Leichte Avionikboxen für Satelliten im 3D-Druckverfahren
Inhaltsübersicht
Einführung: Revolutionierung des Satellitendesigns mit 3D-gedruckten Avionikgehäusen
Die letzte Grenze, der Weltraum, stellt unvergleichliche Herausforderungen an Technik und Design. Jedes Gramm, das in die Umlaufbahn geschossen wird, kostet Tausende von Dollar, so dass die Gewichtsreduzierung vor allem bei Satellitenkomponenten von größter Bedeutung ist. Avionikgehäuse, die empfindliche elektronische Geräte zur Steuerung der Satellitenfunktionen schützen, sind besonders geeignet für eine Optimierung. Traditionell werden diese Gehäuse mit subtraktiven Methoden wie der CNC-Bearbeitung von Knüppeln hergestellt und weisen oft ein Übergewicht auf, das eher durch Fertigungsbeschränkungen als durch funktionale Anforderungen bedingt ist. Hier kommt die additive Fertigung von Metall (AM) ins Spiel, allgemein bekannt als 3D-Druck. Diese transformative Technologie verändert die Art und Weise, wie wir komplexe, hochleistungsfähige Teile für anspruchsvolle Umgebungen entwerfen und produzieren, rapide, insbesondere in der Luft- und Raumfahrtbranche. Durch den schichtweisen Aufbau von Komponenten direkt aus digitalen Modellen eröffnet Metall-AM eine nie dagewesene Designfreiheit und ermöglicht die Herstellung hoch optimierter, leichter und komplizierter Avionikgehäuse, deren Herstellung bisher unmöglich oder unerschwinglich war. Dieser Wandel ist nicht nur schrittweise, sondern stellt einen grundlegenden Wandel in der Herangehensweise dar, der es Satellitenkonstrukteuren und Beschaffungsspezialisten in der Luft- und Raumfahrt ermöglicht, erhebliche Masseneinsparungen zu erzielen, Teile zu konsolidieren, das Wärmemanagement zu verbessern und die Entwicklungszeiten zu verkürzen. Für Satellitenhersteller, die Wettbewerbsvorteile und verbesserte Missionsfähigkeiten anstreben, ist das Verständnis und die Nutzung des 3D-Metalldrucks für kritische Komponenten wie Avionikgehäuse nicht mehr optional, sondern unerlässlich. Unternehmen, die sich auf fortschrittliche Metall-Additiv-Fertigungwie Met3dp bieten das Fachwissen, die Hochleistungsmaterialien und die modernsten Drucktechnologien, die erforderlich sind, um diese fortschrittlichen Entwürfe in flugtaugliche Hardware umzusetzen. Die Fähigkeit, komplexe interne Merkmale, konforme Kühlkanäle und organisch optimierte Formen herzustellen, bedeutet, dass Avionikgehäuse leichter, stärker und thermisch effizienter sein können, was direkt zu einer längeren Lebensdauer, einer höheren Nutzlastkapazität und der Gesamtleistung des Satelliten beiträgt. In diesem einführenden Abschnitt wird erläutert, wie sich Metall-AM speziell auf die Konstruktion und Produktion von Avionikgehäusen für Satelliten auswirkt, und es werden die Voraussetzungen für eine eingehendere Untersuchung der beteiligten Technologien, Materialien und Überlegungen geschaffen. Wir werden untersuchen, warum diese Fertigungsrevolution für Satelliteningenieure, Systemintegratoren und die gesamte Lieferkette für Luft- und Raumfahrtkomponenten, die nach innovativen und effizienten Lösungen suchen, von großer Bedeutung ist.
Die Anforderungen an Satellitenkomponenten sind extrem: Sie müssen enormen Startkräften standhalten, zuverlässig im Vakuum des Weltraums funktionieren, extremen Temperaturschwankungen standhalten und strahlungsbeständig sein, und das alles bei möglichst geringem Gewicht. Avionikboxen, die alles von Kommando- und Datenverarbeitungssystemen bis hin zu Stromverteilungseinheiten und Kommunikationstransceivern beherbergen, sind von zentraler Bedeutung für den Betrieb eines Satelliten. Ihre strukturelle Integrität ist entscheidend für den Schutz der empfindlichen Elektronik, während ihre thermischen Eigenschaften entscheidend für die Ableitung der von diesen Systemen erzeugten Wärme sind. Bei der herkömmlichen Herstellung werden oft mehrere Teile aus Aluminiumblöcken gefertigt und dann zusammengebaut, was zu potenziellen Fehlerstellen, zusätzlichem Gewicht durch Befestigungselemente und Kompromissen bei der Konstruktion aufgrund der Zugänglichkeit der Werkzeuge führt. Die Metall-AM überwindet diese Einschränkungen grundlegend. Anstatt Material abzutragen, wird es genau dort hinzugefügt, wo es benötigt wird. Dabei wird es von einer hochentwickelten Simulations- und Optimierungssoftware gesteuert. Dies ermöglicht es Ingenieuren,:
- Drastische Reduzierung der Masse: Mithilfe von Techniken wie Topologieoptimierung und generativem Design können Ingenieure Strukturen schaffen, bei denen Material nur in den tragenden Pfaden verwendet wird, was zu erheblichen Gewichtseinsparungen (oft 30-50 % oder mehr) im Vergleich zu konventionell bearbeiteten Gegenstücken führt. Gitterstrukturen können intern integriert werden, um die Steifigkeit zu erhöhen und gleichzeitig die Masse zu minimieren.
- Verbessern Sie das Wärmemanagement: AM ermöglicht die Integration komplexer interner Kühlkanäle, Kühlkörper oder Wärmerohre direkt in die Struktur des Avionikgehäuses. Diese Merkmale können sich genau an die wärmeerzeugenden Komponenten anpassen und die Wärmeableitungseffizienz weit über das hinaus verbessern, was mit aufgeschraubten oder maschinell bearbeiteten Lösungen erreicht werden kann.
- Teile konsolidieren: Mehrere Komponenten, die zuvor separat hergestellt und zusammengebaut wurden (z. B. Halterungen, Befestigungen, Abdeckungen, Chassis), können oft in ein einziges, monolithisches 3D-gedrucktes Teil integriert werden. Dies reduziert die Montagezeit, eliminiert Befestigungselemente (potenzielle Fehlerquellen und zusätzliches Gewicht), vereinfacht die Lieferkette und verbessert die strukturelle Gesamtintegrität.
- Komplexe Geometrien aktivieren: Die schichtweise Herstellung von AM-Gehäusen ermöglicht hochkomplexe innere und äußere Merkmale, wie z. B. konturierte Oberflächen, komplizierte innere Trennwände und integrierte Wellenleiter oder Antennenhalterungen, ohne die Beschränkungen des herkömmlichen Werkzeugzugangs. Diese Designfreiheit ermöglicht multifunktionale Gehäuse, die eher auf Leistung als auf Herstellbarkeit optimiert sind.
- Beschleunigen Sie das Prototyping und die Iteration: Neue Entwürfe oder Änderungen können viel schneller gedruckt und getestet werden als die Herstellung von Werkzeugen für die herkömmliche Fertigung. Dieser schnelle Iterationszyklus ist in der schnelllebigen Satellitenentwicklung von unschätzbarem Wert, da er es den Ingenieuren ermöglicht, Leistungsverbesserungen schnell zu validieren.
Die Auswirkungen auf die Lieferkette der Luft- und Raumfahrtindustrie sind erheblich. Beschaffungsmanager können hoch optimierte Komponenten schneller beschaffen, wodurch die Abhängigkeit von umfangreichen Werkzeuginvestitionen und langen Vorlaufzeiten, die mit traditionellen Methoden verbunden sind, verringert werden kann. Lieferanten von Großsatellitenkomponenten wenden sich zunehmend an AM-Partner, um diese fortschrittlichen, leichten Lösungen zu liefern. Der Schwerpunkt verlagert sich von der Beschaffung maschinell bearbeiteter Standardblöcke auf die Zusammenarbeit mit spezialisierten AM-Anbietern wie Met3dp, die über das notwendige Fachwissen in den Bereichen Werkstoffkunde, Prozesskontrolle und Qualitätssicherung verfügen, das für Raumfahrthardware entscheidend ist. Met3dp, mit Hauptsitz in Qingdao, China, verfügt über jahrzehntelange Erfahrung und hochmoderne Anlagen, einschließlich branchenführender Gaszerstäubungs- und Plasma-Rotations-Elektroden-Verfahren (PREP) zur Herstellung von Metallpulvern mit hoher Sphärizität und Fließfähigkeit, die für einen zuverlässigen Druck unerlässlich sind. Ihre Spezialisierung auf Hochleistungslegierungen in Kombination mit fortschrittlichen SEBM-Druckern (Selective Electron Beam Melting), die für ihre Genauigkeit und Zuverlässigkeit bekannt sind, macht sie zu einem wichtigen Partner für Luft- und Raumfahrtunternehmen, die Satelliten-Hardware der nächsten Generation einsetzen wollen. Wenn wir uns in den folgenden Abschnitten mit den spezifischen Anwendungen, Materialien und Designüberlegungen befassen, wird das transformative Potenzial von Metal AM für Satelliten-Avionikgehäuse immer deutlicher.
Die kritische Rolle von Avionikboxen bei Satellitenmissionen
Avionikboxen, die oft auch als Elektronikgehäuse bezeichnet werden, sind grundlegende Subsysteme in jeder Satellitenarchitektur. Auch wenn sie als einfache Behälter erscheinen mögen, ist ihre Rolle alles andere als trivial; sie sind missionskritische Komponenten, die das empfindliche elektronische Gehirn und Nervensystem des Raumfahrzeugs schützen. Ohne robuste und zuverlässige Avionikgehäuse würde die komplexe Anordnung von Prozessoren, Sensoren, Kommunikationsgeräten und Energieverwaltungssystemen, die einen Satelliten in die Lage versetzen, die ihm zugedachte Funktion zu erfüllen - sei es Erdbeobachtung, Telekommunikation, Navigation oder wissenschaftliche Forschung -, die raue Reise in die Umlaufbahn und die unnachgiebige Umgebung des Weltraums nicht überstehen. Das Verständnis der vielfältigen Funktionen dieser Gehäuse ist der Schlüssel dazu, warum die Optimierung ihres Designs und ihrer Herstellung durch Methoden wie die additive Fertigung von Metallen den Satellitenherstellern und den Beschaffungsteams in der Luft- und Raumfahrt so bedeutende Vorteile bietet.
Die Hauptfunktion einer Avionikbox ist im Wesentlichen physischer Schutz. Dies umfasst mehrere Aspekte:
- Strukturelle Unterstützung: Das Gehäuse muss eine starre und stabile Plattform für die Montage von Leiterplatten, Steckern, Netzteilen und anderen elektronischen Komponenten bieten. Es muss seine strukturelle Integrität unter erheblichen mechanischen Belastungen beibehalten, einschließlich der starken Vibrationen und des akustischen Drucks, die beim Start an der Spitze einer Rakete auftreten. Jede Verformung oder jedes Versagen könnte zu katastrophalen Schäden an der internen Elektronik führen.
- Umweltfreundliche Versiegelung: Je nach Missionsprofil und internen Komponenten muss die Box möglicherweise eine geschlossene Umgebung bieten. Dies könnte der Fall sein, um einen bestimmten Innendruck aufrechtzuerhalten, das Ausgasen von Verunreinigungen aus empfindlichen Optiken oder Sensoren an anderen Stellen des Raumfahrzeugs zu verhindern oder die internen Komponenten vor dem Aufprall von Mikrometeoroiden oder orbitalen Trümmern zu schützen, insbesondere bei nach außen gerichteten Einheiten.
- Elektromagnetische Verträglichkeit (EMV): Satelliten sind vollgepackt mit elektronischen Systemen, die elektromagnetische Signale erzeugen und empfangen. Avionikboxen spielen eine entscheidende Rolle bei der Abschirmung elektromagnetischer Interferenzen (EMI). Sie müssen verhindern, dass intern erzeugtes Rauschen andere Teilsysteme des Satelliten stört, und die empfindliche interne Elektronik vor externer elektromagnetischer Strahlung schützen, die im Weltraum vorherrscht (z. B. galaktische kosmische Strahlung, solare Teilchen) oder von anderen Teilen des Satelliten ausgeht. Die Wahl des Materials und die Konstruktion des Gehäuses (einschließlich Erdung und Abdichtung) sind für eine wirksame EMV entscheidend.
Neben dem physischen Schutz sind Avionikboxen ein wesentlicher Bestandteil von Wärmemanagement. Elektronische Bauteile erzeugen während des Betriebs erhebliche Wärme. Im Vakuum des Weltraums ist Konvektion keine Option für die Kühlung; die Wärme muss hauptsächlich durch Leitung und Strahlung abgeführt werden. Das Avionikgehäuse ist ein wichtiger Teil dieses Wärmewegs:
- Wärmeleitung: Das Gehäusematerial muss die Wärme effizient von den Hochleistungskomponenten (wie Prozessoren oder Leistungstransistoren) zu den vorgesehenen Wärmeschnittstellen oder Kühlern ableiten. Die Montageflächen für Leiterplatten und wärmeerzeugende Komponenten müssen für einen optimalen Wärmekontakt ausgelegt sein.
- Wärmestrahlung: Die Außenflächen des Avionikgehäuses wirken oft als Strahler, die die Wärme in den Weltraum oder in kältere Teile des Satelliten ableiten. Die Oberflächen und Beschichtungen (z. B. optische Sonnenreflektoren, Farben mit hohem Emissionsgrad) werden sorgfältig ausgewählt, um die Strahlungseigenschaften entsprechend dem thermischen Design des Satelliten zu optimieren.
- Aufrechterhaltung der Betriebstemperaturen: Das Gehäuse trägt in Verbindung mit dem gesamten Wärmekontrollsystem des Satelliten (Heizungen, Kühler, Wärmedecken) dazu bei, die interne Elektronik innerhalb ihres spezifizierten Betriebstemperaturbereichs zu halten, der je nach Umlaufbahn (z. B. erdnahe Umlaufbahn vs. geostationäre Umlaufbahn) und Ausrichtung zur Sonne erheblich variieren kann. Ein unzureichendes Wärmemanagement kann zur Beeinträchtigung der Komponenten, zu Fehlfunktionen oder zum vollständigen Ausfall führen.
Außerdem dienen Avionikboxen als kritische systemintegration funktionen:
- Definierte Schnittstellen: Sie bieten standardisierte Montagepunkte, Steckerausschnitte und Zugangsklappen und erleichtern so die Integration der elektronischen Nutzlast in die größere Satellitenstruktur. Präzise Schnittstellen sind entscheidend für die Verbindung mit Kabelbäumen, Datenbussen und Stromleitungen.
- Modularität und Wartungsfreundlichkeit: Da die meisten Satelliten nur selten in der Umlaufbahn gewartet werden, ist es wichtig, die Avionikboxen so zu konstruieren, dass sie am Boden leichter getestet und integriert werden können und mögliche Reparaturen oder Aufrüstungen vor dem Start möglich sind.
Angesichts dieser kritischen Aufgaben - strukturelle Integrität, Umweltschutz, EMV-Abschirmung, Wärmeregulierung und Systemintegration - unterliegen die Entwicklung und Herstellung von Avionikgehäusen strengen Anforderungen und Qualifizierungsprozessen. Traditionell waren Luft- und Raumfahrtingenieure, die diese Gehäuse mit Hilfe der subtraktiven Fertigung entwarfen, mit Einschränkungen konfrontiert. Material konnte nur dort abgetragen werden, wo die Schneidwerkzeuge hinkamen, was oft zu sperrigen Konstruktionen mit dicken Wänden führte, um Steifigkeit und Festigkeit zu gewährleisten, selbst wenn die Belastungen lokal begrenzt waren. Die Integration komplexer thermischer Funktionen oder die Erzielung einer optimalen EMI-Abschirmung erforderten oft mehrteilige Baugruppen mit zusätzlichen Befestigungselementen und Schnittstellenmaterialien, was die Komplexität, das Gewicht und potenzielle Fehlerquellen erhöhte. Die Suche nach zuverlässigen Lieferanten für Luft- und Raumfahrtelektronik und Beschaffungslösungen für Satellitenhardware konzentrierte sich oft auf die Suche nach Werkstätten, die in der Lage waren, enge Toleranzen bei relativ einfachen Geometrien einzuhalten. Metall-AM durchbricht dieses Paradigma, indem es Konstruktionen ermöglicht, die sich ausschließlich an Leistungsanforderungen und nicht an Fertigungsbeschränkungen orientieren. Dadurch können diese kritischen Funktionen effizienter und zuverlässiger ausgeführt werden, was sich direkt auf den Gesamterfolg und die Langlebigkeit von Satellitenmissionen auswirkt.
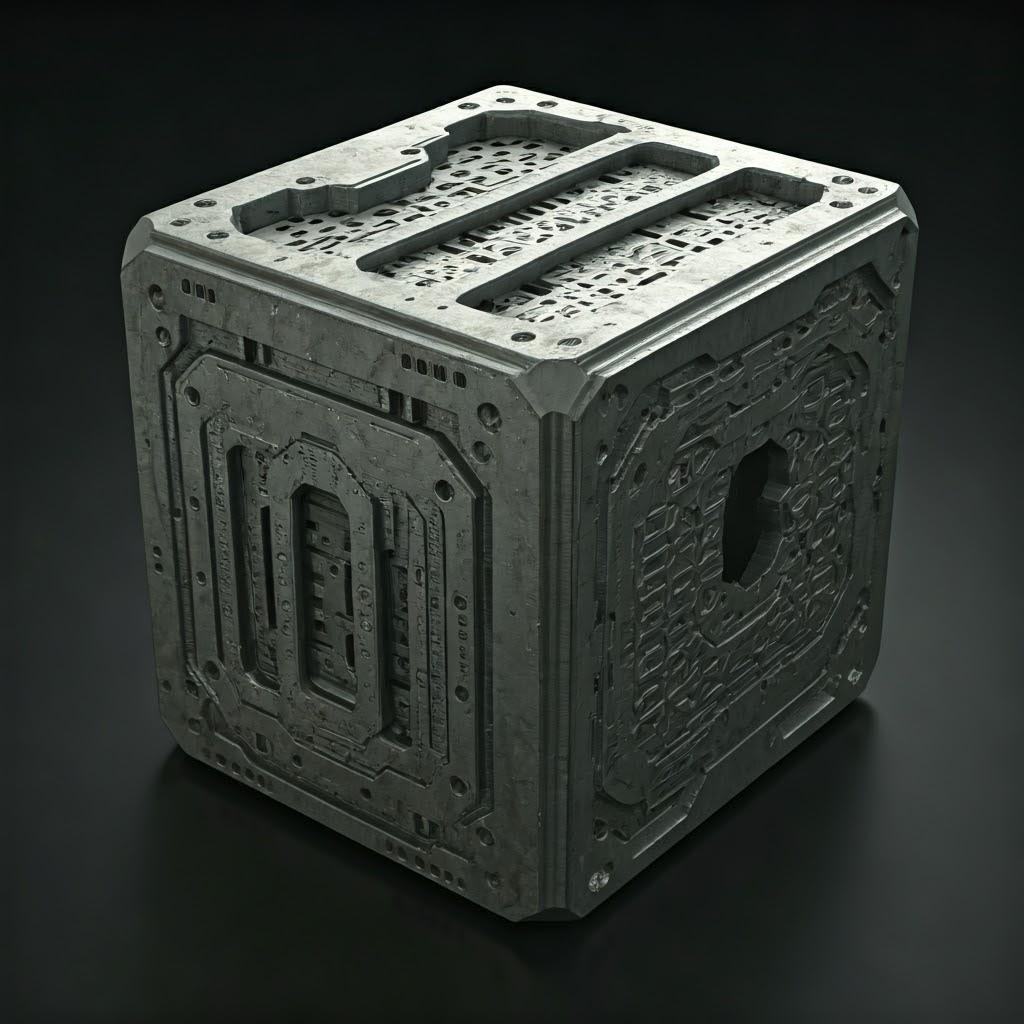
Warum die additive Fertigung von Metall ideal für Satelliten-Avionikboxen ist
Aufgrund der hohen Anforderungen von Raumfahrtanwendungen, insbesondere des unablässigen Strebens nach Massenreduzierung und Leistungssteigerung, eignen sich die Gehäuse der Satellitenavionik besonders gut für die Herstellung mittels additiver Fertigung (AM) von Metall. Während herkömmliche Methoden wie die CNC-Bearbeitung von Knüppeln der Industrie seit Jahrzehnten gute Dienste leisten, bietet AM eine Reihe von Vorteilen, die direkt auf die wichtigsten Herausforderungen von Satellitenkonstrukteuren, -herstellern und Beschaffungsspezialisten in der Luft- und Raumfahrt eingehen. Bei der Entscheidung für den 3D-Metalldruck geht es nicht nur um die Einführung einer neuen Technologie, sondern um eine strategische Entscheidung, die spürbare Verbesserungen in Bezug auf Gewicht, Leistung, Vorlaufzeit und Konstruktionsmöglichkeiten ermöglicht und letztlich zu leistungsfähigeren und kostengünstigeren Satellitenmissionen beiträgt.
Lassen Sie uns die überzeugenden Vorteile der Verwendung von Metall-AM für diese kritischen Komponenten aufschlüsseln:
- Unübertroffenes Leichtbaupotenzial:
- Topologie-Optimierung: AM ermöglicht es den Ingenieuren, Algorithmen zu verwenden, die die Struktur der Avionikboxen formen, indem sie Material aus wenig beanspruchten Bereichen entfernen und gleichzeitig kritische Lastpfade verstärken. Das Ergebnis sind organisch anmutende, hocheffiziente Strukturen, die die Anforderungen an Steifigkeit und Festigkeit bei minimaler Masse erfüllen. Es wird häufig von Gewichtseinsparungen von 30-50 % oder sogar mehr im Vergleich zu traditionell bearbeiteten Konstruktionen berichtet, was sich direkt in Einsparungen bei den Startkosten oder einer höheren Nutzlastkapazität niederschlägt.
- Gitterförmige Strukturen: AM ermöglicht die Integration komplexer interner Gitter- oder Kreiselstrukturen in die Wände oder den Boden des Gehäuses. Diese Strukturen bieten ein hervorragendes Verhältnis zwischen Steifigkeit und Gewicht, wodurch die Masse weiter reduziert wird, ohne die strukturelle Integrität zu beeinträchtigen. Sie können auch so gestaltet werden, dass sie die Schwingungsdämpfung oder das Wärmemanagement unterstützen.
- Materialeffizienz: Im Gegensatz zur subtraktiven Fertigung, bei der eine beträchtliche Menge an teurem, für die Luft- und Raumfahrt geeignetem Material in Form von Spänen verschwendet werden kann, wird bei der AM das Material nur dort verwendet, wo es benötigt wird. Dies führt zu einem besseren Verhältnis zwischen Anschaffung und Fertigung und zu geringeren Rohmaterialkosten, insbesondere bei komplexen Teilen oder teuren Legierungen wie Scalmalloy®.
- Designfreiheit für mehr Leistung:
- Teil Konsolidierung: Mehrere Einzelkomponenten (z. B. Gehäuse, Halterungen, Abdeckungen, Thermobänder), die traditionell separat bearbeitet und mit Hilfe von Befestigungselementen zusammengebaut würden, können in ein einziges, monolithisches 3D-gedrucktes Teil integriert werden. Dies reduziert die Anzahl der Teile, die Montagezeit und die Komplexität erheblich. Entscheidend ist, dass keine Verbindungselemente mehr benötigt werden, die Gewicht und potenzielle Fehlerquellen (z. B. Lockerung durch Vibrationen) darstellen.
- Integriertes Wärmemanagement: AM ermöglicht die Herstellung hochkomplexer interner Merkmale, die sich nicht maschinell bearbeiten lassen. Dazu gehören konforme Kühlkanäle, die genau den Konturen der wärmeerzeugenden elektronischen Komponenten folgen, integrierte Kühlkörper mit optimierten Rippengeometrien oder eingebettete Wärmerohrstrukturen. Dies führt zu einer weitaus effizienteren Wärmeableitung im Vergleich zu aufgeschraubten Lösungen, was die Zuverlässigkeit der Elektronik verbessert und potenziell höhere Leistungsdichten ermöglicht.
- Komplexe Geometrien und funktionale Integration: Merkmale wie eine komplizierte interne Unterteilung zur EMI-Abschirmung, integrierte Wellenleiterstrukturen, kundenspezifische Steckergehäuse, präzise geformte Montagemerkmale für nicht standardisierte Komponenten und gekrümmte oder organische äußere Formen (aufgrund von Optimierungs- oder Verpackungsbeschränkungen) werden herstellbar. Dadurch kann das Avionikgehäuse mehrere Funktionen in einem kompakten Gehäuse effektiver erfüllen.
- Beschleunigte Entwicklung und verkürzte Vorlaufzeiten:
- Rapid Prototyping: Funktionale Metallprototypen können innerhalb weniger Tage direkt aus CAD-Modellen gedruckt werden, anstatt Wochen oder Monate für den Aufbau von Werkzeugen und die Bearbeitung zu benötigen. Dies ermöglicht es den Entwicklungsteams, Entwürfe viel schneller zu überarbeiten und Passformprüfungen, strukturelle Tests und thermische Validierungen früher im Entwicklungszyklus durchzuführen.
- Beseitigung von Werkzeugen: AM ist ein direktes digitales Fertigungsverfahren, das teure und zeitaufwändige Formen, Gesenke oder Vorrichtungen überflüssig macht, die beim Gießen oder bei komplexen Bearbeitungsvorgängen benötigt werden. Dadurch werden die Vorlaufkosten und -zeiten drastisch reduziert, insbesondere bei der für Satellitenprogramme typischen Produktion kleiner bis mittlerer Stückzahlen.
- Fertigung auf Abruf: AM ermöglicht eine dezentralisierte oder bedarfsorientierte Produktion. Ersatzteile oder Designvarianten können je nach Bedarf gedruckt werden, was den Lagerbestand reduziert und die Reaktionsfähigkeit der Lieferkette verbessert - ein wichtiger Aspekt für Fertigungspartner in der Luft- und Raumfahrt und Lieferanten von Satellitenkomponenten.
- Potenzial für verbesserte Materialeigenschaften:
- Optimierte Mikrostrukturen: Das schnelle Schmelzen und Erstarren in Verfahren wie dem Selektiven Laserschmelzen (SLM) oder dem Selektiven Elektronenstrahlschmelzen (SEBM) kann zu feinkörnigen Mikrostrukturen führen. Bei bestimmten Legierungen wie Scalmalloy® ist diese schnelle Erstarrung entscheidend für das Erreichen ihrer außergewöhnlich hohen Festigkeit.
- Fortschrittliche Legierungen: AM-Prozesse können häufig fortschrittliche Legierungen oder Metallmatrix-Verbundwerkstoffe verarbeiten, die speziell für die additive Fertigung entwickelt wurden und im Vergleich zu herkömmlichen Knet- oder Gusslegierungen bessere Eigenschaften aufweisen (z. B. ein besseres Verhältnis von Festigkeit zu Gewicht oder eine bessere Hochtemperaturleistung). Der Zugang zu diesen fortschrittlichen Werkstoffen über zuverlässige Metallpulverlieferanten wie Met3dp ist von entscheidender Bedeutung.
AM vs. CNC-Bearbeitung für Avionik-Gehäuse:
Merkmal | Additive Fertigung von Metall (AM) | Traditionelle CNC-Bearbeitung | Vorteil für Avionikboxen |
---|---|---|---|
Gewicht | Signifikantes Potenzial durch Topologie-Optik, Gitternetze | Begrenzt durch subtraktiven Charakter, Zugang | AM (Massenreduzierung ist das A und O) |
Komplexität | Hohe geometrische Freiheit, einfache interne Merkmale | Begrenzt durch den Zugang zu Werkzeugen und die Komplexität der Einrichtung | AM (Ermöglicht Integration, Optimierung) |
Anzahl der Teile | Ermöglicht die Konsolidierung in monolithische Teile | Erfordert oft mehrteilige Baugruppen | AM (Reduziert Gewicht, Montage, Risiko) |
Wärmemanagement | Integrierte konforme Kanäle, komplexe Wärmesenken | Angeschraubte Lösungen, begrenzte Geometrie | AM (Hervorragende thermische Leistung) |
Vorlaufzeit (Proto) | Fasten (Tage) | Langsamer (Wochen/Monate aufgrund von Einrichtung/Tooling) | AM (Beschleunigt die Entwicklung) |
Vorlaufzeit (Prod) | Kann wettbewerbsfähig sein, abhängig von Volumen/Komplexität | Etabliert, effizient für hohes Volumen | Kommt darauf an (AM oft schneller bei niedrigem Volumen) |
Materialabfälle | Niedrig (additives Verfahren) | Hoch (subtraktives Verfahren) | AM (Besseres Kauf-zu-Flug-Verhältnis) |
Anfängliche Kosten | Keine Werkzeugkosten, potenziell höhere Kosten pro Teil | Werkzeug-/Rüstkosten, geringere Kosten pro Teil bei hohen Stückzahlen | AM (Niedrigere Schranke für geringe Mengen) |
Entwurf Iteration | Einfache und schnelle Änderungen | Erfordert Neuprogrammierung, möglicherweise neue Werkzeuge | AM (Unterstützt agile Entwicklung) |
In Blätter exportieren
Während die CNC-Bearbeitung nach wie vor unerlässlich ist, um sehr hohe Toleranzen bei Gegenflächen oder spezifischen Merkmalen zu erreichen (und oft als Nachbearbeitungsschritt für AM-Teile verwendet wird), bietet die Metall-AM eine überlegene primäre Fertigungsroute, um die leichten, hoch integrierten und leistungsoptimierten Designs zu erreichen, die für moderne Satelliten-Avionikboxen erforderlich sind. Unternehmen wie Met3dp, die umfassende Lösungen für fortschrittliche Druckverfahrenhochwertige Pulver und Anwendungsunterstützung sind entscheidend, um Kunden aus der Luft- und Raumfahrt dabei zu helfen, diese Vorteile effektiv zu nutzen. Die strategische Übernahme von AM durch Ingenieure und Beschaffungsmanager in der Luft- und Raumfahrt treibt Innovation und Effizienz in der Entwicklung von Satellitenhardware voran.
Werkstoff-Fokus: Scalmalloy® und AlSi10Mg für Raumfahrtanwendungen
Die Auswahl des richtigen Materials ist absolut entscheidend für den Erfolg jeder weltraumgebundenen Komponente, und 3D-gedruckte Satelliten-Avionikboxen bilden da keine Ausnahme. Das Material muss nicht nur die erforderlichen mechanischen Eigenschaften (Festigkeit, Steifigkeit, Ermüdungsbeständigkeit) aufweisen, um den Startbelastungen standzuhalten und die strukturelle Integrität zu erhalten, sondern auch strenge Anforderungen an eine geringe Dichte, gute Wärmeleitfähigkeit, Korrosionsbeständigkeit und oft auch spezifische Ausgasungs- und Strahlungsbeständigkeitseigenschaften erfüllen. Für die additive Fertigung von Avionikgehäusen sind zwei Aluminiumlegierungen aufgrund ihrer günstigen Kombination von Eigenschaften, Verarbeitbarkeit und ihrer wachsenden Flugerfahrung besonders geeignet: Scalmalloy® und AlSi10Mg. Für die Entwicklung und Beschaffung leistungsfähiger Satellitenhardware ist es wichtig, die einzigartigen Eigenschaften der einzelnen Produkte zu verstehen und zu wissen, warum sie von Raumfahrtingenieuren bevorzugt und von spezialisierten Metallpulverlieferanten bezogen werden.
Scalmalloy®: Der Hochleistungskandidat
Scalmalloy® ist eine patentierte Hochleistungs-Aluminium-Magnesium-Scandium-Legierung (Al-Mg-Sc), die von APWORKS, einer Tochtergesellschaft von Airbus, speziell für die additive Fertigung entwickelt wurde. Aufgrund seiner außergewöhnlichen Eigenschaften, insbesondere seiner spezifischen Festigkeit (Verhältnis von Festigkeit zu Gewicht), die die vieler herkömmlicher hochfester Aluminiumlegierungen übertrifft und in einigen Bereichen sogar an Titan heranreicht, hat es in anspruchsvollen Branchen wie der Luft- und Raumfahrt und dem Motorsport rasch an Bedeutung gewonnen.
- Wichtige Eigenschaften & Vorteile:
- Außergewöhnliche spezifische Stärke: Dies ist die entscheidende Eigenschaft von Scalmalloy®. Seine hohe Streck- und Zugfestigkeit in Verbindung mit der geringen Dichte (≈2,67 g/cm3) führt zu Bauteilen, die bei gleicher Steifigkeit oder Festigkeit deutlich leichter sind als solche aus herkömmlichen Aluminiumlegierungen für die Luft- und Raumfahrt (wie 6061 oder 7075). Dies ist ein enormer Vorteil für Satellitenkomponenten, bei denen die Masse entscheidend ist.
- Ausgezeichnete Duktilität und Schweißbarkeit: Im Gegensatz zu einigen hochfesten Aluminiumlegierungen der 7xxx-Serie weist Scalmalloy® eine gute Duktilität auf und ist gut schweißbar (wichtig für mögliche Nachbearbeitungs- oder Integrationsschritte).
- Gute Korrosionsbeständigkeit: Die Legierung weist eine gute Korrosionsbeständigkeit auf, ein wichtiger Faktor für die Bodenabfertigung und die langfristige Zuverlässigkeit der Mission.
- Hohe Ermüdungsfestigkeit: Es bietet eine hervorragende Ermüdungsbeständigkeit, die für Bauteile, die während des Starts und des Betriebs zyklischen Belastungen ausgesetzt sind, von entscheidender Bedeutung ist.
- Entwickelt für AM: Seine Zusammensetzung ist auf das Laser Powder Bed Fusion (LPBF, auch bekannt als SLM) Verfahren zugeschnitten, was zu einer guten Verarbeitbarkeit und der Fähigkeit führt, dichte, hochintegrierte Teile herzustellen. Die schnelle Erstarrung während des LPBF-Verfahrens ist der Schlüssel zum Erreichen des feinkörnigen Gefüges und der hohen Festigkeit.
- Erwägungen:
- Kosten: Scalmalloy®-Pulver ist in der Regel teurer als Standard-Aluminiumlegierungen wie AlSi10Mg, da es Scandium und Lizenz-/Patentfaktoren enthält.
- Wärmeleitfähigkeit: Seine Wärmeleitfähigkeit ist im Allgemeinen geringer als die von Standard-Aluminiumlegierungen, was ein Problem darstellen kann, wenn die passive Wärmeableitung durch die Gehäusestruktur die primäre Kühlmethode ist. AM ermöglicht jedoch die Integration hocheffizienter spezieller thermischer Funktionen, um dies auszugleichen.
- Verfügbarkeit: Sie sind zwar zunehmend bei lizenzierten Anbietern erhältlich, aber die Lieferkette ist möglicherweise weniger weit verbreitet als bei Standardlegierungen.
- Warum das für Avionikboxen wichtig ist: Mit Scalmalloy® können Konstrukteure die Gewichtsreduzierung auf die Spitze treiben und gleichzeitig die strukturelle Robustheit beibehalten. Scalmalloy® eignet sich ideal für hoch optimierte, leistungskritische Gehäuse, bei denen die Minimierung der Masse absolute Priorität hat und die höheren Materialkosten rechtfertigt. Seine Festigkeit ermöglicht dünnere Wände und kompliziertere, gewichtssparende Merkmale, die durch Topologieoptimierung entwickelt wurden.
AlSi10Mg: Das bewährte Arbeitspferd
AlSi10Mg ist eine weit verbreitete Aluminiumlegierung, die Silizium und Magnesium enthält. Es ist im Wesentlichen das AM-Äquivalent zu einer gängigen Gusslegierung (A360). Es ist eines der ausgereiftesten und am besten charakterisierten Materialien für Metall-AM, insbesondere LPBF, und bietet ein gutes Gleichgewicht von Eigenschaften, ausgezeichneter Verarbeitbarkeit und Kosteneffizienz.
- Wichtige Eigenschaften & Vorteile:
- Gutes Verhältnis von Stärke zu Gewicht: AlSi10Mg ist zwar nicht so hoch wie Scalmalloy®, bietet aber eine gute Kombination aus Festigkeit und geringer Dichte (≈2,68 g/cm3), was zu erheblichen Gewichtseinsparungen im Vergleich zu vielen traditionell verwendeten Materialien führt.
- Ausgezeichnete Wärmeleitfähigkeit: Im Vergleich zu Scalmalloy® und vielen Titan- oder Stahllegierungen hat AlSi10Mg eine deutlich bessere Wärmeleitfähigkeit. Dies macht es zu einer hervorragenden Wahl für Avionikgehäuse, bei denen eine effiziente Wärmeableitung durch die Struktur selbst eine primäre Designanforderung ist.
- Hervorragende Verarbeitbarkeit: Es ist bekannt für seine einfache Verarbeitung mittels LPBF, die hohe Fertigungsgeschwindigkeiten und eine gute Teilequalität mit gut etablierten Parametersätzen ermöglicht. Dies trägt zu niedrigeren Herstellungskosten und Vorlaufzeiten bei.
- Kosten-Nutzen-Verhältnis: AlSi10Mg-Pulver ist erheblich preiswerter als Scalmalloy® und daher eine wirtschaftlichere Wahl für weniger gewichtskritische Anwendungen oder größere Produktionsserien.
- Breite Verfügbarkeit: Als Standard-AM-Legierung ist AlSi10Mg-Pulver bei zahlreichen Metallpulverhändlern und -herstellern erhältlich, darunter Spezialisten wie Met3dp, die durch fortschrittliche Zerstäubungstechniken eine hohe Qualität gewährleisten.
- Erwägungen:
- Geringere absolute Stärke: Seine Streck- und Zugfestigkeit ist geringer als die von Scalmalloy®, was bedeutet, dass die Bauteile unter Umständen etwas dicker sein oder mehr strukturelle Merkmale aufweisen müssen, um die gleiche Tragfähigkeit zu erreichen, was die Gewichtseinsparungen bei stark beanspruchten Teilen möglicherweise wieder wettmacht.
- Geringere Duktilität: Weist im Vergleich zu Scalmalloy® in der Regel eine geringere Duktilität auf, was bei Anwendungen, die eine hohe Zähigkeit oder Verformungstoleranz erfordern, ein Faktor sein kann. Zur Optimierung der mechanischen Eigenschaften sind häufig Wärmebehandlungen (wie T6) erforderlich.
- Warum das für Avionikboxen wichtig ist: AlSi10Mg ist aufgrund seiner Ausgereiftheit, Kosteneffizienz und hervorragenden thermischen Eigenschaften häufig die Standardwahl für 3D-gedruckte Aluminiumkomponenten. Es ist ideal für Avionikgehäuse, bei denen das Wärmemanagement eine wichtige Rolle spielt oder bei denen die absolut höchste spezifische Festigkeit von Scalmalloy® nicht unbedingt erforderlich ist, um die Einsatzanforderungen zu erfüllen. Aufgrund seiner Verarbeitbarkeit ist es für komplexe Geometrien und eine relativ schnelle Produktion geeignet.
Tabelle zum Materialvergleich:
Eigentum | Scalmalloy® | AlSi10Mg | Relevanz für Avionikboxen |
---|---|---|---|
Primärer Vorteil | Höchste spezifische Festigkeit | Hervorragende Wärmeleitfähigkeit, Kosten | Kompromiss zwischen Masse und Wärmeleistung |
Dichte | ≈2,67g/cm3 | ≈2,68g/cm3 | Beide bieten einen erheblichen Gewichtsvorteil gegenüber Stahl/Titan |
Streckgrenze (typisch) | Sehr hoch (≈450-500+ MPa) | Gut (≈230-280 MPa, im eingebauten Zustand) | Scalmalloy® ermöglicht dünnere/leichtere Strukturen bei gleicher Belastung |
Zugfestigkeit (typisch) | Sehr hoch (≈500-550+ MPa) | Gut (≈350-450 MPa, im eingebauten Zustand) | Höhere Festigkeit erhöht die strukturellen Sicherheitsreserven |
Duktilität (Dehnung) | Gut (≈10-15%) | Mäßig (≈3-10%, im Ist-Zustand) | Wichtig für Zähigkeit und Bruchsicherheit |
Wärmeleitfähigkeit | Mäßig (≈110-130W/m⋅K) | Gut (≈130-180W/m⋅K) | AlSi10Mg besser für passive Wärmeausbreitung über die Struktur |
Verarbeitbarkeit (LPBF) | Gut (spezifische Parameter erforderlich) | Ausgezeichnet (gut etabliert) | AlSi10Mg kann einen schnelleren/günstigeren Druck ermöglichen |
Korrosionsbeständigkeit | Gut | Gut | Geeignet für Weltraumumgebung und Bodenabfertigung |
Kosten | Hoch | Mäßig | Wesentlicher Faktor für Beschaffung und Projektbudget |
Typischer Anwendungsfall | Maximale Gewichtsreduzierung, stark beanspruchte Teile | Wärmemanagement kritisch, kostensensibel | Anpassung des Materials an die wichtigsten Designfaktoren |
In Blätter exportieren
Die Rolle von Pulverqualität und Lieferantenkompetenz
Unabhängig von der gewählten Legierung ist die Qualität des Metallpulvers ausschlaggebend für die Herstellung zuverlässiger, leistungsstarker und weltraumtauglicher AM-Teile. Pulvereigenschaften wie Partikelgrößenverteilung (PSD), Morphologie (Sphärizität), Fließfähigkeit und Reinheit wirken sich direkt auf die Dichte, die mechanischen Eigenschaften und die Oberflächenbeschaffenheit der endgültigen gedruckten Komponente aus. Defekte wie Porosität können durch schlechte Pulverqualität verursacht werden und die Integrität des Avionikgehäuses beeinträchtigen.
Hier sind spezialisierte Anbieter wie Met3dp spielen eine entscheidende Rolle. Met3dp verwendet branchenführende Technologien zur Pulverherstellung:
- Gaszerstäubung: Durch die Verwendung einzigartiger Düsen- und Gasströmungsdesigns werden hochkugelförmige Metallpulver mit hervorragender Fließfähigkeit erzeugt, die für gleichmäßige Pulverbettschichten in LPBF- und SEBM-Verfahren entscheidend sind.
- Plasma-Rotations-Elektroden-Verfahren (PREP): Bekannt für die Herstellung von Pulvern mit außergewöhnlich hoher Reinheit und Sphärizität, besonders geeignet für anspruchsvolle Anwendungen und reaktive Materialien.
Met3dp fertigt eine breite Palette von hochwertige Metallpulverdazu gehören auch Aluminiumlegierungen, die für Luft- und Raumfahrtanwendungen geeignet sind und die strengen Spezifikationen erfüllen, die für den Druck von einsatzkritischen Teilen wie Satelliten-Luftfahrtelektronikboxen erforderlich sind. Das Know-how des Unternehmens geht über die Pulverherstellung hinaus und umfasst den gesamten additiven Fertigungsablauf, einschließlich der Prozessoptimierung auf den modernen SEBM-Druckern und umfassender Anwendungsentwicklungsdienste. Die Zusammenarbeit mit einem sachkundigen Lieferanten, der sowohl die Materialwissenschaft als auch die AM-Verarbeitung versteht, ist für Luft- und Raumfahrtingenieure und Beschaffungsmanager, die zuverlässige, leistungsstarke 3D-gedruckte Komponenten suchen, von entscheidender Bedeutung. Die Entscheidung zwischen Scalmalloy® und AlSi10Mg erfordert eine sorgfältige Analyse der spezifischen Einsatzanforderungen, wobei die Notwendigkeit einer extremen Gewichtsreduzierung gegen die Anforderungen an die thermische Leistung und die Budgeteinschränkungen abzuwägen ist, unterstützt durch fachkundige Material- und Fertigungsberatung. Quellen und verwandte Inhalte
Design for Additive Manufacturing (DfAM) Prinzipien für Avionikgehäuse
Der Übergang von traditionellen Fertigungsparadigmen zur additiven Fertigung (AM) von Metallen erfordert mehr als nur die Konvertierung einer vorhandenen CAD-Datei. Um das transformative Potenzial von AM für Satelliten-Avionikboxen wirklich zu erschließen und ein Maximum an Gewichtsreduzierung, Leistungssteigerung und Kosteneffizienz zu erreichen, müssen die Ingenieure folgende Aspekte berücksichtigen Design für additive Fertigung (DfAM) grundsätze. DfAM ist eine Designphilosophie und eine Reihe von Methoden, die die Fähigkeiten und Einschränkungen des gewählten AM-Prozesses (wie Laser Powder Bed Fusion – LPBF, oder Selective Electron Beam Melting – SEBM) und des Materials (wie Scalmalloy® oder AlSi10Mg) bereits in den frühesten Stadien der Konzeptentwicklung explizit berücksichtigen. Das Ignorieren von DfAM führt oft zu suboptimalen Ergebnissen: Teile, die nur schwer oder gar nicht erfolgreich gedruckt werden können, übermäßige Stützstrukturen erfordern, eine komplexe Nachbearbeitung notwendig machen oder die einzigartigen Vorteile, die AM bietet, nicht ausschöpfen. Für Luft- und Raumfahrtingenieure und Beschaffungsmanager, die mit der Beschaffung von Satellitenhardware der nächsten Generation befasst sind, ist das Verständnis und die Umsetzung von DfAM entscheidend für die Maximierung der Investitionsrendite der additiven Technologie. Es geht um ein grundlegendes Umdenken wie ein Teil ist so konzipiert, dass es am besten zu wie wird es gemacht werden.
Ein wirksames DfAM für Satellitenavionikboxen umfasst mehrere Schlüsselstrategien:
- Topologie-Optimierung: Dies ist wohl eines der leistungsstärksten DfAM-Werkzeuge, um eine drastische Verschlankung zu erreichen.
- Prozess: Die Topologie-Optimierungssoftware nutzt die Finite-Elemente-Analyse (FEA), um die Belastungen (mechanisch, thermisch) zu simulieren, denen die Avionikbox während ihres Lebenszyklus ausgesetzt ist (Startvibrationen, Betriebsbelastungen, thermische Ausdehnung/Kontraktion). Basierend auf definierten Designräumen, Lastfällen, Einschränkungen (z.B. Sperrzonen für Elektronik, Montagepunkte) und Optimierungszielen (z.B. Minimierung der Masse, Maximierung der Steifigkeit) entfernt der Algorithmus iterativ Material aus Bereichen, in denen es nicht wesentlich zur Leistung beiträgt.
- Das Ergebnis: Das Ergebnis ist oft eine organische, knochenähnliche Struktur, bei der das Material nur entlang der Hauptbelastungspfade vorhanden ist. Dies kann zu einer Gewichtseinsparung von 30-70 % im Vergleich zu herkömmlich konstruierten Teilen führen, was sich direkt auf die Startkosten und die Leistung des Satelliten auswirkt.
- Erwägungen: Die Ingenieure müssen alle relevanten Lastfälle genau definieren. Die sich daraus ergebenden komplexen Geometrien müssen sorgfältig validiert und möglicherweise geglättet werden, damit sie im Rahmen der Einschränkungen des AM-Prozesses herstellbar sind (z. B. Vermeidung von Merkmalen, die zu dünn sind, um zuverlässig gedruckt zu werden). Die Integration mit der thermischen Analyse ist ebenfalls entscheidend, um sicherzustellen, dass optimierte Strukturen keine thermischen Engpässe verursachen.
- Gitterstrukturen und Ausfachungen: AM ermöglicht in einzigartiger Weise die Schaffung komplexer innerer Strukturen innerhalb fester Volumen.
- Typen: Es können verschiedene Gittertopologien verwendet werden, darunter strebenbasierte Gitter (wie kubisches oder Oktett-Fachwerk) oder oberflächenbasierte Gitter, die von dreifach periodischen Minimalflächen (TPMS) abgeleitet sind, wie Kreisel oder Schwarzite. Verschiedene Gittertypen bieten ein unterschiedliches Gleichgewicht von Steifigkeit, Festigkeit, Gewicht und möglicherweise anderen funktionellen Eigenschaften.
- Vorteile:
- Gewichtsreduzierung: Das Ersetzen von massiven Innenvolumina durch Gitter mit geringer Dichte führt zu einer erheblichen Verringerung der Masse bei gleichzeitiger Beibehaltung der erforderlichen strukturellen Unterstützung und Steifigkeit.
- Schwingungsdämpfung: Bestimmte Gitterstrukturen können hervorragende Energieabsorptions- und Vibrationsdämpfungseigenschaften aufweisen, was für den Schutz empfindlicher Elektronik beim Start von Vorteil sein kann.
- Verbesserte Wärmeübertragung: Insbesondere TPMS-Gitter bieten ein sehr hohes Verhältnis von Oberfläche zu Volumen und verschlungene Pfade, die bei Bedarf für eine verbesserte passive Kühlung oder die Entwicklung integrierter Wärmetauscher in den Wänden der Avionikbox genutzt werden können.
- Integration: Gitterstrukturen können selektiv in Wänden, Böden oder spezifischen Merkmalen des Avionikgehäuses angebracht werden, oft unter Berücksichtigung von Spannungsanalysen oder thermischen Anforderungen. Software-Tools ermöglichen fließende Übergänge zwischen massiven Abschnitten und gitterartigen Regionen. Die Entfernung von Pulver aus komplexen inneren Gittern muss sorgfältig bedacht werden.
- Teil Konsolidierung: Dieses DfAM-Prinzip nutzt die Fähigkeit von AM, komplexe, monolithische Komponenten zu erstellen.
- Konzept: Anstatt ein Avionikgehäuse als eine Baugruppe aus mehreren maschinell bearbeiteten Teilen (z. B. Hauptgehäuse, Deckel, Montagehalterungen, innere Trennwände, Anschlussplatten) zu konstruieren, die durch Befestigungselemente zusammengehalten werden, können Ingenieure es als eine einzige integrierte Struktur neu konstruieren.
- Vorteile:
- Reduzierte Teileanzahl: Vereinfacht das Bestands-, Logistik- und Lieferkettenmanagement - ein entscheidender Vorteil für die Beschaffung in der Luft- und Raumfahrt.
- Haben sie optimale Druckparameter speziell für die von ihnen angebotenen Marinelegierungen entwickelt und validiert, um dichte, hochleistungsfähige Teile zu gewährleisten? Fragen Sie nach Materialdatenblättern, die auf ihren gedruckten Exemplaren basieren. Spart Gewicht (Verbindungselemente fügen Masse hinzu) und eliminiert potenzielle Fehlerquellen (Verbindungselemente können sich bei Vibrationen lösen).
- Reduzierte Montagezeit und -kosten: Die Herstellung eines einzigen Teils ist oft schneller und insgesamt billiger als die Herstellung mehrerer Teile und deren Zusammenbau.
- Verbesserte strukturelle Integrität: Monolithische Strukturen können stärker und steifer sein als Baugruppen mit Verbindungen.
- Verbesserte Versiegelung/Abschirmung: Die Beseitigung von Nähten und Fugen kann die Umweltabdichtung und die Wirksamkeit der EMI-Abschirmung verbessern.
- Beispiel: Bei einem Avionikgehäuse können die Montagefüße, die internen Leiterplattenführungen, die Kühlkörper und sogar komplexe Steckerschnittstellen als integraler Bestandteil des Hauptgehäuses gedruckt werden.
- Integriertes Wärmemanagement Merkmale: DfAM ermöglicht den Aufbau von Wärmemanagementlösungen in der Struktur, anstatt sie zu ergänzen.
- Konforme Kühlkanäle: Kanäle, die flüssiges Kühlmittel führen (in fortschrittlichen Systemen) oder die Wärmeausbreitung erleichtern, können so gestaltet werden, dass sie den Konturen von wärmeerzeugenden Bauteilen oder Bereichen, die eine gleichmäßige Temperatur erfordern, genau folgen, was die Kühleffizienz im Vergleich zu geraden, gebohrten Kanälen oder angebrachten Kühlplatten drastisch verbessert.
- Optimierte Kühlkörper: Kühlrippen können mit komplexen, optimierten Geometrien (z. B. variable Dicke/Teilung, gekrümmte Profile, Stiftrippen) entworfen werden, die direkt in die Gehäusewände oder den Boden integriert sind und die Oberfläche für die Strahlungs- oder Leitungswärmeübertragung innerhalb der Verpackungsbeschränkungen maximieren. Gitterstrukturen können auch innerhalb der Rippen zur Gewichtsreduzierung eingesetzt werden.
- Eingebettete Heatpipes: AM bietet die Möglichkeit, Strukturen oder Hohlräume, die als Wärmerohre fungieren, direkt in die Gehäusewände einzubetten, was einen hocheffizienten passiven Wärmetransport ermöglicht.
- AM-Prozess-spezifische Designregeln: Effektives Design bedeutet auch, dass die Nuancen des gewählten AM-Verfahrens (LPBF oder SEBM) berücksichtigt werden müssen.
- Minimale Featuregröße: Es gibt Grenzen, wie dünne Wände oder feine Merkmale zuverlässig gedruckt werden können, die durch die Spotgröße des Laser-/Elektronenstrahls, die Größe der Pulverpartikel und die Dynamik des Schmelzbades bestimmt werden. Die Konstrukteure müssen sich an die Richtlinien für die Mindestwandstärke halten (z. B. typischerweise >0,4-0,5 mm für Al-Legierungen, jedoch abhängig von der Höhe und Ausrichtung der Merkmale).
- Überhänge und selbsttragende Winkel: Merkmale, die deutlich über die vertikale Achse hinausragen, erfordern in der Regel Stützstrukturen während der Konstruktion, die später wieder entfernt werden müssen. Konstrukteure sollten möglichst selbsttragende Winkel (bei Aluminiumlegierungen typischerweise >45 Grad aus der Horizontalen) verwenden, um den Bedarf an Stützen zu minimieren. Anstelle von scharfen horizontalen Überhängen können Fasen und Verrundungen verwendet werden.
- Ausrichtung der Löcher: Horizontale Löcher werden oft mit besserer Maßgenauigkeit gedruckt als vertikale Löcher (relativ zur Bauplatte). Kleine vertikale Löcher benötigen möglicherweise keine Unterstützung, können aber rauere Innenflächen haben.
- Entfernung von Puder: Eingeschlossenes Pulver in inneren Hohlräumen oder komplexen Kanälen kann problematisch sein. Die Entwürfe müssen strategisch platzierte Austrittslöcher enthalten, damit das ungeschmolzene Pulver bei der Nachbearbeitung vollständig entfernt werden kann. Dies ist besonders kritisch bei Gitterstrukturen.
- Design für Inspektionen: Komplexe interne Merkmale, die durch AM ermöglicht werden, können mit herkömmlichen Methoden schwer zu prüfen sein. Die DfAM sollte überlegen, wie kritische Merkmale überprüft werden können (z. B. Gestaltung von Zugangsöffnungen für Endoskope, Sicherstellung, dass die Merkmale durch CT-Scans auflösbar sind).
- Strategie der Unterstützungsstruktur: Die Minimierung von Stützen ist zwar ideal, aber oft notwendig.
- Zweck: Stützen verankern das Teil auf der Bauplatte, verhindern Verformungen aufgrund von Wärmespannungen und stützen überhängende Merkmale.
- Designauswirkungen: Die Lage der Stützen wirkt sich auf die Oberflächenbeschaffenheit der Kontaktstellen aus (in der Regel rauher). Eine einfache Entfernung ist von entscheidender Bedeutung; Stützen in unzugänglichen internen Bereichen sollten nach Möglichkeit durch eine Umgestaltung vermieden werden. Verschiedene Arten von Stützen (z. B. massive Blöcke, dünne Wände, baumartige Strukturen) haben unterschiedliche Auswirkungen auf die Druckzeit, den Materialverbrauch und den Entfernungsaufwand.
- Kollaboration: Eine enge Zusammenarbeit zwischen dem Konstrukteur und dem AM-Dienstleister, wie Met3dp, ist unerlässlich, um eine optimale Unterstützungsstrategie zu entwickeln, die Druckbarkeit, Teilequalität und Nachbearbeitungsaufwand in Einklang bringt. Die Anwendungsentwicklungsdienste von Met3dp’ können entscheidende Hinweise zu den DfAM-Prinzipien und zu den auf ihre Anlagen und Materialien zugeschnittenen Unterstützungsstrategien liefern.
Durch die Integration dieser DfAM-Prinzipien können Satelliten-Avionikboxen von einfachen Gehäusen in hochgradig optimierte, multifunktionale Komponenten verwandelt werden, die die Leistung und Zuverlässigkeit von Satelliten erheblich verbessern. Dies erfordert ein Umdenken der Konstrukteure und eine frühzeitige Zusammenarbeit mit erfahrenen AM-Partnern.
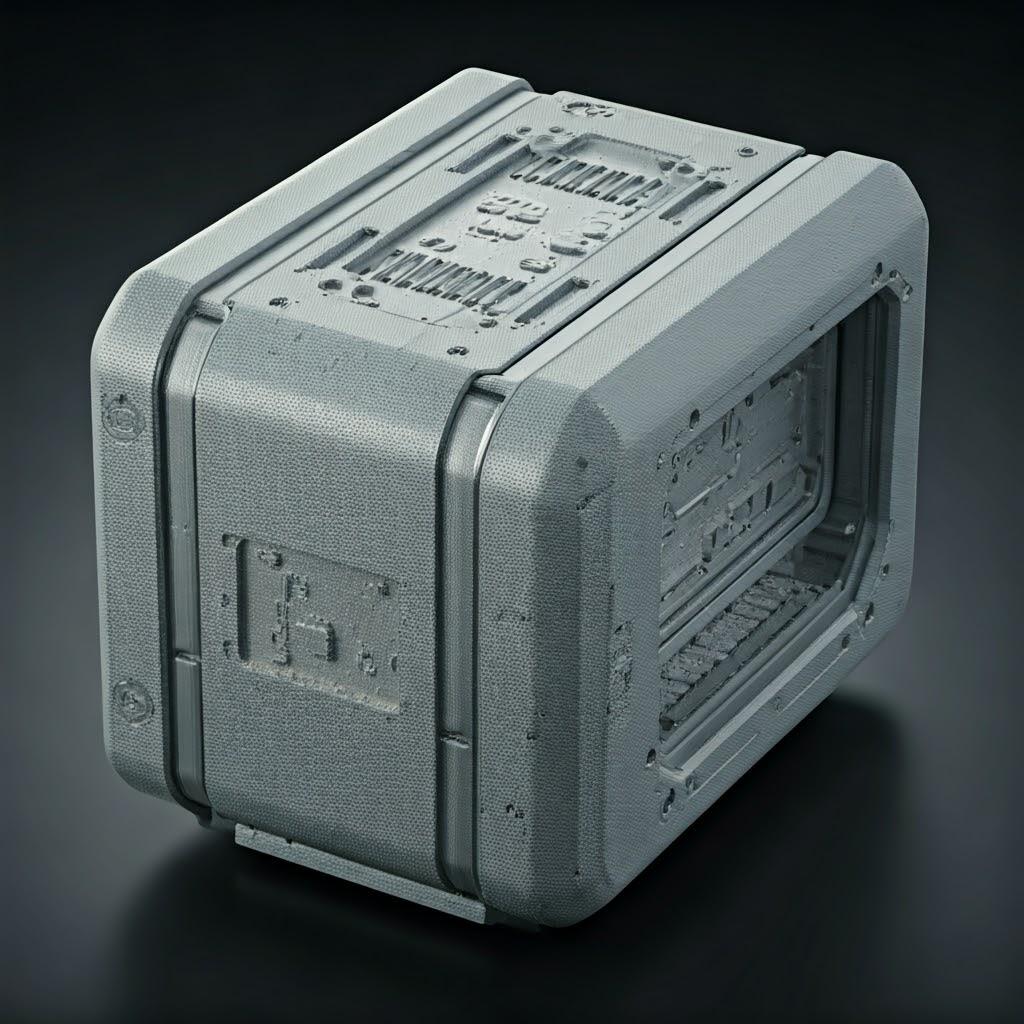
Erreichen von Präzision: Toleranz, Oberflächengüte und Maßgenauigkeit in der AM-Luftfahrtelektronik
Die additive Fertigung von Metallen bietet zwar unvergleichliche Designfreiheit und Leichtbaupotenziale, doch ein entscheidender Faktor für Ingenieure und Beschaffungsmanager in der Luft- und Raumfahrt ist das erreichbare Präzisionsniveau. Satelliten-Avionikgehäuse haben oft enge Anforderungen an die Schnittstellen zu anderen Komponenten, die Montage von Elektronik, die Gewährleistung einer ordnungsgemäßen Abdichtung und den Einbau in begrenzte Volumina. Das Verständnis der typischen Toleranzen, Oberflächengüten und der allgemeinen Maßgenauigkeit, die mit Metall-AM-Verfahren wie LPBF und SEBM, insbesondere mit Materialien wie Scalmalloy® und AlSi10Mg, erreicht werden können, ist für die Festlegung realistischer Erwartungen und der notwendigen Nachbearbeitungsschritte unerlässlich. Darüber hinaus kann die Rolle einer strengen Qualitätskontrolle und Messtechnik bei der Herstellung missionskritischer Fluggeräte nicht hoch genug eingeschätzt werden.
Toleranzen bei Metall-AM:
Metall-AM-Verfahren sind von Natur aus mit schnellem Schmelzen und Erstarren verbunden, was zu thermischen Spannungen und möglicher Schrumpfung führt, die die Maßgenauigkeit beeinträchtigen. Die direkt aus dem Drucker erreichbaren Toleranzen werden zwar ständig verbessert, sind aber im Allgemeinen größer als bei der CNC-Präzisionsbearbeitung erwartet.
- Allgemeine Toleranzen: Für die Gesamtabmessungen von Teilen liegen die typischen erreichbaren Toleranzen für LPBF- und SEBM-Verfahren oft im Bereich der ISO 2768 Klasse m (mittel) oder manchmal Klasse f (fein). Dies kann ±0,1 mm bis ±0,3 mm oder mehr für kleinere Merkmale (z. B. < 100 mm) und möglicherweise ±0,5 mm oder einen Prozentsatz der Abmessung (z. B. ±0,2 %) für größere Abmessungen bedeuten. Diese Werte sind in hohem Maße von der jeweiligen Maschine, dem Material, der Teilegeometrie, der Bauausrichtung und den verwendeten Prozessparametern abhängig.
- Merkmalspezifische Toleranzen: Kleinere Merkmale, Löcher und komplizierte Details können aufgrund von Faktoren wie der Dynamik des Schmelzbads und der Wärmeakkumulation schwieriger präzise zu steuern sein. Die Toleranzen für Lochdurchmesser, Wandstärken und die Positionierung feiner Merkmale können größer sein als die allgemeinen Maßtoleranzen.
- Auswirkungen der Nachbearbeitung: Es ist wichtig zu verstehen, dass kritische Toleranzen die für Passflächen, Lagerschnittstellen, Dichtungsnuten oder präzise Ausrichtungen von Steckern erforderlich sind, sind in der Regel durch Nachbearbeitung erreicht. AM wird eingesetzt, um die endkonturnahe Form mit ihren komplexen Merkmalen und der leichten Struktur zu erzeugen, und die CNC-Bearbeitung sorgt für die endgültige Präzision, wo sie benötigt wird. Bei der Konstruktion für AM wird häufig zusätzliches Material (Bearbeitungszugabe) speziell in Bereichen hinzugefügt, die enge Toleranzen erfordern.
Oberflächengüte (Oberflächenrauhigkeit):
Der schichtweise Aufbau von AM führt zu einer charakteristischen Oberflächenstruktur, die häufig durch den Rauheitsmittelwert (Ra) beschrieben wird. Die erreichbare Oberflächengüte hängt stark von mehreren Faktoren ab:
- Prozess: LPBF erzeugt im Allgemeinen feinere Oberflächen als SEBM, da die Pulverpartikelgröße und die Schichtdicke geringer sind.
- Orientierung: Oberflächen, die während der Bauphase nach oben zeigen, weisen in der Regel die beste Oberfläche auf. Vertikale Wände haben einen spürbaren Schichtabstufungseffekt. Nach unten gerichtete Oberflächen (gestützte Oberflächen) weisen aufgrund der Kontaktpunkte mit der Tragstruktur und des Schmelzbadverhaltens bei Überhängen in der Regel die schlechteste Oberfläche auf.
- Parameter: Schichtdicke, Laser-/Strahlleistung, Scangeschwindigkeit und Pulvereigenschaften beeinflussen alle Ra. Typische Ra-Werte für LPBF-Aluminiumlegierungen liegen zwischen 6 und 15 µm (Mikrometer) auf vertikalen oder aufwärts gerichteten Oberflächen und können auf abwärts gerichteten Oberflächen auf 20 bis 30 µm oder mehr ansteigen. SEBM führt typischerweise zu raueren Oberflächen.
- Auswirkungen: Bei unkritischen Oberflächen oder inneren Merkmalen kann die Oberflächenbeschaffenheit wie im Werk akzeptabel sein. Für Dichtungsflächen, ermüdungskritische Bereiche oder Oberflächen, die besondere thermische/optische Eigenschaften erfordern, ist jedoch eine Nachbearbeitung (z. B. Perlstrahlen, Trommeln, Polieren, maschinelle Bearbeitung) erforderlich, um glattere Oberflächen zu erzielen (z. B. Ra < 3,2 µm, < 1,6 µm oder noch niedriger).
Maßgenauigkeit und Reproduzierbarkeit:
Für die Serienproduktion von Satellitenkomponenten ist eine gleichbleibende Maßgenauigkeit von Bau zu Bau (Wiederholbarkeit) unerlässlich.
- Faktoren, die die Genauigkeit beeinflussen:
- Thermische Effekte: Durch ungleichmäßige Erwärmung und Abkühlung während des Bauprozesses kommt es zu Ausdehnung und Kontraktion, was zu Eigenspannungen und möglichem Verzug (Warping) führt. Ein sorgfältiges Wärmemanagement, optimierte Scan-Strategien und eine spannungsfreie Nachbearbeitung sind entscheidend.
- Schrumpfung: Materialien schrumpfen beim Erstarren und Abkühlen; dies muss in der Software zur Bauvorbereitung kompensiert werden (Skalierungsfaktor).
- Kalibrierung der Maschine: Eine genaue Laser-/Strahlpositionierung, gleichmäßige Energiezufuhr und ein ebenes Pulverbett sind unerlässlich. Regelmäßige Kalibrierung und Wartung der Maschine sind entscheidend.
- Teilegeometrie und -ausrichtung: Komplexe Geometrien mit großen Überhängen oder unterschiedlichen Querschnitten sind anfälliger für Verformungen. Die Bauausrichtung hat erhebliche Auswirkungen auf das thermische Verhalten und die Anforderungen an die Unterstützung.
- Erreichen von Verlässlichkeit: Die Zusammenarbeit mit erfahrenen AM-Dienstleistern wie Met3dp ist entscheidend. Met3dp arbeitet mit branchenführenden Druckern, die für ihre Genauigkeit und Zuverlässigkeitdie für die Herstellung einsatzkritischer Teile für die Luft- und Raumfahrt unerlässlich sind. Ihr Fachwissen in der Prozessoptimierung und ihre strengen Qualitätskontrollmaßnahmen tragen dazu bei, dass die Maßgenauigkeit und Wiederholbarkeit von Bau zu Bau gewährleistet ist. Weitere Informationen zu den Fähigkeiten des Unternehmens finden Sie auf der Website Über uns Seite.
Qualitätskontrolle und Metrologie:
Angesichts der Kritikalität von Satellitenkomponenten sind strenge Inspektionen und Validierungen nicht verhandelbar.
- Prüfung der Abmessungen: Koordinatenmessmaschinen (CMM) und hochauflösende 3D-Scanner werden eingesetzt, um kritische Abmessungen anhand des CAD-Modells und der Zeichnungen zu überprüfen und sicherzustellen, dass die Toleranzen eingehalten werden, insbesondere nach der Nachbearbeitung.
- Interne Merkmalsüberprüfung: Für komplexe interne Kanäle oder Gitterstrukturen, die durch AM entstehen, reicht die herkömmliche Messtechnik möglicherweise nicht aus. Die Computertomografie (CT) wird zunehmend zur zerstörungsfreien Inspektion der inneren Geometrie, zur Prüfung auf eingeschlossenes Pulver und zur Erkennung von inneren Defekten wie Porosität eingesetzt.
- Messung der Oberflächenrauhigkeit: Zur Quantifizierung der Oberflächengüte (Ra) werden bei Bedarf Taststiftprofilometer oder optische Profilometer eingesetzt.
- Prozessüberwachung: In-situ-Überwachungstechnologien (z. B. Schmelzbadüberwachung) werden immer häufiger eingesetzt und liefern während der Fertigung Echtzeitdaten zur Erkennung potenzieller Anomalien, die die Qualität und Maßhaltigkeit der Teile beeinträchtigen könnten.
Zusammenfassend lässt sich sagen, dass AM-Teile aus Metall zwar größere Toleranzen und rauere Oberflächen aufweisen als präzisionsgefertigte Komponenten, dass diese Eigenschaften aber gut verstanden werden und beherrschbar sind. Durch die Kombination von intelligentem DfAM, die Auswahl von fähigen AM-Partnern mit zuverlässigen Anlagen und Prozessen (wie Met3dp), die Einbeziehung geplanter Nachbearbeitungsschritte (insbesondere die Bearbeitung kritischer Schnittstellen) und die Umsetzung einer strengen Qualitätskontrolle und Messtechnik können hochpräzise und zuverlässige Satelliten-Avionikboxen erfolgreich mit additiven Technologien hergestellt werden. Beschaffungsmanager sollten sicherstellen, dass in Angeboten und Spezifikationen die Akzeptanzkriterien für Toleranzen und Oberflächenbeschaffenheit klar definiert werden, wobei sowohl der Ist-Zustand als auch der endgültige, nachbearbeitete Zustand berücksichtigt wird.
Wichtige Nachbearbeitungsschritte für 3D-gedruckte Satellitenhardware
Die Herstellung einer Satelliten-Avionikbox mit Hilfe der additiven Fertigung von Metall endet nicht, wenn der Drucker anhält. Das Teil, das frisch von der Bauplatte kommt, stellt eine Zwischenstufe dar. Um dieses Rohteil in eine flugtaugliche Hardware zu verwandeln, die den strengen Anforderungen von Raumfahrtanwendungen gerecht wird, sind in der Regel eine Reihe von wichtigen Nachbearbeitungsschritten erforderlich. Diese Schritte sind ausschlaggebend für den Abbau innerer Spannungen, das Entfernen von Stützstrukturen, das Erreichen der gewünschten mechanischen Eigenschaften, die Gewährleistung präziser Abmessungen und Oberflächengüte sowie die Überprüfung der Gesamtintegrität des Teils. Das Verständnis dieses Nachbearbeitungsablaufs ist für Luft- und Raumfahrtingenieure, die die Teile entwerfen, und für Beschaffungsmanager, die AM-Dienstleistungen beschaffen, von entscheidender Bedeutung, da sich diese Schritte erheblich auf die Endkosten, die Vorlaufzeit und die Leistung des Bauteils auswirken.
Im Folgenden finden Sie eine Übersicht über die üblichen Nachbearbeitungsschritte für 3D-gedruckte Avionikgehäuse aus Metall, die aus Legierungen wie AlSi10Mg oder Scalmalloy® hergestellt werden:
- Stressabbau Wärmebehandlung:
- Zweck: Dies ist oft der erste Schritt, nachdem das Teil von der Bauplatte entfernt wurde (manchmal auch während es noch befestigt ist). Die schnellen Erwärmungs- und Abkühlungszyklen bei LPBF und SEBM erzeugen erhebliche Eigenspannungen im Bauteil. Diese Spannungen können Verwerfungen oder Verformungen verursachen, insbesondere wenn das Teil von der starren Bauplatte abgetrennt wird, und sich negativ auf die mechanischen Eigenschaften auswirken. Beim Spannungsabbau wird das Bauteil auf eine bestimmte Temperatur (unterhalb der Alterungs- oder Lösungstemperatur) erwärmt und für eine gewisse Zeit gehalten, gefolgt von einer kontrollierten Abkühlung. Auf diese Weise können die inneren Spannungen abgebaut werden, ohne die Mikrostruktur wesentlich zu verändern.
- Typische Zyklen: Bei AlSi10Mg kann der Spannungsabbau ein Erhitzen auf etwa 300°C für 1-2 Stunden beinhalten. Für Scalmalloy® sollten die vom Materiallieferanten/Entwickler (APWORKS) empfohlenen spezifischen Zyklen befolgt werden, die oft etwas höhere Temperaturen beinhalten.
- Wichtigkeit: Das Auslassen oder die unsachgemäße Durchführung des Spannungsabbaus kann zu Instabilität der Abmessungen und vorzeitigem Versagen führen.
- Entnahme von der Bauplatte:
- Methode: Das Teil wird normalerweise auf eine dicke Metallplatte gedruckt. Die Trennung erfolgt in der Regel durch Drahterodieren (EDM) oder Sägen. Es muss darauf geachtet werden, dass das Teil während dieses Prozesses nicht beschädigt wird.
- Erwägung: Die Grenzschicht zwischen dem Teil und der Platte sowie alle mit der Platte verbundenen Stützstrukturen müssen sauber entfernt werden.
- Entfernung der Stützstruktur:
- Zweck: Stützen verankern das Teil und verhindern Verformungen während des Drucks, sind aber nicht Teil des endgültigen Designs.
- Methoden: Je nach Art, Größe und Lage der Stützen kann die Entfernung manuell erfolgen (Brechen oder Schneiden von relativ gut zugänglichen Stützen), mit Hilfe von CNC-Bearbeitung oder manchmal auch mit Drahterodieren für komplizierte oder schwer zugängliche Bereiche.
- Herausforderungen: Das Entfernen von Halterungen kann arbeitsintensiv sein und birgt das Risiko, die Oberfläche des Teils zu beschädigen. Spuren oder Narben an den Stellen, an denen Stützen angebracht waren, sind üblich und erfordern möglicherweise eine weitere Nachbearbeitung. DfAM spielt hier eine Schlüsselrolle - die Konstruktion von Teilen, die so gestaltet sind, dass möglichst wenig Stützen vorhanden sind oder dass sie leicht zugänglich sind, vereinfacht diesen Schritt erheblich.
- Pulverentfernung (Depowdering):
- Zweck: Ungeschmolzenes Metallpulver, das in internen Kanälen, Hohlräumen oder Gitterstrukturen eingeschlossen ist, muss gründlich entfernt werden. Eingeschlossenes Pulver erhöht das Gewicht und kann später zu einer losen Verunreinigung werden.
- Methoden: Dazu gehören in der Regel das Abblasen mit Druckluft, Vibrationen und eine sorgfältige Ausrichtung des Teils, damit das Pulver durch die vorgesehenen Austrittslöcher entweichen kann. Komplexe Innengeometrien können spezielle Reinigungsverfahren erfordern.
- Verifizierung: In manchen Fällen kann mit Hilfe eines CT-Scans überprüft werden, ob das Pulver vollständig aus den kritischen inneren Passagen entfernt wurde.
- Lösungsglühen und Alterungswärmebehandlungen (Optimierung der Werkstoffeigenschaften):
- Zweck: AM-Materialien weisen oft nicht die optimalen mechanischen Eigenschaften (Festigkeit, Duktilität, Härte) auf, die sie im Endzustand haben. Es sind spezielle Wärmebehandlungszyklen erforderlich, um die gewünschte Mikrostruktur und Leistung zu entwickeln.
- AlSi10Mg: Erfordert oft ein T6-Glühen (Lösungsglühen mit anschließender künstlicher Alterung), um seine Festigkeit und Härte deutlich zu erhöhen, obwohl dies die Duktilität im Vergleich zum eingebauten oder spannungsfreien Zustand verringern kann. Ein typisches T6-Glühen umfasst eine Lösungsglühung bei ~500-540 °C, ein Abschrecken und eine anschließende Alterung bei ~150-170 °C.
- Scalmalloy®: Erfordert spezifische Alterungsbehandlungen, die darauf zugeschnitten sind, das charakteristische Gleichgewicht zwischen hoher Festigkeit und Duktilität zu erreichen. Die genauen Parameter sind oft geschützt oder vom Materiallieferanten vorgegeben und hängen von den gewünschten Endeigenschaften ab.
- Kontrolle: Diese Wärmebehandlungen müssen in kalibrierten Öfen mit kontrollierter Atmosphäre (z. B. Vakuum oder Inertgas) durchgeführt werden, um Oxidation zu verhindern und eine gleichmäßige Temperaturverteilung zu gewährleisten.
- CNC-Bearbeitung (kritische Abmessungen und Merkmale):
- Zweck: Zur Erzielung enger Toleranzen (oft enger als ±0,1 mm), spezifischer Oberflächengüten (z. B. Ra < 1,6 µm) und präziser geometrischer Merkmale (z. B. Ebenheit, Rechtwinkligkeit), die für Gegenflächen, Steckerschnittstellen, Montagebohrungen, O-Ring-Nuten oder Lagersitze erforderlich sind.
- Prozess: das 3-, 4- oder 5-Achsen-CNC-Fräsen oder -Drehen wird für die Bearbeitung bestimmter Bereiche des AM-Teils verwendet. Bei diesem hybriden Ansatz (AM + CNC) werden die Stärken beider Technologien genutzt.
- Erwägung: Erfordert ein sorgfältiges Vorrichtungsdesign, um das potenziell komplexe AM-Teil sicher und ohne Verformung zu halten. Beim ursprünglichen AM-Design müssen Bearbeitungszugaben berücksichtigt werden.
- Oberflächenveredelung:
- Zweck: Zur Verbesserung der Oberflächenrauheit im eingebauten Zustand, zur Beseitigung von Abdrücken, zur Erhöhung der Ermüdungsfestigkeit, zur Vorbereitung der Beschichtung oder zur Erzielung einer gewünschten Ästhetik.
- Methoden:
- Abrasives Strahlen (Perlen-/Sandstrahlen): Sorgt für eine gleichmäßige matte Oberfläche, entfernt lose Partikel und kann die Ermüdungseigenschaften durch Druckspannung leicht verbessern.
- Taumeln/Gleitschleifen: Verwendet Schleifmittel in einer rotierenden oder vibrierenden Trommel zum Entgraten von Kanten und zum Glätten von Oberflächen, besonders effektiv bei Chargen von kleineren Teilen.
- Polieren: Durch mechanisches oder elektrochemisches Polieren können bei Bedarf sehr glatte, spiegelglatte Oberflächen erzielt werden (z. B. bei optischen Schnittstellen, jedoch weniger häufig bei Avionikgehäusen).
- Mikro-Bearbeitung/Entgraten: Manuelle oder automatische Entfernung von feinen Graten oder scharfen Kanten.
- Reinigung:
- Zweck: Endreinigung zur Beseitigung von Rückständen von Bearbeitungskühlmitteln, Poliermitteln, Fingerabdrücken oder anderen Verunreinigungen vor der Endkontrolle, Beschichtung oder Montage.
- Methoden: Üblicherweise werden Ultraschallbäder mit geeigneten Lösungsmitteln oder Reinigungsmitteln verwendet.
- Beschichtung oder Plattierung (optional, aber üblich):
- Zweck: Verbesserung spezifischer Oberflächeneigenschaften, die für die Weltraumumgebung erforderlich sind.
- Thermisch kontrollierte Beschichtungen: Spezielle Anstriche oder Oberflächenbehandlungen (z. B. Eloxieren mit speziellen Farbstoffen, chemische Umwandlungsbeschichtungen wie Alodin/Iridit, optische Sonnenreflektoren) werden auf die Außenflächen aufgebracht, um die gewünschten Werte für das solare Absorptionsvermögen (α) und das thermische Emissionsvermögen (ϵ) zu erreichen, die für die Wärmebilanz des Satelliten entscheidend sind.
- EMI-Abschirmung: Während das Metall selbst für die Abschirmung sorgt, können Beschichtungen wie Vernickelung oder Versilberung die Leitfähigkeit und die Wirksamkeit der Abschirmung erhöhen, insbesondere in bestimmten Frequenzbereichen oder gegebenenfalls an Nähten/Verbindungen.
- Korrosionsschutz: Eloxal- oder Konversionsbeschichtungen bieten einen besseren Schutz gegen Korrosion während der Bodenabfertigung und Lagerung.
- Prozess: Erfordert spezielle Einrichtungen und eine sorgfältige Oberflächenvorbereitung.
- Zweck: Verbesserung spezifischer Oberflächeneigenschaften, die für die Weltraumumgebung erforderlich sind.
- Abschließende Inspektion und Prüfung:
- Zweck: Überprüfung, ob das vollständig verarbeitete Teil alle Anforderungen an Abmessungen, Materialeigenschaften und Qualität erfüllt, bevor es als Fluggerät akzeptiert wird.
- Methoden: Dazu gehören abschließende Maßprüfungen (CMM, 3D-Scannen), Überprüfung der Oberflächenbeschaffenheit, zerstörungsfreie Prüfungen (NDT) wie Farbeindringprüfung (zur Erkennung von Oberflächenrissen) oder CT-Scannen (zur Überprüfung der inneren Unversehrtheit) und möglicherweise zerstörende Prüfungen an repräsentativen Prüfstücken, die neben dem Teil hergestellt werden (z. B. Zugversuche zur Überprüfung des Erfolgs der Wärmebehandlung).
Diese umfassende Nachbearbeitungssequenz verdeutlicht, dass die Herstellung einer 3D-gedruckten Avionikbox ein mehrstufiger Prozess ist, der verschiedene Fähigkeiten und eine sorgfältige Koordination erfordert. Dienstleister wie Met3dp verstehen diesen kompletten Arbeitsablauf und bieten nicht nur qualitativ hochwertigen Druck, sondern auch die Verwaltung oder Koordinierung dieser wichtigen nachgelagerten Schritte, um vollständig fertige, einsatzbereite Komponenten zu liefern. Beschaffungsentscheidungen müssen den Zeit- und Kostenaufwand berücksichtigen, der mit diesen notwendigen Nachbearbeitungsaktivitäten verbunden ist.
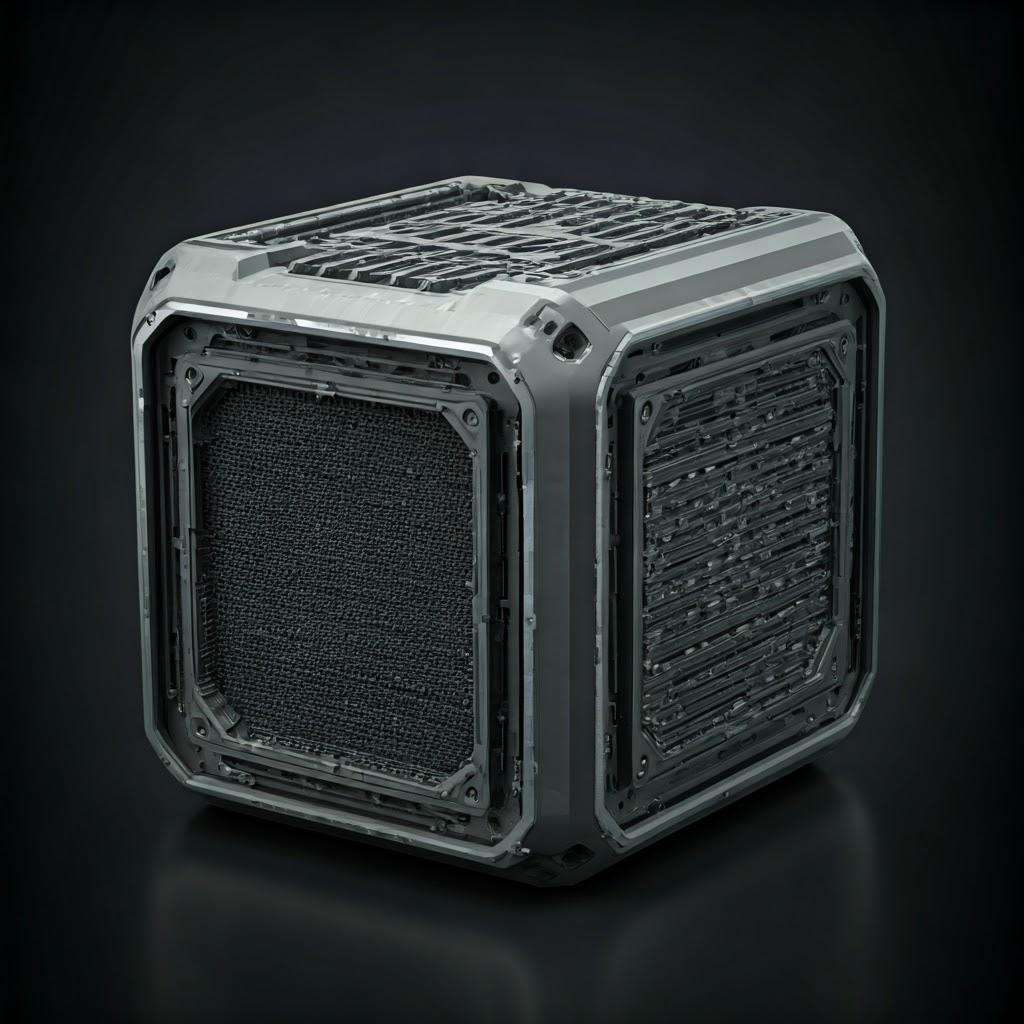
Überwindung allgemeiner Herausforderungen beim 3D-Druck von Avionikgehäusen
Die additive Fertigung von Metallen bietet zwar erhebliche Vorteile für die Herstellung leichter und komplexer Satelliten-Avionikgehäuse, doch die Technologie ist nicht ohne Herausforderungen. Der erfolgreiche Druck von hochintegrierten, missionskritischen Komponenten erfordert ein tiefes Verständnis der potenziellen Probleme, die während des Herstellungsprozesses auftreten können, und die Umsetzung wirksamer Strategien zur Schadensbegrenzung. Luft- und Raumfahrtingenieure und Beschaffungsteams sollten sich dieser allgemeinen Herausforderungen bewusst sein, um bessere Designentscheidungen zu treffen, fähige Fertigungspartner auszuwählen und eine realistische Projektplanung zu gewährleisten. Vorgewarnt ist gewarnt, und viele potenzielle Probleme können mit dem richtigen Fachwissen und der richtigen Prozesssteuerung vermieden oder überwunden werden.
Im Folgenden werden einige häufige Herausforderungen beim 3D-Druck von Avionikgehäusen aus Metall und deren typische Lösungen vorgestellt:
- Verformung und Verzerrung:
- Herausforderung: Erhebliche Temperaturunterschiede zwischen dem geschmolzenen Material und den umgebenden festen Schichten führen zu inneren Spannungen. Da sich diese Spannungen über viele Schichten hinweg akkumulieren, können sie dazu führen, dass sich das Teil verzieht, sich von der Bauplatte abrollt oder von der vorgesehenen Geometrie abweicht, insbesondere bei großen, flachen Abschnitten oder dünnen Merkmalen.
- Lösungen:
- Optimierte Gebäudeausrichtung: Die Ausrichtung des Teils auf der Bauplatte kann helfen, große ebene Flächen parallel zur Platte zu minimieren und thermische Gradienten zu reduzieren.
- Robuste Stützstrukturen: Gut konzipierte Halterungen verankern das Teil sicher auf der Bauplatte und halten den durch die thermische Belastung erzeugten Zugkräften stand. Simulationswerkzeuge können helfen, die Platzierung und Stärke der Stützen zu optimieren.
- Optimierte Prozessparameter: Die Feinabstimmung von Laser-/Strahlleistung, Scan-Geschwindigkeit und Scan-Strategien (z. B. Insel-Scanning, Schichtschraffuren) kann dazu beitragen, den Wärmeeintrag zu steuern und die Stressakkumulation zu reduzieren.
- Stressabbau Wärmebehandlung: Die Durchführung eines geeigneten Entlastungszyklus unmittelbar nach dem Druck ist von entscheidender Bedeutung, um innere Spannungen abzubauen, bevor das Teil von der Bauplatte entfernt wird.
- Simulationsgestützter Entwurf: Durch den Einsatz von Prozesssimulationssoftware in der Entwurfsphase können Bereiche mit hoher Belastung und potenzieller Verformung vorhergesagt werden, so dass vor dem Druck Änderungen am Design vorgenommen werden können (z. B. Hinzufügen von Versteifungsrippen, Änderung der Topologie).
- Eigenspannung:
- Herausforderung: Selbst wenn ein erheblicher Verzug vermieden wird, können im gedruckten Teil hohe Restspannungen verbleiben. Dies kann sich im Laufe der Zeit negativ auf die Ermüdungsfestigkeit, Bruchzähigkeit und Dimensionsstabilität des Teils auswirken. In extremen Fällen kann dies zu Rissen während des Drucks oder der Nachbearbeitung führen.
- Lösungen: Ähnlich wie bei der Verringerung des Verzugs gehören zu den wirksamen Lösungen eine optimierte Ausrichtung, Unterstützungsstrategien, die Abstimmung der Prozessparameter (insbesondere die Steuerung der thermischen Gradienten) und die obligatorische Spannungsreduzierungswärmebehandlung. Heißisostatisches Pressen (HIP) kann ebenfalls dazu beitragen, Eigenspannungen zu reduzieren und gleichzeitig die innere Porosität zu schließen. Konstruktionsmerkmale wie allmähliche Dickenänderungen können ebenfalls zur Beherrschung von Spannungskonzentrationen beitragen.
- Porosität:
- Herausforderung: Im gedruckten Material können sich aufgrund verschiedener Mechanismen kleine Hohlräume oder Poren bilden:
- Lack-of-Fusion-Porosität: Bei unzureichendem Energieeintrag werden die Pulverpartikel nicht vollständig geschmolzen oder benachbarte Schichten/Spuren verschmolzen, so dass Lücken entstehen.
- Schlüsselloch-Porosität: Durch die übermäßige Energiedichte entsteht ein instabiles, tiefes Schmelzbad, das kollabieren kann, wobei Dampf/Gas eingeschlossen wird und kugelförmige Poren entstehen.
- Gas Porosität: Im Metallpulver gelöste oder zwischen Partikeln eingeschlossene Gase können beim Schmelzen und Erstarren Poren bilden.
- Auswirkungen: Porosität wirkt wie ein Spannungskonzentrator, der die Festigkeit, Duktilität und Ermüdungslebensdauer des Materials erheblich reduziert. Dies ist ein kritischer Defekt für Komponenten in der Luft- und Raumfahrt.
- Lösungen:
- Optimierte Prozessparameter: Eine präzise Steuerung der Energiedichte (Leistung, Geschwindigkeit, Schichtdicke, Schraffurabstand) ist der Schlüssel zum Erreichen eines vollständigen Schmelzens ohne Keyholing. Die Entwicklung der Parameter ist für jedes Material und jede Maschine entscheidend.
- Hochwertiges Pulver: Die Verwendung von Pulver mit hoher Sphärizität, kontrollierter Partikelgrößenverteilung, guter Fließfähigkeit und geringem internen Gasgehalt ist entscheidend. Der Bezug von Pulver von renommierten Lieferanten wie Met3dp, die eine fortschrittliche Zerstäubung (Gaszerstäubung, PREP) und Qualitätskontrolle einsetzen, verringert das Risiko von pulverbedingter Porosität erheblich.
- Kontrollierte Bauatmosphäre: Die Aufrechterhaltung einer hochreinen Inertgasatmosphäre (Argon oder Stickstoff für LPBF, Vakuum für SEBM) minimiert Oxidation und Verunreinigung, die zur Porosität beitragen können.
- Heiß-Isostatisches Pressen (HIP): Bei diesem Nachbearbeitungsschritt wird das Teil einer hohen Temperatur und einem hohen isostatischen Druck (unter Verwendung eines Inertgases wie Argon) ausgesetzt. Dabei werden innere Hohlräume (Schmelzmangel, Gasporosität) durch Diffusionsbindung und plastische Verformung wirksam geschlossen, was die Dichte und die mechanischen Eigenschaften erheblich verbessert. Es wird häufig für kritische Teile in der Luft- und Raumfahrt eingesetzt.
- Erkennung: Das CT-Scannen ist die wichtigste ZfP-Methode zur Feststellung der inneren Porosität.
- Herausforderung: Im gedruckten Material können sich aufgrund verschiedener Mechanismen kleine Hohlräume oder Poren bilden:
- Schwierigkeit der Entfernung von Stützstrukturen und Beschädigung von Teilen:
- Herausforderung: Unterstützungen sind zwar notwendig, können aber schwierig und zeitaufwändig zu entfernen sein, insbesondere komplexe Unterstützungen oder solche, die sich in internen Kanälen oder schwer zugänglichen Bereichen befinden. Aggressives Entfernen kann die Oberfläche des Teils oder empfindliche Merkmale beschädigen.
- Lösungen:
- DfAM für die Minimierung der Unterstützung: Die Konstruktion mit selbsttragenden Winkeln, die Vermeidung scharfer Überhänge und die Optimierung der Ausrichtung können den Bedarf an Stützen drastisch reduzieren.
- Optimiertes Support-Design: Verwendung von leicht entfernbaren Stützentypen (z. B. dünnwandige, perforierte oder spezielle Baumstützen mit kleinen Kontaktpunkten), wo dies möglich ist. Simulationswerkzeuge können bei der Optimierung von Stützstrukturen im Hinblick auf Stabilität und Demontierbarkeit helfen.
- Sorgfältige Entfernungstechniken: Der Einsatz geeigneter Werkzeuge (Handwerkzeuge, maschinelle Bearbeitung, Drahterodieren) und Techniken ist entscheidend. Ausbildung und Erfahrung sind wichtig.
- Design für den Zugang: Sicherstellung eines ausreichenden Freiraums um die gestützten Elemente, damit die Werkzeuge die Stützen erreichen und entfernen können.
- Feine Merkmale und dünne Wände erreichen:
- Herausforderung: Aufgrund der physikalischen Gegebenheiten beim Schmelzen von Pulver mit einem Laser- oder Elektronenstrahl sind der Mindestgröße der Merkmale (z. B. dünne Wände, kleine Löcher, scharfe Kanten), die zuverlässig mit guter Auflösung und Genauigkeit hergestellt werden können, Grenzen gesetzt.
- Lösungen:
- Prozessauswahl & Parameter: LPBF bietet im Allgemeinen eine feinere Strukturauflösung als SEBM, da die Strahl-/Punktgrößen kleiner sind. Eine Optimierung der Parameter (z. B. geringere Leistung, feineres Pulver) kann helfen, geht aber oft auf Kosten der Baugeschwindigkeit.
- Entwurfsentschädigung: Verstehen der spezifischen Maschinen-/Prozessgrenzen und Entwerfen von Merkmalen, die etwas größer oder dicker als die theoretische Mindestgrenze sind, um sicherzustellen, dass sie zuverlässig gebaut werden. Vermeiden von Messerkanten und Festlegen von Mindestradien.
- Hybrid-Ansatz: Drucken der komplexen Gesamtform und anschließende Mikrobearbeitung oder Funkenerosion als Nachbearbeitungsschritt, um bei Bedarf sehr feine Merkmale zu erzeugen.
- Kontrolle der Oberflächenrauhigkeit:
- Herausforderung: Die Oberflächenbeschaffenheit von AM-Teilen ist im Allgemeinen rauer als bei maschinell bearbeiteten Oberflächen und variiert je nach Ausrichtung. Dies kann sich negativ auf die Ermüdungsfestigkeit, die Dichtungsfähigkeit oder die thermischen/optischen Eigenschaften auswirken.
- Lösungen:
- Orientierungsstrategie: Wenn kritische Oberflächen vertikal oder nach oben gerichtet gebaut werden, führt dies zu besseren Ergebnissen.
- Optimierung der Parameter: Feinere Schichtdicken und optimierte Scan-Strategien können das Finish verbessern, verlängern aber die Bauzeit.
- Nachbearbeiten: Die Anwendung geeigneter Oberflächenbearbeitungsverfahren (Strahlen, Trowalisieren, Polieren, Bearbeiten), wie im vorherigen Abschnitt beschrieben, ist die gängigste Methode, um die erforderliche Glätte auf kritischen Oberflächen zu erreichen.
- Materialcharakterisierung und -qualifizierung:
- Herausforderung: Um sicherzustellen, dass das 3D-gedruckte Material die anspruchsvollen Anforderungen an die mechanischen Eigenschaften und die Zuverlässigkeit von Raumfahrthardware durchgängig erfüllt, sind strenge Prozesskontrollen, Tests und Qualifikationen erforderlich. Die Eigenschaften können von der Maschinenkalibrierung, den Schwankungen der Pulverchargen und der Konsistenz der Nachbearbeitung abhängen.
- Lösungen:
- Robuste Prozesskontrolle: Einführung strenger Qualitätsmanagementsysteme (z. B. AS9100), die die Handhabung von Pulver, den Maschinenbetrieb, die Kontrolle der Parameter und die Nachbearbeitung abdecken.
- Materialprüfung: Ausgiebige Tests von Prüfstücken, die zusammen mit den tatsächlichen Teilen hergestellt werden (Zugfestigkeit, Ermüdung, Mikrostrukturanalyse), um die Eigenschaften für jede Produktion oder Charge zu überprüfen.
- ZFP: Umfassende zerstörungsfreie Prüfung (z. B. CT-Scan) zur Gewährleistung der inneren Unversehrtheit.
- Partnerschaften mit erfahrenen Lieferanten: Die Zusammenarbeit mit etablierten AM-Dienstleistern wie Met3dp, die über ein tiefes Verständnis der Werkstoffkunde und der Prozesssteuerung für die Anforderungen der Luft- und Raumfahrt verfügen und eine Erfolgsbilanz bei der Herstellung zuverlässiger, hochwertiger Teile vorweisen können, ist für die Minderung von Qualifikationsrisiken von entscheidender Bedeutung.
Die Bewältigung dieser Herausforderungen erfordert eine Kombination aus intelligentem Design (DfAM), sorgfältiger Prozesskontrolle, angemessener Nachbearbeitung, strenger Prüfung und oft auch enger Zusammenarbeit zwischen dem Designteam und dem Fertigungspartner. Wenn Ingenieure und Beschaffungsspezialisten diese potenziellen Probleme proaktiv berücksichtigen, können sie die Einführung von Metall-AM für anspruchsvolle Anwendungen wie Satelliten-Avionikboxen besser steuern.
Auswahl des richtigen Metall-AM-Partners für Luft- und Raumfahrtkomponenten
Die Entscheidung, die additive Fertigung von Metall für kritische Komponenten wie Satellitenavionikgehäuse zu nutzen, ist eine wichtige strategische Entscheidung. Der Erfolg dieser Entscheidung hängt jedoch entscheidend von der Auswahl des richtigen Fertigungspartners ab. Das Angebot an AM-Dienstleistern ist vielfältig und reicht von generalistischen Job-Shops bis hin zu hochspezialisierten Büros, die sich auf die Luft- und Raumfahrt spezialisiert haben. Bei missionskritischer Raumfahrt-Hardware, bei der Qualität, Zuverlässigkeit und Rückverfolgbarkeit an erster Stelle stehen, muss der Auswahlprozess streng sein und auf klar definierten Kriterien basieren. Einfach den Anbieter mit dem niedrigsten Angebot zu wählen, kann zu erheblichen Risiken führen, einschließlich schlechter Teilequalität, Zeitverzögerungen und sogar dem Scheitern der Mission. Luft- und Raumfahrtingenieure und Beschaffungsmanager müssen potenzielle Partner ganzheitlich bewerten und sicherstellen, dass sie über die erforderlichen Fachkenntnisse, Zertifizierungen, Ausrüstungen und Qualitätssysteme verfügen, um die einzigartigen Anforderungen der Raumfahrtindustrie zu erfüllen.
Hier sind die wichtigsten Kriterien, die bei der Bewertung und Auswahl eines Metall-AM-Partners für Luft- und Raumfahrtkomponenten zu berücksichtigen sind:
- Fachwissen und Zertifizierungen in der Luft- und Raumfahrt:
- AS9100-Zertifizierung: Dies ist die international anerkannte Norm für Qualitätsmanagementsysteme (QMS) in der Luft- und Raumfahrtindustrie. Die Einhaltung (oder idealerweise die Zertifizierung) zeigt, dass man sich zu strenger Qualitätskontrolle, Prozessdokumentation und Rückverfolgbarkeit verpflichtet hat, was für Lieferanten von Fluggeräten oft eine nicht verhandelbare Anforderung ist.
- Erbe der Raumfahrt: Hat der Anbieter erfolgreich Teile hergestellt, die bei früheren Raumfahrtmissionen mitgeflogen sind? Nachgewiesene Erfahrung verringert das Risiko des Prozesses erheblich.
- Branchenverständnis: Verstehen sie die besonderen Herausforderungen der Weltraumumgebung (Strahlung, Vakuum, Temperaturwechsel, Ausgasung)? Verstehen sie die entscheidende Bedeutung von Zuverlässigkeit und geringem Gewicht?
- ITAR-Konformität: Bei verteidigungsrelevanten Satellitenprojekten, die den U.S. International Traffic in Arms Regulations unterliegen, ist sicherzustellen, dass der Anbieter die ITAR-Registrierungs- und Compliance-Anforderungen erfüllt.
- Sachkenntnis:
- Spezifische Legierungserfahrung: Nachgewiesene Erfolgsbilanz bei der Verarbeitung genau der gewünschten Legierung (z. B. Scalmalloy®, AlSi10Mg). Dazu gehören validierte Parametersätze für die Herstellung dichter, fehlerfreier Teile mit den gewünschten Mikrostrukturen und mechanischen Eigenschaften.
- Handhabung und Management von Pulver: Strenge Verfahren für die Beschaffung von Pulver (von qualifizierten Lieferanten), die Lagerung (zur Vermeidung von Verunreinigungen und Feuchtigkeitsaufnahme), die Handhabung, das Recycling (falls zutreffend) und die Rückverfolgbarkeit der Chargen sind für eine gleichbleibende Materialqualität entscheidend. Unternehmen wie Met3dpdie ihre eigenen hochwertigen Pulver mit fortschrittlichen Techniken herstellen, wie PREP und Gaszerstäubungbieten einen Vorteil bei der Kontrolle dieser kritischen Eingangsgröße. Ihr Portfolio umfasst innovative Legierungen, die für anspruchsvolle Anwendungen geeignet sind.
- Wissen über Wärmebehandlung: Fachwissen über die spezifischen Spannungsabbau-, Lösungsglüh- und Alterungszyklen, die für die gewählte Legierung erforderlich sind, um optimale Eigenschaften zu erzielen, zusammen mit kalibrierten Ofenkapazitäten.
- Ausrüstungskapazitäten und Technologie:
- Geeignete AM-Technologie: Verwenden sie die am besten geeignete Technologie (z. B. LPBF für feine Merkmale, SEBM für hohe Produktivität/geringe Belastung)? Met3dp ist spezialisiert auf selektives Elektronenstrahlschmelzen (SEBM)sie eignen sich besonders für bestimmte Luft- und Raumfahrtanwendungen, die eine hohe Produktivität und gute Materialeigenschaften im Vakuum erfordern.
- Qualität und Wartung der Maschinen: Verwendung von gut gewarteten, industrietauglichen AM-Systemen von namhaften Herstellern. Konsistente Kalibrierungspläne sind für die Wiederholbarkeit unerlässlich.
- Bauvolumen: Stellen Sie sicher, dass der Bauraum der Maschine die Größe der Avionikbox aufnehmen kann oder eine effiziente Verschachtelung mehrerer Teile ermöglicht.
- Kapazität: Verfügt der Anbieter über ausreichende Maschinenkapazitäten, um die Projektfristen einzuhalten, einschließlich einer möglichen Skalierung für die Produktion von Kleinserien?
- Prozesskontrolle und Qualitätsmanagementsysteme (QMS):
- Robustes QMS über AS9100 hinaus: Achten Sie auf den Nachweis umfassender Qualitätsverfahren, die jeden Schritt vom Auftragseingang bis zur Auslieferung abdecken.
- Rückverfolgbarkeit: Eine lückenlose Rückverfolgbarkeit vom Pulverrohstoff über die Druckparameter, Nachbearbeitungsschritte und Prüfergebnisse bis hin zum ausgelieferten Endprodukt ist für Hardware in der Luft- und Raumfahrt unerlässlich.
- Prozessüberwachung: Nutzung verfügbarer In-situ-Überwachungsinstrumente (z. B. Schmelzbadüberwachung, Wärmebildtechnik) zur Erkennung von Bauanomalien in Echtzeit.
- Konfigurationsmanagement: Verfahren zur Kontrolle von Entwurfsänderungen und zur Gewährleistung, dass die richtige Version hergestellt wird.
- Nachbearbeitungsmöglichkeiten:
- Integrierte Dienstleistungen: Bietet der Anbieter kritische Nachbearbeitungsschritte im eigenen Haus an (z. B. Wärmebehandlung, Grundveredelung) oder unterhält er Beziehungen zu qualifizierten Partnern für Dienstleistungen wie Präzisions-CNC-Bearbeitung, spezialisierte zerstörungsfreie Prüfung (CT-Scannen) und Beschichtungen in Luft- und Raumfahrtqualität? Die Verwaltung einer fragmentierten Lieferkette kann komplex und riskant sein.
- Kompetenz in der Endbearbeitung von AM-Teilen: Verständnis der spezifischen Anforderungen für die Endbearbeitung von AM-Komponenten (z. B. Konstruktion von Vorrichtungen für die Bearbeitung komplexer Formen, geeignete Oberflächenbehandlungen).
- Engineering und Anwendungsunterstützung:
- DfAM-Fachwissen: Fähigkeit zur fachkundigen Beratung bei der Optimierung des Avionikbox-Designs für die additive Fertigung, einschließlich Topologieoptimierung, Support-Strategie und Feature-Design. Met3dp bietet umfassende Dienstleistungen zur Anwendungsentwicklung, in Partnerschaft mit Organisationen, um den 3D-Druck effektiv zu implementieren.
- Simulationsfähigkeiten: Zugang zu Tools für die Prozesssimulation, um potenzielle Probleme wie Verzug oder Eigenspannungen vorherzusagen und zu mindern.
- Kollaborativer Ansatz: Bereitschaft zur engen Zusammenarbeit mit dem technischen Team des Kunden, um Probleme zu lösen und optimale Ergebnisse zu erzielen.
- Erfolgsbilanz und Reputation:
- Fallstudien und Referenzen: Bitten Sie um Beispiele für ähnliche, erfolgreich abgeschlossene Projekte, insbesondere im Bereich der Luft- und Raumfahrt. Prüfen Sie nach Möglichkeit Referenzen.
- Ruf der Industrie: Bewertung ihres Ansehens innerhalb der AM- und Luft- und Raumfahrtgemeinschaft.
- Kommunikation und Projektmanagement:
- Reaktionsfähigkeit: Eine klare und rechtzeitige Kommunikation ist während des gesamten Projektlebenszyklus von entscheidender Bedeutung.
- Projektleitung: Fest zugeordnete Ansprechpartner und strukturierte Projektmanagementprozesse.
- Transparenz: Offenheit in Bezug auf Fähigkeiten, Grenzen und potenzielle Risiken.
Bei der Auswahl eines Partners geht es nicht nur um die Beschaffung, sondern auch um den Aufbau einer technischen Zusammenarbeit. Unternehmen wie Met3dp, die End-to-End-Lösungen von fortschrittlichen Metallpulver und hochmodernen SEBM-Druckern bis hin zu fundiertem Anwendungs-Know-how, stellen die Art von umfassendem Partner dar, der für die erfolgreiche Umsetzung von Metall-AM für anspruchsvolle Luft- und Raumfahrtkomponenten wie Satelliten-Avionikboxen benötigt wird. Wenn Sie sich die Zeit nehmen, potenzielle Lieferanten anhand dieser Kriterien gründlich zu prüfen, wird sich die Wahrscheinlichkeit eines Projekterfolgs deutlich erhöhen und zuverlässige, leistungsstarke Flughardware liefern.
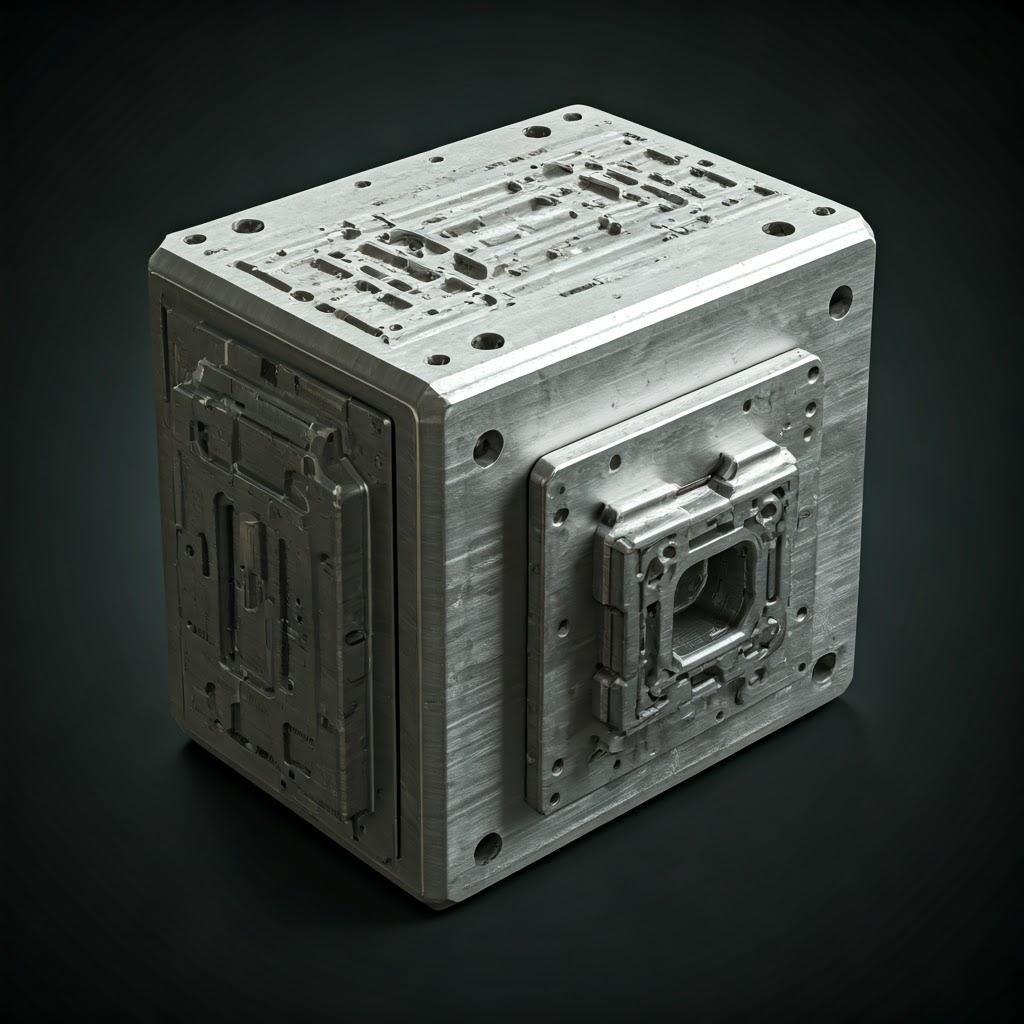
Kostenanalyse und Vorlaufzeitüberlegungen für AM Avionikboxen
Die technischen Vorteile der additiven Fertigung aus Metall für Satelliten-Avionikgehäuse - Gewichtsreduzierung, Teilekonsolidierung, verbessertes Wärmemanagement - sind zwar überzeugend, aber die praktische Umsetzung hängt von der Kenntnis der damit verbundenen Kosten und Vorlaufzeiten ab. Projektleiter in der Luft- und Raumfahrt und Beschaffungsspezialisten benötigen realistische Schätzungen, um Geschäftsszenarien zu erstellen, Budgets zu verwalten und die Fertigungszeitpläne mit den allgemeinen Zeitplänen für die Satellitenintegration abzustimmen. Sowohl die Kosten als auch die Vorlaufzeit für AM-Teile werden durch ein komplexes Zusammenspiel von Faktoren beeinflusst, die über einfache Materialmengenberechnungen hinausgehen.
Faktoren, die die Kosten von 3D-gedruckten Avionikboxen beeinflussen:
- Materialart und Verbrauch:
- Pulverkosten: Hochleistungslegierungen wie Scalmalloy® sind aufgrund der Legierungselemente (Scandium) und der Lizenzierung pro Kilogramm erheblich teurer als Standard-AlSi10Mg. Die Kosten für das Rohpulver sind ein wichtiger Faktor.
- Teil Volumen/Masse: Die tatsächliche Menge an Material, die zur Herstellung des Teils verschmolzen wird, wirkt sich direkt auf die Kosten aus. Topologieoptimierung und Gitterstrukturen erhöhen zwar die Komplexität des Designs, verringern aber den Materialverbrauch.
- Unterstützungsstruktur Volumen: Das für die Stützstrukturen verwendete Material trägt ebenfalls zu den Kosten bei, sowohl in Bezug auf den Pulververbrauch als auch auf die Druckzeit. Effizientes DfAM minimiert den Bedarf an Stützstrukturen.
- Buy-to-Fly-Verhältnis: AM hat in der Regel ein viel besseres Verhältnis zwischen Einkauf und Fertigung (Verhältnis zwischen dem gekauften Rohmaterial und dem Gewicht des fertigen Teils) als die traditionelle subtraktive Bearbeitung, insbesondere bei komplexen Teilen, was die höheren Kosten pro Kilogramm Pulver im Vergleich zu Knüppelmaterial ausgleichen kann.
- AM Machine Time:
- Stundensatz: Industrielle Metall-AM-Maschinen stellen eine beträchtliche Investition dar, und die Dienstleister berechnen in der Regel einen Stundensatz für die Maschinennutzung. Die Preise variieren je nach Maschinentyp (LPBF, SEBM), Größe und Anbieter.
- Druckzeit: Dies ist oft der größte Teil der Kosten für die Maschinenzeit. Sie wird bestimmt durch:
- Teilhöhe: Der Haupttreiber, da der Druck schichtweise erfolgt.
- Teilevolumen und Querschnittsfläche: Je mehr Material pro Schicht, desto länger dauert das Schmelzen.
- Komplexität: Komplizierte Details und Abtaststrategien können die Geschwindigkeit beeinflussen.
- Unterstützende Strukturen: Das Drucken von Unterstützungen kostet Zeit.
- Verschachtelung: Das gleichzeitige Drucken mehrerer Teile in einem Arbeitsgang kann die effektiven Maschinenzeitkosten pro Teil erheblich senken.
- Entwurf und Vorbereitung der Arbeit:
- DfAM und Optimierung: Entwicklungszeit für die Optimierung des Designs für AM.
- Vorbereitung des Baus: Arbeitsaufwand für die Erstellung der Build-Datei, die Erzeugung von Stützstrukturen und die Durchführung von Prozesssimulationen. Diese Kosten werden normalerweise über die Anzahl der produzierten Teile amortisiert.
- Nachbearbeitungsintensität: Dies kann einen beträchtlichen Teil der Gesamtkosten ausmachen, der manchmal sogar die Druckkosten selbst übersteigt.
- Stressabbau und Wärmebehandlung: Zeit- und Energiekosten des Ofens. Spezifische Zyklen für Luft- und Raumfahrtlegierungen erfordern kalibrierte Geräte.
- Support Removal & Depowdering: Arbeitsintensiv, insbesondere bei komplexen Teilen oder schwer zu entfernenden Halterungen.
- CNC-Bearbeitung: Die Kosten hängen von der Anzahl der zu bearbeitenden Merkmale, den vorgegebenen Toleranzen, der Komplexität der Vorrichtungen und der Bearbeitungszeit ab.
- Oberflächenveredelung: Die Kosten variieren stark je nach Methode (z. B. einfaches Perlstrahlen oder mehrstufiges Polieren) und behandelter Fläche.
- ZfP und Inspektion: Arbeits- und Ausrüstungskosten für CMM, 3D-Scannen, CT-Scannen (das besonders teuer sein kann), Farbeindringprüfung usw.
- Beschichtung/Galvanisierung: Spezialisierte Prozesse mit den damit verbundenen Kosten für Material, Arbeit und Gebäudenutzung.
- Qualitätssicherung und Dokumentation:
- Der Umfang der Dokumentation, Rückverfolgbarkeit und Zertifizierung, der für Luft- und Raumfahrtkomponenten erforderlich ist, verursacht zusätzliche Kosten für Personal und Systeme des Qualitätsmanagements. Flugqualifizierungspakete erfordern einen erheblichen Aufwand.
- Auftragsvolumen:
- Prototypen vs. Serien: Die Kosten pro Teil sind bei einmaligen Prototypen aufgrund der Einrichtungskosten in der Regel höher. Skaleneffekte können bei größeren Chargen durch Verschachtelung und amortisierte Einrichtungs-/Programmierungskosten erzielt werden, auch wenn das Verhältnis weniger ausgeprägt ist als bei traditionellen Massenproduktionstechnologien wie Gießen. Die Stärke von AM’ liegt in der Kosteneffizienz bei kleinen bis mittleren Stückzahlen, bei denen die Herstellung von Werkzeugen unerschwinglich ist.
Faktoren, die die Vorlaufzeit beeinflussen:
Die Vorlaufzeit ist die Gesamtdauer von der Auftragserteilung bis zur Auslieferung des endgültigen Teils.
- Entwurfsprüfung und Bauvorbereitung: (1-5 Tage) Überprüfung des Entwurfs auf Herstellbarkeit (DfAM-Check), Optimierung der Ausrichtung, Erzeugung von Halterungen, Slicing und Bahnplanung. Kann ein Hin- und Hergehen mit dem Kunden beinhalten.
- Warteschlangenzeit der Maschine: (Variabel: 1 Tag bis 2+ Wochen) Warten, bis eine geeignete Maschine beim Dienstleister verfügbar ist. Hängt vom Rückstand und der Kapazität des Anbieters ab.
- Druckzeit: (Variabel: 12 Stunden bis 7+ Tage) Hängt stark von der Höhe, dem Volumen, der Komplexität, dem Material und der Verschachtelungseffizienz des Teils ab. Der Druck von großen oder komplexen Avionikboxen kann leicht mehrere Tage dauern.
- Abkühlung und Entfernung der Teile: (0,5-1 Tag) Ausreichende Abkühlung der Baukammer und des Teils vor der Entnahme.
- Nachbearbeiten: (Variabel: 3 Tage bis 3+ Wochen) Dies ist oft die variabelste und potenziell längste Phase. Beinhaltet:
- Stressabbau (bald nach dem Druck erforderlich)
- Ausbau der Bauplatte & Ausbau der Stütze
- Wärmebehandlungszyklen (kann Stunden bis Tage pro Zyklus dauern, einschließlich Hochfahren/Abkühlen)
- CNC-Bearbeitung (Einricht- und Bearbeitungszeit)
- Oberflächenveredelung
- NDT & Inspektion
- Beschichtung/Plattierung (oft ausgelagert, was zusätzliche Transit- und Wartezeiten bedeutet)
- Versand: (Variabel: 1 Tag bis 1+ Woche) Je nach Standort und Versandart.
Typische Vorlaufzeitspannen (Schätzungen):
- Funktionsprototyp (grundlegende Nachbearbeitung): 1 – 4 Wochen
- Flugtaugliches Teil (vollständige Nachbearbeitung & QA): 4 – 10 Wochen oder länger
Best Practices für Angebotsanfragen (RFQ):
Um genaue Angebote und realistische Vorlaufzeiten für Ihre 3D-gedruckte Avionikbox zu erhalten, sollten Sie potenziellen Lieferanten diese Informationen zur Verfügung stellen:
- CAD-Modell: In einem Standardformat (z. B. STEP).
- Technische Zeichnung: Klare Angabe von kritischen Abmessungen, Toleranzen (unter Verwendung von Geometric Dimensioning and Tolerancing – GD&T), Anforderungen an die Oberflächengüte und Materialspezifikationen.
- Spezifikation des Materials: Geben Sie die genaue Legierung (z. B. Scalmalloy®, AlSi10Mg) und den gewünschten Härtegrad/Zustand an.
- Nachbearbeitungsanforderungen: Geben Sie alle erforderlichen Schritte an (Wärmebehandlungen, spezifische Bearbeitungsvorgänge, Oberflächenbehandlungen, Beschichtungen).
- Qualitätsanforderungen: Geben Sie die erforderlichen Zertifizierungen (AS9100), Inspektionsmethoden (z. B. CT-Scan erforderlich?), Dokumentationspakete und Testanforderungen (z. B. Zeugencoupons) an.
- Menge: Anzahl der benötigten Teile.
- Gewünschtes Lieferdatum: Gewünschter Zeitrahmen.
Das Verständnis der Kostentreiber und Vorlaufzeitkomponenten ermöglicht eine bessere Planung und Budgetierung. Auch wenn die anfänglichen Kosten pro Teil im Vergleich zu einer einfachen maschinell gefertigten Box höher sein können (insbesondere bei höheren Stückzahlen), bieten die Vorteile auf Systemebene, die durch AM erschlossen werden (Gewichtseinsparungen, die zu einer Senkung der Startkosten führen, verbesserte Leistung, Beschleunigung des Zeitplans durch schnellere Iteration), oft einen überzeugenden Gesamtwertbeitrag für Satellitenprogramme. Erkundung verschiedener Druckverfahren und die Erörterung von Projektspezifika mit sachkundigen Anbietern wie Met3dp kann zur Optimierung des Ansatzes beitragen.
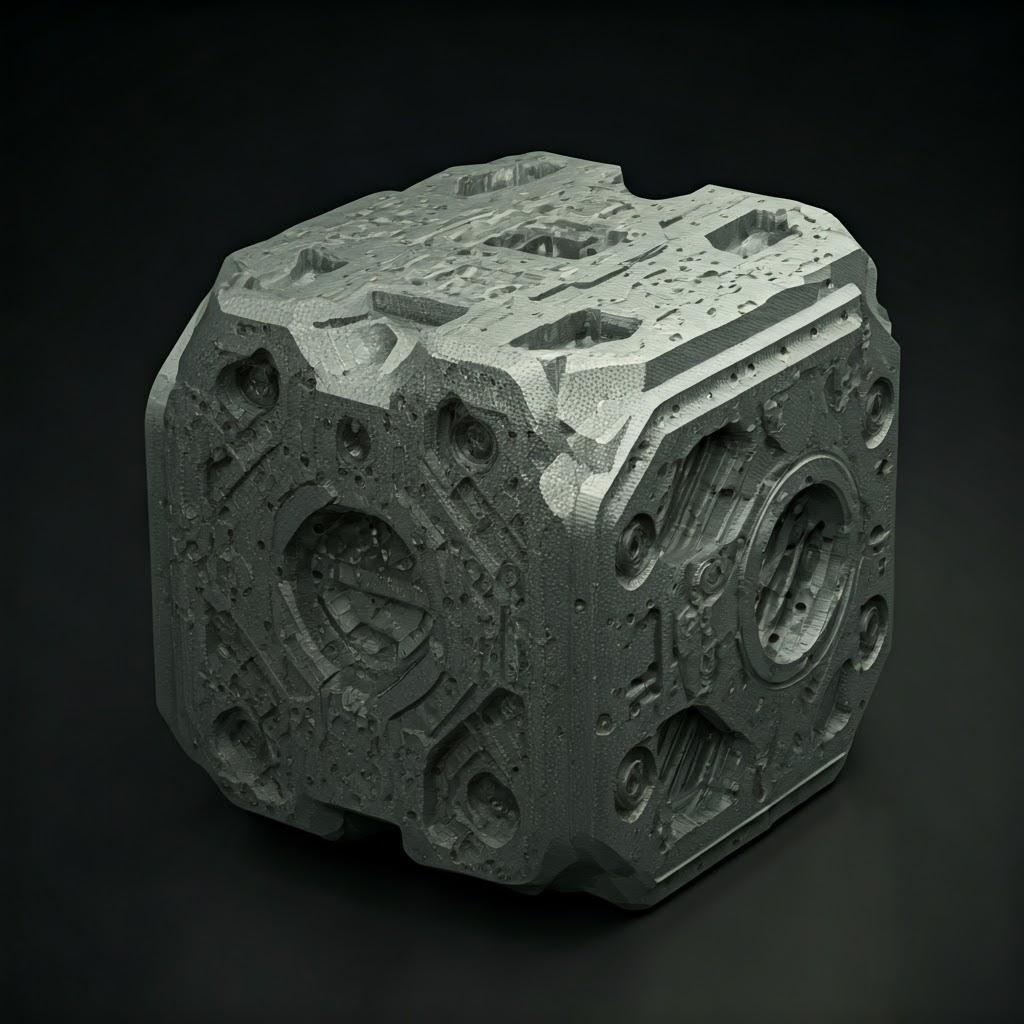
Häufig gestellte Fragen (FAQ) zu 3D-gedruckten Avionikboxen
Da die additive Fertigung von Metallen immer häufiger für kritische Komponenten in der Luft- und Raumfahrt eingesetzt wird, haben Ingenieure, Konstrukteure und Beschaffungsspezialisten oft Fragen zu den Möglichkeiten, Grenzen und Implementierungsspezifika, insbesondere bei Flughardware wie Satellitenavionikboxen. Hier finden Sie Antworten auf einige häufig gestellte Fragen:
1. Können 3D-gedruckte Avionikgehäuse aus Scalmalloy® oder AlSi10Mg die strengen Qualifikationsstandards für die Raumfahrt erfüllen?
Antwort: Ja, absolutaber es erfordert einen sorgfältigen und gut dokumentierten Ansatz. Um die Weltraumqualifikation für eine AM-Komponente zu erreichen, muss nachgewiesen werden, dass sie alle Leistungs-, Zuverlässigkeits- und Sicherheitsanforderungen für die jeweilige Einsatzumgebung erfüllt. Dies umfasst in der Regel:
- Überprüfung der Materialeigenschaften: Nachweis, dass die mechanischen Eigenschaften (Zugfestigkeit, Streckgrenze, Dehnung, Ermüdungslebensdauer, Bruchzähigkeit) des gedruckten und nachbearbeiteten Materials durchweg die Konstruktionsanforderungen erfüllen oder übertreffen. Dies beinhaltet umfangreiche Tests an Prüfkörpern, die neben den eigentlichen Teilen unter kontrollierten Bedingungen hergestellt werden.
- Prozesskontrolle & Validierung: Der Nachweis, dass der gesamte Herstellungsprozess - von der Pulverhandhabung und den Druckparametern bis hin zu den Wärmebehandlungen und der maschinellen Bearbeitung - streng kontrolliert, wiederholbar und validiert ist, um einheitliche Ergebnisse zu erzielen. Dies hängt in hohem Maße von robusten Qualitätsmanagementsystemen (wie AS9100) ab.
- Zerstörungsfreie Prüfung (NDT): Einsatz von Methoden wie Computertomographie (CT) zur Sicherstellung der inneren Integrität (Überprüfung auf Porosität, Einschlüsse oder Fusionsmängel) und möglicherweise Farbeindring- oder Ultraschallprüfung für Oberflächen- und Untergrundfehler.
- Umweltprüfungen: Das Bauteil (oder repräsentative Prüfgegenstände) wird simulierten Start- und Weltraumumgebungen ausgesetzt, einschließlich Vibrationstests, Akustiktests, thermischen Zyklen und möglicherweise Thermalvakuumtests (TVAC), um seine Leistung unter Betriebsbedingungen zu überprüfen.
- Rückverfolgbarkeit und Dokumentation: Lückenlose Rückverfolgbarkeit von der Rohpulvercharge bis zum fertigen Bauteil mit umfassender Dokumentation aller Herstellungsschritte, Kontrollen und Testergebnisse.
Der Qualifizierungsprozess ist zwar anspruchsvoll, aber die zunehmende Verbreitung von AM-Komponenten, einschließlich Strukturteilen und Gehäusen aus Scalmalloy® und AlSi10Mg, beweist die Machbarkeit. Die Zusammenarbeit mit einem erfahrenen Anbieter wie Met3dp, der Wert auf hochwertige Pulver, zuverlässige Drucksysteme (wie seine fortschrittlichen SEBM-Drucker) und Prozesskontrolle legt und Qualifizierungsprotokolle für die Luft- und Raumfahrt unterstützt, ist für den Erfolg entscheidend.
2. Wie hoch ist die typische Gewichtseinsparung bei der Neukonstruktion eines Avionikgehäuses für Metall-AM?
Antwort: Die erreichbare Gewichtseinsparung ist sehr variabel und hängt stark von mehreren Faktoren ab: der Komplexität und Effizienz des ursprünglichen (Basis-)Designs, den spezifischen Lastfällen und Leistungsanforderungen, dem gewählten AM-Material (Scalmalloy® ermöglicht aufgrund seiner höheren spezifischen Festigkeit im Allgemeinen größere Einsparungen als AlSi10Mg) und dem Ausmaß, in dem DfAM-Prinzipien (insbesondere Topologieoptimierung und Gitterstrukturen) angewendet werden.
Allerdings, typische Gewichtseinsparungen, die in Fallstudien für die Luft- und Raumfahrt berichtet werden, liegen oft zwischen 30 und 50 % im Vergleich zu traditionell hergestellten (z. B. maschinell bearbeiteten Knüppeln) Gegenstücken. In einigen aggressiv optimierten Beispielen, insbesondere solchen, die Scalmalloy® und fortschrittliche Topologieoptimierung für Strukturkomponenten nutzen, einsparungen von mehr als 70 % sind nachgewiesen worden.
Es ist wichtig zu beachten, dass die Maximierung der Gewichtseinsparungen eine Neukonstruktion des Teils speziell für AM erfordert, anstatt einfach ein bestehendes Design zu drucken. Die größten Vorteile werden erzielt, wenn Ingenieure die Designfreiheit, die die Technologie bietet, voll ausschöpfen, um hoch optimierte, lastpfadgesteuerte Strukturen zu schaffen.
3. Wie hoch sind die Kosten eines 3D-gedruckten Avionikgehäuses im Vergleich zu einem traditionell CNC-gefrästen Knüppelgehäuse?
Antwort: Es gibt keine einheitliche Antwort, da der Kostenvergleich stark von der Komplexität der Teile, dem Auftragsvolumen und den spezifischen Anforderungen abhängt:
- Prototypen und geringe Stückzahlen (z. B. 1-10 Stück): Metall-AM ist oft kostengünstiger für Prototypen und sehr kleine Produktionsserien. Das liegt vor allem daran, dass bei AM keine teuren Werkzeuge, Vorrichtungen oder komplexen Programmiereinrichtungen wie bei der CNC-Bearbeitung benötigt werden. Die Möglichkeit, direkt vom CAD zum Bauteil zu gelangen, reduziert die Vorlaufkosten und Vorlaufzeiten für Einzelstücke oder Artikel mit geringer Stückzahl erheblich.
- Hohe Komplexität: Für Teile mit extrem komplexen Geometrien (z. B. komplizierte interne Kanäle, konsolidierte Baugruppen, topologieoptimierte Formen), die nur schwer oder gar nicht durch CNC-Bearbeitung hergestellt werden können, wird AM zu einem grundlagentechnologiedadurch werden Kostenvergleiche weniger relevant, da das Design selbst möglicherweise nur durch AM hergestellt werden kann.
- Mittlere bis hohe Stückzahlen (z. B. mehr als 50 identische Einheiten): Bei relativ einfachen Geometrien, die in größeren Stückzahlen produziert werden, erreicht die traditionelle CNC-Bearbeitung oft eine geringere Kosten pro Teil aufgrund der schnelleren Zykluszeiten und der nachgewiesenen Effizienz, sobald sich die anfänglichen Einrichtungskosten amortisiert haben.
- Materialausnutzung (Buy-to-Fly-Ratio): AM nutzt das Material in der Regel viel effizienter als die subtraktive Bearbeitung, bei der erhebliche Abfälle (Späne) anfallen können. Bei teuren Werkstoffen wie Aluminium für die Luft- und Raumfahrt oder Scalmalloy® kann das bessere Verhältnis zwischen Anschaffung und Fertigung die höheren Bearbeitungskosten ausgleichen.
- Gesamtwert-Angebot: Ein direkter Kostenvergleich pro Teil kann irreführend sein. Der Wert eines AM-Teils kann in den Vorteilen auf Systemebene liegen, die die potenziell höheren Komponentenkosten überwiegen. So kann beispielsweise die durch AM erzielte erhebliche Gewichtseinsparung zu einer beträchtlichen Senkung der Startkosten führen oder eine höhere Nutzlastkapazität ermöglichen, was einen weitaus größeren wirtschaftlichen Nutzen darstellt als eine kleine Einsparung bei den Herstellungskosten des Bauteils. Auch die Konsolidierung von Teilen reduziert den Arbeitsaufwand bei der Montage und verbessert die Zuverlässigkeit.
Daher sollte die Entscheidung auf einer Analyse der Gesamtbetriebskosten beruhen, bei der die Komplexität des Designs, das Produktionsvolumen, die Materialkosten, die Vorlaufzeit und die Auswirkungen der durch AM ermöglichten Leistungsverbesserungen auf Systemebene berücksichtigt werden.
4. Was sind die Hauptunterschiede zwischen LPBF (Laser Powder Bed Fusion) und SEBM (Selective Electron Beam Melting) beim Bedrucken von Avionikgehäusen aus Aluminium?
Antwort: Sowohl LPBF (auch bekannt als SLM) als auch SEBM sind Pulverbettschmelzverfahren, mit denen hochwertige Metallteile, einschließlich Avionikgehäuse aus Aluminiumlegierungen, hergestellt werden können. Sie weisen jedoch unterschiedliche Merkmale auf:
Merkmal | LPBF (Laser-Pulver-Bett-Fusion) | SEBM (Selektives Elektronenstrahlschmelzen) | Relevanz für Avionikboxen |
---|---|---|---|
Energiequelle | Laser | Elektronenstrahl | Unterschiedliche Schmelzbaddynamik und Materialinteraktionen |
Atmosphäre | Inertes Gas (Argon, Stickstoff) | Hochvakuum | Vakuum ist besser für reaktive Materialien; verringert die Gasporosität |
Bau-Temp. | Relativ niedrig (<200°C typisch) | Hoch (z. B. 400-600°C+ für Al-Legierungen) | Hohe Temperaturen reduzieren Eigenspannungen in SEBM |
Eigenspannung | Höher (erfordert oft sofortigen Stressabbau) | Niedriger (kann den Bedarf an Stressabbau verringern oder beseitigen) | SEBM vereinfacht potenziell den Nachbearbeitungsprozess |
Oberfläche | Im Allgemeinen besser (feinerer Ra) | Im Allgemeinen gröber (größeres Pulver, höhere Energie) | LPBF wird bevorzugt, wenn die Ausführung im Ist-Zustand kritisch ist |
Merkmal Auflösung | Im Allgemeinen feiner (kleinere Laserpunktgröße) | Im Allgemeinen gröber (größerer Lichtpunkt) | LPBF kann für sehr feine Details besser geeignet sein |
Baugeschwindigkeit | Kann schnell sein, wird aber oft durch das Wärmemanagement eingeschränkt | In der Regel schneller (höhere Leistung, schnelleres Scannen) | SEBM bietet potenziell eine höhere Produktivität |
Größe des Pulvers | Typischerweise feiner | Typischerweise gröber | Beeinflusst Oberflächengüte und Fließfähigkeit |
Erforderliches Material | Breiteres Spektrum an verarbeitbaren Materialien | Erfordert elektrisch leitfähige Materialien | Beide funktionieren gut für AlSi10Mg und Scalmalloy® |
Vor-/Nachbearbeitung | Erfordert oft Stressabbau | Kann weniger Stressabbau erfordern, Pulverhandling empfindlich | Der gesamte Arbeitsablauf kann unterschiedlich sein |
In Blätter exportieren
Met3dp ist spezialisiert auf SEBM-Technologiedie Vorteile wie potenziell höhere Fertigungsgeschwindigkeiten und geringere Eigenspannungen werden für die Herstellung zuverlässiger, einsatzkritischer Teile genutzt. Die Wahl zwischen LPBF und SEBM hängt oft von der spezifischen Teilegeometrie, den erforderlichen Toleranzen, den Anforderungen an die Oberflächengüte, dem Produktionsvolumen und dem verwendeten Material ab. Beide sind praktikable Optionen für hochwertige Aluminium-Avionikgehäuse, wenn die Prozesse richtig gesteuert werden.
Schlussfolgerung: Die Zukunft ist leicht - Additive Fertigung für Satelliten der nächsten Generation
Das unablässige Streben nach leichteren, leistungsfähigeren und kostengünstigeren Satelliten treibt die Innovation in der gesamten Luft- und Raumfahrtindustrie voran. In diesem Bestreben hat sich die additive Fertigung von Metallen nicht nur als neuartige Technologie erwiesen, sondern auch als grundlegender Wegbereiter für die Erreichung der nächsten Leistungsgeneration. Wie wir in dieser Diskussion erörtert haben, ist die Anwendung der Metall-AM, insbesondere unter Verwendung fortschrittlicher Materialien wie Scalmalloy® und das Arbeitspferd AlSi10Mgbietet transformative Vorteile für kritische Komponenten wie satellitenavionikboxen.
Dank der Möglichkeit, die Beschränkungen der traditionellen Fertigung zu überwinden, können die Ingenieure Gehäuse entwerfen, die durch topologieoptimierung und Gitterstrukturen, was sich unmittelbar in geringeren Startkosten oder einer höheren Nutzlastkapazität niederschlägt. Die Website Gestaltungsfreiheit inhärent in AM erleichtert die konsolidierung von mehreren Teilen in einzelne, monolithische Strukturen zu integrieren, was die Montagezeit, das Gewicht und mögliche Fehlerquellen reduziert. Außerdem ist die Fähigkeit zur Integration komplexe Wärmemanagementfunktionenwie z. B. konforme Kühlkanäle oder optimierte Kühlkörper, direkt in die Gehäusestruktur integriert sind, erhöhen die Zuverlässigkeit und Leistung der darin untergebrachten empfindlichen Elektronik.
Um diese Vorteile zu nutzen, bedarf es jedoch mehr als nur des Zugangs zu einem 3D-Drucker. Es erfordert einen ganzheitlichen Ansatz, der Folgendes umfasst Design für additive Fertigung (DfAM) grundsätze, sorgfältige Materialauswahl auf der Grundlage von Leistungsanforderungen, einem gründlichen Verständnis der notwendigen Nachbearbeitungsschritte (von der Wärmebehandlung bis zur Präzisionsbearbeitung), und strenge Qualitätskontrolle geeignet für die Anforderungen der Raumfahrt. Die Bewältigung potenzieller Herausforderungen wie Eigenspannungen, Porosität und das Erreichen enger Toleranzen erfordert Fachwissen und eine robuste Prozesssteuerung.
Der Erfolg hängt entscheidend von der Wahl des richtigen Fertigungspartners ab. Der ideale Partner ist nicht nur ein Zulieferer, sondern ein Partner, der über fundiertes Fachwissen in der Luft- und Raumfahrt, validierte Material- und Prozesskenntnisse, zertifizierte Qualitätssysteme (wie AS9100) und die richtigen technologischen Fähigkeiten verfügt. Met3dp ist ein Paradebeispiel für einen solchen Partner und bietet umfassende Lösungen zur additiven Metallfertigung. Mit branchenführenden Fähigkeiten, die die Entwicklung und Herstellung von hochwertigen Metallpulvern (über PREP und Gaszerstäubung), fortschrittlich und zuverlässig SEBM-Drucksystemeund Experte Anwendungsentwicklungsdienstemet3dp ermöglicht es Unternehmen, die Komplexität von AM zu bewältigen und es erfolgreich für ihre anspruchsvollsten Anwendungen einzusetzen.
Für Luft- und Raumfahrtingenieure, die die Grenzen der Satellitenkonstruktion erweitern wollen, und für Beschaffungsmanager, die nach zuverlässigen Lieferanten für fortschrittliche, leichte Komponenten suchen, ist die additive Fertigung von Metallen ein unverzichtbares Werkzeug. Durch den Einsatz von DfAM, die Nutzung fortschrittlicher Werkstoffe und die Zusammenarbeit mit erfahrenen Anbietern wie Met3dp kann die Luft- und Raumfahrtindustrie ihren Weg zu leichteren, besser integrierten und leistungsfähigeren Satelliten fortsetzen und die Zukunft der Raumfahrttechnologie wirklich gestalten. Die Zukunft der Satellitenhardware ist unbestreitbar leicht, und die additive Fertigung ebnet den Weg.
Teilen auf
MET3DP Technology Co., LTD ist ein führender Anbieter von additiven Fertigungslösungen mit Hauptsitz in Qingdao, China. Unser Unternehmen ist spezialisiert auf 3D-Druckgeräte und Hochleistungsmetallpulver für industrielle Anwendungen.
Fragen Sie an, um den besten Preis und eine maßgeschneiderte Lösung für Ihr Unternehmen zu erhalten!
Verwandte Artikel
Über Met3DP
Aktuelles Update
Unser Produkt
KONTAKT US
Haben Sie Fragen? Senden Sie uns jetzt eine Nachricht! Wir werden Ihre Anfrage mit einem ganzen Team nach Erhalt Ihrer Nachricht bearbeiten.
Holen Sie sich Metal3DP's
Produkt-Broschüre
Erhalten Sie die neuesten Produkte und Preislisten
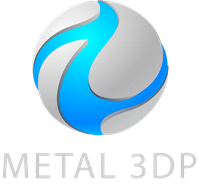
Metallpulver für 3D-Druck und additive Fertigung