3D-Druck von Aluminium-Radnaben
Inhaltsübersicht
Einführung
Die Automobilindustrie steht an der Schwelle zu einer neuen Ära, die von dem unermüdlichen Streben nach höherer Leistung, besserem Kraftstoffverbrauch und geringerer Umweltbelastung angetrieben wird. Ein entscheidender Aspekt zur Erreichung dieser Ziele liegt in der Optimierung der Fahrzeugkomponenten, wobei der Leichtbau eine zentrale Rolle spielt. Da die Hersteller bestrebt sind, die Gesamtmasse des Fahrzeugs zu verringern, werden die für die einzelnen Teile verwendeten Werkstoffe und Herstellungsverfahren einer intensiven Prüfung unterzogen. Die Radnabe, ein scheinbar unscheinbares, aber entscheidendes Bindeglied zwischen dem Rad und der Aufhängung des Fahrzeugs, ist eine der wichtigsten Komponenten und bietet eine große Chance für Innovationen. Traditionelle Herstellungsmethoden für Radnaben, wie Gießen und Schmieden, haben sich in der Industrie seit Jahrzehnten bewährt. Sie sind jedoch oft mit Einschränkungen verbunden, was die Komplexität des Designs, die Verwendung von Materialien und die Fähigkeit zur schnellen Iteration und Anpassung von Lösungen angeht.
Hier kommt der 3D-Druck von Metall ins Spiel, auch bekannt als additive Fertigung von Metall (AM). Diese bahnbrechende Technologie revolutioniert die Art und Weise, wie komplexe Metallteile in verschiedenen Sektoren wie der Luft- und Raumfahrt, der Medizintechnik und jetzt auch zunehmend in der Automobilindustrie konzipiert, entworfen und hergestellt werden. Metall 3D-Druck bietet eine noch nie dagewesene Designfreiheit und ermöglicht die Herstellung komplizierter Geometrien und innerer Strukturen, die mit konventionellen Techniken bisher nicht oder nur mit hohem Kostenaufwand zu realisieren waren. Dies ermöglicht die Entwicklung leichterer und gleichzeitig stabilerer Radnaben, die für bestimmte Leistungsanforderungen und Fahrzeugplattformen optimiert sind. Darüber hinaus erleichtert die additive Fertigung das Rapid Prototyping und die Produktion von kundenspezifischen Teilen oder Kleinserien mit höherer Effizienz, wodurch die Lieferkette gestrafft und die Markteinführungszeit für neue Automobilkonstruktionen verkürzt werden kann. Da die Nachfrage nach leistungsstarken und leichten Fahrzeugen weiter steigt, wird der 3D-Metalldruck zu einem unverzichtbaren Werkzeug für Automobilingenieure und Beschaffungsmanager, die nach innovativen Lösungen für kritische Komponenten wie Radnaben suchen. Unternehmen wie Metall3DP stehen an der Spitze dieser Revolution und bieten fortschrittliche 3D-Druckgeräte und Hochleistungsmetallpulver an, die auf die anspruchsvollen Anforderungen des Automobilsektors zugeschnitten sind.
Wozu dient eine Radnabe?
Die Radnabe ist ein zentraler Bestandteil des Fahrzeugrads und bildet die entscheidende Schnittstelle zwischen dem sich drehenden Rad und dem stationären Aufhängungssystem. Ihre Hauptfunktion besteht darin, einen sicheren Befestigungspunkt für das Rad und den Reifen zu bieten und sicherzustellen, dass sie fest mit dem Fahrzeug verbunden sind. Neben dieser grundlegenden Funktion spielt die Radnabe noch weitere wichtige Rollen für den Betrieb, die Sicherheit und die Leistung eines Fahrzeugs. In der Regel beherbergt sie die Radlager, die dafür sorgen, dass sich das Rad reibungslos und mit minimaler Reibung um die Achse drehen kann. Diese Lager sind entscheidend für den Fahrkomfort und die Langlebigkeit der Radbaugruppe. Die Radnabe enthält häufig auch Elemente zur Befestigung von Bremsscheiben oder -trommeln, damit das Bremssystem das Fahrzeug effektiv abbremsen oder anhalten kann. Die präzise und robuste Verbindung der Radnabe ist für die Stabilität, das Fahrverhalten und die Bremswirkung des Fahrzeugs von größter Bedeutung. Jeder Ausfall oder jede Beeinträchtigung der Radnabe kann schwerwiegende Folgen für die Sicherheit und Kontrolle des Fahrzeugs haben.
Traditionell werden Radnaben mit Hilfe von Großserienverfahren wie Gießen (z. B. Aluminium- oder Eisenguss) und Schmieden (z. B. Stahl- oder Aluminiumschmieden) hergestellt. Diese Verfahren sind gut etabliert und in der Lage, starke und haltbare Teile in großem Maßstab herzustellen. Beim Gießen wird geschmolzenes Metall in eine Form gegossen, beim Schmieden wird das Metall unter hohem Druck geformt. Obwohl diese Verfahren für die Massenproduktion geeignet sind, können sie in Bezug auf die Komplexität des Designs und die Materialeffizienz Einschränkungen aufweisen. Die Werkzeugkosten für Gießen und Schmieden können beträchtlich sein, so dass sie für Kleinserien oder stark kundenspezifische Anwendungen weniger wirtschaftlich sind. Darüber hinaus erlauben diese Verfahren nicht immer die Schaffung optimierter interner Strukturen oder die Verwendung funktional abgestufter Materialien. Da die Automobilindustrie zunehmend leichtere, effizientere und häufig individuellere Fahrzeugdesigns fordert, werden die Grenzen traditioneller Fertigungsmethoden für Komponenten wie Radnaben immer deutlicher und ebnen den Weg für innovative Lösungen wie den 3D-Druck von Metallen, die überzeugende Alternativen bieten.
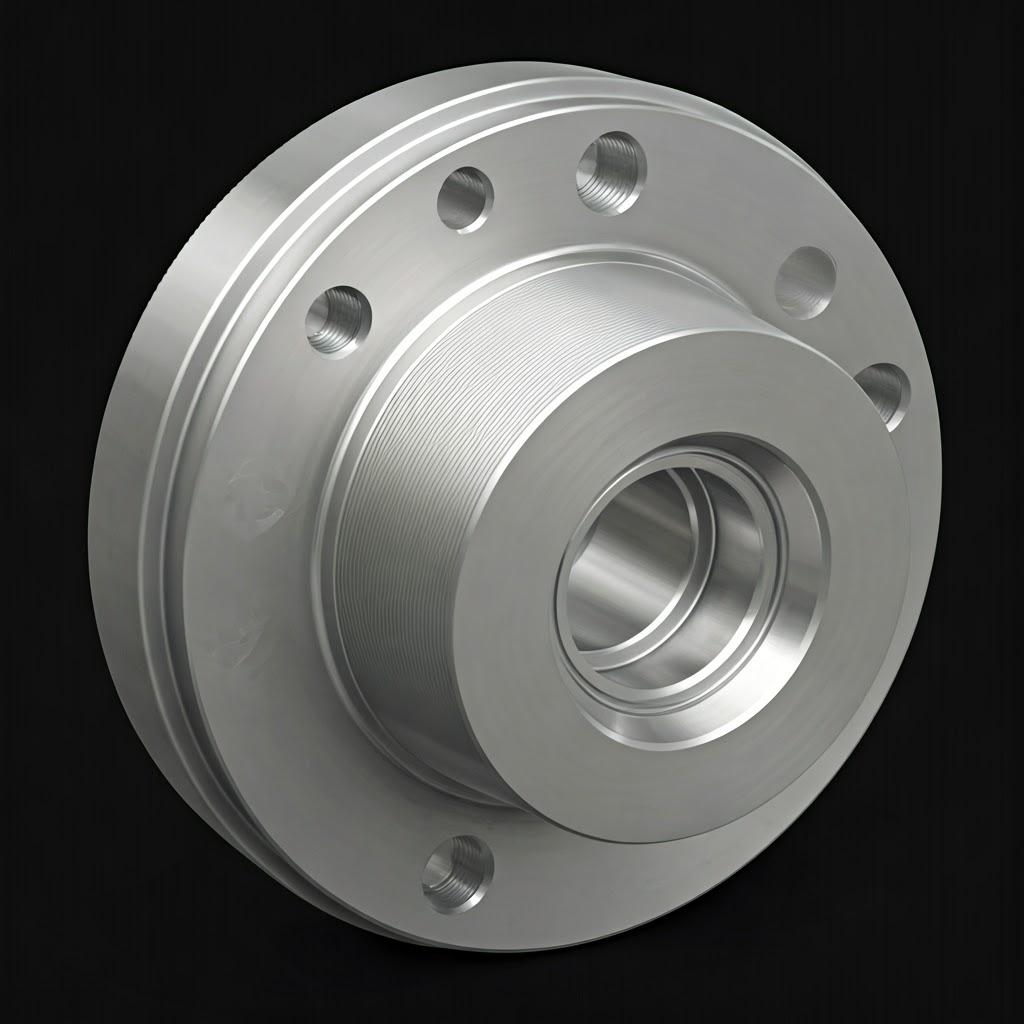
Warum 3D-Metalldruck für Radnaben verwenden?
Der Einsatz von 3D-Metalldruck für die Produktion von Radnaben für die Automobilindustrie bietet eine Reihe von Vorteilen gegenüber herkömmlichen Fertigungsmethoden und erfüllt die sich entwickelnden Anforderungen der Branche in Bezug auf Leichtbau, Leistungsverbesserung und Designflexibilität.
- Verbesserte Gestaltungsfreiheit: Der 3D-Metalldruck befreit die Ingenieure von den Konstruktionszwängen, die beim Gießen und Schmieden bestehen. Die additive Fertigung ermöglicht die Herstellung komplexer Geometrien, komplizierter interner Strukturen wie Gitterstrukturen und optimierter Formen, die das Gewicht der Radnabe erheblich reduzieren können, ohne ihre strukturelle Integrität zu beeinträchtigen. Diese Designfreiheit ermöglicht die Entwicklung von Radnaben, die auf die spezifischen Leistungsanforderungen eines Fahrzeugs zugeschnitten sind und so das Fahrverhalten, die Beschleunigung und die Kraftstoffeffizienz verbessern können.
- Materialoptimierung und Abfallvermeidung: Im Gegensatz zu subtraktiven Fertigungsverfahren, bei denen Material aus einem massiven Block entfernt wird, werden beim 3D-Metalldruck Teile Schicht für Schicht aufgebaut, wobei nur das benötigte Material verwendet wird. Dadurch wird der Materialabfall erheblich reduziert, was zu einer kosteneffizienteren Produktion führt, insbesondere bei teuren Werkstoffen wie Aluminiumlegierungen in Luft- und Raumfahrtqualität. Darüber hinaus eröffnet die additive Fertigung die Möglichkeit, funktional abgestufte Werkstoffe zu verwenden oder Radnaben aus mehreren Werkstoffen mit maßgeschneiderten Eigenschaften in verschiedenen Abschnitten des Bauteils herzustellen.
- Schnelles Prototyping und individuelle Anpassung: Der 3D-Metalldruck eignet sich hervorragend für das Rapid Prototyping und ermöglicht es Automobilingenieuren, Entwürfe schnell zu überarbeiten und Funktionsprototypen von Radnaben zu testen, und zwar mit deutlich kürzeren Vorlaufzeiten als bei herkömmlichen, werkzeugabhängigen Verfahren. Diese Agilität beschleunigt den Design- und Entwicklungszyklus. Darüber hinaus ermöglicht die additive Fertigung die Herstellung kundenspezifischer Radnaben für Nischenmodelle, Motorsportanwendungen oder sogar individuelle Fahrzeugmodifikationen, ohne dass teure Werkzeugänderungen erforderlich sind, was die Produktion von Kleinserien oder hochspezifischen Produkten wirtschaftlich macht.
- Integration von Funktionen und Reduzierung der Montage: Der 3D-Druck von Metall ermöglicht die Konsolidierung mehrerer Komponenten in einem einzigen, komplexen Teil. So könnten beispielsweise Merkmale für die Befestigung des Bremsrotors oder die Integration von Sensoren direkt in das Design der 3D-gedruckten Radnabe integriert werden, wodurch die Anzahl der Einzelteile, Befestigungselemente und Montageschritte reduziert wird. Diese Vereinfachung kann zu niedrigeren Herstellungskosten, höherer Zuverlässigkeit und geringerem Gewicht führen.
- On-Demand-Produktion und Optimierung der Lieferkette: Die additive Fertigung bietet das Potenzial für eine bedarfsgerechte Produktion von Radnaben, was den Bedarf an großen Lagerbeständen verringert und eine flexiblere und reaktionsschnellere Lieferkette ermöglicht. Dies kann besonders bei Teilen für den Ersatzteilmarkt oder bei der Bewältigung von Nachfrageschwankungen vorteilhaft sein. Durch die Nutzung der Fähigkeiten fortschrittlicher 3D-Druckdienstleister für Metall wie Metall3DPdie Automobilhersteller können diese Vorteile nutzen, ohne dass erhebliche Vorabinvestitionen in Ausrüstung und Know-how erforderlich sind.
Empfohlene Materialien und warum sie wichtig sind
Für den 3D-Druck von Kfz-Radnaben zeichnen sich zwei Aluminiumlegierungen durch ein hervorragendes Gleichgewicht aus leichten Eigenschaften, hoher Festigkeit und Eignung für anspruchsvolle Kfz-Anwendungen aus: AlSi10Mg und A7075. Metal3DP’s Portfolio an hochwertigen Metallpulvern enthält diese fortschrittlichen Materialien, die optimale Leistung und Zuverlässigkeit für 3D-gedruckte Radnaben gewährleisten.
AlSi10Mg: Diese Aluminiumlegierung, die hauptsächlich aus Aluminium mit Zusätzen von Silizium (Si) und Magnesium (Mg) besteht, wird aufgrund ihrer außergewöhnlichen Druckbarkeit und ihrer günstigen mechanischen Eigenschaften häufig für den 3D-Metalldruck verwendet.
- Wichtige Eigenschaften und Vorteile für Radnaben:
- Ausgezeichnetes Verhältnis von Stärke zu Gewicht: AlSi10Mg bietet eine gute Kombination aus hoher Festigkeit und geringer Dichte, was entscheidend für die Verringerung der ungefederten Masse des Fahrzeugs ist, was sich positiv auf das Fahrverhalten und die Kraftstoffeffizienz auswirken kann.
- Gute Duktilität und Zähigkeit: Es ist nicht nur stabil, sondern weist auch eine ausreichende Dehnbarkeit und Zähigkeit auf, um den im Fahrzeugbetrieb auftretenden Belastungen und Stößen standzuhalten.
- Hohe Wärmeleitfähigkeit: Diese Eigenschaft hilft bei der Ableitung der vom Bremssystem erzeugten Wärme und trägt so zu einer verbesserten Bremsleistung und Langlebigkeit bei.
- Gute Korrosionsbeständigkeit: Aluminiumlegierungen verfügen von Natur aus über eine gute Korrosionsbeständigkeit, die für die Aufrechterhaltung der strukturellen Integrität von Radnaben, die verschiedenen Umweltbedingungen ausgesetzt sind, unerlässlich ist.
- Schweißbarkeit und Bearbeitbarkeit: AlSi10Mg kann leicht geschweißt und für die Nachbearbeitung bearbeitet werden, was eine präzise Nachbearbeitung von kritischen Schnittstellen ermöglicht.
A7075: Diese Aluminiumlegierung ist für ihre außergewöhnlich hohe Festigkeit bekannt und eignet sich daher hervorragend für Anwendungen, bei denen es auf maximale strukturelle Integrität ankommt.
- Wichtige Eigenschaften und Vorteile für Radnaben:
- Ultra-Hochfest: A7075 weist eine der höchsten Zugfestigkeiten unter den Aluminiumlegierungen auf und eignet sich daher ideal für den Leichtbau von hochbelasteten Komponenten wie leistungsorientierten Radnaben.
- Ausgezeichnete Ermüdungsbeständigkeit: Radnaben sind während des Fahrzeugbetriebs zyklischen Belastungen ausgesetzt. Die hohe Ermüdungsfestigkeit von A7075’ gewährleistet eine lange Lebensdauer unter diesen Bedingungen.
- Gute Bearbeitbarkeit: A7075 bietet zwar eine höhere Festigkeit, kann aber dennoch so bearbeitet werden, dass die für Nabenschnittstellen erforderlichen engen Toleranzen und glatten Oberflächen erreicht werden.
- Leichtes Gewicht: Trotz seiner hohen Festigkeit ist A7075 ein leichtes Material, das zur Reduzierung des Fahrzeuggewichts beiträgt.
Die Auswahl des geeigneten Pulvers hängt von den spezifischen Leistungsanforderungen und Konstruktionszielen für die Radnabe ab. AlSi10Mg bietet ein ausgewogenes Verhältnis von Eigenschaften für ein breites Spektrum von Automobilanwendungen, während A7075 besonders vorteilhaft ist, wenn Endfestigkeit und Leichtbau im Vordergrund stehen, wie bei Hochleistungsfahrzeugen oder im Motorsport. Metal3DP’s fortschrittliches Pulverherstellungssystem stellt sicher, dass diese Aluminiumpulver eine hohe Sphärizität und eine gute Fließfähigkeit aufweisen, was für die Herstellung dichter, hochwertiger 3D-gedruckter Teile mit hervorragenden mechanischen Eigenschaften entscheidend ist.
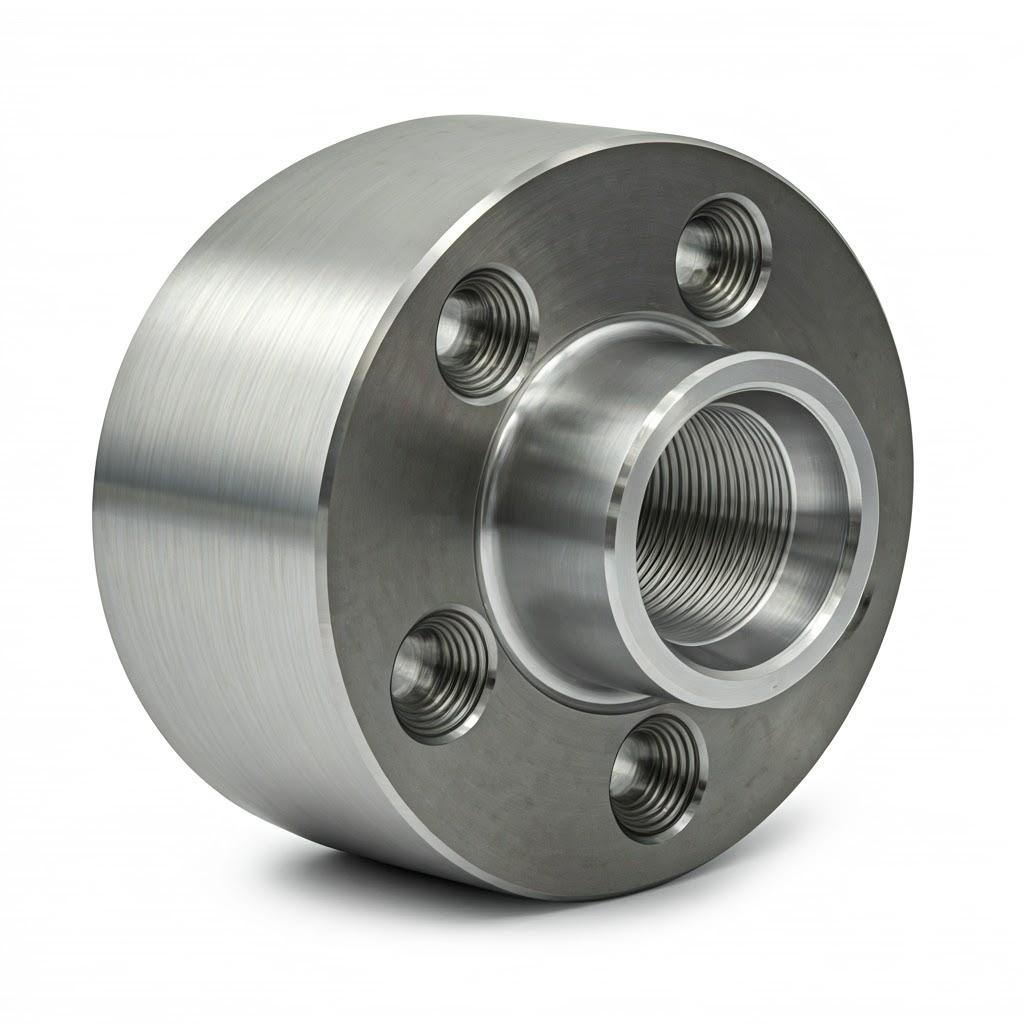
Konstruktionsüberlegungen zur additiven Fertigung
Die Entwicklung von Fahrzeugradnaben für den 3D-Metalldruck erfordert ein Umdenken im Vergleich zu herkömmlichen Fertigungsverfahren. Der schichtweise Aufbau der additiven Fertigung bietet einzigartige Möglichkeiten zur Designoptimierung, erfordert aber auch eine sorgfältige Berücksichtigung spezifischer Designprinzipien, um die Qualität der Teile, die strukturelle Integrität und einen effizienten Druck zu gewährleisten.
- Topologie-Optimierung: Einer der größten Vorteile des 3D-Metalldrucks ist die Möglichkeit der Topologieoptimierung. Dieser rechnergestützte Entwurfsansatz ermittelt die effizienteste Materialverteilung für eine gegebene Reihe von Lasten und Einschränkungen, was zu leichten und dennoch strukturell soliden Teilen führt. Bei Radnaben kann die Topologieoptimierung zu organischen, nicht intuitiven Formen führen, die unnötiges Material einsparen und gleichzeitig die Steifigkeit und Festigkeit erhalten oder sogar verbessern.
- Gitterförmige Strukturen: Interne Gitterstrukturen können strategisch in das Design von 3D-gedruckten Radnaben integriert werden, um das Gewicht weiter zu reduzieren, ohne die mechanische Leistung zu beeinträchtigen. Diese komplizierten Netzwerke aus miteinander verbundenen Streben und Knoten bieten ein hervorragendes Verhältnis von Steifigkeit zu Gewicht und können auf bestimmte Belastungsszenarien zugeschnitten werden. Verschiedene Gittermuster (z. B. gyroid, kubisch, octet) bieten unterschiedliche mechanische Eigenschaften und können je nach den Anforderungen der Anwendung ausgewählt werden.
- Minimierung des Trägermaterials: Beim 3D-Druck von Metall sind häufig Stützstrukturen erforderlich, um Überhänge zu vermeiden und die Stabilität des Teils während des Bauprozesses zu gewährleisten. Übermäßiges Stützmaterial kann jedoch die Druckzeit, den Materialverbrauch und den Nachbearbeitungsaufwand erhöhen. Durch die Konstruktion von Radnaben mit selbsttragenden Winkeln (in der Regel 45 Grad oder weniger) und die strategische Ausrichtung des Teils in der Baukammer kann der Bedarf an umfangreichen Stützstrukturen minimiert werden. Merkmale wie integrierte Stützstrukturen, die leicht entfernt werden können, sind ebenfalls von Vorteil.
- Wandstärke und Riffelung: Um die gewünschte Festigkeit und Steifigkeit einer 3D-gedruckten Radnabe zu erreichen, ist eine sorgfältige Auswahl der Wandstärke entscheidend. Dünne Wände können das Gewicht reduzieren, aber die strukturelle Integrität beeinträchtigen, während zu dicke Wände unnötige Masse hinzufügen. Durch die Integration von Rippen und Versteifungselementen kann eine lokale Verstärkung in kritischen Bereichen erreicht werden, ohne das Gesamtgewicht wesentlich zu erhöhen.
- Merkmal Integration: Der 3D-Metalldruck ermöglicht die direkte Integration von Merkmalen wie Befestigungspunkten für Bremsscheiben, Sensorgehäusen oder sogar Kühlkanälen in das Radnabendesign. Dadurch wird der Bedarf an separaten Komponenten und Montageprozessen reduziert, was zu potenziellen Kosteneinsparungen und höherer Zuverlässigkeit führt.
- Überlegungen zur Oberflächenbeschaffenheit: Die Oberflächenbeschaffenheit eines 3D-gedruckten Metallteils kann je nach Druckverfahren und Parametern variieren. Die Gestaltung kritischer Schnittstellen, wie z. B. Lagersitze oder Montageflächen, unter Berücksichtigung nachfolgender Bearbeitungs- oder Endbearbeitungsprozesse ist für das Erreichen der geforderten Toleranzen und Oberflächenqualität von entscheidender Bedeutung.
Durch die Berücksichtigung dieser Designüberlegungen können Automobilingenieure die Möglichkeiten des 3D-Metalldrucks voll ausschöpfen, um innovative, leistungsstarke Aluminiumradnaben zu entwickeln, die konventionell hergestellte Teile übertreffen.
Toleranzen, Oberflächengüte und Maßgenauigkeit
Das Erreichen der geforderten Toleranzen, Oberflächengüte und Maßgenauigkeit ist für die Funktionsfähigkeit und Sicherheit von Kfz-Radnaben von größter Bedeutung. Die 3D-Drucktechnologien für Metall haben in diesen Bereichen erhebliche Fortschritte gemacht, und mit einer sorgfältigen Prozesssteuerung und Nachbearbeitung können die strengen Standards der Automobilindustrie erfüllt werden.
- Verträglichkeit: Die erreichbare Maßtoleranz beim 3D-Metalldruck hängt von der jeweiligen Drucktechnologie (z. B. Laser Powder Bed Fusion (LPBF) oder Electron Beam Powder Bed Fusion (EBPF)), dem verwendeten Material sowie der Größe und Geometrie des Teils ab. Bei LPBF können für kritische Abmessungen in der Regel Toleranzen im Bereich von ±0,1 mm bis ±0,05 mm erreicht werden. Mit EBPF, das häufig für größere Teile verwendet wird, können ähnliche Genauigkeiten erreicht werden. Faktoren wie die Wärmeausdehnung und -kontraktion während des Druckprozesses und die Präzision des Bewegungssystems der Maschine beeinflussen die endgültige Maßgenauigkeit. Die richtige Bauausrichtung, das Design der Stützstruktur und die Optimierung der Prozessparameter sind entscheidend für die Minimierung von Abweichungen von den geplanten Abmessungen.
- Oberfläche: Die gedruckte Oberfläche im 3D-Metalldruck ist im Allgemeinen rauer als die bearbeitete Oberfläche. Die Oberflächenrauheit (Ra) liegt typischerweise zwischen 5 und 20 µm bei LPBF und kann bei EBPF etwas höher sein. Der Treppeneffekt, der durch den schichtweisen Aufbau verursacht wird, trägt zu dieser Rauheit bei. Für unkritische Oberflächen kann die gedruckte Oberfläche akzeptabel sein. Für Schnittstellen, die glatte Oberflächen erfordern, wie z. B. Lagersitze oder Dichtungsflächen, sind jedoch Nachbearbeitungsmethoden wie Bearbeiten, Schleifen oder Polieren erforderlich.
- Maßgenauigkeit: Die Maßgenauigkeit bezieht sich auf das Ausmaß, in dem das gedruckte Teil mit dem vorgesehenen CAD-Modell übereinstimmt. Das Erreichen einer hohen Maßgenauigkeit erfordert eine sorgfältige Kalibrierung des 3D-Druckers, optimierte Prozessparameter und die Berücksichtigung der Materialschrumpfung während der Verfestigung. Mit Hilfe von Simulationswerkzeugen lassen sich mögliche Verformungen vorhersagen und ausgleichen. Metal3DP’s Verpflichtung zu branchenführender Genauigkeit stellt sicher, dass ihre Druckverfahren und -geräte so konzipiert sind, dass sie Teile mit hoher Maßhaltigkeit liefern. Darüber hinaus sind Qualitätskontrollmaßnahmen, einschließlich der prozessbegleitenden Überwachung und der Prüfung nach dem Druck mit Koordinatenmessgeräten (KMG) oder Laserscannern, unerlässlich, um die Maßhaltigkeit und die Einhaltung der Spezifikationen zu überprüfen. Durch die Kombination fortschrittlicher 3D-Metalldrucktechnologien mit geeigneter Nachbearbeitung und strenger Qualitätskontrolle können Automobilhersteller Aluminiumradnaben herstellen, die den anspruchsvollen Anforderungen der Branche in Bezug auf Abmessungen und Oberflächengüte entsprechen.
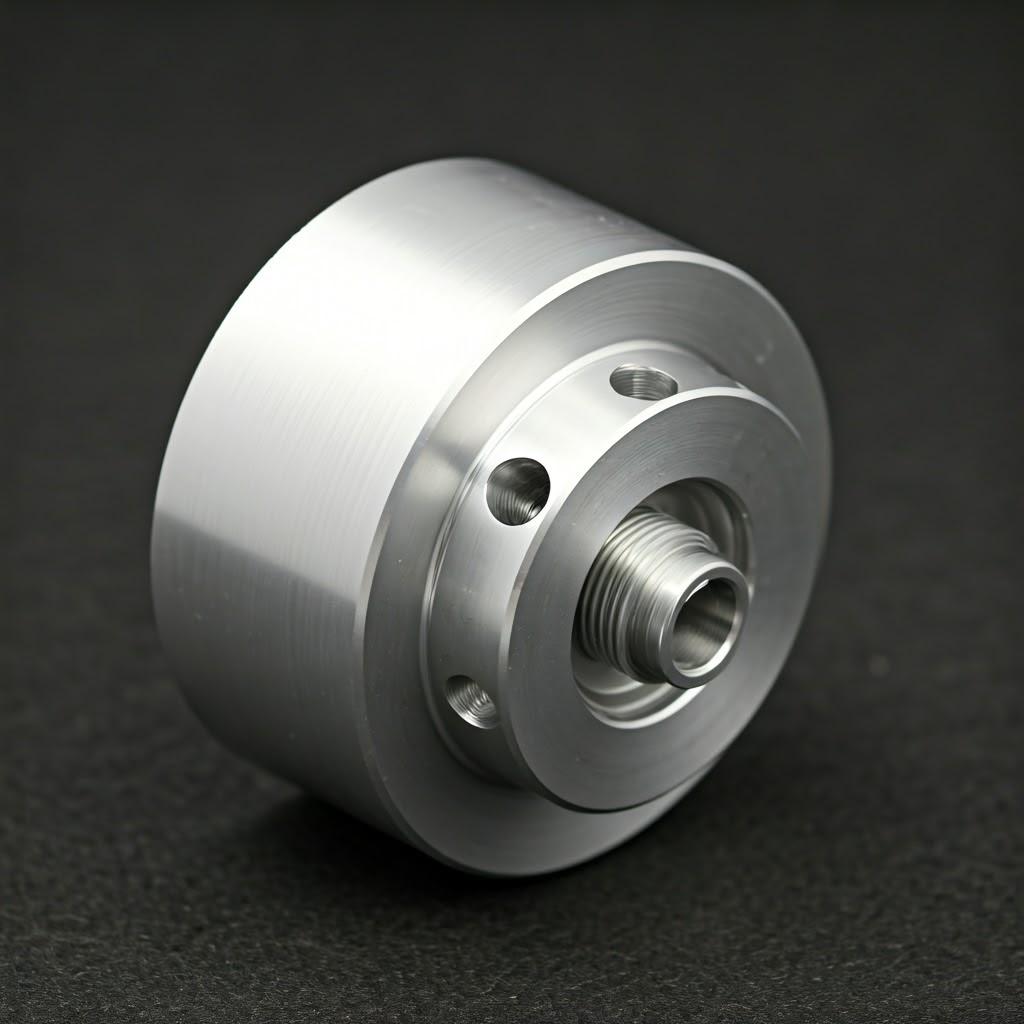
Nachbearbeitungsanforderungen
Der 3D-Metalldruck bietet zwar erhebliche Vorteile bei der Erstellung komplexer Geometrien, doch sind häufig Nachbearbeitungsschritte erforderlich, um die endgültigen funktionalen Anforderungen von Kfz-Radnaben zu erfüllen. Diese Schritte können die mechanischen Eigenschaften verbessern, die Oberflächengüte erhöhen und die Maßhaltigkeit sicherstellen.
- Wärmebehandlung: Spannungsabbau ist eine gängige Wärmebehandlung, die bei 3D-gedruckten Metallteilen angewandt wird, um innere Eigenspannungen zu reduzieren, die sich während der schnellen Aufheiz- und Abkühlzyklen des Druckprozesses aufbauen können. Bei Aluminiumlegierungen wie AlSi10Mg und A7075 können spezifische Wärmebehandlungszyklen auch zur Optimierung der mechanischen Eigenschaften eingesetzt werden, z. B. zur Erhöhung der Festigkeit und Härte. Das spezifische Wärmebehandlungsprotokoll hängt von der Legierung und den gewünschten Endeigenschaften ab.
- Unterstützung bei der Entfernung: Stützstrukturen, die häufig während des Druckvorgangs erforderlich sind, müssen nach Abschluss des Bauprozesses entfernt werden. Die Methode zur Entfernung von Stützstrukturen hängt vom Stützmaterial und der Teilegeometrie ab. Sie kann manuelles Brechen, Schneiden mit Spezialwerkzeugen oder in einigen Fällen die Verwendung von auflösbaren Stützmaterialien beinhalten. Eine sorgfältige Konstruktion und Ausrichtung des Teils kann die Menge der benötigten Halterung minimieren und den Entfernungsprozess vereinfachen.
- CNC-Bearbeitung: Für kritische Schnittstellen, die sehr enge Toleranzen und glatte Oberflächen erfordern, wie z. B. Lagersitze, Schraubenlöcher und Montageflächen, wird häufig eine CNC-Bearbeitung als Nachbearbeitungsschritt eingesetzt. Durch die Präzisionsbearbeitung kann das hohe Maß an Genauigkeit und Oberflächenqualität erreicht werden, das für diese Funktionsbereiche der Radnabe erforderlich ist.
- Oberflächenveredelung: Zur Verbesserung der gesamten Oberflächenbeschaffenheit der 3D-gedruckten Radnabe können verschiedene Techniken eingesetzt werden, darunter:
- Media Blasting: Bei diesem Verfahren werden Schleifmittel eingesetzt, um Oberflächenoxide zu entfernen und die Rauheit zu verringern, so dass eine gleichmäßigere und ästhetisch ansprechendere Oberfläche entsteht.
- Polieren: Für Anwendungen, die eine sehr glatte oder spiegelglatte Oberfläche erfordern, kann poliert werden. Dies kann insbesondere für exponierte Oberflächen von Spezial- oder Hochleistungsradnaben relevant sein.
- Beschichtungen: Je nach Anwendung und Umgebungsbedingungen können Beschichtungen auf die Radnaben aufgetragen werden, um die Korrosionsbeständigkeit und die Verschleißfestigkeit zu erhöhen oder ein bestimmtes ästhetisches Aussehen zu erzielen. Übliche Beschichtungen sind Eloxierungen für Aluminiumlegierungen.
- Inspektion und Qualitätskontrolle: Nach der Nachbearbeitung ist eine gründliche Prüfung mit Techniken wie Koordinatenmessgeräten (KMG), zerstörungsfreien Prüfverfahren (z. B. Ultraschallprüfung oder Farbeindringprüfung) und Messungen der Oberflächenrauheit von entscheidender Bedeutung, um sicherzustellen, dass das fertige Teil die erforderlichen Spezifikationen und Qualitätsstandards erfüllt.
Die spezifischen Nachbearbeitungsschritte, die für eine 3D-gedruckte Aluminiumradnabe erforderlich sind, hängen vom Design, der geplanten Anwendung und den erforderlichen Leistungsmerkmalen ab. Bei einer umfassenden Fertigungsstrategie werden diese Nachbearbeitungsanforderungen bereits in der ersten Entwurfsphase berücksichtigt.
Häufige Herausforderungen und wie man sie vermeidet
Der 3D-Metalldruck bietet zwar zahlreiche Vorteile, aber es gibt auch potenzielle Herausforderungen, die bewältigt werden müssen, um die erfolgreiche Produktion von hochwertigen Radnaben für Kraftfahrzeuge zu gewährleisten. Es ist entscheidend, diese Herausforderungen zu verstehen und geeignete Strategien zu ihrer Vermeidung zu entwickeln.
- Verformung und Verzerrung: Thermische Spannungen, die während der schnellen Aufheiz- und Abkühlzyklen des Druckprozesses entstehen, können zu einer Verformung oder einem Verzug des Teils führen, insbesondere bei großen oder komplexen Geometrien.
- Wie man es vermeidet: Durch die Optimierung der Bauausrichtung, die Verwendung von Stützstrukturen zur Verankerung des Teils auf der Bauplatte und die sorgfältige Steuerung der Druckparameter (z. B. Laserleistung, Scangeschwindigkeit, Temperatur der Bauplatte) können thermische Spannungen und Verformungen minimiert werden. Simulationswerkzeuge können auch dazu beitragen, mögliche Verformungen vorherzusagen und zu kompensieren.
- Unterstützung bei der Entfernung von Problemen: Das Entfernen von Stützstrukturen kann manchmal eine Herausforderung sein, insbesondere bei komplizierten inneren Merkmalen oder empfindlichen Geometrien. Eine unsachgemäße Entfernung von Stützstrukturen kann die Oberfläche des Teils beschädigen.
- Wie man es vermeidet: Die Konstruktion von Teilen mit selbsttragenden Winkeln, die Verwendung optimierter Stützstrukturen mit Ausbruchsmerkmalen und die Anwendung geeigneter Techniken zur Entfernung von Stützen (z. B. Drahterodieren für schwer zugängliche Stützen) können diese Probleme entschärfen.
- Porosität und Dichte: Das Erreichen einer hohen Dichte und die Minimierung der Porosität sind entscheidend für die mechanische Leistung von 3D-gedruckten Metallteilen. Porosität kann das Material schwächen und zu vorzeitigem Versagen führen.
- Wie man es vermeidet: Die Verwendung hochwertiger Metallpulver mit guter Fließfähigkeit, die Optimierung der Druckparameter, um ein ordnungsgemäßes Aufschmelzen und Erstarren zu gewährleisten, und der Einsatz von Nachbearbeitungstechniken wie dem Heiß-Isostatischen Pressen (HIP) können die Porosität erheblich reduzieren und die Dichte erhöhen. Metal3DP’s fortschrittliches Pulverherstellungssystem ist für die Herstellung von Pulvern mit minimaler Porosität konzipiert.
- Oberflächenrauhigkeit: Wie bereits erwähnt, kann die gedruckte Oberfläche rau sein, was nicht für alle Anwendungen geeignet ist.
- Wie man es vermeidet: Die Planung geeigneter Nachbearbeitungsschritte wie Bearbeitung, Strahlen oder Polieren im Fertigungsablauf ist für das Erreichen der gewünschten Oberflächengüte unerlässlich. Auch die Optimierung von Druckparametern wie Schichtdicke und Scan-Strategien kann die gedruckte Oberflächenrauheit bis zu einem gewissen Grad beeinflussen.
- Variabilität der Materialeigenschaften: Die mechanischen Eigenschaften von 3D-gedruckten Metallteilen können in Abhängigkeit von der Bauausrichtung und den Prozessparametern Schwankungen aufweisen.
- Wie man es vermeidet: Eine gründliche Materialcharakterisierung und Prozessoptimierung sind entscheidend, um konsistente und vorhersehbare mechanische Eigenschaften zu gewährleisten. Die Einhaltung bewährter Verfahren für den 3D-Druck von Metall und die Zusammenarbeit mit erfahrenen Dienstleistern wie Metall3DP kann dazu beitragen, diese Herausforderung zu bewältigen.
- Kostenüberlegungen: Der 3D-Druck von Metall kann zwar für bestimmte Anwendungen kosteneffizient sein, aber die Anfangsinvestitionen in die Ausrüstung und die Kosten pro Teil können höher sein als bei herkömmlichen Verfahren für die Großserienproduktion.
- Wie man es vermeidet: Eine sorgfältige Bewertung der Gesamtbetriebskosten unter Berücksichtigung von Faktoren wie Designkomplexität, Materialverbrauch, Nachbearbeitungsanforderungen und Produktionsvolumen ist unerlässlich. Bei geringeren Stückzahlen oder hochkomplexen Teilen kann der 3D-Metalldruck im Vergleich zu herkömmlichen, werkzeugintensiven Verfahren eine wirtschaftlichere Lösung bieten.
Indem sie diese potenziellen Herausforderungen durch sorgfältiges Design, Prozessoptimierung und Zusammenarbeit mit erfahrenen Metall-3D-Druckpartnern proaktiv angehen, können Automobilhersteller die Vorteile der additiven Fertigung für die Herstellung von Hochleistungs-Aluminiumradnaben erfolgreich nutzen.
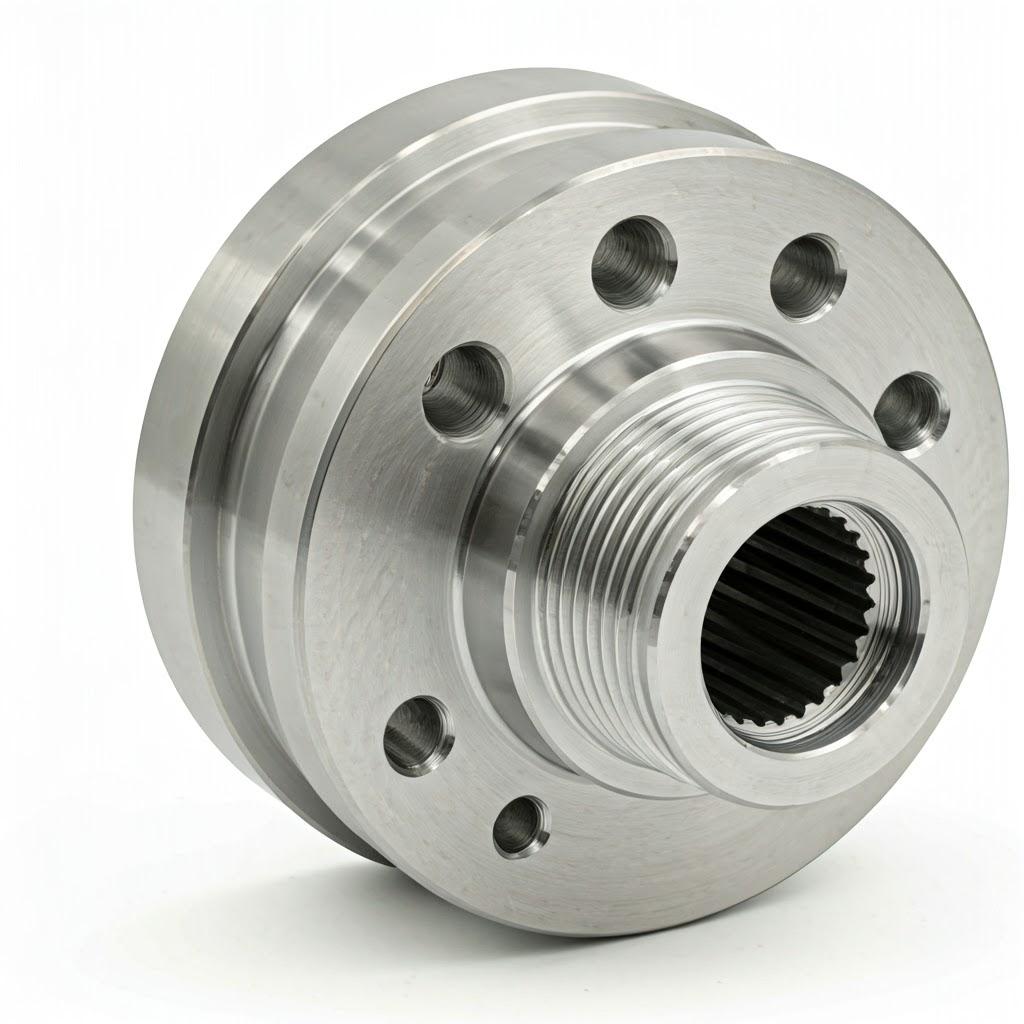
Wie Sie den richtigen 3D-Druckdienstleister für Metall auswählen
Die Auswahl des richtigen 3D-Druckdienstleisters für Metall ist eine wichtige Entscheidung, die sich erheblich auf die Qualität, die Kosten und die Vorlaufzeit Ihrer 3D-gedruckten Aluminiumradnaben auswirken kann. Hier sind die wichtigsten Faktoren, die Sie bei der Bewertung potenzieller Anbieter berücksichtigen sollten:
- Materielle Fähigkeiten: Vergewissern Sie sich, dass der Dienstleister Erfahrung im Umgang mit den für Ihre Anwendung erforderlichen Aluminiumlegierungen wie AlSi10Mg und A7075 hat. Vergewissern Sie sich, dass er über eine zuverlässige Versorgung mit hochwertigen Metallpulvern verfügt und die Feinheiten des Drucks dieser Materialien kennt, um optimale mechanische Eigenschaften zu erzielen. Metal3DP stellt eine breite Palette hochwertiger Metallpulver her optimiert für verschiedene additive Fertigungsverfahren.
- Ausrüstung und Technologie: Informieren Sie sich über die Arten der vom Anbieter verwendeten 3D-Drucktechnologien für Metall (z. B. LPBF, DED, Binder Jetting). Die Wahl der Technologie kann die erreichbare Genauigkeit, Oberflächengüte und das Produktionsvolumen beeinflussen. Erkundigen Sie sich nach den Spezifikationen und Fähigkeiten der 3D-Drucker, einschließlich Bauvolumen und Präzision. Metal3DP’s Drucker liefern branchenführende Druckvolumen, Genauigkeit und Zuverlässigkeit.
- Fachwissen und Erfahrung: Suchen Sie nach einem Dienstleister mit einer nachgewiesenen Erfolgsbilanz im 3D-Metalldruck, idealerweise mit Erfahrung in der Automobilindustrie oder ähnlichen anspruchsvollen Branchen. Ihr Fachwissen in den Bereichen Designoptimierung für die additive Fertigung, Entwicklung von Prozessparametern und Nachbearbeitungstechniken ist von unschätzbarem Wert. Metal3DP verfügt über jahrzehntelange Erfahrung in der additiven Fertigung von Metallen und bietet umfassende Lösungen.
- Qualitätssicherung und Zertifizierungen: Erkundigen Sie sich nach dem Qualitätsmanagementsystem des Anbieters und allen relevanten Zertifizierungen (z. B. ISO 9001, AS9100 für die Luft- und Raumfahrt). Robuste Qualitätskontrollprozesse, einschließlich Materialtests, prozessbegleitender Überwachung und abschließender Teileprüfung, sind unerlässlich, um die Zuverlässigkeit und Leistung der 3D-gedruckten Radnaben zu gewährleisten.
- Post-Processing-Dienste: Stellen Sie fest, ob der Dienstleister die erforderlichen Nachbearbeitungsdienste intern oder über vertrauenswürdige Partner anbietet. Dazu gehören Wärmebehandlung, Entgraten, CNC-Bearbeitung, Oberflächenveredelung und Beschichtungen. Ein umfassendes Serviceangebot kann den Produktionsprozess rationalisieren.
- Designunterstützung und Beratung: Ein guter Dienstleister sollte in der Lage sein, Designanleitungen und Beratung anzubieten, um Ihr Radnabendesign für die additive Fertigung zu optimieren, wobei Faktoren wie Leichtbau, Funktionsintegration und Druckbarkeit berücksichtigt werden.
- Kommunikation und Projektmanagement: Eine effektive Kommunikation und ein transparentes Projektmanagement sind entscheidend für eine erfolgreiche Zusammenarbeit. Beurteilen Sie die Reaktionsfähigkeit des Anbieters, die Klarheit der Kommunikation und seine Fähigkeit, Ihre Zeitvorgaben und Anforderungen einzuhalten.
- Kosten und Vorlaufzeit: Holen Sie klare und detaillierte Kostenvoranschläge ein, in denen alle anfallenden Kosten, einschließlich Druck, Materialien, Nachbearbeitung und Versand, aufgeführt sind. Informieren Sie sich über die typischen Vorlaufzeiten für die Produktion und stellen Sie sicher, dass diese mit Ihrem Projektplan übereinstimmen.
- Skalierbarkeit und Produktionskapazität: Wenn Sie in Zukunft größere Mengen produzieren wollen, erkundigen Sie sich nach der Skalierbarkeit des Anbieters und seiner Fähigkeit, größere Aufträge zu bearbeiten.
Durch eine sorgfältige Bewertung potenzieller 3D-Metalldruck-Dienstleister auf der Grundlage dieser Faktoren können Sie einen Partner auswählen, der Ihren spezifischen Anforderungen gerecht wird und die erfolgreiche Produktion hochwertiger Aluminiumradnaben gewährleistet.
Kostenfaktoren und Vorlaufzeit
Die Kosten und die Vorlaufzeit für den 3D-Druck von Aluminiumradnaben werden von mehreren Faktoren beeinflusst. Das Verständnis dieser Faktoren kann bei der Budgetierung und der effektiven Planung Ihres Projekts helfen.
Kostenfaktoren:
- Materialkosten: Die Kosten für das Aluminiumpulver (z. B. AlSi10Mg, A7075) sind ein wichtiger Faktor. Speziallegierungen oder kundenspezifische Pulvermischungen sind in der Regel mit höheren Kosten verbunden. Die Menge des für jedes Teil verwendeten Materials, die von der Konstruktion und dem Bedarf an Stützstrukturen beeinflusst wird, wirkt sich ebenfalls auf die Gesamtmaterialkosten aus.
- Druckzeit: Die Dauer des Druckprozesses hängt von der Größe und Komplexität der Radnabe, der verwendeten Schichthöhe und der Ausnutzung des Bauvolumens ab. Längere Druckzeiten führen zu höheren Maschinenbetriebskosten.
- Maschinenkosten und Gemeinkosten: Die Kosten für die 3D-Druckausrüstung, die Wartung, den Energieverbrauch und die Gemeinkosten der Einrichtung werden von den Dienstleistern in ihre Preise einbezogen.
- Nachbearbeitungskosten: Das Ausmaß der erforderlichen Nachbearbeitung (z. B. Wärmebehandlung, Entfernen von Halterungen, maschinelle Bearbeitung, Oberflächenveredelung) wirkt sich erheblich auf die Endkosten pro Teil aus. Komplexere oder zeitaufwändigere Nachbearbeitungsschritte erhöhen die Gesamtkosten.
- Arbeitskosten: Der Arbeitsaufwand für die Optimierung des Designs, die Einrichtung des Drucks, die Bedienung der Maschine, die Nachbearbeitung und die Qualitätskontrolle ist ebenfalls ein Bestandteil der Gesamtkosten.
- Menge und Volumen: Im Allgemeinen sinken die Kosten pro Teil aufgrund von Skaleneffekten, wenn das Produktionsvolumen steigt. Der 3D-Metalldruck kann jedoch auch bei geringen bis mittleren Stückzahlen kosteneffizient sein, insbesondere bei komplexen Geometrien, bei denen die herkömmlichen Werkzeugkosten hoch wären.
- Komplexität des Designs: Kompliziertere Designs, die umfangreiche Stützstrukturen erfordern oder Merkmale aufweisen, die die Druckzeit verlängern, sind in der Regel teurer in der Herstellung.
Vorlaufzeit:
- Entwurf und Optimierung: Die erste Entwurfsphase, einschließlich der Optimierung für die additive Fertigung, kann je nach Komplexität und der Notwendigkeit von Iterationen einige Zeit in Anspruch nehmen.
- Bauzeit: Die tatsächliche Druckdauer ist ein wesentlicher Bestandteil der Vorlaufzeit. Sie wird bestimmt durch die Größe des Teils, das Volumen und die gewählten Druckparameter.
- Nachbearbeitungszeit: Der Zeitaufwand für Nachbearbeitungsschritte kann je nach Komplexität und Anzahl der beteiligten Schritte erheblich variieren. Wärmebehandlungszyklen, Bearbeitungsvorgänge und komplizierte Oberflächenbehandlungen können die Gesamtvorlaufzeit erheblich verlängern.
- Qualitätskontrolle und Inspektion: Bevor die Teile versandt werden können, sind gründliche Qualitätsprüfungen und Inspektionen erforderlich, was die Vorlaufzeit verlängert.
- Versand und Logistik: Der Zeitaufwand für die Verpackung und den Versand der fertigen Teile muss ebenfalls berücksichtigt werden.
Wenn Sie diese Kosten- und Vorlaufzeitfaktoren kennen, können Sie fundierte Gespräche mit potenziellen Dienstleistern für den 3D-Metalldruck führen und die effizienteste Wahl für die Produktion Ihrer Fahrzeugradnaben treffen.
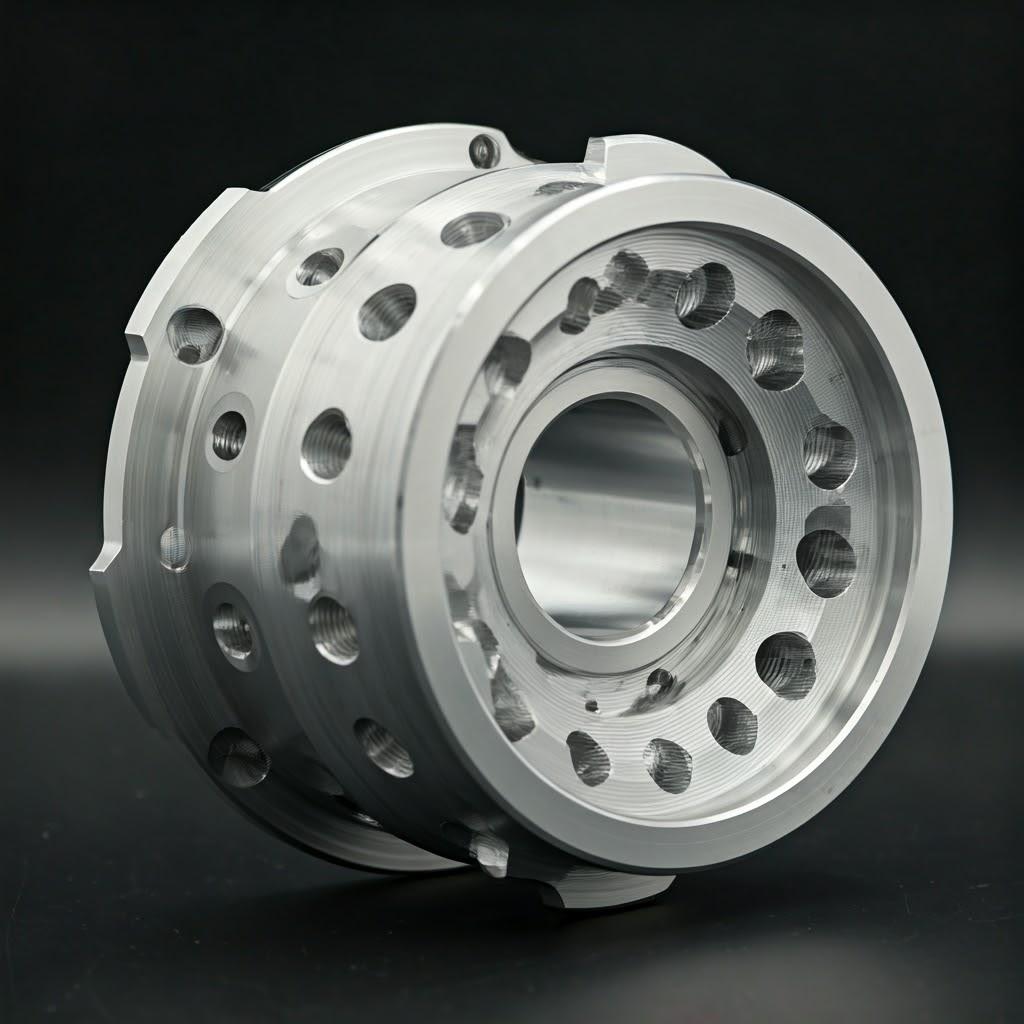
Häufig gestellte Fragen (FAQ)
- Können 3D-gedruckte Aluminiumradnaben die Sicherheitsstandards für Autos erfüllen? Ja, 3D-gedruckte Radnaben aus Aluminium können die strengen Sicherheitsstandards der Automobilindustrie erfüllen, wenn sie aus hochwertigen Materialien wie AlSi10Mg oder A7075, optimierten Designs, kontrollierten Druckverfahren und strengen Nachbearbeitungs- und Prüfverfahren hergestellt werden. Es ist entscheidend, mit erfahrenen Anbietern zusammenzuarbeiten, die sich mit den Materialeigenschaften und der Qualitätskontrolle im Automobilsektor auskennen.
- Sind 3D-gedruckte Metallradnaben leichter als herkömmlich hergestellte? Ja, oft deutlich leichter. Der 3D-Metalldruck ermöglicht eine Optimierung des Designs, z. B. die Optimierung der Topologie und die Integration von Gitterstrukturen, wodurch der Materialverbrauch und das Gesamtgewicht reduziert werden können, ohne die strukturelle Integrität zu beeinträchtigen. Diese Gewichtsreduzierung trägt zu einer verbesserten Fahrzeugleistung und Kraftstoffeffizienz bei.
- Wie hoch ist die typische Lebensdauer einer 3D-gedruckten Aluminiumradnabe? Die Lebensdauer einer 3D-gedruckten Aluminiumradnabe, die mit geeigneten Materialien und Verfahren hergestellt wurde, sollte mit der von herkömmlich hergestellten Aluminiumradnaben vergleichbar sein. Faktoren wie Materialermüdung, Korrosion und die spezifischen Betriebsbedingungen des Fahrzeugs werden die Lebensdauer beeinflussen. Die richtige Materialauswahl, Konstruktionsüberlegungen und Nachbehandlungen (z. B. Beschichtungen) sind für die Gewährleistung einer langfristigen Haltbarkeit von entscheidender Bedeutung.
Schlussfolgerung
Der 3D-Druck von Metall bietet einen neuen Ansatz für das Design und die Herstellung von Radnaben für die Automobilindustrie. Die Möglichkeit, komplexe, leichte Designs mit optimiertem Materialeinsatz zu erstellen, bietet in Verbindung mit schnellem Prototyping und individuellen Anpassungsmöglichkeiten erhebliche Vorteile gegenüber herkömmlichen Fertigungsmethoden. Legierungen wie AlSi10Mg und A7075, die als hochwertige Pulver von Anbietern wie Metall3DPbieten das erforderliche Verhältnis von Festigkeit zu Gewicht und Haltbarkeit für anspruchsvolle Automobilanwendungen.
Zwar müssen Herausforderungen wie das Erreichen enger Toleranzen, das Management der Oberflächenbeschaffenheit und die Sicherstellung konsistenter Materialeigenschaften sorgfältig bedacht werden, doch die Fortschritte in der 3D-Drucktechnologie für Metall und das Know-how erfahrener Dienstleister überwinden diese Hürden kontinuierlich. Wenn Automobilingenieure und Beschaffungsmanager die Designüberlegungen, Nachbearbeitungsanforderungen und die Auswahl des richtigen Partners verstehen, können sie die Möglichkeiten der additiven Fertigung von Metall nutzen, um innovative, leistungsstarke Aluminiumradnaben zu entwickeln, die zur nächsten Fahrzeuggeneration beitragen. Kontaktieren Sie Metal3DP noch heute um zu erfahren, wie ihre umfassenden Metall-AM-Lösungen die Ziele Ihres Unternehmens im Bereich der additiven Fertigung unterstützen können.
Teilen auf
MET3DP Technology Co., LTD ist ein führender Anbieter von additiven Fertigungslösungen mit Hauptsitz in Qingdao, China. Unser Unternehmen ist spezialisiert auf 3D-Druckgeräte und Hochleistungsmetallpulver für industrielle Anwendungen.
Fragen Sie an, um den besten Preis und eine maßgeschneiderte Lösung für Ihr Unternehmen zu erhalten!
Verwandte Artikel
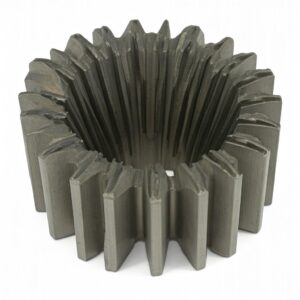
Hochleistungs-Düsenschaufelsegmente: Revolutionierung der Turbineneffizienz mit 3D-Metalldruck
Mehr lesen "Über Met3DP
Aktuelles Update
Unser Produkt
KONTAKT US
Haben Sie Fragen? Senden Sie uns jetzt eine Nachricht! Wir werden Ihre Anfrage mit einem ganzen Team nach Erhalt Ihrer Nachricht bearbeiten.
Holen Sie sich Metal3DP's
Produkt-Broschüre
Erhalten Sie die neuesten Produkte und Preislisten