Additiv gefertigte Lagerschilde
Inhaltsübersicht
Einführung - Die wachsende Bedeutung fortschrittlicher Materialien für Elektromotoren
Die Elektromotorenbranche befindet sich in einem tiefgreifenden Wandel, der durch die zunehmende Nachfrage nach höherer Effizienz, geringerem Gewicht und kompakteren Konstruktionen in verschiedenen Sektoren wie der Automobilbranche, der Luft- und Raumfahrt und der industriellen Automatisierung angetrieben wird. Da diese Anforderungen zunehmen, spielen fortschrittliche Werkstoffe und innovative Fertigungstechniken eine immer wichtigere Rolle. Unter diesen innovativen Ansätzen erweist sich die additive Fertigung von Metallen, allgemein bekannt als 3D-Metalldruck, als eine leistungsstarke Lösung für die Herstellung komplexer Komponenten mit verbesserten Leistungsmerkmalen. Dieser Blogbeitrag befasst sich mit der Anwendung von Metall 3D-Druck für die Herstellung von Lagerschilden für Elektromotoren, kritische Komponenten, die eine entscheidende Rolle für die Gesamtfunktionalität und Haltbarkeit von Elektromotoren spielen. Durch die Nutzung der Designfreiheit und der Materialvielfalt, die Metall-AM bietet, können Hersteller die Leistung von Lagerschilden erheblich verbessern, was letztlich zu effizienteren und zuverlässigeren Elektromotorsystemen beiträgt. Unternehmen wie Metall3DPein führender Anbieter von additiven Fertigungslösungen mit Hauptsitz in Qingdao, China, steht an der Spitze dieser Revolution und bietet branchenführende Druckvolumen, Genauigkeit und Zuverlässigkeit für unternehmenskritische Teile. Ihr Fachwissen in Bezug auf 3D-Druckgeräte und Hochleistungsmetallpulver macht sie zu einem zuverlässigen Partner für Unternehmen, die fortschrittliche Fertigungstechniken einsetzen möchten.
Was sind Lagerschilde für Elektromotoren und ihre wichtigen Funktionen?
Die Lagerschilde von Elektromotoren, auch als Lagerschalen oder Lagergehäuse bezeichnet, sind strukturelle Komponenten, die sich an beiden Enden eines Elektromotors befinden. Diese scheinbar einfachen Teile erfüllen mehrere wichtige Funktionen, die für den Betrieb und die Langlebigkeit des Motors unerlässlich sind. In erster Linie bieten die Lagerschilde mechanische Unterstützung für die Lager des Motors und sorgen dafür, dass sich der Rotor reibungslos und mit minimaler Reibung dreht. Sie spielen auch eine wichtige Rolle beim Schutz der internen Komponenten des Motors, wie z. B. der Statorwicklungen und des Rotors, vor externen Verunreinigungen wie Staub, Feuchtigkeit und Schutt. Darüber hinaus kann das Design der Lagerschilde zum Wärmemanagement des Motors beitragen, indem es die Wärmeableitung erleichtert. In einigen Anwendungen können in den Lagerschilden auch Sensoren oder andere Zusatzkomponenten untergebracht werden. Die Unversehrtheit und der präzise Sitz der Lagerschilde sind entscheidend für die Ausrichtung des Motors, die Reduzierung von Vibrationen und Geräuschen sowie die Gewährleistung der allgemeinen Betriebseffizienz und Haltbarkeit. Angesichts dieser kritischen Funktionen ist die Herstellung hochwertiger, maßgenauer Lagerschilde von größter Bedeutung. Mehr über fortschrittliche Fertigungstechniken für Motorkomponenten erfahren Sie auf der Website Metall3DP website.
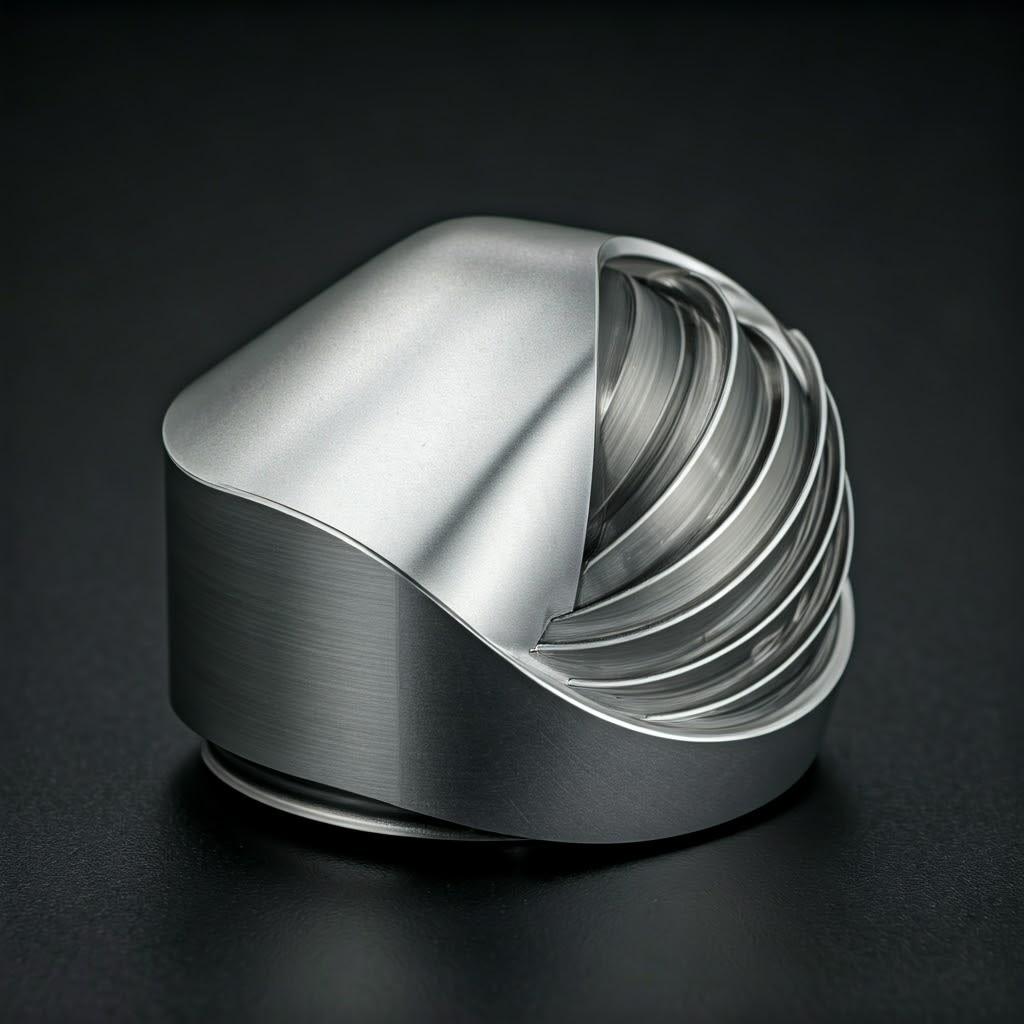
Warum 3D-Metalldruck für die Herstellung von Lagerschilden für Elektromotoren?
Herkömmliche Herstellungsverfahren für Lagerschilde von Elektromotoren, wie Druckguss oder maschinelle Bearbeitung, sind oft mit erheblichen Werkzeugkosten, Designbeschränkungen und Materialabfall verbunden. Der 3D-Metalldruck bietet eine überzeugende Alternative mit zahlreichen Vorteilen, die diese Herausforderungen angehen und neue Möglichkeiten für Design und Leistung von Lagerschilden eröffnen.
- Gestaltungsfreiheit und Komplexität: Die additive Fertigung ermöglicht die Herstellung komplizierter Geometrien und interner Merkmale, die mit herkömmlichen Methoden nur schwer oder gar nicht zu erreichen sind. Diese Designfreiheit ermöglicht es Ingenieuren, das Design von Endschilden im Hinblick auf Gewichtsreduzierung, verbesserte Wärmeableitung durch integrierte Kühlkanäle und erhöhte strukturelle Steifigkeit zu optimieren.
- Vielseitigkeit der Materialien: Der 3D-Metalldruck ist mit einer breiten Palette von Hochleistungsmetalllegierungen kompatibel, so dass die Hersteller Materialien auswählen können, die auf spezifische Anwendungsanforderungen zugeschnitten sind. Für Lagerschilde von Elektromotoren bieten Materialien wie AlSi10Mg ein hervorragendes Verhältnis von Festigkeit zu Gewicht und Wärmeleitfähigkeit, während CuCrZr eine hohe elektrische und thermische Leitfähigkeit bietet, die für bestimmte Motorkonstruktionen entscheidend ist. Metall3DP stellt eine breite Palette an hochwertigen Metallpulvern her, die für verschiedene 3D-Druckverfahren optimiert sind, darunter auch diese fortschrittlichen Legierungen.
- Personalisierung und Kleinserienproduktion: Im Gegensatz zu herkömmlichen Verfahren, die große Produktionsserien erfordern, um kosteneffektiv zu sein, ermöglicht der 3D-Metalldruck die wirtschaftliche Produktion von kundenspezifischen Lagerschilden oder Kleinserien. Dies ist besonders vorteilhaft für spezielle Motoranwendungen oder für das Rapid Prototyping und Design-Iterationen.
- Reduzierte Montage: Komplexe Endschildkonstruktionen können in einem einzigen 3D-gedruckten Teil zusammengefasst werden, wodurch die Notwendigkeit mehrerer Komponenten und Montageschritte reduziert wird. Dies vereinfacht nicht nur den Herstellungsprozess, sondern verbessert auch die Zuverlässigkeit und strukturelle Integrität des Endprodukts.
- Gewichtsreduzierung: Durch die Optimierung des Designs und die Verwendung von Leichtbaumaterialien wie AlSi10Mg kann der 3D-Metalldruck das Gewicht der Lagerschilde erheblich reduzieren und so zur Gesamteffizienz des Motors beitragen, was insbesondere bei Anwendungen wie Elektrofahrzeugen und in der Luft- und Raumfahrt entscheidend ist.
- Rapid Prototyping und Iteration: Der 3D-Metalldruck beschleunigt den Design- und Entwicklungszyklus, indem er es den Ingenieuren ermöglicht, in einem Bruchteil der Zeit im Vergleich zu herkömmlichen Werkzeugverfahren schnell Prototypen herzustellen, verschiedene Designs zu testen und notwendige Änderungen vorzunehmen.
In Anbetracht dieser Vorteile stellt der 3D-Metalldruck einen neuen Ansatz für die Herstellung von Lagerschilden für Elektromotoren dar, der eine verbesserte Leistung, Designflexibilität und Kosteneffizienz für verschiedene Anwendungen bietet.
Materialauswahl: AlSi10Mg und CuCrZr für optimale Leistung
Die Auswahl des geeigneten Metallpulvers ist entscheidend, um die gewünschten Eigenschaften und Leistungsmerkmale von 3D-gedruckten Elektromotor-Lagerschilden zu erreichen. Metall3DP bietet eine Reihe hochwertiger Metallpulver an, darunter AlSi10Mg und CuCrZr, die sich besonders gut für diese Anwendung eignen.
AlSi10Mg
AlSi10Mg ist eine weit verbreitete Aluminiumlegierung für den 3D-Metalldruck, da sie eine hervorragende Kombination aus mechanischen Eigenschaften, Wärmeleitfähigkeit und Verarbeitbarkeit aufweist.
- Wichtigste Eigenschaften und Vorteile:
- Hohes Verhältnis von Festigkeit zu Gewicht: AlSi10Mg bietet im Vergleich zu herkömmlichen Werkstoffen wie Stahl eine erhebliche Gewichtsreduzierung, was für die Verbesserung des Gesamtwirkungsgrads und der Leistung von Elektromotoren entscheidend ist, insbesondere bei gewichtssensiblen Anwendungen.
- Gute Wärmeleitfähigkeit: Diese Legierung weist hervorragende Wärmeableitungseigenschaften auf, was für die Bewältigung der beim Motorbetrieb entstehenden Wärme und die Vermeidung der Überhitzung kritischer Komponenten von entscheidender Bedeutung ist.
- Ausgezeichnete Verarbeitbarkeit: AlSi10Mg weist eine gute Fließfähigkeit und Laserabsorption während des 3D-Druckverfahrens auf, was zu dichten, hochwertigen Teilen mit gleichbleibenden mechanischen Eigenschaften führt.
- Korrosionsbeständigkeit: Die Legierung bietet eine gute Korrosionsbeständigkeit und gewährleistet die langfristige Zuverlässigkeit der Lagerschilde in verschiedenen Betriebsumgebungen.
- Anwendungen: Ideal für Lagerschilde, bei denen geringes Gewicht und effiziente Wärmeableitung entscheidend sind, wie z. B. bei Elektromotoren in der Automobil- und Luftfahrtindustrie.
CuCrZr
CuCrZr ist eine Kupferbasislegierung, die für ihre hohe elektrische und thermische Leitfähigkeit in Verbindung mit einer guten Festigkeit und Härte bekannt ist.
- Wichtigste Eigenschaften und Vorteile:
- Hohe elektrische Leitfähigkeit: Dadurch eignet sich CuCrZr für Lagerschildkonstruktionen, die leitende Elemente enthalten können oder eine hervorragende elektrische Erdung erfordern.
- Hohe Wärmeleitfähigkeit: CuCrZr leitet die Wärme hervorragend ab und ist daher ideal für Hochleistungsmotoren, bei denen das Wärmemanagement eine wichtige Rolle spielt.
- Gute Festigkeit und Härte: Trotz seiner hohen Leitfähigkeit verfügt CuCrZr über eine gute mechanische Festigkeit und Härte, die die strukturelle Integrität des Endschildes gewährleisten.
- Abnutzungswiderstand: Die Legierung bietet eine gute Verschleißfestigkeit und trägt so zur Langlebigkeit des Motors bei.
- Anwendungen: Gut geeignet für Lagerschilde in Hochleistungs-Industriemotoren, Servomotoren und Anwendungen, bei denen effiziente Wärme- und elektrische Leitfähigkeit von größter Bedeutung sind.
Metall3DP nutzt branchenführende Gaszerstäubungs- und PREP-Technologien zur Herstellung dieser und anderer hochwertiger Metallpulver für den 3D-Druck, die eine hohe Sphärizität und gute Fließfähigkeit für optimale Druckergebnisse gewährleisten. Ihr fortschrittliches Pulverherstellungssystem ist ein Beweis für ihr Engagement, überlegene Materialien für die additive Fertigung von Metallen zu liefern. Sie können ihr Angebot an hochwertigen Metallpulvern auf der Website Metal3DP-Produktseite.
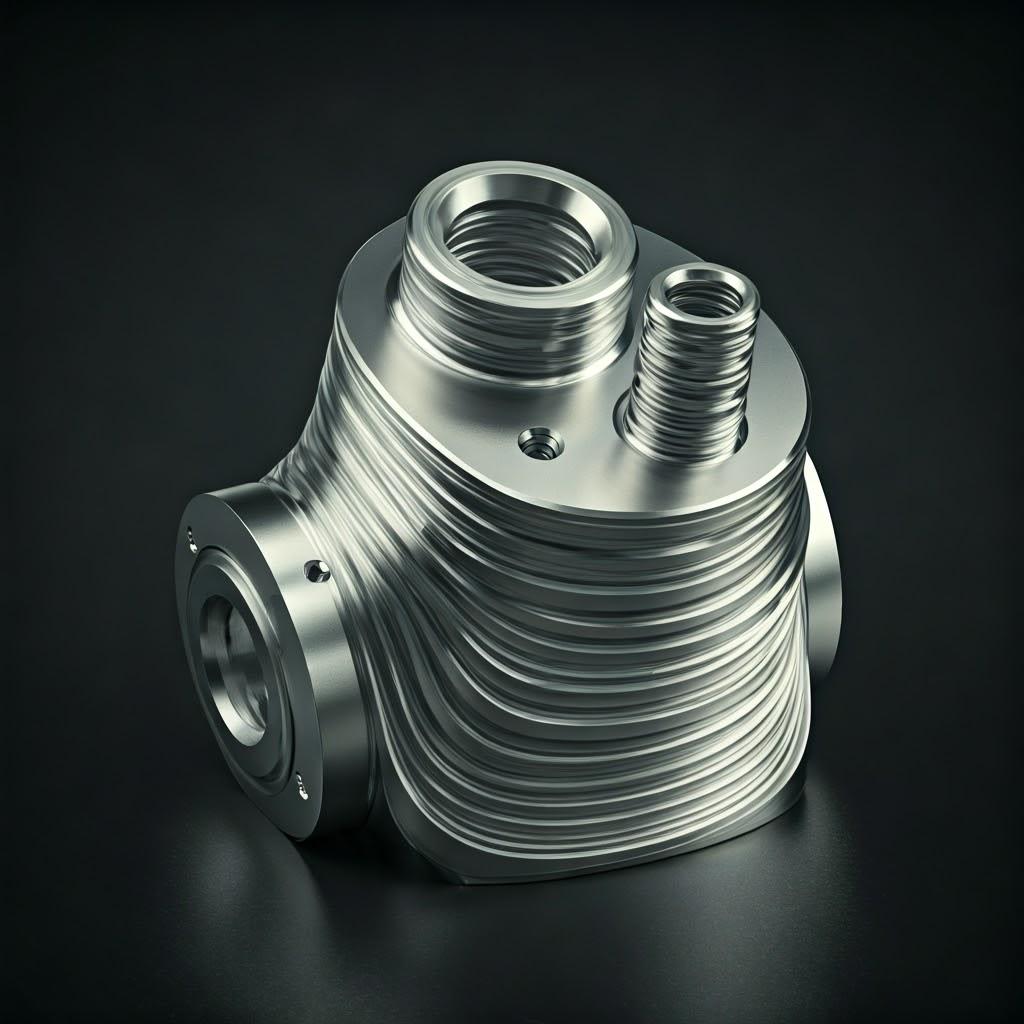
Design-Optimierung für 3D-gedruckte Elektromotor-Lagerschilde
Die Konstruktion für die additive Fertigung von Metall erfordert eine andere Denkweise als bei herkömmlichen Fertigungsverfahren. Um die Möglichkeiten des 3D-Metalldrucks für Motorlagerschilder voll auszuschöpfen, müssen Ingenieure einige wichtige Konstruktionsprinzipien berücksichtigen:
- Topologie-Optimierung: Diese Rechentechnik ermöglicht die Erstellung hocheffizienter Konstruktionen, indem Material aus wenig beanspruchten Bereichen entfernt wird, während die strukturelle Integrität erhalten bleibt. Die Anwendung der Topologieoptimierung auf Lagerschilde kann zu einer erheblichen Gewichtsreduzierung und verbesserten Materialausnutzung führen, ohne die Leistung zu beeinträchtigen.
- Gitterförmige Strukturen: Die Einbeziehung von Gitterstrukturen in die Konstruktion des Lagerschilds kann das Gewicht weiter reduzieren und gleichzeitig für Steifigkeit und Unterstützung sorgen. Diese komplizierten, miteinander verbundenen Netze aus Streben und Knoten können auf spezifische Lastaufnahmeanforderungen zugeschnitten werden.
- Integrierte Funktionen: Der 3D-Druck von Metall ermöglicht die Integration mehrerer Funktionen in ein einziges Teil. Bei Lagerschilden für Elektromotoren könnte dies integrierte Kühlkanäle für ein verbessertes Wärmemanagement, Montagefunktionen oder sogar Sensorgehäuse umfassen, wodurch sich der Bedarf an separaten Komponenten und die Montage verringern.
- Wandstärke und Riffelung: Durch die Optimierung der Wandstärke und den Einbau von strategisch platzierten Rippen kann die strukturelle Steifigkeit des Lagerschilds erhöht werden, ohne dass das Gewicht übermäßig steigt. Die sorgfältige Berücksichtigung des Druckverfahrens und der Materialeigenschaften ist entscheidend für die Bestimmung der minimal erreichbaren Wandstärke und des optimalen Rippendesigns.
- Unterstützende Strukturen: Der 3D-Druck bietet zwar Gestaltungsfreiheit, aber überhängende Merkmale und komplexe Geometrien können während des Druckvorgangs Stützstrukturen erfordern. Die Konstruktion von Teilen mit selbsttragenden Winkeln und die Minimierung des Bedarfs an umfangreichen Stützen kann den Materialabfall und die Nachbearbeitungszeit reduzieren.
- Orientierung und Aufbaustrategie: Die Ausrichtung des Teils auf der Bauplattform und die gewählten Druckparameter können sich erheblich auf die Oberflächengüte, die Maßgenauigkeit und die mechanischen Eigenschaften des fertigen Endschilds auswirken. Eine sorgfältige Berücksichtigung dieser Faktoren in der Entwurfsphase ist daher unerlässlich.
Durch die Berücksichtigung dieser Designüberlegungen können Ingenieure das volle Potenzial des 3D-Metalldrucks ausschöpfen, um leistungsstarke, leichte und funktional integrierte Elektromotor-Lagerschilde zu entwickeln. Metall3DP‘s Expertise in der Anwendungsentwicklung kann Unternehmen bei der Optimierung ihrer Designs für die additive Fertigung unterstützen.
Erreichen von Präzision: Toleranz, Oberflächengüte und Maßgenauigkeit bei AM-Lagerschilden
Bei Elektromotoren sind präzise Toleranzen, glatte Oberflächen und eine hohe Maßgenauigkeit der Lagerschilde entscheidend, um die richtige Ausrichtung der Lager zu gewährleisten, die Reibung zu minimieren, Geräusche und Vibrationen zu reduzieren und letztendlich die Effizienz und Lebensdauer des Motors zu maximieren. Die 3D-Drucktechnologien für Metall haben erhebliche Fortschritte bei der Erreichung dieses Präzisionsniveaus gemacht.
- Toleranzfähigkeiten: Moderne Metall-3D-Drucker, wie sie von Metall3DPkönnen enge Toleranzen erreicht werden, oft im Bereich von ±0,1 bis ±0,05 mm, je nach Material, Teilegeometrie und Druckparametern. Diese Genauigkeit ist entscheidend, um eine präzise Passung mit anderen Motorkomponenten und einen ordnungsgemäßen Lagersitz zu gewährleisten.
- Oberfläche: Die Oberflächenbeschaffenheit eines 3D-gedruckten Teils wird von Faktoren wie der Pulverpartikelgröße, der Schichtdicke und dem Druckverfahren beeinflusst. Während gedruckte Oberflächen eine Nachbearbeitung erfordern können, um glattere Oberflächen zu erhalten, ermöglichen Fortschritte in der Drucktechnik und die Verwendung von feinem Pulver relativ glatte Oberflächen direkt aus dem Drucker. Techniken wie Kugelstrahlen oder Polieren können die Oberflächenrauhigkeit weiter verbessern, um spezifische Anforderungen zu erfüllen.
- Maßgenauigkeit: Das Erreichen einer hohen Maßgenauigkeit erfordert eine sorgfältige Kalibrierung des 3D-Druckers, optimierte Druckparameter und die Berücksichtigung der Materialschrumpfung während des Verfestigungsprozesses. Metall3DP‘s branchenführende Druckgenauigkeit stellt sicher, dass die hergestellten Lagerschilde die strengen Maßanforderungen erfüllen.
- Post-Processing für mehr Präzision: In Fällen, in denen extrem enge Toleranzen oder besondere Anforderungen an die Oberflächengüte erforderlich sind, können Nachbearbeitungstechniken wie CNC-Bearbeitung, Schleifen oder Polieren eingesetzt werden, um die gewünschte Präzision zu erreichen.
Durch die sorgfältige Steuerung des Druckprozesses und die Anwendung geeigneter Nachbearbeitungsmethoden können mit dem 3D-Metalldruck Lagerschilde für Elektromotoren hergestellt werden, die die hohen Präzisionsanforderungen verschiedener Motoranwendungen erfüllen.
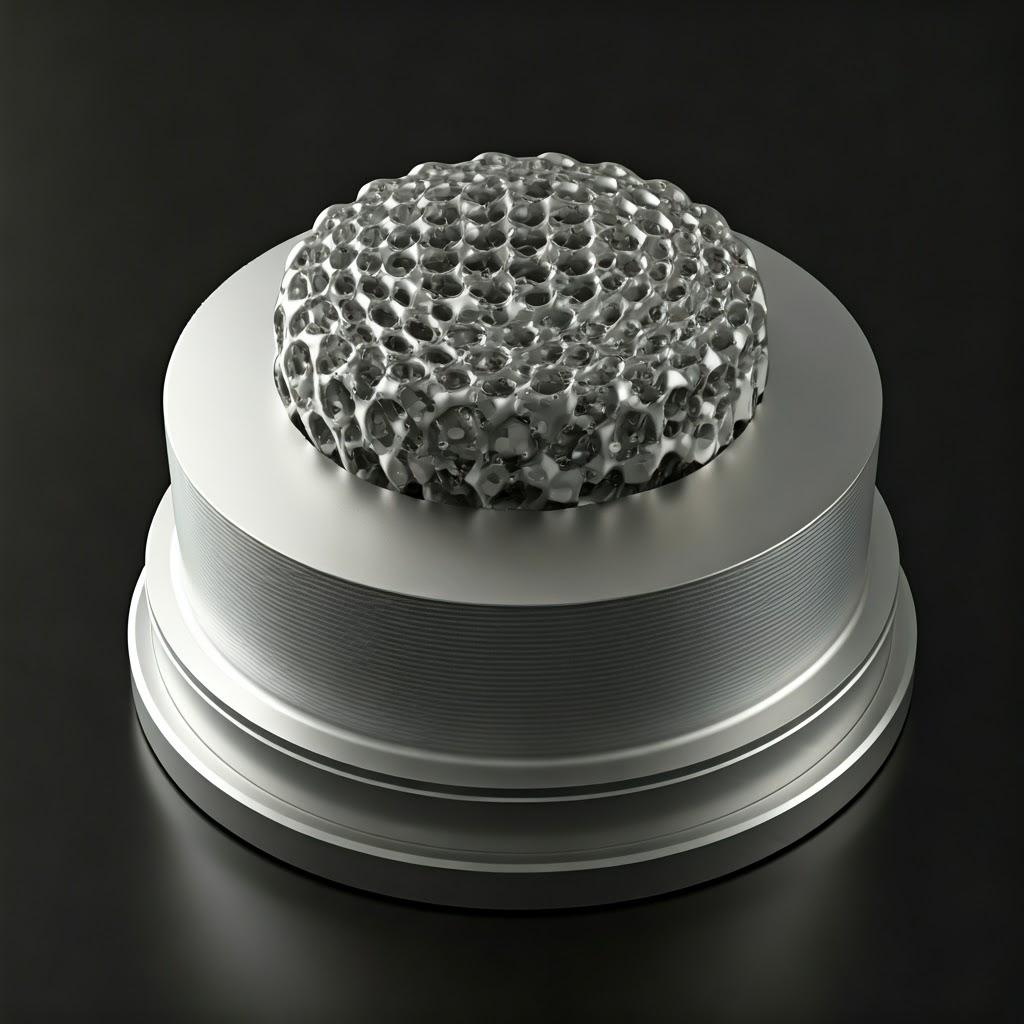
Rationalisierung der Produktion: Nachbearbeitungstechniken für 3D-gedruckte Endschilde aus Metall
Der 3D-Metalldruck bietet zwar erhebliche Vorteile in Bezug auf Designfreiheit und Komplexität, doch sind häufig Nachbearbeitungsschritte erforderlich, um die gewünschten endgültigen Eigenschaften, die Oberflächenbeschaffenheit und die Maßhaltigkeit der gedruckten Teile zu erreichen. Bei Lagerschilden für Elektromotoren sind folgende Nachbearbeitungstechniken üblich:
- Unterstützung bei der Entfernung: Stützstrukturen, die während des Druckprozesses oft notwendig sind, um überhängende Merkmale zu stützen, müssen nach dem Druck sorgfältig entfernt werden. Dies kann je nach Trägermaterial und Teilegeometrie manuell, mechanisch oder durch chemisches Auflösen erfolgen.
- Wärmebehandlung: Um die mechanischen Eigenschaften der 3D-gedruckten Lagerschilde zu verbessern, innere Spannungen zu reduzieren und ihre Gesamtleistung und Haltbarkeit zu erhöhen, können Wärmebehandlungsverfahren wie Spannungsarmglühen oder Glühen erforderlich sein.
- Oberflächenveredelung: Zur Erzielung glatterer Oberflächen und zur Erfüllung spezifischer ästhetischer oder funktionaler Anforderungen können verschiedene Techniken der Oberflächenbearbeitung eingesetzt werden, darunter
- Media Blasting: Dient zur Entfernung von losem Pulver und zur Verbesserung der Oberflächengleichmäßigkeit.
- Polieren: Ermöglicht sehr glatte Oberflächen für bessere Ästhetik und geringere Reibung.
- Vibrationsgleitschleifen: Eine kostengünstige Methode zum gleichzeitigen Glätten und Entgraten mehrerer Teile.
- CNC-Bearbeitung: Bei Anwendungen, die extrem enge Toleranzen oder spezifische Merkmale erfordern, die sich nur schwer direkt durch 3D-Druck erreichen lassen, kann die CNC-Bearbeitung als Sekundärprozess eingesetzt werden, um präzise Merkmale hinzuzufügen oder die Maßgenauigkeit zu verbessern.
- Beschichtungen und Oberflächenbehandlungen: Je nach Anwendungsumgebung können die Lagerschilde mit Beschichtungen wie Korrosionsschutzschichten oder verschleißfesten Beschichtungen versehen werden, um ihre Haltbarkeit und Leistung zu erhöhen.
Die spezifischen Nachbearbeitungsanforderungen für ein 3D-gedrucktes Elektromotor-Lagerschild hängen vom Material, der beabsichtigten Anwendung sowie den gewünschten Endeigenschaften und der Oberflächenbeschaffenheit ab. Die Kenntnis dieser Anforderungen zu Beginn des Konstruktionsprozesses ist entscheidend für die Optimierung des gesamten Fertigungsablaufs. Weitere Informationen über verschiedene 3D-Druckverfahren und ihre typischen Nachbearbeitungsanforderungen finden Sie auf der Website Seite Metall3DP-Druckverfahren.
Überwindung von Herausforderungen bei der Metall-AM von Elektromotorkomponenten
Der 3D-Metalldruck bietet zwar zahlreiche Vorteile, aber es gibt auch potenzielle Herausforderungen, die für eine erfolgreiche Herstellung von Elektromotorkomponenten wie Lagerschilden bewältigt werden müssen:
- Verformung und Verzerrung: Thermische Spannungen während des Druckvorgangs können zu einer Verformung oder Verzerrung des Teils führen, insbesondere bei komplexen Geometrien oder großen Teilen. Die Optimierung der Teileausrichtung, die Verwendung geeigneter Stützstrukturen und die Kontrolle der Baukammertemperatur können dazu beitragen, diese Probleme zu mildern.
- Porosität: Ein ungleichmäßiges Aufschmelzen oder eine unzureichende Verfestigung des Pulvers kann zu Porosität im gedruckten Teil führen, was sich negativ auf dessen mechanische Eigenschaften auswirken kann. Die Optimierung der Druckparameter wie Laserleistung, Scangeschwindigkeit und Schichtdicke sowie die Verwendung hochwertiger Metallpulver mit guter Fließfähigkeit, wie sie von Metall3DPsind entscheidend für die Minimierung der Porosität.
- Entfernung der Stützstruktur: Das Entfernen von Stützstrukturen von komplizierten Geometrien kann schwierig sein und Oberflächenfehler hinterlassen. Die Konstruktion von Teilen mit selbsttragenden Winkeln und die sorgfältige Planung der Platzierung von Stützen können den Entfernungsprozess vereinfachen.
- Oberfläche: Es kann schwierig sein, eine glatte Oberfläche direkt aus dem 3D-Drucker zu erzielen, und es können Nachbearbeitungsschritte erforderlich sein, um bestimmte Anforderungen zu erfüllen. Die Optimierung der Druckparameter und die Berücksichtigung der Anforderungen an die Oberflächengüte in der Entwurfsphase können dazu beitragen, die Notwendigkeit umfangreicher Nachbearbeitungen zu minimieren.
- Materialeigenschaften: Die mechanischen Eigenschaften von 3D-gedruckten Metallen können manchmal von denen konventionell hergestellter Materialien abweichen. Eine sorgfältige Materialauswahl, optimierte Druckparameter und geeignete Wärmebehandlungen in der Nachbearbeitung sind entscheidend, um die gewünschte mechanische Leistung zu erzielen.
- Kosten und Skalierbarkeit: Während der 3D-Metalldruck bei geringen bis mittleren Stückzahlen und komplexen Teilen kosteneffizient ist, können die Kosten pro Teil bei sehr großen Produktionsserien im Vergleich zu herkömmlichen Verfahren höher sein. Mit den Fortschritten der Technologie und den steigenden Produktionsvolumina verbessern sich die Skalierbarkeit und die Kosteneffizienz der Metall-AM kontinuierlich.
Wenn die Hersteller diese potenziellen Herausforderungen verstehen und geeignete Konstruktionsstrategien und Prozesskontrollen implementieren, können sie den 3D-Metalldruck effektiv zur Herstellung hochwertiger Elektromotor-Lagerschilde nutzen.
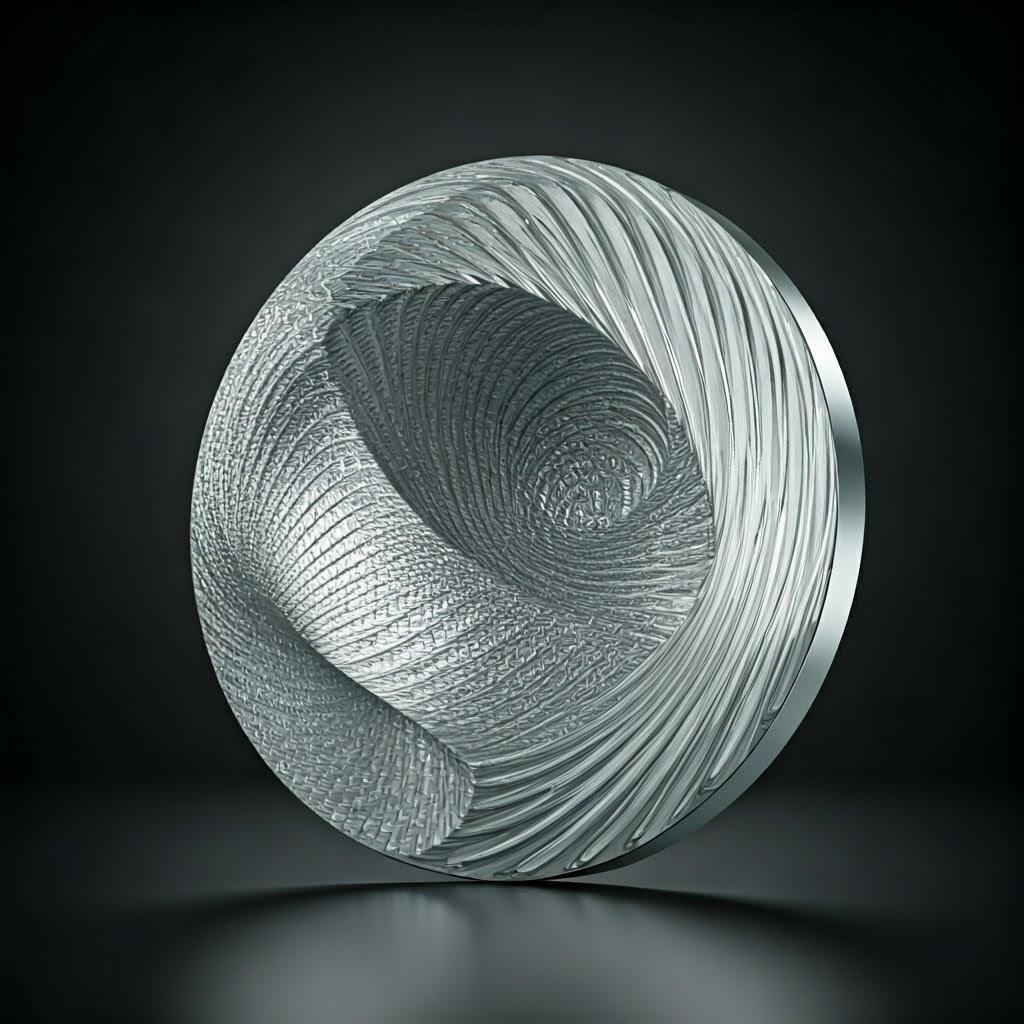
Auswahl eines zuverlässigen 3D-Druckdienstleisters für Endschilde aus Metall
Die Wahl des richtigen 3D-Druckdienstleisters für Metall ist entscheidend für die erfolgreiche Herstellung von qualitativ hochwertigen Elektromotor-Lagerschilden. Bei der Bewertung potenzieller Anbieter sollten mehrere Schlüsselfaktoren berücksichtigt werden:
- Materielle Fähigkeiten: Vergewissern Sie sich, dass der Dienstleister Erfahrung in der Verarbeitung der für Ihre Anwendung erforderlichen Metallpulver hat, wie z. B. AlSi10Mg oder CuCrZr. Metall3DP bietet eine breite Palette von Hochleistungsmetallpulvern an und beweist damit sein Know-how in der Materialwissenschaft.
- Ausrüstung und Technologie: Erkundigen Sie sich nach den Arten von 3D-Metalldruckern, die der Anbieter einsetzt. Hochmoderne Maschinen mit präziser Steuerung der Druckparameter sind für das Erreichen enger Toleranzen und hochwertiger Teile unerlässlich. Metall3DPdas branchenweit führende Druckvolumen, die Genauigkeit und die Zuverlässigkeit unterstreichen ihre fortschrittlichen technologischen Fähigkeiten.
- Qualitätskontrolle und Zertifizierungen: Prüfen Sie, ob der Anbieter über solide Qualitätskontrollverfahren verfügt, einschließlich Materialprüfung und Maßkontrolle. Einschlägige Zertifizierungen, wie z. B. ISO 9001, können eine Garantie für das Qualitätsbewusstsein des Anbieters sein.
- Unterstützung bei Design und Technik: Ein guter Dienstleister sollte Design-Optimierung und technische Unterstützung anbieten, um Ihnen dabei zu helfen, Ihre Endshield-Designs für die additive Fertigung anzupassen, die Leistung zu maximieren und mögliche Probleme zu minimieren. Metall3DP bietet umfassende Lösungen, die SEBM-Drucker, moderne Metallpulver und Anwendungsentwicklungsdienste umfassen, 1 was auf ihre starken Unterstützungsfähigkeiten hinweist. 1. met3dp.sg met3dp.sg
- Post-Processing-Dienste: Stellen Sie fest, ob der Anbieter die erforderlichen Nachbearbeitungsdienste, wie z. B. die Entfernung von Halterungen, Wärmebehandlung, Oberflächenveredelung und CNC-Bearbeitung, anbietet, um Ihre spezifischen Anforderungen zu erfüllen.
- Erfahrung und Fachwissen: Suchen Sie nach einem Anbieter mit einer nachgewiesenen Erfolgsbilanz im 3D-Metalldruck, vorzugsweise mit Erfahrung in der Herstellung von Komponenten für ähnliche Branchen (z. B. Luft- und Raumfahrt, Automobilindustrie, Medizintechnik, Industrie).
- Vorlaufzeiten und Produktionskapazität: Erkundigen Sie sich nach den üblichen Vorlaufzeiten für die Produktion und nach der Kapazität für die von Ihnen benötigten Mengen.
- Kosten und Preisstruktur: Informieren Sie sich über das Preismodell des Anbieters und lassen Sie sich ein detailliertes Angebot erstellen, das alle Kosten, z. B. für Druck, Material und Nachbearbeitung, enthält.
Durch eine sorgfältige Bewertung dieser Faktoren können Sie einen zuverlässigen 3D-Metalldruck-Dienstleister auswählen, der hochwertige Elektromotor-Lagerschilde liefern kann, die Ihren spezifischen Leistungs- und Anwendungsanforderungen entsprechen.
Die Wirtschaftlichkeit verstehen: Kostenfaktoren und Vorlaufzeit für die Produktion von AM-Endschilden
Die Kosten und die Vorlaufzeit für die Herstellung von Lagerschilden für Elektromotoren im 3D-Metalldruck werden von mehreren Faktoren beeinflusst:
- Materialkosten: Die Art und Menge des verwendeten Metallpulvers wirkt sich erheblich auf die Gesamtkosten aus. Moderne Legierungen wie CuCrZr sind in der Regel teurer als gängige Legierungen wie AlSi10Mg.
- Bauvolumen und Teilegröße: Größere Teile, die mehr Bauvolumen beanspruchen und längere Druckzeiten erfordern, sind im Allgemeinen teurer.
- Komplexität des Designs: Komplizierte Designs mit komplexen Geometrien und die Notwendigkeit umfangreicher Stützstrukturen können sowohl die Druckzeit als auch den Materialverbrauch erhöhen und damit die Kosten beeinflussen.
- Nachbearbeitungsanforderungen: Der Umfang der erforderlichen Nachbearbeitung (z. B. Entfernen von Trägern, Wärmebehandlung, Oberflächenbearbeitung, maschinelle Bearbeitung) erhöht die Gesamtkosten und die Vorlaufzeit.
- Produktionsvolumen: Während der 3D-Druck von Metall bei kleinen bis mittleren Stückzahlen vorteilhaft ist, können die Kosten pro Teil bei größeren Produktionsläufen aufgrund von Skaleneffekten sinken.
- Maschinenzeit und Arbeit: Die Zeit, die für den Druck eines Teils benötigt wird, und die Arbeit, die mit der Vorverarbeitung, dem Druck und der Nachbearbeitung verbunden ist, tragen zu den Gesamtkosten bei.
- Preisstruktur des Dienstanbieters’ Verschiedene Dienstleister haben unterschiedliche Preismodelle, die auf Faktoren wie Maschinenauslastung, Materialaufschlag und Gemeinkosten basieren.
Vorlaufzeit ist in erster Linie betroffen von:
- Bauzeit: Die Zeit, die der 3D-Drucker für die Herstellung des Teils benötigt. Sie hängt von der Größe und Komplexität des Teils sowie von der Anzahl der gleichzeitig gedruckten Teile ab.
- Nachbearbeitungszeit: Die Zeit, die für die Entfernung der Auflage, die Wärmebehandlung, die Oberflächenbearbeitung und andere Nachbearbeitungsschritte benötigt wird.
- Terminplanung und Kapazität: Die aktuelle Auslastung und Produktionskapazität des Dienstleisters kann die Vorlaufzeit beeinflussen.
- Versandzeit: Die Zeit, die für den Transport der fertigen Teile zum Kunden benötigt wird.
Die Kenntnis dieser Kostenfaktoren und Vorlaufzeiten ist für die Budgetierung und Planung Ihrer Elektromotoren-Lagerschildproduktion mit Hilfe der additiven Metallfertigung von entscheidender Bedeutung. Kontaktaufnahme mit Metall3DP um deren Möglichkeiten zu erkunden, können Sie spezifische Einblicke in Kosten und Vorlaufzeiten für Ihre Anwendung erhalten.
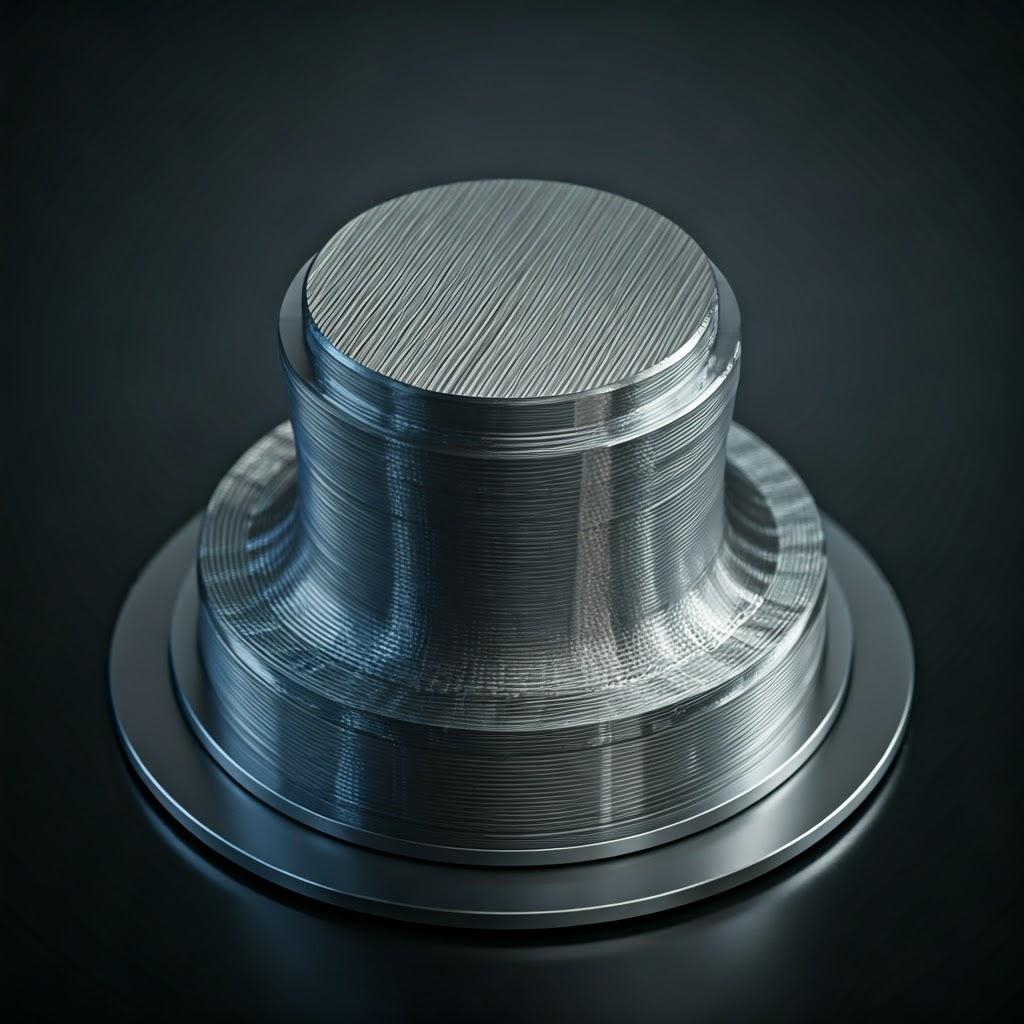
Häufig gestellte Fragen (FAQ)
- Welche Materialien werden typischerweise für 3D-gedruckte Elektromotor-Lagerschilde verwendet? Zu den gängigen Werkstoffen gehören Aluminiumlegierungen wie AlSi10Mg wegen ihres geringen Gewichts und ihrer thermischen Eigenschaften sowie Kupferlegierungen wie CuCrZr wegen ihrer hohen elektrischen und thermischen Leitfähigkeit. Metall3DP bietet eine Reihe von hochwertigen Metallpulvern an, die für diese Anwendung geeignet sind.
- Kann der 3D-Druck von Metall die engen Toleranzen erreichen, die für Motorlager erforderlich sind? Ja, mit modernen 3D-Drucktechnologien für Metall können enge Toleranzen erreicht werden, die oft innerhalb von ±0,1 bis ±0,05 mm liegen. Bei extrem anspruchsvollen Anwendungen können Nachbearbeitungstechniken wie die CNC-Bearbeitung die Maßhaltigkeit weiter verbessern.
- Ist der 3D-Druck von Metall für die Massenproduktion von Lagerschilden kosteneffizient? Der 3D-Druck von Metall ist besonders kosteneffizient bei kleinen bis mittleren Stückzahlen und komplexen Designs. Bei sehr hohen Stückzahlen sind herkömmliche Verfahren zwar immer noch wirtschaftlicher, aber die Vorteile in Bezug auf Designfreiheit und Individualisierung überwiegen bei Spezialanwendungen oft.
- Welche Art von Oberflächengüte kann von einem 3D-gedruckten Metall-Lagerschild erwartet werden? Die Oberflächenbeschaffenheit im Druckzustand hängt vom Druckverfahren und vom Material ab. Sie kann zwar rauer sein als maschinell bearbeitete Oberflächen, aber durch verschiedene Nachbearbeitungstechniken wie Polieren und Strahlen lassen sich glattere Oberflächen erzielen.
- Wie trägt der 3D-Metalldruck zur Verbesserung der Effizienz von Elektromotoren bei? Der 3D-Metalldruck ermöglicht die Konstruktion von leichteren Lagerschilden aus Materialien wie AlSi10Mg, wodurch das Gesamtgewicht des Motors reduziert wird. Er ermöglicht auch die Integration von Kühlkanälen für ein besseres Wärmemanagement, was zu einer verbesserten Effizienz und Leistung beiträgt.
Schlussfolgerung: Die Zukunft der Lagerschilde von Elektromotoren liegt in der additiven Fertigung von Metall
Die additive Fertigung von Metallen revolutioniert die Art und Weise, wie Elektromotorkomponenten, einschließlich Lagerschilden, entworfen und hergestellt werden. Die Möglichkeit, komplexe Geometrien zu erstellen, Hochleistungswerkstoffe wie AlSi10Mg und CuCrZr zu verwenden und kundenspezifische Lösungen zu erzielen, bietet erhebliche Vorteile gegenüber herkömmlichen Fertigungsmethoden. Unternehmen wie Metall3DP stehen an der Spitze dieser Innovation und bieten hochmoderne 3D-Druckgeräte und hochwertige Metallpulver an, mit denen Hersteller effizientere, leichtere und haltbarere Elektromotoren für eine Vielzahl von Branchen entwickeln können, von der Luft- und Raumfahrt über die Automobilindustrie bis hin zur Medizintechnik und Industrieautomation. Mit dem weiteren Fortschritt der Technologie ist zu erwarten, dass sich der 3D-Metalldruck in der Elektromotorenbranche noch stärker durchsetzen wird, um weitere Innovationen voranzutreiben und die Grenzen des Möglichen bei der Konstruktion und Leistung von Motoren zu verschieben. Unternehmen, die das Potenzial des Metall-3D-Drucks für ihre Elektromotorkomponenten ausloten möchten, sollten sich mit erfahrenen Anbietern wie Metall3DP ist ein entscheidender Schritt zur Erschließung der Zukunft der Fertigung. Auf der Website des Unternehmens erfahren Sie mehr über seine umfassenden Lösungen: https://met3dp.com/.
Teilen auf
MET3DP Technology Co., LTD ist ein führender Anbieter von additiven Fertigungslösungen mit Hauptsitz in Qingdao, China. Unser Unternehmen ist spezialisiert auf 3D-Druckgeräte und Hochleistungsmetallpulver für industrielle Anwendungen.
Fragen Sie an, um den besten Preis und eine maßgeschneiderte Lösung für Ihr Unternehmen zu erhalten!
Verwandte Artikel
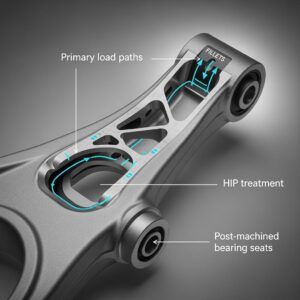
Metal 3D Printing for U.S. Automotive Lightweight Structural Brackets and Suspension Components
Mehr lesen "Über Met3DP
Aktuelles Update
Unser Produkt
KONTAKT US
Haben Sie Fragen? Senden Sie uns jetzt eine Nachricht! Wir werden Ihre Anfrage mit einem ganzen Team nach Erhalt Ihrer Nachricht bearbeiten.
Holen Sie sich Metal3DP's
Produkt-Broschüre
Erhalten Sie die neuesten Produkte und Preislisten