Rocket Engine Baffles via Additive Manufactured Superalloys
Inhaltsübersicht
Introduction: The Critical Role of Baffles in Modern Rocket Propulsion
The relentless pursuit of higher performance, efficiency, and reliability in rocket propulsion systems drives continuous innovation across the aerospace industry. From interplanetary missions to commercial satellite launches and defense applications, the demands placed on rocket engines are immense. These complex machines operate under conditions of extreme temperature, pressure, and vibration, necessitating components designed and manufactured to withstand the harshest environments imaginable. Among the critical elements within a rocket engine’s thrust chamber assembly are baffles – seemingly simple components that play a profoundly important role in ensuring stable and efficient combustion.
Rocket engine baffles are strategically placed structures, often within the injector faceplate or combustion chamber, designed primarily to suppress combustion instabilities. These instabilities, manifesting as high-frequency pressure oscillations, can severely degrade engine performance, damage critical hardware, and even lead to catastrophic failure. By interrupting acoustic wave propagation pathways and altering flow dynamics, baffles act as crucial dampers, ensuring the smooth, controlled release of energy that propels spacecraft. Furthermore, baffles can contribute to thermal management, protecting sensitive components like the injector face from the intense heat of combustion, and influencing fuel-oxidizer mixing patterns. As launch vehicle manufacturers and space exploration agencies push the boundaries of performance, the design and production of sophisticated, highly resilient baffles become paramount. Traditionally, manufacturing these components involved complex machining, joining, and assembly processes, often limiting design possibilities and incurring significant lead times and costs. However, the advent of 3D-Druck von Metall, or additive manufacturing (AM), particularly using high-performance superalloys, is revolutionizing how rocket engine baffles are conceived, designed, and produced. This technology unlocks unprecedented design freedom, enabling the creation of intricate internal cooling channels, complex geometries optimized for acoustic damping, and consolidated part designs that were previously impossible or impractical to manufacture. Companies seeking reliable aerospace component suppliers and manufacturers are increasingly turning to AM specialists capable of handling demanding superalloys and meeting stringent quality requirements. This shift signifies a major leap forward in propulsion technology, promising lighter, more efficient, and more reliable rocket engines for the future of space exploration and utilization. This article delves into the specifics of using additive manufacturing, particularly with advanced superalloys like IN718 and Haynes 282, to produce high-performance rocket engine baffles, exploring the applications, benefits, material considerations, and manufacturing nuances involved.
The challenge of combustion instability has plagued rocket engine development since its inception. Early liquid-propellant rocket engines, particularly larger ones, frequently encountered destructive oscillations that baffled engineers. Understanding and mitigating these instabilities became a primary focus of research and development. Baffles emerged as one of the most effective passive control devices. Their effectiveness lies in their ability to interfere with the feedback loop that sustains combustion instabilities. This loop typically involves coupling between the combustion process (heat release fluctuations) and the chamber acoustics (pressure waves). Pressure waves generated by combustion can travel through the chamber, reflect off surfaces, and return to the combustion zone, influencing further heat release in a way that reinforces the oscillations. Baffles introduce acoustic impedance mismatches and damping, effectively breaking this resonant coupling. They achieve this through several mechanisms:
- Acoustic Damping: Baffles act as physical barriers that absorb, scatter, and dissipate acoustic energy. Their geometry, placement, and internal structure (if any) are carefully designed to target specific instability modes (frequencies and shapes) predicted by computational fluid dynamics (CFD) and acoustic modeling.
- Flow Disruption: By protruding into the combustion chamber or segmenting the injector face, baffles alter the flow patterns of propellants and combustion gases. This can disrupt the organized structures of vortices or recirculation zones that might otherwise contribute to instability coupling.
- Compartmentalization: In some designs, particularly on the injector face, baffles create compartments that isolate different regions of combustion. This prevents instabilities originating in one zone from easily propagating and amplifying across the entire chamber.
Beyond stability control, baffles often serve secondary but vital roles:
- Thermal Protection: Injector faceplates are subjected to intense heat flux. Baffles can shield portions of the faceplate or incorporate internal cooling channels (made possible by AM) to manage temperatures and prevent overheating or erosion.
- Mixing Enhancement/Control: The placement and shape of baffles can influence how fuel and oxidizer streams mix near the injector, potentially affecting combustion efficiency and performance, although stability remains their primary function.
The traditional manufacturing approaches for baffles, such as machining from billet stock or casting followed by machining and welding/brazing, face significant limitations, especially as baffle designs become more complex to handle higher performance engines:
- Geometric Constraints: Machining intricate internal features like curved cooling channels or fine acoustic damping structures is extremely difficult, costly, and sometimes impossible. Complex undercuts and internal voids are often non-manufacturable.
- Materialabfälle: Subtractive processes like machining can generate substantial material waste, particularly when starting with large billets of expensive superalloys.
- Joining Processes: Assembling baffles from multiple machined or cast pieces introduces potential weak points at joints (welds or brazes), which must withstand extreme stress and temperature gradients. These joints require rigorous inspection and can complicate thermal management.
- Vorlaufzeiten: The multi-step nature of traditional manufacturing, involving tooling, casting, machining, joining, and inspection, results in long lead times, hindering rapid design iteration and development cycles crucial in the aerospace industry.
Additive manufacturing directly addresses these limitations. By building baffles layer by layer from metal powder, AM offers:
- Unerreichte Gestaltungsfreiheit: Enabling complex internal channels, optimized topologies, lattice structures for lightweighting and enhanced damping, and conformal cooling pathways that closely follow the baffle’s surfaces.
- Teil Konsolidierung: Allowing multiple components of a baffle assembly to be printed as a single, monolithic part, eliminating joints, reducing weight, and simplifying assembly.
- Geringerer Materialabfall: Using material only where needed, making AM a more sustainable option, especially with costly superalloys.
- Beschleunigte Entwicklung: Facilitating rapid prototyping and design iterations, significantly shortening the development cycle for new engine components.
The integration of additive manufacturing into the production of critical components like rocket engine baffles represents a paradigm shift, empowering aerospace engineers to design and build propulsion systems that are more robust, efficient, and capable than ever before. As specialist AM providers like Met3dp refine processes for superalloys and demonstrate consistent quality and reliability, the adoption of AM for such demanding applications will only continue to grow, pushing the frontiers of space technology. Met3dp, headquartered in Qingdao, China, leverages its expertise in advanced powder manufacturing and metal 3D-Druck systems to support precisely these kinds of demanding aerospace applications, offering high-quality superalloy powders and printing services.
What Are Rocket Engine Baffles Used For? Defining Function and Importance
Rocket engine baffles are integral components within the combustion chamber or injector assembly, primarily tasked with ensuring the stability and efficiency of the combustion process. Their function is critical, as uncontrolled combustion can lead to mission failure. Understanding their specific roles requires delving into the physics of rocket propulsion and the challenges inherent in burning massive amounts of propellant under extreme conditions.
Primary Function: Suppression of Combustion Instabilities
The core purpose of nearly all rocket engine baffles is to prevent or suppress combustion instabilities. These are self-sustaining oscillations in chamber pressure, often coupled with fluctuations in heat release rate from the burning propellants. They can range from relatively low-frequency “chugging” to damaging high-frequency “screeching” or “screaming.”
- Mechanism of Instability: In a simplified view, imagine a small, random increase in pressure within the chamber. This pressure wave travels, reflects, and potentially returns to the combustion zone. If it arrives at a moment when it encourages more propellant to burn (e.g., by increasing mixing or reaction rates), this generates an even stronger pressure pulse. If the timing (phase) is right, this feedback loop amplifies, leading to large-scale, potentially destructive oscillations. The chamber geometry, propellant types, injection method, and operating conditions all influence which frequencies are most prone to instability.
- How Baffles Intervene: Baffles act as acoustic dampers and flow disruptors to break this feedback cycle.
- Acoustic Damping: They introduce physical barriers that increase the acoustic losses within the chamber. Sound waves reflecting off or passing through baffle structures lose energy due to viscous effects, thermal conduction at surfaces, and geometric scattering. Complex internal structures within baffles, manufacturable via AM, can be specifically tuned to dampen problematic frequencies. Think of them like acoustic tiles in a recording studio, but designed for a hellishly energetic environment.
- Flow Field Modification: By physically dividing the injector face or protruding into the chamber, baffles alter the paths of propellant streams and combustion gases. This can prevent the formation of large, coherent structures (like swirling vortexes) that might otherwise couple strongly with acoustic modes. They effectively compartmentalize the combustion process, making it harder for localized disturbances to grow into chamber-wide instabilities.
Types of Baffles and Their Placement:
The specific design and location of baffles depend heavily on the engine type (e.g., liquid bipropellant, solid rocket motor), the specific instability modes anticipated, and the overall engine architecture. Common types include:
- Injector Face Baffles: These are perhaps the most common type in liquid bipropellant engines. They often consist of radial “spokes” or a “hub-and-spoke” pattern mounted directly onto the injector faceplate. This arrangement divides the injection area into smaller segments (pie-shaped or annular), limiting the cross-chamber communication of acoustic waves and disrupting transverse instability modes. They can be integrated directly into the injector design or attached as separate components. AM allows for intricate cooling channels to be embedded within these baffles to protect them and the underlying injector face.
- Acoustic Cavities/Resonators: Sometimes, instead of solid baffles, designers incorporate cavities or Helmholtz resonators into the chamber walls or injector face. These act like tuned absorbers, damping specific resonant frequencies. AM enables the precise fabrication of these complex resonant geometries.
- Chamber Baffles: Less common in liquid engines but sometimes used, these might be annular rings or other structures placed further down in the combustion chamber itself to interfere with longitudinal or bulk instability modes.
- Solid Rocket Motor (SRM) Baffles: SRMs can also experience instabilities, often driven by interactions between gas flow and the burning propellant surface (propellant grain). Fins or other baffle-like structures might be incorporated into the grain design or chamber insulation to disrupt acoustic modes, though the mechanisms differ somewhat from liquid engines.
Secondary Functions:
While stability is paramount, baffles contribute to other aspects of engine operation:
- Wärmemanagement: Injector faces, especially near the center, experience extreme heat loads. Baffles can physically shield parts of the injector or, more effectively with AM, incorporate sophisticated internal cooling channels using propellant flow (regenerative cooling) or a separate coolant circuit. This prevents material degradation and ensures the injector’s structural integrity and functional longevity. Designing conformal cooling channels that precisely follow the contours of the baffle, enabled by AM, maximizes cooling efficiency.
- Mixing Control: The presence of baffles inevitably influences the local flow field near the injectors. While not typically their primary design goal, this interaction can subtly affect propellant mixing efficiency. Designers must account for this to ensure performance targets are met alongside stability requirements. Poorly designed baffles could potentially hinder efficient mixing, leading to performance losses.
- Strukturelle Unterstützung: In some integrated designs, baffles might provide structural reinforcement to the injector faceplate itself.
Importance in the Aerospace Context:
The reliability demanded of rocket engines, particularly for human spaceflight and high-value payloads, makes effective baffle design non-negotiable.
- Mission Success: Combustion instabilities can lead to reduced thrust, inefficient propellant consumption, severe vibrations damaging the engine or spacecraft, and, in worst-case scenarios, rapid engine destruction. Baffles are a primary line of defense against these failure modes.
- Performance Enablement: As engineers push for higher chamber pressures and more energetic propellants to increase engine performance (thrust and specific impulse), the tendency towards instability often increases. Advanced baffle designs, enabled by AM, are crucial for achieving these higher performance levels reliably.
- Cost and Schedule: Engine failures during testing or flight are incredibly expensive. Robust stability margins, ensured by effective baffles, reduce the risk of costly setbacks during development and operation. While baffle manufacturing itself has costs, it pales in comparison to the cost of an engine failure. Utilizing AM can potentially shorten development cycles through faster iteration on baffle designs compared to traditional methods.
Procurement managers and engineers sourcing components for aerospace projects must recognize the criticality of baffles. They are not merely passive pieces of metal; they are carefully engineered devices essential for the safe and effective operation of the entire propulsion system. Partnering with suppliers who possess deep expertise in both materials science (especially superalloys) and advanced manufacturing techniques like AM is crucial. Met3dp, with its focus on high-performance metal powders and industrial 3D printing solutions, aligns perfectly with the needs of aerospace manufacturers seeking cutting-edge baffle production capabilities. Their understanding of material properties and process control is vital for producing baffles that meet the stringent demands of rocket propulsion.
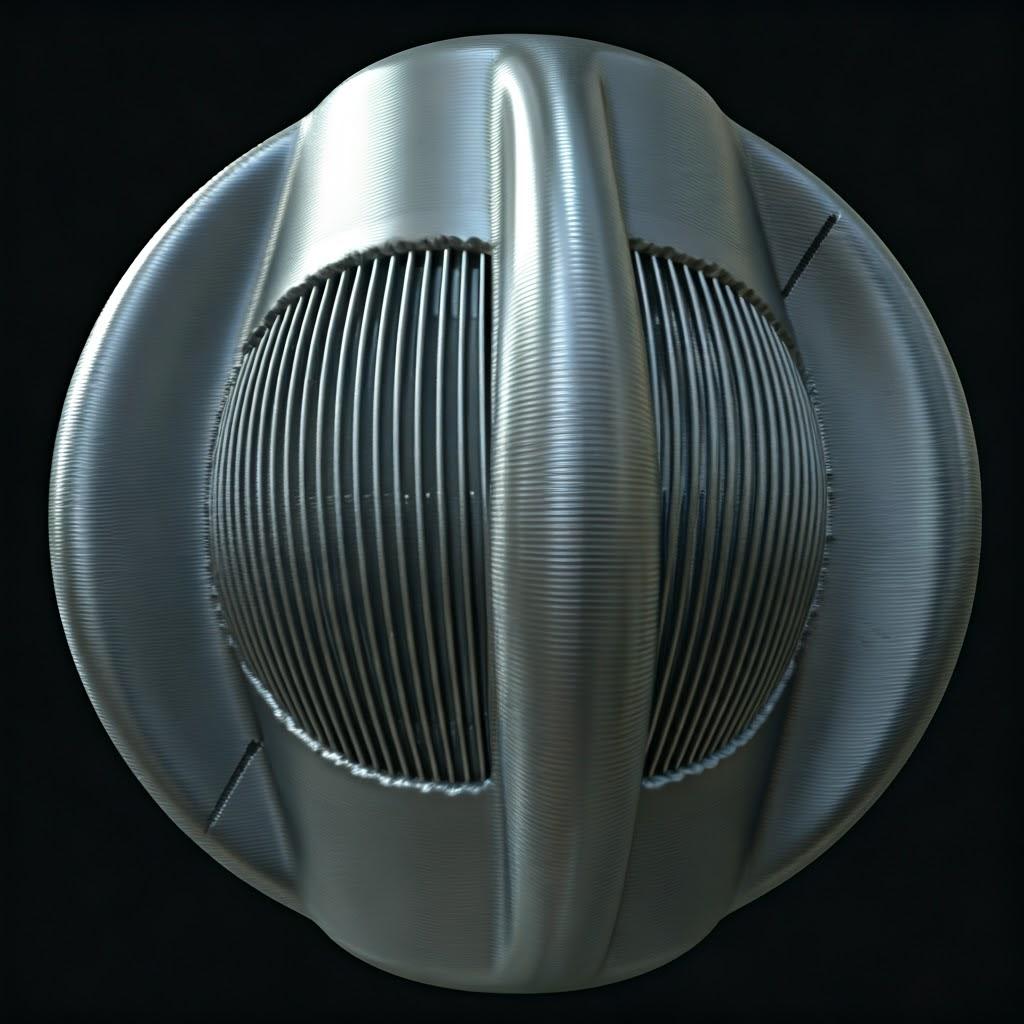
Why Metal 3D Printing for Rocket Engine Baffles? Advantages Over Conventional Methods
The decision to adopt metal additive manufacturing (AM) for critical components like rocket engine baffles isn’t merely about embracing novelty; it’s driven by tangible engineering and economic advantages that directly address the shortcomings of traditional manufacturing techniques (casting, forging, machining, brazing/welding). For aerospace engineers and procurement managers evaluating production methods, understanding these benefits is key to leveraging AM’s full potential, especially when dealing with complex geometries and high-performance superalloys like IN718 and Haynes 282.
1. Unprecedented Design Freedom and Geometric Complexity:
- Traditional Limitations: Machining struggles with internal features, undercuts, and complex curves. Imagine trying to machine intricate, smoothly curving cooling channels deep inside a solid block of metal. Casting can achieve some complexity but often lacks precision and requires secondary machining. Joining multiple simple parts introduces weak points and increases assembly complexity.
- AM Vorteil: AM builds parts layer by layer directly from a 3D CAD model. This fundamental difference liberates designers from many traditional manufacturing constraints.
- Interne Kanäle: AM excels at creating complex internal cooling channels that conform precisely to the baffle’s shape (conformal cooling). This allows for highly efficient thermal management, critical for protecting baffles and injector faces from extreme temperatures. Channels can follow curved paths, vary in cross-section, and reach areas inaccessible by drills or mills.
- Optimized Topologies: Designers can use topology optimization software to remove material from low-stress areas, creating lightweight yet strong baffle structures. This often results in organic, lattice-like geometries that are impossible to machine conventionally but straightforward for AM. Lightweighting is crucial in aerospace for maximizing payload capacity.
- Acoustic Tuning: The geometry of baffles significantly influences their acoustic damping properties. AM allows the creation of intricate internal features, resonant chambers, or specific surface textures designed to absorb or scatter acoustic energy at targeted instability frequencies more effectively than simple solid shapes.
- Integrierte Funktionen: Features like mounting points, sensor ports, or flow guides can be directly integrated into the baffle during the printing process, reducing part count and assembly steps.
2. Part Consolidation:
- Traditional Approach: Complex baffle assemblies might consist of multiple machined or cast pieces that need to be precisely fitted and joined (e.g., welded or brazed). Each joint represents a potential failure point, requires inspection, and adds weight and assembly time.
- AM Vorteil: AM enables the printing of an entire complex baffle assembly as a single, monolithic component.
- Elimination of Joints: This removes the risks associated with welds or brazes in high-stress, high-temperature environments. Monolithic parts are often structurally superior.
- Reduzierte Teileanzahl: Simplifies inventory management, supply chain logistics, and final engine assembly.
- Gewichtsreduzierung: Eliminating fasteners, flanges, and overlapping material needed for joining contributes to overall weight savings.
3. Accelerated Development and Rapid Prototyping:
- Traditional Timelines: Creating tooling for casting or complex machining setups takes significant time and investment. Iterating on a design traditionally involves repeating these lengthy processes.
- AM Vorteil: AM is a tool-less process. Going from a revised CAD model to a physical prototype can often be done in days or weeks, rather than months.
- Faster Iteration: Engineers can quickly test different baffle geometries (e.g., varying spoke count, channel designs, damping features) to find the optimal configuration for stability and thermal performance. This rapid feedback loop significantly shortens the engine development cycle.
- Geringere Entwicklungskosten: While individual AM parts might seem expensive initially, the ability to iterate quickly and avoid tooling costs can dramatically lower overall development program expenses.
4. Material Efficiency and Reduced Waste:
- Traditional Waste: Subtractive manufacturing, especially machining from billet, can generate significant amounts of material waste (chips and shavings). With expensive superalloys like IN718 or Haynes 282, this waste represents a substantial cost.
- AM Vorteil: AM is an additive process, using only the material needed to build the part, plus some support structures. While some powder management and support removal are necessary, the overall material utilization is typically much higher than subtractive methods.
- Einsparmaßnahmen: Reduced raw material consumption directly translates to lower component costs, particularly for buy-to-fly ratios common in aerospace.
- Nachhaltigkeit: Less waste generation contributes to more environmentally conscious manufacturing practices.
5. Suitability for High-Performance Materials:
- Herausforderungen bei der Bearbeitung: Superalloys like IN718 and Haynes 282 are notoriously difficult to machine due to their high strength, toughness, and work-hardening characteristics. This leads to slow machining rates, rapid tool wear, and increased manufacturing costs.
- AM Vorteil: While printing superalloys presents its own set of challenges (requiring careful process control), AM processes like Laser Powder Bed Fusion (L-PBF) and Electron Beam Melting (EBM) are well-suited for melting and fusing these high-temperature materials layer by layer.
- Process Adaptability: AM parameters (laser power, scan speed, beam focus, layer thickness, chamber temperature) can be precisely controlled and optimized for specific superalloys to achieve dense, high-quality parts with desirable microstructures and mechanical properties. Companies like Met3dp specialize in optimizing these parameters using their advanced printing systems and high-quality metal powders.
Comparative Summary Table:
Merkmal | Traditional Manufacturing (Machining/Casting/Joining) | Additive Fertigung von Metall (AM) | Advantage of AM for Baffles |
---|---|---|---|
Geometrische Komplexität | Begrenzte, insbesondere interne Funktionen | High, enables complex internal channels, lattices | Optimized cooling, acoustic damping, lightweighting possible |
Teil Konsolidierung | Requires joining multiple parts | Enables monolithic single-piece construction | Eliminates joints (weak points), reduces part count, simplifies assembly |
Development Speed | Slow (tooling, multi-step process) | Fast (tool-less, direct from CAD) | Rapid prototyping and design iteration, shorter development cycles |
Materialabfälle | High (subtractive processes) | Niedrig (additives Verfahren) | Cost savings on expensive superalloys, more sustainable |
Vorlaufzeit | Long (tooling, multiple operations) | Potentially Shorter (especially for complex parts) | Faster delivery for prototypes and potentially low-volume production |
Superalloy Handling | Difficult and costly to machine | Well-suited (L-PBF, EBM), though requires expertise | Enables use of ideal high-temp materials without extreme machining costs |
Initial Cost (Single) | Can be lower for very simple shapes/high volume | Can be higher for simple parts, competitive for complex | Cost-effective for complex geometries, part consolidation benefits |
Werkzeugkosten | High (molds, dies, fixtures) | Keiner | Eliminates major upfront investment, flexible production |
In Blätter exportieren
Conclusion for Procurement and Engineering:
For rocket engine baffles, where complex geometries for thermal management and acoustic damping are increasingly necessary, and where high-temperature superalloys are essential, the advantages of metal AM are compelling. It enables the creation of components that are potentially lighter, more efficient, more reliable (due to part consolidation), and faster to develop than those made conventionally. While expertise in process control, material science, and post-processing is crucial, partnering with a knowledgeable AM provider like Met3dp, which offers both advanced printing equipment and optimized hochwertige Metallpulver, allows aerospace companies to fully exploit these benefits. The transition towards AM for such critical parts is not just a trend; it’s a strategic move to enhance propulsion system capability and competitiveness in the demanding aerospace sector.
Material Focus: IN718 and Haynes 282 Superalloys for Extreme Environments
The selection of materials for rocket engine components is dictated by the extraordinarily harsh operating environment: extreme temperatures (often exceeding 1000°C, potentially reaching >3000°C in the combustion core), high pressures, severe thermal cycling, intense vibrations, and exposure to corrosive combustion products. Rocket engine baffles, situated directly in or near this hostile zone, demand materials that retain exceptional mechanical properties and environmental resistance under these conditions. Nickel-based superalloys are the workhorses for such applications, and among them, Inconel 718 (IN718) and Haynes 282 stand out as prime candidates, particularly well-suited for additive manufacturing. Understanding their properties is crucial for engineers designing baffles and procurement managers sourcing materials and manufacturing services.
What are Superalloys?
Superalloys are metallic alloys, typically based on nickel, cobalt, or iron, engineered to exhibit outstanding mechanical strength, resistance to creep (deformation under long-term stress at high temperature), good surface stability, and exceptional resistance to corrosion and oxidation at elevated temperatures (generally above 540°C or 1000°F). Their performance relies on complex microstructures, often featuring a face-centered cubic (FCC) austenite matrix strengthened by precipitates (like gamma prime γ’ and gamma double-prime γ”) and solid-solution strengthening elements.
Inconel 718 (IN718 / Alloy 718): The Established Workhorse
IN718 is arguably the most widely used nickel-based superalloy due to its excellent combination of properties, good fabricability (including weldability and printability), and relatively lower cost compared to some other high-performance superalloys.
- Zusammensetzung: Primarily Nickel (Ni), Chromium (Cr), Iron (Fe), Niobium+Tantalum (Nb+Ta), Molybdenum (Mo), Titanium (Ti), Aluminum (Al). The key strengthening comes from the precipitation of γ” (Ni3Nb) and γ’ (Ni3(Al,Ti)) phases within the FCC matrix.
- Wichtige Eigenschaften:
- Hohe Festigkeit: Excellent tensile, yield, creep, and rupture strength up to about 700°C (1300°F). Its strength is largely derived from the precipitation of the γ” phase, which requires a specific heat treatment cycle.
- Gute Korrosionsbeständigkeit: The high chromium content provides good resistance to oxidation and corrosion in various environments, including combustion atmospheres.
- Excellent Weldability/Printability: Compared to many other precipitation-strengthened superalloys, IN718 exhibits superior resistance to strain-age cracking during welding or the layer-by-layer thermal cycles of AM. This makes it relatively easier to process via L-PBF and EBM, achieving dense, crack-free parts.
- Good Fatigue Life: Important for components subjected to vibrational loads.
- Wide Availability and Database: Extensive data exists on its properties and processing, providing confidence for designers and manufacturers.
- Additive Manufacturing Considerations:
- IN718 is one of the most mature materials for metal AM. Optimized parameters for L-PBF and EBM are well-established.
- Requires post-processing heat treatments (solution annealing and aging) to develop the desired microstructure and achieve optimal mechanical properties. Hot Isostatic Pressing (HIP) is often employed to close any residual internal porosity and further enhance fatigue properties.
- Met3dp produces high-quality, gas-atomized IN718 powder specifically optimized for AM processes, ensuring high sphericity, good flowability, and controlled particle size distribution, which are critical for achieving consistent, high-density prints.
- Beschränkungen: While excellent, its strength begins to drop off more significantly above 700°C compared to some more advanced superalloys. For components experiencing even higher sustained temperatures, alternatives might be necessary.
Haynes 282: The Advanced Contender for Higher Temperatures
Haynes 282 is a newer generation gamma-prime (γ’) strengthened superalloy developed specifically for improved creep strength, thermal stability, fabricability, and weldability compared to other high-strength alloys like Waspaloy or R-41, targeting applications in the 650-930°C (1200-1700°F) range.
- Zusammensetzung: Primarily Nickel (Ni), Chromium (Cr), Cobalt (Co), Molybdenum (Mo), Titanium (Ti), Aluminum (Al), with additions like Boron (B) for enhanced creep resistance. Its strengthening relies heavily on the precipitation of the γ’ phase.
- Wichtige Eigenschaften:
- Superior Creep Strength: Offers significantly better creep resistance than IN718 and Waspaloy, particularly in the 750°C – 900°C range. This is crucial for components under sustained load at very high temperatures.
- Ausgezeichnete thermische Stabilität: Resists microstructural degradation during long exposures to high temperatures.
- Gute Oxidationsbeständigkeit: Comparable or superior to other high-performance superalloys.
- Good Fabricability: Designed for improved weldability and resistance to strain-age cracking compared to similarly strong alloys like Waspaloy, making it amenable to AM.
- Good Fatigue Life: Retains strength well under cyclic loading at high temperatures.
- Additive Manufacturing Considerations:
- While newer than IN718 in the AM space, process development for Haynes 282 is rapidly maturing. Achieving optimal properties requires careful control over AM parameters and post-processing heat treatments (solution anneal + multi-step aging).
- Its good weldability translates to relatively good printability, though potentially requiring more stringent process control than IN718 to manage residual stresses and avoid defects.
- The availability of high-quality Haynes 282 powder suitable for AM is crucial. Suppliers focusing on advanced powder production, like Met3dp utilizing gas atomization and PREP technologies, are essential for providing powders with the necessary purity, sphericity, and particle size distribution for demanding applications.
- Application Niche: Ideal for baffles or other engine components that operate consistently at temperatures where IN718’s creep strength becomes marginal, pushing performance envelopes further.
Material Selection Rationale for Baffles:
The choice between IN718 and Haynes 282 for a specific rocket engine baffle depends on a detailed analysis of the operating conditions:
- Peak and Sustained Temperatures: If operating temperatures consistently exceed ~700-750°C, especially under significant mechanical load (pressure differences, vibrations), Haynes 282’s superior creep strength becomes highly advantageous.
- Complexity and Printability: IN718 currently has a more established and potentially more forgiving processing window for AM, which might be preferred for extremely complex geometries where minimizing print defects is paramount, assuming its properties are sufficient.
- Kosten: IN718 is generally less expensive than Haynes 282, both in raw material cost and potentially in processing maturity. If IN718 meets the performance requirements, it may be the more economical choice.
- Fähigkeit der Lieferanten: The ability of the chosen AM service provider to reliably process the selected alloy is critical. This includes having validated process parameters, appropriate post-processing capabilities (vacuum furnaces for heat treatment, HIP), and rigorous quality control.
Met3dp’s Role in Material Provision:
A company like Met3dp plays a vital role in enabling the use of these advanced materials. Their capabilities are crucial at the foundation of the AM process:
- Fortschrittliche Pulverproduktion: Utilizing industry-leading techniques like Vacuum Induction Melting Gas Atomization (VIGA) and Plasma Rotating Electrode Process (PREP), Met3dp can produce superalloy powders (including IN718 and potentially Haynes 282 or custom variants) with:
- Hohe Reinheit: Minimizing contaminants that could compromise material properties.
- Hohe Sphärizität: Ensuring good powder flowability in AM machines, leading to uniform layer spreading and consistent melt pool behavior.
- Kontrollierte Partikelgrößenverteilung (PSD): Optimizing PSD for high packing density and predictable melting characteristics.
- Niedriger Satellitengehalt: Reducing issues related to powder spreading and potential defects.
- Sachkenntnis: Decades of collective expertise in metal AM means Met3dp understands the nuances of printing challenging materials like superalloys, potentially offering guidance on material selection and process optimization.
- Integrierte Lösungen: By offering both high-quality powders and advanced printing systems (like their SEBM printers, known for handling high-temperature alloys and reducing residual stress), Met3dp provides a comprehensive solution for aerospace manufacturers looking to implement AM for critical components like baffles.
In summary, IN718 and Haynes 282 represent excellent material choices for additively manufactured rocket engine baffles, offering the necessary high-temperature strength and environmental resistance. IN718 provides a proven, reliable, and cost-effective solution for many applications, while Haynes 282 pushes the temperature capability further for more demanding scenarios. The success of manufacturing baffles from these materials via AM heavily relies on the quality of the input powder and the expertise of the manufacturing partner, highlighting the importance of specialized suppliers in the aerospace supply chain. Sources and related content
Design for Additive Manufacturing (DfAM): Optimizing Baffles for 3D Printing
Transitioning from traditional manufacturing paradigms to additive manufacturing (AM) requires more than simply converting an existing CAD file. To truly unlock the benefits of metal 3D printing for complex components like rocket engine baffles, engineers must embrace Design for Additive Manufacturing (DfAM). DfAM is a methodology that involves designing parts specifically to leverage the unique capabilities and account for the constraints of AM processes like Laser Powder Bed Fusion (L-PBF) and Electron Beam Melting (EBM). Applying DfAM principles to rocket engine baffles can lead to significant improvements in performance (thermal management, acoustic damping), weight reduction, and manufacturing efficiency. Collaborating with an experienced AM service provider, who understands the nuances of various Druckverfahren, is often crucial for successful DfAM implementation.
Key DfAM Principles for Rocket Engine Baffles:
- Leveraging Geometric Freedom for Functional Enhancement:
- Konforme Kühlkanäle: This is one of the most powerful applications of AM for thermally loaded components. Instead of straight drilled holes, AM allows cooling channels to precisely follow the complex contours of the baffle surfaces, maintaining a consistent distance from the hot combustion gases.
- Überlegungen zum Design: Channel diameter (typically >0.5-1mm for cleanability), aspect ratio, minimum bend radii, smooth transitions, and designing for support-free printing where possible are critical. CFD analysis is used to optimize channel paths for maximum heat extraction where needed most.
- Nutzen: Significantly improved cooling efficiency, leading to lower baffle surface temperatures, increased component life, and potentially allowing for higher engine operating temperatures or the use of materials with slightly lower temperature limits.
- Optimized Acoustic Damping Features: Simple solid baffles provide some damping, but AM allows for far more sophisticated designs.
- Gitterförmige Strukturen: Incorporating internal lattice or gyroid structures can dramatically increase the surface area within the baffle, enhancing acoustic energy dissipation through viscous effects. The density and cell type of the lattice can be graded throughout the part to target specific frequencies or provide structural support where needed.
- Resonant Chambers: Designing internal Helmholtz resonators or complex cavity networks tuned to specific problematic instability frequencies can provide highly targeted acoustic damping.
- Nutzen: More effective suppression of combustion instabilities across a wider range of operating conditions, leading to more stable and reliable engine performance.
- Optimierung der Fließwege: The shape of the baffle influences local propellant mixing and gas flow. AM allows for aerodynamically optimized shapes, potentially incorporating features like flow straighteners or controlled turbulence generators if needed, integrated directly into the baffle structure.
- Konforme Kühlkanäle: This is one of the most powerful applications of AM for thermally loaded components. Instead of straight drilled holes, AM allows cooling channels to precisely follow the complex contours of the baffle surfaces, maintaining a consistent distance from the hot combustion gases.
- Teil Konsolidierung:
- Strategie: Identify baffle assemblies previously made from multiple brazed or welded components. Redesign them as a single, monolithic AM part.
- Erwägungen: Ensure the consolidated design is manufacturable via AM (e.g., access for powder removal from internal cavities). Analyze stress concentrations to ensure the monolithic design is robust.
- Nutzen: Eliminates joint failures, reduces weight, simplifies assembly, shortens supply chain, improves structural integrity.
- Lightweighting through Topology Optimization:
- Strategie: Use Finite Element Analysis (FEA) to understand the stress distribution within the baffle under operational loads (pressure, vibration, thermal stress). Employ topology optimization software to systematically remove material from low-stress regions while maintaining structural integrity and functional surfaces.
- Ergebnis: Often produces organic, load-path-optimized structures that are significantly lighter than traditional designs. These complex shapes are ideally suited for AM.
- Nutzen: Reduced component weight is critical in aerospace to increase payload capacity and reduce launch costs.
- Designing for Manufacturability (AM Constraints):
- Support Structure Minimization: Support structures are often necessary in L-PBF and EBM to anchor the part to the build plate, support overhanging features, and conduct heat away. However, supports consume extra material, add print time, require removal (which can be difficult, especially for internal channels), and can affect surface finish.
- Techniques: Orient the part strategically on the build plate to minimize overhangs. Utilize self-supporting angles (typically >40-45° from the horizontal for many processes/materials, though this varies). Design internal channels with diamond or teardrop cross-sections instead of circular to make them self-supporting. Employ sacrificial features or structures designed for easier break-off.
- Minimum Feature Size and Wall Thickness: AM processes have limitations on the smallest features they can reliably produce. Walls that are too thin may warp or not resolve properly. Typical minimum wall thicknesses are often in the range of 0.3-0.5 mm, but depend heavily on the specific machine, material, and feature geometry.
- Entfernung von Puder: For designs with internal cavities or complex channels, ensure there are adequate openings designed for removing unfused powder after the build. Trapped powder adds weight and can be detrimental. Consider vibration or airflow paths for powder evacuation.
- Thermal Management During Build: Very large or dense parts can accumulate significant thermal stress. DfAM might involve designing relief features or optimizing the build layout to mitigate warping and distortion. EBM, with its high-temperature build environment, inherently reduces thermal gradients and residual stress compared to L-PBF.
- Support Structure Minimization: Support structures are often necessary in L-PBF and EBM to anchor the part to the build plate, support overhanging features, and conduct heat away. However, supports consume extra material, add print time, require removal (which can be difficult, especially for internal channels), and can affect surface finish.
DfAM Workflow Considerations:
- Close Collaboration: Effective DfAM requires close collaboration between design engineers (who understand the functional requirements) and AM specialists (who understand the process capabilities and limitations). Providers like Met3dp, with deep expertise in materials and printing processes, can offer invaluable input during the design phase.
- Simulationsgestützter Entwurf: Utilizing CFD for thermal and flow analysis, FEA for structural and stress analysis, and AM process simulation to predict potential issues like distortion or overheating during the build is highly recommended.
- Iterative Approach: DfAM is often an iterative process. Initial designs are evaluated for manufacturability and performance, then refined based on simulation results or feedback from the AM provider. The rapid prototyping capability of AM facilitates this iterative loop.
By thoughtfully applying DfAM principles, engineers can move beyond simply replicating traditionally designed baffles with AM, instead creating next-generation components that offer superior performance, lower weight, and enhanced reliability, fully capitalizing on the transformative potential of additive manufacturing in aerospace propulsion.
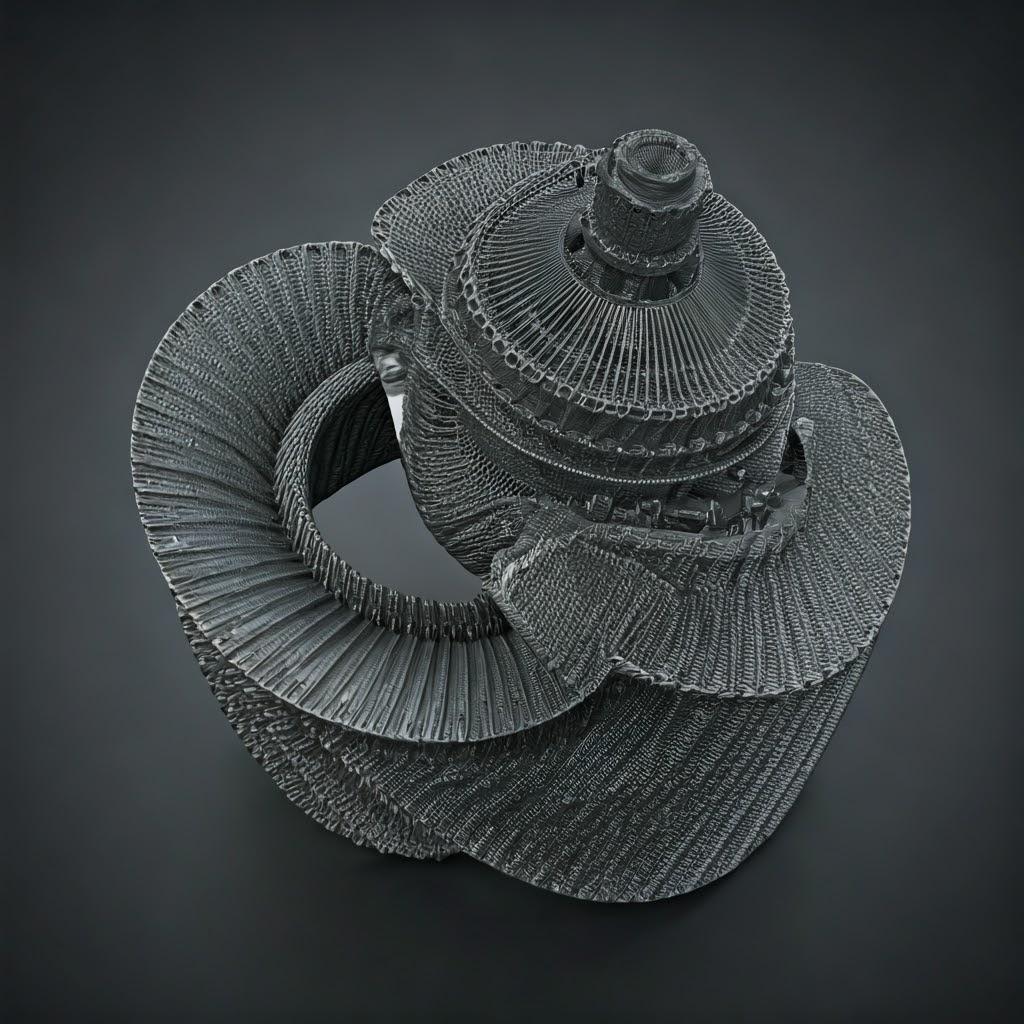
Achievable Tolerances, Surface Finish, and Dimensional Accuracy in AM Baffles
While additive manufacturing offers unparalleled design freedom, it’s crucial for engineers and procurement managers to have realistic expectations regarding the achievable tolerances, surface finish, and overall dimensional accuracy of AM-produced components, particularly for critical applications like rocket engine baffles made from superalloys. These factors directly impact component fit, sealing, fluid dynamics, thermal performance, and the need for subsequent finishing operations. The specific outcomes depend heavily on the chosen AM process (L-PBF vs. EBM), the material (IN718, Haynes 282), machine calibration, part geometry, and post-processing steps.
Maßgenauigkeit und Toleranzen:
Dimensional accuracy refers to how closely the final part dimensions match the nominal dimensions specified in the CAD model. Tolerance defines the permissible range of variation for a given dimension.
- Typische As-Built-Toleranzen:
- L-PBF (Laser Powder Bed Fusion): Generally considered capable of higher accuracy and finer features than EBM. Typical achievable tolerances for well-controlled processes are often in the range of ±0.1 mm to ±0.2 mm (±0.004″ to ±0.008″) for smaller dimensions, potentially increasing slightly for larger parts (e.g., ±0.1% to ±0.2% of the overall dimension). Specific machines and optimized processes might achieve even tighter tolerances locally.
- EBM (Electron Beam Melting): EBM operates at higher temperatures, which reduces residual stress but can sometimes lead to slightly lower dimensional accuracy compared to L-PBF due to factors like thermal expansion/contraction and potential powder sintering effects. Typical tolerances might range from ±0.2 mm to ±0.4 mm (±0.008″ to ±0.016″), though improvements are continually being made.
- Faktoren, die die Genauigkeit beeinflussen:
- Kalibrierung der Maschine: Regular and precise calibration of the scanner system, beam focus, and build platform is essential.
- Thermische Effekte: Non-uniform heating and cooling during the build can cause warping and distortion, affecting final dimensions. Process parameters, scan strategies, and build chamber temperature control (especially EBM’s elevated temperature) play a role.
- Part Geometry and Size: Large, bulky parts or those with significant variations in cross-section are more prone to thermal distortion. Internal stresses accumulating over many layers can affect accuracy.
- Materialeigenschaften: Thermal conductivity, expansion coefficient, and melt pool behavior of the specific superalloy influence the process.
- Unterstützende Strukturen: How the part is supported can influence stress accumulation and potential distortion upon removal.
- Nachbearbeiten: Stress relief and HIP cycles can cause minor, generally predictable dimensional changes that need to be accounted for.
- Erzielung engerer Toleranzen: For critical features like mating surfaces, sealing diameters, or interfaces requiring high precision, as-built AM tolerances may not be sufficient. In these cases, post-machining is employed. Areas requiring tight tolerances are often designed with extra material (machining allowance or “stock”) that is precisely removed using CNC machining after the AM build and heat treatment. Tolerances achievable via post-machining are comparable to conventional machining standards (e.g., ±0.01 mm to ±0.05 mm or better).
Oberflächengüte (Rauhigkeit):
Surface finish, typically quantified by average roughness (Ra), describes the texture of the part’s surfaces. AM parts inherently have a rougher finish than machined surfaces due to the layer-by-layer construction and partially melted powder particles adhering to the surface.
- Typical As-Built Surface Roughness (Ra):
- L-PBF: Generally produces a better surface finish than EBM. Ra values often range from 6 µm to 15 µm (approx. 240 µin to 600 µin) on vertical or near-vertical walls, but can be significantly rougher (e.g., >20 µm) on upward-facing and especially downward-facing surfaces (supported surfaces).
- EBM: Typically results in rougher surfaces compared to L-PBF, often with Ra values ranging from 20 µm to 40 µm (approx. 800 µin to 1600 µin) or higher. This is partly due to the larger beam spot size and higher energy input leading to more powder sintering.
- Factors Influencing Surface Finish:
- Schichtdicke: Thinner layers generally lead to smoother surfaces, especially on sloped features, but increase build time.
- Partikelgrößenverteilung (PSD): Finer powders can contribute to a better finish but may pose challenges for flowability and handling.
- Prozessparameter: Laser/electron beam power, scan speed, and hatch spacing affect melt pool dynamics and surface melt quality.
- Teil Orientierung: Vertical walls tend to be smoother than angled or horizontal surfaces. Downward-facing surfaces supported by structures are usually the roughest after support removal.
- Gas Flow (L-PBF): In L-PBF, the flow of inert gas to remove processing byproducts can influence surface quality.
- Implications of Surface Roughness:
- Fluiddynamik: Rough internal channel surfaces can increase pressure drop and affect flow characteristics.
- Thermal Transfer: Surface roughness can influence heat transfer coefficients.
- Müdigkeit Leben: Rough surfaces can act as initiation sites for fatigue cracks, potentially reducing component life under cyclic loading. HIP processing is crucial for mitigating the effects of surface and subsurface porosity linked to roughness.
- Versiegeln: As-built surfaces are generally unsuitable for dynamic or high-pressure seals.
- Verbesserung der Oberflächengüte: When smoother surfaces are required:
- Nachbearbeiten: Most effective for external surfaces or accessible internal features requiring high smoothness and tight tolerances.
- Abrasive Fließbearbeitung (AFM): Used to polish internal channels and complex passages by flowing abrasive media through them.
- Mass Finishing: Techniques like tumbling or vibratory finishing can improve general surface smoothness but may not be suitable for delicate features or maintaining sharp edges.
- Elektropolieren: Can provide a very smooth finish but requires specific electrolytes and process control.
Das Engagement von Met3dp:
Achieving consistent dimensional accuracy and managing surface finish requires deep process understanding and robust quality control. Companies like Met3dp, focusing on industrial applications in sectors like aerospace, prioritize:
- Hochwertige Pulver: Using powders with controlled sphericity and PSD contributes to more stable melt pools and better surface quality.
- Advanced Printing Systems: Utilizing printers with precise calibration, stable thermal management (including SEBM capabilities beneficial for superalloys), and optimized process parameters.
- Prozesssteuerung und -überwachung: Implementing rigorous quality checks and potentially in-situ monitoring to ensure consistency from build to build.
- Post-Processing Expertise: Understanding the effects of heat treatment and HIP on dimensions and offering integrated post-machining solutions.
Summary Table: AM Baffle Tolerances & Finish
Parameter | Typical L-PBF Range | Typical EBM Range | Wichtige Einflussfaktoren | Improvement Methods |
---|---|---|---|---|
Tolerance (As-Built) | ±0.1 to ±0.2 mm (or ±0.1-0.2%) | ±0.2 to ±0.4 mm (or ±0.2-0.4%) | Machine calibration, thermal effects, geometry, material | Process optimization, Post-Machining (for critical) |
Surface Finish Ra (As-Built) | 6-15 µm (vertical walls) >20 µm (down-facing) | 20-40+ µm | Layer thickness, PSD, parameters, orientation, process type | Post-Machining, AFM, Mass Finishing, Polishing |
In Blätter exportieren
Engineers designing AM rocket baffles must specify required tolerances and surface finishes based on functional requirements, understanding that tighter specifications often necessitate post-processing steps, adding cost and lead time. Clear communication with the AM provider regarding critical features and acceptance criteria is essential for successful component manufacturing.
Essential Post-Processing Steps for Additively Manufactured Baffles
Simply removing a metal 3D printed rocket engine baffle from the build plate is far from the end of the manufacturing journey. For critical aerospace components fabricated from superalloys like IN718 or Haynes 282, a series of essential post-processing steps are required to relieve internal stresses, remove support structures, achieve the desired material microstructure and mechanical properties, ensure dimensional accuracy, attain the required surface finish, and verify part integrity. These steps are non-negotiable for ensuring the safety, reliability, and performance of the final component in the demanding environment of a rocket engine. Neglecting or improperly executing any of these stages can compromise the entire component.
Typical Post-Processing Workflow for AM Superalloy Baffles:
- Stressabbau:
- Zweck: The rapid heating and cooling cycles inherent in L-PBF and, to a lesser extent, EBM create significant residual stresses within the printed part. These stresses can cause distortion (especially after removal from the build plate), cracking, and reduced mechanical performance. Stress relief is a thermal cycle designed to relax these internal stresses before the part is removed from the build plate or undergoes significant handling/machining.
- Prozess: Typically involves heating the part (often while still attached to the build plate) in a controlled atmosphere furnace (inert gas like Argon or vacuum to prevent oxidation) to a temperature below the aging or solution annealing temperatures, holding it for a specific duration, and then slowly cooling it. Exact parameters depend on the alloy and part geometry. EBM parts, built at higher temperatures, generally have lower residual stress but may still benefit from a stress relief cycle.
- Wichtigkeit: Critical first step to prevent cracking or warping during subsequent handling and support removal.
- Entfernen des Teils von der Bauplatte:
- Prozess: Usually achieved using wire EDM (Electrical Discharge Machining), sawing, or sometimes milling/grinding, depending on the part geometry and material.
- Erwägungen: Must be done carefully to avoid damaging the part. The interface layer between the part and the plate is often designed for easier separation.
- Entfernung der Stützstruktur:
- Zweck: Remove the temporary structures used during the build process.
- Prozess: Can range from simple manual breaking/cutting for accessible supports to more complex machining (milling, grinding) or EDM for supports in intricate or internal locations. This can be one of the most labor-intensive and challenging post-processing steps, especially for baffles with complex internal channels or lattice structures.
- Herausforderungen: Risk of damaging the part surface, difficulty accessing internal supports, ensuring complete removal. DfAM plays a crucial role in designing easily removable supports.
- Heat Treatment (Microstructure and Property Development):
- Zweck: As-built AM superalloys typically do not possess the optimal microstructure or mechanical properties (strength, ductility, creep resistance) required for demanding applications. Heat treatment homogenizes the microstructure, dissolves undesirable phases formed during printing, and precipitates the strengthening phases (γ’ and/or γ”) in a controlled manner.
- Process (Example for IN718):
- Lösungsglühen: Heating to a high temperature (e.g., ~980°C – 1065°C depending on desired properties) to dissolve existing precipitates and homogenize the matrix, followed by rapid cooling.
- Behandlung der Alterung: A two-step aging process (e.g., ~720°C followed by ~620°C) to precipitate the γ’ and γ” strengthening phases in the optimal size and distribution.
- Process (Example for Haynes 282): Typically involves a higher solution annealing temperature (e.g., ~1135°C – 1177°C) followed by a multi-step aging process (e.g., ~1010°C followed by ~790°C).
- Umwelt: Must be performed in a vacuum or controlled inert atmosphere furnace to prevent oxidation, especially at the high temperatures involved. Precise temperature control and quench rates are critical.
- Wichtigkeit: Absolutely essential to achieve the required mechanical properties (tensile strength, yield strength, creep resistance, fatigue life) specified for the application. As-built properties are generally inferior.
- Heiß-Isostatisches Pressen (HIP):
- Zweck: To close internal porosity (micro-voids) that may remain after the AM process due to factors like trapped gas or incomplete fusion. Porosity acts as stress concentrators and significantly degrades mechanical properties, particularly fatigue life and fracture toughness. HIP densifies the material, improving its integrity.
- Prozess: The part is subjected to both high temperature (typically just below the solution annealing temperature) and high pressure (e.g., 100-200 MPa or 15,000-30,000 psi) using an inert gas (usually Argon) within a specialized HIP vessel. The combination of heat and pressure causes internal voids to collapse and metallurgically bond shut.
- Wichtigkeit: Widely considered mandatory for critical aerospace components, especially those subjected to fatigue loading. It significantly improves mechanical properties, reduces data scatter, and enhances inspectability. Often performed before or integrated with the solution annealing step of heat treatment.
- Oberflächenveredelung:
- Zweck: To achieve the required surface roughness for functional reasons (e.g., fluid flow, sealing) or to remove surface imperfections that could act as fatigue initiation sites.
- Processes (as needed):
- CNC-Bearbeitung: For critical dimensions, tolerances, and smooth finishes on specific features (e.g., mating faces, seal grooves). Requires careful fixture design for potentially complex AM shapes.
- Abrasive Flow Machining (AFM), Extrude Hone: For smoothing internal channels and passages.
- Mass Finishing (Tumbling, Vibratory): For general deburring and smoothing, if appropriate for the part geometry.
- Manuelles Schleifen/Polieren: For localized finishing or complex shapes.
- Inspection and Non-Destructive Testing (NDT):
- Zweck: To verify the integrity of the final part and ensure it meets all specifications and quality standards before entering service.
- Common Techniques for AM Aerospace Parts:
- Prüfung der Abmessungen: Using CMM (Coordinate Measuring Machines), laser scanning, or structured light scanning to verify dimensions and tolerances against the CAD model.
- Computertomographie (CT) Scannen: X-ray based method providing a 3D view of the part’s internal structure, capable of detecting internal voids, inclusions, cracks, and verifying internal channel geometry. Increasingly vital for complex AM parts.
- Farbeindringprüfung (Dye Penetrant Inspection, DPI) oder Fluorescent Penetrant Inspection (FPI): To detect surface-breaking cracks or porosity.
- Ultraschallprüfung (UT): Can detect subsurface flaws, though complex geometries can be challenging.
- Visuelle Inspektion: Thorough examination under magnification.
- Wichtigkeit: Final quality gate to ensure the baffle is free from critical defects and meets all engineering requirements. Rigorous NDT is standard practice for flight-critical aerospace hardware.
Fähigkeit der Lieferanten:
Executing this complex sequence of post-processing steps requires significant expertise, specialized equipment (vacuum furnaces, HIP units, NDT systems), and robust quality management systems (e.g., AS9100 certification). When selecting an AM service provider for rocket engine baffles, it is crucial to verify their in-house capabilities or their established relationships with certified partners for all necessary post-processing stages. A provider like Met3dp, focused on delivering end-to-end solutions for industrial applications, understands the criticality of these steps and integrates them into their quality assurance protocols. Their knowledge extends beyond printing to encompass the entire manufacturing chain required for aerospace-grade components.
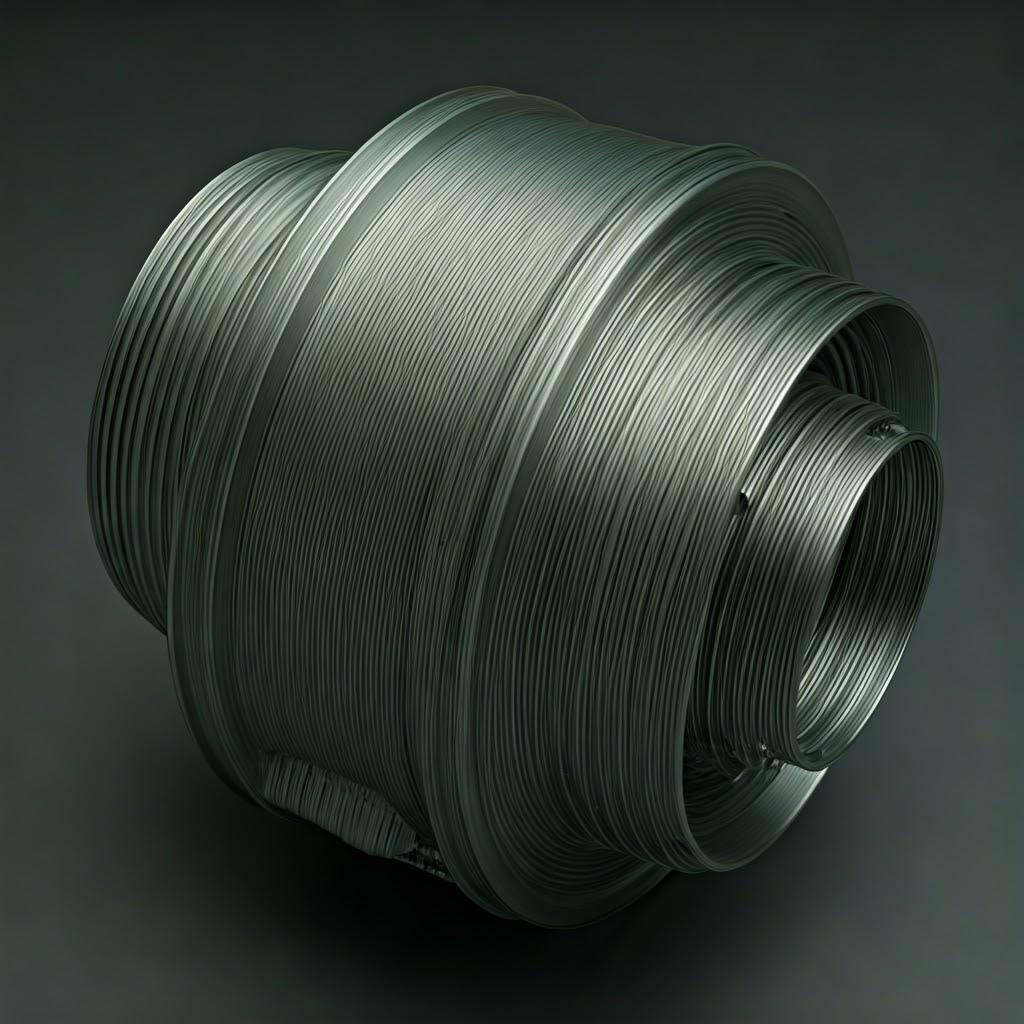
Overcoming Common Challenges in 3D Printing Rocket Engine Baffles
While metal additive manufacturing unlocks significant potential for producing advanced rocket engine baffles, the process is not without its challenges, particularly when dealing with complex geometries and demanding superalloys like IN718 and Haynes 282. Successfully manufacturing flight-worthy components requires anticipating, understanding, and mitigating these potential issues through careful design, rigorous process control, and advanced material science knowledge. Aerospace manufacturers and suppliers must be adept at navigating these hurdles.
1. Residual Stress and Distortion:
- Herausforderung: The rapid, localized heating and cooling inherent in L-PBF and EBM creates steep thermal gradients, leading to the build-up of internal residual stresses as layers solidify and contract. Excessive stress can cause:
- Distortion/Warping: The part deforms during the build or after removal from the build plate, leading to dimensional inaccuracies.
- Knacken: Stresses exceeding the material’s strength at elevated temperatures can cause solidification or liquation cracks during the build.
- Reduced Performance: High residual stresses can negatively impact fatigue life and fracture toughness.
- Strategien zur Schadensbegrenzung:
- Optimierte Scan-Strategien: Using techniques like island scanning, sectoring, or adjusting scan vector lengths and orientations helps distribute heat more evenly and reduce localized stress peaks.
- Build Plate Heating (L-PBF): Pre-heating the build plate reduces the thermal gradient between the solidified material and the new layer, lowering stress accumulation.
- High-Temperature Environment (EBM): EBM inherently operates with the build chamber at elevated temperatures (several hundred °C), significantly reducing thermal gradients and residual stresses compared to most L-PBF systems. This is a key advantage for processing crack-sensitive alloys or large, complex parts.
- Entwurf der Stützstruktur: Supports act as heat sinks and mechanical anchors, influencing stress. Careful design is needed to balance support effectiveness with ease of removal.
- Thermal Post-Processing: Mandatory stress relief cycles (often performed on the build plate) are crucial for relaxing accumulated stresses before part removal. HIP also helps reduce residual stresses.
- AM Process Simulation: Software tools can predict stress accumulation and distortion based on part geometry and process parameters, allowing for design or process adjustments before printing.
2. Support Structure Design and Removal:
- Herausforderung: Baffles often feature complex internal passages, overhangs, and lattice structures that require support during the build. Designing supports that are effective (preventing collapse, conducting heat) yet easily and completely removable without damaging the part is difficult. Internal supports can be particularly challenging or impossible to remove mechanically.
- Strategien zur Schadensbegrenzung:
- DfAM for Support Reduction: Designing features to be self-supporting (using appropriate angles, teardrop/diamond channels) is the most effective approach. Orienting the part optimally on the build plate is key.
- Optimiertes Support-Design: Using support types (e.g., block, cone, tree) and parameters (e.g., density, fragmentation) that balance strength with breakability. Specialized software aids in generating efficient supports.
- Wahl des Materials: Some support materials are designed to be chemically dissolved, though this is less common for high-temperature superalloys.
- Access for Removal: Designing access ports or pathways for removing internal supports or trapped powder.
- Post-Processing Methods: Utilizing CNC machining, EDM, or AFM for precise support removal in difficult areas. Thorough inspection (e.g., borescope, CT scan) is needed to verify complete removal.
3. Powder Quality Management and Handling:
- Herausforderung: The quality and consistency of the metal powder feedstock (IN718, Haynes 282) are paramount. Issues include:
- Kontamination: Introduction of foreign particles or cross-contamination with other alloys can create defects and compromise material properties.
- Abbau des Pulvers: Repeated reuse of powder can alter its chemistry (e.g., oxygen pickup) or morphology (particle shape/size distribution), affecting processability and part quality.
- Flowability Issues: Poor powder flow can lead to uneven layer spreading, causing defects.
- Sicherheit: Handling fine metal powders requires appropriate safety precautions (inert atmospheres, grounding, personal protective equipment) to mitigate explosion or inhalation risks.
- Strategien zur Schadensbegrenzung:
- High-Quality Virgin Powder: Sourcing powder from reputable suppliers like Met3dp, who utilize advanced atomization techniques (VIGA, PREP) and rigorous quality control to ensure high purity, sphericity, controlled PSD, and low satellite content. Information über uns and our commitment to quality powder can be found on our website.
- Strict Powder Handling Protocols: Dedicated equipment, controlled environments (e.g., glove boxes), sieving procedures, and careful tracking of powder batches and reuse cycles.
- Charakterisierung des Pulvers: Regularly testing virgin and reused powder (chemistry, PSD, flowability, morphology) to ensure it remains within specification.
- Atmosphärenkontrolle: Maintaining high-purity inert gas atmospheres (Argon, Nitrogen) in the printer and handling systems to minimize oxygen/moisture pickup.
4. Porosität:
- Herausforderung: The presence of small internal voids (pores) within the printed material. Porosity significantly degrades mechanical properties, especially fatigue life. Causes include:
- Gas Porosität: Trapped gas within the powder particles or dissolved gas in the melt pool coming out of solution during solidification.
- Fehlende Fusionsporosität: Insufficient energy input or improper melt pool overlap leading to incomplete melting between layers or adjacent scan tracks.
- Schlüsselloch-Porosität: Excessive energy density causing vaporization of the metal, leading to instability and gas entrapment when the vapor cavity collapses.
- Strategien zur Schadensbegrenzung:
- Optimierte Prozessparameter: Careful control of laser/beam power, scan speed, layer thickness, hatch spacing, and focus ensures stable melting and complete fusion. Parameter development is alloy-specific.
- Hochwertiges Pulver: Using powder with low internal gas content. Vacuum Induction Melting (VIM) during atomization helps minimize dissolved gases.
- Atmosphärenkontrolle: Ensuring a clean, high-purity inert gas environment in the build chamber.
- Heiß-Isostatisches Pressen (HIP): The most effective method for closing residual porosity (Lack of Fusion and Gas pores) after printing. It’s considered essential for critical components.
5. Cracking:
- Herausforderung: Formation of cracks during solidification (solidification cracking) or in the heat-affected zone during subsequent thermal cycles (liquation cracking). Superalloys, especially highly alloyed ones, can be susceptible due to their wide solidification range and precipitation behavior.
- Strategien zur Schadensbegrenzung:
- Auswahl der Legierung: IN718 and Haynes 282 are generally considered to have relatively good resistance to cracking during AM compared to some other superalloys, which is why they are favored.
- Optimierung der Parameter: Controlling energy input and cooling rates via scan strategy and parameters can minimize cracking susceptibility.
- Wärmemanagement: Build plate heating (L-PBF) or high-temperature operation (EBM) reduces thermal gradients and cracking risk.
- Geeignete Wärmebehandlung: Post-build heat treatments must be carefully selected to avoid detrimental phase precipitation or relaxation mechanisms that could lead to cracking.
Successfully navigating these challenges requires a combination of robust machine technology, high-quality materials, optimized process parameters developed through rigorous experimentation, meticulous process control, comprehensive post-processing, and deep metallurgical expertise. Partnering with an experienced AM service provider equipped with the right tools and knowledge is crucial for producing reliable, high-performance rocket engine baffles that meet the stringent demands of the aerospace industry.
Die Wahl Ihres Partners: Die Auswahl des richtigen Metall-AM-Dienstleisters für Luft- und Raumfahrtkomponenten
The successful adoption of additive manufacturing for flight-critical components like rocket engine baffles hinges not only on advanced design and materials but critically on the capabilities and reliability of the chosen manufacturing partner. Selecting the right metal AM service provider is a crucial decision for aerospace engineers and procurement managers. The stakes are incredibly high, demanding a supplier who demonstrates not just technical proficiency but also an unwavering commitment to quality, traceability, and process control, commensurate with aerospace industry standards. Evaluating potential partners requires a multi-faceted approach, looking beyond mere printing capabilities.
Key Criteria for Evaluating Aerospace AM Suppliers:
- Certifications and Quality Management System (QMS):
- AS9100-Zertifizierung: This is the internationally recognized QMS standard for the aviation, space, and defense industries. AS9100 incorporates ISO 9001 requirements but adds more stringent criteria specific to aerospace, covering aspects like configuration management, risk management, traceability, and verification of purchased products. For flight-critical hardware, partnering with an AS9100 certified supplier is often mandatory or highly preferred. It demonstrates a commitment to rigorous quality control processes.
- Zertifizierung nach ISO 9001: A foundational quality management standard, indicating robust processes for consistency and customer satisfaction.
- Documented QMS: Even beyond certifications, the supplier should have a well-documented and consistently implemented QMS covering all stages from powder handling to final inspection and shipping.
- Technische Kompetenz und Erfahrung:
- Werkstoffkunde: Deep understanding of metallurgy, especially for nickel-based superalloys like IN718 and Haynes 282. This includes knowledge of their behavior during AM processing, required heat treatments, and achievable properties.
- Process Expertise (L-PBF/EBM): Proven capability in operating and optimizing the specific AM technology (e.g., L-PBF, EBM) required for the baffle. Experience with the selected superalloy is paramount. Ask for case studies or evidence of successful projects with similar materials and complexity.
- DfAM-Unterstützung: The ideal partner can collaborate on Design for Additive Manufacturing, providing feedback on design feasibility, suggesting optimizations for printability, support reduction, or performance enhancement.
- Aerospace Application Experience: Demonstrated track record in producing components for aerospace or similarly demanding industries. Understanding the specific requirements and challenges of propulsion systems is a significant advantage.
- Equipment, Technology, and Facilities:
- Appropriate AM Systems: Possessing well-maintained, industrial-grade L-PBF or EBM machines suitable for processing reactive superalloys. Factors include build volume, laser/beam power, atmosphere control, thermal management capabilities (e.g., high build plate heating for L-PBF, high chamber temperature for EBM like Met3dp’s SEBM systems), and monitoring capabilities.
- Handhabung des Pulvers: Dedicated, controlled environment and procedures for handling, storing, sieving, and managing superalloy powders to prevent contamination and ensure consistency.
- Post-Processing Equipment: In-house or tightly controlled access through certified partners for all necessary post-processing steps: stress relief furnaces, vacuum heat treatment furnaces, Hot Isostatic Pressing (HIP) units, CNC machining centers, surface finishing tools, and comprehensive NDT equipment.
- Calibration and Maintenance: Regular, documented calibration and preventative maintenance schedules for all critical equipment (AM machines, furnaces, inspection tools).
- Umfassende Nachbearbeitungsmöglichkeiten:
- As detailed previously, post-processing is critical. Verify the supplier’s capability to manage the entire workflow, including:
- Entspannung
- Support Removal Expertise (especially for complex internal features)
- Precision Heat Treatment (vacuum/inert atmosphere, accurate temperature control)
- HIP Processing (access to certified facilities)
- CNC Machining (for tight tolerances and critical features)
- Surface Finishing (including internal channels if required, e.g., AFM)
- As detailed previously, post-processing is critical. Verify the supplier’s capability to manage the entire workflow, including:
- Rigorous Inspection and NDT Capabilities:
- In-house or partnered access to essential NDT methods like CT Scanning, FPI/DPI, UT, and dimensional inspection tools (CMM, scanners).
- Qualified NDT personnel certified to relevant standards (e.g., NAS 410 / EN 4179).
- Robust inspection protocols integrated throughout the manufacturing process.
- Rückverfolgbarkeit von Materialien:
- Ability to provide complete “cradle-to-grave” traceability for materials, linking the final part back to specific powder batches, processing parameters, heat treatment cycles, and inspection results. This is a fundamental requirement of AS9100.
- Kapazität, Vorlaufzeit und Kommunikation:
- Sufficient machine capacity and workforce to meet project timelines reliably.
- Transparent communication regarding lead times, potential risks, and project status.
- Responsiveness and willingness to collaborate closely with the customer’s engineering team.
Warum eine Partnerschaft mit Met3dp?
While specific certifications should always be verified based on current project requirements, Met3dp embodies many qualities sought in a high-caliber aerospace AM partner:
- Foundation in Materials: As a developer and manufacturer of high-quality metal powders using advanced VIGA and PREP technologies, Met3dp possesses a fundamental understanding of material properties and their interaction with the AM process. This expertise extends to demanding superalloys like IN718.
- Fortgeschrittene AM-Systeme: Offering industrial printers, including Selective Electron Beam Melting (SEBM) technology known for its advantages in processing high-temperature, crack-prone alloys due to its high-temperature build environment, reducing residual stress.
- Integrierte Lösungen: Met3dp positions itself as providing comprehensive solutions, encompassing printers, powders, and application development services, suggesting a capacity for supporting customers from design through production.
- Focus on Industrial Applications: Their target industries include aerospace, medical, and automotive, indicating experience with high-specification requirements and quality expectations.
- Commitment to Quality: Their emphasis on industry-leading accuracy and reliability points towards a culture focused on meeting the stringent demands of sectors like aerospace.
Choosing the right supplier is an exercise in risk management. A thorough evaluation based on these criteria will help ensure that your additively manufactured rocket engine baffles are produced to the highest standards of quality, reliability, and performance, leveraging the full capabilities of this transformative technology.

Understanding Cost Drivers and Lead Times for AM Rocket Baffles
While additive manufacturing offers significant technical advantages for producing complex rocket engine baffles, it’s essential for procurement managers and engineers to understand the factors that influence cost and lead time. A clear picture of these elements allows for better budgeting, planning, and comparison with traditional manufacturing methods or alternative AM suppliers. The cost structure for AM differs from traditional methods, often involving higher initial per-part costs for simple items but becoming competitive or even advantageous for highly complex or consolidated designs, especially when considering total lifecycle and development costs.
Major Cost Drivers for AM Rocket Baffles:
- Materialkosten:
- Pulver Preis: Nickel-based superalloys like IN718 and Haynes 282 are inherently expensive raw materials compared to standard steels or aluminum alloys. Haynes 282 is generally more costly than IN718. Powder quality (purity, sphericity, PSD) also influences price.
- Volume Used: The actual volume of the baffle, plus the volume of required support structures, determines the amount of powder consumed directly in the part.
- Powder Loss/Recycling Efficiency: Some powder is inevitably lost during handling, printing, and recovery. The efficiency of powder sieving and recycling processes impacts the overall material cost per part. Strict quality control on reused powder is necessary, adding some overhead.
- Buy-to-Fly Ratio: AM generally has a much better buy-to-fly ratio (weight of raw material purchased vs. weight of the final part) compared to subtractive machining, which is a significant advantage for expensive materials.
- AM Machine Time:
- Bauzeit: This is often the most significant cost driver. It’s determined by:
- Teil Volumen & Höhe: Larger and taller parts take longer to print.
- Komplexität: Intricate features, thin walls, and lattice structures can require slower scan speeds or specific strategies, increasing time.
- Anzahl der Teile pro Build: Printing multiple parts simultaneously (nesting) can significantly reduce the effective machine time cost per part by optimizing the use of the build platform area and setup time.
- Schichtdicke: Thinner layers improve resolution and surface finish on slopes but increase the number of layers and thus build time.
- Maschine Stundensatz: This rate incorporates machine depreciation, energy consumption, maintenance, facility overheads, and inert gas consumption. Industrial metal AM systems represent a significant capital investment.
- Bauzeit: This is often the most significant cost driver. It’s determined by:
- Arbeitskosten:
- Setup & Teardown: Preparing the machine, loading powder, setting up the build file, and then removing the completed build, cleaning the machine, and harvesting parts requires skilled labor.
- Nachbearbeitungsarbeiten: Dies kann erheblich sein, insbesondere für:
- Unterstützung bei der Entfernung: Manual or semi-automated removal of supports, particularly complex internal ones, can be time-consuming.
- Basic Finishing: Initial surface cleaning or smoothing.
- Inspektion und Qualitätssicherung: Labor associated with dimensional checks, NDT preparation, and documentation.
- Post-Processing Costs (External or Internal):
- Thermische Behandlungen: Stress relief, solution annealing, aging, and HIP cycles require specialized furnaces and HIP units. These processes add significant cost due to equipment operation (energy, inert gas) and cycle time. HIP is particularly costly but often mandatory.
- Bearbeitungen: If tight tolerances or specific finishes are required on certain features, CNC machining adds cost based on complexity, setup time, and machining time. Machining superalloys is inherently slower and requires more robust tooling.
- Oberflächenveredelung: Costs associated with AFM, polishing, or other finishing methods depend on the level required and the complexity of accessing surfaces (especially internal).
- NDT: Costs associated with running CT scans, FPI, UT, etc., including equipment time and certified operator labor.
- Design and Engineering Costs:
- DfAM: If significant redesign or optimization for AM is required, engineering time adds to the initial project cost, though it often pays off in reduced manufacturing costs or improved performance.
- Simulation: Costs associated with running AM process simulations or CFD/FEA for design validation.
- Qualitätssicherung und Zertifizierung:
- Maintaining AS9100 certification and adhering to its rigorous documentation, traceability, and process control requirements adds overhead cost, reflected in the final part price. This investment, however, is crucial for ensuring aerospace-grade quality and reliability.
Typical Lead Times for AM Rocket Baffles:
Lead time is the total time from order placement to part delivery. For complex AM superalloy components, it can range from a few weeks to several months, depending on various factors:
- Design Finalization & Preparation: Time required for final DfAM checks, support generation, build file preparation, and simulation (if performed). (Days)
- Machine Queue & Scheduling: Availability of the appropriate AM machine. High demand or maintenance can create backlogs. (Days to Weeks)
- Druckzeit: Actual time the part spends building in the machine. Can range from ~24 hours to over a week or more for large/complex builds. (Days to Weeks)
- Nachbearbeiten: This often constitutes a significant portion of the lead time:
- Cooling & Stress Relief: (1-2 Days)
- Entfernen und Reinigen von Teilen: (1 Day)
- Heat Treatment & HIP: Often involves batching parts and long furnace/HIP cycles, plus transport time if outsourced. (1-3 Weeks)
- Support Removal & Machining: Dependent on complexity. (Days to Weeks)
- Finishing & NDT: (Days to Week)
- Versand: (Days)
Faktoren, die die Vorlaufzeit beeinflussen:
- Teil Komplexität: More complex parts require longer print times and more intensive post-processing.
- Supplier Capacity & Backlog: Current workload of the AM service provider.
- Post-Processing Chain: Efficiency and scheduling of in-house and external post-processing steps (HIP cycles, heat treatment batches).
- Menge: Prototyping single parts might be faster initially, but optimizing builds with multiple parts can reduce pro Teil lead time in production scenarios, though the overall batch time might be longer.
- Quality Requirements: More stringent inspection and documentation requirements add time.
Zusammenfassung:
Understanding the interplay of material costs, machine time, labor, extensive post-processing, and quality assurance is key to accurately estimating the cost and lead time for additively manufactured rocket engine baffles. While AM can accelerate the development phase through rapid prototyping, the manufacturing lead time for production-quality parts involves numerous steps beyond just printing. Clear communication with suppliers like Met3dp regarding expectations, specifications, and schedules is essential for successful project execution.
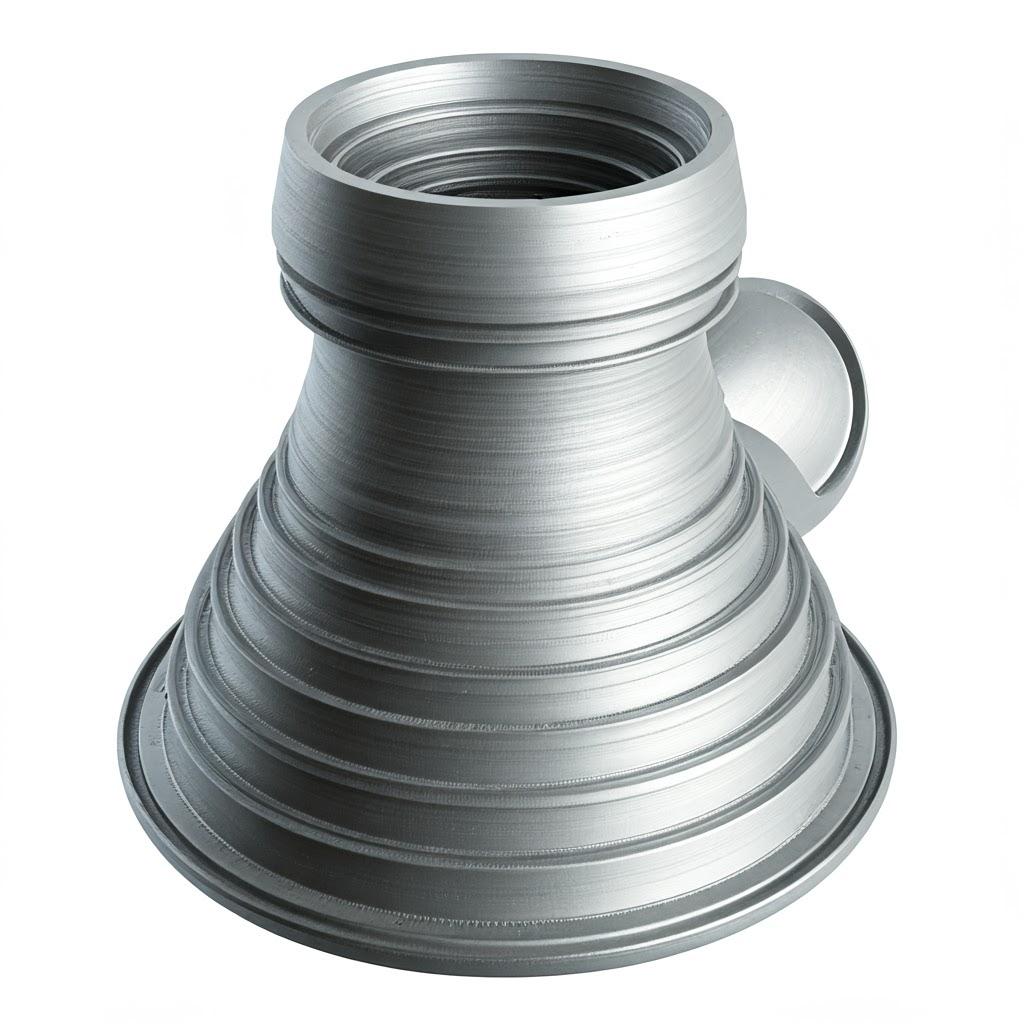
Frequently Asked Questions (FAQ) about AM Rocket Engine Baffles
When considering additive manufacturing for critical components like rocket engine baffles using superalloys, engineers and procurement managers often have specific questions regarding performance, quality, and process specifics. Here are answers to some common inquiries:
1. How does the reliability and fatigue life of AM baffles (IN718, Haynes 282) compare to traditionally manufactured ones?
- Antwort: When manufactured using well-controlled and optimized AM processes, followed by appropriate post-processing including Heiß-Isostatisches Pressen (HIP) and rigorous heat treatment, the mechanical properties (including tensile strength, creep resistance, and fatigue life) of AM superalloy baffles can meet or even exceed those of components made via traditional methods like casting or forging.
- Key Factors: Achieving properties equivalent or superior to wrought material relies heavily on achieving full material density (HIP is crucial for closing internal porosity), obtaining the correct microstructure through heat treatment, and minimizing defects.
- Advantages of AM: Part consolidation eliminates joints (welds/brazes), which are often weak points or fatigue initiation sites in traditional assemblies. DfAM can enable optimized designs with better stress distribution.
- Erfordernis: Rigorous process validation, material testing (using test coupons printed alongside parts), and non-destructive testing (NDT) are essential to guarantee reliability for flight-critical hardware.
2. What level of material traceability is provided for AM aerospace parts, and why is it important?
- Antwort: For aerospace components produced by qualified suppliers (especially those certified to AS9100), full material traceability is standard and mandatory. This means:
- Powder Batch Tracking: Every batch of metal powder (virgin or reused) is tracked with unique identifiers, including its source, chemistry certification, and processing history.
- Build Linkage: Each printed part is linked to the specific AM machine used, the build file containing all process parameters, the specific powder batches loaded, and the date/time of the build.
- Post-Processing Records: All subsequent steps (stress relief, heat treatment, HIP, machining, NDT) are documented and linked to the part or build batch, including furnace charts, HIP logs, machining records, and NDT reports.
- Wichtigkeit: Traceability is crucial for quality control, allowing manufacturers to investigate any potential issues back to their source (e.g., a specific powder batch or process deviation). It provides assurance to the end-user (the rocket engine manufacturer) that the part was produced according to specification using qualified materials and processes.
3. Can existing baffle designs, originally made for traditional manufacturing, be directly printed using AM?
- Antwort: Technically, it is often possible to print an existing design directly using AM. However, doing so rarely leverages the key advantages of additive manufacturing and may even be suboptimal or inefficient.
- Missed Opportunities: Direct printing doesn’t utilize AM’s ability to create complex internal cooling channels, optimized lattice structures, or consolidated assemblies. The design likely includes compromises made specifically for traditional manufacturing limitations (e.g., straight drillable cooling holes, multiple parts needing assembly).
- Potential Issues: Designs intended for casting or machining might have features (e.g., large overhangs, thin unsupported walls) that are difficult or inefficient to print using AM, requiring extensive support structures.
- Empfehlung: While direct printing might be used for initial assessments or non-critical prototypes, redesigning the baffle using DfAM principles is highly recommended to fully benefit from AM’s capabilities in terms of performance enhancement (better cooling, damping), weight reduction, and potentially reduced manufacturing complexity (part consolidation).
4. What are the most critical quality inspection methods used to qualify AM rocket engine baffles for flight?
- Antwort: Qualifying AM baffles involves a comprehensive suite of inspection and NDT methods to ensure both geometric conformity and internal integrity. Key methods include:
- Prüfung der Abmessungen: Using high-precision CMMs or 3D scanning to verify all critical dimensions and tolerances against the engineering drawing and CAD model.
- Computertomographie (CT) Scannen: Considered essential for complex AM parts. Provides a detailed 3D X-ray view to non-destructively inspect internal features (like cooling channels), detect internal defects (porosity, inclusions, cracks), and verify overall geometric integrity.
- Fluoreszierende Eindringprüfung (FPI): Used to detect surface-breaking cracks, pores, or other discontinuities. A standard NDT method for critical metallic components.
- Materialprüfung: Destructive testing of representative samples or “witness coupons” printed alongside the actual parts (often on the same build plate) to verify tensile properties, microstructure (metallography), and potentially fatigue or creep properties meet specifications after post-processing.
- Proof Testing/Functional Testing: Depending on the component’s criticality, pressure testing or flow testing might be performed to verify functional performance under simulated operating conditions.
Conclusion: Propelling Aerospace Innovation with Additively Manufactured Baffles
The journey into the heart of a rocket engine reveals components subjected to some of the most extreme conditions engineered systems face. Among these, the baffle stands as a critical enabler of stable and efficient combustion. Traditionally constrained by the limitations of subtractive manufacturing and assembly, baffle design is now entering a new era powered by metal additive manufacturing.
As explored throughout this article, utilizing advanced AM processes like Laser Powder Bed Fusion (L-PBF) and Electron Beam Melting (EBM), combined with high-performance superalloys such as IN718 and Haynes 282, offers transformative advantages for rocket engine baffles:
- Unerreichte Designfreiheit: Enabling complex internal cooling channels, acoustically optimized geometries, and lightweight lattice structures previously unattainable.
- Verbesserte Leistung: Leading to superior thermal management, more effective combustion instability suppression, and potentially higher engine performance ceilings.
- Teil Konsolidierung: Reducing complexity, weight, and potential failure points by integrating multiple components into a single, monolithic part.
- Beschleunigte Entwicklung: Facilitating rapid design iteration and prototyping cycles crucial for the fast-paced aerospace industry.
However, realizing these benefits demands more than just access to a 3D printer. It requires a holistic approach encompassing:
- Design for Additive Manufacturing (DfAM): Rethinking design strategies to fully leverage AM capabilities.
- Hochwertige Materialien: Utilizing premium superalloy powders with controlled characteristics.
- Rigorous Process Control: Optimizing and meticulously managing AM parameters.
- Comprehensive Post-Processing: Implementing essential steps like stress relief, heat treatment, HIP, and precision finishing.
- Stringent Quality Assurance: Employing thorough NDT and inspection protocols.
Navigating this complex landscape necessitates strong partnerships. Collaborating with an experienced and capable metal AM service provider – one with deep expertise in materials, processes, post-processing, and the stringent quality demands of the aerospace sector – is paramount. Companies like Met3dp, with their foundation in advanced powder manufacturing, cutting-edge printing technologies (including SEBM), and focus on comprehensive industrial solutions, represent the type of partner needed to successfully implement AM for critical applications like rocket engine baffles.
Additive manufacturing is not just an alternative production method; it is a catalyst for innovation in propulsion technology. By enabling the creation of more sophisticated, reliable, and efficient components, metal AM is helping to shape the future of space exploration and utilization. As the technology continues to mature and adoption grows, we can expect to see additively manufactured parts playing an increasingly vital role in propelling the next generation of launch vehicles and spacecraft.
To explore how Met3dp’s advanced metal additive manufacturing capabilities can power your organization’s aerospace projects, visit our website or contact our team today. https://met3dp.com/
Teilen auf
MET3DP Technology Co., LTD ist ein führender Anbieter von additiven Fertigungslösungen mit Hauptsitz in Qingdao, China. Unser Unternehmen ist spezialisiert auf 3D-Druckgeräte und Hochleistungsmetallpulver für industrielle Anwendungen.
Fragen Sie an, um den besten Preis und eine maßgeschneiderte Lösung für Ihr Unternehmen zu erhalten!
Verwandte Artikel
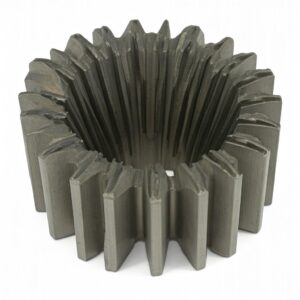
Hochleistungs-Düsenschaufelsegmente: Revolutionierung der Turbineneffizienz mit 3D-Metalldruck
Mehr lesen "Über Met3DP
Aktuelles Update
Unser Produkt
KONTAKT US
Haben Sie Fragen? Senden Sie uns jetzt eine Nachricht! Wir werden Ihre Anfrage mit einem ganzen Team nach Erhalt Ihrer Nachricht bearbeiten.
Holen Sie sich Metal3DP's
Produkt-Broschüre
Erhalten Sie die neuesten Produkte und Preislisten
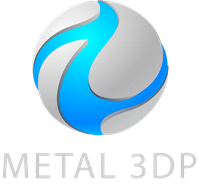
Metallpulver für 3D-Druck und additive Fertigung
UNTERNEHMEN
PRODUKT
cONTACT INFO
- Qingdao Stadt, Shandong, China
- [email protected]
- [email protected]
- +86 19116340731