Jet Engine Combustors via 3D Printed Superalloys: The Future of Aerospace Propulsion
Inhaltsübersicht
The relentless pursuit of higher performance, improved fuel efficiency, and reduced environmental impact defines the trajectory of the modern aerospace industry. At the heart of this quest lies the jet engine, a marvel of complex engineering operating under extreme conditions. Within the engine, the combustor plays a pivotal, defining role – it’s the furnace where chemical energy is converted into the thermal power that drives propulsion. The demands placed upon this single component are immense: scorching temperatures exceeding 1500∘C, intense pressures, highly corrosive environments, and relentless thermal cycling. For decades, manufacturing these critical components involved intricate, multi-stage processes using traditional techniques like casting, forging, and fabrication. While reliable, these methods often encountered limitations in geometric complexity, lead times, and material utilization, especially when dealing with the high-performance superalloys required to survive the combustor’s harsh reality.
Enter Additive Manufacturing (AM), commonly known as 3D-Druck. This transformative technology is rapidly reshaping the landscape of aerospace manufacturing, offering unprecedented design freedom and production agility. Specifically for jet engine combustors, metal AM enables the creation of highly intricate internal cooling channels, consolidated part designs, and optimized geometries that were previously impossible or prohibitively expensive to produce. By leveraging advanced superalloy powders like IN738LC and Haynes 282, engineered specifically for high-temperature strength and durability, AM allows engineers to push the boundaries of engine performance. This synergy between advanced materials and cutting-edge manufacturing processes promises lighter, more efficient, and potentially more reliable combustors, directly contributing to the next generation of aerospace propulsion systems.
Companies at the forefront of this technological shift, such as Met3dp, are crucial enablers. Specializing in both advanced metal AM systems, including Selective Electron Beam Melting (SEBM), and the production of high-quality, gas-atomized spherical metal powders, Met3dp provides the foundational elements required to successfully implement AM for mission-critical applications. Their expertise in materials science and powder manufacturing ensures that aerospace engineers and procurement managers have access to materials like IN738LC and Haynes 282 with the precise characteristics needed for demanding environments. As we delve deeper into the intricacies of 3D printed combustors, the advantages of this approach – from design innovation to supply chain efficiency – become increasingly clear, marking a significant step forward in aerospace engineering. This isn’t just an alternative manufacturing method; it’s a fundamental enabler for achieving future goals in thrust, efficiency, and sustainability.
The Critical Role of Combustors in Jet Engine Performance
The combustor, often referred to as the combustion chamber, is arguably the most critical component within the hot section of a gas turbine engine. Its primary function is fundamental yet immensely challenging: to efficiently burn large quantities of fuel with compressed air, releasing tremendous thermal energy in a controlled manner. This high-temperature, high-pressure gas stream is then directed towards the turbine section, providing the energy needed to drive both the turbine itself (which in turn drives the compressor) and ultimately generate thrust. The performance of the entire engine – its power output, fuel consumption, and emissions profile – is inextricably linked to the effectiveness and design integrity of the combustor.
Let’s break down the process and the associated challenges:
- Air Intake and Compression: Air enters the engine and is drawn into the compressor stages, where its pressure and temperature are significantly increased.
- Entry into Combustor: This highly compressed air flows into the combustor. A portion is directed into the primary combustion zone, while the rest is used for cooling the combustor walls and shaping the combustion process downstream.
- Kraftstoffeinspritzung: Precisely metered fuel is sprayed into the primary zone through specialized fuel nozzles, ensuring atomization for efficient mixing with the incoming compressed air.
- Ignition and Combustion: An ignition source (initially) starts the combustion process. The fuel-air mixture burns intensely, rapidly increasing the temperature of the gases to levels often exceeding 2000∘C locally, although bulk gas temperatures entering the turbine are typically managed to around 1500−1700∘C in modern engines.
- Mixing and Dilution: The extremely hot gases from the primary zone are mixed with the remaining compressor air (dilution and cooling air) flowing through intricate patterns of holes and slots in the combustor liner. This process serves two vital purposes:
- It cools the gas to a temperature that the downstream turbine blades can withstand.
- It ensures a relatively uniform temperature profile at the turbine inlet, preventing hot spots that could damage turbine components.
- Exhaust to Turbine: The resulting high-temperature, high-pressure gas stream exits the combustor and flows into the turbine section.
Operating Environment – A Crucible of Extremes:
The environment within a jet engine combustor is one of the harshest encountered in any engineered system:
- Extreme Temperaturen: Gas temperatures can locally exceed the melting point of many metals. The combustor liners themselves must survive sustained temperatures that challenge even the most advanced superalloys. Effective cooling is not just beneficial; it’s essential for survival.
- High Pressure: The combustion process occurs under significant pressure built up by the compressor stages. This pressure exerts substantial mechanical stress on the combustor structure.
- Thermal Cycling: Engines undergo frequent start-up, throttle adjustment, and shutdown cycles. This results in rapid temperature fluctuations, inducing thermal fatigue stresses that can lead to cracking over time.
- Oxidative and Corrosive Atmosphere: The combination of high temperatures and combustion byproducts (including potential contaminants from fuel or ingested air) creates a highly oxidative and corrosive environment, demanding materials with exceptional resistance.
- Vibrations and Acoustics: The turbulent combustion process and overall engine operation generate significant vibrations and acoustic loads that the structure must withstand.
Impact on Engine Performance Metrics:
The design and execution of the combustor directly influence key engine performance parameters sought after by aerospace manufacturers and operators:
- Combustion Efficiency: How completely is the fuel burned? Incomplete combustion wastes fuel (increasing specific fuel consumption – SFC) and produces harmful emissions like carbon monoxide (CO) and unburned hydrocarbons (UHCs). Modern combustors achieve efficiencies well over 99%.
- Temperature Profile (Pattern Factor): The uniformity of the gas temperature entering the turbine is critical. Hot spots can drastically reduce turbine blade life. A well-designed combustor minimizes these variations.
- Pressure Drop: While some pressure drop across the combustor is unavoidable, minimizing it is crucial for overall engine efficiency. Complex internal geometries needed for mixing and cooling must be carefully designed to avoid excessive pressure losses.
- Emissionen: Global environmental regulations strictly limit the emission of pollutants like oxides of nitrogen (NOx), CO, UHCs, and soot (smoke). Combustor design, particularly the stoichiometry and mixing in the primary zone and the residence time at high temperatures, is the primary determinant of these emissions. Lean-burn combustion strategies, often requiring complex fuel-air mixing schemes, are key to reducing NOx.
- Reliability and Durability: The combustor must maintain its structural integrity and performance over thousands of flight hours and cycles. Material selection, cooling effectiveness, and robust design are paramount for ensuring long service life and minimizing maintenance requirements for aerospace MRO providers.
- Operability: The combustor must ignite reliably across a range of altitudes and ambient conditions and maintain stable combustion without flameout during rapid throttle changes or maneuvers.
Understanding these critical functions and the brutal operating conditions underscores why combustor design and manufacturing are so challenging, and why advanced materials and manufacturing techniques like AM are becoming increasingly vital. The ability to precisely control geometry and utilize materials capable of withstanding these extremes is key to unlocking the next level of jet engine performance.
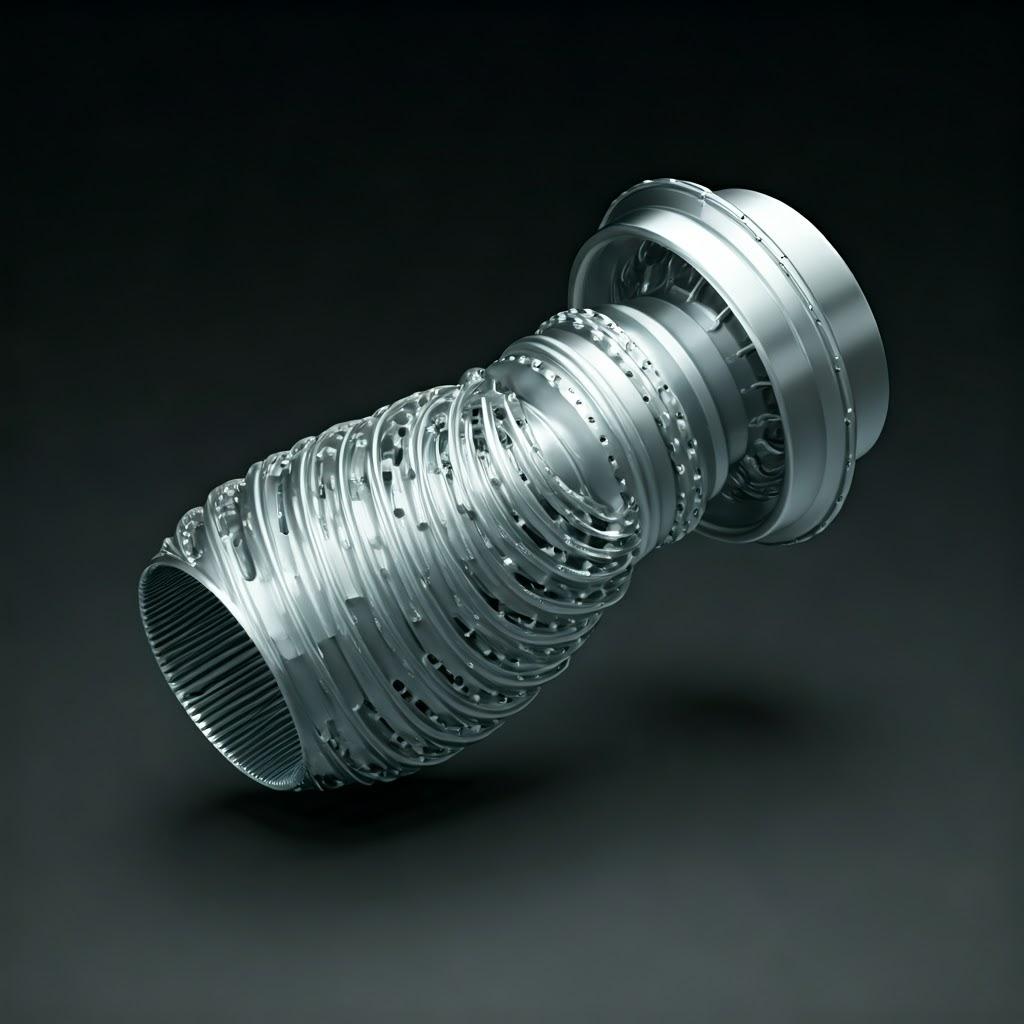
Why Aerospace Demands Additive Manufacturing for Combustor Production
The aerospace industry has always been at the forefront of adopting advanced manufacturing technologies, driven by stringent requirements for performance, safety, reliability, and weight reduction. While traditional manufacturing methods like investment casting, forging, CNC machining, and sheet metal fabrication have served the industry well for decades in producing combustor components, they inherently possess limitations that Additive Manufacturing (AM) can overcome. The complex operational demands of modern jet engine combustors – higher temperatures, better efficiency, lower emissions – necessitate designs that are increasingly intricate, pushing traditional methods to their limits. Metal AM, particularly powder bed fusion techniques like Selective Laser Melting (SLM) or Laser Powder Bed Fusion (L-PBF) and Selective Electron Beam Melting (SEBM), offers a compelling suite of advantages perfectly suited to these challenges, making it not just a viable alternative but often a superior choice for combustor production and development.
Limitations of Traditional Manufacturing for Combustors:
- Geometric Constraints: Investment casting, while capable of complex shapes, struggles with extremely fine, intricate internal passages needed for advanced cooling schemes (e.g., micro-channel cooling, complex effusion patterns). Creating these features often requires complex ceramic cores that are difficult to produce and remove. Machining internal features is often impossible. Fabricated sheet metal liners involve numerous welds, which act as potential stress concentration points and failure sites.
- Long Lead Times & High Tooling Costs: Creating molds for casting or dies for forging involves significant upfront investment and time. Design iterations become slow and expensive, hindering rapid development cycles crucial for staying competitive.
- Materialabfälle: Subtractive processes like CNC machining start with a larger block of material and remove excess, leading to significant waste (buy-to-fly ratio), especially costly with expensive superalloys. While casting is more efficient, it still requires downstream machining.
- Part Count & Assembly Complexity: Traditional combustors are often assemblies of multiple individually manufactured components (liners, domes, fuel nozzle interfaces, mounting bosses) joined by welding or brazing. Each joint represents a potential leak path or failure point and adds weight and assembly time.
- Design Iteration Barriers: The high cost and long lead times associated with tooling make engineers hesitant to explore truly radical design changes or perform numerous optimization iterations.
Advantages of Additive Manufacturing for Combustors:
Metal AM addresses these limitations directly, offering transformative benefits for aerospace component suppliers and engine manufacturers:
- Beispiellose Designfreiheit: This is arguably the most significant advantage. AM builds parts layer by layer, enabling the creation of geometries unachievable by other means:
- Highly Complex Internal Cooling Channels: Engineers can design intricate, optimized cooling networks, including conformal channels that follow the contour of the combustor walls, lattice structures for enhanced heat transfer and lightweighting, and precisely shaped effusion holes for superior film cooling. This allows for higher operating temperatures, boosting thermodynamic efficiency.
- Integrierte Funktionen: Fuel nozzle tips, swirlers, mounting brackets, and sensors can be integrated directly into the combustor body during the printing process.
- Topologie-Optimierung: Algorithms can be used to remove material from non-critical areas while maintaining structural integrity, leading to significant weight savings – a crucial factor in aerospace.
- Drastic Lead Time Reduction: AM eliminates the need for traditional tooling. Prototypes and design iterations can be produced in days or weeks, rather than months. This accelerates the development cycle, allowing engineers to test and refine designs much faster. For the Maintenance, Repair, and Overhaul (MRO) sector, AM enables on-demand printing of spare parts, reducing inventory costs and aircraft downtime. This directly addresses the need for aerospace component lead time reduction und supply chain optimization aerospace.
- Teil Konsolidierung: AM allows multiple components of a traditional assembly to be printed as a single, monolithic part. For a combustor, this could mean integrating the inner liner, outer liner, and dome into one piece. This offers several benefits:
- Reduziertes Gewicht: Eliminates flanges, fasteners, and weld material.
- Verbesserte Verlässlichkeit: Fewer joints mean fewer potential failure points.
- Simplified Assembly: Reduces assembly time and logistical complexity.
- Verbesserte Leistung: Eliminates leakage between traditionally separate components.
- Verbesserte Materialausnutzung: AM is an additive process, building parts layer by layer using only the necessary material. While some support structures are often required and subsequently removed, the overall material waste (buy-to-fly ratio) is typically much lower than subtractive machining, representing significant cost savings for expensive superalloys like IN738LC and Haynes 282. Unused powder in the build chamber can often be recycled and reused, further enhancing sustainability.
- Enhanced Performance Potential: The combination of optimized cooling, reduced weight, and potentially novel combustion features enabled by AM’s design freedom can lead to tangible performance gains: higher thrust-to-weight ratios, lower specific fuel consumption (SFC), and reduced emissions through more effective fuel-air mixing and temperature control.
Leveraging Expertise for AM Success:
Achieving these benefits requires not only the right equipment but also deep expertise in materials science, process parameter optimization, and post-processing. Companies like Met3dp play a vital role by providing both high-performance AM systems, such as their SEBM printers known for producing parts with low residual stress, and crucially, the high-quality metal powders essential for reliable and repeatable results. Their understanding of powder characteristics and how they interact with the AM process ensures that the superalloys used retain their desired properties in the final printed component. The transition to AM for critical parts like combustors necessitates collaboration with knowledgeable partners who understand the nuances of the technology and the demanding requirements of the aerospace industry. The compelling advantages – from faster innovation cycles driven by schneller Prototypenbau to superior performing, lighter components achieved through Herstellung komplexer Geometrien – solidify AM’s position as a cornerstone technology for the future of jet engine combustor production.
IN738LC & Haynes 282: Superalloy Powders Engineered for Extreme Environments
The selection of materials for jet engine combustors is dictated by the extreme operating conditions: temperatures routinely exceeding 1000∘C (with gas temperatures far higher), significant mechanical stresses from pressure and vibration, thermal fatigue from cycling, and a highly oxidative/corrosive environment. Only a select class of materials, known as superalloys, possess the necessary combination of properties to survive and perform reliably under such duress. Traditionally, these components were made from cast or wrought nickel-based or cobalt-based superalloys. With the advent of Additive Manufacturing, the focus shifts to developing and utilizing powder forms of these high-performance alloys, specifically optimized for processes like Laser Powder Bed Fusion (L-PBF) and Selective Electron Beam Melting (SEBM). Among the leading candidates for 3D printed combustors are IN738LC and Haynes 282, each offering a unique blend of characteristics highly desirable for this demanding application. Sourcing these materials from reputable metal powder suppliers aerospace ensures quality and consistency.
What are Superalloys?
Superalloys are metallic alloys, typically based on nickel (Ni), cobalt (Co), or nickel-iron (Ni-Fe), designed to exhibit exceptional mechanical strength, resistance to thermal creep deformation, good surface stability (oxidation and corrosion resistance), and fatigue life, particularly at elevated temperatures (typically above 650∘C or 1200∘F). Their remarkable properties derive from complex chemistries and carefully controlled microstructures, often featuring:
- A Face-Centered Cubic (FCC) Austenite Matrix: Provides good baseline ductility and toughness.
- Verstärkung der Niederschläge: Formation of finely dispersed secondary phases, such as gamma prime (γ′) [Ni$_3$(Al,Ti)] in nickel-based alloys, which impede dislocation movement, thereby increasing strength, especially at high temperatures.
- Solid Solution Strengthening: Alloying elements like Molybdenum (Mo), Tungsten (W), Rhenium (Re), and Cobalt (Co) dissolve into the matrix, distorting the crystal lattice and hindering dislocation motion.
- Grain Boundary Strengthening: Elements like Boron (B), Zirconium (Zr), and Hafnium (Hf) segregate to grain boundaries, improving creep resistance and ductility by strengthening these interfaces.
- Oxidation/Corrosion Resistance: Elements like Chromium (Cr) and Aluminum (Al) form protective oxide scales (e.g., Cr2O3, Al2O3) on the surface, shielding the alloy from the harsh environment.
IN738LC: The Established High-Temperature Performer
IN738LC (Low Carbon variant of Inconel 738) is a vacuum-cast, precipitation-hardenable nickel-based superalloy that has long been a workhorse material for turbine blades and other hot-section components in industrial and aero gas turbines, primarily produced via investment casting. Its reputation is built on an excellent combination of high-temperature strength, creep resistance, and particularly strong hot corrosion resistance, making it inherently suitable for the conditions within a combustor.
- Compositional Highlights (Nominal wt%): Ni (Balance), Cr (16%), Co (8.5%), Mo (1.7%), W (2.6%), Ta (1.7%), Nb (0.9%), Al (3.4%), Ti (3.4%), C (0.10%), B (0.01%), Zr (0.05%).
- Key Properties & Benefits for Combustors:
- Excellent Creep Strength: Resists deformation under sustained load at high temperatures (up to approx. 980∘C). This is critical for maintaining the shape and integrity of the combustor liner over long operational periods.
- Superior Hot Corrosion Resistance: High Chromium content provides excellent resistance to sulfidation and other forms of corrosion caused by combustion byproducts and contaminants, a common degradation mechanism in combustors.
- Gute Oxidationsbeständigkeit: Forms a protective oxide scale.
- Hohe Festigkeit: Strengthened primarily by the γ′ phase.
- AM Überlegungen: IN738LC was originally developed for casting, and its high γ′ content and complex composition can make it susceptible to solidification cracking and micro-segregation during the rapid heating/cooling cycles inherent in AM processes like L-PBF. Producing high-quality, crack-free IN738LC parts via AM requires careful optimization of process parameters (laser power, scan speed, layer thickness, pre-heating) and potentially post-processing like Hot Isostatic Pressing (HIP) to close internal porosity and homogenize the microstructure. The quality of the starting powder – its chemistry, Particle Size Distribution (PSD), flowability, and low presence of detrimental satellite particles – is paramount for processability.
Haynes 282: Designed for Strength and Fabricability
Haynes 282 is a newer generation, precipitation-strengthened nickel-based superalloy specifically developed to offer an exceptional combination of creep strength, thermal stability, good weldability, and fabricability – characteristics that make it particularly attractive for AM. Its development aimed to bridge the gap between alloys with excellent strength but poor fabricability and those with good fabricability but lower strength capabilities.
- Compositional Highlights (Nominal wt%): Ni (Balance), Cr (19.5%), Co (10%), Mo (8.5%), Ti (2.1%), Al (1.5%), C (0.06%), B (0.005%), Mn (0.3%), Si (0.15%).
- Key Properties & Benefits for Combustors:
- Outstanding Creep Strength: Offers creep strength exceeding that of alloys like Waspaloy and approaching that of R-41, making it suitable for very demanding high-temperature structural applications.
- Excellent Fabricability/Weldability: Compared to other superalloys of similar strength (like Waspaloy or R-41), Haynes 282 exhibits significantly better resistance to strain-age cracking (a common issue during welding or post-weld heat treatment), which translates to improved processability during AM. This reduces the risk of cracking during the layer-by-layer build process.
- Good Thermal Stability: Resists the formation of detrimental phases during long exposures at high temperatures.
- Very Good Oxidation Resistance: High Cr and presence of Al ensure formation of a protective scale.
- AM Überlegungen: Haynes 282’s enhanced fabricability makes it inherently more suitable for AM processes compared to notoriously difficult-to-process alloys like IN738LC or CM247LC. It generally exhibits a wider processing window and lower susceptibility to defects like solidification cracking. This makes it a prime candidate for complex AM components like combustors, potentially requiring less stringent process control or simpler post-processing routes compared to IN738LC, while still delivering exceptional high-temperature mechanical properties.
The Critical Role of Powder Quality
Regardless of the chosen alloy, the success of producing high-integrity 3D printed combustors hinges critically on the quality of the metal powder feedstock. Key powder characteristics significantly influence the AM process and the final part’s properties:
- Sphärizität: Highly spherical powder particles ensure good flowability and high packing density in the powder bed. This leads to more uniform energy absorption during melting, stable melt pool dynamics, and lower porosity in the final part.
- Fließfähigkeit: Dictates how easily and uniformly the powder spreads across the build platform in thin layers. Poor flowability can lead to uneven layers, voids, and process interruptions.
- Partikelgrößenverteilung (PSD): The range and distribution of particle sizes affect packing density and melt behavior. A controlled PSD, optimized for the specific AM machine (e.g., L-PBF typically uses finer powders than SEBM), is crucial.
- Reinheit und Chemie: The powder must meet the exact chemical specifications of the alloy standard. Impurities (like oxygen, nitrogen) or deviations in alloying elements can degrade mechanical properties and corrosion resistance. Low levels of entrapped gas (e.g., Argon from atomization) are also important.
- Niedriger Satellitengehalt: Satellites are smaller particles attached to larger ones, which can hinder flowability and packing density.
Met3dp’s Contribution to Material Excellence:
This is where specialized powder manufacturers like Met3dp add significant value. Utilizing advanced production techniques such as Vacuum Induction Melting Gas Atomization (VIGA) and Plasma Rotating Electrode Process (PREP), Met3dp engineers metal powders with characteristics optimized for AM:
- High Sphericity & Flowability: Their unique gas atomization nozzle and gas flow designs promote the formation of highly spherical particles with minimal satellites, ensuring excellent processability.
- Controlled PSD: Precise sieving and classification allow tailoring the PSD to customer requirements and specific AM systems.
- Hohe Reinheit: Strict process controls minimize contamination, ensuring the chemical integrity of alloys like IN738LC and Haynes 282.
- Broad Portfolio: Met3dp manufactures a wide range of hochwertige Metallpulver, including standard superalloys and innovative custom compositions, catering to diverse industrial needs.
By ensuring a supply of high-quality, consistent superalloy powders like IN738LC and Haynes 282, Met3dp empowers aerospace manufacturers to fully leverage the benefits of AM for producing next-generation jet engine combustors with enhanced performance and reliability. The choice between IN738LC and Haynes 282 will depend on the specific balance of required properties (creep, corrosion, fabricability) and the maturity of the AM process parameters for each alloy.
Table: Comparison of IN738LC and Haynes 282 for AM Combustors
Merkmal | IN738LC | Haynes 282 | Significance for Combustors |
---|---|---|---|
Primary Strengths | Excellent Hot Corrosion Resistance, Good Creep | Excellent Creep Strength, Excellent Fabricability | Both offer high-temp strength; IN738LC excels in corrosive environments, H282 excels in AM ease |
Kriechfestigkeit | Very Good (up to ~980°C) | Excellent (Comparable to R-41 in some regimes) | Critical for maintaining structural integrity under sustained high-temperature load. |
Hot Corrosion Resist. | Excellent (High Cr) | Good to Very Good | Resists degradation from fuel impurities/combustion byproducts. Important for longevity. |
Oxidation Resist. | Gut | Sehr gut | Protects against high-temperature reaction with oxygen. |
AM Verarbeitbarkeit | Challenging (Prone to cracking) | Excellent (Designed for fabricability/weldability) | Impacts ease of printing complex geometries, defect rates, and process window robustness. |
Typical AM Method | L-PBF (with care), potentially SEBM | L-PBF, SEBM | H282 offers more flexibility in process choice and parameter optimization. |
Strengthening Phase | γ′ (High Volume Fraction) | γ′ (Moderate Volume Fraction) | γ′ provides high-temperature strength; higher volume fraction can reduce weldability. |
Development Era | 1960s (Casting focused) | 2000s (Fabricability considered) | H282 benefits from decades of alloy design knowledge aimed at improving manufacturability. |
In Blätter exportieren
This table provides a high-level comparison. The optimal choice requires detailed analysis of the specific combustor design, operating conditions, and the manufacturer’s qualified AM processes and post-processing capabilities. Partnering with material experts and AM service providers like Met3dp is crucial for making the right selection and ensuring successful implementation.
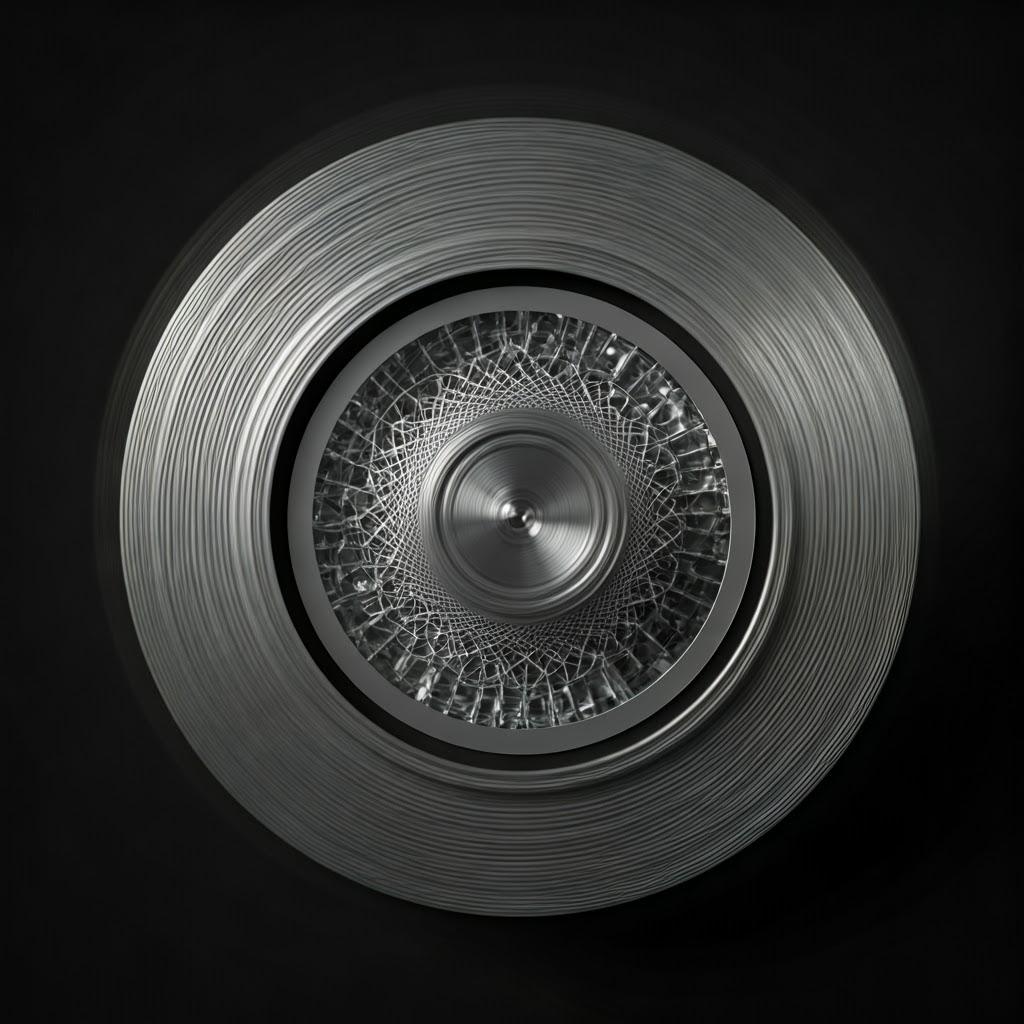
Design for Additive Manufacturing (DfAM) Strategies for Optimal Combustor Performance
Simply replicating a traditionally manufactured combustor design using Additive Manufacturing often fails to capture the true potential of the technology. The real revolution lies in rethinking the design from the ground up, leveraging the unique capabilities of AM. This approach is known as Design for Additive Manufacturing (DfAM). Unlike traditional Design for Manufacturing (DfM), which focuses on optimizing designs for processes like casting, machining, or forming, DfAM encourages engineers to exploit the layer-by-layer nature of AM to create parts with enhanced functionality, reduced weight, and consolidated complexity – features previously unattainable. For jet engine combustors operating in extreme conditions, DfAM is not just an optimization strategy; it’s a critical enabler for achieving next-generation performance targets in efficiency, emissions, and durability. Implementing effective DfAM aerospace components strategies requires a shift in mindset and the utilization of advanced design tools.
Core DfAM Principles Applied to Combustors:
- Exploiting Geometric Freedom for Thermal Management: This is perhaps the most impactful application of DfAM in combustors. AM allows the creation of highly sophisticated cooling schemes far beyond the limitations of drilled holes or cast passages:
- Konforme Kühlkanäle: Channels that precisely follow the complex contours of the combustor liner walls, maintaining an optimal distance for efficient heat extraction exactly where needed. This contrasts with traditional straight-drilled channels that result in uneven cooling.
- Micro-Channel and Fin Structures: Integrating extremely fine channels or internal fins directly into the walls to dramatically increase the surface area for heat transfer, allowing for more effective cooling with potentially less cooling air bleed from the compressor (improving engine efficiency).
- Lattice Structures and TPMS: Utilizing engineered porous structures, such as Triply Periodic Minimal Surfaces (TPMS) like gyroids or Schwarzites, within the combustor walls. These structures offer high surface area-to-volume ratios, promoting convective heat transfer while maintaining structural integrity and potentially reducing weight. They can create complex, tortuous paths for cooling air, maximizing heat absorption. The use of lattice structures cooling is a hallmark of advanced DfAM.
- Optimized Effusion Cooling Holes: Moving beyond simple cylindrical holes, AM allows for precisely shaped effusion holes (e.g., fan-shaped, laidback) designed using computational fluid dynamics (CFD) to improve the spread and effectiveness of the cooling air film along the liner surface, providing better protection with less air.
- Part Consolidation for Simplification and Reliability: As mentioned previously, AM enables the integration of multiple traditionally separate components into a single, monolithic printed part. For a combustor, this could involve:
- Printing the inner liner, outer liner, and combustor dome as one unit.
- Integrating fuel nozzle guide vanes or swirlers directly into the dome structure.
- Incorporating mounting bosses, brackets, or flanges into the main body. This consolidation drastically reduces part count, eliminates failure-prone joints (welds, brazes), simplifies assembly logistics, reduces sealing requirements, and often lowers overall weight.
- Topologie-Optimierung für Lightweighting: Aerospace applications perpetually demand weight reduction to improve fuel efficiency and payload capacity. DfAM enables the use of topology optimization software. Engineers define load cases, boundary conditions, and performance targets (e.g., stiffness); the software then iteratively removes material from areas where it doesn’t contribute significantly to structural performance, resulting in highly organic, load-path-optimized shapes that are significantly lighter than traditional designs while meeting or exceeding structural requirements. Applying topology optimization combustor techniques can yield substantial weight savings.
- Designing for Manufacturability (AM Context): While AM offers immense freedom, it still has constraints that must be considered during design:
- Unterstützende Strukturen: Powder Bed Fusion (PBF) processes typically require support structures for overhanging features (usually below 45 degrees from the horizontal) and to conduct heat away from the melt zone. DfAM involves designing parts to be self-supporting where possible (using angles >45∘), minimizing the volume of supports needed, and designing supports that are easily accessible and removable without damaging critical surfaces. Sometimes, supports can even be designed as functional lattice structures that remain part of the final component. Effective support structure design AM is crucial for cost-effective production.
- Orientierung aufbauen: The orientation of the part on the build plate significantly impacts build time, support requirements, surface finish (especially stair-stepping on curved surfaces), residual stresses, and potentially anisotropic mechanical properties. DfAM includes considering the optimal orientation early in the design phase.
- Merkmal Auflösung: AM processes have limitations on the minimum wall thickness, hole diameter, and feature size they can reliably produce. Designs must respect these limits, which depend on the specific machine and material.
- Merkmal Integration: Beyond structural elements, DfAM allows for the integration of functional features like optimized mixing channels for fuel and air, pathways for sensors, or textured surfaces to enhance heat transfer or flow characteristics.
Tools and Workflow:
Effective DfAM relies heavily on advanced software tools integrated into the design workflow:
- CAD Software: Modern CAD platforms increasingly incorporate DfAM-specific features, including lattice generation tools and topology optimization modules.
- Simulation Software (FEA/CFD): Finite Element Analysis (FEA) is used to predict structural and thermal performance under load, guiding topology optimization and validating design integrity. Computational Fluid Dynamics (CFD) is essential for simulating internal flows, combustion processes, and cooling effectiveness, allowing engineers to optimize channel designs and effusion patterns before printing. This simulation-driven design approach minimizes costly physical trial-and-error.
- Build Preparation Software: Software used to slice the CAD model into layers, generate scan paths for the laser or electron beam, and create support structures. Understanding the capabilities and limitations of this software is part of the DfAM process.
Successfully implementing these DfAM strategies requires expertise not only in design principles but also in the nuances of the chosen AM process (L-PBF, SEBM) and the behavior of the selected superalloy (IN738LC, Haynes 282). The ability to realize these intricate, optimized designs relies fundamentally on the precision and reliability of the additive manufacturing system and the quality consistency of the feedstock powder. High-end systems and powders, like those developed by specialists such as Met3dp, provide the necessary foundation of accuracy and material integrity, enabling engineers to confidently push the boundaries of combustor design and unlock significant performance improvements for the next generation of jet engines.
Achieving Precision: Tolerance, Surface Finish, and Accuracy in 3D Printed Combustors
While Additive Manufacturing unlocks unparalleled design freedom, engineers and procurement managers must have realistic expectations regarding the dimensional accuracy, tolerances, and surface finish achievable directly from the AM process, especially when dealing with high-performance superalloys like IN738LC and Haynes 282. Understanding these aspects is crucial for determining necessary post-processing steps, ensuring proper assembly fit, and meeting the stringent functional requirements of jet engine combustors. While AM technology is continuously improving, achieving the ultra-high precision associated with finish machining often requires secondary operations. Sourcing from a precision manufacturing supplier with strong AM capabilities and metrology is key.
Maßgenauigkeit und Toleranzen:
- Definition: Dimensional accuracy refers to how closely the printed part conforms to the nominal dimensions specified in the CAD model. Tolerance is the permissible range of variation for a given dimension.
- Typical Achievable Tolerances: Metal AM processes like L-PBF and SEBM can typically achieve dimensional tolerances in the range of ±0.1 mm to ±0.3 mm (±0.004 in to ±0.012 in) for smaller features, with potentially larger deviations (e.g., ±0.5 mm or ±0.2%) over larger dimensions. However, these are general guidelines, and achievable tolerances are highly dependent on several factors:
- Kalibrierung und Zustand der Maschine: Regular calibration and maintenance are critical.
- Materialeigenschaften: Thermal expansion and contraction behavior of the specific superalloy.
- Geometrie und Größe des Teils: Large or complex parts are more prone to thermal distortion.
- Orientierung aufbauen: Can affect thermal stresses and resulting warpage.
- Wärmemanagement: Effectiveness of build plate heating (inherent in SEBM) or process temperature control.
- Scan-Strategie: The pattern used by the laser/electron beam affects heat input and stress buildup.
- Nachbearbeiten: Stress relief and HIP can sometimes cause minor dimensional changes.
- Vergleich: As-built AM tolerances are generally looser than those achievable with multi-axis CNC machining but can be comparable to or better than investment casting for certain features.
- Meeting Requirements: For critical interfaces, sealing surfaces, or features requiring very tight tolerances (e.g., < ±0.05 mm), post-process machining is almost always necessary. DfAM principles should account for adding machining stock in these specific areas. Dimensional accuracy 3D printing capabilities should be clearly specified and verified by the AM provider.
Oberflächengüte (Rauhigkeit):
- Inherent Nature: The layer-by-layer construction and the use of powder feedstock result in an inherent surface roughness on as-built AM parts. This is caused by partially melted powder particles adhering to the surface and the “stair-stepping” effect on surfaces angled relative to the build direction.
- Messung: Surface roughness is typically quantified using parameters like Ra (average roughness) or Rz (average maximum height of the profile).
- Typische Werte:
- L-PBF: As-built Ra values often range from 6 µm to 20 µm (240 µin to 800 µin), depending on material, parameters, and surface orientation (up-facing vs. down-facing vs. vertical walls). Down-facing surfaces supported by powder typically exhibit higher roughness.
- SEBM: Due to the higher processing temperatures and different melt pool dynamics, SEBM parts often exhibit a smoother as-built surface finish compared to L-PBF, potentially in the Ra 10 µm to 35 µm range, although this can vary significantly. Surface morphology can also appear different.
- Significance for Combustors:
- Aerodynamics: Roughness inside cooling passages or effusion holes can increase pressure drop and reduce cooling effectiveness. Smooth internal surfaces are often desirable.
- Müdigkeit Leben: Surface roughness can act as initiation sites for fatigue cracks, particularly under high cyclic loading. Smoother finishes generally improve fatigue performance.
- Wärmeübertragung: Surface roughness can influence convective heat transfer coefficients.
- Versiegeln von Oberflächen: Rough surfaces are unsuitable for creating effective seals.
- Improvement: Various post-processing techniques (discussed in the next section) are used to improve the as-built surface finish when required by the application. Surface finish standards aerospace often dictate specific requirements for different component zones.
Qualitätskontrolle und -überprüfung:
Ensuring that 3D printed combustors meet the required precision is paramount for safety and performance. A robust quality control process is essential:
- Prozessbegleitende Überwachung: Advanced AM systems incorporate sensors to monitor aspects like melt pool temperature, layer deposition, and thermal conditions during the build, helping to detect anomalies in real-time.
- Post-Build Metrology:
- Coordinate Measuring Machines (CMMs): Provide high-accuracy dimensional measurements of specific features.
- 3D Scanning (Laser or Structured Light): Capture the full geometry of the part, allowing comparison to the original CAD model and verification of overall form and complex surfaces.
- Zerstörungsfreie Prüfung (NDT): Crucial for verifying internal integrity, especially for critical components:
- Computertomographie (CT) Scannen: Provides detailed 3D X-ray images, allowing inspection of internal channels, detection of porosity or inclusions, and verification of wall thicknesses without destroying the part. This is invaluable for validating complex DfAM features. NDT aerospace protocols are rigorously applied.
- Fluoreszierende Eindringprüfung (FPI): Used to detect surface-breaking cracks or defects.
- Ultraschallprüfung (UT): Can be used for detecting subsurface flaws.
Achieving the required precision for demanding applications like jet engine combustors requires a holistic approach, combining careful DfAM, optimized AM processing, appropriate post-processing, and rigorous quality control AM parts methodologies. Collaboration with an experienced AM service provider equipped with advanced metrology and NDT capabilities is essential for validating that the final components meet all specifications.
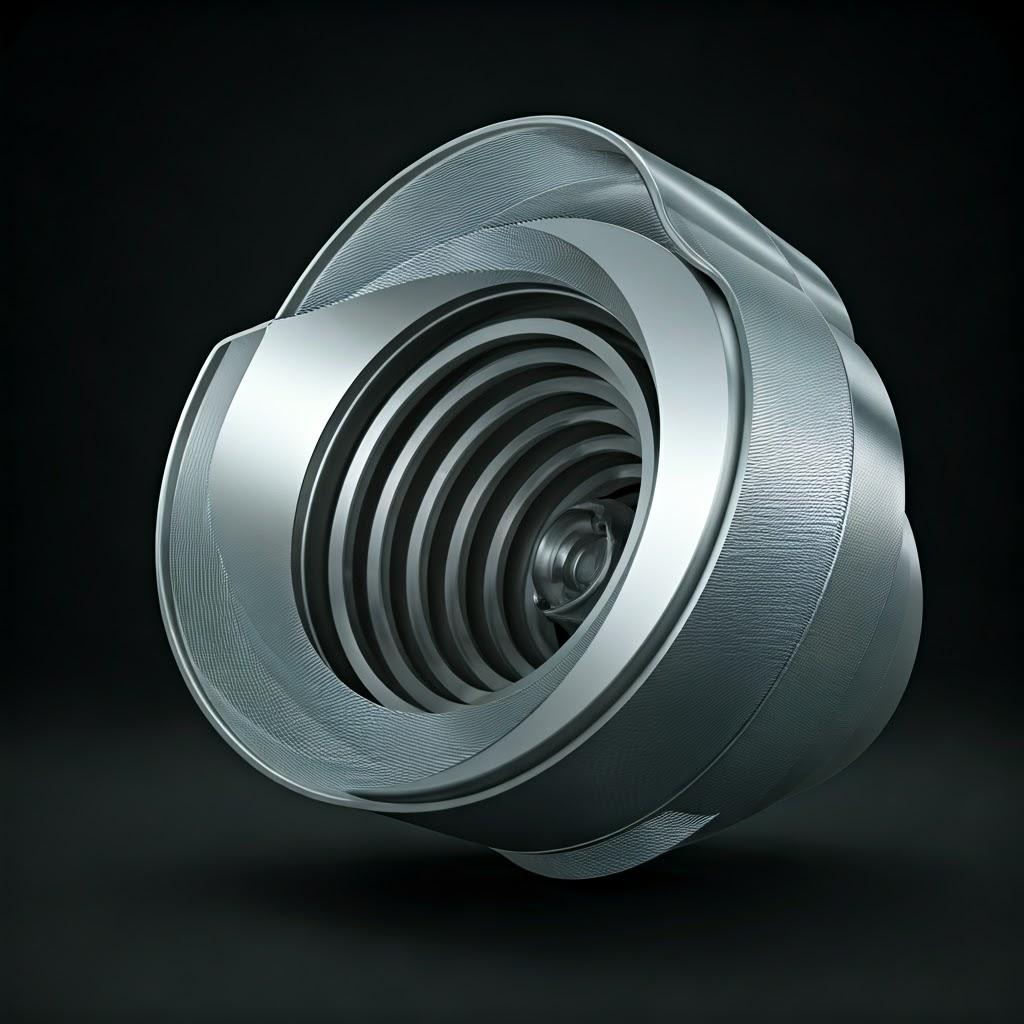
Essential Post-Processing Steps for Mission-Critical Combustor Components
Producing a jet engine combustor using Additive Manufacturing is rarely a single-step process. The “as-built” part emerging from the L-PBF or SEBM machine, while geometrically complex, typically requires a series of carefully controlled post-processing steps to achieve the necessary material properties, dimensional tolerances, surface finish, and overall integrity demanded by this critical aerospace application. These steps are not merely finishing touches; they are integral parts of the manufacturing workflow, essential for transforming the raw AM part into a flight-worthy component. Engaging with an AM supplier offering comprehensive post-processing services AM ist entscheidend für den Erfolg.
Common Post-Processing Workflow for AM Superalloy Combustors:
- Stressabbau:
- Zweck: To relax the internal residual stresses induced during the rapid heating and cooling cycles of the AM process, particularly significant in L-PBF. High residual stress can lead to distortion during or after the build, cracking, and reduced fatigue life.
- Methode: Typically involves heating the part to a specific temperature (below the aging temperature range) for a set duration, followed by controlled cooling. This is often performed while the part is still attached to the build plate to minimize warpage. SEBM parts generally have lower residual stress due to the high, uniform build chamber temperature, but stress relief may still be beneficial or required depending on the alloy and part complexity.
- Entfernen des Teils von der Bauplatte:
- Zweck: To separate the printed component(s) from the base plate they were built upon.
- Methode: Commonly done using wire Electrical Discharge Machining (EDM) or band sawing. Care must be taken to avoid damaging the part.
- Entfernung der Stützstruktur:
- Zweck: To remove the temporary structures generated during the build to support overhanging features and facilitate heat transfer.
- Methode: Can range from manual breaking and grinding (for accessible supports) to more precise methods like CNC machining or potentially electrochemical machining for internal or delicate supports. This step can be labor-intensive and requires careful execution. DfAM strategies aim to minimize and simplify support removal.
- Heat Treatment (Solution Annealing & Aging):
- Zweck: This is arguably the most critical post-processing step for achieving the target mechanical properties (strength, creep resistance, ductility) in precipitation-hardenable superalloys like IN738LC and Haynes 282. The as-built microstructure is often non-optimal.
- Methode: Typically involves a multi-stage process:
- Lösungsglühen: Heating the part to a high temperature (e.g., 1120−1200∘C) to dissolve existing precipitates and homogenize the microstructure, followed by rapid cooling (quenching).
- Aging Treatment(s): Heating the part to one or more intermediate temperatures (e.g., 760−900∘C) for specific durations to precipitate the strengthening phases (like γ′) in a controlled size and distribution. The exact cycles are alloy-specific and critical for performance. Heat treatment superalloys requires precise furnace control and adherence to specifications.
- Heiß-Isostatisches Pressen (HIP):
- Zweck: To eliminate internal microporosity (both gas porosity and lack-of-fusion voids) that can remain after the AM process. Densification improves fatigue life, ductility, and overall material integrity, which is often mandatory for critical rotating or structural aerospace parts.
- Methode: The part is subjected to high temperature (typically near the solution annealing temperature) and high inert gas pressure (e.g., 100-200 MPa or 15-30 ksi) simultaneously in a specialized HIP vessel. The pressure collapses internal voids, diffusion bonding the material across the pore interfaces. HIPing aerospace parts is a standard step for highest quality components.
- Oberflächenveredelung / Glättung:
- Zweck: To reduce the as-built surface roughness (Ra) for improved aerodynamic performance, fatigue life, or cleanability.
- Methode: Various techniques can be employed depending on the required finish and accessibility:
- Abrasive Blasting (Grit/Bead Blasting): Cleans surfaces and provides a uniform matte finish.
- Shot Peening: Imparts compressive residual stresses on the surface to improve fatigue life, often used after final machining.
- Taumeln / Vibrationsgleitschleifen: Uses abrasive media in a tumbling barrel or vibratory bowl to smooth external surfaces and edges.
- Electrochemical Polishing (Electropolishing): An electrochemical process that preferentially removes material from peaks, resulting in a very smooth and clean surface, effective even for complex geometries.
- Abrasive Fließbearbeitung (AFM): Forces abrasive-laden putty through internal passages to smooth them.
- Manuelles Schleifen/Polieren: For specific areas requiring high finish or defect removal. Surface treatment aerospace requirements often drive the selection of method.
- CNC-Bearbeitung:
- Zweck: To achieve tight tolerances, critical dimensions, specific surface finishes, or geometric features (e.g., threaded holes, O-ring grooves, mating flanges) that cannot be produced accurately enough by the AM process alone.
- Methode: Utilizes traditional multi-axis CNC milling or turning centers. Machining stock must be included in the DfAM design for these features. CNC-Bearbeitung von 3D-Drucken requires careful fixture design and awareness of the potentially different machinability of AM materials compared to their wrought/cast counterparts.
- Application of Coatings:
- Zweck: To provide additional protection against the extreme temperatures and corrosive environment within the combustor.
- Methode:
- Wärmedämmschichten (TBCs): Ceramic coatings (typically Yttria-Stabilized Zirconia – YSZ) applied over a metallic bond coat. They provide thermal insulation, reducing the temperature experienced by the underlying superalloy substrate, allowing for higher gas temperatures or extending part life.
- Environmental Barrier Coatings (EBCs): Similar concept but designed to protect against steam and combustion byproducts, especially relevant for advanced engine designs or ceramic matrix composite (CMC) components, but also used on superalloys. Application methods include plasma spray or electron beam physical vapor deposition (EB-PVD). Coating technologies turbine components are essential for maximizing performance and durability.
- Final Inspection and Cleaning:
- Zweck: To verify all dimensions and features are within specification after all processing steps and to ensure the part is free from contaminants before assembly.
- Methode: Includes final dimensional checks (CMM, scanning), NDT (FPI, CT if required), visual inspection, and specialized cleaning procedures.
This comprehensive sequence highlights that producing a functional, reliable 3D printed combustor involves a significant amount of post-processing expertise, specialized equipment, and rigorous quality control, extending far beyond the initial printing stage.
Overcoming Challenges in Superalloy Additive Manufacturing for Combustors
While the potential benefits of using AM for jet engine combustors are substantial, manufacturing these complex components from demanding superalloys like IN738LC and Haynes 282 using processes like L-PBF and SEBM is not without its challenges. These materials are inherently difficult to work with due to their high strength at elevated temperatures and complex metallurgy. The rapid solidification and thermal gradients inherent in AM can exacerbate these difficulties. Successfully producing high-integrity combustors requires a deep understanding of these potential issues and the implementation of effective mitigation strategies, often involving close collaboration between designers, materials scientists, and manufacturing engineers. Accessing detailed information on Metal 3D Printing methods can provide further context on process specifics.
Gemeinsame Herausforderungen und Abhilfestrategien:
- Eigenspannung, Verformung und Verzerrung:
- Herausforderung: The intense, localized heating from the laser or electron beam followed by rapid cooling creates steep thermal gradients within the part and between the part and the build plate. This leads to the buildup of internal residual stresses. If these stresses exceed the material’s yield strength at temperature, they can cause warping or distortion during the build, cracking upon cooling, or distortion after removal from the build plate.
- Milderung:
- Optimierte Scan-Strategien: Using techniques like island scanning, sector scanning, or rotating scan vectors between layers helps distribute heat more evenly and reduce long-range stress buildup.
- Build Plate Heating: Pre-heating the build plate (common in L-PBF, inherent and higher temp in SEBM) reduces thermal gradients between the part and the plate, lowering stress. SEBM’s high-temperature environment (>600∘C) significantly reduces residual stress compared to L-PBF.
- Robuste Stützstrukturen: Well-designed supports anchor the part firmly to the build plate, resisting warpage, and also help conduct heat away efficiently.
- Stressabbau nach der Bauphase: Performing a thermal stress relief cycle before removing the part from the build plate is crucial, especially for L-PBF parts.
- Simulation: Using process simulation software to predict stress accumulation and distortion, allowing for pre-compensation in the design or optimization of build parameters. Effective residual stress management is key. Addressing warping distortion AM requires a multi-faceted approach.
- Cracking (Solidification and Solid-State):
- Herausforderung: Superalloys, particularly high γ′ content alloys like IN738LC, can be susceptible to cracking during AM.
- Erstarrungsrisse: Occurs in the melt pool or during the final stages of solidification due to thermal stresses acting on the weak, semi-solid material. Impurities segregating to grain boundaries can exacerbate this.
- Solid-State Cracking (e.g., Strain Age Cracking): Can occur during cooling or subsequent heat treatments (like welding or aging) due to precipitation effects combined with residual stresses. Haynes 282 was specifically designed for improved resistance to this compared to alloys like Waspaloy.
- Milderung:
- Auswahl der Legierung: Choosing alloys with better inherent “printability” or weldability (like Haynes 282) where performance requirements allow.
- Qualitätskontrolle des Pulvers: Using high-purity powders with low levels of detrimental elements (e.g., S, P) minimizes segregation effects.
- Optimierung der Parameter: Carefully controlling energy input (power, speed, hatch spacing) to manage melt pool size, cooling rates, and thermal gradients. Reduced energy density might be needed for crack-prone alloys.
- Vorheizen: Higher build chamber temperatures (as in SEBM) reduce thermal shock and stress, mitigating cracking risk.
- Optimized Heat Treatments: Developing specific heat treatment cycles suitable for the AM microstructure, potentially different from cast/wrought counterparts. Addressing cracking in superalloy AM often involves careful tuning of the entire process chain.
- Herausforderung: Superalloys, particularly high γ′ content alloys like IN738LC, can be susceptible to cracking during AM.
- Porosity (Gas and Lack-of-Fusion):
- Herausforderung: Internal pores act as stress concentrators, significantly degrading fatigue life and mechanical properties.
- Gas Porosität: Caused by gas (e.g., argon used in atomization or shielding gas) trapped within the melt pool during solidification, or by the volatilization of certain elements.
- Lack-of-Fusion (LoF) Porosity: Irregularly shaped voids occurring between adjacent melt tracks or layers due to insufficient melting and fusion, often caused by inadequate energy density or poor powder spreading.
- Milderung:
- Hochwertiges Pulver: Using powders with low internal gas content and good flowability/packing density. Met3dp’s advanced atomization techniques aim to minimize trapped gas.
- Optimierung der Parameter: Ensuring sufficient energy density for complete melting and fusion, while avoiding excessive energy that could lead to keyholing (vapor depression instability) which can trap gas.
- Optimized Shielding Gas Flow: Ensuring proper removal of processing fumes without disturbing the powder bed.
- Heiß-Isostatisches Pressen (HIP): Highly effective at closing both gas and LoF pores, significantly improving density and material integrity. Porosity control metal 3D printing is essential for critical parts.
- Herausforderung: Internal pores act as stress concentrators, significantly degrading fatigue life and mechanical properties.
- Entfernung der Stützstruktur:
- Herausforderung: Supports made from high-strength superalloys can be extremely difficult and time-consuming to remove, especially complex internal supports within cooling channels. Removal processes can potentially damage the part surface.
- Milderung:
- DfAM for Support Reduction: Designing self-supporting features (angles >45∘), choosing optimal build orientations.
- Easily Removable Support Designs: Using specialized support structures (e.g., thin tips, perforation points, lower density supports where possible) that are designed to break away more easily.
- Erweiterte Entfernungstechniken: Utilizing wire EDM, electrochemical machining (ECM), or abrasive flow machining for challenging supports.
- Microstructure Control and Anisotropy:
- Herausforderung: The directional solidification inherent in AM often leads to columnar grain structures growing parallel to the build direction. This can result in anisotropic mechanical properties (properties differ depending on the testing direction relative to the build direction). The as-built microstructure (grain size, precipitate morphology) may also differ from conventionally processed materials.
- Milderung:
- Scan Strategy Manipulation: Techniques like scan vector rotation between layers can help disrupt epitaxial growth and promote more equiaxed grain structures, although complete elimination of anisotropy is difficult.
- Post-Build Heat Treatments: Solution annealing and aging treatments are critical for homogenizing the microstructure and precipitating the desired strengthening phases, reducing anisotropy to some extent.
- Prozessauswahl: SEBM’s higher temperature processing can sometimes promote different grain structures compared to L-PBF.
- Entwurfsüberlegungen: Understanding the directionality of properties and aligning the part orientation so that the most critical stress axes correspond to the strongest material direction.
- Reproducibility and Qualification:
- Herausforderung: Ensuring consistent part quality across multiple builds, different machines, and over time is crucial for aerospace certification. Minor variations in powder batches, machine calibration, or ambient conditions can potentially affect outcomes.
- Milderung:
- Robust Process Monitoring & Control: Implementing real-time monitoring of key process parameters (laser power, melt pool characteristics, temperature).
- Strict Quality Management Systems (QMS): Adhering to aerospace standards like AS9100.
- Thorough Powder Management: Rigorous testing, tracking, blending, and recycling protocols for metal powders.
- Comprehensive Process Qualification: Statistically validating the process window and demonstrating repeatable outcomes through rigorous testing protocols (material characterization, NDT, dimensional analysis). Process parameter optimization and validation are continuous efforts. Effectively troubleshooting metal AM defects requires systematic analysis and control.
Overcoming these challenges requires significant investment in technology, process control, materials science expertise, and rigorous quality assurance protocols. Partnering with experienced AM providers like Met3dp, who possess both advanced equipment (like SEBM printers beneficial for stress reduction) and deep knowledge of materials and process optimization, is essential for successfully navigating the complexities of producing mission-critical components like jet engine combustors via additive manufacturing.
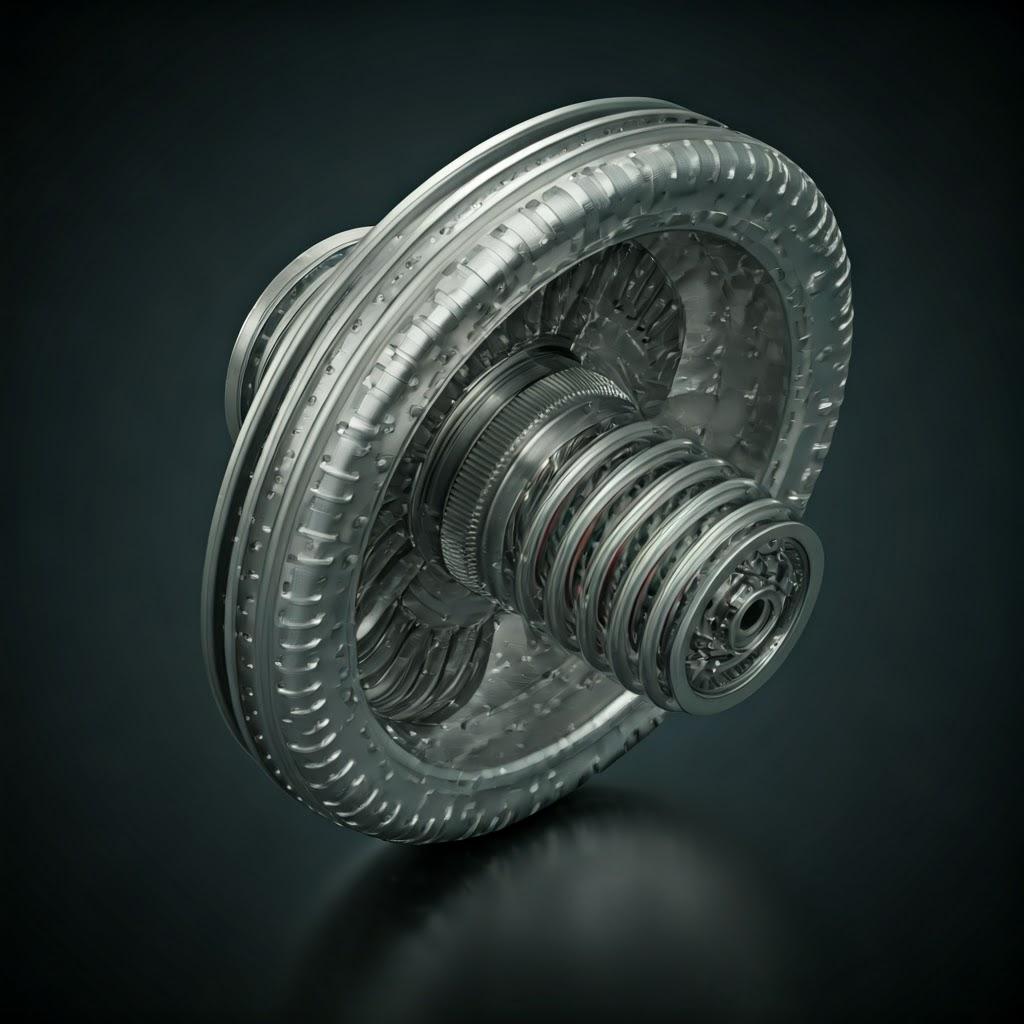
Selecting Your Aerospace Metal AM Partner: Key Evaluation Criteria
Choosing the right additive manufacturing service provider is a critical decision when embarking on the production of high-stakes components like jet engine combustors using advanced superalloys. This decision extends beyond simply finding a vendor with a 3D printer; it involves selecting a strategic partner with the technical depth, process rigor, quality certifications, and collaborative mindset necessary to navigate the complexities of aerospace AM. For procurement managers and engineering leads, a thorough evaluation process is essential to ensure the chosen partner can reliably deliver flight-worthy hardware that meets stringent performance and safety standards. Simply put, the success of your AM project heavily relies on the capabilities and expertise of your chosen provider.
Why Partnership Matters:
Manufacturing mission-critical aerospace components via AM, especially with challenging materials like IN738LC or Haynes 282, often requires close collaboration. The ideal partner acts as an extension of your engineering team, providing insights on Design for Additive Manufacturing (DfAM), material selection trade-offs, process optimization, and qualification strategies. They should be transparent about their capabilities and limitations, working with you to mitigate risks and ensure project success.
Key Evaluation Criteria for Aerospace Metal AM Providers:
When evaluating potential partners for your combustor project, consider the following critical factors:
- Aerospace Certifications and Compliance:
- AS9100-Zertifizierung: This is the fundamental requirement for aerospace manufacturing, indicating a robust Quality Management System (QMS) tailored to the industry’s demands. Do not proceed without verifying current AS9100 certification.
- NADCAP Accreditations: The National Aerospace and Defense Contractors Accreditation Program provides specific accreditations for special processes. Look for NADCAP accreditation relevant to your project, such as Heat Treating, Non-Destructive Testing (NDT), Welding (if applicable for post-processing), and Coatings. Having these aerospace certifications AM (AS9100) and NADCAP approvals demonstrates a commitment to industry best practices and process control.
- Demonstrated Technical Expertise and Experience:
- Superalloy Experience: Proven success in printing with the specific superalloys required (IN738LC, Haynes 282, etc.). Ask for case studies, material property data from builds, and evidence of parameter development for these alloys.
- Aerospace Application Experience: Have they successfully produced similar aerospace components (hot section parts, complex geometries)? Understanding the specific demands and qualification pathways of aerospace is crucial.
- Technische Unterstützung: Availability of experienced AM engineers and materials scientists who can assist with DfAM, simulation (thermal, stress, fluid dynamics), build preparation, and troubleshooting. Technical expertise AM provider capabilities are non-negotiable.
- Equipment Capabilities and Technology:
- Geeignete AM-Technologie: Do they operate well-maintained L-PBF and/or SEBM machines suitable for your chosen material and part complexity? Understand the pros and cons of each technology for your application. For instance, SEBM, like the systems developed by Met3dp, operates at higher temperatures, which can be highly advantageous for reducing residual stress in complex superalloy parts, potentially simplifying post-processing.
- Machine Fleet & Condition: Assess the number, size, age, and maintenance/calibration protocols for their AM machines. Redundancy can be important for meeting production schedules. Evaluate their equipment capabilities (SEBM, L-PBF) thoroughly.
- Prozessbegleitende Überwachung: Do their machines incorporate advanced monitoring systems (melt pool monitoring, thermal imaging) for enhanced quality control?
- Materialkenntnis und Rückverfolgbarkeit:
- Pulverbeschaffung und -handhabung: Rigorous procedures for sourcing high-quality powder from approved suppliers (or producing it in-house, like Met3dp), incoming powder inspection, controlled storage, handling, recycling/rejuvenation, and batch tracking.
- Materialqualifikation: Documented processes for qualifying specific machine-material combinations, ensuring consistent and predictable material properties.
- Full Traceability: Ability to provide complete material traceability supplier documentation from the raw powder batch to the final shipped part, essential for aerospace requirements. Companies like Met3dp, with deep expertise in both 3D-Druck von Metall and powder manufacturing, often excel here.
- Umfassende Nachbearbeitungsmöglichkeiten:
- Integrierter Arbeitsablauf: Ideally, the partner should offer a wide range of necessary post-processing steps in-house or through a tightly controlled network of NADCAP-approved suppliers. This includes stress relief, heat treatment, HIP, support removal, precision CNC machining, surface finishing, NDT, and coating application. Managing multiple disparate vendors increases complexity and risk.
- Robustes Qualitätsmanagementsystem (QMS):
- Beyond Certification: Look for evidence of a mature QMS ingrained in their culture, encompassing process control, data logging, statistical process control (SPC) where applicable, rigorous inspection protocols (including advanced NDT like CT scanning), clear documentation practices, and effective non-conformance management.
- Capacity, Scalability, and Financial Stability:
- Meeting Demand: Can the provider handle your required volumes, from initial prototypes to potential low-rate or full-scale production? Assess their current workload and expansion plans.
- Financial Health: Ensure the provider is financially stable to mitigate supply chain risks associated with long aerospace program lifecycles.
- Communication, Responsiveness, and Project Management:
- Clear Communication: Open and transparent communication channels are vital.
- Reaktionsfähigkeit: Timely responses to inquiries, technical questions, and request for quote (RFQ) aerospace AM submissions.
- Projektleitung: Dedicated project managers who understand aerospace requirements and can effectively manage timelines and deliverables.
Summary Table: Partner Evaluation Checklist
Kriterien | Wichtige Überlegungen | Why It Matters for Combustors |
---|---|---|
Zertifizierungen | AS9100 (Mandatory), NADCAP (Heat Treat, NDT, etc.) | Ensures adherence to aerospace quality standards and process control. |
Technisches Fachwissen | Superalloy AM experience, Aerospace application knowledge, DfAM support | Crucial for handling difficult materials, complex designs, and navigating qualification. |
Ausrüstung und Technologie | L-PBF/SEBM suitability, Machine condition & calibration, In-process monitoring | Ensures capability to produce the part accurately and reliably; SEBM may offer stress advantages. |
Material Expertise & Traceability | Powder quality control, Material qualification data, Full traceability records | Guarantees material integrity and compliance, essential for flight safety. |
Nachbearbeitung | In-house/controlled network for Heat Treat, HIP, Machining, NDT, Coating | Streamlines workflow, ensures consistent quality control throughout all manufacturing stages. |
Quality Management System | Mature QMS, Process monitoring, Rigorous inspection (CT, FPI), Data logging | Provides confidence in part quality, consistency, and defect detection. |
Capacity & Scalability | Ability to meet prototype and production volumes | Ensures supply chain reliability as program needs evolve. |
Communication & Project Mgmt. | Responsiveness, Clarity, Dedicated points of contact | Facilitates effective collaboration and smooth project execution. |
Company Background | Visit provider’s info page (e.g., Met3dp’s Über uns) for stability & focus clues | Understand their core business, history, and long-term commitment to aerospace AM. |
In Blätter exportieren
Selecting the right metal AM partner is a strategic investment. Thorough due diligence using these criteria will significantly increase the likelihood of successfully leveraging additive manufacturing for demanding applications like jet engine combustors.
Understanding Cost Drivers and Lead Times for 3D Printed Combustors
While additive manufacturing offers compelling advantages for producing complex jet engine combustors, understanding the factors that influence cost and lead time is crucial for accurate project planning, budgeting, and managing expectations within the B2B procurement additive manufacturing process. Unlike mass-produced simple parts, AM components made from superalloys involve sophisticated processes and materials, leading to different cost structures and timelines compared to traditional methods.
Key Cost Drivers for AM Combustors:
The final price of a 3D printed combustor is influenced by a multitude of factors. A thorough Kostenanalyse für den 3D-Druck von Metall should consider:
- Materialkosten:
- Pulver Preis: Aerospace-grade superalloy powders (IN738LC, Haynes 282) are inherently expensive due to their complex compositions (high Ni, Co, refractory elements) and the specialized atomization processes required to produce high-quality spherical particles suitable for AM. Material cost superalloys is often a primary driver.
- Powder Usage: Cost is directly related to the volume/mass of the final part plus any support structures. Material lost during processing or unsieved powder also contributes. Efficient DfAM (topology optimization, reducing supports) can help minimize material consumption.
- AM Machine Time:
- Hourly Rates: Metal AM machines represent significant capital investment, and their operating costs (energy, inert gas, maintenance, labor) contribute to high hourly rates.
- Bauzeit: This is determined by the part’s height (number of layers), the volume of material being melted in each layer (influenced by part geometry and nesting density on the build plate), and the specific scan strategy parameters used. Tall, bulky, or highly complex parts take longer to print.
- Part Complexity and Design (DfAM Impact):
- Geometric Complexity: While AM excels at complexity, extremely intricate features or very thin walls might require slower printing speeds or specialized parameters, potentially increasing time.
- Unterstützende Strukturen: The volume of required support material adds to both material cost and build time. Furthermore, complex internal supports increase the labor cost associated with their removal in post-processing. Effective DfAM aims to minimize reliance on supports.
- Nachbearbeitungsintensität:
- Mandatory Steps: Stress relief, heat treatments (solution + aging), and HIP are often standard for critical superalloy parts and represent significant time and cost additions due to furnace cycles and specialized equipment (HIP).
- Finishing Requirements: The extent of surface finishing (blasting, polishing, AFM for internal channels) and precision CNC machining required to meet final tolerance and surface specifications heavily impacts cost. Each additional step adds labor, machine time, and potential tooling costs.
- Beschichtungen: Application of TBCs or EBCs is a specialized, costly process.
- Qualitätssicherung und Inspektion:
- NDT Requirements: Rigorous non-destructive testing, especially CT scanning for internal integrity verification, adds substantial cost due to equipment time and specialized analysis.
- Dokumentation: Extensive documentation required for aerospace traceability and qualification contributes to overhead costs.
- Arbeit und Fachwissen:
- Highly skilled engineers and technicians are needed for DfAM, build preparation, machine operation, post-processing, and quality control, impacting labor costs.
- Order Volume (Economies of Scale):
- Prototypes vs. Production: One-off prototypes incur high setup and qualification costs per part. As production volume scaling AM occurs, costs per part generally decrease due to amortization of setup, optimized build nesting, and more efficient workflows. However, AM cost reduction with volume is typically less dramatic than with traditional high-volume methods like casting with permanent tooling.
Faktoren für die Vorlaufzeit:
The total time required from order placement to receiving a finished, qualified combustor (lead time estimation aerospace components) is also influenced by multiple stages:
- Vorverarbeitung:
- Design Consultation & DfAM: Initial discussions, design optimization for AM (can take days to weeks).
- Simulation: Performing FEA/CFD analysis if required (days to weeks).
- Build File Preparation: Creating the build layout, defining scan strategies, generating support structures (hours to days).
- AM Machine Queue & Scheduling:
- The selected AM service provider’s backlog and machine availability will impact when the build can start (can range from days to several weeks).
- Printing (Build Time):
- The actual time the part spends printing in the AM machine (typically 1-5 days for reasonably sized combustor components, but can be longer).
- Nachbearbeiten:
- Cooling & Stress Relief: Hours to a day.
- Teil/Träger entfernen: Hours to days, depending on complexity.
- Heat Treatment Cycles: Can take 1-3 days, including furnace time and controlled cooling.
- HIP Cycle: Typically takes 1-2 days (including loading, cycle time, unloading).
- Bearbeitungen: Setup and machining time can range from days to weeks, depending on complexity and machine availability.
- Surface Finishing/Coating: Days to weeks, depending on the process.
- Inspektion und Qualitätskontrolle:
- NDT (CT, FPI) and dimensional inspection (CMM, scanning) can take several days, including analysis and reporting.
- Versand:
- Transit time to the customer’s facility.
Overall Timeline: Considering all these factors, the realistic lead time for a complex, fully post-processed and inspected 3D printed superalloy combustor is typically measured in weeks to months, rather than days. While potentially faster than the months or even year+ lead times sometimes associated with developing new casting tooling, it’s significantly longer than printing simple polymer prototypes. Effective project management and clear communication with the AM provider are essential for managing these timelines.
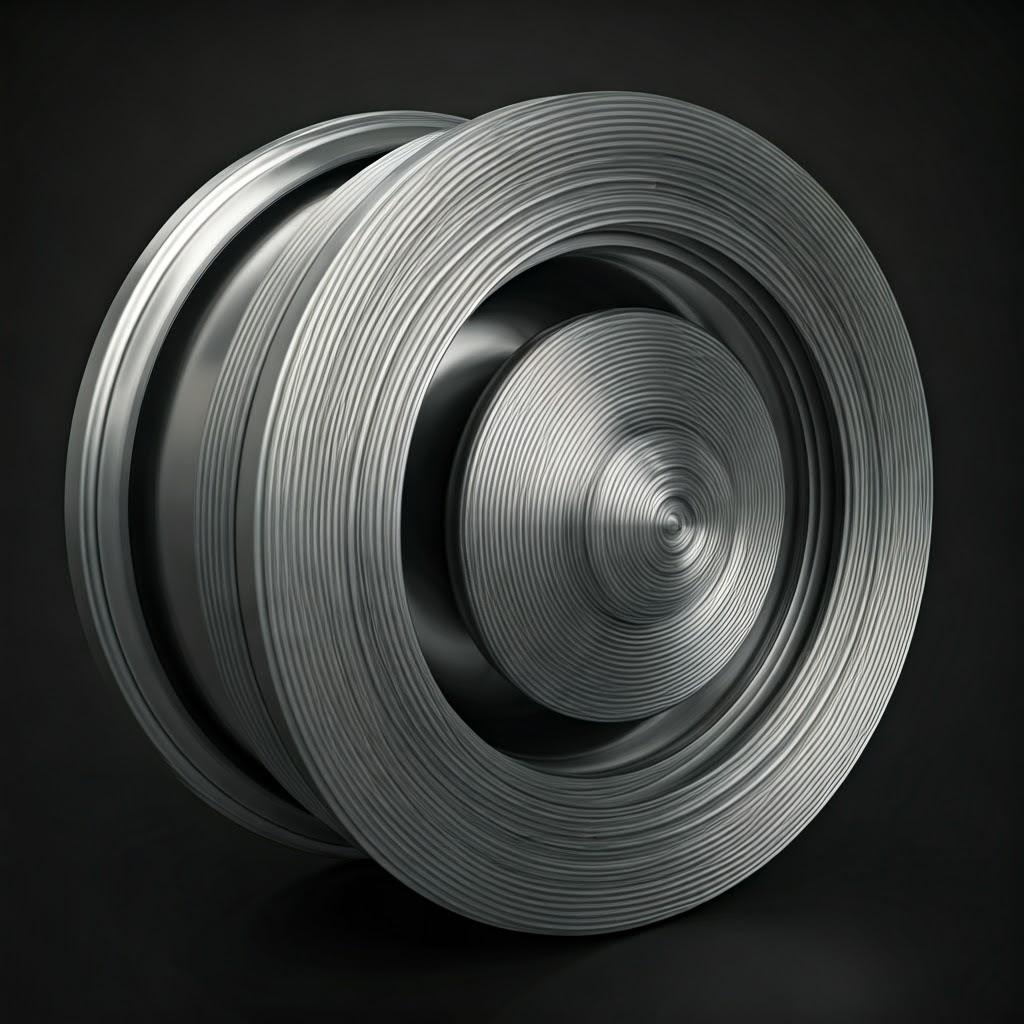
Frequently Asked Questions (FAQ) about 3D Printed Jet Engine Combustors
As additive manufacturing becomes increasingly adopted for critical aerospace components, engineers, designers, and procurement specialists often have specific questions regarding its application for jet engine combustors. Here are answers to some frequently asked questions:
1. How does the lifespan/durability of a 3D printed combustor compare to a traditionally manufactured one?
With appropriate DfAM, careful selection of high-quality materials (like IN738LC or Haynes 282), meticulously optimized AM process parameters, comprehensive post-processing (including HIP and proper heat treatments), and rigorous quality control, 3D printed combustors can be designed and manufactured to meet or even exceed the lifespan and durability requirements of traditionally manufactured counterparts. The key lies in understanding the unique microstructure produced by AM and ensuring through extensive testing (creep, fatigue, thermal-mechanical fatigue, corrosion/oxidation) that it meets the demands of the harsh operating environment. Qualification data, not just the manufacturing method, determines the 3D printed combustor lifetime Leistung.
2. What is the certification process for flight-critical 3D printed components like combustors?
Die certification process AM parts for flight is rigorous and follows established frameworks from aviation authorities like the FAA and EASA, adapted for AM specifics. It typically involves:
- Prozessqualifizierung: Demonstrating stability and repeatability of the entire process chain (powder handling, printing, post-processing) through statistical methods.
- Materialcharakterisierung: Extensive testing to establish material property allowables (strength, fatigue, creep, etc.) specific to the chosen machine, material batch, and processing route. This often involves building and testing numerous material coupons.
- Component Testing: Functional testing of the actual component under simulated or real operating conditions, including validation of cooling performance, structural integrity, and durability.
- Non-Destructive Inspection (NDI/NDT): Establishing reliable NDI techniques (like CT scanning) and acceptance criteria to ensure internal and external quality.
- Quality Management System: Adherence to AS9100 and stringent documentation control. Initially, certification often follows a “point design qualification,” where a specific part design manufactured via a specific, locked-down process is certified. Broader “equivalency” or “family of parts” certifications are evolving as the industry gains more experience and data.
3. Is 3D printing more expensive than casting or fabricating combustors?
Die cost comparison AM vs casting/fabrication is complex and depends heavily on several factors:
- Komplexität: For highly intricate designs with features difficult or impossible to cast/fabricate (e.g., complex internal cooling, integrated features), AM can be more cost-effective, especially when considering the performance benefits enabled by the design freedom.
- Teil Konsolidierung: If AM allows reducing a multi-part assembly to a single component, the savings in assembly labor, joining processes, and potential failure points can offset higher AM part costs.
- Lautstärke: For very high production volumes of relatively simple designs, traditional methods with established tooling often remain cheaper per part. AM typically finds its “sweet spot” in low-to-medium volume production, prototyping, and complex geometries where tooling costs for traditional methods would be prohibitive or lead times excessive.
- Total Cost of Ownership: Consider factors beyond initial part cost, such as potential weight savings (fuel efficiency), improved performance (efficiency, emissions), and reduced development time.
4. Are superalloy powders like IN738LC and Haynes 282 readily available for AM?
Die material availability superalloys specifically processed and quality-controlled for additive manufacturing has improved significantly in recent years. Specialized metal powder producers, such as Met3dp which employs advanced gas atomization and PREP technologies, focus on manufacturing these high-performance powders with the necessary characteristics (sphericity, flowability, PSD, purity) for reliable AM. While availability is generally good from these specialized suppliers, ensuring a consistent, large-scale supply chain for major production programs still requires careful planning and strong supplier relationships. Quality control and batch consistency remain paramount.
5. Can AM be used to repair existing combustors?
Ja, AM repair strategies aerospace are a rapidly growing field. Techniques like Directed Energy Deposition (DED), where powder or wire is fed into a melt pool created by a laser or electron beam, are particularly well-suited for adding material to repair worn or damaged areas of high-value components like combustors. Laser Powder Bed Fusion (L-PBF) can also sometimes be adapted for repair tasks. AM repair offers the potential to restore components to service that might otherwise be scrapped, significantly reducing costs and downtime compared to replacement, especially for complex legacy parts where original manufacturing methods may no longer be available. Certification of AM repairs follows similarly rigorous pathways as new part production.
Conclusion: Revolutionizing Propulsion with Additive Manufacturing and Advanced Materials
The journey through the intricacies of manufacturing jet engine combustors via additive manufacturing reveals a clear picture: AM, when coupled with advanced superalloys like IN738LC and Haynes 282, represents a truly revolutionary force in aerospace propulsion technology. We’ve moved beyond the realm of simple prototyping; metal AM is now a proven, viable, and increasingly preferred method for producing flight-critical hardware capable of withstanding the extreme conditions found within the heart of a jet engine.
The value proposition is compelling. AM unshackles designers from the constraints of traditional manufacturing, enabling the creation of highly optimized combustors with intricate cooling schemes, consolidated part counts, and reduced weight. These design advantages translate directly into tangible performance benefits: improved fuel efficiency, reduced emissions, higher thrust-to-weight ratios, and potentially longer component life. The ability to rapidly iterate designs and significantly shorten lead times compared to tooling-intensive methods accelerates innovation cycles, allowing engine manufacturers to bring next-generation technology to market faster. This is pivotal in the ongoing drive towards more sustainable propulsion technology and maintaining a competitive edge in the demanding Zukunft der Luft- und Raumfahrtindustrie.
However, realizing this potential demands a holistic approach. Success hinges on the critical synergy between cutting-edge manufacturing processes and high-performance materials. This includes:
- Nutzung von Design für additive Fertigung (DfAM) principles to fully exploit geometric freedom.
- Utilizing precise and reliable Additive Manufacturing Systems, such as the Selective Electron Beam Melting (SEBM) technology offered by companies like Met3dp, known for handling challenging superalloys effectively due to better thermal management.
- Sourcing exceptionally Hochwertige Metallpulver with optimized characteristics (sphericity, purity, flowability), like those produced through Met3dp’s advanced atomization techniques.
- Implementing rigorous Post-Processing and Quality Assurance protocols, including heat treatment, HIP, NDT, and meticulous inspection.
The path involves overcoming challenges related to residual stress, material behavior, precision, and qualification. This underscores the importance of strategic sourcing AM parts und partnering with AM experts who possess the necessary certifications, technical depth, and integrated capabilities spanning materials, processes, and quality control.
As the aerospace industry continues its relentless pursuit of innovation in jet engines, additive manufacturing stands out as a cornerstone technology. It offers not just incremental improvements but the potential for step-changes in performance and efficiency. For engineers and procurement managers looking to push the boundaries of propulsion systems, exploring the possibilities of 3D printed combustors with advanced superalloys is no longer optional – it’s essential.
To explore how Met3dp’s integrated solutions – encompassing advanced SEBM printers and high-performance metal powders – can empower your organization’s additive manufacturing goals for critical aerospace components, visit our main website at Met3dp. Let’s build the future of flight, together.
Teilen auf
MET3DP Technology Co., LTD ist ein führender Anbieter von additiven Fertigungslösungen mit Hauptsitz in Qingdao, China. Unser Unternehmen ist spezialisiert auf 3D-Druckgeräte und Hochleistungsmetallpulver für industrielle Anwendungen.
Fragen Sie an, um den besten Preis und eine maßgeschneiderte Lösung für Ihr Unternehmen zu erhalten!
Verwandte Artikel
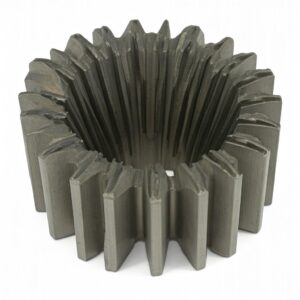
Hochleistungs-Düsenschaufelsegmente: Revolutionierung der Turbineneffizienz mit 3D-Metalldruck
Mehr lesen "Über Met3DP
Aktuelles Update
Unser Produkt
KONTAKT US
Haben Sie Fragen? Senden Sie uns jetzt eine Nachricht! Wir werden Ihre Anfrage mit einem ganzen Team nach Erhalt Ihrer Nachricht bearbeiten.
Holen Sie sich Metal3DP's
Produkt-Broschüre
Erhalten Sie die neuesten Produkte und Preislisten
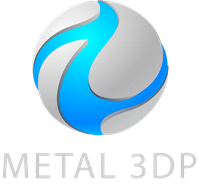
Metallpulver für 3D-Druck und additive Fertigung
UNTERNEHMEN
PRODUKT
cONTACT INFO
- Qingdao Stadt, Shandong, China
- [email protected]
- [email protected]
- +86 19116340731