3D-gedruckte Automobilscharniere für mehr Stabilität und Gewichtseinsparungen
Inhaltsübersicht
Revolutionierung des Automobildesigns: Leistungsstarke Scharniere durch 3D-Druck von Metall
Die Automobilindustrie befindet sich in ständiger Entwicklung, angetrieben durch den unablässigen Druck, die Leistung zu steigern, die Kraftstoffeffizienz (oder die Batteriereichweite bei Elektrofahrzeugen) zu verbessern und immer strengere Sicherheits- und Umweltvorschriften zu erfüllen. Das Konzept des Leichtbaus - die Verringerung der Gesamtmasse eines Fahrzeugs ohne Beeinträchtigung der strukturellen Integrität oder Sicherheit - ist von zentraler Bedeutung, um diese Ziele zu erreichen. Jedes eingesparte Kilogramm bringt greifbare Vorteile mit sich, sei es eine schnellere Beschleunigung, ein besseres Fahrverhalten, eine größere Reichweite oder geringere Emissionen. Während großen Komponenten wie dem Fahrgestell und den Karosserieblechen große Aufmerksamkeit geschenkt wird, ist das kumulative Gewichtseinsparungspotenzial kleinerer, oft übersehener Komponenten wie Scharniere beträchtlich, insbesondere in den Segmenten der Hochleistungs-, Luxus- und Elektrofahrzeuge, in denen Innovation und Optimierung an erster Stelle stehen.
Hochleistungsscharniere für Kraftfahrzeuge sind weit mehr als nur einfache Drehpunkte; sie sind entscheidende Strukturkomponenten, die für die zuverlässige und sichere Funktion von Türen, Motorhauben, Kofferräumen (Heckklappen) und zunehmend auch von komplexen beweglichen Elementen wie aktiven aerodynamischen Flügeln oder ausfahrbaren Spoilern verantwortlich sind. Diese Bauteile müssen während der gesamten Lebensdauer des Fahrzeugs erheblichen statischen und dynamischen Belastungen standhalten, unzählige Öffnungs- und Schließzyklen überstehen, Umwelteinflüssen wie Korrosion widerstehen und jedes Mal reibungslos und präzise funktionieren. Bei Hochleistungsfahrzeugen kann ein Scharnierversagen katastrophale Folgen haben und nicht nur den Komfort, sondern möglicherweise auch die Sicherheit und die Fahrzeugdynamik beeinträchtigen. Bei Luxusfahrzeugen tragen Haptik und Klang eines Scharniers wesentlich zur Qualitätswahrnehmung bei. Bei Elektrofahrzeugen ist die Minimierung des Gewichts aller Komponenten, einschließlich der Scharniere, entscheidend für die Maximierung der Batteriereichweite - ein wichtiger Kauffaktor für die Verbraucher.
Traditionell werden Scharniere für Kraftfahrzeuge mit Methoden wie Stanzen, Gießen oder Schmieden hergestellt, wobei in der Regel Stahl oder herkömmliche Aluminiumlegierungen verwendet werden. Diese Methoden sind zwar robust und kostengünstig für die Massenproduktion, führen aber oft zu Teilen, die schwerer als nötig sind und die Komplexität der Konstruktion erheblich einschränken. Die Werkzeugkosten für das Stanzen und Schmieden sind beträchtlich, so dass sie sich weniger für Kleinserien oder kundenspezifische Anwendungen eignen. Das Gießen bietet zwar mehr geometrische Freiheit, kann aber unter geringeren Festigkeitseigenschaften oder Porositätsproblemen leiden, wenn es nicht sorgfältig kontrolliert wird. Die spanabhebende Bearbeitung von Knüppeln bietet Präzision und Festigkeit, verursacht aber einen erheblichen Materialabfall und kann zeitaufwändig sein.
Der Einstieg in die additive Fertigung von Metall (AM), allgemein bekannt als Metall 3D-Druck. Diese transformative Technologie baut Teile Schicht für Schicht direkt aus einem digitalen Modell unter Verwendung von Hochleistungsmetallpulvern auf. Für Hochleistungs-Automobilscharniere bietet die Metall-AM einen Paradigmenwechsel, der Möglichkeiten eröffnet, die mit konventioneller Fertigung bisher unerreichbar waren. Es ermöglicht den Ingenieuren, sich von den durch herkömmliche Methoden auferlegten Designbeschränkungen zu lösen und hoch optimierte, leichte Strukturen mit komplizierten Geometrien zu schaffen, die genau auf ihre funktionalen Anforderungen zugeschnitten sind. Technologien wie das Selektive Laserschmelzen (SLM) und das Direkte Metall-Lasersintern (DMLS), Formen des Laser Powder Bed Fusion (L-PBF), nutzen leistungsstarke Laser, um feine Metallpulver Schicht für Schicht zu verschmelzen und dichte, hochfeste Metallteile zu erzeugen. Diese Fähigkeit ist besonders wichtig für die Herstellung von Automobilscharnieren, die die anspruchsvollen Anforderungen von Hochleistungsfahrzeugen, Motorsportanwendungen, Elektrofahrzeugen und Luxusautos erfüllen. Die Fähigkeit, mehrere Komponenten in einem einzigen gedruckten Teil zu konsolidieren, Strukturen mithilfe von Topologieoptimierung zu optimieren und Designs schnell zu prototypisieren und zu iterieren, macht 3D-Druck von Metall eine zunehmend attraktive Lösung für vorausschauende Automobilingenieure und Beschaffungsmanager, die einen Wettbewerbsvorteil durch fortschrittliche Fertigung suchen. Unternehmen, die sich auf additive Fertigungslösungen spezialisiert haben, wie Met3dp, bieten die notwendige Ausrüstung, hochwertige Materialien und das Fachwissen, um diese Technologie effektiv für die Herstellung robuster, leichter und innovativer Automobilkomponenten, einschließlich Scharnieren der nächsten Generation, zu nutzen.
Wichtige Anwendungen & Funktionen: Wo 3D-gedruckte Scharniere in der Automobilindustrie überzeugen
Der Anwendungsbereich für 3D-gedruckte Hochleistungs-Automobilscharniere geht weit über das Standard-Türscharnier hinaus und berührt zahlreiche Bereiche, in denen Festigkeit, Gewicht, Präzision und Designkomplexität entscheidende Faktoren sind. Die additive Fertigung ermöglicht maßgeschneiderte Lösungen, die spezifische, oft anspruchsvolle funktionale Anforderungen in verschiedenen Fahrzeugsegmenten erfüllen.
- Türscharniere: Dies ist vielleicht die offensichtlichste Anwendung, aber auch hier bietet AM erhebliche Vorteile.
- Standard-Türen: Die Gewichtsreduzierung von Standard-Türscharnieren trägt erheblich zur Verringerung der Gesamtmasse des Fahrzeugs bei, insbesondere bei vier oder mehr Türen. Optimierte Konstruktionen können die Festigkeit beibehalten oder sogar erhöhen und gleichzeitig Gewicht einsparen. Dies ist entscheidend für die Verbesserung des Kraftstoffverbrauchs von Fahrzeugen mit Verbrennungsmotor (ICE) und die Erhöhung der Reichweite von Elektrofahrzeugen.
- Spezialtüren (Flügeltür, Scherentür, Selbstmördertür): Diese komplexen Mechanismen erfordern oft eine komplizierte Kinematik, hohe Festigkeit, um potenziell schwerere Türen zu tragen, und einzigartige Verpackungslösungen. AM ermöglicht die Entwicklung maßgeschneiderter Scharniersysteme mit komplexen Geometrien, die sich nahtlos in die Karosseriestruktur des Fahrzeugs einfügen, was mit Standardscharnieren von der Stange oder traditionell hergestellten Scharnieren nur schwer oder gar nicht zu erreichen ist. Die Möglichkeit, organische, lastpfadoptimierte Formen zu schaffen, ist ein großer Vorteil. Fahrzeugbauer und Hersteller von Luxus- und Hochleistungsfahrzeugen mit kleinen Stückzahlen finden AM hier besonders wertvoll.
- Scharniere für die Motorhaube: Motorhauben, insbesondere bei leistungsstarken Autos oder Lastwagen, können groß und relativ schwer sein. Ihre Scharniere müssen dieses Gewicht sicher tragen, ein leichtes Öffnen und Schließen ermöglichen und oft Sicherheitsverriegelungsmechanismen enthalten. mit Hilfe des 3D-Drucks können starke und dennoch leichte Motorhaubenscharniere hergestellt werden, wobei durch geschickte Konstruktion Funktionen wie Federunterstützungsmechanismen oder Soft-Close-Funktionen in den Scharnierkörper selbst integriert werden können. Eine Gewichtsreduzierung im vorderen Bereich des Fahrzeugs wirkt sich auch positiv auf die Fahrdynamik aus.
- Scharniere Kofferraum/Heckklappe: Ähnlich wie Motorhauben benötigen auch Kofferräume und Heckklappen robuste Scharniere. Bei Geländewagen und Schräghecklimousinen sorgen elektrisch betriebene Heckklappen für zusätzliche Komplexität und erfordern Scharniere, die den von den Aktuatoren ausgeübten Kräften standhalten und gleichzeitig leicht sind. AM ermöglicht die Konstruktion kompakter, stabiler Scharniere, die für die Unterbringung in engen Räumen optimiert sind und Befestigungspunkte für Streben und Aktuatoren integrieren können. Bei leistungsstarken Fahrzeugen trägt die Verkleinerung des Hecks zu einer besseren Gewichtsverteilung bei.
- Handschuhfach & Scharniere der Mittelkonsole: Scharniere in diesen Bereichen sind zwar weniger belastbar, tragen aber zur wahrgenommenen Qualität des Fahrzeuginnenraums bei. AM kann Scharniere mit komplexer Kinematik für eine sanfte, gedämpfte Bewegung herstellen, möglicherweise unter Verwendung fortschrittlicher Materialien oder integrierter Funktionen, die bei einfachen gestanzten Metall- oder Kunststoffscharnieren nicht möglich sind, und so das Gefühl von Luxus verstärken.
- Klappbare Sitzscharniere: Vor allem in Vans, Geländewagen und Transportern beinhalten Klappsitzmechanismen komplexe Scharniere und Verriegelungen, die aus Sicherheits- und Komfortgründen sowohl stabil als auch zuverlässig sein müssen. AM ermöglicht die Konsolidierung von Teilen, wodurch die Anzahl der einzelnen Komponenten in einem Sitzklappmechanismus reduziert wird, was wiederum das Gewicht, die Montagezeit und potenzielle Fehlerquellen verringert. Festigkeit und Langlebigkeit sind hier das A und O.
- Aktive aerodynamische Elemente: Dies ist ein schnell wachsender Bereich bei Hochleistungsfahrzeugen. Scharniere und Aktuatoren für aktive Spoiler, Heckflügel, Frontsplitter oder Kühlklappen müssen leicht, stabil und in der Lage sein, sich unter erheblichen aerodynamischen Belastungen präzise und schnell zu bewegen. Metall-AM ist ideal geeignet, um die komplexen, aerodynamisch effizienten und hochbelasteten Scharnierkomponenten herzustellen, die für diese Systeme erforderlich sind. Die Optimierung der Topologie kann maximale Steifigkeit und Festigkeit bei minimalem Gewicht gewährleisten.
Funktionale Anforderungen & Begünstigte Branchen:
Unabhängig von der spezifischen Anwendung müssen 3D-gedruckte Automobilscharniere strenge funktionale Anforderungen erfüllen:
- Tragfähigkeit: Sie müssen dem statischen Gewicht und den dynamischen Kräften während des Betriebs und möglichen Aufprallszenarien standhalten. Die FEA (Finite-Elemente-Analyse) ist in der Entwurfsphase von entscheidender Bedeutung.
- Dauerhaftigkeit & Ermüdungslebensdauer: Sie müssen Zehntausende, wenn nicht Hunderttausende von Zyklen ohne Ausfall oder übermäßigen Verschleiß überstehen. Die Wahl des Materials (wie A7075) und die Nachbearbeitung (Wärmebehandlung) sind entscheidend.
- Korrosionsbeständigkeit: Da sie Feuchtigkeit, Streusalz und unterschiedlichen Temperaturen ausgesetzt sind, ist eine gute Korrosionsbeständigkeit erforderlich. Die Materialauswahl (AlSi10Mg bietet eine gute Beständigkeit) und die Oberflächenbehandlung (Eloxieren, Beschichtungen) sind wichtig.
- Leichtgängig & Präzise Bedienung: Die Kinematik der Scharniere muss genau sein, um eine korrekte Ausrichtung der Türen/Paneele, eine gute Abdichtung und ein gutes Gefühl zu gewährleisten. Toleranzen und Oberflächengüte sind entscheidend.
- Verpackung & Integration: Scharniere müssen oft in enge Räume passen und sich nahtlos in die umgebenden Karosseriestrukturen und Mechanismen integrieren. Die Designfreiheit von AM’ ist hier ein großer Vorteil.
Zu den Branchen und Akteuren, die von der Einführung von 3D-gedruckten Scharnieren erheblich profitieren werden, gehören:
- Originalausrüstungshersteller (OEMs): Vor allem diejenigen, die sich auf Leistung, Luxus und Elektrofahrzeuge konzentrieren und Leichtbau, Differenzierung und fortschrittliche Funktionen anstreben.
- Tier-1-Lieferanten: Unternehmen, die komplette Modulbaugruppen (z. B. Türen, Sitze, Verschlüsse) entwickeln und liefern, können AM nutzen, um OEMs innovative, wertsteigernde Lösungen anzubieten.
- Motorsport-Teams: Hier bieten Gewichtsreduzierung und die schnelle Entwicklung maßgeschneiderter, hochfester Komponenten einen direkten Wettbewerbsvorteil.
- Custom Car Builders & Tuner: Ermöglicht die Schaffung einzigartiger, hochwertiger Scharnierlösungen für maßgeschneiderte Fahrzeugprojekte.
- Lieferanten für Aftermarket-Leistungsteile: Wir bieten leichte, hochfeste Scharnier-Upgrades für gängige Fahrzeugmodelle an.
- Hersteller von Spezialfahrzeugen: Hersteller von gepanzerten Fahrzeugen, Freizeitfahrzeugen oder Industriefahrzeugen, bei denen kundenspezifische, dauerhafte Scharnierlösungen benötigt werden können.
Durch die Zusammenarbeit mit sachkundigen Metall-AM-Dienstleistern und die Verwendung fortschrittlicher Materialien können diese Branchenakteure den 3D-Druck effektiv nutzen, um hochwertige Scharnierkomponenten für die Automobilindustrie herzustellen. Beschaffungsmanager, die zuverlässige lieferanten für kundenspezifische Automobilscharniere oder zulieferer für die Automobilindustrie die auf fortschrittliche Fertigung spezialisiert sind, sollten sich nach Anbietern umsehen, die nachweislich über Erfahrung in 3D-Druck von Metall für die Automobilindustrie Anwendungen.
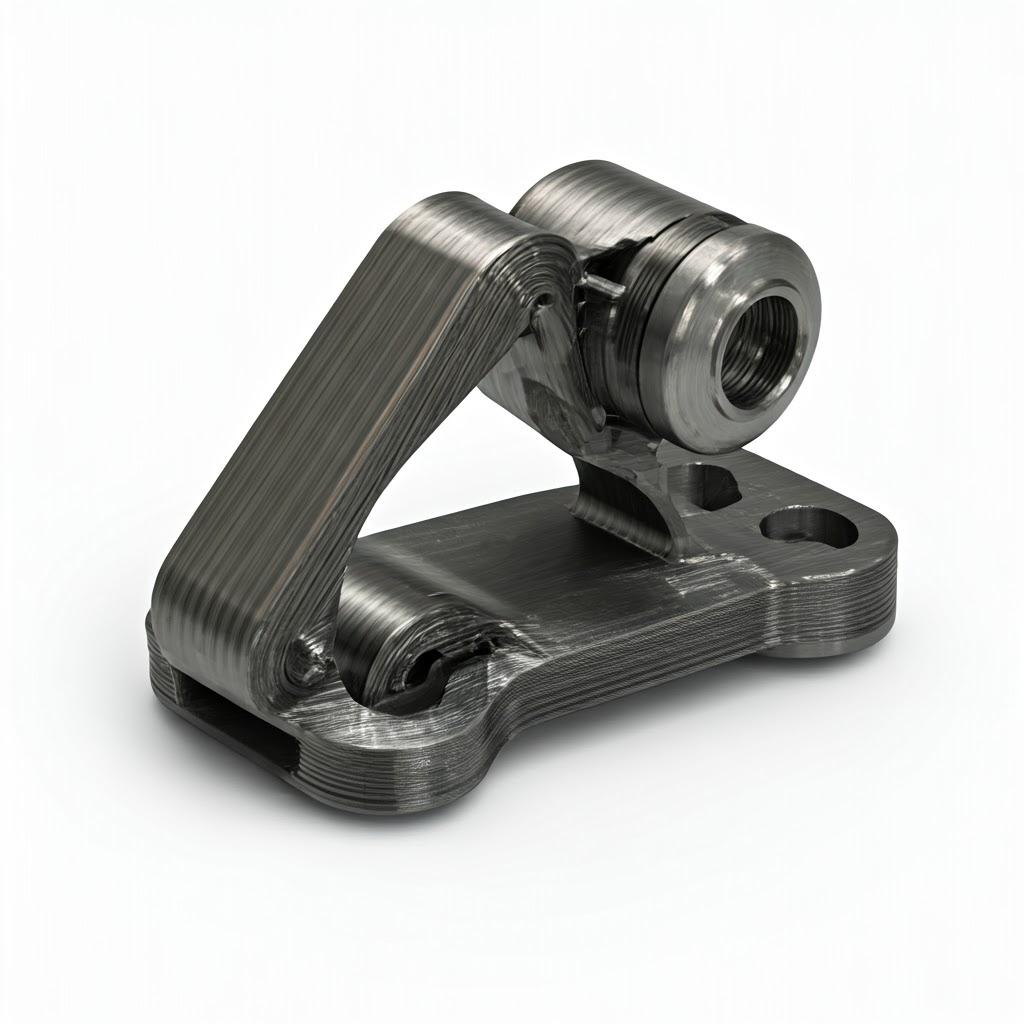
Der Additiv-Vorteil: Warum Metall-3D-Druck für Automobilscharniere?
Herkömmliche Fertigungsmethoden haben sich in der Automobilindustrie zwar seit Jahrzehnten bewährt, weisen jedoch inhärente Grenzen auf, insbesondere bei der Herstellung von Hochleistungsscharnieren, bei denen Komplexität, individuelle Anpassung und Gewicht entscheidend sind. Die additive Fertigung von Metall (AM) bietet eine Reihe von Vorteilen, die diese Einschränkungen direkt angehen und sie in vielen Szenarien als überlegene Wahl für die Entwicklung und Produktion der nächsten Generation von Scharnieren positionieren.
Vergleich mit traditionellen Methoden:
- Stanzen: Hervorragend geeignet für die Großserienproduktion von relativ einfachen Scharnierteilen auf Blechbasis. Es erfordert jedoch extrem teure Werkzeuge (Matrizen), bietet eine begrenzte geometrische Komplexität (hauptsächlich 2,5D-Formen) und ist aufgrund der Werkzeugkosten und Vorlaufzeiten schlecht für kleine bis mittlere Stückzahlen oder Designwiederholungen geeignet. Auch die Materialauswahl ist etwas eingeschränkt.
- Gießen: Ermöglicht komplexere Formen als das Stanzen und kann bei moderaten Stückzahlen kostengünstig sein. Um eine hohe Festigkeit zu erreichen, sind jedoch oft spezielle Legierungen und Verfahren erforderlich, die Porosität kann die strukturelle Integrität beeinträchtigen, und für Präzisionsmerkmale ist in der Regel eine Nachbearbeitung erforderlich. Die Herstellung von Werkzeugen (Gussformen) stellt immer noch eine erhebliche Vorabinvestition und Vorlaufzeit dar. Es kann eine Herausforderung sein, die mit AM möglichen dünnen Wände und komplizierten Details zu erreichen.
- Schmieden: Erzeugt Teile mit ausgezeichneten Festigkeits- und Ermüdungseigenschaften aufgrund der Verfeinerung der Kornstruktur. Allerdings ist das Schmieden im Vergleich zum Gießen oder AM in der Regel auf einfachere Geometrien beschränkt, erfordert teure Werkzeuge und erfordert oft eine erhebliche Nachbearbeitung, was zu Materialabfall führt. Am besten geeignet für hochbelastete, einfachere Scharnierkomponenten in sehr hohen Stückzahlen.
- CNC-Bearbeitung (aus Billet): Bietet hohe Präzision und hervorragende Materialeigenschaften (ausgehend vom Vollmaterial). Allerdings entsteht dabei ein erheblicher Materialabfall (das Verhältnis zwischen Einkauf und Fertigung kann schlecht sein), es kann bei komplexen Geometrien langsam sein und wird bei komplizierten Teilen oder großen Produktionsserien aufgrund von Maschinenzeit und Werkzeugverschleiß teuer.
Vorteile der additiven Metallfertigung für Scharniere:
Metall-AM, insbesondere L-PBF-Verfahren wie SLM/DMLS, überwindet viele dieser Hürden:
- Unerreichte Designfreiheit: Dies ist wohl der bedeutendste Vorteil. AM baut Teile Schicht für Schicht auf und befreit die Konstrukteure von den Zwängen der Formen, Gesenke oder des Werkzeugzugangs. Dies ermöglicht:
- Komplexe Geometrien: Herstellung komplizierter innerer Strukturen, konformer Kanäle (z. B. für die Schmierung oder integrierte Verdrahtung) und organischer Formen, die auf herkömmliche Weise nicht hergestellt werden können.
- Topologie-Optimierung: Mithilfe von Software werden Lastpfade analysiert und Material in unkritischen Bereichen entfernt. Das Ergebnis sind Scharniere, die deutlich leichter sind (oft 30-60 % Gewichtsreduzierung) und gleichzeitig die Steifigkeit und Festigkeit genau dort beibehalten oder sogar erhöhen, wo sie benötigt werden.
- Gitterförmige Strukturen: Der Einbau interner Gitterstrukturen führt zu einer weiteren Gewichts- und Materialeinsparung und bietet gleichzeitig eine maßgeschneiderte strukturelle Unterstützung.
- Signifikante Gewichtsreduzierung: In direktem Zusammenhang mit der Designfreiheit zeichnet sich AM durch die Schaffung leichter Strukturen aus. Topologieoptimierung und Gitterstrukturen ermöglichen eine radikale Verringerung der Masse im Vergleich zu massiven Teilen, die durch Gießen, Schmieden oder maschinelle Bearbeitung hergestellt werden, und tragen so direkt zur Effizienz und Leistung von Fahrzeugen bei.
- Teil Konsolidierung: Komplexe Scharnierbaugruppen bestehen oft aus mehreren Einzelteilen (Halterungen, Arme, Stifte, Befestigungen), die separat hergestellt und dann zusammengebaut werden müssen. AM ermöglicht es den Konstrukteuren, mehrere Funktionen in einem einzigen, monolithisch gedruckten Teil zusammenzufassen. Dies reduziert die Anzahl der Teile, vereinfacht die Montage, minimiert Toleranzprobleme, senkt die Arbeitskosten für die Montage und eliminiert potenzielle Fehlerstellen an Gelenken oder Befestigungselementen.
- Rapid Prototyping und Iteration: Die Erstellung physischer Prototypen neuer Scharnierdesigns ist mit AM wesentlich schneller als das Warten auf herkömmliche Werkzeuge. Ingenieure können Scharnierprototypen innerhalb von Tagen statt Wochen oder Monaten entwerfen, drucken, testen und verfeinern. Dies beschleunigt den Entwicklungszyklus, ermöglicht mehr Designuntersuchungen und verringert das Risiko, das mit einer zu frühen Festlegung auf teure Werkzeuge verbunden ist. Diese Agilität ist von unschätzbarem Wert für rapid Prototyping von Automobilscharnieren.
- Materialeffizienz (Near-Net-Shape): Bei AM-Verfahren wie L-PBF wird in der Regel nur das Material verwendet, das für die Herstellung des Teils und seiner Halterungen benötigt wird, was im Vergleich zur subtraktiven Fertigung (CNC-Bearbeitung) zu deutlich weniger Abfall führt. Zwar ist das Recycling von Pulver unerlässlich, doch ist das Verhältnis zwischen Anschaffung und Verbrauch in der Regel viel besser, was das Verfahren bei teuren Legierungen nachhaltiger und kostengünstiger macht.
- Tragfähige On-Demand & Kleinserienproduktion: Da keine physischen Werkzeuge mehr benötigt werden, ist AM für die Herstellung von Kleinserien spezieller Scharniere, Sonderanfertigungen für Spezialfahrzeuge oder Teile für den Ersatzteilmarkt wirtschaftlich. Hersteller können Scharniere produzieren abrufbar unterdadurch werden die Lagerkosten gesenkt und Strategien zur Massenanpassung ermöglicht. Dies ist ideal für kleinserienfertigung von Automobilscharnieren.
- Werkzeuglose Fertigung: AM erfordert keine teilespezifischen Werkzeuge (Gussformen, Matrizen). Die Entwürfe werden direkt vom CAD auf die Maschine übertragen, wodurch sich die Vorlaufzeiten für die ersten Teile drastisch verkürzen und die Werkzeugkosten entfallen, die bei herkömmlichen Verfahren zwischen Tausenden und Hunderttausenden von Dollar liegen können.
Auch wenn AM nicht für jedes Scharnier in jedem Fahrzeug die traditionellen Methoden ersetzen kann (vor allem nicht für Standardscharniere in hochvolumigen, kostensensitiven Modellen), so machen seine Vorteile es doch zur klaren Wahl für Anwendungen, die maximale Leistung, minimales Gewicht, komplexe Funktionalität oder schnelle Anpassung erfordern. Die vorteile der additiven Fertigung in der Automobilindustrie sind bei Hochleistungsscharnieren besonders ausgeprägt und ermöglichen Konstruktionen und Leistungsniveaus, die bisher unerreichbar waren. Unternehmen, die nach produktion von Automobilteilen auf Abruf oder metall AM vs. Guss vergleiche für komplexe Bauteile werden zwingende Gründe finden, additive Lösungen zu erforschen.
Werkstoff-Fokus: A7075 & AlSi10Mg-Aluminiumlegierungen für anspruchsvolle Scharnieranwendungen
Die Leistung eines 3D-gedruckten Kfz-Scharniers wird im Wesentlichen durch das verwendete Material bestimmt. Zwar können verschiedene Metalle mit Hilfe der additiven Fertigung verarbeitet werden, doch werden für Automobilanwendungen häufig Aluminiumlegierungen gewählt, da sie ein hervorragendes Gleichgewicht zwischen geringer Dichte, guten mechanischen Eigenschaften und Korrosionsbeständigkeit bieten. Für Hochleistungsscharniere, die eine überragende Festigkeit oder ein Gleichgewicht der Eigenschaften erfordern, sind zwei Legierungen im Bereich des Laser Powder Bed Fusion (L-PBF) hervorzuheben: A7075 (eine Aluminium-Zink-Legierung) und AlSi10Mg (eine Aluminium-Silizium-Magnesium-Legierung). Die Auswahl des richtigen Materials ist entscheidend und hängt stark von den spezifischen Belastungsanforderungen, der Betriebsumgebung und den Leistungszielen des Scharniers ab.
A7075-Aluminiumlegierung:
A7075 ist in der Luft- und Raumfahrt sowie in der Hochleistungs-Automobilindustrie für sein außergewöhnliches Verhältnis von Festigkeit zu Gewicht bekannt, das oft mit dem einiger anderer Stähle vergleichbar ist, jedoch bei etwa einem Drittel der Dichte. Es handelt sich um eine Aluminiumlegierung, die hauptsächlich mit Zink sowie kleineren Mengen von Magnesium und Kupfer legiert ist.
- Wichtige Eigenschaften:
- Hohe Festigkeit: Weist eine sehr hohe Streck- und Zugfestigkeit auf, insbesondere nach einer geeigneten Wärmebehandlung (typischerweise im Zustand T6). Dadurch ist es für Scharniere geeignet, die erheblichen statischen und dynamischen Belastungen ausgesetzt sind.
- Gute Ermüdungsfestigkeit: Widersteht Versagen bei zyklischer Belastung, was für Bauteile wie Tür- oder Motorhaubenscharniere, die wiederholt geöffnet und geschlossen werden, entscheidend ist.
- Gute Bearbeitbarkeit: Kann nach dem Druck bearbeitet werden, um enge Toleranzen auf kritischen Oberflächen zu erreichen.
- Geringere Korrosionsbeständigkeit (im Vergleich zu anderen Al-Legierungen): Sie sind anfälliger für Korrosion, insbesondere Spannungsrisskorrosion, wenn sie nicht ordnungsgemäß geschützt sind (z. B. durch Eloxieren oder Lackieren).
- Schweißeignung: Wird im Allgemeinen als schlecht zum Schweißen geeignet angesehen.
- Typische Automobilanwendungen (Traditionell & AM): Hochbeanspruchte Strukturkomponenten, Aufhängungsteile, Fahrwerkselemente und Anwendungen, bei denen es auf maximale Festigkeit bei minimalem Gewicht ankommt. In AM wird es für tragende Scharniere im Motorsport, für Hochleistungsfahrzeuge oder sicherheitskritische Anwendungen eingesetzt.
- Überlegungen zur AM-Verarbeitung: Das Drucken von A7075 mittels L-PBF kann eine Herausforderung darstellen, da das Pulver während der schnellen Aufheiz- und Abkühlzyklen des Prozesses zu Heißrissen neigt. Um dichte, rissfreie Teile zu erhalten, sind sorgfältig kontrollierte Prozessparameter, spezielle Maschinenkapazitäten und häufig spezifische Pulvereigenschaften erforderlich. Eine Wärmebehandlung nach dem Druck (Lösungsglühen, Abschrecken und Aushärten - T6-Temperierung) ist unerlässlich, um das volle Festigkeitspotenzial des Materials zu entwickeln. Die Suche nach einem A7075 3D-Druck-Dienstleistung mit nachgewiesener Erfahrung in der Verarbeitung dieser Legierung ist entscheidend.
AlSi10Mg-Aluminiumlegierung:
AlSi10Mg ist eine der am häufigsten verwendeten Aluminiumlegierungen in der additiven Fertigung von Metallen, insbesondere L-PBF. Es handelt sich im Wesentlichen um eine für AM angepasste Gusslegierung, die für ihre hervorragende Druckbarkeit und ausgewogenen Eigenschaften bekannt ist.
- Wichtige Eigenschaften:
- Gute Festigkeit & Härte: Bietet eine gute Kombination aus Festigkeit und Härte und eignet sich für viele strukturelle Anwendungen in der Automobilindustrie, wenngleich die Festigkeit in der Regel geringer ist als bei optimal wärmebehandeltem A7075.
- Ausgezeichnete Druckbarkeit: Relativ leicht über L-PBF zu verarbeiten, weniger rissanfällig als hochfeste Legierungen wie A7075, was die zuverlässige Herstellung komplexer Geometrien ermöglicht.
- Gute Korrosionsbeständigkeit: Bietet eine bessere inhärente Korrosionsbeständigkeit als A7075.
- Gute thermische Eigenschaften: Geeignet für Anwendungen, die mäßigen Temperaturschwankungen ausgesetzt sind.
- Gut schweißbar: Kann leichter geschweißt werden als A7075.
- Gemeinsame AM-Anwendungen: Weit verbreitet für Motorkomponenten (Kolben, Blöcke - wenn auch weniger häufig für Scharniere), Wärmetauscher, Gehäuse, Halterungen und allgemeine Strukturkomponenten, bei denen ein ausgewogenes Verhältnis zwischen Druckbarkeit, Festigkeit und Gewicht erforderlich ist. Es ist ein Arbeitspferd Legierung für viele AlSi10Mg Automobilzulieferer.
- Überlegungen zur AM-Verarbeitung: Obwohl es einfacher zu drucken ist als A7075, erfordert das Erreichen optimaler mechanischer Eigenschaften immer noch eine sorgfältige Kontrolle der Parameter und in der Regel eine Wärmebehandlung nach dem Druck (Spannungsabbau und/oder Alterung, ähnlich wie bei T6, aber auf den Si-Gehalt zugeschnitten), um die Festigkeit und Duktilität zu maximieren.
Vergleichende Analyse für Scharnieranwendungen:
Merkmal | A7075 | AlSi10Mg | Überlegungen zu Scharnieren |
---|---|---|---|
Stärke | Sehr hoch (nach T6-Behandlung) | Gut bis Hoch (nach der Wärmebehandlung) | Wählen Sie A7075 für maximale Belastbarkeit oder extreme Ermüdungsanforderungen. AlSi10Mg ist für viele Standard-/Mittellastscharniere ausreichend. |
Gewicht | Niedrige Dichte | Niedrige Dichte (etwas niedriger als A7075) | Beide bieten erhebliche Gewichtseinsparungen gegenüber Stahl. AlSi10Mg hat einen leichten Vorteil bei der Dichte. |
Druckbarkeit | Herausfordernd (erfordert Fachwissen) | Ausgezeichnet (etablierter Prozess) | AlSi10Mg ermöglicht im Allgemeinen einen einfacheren, potenziell schnelleren und zuverlässigeren Druck. |
Korrosionsbeständigkeit. | Mäßig (erfordert Schutz) | Gut | AlSi10Mg erfordert möglicherweise eine weniger aggressive Oberflächenbehandlung für den Korrosionsschutz. |
Ermüdungsfestigkeit | Gut | Mäßig bis gut | A7075 bietet in der Regel bessere Ermüdungseigenschaften bei hohen Belastungszyklen. |
Kosten | Höher (Pulver & Komplexität der Verarbeitung) | Mäßig | AlSi10Mg ist aufgrund der einfacheren Verarbeitung und der größeren Verfügbarkeit oft kostengünstiger. |
Nachbearbeitung | T6 Wärmebehandlung unerlässlich für die Festigkeit | Empfohlene Wärmebehandlung für Eigenschaften | Beide erfordern ähnliche Schritte (Entfernen der Auflage, Bearbeitung), aber die Wärmebehandlung nach A7075 ist entscheidend. |
In Blätter exportieren
Die Bedeutung der Puderqualität:
Unabhängig von der gewählten Legierung ist die Qualität des Metallpulvers, das im L-PBF-Verfahren verwendet wird, von entscheidender Bedeutung für die Herstellung hochwertiger und zuverlässiger Scharniere. Die Pulverpartikel müssen sein:
- Sphärisch: Gewährleistet eine gute Fließfähigkeit des Pulvers im Wiederbeschichtungsmechanismus des Druckers und eine dichte Packung im Pulverbett, was zu einem gleichmäßigen Schmelzen und einer geringeren Porosität führt.
- Kontrollierte Partikelgrößenverteilung (PSD): Für eine optimale Packungsdichte und ein optimales Schmelzverhalten bei einem bestimmten Satz von Laserparametern ist eine bestimmte PSD erforderlich.
- Hohe Reinheit: Frei von Verunreinigungen, die die mechanischen Eigenschaften beeinträchtigen oder Defekte im fertigen Teil verursachen könnten.
- Niedriger Feuchtigkeits- und Sauerstoffgehalt: Verhindert Oxidation und Porosität während des Hochtemperaturdruckverfahrens.
Dies ist der Ort, an dem spezialisierte lieferanten von 3D-Druckpulver aus Metall eine entscheidende Rolle spielen. Unternehmen wie Met3dpunter Verwendung fortschrittlicher Pulverherstellungstechniken wie branchenführende Technologien zur Gaszerstäubung und zum Plasma-Rotations-Elektroden-Verfahren (PREP)sind wichtige Partner. Die Fähigkeit von Met3dp’, hochwertige, kugelförmige Metallpulver zu erforschen und herzustellen, einschließlich Aluminiumlegierungen, die für AM optimiert sind, stellt sicher, dass Hersteller Zugang zu den konsistenten, leistungsstarken Materialien haben, die für die zuverlässige Herstellung anspruchsvoller Komponenten wie Automobilscharniere erforderlich sind. Die Konzentration auf einzigartige Düsen- und Gasströmungsdesigns bei der Gaszerstäubung führt zu Pulvern mit der hohen Sphärizität und Fließfähigkeit, die für den erfolgreichen L-PBF-Druck von Legierungen wie A7075 und AlSi10Mg entscheidend sind. Die Zusammenarbeit mit einem Anbieter wie Met3dp, der sowohl die Pulverherstellung als auch den Druckprozess kontrolliert, bietet einen bedeutenden Vorteil bei der Sicherstellung einer durchgängigen Qualität und Leistung für kritische Automobilanwendungen. Beschaffungsmanager, die eine aluminiumlegierungen AM strategie sollte Lieferanten mit nachweislichem Know-how in der Pulvermetallurgie und -verarbeitung den Vorzug geben.
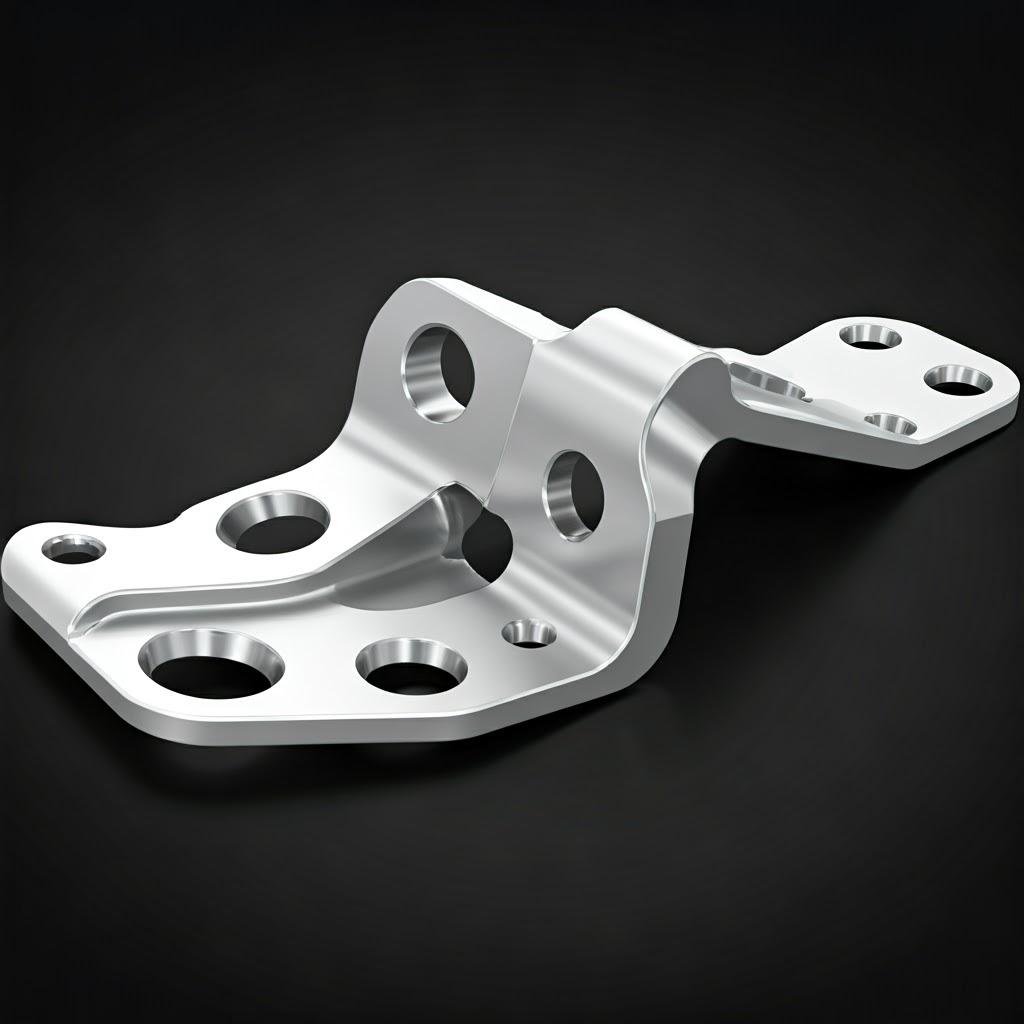
Design für additive Fertigung (DfAM): Optimierung von Scharnieren für den Erfolg im 3D-Druck
Eine der tiefgreifendsten Veränderungen, die durch die additive Fertigung von Metallen ermöglicht wird, ist die Befreiung von traditionellen Designbeschränkungen. Wenn man jedoch ein Scharnierdesign, das für Guss oder Bearbeitung vorgesehen ist, einfach an einen 3D-Drucker schickt, wird das volle Potenzial von AM selten ausgeschöpft. Um die Vorteile der Optimierung des Verhältnisses von Festigkeit zu Gewicht, der Konsolidierung von Teilen und der verbesserten Funktionalität wirklich nutzen zu können, müssen Ingenieure die folgenden Aspekte berücksichtigen Design für additive Fertigung (DfAM) grundsätze. Bei DfAM geht es nicht nur darum, einen Teil druckbares geht darum, das Design grundlegend zu überdenken, um die einzigartigen Möglichkeiten der Schicht-für-Schicht-Fertigung zu nutzen. Für Hochleistungs-Automobilscharniere ist die Anwendung von DfAM nicht nur vorteilhaft - sie ist unerlässlich, um Wettbewerbsvorteile in Bezug auf Gewicht, Leistung und Kosteneffizienz zu erzielen.
Die Nichtanwendung von DfAM-Prinzipien kann zu suboptimalen Ergebnissen führen: Teile, die übermäßige Stützstrukturen erfordern (was die Druckzeit, den Materialverbrauch und den Nachbearbeitungsaufwand erhöht), nicht erreichtes Gewichtseinsparungspotenzial, höhere innere Spannungen, die zu einem potenziellen Versagen führen, oder sogar Druckfehler insgesamt. Eine gut ausgeführte DfAM-Strategie, die oft in Zusammenarbeit mit erfahrenen AM-Dienstleistern entwickelt wird, stellt dagegen sicher, dass das endgültige Scharnierbauteil leichter, stabiler, funktioneller und kostengünstiger mittels AM hergestellt werden kann.
Die wichtigsten DfAM-Prinzipien für Kfz-Scharniere:
- Topologie-Optimierung: Dies ist ein Eckpfeiler der Leichtbauweise bei AM. Die Topologie-Optimierungssoftware nutzt die Finite-Elemente-Analyse (FEA), um die Belastungen und Beanspruchungen zu simulieren, denen ein Scharnier während seiner Lebensdauer ausgesetzt ist (z. B. Unterstützung des Türgewichts, Aushalten von Schließkräften). Auf der Grundlage dieser Simulationen entfernt die Software auf intelligente Weise Material aus Bereichen, die nicht wesentlich zur strukturellen Integrität des Teils beitragen, und hinterlässt eine organische, lastpfadoptimierte Struktur.
- Prozess: Definieren Sie den Konstruktionsraum, die Lasten, die Randbedingungen (z. B. Befestigungspunkte, Drehpunkte, Sperrzonen) und die Optimierungsziele (z. B. Minimierung der Masse, Maximierung der Steifigkeit).
- Software-Beispiele: Altair OptiStruct, ANSYS Discovery, Dassault Systèmes SOLIDWORKS Simulation/CATIA Generative Design, Autodesk Fusion 360 Generative Design, nTopology.
- Vorteile für Scharniere: Erhebliche Gewichtsreduzierung (oft 30-60 % oder mehr im Vergleich zu einer massiven Konstruktion) unter Beibehaltung oder Übertreffen der ursprünglichen Festigkeits-/Steifigkeitsanforderungen. Schafft hocheffiziente Strukturen, die perfekt auf ihren spezifischen Lastfall zugeschnitten sind. Unverzichtbar für leichtes Scharnierdesign.
- Erwägungen: Optimierte Formen können komplex sein und erfordern möglicherweise eine Glättung oder Interpretation für die Herstellbarkeit, sogar mit AM. Es ist entscheidend, dass die Lastfälle die realen Bedingungen genau widerspiegeln.
- Gitterstrukturen & Infill-Strategien: Über die Optimierung der Gesamtform hinaus ermöglicht DfAM die Einbindung interner Gitterstrukturen in die feste Schale des Scharniers. Diese sich wiederholenden geometrischen Muster (z. B. auf der Basis von Streben wie kubische oder Oktett-Fachwerke oder auf der Basis von Oberflächen wie Kreisel oder andere dreifach periodische Minimalflächen – TPMS) ersetzen massives Material, wodurch Gewicht und Materialverbrauch drastisch reduziert werden, während gleichzeitig eine maßgeschneiderte strukturelle Unterstützung und potenziell andere Vorteile wie Energieabsorption oder Schwingungsdämpfung geboten werden.
- Typen: In verschiedenen Regionen des Gelenks können unterschiedliche Dichten und Zelltypen verwendet werden, je nach örtlichem Stressniveau.
- Vorteile: Weitere Gewichtsreduzierung über die reine Topologieoptimierung hinaus, Potenzial für verbesserte Stoßdämpfung (relevant für die Crashsicherheit), verbessertes Wärmemanagement bei richtiger Konstruktion.
- Herausforderungen: Sicherstellung der Druckbarkeit feiner Gitterstreben, wirksame Entfernung von eingeschlossenem Pulver aus inneren Hohlräumen (entscheidend!), mögliche Spannungskonzentrationen an Knotenpunkten, wenn nicht sorgfältig entworfen. Erfordert spezielle Softwarefunktionen (z. B. nTopology, Materialise 3-matic).
- Mindestwanddicke und Größe der Merkmale: Bei AM-Prozessen gibt es Grenzen für die Mindestgröße von Merkmalen, die sie zuverlässig herstellen können. Dies wird durch die Größe des Laserspots, die Größe der Pulverpartikel und die Dynamik des Schmelzbads beeinflusst. Bei L-PBF-Verfahren, die mit Aluminiumlegierungen wie A7075 und AlSi10Mg eingesetzt werden, liegen die minimalen druckbaren Wandstärken in der Regel im Bereich von 0,4 mm bis 0,8 mm, obwohl dickere Wände für die strukturelle Integrität im Allgemeinen empfohlen werden. Bei kleinen Merkmalen wie Drehzapfen oder feinen Details müssen diese Einschränkungen beachtet werden. Die Gestaltung von zu dünnen Wänden oder Merkmalen kann zu unvollständiger Formgebung, Verformung oder Versagen während des Drucks oder der Verwendung führen.
- Relevanz der Scharniere: Entscheidend für die Konstruktion dünner Verstärkungsrippen, leichter Arme oder kleiner integrierter Merkmale innerhalb der Scharnierbaugruppe.
- Design für minimale Unterstützungsstrukturen: L-PBF-Prozesse erfordern Stützstrukturen für Überhänge (Oberflächen mit einem Winkel von weniger als ~45 Grad zur horizontalen Bauplatte) und zur Verankerung des Teils auf der Bauplatte, zur Bewältigung von Wärmespannungen und zur Vermeidung von Verformungen. Stützstrukturen verlängern jedoch die Druckzeit, verbrauchen Material, erfordern einen erheblichen Nachbearbeitungsaufwand für die Entfernung und können die Oberflächenbeschaffenheit an den Stellen, an denen sie angebracht sind, negativ beeinflussen. Effektives DfAM zielt darauf ab minimierung der Stützstrukturen AM von:
- Orientierungsstrategie: Ausrichten des Scharniers auf der Bauplatte, um die selbsttragenden Winkel zu maximieren. Komplexe Scharniere erfordern unter Umständen eine sorgfältige Analyse, um die optimale Ausrichtung zu finden, die den Bedarf an Unterstützung, die Druckzeit und die Anforderungen an die Oberflächenqualität ausgleicht.
- Entwurf von selbsttragenden Funktionen: Anstelle von scharfen horizontalen Auskragungen sollten nach Möglichkeit Fasen oder Verrundungen verwendet werden. Die Verwendung von Rauten- oder Tropfenformen für horizontale Löcher anstelle von einfachen Kreisen kann sie selbsttragend machen.
- Unterstützung von Optimierungssoftware: Verwendung von Software für die Bauvorbereitung zur Erzeugung effizienter Stützstrukturen (z. B. Baumstützen, Blockstützen mit optimierten Schnittstellen), die leichter zu entfernen sind.
- Teil Konsolidierung: Wie bereits erwähnt, ermöglicht AM’s Fähigkeit, komplexe Geometrien zu erzeugen, dass mehrere Komponenten einer traditionellen Scharnierbaugruppe (z.B. Scharnierkörper, Montagebügel, Verstärkungsplatten, Federteller) neu entworfen und als ein einziges, monolithisches Teil gedruckt werden können.
- Vorteile: Geringere Anzahl von Teilen, vereinfachte Montage, geringerer Bedarf an Lagerbeständen, Wegfall von Befestigungselementen/Verbindungen (potenzielle Fehlerquellen), verbesserte strukturelle Integrität, häufig geringeres Gesamtgewicht.
- Beispiel: Entwicklung eines Türscharniers, bei dem die Karosseriestruktur, der Befestigungsflansch für die A-Säule und die Befestigungspunkte für eine Gasdruckfeder in einem einzigen gedruckten Bauteil integriert sind.
- Berücksichtigung von Kinematik und Spielraum: Scharniere sind dynamische Bauteile. DfAM muss die Bewegung der Scharnierteile relativ zueinander und zur umgebenden Fahrzeugstruktur berücksichtigen.
- Pivot Design: Konstruktion von Drehpunkten (Bohrungen, Stifte) mit angemessenen Abständen, um eine reibungslose Bewegung ohne Bindung zu ermöglichen, unter Berücksichtigung der erreichbaren Toleranzen des AM-Prozesses und der geplanten Nachbearbeitungsschritte.
- Passende Oberflächen: Sicherstellung eines ausreichenden Abstands zwischen den beweglichen Teilen über den gesamten Bewegungsbereich.
- Simulation: Verwendung von CAD-Tools zur Simulation der kinematischen Bewegung des Scharniers, um frühzeitig in der Entwurfsphase auf Störungen oder unerwünschte Bewegungsmuster zu prüfen.
Kollaboration und Software:
Effektives DfAM beinhaltet oft einen iterativen Prozess, bei dem eine Reihe von Softwaretools zum Einsatz kommt - beginnend mit CAD für die anfängliche Geometrie, über FEA und Topologieoptimierung für die strukturelle Effizienz, möglicherweise unter Verwendung spezieller Werkzeuge für das Gitterdesign, bis hin zum Einsatz von Software für die Bauvorbereitung (z. B. Materialise Magics, Autodesk Netfabb), um das Teil auszurichten, Stützen zu erzeugen und das Modell für den Drucker zu schneiden. Die Zusammenarbeit zwischen den Automobilkonstrukteuren und dem AM-Dienstleister wird dringend empfohlen. Anbieter wie Met3dp verfügen über Fachwissen über alle Materialien, Lösungen für die additive Fertigungund DfAM können in der Konstruktionsphase einen unschätzbaren Beitrag leisten, um sicherzustellen, dass das Scharnier für eine erfolgreiche und effiziente Produktion optimiert wird, indem sie ihr umfassendes Wissen über Prozessmöglichkeiten und Materialverhalten nutzen. Ihre Erfahrung kann dazu beitragen, häufige Fallstricke zu vermeiden und die Vorteile zu maximieren, die durch folgende Maßnahmen erzielt werden können DfAM-Aluminiumteile.
Erreichen von Präzision: Toleranz, Oberflächengüte und Maßgenauigkeit bei 3D-gedruckten Scharnieren
Während Metall-AM eine unglaubliche Designfreiheit bietet, erfordert das Erreichen der erforderlichen Präzision für funktionale Komponenten wie Automobilscharniere ein gründliches Verständnis der Möglichkeiten des Prozesses in Bezug auf Toleranzen, Oberflächengüte und allgemeine Maßgenauigkeit. Scharniere sind für einen reibungslosen, zuverlässigen Betrieb und eine ordnungsgemäße Abdichtung von Türen oder Verkleidungen auf eine präzise Ausrichtung und einen ausreichenden Abstand angewiesen. Das Verständnis dessen, was L-PBF-Verfahren leisten können und wie verschiedene Faktoren das Ergebnis beeinflussen, ist entscheidend für die Festlegung realistischer Erwartungen und die Planung der erforderlichen Nachbearbeitungsschritte.
Toleranzen bei Metall-AM:
Im Gegensatz zur herkömmlichen CNC-Bearbeitung, bei der Toleranzen im zweistelligen Mikrometerbereich erreicht werden können, sind die Toleranzen bei gedruckten AM-Metallteilen im Allgemeinen geringer. Während spezifische Normen noch in der Entwicklung sind, wird ein gemeinsamer Bezugspunkt oft von allgemeinen Bearbeitungstoleranzen (wie ISO 2768-m oder -f) übernommen, aber spezielle AM-Normen wie ISO/ASTM 52902 bieten eine bessere Anleitung zur geometrischen Dimensionierung und Toleranz (GD&T) für additive Teile.
- Typische erreichbare Toleranzen (L-PBF, A7075/AlSi10Mg):
- Für kleinere Merkmale (z. B. bis zu 100 mm): Normalerweise im Bereich von +/- 0,1 mm bis +/- 0,3 mm.
- Für größere Abmessungen: Oft als Prozentsatz ausgedrückt, z. B. +/- 0,1 % bis 0,2 % des Nennmaßes.
- Anmerkung: Dies sind allgemeine Leitlinien. Die erreichbaren Toleranzen hängen stark von den unten aufgeführten Faktoren ab. Engere Toleranzen erfordern häufig eine Nachbearbeitung.
Faktoren, die die Maßgenauigkeit beeinflussen:
Erreichen einer konsistenten Maßhaltigkeit additive Fertigung ist komplex und wird von zahlreichen interagierenden Faktoren beeinflusst:
- Kalibrierung der Maschine: Die Genauigkeit des Laserscannersystems, die Ebenheit und Nivellierung der Bauplatte und die präzise Steuerung der Z-Achse (Schichthöhe) sind von grundlegender Bedeutung. Regelmäßige Kalibrierung und Wartung sind unerlässlich. Met3dp hebt die Genauigkeit und Zuverlässigkeit seiner Drucker hervor, die für gleichbleibende Ergebnisse entscheidend sind.
- Prozessparameter: Einstellungen wie Laserleistung, Scangeschwindigkeit, Schraffurabstand und Schichtdicke wirken sich direkt auf die Größe und Stabilität des Schmelzbades aus und beeinflussen Schrumpfung, Eigenspannung und die endgültigen Abmessungen des Teils. Optimierte Parametersätze, die auf das jeweilige Material (A7075 und AlSi10Mg verhalten sich unterschiedlich) und die Maschine abgestimmt sind, sind entscheidend.
- Materialeigenschaften: Jede Legierung hat einzigartige thermische Eigenschaften (Leitfähigkeit, Ausdehnungskoeffizient) und ein Schrumpfungsverhalten beim Erstarren und Abkühlen. Diese müssen bei der Prozessplanung berücksichtigt werden, was manchmal Skalierungsanpassungen in der Software für die Bauvorbereitung erfordert.
- Teilegeometrie und -ausrichtung:
- Thermische Masse: Große, massive Abschnitte speichern die Wärme anders als dünne Wände, was zu einer unterschiedlichen Schrumpfung und möglichen Verformungen führt.
- Orientierung: Die Ausrichtung auf der Bauplatte wirkt sich auf die Wärmeverteilung, den Stützbedarf und die Schrumpfung der einzelnen Schichten aus.
- Überhänge: Auf Stützen gebaute Flächen weisen oft ein leicht abweichendes Maßverhalten und Oberflächeneigenschaften auf.
- Strategie unterstützen: Die Art, die Dichte und die Position der Stützstrukturen beeinflussen die Wärmeableitung und die Verankerung und wirken sich auf den Spannungsaufbau und mögliche Verformungen während und nach dem Druck aus.
- Thermische Spannungen: Die schnelle Erwärmung und Abkühlung, die mit der Laser-Pulverbett-Fusion erzeugen innere Spannungen. Wenn diese Spannungen nicht richtig gehandhabt werden (durch Parameter, Stützen, Spannungsabbau), können sie zu Verformungen während des Aufbaus oder zum Verzug nach dem Entfernen von der Bauplatte führen.
- Nachbearbeiten:
- Wärmebehandlung: Spannungsabbau und Alterungszyklen können zu leichten Dimensionsänderungen (Schrumpfung oder Wachstum) führen, mit denen gerechnet werden muss. Das Abschrecken (insbesondere bei A7075 T6) kann zu Verformungen führen, wenn es nicht sorgfältig kontrolliert wird (z. B. mit Hilfe von Spannvorrichtungen).
- Bearbeitung/Fertigstellung: Jeder Abtragsschritt verändert natürlich die Abmessungen und muss genau kontrolliert werden, um die endgültigen Toleranzanforderungen zu erfüllen.
Oberflächengüte (Rauhigkeit - Ra):
Die Oberflächenbeschaffenheit von gedruckten AM-Metallteilen ist aufgrund des schichtweisen Verfahrens und der teilweise geschmolzenen Pulverpartikel, die an der Oberfläche haften, von Natur aus rauer als bearbeitete Oberflächen. Die Oberflächenrauhigkeit wird in der Regel als Ra (durchschnittliche Rauheit) gemessen.
- Wie-gedruckt-Ra-Werte (L-PBF): Im Allgemeinen liegen sie zwischen 5 µm und 25 µm Ra.
- Faktoren, die Ra beeinflussen:
- Oberflächenausrichtung: Vertikale Wände sind in der Regel glatter als die oberen (oberen) Oberflächen. Untere (untere) Oberflächen, die auf Stützen ruhen, sind aufgrund der Kontaktpunkte mit den Stützen in der Regel am rauesten.
- Schichtdicke: Dünnere Schichten ergeben im Allgemeinen etwas glattere Oberflächen.
- Prozessparameter: Laserleistung, Scangeschwindigkeit und Pulvereigenschaften beeinflussen das Schmelzverhalten der Oberfläche.
- Auswirkungen auf die Scharniere: Eine hohe Rauheit, insbesondere auf den Drehzapfen oder den Gegenflächen, kann übermäßige Reibung und Verschleiß verursachen und einen reibungslosen Betrieb verhindern. Raue Oberflächen können auch Anfänge für Ermüdungsrisse sein und die Dichtigkeit beeinträchtigen.
- Verbesserung der Oberflächengüte: Nachbearbeitungsschritte wie Perlstrahlen, Trommeln, Polieren oder CNC-Bearbeitung sind in der Regel erforderlich, um glattere Oberflächen (oft ist 1 µm Ra mit Bearbeitung/Polieren möglich) auf kritischen Scharnieroberflächen zu erzielen.
Die Bedeutung von Präzision bei Scharnieren:
Bei einem Autoscharnier sind Maßgenauigkeit und eine angemessene Oberflächenbeschaffenheit nicht nur ein ästhetisches Anliegen, sondern entscheidend für Funktion und Sicherheit:
- Pivot-Ausrichtung: Die genaue Positionierung und Dimensionierung der Drehzapfenbohrungen und -stifte gewährleistet eine reibungslose Drehung ohne Bindung oder übermäßiges Spiel.
- Freiräume: Korrekte Abstände zwischen beweglichen Teilen verhindern Interferenzen und ermöglichen Schmierung oder Wärmeausdehnung.
- Montage-Schnittstellen: Die exakte Positionierung und die Ebenheit der Montageflächen stellen sicher, dass das Scharnier korrekt an der Fahrzeugkarosserie (A-Säule, Türrahmen usw.) ausgerichtet ist, was ein ordnungsgemäßes Schließen der Tür/Platte, Abdichtung und Lastverteilung ermöglicht.
- Versiegeln: Glatte Anschlussflächen können erforderlich sein, wenn das Scharnier Teil einer Wetterdichtung ist.
Metrologie und Qualitätskontrolle:
Um sicherzustellen, dass Scharniere die vorgegebenen Toleranzen einhalten, ist eine robuste Messtechnik erforderlich. Koordinatenmessgeräte (KMG) liefern hochpräzise Punktmessungen, während berührungsloses 3D-Scannen (Laser oder strukturiertes Licht) die vollständige Teilegeometrie erfasst und einen Vergleich mit dem ursprünglichen CAD-Modell ermöglicht (Scan-to-CAD). Oberflächenrauhigkeitsprüfer quantifizieren die Oberflächengüte. Die Einführung eines strengen Qualitätsmanagementsystems (QMS), das die Prozessüberwachung, die Rückverfolgbarkeit von Materialien und die Endkontrolle umfasst, ist für Lieferanten von kritischen präzision bei Automobilkomponenten teile wie Scharniere. Seriöse Dienstleister haben etablierte Verfahren für CMM-Prüfung AM-Teile und andere notwendige Qualitätskontrollen.
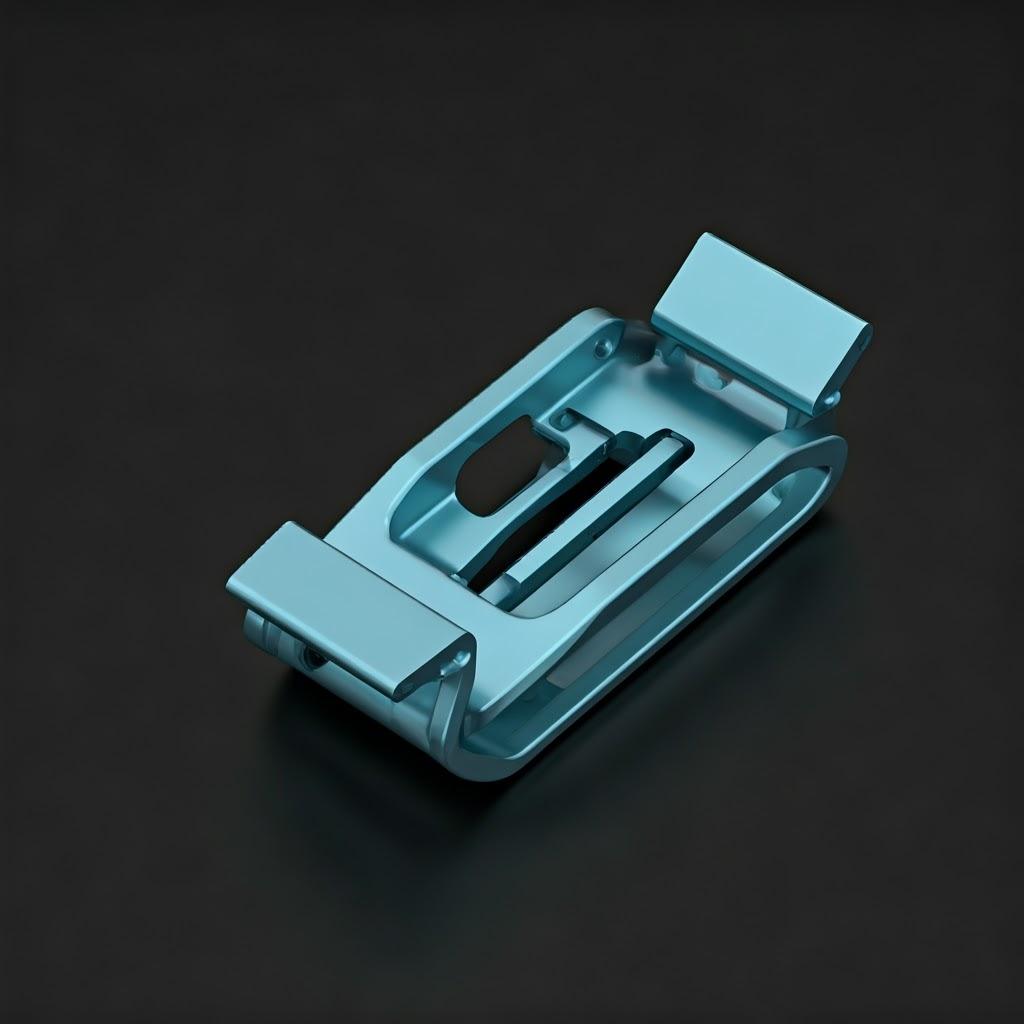
Über das Drucken hinaus: Wichtige Nachbearbeitungsschritte für Automobilscharniere
Ein weit verbreiteter Irrglaube über den 3D-Druck von Metall ist, dass das aus dem Drucker kommende Teil das Endprodukt ist. In Wirklichkeit ist die Druckphase bei anspruchsvollen Anwendungen wie Hochleistungs-Automobilscharnieren aus A7075 oder AlSi10Mg nur ein Teil eines mehrstufigen Fertigungsablaufs. Die Nachbearbeitung ist nicht optional, sondern eine kritische Abfolge von Vorgängen, die erforderlich sind, um das gedruckte Rohteil in eine funktionelle, zuverlässige und dauerhafte Komponente zu verwandeln, die den technischen Spezifikationen entspricht. Diese Schritte sind unerlässlich, um Spannungen abzubauen, die gewünschten Materialeigenschaften zu erzielen, temporäre Strukturen zu entfernen, die erforderlichen Toleranzen und Oberflächengüten zu erreichen und die langfristige Leistungsfähigkeit durch Behandlungen wie eloxieren von Aluminiumscharnieren.
Die spezifischen Nachbearbeitungsschritte, die erforderlich sind, hängen vom Material, der Designkomplexität und den Anwendungsanforderungen ab. Ein typischer Arbeitsablauf für L-PBF-Aluminiumscharniere umfasst jedoch Folgendes:
- Stressabbau / Wärmebehandlung: Dies ist oft der erste entscheidende Schritt nach dem Druck, der manchmal durchgeführt wird, während das Teil noch auf der Bauplatte befestigt ist.
- Zweck: Die schnellen Erwärmungs-/Abkühlungszyklen während des L-PBF-Verfahrens erzeugen erhebliche innere Spannungen im gedruckten Teil. Diese Spannungen können bei der Entnahme aus der Bauplatte Verformungen verursachen oder sogar zu Rissen im späteren Leben des Teils führen, wenn sie nicht abgebaut werden. Durch die Wärmebehandlung wird auch die Mikrostruktur homogenisiert und die gewünschten mechanischen Eigenschaften (Festigkeit, Duktilität, Härte) entwickelt.
- Verfahren für AlSi10Mg:
- Stressabbau: In der Regel erfolgt eine Erhitzung auf etwa 300 °C für etwa 2 Stunden, gefolgt von einer langsamen Abkühlung. Dies reduziert die inneren Spannungen bei minimaler Auswirkung auf die Härte.
- Lösungsglühen & Alterung (T6-ähnlich): Für eine höhere Festigkeit können die Teile einer Lösungsbehandlung bei höheren Temperaturen (~500-540 °C) unterzogen werden, gefolgt von einem Abschrecken und einer künstlichen Alterung (~150-170 °C für mehrere Stunden). Die spezifischen Parameter hängen von dem gewünschten Gleichgewicht zwischen Festigkeit und Duktilität ab.
- Verfahren für A7075: Um die hohe Festigkeit zu erreichen, für die A7075 bekannt ist, bedarf es unbedingt einer T6-Wärmebehandlung:
- Lösung Behandlung: Erhitzen auf ~470-490°C für eine bestimmte Dauer, um die Legierungselemente in der Aluminiummatrix aufzulösen.
- Abschrecken: Schnelles Abkühlen (normalerweise in Wasser), um die Elemente in Lösung zu halten. Dieser Schritt kann zu erheblichen Verformungen führen, wenn er nicht sorgfältig gehandhabt wird (z. B. kontrollierte Abschreckgeschwindigkeit, mögliche Verwendung von Vorrichtungen für komplexe Geometrien).
- Künstliche Alterung: Erhitzen auf eine niedrigere Temperatur (~120 °C) über einen längeren Zeitraum (z. B. 24 Stunden), um Verfestigungsphasen auszufällen.
- Atmosphäre: Wärmebehandlungen werden in der Regel in Inertgas- (Argon, Stickstoff) oder Vakuumöfen durchgeführt, um eine Oxidation zu verhindern.
- Entfernen des Teils von der Bauplatte: Sobald das gedruckte Scharnier abgekühlt (und möglicherweise entspannt) ist, muss es von der Metallbauplatte getrennt werden, mit der es verschmolzen wurde. Dies geschieht in der Regel mit:
- Draht-Elektroerosion (Wire EDM): Präzises Verfahren, gut geeignet für komplexe Schnittstellen.
- Bandsägen: Schneller, aber weniger präzise, geeignet für einfachere Geometrien.
- Entfernung der Stützstruktur: Die beim Druck entstandenen Auflagen müssen entfernt werden. Dies ist oft ein arbeitsintensiver Prozess.
- Methoden: Manuelles Brechen/Schneiden mit Handwerkzeugen (für zugängliche Träger), CNC-Bearbeitung (für präzises Entfernen oder schwer zugängliche Bereiche), manchmal elektrochemische Bearbeitung oder abrasive Fließbearbeitung für interne Kanäle.
- Herausforderungen: Kann Spuren oder raue Oberflächen hinterlassen, die eine weitere Nachbearbeitung erfordern. Das Entfernen von Stützen von empfindlichen Merkmalen oder komplexen Innengeometrien (wie Gittern) erfordert eine sorgfältige Planung und Ausführung. Effektiv Abstützung Metall AM techniken sind der Schlüssel zu einer effizienten Nachbearbeitung.
- Oberflächenveredelung: Unbedruckte Oberflächen sind in der Regel rau und können teilweise gesinterte Partikel aufweisen. Es werden verschiedene Techniken angewandt, um die gewünschte Oberfläche für die Ästhetik, die Reibungsreduzierung oder die Vorbereitung für die Beschichtung zu erreichen.
- Reinigung: Gründliche Entfernung von losem oder eingeschlossenem Pulver, oft mit Hilfe von Druckluft, Bürsten oder Ultraschallreinigung, besonders kritisch bei internen Kanälen oder Gitterstrukturen.
- Gedruckte Oberflächen sind typischerweise rau und können teilsinterte Partikel zurückhalten. Verschiedene Techniken werden verwendet, um die gewünschte Oberfläche zu erzielen: Schleudern von Schleifmitteln auf die Oberfläche, um lose Partikel zu entfernen, eine gleichmäßige matte Textur zu erzeugen und die Ermüdungseigenschaften durch Einbringen von Druckspannungen leicht zu verbessern. Die Wahl des Mediums beeinflusst das endgültige Finish.
- Taumeln / Vibrationsgleitschleifen: Das Einlegen von Teilen in einen Tumbler mit Schleifmitteln zum Entgraten von Kanten, Glätten von Oberflächen und Erzielen eines gleichmäßigen Finishs, besonders effektiv bei Chargen kleinerer Komponenten.
- Polieren: Verwendung immer feinerer Schleifmittel (manuell oder maschinell) zur Erzielung sehr glatter, spiegelähnlicher Oberflächen (Ra < 1 µm), wenn dies für geringe Reibung (Drehpunkte) oder hohen ästhetischen Wert erforderlich ist.
- Eloxieren: Ein elektrochemischer Prozess, der speziell für Aluminium und seine Legierungen gilt. Es bildet eine kontrollierte Oxidschicht auf der Oberfläche, die die Korrosionsbeständigkeit (wichtig für A7075) und die Verschleißfestigkeit erheblich verbessert. Typ-II-Eloxal bietet einen guten Schutz und kann in verschiedenen Farben eingefärbt werden. Beim Eloxieren des Typs III (Hardcoat) entsteht eine viel dickere, härtere Schicht für extreme Verschleißfestigkeit, die jedoch die Ermüdungslebensdauer etwas beeinträchtigen kann.
- Anstrich/Pulverbeschichtung: Aufbringen von organischen Beschichtungen für ästhetische Farbauswahl oder zusätzliche Umweltschutzschichten über Eloxal- oder Konversionsbeschichtungen.
- CNC-Bearbeitung: Selbst bei optimierten AM-Prozessen erfordert das Erreichen engster Toleranzen (z. B. für Drehzapfenbohrungen, Lagersitze, kritische Montageflächen) oft sekundäre CNC-Bearbeitung von AM-Komponenten.
- Zweck: Bearbeitung von kritischen Merkmalen mit Endmaßen und Toleranzen, die über die drucktechnischen Möglichkeiten hinausgehen. Erstellen von präzisen Gewinden, O-Ring-Nuten oder Sicherstellen der Ebenheit/Parallelität von Gegenflächen.
- Erwägungen: Erfordert eine genaue Fixierung des potenziell komplexen AM-Teils. In der DfAM-Phase müssen Bearbeitungszugaben berücksichtigt werden.
- Inspektion und Qualitätskontrolle (QC): Abschließende Überprüfung, ob das Scharnier alle Spezifikationen erfüllt.
- Methoden: Maßprüfungen (CMM, 3D-Scannen), Messung der Oberflächenbeschaffenheit, visuelle Inspektion, Überprüfung der Materialeigenschaften (wenn nebenbei Testcoupons gedruckt wurden), möglicherweise NDT (z. B. CT-Scannen zur Erkennung interner Fehler in kritischen Teilen).
Auswirkungen auf Kosten, Vorlaufzeit & Eigenschaften:
Jeder Nachbearbeitungsschritt verursacht zusätzliche Kosten (Arbeit, Maschinenzeit, Verbrauchsmaterial) und verlängert die Gesamtvorlaufzeit. Komplexe Anforderungen an die Endbearbeitung oder enge Toleranzen, die eine umfangreiche Bearbeitung erfordern, wirken sich erheblich auf den Endpreis des Stücks aus. Die Wärmebehandlung ist zwar für die Eigenschaften wichtig, erfordert jedoch Ofenzeit und sorgfältige Handhabung. Daher ist die Optimierung der Konstruktion (DfAM) zur Minimierung komplexer Stützstrukturen und zur Verringerung des Bedarfs an umfangreichen Bearbeitungen entscheidend für eine kosteneffiziente Produktion. Die Zusammenarbeit mit einem Dienstleister wie Met3dp, der ein umfassendes Paket von In-House Nachbearbeitung bei der additiven Fertigung funktionen neben dem Druck können den Arbeitsablauf straffen, die Qualitätskontrolle verbessern und die Gesamtvorlaufzeiten im Vergleich zur Verwaltung mehrerer Anbieter möglicherweise verkürzen. Für Beschaffungsmanager ist es wichtig, das Zusammenspiel von Design, Druck und Nachbearbeitung zu verstehen, wenn sie Folgendes bewerten oberflächenbearbeitung von Automobilteilen Lieferanten.
Herausforderungen meistern: Häufige Probleme bei 3D-Druckscharnieren und Strategien zur Abhilfe
Die additive Fertigung von Metall bietet zwar ein immenses Potenzial für die Herstellung von Hochleistungsscharnieren für Kraftfahrzeuge, ist aber auch nicht ohne Herausforderungen. Das Verständnis dieser potenziellen Probleme und der Strategien zu ihrer Entschärfung ist entscheidend für die erfolgreiche Implementierung der AM-Technologie. Automobilingenieure und Beschaffungsmanager sollten sich dieser Komplexität bewusst sein, wenn sie Teile spezifizieren und Fertigungspartner auswählen. Die Herstellung von zuverlässigen A7075- und AlSi10Mg-Scharnieren mittels L-PBF erfordert eine sorgfältige Kontrolle zahlreicher Variablen.
Häufige Herausforderungen und wie man sie vermeidet:
- Verformung und Verzerrung:
- Die Ursache: Eine ungleichmäßige Erwärmung und Abkühlung während des schichtweisen Prozesses führt zum Aufbau innerer thermischer Spannungen. Wenn das Teil aus der Verankerung der Bauplatte gelöst wird, können diese Spannungen dazu führen, dass es sich verzieht oder verformt und von der beabsichtigten Geometrie abweicht. Dies ist eine erhebliche metall AM Herausforderungen Automotive problem.
- Milderung:
- Optimierte Teileausrichtung: Platzierung des Teils auf der Bauplatte, um große, flache Oberflächen parallel zur Platte zu minimieren und thermische Gradienten zu reduzieren.
- Robuste Stützstrukturen: Richtig konstruierte Stützen verankern das Teil sicher und leiten die Wärme ab, wodurch die Spannungsakkumulation verringert wird.
- Build Plate Heating: Durch das Vorheizen der Bauplatte wird der Temperaturunterschied zwischen dem erstarrten Material und der neuen Schicht verringert, was zu einer geringeren Belastung führt.
- Prozess-Simulation: Verwendung von Software zur Vorhersage des thermischen Verhaltens und möglicher Verformungen vor dem Druck, wodurch Anpassungen der Ausrichtung oder der Stützen möglich werden.
- Optimierte Scan-Strategien: Verwendung spezieller Laserabtastmuster (z. B. Inselabtastung, Schachbrettmuster), um die Wärme gleichmäßiger zu verteilen.
- Unmittelbarer Stressabbau: Durchführung eines Wärmebehandlungszyklus zum Spannungsabbau unmittelbar nach dem Druck, manchmal vor der Entnahme aus der Bauplatte.
- Eigenspannung:
- Die Ursache: Ähnlich wie beim Verziehen sind Eigenspannungen aufgrund der schnellen thermischen Zyklen unvermeidlich. Selbst wenn sie keine unmittelbare Verformung verursachen, können sich hohe Eigenspannungen negativ auf die Ermüdungslebensdauer, die Bruchzähigkeit und die Anfälligkeit für Spannungsrisskorrosion (insbesondere bei Legierungen wie A7075) auswirken.
- Milderung:
- Wirksame Wärmebehandlung zum Stressabbau: Unbedingt erforderlich. Die Parameter müssen auf der Grundlage der Legierung und der gewünschten Endeigenschaften sorgfältig ausgewählt werden.
- Optimierte Prozessparameter & Scan-Strategien: Wie bereits erwähnt, zur Kontrolle des Verzugs.
- Heiß-Isostatisches Pressen (HIP): Ein Nachbearbeitungsschritt bei hoher Temperatur und hohem Druck (unter Verwendung eines Inertgases wie Argon). HIP kann die innere Porosität und die Eigenspannungen erheblich reduzieren und so die mechanischen Eigenschaften verbessern, verursacht aber zusätzliche Kosten und Vorlaufzeiten. Es wird oft für kritische Anwendungen mit hoher Ermüdung in Betracht gezogen.
- Porosität:
- Die Ursache: Kleine Hohlräume oder Poren innerhalb des gedruckten Materials. Sie können durch Gaseinschlüsse im Pulver oder Schmelzbad (Gasporosität) oder durch unvollständiges Schmelzen und Verschmelzen zwischen Schichten oder Scannerspuren (Fehlluftporosität) verursacht werden. Schlechte Pulverqualität (hoher Gasgehalt, unregelmäßige Formen) oder nicht optimierte Prozessparameter (falsche Laserleistung/-geschwindigkeit, schlechter Strahlfokus) sind häufig die Ursache.
- Auswirkungen: Porosität wirkt wie ein Spannungskonzentrator, der die Zugfestigkeit, die Duktilität und insbesondere die Ermüdungslebensdauer des Scharniers erheblich reduziert. Sie kann ein kritischer Fehlerpunkt sein.
- Milderung:
- Hochwertiges Pulver: Die Verwendung von Pulvern mit kontrollierter Sphärizität, PSD und geringem Gasgehalt (wie sie mit der fortschrittlichen Zerstäubung von Met3dp hergestellt werden) ist grundlegend für Porositätskontrolle bei der additiven Fertigung.
- Optimierte Prozessparameter: Umfassende Prozessentwicklung zur Festlegung von Parametern, die ein vollständiges Schmelzen und Aufschmelzen gewährleisten.
- Kontrolle der inerten Atmosphäre: Aufrechterhaltung einer hochreinen Inertgasumgebung (Argon oder Stickstoff) in der Baukammer, um Oxidation und Gasaufnahme zu minimieren.
- HIP: Kann die inneren Poren wirksam schließen (allerdings nicht die zur Oberfläche hin offenen).
- Prozessüberwachung: Moderne Systeme können den Schmelzesee während des Drucks überwachen, um mögliche Anomalien zu erkennen.
- Support Removal Difficulty & Oberflächenqualität:
- Die Ursache: Halterungen sind zwar notwendig, können aber schwierig und zeitaufwändig zu entfernen sein, insbesondere bei komplexen Innengeometrien (Gitter, Kanäle) oder empfindlichen Merkmalen. Entnahmeverfahren können das Teil beschädigen oder grobe Spuren hinterlassen.
- Milderung:
- DfAM Fokus: Das Scharnier sollte so selbsttragend wie möglich sein und so wenig wie möglich auf Stützen angewiesen sein. Strategische Ausrichtung des Teils.
- Optimiertes Support-Design: Verwendung von Software für die Bauvorbereitung, um Stützen zu erzeugen, die während des Baus stark genug sind, aber leichter entfernt werden können (z. B. bestimmte Schnittstellenschichten, Perforationspunkte).
- Zugangsplanung: Planung von Zugangslöchern oder -kanälen, wenn interne Stützen unvermeidbar sind und manuell entfernt oder gespült werden müssen.
- Erweiterte Entfernungstechniken: Gegebenenfalls unter Einsatz von CNC-Bearbeitung, elektrochemischem Polieren oder abrasiver Fließbearbeitung.
- Erzielung konsistenter Materialeigenschaften:
- Die Ursache: Geringfügige Schwankungen in der lokalen thermischen Entwicklung, den Pulvereigenschaften oder den Prozessparametern können zu Unstimmigkeiten in der Mikrostruktur und den mechanischen Eigenschaften innerhalb eines einzelnen Teils oder zwischen verschiedenen Fertigungen führen.
- Milderung:
- Strenge Prozesskontrolle: Strenge Kontrolle aller Parameter (Laserleistung, Geschwindigkeit, Schichtdicke, Gasfluss, Temperatur).
- Kalibrierung und Wartung von Maschinen: Sicherstellung einer konsistenten Leistung des AM-Systems.
- Pulverqualitätsmanagement: Verwendung von Pulver von qualifizierten Lieferanten mit gleichbleibenden Eigenschaften von Charge zu Charge. Implementierung von Protokollen für die Handhabung und das Recycling von Pulver, um eine Verschlechterung oder Verunreinigung zu verhindern.
- Standardisierte Nachbearbeitung: Anwendung einheitlicher Wärmebehandlungs- und Endbearbeitungsverfahren für alle Teile.
- Gutscheine bezeugen: Drucken von standardisierten Testcoupons neben den tatsächlichen Teilen in jeder Ausführung für anschließende mechanische Tests zur Überprüfung der Eigenschaften.
- Rissbildung (insbesondere bei hochfesten Legierungen wie A7075):
- Die Ursache: Legierungen wie A7075 haben einen weiten Gefrierbereich und sind anfällig für Erstarrungsrisse oder Heißrisse während der schnellen Abkühlphase in L-PBF. Die hohen thermischen Spannungen verschärfen diese Tendenz noch. Warmrissbildung A7075 AM ist eine bekannte Herausforderung.
- Milderung:
- Spezielle Prozessparameter: Erfordert hochgradig optimierte, oft firmeneigene Parametersätze, die speziell für die Bearbeitung dieser anspruchsvollen Legierung entwickelt wurden (z. B. spezifische Vorwärmung, Modulation der Laserleistung, Scanstrategien).
- Pulverchemiekontrolle: Während Standardqualitäten verwendet werden, können geringfügige Abweichungen oder speziell angepasste Pulverzusammensetzungen leichte Verbesserungen bieten (weniger häufig).
- Fachwissen: Das erfolgreiche und zuverlässige Drucken von A7075 erfordert ein hohes Maß an Prozesswissen und Erfahrung. Die Zusammenarbeit mit einem Anbieter wie Met3dp, der über fundierte materialwissenschaftliche Kenntnisse und fortschrittliche Anlagen verfügt, ist für die Arbeit mit solchen Legierungen von entscheidender Bedeutung.
Die Bewältigung dieser Herausforderungen erfordert eine Kombination aus fortschrittlicher Technologie, materialwissenschaftlichem Know-how, strenger Prozesskontrolle und einer DfAM-Mentalität. Verlassen Sie sich auf erfahrene Partner mit branchenführendes Druckvolumen, Genauigkeit und Zuverlässigkeitwie Met3dp, erhöht die Wahrscheinlichkeit der erfolgreichen Herstellung von robusten, hochleistungsfähigen 3D-gedruckten Automobilscharnieren erheblich, während entschärfung von Fehlern beim 3D-Druck. Ihr Fokus auf hochwertige Metallpulver und umfassend qualitätskontrolle Metall AM verfahren bietet eine solide Grundlage für die Bewältigung dieser inhärenten Prozesskomplexität.
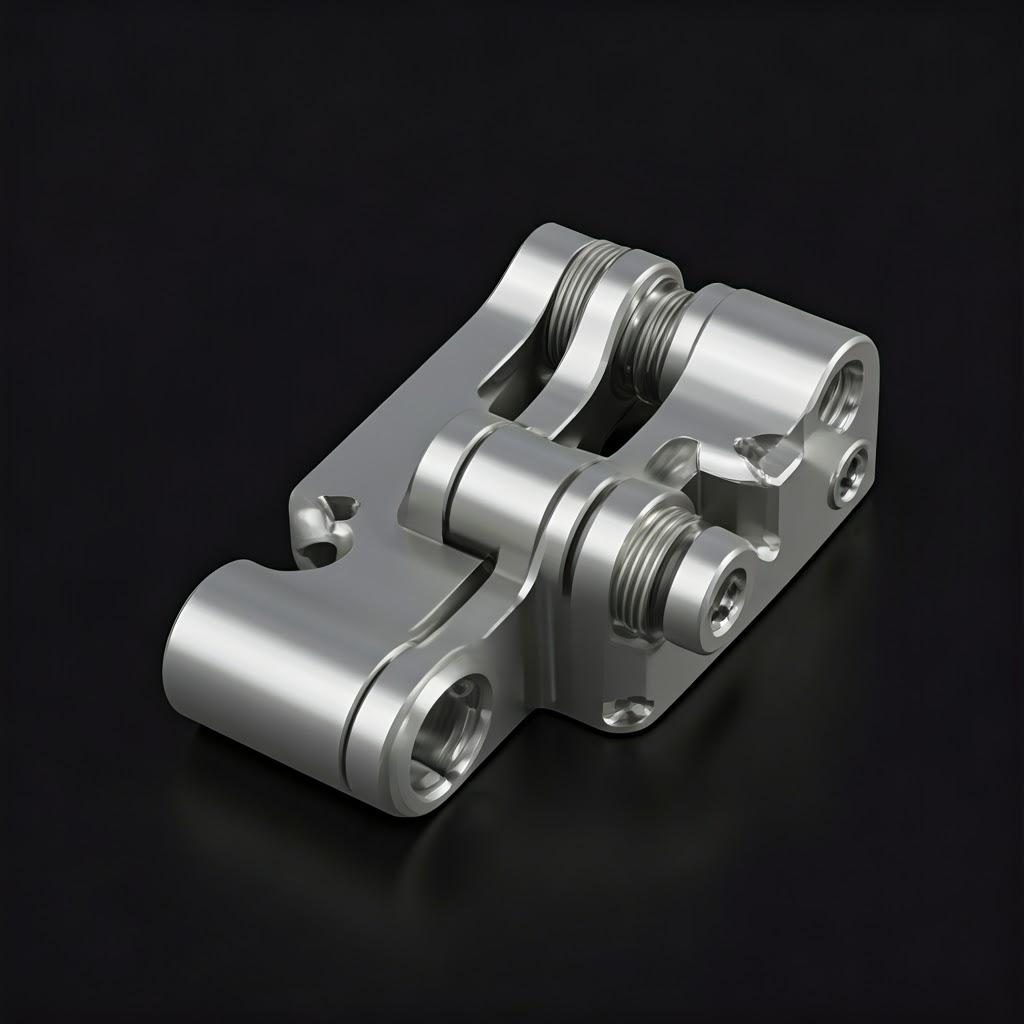
Auswahl der Partner: Die Wahl des richtigen 3D-Druckdienstleisters für Automobilscharniere
Die erfolgreiche Nutzung der additiven Fertigung von Metall für kritische Komponenten wie Hochleistungsscharniere für Kraftfahrzeuge geht über den einfachen Zugang zu einem 3D-Drucker hinaus. Die Qualität, Zuverlässigkeit und Leistung des endgültigen Teils sind untrennbar mit dem Know-how, den Fähigkeiten und den Qualitätssystemen des von Ihnen gewählten Fertigungspartners verbunden. Die Auswahl des richtigen metall-3D-Druck-Dienstleister Automotive das Vertrauen der Spezialisten ist wohl eine der wichtigsten Entscheidungen im Einführungsprozess. Es geht nicht nur darum, einen Anbieter zu finden, der Metall drucken kann; es geht darum, einen strategischen Partner zu finden, der die Feinheiten der Technologie, die Materialien und die anspruchsvollen Anforderungen der Automobilindustrie versteht.
Eine falsche Entscheidung kann zu suboptimalen Teilen, Verzögerungen, Budgetüberschreitungen und letztlich zu einer negativen Wahrnehmung der AM-Technologie selbst führen. Eine Partnerschaft mit einem fähigen und erfahrenen Anbieter sichert dagegen den Zugang zu modernster Technologie, Materialkenntnis, Prozesskontrolle und die Unterstützung bei der Zusammenarbeit, die für eine echte Optimierung der Scharnierkonstruktion und das Erreichen der gewünschten Ergebnisse erforderlich ist. Für Ingenieure und Beschaffungsmanager, die potenzielle Lieferanten evaluieren, insbesondere für diejenigen, die 3D-Druckdienste für den Großhandel oder eine langfristige automobilzuliefererist ein strenges Bewertungsverfahren auf der Grundlage von Schlüsselkriterien unerlässlich.
Kriterien für die Bewertung von Anbietern von Metall-AM-Dienstleistungen:
- Werkstoff- und Verfahrenskenntnisse (A7075 & AlSi10Mg L-PBF):
- Verfügt der Anbieter über dokumentierte Erfahrungen mit dem erfolgreichen Druck der benötigten Aluminiumlegierung (A7075 und/oder AlSi10Mg) mittels Laser Powder Bed Fusion (L-PBF/SLM/DMLS)?
- Können sie ihr Fachwissen bei der Entwicklung und Kontrolle von Prozessparametern für diese Legierungen unter Beweis stellen, um dichte Teile mit geringer Porosität und gleichbleibenden mechanischen Eigenschaften zu erhalten?
- Kennen sie die spezifischen Herausforderungen, die mit jeder Legierung verbunden sind (z. B. Heißrissbildung bei A7075), und verfügen sie über bewährte Strategien zur Abhilfe?
- Fragen Sie nach Materialdatenblättern, die auf ihren tatsächlichen Druck- und Nachbearbeitungsergebnissen basieren, und nicht nur nach allgemeinen Pulverspezifikationen. Fordern Sie Fallstudien oder Musterteile an, die ihre Fähigkeiten mit diesen spezifischen Materialien demonstrieren.
- Branchenerfahrung (Schwerpunkt Automobilindustrie):
- Hat der Anbieter Erfahrung in der Zusammenarbeit mit Automobil-OEMs, Tier-1-Zulieferern oder Motorsportteams?
- Sind sie mit den Qualitätserwartungen der Automobilindustrie, den Dokumentationsanforderungen (auch wenn sie nicht vollständig nach IATF 16949 zertifiziert sind) und den gängigen Anwendungen vertraut?
- Erfahrungen in angrenzenden anspruchsvollen Branchen wie der Luft- und Raumfahrt (AS9100-Zertifizierung ist ein großes Plus) deuten oft auf ausgereifte Prozesse und strenge Qualitätskontrollen hin, die sich auf die Anforderungen der Automobilindustrie übertragen lassen.
- Zertifizierungen und Qualitätsmanagementsystem (QMS):
- ISO 9001: Diese Zertifizierung für Qualitätsmanagementsysteme ist eine grundlegende Anforderung, die auf standardisierte Prozesse für Konsistenz und Qualität hinweist.
- AS9100 (Luft- und Raumfahrt): Diese Zertifizierung ist zwar spezifisch für die Luft- und Raumfahrt, bedeutet aber ein sehr hohes Maß an QMS-Reife, Prozesskontrolle und Rückverfolgbarkeit, das oft über die Anforderungen der Norm ISO 9001 hinausgeht. Sehr wünschenswert für kritische Komponenten.
- IATF 16949-Bewusstsein: Während eine vollständige Zertifizierung für reine AM-Servicebüros selten ist, ist es von Vorteil, das Bewusstsein und die Ausrichtung an den Grundsätzen des QMS für die Automobilindustrie zu demonstrieren.
- Robustes QMS: Erkundigen Sie sich unabhängig von den spezifischen Zertifizierungen nach den Einzelheiten ihres QMS: Wie wird die Rückverfolgbarkeit von Materialien sichergestellt (Verfolgung von Pulverchargen von der Quelle bis zum fertigen Teil)? Wie werden die Prozesse dokumentiert und kontrolliert? Wie werden die Geräte kalibriert und gewartet? Wie wird die Bedienerschulung gehandhabt?
- Maschinenpark und technische Möglichkeiten:
- Mit welchen Typen und Marken von L-PBF-Maschinen arbeiten sie? Sind sie gut gewartet und kalibriert?
- Wie hoch ist ihre Produktionskapazität? Können sie die Größe der benötigten Scharniere, möglicherweise in Chargen, herstellen? Suchen Sie nach Anbietern, die Folgendes erwähnen branchenführendes Druckvolumen, Genauigkeit und Zuverlässigkeit.
- Verfügen ihre Maschinen über fortschrittliche Funktionen wie In-situ-Prozessüberwachung (z. B. Schmelzbadüberwachung) für eine verbesserte Qualitätskontrolle?
- Wie hoch ist ihre Gesamtproduktionskapazität und Redundanz? Können sie schwankende Nachfrage oder dringende Aufträge bewältigen?
- Hausinterne Nachbearbeitungsmöglichkeiten:
- Bietet der Anbieter ein umfassendes Angebot an Nachbearbeitungsdienstleistungen für Aluminiumscharniere aus einer Hand? Dies beinhaltet:
- Spannungsarmglühen und kritische Wärmebehandlung (insbesondere T6 für A7075) mit kalibrierten Öfen.
- Effiziente Techniken zum Entfernen der Unterstützung.
- CNC-Bearbeitung für enge Toleranzen bei kritischen Merkmalen.
- Verschiedene Möglichkeiten der Oberflächenbearbeitung (Strahlen, Trommeln, Polieren, eloxieren von Aluminiumscharnieren).
- Mess- und Prüfgeräte (CMM, 3D-Scanning, Oberflächenprofilometrie).
- Die Bereitstellung dieser Funktionen im eigenen Haus strafft den Arbeitsablauf, gewährleistet eine bessere Prozesskontrolle, verkürzt potenziell die Vorlaufzeiten und vereinfacht das Lieferkettenmanagement im Vergleich zur Koordinierung mehrerer Anbieter. Suchen Sie nach Anbietern, die damit werben umfassende Lösungen.
- Bietet der Anbieter ein umfassendes Angebot an Nachbearbeitungsdienstleistungen für Aluminiumscharniere aus einer Hand? Dies beinhaltet:
- Designunterstützung und DfAM-Fachwissen:
- Bietet der Anbieter eine Beratung zu Design for Additive Manufacturing (DfAM) an?
- Können deren Ingenieure mit Ihrem Konstruktionsteam zusammenarbeiten, um das Scharnierdesign im Hinblick auf Leichtbau, Teilekonsolidierung, minimale Stützen und allgemeine Herstellbarkeit durch AM zu optimieren?
- Dieser kooperative Ansatz ist oft der Schlüssel zur Maximierung der Vorteile der Technologie.
- Erfolgsbilanz, Reputation und Kommunikation:
- Fragen Sie nach Kundenreferenzen oder Zeugnissen, insbesondere in der Automobilindustrie oder verwandten Branchen.
- Beurteilen Sie die Kommunikationsbereitschaft, die Transparenz und das Projektmanagement des Unternehmens. Ist es einfach, mit ihnen zu arbeiten? Bietet er klare Angebote und regelmäßige Aktualisierungen?
- Bedenken Sie ihre Stabilität und Langlebigkeit auf dem sich schnell entwickelnden AM-Markt.
Finden und Auswählen eines Partners:
Potenzielle Lieferanten können über Online-Fertigungsverzeichnisse (stellen Sie sicher, dass sie auf Metall-AM spezialisiert sind), Branchenmessen (wie Formnext), berufliche Netzwerke und Empfehlungen gefunden werden. Es ist wichtig, zwischen Maklern (die Arbeiten an Unterauftragnehmer vergeben), kleinen Werkstätten (die möglicherweise nur über begrenzte Kapazitäten oder Fachkenntnisse verfügen) und etablierten, vertikal integrierten Anbietern zu unterscheiden.
Für Unternehmen, die einen zuverlässigen, kompetenten Partner für anspruchsvolle Anwendungen wie Hochleistungsscharniere für die Automobilindustrie suchen, Met3dp auszeichnet. Met3dp hat seinen Hauptsitz in Qingdao, China, und ist auf additive Fertigungslösungen spezialisiert, die sowohl hochmoderne 3D-Druckanlagen als auch die Herstellung von Hochleistungsmetallpulvern umfassen. Das Unternehmen konzentriert sich darauf, branchenführende Druckvolumen, Genauigkeit und Zuverlässigkeit zu liefern, wodurch sich seine Systeme ideal für unternehmenskritische Teile in den Bereichen Automobil, Luft- und Raumfahrt sowie Medizin eignen. Entscheidend ist, dass Met3dp fortschrittliche Pulverherstellungstechnologien wie Gaszerstäubung und PREP einsetzt und so die hochwertige Metallpulver (einschließlich optimiertem A7075 und AlSi10Mg), die für eine hervorragende Teilequalität erforderlich sind. Mit jahrzehntelanger kollektiver Erfahrung, Met3dp bietet umfassende Lösungen damit ist das Unternehmen ein kompetenter Partner, der seine Kunden durch den gesamten Prozess von der Designoptimierung bis zum fertigen Teil begleitet. Ihr partnerschaftlicher Ansatz zielt darauf ab, Unternehmen in die Lage zu versetzen, den 3D-Druck effektiv zu implementieren und ihre digitale Fertigungstransformation zu beschleunigen, was sie zu einer idealen Wahl macht, wenn auswahl des AM-Lieferanten für kritische Automobilkomponenten.
Die Investition verstehen: Kostenfaktoren und Vorlaufzeiten für 3D-gedruckte Automobilscharniere
Eine der häufigsten Fragen zur additiven Fertigung von Metallteilen betrifft die Kosteneffizienz im Vergleich zu herkömmlichen Verfahren. Zwar entfallen bei der AM die oft beträchtlichen Vorabinvestitionen in Werkzeuge (Gussformen, Matrizen), doch die Kostenstruktur für die Herstellung von Teilen ist anders und wird in erster Linie durch den Materialverbrauch, die Maschinenzeit und die Nachbearbeitungsarbeit bestimmt. Das Verständnis der wichtigsten Kostentreiber und typischen Vorlaufzeiten ist für die Budgetierung, Projektplanung und fundierte Entscheidungen darüber, wann und wo AM für Automobilscharniere eingesetzt werden soll, unerlässlich.
Aufschlüsselung der Kostentreiber:
Das Finale 3D-gedrucktes Scharnier Preis wird durch eine Kombination von Faktoren beeinflusst:
Kostentreiber | Beschreibung & Auswirkungen | Wie man mindert/optimiert |
---|---|---|
Materialkosten | Kosten pro Kilogramm des gewählten Pulvers (z. B. ist A7075 in der Regel teurer als AlSi10Mg). Das Gesamtvolumen des Teils und seiner Stützstrukturen bestimmt direkt den Materialverbrauch. | Wenden Sie Topologieoptimierung und Gitterstrukturen (DfAM) an, um das Teilevolumen zu minimieren. Wählen Sie das kostengünstigste Material, das die Anforderungen erfüllt. |
Maschinenzeit | Wird pro Betriebsstunde der Maschine abgerechnet. Beeinflusst durch das Volumen/die Höhe des Teils (mehr Schichten = mehr Zeit), die Komplexität und die gewählten Druckparameter (z. B. erhöhen feinere Schichten die Zeit). | Optimieren Sie die Teileausrichtung für die Z-Höhe. Maximieren Sie die Anzahl der Teile pro Bauplatte (Verschachtelung), um die Rüst-/Abkühlzeit zu teilen. Vermeiden Sie unnötig feine Parameter. |
Arbeitskosten | Beinhaltet das Einrichten und Abrüsten der Maschine, die Handhabung des Pulvers, eine umfangreiche Nachbearbeitung (Entfernen von Halterungen, Endbearbeitung, maschinelle Bearbeitung) und die Qualitätskontrolle. Kann eine erhebliche Kostenkomponente sein. | Entwurf für minimale Stützen (DfAM). Geben Sie nur die notwendigen Toleranzen/Bearbeitungen an, um die Bearbeitung/Polieren zu reduzieren. Automatisieren Sie die Nachbearbeitung wo möglich. |
Teil Komplexität | Komplizierte Geometrien können langsamere Druckgeschwindigkeiten oder komplexere Unterstützungsstrategien erfordern, was sowohl die Maschinenzeit als auch den Nachbearbeitungsaufwand (insbesondere die Entfernung der Unterstützung) erhöht. | Vereinfachen Sie das Design, wo immer möglich, ohne die Funktion zu beeinträchtigen (DfAM). Entwerfen Sie interne Kanäle/Gitter für die Zugänglichkeit (Pulver-/Stützentfernung). |
Toleranzen & Oberfläche | Bei sehr engen Toleranzen ist eine umfangreiche CNC-Bearbeitung erforderlich. Hochwertige Oberflächenbearbeitungen (z. B. Polieren) sind arbeitsintensiv. | Spezifizieren Sie Toleranzen/Ausführungen nur so eng wie funktionell erforderlich. Nutzen Sie unbedruckte Oberflächen, wo dies akzeptabel ist. |
Menge bestellen | Die Rüstkosten amortisieren sich über mehr Teile in größeren Chargen. Bauplatten können für eine höhere Dichte optimiert werden. Potenzielle Mengenrabatte auf Pulver oder Verarbeitung sind möglich. | Konsolidieren Sie die Nachfrage wo möglich. Diskutieren Sie mit den Anbietern von Mengenrabatten 3D-Druckdienste für den Großhandel. |
Nachbearbeitungsschritte | Jeder Schritt (Wärmebehandlung, Strahlen, maschinelle Bearbeitung, Eloxieren) verursacht zusätzliche Kosten (Gerätezeit, Arbeitsaufwand, Verbrauchsmaterial). Komplexe mehrstufige Prozesse erhöhen die Gesamtkosten. | Minimieren Sie die erforderlichen Schritte durch intelligentes Design (DfAM). Wählen Sie integrierte Lieferanten, um den logistischen Aufwand zu reduzieren. |
Qualitätssicherung | Der Grad der erforderlichen Inspektion (visuell, Basisabmessungen, CMM, NDT wie CT-Scanning) erhöht den Zeitaufwand für Arbeit und Ausrüstung. | Definieren Sie qualitätskritische Merkmale, die ein höheres Prüfniveau erfordern, und verwenden Sie Standardprüfungen an anderer Stelle. |
In Blätter exportieren
Schätzung der Kosten:
Erlangung einer genauen kostenvoranschlag AM-Teile erfordert die Übermittlung eines detaillierten RFQ (Request for Quote) an potenzielle Lieferanten, einschließlich:
- Endgültiges 3D-CAD-Modell (vorzugsweise im STEP-Format).
- Werkstoffspezifikation (A7075 oder AlSi10Mg).
- Erforderliche Toleranzen (auf den Zeichnungen deutlich mit GD&T angegeben).
- Anforderungen an die Oberflächenbeschaffenheit für verschiedene Merkmale.
- Anforderungen an die Nachbearbeitung (Härtegrad der Wärmebehandlung, Art der Eloxierung usw.).
- Erforderliche Menge (einschließlich möglicher künftiger Mengen).
- Prüf- und Inspektionsanforderungen.
Seriöse Anbieter wie Met3dp können auf der Grundlage dieser Informationen detaillierte Kostenvoranschläge erstellen. Seien Sie vorsichtig mit sofortigen Online-Angeboten für komplexe Metallteile, da sie oft nicht den vollen Umfang der Nachbearbeitung und Qualitätsanforderungen erfassen.
Vorlaufzeiten für 3D-gedruckte Scharniere:
Die Vorlaufzeit der additiven Fertigung unterscheidet sich auch von den traditionellen Methoden, insbesondere durch die fehlende Vorlaufzeit für die Werkzeuge.
- Prototypen: Für Einzelteile oder sehr kleine Chargen mit minimaler Nachbearbeitung können die Vorlaufzeiten relativ kurz sein und liegen oft zwischen einige Tage bis 1-2 Wochenje nach Verfügbarkeit der Maschine und Komplexität des Teils. Dies ermöglicht eine schnelle Design-Iteration.
- Produktion von Kleinserien: Für die Serienproduktion (Dutzende bis Hunderte von Teilen) sind die Vorlaufzeiten in der Regel länger und liegen oft im Bereich von 2 bis 6 Wochen oder länger. Dies ist auf Folgendes zurückzuführen:
- Einplanung von Teilen in die Maschinenwarteschlange.
- Längere Druckzeiten für volle Bauplatten.
- Stapelverarbeitung für Schritte wie Wärmebehandlung und Oberflächenbehandlung.
- Für Produktionsteile ist eine umfangreichere Nachbearbeitung (maschinelle Bearbeitung, Endbearbeitung) erforderlich.
- Strenge Qualitätssicherungsverfahren.
- Faktoren, die die Vorlaufzeit beeinflussen:
- Aktuelle Maschinenwarteschlange: Wie beschäftigt der Dienstanbieter ist.
- Druckzeit: Bestimmt durch Größe, Komplexität und Anzahl der Teile.
- Komplexität der Nachbearbeitung: Anzahl und Dauer der erforderlichen Arbeitsschritte (Wärmebehandlungszyklen, Bearbeitungszeit, Nachbearbeitungsprozesse).
- Qualitätssicherungsanforderungen: Zeit, die für eine gründliche Inspektion und Dokumentation benötigt wird.
- Versandlogistik.
Eine klare Kommunikation mit dem Lieferanten über die erforderlichen Liefertermine ist während des Angebots- und Bestellprozesses unerlässlich. Das Verständnis des Zusammenspiels zwischen Kostentreibern und Vorlaufzeitfaktoren hilft dabei, die Erwartungen für kosten der Kleinserienfertigung in der Automobilindustrie und Zeitvorgaben bei der Verwendung von Metall-AM.
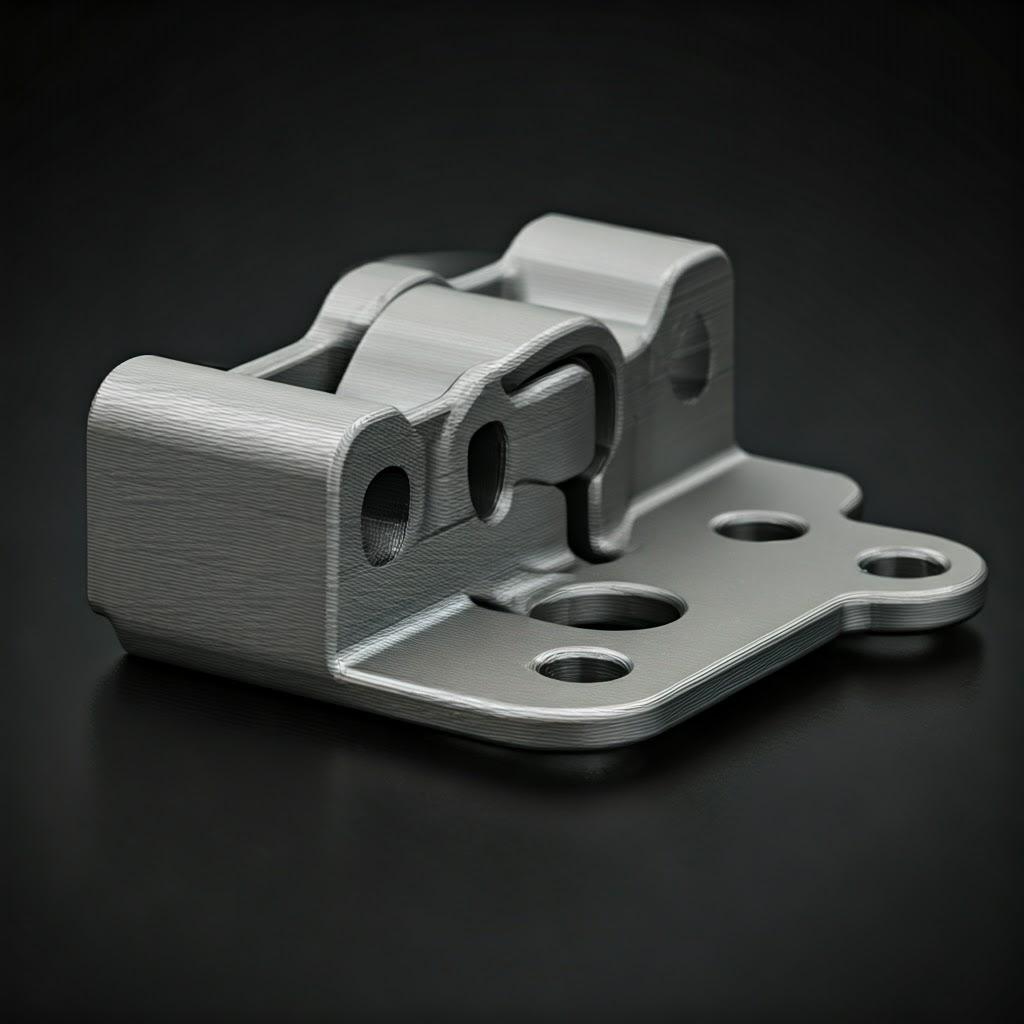
Häufig gestellte Fragen (FAQ) zu 3D-gedruckten Autoscharnieren
Da sich die additive Fertigung von Metallen im Automobilsektor immer mehr durchsetzt, haben Ingenieure, Konstrukteure und Beschaffungsmanager oft Fragen zu den Möglichkeiten und der Eignung für Komponenten wie Scharniere. Hier finden Sie Antworten auf einige häufig gestellte Fragen:
Q1: Sind 3D-gedruckte Aluminiumscharniere (A7075 / AlSi10Mg) stabil genug für Autotüren/Hauben?
A: Ja, absolut, wenn sie richtig entworfen, hergestellt und verarbeitet werden.
- A7075: Bei richtiger Bedruckung und Wärmebehandlung im T6-Zustand weist A7075 eine außergewöhnlich hohe Festigkeit auf, die oft mit den üblichen Automobilstählen vergleichbar oder ihnen sogar überlegen ist, jedoch bei deutlich geringerem Gewicht. Seine Streckgrenze kann 500 MPa übersteigen. Dadurch eignet er sich für hoch belastete Scharniere an Türen, Motorhauben und Heckklappen, insbesondere bei Hochleistungsanwendungen.
- AlSi10Mg: Obwohl es im Allgemeinen nicht so fest ist wie A7075 mit Spitzenalterung, bietet wärmebehandeltes AlSi10Mg eine gute Festigkeit (Streckgrenze typischerweise 250-300+ MPa) und Härte, die für viele Standardscharnieranwendungen, Halterungen und Gehäuse ausreicht, mit dem zusätzlichen Vorteil einer besseren Druckbarkeit und Korrosionsbeständigkeit.
- Schlüsselfaktoren: Das Erreichen dieser Stärke hängt in hohem Maße davon ab:
- Richtiges DfAM: Sicherstellen, dass die Konstruktion die Lasten effektiv verteilt.
- Optimiertes Drucken: Erzielung einer hohen Dichte (>99,7 %) und Minimierung interner Defekte wie Porosität.
- Korrekte Wärmebehandlung: Wesentlich für die Entwicklung der vollen mechanischen Eigenschaften der Legierung (insbesondere T6 für A7075).
- Qualitätskontrolle: Überprüfung der Materialeigenschaften und der Integrität der Teile. Die Website 3D-gedruckte Scharnierstärke ist daher in hohem Maße von der Materialauswahl und der sorgfältigen Prozesskontrolle abhängig.
F2: Wie hoch sind die Kosten für ein 3D-gedrucktes Scharnier im Vergleich zu einem herkömmlich hergestellten Scharnier?
A: Die direkte kostenvergleich AM vs. traditionell methoden hängt stark vom Volumen, der Komplexität und der spezifischen traditionellen Methode ab.
- Großes Volumen (z.B. >10.000 Teile/Jahr): Für einfache Scharniere sind traditionelle Methoden wie Stanzen oder Gießen fast immer billiger pro Teil aufgrund von Skaleneffekten, trotz hoher anfänglicher Werkzeugkosten.
- Geringes bis mittleres Volumen (z.B. <1.000 – 5.000 Teile/Jahr): AM wird viel wettbewerbsfähiger. Der Wegfall der Werkzeugkosten (die in die Zehn- oder Hunderttausende von Dollar gehen können) kann AM insgesamt billiger machen, insbesondere bei komplexen Designs.
- Komplexität: Für hochkomplexe oder topologieoptimierte Scharniere, die sich nur schwer oder gar nicht gießen oder bearbeiten lassen, könnte AM die richtige Lösung sein nur machbare Herstellungsmethode, so dass ein direkter Kostenvergleich weniger relevant ist.
- Gesamtwert-Angebot: Es ist wichtig, Faktoren zu berücksichtigen, die über den Preis pro Teil hinausgehen:
- Keine Werkzeugkosten: Erhebliche Einsparungen und kürzere Zeit bis zum ersten Teil.
- Gewichtseinsparung: Das bedeutet Kraftstoffeinsparung/Reichweite oder verbesserte Leistung, was sich über die gesamte Lebensdauer des Fahrzeugs auszahlt.
- Teil Konsolidierung: Reduziert die Montagekosten und mögliche Fehlerquellen.
- Gestaltungsfreiheit: Ermöglicht Leistungen oder Funktionen, die sonst nicht möglich wären.
- Produktion auf Abruf: Reduziert die Lagerhaltungskosten. Auch wenn der Preis pro AM-Teil manchmal höher ist, können der Gesamtwert und die Kosteneffizienz, insbesondere bei geringeren Stückzahlen und Hochleistungsanwendungen, höher sein.
F3: Wie hoch ist die typische Lebensdauer oder Haltbarkeit eines 3D-gedruckten Autoscharniers?
A: Die haltbarkeit additiv gefertigter Teile wie Scharniere erreichen können, ist so konzipiert, dass sie die typischen Anforderungen der Automobilindustrie erfüllen oder übertreffen, wenn sie richtig konstruiert sind.
- Müdigkeit Leben: Dies ist entscheidend für Scharniere, die zyklischen Belastungen ausgesetzt sind. A7075-T6 bietet eine gute Ermüdungsfestigkeit. Ein geeignetes Design (Vermeidung von Spannungskonzentrationen), ein hochdichter Druck (Minimierung der Porosität) und eine geeignete Oberflächenbehandlung sind entscheidend. Scharniere können so konstruiert und validiert werden (durch Simulation und physische Tests), dass sie Hunderttausenden oder sogar Millionen von Zyklen standhalten, die von den Automobilstandards gefordert werden.
- Abnutzungswiderstand: Drehpunkte sind dem Verschleiß unterworfen. Die Wahl des Materials (Härte) und die Oberflächenbehandlung (z. B. Hartanodisierung Typ III bei Aluminium) erhöhen die Verschleißfestigkeit erheblich. Geeignete Schmierungsstrategien, die möglicherweise durch integrierte Kanäle mittels AM ermöglicht werden, tragen ebenfalls dazu bei.
- Korrosionsbeständigkeit: Wesentlich für die Langlebigkeit. AlSi10Mg bietet eine gute inhärente Beständigkeit. A7075 erfordert Schutzbeschichtungen wie Eloxierung oder Farbe, insbesondere in rauen Umgebungen.
- Insgesamt: Ein gut konzipiertes, ordnungsgemäß hergestelltes und angemessen nachbearbeitetes AM-Metallscharnier aus A7075 oder AlSi10Mg wird voraussichtlich die typische Lebensdauer eines Fahrzeugs überdauern. Validierungstests unter realistischen Belastungs- und Umgebungsbedingungen sind bei kritischen Komponenten gängige Praxis.
F4: Können bestehende Scharnierdesigns (für Guss/Bearbeitung) direkt in 3D gedruckt werden?
A: Obwohl es technisch möglich ist, eine für ein anderes Verfahren konzipierte Geometrie zu drucken, ist es höchst unratsam und geht an den Hauptvorteilen von AM vorbei.
- Suboptimales Design: Entwürfe, die für das Gießen (z. B. Entformungswinkel, einheitliche Wandstärke) oder die Bearbeitung (z. B. Zugänglichkeit für Schneidwerkzeuge) optimiert wurden, sind nicht für den schichtbasierten Ansatz von AM’s optimiert. Der Direktdruck führt oft zu übermäßigem Gewicht, unnötigen Stützstrukturen und suboptimaler Leistung.
- DfAM-Notwendigkeit: Um die Vorteile von AM (Leichtbau, Komplexität, Konsolidierung) zu nutzen, muss das Scharnier muss umgestaltet werden DfAM-Notwendigkeit grundsätze. Dazu gehören die Optimierung der Topologie, möglicherweise Gitterstrukturen, die Gestaltung selbsttragender Winkel und die Integration von Merkmalen.
- Kollaboration: Die Zusammenarbeit mit AM-Experten während der Umgestaltungsphase ist von entscheidender Bedeutung, um sicherzustellen, dass das Teil im Hinblick auf Druckbarkeit, Leistung und Kosteneffizienz durch AM optimiert ist.
F5: Welche Maßnahmen zur Qualitätskontrolle gewährleisten die Zuverlässigkeit von 3D-gedruckten Scharnieren?
A: Um die Zuverlässigkeit kritischer AM-Komponenten zu gewährleisten, ist ein vielschichtiges qualitätskontrolle Metall 3D-Druck strategie des Dienstanbieters:
- Materialkontrolle: Strenge Eingangskontrolle von Metallpulver (Chemie, PSD, Morphologie, Fließfähigkeit), kontrollierte Lagerung, Rückverfolgbarkeit der Chargen während des gesamten Prozesses.
- Prozessvalidierung & Überwachung: Validierte Druckparameter für jede Material/Maschinen-Kombination, Echtzeit-Überwachung der wichtigsten Prozessvariablen (Laserleistung, Sauerstoffgehalt, Schmelzbadcharakteristik, sofern vorhanden), dokumentierte Verfahren.
- Kontrolle nach dem Druck: Gründliche Reinigung und visuelle Inspektion, präzise Maßprüfung mit CMM oder 3D-Scanning anhand des CAD-Modells und der GD&T-Spezifikationen.
- Überprüfung der Materialeigenschaften: Regelmäßiges Drucken und Prüfen von Prüfmustern zusammen mit den Teilen (Zugversuche, Härtetests), um zu überprüfen, ob das Verfahren die erwarteten mechanischen Eigenschaften erzielt.
- Zerstörungsfreie Prüfung (NDT): Bei hochkritischen Scharnieren können CT-Scans (Computertomographie) oder Röntgenaufnahmen eingesetzt werden, um die inneren Strukturen auf Porosität oder Fusionsfehler zu untersuchen, ohne das Teil zu zerstören.
- Robustes QMS: Alle Verfahren sollten durch ein umfassendes Qualitätsmanagementsystem (z. B. ISO 9001, AS9100) geregelt werden.
Schlussfolgerung: Die Zukunft der Automobilkomponenten mit 3D-gedruckten Scharnieren
Die Reise durch die Feinheiten der Konstruktion, Herstellung und Implementierung von Hochleistungsscharnieren für Kraftfahrzeuge mit Hilfe der additiven Fertigung von Metallen offenbart eine Technologie, die die Produktion von Automobilkomponenten neu gestalten wird. Metall-AM, insbesondere unter Verwendung fortschrittlicher Aluminiumlegierungen wie A7075 und AlSi10Mg durch Laser Powder Bed Fusion, bietet einen überzeugenden Weg, der die Grenzen herkömmlicher Methoden überwindet. Es ermöglicht den Ingenieuren eine unvergleichliche Synergie von festigkeit, Leichtgewichtigkeit und Komplexität der Konstruktiondiese Eigenschaften sind entscheidend für das unermüdliche Streben nach verbesserter Fahrzeugleistung, Effizienz und Innovation, insbesondere in den anspruchsvollen Segmenten Elektrofahrzeuge, Performance und Luxus.
Wir haben erforscht, wie die DfAM-Prinzipien radikale Topologieoptimierung und Teilkonsolidierungdies führt zu Scharnieren, die deutlich leichter, aber genauso stark, wenn nicht sogar stärker, sind als ihre herkömmlichen Gegenstücke. Wir haben gesehen, wie Legierungen wie A7075 eine stahlähnliche Festigkeit für hochbelastete Anwendungen bieten, während AlSi10Mg eine robuste und bedruckbare Lösung für ein breites Spektrum von Anwendungen darstellt. Die Möglichkeit, Prototypen schnell und in kleinen Stückzahlen ohne Investitionen in Werkzeuge herzustellen, beschleunigt die Entwicklungszyklen und ermöglicht eine Anpassung an Kundenwünsche, die zuvor unvorstellbar war.
Die Ausschöpfung dieses Potenzials erfordert jedoch während des gesamten Arbeitsablaufs viel Liebe zum Detail - von der fachkundigen DfAM und der präzisen Prozesssteuerung während des Drucks bis hin zu kritischen Nachbearbeitungsschritten wie Wärmebehandlung, Bearbeitung und Oberflächenveredelung. Die Bewältigung von Herausforderungen wie Eigenspannungen, Porosität und das Erreichen enger Toleranzen erfordert fundiertes Fachwissen und ein solides Qualitätsmanagement. Dies unterstreicht, wie wichtig es ist, den richtigen Fertigungspartner auszuwählen - einen Partner mit nachgewiesener Erfahrung, fortschrittlichen Fähigkeiten und einer Verpflichtung zur Qualität.
Die zukünftigen Automobilbau die Landschaft wird zunehmend von Metall-AM geprägt sein, und zwar nicht als Nischenwerkzeug für den Prototypenbau, sondern als praktikable Lösung für die Serienproduktion komplexer, hochwertiger Komponenten. Die innovation Automobilkomponenten die Entwicklung, die Scharniere durchlaufen, wird durch AM vorangetrieben und trägt direkt zu Fortschritten in der Fahrzeugdynamik, der Erweiterung der Reichweite und neuen Funktionen bei. Da die Technologie reift und die Kosten weiter steigen, werden die metall AM Einführung Automotive industrie wird sich weiter beschleunigen.
Für Automobilingenieure und Beschaffungsmanager, die vor der Herausforderung stehen, Gewicht zu reduzieren, die Leistung von Komponenten zu verbessern oder die Entwicklung komplexer Baugruppen zu beschleunigen, stellt die additive Fertigung von Metallen eine leistungsstarke Lösung dar. Wenn Sie herausfinden möchten, wie 3D-gedruckte Scharniere oder andere Komponenten Ihr nächstes Fahrzeugprojekt aufwerten können, ist die Zusammenarbeit mit einem führenden Unternehmen auf diesem Gebiet von größter Bedeutung.
Met3dpmit seiner Grundlage sowohl in der fortschrittlichen Metallpulverproduktion als auch in modernsten Drucksystemen ist ein solcher Marktführer. Umfassendes Angebot Met3dp-Lösungen die Materialwissenschaft, zuverlässige Druckanlagen und Fachwissen in der Anwendungsentwicklung umfassen, sind sie ideal positioniert, um Ihrem Unternehmen zu helfen, die transformative Kraft der additiven Fertigung zu nutzen. Wir ermutigen Sie kontakt zum 3D-Drucker für Metall Met3dp, um Ihre spezifischen Anwendungsanforderungen zu besprechen und herauszufinden, wie das Unternehmen Ihre digitale Transformation in der Fertigung vorantreiben kann.
Teilen auf
MET3DP Technology Co., LTD ist ein führender Anbieter von additiven Fertigungslösungen mit Hauptsitz in Qingdao, China. Unser Unternehmen ist spezialisiert auf 3D-Druckgeräte und Hochleistungsmetallpulver für industrielle Anwendungen.
Fragen Sie an, um den besten Preis und eine maßgeschneiderte Lösung für Ihr Unternehmen zu erhalten!
Verwandte Artikel
Über Met3DP
Aktuelles Update
Unser Produkt
KONTAKT US
Haben Sie Fragen? Senden Sie uns jetzt eine Nachricht! Wir werden Ihre Anfrage mit einem ganzen Team nach Erhalt Ihrer Nachricht bearbeiten.
Holen Sie sich Metal3DP's
Produkt-Broschüre
Erhalten Sie die neuesten Produkte und Preislisten
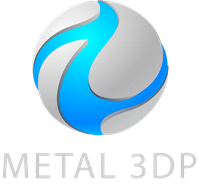
Metallpulver für 3D-Druck und additive Fertigung