3D-gedruckte Gehäuse für Wärmerohre in Raumfahrtsystemen
Inhaltsübersicht
Einführung: Revolutionierung des Wärmemanagements von Raumfahrzeugen mit 3D-gedruckten Wärmerohrgehäusen
Der Weltraum stellt unvergleichliche Herausforderungen dar, nicht zuletzt die Bewältigung extremer Temperaturen. Raumfahrzeuge, die die Erde umkreisen, ferne Planeten erforschen oder menschliche Besatzungen an Bord haben, arbeiten in Umgebungen, in denen die Temperaturen zwischen direktem Sonnenlicht und Schatten um Hunderte von Grad Celsius schwanken können. Ein effektives Wärmemanagement ist nicht nur wünschenswert, sondern auch entscheidend für den Einsatz. Empfindliche Elektronik, optische Instrumente, Antriebssysteme und Lebenserhaltungssysteme hängen alle von der Aufrechterhaltung stabiler Betriebstemperaturen ab. Gelingt dies nicht, kann es zu Leistungseinbußen, zum Ausfall von Komponenten und schließlich zum Verlust der Mission kommen. Unter den hochentwickelten Werkzeugen, die in thermischen Kontrollsystemen (TCS) für Raumfahrzeuge eingesetzt werden, zeichnen sich Wärmerohre durch ihre Effizienz und Zuverlässigkeit bei der passiven Übertragung großer Wärmemengen über große Entfernungen mit minimalem Temperaturabfall aus. Die effektive Integration dieser Heatpipes erfordert jedoch häufig komplexe Gehäuse, die strukturelle Unterstützung, Schutz und optimierte thermische Schnittstellen bieten. Traditionell erforderte die Herstellung dieser Gehäuse komplexe mehrteilige Baugruppen, umfangreiche Bearbeitungen von Knüppelmaterialien oder komplizierte Lötverfahren - Methoden, die oft durch geometrische Einschränkungen, lange Vorlaufzeiten und erheblichen Materialabfall begrenzt waren.
Der Einstieg in die additive Fertigung von Metall (AM), allgemein bekannt als Metall 3D-Druck. Diese transformative Technologie verändert die Art und Weise, wie Ingenieure Komponenten für die anspruchsvollsten Anwendungen, einschließlich der Luft- und Raumfahrt, entwerfen und herstellen. Durch den schichtweisen Aufbau von Teilen direkt aus digitalen Modellen unter Verwendung von Hochleistungsmetallpulvern eröffnet AM eine nie dagewesene Designfreiheit. Auf diese Weise lassen sich hochkomplexe, leichte und funktional integrierte Wärmerohrgehäuse herstellen, deren Produktion bisher unmöglich oder unerschwinglich war. Der 3D-Metalldruck ermöglicht Merkmale wie konforme Kühlkanäle, komplizierte interne Strukturen für eine optimierte Flüssigkeitsströmung (in Wärmerohrkreisläufen oder CPLs, die oft in Gehäusen untergebracht sind), dünne Wände zur Gewichtsreduzierung und konsolidierte Designs, die mehrere Funktionen in einer einzigen Komponente vereinen. Dies revolutioniert nicht nur die Komponente selbst, sondern auch das gesamte Systemdesign, die Integration und die Leistung.
Die Vorteile gehen über die reine Geometrie hinaus. Die additive Fertigung erleichtert das Rapid Prototyping und die Design-Iteration und verkürzt so die Entwicklungszyklen erheblich - ein entscheidender Vorteil in der schnelllebigen Luft- und Raumfahrtbranche. Es ermöglicht den Ingenieuren, mehrere Designvarianten schnell zu testen und die thermische Leistung und strukturelle Integrität auf der Grundlage von Simulationen und empirischen Daten zu optimieren. Darüber hinaus können beim AM fortschrittliche Materialien verwendet werden, die speziell für ihre Wärmeleitfähigkeit, ihr Verhältnis von Festigkeit zu Gewicht und ihre Widerstandsfähigkeit in der rauen Weltraumumgebung ausgewählt wurden. Diese Einführung untersucht die kritische Rolle von Wärmerohrgehäusen im Wärmemanagement von Raumfahrzeugen und zeigt auf, wie der 3D-Metalldruck zu einem unverzichtbaren Werkzeug für die Entwicklung von thermischen Hochleistungslösungen der nächsten Generation wird, die den Weg für leistungsfähigere und ehrgeizigere Raumfahrtmissionen ebnen. Unternehmen wie Met3dpmit ihrem umfassenden Fachwissen im Bereich der additiven Fertigungstechnologien für Metalle und der Herstellung hochwertiger Materialien an der Spitze dieser Entwicklung und bieten die für die Realisierung dieser fortschrittlichen Komponenten erforderlichen Fähigkeiten.
Anwendungen: Wo werden 3D-gedruckte Heatpipe-Gehäuse in Raumfahrtsystemen eingesetzt?
Der Anwendungsbereich für 3D-gedruckte Wärmerohrgehäuse in Raumfahrtsystemen ist breit gefächert und wird mit zunehmender Reife und Flugerfahrung der Technologie ständig erweitert. Ihre Fähigkeit, maßgeschneiderte thermische Leistung, strukturelle Integration und Massenreduzierung zu bieten, macht sie für verschiedene Raumfahrzeugplattformen und Subsysteme von unschätzbarem Wert. Beschaffungsmanager und Ingenieure, die für Lieferanten von thermischen Kontrollsystemen für Raumfahrzeuge, Satellitenhersteller und Beschaffungsabteilungen für Luft- und Raumfahrtkomponenten arbeiten, wenden sich zunehmend an AM, um Lösungen zu finden, die mit konventionellen Methoden nicht effizient geliefert werden können.
Wichtigste Anwendungsbereiche:
- Satellitenplattformen (LEO, MEO, GEO):
- Kühlung der Elektronik: Satelliten sind vollgepackt mit Elektronik mit hoher Leistungsdichte für Kommunikationsnutzlasten, Datenverarbeitungseinheiten und Stromverteilungssysteme. Mittels AM gefertigte Heatpipe-Gehäuse können so gestaltet werden, dass sie genau dem Layout der elektronischen Komponenten entsprechen und die Wärme effizient ableiten und über angebrachte Kühlerplatten ins All abstrahlen. der 3D-Druck ermöglicht integrierte Montagefunktionen und optimierte Wärmewege innerhalb des Gehäuses selbst, wodurch der Wärmewiderstand minimiert wird.
- Thermisches Management der Batterie: Batteriemodule erzeugen insbesondere während der Lade-/Entladezyklen erhebliche Wärme. Sie in einem engen optimalen Temperaturbereich zu halten, ist entscheidend für Leistung und Lebensdauer. AM-Gehäuse können komplexe interne Strukturen oder Kanäle (für Wärmerohre) zur gleichmäßigen Kühlung von Batteriearrays aufweisen.
- Thermische Stabilität der optischen Nutzlast: Teleskope und empfindliche optische Instrumente benötigen eine außergewöhnliche thermische Stabilität, um den Fokus und die Ausrichtung beizubehalten. in 3D-gedruckten Gehäusen können Wärmerohre untergebracht werden, die die Temperatur von Detektoranordnungen, Linsen und strukturellen Halterungen präzise steuern, häufig unter Verwendung von Materialien mit niedrigem Wärmeausdehnungskoeffizienten (WAK) oder maßgeschneiderter Wärmeleitfähigkeit.
- Strukturelle Integration: Bei Kleinsatelliten (CubeSats, SmallSats), bei denen Volumen und Masse stark eingeschränkt sind, können AM-Gehäuse einen doppelten Zweck erfüllen: Sie bieten Wärmemanagement über Wärmerohre und die als primäre oder sekundäre Strukturelemente, Befestigungspunkte oder Strahlungsabschirmung dienen.
- Sonden und Rover für den Weltraum:
- Überleben bei extremen Temperaturen: Missionen, die in die Tiefen des Weltraums vorstoßen oder auf Himmelskörpern landen, sind extremen Hitze- und Kältezyklen ausgesetzt. Wärmerohre in robusten AM-Gehäusen helfen bei der Bewältigung dieser Temperaturschwankungen und sorgen dafür, dass kritische Systeme auch bei langen Transits oder rauen Oberflächenbedingungen betriebsbereit bleiben (z. B. um die Elektronik in Mondnächten oder im Winter auf dem Mars warm zu halten).
- Mechanismen für den Einsatz von Heizkörpern: Gehäuse könnten mit Mechanismen integriert werden, die größere Heizflächen entfalten und Wärmerohre verwenden, um die Abwärme effizient zu diesen entfaltbaren Elementen zu transportieren. AM ermöglicht komplexe, leichte Scharniere und strukturelle Schnittstellen innerhalb des Gehäuses.
- Thermische Kontrolle der Instrumente: Wissenschaftliche Instrumente haben oft sehr spezifische und stabile Temperaturanforderungen. Maßgeschneiderte AM-Gehäuse mit Wärmerohren sorgen für eine präzise thermische Kontrolle von Spektrometern, Kameras und Sensoren und ermöglichen eine genaue Datenerfassung.
- Bemannte Raumfahrzeuge und Raumstationen:
- Lebenserhaltende Systeme: Umweltkontroll- und Lebenserhaltungssysteme (Environmental Control and Life Support Systems, ECLSS) umfassen das Management der von Geräten und Bewohnern erzeugten Wärme. Wärmerohrbaugruppen mit AM-Gehäusen tragen zur effizienten Wärmeabfuhr bei und sorgen für eine bewohnbare Umgebung.
- Avionik-Kühlung: Komplexe Avioniksysteme zur Steuerung von Navigations-, Lenk- und Kommunikationssystemen erfordern ein robustes Wärmemanagement. Konforme AM-Gehäuse mit integrierten Wärmerohren bieten effiziente Kühllösungen in dicht gepackten Avionikbuchten.
- Experimentiermodule: Wissenschaftliche Experimente, die in der Mikrogravitation durchgeführt werden, erfordern oft eine präzise Temperaturkontrolle. AM-Gehäuse können für spezifische Experiment-Hardware maßgeschneidert werden, wobei Wärmerohre für stabile thermische Bedingungen integriert werden.
B2B-Kontext und Schlüsselwörter:
Für Unternehmen, die in der Lieferkette der Luft- und Raumfahrt tätig sind, ist das Verständnis dieser Anwendungen von entscheidender Bedeutung. Zu den für B2B-Interaktionen relevanten Schlüsselwörtern gehören:
- Anbieter von Wärmemanagementlösungen für die Luft- und Raumfahrt
- Hersteller von Raumfahrzeugkomponenten
- Beschaffung von Wärmekontrollsystemen für Satelliten
- Kundenspezifische Fertigung von Wärmerohrbaugruppen
- Additive Fertigung für Luft- und Raumfahrtstrukturen
- Hochleistungs-Wärmeschränke B2B
- Beschaffung von weltraumtauglichen Komponenten
- 3D-Druck von Metall für Satelliten
- Anbieter von Leichtbaukomponenten für die Luft- und Raumfahrt
Der Trend ist eindeutig: Je leistungsfähiger die Raumfahrzeuge und je ehrgeiziger die Missionen werden, desto höher sind die Anforderungen an die thermischen Kontrollsysteme. Herkömmliche Fertigungsverfahren haben oft Schwierigkeiten, die Anforderungen an Komplexität, Leistung und Gewichtsoptimierung zu erfüllen. Der 3D-Metalldruck bietet eine leistungsstarke Alternative und ermöglicht die Entwicklung und Herstellung von Wärmerohrgehäusen, die speziell auf die einzigartigen Herausforderungen jeder Raumfahrtmission zugeschnitten sind. Diese Fähigkeit macht AM zu einem entscheidenden Faktor für die künftige Erforschung und Kommerzialisierung des Weltraums, so dass Partner, die diese Technologie beherrschen, bei Hauptauftragnehmern und Systemintegratoren in der Luft- und Raumfahrt sehr gefragt sind.
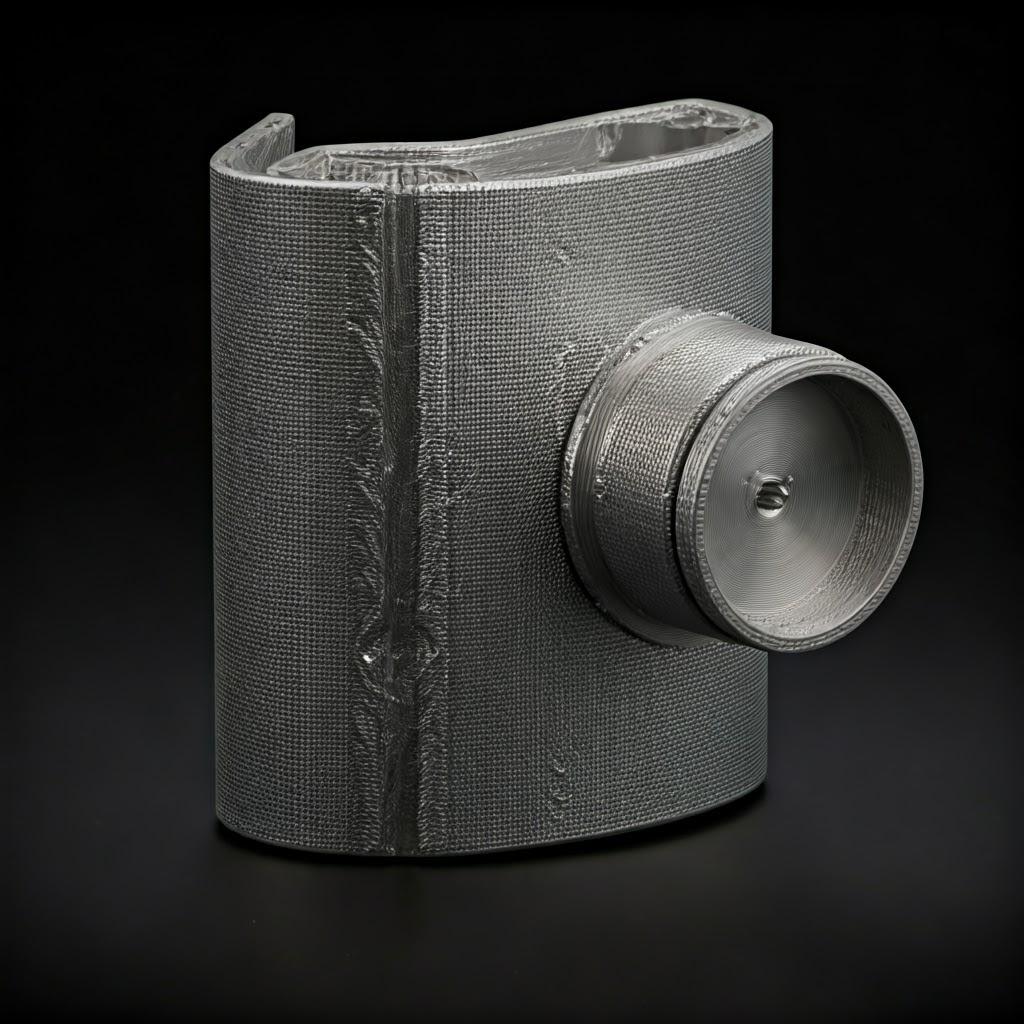
Warum Metall-Additive Fertigung für Wärmerohrgehäuse?
Die Entscheidung, für die Herstellung von Wärmerohrgehäusen in Raumfahrtsystemen die additive Fertigung von Metallen zu nutzen, ergibt sich aus einem Zusammenspiel von überzeugenden Vorteilen, die die Grenzen herkömmlicher Fertigungsmethoden wie Zerspanung, Gießen oder Löten/Schweißen komplexer Baugruppen direkt ansprechen. Diese Vorteile schlagen sich in spürbaren Verbesserungen bei Leistung, Gewicht, Kosten und Entwicklungszeit nieder und machen AM zu einer zunehmend bevorzugten Wahl für Fertigungslösungen in der Luft- und Raumfahrt und für die Herstellung fortschrittlicher Komponenten.
Vergleich: Metall-AM vs. traditionelle Fertigung für Heatpipe-Gehäuse
Merkmal | Traditionelle Fertigung (Zerspanung, Löten, Gießen) | Additive Fertigung von Metallen (LPBF, SEBM) | Vorteil für Heat Pipe Enclosures (Space) |
---|---|---|---|
Entwurfskomplexität | Begrenzt durch Werkzeugzugang, Entformungswinkel, Verbindungsmethoden. Komplexe innere Merkmale schwierig/unmöglich. | Hochkomplexe Geometrien, komplizierte interne Kanäle, konforme Formen, organische Formen sind leicht realisierbar. | Ermöglicht optimierte thermische Pfade, integrierte Flüssigkeitskanäle (LHP/CPL), konforme Designs, die in enge Räume passen, verbesserte thermische Leistung. |
Teil Konsolidierung | Oft müssen mehrere Komponenten zusammengebaut werden (Löten, Schweißen, Befestigungen), was die Anzahl der Teile, das Gewicht und mögliche Fehlerquellen erhöht. | Fähigkeit, komplexe, multifunktionale Komponenten als ein einziges Stück zu drucken. | Geringere Anzahl von Teilen, weniger Montageaufwand, geringeres Gewicht, höhere Zuverlässigkeit (weniger Verbindungen), vereinfachte Lieferkette. |
Gewichtsreduzierung | Materialabtragungsprozesse können verschwenderisch sein. Die Wanddicke ist durch Bearbeitungszwänge begrenzt. Es ist schwierig, eine optimale Topologie zu erreichen. | Material wird nur dort hinzugefügt, wo es benötigt wird. Ermöglicht Topologie-Optimierung, Gitterstrukturen, dünne Wände und reduziert die Masse erheblich. | Entscheidend für Raumfahrtanwendungen, bei denen die Startkosten hoch sind (Tausende Dollar pro kg). Verbesserte Nutzlastkapazität oder geringere Anforderungen an Trägerraketen. |
Materialnutzung | Bei subtraktiven Verfahren (spanabhebende Bearbeitung) fallen erhebliche Materialabfälle (Späne) an. Beim Gießen fallen Anschnitt-/Speiserabfälle an. | Beim additiven Verfahren wird das Material hauptsächlich für das Teil selbst verwendet. Durch die Wiederverwendung des Pulvers wird der Abfall minimiert (auch wenn etwas Trägermaterial verwendet wird). | Nachhaltigere, geringere Rohstoffkosten, besonders wichtig bei teuren Legierungen für die Luft- und Raumfahrt. |
Vorlaufzeit (Prototyping) | Erfordert Werkzeuge, Vorrichtungen, mehrstufige Prozesse. Iteration ist langsam und kostspielig. | Direkte digitale Fertigung (CAD-zu-Teil). Rapid Prototyping und Design-Iteration innerhalb von Tagen/Wochen möglich. | Beschleunigung der Entwicklungszyklen, schnellere Prüfung und Optimierung von thermischen Designs, schnellere Reaktion auf Designänderungen. |
Vorlaufzeit (Produktion) | Kann bei großen Mengen effizient sein wenn werkzeuge vorhanden sind. Die Rüstzeiten können bei komplexen Teilen lang sein. | Potenziell langsamere Bauzeit pro Teil, erfordert aber keine Werkzeugausstattung. Skalierbar durch Hinzufügen von Maschinen. Schneller für kleine bis mittlere Stückzahlen oder hochkomplexe Teile. | Kürzere Durchlaufzeiten für einzigartige oder kleinvolumige Raumfahrtkomponenten. Geringerer Bedarf an Lagerbeständen (Fertigung auf Abruf). |
Personalisierung | Hohe Kosten und lange Vorlaufzeiten für kundenspezifische Teile oder Teile in kleinen Stückzahlen. | Ideal für die kosteneffiziente Herstellung einzigartiger oder hochgradig kundenspezifischer Teile. | Ermöglicht missionsspezifische Gehäusedesigns, die auf einzigartige thermische Belastungen, Schnittstellen und Volumenbeschränkungen zugeschnitten sind, ohne dass hohe Werkzeugkosten anfallen. |
Thermische Leistung | Begrenzt durch realisierbare Geometrien und Verbindungswiderstände (in Baugruppen). | Komplexe interne Merkmale (Rippen, Kanäle) und konforme Designs optimieren die Wärmeübertragung. Geringerer Wärmewiderstand durch Teilekonsolidierung. | Verbesserte Wärmeableitung, verbesserte Temperaturgleichmäßigkeit, bessere Gesamteffizienz des Wärmekontrollsystems. |
Interne Merkmale | Extrem schwierig oder unmöglich, komplexe interne Kanäle oder Strukturen zu bearbeiten. | Relativ einfach lassen sich komplizierte interne Kühlkanäle, poröse Strukturen (für Dochte) oder Strömungswege einbauen. | Wesentlich für fortschrittliche Wärmerohrkonstruktionen (z. B. Loop Heat Pipes, Capillary Pumped Loops), die oft in Gehäuse integriert sind. Verbesserte Dochtstrukturen. |
In Blätter exportieren
Spezifische Vorteile, die ausgearbeitet wurden:
- Unerreichte Designfreiheit: AM befreit die Ingenieure von den Zwängen der traditionellen Fertigung. Bei Wärmerohrgehäusen bedeutet dies, dass komplexe interne Passagen entworfen werden, die genau den Wärmequellen folgen, dass optimierte Rippenstrukturen innerhalb des Gehäuses für die Wärmeableitung geschaffen werden oder dass Montagehalterungen, Sensoranschlüsse und strukturelle Verstärkungen direkt in das einzelne gedruckte Teil integriert werden. Dies ermöglicht Gehäuse, die perfekt an die zu kühlenden Komponenten angepasst sind, wodurch der thermische Schnittstellenwiderstand minimiert und der volumetrische Wirkungsgrad maximiert wird - was in eng gepackten Raumfahrzeugen von entscheidender Bedeutung ist.
- Signifikante Gewichtsreduzierung: Mithilfe von Techniken wie der Topologieoptimierung (Entfernen von Material aus unkritischen Bereichen unter Beibehaltung der strukturellen Integrität) und der Einbeziehung interner Gitterstrukturen kann AM die Masse von Wärmerohrgehäusen im Vergleich zu maschinell gefertigten Pendants drastisch reduzieren. Jedes eingesparte Kilogramm schlägt sich direkt in niedrigeren Startkosten oder einer höheren Kapazität für wissenschaftliche Instrumente oder Treibstoff nieder.
- Reduktion der Teileanzahl: Eine komplexe Heatpipe-Gehäusebaugruppe kann traditionell aus einem maschinell bearbeiteten Gehäuse, gelöteten oder geschweißten Endkappen, Montageflanschen und internen Stützstrukturen bestehen. Metall-AM kann diese verschiedenen Teile oft zu einer einzigen, monolithischen Komponente zusammenfassen. Dies vereinfacht die Lieferkette, reduziert die Montagezeit und -kosten, beseitigt potenzielle Leckagepfade oder Fehlerstellen an den Verbindungsstellen und verbessert die strukturelle Integrität und die thermische Kontinuität von Natur aus.
- Beschleunigte Entwicklung: Die Möglichkeit, direkt von einem CAD-Modell zu einem physischen Metallteil überzugehen, ermöglicht eine schnelle Iteration. Ingenieure können ein Gehäuse entwerfen, einen Prototyp drucken, seine thermische und strukturelle Leistung testen und Änderungen schnell in die nächste Entwurfsiteration einfließen lassen. Dies verkürzt den Entwicklungszyklus drastisch im Vergleich zum Warten auf herkömmliche Werkzeug- oder Bearbeitungsvorrichtungen und ermöglicht eine schnellere Optimierung und Qualifizierung von Raumfahrthardware. Unternehmen, die spezialisiert sind auf 3D-Druck von Metall dienste können diesen Prozess durch gestraffte Arbeitsabläufe weiter beschleunigen.
- Ermöglichung fortschrittlicher thermischer Designs: Bestimmte fortschrittliche Wärmemanagementkonzepte wie Loop Heat Pipes (LHPs) oder Capillary Pumped Loops (CPLs) beruhen auf komplizierten internen Verdampfer- und Verflüssigerstrukturen mit feinen Kapillardochten. Metall-AM ist in einzigartiger Weise in der Lage, diese komplexen internen Geometrien und porösen Dochtstrukturen direkt im Gehäusekörper herzustellen, was mit herkömmlichen Methoden praktisch unmöglich ist.
Zusammenfassend lässt sich sagen, dass die additive Fertigung von Metallen einen Paradigmenwechsel bei der Entwicklung und Herstellung von Wärmerohrgehäusen für Raumfahrtsysteme darstellt. Sie überwindet die Grenzen subtraktiver und formgebender Verfahren und ermöglicht die Entwicklung leichterer, komplexerer, leistungsfähigerer und schnell entwickelter Wärmemanagementlösungen, die für den Erfolg moderner und künftiger Raumfahrtmissionen unerlässlich sind.
Werkstoff-Fokus: AlSi10Mg- und CuCrZr-Pulver für optimale Leistung
Bei der Entwicklung von Komponenten für die anspruchsvollen Umgebungsbedingungen im Weltraum ist die Wahl des Materials von entscheidender Bedeutung, und 3D-gedruckte Wärmerohrgehäuse bilden hier keine Ausnahme. Das Material muss eine geeignete Kombination aus Wärmeleitfähigkeit, mechanischer Festigkeit, geringer Dichte, Beständigkeit gegenüber der Weltraumumgebung (Vakuum, Strahlung, Temperaturwechsel) und Kompatibilität mit dem gewählten additiven Fertigungsverfahren aufweisen. Für Heatpipe-Gehäuse sind zwei Metallpulver besonders gut geeignet und werden häufig empfohlen: Aluminiumlegierung AlSi10Mg und Kupferlegierung CuCrZr. Die Qualität und die Eigenschaften des verwendeten Metallpulvers sind von grundlegender Bedeutung, um die gewünschten Eigenschaften des Endprodukts zu erreichen. Daher sind Partnerschaften mit erfahrenen Pulverherstellern wie Met3dp von entscheidender Bedeutung. Met3dp nutzt branchenführende Gaszerstäubungs- und Plasma-Rotations-Elektroden-Verfahren (PREP) zur Herstellung von Metallpulvern mit hoher Sphärizität und Fließfähigkeit, die für AM-Verfahren wie Laser Powder Bed Fusion (LPBF) und Selective Electron Beam Melting (SEBM) optimiert sind.
1. Aluminium-Legierung AlSi10Mg:
AlSi10Mg ist eine in der additiven Fertigung weit verbreitete Aluminiumlegierung, die für ihre hervorragende Kombination aus geringer Dichte, guten mechanischen Eigenschaften, guter Wärmeleitfähigkeit (im Vergleich zu anderen AM-Legierungen wie Titan oder Edelstahl) und ausgezeichneter Druckbarkeit bekannt ist.
- Eigenschaften und Vorteile:
- Geringe Dichte: ~2,67g/cm3. Dies ist einer der Hauptgründe für seine Verwendung in der Luft- und Raumfahrt, da es direkt zur Gewichtsreduzierung und zur Senkung der Startkosten beiträgt.
- Gute Wärmeleitfähigkeit: Normalerweise etwa 120-150 W/(m⋅K) nach entsprechender Wärmebehandlung. Dieser Wert ist zwar nicht so hoch wie der von reinem Aluminium oder Kupfer, reicht aber für viele Wärmeübertragungsanwendungen aus, insbesondere dort, wo auch die strukturelle Leistung eine Rolle spielt.
- Gute mechanische Festigkeit: Bietet ein ausgewogenes Verhältnis zwischen Zugfestigkeit (bis zu 450 MPa) und Streckgrenze (bis zu 280 MPa) nach der Wärmebehandlung (z. B. T6) und sorgt für die notwendige strukturelle Integrität des Gehäuses.
- Ausgezeichnete Druckbarkeit: Schmelzt und erstarrt gut während LPBF-Prozessen und ermöglicht die Herstellung komplexer Geometrien mit feinen Merkmalen und relativ geringen Eigenspannungen im Vergleich zu einigen anderen Legierungen.
- Korrosionsbeständigkeit: Weist eine gute Korrosionsbeständigkeit auf.
- Kosten-Nutzen-Verhältnis: Im Allgemeinen kostengünstiger als Titan oder Hochleistungs-Kupferlegierungen.
- Eignung für Heat Pipe Enclosures:
- Ideal für Anwendungen, bei denen leichtbau ist die wichtigste Triebfederund eine mäßige Wärmeleitfähigkeit sind akzeptabel.
- Geeignet für strukturell integrierte Gehäuse, die neben der Unterbringung des Wärmerohrs auch mechanischen Belastungen standhalten müssen.
- Wird häufig für Gehäuse verwendet, die in moderaten Temperaturbereichen arbeiten, in denen die thermischen Belastungen nicht extrem sind.
- Kann nachbearbeitet (maschinell bearbeitet, beschichtet) werden, um spezifische Schnittstellen- oder Oberflächenanforderungen zu erfüllen.
- Erwägungen:
- Die Wärmeleitfähigkeit ist geringer als bei Kupferlegierungen.
- Die mechanischen Eigenschaften nehmen bei höheren Temperaturen (über ~150-200°C) ab.
- Erfordert eine angemessene Wärmebehandlung (Lösen und Altern), um optimale mechanische Eigenschaften zu erzielen.
2. Kupferlegierung CuCrZr (Chrom-Zirkonium-Kupfer):
CuCrZr ist eine Hochleistungs-Kupferlegierung, die speziell entwickelt wurde, um im Vergleich zu Aluminiumlegierungen eine deutlich höhere thermische und elektrische Leitfähigkeit zu bieten und gleichzeitig eine gute mechanische Festigkeit zu gewährleisten, insbesondere bei erhöhten Temperaturen.
- Eigenschaften und Vorteile:
- Ausgezeichnete Wärmeleitfähigkeit: Übersteigt nach der Wärmebehandlung in der Regel 300 W/(m⋅K) und ist damit in Bezug auf die effiziente Wärmeübertragung AlSi10Mg weit überlegen. Dies ist entscheidend für die Minimierung von Temperaturgradienten und die Maximierung der Leistung von Wärmerohren.
- Hohe elektrische Leitfähigkeit: Außerdem weist es eine ausgezeichnete elektrische Leitfähigkeit auf, was von Vorteil sein kann, wenn das Gehäuse eine elektrische Erdung oder Abschirmung bieten muss.
- Gute mechanische Festigkeit: Behält eine gute Festigkeit und Härte, insbesondere bei erhöhten Temperaturen, bei denen Aluminiumlegierungen erweichen können. Die Zugfestigkeit kann bei entsprechender Wärmebehandlung 450-550 MPa erreichen.
- Gute Hochtemperaturleistung: Behält seine Festigkeit bei und wird bei Temperaturen bis zu ~450-500°C nicht weich.
- Gute Abriebfestigkeit: Bietet im Vergleich zu Aluminiumlegierungen eine bessere Verschleißfestigkeit.
- Eignung für Heat Pipe Enclosures:
- Die bevorzugte Wahl für Anwendungen, die maximale thermische Leistung erfordern und effiziente Wärmeableitung, z. B. bei der Kühlung von Hochleistungselektronik oder der Bewältigung großer thermischer Lasten.
- Geeignet für Gehäuse, die bei höheren Temperaturen betrieben werden, bei denen sich die Eigenschaften von AlSi10Mg verschlechtern würden.
- Ideal für Kühlkörper oder thermische Spreizer, die in das Gehäusedesign integriert sind.
- Erwägungen:
- Höhere Dichte: ~8,8-8,9g/cm3. Erheblich schwerer als AlSi10Mg, was sich auf die Bemühungen um Leichtbau auswirkt. Der Leistungsgewinn muss den Gewichtsnachteil rechtfertigen.
- Anspruchsvollere Druckbarkeit: Kupferlegierungen haben ein hohes Reflexionsvermögen und eine hohe Wärmeleitfähigkeit, was ihre zuverlässige Bearbeitung mit LPBF im Vergleich zu Aluminium oder Stahl erschwert. Sie erfordern optimierte Laserparameter, spezielle Maschineneinstellungen und eine sorgfältige Prozesskontrolle. Das Fachwissen von Anbietern wie Met3dp, die Erfahrung mit verschiedenen Materialien haben, ist hier entscheidend.
- Höhere Kosten: Kupferlegierungspulver sind im Allgemeinen teurer als AlSi10Mg.
- Oxidation: Kupferlegierungen können anfälliger für Oxidation sein und erfordern möglicherweise Schutzbeschichtungen oder eine sorgfältige Handhabung, obwohl CuCrZr eine angemessene Beständigkeit aufweist.
Auswahlkriterien & Pulverqualität:
Die Wahl zwischen AlSi10Mg und CuCrZr hängt von den spezifischen Anforderungen des Einsatzes ab, wobei die Anforderungen an die thermische Leistung mit den Massenbeschränkungen und dem Budget abzuwägen sind.
- Bevorzugen Sie AlSi10Mg, wenn: Leichtgewichtigkeit ist von größter Bedeutung, die thermische Belastung ist moderat, die strukturelle Leistung ist entscheidend und die Kosten sind ein wichtiger Faktor.
- Bevorzugen Sie CuCrZr, wenn: Maximale Wärmeübertragungseffizienz ist entscheidend, die Betriebstemperaturen sind hoch, und der Massennachteil ist akzeptabel oder wird durch optimiertes Design gemildert.
Unabhängig von der gewählten Legierung ist die qualität des Metallpulvers ist grundlegend. Zu den wichtigsten Pulvereigenschaften, die die Qualität des Endprodukts beeinflussen, gehören:
- Partikelgrößenverteilung (PSD): Beeinflusst die Dichte des Pulverbetts, die Fließfähigkeit sowie die Auflösung und Dichte des fertigen Teils.
- Sphärizität: Hochkugelförmige Pulver fließen besser, was zu gleichmäßigen Pulverschichten und dichteren, konsistenteren Teilen führt.
- Fließfähigkeit: Entscheidend für die gleichmäßige Verteilung der Pulverschichten während des Druckvorgangs.
- Reinheit/Chemie: Eine strenge Kontrolle der Legierungszusammensetzung und die Minimierung von Verunreinigungen (wie Sauerstoff und Stickstoff) sind für das Erreichen der gewünschten mechanischen und thermischen Eigenschaften und die Gewährleistung der Prozessstabilität von entscheidender Bedeutung.
- Abwesenheit von Satelliten: Kleine Partikel, die an größeren Partikeln haften, können die Fließfähigkeit und Packungsdichte beeinträchtigen.
Das Engagement von Met3dp’s für Qualität und der Einsatz fortschrittlicher Fertigungstechniken wie Vakuum-Induktionsschmelz-Gaszerstäubung (VIGA) und PREP stellen sicher, dass ihre Metallpulver die strengen Anforderungen für Luft- und Raumfahrtanwendungen erfüllen. Das Portfolio umfasst nicht nur Standardlegierungen, sondern auch die Möglichkeit, innovative Werkstoffe zu entwickeln, die auf spezifische Kundenanforderungen zugeschnitten sind. Die Sicherstellung einer zuverlässigen Versorgung mit hochwertigem, für die Luft- und Raumfahrt geeignetem Pulver ist der erste entscheidende Schritt zur erfolgreichen Herstellung anspruchsvoller Komponenten wie Wärmerohrgehäuse. Bei der Erkundung von Materialoptionen sollten Sie die detaillierten Spezifikationen konsultieren, die auf Ressourcen wie Met3dp’s produktseiten kann wertvolle Einblicke in die verfügbaren Pulver und ihre zertifizierten Eigenschaften geben.
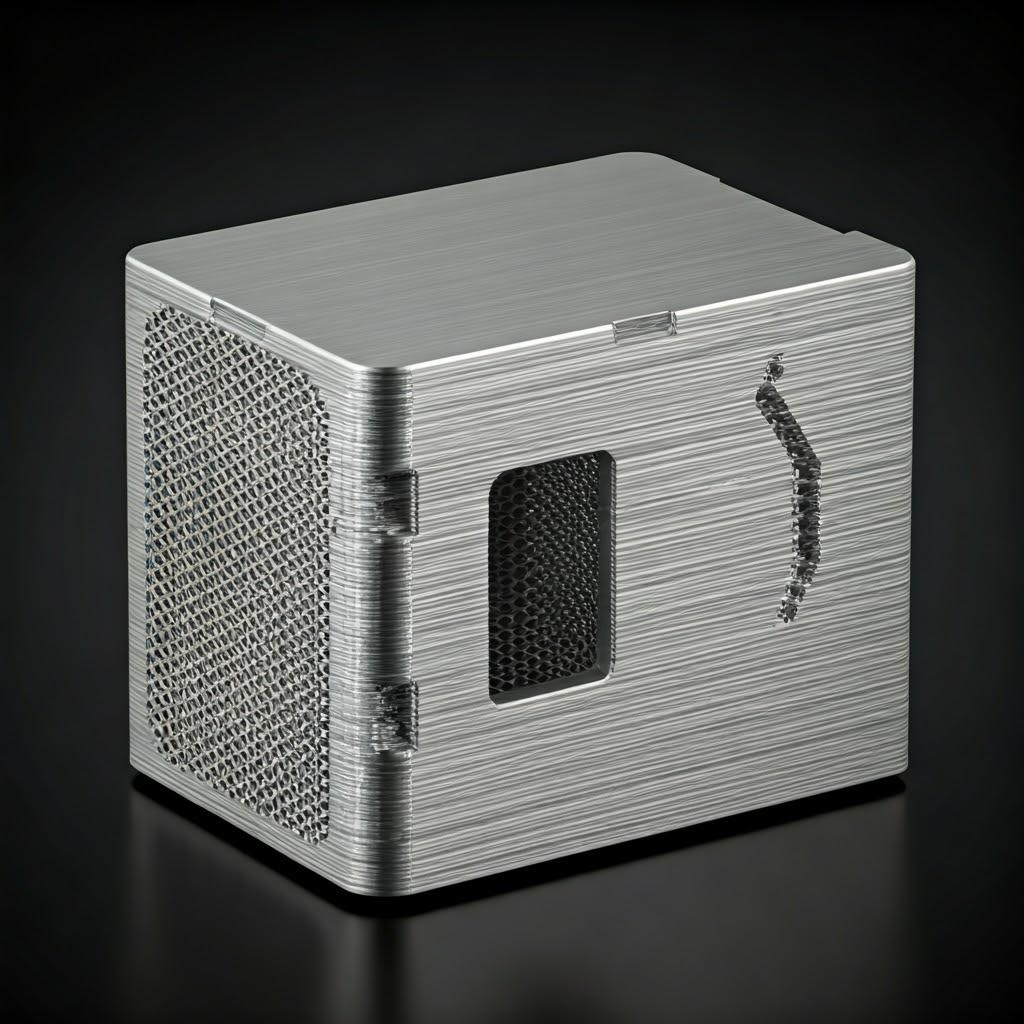
Entwurf für additive Fertigung (DfAM): Optimierung von Wärmerohrgehäusen für den 3D-Druck
Die einfache Nachbildung eines Designs, das für die herkömmliche Fertigung vorgesehen ist, mit Hilfe der additiven Fertigung führt selten zu optimalen Ergebnissen. Um die Vorteile des 3D-Drucks von Metall für Wärmerohrgehäuse in Raumfahrtsystemen wirklich zu nutzen, müssen Ingenieure folgende Aspekte berücksichtigen Design für additive Fertigung (DfAM) grundsätze. DfAM ist nicht nur eine Reihe von Regeln, sondern eine neue Denkweise, die sich darauf konzentriert, die einzigartigen Fähigkeiten von AM - kostenlose Komplexität, Bauteilkonsolidierung, Leichtbaupotenzial - zu nutzen und gleichzeitig die inhärenten Beschränkungen zu respektieren, wie z. B. Stützstrukturen, Bauausrichtung und minimale Featuregrößen. Die Optimierung eines Wärmerohrgehäuses mit DfAM kann zu erheblichen Verbesserungen der thermischen Leistung, der strukturellen Effizienz, der Massenreduzierung und der gesamten Systemintegration führen.
Die wichtigsten DfAM-Prinzipien für Wärmerohrgehäuse:
- Topologie-Optimierung:
- Konzept: Softwaregesteuerter Prozess, der die Materialverteilung innerhalb eines definierten Konstruktionsraums unter Berücksichtigung gegebener Lasten, Randbedingungen und Einschränkungen (z. B. Maximierung der Steifigkeit für eine bestimmte Masse) mathematisch optimiert.
- Anwendung: Bei Wärmerohrgehäusen kann die Topologieoptimierung nicht benötigte Materialien identifizieren, die entfernt werden können, was zu organischen, dem Lastpfad folgenden Strukturen führt, die deutlich leichter sind als konventionell konstruierte Teile und gleichzeitig die strukturellen Anforderungen erfüllen oder übertreffen. Dies ist für die Senkung der Startkosten von entscheidender Bedeutung.
- Nutzen: Maximiert das Verhältnis von Festigkeit zu Gewicht, schafft hocheffiziente Strukturen, ideal für die Entwicklung erster Leichtbaukonzepte.
- Erwägung: Optimierte Formen können komplex sein und erfordern möglicherweise eine sorgfältige Berücksichtigung der Herstellbarkeit (z. B. Überhänge, die unterstützt werden müssen). Für den praktischen Druck ist oft eine gewisse Glättung oder Interpretation erforderlich.
- Gitterstrukturen und Ausfachungen:
- Konzept: Ersetzen fester Volumina durch innere Gitterstrukturen (z. B. Waben-, Kreisel- oder Fachwerkstrukturen) oder gemusterte Ausfachungen.
- Anwendung: Verringert die Masse und erhält gleichzeitig eine angemessene strukturelle Unterstützung. Bestimmte Gittertypen (wie TPMS – Triply Periodic Minimal Surfaces, z. B. Kreisel) können auch die thermische Leistung verbessern, indem sie die Oberfläche für die Wärmeübertragung vergrößern oder die Flüssigkeitsströmung in integrierten Kanälen (falls zutreffend) beeinflussen.
- Nutzen: Signifikante Gewichtsreduzierung, Potenzial für maßgeschneiderte mechanische Eigenschaften (z. B. Energieabsorption), mögliche thermische Vorteile.
- Erwägung: Bei komplexen Gittern kann es schwierig sein, sie ohne Defekte zu drucken, sie können Pulver einschließen, was eine sorgfältige Planung der Entwässerung erfordert, und die Analyse kann rechenintensiv sein. Die Oberflächenrauhigkeit innerhalb von Gittern kann hoch sein.
- Konformes Design und Kanaloptimierung:
- Konzept: Gestaltung von Merkmalen, insbesondere von internen Kanälen oder Wärmeleitbahnen, die den Konturen der Komponenten, mit denen sie verbunden sind, oder dem optimalen Pfad für den Wärme-/Flüssigkeitsstrom genau entsprechen.
- Anwendung: Bei Heatpipe-Gehäusen zur Kühlung von Elektronik können die internen Durchgänge oder die äußere Form genau an die wärmeerzeugenden Komponenten angepasst werden, um den Widerstand der thermischen Schnittstelle zu minimieren. Bei Wärmerohrgehäusen können die Verdampfer- und Verflüssigerkanäle für die Fluiddynamik und die Wärmeübertragung optimiert werden, wobei glatte Biegungen und variable Querschnitte möglich sind, die durch Bohren oder Fräsen nicht möglich sind.
- Nutzen: Verbesserter Wärmewirkungsgrad, geringerer Druckverlust (in Flüssigkeitssystemen), höhere Packungsdichte.
- Erwägung: Erfordert eine genaue Modellierung der Schnittstellenkomponenten; komplexe interne Kanäle erfordern robuste Strategien zur Pulverentfernung.
- Teil Konsolidierung:
- Konzept: Umgestaltung einer Baugruppe aus mehreren traditionell hergestellten Teilen in eine einzige, integrierte Komponente, die mittels AM druckbar ist.
- Anwendung: Kombination des Hauptgehäuses, der Montageflansche, der Halterungen, der internen Stützen und möglicherweise sogar der Elemente der Dochtstruktur des Wärmerohrs (unter Verwendung poröser AM-Techniken) in einem einzigen monolithischen Teil.
- Nutzen: Reduziert die Anzahl der Teile, die Montagezeit, das Gewicht und potenzielle Fehlerstellen (Verbindungen, Befestigungselemente, Schweißnähte, Lötstellen). Verbessert die strukturelle und thermische Kontinuität.
- Erwägung: Erhöht die Komplexität des Einzelteils; der Ausfall des Einzelteils erfordert den Austausch der gesamten integrierten Komponente. Erfordert eine sorgfältige Konstruktion, um sicherzustellen, dass alle Funktionsanforderungen der ursprünglichen Baugruppe erfüllt werden.
- Wanddicke und Größe der Merkmale:
- Konzept: Entwurf von Wänden und Merkmalen, die für den jeweiligen AM-Prozess (z. B. LPBF, SEBM) und das verwendete Material geeignet sind.
- Anwendung: Sicherstellen, dass die Wände dick genug sind, um die strukturelle Integrität und die Druckbarkeit zu gewährleisten (typischerweise >0,4-0,5 mm für viele Prozesse, obwohl die Spezifika variieren), aber Minimierung der Dicke, wo dies möglich ist, um das Gewicht zu reduzieren. Berücksichtigung der Mindestgröße auflösbarer Merkmale für kleine Details wie Stifte oder dünne Rippen.
- Nutzen: Ausgewogenes Verhältnis zwischen struktureller Leistung, Gewicht und Herstellbarkeit. Verhindert Druckfehler aufgrund von zu kleinen Merkmalen oder zu dünnen Wänden.
- Erwägung: Die optimale Dicke hängt vom Material, dem Lastfall, den thermischen Anforderungen und den Druckereigenschaften ab. Sehr dünne Wände können anfällig für Verformungen sein.
- Unterstützung der Strategie und der Gebäudeausrichtung:
- Konzept: Gestaltung des Teils und Wahl seiner Ausrichtung in der Baukammer, um den Bedarf an Stützstrukturen zu minimieren, insbesondere in kritischen oder schwer zugänglichen Bereichen, und gleichzeitig die Druckbarkeit zu gewährleisten. Überhängende Features (typischerweise unter 45 Grad von der Horizontalen) erfordern Unterstützung.
- Anwendung: Ausrichtung des Gehäuses, um nach unten gerichtete Flächen zu minimieren, oder Gestaltung von Merkmalen, die selbsttragend sind (z. B. Verwendung von Abschrägungen anstelle von scharfen Überhängen). Konstruktion von Stützstrukturen, die leicht zu entfernen sind, ohne das Teil zu beschädigen, und Minimierung von Kontaktpunkten an kritischen Oberflächen.
- Nutzen: Reduziert die Nachbearbeitungszeit und -kosten, verbessert die Oberflächengüte auf unterstützten Oberflächen und verringert das Risiko einer Beschädigung der Teile beim Entfernen.
- Erwägung: Die Ausrichtung des Bauwerks wirkt sich auf die Eigenspannung, die Anisotropie (Richtungseigenschaften) und die Oberflächenrauheit auf verschiedenen Flächen aus. Interne Stützen in komplexen Kanälen können sehr schwierig oder unmöglich zu entfernen sein und erfordern eine sorgfältige DfAM-Planung (z. B. Entwässerungslöcher, Verwendung löslicher Stützen, falls vorhanden, oder Ausrichtung zur Vermeidung interner Überhänge).
- Integration des Wärmemanagements:
- Konzept: Direkte Integration von Wärmemanagementfunktionen wie Rippen, Stifte oder optimierte Leiterbahnen in das Gehäusedesign.
- Anwendung: Gestaltung externer Rippen direkt auf der Gehäuseoberfläche zur Vergrößerung der Oberfläche für die Abstrahlung in den Raum. Schaffung interner Strukturen oder optimierter fester Bahnen zur effizienten Wärmeleitung von der Quelle zum Verdampferabschnitt des Wärmerohrs oder vom Verflüssigerabschnitt zu einer Heizkörperschnittstelle.
- Nutzen: Verbesserte thermische Leistung, geringerer Wärmewiderstand, möglicher Verzicht auf separate Kühlkörper oder Spreader.
- Erwägung: Komplexe Rippen verlängern die Druckzeit und erhöhen möglicherweise den Bedarf an Stützen. Die thermische Leistung muss durch Simulation und Tests validiert werden.
DfAM Arbeitsablauf:
Ein typischer DfAM-Arbeitsablauf umfasst:
- Definition der Anforderungen: Klare Angaben zu thermischen Belastungen, strukturellen Zwängen, Schnittstellen, Massenzielen und Umweltbedingungen.
- Konzeptionelle Gestaltung: Nutzung von Topologieoptimierung, generativem Design oder Expertenwissen zur Erstellung erster AM-zentrierter Konzepte.
- Detaillierter Entwurf und Simulation: Verfeinerung der Geometrie mit Hilfe von CAD-Werkzeugen unter Berücksichtigung der DfAM-Grundsätze (Wandstärke, Stützen usw.). Durchführung von thermischen und strukturellen Finite-Elemente-Analysen (FEA) zur Validierung der Leistung.
- Prüfungen der Herstellbarkeit: Verwendung spezieller Software oder Checklisten, um sicherzustellen, dass der Entwurf druckbar ist, die Halterungen machbar sind und das Pulver entfernt werden kann. Eine frühzeitige Beratung mit dem AM-Dienstleister (wie Met3dp) in der Entwurfsphase wird dringend empfohlen.
- Iteration: Verfeinerung des Entwurfs auf der Grundlage von Simulationsergebnissen und Rückmeldungen zur Herstellbarkeit.
Durch die durchdachte Anwendung von DfAM können Ingenieure das volle Potenzial des 3D-Metalldrucks ausschöpfen und Wärmerohrgehäuse schaffen, die nicht nur anders hergestellt werden, sondern grundlegend besser sind - leichter, effizienter und perfekt auf die extremen Anforderungen des Weltraums zugeschnitten.
Erreichen von Präzision: Toleranz, Oberflächengüte und Maßgenauigkeit bei AM-Gehäusen
Während die additive Fertigung von Metallen eine unglaubliche geometrische Komplexität ermöglicht, ist das Verständnis und die Kontrolle der erreichbaren Präzision - einschließlich der Maßgenauigkeit, der Toleranzen und der Oberflächenbeschaffenheit - für funktionale Raumfahrt-Hardware wie Wärmerohr-Gehäuse entscheidend. Schnittstellen müssen perfekt ausgerichtet sein, Dichtungen müssen korrekt funktionieren und der thermische Kontaktwiderstand muss minimiert werden. Die Fähigkeiten des AM-Prozesses selbst, das gewählte Material, das Design des Teils und die nachfolgenden Nachbearbeitungsschritte beeinflussen alle die endgültige Präzision.
Maßgenauigkeit und Toleranzen:
- As-Built-Genauigkeit: Metall-AM-Verfahren wie Laser Powder Bed Fusion (LPBF) und Selective Electron Beam Melting (SEBM) erreichen in der Regel Maßgenauigkeiten im Bereich von ±0,1 mm bis ±0,2 mm für kleinere Merkmale (z. B. bis zu 100 mm), oder ±0,1 % bis ±0,2 % des Nennmaßes für größere Teile. Dies kann jedoch durch Faktoren wie folgende beeinflusst werden:
- Thermische Effekte: Eigenspannungen, die sich während des Drucks ansammeln, können zu Verformungen oder Verzerrungen führen und die Gesamtgenauigkeit beeinträchtigen. Das Teiledesign, die Unterstützungsstrategie und die Bauparameter spielen eine entscheidende Rolle.
- Material: Verschiedene Werkstoffe weisen ein unterschiedliches Maß an Schrumpfung und Spannungsakkumulation auf (z. B. kann CuCrZr eine größere Herausforderung darstellen als AlSi10Mg).
- Kalibrierung der Maschine: Die Genauigkeit und Kalibrierung des spezifischen AM-Systems sind von grundlegender Bedeutung. Hochwertige Industriedrucker, wie sie möglicherweise von Anbietern wie Met3dp verwendet werden, die für branchenführende Genauigkeit und Zuverlässigkeitbieten im Allgemeinen eine bessere Konsistenz.
- Teilegeometrie und -ausrichtung: Große flache Abschnitte oder freitragende Überhänge sind anfälliger für Abweichungen.
- Erreichbare Toleranzen: Während die allgemeine Genauigkeit eine Grundlage bildet, sind bei bestimmten kritischen Merkmalen (z. B. Montagebohrungen, Schnittstellenflächen, Dichtungsnuten) häufig engere Toleranzen erforderlich.
- Wie gedruckt: Toleranzen, die enger sind als die allgemeine Genauigkeit, erfordern oft eine sorgfältige Prozesskontrolle und möglicherweise eine Kompensation der Merkmale in der Konstruktionsdatei. Das Erreichen von Toleranzen unter ±0,1 mm direkt beim Drucken kann eine Herausforderung sein und ist über das gesamte Teil uneinheitlich.
- Nachbearbeitet: Für Merkmale, die eine hohe Präzision erfordern (z. B. ±0,01 mm bis ±0,05 mm), postprozessorische Bearbeitung (CNC-Fräsen, Drehen, Schleifen) ist in der Regel erforderlich. Kritische Schnittstellen, Dichtungsflächen und präzise Lochdurchmesser/-positionen werden in der Regel nach dem Druck mit subtraktiven Verfahren bearbeitet.
Oberflächengüte (Rauhigkeit):
Die Oberflächenbeschaffenheit, die häufig durch die durchschnittliche Rauheit (Ra) quantifiziert wird, ist ein weiterer Schlüsselaspekt der Präzision und besonders wichtig für den thermischen Kontaktwiderstand und die Abdichtung.
- Oberflächenrauhigkeit im Ist-Zustand:
- Obere Oberflächen: Oberflächen, die während des Aufbaus nach oben zeigen, haben im Allgemeinen die geringste Rauheit, oft Ra 5-15 µm, je nach Pulvergröße und Schichtdicke.
- Vertikale Mauern: Die Seitenwände weisen aufgrund der schichtweisen Beschaffenheit in der Regel eine etwas höhere Rauheit auf, typischerweise Ra 10-20 µm.
- Unterstützte Oberflächen: Nach unten gerichtete Oberflächen, für die Stützstrukturen erforderlich waren, weisen die höchste Rauheit auf, oft Ra 20-50 µm oder mehr, je nach Art der Stütze und des Entfernungsverfahrens. Die Stellen, an denen die Stützen angebracht werden, hinterlassen Spuren, die oft nachbearbeitet werden müssen.
- Interne Kanäle: Die Rauheit in komplexen inneren Kanälen kann sehr hoch sein und lässt sich ohne spezielle Techniken (z. B. abrasive Fließbearbeitung) nur schwer deutlich verbessern.
- Auswirkungen auf die Leistung:
- Thermischer Kontaktwiderstand (TCR): Durch raue Oberflächen entstehen beim Zusammenfügen zweier Komponenten mikroskopisch kleine Lücken, in denen Luft (ein schlechter Leiter) eingeschlossen wird und die den Widerstand gegen den Wärmefluss an der Schnittstelle erheblich erhöhen. Bei Wärmerohrgehäusen, die mit Wärmequellen oder Heizkörpern verbunden sind, ist die Minimierung des TCR entscheidend. Glatte Oberflächen (niedrige Ra), die durch Bearbeitung oder Polieren erreicht werden, sind an diesen Schnittstellen oft erforderlich.
- Versiegeln: Raue Oberflächen können die Wirksamkeit von Dichtungen (z. B. O-Ringe, metallische Dichtungen) beeinträchtigen, was zu potenziellen Leckagen führen kann - inakzeptabel für eingeschlossene Flüssigkeiten oder die Aufrechterhaltung der Vakuumintegrität. Dichtungsoberflächen müssen fast immer nachbearbeitet oder poliert werden.
- Strahlungseigenschaften: Die Oberflächenrauhigkeit wirkt sich auf das Emissions- und Absorptionsvermögen der Außenflächen des Gehäuses aus und beeinflusst so dessen Fähigkeit, Wärme in den Raum abzustrahlen. Während Beschichtungen häufig zur präzisen Steuerung dieser Eigenschaften verwendet werden, kann auch die zugrunde liegende Rauheit eine Rolle spielen.
- Fluid Flow: Hohe Rauheit in internen Kanälen (z. B. in LHPs) kann den Druckverlust erhöhen.
- Verbesserung der Oberflächengüte: Zu den gängigen Nachbearbeitungsmethoden gehören:
- Spanende Bearbeitung (Fräsen, Drehen): Erzeugt sehr glatte, präzise Oberflächen (Ra < 1 µm möglich).
- Polieren: Mechanisches oder elektrochemisches Polieren für sehr niedrige Ra-Werte.
- Abrasives Strahlen (Sandstrahlen, Perlstrahlen): Erzeugt eine gleichmäßige, matte Oberfläche, kann kleinere Unebenheiten beseitigen, erhöht aber in der Regel die Ra im Vergleich zur maschinellen Bearbeitung.
- Abrasive Fließbearbeitung (AFM): Zum Glätten von inneren Kanälen, indem eine abrasive Spachtelmasse durch sie hindurchfließt.
- Massenabfertigung (Tumbling): Kann Außenflächen glätten und Kanten entgraten, aber weniger präzise Kontrolle.
Präzision erreichen – Ein ganzheitlicher Ansatz:
Die erforderliche Präzision für ein 3D-gedrucktes Wärmerohrgehäuse muss gewährleistet sein:
- Entwurf: Konstruktion von kritischen Merkmalen mit Aufmaß für die Bearbeitung, wenn enge Toleranzen oder glatte Oberflächen erforderlich sind. Vermeidung komplexer interner Stützen, wenn möglich.
- Material & Prozessauswahl: Auswahl des geeigneten AM-Prozesses und Materials, Verständnis der inhärenten Genauigkeits- und Rauheitseigenschaften.
- Optimierung der Parameter: Zusammenarbeit mit einem erfahrenen AM-Anbieter zur Optimierung der Fertigungsparameter für Dichte, Genauigkeit und minimale Belastung.
- Nachbearbeitungsplan: Festlegung der erforderlichen Bearbeitungs-, Polier- oder anderen Endbearbeitungsschritte für kritische Merkmale während der Konstruktionsphase.
- Qualitätskontrolle: Anwendung strenger Prüfverfahren (CMM-Messungen, Oberflächenprofilometrie, CT-Scanning) zur Überprüfung von Abmessungen und Oberflächeneigenschaften.
Durch die sorgfältige Berücksichtigung dieser Faktoren können Ingenieure mit Zuversicht Metall-AM zur Herstellung von Wärmerohrgehäusen nutzen, die den strengen Präzisionsanforderungen von Raumfahrtanwendungen entsprechen.
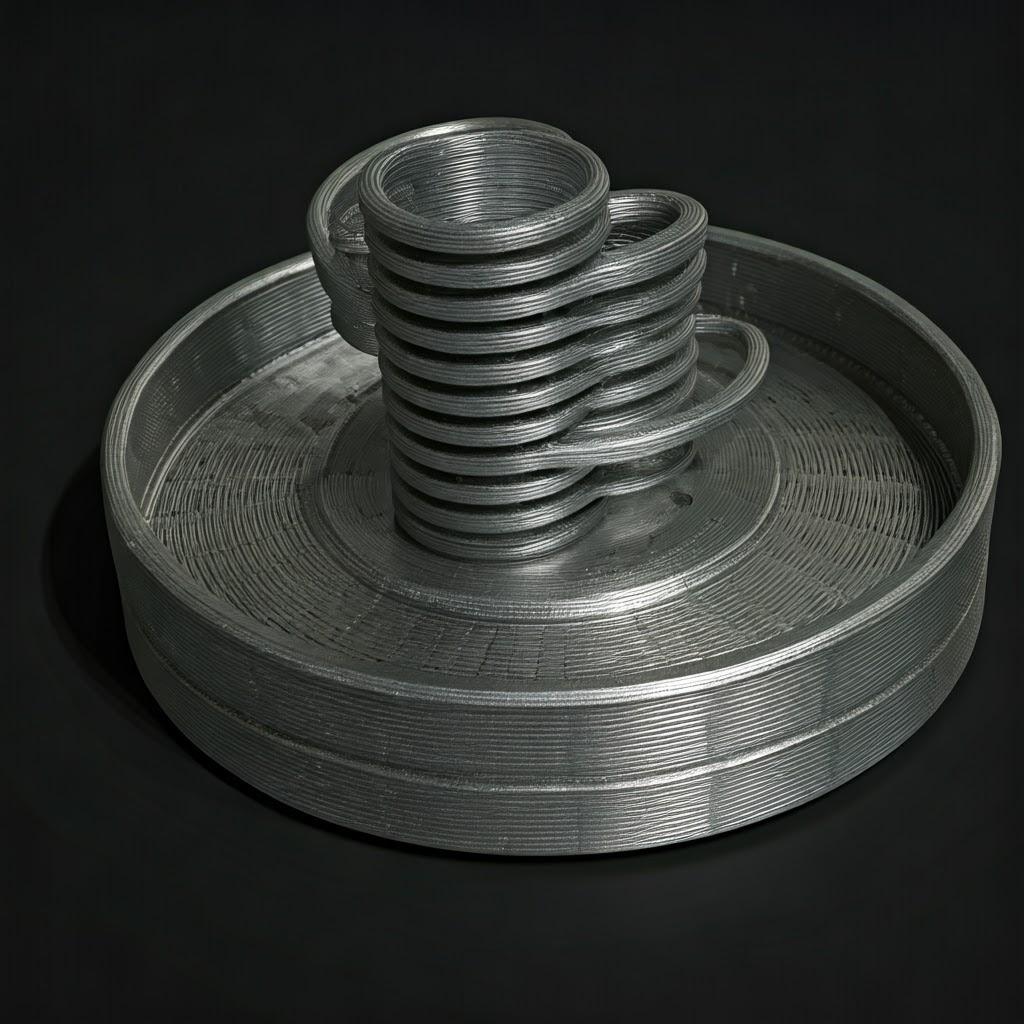
Jenseits des Drucks: Unverzichtbare Nachbearbeitung für weltraumtaugliche Gehäuse
Die Reise eines 3D-gedruckten Wärmerohrgehäuses aus Metall endet nicht, wenn es aus dem Drucker kommt. Das fertige Teil erfordert mehrere entscheidende Nachbearbeitungsschritte, um es von einem rohen Druck in eine flugtaugliche, funktionale Komponente zu verwandeln. Diese Schritte sind unerlässlich, um Spannungen abzubauen, die erforderliche Maßgenauigkeit und Oberflächengüte zu erreichen, sicherzustellen, dass die Materialeigenschaften den Spezifikationen entsprechen, und die Sauberkeit für die Weltraumumgebung zu gewährleisten. Das Auslassen oder die unsachgemäße Durchführung dieser Schritte kann die Integrität und Leistung des Teils beeinträchtigen.
Gemeinsame Nachbearbeitungsschritte für AM-Heatpipe-Gehäuse:
- Entpudern / Reinigen (Initial):
- Zweck: Entfernen Sie den Großteil des ungeschmolzenen Metallpulvers, das das Teil umgibt und möglicherweise im Inneren eingeschlossen ist, nachdem der Bau abgeschlossen ist.
- Methoden: Manuelles Bürsten, Abblasen mit Druckluft, Vibration, Perlstrahlen (vorsichtig, um Oberflächenschäden zu vermeiden). Bei komplexen inneren Kanälen können spezielle Pulverentfernungssysteme oder eine vorsichtige Handhabung erforderlich sein.
- Wichtigkeit: Pulverreste können nachfolgende Schritte (Wärmebehandlung, Bearbeitung) beeinträchtigen, zusätzliches Gewicht verursachen und möglicherweise später zu einer losen Verunreinigung werden. Die vollständige Entfernung von Pulver aus komplizierten Innengeometrien ist eine große Herausforderung, die eine sorgfältige DfAM erfordert.
- Stressabbau Wärmebehandlung:
- Zweck: Abbau von inneren Spannungen, die während der schnellen Heiz- und Kühlzyklen des schichtweisen AM-Prozesses entstehen. Diese Spannungen können nach der Entnahme des Teils aus der Bauplatte oder bei der anschließenden Bearbeitung zu Verformungen (Verzug) führen und die mechanischen Eigenschaften negativ beeinflussen.
- Methoden: Erhitzen des Teils (oft noch auf der Bauplatte) in einem Ofen mit kontrollierter Atmosphäre auf eine bestimmte Temperatur unterhalb des Alterungs- oder Schmelzpunkts der Legierung, Halten des Teils für eine bestimmte Zeit und anschließendes langsames Abkühlen. Die Parameter (Temperatur, Zeit, Atmosphäre) sind spezifisch für die jeweilige Legierung (AlSi10Mg, CuCrZr).
- Wichtigkeit: Obligatorischer Schritt für fast alle metallischen AM-Teile, insbesondere für solche mit komplexen Geometrien oder engen Toleranzen, um Maßhaltigkeit zu gewährleisten und Rissbildung zu verhindern.
- Entfernen von der Bauplatte und Entfernen der Stützstruktur:
- Zweck: Trennen Sie das/die gedruckte(n) Teil(e) von der Grundplatte, auf der es/sie aufgebaut wurde(n), und entfernen Sie die Stützstrukturen, die zur Verankerung des Teils verwendet wurden und verhindern, dass die Überhänge während des Drucks zusammenbrechen.
- Methoden:
- Entfernen der Bauplatte: Drahterodieren (Electrical Discharge Machining), Sägen oder Zerspanen.
- Unterstützung bei der Entfernung: Manuelles Brechen/Schneiden (für leicht zugängliche Träger), CNC-Bearbeitung, Schleifen, Drahterodieren (für empfindliche oder schwer zugängliche Träger).
- Wichtigkeit: Die Stützen sind für den Druck erforderlich, werden aber geopfert. Sie müssen vorsichtig entfernt werden, um die Oberfläche des Teils nicht zu beschädigen. Bereiche, an denen Stützen angebracht waren, haben in der Regel eine rauere Oberfläche und müssen weiter behandelt werden. Die einfache Entfernung der Stützen sollte ein wichtiger Aspekt der DfAM sein.
- Weitere Wärmebehandlung (Solutionizing & Aging / Annealing):
- Zweck: Optimierung der Mikrostruktur des Materials, um die gewünschten mechanischen Eigenschaften (Festigkeit, Duktilität, Härte) und Wärmeleitfähigkeit zu erreichen.
- Methoden:
- AlSi10Mg: In der Regel ist eine T6-Wärmebehandlung erforderlich, die eine Lösungsglühung (Erhitzung zur Auflösung von Si und Mg in der Al-Matrix), gefolgt von einer Abschreckung und künstlichen Alterung (Erhitzung bei niedrigeren Temperaturen zur Ausscheidung von Verfestigungsphasen) umfasst.
- CuCrZr: Oft ist ein Lösungsglühen mit anschließendem Abschrecken und Ausscheidungshärten (Alterung) erforderlich, um die Festigkeit und Leitfähigkeit zu maximieren.
- Parameter: Spezifische Temperaturen, Haltezeiten, Abschreckraten und Alterungsparameter sind von entscheidender Bedeutung und hängen von der Legierung und den gewünschten Eigenschaften ab, wobei häufig Spezifikationen aus der Luft- und Raumfahrt Anwendung finden. Um Oxidation zu verhindern, sind in der Regel Öfen mit kontrollierter Atmosphäre oder Vakuumöfen erforderlich.
- Wichtigkeit: Wesentlich für die Erfüllung der im Entwurf festgelegten Leistungsanforderungen. Ungedruckte oder nur spannungsarm gefertigte Teile weisen im Allgemeinen nicht die optimalen Materialeigenschaften auf.
- Spanende Bearbeitung (CNC):
- Zweck: Erzielen Sie enge Toleranzen bei kritischen Abmessungen, erstellen Sie präzise Schnittstellen (für zusammenpassende Teile, thermischen Kontakt), erzeugen Sie glatte Dichtungsflächen und bearbeiten Sie Merkmale, die sich nur schwer oder gar nicht präzise drucken lassen (z. B. Gewindebohrungen).
- Methoden: Fräsen, Drehen, Schleifen, Bohren, Gewindeschneiden.
- Wichtigkeit: Schließt die Lücke zwischen der geometrischen Freiheit von AM’s und der hohen Präzision, die oft für funktionale Schnittstellen erforderlich ist. Unerlässlich für die Gewährleistung einer ordnungsgemäßen Montage, Abdichtung und effizienten Wärmeübertragung an den Kontaktpunkten. Erfordert ein sorgfältiges Vorrichtungsdesign, um das potenziell komplexe AM-Teil sicher und ohne Verformung zu halten.
- Oberflächenveredelung:
- Zweck: Verbesserung der Oberflächenrauheit aus thermischen, abdichtenden oder ästhetischen Gründen, Entgraten von Kanten, Vorbereitung von Oberflächen für Beschichtungen oder Aufbringen bestimmter Oberflächeneigenschaften (z. B. kontrollierter Emissionsgrad/Absorptionsgrad).
- Methoden: Strahlen (verschiedene Medien), Trommeln/Massenschliff, mechanisches Polieren, Elektropolieren, Mikrobearbeitung, eventuell Eloxieren (für Aluminiumlegierungen) oder anwendungsspezifische Beschichtungen (z. B. Wärmeschutzbeschichtungen wie weiße Farbe, schwarze Farbe, optische Sonnenreflektoren oder spezielle ausgasungsarme Beschichtungen für die Luft- und Raumfahrt).
- Wichtigkeit: Maßgeschneiderte Oberflächeneigenschaften zur Erfüllung funktionaler Anforderungen, die über die grundlegende Geometrie und Maßgenauigkeit hinausgehen. Beschichtungen sind für thermische Kontrollflächen im Weltraum sehr verbreitet.
- Endreinigung & Inspektion:
- Zweck: Entfernen Sie alle Rückstände von Bearbeitungsflüssigkeiten, Polierpasten, Ablagerungen oder Verunreinigungen bei der Handhabung, um die strengen Sauberkeitsstandards der Luft- und Raumfahrt zu erfüllen (Vermeidung von Ausgasungen oder Partikelverunreinigungen im Weltraum). Führen Sie eine abschließende Qualitätsprüfung durch.
- Methoden: Mehrstufige Reinigungsverfahren (Ultraschallbäder mit spezifischen Lösungsmitteln/Reinigungsmitteln), Präzisionsreinigungsprotokolle, Endkontrolle unter Vergrößerung oder mit Spezialgeräten. Die zerstörungsfreie Prüfung (NDT) ist entscheidend:
- Computertomographie (CT) Scannen: Erkennt interne Hohlräume, Porosität und Risse und prüft komplexe interne Geometrien und Pulverentfernung.
- Prüfung der Abmessungen: Koordinatenmessmaschine (CMM) zur Überprüfung kritischer Abmessungen und Toleranzen.
- Messung der Oberflächenrauhigkeit: Profilometrie zur Bestätigung der Anforderungen an die Oberflächengüte.
- Materialprüfung: Zugversuch, Härteprüfung, chemische Analyse auf neben dem Teil gedruckten Prüfstücken.
- Druck-/Leckprüfung: Wenn das Gehäuse für den Einschluss konzipiert ist.
- Wichtigkeit: Stellt sicher, dass das fertige Teil frei von Mängeln ist, alle Spezifikationen erfüllt und sicher für den Flug ist.
Die spezifische Abfolge und Notwendigkeit dieser Schritte hängt stark von der Konstruktion des Teils, dem Material und den Anwendungsanforderungen ab. Die Zusammenarbeit mit einem sachkundigen AM-Dienstleister, der Erfahrung mit Anwendungen in der Luft- und Raumfahrt hat, ist von entscheidender Bedeutung, um sicherzustellen, dass alle erforderlichen Nachbearbeitungsschritte korrekt identifiziert, geplant und ausgeführt werden, damit ein zuverlässiges, weltraumtaugliches Wärmerohrgehäuse entsteht.
Herausforderungen meistern: Überwindung von Hürden beim 3D-Druck von Wärmerohrgehäusen
Die additive Fertigung von Metallen bietet zwar entscheidende Vorteile für die Herstellung komplexer Wärmerohrgehäuse, aber die Technologie ist auch mit einigen Herausforderungen verbunden, insbesondere bei der Herstellung von Komponenten für Raumfahrtsysteme, bei denen viel auf dem Spiel steht. Das Verständnis dieser potenziellen Hürden und die Umsetzung wirksamer Abhilfestrategien sind entscheidend für eine erfolgreiche Einführung. Erfahrene AM-Anbieter entwickeln robuste Prozesse, um diese allgemeinen Probleme zu lösen.
Gemeinsame Herausforderungen und Abhilfestrategien:
- Eigenspannung und Verzug:
- Herausforderung: Die schnelle, örtlich begrenzte Erwärmung und Abkühlung beim Pulverbettschmelzen führt zu erheblichen Temperaturgradienten, die zu inneren Spannungen im gedruckten Teil führen. Diese Spannungen können während oder nach der Herstellung zu Verformungen (Verzug) führen, insbesondere bei großen oder geometrisch komplexen Teilen, wodurch die Maßhaltigkeit beeinträchtigt wird.
- Milderung:
- Simulation: Einsatz von Prozesssimulationssoftware zur Vorhersage von Spannungsakkumulation und Verformung, um Konstruktions- oder Parameteranpassungen zu ermöglichen.
- Strategie aufbauen: Optimierung der Teileausrichtung unter Verwendung geeigneter Laser-/Elektronenstrahl-Abtaststrategien (z. B. Inselabtastung, Sektorierung), um den Wärmeeintrag zu steuern.
- Unterstützende Strukturen: Entwicklung robuster Stützstrukturen, um das Teil sicher auf der Bauplatte zu verankern und Verformungskräften entgegenzuwirken.
- Wärmemanagement: Das Vorheizen der Bauplatte (üblich bei LPBF, inhärent bei SEBM) reduziert thermische Gradienten.
- Obligatorischer Stressabbau: Unmittelbar nach dem Druck und häufig vor der Entnahme des Teils von der Bauplatte ist eine Spannungsarmglühung erforderlich.
- Porosität:
- Herausforderung: Im gedruckten Material können sich kleine Hohlräume oder Poren bilden, die durch eingeschlossenes Gas (Gasporosität) oder unvollständiges Aufschmelzen/Verschmelzen zwischen Schichten oder Scannerspuren (Lack-of-Fusion-Porosität) entstehen. Porosität verschlechtert die mechanischen Eigenschaften (insbesondere die Ermüdungsfestigkeit), kann die Wärmeleitfähigkeit verringern und kann als Rissauslöser dienen. Die Normen für die Luft- und Raumfahrt haben in der Regel sehr strenge Grenzwerte für die zulässige Porosität.
- Milderung:
- Optimierung der Parameter: Entwicklung und sorgfältige Kontrolle von Prozessparametern (Laser-/Strahlleistung, Scangeschwindigkeit, Schichtdicke, Schraffurabstand), die speziell auf das Material (AlSi10Mg, CuCrZr) und die Maschine abgestimmt sind, um eine Dichte von >99,5 % (häufig >99,9 %) zu erreichen. Dies erfordert erhebliches Fachwissen.
- Qualität des Pulvers: Die Verwendung von hochwertigem, trockenem, kugelförmigem Pulver mit kontrollierter Partikelgrößenverteilung minimiert den Gaseinschluss. Die ordnungsgemäße Handhabung und Lagerung des Pulvers ist entscheidend.
- Prozessüberwachung: Einsatz von In-situ-Überwachungsinstrumenten (z. B. Schmelzbadüberwachung) zur Erkennung potenzieller Anomalien während der Bauphase.
- Heiß-Isostatisches Pressen (HIP): Ein Nachbearbeitungsschritt, bei dem das Teil einer hohen Temperatur und einem hohen Inertgasdruck ausgesetzt wird. HIP kann innere Poren (mit Ausnahme der oberflächenverbundenen) wirksam schließen und so die Dichte und die mechanischen Eigenschaften erheblich verbessern. Häufig erforderlich für kritische Bauteile in der Luft- und Raumfahrt.
- Entfernung der Stützstruktur:
- Herausforderung: Wenn nötig, müssen Stützstrukturen entfernt werden. Dies kann zeitaufwändig und kostspielig sein, insbesondere bei komplexen internen Stützen in Kanälen oder schwer zugänglichen Bereichen. Eine aggressive Entfernung kann die Oberfläche des Teils beschädigen, während eine unvollständige Entfernung unerwünschte Vorsprünge oder potenzielle Verunreinigungsfallen hinterlässt.
- Milderung:
- DfAM: Konstruktion von Teilen, die möglichst selbsttragend sind, Minimierung von Überhangwinkeln und Konstruktion von Stützen für einen leichteren Zugang und Ausbau (z. B. Verwendung von Stützen mit geringerer Dichte, die leicht zerbrechlich sind, wo dies angebracht ist).
- Orientierung: Wahl von Bauausrichtungen, die den Bedarf an kritischen internen Stützen minimieren.
- Erweiterte Entfernungstechniken: Einsatz von Methoden wie Drahterodieren oder Spezialbearbeitung für empfindliche oder unzugängliche Träger.
- Lösliche/chemisch entfernbare Stützen: Die Forschung ist im Gange, aber bei AM für Strukturmetalle derzeit weniger verbreitet.
- Validierung und Konsistenz von Materialeigenschaften:
- Herausforderung: Sicherstellung, dass die mechanischen, thermischen und chemischen Eigenschaften des gedruckten und nachbearbeiteten Endprodukts durchgängig den strengen Spezifikationen für Raumfahrtanwendungen genügen. Die Eigenschaften können durch die Bauparameter, die Lage in der Baukammer, unterschiedliche Pulverchargen und Wärmebehandlungszyklen beeinflusst werden. Auch Anisotropie (mit der Baurichtung variierende Eigenschaften) kann auftreten.
- Milderung:
- Strenge Prozesskontrolle: Strenge Kontrolle aller Prozessvariablen (Maschinenkalibrierung, Parameter, Pulverqualität, Atmosphäre, Wärmebehandlung).
- Gutscheine bezeugen: Drucken von standardisierten Testcoupons neben den tatsächlichen Teilen in jedem Bauzyklus. Diese Coupons werden einer zerstörenden Prüfung unterzogen (Zugversuche, Härtetests, Metallografie, chemische Analyse), um die in diesem spezifischen Bauzyklus erzielten Eigenschaften zu überprüfen.
- Datenbank-Entwicklung: Aufbau einer statistischen Datenbank für Materialeigenschaften auf der Grundlage einheitlicher Prozessparameter.
- Qualifikationsprotokolle: Einhaltung etablierter Qualifizierungsverfahren in der Luft- und Raumfahrt (z. B. Prozessqualifizierung, Teilequalifizierung), die umfangreiche Tests beinhalten.
- Kontrolle der Kontamination:
- Herausforderung: Metall-AM-Prozesse, insbesondere die Pulververarbeitung, erfordern saubere Umgebungen. Verunreinigungen durch Fremdpartikel, Feuchtigkeit oder Kreuzkontaminationen zwischen verschiedenen Pulversorten können zu Defekten am fertigen Teil führen oder dessen Leistung im Vakuum des Weltraums beeinträchtigen (z. B. Ausgasung).
- Milderung:
- Dedizierte Ausrüstung: Einsatz von Maschinen für bestimmte Materialien oder Materialfamilien (z. B. eine Maschine für Aluminium, eine andere für Kupfer).
- Strenge Handhabung des Pulvers: Einführung strenger Verfahren für die Lagerung, das Einfüllen, das Sieben und das Recycling von Pulver in kontrollierten Umgebungen (z. B. Inertgas-Handschuhboxen).
- Umgebung der Baukammer: Aufrechterhaltung einer hochreinen Inertgasatmosphäre (Argon, Stickstoff) in der Baukammer, um Oxidation zu verhindern.
- Reinigungsprotokolle: Gründliche Reinigung der Teile nach dem Druck und der Nachbearbeitung, um die Reinheitsstandards der Luft- und Raumfahrt zu erfüllen.
- Einschränkungen der Oberflächenbeschaffenheit:
- Herausforderung: Die Oberflächenrauhigkeit im Ist-Zustand, insbesondere auf gestützten Oberflächen oder in internen Kanälen, entspricht möglicherweise nicht den Anforderungen an thermische Schnittstellen, Dichtungen oder Flüssigkeitsdurchfluss ohne erheblichen Nachbearbeitungsaufwand.
- Milderung:
- DfAM & Ausrichtung: Entwurf und Ausrichtung von Teilen, um kritische Oberflächen so zu platzieren, dass sie auf natürliche Weise eine bessere Oberfläche ergeben (z. B. nach oben gerichtet oder vertikal).
- Gezielte Nachbearbeitung: Aufnahme der erforderlichen Bearbeitungs-, Polier- oder AFM-Schritte in den Fertigungsplan speziell für kritische Oberflächen.
- Realistische Erwartungen: Verstehen der inhärenten Rauheitsgrenzen des gewählten AM-Prozesses und entsprechende Planung.
Die erfolgreiche Bewältigung dieser Herausforderungen erfordert ein tiefes Verständnis der Materialwissenschaft, der Physik des AM-Prozesses, der DfAM-Prinzipien und robuster Qualitätsmanagementsysteme. Die Partnerschaft mit einem etablierten Metall-AM-Anbieter wie Met3dp, der über jahrzehntelange kollektive Erfahrung verfügt und fortschrittliche Anlagen und Pulverherstellungstechnologien wie die verschiedene Druckverfahrender Prozess wird dadurch erheblich entschärft und die Wahrscheinlichkeit erhöht, dass hochwertige und zuverlässige Wärmerohrgehäuse für anspruchsvolle Raumfahrtanwendungen hergestellt werden.
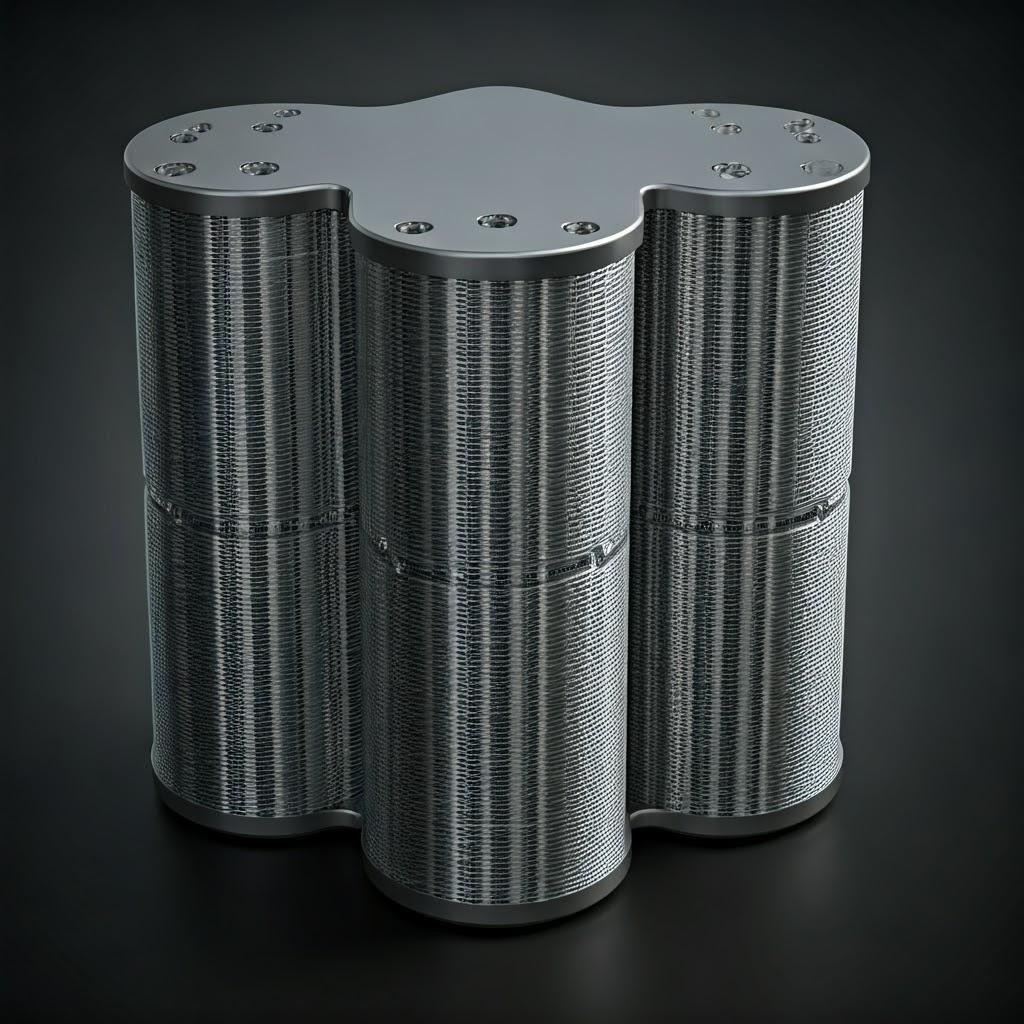
Auswahl der Lieferanten: Die Wahl des richtigen Metall-AM-Partners für Luft- und Raumfahrtkomponenten
Die Auswahl des richtigen Dienstleisters für die additive Fertigung ist ebenso entscheidend wie die Wahl des Designs und des Materials, insbesondere bei anspruchsvollen Anwendungen in der Luft- und Raumfahrt, wie z. B. Wärmerohrgehäusen. Der Unterschied zwischen einem erfolgreichen, flugtauglichen Teil und einem kostspieligen Fehlschlag liegt oft in den Fähigkeiten, der Erfahrung und den Qualitätssystemen Ihres Fertigungspartners. Beschaffungsmanager und -ingenieure, die diese kritischen Komponenten beschaffen, müssen potenzielle Lieferanten anhand einer umfassenden Reihe von Kriterien gründlich bewerten. Die Wahl eines ungeeigneten Partners kann zu Verzögerungen, Budgetüberschreitungen, nicht qualifizierten Teilen und letztlich zu einem Einsatzrisiko führen.
Schlüsselkriterien für die Bewertung von Metall-AM-Anbietern für Raumfahrtanwendungen:
- Zertifizierungen und Konformität in der Luft- und Raumfahrt:
- AS9100: Dies ist die Standardanforderung an ein Qualitätsmanagementsystem (QMS) für die Luft-, Raumfahrt- und Verteidigungsindustrie. Die Zertifizierung nach AS9100 zeigt das Engagement eines Anbieters für Qualität, Rückverfolgbarkeit, Risikomanagement und kontinuierliche Verbesserung, zugeschnitten auf die strengen Anforderungen des Sektors. Sie ist oft eine nicht verhandelbare Anforderung für Hauptauftragnehmer und OEMs.
- Nadcap: Die Nadcap-Akkreditierung ist zwar eher für bestimmte Verfahren wie Wärmebehandlung oder zerstörungsfreie Prüfung (NDT) üblich, bedeutet aber in den entsprechenden Bereichen die Einhaltung der von der Industrie gehandhabten speziellen Prozessstandards.
- Einhaltung der Exportkontrolle: Vertrautheit mit und Einhaltung von Vorschriften wie ITAR (International Traffic in Arms Regulations) oder EAR (Export Administration Regulations), sofern diese auf die Art und den Standort des Projekts anwendbar sind.
- Nachgewiesene Weltraumerfahrung und -erfahrung:
- Erfolgsbilanz: Hat der Lieferant erfolgreich Komponenten hergestellt, die derzeit in Satelliten, Sonden oder anderen Raumfahrzeugen fliegen? Nachgewiesene Erfahrung mit weltraumtauglichen Teilen schafft Vertrauen in das Verständnis der besonderen Anforderungen (z. B. Ausgasung, Strahlungsbeständigkeit, thermische Vakuumtests).
- Fallstudien: Suchen Sie nach Beispielen für ähnliche Projekte, Materialien und Komplexitäten, die sie bearbeitet haben.
- Verständnis des Platzbedarfs: Verstehen sie die Reinheitsgrade, die Rückverfolgbarkeit von Materialien, den Dokumentationsbedarf und die Qualifizierungsprozesse, die für Raumfahrt-Hardware spezifisch sind?
- Werkstoffkompetenz (AlSi10Mg, CuCrZr und darüber hinaus):
- Spezifische Legierungserfahrung: Tiefgreifende Kenntnisse über die Verarbeitung der erforderlichen spezifischen Legierungen (AlSi10Mg, CuCrZr). Dazu gehören optimierte Fertigungsparameter, geeignete Wärmebehandlungszyklen und das Verständnis potenzieller Herausforderungen wie die Reflektivität von Kupfer oder die Rissanfälligkeit von Aluminium.
- Pulverbehandlung & Qualität: Robuste Verfahren für die Handhabung, Lagerung, Siebung und das Recycling von Metallpulvern in Luft- und Raumfahrtqualität, um die Reinheit zu erhalten und Verunreinigungen zu vermeiden. Im Idealfall beziehen sie es von seriösen Lieferanten oder, wie Met3dpwir verfügen über firmeneigene Kapazitäten zur Herstellung hochwertiger sphärischer Pulver unter Verwendung fortschrittlicher Methoden wie Gaszerstäubung oder PREP, die die Konsistenz und Rückverfolgbarkeit der Pulver gewährleisten.
- Breiteres Portfolio: Auch wenn spezifische Legierungserfahrungen von entscheidender Bedeutung sind, deutet ein breiteres Portfolio (z. B. Titanlegierungen, Nickelsuperlegierungen, Spezialmetalle wie TiNi, TiTa, wie von Met3dp angeboten) oft auf eine tiefere materialwissenschaftliche Kompetenz hin.
- Technologie, Ausrüstung und Kapazität:
- Prozess-Fähigkeit: Beherrschung des jeweiligen AM-Verfahrens (in der Regel LPBF für feine Merkmale und gute Oberflächengüte, manchmal SEBM für bestimmte Materialien wie Titan oder rissanfällige Legierungen).
- Maschinenqualität und -wartung: Verwendung von industriellen, gut gewarteten und kalibrierten AM-Systemen namhafter Hersteller. Eine gleichbleibende Maschinenleistung ist entscheidend für die Qualität der Teile.
- Kapazität & Redundanz: Ausreichende Maschinenkapazität, um die Anforderungen an die Vorlaufzeit zu erfüllen, möglicherweise mit mehreren Maschinen für Redundanz und Skalierbarkeit.
- Umweltkontrolle: Bauumgebungen mit kontrollierten Inertgasatmosphären (Argon/Stickstoff) und Temperaturmanagement.
- Robustes Qualitätsmanagementsystem (QMS):
- Rückverfolgbarkeit: Durchgängige Rückverfolgbarkeit von Materialien (Pulverchargen), Prozessparametern, Bedieneraktionen und Prüfergebnissen für jedes Teil.
- Inspektionskapazitäten: Zugang zu den erforderlichen Prüfgeräten im eigenen Haus oder durch zertifizierte Dritte: CMM für Maßkontrollen, Oberflächenprofilometrie, NDT-Methoden (CT-Scanning ist für die Validierung interner AM-Merkmale sehr wertvoll), Materialanalysetools.
- Dokumentation: Fähigkeit zur Bereitstellung umfassender Dokumentationspakete, die für die Qualifikation in der Luft- und Raumfahrt erforderlich sind (z. B. Konformitätszertifikate, Materialzertifikate, Prozessprotokolle, Prüfberichte).
- DfAM und technische Unterstützung:
- Kollaboration: Bereitschaft und Fähigkeit zur Zusammenarbeit mit dem Konstruktionsteam des Kunden und Bereitstellung von DfAM-Feedback zur Optimierung des Teils hinsichtlich Herstellbarkeit, Kosten und Leistung.
- Fachwissen: Zugang zu erfahrenen AM-Ingenieuren und Metallurgen, die über Konstruktionsregeln, Stützstrategien, Materialauswahl und Nachbearbeitungsoptionen beraten können.
- In-House vs. Managed Post-Processing:
- Integrierte Dienstleistungen: Bietet der Lieferant kritische Nachbearbeitungsschritte (Spannungsarmglühen, Wärmebehandlung, Entfernen von Stützen, Grundbearbeitung) im eigenen Haus an? Dies kann den Arbeitsablauf straffen und die Kontrolle verbessern.
- Verwaltetes Netzwerk: Wenn sie die Nachbearbeitung auslagern (z. B. komplexe Bearbeitung, spezielle Beschichtungen, HIP, fortschrittliche zerstörungsfreie Prüfung), verfügen sie dann über ein Netz qualifizierter und vertrauenswürdiger Partner, die diesen Prozess nahtlos verwalten?
- Vorlaufzeiten und Reaktionsfähigkeit:
- Zitiergeschwindigkeit: Fähigkeit zur rechtzeitigen und genauen Erstellung von Kostenvoranschlägen.
- Produktionsvorlaufzeiten: Realistische und zuverlässige Schätzungen der Vorlaufzeiten für Prototypen und Produktionsteile.
- Kommunikation: Klare und proaktive Kommunikation während des gesamten Entwurfs-, Herstellungs- und Lieferprozesses.
- Wettbewerbsfähigkeit bei den Kosten:
- Die Kosten sind zwar immer ein Faktor, doch sollten sie im Zusammenhang mit den anderen Kriterien bewertet werden. Die billigste Option bietet möglicherweise nicht die nötige Qualität, Zuverlässigkeit oder Expertise für kritische Raumfahrtkomponenten. Achten Sie auf den Wert - ein ausgewogenes Verhältnis von Kosten, Qualität und Service.
Checkliste zur Lieferantenbewertung (Beispiel):
Kriterien | Frage | Wichtigkeit (Hoch/Mittel/Niedrig) | Anmerkungen / Ziel |
---|---|---|---|
Zertifizierungen | AS9100 zertifiziert? | Hoch | Obligatorisch für viele Programme |
Erleben Sie | Nachgewiesene Erfahrung mit Raumfahrt-Hardware? Sind Fallstudien verfügbar? | Hoch | Suche nach relevanten Beispielen (Thermik, Materialien) |
Werkstoffkompetenz (AlSi10Mg) | Nachgewiesener Erfolg beim Drucken von AlSi10Mg nach Spezifikationen der Luft- und Raumfahrt? Optimierte Parameter? T6-Behandlung möglich? | Hoch | Überprüfung der Prozesskontrolle, Eigenschaftsdaten |
Werkstoffkompetenz (CuCrZr) | Erfahrung mit dem Druck von anspruchsvollen Kupferlegierungen? Kontrolle der Parameter? Fähigkeit zur Wärmebehandlung? | Hoch | Erfordert spezielles Fachwissen |
Qualität des Pulvers | Strenge Pulverhandhabung/Beschaffung/QC? Eigene Pulverproduktion (z. B. Met3dp)? | Hoch | Grundlegend für die Teilequalität |
Technologie | Geeignete AM-Maschinen (LPBF/SEBM)? Gut gewartet? | Hoch | Maschinenqualität wirkt sich auf die Konsistenz aus |
QMS & Rückverfolgbarkeit | Robustes QMS? Vollständige Rückverfolgbarkeit? Umfassende Dokumentation? | Hoch | Wesentlich für die Qualifikation |
Inspektion/NDT | Eigene CMM, Oberflächenanalyse? Zugang zu CT-Scans? | Hoch | Überprüfung der Übereinstimmung von Fähigkeiten und Anforderungen |
DfAM-Unterstützung | Bietet er Entwurfsprüfung/Feedback an? Erfahrene AM-Ingenieure? | Mittel-Hoch | Wertschöpfung, verbesserte Herstellbarkeit |
Nachbearbeitung | Wichtige Schritte im Haus (Wärmebehandlung, Bearbeitung)? Qualifiziertes Netzwerk? | Mittel-Hoch | Rationalisierung des Prozesses, Sicherung der Qualität |
Vorlaufzeit | Zuverlässige Kostenvoranschläge & Produktionsfristen? | Med | Gleichgewicht mit Qualität; Engpässe verstehen |
Empfänglichkeit | Gute Kommunikation? Proaktive Problemlösung? | Med | Wichtig für eine reibungslose Projektdurchführung |
Kosten | Wettbewerbsfähige Preise im Verhältnis zum Wert/zur Qualität? | Med | Bewertung der Gesamtbetriebskosten, einschließlich Risiko |
In Blätter exportieren
Die Wahl eines Partners wie Met3dpdas seine Bedeutung für die branchenführendes Druckvolumen, Genauigkeit und Zuverlässigkeit neben der fortschrittlichen Pulverherstellung und den umfassenden Lösungen auch diese kritischen Auswahlkriterien für anspruchsvolle Luft- und Raumfahrtprojekte erfüllt. Gründliche Sorgfalt bei der Lieferantenauswahl ist eine wichtige Investition, um den Erfolg und die Zuverlässigkeit von 3D-gedruckten Wärmerohrgehäusen für Raumfahrtsysteme zu gewährleisten.
Die Investition verstehen: Kostenfaktoren und Vorlaufzeiten für AM Heat Pipe Enclosures
Obwohl die additive Fertigung von Metall erhebliche Leistungs- und Designvorteile bietet, ist es für Beschaffungsmanager und Ingenieure wichtig, die Faktoren zu verstehen, die die Kosten und die Vorlaufzeit für die Herstellung von 3D-gedruckten Wärmerohrgehäusen beeinflussen. Ein klares Verständnis ermöglicht eine bessere Budgetierung, Projektplanung und einen Vergleich mit traditionellen Fertigungsalternativen, wo dies möglich ist. Die Kosten pro Teil sind in der Regel höher als bei einfachen Massenprodukten, können aber bei komplexen Hochleistungskomponenten mit geringen Stückzahlen, wie sie in der Raumfahrt verwendet werden, sehr wettbewerbsfähig sein.
Die wichtigsten Kostentreiber für Metall-AM-Heatpipe-Gehäuse:
- Materialart und Verbrauch:
- Wahl der Legierung: Pulver aus Kupferlegierungen (CuCrZr) sind im Allgemeinen wesentlich teurer als Pulver aus Aluminiumlegierungen (AlSi10Mg).
- Qualität des Pulvers: Hochwertige, für die Luft- und Raumfahrt geeignete Pulver mit spezifischen Partikelgrößenverteilungen und Reinheitsgraden erzielen höhere Preise.
- Part Volume & Support Volume: Die Gesamtmenge des geschmolzenen Materials (Teilevolumen) und die für Stützstrukturen verwendete Menge wirken sich direkt auf die Kosten aus. Die Bemühungen des DfAM, das Volumen und die Stützstrukturen zu minimieren, tragen zur Senkung des Materialverbrauchs bei.
- Wiederverwendung von Pulver: Effiziente Verfahren für das Pulverrecycling durch den Lieferanten können zur Kostensenkung beitragen, erfordern aber eine sorgfältige Qualitätskontrolle.
- Maschinenzeit (Bauzeit):
- Teilhöhe (Z-Höhe): Die Bauzeit korreliert stark mit der Anzahl der Schichten, was bedeutet, dass größere Teile unabhängig von ihrer Grundfläche länger brauchen. Der gleichzeitige Bau mehrerer Teile kann die Maschinenzeit optimieren, wenn sie in den Bauraum passen.
- Teilband: Bei größeren Teilen muss mehr Material pro Schicht geschmolzen werden, was die Scanzeit verlängert.
- Komplexität: Hochkomplexe Geometrien, dünne Wände und komplizierte Merkmale erfordern oft langsamere Scangeschwindigkeiten oder spezielle Strategien, was die Bauzeit verlängert.
- AM-Prozess: Die Druckgeschwindigkeiten können zwischen verschiedenen AM-Technologien (z. B. LPBF vs. SEBM) und bestimmten Maschinenmodellen variieren.
- Maschinentarif: Die stündlichen Betriebskosten des industriellen Metall-AM-Systems unter Berücksichtigung von Abschreibung, Energie, Wartung und Verbrauchsmaterialien (Gas, Filter).
- Arbeitskosten:
- Vorbereitung der Datei: Die Vorbereitung der CAD-Datei für den Druck, die Erzeugung von Stützstrukturen und die Erstellung des Bau-Layouts erfordert qualifizierte Arbeitskräfte.
- Maschineneinrichtung & Überwachung: Laden des Pulvers, Einrichten der Anlage, Überwachen des Prozesses und Entladen des fertigen Teils.
- Nachbearbeitungsarbeiten: Das Entpulvern, die Entfernung der Halterung, die Wärmebehandlung, die Bearbeitung, die Endbearbeitung, die Reinigung und die Inspektion sind mit erheblichem Arbeitsaufwand verbunden. Die Komplexität des Teils hat großen Einfluss auf diese Kostenkomponente.
- Technik/DfAM-Unterstützung: Wenn es sich um eine kollaborative Designoptimierung handelt, fallen die damit verbundenen Arbeitskosten für Ingenieure an.
- Komplexität der Nachbearbeitung:
- Wärmebehandlung: Kosten in Verbindung mit Ofenzeit, Energie und kontrollierten Atmosphären. Komplexe oder mehrstufige Zyklen verursachen zusätzliche Kosten.
- Unterstützung bei der Entfernung: Schwer zugängliche Halterungen erfordern mehr manuelle Arbeit oder fortschrittliche Techniken (EDM, Bearbeitung), was die Kosten erhöht.
- Bearbeitungen: Der Umfang und die Präzision der erforderlichen CNC-Bearbeitung wirken sich erheblich auf die Kosten aus (Anzahl der Aufspannungen, Bearbeitungszeit, Werkzeuge).
- Oberflächenveredelung: Polieren, Strahlen oder spezielle Beschichtungen verursachen zusätzliche Kosten, die sich nach dem Verfahren und der behandelten Fläche richten.
- HIP: Das heißisostatische Pressen ist mit erheblichen Mehrkosten verbunden, kann aber bei kritischen Anwendungen, die eine maximale Dichte und Ermüdungsfestigkeit erfordern, erforderlich sein.
- ZfP und Inspektion: Kosten im Zusammenhang mit CT-Scans, CMM-Messungen, Oberflächenanalysen und anderen erforderlichen Qualitätsprüfungen.
- Qualifizierung und Dokumentation:
- Prüfung: Wenn spezielle Teilequalifizierungstests (z. B. thermisches Vakuum, Vibration, Probeläufe) erforderlich sind, werden diese Kosten hinzugerechnet.
- Dokumentationspaket: Die Erstellung einer umfassenden Rückverfolgbarkeits- und Qualitätsdokumentation für Luft- und Raumfahrtnormen ist mit erheblichem Aufwand und zusätzlichen Kosten verbunden.
- Auftragsvolumen:
- Skalenvorteile: AM eignet sich zwar für niedrige Stückzahlen, aber es gibt einige Größenvorteile. Die Einrichtungskosten amortisieren sich über mehr Teile in größeren Chargen. Das Drucken mehrerer Teile in einem einzigen Arbeitsgang optimiert die Maschinenauslastung. Allerdings flacht die Kostenreduzierung pro Teil in der Regel viel früher ab als bei herkömmlichen Massenproduktionsverfahren.
Typische Vorlaufzeiten:
Die Lieferzeiten für 3D-gedruckte Metallgehäuse für Wärmerohre können aufgrund verschiedener Faktoren stark variieren:
- Prototyping: Einfache Prototypen mit minimaler Nachbearbeitung lassen sich in 1-3 Wochen.
- Funktionale Prototypen: Teile, die eine Wärmebehandlung und eine einfache Bearbeitung erfordern, können 3-6 Wochen.
- Produktionsteile (nicht qualifiziert): Komplexe Teile mit umfangreicher Nachbearbeitung (Zerspanung, Endbearbeitung), aber ohne formale Qualifikation, können sein 6-10 Wochen.
- Flugtaugliche Teile: Teile, die eine vollständige Qualifizierung für die Luft- und Raumfahrt erfordern, einschließlich umfangreicher Nachbearbeitung, strenger zerstörungsfreier Prüfung, möglicher HIP und umfassender Dokumentation, können Vorlaufzeiten von 10-20 Wochen oder mehrje nach Komplexität des Qualifizierungsprozesses und der Prüfanforderungen.
Faktoren, die die Vorlaufzeit beeinflussen:
- Lieferanten-Warteschlange: Aktuelle Auslastung und Maschinenverfügbarkeit bei dem gewählten Dienstleister.
- Komplexität des Designs: Komplexere Teile benötigen mehr Zeit für den Druck und die Nachbearbeitung.
- Bauhöhe: Höhere Teile brauchen länger zum Drucken.
- Nachbearbeitungsanforderungen: Jeder Schritt (Wärmebehandlung, Bearbeitung, Beschichtung, HIP, NDT) kostet Zeit. Ausgelagerte Schritte können zu weiteren Verzögerungen führen.
- Qualifizierungsprozess: Iterationen, Testpläne und Dokumentationsprüfungen bedeuten einen erheblichen Zeitaufwand.
- Materialverfügbarkeit: Sicherstellen, dass das spezielle Pulver für die Luft- und Raumfahrt auf Lager ist oder eine akzeptable Beschaffungszeit hat.
Es ist von entscheidender Bedeutung, die Kostentreiber und die Erwartungen an die Vorlaufzeit mit potenziellen Lieferanten in einem frühen Stadium des Projekts transparent zu besprechen. Durch eine klare Definition der Anforderungen, einschließlich CAD-Modellen, Materialspezifikationen, Toleranz-/Fertigstellungsanforderungen, Nachbearbeitungsbedarf und erforderlicher Dokumentation, können die Lieferanten genauere Angebote und realistische Zeitpläne erstellen.
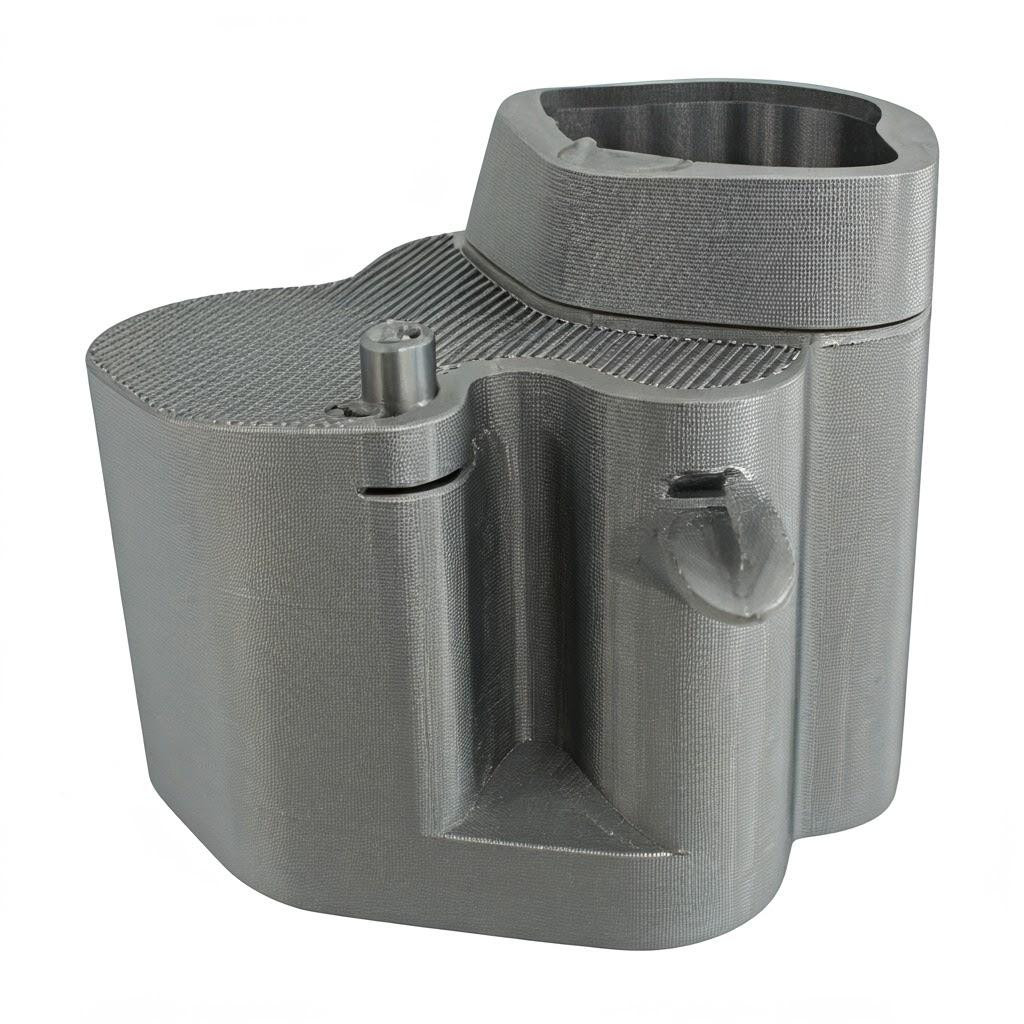
Häufig gestellte Fragen (FAQ) zu 3D-gedruckten Wärmerohrgehäusen
Hier finden Sie Antworten auf einige häufig gestellte Fragen zur Verwendung der additiven Fertigung von Metall für Wärmerohrgehäuse in Raumfahrtsystemen:
- Wie ist die thermische Leistung eines 3D-gedruckten Wärmerohrgehäuses im Vergleich zu einem traditionell hergestellten?
- Die Leistung kann sein gleich oder deutlich besserje nach Design. Metall-AM ermöglicht hochgradig optimierte Designs, die auf herkömmliche Weise nicht hergestellt werden können. Merkmale wie konforme Kanäle, integrierte Rippen, optimierte interne Dochtstrukturen (für LHPs/CPLs) und konsolidierte Baugruppen (die den Wärmewiderstand an den Verbindungsstellen verringern) können die Wärmeübertragungseffizienz verbessern. Auch wenn die Wärmeleitfähigkeit eines AM-Materials aufgrund der Mikrostruktur geringfügig niedriger ist als die seines Knetäquivalents, wird dies durch die Designfreiheit oft mehr als kompensiert, was zu einer besseren thermischen Gesamtleistung in der endgültigen Baugruppe führt. Eine sorgfältige Materialauswahl (z. B. CuCrZr mit hoher Leitfähigkeit, wo erforderlich) und DfAM sind entscheidend.
- Wie hoch ist der Technology Readiness Level (TRL) für metallische AM-Komponenten wie Heatpipe-Gehäuse im Weltraum?
- Die Metall-AM für Raumfahrtanwendungen hat sich erheblich weiterentwickelt. Für viele Anwendungen, insbesondere bei gut charakterisierten Legierungen wie AlSi10Mg und Ti6Al4V, gilt die TRL als hoch (TRL 7-9)das bedeutet, dass die Technologie in operationellen Umgebungen (d.h. im Weltraum) demonstriert und bewährt wurde. Es gibt zahlreiche Beispiele für unkritische und zunehmend kritische strukturelle und thermische Komponenten, die mittels AM auf Satelliten und Raumfahrzeugen hergestellt werden. Für neuere Legierungen (wie potenziell AM CuCrZr in einigen spezifischen komplexen Geometrien) oder hochkritische Primärstrukturen könnte die TRL etwas niedriger sein (TRL 5-7), was eine weitere Qualifizierung und Demonstration für spezifische Missionskontexte erfordert. Die Verifizierung hängt immer von dem jeweiligen Teil, dem Material, dem Prozess und den Einsatzanforderungen ab.
- Sind 3D-gedruckte AlSi10Mg- und CuCrZr-Gehäuse für Langzeit-Weltraummissionen geeignet, wenn man Strahlung, Vakuum und Temperaturwechsel berücksichtigt?
- Ja, im Allgemeinen.
- Vakuum: Sowohl AlSi10Mg als auch CuCrZr sind metallische Legierungen mit sehr geringen Ausgasungseigenschaften (bei ordnungsgemäßer Reinigung), was sie für Vakuumumgebungen geeignet macht. Bei der Materialauswahl sind der Dampfdruck und die Ausgasungsrate zu berücksichtigen, um eine Kontamination empfindlicher Oberflächen zu vermeiden.
- Strahlung: Metallische Strukturen bieten eine inhärente Strahlungsabschirmung. Obwohl extreme Strahlung bei sehr langen Missionen zu einer Verschlechterung der Materialeigenschaften führen kann, werden Aluminium- und Kupferlegierungen üblicherweise für Weltraumstrukturen verwendet und gelten im Allgemeinen als geeignet. Die spezifischen Auswirkungen hängen von der Umlaufbahn, der Dauer der Mission und dem Design der Abschirmung ab.
- Thermisches Zyklieren: Beide Legierungen können den im Weltraum auftretenden Temperaturschwankungen standhalten, obwohl eine sorgfältige Konstruktion und Spannungsentlastung entscheidend sind, um Ermüdungsversagen aufgrund von Expansions-/Kontraktionsspannungen über viele Zyklen zu verhindern. Die Materialeigenschaften bei extremen Betriebstemperaturen müssen bei der Konstruktion berücksichtigt werden. Strenge Tests (thermische Zyklen, thermisches Vakuum) sind Teil des Standardqualifizierungsprozesses für die Raumfahrt.
- Ja, im Allgemeinen.
- Welche Informationen benötigt ein AM-Lieferant, um ein genaues Angebot für ein 3D-gedrucktes Wärmerohr-Gehäuse zu erstellen?
- Um einen möglichst genauen Kostenvoranschlag zu erhalten, sollten Sie so viele Details wie möglich angeben:
- 3D-CAD-Modell: Eine STEP-Datei ist Standard.
- Spezifikation des Materials: Geben Sie eindeutig die erforderliche Legierung (z. B. AlSi10Mg oder CuCrZr) und alle spezifischen Materialnormen (z. B. AMS-Spezifikationen) an.
- Technische Zeichnung: Dazu gehören kritische Abmessungen, Toleranzen, Anforderungen an die Oberflächengüte (Ra-Werte) für bestimmte Merkmale und Stellen, die nachbearbeitet werden müssen.
- Nachbearbeitungsanforderungen: Geben Sie die erforderlichen Wärmebehandlungen (Spannungsabbau, Alterung), Oberflächenbehandlungen (Beschichtungen, Polieren) und HIP (falls erforderlich) an.
- Menge: Anzahl der benötigten Teile.
- Qualität & Dokumentationsanforderungen: Spezifizieren Sie die erforderlichen Zertifizierungen (z. B. AS9100), Prüfmethoden (ZfP-Anforderungen wie CT-Scanning) und Dokumentationspakete (CofC, Materialzertifikate, Prüfberichte).
- Anwendungskontext (fakultativ, aber hilfreich): Eine kurze Beschreibung der Anwendung hilft dem Lieferanten, die Kritikalität und die funktionalen Anforderungen zu verstehen.
- Um einen möglichst genauen Kostenvoranschlag zu erhalten, sollten Sie so viele Details wie möglich angeben:
Schlussfolgerung: Die Zukunft der thermischen Kontrolle - Fortschrittliche Fertigung mit Met3dp
Die effektive Bewältigung thermischer Belastungen ist nach wie vor eine der größten Herausforderungen bei der Entwicklung und dem Betrieb zuverlässiger, leistungsstarker Raumfahrzeuge. Wärmerohre sind dabei unverzichtbare Werkzeuge, und die Gehäuse, in denen sie untergebracht und integriert sind, entwickeln sich dank der transformativen Fähigkeiten der additiven Fertigung von Metallen rasch weiter. Wie wir erforscht haben, ermöglicht der Einsatz von AM-Technologien wie Laser Powder Bed Fusion (LPBF) mit fortschrittlichen Materialien wie leichtem AlSi10Mg oder hochleitfähigem CuCrZr den Ingenieuren, sich von den Beschränkungen der traditionellen Fertigung zu lösen.
Die Vorteile sind überzeugend: beispiellose Designfreiheit, die komplexe, konforme Geometrien und integrierte Funktionen ermöglicht; erhebliche Gewichtsreduzierung durch Topologieoptimierung und Gitterstrukturen, was sich direkt auf die Startkosten auswirkt; Bauteilkonsolidierung, die zu geringerer Komplexität, Montagezeit und potenziellen Fehlerpunkten führt; und beschleunigte Entwicklungszyklen durch Rapid Prototyping und Iteration. Diese Vorteile führen direkt zu effizienteren, kompakteren und zuverlässigeren thermischen Kontrollsystemen, die den Weg für ehrgeizigere wissenschaftliche Missionen, dichtere Satellitennutzlasten und nachhaltige Weltraumforschung über lange Zeiträume ebnen.
Um diese Vorteile erfolgreich zu nutzen, ist jedoch ein ganzheitlicher Ansatz erforderlich. Dazu gehört, dass die Grundsätze des Design for Additive Manufacturing (DfAM) von Anfang an berücksichtigt werden, dass das optimale Material für die spezifischen thermischen und strukturellen Anforderungen sorgfältig ausgewählt wird, dass die notwendigen Nachbearbeitungsschritte (von der Wärmebehandlung bis zur Präzisionsbearbeitung und strengen Inspektion) verstanden und geplant werden und dass die inhärenten Herausforderungen des AM-Prozesses durch eine robuste Prozesskontrolle und Qualitätssicherung gemeistert werden.
Entscheidend für den Erfolg ist die Zusammenarbeit mit dem richtigen Fertigungspartner. Die Wahl eines Zulieferers mit nachgewiesener Erfahrung in der Luft- und Raumfahrt, umfassenden Material- und Prozesskenntnissen, strengen Qualitätszertifizierungen (wie AS9100), umfassenden Fähigkeiten, die von der DfAM-Unterstützung bis zur Endkontrolle reichen, und einer Verpflichtung zur Qualität - wie Met3dp - ist von größter Bedeutung. Met3dp mit Hauptsitz in Qingdao, China, ist ein führender Anbieter von Lösungen für die additive Fertigung, der sich sowohl auf fortschrittliche 3D-Druckanlagen als auch auf Hochleistungsmetallpulver spezialisiert hat, die für industrielle Anwendungen in der Luft- und Raumfahrt, der Medizintechnik und der Automobilindustrie unerlässlich sind. Der Einsatz von branchenführenden Gaszerstäubungs- und PREP-Technologien gewährleistet die Herstellung von Metallpulvern mit hoher Sphärizität und Fließfähigkeit, einschließlich innovativer Legierungen, die es den Kunden ermöglichen, dichte, hochwertige Teile mit hervorragenden Eigenschaften zu drucken. Mit seiner jahrzehntelangen Erfahrung bietet Met3dp umfassende Lösungen an und arbeitet mit Unternehmen zusammen, um deren digitalen Wandel in der Fertigung zu beschleunigen.
Die additive Fertigung von Metallen ist nicht länger eine futuristische Neuheit für die Raumfahrt, sondern ermöglicht bereits heute die Fähigkeiten der nächsten Generation. Für Wärmemanagementsysteme stellen 3D-gedruckte Wärmerohrgehäuse einen bedeutenden Sprung nach vorn dar und bieten Leistungs- und Integrationsmöglichkeiten, die zuvor unerreichbar waren. Da die Raumfahrtindustrie die Grenzen immer weiter hinausschiebt, werden fortschrittliche Fertigungstechniken und fachkundige Partner wie Met3dp bei der Realisierung innovativer thermischer Lösungen, die für den Erfolg von Missionen erforderlich sind, eine entscheidende Rolle spielen.
Teilen auf
MET3DP Technology Co., LTD ist ein führender Anbieter von additiven Fertigungslösungen mit Hauptsitz in Qingdao, China. Unser Unternehmen ist spezialisiert auf 3D-Druckgeräte und Hochleistungsmetallpulver für industrielle Anwendungen.
Fragen Sie an, um den besten Preis und eine maßgeschneiderte Lösung für Ihr Unternehmen zu erhalten!
Verwandte Artikel
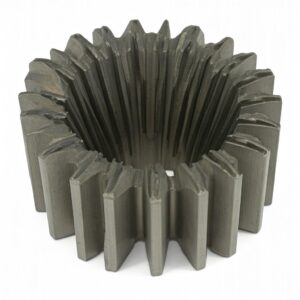
Hochleistungs-Düsenschaufelsegmente: Revolutionierung der Turbineneffizienz mit 3D-Metalldruck
Mehr lesen "Über Met3DP
Aktuelles Update
Unser Produkt
KONTAKT US
Haben Sie Fragen? Senden Sie uns jetzt eine Nachricht! Wir werden Ihre Anfrage mit einem ganzen Team nach Erhalt Ihrer Nachricht bearbeiten.
Holen Sie sich Metal3DP's
Produkt-Broschüre
Erhalten Sie die neuesten Produkte und Preislisten
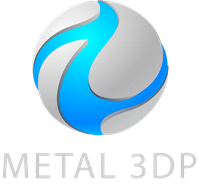
Metallpulver für 3D-Druck und additive Fertigung