3D-gedruckte Halterungen für Kfz-Radarsensoren: Präzision und Leistung
Inhaltsübersicht
Einführung – Revolutionierung der Integration von Automobilsensoren mit Metalldruck im 3D-Verfahren
Die Integration von fortschrittlichen Fahrerassistenzsystemen (ADAS) und Technologien für autonomes Fahren verändert die Automobilindustrie rasant. Im Mittelpunkt dieser Systeme stehen kritische Sensoren, darunter Radar, die präzise und zuverlässige Montagelösungen erfordern. Herkömmliche Herstellungsverfahren für diese Kfz-Radarsensorhalterungen stoßen oft auf Einschränkungen in Bezug auf Designflexibilität, Gewichtsoptimierung und Rapid Prototyping. Der Metalldruck im 3D-Verfahren, auch bekannt als additive Metallfertigung, bietet eine bahnbrechende Alternative, die die Erstellung komplexer Geometrien mit verbesserten Leistungseigenschaften ermöglicht. Dieser Blogbeitrag befasst sich mit den Vorteilen der Verwendung von Metall 3D-Druck für Kfz-Radarsensorhalterungen, wobei Materialbetrachtungen, Designoptimierung und die entscheidende Rolle erfahrener Dienstleister wie Metal3DP Technology Co. LTD.
Wofür wird dieses Produkt verwendet? – Ermöglichung von erweiterten Fahrerassistenzsystemen und autonomem Fahren
Kfz-Radarsensorhalterungen dienen als entscheidende Schnittstelle zwischen den Radarsensoren und der Fahrzeugstruktur. Ihre Hauptfunktion besteht darin, die Radareinheiten sicher zu positionieren und auszurichten, um eine genaue Datenerfassung für verschiedene ADAS-Funktionen wie adaptive Geschwindigkeitsregelung, Totwinkel-Erkennung, Spurhalteassistent und automatische Notbremsung zu gewährleisten. Da die Automobilindustrie in Richtung höherer Autonomiestufen voranschreitet, steigen die Anforderungen an diese Halterungen. Sie müssen rauen Umgebungsbedingungen standhalten, einschließlich Vibrationen, Temperaturschwankungen und der Einwirkung von Feuchtigkeit und Straßenschmutz, während sie die Dimensionsstabilität beibehalten, um eine konsistente Sensorleistung zu gewährleisten. Darüber hinaus wirkt sich das Design dieser Halterungen erheblich auf das Sichtfeld des Sensors und die Gesamteffizienz des Systems aus. Der Metalldruck im 3D-Verfahren ermöglicht die Erstellung komplizierter Halterungsdesigns, die auf spezifische Fahrzeugarchitekturen und Sensoranforderungen zugeschnitten sind, wodurch sowohl die Funktionalität als auch die Integration optimiert werden.
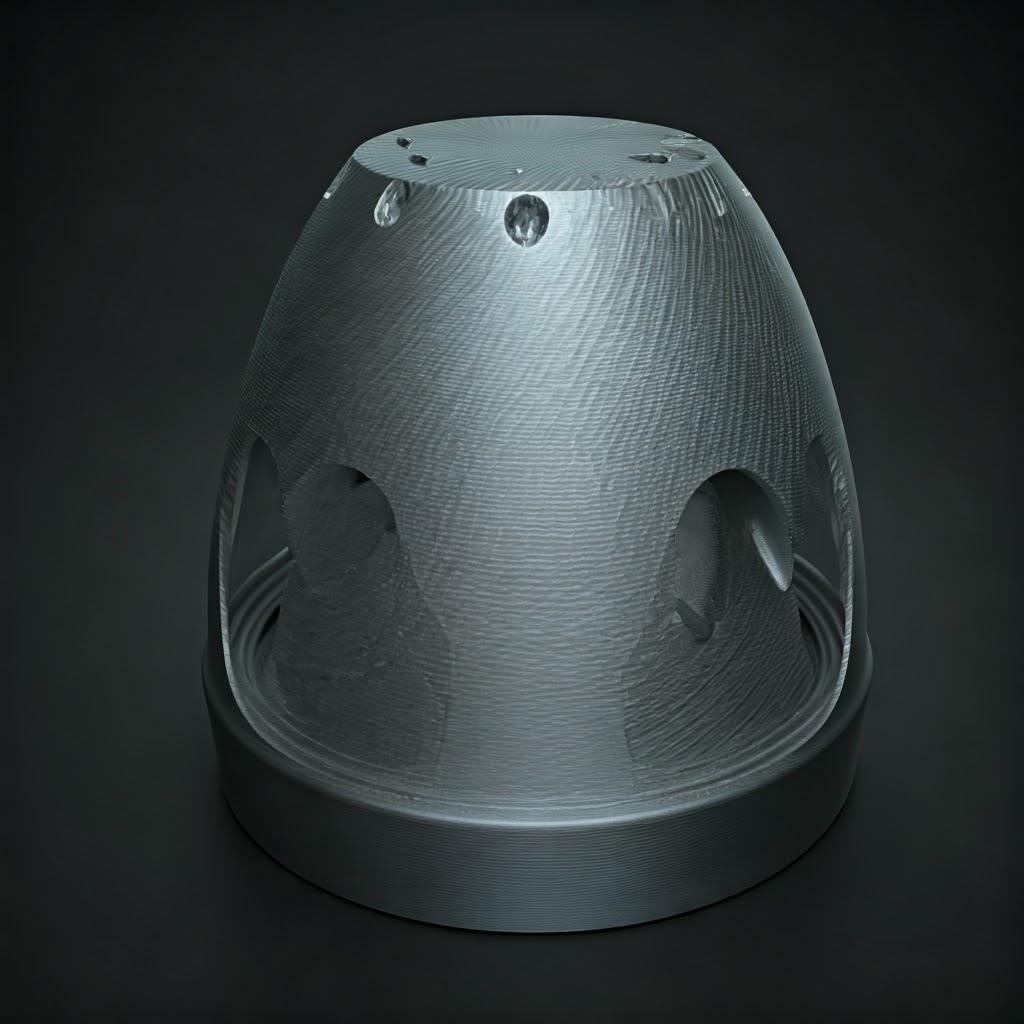
Warum Metalldruck im 3D-Verfahren für dieses Produkt verwenden? – Designfreiheit und Leistungsvorteile freisetzen
Die Entscheidung für den Metalldruck im 3D-Verfahren gegenüber herkömmlichen Herstellungsverfahren für Kfz-Radarsensorhalterungen bietet eine Vielzahl überzeugender Vorteile:
- Flexibilität bei der Gestaltung: Die additive Fertigung befreit Ingenieure von den Einschränkungen herkömmlicher Werkzeuge und ermöglicht die Erstellung komplexer Geometrien, komplizierter Innenstrukturen und kundenspezifischer Merkmale, die mit Zerspanung oder Gießen nur schwer oder gar nicht zu erreichen wären. Diese Designfreiheit ermöglicht eine optimierte Sensorplatzierung, eine verbesserte aerodynamische Leistung und integrierte Funktionen wie Kühlkanäle oder Kabelführung.
- Optimierung des Gewichts: In der Automobilindustrie ist die Reduzierung des Fahrzeuggewichts von größter Bedeutung, um die Kraftstoffeffizienz zu verbessern und die Emissionen zu senken. Der Metalldruck im 3D-Verfahren erleichtert die Erstellung leichter und dennoch strukturell robuster Halterungen durch Techniken wie Topologieoptimierung und Gitterstrukturen. Durch die strategische Verteilung von Material nur dort, wo es benötigt wird, können erhebliche Gewichtseinsparungen erzielt werden, ohne die Leistung zu beeinträchtigen.
- Rapid Prototyping und Iteration: Die Fähigkeit, Designs schnell zu wiederholen und Funktionsprototypen herzustellen, ist ein erheblicher Vorteil des Metalldrucks im 3D-Verfahren. Dies beschleunigt den Entwicklungszyklus und ermöglicht es Automobilherstellern, Sensorhalterungsdesigns effizient zu testen und zu verfeinern, wodurch die Markteinführungszeit und die Entwicklungskosten reduziert werden.
- Materialeffizienz: Additive Fertigungsverfahren beinhalten typischerweise weniger Materialabfall als subtraktive Verfahren wie die Zerspanung, bei denen ein erheblicher Teil des Rohmaterials entfernt wird. Dies kann zu Kosteneinsparungen führen, insbesondere bei der Arbeit mit teuren Speziallegierungen.
- Personalisierung und Kleinserienproduktion: Der Metalldruck im 3D-Verfahren eignet sich besonders gut für die Herstellung kundenspezifischer Halterungen für bestimmte Fahrzeugmodelle oder Kleinserien, bei denen die Kosten für herkömmliche Werkzeuge prohibitiv wären. Diese Agilität ist in der sich entwickelnden Automobillandschaft mit vielfältigen Fahrzeugplattformen und Nischenmärkten von zunehmender Bedeutung.
- Verbesserte Leistung: Durch die Auswahl des geeigneten Metallpulvers und die Optimierung des Designs für die additive Fertigung ist es möglich, Sensorhalterungen mit überlegenen mechanischen Eigenschaften zu erstellen, wie z. B. einem erhöhten Festigkeits-Gewichts-Verhältnis, verbesserter Steifigkeit und erhöhter Haltbarkeit in anspruchsvollen Automobilumgebungen. 3D-Druck von Metall von erfahrenen Anbietern wie Metal3DP stellen sicher, dass diese Leistungsvorteile durch optimierte Druckparameter und Nachbearbeitungstechniken realisiert werden.
Empfohlene Materialien und warum sie wichtig sind – AlSi10Mg und A7075 für optimale Leistung
Die Materialauswahl ist entscheidend für die Leistung und Zuverlässigkeit von Kfz-Radarsensorhalterungen. Metal3DP empfiehlt die Aluminiumlegierungen AlSi10Mg und A7075 für diese Anwendung aufgrund ihrer außergewöhnlichen Kombination von Eigenschaften:
- AlSi10Mg: Diese Aluminiumlegierung wird aufgrund ihres ausgezeichneten Festigkeits-Gewichts-Verhältnisses, ihrer guten Wärmeleitfähigkeit und Korrosionsbeständigkeit häufig im Metalldruck im 3D-Verfahren eingesetzt. Ihr hoher Siliziumgehalt verbessert ihre Bedruckbarkeit und führt zu Teilen mit guter Oberflächenbeschaffenheit und hoher Dichte. Diese Eigenschaften machen AlSi10Mg zu einem idealen Kandidaten für Radarsensorhalterungen, die eine leichte Konstruktion und zuverlässige Leistung bei unterschiedlichen Temperaturen erfordern. Metal3DP verwendet fortschrittliche Pulverherstellungssysteme, um die hohe Sphärizität und Fließfähigkeit seines AlSi10Mg-Pulvers zu gewährleisten, was für das Erreichen dichter und konsistenter 3D-gedruckter Teile unerlässlich ist. | Eigenschaft | Wert | Vorteil | Relevanz für Radarhalterungen | | :—————————- | :———————————- | :———————————————————————- | :—————————————————————————- | | Zugfestigkeit (MPa) | ~450 | Hohe strukturelle Integrität unter Last | Gewährleistet eine sichere Sensormontage während des Fahrzeugbetriebs. | | Streckgrenze (MPa) | ~300 | Beständigkeit gegen bleibende Verformung | Behält die präzise Sensorausrichtung im Laufe der Zeit bei. | | Dichte (g/cm³) | ~2,67 | Leichte Konstruktion | Trägt zur Gewichtsreduzierung und Kraftstoffeffizienz des Fahrzeugs bei. | | Wärmeleitfähigkeit (W/m·K) | ~160 | Effiziente Wärmeableitung | Hilft, die Sensortemperatur für eine optimale Leistung zu regulieren. | | Korrosionsbeständigkeit | Gut | Fähigkeit, rauen Automobilumgebungen standzuhalten | Gewährleistet langfristige Zuverlässigkeit und verhindert die Zersetzung der Halterung. | | Bedruckbarkeit | Ausgezeichnet | Ermöglicht die Erstellung komplexer Geometrien mit hoher Genauigkeit. | Erleichtert optimierte Designs für Sensorintegration und -leistung. | | Anwendungen | Automobil, Luft- und Raumfahrt, Medizin | Bewährte Erfolgsbilanz in anspruchsvollen Industrieanwendungen. | Zeigt die Eignung des Materials für kritische Automobilkomponenten. | | Metal3DP-Pulver Vorteil | Hohe Sphärizität und gute Fließfähigkeit | Gewährleistet eine gleichmäßige Pulverzuführung und hochdichte, fehlerfreie Drucke. | Führt zu zuverlässigen und leistungsstarken Radarsensorhalterungen. |
- A7075: Diese Aluminiumlegierung ist bekannt für ihr außergewöhnlich hohes Festigkeits-Gewichts-Verhältnis, was sie ideal für Anwendungen macht, bei denen maximale Festigkeit bei gleichzeitiger Minimierung des Gewichts erforderlich ist. Obwohl sie im 3D-Druck schwieriger zu verarbeiten ist als AlSi10Mg, ermöglichen Fortschritte in den Metall-AM-Verfahren und die Expertise von Metal3DP in hochwertige Metallpulver die Herstellung von Hochleistungs-A7075-Radarsensorhalterungen. Diese Halterungen bieten eine überlegene Beständigkeit gegen mechanische Belastungen und Vibrationen, die in Automobilumgebungen auftreten. | Eigenschaft | Wert | Vorteil | Relevanz für Radarhalterungen | | :——̵ Metal3DP-Pulver Vorteil | Optimiert für Pulverbettfusion | Gewährleistet einen konsistenten und zuverlässigen Druck von hochfesten Komponenten. | Liefert A7075-Radarsensormontagen mit überlegener mechanischer Leistung. |
Durch die sorgfältige Auswahl des geeigneten Pulvers, sei es die hervorragende Allround-Leistung von AlSi10Mg oder die ultrahohe Festigkeit von A7075, und die Nutzung des Fachwissens eines Metall-3D-Druckdienstleisters wie Metal3DP können Automobilhersteller Radarsensormontagen herstellen, die den anspruchsvollen Anforderungen moderner Fahrzeuge gerecht werden. Ihre branchenführendes Druckvolumen, Genauigkeit und Zuverlässigkeit festigen ihre Position als zuverlässiger Partner in der additiven Metallfertigung weiter.

Designüberlegungen für die additive Fertigung – Optimierung von Geometrie, Wandstärke und Stützstrukturen
Das Konstruieren für den Metall-3D-Druck erfordert eine andere Denkweise im Vergleich zur traditionellen Fertigung. Um die Möglichkeiten der additiven Fertigung für Radarsensormontagen im Automobilbereich voll auszuschöpfen, müssen Ingenieure bestimmte Konstruktionsprinzipien berücksichtigen:
- Topologie-Optimierung: Diese Berechnungsmethode kann eingesetzt werden, um die effizienteste Materialverteilung für eine bestimmte Last und Randbedingungen zu ermitteln. Durch das Entfernen von unnötigem Material führt die Topologieoptimierung zu leichten Konstruktionen mit erhöhter struktureller Integrität, ein entscheidender Faktor für Anwendungen in der Automobilindustrie. Das Fachwissen von Metal3DP kann Ingenieure bei der effektiven Anwendung der Topologieoptimierung für ihre spezifischen Anforderungen an Radarsensormontagen unterstützen.
- Gitterförmige Strukturen: Die Integration von Gitterstrukturen in das Design der Halterung kann das Gewicht weiter reduzieren, ohne die Steifigkeit zu beeinträchtigen. Diese komplizierten, sich wiederholenden Zellstrukturen bieten hohe Festigkeits-Gewichts-Verhältnisse und können an bestimmte lasttragende Bereiche angepasst werden. Die Designfreiheit des Metall-3D-Drucks macht die Erstellung komplexer Gittergeometrien machbar.
- Wanddicke: Eine sorgfältige Berücksichtigung der Wandstärke ist unerlässlich, um die gewünschte Festigkeit und Steifigkeit zu erreichen und gleichzeitig den Materialverbrauch und die Druckzeit zu minimieren. Die optimale Wandstärke hängt von der spezifischen Legierung, der Größe und Form der Halterung sowie den erwarteten Belastungen ab. Die Erfahrung von Metal3DP mit verschiedenen Metallpulvern und Druckparametern ermöglicht die Bestimmung optimaler Wandstärken für verschiedene Anwendungen.
- Unterstützende Strukturen: Metall-3D-Druckverfahren erfordern oft Stützstrukturen, um Verformungen zu verhindern, die Maßgenauigkeit zu gewährleisten und überhängende Merkmale während des Aufbaus zu verankern. Das Konstruieren unter Berücksichtigung minimaler Stützstrukturanforderungen ist entscheidend, um Materialverschwendung, Nachbearbeitungszeit und Probleme mit der Oberflächenbeschaffenheit zu reduzieren. Konstruktionsmerkmale wie selbsttragende Winkel und eine strategische Teileausrichtung können den Bedarf an umfangreichen Stützen minimieren.
- Orientierung: Die Ausrichtung des Teils auf der Bauplattform hat erhebliche Auswirkungen auf die Oberflächenbeschaffenheit, die Stützstrukturanforderungen und die mechanischen Eigenschaften. Eine sorgfältige Berücksichtigung der Belastungsrichtungen und kritischen Funktionsflächen kann die optimale Bauausrichtung leiten. Die Anwendungsentwicklung von Metal3DP bietet Anleitung zur Teileausrichtung, um das bestmögliche Ergebnis zu erzielen.
- Merkmal Integration: Der Metall-3D-Druck ermöglicht die Integration mehrerer Funktionalitäten in einem einzigen Teil. Bei Radarsensormontagen könnten dies integrierte Kühlkanäle, Kabelführungspfade oder Befestigungsmerkmale für andere Komponenten sein. Die Konsolidierung von Teilen reduziert die Montagezeit und potenzielle Fehlerquellen.
- Minimierung der Stresskonzentration: Scharfe Ecken und abrupte Querschnittsänderungen können unter Belastung zu Spannungskonzentrationen führen. Das Konstruieren mit sanften Übergängen und großzügigen Rundungen kann die strukturelle Integrität und die Lebensdauer der 3D-gedruckten Halterung verbessern.
Durch die Einhaltung dieser Konstruktionsüberlegungen und die Zusammenarbeit mit erfahrenen Metall-3D-Druckanbietern wie Metal3DP können Automobilingenieure hochoptimierte und funktionale Radarsensormontagen erstellen.
Toleranz, Oberflächenbeschaffenheit und Maßgenauigkeit – Präzision im Metall-3D-Druck erreichen
Die Präzision von Radarsensormontagen im Automobilbereich ist von größter Bedeutung, um genaue Sensorwerte und den zuverlässigen Betrieb von ADAS-Systemen zu gewährleisten. Metall-3D-Drucktechnologien haben sich in ihrer Fähigkeit, enge Toleranzen, gute Oberflächenbeschaffenheiten und hohe Maßgenauigkeit zu erreichen, erheblich weiterentwickelt. Diese Faktoren werden jedoch von mehreren Variablen beeinflusst:
- Druckertechnologie: Verschiedene Metall-3D-Drucktechnologien, wie z. B. Selektives Laserschmelzen (SLM) und Elektronenstrahlschmelzen (EBM), bieten unterschiedliche Präzisionsniveaus. SLM liefert im Allgemeinen feinere Details und engere Toleranzen, während EBM für größere Teile und bestimmte Materialien von Vorteil sein kann. Metal3DP verwendet sowohl SEBM-Drucker als auch andere fortschrittliche Technologien, um den vielfältigen Anwendungsanforderungen gerecht zu werden.
- Auswahl der Materialien: Das gewählte Metallpulver kann sich auf die erreichbare Toleranz und Oberflächenbeschaffenheit auswirken. Legierungen mit feineren Pulverpartikelgrößenverteilungen neigen dazu, glattere Oberflächen und feinere Merkmale zu erzeugen. Das Sortiment an hochwertigen Metallpulvern von Metal3DP ist für die Erzielung hoher Genauigkeit und Oberflächenqualität optimiert.
- Prozessparameter: Druckparameter, einschließlich Laserleistung, Scangeschwindigkeit, Schichtdicke und Bauumgebung, spielen eine entscheidende Rolle für die Genauigkeit und Oberflächenbeschaffenheit des fertigen Teils. Erfahrene Metall-3D-Druckdienstleister wie Metal3DP kontrollieren diese Parameter sorgfältig, um konsistente und qualitativ hochwertige Ergebnisse zu gewährleisten.
- Nachbearbeiten: Nachbearbeitungstechniken wie CNC-Bearbeitung, Polieren und Oberflächenbehandlungen können die Maßgenauigkeit und Oberflächenbeschaffenheit von 3D-gedruckten Teilen bei Bedarf für kritische Anwendungen weiter verbessern. Metal3DP bietet umfassende Nachbearbeitungsdienstleistungen, um die spezifischen Kundenbedürfnisse zu erfüllen.
Während die Erzielung extrem enger Toleranzen, die mit der Präzisionsbearbeitung vergleichbar sind, möglicherweise eine Nachbearbeitung erfordert, kann der Metall-3D-Druck funktionale Prototypen und Endanwendungsteile für Radarsensormontagen im Automobilbereich mit akzeptablen Toleranzen und Oberflächenbeschaffenheiten für viele Anwendungen herstellen. Die Zusammenarbeit mit einem sachkundigen Partner wie Metal3DP stellt sicher, dass die erreichbare Präzision den spezifischen Anforderungen des Sensors und des Gesamtsystems entspricht.
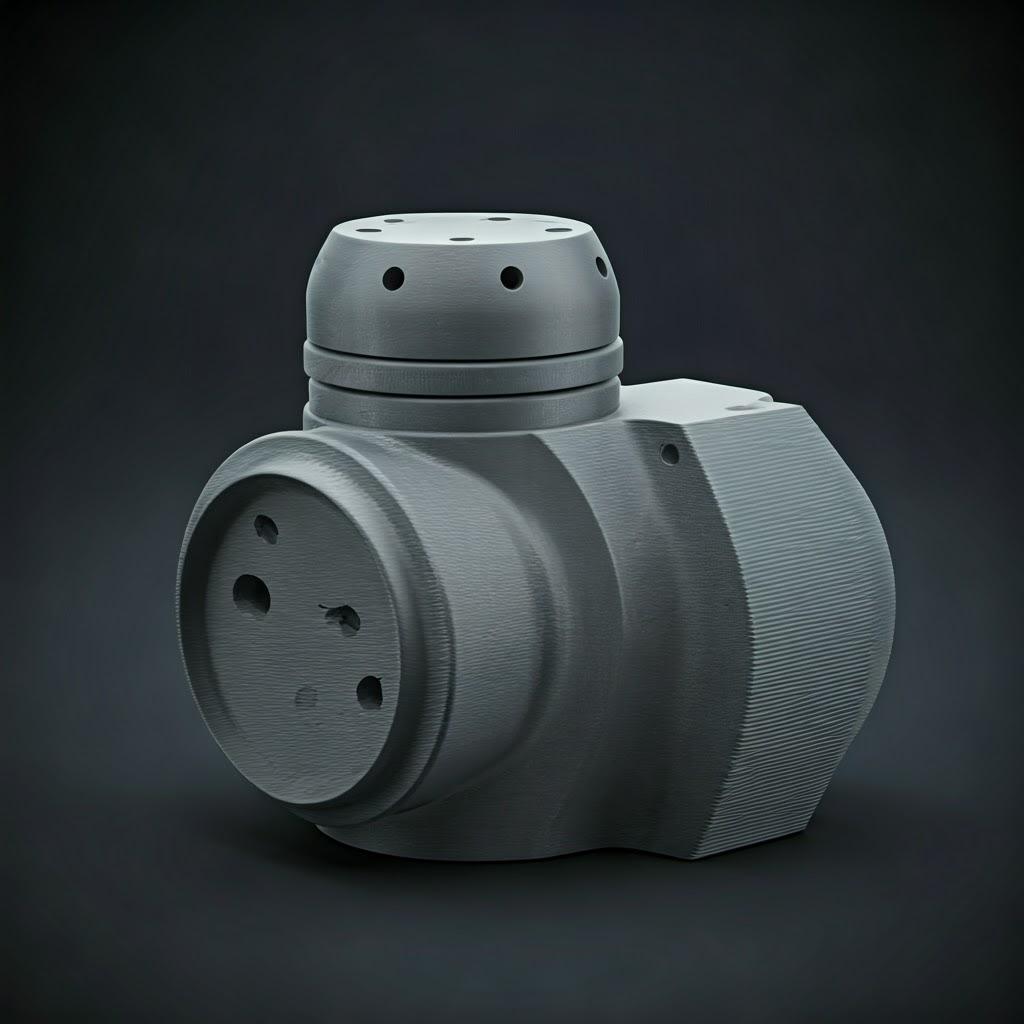
Nachbearbeitungsanforderungen – Verfeinern von 3D-gedruckten Radarsensormontagen
Während der Metall-3D-Druck Teile in nahezu endgültiger Form herstellt, sind oft Nachbearbeitungsschritte erforderlich, um die endgültigen gewünschten Eigenschaften, die Oberflächenbeschaffenheit und die Maßgenauigkeit für Radarsensormontagen im Automobilbereich zu erreichen. Zu den üblichen Nachbearbeitungsanforderungen gehören:
- Unterstützung bei der Entfernung: Stützstrukturen, die während des Druckprozesses unerlässlich sind, müssen sorgfältig entfernt werden, ohne die Geometrie des Teils zu beschädigen. Dies kann manuelles Brechen, Schneiden oder die Verwendung spezieller Werkzeuge und Maschinen umfassen.
- Wärmebehandlung: Wärmebehandlungsverfahren werden oft angewendet, um innere Spannungen abzubauen, die mechanischen Eigenschaften (wie Härte und Festigkeit) zu verbessern und die gewünschte Mikrostruktur des Metalls zu erreichen. Der spezifische Wärmebehandlungszyklus hängt von der Legierung und den Anwendungsanforderungen ab.
- Oberflächenveredelung: Je nach Anwendung und ästhetischen Anforderungen können verschiedene Oberflächenveredelungstechniken eingesetzt werden. Diese beinhalten:
- Media Blasting: Wird verwendet, um Restpulver zu entfernen und die Oberflächenrauheit zu verbessern.
- Polieren: Um eine glattere Oberflächenbeschaffenheit zu erzielen, was für die Sensorleistung und Ästhetik wichtig sein kann.
- CNC-Bearbeitung: Zum Erreichen sehr enger Toleranzen bei kritischen Merkmalen, wie z. B. Befestigungslöchern oder Schnittstellen mit dem Sensor.
- Beschichtungen und Oberflächenbehandlungen: Beschichtungen können aufgetragen werden, um die Korrosionsbeständigkeit, die Verschleißfestigkeit oder andere spezifische Eigenschaften zu verbessern. Beispiele sind Eloxieren für Aluminiumlegierungen oder Lackieren für ästhetische Zwecke.
Metal3DP bietet eine umfassende Palette an Nachbearbeitungsdienstleistungen, um sicherzustellen, dass die 3D-gedruckten Radarsensormontagen die erforderlichen Spezifikationen für Form, Passung und Funktion erfüllen. Ihr Fachwissen in Materialwissenschaft und Fertigungsprozessen garantiert, dass die gewählten Nachbearbeitungsmethoden für die spezifische Legierung und Anwendung geeignet sind.
Häufige Herausforderungen und wie man sie vermeidet – Sicherstellung erfolgreicher Metall-3D-Druckergebnisse
Während der Metall-3D-Druck erhebliche Vorteile bietet, können während des Prozesses bestimmte Herausforderungen auftreten. Das Verständnis dieser potenziellen Probleme und die Umsetzung von Präventivmaßnahmen ist entscheidend, um erfolgreiche Ergebnisse für Radarsensormontagen im Automobilbereich zu erzielen:
- Verformung und Verzerrung: Thermische Spannungen während des Druckprozesses können zu Verformungen oder Verzerrungen führen, insbesondere bei Teilen mit komplexen Geometrien oder dünnen Wänden.
- Wie man es vermeidet: Optimieren Sie die Teileausrichtung, verwenden Sie geeignete Stützstrukturen und kontrollieren Sie die Bauparameter sorgfältig. Simulationstools können auch helfen, potenzielle Verzerrungen vorherzusagen und zu mildern.
- Unterstützung bei der Entfernung von Problemen: Aggressives Entfernen von Stützen kann empfindliche Merkmale beschädigen oder unerwünschte Oberflächenmarkierungen hinterlassen.
- Wie man es vermeidet: Konstruieren Sie Teile mit minimalen Stützstrukturanforderungen, verwenden Sie gegebenenfalls auflösbare Stützmaterialien und setzen Sie qualifizierte Techniker für die Stützenentfernung ein.
- Probleme mit Porosität und Dichte: Unzureichendes Schmelzen oder Erstarren kann zu Porosität innerhalb des gedruckten Teils führen, was seine mechanischen Eigenschaften beeinträchtigt.
- Wie man es vermeidet: Optimieren Sie die Laserleistung, die Scangeschwindigkeit und die Vorbereitung des Pulverbettes. Hochwertige Metallpulver mit guter Fließfähigkeit, wie sie von Metal3DP angeboten werden, sind ebenfalls unerlässlich.
- Oberflächengüte Rauheit: Die gedruckten Metalloberflächen können rauer sein als die durch traditionelle Bearbeitung hergestellten.
- Wie man es vermeidet: Optimieren Sie die Druckparameter, verwenden Sie feinere Pulverpartikelgrößen und wenden Sie geeignete Nachbearbeitungstechniken wie Strahlen oder Polieren an.
- Maßliche Ungenauigkeiten: Abweichungen von den beabsichtigten Abmessungen können aufgrund von Schrumpfung, Wärmeausdehnung oder falscher Kalibrierung auftreten.
- Wie man es vermeidet: Kalibrieren Sie den 3D-Drucker regelmäßig, optimieren Sie die Bauparameter für das jeweilige Material und erwägen Sie die Verwendung von Schrumpfungskompensationstechniken in der Designphase.
- Variationen der Materialeigenschaften: Ungleichmäßiges Schmelzen oder Erstarren kann zu Schwankungen der mechanischen Eigenschaften des gesamten gedruckten Teils führen.
- Wie man es vermeidet: Verwenden Sie etablierte Druckparameter, sorgen Sie für eine stabile Bauumgebung und arbeiten Sie mit renommierten Materiallieferanten wie Metal3DP zusammen, die strenge Qualitätskontrollprozesse für ihre Metallpulver haben.
Durch das Verständnis dieser häufigen Herausforderungen und die Umsetzung geeigneter Konstruktionsstrategien und Prozesskontrollen in Zusammenarbeit mit erfahrenen Metall-3D-Druckdienstleistern wie Metal3DP können Automobilhersteller Risiken mindern und zuverlässige und leistungsstarke Radarsensormontagen erzielen. Ihre fortschrittliches Pulverherstellungssystem gewährleistet die gleichbleibende Qualität ihrer Materialien und trägt zu erfolgreichen Druckergebnissen bei.
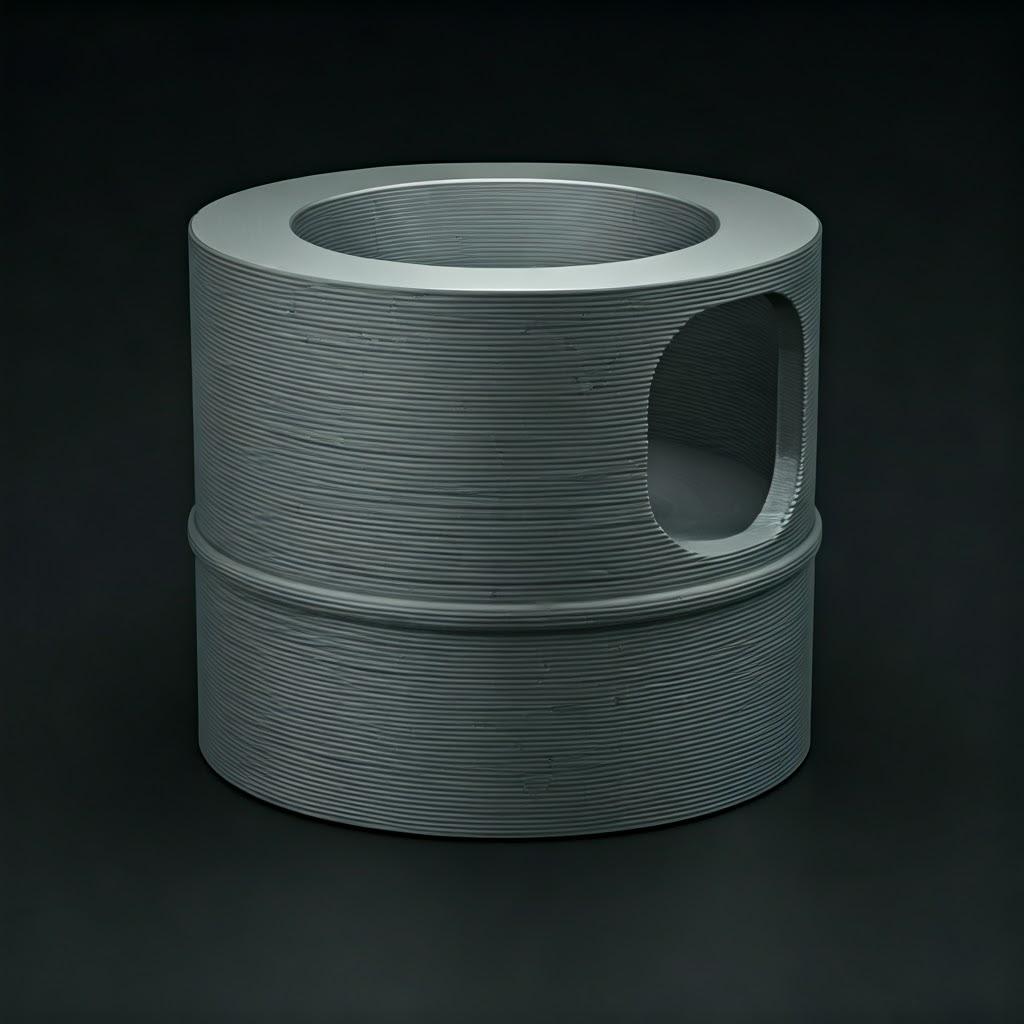
So wählen Sie den richtigen Metall-3D-Druckdienstleister aus – Bewertung von Fachwissen und Fähigkeiten
Die Auswahl des geeigneten Metall-3D-Druckdienstleisters ist eine entscheidende Entscheidung, die den Erfolg Ihres Radarsensormontageprojekts im Automobilbereich erheblich beeinflusst. Berücksichtigen Sie die folgenden Faktoren bei der Bewertung potenzieller Partner:
- Materielle Fähigkeiten: Stellen Sie sicher, dass der Anbieter die empfohlenen Materialien (AlSi10Mg und A7075) anbietet und nachweislich erfolgreich verarbeitet. Erkundigen Sie sich nach ihren Daten zur Materialcharakterisierung und ihren Qualitätskontrollprozessen. Metal3DP stellt eine breite Palette hochwertiger Metallpulver her, einschließlich der idealen für Automobilanwendungen.
- Technologie und Ausrüstung: Verstehen Sie die Arten von Metall-3D-Drucktechnologien, die der Anbieter verwendet (z. B. SLM, DMLS, EBM). Die Wahl der Technologie kann die erreichbare Präzision, Oberflächenbeschaffenheit und Materialeigenschaften beeinflussen. Die Spezialisierung von Metal3DP auf SEBM-Drucker und andere fortschrittliche Systeme positioniert sie als führend im Bereich der Metall-AM-Ausrüstung. Sie können mehr über verschiedene Druckverfahren erfahren auf ihrer Website.
- Fachwissen und Erfahrung: Bewerten Sie die Erfahrung des Anbieters im Metall-3D-Druck, insbesondere in der Automobilindustrie oder ähnlichen anspruchsvollen Branchen. Suchen Sie nach Fallstudien oder Erfahrungsberichten, die ihre Fähigkeit demonstrieren, komplexe Geometrien und strenge Anforderungen zu bewältigen. Metal3DP verfügt über jahrzehntelange Erfahrung in der additiven Metallfertigung.
- Unterstützung bei Design und Technik: Ein starker Dienstleister sollte Designberatung und technische Unterstützung anbieten, um Ihre Radarsensormontage für die additive Fertigung zu optimieren. Dies beinhaltet Anleitungen zur Topologieoptimierung, Materialauswahl und Design für die Herstellbarkeit. Metal3DP bietet umfassende Lösungen, die Geräte, Pulver und Anwendungsentwicklungsdienste umfassen.
- Post-Processing-Dienste: Bestimmen Sie, ob der Anbieter die erforderlichen Nachbearbeitungsdienstleistungen anbietet, wie z. B. Stützenentfernung, Wärmebehandlung, Oberflächenveredelung und Qualitätsprüfung. Ein umfassendes Serviceangebot rationalisiert den Produktionsprozess.
- Qualitätssicherung und Zertifizierungen: Erkundigen Sie sich nach dem Qualitätsmanagementsystem des Anbieters und allen relevanten Zertifizierungen (z. B. ISO 9001, AS9100 für die Luft- und Raumfahrt). Dies gewährleistet die Einhaltung von Qualitätsstandards und die Rückverfolgbarkeit.
- Kommunikation und Kundenbetreuung: Eine effektive Kommunikation und ein reaktionsschneller Kundensupport sind für ein reibungsloses und erfolgreiches Projekt entscheidend. Beurteilen Sie die Reaktionsfähigkeit und die Bereitschaft zur Zusammenarbeit des Anbieters.
- Vorlaufzeiten und Produktionskapazität: Verstehen Sie die typischen Vorlaufzeiten des Anbieters für ähnliche Projekte und seine Produktionskapazität, um Ihre Volumenanforderungen zu erfüllen.
- Kostenstruktur: Holen Sie sich eine klare Aufschlüsselung der beteiligten Kosten, einschließlich Druck, Materialien, Nachbearbeitung und etwaiger Konstruktionsgebühren. Vergleichen Sie Angebote von mehreren Anbietern und berücksichtigen Sie dabei den Gesamtwert und das angebotene Fachwissen.
Durch die sorgfältige Bewertung dieser Faktoren können Sie einen Metall-3D-Druckdienstleister wie Metal3DP auswählen, der hochwertige, zuverlässige Radarsensormontagen für den Automobilbereich liefern kann, die Ihren spezifischen Anforderungen entsprechen.
Kostenfaktoren und Vorlaufzeit – Die Wirtschaftlichkeit des Metall-3D-Drucks verstehen
Die Kosten und die Vorlaufzeit für die Herstellung von Radarsensormontagen im Automobilbereich mit Metall-3D-Druck werden von mehreren Faktoren beeinflusst:
- Materialkosten: Die Kosten für das Metallpulver (z. B. AlSi10Mg, A7075) sind ein wesentlicher Faktor. Speziallegierungen oder solche mit komplexen Zusammensetzungen sind tendenziell teurer. Die Materialmenge, die für das Teil benötigt wird, wirkt sich ebenfalls auf die Gesamtkosten aus.
- Bauvolumen und Komplexität: Größere Teile, die mehr Bauvolumen beanspruchen, und komplizierte Designs, die umfangreiche Stützstrukturen erfordern,
- Druckzeit: Die Dauer des Druckprozesses hängt von der Größe und Komplexität des Teils, der Schichthöhe und der gewählten Drucktechnologie ab. Längere Druckzeiten führen zu höheren Maschinenbetriebskosten.
- Nachbearbeitungsanforderungen: Der Umfang der erforderlichen Nachbearbeitung (z. B. Entfernung von Stützstrukturen, Wärmebehandlung, Bearbeitung, Beschichtung) wirkt sich erheblich auf die Gesamtkosten und die Vorlaufzeit aus. Komplexe Nachbearbeitungsschritte erhöhen sowohl den Zeit- als auch den Arbeitsaufwand.
- Menge und Volumen: Während der Metall-3D-Druck für die Produktion von kleinen bis mittleren Stückzahlen und die kundenspezifische Fertigung von Vorteil ist, können höhere Stückzahlen von Skaleneffekten profitieren. Im Gegensatz zur traditionellen Fertigung fallen beim 3D-Druck jedoch in der Regel keine Werkzeugkosten an, was bei kleineren Chargen ein erheblicher Vorteil sein kann.
- Kosten für Dienstanbieter: Die Preisstruktur des Metall-3D-Druck-Dienstleisters, einschließlich seiner Gemeinkosten, seines Fachwissens und seiner Gewinnspannen, beeinflusst die endgültigen Kosten.
- Vorlaufzeit: Die gesamte Vorlaufzeit umfasst die Designfinalisierung, die Druckvorbereitung, die Druckzeit, die Nachbearbeitung und die Qualitätskontrolle. Diese kann je nach Komplexität des Teils, der Arbeitsauslastung des Dienstleisters und den erforderlichen Nachbearbeitungsschritten variieren.
Es ist wichtig, die Erwartungen an Kosten und Vorlaufzeit frühzeitig im Projekt mit potenziellen Dienstleistern zu besprechen. Detaillierte Angebote einzuholen und die Faktoren zu verstehen, die die Preisgestaltung beeinflussen, hilft bei fundierten Entscheidungen. Metal3DP kann detaillierte Kostenaufschlüsselungen und Vorlaufzeitschätzungen basierend auf Ihren spezifischen Anforderungen erstellen.
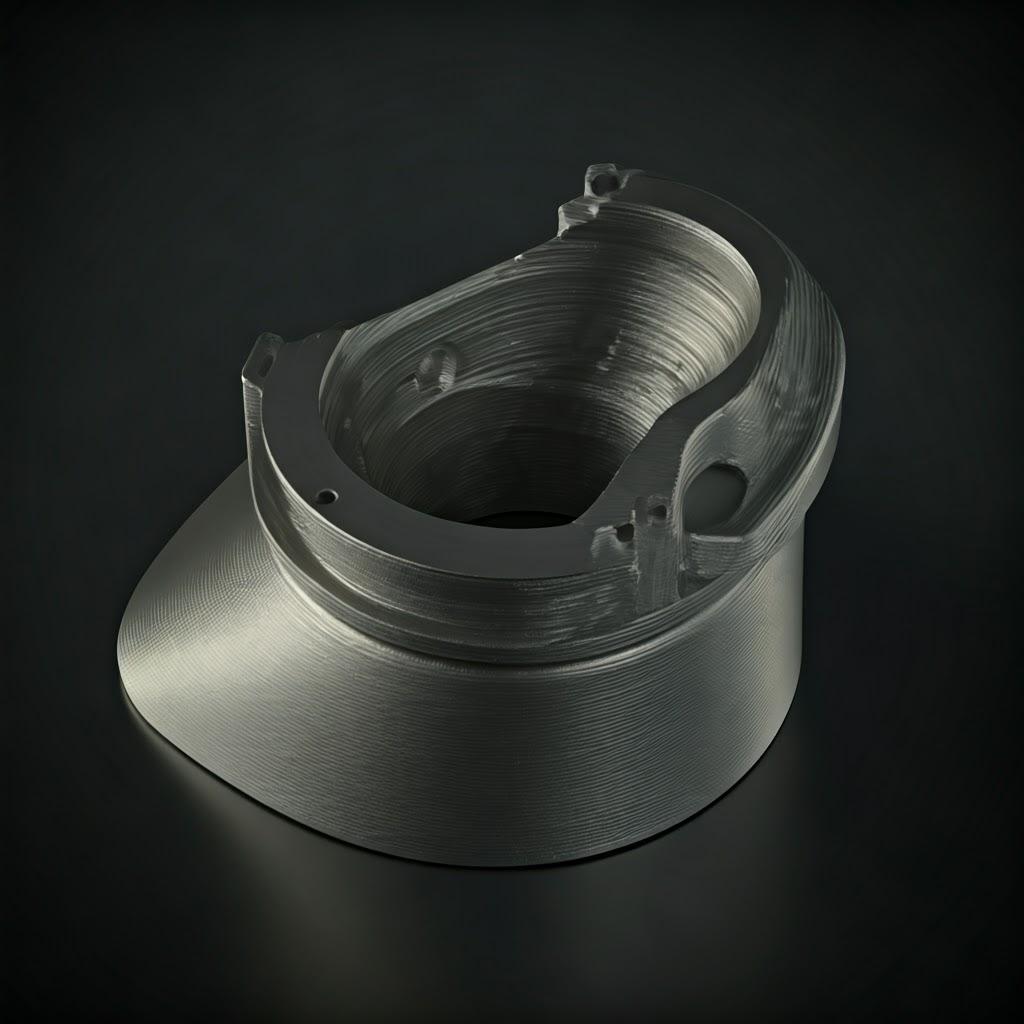
Häufig gestellte Fragen (FAQ)
- Welche typischen Toleranzen sind mit dem Metall-3D-Druck für Automobilteile erreichbar? Während die Toleranzen je nach Drucktechnologie, Material und Teilegeometrie variieren, kann der Metall-3D-Druck in der Regel Toleranzen im Bereich von ±0,1 bis ±0,5 mm für funktionale Automobilteile erreichen. Engere Toleranzen können durch Nachbearbeitung wie CNC-Bearbeitung erreicht werden.
- Ist der Metall-3D-Druck für die Großserienproduktion von Radarsensormontagen kosteneffektiv? Der Metall-3D-Druck ist im Allgemeinen am kosteneffektivsten für die Produktion von kleinen bis mittleren Stückzahlen, komplexe Geometrien und kundenspezifische Teile, bei denen die traditionellen Werkzeugkosten hoch wären. Für sehr hohe Stückzahlen können traditionelle Fertigungsverfahren wie das Druckgießen wirtschaftlicher sein. Die Vorteile der Designflexibilität und der schnellen Iteration, die der 3D-Druck bietet, können jedoch in den frühen Entwicklungs- und Kleinserienproduktionsphasen immer noch wertvoll sein.
- Welche Oberflächengüte ist von einer 3D-gedruckten Metall-Radarsensormontage zu erwarten? Die Oberfläche von 3D-gedruckten Metallteilen ist in der Regel rauer als die von bearbeiteten Oberflächen. Verschiedene Nachbearbeitungstechniken wie Strahlen, Polieren und chemisches Ätzen können jedoch eingesetzt werden, um glattere Oberflächen zu erzielen, die für die Anwendung erforderlich sind.
- Können 3D-gedruckte Metall-Radarsensormontagen rauen Umgebungsbedingungen in der Automobilindustrie standhalten? Ja, durch die Auswahl geeigneter Materialien wie AlSi10Mg und A7075 und den Einsatz geeigneter Nachbehandlungen wie Wärmebehandlung und Schutzbeschichtungen können 3D-gedruckte Metall-Radarsensormontagen so konstruiert werden, dass sie den Temperaturschwankungen, Vibrationen, der Feuchtigkeit und der Einwirkung von Chemikalien, die in der Automobilindustrie üblich sind, standhalten.
Fazit – Innovation im Bereich der Automobilsensorik durch Metall-3D-Druck
Der Metall-3D-Druck bietet einen transformativen Ansatz für das Design und die Herstellung von Radarsensormontagen für die Automobilindustrie. Die Fähigkeit, komplexe, leichte und leistungsstarke Komponenten mit schnellen Iterationszyklen zu erstellen, bietet der Automobilindustrie erhebliche Vorteile für die laufenden Fortschritte in den Bereichen ADAS und autonomes Fahren. Durch die Nutzung der Designfreiheit, der Materialeffizienz und der Anpassungsmöglichkeiten der additiven Metallfertigung und die Zusammenarbeit mit erfahrenen Anbietern wie Metal3DP Technology Co. LTD, können Automobilhersteller Innovationen beschleunigen, die Fahrzeugleistung optimieren und den Weg für die Zukunft der Mobilität ebnen. Kontaktieren Sie Metal3DP noch heute, um zu erfahren, wie ihre hochmodernen Systeme und hochwertigen Metallpulver die additiven Fertigungsziele Ihres Unternehmens unterstützen können.
Teilen auf
MET3DP Technology Co., LTD ist ein führender Anbieter von additiven Fertigungslösungen mit Hauptsitz in Qingdao, China. Unser Unternehmen ist spezialisiert auf 3D-Druckgeräte und Hochleistungsmetallpulver für industrielle Anwendungen.
Fragen Sie an, um den besten Preis und eine maßgeschneiderte Lösung für Ihr Unternehmen zu erhalten!
Verwandte Artikel
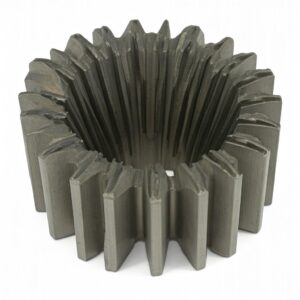
Hochleistungs-Düsenschaufelsegmente: Revolutionierung der Turbineneffizienz mit 3D-Metalldruck
Mehr lesen "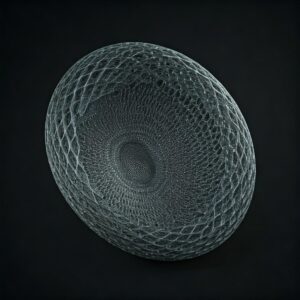
Korrosionsbeständige Gehäuse für Hydrophone: Fortschritte in der Unterwasser-Akustiktechnologie
Mehr lesen "Über Met3DP
Aktuelles Update
Unser Produkt
KONTAKT US
Haben Sie Fragen? Senden Sie uns jetzt eine Nachricht! Wir werden Ihre Anfrage mit einem ganzen Team nach Erhalt Ihrer Nachricht bearbeiten.
Holen Sie sich Metal3DP's
Produkt-Broschüre
Erhalten Sie die neuesten Produkte und Preislisten
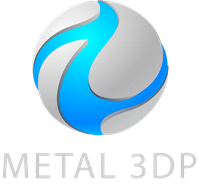
Metallpulver für 3D-Druck und additive Fertigung