geht dies direkt an, indem sie Material aus nicht-kritischen Bereichen entfernt, was zu organischen, knochenartigen Strukturen führt, die unglaublich effizient sind.
- Umsetzung:
- Definieren Sie den Planungsraum (maximal zulässiges Volumen).
- Spezifizieren Sie „Keep-in“-Zonen (z. B. Montagepunkte, Fingerkontaktflächen).
- Erwartete Lasten anwenden (Klemmkraft, Nutzlastgewicht, Beschleunigungskräfte).
- Beschränkungen definieren (Materialeigenschaften, Fertigungsbeschränkungen).
- Das Optimierungsziel festlegen (z. B. Masse für eine bestimmte Steifigkeit minimieren).
- Die Software generiert eine optimierte, oft komplexe Geometrie, die für AM nachfolgend geglättet und verfeinert werden muss.
- Nutzen: Deutliche Gewichtsreduzierungen (oft 30-60 % oder mehr im Vergleich zu konventionell konstruierten Teilen) bei gleichzeitiger Beibehaltung oder Verbesserung der mechanischen Leistung.
2. Gitterstrukturen nutzen:
- Was sie sind: Gitter sind sich wiederholende Netzwerke aus miteinander verbundenen Streben oder Oberflächen (wie TPMS – Triply Periodic Minimal Surfaces), die zur Füllung interner Volumina verwendet werden.
- Warum sie verwenden:
- Weitere Gewichtsreduzierung: Kann feste Innenabschnitte ersetzen, die durch Topologieoptimierung identifiziert wurden, oder allgemeine Hohlräume füllen.
- Einstellbare Eigenschaften: Verschiedene Gittertypen und -dichten bieten unterschiedliche Steifigkeiten, Festigkeiten, Energieabsorption und sogar Schwingungsdämpfungseigenschaften.
- Verbesserte Funktionalität: Kann den Flüssigkeitsfluss (für Kühlung/Pneumatik) oder die Wärmeableitung erleichtern.
- Erwägungen: Stellen Sie sicher, dass die Streben-Durchmesser oder Wandstärken innerhalb der druckbaren Grenzen des gewählten AM-Verfahrens und -Materials liegen. Berücksichtigen Sie den Zugang zur Pulverentfernung aus geschlossenen Gitterzellen.
3. Maximierung der Teilekonsolidierung:
- Das Ziel: Baugruppen aus mehreren traditionell gefertigten Komponenten in ein einziges, integriertes AM-Teil umgestalten.
- Greiferbeispiele:
- Montagehalterungen, Sensorhalter oder pneumatische Anschlüsse direkt in den Greifkörper integrieren.
- Greiferfinger und die Basis in einer Komponente kombinieren.
- Multifunktionale Greifer erstellen (z. B. Greifen + Vakuumsaugen) in einem einzigen Druck.
- Vorteile:
- Reduzierte Teileanzahl führt zu einfacherer Inventur und Montage.
- Eliminiert Verbindungen und Befestigungselemente, die potenzielle Fehlerquellen oder Ursachen für Fehlausrichtungen sein können.
- Führt oft zu einer leichteren, steiferen Gesamtbaugruppe.
- Ermöglicht kompaktere Designs.
4. Konstruktion für interne Kanäle (Kühlung, Pneumatik, Vakuum):
- AM Vorteil: Die Fähigkeit, komplexe, konforme interne Kanäle zu erstellen, die den Konturen des Greifers folgen, ist ein großer Vorteil gegenüber dem Bohren gerader Löcher.
- Anwendungen:
- Konforme Kühlung: Kanäle, die den Fingeroberflächen oder wärmeerzeugenden Bereichen für eine effiziente Temperaturkontrolle beim Umgang mit heißen Teilen oder der Integration von Elektronik eng folgen.
- Pneumatische Betätigung: Integrierte Luftleitungen für die Fingerbetätigung, wodurch externe Schläuche und potenzielle Leckstellen reduziert werden.
- Vakuumgreifen: Interne Vakuumkanäle, die direkt zu Saugern oder porösen Oberflächen führen, die in die Greiferfläche integriert sind.
- Designtipps:
- Stellen Sie sicher, dass die Kanal-Durchmesser groß genug für einen effektiven Durchfluss und eine effektive Reinigung sind (berücksichtigen Sie die minimal druckbaren Merkmalsgrößen).
- Konstruieren Sie Kanäle nach Möglichkeit mit selbsttragenden Winkeln (typischerweise > 45° zur Horizontalen), um interne Stützen zu minimieren.
- Planen Sie Zugänge zur Pulverentfernung ein.
- Berücksichtigen Sie die Anforderungen an die Oberflächenbeschaffenheit innerhalb der Kanäle, was möglicherweise eine Nachbearbeitung wie Abrasivstrahlen oder Elektropolieren erfordert.
5. Minimierung und Optimierung von Stützstrukturen:
- Warum benötigt: Metall-AM-Verfahren wie LPBF und SEBM erfordern Stützstrukturen, um das Teil an der Bauplatte zu verankern, überhängende Merkmale (typischerweise Winkel < 45° zur Horizontalen) zu unterstützen und thermische Spannungen zu bewältigen.
- Designauswirkungen: Stützen verbrauchen zusätzliches Material, erhöhen die Druckzeit, erfordern Aufwand für die Entfernung (Nachbearbeitung) und können die Teileoberfläche dort beschädigen, wo sie verbunden sind.
- Strategien:
- Orientierung: Wählen Sie die Bauausrichtung sorgfältig aus, um das Ausmaß von Überhängen und nach unten gerichteten Oberflächen zu minimieren. Analysieren Sie Kompromisse (z. B. Oberflächenbeschaffenheit vs. Stützvolumen).
- Feature-Design: Selbsttragende Winkel (> 45°) einbauen, Fasen oder Rundungen anstelle von scharfen horizontalen Überhängen verwenden, wo immer möglich, und Merkmale wie rauten- oder tropfenförmige Löcher anstelle von rein horizontalen Löchern konstruieren.
- Optimierung der Unterstützung: Verwenden Sie spezielle Software, um Stützen zu generieren, die dort stark sind, wo sie benötigt werden, aber leichter zu entfernen sind (z. B. Verwendung von konischen Kontaktpunkten, perforierten Strukturen). Konstruieren Sie einen Zugang für Werkzeuge zur Entfernung.
6. Einhaltung von Wandstärke- und Merkmalsgrößenbeschränkungen:
- Mindestanforderungen: Jede AM-Verfahrens-/Materialkombination hat minimale druckbare Wandstärken und Merkmalsgrößen (z. B. kleine Stifte, dünne Wände). Wenn Sie unter diesen Grenzen konstruieren, kann dies zu Druckfehlern oder spröden Teilen führen. Wenden Sie sich an Ihren AM-Anbieter, um spezifische Richtlinien zu erhalten.
- Maxima: Sehr dicke Abschnitte können Restspannungen ansammeln und potenziell zu Verformungen oder Rissen führen. Erwägen Sie das Aushöhlen oder die Verwendung von Gitterstrukturen für sperrige Abschnitte.
- Einheitlichkeit: Streben Sie nach Möglichkeit relativ gleichmäßige Wandstärken an, um ein gleichmäßiges Erhitzen und Abkühlen während des Baus zu fördern und Spannungen zu reduzieren.
7. Berücksichtigung materialspezifischer Konstruktionsregeln:
- 17-4PH: Da Konstruktionen sehr stark, aber dicht sind, konzentrieren sie sich oft stark auf die Topologieoptimierung und die Teilekonsolidierung, um das Gewicht zu bewältigen und gleichzeitig ihre Festigkeit für tragende Merkmale zu nutzen. Stützstrategien müssen die höhere thermische Masse berücksichtigen.
- AlSi10Mg: Seine geringere Dichte ermöglicht bei Bedarf voluminösere Konstruktionen, aber seine geringere Festigkeit erfordert eine sorgfältige Strukturanalyse und möglicherweise dickere Abschnitte oder eine aufwändigere Optimierung im Vergleich zu Stahl für die gleiche Last. Seine thermischen Eigenschaften beeinflussen auch die Stütz- und Ausrichtungsstrategien.
Tabelle: DfAM-Prinzipien für Greifer
DfAM-Prinzip | Ziel | Schlüsseltechniken | Vorteil für Greifer |
---|---|---|---|
Topologieoptimierung | Maximierung des Steifigkeits-/Festigkeits-Gewichts-Verhältnisses | Softwaregesteuerte Materialentfernung | Leichtere, schnellere, effizientere EOAT |
Gitterförmige Strukturen | Reduzierung des Gewichts, Hinzufügen von Funktionalität | Interne Streben-/Oberflächennetzwerke | Weitere Gewichtsreduzierung, Dämpfung, Wärmemanagement |
Teil Konsolidierung | Reduzierung der Teileanzahl, Vereinfachung der Montage | Integration mehrerer Komponenten in ein AM-Teil | Weniger Fehlerquellen, weniger Montage, kompaktes Design |
Interne Kanäle | Integration des Flüssigkeits-/Luftstroms | Konforme Kühlung, pneumatische/Vakuumkanäle | Verbesserte Temperaturkontrolle, weniger externe Leitungen |
Minimierung der Unterstützung | Reduzierung der Druckzeit, der Kosten, der Nachbearbeitung | Optimierung der Ausrichtung, Gestaltung selbsttragender Merkmale | Einfachere Herstellung, bessere Oberflächenbeschaffenheit |
Feature-Einschränkungen | Gewährleistung der Herstellbarkeit, Integrität | Einhaltung der minimalen/maximalen Wandstärke, Merkmalsgröße | Erfolgreiche Drucke, robuste Teile |
In Blätter exportieren
Durch sorgfältige Anwendung dieser DfAM-Prinzipien können Ingenieure über das bloße Drucken bestehender Greiferkonstruktionen hinausgehen und wirklich innovative, leistungsstarke EOAT-Lösungen entwickeln, die neue Ebenen der Automatisierungseffizienz erschließen. Dieser designorientierte Ansatz, unterstützt durch das Fachwissen von Metall-AM-Lösungsanbietern, ist der Schlüssel zur Realisierung des vollen Potenzials von 3D-gedruckten Robotergreifern.
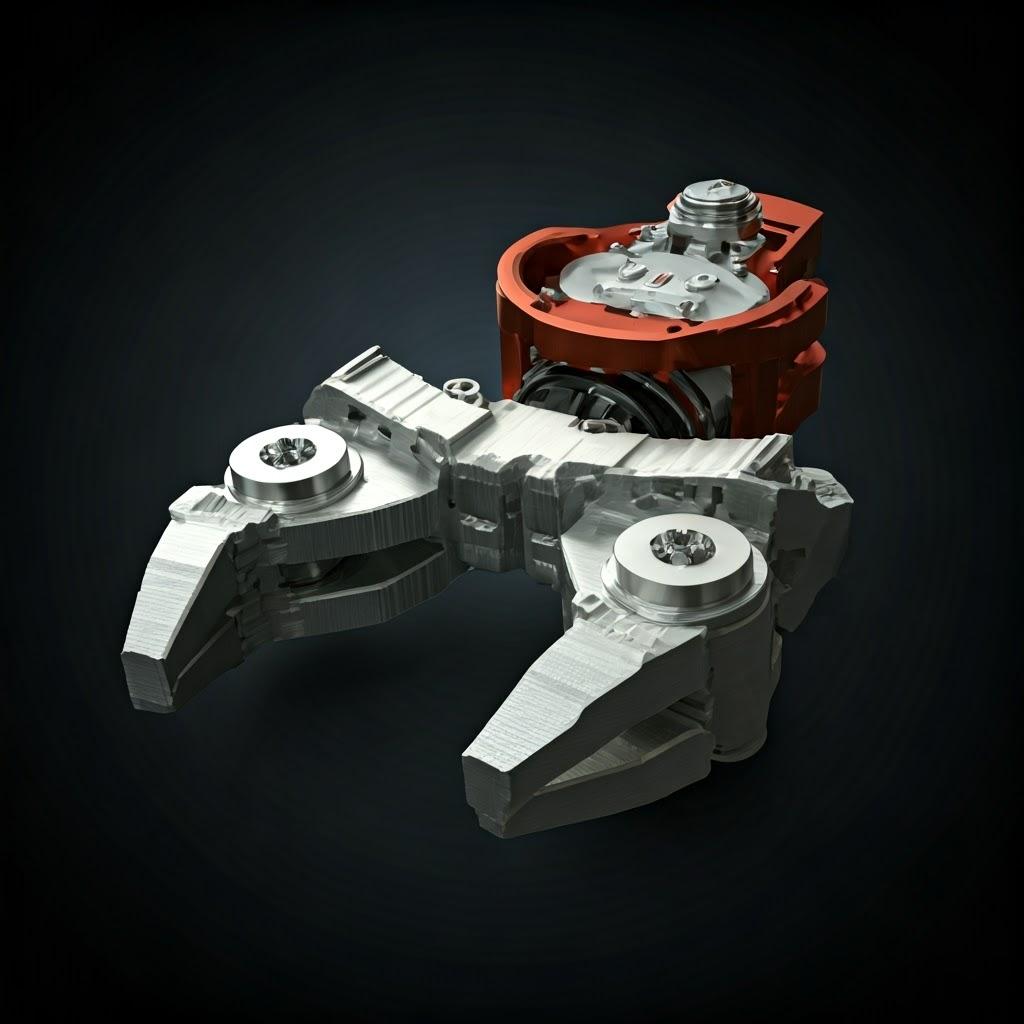
Erzielung von Präzision: Toleranz, Oberflächenbeschaffenheit und Maßgenauigkeit in 3D-gedruckten Greifern
Während die additive Metallfertigung eine beispiellose Designfreiheit bietet, ist es für Ingenieure und Beschaffungsmanager, die 3D-gedruckte Robotergreifer beziehen, unerlässlich, realistische Erwartungen hinsichtlich der erreichbaren Präzision zu haben – einschließlich Maßtoleranzen, Oberflächenbeschaffenheit und Gesamtgenauigkeit. Metall-AM-Teile, insbesondere im ungedruckten Zustand, erreichen im Allgemeinen nicht das gleiche Präzisionsniveau wie Komponenten, die durch hochpräzise CNC-Bearbeitung ohne Sekundäroperationen hergestellt werden. Das Verständnis der typischen Fähigkeiten und der Faktoren, die die Präzision beeinflussen, ermöglicht jedoch ein effektives Design und eine effektive Spezifikation, wodurch sichergestellt wird, dass der endgültige Greifer die funktionalen Anforderungen erfüllt. Unternehmen wie Met3dp betonen die Genauigkeit und Zuverlässigkeit ihrer Drucksysteme, was für das Erzielen konsistenter Ergebnisse, insbesondere bei einsatzkritischen Teilen, von entscheidender Bedeutung ist.
1. Allgemeine Maßtoleranzen:
- Ungedruckter Zustand: Typische Toleranzen für Metallpulverbett-Schmelzverfahren (LPBF, SEBM) liegen oft im Bereich von ±0,1 mm bis ±0,2 mm für kleinere Merkmale (z. B. bis zu 25-50 mm) plus zusätzliche ±0,002 mm/mm bis ±0,005 mm/mm für größere Abmessungen. Dies ist jedoch eine allgemeine Richtlinie und kann je nach Folgendem erheblich variieren:
- AM-Technologie: Verschiedene Maschinen und Verfahren haben inhärente Genauigkeitsgrade.
- Material: Thermische Eigenschaften (Ausdehnung, Schrumpfung) beeinflussen die endgültigen Abmessungen.
- Größe und Geometrie des Teils: Größere Teile und komplexe Geometrien sind anfälliger für Abweichungen.
- Orientierung aufbauen: Die Ausrichtung beeinflusst die thermische Historie und die Wechselwirkungen mit der Stütze.
- Thermische Belastung: Restspannungen können Verformungen und Verzerrungen verursachen.
- Kalibrierung & Prozesskontrolle: Maschinen-Genauigkeit und Prozessparameter-Stabilität sind entscheidend.
- Vergleich mit CNC: Hochpräzise CNC-Bearbeitung kann problemlos Toleranzen von ±0,01 mm bis ±0,05 mm oder sogar enger für kritische Merkmale erreichen.
- Design-Implikation: Identifizieren Sie kritische Merkmale am Greifer (z. B. Montageschnittstellen, präzise Fingerkontaktflächen, Lagerbohrungen), die engere Toleranzen erfordern, als im ungedruckten Zustand erreichbar sind. Diese Merkmale müssen für die Nachbearbeitung geplant werden. Nicht kritische Abmessungen können oft ungedruckte Toleranzen akzeptieren.
2. Maßgenauigkeit & Verformung:
- Genauigkeit vs. Toleranz: Toleranz bezieht sich auf die zulässige Abweichung in einer Abmessung, während Genauigkeit sich darauf bezieht, wie nah die durchschnittliche gemessene Abmessung an der nominalen Designabsicht liegt.
- Verformung & Verzerrung: Die größte Herausforderung für die Genauigkeit in der Metall-AM ist die Verformung, die durch Restwärmespannungen verursacht wird, die während der schichtweisen Erhitzungs- und Abkühlzyklen akkumuliert werden. Dies kann dazu führen, dass sich Teile während des Baus, nach dem Entfernen von der Bauplatte oder nach dem Entfernen der Stütze verformen.
- Strategien zur Schadensbegrenzung:
- Simulation: Verwendung von Prozesssimulationssoftware zur Vorhersage von Verformungen und potenzieller Anwendung von Kompensationsfaktoren auf die Bau-Datei.
- Optimierte Orientierung und Stützen: Strategische Ausrichtung des Teils und Gestaltung effektiver Stützstrukturen zur Bewältigung der Wärme und zur sicheren Verankerung des Teils.
- Prozessparameter: Verwendung validierter Parameter, die für das spezifische Material und die Geometrie optimiert sind.
- Umgebung der Baukammer: Aufrechterhaltung stabiler thermischer Bedingungen (z. B. beheizte Bauplatten, kontrollierte Atmosphäre). Technologien wie SEBM, die bei höheren Temperaturen arbeiten, können manchmal dazu beitragen, Restspannungen für bestimmte Materialien/Geometrien zu reduzieren.
- Stressabbau: Die Durchführung einer Wärmebehandlung zur Spannungsarmglühen nach dem Bau vor dem Entfernen der Teile von der Bauplatte ist entscheidend für die Stabilisierung der Abmessungen.
3. Oberflächenbeschaffenheit (Rauheit):
- Ungedruckte Rauheit (Ra): Die Oberflächenbeschaffenheit von ungedruckten Metall-AM-Teilen ist deutlich rauer als bei bearbeiteten Oberflächen. Typische Ra-Werte variieren stark:
- Seitenwände (vertikal): Oft Ra 6 µm – 15 µm (240 µin – 600 µin). Schichtlinien sind in der Regel sichtbar.
- Nach oben gerichtete Oberflächen (Oberseite): Im Allgemeinen glatter, potenziell Ra 5 µm – 10 µm (200 µin – 400 µin).
- Nach unten gerichtete Oberflächen (Überhänge/Unterstützt): Typischerweise am rauesten, oft Ra 15 µm – 25 µm (600 µin – 1000 µin) oder mehr, aufgrund von Kontaktpunkten der Stützen und der Art der Bildung von Überhängen.
- Faktoren, die Ra beeinflussen: Schichtdicke, Pulverpartikelgröße, Laser-/Strahlparameter, Ausrichtung und Stützstrategie.
- Vergleich mit CNC: Bearbeitete Oberflächen erreichen üblicherweise Ra 0,8 µm – 3,2 µm (32 µin – 125 µin), wobei Polieren deutlich glattere Oberflächen erzielt (Ra < 0,4 µm / 16 µin).
- Auswirkungen auf den Greifer:
- Raue Oberflächen können die Reibung oder den Verschleiß an den gehandhabten Teilen erhöhen.
- Rauheit kann sich auf Dichtflächen auswirken (z. B. O-Ring-Nuten).
- Ästhetik kann für einige Anwendungen inakzeptabel sein.
- Interne Kanäle weisen ebenfalls raue Oberflächen auf, was sich potenziell auf den Fluss auswirkt.
4. Erreichen engerer Toleranzen und glatterer Oberflächen:
- Die Rolle der Nachbearbeitung: Für Merkmale, die eine Präzision erfordern, die über die Möglichkeiten des Drucks hinausgeht, ist die Nachbearbeitung unerlässlich. Dies beinhaltet typischerweise:
- CNC-Bearbeitung: Fräsen, Drehen, Bohren, Gewindeschneiden oder Schleifen bestimmter Merkmale, um enge Toleranzen (±0,01 bis ±0,05 mm) und verbesserte Oberflächengüten (Ra 0,8 – 3,2 µm) zu erzielen. Konstruieren Sie Teile mit ausreichendem Rohteilmaterial (z. B. 0,5 – 1,0 mm) auf Oberflächen, die für die Bearbeitung vorgesehen sind.
- Oberflächenveredelung: Techniken wie Strahlen, Trommeln, Polieren oder Elektropolieren können die allgemeine Oberflächenglätte und Ästhetik erheblich verbessern, obwohl sie die Maßtoleranzen über große Merkmale im Allgemeinen nicht signifikant verbessern (außer bei Materialabtragsprozessen wie Schleifen/Polieren).
Tabelle: Typischer Präzisionsvergleich (allgemeine Richtlinie)
Parameter | Metall-AM (gedruckt) | Standard-CNC-Bearbeitung | Hochpräzisions-CNC-Bearbeitung |
---|---|---|---|
Toleranz (Kleine Merkmale) | ±0,1 bis ±0,2 mm | ±0,05 bis ±0,1 mm | ±0,01 bis ±0,025 mm |
Toleranz (Große Merkmale) | + ±0,002 bis ±0,005 mm/mm | + ±0,001 mm/mm | + ±0,0005 mm/mm |
Oberflächengüte (Ra) | 5 µm – 25 µm+ (variiert je nach Oberfläche) | 0,8 µm – 3,2 µm | < 0,8 µm |
In Blätter exportieren
5. Messtechnik und Inspektion:
- Wichtigkeit: Es ist entscheidend zu überprüfen, ob der endgültige Greifer (nach der gesamten Nachbearbeitung) die angegebenen Maß- und Toleranzanforderungen erfüllt.
- Methoden: Koordinatenmessgeräte (KMG), 3D-Laserscanning, optische Komparatoren und herkömmliche Messwerkzeuge werden zur Inspektion verwendet.
Fazit zur Präzision: Ingenieure, die entwerfen 3D-gedruckte Metallgreifer müssen einen hybriden Ansatz verfolgen. Nutzen Sie AM für komplexe Geometrien, Leichtbau und Teilekonsolidierung, während Sie strategisch kritische Merkmale identifizieren, die die Präzision der Nachbearbeitung erfordern. Die klare Kommunikation von Toleranzanforderungen und Inspektionskriterien an die Metall-AM-Dienstleister ist für erfolgreiche Ergebnisse unerlässlich. Das Verständnis der inhärenten Fähigkeiten und Einschränkungen des gedruckten Zustands ermöglicht ein effizientes Design und verhindert unrealistische Erwartungen.
Anforderungen an die Nachbearbeitung für eine optimale Greiferleistung
Ein weit verbreitetes Missverständnis über die additive Fertigung von Metallen ist, dass Teile unmittelbar nach Abschluss des Druckzyklus einsatzbereit sind. In Wirklichkeit ist der Druckprozess für Hochleistungsanwendungen wie Robotergreifer nur der erste Schritt. Eine Reihe von entscheidenden Nachbearbeitung Schritte sind in der Regel erforderlich, um die gedruckte Komponente in ein funktionelles, langlebiges und präzises Werkzeug zu verwandeln. Diese Schritte sind unerlässlich, um Spannungen abzubauen, temporäre Strukturen zu entfernen, die gewünschten Materialeigenschaften zu erzielen, Maßtoleranzen einzuhalten, geeignete Oberflächengüten zu erreichen und die Gesamtqualität sicherzustellen. Die Planung dieser Vorgänge ist unerlässlich, um die Kosten und Vorlaufzeiten bei der Beschaffung von kundenspezifischen 3D-gedruckten Greifern.
Hier ist eine Aufschlüsselung der gängigen Nachbearbeitungsanforderungen für Robotergreifer aus Metall-AM, insbesondere für solche aus Materialien wie 17-4PH und AlSi10Mg:
1. Spannungsarmglühen:
- Warum? Das schnelle Erhitzen und Abkühlen, das den Pulverbett-Schmelzprozessen innewohnt, induziert erhebliche Eigenspannungen innerhalb des gedruckten Teils. Diese Spannungen können während des Druckens, nach dem Entfernen von der Bauplatte oder später im Lebenszyklus des Teils zu Verformungen oder sogar Rissen führen.
- Wann: Typischerweise durchgeführt während das Teil noch an der Bauplatte befestigt ist in einem separaten Ofen oder einem Ofen mit kontrollierter Atmosphäre.
- Prozess: Beinhaltet das Erhitzen des Teils und der Bauplatte auf eine bestimmte Temperatur unterhalb des Transformationspunkts des Materials, das Halten für einen bestimmten Zeitraum und anschließendes langsames Abkühlen. Die Parameter hängen stark vom Material ab (z. B. erfordert 17-4PH andere Zyklen als AlSi10Mg) und von der Teilegeometrie/Masse.
- Wichtigkeit: Absolut entscheidend für die Dimensionsstabilität und zur Vermeidung von vorzeitigem Versagen. Das Überspringen oder unsachgemäße Durchführen des Spannungsarmglühens ist eine häufige Ursache für Probleme.
2. Entfernen des Teils von der Bauplatte:
- Methoden:
- Drahterodieren (Electrical Discharge Machining): Präzise Methode, oft verwendet für Teile mit komplexen oder empfindlichen Schnittstellen zur Bauplatte. Hinterlässt einen sauberen Schnitt.
- Sägen/Schneiden: Verwendung einer Bandsäge oder anderer Schneidwerkzeuge. Schneller, aber weniger präzise, erfordert ausreichend Freiraum.
- Bearbeitungen: Fräsen des Teils von der Platte.
- Erwägung: Die gewählte Methode hängt von der Teilegeometrie, der erforderlichen Präzision an der Basis und der Losgröße ab.
3. Entfernung der Stützstruktur:
- Warum? Stützstrukturen sind während des Baus erforderlich, müssen aber anschließend entfernt werden.
- Herausforderungen: Stützen bestehen aus demselben dichten Metall wie das Teil und können schwierig und zeitaufwändig zu entfernen sein, insbesondere interne Stützen oder solche in schwer zugänglichen Bereichen.
- Methoden:
- Manuelles Brechen/Abtragen: Möglicherweise für gut gestaltete, zugängliche Stützen mit minimalen Kontaktpunkten. Erfordert eine sorgfältige Handhabung, um eine Beschädigung des Teils zu vermeiden.
- Handwerkzeuge: Zangen, Schleifmaschinen, Meißel. Arbeitsintensiv und erfordert Geschick.
- Bearbeitung (Fräsen/Schleifen): Präzisere Entfernung, oft verwendet für Stützkontaktpunkte auf kritischen Oberflächen.
- Drahterodieren: Kann für einige interne oder komplizierte Stützstrukturen verwendet werden.
- DfAM-Link: Das Konstruieren zur Minimierung der Stützen und zum einfachen Zugang während der DfAM-Phase reduziert den Nachbearbeitungsaufwand und die Kosten erheblich.
4. Wärmebehandlung (Lösungsglühen, Aushärten, Härten):
- Warum? Um die endgültigen gewünschten mechanischen Eigenschaften (Festigkeit, Härte, Duktilität, Zähigkeit) zu erzielen. Gedruckte Mikrostrukturen stellen oft nicht das volle Potenzial des Materials dar.
- Prozessbeispiele:
- 17-4PH: Erfordert Lösungsglühen gefolgt von Ausscheidungshärtung (Aushärten). Gängige Aushärtebehandlungen wie H900 (hohe Festigkeit, moderate Zähigkeit) oder H1025/H1075 (geringere Festigkeit, höhere Zähigkeit) beinhalten das Erhitzen auf bestimmte Temperaturen (z. B. 482 °C für H900) für eine bestimmte Dauer (z. B. 1-4 Stunden) gefolgt von Luftkühlung. Dieser Schritt ist entscheidend für 17-4PH-Greifer, die eine hohe Festigkeit und Verschleißfestigkeit benötigen.
- AlSi10Mg: Unterliegt oft einer T6-Wärmebehandlung (Lösungsglühen gefolgt von künstlichem Aushärten), um die Festigkeit und Härte im Vergleich zum gedruckten Zustand deutlich zu erhöhen.
- Atmosphäre: Wärmebehandlungen werden typischerweise in Vakuum- oder Inertgasöfen durchgeführt, um Oxidation zu verhindern.
- Wichtigkeit: Unverzichtbar, um sicherzustellen, dass der Greifer die Leistungsspezifikationen erfüllt. Die Eigenschaften können basierend auf dem gewählten Zyklus angepasst werden.
5. Bearbeitung (Sekundärbearbeitung):
- Warum? Um enge Toleranzen an kritischen Merkmalen zu erzielen, glatte Oberflächen zum Abdichten oder Anpassen zu erzeugen, Gewindebohrungen zu erstellen oder Merkmale hinzuzufügen, die während des Druckens nicht möglich sind.
- Gängige Anwendungen an Greifern:
- Bearbeiten von Montageflächen flach und parallel.
- Bohren von Löchern für Lager oder Präzisionsstifte.
- Fräsen von Fingerkontaktflächen auf präzise Abmessungen oder Profile.
- Schneiden von O-Ring-Nuten oder anderen Dichtungsmerkmalen.
- Gewindeschneiden von Gewindebohrungen für Befestigungselemente oder pneumatische Anschlüsse.
- Erwägung: Erfordert eine sorgfältige Vorrichtungsgestaltung, um das oft komplexe AM-Teil zu halten. Auf Merkmalen, die für die Bearbeitung vorgesehen sind, muss während der Konstruktionsphase ausreichend Materialvorrat verbleiben.
6. Oberflächenveredelung:
- Warum? Zur Verbesserung der Oberflächenglätte (Reduzierung von Ra), zur Verbesserung der Ästhetik, zum Entfernen von Stützresten, zum Entgraten von Kanten oder zur Vorbereitung auf Beschichtungen.
- Gängige Methoden:
- Medienstrahlen (Kugel-, Sand-, Körnchenstrahlen): Erzeugt eine gleichmäßige matte Oberfläche, entfernt loses Pulver und kann kleinere Unvollkommenheiten ausblenden. Unterschiedliche Medien erzielen unterschiedliche Texturen.
- Taumeln / Vibrationsgleitschleifen: Teile werden in einer Maschine mit Medien (Keramik, Kunststoff, organisch) verarbeitet, um Oberflächen zu glätten und Kanten abzurunden. Gut für die Chargenverarbeitung kleinerer Greifer.
- Manuelles Entgraten und Polieren: Verwendung von Handwerkzeugen, Feilen, Schleiftüchern oder motorbetriebenen Polierwerkzeugen für bestimmte Bereiche, die eine hohe Glätte oder das Entfernen scharfer Kanten erfordern.
- Elektropolieren (für Edelstähle): Elektrochemischer Prozess, der eine dünne Materialschicht entfernt, was zu einer sehr glatten, sauberen und oft korrosionsbeständigeren Oberfläche führt. Hervorragend für interne Kanäle.
- Abrasive Fließbearbeitung (AFM): Schieben von Schleifkitt durch interne Kanäle, um deren Oberflächen zu glätten.
7. Beschichtungen und Oberflächenbehandlungen:
- Warum? Zur Verbesserung spezifischer Oberflächeneigenschaften über die Fähigkeiten des Basismaterials hinaus.
- Beispiele für Greifer:
- Abnutzungswiderstand: Hartverchromung, Nitrieren, PVD-Beschichtungen (z. B. TiN, CrN), WC-Co-Beschichtungen, die durch thermisches Spritzen aufgebracht werden. Unverzichtbar für Greifer, die abrasive Materialien handhaben oder solche mit hohen Zyklenzahlen.
- Gleitfähigkeit: Beschichtungen mit geringer Reibung (z. B. DLC – diamantartiger Kohlenstoff, MoS2) für Gleitkomponenten oder empfindliche Handhabung.
- Korrosionsbeständigkeit: Eloxieren (für Aluminium), Passivierung oder Elektropolieren (für Edelstahl), Spezialfarben oder -beschichtungen für extreme Umgebungen.
- Elektrische Isolierung: Polymer- oder Keramikbeschichtungen, wenn der Greifer elektrisch empfindliche Komponenten handhaben muss.
- Nicht-Beschädigung: Auftragen weicherer Beschichtungsmaterialien (z. B. Urethan) auf Kontaktflächen für die empfindliche Teilehandhabung.
8. Reinigung und Inspektion:
- Warum? Stellen Sie sicher, dass das Teil frei von Verunreinigungen (Pulver, Kühlflüssigkeiten, Medien) ist und alle Spezifikationen vor dem Einsatz erfüllt.
- Methoden: Ultraschallreinigung, Lösungsmittelwäsche, Sichtprüfung, Dimensionsprüfung (KMG, Scannen), Materialprüfung (falls erforderlich).
Typisches Workflow-Beispiel (17-4PH-Greifer):
Drucken -> Spannungsarmglühen (auf Platte) -> Entfernen von der Platte (Draht-EDM) -> Grobe Stützenentfernung -> Lösungsglühen -> Endgültige Stützenentfernung / Grobbearbeitung -> Aushärten (z. B. H900) -> Feinbearbeitung (kritische Merkmale) -> Oberflächenveredelung (z. B. Kugelstrahlen) -> Beschichtung (optional) -> Reinigung -> Endkontrolle.
Das Verständnis dieses umfassenden Nachbearbeitungs-Workflows ist für Einkaufsmanager und Ingenieure von entscheidender Bedeutung. Er wirkt sich auf die endgültigen Kosten, die Vorlaufzeit und die Leistung des 3D-gedruckten Robotergreifers. Die Zusammenarbeit mit einem Full-Service- Metall-AM-Anbieter , der diese Schritte verwalten oder beraten kann, ist von großem Vorteil.
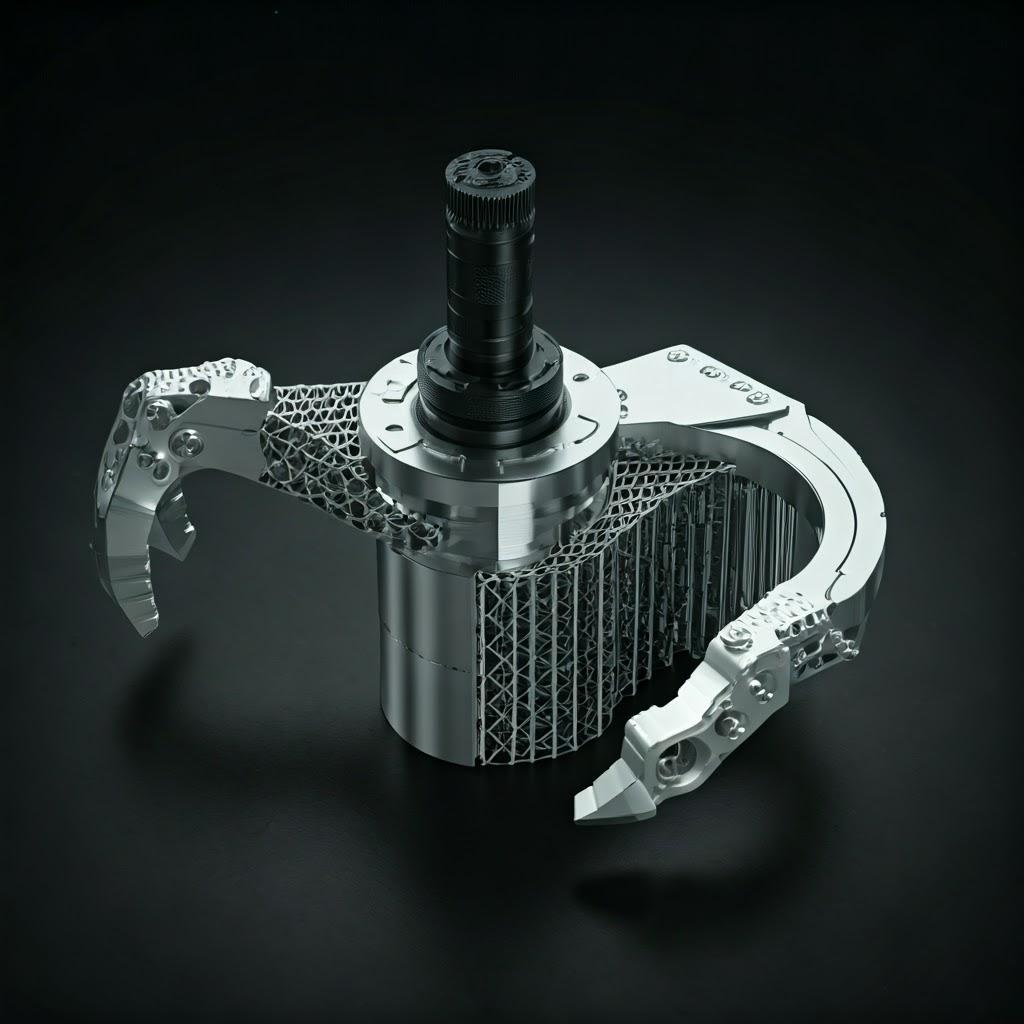
Häufige Herausforderungen beim 3D-Druck von Greifern und effektive Lösungen
Obwohl die additive Fertigung von Metallen erhebliche Vorteile für Robotergreifer bietet, ist sie nicht ohne potenzielle Herausforderungen. Das Bewusstsein für diese häufigen Probleme und die Umsetzung proaktiver Lösungen – oft basierend auf robusten DfAM-Praktiken, sorgfältiger Prozesskontrolle und der Zusammenarbeit mit erfahrenen AM-Dienstleister – ist der Schlüssel, um durchweg erfolgreiche Ergebnisse zu erzielen. Für Unternehmen, die sich auf Komponentenlieferanten für Industrieroboter verlassen, hilft das Verständnis dieser potenziellen Hürden bei der Bewertung der Lieferantenfähigkeiten und der Festlegung realistischer Projekterwartungen.
Hier sind einige häufige Herausforderungen, die beim 3D-Druck von Metall-Robotergreifern auftreten, sowie Strategien zu deren Bewältigung:
1. Verzug und Verzerrung:
- Herausforderung: Restliche thermische Spannungen führen dazu, dass sich der Greifer während oder nach dem Druck verzieht, was zu Maßungenauigkeiten oder sogar zum Fehlschlagen des Aufbaus (z. B. Kollisionen der Beschichterklinge) führt. Dies ist besonders relevant für große flache Abschnitte oder komplexe Geometrien.
- Die Ursachen: Ungleichmäßiges Erhitzen/Abkühlen, unzureichende Unterstützung, große Temperaturgradienten, ungeeignete Prozessparameter.
- Lösungen:
- DfAM: Konstruktion zur Reduzierung der Spannung (Vermeidung großer Massivblöcke, Verwendung von Gittern, Hinzufügen von Opferrippen).
- Orientierung: Optimieren Sie die Bauausrichtung, um große flache, nach unten gerichtete Bereiche zu minimieren und die Wärmeverteilung zu steuern.
- Strategie unterstützen: Verwenden Sie robuste Stützen, die nicht nur für die Schwerkraft ausgelegt sind, sondern auch thermischen Spannungen entgegenwirken und das Teil effektiv verankern. Verwenden Sie Simulationstools, um die Platzierung der Stützen zu optimieren.
- Prozessparameter: Verwenden Sie validierte Parameter, die für das Material, die Maschine und die Geometrie spezifisch sind. Stellen Sie ein stabiles Wärmemanagement der Baukammer sicher (die bei erhöhten Temperaturen arbeitenden SEBM-Drucker von Met3dp können inhärent dazu beitragen, die Spannung für bestimmte Materialien zu reduzieren).
- Stressabbau: Führen Sie einen ordnungsgemäßen Spannungsabbauzyklus durch vor Entfernen des Teils von der Bauplatte.
2. Porosität:
- Herausforderung: Kleine Hohlräume oder Poren innerhalb des gedruckten Materials können die mechanischen Eigenschaften, insbesondere die Ermüdungsfestigkeit und die Bruchzähigkeit, beeinträchtigen und können Ausgangspunkte für Risse sein.
- Die Ursachen: Eingeschlossenes Gas während des Schmelzens, unvollständiges Schmelzen aufgrund falscher Parameter (Laser-/Strahlleistung, Geschwindigkeit, Fokus), Schlüssellochinstabilität, schlechte Pulverqualität (interne Gasporen, unregelmäßige Morphologie, schlechte Fließfähigkeit).
- Lösungen:
- Optimierte Parameter: Entwickeln und verwenden Sie sorgfältig validierte Druckparameter, die bekanntermaßen dichte Teile erzeugen (typischerweise >99,5 % Dichte erreichbar, oft >99,8 %).
- Hochwertiges Pulver: Verwenden Sie Pulver mit hoher Sphärizität, geringer Porosität und guter Fließfähigkeit, die unter strenger Qualitätskontrolle hergestellt werden (Met3dp betont seine fortschrittlichen Gaszerstäubungs- und PREP-Systeme für die Pulverqualität). Stellen Sie eine ordnungsgemäße Pulverhandhabung und -lagerung sicher, um die Aufnahme von Feuchtigkeit zu vermeiden.
- Prozessüberwachung: Verwenden Sie In-situ-Überwachungswerkzeuge (falls verfügbar), um potenzielle Instabilitäten des Schmelzbades zu erkennen.
- Heiß-Isostatisches Pressen (HIP): Ein Nachbearbeitungsschritt, der ein Inertgas bei hoher Temperatur und hohem Druck beinhaltet, um interne Poren zu schließen. Oft erforderlich für kritische Anwendungen (z. B. Luft- und Raumfahrt, medizinische Implantate), um nahezu 100 % Dichte zu erreichen, was jedoch Kosten und Vorlaufzeit erhöht.
3. Schwierigkeiten beim Entfernen der Stützen:
- Herausforderung: Stützen können schwierig, zeitaufwändig und kostspielig zu entfernen sein, insbesondere interne Stützen oder solche in begrenzten Bereichen. Das Entfernen kann auch die Oberfläche des Teils beschädigen.
- Die Ursachen: Schlechte DfAM (fehlender Zugang, übermäßiges Stützvolumen), übermäßig starke Stützstrukturen, ungeeignete Entfernungstechniken.
- Lösungen:
- DfAM für Barrierefreiheit: Konstruieren Sie Teile, um den Bedarf an Stützen zu minimieren (selbsttragende Winkel) und klare Zugangspfade für Werkzeuge oder Prozesse zum Entfernen sicherzustellen (z. B. Sichtlinie für die Bearbeitung, Fließwege für AFM).
- Optimierte Unterstützungsstrukturen: Verwenden Sie Softwarefunktionen, um Stützen zu erstellen, die leichter zu entfernen sind (z. B. konische Kontakte, Perforationen, spezifische Materialoberflächenparameter).
- Spezialisierte Entfernungstechniken: Verwenden Sie Methoden wie Drahterodieren oder Präzisionsbearbeitung für schwierige Stützen.
- Berücksichtigen Sie die Kosten/Vorlaufzeit: Planen Sie realistisch Zeit und Ressourcen für die Entfernung der Stützen ein.
4. Konsistentes Erreichen der gewünschten mechanischen Eigenschaften:
- Herausforderung: Die endgültigen Teileigenschaften (Festigkeit, Härte, Duktilität) erfüllen möglicherweise nicht die Spezifikationen oder variieren zwischen den Bauteilen.
- Die Ursachen: Porosität, falsche Druckparameter, die die Mikrostruktur beeinflussen, unsachgemäße oder inkonsistente Wärmebehandlungszyklen (Temperatur, Zeit, Atmosphärenkontrolle).
- Lösungen:
- Strenge Prozesskontrolle: Behalten Sie die strenge Kontrolle über alle Druckparameter und die Maschinenkalibrierung bei.
- Pulverqualitätsmanagement: Stellen Sie eine konsistente Pulverchemie, Größenverteilung und Morphologie sicher.
- Validierte Wärmebehandlung: Verwenden Sie präzise gesteuerte, kalibrierte Öfen mit geeigneter Atmosphärenkontrolle. Befolgen Sie validierte Wärmebehandlungsrezepte, die für das AM-Material und den gewünschten Zustand spezifisch sind (z. B. H900 für 17-4PH).
- Materialprüfung: Führen Sie regelmäßige Zugversuche, Härteprüfungen und möglicherweise Mikrostrukturanalyse an Zeugenmustern durch, die zusammen mit den Teilen gedruckt werden, um die Eigenschaften zu überprüfen.
5. Probleme mit der Oberflächenbeschaffenheit:
- Herausforderung: Die Oberfläche des gedruckten Teils ist für die Anwendung (Verschleiß, Abdichtung, Ästhetik) zu rau oder variiert inakzeptabel über verschiedene Teiloberflächen. Stützkontaktpunkte (“Zeugenmarken”) sind problematisch.
- Die Ursachen: Inhärente Natur des schichtweisen Aufbaus, Auswahl der Ausrichtung, Wechselwirkungen der Stützen.
- Lösungen:
- Optimierung der Orientierung: Priorisieren Sie kritische Oberflächen für eine optimale Ausrichtung (z. B. nach oben oder vertikal für die beste Oberfläche).
- Einstellung der Parameter: Durch Feinabstimmung von Parametern wie Konturübergängen kann die Oberflächenbeschaffenheit der Seitenwand leicht verbessert werden.
- Geeignete Nachbearbeitung: Wählen Sie die richtige Oberflächenbearbeitungstechnik (Strahlen, Trommeln, Polieren, Bearbeiten) basierend auf dem erforderlichen Ra-Wert und der Merkmalsposition.
- Konstruktion für die Endbearbeitung: Stellen Sie sicher, dass Merkmale, die eine hohe Oberflächenbeschaffenheit benötigen, für Nachbearbeitungswerkzeuge zugänglich sind. Lassen Sie bei Bedarf Bearbeitungszugabe.
Tabelle: Zusammenfassung der häufigen Herausforderungen und Lösungen
Herausforderung | Häufige Ursachen | Schlüssellösungen |
---|---|---|
Verzug/Verzerrung | Restspannung, unzureichende Unterstützung, Parameter | DfAM, optimierte Ausrichtung & Stützen, validierte Parameter, Spannungsabbau |
Porosität | Parameter, eingeschlossenes Gas, schlechte Pulverqualität | Optimierte Parameter, hochwertiges Pulver (z. B. Met3dp), Prozesskontrolle, HIP (optional) |
Schwierigkeit beim Entfernen der Stütze | Schlechte DfAM, übermäßig starke Stützen | DfAM für den Zugang, optimierte Stützen, spezielle Entfernungsmethoden |
Inkonsistente Eigenschaften | Porosität, falsche Parameter oder Wärmebehandlung | Prozesskontrolle, Pulvermanagement, validierte Wärmebehandlung, Materialprüfung |
Probleme mit der Oberflächenbeschaffenheit | Schichtweise Natur, Ausrichtung, Stützkontakt | Optimieren Sie die Ausrichtung, die Parameteranpassung, die geeignete Nachbearbeitung (Bearbeitung/Endbearbeitung) |
Kostenüberschreitungen | Ineffizientes Design, übermäßige Stützen/Nachbearbeitung. | DfAM für AM, strategische Material-/Prozessauswahl, Zusammenarbeit mit Lieferanten |
Fehlkalkulationen der Vorlaufzeit | Unterschätzung der Nachbearbeitung, Baufehler | Realistische Planung (einschließlich Nachbearbeitung), robuster Prozess, Kommunikation mit dem Lieferanten |
In Blätter exportieren
Die erfolgreiche Bewältigung dieser Herausforderungen erfordert eine Kombination aus guten Konstruktionspraktiken, robuster Prozesskontrolle, geeigneter Nachbearbeitung und oft eine enge Zusammenarbeit mit einem erfahrenen Metall-AM-Dienstleister , der die Nuancen der Technologie und der beteiligten Materialien versteht. Dieser kollaborative Ansatz hilft, Risiken zu mindern und die Lieferung von hochwertigen, zuverlässigen 3D-gedruckten Robotergreifern sicherzustellen.
Auswahl Ihres Metall-AM-Partners: Auswahl des richtigen 3D-Druckdienstleisters für Greifer
Die Auswahl des richtigen Fertigungspartners ist ebenso wichtig wie die Konstruktions- und Materialauswahl, wenn Sie ein Metall-Additivfertigungsprojekt für Robotergreifer in Angriff nehmen. Die Qualität, Leistung, Wirtschaftlichkeit und pünktliche Lieferung Ihrer Komponenten hängen von den Fähigkeiten und der Expertise Ihres gewählten Metall-AM-Dienstleisterab. Für Einkaufsmanager und Ingenieure, die es gewohnt sind, traditionell hergestellte Teile zu beschaffen, erfordert die Bewertung potenzieller AM-Lieferanten die Betrachtung einer bestimmten Reihe von Kriterien, die sich auf Technologie, Prozesskontrolle und Spezialwissen konzentrieren. Hier geht es nicht nur darum, einen Anbieter zu finden; es geht darum, eine kollaborative Partnerschaft mit einem Lieferanten aufzubauen, der die Nuancen des Metall-3D-Drucks und Ihre Anwendungsanforderungen versteht.
Hier ist ein Leitfaden zur Bewertung und Auswahl des richtigen 3D-Druck-Anbieter für Ihre hochfesten Robotergreifer-Anforderungen:
1. Fachwissen und Anwendungserfahrung:
- Fachwissen: Verfügt der Anbieter über fundiertes Fachwissen in Metall-AM-Verfahren (LPBF, SEBM usw.), Metallurgie und DfAM-Prinzipien?
- Relevante Erfahrung: Haben sie Teile, die Ihrem Greifer in Bezug auf Komplexität, Material und Industrieanforderungen ähneln, erfolgreich hergestellt? Bitten Sie um Fallstudien, Musterteile (falls möglich) oder Referenzen. Erfahrung speziell mit Robotik-EOAT oder hochfesten Komponenten ist ein erhebliches Plus.
- Problemlösung: Können sie Lösungen für potenzielle Konstruktionsherausforderungen anbieten oder bei der Optimierung Ihres Greifers für die Additive Fertigung beraten?
2. Ausrüstung, Technologie und Kapazität:
- Angemessene Technologie: Betreiben sie den richtigen AM-Systemtyp (z. B. LPBF für feine Merkmale, SEBM für bestimmte Materialien/Spannungsreduzierung wie die von Met3dp angebotenen Systeme) für Ihr gewähltes Material (17-4PH, AlSi10Mg) und Ihre Konstruktionskomplexität?
- Maschinenqualität und -wartung: Sind ihre Maschinen modern, gut gewartet und ordnungsgemäß kalibriert? Dies wirkt sich direkt auf die Teilequalität, Konsistenz und Zuverlässigkeit aus.
- Bauvolumen: Können ihre Maschinen die Größe Ihres Greifers aufnehmen?
- Kapazität und Durchsatz: Verfügen sie über eine ausreichende Maschinenkapazität, um Ihre erforderlichen Vorlaufzeiten einzuhalten, insbesondere wenn Sie wiederkehrende Bestellungen oder Serienfertigung erwarten?
3. Materialfähigkeiten und Qualitätskontrolle:
- Material-Portfolio: Bieten sie die spezifischen Metalllegierungen an, die Sie benötigen (z. B. 17-4PH, AlSi10Mg) und möglicherweise andere, wenn sich Ihre Anforderungen ändern?
- Pulverbeschaffung und -handhabung: Wo beziehen sie ihre Metallpulver? Verfügen sie über strenge Qualitätskontrollverfahren für die Eingangsprüfung des Pulvers (Chemie, Partikelgrößenverteilung, Morphologie, Fließfähigkeit)? Wie wird das Pulver gelagert, gehandhabt und recycelt, um Konsistenz zu gewährleisten und Kontamination zu vermeiden? Anbieter wie Met3dp, die ihre eigenen herstellen hochwertige Metallpulver unter Verwendung fortschrittlicher Techniken wie Gaszerstäubung und PREP, haben oft einen Vorteil bei der Gewährleistung der Pulverqualität und Rückverfolgbarkeit.
- Materialzertifizierung: Können sie Materialzertifizierungen bereitstellen, die die Pulvercharge bis zum fertigen Teil zurückverfolgen?
4. Inhouse- vs. verwaltete Nachbearbeitung:
- Integrierte Dienstleistungen: Bietet der Anbieter wichtige Nachbearbeitungsschritte intern an (Spannungsabbau, Wärmebehandlung, grundlegende Stützenentfernung, einige Oberflächenbearbeitungen)? Dies kann den Arbeitsablauf rationalisieren, die Vorlaufzeiten verkürzen und das Qualitätsmanagement vereinfachen.
- Managed Services: Wenn sie Schritte wie Bearbeitung, Spezialbeschichtungen oder erweiterte Inspektionen (HIP, CMM) auslagern, verfügen sie über ein Netzwerk qualifizierter, vertrauenswürdiger Partner? Wie verwalten sie Qualität und Logistik in der gesamten Lieferkette?
- Fähigkeitsausrichtung: Stellen Sie sicher, dass ihre verfügbaren oder verwalteten Nachbearbeitungsfähigkeiten genau mit den Anforderungen Ihres Greifers übereinstimmen (z. B. spezifische Wärmebehandlungszyklen wie H900 für 17-4PH, Bearbeitung mit engen Toleranzen, spezifische Oberflächenbeschaffenheit).
5. Qualitätsmanagementsystem (QMS) und Zertifizierungen:
- Formelles QMS: Arbeiten sie im Rahmen eines robusten QMS, wie z. B. ISO 9001? Dies deutet auf ein Bekenntnis zu standardisierten Prozessen, kontinuierlicher Verbesserung und Qualitätssicherung hin.
- Branchenspezifische Zertifizierungen: Hält der Anbieter, falls für Ihre Anwendung erforderlich (z. B. Luft- und Raumfahrt AS9100, Medizin ISO 13485), die relevanten Zertifizierungen?
- Inspektionskapazitäten: Welche Messtechnikgeräte (CMM, 3D-Scanner, Materialprüflabore) haben sie intern oder haben sie Zugriff darauf? Wie sehen ihre Standardinspektionsverfahren aus, und können sie spezifische Inspektionspläne berücksichtigen?
- Rückverfolgbarkeit: Können sie die vollständige Rückverfolgbarkeit vom Rohmaterial bis zum fertigen Teil gewährleisten?
6. Engineering und DfAM-Unterstützung:
- Kollaborativer Ansatz: Sind sie bereit, frühzeitig in der Konstruktionsphase mit Ihrem Engineering-Team zusammenzuarbeiten, um den Greifer für AM zu optimieren? Diese kollaborative DfAM-Anstrengung ist entscheidend, um die Vorteile von AM zu nutzen und die Kosten zu kontrollieren.
- Fachwissen: Verfügen sie über Anwendungstechniker mit praktischer Erfahrung in der Konstruktion für den spezifischen AM-Prozess, den sie verwenden? Können sie zu Topologieoptimierung, Stützstrategien, Feature-Einschränkungen und Kompromissen bei der Materialauswahl beraten?
7. Kommunikation, Transparenz und Kundenservice:
- Reaktionsfähigkeit: Sind sie in ihrer Kommunikation zeitnah und klar?
- Transparenz: Sind sie offen in Bezug auf ihre Prozesse, Fähigkeiten und potenziellen Herausforderungen? Stellen sie klare und detaillierte Angebote zur Verfügung?
- Projektleitung: Haben sie einen dedizierten Ansprechpartner für Ihr Projekt? Wie gehen sie mit Projektaktualisierungen und potenziellen Problemen um?
8. Vorlaufzeiten und Wettbewerbsfähigkeit der Kosten:
- Realistische Zeitpläne: Stellen sie klare, realistische Schätzungen der Vorlaufzeit zur Verfügung, die den Druck berücksichtigen und alle notwendigen Nachbearbeitungsschritte?
- Preisstruktur: Ist ihre Preisgestaltung transparent und wettbewerbsfähig für den angebotenen Wert (unter Berücksichtigung von Qualität, Fachwissen und Service)? Verstehen Sie, was im Angebot enthalten ist. Während die Kosten wichtig sind, kann die Auswahl des billigsten Anbieters ohne Berücksichtigung der oben genannten Faktoren zu minderwertigen Teilen, Verzögerungen und höheren Gesamtkosten führen.
9. Unternehmensstabilität und Hintergrund:
- Erfolgsbilanz: Wie lange sind sie im Metall-AM-Bereich tätig? Welchen Ruf haben sie in der Branche? Die Untersuchung des Hintergrunds des Unternehmens, wie z. B. auf der Seite von Met3dp,
[about-us](https://met3dp.com/about-us/)
kann Einblicke in ihre Geschichte, Mission und ihren Fokus geben. - Standort und Logistik: Berücksichtigen Sie die Auswirkungen ihres Standorts auf Versandzeiten, -kosten und die einfache Kommunikation oder Standortbesuche, falls erforderlich.
Checklisten-Tabelle: Wichtige Kriterien zur Lieferantenbewertung
Kriterium | Zentrale Fragen | Bedeutung |
---|---|---|
Technisches Fachwissen | Relevante Erfahrung? DfAM-Kenntnisse? Fähigkeiten zur Problemlösung? | Sehr hoch |
Ausrüstung und Technologie | Richtiger AM-Prozess? Maschinenqualität/Alter? Bauvolumen? Kapazität? | Sehr hoch |
Materialqualität & Kontrolle | Bietet benötigte Legierungen an? Pulver-QC? Handhabungsverfahren? Zertifizierung? | Sehr hoch |
Nachbearbeitung | Inhouse oder verwaltet? Auf Bedürfnisse abgestimmt? Qualitätskontrolle? | Sehr hoch |
Qualitätssystem/Zertifikate | ISO 9001? Branchenspezifische Zertifizierungen? Inspektionsfähigkeiten? Rückverfolgbarkeit? | Hoch bis sehr hoch |
Technische Unterstützung | DfAM-Beratung angeboten? Kooperativer Ansatz? | Hoch |
Kommunikation und Service | Reaktionsschnell? Transparent? Klare Angebote? Projektmanagement? | Hoch |
Lieferzeit und Kosten | Realistische Zeitpläne? Wettbewerbsfähige Preise? Preis-Leistungs-Verhältnis? | Hoch |
Hintergrund des Unternehmens | Erfolgsbilanz? Stabilität? Standort Eignung? | Mittel bis Hoch |
In Blätter exportieren
Die Wahl des richtigen Metall-AM-Fertigungspartner ist eine strategische Entscheidung. Durch die gründliche Bewertung potenzieller Lieferanten anhand dieser Kriterien können Sie eine Beziehung zu einem Anbieter aufbauen, der konsequent hochwertige, hochleistungsfähige 3D-gedruckte Robotergreifer liefern kann, die auf Ihre spezifischen Bedürfnisse zugeschnitten sind und letztendlich Ihre Automatisierungsfähigkeiten verbessern.
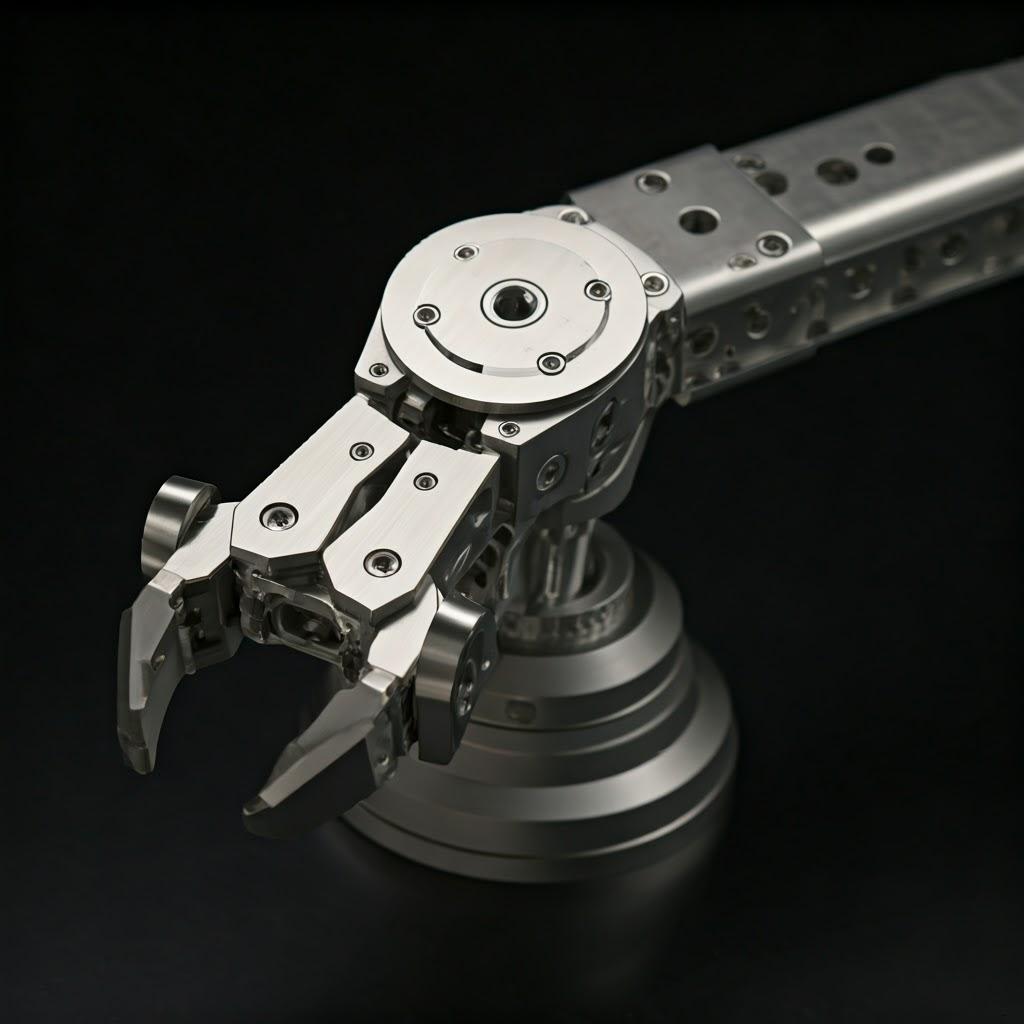
Kostenfaktoren und Vorlaufzeiten für kundenspezifische 3D-gedruckte Robotergreifer
Das Verständnis der Faktoren, die die Kosten und die Vorlaufzeit von kundenspezifischen 3D-gedruckten Metall-Robotergreifern beeinflussen, ist für eine genaue Budgetierung, Projektplanung und das Management von Erwartungen unerlässlich. Im Gegensatz zur traditionellen Fertigung, bei der die Werkzeugkosten oft die anfänglichen Kosten dominieren, sind die Preise für Metall-AM stärker an den Materialverbrauch, die Maschinenzeit und den Umfang der erforderlichen Nachbearbeitung gebunden. Auch die Vorlaufzeiten werden durch einen mehrstufigen Arbeitsablauf bestimmt, der über die Druckdauer hinausgeht.
Wichtige Kostenfaktoren:
- Materialart und Verbrauch:
- Pulverkosten: Die Rohmaterialpulverkosten variieren erheblich zwischen den Legierungen. Hochleistungslegierungen wie Titan oder spezielle Superlegierungen sind viel teurer als Edelstähle (wie 17-4PH) oder Aluminiumlegierungen (wie AlSi10Mg).
- Verwendetes Volumen: Der primäre Kostentreiber ist oft das Volumen (und damit das Gewicht) des fertigen Teils plus das Volumen der benötigten Stützstrukturen. Größere und dichtere Teile verbrauchen mehr teures Pulver. DfAM-Techniken wie Topologieoptimierung und Gitterstrukturen reduzieren den Materialverbrauch und damit die Kosten direkt.
- Komplexität des Teiledesigns und Bounding Box:
- Bounding Box: Die Gesamtabmessungen (Länge x Breite x Höhe) des Teils beeinflussen, wie viel Platz es auf der Bauplatte einnimmt und potenziell wie lange der Druck dauert (insbesondere die Höhe). Größere Teile binden die Maschine länger.
- Geometrische Komplexität: Während AM mit Komplexität gut umgehen kann, sind extrem komplizierte Designs möglicherweise umfangreichere Stützstrukturen oder eine anspruchsvollere Nachbearbeitung (z. B. Reinigung interner Kanäle) erforderlich, was die Kosten erhöhen kann. Komplexität, die eine Teilekonsolidierung ermöglicht, führt jedoch oft zu Einsparungen bei den Gesamtsystemkosten.
- Maschinenzeit (Druckzeit):
- Kalkulation: Basierend auf der Höhe des Teils (Anzahl der Schichten) und der zu scannenden Fläche pro Schicht. Zu den Faktoren gehören die Schichtdicke, die Scangeschwindigkeit und die Wiederbeschichtungszeit.
- Kostenzuordnung: AM-Maschinen stellen erhebliche Kapitalinvestitionen dar, daher führen längere Druckzeiten direkt zu höheren Kosten, die dem Teil zugewiesen werden. Das Füllen einer Bauplatte mit mehreren Teilen kann die Maschinenauslastung verbessern und möglicherweise die Stückkosten senken, verglichen mit dem Drucken eines einzelnen Teils allein.
- Unterstützende Strukturen:
- Materialabfälle: Stützen werden mit demselben teuren Metallpulver wie das Teil gedruckt, aber letztendlich entfernt und oft nur teilweise recycelbar.
- Entfernungskosten: Der Arbeits- und Zeitaufwand für die Stützenentfernung (manuell, maschinell, EDM) erhöht die Kosten erheblich. Die Minimierung von Stützen durch DfAM ist eine wichtige Strategie zur Kostensenkung.
- Nachbearbeitungsanforderungen:
- Umfang & Komplexität: Dies ist oft eine Hauptkostenkomponente. Jeder Schritt – Spannungsarmglühen, Wärmebehandlung, Bearbeitung, Oberflächenveredelung, Beschichtung, Inspektion – erhöht den Arbeitsaufwand, die Maschinenzeit und möglicherweise die Kosten für Spezialwerkzeuge.
- Toleranz & Finish: Engere Toleranzen, die eine umfangreiche Mehrachsen-CNC-Bearbeitung oder sehr feine Oberflächen erfordern, die ein manuelles Polieren erfordern, erhöhen die Kosten erheblich im Vergleich zu Teilen, die nur eine einfache Stützenentfernung und ein Kugelstrahlen benötigen. Wärmebehandlungen, die bestimmte Atmosphären und kalibrierte Öfen erfordern, erhöhen ebenfalls die Kosten.
- Arbeit:
- Qualifizierte Arbeitskräfte: Zu den Kosten gehören DfAM-Beratung, Bauvorbereitung, Maschinenbedienung, Teileentfernung, alle Nachbearbeitungsschritte, Qualitätskontrolle und Projektmanagement. Metall-AM erfordert qualifizierte Techniker und Ingenieure.
- Qualitätssicherung und Inspektion:
- Grad der Prüfung: Einfache Maßkontrollen sind Standard. Strengere Anforderungen wie detaillierte CMM-Berichte, Materialtests (Zug, Härte), CT-Scannen auf interne Defekte oder die Einhaltung bestimmter Branchenzertifizierungen erhöhen die Kosten erheblich.
- Bestellmenge:
- Skalenvorteile: Während AM die Werkzeugkosten eliminiert und kleine Chargen rentabel macht, gelten immer noch einige Skaleneffekte. Das Einrichten eines Baus ist weitgehend ein fester Aufwand, sodass das gleichzeitige Drucken mehrerer Teile (wenn sie auf eine Bauplatte passen) die Einrichtungskosten pro Teil reduziert. Auch die Stapelverarbeitung während der Nachbearbeitungsschritte (wie Wärmebehandlung oder Trommeln) kann Einsparungen bringen. Die Kostenreduzierung pro Teil ist jedoch in der Regel weniger dramatisch als in der traditionellen Großserienfertigung.
Wichtige Vorlaufzeitfaktoren:
- Design- und Angebotsphase: Zeit für die Designfinalisierung, DfAM-Beratung (falls erforderlich) und Angebotsgenerierung/-genehmigung. (Kann von Tagen bis zu Wochen dauern).
- Zeit in der Warteschlange: Warten auf einen verfügbaren Maschinenslot beim Dienstleister. Dies kann je nach Arbeitsauslastung des Anbieters stark variieren. (Kann von Tagen bis zu mehreren Wochen dauern).
- Druckzeit: Die tatsächliche Zeit, die das Teil in der AM-Maschine verbringt. (Typischerweise 12 Stunden bis mehrere Tage, abhängig von Größe, Höhe und Anzahl der Teile).
- Nachbearbeiten: Oft der längste und variabelste Teil der Vorlaufzeit.
- Abkühlen & Spannungsarmglühen: Abkühlen der Bauplatte, gefolgt vom Spannungsarmglühzyklus (kann 12-48 Stunden dauern).
- Teil/Träger entfernen: Kann je nach Komplexität Stunden bis Tage dauern.
- Wärmebehandlung: Zyklen (z. B. Lösung + Alterung für 17-4PH) können 1-3 Tage dauern, einschließlich Ofenzeit und kontrollierter Abkühlung.
- Bearbeitungen: Einrichtungs- und Bearbeitungszeit variiert stark je nach Komplexität und Toleranzanforderungen (kann Tage bis Wochen dauern).
- Oberflächenveredelung/Beschichtung: Kann je nach Verfahren und Lieferzeiten des Lieferanten mehrere Tage bis Wochen dauern.
- Inspektion: Zeit, die für die erforderlichen Qualitätskontrollen benötigt wird.
- Versand: Transitzeit vom Lieferanten zu Ihrem Standort.
Tabelle: Zusammenfassung der Kosten- und Vorlaufzeittreiber
Treiber | Auswirkungen auf die Kosten | Auswirkungen auf die Vorlaufzeit | Strategie zur Risikominderung |
---|---|---|---|
Material Volumen | Hoch (Pulverkosten + Stützen) | Mäßig (Druckzeit) | DfAM (Topologie Opt., Gitter), Minimierung von Stützen |
Teil Komplexität | Variabel (Kann die Nachbearbeitungskosten erhöhen) | Variabel (Kann die Druck-/Nachbearbeitungszeit erhöhen) | DfAM (Teilekonsolidierung kann reduzieren Gesamtkosten) |
Maschinenzeit | Hoch (Maschinenamortisation, Betrieb) | Hoch (Wirkt sich direkt auf den Zeitplan aus) | Ausrichtung optimieren, Teile verschachteln, DfAM |
Stützvolumen | Mittel (Materialverschwendung + Arbeitsaufwand für die Entfernung) | Mittel (Entfernungszeit) | DfAM (Selbsttragende Merkmale), Ausrichtung |
Nachbearbeitung | Sehr hoch (Arbeit, Spezialausrüstung, Verbrauchsmaterialien) | Sehr hoch (Oft die längste Phase) | Design für minimale Nachbearbeitung, Anforderungen klar definieren |
Qualitätsanforderungen | Hoch (Inspektionszeit, Ausrüstung, Dokumentation) | Mäßig (Inspektionszeit) | Nur notwendige Toleranzen/Prüfungen angeben |
Menge | Mäßig (Stückkosten sinken leicht mit dem Volumen) | Mäßig (Chargeneffizienz vs. längerer Gesamtdruck) | Bauplattenausnutzung optimieren, Bestellungen sorgfältig planen |
In Blätter exportieren
Typische Vorlaufzeiten (beispielhaft):
- Einfacher Greifer (Grundausführung): 1,5 – 3 Wochen
- Komplexer Greifer (Wärmebehandlung + Grundbearbeitung): 3 – 5 Wochen
- Hochkomplexer Greifer (Wärmebehandlung + umfangreiche Bearbeitung + Beschichtung): 4 – 8+ Wochen
Fazit zu Kosten/Zeit: Metall-AM bietet überzeugende technische Vorteile, erfordert aber eine sorgfältige Abwägung von Kosten und Vorlaufzeiten. Eine genaue Schätzung erfordert ein klares Verständnis des gesamten Prozesses, vom Design bis zum fertigen Teil. Die frühzeitige Zusammenarbeit mit erfahrenen Metall-AM-Dienstleister Experten hilft, Designs kosteneffektiv zu optimieren und realistische Zeitpläne auf der Grundlage der spezifischen Anforderungen Ihres Robotergreiferprojekts zu erstellen.
Häufig gestellte Fragen (FAQ) zu 3D-gedruckten Robotergreifern
Hier sind Antworten auf einige häufige Fragen, die sich Ingenieure und Beschaffungsmanager stellen, wenn sie den Metall-3D-Druck für Robotergreifer in Betracht ziehen:
F1: Wie stark sind 3D-gedruckte Metallgreifer im Vergleich zu herkömmlich bearbeiteten Greifern?
A: Die Festigkeit hängt stark vom gewählten Material, der Qualität des Druckprozesses (Erreichen hoher Dichte), der Nachbearbeitung (insbesondere Wärmebehandlung) und dem Design selbst ab.
- Materialvergleich: Ein 3D-gedruckter Greifer aus 17-4PH-Edelstahl , der ordnungsgemäß wärmebehandelt wurde (z. B. auf H900-Zustand), kann Zug- und Streckgrenzen erreichen, die mit vielen herkömmlich bearbeiteten Stahllegierungen vergleichbar oder sogar überlegen sind.
- Aluminiumlegierung AlSi10Mg, ist zwar leichter, aber nicht so stark wie Stahl, bietet aber ein ausgezeichnetes Festigkeits-Gewichts-Verhältnis, oft vergleichbar mit Aluminiumgussteilen nach der Wärmebehandlung T6.
- Optimierung des Designs: Durch die Nutzung von DfAM-Techniken wie Topologieoptimierung können AM-Teile die erforderlichen Festigkeits- und Steifigkeitsziele mit deutlich weniger Material (und Gewicht) erreichen als ein herkömmlich konstruiertes, bearbeitetes Teil.
- Schlussfolgerung: Ordnungsgemäß konstruierte, gedruckte und nachbearbeitete Metall-AM-Greifer können die Festigkeitsanforderungen anspruchsvoller Roboteranwendungen absolut erfüllen oder übertreffen und bieten oft Vorteile in Bezug auf Gewicht und Komplexität.
F2: Wie ist die typische Lebensdauer oder Haltbarkeit eines 3D-gedruckten Metallgreifers?
A: Die Haltbarkeit ist eine Funktion der Materialauswahl, der Konstruktion unter Last (insbesondere Ermüdungsaspekte), der Druckqualität (Dichte, Mangel an Defekten), der Nachbearbeitung und der spezifischen Anwendungsumgebung (Verschleiß, Stoß, Temperatur, Chemikalien).
- Hochwertige Produktion: Ein gut gedruckter Greifer mit hoher Dichte aus einem haltbaren Material wie wärmebehandeltem 17-4PH, die unter Berücksichtigung der Ermüdungsgrenzen konstruiert wurden, eine ausgezeichnete Lebensdauer bieten können, die mit der von traditionell hergestellten Gegenstücken vergleichbar oder diesen überlegen ist. Ihre Härte sorgt für eine gute Verschleißfestigkeit.
- Oberflächenbehandlungen: Für Anwendungen mit starkem Verschleiß oder Abrieb kann das Hinzufügen von Nachbearbeitungsbeschichtungen (z. B. PVD, Nitrieren) die Lebensdauer des Greifers erheblich verlängern.
- AlSi10Mg: Obwohl weniger verschleißfest als Stahl, eignet es sich für viele Anwendungen. Seine Ermüdungslebensdauer ist für Aluminiumlegierungen im Allgemeinen gut, erfordert aber bei zyklischer Belastung eine sorgfältige Konstruktionsbetrachtung.
- Schlussfolgerung: Es gibt keine allgemeingültige Antwort, aber Metall-AM-Greifer sind nicht von Natur aus weniger haltbar. Mit der richtigen Konstruktion und Fertigung können sie robuste, langlebige Komponenten sein, die für raue Industrieumgebungen geeignet sind.
F3: Können interne Kanäle für Luft, Vakuum oder Kühlung zuverlässig gedruckt und gereinigt werden?
A: Ja, dies ist einer der Hauptvorteile von Metall-AM. Interne Kanäle können zuverlässig gedruckt werden, aber der Erfolg hängt ab von:
- DfAM: Die Konstruktion von Kanälen mit selbsttragenden Winkeln (typischerweise >45° zur Horizontalen) minimiert die Notwendigkeit von internen Stützen, deren Entfernung sehr schwierig ist. Mindestdruckbare Kanalduchmesser-Grenzwerte müssen eingehalten werden (wenden Sie sich an Ihren AM-Anbieter). Glatte Biegungen sind scharfen Ecken vorzuziehen.
- Entfernung von Puder: Die Konstruktion von Zugangspunkten zur Entfernung von ungeschmolzenem Pulver nach dem Drucken ist entscheidend. Komplexe, gewundene Pfade können Pulver einschließen.
- Reinigung & Veredelung: Während die Pulverentfernung Standard ist, kann das Erreichen einer sehr glatten Innenoberfläche zusätzliche Verfahren wie Abrasivstrombearbeitung (AFM) oder Elektropolieren (für kompatible Materialien wie Edelstahl) erfordern, falls dies für einen optimalen Fluss oder Sauberkeit erforderlich ist.
- Schlussfolgerung: Zuverlässiges Drucken und grundlegende Pulverentfernung sind Standard. Das Erreichen bestimmter Innenoberflächenglätte- oder Sauberkeitsgrade erfordert eine sorgfältige Konstruktion und möglicherweise spezielle Nachbearbeitung.
F4: Ist der 3D-Metalldruck kosteneffektiv für die Herstellung von Robotergreifern?
A: Metall-AM ist unter bestimmten Umständen am kosteneffektivsten:
- Hohe Komplexität / Individualisierung: Wenn das Greiferdesign sehr komplex ist, interne Merkmale aufweist oder stark an ein bestimmtes Teil angepasst werden muss, vermeidet AM die hohen Werkzeugkosten und die Bearbeitungsherausforderungen herkömmlicher Methoden.
- Geringes bis mittleres Volumen: Für Einzelanfertigungen, Prototypen oder Kleinserien vermeidet AM die hohen Einrichtungs- und Werkzeugkosten, die mit Gießen oder Spritzgießen verbunden sind.
- Teil Konsolidierung: Wenn AM es Ihnen ermöglicht, mehrere Komponenten in einem einzigen Druck zu kombinieren, können die Einsparungen bei der Montagezeit, dem Lagerbestand und den potenziellen Fehlerpunkten die höheren Druckkosten pro Teil überwiegen.
- Leistungssteigerungen durch Gewichtsreduzierung: Wenn die durch AM erreichte Gewichtsreduzierung höhere Robotegeschwindigkeiten oder den Einsatz kleinerer Roboter ermöglicht, können die Betriebskosteneinsparungen höhere Komponenten kosten rechtfertigen.
- Wenn es weniger kosteneffektiv ist: Für sehr einfache Greiferdesigns, die in großen Mengen benötigt werden, werden herkömmliche CNC-Bearbeitung oder Gießen aufgrund der geringeren Stückkosten in großem Maßstab wahrscheinlich wirtschaftlicher bleiben.
- Schlussfolgerung: Bewerten Sie die Kosten basierend auf der Gesamtnutzenversprechen, einschließlich Designfreiheit, Leistungssteigerungen und Systemvereinfachung, nicht nur auf den Stückkosten für die Herstellung.
F5: Welche Informationen muss ich angeben, um ein genaues Angebot für einen 3D-gedruckten Greifer zu erhalten?
A: Um ein zeitnahes und genaues Angebot von einem Metall-AM-Dienstleister wie Met3dp zu erhalten, sollten Sie Folgendes angeben:
- 3D-CAD-Modell: Ein hochwertiges 3D-Modell, typischerweise im STEP-Format (.stp oder .step). Vermeiden Sie nach Möglichkeit Mesh-Dateien (wie STL) für die Angebotserstellung von Metallteilen, da ihnen die erforderliche präzise Geometrie fehlt.
- Spezifikation des Materials: Geben Sie die gewünschte Metalllegierung (z. B. 17-4PH, AlSi10Mg) und den erforderlichen Endzustand (z. B. Wärmebehandlungsspezifikation wie H900 für 17-4PH oder T6 für AlSi10Mg) deutlich an.
- Kritische Abmessungen und Toleranzen: Identifizieren Sie alle kritischen Abmessungen eindeutig und geben Sie die erforderlichen Toleranzen auf einer 2D-Zeichnung oder einem annotierten 3D-Modell an. Unterscheiden Sie zwischen den gedruckten und (falls erforderlich) nachbearbeiteten Toleranzen.
- Anforderungen an die Oberflächenbeschaffenheit: Geben Sie alle erforderlichen Oberflächenrauheitswerte (Ra) für das gesamte Teil oder bestimmte Merkmale an. Geben Sie Bereiche an, die poliert, strahlgestrahlt usw. werden müssen.
- Menge: Die Anzahl der benötigten Greifer (für diese Bestellung und die geschätzte jährliche Nutzung).
- Details zur Anwendung: Beschreiben Sie kurz die Funktion des Greifers, die Belastungen, denen er ausgesetzt ist, die Betriebsumgebung (Temperatur, Chemikalien) und alle kritischen Leistungsanforderungen. Dies hilft dem Anbieter, die Machbarkeit zu beurteilen und Optimierungen zu empfehlen.
- Post-Processing-Bedarf: Listen Sie alle erforderlichen Beschichtungen, spezifischen Inspektionskriterien oder Zertifizierungen auf.
Die Bereitstellung umfassender Informationen im Voraus ermöglicht es dem AM-Lieferant , die Fertigungsanforderungen genau zu beurteilen, die notwendigen Schritte zu planen und ein zuverlässiges Angebot und eine Vorlaufzeitschätzung abzugeben.
Fazit: Die Zukunft der Robotik, verbessert durch die additive Fertigung von Metallen
Die Integration der additiven Fertigung von Metallen in den Bereich der Robotik, insbesondere für kritische Komponenten wie Greifer, stellt einen bedeutenden Fortschritt dar. Wie wir untersucht haben, eröffnet das Überschreiten der Grenzen der traditionellen Fertigung eine neue Welt der Möglichkeiten für die Gestaltung von End-of-Arm-Werkzeugen, die stärker, leichter, komplexer und perfekt auf ihre spezifische Aufgabe zugeschnitten sind. Die Fähigkeit, hochfeste Materialien wie Edelstahl 17-4PH und Leichtmetalllegierungen wie AlSi10Mgzu nutzen, in Kombination mit der geometrischen Freiheit, die der 3D-Druck bietet, ermöglicht es Ingenieuren, Greifer zu erstellen, deren Herstellung zuvor unmöglich oder unpraktisch war.
Die wichtigsten Erkenntnisse sind klar: Metall-AM ermöglicht beispiellose Designfreiheit durch Topologieoptimierung und Integration interner Kanäle; erleichtert erhebliche Gewichtsreduzierung für schnellere, effizientere Roboteroperationen; ermöglicht schnelle Anpassung und Prototyping; ermöglicht Teilkonsolidierung für einfachere, robustere Baugruppen; und liefert Komponenten mit hervorragende mechanische Eigenschaften , die für anspruchsvolle Industrieumgebungen geeignet sind.
Um diese Vorteile zu realisieren, ist jedoch ein ganzheitlicher Ansatz erforderlich. Der Erfolg hängt davon ab, Design für additive Fertigung (DfAM) Prinzipien zu übernehmen, das geeignete Material sorgfältig auszuwählen, die notwendigen Nachbearbeitung Schritte zu verstehen und zu planen und vor allem das Richtige Metall-AM-Fertigungspartnerauszuwählen. Ein erfahrener Anbieter wie Met3dp bietet nicht nur Druckkapazität, sondern auch entscheidendes Fachwissen in Materialwissenschaft, Prozessoptimierung und Qualitätskontrolle, untermauert durch seine Fähigkeiten in der Herstellung von branchenführenden SEBM-Druckern und fortschrittlichen Metallpulvern.
Die Herausforderungen im Zusammenhang mit Präzision, Oberflächenbeschaffenheit und Prozesskontrolle werden durch technologische Fortschritte und ein strenges Qualitätsmanagement aktiv angegangen. Da sich Metall-AM weiterentwickelt, können wir mit einer noch breiteren Akzeptanz, neuen Materialinnovationen und einer tieferen Integration in automatisierte Systeme rechnen, wodurch die Fähigkeiten und die Effizienz der Robotik in den Bereichen Luft- und Raumfahrt, Automobil, Medizin und Industrie weiter verbessert werden.
Die Zukunft der Robotik ist untrennbar mit den Fortschritten in der Fertigungstechnologie verbunden. Der 3D-Metalldruck ist nicht länger ein Nischen-Prototyping-Werkzeug, sondern eine leistungsstarke Produktionsmethode, die in der Lage ist, Endanwendungs- und Hochleistungskomponenten wie Robotergreifer zu liefern, die Effizienz und Innovation vorantreiben.
Sind Sie bereit, zu erkunden, wie die additive Fertigung von Metallen Ihre Robotergreiferanwendungen revolutionieren kann? Kontaktieren Sie die Experten von Met3dp noch heute, um Ihre Projektanforderungen zu besprechen und zu erfahren, wie ihre umfassenden Metall-AM-Lösungen Ihnen helfen können, Ihre Automatisierungsziele zu erreichen.
Teilen auf
MET3DP Technology Co., LTD ist ein führender Anbieter von additiven Fertigungslösungen mit Hauptsitz in Qingdao, China. Unser Unternehmen ist spezialisiert auf 3D-Druckgeräte und Hochleistungsmetallpulver für industrielle Anwendungen.
Fragen Sie an, um den besten Preis und eine maßgeschneiderte Lösung für Ihr Unternehmen zu erhalten!
Verwandte Artikel
Über Met3DP
Aktuelles Update
Unser Produkt
KONTAKT US
Haben Sie Fragen? Senden Sie uns jetzt eine Nachricht! Wir werden Ihre Anfrage mit einem ganzen Team nach Erhalt Ihrer Nachricht bearbeiten.
Holen Sie sich Metal3DP's
Produkt-Broschüre
Erhalten Sie die neuesten Produkte und Preislisten
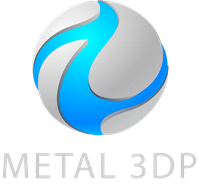
Metallpulver für 3D-Druck und additive Fertigung