Korrosionsbeständige Bootsteile über AM
Inhaltsübersicht
Revolutionierung von Schiffskomponenten: Die Kraft der additiven Fertigung von Metall für korrosionsbeständige Bootsteile
Die Meeresumwelt ist eine der anspruchsvollsten Umgebungen für technische Komponenten. Die ständige Einwirkung von Salzwasser, die unerbittliche UV-Strahlung, die dynamische Belastung durch Wellen und Wind und das Potenzial für galvanische Korrosion schaffen einen perfekten Sturm, der die Grenzen von Materialien und Design testet. Bootshardware - von einfachen Klampen und Scharnieren bis hin zu komplexen Propellerhalterungen und strukturellen Verbindungsstücken - bildet die kritische Schnittstelle zwischen dem Schiff, seinen Systemen und den rauen Elementen. Die Zuverlässigkeit und Langlebigkeit dieser Beschläge sind nicht nur eine Frage der Wartungskosten, sondern von grundlegender Bedeutung für die Sicherheit, Leistung und Betriebsintegrität eines jeden Schiffes, ganz gleich, ob es sich um eine Freizeityacht, ein robustes Fischerboot, einen kommerziellen Frachter oder ein Patrouillenboot der Marine handelt.
Jahrzehntelang waren traditionelle Fertigungsmethoden wie Gießen, Schmieden und maschinelle Bearbeitung die Hauptstützen für die Herstellung von Bootsteilen. Diese Methoden sind zwar effektiv, stoßen aber oft an ihre Grenzen, insbesondere was die Komplexität des Designs, den Materialabfall (insbesondere bei der subtraktiven Bearbeitung), die Vorlaufzeiten für kundenspezifische Teile und die wirtschaftliche Machbarkeit von Kleinserien angeht. Darüber hinaus hängt das Erreichen einer optimalen Korrosionsbeständigkeit oft stark von der Materialauswahl und der Oberflächenbehandlung ab, was manchmal die Designmöglichkeiten einschränkt oder erhebliche Kosten verursacht.
Hier kommt die Additive Fertigung von Metall (AM) ins Spiel, besser bekannt als 3D-Druck von Metall. Diese transformative Technologie geht schnell über das Prototyping hinaus und dringt in den Bereich der funktionalen Produktion von Endverbrauchsteilen in anspruchsvollen Branchen wie der Luft- und Raumfahrt, der Medizintechnik, der Automobilindustrie und zunehmend auch der Schifffahrt vor. Metall-AM baut Teile Schicht für Schicht direkt aus digitalen Modellen unter Verwendung von Hochleistungsmetallpulvern auf. Dieser Ansatz verändert das Fertigungsparadigma grundlegend und bietet beispiellose Möglichkeiten zur Herstellung von Bootsteilen, die nicht nur außergewöhnlich korrosionsbeständig sind, sondern auch in Bezug auf Gewicht, Festigkeit und Funktionalität in bisher unerreichter Weise optimiert wurden.
Im Mittelpunkt dieser Revolution stehen fortschrittliche Werkstoffe, die speziell für die Herausforderungen des Meeres geeignet sind. Zwei herausragende Kandidaten, die häufig in der Metall-AM für Schiffsanwendungen eingesetzt werden, sind Edelstahl 316L und Ti-6Al-4V (Grad 5) Titanlegierung. 316L ist bekannt für seine hervorragende Beständigkeit gegen Lochfraß und Spaltkorrosion in chloridreichen Umgebungen (wie Meerwasser), während Ti-6Al-4V eine unvergleichliche Kombination aus hoher Festigkeit, geringem Gewicht und weitgehender Immunität gegen Meerwasserkorrosion bietet. Die Verwendung dieser Materialien mit der Präzision von AM-Prozessen eröffnet neue Möglichkeiten für das Design und die Leistung von Schiffshardware.
Dieser Artikel richtet sich an ingenieure, Konstrukteure, Schiffbauingenieure und Beschaffungsmanager in der Schifffahrtsindustrie - Fachleute, die ständig auf der Suche nach innovativen Lösungen sind, um die Leistung, Haltbarkeit und Kosteneffizienz von Schiffen zu verbessern. Ob Sie nun an der Beschaffung von Komponenten für Neubauten beteiligt sind, Nachrüstungen und Reparaturen verwalten oder nach zuverlässigen großhandel mit Bootshardware Lieferanten die in der Lage sind, kundenspezifische, leistungsstarke Teile zu liefern, ist das Verständnis der Möglichkeiten von Metall-AM entscheidend. Wir werden die spezifischen Anwendungen untersuchen, bei denen sich 3D-gedruckte Bootsteile auszeichnen, die eindeutigen Vorteile, die AM gegenüber herkömmlichen Methoden bietet, die entscheidende Rolle der Materialauswahl (mit Schwerpunkt auf 316L und Ti-6Al-4V) und die wichtigsten Überlegungen für die Entwicklung, Herstellung und Beschaffung dieser fortschrittlichen Komponenten. Seien Sie dabei, wenn wir uns ansehen, wie Metall-AM die Zukunft korrosionsbeständiger Bootsteile neu gestaltet und dauerhafte, optimierte Lösungen für die anspruchsvollsten maritimen Herausforderungen bietet. Unternehmen wie Met3dp, die über umfassendes Fachwissen sowohl in der modernen Pulverherstellung als auch bei Metall-AM-Systemen verfügen, stehen an vorderster Front, um diesen Wandel zu ermöglichen. Sie bieten die hochwertigen Materialien und technologischen Fähigkeiten, die erforderlich sind, um das volle Potenzial von 3D-gedruckt marine Komponenten.
Wesentliche Anwendungen: Wo macht 3D-gedruckte Bootshardware Furore?
Die Vielseitigkeit der additiven Fertigung von Metallen ermöglicht die Herstellung eines breiten und wachsenden Spektrums von Bootsteilen, die über den einfachen Ersatz hinausgehen, bis hin zu Komponenten, die für eine verbesserte Leistung und Integration neu konzipiert werden. Die Technologie bietet sich vor allem dort an, wo Komplexität, individuelle Anpassung, Gewichtsreduzierung oder schnelle Verfügbarkeit im Vordergrund stehen. Beschaffungsmanager, die zulieferer von Schiffskomponenten die in der Lage sind, unterschiedliche Anforderungen zu erfüllen, von Einzelstücken nach Maß bis hin zur Kleinserienfertigung für Spezialbehälter, werden AM besonders vorteilhaft finden.
Hier sind einige Schlüsselbereiche, in denen 3D-gedruckte Bootshardware einen erheblichen Wert darstellt:
1. Individuelle und komplexe Beschläge:
- Einzigartige Deck Hardware: Klampen, Unterlegkeile, Klüsen, Poller und Ösen, die für spezifische Rumpfkonturen, einzigartige Belastungswinkel oder ästhetische Anforderungen entwickelt wurden, die durch Guss- oder Schmiedeformen nur schwer oder teuer zu erreichen sind.
- Spezialisierte Montagehalterungen: Halterungen für die Montage von Navigationsgeräten, Sensoren, Solarpanels, Antennen oder Spezialausrüstung, die oft komplexe Geometrien erfordern, um sich nahtlos in bestehende Strukturen zu integrieren oder den Luftwiderstand zu minimieren. AM ermöglicht die Optimierung der Topologie und schafft leichte und dennoch stabile Halterungen, die auf bestimmte Lastpfade zugeschnitten sind.
- Durch-Rumpf-Armaturen: Maßgeschneiderte Gehäuse für Messwandler, Zuläufe oder Abflüsse, die möglicherweise mehrere Funktionen integrieren oder die Durchflusseigenschaften optimieren. Materialien wie 316L und Ti-6Al-4V gewährleisten eine hervorragende Korrosionsbeständigkeit, die für Anwendungen unterhalb der Wasserlinie entscheidend ist.
2. Gewichtsempfindliche Komponenten:
- Leistungsstarke Yacht-Hardware: Bei Regattayachten oder Performance-Cruisern ist die Gewichtsreduzierung von größter Bedeutung. AM, insbesondere mit Ti-6Al-4V, ermöglicht die Herstellung von Beschlägen wie Mastbeschlägen, Kettenplatten, Rungensockeln und Ruderkomponenten, die deutlich leichter sind als ihre herkömmlichen Gegenstücke, ohne dass die Festigkeit darunter leidet. Topologie-Optimierungstools, die oft in Verbindung mit AM eingesetzt werden, helfen dabei, Material aus Bereichen mit geringer Belastung zu entfernen, um organisch aussehende, hocheffiziente Strukturen zu erhalten.
- Strukturelle Knotenpunkte: Komplexe Verbindungen, bei denen mehrere Rohre oder Strukturelemente zusammentreffen (z. B. in Spaceframes für Türme oder Hardtops), können als einzelne, optimierte Teile 3D-gedruckt werden, wodurch sich die Anzahl der Teile verringert, Schweißarbeiten (und die damit verbundenen wärmebeeinflussten Zonen oder Verformungen) entfallen und Gewicht eingespart wird.
3. Teil Konsolidierung:
- Integrierte Baugruppen: Mit AM können Konstrukteure mehrere Einzelteile (z. B. eine Halterung, ein Scharnier und einen Verriegelungsmechanismus) zu einer einzigen, monolithisch gedruckten Komponente kombinieren. Dies reduziert den Zeit- und Arbeitsaufwand für die Montage, beseitigt potenzielle Fehlerstellen an Verbindungen oder Befestigungselementen und vereinfacht die Bestandsverwaltung für bootszubehör-Händlerund kann die strukturelle Integrität insgesamt verbessern.
4. Rapid Prototyping und Funktionstests:
- Während sich dieser Artikel auf Endverbrauchsteile konzentriert, ist die Geschwindigkeit von AM von unschätzbarem Wert für die Erstellung funktionaler Metallprototypen neuer Hardware-Designs. Ingenieure können Entwürfe schnell wiederholen, Konzepte unter realistischen Belastungsbedingungen (unter Verwendung des tatsächlichen Endverbrauchsmaterials wie 316L oder Ti-6Al-4V) physisch testen und die Geometrie verfeinern, bevor sie sich zu größeren Produktionsläufen verpflichten oder den Werkzeugbau für herkömmliche Methoden abschließen, wenn eine erhebliche Skalierung erforderlich ist. Dadurch wird der Entwicklungszyklus für neue Behälterdesigns oder Hardware-Innovationen beschleunigt.
5. Ersatz für veraltete und überholte Teile:
- Es kann eine große Herausforderung sein, Ersatz für die Hardware älterer Schiffe zu finden, deren Originalhersteller möglicherweise nicht mehr existieren oder deren Werkzeuge verloren gegangen sind. Metall-AM bietet eine Lösung, indem es Reverse Engineering (mit 3D-Scanning) und die direkte digitale Herstellung von Ersatzteilen ermöglicht, oft mit Verbesserungen bei Material oder Design auf der Grundlage moderner Analysetechniken. Dies ist von entscheidender Bedeutung für die Instandhaltung klassischer Yachten oder die Verlängerung der Nutzungsdauer von Handels- und Marineflotten. Beschaffung für die Schiffsherstellung kann AM nutzen, um kritische Veralterungsprobleme zu lösen.
6. Propeller- und Propulsionskomponenten:
- Während große Propeller in der Regel gegossen werden, können kleinere Propeller, Impeller für Wasserdüsen, Propellerwellenhalterungen (P-Halterungen) und Kort-Düsenkomponenten mit AM hergestellt werden. Dies ermöglicht hochgradig maßgeschneiderte Blattgeometrien, die für die spezifische Hydrodynamik von Schiffen optimiert sind, was die Effizienz verbessern und Kavitation reduzieren kann. Die Verwendung korrosionsbeständiger Legierungen wie Ti-6Al-4V oder spezieller Bronzen (auch druckbar) ist hier unerlässlich.
Branchenspezifische Beispiele:
- Freizeitschifffahrt: Maßgefertigte Ankerrollen, leichte Masthalterungen, maßgeschneiderte Windengriffe, ästhetische Verkleidungsteile.
- Kommerzieller Versand: Spezielle Halterungen für Containerzurrpunkte, robuste Sensorgehäuse, Komponenten für Abgasanlagen, die Korrosions- und Hitzebeständigkeit erfordern.
- Anwendungen in der Marine: Leichte Waffenträger, Gehäuse für elektronische Kampfführungssysteme, Armaturen zur Schadensbegrenzung, Komponenten für unbemannte Über- und Unterwasserfahrzeuge (USVs/UUVs), bei denen Gewicht und komplexe Integration entscheidend sind.
- Offshore-Strukturen: Spezielle Steckverbinder, Ventilkomponenten, Hardware für den Sensoreinsatz, die extremen Meeresbedingungen ausgesetzt sind.
Der Anwendungsbereich erweitert sich ständig, je mehr Designer und Ingenieure mit den Möglichkeiten von DfAM (Design for Additive Manufacturing) vertraut werden und je ausgereifter die Technologie wird. Die Zusammenarbeit mit einem erfahrenen industrielle Schiffskomponenten ein Anbieter wie Met3dp, der sowohl die Materialwissenschaft als auch die Druckverfahren versteht, ist der Schlüssel zur erfolgreichen Implementierung von AM für diese anspruchsvollen Anwendungen.
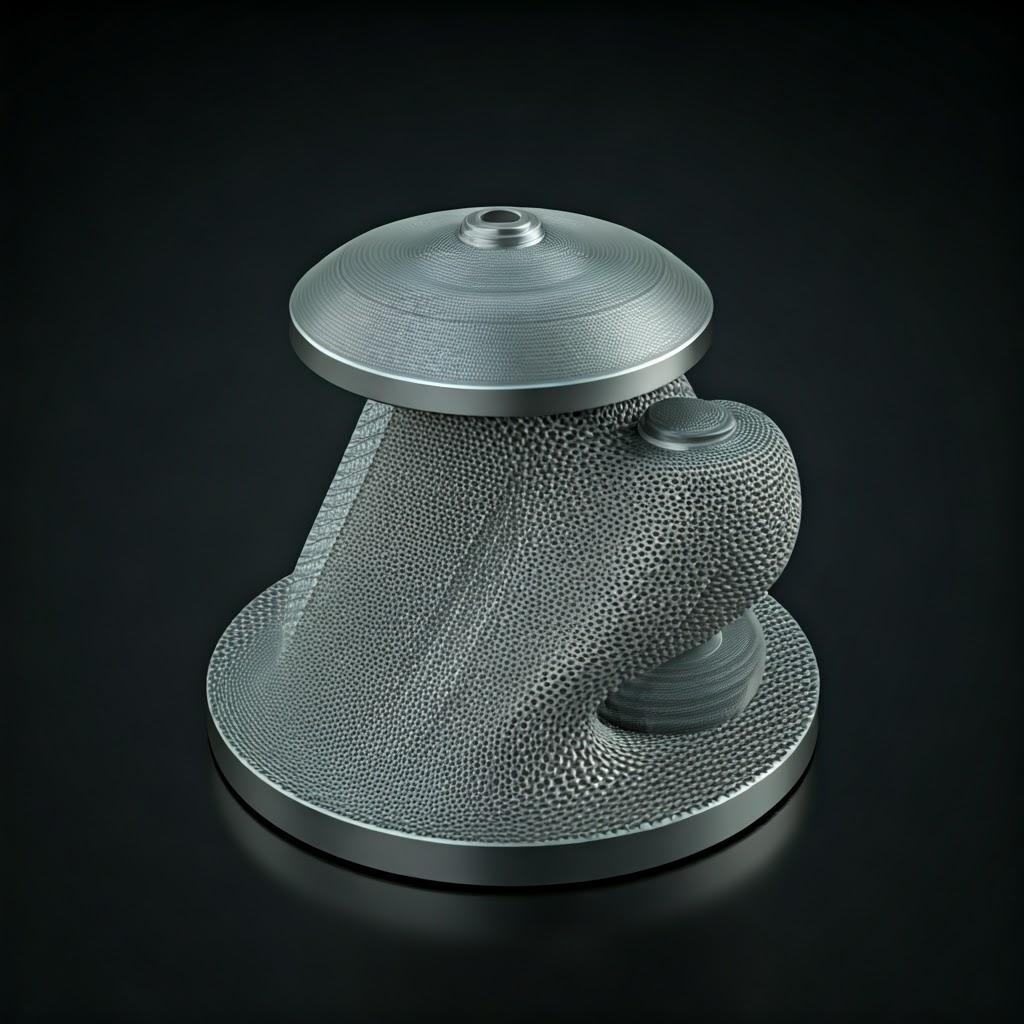
Der AM-Vorteil: Warum Metall-3D-Druck für die Produktion von Bootsteilen?
Während sich die traditionellen Fertigungsmethoden in der Schifffahrtsindustrie bewährt haben, bietet die additive Fertigung von Metallen eine ganze Reihe von Vorteilen, insbesondere für die Arten von komplexen, leistungsstarken oder kundenspezifischen Komponenten, die im Bootsbau und bei der Wartung häufig benötigt werden. Für Ingenieure, die sich auf die Leistung konzentrieren, und für Beschaffungsmanager, die sich auf die Gesamtbetriebskosten und die Stabilität der Lieferkette konzentrieren, ist das Verständnis dieser Vorteile von entscheidender Bedeutung, wenn sie die Produktionsmethoden für Bootsteile bewerten.
Vergleichen wir AM direkt mit traditionellen Techniken wie Gießen, Schmieden und Zerspanen:
1. Unerreichte Designfreiheit:
- AM: Ermöglicht die Erstellung hochkomplexer Geometrien, interner Kanäle (z. B. für Kühlung oder Flüssigkeitsströmung), komplizierter Gitterstrukturen zur Gewichtsreduzierung und organischer Formen, die durch Topologieanalyse optimiert werden. Das Design wird durch die Funktion bestimmt und ist nicht durch Werkzeugbeschränkungen (Gussformen, Matrizen) oder den Zugang zu Werkzeugen (Bearbeitung) begrenzt.
- Traditionell: Für das Gießen sind Formen erforderlich, die die Komplexität einschränken und häufig eine Nachbearbeitung erfordern. Das Schmieden erfordert teure Formen und eignet sich am besten für einfachere Formen, die in großen Mengen hergestellt werden. Die maschinelle Bearbeitung ist subtraktiv, begrenzt die inneren Merkmale und erzeugt erheblichen Abfall von Knüppeln oder Schmiedeteilen.
- Nutzen für die Marine: Ermöglicht eine wirklich optimierte Hardware - leichter, stabiler, möglicherweise mit mehreren Funktionen in einem Teil, was zu einer besseren Leistung des Schiffes und einer geringeren Anzahl von Teilen führt.
2. Materialeffizienz & Abfallreduzierung:
- AM: In der Regel handelt es sich um ein additives Verfahren, bei dem nur das Material verwendet wird, das für die Herstellung des Teils und seiner Träger benötigt wird. Zwar ist ein Teil des Pulvers nicht wiederverwendbar oder muss recycelt werden, doch ist das Verhältnis zwischen Einkauf und Fertigung (Verhältnis zwischen dem gekauften Rohmaterial und dem Gewicht des fertigen Teils) oft deutlich besser als bei subtraktiven Verfahren.
- Traditionell: Die maschinelle Bearbeitung, insbesondere von Knüppeln, kann zu erheblichem Materialabfall (Späne) führen, der bei komplexen Teilen für die Luft- und Raumfahrt oder die Schifffahrt manchmal mehr als 80-90 % beträgt. Gießen und Schmieden sind effizienter, erzeugen aber immer noch Abfall durch Angüsse, Angusskanäle, Anschnitte und Grate sowie nachträgliche Bearbeitungszugaben.
- Nutzen für die Marine: Reduziert die Kosten für teure Rohstoffe wie rostfreien Stahl und insbesondere Titanlegierungen. Trägt zu nachhaltigeren Herstellungspraktiken bei.
3. Rapid Prototyping & Beschleunigte Innovation:
- AM: Ermöglicht es den Konstrukteuren, innerhalb von Tagen statt Wochen oder Monaten von einem CAD-Modell zu einem funktionalen Metallteil zu gelangen. Dies ermöglicht schnelle Design-Iterationen, physische Tests und schnellere Verfeinerungszyklen.
- Traditionell: Die Herstellung von Formen oder Gesenken für das Gießen/Schmieden ist zeit- und kostenaufwändig, so dass das Prototyping langsam und kostspielig ist. Auch das Einrichten komplexer Bearbeitungsaufgaben kostet Zeit.
- Nutzen für die Marine: Beschleunigt den Entwicklungsprozess für neue Schiffsentwürfe, kundenspezifische Hardwarelösungen oder Leistungsverbesserungen. Ermöglicht eine schnellere Validierung von neuen Konzepten.
4. Produktion auf Abruf & Digitale Bestandsaufnahme:
- AM: Die Teile werden direkt aus digitalen Dateien hergestellt. Dies ermöglicht ein digitales Lagerkonzept, bei dem die Entwürfe elektronisch gespeichert und nur bei Bedarf gedruckt werden. Ideal für Ersatzteile, veraltete Komponenten oder kundenspezifische Aufträge.
- Traditionell: In der Regel muss ein physischer Bestand gehalten werden, was Kapital bindet, Lagerraum erfordert und das Risiko der Veralterung birgt. Aufgrund der Einrichtungskosten sind oft Mindestbestellmengen erforderlich.
- Nutzen für die Marine: Reduziert die Lagerhaltungskosten, minimiert den Abfall durch unverkaufte Bestände und gewährleistet die Verfügbarkeit wichtiger Ersatzteile, auch für ältere Schiffe. Ermöglicht produktion von Bootshardware auf Abruf die auf die spezifischen Bedürfnisse der Nachrüstung oder Reparatur zugeschnitten sind.
5. Teil Konsolidierung:
- AM: Komplexe Baugruppen, für die bisher mehrere Komponenten, Verbindungselemente und Montageschritte erforderlich waren, können oft neu entworfen und als ein einziges, monolithisches Teil gedruckt werden.
- Traditionell: Erfordert die Herstellung einzelner Komponenten und deren anschließende Montage, was zu potenziellen Fehlerquellen, höherem Gewicht und zusätzlichen Arbeitskosten führt.
- Nutzen für die Marine: Vereinfachung der Lieferketten (weniger zu beschaffende Teile für großhandel mit Schiffskomponenten), reduziert die Montagezeit und die Fehleranfälligkeit, senkt das Gesamtgewicht und kann die strukturelle Integrität durch den Wegfall von Verbindungen verbessern.
6. Die Herstellung des “Unmöglichen”:
- AM: Es können Merkmale wie konforme Kühlkanäle, komplexe innere Gitter und negative Entformungswinkel erzeugt werden, die durch Gießen, Schmieden oder maschinelle Bearbeitung nicht oder nur mit unverhältnismäßig hohem Aufwand herstellbar sind.
- Traditionell: Begrenzt durch Form-/Gesenkbeschränkungen oder Werkzeugzugang.
- Nutzen für die Marine: Öffnet die Tür zu neuartigen Hardware-Designs mit verbesserter Funktionalität - z. B. Hardware mit integrierten Sensorikfunktionen, optimierter Fluiddynamik oder besserer Wärmeableitung.
7. Wirtschaftliche Rentabilität für kleine bis mittlere Volumina & Personalisierung:
- AM: Die Einrichtungskosten sind im Vergleich zu den Werkzeugkosten beim Gießen/Schmieden relativ niedrig. Die Kosten pro Teil sind weniger volumenabhängig, was AM für Einzelstücke, Prototypen und kleine bis mittlere Losgrößen (je nach Komplexität und Größe bis zu Hunderten oder manchmal Tausenden von Teilen) äußerst wettbewerbsfähig macht.
- Traditionell: Die hohen Werkzeugkosten für Guss- und Schmiedeteile machen kleine Stückzahlen sehr teuer pro Teil. Bei der maschinellen Bearbeitung werden zwar keine Werkzeuge benötigt, aber komplexe Teile erfordern einen erheblichen Programmier- und Maschinenaufwand, was die Kosten für kleine Serien in die Höhe treibt.
- Nutzen für die Marine: Macht maßgeschneiderte Bootsteile wirtschaftlich machbar. Ideal für den maßgeschneiderten Yachtbau, spezialisierte Handelsschiffe oder die Herstellung von Ersatzteilen, die nicht in großen Stückzahlen gefertigt werden müssen. Erfüllt die Anforderungen von lieferanten für kundenspezifische Bootsbeschläge.
Zusammenfassende Vergleichstabelle:
Merkmal | Additive Fertigung von Metall (AM) | Traditionelles Gießen/Schmieden | Traditionelle Bearbeitung |
---|---|---|---|
Entwurfskomplexität | Sehr hoch (Komplexe Einbauten, Gitter) | Mäßig (Begrenzt durch Schimmel/Würfel) | Hoch (begrenzt durch Werkzeugzugang) |
Materialabfälle | Gering bis mäßig (additiv) | Moderat (Läufer, Tore, Blitzlicht) | Hoch (subtraktiv) |
Werkzeugkosten | Keine / Minimal | Hoch (Gussformen, Matrizen) | Minimal (Vorrichtungen) |
Vorlaufzeit (Proto) | Sehr schnell (Tage) | Langsam (Wochen/Monate) | Mäßig bis schnell (Tage/Wochen) |
Vorlaufzeit (Prod) | Mäßig (abhängig von der Größe/Menge des Gebäudes) | Schnell (hohe Lautstärke) | Mittel bis schnell |
Ideales Volumen | Niedrig bis mittel, benutzerdefiniert | Hoch | Niedrig bis hoch (variiert) |
Teil Konsolidierung | Ausgezeichnet | Schlecht | Schlecht |
Leichte Anpassbarkeit | Sehr hoch | Gering (Erfordert neue Werkzeuge) | Mäßig (Erfordert Neuprogrammierung) |
Material-Optionen | Wachsende Auswahl an schweißbaren Legierungen | Große Auswahl an Guss-/Schmiedelegierungen | Große Auswahl an bearbeitbaren Legierungen |
In Blätter exportieren
Obwohl AM überzeugende Vorteile bietet, ist es nicht immer die beste Lösung für jedes Teil der Bootshardware. Die Großserienproduktion von einfachen, standardisierten Komponenten kann mit herkömmlichen Methoden immer noch kostengünstiger sein. Für korrosionsbeständige Beschläge, die komplexe Formen, kundenspezifische Anpassungen, geringes Gewicht oder schnelle Verfügbarkeit erfordern, stellt Metall-AM jedoch eine leistungsstarke und zunehmend praktikable Fertigungsalternative dar. Die Zusammenarbeit mit einem kompetenten Anbieter wie Met3dp sichert den Zugang zu modernsten Anlagen und Materialkenntnissen, um diese Vorteile effektiv zu nutzen.
Das Material ist entscheidend: Die Auswahl von 316L und Ti-6Al-4V für eine überlegene Leistung in der Schifffahrt
Die außergewöhnliche Leistung von 3D-gedruckten Bootsteilen in rauen Meeresumgebungen hängt entscheidend von der Auswahl des richtigen Materials ab. Die Metall-AM-Technologie kann zwar eine Vielzahl von Legierungen verarbeiten, aber zwei zeichnen sich durch ihre bewährte Erfolgsbilanz und ihre Eignung für Salzwasser aus: 316L-Edelstahl und Ti-6Al-4V (Grad 5) Titanlegierung. Das Verständnis ihrer Eigenschaften, Vorteile und AM-spezifischen Überlegungen ist für Ingenieure, die Komponenten entwerfen, und für Beschaffungsmanager, die sie von anbieter von Schiffslegierungen.
1. 316L-Edelstahl: Das Arbeitspferd der Schiffsindustrie
- Zusammensetzung und Eigenschaften: 316L ist eine austenitische rostfreie Stahllegierung, die Chrom (Cr), Nickel (Ni) und Molybdän (Mo) enthält. Das ‘L’ steht für einen niedrigen Kohlenstoffgehalt (typischerweise <0,03%), der für die Minimierung der Sensibilisierung (Ausscheidung von Chromkarbiden an den Korngrenzen) während des Schweißens oder der thermischen Zyklen bei AM-Verfahren entscheidend ist. Dadurch bleibt die hervorragende Korrosionsbeständigkeit erhalten, insbesondere nach thermischer Belastung.
- Wichtige Eigenschaften:
- Ausgezeichnete Korrosionsbeständigkeit: Der Molybdängehalt erhöht die Widerstandsfähigkeit gegen Lochfraß und Spaltkorrosion, die durch die im Meerwasser vorkommenden Chloride verursacht werden, erheblich. In Meeresumgebungen schneidet er wesentlich besser ab als Edelstahl 304.
- Gute Festigkeit und Duktilität: Bietet ein ausgewogenes Verhältnis von mechanischen Eigenschaften, die für viele Hardware-Anwendungen geeignet sind.
- Gute Umformbarkeit und Schweißbarkeit: Obwohl es für die AM selbst weniger relevant ist, liefert sein bekanntes Verhalten bei der traditionellen Herstellung einen Kontext. Seine Eignung für die AM-Pulverzerstäubung und -Schmelzung ist gut bekannt.
- Nicht-magnetisch: Im Allgemeinen nicht magnetisch im geglühten Zustand.
- Hygienisch und ästhetisch: Bietet eine saubere, helle Oberfläche, die oft für Deckbeschläge gewünscht wird.
- Wichtige Eigenschaften:
- Warum es ein Marine Standard ist: 316L (und seine Varianten) ist seit Jahrzehnten ein beliebtes Material für Bootsbeschläge, Geländer, Befestigungselemente und architektonische Elemente, da es zuverlässig funktioniert und im Vergleich zu exotischeren Legierungen kostengünstig ist.
- AM-spezifische Überlegungen:
- Druckbarkeit: 316L ist einer der gängigsten und bekanntesten Werkstoffe für Pulverbettschmelzverfahren (PBF-LB/SLM). Die Parameter sind im Allgemeinen gut etabliert.
- Mikrostruktur: Mit AM können feinkörnige Mikrostrukturen in 316L erzeugt werden, die die Festigkeit im Vergleich zu gegossenen oder geglühten Knetformen erhöhen können.
- Nachbearbeiten: Nach dem Druck ist in der Regel eine Spannungsarmglühung erforderlich, um Eigenspannungen zu reduzieren und die Korrosionsbeständigkeit zu optimieren. Oberflächenveredelungstechniken wie Elektropolieren können die Korrosionsbeständigkeit und Glätte weiter verbessern. Auch eine Passivierung wird empfohlen.
- Met3dp’s 316L-Pulver: Met3dp nutzt fortschrittliche Gaszerstäubungstechniken zur Herstellung hochwertiger 316L-Pulver mit hoher Sphärizität, guter Fließfähigkeit und kontrollierter Partikelgrößenverteilung. Dies gewährleistet ein gleichmäßiges Schmelzverhalten während des AM-Prozesses und führt zu dichten, hochintegrierten Teilen mit vorhersehbaren mechanischen Eigenschaften, die für eine zuverlässige marinestahl AM Komponenten.
2. Ti-6Al-4V (Grad 5) Titan: Der High-Performance-Champion
- Zusammensetzung und Eigenschaften: Ti-6Al-4V ist die am häufigsten verwendete Alpha-Beta-Titanlegierung, die etwa 6 % Aluminium und 4 % Vanadium enthält. Sie dominiert Anwendungen in der Luft- und Raumfahrt und wird zunehmend in der Schifffahrt bevorzugt, wo die Leistung entscheidend ist.
- Wichtige Eigenschaften:
- Außergewöhnliches Verhältnis von Stärke zu Gewicht: Deutlich leichter als Stahl (ca. 40-45 % weniger Dichte), aber mit vergleichbarer oder sogar höherer Festigkeit, wodurch es sich ideal für gewichtskritische Anwendungen eignet.
- Hervorragende Korrosionsbeständigkeit: Bildet eine stabile, passive Oxidschicht, die es praktisch immun gegen Korrosion in Meerwasser, Salzlake und Meeresatmosphäre macht, selbst bei erhöhten Temperaturen oder in verschmutzten Gewässern. Unter hochaggressiven Bedingungen besser als 316L.
- Ausgezeichnete Ermüdungsfestigkeit: Gute Leistung bei zyklischer Belastung, wie sie auf Schiffen üblich ist.
- Biokompatibilität: Obwohl es für die meisten Bootsteile weniger relevant ist, unterstreicht seine Biokompatibilität seine Trägheit.
- Geringe thermische Ausdehnung: Formstabil bei Temperaturschwankungen.
- Wichtige Eigenschaften:
- Anwendungen, bei denen sich Titan auszeichnet: Ideal für hochbelastete, gewichtsempfindliche Komponenten wie Ruderschäfte und -lager, Propellerwellen (kleinere Schiffe), Kettenplatten, Mastbeschläge, Hochleistungswinden und Strukturelemente, bei denen eine Gewichtsreduzierung auf der Oberseite die Stabilität verbessert. Häufig spezifiziert von beschaffung für die Schiffsherstellung mit Schwerpunkt auf Hochleistungsschiffen.
- AM-spezifische Überlegungen:
- Reaktivität: Titan ist bei hohen Temperaturen reaktiv und erfordert eine sorgfältige Kontrolle der Fertigungsatmosphäre (Inertgas wie Argon) während der AM, um die Aufnahme von Sauerstoff oder Stickstoff zu verhindern, die das Material verspröden kann.
- Thermische Eigenschaften: Seine im Vergleich zu Stahl geringere Wärmeleitfähigkeit erfordert ein sorgfältiges Management der thermischen Spannungen während des Bauprozesses.
- Nachbearbeiten: Spannungsabbau ist unerlässlich. Heiß-Isostatisches Pressen (HIP) wird häufig für kritische Anwendungen empfohlen, um interne Mikroporosität zu schließen und die Ermüdungslebensdauer zu maximieren. Die Bearbeitung von Titan erfordert aufgrund seiner Zähigkeit spezielle Werkzeuge und Techniken.
- Met3dp’s Ti-6Al-4V-Pulver: Met3dp ist sich der kritischen Natur von Titananwendungen bewusst und setzt neben der fortschrittlichen Gaszerstäubung auch branchenführende Technologien wie das Plasma Rotating Electrode Process (PREP) ein. PREP eignet sich besonders für die Herstellung hochgradig kugelförmiger Titanpulver mit sehr geringen Satellitenpartikeln und hervorragender Reinheit, die für das Erreichen hervorragender mechanischer Eigenschaften und Ermüdungsbeständigkeit in anspruchsvollen Anwendungen entscheidend sind, wie Ti-6Al-4V Seewasserbeständigkeit komponenten. Die strenge Qualitätskontrolle von Met3dp’ stellt sicher, dass diese fortschrittlichen Pulver den strengen Anforderungen der Schifffahrt und anderer High-Tech-Industrien entsprechen.
Tabelle zum Materialvergleich:
Eigentum | 316L-Edelstahl | Ti-6Al-4V (Grad 5) Titan | Einheit | Anmerkungen |
---|---|---|---|---|
Dichte | ~7.9 – 8.0 | ~4.43 | g/cm³ | Titan ist ca. 45% leichter. |
Typische Zugfestigkeit (AM, As-Built/Stress Relieved) | 500 – 650 | 900 – 1100 | MPa | Variiert je nach Bauparameter/Nachbearbeitung. Ti-6Al-4V deutlich stärker. |
Streckgrenze (0,2% Offset) | 250 – 450 | 800 – 1000 | MPa | Entscheidend für die Konstruktion gegen bleibende Verformung. |
Elastischer Modul | ~190 – 200 | ~110 – 115 | GPa | Stahl ist steifer. |
Korrosion durch Meerwasser | Ausgezeichnet (gute Lochfraß-/Spaltfestigkeit) | Hervorragend (Praktisch immun) | Bewertung | Titan überlegen, insbesondere in stehendem oder verschmutztem Wasser. |
Relativer Kostenindex (Pulver) | 1x | ~5x – 10x+ | Index | Titanpulver ist wesentlich teurer. |
Druckbarkeit (PBF-LB) | Ausgezeichnet | Gut (Erfordert strenge Atmosphäre ctrl) | Bewertung | Beide sind bedruckbar, Ti erfordert mehr Prozesskontrolle. |
Typische Nachbearbeitungen | Stressabbau, optional Polieren/Passivieren | Stressabbau, optional HIP/Bearbeitung | Prozess | Beide erfordern Stressabbau. HIP wird oft für Titan empfohlen. |
In Blätter exportieren
Anleitung zur Auswahl:
- Wählen Sie 316L wenn gute Korrosionsbeständigkeit, mittlere Festigkeit und Kosteneffizienz im Vordergrund stehen. Hervorragend geeignet für allgemeine Deckbeschläge, Geländer, Halterungen und nicht gewichtskritische Beschläge.
- Wählen Sie Ti-6Al-4V wenn maximale Korrosionsbeständigkeit, höchstes Verhältnis von Festigkeit zu Gewicht und Leistung unter hohen Belastungen oder Ermüdungsbedingungen von größter Bedeutung sind. Gerechtfertigt für kritische Strukturkomponenten, gewichtssensible Anwendungen (Rennyachten, Sportboote) und Hardware in extrem aggressiven Umgebungen.
Letztendlich hängt die Wahl von den spezifischen Anwendungsanforderungen, den Leistungszielen und den Budgetbeschränkungen ab. Die Beratung durch Materialexperten und erfahrene AM-Dienstleister wie Met3dp, die über fundierte Kenntnisse sowohl der 316L Marinestahl AM und Ti-6Al-4V verarbeitung, ist der Schlüssel zur optimalen Auswahl für Ihren Bedarf an korrosionsbeständigen Bootsteilen.
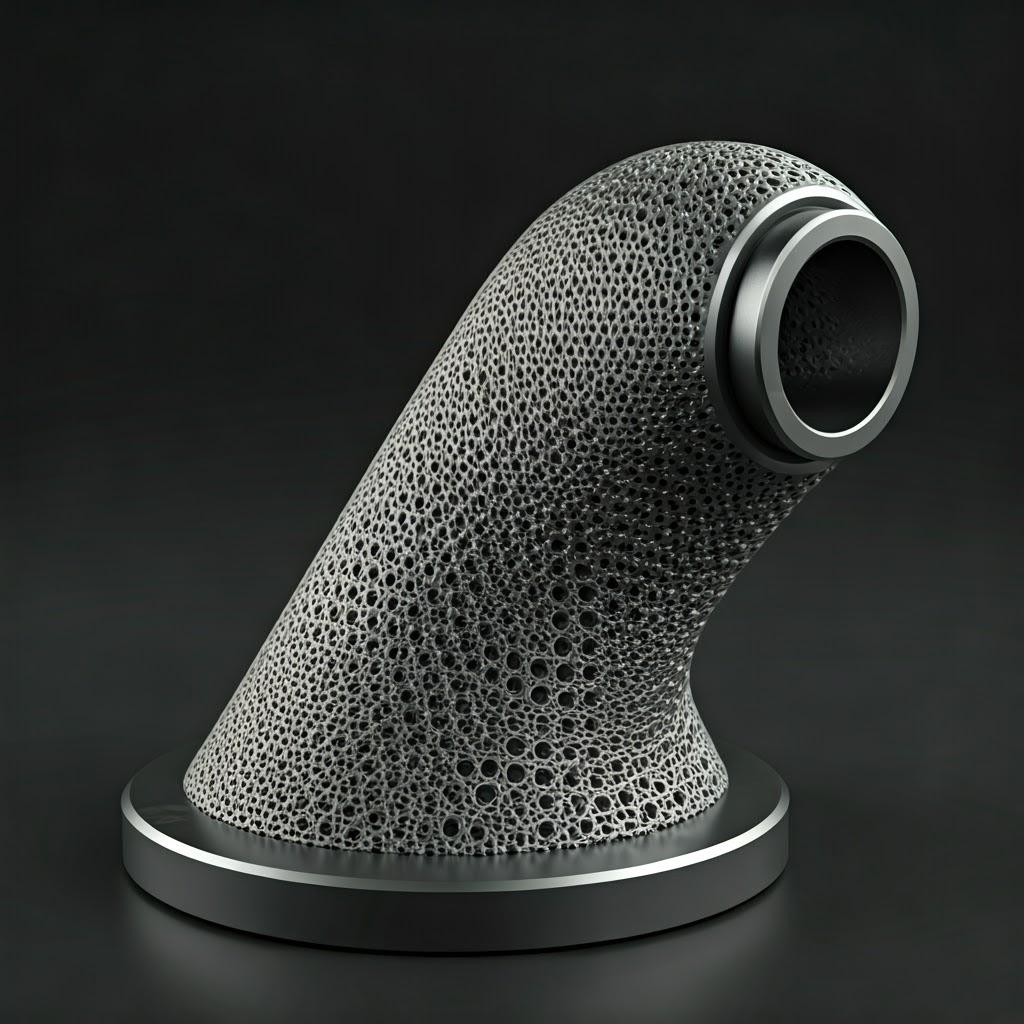
Design für additive Fertigung (DfAM): Optimierung von Bootshardware für den 3D-Druck
Wenn man einen Entwurf, der für das Gießen oder die maschinelle Bearbeitung vorgesehen ist, einfach an einen 3D-Metalldrucker schickt, erzielt man selten die besten Ergebnisse. Um die Vorteile der additiven Fertigung für Bootsteile wirklich nutzen zu können, müssen Ingenieure und Designer die folgenden Punkte berücksichtigen Design für additive Fertigung (DfAM) grundsätze. Bei DfAM geht es nicht nur um die Herstellung eines Teils druckbares geht darum, die einzigartigen Fähigkeiten von AM zu nutzen, um Komponenten zu schaffen, die leichter, stärker, funktioneller und potenziell kostengünstiger zu produzieren sind als ihre traditionell hergestellten Gegenstücke. Für Beschaffungsmanager, die Angebote von additive Fertigungsdesigndienstleistungen oder Lieferanten, ist das Verständnis, ob die DfAM-Prinzipien angewandt wurden, der Schlüssel zur Beurteilung des potenziellen Wertes, den AM bietet.
Im Folgenden finden Sie wichtige DfAM-Überlegungen, die speziell für die Optimierung von Bootshardware relevant sind:
1. Topologie-Optimierung und Gewichtsreduzierung:
- Konzept: Verwendung von Software-Algorithmen zur Entfernung von Material aus Bereichen, in denen es strukturell nicht notwendig ist, basierend auf definierten Lastfällen, Einschränkungen und Leistungszielen. Das Ergebnis sind oft organische, gitterartige Strukturen, die das Gewicht minimieren und gleichzeitig die Steifigkeit und Festigkeit erhalten oder sogar erhöhen.
- Anwendung in der Schifffahrt: Ideal für die Gewichtsreduzierung an der Oberseite von Schiffen (Verbesserung der Stabilität), die Minimierung der Masse rotierender oder beweglicher Komponenten (wie Ruderbeschläge oder Winden) und die Schaffung hocheffizienter Strukturknoten. Besonders vorteilhaft bei der Verwendung dichterer Materialien wie 316L, aber auch zur Maximierung der Vorteile von natürlich leichten Materialien wie Ti-6Al-4V.
- Werkzeuge: Software wie Altair Inspire, nTopology, Siemens NX und Autodesk Fusion 360 enthalten Module zur Topologieoptimierung.
- Erwägung: Optimierte Entwürfe können im Vergleich zu herkömmlichen Teilen unkonventionell aussehen, was die Akzeptanz der Endnutzer oder die Einbindung in die Ästhetik des Schiffes erfordert. Die Komplexität kann sich auch auf die Druckzeit und die Nachbearbeitungsanforderungen auswirken.
2. Teil Konsolidierung:
- Konzept: Neugestaltung von Baugruppen aus mehreren Komponenten, die als ein einziges, monolithisches Teil gedruckt werden sollen.
- Anwendung in der Schifffahrt: Die Kombination von Halterungen mit ihren Montageplatten, die Integration von Scharnieren direkt in Luken oder Zugangsklappen, die Schaffung komplexer Fairleads mit integrierten Befestigungspunkten.
- Vorteile: Reduziert die Anzahl der Teile (vereinfacht die Beschaffung und den Bestand für bootszubehör-Händler), eliminiert Verbindungselemente (potenzielle Korrosionsstellen und Fehlerquellen), reduziert den Montageaufwand und kann durch den Wegfall von Verbindungen die Gesamtfestigkeit und Steifigkeit verbessern.
- Erwägung: Erfordert ein Überdenken des gesamten Baugruppendesigns. Kann Reparaturen komplizierter machen (Austausch des gesamten integrierten Teils anstelle eines einzelnen Bauteils), was jedoch häufig durch die erhöhte Haltbarkeit ausgeglichen wird.
3. Design für minimale Unterstützungsstrukturen:
- Konzept: Metall-AM-Verfahren, insbesondere das Pulverbettschmelzen (PBF-LB/SLM), erfordern Stützstrukturen für überhängende Merkmale (typischerweise mehr als 45 Grad aus der Senkrechten) und zur Verankerung des Teils auf der Bauplatte, um die thermische Belastung zu bewältigen. Diese Stützen verbrauchen Material, verlängern die Druckzeit und müssen in der Nachbearbeitung entfernt werden (ein erheblicher Kostenfaktor). DfAM zielt darauf ab, den Bedarf an Stützen zu minimieren oder zu eliminieren.
- Strategien:
- Orientierung: Auswahl der optimalen Bauausrichtung für das Teil.
- Selbsttragende Winkel: Planung von Überhängen, die kleiner als der kritische Winkel sind (oft ~45 Grad).
- Fasen und Filets: Verwendung von Abschrägungen anstelle von scharfen horizontalen Überhängen an der Unterseite von Elementen. Das Einfügen von Verrundungen an scharfen Ecken reduziert Spannungskonzentrationen und kann manchmal die Notwendigkeit von Stützen überflüssig machen.
- Interne Kanäle: Gestaltung von Innenkanälen in Tropfen- oder Rautenform, damit sie selbsttragend sind.
- Anwendung in der Schifffahrt: Entscheidend für die Reduzierung der Kosten und der Vorlaufzeit für den Druck komplexer Hardware wie kundenspezifische Halterungen oder Gehäuse. Sorgt für saubere Oberflächen, wo Stützen vermieden werden.
4. Feature Design Regeln:
- Wanddicke: Die minimale druckbare Wandstärke hängt vom Material, der Maschine und den Parametern ab (typischerweise 0,4 mm – 1,0 mm), aber dickere Wände sind in der Regel für die strukturelle Integrität erforderlich. Vermeiden Sie abrupte Dickenänderungen, die zu Spannungskonzentrationen führen können.
- Design der Löcher: Horizontal gedruckte Löcher sind aufgrund von Schichteffekten oft leicht elliptisch; vertikale Löcher sind im Allgemeinen genauer. Ziehen Sie in Erwägung, für kritische Löcher, die nach dem Druck aufgerieben oder maschinell bearbeitet werden sollen, Opfermaterial hinzuzufügen. Die minimale druckbare Lochgröße liegt normalerweise bei 0,5 mm – 1,0 mm.
- Kanäle: Interne Kanäle müssen sorgfältig entworfen werden, damit das Pulver nach dem Druck entfernt werden kann. Entweichungslöcher sind unerlässlich. Komplexe interne Kanäle sind eine wesentliche Stärke von AM, erfordern aber eine gute Planung.
- Fäden: Während Feingewinde manchmal direkt gedruckt werden können, ist es oft zuverlässiger und kostengünstiger, Löcher mit Untermaß zu drucken und sie dann konventionell zu schneiden oder Gewindeeinsätze nach dem Druck zu verwenden, insbesondere bei hochfesten Verbindungen.
5. Nutzung von AM-spezifischen Funktionen:
- Interne Gitternetze: Durch den Einbau interner Gitterstrukturen lassen sich Gewicht und Materialverbrauch bei gleichbleibender struktureller Leistung erheblich reduzieren. Nützlich für Auftriebskomponenten oder Teile, die besondere Steifigkeitseigenschaften erfordern.
- Konforme Kühl-/Heizkanäle: Die Möglichkeit, interne Kanäle zu drucken, die sich an die Oberfläche des Teils anpassen, ist bei Standard-Bootsbauteilen zwar weniger verbreitet, könnte aber bei speziellen Anwendungen genutzt werden, z. B. für das Wärmemanagement in hochbelasteten Windenlagern oder die Integration von Enteisungsfunktionen.
- Oberflächentexturen: Einzigartige Oberflächentexturen können direkt in das Teil eingearbeitet werden, um die Griffigkeit (z. B. an Griffen oder Stufen) oder die Ästhetik zu verbessern oder möglicherweise den Flüssigkeitsfluss zu beeinflussen (allerdings gelten hier Einschränkungen für die Oberflächenbeschaffenheit).
6. Simulation und Validierung:
- Konzept: Einsatz der Finite-Elemente-Analyse (FEA) zur Simulation der Leistung des DfAM-optimierten Entwurfs unter den zu erwartenden Schiffsbelastungen (statisch, dynamisch, Ermüdung). Außerdem werden AM-Prozess-Simulationstools verwendet, um potenzielle Probleme bei der Herstellung wie Verformung, Eigenspannung und Anforderungen an die Stützstruktur vorherzusagen, bevor der Druckauftrag erteilt wird.
- Anwendung in der Schifffahrt: Unverzichtbar für die Validierung der strukturellen Integrität kritischer Hardware, um sicherzustellen, dass die Bemühungen um Gewichtsreduzierung oder Teilekonsolidierung die Sicherheit oder Leistung nicht beeinträchtigt haben. Die Prozesssimulation hilft bei der Optimierung des Build-Setups, reduziert Versuch und Irrtum und erhöht die Erfolgsquote beim ersten Druck.
Durch die durchdachte Anwendung dieser DfAM-Prinzipien können Hersteller nicht nur vorhandene Bootsteile durch 3D-gedruckte Versionen ersetzen, sondern stattdessen echte Komponenten der nächsten Generation schaffen, die für die anspruchsvollen Bedingungen auf See optimiert sind. Die Zusammenarbeit mit AM-Experten, die sich mit DfAM auskennen, ist entscheidend, um diese Vorteile zu maximieren.
Erreichen von Präzision: Verständnis von Toleranz, Oberflächengüte und Genauigkeit bei AM-Bootsteilen
Während Metall-AM eine unglaubliche Designfreiheit bietet, ist es für Ingenieure und Beschaffungsmanager wichtig, realistische Erwartungen hinsichtlich der erreichbaren Präzision, Maßhaltigkeit und Oberflächenbeschaffenheit von 3D-gedruckten Bootsteilen zu haben. Diese Faktoren wirken sich direkt auf die Passform, die Funktion, die Leistung (insbesondere hinsichtlich Korrosion und Ermüdung) und die Ästhetik des Teils aus. Sie beeinflussen auch die Notwendigkeit und die Kosten von Nachbearbeitungsprozessen.
1. Maßgenauigkeit und Toleranzen:
- Was ist realisierbar? Typische Maßtoleranzen für das Metallpulverbettschmelzen (PBF-LB/SLM), ein gängiges Verfahren für 316L und Ti-6Al-4V, liegen oft im Bereich von ±0,1 mm bis ±0,2 mm für kleinere Merkmale oder ±0,1 % bis ±0,2 % des Gesamtmaßes für größere Teile. Dies kann jedoch erheblich variieren. Das Elektronenstrahlschmelzen (EBM), ein weiteres PBF-Verfahren, das manchmal für Ti-6Al-4V verwendet wird, kann etwas engere Toleranzen, aber geringere Eigenspannungen aufweisen. Sie können verschiedene Druckverfahren und ihre Eigenschaften.
- Faktoren, die die Genauigkeit beeinflussen:
- Kalibrierung der Maschine: Präzision des Laser-/Elektronenstrahlsystems, Scannergenauigkeit, Schichtdickenkontrolle.
- Materialeigenschaften: Wärmeausdehnung/Kontraktion, Pulvereigenschaften (Fließfähigkeit, Partikelgrößenverteilung). Hochwertige Pulver, wie die von Met3dp hergestellten, tragen zu einem besser vorhersehbaren Schmelzen und Erstarren bei, was der Genauigkeit zugute kommt.
- Parameter aufbauen: Laserleistung, Scangeschwindigkeit, Schraffurabstand und Schichtdicke beeinflussen die Stabilität des Schmelzbades und die resultierenden Abmessungen.
- Thermische Belastung: Eine ungleichmäßige Erwärmung und Abkühlung kann zu Verzug und Verwerfungen führen, die sich auf die endgültigen Abmessungen auswirken. Die Ausrichtung der Teile und die Unterstützungsstrategie spielen hier eine große Rolle.
- Teilegeometrie und -größe: Größere Teile und komplexe Geometrien sind im Allgemeinen anfälliger für Verformungen.
- Nachbearbeiten: Wärmebehandlungen zum Spannungsabbau können manchmal geringfügige Änderungen der Abmessungen verursachen. Die maschinelle Bearbeitung wird eingesetzt, um engere Toleranzen bei bestimmten Merkmalen zu erreichen.
- Erwartungen setzen: Gehen Sie von Standard-AM-Toleranzen aus, es sei denn, engere Anforderungen werden ausdrücklich diskutiert und angegeben. Kritische Abmessungen, die engere Toleranzen als ~±0,1 mm erfordern, müssen wahrscheinlich nachbearbeitet werden. Definieren Sie kritische Abmessungen und Toleranzen klar auf den Zeichnungen, die dem 3D-Druck-Dienstleister für Metall.
2. Oberflächengüte (Rauhigkeit):
- Ist-Zustand: AM-Teile aus Metall haben von Natur aus eine rauere Oberfläche als maschinell bearbeitete Teile. Die Rauheit hängt ab von:
- Prozess: PBF-LB führt in der Regel zu glatteren Oberflächen als EBM.
- Schichtdicke: Dünnere Schichten ergeben im Allgemeinen feinere Oberflächen auf geneigten Flächen.
- Partikelgröße: Feinere Metallpulver können zu glatteren Oberflächen beitragen.
- Orientierung: Nach oben weisende Flächen sind in der Regel glatter als Seitenwände oder nach unten weisende Flächen (die durch Stützkontakte beeinflusst werden). Steil abfallende Oberflächen sind aufgrund des Treppeneffekts der Schichtung tendenziell rauer.
- Typische Ra-Werte: Die Oberflächenrauhigkeit (Ra) von PBF-LB-Teilen liegt oft zwischen 6 µm und 15 µm (Mikrometer). EBM-Teile sind in der Regel rauher. Zum Vergleich: Eine Standardbearbeitung kann 1,6µm bis 6,3µm Ra erreichen, während Schleifen oder Polieren <1µm Ra erreichen kann.
- Auswirkungen auf die Leistung:
- Korrosion: Rauere Oberflächen haben mehr Oberfläche und potenzielle Spalten, in denen Korrosion, insbesondere Spaltkorrosion, entstehen kann. Glattere Oberflächen sind im Allgemeinen besser für Meeresumgebungen geeignet.
- Müdigkeit Leben: Oberflächenrauhigkeit wirkt als Spannungskonzentrator und kann die Lebensdauer von Bauteilen bei zyklischer Belastung verringern.
- Ästhetik: Bei funktionalen, verdeckten Teilen kann die Ausführung im Ist-Zustand akzeptabel sein, bei sichtbaren Deckbeschlägen ist jedoch oft eine Verbesserung erforderlich.
- Passende Oberflächen: Die Rauheit wirkt sich auf den Sitz und den Verschleiß von Pass- oder Dichtflächen aus.
3. Erreichen der gewünschten Präzision und Ausführung:
- Entwurfsphase: Berücksichtigen Sie Toleranzen und Anforderungen an die Oberflächenbeschaffenheit während der DfAM. Legen Sie kritische Merkmale klar fest. Vermeiden Sie die Konstruktion von Merkmalen, die unnötig schwer genau zu drucken oder glatt zu bearbeiten sind.
- Prozessauswahl: Besprechen Sie mit Ihrem AM-Anbieter, welches Verfahren (z.B. PBF-LB vs. EBM, falls zutreffend) und welcher Parametersatz für Ihre Anforderungen am besten geeignet ist.
- Nachbearbeiten: Dies ist der Schlüssel zum Erreichen enger Toleranzen und glatter Oberflächen.
- CNC-Bearbeitung: Wird für kritische Abmessungen, Passflächen, Dichtflächen und Gewindebohrungen verwendet. Unverzichtbar, wenn Toleranzen erforderlich sind, die über die Standard-AM-Fähigkeiten hinausgehen.
- Strahlen / Shot Peening: Kann eine gleichmäßige matte Oberfläche erzeugen und die Ermüdungsfestigkeit verbessern (Kugelstrahlen erzeugt Druckspannungen).
- Taumeln / Vibrationsgleitschleifen: Verbessert die Oberflächenglätte und entgratet die Kanten, geeignet für Chargen von kleineren Teilen.
- Elektropolieren (für 316L): Verbessert die Oberflächenglätte erheblich (bis zu <1µm Ra möglich) und erhöht die Korrosionsbeständigkeit durch Entfernen der äußeren Schicht und Anreicherung von Chrom an der Oberfläche. Ideal für High-End-Schiffsteile.
- Manuelle Endbearbeitung / Polieren: Zur Erzielung bestimmter ästhetischer Ergebnisse, einschließlich Spiegelpolituren, ist jedoch arbeitsintensiv.
Zusammenfassende Tabelle: Toleranz und Ausführung:
Parameter | As-Built Metall AM (PBF-LB) | Nachbearbeitet (typisch) | Anmerkungen |
---|---|---|---|
Abmessungstoleranz | ±0,1 bis ±0,2 mm / ±0,1% bis ±0,2% | ±0,05 mm (maschinelle Bearbeitung) | Engere Toleranzen erfordern eine spezielle Nachbearbeitung. |
Oberflächenrauhigkeit (Ra) | 6 – 15 µm | 1 – 6 µm (Strahlen/Taumeln) < 1 µm (Polieren/Elektropolieren) | Erhebliche Verbesserungen durch verschiedene Nachbearbeitungsschritte möglich. |
Einstellung der Anforderungen | Definieren Sie kritische Dimensionen & beenden Sie frühzeitig | Nachbearbeitung in Kosten/Durchlaufzeit einkalkulieren | Eine klare Kommunikation mit dem Lieferanten ist unerlässlich. |
In Blätter exportieren
Das Verständnis dieser Aspekte ermöglicht eine bessere Planung, eine realistische Kostenabschätzung (da die Nachbearbeitung zusätzliche Kosten verursacht) und stellt sicher, dass die endgültige 3D-gedruckte Bootshardware die erforderlichen Anforderungen erfüllt präzisionsschiffshardware spezifikationen für Passform, Funktion und Langlebigkeit in der anspruchsvollen Meeresumgebung.
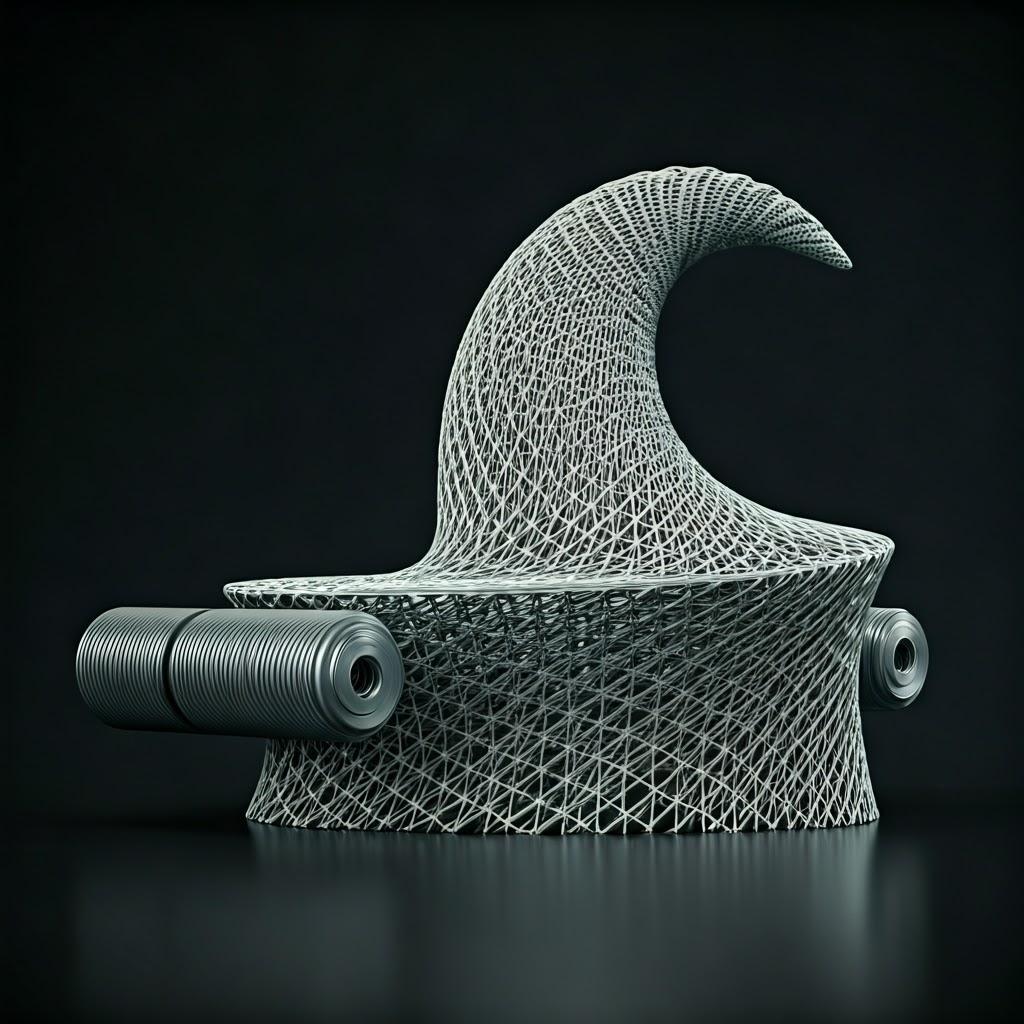
Über den Bau hinaus: Wichtige Nachbearbeitungsschritte für 3D-gedruckte Bootsteile
Die Reise eines 3D-gedruckten Bootsteils aus Metall ist nicht zu Ende, wenn es aus dem Drucker kommt. Die Nachbearbeitung ist eine kritische Phase, in der das rohe, fertige Bauteil in funktionale, zuverlässige und ästhetisch ansprechende Hardware verwandelt wird, die für die harten Bedingungen der maritimen Umgebung bereit ist. Diese Schritte sind für das Erreichen der gewünschten mechanischen Eigenschaften, Maßgenauigkeit, Oberflächenbeschaffenheit und Korrosionsbeständigkeit von entscheidender Bedeutung. Das Verständnis dieser Prozesse ist sowohl für Ingenieure, die die Teile spezifizieren, als auch für Beschaffungsmanager, die das Budget für metall-AM-Nachbearbeitungsdienste.
Zu den üblichen Nachbearbeitungsschritten für Bootsteile aus 316L und Ti-6Al-4V gehören:
1. Entfernung von Puder:
- Prozess: Unmittelbar nach Abschluss der Fertigung wird das Teil aus dem Bett aus ungeschmolzenem Metallpulver ausgehoben. Loses Pulver muss sorgfältig von allen Oberflächen, einschließlich der inneren Kanäle und komplexen Merkmale, entfernt werden.
- Methoden: Bürsten, Staubsaugen, Ausblasen mit Druckluft, manchmal spezielle Entleerungsstationen.
- Wichtigkeit: Es wird sichergestellt, dass kein eingeschlossenes Pulver die nachfolgenden Schritte oder die Funktion des Teils beeinträchtigt. Eine effiziente Pulverrückgewinnung ist auch für die Kosteneffizienz und Nachhaltigkeit wichtig (Wiederverwendung von ungeschmolzenem Pulver).
2. Stressabbau / Wärmebehandlung:
- Prozess: Erhitzen des gedruckten Teils in einer kontrollierten Ofenatmosphäre auf bestimmte Temperaturen und Haltezeiten, gefolgt von einer kontrollierten Abkühlung.
- Zweck:
- Reduziert Eigenspannung: Durch die schnellen Erwärmungs- und Abkühlungszyklen beim AM werden innere Spannungen aufgebaut. Die Spannungsentlastung minimiert diese Spannungen und verringert so das Risiko von Verformungen bei der nachfolgenden Bearbeitung oder von Rissen/Versagen im Betrieb. Entscheidend sowohl für 316L als auch für Ti-6Al-4V.
- Optimiert die Mikrostruktur: Kann das Mikrogefüge homogenisieren, unerwünschte Phasen auflösen und die Duktilität und Zähigkeit verbessern.
- Verbessert die Korrosionsbeständigkeit: Besonders wichtig bei 316L, um eine gute Chromverteilung zu gewährleisten und eine Sensibilisierung zu verhindern.
- Erwägungen: Spezifische Temperaturprofile hängen von der Legierung ab (z. B. unterschiedliche Zyklen für 316L gegenüber Ti-6Al-4V). Die Teile werden häufig wärmebehandelt, während sie noch auf der Bauplatte befestigt sind, um Verformungen zu vermeiden. Erforderlich sind Öfen mit präziser Temperaturregelung und häufig inerten Atmosphären (insbesondere für Titan).
3. Entfernung der Stützstruktur:
- Prozess: Physikalisches Entfernen der Stützstrukturen, die das Teil verankern und Überhänge während des Drucks stützen sollen.
- Methoden: Stützen werden in der Regel manuell mit Drahtschneidern, Zangen, Sägen oder manchmal auch durch CNC-Bearbeitung oder Drahterodieren (Electrical Discharge Machining) für schwer zugängliche Bereiche oder empfindliche Teile entfernt.
- Wichtigkeit: Stützen sind nicht funktionsfähig und müssen entfernt werden. Die Leichtigkeit des Ausbaus hängt stark von den verwendeten DfAM-Prinzipien ab.
- Herausforderungen: Kann arbeitsintensiv und zeitaufwendig sein. Unsachgemäßes Entfernen kann die Oberfläche des Teils beschädigen und Spuren hinterlassen, die eine weitere Nachbearbeitung erforderlich machen können.
4. Heißisostatisches Pressen (HIP) – Optional, hauptsächlich für Ti-6Al-4V:
- Prozess: Das Teil wird gleichzeitig einer hohen Temperatur (unter dem Schmelzpunkt) und einem hohen isostatischen Gasdruck (in der Regel Argon) ausgesetzt.
- Zweck: Schließt die interne Mikroporosität, die nach dem Druck vorhanden sein könnte. Dadurch werden Ermüdungsfestigkeit, Duktilität und Bruchzähigkeit deutlich verbessert.
- Anwendung in der Schifffahrt: Häufig für hochkritische Titankomponenten spezifiziert, die hohen zyklischen Belastungen ausgesetzt sind (z. B. Ruderlager, kritische Strukturelemente), um maximale Materialintegrität zu gewährleisten. Weniger häufig für allgemeine 316L-Bauteile, es sei denn, Ermüdung ist ein wichtiges Thema.
- Erwägungen: Erhöht die Kosten und die Vorlaufzeit erheblich. Erfordert spezielle HIP-Ausrüstung.
5. Oberflächenveredelung:
- Zweck: Zur Verbesserung der Oberflächenglätte, der Ästhetik, zur Beseitigung von Abdrücken und zur Verbesserung der Funktionsfähigkeit (Korrosionsbeständigkeit, Ermüdungsfestigkeit).
- Gängige Methoden:
- Strahlen von Medien (Sandstrahlen, Perlstrahlen): Schleudern von Schleifmitteln (Sand, Glasperlen, Keramikperlen) gegen die Oberfläche. Erzeugt eine gleichmäßige matte Oberfläche, entfernt Verunreinigungen und kann kleinere Unebenheiten ausgleichen.
- Shot Peening: Ähnlich wie beim Strahlen, jedoch werden kleine kugelförmige Kugeln verwendet, um Druckspannungen auf der Oberfläche zu erzeugen, was die Ermüdungslebensdauer erheblich verbessert. Wird häufig für dynamisch belastete Teile verwendet.
- Taumeln / Vibrationsgleitschleifen: Einlegen der Teile in eine Wanne mit abrasiven Medien, die vibrieren oder taumeln. Gut geeignet zum Glätten von Oberflächen und Entgraten von Kanten bei Chargen kleinerer, robuster Teile.
- CNC-Bearbeitung: Wird nicht nur für Toleranzen verwendet, sondern auch zur Erzielung bestimmter glatter Oberflächen auf Funktionsflächen (z. B. Dichtflächen, Lagerzapfen).
- Elektropolieren (hauptsächlich 316L): Ein elektrochemisches Verfahren, bei dem eine mikroskopisch kleine Materialschicht entfernt wird, wobei die Spitzen bevorzugt angegriffen werden. Das Ergebnis ist eine sehr glatte, glänzende, hoch korrosionsbeständige Oberfläche. Ideal für hochwertige Decksbeschläge.
- Passivierung (hauptsächlich 316L): Eine chemische Behandlung (in der Regel Salpeter- oder Zitronensäure), die freies Eisen von der Oberfläche entfernt und die natürliche passive Chromoxidschicht verstärkt, wodurch die Korrosionsbeständigkeit maximiert wird. Wird oft nach der Bearbeitung oder dem Strahlen durchgeführt.
- Bürsten/Schleifen/Polieren: Manuelle oder automatisierte Verfahren unter Verwendung von Schleifbändern, -rädern oder -mitteln zur Erzielung bestimmter Glättegrade oder ästhetischer Oberflächen (z. B. Satinieren, Hochglanzpolieren). Arbeitsintensiv.
- Beschichtung/Malerei: Während 316L und Ti-6Al-4V von Haus aus eine ausgezeichnete Korrosionsbeständigkeit aufweisen, können Beschichtungen (z. B. PVD, Pulverbeschichtung) oder Lacke aus ästhetischen Gründen, als Bewuchsschutz oder als zusätzliche Abriebfestigkeit in bestimmten Bereichen eingesetzt werden.
6. Inspektion und Qualitätskontrolle (QC):
- Prozess: Überprüfung, ob das fertige Teil alle vorgegebenen Anforderungen erfüllt.
- Methoden:
- Prüfung der Abmessungen: Verwendung von Messschiebern, Mikrometern, CMMs (Coordinate Measuring Machines) oder 3D-Scans zur Überprüfung von Abmessungen und Toleranzen.
- Visuelle Inspektion: Prüfung auf Oberflächenfehler, vollständige Entfernung von Stützen und allgemeine Oberflächenqualität.
- Zerstörungsfreie Prüfung (NDT): Methoden wie Röntgen- oder CT-Scannen (zur Prüfung auf innere Porosität/Defekte, insbesondere nach HIP), Farbeindringprüfung (zur Prüfung auf Oberflächenrisse) oder Ultraschallprüfung. Der Umfang der zerstörungsfreien Prüfung hängt von der Kritikalität des Teils ab.
- Materialprüfung (zerstörend): Wird manchmal an repräsentativen Mustern durchgeführt, die neben den Hauptteilen gedruckt werden, um die mechanischen Eigenschaften (Zugfestigkeit, Streckgrenze, Dehnung) zu überprüfen.
- Wichtigkeit: Stellt sicher, dass die Hardware für den Zweck geeignet ist und die in der Schifffahrtsindustrie erwarteten Sicherheits- und Leistungsstandards erfüllt. Unverzichtbar für zuverlässige zulieferer von Schiffskomponenten.
Welche Nachbearbeitungsschritte erforderlich sind, hängt stark vom gewählten Material, der Komplexität des Teils, der vorgesehenen Anwendung und den vorgegebenen Toleranz- und Oberflächenanforderungen ab. Jeder Schritt bedeutet einen zusätzlichen Zeit- und Kostenaufwand. Daher ist es immer von Vorteil, die Konstruktion (DfAM) zu optimieren, um komplexe Nachbearbeitungsschritte zu minimieren.
Herausforderungen meistern: Allgemeine Probleme bei Metall-AM für Schiffsteile und Lösungen
Die additive Fertigung von Metallen bietet zwar erhebliche Vorteile für die Herstellung korrosionsbeständiger Bootsteile, ist aber auch nicht ohne Herausforderungen. Das Verständnis dieser potenziellen Probleme und deren Abschwächung ist entscheidend für die Gewährleistung erfolgreicher Ergebnisse, gleichbleibender Qualität und kostengünstiger Produktion. Sowohl die Ingenieure, die die Teile entwerfen, als auch die Beschaffungsmanager, die die Lieferanten auswählen, müssen sich dieser potenziellen Hürden bewusst sein.
1. Verformung und Eigenspannung:
- Ausgabe: Die intensive, örtlich begrenzte Erwärmung durch den Laser- oder Elektronenstrahl und die anschließende schnelle Abkühlung führt während des Bauprozesses zu erheblichen Temperaturgradienten innerhalb des Teils. Dies führt zu inneren Spannungen (Eigenspannungen), die dazu führen können, dass sich das Teil entweder während des Bauprozesses oder nach der Entnahme aus der Bauplatte verzieht, verformt oder sogar reißt. Dies ist besonders bei großen Teilen oder Teilen mit erheblichen Querschnittsschwankungen von Bedeutung.
- Strategien zur Schadensbegrenzung:
- DfAM: Entwerfen Sie Teile mit allmählichen Übergängen in der Dicke. Vermeiden Sie große, flache freitragende Bereiche.
- Orientierung und Unterstützung aufbauen: Eine strategische Ausrichtung kann die Stressakkumulation minimieren. Robuste Stützstrukturen sind wichtig, um das Teil zu verankern und die Wärme abzuleiten.
- Optimierte Build-Parameter: Eine sorgfältige Steuerung der Laser-/Strahlleistung, der Scan-Geschwindigkeit und der Scan-Strategie (z. B. Verwendung eines Insel-Scanmusters) kann dazu beitragen, den Wärmeeintrag zu steuern und die Belastung zu reduzieren.
- Thermische Simulation: Prozesssimulationssoftware kann Bereiche mit hoher Belastung und potenzieller Verformung vorhersagen, so dass vor dem Druck Design- oder Einrichtungsanpassungen vorgenommen werden können.
- Stressabbau Wärmebehandlung: Die Anwendung eines geeigneten Wärmebehandlungszyklus nach der Herstellung ist für den Abbau der angesammelten Spannungen unerlässlich.
2. Schwierigkeiten beim Entfernen der Stützen:
- Ausgabe: Stützstrukturen sind zwar notwendig, können aber schwierig und zeitaufwändig zu entfernen sein, insbesondere bei inneren Kanälen oder komplexen Geometrien. Bei der manuellen Entfernung besteht die Gefahr, dass die Oberfläche des Teils beschädigt wird oder unerwünschte Markierungen zurückbleiben.
- Strategien zur Schadensbegrenzung:
- DfAM: Minimieren Sie den Bedarf an Stützen, indem Sie selbsttragende Winkel (typischerweise <45°) konstruieren, Verrundungen verwenden und die Ausrichtung der Teile optimieren. Entwerfen Sie Stützen für leichteren Zugang und Ausbrechpunkte, wo immer möglich.
- Spezialisierte Unterstützungsstrukturen: Verwenden Sie Softwarefunktionen, die Stützstrukturen (z. B. Baumstützen, Blockstützen) erzeugen, die für eine leichtere Entfernung und minimale Kontaktpunkte optimiert sind.
- Nachbearbeitungstechniken: Verwendung geeigneter Werkzeuge (Handwerkzeuge, CNC-Bearbeitung, Drahterodieren) für die Entfernung. Berücksichtigen Sie Zeit und Aufwand für die Demontage bei der Kostenschätzung.
3. Konsistente Materialeigenschaften erreichen:
- Ausgabe: Es kann eine Herausforderung sein, sicherzustellen, dass die mechanischen Eigenschaften (Festigkeit, Duktilität, Ermüdungsfestigkeit) und die Korrosionsbeständigkeit des AM-Teils durchgängig konsistent sind und den Spezifikationen des Knet- oder Gussäquivalents entsprechen. Die Eigenschaften können durch Prozessparameter, Pulverqualität, Fertigungsatmosphäre und Nachbearbeitung beeinflusst werden.
- Strategien zur Schadensbegrenzung:
- Qualitätskontrolle des Pulvers: Verwenden Sie hochwertige, konsistente Metallpulver mit bekannten Eigenschaften (Sphärizität, Fließfähigkeit, Partikelgrößenverteilung, Chemie). Beschaffung bei renommierten Lieferanten wie Met3dpdie eine fortschrittliche Zerstäubung (Gaszerstäubung, PREP) und eine strenge Qualitätskontrolle anwenden, ist entscheidend.
- Optimierung der Prozessparameter: Entwicklung und strikte Einhaltung von validierten Bauparametern, die für das Material, die Maschine und die gewünschten Eigenschaften spezifisch sind. Aufrechterhaltung einer strengen Kontrolle der Bauumgebung (Reinheit des Inertgases, Sauerstoffgehalt).
- Geeignete Nachbearbeitung: Durchführung der richtigen Wärmebehandlungszyklen (Spannungsabbau, ggf. HIP) zur Optimierung der Eigenschaften für die jeweilige Legierung und Anwendung.
- Prüfung und Validierung: Führen Sie Materialtests an repräsentativen Mustern oder Coupons durch, die mit jeder Konstruktion gedruckt werden, um zu überprüfen, ob die Eigenschaften den Anforderungen entsprechen.
4. Porositätskontrolle:
- Ausgabe: Im gedruckten Teil können sich manchmal kleine Hohlräume oder Poren bilden, die auf eine unvollständige Verschmelzung zwischen den Schichten, auf Gaseinschlüsse während des Schmelzvorgangs oder auf Pulververunreinigungen/Feuchtigkeit zurückzuführen sind. Poren können die mechanischen Eigenschaften, insbesondere die Ermüdungsfestigkeit, erheblich verschlechtern und potenziell als Ansatzpunkte für Korrosion dienen.
- Strategien zur Schadensbegrenzung:
- Optimierte Prozessparameter: Die Feinabstimmung von Laser-/Strahlleistung, Scangeschwindigkeit und Schraffurabständen ist entscheidend, um ein vollständiges Schmelzen und Verschmelzen zu gewährleisten.
- Qualität und Handhabung des Pulvers: Verwenden Sie hochwertiges, trockenes Pulver mit guter Fließfähigkeit. Sorgen Sie für eine ordnungsgemäße Handhabung und Lagerung des Pulvers, um Feuchtigkeitsaufnahme und Kontamination zu vermeiden. Met3dp’s Fokus auf die Sphärizität und Reinheit des Pulvers hilft, das Porositätsrisiko zu minimieren.
- Atmosphärenkontrolle aufbauen: Sorgen Sie während des Drucks für eine hochreine Inertgasumgebung, um Gaseinschlüsse zu vermeiden.
- Heiß-Isostatisches Pressen (HIP): Wirksam beim Schließen interner Gasporosität, besonders wichtig für ermüdungskritische Teile aus Titan.
- NDT-Inspektion: Verwenden Sie Röntgen- oder CT-Scans für kritische Teile, um interne Porosität zu erkennen und zu quantifizieren.
5. Oberflächenfehler und Konsistenz der Oberfläche:
- Ausgabe: Die fertige Oberfläche kann Defekte wie teilweise geschmolzene und auf die Oberfläche gesinterte Pulverpartikel (Balling), Schichtlinien und Abdrücke von Stützstrukturen aufweisen. Das Erreichen einer gleichmäßig glatten und fehlerfreien Oberfläche bei komplexen Geometrien kann eine Herausforderung sein.
- Strategien zur Schadensbegrenzung:
- Optimierung der Parameter: Feinabstimmung der Oberflächenkonturparameter während des Drucks.
- DfAM & Ausrichtung: Wenn Sie kritische Oberflächen vertikal oder nach oben ausrichten, erzielen Sie im Allgemeinen bessere Ergebnisse. Minimieren Sie nach unten gerichtete Flächen, die Unterstützung benötigen.
- Effektive Nachbearbeitung: Anwendung geeigneter Oberflächenbearbeitungsverfahren (Strahlen, Trommeln, Polieren, Elektropolieren), die auf das Material und das gewünschte Ergebnis zugeschnitten sind. Berücksichtigen Sie die Anforderungen an die Endbearbeitung bei der Konstruktion und Kalkulation.
6. Kosten-Nutzen-Verhältnis:
- Ausgabe: Metall-AM bietet zwar viele Vorteile, ist aber manchmal pro Teil teurer als herkömmliche Verfahren, insbesondere bei einfachen Teilen, die in sehr hohen Stückzahlen hergestellt werden. Die Kosten werden durch teure Maschinen, relativ langsame Fertigungsgeschwindigkeiten, teure Rohstoffe (insbesondere Titanpulver) und notwendige Nachbearbeitungsschritte verursacht.
- Strategien zur Schadensbegrenzung:
- Geeignete Anwendungen: Konzentrieren Sie sich auf Teile, bei denen die Vorteile von AM (Komplexität, Anpassung, Konsolidierung, Gewichtsreduzierung) einen erheblichen Wert darstellen, der die potenziellen Kostenaufschläge aufwiegt.
- DfAM zur Kostenreduzierung: Optimieren Sie Designs, um den Materialverbrauch, die Druckzeit (z. B. Aushöhlung, Gitter) und das Volumen der Stützstruktur bzw. den Aufwand für deren Entfernung zu minimieren. Konsolidieren Sie Teile, um Montagekosten zu sparen.
- Verschachtelung und Optimierung der Erstellung: Maximieren Sie die Anzahl der auf einer einzigen Bauplatte gedruckten Teile, um die Maschinenauslastung zu verbessern.
- Arbeiten Sie mit erfahrenen Anbietern zusammen: Arbeiten mit Metall-AM-Dienstleister die über optimierte Arbeitsabläufe und effiziente Nachbearbeitungsmöglichkeiten verfügen und möglicherweise Mengenrabatte für 3D-Druck im Großhandel. Bewerten Sie die Gesamtbetriebskosten, einschließlich reduzierter Montage- und Lagerhaltungskosten und potenzieller Leistungssteigerungen, und nicht nur die Druckkosten pro Teil.
Durch die Anerkennung dieser Herausforderungen und die proaktive Umsetzung von Abhilfestrategien durch sorgfältiges Design, Prozesskontrolle, hochwertige Materialien, geeignete Nachbearbeitung und die Zusammenarbeit mit erfahrenen Partnern wie Met3dp kann das volle Potenzial der Metall-AM für die Herstellung von hochleistungsfähiger, korrosionsbeständiger Bootshardware erfolgreich genutzt werden.
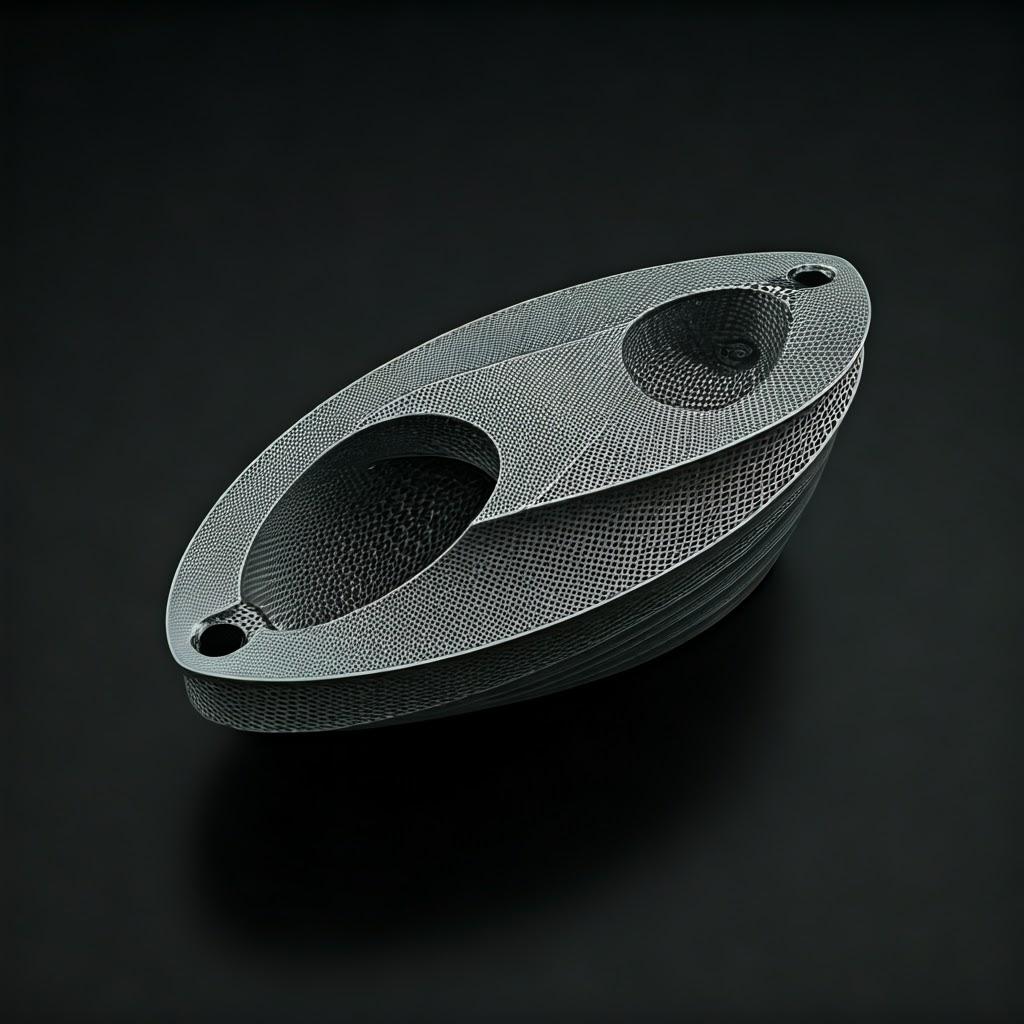
Die Auswahl Ihres Partners: So wählen Sie den richtigen 3D-Druckdienstleister für Bootsteile aus Metall
Die Wahl des richtigen Partners für die additive Fertigung ist ebenso wichtig wie die Auswahl des richtigen Materials oder die Optimierung des Designs. Die Qualität, Zuverlässigkeit und Kosteneffizienz Ihrer 3D-gedruckten Bootshardware hängt in hohem Maße von der Expertise, den Fähigkeiten und den Qualitätssystemen des gewählten Dienstleisters ab. Beschaffungsmanager und Ingenieurteams, die sich an AM für Schiffsanwendungen wagen, müssen bei der Bewertung potenzieller Lieferanten mehr als nur den Preis berücksichtigen. Hier finden Sie eine Checkliste mit Kriterien, die Sie bei der Auswahl eines 3D-Druck-Dienstleister für die Schifffahrt:
1. Fachwissen über maritime Anwendungen und Materialien:
- Erfordernis: Hat der Anbieter nachweislich Erfahrung in der Arbeit mit Kunden aus der Schifffahrtsbranche oder in ähnlich anspruchsvollen Umgebungen? Sind sie mit den Herausforderungen von Korrosion, Ermüdung und struktureller Integrität in der Schifffahrt bestens vertraut?
- Schwerpunkt Materialien: Sind sie auf den Druck von Schiffslegierungen spezialisiert oder haben sie umfangreiche Erfahrungen mit diesen Legierungen wie Edelstahl 316L und Ti-6Al-4V-Titan? Erkundigen Sie sich nach der Entwicklung der Parameter, den Daten zur Materialcharakterisierung und dem Verständnis der Auswirkungen von AM auf die Korrosionsbeständigkeit dieser spezifischen Legierungen.
- Warum das wichtig ist: Ein Anbieter, der mit den Anforderungen der Schifffahrt vertraut ist, versteht besser, wie wichtig die Materialeigenschaften, die Oberflächenbeschaffenheit und die Nachbearbeitung für die Langlebigkeit auf See sind.
2. Angebot an AM-Technologien und -Ausrüstung:
- Erfordernis: Welche Metall-AM-Technologien bieten sie an? Vor allem Pulverbettschmelzen (PBF-LB/SLM) ist für 316L und Ti-6Al-4V üblich und bietet eine hohe Auflösung. Verfügt das Unternehmen über moderne, gut gewartete Drucker für den industriellen Einsatz? Beurteilen Sie deren Kapazitäten für die Herstellung von Volumen - können sie die Größe Ihrer Hardware aufnehmen? Erkundigen Sie sich bei Anbietern wie Met3dp, die nicht nur Dienstleistungen anbieten, sondern auch moderne Drucker herstellen, was auf ein tiefes technisches Verständnis schließen lässt.
- Warum das wichtig ist: Verschiedene Technologien können für bestimmte Geometrien oder Materialien etwas besser geeignet sein. Der Zugang zu moderner Ausrüstung bedeutet in der Regel eine höhere Genauigkeit, Zuverlässigkeit und potenziell schnellere Bauzeiten.
3. Qualitätskontrolle und Rückverfolgbarkeit von Materialien:
- Erfordernis: Wie beschaffen, handhaben, prüfen und lagern sie ihre Metallpulver? Verfügen sie über strenge Qualitätskontrollverfahren für eingehende Pulverchargen (Überprüfung von Chemie, Partikelgrößenverteilung, Morphologie, Fließfähigkeit)? Wie wird die Wiederverwendung von Pulver gehandhabt und eine Kreuzkontamination verhindert? Gibt es eine vollständige Rückverfolgbarkeit von der Rohpulvercharge bis zum fertigen Teil?
- Met3dp Vorteil: Unternehmen wie Met3dp, die ihre eigenen hochwertigen Pulver mit fortschrittlichen Methoden wie Gaszerstäubung und PREP herstellen, haben von Anfang an eine inhärente Kontrolle über die Pulverqualität und gewährleisten so die für anspruchsvolle Anwendungen wichtige Konsistenz. Suchen Sie nach Lieferanten, die ihre Pulvermanagement-Protokolle priorisieren und dokumentieren können.
- Warum das wichtig ist: Die Qualität des Pulvers wirkt sich direkt auf die Dichte, das Gefüge, die mechanischen Eigenschaften und die Fehlerquote des Endprodukts aus. Die Rückverfolgbarkeit ist für die Qualitätssicherung und Zertifizierung unerlässlich.
4. Bewährte Erfolgsbilanz und Fallstudien:
- Erfordernis: Kann der Anbieter Beispiele für ähnliche Projekte nennen, die er erfolgreich abgeschlossen hat? Achten Sie auf Fallstudien, Zeugnisse oder Referenzen, insbesondere in den Bereichen Schifffahrt, Luft- und Raumfahrt oder Medizin, in denen oft vergleichbare Qualitätsanforderungen gelten.
- Warum das wichtig ist: Die bisherige Leistung ist ein starker Indikator für Leistungsfähigkeit und Zuverlässigkeit. Sie zeigt, dass sie technische Anforderungen in qualitativ hochwertige Fertigteile umsetzen können.
5. Zertifizierungen und Qualitätsmanagementsystem (QMS):
- Erfordernis: Verfügt der Anbieter über einschlägige Zertifizierungen? ISO 9001 zertifizierung ist ein grundlegender Indikator für ein robustes QMS. Je nach Kritikalität Ihrer Hardware können zusätzliche Zertifizierungen von Vorteil sein (z. B. AS9100 für die Luft- und Raumfahrt, was sehr hohe Standards voraussetzt, oder potenziell schiffsspezifische Zertifizierungen wie DNV- oder ABS-Prozesszulassungen, obwohl diese für AM noch in der Entwicklung sind).
- Warum das wichtig ist: Zertifizierungen belegen das Engagement für Qualität, Prozesskontrolle, Dokumentation und kontinuierliche Verbesserung - eine wesentliche Voraussetzung für die Herstellung zuverlässiger, unternehmenskritischer Hardware.
6. Hausinterne Nachbearbeitungsmöglichkeiten:
- Erfordernis: Kann der Anbieter die erforderlichen Nachbearbeitungsschritte selbst durchführen (Spannungsabbau, Entfernen von Stützen, einfache Endbearbeitung)? Oder ist er in hohem Maße auf Zulieferer angewiesen? Wie hoch ist ihre Kompetenz bei speziellen Verfahren wie CNC-Bearbeitung von AM-Teilen, HIP, Elektropolieren oder Passivieren?
- Warum das wichtig ist: Interne Kapazitäten führen in der Regel zu einer besseren Kontrolle über den gesamten Arbeitsablauf, zu potenziell kürzeren Vorlaufzeiten und zu einer optimierten Verantwortlichkeit. Wenn das Unternehmen Unteraufträge vergibt, sollten Sie den Prozess des Lieferantenmanagements kennen.
7. Technische Unterstützung und DfAM-Fachwissen:
- Erfordernis: Bietet der Anbieter technische Unterstützung an? Kann er Sie bei der Optimierung Ihres Designs für die additive Fertigung (DfAM) unterstützen? Verfügt der Anbieter über Ingenieure, die sowohl die Grundsätze der Schiffstechnik als auch die Grenzen und Möglichkeiten des AM-Prozesses kennen?
- Warum das wichtig ist: Die Zusammenarbeit bei DfAM kann die Leistung der Teile erheblich verbessern, die Kosten senken und die Herstellbarkeit sicherstellen. Dies ist besonders wertvoll, wenn Ihr Team neu im Design für AM ist.
8. Kapazität, Vorlaufzeiten und Skalierbarkeit:
- Erfordernis: Ist der Anbieter in der Lage, die von Ihnen erwarteten Mengen und Vorlaufzeiten zu erfüllen? Wie wird die Terminplanung gehandhabt? Kann er die Produktion hoch- oder runterfahren, wenn sich Ihre Anforderungen ändern? Erörtern Sie die typischen vorlaufzeit der additiven Fertigung für Bootsteile.
- Warum das wichtig ist: Gewährleistet die rechtzeitige Lieferung und die Fähigkeit, Ihre Produktions- oder MRO (Maintenance, Repair, Overhaul)-Zeitpläne zu unterstützen. Wichtig für Beschaffungsmanager abgleich von Bestandsaufnahme und Projektzeitplänen.
9. Kommunikation und Kundenbetreuung:
- Erfordernis: Sind sie reaktionsschnell, transparent und leicht zu erreichen? Liefern sie klare Kostenvoranschläge und Aktualisierungen?
- Warum das wichtig ist: Eine starke Arbeitsbeziehung, die auf einer klaren Kommunikation beruht, ist für die Bewältigung der komplexen AM-Projekte unerlässlich.
Evaluierung potenzieller Lieferanten – Schlüsselfragen für die Beschaffung:
- Erkundigen Sie sich nach den Erfahrungen mit 316L und Ti-6Al-4V für den Einsatz im Meer oder in korrosiven Umgebungen.
- Erkundigen Sie sich nach der Beschaffung des Pulvers, den Qualitätskontrollverfahren und den Methoden der Rückverfolgbarkeit.
- Erkundigen Sie sich nach ihren QMS-Zertifizierungen (fordern Sie Kopien an).
- Überprüfen Sie die Ausrüstungsliste und die angegebenen Toleranzen/Ausführungen.
- Fragen Sie nach einschlägigen Fallstudien oder Referenzen.
- Klärung der Frage, ob die Nachbearbeitung im eigenen Haus oder bei einem Zulieferer erfolgt.
- Den DfAM-Unterstützungsprozess zu verstehen.
- Fordern Sie detaillierte Angebote an, in denen alle Kosten (Material, Druckzeit, Nachbearbeitung, Qualitätskontrolle) aufgeführt sind.
- Bestätigen Sie die Vorlaufzeiten und die Kapazität für Ihr geplantes Volumen.
Die Wahl des richtigen Partners ist eine Investition in Qualität und Zuverlässigkeit. Gründliche Prüfung potenzieller metall-AM-Lieferanten die Anwendung dieser Kriterien erhöht die Wahrscheinlichkeit einer erfolgreichen Nutzung der additiven Fertigung für Ihren Bedarf an hochleistungsfähigen, korrosionsbeständigen Bootsteilen erheblich.
Budgetierung und Zeitpläne: Kostenfaktoren und Vorlaufzeiten für AM Boat Hardware verstehen
Während die additive Fertigung von Metallteilen erhebliche technische Vorteile für die Bootshardware mit sich bringt, ist das Verständnis der damit verbundenen Kosten und Produktionsfristen für eine effektive Projektplanung, Budgetierung und das Management der Lieferkette von entscheidender Bedeutung. Sowohl Ingenieure, die Teile anfordern, als auch Beschaffungsmanager, die Bestellungen ausstellen, brauchen ein klares Bild davon, was den Endpreis und den Lieferplan bestimmt.
Faktoren, die die Kosten für AM-Bootsteile beeinflussen:
- Teilvolumen und Bounding Box:
- Materialverbrauch: Größere Teile verbrauchen natürlich mehr teures Metallpulver (insbesondere Ti-6Al-4V). Eine Optimierung des Designs (Aushöhlung, Gitter über DfAM) kann den Materialverbrauch erheblich reduzieren.
- Druckzeit: Größere Teile oder Teile mit größeren Querschnittsflächen pro Schicht brauchen länger zum Drucken, was die Kosten für die Maschinenzeit erhöht. Die Gesamthöhe des Teils in der Baukammer ist ein wichtiger Faktor für die Druckdauer.
- Auslastung der Maschine: Wie effizient das Bauvolumen gepackt wird (Verschachtelung mehrerer Teile), wirkt sich auf die amortisierten Kosten der Maschinenzeit pro Teil aus. Preise für 3D-Druck im Großhandel profitiert oft von effizient gepackten Bauplatten.
- Teil Komplexität:
- Geometrische Komplexität: Während AM die Komplexität gut bewältigen kann, erfordern hochkomplexe Designs möglicherweise umfangreichere Stützstrukturen oder eine anspruchsvollere Nachbearbeitung, was zusätzliche Kosten verursacht. Allerdings wird AM oft mehr mit zunehmender Komplexität kostengünstiger als herkömmliche Methoden.
- Unterstützende Strukturen: Das Volumen des benötigten Stützmaterials erhöht die Druckzeit und die Materialkosten. Noch wichtiger ist, dass der Zeit- und Arbeitsaufwand für das Entfernen der Stützen einen großen Kostenfaktor darstellen kann, insbesondere bei komplexen internen Stützen. Der Fokus von DfAM liegt auf der Minimierung von Stützen.
- Materialart und Kosten:
- Pulver Preis: Die Rohstoffkosten schwanken erheblich. Ti-6Al-4V-Pulver ist wesentlich teurer (oft 5-10x oder mehr) als 316L-Edelstahlpulver. Dies ist ein wesentlicher Unterschied bei den Endkosten der Teile.
- Assoziierte Verarbeitung: Der Titandruck erfordert oft eine strengere Kontrolle der Atmosphäre und möglicherweise eine aufwändigere Nachbearbeitung (wie HIP), was die Kosten im Vergleich zu Edelstahl erhöht.
- Druckzeit (Maschinenstundensatz):
- Industrielle Metall-AM-Maschinen stellen eine beträchtliche Kapitalinvestition dar, und ihre Betriebskosten (Energie, Inertgas, Wartung) sind beträchtlich. Dienstleister berechnen einen Stundensatz für die Maschinennutzung in ihre Preise ein. Längere Druckzeiten erhöhen direkt die Kosten.
- Nachbearbeitungsanforderungen:
- Dies ist oft ein einen erheblichen Teil der Endkosten. Jeder Schritt bedeutet zusätzlichen Arbeitsaufwand, Maschinenzeit (bei CNC-Bearbeitung) und möglicherweise Kosten für Spezialausrüstung.
- Grundlegend: Entstaubung, Stressabbau, Abstützung.
- Zwischenstufe: Strahlen, Taumeln.
- Fortgeschritten/Kostspielig: CNC-Bearbeitung für enge Toleranzen, HIP, Elektropolieren, manuelles Polieren für kosmetische Veredelungen.
- Der Grad der geforderten Endbearbeitung (von funktionaler Toleranz bis hin zu hochglänzender maritimer Ästhetik) wirkt sich dramatisch auf den Preis aus.
- Qualitätssicherung und Inspektion:
- Der Umfang der erforderlichen Inspektion (Sichtprüfung, Maßprüfung, zerstörungsfreie Prüfung wie Röntgen/CT-Scannen, Materialprüfung) verursacht zusätzliche Kosten, die sich nach dem erforderlichen Zeitaufwand, der Ausrüstung und dem Fachwissen richten. Kritische Komponenten erfordern natürlich strengere und kostspieligere Qualitätssicherungsverfahren.
- Bestellmenge:
- AM eignet sich zwar hervorragend für die Anpassung an Kundenwünsche und geringe Stückzahlen, aber es fallen immer noch Einrichtungskosten an (Bauvorbereitung, Programmierung). Durch die Verteilung dieser Kosten auf eine größere Charge kann der Preis pro Teil gesenkt werden. Einige Anbieter bieten Mengenrabatte an, aber die Kurve ist im Allgemeinen flacher als bei traditionellen Massenproduktionsverfahren. Erörtern Sie das Potenzial für 3D-gedruckte Bootsteile als Massenware preisgestaltung.
Typische Vorlaufzeiten für AM Boat Hardware:
Die Vorlaufzeit ist die Gesamtzeit von der Auftragserteilung bis zur Lieferung des Teils. Sie kann je nach Komplexität, Menge, aktueller Auslastung des Lieferanten und erforderlicher Nachbearbeitung stark variieren.
- Auftragsabwicklung & Entwurfsprüfung (1-3 Tage): Bestätigung der Anforderungen, Überprüfung des Entwurfs auf Herstellbarkeit (DfAM-Check), Fertigstellung des Angebots.
- Druckeinrichtung & Terminierung (1-5 Tage): Vorbereitung der Bauakte, Verschachtelung der Teile auf der Bauplatte, Terminierung des Auftrags auf einer verfügbaren Maschine. Der Rückstand der Lieferanten beeinflusst diese Phase stark.
- Druck-/Herstellungszeit (1-7+ Tage): Äußerst variabel. Hängt von der Höhe des Teils, dem Volumen und der Anzahl der verschachtelten Teile ab. Ein großes, einzelnes Teil kann mehrere Tage in Anspruch nehmen; eine Platte mit vielen kleinen Teilen kann zwar schneller pro Teil gedruckt werden, aber die Maschine ist trotzdem einen Tag oder länger beschäftigt.
- Abklingzeit & Auspowern (0,5-1 Tag): Lassen Sie die Baukammer abkühlen, bevor Sie Teile und Pulver sicher entfernen.
- Nachbearbeitung (2-10+ Tage): Dies ist oft der längste und variabelste Teil der Vorlaufzeit.
- Stressabbau: ~1 Tag (einschließlich Ofenzeit und Abkühlung).
- Entfernung der Unterstützung: Sehr variabel (Stunden bis Tage).
- Bearbeitungen: Abhängig von der Komplexität und der Verfügbarkeit der Maschinenhalle (Tage).
- Endbearbeitung (Strahlen, Polieren usw.): Variabel (Stunden bis Tage).
- HIP (falls erforderlich): Kann aufgrund der speziellen Zykluszeiten und der Logistik mehrere Tage in Anspruch nehmen.
- Qualitätskontrolle & Inspektion (1-3 Tage): Je nach Bedarf.
- Versand (1-5 Tage): Je nach Standort und Versandart.
Geschätzte Gesamtvorlaufzeit: Für ein typisches Metall-AM-Bootsteil, das eine Standard-Nachbearbeitung erfordert, sind Vorlaufzeiten von 1.5 bis 4 Wochen. Teile, die eine umfangreiche Bearbeitung, eine komplexe Endbearbeitung oder HIP erfordern oder in Zeiten hoher Nachfrage beschafft werden, könnten länger dauern.
Vergleich mit traditionellen Methoden:
- Für komplexe Teile nach Maß oder in Kleinseriesind die AM-Vorlaufzeiten oft erheblich kürzer als auf maßgeschneiderte Gussformen oder Schmiedegesenke zu warten (was Monate dauern kann).
- Für hochvolumige, einfache Teileherkömmliche Verfahren mit vorhandenen Werkzeugen sind in der Regel schneller in der Massenproduktion, wobei jedoch die anfängliche Vorlaufzeit für die Werkzeuge berücksichtigt werden muss.
Tipp zur Budgetierung: Fordern Sie immer detaillierte Angebote an, in denen die Kosten für Einrichtung, Material, Druck und jeden wichtigen Nachbearbeitungsschritt aufgeschlüsselt sind. Diese Transparenz hilft dabei, die Kostenfaktoren zu verstehen und fundierte Entscheidungen über Designänderungen oder Nachbearbeitungsanforderungen zu treffen. Genaue benutzerdefinierte Boot Hardware Kostenvoranschlag erfordert klare Spezifikationen und Kommunikation mit Ihrem AM-Partner.
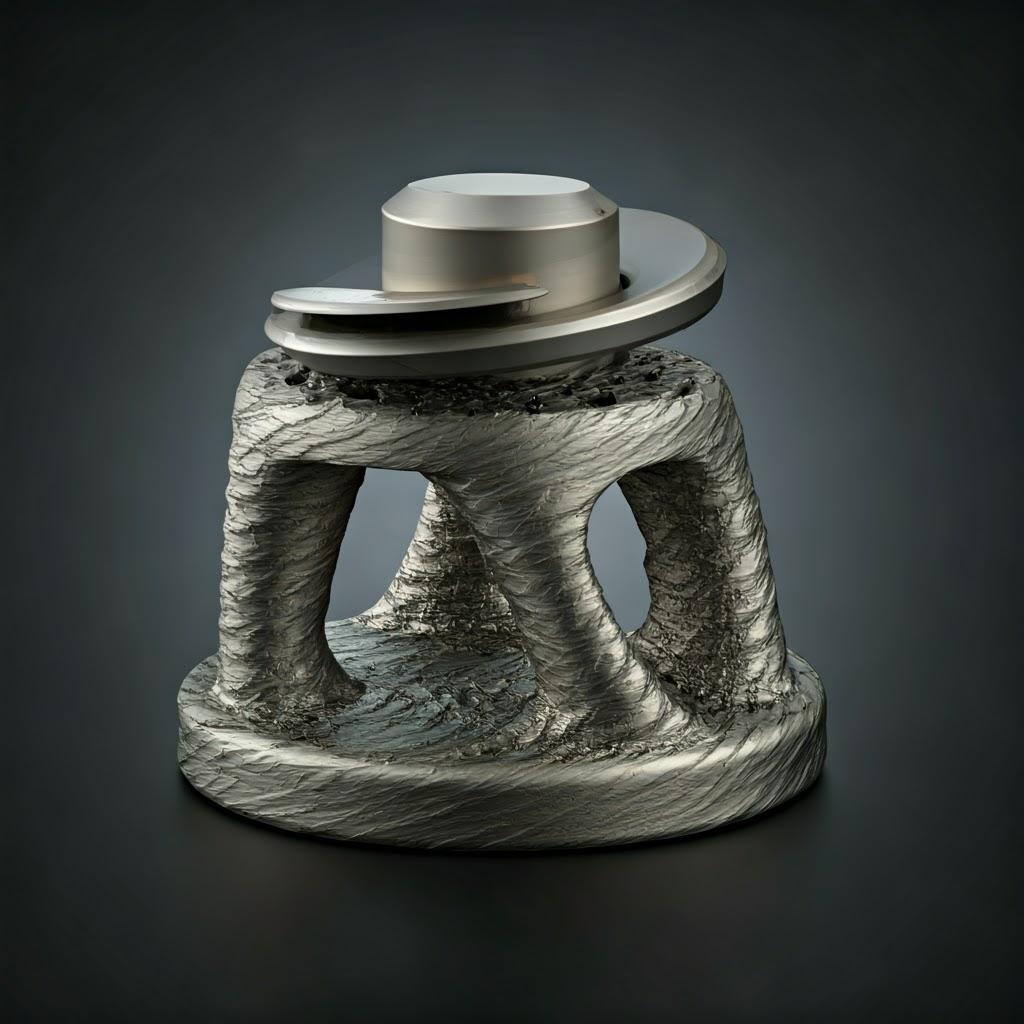
Häufig gestellte Fragen (FAQ) über 3D-gedruckte Bootsteile
Hier finden Sie Antworten auf einige häufig gestellte Fragen von Ingenieuren und Beschaffungsmanagern zum Einsatz der additiven Fertigung von Metall für Bootsteile:
F1: Sind 3D-gedruckte Bootsteile genauso stabil und korrosionsbeständig wie traditionell hergestellte Teile (z. B. gegossene oder geschmiedete)?
A: Ja, möglicherweise sogar noch besser, wenn die richtigen Materialien, Prozesskontrollen und Nachbearbeitungen verwendet werden.
- Stärke: AM-Metallteile können, insbesondere nach einer geeigneten Wärmebehandlung (und HIP für ermüdungskritisches Ti-6Al-4V), mechanische Eigenschaften (Zugfestigkeit, Streckgrenze) erreichen, die denen von gleichwertigen Gusswerkstoffen entsprechen oder sie übertreffen und mit denen von Knetwerkstoffen vergleichbar sind. Das feinkörnige Mikrogefüge, das bei der AM häufig erreicht wird, kann manchmal zu einer höheren Festigkeit führen.
- Korrosionsbeständigkeit: Die Verwendung von Legierungen in Marinequalität wie 316L und Ti-6Al-4V ist entscheidend. Geeignete Druckparameter, um die volle Dichte (>99,5 %) zu erreichen, und eine angemessene Nachbearbeitung (z. B. Spannungsabbau bei beiden, Passivierung und Elektropolieren bei 316L) sind für die Maximierung der Korrosionsbeständigkeit von entscheidender Bedeutung und gewährleisten eine Leistung, die der herkömmlicher Gegenstücke entspricht oder diese übertrifft. Ti-6Al-4V bietet im Allgemeinen eine bessere Korrosionsbeständigkeit als 316L in den meisten maritimen Umgebungen.
F2: Wie groß ist der typische Kostenunterschied zwischen AM und Guss/Bearbeitung für Bootsteile?
A: Sie hängt stark von der Komplexität der Teile und dem Auftragsvolumen ab.
- Geringes Volumen / hohe Komplexität: Für einmalige kundenspezifische Teile, Prototypen oder Kleinserien (Dutzende bis wenige Hunderte) komplexer Geometrien ist AM oft kostengünstiger weil es hohe Werkzeugkosten (Gießen/Schmieden) oder umfangreiche Programmier- und Bearbeitungszeiten vermeidet.
- Großes Volumen / Einfache Teile: Bei Tausenden von identischen, relativ einfachen Teilen sind die Kosten pro Teil bei traditionellen Verfahren wie Gießen oder Schmieden aufgrund von Skaleneffekten in der Regel niedriger, trotz der anfänglichen Investitionen in die Werkzeuge.
- Faustformel: AM bietet sich dort an, wo die Komplexität des Entwurfs hoch ist, eine kundenspezifische Anpassung erforderlich ist, die Vorlaufzeiten für die Werkzeugherstellung unerschwinglich sind oder die Konsolidierung von Teilen erhebliche nachgelagerte Einsparungen ermöglicht (Montage, Lagerbestand). Holen Sie immer Angebote für beide Methoden ein, wenn Volumen und Komplexität grenzwertig sind.
F3: Können bestehende Bootsbeschlagsentwürfe (ursprünglich für Guss/Bearbeitung) direkt in 3D gedruckt werden?
A: Obwohl technisch möglich, ist es oft nicht optimal. Der direkte Druck eines Designs, das für den Guss oder die maschinelle Bearbeitung vorgesehen ist, nutzt die Hauptvorteile von AM nicht und kann sogar weniger effizient sein.
- Empfehlung: Bestehende Entwürfe sollten idealerweise überprüft und möglicherweise neu gestaltet werden, indem Design für additive Fertigung (DfAM) prinzipien. Dies ermöglicht eine Gewichtsreduzierung (Topologieoptimierung), die Konsolidierung von Teilen, die Minimierung von Stützstrukturen und das Hinzufügen komplexer Merkmale, die die Leistung verbessern - Vorteile, die sich bei einer direkten Übersetzung nicht ergeben würden. Ein guter AM-Dienstleister kann Sie bei diesem Umgestaltungsprozess unterstützen.
F4: Auf welche Zertifizierungen sollte ich bei einem Metall-AM-Anbieter für Schiffskomponenten achten?
A: Die Zertifizierungsanforderungen hängen von der Kritikalität der Hardware ab.
- Grundlegend: ISO 9001:2015 weist ein funktionierendes Qualitätsmanagementsystem nach, das für die Konsistenz und Rückverfolgbarkeit entscheidend ist.
- Luft- und Raumfahrt Äquivalent (hoher Standard): AS9100 weist auf sehr ausgereifte Verfahren hin, die häufig auf kritische Komponenten anwendbar sind.
- Meeresspezifisch: Zertifizierungen von Schiffsklassifikationsgesellschaften (z. B. DNV, ABS, Lloyd’s Register) für AM-Prozesse, -Materialien oder -Anlagen werden immer häufiger, sind aber noch nicht weit verbreitet. Ihre Relevanz hängt davon ab, ob die spezifische Hardware eine Klassenzulassung erfordert (z. B. kritische Struktur- oder Sicherheitskomponenten auf klassifizierten Schiffen). Fragen Sie potenzielle Lieferanten nach ihren Erfahrungen mit Teilen, die eine Klassenzulassung erfordern, auch wenn die Anlage selbst noch nicht vollständig zertifiziert ist.
F5: Wie gewährleistet Met3dp die Qualität seiner Metallpulver für Schiffsanwendungen?
A: Met3dp legt größten Wert auf die Qualität des Pulvers, da sie die Grundlage für leistungsstarke AM-Teile darstellt. Ihr Ansatz umfasst:
- Fortgeschrittene Produktionsmethoden: Durch den Einsatz der branchenführenden Gaszerstäubung (für Legierungen wie 316L) und des Plasma-Rotations-Elektroden-Verfahrens (PREP – insbesondere für reaktive Legierungen wie Ti-6Al-4V) werden eine hohe Sphärizität, ein geringer Satellitengehalt, eine gute Fließfähigkeit und eine hohe Reinheit erreicht.
- Strenge Qualitätskontrolle: Einführung strenger Prüfprotokolle für jede Pulvercharge, die die chemische Zusammensetzung, die Partikelgrößenverteilung (PSD), die Morphologie (Form), die Fließgeschwindigkeit und die Schütt-/Hahndichte analysieren.
- Optimiert für AM-Prozesse: Sicherstellen, dass die Pulver für Pulverbettschmelzverfahren (PBF-LB/SLM, EBM) maßgeschneidert sind, was zu einem gleichmäßigen Schmelzverhalten, einer hohen Teiledichte (>99,5 %) und vorhersehbaren mechanischen Eigenschaften führt.
- Material-Portfolio: Wir bieten eine Reihe relevanter Marinewerkstoffe an, darunter hochwertiges 316L und Ti-6Al-4V sowie andere fortschrittliche Legierungen. Sie können deren spezifisches Pulver erkunden Produkt Angebote.
- Fachwissen: Ihre jahrzehntelange Erfahrung in der Metallurgie und der additiven Fertigung fließt in ihre Pulverentwicklung und ihre Produktionsprozesse ein.
Diese Konzentration auf die Qualität des Pulvers führt direkt zu zuverlässigeren, fehlerfreien und leistungsstarken 3D-gedruckten Schiffskomponenten für ihre Kunden.
Schlussfolgerung: Segel setzen mit fortschrittlicher Fertigung - Die Zukunft der Bootshardware ist additiv
In der maritimen Welt sind Komponenten gefragt, die den unerbittlichen Kräften der Natur standhalten und gleichzeitig eine unerschütterliche Leistung und Sicherheit bieten. Wie wir erforscht haben, ist die additive Fertigung von Metallen unter Verwendung robuster Materialien wie Edelstahl 316L als auch Hochleistungs- Ti-6Al-4V-Titanlegierungist nicht länger ein futuristisches Konzept, sondern eine praktische und leistungsstarke Lösung für die Herstellung hochwertiger Bootshardware.
Von maßgefertigten Klampen, die für spezifische Rumpfkonturen entwickelt wurden, bis hin zu topologisch optimierten Halterungen, die kritisches Gewicht einsparen, und von konsolidierten Baugruppen, die die Komplexität reduzieren, bis hin zum bedarfsgerechten Ersatz veralteter Teile - Metall-AM bietet für eine wachsende Anzahl von Schiffsanwendungen überzeugende Vorteile gegenüber herkömmlichen Methoden. Die Fähigkeit zu erreichen beispiellose Designfreiheitdies ermöglicht Teile, die hinsichtlich Festigkeit, Gewicht und Funktion optimiert sind, kombiniert mit dem Potenzial für schnelles Prototyping, kürzere Vorlaufzeiten für kundenspezifische Teile und verbesserte Materialeigenschaftenmacht AM zu einem transformativen Werkzeug für Schiffsingenieure und Hersteller.
Zu den wichtigsten Erkenntnissen gehören:
- Korrosionsbeständigkeit: AM-Teile aus 316L und Ti-6Al-4V erfüllen oder übertreffen bei ordnungsgemäßer Verarbeitung die Korrosionsbeständigkeitsstandards, die für raue Meeresumgebungen erforderlich sind.
- Leistungsverbesserung: Die DfAM-Prinzipien ermöglichen eine leichtere und stabilere Hardware durch Topologieoptimierung und Teilekonsolidierung, was die Leistung und Effizienz von Schiffen verbessert.
- Flexibilität der Lieferkette: Produktionsmöglichkeiten auf Abruf reduzieren den Lagerbedarf und bieten Lösungen für Ersatzteile und Veralterung.
- Anpassungen: AM macht maßgeschneiderte Hardware wirtschaftlich realisierbar und erfüllt die einzigartigen Bedürfnisse von Yachtbauern, spezialisierten Handelsschiffen und Nachrüstungsprojekten.
Zwar gibt es Herausforderungen im Zusammenhang mit den Kosten für hohe Stückzahlen, der Prozesskontrolle und der Nachbearbeitung, doch werden diese durch technologische Fortschritte, verbesserte DfAM-Praktiken und das wachsende Fachwissen spezialisierter Dienstleistungsanbieter aktiv angegangen. Die Zusammenarbeit mit einem sachkundigen Lieferanten, der über fortschrittliche Technologie, strenge Qualitätskontrollen (angefangen beim Pulver) und Fachwissen über Schiffsanwendungen verfügt, ist von entscheidender Bedeutung für den Erfolg.
Der Weg zur Einführung der additiven Fertigung erfordert ein Umdenken - man muss sich auf neue Designmöglichkeiten einlassen und die Feinheiten der Technologie verstehen. Aber die Belohnungen - haltbarere, effizientere und innovativere Schiffskomponenten - sind die Reise allemal wert.
Sind Sie bereit zu erfahren, wie die additive Fertigung von Metallen Ihre Bootsteile revolutionieren kann? Ganz gleich, ob Sie Schiffe der nächsten Generation entwerfen, nach Leistungsverbesserungen suchen oder zuverlässige Lösungen für die Beschaffung von Schiffskomponenten benötigen - die Möglichkeiten von AM sind zum Greifen nah.
Kontaktieren Sie Met3dp noch heute um Ihre spezifischen Anforderungen zu besprechen. Mit unserem branchenführenden Know-how in der Herstellung hochwertiger Metallpulver (einschließlich 316L und Ti-6Al-4V in Marinequalität), fortschrittlichen SEBM- und PBF-LB-Drucklösungen und umfassender Anwendungsunterstützung sind wir bereit, Ihnen bei der Navigation in der Welt der additiven Fertigung zu helfen und ihr volles Potenzial für Ihre Marineprojekte zu nutzen. Besuchen Sie unsere Website unter https://met3dp.com/ um mehr über unsere Möglichkeiten zu erfahren und loszulegen.
Teilen auf
MET3DP Technology Co., LTD ist ein führender Anbieter von additiven Fertigungslösungen mit Hauptsitz in Qingdao, China. Unser Unternehmen ist spezialisiert auf 3D-Druckgeräte und Hochleistungsmetallpulver für industrielle Anwendungen.
Fragen Sie an, um den besten Preis und eine maßgeschneiderte Lösung für Ihr Unternehmen zu erhalten!
Verwandte Artikel
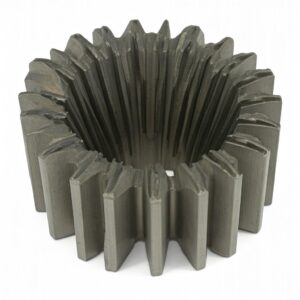
Hochleistungs-Düsenschaufelsegmente: Revolutionierung der Turbineneffizienz mit 3D-Metalldruck
Mehr lesen "Über Met3DP
Aktuelles Update
Unser Produkt
KONTAKT US
Haben Sie Fragen? Senden Sie uns jetzt eine Nachricht! Wir werden Ihre Anfrage mit einem ganzen Team nach Erhalt Ihrer Nachricht bearbeiten.
Holen Sie sich Metal3DP's
Produkt-Broschüre
Erhalten Sie die neuesten Produkte und Preislisten
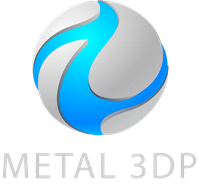
Metallpulver für 3D-Druck und additive Fertigung