Additive Fertigung von Batterie-Thermoplatten: Verbesserte EV-Leistung durch 3D-Druck von Metall
Inhaltsübersicht
Einführung - Revolutionierung des Wärmemanagements von EV-Batterien mit 3D-Metalldruck
Die Revolution der Elektrofahrzeuge (EV) führt zu einer beispiellosen Nachfrage nach fortschrittlichen Batterietechnologien. Das Herzstück der Leistung, Effizienz und Sicherheit von Elektrofahrzeugen ist das Wärmemanagement, das eine entscheidende Rolle spielt. Batterie-Thermoplatten sind wesentliche Komponenten zur Regulierung der Temperatur von Batteriepaketen, um optimale Betriebsbedingungen zu gewährleisten und die Lebensdauer der Batterie zu verlängern. Herkömmliche Herstellungsmethoden für diese Platten stoßen oft an Grenzen, was die Komplexität des Designs, die Materialauswahl und die Produktionseffizienz betrifft. Dennoch, Metall 3D-Druckauch bekannt als metalladditive Fertigung, bietet einen transformativen Ansatz für die Herstellung von Batterie-Thermoplatten. Diese innovative Technologie ermöglicht die Herstellung komplizierter Geometrien, die Verwendung von Hochleistungswerkstoffen wie AlSi10Mg und CuCrZr sowie das Potenzial für erhebliche Verbesserungen bei Design und Leistung von Wärmemanagementsystemen. Unter https://met3dp.com/wir sind führend in der Bereitstellung modernster 3D-Drucklösungen aus Metall, die es Branchen wie der Automobilindustrie ermöglichen, die Grenzen der EV-Technologie zu erweitern.
Wozu werden Batterie-Thermoplatten verwendet? - Kritische Funktionen in Batteriesystemen für Elektrofahrzeuge
Batterie-Thermoplatten sind ein wesentlicher Bestandteil für den effektiven Betrieb von EV-Batteriepacks. Ihre Hauptfunktion besteht darin, die Wärmeabfuhr von den Batteriezellen während des Betriebs und des Ladevorgangs zu erleichtern und in einigen Fällen für eine thermische Isolierung oder kontrollierte Heizung in kalten Klimazonen zu sorgen. Überhitzung kann zu verminderter Batterieleistung, beschleunigter Degradation und Sicherheitsrisiken führen, während zu niedrige Temperaturen auch die Effizienz und die Ladefähigkeit beeinträchtigen können.
Hier sind die wichtigsten Anwendungsfälle und Funktionen von Batterie-Thermoplatten:
- Wärmeableitung: Während der Lade- und Entladezyklen erzeugen Lithium-Ionen-Batterien aufgrund des Innenwiderstands Wärme. Wärmeplatten, die häufig mit Kühlkanälen ausgestattet sind, leiten diese Wärme von den Zellen weg zu einem (flüssigen oder luftbasierten) Kühlsystem.
- Gleichmäßigkeit der Temperatur: Die Aufrechterhaltung einer gleichmäßigen Temperatur über alle Batteriezellen innerhalb eines Akkupacks ist entscheidend für die Maximierung der Gesamtleistung und Lebensdauer. Thermoplatten helfen, die Wärme gleichmäßig zu verteilen und verhindern so lokale Hot Spots.
- Strukturelle Unterstützung: In vielen Akkupack-Konstruktionen dienen die Wärmeleitbleche auch als strukturelle Komponenten, die den Akkumodulen Halt und Schutz bieten.
- Thermische Schnittstelle: Die Wärmeplatte fungiert als kritische Schnittstelle zwischen den Batteriezellen oder -modulen und dem Kühl-/Heizsystem und sorgt für eine effiziente Wärmeübertragung über diese Grenze.
- Integration von Kühlkanälen: Die additive Fertigung ermöglicht die Konstruktion und Herstellung komplexer interner Kühlkanäle direkt in der Wärmeplatte, wodurch der Kühlmittelfluss optimiert und die Effizienz des Wärmeaustauschs verbessert wird.
- Gewichtsreduzierung: Im Vergleich zu herkömmlichen Materialien und Konstruktionen kann der 3D-Druck von Metallen mit leichten Legierungen wie AlSi10Mg zu einer allgemeinen Gewichtsreduzierung des Batteriepakets beitragen und so die Fahrzeugeffizienz verbessern.
Zu den Branchen, die in erheblichem Maße von der fortschrittlichen Batterie-Thermoplatten-Technologie profitieren, gehören:
- Automobilindustrie: Elektrofahrzeuge, Hybridelektrofahrzeuge (HEVs) und Plug-in-Hybridelektrofahrzeuge (PHEVs) sind im Hinblick auf Leistung, Reichweite und Sicherheit in hohem Maße auf ein effizientes Wärmemanagement der Batterien angewiesen.
- Luft- und Raumfahrt: Senkrecht startende und landende Elektroflugzeuge (eVTOL) und elektrische Antriebssysteme erfordern leichte und leistungsstarke Wärmemanagementlösungen für Batterien.
- Medizinisch: Tragbare medizinische Geräte und Ausrüstungen, die mit Batterien betrieben werden, benötigen ein zuverlässiges Wärmemanagement für einen konstanten Betrieb und Sicherheit.
- Industrielle Fertigung: Batteriebetriebene Industrieausrüstungen wie Gabelstapler und Roboter profitieren von einem optimierten Wärmemanagement für längere Betriebszeiten und Langlebigkeit.
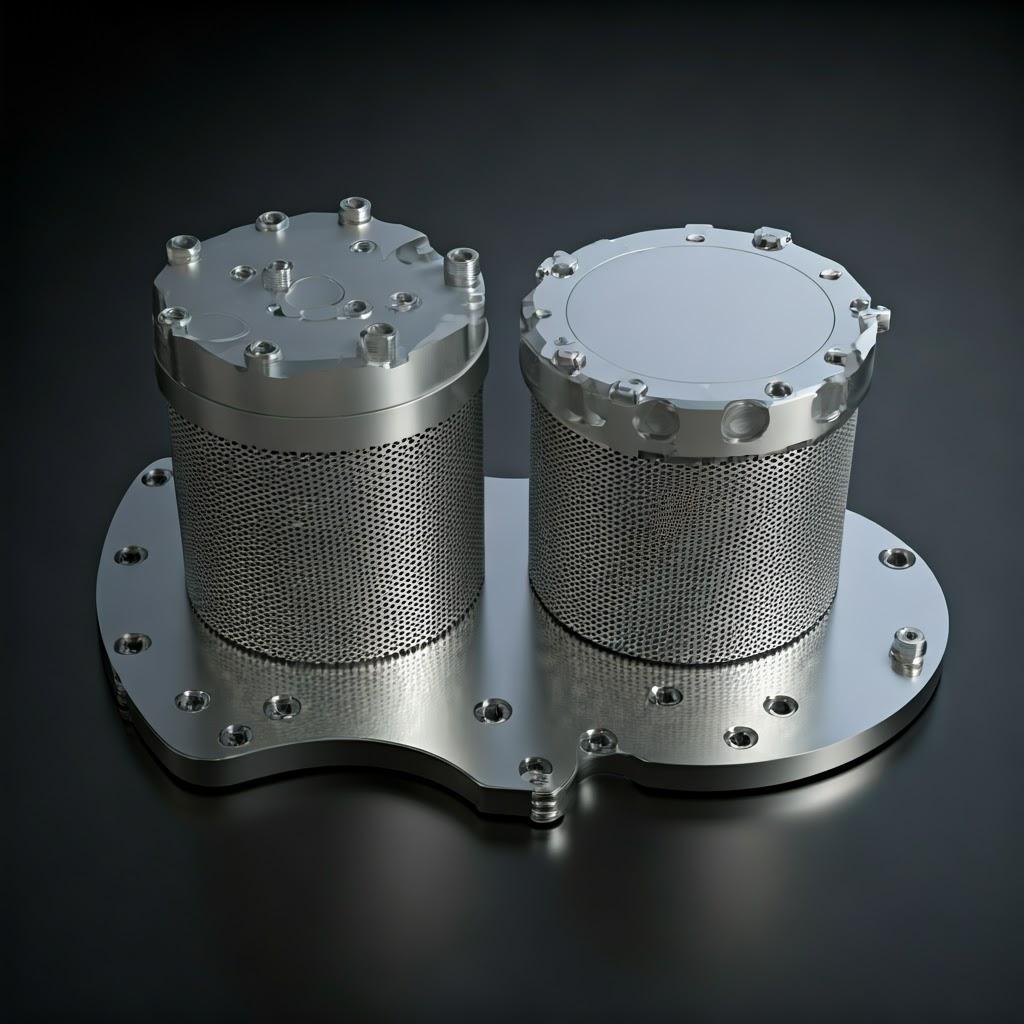
Warum 3D-Metalldruck für Batterie-Thermoplatten verwenden? - Vorteile gegenüber traditioneller Fertigung
Der 3D-Druck von Metall bietet eine überzeugende Alternative zu herkömmlichen Fertigungsmethoden wie Bearbeitung, Gießen oder Extrusion für die Herstellung von Batterie-Thermoplatten. Die einzigartigen Fähigkeiten der additiven Fertigung bieten mehrere entscheidende Vorteile:
- Gestaltungsfreiheit und Komplexität: der 3D-Druck ermöglicht die Erstellung komplizierter interner Geometrien, wie z. B. optimierte Kühlkanäle mit komplexen Strömungswegen, die mit herkömmlichen Methoden nur schwer oder gar nicht zu realisieren sind. Diese Designflexibilität ermöglicht eine verbesserte Wärmeübertragungseffizienz und kompaktere Wärmemanagementsysteme.
- Optimierung der Materialien: Der 3D-Metalldruck ist mit einer Vielzahl von Hochleistungswerkstoffen kompatibel, darunter Aluminiumlegierungen wie AlSi10Mg, die für ihre hervorragende Wärmeleitfähigkeit und ihr geringes Gewicht bekannt sind, und Kupferlegierungen wie CuCrZr, die eine ausgewogene Kombination aus hoher Wärme- und elektrischer Leitfähigkeit und Festigkeit bieten. Metall3DP bietet ein umfassendes Portfolio an fortschrittlichen Metallpulvern, darunter diese empfohlenen Materialien, die speziell für additive Fertigungsverfahren optimiert sind. Unser fortschrittliches Pulverherstellungssystem gewährleistet eine hohe Sphärizität und Fließfähigkeit, die für die Herstellung dichter, hochwertiger Teile entscheidend sind.
- Gewichtsreduzierung: Durch die Optimierung des Designs und die Verwendung leichter Materialien kann der 3D-Metalldruck das Gewicht von Batterie-Thermoplatten erheblich reduzieren und so zu einer verbesserten Energieeffizienz und Reichweite von Elektrofahrzeugen beitragen.
- Teil Konsolidierung: Komplexe Baugruppen aus mehreren Komponenten können in einem einzigen 3D-gedruckten Teil zusammengefasst werden, wodurch die Anzahl der Verbindungen, Befestigungselemente und Fertigungsschritte reduziert wird, was zu einer höheren Zuverlässigkeit und geringeren Kosten führt.
- Personalisierung und Kleinserienproduktion: Die additive Fertigung ist ideal für die Herstellung kundenspezifischer Wärmeleitbleche für bestimmte Batteriepacks oder für Kleinserien, ohne dass teure Werkzeuge benötigt werden. Diese Flexibilität ist besonders auf dem sich schnell entwickelnden Markt für Elektrofahrzeuge von Vorteil.
- Rapid Prototyping und Iteration: Der 3D-Metalldruck ermöglicht ein schnelles Prototyping verschiedener Thermoplatten-Designs, so dass Ingenieure ihre Konzepte schnell testen und überarbeiten können, um die Leistung vor der Massenproduktion zu optimieren.
- Geringerer Materialabfall: Bei additiven Fertigungsverfahren fällt in der Regel weniger Materialabfall an als bei subtraktiven Verfahren wie der maschinellen Bearbeitung, da das Material nur dort eingesetzt wird, wo es für die Herstellung des Teils benötigt wird.
Empfohlene Materialien und warum sie wichtig sind - AlSi10Mg und CuCrZr für optimale thermische Leistung
Die Wahl des Materials ist entscheidend für die Leistung von Batterie-Thermoplatten. Der 3D-Metalldruck bietet die Flexibilität, fortschrittliche Materialien zu verwenden, die auf spezifische thermische und mechanische Anforderungen zugeschnitten sind. Zwei besonders vielversprechende Materialien für EV-Batterie-Thermoplatten sind AlSi10Mg und CuCrZr.
AlSi10Mg: Leicht und wärmeleitend
AlSi10Mg ist eine Aluminiumlegierung, die aufgrund ihrer hervorragenden Eigenschaftskombination in der additiven Fertigung weit verbreitet ist:
Eigentum | Wert | Bedeutung für Thermoplatten |
---|---|---|
Dichte | ~2,68 g/cm³ | Leichtes Gewicht, das zur Gesamteffizienz des Fahrzeugs beiträgt. |
Wärmeleitfähigkeit | ~150 W/m-K | Effiziente Wärmeableitung von den Batteriezellen. |
Zugfestigkeit (wie gebaut) | ~430 MPa | Sorgt für die strukturelle Integrität des Akkupacks. |
Streckgrenze (wie gebaut) | ~270 MPa | Widerstandsfähigkeit gegen Verformung unter Belastung. |
Korrosionsbeständigkeit | Ausgezeichnet in neutralen wässrigen Umgebungen | Geeignet für den Einsatz in Kühlsystemen mit Kühlmitteln auf Wasserbasis. |
Druckbarkeit | Ausgezeichnet | Produziert dichte Teile mit guter Oberflächengüte unter Verwendung von Pulverbettschmelzverfahren wie Selective Laser Melting (SLM) und Direct Metal Laser Sintering (DMLS). |
In Blätter exportieren
Der hohe Siliziumgehalt in AlSi10Mg verbessert die Fließfähigkeit während des Druckvorgangs und erhöht die Festigkeit und Härte des Materials. Der Zusatz von Magnesium erhöht die Festigkeit durch Mischkristallverfestigung und Ausscheidungshärtung weiter. Metal3DPs AlSi10Mg-Pulver ist speziell für die additive Fertigung optimiert und gewährleistet eine hervorragende Fließfähigkeit und gleichbleibende Materialeigenschaften im fertigen Druckteil. Nähere Informationen zu den Eigenschaften unseres AlSi10Mg-Pulvers finden Sie unter https://met3dp.sg/product/alsi10mg-powder/.
CuCrZr: Hohe thermische und elektrische Leitfähigkeit und Festigkeit
CuCrZr ist eine Kupferlegierung, die für ihre einzigartige Kombination aus hoher thermischer und elektrischer Leitfähigkeit mit guter Festigkeit und Beständigkeit gegen Erweichung bei erhöhten Temperaturen bekannt ist:
Eigentum | Wert | Bedeutung für Thermoplatten |
---|---|---|
Dichte | ~8,8 g/cm³ | Höhere Dichte als Aluminium, aber mit besserer Leitfähigkeit. |
Wärmeleitfähigkeit | 200 - 300 W/m-K | Ausgezeichnete Wärmeableitung, bei bestimmten Anwendungen möglicherweise besser als Aluminiumlegierungen. |
Elektrische Leitfähigkeit | 22 - 48% INVEKOS | Kann in Batteriepacks von Vorteil sein, bei denen die Wärmeplatten auch eine Rolle bei der elektrischen Erdung oder Stromverteilung spielen. |
Streckgrenze (wärmebehandelt) | 350 - 650 MPa | Hohe Festigkeit, die dünnere und leichtere Konstruktionen ermöglicht, ohne die strukturelle Integrität zu beeinträchtigen. |
Oxidationsbeständigkeit | Gut bis zu 900°C | Geeignet für Umgebungen mit hohen Temperaturen und mit langer Lebensdauer. |
Druckbarkeit | Gut | Kann mit Pulverbettschmelzverfahren verarbeitet werden, wobei optimierte Parameter erforderlich sind, um eine hohe Dichte und Leitfähigkeit zu erreichen. |
In Blätter exportieren
Der Mechanismus der Ausscheidungshärtung in CuCrZr ermöglicht es, eine hohe Festigkeit zu erreichen und gleichzeitig eine hohe Leitfähigkeit beizubehalten. Chrom und Zirkonium bilden in der Kupfermatrix Ausscheidungen, die die Versetzungsbewegung behindern und die Festigkeit erhöhen. Dies macht CuCrZr zu einer ausgezeichneten Wahl für Anwendungen, die sowohl eine effiziente Wärmeübertragung als auch mechanische Robustheit erfordern. Metall3DP bietet hochwertiges CuCrZr-Pulver an, das für die additive Fertigung geeignet ist und die Herstellung von Hochleistungs-Thermoplatten für Batterien ermöglicht. Erfahren Sie mehr über unser Angebot an CuCrZr-Pulvern unter https://met3dp.sg/product/cucrzr-powder/.
Die Wahl zwischen AlSi10Mg und CuCrZr hängt von den spezifischen Anforderungen des Wärmemanagementsystems der Batterie ab, einschließlich der gewünschten Balance zwischen Gewicht, Wärmeleitfähigkeit, elektrischer Leitfähigkeit und Kosten. Der 3D-Metalldruck ermöglicht es den Ingenieuren, das optimale Material für ihre Anwendung auszuwählen und komplizierte Wärmeleitbleche zu entwerfen, die die Leistung und Effizienz maximieren. Quellen und verwandte Inhalte
Designüberlegungen für die additive Fertigung von Batterie-Thermoplatten - Optimierung von Geometrie und Struktur
Die Entwicklung von Batterie-Thermoplatten für den 3D-Metalldruck erfordert einen anderen Ansatz als herkömmliche Herstellungsverfahren. Der schichtweise Aufbau der additiven Fertigung eröffnet neue Möglichkeiten zur Optimierung der Geometrie, der inneren Merkmale und der Gesamtleistung. Hier sind die wichtigsten Designüberlegungen:
- Topologie-Optimierung: Mit dieser Berechnungsmethode lässt sich die effizienteste Materialverteilung für Wärmeübertragung und strukturelle Unterstützung ermitteln. Durch die Definition des Designraums, der Lasten und der thermischen Randbedingungen kann die Topologieoptimierungssoftware komplexe, organisch anmutende Geometrien erzeugen, die die Leistung maximieren und gleichzeitig den Materialverbrauch und das Gewicht minimieren. Der 3D-Metalldruck eignet sich hervorragend für die Herstellung dieser komplizierten Konstruktionen.
- Interne Kühlungskanäle: Einer der wichtigsten Vorteile des 3D-Metalldrucks ist die Möglichkeit, komplexe interne Kühlkanäle innerhalb der Wärmeplatte zu erstellen. Diese Kanäle können mit optimierten Strömungswegen, einer vergrößerten Oberfläche für den Wärmeaustausch und Merkmalen wie Turbulatoren zur Verbesserung der Kühlmittelmischung und der Wärmeübertragungseffizienz entworfen werden. Beachten Sie bei der Gestaltung von Kühlkanälen Folgendes:
- Form und Größe der Kanäle: Optimieren Sie die Querschnittsform (z. B. kreisförmig, rechteckig, konform) und die Größe der Kanäle, um Druckverlust und Wärmeübertragung auszugleichen.
- Kanal-Layout: Entwerfen Sie das Kanalnetz so, dass eine gleichmäßige Kühlung der Batteriezellen gewährleistet ist, und vermeiden Sie stagnierende Zonen und heiße Stellen.
- Oberflächenveredelung: Integrieren Sie Merkmale wie Rippen, Rippen oder Stiftrippen in die Kanäle, um die Oberfläche für die Wärmeübertragung zu vergrößern.
- Verteilerdesign: Konstruieren Sie die Ein- und Auslassverteiler sorgfältig, um eine gleichmäßige Verteilung des Kühlmittelflusses auf alle Kanäle zu gewährleisten.
- Wanddicke: Optimieren Sie die Wandstärke, um ein Gleichgewicht zwischen Wärmeleitfähigkeit, struktureller Integrität und Gewicht herzustellen. Dünnere Wände können die Wärmeübertragung verbessern, aber die Festigkeit beeinträchtigen. Erwägen Sie die Verwendung variabler Wandstärken, um die Leistung auf bestimmte Bereiche der Platte zuzuschneiden.
- Unterstützende Strukturen: Der 3D-Druck von Metall erfordert häufig Stützstrukturen, um ein Verziehen, Durchhängen und Zusammenbrechen von überhängenden Elementen während des Bauprozesses zu verhindern. Entwerfen Sie, wann immer möglich, Teile mit selbsttragenden Geometrien, um den Bedarf an Stützen zu minimieren. Wenn Stützen erforderlich sind, planen Sie deren effiziente Entfernung und berücksichtigen Sie die Auswirkungen auf die Oberflächengüte. Software-Tools können helfen, die Erzeugung von Stützen zu optimieren.
- Thermische Schnittstellengestaltung: Die Schnittstelle zwischen der Wärmeplatte und den Batteriezellen oder dem Kühlsystem ist entscheidend für eine effiziente Wärmeübertragung. Erwägen Sie die Integration von Merkmalen wie:
- Flache und glatte Oberflächen: Achten Sie auf einen guten Kontakt zwischen den zueinander passenden Oberflächen, um den Wärmewiderstand zu minimieren.
- Integrierte Befestigungsmerkmale: Konstruktionsmerkmale für eine sichere und zuverlässige Befestigung an den Batteriemodulen und dem Kühlsystem.
- Oberflächenbehandlungen: Erforschung von Oberflächenbehandlungen oder -beschichtungen zur Verbesserung der thermischen Kontaktleitfähigkeit.
- Merkmal Integration: Die additive Fertigung ermöglicht die Integration mehrerer Funktionen in ein einziges Teil. Ziehen Sie in Erwägung, Funktionen wie Montagevorsprünge, Sensorgehäuse oder elektrische Leitungen direkt in das Design der Wärmeplatte zu integrieren.
- Orientierung und Gebäuderichtung: Die Ausrichtung des Teils auf der Bauplattform und die Baurichtung können sich erheblich auf die Oberflächengüte, die mechanischen Eigenschaften und den Bedarf an Stützstrukturen auswirken. Optimieren Sie die Ausrichtung, um den Unterstützungsbedarf zu minimieren und die gewünschten Leistungsmerkmale zu erzielen.
- Materialauswahl für Design: Wie bereits erwähnt, hat die Wahl des Werkstoffs (AlSi10Mg oder CuCrZr) erheblichen Einfluss auf die thermischen und mechanischen Konstruktionsüberlegungen. Die Konstruktionsparameter sollten auf die spezifischen Eigenschaften des gewählten Pulvers zugeschnitten sein. Metal3DPs fachwissen im Bereich der additiven Fertigung von Metallen kann wertvolle Einblicke in die Materialauswahl und Konstruktionsoptimierung für Ihre spezifische Anwendung liefern.
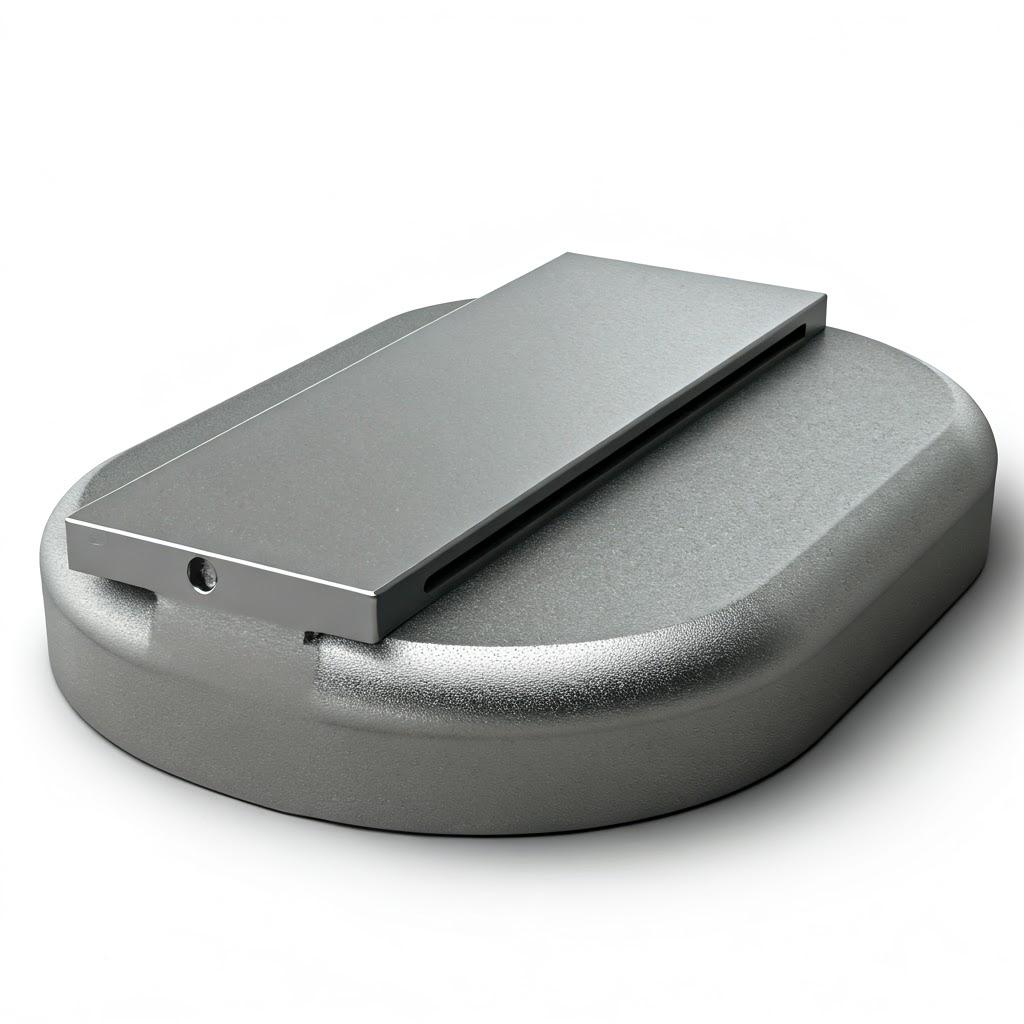
Toleranz, Oberflächenbeschaffenheit und Maßgenauigkeit von 3D-gedruckten Thermoplatten
Das Verständnis der erreichbaren Toleranzen, der Oberflächenbeschaffenheit und der Maßgenauigkeit von 3D-gedruckten Metallteilen ist entscheidend für die Integration von Batteriekühlplatten in komplexe EV-Batteriesysteme. Diese Faktoren beeinflussen die Passform, Leistung und Zuverlässigkeit der endgültigen Baugruppe.
- Maßgenauigkeit: Metallische 3D-Druckverfahren wie Selective Laser Melting (SLM) und Direct Metal Laser Sintering (DMLS) können eine relativ hohe Maßgenauigkeit erreichen. Allerdings sind die Toleranzen in der Regel breiter als bei der herkömmlichen Bearbeitung. Zu den Faktoren, die die Maßgenauigkeit beeinflussen, gehören:
- Maschinengenauigkeit: Die inhärente Genauigkeit des 3D-Druckers. Metal3DPs drucker sind so konstruiert, dass sie eine branchenführende Genauigkeit für unternehmenskritische Teile bieten.
- Schrumpfung des Materials: Metalle schrumpfen, wenn sie nach dem Schmelzen erstarren. Diese Schrumpfung ist vorhersehbar, muss aber bei der Konstruktion und den Prozessparametern berücksichtigt werden.
- Orientierung aufbauen: Die Ausrichtung des Teils während des Drucks kann die Maßgenauigkeit in verschiedenen Achsen beeinflussen.
- Größe und Komplexität der Teile: Größere und komplexere Teile können größere Abweichungen in der Maßhaltigkeit aufweisen.
- Nachbearbeiten: Verfahren wie die Spannungsarmglühung können die endgültigen Abmessungen beeinflussen.
- Erreichbare Toleranzen: Typische erreichbare Toleranzen für 3D-gedruckte Metallteile reichen von ±0,1 mm bis ±0,5 mm, abhängig von den oben genannten Faktoren. Engere Toleranzen können durch sorgfältige Prozessoptimierung und Nachbearbeitungsschritte wie CNC-Bearbeitung erreicht werden.
- Oberfläche: Die Oberflächenbeschaffenheit von 3D-gedruckten Metallteilen ist in der Regel rauer als bei maschinell bearbeiteten Oberflächen. Der schichtweise Aufbauprozess führt zu einer Oberflächentextur, die aus teilweise geschmolzenen Pulverpartikeln besteht. Zu den Faktoren, die die Oberflächenbeschaffenheit beeinflussen, gehören:
- Pulver Partikelgröße: Feinere Pulver führen im Allgemeinen zu glatteren Oberflächen. Metal3DPs das fortschrittliche Pulverherstellungssystem gewährleistet eine hohe Sphärizität und eine kontrollierte Partikelgrößenverteilung für eine optimale Oberflächengüte.
- Schichtdicke: Dünnere Schichten können glattere Oberflächen erzeugen, verlängern aber die Bauzeit.
- Orientierung aufbauen: Nach unten gerichtete Oberflächen sind aufgrund der Stützstrukturen eher rau.
- Nachbearbeiten: Zur Verbesserung der Oberflächengüte können verschiedene Nachbearbeitungstechniken eingesetzt werden, darunter:
- Media Blasting: Verwendet abrasive Medien, um teilweise gesinterte Partikel zu entfernen und die Oberflächenrauheit zu verringern.
- Polieren: Durch mechanisches oder chemisches Polieren lassen sich sehr glatte Oberflächen erzielen.
- CNC-Bearbeitung: Für kritische Oberflächen, die enge Toleranzen und glatte Oberflächen erfordern, kann die Bearbeitung als sekundärer Arbeitsgang durchgeführt werden.
- Auswirkungen auf Batterie-Thermoplatten: Bei Batterie-Thermoplatten ist die Maßgenauigkeit entscheidend für die richtige Passform und Integration in das Batteriepack und das Kühlsystem. Glatte Oberflächen an der thermischen Schnittstelle sind für die Maximierung der Wärmeübertragungseffizienz von entscheidender Bedeutung, da sie einen guten Kontakt mit den Batteriezellen oder Kühlelementen gewährleisten. Berücksichtigen Sie die kritischen Abmessungen und die Anforderungen an die Oberflächenbeschaffenheit je nach den Bedürfnissen der Anwendung. Metall-3D-Druck-Dienstleister wie Metall3DP kann Sie über erreichbare Toleranzen und Oberflächengüten für bestimmte Materialien und Geometrien beraten.
Nachbearbeitungsanforderungen für 3D-gedruckte Batterie-Thermoplatten aus Metall
Der 3D-Metalldruck bietet zwar erhebliche Vorteile, doch sind häufig Nachbearbeitungsschritte erforderlich, um die endgültigen gewünschten Eigenschaften, Abmessungen und Oberflächenbeschaffenheit der Batterie-Thermoplatten zu erreichen. Zu den üblichen Nachbearbeitungsanforderungen gehören:
- Entfernung von Puder: Nach dem Druckvorgang muss loses und teilweise gesintertes Pulver aus der Baukammer und allen internen Kanälen oder Hohlräumen innerhalb der Wärmeplatte entfernt werden. Dies geschieht in der Regel mit Druckluft, Bürsten oder Vakuumsystemen. Für komplizierte interne Kühlkanäle können spezielle Techniken erforderlich sein.
- Entfernung der Stützstruktur: Stützstrukturen, die oft notwendig sind, um Verformungen während des Drucks zu verhindern, müssen sorgfältig entfernt werden, ohne das Teil zu beschädigen. Dies kann manuell mit Schneidwerkzeugen oder durch automatisierte Verfahren wie maschinelle Bearbeitung oder растворение (Auflösen) für bestimmte Materialien erfolgen. Die Gestaltung der Stützstrukturen sollte auf eine einfache und saubere Entfernung abzielen.
- Stressabbau Wärmebehandlung: 3D-gedruckte Metallteile enthalten aufgrund der schnellen Erwärmungs- und Abkühlungszyklen während des Druckvorgangs häufig Restspannungen. Bei der Entspannungswärmebehandlung wird das Teil auf eine bestimmte Temperatur erwärmt und für eine bestimmte Zeit gehalten, um diese inneren Spannungen zu reduzieren und die Dimensionsstabilität und die mechanischen Eigenschaften zu verbessern.
- Heiß-Isostatisches Pressen (HIP): HIP ist ein Verfahren, bei dem hoher Druck und hohe Temperatur gleichzeitig auf das gedruckte Teil einwirken. Dadurch kann die interne Porosität verringert, die Dichte erhöht und die mechanischen Eigenschaften des Materials verbessert werden, insbesondere die Ermüdungsfestigkeit und Duktilität. HIP wird häufig für kritische Anwendungen eingesetzt, die eine hohe Leistung erfordern.
- CNC-Bearbeitung: Für Oberflächen, die sehr enge Toleranzen oder glatte Oberflächen erfordern, die nicht direkt durch 3D-Druck erreicht werden können, kann die CNC-Bearbeitung als sekundärer Vorgang eingesetzt werden. Dies ist besonders wichtig für kritische Passflächen oder Merkmale, die eine hohe Präzision erfordern.
- Oberflächenveredelung: Wie bereits erwähnt, können verschiedene Oberflächenbearbeitungsverfahren eingesetzt werden, um die Oberflächenrauheit von 3D-gedruckten Thermoplatten zu verbessern. Dazu gehören Strahlen, Polieren (mechanisch, chemisch, elektrochemisch) und Beschichten. Die Wahl der Oberflächenbehandlung hängt von den Anforderungen an den Wärmekontakt, die Korrosionsbeständigkeit und die Integration mit anderen Komponenten ab.
- Beschichtung: Beschichtungen können auf 3D-gedruckte Thermoplatten aus Metall aufgebracht werden, um deren Eigenschaften zu verbessern, wie Korrosionsbeständigkeit, Wärmeleitfähigkeit oder elektrische Isolierung. Beispiele sind die Eloxierung von Aluminiumlegierungen oder spezielle Materialien für thermische Schnittstellen.
- Qualitätsinspektion: Nach der Nachbearbeitung ist eine gründliche Qualitätsprüfung unerlässlich, um sicherzustellen, dass die Thermobleche die erforderliche Maßgenauigkeit, Oberflächenbeschaffenheit und Materialeigenschaften aufweisen. Dies kann visuelle Inspektionen, Messungen mit Koordinatenmessgeräten (KMG), zerstörungsfreie Prüfverfahren (ZfP) wie Ultraschall- oder Röntgenprüfungen und Materialprüfungen umfassen.
Die spezifischen Nachbearbeitungsanforderungen für eine 3D-gedruckte Batterie-Thermoplatte aus Metall hängen vom Material, der geplanten Anwendung und den gewünschten Leistungsmerkmalen ab. Die Zusammenarbeit mit einem erfahrenen Metall-3D-Druck-Dienstleister wie Metall3DP stellt sicher, dass die richtigen Nachbearbeitungsschritte durchgeführt werden, um qualitativ hochwertige und zuverlässige Komponenten zu erhalten. Unsere umfassenden Lösungen decken den gesamten Herstellungsprozess ab, von der Materialauswahl und Designoptimierung bis hin zum Druck und der Nachbearbeitung.
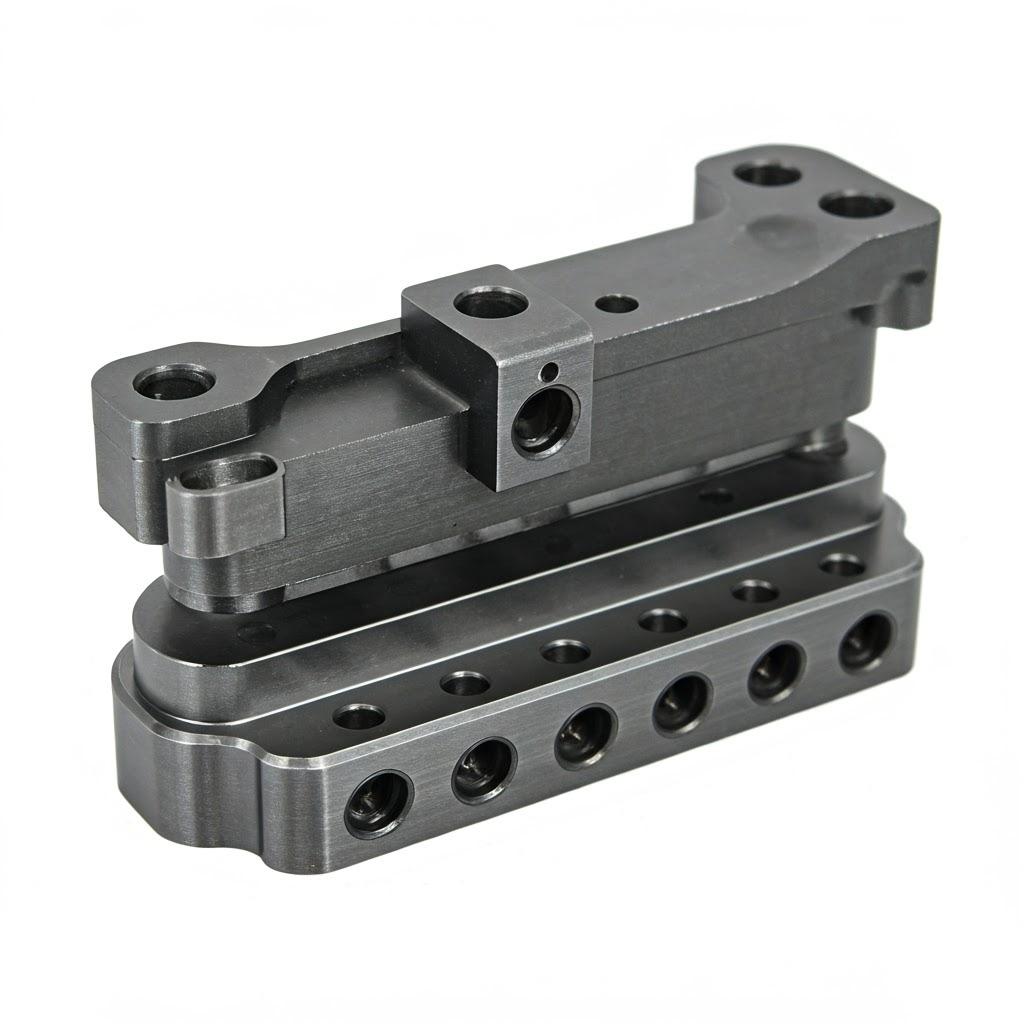
Häufige Herausforderungen und deren Vermeidung beim 3D-Druck von Thermoplatten aus Metall
Der 3D-Metalldruck bietet zwar zahlreiche Vorteile, doch bei der Herstellung von Batterie-Thermoplatten können verschiedene Probleme auftreten. Das Verständnis dieser potenziellen Probleme und die Umsetzung geeigneter Strategien können helfen, sie zu vermeiden und erfolgreiche Ergebnisse zu gewährleisten:
- Verformung und Verzerrung: Thermische Spannungen, die während des Druckvorgangs entstehen, können insbesondere bei großen oder komplexen Geometrien zu Verwerfungen und Verzerrungen des Teils führen.
- Wie man es vermeidet: Optimieren Sie die Teileausrichtung, verwenden Sie geeignete Stützstrukturen, setzen Sie eine Wärmebehandlung zum Spannungsabbau ein und kontrollieren Sie die Prozessparameter sorgfältig. Konstruieren Sie nach den Prinzipien der additiven Fertigung, um große flache Bereiche und Überhänge zu minimieren.
- Schwierigkeiten bei der Beseitigung von Stützstrukturen: Das Entfernen von Stützstrukturen kann bei komplizierten Geometrien oder empfindlichen Merkmalen eine Herausforderung darstellen, da die Oberfläche des Teils beschädigt werden könnte.
- Wie man es vermeidet: Entwerfen Sie, wann immer möglich, selbsttragende Geometrien, optimieren Sie das Design der Stützstruktur für eine einfache Entfernung und ziehen Sie gegebenenfalls die Verwendung von auflösbaren Stützmaterialien in Betracht.
- Probleme mit Porosität und Dichte: Unvollständiges Aufschmelzen oder unzureichende Verfestigung der Pulverpartikel kann zu Porosität im gedruckten Teil führen und dessen mechanische und thermische Eigenschaften beeinträchtigen.
- Wie man es vermeidet: Optimieren Sie Prozessparameter wie Laserleistung, Scangeschwindigkeit und Schichtdicke. Verwenden Sie hochwertige Metallpulver mit guter Fließfähigkeit, wie sie beispielsweise von Metall3DP. Ziehen Sie Nachbearbeitungstechniken wie das heißisostatische Pressen (HIP) in Betracht, um die Porosität zu verringern.
- Oberflächenrauhigkeit: Wie bereits erwähnt, können 3D-gedruckte Metalloberflächen rau sein, was für thermische Schnittstellen, die einen guten Kontakt erfordern, unerwünscht sein kann.
- Wie man es vermeidet: Optimieren Sie die Herstellungsparameter, verwenden Sie feineres Pulver und setzen Sie geeignete Nachbearbeitungstechniken wie Strahlen, Polieren oder Bearbeiten ein.
- Maßliche Ungenauigkeit: Das Erreichen enger Toleranzen kann aufgrund von Materialschwund und anderen Prozessschwankungen eine Herausforderung sein.
- Wie man es vermeidet: Kompensieren Sie die Materialschrumpfung bei der Konstruktion, optimieren Sie die Ausrichtung der Bauteile und ziehen Sie die Nachbearbeitung kritischer Abmessungen in Betracht. Metal3DPs unsere Erfahrung im 3D-Präzisionsmetalldruck gewährleistet eine sorgfältige Prozesskontrolle, um Maßabweichungen zu minimieren.
- Variationen der Materialeigenschaften: Ungleichmäßiges Schmelzen und Erstarren kann zu Schwankungen der Materialeigenschaften im gesamten gedruckten Teil führen.
- Wie man es vermeidet: Verwenden Sie gut kalibrierte 3D-Druckgeräte und optimierte Prozessparameter. Gewährleisten Sie eine gleichbleibende Qualität und Handhabung des Pulvers.
- Kostenüberlegungen: Der 3D-Druck von Metall kann bei hohen Stückzahlen teurer sein als herkömmliche Fertigungsmethoden.
- Wie man es vermeidet: Optimieren Sie das Teiledesign für effizienten Druck und Materialeinsatz. Ziehen Sie eine Teilekonsolidierung in Betracht, um die Montagekosten zu senken. Bewerten Sie bei hohen Stückzahlen die Gesamtkosten-Nutzen-Analyse, einschließlich Faktoren wie Werkzeugkosten und Vorlaufzeiten, die mit herkömmlichen Methoden verbunden sind.
- Skalierbarkeit: Die Skalierung der Produktion von 3D-gedruckten Metallteilen zur Deckung des Bedarfs an hohen Stückzahlen kann eine Herausforderung in Bezug auf die Bauzeit und die Anlagenkapazität darstellen.
- Wie man es vermeidet: Planen Sie den parallelen Druck auf mehreren Maschinen, optimieren Sie Build-Layouts, um die Anzahl der Teile pro Build zu maximieren, und untersuchen Sie Technologien für den kontinuierlichen 3D-Druck.
Durch das Verständnis dieser gemeinsamen Herausforderungen und die Implementierung geeigneter Design- und Prozessstrategien können Hersteller den Metall-3D-Druck effektiv nutzen, um leistungsstarke Batterie-Thermoplatten für Elektrofahrzeuge herzustellen. Die Zusammenarbeit mit erfahrenen Metall-3D-Druck-Dienstleistern wie Metall3DP kann bei der Bewältigung dieser Herausforderungen wertvolles Fachwissen und Unterstützung bieten.
Wie man den richtigen 3D-Druckdienstleister für Batterie-Thermoplatten aus Metall auswählt
Die Auswahl des richtigen 3D-Druckdienstleisters für Metall ist entscheidend für die erfolgreiche Herstellung von hochwertigen Batterie-Thermoplatten. Das Fachwissen, die Fähigkeiten und die Qualitätsstandards des Anbieters wirken sich direkt auf die Leistung und Zuverlässigkeit der fertigen Komponenten aus. Hier sind die wichtigsten Faktoren, die bei der Bewertung potenzieller Anbieter zu berücksichtigen sind:
- Materielle Fähigkeiten: Stellen Sie sicher, dass der Dienstleister Erfahrung in der Verarbeitung der empfohlenen Materialien für Batterie-Thermoplatten hat, insbesondere AlSi10Mg und CuCrZr. Vergewissern Sie sich, dass der Dienstleister über Fachwissen bei der Optimierung der Druckparameter für diese Materialien verfügt, um die gewünschten thermischen und mechanischen Eigenschaften zu erzielen. Metall3DP verfügt über umfangreiche Erfahrungen mit einer breiten Palette von Hochleistungsmetallpulvern, die sich auch für EV-Batterieanwendungen eignen. Unser Team berät Sie gerne bei der Materialauswahl auf der Grundlage Ihrer spezifischen Anforderungen.
- Drucktechnik und Ausrüstung: Informieren Sie sich über die Arten von 3D-Drucktechnologien für Metall, die der Anbieter einsetzt (z. B. SLM, DMLS, EBM). Jede Technologie hat ihre eigenen Stärken und Grenzen in Bezug auf die erreichbare Genauigkeit, Oberflächengüte und Materialkompatibilität. Erkundigen Sie sich nach den spezifischen Druckern, die der Anbieter einsetzt, und nach deren Produktionsvolumen, insbesondere wenn Sie größere thermische Platten oder höhere Produktionsvolumina benötigen. Metall3DP setzt hochmoderne SEBM-Drucker (Selective Electron Beam Melting) ein, die für ihr branchenführendes Druckvolumen, ihre Genauigkeit und Zuverlässigkeit bekannt sind. Mehr über unsere Druckverfahren erfahren Sie unter https://met3dp.com/printing-methods/.
- Fachwissen im Bereich Design für additive Fertigung (DfAM): Ein kompetenter Dienstleister sollte Sie bei der Optimierung Ihres Thermoplattenentwurfs für den 3D-Metalldruckprozess unterstützen. Dazu gehören Überlegungen zu Geometrie, Stützstrukturen, Materialauswahl und Nachbearbeitungsanforderungen. Ihr Fachwissen im Bereich DfAM kann zu einer verbesserten Leistung, einem geringeren Materialverbrauch und niedrigeren Herstellungskosten führen. Metal3DPs team verfügt über jahrzehntelange Erfahrung in der additiven Fertigung von Metallen und kann Ihnen umfassende Anwendungsentwicklungsdienste anbieten, um Sie bei der Optimierung Ihrer Designs zu unterstützen.
- Nachbearbeitungsmöglichkeiten: Wie bereits erwähnt, ist die Nachbearbeitung für 3D-gedruckte Metallteile oft unerlässlich. Prüfen Sie die Fähigkeiten des Anbieters in Bezug auf Pulverentfernung, Trägerentfernung, Wärmebehandlung, Oberflächenbehandlung, Bearbeitung und Beschichtung. Vergewissern Sie sich, dass der Anbieter über die erforderliche Ausrüstung und das Fachwissen verfügt, um Ihre spezifischen Nachbearbeitungsanforderungen zu erfüllen.
- Qualitätssicherung und Zertifizierungen: Erkundigen Sie sich nach dem Qualitätsmanagementsystem des Anbieters und allen relevanten Zertifizierungen (z. B. ISO 9001, AS9100 für die Luft- und Raumfahrt). Robuste Qualitätskontrollverfahren, einschließlich Materialprüfung, Maßkontrolle und zerstörungsfreie Prüfung, sind entscheidend für die Zuverlässigkeit von Batterie-Thermoplatten, insbesondere für anspruchsvolle Anwendungen in der Automobil- und Luftfahrtindustrie.
- Erfahrung und Portfolio: Prüfen Sie die Erfahrung des Dienstleisters in der Herstellung ähnlicher Komponenten oder in der Zusammenarbeit mit der Automobilindustrie, der Luft- und Raumfahrt, der Medizintechnik oder der industriellen Fertigung. Prüfen Sie das Portfolio früherer Projekte, um die Qualität und Komplexität der Arbeit zu beurteilen.
- Kommunikation und Kundenbetreuung: Eine effektive Kommunikation und ein reaktionsschneller Kundensupport sind für ein reibungsloses und erfolgreiches Projekt unerlässlich. Bewerten Sie die Reaktionsfähigkeit des Anbieters auf Anfragen, seine Fähigkeit, technische Unterstützung zu leisten, und seine allgemeine Professionalität.
- Vorlaufzeiten und Produktionskapazität: Besprechen Sie die Vorlaufzeiten für die Prototypenerstellung und die Produktion sowie die Kapazität des Unternehmens, die erwarteten Mengen zu bewältigen. Stellen Sie sicher, dass der Zeitplan mit Ihrem Projektplan übereinstimmt.
- Kostenstruktur und Transparenz: Verstehen Sie das Preismodell des Anbieters, einschließlich der Kosten für Druck, Material und Nachbearbeitung. Fordern Sie ein detailliertes Angebot an und sorgen Sie für Transparenz in der Preisstruktur.
- Vertraulichkeit und Schutz des geistigen Eigentums: Wenn Ihr Wärmeplattenentwurf urheberrechtlich geschützt ist, stellen Sie sicher, dass der Dienstleister über solide Vertraulichkeitsvereinbarungen und Maßnahmen zum Schutz Ihres geistigen Eigentums verfügt.
Wenn Sie diese Faktoren sorgfältig abwägen, können Sie einen 3D-Druckdienstleister für Metall auswählen, wie Metall3DP die qualitativ hochwertige Batterie-Thermoplatten liefern können, die auf Ihre spezifischen Bedürfnisse zugeschnitten sind und Ihre EV-Entwicklungs- und Fertigungsprozesse beschleunigen. Wir sind bestrebt, hochmoderne Systeme und Pulver für die Herstellung der nächsten Generation zu liefern. Kontaktieren Sie uns unter https://met3dp.com/contact-us/ um herauszufinden, wie unsere Fähigkeiten die Ziele Ihres Unternehmens im Bereich der additiven Fertigung unterstützen können.
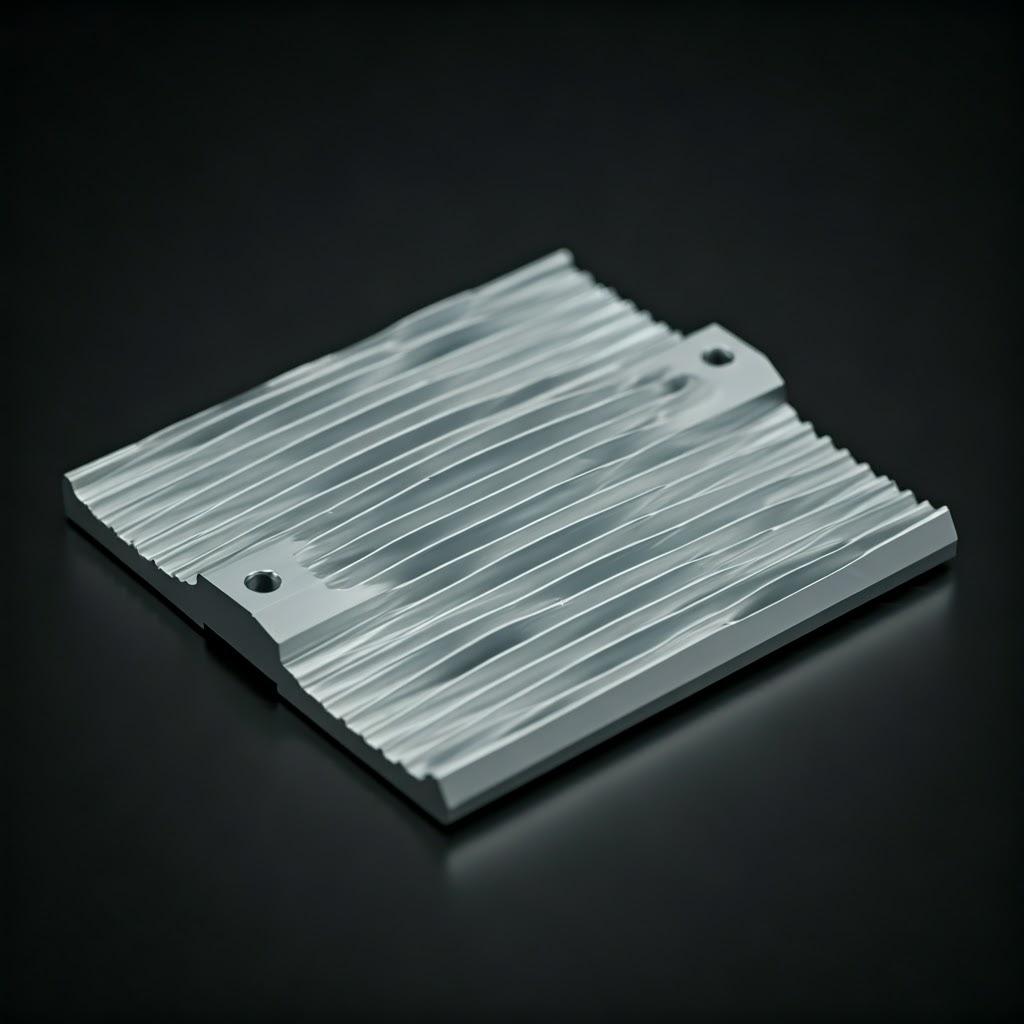
Kostenfaktoren und Vorlaufzeit für 3D-gedruckte Batterie-Thermoplatten aus Metall
Das Verständnis der Faktoren, die die Kosten und die Vorlaufzeit für 3D-gedruckte Batterie-Thermoplatten aus Metall beeinflussen, ist für die Projektplanung und Budgetierung von entscheidender Bedeutung. Diese Parameter können in Abhängigkeit von mehreren Variablen erheblich variieren:
Kostenfaktoren:
- Materialkosten: Die Kosten für das Metallpulver (z. B. AlSi10Mg, CuCrZr) sind ein wichtiger Faktor. Speziallegierungen oder Pulver mit höherem Reinheitsgrad haben im Allgemeinen höhere Kosten pro Kilogramm. Die für jedes Teil benötigte Materialmenge, die durch das Volumen und die Dichte des Teils beeinflusst wird, wirkt sich ebenfalls auf die Gesamtmaterialkosten aus.
- Bauzeit: Die Zeit, die für den Druck einer Thermoplatte benötigt wird, hängt von deren Größe, Komplexität und der gewählten Schichtdicke ab. Längere Bauzeiten führen zu höheren Betriebskosten der Maschine.
- Betriebskosten der Maschine: Diese Kosten umfassen den Energieverbrauch, die Wartung und die Abschreibung der 3D-Druckausrüstung.
- Kosten der Unterstützungsstruktur: Der Umfang und die Komplexität der erforderlichen Stützstrukturen beeinflussen den Materialverbrauch und die Nachbearbeitungszeit und wirken sich somit auf die Gesamtkosten aus.
- Nachbearbeitungskosten: Der Umfang und die Komplexität der Nachbearbeitungsschritte (Pulverentfernung, Trägerentfernung, Wärmebehandlung, Oberflächenveredelung, maschinelle Bearbeitung, Beschichtung) tragen zu den Endkosten bei. Verfahren wie HIP oder eine umfangreiche Bearbeitung können besonders kostenintensiv sein.
- Arbeitskosten: Der Arbeitsaufwand für die Designoptimierung, die Druckeinrichtung, den Maschinenbetrieb, die Nachbearbeitung und die Qualitätskontrolle trägt zu den Gesamtkosten bei.
- Menge und Volumen: Der 3D-Druck von Metall eignet sich hervorragend für die Produktion von kleinen bis mittleren Stückzahlen und für die individuelle Anpassung, wobei die Kosten pro Teil bei größeren Produktionsläufen aufgrund von Skaleneffekten bei der Materialbeschaffung und Prozessoptimierung sinken können. Bei sehr hohen Stückzahlen können jedoch herkömmliche Fertigungsmethoden immer noch kostengünstiger sein.
- Komplexität des Designs: Komplizierte Entwürfe mit internen Kanälen oder komplexen Geometrien können längere Bauzeiten und eine komplexere Nachbearbeitung erfordern, was die Kosten erhöht.
- Qualitätsanforderungen: Strenge Qualitätskontrollmaßnahmen, einschließlich umfangreicher Tests und Kontrollen, erhöhen die Gesamtkosten.
Faktoren für die Vorlaufzeit:
- Design und Technik: Die Zeit, die für die Optimierung des Designs, die Simulation und die Erstellung der Build-Dateien benötigt wird.
- Materialbeschaffung: Die Vorlaufzeit für die Beschaffung des spezifischen Metallpulvers, insbesondere bei Speziallegierungen. Metall3DP hält einen Vorrat an hochwertigen Metallpulvern vor, wodurch die Vorlaufzeiten für das Material verkürzt werden können.
- Druckzeit: Die tatsächliche Dauer des 3D-Druckverfahrens, die von der Größe und Komplexität des Teils abhängt.
- Nachbearbeitungszeit: Die für jeden Nachbearbeitungsschritt erforderliche Zeit, die je nach Komplexität und Anzahl der zu bearbeitenden Teile variieren kann.
- Qualitätsinspektion: Die Zeit, die für gründliche Qualitätskontrollen und Tests benötigt wird.
- Versand und Logistik: Die Zeit für die Verpackung und den Transport der fertigen Teile.
Metall3DP ist bestrebt, transparente und wettbewerbsfähige Preise für unsere 3D-Metalldruckdienste anzubieten. Wir bewerten jedes Projekt sorgfältig, um einen genauen Kostenvoranschlag und realistische Vorlaufzeiten auf der Grundlage Ihrer spezifischen Anforderungen zu erstellen. Dabei werden Faktoren wie Materialauswahl, Teilegeometrie, gewünschte Stückzahl und Nachbearbeitungsbedarf berücksichtigt. Wir arbeiten eng mit unseren Kunden zusammen, um Konstruktionen und Produktionsprozesse zu optimieren und so eine kosteneffiziente und pünktliche Lieferung von Hochleistungs-Thermoblechen für Batterien zu erreichen. Wenn Sie ein detailliertes Angebot und einen Kostenvoranschlag für Ihr Projekt wünschen, kontaktieren Sie uns bitte über unsere Website.
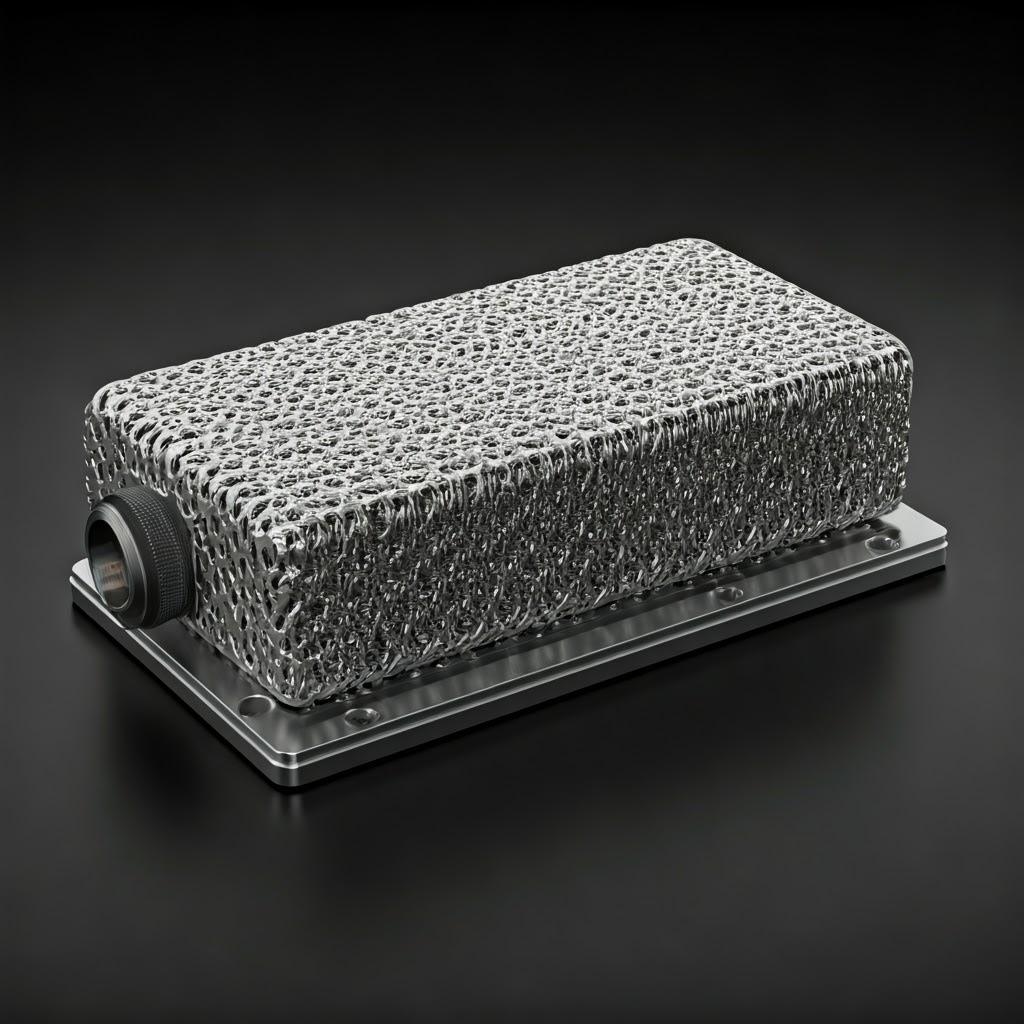
Häufig gestellte Fragen (FAQ)
- Was sind die wichtigsten Vorteile des 3D-Metalldrucks für Wärmeplatten von Elektroautos?
- Der 3D-Metalldruck bietet Designfreiheit für optimierte Kühlkanäle, Leichtbaupotenzial mit Materialien wie AlSi10Mg, Teilekonsolidierung, Rapid Prototyping und die Möglichkeit, Hochleistungsmaterialien wie CuCrZr für eine verbesserte Wärmeleitfähigkeit zu verwenden.
- Welche Materialien empfiehlt Metal3DP für Batterie-Thermoplatten?
- Wir empfehlen AlSi10Mg wegen seiner hervorragenden Wärmeleitfähigkeit und seines geringen Gewichts und CuCrZr wegen seiner hohen thermischen und elektrischen Leitfähigkeit in Verbindung mit guter Festigkeit. Metall3DP bietet hochwertige Pulver aus diesen beiden Materialien an, die für die additive Fertigung optimiert sind.
- Welche Toleranzen und Oberflächengüten sind bei 3D-gedruckten Thermoplatten aus Metall zu erwarten?
- Die erreichbaren Toleranzen liegen in der Regel zwischen ±0,1 mm und ±0,5 mm, je nach Geometrie und Verfahren. Die Oberflächenbeschaffenheit ist im Allgemeinen rauer als bei maschinell bearbeiteten Oberflächen, kann aber durch Nachbearbeitungstechniken wie Strahlen, Polieren oder Bearbeiten verbessert werden. Metall3DP kann Sie über erreichbare Toleranzen und Oberflächengüten für bestimmte Anwendungen beraten.
- Ist der 3D-Druck von Metall für die Massenproduktion von Batterie-Thermoplatten kosteneffizient?
- Der 3D-Druck von Metall ist oft kosteneffizient für kleine bis mittlere Produktionsmengen, komplexe Designs und Rapid Prototyping. Bei sehr hohen Stückzahlen können herkömmliche Fertigungsmethoden wirtschaftlicher sein. Die Vorteile der Designoptimierung und Teilekonsolidierung können jedoch zu Gesamtkosteneinsparungen führen.
- Welche Nachbearbeitungsschritte sind typischerweise für 3D-gedruckte Batterie-Thermoplatten aus Metall erforderlich?
- Zu den üblichen Nachbearbeitungsschritten gehören die Pulverentfernung, die Entfernung von Trägern, die Spannungsarmglühung und je nach Anwendungsanforderungen möglicherweise die Oberflächenbearbeitung oder die maschinelle Bearbeitung. Metall3DP bietet umfassende Nachbearbeitungsdienste an, um sicherzustellen, dass die fertigen Teile Ihren Spezifikationen entsprechen.
Fazit - Die Zukunft der Elektrofahrzeuge mit fortschrittlichen Metall-AM-Thermolösungen vorantreiben
Der 3D-Metalldruck revolutioniert das Design und die Herstellung von Batteriekühlplatten für Elektrofahrzeuge. Die Möglichkeit, komplizierte interne Kühlkanäle zu erstellen, Hochleistungsmaterialien wie AlSi10Mg und CuCrZr zu verwenden und leichte Konstruktionen zu realisieren, bietet erhebliche Vorteile in Bezug auf die Leistung, Effizienz und Sicherheit der Batterie. Metall3DP ist ein führender Anbieter von Lösungen für die additive Fertigung von Metallen und bietet branchenführende SEBM-Drucker und ein umfassendes Portfolio an hochwertigen Metallpulvern. Unser Fachwissen in den Bereichen Designoptimierung, Materialauswahl und Nachbearbeitung stellt sicher, dass unsere Kunden das volle Potenzial des metallischen 3D-Drucks für die Entwicklung und Herstellung fortschrittlicher Batterie-Thermomanagementsysteme nutzen können. Durch die Partnerschaft mit Metall3DPkönnen Unternehmen in der Automobil-, Luft- und Raumfahrt- und anderen Branchen ihre Innovationszyklen beschleunigen und die Zukunft der Elektromobilität vorantreiben. Setzen Sie sich noch heute mit uns in Verbindung, um zu erfahren, wie unsere 3D-Drucklösungen für Metall Ihr Unternehmen unterstützen können.
Teilen auf
MET3DP Technology Co., LTD ist ein führender Anbieter von additiven Fertigungslösungen mit Hauptsitz in Qingdao, China. Unser Unternehmen ist spezialisiert auf 3D-Druckgeräte und Hochleistungsmetallpulver für industrielle Anwendungen.
Fragen Sie an, um den besten Preis und eine maßgeschneiderte Lösung für Ihr Unternehmen zu erhalten!
Verwandte Artikel
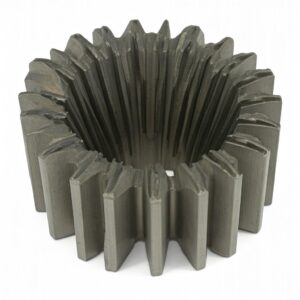
Hochleistungs-Düsenschaufelsegmente: Revolutionierung der Turbineneffizienz mit 3D-Metalldruck
Mehr lesen "Über Met3DP
Aktuelles Update
Unser Produkt
KONTAKT US
Haben Sie Fragen? Senden Sie uns jetzt eine Nachricht! Wir werden Ihre Anfrage mit einem ganzen Team nach Erhalt Ihrer Nachricht bearbeiten.
Holen Sie sich Metal3DP's
Produkt-Broschüre
Erhalten Sie die neuesten Produkte und Preislisten
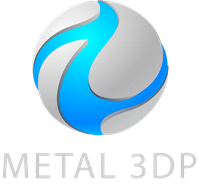
Metallpulver für 3D-Druck und additive Fertigung