3D-gedruckte Abstandshalter für die Luft- und Raumfahrt für enge Toleranzen
Inhaltsübersicht
Einführung: Präzisionsabstandshalter für die Luft- und Raumfahrt durch additive Fertigung neu definiert
Im anspruchsvollen Bereich der Luft- und Raumfahrttechnik spielt jede Komponente, unabhängig von ihrer Größe, eine entscheidende Rolle bei der Gewährleistung von Flugsicherheit, Zuverlässigkeit und Leistung. Zu diesen lebenswichtigen Teilen gehören Abstandshalter für die Luft- und Raumfahrt - scheinbar einfache Komponenten mit komplexen Aufgaben, die von der Aufrechterhaltung präziser Abstände zwischen Baugruppen bis hin zur Gewährleistung einer korrekten Ausrichtung und Lastverteilung reichen. Traditionell werden sie mit subtraktiven Methoden wie der CNC-Bearbeitung hergestellt. Die Produktion von kundenspezifischen Abstandshaltern, insbesondere von solchen mit komplizierten Designs oder solchen, die Hochleistungsmaterialien erfordern, steht oft vor Herausforderungen in Bezug auf Kosten, Vorlaufzeit und geometrische Einschränkungen. Hier kommt die additive Fertigung von Metallen (AM) oder der 3D-Druck ins Spiel, eine transformative Technologie, die die Art und Weise, wie Komponenten für die Luft- und Raumfahrt, einschließlich Abstandshalter, entworfen und hergestellt werden, grundlegend verändert. Für Luft- und Raumfahrtingenieure und Beschaffungsmanager, die überlegene Leistung, Designfreiheit und Flexibilität in der Lieferkette anstreben, ist das Verständnis der Möglichkeiten von Metall-AM von entscheidender Bedeutung.
Metall 3D-Druck ermöglicht die schichtweise Herstellung von Abstandshaltern direkt aus digitalen Modellen unter Verwendung von Hochleistungsmetallpulvern. Dieser Ansatz eröffnet nie dagewesene Möglichkeiten:
- Komplexe Geometrien: Die Herstellung komplizierter interner Kanäle für die Kühlung oder leichter Gitterstrukturen innerhalb des Abstandshalters, die bisher unmöglich oder unerschwinglich waren.
- Materialeffizienz: Verwendung von Werkstoffen wie Titanlegierungen (z. B. Ti-6Al-4V) und hochfesten Edelstählen (z. B. 17-4PH) mit minimalem Ausschuss im Vergleich zu subtraktiven Verfahren.
- Schnelle Prototypenerstellung und Anpassung: Schnelle Iteration von Entwürfen und Herstellung hochgradig kundenspezifischer Abstandshalter, die auf spezifische Anwendungsanforderungen zugeschnitten sind, ohne dass teure Werkzeuge benötigt werden.
- Konsolidierung: Neugestaltung von Baugruppen zur Integration von Abstandshalterfunktionen in größere Komponenten, wodurch die Anzahl der Teile, das Gewicht und potenzielle Fehlerquellen reduziert werden.
- Enge Toleranzen: Sie erreichen die hohe Präzision, die in der Luft- und Raumfahrt gefordert wird, und übertreffen in Kombination mit einer geeigneten Nachbearbeitung oft die traditionellen Methoden.
Unternehmen wie Met3dp stehen an der Spitze dieses technologischen Wandels. Met3dp mit Hauptsitz in Qingdao, China, ist auf industrielle 3D-Drucklösungen aus Metall spezialisiert und bietet sowohl fortschrittliche Druckgeräte als auch eine breite Palette von Hochleistungsmetallpulvern an, die für Luft- und Raumfahrtanwendungen optimiert sind. Unsere Erfahrung mit Verfahren wie dem selektiven Laserschmelzen (SLM) und dem Elektronenstrahlschmelzen (EBM) in Kombination mit den branchenführenden Technologien der Gaszerstäubung und des Plasma-Rotations-Elektroden-Verfahrens (PREP) für die Pulverherstellung gewährleistet, dass wir Komponenten liefern, die den strengen Qualitäts- und Leistungsstandards der Luft- und Raumfahrtbranche entsprechen. Dieser Beitrag befasst sich mit den Besonderheiten des 3D-Metalldrucks für kundenspezifische Abstandshalter für die Luft- und Raumfahrt, mit Anwendungen, Materialauswahl, Designüberlegungen und der Frage, wie man mit einem qualifizierten Lieferanten zusammenarbeitet, um diese leistungsstarke Technologie zu nutzen. Wir möchten B2B-Einkäufern, Luft- und Raumfahrtzulieferern und Ingenieurteams, die ihre Beschaffungs- und Fertigungsstrategien für Komponenten optimieren möchten, wertvolle Einblicke bieten.
Kritische Funktionen: Wofür werden kundenspezifische Abstandshalter für die Luft- und Raumfahrt verwendet?
Abstandshalter für die Luft- und Raumfahrt sind unverzichtbare Komponenten, die in Flugzeugen, Raumfahrzeugen und verwandten Subsystemen zu finden sind. Ihre Hauptfunktion besteht darin, einen bestimmten, kontrollierten Abstand zwischen zwei anderen Komponenten oder Oberflächen zu schaffen und aufrechtzuerhalten. Ihre Rolle geht jedoch oft über den einfachen Abstand hinaus und umfasst eine Vielzahl von kritischen Funktionen, die für die strukturelle Integrität, die Systemleistung und die Betriebssicherheit wichtig sind. Das Verständnis dieser vielfältigen Anwendungen macht deutlich, warum Präzision, Materialeigenschaften und Fertigungszuverlässigkeit nicht verhandelbar sind.
Wichtige Funktionen und Anwendungen:
- Genaue Einhaltung von Abständen und Freiräumen:
- Funktion: Gewährleistung eines angemessenen Raums für die Wärmeausdehnung, die Schwingungsdämpfung, die elektrische Isolierung, den Flüssigkeitsfluss oder die Vermeidung von Kontakt und Verschleiß zwischen beweglichen Teilen.
- Anwendungen: Montage von Elektronikgehäusen (Avionik) an Strukturen, Trennung von Hydraulik- oder Kraftstoffleitungen, Sicherstellung von Spielraum in Fahrwerksmechanismen, Abstand von Turbinenschaufeln oder Triebwerkskomponenten.
- Wichtigkeit: Falsche Abstände können zu Überhitzung, Kurzschlüssen, Flüssigkeitslecks, vorzeitigem Verschleiß oder katastrophalem mechanischen Versagen führen.
- Sicherstellung einer genauen Ausrichtung:
- Funktion: Ausrichten von zusammenpassenden Komponenten während der Montage, Sicherstellen der korrekten Verteilung von Lastpfaden und Aufrechterhalten der geometrischen Genauigkeit komplexer Baugruppen.
- Anwendungen: Ausrichten von Strukturspanten oder Rumpfabschnitten, Positionieren von Aktuatoren oder Sensoren, Sicherstellen des Rundlaufs rotierender Maschinenhalterungen, Einstellen der Lagervorspannung.
- Wichtigkeit: Eine Fehlausrichtung kann zu Spannungskonzentrationen führen, die Ermüdungslebensdauer verringern, die aerodynamische Effizienz beeinträchtigen oder Fehlfunktionen des Systems verursachen.
- Lastverteilung und Stressmanagement:
- Funktion: Verteilung konzentrierter Lasten auf eine größere Fläche, Vermeidung lokaler Spannungsspitzen in den darunter liegenden Strukturen und in einigen Fällen die Funktion eines Opferelements.
- Anwendungen: Unterhalb von Befestigungselementen (Bolzen, Nieten), um das Durchziehen oder Quetschen von Verbundwerkstoffen zu verhindern, zwischen strukturellen Verbindungen, bei der Montage schwerer Geräte.
- Wichtigkeit: Verhindert Schäden an kritischen Strukturen, erhöht die Ermüdungsfestigkeit und stellt sicher, dass die Baugruppe betrieblichen Belastungen standhalten kann.
- Thermische und elektrische Isolierung:
- Funktion: Sie dienen als thermische Trennung zur Begrenzung der Wärmeübertragung zwischen Bauteilen oder zur elektrischen Isolierung, um Kurzschlüsse oder galvanische Korrosion zu verhindern.
- Anwendungen: Abstandshalter aus Materialien mit spezifischen thermischen oder elektrischen Eigenschaften, die in der Nähe von Motoren, Abgasanlagen, Stromverteilungseinheiten oder empfindlicher Elektronik verwendet werden.
- Wichtigkeit: Schützt die Komponenten vor extremen Temperaturen, gewährleistet die elektromagnetische Verträglichkeit (EMV) und verhindert Ausfälle des elektrischen Systems.
- Schwingungsdämpfung:
- Funktion: Verwendung spezieller Geometrien oder Materialien zur Absorption oder Dämpfung der zwischen den Bauteilen übertragenen Schwingungen.
- Anwendungen: Montage empfindlicher Geräte, Reduzierung von Resonanzfrequenzen in Strukturplatten, Isolierung vibrierender Maschinen.
- Wichtigkeit: Verbessert den Fahrgastkomfort, verlängert die Lebensdauer empfindlicher elektronischer Komponenten und verbessert die strukturelle Integrität, indem Ermüdungsschäden verringert werden.
Branchen & Teilsysteme:
Kundenspezifische Abstandshalter für die Luft- und Raumfahrt sind in verschiedenen Segmenten allgegenwärtig:
- Kommerzielle Luftfahrt: Rumpfstrukturen, Tragflächen, Triebwerkspylone, Fahrwerk, Kabineninnenraum, Avionikräume.
- Verteidigung & Militär: Kampfflugzeuge, Transportflugzeuge, Hubschrauber, Raketensysteme, UAVs - oft werden hochtemperaturbeständige oder hochfeste Materialien benötigt.
- Erforschung des Weltraums: Satelliten, Trägerraketen, Raumstationen - hier sind extreme Zuverlässigkeit, geringes Gewicht und Beständigkeit gegen raue Umgebungsbedingungen (Strahlung, Vakuum, Temperaturwechsel) gefragt.
- Avionik & Elektronik: Montage von Leiterplatten, Steckverbindern, Netzteilen und Anzeigegeräten.
Der Bedarf an benutzerdefinierte abstandshalter ergeben sich aus den einzigartigen Anforderungen der jeweiligen Anwendung. Faktoren wie spezifische Spaltmaße, komplexe Schnittstellengeometrien, Gewichtsbeschränkungen, Betriebstemperaturen, Belastungsprofile und Materialkompatibilität erfordern häufig maßgeschneiderte Lösungen anstelle von Teilen von der Stange. Hier kommt die Flexibilität des 3D-Metalldrucks den Herstellern von Luft- und Raumfahrtprodukten und ihren Partnern in der Lieferkette besonders zugute. Beschaffungsmanager, die diese kritischen Komponenten beschaffen, brauchen zuverlässige Lieferanten, die in der Lage sind, maßgeschneiderte Teile zu liefern, die die anspruchsvollen Spezifikationen durchgehend erfüllen.
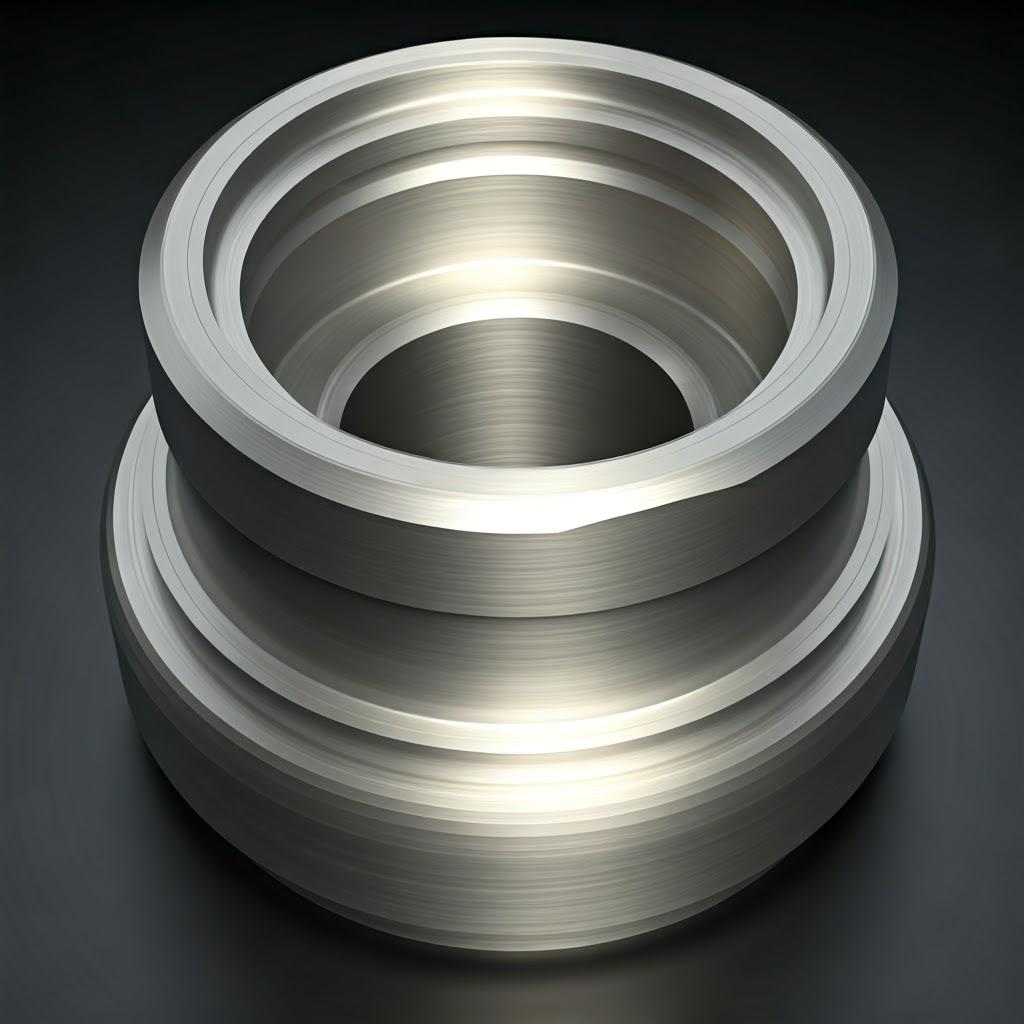
Der additive Vorteil: Warum 3D-Metalldruck für Abstandshalter in der Luft- und Raumfahrt?
Während herkömmliche Fertigungsverfahren wie die CNC-Bearbeitung lange Zeit der Standard für die Herstellung von Abstandshaltern für die Luft- und Raumfahrt waren, bietet die additive Fertigung von Metallen überzeugende Vorteile, insbesondere für komplexe, kundenspezifische oder in kleinen bis mittleren Stückzahlen hergestellte Teile. Mit diesen Vorteilen lassen sich die wichtigsten Herausforderungen angehen, mit denen Ingenieure und Beschaffungsexperten in der Luft- und Raumfahrt konfrontiert sind, wie z. B. Kostensenkung, Verkürzung der Vorlaufzeit, Leistungssteigerung und Optimierung der Lieferkette. Das Verständnis dieser Vorteile ist entscheidend für die Entscheidung, wann und warum man sich für die 3D-Druck von Metall für die Herstellung von Abstandshaltern.
Vergleich: Metall-AM vs. herkömmliche Bearbeitung für Distanzstücke
Merkmal | Additive Fertigung von Metallen (z. B. SLM, EBM) | Traditionelle CNC-Bearbeitung | Hauptvorteil von AM für Abstandshalter |
---|---|---|---|
Geometrische Komplexität | Hoch (Interne Kanäle, Gitter, organische Formen machbar) | Mäßig bis hoch (eingeschränkt durch den Zugang zu Werkzeugen und die Komplexität der Einrichtung) | Ermöglicht hochgradig optimierte, leichte Konstruktionen & Konsolidierung von Teilen, die bei der maschinellen Bearbeitung nicht möglich ist. |
Materialabfälle | Gering (Pulver wiederverwendet) | Hoch (Material aus dem Knüppel entfernt) | Erhebliche Kosteneinsparungen bei teuren Werkstoffen für die Luft- und Raumfahrt (Ti, Inconel); mehr Nachhaltigkeit. |
Vorlaufzeit (kundenspezifisch) | Kurz (Keine Werkzeuge erforderlich, direkt aus CAD) | Mäßig bis lang (Erfordert Vorrichtungen, Programmierung) | Schnellere Iteration, schnellere Lieferung bei dringendem Bedarf (AOG) & Entwicklungszyklen. |
Werkzeugkosten | Keiner | Hoch (Vorrichtungen, Spezialwerkzeuge) | Wirtschaftlich für die Produktion von Kleinserien, Prototypen und stark kundenspezifischen Teilen. |
Teil Konsolidierung | Hohes Potenzial | Geringes Potenzial | Reduziert die Anzahl der Teile, die Montagezeit, das Gewicht und mögliche Fehlerquellen durch die Integration von Abstandshaltern. |
Gewichtsreduzierung | Hervorragend (Topologieoptimierung, Netze) | Begrenzt (vor allem Taschengeld) | Entscheidend für die Treibstoffeffizienz und Nutzlastkapazität in der Luft- und Raumfahrt; AM ermöglicht optimale Strukturen. |
Materialeignung | Wachsendes Angebot an Legierungen für die Luft- und Raumfahrt (Ti, Ni, Al, Stahl) | Große Auswahl an bearbeitbaren Metallen | Optimierte Pulver (wie die von Met3dp) gewährleisten qualitativ hochwertige AM-Teile aus den wichtigsten Werkstoffen der Luft- und Raumfahrt. |
Mindestbestellmenge | Niedrig (kostengünstig für Einzelteile) | Höher (Rüstkosten begünstigen größere Chargen) | Ideal für Sonderanfertigungen, Ersatzteile und erste Produktionsläufe. |
In Blätter exportieren
Die wichtigsten Vorteile, die die Einführung von AM für Abstandshalter vorantreiben:
- Unerreichte Designfreiheit: AM befreit Designer von den Zwängen der traditionellen Fertigung. Abstandshalter können mit komplexen internen Strukturen zur Gewichtsreduzierung (durch Topologieoptimierung oder Gitterstrukturen) entworfen werden, ohne die Festigkeit zu beeinträchtigen. Merkmale wie integrierte Kühlkanäle oder spezielle schwingungsdämpfende Geometrien werden machbar.
- Erhebliche Möglichkeiten zur Gewichtsreduzierung: In der Luft- und Raumfahrt ist das Gewicht ein entscheidender Faktor. Metall-AM ermöglicht die Herstellung von Abstandshaltern, die deutlich leichter sind als ihre maschinell gefertigten Gegenstücke und gleichzeitig die strukturellen Anforderungen erfüllen oder übertreffen. Dies führt direkt zu Treibstoffeinsparungen, erhöhter Nutzlastkapazität oder verbesserter Leistung.
- Geringerer Materialabfall & Kosten: Luft- und Raumfahrtmaterialien wie Ti-6Al-4V sind teuer. Bei der maschinellen Bearbeitung kann erheblicher Abfall entstehen (bis zu 80-90 % bei komplexen Teilen). AM-Verfahren wie das Pulverbettschmelzen nutzen das Material weitaus effizienter, indem sie nur das für das Teil und die Halterungen benötigte Pulver schmelzen, wobei nicht verwendetes Pulver weitgehend recycelbar ist. Dadurch wird das Verhältnis zwischen Anschaffung und Verbrauch erheblich reduziert und die Materialkosten werden gesenkt, was für die Beschaffungsteams ein wichtiger Aspekt ist.
- Beschleunigte Entwicklung und Produktion: Durch den Verzicht auf kundenspezifische Werkzeuge (Vorrichtungen) werden die Vorlaufzeiten drastisch verkürzt, insbesondere bei neuen oder kundenspezifischen Abstandshalterkonstruktionen. Prototypen können schnell hergestellt und getestet werden, was den Design-Iterationszyklus beschleunigt. Für dringende MRO-Bedürfnisse (Wartung, Reparatur, Überholung) oder Kleinserien bietet AM im Vergleich zur Einrichtung eines herkömmlichen Bearbeitungsprozesses wesentlich kürzere Durchlaufzeiten.
- Vereinfachung der Lieferkette: AM ermöglicht eine bedarfsgerechte Produktion näher am Ort des Bedarfs, wodurch die Abhängigkeit von komplexen globalen Lieferketten verringert und die Kosten für die Lagerhaltung minimiert werden können. Ersatzteile, einschließlich kundenspezifischer Abstandshalter, können nach Bedarf gedruckt werden.
- Teil Konsolidierung: In einigen Fällen kann die Funktion eines Abstandshalters und benachbarter Komponenten in einem einzigen, komplexeren 3D-gedruckten Teil kombiniert werden. Dadurch verringert sich die Gesamtzahl der Teile in einer Baugruppe, was die Logistik vereinfacht, die Montagezeit und den Arbeitsaufwand minimiert und potenzielle Fehlerstellen an den Verbindungsstellen eliminiert.
Met3dp nutzt den neuesten Stand der Technik Druckverfahren wie Selective Electron Beam Melting (SEBM) und Selective Laser Melting (SLM), die sich besonders gut für die Verarbeitung reaktiver Materialien wie Titanlegierungen eignen, die in der Luft- und Raumfahrt häufig verwendet werden. Unsere Drucker zeichnen sich durch branchenführende Fertigungsvolumina, Genauigkeit und Zuverlässigkeit aus und stellen sicher, dass die theoretischen Vorteile von AM in greifbare Vorteile für unternehmenskritische Komponenten wie Abstandshalter für die Luft- und Raumfahrt umgesetzt werden. Durch die Zusammenarbeit mit einem erfahrenen Anbieter wie Met3dp können Luft- und Raumfahrtunternehmen die Vorteile der additiven Fertigung für ihre Abstandshalteranforderungen nutzen.
Das Material ist wichtig: Empfohlene Pulver (Ti-6Al-4V & 17-4PH) für optimale Leistung
Die Wahl des Materials ist von grundlegender Bedeutung für die Leistung und Zuverlässigkeit eines jeden Bauteils in der Luft- und Raumfahrt, und Abstandshalter bilden hier keine Ausnahme. Der 3D-Metalldruck bietet die Möglichkeit, mit Hochleistungslegierungen zu arbeiten, die den hohen Anforderungen der Luft- und Raumfahrt gerecht werden. Bei Abstandshaltern zeichnen sich zwei Werkstoffe häufig durch ein hervorragendes Gleichgewicht ihrer Eigenschaften aus: Titanlegierung Ti-6Al-4V (Grad 5) und ausscheidungshärtender rostfreier Stahl 17-4PH. Die Kenntnis ihrer Eigenschaften ist der Schlüssel zur Auswahl des richtigen Materials für eine bestimmte Abstandshalteranwendung.
Ti-6Al-4V (Titan Grad 5): Das Arbeitspferd der Luft- und Raumfahrt
Ti-6Al-4V ist wohl die in der Luft- und Raumfahrt am häufigsten verwendete Titanlegierung, die für ihr außergewöhnliches Verhältnis von Festigkeit zu Gewicht, ihre hervorragende Korrosionsbeständigkeit und ihre gute Leistung bei mäßig hohen Temperaturen bekannt ist.
- Wichtige Eigenschaften:
- Hohes Verhältnis von Festigkeit zu Gewicht: Erheblich leichter als Stahl (ca. 40-50 %), aber mit vergleichbarer oder höherer Festigkeit, wodurch es sich ideal für gewichtskritische Anwendungen eignet.
- Ausgezeichnete Korrosionsbeständigkeit: Bildet eine stabile, passive Oxidschicht, die eine hervorragende Beständigkeit gegen korrosive Umgebungen, einschließlich Salzwasser, Industriechemikalien und oxidierende Säuren, bietet.
- Gute Hochtemperatureignung: Behält seine nützliche Festigkeit bis zu ca. 315∘C (600∘F) bei und eignet sich für viele Anwendungen von Flugzeugzellen und Triebwerkskomponenten.
- Biokompatibilität: Während es für die meisten Abstandshalter weniger relevant ist, eignet es sich aufgrund seiner Biokompatibilität für bestimmte spezialisierte Luft- und Raumfahrtanwendungen, bei denen menschliche Faktoren oder spezifische Umweltkontrollen eine Rolle spielen.
- Gute Ermüdungsfestigkeit: Gute Leistung unter zyklischen Belastungsbedingungen, wie sie in Flugzeugstrukturen üblich sind.
- Warum für Abstandshalter verwenden?
- Gewichtsreduzierung: Hauptantrieb; reduziert das Gesamtgewicht des Flugzeugs.
- Korrosionsschutz: Ideal für Abstandshalter, die im Außenbereich, in der Nähe ungleicher Metalle (Verringerung des galvanischen Korrosionspotenzials) oder in feuchten/korrosiven Umgebungen verwendet werden.
- Anwendungen bei moderaten Temperaturen: Geeignet für Abstandshalter in der Nähe von Motoren oder anderen Wärmequellen innerhalb seines Betriebsbereichs.
- Strukturelle Angleichung: Seine hohe Steifigkeit gewährleistet eine genaue Einhaltung der Lücken und der Ausrichtung unter Last.
17-4PH-Edelstahl: Festigkeit, Härte und Korrosionsbeständigkeit
17-4PH ist ein ausscheidungshärtender Chrom-Nickel-Kupfer-Stahl, der für seine hohe Festigkeit, Härte, gute Korrosionsbeständigkeit (in vielen Umgebungen vergleichbar mit Edelstahl 304) und hervorragende mechanische Eigenschaften bekannt ist, die durch Wärmebehandlung angepasst werden können.
- Wichtige Eigenschaften:
- Hohe Festigkeit und Härte: Erreicht nach entsprechender Wärmebehandlung (z. B. Zustand H900) eine hohe Zug- und Streckgrenze und eignet sich daher für hochbelastete Anwendungen.
- Gute Korrosionsbeständigkeit: Bietet eine bessere Korrosionsbeständigkeit als martensitische Standard-Edelstähle (wie 410) und ist für viele atmosphärische und chemische Umgebungen geeignet.
- Gute Zähigkeit: Behält auch bei hoher Festigkeit eine angemessene Zähigkeit bei.
- Moderate Temperaturfähigkeit: Kann bis zu etwa 315∘C (600∘F) verwendet werden, ähnlich wie Ti-6Al-4V, obwohl die Festigkeit am oberen Ende stärker abnimmt.
- Magnetisch: Es ist ferromagnetisch.
- Warum für Abstandshalter verwenden?
- Anwendungen mit hoher Belastung: Ideal für Abstandshalter, die erheblichen Druck- oder Scherbelastungen ausgesetzt sind, bei denen es auf hohe Festigkeit und Härte ankommt (z. B. unter großen Befestigungselementen, in Fahrwerken).
- Kosten-Nutzen-Verhältnis: In der Regel preiswerter als Titanlegierungen, was es zu einer guten Wahl macht, wenn die extreme Leichtigkeit von Ti-6Al-4V nicht der Hauptgrund ist.
- Abnutzungswiderstand: Seine Härte bietet bei bestimmten Anwendungen eine gute Beständigkeit gegen Verschleiß und Abrieb.
- Kompatibilität: Wird häufig für die Verbindung mit anderen Stahlbauteilen verwendet.
Vergleich der Materialeigenschaften (typische Werte für AM-Teile, nachbearbeitet):
Eigentum | Ti-6Al-4V (geglüht) | 17-4PH (H900 Wärmebehandlung) | Einheit | Anmerkungen |
---|---|---|---|---|
Dichte | ≈4.43 | ≈7.75-7.80 | g/cm3 | Ti-6Al-4V ist wesentlich leichter. |
Endgültige Zugfestigkeit | ≈950-1100 | ≈1310-1450 | MPa | 17-4PH (H900) ist in der Regel stärker. |
Streckgrenze (0.2%) | ≈830-1000 | ≈1170-1300 | MPa | 17-4PH (H900) hat eine höhere Streckgrenze. |
Dehnung beim Bruch | ≈10-18 | ≈10-16 | % | Ähnlicher Duktilitätsbereich. |
Härte | ≈30-36 | ≈40-45 | HRC | 17-4PH (H900) ist härter. |
Maximale Betriebstemperatur | ≈315 (600) | ≈315 (600) | ∘C (∘F) | Ähnliche Obergrenzen, spezifische Daten prüfen. |
Korrosionsbeständigkeit | Ausgezeichnet | Gut | – | Ti-6Al-4V im Allgemeinen überlegen. |
In Blätter exportieren
Met3dp’s Material Vorteil:
Die Wahl des richtigen Materials ist nur ein Teil der Gleichung; die Qualität des für den 3D-Druck verwendeten Metallpulvers ist ebenso entscheidend. Met3dp zeichnet sich in diesem Bereich aus. Wir verwenden branchenführende Gaszerstäubungs- und PREP-Technologien zur Herstellung von hochsphärischen Metallpulvern mit kontrollierter Partikelgrößenverteilung und hervorragender Fließfähigkeit. Dies gewährleistet:
- High Density Parts: Minimierung der Porosität und Erreichen einer nahezu vollständigen theoretischen Dichte für hervorragende mechanische Eigenschaften.
- Gleichbleibende Qualität: Die Konsistenz von Charge zu Charge ist für Luft- und Raumfahrtanwendungen entscheidend.
- Optimale Druckbarkeit: Pulver, die so konzipiert sind, dass sie in SLM- und SEBM-Verfahren zuverlässig funktionieren.
Unser Produkt portfolio umfasst optimierte Ti-6Al-4V- und 17-4PH-Pulver sowie andere innovative Legierungen wie TiNi, TiTa, CoCrMo und verschiedene Superlegierungen, die für anspruchsvolle Umgebungen geeignet sind. Durch den Einsatz der hochwertigen Pulver und fortschrittlichen Drucksysteme von Met3dp’ können Luft- und Raumfahrtunternehmen mit diesen außergewöhnlichen Werkstoffen sicher kundenspezifische Abstandshalter herstellen, die strenge Leistungs- und Zuverlässigkeitsanforderungen erfüllen. Eine Beratung durch unsere Experten für Werkstoffkunde kann Ihnen dabei helfen, das optimale Pulver und die optimalen Verarbeitungsparameter für Ihre spezifische Abstandshalteranwendung auszuwählen, damit Sie das volle Potenzial dieser fortschrittlichen Legierungen ausschöpfen können.

Design für additive Fertigung (DfAM): Optimierung der Abstandshaltergeometrie
Die einfache Nachbildung eines traditionell konstruierten Abstandshalters im 3D-Metalldruck schöpft oft nicht das gesamte Potenzial der additiven Fertigung aus. Um die Vorteile der additiven Fertigung - Leichtbau, verbesserte Leistung und Kosteneffizienz - wirklich zu nutzen, müssen die Komponenten für den Prozess. Die Grundsätze des Design for Additive Manufacturing (DfAM) sind bei der Entwicklung kundenspezifischer Abstandshalter für die Luft- und Raumfahrt, die für den 3D-Druck bestimmt sind, von entscheidender Bedeutung. Die Anwendung von DfAM gewährleistet eine bessere Druckbarkeit, reduziert den Bedarf an umfangreichen Stützstrukturen, minimiert den Nachbearbeitungsaufwand und ermöglicht Leistungssteigerungen, die mit herkömmlichen Konstruktionen nicht erreicht werden können.
Hier sind die wichtigsten DfAM-Überlegungen für Abstandshalter in der Luft- und Raumfahrt:
1. Überdenken Sie die traditionellen Design-Zwänge:
- Umfassen Sie die Komplexität: Anders als bei der maschinellen Bearbeitung muss die Komplexität bei AM nicht zwangsläufig mit deutlich höheren Kosten einhergehen. Ziehen Sie die Integration von Merkmalen in Betracht, die die Funktion verbessern, aber bisher zu schwierig zu bearbeiten waren, wie z. B.:
- Interne Gitternetze: Ersetzen Sie Vollmaterial durch optimierte Gitterstrukturen (z. B. Kreisel, Oktett-Fachwerke), um das Gewicht drastisch zu reduzieren und gleichzeitig die erforderliche Steifigkeit und Festigkeit zu erhalten. Software-Tools können diese auf der Grundlage von Lastfällen generieren.
- Konforme Kanäle: Integrieren Sie interne Kanäle, die den Konturen des Abstandshalters folgen, für eine mögliche Kühlung, einen Flüssigkeitsdurchlass oder die Unterbringung von Sensoren/Verdrahtung, um Funktionen zu konsolidieren.
- Organische Formen: Glatte, gekrümmte und topologieoptimierte Formen lassen sich leicht herstellen und ermöglichen Konstruktionen, die den Belastungspfaden natürlicher folgen, was die Ermüdungslebensdauer verbessert.
2. Stützstrukturen minimieren: Stützstrukturen sind bei Pulverbettschmelzverfahren (wie SLM und SEBM) oft notwendig, um das Teil auf der Bauplatte zu verankern, überhängende Merkmale zu stützen und Wärme abzuführen. Sie verbrauchen jedoch zusätzliches Material, verlängern die Druckzeit und müssen manuell entfernt werden, was zusätzliche Kosten verursacht und die Oberflächengüte beeinträchtigen kann.
- Selbsttragende Winkel: Konstruieren Sie Features mit einem Winkel von typischerweise mehr als 45 Grad relativ zur Bauplatte, um den Bedarf an Stützen zu minimieren. Die optimale Ausrichtung des Spacers auf der Bauplattform während der Druckvorbereitung ist ebenfalls entscheidend.
- Fräsungen und Fasen einarbeiten: Glätten Sie die Übergänge zwischen den Elementen und vermeiden Sie scharfe Überhänge. Ersetzen Sie horizontale Überhänge nach Möglichkeit durch abgeschrägte oder abgerundete Kanten.
- Design-In Unterstützt: Bei Merkmalen, die eine Unterstützung benötigen, sollten Sie diese als integrierte, leicht entfernbare Elemente konzipieren, anstatt sich ausschließlich auf softwaregenerierte Gitterstützen zu verlassen.
- Überbrückung: Informieren Sie sich über die Überbrückungsmöglichkeiten des gewählten Maschinen-/Materialsystems - die maximale horizontale Entfernung, die der Drucker ohne Stützen überbrücken kann. Entwerfen Sie entsprechend kleine Lücken oder Kanäle.
3. Optimieren Sie die Wandstärke und die Größe der Elemente: Bei AM-Prozessen gibt es Grenzen für die Mindestgröße von Merkmalen und Wandstärken, die sie zuverlässig herstellen können.
- Mindestwanddicke: Stellen Sie sicher, dass die Wände dick genug sind, um zuverlässig zu drucken und der Handhabung und den betrieblichen Belastungen standzuhalten. Dies ist je nach Material und Maschine unterschiedlich, liegt aber häufig im Bereich von 0,4 mm bis 1,0 mm. Extrem dünne Wände können sich während des Drucks verziehen oder versagen.
- Bohrungsdurchmesser: Kleine Löcher (typischerweise < 6-$8$mm, je nach Ausrichtung und Tiefe) können aufgrund der Schmelzbaddynamik und Pulverhaftung leicht unterdimensioniert oder mit raueren Innenflächen gedruckt werden. Entwerfen Sie Löcher leicht überdimensioniert, wenn eine enge Toleranz beim Druck erforderlich ist, oder planen Sie eine Nachbearbeitung (Aufbohren, Bohren) ein. Horizontale Löcher erfordern im Allgemeinen eine Unterstützung oder sollten als Tropfen- oder Rautenform entworfen werden, um selbsttragend zu sein.
- Aspekt-Verhältnisse: Hohe, dünne Merkmale können während des Drucks zu Vibrationen oder Verformungen führen. Erwägen Sie das Hinzufügen von temporären Verstrebungen oder die Optimierung des Designs/der Ausrichtung, wenn hohe Seitenverhältnisse unvermeidbar sind.
4. Erwägen Sie die Entfernung von Puder: Bei Abstandshaltern mit inneren Kanälen oder komplexen Hohlkörpern ist es entscheidend, dass das nicht verschmolzene Pulver nach dem Druck vollständig entfernt wird. Eingeschlossenes Pulver erhöht das Gewicht und kann ein Risiko darstellen, wenn es sich während des Betriebs verlagert.
- Fluchtlöcher entwerfen: Bringen Sie an strategischen Stellen ausreichend große Öffnungen (Austrittslöcher) an, damit ungeschmolzenes Pulver leicht durch Vibration, Druckluft oder Spülung entfernt werden kann.
- Vermeiden Sie Pulverfallen: Entwerfen Sie die Innengeometrien so, dass sie glatt und frei fließend sind, und vermeiden Sie scharfe Innenecken oder Sackgassen, in denen sich das Pulver festsetzen kann.
- Simulation: Nutzen Sie Simulationswerkzeuge, um die Herausforderungen bei der Pulverentfernung bereits in der Entwurfsphase vorherzusagen.
5. Nutzen Sie Topologieoptimierung und generatives Design: Diese leistungsstarken Software-Tools verwenden Algorithmen zur Optimierung der Materialverteilung auf der Grundlage definierter Lastfälle, Einschränkungen und angestrebter Gewichtsreduzierungen.
- Topologie-Optimierung: Beginnt mit einem grundlegenden Designraum und entfernt Material dort, wo es nicht benötigt wird, was zu oft organisch aussehenden, hocheffizienten Strukturen führt. Ideal für die Gewichtsreduzierung von Abstandshaltern bei gleichbleibender Steifigkeit.
- Generatives Design: Untersucht mehrere Designlösungen auf der Grundlage von funktionalen Anforderungen und Einschränkungen und bietet neuartige und leistungsstarke Optionen, die ein menschlicher Designer vielleicht nicht erdenken würde.
Die Anwendung dieser DfAM-Grundsätze erfordert ein Umdenken gegenüber den traditionellen Entwurfspraktiken. Eine enge Zusammenarbeit mit einem erfahrenen AM-Dienstleister wie Met3dp zu einem frühen Zeitpunkt in der Entwurfsphase wird dringend empfohlen. Unsere Ingenieure verfügen über umfassendes Fachwissen im Bereich DfAM und können Ihnen wertvolles Feedback zur Optimierung Ihres Spacer-Designs im Hinblick auf Druckbarkeit, Leistung und Kosteneffizienz geben, damit Sie die Vorteile der additiven Fertigung voll ausschöpfen können.
Erreichen von Präzision: Toleranz, Oberflächengüte und Maßgenauigkeit bei 3D-gedruckten Abstandhaltern
Luft- und Raumfahrtanwendungen erfordern ein hohes Maß an Präzision. Trotz ihrer scheinbaren Einfachheit haben Abstandhalter oft enge Toleranzen bei kritischen Abmessungen wie Dicke, Parallelität, Ebenheit und Lochdurchmesser/-positionen, um die korrekte Passform und Funktion der Baugruppe zu gewährleisten. Die 3D-Drucktechnologie für Metalle hat sich zwar erheblich weiterentwickelt, doch die Kenntnis der erreichbaren Toleranzen, Oberflächengüte und Maßgenauigkeit ist entscheidend für die Festlegung realistischer Erwartungen und die Planung der erforderlichen Nachbearbeitungsschritte.
Toleranzen:
- Toleranzen wie gedruckt: Die direkt mit dem Drucker erreichbaren Toleranzen hängen von mehreren Faktoren ab, darunter das spezifische AM-Verfahren (SLM, EBM), die Maschinenkalibrierung, die Materialeigenschaften, die Teilegröße und -geometrie sowie die Bauausrichtung.
- Typische Werte: Allgemeine Toleranzen für gut kalibrierte Systeme werden oft im Bereich von $\pm 0,1$mm bis $\pm 0,2$mm für kleinere Abmessungen (z.B. bis zu 100mm) angegeben, mit möglicherweise größeren Abweichungen (±0,1% bis ±0,2% der Abmessung) für größere Teile.
- Prozessunterschiede: SEBM (Selective Electron Beam Melting), das von Met3dp häufig für Materialien wie Ti-6Al-4V verwendet wird, arbeitet mit höheren Temperaturen, was zur Verringerung von Eigenspannungen beitragen kann, aber im Vergleich zum SLM (Selective Laser Melting) manchmal zu etwas geringeren Toleranzen beim Druck führt. Mit beiden Verfahren kann jedoch eine hohe Genauigkeit erreicht werden.
- Faktoren, die die Verträglichkeit beeinflussen: Thermische Spannungen während des Drucks und der Abkühlung, die Schichtdicke, die Größe des Strahlflecks, die Pulvereigenschaften und die Trägerstrategie spielen alle eine Rolle. Auch die Schrumpfung während der Abkühlung und Wärmebehandlungen zum Spannungsabbau müssen berücksichtigt werden.
- Kritische Toleranzen: Für Merkmale, die engere Toleranzen erfordern als die typischen Möglichkeiten des Drucks (z. B. Passflächen, präzise Lochdurchmesser), ist in der Regel eine Nachbearbeitung (CNC-Fräsen, Drehen, Schleifen) erforderlich.
Oberflächengüte (Rauhigkeit):
- Wie gedruckt Oberflächenbehandlung: AM-Teile aus Metall haben im Vergleich zu maschinell gefertigten Bauteilen von Natur aus eine rauere Oberfläche, was auf den schichtweisen Prozess und die teilweise geschmolzenen Pulverpartikel zurückzuführen ist, die an den Oberflächen haften.
- Typische Werte (Ra): Die Rauheit (Ra) der gedruckten Oberfläche liegt in der Regel zwischen 5μm und 25μm (200μin bis 1000μin) und hängt stark von der Ausrichtung der Oberfläche in Bezug auf die Aufbaurichtung, das Material, die Schichtdicke und die Prozessparameter ab. Nach unten gerichtete Oberflächen, die von Strukturen getragen werden, sind tendenziell rauer.
- Interne Oberflächen: Innenliegende Kanäle und komplexe Merkmale weisen oft höhere Rauheitswerte auf und können schwierig zu bearbeiten sein.
- Verbesserung der Oberflächengüte: Die Nachbearbeitung ist unerlässlich, um glattere Oberflächen zu erzielen, die für die Abdichtung, die Verschleißfestigkeit, die Ermüdungsleistung oder die Ästhetik erforderlich sind. Zu den gängigen Methoden gehören:
- Perlstrahlen / Shot Peening: Verbessert die Gleichmäßigkeit und entfernt lose Partikel, wobei in der Regel Ra 3μm-10μm erreicht werden. Shotpeening kann auch positive Druckspannungen erzeugen.
- Taumeln / Vibrationsgleitschleifen: Effektiv zum Glätten von Außenflächen und Entgraten von Kanten bei Chargen kleinerer Teile.
- CNC-Bearbeitung: Bietet die beste Oberflächengüte bei bestimmten Merkmalen und erreicht Ra <1μm.
- Polieren: Durch manuelles oder automatisiertes Polieren lassen sich bei Bedarf sehr glatte, spiegelglatte Oberflächen (Ra <0,1μm) erzielen.
Maßgenauigkeit:
Die Maßgenauigkeit bezieht sich darauf, wie genau das endgültige Teil mit den im CAD-Modell angegebenen Nennmaßen übereinstimmt. Sie ist eng mit der Toleranz verbunden, umfasst aber auch Formfehler wie Ebenheit, Parallelität und Rundheit.
- Erzielung von Genauigkeit: Erfordert eine sorgfältige Prozesssteuerung, Maschinenkalibrierung, Wärmemanagementsimulation (zur Vorhersage und Kompensation von Verformungen), geeignete Stützstrategien und kontrollierte Nachbearbeitung (insbesondere Spannungsabbau und Bearbeitung).
- Metrologie und Inspektion: Eine strenge Qualitätskontrolle mit Hilfe von CMM (Coordinate Measuring Machines), 3D-Scanning und anderen Messinstrumenten ist unerlässlich, um sicherzustellen, dass der fertige Abstandhalter alle Maßvorgaben erfüllt. Anwendungen in der Luft- und Raumfahrt erfordern eine gründliche Prüfung und Dokumentation.
Erwartungen managen:
Für Konstrukteure und Beschaffungsmanager ist es wichtig zu verstehen, dass das Erreichen engster Toleranzen in der Luft- und Raumfahrt und feinster Oberflächen mit Metall-AM in der Regel eine Kombination aus präzisem Druck und gezielter Nachbearbeitung erfordert. Es ist von entscheidender Bedeutung, dem AM-Dienstleister die kritischen Abmessungen und Oberflächenanforderungen bereits in einem frühen Stadium des Projekts klar mitzuteilen. Erfahrene Anbieter wie Met3dp nutzen fortschrittliche Simulationswerkzeuge, sorgfältige Prozesskontrolle und integrierte Nachbearbeitungsmöglichkeiten, um kundenspezifische Abstandshalter für die Luft- und Raumfahrt zu liefern, die die hohen Präzisionsanforderungen zuverlässig erfüllen.
Zusammenfassung der Toleranzen und Oberflächengüte:
Parameter | Wie gedruckt (typisch) | Nachbearbeitet (typischer Bereich) | Methode zur Verbesserung |
---|---|---|---|
Toleranz | ±0,1 bis ±0,2 mm / ±0,1-0,2% | ±0,01 bis ±0,05 mm (maschinell bearbeitet) | CNC-Bearbeitung, Schleifen |
Oberflächenrauhigkeit (Ra) | 5-25μm | 1-10μm (gestrahlt/getrommelt) | Strahlen, Trommeln, Polieren, Bearbeiten |
<1μm (bearbeitet/poliert) | |||
Ebenheit/Parallelität | Abhängig von Größe/Orientierung | Hoch (über Bearbeitung/Schleifen) | Spanende Bearbeitung, Läppen, Schleifen |
In Blätter exportieren
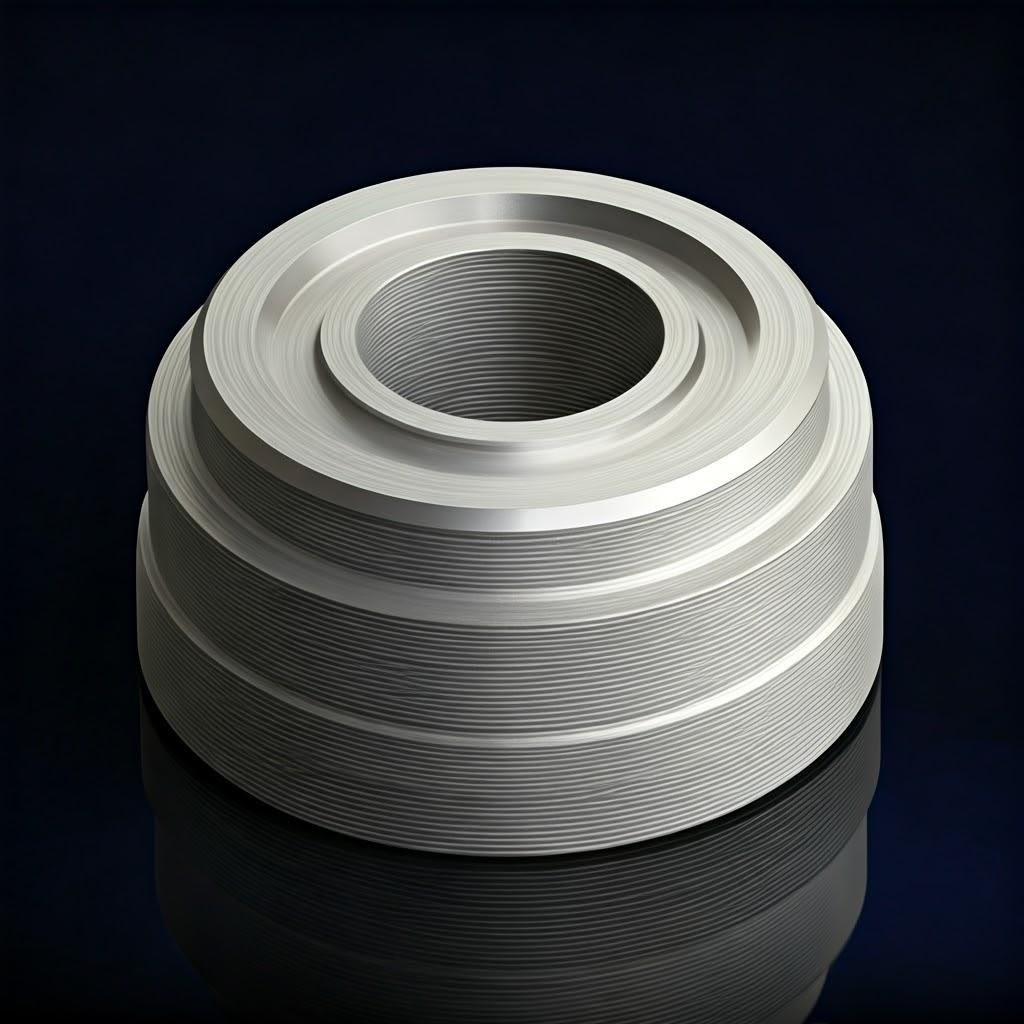
Über das Drucken hinaus: Wesentliche Nachbearbeitungsschritte für Abstandshalter in der Luft- und Raumfahrt
Die Reise eines 3D-gedruckten Abstandhalters aus Metall für die Luft- und Raumfahrt endet nicht, wenn er die Bauplatte verlässt. In der Regel sind eine Reihe wichtiger Nachbearbeitungsschritte erforderlich, um das gedruckte Teil in ein flugtaugliches Bauteil zu verwandeln, das die strengen Luft- und Raumfahrtnormen für mechanische Eigenschaften, Maßhaltigkeit, Oberflächenqualität und Sicherheit erfüllt. Das Verständnis dieser Schritte ist für die Projektplanung, die Kostenabschätzung und die Auswahl eines kompetenten Fertigungspartners unerlässlich.
Gemeinsamer Post-Processing-Workflow für AM Aerospace Spacers:
- Entpudern:
- Prozess: Sorgfältiges Entfernen des gesamten ungeschmolzenen Metallpulvers vom Teil und der Baukammer, insbesondere aus internen Kanälen und komplexen Geometrien. Dies geschieht häufig mit Bürsten, Vakuumsystemen, Druckluft und Vibration.
- Wichtigkeit: Es wird sichergestellt, dass kein loses Pulver zurückbleibt, das das Gewicht erhöhen, die Leistung beeinträchtigen oder zu Verunreinigungen führen könnte. Entscheidend für Teile mit inneren Merkmalen.
- Stressabbau:
- Prozess: Erhitzen des Teils (oft noch auf der Bauplatte) in einem Ofen mit kontrollierter Atmosphäre auf eine bestimmte Temperatur unterhalb des Umwandlungspunkts des Materials, Halten des Teils und anschließendes langsames Abkühlen.
- Wichtigkeit: Verringert die inneren Spannungen, die während der schnellen Heiz- und Kühlzyklen des Druckprozesses entstehen. Minimiert das Risiko von Verformungen oder Rissen bei nachfolgenden Schritten (z. B. bei der Entnahme von der Bauplatte) oder später im Betrieb. Wesentlich für die Dimensionsstabilität.
- Entfernen des Teils von der Bauplatte:
- Prozess: Trennen des/der gedruckten Abstandshalter(s) von der Bauplatte. Dies geschieht in der Regel durch Drahterodieren (Electrical Discharge Machining), Sägen oder Zerspanen.
- Wichtigkeit: Um eine Beschädigung des Teils zu vermeiden, ist eine sorgfältige Entfernung erforderlich. Die Methode hängt von der Teilegeometrie, dem Material und der Unterstützungsstrategie ab.
- Entfernung der Stützstruktur:
- Prozess: Entfernen der temporären Stützstrukturen, die während des Drucks entstanden sind. Dies kann durch manuelles Brechen/Clipping (bei leicht zugänglichen Stützen), maschinelles Bearbeiten, Schleifen oder Erodieren erfolgen.
- Wichtigkeit: Stützen sind nicht funktionsfähig und müssen vollständig entfernt werden. Dieser Schritt erfordert Sorgfalt, um eine Beschädigung der Teileoberfläche zu vermeiden, und kann bei komplexen Geometrien arbeitsintensiv sein. DfAM spielt eine Schlüsselrolle bei der Minimierung des Unterstützungsbedarfs.
- Wärmebehandlung (Lösungsglühen, Alterung, HIP):
- Prozess: Spezifische, auf das Material (Ti-6Al-4V, 17-4PH) zugeschnittene Wärmebehandlungszyklen zur Erzielung der gewünschten endgültigen mechanischen Eigenschaften (Festigkeit, Duktilität, Härte, Ermüdungsfestigkeit).
- Lösungsglühen & Alterung (z. B. für 17-4PH): Löst Ausfällungen auf und formt sie anschließend kontrolliert um, um bestimmte Festigkeitsstufen zu erreichen (z. B. H900, H1025).
- Glühen (z. B. für Ti-6Al-4V): Verbessert die Duktilität und Bruchzähigkeit.
- Heiß-Isostatisches Pressen (HIP): Ein entscheidender Schritt für viele kritische Teile in der Luft- und Raumfahrt. Er umfasst die gleichzeitige Anwendung von hohen Temperaturen und hohem Inertgasdruck (Argon).
- Wichtigkeit:
- Homogenisiert die Mikrostruktur: Verfeinert die beim Druck entstandene Kornstruktur.
- Optimiert die mechanischen Eigenschaften: Stellt sicher, dass das Material den technischen Spezifikationen entspricht.
- Schließt die innere Porosität (HIP): HIP beseitigt effektiv die verbleibende interne Mikroporosität und verbessert dadurch die Ermüdungslebensdauer, die Bruchzähigkeit und die allgemeine Materialintegrität, was für kritische Komponenten in der Luft- und Raumfahrt oft unerlässlich ist. Met3dp empfiehlt HIP für anspruchsvolle Anwendungen und kann diese erleichtern.
- Prozess: Spezifische, auf das Material (Ti-6Al-4V, 17-4PH) zugeschnittene Wärmebehandlungszyklen zur Erzielung der gewünschten endgültigen mechanischen Eigenschaften (Festigkeit, Duktilität, Härte, Ermüdungsfestigkeit).
- Spanende Bearbeitung (für kritische Toleranzen & Merkmale):
- Prozess: Einsatz von CNC-Fräsen, -Drehen, -Schleifen oder -Bohren zur Erzielung von Endmaßen, Toleranzen und Oberflächengüten bei bestimmten Merkmalen, die mit dem AM-Verfahren allein nicht angemessen hergestellt werden können.
- Wichtigkeit: Garantiert Präzision für Passflächen, Lagerschnittstellen, Befestigungsbohrungen, Dichtungsflächen usw. Unverzichtbar für die Einhaltung strenger Zeichnungsspezifikationen in der Luft- und Raumfahrt.
- Oberflächenveredelung:
- Prozess: Verbesserung der Oberflächenqualität und Beseitigung von Spuren, die beim Entfernen von Trägern oder bei der Handhabung entstanden sind. Zu den Methoden gehören Perlstrahlen, Kugelstrahlen, Trowalisieren, Polieren, Elektropolieren oder spezielle Behandlungen.
- Wichtigkeit: Erzielt die erforderliche Oberflächenrauheit (Ra), verbessert die Ermüdungsleistung (Kugelstrahlen induziert Druckspannungen), gewährleistet die Reinigungsfähigkeit, verbessert die Ästhetik oder bereitet die Oberfläche für nachfolgende Beschichtungen vor.
- Reinigung und Inspektion:
- Prozess: Endreinigung zur Entfernung von Bearbeitungsflüssigkeiten, Strahlmitteln oder Verunreinigungen. Anschließend erfolgt eine strenge Inspektion mit Techniken wie CMM, 3D-Scanning, Sichtprüfung, NDT (Non-Destructive Testing – z. B. CT-Scanning für innere Integrität, FPI/MPI für Oberflächenfehler) gemäß den Normen der Luft- und Raumfahrt.
- Wichtigkeit: Überprüft vor der Lieferung und dem Einbau, ob der endgültige Abstandhalter alle Maß-, Material- und Qualitätsanforderungen erfüllt.
Die spezifische Abfolge und Kombination dieser Nachbearbeitungsschritte hängt stark von der Komplexität des Designs, der Materialwahl und den Anwendungsanforderungen des Abstandshalters ab. Die Zusammenarbeit mit einem Full-Service-Anbieter wie Met3dp, der über Fachwissen und Fähigkeiten (oder etablierte Partnerschaften) für den gesamten Arbeitsablauf vom Druck bis zur Endbearbeitung und Prüfung verfügt, rationalisiert den Prozess und gewährleistet eine durchgehende Qualitätskontrolle, die für die Beschaffung in der Luft- und Raumfahrt entscheidend ist.
Herausforderungen meistern: Häufige Fallstricke bei Metall-AM für Abstandshalter und Lösungen
Die additive Fertigung von Metall bietet zwar erhebliche Vorteile für die Herstellung von Abstandshaltern für die Luft- und Raumfahrt, ist aber auch nicht ohne Herausforderungen. Das Verständnis potenzieller Fallstricke und der Umgang mit ihnen durch erfahrene Anbieter ist entscheidend für die Gewährleistung erfolgreicher Ergebnisse und zuverlässiger Teile. Dieses Wissen hilft Konstrukteuren, ihre Teile zu optimieren, und Beschaffungsmanagern, bei der Auswahl eines Lieferanten die richtigen Fragen zu stellen.
Gemeinsame Herausforderungen und Abhilfestrategien:
- Verformung und Verzerrung:
- Herausforderung: Durch ungleichmäßige Erwärmung und Abkühlung während des Drucks entstehen innere Spannungen, die dazu führen können, dass sich das Teil verzieht oder verformt, insbesondere bei großen oder geometrisch komplexen Abstandhaltern.
- Lösungen:
- Thermische Simulation: Einsatz von Software zur Vorhersage des Spannungsaufbaus und der Verformung, wodurch Konstruktionsanpassungen oder optimierte Bauausrichtung und Stützstrategien möglich werden.
- Optimierte Unterstützungsstrukturen: Strategisch platzierte Stützen verankern das Teil und helfen bei der Wärmeableitung.
- Kontrolle der Prozessparameter: Feinabstimmung von Laser-/Elektronenstrahlleistung, Scangeschwindigkeit und Schichtdicke zur Minimierung von Temperaturgradienten.
- Stressabbau-Zyklen: Durchführung geeigneter Wärmebehandlungen zum Spannungsabbau unmittelbar nach dem Druck.
- Build Plate Heating: Durch die Aufrechterhaltung einer hohen, gleichmäßigen Temperatur auf der Bauplatte (wie beim SEBM üblich) werden thermische Gradienten reduziert.
- Eigenspannung:
- Herausforderung: Selbst wenn der Verzug kontrolliert wird, können erhebliche Eigenspannungen im Teil verbleiben, die die Ermüdungslebensdauer und die Dimensionsstabilität im Laufe der Zeit beeinträchtigen oder bei der Nachbearbeitung oder im Betrieb zu Rissen führen können.
- Lösungen:
- Wirksamer Stressabbau: Die Durchführung ordnungsgemäßer thermischer Entlastungszyklen ist von größter Bedeutung.
- Heiß-Isostatisches Pressen (HIP): HIP ist hochwirksam beim Abbau von Eigenspannungen und schließt gleichzeitig die Porosität.
- Optimierte Scan-Strategien: Die Verwendung spezieller Laser-/Strahlabtastmuster (z. B. Inselabtastung, wechselnde Richtungen) kann dazu beitragen, die Spannungsakkumulation zu verringern.
- Überlegungen zum Design: Die Vermeidung großer Querschnittsschwankungen und die Verwendung von Verrundungen können dazu beitragen, Spannungskonzentrationen zu vermeiden.
- Porosität:
- Herausforderung: Im gedruckten Material können sich kleine Hohlräume oder Poren bilden, die durch eingeschlossenes Gas, unvollständige Verschmelzung zwischen den Schichten oder Unregelmäßigkeiten im Pulver entstehen. Porosität verschlechtert die mechanischen Eigenschaften, insbesondere die Ermüdungsfestigkeit.
- Lösungen:
- Hochwertiges Pulver: Verwendung von Pulvern mit hoher Sphärizität, kontrollierter Partikelgrößenverteilung und geringem internen Gasgehalt (wie die von Met3dp’s fortschrittlicher Zerstäubung produzierten). Die richtige Handhabung und Lagerung des Pulvers ist ebenfalls entscheidend.
- Optimierte Prozessparameter: Einstellung der Energiedichte (Strahlleistung, Geschwindigkeit, Lukenabstand), um ein vollständiges Schmelzen und Verschmelzen zu gewährleisten.
- Kontrolle der inerten Atmosphäre: Aufrechterhaltung einer hochreinen Inertgasumgebung (Argon oder Stickstoff für SLM, Vakuum für EBM), um Oxidation und Gaseinschlüsse zu verhindern.
- Heiß-Isostatisches Pressen (HIP): Die wirksamste Methode zur Beseitigung von inneren Porositäten in kritischen Teilen.
- Unterstützung bei der Beseitigung von Schwierigkeiten:
- Herausforderung: Halterungen in schwer zugänglichen Bereichen oder auf komplexen Oberflächen können schwierig und zeitaufwändig zu entfernen sein, ohne die Oberfläche des Teils zu beschädigen. Rückstände von Abstützungen können die Oberflächengüte beeinträchtigen.
- Lösungen:
- DfAM: Die beste Lösung ist es, die Teile so selbsttragend wie möglich zu gestalten.
- Optimiertes Support-Design: Verwendung spezieller Stützstrukturen (z. B. dünne, leicht zerbrechliche Schnittstellen, Baumstützen), die von fortschrittlicher Software erzeugt werden.
- Strategische Ausrichtung: Wahl einer Bauausrichtung, die den Bedarf an Stützen auf kritischen Oberflächen minimiert.
- Nachbearbeitungstechniken: Einsatz geeigneter Werkzeuge und Techniken (Bearbeitung, Schleifen, Verschneiden) zur sauberen Entfernung und Wiederherstellung der Oberfläche.
- Konsistenz der Oberflächenbeschaffenheit:
- Herausforderung: Es kann schwierig sein, eine einheitliche Oberflächenbeschaffenheit in allen Bereichen eines komplexen Abstandshalters zu erreichen, da die Rauheit mit der Ausrichtung der Oberfläche relativ zur Baurichtung variiert.
- Lösungen:
- Gezielte Nachbearbeitung: Anwendung geeigneter Endbearbeitungstechniken (Strahlen, Trommeln, Polieren) entsprechend den Anforderungen. Kritische Oberflächen müssen möglicherweise bearbeitet werden.
- Orientierung aufbauen: Die Optimierung der Ausrichtung kann dazu beitragen, die Oberflächenqualität auf wichtigen Flächen zu verbessern.
- Abstimmung der Prozessparameter: Die Feinabstimmung der Parameter kann manchmal die Oberflächenqualität beeinflussen, obwohl die Nachbearbeitung in der Regel die wichtigste Methode zur Erzielung bestimmter Oberflächen ist.
- Pulverentfernung von internen Merkmalen:
- Herausforderung: Sicherstellung der vollständigen Entfernung von ungeschmolzenem Pulver aus komplizierten internen Kanälen oder Hohlräumen.
- Lösungen:
- DfAM: Angemessene Fluchtlöcher und glatte innere Wege.
- Gründliche Reinigungsverfahren: Mehrstufige Reinigungsverfahren mit Vibration, Ultraschallbädern, Druckluft und manchmal Lösungsmittelspülung.
- Inspektion: Einsatz von Endoskopen oder CT-Scans (für kritische Teile) zur Überprüfung der vollständigen Pulverentfernung.
Die erfolgreiche Bewältigung dieser Herausforderungen erfordert ein tiefes Verständnis der Materialwissenschaft, der Physik des AM-Prozesses, der thermischen Dynamik und der sorgfältigen Prozesskontrolle. Dies ist der Punkt, an dem die Zusammenarbeit mit einem etablierten Experten wie Met3dp von unschätzbarem Wert ist. Unsere jahrzehntelange Erfahrung in der additiven Fertigung von Metallen in Kombination mit unseren fortschrittlichen SEBM-Druckern, einer hochwertigen Pulverproduktion und robusten Qualitätsmanagementsystemen ermöglicht es uns, diese Herausforderungen zu antizipieren und zu entschärfen und zuverlässige, leistungsstarke Abstandshalter für die Luft- und Raumfahrt zu liefern, die die strengsten Industriestandards erfüllen.
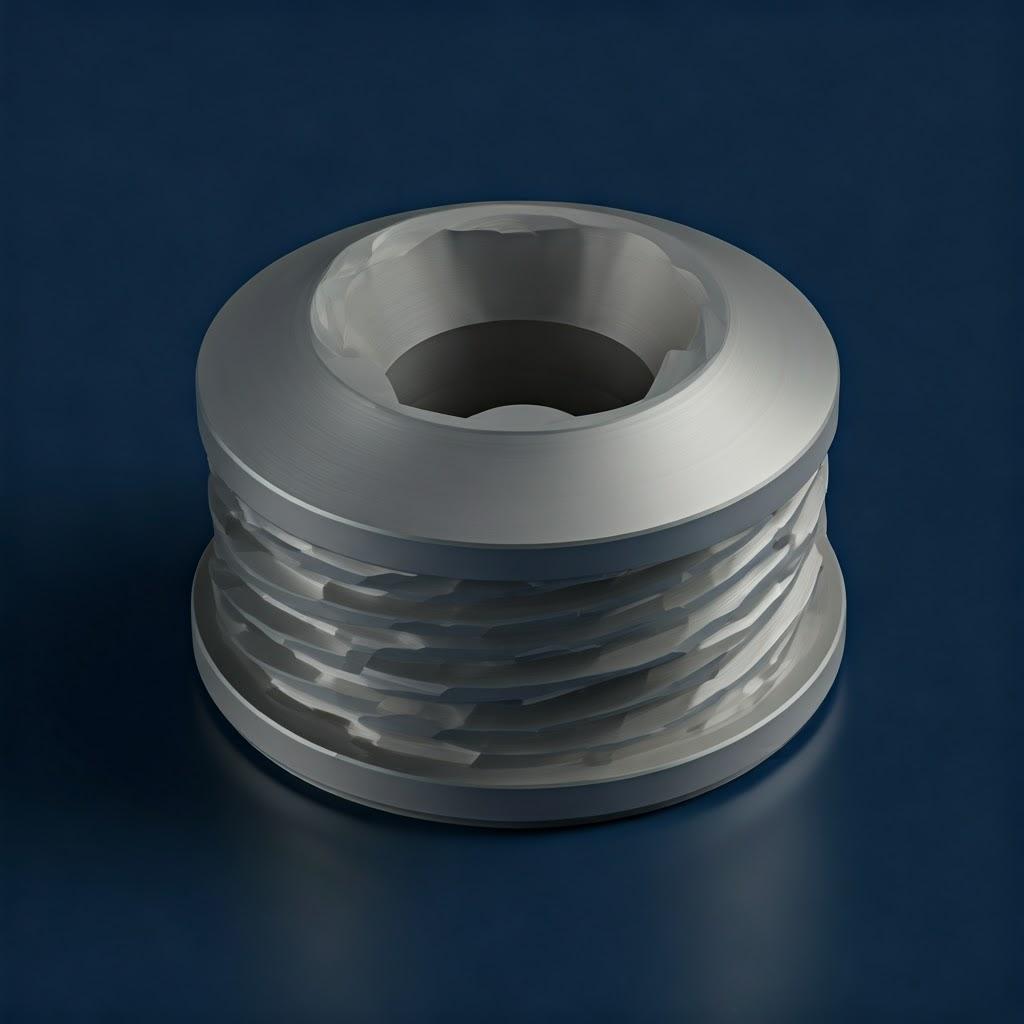
Lieferantenauswahl: So wählen Sie den richtigen Partner für den 3D-Druck von Metall
Die Auswahl des richtigen Fertigungspartners ist ebenso wichtig wie die Technologie selbst, insbesondere in der Luft- und Raumfahrtindustrie, wo Qualität, Zuverlässigkeit und Rückverfolgbarkeit von größter Bedeutung sind. Nicht alle Metall-3D-Druck-Dienstleister sind für die strengen Anforderungen der Fertigung von Luft- und Raumfahrtkomponenten gerüstet. Beschaffungsmanager und Ingenieure benötigen einen systematischen Ansatz, um potenzielle Lieferanten für kundenspezifische Abstandshalter für die Luft- und Raumfahrt zu bewerten.
Schlüsselkriterien für die Bewertung von Metall-AM-Anbietern:
- Zertifizierungen für die Luft- und Raumfahrt und Qualitätsmanagementsystem (QMS):
- Erfordernis: Suchen Sie nach Lieferanten mit einschlägigen Zertifizierungen für die Luft- und Raumfahrt, vor allem AS9100. Diese Zertifizierung weist ein robustes QMS nach, das auf die spezifischen Anforderungen der Luft-, Raumfahrt- und Verteidigungsindustrie zugeschnitten ist. ISO 9001 ist eine Grundvoraussetzung, aber AS9100 zeigt ein höheres Niveau der Prozesskontrolle, der Rückverfolgbarkeit und des Risikomanagements.
- Verifizierung: Verlangen Sie einen Zertifizierungsnachweis und erkundigen Sie sich nach dem Qualitätshandbuch, der Dokumentation zur Prozesskontrolle und den Verfahren zur Rückverfolgbarkeit der Chargen.
- Materialkenntnis und Handhabung:
- Erfordernis: Der Lieferant muss nachweislich Erfahrung im Umgang mit den spezifischen Legierungen für die Luft- und Raumfahrt haben (z. B. Ti-6Al-4V, 17-4PH, Inconels). Dazu gehört die Kenntnis der einzigartigen Druckeigenschaften, der erforderlichen Nachbearbeitung (insbesondere Wärmebehandlungen wie HIP) und der richtigen Handhabungsprotokolle zur Vermeidung von Kontaminationen.
- Verifizierung: Sprechen Sie mit dem Unternehmen über seine Erfahrungen mit dem von Ihnen gewählten Material, sehen Sie sich Fallstudien oder Beispiele ähnlicher Teile an, die es hergestellt hat, und erkundigen Sie sich nach den Verfahren für die Beschaffung, Prüfung, Handhabung und das Recycling von Pulver. Vergewissern Sie sich, dass das Unternehmen die Rückverfolgbarkeit der Materialchargen gewährleistet.
- Technologie und Ausrüstung:
- Erfordernis: Beurteilen Sie, ob der Druckerpark (z. B. SLM, SEBM) für Ihre Material- und Teileanforderungen (Größe, Komplexität, Genauigkeit) geeignet ist. Stellen Sie sicher, dass sie über gut gewartete, kalibrierte Maschinen in Industriequalität verfügen. Entscheidend ist auch der Zugang zu den erforderlichen Nachbearbeitungsanlagen (Wärmebehandlungsöfen, HIP-Einheiten, CNC-Maschinen, Endbearbeitungswerkzeuge, Messlabors), entweder intern oder über qualifizierte Partner.
- Verifizierung: Erkundigen Sie sich nach den spezifischen Maschinenmodellen, der Größe des Bauraums, den Wartungsplänen und den Kalibrierungsverfahren. Erkundigen Sie sich nach den internen und externen Nachbearbeitungsmöglichkeiten.
- Technisches Fachwissen und technische Unterstützung:
- Erfordernis: Der ideale Partner ist mehr als nur ein Druckdienstleister. Suchen Sie nach Lieferanten mit erfahrenen Ingenieuren und Metallurgen, die DfAM-Unterstützung bieten, bei der Materialauswahl beraten, die Druckausrichtung und -parameter optimieren und mögliche Probleme beheben können.
- Verifizierung: Besprechen Sie Ihre Projektanforderungen mit dem technischen Team des Unternehmens. Prüfen Sie das Verständnis für die Herausforderungen der Luft- und Raumfahrt und die Bereitschaft zur Zusammenarbeit bei der Designoptimierung. Erkundigen Sie sich nach dem Hintergrund und der Erfahrung des Teams.
- Prozesskontrolle und Reproduzierbarkeit:
- Erfordernis: Konsistenz ist der Schlüssel. Der Lieferant muss eine strenge Prozessüberwachung und -kontrolle während des gesamten Arbeitsablaufs nachweisen - von der Handhabung des Pulvers bis zum Druck, der Nachbearbeitung und der Inspektion - um die Wiederholbarkeit von Teil zu Teil zu gewährleisten.
- Verifizierung: Erkundigen Sie sich nach ihren Bauüberwachungssystemen (z. B. Schmelzepool-Überwachung), der Datenprotokollierung, der Parametersteuerung und den Methoden der statistischen Prozesskontrolle (SPC), falls zutreffend.
- Inspektions- und Metrologiekapazitäten:
- Erfordernis: Der Lieferant muss über die notwendige Ausrüstung und das Fachwissen verfügen, um eine gründliche Maßprüfung (CMM, 3D-Scanning) und möglicherweise eine zerstörungsfreie Prüfung (NDT, z. B. CT-Scanning, FPI) durchzuführen, um die Qualität der Teile und die Einhaltung der Spezifikationen zu überprüfen.
- Verifizierung: Erkundigen Sie sich nach der Liste der Prüfmittel, den Kalibrierungsstandards und den Berichtsmöglichkeiten. Vergewissern Sie sich, dass das Unternehmen die erforderliche Dokumentation vorlegen kann (z. B. Konformitätsbescheinigungen, Materialzertifikate, Berichte über Maßprüfungen).
- Erfolgsbilanz und Reputation:
- Erfordernis: Suchen Sie nach Lieferanten, die nachweislich erfolgreich hochwertige Teile für die Luft- und Raumfahrt oder ähnlich anspruchsvolle Branchen geliefert haben.
- Verifizierung: Fordern Sie Referenzen, Fallstudien oder Zeugnisse von anderen Kunden aus der Luft- und Raumfahrt an. Bewerten Sie die Reaktionsfähigkeit, die Kommunikation und den Projektmanagementansatz des Unternehmens.
Warum sollte man Met3dp in Betracht ziehen?
Met3dp verkörpert diese entscheidenden Lieferanteneigenschaften. Als führender Anbieter von additiven Fertigungslösungen, der sich auf den industriellen Metall-3D-Druck spezialisiert hat, bieten wir:
- Fortschrittliche Technologie: Wir setzen branchenführende SEBM- und SLM-Drucker ein, die für ihre Genauigkeit und Zuverlässigkeit bekannt sind, ergänzt durch eine hochentwickelte Pulverproduktion mittels Gaszerstäubung und PREP.
- Sachkenntnis: Unser Portfolio umfasst eine breite Palette an hochwertigen Metallpulvern, darunter Ti-6Al-4V und 17-4PH in Luft- und Raumfahrtqualität, die für AM-Prozesse optimiert sind. Sie können mehr erfahren Über uns und unser Engagement in der Materialwissenschaft.
- Umfassende Lösungen: Mit unserer jahrzehntelangen Erfahrung bieten wir eine umfassende Unterstützung, von der DfAM-Beratung über den Druck bis hin zur Nachbearbeitungskoordination und Qualitätssicherung.
- Schwerpunkt Qualität: Wir verpflichten uns zu einer strengen Qualitätskontrolle während des gesamten Fertigungsprozesses, um sicherzustellen, dass die Teile die anspruchsvollen Spezifikationen erfüllen. (Spezifische Zertifizierungen wie AS9100 sollten zwar direkt auf der Grundlage des aktuellen Status bestätigt werden, aber unser Schwerpunkt liegt auf den besten Praktiken der Branche).
Die Wahl des richtigen Partners ist eine Investition in Qualität und Zuverlässigkeit. Durch eine sorgfältige Bewertung potenzieller Lieferanten anhand dieser Kriterien können Luft- und Raumfahrtunternehmen Metall-AM für die Herstellung kundenspezifischer Hochleistungs-Abstandshalter vertrauensvoll nutzen.
Die Investition verstehen: Kostenfaktoren und Vorlaufzeit für 3D-gedruckte Abstandshalter für die Luft- und Raumfahrt
Der 3D-Metalldruck bietet zwar zahlreiche Vorteile, doch das Verständnis der Faktoren, die Kosten und Vorlaufzeit beeinflussen, ist für eine effektive Projektplanung und Budgetierung unerlässlich, insbesondere für Beschaffungsexperten, die Lieferketten in der Luft- und Raumfahrt verwalten. Die Preisgestaltung für AM-Teile ist in der Regel komplexer als bei herkömmlichen Methoden und hängt von einer Kombination von Faktoren ab.
Die wichtigsten Kostentreiber für 3D-gedruckte Abstandshalter:
- Materialtyp und Volumen:
- Materialkosten: Hochleistungslegierungen für die Luft- und Raumfahrt wie Ti-6Al-4V sind von Natur aus teurer als Standardstähle wie 17-4PH. Die Kosten für das Rohpulver sind ein wichtiger Faktor.
- Teilband: Das tatsächliche Materialvolumen, das zum Drucken des Teils verwendet wird, wirkt sich direkt auf die Kosten aus. Größere oder massive Abstandshalter kosten mehr als kleinere oder leichtgewichtige Designs.
- Wiederverwendung von Pulver: Pulver ist zwar weitgehend wiederverwendbar, aber Faktoren wie die Degradation über die Zyklen und die Qualifizierungsprozesse verursachen einen gewissen Mehraufwand.
- Teil Komplexität und Design:
- Geometrische Komplexität: Hochkomplexe Designs mit Merkmalen wie internen Gittern oder konformen Kanälen können anspruchsvollere Druckstrategien und möglicherweise mehr Unterstützung erfordern, was die Druckzeit und den Nachbearbeitungsaufwand leicht erhöht. Die Komplexität wirkt sich jedoch nicht so dramatisch auf die Kosten aus wie bei der Bearbeitung.
- Unterstützungsstruktur Volumen: Die Menge des benötigten Stützmaterials erhöht die Druckzeit und den Materialverbrauch sowie den Nachbearbeitungsaufwand für die Entfernung. Designs, die mit DfAM optimiert wurden, um die Anzahl der Stützen zu minimieren, sind kostengünstiger.
- Druckzeit (Maschinenzeit):
- Teilhöhe (Z-Höhe): Die Druckzeit hängt im Wesentlichen von der Anzahl der Schichten ab, d. h. höhere (vertikal ausgerichtete) Teile brauchen länger als flachere Teile, die die gleiche Fläche abdecken.
- Dichte der Teile auf der Bauplatte: Wie viele Teile effizient auf einer einzigen Bauplatte verschachtelt werden können, beeinflusst die Maschinenzeit pro Teil. Eine höhere Verschachtelungsdichte senkt im Allgemeinen die Kosten pro Teil.
- Schichtdicke & Parameter: Dickere Schichten werden schneller gedruckt, führen aber zu einer raueren Oberfläche und möglicherweise zu einer geringeren Detailauflösung. Feinere Schichten verlängern die Druckzeit.
- Nachbearbeitungsanforderungen:
- Wärmebehandlungen: Spannungsarmglühen ist Standard. Komplexere Zyklen wie Lösungsglühen, Altern oder insbesondere HIP verursachen aufgrund der Ofenzeit und der Anforderungen an die Spezialausrüstung erhebliche Mehrkosten.
- Entfernen von Stützen & Bearbeitung: Arbeitsintensive Stützentfernungen für komplexe Teile oder umfangreiche CNC-Bearbeitungen für enge Toleranzen sind wichtige Kostenfaktoren.
- Oberflächenveredelung: Der Grad des erforderlichen Finishs (z. B. einfaches Perlstrahlen oder mehrstufiges Polieren) wirkt sich auf den Arbeitsaufwand und die Bearbeitungszeit aus.
- Qualitätssicherung und Inspektion:
- Inspektionsstufe: Grundlegende Maßprüfungen kosten weniger als umfassende CMM-Berichte, NDT (CT, FPI) und vollständige Dokumentationspakete für die Luft- und Raumfahrt. Die Anforderungen müssen klar spezifiziert werden.
- Auftragsvolumen (Menge):
- Einrichtungskosten: Während bei AM keine Werkzeugkosten anfallen, gibt es immer noch Einrichtungskosten, die mit der Vorbereitung der Build-Datei, dem Beladen der Maschine und den ersten Nachbearbeitungsschritten verbunden sind. Diese Kosten werden über die Losgröße amortisiert.
- Massen-/Großhandelspreise: Die Herstellung von Abstandshaltern in größeren Serien senkt im Allgemeinen die Kosten pro Teil im Vergleich zum Druck von Einzelstücken oder sehr kleinen Mengen. Sprechen Sie mit Ihrem Lieferanten über Mengenrabatte.
Typische Vorlaufzeiten:
Die Vorlaufzeit für 3D-gedruckte Abstandshalter für die Luft- und Raumfahrt kann je nach den oben genannten Faktoren sowie der aktuellen Kapazität des Lieferanten erheblich variieren.
- Rapid Prototyping: Einfache Abstandshalter mit minimaler Nachbearbeitung können geliefert werden in 1-2 Wochen.
- Produktionsteile (Standard-Nachbearbeitung): Teile, die einen Spannungsabbau, die Entfernung von Stützen, eine einfache Endbearbeitung und eine Standardprüfung erfordern, benötigen in der Regel 3-6 Wochen.
- Komplexe Teile (umfangreiche Nachbearbeitung): Abstandshalter, die HIP, eine umfangreiche CNC-Bearbeitung, eine komplexe Endbearbeitung und eine strenge zerstörungsfreie Prüfung/Inspektion erfordern, können Vorlaufzeiten von 6-10 Wochen oder länger.
Faktoren, die die Vorlaufzeit beeinflussen:
- Druckwarteschlange beim Dienstanbieter.
- Komplexität und Dauer des Druckvorgangs selbst.
- Verfügbarkeit und Zeitplanung von Nachbearbeitungsanlagen (insbesondere HIP und Spezialbearbeitung).
- Erforderliche Inspektionsstufe und Dokumentationsumlaufzeit.
- Versandlogistik.
Es ist von entscheidender Bedeutung, die spezifischen Anforderungen mit dem AM-Dienstleister zu besprechen, um ein genaues Angebot und eine realistische Vorlaufzeitschätzung zu erhalten. Die Vorlage einer klaren Arbeitsbeschreibung mit CAD-Modellen, Materialspezifikationen, Toleranzanforderungen, Anforderungen an die Oberflächenbeschaffenheit und erforderlichen Zertifizierungen/Dokumenten beschleunigt den Angebotsprozess.
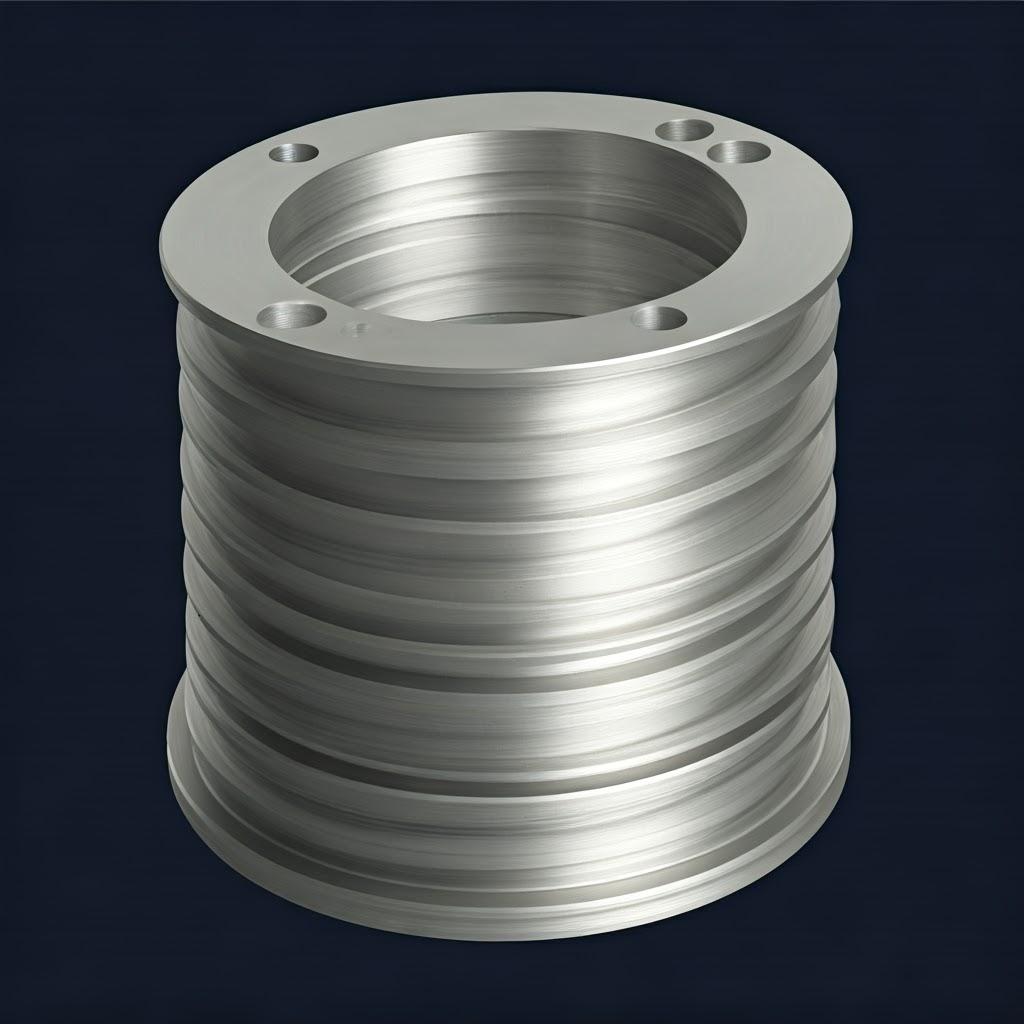
Häufig gestellte Fragen (FAQ) zu 3D-gedruckten Abstandhaltern für die Luft- und Raumfahrt
Hier finden Sie Antworten auf einige häufig gestellte Fragen von Ingenieuren und Beschaffungsmanagern zum Einsatz von Metall-AM für Abstandshalter in der Luft- und Raumfahrt:
1. Wie groß ist der typische Kostenunterschied zwischen 3D-Druck und CNC-Bearbeitung für kundenspezifische Abstandshalter für die Luft- und Raumfahrt?
- Darauf gibt es keine einheitliche Antwort, da dies stark von der Komplexität, dem Material und der Menge abhängt.
- Für einfache Abstandshalter in großen Mengen: Die CNC-Bearbeitung ist aufgrund etablierter Prozesse und schnellerer Zykluszeiten pro Teil nach dem Einrichten oft kostengünstiger.
- Für hochkomplexe Abstandshalter (z. B. mit inneren Gittern, konforme Kanäle): der 3D-Druck kann erheblich billiger sein, da diese Merkmale nur schwer oder gar nicht maschinell zu bearbeiten sind. Auch die Materialeinsparungen durch AM (insbesondere bei teuren Legierungen wie Titan) können die Wettbewerbsfähigkeit erhöhen.
- Für geringe Stückzahlen (Prototypen, 1-100 Teile): der 3D-Druck ist häufig wirtschaftlicher, weil er die hohen Vorlaufkosten für Werkzeuge und Programmierung vermeidet, die bei der CNC-Bearbeitung anfallen.
- Empfehlung: Holen Sie Angebote für beide Verfahren auf der Grundlage Ihrer spezifischen Design- und Mengenanforderungen ein, um einen direkten Vergleich anzustellen. Berücksichtigen Sie den Gesamtwertbeitrag, einschließlich der Vorlaufzeit und der potenziellen Leistungsvorteile (z. B. Gewichtsreduzierung) von AM.
2. Können bestehende Abstandshalter, die ursprünglich für die maschinelle Bearbeitung entwickelt wurden, direkt in 3D gedruckt werden?
- Technisch gesehen kann ein vorhandenes CAD-Modell für den 3D-Druck eines Abstandshalters verwendet werden. Bei diesem Ansatz werden jedoch oft die wichtigsten Vorteile von AM nicht genutzt. Der direkte Druck eines für die Bearbeitung optimierten Designs könnte dies tun:
- Unnötig schwer oder sperrig sein im Vergleich zu einem AM-optimierten Design.
- Erfordern erhebliche Unterstützungsstrukturen, die mit DfAM hätten minimiert werden können.
- Keine Leistungsverbesserungen, die mit AM möglich sind (z. B. interne Funktionen).
- Die Kosten für Druck und Nachbearbeitung sind möglicherweise höher als nötig.
- Empfehlung: Während der Direktdruck für schnellen Ersatz oder erste Tests möglich ist, wird dringend empfohlen, bestehende Abstandshalter zu überprüfen und möglicherweise unter Verwendung von DfAM-Prinzipien neu zu entwerfen, um die Möglichkeiten des Metall-3D-Drucks voll auszuschöpfen, insbesondere für Produktionsanwendungen. Die Zusammenarbeit mit AM-Experten wie denen von Met3dp ist in dieser Phase der Neuentwicklung von Vorteil.
3. Welche Qualitätsdokumentation wird normalerweise mit 3D-gedruckten Abstandhaltern für die Luft- und Raumfahrt geliefert?
- Der Umfang der Dokumentation hängt von den Anforderungen des Kunden und der Kritikalität der Anwendung ab. Zu den üblichen Dokumenten gehören:
- Konformitätszertifikat (CoC): Feststellung, dass die Teile den Zeichnungsanforderungen und Normen entsprechen.
- Materialzertifizierung: Rückverfolgbarkeitsdokumente, die den Typ, die Spezifikation und die Chargen-/Losnummer des verwendeten Metallpulvers bestätigen. Chemische Analyseberichte für die Pulvercharge können beigefügt werden.
- Bericht zur Maßprüfung: Daten mit Messungen kritischer Maße, oft von CMM oder 3D-Scans, die mit Zeichnungstoleranzen verglichen werden.
- Wärmebehandlungsaufzeichnungen: Tabellen oder Bescheinigungen, aus denen hervorgeht, dass Spannungsarmglühen, HIP oder andere Wärmebehandlungen gemäß den vorgegebenen Parametern durchgeführt wurden.
- NDT-Berichte (falls zutreffend): Ergebnisse aller erforderlichen zerstörungsfreien Prüfungen (z. B. CT-Scan-Berichte mit Porositätsanalyse, FPI-Berichte für Oberflächenfehler).
- Erfordernis: Kunden aus der Luft- und Raumfahrtindustrie sollten das erforderliche Dokumentationspaket in ihrer Bestellung oder Arbeitsanweisung klar angeben. Seriöse Lieferanten wie Met3dp, die mit der Luft- und Raumfahrtindustrie vertraut sind, wissen um die Bedeutung einer umfassenden Dokumentation und Rückverfolgbarkeit.
Schlussfolgerung: Verbessern Sie Ihre Luft- und Raumfahrtdesigns mit 3D-gedruckten Präzisionsmetallabstandshaltern
Kundenspezifische Abstandshalter für die Luft- und Raumfahrt sind zwar oft klein, aber dennoch kritische Komponenten, bei denen Präzision, Materialleistung und Zuverlässigkeit nicht verhandelbar sind. Die additive Fertigung von Metallen hat sich zu einer leistungsstarken Technologie entwickelt, die die Herstellung dieser wichtigen Teile mit beispiellosen Vorteilen gegenüber herkömmlichen Methoden ermöglicht. Durch den Einsatz von Verfahren wie Selective Laser Melting (SLM) und Selective Electron Beam Melting (SEBM) können Hersteller Abstandshalter aus Hochleistungslegierungen wie Ti-6Al-4V und 17-4PH herstellen:
- Enge Toleranzen: Erfüllung anspruchsvoller Luft- und Raumfahrtspezifikationen durch präzisen Druck und gezielte Nachbearbeitung.
- Komplexe Geometrien: Realisierung komplizierter Designs, interner Merkmale und leichter Gitterstrukturen, die mit maschineller Bearbeitung unmöglich oder unpraktisch sind.
- Optimierte Leistung: Topologieoptimierung und fortschrittliche Materialien sorgen für ein hervorragendes Verhältnis von Festigkeit zu Gewicht und maßgeschneiderte Funktionalität.
- Reduzierte Vorlaufzeiten: Beschleunigung des Prototyping und schnellere Lieferung von kundenspezifischen Teilen und Kleinserien ohne Werkzeugbeschränkungen.
- Materialeffizienz: Minimierung des Abfalls, insbesondere bei teuren Legierungen für die Luft- und Raumfahrt, was zu Kosteneinsparungen und Nachhaltigkeit beiträgt.
Um diese Vorteile erfolgreich zu nutzen, bedarf es einer Kombination aus intelligentem Design (DfAM), sorgfältiger Materialauswahl, kontrollierter Verarbeitung, sorgfältiger Nachbearbeitung und strenger Qualitätssicherung. Die Zusammenarbeit mit einem erfahrenen Metall-AM-Anbieter ist entscheidend, um die Komplexität zu bewältigen und flugtaugliche Komponenten zu gewährleisten.
Met3dp ist bereit, dieser Partner zu sein. Mit unseren fortschrittlichen 3D-Metalldrucksystemen, hochwertigen sphärischen Metallpulvern aus eigener Herstellung, einem umfassenden Nachbearbeitungsnetzwerk und fundiertem Fachwissen über Anwendungen in der Luft- und Raumfahrt bieten wir End-to-End-Lösungen für Ihren Bedarf an kundenspezifischen Abstandshaltern. Wir helfen Ihnen, die Grenzen der traditionellen Fertigung zu überwinden und Ihre Designs zu verbessern.
Sind Sie bereit zu erfahren, wie der 3D-Druck von Metall Ihre kundenspezifischen Abstandhalter für die Luft- und Raumfahrt optimieren kann?
Wenden Sie sich noch heute an Met3dp, um Ihre Projektanforderungen mit unseren technischen Experten zu besprechen und herauszufinden, wie unsere Fähigkeiten die Ziele Ihres Unternehmens im Bereich der additiven Fertigung unterstützen können.
Teilen auf
MET3DP Technology Co., LTD ist ein führender Anbieter von additiven Fertigungslösungen mit Hauptsitz in Qingdao, China. Unser Unternehmen ist spezialisiert auf 3D-Druckgeräte und Hochleistungsmetallpulver für industrielle Anwendungen.
Fragen Sie an, um den besten Preis und eine maßgeschneiderte Lösung für Ihr Unternehmen zu erhalten!
Verwandte Artikel
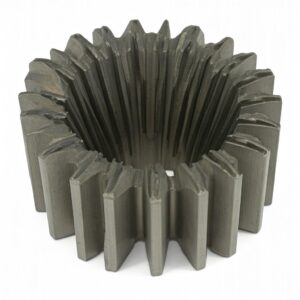
Hochleistungs-Düsenschaufelsegmente: Revolutionierung der Turbineneffizienz mit 3D-Metalldruck
Mehr lesen "Über Met3DP
Aktuelles Update
Unser Produkt
KONTAKT US
Haben Sie Fragen? Senden Sie uns jetzt eine Nachricht! Wir werden Ihre Anfrage mit einem ganzen Team nach Erhalt Ihrer Nachricht bearbeiten.
Holen Sie sich Metal3DP's
Produkt-Broschüre
Erhalten Sie die neuesten Produkte und Preislisten
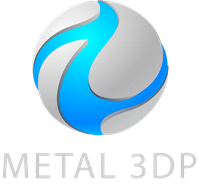
Metallpulver für 3D-Druck und additive Fertigung