Leichte Zugangsluken für die Luft- und Raumfahrt: Die Zukunft des Flugzeugdesigns
Inhaltsübersicht
Einleitung - Die entscheidende Rolle von Zugangsluken in der Luft- und Raumfahrt und der Wunsch nach Leichtbau
Im anspruchsvollen Bereich der Luft- und Raumfahrttechnik spielt jedes Bauteil eine entscheidende Rolle bei der Gewährleistung der Sicherheit, Effizienz und Leistung von Flugzeugen. Zu diesen wesentlichen Elementen gehören auch die Zugangsluken, scheinbar einfache, aber lebenswichtige Teile, die für Inspektion, Wartung und Zugang zu kritischen Systemen innerhalb der Flugzeugstruktur erforderlich sind. Von Rumpfverkleidungen bis hin zu Flügelabteilen und verschiedenen Innenteilen müssen diese Luken strenge Anforderungen an strukturelle Integrität, Abdichtung und Haltbarkeit erfüllen und gleichzeitig das Gewicht minimieren.
Die Luft- und Raumfahrtindustrie steht unter dem ständigen Zwang zur Gewichtsreduzierung. Die Verringerung des Gesamtgewichts eines Flugzeugs bringt zahlreiche Vorteile mit sich, wie z. B. einen geringeren Kraftstoffverbrauch, eine größere Flugreichweite, eine höhere Nutzlastkapazität und geringere Emissionen. Folglich werden Konstruktion und Fertigung selbst scheinbar unbedeutender Komponenten wie Einstiegsluken ständig auf mögliche Gewichtseinsparungen ohne Beeinträchtigung der Sicherheit oder Funktionalität hin überprüft. Herkömmliche Fertigungsmethoden für diese Teile umfassen häufig subtraktive Verfahren wie die Bearbeitung von massiven Aluminiumknüppeln oder anderen für die Luft- und Raumfahrt geeigneten Legierungen. Mit diesen Verfahren können zwar qualitativ hochwertige Teile hergestellt werden, sie führen jedoch häufig zu erheblichem Materialabfall und konstruktiven Einschränkungen, die eine Gewichtsoptimierung verhindern.
Betreten Sie Metall 3D-Druckauch bekannt als additive Fertigung von Metall (AM). Diese transformative Technologie bietet einen Paradigmenwechsel bei der Realisierung komplexer Geometrien und ermöglicht die Schaffung komplizierter interner Strukturen und optimierter Designs, die mit herkömmlichen Techniken einfach nicht zu erreichen sind. Durch den schichtweisen Aufbau von Teilen aus Metallpulvern ermöglicht der 3D-Metalldruck die Herstellung von leichten Zugangsklappen für die Luft- und Raumfahrt mit maßgeschneiderten Eigenschaften und minimiertem Materialverbrauch. Unternehmen wie Metall3DPdas Unternehmen mit Hauptsitz in Qingdao, China, ist führend bei der Bereitstellung dieser fortschrittlichen additiven Fertigungslösungen und kombiniert branchenführende Druckvolumen, Genauigkeit und Zuverlässigkeit, um die anspruchsvollen Anforderungen der Luft- und Raumfahrtbranche zu erfüllen. Ihr Fachwissen über 3D-Druckanlagen und Hochleistungsmetallpulver macht sie zu einem zuverlässigen Partner für Luft- und Raumfahrtunternehmen, die die Vorteile der Metall-AM nutzen möchten.
Wofür werden leichte Zugangsluken in der Luft- und Raumfahrt verwendet? - Anwendungen in allen Luftfahrtsystemen
Leichte Zugangsluken für die Luft- und Raumfahrt erfüllen eine Vielzahl wichtiger Funktionen in verschiedenen Flugzeugsystemen. Ihr Hauptzweck besteht darin, kontrollierten Zugang zu internen Komponenten und Bereichen für wichtige Aktivitäten wie Inspektion, Wartung, Reparatur und Upgrades zu ermöglichen. Das spezifische Design und die Platzierung dieser Luken werden von der Architektur des Flugzeugs und den Systemen, zu denen sie Zugang bieten, bestimmt. Hier sind einige wichtige Anwendungen:
- Zugang zum Rumpf: Luken an der Rumpfaußen- und -innenseite ermöglichen den Wartungsmannschaften den Zugang zu Kabeln, Hydraulikleitungen, Steuerkabeln, Isolierung und Strukturelementen für Routinekontrollen und Reparaturen. Leichtbaukonstruktionen sind hier entscheidend, um das Gesamtgewicht der Flugzeughaut zu minimieren.
- Zugang zum Flügel: In den Flügeln befinden sich kritische Systeme wie Treibstofftanks, Steuerflächenaktuatoren und Hochauftriebsvorrichtungen. Zugangsluken auf den Flügeloberflächen und innerhalb der Flügelstruktur ermöglichen die Inspektion und Wartung dieser wichtigen Komponenten. Die Gewichtsreduzierung in diesen Bereichen trägt zur Verbesserung der aerodynamischen Effizienz bei.
- Zugang zur Motorgondel: Luken an den Triebwerksgondeln ermöglichen den Zugang zur Inspektion und Wartung der Triebwerke selbst und der zugehörigen Systeme wie Verkabelung und Rohrleitungen. Leichte Materialien in diesen Luken können zu einer besseren Motorleistung und Kraftstoffeffizienz beitragen.
- Zugang zum Fahrwerksschacht: Der Zugang zu den Ein- und Ausfahrmechanismen des Fahrwerks sowie zu den Hydrauliksystemen in den Fahrwerksschächten ist für die Sicherheit und die Einsatzbereitschaft von entscheidender Bedeutung. Leichte Luken in diesen Bereichen reduzieren das nicht benötigte Gewicht.
- Zugang zur Avionikbucht: Luken bieten sicheren Zugang zu den hochentwickelten Avioniksystemen des Flugzeugs für Wartung, Aufrüstung und Fehlersuche. Die Minimierung des Gewichts dieser Zugangsklappen ist wichtig für die Gesamtbalance und Leistung des Flugzeugs.
- Zugang zum Laderaum: In Frachtflugzeugen ermöglichen Zugangsluken die Inspektion und Wartung der Frachtabfertigungssysteme und der strukturellen Integrität des Frachtraums. Leichte und dennoch robuste Luken sind für einen effizienten Betrieb erforderlich.
- Zugang zum Heckbereich: Luken im Leitwerk ermöglichen den Zugang zu den Stellmotoren der Steuerflächen und anderen Systemen in den Höhen- und Seitenleitwerken. Eine Gewichtsreduzierung im Heckbereich kann sich positiv auf die Stabilität und Kontrolle des Flugzeugs auswirken.
Bei jeder dieser Anwendungen ist der Bedarf an Leichtbau von größter Bedeutung. Durch den Einsatz des 3D-Drucks von Metall können Hersteller Zugangsklappen mit optimierten Designs herstellen, bei denen nur dort Material verwendet wird, wo es strukturell notwendig ist, und die Merkmale wie interne Gitter oder topologisch optimierte Geometrien enthalten. Dies reduziert nicht nur das Gewicht, sondern kann auch die strukturelle Leistung der Luke selbst verbessern. Metal3DPs metall-3D-Drucker und hochwertige Metallpulver eignen sich ideal für die Herstellung dieser komplexen, leichten Luft- und Raumfahrtkomponenten.
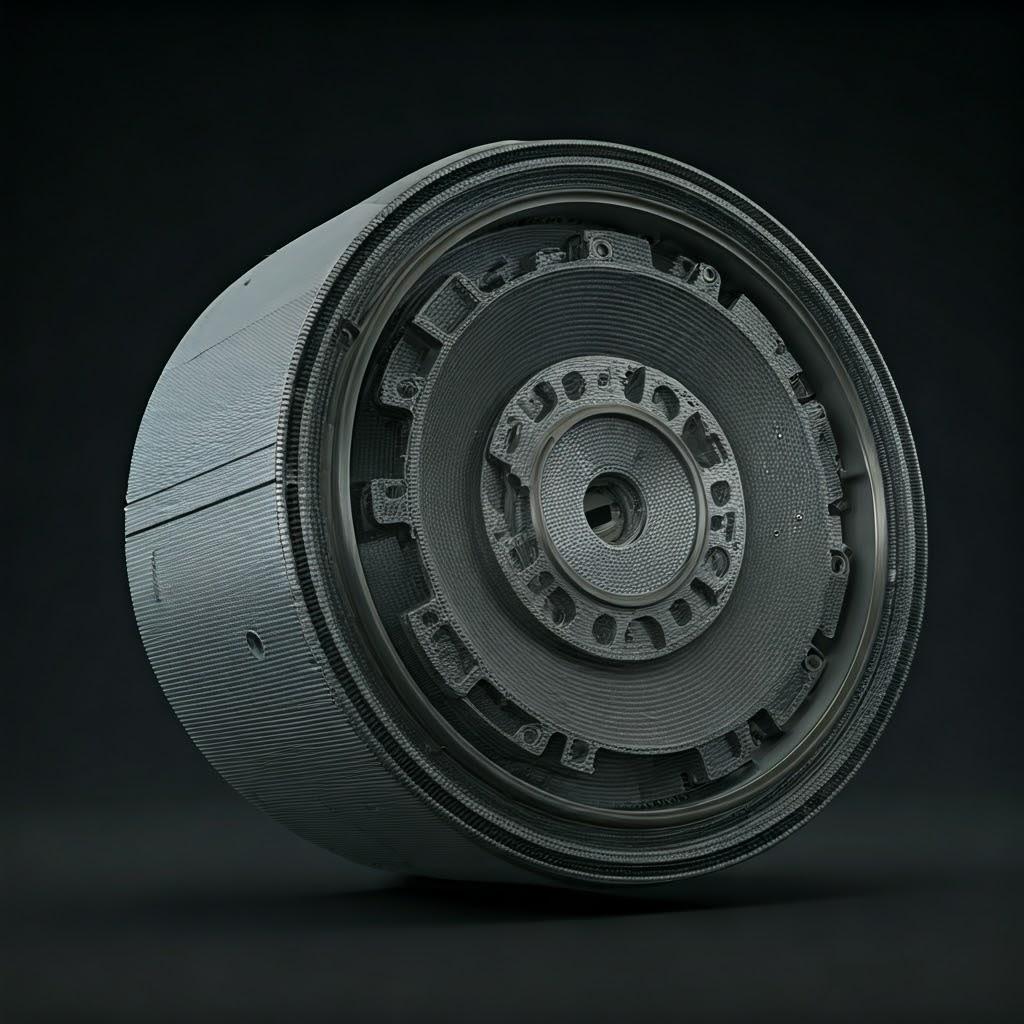
Warum 3D-Metalldruck für Zugangsöffnungen in der Luft- und Raumfahrt? - Vorteile gegenüber traditioneller Fertigung
Der Einsatz von 3D-Metalldruck für die Herstellung von Zugangsklappen in der Luft- und Raumfahrt bietet eine Reihe von Vorteilen gegenüber herkömmlichen Fertigungsmethoden wie Bearbeitung, Gießen oder Blechumformung. Diese Vorteile kommen den kritischen Bedürfnissen der Luft- und Raumfahrtindustrie nach Gewichtsreduzierung, Leistungssteigerung und Kosteneffizienz direkt entgegen:
- Signifikante Gewichtsreduzierung: Der 3D-Metalldruck ermöglicht die Herstellung komplexer Geometrien und interner Strukturen, wie z. B. Gitter und Waben, die mit herkömmlichen Methoden nicht oder nur zu einem sehr hohen Preis hergestellt werden können. Durch Optimierung des Designs und der Materialverteilung können mit 3D-gedruckten Einstiegsluken erhebliche Gewichtseinsparungen erzielt werden, ohne die strukturelle Integrität zu beeinträchtigen. Dies trägt direkt zu einer verbesserten Treibstoffeffizienz und Nutzlastkapazität bei.
- Gestaltungsfreiheit und Komplexität: Die additive Fertigung bietet eine unvergleichliche Designfreiheit. Ingenieure können hochgradig individuelle Einstiegsluken entwerfen, die auf bestimmte Flugzeugbereiche und Funktionsanforderungen zugeschnitten sind. Komplexe Merkmale wie integrierte Versteifungen, Scharniere oder Verriegelungsmechanismen können direkt in das Design integriert werden, wodurch der Bedarf an mehreren Teilen und Befestigungselementen reduziert wird, was wiederum zu Gewichtseinsparungen und einer vereinfachten Montage beiträgt.
- Materialeffizienz: Im Gegensatz zu subtraktiven Fertigungsverfahren wie der maschinellen Bearbeitung, bei denen Material aus einem massiven Block abgetragen wird, wird beim 3D-Metalldruck Material Schicht für Schicht hinzugefügt. Dadurch wird der Materialabfall erheblich reduziert, was zu niedrigeren Materialkosten führt, insbesondere bei der Verwendung teurer Legierungen in Luft- und Raumfahrtqualität. Metal3DPs das fortschrittliche Pulverherstellungssystem gewährleistet eine hohe Sphärizität und Fließfähigkeit der Metallpulver und optimiert so deren Eignung für effiziente 3D-Druckverfahren.
- Fertigung auf Abruf und kundenspezifische Anpassung: Der 3D-Metalldruck ermöglicht die Herstellung von Einstiegsluken auf Anfrage und in genau der benötigten Menge. Dadurch entfallen die Notwendigkeit großer Produktionsserien und die Lagerhaltung, was insbesondere für Ersatzteile oder kundenspezifische Flugzeugkonfigurationen von Vorteil ist. Jede Luke kann auf spezifische Anforderungen zugeschnitten werden, ohne dass neue Werkzeuge benötigt werden, was eine größere Flexibilität und Reaktionsfähigkeit ermöglicht.
- Verbesserte Leistung: Durch optimierte Konstruktionen und die Verwendung fortschrittlicher Materialien können 3D-gedruckte Zugangsluken verbesserte Leistungsmerkmale bieten. So können beispielsweise interne Gitterstrukturen ein hervorragendes Verhältnis von Festigkeit zu Gewicht und eine verbesserte Steifigkeit bieten. Die präzise Steuerung der Materialeigenschaften, die mit Metall-AM möglich ist, kann auch zu einer verbesserten Ermüdungsbeständigkeit und Haltbarkeit führen.
- Geringere Montagezeit und -kosten: Durch die Integration mehrerer Komponenten in ein einziges 3D-gedrucktes Teil können die Anzahl der Montageschritte und die damit verbundenen Arbeitskosten erheblich reduziert werden. Dieser rationalisierte Herstellungsprozess kann zu kürzeren Produktionszeiten und niedrigeren Gesamtkosten führen.
- Rapid Prototyping und Iteration: Der 3D-Metalldruck ist ideal für das Rapid Prototyping. Luft- und Raumfahrtingenieure können Entwürfe schnell überarbeiten, funktionale Prototypen von Zugangsluken herstellen und deren Leistung testen, bevor sie sich für eine Serienfertigung entscheiden. Dieser beschleunigte Designzyklus kann zu schnelleren Innovationen und verbesserten Endprodukten führen.
Durch die Nutzung der Möglichkeiten des 3D-Metalldrucks können Hersteller in der Luft- und Raumfahrt die Grenzen herkömmlicher Methoden überwinden und leichte, leistungsstarke Einstiegsluken herstellen, die zu effizienteren und nachhaltigeren Flugzeugen beitragen. Metal3DPs umfassende Lösungen, die Selective Electron Beam Melting (SEBM)-Drucker und fortschrittliche Metallpulver umfassen, ermöglichen es Luft- und Raumfahrtunternehmen, diese Vorteile zu nutzen.
Empfohlene Materialien und warum sie wichtig sind - AlSi10Mg und Scalmalloy® für optimale Leistung
Die Wahl des Materials ist bei der Herstellung von Zugangsklappen für die Luft- und Raumfahrt von entscheidender Bedeutung, da es sich direkt auf das Gewicht, die Festigkeit, die Haltbarkeit und die Gesamtleistung der Komponente in anspruchsvollen Betriebsumgebungen auswirkt. Der 3D-Metalldruck bietet die Flexibilität, eine Reihe von Hochleistungsmetallpulvern zu verwenden, die auf spezifische Anwendungsanforderungen zugeschnitten sind. Für leichte Zugangsklappen in der Luft- und Raumfahrt sind zwei Materialien besonders interessant: AlSi10Mg und Scalmalloy®:
AlSi10Mg:
- Beschreibung: AlSi10Mg ist eine im 3D-Metalldruck weit verbreitete Aluminiumlegierung, die für ihr hervorragendes Verhältnis von Festigkeit zu Gewicht, ihre gute Wärmeleitfähigkeit und ihre Korrosionsbeständigkeit bekannt ist. Es handelt sich um ein Pulver mit einer nahezu eutektischen Aluminium-Silizium-Magnesium-Zusammensetzung.
- Warum dies für Zugangsluken wichtig ist:
- Gewichtsreduzierung: Aluminiumlegierungen sind von Natur aus leichter als Stahl oder Titan, was AlSi10Mg zu einer ausgezeichneten Wahl für gewichtssensible Luft- und Raumfahrtanwendungen macht.
- Gute mechanische Eigenschaften: Es bietet ein ausgewogenes Verhältnis von Festigkeit, Härte und Duktilität und eignet sich für Zugangsluken, die betrieblichen Belastungen und Handhabungen standhalten müssen.
- Korrosionsbeständigkeit: Der Magnesiumgehalt erhöht die Korrosionsbeständigkeit, was für Bauteile in der Luft- und Raumfahrt, die verschiedenen Umweltbedingungen ausgesetzt sind, von entscheidender Bedeutung ist.
- Schweißbarkeit und Bearbeitbarkeit: AlSi10Mg-Teile können durch Schweißen oder maschinelle Bearbeitung weiterverarbeitet werden, falls dies für bestimmte Montage- oder Endbearbeitungsanforderungen erforderlich ist.
- Kosten-Nutzen-Verhältnis: Im Vergleich zu einigen anderen für die Luft- und Raumfahrt geeigneten Legierungen kann AlSi10Mg für bestimmte Anwendungen eine kostengünstigere Materialoption darstellen.
Scalmalloy®:
- Beschreibung: Scalmalloy® ist eine Hochleistungslegierung aus Aluminium, Magnesium und Scandium, die speziell für die additive Fertigung entwickelt wurde. Sie zeichnet sich durch ein außergewöhnliches Verhältnis von Festigkeit zu Gewicht aus, das sogar viele Titanlegierungen übertrifft, sowie durch hervorragende Duktilität und Korrosionsbeständigkeit.
- Warum dies für Zugangsluken wichtig ist:
- Ultra-Leichtgewicht: Der Zusatz von Scandium verfeinert das Gefüge, was zu einer deutlich höheren Festigkeit und Steifigkeit im Vergleich zu herkömmlichen Aluminiumlegierungen führt und eine noch größere Gewichtsreduzierung bei der Konstruktion von Einstiegsluken ermöglicht.
- Hervorragende mechanische Eigenschaften: Scalmalloy® weist eine sehr hohe Zugfestigkeit und Streckgrenze auf und eignet sich daher ideal für stark beanspruchte Bauteile von Einstiegsluken.
- Ausgezeichnete Ermüdungsbeständigkeit: Seine überragenden mechanischen Eigenschaften tragen auch zu einer ausgezeichneten Ermüdungsbeständigkeit bei, die für Bauteile, die während des Fluges wiederholt belastet werden, von entscheidender Bedeutung ist.
- Gut schweißbar: Scalmalloy® kann mit geeigneten Techniken geschweißt werden, was die Integration mit anderen Flugzeugstrukturen erleichtert.
- Erstklassige Leistung: Scalmalloy® ist zwar potenziell teurer als AlSi10Mg, aber seine außergewöhnlichen Leistungsmerkmale rechtfertigen seinen Einsatz in kritischen Anwendungen, bei denen maximale Gewichtseinsparungen und Festigkeit von größter Bedeutung sind.
Metall3DP bietet ein umfassendes Portfolio an hochwertigen Metallpulvern, darunter AlSi10Mg und andere fortschrittliche Legierungen, die sich für Luft- und Raumfahrtanwendungen eignen. Die branchenführende Gaszerstäubungstechnologie gewährleistet die Herstellung von kugelförmigen Pulvern mit hoher Sphärizität und Fließfähigkeit, die für die Herstellung dichter, hochwertiger 3D-gedruckter Teile mit hervorragenden mechanischen Eigenschaften unerlässlich sind. Durch die Auswahl des geeigneten Pulvers können Hersteller in der Luft- und Raumfahrtindustrie die Leistung und das Gewicht ihrer 3D-gedruckten Zugangsluken optimieren, um auch den anspruchsvollsten Anforderungen gerecht zu werden.
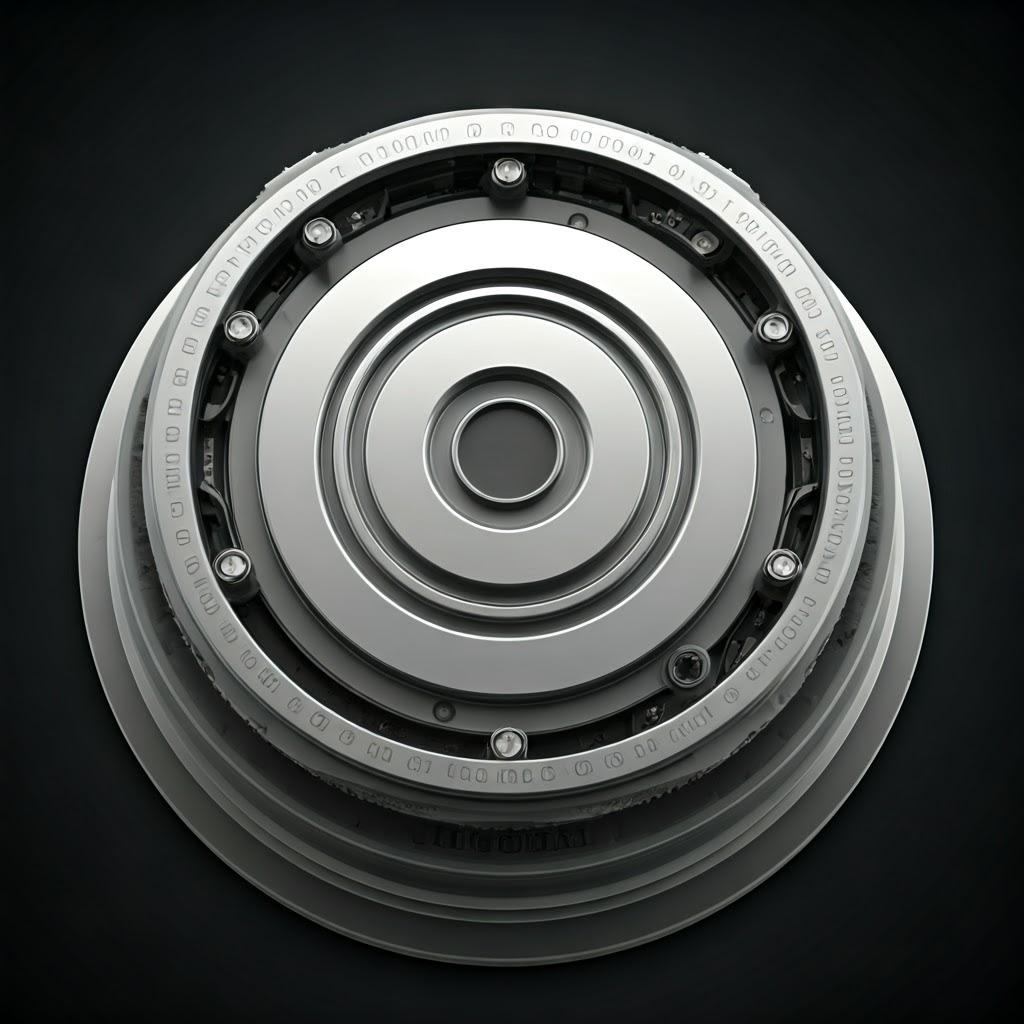
Konstruktionsüberlegungen zur additiven Fertigung von Zugangsluken - Optimierung von Geometrie und Funktionalität
Die Entwicklung von Zugangsklappen für die Luft- und Raumfahrt für den 3D-Druck aus Metall erfordert ein Umdenken im Vergleich zur herkömmlichen Fertigung. Das schichtweise additive Verfahren ermöglicht die Erstellung komplexer Geometrien und interner Merkmale, die die Funktionalität optimieren und das Gewicht minimieren können. Hier sind die wichtigsten Designüberlegungen:
- Topologie-Optimierung: Dieser rechnergestützte Entwurfsansatz ermittelt die effizienteste Materialverteilung für einen bestimmten Satz von Lasten und Einschränkungen. Durch die Entfernung von Material aus wenig beanspruchten Bereichen kann die Topologieoptimierung zu deutlich leichteren Einstiegsluken mit gleicher oder sogar besserer struktureller Leistung führen. Der 3D-Metalldruck ist für die Realisierung dieser komplexen, organisch anmutenden Designs unerlässlich.
- Gitterförmige Strukturen: Der Einbau von internen Gitterstrukturen wie Kreiseln, Waben oder kubischen Gittern in die Einstiegsluke kann ein hervorragendes Verhältnis zwischen Festigkeit und Gewicht bieten. Diese Strukturen bieten Steifigkeit und Halt und reduzieren gleichzeitig die Gesamtmasse des Bauteils erheblich. Die Dichte und Zellengröße des Gitters kann auf die spezifischen Belastungsanforderungen zugeschnitten werden.
- Teil Konsolidierung: Die additive Fertigung ermöglicht die Integration mehrerer Komponenten in ein einziges gedrucktes Teil. So können beispielsweise Scharniere, Verriegelungen und Versteifungen direkt in die Einstiegsluke integriert werden, sodass keine separaten Teile und Befestigungselemente erforderlich sind. Dies reduziert die Montagezeit, mögliche Fehlerquellen und das Gesamtgewicht.
- Wandstärke und Riffelung: Die sorgfältige Berücksichtigung der Wandstärke und die strategische Platzierung von Rippen können die Steifigkeit und Festigkeit der Einstiegsluke erhöhen, ohne dass sie übermäßig schwer wird. Variable Wandstärken können eingesetzt werden, um den Materialeinsatz auf der Grundlage der Spannungsverteilung zu optimieren.
- Unterstützende Strukturen: Während des 3D-Drucks von Metallteilen sind häufig Stützstrukturen erforderlich, um Verformungen und Durchbiegungen zu verhindern und die richtige Ausrichtung der Teile zu gewährleisten. Die Gestaltung des Teils mit selbsttragenden Winkeln und die Minimierung von Überhängen kann die Notwendigkeit umfangreicher Stützstrukturen reduzieren, die nach der Bearbeitung entfernt werden müssen und die Oberflächengüte beeinträchtigen können.
- Gestaltung und Platzierung der Löcher: Bei Bohrungen für Befestigungselemente ist auf die optimale Größe und Platzierung zu achten, um eine sichere Befestigung zu gewährleisten und gleichzeitig Spannungskonzentrationen zu minimieren. Merkmale wie integrierte Buchsen oder verstärkte Lochränder können in der Entwurfsphase berücksichtigt werden.
- Dichtungsmerkmale: Zugangsluken erfordern oft eine wirksame Abdichtung gegen Umwelteinflüsse. Konstruktionsmerkmale wie integrierte Nuten für O-Ringe oder andere Dichtungselemente sollten in das 3D-Modell integriert werden, um eine dichte und zuverlässige Abdichtung zu gewährleisten.
- Ergonomie und Handhabung: Überlegen Sie, wie die Einstiegsluke gehandhabt und bedient werden soll. Merkmale wie ergonomische Griffe oder Hebepunkte können die Benutzerfreundlichkeit und Sicherheit für das Wartungspersonal verbessern.
Durch die sorgfältige Berücksichtigung dieser Konstruktionsaspekte können Luft- und Raumfahrtingenieure die einzigartigen Möglichkeiten des 3D-Metalldrucks nutzen, um leichte, leistungsstarke Zugangsluken mit optimierter Funktionalität und reduzierter Teilezahl zu entwickeln. Die Zusammenarbeit mit erfahrenen Metall-AM-Dienstleistern wie Metall3DP kann wertvolle Einblicke in die Grundsätze und bewährten Verfahren des Designs für die additive Fertigung (DfAM) bieten.
Toleranz, Oberflächengüte und Maßgenauigkeit bei 3D-gedruckten Luken - Erfüllung strenger Luft- und Raumfahrtstandards
Bauteile für die Luft- und Raumfahrt, darunter auch Zugangsklappen, müssen strenge Toleranzen und Anforderungen an die Oberflächenbeschaffenheit einhalten, um Passgenauigkeit, Funktionalität und Zuverlässigkeit zu gewährleisten. Die 3D-Drucktechnologien für Metall haben sich in ihrer Fähigkeit, diese Standards zu erreichen, erheblich weiterentwickelt, aber eine sorgfältige Prozesskontrolle und Nachbearbeitung sind oft erforderlich.
- Toleranzfähigkeiten: Die mit dem 3D-Metalldruck erreichbare Maßgenauigkeit hängt von der jeweiligen Technologie (z. B. Laser Powder Bed Fusion (LPBF) oder Electron Beam Powder Bed Fusion (EBPBF)), dem verwendeten Material und der Teilegeometrie ab. Im Allgemeinen können bei kritischen Abmessungen Toleranzen im Bereich von ±0,1 mm oder noch enger erreicht werden. Zu den Faktoren, die die Toleranz beeinflussen, gehören die Spotgröße des Laser-/Elektronenstrahls, die Größenverteilung der Pulverpartikel, das Wärmemanagement während des Drucks und die Nachbearbeitungsschritte. Metal3DPs SEBM-Drucker sind für ihre hohe Genauigkeit und Zuverlässigkeit bekannt und tragen zur Herstellung von maßgenauen Teilen bei.
- Oberfläche: Die gedruckte Oberfläche von 3D-gedruckten Metallteilen weist aufgrund des schichtweisen Aufbaus und der teilweise gesinterten Pulverpartikel auf der Oberfläche in der Regel einen gewissen Grad an Rauheit auf. Die Oberflächenrauhigkeit (Ra) kann je nach Druckparameter und Material zwischen 5 und 20 µm liegen. Bei Zugangsluken für die Luft- und Raumfahrt können glattere Oberflächen erforderlich sein, um eine ordnungsgemäße Abdichtung zu gewährleisten, den Luftwiderstand zu verringern (bei Außenluken) oder ästhetischen Anforderungen zu genügen.
- Faktoren, die sich auf Genauigkeit und Ausführung auswirken:
- Schichtdicke: Dünnere Schichten führen in der Regel zu glatteren Oberflächen, können aber die Bauzeit verlängern.
- Partikelgröße und -verteilung des Pulvers: Feinere, gleichmäßigere Pulverpartikel führen in der Regel zu dichteren Teilen mit besserer Oberflächenqualität. Metal3DPs das fortschrittliche Pulverherstellungssystem gewährleistet hochwertige Metallpulver mit kontrollierter Partikelgrößenverteilung.
- Orientierung aufbauen: Die Ausrichtung des Teils während des Drucks kann sich erheblich auf die Oberflächengüte bestimmter Merkmale auswirken. Durch die Optimierung der Bauausrichtung kann der Bedarf an Stützstrukturen auf kritischen Oberflächen minimiert werden.
- Prozessparameter: Laserleistung, Scangeschwindigkeit und andere Druckparameter müssen sorgfältig kontrolliert werden, um konsistente und genaue Ergebnisse zu gewährleisten.
- Nachbearbeitung zur Verbesserung von Genauigkeit und Finish:
- Bearbeitungen: Bei kritischen Passflächen oder engen Toleranzen kann die Nachbearbeitung eingesetzt werden, um die erforderliche Genauigkeit und Oberflächengüte zu erreichen.
- Polieren und Schleifen: Verschiedene Polier- und Schleiftechniken können zur Verbesserung der Oberflächengüte von 3D-gedruckten Zugangsluken eingesetzt werden.
- Media Blasting: Durch Strahlen können teilweise gesinterte Pulverpartikel entfernt und eine gleichmäßigere Oberflächenstruktur erzielt werden.
- Chemisches Ätzen: In einigen Fällen kann die Oberfläche durch chemisches Ätzen verfeinert werden.
Um die strengen Toleranz- und Oberflächenanforderungen der Luft- und Raumfahrtindustrie zu erfüllen, müssen das 3D-Metalldruckverfahren, die Materialauswahl und geeignete Nachbearbeitungstechniken sorgfältig geprüft werden. Die Zusammenarbeit mit einem seriösen Metall-AM-Dienstleister mit Erfahrung in der Luft- und Raumfahrt ist entscheidend, um sicherzustellen, dass die endgültigen Teile die erforderlichen Spezifikationen erfüllen.
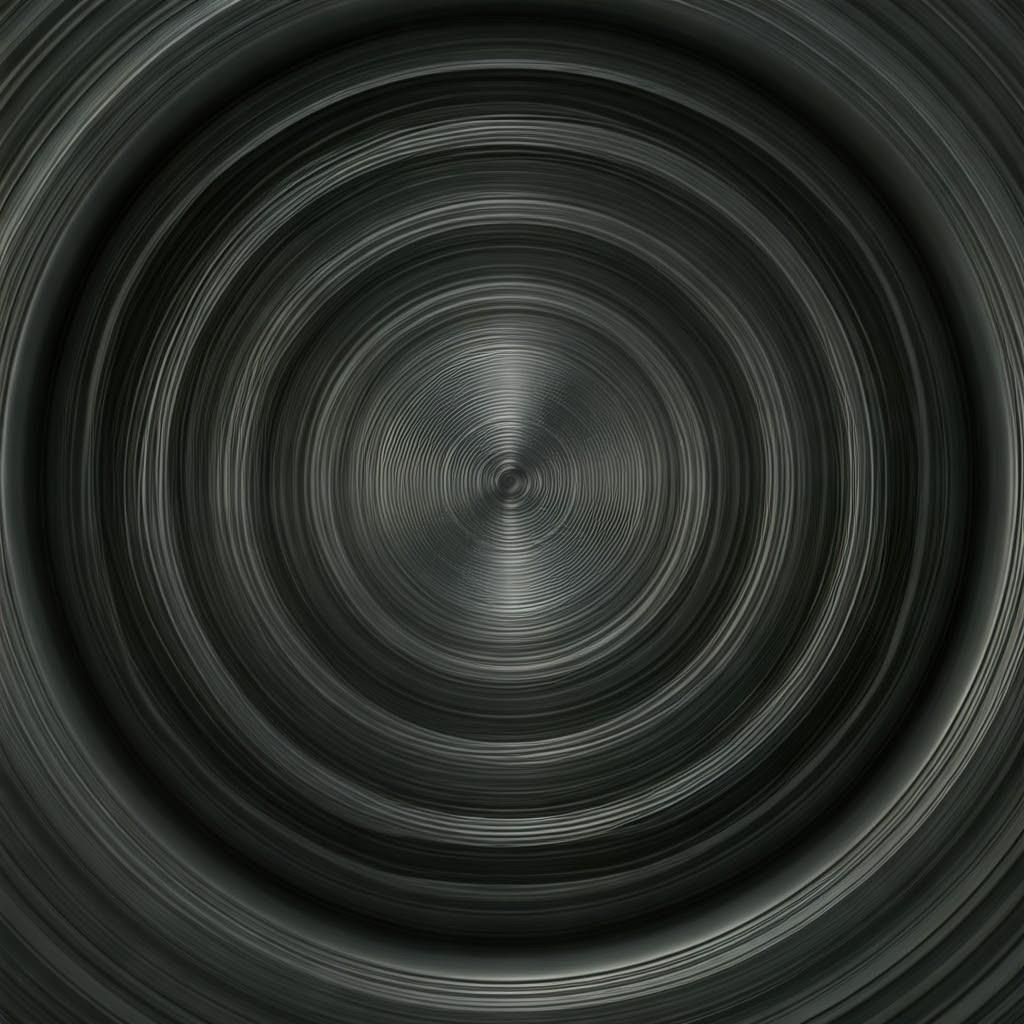
Nachbearbeitungsanforderungen für Zugangsklappen für die Luft- und Raumfahrt - Sicherstellung von Haltbarkeit und Verlässlichkeit
Während der 3D-Metalldruck erhebliche Vorteile bei der Erstellung komplexer Geometrien bietet, sind Nachbearbeitungsschritte oft unerlässlich, um die endgültigen Eigenschaften, die Oberflächenbeschaffenheit und die Maßgenauigkeit zu erreichen, die für für die Luft- und Raumfahrt geeignete Zugangsluken erforderlich sind. Diese Schritte gewährleisten die Haltbarkeit, Zuverlässigkeit und Leistung der Komponenten in anspruchsvollen Luft- und Raumfahrtumgebungen. Zu den üblichen Nachbearbeitungsanforderungen gehören:
- Entfernung der Stützstruktur: 3D-gedruckte Metallteile benötigen oft Stützstrukturen, um Verformungen während des Bauprozesses zu verhindern. Diese Stützstrukturen müssen nach dem Druck sorgfältig entfernt werden, in der Regel durch Bearbeitung, Schleifen oder Drahterodieren (EDM). Die Konstruktion des Teils sollte darauf abzielen, die Notwendigkeit umfangreicher Stützstrukturen zu minimieren, um den Nachbearbeitungsaufwand und mögliche Oberflächenschäden zu verringern.
- Stressabbau Wärmebehandlung: In 3D-gedruckten Metallteilen können sich aufgrund der schnellen Erwärmungs- und Abkühlungszyklen während des Druckvorgangs Eigenspannungen aufbauen. Eine Wärmebehandlung zum Spannungsabbau ist oft notwendig, um diese inneren Spannungen zu reduzieren, Verformungen zu verhindern und die allgemeinen mechanischen Eigenschaften und die Dimensionsstabilität der Zugangsluken zu verbessern.
- Heiß-Isostatisches Pressen (HIP): HIP ist ein Verfahren, bei dem das 3D-gedruckte Teil unter hohem Druck und bei hoher Temperatur in einer Inertgasumgebung hergestellt wird. Dieses Verfahren trägt dazu bei, interne Porosität zu beseitigen, die Dichte des Materials zu erhöhen und seine mechanischen Eigenschaften zu verbessern, insbesondere die Ermüdungsfestigkeit, die für Bauteile in der Luft- und Raumfahrt entscheidend ist.
- Oberflächenveredelung: Wie bereits erwähnt, entspricht die Oberfläche im gedruckten Zustand möglicherweise nicht den Anforderungen aller Luft- und Raumfahrtanwendungen. Nachbearbeitungstechniken wie Bearbeiten, Schleifen, Polieren oder Strahlen können erforderlich sein, um die gewünschte Glätte für Dichtungsflächen, aerodynamische Leistung oder aus ästhetischen Gründen zu erreichen.
- Wärmebehandlung für spezifische Eigenschaften: Je nach Werkstoff und Verwendungszweck können weitere Wärmebehandlungen erforderlich sein, um bestimmte mechanische Eigenschaften zu erzielen, z. B. eine höhere Härte oder Festigkeit. Die spezifischen Wärmebehandlungszyklen sind auf die verwendete Legierung zugeschnitten.
- Zerstörungsfreie Prüfung (NDT): Bauteile für die Luft- und Raumfahrt werden häufig strengen zerstörungsfreien Prüfungen unterzogen, wie z. B. Farbeindringprüfung, Magnetpulverprüfung, Ultraschallprüfung oder Durchstrahlungsprüfung, um sicherzustellen, dass sie keine kritischen Mängel wie Risse oder Porosität aufweisen. Diese Prüfungen werden nach der Nachbearbeitung durchgeführt, um die Integrität der hergestellten Zugangsluken zu überprüfen.
- Oberflächenbeschichtungen und -behandlungen: Je nach Anwendung und Umgebungsbedingungen können Oberflächenbeschichtungen oder -behandlungen erforderlich sein, um die Korrosionsbeständigkeit, Verschleißfestigkeit oder andere spezifische Eigenschaften zu verbessern. Beispiele hierfür sind die Eloxierung von Aluminiumlegierungen oder die Lackierung zu Schutz- und ästhetischen Zwecken.
- Prüfung der Abmessungen: Nach Abschluss aller Nachbearbeitungsschritte ist eine gründliche Maßkontrolle mit Hilfe von Koordinatenmessgeräten (KMG) oder anderen Messgeräten unerlässlich, um zu überprüfen, ob die Durchstiegsluken den vorgegebenen Toleranzen und der Maßgenauigkeit entsprechen.
Die spezifischen Nachbearbeitungsanforderungen für 3D-gedruckte Zugangsluken für die Luft- und Raumfahrt hängen vom Material, dem verwendeten Druckverfahren, der Komplexität des Designs und den Anwendungsanforderungen ab. Die Zusammenarbeit mit einem erfahrenen Metall-AM-Dienstleister wie Metall3DPdie über Fachwissen auf dem Gebiet der Nachbearbeitungsverfahren und der Qualitätskontrolle in der Luft- und Raumfahrt verfügt, ist für die Herstellung zuverlässiger und leistungsstarker Bauteile von entscheidender Bedeutung.
Häufige Herausforderungen und deren Vermeidung beim 3D-Druck von Luft- und Raumfahrtkomponenten
Der 3D-Metalldruck bietet zwar zahlreiche Vorteile für die Herstellung von Bauteilen für die Luft- und Raumfahrt, doch können während des Prozesses auch verschiedene Herausforderungen auftreten. Das Verständnis dieser potenziellen Probleme und die Implementierung geeigneter Strategien zu ihrer Vermeidung sind entscheidend für die erfolgreiche Produktion hochwertiger Zugangsluken für die Luft- und Raumfahrt:
- Verformung und Verzerrung: Thermische Spannungen während des schichtweisen Druckvorgangs können zu Verwerfungen oder Verzerrungen des Teils führen, insbesondere bei komplexen Geometrien oder großen Teilen.
- Wie man es vermeidet: Optimieren Sie die Ausrichtung der Teile, um Überhänge und Spannungskonzentrationen zu minimieren. Verwenden Sie geeignete Stützstrukturen. Sorgfältige Kontrolle der Bauparameter und der Temperatur in der Baukammer. Erwägen Sie eine Wärmebehandlung zum Spannungsabbau nach dem Druck.
- Probleme mit Porosität und Dichte: Unzureichendes Schmelzen oder Schmelzen des Metallpulvers kann zu Porosität im gedruckten Teil führen, was sich negativ auf die mechanischen Eigenschaften auswirken kann.
- Wie man es vermeidet: Optimieren Sie die Laser- oder Elektronenstrahlleistung und die Scangeschwindigkeit. Achten Sie auf die Verwendung von hochwertigen Metallpulvern mit guter Fließfähigkeit, wie sie beispielsweise von Metall3DP. Erwägen Sie das heißisostatische Pressen (HIP) als Nachbearbeitungsschritt, um die Porosität zu reduzieren und die Dichte zu erhöhen.
- Oberflächenrauhigkeit: Die gedruckte Oberfläche kann für bestimmte Anwendungen in der Luft- und Raumfahrt zu rau sein und die Dichtigkeit oder die aerodynamische Leistung beeinträchtigen.
- Wie man es vermeidet: Optimieren Sie die Bauparameter, z. B. die Schichtdicke. Ziehen Sie Nachbearbeitungstechniken wie Bearbeitung, Polieren oder Strahlen in Betracht, um die gewünschte Oberflächengüte zu erreichen.
- Schäden bei der Beseitigung von Stützstrukturen: Das Entfernen von Stützstrukturen kann manchmal Spuren hinterlassen oder die Oberfläche des Teils beschädigen, insbesondere bei komplizierten Geometrien.
- Wie man es vermeidet: Konstruieren Sie Teile mit selbsttragenden Eigenschaften, um den Bedarf an Stützen zu minimieren. Planen Sie die Platzierung der Stützen sorgfältig und wenden Sie geeignete Entfernungsmethoden an. Erwägen Sie die Verwendung von auflösbaren Stützmaterialien, falls für das gewählte Metall verfügbar.
- Maßliche Ungenauigkeit: Das Erreichen enger Toleranzen kann eine Herausforderung sein, insbesondere bei komplexen Teilen oder großen Produktionsmengen.
- Wie man es vermeidet: Kalibrieren und warten Sie die 3D-Druckausrüstung regelmäßig. Optimieren Sie die Bauausrichtung und berücksichtigen Sie bei der Konstruktion den Schrumpfungsausgleich. Nutzen Sie die Nachbearbeitung für kritische Abmessungen. Metal3DPs hochpräzisionsdrucker sind darauf ausgelegt, Maßabweichungen zu minimieren.
- Variabilität der Materialeigenschaften: Ungleichmäßiges Schmelzen oder Erstarren während des Druckvorgangs kann zu Schwankungen der mechanischen Eigenschaften des gesamten Teils führen.
- Wie man es vermeidet: Optimieren Sie die Prozessparameter, um einen gleichmäßigen Energieeintrag zu gewährleisten. Verwenden Sie hochwertige Metallpulver mit gleichmäßiger Partikelgrößenverteilung. Erwägen Sie Prozessüberwachungsmethoden, um Unstimmigkeiten zu erkennen und abzumildern.
- Kosten der Produktion: Der 3D-Druck von Metall kann teuer sein, insbesondere bei großen Produktionsmengen oder komplexen Teilen, die eine umfangreiche Nachbearbeitung erfordern.
- Wie man es vermeidet: Optimieren Sie das Teiledesign für effizientes Drucken und minimalen Materialverbrauch. Sondieren Sie Möglichkeiten zur Teilekonsolidierung. Sorgfältige Bewertung der Kosten-Nutzen-Analyse im Vergleich zu herkömmlichen Fertigungsmethoden für die jeweilige Anwendung.
- Qualifizierung und Zertifizierung: Bauteile für die Luft- und Raumfahrt unterliegen strengen Qualifikations- und Zertifizierungsanforderungen. Die Entwicklung eines robusten und wiederholbaren 3D-Druckverfahrens für Metall, das diese Standards erfüllt, kann eine Herausforderung sein.
- Wie man es vermeidet: Arbeiten Sie mit erfahrenen Metall-AM-Dienstleistern zusammen, die sich mit Qualitätsmanagementsystemen und Zertifizierungsverfahren in der Luft- und Raumfahrt auskennen. Implementieren Sie strenge Prozesskontroll- und Qualitätssicherungsverfahren.
Durch die proaktive Bewältigung dieser potenziellen Herausforderungen durch sorgfältiges Design, optimierte Prozessparameter, geeignete Nachbearbeitung und die Zusammenarbeit mit erfahrenen Partnern wie Metall3DPkönnen Hersteller in der Luft- und Raumfahrtindustrie die Vorteile des 3D-Metalldrucks erfolgreich für die Produktion von leistungsstarken Zugangsluken und anderen kritischen Komponenten nutzen.
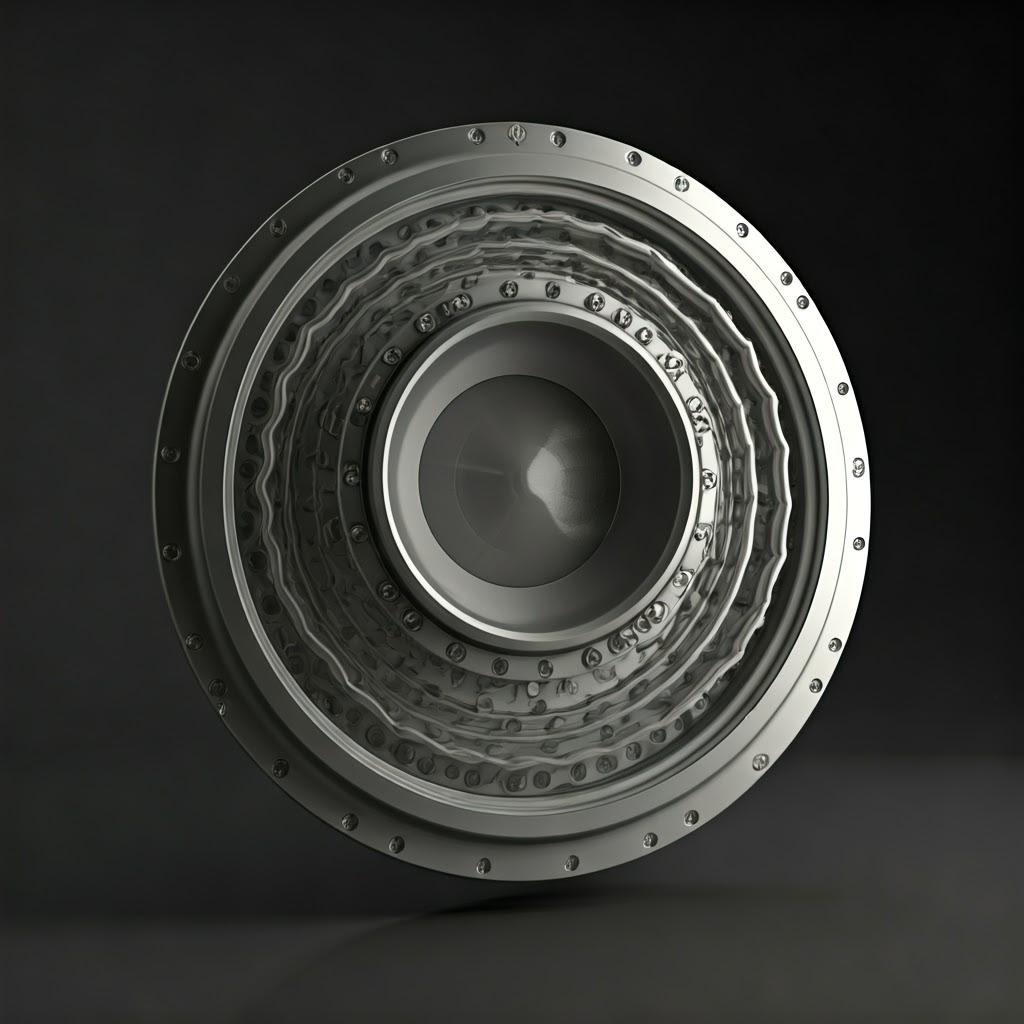
Wie man den richtigen 3D-Druckdienstleister für die Luft- und Raumfahrt auswählt
Die Auswahl des richtigen 3D-Druckdienstleisters für Metall ist eine wichtige Entscheidung für Luft- und Raumfahrtunternehmen, die die Vorteile der additiven Fertigung für Zugangsluken und andere Komponenten nutzen möchten. Der ausgewählte Anbieter sollte über das Fachwissen, die Fähigkeiten und die Qualitätsstandards verfügen, die erforderlich sind, um die strengen Anforderungen der Luft- und Raumfahrtindustrie zu erfüllen. Hier sind einige Schlüsselfaktoren zu berücksichtigen:
- Erfahrung und Zertifizierungen in der Luft- und Raumfahrt: Suchen Sie nach einem Dienstleister, der nachweislich mit Kunden aus der Luft- und Raumfahrtindustrie zusammengearbeitet hat und die spezifischen Anforderungen dieser Branche genau kennt. Einschlägige Zertifizierungen wie AS9100 oder Nadcap zeugen von einer Verpflichtung zu Qualität und Prozesskontrolle.
- Materielle Fähigkeiten: Vergewissern Sie sich, dass der Anbieter die für Ihre Anwendung erforderlichen spezifischen Metallpulver in Luft- und Raumfahrtqualität anbietet, wie z. B. AlSi10Mg und Scalmalloy®, und dass er Erfahrung in der Verarbeitung dieser Materialien hat. Erkundigen Sie sich nach den Möglichkeiten der Materialcharakterisierung und -prüfung. Metall3DP verfügt über eine breite Palette an hochwertigen Metallpulvern, die für verschiedene Anwendungen optimiert sind.
- Technologie und Ausrüstung: Prüfen Sie, welche Arten von Metall-3D-Drucktechnologien der Anbieter einsetzt (z. B. LPBF, EBPBF). Vergewissern Sie sich, dass der Anbieter über gut gewartete, hochpräzise Anlagen verfügt, die für die Herstellung der Größe und Komplexität Ihrer Zugangsluken geeignet sind. Metal3DPs die branchenführenden SEBM-Drucker bieten ein hohes Druckvolumen, Genauigkeit und Zuverlässigkeit.
- Fachwissen im Bereich Design für additive Fertigung (DfAM): Ein kompetenter Dienstleister sollte Sie bei der Optimierung Ihrer Lukendesigns für den 3D-Metalldruck beraten und unterstützen. Seine Erfahrung mit den DfAM-Prinzipien kann Ihnen helfen, Gewicht zu reduzieren, Teile zu konsolidieren und die Leistung zu verbessern.
- Nachbearbeitungsmöglichkeiten: Erkundigen Sie sich nach den betriebsinternen Nachbearbeitungsdiensten, wie z. B. Entfernen von Stützen, Wärmebehandlung (einschließlich Spannungsabbau und HIP), Oberflächenbearbeitung und zerstörungsfreie Prüfung. Ein umfassendes Angebot an Nachbearbeitungsmöglichkeiten kann den Fertigungsprozess rationalisieren.
- Qualitätskontrolle und Inspektion: Robuste Qualitätskontrollverfahren und Inspektionsmöglichkeiten sind in der Luft- und Raumfahrt von entscheidender Bedeutung. Vergewissern Sie sich, dass der Anbieter über strenge Qualitätsmanagementsysteme verfügt, einschließlich Maßkontrolle, Materialprüfung und Rückverfolgbarkeit.
- Skalierbarkeit und Produktionskapazität: Berücksichtigen Sie die Fähigkeit des Anbieters, Ihr aktuelles und zukünftiges Produktionsvolumen zu bewältigen. Ist er in der Lage, die Produktion zu erhöhen, wenn Ihr Bedarf steigt?
- Vorlaufzeiten und Lieferung: Erörtern Sie typische Vorlaufzeiten für ähnliche Komponenten für die Luft- und Raumfahrt und stellen Sie sicher, dass diese mit Ihren Projektzeitplänen übereinstimmen. Ein zuverlässiger Anbieter sollte über effiziente Produktionsprozesse und Logistik verfügen.
- Kommunikation und Kollaboration: Effektive Kommunikation und ein kooperativer Ansatz sind für eine erfolgreiche Partnerschaft unerlässlich. Wählen Sie einen Anbieter, der reaktionsschnell und transparent ist und eng mit Ihrem Team zusammenarbeiten möchte. 1 1. inbouncy.com inbouncy.com
- Vertraulichkeit und Schutz des geistigen Eigentums: Vergewissern Sie sich, dass der Dienstleister zuverlässige Maßnahmen zum Schutz Ihrer vertraulichen Informationen und Ihres geistigen Eigentums getroffen hat.
Durch eine sorgfältige Bewertung dieser Faktoren können Sie einen 3D-Druckdienstleister für Metall auswählen, der gut gerüstet ist, um die anspruchsvollen Anforderungen Ihres Zugangslukenprojekts für die Luft- und Raumfahrt zu erfüllen und zu den Zielen Ihres Unternehmens im Bereich der additiven Fertigung beizutragen.
Kostenfaktoren und Vorlaufzeit für 3D-gedruckte Zugangsluken für die Luft- und Raumfahrt
Das Verständnis der Kostentreiber und typischen Vorlaufzeiten im Zusammenhang mit dem 3D-Metalldruck von Zugangsluken für die Luft- und Raumfahrt ist für die Budgetierung und Projektplanung von entscheidender Bedeutung. Mehrere Faktoren beeinflussen die Gesamtkosten und den Produktionszeitplan:
- Materialkosten: Die Kosten für das Metallpulver sind ein wichtiger Faktor. Für die Luft- und Raumfahrt geeignete Legierungen wie Scalmalloy® können teurer sein als Standard-Aluminiumlegierungen wie AlSi10Mg. Auch die Menge des für jedes Teil benötigten Materials wirkt sich auf die Kosten aus. Optimierte Konstruktionen, die den Materialverbrauch minimieren, können hier Abhilfe schaffen.
- Bauzeit: Die Zeit, die für den Druck einer Zugangsluke benötigt wird, hängt von der Größe, der Komplexität und den gewählten Druckparametern (z. B. Schichtdicke, Scangeschwindigkeit) ab. Längere Bauzeiten führen zu höheren Maschinennutzungskosten.
- Kosten der Maschinenbenutzung: 3D-Druckanlagen aus Metall haben hohe Investitions- und Betriebskosten (z. B. Energieverbrauch, Wartung). Diese Kosten werden von den Dienstleistern in ihre Preise eingerechnet.
- Nachbearbeitungskosten: Das Ausmaß der erforderlichen Nachbearbeitung (Entfernen von Stützen, Wärmebehandlung, Oberflächenbearbeitung, Inspektion) hat erhebliche Auswirkungen auf die Gesamtkosten und die Vorlaufzeit. Komplexe Geometrien erfordern oft eine umfangreichere Nachbearbeitung.
- Entwurfskomplexität und Optimierung: Der 3D-Druck ermöglicht zwar komplexe Entwürfe, doch hochkomplexe Geometrien können einen höheren Entwurfsaufwand und längere Bauzeiten erfordern, was die Kosten in die Höhe treiben kann. Die Gestaltung für einen effizienten Druck kann zur Kostenoptimierung beitragen.
- Menge und Umfang: Die Kosten pro Teil sinken in der Regel mit steigendem Produktionsvolumen aufgrund von Skaleneffekten. Der 3D-Metalldruck ist jedoch oft am kosteneffizientesten für die Produktion kleiner bis mittlerer Stückzahlen oder stark individualisierter Teile.
- Qualitätssicherung und Prüfung: Die strengen Qualitätskontroll- und Prüfverfahren, die für Luft- und Raumfahrtkomponenten erforderlich sind, erhöhen die Gesamtkosten.
- Faktoren für die Vorlaufzeit:
- Design und Technik: Die Zeit, die für die Designoptimierung und die Vorbereitung für den 3D-Druck benötigt wird.
- Druckzeit: Die tatsächliche Bauzeit auf dem 3D-Drucker.
- Nachbearbeitungszeit: Die Zeit, die für das Entfernen der Auflage, die Wärmebehandlung, die Oberflächenbearbeitung und andere Nachbearbeitungsschritte benötigt wird.
- Qualitätsinspektion: Die Zeit für gründliche Maß- und Materialprüfungen.
- Versand und Logistik: Der Zeitpunkt für die endgültige Lieferung der Teile.
Die Vorlaufzeiten für 3D-gedruckte Einstiegsluken aus Metall für die Luft- und Raumfahrt können je nach diesen Faktoren erheblich variieren und reichen von wenigen Tagen für einfache Prototypen bis zu mehreren Wochen für komplexe Großserien mit umfangreicher Nachbearbeitung und strengen Qualitätsprüfungen. Es ist wichtig, diese Faktoren im Detail mit dem gewählten 3D-Druckdienstleister zu besprechen, um genaue Kostenschätzungen und Vorlaufzeiten für Ihr spezifisches Projekt zu erhalten.
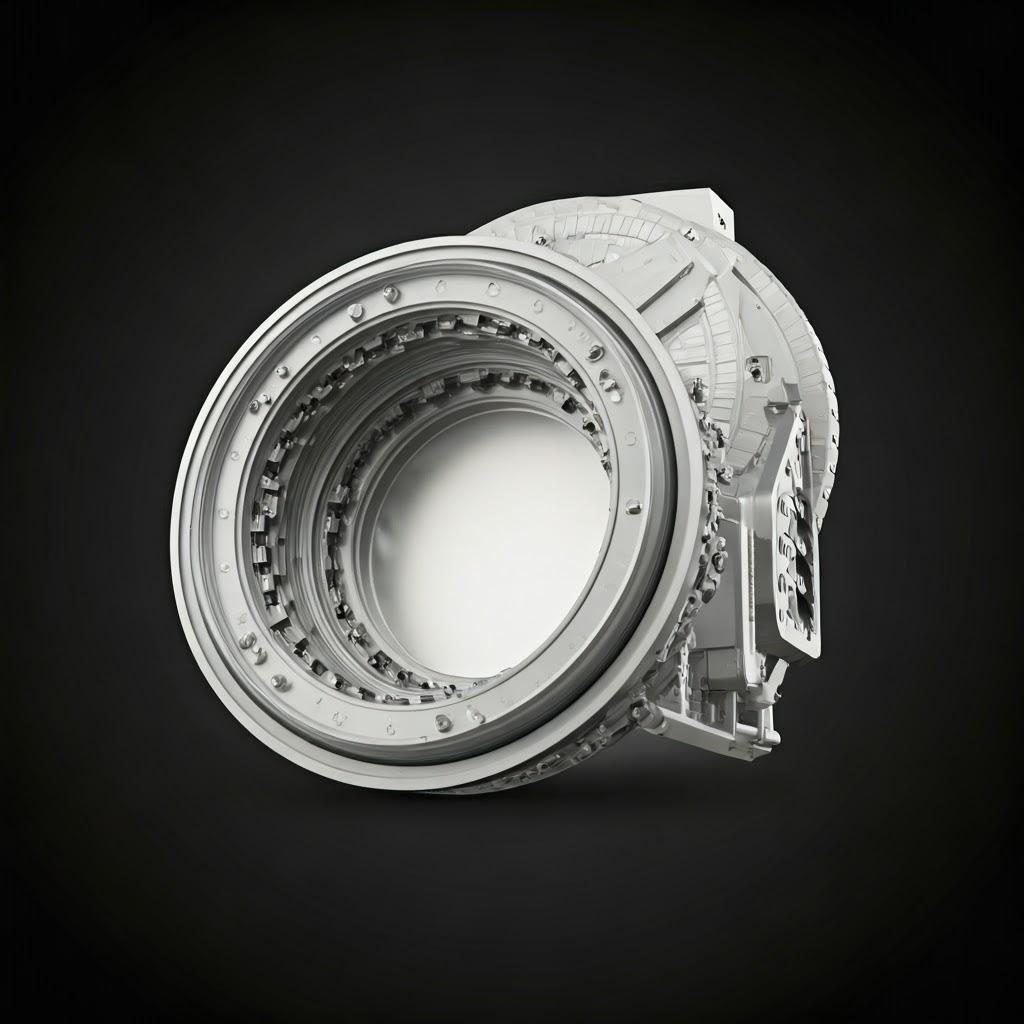
Häufig gestellte Fragen (FAQ)
- F: Können 3D-gedruckte Zugangsluken aus Metall die strukturellen Anforderungen der Luft- und Raumfahrt erfüllen?
- A: Ja, unter Verwendung geeigneter Materialien für die Luft- und Raumfahrt wie AlSi10Mg oder Scalmalloy® und unter Einhaltung strenger Prozesskontrollen und Nachbearbeitungsverfahren können 3D-gedruckte Zugangsluken aus Metall die strukturellen Anforderungen der Luft- und Raumfahrt erfüllen oder sogar übertreffen. Techniken wie das Heiß-Isostatische Pressen (HIP) können ihre mechanischen Eigenschaften weiter verbessern und sicherstellen, dass sie die erforderliche Festigkeit und Ermüdungsbeständigkeit aufweisen.
- F: Wie hoch ist die typische Gewichtseinsparung, die mit 3D-gedruckten Zugangsluken für die Luft- und Raumfahrt im Vergleich zu traditionell hergestellten Luken erzielt werden kann?
- A: Die Gewichtseinsparungen können je nach spezifischem Design und dem Ausmaß der Topologieoptimierung und der Integration der Gitterstruktur variieren. Durch die Nutzung der Designfreiheit, die der 3D-Metalldruck im Vergleich zu herkömmlichen subtraktiven Fertigungsverfahren bietet, sind jedoch häufig Einsparungen von 20-50 % oder mehr möglich.
- F: Ist der 3D-Druck von Metall für die Herstellung von Zugangsklappen für die Luft- und Raumfahrt kostengünstig?
- A: Der 3D-Metalldruck kann kosteneffizient sein, wenn es um die Produktion von kleinen bis mittleren Stückzahlen, hochgradig kundenspezifischen Teilen und komplexen Geometrien geht, bei denen die herkömmliche Fertigung einen erheblichen Materialabfall oder mehrere Montageschritte erfordert. Die Kosteneffizienz wird durch das Potenzial zur Gewichtsreduzierung, Teilekonsolidierung und On-Demand-Fertigung erhöht, was insgesamt zu Einsparungen bei Kraftstoffverbrauch, Montagezeit und Lagerbestand führen kann.
- F: Welche Metalllegierungen werden häufig für den 3D-Druck von Zugangsklappen für die Luft- und Raumfahrt verwendet?
- A: Zu den gebräuchlichen Legierungen gehören Aluminiumlegierungen wie AlSi10Mg und Hochleistungslegierungen wie Scalmalloy® zur Gewichtsreduzierung. Titanlegierungen (z. B. Ti-6Al-4V) und nichtrostende Stähle werden ebenfalls verwendet, je nach den spezifischen Anforderungen an Festigkeit, Korrosionsbeständigkeit und Temperaturverhalten der Anwendung. Metall3DP bietet ein breit gefächertes Angebot an hochwertigen Metallpulvern für Anwendungen in der Luft- und Raumfahrt.
Schlussfolgerung - Einsatz des 3D-Drucks von Metall für die nächste Generation von Zugangsklappen in der Luft- und Raumfahrt
Das unablässige Streben der Luft- und Raumfahrtindustrie nach Leichtbau, verbesserter Leistung und effizienter Fertigung treibt die Einführung innovativer Technologien wie den 3D-Druck von Metall voran. Für Zugangsklappen in der Luft- und Raumfahrt bietet die additive Fertigung von Metall einen transformativen Ansatz, der die Herstellung von leichten, strukturell optimierten Komponenten mit komplexen Geometrien und integrierten Merkmalen ermöglicht, die mit herkömmlichen Methoden bisher unerreichbar waren.
Werkstoffe wie AlSi10Mg und Scalmalloy® bieten ein ausgezeichnetes Gleichgewicht zwischen Gewicht und Festigkeit und sind daher ideal für 3D-gedruckte Zugangsluken. Durch die sorgfältige Berücksichtigung der Prinzipien des Designs für die additive Fertigung, die Einhaltung strenger Qualitätskontrollmaßnahmen und die Zusammenarbeit mit erfahrenen Metall-AM-Dienstleistern wie Metall3DPkönnen die Hersteller der Luft- und Raumfahrtindustrie das volle Potenzial dieser Technologie ausschöpfen.
Von erheblichen Gewichtsreduzierungen und verbesserter Treibstoffeffizienz bis hin zu größerer Designfreiheit und schnelleren Prototyping-Zyklen - der 3D-Metalldruck ist bereit, die Art und Weise zu revolutionieren, wie Einstiegsluken in der Luft- und Raumfahrt entworfen und hergestellt werden. Mit der Weiterentwicklung der Technologie und der Ausweitung der Materialoptionen ist eine noch breitere Anwendung von Metall-AM in der Luft- und Raumfahrt zu erwarten, die den Weg für die nächste Generation von Flugzeugen mit verbesserter Leistung, Nachhaltigkeit und Kosteneffizienz ebnet. Kontakt Metall3DP um herauszufinden, wie die hochmodernen Systeme und die hochwertigen Metallpulver die Ziele Ihres Unternehmens im Bereich der additiven Fertigung für Luft- und Raumfahrtanwendungen unterstützen können.
Teilen auf
MET3DP Technology Co., LTD ist ein führender Anbieter von additiven Fertigungslösungen mit Hauptsitz in Qingdao, China. Unser Unternehmen ist spezialisiert auf 3D-Druckgeräte und Hochleistungsmetallpulver für industrielle Anwendungen.
Fragen Sie an, um den besten Preis und eine maßgeschneiderte Lösung für Ihr Unternehmen zu erhalten!
Verwandte Artikel
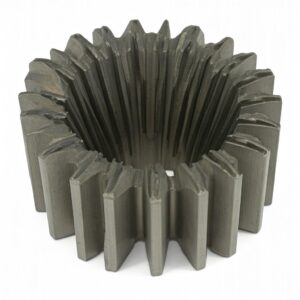
Hochleistungs-Düsenschaufelsegmente: Revolutionierung der Turbineneffizienz mit 3D-Metalldruck
Mehr lesen "Über Met3DP
Aktuelles Update
Unser Produkt
KONTAKT US
Haben Sie Fragen? Senden Sie uns jetzt eine Nachricht! Wir werden Ihre Anfrage mit einem ganzen Team nach Erhalt Ihrer Nachricht bearbeiten.
Holen Sie sich Metal3DP's
Produkt-Broschüre
Erhalten Sie die neuesten Produkte und Preislisten