Leichte Zugangspaneele für die Luft- und Raumfahrt durch 3D-Druck
Inhaltsübersicht
Revolutionierung des Luft- und Raumfahrtdesigns: Leichte Zugangspaneele durch 3D-Metalldruck
Die Luft- und Raumfahrtindustrie ist der Gipfel der technischen Errungenschaften und verschiebt ständig die Grenzen von Leistung, Effizienz und Sicherheit. In diesem anspruchsvollen Umfeld spielt jede noch so klein erscheinende Komponente eine entscheidende Rolle. Zugangspaneele für die Luft- und Raumfahrt werden zwar oft vom zufälligen Beobachter übersehen, sind aber grundlegende Elemente der Flugzeugstruktur und der Wartungsprotokolle. Diese Paneele bieten wichtige Zugangspunkte für Inspektion, Wartung, Reparatur und Überholung (MRO) und schützen die komplizierten Systeme, die sich in der Flugzeugzelle, den Tragflächen, den Triebwerken und anderen kritischen Bereichen befinden. In der Vergangenheit wurden diese Komponenten mit traditionellen Methoden wie CNC-Bearbeitung aus massiven Knüppeln oder Umformung aus Blech hergestellt. Diese Verfahren sind zwar zuverlässig, stoßen aber oft an ihre Grenzen, insbesondere in Bezug auf Gewicht, Designkomplexität und Fertigungszeiten, vor allem bei Kleinserien oder stark kundenspezifischen Anforderungen, die für die Beschaffungszyklen in der Luft- und Raumfahrt typisch sind.
Im unermüdlichen Streben nach verbesserter Treibstoffeffizienz, höherer Nutzlast und geringerer Umweltbelastung bleibt die Gewichtsreduzierung ein vorrangiges Ziel für Ingenieure und Hersteller in der Luft- und Raumfahrt. Jedes eingesparte Kilogramm führt direkt zu erheblichen Einsparungen bei den Betriebskosten und Leistungssteigerungen während der Lebensdauer eines Flugzeugs. Diese Notwendigkeit hat Innovationen in allen Bereichen der Flugzeugkonstruktion vorangetrieben, von fortschrittlichen Verbundwerkstoffstrukturen bis hin zu hoch optimierten Systemen. Jetzt hält eine neue Fertigungstechnologie Einzug in die Produktion von Bauteilen wie z. B. Einstiegsklappen: Additive Fertigung von Metall (AM), besser bekannt als 3D-Druck von Metall. Diese Technologie stellt einen Paradigmenwechsel dar: weg von subtraktiven Methoden (Abtragen von Material) oder formgebenden Methoden (Umformen von Material) hin zu einem additiven Ansatz, bei dem Teile Schicht für Schicht direkt aus digitalen Entwürfen unter Verwendung von speziellen Metallpulvern hergestellt werden.
Das Potenzial der Metall-AM in der Luft- und Raumfahrt ist immens. Es eröffnet eine nie dagewesene Designfreiheit, die es Ingenieuren ermöglicht, hoch optimierte, leichte Strukturen zu schaffen, deren Herstellung bisher unmöglich oder unerschwinglich war. Merkmale wie komplexe Innenkanäle, topologieoptimierte Geometrien, bei denen das Material strategisch nur dort platziert wird, wo es benötigt wird, und integrierte Funktionalitäten können direkt während des Druckprozesses realisiert werden. Für Zugangsplatten bedeutet dies die Möglichkeit, Komponenten zu schaffen, die deutlich leichter sind als ihre traditionell hergestellten Gegenstücke, während die strukturelle Integrität und die Leistungsmerkmale erhalten bleiben oder sogar verbessert werden. Diese Fähigkeit ist nicht nur eine inkrementelle Verbesserung, sondern stellt einen grundlegenden Wandel in der Art und Weise dar, wie Komponenten für die Luft- und Raumfahrt konzipiert, entworfen und produziert werden können.
Die Einführung von Metall-AM beschleunigt sich in der gesamten Branche, angetrieben von Fortschritten in der Maschinentechnologie, der Materialwissenschaft und der Prozesskontrolle. Führende Erstausrüster der Luft- und Raumfahrt, Tier-1-Zulieferer und spezialisierte MRO-Anbieter erforschen und implementieren AM zunehmend für eine wachsende Anzahl von Anwendungen, von nicht kritischen Kabinenkomponenten bis hin zu flugkritischen Strukturteilen. Zugangsverkleidungen sind ein besonders geeigneter Anwendungsbereich, da sie oft ein Gleichgewicht zwischen Festigkeit, Steifigkeit und geringem Gewicht erfordern, kombiniert mit dem Bedarf an geometrischen Variationen je nach ihrer spezifischen Position und Funktion im Flugzeug. Darüber hinaus bietet die Fähigkeit von AM, Teile auf Abruf zu produzieren, erhebliche Vorteile für das Ersatzteilmanagement und die Senkung der Lagerhaltungskosten, ein entscheidender Faktor für die Logistik in der Luft- und Raumfahrt und die Großhandelslieferanten.
Unternehmen wie Met3dp stehen an der Spitze dieser Fertigungsrevolution. Met3dp verfügt über umfassendes Know-how sowohl bei fortschrittlichen Metall-AM-Systemen als auch bei der Herstellung von Hochleistungsmetallpulvern und bietet umfassende Lösungen, die auf die anspruchsvollen Anforderungen des Luft- und Raumfahrtsektors zugeschnitten sind. Unsere branchenführenden Selective Electron Beam Melting (SEBM)-Drucker und unsere hochwertigen gasverdüsten Metallpulver, einschließlich Aluminiumlegierungen in Luft- und Raumfahrtqualität, ermöglichen die Herstellung dichter, zuverlässiger und geometrisch komplexer Teile, wie z. B. leichte Zugangsklappen. Als zuverlässiger Lieferant und Partner arbeiten wir mit Luft- und Raumfahrtingenieuren und Beschaffungsmanagern zusammen, um das volle Potenzial der additiven Fertigung auszuschöpfen, das Komponentendesign zu verändern und die Fertigungsabläufe zu optimieren. Dieser Blogbeitrag befasst sich mit den Besonderheiten der Verwendung von Metall 3D-Druck für Zugangsklappen in der Luft- und Raumfahrt und untersucht die Anwendungen, Vorteile, Materialien, Designüberlegungen und Beschaffungsstrategien, die mit der Einführung dieser Spitzentechnologie verbunden sind.
Kritische Funktionen: Wofür werden Zugangspaneele für die Luft- und Raumfahrt verwendet?
Zugangspaneele für die Luft- und Raumfahrt sind allgegenwärtige und dennoch wesentliche Komponenten, die in praktisch jedem Flugzeugtyp zu finden sind, von kleinen Flugzeugen der allgemeinen Luftfahrt und unbemannten Luftfahrzeugen (UAVs) bis hin zu großen Verkehrsflugzeugen, Hochleistungs-Militärjets und sogar Raumfahrzeugen. Ihr Hauptzweck ist einfach, aber entscheidend: Sie bieten abnehmbare Abschnitte in der Außenhaut oder Struktur des Flugzeugs, die Technikern und Ingenieuren kontrollierten Zugang zu den darunter liegenden Systemen und Fächern für notwendige Aufgaben ermöglichen. Ohne diese Paneele wäre die Durchführung von Routineinspektionen, planmäßigen Wartungsarbeiten, unerwarteten Reparaturen oder Komponenten-Upgrades wesentlich komplexer, zeitaufwändiger und würde möglicherweise die umgebende Struktur beschädigen.
Die spezifischen Funktionen und Einsatzorte von Zugangsklappen sind unglaublich vielfältig und spiegeln die Komplexität moderner Flugzeugsysteme wider. Das Verständnis dieser unterschiedlichen Funktionen ist der Schlüssel zum Verständnis der Konstruktionsanforderungen und der potenziellen Vorteile, die die additive Fertigung bieten kann.
Wichtige Standorte und Funktionen:
- Rumpfpaneele: Entlang des Flugzeugrumpfes befinden sich zahlreiche Zugangsklappen. Sie ermöglichen den Zugang zur Inspektion von Strukturelementen (Spanten, Stringer), Kabelbäumen, Hydraulikleitungen, Kanälen des Umweltkontrollsystems (ECS), Avionikbuchten, Frachträumen und anderen internen Systemen. Bei einigen handelt es sich um einfache Inspektionsöffnungen, bei anderen um größere Türen für den Zugang zur Ausrüstung.
- Flügelzugangspunkte: In den Flügeln befinden sich kritische Systeme wie Treibstofftanks, hydraulische Stellantriebe für die Steuerflächen (Querruder, Klappen, Störklappen), elektrische Leitungen, Enteisungsanlagen und Strukturholme/-rippen. Zugangspaneele an der Ober- und Unterseite der Tragflächen sind für die Wartung des Treibstoffsystems, Strukturinspektionen (insbesondere im Hinblick auf Ermüdung und Korrosion) und die Wartung der Steuerflächenmechanismen unerlässlich. Paneele in der Nähe der Triebwerkspylone ermöglichen auch die Inspektion der Befestigungspunkte.
- Leitwerkspaneele (Heckbereich): Ähnlich wie die Tragflächen enthalten die horizontalen und vertikalen Stabilisatoren Steuerflächenaktuatoren (Höhenruder, Seitenruder), Verkabelung und strukturelle Komponenten, die eine regelmäßige Inspektion und Wartung über spezielle Zugangsklappen erfordern.
- Triebwerksgondel und Pylonverkleidung: Triebwerke müssen häufig inspiziert und gewartet werden. Zugangsklappen an den Gondeln (Triebwerksverkleidungen) und Pylonen (Strukturen, mit denen die Triebwerke am Flügel oder Rumpf befestigt sind) ermöglichen es den Technikern, Triebwerkskomponenten, Hilfstriebwerke (APUs), Zapfluftsysteme, Branderkennungs-/Unterdrückungssysteme und strukturelle Halterungen zu untersuchen. Diese Paneele sind oft hohen Temperaturen und Vibrationen ausgesetzt, was eine robuste Konstruktion und robuste Materialien erfordert.
- Fahrwerksschächte: Die Abteile, in denen das eingefahrene Fahrwerk untergebracht ist, enthalten komplexe Hydrauliksysteme, Ein- und Ausfahrmechanismen, Räder, Bremsen und Strukturelemente. Zugangspaneele in diesen Schächten sind für die Wartung und Inspektion dieser stark beanspruchten Komponenten unerlässlich.
- Avionikbuchten: Konzentrierte Bereiche, oft im vorderen Rumpf oder unter dem Cockpit, beherbergen empfindliche elektronische Geräte (Flugcomputer, Navigationssysteme, Kommunikationsfunkgeräte). Zugangspaneele ermöglichen hier die Fehlersuche, Software-Updates und den Austausch von Line-Replaceable-Units (LRUs). Diese erfordern oft eine spezielle Konstruktion zur Abschirmung elektromagnetischer Störungen (EMI).
- Flüssigkeitsservicepunkte: Kleinere Zugangsstellen sind oft für die Wartung von Hydraulikflüssigkeitsbehältern, Öltanks oder anderen Flüssigkeitssystemen vorgesehen.
Arten von Zugangspaneelen:
Zugangsklappen sind nicht monolithisch; sie unterscheiden sich erheblich in ihrem Design, je nach Funktion, Standort, Häufigkeit der Nutzung und strukturellen Anforderungen:
- Quick-Release-Panels: Konzipiert für häufigen Zugang, oft unter Verwendung von Vierteldrehverschlüssen (z. B. Dzus-Verschlüssen), Riegeln oder Scharniermechanismen zum schnellen Öffnen und Schließen ohne umfangreiche Werkzeuge. Sie werden häufig für Routineinspektionen vor dem Flug oder für häufig zugängliche Wartungsbereiche verwendet.
- Verschraubte Paneele: Wird mit Standardschrauben oder -bolzen befestigt und in der Regel für Bereiche verwendet, die weniger häufig zugänglich sind oder in denen eine höhere Klemmkraft für die strukturelle Integrität oder die Abdichtung erforderlich ist.
- Strukturelle Zugangspaneele: Einige Paneele sind so konstruiert, dass sie als Teil der Flugzeugzelle erhebliche strukturelle Lasten tragen. Ihre Aus- und Einbauverfahren sind kritisch, und ihr Design muss strenge Festigkeits- und Steifigkeitsanforderungen erfüllen. Diese sind erstklassige Kandidaten für die Optimierung durch AM.
- Versiegelte Paneele: Paneele, die Zugang zu druckbeaufschlagten Zonen, Kraftstofftanks oder umweltsensiblen Bereichen bieten, erfordern spezielle Dichtungen (z. B. O-Ringe, Form-in-Place-Dichtungen), um Leckagen zu verhindern. Die Ebenheit und Oberflächenbeschaffenheit der Platte und der umgebenden Struktur sind entscheidend.
- Belüftete/gerasterte Paneele: Einige Paneele sind mit Lüftungsöffnungen oder Jalousien ausgestattet, um einen Luftstrom, die Kühlung von Komponenten oder einen Druckausgleich zu ermöglichen.
Variationen zwischen den Flugzeugtypen:
Die spezifischen Anforderungen an Zugangsklappen unterscheiden sich auch je nach Einsatzprofil des Flugzeugs:
- Kommerzielle Verkehrsflugzeuge: Der Schwerpunkt liegt auf Langlebigkeit, Zuverlässigkeit, Wartungsfreundlichkeit zur Minimierung der Abfertigungszeiten (AOG – Aircraft on Ground-Situationen sind extrem kostspielig) und der Einhaltung der strengen Vorschriften der Zivilluftfahrt (FAA, EASA). Gewichtseinsparungen sind entscheidend für die Treibstoffeffizienz.
- Militärische Flugzeuge: Der Schwerpunkt liegt auf Robustheit, schnellen Wartungsmöglichkeiten vor Ort, geringer Erkennbarkeit (Tarnkappencharakter), wo anwendbar (was spezielle Formen und Beschichtungen erfordert), Widerstandsfähigkeit gegen raue Betriebsbedingungen (Vibrationen, G-Belastungen, potenzielle Gefechtsschäden) und potenziellen ballistischen Schutzanforderungen für bestimmte Platten.
- Allgemeine Luftfahrt: Kosteneffizienz und Einfachheit sind oft die wichtigsten Faktoren, doch Sicherheit und Zuverlässigkeit stehen weiterhin an erster Stelle.
- UAVs/Drohnen: Das Gewicht ist oft ein entscheidender Faktor für die Lebensdauer und die Nutzlastkapazität. Miniaturisierung und Integration von Funktionalitäten sind höchst wünschenswert.
- Raumfahrzeuge/Trägerraketen: Extreme Umweltbedingungen (Vakuum, Strahlung, thermische Zyklen), höchste Anforderungen an die Zuverlässigkeit und ein extrem geringes Gewicht sind erforderlich. Die Zugänglichkeit während der Verarbeitung am Boden ist entscheidend, aber die Paneele müssen auch den Belastungen beim Start standhalten.
Die schiere Vielfalt und der kritische Charakter dieser Komponenten unterstreichen, warum die Optimierung ihrer Konstruktion und ihres Herstellungsprozesses so wichtig ist. Für Beschaffungsmanager und Zulieferer von Luft- und Raumfahrtkomponenten ist die Sicherstellung einer zuverlässigen Quelle für qualitativ hochwertige, konforme Zugangsklappen sowohl für neue Flugzeugproduktionslinien als auch für den laufenden MRO-Betrieb weltweit unerlässlich. Die Grenzen der herkömmlichen Fertigung bei der Erfüllung der kombinierten Anforderungen an Leichtbau, komplexe Geometrien (insbesondere für die Integration von Merkmalen oder die Anpassung an gekrümmte Oberflächen) und die Verfügbarkeit auf Abruf ebnen den Weg für die Erforschung fortschrittlicher Lösungen wie den 3D-Druck von Metall.
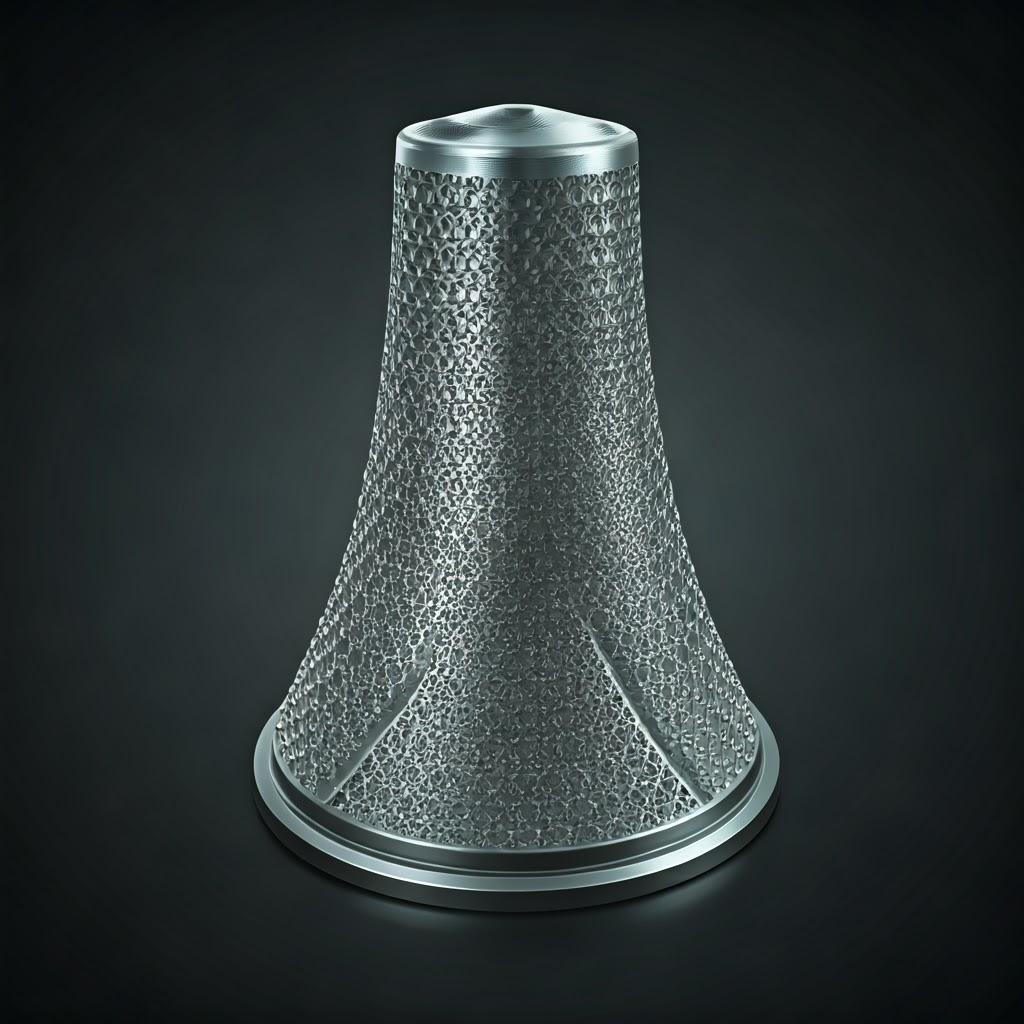
Der Additiv-Vorteil: Warum 3D-Metalldruck für Zugangspaneele in der Luft- und Raumfahrt verwenden?
Herkömmliche Fertigungsverfahren wie die CNC-Bearbeitung von Aluminiumblöcken oder die Blechumformung haben sich in der Luft- und Raumfahrtindustrie zwar seit Jahrzehnten bewährt, weisen aber naturgemäß Einschränkungen auf, die durch die additive Fertigung von Metallen überwunden werden können, was insbesondere bei Komponenten wie Zugangsklappen überzeugende Vorteile bietet. Die Entscheidung, auf AM umzusteigen, wird durch eine Kombination von Faktoren angetrieben, die darauf abzielen, die Leistung zu verbessern, die Kosten zu senken und die Lieferkette zu rationalisieren. Vergleicht man AM, insbesondere Pulverbettschmelzverfahren (Powder Bed Fusion, PBF) wie Selective Laser Melting (SLM) oder Selective Electron Beam Melting (SEBM), mit herkömmlichen Verfahren, wird deutlich, warum Hersteller, Konstrukteure und Großabnehmer in der Luft- und Raumfahrtindustrie diese Technologie zunehmend einsetzen.
Vergleich: Metall-AM vs. traditionelle Fertigung für Zugangspaneele
Merkmal | Metallbasierte additive Fertigung (PBF) | Traditionell (CNC-Bearbeitung) | Traditionell (Blechumformung) |
---|---|---|---|
Gewichtsreduzierung | Ausgezeichnet: Ermöglicht Topologieoptimierung, Gitterstrukturen, generatives Design für erhebliche Gewichtseinsparungen (oft 20-50 %+). | Begrenzt: Der Materialabtrag wird durch den Zugang zum Werkzeug und die ursprüngliche Form des Knüppels eingeschränkt. Die Optimierung ist weniger radikal. | Mäßig: Leichtes Basismaterial, aber die Geometrie ist durch das Umformverfahren begrenzt. Begrenzte Optimierung. |
Entwurfskomplexität | Sehr hoch: Kann komplexe innere Merkmale, konforme Formen, integrierte Funktionen (Scharniere, Versteifungen) erstellen, die sonst nicht möglich wären. | Mäßig: Begrenzt durch die Werkzeuggeometrie, die Bewegungsachse und den möglichen Bedarf an mehreren Aufspannungen. Hinterschneidungen schwierig. | Niedrig: In erster Linie 2,5D-Formen, die durch Biegeradien, Ziehtiefe und die Möglichkeit des Reißens/Faltens begrenzt sind. |
Teil Konsolidierung | Ausgezeichnet: Mehrere Komponenten (z. B. Platte + Versteifungen + Halterungen) können oft als ein einziges, monolithisches Teil gedruckt werden. | Schlecht: Erfordert den Zusammenbau von mehreren bearbeiteten Teilen. | Schlecht: Erfordert die Montage von Formteilen und Verbindungselementen. |
Materialnutzung | Gut: Verwendet Pulver hauptsächlich dort, wo es benötigt wird; nicht verwendetes Pulver ist weitgehend recycelbar. Einige Abfälle von Trägern. | Schlecht: Hoher Materialabfall (das Verhältnis von Kauf- zu Flugmaterial kann hoch sein, z. B. 10:1 oder mehr), da das Material von einem festen Block abgeschnitten wird. | Gut: Relativ geringer Ausschuss, wenn die Verschachtelung optimiert wird, aber dennoch Verschnitt entsteht. |
Werkzeugkosten | Keine: Die direkte digitale Fertigung erfordert keine teilespezifischen Werkzeuge, Gussformen oder Matrizen. | Gering-Mäßig: Erfordert Vorrichtungen und Schneidwerkzeuge. | Hoch: Erfordert teure kundenspezifische Matrizen, Stanzen und Formwerkzeuge, insbesondere für komplexe Formen. |
Vorlaufzeit (Prototyp) | Schnell: Tage bis ein paar Wochen, ideal für schnelle Iterationen und Designvalidierung. | Mäßig: Wochen, je nach Komplexität und Maschinenverfügbarkeit. | Langsam: Monate, bedingt durch die Konstruktion der Werkzeuge und die Herstellungszeit. |
Vorlaufzeit (Produktion) | Mäßig: Geeignet für geringe bis mittlere Stückzahlen; die Geschwindigkeit hängt von der Größe/Komplexität der Teile und der Anzahl der Maschinen ab. | Schnell: Gut geeignet für die Produktion hoher Stückzahlen, sobald sie eingerichtet ist. | Schnell: Sehr effizient für die Großserienproduktion von einfacheren Teilen, sobald die Werkzeuge hergestellt sind. |
Eignung für Anpassungen | Ausgezeichnet: Jeder Druck kann einzigartig sein, ohne dass das Werkzeug gewechselt werden muss. Ideal für maßgeschneiderte oder kleinvolumige Varianten. | Mäßig: Erfordert Neuprogrammierung und möglicherweise neue Vorrichtungen. | Schlecht: Erfordert teure Werkzeugänderungen oder neue Werkzeuge. |
In Blätter exportieren
Die wichtigsten Vorteile werden herausgearbeitet:
- Beispiellose Leichtbauweise: Dies ist wohl der wichtigste Antrieb für AM in der Luft- und Raumfahrt. Zugangspaneele müssen zwar robust sein, benötigen aber oft nicht die Masse von Teilen, die aus Standardmaterial gefertigt werden, oder die geometrischen Beschränkungen von Blechen.
- Topologie-Optimierung: Software-Algorithmen analysieren die Belastungspfade und Spannungen auf einer Platte und entfernen Material aus unkritischen Bereichen. Das Ergebnis sind organisch aussehende, hocheffiziente Strukturen, die die Leistungsanforderungen bei minimaler Masse erfüllen.
- Gitterförmige Strukturen: AM ermöglicht den Einbau interner Gitterstrukturen (Bienenwaben, stochastische Schäume, Kreisel) in das Plattenvolumen. Diese bieten ein hervorragendes Verhältnis von Steifigkeit zu Gewicht und können für bestimmte Belastungsbedingungen oder zur Schwingungsdämpfung maßgeschneidert werden.
- Generatives Design: Ingenieure definieren funktionale Anforderungen, Lasten und Einschränkungen, und die Software generiert mehrere optimierte Konstruktionslösungen, wobei sie oft nicht-intuitive Wege findet, um das Gewicht zu reduzieren und gleichzeitig die Leistungsziele zu erreichen.
- Teil Konsolidierung: Herkömmliche Revisionsklappen bestehen oft aus der eigentlichen Klappe und separaten Versteifungen, Halterungen, Aufdopplungen oder Befestigungselementen, die einzeln hergestellt und dann zusammengebaut werden müssen (z. B. durch Nieten, Kleben oder Schweißen). Dies erhöht die Anzahl der Teile, die Montagezeit, das Gewicht (aufgrund von Verbindungselementen und Überlappungen) und potenzielle Fehlerquellen. Metall-AM ermöglicht es den Konstrukteuren, viele dieser Merkmale direkt in ein einziges, monolithisch gedrucktes Teil zu integrieren. Dies reduziert:
- Arbeitskosten bei der Montage
- Komplexität der Lieferkette (weniger zu beschaffende, zu verfolgende und zu lagernde Teile)
- Gesamtgewicht
- Potenzielle Fehlerstellen in Verbindung mit Verbindungen und Befestigungselementen
- Geometrische Freiheit: AM befreit Designer von den Beschränkungen, die ihnen durch traditionelle Fertigungswerkzeuge und -verfahren auferlegt werden. Zugangspaneele müssen sich oft an die komplexen Krümmungen der Außenhaut eines Flugzeugs anpassen.
- Konforme Formen: Der Druck ermöglicht die perfekte Anpassung der Paneele an gekrümmte Rumpf- oder Flügeloberflächen ohne teure Formwerkzeuge oder komplexe Bearbeitungsvorrichtungen.
- Integrierte Funktionen: Scharniere, Verriegelungsmechanismen, unverlierbare Verschlüsse, Flüssigkeitskanäle (zur Kühlung oder Abdichtung) oder sogar integrierte EMI-Abschirmungspfade können potenziell direkt in die Plattenstruktur integriert werden.
- Komplexe Versteifung: Rippen und Versteifungen müssen nicht mehr geraden Linien oder einfachen Kurven folgen; sie können organisch geformt und genau dort platziert werden, wo sie für maximale Effizienz benötigt werden.
- Rapid Prototyping und Iteration: Bevor teure Werkzeuge (für die Umformung) oder langwierige Bearbeitungen notwendig werden, können Ingenieure mit AM schnell funktionale Prototypen von Zugangsklappen herstellen. Diese können für Passgenauigkeitsprüfungen, Funktionstests und Designvalidierung verwendet werden und ermöglichen schnelle Designiterationen und Verbesserungen innerhalb von Tagen oder Wochen statt Monaten.
- Eliminierung von Werkzeugen: Die Herstellung von Formen oder Gesenken für die Blechumformung oder von komplexen Vorrichtungen für die mehrachsige CNC-Bearbeitung stellt eine erhebliche Vorabinvestition in Form von Kosten und Zeit dar. Bei den relativ geringen Stückzahlen, die für viele spezifische Zugangsklappen für die Luft- und Raumfahrt typisch sind (insbesondere für bestimmte Flugzeugmodelle oder Ersatzteile), können diese Werkzeugkosten unerschwinglich sein. Metall-AM ist ein werkzeugloses Verfahren; die Komplexität wird von der Maschine direkt aus der digitalen Datei übernommen, was es für die Produktion kleiner bis mittlerer Stückzahlen und hochgradig individueller Designs wirtschaftlich macht.
- Fertigung auf Abruf und MRO: Die Lebensdauer von Flugzeugen kann sich über Jahrzehnte erstrecken und erfordert eine langfristige Versorgung mit Ersatzteilen. Es ist kostspielig und ineffizient, große Bestände an Zugangsklappen für jede Variante eines jeden Flugzeugmodells zu führen. Metal AM ermöglicht eine digitale Bestandsaufnahme. Die Entwürfe der Paneele werden digital gespeichert, und die Teile können bei Bedarf von MRO-Anbietern oder Fluggesellschaften gedruckt werden. Dadurch werden die Lagerkosten drastisch gesenkt, der Abfall durch veraltete Bestände minimiert und die Vorlaufzeiten für wichtige Ersatzteile erheblich verkürzt, so dass Flugzeuge schneller wieder in Betrieb genommen werden können. Diese Fähigkeit verändert die MRO-Lieferkette in der Luft- und Raumfahrt und kommt sowohl den MRO-Anbietern als auch den Großhändlern, die sie unterstützen, zugute.
Obwohl Metal AM zahlreiche Vorteile bietet, ist es entscheidend, mit einem erfahrenen Anbieter wie Met3dp. Unser Know-how in der Optimierung von Prozessparametern, der Materialwissenschaft und der Nachbearbeitung stellt sicher, dass die Vorteile von AM - insbesondere Leichtbau und komplexe Geometrien - voll zum Tragen kommen und gleichzeitig die strengen Qualitäts- und Leistungsstandards der Luft- und Raumfahrtindustrie erfüllt werden. Wir setzen fortschrittliche Drucktechnologien ein, um Komponenten zu liefern, die die Möglichkeiten in der Luft- und Raumfahrt neu definieren.
Materialfragen: Empfohlene Metallpulver für 3D-gedruckte Zugangspaneele
Die Auswahl des richtigen Materials ist in der Luft- und Raumfahrttechnik von entscheidender Bedeutung und wirkt sich direkt auf die Leistung, Sicherheit und Lebensdauer der Komponenten aus. Bei 3D-gedruckten Zugangsklappen aus Metall entscheidet die Wahl der Pulverlegierung über entscheidende Eigenschaften wie das Verhältnis von Festigkeit zu Gewicht, Ermüdungsfestigkeit, Korrosionsbeständigkeit, thermische Stabilität und Schweißbarkeit/Reparaturfähigkeit. Während verschiedene Legierungen mit Hilfe der additiven Fertigung verarbeitet werden können, zeichnen sich zwei Aluminiumlegierungen aufgrund ihrer ausgezeichneten Eigenschaften und ihrer etablierten Verwendung in der Industrie als Hauptkandidaten für leichte Zugangsklappen für die Luft- und Raumfahrt aus: AlSi10Mg und Scalmalloy®.
Die Kenntnis der Eigenschaften dieser Materialien ist für die Ingenieure, die die Paneele entwerfen, und für die Beschaffungsmanager, die sie von qualifizierten Metall-AM-Lieferanten beziehen, von wesentlicher Bedeutung.
1. AlSi10Mg:
- Beschreibung: AlSi10Mg ist eine weit verbreitete Aluminiumlegierung, die Silizium und Magnesium enthält. Sie ist bekannt für ihre gute Festigkeit, ihre hervorragenden thermischen Eigenschaften, ihre Korrosionsbeständigkeit und vor allem für ihre ausgezeichnete Verarbeitbarkeit in Laser Powder Bed Fusion (LPBF/SLM) Systemen. Es handelt sich im Wesentlichen um eine gegossene Legierungszusammensetzung, die für die additive Fertigung geeignet ist.
- Wichtige Eigenschaften & Relevanz für die Luft- und Raumfahrt:
- Geringe Dichte: Ungefähr 2,67 g/cm3, was erheblich zur Gewichtsreduzierung beiträgt.
- Gute Festigkeit & Härte (nach Wärmebehandlung): AlSi10Mg ist zwar im Ausgangszustand mäßig, spricht aber sehr gut auf Wärmebehandlungen an (typischerweise T6: Lösungsglühen und künstliche Alterung). Nach einem T6-Zyklus kann es eine Streckgrenze von etwa 230-270 MPa und eine Zugfestigkeit von 330-430 MPa erreichen, kombiniert mit einer guten Härte. Dies bietet eine ausreichende Festigkeit für viele halbstrukturelle oder nichtstrukturelle Zugangsplatten.
- Ausgezeichnete Druckbarkeit: Es ist eine der am einfachsten mit LPBF zu verarbeitenden Aluminiumlegierungen, mit gut verstandenen Parametersätzen, die zu Teilen mit hoher Dichte (>99,8 %) und guter Oberflächengüte (im Vergleich zu anderen AM-Metallen) führen. Diese Zuverlässigkeit ist für eine konsistente Fertigung entscheidend.
- Gute Korrosionsbeständigkeit: Geeignet für typische Betriebsumgebungen in der Luft- und Raumfahrt.
- Wärmeleitfähigkeit: Besitzt eine gute Wärmeleitfähigkeit, was von Vorteil sein kann, wenn sich die Platte in der Nähe von Wärmequellen befindet.
- Erwägungen:
- Duktilität/Ermüdung: Im Vergleich zu Aluminium-Knetlegierungen oder speziellen AM-Legierungen wie Scalmalloy® weist AlSi10Mg im Allgemeinen eine geringere Duktilität (Bruchdehnung oft 3-10 % nach T6) und Ermüdungsfestigkeit auf. Daher eignet es sich weniger für Platten, die sehr hohen zyklischen Belastungen oder potenziellen Stößen ausgesetzt sind, es sei denn, sie sind mit entsprechenden Sicherheitsfaktoren ausgelegt.
- Temperaturbeschränkungen: Seine mechanischen Eigenschaften neigen dazu, sich bei höheren Temperaturen (über ~150-200°C) erheblich zu verschlechtern, was seine Verwendung in Hochtemperaturbereichen wie Motorgondeln ohne sorgfältiges Wärmemanagement einschränkt.
- Anwendungen: Ideal für statische oder mäßig belastete Zugangsklappen, Inspektionsabdeckungen, Halterungen, Gehäuse und Komponenten, bei denen geringes Gewicht und einfache Herstellung im Vordergrund stehen und die Ermüdungsanforderungen nicht extrem sind. Häufig verwendet in Rumpf, Flügel (nicht primäre Struktur) und Systemgehäusen.
2. Scalmalloy®:
- Beschreibung: Scalmalloy® ist eine patentierte Hochleistungs-Aluminium-Magnesium-Scandium-Legierung, die von der APWORKS GmbH speziell für die additive Fertigung entwickelt wurde. Durch den Zusatz von Scandium entstehen feine Ausscheidungen, die die mechanischen Eigenschaften der Legierung im Vergleich zu herkömmlichen Al-Si-Legierungen deutlich verbessern.
- Wichtige Eigenschaften & Relevanz für die Luft- und Raumfahrt:
- Geringe Dichte: Ähnlich wie bei anderen Aluminiumlegierungen (~2,67g/cm3), wodurch der Vorteil des geringen Gewichts erhalten bleibt.
- Außergewöhnliches Verhältnis von Stärke zu Gewicht: Dies ist das bestimmende Merkmal von Scalmalloy®’. Es bietet im Vergleich zu AlSi10Mg eine deutlich höhere Streckgrenze (bis zu 450-500 MPa) und Zugfestigkeit (bis zu 500-540 MPa) und nähert sich damit der Festigkeit einiger traditioneller hochfester Aluminiumlegierungen der Serie 7xxx an, verfügt aber über bessere Schweißbarkeitseigenschaften, die für AM typisch sind.
- Ausgezeichnete Duktilität & Ermüdungsfestigkeit: Im Gegensatz zu vielen hochfesten Aluminiumlegierungen behält Scalmalloy® eine gute Duktilität (Dehnung typischerweise >12%) und weist im Vergleich zu AlSi10Mg eine deutlich verbesserte Ermüdungsleistung auf. Dadurch eignet es sich für dynamisch belastete Bauteile und Strukturen, die eine hohe Schadenstoleranz erfordern.
- Gute Korrosionsbeständigkeit & Schweißbarkeit: Bietet robuste Leistung in typischen Luft- und Raumfahrtumgebungen.
- Hohe Prozessrobustheit: Es wurde für AM entwickelt und lässt sich im Allgemeinen gut in LPBF-Systemen verarbeiten, wodurch Teile mit hoher Dichte entstehen.
- Erwägungen:
- Kosten: Scandium ist ein teures Legierungselement, weshalb Scalmalloy®-Pulver wesentlich teurer ist als AlSi10Mg.
- Verfügbarkeit: Obwohl es immer häufiger vorkommt, ist seine Lieferkette möglicherweise weniger weit verbreitet als die des allgegenwärtigen AlSi10Mg. Erfordert lizenzierte Lieferanten.
- Wärmebehandlung: Erfordert spezifische Wärmebehandlungszyklen, die für die Legierung optimiert sind, um ihre besten Eigenschaften zu erreichen.
- Anwendungen: Bestens geeignet für anspruchsvolle Anwendungen in der Luft- und Raumfahrt, bei denen ein maximales Verhältnis von Festigkeit zu Gewicht, hohe Ermüdungsbeständigkeit und strukturelle Integrität entscheidend sind. Dazu gehören tragende Zugangsklappen, strukturelle Halterungen, die maschinell bearbeitete Komponenten ersetzen, Komponenten, die erheblichen Vibrationen oder zyklischen Belastungen ausgesetzt sind, sowie leistungsrelevante Anwendungen, bei denen die höheren Materialkosten durch Leistungssteigerungen gerechtfertigt sind.
Vergleich der Materialeigenschaften (typische Werte nach optimierter Wärmebehandlung):
Eigentum | AlSi10Mg (Zustand T6) | Scalmalloy® (Optimierter Zustand) | Einheit | Bedeutung für die Luft- und Raumfahrt |
---|---|---|---|---|
Dichte | ~2.67 | ~2.67 | g/cm³ | Grundlegend für den Leichtbau |
Streckgrenze (Rp0,2) | 230 – 270 | 450 – 500 | MPa | Widerstand gegen bleibende Verformung unter Last |
Höchstzugkraft (Rm) | 330 – 430 | 500 – 540 | MPa | Maximale Spannung vor dem Bruch |
Bruchdehnung (A) | 3 – 10 | > 12 | % | Duktilität; Fähigkeit, sich zu verformen, bevor sie bricht |
Elastizitätsmodul (E) | ~70 | ~70 | GPa | Steifigkeit; Widerstand gegen elastische Verformung |
Ermüdungsfestigkeit | Mäßig | Hoch | (variiert) | Widerstand gegen Versagen bei zyklischer Belastung |
Maximale Betriebstemperatur | ~150 – 200 | ~200 – 250 | °C | Temperaturgrenze für die Beibehaltung der mechanischen Eigenschaften |
Druckbarkeit (LPBF) | Ausgezeichnet | Sehr gut | – | Einfachheit und Zuverlässigkeit des AM-Prozesses |
Relative Kosten | Unter | Höher | – | Kosten der Materialbeschaffung |
In Blätter exportieren
Die Rolle von Met3dp bei der Materialexzellenz:
Die Wahl der richtigen Legierung ist nur ein Teil der Gleichung. Die Qualität des Metallpulvers selbst ist entscheidend, um die gewünschten mechanischen Eigenschaften zu erreichen und fehlerfreie Teile zu gewährleisten. Met3dp nutzt die branchenführenden Technologien der Gaszerstäubung und des Plasma-Rotations-Elektroden-Verfahrens (PREP) zur Herstellung von hochwertige Metallpulver optimiert für AM-Verfahren wie LPBF und SEBM.
- Hohe Sphärizität & Fließfähigkeit: Unsere fortschrittlichen Zerstäubungstechniken mit einzigartigen Düsen- und Gasströmungsdesigns ergeben Metallpulver mit hoher Sphärizität und ausgezeichneter Fließfähigkeit. Dies gewährleistet eine gleichmäßige Schichtung des Pulverbetts im 3D-Drucker, was für eine hohe Teiledichte und gleichbleibende Materialeigenschaften entscheidend ist.
- Kontrollierte Partikelgrößenverteilung (PSD): Wir steuern das PSD sorgfältig, um die spezifischen Anforderungen der verschiedenen AM-Maschinen und -Anwendungen zu erfüllen und die Packungsdichte und das Schmelzverhalten zu optimieren.
- Niedrige Verunreinigungswerte: Strenge Qualitätskontrollen minimieren den Gehalt an Sauerstoff und anderen Verunreinigungen, die sich negativ auf die mechanischen Eigenschaften und die Ermüdungslebensdauer des Endprodukts auswirken können.
- Material-Portfolio: Met3dp konzentriert sich auf Legierungen wie TiNi, TiTa, TiAl, CoCrMo, rostfreie Stähle und Superlegierungen und verfügt über die Fähigkeit und das Fachwissen, Aluminiumlegierungen in Luft- und Raumfahrtqualität wie AlSi10Mg herzustellen, die den strengen Spezifikationen der Industrie entsprechen. Unser Team arbeitet eng mit Kunden aus der Luft- und Raumfahrtindustrie zusammen, um sicherzustellen, dass das gelieferte Pulver die genauen Anforderungen für ihre Anwendungen für Zugangsplatten erfüllt.
Durch die Kombination von fortschrittlichen Pulverherstellungsfähigkeiten mit modernsten Druckanlagen und fundiertem Anwendungswissen ermöglicht Met3dp Luft- und Raumfahrtunternehmen, Metall-AM für anspruchsvolle Komponenten wie leichte Zugangsklappen einzusetzen und dabei die besten Materialien für optimale Leistung und Zuverlässigkeit zu nutzen. Die Wahl zwischen AlSi10Mg und Scalmalloy® hängt letztlich von einer detaillierten Analyse der strukturellen Anforderungen, der Betriebsumgebung, des Ermüdungslastspektrums und der Kostenziele der jeweiligen Platte ab.
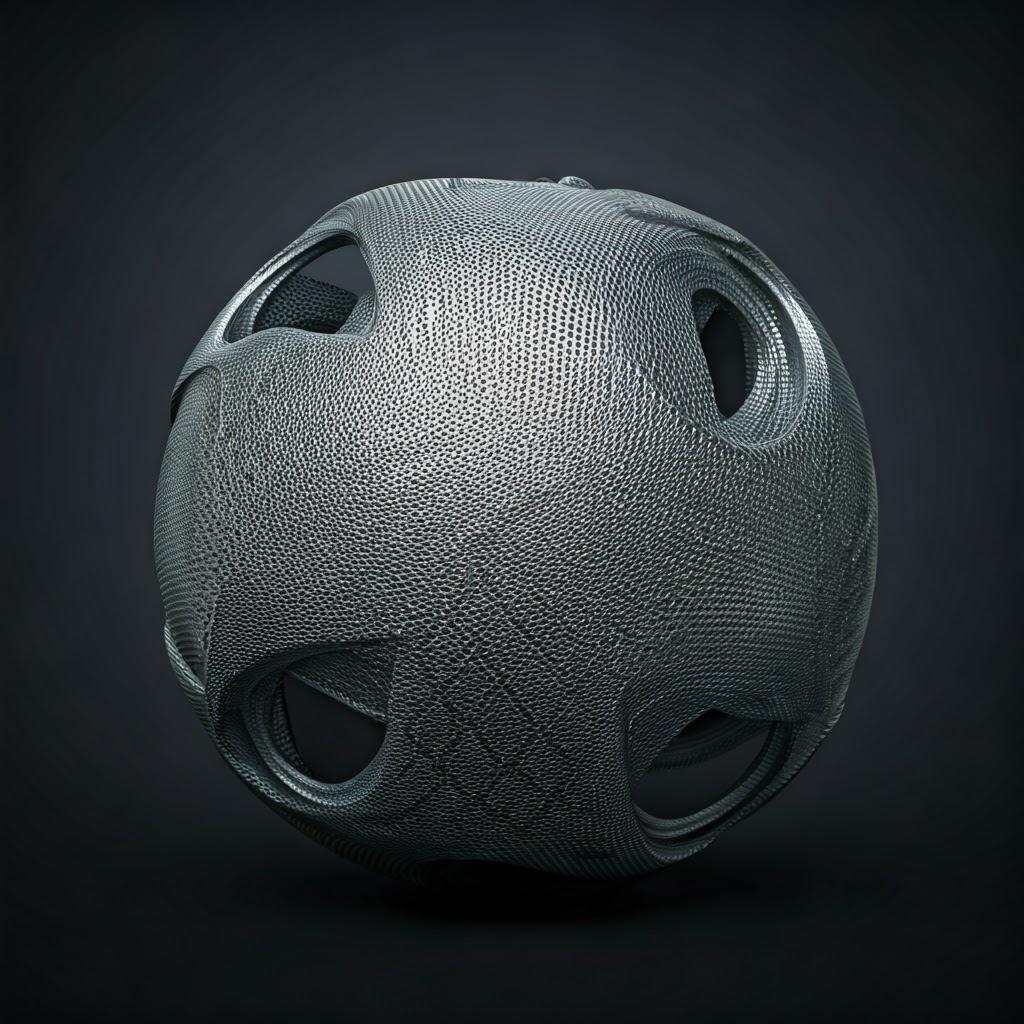
Design für additive Fertigung (DfAM): Optimierung von Zugangspaneelen für den 3D-Druck
Die einfache Nachbildung eines Designs, das für die herkömmliche Fertigung (z. B. CNC-Bearbeitung oder Blechumformung) vorgesehen ist, mit Hilfe der additiven Fertigung schöpft selten das volle Potenzial der Technologie aus. Um die Vorteile des 3D-Metalldrucks für Zugangspaneele in der Luft- und Raumfahrt wirklich nutzen zu können - insbesondere zur Erzielung einer erheblichen Gewichtsreduzierung, Funktionsintegration und Leistungsverbesserung - müssen die Ingenieure folgende Punkte berücksichtigen Design für additive Fertigung (DfAM) grundsätze. DfAM ist eine Methode, bei der Teile unter Berücksichtigung der Fähigkeiten und Einschränkungen des gewählten AM-Prozesses, der Materialien und der Nachbearbeitungsschritte entworfen werden. Für Bauteile in der Luft- und Raumfahrt bedeutet dies, über das konventionelle Designdenken hinauszugehen und die einzigartige geometrische Freiheit zu nutzen, die die schichtweise Fertigung bietet.
Die Anwendung von DfAM auf Zugangskontrollen umfasst mehrere Schlüsselstrategien:
- Topologie-Optimierung: Dies ist oft der Ausgangspunkt für eine radikale Gewichtsreduzierung.
- Prozess: Ingenieure definieren den Konstruktionsraum (das maximal zulässige Volumen für die Platte), legen Lastfälle fest (Kräfte, Drücke, Vibrationen, denen die Platte im Betrieb ausgesetzt ist), definieren Einschränkungen (Montagepunkte, Sperrzonen, Mindestdicke) und setzen Leistungsziele (z. B. maximal zulässige Durchbiegung, Spannungsgrenzen). Eine spezielle Software entfernt dann iterativ Material aus Bereichen mit geringer Belastung und hinterlässt eine optimierte tragende Struktur.
- Das Ergebnis: Das Ergebnis ist oft eine organische, knochenähnliche Struktur, die alle Leistungsanforderungen bei möglichst geringer Masse erfüllt. Für eine Zugangsklappe kann dies bedeuten, dass sie an den Rändern zur Abdichtung und Befestigung aus massivem Material besteht, an den Stellen mit der höchsten Belastung (z. B. in der Nähe von Verschlüssen oder Scharnieren) dicker ist und im Hauptteil der Klappe eine hoch optimierte, möglicherweise stegartige Struktur aufweist.
- Nutzen: Reduziert das Gewicht erheblich (oft 20-50% oder mehr im Vergleich zu einer massiven Platte) und gewährleistet gleichzeitig die strukturelle Integrität.
- Gitterstrukturen und Infill-Strategien: Während bei der Topologieoptimierung große Teile des Materials entfernt werden können, können Gitterstrukturen feste Volumen durch leichte, aber steife Innengeometrien ersetzen.
- Typen: Es gibt verschiedene Gittertypen (z. B. Wabe, kubisch, Oktett-Fachwerk, Kreisel, stochastische Schäume), die jeweils unterschiedliche mechanische Eigenschaften aufweisen (Steifigkeit, Energieabsorption, Wärmeleitfähigkeit).
- Anwendung: Bei einer Zugangsplatte könnte eine Gitterfüllung zwischen der massiven Ober- und Unterschale verwendet werden, um eine leichte Sandwichstruktur zu schaffen. Dies erhöht die Biegesteifigkeit des Paneels bei minimalem Gewichtsverlust im Vergleich zu einem massiven Paneel der gleichen Dicke erheblich. Je nach lokaler Beanspruchung könnten sogar unterschiedliche Gitterdichten oder -typen in verschiedenen Bereichen desselben Paneels verwendet werden.
- Nutzen: Bietet ein hervorragendes Verhältnis von Steifigkeit zu Gewicht, ein Potenzial zur Schwingungsdämpfung und lässt sich nahtlos in den AM-Bauprozess integrieren.
- Generatives Design: Generative Designtools gehen bei der Optimierung noch einen Schritt weiter und ermöglichen es Ingenieuren, hochrangige funktionale Anforderungen, Materialauswahl, Fertigungsmethoden (einschließlich AM-Einschränkungen) und Leistungsziele einzugeben. Die Software generiert und bewertet dann selbstständig Hunderte oder Tausende potenzieller Designlösungen, die oft innovative und nicht intuitive Formen ergeben, die die Kriterien erfüllen. Dies kann besonders bei komplexen Zugangsplatten mit mehreren integrierten Funktionen oder schwierigen Belastungsbedingungen nützlich sein.
- Minimierungs- und Orientierungsstrategie für Stützstrukturen: Metall-AM-Verfahren wie das Pulverbettschmelzen (Powder Bed Fusion, PBF), einschließlich Laser-PBF (LPBF/SLM) und Elektronenstrahl-PBF (EBPF/SEBM), erfordern in der Regel Stützstrukturen, um das Teil auf der Bauplatte zu verankern, überhängende Merkmale zu stützen und thermische Spannungen während des Bauprozesses zu bewältigen. Diese Stützen verbrauchen zusätzliches Material, verlängern die Bauzeit und müssen bei der Nachbearbeitung entfernt werden, was zusätzliche Arbeitskosten verursacht und die Oberflächengüte beeinträchtigen kann. Effektives DfAM zielt darauf ab, die Abhängigkeit von Stützen zu minimieren.
- Selbsttragende Winkel: Das Design von Features mit Überhangwinkeln von typischerweise mehr als 45 Grad (relativ zur Bauplatte) ermöglicht es oft, sie ohne Stützen zu drucken. Zugangspaneele sollten in der Baukammer so ausgerichtet werden, dass die Anzahl der selbsttragenden Flächen maximiert wird.
- Feature-Design: Wenn scharfe horizontale Überhänge mit Fasen oder Hohlkehlen versehen werden, kann die Notwendigkeit von Stützen in diesen Bereichen entfallen.
- Orientierung aufbauen: Die Ausrichtung der Platte hat einen erheblichen Einfluss auf die Anforderungen an die Halterung, die Bauzeit, die Oberflächenqualität (insbesondere nach unten gerichtete Oberflächen) und möglicherweise auf die mechanischen Eigenschaften aufgrund von Anisotropie. Die Wahl der optimalen Ausrichtung ist ein entscheidender DfAM-Schritt, bei dem oft Kompromisse eingegangen werden müssen. Wird eine Platte beispielsweise flach gedruckt, kann die Bauhöhe (und die Bauzeit) minimiert, der Stützbedarf für die Unterseite jedoch maximiert werden, während der vertikale Druck zwar die Stützung reduziert, aber die Bauzeit verlängert und möglicherweise Anisotropieprobleme verursacht. Simulationswerkzeuge können helfen, das Ergebnis der verschiedenen Ausrichtungen vorherzusagen.
- Integrierte Unterstützungen: Manchmal können Stützen als funktionale Merkmale entworfen werden, die Teil des endgültigen Bauteils bleiben, wodurch der Schritt des Entfernens entfällt.
- Feature-Integration und Teilekonsolidierung: Wie bereits erwähnt, ermöglicht AM die Kombination mehrerer, traditionell getrennter Teile zu einer einzigen gedruckten Komponente. DfAM für Zugangsklappen bedeutet, aktiv nach diesen Möglichkeiten zu suchen:
- Integrierte Versteifungen: Rippen und Versteifungselemente können direkt in das Paneel eingearbeitet werden und passen sich perfekt an die optimierten Belastungspfade an, anstatt als separate genietete oder geklebte Elemente zu dienen.
- Eingebaute Befestigungspunkte: Vorsprünge für Gewindeeinsätze, Montageflansche oder sogar Merkmale, die mit bestimmten Schnellverschlüssen funktionieren, können direkt integriert werden.
- Scharnier & Verriegelung Merkmale: Einfache Scharniergelenke oder vorläufige Merkmale für Verriegelungsmechanismen können als Teil der Platte gedruckt werden, was die Komplexität der Montage verringert.
- Dichtungsnuten: Nuten für O-Ringe oder Form-in-Place-Dichtungen können mit hoher Präzision direkt in die Plattenkante gedruckt werden.
- Entwerfen für die Nachbearbeitung: DfAM muss auch nachgelagerte Fertigungsschritte berücksichtigen.
- Zugänglichkeit der Stützen: Wenn Stützen unvermeidlich sind, müssen sie so konstruiert sein, dass sie physisch erreicht und entfernt werden können, ohne das Teil zu beschädigen. Interne Kanäle, die eine Abstützung erfordern, können eine besondere Herausforderung darstellen.
- Zulagen für die Bearbeitung: Wenn bestimmte Oberflächen eine hohe Präzision oder spezielle Oberflächengüten erfordern, die nur durch CNC-Bearbeitung erreicht werden können (z. B. Dichtungsflächen, Montageschnittstellen), muss diesen Merkmalen in der AM-Konstruktionsdatei zusätzliches Material hinzugefügt werden, um den Materialabtrag während der Bearbeitung zu ermöglichen.
- Zugang zur Inspektion: Die Merkmale müssen so konstruiert sein, dass die erforderlichen Prüfungen möglich sind, sei es visuell, maßlich (Zugang mit dem CMM-Taster) oder zerstörungsfrei (z. B. um sicherzustellen, dass die Merkmale keine toten Winkel für Röntgenstrahlen bilden).
Die erfolgreiche Umsetzung von DfAM erfordert nicht nur Fachwissen über Gestaltungsprinzipien, sondern auch ein tiefes Verständnis für die spezifischen Metall-3D-Druckverfahren und das Verhalten des gewählten Materials sowie den gesamten Arbeitsablauf. Die Zusammenarbeit mit einem erfahrenen AM-Dienstleister wie Met3dp kann von unschätzbarem Wert sein. Unsere Ingenieurteams verfügen über umfassende DfAM-Kenntnisse, die speziell für Luft- und Raumfahrtanwendungen und unsere fortschrittlichen Drucktechnologien (einschließlich LPBF und SEBM) gelten. Wir arbeiten eng mit den Konstruktionsteams unserer Kunden zusammen und bieten Beratung und Analysen zur Optimierung von Zugangsplattenentwürfen für maximalen Leichtbau, Leistung und Herstellbarkeit, um sicherzustellen, dass die theoretischen Vorteile von AM in greifbare Ergebnisse umgesetzt werden.
Definierte Präzision: Toleranz, Oberflächengüte und Maßgenauigkeit bei AM Access Panels
Während die additive Fertigung eine beispiellose Designfreiheit bietet, müssen die für die Luft- und Raumfahrtindustrie hergestellten Komponenten strenge Anforderungen an die Maßgenauigkeit, Toleranzen und Oberflächenbeschaffenheit einhalten. Zugangspaneele, insbesondere solche, die Teil der aerodynamischen Haut sind, eine Abdichtung bieten oder eine Schnittstelle zu anderen Strukturen und Verriegelungsmechanismen bilden, erfordern eine präzise Kontrolle ihrer Geometrie und Oberflächeneigenschaften. Das Verständnis der mit Metall-AM-Verfahren wie Powder Bed Fusion (PBF) erreichbaren Präzisionsniveaus ist sowohl für Konstrukteure als auch für Beschaffungsmanager, die potenzielle Lieferanten bewerten, von entscheidender Bedeutung.
Maßgenauigkeit und Toleranzen:
- Allgemeine Toleranzen: Als allgemeine Richtlinie kann man sagen, dass Metall-PBF-Verfahren in der Regel eine mit dem Metallfeinguss vergleichbare Maßgenauigkeit erreichen. Die erreichbaren Standardtoleranzen liegen oft im Bereich der ISO 2768-m (mittel) oder manchmal auch der ISO 2768-f (fein) für die Gesamtabmessungen des Teils. Dies bedeutet in der Regel Toleranzen von etwa ±0,1 mm bis ±0,3 mm für kleinere Teile (bis zu ~100 mm) und möglicherweise ±0,5 mm oder mehr für größere Abmessungen, was stark von der spezifischen Geometrie, dem Material und der Maschinenkalibrierung abhängt.
- Faktoren, die die Genauigkeit beeinflussen: Mehrere Faktoren tragen zur endgültigen Maßhaltigkeit eines gedruckten Metallteils bei:
- Kalibrierung der Maschine: Die regelmäßige Kalibrierung des Laser-/Elektronenstrahl-Abtastsystems des Druckers, des Pulverbeschichtungsmechanismus und der Nivellierung der Bauplattform ist unerlässlich.
- Prozessparameter: Schichtdicke, Strahlleistung, Scangeschwindigkeit und Schraffurabstand wirken sich erheblich auf die Dynamik des Schmelzbades, die Schrumpfung und die endgültigen Abmessungen aus. Optimierte Parameter sind der Schlüssel.
- Thermische Effekte: Eigenspannungen, die sich während der Erwärmungs- und Abkühlungszyklen aufbauen, können Verformungen und Verzerrungen verursachen, die die Genauigkeit beeinträchtigen, insbesondere bei großen oder komplexen Teilen. Ein wirksames Wärmemanagement (z. B. die Beheizung der Bauplatte beim SEBM) und eine Spannungsentlastung nach der Bearbeitung sind entscheidend.
- Materialeigenschaften: Die verschiedenen Legierungen weisen unterschiedliche Schrumpfungsraten und Wärmeleitfähigkeiten auf, was sich auf die endgültigen Abmessungen auswirkt.
- Teilegeometrie und -ausrichtung: Große ebene Flächen sind anfälliger für Verformungen als komplizierte Strukturen. Die Ausrichtung wirkt sich auf den thermischen Verlauf und die Position der Stützen aus, was sich auf die Genauigkeit auswirkt.
- Strategie unterstützen: Stützen helfen, das Teil zu verankern und Verformungen zu vermeiden, aber ihre Entfernung kann manchmal die Abmessungen oder die Oberflächenqualität an den Kontaktpunkten beeinträchtigen.
- Erzielung engerer Toleranzen: Für kritische Merkmale wie Montagebohrungen, Passflächen oder Dichtungsnuten, die engere Toleranzen als die Standard-PBF-Prozessfähigkeit erfordern (z. B. ±0,05 mm oder weniger), wird in der Regel eine CNC-Nachbearbeitung eingesetzt. Das DfAM-Verfahren muss dies berücksichtigen, indem im 3D-Modell ein ausreichendes Bearbeitungsmaterial für diese spezifischen Merkmale vorgesehen wird.
Oberflächengüte (Rauhigkeit):
- Oberflächenrauhigkeit im Ist-Zustand: Die Oberflächenbeschaffenheit von AM-Metallteilen ist von Natur aus rauer als die von bearbeiteten Oberflächen. Dies ist auf den schichtweisen Prozess und die teilweise geschmolzenen Pulverpartikel zurückzuführen, die an der Oberfläche haften. Typische Werte für die Oberflächenrauhigkeit (Ra) bei PBF-Prozessen liegen im Bereich von:
- Nach oben gerichtete Oberflächen: Im Allgemeinen glatter, oft Ra 6-15 µm.
- Seitenwände (vertikale Flächen): Schichtlinien anzeigen, typischerweise Ra 10-20 µm. Der genaue Wert hängt von der Schichtdicke und der Orientierung relativ zur Aufbaurichtung ab (Treppeneffekt bei schrägen Oberflächen).
- Nach unten gerichtete Oberflächen (unterstützt): Sie sind in der Regel am rauesten, oft mit Ra 15-30 µm oder mehr, was auf den Kontakt mit Stützstrukturen oder teilweise gesintertem Pulver zurückzuführen ist.
- Verbesserung der Oberflächengüte: Für viele Zugangsklappen kann die Oberfläche im Ist-Zustand akzeptabel sein, insbesondere bei unkritischen Innenflächen. Für aerodynamische Außenflächen, Dichtungsflächen oder Bereiche, die eine verbesserte Dauerfestigkeit oder Ästhetik erfordern, ist jedoch eine Nachbearbeitung erforderlich. Zu den gängigen Methoden gehören:
- Perlstrahlen/Shot Peening: Verbessert die Gleichmäßigkeit, entfernt loses Pulver, verleiht eine matte Oberfläche und kann Druckspannungen erzeugen, die sich positiv auf die Ermüdungsfestigkeit auswirken. Kann Ra-Werte erreichen, die typischerweise im Bereich von 5-10 µm liegen.
- Taumeln/Gleitschleifen: Verwendet Schleifmittel in einer rotierenden oder vibrierenden Trommel, um Oberflächen zu glätten und Kanten zu entgraten. Effektiv für Chargen von kleineren Teilen, kann Ra ~1-5 µm erreichen.
- CNC-Bearbeitung: Bietet die beste Oberflächengüte und -genauigkeit für spezifische Merkmale und erreicht leicht Ra < 1,6 µm oder sogar weniger (Spiegelglanz mit Polieren).
- Polieren (manuell oder automatisiert): Es können sehr glatte, spiegelähnliche Oberflächen (Ra < 0,4 µm) erzielt werden, wenn dies für bestimmte Anwendungen erforderlich ist (z. B. für die Optik oder den Flüssigkeitsfluss).
- Spezifikation: Die Anforderungen an die Oberflächenbeschaffenheit sollten in den technischen Zeichnungen unter Verwendung von Standard-Ra- oder -Rz-Bezeichnungen für die verschiedenen Oberflächen der Zugangsklappe deutlich angegeben werden.
Metrologie und Qualitätskontrolle:
Die Überprüfung, ob 3D-gedruckte Zugangsklappen die spezifizierten Anforderungen an die Abmessungen und die Oberflächenbeschaffenheit erfüllen, ist ein wichtiger Teil des Qualitätssicherungsprozesses in der Luft- und Raumfahrt.
- Koordinatenmessmaschinen (KMG): Hochpräzise Punktmessungen zur Überprüfung kritischer Abmessungen, Lochpositionen, Ebenheit und geometrischer Bemaßungen und Toleranzen (GD&T)-Angaben. Erfordert physisches Antasten.
- 3D-Laserscanning/Strukturiertes Licht-Scanning: Berührungslose Methoden, die Millionen von Punkten erfassen, um eine digitale 3D-Karte der gesamten Teileoberfläche zu erstellen. Dies ermöglicht den Vergleich mit dem ursprünglichen CAD-Modell (Abweichungsanalyse), die Überprüfung der Gesamtform und komplexer Krümmungen sowie die Durchführung von GD&T-Prüfungen. Sie werden zunehmend für komplexe AM-Teile verwendet.
- Oberflächenrauhigkeitsprüfgeräte (Profilometer): Kontaktstiftinstrumente zur Messung von Ra- oder Rz-Werten auf bestimmten Oberflächen.
- Computertomographie (CT) Scannen: Kann nicht nur für die Erkennung interner Defekte verwendet werden (siehe Abschnitt Herausforderungen), sondern auch für die Dimensionsanalyse, insbesondere bei komplexen internen Merkmalen, die für KMG-Taster oder -Scanner unzugänglich sind.
Das Engagement von Met3dp für Präzision:
Unter Met3dpwir wissen, dass Präzision in der Luft- und Raumfahrt nicht verhandelbar ist. Unsere Investitionen in branchenführende Metall-AM-Systeme, darunter hochauflösende LPBF- und robuste SEBM-Drucker, in Kombination mit strengen Prozesskontroll- und Kalibrierungsroutinen, ermöglichen uns die Herstellung von Teilen mit hoher Maßgenauigkeit und Konsistenz. Wir arbeiten eng mit unseren Kunden zusammen, um die erreichbaren Toleranzen und Oberflächen zu definieren, und empfehlen geeignete Nachbearbeitungsschritte wie CNC-Bearbeitung, wenn bei bestimmten Merkmalen höchste Präzision erforderlich ist. Unser Qualitätsmanagementsystem umfasst fortschrittliche Messtechniken, um sicherzustellen, dass jede gelieferte Zugangsplatte die strengen Spezifikationen der Luft- und Raumfahrtindustrie erfüllt. Die Zusammenarbeit mit einem kompetenten Partner wie Met3dp gewährleistet, dass die Präzisionsanforderungen effizient und zuverlässig erfüllt werden.
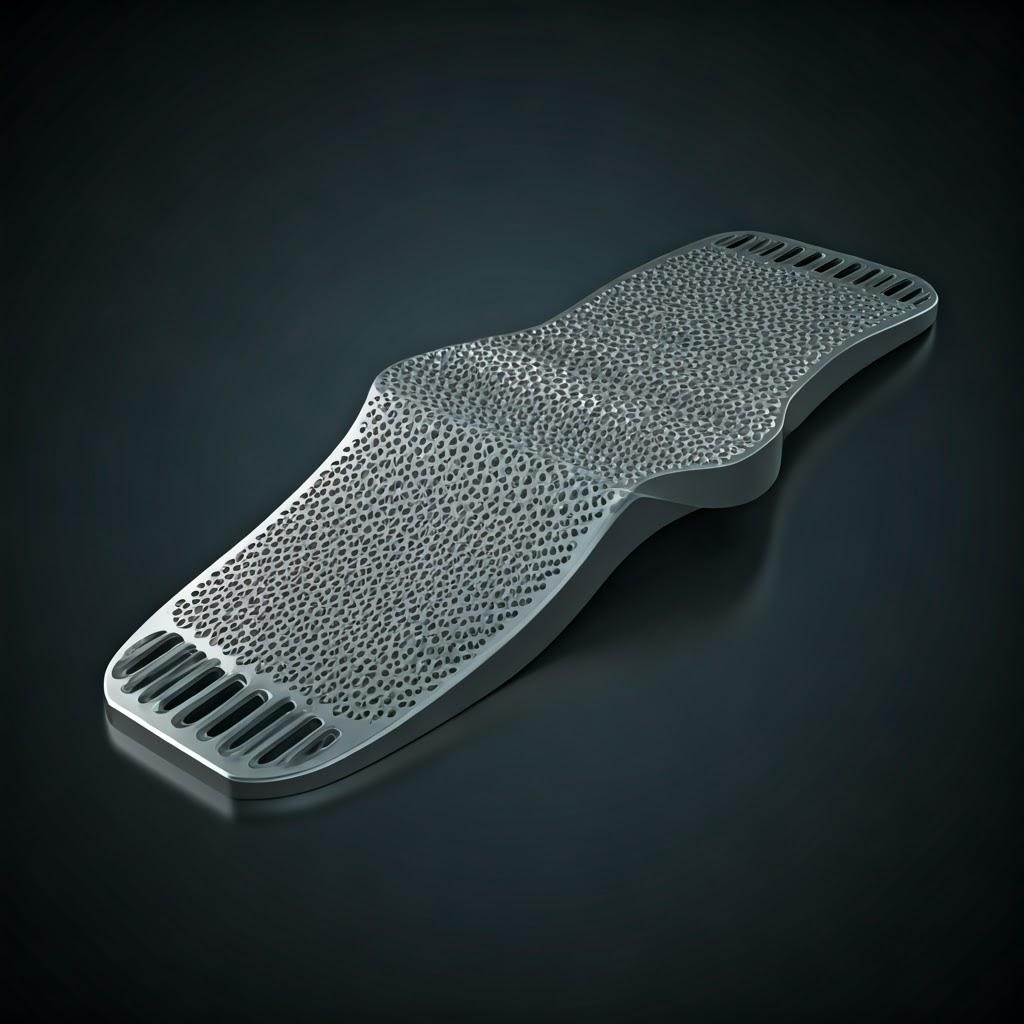
Über den Bau hinaus: Nachbearbeitungsanforderungen für 3D-gedruckte Luft- und Raumfahrtpaneele
Die Reise einer 3D-gedruckten Zugangsplatte aus Metall für die Luft- und Raumfahrt endet nicht, wenn der Drucker anhält. Das frisch aus der Maschine kommende Teil erfordert eine Reihe wichtiger Nachbearbeitungsschritte, um es in ein funktionales, flugtaugliches Bauteil zu verwandeln. Diese Schritte sind entscheidend für das Erreichen der gewünschten mechanischen Eigenschaften, der Maßgenauigkeit, der Oberflächengüte und der Gesamtqualität, die für Luft- und Raumfahrtanwendungen erforderlich sind. Das Verständnis dieses Arbeitsablaufs ist entscheidend für die Planung von Produktionszeiten und -kosten.
Die typische Nachbearbeitungskette für eine AM-Zugangsplatte aus Metall (insbesondere bei Verwendung von PBF mit Aluminiumlegierungen wie AlSi10Mg oder Scalmalloy®) umfasst Folgendes:
- Stressabbauende Wärmebehandlung (optional, aber empfohlen):
- Zweck: Die schnellen Erwärmungs- und Abkühlungszyklen im PBF-Verfahren führen zu erheblichen Eigenspannungen im gedruckten Teil. Diese Spannungen können Verwerfungen oder Verformungen verursachen, insbesondere nachdem das Teil von der starren Bauplatte entfernt wurde, und können die mechanischen Eigenschaften negativ beeinflussen. Zum Spannungsabbau wird das Teil (während es noch auf der Bauplatte befestigt ist) für eine bestimmte Dauer auf eine moderate Temperatur (unterhalb der Alterungstemperatur) erhitzt und anschließend langsam abgekühlt.
- Nutzen: Verringert die inneren Spannungen, verbessert die Dimensionsstabilität für die nachfolgenden Schritte und minimiert das Risiko der Rissbildung. Der spezifische Zyklus hängt von der Legierung und der Teilegeometrie ab.
- Entfernen des Teils von der Bauplatte:
- Methode: Die Teile werden normalerweise auf eine dicke Metallplatte gedruckt. Sie müssen sorgfältig getrennt werden. Zu den gängigen Methoden gehören:
- Draht-Elektroerosion (Wire EDM): Bietet einen präzisen Schnitt mit geringem Kraftaufwand und minimiert die Belastung des Werkstücks. Ideal für empfindliche oder komplexe Geometrien.
- Bandsägen: Eine schnellere und kostengünstigere Methode für einfachere Geometrien, die jedoch eine sorgfältige Handhabung erfordert, um eine Beschädigung des Teils zu vermeiden.
- Erwägung: Die Oberfläche, an der das Teil an der Platte befestigt war (und alle mit der Platte verbundenen Stützstrukturen), muss später nachbearbeitet werden.
- Methode: Die Teile werden normalerweise auf eine dicke Metallplatte gedruckt. Sie müssen sorgfältig getrennt werden. Zu den gängigen Methoden gehören:
- Entfernung der Stützstruktur:
- Zweck: Entfernen der temporären Stützstrukturen, die während des Druckvorgangs entstanden sind.
- Methoden: Dabei handelt es sich häufig um einen manuellen oder halbautomatischen Prozess, der unter Umständen mit einem Aufwand verbunden ist:
- Handwerkzeuge: Entfernen von zugänglichen Halterungen mit Zangen, Schneidegeräten oder Schleifmaschinen. Erfordert Geschicklichkeit, um die Oberfläche des Teils nicht zu beschädigen.
- Bearbeitung (Fräsen/Schleifen): Wird für robustere Stützen verwendet oder wenn eine bestimmte Oberflächenbeschaffenheit an den Schnittstellen der Stützen erforderlich ist (“Zeugenmarken”).
- EDM: Kann manchmal für interne oder schwer zugängliche Stützen verwendet werden.
- Herausforderungen: Kann arbeitsintensiv sein, insbesondere bei komplexen inneren Gittern oder Merkmalen. Schlecht konstruierte Halterungen lassen sich nur schwer oder gar nicht vollständig entfernen. DfAM spielt eine Schlüsselrolle bei der Minimierung und Optimierung von Halterungen für eine leichtere Entfernung.
- Lösungsglühen und Alterungswärmebehandlung (z. B. T6 für Al-Legierungen):
- Zweck: Dies ist ein entscheidender Schritt zur Entwicklung der endgültigen, gewünschten mechanischen Eigenschaften (Festigkeit, Härte, Duktilität) von Aluminiumlegierungen wie AlSi10Mg und Scalmalloy®.
- Lösungsglühen: Erhitzen des Teils auf eine hohe Temperatur (z. B. ~500-540 °C für Al-Legierungen), um Legierungselemente in einer festen Lösung aufzulösen.
- Abschrecken: Schnelles Abkühlen des Teils (normalerweise in Wasser oder Polymer), um die Elemente in Lösung zu halten.
- Künstliche Alterung: Wiedererwärmung des Teils auf eine niedrigere Temperatur (z.B. ~150-180°C) für einen längeren Zeitraum, was eine kontrollierte Ausscheidung von Verfestigungsphasen innerhalb der Aluminiummatrix ermöglicht.
- Kontrolle: Erfordert genau kontrollierte Öfen mit gleichmäßiger Erwärmung und geeigneten Atmosphären (z. B. Schutzgas oder Vakuum), um Oxidation zu verhindern. Auch die Abschreckparameter sind entscheidend, um den Verzug zu minimieren.
- Das Ergebnis: Überführt das Material von einem relativ weichen Zustand in den hochfesten Zustand, der für die Verwendung in der Luft- und Raumfahrt geeignet ist. Die spezifischen T6-Zyklen hängen von der Legierung und dem gewünschten Eigenschaftsgleichgewicht ab.
- Zweck: Dies ist ein entscheidender Schritt zur Entwicklung der endgültigen, gewünschten mechanischen Eigenschaften (Festigkeit, Härte, Duktilität) von Aluminiumlegierungen wie AlSi10Mg und Scalmalloy®.
- Bearbeitung (kritische Merkmale):
- Zweck: Zur Erzielung enger Toleranzen, spezifischer Oberflächengüten oder geometrischer Merkmale, die mit dem AM-Verfahren allein nicht genau hergestellt werden können.
- Anwendungen: Üblich für Dichtungsflächen von Zugangsklappen, Befestigungslöcher, die genaue Durchmesser und Positionen erfordern, Schnittstellen mit Verschlüssen oder Scharnieren und zur Gewährleistung der Gesamtebenheit, falls erforderlich.
- Prozess: Beinhaltet in der Regel 3- oder 5-Achsen-CNC-Fräsen oder -Drehen. Erfordert ein sorgfältiges Vorrichtungsdesign, um die oft komplexe AM-Teilegeometrie sicher und ohne Verzug zu halten. DfAM stellt sicher, dass genügend Material für diese Vorgänge übrig bleibt.
- Oberflächenveredelung:
- Zweck: Zur Erzielung der gewünschten Oberflächenstruktur, zur Beseitigung kleinerer Unvollkommenheiten, zur Verbesserung der Ermüdungsfestigkeit oder zur Vorbereitung der Oberfläche für nachfolgende Beschichtungen.
- Methoden (wie im vorherigen Abschnitt beschrieben):
- Perlstrahlen / Shot Peening
- Taumeln / Vibrationsgleitschleifen
- Polieren
- Auswahl: Die Methode hängt von den Anforderungen an bestimmte Oberflächen der Platte ab (z. B. äußere aerodynamische Oberfläche vs. innere unkritische Oberfläche).
- Reinigung und Inspektion:
- Zweck: Gründliche Reinigung des Teils, um alle Bearbeitungsflüssigkeiten, Strahlmittel oder Verunreinigungen zu entfernen. Anschließend erfolgt die abschließende Maßprüfung (CMM, Scannen) und die zerstörungsfreie Prüfung (NDT).
- ZfP für die Luft- und Raumfahrt: Entscheidend für die Gewährleistung der internen Integrität und die Erkennung von Fehlern wie Porosität oder Rissen, die während des Drucks oder der Nachbearbeitung entstanden sind. Zu den gängigen Methoden gehören:
- Visuelle Inspektion (VT): Grundlegende Prüfung auf Oberflächenfehler.
- Flüssigkeitseindringprüfung (LPI/FPI): Erkennt Risse, die die Oberfläche durchbrechen.
- Röntgenuntersuchung (X-Ray) / Computertomographie (CT): Unverzichtbar für die Erkennung von inneren Hohlräumen, Porosität, Einschlüssen und die Überprüfung komplexer innerer Geometrien. Das CT-Scannen bietet eine vollständige 3D-Ansicht der inneren Strukturen.
- Ultraschallprüfung (UT): Kann Fehler unter der Oberfläche erkennen.
- Beschichtung / Lackierung:
- Zweck: Zum Schutz vor Korrosion, zur Verbesserung der Verschleißfestigkeit, zur Erfüllung spezifischer Anforderungen an die Oberflächenleitfähigkeit oder zum Auftragen der für die Luft- und Raumfahrt erforderlichen Farbschemata.
- Gängige Luft- und Raumfahrtbeschichtungen für Aluminium:
- Eloxieren (z. B. Schwefelsäure-Eloxieren – Typ II, Hart-Eloxieren – Typ III): Bietet hervorragende Korrosions- und Verschleißfestigkeit.
- Chemische Konversionsbeschichtung (z. B. auf Alodin-, Chromat- oder Nichtchromatbasis): Bietet Korrosionsbeständigkeit und dient als hervorragende Grundierung.
- Grundierung und Deckbeschichtung: Auftragen von speziellen Grundierungen und Lacken für die Luft- und Raumfahrt zum endgültigen Schutz und zur Lackierung.
Die Komplexität dieser Nachbearbeitungskette verdeutlicht den Bedarf an einer umfassenden Fertigungslösung. Es reicht nicht aus, nur einen 3D-Drucker zu haben. Die Zulieferer von Luft- und Raumfahrtkomponenten müssen über starke Partnerschaften für Wärmebehandlung, Präzisionsbearbeitung, Oberflächenbehandlung, zerstörungsfreie Prüfung und Beschichtung verfügen, die alle im Rahmen eines robusten Qualitätssystems wie AS9100 verwaltet werden. Met3dp versteht dieses Ökosystem. Unsere Hauptstärken liegen in der fortgeschrittenen AM-Ausrüstung und Pulverherstellungwir bieten umfassende Lösungen an, indem wir den gesamten Arbeitsablauf von der Designoptimierung bis zur Endkontrolle und Endbearbeitung verwalten. So stellen wir sicher, dass die an unsere Kunden aus der Luft- und Raumfahrtindustrie gelieferten 3D-gedruckten Zugangsklappen für die Integration bereit sind.
Herausforderungen meistern: Häufige Probleme beim 3D-Druck - Zugangspaneele und Lösungen
Die additive Fertigung von Metallen bietet zwar ein transformatives Potenzial für Zugangsplatten in der Luft- und Raumfahrt, ist aber nicht ohne technische Herausforderungen. Die erfolgreiche Herstellung hochwertiger, zuverlässiger AM-Komponenten erfordert ein tiefes Verständnis der Prozessphysik, der Materialwissenschaft und möglicher Fallstricke. Sowohl für den AM-Dienstleister als auch für den Endanwender ist es wichtig, sich dieser allgemeinen Probleme bewusst zu sein und wirksame Strategien zur Abhilfe zu entwickeln.
Gemeinsame Herausforderungen und Lösungen:
- Verformung und Verzerrung:
- Ausgabe: Erhebliche Temperaturgradienten während des PBF-Prozesses (schnelles Schmelzen und Erstarren) führen zum Aufbau von inneren Eigenspannungen. Diese Spannungen können dazu führen, dass sich die Zugangsplatte, insbesondere wenn sie groß und relativ dünn ist, während des Baus oder nach der Entnahme aus der Bauplatte verzieht oder verformt.
- Die Ursachen: Hohe thermische Gradienten, unzureichende Verankerung der Teile, ungeeignete Scanstrategien, große Querschnittsflächen.
- Lösungen:
- Prozess-Simulation: Einsatz von Simulationssoftware (z. B. Finite-Elemente-Analyse – FEA) zur Vorhersage des thermischen Verhaltens und der Spannungsakkumulation vor dem Druck, wodurch Anpassungen der Ausrichtung oder der Stützstrategie möglich sind.
- Optimierte Unterstützungsstrukturen: Strategisch platzierte Stützen verankern das Teil effektiv und tragen zur Wärmeableitung bei.
- Bauen Sie eine Plattenheizung (insbesondere in SEBM): Durch die Aufrechterhaltung einer hohen Temperatur in der Baukammer werden thermische Gradienten reduziert.
- Optimierte Scan-Strategien: Die Verwendung spezieller Laser-/Elektronenstrahl-Abtastmuster (z. B. Inselabtastung, Schachbrettmuster) kann dazu beitragen, die Wärme gleichmäßiger zu verteilen und die Belastung zu verringern.
- DfAM: Konstruktion von Teilen mit Merkmalen, die von Natur aus die Spannungskonzentration verringern (z. B. Vermeidung großer ebener Flächen, Verwendung gerippter Strukturen).
- Stressabbau Wärmebehandlung: Dieser Schritt muss unbedingt durchgeführt werden, bevor das Teil von der Bauplatte entfernt wird.
- Reststress-Management:
- Ausgabe: Selbst wenn ein erheblicher Verzug vermieden wird, können hohe Eigenspannungen im Teil eingeschlossen bleiben. Diese Spannungen können die Ermüdungslebensdauer verringern, bei der Nachbearbeitung (z. B. bei der maschinellen Bearbeitung) Risse verursachen oder zu langfristiger Instabilität der Abmessungen führen.
- Die Ursachen: Dasselbe wie bei der Verformung (thermische Gradienten).
- Lösungen:
- Obligatorischer Stressabbau: Für die meisten AM-Teile in der Luft- und Raumfahrt ist die Durchführung eines geeigneten Spannungsarmglühzyklus unverzichtbar.
- Optimierung der Prozessparameter: Die Feinabstimmung von Parametern wie Strahlleistung, Geschwindigkeit und Schichtdicke kann den Eigenspannungszustand beeinflussen.
- Entspannung nach der Bauphase: Verfahren wie das Kugelstrahlen können günstige Druckeigenspannungen in die Oberfläche einbringen und so schädlichen Zugspannungen entgegenwirken.
- Unterstützung bei der Beseitigung von Schwierigkeiten:
- Ausgabe: Obwohl notwendig, kann das Entfernen von Stützstrukturen schwierig und zeitaufwändig sein, insbesondere bei komplexen Innengeometrien (wie Gitterstrukturen) oder empfindlichen Merkmalen. Eine unsachgemäße Entfernung kann die Oberfläche des Teils beschädigen oder unerwünschte Abdrücke hinterlassen.
- Die Ursachen: Schlechte DfAM (unzugängliche Stützen), zu dichte oder starke Stützstrukturen, komplexe interne Kanäle.
- Lösungen:
- DfAM Fokus: Entwurf für minimale Unterstützung, Verwendung selbsttragender Winkel und Gewährleistung der Zugänglichkeit von Stützen. Software-Tools können helfen, leicht entfernbare Stützen (z. B. perforierte oder konische Schnittstellen) zu erzeugen.
- Optimierte Stützenparameter: Verwendung von Trägerstrukturen, die dicht genug sind, um zu funktionieren, aber für eine leichtere Entfernung optimiert sind (z. B. geringere Dichte, spezifische Schnittstellenschichten).
- Erweiterte Entfernungstechniken: Einsatz von Verfahren wie elektrochemische Bearbeitung oder abrasive Fließbearbeitung für interne Halterungen, die jedoch zusätzliche Kosten und Komplexität verursachen.
- Qualifizierte Techniker: Lassen Sie erfahrene Techniker die manuelle Entfernung sorgfältig durchführen.
- Porosität:
- Ausgabe: Im gedruckten Material können sich kleine Hohlräume oder Poren bilden. Ein hohes Maß an Porosität kann die mechanischen Eigenschaften, insbesondere die Ermüdungsfestigkeit und Bruchzähigkeit, erheblich beeinträchtigen, was für Bauteile in der Luft- und Raumfahrt nicht akzeptabel ist.
- Die Ursachen:
- Gas Porosität: Eingeschlossenes Argon (in LPBF) oder atmosphärische Gase, wenn die Abschirmung unzureichend ist. Kann auch von gelösten Gasen im Pulverrohstoff stammen.
- Lack-of-Fusion-Porosität: Unzureichender Energieeintrag, der zu unvollständigem Schmelzen zwischen den Schichten oder benachbarten Scanspuren führt, wodurch unregelmäßig geformte Hohlräume entstehen.
- Schlüsselloch-Porosität: Übermäßige Energiedichte, die zur Verdampfung des Metalls führt, was zu instabilen Schmelzbädern und Gaseinschlüssen beim Zusammenbruch führt.
- Fragen zur Pulverqualität: Schlechte Pulvermorphologie, interne Gasporen in den Pulverpartikeln oder Verunreinigungen.
- Lösungen:
- Strenge Kontrolle der Parameter: Entwicklung und strenge Kontrolle von validierten Prozessparametern (Leistung, Geschwindigkeit, Schichtdicke, Gasfluss) für das spezifische Material und die Maschine.
- Hochwertiges Pulver: Verwendung von hochreinen, kugelförmigen Metallpulvern mit kontrollierter Partikelgrößenverteilung und geringem internen Gasgehalt. Met3dp's die fortschrittlichen Gaszerstäubungs- und PREP-Prozesse sind darauf ausgelegt, Pulver zu produzieren, die diese Risiken minimieren.
- Optimierte Scan-Strategien: Sicherstellung einer ausreichenden Überlappung zwischen Scannerspuren und Ebenen.
- Kontrolle der inerten Atmosphäre: Aufrechterhaltung einer hochreinen Inertgasumgebung (Argon oder Stickstoff in LPBF) oder Hochvakuum (in SEBM).
- Zerstörungsfreie Prüfung (NDT): Für die Qualitätssicherung in der Luft- und Raumfahrt ist der Einsatz von CT-Scans oder hochempfindlichen UT zur Erkennung und Quantifizierung der inneren Porosität unerlässlich. Heiß-Isostatisches Pressen (HIP) kann manchmal als Nachbearbeitung zum Schließen der inneren Poren verwendet werden, verursacht aber zusätzliche Kosten und Komplexität.
- Oberflächenmängel:
- Ausgabe: Unvollkommenheiten auf der Oberfläche des Teils, die über die allgemeine Rauheit hinausgehen, wie z. B. teilweise gesintertes Pulver, Krätzebildung, Treppenstufen auf abgewinkelten Oberflächen oder Abdrücke von Stützen.
- Die Ursachen: Prozessinstabilitäten, Pulverspritzer, suboptimale Ausrichtung, Wechselwirkungen mit dem Träger.
- Lösungen:
- Optimierung der Parameter: Feinabstimmung der Parameter, um Spritzer zu minimieren und ein stabiles Schmelzen zu gewährleisten.
- Optimierte Ausrichtung: Wahl von Bauausrichtungen, die das Treppentreten auf kritischen Flächen minimieren.
- Effektiver Schutzgasfluss: Zum Entfernen von Spritzern und Dämpfen aus dem Arbeitsbereich (LPBF).
- Nachbearbeiten: Oberflächenbearbeitungsverfahren (Strahlen, Bearbeiten, Polieren) sind häufig erforderlich, um diese Mängel zu beseitigen oder abzumildern.
- Qualifikations- und Zertifizierungshürden:
- Ausgabe: In der Luft- und Raumfahrtindustrie gelten äußerst strenge Qualitäts- und Zertifizierungsstandards (z. B. AS9100). Die Qualifizierung eines neuen Fertigungsverfahrens wie AM, bestimmter Materialien, Maschinen und Nachbearbeitungsschritte erfordert erheblichen Aufwand, Tests und Dokumentation, um die Prozessstabilität, Wiederholbarkeit und die Gleichwertigkeit oder Überlegenheit der Teileleistung gegenüber herkömmlichen Methoden nachzuweisen.
- Lösungen:
- Robustes Qualitätsmanagementsystem (QMS): Umsetzung und Einhaltung von AS9100 oder gleichwertigen Normen.
- Prozess-Validierung: Rigorose Tests (Materialcharakterisierung, mechanische Tests, NDT) zur Ermittlung der Prozessfähigkeiten und zur Erstellung eines statistisch signifikanten Datensatzes.
- Rückverfolgbarkeit von Materialien: Aufrechterhaltung der vollständigen Rückverfolgbarkeit von Pulverchargen von der Quelle über die Produktion bis zum fertigen Teil.
- Konfigurationskontrolle: Strenge Kontrolle der Maschinenparameter, der Softwareversionen und der Nachbearbeitungsprozesse.
- Partnerschaft mit erfahrenen Zulieferern: Die Zusammenarbeit mit AM-Dienstleistern wie Met3dp, die Erfahrung mit Qualifizierungsprozessen in der Luft- und Raumfahrt haben und über die erforderlichen Zertifizierungen und Fachkenntnisse verfügen, ist entscheidend für die Risikominderung und die Beschleunigung der Einführung.
Um diese Herausforderungen erfolgreich zu meistern, bedarf es einer Kombination aus fortschrittlicher Technologie, werkstoffwissenschaftlichem Wissen, strenger Prozesskontrolle, umfassender Qualitätssicherung und qualifiziertem Personal. Wenn diese potenziellen Probleme proaktiv durch sorgfältiges Design, Simulation, Prozessoptimierung und Partnerschaft mit kompetenten Lieferanten angegangen werden, können die erheblichen Vorteile von Metall-AM für Zugangsklappen in der Luft- und Raumfahrt zuverlässig erreicht werden.
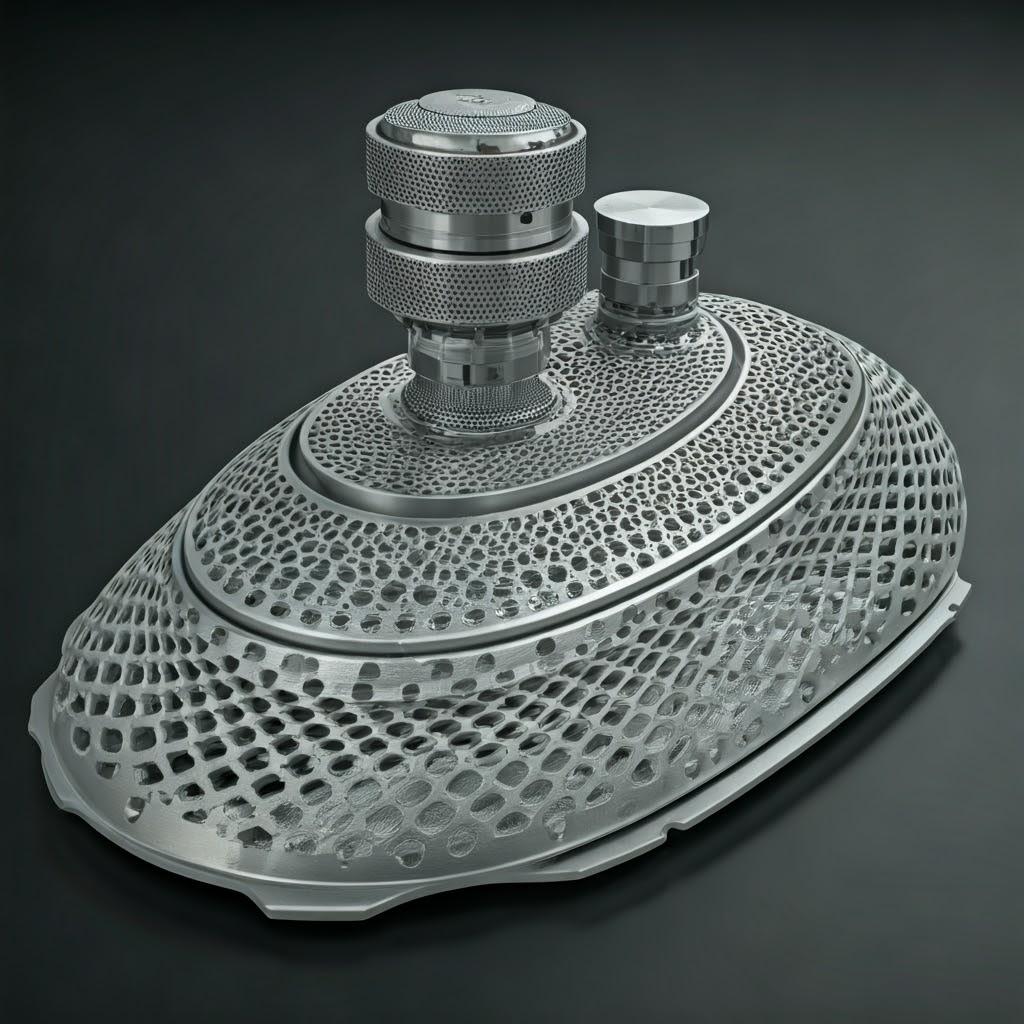
Erfolgreich beschaffen: Wie man den richtigen 3D-Druckdienstleister für Luft- und Raumfahrtkomponenten auswählt
Die Auswahl des richtigen Fertigungspartners ist in der Luft- und Raumfahrtindustrie, in der Qualität, Zuverlässigkeit und Rückverfolgbarkeit an erster Stelle stehen, immer entscheidend. Bei der Beschaffung von 3D-gedruckten Metallkomponenten wie Zugangsklappen ist die Wahl eines fähigen und zertifizierten Dienstleisters für die Additive Fertigung (AM) aufgrund der relativen Neuheit der Technologie und des erforderlichen Fachwissens wohl noch wichtiger. Eine falsche Wahl kann zu Projektverzögerungen, Kostenüberschreitungen, minderwertiger Komponentenqualität und potenziellen Risiken für die Lufttüchtigkeit führen. Beschaffungsmanager und Ingenieurteams müssen eine gründliche Due-Diligence-Prüfung durchführen und potenzielle Lieferanten anhand einer Reihe strenger, auf die Anforderungen der Luft- und Raumfahrt zugeschnittener Kriterien bewerten.
Schlüsselkriterien für die Bewertung von Metall-AM-Lieferanten für Zugangspaneele in der Luft- und Raumfahrt:
- Zertifizierung für die Luft- und Raumfahrt (AS9100):
- Erfordernis: Dies ist nicht verhandelbar. Potenzielle Lieferanten MÜSSEN über eine aktuelle AS9100-Zertifizierung (oder eine gleichwertige Zertifizierung wie EN9100) verfügen. Diese international anerkannte Norm baut auf ISO 9001 auf, enthält jedoch spezifische Anforderungen für Qualitätsmanagementsysteme in der Luft-, Raumfahrt- und Verteidigungsindustrie.
- Bedeutsamkeit: AS9100 demonstriert das Engagement eines Zulieferers für strenge Qualitätskontrolle, Prozessmanagement, Rückverfolgbarkeit, Risikomanagement und kontinuierliche Verbesserung, die alle für die Herstellung flugtauglicher Komponenten unerlässlich sind. Die Überprüfung der Gültigkeit und des Umfangs des Zertifikats ist von entscheidender Bedeutung.
- Nachgewiesene Erfahrung in der Luft- und Raumfahrt & Erfolgsbilanz:
- Erfordernis: Schauen Sie nicht nur auf das Zertifikat. Hat der Anbieter nachweislich Erfahrung mit der Herstellung von Bauteilen für andere Kunden aus der Luft- und Raumfahrt, insbesondere mit Metall-AM? Kann er relevante Fallstudien oder Referenzen vorlegen (innerhalb der Vertraulichkeitsgrenzen)?
- Bedeutsamkeit: Die Erfahrung zeigt, dass Sie mit den Leistungserwartungen in der Luft- und Raumfahrt, den Dokumentationsanforderungen (z. B. First Article Inspection Reports – FAIR), den Materialspezifikationen (AMS-Standards) und der allgemeinen Industriekultur der Präzision und Sicherheit vertraut sind. Erfahrung speziell mit Zugangsklappen oder ähnlichen strukturellen/halbstrukturellen Komponenten ist ein Plus.
- Maschinenfähigkeiten und Technologie:
- Erfordernis: Verfügt der Anbieter über die geeignete AM-Technologie (z. B. Laser Powder Bed Fusion – LPBF/SLM, Electron Beam Powder Bed Fusion – EBPF/SEBM), die für das gewählte Material (AlSi10Mg, Scalmalloy®) und die Anforderungen an das Teil geeignet ist? Beurteilen Sie den Maschinenpark: spezifische Modelle, Bauraumgrößen (können sie Ihre Plattenabmessungen aufnehmen?), Maschinenzustand, Wartungspläne und Prozessüberwachungsmöglichkeiten (z. B. Schmelzbadüberwachung).
- Bedeutsamkeit: Verschiedene Maschinen haben unterschiedliche Stärken. SEBM arbeitet zum Beispiel bei höheren Temperaturen, wodurch die Eigenspannung bei bestimmten Legierungen verringert werden kann, hat aber möglicherweise andere Oberflächeneigenschaften als LPBF. Vergewissern Sie sich, dass die Technologie mit Ihren Anforderungen an Präzision, Oberflächengüte und Materialauswahl übereinstimmt.
- Materialkenntnis und Handhabung:
- Erfordernis: Tiefgreifende Kenntnisse der angegebenen Materialien (AlSi10Mg, Scalmalloy®) sind unerlässlich. Wie werden die Metallpulver beschafft, geprüft, gehandhabt, gelagert und recycelt? Verfügen sie über solide Verfahren zur Vermeidung von Kreuzkontaminationen zwischen verschiedenen Legierungen? Können sie Materialzertifikate vorlegen und die Rückverfolgbarkeit für jede verwendete Pulvercharge nachweisen? Verfügen sie über Erfahrung mit den erforderlichen Wärmebehandlungszyklen für diese spezifischen Legierungen?
- Bedeutsamkeit: Die Materialeigenschaften sind untrennbar mit der Pulverqualität und den Handhabungsverfahren verbunden. Unsachgemäße Lagerung (z. B. Feuchtigkeitsaufnahme), Verunreinigung oder falsche Wiederverwendung können die Integrität des fertigen Teils beeinträchtigen. Fachwissen über die Wärmebehandlung nach dem Druck ist entscheidend für das Erreichen der angegebenen mechanischen Eigenschaften.
- Robustes Qualitätsmanagementsystem (QMS):
- Erfordernis: Über AS9100 hinaus sollten Sie sich mit den spezifischen QMS-Verfahren des Unternehmens befassen. Wie wird die Prozesskontrolle gehandhabt (Parametervalidierung, Überwachung)? Welche Verfahren gibt es für das Management von Nichtkonformitäten, Korrekturmaßnahmen und Dokumentation? Wie wird die Wiederholbarkeit von Fertigung zu Fertigung sichergestellt?
- Bedeutsamkeit: Ein leistungsfähiges QMS bietet die Gewissheit, dass die Teile jedes Mal gemäß den Spezifikationen hergestellt werden. Dazu gehört die Konfigurationskontrolle für digitale Dateien, Prozessparameter und Maschineneinstellungen.
- Technische Unterstützung (DfAM & Simulation):
- Erfordernis: Bietet der Lieferant technische Unterstützung an, insbesondere Know-how im Bereich Design for Additive Manufacturing (DfAM)? Kann er bei der Optimierung des Zugangsplatten-Designs im Hinblick auf Leichtbau, Minimierung der Stützen und Herstellbarkeit helfen? Nutzt er Tools zur Prozesssimulation, um potenzielle Probleme wie Verzug vorherzusagen und zu mindern?
- Bedeutsamkeit: Ein Zulieferer, der als echter Partner agiert, kann einen erheblichen Mehrwert schaffen, indem er hilft, Designs für AM zu verfeinern, was zu einer besseren Leistung, niedrigeren Kosten und einer schnelleren Produktion führen kann. Dieser kooperative Ansatz ist oft entscheidend für die Maximierung der Vorteile von AM.
- Eigene vs. partnerschaftliche Nachbearbeitungskapazitäten:
- Erfordernis: Beurteilen Sie die Fähigkeiten des Unternehmens für den gesamten erforderlichen Arbeitsablauf: Spannungsentlastung, Entfernen von Teilen/Trägern, Wärmebehandlung (mit kalibrierten Öfen für die Luft- und Raumfahrt), CNC-Bearbeitung, Oberflächenbehandlung, zerstörungsfreie Prüfung und Beschichtung. Werden diese Arbeiten intern durchgeführt oder von qualifizierten Unterauftragnehmern übernommen? Falls Unteraufträge vergeben werden, wie verwaltet der Lieferant die Qualität und Rückverfolgbarkeit in der gesamten Lieferkette?
- Bedeutsamkeit: Eigene Kapazitäten bieten oft eine bessere Kontrolle über Vorlaufzeiten und Qualitätsintegration. Aber auch gut geführte Partnerschaften können effektiv sein. Es ist wichtig, den gesamten Arbeitsablauf zu verstehen und zu wissen, wer die einzelnen Schritte durchführt.
- Ressourcen für Inspektion und zerstörungsfreie Prüfung (NDT):
- Erfordernis: Verfügen sie über die erforderlichen Messgeräte (CMMs, 3D-Scanner, Oberflächenprofilometer) und qualifiziertes ZfP-Personal (z. B. zertifizierte Prüfer der Stufe II/III) für AM-relevante Verfahren (insbesondere CT-Scanning für innere Fehler, FPI für Oberflächenrisse)?
- Bedeutsamkeit: Ordnungsgemäße Inspektion und zerstörungsfreie Prüfung sind unverzichtbar, um die Qualität der Teile zu überprüfen und die Einhaltung der Luft- und Raumfahrtnormen zu gewährleisten.
- Kapazität, Skalierbarkeit und Vorlaufzeitzuverlässigkeit:
- Erfordernis: Kann der Lieferant die von Ihnen benötigten Produktionsmengen bewältigen (Prototypen, Kleinserien, Serienproduktion)? Verfügt er über ausreichende Maschinenkapazitäten und Arbeitskräfte? Wie sieht es mit der Liefertreue aus?
- Bedeutsamkeit: Damit wird sichergestellt, dass sie Ihre Projektfristen einhalten und bei Bedarf die Produktion skalieren können. Die Verlässlichkeit bei der Angabe genauer Vorlaufzeiten ist für die Projektplanung entscheidend.
- Kommunikation und Projektmanagement:
- Erfordernis: Wie reaktionsschnell und transparent ist der Anbieter? Bietet er klare Kommunikationskanäle und engagierte Unterstützung beim Projektmanagement?
- Bedeutsamkeit: Eine gute Kommunikation ist unerlässlich, um technische Fragen zu klären, Änderungen zu verwalten und einen reibungslosen Projektablauf von der Bestellung bis zur Lieferung zu gewährleisten.
Met3dp als Ihr Partner für AM in der Luft- und Raumfahrt:
Met3dp ist strategisch gut positioniert, um diese anspruchsvollen Kriterien zu erfüllen. Als führender Anbieter von additiven Fertigungslösungen detailliert weiter über unsbieten wir:
- Fortschrittliche Technologie: Branchenführende SEBM- und LPBF-Drucker, die Legierungen für die Luft- und Raumfahrt wie AlSi10Mg mit hoher Genauigkeit und Zuverlässigkeit verarbeiten können.
- Material Exzellenz: Eigene Herstellung von hochwertigen, kugelförmigen Metallpulvern unter Verwendung fortschrittlicher Gaszerstäubungs- und PREP-Technologien, die ein optimales Ausgangsmaterial für anspruchsvolle Anwendungen gewährleisten. Strenge Pulverhandhabungs- und Rückverfolgbarkeitsprotokolle sind Standard.
- Umfassende Lösungen: Wir sind zwar auf Anlagen und Pulver spezialisiert, arbeiten aber mit unseren Kunden zusammen, um End-to-End-Lösungen anzubieten, einschließlich DfAM-Unterstützung, Prozessoptimierung und Koordinierung der erforderlichen Nachbearbeitungs- und Qualitätssicherungsschritte durch ein Netzwerk von qualifizierten Partnern, wo dies erforderlich ist.
- Schwerpunkt Luft- und Raumfahrt: Unsere jahrzehntelange Erfahrung in der Metall-AM in anspruchsvollen Sektoren, einschließlich der Luft- und Raumfahrt, ermöglicht es uns, die spezifischen Anforderungen der Industrie an Qualität, Leistung und Dokumentation zu verstehen und zu erfüllen.
- Kollaborativer Ansatz: Wir arbeiten eng mit unseren Kunden zusammen, um die erfolgreiche Implementierung der AM-Technologie zu gewährleisten, indem wir Designs und Prozesse optimieren, um die bestmöglichen Ergebnisse zu erzielen.
Die Wahl des richtigen Lieferanten ist eine strategische Entscheidung. Durch die sorgfältige Bewertung potenzieller Partner anhand dieser Kriterien können Luft- und Raumfahrtunternehmen den 3D-Metalldruck vertrauensvoll zur Herstellung innovativer, leichter und leistungsstarker Zugangsklappen nutzen und sich so einen Wettbewerbsvorteil in der sich schnell entwickelnden Fertigungslandschaft sichern.
Die Investition verstehen: Kostenfaktoren und Vorlaufzeiten für 3D-gedruckte Zugangspaneele
Die technischen Vorteile des 3D-Metalldrucks für Zugangsklappen in der Luft- und Raumfahrt sind zwar überzeugend, aber das Verständnis der damit verbundenen Kosten und Produktionsfristen ist für die Budgetierung von Projekten, Beschaffungsentscheidungen und die Rechtfertigung des Geschäftsmodells insgesamt von entscheidender Bedeutung. Sowohl die Kosten als auch die Vorlaufzeit werden durch ein komplexes Zusammenspiel von Faktoren beeinflusst, die mit dem Teiledesign, der Materialauswahl, den Prozessspezifika, dem erforderlichen Qualitätsniveau und dem Auftragsvolumen zusammenhängen.
Die wichtigsten Kostentreiber für 3D-gedruckte Zugangspaneele aus Metall:
- Materialkosten:
- Pulvertyp: Die Grundkosten des Metallpulvers wirken sich erheblich auf den Preis aus. Hochleistungslegierungen wie Scalmalloy® sind aufgrund der Kosten für Legierungselemente wie Scandium wesentlich teurer als Standard-AlSi10Mg.
- Part Volume & Support Volume: Die Gesamtmenge des verbrauchten Pulvers steht in direktem Zusammenhang mit dem Volumen des fertigen Teils plus dem Volumen der erforderlichen Stützstrukturen. Effizientes DfAM, das das Teilevolumen (durch Topologieoptimierung, Gitter) und die Stützstrukturen minimiert, reduziert direkt die Materialkosten.
- Pulver-Recycling/Auffrischungsrate: Während unbenutztes Pulver weitgehend wiederverwertbar ist, muss es in der Regel mit frischem Pulver gemischt werden, um die optimalen Eigenschaften über mehrere Bauphasen hinweg zu erhalten, was mit geringen Zusatzkosten verbunden ist.
- Maschinenzeit (Bauzeit):
- Vorbereitung des Baus: Erforderliche Zeit für das Laden der digitalen Datei, das Einstellen der Bauparameter, die Vorbereitung der Bauplattform und das Laden des Pulvers.
- Druckzeit: Dies ist oft der größte Einzelposten bei den Maschinenkosten. Er wird hauptsächlich durch die höhe des Aufbaus (Anzahl der Schichten) und die Band des in jeder Schicht gesinterten/geschmolzenen Materials (bezogen auf die Querschnittsfläche und die Scangeschwindigkeit). Komplexe Geometrien mit komplizierten Merkmalen oder umfangreichen Stützstrukturen können die Scanzeit pro Schicht erhöhen.
- Abkühlzeit: Zeit, die benötigt wird, um die Baukammer und die Teile vor der Entnahme ausreichend abzukühlen, besonders wichtig bei Verfahren wie SEBM, die mit hohen Temperaturen arbeiten.
- Maschine Stundensatz: Die Dienstleister rechnen die Abschreibung der Maschinen, die Wartung, den Energieverbrauch, die Gemeinkosten der Einrichtung und die Softwarelizenzen in einen Stundensatz für ihre AM-Geräte ein.
- Arbeitskosten:
- Techniker Zeit: Für das Einrichten der Maschine, den Betrieb, die Überwachung, die Handhabung des Pulvers, die Entnahme der Teile, die Entfernung der Halterung, die Oberflächenbearbeitung, die Inspektion und die Verpackung sind qualifizierte Arbeitskräfte erforderlich. Insbesondere das Entfernen von Halterungen kann bei komplexen Teilen sehr arbeitsintensiv sein.
- Technik/CAM Zeit: Zeit, die von Ingenieuren oder CAM-Spezialisten für die Vorbereitung der Konstruktion, die Optimierung der Ausrichtung, die Erzeugung von Unterstützung und die Prozesssimulation aufgewendet wird, insbesondere bei neuen oder komplexen Konstruktionen.
- Nachbearbeitungskosten:
- Stressabbau und Wärmebehandlung: Kosten im Zusammenhang mit der Ofenzeit, dem Energieverbrauch und den erforderlichen kontrollierten Atmosphären (Inertgas, Vakuum).
- Bearbeitungen: Die Kosten hängen von der Komplexität der erforderlichen Bearbeitungsvorgänge, der Anzahl der zu bearbeitenden Merkmale, den erforderlichen Toleranzen, der CNC-Maschinenzeit und der Programmier-/Einrichtungszeit ab.
- Oberflächenveredelung: Die Kosten variieren erheblich je nach Methode (Strahlen ist relativ billig, mehrstufiges Polieren ist teuer) und der zu behandelnden Oberfläche.
- Beschichtung/Malerei: Die Kosten hängen von der Art der Beschichtung, der erforderlichen Oberflächenvorbereitung und der Komplexität der erforderlichen Abdeckungen ab.
- Qualitätssicherung & Inspektionskosten:
- Metrologie: Zeit und Ressourcen für CMM-Messungen, 3D-Scannen und Datenanalyse.
- ZFP: Kosten im Zusammenhang mit der Durchführung und Interpretation von ZfP-Ergebnissen (FPI, Röntgen, CT-Scanning). Das CT-Scannen liefert zwar wertvolle interne Daten, ist aber in der Regel die teuerste ZfP-Methode.
- Dokumentation: Zeitaufwand für die Erstellung der erforderlichen Dokumentation, wie z. B. Materialzertifikate, Konformitätsbescheinigungen und Erstmusterprüfberichte (FAIR).
- Auftragsvolumen:
- Skalenvorteile: Wie die meisten Fertigungsverfahren profitiert auch AM von Skaleneffekten, wenn auch vielleicht anders als die traditionelle Massenproduktion. Durch das Drucken mehrerer Exemplare einer Platte in einem Arbeitsgang (Nesting) wird die Maschinenzeit effektiver genutzt, und die Einrichtungskosten verteilen sich auf mehr Teile. Höhere Gesamtauftragsvolumina können eine Prozessoptimierung und potenziell niedrigere Preise pro Teil ermöglichen. Die Hauptkostentreiber (Material, Maschinenzeit pro Teil) sind jedoch nach wie vor erheblich.
Faktoren für die Vorlaufzeit:
Die Vorlaufzeit ist die Gesamtzeit, die von der Auftragserteilung bis zum Erhalt der fertigen Teile vergeht. Bei AM-Zugangsklappen aus Metall umfasst sie mehrere Phasen:
- Angebotserstellung und Auftragsbestätigung: Erste Prüfung der CAD-Datei, DfAM-Beratung (falls erforderlich), Kostenkalkulation und formale Auftragserteilung (kann einige Tage dauern).
- Engineering & Bauvorbereitung: Endgültige Entwurfsprüfungen, Planung des Baulayouts (Verschachtelung mehrerer Teile), Generierung von Supports, Erstellung von Slice-Dateien und Maschinenplanung (kann je nach Komplexität und Warteschlange 1-5 Tage dauern).
- Drucken: Die Zeit, die das Teil tatsächlich in der AM-Maschine verbringt. Sie kann von einigen Stunden für eine kleine, einfache Platte bis zu mehreren Tagen oder sogar über einer Woche für sehr große, komplexe Teile oder eine komplette Bauplatte mit verschachtelten Komponenten reichen.
- Abkühlung und Entfettung: Abkühlung des Baus und vorsichtige Entnahme der Teile aus dem Pulverbett (in der Regel Stunden bis zu einem Tag).
- Nachbearbeiten: Dies kann einen erheblichen Teil der Gesamtvorlaufzeit ausmachen.
- Stressabbau/Wärmebehandlung: 1-3 Tage (einschließlich Ofenzeit und Abkühlung).
- Entfernung von Teilen/Trägern: Stunden bis mehrere Tage, je nach Komplexität.
- Bearbeitung: Tage bis Wochen, je nach Komplexität und Maschinenverfügbarkeit.
- Endbearbeitung/Beschichtung: Tage bis Wochen, je nach Verfahren und Vorlaufzeiten der Lieferanten.
- Qualitätssicherung und Inspektion: Durchführung von Maßkontrollen und NDT (kann je nach Anforderungen 1-5 Tage dauern).
- Versand: Transportzeit zum Standort des Kunden.
Typische Vorlaufzeitspannen:
- Prototypen (1-5 Einheiten): Häufig 1 bis 4 Wochen, abhängig von der Komplexität und den erforderlichen Nachbearbeitungsschritten. Rapid-Prototyping-Dienste können eine schnellere Durchlaufzeit für einfachere Teile mit minimaler Nachbearbeitung bieten.
- Kleinserienproduktion (10-100 Einheiten): In der Regel 4 bis 8 Wochen, was eine optimierte Verschachtelung, Chargennachbearbeitung und gründliche Qualitätsprüfungen ermöglicht.
- Höhere Volumina: Die Vorlaufzeiten müssen sorgfältig geplant werden und hängen in hohem Maße von den Kapazitäten des Lieferanten und den spezifischen Anforderungen an das Teil bzw. den Prozess ab.
Schlussfolgerung zu Kosten & Vorlaufzeit:
Auch wenn sie potenziell einen höheren pro Teil kosten als herkömmliche Methoden für sehr einfache Designs oder extrem hohe Stückzahlen, wird Metall-AM sehr wettbewerbsfähig und oft vorteilhaft für Zugangspaneele, die sich durch ihre Eigenschaften auszeichnen:
- Hohe Komplexität: Wenn die Bearbeitung mehrere Aufspannungen oder einen umfangreichen Materialabtrag erfordern würde.
- Erhebliches Potenzial zur Gewichtsreduzierung: Wenn der Wert der Gewichtseinsparung (Kraftstoffeffizienz, Leistung) die potenziell höheren Bauteilkosten überwiegt.
- Teil Konsolidierung: Der Wegfall von Montageschritten spart erhebliche Arbeitskosten und reduziert den Aufwand in der Lieferkette.
- Geringes bis mittleres Aufkommen: Wo die hohen Kosten für herkömmliche Werkzeuge (z. B. für die Umformung) vermieden werden.
- Rapid-Prototyping-Bedarf: Wenn Geschwindigkeit für die Entwurfsvalidierung entscheidend ist.
- Ersatzteile auf Abruf: Wenn die Kosten für die Vorratshaltung hoch sind.
Die Einholung genauer Angebote von qualifizierten Anbietern wie Met3dp, die auf ausgereiften Designs und klar definierten Anforderungen basieren, ist der beste Weg, um die spezifischen Kosten und die Vorlaufzeit für Ihr Projekt für Zugangsverkleidungen in der Luft- und Raumfahrt zu ermitteln.
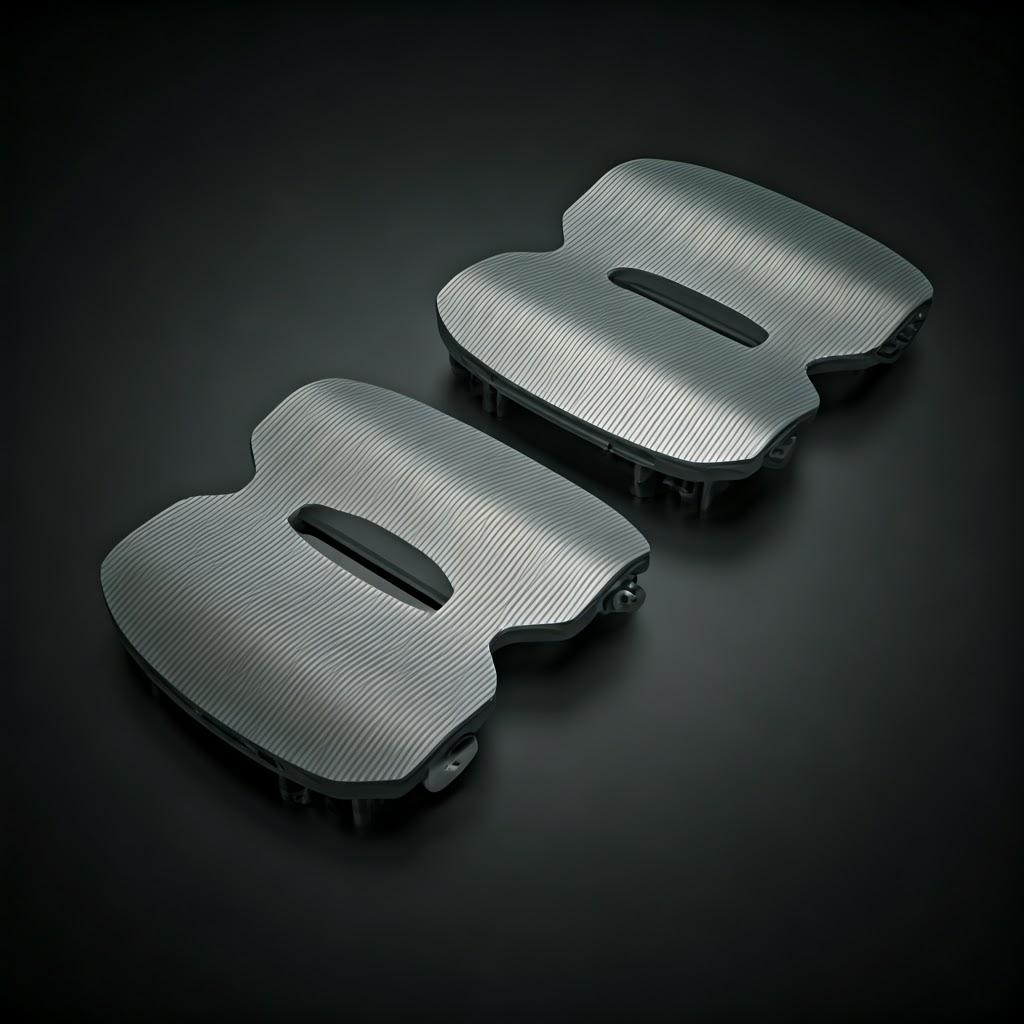
Häufig gestellte Fragen (FAQ) zu 3D-gedruckten Zugangspaneelen für die Luft- und Raumfahrt
Da sich die additive Fertigung von Metallen in der Luft- und Raumfahrt immer mehr durchsetzt, haben Ingenieure, Konstrukteure und Beschaffungsfachleute oft Fragen zu ihrer Anwendung für Komponenten wie Zugangsverkleidungen. Hier finden Sie Antworten auf einige häufig gestellte Fragen:
1. Sind 3D-gedruckte Metallzugangsklappen genauso stabil und zuverlässig wie traditionell bearbeitete oder geformte?
- Antwort: Ja, vorausgesetzt, sie werden unter Verwendung geeigneter Materialien und validierter Verfahren korrekt entworfen, hergestellt und nachbearbeitet. Der Schlüssel liegt im Erreichen der vollen Materialdichte (in der Regel >99,8 %) und der Entwicklung der erforderlichen Mikrostruktur durch Wärmebehandlung.
- Stärke: Mit Legierungen wie Scalmalloy® können 3D-gedruckte Komponenten ein Festigkeits-Gewichts-Verhältnis erreichen, das über dem vieler traditioneller Aluminium-Knetlegierungen liegt, die für Zugangsklappen verwendet werden. Bei AlSi10Mg führt eine Wärmebehandlung nach T6 zu Festigkeiten, die für viele mäßig belastete Paneele geeignet sind und mit denen von Aluminiumgussteilen vergleichbar sind.
- Müdigkeit: Die Ermüdungsleistung hängt in hohem Maße von der Wahl des Werkstoffs, den Prozessparametern (die sich auf die Defektpopulation wie Porosität auswirken), der Oberflächenbeschaffenheit (glattere Oberflächen verbessern im Allgemeinen die Ermüdungslebensdauer) und dem Eigenspannungszustand ab. Scalmalloy® bietet eine deutlich bessere Ermüdungslebensdauer als AlSi10Mg. Nachbearbeitungsprozesse wie das Kugelstrahlen können die Ermüdungsbeständigkeit weiter verbessern, indem sie Druckspannungen auf der Oberfläche erzeugen. Eine sorgfältige zerstörungsfreie Prüfung (z. B. CT-Scannen) ist entscheidend, um sicherzustellen, dass die innere Qualität den Ermüdungsanforderungen entspricht.
- Verlässlichkeit: Zuverlässigkeit ist das Ergebnis von Prozesskontrolle und Qualitätssicherung. Die Zusammenarbeit mit einem AS9100-zertifizierten Lieferanten, der validierte Prozesse, hochwertiges Pulver, strenge zerstörungsfreie Prüfungen und eine umfassende Dokumentation einsetzt, stellt sicher, dass die gedruckten Platten die anspruchsvollen Zuverlässigkeitsstandards der Luft- und Raumfahrt erfüllen. Bei richtiger Ausführung können AM-Teile genauso zuverlässig oder sogar zuverlässiger sein als herkömmliche Teile, insbesondere wenn durch die Konsolidierung der Teile potenzielle Fehlerstellen an den Verbindungsstellen vermieden werden.
2. Wie sieht das Verfahren zur Zertifizierung von 3D-gedruckten Zugangsklappen für den Flug aus?
- Antwort: Die Zertifizierung eines jeden Flugzeugteils, unabhängig von der Herstellungsmethode, ist ein strenges Verfahren, das von den Luftfahrtbehörden (FAA, EASA usw.) geregelt wird. Für AM-Teile beinhaltet das Verfahren den Nachweis der Gleichwertigkeit oder Überlegenheit gegenüber bereits zertifizierten Teilen oder die Qualifizierung der neuen Teile-/Prozesskombination. Zu den wichtigsten Schritten gehören in der Regel:
- Qualifizierungsplan: Festlegung des Umfangs, der Anforderungen, der Materialien, der Herstellungsprozesse (einschließlich spezifischer AM-Maschinen, Parameter, Nachbearbeitung), der Prüfprotokolle und der Abnahmekriterien.
- Materialcharakterisierung: Ausführliche Prüfung des gewählten AM-Materials (z. B. AlSi10Mg oder Scalmalloy®, das mit der spezifischen AM-Methode verarbeitet wurde) zur Ermittlung statistisch signifikanter zulässiger Konstruktionswerte (z. B. A-Basis- oder B-Basis-Werte für Festigkeit, Ermüdung usw.). Dies erfordert häufig die Prüfung zahlreicher Proben, die unter verschiedenen Bedingungen hergestellt wurden.
- Prozess-Spezifikation: Festhalten und Dokumentieren aller kritischen Prozessparameter - vom Pulverhandling und der Maschineneinrichtung bis hin zu den Druckparametern (Laserleistung, Geschwindigkeit, Schichtdicke usw.) und allen Nachbearbeitungsschritten (Wärmebehandlungszyklen, Bearbeitungseinstellungen, Endbearbeitungsverfahren).
- Validierung von Teilen: Herstellung mehrerer konformer Teile unter Verwendung der gesperrten Prozessspezifikation und Durchführung umfangreicher Tests, einschließlich Dimensionsprüfung, zerstörungsfreier Prüfung, statischer Belastungstests, Ermüdungstests und potenzieller Umwelttests, um nachzuweisen, dass sie alle Leistungsanforderungen erfüllen.
- Dokumentation & Audits: Zusammenstellung aller Daten, Berichte (einschließlich FAIR) und Prozessunterlagen zur Überprüfung durch die Zertifizierungsbehörde oder den Hauptauftragnehmer. Audits der Produktionsstätte und der Prozesse sind Standard.
- Zusammenarbeit mit Experten: Dieser Prozess ist komplex und erfordert erhebliche Investitionen. Die Zusammenarbeit mit erfahrenen AM-Anbietern wie Met3dp, die sich mit den Qualifikationsanforderungen der Luft- und Raumfahrt auskennen, kann diesen Prozess rationalisieren.
3. Wie hoch sind die Kosten des 3D-Drucks im Vergleich zu herkömmlichen Methoden (CNC-Bearbeitung, Blechumformung) für Zugangsklappen?
- Antwort: Es gibt keine einfache Antwort; sie hängt stark von der Komplexität, der Größe, dem Material und dem Volumen der Teile ab.
- Einfache, großvolumige Paneele: Bei sehr einfachen, in hohen Stückzahlen produzierten Plattenentwürfen wird die herkömmliche Blechumformung (sobald sich die Werkzeuge amortisiert haben) oder die Hochgeschwindigkeits-CNC-Bearbeitung von Standardmaterial wahrscheinlich weiterhin günstiger pro Teil sein.
- Komplexe Paneele mit geringem bis mittlerem Volumen: Metall-AM wird äußerst wettbewerbsfähig oder sogar billiger, wenn:
- Die Geometrie der Platten ist sehr komplex (z. B. optimierte Topologie, konforme Formen, integrierte Merkmale), was die Bearbeitung schwierig/zeitaufwändig macht oder teure Umformwerkzeuge erfordert.
- Es wird eine erhebliche Gewichtsreduzierung erreicht, bei der der Wert des über die Lebensdauer des Flugzeugs eingesparten Gewichts die höheren Anschaffungskosten für das Teil rechtfertigt.
- Durch die Teilekonsolidierung entfallen mehrere traditionelle Teile und Montageschritte.
- Die Stückzahlen sind gering bis mittelgroß, wodurch hohe Werkzeugkosten für die Umformung vermieden werden.
- Rapid Prototyping oder die Produktion von Ersatzteilen auf Abruf ist erforderlich, wobei die Geschwindigkeit und die werkzeuglose Natur von AM’ genutzt werden.
- Break-Even-Punkt: Der Break-even-Punkt hängt von diesen Faktoren ab. Eine gründliche Kostenanalyse, in der AM mit traditionellen Methoden für das spezifische Design und Produktionsszenario der Zugangsplatte verglichen wird, ist notwendig. Denken Sie daran, Werkzeuge, Montage und mögliche Gewichtseinsparungen in den Vergleich einzubeziehen.
4. Welches Material (AlSi10Mg vs. Scalmalloy®) ist besser für meine spezifische Anwendung der Zugangsplatte?
- Antwort: Die Wahl hängt von den Leistungsanforderungen und dem Budget ab:
- Wählen Sie AlSi10Mg, wenn:
- Die Platte ist nicht-strukturell oder halb-strukturell mit mäßigen Belastungsanforderungen.
- Die Ermüdungsbeanspruchung ist nicht der primäre Konstruktionsfaktor.
- Die Betriebstemperaturen bleiben unter ~150°C.
- Das Kosten-Nutzen-Verhältnis ist eine wichtige Priorität.
- Gute Bedruckbarkeit und festgelegte Prozessparameter sind erwünscht.
- Wählen Sie Scalmalloy®, wenn:
- Die Platte ist strukturell kritisch oder trägt erhebliche Lasten.
- Hohe Ermüdungsfestigkeit und Schadenstoleranz sind erforderlich.
- Ein maximales Verhältnis zwischen Stärke und Gewicht ist unerlässlich.
- Die höheren Materialkosten sind durch Leistungssteigerungen oder Gewichtseinsparungen gerechtfertigt.
- Die Betriebstemperaturen können die für AlSi10Mg geeigneten Temperaturen leicht überschreiten (bis zu ~200-250°C).
- Konsultation: Die Erörterung der spezifischen Belastungsfälle, der Betriebsumgebung und der Leistungsziele mit den Materialexperten eines AM-Anbieters wie Met3dp kann dabei helfen, die optimale Auswahl zu treffen.
- Wählen Sie AlSi10Mg, wenn:
5. Welcher Grad an Detailgenauigkeit und geometrischer Komplexität kann bei Zugangsklappen mit dem 3D-Druck von Metall realistisch erreicht werden?
- Antwort: Metall-AM, insbesondere PBF, bietet eine sehr große geometrische Freiheit.
- Minimale Featuregröße: Abhängig von der Maschine und den Parametern liegen die kleinsten druckbaren Merkmale (z. B. Wandstärke, Lochdurchmesser) in der Regel bei 0,4 – 0,8 mm. Dünne, freitragende Wände unter 0,5-1,0 mm können aufgrund von thermischer Belastung und Handhabung eine Herausforderung darstellen.
- Komplexität: Extrem komplexe Geometrien, einschließlich interner Kanäle (für Kühlung, Verdrahtung oder Leichtbau), komplizierte Gitterstrukturen, konforme Formen, die zu gekrümmten Oberflächen passen, und hochgradig topologieoptimierte Formen sind leicht realisierbar. Merkmale wie integrierte Scharniere, Vorsprünge und Versteifungen können direkt eingebaut werden.
- Beschränkungen: Zu den praktischen Einschränkungen gehören die Notwendigkeit von Stützkonstruktionen für Überhänge mit geringem Winkel (<45 Grad) und die Schwierigkeit, Stützen von sehr langen, schmalen Innenkanälen zu entfernen. Die Oberflächenbeschaffenheit der nach unten gerichteten oder abgestützten Flächen ist rauer als in anderen Bereichen, sofern sie nicht nachbearbeitet werden. Die DfAM-Prinzipien sind der Schlüssel zur Nutzung der Komplexität bei gleichzeitiger Gewährleistung der Herstellbarkeit. Die Diskussion der Designabsicht mit einem AM-Experten kann klären, was machbar ist und wie man komplexe Merkmale am besten zuverlässig erreicht.
Schlussfolgerung: Aufwertung von Luft- und Raumfahrtkomponenten durch fortschrittliche additive Fertigung
Das ständige Streben der Luft- und Raumfahrtindustrie nach leichteren, stärkeren und effizienteren Flugzeugen hat in der additiven Fertigung von Metallen einen starken Verbündeten gefunden. Wie wir in dieser Diskussion erörtert haben, bietet die Anwendung des 3D-Metalldrucks auf Komponenten wie Zugangsklappen eine überzeugende Reihe von Vorteilen, die direkt auf die zentralen Herausforderungen der Branche eingehen. Durch die Überwindung der Beschränkungen der traditionellen Fertigung eröffnet AM eine neue Dimension von Designmöglichkeiten und ermöglicht die Erstellung von Komponenten, die in Bezug auf Leistung und Herstellbarkeit auf bisher unvorstellbare Weise optimiert sind.
Die wichtigsten Erkenntnisse liegen auf der Hand: Der 3D-Metalldruck ermöglicht es den Ingenieuren in der Luft- und Raumfahrt, Zugangsklappen zu entwerfen, die deutlich kleiner sind Feuerzeug durch ausgeklügelte Techniken wie Topologieoptimierung und interne Gitterstrukturen, was direkt zu Treibstoffeinsparungen und einer höheren Nutzlastkapazität beiträgt. Es ermöglicht eine noch nie dagewesene Gestaltungsfreiheitund ermöglicht die Erstellung komplexer, konformer Formen und die konsolidierung von mehreren Teilen in einzelne, monolithische Komponenten, wodurch die Montagezeit, das Gewicht und potenzielle Fehlerpunkte reduziert werden. Außerdem ist die werkzeuglose Natur von AM rationalisiert das Prototyping, beschleunigt die Design-Iteration und revolutioniert die MRO-Lieferkette durch die On-Demand-Produktion von Ersatzteilen, wodurch Lagerkosten und Ausfallzeiten von Flugzeugen minimiert werden.
Um diese Vorteile zu nutzen, ist jedoch mehr erforderlich als nur der Zugang zu einem 3D-Drucker. Der Erfolg hängt von einem ganzheitlichen Ansatz ab, der Folgendes umfasst:
- Intelligentes Design (DfAM): Überdenken des Komponentendesigns zur gezielten Nutzung der AM-Fähigkeiten unter Berücksichtigung der damit verbundenen Beschränkungen.
- Strategische Materialauswahl: Auswahl des optimalen Metallpulvers (wie AlSi10Mg oder das Hochleistungsmetall Scalmalloy®) auf der Grundlage einer strengen Analyse der Leistungsanforderungen und Betriebsbedingungen.
- Kontrolliertes Post-Processing: Durchführung wichtiger Schritte wie Wärmebehandlung, Bearbeitung und Endbearbeitung, um die erforderlichen mechanischen Eigenschaften, Maßgenauigkeit und Oberflächenbeschaffenheit zu erreichen.
- Strenge Qualitätssicherung: Einhaltung strenger Luft- und Raumfahrtnormen (AS9100) durch umfassende Prozesskontrolle, Materialrückverfolgbarkeit und zerstörungsfreie Prüfung.
Um die Komplexität der Materialwissenschaft, der Prozessoptimierung und des Qualitätsmanagements zu bewältigen, ist die Zusammenarbeit mit einem sachkundigen und erfahrenen Partner erforderlich. Die Auswahl eines Metall-AM-Dienstleisters ist eine wichtige Entscheidung, die sich direkt auf den Projekterfolg auswirkt. Die Anbieter müssen nicht nur über die richtige Technologie und die entsprechenden Zertifizierungen verfügen, sondern auch über fundiertes Fachwissen in den Bereichen Luft- und Raumfahrtanwendungen, Werkstoffe, DfAM und den gesamten durchgängigen Fertigungsablauf.
Met3dp ist bereit, dieser strategische Partner zu sein. Mit unserer Grundlage in der Herstellung von hochwertigen, spezialisierten Metallpulvern unter Verwendung modernster Zerstäubungstechniken und unserem Betrieb von branchenführenden additiven Fertigungssystemen bieten wir die Kernelemente für den Erfolg. Das kollektive Fachwissen unseres Teams auf dem Gebiet der Metall-AM, kombiniert mit unserem Engagement für Qualität und Zusammenarbeit, ermöglicht es uns, Luft- und Raumfahrtunternehmen bei der effektiven Nutzung dieser transformativen Technologie zu unterstützen. Wir arbeiten mit Ihren Ingenieuren und Beschaffungsteams zusammen, um Entwürfe zu optimieren, die richtigen Materialien auszuwählen, den Fertigungsprozess zu steuern und flugfertige Komponenten zu liefern, die den höchsten Ansprüchen an Leistung und Zuverlässigkeit gerecht werden.
Die Zukunft der Luft- und Raumfahrtfertigung ist zunehmend digital und additiv. Der 3D-Metalldruck ist nicht nur ein Werkzeug für das Prototyping, sondern eine praktikable, wertschöpfende Produktionstechnologie, die greifbare Vorteile für Komponenten wie Zugangsklappen und darüber hinaus bietet. Durch die Nutzung von AM und die Zusammenarbeit mit kompetenten Zulieferern können Luft- und Raumfahrtunternehmen Innovationen beschleunigen, die Leistung von Flugzeugen verbessern und sich einen Wettbewerbsvorteil am Himmel von morgen sichern.
Sind Sie bereit zu erfahren, wie die additive Fertigung von Metallen Ihre Komponenten für die Luft- und Raumfahrt revolutionieren kann? Kontaktieren Sie Met3dp noch heute um Ihre spezifischen Anforderungen zu besprechen und zu erfahren, wie unsere fortschrittlichen Pulver- und Drucklösungen die Ziele Ihres Unternehmens im Bereich der additiven Fertigung unterstützen können.
Teilen auf
MET3DP Technology Co., LTD ist ein führender Anbieter von additiven Fertigungslösungen mit Hauptsitz in Qingdao, China. Unser Unternehmen ist spezialisiert auf 3D-Druckgeräte und Hochleistungsmetallpulver für industrielle Anwendungen.
Fragen Sie an, um den besten Preis und eine maßgeschneiderte Lösung für Ihr Unternehmen zu erhalten!
Verwandte Artikel
Über Met3DP
Aktuelles Update
Unser Produkt
KONTAKT US
Haben Sie Fragen? Senden Sie uns jetzt eine Nachricht! Wir werden Ihre Anfrage mit einem ganzen Team nach Erhalt Ihrer Nachricht bearbeiten.
Holen Sie sich Metal3DP's
Produkt-Broschüre
Erhalten Sie die neuesten Produkte und Preislisten
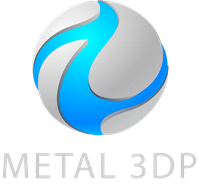
Metallpulver für 3D-Druck und additive Fertigung