Leichte Flugzeugverschlüsse aus 3D-Aluminium gedruckt
Inhaltsübersicht
Einführung: Revolutionierung von Luft- und Raumfahrtkomponenten mit 3D-gedruckten Aluminiumverschlüssen
Die Luft- und Raumfahrtindustrie arbeitet auf dem neuesten Stand der Technik und ist ständig auf der Suche nach Materialien und Fertigungsverfahren, die die Leistung erhöhen, die Sicherheit verbessern und die Betriebskosten senken. Von zentraler Bedeutung für die Funktion von Flugzeugen, aber oft übersehen, sind Komponenten wie Verschlüsse. Diese Mechanismen, die für die Sicherung von Kabinentüren und Zugangsklappen bis hin zu Laderäumen und Innenausstattungen zuständig sind, sind für einen sicheren und zuverlässigen Flugbetrieb von entscheidender Bedeutung. Diese Komponenten, die traditionell durch maschinelle Bearbeitung oder Gießen hergestellt wurden, erfahren nun dank der Fortschritte in der Technik einen bedeutenden Wandel Additive Fertigung (AM), allgemein bekannt als 3D-Druck.
Der 3D-Metalldruck, insbesondere unter Verwendung von leichten und dennoch robusten Aluminiumlegierungen, bietet ungeahnte Möglichkeiten zur Optimierung von Flugzeugverschlüssen. Diese Technologie ermöglicht es den Ingenieuren, sich von den Beschränkungen der traditionellen Fertigung zu lösen und komplexe, topologieoptimierte Designs zu entwickeln, deren Herstellung bisher unmöglich oder unerschwinglich war. Der Hauptgrund für die Einführung von Aluminium-3D-Druck in Luft- und Raumfahrtkomponenten ist das unerbittliche Streben nach Leichtbau. Jedes eingesparte Kilogramm schlägt sich direkt in einer verbesserten Treibstoffeffizienz, einer höheren Nutzlast oder einer größeren Reichweite nieder - entscheidende Kriterien für die Wirtschaftlichkeit der Luft- und Raumfahrt.
Darüber hinaus erleichtert die additive Fertigung die Konsolidierung von Teilen, indem sie die Anzahl der für eine Schlossbaugruppe benötigten Einzelteile reduziert. Diese Vereinfachung verringert nicht nur das Gewicht, sondern minimiert auch potenzielle Fehlerquellen und strafft die Lieferkette, was erhebliche Vorteile bietet für B2B-Luftfahrtzulieferung ketten und Beschaffungsmanager, die nach innovativen Lösungen für die Luft- und Raumfahrtfertigung.
An der Spitze dieses technologischen Wandels steht Met3dp. Als führender Anbieter umfassender Lösungen für die additive Fertigung hat das Unternehmen seinen Hauptsitz in Qingdao, China, Met3dp ist spezialisiert auf hochmoderne 3D-Druckanlagen und die Herstellung von Hochleistungsmetallpulvern, die speziell auf anspruchsvolle industrielle Anwendungen, einschließlich der Luft- und Raumfahrt, zugeschnitten sind. Mit seiner jahrzehntelangen Erfahrung arbeitet Met3dp mit Luft- und Raumfahrtunternehmen zusammen, um Metall-AM zu implementieren, ihren Weg zur digitalen Transformation der Fertigung zu beschleunigen und die hochwertigen Materialien zu liefern, die für wichtige Komponenten wie leichte Flugzeugverschlüsse benötigt werden. Dieser Artikel befasst sich mit den Besonderheiten des 3D-Drucks von Aluminium für Flugzeugverschlüsse und untersucht die Anwendungen, Vorteile, Materialien und wichtigsten Überlegungen für Ingenieure und Beschaffungsexperten.
Die kritische Rolle von Verschlüssen in Flugzeugen: Anwendungen und Anforderungen
Flugzeugverschlüsse sind allgegenwärtige, aber wichtige Komponenten, die in der Struktur und im Inneren eines Flugzeugs zu finden sind. Ihre Hauptfunktion besteht darin, bewegliche Teile sicher zu befestigen und ihre Integrität während aller Flugphasen zu gewährleisten. Selbst der Ausfall eines scheinbar unbedeutenden Verschlusses kann erhebliche Folgen haben, weshalb ihre Zuverlässigkeit von größter Bedeutung ist. Das Verständnis der vielfältigen Anwendungen und des anspruchsvollen Betriebsumfelds macht deutlich, warum fortschrittliche Werkstoffe und Fertigungsmethoden von den folgenden Unternehmen zunehmend nachgefragt werden Raumfahrttechnik Teams und beschaffung in der Luft- und Raumfahrt spezialisten.
Schlüsselanwendungen von Flugzeugverschlüssen:
- Außentüren: Hauptkabinentüren, Notausstiege und Wartungstüren erfordern robuste Verriegelungssysteme, die erheblichen Druckunterschieden standhalten und eine luftdichte Abdichtung gewährleisten.
- Frachttüren: Große Frachttüren erfordern hochbelastbare Verschlüsse, die sperrige und schwere Lasten unter dynamischen Flugbedingungen sichern können. Zuverlässigkeit ist entscheidend für die Sicherheit des Bodenpersonals und die Vermeidung von Zwischenfällen während des Fluges.
- Zugangspaneele: Zahlreiche Verkleidungen am Rumpf, an den Flügeln und am Leitwerk ermöglichen den Zugang zu Inspektions- und Wartungszwecken. Die Verschlüsse dieser Paneele müssen sicher sein und dennoch vom Wartungspersonal leicht bedient werden können.
- Fahrwerksklappen: Diese Türen schützen den Fahrwerksmechanismus und müssen aerodynamischen Kräften und Trümmereinschlägen standhalten. Ihre Verriegelungen sind für das ordnungsgemäße Einfahren und Ausfahren des Fahrwerks von entscheidender Bedeutung.
- Innenausstattung: Ablagefächer, Kabinentrennwände, Bordküchenkomponenten und Toilettentüren sind mit verschiedenen Verriegelungsmechanismen ausgestattet. Obwohl sie weniger kritisch sind als äußere Verschlüsse, wirkt sich ihre Funktionalität auf die Erfahrung und Sicherheit der Passagiere aus.
- Motorhauben: Für die Sicherung von Motorverkleidungen sind Verschlüsse erforderlich, die hohen Temperaturen, Vibrationen und aerodynamischen Belastungen standhalten und gleichzeitig den Zugang für die Motorwartung ermöglichen.
Anspruchsvolles operatives Umfeld:
Flugzeugverschlüsse arbeiten unter weitaus extremeren Bedingungen als typische Industriekomponenten:
- Vibrationen: Die ständigen Vibrationen von Motoren und aerodynamischen Kräften erfordern eine hohe Ermüdungsfestigkeit, um ein Lösen oder Versagen mit der Zeit zu verhindern.
- Temperaturschwankungen: Verschlüsse, insbesondere Außenverschlüsse, sind einem breiten Temperaturspektrum ausgesetzt, das vom Einfrieren in großen Höhen bis hin zu hohen Temperaturen in der Nähe von Motoren oder während des Bodenbetriebs in heißen Klimazonen reicht. Die Materialstabilität bei diesen Temperaturen ist entscheidend.
- Druckunterschiede: Im Rumpf montierte Verschlüsse müssen in der Höhe erheblichen Druckunterschieden zwischen der Druckkabine und der Außenatmosphäre standhalten.
- Belastungen und Spannungen: Die Verschlüsse müssen die Bauteile sicher gegen aerodynamische Belastungen, Trägheitskräfte bei Manövern und betriebliche Belastungen (z. B. Gewicht in Gepäckfächern) halten.
- Korrosion: Da sie Feuchtigkeit, Enteisungsflüssigkeiten und unterschiedlichen atmosphärischen Bedingungen ausgesetzt sind, ist eine ausgezeichnete Korrosionsbeständigkeit erforderlich, um die Funktionalität und strukturelle Integrität zu erhalten.
- Sicherheitskritikalität: Viele Verriegelungsanwendungen werden klassifiziert als sicherheitskritische Teile. Ein Versagen könnte die strukturelle Integrität des Flugzeugs, seine Steuerbarkeit oder die Sicherheit von Passagieren und Besatzung gefährden. Strenge Tests und Zertifizierungen sind daher obligatorisch.
Angesichts dieser strengen Anforderungen müssen die für Flugzeugverschlüsse verwendeten Werkstoffe und Herstellungsverfahren eine außergewöhnliche Zuverlässigkeit, Haltbarkeit und Leistung gewährleisten. Dieser anspruchsvolle Kontext macht die potenziellen Vorteile der additiven Fertigung von Metallen für die Luft- und Raumfahrtbranche besonders attraktiv.
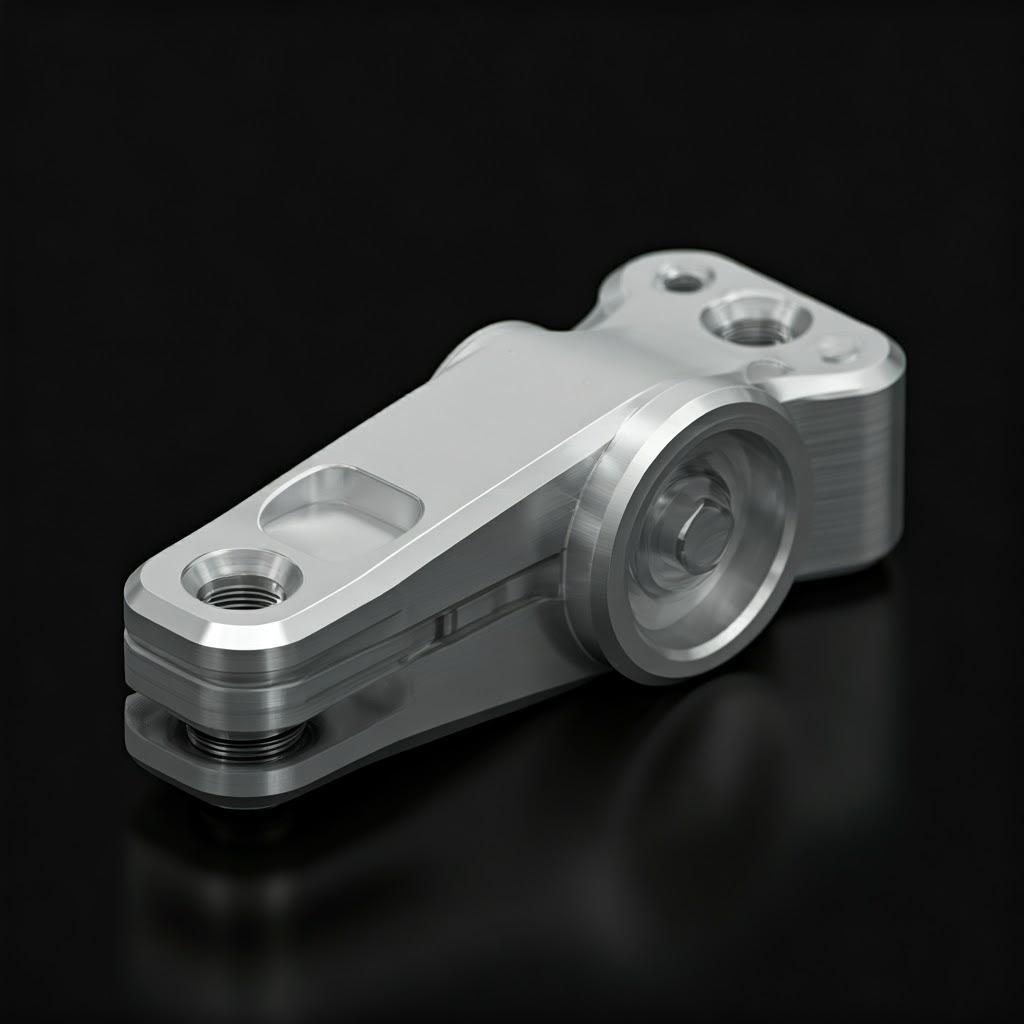
Warum 3D-Metalldruck für die Produktion von Flugzeugverschlüssen?
Herkömmliche Fertigungsverfahren wie die CNC-Bearbeitung von Knüppeln oder Gussteilen werden in der Luft- und Raumfahrtindustrie schon seit langem eingesetzt, Additive Fertigung von Metall (AM) bietet überzeugende Vorteile, insbesondere für Komponenten wie Flugzeugverschlüsse, bei denen Gewicht, Komplexität und Leistung entscheidend sind. Das Laser Powder Bed Fusion (LPBF), das Verfahren wie Selective Laser Melting (SLM) und Direct Metal Laser Sintering (DMLS) umfasst, eignet sich besonders gut für die Herstellung hochauflösender Aluminiumteile. Hier erfahren Sie, warum Hersteller und Zulieferer in der Luft- und Raumfahrt zunehmend auf AM setzen:
- Unerreichte Gestaltungsfreiheit und Komplexität: AM baut Teile Schicht für Schicht direkt aus einem 3D-CAD-Modell auf. Dies befreit die Konstrukteure von den Beschränkungen, die bei herkömmlichen Methoden gelten (z. B. Werkzeugzugang für die Bearbeitung, Entformungswinkel für das Gießen). Es ermöglicht:
- Komplexe Geometrien: Komplizierte interne Kanäle, wabenförmige Strukturen und sehr organische Formen können geschaffen werden, um die Funktion zu optimieren und das Gewicht zu minimieren.
- Topologie-Optimierung: Mithilfe von Software kann die effizienteste Materialverteilung zur Erfüllung der Belastungsanforderungen ermittelt werden, wodurch unnötiges Material entfernt und hoch optimierte, leichte Strukturen geschaffen werden, die auf herkömmliche Weise nicht zu bearbeiten sind.
- Erhebliches Potenzial zur Gewichtsreduzierung: Wie bereits erwähnt, ist die Gewichtsreduzierung in der Luft- und Raumfahrt von größter Bedeutung. AM ermöglicht:
- Materialeffizienz: Im Gegensatz zur subtraktiven Bearbeitung, bei der von einem größeren Block ausgegangen wird, wird nur das Material verwendet, das für das endgültige Teil benötigt wird (plus Stützen).
- Optimierte Strukturen: Topologieoptimierung und Gitterstrukturen ermöglichen eine drastische Gewichtsreduzierung bei gleichbleibender oder sogar höherer Festigkeit und Steifigkeit im Vergleich zu sperrigen, traditionell hergestellten Gegenstücken.
- Teil Konsolidierung: Komplexe Baugruppen erfordern oft die Herstellung mehrerer Einzelteile, die dann zusammengefügt (geschweißt, geschraubt, genietet) werden müssen. AM ermöglicht es den Konstrukteuren, mehrere Teile zu einem einzigen, monolithischen Bauteil zusammenzufassen. Dies bietet mehrere Vorteile:
- Reduzierte Teileanzahl vereinfacht die Inventur und beschaffung in der Luft- und Raumfahrt.
- Es gibt keine Verbindungsstellen mehr, die potenzielle Fehlerquellen darstellen und zusätzliches Gewicht verursachen.
- Reduziert die Montagezeit und die Arbeitskosten.
- Rapid Prototyping und Iteration: AM ermöglicht die schnelle Herstellung von Prototypen direkt aus digitalen Dateien. Designänderungen können schnell umgesetzt und getestet werden, was den Entwicklungszyklus für neue Verschlussdesigns oder Änderungen beschleunigt. Diese Flexibilität ist in der schnelllebigen Luft- und Raumfahrtbranche von entscheidender Bedeutung.
- On-Demand-Fertigung & Verkürzte Vorlaufzeiten: Bei Kleinserien oder Ersatzteilen kann AM oft kürzere Vorlaufzeiten bieten als die Einrichtung herkömmlicher Werkzeug- und Bearbeitungsprozesse. Dies erleichtert die luft- und Raumfahrtteile auf Abruf verfügbarkeit, Verbesserung der Wartungspläne und Verringerung der Ausfallzeiten von Flugzeugen.
- Materielle Möglichkeiten: Dieser Beitrag konzentriert sich zwar auf Aluminium, aber AM-Prozesse können mit einer Vielzahl von für die Luft- und Raumfahrt geeigneten Werkstoffen eingesetzt werden, darunter Titanlegierungen, Nickelsuperlegierungen und rostfreie Stähle, und bieten somit Flexibilität für verschiedene Komponentenanforderungen.
Vergleich: AM vs. traditionelle Bearbeitung für Verschlüsse
Merkmal | Additive Fertigung aus Metall (LPBF) | Traditionelle CNC-Bearbeitung |
---|---|---|
Gestaltungsfreiheit | Sehr hoch (komplexe interne Merkmale, Topologie usw.) | Mäßig (begrenzt durch Werkzeugzugang, Einrichtung) |
Gewichtsreduzierung | Hervorragendes Potenzial durch Optimierung | Begrenzt durch subtraktiven Charakter |
Teil Konsolidierung | Hohes Potenzial | Geringes Potenzial |
Materialabfälle | Gering (Pulver ist weitgehend recycelbar) | Hoch (erheblicher Spanabfall) |
Komplexität Kosten | Weniger empfindlich gegenüber Komplexität | Die Kosten steigen erheblich mit der Komplexität |
Vorlaufzeit (Proto) | Schnell | Moderat (erfordert Programmierung, Einrichtung) |
Vorlaufzeit (Prod) | Wettbewerbsfähig bei geringem bis mittlerem Volumen | Effizient für hohe Stückzahlen |
Erstausstattung mit Werkzeugen | Keine (digitale Fertigung) | Vorrichtungen, Spezialwerkzeuge können erforderlich sein |
Oberfläche | Grober Bestandszustand, erfordert Nachbearbeitung | Im Allgemeinen glatter als bearbeitet |
In Blätter exportieren
Während AM zahlreiche Vorteile bietet, ist es wichtig zu beachten, dass eine Nachbearbeitung (wie Wärmebehandlung und Oberflächenveredelung) in der Regel erforderlich ist, um die endgültigen gewünschten Eigenschaften und Toleranzen zu erreichen, was zusätzliche Schritte im Vergleich zu einigen traditionellen Arbeitsabläufen bedeutet. Bei komplexen, leichten und leistungskritischen Bauteilen wie Flugzeugverschlüssen überwiegen die Vorteile des 3D-Metalldrucks jedoch oft diese Überlegungen und bieten überlegene Lösungen für die Luft- und Raumfahrtfertigung.
Aluminiumlegierungen für AM in der Luft- und Raumfahrt: Im Blickpunkt: AlSi10Mg und Scalmalloy®
Die Auswahl des richtigen Materials ist für den Erfolg jeder Komponente in der Luft- und Raumfahrt, einschließlich 3D-gedruckter Verschlüsse, von grundlegender Bedeutung. Aluminiumlegierungen sind in der Luft- und Raumfahrt aufgrund ihrer geringen Dichte in Kombination mit guten mechanischen Eigenschaften und Korrosionsbeständigkeit sehr beliebt. Für die additive Fertigung wurden spezielle Pulver aus Aluminiumlegierungen entwickelt und für Verfahren wie LPBF optimiert. Zwei führende Kandidaten für den Druck von Flugzeugverschlüssen sind AlSi10Mg und Scalmalloy®. Das Verständnis ihrer unterschiedlichen Eigenschaften ist für Ingenieure bei der Materialauswahl von entscheidender Bedeutung.
Als geübter aluminium 3D-Druck Pulver Lieferantmet3dp ist sich der Bedeutung von Materialqualität und -konsistenz bewusst. Unser Unternehmen nutzt branchenführende Gaszerstäubungstechniken zur Herstellung von Metallpulvern mit hoher Sphärizität und Fließfähigkeit, die eine optimale Leistung während des Druckprozesses und hervorragende mechanische Eigenschaften des fertigen Teils gewährleisten. Wir bieten sowohl Standard- als auch kundenspezifische aluminium für die Luft- und Raumfahrt pulver, um spezifische Kundenanforderungen zu erfüllen.
AlSi10Mg:
AlSi10Mg ist eine der am häufigsten verwendeten Aluminiumlegierungen in der additiven Fertigung. Es handelt sich im Wesentlichen um eine Aluminium-Silizium-Magnesium-Gusslegierung, die für das Pulverbettschmelzen angepasst wurde. Seine Beliebtheit beruht auf seiner guten Ausgewogenheit der Eigenschaften und der relativ einfachen Verarbeitung.
- Wesentliche Merkmale:
- Gutes Verhältnis zwischen Stärke und Gewicht.
- Ausgezeichnete thermische Eigenschaften und Leitfähigkeit.
- Gute Korrosionsbeständigkeit.
- Gilt als relativ einfach zu bedrucken mit guter Detailauflösung.
- Schweißbar (dies ist wichtig, wenn kleinere Reparaturen nach der Bearbeitung erforderlich sind, was bei Verschlüssen jedoch unwahrscheinlich ist).
- Bedeutung für Luftfahrzeugverschlüsse: Geeignet für Verschlüsse, bei denen eine mittlere Festigkeit ausreicht und Faktoren wie thermische Stabilität oder komplizierte Details wichtig sind. Im Vergleich zu leistungsfähigeren Legierungen ist es oft eine kostengünstige Wahl. Die Nachbearbeitung, insbesondere die Wärmebehandlung (z. B. T6-Anlassen), ist für das Erreichen optimaler mechanischer Eigenschaften unerlässlich.
Scalmalloy®:
Scalmalloy® wurde von APWORKS (einer Airbus-Tochter) speziell für die additive Fertigung entwickelt und ist eine Hochleistungslegierung aus Aluminium, Magnesium und Scandium. Sie überschreitet die Grenzen dessen, was Aluminiumlegierungen erreichen können, und bietet Eigenschaften, die denen einiger Titansorten nahe kommen.
- Wesentliche Merkmale:
- Sehr hohe spezifische Festigkeit (Verhältnis von Festigkeit zu Gewicht). Deutlich stärker als AlSi10Mg, insbesondere nach entsprechender Wärmebehandlung.
- Ausgezeichnete Duktilität und Zähigkeit, auch bei kryogenen Temperaturen.
- Hohe Ermüdungsfestigkeit, entscheidend für Komponenten, die zyklischen Belastungen ausgesetzt sind, wie z. B. Verschlüsse.
- Gute Korrosionsbeständigkeit.
- Behält seine Eigenschaften auch bei mäßig erhöhten Temperaturen bei.
- Bedeutung für Luftfahrzeugverschlüsse: Ideal für hochbelastete oder sicherheitskritische Verschlussanwendungen, bei denen maximale Festigkeit, Haltbarkeit und Ermüdungsbeständigkeit erforderlich sind, während gleichzeitig von der geringen Dichte von Aluminium profitiert wird. Es ermöglicht eine erhebliche Gewichtsreduzierung, selbst im Vergleich zu optimierten AlSi10Mg-Konstruktionen. Der Scandiumgehalt trägt wesentlich zu den verbesserten Eigenschaften bei, macht es aber auch zu einem höherpreisigen Material.
Vergleich der Materialeigenschaften (typische Werte nach der Wärmebehandlung):
Eigentum | Einheit | AlSi10Mg (T6 wärmebehandelt) | Scalmalloy® (wärmebehandelt) | Bedeutung für Verschlüsse |
---|---|---|---|---|
Dichte | g/cm3 | ~2.67 | ~2.68 | Geringe Dichte ermöglicht Leichtbauweise. |
Höchstzugkraft (UTS) | MPa | 330 – 430 | 500 – 540 | Ein höherer UTS-Wert weist auf die Fähigkeit hin, höheren Belastungen standzuhalten. |
Streckgrenze (YS) | MPa | 230 – 330 | 450 – 500 | Ein höherer YS-Wert bedeutet eine geringere Wahrscheinlichkeit einer dauerhaften Verformung. |
Dehnung beim Bruch | % | 6 – 10 | 10 – 15 | Eine höhere Dehnung weist auf eine bessere Duktilität/Zähigkeit hin. |
Ermüdungsfestigkeit | MPa | Mäßig | Hoch | Entscheidend für Bauteile, die zyklischen Belastungen (Vibrationen) ausgesetzt sind. |
Max. Betriebstemperatur | ∘C | ~150 | ~200-250 | Wichtig bei Verschlüssen in der Nähe von Motoren oder heißen Oberflächen. |
In Blätter exportieren
(Hinweis: Die genauen Eigenschaften können je nach den spezifischen Druckparametern, der Bauausrichtung und den Wärmebehandlungszyklen variieren. Beachten Sie immer die Datenblätter der Lieferanten für spezifische Anwendungen)
Die Wahl zwischen AlSi10Mg und Scalmalloy®:
- AlSi10Mg: Eine zuverlässige Arbeitslegierung, die sich für viele Verriegelungsanwendungen eignet und ein gutes Gleichgewicht zwischen Leistung, Druckfähigkeit und Kosten bietet.
- Scalmalloy®: Die erste Wahl für anspruchsvolle Anwendungen, die maximale Festigkeit, Ermüdungsfestigkeit und Gewichtseinsparungen erfordern. Seine überlegenen Eigenschaften rechtfertigen die höheren Kosten bei sicherheitskritischen oder hoch optimierten Komponenten.
Beratung durch einen erfahrenen 3D-Druck-Dienstleister für Metall wie Met3dp, mit Fachwissen sowohl in der Materialwissenschaft als auch in der Luft- und Raumfahrt, wird empfohlen. Wir können Ihnen helfen, die spezifischen Anforderungen Ihres Flugzeugverschlussdesigns zu bewerten und Sie bei der Wahl der optimalen Aluminiumlegierung zu unterstützen - sei es AlSi10Mg, Scalmalloy® oder ein anderes spezialisiertes Pulver aus unserem Portfolio - um sicherzustellen, dass Sie das beste Material für Leistung, Sicherheit und Kosteneffizienz nutzen.
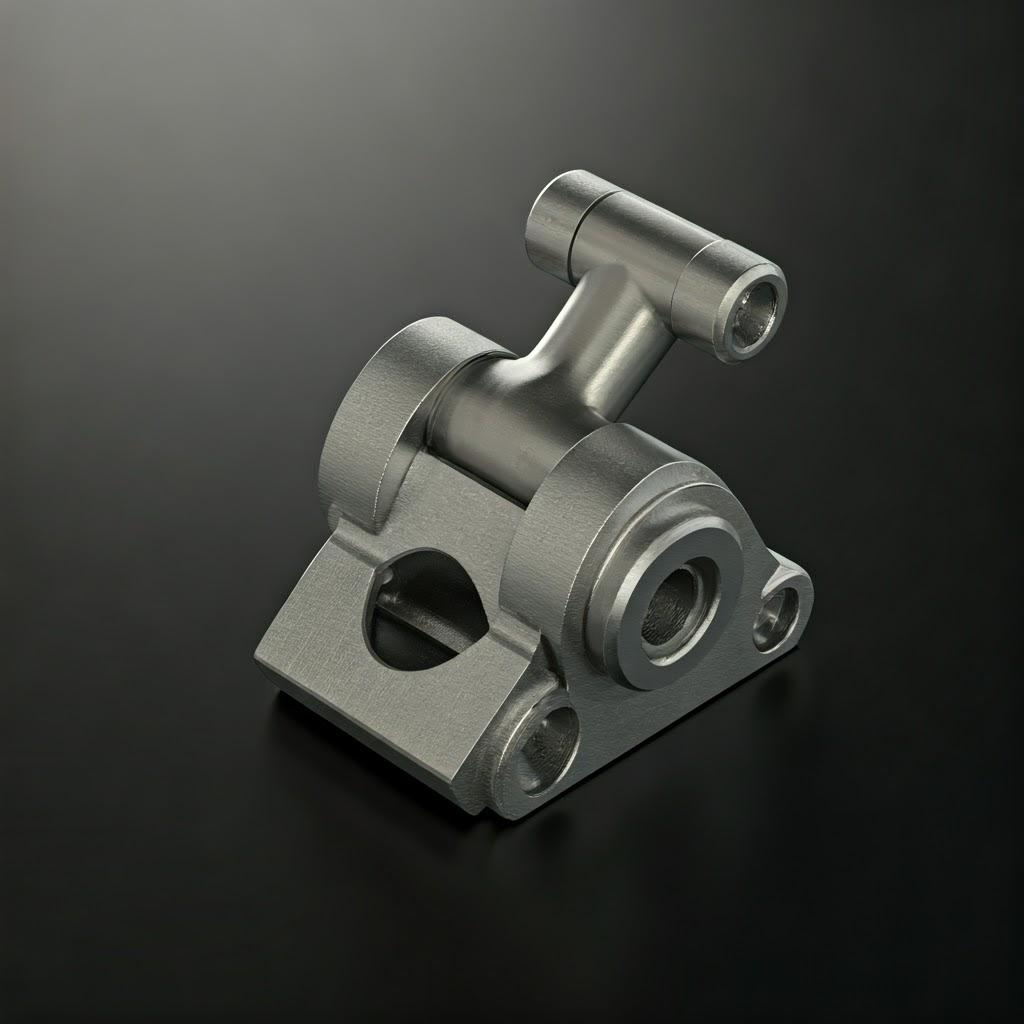
Entwurf für additive Fertigung (DfAM): Optimierung von Flugzeugverschlüssen
Die einfache Nachbildung eines herkömmlich konstruierten Flugzeugverschlusses mit Hilfe des 3D-Drucks schöpft oft nicht das gesamte Potenzial der additiven Fertigung aus. Um die Vorteile der Leichtbauweise, der Teilekonsolidierung und der Leistungssteigerung wirklich zu nutzen, müssen die Ingenieure die folgenden Aspekte berücksichtigen Design für additive Fertigung (DfAM) grundsätze. DfAM bedeutet, den Designprozess von Grund auf neu zu überdenken und dabei die einzigartigen Fähigkeiten und Einschränkungen des gewählten AM-Prozesses, wie z. B. Laser Powder Bed Fusion (LPBF) für Aluminiumlegierungen, zu berücksichtigen. Die Optimierung des Designs eines Flugzeugverschlusses für AM erfordert eine sorgfältige Berücksichtigung der Geometrie, der Stützstrukturen, der Materialeigenschaften und der funktionalen Anforderungen.
Die wichtigsten DfAM-Prinzipien für 3D-gedruckte Verschlüsse:
- Topologie-Optimierung: Dies ist wohl eines der leistungsfähigsten DfAM-Werkzeuge für Luft- und Raumfahrtkomponenten. Mithilfe einer speziellen Software definieren die Ingenieure Lastpfade, Randbedingungen und Ziele für die Gewichtsreduzierung. Die Software entfernt dann rechnerisch Material aus unkritischen Bereichen. Das Ergebnis sind hochgradig organische, tragende Strukturen, die deutlich leichter sind und dennoch die erforderliche Festigkeit und Steifigkeit erfüllen oder übertreffen. Anwendung von topologieoptimierung Luft- und Raumfahrt techniken an Verriegelungskörpern oder Hebeln können zu erheblichen Gewichtseinsparungen führen.
- Stützstrukturen minimieren: LPBF-Prozesse erfordern Stützstrukturen für überhängende Merkmale (typischerweise Winkel unter 45 Grad zur horizontalen Ebene) und zur Verankerung des Teils auf der Bauplatte, um thermische Spannungen zu bewältigen. Stützstrukturen verursachen jedoch zusätzliche Materialkosten, verlängern die Druckzeit und erfordern einen Nachbearbeitungsaufwand für die Entfernung, was in komplexen internen Bereichen eines Verriegelungsmechanismus eine Herausforderung darstellen kann. Wirksame DfAM-Strategien umfassen:
- Optimierung der Orientierung: Durch die Wahl der optimalen Bauausrichtung kann der Bedarf an Stützen erheblich reduziert werden.
- Selbsttragende Winkel: Gestaltung von Überhängen mit Winkeln von mehr als 45 Grad, wo immer dies möglich ist.
- Opfernde Merkmale einbauen: Entwurf von Merkmalen, die kritische Bereiche unterstützen, aber später leicht entfernt werden können.
- Design für den Zugang: Sicherstellen, dass die Stützstrukturen für die Entfernung zugänglich sind, ohne das Teil zu beschädigen.
- Teil Konsolidierung: Analysieren Sie die vorhandene Verriegelungsbaugruppe. Können mehrere Komponenten (Halterungen, Hebel, Federgehäuse) neu entworfen und als ein einziges, integriertes Teil gedruckt werden? Dies reduziert die Komplexität der Baugruppe, das Gewicht und mögliche Fehlerquellen. DfAM fördert das Denken in Funktionen und nicht in einzelnen traditionellen Teilen.
- Interne Kanäle und komplexe Merkmale: Nutzen Sie die Fähigkeit von AM’s, komplizierte interne Geometrien zu schaffen. Dies könnte die Konstruktion interner Kanäle für die Schmierung, integrierte Federmechanismen oder leichte interne Gitterstrukturen innerhalb dickerer Abschnitte des Verschlusskörpers umfassen. Diese Merkmale sind bei der herkömmlichen Bearbeitung oft nicht oder nur sehr schwer zu erreichen.
- Wanddicke und Größe der Merkmale: Verstehen Sie die Grenzen des gewählten LPBF-Systems und des Materials in Bezug auf die Mindestwandstärke und die Auflösung der Merkmale. Stellen Sie sicher, dass die kritischen Merkmale für den Druckprozess und die Endanwendung robust genug sind. Dünne Wände können sich verziehen oder nicht genau aufgelöst werden. Gestalten Sie die Übergänge zwischen dicken und dünnen Abschnitten fließend, um thermische Spannungen zu bewältigen.
- Überlegungen zur Anisotropie: Die Materialeigenschaften von AM-Teilen können manchmal je nach Baurichtung (X, Y vs. Z) leicht variieren. Während dieser Effekt bei Aluminiumlegierungen wie AlSi10Mg und Scalmalloy® im Allgemeinen mit einer angemessenen Prozesssteuerung beherrschbar ist, sollten kritische Belastungspfade innerhalb des Riegels idealerweise mit der Richtung der optimalen Materialeigenschaften ausgerichtet sein, häufig parallel zur Bauplatte (X-Y-Ebene).
Tipps für Konstrukteure in der Luft- und Raumfahrt:
- Funktional denken: Denken Sie nicht nur über die bestehende Form nach, sondern auch darüber, wie der Riegel funktionieren muss, und entwerfen Sie die optimale Form, die durch AM ermöglicht wird.
- Frühzeitig zusammenarbeiten: Engagieren Sie sich mit Ihrem gewählten Metall-AM-Dienstleisterwie Met3dp frühzeitig in der Entwurfsphase. Ihr Fachwissen in den Bereichen DfAM, Materialverhalten und Prozesssimulation kann spätere kostspielige Umgestaltungen verhindern.
- Nutzen Sie die Simulation: Einsatz von Simulationswerkzeugen (thermisch, strukturell) zur Vorhersage von Druckspannungen, potenzieller Verformung und der endgültigen Leistung des Teils, bevor ein Bauauftrag erteilt wird.
- Design für die Nachbearbeitung: Überlegen Sie, wie das Teil wärmebehandelt werden soll, wie Stützen entfernt werden sollen und welche Oberflächen möglicherweise nachbearbeitet oder nachgearbeitet werden müssen. Sorgen Sie für den notwendigen Zugang und einen ausreichenden Materialvorrat, falls erforderlich.
Durch die Anwendung dieser DfAM-Prinzipien können Ingenieure Standard-Flugzeugverschlüsse in hochgradig optimierte, leichte und funktionell überlegene Komponenten umwandeln und so die Vorteile von Aluminium-3D-Druck.
Erreichbare Toleranzen, Oberflächengüte und Maßgenauigkeit bei Aluminium-AM
Ingenieure und Beschaffungsmanager, die Metall-AM für Flugzeugverschlüsse evaluieren, müssen die erreichbaren Präzisionsniveaus verstehen. Während AM eine unglaubliche Designfreiheit bietet, unterscheidet es sich von Natur aus von der Präzision, die typischerweise mit der mehrachsigen CNC-Bearbeitung im "as-built"-Zustand verbunden ist. Mit einer angemessenen Prozesssteuerung und oft in Kombination mit Nachbearbeitung ist dies jedoch möglich, Toleranzen beim 3D-Druck von Metall kann die anspruchsvollen Anforderungen vieler Anwendungen in der Luft- und Raumfahrt erfüllen.
Maßgenauigkeit:
Die endgültige Maßhaltigkeit eines LPBF-gedruckten Aluminiumteils hängt von mehreren Faktoren ab:
- Drucker-Kalibrierung: Die Genauigkeit und Kalibrierung des verwendeten 3D-Druckers sind von grundlegender Bedeutung. Seriöse Anbieter wie Met3dp stellen sicher, dass ihre Maschinen, einschließlich branchenführender Drucker, die für ihre Genauigkeit und Zuverlässigkeit bekannt sind, sorgfältig gewartet und kalibriert werden.
- Materialeigenschaften: Das thermische Verhalten der spezifischen Aluminiumlegierung (AlSi10Mg vs. Scalmalloy®) beeinflusst die Schrumpfung und den möglichen Verzug.
- Geometrie und Größe des Teils: Größere Teile und komplexe Geometrien mit unterschiedlichen Querschnitten sind anfälliger für thermische Spannungen und mögliche Abweichungen.
- Orientierung und Unterstützung aufbauen: Die Art und Weise, wie das Teil ausgerichtet und gestützt wird, hat einen erheblichen Einfluss auf das Wärmemanagement und die endgültige Genauigkeit.
- Prozessparameter: Laserleistung, Scangeschwindigkeit, Schichtdicke und andere Parameter müssen für das jeweilige Material und die Geometrie optimiert werden.
Als allgemeine Richtlinie gelten für gut kontrollierte LPBF-Prozesse mit AlSi10Mg oder Scalmalloy® typische erreichbare Toleranzen Ist-Zustand liegen oft in der Größenordnung von:
- ± 0,1 mm bis ± 0,3 mm für kleinere Merkmale (z. B. bis zu 50 mm)
- ± 0,2% bis ± 0,5% des Nennmaßes für größere Merkmale.
Es ist wichtig zu wissen, dass engere Toleranzen für bestimmte kritische Merkmale (z. B. Passflächen, Drehpunkte in einem Verriegelungsmechanismus) oft durch gezielte Nachbearbeitung erreicht werden können.
Oberflächengüte (Rauhigkeit):
Die Oberflächenbeschaffenheit von LPBF-Bauteilen ist aufgrund der schichtweisen Verschmelzung der Pulverpartikel von Natur aus rauer als bei maschinell bearbeiteten Oberflächen.
- Typische As-Built Ra: Die Werte der Oberflächenrauheit (Ra) liegen typischerweise im Bereich von 6 µm bis 20 µm (240 µin bis 800 µin)dies hängt von der Ausrichtung der Oberfläche in Bezug auf die Baurichtung (nach oben gerichtete Oberflächen sind in der Regel glatter als nach unten gerichtete oder Seitenwände) und den verwendeten Prozessparametern ab.
- Auswirkungen auf Verschlüsse: Für einige Oberflächen eines Riegels kann dieses Finish akzeptabel sein. Für Passflächen, gleitende Teile oder Bereiche, die besondere Dichtungseigenschaften erfordern, ist jedoch eine Nachbearbeitung erforderlich.
- Erzielung glatterer Oberflächen: Verschiedene Nachbearbeitungstechniken wie Perlstrahlen, Sandstrahlen, Trommeln, Polieren oder CNC-Bearbeitung können die Oberflächenbeschaffenheit erheblich verbessern und Ra-Werte erzielen, die mit den traditionellen Verfahren vergleichbar oder sogar besser sind. Das Eloxieren, das häufig für Aluminiumteile in der Luft- und Raumfahrt zum Korrosionsschutz verwendet wird, erfordert in der Regel ebenfalls eine glattere Ausgangsoberfläche.
Qualitätskontrolle und -sicherung:
Angesichts der kritischen Natur der spezifikationen für Luft- und Raumfahrtkomponenteneine strenge Qualitätskontrolle (QC) ist nicht verhandelbar. Dies beinhaltet:
- Prozessbegleitende Überwachung: Moderne AM-Systeme umfassen die Überwachung des Schmelzbades, der Schichtkonsistenz und der Umgebungsbedingungen.
- Rückverfolgbarkeit von Materialien: Strenge Rückverfolgung der Pulverchargen von der Produktion bis zum fertigen Teil. Met3dp gewährleistet die vollständige Rückverfolgbarkeit seiner hochwertigen Metallpulver.
- Inspektion nach der Fertigstellung: Überprüfung der Abmessungen mittels CMM (Coordinate Measuring Machines) oder 3D-Scanning.
- Zerstörungsfreie Prüfung (NDT): Verfahren wie die Computertomographie (CT) können eingesetzt werden, um interne Defekte wie Porosität oder fehlende Verschmelzung zu erkennen, insbesondere bei kritischen Bauteilen.
Bei der Spezifikation von 3D-gedruckten Flugzeugverschlüssen sollten die Ingenieure kritische Abmessungen, Toleranzen und erforderliche Oberflächenbeschaffenheiten in Zeichnungen klar definieren und angeben, welche Merkmale eine Präzision wie bei der Herstellung erfordern und welche durch Nachbearbeitung erreicht werden sollen. Die Zusammenarbeit mit einem AM-Lieferanten mit robusten qualitätskontrolle AM verfahren und Zertifizierungen in der Luft- und Raumfahrt (wie AS9100) sind unerlässlich.
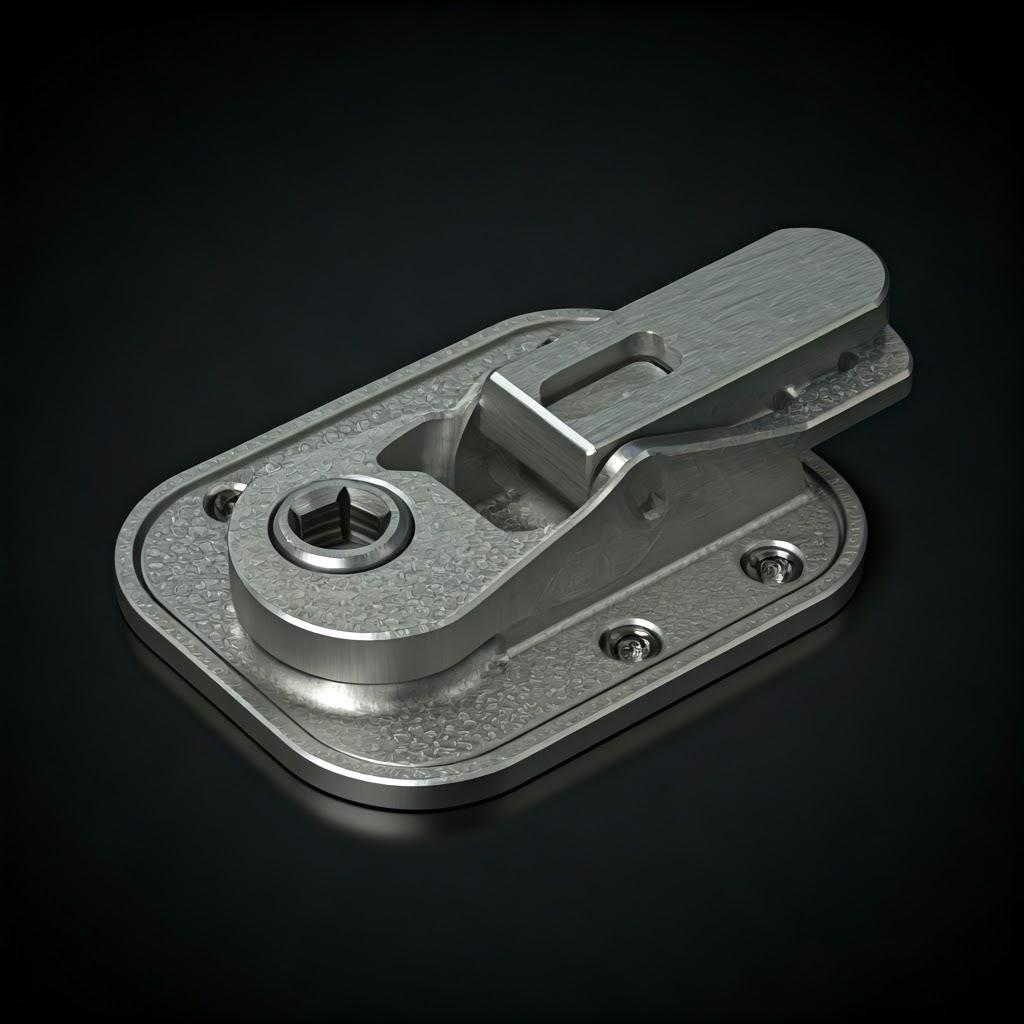
Wesentliche Nachbearbeitungsschritte für 3D-gedruckte Luftfahrzeugverschlüsse
Ein mit LPBF und AlSi10Mg oder Scalmalloy® gedruckter Flugzeugverschluss ist selten direkt von der Bauplatte aus einsatzbereit. Die Nachbearbeitung ist eine kritische Phase im additive Fertigung arbeitsabläufe, die erforderlich sind, um innere Spannungen abzubauen, Stützstrukturen zu entfernen, die erforderlichen Maßtoleranzen und Oberflächengüten zu erreichen und sicherzustellen, dass die Materialeigenschaften den Anforderungen entsprechen Luft- und Raumfahrt spezifikationen. Die einzelnen Schritte können je nach Komplexität des Designs, des Materials und der Anwendungsanforderungen variieren.
Gemeinsamer Nachbearbeitungs-Workflow für Aluminium-AM-Latches:
- Stressabbau / Wärmebehandlung: Dies ist wohl der kritischste Schritt, insbesondere bei Aluminiumlegierungen. Die schnellen Erwärmungs- und Abkühlungszyklen während des LPBF-Verfahrens führen zu erheblichen Eigenspannungen innerhalb des Teils.
- Zweck: Um diese inneren Spannungen zu entspannen, um Verformungen oder Risse bei der Entfernung der Halterung oder bei der anschließenden Bearbeitung zu vermeiden, und um die Mikrostruktur zu homogenisieren.
- Verfahren: Die Teile werden in der Regel in einem Ofen mit kontrollierter Atmosphäre wärmebehandelt, während sie noch auf der Bauplatte befestigt sind. Die spezifischen Zyklen (Temperatur und Dauer) hängen von der Legierung (die Zyklen für AlSi10Mg unterscheiden sich von denen für Scalmalloy®) und den gewünschten Endeigenschaften ab (z. B. Erreichen eines T6-Zustands für AlSi10Mg). Met3dp verfügt über ein umfangreiches Wissen über optimale Wärmebehandlungsprotokolle für verschiedene Legierungen, die mit unterschiedlichen Druckverfahren.
- Entfernen des Teils von der Bauplatte: Nach der Wärmebehandlung wird das Teil (zusammen mit seinen Stützstrukturen) in der Regel mit Methoden wie Drahterodieren (Electrical Discharge Machining) oder Bandsägen aus der Bauplatte geschnitten.
- Entfernung der Stützstruktur: Dies kann einer der arbeitsintensivsten Schritte sein, je nach Komplexität der in der DfAM-Phase entworfenen Stützen.
- Methoden: Stützen werden manuell abgebrochen, abgefräst oder mit Spezialwerkzeugen entfernt. Dabei ist eine sorgfältige Handhabung erforderlich, um die Oberfläche des Teils nicht zu beschädigen. Der Zugang zu internen Stützen kann besonders schwierig sein.
- Die Bedeutung des DfAM: Gute DfAM-Praktiken, die den Support minimieren, reduzieren den mit diesem Schritt verbundenen Zeit- und Kostenaufwand erheblich.
- Sekundär-Bearbeitung (CNC): Während AM darauf abzielt, die maschinelle Bearbeitung zu minimieren, ist sie oft für kritische Merkmale erforderlich, die sehr enge Toleranzen oder spezifische Oberflächengüten erfordern, die durch AM allein nicht erreicht werden können.
- Anwendungen: Bearbeitung von Passflächen, Lagerschnittstellen, präzisen Lochdurchmessern, Gewinden oder kritischen Dichtflächen am Verschluss.
- Erwägungen: Für diese Merkmale muss in der AM-Konstruktion ausreichend Materialvorrat vorhanden sein (Bearbeitungszugabe). Auch die korrekte Befestigung komplexer AM-Geometrien ist wichtig.
- Oberflächenveredelung: Die LPBF-Oberflächen sind im Auslieferungszustand relativ rau. Um die gewünschte Oberfläche zu erreichen, können verschiedene Techniken eingesetzt werden:
- Sprengen: Perlstrahlen oder Sandstrahlen sorgt für ein gleichmäßiges, mattes Finish und entfernt halbgesinterte Partikel.
- Taumeln/Gleitschleifen: Geeignet zum Entgraten und Glätten von kleineren Teilen.
- Polieren: Durch manuelles oder automatisiertes Polieren können bei Bedarf sehr glatte, spiegelnde Oberflächen erzielt werden, was bei funktionalen Verschlüssen jedoch oft nicht erforderlich ist.
- Eloxieren: Eine gemeinsame oberflächenbehandlung Luft- und Raumfahrt die Eloxierung ist eine der wichtigsten Anforderungen an Aluminiumteile und sorgt für Korrosionsbeständigkeit und eine dauerhafte Oberflächenbeschaffenheit. Das Eloxieren erfordert häufig eine vorbehandelte (z. B. gestrahlte oder leicht bearbeitete) Oberfläche für eine gleichmäßige Beschichtung.
- Reinigung und Inspektion: Eine gründliche Reinigung ist erforderlich, um alle Reste von Pulver, Bearbeitungsflüssigkeiten oder Strahlmitteln zu entfernen. Die Endkontrolle umfasst:
- Maßkontrollen: Verwendung von CMM, Messgeräten oder 3D-Scannern zur Überprüfung der Konformität mit Zeichnungen.
- Visuelle Inspektion: Überprüfung auf Oberflächenfehler.
- NDT (falls erforderlich): CT-Scan, Ultraschallprüfung oder Farbeindringprüfung, um die innere Unversehrtheit sicherzustellen und auf Risse oder Porosität zu prüfen, insbesondere bei flugkritischen Verschlüssen.
Diese zu verstehen AM-Nachbearbeitung Luft- und Raumfahrt bei der Beschaffung von 3D-gedruckten Flugzeugverschlüssen ist eine genaue Kostenschätzung und Planung der Vorlaufzeit entscheidend. Die Zusammenarbeit mit einem vertikal integrierten Anbieter wie Met3dp, der sowohl den Druck als auch umfassende Nachbearbeitungsfunktionen anbietet, kann den Produktionsprozess erheblich rationalisieren.
Überwindung gängiger Herausforderungen beim 3D-Druck von Aluminiumverschlüssen
Während 3D-Druck von Metall bietet zwar erhebliche Vorteile für die Herstellung von Flugzeugverschlüssen, ist aber auch nicht ohne Herausforderungen. Das Bewusstsein für potenzielle Probleme und die Zusammenarbeit mit einem erfahrenen Anbieter, der robuste Abhilfestrategien einsetzt, sind der Schlüssel zur erfolgreichen Implementierung dieser Technologie für anspruchsvolle Luft- und Raumfahrtanwendungen. Met3dp nutzt sein tiefes Verständnis von Materialwissenschaft und Prozesssteuerung, das es durch umfangreiche Forschung und Entwicklung mit seinen fortschrittlichen Pulverherstellungssystemen und SEBM/LPBF-Druckern erworben hat, um diese allgemeinen Hürden zu überwinden.
Zentrale Herausforderungen und Strategien zur Abhilfe:
- Eigenspannung und Verformung:
- Herausforderung: Die hohen thermischen Gradienten, die LPBF inhärent sind, können dazu führen, dass sich innere Spannungen aufbauen, die während des Aufbaus oder nach der Entnahme von der Bauplatte zu einer Verformung des Teils führen können. Dies ist bei Aluminiumlegierungen aufgrund ihrer thermischen Eigenschaften besonders relevant.
- Milderung:
- Optimierte Support-Strategien: Richtig konstruierte Stützen verankern das Teil und tragen zur Wärmeableitung bei.
- Kontrolle der Prozessparameter: Die Feinabstimmung der Laserparameter (Leistung, Geschwindigkeit, Scanstrategie) minimiert die Ansammlung thermischer Spannungen.
- Simulation: Der Einsatz von Simulationssoftware zur Vorhersage von Spannungen und Verformungen ermöglicht eine Anpassung der Konstruktion oder der Ausrichtung vor der Fertigung.
- Stressabbau Wärmebehandlung: Bei Aluminiumteilen ist es wichtig, diesen Schritt durchzuführen, bevor das Teil von der Bauplatte entfernt wird.
- Porosität:
- Herausforderung: Im gedruckten Material können sich manchmal kleine Hohlräume oder Poren bilden, die durch eingeschlossenes Gas oder unvollständige Verschmelzung entstehen. Eine übermäßige Porosität kann die mechanischen Eigenschaften wie die Ermüdungsfestigkeit beeinträchtigen, die für Verschlüsse entscheidend ist.
- Milderung:
- Hochwertiges Pulver: Die Verwendung von Pulver mit kontrollierter Partikelgrößenverteilung, hoher Sphärizität und geringem Gehalt an eingeschlossenen Gasen (wie bei der fortschrittlichen Gaszerstäubung von Met3dp’) ist unerlässlich.
- Optimierte Parameter: Die Sicherstellung der richtigen Laserenergiedichte und des Schutzgasflusses (z. B. Argon) minimiert die Porositätsbildung.
- Heiß-Isostatisches Pressen (HIP): Bei hochkritischen Anwendungen kann die HIP-Nachbearbeitung zum Schließen der inneren Poren eingesetzt werden, wodurch sich die Materialdichte und die Ermüdungsleistung deutlich verbessern.
- Unterstützung bei der Beseitigung von Schwierigkeiten:
- Herausforderung: Das Entfernen von Stützstrukturen, insbesondere von komplexen inneren Geometrien innerhalb eines Verriegelungsmechanismus, kann schwierig und zeitaufwändig sein und das Risiko bergen, das Teil zu beschädigen.
- Milderung:
- DfAM: Am besten ist es, die Teile so zu konstruieren, dass sie selbsttragend sind, oder den Bedarf an Stützen in unzugänglichen Bereichen zu minimieren.
- Optimiertes Support-Design: Verwendung von Stützkonstruktionen (z. B. Kegel- oder Baumstützen), die während der Bauphase ausreichend stabil sind, sich aber leicht entfernen lassen.
- Qualifizierte Techniker: Verlassen Sie sich auf erfahrene Techniker für die sorgfältige manuelle Entfernung oder nutzen Sie Techniken wie elektrochemische Bearbeitung für empfindliche Bereiche.
- Pulverentfernung aus internen Kanälen:
- Herausforderung: Es kann schwierig sein, das gesamte ungeschmolzene Pulver aus den komplizierten internen Kanälen oder Hohlprofilen zu entfernen, die zur Gewichtsreduzierung in den Verschluss eingebaut wurden. Eingeschlossenes Pulver erhöht das Gewicht und könnte ein Kontaminationsrisiko darstellen.
- Milderung:
- DfAM: Gestaltung von Innenkanälen mit ausreichenden Austrittslöchern für die Entleerung des Pulvers.
- Gründliche Nachbearbeitung: Einsatz von Druckluft, Vibrationssystemen und geeigneten Reinigungsverfahren in den Nachbearbeitungsphasen.
- Inspektion: Einsatz von Methoden wie Endoskopie oder CT-Scanning zur Überprüfung der vollständigen Entfernung des Pulvers, falls erforderlich.
- Erzielung konsistenter Materialeigenschaften:
- Herausforderung: Die Sicherstellung gleichmäßiger, homogener Materialeigenschaften im gesamten Bauteil und zwischen verschiedenen Fertigungsschritten erfordert eine strenge Prozesskontrolle.
- Milderung:
- Strenge Prozesskontrolle: Aufrechterhaltung einer konstanten Pulverqualität, Laserkalibrierung, Schutzgasumgebung und Wärmemanagement.
- Standardisierte Wärmebehandlung: Anwendung von konsistenten, validierten Wärmebehandlungszyklen.
- Regelmäßige Tests: Durchführung von routinemäßigen Zugversuchen und Mikrostrukturanalysen an Prüfmustern, die neben echten Teilen gedruckt werden.
Erfolgreiche Navigation in diesen metall-AM-Herausforderungen erfordert eine Kombination aus fortschrittlicher Technologie, materialwissenschaftlichem Fachwissen, strenger Prozesskontrolle und praktischer Erfahrung. Die Wahl eines Partners wie Met3dp, der sich für Qualität und kontinuierliche Verbesserung in 3D-Druck von Metalldadurch werden die Risiken, die mit der Einführung dieser Technologie für kritische Bauteile wie Flugzeugverschlüsse verbunden sind, erheblich verringert.
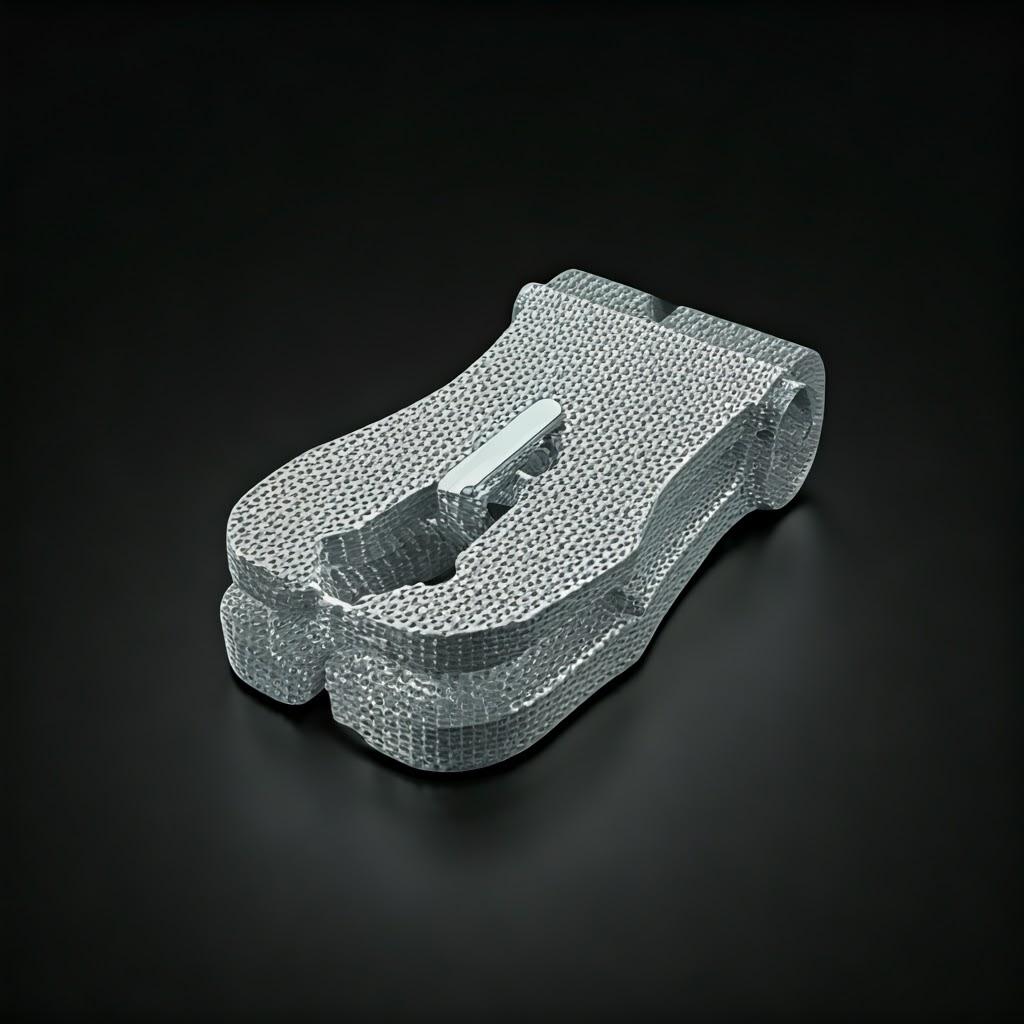
Auswahl des richtigen 3D-Druckdienstleisters für Luft- und Raumfahrtkomponenten aus Metall
Die Wahl des richtigen Fertigungspartners ist bei der Beschaffung von sicherheitskritischen Komponenten wie Flugzeugverschlüssen von entscheidender Bedeutung, insbesondere wenn fortschrittliche Technologien wie die additive Fertigung eingesetzt werden. Die Qualität, Zuverlässigkeit und Lufttüchtigkeit des Endprodukts hängen in hohem Maße vom Know-how, den Verfahren und den Qualitätssystemen des Lieferanten ab. Für Beschaffungsmanager und Ingenieure, die sich mit B2B-Beschaffung im Bereich der additiven Fertigungbewertung des Potenzials lieferanten für 3D-Druck in der Luft- und Raumfahrt erfordert eine gründliche Bewertung, die über den reinen Preis hinausgeht.
Schlüsselkriterien für die Bewertung eines Metall-AM-Dienstleisters:
- Zertifizierungen für die Luft- und Raumfahrt: Bei Flugkomponenten ist dies nicht verhandelbar. Achten Sie auf Lieferanten, die über entsprechende Zertifizierungen verfügen, vor allem AS9100. Diese Norm passt ISO 9001 speziell für die Luft- und Raumfahrtindustrie an und weist auf ein robustes Qualitätsmanagementsystem (QMS) hin, das auf die strengen Anforderungen des Sektors hinsichtlich Sicherheit, Zuverlässigkeit und Rückverfolgbarkeit zugeschnitten ist.
- Nachgewiesene Erfahrung in der Luft- und Raumfahrt: Hat der Lieferant eine Erfolgsbilanz bei der Herstellung von Teilen für Luft- und Raumfahrtanwendungen? Fragen Sie nach Fallstudien, Beispielen für ähnliche Komponenten (wie Halterungen, Gehäuse oder andere Strukturteile) und Referenzen in der Branche. Erfahrungen mit den spezifischen Herausforderungen und Anforderungen der Luft- und Raumfahrt sind von unschätzbarem Wert.
- Materialexpertise & Rückverfolgbarkeit: Der Anbieter muss fundierte Kenntnisse über die angegebenen Aluminiumlegierungen (AlSi10Mg, Scalmalloy®) nachweisen. Dazu gehört das Verständnis der optimalen Druckparameter, Wärmebehandlungsprotokolle und potenzieller Defekte. Entscheidend ist, dass sie über strenge Systeme verfügen für materialrückverfolgbarkeit Luft- und Raumfahrt standards verlangen, die Rückverfolgung von Pulverchargen von der Beschaffung bis zum fertigen Teil. Met3dp beispielsweise verwendet nicht nur hochreine Metallpulver, sondern stellt diese auch selbst her und bietet damit eine zusätzliche Ebene der Kontrolle und Rückverfolgbarkeit. Erfahren Sie mehr über unser Engagement für Qualität und Fachwissen auf unserer Über uns Seite.
- Robustes Qualitätsmanagementsystem (QMS): Bewerten Sie über AS9100 hinaus das gesamte QMS des Unternehmens. Wie werden Prozesskontrolle, Gerätekalibrierung, Meldung von Abweichungen, Korrekturmaßnahmen und Endkontrolle gehandhabt? Achten Sie auf Belege für die statistische Prozesskontrolle und kontinuierliche Verbesserungsmaßnahmen.
- Technisches Fachwissen & DfAM-Unterstützung: Der ideale Partner agiert als Kooperationspartner, nicht nur als Auftragsfertiger. Verfügt er über Ingenieure, die sich mit den DfAM-Prinzipien auskennen und Feedback zu Ihrem Verriegelungsdesign geben können, um optimale Druckbarkeit, Leistung und Kosteneffizienz zu erzielen? Können sie bei der Simulation oder Topologieoptimierung helfen?
- Kapazität der Ausrüstung & Kapazität: Vergewissern Sie sich, dass der Lieferant über gut gewartete, industrietaugliche LPBF-Maschinen verfügt, die für Aluminiumlegierungen geeignet sind. Vergewissern Sie sich, dass die Kapazität ausreicht, um die von Ihnen geforderten Vorlaufzeiten einzuhalten, sowohl für Prototypen als auch für die potenzielle Serienproduktion. Met3dp ist stolz auf den Einsatz branchenführender Maschinen, die eine hohe Genauigkeit und Zuverlässigkeit bieten.
- Nachbearbeitungsmöglichkeiten: Bietet der Lieferant interne Nachbearbeitungsdienste an (Wärmebehandlung, Bearbeitung, Endbearbeitung, NDT)? Die Verwendung eines einzigen Anbieters kann den Arbeitsablauf rationalisieren, die Verantwortlichkeit verbessern und möglicherweise die Vorlaufzeiten im Vergleich zur Verwaltung mehrerer Anbieter verkürzen.
- Vertraulichkeit und Datensicherheit: In Anbetracht des sensiblen Charakters von Entwürfen für die Luft- und Raumfahrt sollten Sie sich vergewissern, dass der Anbieter über strenge Protokolle zum Schutz des geistigen Eigentums (IP) und zum sicheren Umgang mit digitalen Dateien verfügt.
Met3dp als Ihr zuverlässiger Partner:
Met3dp verkörpert diese entscheidenden Eigenschaften. Mit unserem Hauptsitz in Qingdao, China, bieten wir umfassende Lösungen für die additive Fertigung, einschließlich:
- Erweiterte Ausrüstung: Verwendung von SEBM- und LPBF-Druckern, die für branchenführendes Volumen, Genauigkeit und Zuverlässigkeit bekannt sind.
- Hochwertige Materialien: Herstellung von Metallpulvern für die Luft- und Raumfahrt (einschließlich Aluminiumlegierungen, Titanlegierungen, Superlegierungen) mit hervorragenden Eigenschaften durch fortschrittliche Zerstäubungsprozesse.
- Fachwissen: Wir verfügen über jahrzehntelange Erfahrung in der Metall-AM und bedienen anspruchsvolle Branchen wie die Luft- und Raumfahrt, die Medizintechnik und die Automobilindustrie.
- Integrierte Lösungen: Das Dienstleistungsangebot umfasst DfAM-Beratung, Druck, Nachbearbeitung und Unterstützung bei der Anwendungsentwicklung.
Die Entscheidung für Met3dp bedeutet, mit einem Unternehmen zusammenzuarbeiten, das die Grenzen der Metall-AM verschiebt und Komponenten liefert, die den höchsten Qualitäts- und Leistungsstandards entsprechen, die für spezifikationen für Luft- und Raumfahrtkomponenten.
Verständnis der Kostentreiber und Vorlaufzeiten für AM-Flugzeugverschlüsse
Während der 3D-Metalldruck erhebliche technische Vorteile für Flugzeugverschlüsse bietet, ist das Verständnis der wirtschaftlichen Faktoren entscheidend für die Projektplanung und B2B AM-Angebote. Die Kosten und die Vorlaufzeit für die Herstellung von AM-Teilen werden durch eine Reihe von Variablen beeinflusst, die sich von denen der traditionellen Fertigung unterscheiden.
Die wichtigsten Kostenfaktoren für 3D-gedruckte Aluminiumverschlüsse:
- Materialverbrauch: Dies umfasst das Volumen des endgültigen Teils plus etwaige Stützstrukturen. Komplexere oder größere Verschlüsse erfordern natürlich mehr Material (AlSi10Mg oder Scalmalloy®-Pulver). Obwohl Pulver bis zu einem gewissen Grad recycelbar ist, sind die Kosten pro Kilogramm, insbesondere für Speziallegierungen wie Scalmalloy®, ein wichtiger Faktor.
- Maschinenzeit: Dies ist oft der größte Kostenfaktor. Sie wird bestimmt durch:
- Teil Volumen & Höhe: Größere Teile oder höhere Bauwerke brauchen länger.
- Schichtdicke: Dünnere Schichten bieten eine bessere Auflösung, verlängern aber die Bauzeit.
- Suchstrategie und Parameter: Optimierte Parameter sichern die Qualität, beeinträchtigen aber die Geschwindigkeit.
- Verschachtelung: Das gleichzeitige Drucken mehrerer Teile in einem Bauvorgang kann die Kosten für die Maschinenzeit pro Teil senken. Effiziente Verschachtelung erfordert Fachwissen.
- Teil Komplexität: Während AM die Komplexität gut handhabt, können sehr komplizierte Designs umfangreichere Stützstrukturen oder eine sorgfältigere Ausrichtungsplanung erfordern, was sich indirekt auf die Maschinenzeit und den Nachbearbeitungsaufwand auswirkt. Designs, die umfangreiche interne Stützen erfordern, die schwer zu entfernen sind, erhöhen die Arbeitskosten.
- Nachbearbeitungsintensität: Der Umfang der erforderlichen Nachbearbeitung wirkt sich erheblich auf die Kosten aus. Dazu gehören:
- Wärmebehandlung (Zeit und Energie des Ofens).
- Unterstützung bei der Entfernung (manuelle Arbeit oder spezialisierte Prozesse).
- CNC-Bearbeitung (Maschinenzeit, Programmierung, Vorrichtungen).
- Oberflächenbearbeitung (Arbeit und Verbrauchsmaterial für Strahlen, Polieren, Eloxieren).
- Qualitätssicherungsanforderungen: Der Umfang der erforderlichen Inspektion (standardmäßige Maßkontrollen im Vergleich zu umfangreichen NDT-Verfahren wie CT-Scans) verursacht zusätzliche Kosten. Komponenten für die Luft- und Raumfahrt erfordern in der Regel eine strenge Qualitätskontrolle.
- Auftragsvolumen: Wie bei den meisten Fertigungsverfahren gibt es auch hier Größenvorteile. Während AM bei Prototypen und geringen Stückzahlen wettbewerbsfähig ist, ist die kosten pro Teil 3D-Druck sinkt bei größeren Losgrößen aufgrund der besseren Maschinenauslastung und der Amortisation der Einrichtung. Diskutieren Sie aM-Großhandelspreise optionen mit Ihrem Lieferanten für größere Mengen.
Schätzung der Vorlaufzeit:
Die Vorlaufzeiten für AM-Flugzeugverschlüsse können erheblich variieren, sind aber bei Prototypen und geringen Stückzahlen oft kürzer als bei herkömmlichen Methoden, insbesondere wenn für letztere Werkzeuge benötigt werden.
- Prototyping: Je nach Komplexität, aktueller Maschinenauslastung und Nachbearbeitungsbedarf dauert es in der Regel zwischen einigen Tagen und 2-3 Wochen.
- Produktion von Kleinserien: Je nach Chargengröße, Komplexität und Umfang der Nachbearbeitung und Qualitätssicherung können 3 bis 6 Wochen oder mehr vergehen.
- Faktoren, die die Vorlaufzeit beeinflussen: Die Druckzeit, die Warteschlange für die Nachbearbeitung, die Qualitätssicherungsverfahren und die Kapazität der Lieferanten sind die wichtigsten Faktoren.
Erlangung genauer preise für additive Fertigung in der Luft- und Raumfahrt für die Erstellung von Angeboten ist es erforderlich, potenziellen Lieferanten wie Met3dp detaillierte 3D-CAD-Modelle und technische Zeichnungen mit Angaben zu Materialien, Toleranzen, Oberflächen und Qualitätssicherungsanforderungen zu übermitteln. Wir können detaillierte Angebote mit Kosten und geschätzten Vorlaufzeiten für Ihr spezifisches Flugzeugverschlussprojekt erstellen.
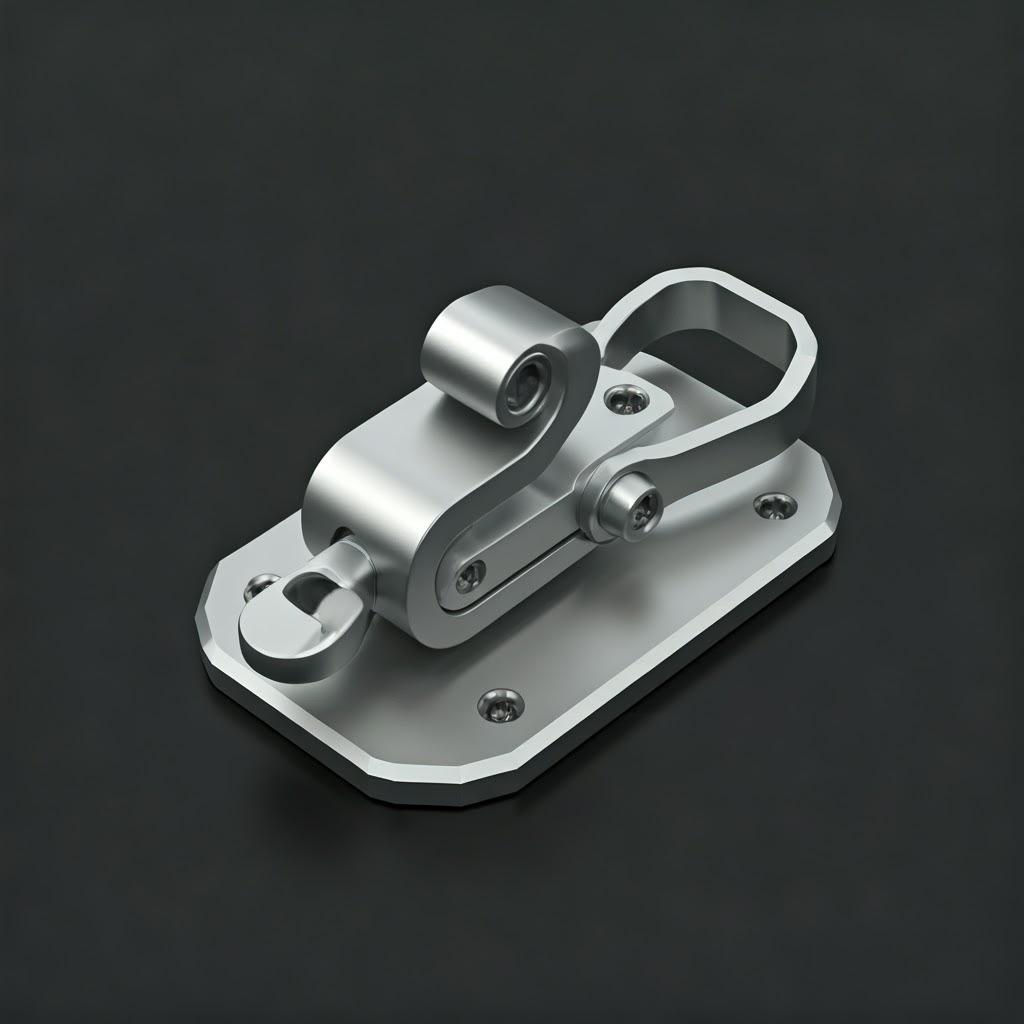
Häufig gestellte Fragen (FAQ) zu 3D-gedruckten Aluminium-Flugzeugverschlüssen
Hier finden Sie Antworten auf einige häufig gestellte Fragen von Ingenieuren und Beschaffungsexperten zum Einsatz von AM für Flugzeugverschlüsse:
- F1: Sind 3D-gedruckte Aluminiumverschlüsse genauso stabil und zuverlässig wie maschinell hergestellte?
- A: Ja, bei korrekter Herstellung mit optimierten Parametern, hochwertigen Pulvern (wie AlSi10Mg oder Scalmalloy®) und geeigneter Nachbearbeitung (insbesondere Wärmebehandlung) können 3D-gedruckte Aluminiumteile die mechanischen Eigenschaften (Festigkeit, Ermüdungsbeständigkeit) von gleichwertigen Knet- oder Gussaluminiumlegierungen erreichen oder sogar übertreffen. Insbesondere Scalmalloy® bietet eine außergewöhnlich hohe Festigkeit, die mit der einiger Stähle oder Titanlegierungen vergleichbar ist, jedoch bei gleichem Gewicht wie Aluminium. Strenge Prozesskontrolle und Qualitätssicherung gemäß Standards wie AS9100 gewährleisten, dass die Zuverlässigkeit den Anforderungen der Luft- und Raumfahrt entspricht.
- F2: Was sind die Hauptvorteile von Scalmalloy® gegenüber AlSi10Mg für Flugzeugverschlüsse?
- A: Die wichtigsten Vorteile von Scalmalloy vs. AlSi10Mg Luft- und Raumfahrt anwendungen sind die deutlich höhere Zugfestigkeit, Streckgrenze und Ermüdungsfestigkeit. Dies ermöglicht einen potenziell größeren Leichtbau durch optimiertes Design oder bietet höhere Sicherheitsmargen für kritische, hoch belastete Verschlüsse. Scalmalloy® bietet im Vergleich zu AlSi10Mg auch eine bessere Duktilität und Leistung bei extremen Temperaturen. Der Nachteil sind die höheren Materialkosten aufgrund des Scandiumgehalts. AlSi10Mg bleibt eine leistungsfähige und kostengünstigere Option für weniger anspruchsvolle Verriegelungsanwendungen.
- F3: Ist der 3D-Druck von Metall für die Massenproduktion von Flugzeugverschlüssen kosteneffizient?
- A: Die Kosteneffizienz hängt vom Volumen, der Komplexität und dem Vergleichspunkt ab. Bei hochkomplexen Verschlüssen, topologieoptimierten Designs oder konsolidierten Baugruppen kann AM selbst bei moderaten Stückzahlen im Vergleich zu mehrteiligen, maschinell bearbeiteten Baugruppen kosteneffizient sein. Bei einfachen Verschlussdesigns, die in sehr hohen Stückzahlen produziert werden, kann die traditionelle Bearbeitung oder das Gießen pro Teil immer noch günstiger sein. Die Gesamtbetriebskosten (unter Berücksichtigung von Gewichtseinsparungen, geringerem Montageaufwand und kürzerer Entwicklungszeit) sprechen jedoch oft für AM, insbesondere wenn die Technologie ausgereift ist und die Kosten sinken. Das Break-even-Volumen verschiebt sich kontinuierlich zugunsten von AM.
- F4: Welche Zertifizierungen sind für einen Anbieter von 3D-gedruckten Teilen für Fluganwendungen wichtig?
- A: Die wichtigste Zertifizierung ist AS9100. Dies zeigt, dass das QMS des Lieferanten speziell auf die strengen Qualitäts-, Sicherheits- und Rückverfolgbarkeitsanforderungen der Luft- und Raumfahrtindustrie zugeschnitten ist. Je nach Kunde und spezifischer Anwendung können auch andere Zertifizierungen oder Qualifikationen (z. B. Nadcap für bestimmte Prozesse wie Wärmebehandlung oder NDT) erforderlich sein. Überprüfen Sie immer die aktuellen Zertifizierungen eines Lieferanten.
- F5: Wie sieht die Oberflächenbeschaffenheit von AM-Verschlüssen im Vergleich zu herkömmlichen Verfahren aus, und kann sie verbessert werden?
- A: LPBF-Teile haben eine rauere Oberflächenbeschaffenheit (typischerweise 6-20 µm Ra) als maschinell bearbeitete Teile. Während dies für einige Oberflächen geeignet ist, müssen kritische Pass- oder Gleitflächen in der Regel verbessert werden. Nachbearbeitungstechniken wie Perlstrahlen erzeugen eine gleichmäßige, matte Oberfläche, während die CNC-Bearbeitung sehr glatte Oberflächen (unter 1 µm Ra) auf bestimmten Merkmalen erzielen kann. Das Eloxieren, das bei Aluminiumteilen für die Luft- und Raumfahrt üblich ist, erfordert ebenfalls eine geeignete Oberflächenvorbereitung. Lieferanten wie Met3dp bieten eine Reihe von Endbearbeitungsoptionen an, um die auf der Bauteilzeichnung angegebenen Spezifikationen zu erfüllen. Sie können verschiedene Materialoptionen und Oberflächenbehandlungen in unserem Produkt Angebote.
Schlussfolgerung: Die Zukunft der Herstellung von Flugzeugverschlüssen ist additiv
Das unablässige Streben der Luft- und Raumfahrtindustrie nach leichteren, stärkeren und effizienteren Flugzeugen erfordert kontinuierliche Innovationen bei Materialien und Fertigungsverfahren. Für Komponenten wie Flugzeugverschlüsse, Metall-Additiv-Fertigung die Verwendung von Hochleistungsaluminiumlegierungen wie AlSi10Mg und Scalmalloy® stellt einen bedeutenden Fortschritt dar. Die Fähigkeit zur Nutzung von DfAM prinzipien zur Topologieoptimierung und Teilekonsolidierung ermöglichen es den Ingenieuren, Verschlüsse zu entwerfen, die nicht nur wesentlich leichter, sondern auch robuster und zuverlässiger sind als ihre traditionell hergestellten Vorgänger.
Von der Verbesserung der Kraftstoffeffizienz durch leichtbaulösungen zur Rationalisierung der Lieferketten durch luft- und Raumfahrtteile auf Abruf produktion, sind die Vorteile überzeugend. Es gibt zwar Herausforderungen, aber diese werden durch sorgfältiges Design, fortschrittliche Prozesskontrolle, rigorose Nachbearbeitung und strenge Qualitätssicherungsprotokolle von erfahrenen Anbietern effektiv gemeistert.
Der Schlüssel zur Erschließung des vollen Potenzials dieser digitale Fertigung Luft- und Raumfahrt technologie liegt in der Zusammenarbeit. Die Partnerschaft mit einem sachkundigen und fähigen Metall-AM-Dienstleister ist entscheidend. Met3dp ist bereit, dieser Partner zu sein und bietet End-to-End-Lösungen an, die fortschrittliche Drucktechnologie, hochwertige Metallpulver, DfAM-Fachwissen, umfassende Nachbearbeitung und eine unerschütterliche Verpflichtung zu Qualitätsstandards in der Luft- und Raumfahrt umfassen.
Wir blicken auf die zukünftige Luft- und Raumfahrtproduktion landschaft wird die additive Fertigung eine immer wichtigere Rolle bei der Herstellung innovativer, leistungsstarker Komponenten spielen. Leichte, 3D-gedruckte Aluminiumverschlüsse sind nur ein Beispiel dafür, wie diese Technologie die Branche umgestaltet.
Möchten Sie herausfinden, wie die additiven Fertigungsmöglichkeiten von Met3dp’ Ihre Flugzeugkomponentenkonstruktionen revolutionieren können? Setzen Sie sich noch heute mit uns in Verbindung, um Ihre Projektanforderungen zu besprechen und zu erfahren, wie wir Ihnen helfen können, Ihre Ziele in Bezug auf Leichtbau und Leistung zu erreichen.
Teilen auf
MET3DP Technology Co., LTD ist ein führender Anbieter von additiven Fertigungslösungen mit Hauptsitz in Qingdao, China. Unser Unternehmen ist spezialisiert auf 3D-Druckgeräte und Hochleistungsmetallpulver für industrielle Anwendungen.
Fragen Sie an, um den besten Preis und eine maßgeschneiderte Lösung für Ihr Unternehmen zu erhalten!
Verwandte Artikel
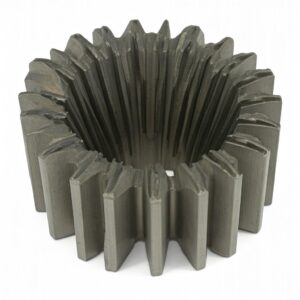
Hochleistungs-Düsenschaufelsegmente: Revolutionierung der Turbineneffizienz mit 3D-Metalldruck
Mehr lesen "Über Met3DP
Aktuelles Update
Unser Produkt
KONTAKT US
Haben Sie Fragen? Senden Sie uns jetzt eine Nachricht! Wir werden Ihre Anfrage mit einem ganzen Team nach Erhalt Ihrer Nachricht bearbeiten.
Holen Sie sich Metal3DP's
Produkt-Broschüre
Erhalten Sie die neuesten Produkte und Preislisten
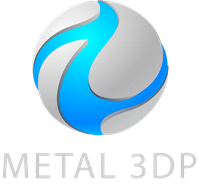
Metallpulver für 3D-Druck und additive Fertigung