Komponenten für Hochtemperaturabschirmungen durch additive Fertigung von Metallen
Inhaltsübersicht
Einleitung: Definition von Hochtemperatur-Wärmeschutzschilden und ihre entscheidende Rolle
In den anspruchsvollen Bereichen der Luft- und Raumfahrt, der Automobiltechnik, der Energieerzeugung und fortschrittlicher industrieller Prozesse sind Komponenten regelmäßig extremen Temperaturen ausgesetzt, die oft Hunderte oder sogar Tausende von Grad Celsius überschreiten. Ein zuverlässiger Betrieb unter solchen Bedingungen ist für Sicherheit, Effizienz und Leistung von größter Bedeutung. Dies ist der Punkt hitzeschild-Komponenten spielen eine unverzichtbare, oft unsichtbare, aber äußerst wichtige Rolle. Im Kern sind Hitzeschilde Barrieren, die speziell zum Schutz empfindlicher Geräte, Strukturelemente oder Personen vor den schädlichen Auswirkungen übermäßiger Hitze entwickelt wurden, sei es durch Motoren, Abgase, Verbrennungsprozesse oder andere Hochtemperaturquellen. Ihre Hauptfunktion besteht darin, thermische Energie zu managen - sie zu reflektieren, zu isolieren oder manchmal auch sorgfältig von geschützten Bereichen wegzuleiten.
Die Bedeutung dieser Komponenten kann gar nicht hoch genug eingeschätzt werden. In der Luft- und Raumfahrt schützen sie empfindliche Elektronik, Kraftstoffleitungen und strukturelle Teile der Flugzeugzelle vor der starken Hitze von Düsentriebwerken oder dem Wiedereintritt in die Atmosphäre. In der Automobilindustrie schützen sie Unterbodenkomponenten, Kraftstofftanks und Fahrgasträume vor heißen Abgassystemen und Motorräumen und tragen so zur Fahrzeugsicherheit und zum Fahrkomfort bei. In Stromerzeugungsturbinen schützen sie kritische Schaufeln und Gehäuse vor extremen Verbrennungstemperaturen, was sich direkt auf die Langlebigkeit und die Betriebseffizienz der Turbine auswirkt. Industrieöfen sind auf eine robuste thermische Abschirmung angewiesen, um die Prozesstemperaturen aufrechtzuerhalten und gleichzeitig die umliegende Infrastruktur zu schützen und die Sicherheit der Mitarbeiter zu gewährleisten. Das Versagen eines Hitzeschilds kann katastrophale Folgen haben, die von der Beeinträchtigung von Bauteilen und dem Ausfall von Systemen bis hin zu erheblichen Sicherheitsrisiken reichen.
Für die Herstellung dieser kritischen Teile werden traditionell Verfahren wie Stanzen, Umformen, Gießen und umfangreiche mechanische Bearbeitung eingesetzt, häufig unter Verwendung spezieller Hochtemperaturlegierungen. Diese Methoden sind zwar effektiv, stoßen aber an ihre Grenzen, insbesondere wenn es um immer komplexere Geometrien geht, die für ein optimiertes Wärmemanagement, Leichtbauinitiativen oder integrierte Funktionen erforderlich sind. Die moderne Technik verlangt nach Komponenten, die nicht nur hitzebeständig, sondern auch leicht sind, die für maximale Effizienz komplex geformt sind und die mit angemessenen Vorlaufzeiten und Kosten hergestellt werden können, insbesondere für kleine bis mittlere Produktionsserien oder schnelle Prototyping-Zyklen. Diese sich wandelnden Anforderungen haben den Weg für innovative Fertigungstechniken geebnet und die Voraussetzungen für die Einführung der additiven Fertigung von Metallen (AM) geschaffen, oder 3D-Druckals transformative Lösung für die Produktion der nächsten Generation hochtemperaturschutz systeme. Diese Technologie bietet eine beispiellose Designfreiheit und Materialeigenschaften, die sich ideal für die einzigartigen Herausforderungen eignen, die sich bei der Entwicklung effektiver und zuverlässiger kritische Industrieteile für extreme thermische Umgebungen entwickelt und ermöglichen Fortschritte in der wärmemanagement in der Luft- und Raumfahrt und die Optimierung der Leistung in Systemen wie Autoabgassysteme. Unternehmen, die auf der Suche nach zuverlässigen Lieferanten für diese spezialisierten Komponenten sind, suchen häufig nach Herstellern, die über bewährte Fachkenntnisse sowohl in Bezug auf fortschrittliche Materialien als auch auf modernste Produktionstechniken verfügen, um die für diese Anwendungen erforderliche Integrität und Leistung zu gewährleisten.
Branchenübergreifende Anwendungen: Wo werden 3D-gedruckte Wärmeschutzschilde aus Metall eingesetzt?
Die einzigartigen Vorteile der additiven Fertigung von Metallen - komplexe Geometrien, Materialeffizienz, Eignung für Hochleistungslegierungen und schnelle Iteration - haben sie zu einer zunehmend attraktiven Lösung für die Herstellung von Hitzeschilden in einer Vielzahl anspruchsvoller Branchen gemacht. Die Fähigkeit, komplizierte interne Kühlkanäle, konform geformte Abschirmungen und leichte, aber dennoch steife Strukturen zu schaffen, eröffnet neue Möglichkeiten, die mit herkömmlichen Methoden nur schwer oder gar nicht zu erreichen sind. Beschaffungsmanager und Ingenieure in verschiedenen Sektoren erkennen das Potenzial von AM zur Steigerung der Leistung, zur Gewichtsreduzierung und zur Konsolidierung von Teilen in Hochtemperaturanwendungen.
Im Folgenden finden Sie eine Aufschlüsselung der wichtigsten Branchen und spezifischen Anwendungen, die 3D-gedruckte Hitzeschilde aus Metall nutzen:
- Luft- und Raumfahrt und Verteidigung: Dieser Sektor ist wohl der bedeutendste Anwender, der durch den ständigen Bedarf an Gewichtsreduzierung und Leistungsverbesserung in extremen Umgebungen angetrieben wird.
- Gasturbinentriebwerke: Schutz von Brennkammerauskleidungen, Turbinenschaufeln, Düsenleitschaufeln und Motorgehäusen vor extremen Verbrennungstemperaturen. AM ermöglicht integrierte Kühlkanäle und komplexe Bohrungsgeometrien für die Filmkühlung und verbessert so die Effizienz und Haltbarkeit von Motoren. Zu den spezifischen Anwendungen gehören thermische Abschirmung für die Luft- und Raumfahrt für Niederdruckturbinengehäuse und Brennkammer-Hitzeschilde.
- Raketentriebwerke und Trägerraketen: Abschirmung empfindlicher Komponenten während des Starts und des Aufstiegs, wo die Temperaturen drastisch schwanken können. Schutz von Düsenverlängerungen und Brennkammern.
- Hyperschall-Fahrzeuge: Bewältigung der extremen aerodynamischen Erwärmung während des Hochgeschwindigkeitsfluges, Schutz der Vorderkanten und der inneren Strukturen.
- Avionik- und Elektronikbuchten: Abschirmung empfindlicher elektronischer Geräte vor der von Motoren oder Umwelteinflüssen erzeugten Hitze.
- Lieferanten und Hersteller: OEMs der Luft- und Raumfahrtindustrie und Tier-1-Zulieferer suchen aktiv nach qualifizierten Metall-AM-Anbietern, die in der Lage sind, die strengen AS9100-Qualitätsstandards für diese Gasturbinenkomponenten.
- Automobilindustrie: Die Kostensensibilität ist zwar höher, aber die Vorteile von AM für bestimmte Hochleistungsanwendungen oder Spezialanwendungen treiben die Akzeptanz voran.
- Hochleistungs- und Rennfahrzeuge: Leichtgewicht auto-Hitzeschilder für Abgaskrümmer, Turbolader und Katalysatoren. AM ermöglicht komplexe Formen, die eng in enge Motorräume passen und das Wärmemanagement und die Leistung verbessern.
- Elektrofahrzeuge (EVs): EVs erzeugen zwar weniger Wärme als ICEs, erfordern aber dennoch ein Wärmemanagement für Akkus und Leistungselektronik, insbesondere beim schnellen Laden/Entladen. Kundenspezifische AM-Abschirmungen können gezielten Wärmeschutz bieten.
- Auspuffanlagen: Erstellung haltbarer, komplexer Abschirmungen für Fallrohre, Schalldämpfer und Bereiche in der Nähe des Kraftstofftanks oder des Fahrgestells, insbesondere dort, wo der Platz begrenzt ist oder eine komplexe Verlegung erforderlich ist.
- Prototyping: Schnelles Erstellen und Testen verschiedener Hitzeschilddesigns während der Fahrzeugentwicklungszyklen.
- Energie und Stromerzeugung: Effizienz und Langlebigkeit sind die wichtigsten Faktoren in diesem Sektor.
- Industrielle Gasturbinen (IGTs): Ähnlich wie bei Luft- und Raumfahrtturbinen, aber oft in größerem Maßstab. AM wird für Brennkammerauskleidungen, Übergangsstücke und Schaufelabschirmungen verwendet, um hohen Betriebstemperaturen standzuhalten und die Effizienz und Emissionskontrolle zu verbessern.
- Kernenergie: Herstellung spezieller Abschirmungskomponenten für Reaktoren oder die Abfallbehandlung, wo hohe Temperaturen und Strahlungsbeständigkeit erforderlich sind.
- Erneuerbare Energien: Komponenten in Solarkraftwerken (CSP) oder geothermischen Anlagen, die hohen Temperaturen ausgesetzt sind.
- Industrielle Fertigung: Verschiedene Hochtemperaturprozesse profitieren von einem maßgeschneiderten Wärmeschutz.
- Öfen und Brennöfen: Herstellung langlebiger, individuell geformter Teile für Industrieöfen wie interne Abschirmungen, Ablenkbleche oder Sensorschutz für die Wärmebehandlung von Metallen, die Glasherstellung oder das Brennen von Keramik. AM ermöglicht optimierte Formen und die Integration von Merkmalen.
- Chemische Verarbeitung: Schutz von Reaktoren, Rohrleitungen und Sensoren in chemischen Hochtemperaturprozessen mit korrosiven Medien. Die Wahl spezifischer Legierungen wie IN625 über AM ist hier entscheidend.
- Leistungsstarke Maschinen: Abschirmkomponenten in Spezialgeräten wie Plasmaschneidern, Schweißanlagen oder Werkzeugen für die Halbleiterherstellung.
- Medizinisch: Weniger häufig ist dies bei thermisch abschirmende, hochtemperaturbeständige Materialien, die mittels AM gedruckt werden, werden für Sterilisationstrays oder Komponenten in medizinischen Geräten verwendet, die wiederholt Hochtemperatur-Sterilisationszyklen unterzogen werden.
Allen diesen Anwendungen gemeinsam ist der Bedarf an Komponenten, die zuverlässig schweren thermischen Belastungen standhalten, oft in Kombination mit mechanischer Beanspruchung und korrosiven Umgebungen. Der 3D-Druck von Metallen, insbesondere von Hochleistungssuperlegierungen, die von Experten Lieferanten für additive Fertigungbietet Ingenieuren die Möglichkeit, Hitzeschilde zu entwerfen und zu produzieren, die diese anspruchsvollen Anforderungen erfüllen und oft die Möglichkeiten herkömmlicher Fertigungsverfahren übersteigen. Die Möglichkeit, diese fortschrittlichen Komponenten von spezialisierten Hochleistungsmaschinen teilanbietern wird immer wichtiger, um einen Wettbewerbsvorteil zu behalten.
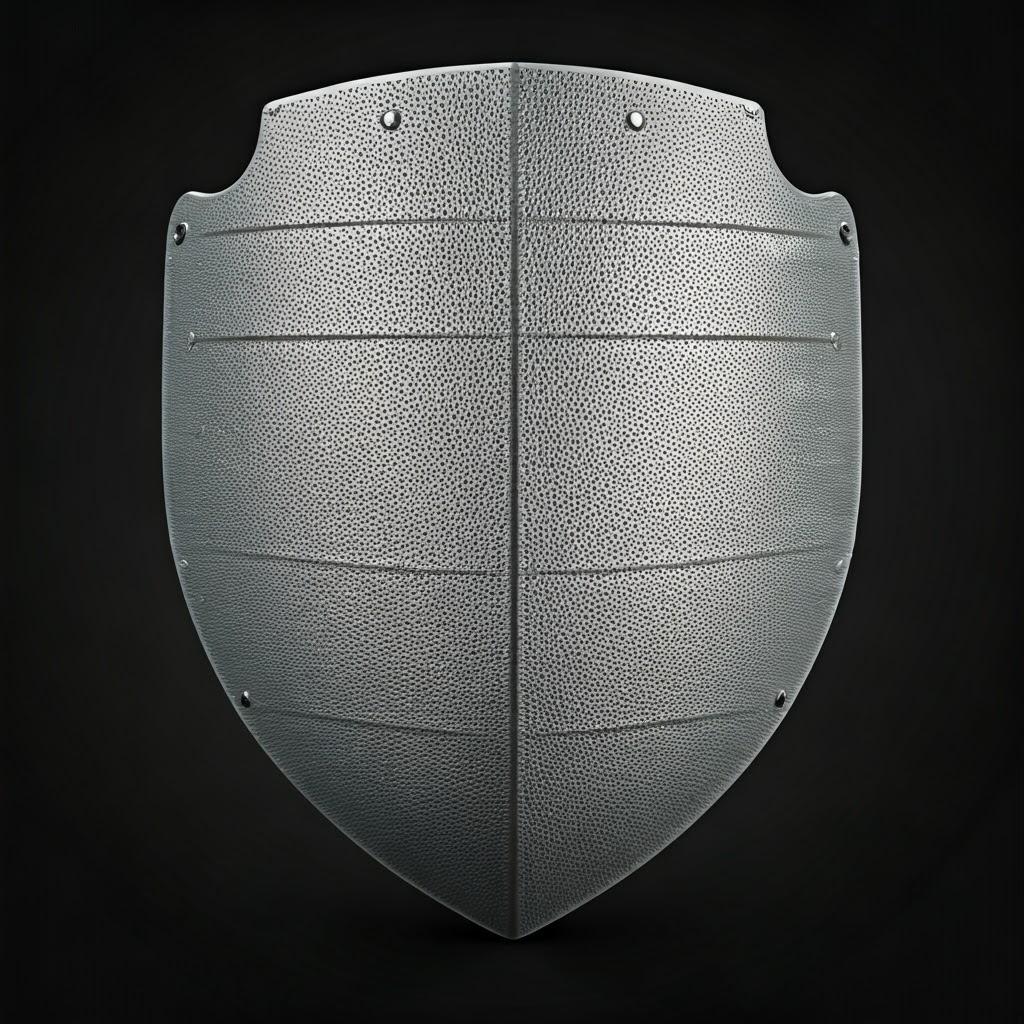
Der Additiv-Vorteil: Warum sollten Sie sich für den 3D-Druck von Metall für Wärmeschutzschilde entscheiden?
Während herkömmliche Fertigungsverfahren wie Stanzen, Gießen und CNC-Bearbeitung der Industrie bei der Herstellung von Hitzeschilden seit langem gute Dienste leisten, bietet die additive Fertigung (AM) von Metallen eine Reihe überzeugender Vorteile, insbesondere für komplexe, leistungsstarke oder in kleinen Stückzahlen hergestellte Komponenten. Diese Vorteile ergeben sich direkt aus dem schichtweisen Herstellungsprozess, der der additiven Fertigung innewohnt und beispiellose Freiheiten und Möglichkeiten bietet, die viele Beschränkungen konventioneller Techniken aufheben. Für Ingenieure und Beschaffungsspezialisten, die Produktionsmethoden für anspruchsvolle thermische Anwendungen evaluieren, ist es wichtig, diese Vorteile zu verstehen vorteile der additiven Fertigung ist entscheidend.
Hauptvorteile von Metal AM für thermische Abschirmungen:
- Unerreichte Gestaltungsfreiheit und Komplexität:
- Verschlungene Geometrien: AM eignet sich hervorragend für die Herstellung hochkomplexer Formen, die subtraktiv oder durch Umformung nur schwer, kostspielig oder gar nicht hergestellt werden können. Dazu gehören interne Kühlkanäle, die sich der Oberfläche des Schildes anpassen, komplexe Gitterstrukturen für optimierte Wärmeableitung oder strukturelle Unterstützung bei minimalem Gewicht sowie dünne, organisch geformte Wände.
- Teil Konsolidierung: Mehrere Komponenten einer herkömmlichen Hitzeschildbaugruppe (z. B. Halterungen, Abstandshalter, Abschirmplatten) können oft neu entworfen und als ein einziges, integriertes Teil gedruckt werden. Dies reduziert die Montagezeit, potenzielle Fehlerquellen (wie Schweißnähte oder Befestigungselemente) und das Gesamtgewicht des Systems.
- Topologie-Optimierung: Ingenieure können mit Hilfe von Software-Tools die Materialverteilung innerhalb der Abschirmung optimieren und das Material nur dort platzieren, wo es strukturell oder thermisch notwendig ist. Dies führt zu erheblichen leichtgewichtige Hitzeschilde ohne Leistungseinbußen - ein entscheidender Faktor in der Luft- und Raumfahrt und bei Hochleistungsanwendungen in der Automobilindustrie.
- Rapid Prototyping und Iteration:
- Geschwindigkeit zum ersten Teil: AM ermöglicht die Erstellung von Funktionsprototypen direkt aus CAD-Daten in wenigen Tagen statt in Wochen oder Monaten, die oft für die Herstellung von Werkzeugen (z. B. für das Gießen oder Stanzen) erforderlich sind. Dies beschleunigt die Designvalidierung und die Testzyklen für rapid Prototyping von Hochtemperaturteilen.
- Erleichterung von Designänderungen: Änderungen am Design können schnell umgesetzt werden, indem einfach das digitale Modell geändert und eine neue Iteration gedruckt wird, ohne dass teure Werkzeuganpassungen erforderlich sind. Diese Flexibilität ist während der Entwicklungsphasen von unschätzbarem Wert.
- Materialeffizienz und Abfallvermeidung:
- Produktion in nahezu endkonturnaher Form: AM baut Teile schichtweise auf, wobei nur das Material verwendet wird, das für das Bauteil selbst und die notwendigen Stützstrukturen benötigt wird. Dies steht in scharfem Gegensatz zur subtraktiven Fertigung (maschinelle Bearbeitung), die mit einem größeren Materialblock beginnt und einen Großteil davon als Abfall (Späne) entfernt. Dies ist besonders vorteilhaft bei der Arbeit mit teuren Hochtemperatur-Superlegierungen wie IN625 oder Haynes 282.
- Nachhaltigkeit: Die Verringerung des Materialabfalls trägt zu nachhaltigeren Produktionsverfahren bei.
- Zugang zu fortgeschrittenen Materialien:
- Hochleistungslegierungen: AM-Verfahren, insbesondere Pulverbettschmelzverfahren (Powder Bed Fusion, PBF) wie das selektive Elektronenstrahlschmelzen (Selective Electron Beam Melting, SEBM) und das selektive Laserschmelzen (Selective Laser Melting, SLM), eignen sich gut für die Verarbeitung von Hochleistungs-Superlegierungen auf Nickelbasis, Kobalt-Chrom, Titanlegierungen und Refraktärmetallen, die für extreme Temperaturbeständigkeit unerlässlich sind. Unternehmen wie Met3dp sind auf die Herstellung und Verarbeitung dieser anspruchsvollen Materialien spezialisiert.
- Maßgeschneiderte Mikrostrukturen: Die Prozessparameter in der AM können manchmal so eingestellt werden, dass sie die resultierende Mikrostruktur des Materials beeinflussen, wodurch bestimmte Eigenschaften wie Kriechfestigkeit oder thermische Ermüdungsfestigkeit verbessert werden können.
- Optimierung der Lieferkette und Produktion auf Abruf:
- Beseitigung von Werkzeugen: AM umgeht den Bedarf an speziellen Werkzeugen und reduziert so die Vorabinvestitionen und Vorlaufzeiten, insbesondere bei kleinen bis mittleren Produktionsserien oder Ersatzteilen.
- Verteilte Fertigung: Teile können potenziell näher am Ort des Bedarfs gedruckt werden, was Transportkosten und Vorlaufzeiten reduziert und dazu beiträgt Optimierung der Lieferkette.
- Digitales Inventar: Die Entwürfe werden digital gespeichert, so dass die Teile auf Abruf gedruckt werden können, was den Bedarf an großen physischen Lagerbeständen von Ersatzteilen verringert.
Vergleich zwischen traditioneller und additiver Fertigung für thermische Abschirmungen:
Merkmal | Herkömmliche Verfahren (Stanzen, Gießen, maschinelle Bearbeitung) | Additive Fertigung von Metallen (z. B. SEBM, SLM) | Vorteil Anmerkungen |
---|---|---|---|
Entwurfskomplexität | Begrenzt durch Werkzeuge, Umformung, Bearbeitungsmöglichkeiten | Sehr hoch (interne Kanäle, Gitter, organische Formen) | AM ermöglicht optimierte Leistung durch komplexe Designs. |
Teil Konsolidierung | Schwierig; erfordert oft Montage | Hohes Potenzial | Reduziert das Gewicht, die Montagezeit und mögliche Fehlerquellen. |
Gewichtsreduzierung | Begrenzt; oft gleichmäßige Dicke | Hohes Potenzial durch Topologie-Optimierung, Gitternetze | Entscheidend für die Treibstoffeffizienz in der Luft- und Raumfahrt und in der Automobilindustrie. |
Vorlaufzeit (Proto) | Wochen/Monate (Werkzeugbau oft erforderlich) | Tage/Wochen | Die Entwicklungszyklen werden erheblich beschleunigt. |
Vorlaufzeit (Prod.) | Schnell für hohe Stückzahlen (Stanzen); Langsam (Gießen) | Mäßig; Verbesserung mit schnelleren Maschinen | Wettbewerbsfähig für kleine bis mittlere Mengen, Ersatzteile. |
Materialabfälle | Mäßig (Stanzen) bis hoch (Bearbeitung) | Niedrig (Fast-Netzform) | Kosteneinsparungen, vor allem bei teuren Superlegierungen; mehr Nachhaltigkeit. |
Werkzeugkosten | Hoch (Matrizen, Gussformen) | Keiner | Erhebliche Kosteneinsparungen bei geringen Stückzahlen und Prototypen. |
Material-Optionen | Große Reichweite, aber prozessbegrenzt | Wachsende Produktpalette, hervorragend geeignet für Hochtemperatur-Superlegierungen | AM eignet sich gut für Materialien, die in extremen Umgebungen benötigt werden. |
Minimale Chargengröße | Oft hoch aufgrund der Werkzeugausstattung | Eine | Ideal für Anpassungen, Prototypen und Ersatzteile. |
Oberfläche | Variabel (gut im Originalzustand/gestempelt, ausgezeichnet bearbeitet) | Typischerweise rauer als gedruckt; erfordert Nachbearbeitung | Für glatte Oberflächen oder enge Toleranzen ist oft eine Nachbearbeitung erforderlich. |
Interne Merkmale | Schwierig/unmöglich | Relativ einfach | Ermöglicht integrierte Kühlung, komplexe interne Umlenkungen. |
In Blätter exportieren
Während AM erhebliche Vorteile bietet, ist es wichtig zu beachten, dass es nicht allgemein überlegen ist für alle hitzeschildanwendungen. Einfache Abschirmungen in hohen Stückzahlen lassen sich vielleicht immer noch kostengünstiger durch Stanzen herstellen. Bei Komponenten, die komplexe Geometrien, geringes Gewicht, schnelle Entwicklung oder die Verwendung fortschrittlicher Superlegierungen erfordern, bietet der 3D-Metalldruck jedoch einen entscheidenden Vorteil und verändert die Art und Weise, wie Ingenieure an die Konstruktion und Produktion kritischer Hochtemperatur-Hardware herangehen. Die Zusammenarbeit mit einem erfahrenen AM-Anbieter stellt sicher, dass diese Vorteile voll zum Tragen kommen.
Materialschwerpunkt: IN625 und Haynes 282 für extreme Umgebungen
Die Auswahl des geeigneten Materials ist wohl die wichtigste Entscheidung bei der Entwicklung und Herstellung von Hitzeschilden für den Hochtemperaturbetrieb. Das Material muss nicht nur extremer Hitze standhalten, sondern oft auch Oxidation, Korrosion, Kriechen (Verformung unter anhaltender Belastung bei hoher Temperatur) und thermischer Ermüdung (Versagen aufgrund zyklischer Temperaturänderungen) widerstehen. Für viele anspruchsvolle Anwendungen in der Luft- und Raumfahrt, der Energieerzeugung und bei industriellen Prozessen sind Superlegierungen auf Nickelbasis aufgrund ihrer außergewöhnlichen Kombination aus Hochtemperaturfestigkeit, Umweltbeständigkeit und Verarbeitbarkeit die Materialien der Wahl. Dazu gehören, IN625 (Inconel® 625) und Haynes® 282® zeichnen sich als Hauptkandidaten aus, die häufig in der additiven Metallfertigung für Hitzeschilde eingesetzt werden.
Die Kenntnis der Eigenschaften und Vorteile dieser spezifischen Legierungen hilft Ingenieuren und Beschaffungsexperten, das richtige Material für ihre Anwendung zu spezifizieren und zu verstehen, warum die Zusammenarbeit mit einem sachkundigen anbieter von Metallpulvern wie Met3dp, das hochwertige Versionen dieser Materialien anbietet, ist entscheidend.
Inconel® 625 (IN625 / Legierung 625)
IN625 ist eine weit verbreitete und vielseitige Nickel-Chrom-Molybdän-Niob-Legierung, die für ihre hervorragende Verarbeitbarkeit und Beständigkeit in einer Vielzahl von korrosiven Umgebungen bekannt ist, verbunden mit einer ausgezeichneten Festigkeit bei kryogenen Temperaturen bis zu etwa 815∘C (1500∘F) und einer nützlichen Oxidationsbeständigkeit bei noch höheren Temperaturen.
- Wichtige Eigenschaften & Vorteile für Wärmeschutzschilde:
- Hohe Temperaturbeständigkeit: Sie ist zwar bei den höchsten Temperaturen nicht die stärkste Superlegierung, weist aber bis zu mäßig hohen Temperaturen eine beträchtliche Festigkeit und Zähigkeit auf, so dass sie sich für viele Abgaskomponenten und Turbinenteile eignet.
- Ausgezeichnete Korrosionsbeständigkeit: Bietet eine hervorragende Beständigkeit sowohl gegen allgemeine Korrosion als auch gegen lokale Angriffe (Lochfraß, Spaltkorrosion) in verschiedenen Medien, einschließlich Seewasser, Säuren und alkalischen Umgebungen. Dies ist vorteilhaft für Abschirmungen, die Verbrennungsnebenprodukten oder aggressiven Industriechemikalien ausgesetzt sind.
- Oxidationsbeständigkeit: Bildet eine schützende Oxidschicht, die eine gute Beständigkeit gegen Verzunderung und Oxidation bei erhöhten Temperaturen bietet.
- Ermüdungsfestigkeit: Weist eine hohe Ermüdungs- und Thermoermüdungsfestigkeit auf, was für Bauteile, die zyklischer Erwärmung und Abkühlung ausgesetzt sind, von entscheidender Bedeutung ist.
- Verarbeitbarkeit & Schweißeignung: Bekannt für seine relativ einfache Herstellung im Vergleich zu anderen Superlegierungen, sowohl traditionell als auch durch additive Fertigung. Er weist im Allgemeinen eine gute Druckbarkeit in PBF-Verfahren auf.
- Kosten-Nutzen-Verhältnis: Oft kostengünstiger als leistungsfähigere Superlegierungen wie Haynes 282.
- Typische Wärmeschutzanwendungen: Abgassysteme für Luft- und Raumfahrtmotoren, Hochleistungsabgaskomponenten für Kraftfahrzeuge, Abschirmung von Industrieöfen, Schutz von chemischen Verarbeitungsanlagen, Bälge und Kompensatoren.
Haynes® 282®
Haynes 282 ist eine neue Generation von Gamma-Prime (γ′)-verstärkten Nickelbasis-Superlegierungen, die speziell für Hochtemperatur-Strukturanwendungen, insbesondere in Gasturbinen, entwickelt wurden. Im Vergleich zu anderen Legierungen wie Waspaloy oder R-41 bietet es eine hervorragende Kombination aus Kriechfestigkeit, thermischer Stabilität, Verarbeitbarkeit und Schweißbarkeit.
- Wichtige Eigenschaften & Vorteile für Wärmeschutzschilde:
- Außergewöhnliche Kriechfestigkeit: Sein Hauptvorteil liegt in seiner hervorragenden Kriechbeständigkeit bei Temperaturen von bis zu 927∘C (1700∘F), die viele andere verarbeitbare Superlegierungen übertrifft. Dies ist von entscheidender Bedeutung für tragende Bauteile oder Abschirmungen, die bei hohen Temperaturen dauerhaft belastet werden, wie Turbinengehäuse oder Brennkammerauskleidungen.
- Ausgezeichnete thermische Stabilität: Widersteht der Versprödung durch Alterung bei langer Einwirkung von hohen Temperaturen.
- Gute Oxidationsbeständigkeit: Bietet eine gute Beständigkeit gegen Hochtemperaturoxidation.
- Hervorragende Verarbeitbarkeit (für seine Klasse): Entwickelt für eine verbesserte Verarbeitbarkeit und Schweißbarkeit im Vergleich zu ähnlich starken Legierungen, wodurch es sich besser für komplexe Fertigungsverfahren, einschließlich AM, eignet. Es zeigt eine gute Druckbarkeit in PBF-Systemen, obwohl die Optimierung der Prozessparameter entscheidend ist.
- Hohe Ermüdungsfestigkeit: Behält eine gute Ermüdungsbeständigkeit unter anspruchsvollen thermischen Zyklen bei.
- Typische Wärmeschutzanwendungen: Kritische Gasturbinenkomponenten (Luft- und Raumfahrt und Industrie) wie Brennkammerauskleidungen, Übergangskanäle, Gehäuse, Ummantelungen und Abgasstrukturen, die maximale Festigkeit und Kriechfestigkeit bei höchsten Betriebstemperaturen erfordern.
Vergleich der Materialeigenschaften (typische Werte):
Eigentum | IN625 | Haynes® 282® | Einheiten | Anmerkungen |
---|---|---|---|---|
Nominale Zusammensetzung (Gew.-%) | Ni: 58 min, Cr: 20-23, Mo: 8-10, Nb: 3,15-4,15 | Ni: Bal, Cr: 19-21, Co: 9-11, Mo: 8-9, Ti: 1,9-2,3, Al: 1,3-1,7 | – | Die wichtigsten Verstärkungselemente unterscheiden sich erheblich. |
Dichte | 8.44 | 8.33 | g/cm3 | Haynes 282 ist etwas leichter. |
Schmelzbereich | 1290 – 1350 | 1307 – 1356 | ∘C | Ähnliche Schmelzpunkte. |
Max. Empfohlene Betriebstemp. | ~815∘C (für Stärke) | ~927∘C (für Stärke/Kriechen) | ∘C | Haynes 282 zeichnet sich durch höhere Temperaturen unter Belastung aus. |
Streckgrenze (RT, geglüht) | ~520 | ~690 (gealtert) | MPa | Haynes 282 (wärmebehandelt) ist wesentlich stärker. |
Streckgrenze (871$^{\circ}C/1600^{\circ}$F) | ~300 | ~550 (gealtert) | MPa | Zeigt die überragende Hochtemperaturfestigkeit des Haynes 282’s. |
1000-Stunden-Kriechbruchfestigkeit (815$^{\circ}C/1500^{\circ}$F) | ~80 | ~170 | MPa | Hervorzuheben ist die deutlich bessere Kriechfestigkeit des Haynes 282’. |
Druckbarkeit (PBF) | Im Allgemeinen gut | Gut (Erfordert eine sorgfältige Kontrolle der Parameter) | – | Beide sind bedruckbar, Haynes 282 kann empfindlicher auf Prozessparameter reagieren. |
In Blätter exportieren
Warum die Materialqualität bei AM wichtig ist:
Der Erfolg der Herstellung hochintegrierter Hitzeschilde mittels AM hängt stark von der Qualität des eingesetzten Metallpulvers ab. Faktoren wie:
- Partikelgrößenverteilung (PSD): Beeinflusst die Dichte und die Fließfähigkeit des Pulverbettes, was sich auf die Dichte und die Oberflächengüte des Endproduktes auswirkt.
- Sphärizität: Hochgradig kugelförmige Pulver, wie sie mit den fortschrittlichen Gaszerstäubungs- und PREP-Technologien von Met3dp’ hergestellt werden, gewährleisten einen guten Pulverfluss und eine gleichmäßige Verteilung, wodurch Defekte minimiert werden.
- Chemische Reinheit: Verunreinigungen können zu Defekten führen und die Hochtemperatureigenschaften und die Korrosionsbeständigkeit des Materials beeinträchtigen.
- Niedriger Sauerstoff-/Stickstoffgehalt: Ein Übermaß an Zwischengitterelementen kann das Endprodukt verspröden.
Met3dp bietet eine Reihe von hochwertige Metallpulvereinschließlich nickelbasierter Superlegierungen wie IN625, die für additive Fertigungsverfahren optimiert sind. Unser Engagement für fortschrittliche Pulverproduktionstechniken gewährleistet eine hohe Sphärizität, kontrollierte PSD und chemische Reinheit, die es unseren Kunden ermöglichen, dichte, zuverlässige Hitzeschilde und andere kritische Komponenten mit überlegenen mechanischen Eigenschaften zu drucken, die für extreme Umgebungen erforderlich sind. Die Wahl eines Anbieters wie Met3dp, der über Fachwissen sowohl in der Materialwissenschaft als auch in der AM-Bearbeitung verfügt, ist entscheidend für die erfolgreiche Nutzung von IN625 3D-Druck-Pulver oder Haynes 282 Additive Fertigung Fähigkeiten.
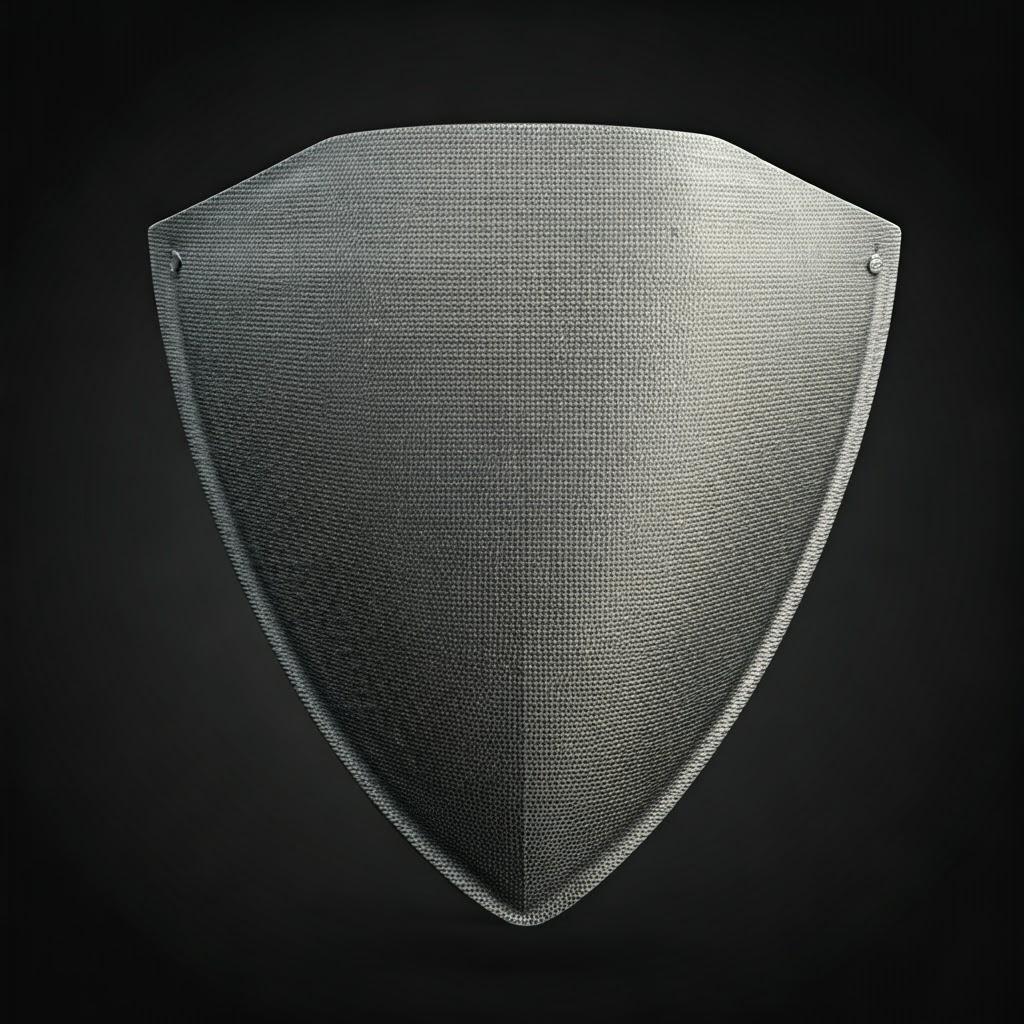
Entwurf für additive Fertigung (DfAM): Optimierung der Leistung von Wärmeschilden
Das wahre Potenzial der additiven Fertigung von Metallen wird nicht nur durch die Replikation von Designs erschlossen, die für traditionelle Methoden vorgesehen sind, sondern auch durch Design für additive Fertigung (DfAM). DfAM ist eine Design-Philosophie und eine Reihe von Praktiken, die die einzigartigen Fähigkeiten von AM-Prozessen nutzen und deren spezifische Einschränkungen berücksichtigen. Bei der Anwendung auf Hochtemperatur-Thermoschilde ermöglicht DfAM den Ingenieuren die Entwicklung von Bauteilen mit deutlich verbesserter Leistung, geringerem Gewicht und integrierter Funktionalität, die auf andere Weise einfach nicht zu erreichen wäre. Es erfordert ein Umdenken, das über die Grenzen von Formen, Gesenken und Schneidwerkzeugen hinausgeht und die Freiheit des schichtweisen Aufbaus nutzt. Die Zusammenarbeit mit einem AM-Experten wie Met3dp, der sich sowohl mit den Materialien als auch mit den 3D-Druck von Metall für eine wirksame Umsetzung von DfAM unerlässlich ist.
Die wichtigsten DfAM-Prinzipien für Wärmeschutzschilde:
- Ausnutzung der geometrischen Komplexität für das Wärmemanagement:
- Konforme Kühl-/Heizkanäle: Die vielleicht leistungsfähigste DfAM-Anwendung für das Wärmemanagement. Anstatt gerade Kühllöcher zu bohren, ermöglicht AM die Schaffung von Kanälen, die den komplexen Konturen der Oberfläche der Abschirmung genau folgen, auch im Inneren. Dies gewährleistet eine gleichmäßigere Temperaturverteilung, reduziert Hot Spots und ermöglicht eine effizientere Wärmeabfuhr oder -verteilung genau dort, wo sie benötigt wird.
- Optimierung: CFD-Simulationen (Computational Fluid Dynamics) können in der Entwurfsphase eingesetzt werden, um den Verlauf, den Durchmesser und die internen Merkmale (wie Turbulatoren) dieser Kanäle für maximale thermische Leistung zu optimieren.
- Herausforderung: Die Konstruktion von Rinnen, die selbsttragend sind oder nur minimale, leicht entfernbare interne Stützen benötigen, ist von entscheidender Bedeutung.
- Integrierter Wärmetauscher Merkmale: Bei Abschirmungen, die für eine aktive Wärmeableitung ausgelegt sind, können komplizierte Rippenstrukturen, Pin-Arrays oder komplexe Umlenkungen direkt in den Abschirmungskörper integriert werden, um die Oberfläche für die konvektive oder strahlende Wärmeübertragung bei minimalem Volumen zu maximieren.
- Doppelwandige Strukturen: Die Schaffung hohler oder doppelwandiger Abschirmungen mit internen Strukturen kann für Isolierung sorgen, eine Kühlung durch Luftströmung ermöglichen oder die Wärmeübertragung durch Leitung verringern.
- Konforme Kühl-/Heizkanäle: Die vielleicht leistungsfähigste DfAM-Anwendung für das Wärmemanagement. Anstatt gerade Kühllöcher zu bohren, ermöglicht AM die Schaffung von Kanälen, die den komplexen Konturen der Oberfläche der Abschirmung genau folgen, auch im Inneren. Dies gewährleistet eine gleichmäßigere Temperaturverteilung, reduziert Hot Spots und ermöglicht eine effizientere Wärmeabfuhr oder -verteilung genau dort, wo sie benötigt wird.
- Gewichtsreduzierung durch optimierte Strukturen:
- Topologie-Optimierung: Mithilfe von Softwarealgorithmen wird Material aus unkritischen Bereichen entfernt, während die strukturelle Integrität unter den zu erwartenden thermischen und mechanischen Belastungen erhalten bleibt. Das Ergebnis sind organisch anmutende, hocheffiziente Strukturen, die das Gewicht der Bauteile erheblich reduzieren - ein wichtiges Anliegen in der Luft- und Raumfahrt sowie in der Automobilindustrie.
- Gitterförmige Strukturen: Ersetzen von Vollprofilen durch innere Gitter- oder Kreiselstrukturen. Diese periodischen, porösen Strukturen bieten ein außergewöhnliches Verhältnis zwischen Steifigkeit und Gewicht. Außerdem können sie auf die thermischen Eigenschaften zugeschnitten werden:
- Isolierung: Bestimmte Gittertopologien können Luft einschließen oder die Wärmeableitung behindern.
- Verbesserte Konvektion: Offenzellige Gitter können die Oberfläche für den Flüssigkeitsstrom (Luft oder flüssiges Kühlmittel) drastisch vergrößern, wenn sie in Kühlsysteme integriert werden.
- Schwingungsdämpfung: Gitter können auch so gestaltet werden, dass sie Schwingungen dämpfen.
- Dünnwandige Konstruktion: AM-Prozesse können viel dünner und komplexer sein dünnwandige Strukturen als das Gießen oder die maschinelle Bearbeitung normalerweise erlauben. Die Konstruktion von Abschirmungen mit variabler Wandstärke, die auf der Grundlage lokaler thermischer Belastungen und struktureller Anforderungen optimiert wird, trägt weiter zur Gewichtseinsparung bei. Die minimale druckbare Wandstärke hängt vom Material, der Maschine (z. B. SEBM, SLM) und der spezifischen Geometrie ab, liegt aber oft im Bereich von 0,3-0,5 mm.
- Teil Konsolidierung:
- Verringerung der Montagekomplexität: DfAM ermutigt Designer, Baugruppen neu zu überdenken. Halterungen, Befestigungen, Strömungsführungen und Abschirmelemente, die zuvor separat hergestellt wurden, können oft in ein einziges, monolithisches 3D-gedrucktes Bauteil integriert werden.
- Vorteile: Dies verringert die Anzahl der Teile, eliminiert Verbindungen (potenzielle Leckagepfade oder Fehlerstellen), vereinfacht die Montage, reduziert die Lagerhaltung und senkt oft das Gesamtgewicht und die Kosten des Systems.
- Design for Manufacturability (AM-Spezifika):
- Minimierung der Stützstrukturen: Beim Pulverbettschmelzen (Powder Bed Fusion, PBF) sind häufig Stützstrukturen erforderlich, um das Teil zu verankern, Verformungen zu verhindern und überhängende Merkmale zu stützen (typischerweise Winkel unter 45 Grad zur Horizontalen). Stützstrukturen verlängern jedoch die Druckzeit, verbrauchen Material, erfordern eine Nachbearbeitung zur Entfernung und können die Oberflächengüte beeinträchtigen. Effektives DfAM zielt darauf ab:
- Orientieren Sie sich an der Rolle: Wählen Sie eine Bauausrichtung, die den Bedarf an Stützen auf kritischen Oberflächen oder in schwer zugänglichen Bereichen (wie internen Kanälen) minimiert.
- Selbsttragende Winkel entwerfen: Anstelle von scharfen horizontalen Auskragungen sollten möglichst Fasen oder Hohlkehlen verwendet werden.
- Nutzen Sie opferbereite Merkmale: Konstruktionsmerkmale, die speziell dafür gedacht sind, später entfernt zu werden, und die möglicherweise die notwendige Unterstützung enthalten.
- Nutzung von Prozessfähigkeiten: Verfahren wie das Selektive Elektronenstrahlschmelzen (SEBM) von Met3dp arbeiten oft bei höheren Temperaturen, wodurch die Eigenspannung reduziert wird und für bestimmte Geometrien möglicherweise weniger Stützen als beim SLM benötigt werden.
- Bewältigung von Reststress: Die Konstruktion von Merkmalen zur Verringerung der Spannungskonzentration, die Vermeidung großer Querschnittsschwankungen und die Berücksichtigung der Bauausrichtung können dazu beitragen, die dem PBF-Prozess innewohnenden Restspannungen zu bewältigen.
- Merkmal Auflösung: Die Kenntnis der Mindestgröße der Merkmale, des Lochdurchmessers und der erreichbaren Toleranzen des gewählten AM-Prozesses und des Materials ist in der Entwurfsphase von entscheidender Bedeutung.
- Minimierung der Stützstrukturen: Beim Pulverbettschmelzen (Powder Bed Fusion, PBF) sind häufig Stützstrukturen erforderlich, um das Teil zu verankern, Verformungen zu verhindern und überhängende Merkmale zu stützen (typischerweise Winkel unter 45 Grad zur Horizontalen). Stützstrukturen verlängern jedoch die Druckzeit, verbrauchen Material, erfordern eine Nachbearbeitung zur Entfernung und können die Oberflächengüte beeinträchtigen. Effektives DfAM zielt darauf ab:
Überlegungen zum DfAM-Workflow:
- CAD & Simulation: Einsatz fortschrittlicher CAD-Werkzeuge, die komplexe Geometrien (wie Gitter und topologieoptimierte Formen) verarbeiten können, und Integration der Finite-Elemente-Analyse (FEA) für strukturelle Integrität und CFD für thermische Simulation AM ist entscheidend.
- Kollaboration: Eine enge Zusammenarbeit zwischen den Konstrukteuren und dem AM-Dienstleister (wie Met3dp) ist unerlässlich, um sicherzustellen, dass das Design für die jeweilige Maschine, das Material (z. B. IN625, Haynes 282) und die Nachbearbeitungsmöglichkeiten optimiert ist.
- Iterative Verfeinerung: Nutzung der Rapid-Prototyping-Fähigkeit von AM’s zum schnellen Drucken, Testen und Verfeinern von Designs auf der Grundlage von Feedback zur realen Leistung.
Indem sie sich die DfAM-Prinzipien zu eigen machen, können die Hersteller über die einfache Substitution hinausgehen und sich die Macht der additive Fertigung um leistungsstarke Hitzeschilde zu entwickeln, die leichter und effizienter sind und über Funktionen verfügen, die bisher als unmöglich galten. Dieser strategische Ansatz ist der Schlüssel für Großabnehmer und Beschaffungsspezialisten, die Komponenten der nächsten Generation für anspruchsvolle Hochtemperaturumgebungen beschaffen wollen.
Auf die Präzision kommt es an: Erzielung enger Toleranzen und hervorragender Oberflächengüte
Während die additive Fertigung von Metallen eine unglaubliche Designfreiheit bietet, dreht sich eine häufige Frage von Ingenieuren und Beschaffungsmanagern um die erreichbare Präzision: Welcher Grad an metall 3D-Druck Toleranz und Oberflächengüte additive Fertigung für Komponenten wie Hitzeschilde erwartet werden kann? Die Kenntnis dieser Aspekte ist von entscheidender Bedeutung, da sie sich direkt auf die Passform, die Dichtungseigenschaften, die aerodynamische Leistung (falls zutreffend) und die Interaktion mit den Gegenstücken auswirken. Die erforderliche Präzision bestimmt oft den Umfang der notwendigen Nachbearbeitung.
Maßgenauigkeit bei Metall-AM:
Die Maßhaltigkeit eines 3D-gedruckten Metallteils hängt von einem komplexen Zusammenspiel von Faktoren ab:
- AM-Prozess: Anders Druckverfahren ergeben unterschiedliche Genauigkeitsgrade. Pulverbettschmelzverfahren (PBF) wie selektives Laserschmelzen (SLM/LPBF) und selektives Elektronenstrahlschmelzen (SEBM) sind bei Hochleistungsmetallen üblich.
- SLM/LPBF: Bietet im Allgemeinen eine etwas bessere Feinauflösung und potenziell engere Toleranzen beim Druck, da der Laserpunkt kleiner ist.
- SEBM: Verwendet einen Elektronenstrahl und arbeitet in einem Vakuum bei erhöhten Temperaturen. Der Strahlfleck ist zwar größer, aber die höhere Temperatur reduziert die Eigenspannung, was bei größeren oder sperrigen Teilen zu weniger Verzug führen kann und die Gesamtgenauigkeit bei bestimmten Geometrien verbessert. SEBM wird häufig für reaktive oder rissanfällige Werkstoffe wie bestimmte Titanlegierungen oder moderne Superlegierungen eingesetzt. Das Fachwissen von Met3dp’ umfasst verschiedene Verfahren und ermöglicht die Auswahl der optimalen Methode.
- Material: Verschiedene Materialien verhalten sich beim Schmelzen und Erstarren unterschiedlich, was sich auf die Schrumpfung und mögliche Verformung auswirkt. Superlegierungen wie IN625 und Haynes 282 erfordern eine sorgfältige Optimierung der Parameter für die Genauigkeit.
- Größe und Geometrie der Teile: Größere Teile oder solche mit erheblichen Querschnittsschwankungen sind anfälliger für thermische Verformung, was die Gesamtgenauigkeit beeinträchtigen kann. Komplexe innere Merkmale können ebenfalls schwierig zu messen und genau zu kontrollieren sein.
- Kalibrierung und Zustand der Maschine: Regelmäßige Kalibrierung und Wartung des AM-Systems sind entscheidend für gleichbleibende Genauigkeit.
- Orientierung schaffen und Unterstützung bieten: Die Ausrichtung des Teils auf der Bauplatte beeinflusst die Maßgenauigkeit aufgrund von Faktoren wie Treppenstufen auf gekrümmten Oberflächen und dem Einfluss von Stützstrukturen.
- Nachbearbeiten: Spannungsabbau und andere Wärmebehandlungen können manchmal geringfügige Maßänderungen verursachen, die berücksichtigt werden müssen. Die maschinelle Bearbeitung wird häufig eingesetzt, um Endtoleranzen bei kritischen Merkmalen zu erreichen.
Typische Toleranzen:
Als allgemeine Leitlinie für PBF-Prozesse:
- Wie gedruckt: Die Toleranzen liegen häufig im Bereich von ±0,1 mm bis ±0,3 mm für kleinere Merkmale (z. B. 100 mm) und können sich bei größeren Abmessungen auf ±0,5 % oder mehr erhöhen. Die spezifischen Möglichkeiten sind je nach Maschine und Anbieter sehr unterschiedlich.
- Nachbearbeitet: Wenn engere Toleranzen für Schnittstellen, Befestigungspunkte oder Dichtungsflächen erforderlich sind, wird die CNC-Bearbeitung nach dem Druck eingesetzt. Durch die maschinelle Bearbeitung können Toleranzen erreicht werden, die mit der konventionellen Fertigung vergleichbar sind, typischerweise ±0,025 mm bis ±0,05 mm oder sogar noch enger, falls erforderlich.
Für Konstrukteure ist es von entscheidender Bedeutung, kritische Toleranzen auf Zeichnungen festzulegen und die Anforderungen mit dem AM-Anbieter frühzeitig im Prozess zu besprechen. Met3dp verwendet branchenführende Ausrüstung, die für ihre Genauigkeit und Zuverlässigkeit bekannt ist, kombiniert mit strengen qualitätskontrolle AM-Teile verfahren, um anspruchsvolle Spezifikationen zu erfüllen, einschließlich derer, die in luft- und Raumfahrtspezifikationen.
Oberflächengüte (Rauhigkeit):
Die gedruckte Oberfläche von AM-Metallteilen ist in der Regel rauer als eine maschinell bearbeitete Oberfläche.
- Faktoren, die die Rauheit (Ra) beeinflussen:
- Schichtdicke: Dickere Schichten führen im Allgemeinen zu einer raueren Oberfläche.
- Pulver Partikelgröße: Die Größe der Metallpulverpartikel beeinflusst das Finish.
- Strahlparameter: Leistung, Geschwindigkeit und Strategie des Laser- oder Elektronenstrahls wirken sich auf das Schmelzbad und die Erstarrung aus und beeinflussen die Oberflächenbeschaffenheit.
- Winkel der Oberfläche: Oberflächen, die in einem Winkel zur Bauplatte gebaut werden, weisen eine Treppentreppe auf, was die Rauheit erhöht. Vertikale Wände sind in der Regel glatter als schräge oder horizontale Flächen. Obere Oberflächen sind oft rauer als Seitenwände.
- Unterstützende Strukturen: Bereiche, an denen Stützkonstruktionen angebracht waren, müssen nach der Entfernung oft nachbearbeitet werden.
- AM-Prozess: Beim SEBM entstehen in der Regel etwas rauere Oberflächen (z. B. Ra 20-35 μm) als beim SLM (z. B. Ra 10-20 μm), was auf größere Schmelzbäder und Pulverpartikel zurückzuführen ist, allerdings variiert dies.
- Typische As-Printed Ra-Werte: Bereich von Ra 5 μm bis Ra 35 μm (200 bis 1400 μin), stark abhängig von den oben genannten Faktoren.
- Erzielung glatterer Oberflächen: Für Anwendungen, die glattere Oberflächen erfordern (z. B. verbesserte Ermüdungsfestigkeit, besondere Fließeigenschaften in Kanälen, Abdichtung), ist eine Nachbearbeitung erforderlich:
- Abrasives Strahlen/Trommeln: Verbessert die Gleichmäßigkeit und entfernt losen Puder, reduziert aber nur geringfügig Ra.
- Bearbeitungen/Schleifen/Polieren: Kann sehr glatte Oberflächen (Ra < 1 μm) auf zugänglichen Oberflächen erzielen.
- Abrasive Fließbearbeitung (AFM) / Elektrochemisches Polieren: Zur Glättung interner Kanäle und komplexer Geometrien.
Qualitätskontrolle und -überprüfung:
Die Gewährleistung von Präzision erfordert robuste Qualitätskontrollmaßnahmen während des gesamten Herstellungsprozesses:
- Analyse des Pulvers: Überprüfung der Qualität und Konsistenz des eingehenden Metallpulvers.
- Prozessbegleitende Überwachung: Einige fortschrittliche AM-Systeme sind mit Sensoren ausgestattet, die den Herstellungsprozess in Echtzeit überwachen.
- Prüfung der Abmessungen: Einsatz von Koordinatenmessmaschinen (CMM) oder 3D-Scanning zur Überprüfung kritischer Abmessungen anhand des CAD-Modells und der Zeichnungsspezifikationen. CMM-Prüfung 3D-Druck ist Standard für kritische Komponenten.
- Messung der Oberflächenrauhigkeit: Verwendung von Profilometern zur Quantifizierung der Oberflächengüte.
- Zerstörungsfreie Prüfung (NDT): Verfahren wie das CT-Scannen sind von unschätzbarem Wert, wenn es darum geht, die Geometrie und Integrität komplexer interner Merkmale (z. B. Kühlkanäle) zu überprüfen, die auf herkömmliche Weise nicht gemessen werden können.
Um die erforderliche Präzision für Hochtemperatur-Hitzeschilde zu erreichen, bedarf es oft einer Kombination aus optimierter AM-Bearbeitung und gezielter Nachbearbeitung. Eine klare Kommunikation zwischen dem Kunden und einem fähigen AM-Lieferanten wie Met3dp, der die Nuancen der verschiedenen Druckverfahren und Materialien wie IN625 und Haynes 282 ist der Schlüssel zur Erfüllung der anspruchsvollen Toleranz- und Oberflächenanforderungen für kritische Anwendungen.
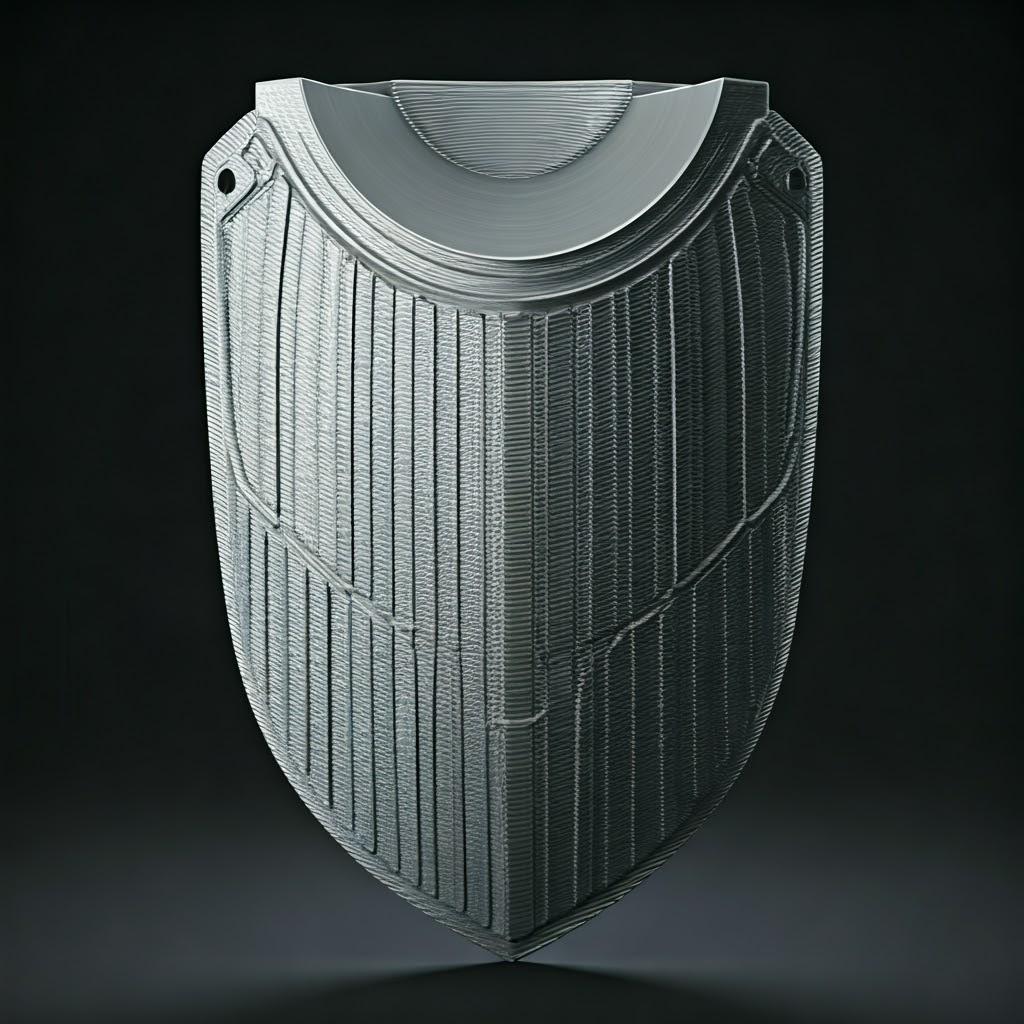
Mehr als der Druck: Unverzichtbare Nachbearbeitung für Wärmeschutzschilder
Ein weit verbreiteter Irrglaube über die additive Fertigung von Metallen ist, dass der Prozess endet, wenn das Teil aus dem Drucker kommt. In Wirklichkeit, insbesondere bei anspruchsvollen Anwendungen mit Hochleistungslegierungen wie IN625 und Haynes 282, die in Hitzeschilden verwendet werden, ist der Druck oft erst der Anfang. Eine Reihe von entscheidenden Nachbearbeitung bei der additiven Fertigung in der Regel sind mehrere Schritte erforderlich, um die gedruckte Komponente in ein funktionsfähiges, zuverlässiges Teil umzuwandeln, das strenge Leistungs- und Qualitätsanforderungen erfüllt. In diesen Schritten werden Eigenspannungen beseitigt, die Mikrostruktur des Materials verfeinert, endgültige Maßtoleranzen und Oberflächengüten erreicht und die Gesamtintegrität des Teils sichergestellt. Das Verständnis dieser Anforderungen ist entscheidend für eine genaue Kostenschätzung, die Planung der Vorlaufzeit und die Gewährleistung, dass das endgültige Bauteil die erwartete Leistung in seiner Hochtemperaturumgebung erbringt.
Gemeinsame Nachbearbeitungsschritte für AM-Wärmeschutzschilde:
- Stressabbau Wärmebehandlung:
- Zweck: Dies ist wohl die am kritischsten erster Schritt für PBF-Teile. Die schnellen Erwärmungs- und Abkühlungszyklen während des Drucks erzeugen erhebliche innere Spannungen im Bauteil. Wenn diese Spannungen nicht abgebaut werden, können sie zu Verformungen oder Rissen führen, wenn das Teil von der Bauplatte entfernt wird oder bei der anschließenden Verarbeitung/Wartung.
- Prozess: Die Teile werden auf eine bestimmte Temperatur erwärmt (unterhalb der Alterungstemperatur für ausscheidungsgehärtete Legierungen), während sie noch auf der Bauplatte befestigt sind, eine Zeit lang gehalten und dann langsam abgekühlt. Die spezifischen Zyklen hängen stark von der Legierung (z. B. haben IN625 und Haynes 282 unterschiedliche Anforderungen) und der Teilegeometrie ab.
- Wichtigkeit: Überspringen oder unsachgemäße Ausführung stressabbau AM Teile kann zu einem katastrophalen Versagen von Teilen führen.
- Entnahme von der Bauplatte:
- Prozess: Nach dem Spannungsabbau werden das Teil und seine Halterungen in der Regel mit einer Drahterodiermaschine oder einer Bandsäge aus der Bauplatte geschnitten. Dabei muss darauf geachtet werden, dass das Teil nicht beschädigt wird.
- Entfernung der Stützstruktur:
- Zweck: Entfernen der temporären Strukturen, die während des Bauprozesses verwendet wurden.
- Methoden: Dies kann von einfachem manuellem Brechen/Schneiden für zugängliche Stützen bis hin zu komplexeren Methoden wie CNC-Bearbeitung oder Schleifen für Stützen auf kritischen Oberflächen oder solche, die eng mit dem Teil integriert sind, reichen. Stützentfernung AM für komplexe interne Geometrien kann besonders schwierig und zeitaufwändig sein.
- Auswirkungen: Dieser Schritt hinterlässt oft Spuren oder raue Stellen auf der Oberfläche, die eine weitere Bearbeitung erfordern können. Das DfAM spielt eine Schlüsselrolle bei der Gestaltung von Stützen für eine leichtere Entfernung.
- Heiß-Isostatisches Pressen (HIP):
- Zweck: HIP ist ein Verfahren, bei dem die Teile gleichzeitig einer hohen Temperatur (unter dem Schmelzpunkt) und einem hohen isostatischen Gasdruck (in der Regel Argon) ausgesetzt werden. Dadurch wird die interne Mikroporosität (Hohlräume), die beim Druck entstehen kann, beseitigt, was die mechanischen Eigenschaften wie Ermüdungsfestigkeit, Duktilität und Bruchzähigkeit deutlich verbessert.
- Vorteile: Führt zu nahezu 100 % dichten Teilen, was für Komponenten mit hoher Belastung oder zyklischer Beanspruchung, wie sie in der Luft- und Raumfahrt und bei Turbinenanwendungen üblich sind, von entscheidender Bedeutung ist. HIP Metall 3D-Druck ist oft eine zwingende Voraussetzung für kritische Fluggeräte.
- Erwägung: HIP kann zu leichten Maßänderungen führen und erfordert eine sorgfältige Planung, insbesondere wenn vor diesem Schritt enge Toleranzen erforderlich sind.
- Weitere Wärmebehandlungen (Lösungsglühen/Alterung):
- Zweck: Um das gewünschte endgültige Gefüge und die mechanischen Eigenschaften zu erreichen, insbesondere bei ausscheidungsgehärteten Superlegierungen wie Haynes 282.
- Lösungsglühen: Löst Ausscheidungen auf und homogenisiert das Gefüge.
- Alterung: Kontrolliertes Erhitzen zur Ausscheidung verfestigender Phasen (wie Gamma Prime in Haynes 282), wodurch die Hochtemperaturfestigkeit und die Kriechbeständigkeit deutlich erhöht werden.
- Wichtigkeit: Anpassung der Materialeigenschaften (Festigkeit, Härte, Kriechfestigkeit) an die spezifischen Anforderungen der Hitzeschildanwendung. Met3dp verfügt über umfassendes Know-how bei der Optimierung von wärmebehandlung von Superlegierungen zyklen für AM-Komponenten.
- Zweck: Um das gewünschte endgültige Gefüge und die mechanischen Eigenschaften zu erreichen, insbesondere bei ausscheidungsgehärteten Superlegierungen wie Haynes 282.
- Spanende Bearbeitung (CNC):
- Zweck: Zur Erzielung enger Maßtoleranzen bei kritischen Merkmalen (z. B. Montageschnittstellen, Dichtungsoberflächen, genaue Durchmesser), die bei einem gedruckten oder wärmebehandelten Teil nicht eingehalten werden können.
- Prozess: Einsatz von mehrachsigen CNC-Fräs- oder Drehzentren zur Bearbeitung spezifischer Oberflächen. Die Befestigung komplexer AM-Geometrien kann eine Herausforderung sein.
- Die Notwendigkeit: Häufig erforderlich für Passflächen, Schraubenlöcher und alle Merkmale, die eine hohe Präzision erfordern, die über die Standard-AM-Möglichkeiten hinausgeht. CNC-Bearbeitung von 3D-gedruckten Schilden gewährleistet die richtige Passform und Funktion innerhalb größerer Baugruppen.
- Techniken der Oberflächenveredelung:
- Zweck: Zur Erzielung der erforderlichen Oberflächenrauhigkeit (Ra) aus aerodynamischen, strömungstechnischen, abdichtenden oder ästhetischen Gründen oder als Vorbereitung für Beschichtungen.
- Methoden:
- Strahlmittel (Sand, Perlen): Reinigt Oberflächen, entfernt losen Puder und sorgt für ein gleichmäßig mattes Finish.
- Taumeln/Gleitschleifen: Glättet Oberflächen und entgratet Kanten, insbesondere bei kleineren Teilen.
- Schleifen/Polieren: Erzielt sehr glatte, spiegelähnliche Oberflächen an zugänglichen Stellen.
- Abrasive Fließbearbeitung (AFM) / Elektrochemisches Polieren (ECP): Spezialisierte Techniken zum Glätten von inneren Kanälen und komplexen, schwer zugänglichen Oberflächen.
- Auswahl: Die Wahl von oberflächenveredelungstechniken hängt von den spezifischen Ra-Anforderungen, der Geometrie und der Zugänglichkeit der Flächen ab.
- Wärmedämmschichten (TBCs):
- Zweck: Äußerst wichtig für Hitzeschilde in den heißesten Umgebungen (z. B. Turbinenbrennkammern, Schaufeln). TBCs sind mehrschichtige keramische Beschichtungen, die auf die Oberfläche von Superlegierungen aufgebracht werden, um eine thermische Isolierung zu erreichen, die die Betriebstemperatur des Metalls erheblich reduziert und die Lebensdauer der Komponenten verlängert.
- Struktur: Sie besteht in der Regel aus einer metallischen Haftschicht (häufig MCrAlY) für die Haftung und den Oxidationsschutz, gefolgt von einer keramischen Deckschicht (häufig Yttriumoxid-stabilisiertes Zirkoniumdioxid – YSZ) zur Isolierung.
- Anwendung: Aufgetragen durch Verfahren wie Air Plasma Spray (APS) oder Electron Beam Physical Vapor Deposition (EB-PVD) nach entsprechender Oberflächenvorbereitung.
- Qualitätssicherungsprüfungen & Inspektionen:
- Zweck: Überprüfung, ob das fertige Teil alle Spezifikationen erfüllt.
- Methoden: Dazu gehören abschließende Maßkontrollen (CMM, Scannen), Messung der Oberflächenbeschaffenheit, NDT (FPI für Oberflächenrisse, Röntgen/CT für innere Unversehrtheit), Materialprüfung (Zug, Härte an Musterkupons) und Sichtprüfung. Qualitätssicherungsprüfungen sorgt für die endgültige Freigabe vor dem Versand.
Der Umfang und die Reihenfolge dieser Nachbearbeitungsschritte variieren erheblich, je nach den Anforderungen der Anwendung, dem gewählten Material, der Komplexität des Teils und dem verwendeten AM-Prozess. Die Integration dieser Schritte in den gesamten Fertigungsplan ist entscheidend für die Lieferung hochwertiger, zuverlässiger 3D-gedruckter Hitzeschilde, die für den anspruchsvollen Einsatz bereit sind. Beschaffungsspezialisten sollten sich vergewissern, dass potenzielle Lieferanten ihre Fähigkeiten in diesem gesamten Spektrum von Nachbearbeitungsaktivitäten unter Beweis gestellt haben.
Herausforderungen meistern: Überwindung von Hürden bei der additiven Fertigung von Hitzeschilden
Die additive Fertigung von Metallen bietet zwar ein transformatives Potenzial für die Herstellung von Hochtemperatur-Hitzeschilden, ist aber nicht ohne Herausforderungen. Diese potenziellen Hürden zu erkennen und die Strategien zu verstehen, die von erfahrenen AM-Anbietern wie Met3dp eingesetzt werden, um sie zu entschärfen, ist entscheidend für eine erfolgreiche Einführung. Ingenieure und Beschaffungsmanager sollten sich dieser Faktoren bewusst sein, wenn sie AM-Komponenten spezifizieren und beschaffen.
Gemeinsame Herausforderungen und Abhilfestrategien:
- Eigenspannung und Verformung:
- Herausforderung: Die intensive, örtlich begrenzte Erwärmung und die schnelle Abkühlung, die den PBF-Prozessen eigen sind, erzeugen erhebliche thermische Gradienten, die zu inneren Spannungen innerhalb des Teils führen. Diese Spannungen können zu Verformungen (Verwerfungen) während der Herstellung, zu Rissen oder zur Instabilität der Abmessungen nach der Entnahme aus der Bauplatte führen. Nickelsuperlegierungen mit ihrem hohen Wärmeausdehnungskoeffizienten und ihrer hohen Festigkeit können besonders anfällig sein.
- Strategien zur Schadensbegrenzung:
- Optimierung der Prozessparameter: Sorgfältige Abstimmung von Laser-/Elektronenstrahlleistung, Scan-Geschwindigkeit, Schichtdicke und Scan-Strategie zur Minimierung von Wärmegradienten.
- Optimierte Unterstützungsstrukturen: Entwicklung robuster Halterungen, um das Teil sicher auf der Bauplatte zu verankern und Verformungskräften zu widerstehen.
- Build Plate Heating: Das Vorheizen der Bauplatte (ein Standardmerkmal beim SEBM, möglich bei einigen SLM-Systemen) reduziert die Temperaturdifferenz und senkt die Eigenspannung.
- Intelligente Scan-Strategien: Verwendung von Techniken wie Inselscannen oder Schachbrettmustern, um die Wärme gleichmäßiger zu verteilen.
- Obligatorischer Stressabbau: Die Durchführung einer ordnungsgemäßen stressabbau AM Teile zyklus unmittelbar nach dem Druck und vor dem Entfernen des Trägers ist unverzichtbar für die Minimierung der eigenspannung Metall AM und verhinderung des Verziehens 3D-Druck.
- DfAM: Konstruktion von Teilen mit allmählichen Dickenübergängen und Vermeidung großer, nicht abgestützter flacher Bereiche.
- Entfernung der Stützstruktur und Auswirkungen auf die Oberfläche:
- Herausforderung: Abstützungen sind oft notwendig, können aber schwierig und zeitaufwändig zu entfernen sein, insbesondere von komplexen Innengeometrien wie Kühlkanälen. Entfernungsprozesse können das Teil möglicherweise beschädigen oder unerwünschte Spuren auf der Oberfläche hinterlassen, die eine weitere Nachbearbeitung erfordern. Unterstützung bei der Entfernung komplexer Teile ist ein erheblicher Kosten- und Zeitfaktor.
- Strategien zur Schadensbegrenzung:
- DfAM für die Minimierung der Unterstützung: Konstruktion von Teilen mit selbsttragenden Winkeln (>45 Grad), Verwendung von Fasen anstelle von scharfen Überhängen und Wahl von Bauausrichtungen, die den Stützbedarf minimieren.
- Optimiertes Support-Design: Verwendung von Stützentypen (z. B. Kegel, Block, Baum) und -dichten, die während des Baus stark genug sind, sich aber später leichter entfernen lassen. Spezialisierte Software hilft bei der Optimierung der Platzierung und Struktur der Stützen.
- Erweiterte Entfernungstechniken: Einsatz präziser Methoden wie Drahterodieren oder spezielle Entgratungswerkzeuge.
- Nachbearbeiten: Planung der notwendigen Oberflächenbearbeitung in den Bereichen, in denen Stützen angebracht wurden.
- Kontrolle der Porosität:
- Herausforderung: Im gedruckten Material können sich kleine Hohlräume oder Poren bilden, die durch eingeschlossenes Gas (aus dem Pulver oder der Atmosphäre) oder unvollständige Verschmelzung zwischen den Schichten (Lack of Fusion – LoF) entstehen. Poren wirken wie Spannungskonzentratoren und verschlechtern die mechanischen Eigenschaften wie Ermüdungsfestigkeit und Duktilität, was für kritische Hitzeschilde nicht akzeptabel ist.
- Strategien zur Schadensbegrenzung:
- Hochwertiges Pulver: Die Verwendung von Pulvern mit hoher Sphärizität, kontrollierter Partikelgrößenverteilung, geringem internen Gasgehalt und hoher Reinheit ist von grundlegender Bedeutung. Met3dp’s fortschrittliche Zerstäubungsprozesse (Gas Atomization, PREP) wurden entwickelt, um solche Pulver zu produzieren, die optimiert sind für superlegierungen mit Porositätskontrolle.
- Optimierte Prozessparameter: Gewährleistung einer ausreichenden Energiedichte (Strahlleistung/-geschwindigkeit), um die Pulverpartikel vollständig zu schmelzen und gelöste Gase vor der Erstarrung aus dem Schmelzbad entweichen zu lassen. Der Betrieb in einer kontrollierten Atmosphäre (Argon/Stickstoff für SLM) oder im Vakuum (SEBM) minimiert die Gasaufnahme.
- Heiß-Isostatisches Pressen (HIP): Wie bereits erwähnt, ist HIP äußerst wirksam beim Schließen der inneren Poren und beim Erreichen der vollen Dichte, was für die sicherstellung der Materialintegrität.
- Materialintegrität, Mikrostruktur und Rissbildung:
- Herausforderung: Die Erzielung eines gleichmäßigen, feinkörnigen, homogenen Gefüges ohne Defekte wie Mikrorisse ist für die Leistungsfähigkeit von Superlegierungen von entscheidender Bedeutung. Einige Legierungen, insbesondere ausscheidungsgehärtete Legierungen wie Haynes 282 oder bestimmte Legierungen mit hohem Gamma-Kalkgehalt, können bei unsachgemäßer Verarbeitung während der Wärmebehandlung zu Erstarrungsrissen oder Rissen durch Reckung neigen.
- Strategien zur Schadensbegrenzung:
- Rigorose Prozessentwicklung: Umfassende Tests und Charakterisierungen zur Ermittlung der optimalen Druckparameter für jede spezifische Legierung.
- Wärmemanagement: Einsatz von Heizplatten und optimierten Scan-Strategien zur Steuerung der Abkühlungsraten und der Mikrostrukturbildung.
- Sorgfältig kontrollierte Wärmebehandlungen: Entwicklung spezifischer Spannungsabbau-, Lösungsglüh- und Alterungszyklen, die auf die einzigartige Mikrostruktur des AM-Materials zugeschnitten sind. Während bestimmter Wärmebehandlungsphasen können langsame Erwärmungs-/Abkühlungsraten erforderlich sein.
- Auswahl/Änderung der Legierung: In einigen Fällen können geringfügige Änderungen der Legierungschemie speziell für AM die Druckfähigkeit verbessern und die Rissanfälligkeit verringern.
- Kostenfaktoren:
- Herausforderung: Metall-AM kann im Vergleich zu herkömmlichen Verfahren höhere Vorlaufkosten pro Teil verursachen, insbesondere bei einfacheren Geometrien oder sehr hohen Stückzahlen, was auf teure Maschinen, spezielle Pulver und oft umfangreiche Nachbearbeitungen zurückzuführen ist.
- Strategien zur Schadensbegrenzung:
- Konzentration auf hochwertige Anwendungen: Ausrichtung auf Komponenten, bei denen die Vorteile von AM (Komplexität, Konsolidierung, Leistung) einen erheblichen Wert darstellen, der den Kostenunterschied aufwiegt (z. B. kritische Teile in der Luft- und Raumfahrt, hochoptimierte Konstruktionen).
- DfAM zur Kostenreduzierung: Einsatz von Topologieoptimierung und Teilekonsolidierung zur Senkung des Materialverbrauchs und der nachgelagerten Montagekosten. Das Design für minimale Stützen reduziert die Druckzeit und den Nachbearbeitungsaufwand.
- Prozess-Effizienz: Einsatz schnellerer Maschinen, Optimierung der Verschachtelung von Bauteilen (gleichzeitiger Druck mehrerer Teile) und Rationalisierung der Nachbearbeitungsabläufe.
- Beschaffung von Großaufträgen: Zusammenarbeit mit Lieferanten wie Met3dp bei Großhandel oder Großbestellung vereinbarungen können Größenvorteile bieten für beschaffung AM-Teile.
- Skalierbarkeit und Vorlaufzeiten:
- Herausforderung: Sie eignen sich zwar hervorragend für Prototypen und kleine Stückzahlen, aber die Ausweitung der Produktion auf Hunderte oder Tausende von Teilen kann erhebliche Investitionen in Maschinen und qualifiziertes Personal erfordern. Die Vorlaufzeiten können manchmal länger sein als bei herkömmlichen Verfahren für etablierte Großserienteile.
- Strategien zur Schadensbegrenzung:
- Kapazität der Lieferanten: Partnerschaften mit etablierten AM-Dienstleistern wie Met3dp, die in mehrere Maschinen und robuste Qualitätssysteme investiert haben, um größere Produktionsmengen zu bewältigen.
- Prozessautomatisierung: Automatisierung der Pulverhandhabung, der Teileentnahme und der Nachbearbeitung zur Verbesserung des Durchsatzes.
- Realistische Planung: Das Verständnis typischer Vorlaufzeit der additiven Fertigung faktoren (Druckzeit, Nachbearbeitung, Qualitätssicherung) zu berücksichtigen und entsprechend zu planen. AM bietet oft kürzere insgesamt vorlaufzeiten, wenn man die Werkzeugkosten für die traditionellen Methoden mit einbezieht.
Erfolgreich fehlersuche bei AM-Fehlern und die Bewältigung dieser Herausforderungen erfordert fundiertes Fachwissen in den Bereichen Materialwissenschaft, Prozessphysik, DfAM und Qualitätskontrolle. Durch die Zusammenarbeit mit einem sachkundigen und erfahrenen Anbieter können Unternehmen Metall-AM vertrauensvoll nutzen, um hochleistungsfähige, zuverlässige Hitzeschilde für die anspruchsvollsten Anwendungen zu produzieren und die traditionellen Probleme zu überwinden metall-AM-Herausforderungen und grenzen der additiven Fertigung.
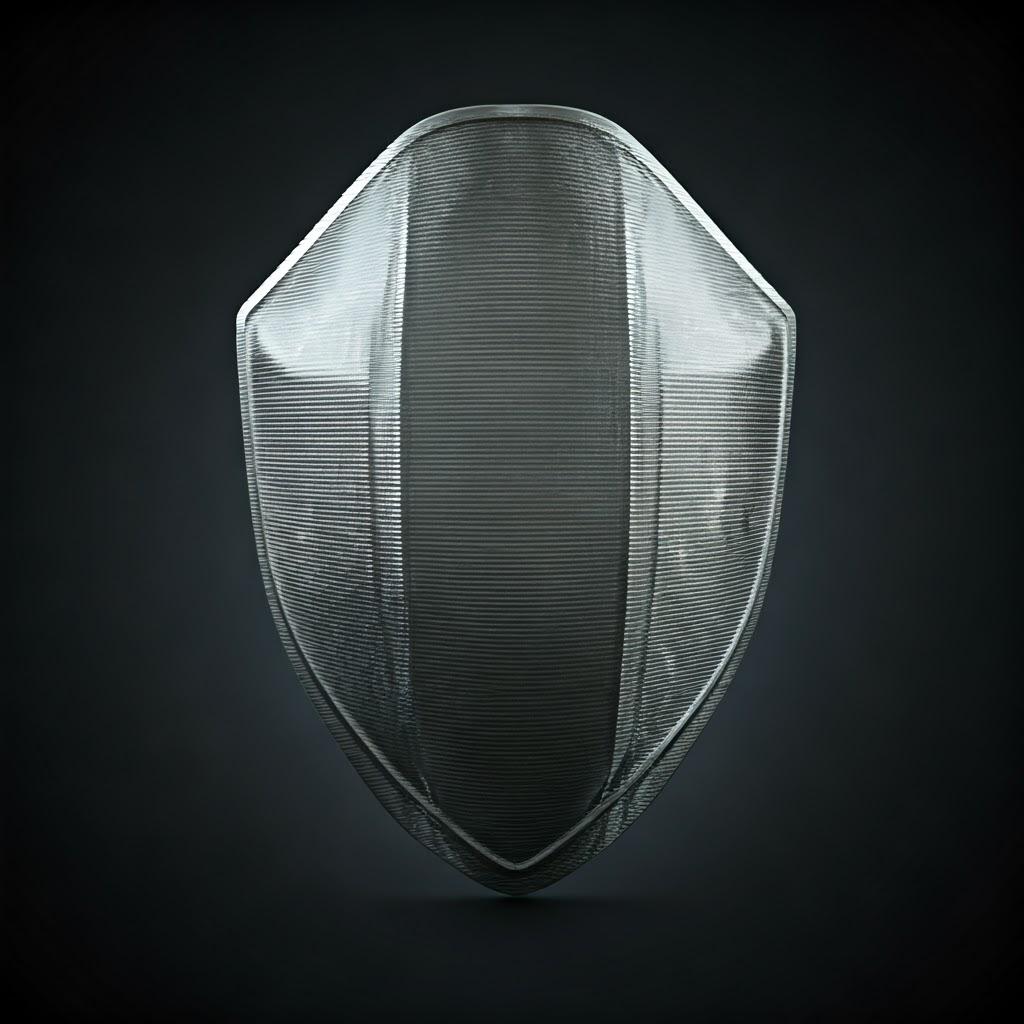
Auswahl der Lieferanten: Die Wahl des richtigen Metall-AM-Partners für Hochtemperaturkomponenten
Der Erfolg des Einsatzes der additiven Fertigung von Metall für kritische Komponenten wie Hochtemperatur-Hitzeschilde hängt wesentlich von der Auswahl des richtigen Fertigungspartners ab. Nicht alle Anbieter von 3D-Metalldruckdiensten verfügen über das spezifische Fachwissen, die Ausrüstung, die Werkstoffkenntnisse und die Qualitätssysteme, die erforderlich sind, um Teile, die für extreme Umgebungen konzipiert sind, unter Verwendung von anspruchsvollen Superlegierungen wie IN625 und Haynes 282 zuverlässig herzustellen. Für Ingenieure und Beschaffungsmanager, bewertung von AM-Lieferanten erfordert eine strenge Bewertung, die über die bloße Angebotsabgabe hinausgeht. Eine Partnerschaft mit einem Unternehmen, das umfassende Lösungen für die additive Fertigung ist von entscheidender Bedeutung.
Hier sind die wichtigsten Kriterien, die bei der Auswahl eines Metall-AM-Partners für Hochtemperatur-Hitzeschilde zu beachten sind:
1. Erfahrung mit Hochtemperatursuperlegierungen:
- Nachgewiesene Erfolgsbilanz: Hat der Lieferant nachweislich Erfahrung mit dem Druck der gewünschten Legierungen (z. B. IN625, Haynes 282, andere Superlegierungen auf Nickelbasis)? Fragen Sie nach Fallstudien oder Beispielen für ähnliche Teile.
- Materialwissenschaftliche Kenntnisse: Kennen sie die besonderen metallurgischen Herausforderungen, die mit dem Druck dieser Legierungen verbunden sind, wie z. B. die Rissanfälligkeit, die erforderlichen Wärmebehandlungen und die erreichbaren Gefüge? Diese kompetenz in Hochtemperaturlegierungen ist nicht verhandelbar.
- Entwicklung der Parameter: Haben sie robuste Druckparameter speziell für diese anspruchsvollen Materialien auf ihren Maschinen entwickelt und validiert?
2. Ausrüstungskapazitäten und Technologie:
- Geeignete AM-Technologie: Betreiben sie die richtige Art von PBF-System (z. B. SLM/LPBF, SEBM), das für das gewählte Material und die Komplexität der Anwendung geeignet ist? Das Angebot von Met3dp’, einschließlich der branchenführenden SEBM-Drucker, die für die Verarbeitung anspruchsvoller Materialien bekannt sind, bietet Flexibilität.
- Qualität und Wartung der Maschinen: Sind die Maschinen gut gewartet und kalibriert, um Prozessstabilität und Wiederholbarkeit zu gewährleisten? Welche Maschinenkapazität und Redundanz haben sie?
- Bauvolumen: Können ihre Maschinen die erforderliche Größe der Hitzeschildkomponente aufnehmen?
3. Qualitätskontrolle und Beschaffung von Pulvern:
- Pulvermanagement: Wie werden Metallpulver gehandhabt, gelagert und recycelt, um die Reinheit zu erhalten und eine Verunreinigung oder Verschlechterung zu verhindern? Dies ist für Superlegierungen von entscheidender Bedeutung.
- Qualitätssicherung: Wird die Qualität der eingehenden Pulver geprüft (z. B. Chemie, Partikelgrößenverteilung (PSD), Morphologie)?
- Vorteil der Eigenproduktion: Lieferanten wie Met3dp, die ihre eigenen Hochleistungspulver mit fortschrittlichen Methoden wie Gaszerstäubung und PREP herstellen, bieten erhebliche Vorteile in Bezug auf Qualitätskontrolle, Konsistenz und Rückverfolgbarkeit direkt ab der Quelle. Diese hersteller von Qualitätskontrollen für Pulver fähigkeit gewährleistet einen optimalen Materialeinsatz.
4. Umfassende Post-Processing-Fähigkeiten:
- Wesentliche Wärmebehandlungen: Verfügen sie über validierte interne oder engmaschig verwaltete externe Kapazitäten für kritischen Spannungsabbau, HIP und spezielle Lösungsglüh-/Alterungszyklen, die für Superlegierungen erforderlich sind?
- Feinmechanische Bearbeitung: Können sie mehrachsige CNC-Bearbeitung durchführen, um enge Toleranzen bei kritischen Merkmalen zu erreichen?
- Oberflächenveredelung & Beschichtung: Bieten sie die erforderliche Oberflächenbearbeitung (Polieren, Strahlen, AFM) und spezielle Beschichtungen wie Wärmedämmschichten (TBCs) an?
- Unterstützung bei der Entfernung von Fachwissen: Verfügen sie über wirksame und nicht schädigende Methoden zur Entfernung komplexer Stützstrukturen?
5. Robustes Qualitätsmanagementsystem (QMS) und Zertifizierungen:
- Einschlägige Zertifizierungen: Sind sie nach Normen zertifiziert, die für Ihre Branche relevant sind, wie z. B. ISO 9001 (allgemeine Qualität) oder, was für die Luft- und Raumfahrt wichtig ist, AS9100? Diese Zertifizierungen belegen die Verpflichtung zu strenger Prozesskontrolle, Dokumentation und Rückverfolgbarkeit. Zertifizierungen in der Luft- und Raumfahrt AM sind für Flugkomponenten oft obligatorisch.
- Prozesskontrolle: Welche Maßnahmen gibt es zur Überwachung und Kontrolle der Druck- und Nachbearbeitungsschritte?
- Inspektionskapazitäten: Verfügen sie über fortschrittliche Prüfwerkzeuge wie CMM, 3D-Scanner, NDT-Ausrüstung (CT, FPI, Röntgen) und Materialprüfungseinrichtungen?
6. Technische Unterstützung und DfAM-Fachwissen:
- Kollaborativer Ansatz: Sind sie bereit und in der Lage, mit Ihrem Ingenieurteam zusammenzuarbeiten, um das Design für die additive Fertigung (DfAM) zu optimieren?
- Anwendungstechnik: Bieten sie technische Unterstützung bei der Auswahl des besten Materials, der Optimierung der Teileausrichtung und der Beratung zu Nachbearbeitungsstrategien? Met3dp ist stolz darauf, neben seinen Anlagen und Materialien auch Dienstleistungen zur Anwendungsentwicklung anzubieten.
7. Erfolgsbilanz, Reputation und Stabilität:
- Erfahrung in der Industrie: Wie lange bieten sie schon Metall-AM-Dienstleistungen an, insbesondere für anspruchsvolle Branchen?
- Kundenreferenzen: Kann er Referenzen von zufriedenen Kunden aus ähnlichen Branchen vorweisen?
- Finanzielle Stabilität: Für langfristige B2B-Beziehungen und die Zuverlässigkeit der Lieferkette ist die Bewertung der Stabilität des Lieferanten wichtig.
8. Kommunikation und Projektmanagement:
- Reaktionsfähigkeit: Wie schnell und klar reagieren sie auf Anfragen und RFQ Metall AM Lieferant anfragen?
- Projektleitung: Verfügen sie über klare Verfahren für die Verwaltung von Projekten, die Bereitstellung von Aktualisierungen und die Bearbeitung von Unterlagen?
Die Auswahl eines Partners wie Met3dpdie fortschrittliche SEBM-Drucktechnologie, hochwertige Pulverherstellung im eigenen Haus, tiefgreifende Materialkenntnisse und einen Fokus auf umfassende Lösungen für die additive Fertigungdadurch wird die Einführung von AM für kritische Hochtemperaturkomponenten erheblich erschwert und der Zugang zu modernsten Fähigkeiten sichergestellt. Eine gründliche Due-Diligence-Prüfung anhand dieser Kriterien ist unerlässlich, bevor Sie sich für einen Lieferanten für die Herstellung von Hitzeschilden entscheiden.
Kosten und Vorlaufzeiten für die B2B-Beschaffung verstehen
Für Beschaffungsmanager und Ingenieure, die eine additive Fertigung von Hitzeschilden aus Metall in Betracht ziehen, ist es wichtig, die damit verbundenen Metall-3D-Druck-Kostenfaktoren und typische vorlaufzeiten der additiven Fertigung ist entscheidend für die Budgetierung, Projektplanung und fundierte Beschaffungsentscheidungen. AM bietet zwar erhebliche technische Vorteile, aber die Kostenstruktur und die Produktionszeiten unterscheiden sich von traditionellen Methoden. Transparenz seitens des AM-Lieferanten in Bezug auf diese Aspekte ist der Schlüssel für eine effektive beschaffung AM-Teile.
Die Kosten von Metal AM aufschlüsseln:
Der Endpreis eines 3D-gedruckten Hitzeschilds aus Metall wird von mehreren miteinander verbundenen Faktoren beeinflusst. Eine typische Aufschlüsselung der AM-Kosten umfasst:
- Materialkosten:
- Pulver Preis: Hochleistungs-Superlegierungen auf Nickelbasis wie IN625 und Haynes 282 sind von Natur aus teure Werkstoffe im Vergleich zu Standardstählen oder Aluminiumlegierungen. Die Kosten werden in der Regel pro Kilogramm berechnet.
- Materialverbrauch: Dies umfasst das Material, aus dem das fertige Teil besteht plus das für Stützstrukturen verwendete Material und den potenziellen Abfall bei der Verarbeitung. DfAM-Techniken, die auf Leichtbau und Minimierung der Stützstrukturen ausgerichtet sind, wirken sich direkt auf diese Kosten aus.
- Maschinenzeit:
- Dauer des Baus: Je länger der Druck eines Teils dauert, desto höher sind die Kosten. Dies wird beeinflusst durch:
- Teilband: Das Gesamtvolumen des zu deponierenden Materials.
- Teilhöhe: Die Erstellungszeit hängt in erster Linie von der Anzahl der Schichten (Höhe) ab.
- Komplexität: Komplizierte Merkmale können langsamere Scangeschwindigkeiten oder komplexere Werkzeugwege erfordern.
- Verschachtelung: Das gleichzeitige Drucken mehrerer Teile in einem Arbeitsgang (Nesting) kann die Maschinenauslastung verbessern und die Kosten pro Teil senken, was insbesondere für folgende Bereiche von Vorteil ist großbestellung AM Preise.
- Maschinentarif: AM-Maschinen stellen eine beträchtliche Investition dar, und die Anbieter berechnen einen Stundensatz, der die Abschreibung, Energie-, Wartungs- und Anlagenkosten abdeckt.
- Dauer des Baus: Je länger der Druck eines Teils dauert, desto höher sind die Kosten. Dies wird beeinflusst durch:
- Arbeitskosten:
- Vorverarbeitung: CAD-Dateivorbereitung, Build-Setup, Simulation und Slicing.
- Betrieb der Maschine: Überwachung des Build-Prozesses.
- Nachbearbeiten: Dies kann ein sehr bedeutend kostenkomponente, die manuelle Arbeit für Reinigung, Entfernung von Halterungen, Oberflächenbearbeitung, Inspektion usw. beinhaltet. Komplexe Teile, die eine umfangreiche Nachbearbeitung oder die Entfernung interner Stützen erfordern, verursachen höhere Arbeitskosten.
- Nachbearbeitungskosten:
- Spezialisierte Prozesse: Kosten im Zusammenhang mit externen oder spezialisierten internen Verfahren wie Spannungsarmglühen, HIP, Vakuumwärmebehandlung (Lösung/Alterung), CNC-Präzisionsbearbeitung und TBC-Anwendung. Diese haben oft feste Chargenkosten oder Kosten pro Teil.
- Qualitätskontrolle & Inspektion:
- Zeit und Ausrüstung: Kosten im Zusammenhang mit der Maßprüfung (CMM, Scannen), der zerstörungsfreien Prüfung (CT, FPI), der Materialprüfung und der Erstellung der Dokumentation. Der Umfang der erforderlichen Qualitätskontrolle wirkt sich auf die Endkosten aus.
- Gemeinkosten und Gewinn: Standardgeschäftskosten und Lieferantenmarge.
Faktoren, die die Endkosten beeinflussen:
- Teil Komplexität & Größe: Komplexere Geometrien oder größere Teile erhöhen in der Regel die Bearbeitungszeit und möglicherweise auch den Nachbearbeitungsaufwand.
- Wahl des Materials: Superlegierungen sind wesentlich teurer als herkömmliche technische Metalle.
- Toleranzen & Anforderungen an die Oberflächengüte: Engere Toleranzen erfordern in der Regel eine Nachbearbeitung; glattere Oberflächen erfordern zusätzliche Bearbeitungsschritte - beides verursacht zusätzliche Kosten.
- Post-Processing-Bedarf: Anforderungen wie HIP oder TBC verursachen erhebliche Kosten.
- Bestellmenge: Beim Prototyping (Einzelteile) sind die Kosten pro Teil am höchsten. Kleine Chargen profitieren von einer gewissen Amortisation der Einrichtung. Größere Mengen (großbestellung AM Preise) ermöglichen eine bessere Maschinenauslastung (Verschachtelung) und potenziell ausgehandelte Rabatte, wodurch die Kosten pro Teil gesenkt werden können.
Verständnis der Vorlaufzeiten:
Vorlaufzeit der additiven Fertigung ist ebenfalls variabel und hängt von mehreren Stufen ab:
- Angebots- und Auftragsabwicklung: Der Erhalt der RFQ Metall 3D-Drucktechnische Prüfung, Angebotserstellung und Auftragsbestätigung (in der Regel 1-5 Arbeitstage).
- Design & Vorbereitung: Abschließende DfAM-Prüfungen, Dateivorbereitung, Planung des Baulayouts, Simulation (falls erforderlich) (in der Regel 1-3 Arbeitstage).
- Maschinenwarteschlange: Wartezeit, bis eine geeignete Maschine verfügbar ist. Dies kann je nach Auslastung des Lieferanten erheblich variieren (möglicherweise 0 Tage bis 2+ Wochen).
- Druckzeit: Tatsächliche Zeit, die das Teil in der Maschine gedruckt wird (reicht von Stunden für kleine Teile bis zu mehreren Tagen oder sogar über eine Woche für große/komplexe Teile).
- Nachbearbeiten: Dies ist oft die längste teil der Vorlaufzeit.
- Kühlung, Entschlackung, Stressabbau: ~1-2 Tage
- Schneiden von der Platte, Entfernen der Stütze: ~1-3 Tage (hängt stark von der Komplexität ab)
- HIP-Zyklus (einschließlich Versand bei Auslagerung): ~3-7 Tage
- Wärmebehandlung (Lösung/Alterung): ~2-4 Tage
- Bearbeitung: ~2-10 Tage (je nach Komplexität und Warteschlange in der Werkstatt)
- Oberflächenveredelung/Beschichtung: ~2-7 Tage
- Inspektion & QA: ~1-3 Tage
- Versand: Abhängig von Standort und Methode.
Typische Vorlaufzeitspannen (Richtwerte):
- Prototypen / Einzelteile: Häufig 1-3 Wochen, wenn man von einer schnellen Nachbearbeitung und der Verfügbarkeit von Maschinen ausgeht.
- Kleinserienproduktion (z. B. 5-20 Teile): In der Regel 4-8 Wochen, was eine effiziente Stapelverarbeitung ermöglicht, aber möglicherweise längere Wartezeiten für spezielle Schritte wie HIP oder Bearbeitung.
- Größere Chargen: Die Vorlaufzeiten müssen sorgfältig geplant werden und hängen von den Kapazitäten der Zulieferer und den Möglichkeiten der Parallelverarbeitung ab; sie können sich über 8 Wochen hinaus erstrecken, allerdings mit geplanten Lieferungen.
Es ist von entscheidender Bedeutung, ein spezifisches Angebot und eine Schätzung der Vorlaufzeit von Ihrem gewählten Lieferanten auf der Grundlage Ihrer detaillierten Anforderungen zu erhalten. Faktoren wie beschleunigte Optionen können zu höheren Kosten verfügbar sein. Das Verständnis der Aufschlüsselung hilft bei der Verhandlung und der Steuerung der Erwartungen für durchlaufzeit der Lieferkette beim Einbau von AM-Komponenten.
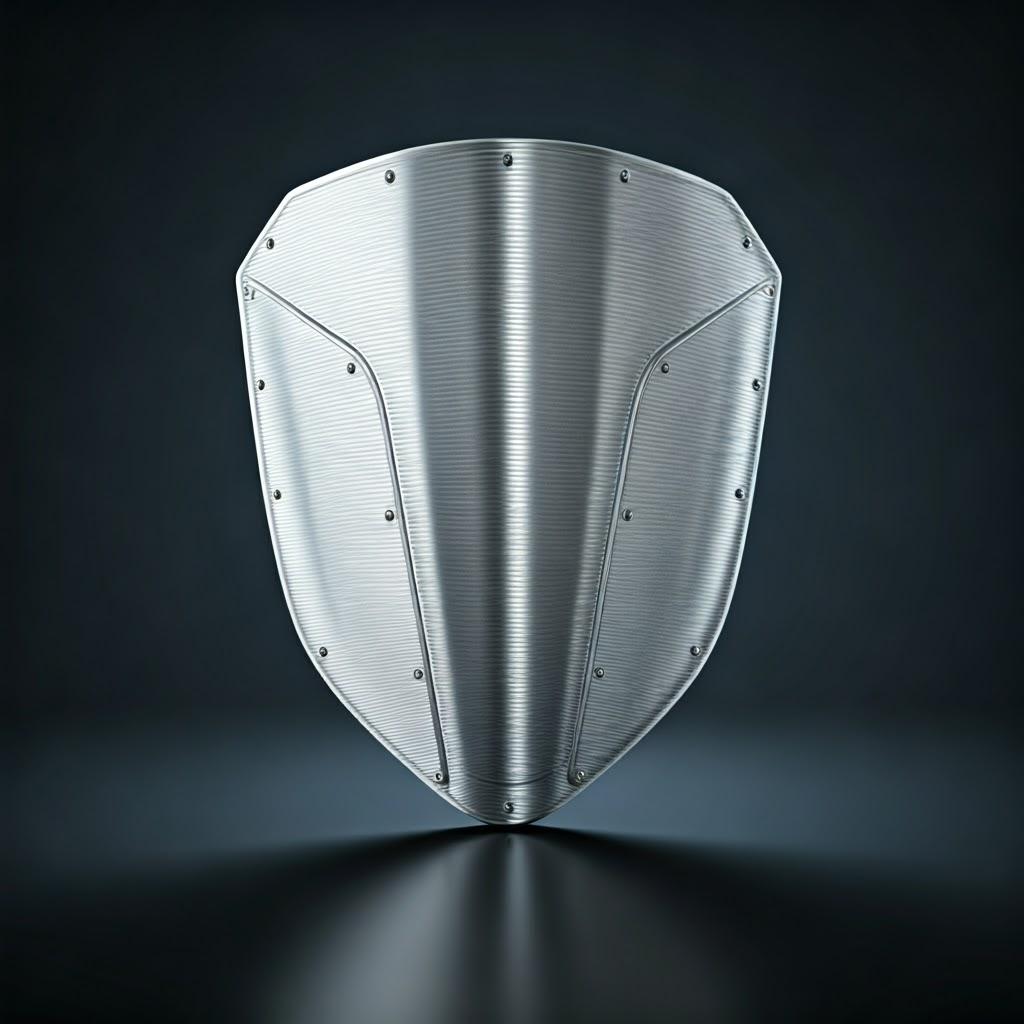
Häufig gestellte Fragen (FAQ) zu 3D-gedruckten Hitzeschilden
Hier finden Sie Antworten auf einige häufig gestellte Fragen von Ingenieuren, Konstrukteuren und Beschaffungsexperten zum Einsatz der additiven Fertigung von Metall für Hochtemperatur-Hitzeschilde:
F1: Wie ist die Festigkeit und Haltbarkeit von 3D-gedruckten Hitzeschilden im Vergleich zu traditionell hergestellten (z. B. gegossenen oder gefrästen)?
- A: Bei korrekter Verarbeitung werden die mechanischen Eigenschaften (einschließlich Festigkeit und haltbarkeit des 3D-Drucks) von AM-Komponenten aus Metall, die aus Legierungen wie IN625 oder Haynes 282 hergestellt werden, können in bestimmten Aspekten (z. B. Ermüdungsfestigkeit) mit Knet- oder Gussbauteilen vergleichbar und manchmal sogar überlegen sein. Zu den Schlüsselfaktoren gehören:
- Die Dichte: Das Erreichen einer nahezu vollständigen Dichte (>99,5 %, häufig >99,9 % mit HIP) ist von entscheidender Bedeutung und bei kritischen Bauteilen Standardpraxis.
- Mikrostruktur: AM erzeugt aufgrund der schnellen Erstarrung ein einzigartiges, feinkörniges Mikrogefüge, das die Festigkeit erhöhen kann. Um dieses Gefüge zu optimieren und die gewünschten Eigenschaften zu erzielen (z. B. Kriechfestigkeit bei Haynes 282), sind geeignete Wärmebehandlungen unerlässlich.
- Nachbearbeiten: Heiß-Isostatisches Pressen (HIP) wird dringend empfohlen (und ist bei kritischen Teilen oft erforderlich), um die verbleibende Mikroporosität zu schließen und die Ermüdungslebensdauer und Duktilität so zu verbessern, dass sie der von Gusswerkstoffen entspricht oder diese übertrifft.
- Entwurf: AM ermöglicht optimierte Konstruktionen (z. B. Topologieoptimierung), die das Verhältnis von Festigkeit und Gewicht über das herkömmlicher Konstruktionen hinaus verbessern können.
- Schlussfolgerung: Mit einer strengen Prozesskontrolle, hochwertigem Pulver und einer angemessenen Nachbearbeitung (insbesondere HIP und Wärmebehandlung) können 3D-gedruckte Hitzeschilde die hohen Anforderungen erfüllen oder sogar übertreffen, die bisher mit herkömmlichen Methoden erfüllt wurden. Beachten Sie immer die Materialdatenblätter der Lieferanten, die auf standardisierten Tests ihres AM-Prozesses basieren.
F2: Wie groß ist der typische Kostenunterschied zwischen Metall-AM und herkömmlichen Methoden zur Herstellung von Hitzeschilden?
- A: Es gibt keine einheitliche Antwort, da die metall-AM-Kostenvergleich hängt stark von mehreren Faktoren ab:
- Komplexität: Bei hochkomplexen Geometrien (interne Kanäle, Gitter, topologieoptimierte Formen), die auf herkömmliche Weise nur schwer oder gar nicht hergestellt werden können, kann AM selbst bei geringen Stückzahlen deutlich kostengünstiger sein, da komplexe Werkzeuge oder umfangreiche Bearbeitungsvorrichtungen vermieden werden.
- Lautstärke: Bei sehr einfachen Formen, die in hohen Stückzahlen (Tausende oder mehr) hergestellt werden, sind herkömmliche Verfahren wie Stanzen oder Gießen aufgrund von Skaleneffekten und einer geringeren Bearbeitungszeit pro Teil oft günstiger, sobald sich die Werkzeuge amortisiert haben.
- Werkzeugkosten: AM macht teure Formen, Gesenke oder komplexe Vorrichtungen, wie sie beim Gießen, Schmieden oder Stanzen benötigt werden, überflüssig. Dies macht AM äußerst wettbewerbsfähig für Prototypen, kleine bis mittlere Serien und Ersatzteile, bei denen die Werkzeugkosten dominieren.
- Material: Bei teuren Superlegierungen reduziert die endkonturnahe Fertigung von AM’ den Materialabfall im Vergleich zur subtraktiven Bearbeitung, was Kosteneinsparungen ermöglicht.
- Total Cost of Ownership: Berücksichtigen Sie Faktoren, die über den Teilepreis hinausgehen, wie z. B. die Verkürzung der Montagezeit (aufgrund der Teilekonsolidierung), die Verbesserung der Leistung (was zu einer höheren Systemeffizienz oder Langlebigkeit führt) und die Verringerung der Lagerkosten (On-Demand-Druck).
- Schlussfolgerung: AM ist in der Regel am kosteneffizientesten für komplexe Teile in kleinen bis mittleren Stückzahlen, für Teile, die ein schnelles Prototyping oder eine kundenspezifische Anpassung erfordern, oder wenn die Nutzung von Designmöglichkeiten wie Teilekonsolidierung und Leichtbau erhebliche Vorteile auf Systemebene bietet. Holen Sie für einen direkten Vergleich immer spezifische Angebote für Ihre Anwendung mit beiden Methoden ein.
F3: Können standardmäßige Wärmedämmschichten (TBCs) auf 3D-gedruckte Hitzeschilde aus Superlegierung aufgebracht werden?
- A: Ja, absolut. Standard TBC-Beschichtung AM-Teile ist ein gängiges Verfahren zur Verbesserung der thermischen Isolierung von Schilden, die unter extremsten Temperaturen arbeiten (z. B. Gasturbinenbrennkammern). Das Verfahren ähnelt der Beschichtung herkömmlich hergestellter Komponenten:
- Vorbereitung der Oberfläche: Die Oberfläche des AM-Teils muss ordnungsgemäß gereinigt und häufig gestrahlt werden, um die richtige Struktur für die Haftung zu schaffen.
- Bond Coat Anwendung: Eine metallische Haftschicht (z. B. MCrAlY) wird in der Regel zuerst mit Methoden wie dem Luftplasmaspritzen (APS) oder dem Hochgeschwindigkeits-Sauerstoffbrennstoff (HVOF) aufgebracht.
- Top Coat Anwendung: Anschließend wird die isolierende keramische Deckschicht (z. B. YSZ) aufgebracht, in der Regel mittels APS oder manchmal auch mittels Elektronenstrahl-PVD (Electron Beam Physical Vapor Deposition) für glattere, dichtere Beschichtungen, die häufig für rotierende Teile bevorzugt werden.
- Erwägungen: Die Oberflächenrauhigkeit von AM-Teilen kann im Vergleich zu glatten, maschinell bearbeiteten Oberflächen etwas andere Vorbereitungsparameter erfordern, aber die grundlegenden Beschichtungsprozesse und Materialien sind kompatibel. Stellen Sie sicher, dass Ihr AM-Lieferant oder Beschichtungspartner Erfahrung mit TBCs auf AM-Superlegierungen hat.
F4: Welche Informationen sind für einen Lieferanten wie Met3dp wichtig, um ein genaues Angebot (RFQ) für ein 3D-gedrucktes Hitzeschild zu erhalten?
- A: Um ein zeitnahes und genaues Angebot zu erhalten, sollten Sie so viele Details wie möglich in Ihrem RFQ Metall 3D-Druck Anforderungen:
- 3D-CAD-Modell: Ein qualitativ hochwertiges Modell in einem neutralen Format (z. B. STEP, Parasolid) ist unerlässlich.
- 2D-Konstruktionszeichnung: Entscheidend für die Spezifizierung:
- Kritische Maße und erforderliche Toleranzen (unter Verwendung von Geometric Dimensioning and Tolerancing – GD&T).
- Anforderungen an die Oberflächengüte (Ra-Werte) für bestimmte Oberflächen.
- Werkstoffspezifikation (z. B. IN625, Haynes 282, UNS-Nummern).
- Identifizierung von kritischen Merkmalen oder Bezugspunkten.
- Spezifikation des Materials: Geben Sie die erforderliche Legierung klar an.
- Menge: Anzahl der benötigten Teile (für Prototypen, Chargen usw.).
- Nachbearbeitungsanforderungen: Spezifizieren Sie die erforderlichen Schritte wie Spannungsabbau, HIP, Wärmebehandlungsbedingungen (falls bekannt, z. B. spezifische AMS-Normen), erforderliche Bearbeitungsvorgänge, Oberflächenbehandlung und Beschichtungsanforderungen (TBCs usw.).
- Qualität & Zertifizierungsanforderungen: Erwähnen Sie alle erforderlichen Branchenzertifizierungen (z. B. AS9100), spezielle Prüfberichte (z. B. CMM-Bericht, NDT-Berichte, Materialzertifikate) oder Prüfanforderungen.
- Anwendungskontext (fakultativ, aber hilfreich): Eine kurze Beschreibung der Funktion des Teils und der Betriebsumgebung kann dem Lieferanten helfen, eine bessere DfAM-Beratung anzubieten oder die Materialeignung zu bestätigen.
F5: Wie stellt Met3dp die Qualität und Konsistenz seiner Hochtemperaturmetallpulver wie IN625 und Haynes 282 für AM sicher?
- A: Met3dp verwendet branchenführende Pulverherstellungstechnologien und strenge Qualitätskontrollverfahren:
- Fortschrittliche Zerstäubung: Durch den Einsatz der firmeneigenen Technologien der Gaszerstäubung (GA) und des Plasma-Rotations-Elektroden-Verfahrens (PREP) werden hochgradig kugelförmige Pulver mit minimalen Satellitenpartikeln hergestellt. Die hohe Sphärizität gewährleistet eine hervorragende Fließfähigkeit und eine gleichmäßige Pulverbettdichte während des Drucks.
- Strenge Kontrolle der Partikelgrößenverteilung (PSD): Maßschneidern des PSD für bestimmte AM-Prozesse (SLM, SEBM) zur Optimierung der Packungsdichte und des Schmelzverhaltens.
- Hoher Reinheitsgrad & Niedriger Gasgehalt: Verwendung von hochreinen Rohstoffen und kontrollierten Inertgas- oder Vakuumzerstäubungsumgebungen zur Minimierung von Verunreinigungen und gelösten Gasen (wie Sauerstoff und Stickstoff), die die Materialeigenschaften beeinträchtigen können.
- Umfassende Tests: Jede Pulvercharge wird gründlichen Tests unterzogen, einschließlich der Analyse der chemischen Zusammensetzung (ICP-OES, LECO), der PSD-Messung (Laserbeugung), der Morphologieanalyse (SEM), der Prüfung der Fließgeschwindigkeit und der Messung der Schütt- und Klopfdichte.
- Rückverfolgbarkeit der Chargen: Einführung einer strengen Chargenverwaltung und Rückverfolgbarkeit von den Rohstoffen bis zum fertig verpackten Pulver, um Konsistenz und Verantwortlichkeit zu gewährleisten.
- Dieses Engagement für hersteller von Qualitätskontrollen für Pulver exzellenz gewährleistet, dass Kunden, die Met3dp-Pulver verwenden, dichte, hochintegrierte AM-Teile mit zuverlässiger und wiederholbarer Qualität herstellen können AM-Materialeigenschaften.
Schlussfolgerung: Die Zukunft der Hochtemperaturkomponenten mit Met3dp
Die Landschaft der Herstellung von Komponenten für extreme thermische Umgebungen unterliegt einem bedeutenden Wandel, der durch die Möglichkeiten der additiven Fertigung von Metallen vorangetrieben wird. Wie wir erforscht haben, ist die Herstellung hochtemperatur-Hitzeschilder die Anwendung von AM, insbesondere bei fortschrittlichen Superlegierungen auf Nickelbasis wie IN625 und Haynes 282, bietet im Vergleich zu herkömmlichen Methoden unvergleichliche Vorteile in Bezug auf Designfreiheit, Leistungsoptimierung, Materialeffizienz und schnelle Iteration.
Metal AM befähigt Ingenieure zu:
- Entwerfen und realisieren Sie komplizierte Geometrien, wie konforme Kühlkanäle und topologieoptimierte Strukturen, die zu leichteren und effizienteren Wärmemanagementlösungen führen.
- Konsolidieren Sie mehrere Teile zu einzelnen, komplexen Komponenten, um Gewicht, Montagezeit und potenzielle Fehlerquellen zu reduzieren.
- Verwendung von Hochleistungsmaterialien, die speziell für ihre außergewöhnliche Festigkeit und Beständigkeit bei extremen Temperaturen ausgewählt wurden.
- Beschleunigung der Entwicklungszyklen durch Rapid Prototyping und werkzeuglose Produktion.
Um diese Vorteile nutzen zu können, ist jedoch ein tiefes Verständnis der gesamten Prozesskette erforderlich: von Design für additive Fertigung (DfAM) prinzipien und einer sorgfältigen Materialauswahl bis hin zu einer präzisen Prozesskontrolle während des Drucks und, was besonders wichtig ist, einer sorgfältigen Nachbearbeitung einschließlich Spannungsabbau, HIP, Wärmebehandlungen und Oberflächenbehandlung. Die Bewältigung potenzieller Herausforderungen wie Eigenspannungen und die Gewährleistung der Maßhaltigkeit erfordern Fachwissen und eine strenge Qualitätskontrolle.
Die Wahl des richtigen Fertigungspartners ist daher von entscheidender Bedeutung. Ein Lieferant muss nicht nur über hochmoderne Anlagen verfügen, sondern auch über fundiertes Fachwissen in der Werkstoffkunde, validierte Verarbeitungsparameter für anspruchsvolle Legierungen, umfassende Nachbearbeitungsmöglichkeiten und robuste Qualitätsmanagementsysteme, die für anspruchsvolle Branchen wie die Luft- und Raumfahrt zertifiziert sind.
Hier ist Met3dp auszeichnet. Als ein führendes Unternehmen mit Hauptsitz in Qingdao, China, bietet Met3dp umfassende Lösungen für die additive Fertigungzu integrieren:
- Branchenführende SEBM-Drucker: Hervorragendes Druckvolumen, Genauigkeit und Zuverlässigkeit für unternehmenskritische Teile.
- Fortschrittliche Metallpulver: Herstellung von hochwertigen, kugelförmigen Pulvern (einschließlich IN625, Haynes 282 und anderen Superlegierungen) unter Verwendung der firmeneigenen Gaszerstäubungs- und PREP-Technologien, die eine optimale Bedruckbarkeit und die endgültigen Bauteileigenschaften gewährleisten.
- Fachwissen über Anwendungen: Jahrzehntelange Erfahrung im Angebot von Anwendungsentwicklungsdiensten, um Partner bei der Implementierung von AM zu unterstützen und ihr Geschäft zu beschleunigen digitale Fertigungstransformation.
Durch die Kontrolle von Schlüsselaspekten des Prozesses, von der Pulverherstellung bis zum Druck, und durch die Nutzung eines umfassenden Anwendungswissens, ermöglicht Met3dp die Herstellung von komponenten der nächsten Generation für die anspruchsvollsten Hochtemperaturanwendungen in der Luft- und Raumfahrt, der Automobilindustrie, dem Energiesektor und der Industrie.
Die zukunft der additiven Fertigung für das Wärmemanagement ist vielversprechend und verspricht Komponenten, die bessere Leistungen erbringen, länger halten und neue Ebenen der Systemeffizienz ermöglichen. Wenn Sie herausfinden möchten, wie Metall-AM Ihre Hochtemperatur-Wärmeschild-Komponenten oder andere kritische Teile revolutionieren kann, laden wir Sie ein, folgende Möglichkeiten zu nutzen Met3dp-Fähigkeiten.
Setzen Sie sich noch heute mit Met3dp in Verbindung, um Ihre spezifischen Anforderungen zu besprechen und herauszufinden, wie unsere hochmodernen Systeme, fortschrittlichen Materialien und unser fachkundiger Support die Ziele Ihres Unternehmens im Bereich der additiven Fertigung unterstützen können.
Teilen auf
MET3DP Technology Co., LTD ist ein führender Anbieter von additiven Fertigungslösungen mit Hauptsitz in Qingdao, China. Unser Unternehmen ist spezialisiert auf 3D-Druckgeräte und Hochleistungsmetallpulver für industrielle Anwendungen.
Fragen Sie an, um den besten Preis und eine maßgeschneiderte Lösung für Ihr Unternehmen zu erhalten!
Verwandte Artikel
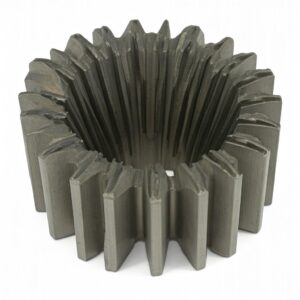
Hochleistungs-Düsenschaufelsegmente: Revolutionierung der Turbineneffizienz mit 3D-Metalldruck
Mehr lesen "Über Met3DP
Aktuelles Update
Unser Produkt
KONTAKT US
Haben Sie Fragen? Senden Sie uns jetzt eine Nachricht! Wir werden Ihre Anfrage mit einem ganzen Team nach Erhalt Ihrer Nachricht bearbeiten.
Holen Sie sich Metal3DP's
Produkt-Broschüre
Erhalten Sie die neuesten Produkte und Preislisten
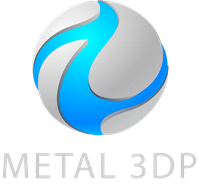
Metallpulver für 3D-Druck und additive Fertigung