3D-gedruckte Gehäuse für Wärmetauscher: Revolutionierung des Wärmemanagements
Inhaltsübersicht
Wärmetauscher sind wichtige Komponenten in einer Vielzahl von Branchen, von der Luft- und Raumfahrt über die Automobilindustrie bis hin zu medizinischen Geräten und der industriellen Verarbeitung. Ihre Effizienz und Zuverlässigkeit wirken sich direkt auf die Systemleistung und die Gesamtbetriebskosten aus. Traditionell hergestellte Gehäuse für diese wichtigen Teile weisen oft Einschränkungen in Bezug auf Designkomplexität, Materialoptimierung und Vorlaufzeiten auf. Mit dem Aufkommen von Metall 3D-Druck, auch bekannt als additive Fertigung von Metallen, läutet eine neue Ära der Möglichkeiten für Wärmetauschergehäuse ein. Diese innovative Technologie ermöglicht die Herstellung komplizierter Geometrien, die Verwendung von Hochleistungswerkstoffen und das Potenzial für erhebliche Verbesserungen sowohl der Funktionalität als auch der Kosteneffizienz. Unter Metall3DPmit unseren innovativen Lösungen für die Herstellung komplexer und hochwertiger Metallgehäuse, die auf die spezifischen Anforderungen von Wärmetauscheranwendungen zugeschnitten sind, stehen wir an der Spitze dieser Revolution.
Wozu werden 3D-gedruckte Gehäuse für Wärmetauscher verwendet?
3D-gedruckte Metallgehäuse für Wärmetauscher erfüllen einen grundlegenden Zweck: Sie enthalten und schützen die Kernkomponenten des Wärmetauschers und ermöglichen gleichzeitig einen effizienten Flüssigkeitsstrom. Durch die Vielseitigkeit der additiven Fertigung wird ihre Funktionalität jedoch erheblich erweitert. Diese Gehäuse können mit optimierten internen Kanälen und Strukturen entworfen werden, um die Fluiddynamik zu verbessern, was zu verbesserten Wärmeübertragungsraten und einem geringeren Druckverlust führt. In Branchen wie der Luft- und Raumfahrt, in denen das Gewicht ein entscheidender Faktor ist, ermöglicht der 3D-Druck die Herstellung von leichten und dennoch robusten Gehäusen mit komplexen inneren Gittern und dünnen Wänden, die mit herkömmlichen Fertigungsmethoden nicht zu erreichen sind. Die Medizinbranche profitiert von der Möglichkeit, maßgeschneiderte Gehäuse für Kühl- oder Heizsysteme in medizinischen Geräten herzustellen, um den Komfort der Patienten und die Wirksamkeit der Geräte zu gewährleisten. Darüber hinaus können 3D-gedruckte Gehäuse in der Automobilbranche und in der Industrie auf bestimmte räumliche Gegebenheiten und anspruchsvolle Umgebungsbedingungen zugeschnitten werden und bieten so ein bisher unerreichtes Maß an Designfreiheit. Die Möglichkeit, schnell Prototypen zu erstellen und Entwürfe zu wiederholen, macht 3D-gedruckte Gehäuse auch für die Forschung und Entwicklung von Wärmemanagementlösungen von unschätzbarem Wert.
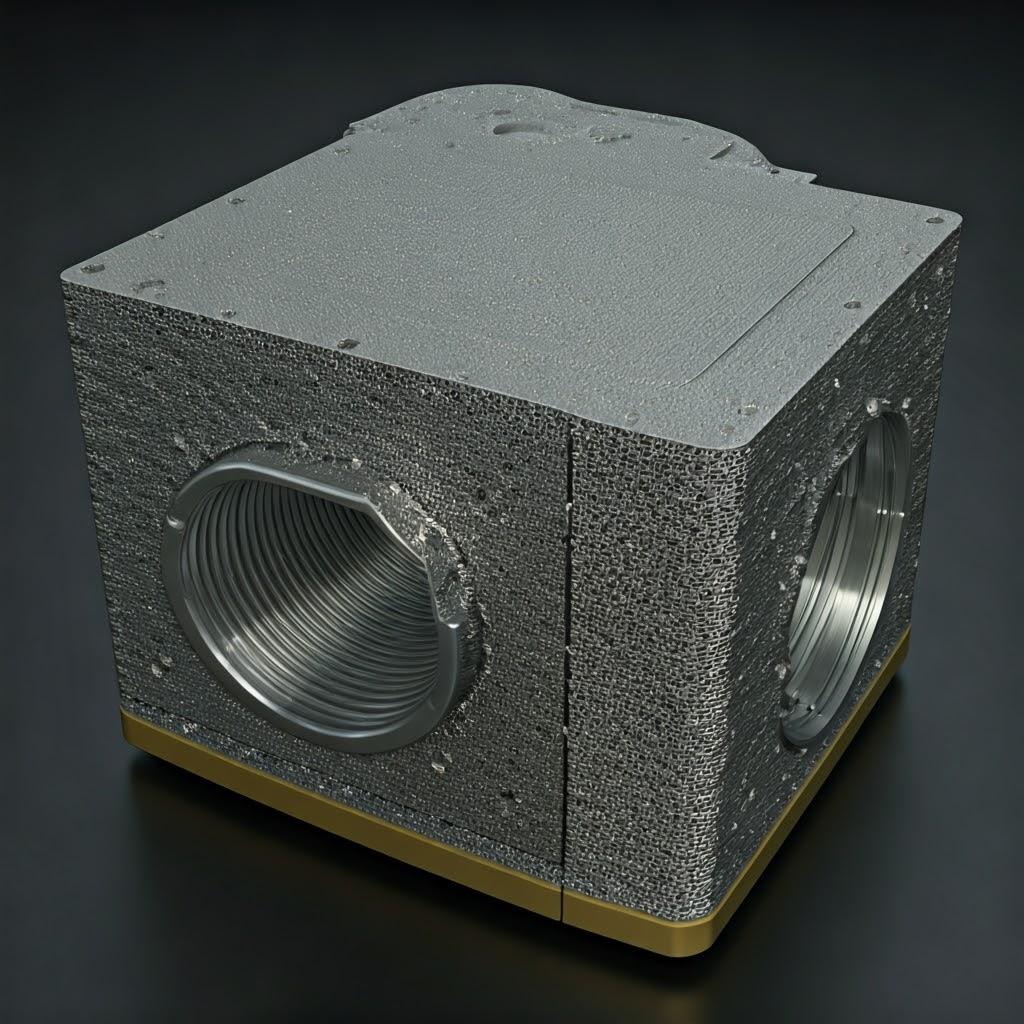
Warum sollten Sie sich für den 3D-Metalldruck von Wärmetauschergehäusen entscheiden?
Die Entscheidung für den 3D-Druck von Wärmetauschergehäusen aus Metall bietet eine ganze Reihe von Vorteilen gegenüber herkömmlichen Fertigungsverfahren wie Zerspanung, Gießen oder Schweißen. Einer der wichtigsten Vorteile ist die unvergleichliche Designfreiheit, die sich daraus ergibt. Ingenieure können komplexe Innengeometrien, komplizierte Kühlkanäle und integrierte Funktionen erstellen, die die Wärmeübertragung optimieren und die Montageschritte reduzieren. Diese Fähigkeit ist besonders wichtig für Anwendungen, die einen hohen Wirkungsgrad und kompakte Designs erfordern. Darüber hinaus ermöglicht der 3D-Metalldruck die Verwendung fortschrittlicher Materialien wie AlSi10Mg und CuCrZr, die eine hervorragende Wärmeleitfähigkeit, ein hervorragendes Verhältnis von Festigkeit zu Gewicht und Korrosionsbeständigkeit bieten - Eigenschaften, die für die anspruchsvollen Umgebungen, in denen Wärmetauscher arbeiten, von entscheidender Bedeutung sind. Unter Metall3DPunsere fortschrittlichen Pulverbettschmelztechnologien gewährleisten, dass diese Materialien zu dichten, hochwertigen Teilen mit hervorragenden mechanischen Eigenschaften verarbeitet werden. Die Möglichkeit, Gehäuse nach Bedarf und in kundenspezifischen Mengen zu produzieren, führt auch zu kürzeren Vorlaufzeiten und geringeren Werkzeugkosten, was sie zu einer wirtschaftlich sinnvollen Lösung sowohl für die Prototypen- als auch für die Serienproduktion macht. Für Unternehmen, die ihre Lieferketten rationalisieren und Innovationen beschleunigen wollen, bietet der 3D-Druck von Metallen eine leistungsstarke und flexible Fertigungsalternative.
Empfohlene Materialien: AlSi10Mg und CuCrZr und ihre Bedeutung
Die Auswahl des richtigen Materials ist für die Leistung und Langlebigkeit von Wärmetauschergehäusen von entscheidender Bedeutung. Bei Metal3DP empfehlen wir AlSi10Mg und CuCrZr als ausgezeichnete Wahl für den 3D-Druck dieser kritischen Komponenten, die jeweils eine Reihe einzigartiger Vorteile bieten.
AlSi10Mg: Diese Aluminiumlegierung ist aufgrund ihrer hervorragenden Eigenschaftskombination in der additiven Fertigung sehr beliebt:
- Hohe Wärmeleitfähigkeit: AlSi10Mg leitet die Wärme effizient ab, was für einen effektiven Wärmeaustausch entscheidend ist.
- Gutes Verhältnis von Stärke zu Gewicht: Es bietet strukturelle Integrität ohne übermäßiges Gewicht, was besonders in der Luft- und Raumfahrt und in der Automobilindustrie von Vorteil ist.
- Ausgezeichnete Korrosionsbeständigkeit: Dies gewährleistet die Langlebigkeit und Zuverlässigkeit des Gehäuses in verschiedenen Betriebsumgebungen.
- Gute Schweißbarkeit und Bearbeitbarkeit: Die Nachbearbeitung, falls erforderlich, ist relativ einfach.
CuCrZr: Diese Kupferbasislegierung zeichnet sich durch ihre außergewöhnliche thermische und elektrische Leitfähigkeit aus:
- Hervorragende Wärmeleitfähigkeit: CuCrZr bietet eine wesentlich höhere Wärmeleitfähigkeit als Aluminiumlegierungen und ist damit ideal für Anwendungen, die eine schnelle Wärmeübertragung erfordern.
- Hohe Festigkeit und Härte: Es behält seine mechanischen Eigenschaften auch bei hohen Temperaturen bei.
- Gute Korrosionsbeständigkeit: Sorgt für Langlebigkeit in anspruchsvollen Umgebungen.
- Hervorragende Abriebfestigkeit: Gewährleistet eine lange Lebensdauer des Gehäuses.
Unser hochwertige Metallpulver sind für das Laser-Pulverbett-Fusionsverfahren (LPBF) und das Elektronenstrahl-Pulverbett-Fusionsverfahren (EBPBF) optimiert und gewährleisten die Herstellung von dichten, fehlerfreien Gehäusen mit den gewünschten Materialeigenschaften. Die Wahl zwischen AlSi10Mg und CuCrZr hängt von den spezifischen Anwendungsanforderungen ab, wobei Faktoren wie Betriebstemperatur, Wärmeübertragungsanforderungen und Gewichtsüberlegungen eine entscheidende Rolle bei der Auswahl spielen. Das Fachwissen von Metal3DP im Bereich der Materialwissenschaft und der additiven Fertigung ermöglicht es uns, unsere Kunden bei der Auswahl des optimalen Pulvers für ihre Anforderungen an Wärmetauschergehäuse zu unterstützen.
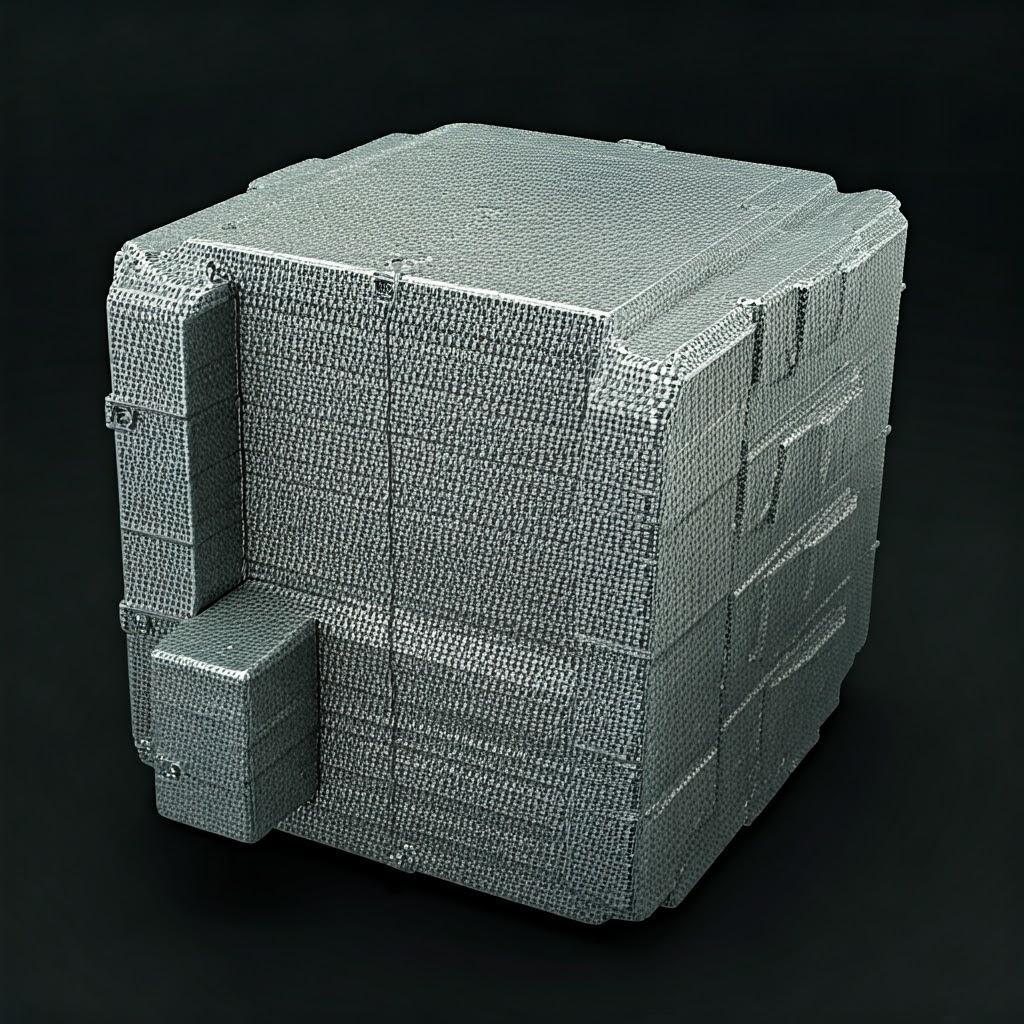
Konstruktionsüberlegungen für die additive Fertigung von Gehäusen
Die Konstruktion für die additive Fertigung von Metallen erfordert eine andere Denkweise als herkömmliche Methoden. Um die Möglichkeiten des 3D-Drucks voll auszuschöpfen und eine optimale Leistung für Wärmetauschergehäuse zu erzielen, müssen mehrere wichtige Designüberlegungen berücksichtigt werden:
- Topologie-Optimierung: Bei dieser fortschrittlichen Konstruktionstechnik werden Algorithmen eingesetzt, um Material in unkritischen Bereichen zu identifizieren und zu entfernen, während die strukturelle Integrität erhalten bleibt. Bei Wärmetauschergehäusen kann die Topologieoptimierung zu einer erheblichen Gewichtsreduzierung und verbesserten Materialeffizienz führen, ohne die Festigkeit oder die thermische Leistung zu beeinträchtigen. Die komplexen, organischen Formen, die mit diesem Verfahren erzeugt werden, sind oft nur durch additive Fertigung zu erreichen.
- Interne Kanalgestaltung: der 3D-Druck ermöglicht die Erstellung komplizierter interner Kanäle mit optimierten Geometrien zur Verbesserung des Flüssigkeitsstroms und der Wärmeübertragung. Gitterstrukturen, konforme Kühlkanäle, die der Form der wärmeerzeugenden Komponenten folgen, und komplexe Rippendesigns können direkt in das Gehäuse integriert werden. Diese Merkmale können die Effizienz und Kompaktheit des Wärmetauschers erheblich verbessern.
- Wanddicke und Stützstrukturen: Die sorgfältige Berücksichtigung der Wanddicke ist entscheidend, um ein Gleichgewicht zwischen Gewichtsreduzierung und struktureller Stabilität herzustellen. Die additive Fertigung ermöglicht die Herstellung dünnwandiger Strukturen, doch sind während des Druckprozesses oft Stützstrukturen erforderlich, um ein Zusammenbrechen oder Verziehen zu verhindern. Die Konstruktion mit selbsttragenden Winkeln und die Minimierung von Überhängen kann den Bedarf an umfangreichen Stützstrukturen verringern, was zu weniger Nachbearbeitung und Materialabfall führt.
- Merkmal Integration: Im Gegensatz zur herkömmlichen Fertigung ermöglicht der 3D-Druck die Integration mehrerer Funktionen in ein einziges Teil. Bei Wärmetauschergehäusen könnte dies integrierte Befestigungselemente, Sensorgehäuse oder Flüssigkeitsanschlüsse umfassen, wodurch der Bedarf an zusätzlichen Komponenten und Montageschritten reduziert wird.
- Überlegungen zur Oberflächenbeschaffenheit: Die durch den 3D-Druck von Metallen erzielte Oberflächenbeschaffenheit kann sich auf den Flüssigkeitsstrom und die Wärmeübertragung auswirken. Während Nachbearbeitungstechniken wie Polieren die Oberflächenrauheit verbessern können, kann die Gestaltung der Oberfläche im gedruckten Zustand bei einigen Anwendungen von Vorteil sein. So kann beispielsweise eine etwas rauere Oberfläche die Turbulenzen erhöhen und die Wärmeübertragung in bestimmten Strömungsregimen verbessern.
- Materialverteilung: Die additive Fertigung bietet in Zukunft das Potenzial für funktional abgestufte Materialien, bei denen die Materialzusammensetzung innerhalb eines einzigen Teils variiert werden kann, um verschiedene Eigenschaften zu optimieren. Dieses Konzept wird zwar noch nicht in großem Umfang für Wärmetauschergehäuse eingesetzt, verdeutlicht aber die langfristigen Gestaltungsmöglichkeiten, die diese Technologie bietet.
Durch die Berücksichtigung dieser Konstruktionsprinzipien können Ingenieure das volle Potenzial des 3D-Metalldrucks ausschöpfen, um leistungsstarke, leichte und hochfunktionale Gehäuse für Wärmetauscher zu entwickeln. Das Fachwissen von Metal3DP im Bereich Design für die additive Fertigung stellt sicher, dass unsere Kunden ihre Entwürfe für die Herstellbarkeit und Leistung auf unseren modernen Drucksystemen optimieren können.
Toleranz, Oberflächengüte und Maßgenauigkeit bei 3D-gedruckten Gehäusen
Das Erreichen der erforderlichen Toleranzen, Oberflächengüte und Maßgenauigkeit ist für die funktionale Integration und Leistung von Wärmetauschergehäusen von größter Bedeutung. 3D-Drucktechnologien für Metall, insbesondere Pulverbettschmelzverfahren (PBF) wie Selective Laser Melting (SLM) und Electron Beam Melting (EBM), bieten ein beeindruckendes Maß an Präzision.
- Maßgenauigkeit: Die Drucker von Metal3DP sind für eine hohe Maßgenauigkeit ausgelegt, die je nach Teilegeometrie und -größe typischerweise im Bereich von ±0,1 bis ±0,2 mm liegt. Diese Genauigkeit stellt sicher, dass die 3D-gedruckten Gehäuse nahtlos mit anderen Komponenten des Wärmetauschersystems zusammenpassen.
- Verträglichkeit: Wir können enge Toleranzen bei kritischen Merkmalen erreichen, oft bis zu ±0,05 mm in lokalisierten Bereichen. Diese Präzision ist für die Gewährleistung der ordnungsgemäßen Abdichtung und des Flüssigkeitsstroms im Wärmetauscher von entscheidender Bedeutung. Zu den Faktoren, die die erreichbaren Toleranzen beeinflussen, gehören das verwendete Material, die Bauausrichtung sowie die Größe und Komplexität des Teils.
- Oberfläche: Die Oberflächenbeschaffenheit im 3D-Metalldruck liegt in der Regel zwischen 5 und 20 µm Ra (Rauheitsmittelwert), wie sie gedruckt wird. Während dies für viele interne Merkmale und einige externe Oberflächen geeignet sein kann, können glattere Oberflächen durch verschiedene Nachbearbeitungsmethoden erreicht werden.
- Nachbearbeitung zur Verbesserung von Finish und Genauigkeit: Für Anwendungen, die glattere Oberflächen oder engere Toleranzen erfordern, bietet Metal3DP eine Reihe von Nachbearbeitungsdiensten an, darunter:
- CNC-Bearbeitung: Zum Erreichen sehr enger Toleranzen bei kritischen Abmessungen und glatten Oberflächen.
- Polieren: Verringerung der Oberflächenrauhigkeit und Verbesserung der Fließeigenschaften.
- Oberflächenbeschichtung: Zur Verbesserung der Korrosionsbeständigkeit oder zur Erzielung bestimmter Oberflächeneigenschaften.
Bei Metal3DP wissen wir, wie wichtig Maßgenauigkeit und Oberflächengüte für die Leistung von Wärmetauschergehäusen sind. Unser erfahrenes Team arbeitet eng mit den Kunden zusammen, um die erforderlichen Spezifikationen zu definieren und die geeigneten Druckparameter und Nachbearbeitungstechniken einzusetzen, um diese Anforderungen zu erfüllen. Unser Engagement für Qualität stellt sicher, dass die von uns produzierten 3D-gedruckten Gehäuse die strengen Anforderungen verschiedener industrieller Anwendungen erfüllen. Mehr über unseren Druckprozess erfahren Sie unter Metal3DP’s Druckmethoden Seite.
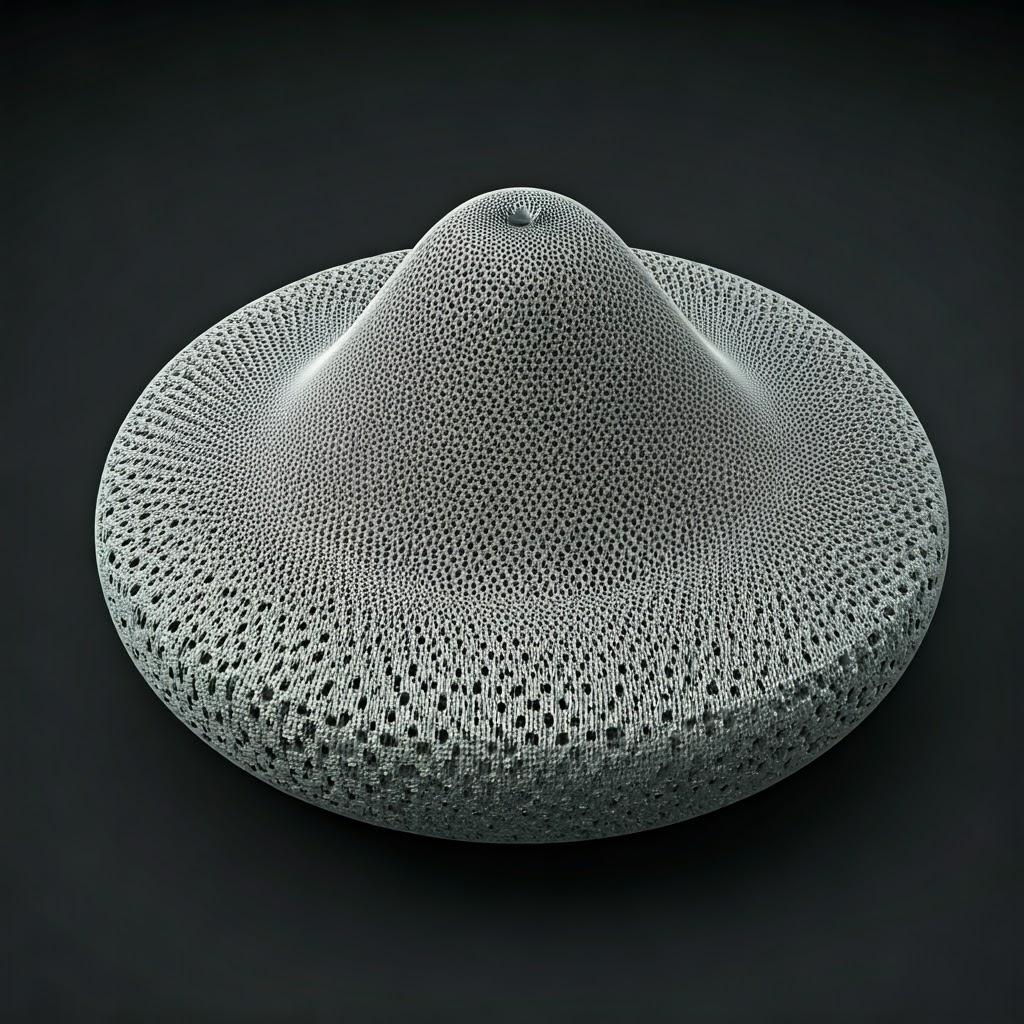
Anforderungen an die Nachbearbeitung von 3D-gedruckten Metallgehäusen
Der 3D-Metalldruck bietet zwar erhebliche Vorteile bei der Erstellung komplexer Geometrien, doch ist häufig eine Nachbearbeitung erforderlich, um die gewünschten endgültigen Eigenschaften und das gewünschte Finish von Wärmetauschergehäusen zu erreichen. Die spezifischen Nachbearbeitungsschritte hängen von den Anwendungsanforderungen, dem verwendeten Material und dem Druckverfahren ab. Zu den üblichen Nachbearbeitungsanforderungen gehören:
- Entfernung der Stützstruktur: Bei Pulverbettfusionsverfahren sind häufig Stützstrukturen erforderlich, um eine Verformung der Teile während des Drucks zu verhindern. Diese Stützen müssen nach Abschluss des Druckvorgangs sorgfältig entfernt werden. Das Design der Stützen und das verwendete Material können die Leichtigkeit des Entfernens und die Oberflächenbeschaffenheit der gestützten Bereiche beeinflussen.
- Wärmebehandlung: Um die inneren Spannungen abzubauen, die während der schnellen Aufheiz- und Abkühlzyklen des 3D-Druckverfahrens entstehen, wird häufig eine Wärmebehandlung durchgeführt. Dieser Prozess kann auch die mechanischen Eigenschaften des Materials verbessern, wie z. B. die Festigkeit und Duktilität, die für die langfristige Zuverlässigkeit von Wärmetauschergehäusen entscheidend sind.
- Oberflächenreinigung: Restliche Pulverpartikel können an der Oberfläche des gedruckten Gehäuses haften und müssen durch Verfahren wie Strahlen oder Ultraschallreinigung entfernt werden. Dies gewährleistet eine saubere Oberfläche für nachfolgende Arbeitsgänge oder für die endgültige Anwendung.
- CNC-Bearbeitung: Bei kritischen Abmessungen und engen Toleranzen, die durch 3D-Druck nur schwer zu erreichen sind, kann die CNC-Bearbeitung als sekundäres Verfahren eingesetzt werden. Dies ist vor allem für Passflächen oder Merkmale relevant, die eine hohe Präzision erfordern.
- Oberflächenveredelung: Je nach Anwendung können verschiedene Techniken der Oberflächenbearbeitung eingesetzt werden. Dazu gehören:
- Polieren: Zur Verringerung der Oberflächenrauhigkeit, zur Verbesserung des Flüssigkeitsflusses und zur Erhöhung der Korrosionsbeständigkeit.
- Media Blasting: Um ein gleichmäßiges, mattes Finish zu erzielen.
- Beschichtung: Sie sollen zusätzlichen Korrosionsschutz bieten, die Verschleißfestigkeit verbessern oder bestimmte thermische Eigenschaften erzielen. Beschichtungen können von einfachen Lacken bis hin zu speziellen Keramik- oder Metallschichten reichen.
- Inspektion und Qualitätskontrolle: Nach der Nachbearbeitung ist eine gründliche Inspektion mit Hilfe von Techniken wie Koordinatenmessmaschinen (KMG), zerstörungsfreien Prüfungen (ZfP) und Oberflächenrauheitsmessungen von entscheidender Bedeutung, um sicherzustellen, dass die Gehäuse die geforderte Maßgenauigkeit, Oberflächengüte und Materialintegrität erfüllen.
Metal3DP bietet umfassende Nachbearbeitungsdienste an, um sicherzustellen, dass unsere 3D-gedruckten Wärmetauschergehäuse die genauen Spezifikationen unserer Kunden erfüllen. Dank unseres Fachwissens in den Bereichen Materialwissenschaft und Fertigungsverfahren können wir die am besten geeigneten Nachbearbeitungsschritte auswählen und durchführen, um die Leistung und Haltbarkeit des Endprodukts zu optimieren.
Häufige Herausforderungen und wie man sie beim 3D-Druck von Gehäusen vermeidet
Der 3D-Metalldruck bietet zwar zahlreiche Vorteile, doch können bei der Erstellung von Wärmetauschergehäusen auch bestimmte Probleme auftreten. Das Verständnis dieser potenziellen Probleme und die Umsetzung von Präventivmaßnahmen sind entscheidend für erfolgreiche Ergebnisse. Häufige Herausforderungen sind:
- Verformung und Verzerrung: Thermische Spannungen während des Druckvorgangs können zu einer Verformung oder einem Verzug des Gehäuses führen, insbesondere bei großen oder komplexen Geometrien.
- Wie man es vermeidet: Die Optimierung der Teileausrichtung, die Verwendung geeigneter Stützstrukturen und die sorgfältige Kontrolle der Baukammertemperatur können diese Probleme minimieren. Die Grundsätze des Designs für die additive Fertigung, wie z. B. die Einbeziehung allmählicher Dickenübergänge, können ebenfalls helfen.
- Porosität und Defekte: Eine unvollständige Verschmelzung der Pulverpartikel kann zu inneren Porositäten oder anderen Defekten führen, die die mechanische Festigkeit und Dichtheit des Gehäuses beeinträchtigen.
- Wie man es vermeidet: Die Wahl der richtigen Druckparameter, die Verwendung von hochwertigen Metallpulvern, wie sie von Metall3DPund die Gewährleistung einer angemessenen atmosphärischen Kontrolle im Drucker sind von entscheidender Bedeutung. Nachbearbeitungstechniken wie das heißisostatische Pressen (HIP) können die Porosität ebenfalls verringern.
- Oberflächenrauhigkeit: Die unbedruckte Oberfläche ist möglicherweise nicht für alle Anwendungen geeignet, da sie den Flüssigkeitsstrom beeinträchtigen und das Korrosionsrisiko erhöhen kann.
- Wie man es vermeidet: Die Optimierung von Druckparametern, wie Schichtdicke und Laserleistung, kann die Oberflächenrauheit beeinflussen. Durch Nachbearbeitungstechniken wie Polieren, Strahlen oder chemisches Ätzen lassen sich glattere Oberflächen erzielen.
- Schäden bei der Beseitigung von Stützstrukturen: Das Entfernen von Stützstrukturen kann manchmal Spuren hinterlassen oder die Oberfläche des Gehäuses beschädigen, insbesondere in Bereichen mit komplexer Geometrie.
- Wie man es vermeidet: Die Konstruktion mit selbsttragenden Winkeln, die Verwendung von auflösbarem Stützmaterial (falls zutreffend) und der Einsatz von Fachkräften für die Entfernung der Stützen können dieses Risiko mindern.
- Eigenspannungen: Die schnellen Erwärmungs- und Abkühlungszyklen beim 3D-Druck können Eigenspannungen im Bauteil hervorrufen, die unter Belastung zu Rissen oder Versagen führen können.
- Wie man es vermeidet: Die Wärmebehandlung nach dem Druck ist entscheidend für den Abbau von Restspannungen und die Verbesserung der mechanischen Eigenschaften des Gehäuses insgesamt.
Bei Metal3DP verfügen wir über umfassende Erfahrung bei der Bewältigung dieser Herausforderungen durch sorgfältige Prozesskontrolle, optimierte Designstrategien und geeignete Nachbearbeitungstechniken. Unser Expertenteam arbeitet eng mit den Kunden zusammen, um potenzielle Probleme bereits in der Entwurfsphase zu erkennen und Lösungen zu implementieren, die die erfolgreiche Herstellung von hochwertigen 3D-gedruckten Wärmetauschergehäusen aus Metall gewährleisten.
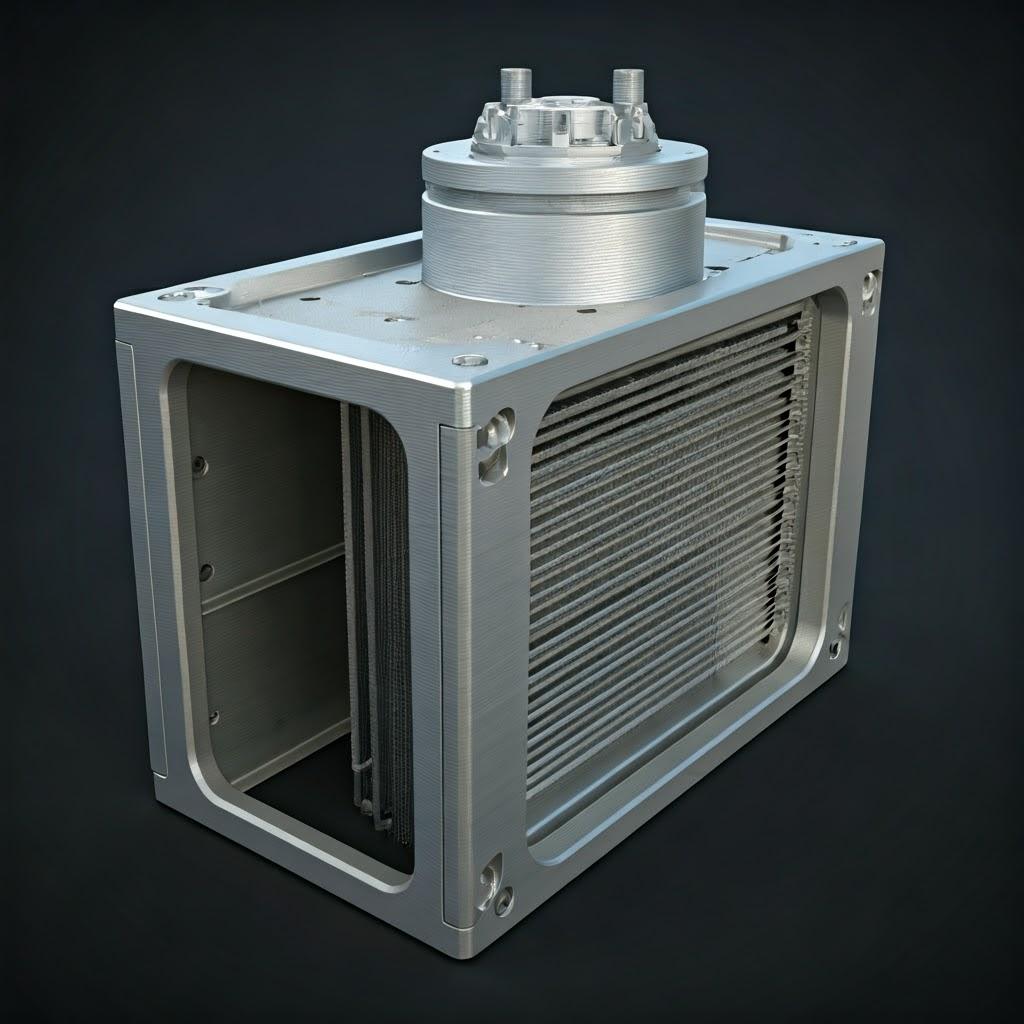
Wie man den richtigen 3D-Druckdienstleister für Metallgehäuse auswählt
Die Auswahl des richtigen 3D-Druckdienstleisters für Metall ist eine wichtige Entscheidung, die sich erheblich auf die Qualität, die Kosten und die Vorlaufzeit Ihrer Wärmetauschergehäuse auswirken kann. Hier sind die wichtigsten Faktoren, die Sie bei der Bewertung potenzieller Anbieter berücksichtigen sollten:
- Materielle Fähigkeiten: Vergewissern Sie sich, dass der Anbieter die spezifischen Metallpulver anbietet, die für Ihre Anwendung benötigt werden, wie z. B. AlSi10Mg und CuCrZr, und dass er diese Materialien nachweislich erfolgreich verarbeitet. Erkundigen Sie sich nach den Verfahren zur Materialcharakterisierung und -prüfung, um die Qualität der gedruckten Teile zu gewährleisten. Metal3DP stellt eine breite Palette hochwertiger Metallpulver her optimiert für verschiedene additive Fertigungsverfahren.
- Technologie und Ausrüstung: Informieren Sie sich über die Arten von 3D-Drucktechnologien für Metall, die der Anbieter einsetzt (z. B. SLM, DMLS, EBM). Die verschiedenen Technologien bieten unterschiedliche Niveaus von Präzision, Oberflächengüte und Bauvolumen. Vergewissern Sie sich, dass die Geräte gut gewartet werden und in der Lage sind, Teile zu produzieren, die Ihren Anforderungen an Maßhaltigkeit und Toleranz entsprechen. Die Drucker von Metal3DP’ liefern ein branchenführendes Druckvolumen, Genauigkeit und Zuverlässigkeit.
- Fachwissen im Bereich Design für additive Fertigung (DfAM): Ein kompetenter Dienstleister sollte Sie bei der Optimierung Ihres Gehäusedesigns für den additiven Fertigungsprozess beraten. Dazu gehört die Beratung zur Topologieoptimierung, zum Design der Stützstruktur und zur Integration von Funktionen, um die Leistung zu verbessern und die Herstellungskosten zu senken. Unser Unternehmen arbeitet mit Unternehmen zusammen, um den 3D-Druck zu implementieren und die Transformation der digitalen Fertigung zu beschleunigen.
- Post-Processing-Dienste: Stellen Sie fest, ob der Anbieter die erforderlichen Nachbearbeitungsdienste anbietet, wie z. B. das Entfernen von Halterungen, Wärmebehandlung, CNC-Bearbeitung, Polieren und Beschichten. Ein umfassendes Angebot an internen Dienstleistungen kann den Produktionsprozess rationalisieren und eine gleichbleibende Qualität gewährleisten.
- Qualitätssicherung und Zertifizierungen: Erkundigen Sie sich nach dem Qualitätsmanagementsystem des Anbieters und allen relevanten Zertifizierungen (z. B. ISO 9001, AS9100 für die Luft- und Raumfahrt). Robuste Qualitätskontrollverfahren sind unerlässlich, um die Zuverlässigkeit und Leistung kritischer Komponenten wie Wärmetauschergehäuse zu gewährleisten.
- Erfahrung und Branchenschwerpunkt: Suchen Sie nach einem Anbieter mit Erfahrung in der Herstellung von Teilen für Ihre spezielle Branche (z. B. Luft- und Raumfahrt, Automobilindustrie, Medizintechnik). Branchenspezifisches Wissen kann zu einem besseren Verständnis Ihrer Anwendungsanforderungen und potenziellen Herausforderungen führen.
- Kommunikation und Kundenbetreuung: Eine effektive Kommunikation und ein reaktionsschneller Kundendienst sind entscheidend für ein reibungsloses und erfolgreiches Projekt. Bewerten Sie die Reaktionsfähigkeit des Anbieters auf Anfragen, seine Bereitschaft zur Zusammenarbeit bei Design und Materialauswahl sowie seine allgemeine Professionalität.
- Vorlaufzeiten und Produktionskapazität: Informieren Sie sich über die typischen Vorlaufzeiten des Anbieters für ähnliche Projekte und seine Produktionskapazitäten, um sicherzustellen, dass er Ihre Projektfristen und Mengenanforderungen einhalten kann.
- Kostenstruktur und Transparenz: Fordern Sie eine detaillierte Aufschlüsselung der anfallenden Kosten an, einschließlich Druck, Material, Nachbearbeitung und anderer damit verbundener Gebühren. Eine transparente Preisstruktur hilft Ihnen bei der genauen Budgetierung Ihres Projekts.
Wenn Sie diese Faktoren sorgfältig abwägen, können Sie einen 3D-Druckdienstleister für Metall auswählen, wie Metall3DP das auf Ihre spezifischen Bedürfnisse abgestimmt ist und die erfolgreiche Produktion von hochwertigen Wärmetauschergehäusen gewährleistet.
Kostenfaktoren und Vorlaufzeit für 3D-gedruckte Gehäuse
Das Verständnis der Faktoren, die die Kosten und die Vorlaufzeit für 3D-gedruckte Wärmetauschergehäuse beeinflussen, ist für eine effektive Projektplanung und Budgetierung unerlässlich.
Kostenfaktoren:
- Materialkosten: Die Kosten für das Metallpulver sind ein wichtiger Faktor. Moderne Legierungen wie CuCrZr können teurer sein als Standardmaterialien wie AlSi10Mg. Die für das Gehäusedesign erforderliche Materialmenge wirkt sich direkt auf die Materialkosten aus. Metal3DP stellt eine breite Palette von hochwertigen Metallpulvern zu wettbewerbsfähigen Preisen her.
- Bauzeit: Die Zeit, die für den Druck des Gehäuses benötigt wird, hängt von dessen Größe, Komplexität und der gewählten Schichtdicke ab. Längere Bauzeiten führen zu höheren Betriebskosten der Maschine.
- Kosten der Maschine: Die Abschreibung und die Betriebskosten des 3D-Metalldruckers werden in die Gesamtkosten pro Teil eingerechnet.
- Nachbearbeitungskosten: Der Umfang der erforderlichen Nachbearbeitung (z. B. Entfernen von Halterungen, Wärmebehandlung, Bearbeitung, Polieren, Beschichtung) beeinflusst die Endkosten erheblich. Komplexe Nachbearbeitungsschritte erhöhen sowohl den Zeitaufwand als auch die Arbeitskosten.
- Arbeitskosten: Für die Bedienung der Maschine, die Einrichtung des Gebäudes, die Nachbearbeitung und die Qualitätskontrolle sind qualifizierte Techniker erforderlich, deren Arbeitskosten in den Gesamtpreis eingerechnet werden.
- Komplexität des Designs: Hochkomplexe Geometrien, die umfangreiche Stützstrukturen oder komplizierte interne Merkmale erfordern, können sowohl die Bauzeit als auch den Nachbearbeitungsaufwand erhöhen und damit die Kosten beeinflussen.
- Auftragsvolumen: Ähnlich wie bei der traditionellen Fertigung können die Kosten pro Teil beim 3D-Druck von Metall aufgrund von Skaleneffekten bei höheren Produktionsmengen sinken.
Vorlaufzeit:
- Vorverarbeitung und Design-Optimierung: Die anfängliche Phase der Designoptimierung für die additive Fertigung und die Bauvorbereitung kann je nach Komplexität des Gehäuses einige Zeit in Anspruch nehmen.
- Druckzeit: Wie bereits erwähnt, hängt die Bauzeit direkt von der Größe und Komplexität des Teils ab.
- Nachbearbeitungszeit: Die Dauer der Nachbearbeitungsschritte variiert je nach den Anforderungen. Die einfache Entfernung von Trägern kann einige Stunden dauern, während umfangreiche Bearbeitungs- oder Beschichtungsprozesse die Vorlaufzeit um mehrere Tage verlängern können.
- Qualitätskontrolle und Inspektion: Eine gründliche Inspektion, um sicherzustellen, dass das Gehäuse den erforderlichen Spezifikationen entspricht, verlängert die Gesamtvorlaufzeit.
- Versand und Logistik: Auch die Zeit, die für den Transport der fertigen Teile an ihren endgültigen Bestimmungsort benötigt wird, muss berücksichtigt werden.
Metal3DP ist bestrebt, transparente und wettbewerbsfähige Preise für seine 3D-Metalldruckdienste anzubieten. Wir arbeiten eng mit unseren Kunden zusammen, um die Entwürfe im Hinblick auf die Kosteneffizienz zu optimieren und genaue Vorlaufzeitschätzungen auf der Grundlage der spezifischen Anforderungen ihrer Wärmetauschergehäuseprojekte zu erstellen. Wenden Sie sich an Metal3DP, um zu erfahren, wie wir die Ziele Ihres Unternehmens im Bereich der additiven Fertigung unterstützen können.
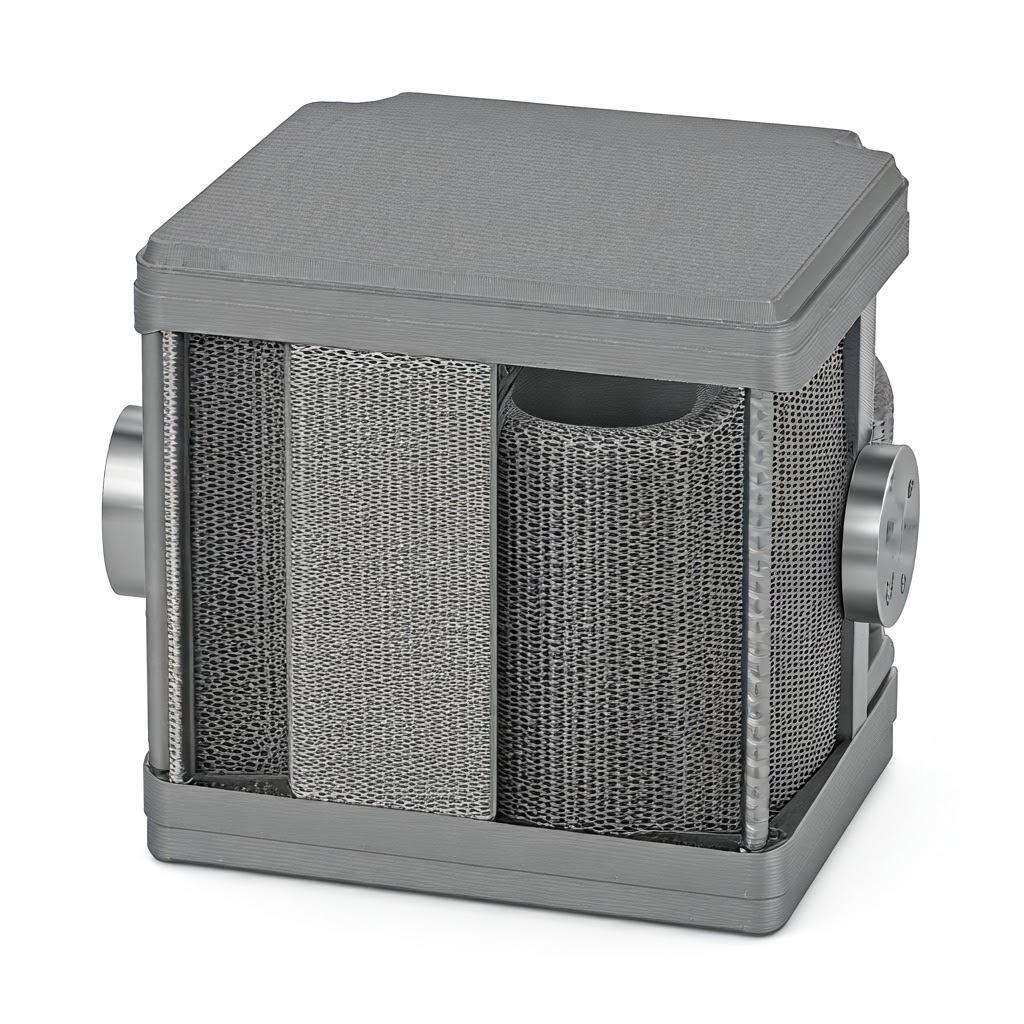
Häufig gestellte Fragen (FAQ)
- Was sind die typischen Anwendungen für 3D-gedruckte Wärmetauschergehäuse?
- 3D-gedruckte Wärmetauschergehäuse werden in einer Vielzahl von Anwendungen eingesetzt, z. B. in der Luft- und Raumfahrt (leichte Kühlsysteme), in der Automobilindustrie (Wärmemanagement für Elektronik und Motoren), in der Medizintechnik (Temperaturkontrolle in Diagnose- und Therapiegeräten) und in der Industrie (effiziente Kühlung kritischer Komponenten). Die Möglichkeit, komplexe Innengeometrien zu schaffen, macht sie ideal für Anwendungen, bei denen Platz und Gewicht begrenzt sind oder eine verbesserte Wärmeübertragung erforderlich ist.
- Können 3D-gedruckte Metallgehäuse hohen Temperaturen und Drücken standhalten?
- Ja, je nach gewähltem Werkstoff und der Konstruktion des Gehäuses. Legierungen wie CuCrZr bieten eine hervorragende Hochtemperaturfestigkeit und Wärmeleitfähigkeit. Durch die richtige Konstruktion, Materialauswahl und Nachbearbeitung (z. B. heißisostatisches Pressen) kann sichergestellt werden, dass die Gehäuse den für viele Wärmetauscheranwendungen typischen Betriebsdrücken und -temperaturen standhalten. Metal3DP bietet ein Portfolio innovativer Legierungen, die für anspruchsvolle Umgebungen geeignet sind.
- Was ist der typische Größenbereich für 3D-gedruckte Wärmetauschergehäuse?
- Der Größenbereich hängt vom Bauvolumen des verwendeten Metall-3D-Druckers ab. Die Drucker von Metal3DP’ bieten branchenführende Druckvolumina, die sowohl die Produktion von kleinen, komplizierten Gehäusen als auch von größeren Komponenten ermöglichen. Wir sind in der Lage, eine Vielzahl von Größen zu produzieren, um verschiedene Anwendungsanforderungen zu erfüllen.
Schlussfolgerung: Die Zukunft von Wärmetauschergehäusen mit 3D-Metalldruck
Der 3D-Metalldruck revolutioniert das Design und die Herstellung von Gehäusen für Wärmetauscher und bietet ein noch nie dagewesenes Maß an Designfreiheit, Materialoptimierung und Funktionsintegration. Die Möglichkeit, komplexe interne Kanäle, leichte Strukturen und kundenspezifische Merkmale mit Hochleistungsmaterialien wie AlSi10Mg und CuCrZr zu erstellen, eröffnet neue Möglichkeiten zur Verbesserung der Effizienz, Leistung und Langlebigkeit von Wärmemanagementsystemen in verschiedenen Branchen.
Wir von Metal3DP Technology Co., LTD mit Hauptsitz in Qingdao, China, sind stolz darauf, ein führender Anbieter von additiven Fertigungslösungen zu sein, der sowohl hochmoderne Metall-3D-Druckanlagen als auch ein umfassendes Sortiment an hochwertigen Metallpulvern anbietet. Unser branchenführendes Druckvolumen, unsere Genauigkeit und Zuverlässigkeit sowie unser Fachwissen in den Bereichen Materialwissenschaft und Anwendungsentwicklung machen uns zu einem idealen Partner für Unternehmen, die die Vorteile des 3D-Metalldrucks für ihre Anforderungen an Wärmetauschergehäuse nutzen möchten.
Wir laden Sie ein, das Potenzial der additiven Fertigung von Metallen mit Metal3DP zu erkunden. Ganz gleich, ob Sie Rapid Prototyping, kundenspezifische Designs oder die Serienproduktion von Hochleistungs-Wärmetauschergehäusen benötigen, unser Team ist bereit, mit Ihnen zusammenzuarbeiten, um Ihre Ziele der digitalen Transformation der Fertigung zu erreichen. Nehmen Sie noch heute Kontakt mit uns auf, um Ihre spezifischen Anforderungen zu besprechen und zu erfahren, wie unsere fortschrittlichen Technologien und Materialien Ihre Innovationen unterstützen können.
Teilen auf
MET3DP Technology Co., LTD ist ein führender Anbieter von additiven Fertigungslösungen mit Hauptsitz in Qingdao, China. Unser Unternehmen ist spezialisiert auf 3D-Druckgeräte und Hochleistungsmetallpulver für industrielle Anwendungen.
Fragen Sie an, um den besten Preis und eine maßgeschneiderte Lösung für Ihr Unternehmen zu erhalten!
Verwandte Artikel
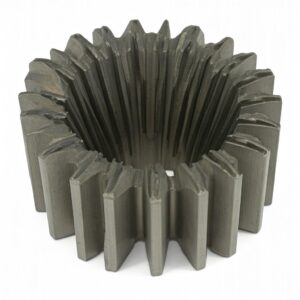
Hochleistungs-Düsenschaufelsegmente: Revolutionierung der Turbineneffizienz mit 3D-Metalldruck
Mehr lesen "Über Met3DP
Aktuelles Update
Unser Produkt
KONTAKT US
Haben Sie Fragen? Senden Sie uns jetzt eine Nachricht! Wir werden Ihre Anfrage mit einem ganzen Team nach Erhalt Ihrer Nachricht bearbeiten.
Holen Sie sich Metal3DP's
Produkt-Broschüre
Erhalten Sie die neuesten Produkte und Preislisten
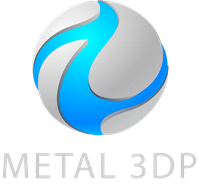
Metallpulver für 3D-Druck und additive Fertigung