Precision Injector Components for Rocket Engines
Inhaltsübersicht
Introduction: The Critical Role of Injectors in Rocket Propulsion and the Additive Manufacturing Advantage
The relentless pursuit of space, whether for exploration, communication, or defense, hinges on the power and reliability of rocket propulsion systems. At the very heart of these powerful engines lies a component of extraordinary complexity and criticality: the injector. Tasked with the precise delivery and mixing of fuel and oxidizer under extreme conditions, the rocket engine injector is paramount to achieving stable combustion, maximizing thrust, and ensuring mission success. Even minute imperfections in its design or manufacture can lead to catastrophic failures. Traditionally, crafting these intricate components involved complex, multi-stage processes like casting, intricate machining, and painstaking brazing or welding of numerous individual pieces. These methods, while proven, often impose significant limitations on design freedom, drive up costs, extend lead times, and introduce potential failure points at joints.
Enter the transformative power of 3D-Druck von Metall, more formally known as Additive Manufacturing (AM). This layer-by-layer fabrication process unlocks unprecedented possibilities for creating highly complex, optimized, and integrated components that were previously impossible or prohibitively expensive to manufacture. For rocket engine injectors, AM offers a paradigm shift. It allows engineers to design and produce monolithic parts with incredibly complex internal geometries, such as conformal cooling channels that precisely follow the contours of combustion surfaces, and sophisticated spray patterns designed through computational fluid dynamics (CFD) to achieve optimal propellant atomization and mixing efficiency. This capability directly translates to enhanced engine performance, improved thermal management, increased reliability through part consolidation, and significantly accelerated development cycles.
The materials used in these demanding applications must withstand hellish environments. Nickel-based superalloys, renowned for their exceptional strength at high temperatures and resistance to oxidation and corrosion, are the materials of choice. Specifically, alloys like Inconel 718 (IN718) and Inconel 625 (IN625) have emerged as primary candidates for additively manufactured injectors due to their proven track record in aerospace and their compatibility with AM processes like Laser Powder Bed Fusion (LPBF). The success of printing these high-performance alloys, however, relies heavily on the quality of the raw material – the metal powder. Achieving the required density, microstructural integrity, and mechanical properties necessitates powders with high sphericity, controlled particle size distribution, and minimal impurities, characteristics that companies like Met3dp, with their advanced gas atomization and PREP technologies, specialize in producing. As the aerospace industry increasingly embraces AM, understanding its application to critical components like injectors is essential for engineers, procurement managers, and manufacturers seeking to push the boundaries of propulsion technology. This article delves into the intricacies of using metal AM for rocket engine injectors, exploring the applications, benefits, materials, design considerations, and supplier selection criteria crucial for harnessing this powerful manufacturing approach.
What Are Rocket Engine Injectors Used For? Functions and Demanding Operational Requirements
The rocket engine injector serves as the sophisticated “carburetor” of the propulsion system, performing the crucial task of introducing and preparing the propellants—fuel and oxidizer—for combustion. Its primary functions are threefold:
- Zerstäubung: Breaking down the liquid propellants into vast clouds of incredibly fine droplets. This dramatically increases the surface area available for reaction, enabling rapid and efficient vaporization and combustion. The size and distribution of these droplets significantly impact combustion stability and engine performance. Poor atomization can lead to incomplete combustion, reduced efficiency, and potentially damaging instabilities.
- Mischen: Ensuring thorough and uniform mixing of the atomized fuel and oxidizer droplets within the combustion chamber. The quality of mixing dictates the completeness of the chemical reaction, directly influencing the energy released (thrust) and the temperature distribution within the engine. Inadequate mixing can create localized hot spots or fuel-rich/oxidizer-rich zones, leading to performance losses and potential hardware damage.
- Distribution: Delivering the propellant mixture evenly across the face of the combustion chamber. This prevents pressure and temperature gradients that could compromise structural integrity or lead to uneven thrust generation.
To achieve these functions reliably under extreme conditions, injectors employ various designs, each with specific characteristics:
- Impinging Jet Injectors: Streams of fuel and oxidizer are directed to collide (impinge) at precise angles, using the impact energy to atomize and mix the propellants. Often arranged in patterns like doublet, triplet, or quadruplet elements.
- Pintle Injectors: One propellant flows through a central post (pintle) and impacts a radially flowing sheet or spray of the other propellant. Known for throttling capability and inherent combustion stability, famously used in the Apollo Lunar Module’s descent engine.
- Coaxial Swirl Injectors: One propellant (often the oxidizer) flows through a central tube, while the other flows through an annular passage around it. Swirl vanes impart a tangential velocity, causing the propellants to exit in conical sheets that interact and atomize. Common in many large liquid-propellant engines.
Regardless of the specific design, all rocket engine injectors operate in arguably one of the most demanding environments imaginable:
- Extreme Temperaturen: Injectors face a staggering thermal gradient. One side might handle cryogenic propellants like liquid hydrogen (-253°C) or liquid oxygen (-183°C), while the other faces the intense heat of combustion, often exceeding 3000°C. Efficient cooling is therefore not just desirable, but essential for survival.
- Hohe Drücke: Propellants are injected at extremely high pressures, sometimes hundreds of atmospheres (e.g., 100-300 bar or 1450-4350 psi), to overcome combustion chamber pressure and ensure proper flow rates. The injector body must withstand these immense pressures without leaking or deforming.
- Corrosive Propellants: Rocket fuels (like RP-1 kerosene, hydrogen) and oxidizers (like liquid oxygen, nitrogen tetroxide) can be highly reactive and corrosive, especially at elevated temperatures. Material selection is critical to prevent degradation over the injector’s operational life.
- High Vibrations and Acoustic Loads: The combustion process itself generates intense noise and vibration (combustion instabilities, acoustic oscillations) that subject the injector to severe mechanical stress and fatigue.
These brutal conditions necessitate components with exceptional material properties, intricate internal features (like cooling channels), and flawless manufacturing quality. The primary industries relying on these high-performance injectors are:
- Commercial Space Launch Providers: Companies launching satellites, cargo, and soon, humans into orbit require reliable and cost-effective engines. AM offers a path to optimize performance and reduce launch costs. Procurement managers in this sector look for suppliers offering consistent quality and competitive lead times for injector assemblies.
- Defense and Military: Ballistic missiles, interceptors, and military spacecraft rely on high-performance propulsion. AM enables rapid development and production of advanced designs for strategic applications, often demanding secure supply chains and certified defense contractor manufacturing partners.
- Satellite Propulsion: Smaller thrusters for satellite station-keeping and orbit adjustments also utilize sophisticated injectors. AM allows for miniaturization, integration, and weight reduction, critical factors for spacecraft design. Suppliers specializing in components for satellite manufacturers are key partners.
The inherent complexity and the extreme operational demands make rocket engine injectors prime candidates for the advanced capabilities offered by metal additive manufacturing, pushing beyond the limitations of traditional fabrication methods.
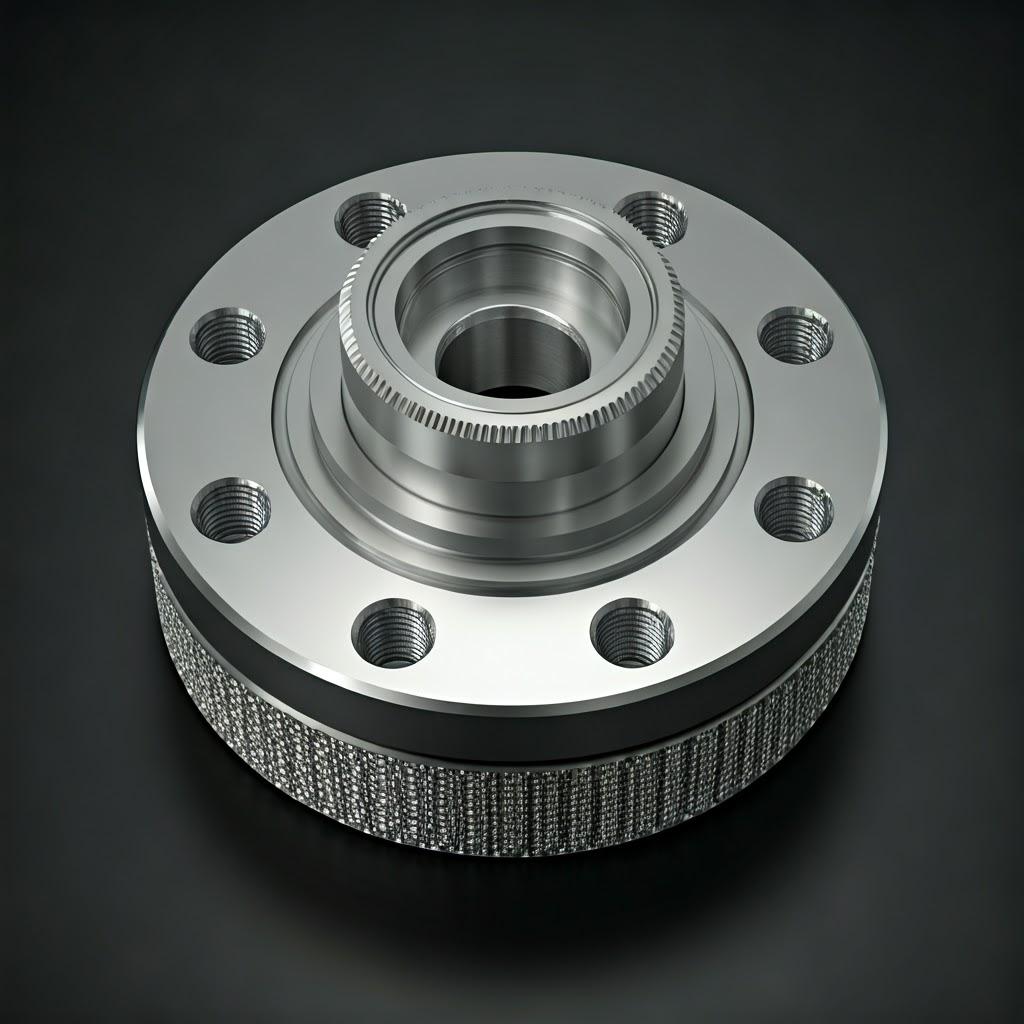
Why Use Metal 3D Printing for Rocket Engine Injectors? Unlocking Performance and Efficiency
For decades, manufacturing rocket engine injectors involved subtractive methods like CNC machining complex manifolds and drilling myriad tiny orifices, or intricate casting processes, often followed by complex brazing or welding operations to join multiple pieces. While these traditional methods have successfully powered rockets for generations, they come with inherent limitations, particularly when pushing the frontiers of performance and efficiency:
- Design Complexity Constraints: Machining struggles with internal, non-linear channels essential for conformal cooling. Casting can achieve some complexity but often requires cores that can be difficult to remove and may compromise internal surface finish. Brazing/welding multiple parts introduces joints that are potential leak paths and stress concentration points, limiting overall structural integrity and thermal performance.
- Long Lead Times & High Tooling Costs: Creating the specialized tooling, jigs, and fixtures required for traditional manufacturing is time-consuming and expensive, especially for complex designs or low-volume production runs typical in aerospace development. Iterating on a design often means starting the tooling process over.
- Assembly Challenges: Joining dozens or even hundreds of small, precision parts requires meticulous assembly processes, increasing labor costs and the risk of errors or joint failures.
- Materialabfälle: Subtractive machining inherently starts with a larger block of expensive material (like superalloys) and removes a significant portion as waste chips.
Metal additive manufacturing fundamentally overcomes these hurdles, offering compelling advantages that are reshaping how rocket injectors are designed and produced:
- Unparalleled Geometric Freedom: This is arguably the most significant advantage. AM, particularly LPBF, builds parts layer by layer, enabling the creation of internal features that are simply impossible to machine or cast as a single piece. This includes:
- Konforme Kühlkanäle: Cooling passages that precisely follow the shape of the injector face and combustion chamber walls, maximizing heat extraction exactly where needed. This allows engines to run hotter and more efficiently or increases component lifespan.
- Optimierte Flusspfade: Smooth, curved internal passages for propellants that minimize pressure drops and improve flow efficiency compared to the sharp angles often necessitated by drilling.
- Integrated Spray Elements: Features like swirlers or orifice geometries can be directly built into the injector body, eliminating complex assemblies and improving atomization precision.
- Teil Konsolidierung: AM allows engineers to redesign multi-part assemblies into a single, monolithic component. A complex injector head that previously consisted of 50, 100, or even more individual pieces can potentially be printed as one unit. This offers tremendous benefits:
- Reduziertes Gewicht: Eliminating flanges, fasteners, and weld/braze material.
- Erhöhte Verlässlichkeit: Removing potential leak paths and failure points associated with joints.
- Simplified Assembly: Drastically reducing touch labor and associated costs.
- Streamlined Supply Chain: Managing one part number instead of many.
- Rapid Prototyping und Iteration: AM eliminates the need for traditional tooling. A new injector design can be printed, tested, modified, and reprinted in a matter of days or weeks, rather than months. This dramatically accelerates the development cycle, allowing aerospace engineers to quickly optimize performance and validate designs – crucial in the fast-moving commercial space race. Aerospace component suppliers leveraging AM can offer significantly faster turnaround times for prototypes and first articles.
- Reduced Lead Times for Production: Once a design is finalized, AM can often produce functional parts faster than the time required to set up a traditional manufacturing line, especially for low-to-mid volume production. This improves responsiveness for procurement managers needing critical components.
- Materialeffizienz: While AM is not waste-free (support structures, some powder loss), it is generally more materially efficient than subtractive manufacturing, particularly for complex parts where machining would remove a large percentage of the initial stock. Unfused powder can often be recycled, further improving sustainability. High-quality powder management and recycling are key operational aspects for AM service providers.
The combination of these advantages makes metal AM an exceptionally powerful tool for aerospace engineers and manufacturers. It doesn’t just offer a new way to make existing designs; it enables entirely new levels of performance and integration, driving innovation in rocket propulsion. By partnering with knowledgeable Additive Fertigungsdienstleistungen providers who understand the nuances of aerospace requirements and materials, companies can leverage AM to build lighter, more efficient, more reliable, and faster-to-market rocket engine injectors.
Recommended Materials (IN718 & IN625) and Why They Excel in Propulsion Applications
The selection of materials for rocket engine injectors is dictated by the extreme operating conditions: searing temperatures adjacent to cryogenic fluids, enormous pressures, corrosive propellants, and intense vibrations. Only a select few materials can reliably withstand this onslaught. Nickel-based superalloys have become the workhorses for these demanding applications due to their unique combination of high-temperature strength, toughness, fatigue resistance, and environmental stability. Among these, Inconel 718 (IN718) and Inconel 625 (IN625) are frequently chosen for additively manufactured injectors, each offering a distinct set of properties suitable for different aspects of the injector’s function or location.
The Need for Superalloys: Standard steels or aluminum alloys simply cannot maintain their structural integrity at the temperatures experienced near the combustion zone. Superalloys, typically based on nickel, cobalt, or nickel-iron, are specifically engineered to operate under severe mechanical stress at temperatures approaching their melting points (often above 650°C or 1200°F). Their performance stems from complex microstructures, often featuring a face-centered cubic (FCC) austenite matrix strengthened by secondary phases like gamma prime (γ′) and gamma double-prime (γ′′) precipitates (in the case of IN718) or solid solution strengthening and carbides/nitrides (more dominant in IN625).
Inconel 718 (UNS N07718): The Versatile Workhorse IN718 is arguably the most widely used nickel-based superalloy in aerospace, prized for its excellent mechanical properties up to about 700°C (1300°F), good fabricability (including weldability and printability), and resistance to post-weld cracking.
- Key Properties & Advantages for Injectors:
- Hohe Festigkeit: Possesses exceptional yield strength, tensile strength, and creep-rupture strength at intermediate temperatures. This is crucial for handling high propellant pressures and mechanical loads.
- Good Fatigue Life: Withstands the cyclic loading caused by engine vibrations and thermal cycles.
- Korrosionsbeständigkeit: Offers good resistance to many corrosive media, though IN625 is generally superior in highly oxidizing or reducing environments.
- Ausgezeichnete Druckbarkeit: Relatively well-understood and characterized for AM processes like LPBF, allowing for the production of dense, high-integrity parts.
- Heat Treatment Response: Develops its high strength through a precipitation hardening heat treatment (solution annealing followed by double aging), which creates the strengthening γ′ and γ′′ phases.
- Typical Injector Applications: Often used for the main injector body, structural manifolds, and elements not directly exposed to the absolute hottest parts of the combustion flame front. Its balance of strength, fabricability, and cost makes it a versatile choice.
Inconel 625 (UNS N06625): The Corrosion and High-Temp Specialist IN625 offers superior performance compared to IN718 in terms of high-temperature strength (especially above 700°C) and, crucially, outstanding corrosion resistance in a wider range of aggressive environments. Its strength comes primarily from the solid solution strengthening effect of molybdenum and niobium within the nickel-chromium matrix.
- Key Properties & Advantages for Injectors:
- Außergewöhnliche Korrosionsbeständigkeit: Highly resistant to oxidation, acids, alkalis, and chloride-ion stress-corrosion cracking. This is vital when dealing with certain aggressive propellants or combustion byproducts.
- Superior High-Temperature Strength: Retains strength at higher temperatures than IN718, making it suitable for components closer to or within the primary combustion zone.
- Ausgezeichnete Ermüdungsfestigkeit: Robust against cyclic stress.
- Good Fabricability: Also readily weldable and printable via LPBF, though parameter optimization might differ slightly from IN718.
- Typical Injector Applications: Ideal for injector faceplates directly exposed to combustion, elements handling particularly corrosive propellants, or designs pushing thermal limits where IN718 might start to lose significant strength.
The Critical Role of Metal Powder Quality: The remarkable properties of AM superalloy parts are only achievable if the process starts with exceptionally high-quality metal powder. This is where specialized powder manufacturers like Met3dp play a vital role. Key powder characteristics impacting the final part include:
- Sphärizität: Highly spherical powder particles flow uniformly and pack densely in the powder bed, minimizing voids and leading to higher density, more consistent melting, and better mechanical properties in the final part. Met3dp utilizes advanced gas atomization and Plasma Rotating Electrode Process (PREP) technologies specifically designed to produce powders with high sphericity.
- Partikelgrößenverteilung (PSD): A controlled PSD ensures good powder bed density and consistent melt pool behavior. Powders tailored for specific AM machines (e.g., LPBF) are crucial.
- Chemische Reinheit: Low levels of impurities, particularly oxygen and nitrogen, are critical. Entrained gases can lead to porosity, while other contaminants can negatively affect mechanical properties or corrosion resistance. Met3dp’s manufacturing processes are designed to minimize contamination.
- Fließfähigkeit: Consistent flow ensures uniform layers are spread across the build plate, preventing defects related to uneven powder distribution.
Überlegungen zur Materialauswahl: The choice between IN718 and IN625 (or potentially other advanced alloys available from suppliers like Met3dp’s product portfolio, which includes various superalloys) depends on a detailed analysis of the specific injector design and operating conditions:
- Temperature Profile: Mapping the expected temperatures across the injector is crucial. IN625 might be necessary for the hottest zones, while IN718 could suffice for cooler sections or structural elements, potentially enabling hybrid material approaches in the future.
- Corrosive Environment: The specific fuel/oxidizer combination dictates the required level of corrosion resistance.
- Mechanical Loads: Stress analysis (FEA) helps determine the strength requirements in different areas.
- Kosten: IN625 powder is typically more expensive than IN718, influencing overall component cost.
By carefully selecting the appropriate superalloy and ensuring the use of premium, aerospace-grade metal powder optimized for AM, manufacturers can produce rocket engine injectors with the demanding performance and reliability required for successful space missions. Partnering with suppliers who possess deep expertise in both materials science and additive manufacturing processes is essential for navigating these critical choices.
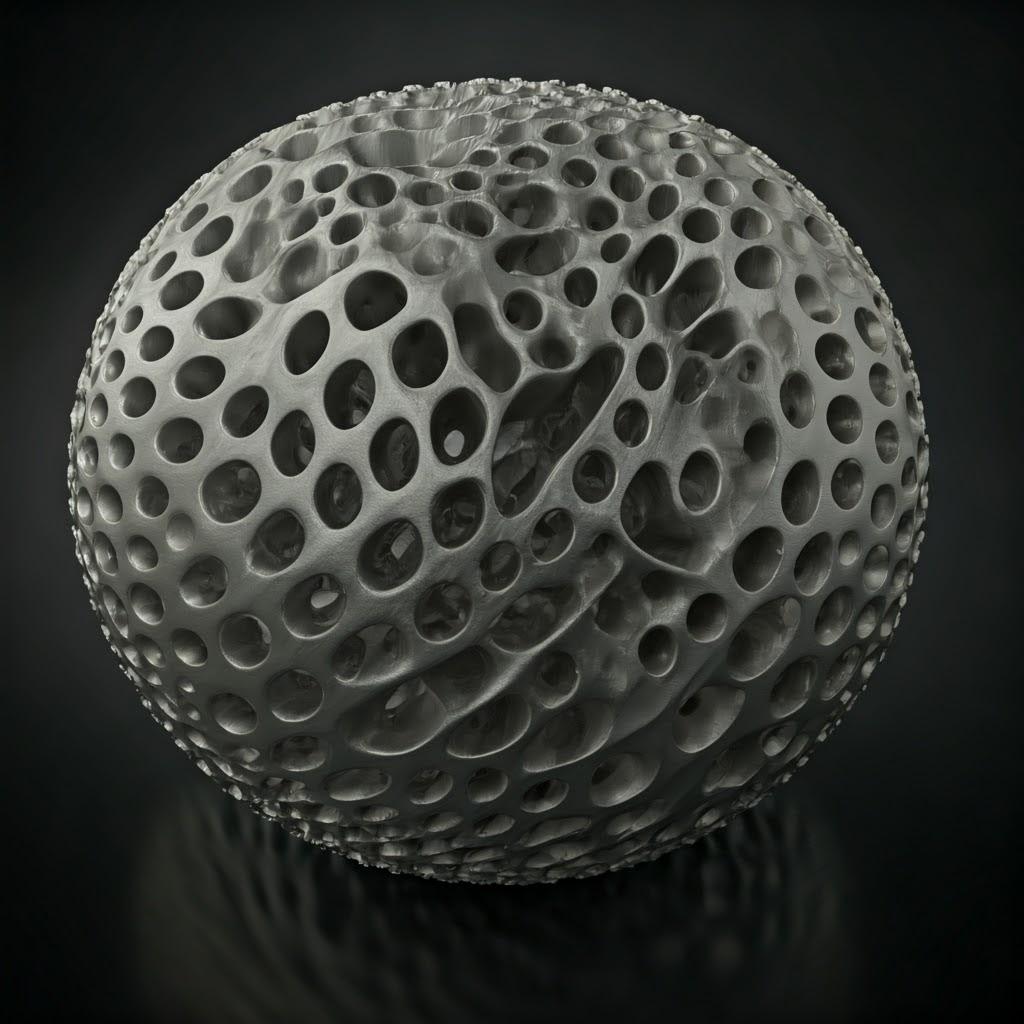
Design Considerations for Additively Manufactured Rocket Injectors: Leveraging DfAM Principles
The true power of metal additive manufacturing for rocket engine injectors lies not just in replicating existing designs more easily, but in enabling radically new designs optimized for performance, weight, and reliability. This requires embracing Design for Additive Manufacturing (DfAM) – a mindset and methodology that leverages the unique capabilities of AM while accounting for its constraints. Designing an injector for AM is fundamentally different from designing one for machining or casting. Engineers must think in terms of layers, thermal management during the build, support structures, and post-processing accessibility right from the conceptual stage.
Key DfAM Principles Applied to Injectors:
- Exploiting Geometric Freedom for Performance:
- Konforme Kühlkanäle: This is a hallmark AM advantage. Instead of drilling straight cooling lines that approximate the required cooling, AM allows channels to precisely follow the complex 3D contours of the injector face and combustion chamber walls. This enables:
- Targeted Heat Extraction: Placing cooling exactly where thermal loads are highest, preventing hot spots and increasing material lifespan or allowing higher combustion temperatures for better performance (Isp).
- Optimized Flow: Designing smooth, curved channels minimizes pressure drop in the coolant circuit, reducing parasitic power losses.
- Reduced Thermal Gradients: More uniform cooling minimizes thermal stresses within the component. Design involves intricate CFD analysis to map thermal loads and determine optimal channel path, size, and shape (e.g., circular, elliptical, rectangular).
- Optimized Injector Elements: The orifices, swirlers, or impinging jets can be designed with complex internal features to enhance atomization efficiency and mixing uniformity. For instance, internal vanes within a coaxial injector can be shaped aerodynamically, or orifice inlets can be smoothly bell-mouthed to improve flow characteristics – features difficult or impossible to achieve conventionally. CFD simulation is indispensable for designing and validating these micro-features.
- Integrated Manifolding: Internal propellant manifolds can be designed with smooth, branching paths that minimize flow stagnation and pressure loss, ensuring uniform propellant delivery to all injection elements.
- Konforme Kühlkanäle: This is a hallmark AM advantage. Instead of drilling straight cooling lines that approximate the required cooling, AM allows channels to precisely follow the complex 3D contours of the injector face and combustion chamber walls. This enables:
- Topology Optimization and Generative Design:
- While the injector face itself is often constrained by fluid dynamics requirements, the supporting structures, flanges, and mounting features can benefit significantly from topology optimization. Algorithms remove material from non-critical areas while ensuring structural requirements (stiffness, strength under pressure and vibration) are met. This can lead to substantial weight savings – a critical factor in aerospace where every kilogram saved translates to increased payload capacity or performance. Generative design tools can propose novel, organic-looking structures that are highly efficient and inherently suitable for AM.
- AM Process Constraints and Considerations:
- Mindestwanddicke: LPBF processes have limits on how thin a feature can be reliably built. For IN718/IN625, this is typically around 0.3-0.5 mm, depending on the specific machine and parameters. Thin walls require careful design to avoid distortion or incomplete formation.
- Selbsttragende Winkel: Overhanging features require support structures unless they are angled relative to the build plate. The typical self-supporting angle for Nickel superalloys is around 45 degrees from the horizontal. Designing features to be self-supporting where possible minimizes support usage, reducing material waste and post-processing time.
- Merkmal Auflösung: The laser spot size and layer thickness limit the smallest positive or negative features (e.g., holes, pins) that can be accurately produced. This is critical for orifice design and small internal passages. Understanding the specific Druckverfahren and machine capabilities of the chosen AM service provider is essential.
- Orientierung aufbauen: How the part is oriented on the build plate significantly impacts support requirements, surface finish on different faces, thermal behavior during the build (affecting residual stress and potential distortion), and overall build time. Optimization often involves trade-offs and should be considered early in the design phase, ideally in collaboration with the AM provider.
- Designing for Support Structures:
- Support structures are often unavoidable, especially for complex internal channels and external overhangs below the self-supporting angle. DfAM involves minimizing the brauchen for supports and designing the erforderlich supports intelligently:
- Minimization: Orienting the part strategically, incorporating sacrificial features or slight design modifications (e.g., changing an overhang angle from 40° to 45°).
- Zugänglichkeit: Ensuring supports, particularly internal ones, can be physically reached and removed during post-processing without damaging the part. This might involve designing specific access ports that are later sealed or integrated into the design.
- Ease of Removal: Using support types (e.g., tree supports vs. block supports) with minimal contact points, optimizing support parameters for easier detachment, potentially using materials or designs that break away more cleanly.
- Surface Finish Impact: Recognizing that surfaces where supports attach will have a rougher finish and require post-processing.
- Support structures are often unavoidable, especially for complex internal channels and external overhangs below the self-supporting angle. DfAM involves minimizing the brauchen for supports and designing the erforderlich supports intelligently:
- Entwerfen für die Nachbearbeitung:
- An AM part is rarely finished when it comes off the build plate. DfAM requires anticipating downstream steps:
- Zulagen für die Bearbeitung: Adding extra material (e.g., 0.5-1.0 mm) to surfaces that require high precision or specific finishes via CNC machining (e.g., sealing faces, interfaces, critical orifice exits).
- Werkstückspannung: Designing features or surfaces that allow the complex AM part to be securely and accurately held during machining operations.
- Internal Channel Access: Ensuring ports or openings exist for effective cleaning, inspection, and potential internal surface finishing (e.g., AFM).
- Inspection Features: Incorporating datum features or reference points required for CMM or scanning verification.
- An AM part is rarely finished when it comes off the build plate. DfAM requires anticipating downstream steps:
- Simulationsgestützter Entwurf:
- The complexity enabled by AM necessitates robust simulation.
- CFD (Computational Fluid Dynamics): Essential for validating injector spray patterns, mixing efficiency, pressure drops, and crucially, the effectiveness of conformal cooling channel designs under operational thermal loads.
- FEA (Finite Element Analysis): Used to verify structural integrity under pressure, analyze vibration modes (critical for combustion stability), predict thermal stresses during operation, and increasingly, to simulate the AM build process itself to predict potential distortion and residual stress.
- This simulation-driven approach, tightly integrated with AM, allows for rapid virtual iteration and optimization before committing to expensive physical prints and tests. Leading AM providers often offer simulation support as part of their engineering services.
- The complexity enabled by AM necessitates robust simulation.
By integrating these DfAM principles, engineers can fully exploit the potential of metal AM to create next-generation rocket engine injectors that are lighter, perform better, are more reliable, and can be developed significantly faster than their conventionally manufactured predecessors. Collaboration between design engineers and AM manufacturing experts, like the team at Met3dp, is key to navigating the intricacies of DfAM for such critical aerospace components.
Achievable Tolerance, Surface Finish, and Dimensional Accuracy in 3D Printed Injectors
While metal additive manufacturing unlocks incredible geometric freedom, it’s crucial for engineers and procurement managers to have realistic expectations regarding the achievable dimensional accuracy, tolerances, and surface finish, especially for demanding aerospace applications like rocket injectors. These factors are influenced by the AM process itself (primarily LPBF for IN718/IN625 injectors), material properties, part geometry, and post-processing steps.
Toleranzen:
- As-Built Tolerances: For typical LPBF processes using well-characterized parameters for IN718 or IN625, general dimensional tolerances often fall within the range of +/- 0.1 mm to +/- 0.2 mm (or +/- 0.004″ to +/- 0.008″) for smaller features, potentially scaling up slightly for larger dimensions (e.g., +/- 0.1% to 0.2% of the dimension). This might correspond to ISO 2768 tolerance class ‘m’ (medium) or sometimes ‘f’ (fine) for general dimensions.
- Faktoren, die die Verträglichkeit beeinflussen:
- Kalibrierung der Maschine: Accuracy of the laser scanning system, layer thickness control, and build platform leveling.
- Prozessparameter: Laser power, scan speed, hatch spacing, layer thickness all affect melt pool size and stability, influencing shrinkage and final dimensions. Providers like Met3dp invest heavily in process parameter optimization for their materials.
- Qualität des Pulvers: Consistent particle size distribution and morphology, as provided by Met3dp’s advanced atomization techniques, contribute to stable melting and predictable shrinkage. Variations in powder can affect dimensional outcomes.
- Thermische Spannungen: Uneven heating and cooling during the build cause internal stresses that can lead to warping or distortion, impacting final dimensions, especially after removal from the build plate.
- Teilegeometrie und -ausrichtung: Large flat surfaces, thin walls, and overhangs are more susceptible to deviation. Orientation affects thermal history and support needs.
- Kritische Toleranzen: Features like propellant orifice diameters, sealing surfaces, and mounting interfaces often require much tighter tolerances than achievable in the as-built state. These are typically achieved through post-processing, specifically CNC machining. It is essential to specify these critical tolerances clearly on engineering drawings using GD&T (Geometric Dimensioning and Tolerancing).
Oberflächengüte (Rauhigkeit):
- As-Built Surface Finish (Ra): The surface roughness of an AM part varies depending on the surface orientation relative to the build layers:
- Nach oben gerichtete Flächen: Generally exhibit the best finish, often in the range of 6-10 µm (240-400 µin) Ra, influenced by the melt pool characteristics.
- Side Walls (Vertical): Show distinct layering effects, typically resulting in roughness of 8-15 µm (320-600 µin) Ra.
- Downward-Facing Surfaces (Overhangs): Require support structures. The points where supports touch leave witness marks, and the surface itself tends to be rougher due to the interaction with supports and less stable melting conditions, often exceeding 15-20 µm (600-800 µin) Ra even after support removal.
- Interne Kanäle: Surface roughness inside intricate cooling channels or flow passages is a significant concern. As-built roughness can be high, impacting fluid flow (increased pressure drop due to friction) and heat transfer efficiency. Achieving smooth internal surfaces often requires specific post-processing steps (see next section).
- Nachbearbeitetes Oberflächenfinish: Various post-processing techniques can significantly improve surface finish:
- CNC-Bearbeitung: Can achieve very smooth finishes, typically <1.6 µm (63 µin) Ra, often down to 0.8 µm (32 µin) Ra or better.
- Polieren/Läppen: Manual or automated polishing can produce mirror-like finishes (<0.1 µm / 4 µin Ra) on accessible external surfaces.
- Abrasive Flow Machining (AFM) / Electro-Chemical Polishing (ECP): Used to smooth internal channels, potentially reducing Ra significantly, though uniformity can be challenging in complex networks.
- Tumbling/Mass Finishing: Can provide general deburring and smoothing for external surfaces, typically resulting in finishes around 1-3 µm (40-120 µin) Ra.
Dimensional Accuracy Verification:
Ensuring that the final injector meets the stringent dimensional requirements of aerospace applications necessitates rigorous inspection and verification protocols:
- Koordinatenmessmaschinen (KMG): Provide high-accuracy point measurements for verifying critical dimensions, flatness, perpendicularity, and other GD&T callouts, particularly after final machining operations.
- Structured Light / Laser Scanning: Offer rapid, non-contact capture of the part’s overall geometry, allowing comparison to the original CAD model. Excellent for verifying complex external shapes and identifying warpage or deviation. Accuracy is typically lower than CMM but much faster for overall form assessment.
- Computertomographie (CT) Scannen: Uniquely powerful for aerospace AM parts, CT scanning uses X-rays to create a complete 3D model of the part, including intern features. This allows for:
- Verification of internal channel dimensions, wall thicknesses, and geometry.
- Detection of internal defects like porosity or inclusions.
- Measurement of features inaccessible by other methods.
- Comparison of the as-built internal geometry against the design intent. CT scanning is becoming increasingly essential for qualifying critical AM components like injectors.
Achieving the required precision for rocket injectors involves a combination of optimized AM process control, careful DfAM, targeted post-processing (especially machining), and comprehensive metrology. Procurement managers should engage with AM suppliers who demonstrate robust quality control systems, advanced metrology capabilities, and a clear understanding of how to achieve and verify the demanding tolerances and surface finishes required for flight hardware.
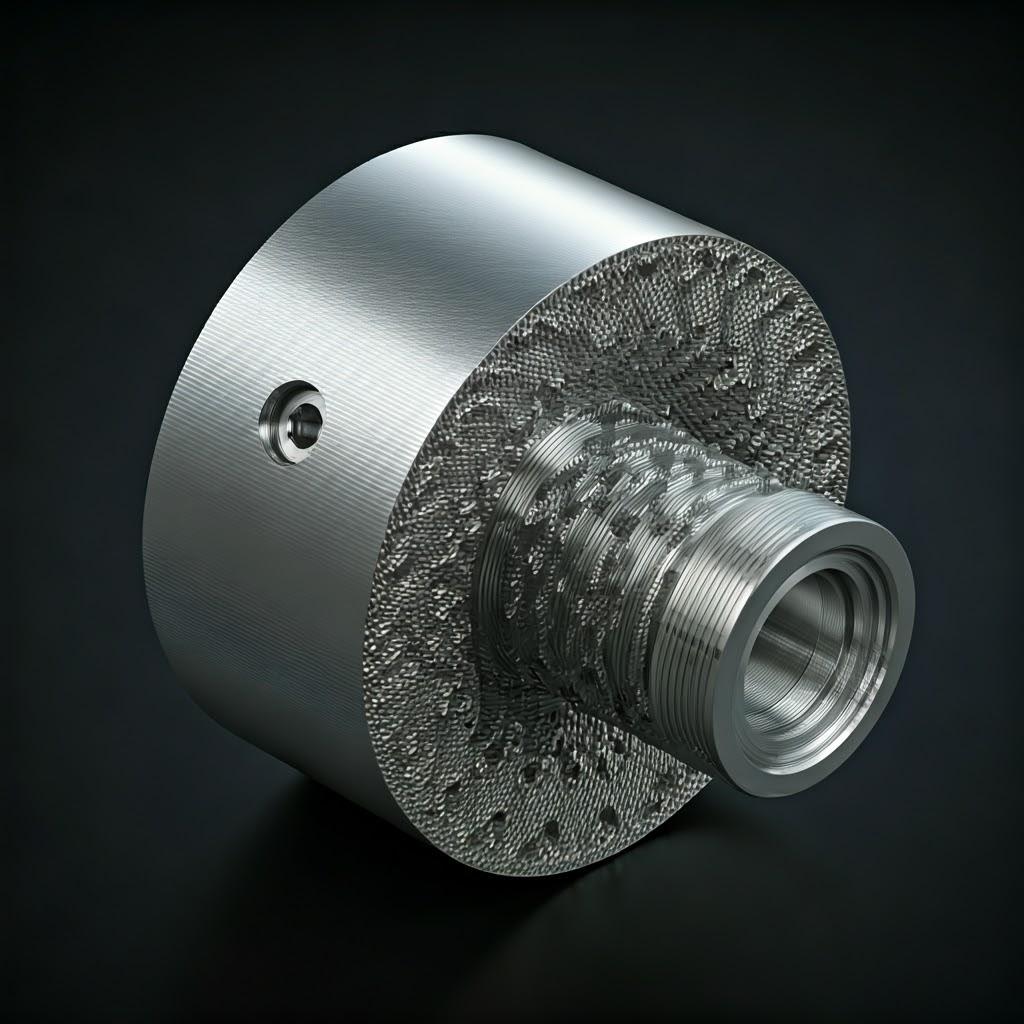
Post-Processing Requirements: From Print Bed to Flight-Ready Component
A common misconception about metal additive manufacturing is that parts are ready to use straight off the printer. For critical applications like rocket engine injectors made from high-performance superalloys like IN718 or IN625, the as-built part represents only an intermediate stage. A series of essential post-processing steps are required to transform the printed component into a flight-ready piece of hardware, ensuring the necessary mechanical properties, dimensional accuracy, surface characteristics, and overall integrity. This multi-stage process requires specialized equipment, expertise, and rigorous process control.
Typical Post-Processing Workflow for AM Superalloy Injectors:
- Stressabbau:
- Zweck: The rapid heating and cooling cycles inherent in LPBF create significant internal stresses within the printed part. These stresses can cause distortion upon removal from the build plate or cracking during subsequent steps. A stress relief heat treatment, performed while the part is still attached to the build plate, is crucial to relax these stresses.
- Prozess: Typically involves heating the part and plate in a controlled atmosphere (vacuum or inert gas like argon) to a specific temperature below the aging temperature range (e.g., ~950-1050°C for IN718, depending on specifics), holding for a period (e.g., 1-2 hours), and then slowly cooling. Parameters must be carefully controlled to avoid unwanted microstructural changes.
- Entnahme von der Bauplatte:
- Zweck: Separating the stress-relieved part(s) from the base plate.
- Prozess: Commonly done using wire Electrical Discharge Machining (EDM) or a bandsaw. Care must be taken to avoid damaging the part itself. The cut surface will require finishing later if it’s a functional surface.
- Heat Treatment (Solution Annealing & Aging):
- Zweck: This is arguably the most critical step for achieving the desired mechanical properties (strength, ductility, hardness, creep resistance) specified for aerospace applications. The as-built microstructure is typically non-optimal. Heat treatment homogenizes the microstructure, dissolves certain phases, and then precipitates the strengthening phases (γ′ and γ′′ for IN718).
- Process (Example for IN718):
- Lösungsglühen: Heating to a high temperature (e.g., 955-1010°C) to dissolve soluble phases and homogenize the structure, followed by rapid cooling (quenching).
- Alterung (Ausscheidungshärtung): A two-step aging process is common for IN718 (e.g., ~720°C for 8 hours, furnace cool to ~620°C, hold for 8 hours, then air cool). This precisely controlled cycle precipitates the fine γ′ and γ′′ phases that give IN718 its high strength.
- Process (Example for IN625): Often used in the solution-annealed condition (~1150°C) for maximum corrosion resistance and ductility, or annealed at lower temperatures (~980°C) for higher fatigue strength. Specific cycles depend heavily on the application requirements.
- Umwelt: These treatments must be performed in high-purity vacuum or inert atmosphere furnaces to prevent oxidation and contamination, which can severely degrade properties. AMS standards (e.g., AMS5662/AMS5663 for IN718 properties, AMS2774 for heat treatment) often dictate requirements.
- Entfernung der Stützstruktur:
- Zweck: Removing the temporary structures used to support overhangs and complex features during the build.
- Prozess: Can be challenging, especially for dense or intricate supports or those within internal channels. Methods include:
- Manuelle Entfernung: Breaking or cutting away accessible supports using hand tools (pliers, cutters, grinders). Requires skill to avoid damaging the part surface.
- CNC-Bearbeitung: Milling or grinding away supports, especially larger block supports or those on surfaces that will be machined later anyway.
- Drahterodieren: Sometimes used for precise removal in tight areas.
- The surfaces where supports were attached will typically be rough and require further finishing.
- Heiß-Isostatisches Pressen (HIP):
- Zweck: To close internal microporosity (e.g., small gas pores or lack-of-fusion voids) that may be present even in a well-controlled AM process. Eliminating porosity significantly improves fatigue life, ductility, and fracture toughness – properties absolutely critical for flight-critical hardware subjected to cyclic loading and extreme stress.
- Prozess: Involves subjecting the part to high temperature (just below the solution annealing temperature, e.g., ~1120-1180°C for IN718/IN625) and high-pressure inert gas (typically Argon at 100-200 MPa / 15,000-30,000 psi) simultaneously in a specialized HIP vessel. The combination of heat and pressure causes internal voids to collapse and metallurgically bond shut.
- Erfordernis: Increasingly considered mandatory by major aerospace primes for Class A / flight-critical AM components. Requires specialized HIP equipment and expertise.
- CNC-Bearbeitung:
- Zweck: To achieve tight tolerances, specific surface finishes, and precise geometric features (GD&T) on critical surfaces that cannot be achieved by AM alone.
- Anwendungen: Machining sealing faces, mounting flanges, threaded holes, mating interfaces, and precisely sizing critical orifice diameters and contours.
- Herausforderungen: Workholding complex AM shapes can be difficult. Machining tough superalloys like IN718/IN625 requires appropriate tooling, speeds, and feeds.
- Oberflächenveredelung:
- Zweck: To achieve the required surface roughness (Ra) for functional reasons (e.g., flow efficiency, heat transfer, sealing) or inspection requirements.
- Methoden:
- Externe Oberflächen: CNC machining, grinding, belt sanding, manual polishing, automated electropolishing, tumbling/vibro-finishing.
- Interne Kanäle: Abrasive Flow Machining (AFM) where a abrasive-laden polymer is forced through channels, Electro-Chemical Machining (ECM) / Polishing (ECP), or chemical etching/polishing processes. Achieving uniform finish in complex internal networks remains challenging.
- Reinigung und Inspektion:
- Zweck: Ensuring the part is completely free of contaminants (powder residues, support material, machining fluids, debris) that could interfere with engine operation or propellant compatibility. Final verification of integrity and dimensional conformance.
- Reinigung: Multi-stage ultrasonic cleaning processes with specialized solvents are often used. Verification of cleanliness is critical.
- Inspection (Non-Destructive Testing – NDT):
- Visuelle Inspektion (VT): Including boroscopic inspection of internal channels.
- Dye Penetrant Inspection (FPI/PT): To detect surface-breaking cracks or defects.
- Computed Tomography (CT): For internal defect detection (porosity, inclusions) and internal geometry verification.
- Ultraschallprüfung (UT): Can detect subsurface flaws.
- Dimensionelle Metrologie: Final CMM or scan verification.
- Dokumentation: Meticulous documentation (material certs, build logs, heat treat/HIP records, NDT reports, dimensional inspection reports) is essential for aerospace traceability and quality assurance.
Executing this complex post-processing chain requires a robust quality management system (ideally AS9100 certified for aerospace work) and often involves a network of specialized service providers coordinated by the primary AM manufacturer or the customer. Understanding these steps is vital for accurately estimating costs, lead times, and ensuring the final injector meets all performance and safety requirements.
Common Challenges in Printing Rocket Injectors and Mitigation Strategies
While metal AM offers transformative potential for rocket injectors, printing these complex components from challenging materials like IN718 and IN625 is not without difficulties. Anticipating and mitigating these common challenges is crucial for achieving successful, reliable, flight-worthy hardware. Collaboration between designers and experienced AM service providers, equipped with robust process controls and diagnostic tools, is key.
- Verformung und Verzerrung:
- Herausforderung: The high energy input and rapid solidification inherent in LPBF generate steep thermal gradients and significant residual stresses within the part. As layers build up, these stresses can accumulate and cause the part to warp, curl, or distort, especially after removal from the build plate. Injectors often feature combinations of thick sections (manifolds) and thin walls (injector face, internal vanes), exacerbating differential shrinkage and stress.
- Milderung:
- Thermische Simulation: Using build process simulation software to predict stress accumulation and distortion patterns based on geometry and orientation.
- Optimierte Gebäudeausrichtung: Selecting an orientation that minimizes large flat overhangs, balances thermal mass, and potentially reduces overall build height.
- Intelligent Support Strategy: Designing robust supports that effectively anchor the part to the build plate, conduct heat away, and counteract shrinkage forces. Support density and placement are critical.
- Optimierte Scan-Strategie: Using specific laser scan patterns (e.g., island scanning, quadrant rotation) to distribute heat input more evenly and reduce localized stress buildup.
- Appropriate Stress Relief Cycle: Performing an effective stress relief heat treatment immediately after the build, before support removal.
- Cracking (Solidification and Liquation):
- Herausforderung: Nickel-based superalloys, particularly those with high Nickel and Chromium content like IN718 and IN625, can be susceptible to cracking during the rapid solidification and reheating cycles of AM. Solidification cracking occurs in the last liquid to solidify in interdendritic regions, while liquation cracking can happen in the heat-affected zone of previously solidified layers if low-melting-point phases or grain boundary segregation exist.
- Milderung:
- Hochwertiges Pulver: Using powders with tightly controlled chemistry, particularly low levels of impurities like Sulfur (S), Phosphorus (P), Silicon (Si), and Boron (B), which can promote cracking. Met3dp’s advanced powder production methods focus on achieving high purity.
- Optimierte Prozessparameter: Carefully developing and validating parameters (laser power, speed, hatch distance) to control the melt pool size, cooling rate, and thermal gradients. Avoiding excessive energy density that can lead to vaporization and instability.
- Preheating: Using build plate heating (common in LPBF) helps reduce thermal gradients, although its effect diminishes with part height.
- Post-Weld Heat Treatment Procedures: Specific heat treatments (like homogenization before aging) can sometimes help heal or mitigate micro-cracking, although preventing them during the build is preferable.
- Porosity (Gas and Lack-of-Fusion):
- Herausforderung: Internal pores are defects that act as stress concentrators, severely degrading fatigue life, ductility, and fracture toughness – unacceptable for critical injector components. Porosity can arise from:
- Gas Porosität: Trapped gas (e.g., Argon from the build chamber, or dissolved gases released from the powder during melting) forming spherical pores.
- Lack-of-Fusion-Porosität: Insufficient energy input or improper beam overlap leading to incomplete melting between layers or adjacent scan tracks, resulting in irregular-shaped voids.
- Schlüsselloch-Porosität: Excessive energy density causing deep vaporization and melt pool instability, leading to trapped gas at the bottom of the melt track.
- Milderung:
- High-Quality, Dry Powder: Using spherical powders with low internal porosity and minimal adsorbed moisture/gas content. Proper powder handling and storage are essential.
- Rigorous Parameter Development: Extensive testing (e.g., building and analyzing density cubes) to establish process windows that ensure full melting and fusion without excessive vaporization. Parameter sets must be validated for specific machines and powder batches.
- Optimierte Scan-Strategien: Ensuring sufficient overlap between scan tracks and layers.
- Shielding Gas Flow: Maintaining proper laminar flow of inert shielding gas (Argon) to remove fumes and prevent melt pool contamination/instability.
- Heiß-Isostatisches Pressen (HIP): As discussed previously, HIP is highly effective at closing both gas and lack-of-fusion porosity, significantly enhancing mechanical properties. It’s often considered mandatory for critical AM aerospace parts.
- Herausforderung: Internal pores are defects that act as stress concentrators, severely degrading fatigue life, ductility, and fracture toughness – unacceptable for critical injector components. Porosity can arise from:
- Unterstützung bei der Beseitigung von Schwierigkeiten:
- Herausforderung: Removing support structures, especially complex lattice or tree supports within intricate internal cooling channels or tightly packed injector elements, can be extremely difficult, time-consuming, and risks damaging the part. Incomplete support removal can obstruct flow paths or act as crack initiation sites.
- Milderung:
- DfAM für Barrierefreiheit: Designing the part with support removal in mind – maximizing self-supporting features, providing clear lines of sight and tool access, potentially incorporating sacrificial bosses or features to aid removal.
- Optimiertes Support-Design: Using support types (e.g., conical, easily breakable interfaces) and parameters that balance support effectiveness with ease of removal. Simulation tools can help optimize support placement and type.
- Spezialisierte Entfernungstechniken: Utilizing micro-machining, wire EDM, or even chemical etching in some cases for inaccessible supports.
- Inspektion: Thorough inspection (visual, boroscopic, potentially CT) to confirm complete support removal.
- Reststress-Management:
- Herausforderung: Even after stress relief, some residual stress remains. High residual stresses can lead to long-term dimensional instability, reduced fatigue life, and increased susceptibility to stress corrosion cracking, especially in the demanding environment of a rocket engine.
- Milderung:
- Process Simulation & Optimization: As mentioned for warping, optimizing orientation and scan strategies to minimize stress buildup.
- Effective Stress Relief & Heat Treatment: Ensuring proper execution of stress relief and subsequent heat treatments (solution/aging, HIP) which further homogenize the structure and reduce stress.
- Überlegungen zum Design: Avoiding sharp corners and abrupt changes in section thickness, which act as stress concentrators. Incorporating generous radii and smooth transitions.
- Surface Roughness in Internal Channels:
- Herausforderung: Achieving a smooth surface finish inside complex, narrow, and often tortuous cooling or propellant passages remains a significant challenge for AM. High roughness increases pressure drop, reduces heat transfer efficiency, and could potentially create sites for undesired chemical reactions or boundary layer effects.
- Milderung:
- Optimierung der Parameter: Tuning process parameters specifically for down-skin surfaces (the underside of overhangs) can sometimes improve finish, but trade-offs exist.
- Orientation Strategies: Orienting channels vertically often yields better internal finishes than horizontal orientations.
- Post-Processing Methods: Employing techniques like Abrasive Flow Machining (AFM), Electro-Chemical Polishing (ECP), or chemical polishing specifically targeted at internal surfaces. The effectiveness and uniformity depend heavily on channel geometry and accessibility.
- Ongoing Research: This remains an active area of research and development within the AM community.
Successfully navigating these challenges requires deep process expertise, rigorous quality control, advanced simulation and diagnostic tools, and a collaborative approach between designers and the AM manufacturing partner. Companies seeking AM solutions for critical components like rocket injectors should prioritize suppliers with demonstrated experience in handling superalloys and overcoming these inherent process complexities.
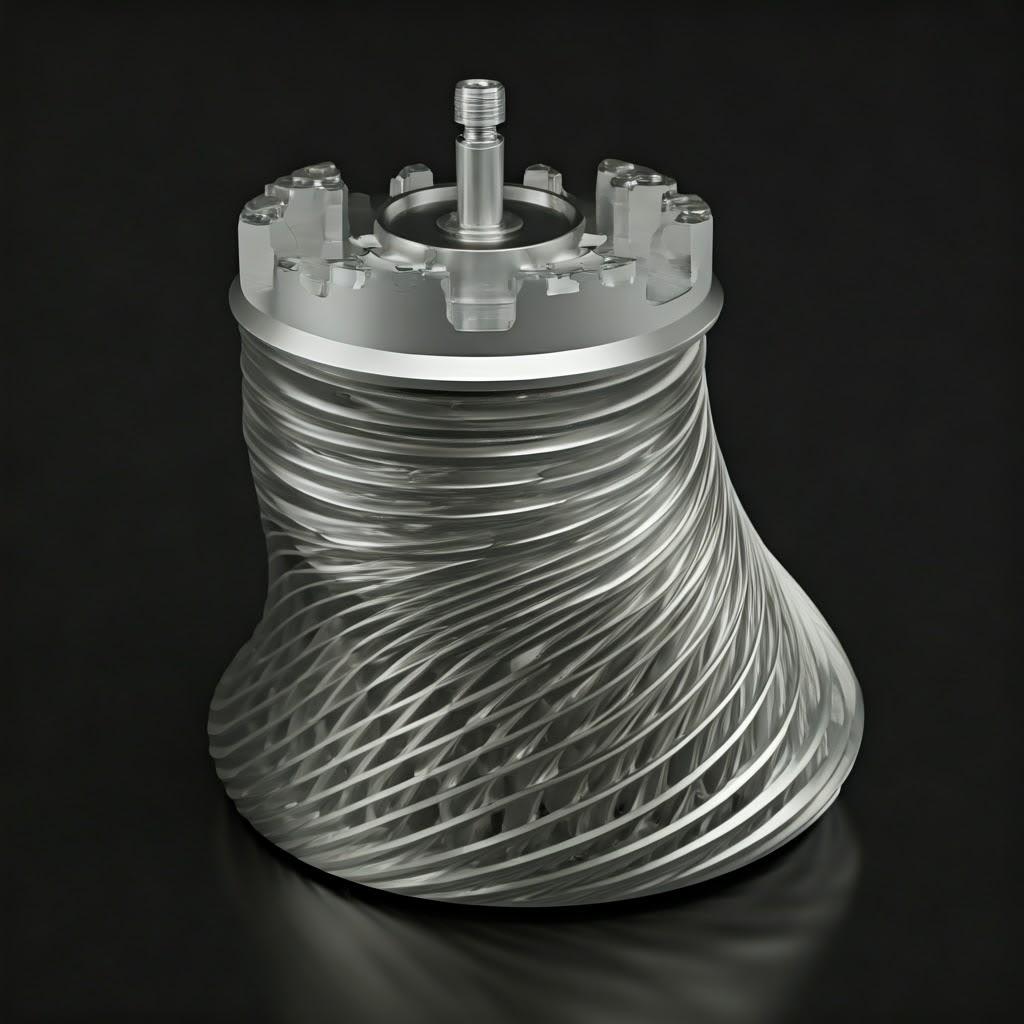
How to Choose the Right Metal 3D Printing Service Provider for Aerospace Components
Selecting a manufacturing partner for flight-critical hardware like rocket engine injectors is one of the most important decisions an aerospace company will make. The stakes are incredibly high, and the required level of expertise, process control, and quality assurance goes far beyond standard industrial manufacturing. Not all metal additive manufacturing service providers are equipped to handle the complexities and stringent requirements of printing nickel-based superalloys like IN718 and IN625 for propulsion applications. Choosing the right partner is crucial for mitigating risks, ensuring component reliability, and achieving mission success.
Here are key criteria procurement managers and engineering teams should use when evaluating potential metal AM suppliers for aerospace components:
- Demonstrated Aerospace Expertise and Experience:
- Look beyond general AM capabilities. Does the supplier have a proven track record of successfully manufacturing complex components specifically for the aerospace or space industry? Can they provide case studies or references related to propulsion systems, high-temperature applications, or parts with similar complexity to your injector?
- Do they understand aerospace qualification processes, testing requirements (e.g., material characterization, life testing), and the documentation rigor involved (e.g., First Article Inspection Reports – FAIR)?
- Deep Material Expertise (IN718, IN625, etc.):
- Proficiency in printing nickel-based superalloys is essential. This includes having thoroughly developed and validated process parameters for IN718 and IN625 on their specific machines to achieve high density (>99.7%, often >99.9% after HIP) and optimal microstructure.
- Expertise extends to powder handling and management protocols crucial for reactive superalloys to prevent contamination and ensure consistency. Companies like Met3dp, which manufacture their own high-quality spherical powders using advanced Gaszerstäubung und PREP-Technologien, often possess a deeper understanding of material behavior during the AM process.
- Appropriate Technology and Comprehensive Capabilities:
- AM Systems: Access to well-maintained, industrial-grade Laser Powder Bed Fusion (LPBF) machines suitable for processing superalloys, potentially with features like controlled atmosphere and build plate heating. Ensure their machine portfolio matches the size and precision requirements of your injector.
- Nachbearbeiten: Assess their in-house capabilities and/or their network of qualified partners for the entire post-processing chain: stress relief, vacuum heat treatment (to AMS standards), Hot Isostatic Pressing (HIP), precision CNC machining (5-axis capabilities often needed), surface finishing (including internal channels via AFM/ECP), and thorough cleaning. Vertical integration can sometimes streamline lead times and quality control.
- Robustes Qualitätsmanagementsystem (QMS):
- AS9100-Zertifizierung: This is the internationally recognized QMS standard for the aerospace industry. For flight-critical hardware, AS9100 certification is generally considered mandatory. It demonstrates a commitment to rigorous process control, risk management, configuration management, and continuous improvement. ISO 9001 is a prerequisite but insufficient on its own for this level of criticality.
- Process Control & Documentation: Evidence of stringent process controls at every step, from powder acceptance testing to final inspection. Meticulous documentation and traceability procedures are paramount.
- Material Sourcing, Quality, and Traceability:
- Does the supplier use powders procured from reputable sources with clear certifications (e.g., chemical analysis, PSD)? Can they provide full lot traceability, linking the specific powder batch used back to the raw materials and forward to the finished part and its processing history? This is non-negotiable for aerospace components. Working with a provider like Met3dp, known for producing high-purity, aerospace-grade powders, can provide added assurance.
- Engineering Support and DfAM Collaboration:
- The ideal partner acts as more than just a print service. Look for suppliers with experienced application engineers who can provide Design for Additive Manufacturing (DfAM) guidance, helping optimize your injector design for printability, performance, and cost-effectiveness. Capabilities in build simulation (thermal, stress) are also highly valuable for predicting and mitigating potential issues.
- Capacity, Scalability, and Lead Time Reliability:
- Can the supplier meet your project timelines, from prototypes through potential low-rate production? Do they have sufficient machine capacity and redundancy to handle potential equipment downtime? Assess their track record for on-time delivery.
- Testing and Validation Capabilities:
- Access to comprehensive testing facilities, either in-house or through certified labs, is crucial for qualifying AM parts. This includes:
- Materialprüfung: Tensile, yield, elongation, hardness, fatigue, creep-rupture testing at relevant temperatures.
- Mikrostrukturanalyse: Metallography to verify grain structure, phase distribution, and check for defects.
- Zerstörungsfreie Prüfung (NDT): Including visual (VT), penetrant (FPI/PT), ultrasonic (UT), and crucially, Computed Tomography (CT) scanning for internal integrity and geometry verification. NADCAP accreditation for special processes (NDT, Heat Treat, HIP, etc.) is often required.
- Access to comprehensive testing facilities, either in-house or through certified labs, is crucial for qualifying AM parts. This includes:
Choosing an AM supplier for rocket injectors requires thorough due diligence. Consider auditing potential suppliers, reviewing their quality manuals, discussing their experience in detail, and potentially starting with a smaller qualification project. A collaborative partnership approach, built on trust and technical competence, is essential for success. Companies like Met3dp, with decades of collective expertise spanning AM systems, advanced metal powders, and application development, position themselves as comprehensive solution providers capable of supporting demanding aerospace projects from concept to qualified hardware.
Cost Factors and Lead Time Considerations for AM Rocket Injectors
While Additive Manufacturing offers significant advantages in terms of design freedom and potential lead time reduction for complex parts, understanding the cost structure and typical timelines is essential for project planning and budgeting, especially for procurement managers sourcing these high-value components. AM injector costs are influenced by a variety of factors, and lead times involve multiple sequential steps.
Breakdown of Cost Drivers:
The total cost of an additively manufactured rocket injector can be broken down into several key components:
Kostenkategorie | Beschreibung | Wichtige Einflussfaktoren |
---|---|---|
Design & Engineering | Initial design work (if not provided), DfAM optimization, build preparation (orientation, supports), simulation (CFD, FEA, process). | Design complexity, level of optimization required, need for simulation. |
Materialkosten | Price per kilogram of aerospace-grade IN718 or IN625 powder (significant cost). Total powder consumed (part weight + support structures). | Material choice (IN625 > IN718), part volume, support volume, powder recyclability rate. |
AM Machine Time | Cost per hour of operating the LPBF machine. Determined by the total build time. | Part height (number of layers), part volume/density within each layer, machine model. |
Arbeit | Skilled technicians for build setup, powder handling, machine operation monitoring, part removal, support removal, post-processing tasks. | Complexity of setup/removal, amount of manual support removal needed. |
Nachbearbeitung | Costs associated with each required step: Stress relief, heat treatment, HIP, CNC machining, surface finishing, cleaning. | Number & complexity of steps, furnace/HIP time, machining hours, finishing specs. |
Qualitätssicherung | Costs for inspection and testing: NDT (CT scanning can be costly), dimensional metrology (CMM, scanning), material testing, documentation. | Level of inspection required (driven by criticality), number of checks, reporting needs. |
Overhead & Profit | Supplier’s operational costs (facility, utilities, administration) and profit margin. | Supplier’s business model, competitive landscape. |
In Blätter exportieren
Key Factors Influencing Overall Cost:
- Teil Komplexität: Highly intricate designs with complex internal channels may increase build time, support requirements, and post-processing difficulty (especially internal finishing).
- Part Size/Volume: Directly impacts material consumption and machine build time.
- Wahl des Materials: Nickel-based superalloys are inherently expensive materials.
- Menge: While AM avoids tooling costs, per-part costs may not decrease as rapidly with volume as in traditional mass production. However, efficiencies in setup and post-processing can provide some volume benefits.
- Tolerance and Quality Requirements: Tighter tolerances necessitate more extensive machining and inspection. Higher quality classifications (e.g., flight critical) demand more rigorous NDT and documentation, adding cost.
Überlegungen zur Vorlaufzeit:
The total lead time for receiving a finished AM injector involves more than just the print time. It’s a sequence of steps, each contributing to the overall duration:
- Design Finalization & Build Prep: (Days to Weeks) Finalizing the DfAM-optimized design, performing simulations, planning build layout, generating support structures, and creating the machine build file.
- Printing (AM Build): (Days to Weeks) The actual layer-by-layer printing process. Build time depends primarily on part height, but also volume and complexity. Multiple parts can often be printed simultaneously on one build plate.
- Post-Processing Queue: (Variable) Parts often need to wait for access to specialized equipment like vacuum furnaces or HIP units, which may be shared resources or require scheduling with external partners. This queuing time can sometimes be a significant portion of the total lead time.
- Post-Processing Execution: (Weeks) Performing the sequence of stress relief, heat treatment, HIP, support removal, machining, finishing, and cleaning. Each step takes time, and complex machining or internal finishing can be particularly lengthy.
- Qualitätssicherung und Inspektion: (Days to Weeks) Thorough NDT, dimensional verification, and final documentation review.
- Versand: (Days)
Total Lead Time: Can range widely, typically from mehrere Wochen bis mehrere Monate, depending heavily on complexity, quantity, post-processing requirements, and supplier/partner capacity and scheduling.
AM vs. Traditional Lead Time:
- Vorteil: AM eliminates the significant upfront lead time required for designing and fabricating complex tooling (molds, cores, jigs, fixtures), which can take many months for traditional methods. This makes AM much faster for prototypes, design iterations, and low-volume production.
- Erwägung: The actual printing and post-processing time per part in AM might be longer than the per-part cycle time in traditional mass production once tooling is established.
Clear communication with the chosen AM supplier regarding expected costs and realistic lead times, including potential bottlenecks, is essential for effective project management and integration into larger aerospace program schedules.

Häufig gestellte Fragen (FAQ)
Here are answers to some common questions engineers and procurement managers have about using metal additive manufacturing for rocket engine injectors:
- Q1: What are the main advantages of using AM for rocket injectors over traditional casting or machining?
- A1: The primary advantages are:
- Beispiellose Designfreiheit: Enabling highly complex internal features like conformal cooling channels and optimized flow paths for improved performance and efficiency.
- Teil Konsolidierung: Reducing component count by integrating multi-part assemblies into a single monolithic print, which decreases weight, eliminates joints (potential leak/failure points), and simplifies assembly.
- Rapid Prototyping & Development: Significantly faster design iteration cycles compared to methods requiring tooling, accelerating engine development and optimization.
- Reduced Lead Times (for Low Volume): Often faster delivery for prototypes and low-volume production runs by eliminating tooling lead times.
- Potential for Weight Reduction: Through topology optimization and part consolidation.
- A1: The primary advantages are:
- Q2: How does the performance of 3D printed IN718/IN625 injectors compare to wrought materials?
- A2: When processed correctly (including optimized printing parameters, appropriate heat treatment, and mandatory HIP), the static mechanical properties (tensile strength, yield strength, elongation) of AM IN718/IN625 can closely match or even exceed minimum specifications for wrought counterparts. HIP is critical for improving dynamic properties like fatigue life and fracture toughness by closing internal porosity, bringing performance much closer to wrought levels. The key advantage AM offers is the ability to create optimized geometries (like conformal cooling) that enhance the component’s overall performance (e.g., thermal management, combustion efficiency) beyond what’s possible with wrought stock shapes, even if base material properties are only comparable. Qualification testing specific to the application is always required.
- Q3: What quality certifications are crucial when selecting an AM supplier for flight-critical hardware like injectors?
- A3: The most critical certification is AS9100, the aerospace industry’s standard for Quality Management Systems. It ensures rigorous controls over processes, documentation, traceability, and risk management. Additionally, NADCAP (National Aerospace and Defense Contractors Accreditation Program) accreditation for special processes performed by the supplier or their subcontractors is highly important. This includes accreditations for Heat Treating, Materials Testing Laboratories, Non-Destructive Testing, Welding (relevant if any joining is done), and potentially Hot Isostatic Pressing if performed under NADCAP scope. ISO 9001 is a foundational QMS but generally insufficient on its own for flight hardware.
- Q4: Can existing injector designs be directly printed, or do they need modification for AM?
- A4: While it’s sometimes possible to print a design originally intended for traditional manufacturing, doing so rarely leverages the full potential of AM and may even introduce printability challenges. To maximize benefits (performance, weight, cost, lead time), existing designs should almost always be redesigned or optimized for additive manufacturing (DfAM). This involves modifying geometries to leverage AM’s strengths (e.g., adding complex internal channels, consolidating parts) and accommodate its constraints (e.g., managing overhangs, planning for support removal, adding machining allowances). Simply “printing the CAD” is usually not the optimal approach.
- Q5: What is the typical lifespan or reusability of an additively manufactured rocket engine injector?
- A5: The lifespan and potential for reusability depend entirely on the specific engine design, mission requirements (expendable vs. reusable launcher), operating conditions (thrust levels, duration, propellant types), and how the injector was designed and qualified. An AM injector designed and rigorously tested for reusability can potentially achieve lifespans comparable to traditionally manufactured counterparts intended for similar missions. This involves extensive testing, including hot-fire testing campaigns that simulate multiple mission duty cycles, followed by detailed inspection (NDT, potentially destructive evaluation of samples) to validate its durability and resistance to failure modes like low-cycle fatigue, creep, and thermal degradation. There isn’t a single “typical” lifespan; it’s application-specific and must be proven through qualification testing.
Conclusion: Propelling the Future of Spaceflight with Additively Manufactured Injectors
Metal Additive Manufacturing has irrevocably transformed the landscape of rocket propulsion engineering. For critical components like injectors, AM is not merely an alternative production method; it is an enabling technology, unlocking unprecedented levels of design complexity, performance optimization, and development speed. The ability to print monolithic injectors from high-performance superalloys like IN718 and IN625, incorporating intricate conformal cooling channels and highly optimized spray geometries, directly translates into more efficient, more reliable, and potentially lighter rocket engines.
Harnessing these benefits requires a holistic approach. It begins with embracing Design for Additive Manufacturing (DfAM) principles to fully leverage geometric freedom while respecting process constraints. It necessitates the use of advanced materials – specifically high-quality, aerospace-grade metal powders with controlled characteristics – and meticulously optimized printing processes. Furthermore, the journey from printed part to flight-ready hardware involves a critical chain of post-processing steps, including stress relief, precise heat treatments, Hot Isostatic Pressing (HIP), and often final machining and rigorous NDT, all governed by stringent aerospace quality standards.
The success of implementing AM for demanding applications hinges significantly on selecting the right manufacturing partner. Expertise in superalloys, AS9100-certified quality systems, comprehensive technological capabilities spanning printing through post-processing and inspection, and a collaborative engineering approach are non-negotiable criteria.
Met3dp stands at the forefront of this technological wave, offering comprehensive additive manufacturing solutions. With industry-leading expertise in developing and producing high-quality metal powders via advanced atomization techniques, coupled with state-of-the-art AM printing systems and a deep understanding of application requirements across aerospace, medical, and automotive sectors, Met3dp is uniquely positioned to support the next generation of manufacturing.
As the space industry continues its rapid evolution towards more capable, reusable, and cost-effective launch systems, metal additive manufacturing will undoubtedly play an increasingly vital role. Additively manufactured injectors are not just a possibility; they are rapidly becoming the standard for achieving the performance and reliability demanded by the future of spaceflight.
Ready to explore how metal additive manufacturing can elevate your aerospace components? Kontaktieren Sie Met3dp noch heute to discuss your project requirements with our team of experts and discover how our advanced powder technology and AM solutions can help you achieve your manufacturing goals.
Teilen auf
MET3DP Technology Co., LTD ist ein führender Anbieter von additiven Fertigungslösungen mit Hauptsitz in Qingdao, China. Unser Unternehmen ist spezialisiert auf 3D-Druckgeräte und Hochleistungsmetallpulver für industrielle Anwendungen.
Fragen Sie an, um den besten Preis und eine maßgeschneiderte Lösung für Ihr Unternehmen zu erhalten!
Verwandte Artikel
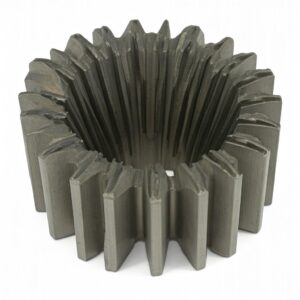
Hochleistungs-Düsenschaufelsegmente: Revolutionierung der Turbineneffizienz mit 3D-Metalldruck
Mehr lesen "Über Met3DP
Aktuelles Update
Unser Produkt
KONTAKT US
Haben Sie Fragen? Senden Sie uns jetzt eine Nachricht! Wir werden Ihre Anfrage mit einem ganzen Team nach Erhalt Ihrer Nachricht bearbeiten.
Holen Sie sich Metal3DP's
Produkt-Broschüre
Erhalten Sie die neuesten Produkte und Preislisten
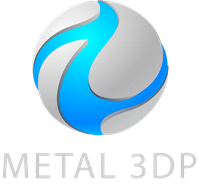
Metallpulver für 3D-Druck und additive Fertigung
UNTERNEHMEN
PRODUKT
cONTACT INFO
- Qingdao Stadt, Shandong, China
- [email protected]
- [email protected]
- +86 19116340731