Chrom-Pulver-Hartlegierungen
Inhaltsübersicht
Stellen Sie sich eine Welt vor, in der Maschinen nicht aufgrund von Verschleiß zum Stillstand kommen. In der Werkzeuge ihre scharfen Kanten länger behalten und Komponenten der Abrieb wie Champions widerstehen. Dies ist die Realität, die Chrompulver-Hartlegierungen bieten.
Diese bemerkenswerten Materialien werden sorgfältig durch die Kombination der Festigkeit von Metallpulvern mit der unglaublichen Härte von Keramikpartikeln hergestellt. Stellen Sie es sich wie ein Superhelden-Team vor – die Metallpulver bilden eine robuste Grundlage, während die Keramikpartikel als ultimative Verteidigung gegen Verschleiß fungieren. Das Ergebnis? Eine wirksame Mischung, die Reibung überwindet und die Lebensdauer Ihrer wichtigsten Industriekomponenten verlängert.
Aber bevor wir tiefer eintauchen, wollen wir die Einzelheiten der Chrompulver-Hartlegierungen aufschlüsseln.
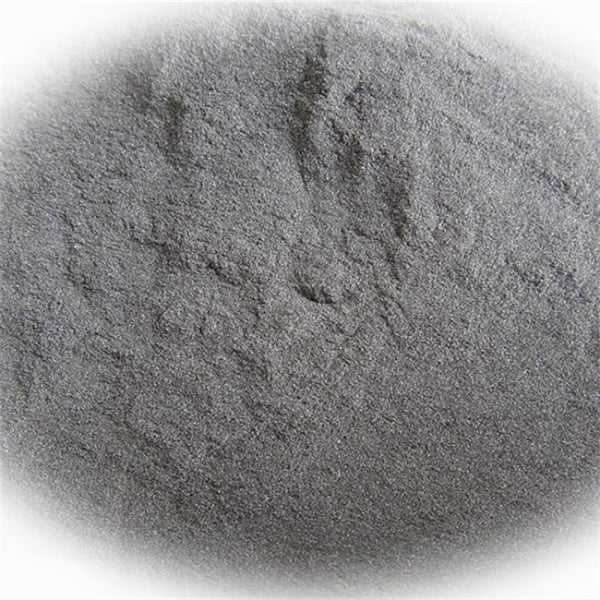
Verständnis Chrompulver-Hartlegierung
Metall-Pulver: Die Basis dieser Legierungen besteht typischerweise aus:
- Nickel: Dieses vielseitige Metall bietet ausgezeichnete Festigkeit, Duktilität und Korrosionsbeständigkeit und bildet das Rückgrat der Legierung.
- Chrom: Stellen Sie sich die Rüstung eines Ritters vor – das ist es, was Chrom in die Gleichung einbringt. Es erhöht die Härte und Oxidationsbeständigkeit der Legierung.
- Eisen: Haben Sie sich jemals gefragt, warum Gusseisenpfannen so haltbar sind? Eisen trägt zur Gesamtfestigkeit und Verschleißfestigkeit der Legierung bei.
- Molybdän: Stellen Sie sich Molybdän als die geheime Zutat für Hochleistungsanwendungen vor. Es erhöht die Beständigkeit der Legierung gegen Erweichung bei erhöhten Temperaturen.
Keramikpartikel: Die Geheimwaffe in diesem Arsenal ist:
- Chromkarbid (Cr3C2): Diese unglaublich harte Keramik wirkt wie mikroskopische Diamanten und erhöht die Abrieb- und Verschleißfestigkeit der Legierung drastisch.
Die Bindungsmagie: Diese einzelnen Komponenten werden dann durch einen Prozess namens Sintern miteinander verschmolzen. Stellen Sie sich vor, winzige Bausteine verwandeln sich auf magische Weise in eine einheitliche Struktur – das ist die Essenz des Sinterns. Das Endprodukt ist eine robuste Legierung mit außergewöhnlicher Verschleißfestigkeit.
Erkundung der vielfältigen Auswahl an Hartmetalllegierungen aus Chrompulver
Lernen wir nun einige der wichtigsten Akteure in der Liga der Hartmetalllegierungen aus Chrompulver kennen, die jeweils einzigartige Eigenschaften für spezifische Anwendungen aufweisen:
- WC-Ni (Wolframkarbid-Nickel): Eine klassische Wahl, die ein fantastisches Gleichgewicht aus Härte, Zähigkeit und Verschleißfestigkeit bietet. Sie zeichnet sich in Anwendungen wie Schneidwerkzeugen, Verschleißplatten und Matrizen aus.
- CrC-Ni (Chromkarbid-Nickel): Diese Legierung glänzt in Hochtemperaturumgebungen aufgrund ihrer überlegenen Oxidationsbeständigkeit. Sie ist ein Champion in Anwendungen wie Ofenkomponenten, Wärmetauschern und Warmstanzwerkzeugen.
- (Fe,Cr)C-Ni ((Eisen, Chrom) Karbid-Nickel): Diese Legierung vereint das Beste aus beiden Welten und bietet ein gutes Gleichgewicht aus Härte, Zähigkeit und Korrosionsbeständigkeit. Sie ist eine vielseitige Wahl für Anwendungen wie Zahnräder, Pumpenwellen und Verschleißauskleidungen.
- Ni-Si (Nickel-Silizium): Diese Legierung priorisiert die Verschleißfestigkeit mit einer geringeren Härte im Vergleich zu anderen. Sie kompensiert dies jedoch mit ausgezeichneter Hochtemperatur-Oxidationsbeständigkeit und Korrosionsbeständigkeit, was sie ideal für Anwendungen wie Auspuffkrümmer und Turboladerkomponenten macht.
- Ni-Al (Nickel-Aluminium): Diese leichte Option zeichnet sich durch gute Verschleißfestigkeit und ausgezeichnete Beständigkeit gegen Oxidation und Sulfidierung aus. Sie ist eine beliebte Wahl für Anwendungen in der Luft- und Raumfahrt- und Automobilindustrie.
- CoCr-WC (Kobalt-Chrom-Wolframkarbid): Stellen Sie sich eine Legierung vor, die speziell für Hochtemperatur- und Hochdruckumgebungen entwickelt wurde. Das ist CoCr-WC, das in Anwendungen wie Gasturbinenkomponenten und Ventilsitzen bevorzugt wird.
- Ni-Mo (Nickel-Molybdän): Diese Legierung priorisiert Festigkeit und Zähigkeit bei erhöhten Temperaturen. Sie ist eine zuverlässige Wahl für Anwendungen wie Dampfturbinenschaufeln und Wärmetauscherkomponenten.
- Fe-Cr-B-Si (Eisen-Chrom-Bor-Silizium): Diese komplexe Legierung bietet außergewöhnliche Verschleißfestigkeit mit guter Zähigkeit. Stellen Sie sie sich als den ultimativen Bodyguard für Komponenten vor, die extremer Abnutzung ausgesetzt sind, was sie ideal für Anwendungen wie Brecherbacken und Verschleißauskleidungen in Bergbauausrüstung macht.
- Ni-Fe-Cr-P (Nickel-Eisen-Chrom-Phosphor): Diese Legierung priorisiert Zähigkeit und Verschleißfestigkeit, insbesondere in Anwendungen mit Gleitverschleiß. Sie ist eine beliebte Wahl für Komponenten wie Zahnräder, Walzwerkswalzen und Verschleißplatten.
- Ni-Cr-Mo-B (Nickel-Chrom-Molybdän-Bor): Stellen Sie sich eine Legierung vor, die speziell für Hochspannungsanwendungen entwickelt wurde. Das ist Ni-Cr-Mo-B, mit ausgezeichneter Verschleißfestigkeit und Beständigkeit gegen Erweichung bei erhöhten Temperaturen. Sie ist ein Champion in Anwendungen wie Warmformgesenken und Extrusionswerkzeugen.
Denken Sie daran, dies ist nur ein Einblick in die vielfältige Welt der Hartmetalllegierungen aus Chrompulver. Jede spezifische Legierung hat ihre eigene einzigartige Zusammensetzung und Eigenschaften, die auf bestimmte Anwendungen zugeschnitten sind.
die Anwendungen von Chrompulver-Hartlegierung
Hartmetalllegierungen aus Chrompulver sind nicht nur eine Reihe von ausgefallenen Namen – sie sind Arbeitstiere in verschiedenen industriellen Anwendungen. Hier zeigen diese bemerkenswerten Materialien ihre wahre Stärke:
Metallschneiden und -formen:
- Schneidewerkzeuge: Stellen Sie sich Bohrer vor, die länger scharf bleiben, wodurch Ausfallzeiten reduziert und die Produktivität verbessert wird. Hartmetalllegierungen aus Chrompulver wie WC-Ni und (Fe,Cr)C-Ni sind perfekt für diese Rolle und bewältigen anspruchsvolle Materialien wie Stahl, Edelstahl und Gusseisen.
- Matrizen und Stempel: Stellen Sie sich diese als die Bildhauer der Metallbearbeitungswelt vor. Hartmetalllegierungen aus Chrompulver wie WC-Ni und Fe-Cr-B-Si zeichnen sich bei Stanz-, Scher- und Umformvorgängen aus, behalten ihre Form und liefern konstante Ergebnisse.
Verschleiß- und Abriebfestigkeit:
- Verschleißplatten und Auskleidungen: In Umgebungen, in denen ständige Reibung herrscht, kommen Hartmetalllegierungen aus Chrompulver zur Rettung. Legierungen wie WC-Ni, (Fe,Cr)C-Ni und Fe-Cr-B-Si sind Champions beim Schutz von Geräten vor Verschleiß und verlängern ihre Lebensdauer erheblich. Stellen Sie sich Förderbänder vor, die mühelos gleiten, und Rutschen, die dem Ansturm von abrasiven Materialien widerstehen – das ist die Kraft dieser Legierungen in Aktion.
- Zahnräder und Walzwerkswalzen: Zahnräder sind die Arbeitstiere vieler Maschinen, und Hartmetalllegierungen aus Chrompulver wie Ni-Fe-Cr-P und Fe-Cr-B-Si sorgen dafür, dass sie reibungslos laufen. Diese Legierungen widerstehen dem Verschleiß durch ständiges Eingreifen und Walzen, wodurch Ausfallzeiten minimiert und eine konstante Leistung aufrechterhalten wird.
Hochtemperaturumgebungen:
- Ofenkomponenten und Wärmetauscher: Stellen Sie sich Komponenten vor, die der feurigen Wut von Industrieöfen standhalten. Hartmetalllegierungen aus Chrompulver wie CrC-Ni und Ni-Si stellen sich der Herausforderung, widerstehen der Oxidation und erhalten ihre strukturelle Integrität bei erhöhten Temperaturen.
- Warmstanzwerkzeuge und -formen: Das Schmieden und Formen von heißen Metallen erfordert Werkzeuge, die der Hitze standhalten können. Legierungen wie CrC-Ni und Ni-Mo zeichnen sich in diesen Anwendungen aus, indem sie Wärme effizient übertragen, ihre Form beibehalten und präzise Ergebnisse liefern.
Andere Anwendungen:
Diese vielseitigen Legierungen erweitern ihren Anwendungsbereich über die genannten Sektoren hinaus. Sie finden Anwendung in:
- Luft- und Raumfahrtindustrie: Leichte Optionen wie Ni-Al reduzieren das Gewicht und verbessern die Kraftstoffeffizienz in Flugzeugkomponenten.
- Bergbau und Bauwesen: Hoch verschleißfeste Legierungen wie Fe-Cr-B-Si schützen vor extremer Abnutzung in Geräten wie Brecherbacken und Verschleißauskleidungen.
- Ausrüstung für die Lebensmittelverarbeitung: Korrosionsbeständige Optionen wie Ni-Si gewährleisten Hygiene und Langlebigkeit in Anwendungen mit Lebensmittelkontakt.
Auswahl der richtigen Hartmetalllegierung aus Chrompulver
Bei einer so vielfältigen Auswahl an Legierungen ist die Auswahl der richtigen von entscheidender Bedeutung. Hier sind einige Schlüsselfaktoren, die berücksichtigt werden müssen:
- Anwendung: Welche spezifische Aufgabe wird die Legierung ausführen? Schneiden, Formen, Verschleißfestigkeit oder Hochtemperaturanwendungen?
- Zu verarbeitendes Material: Das Verständnis des Materials, mit dem die Legierung interagieren wird (Stahl, Aluminium usw.), hilft bei der Bestimmung der erforderlichen Härte und Verschleißfestigkeit.
- Betriebstemperatur: Wird die Legierung extremer Hitze ausgesetzt sein? Legierungen wie CrC-Ni und Ni-Mo sind besser für Hochtemperaturumgebungen geeignet.
- Erforderliche Eigenschaften: Priorisieren Sie die wichtigsten Eigenschaften – Härte, Zähigkeit, Verschleißfestigkeit oder Korrosionsbeständigkeit – basierend auf der Anwendung.
Die Beratung durch einen spezialisierten Materiallieferanten wird dringend empfohlen, um sicherzustellen, dass Sie die optimale Hartmetalllegierung aus Chrompulver für Ihre spezifischen Anforderungen auswählen.
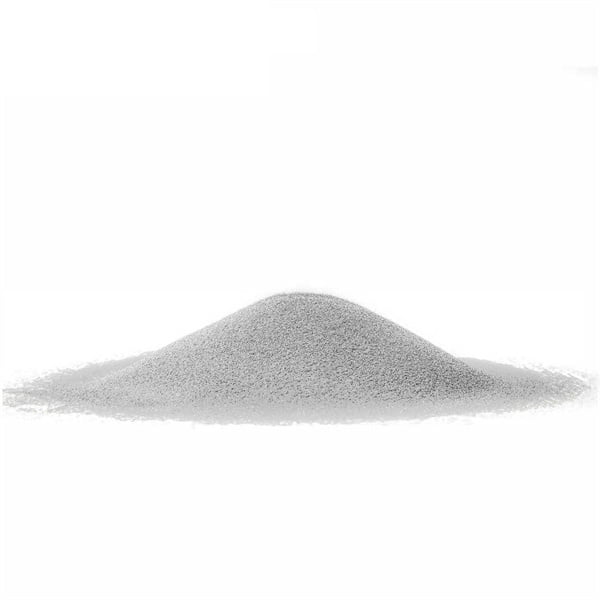
Vorteile und Beschränkungen
Hartmetalllegierungen aus Chrompulver bieten eine überzeugende Reihe von Vorteilen:
- Außergewöhnliche Abriebfestigkeit: Sie übertreffen traditionelle Materialien deutlich, verlängern die Lebensdauer der Komponenten und reduzieren Ausfallzeiten.
- Hohe Härte: Diese Legierungen bewältigen anspruchsvolle Materialien mit Leichtigkeit, behalten ihre Schneidkante bei und liefern präzise Ergebnisse.
- Überlegene Stärke und Zähigkeit: Sie halten hohen Belastungen stand und widerstehen Rissen, wodurch eine zuverlässige Leistung in anspruchsvollen Anwendungen gewährleistet wird.
- Leistung bei hohen Temperaturen: Bestimmte Legierungen zeichnen sich in heißen Umgebungen aus, indem sie ihre strukturelle Integrität und Funktionalität beibehalten.
- Korrosionsbeständigkeit: Spezifische Optionen sind korrosionsbeständig, was sie ideal für Anwendungen mit aggressiven Chemikalien oder Umgebungen macht.
Es ist jedoch wichtig, ihre Einschränkungen anzuerkennen:
- Kosten: Diese Legierungen können im Voraus teurer sein als herkömmliche Materialien. Ihre längere Lebensdauer und die reduzierten Ausfallzeiten rechtfertigen jedoch oft die Anfangsinvestition.
- Zerbrechlichkeit: Einige Legierungen können spröde sein, was bedeutet, dass sie bei übermäßiger Belastung reißen können. Eine sorgfältige Auswahl basierend auf der Anwendung ist von entscheidender Bedeutung.
- Bearbeitbarkeit: Bestimmte Legierungen können schwierig zu bearbeiten sein und erfordern spezielle Techniken.
Spezifikationen, Größen und Normen
Verstehen der technischen Spezifikationen von Hartmetalllegierungen aus Chrompulver ermöglicht eine fundierte Entscheidungsfindung. Hier ist eine Aufschlüsselung der wichtigsten Parameter:
Chemische Zusammensetzung:
Jede Legierung zeichnet sich durch eine einzigartige Mischung aus Metallpulvern und Keramikpartikeln aus. Die spezifischen Prozentsätze dieser Bestandteile bestimmen die endgültigen Eigenschaften der Legierung. Materiallieferanten stellen in der Regel detaillierte Datenblätter zur Verfügung, in denen die genaue Zusammensetzung für jede von ihnen angebotene Legierung aufgeführt ist.
Härte:
Gemessen in Einheiten wie Rockwell-Härte (HR) oder Vickers-Härte (HV) gibt dieser Wert die Beständigkeit des Materials gegen dauerhafte Eindrücke an. Höhere Härtewerte bedeuten eine bessere Verschleißfestigkeit. Verschiedene Legierungen innerhalb der Hartmetalllegierungsfamilie aus Chrompulver bieten unterschiedliche Härtegrade, die auf spezifische Anwendungen zugeschnitten sind.
Die Dichte:
Dieser Parameter spiegelt die Masse pro Volumeneinheit der Legierung wider. Er beeinflusst das Gesamtgewicht der Komponente und könnte in bestimmten Anwendungen, insbesondere in gewichtsempfindlichen Branchen wie der Luft- und Raumfahrt, eine Rolle spielen.
Elastizitätsmodul:
Dieser Wert stellt die Steifigkeit des Materials dar – seinen Widerstand gegen elastische Verformung unter Belastung. Ein höherer Elastizitätsmodul zeigt an, dass sich die Legierung unter Belastung weniger verformt, was sie für Anwendungen geeignet macht, die Dimensionsstabilität erfordern.
Wärmeausdehnungskoeffizient (CTE):
Dieser Parameter beschreibt, wie stark sich die Legierung bei steigender Temperatur ausdehnt. Die Anpassung des Wärmeausdehnungskoeffizienten (WAK) der Legierung an das Material, mit dem sie interagieren wird, minimiert thermische Spannungen, die zu Rissen oder Verformungen führen können.
Größen und Güteklassen:
Hartmetalllegierungen aus Chrompulver sind in verschiedenen Formen und Größen erhältlich. Gängige Formen sind:
- Pulver: Wird für thermische Spritzanwendungen verwendet, bei denen die Legierung auf ein Substrat aufgetragen wird, um eine verschleißfeste Beschichtung zu erzeugen.
- Rundstäbe: Ideal für die Herstellung von zylindrischen Komponenten wie Wellen, Stiften und Buchsen.
- Flachstäbe: Geeignet für die Herstellung von Verschleißplatten, Auskleidungen und anderen flachen Komponenten.
- Formen: Komplexere Geometrien können durch Verfahren wie das formnahe Pressen oder die Bearbeitung von größeren Rohlingen hergestellt werden.
Die spezifische Größe und der Grad (Feinheit) des Pulvers hängen von der beabsichtigten Anwendung ab. Beispielsweise werden feinere Pulver für das thermische Spritzen bevorzugt, während gröbere Pulver für Verfahren wie das Heißpressen geeignet sein könnten.
Normen:
Mehrere internationale Normen regeln die Spezifikationen und Testverfahren für Hartmetalllegierungen aus Chrompulver. Diese Normen gewährleisten Konsistenz und Qualität über verschiedene Hersteller hinweg. Einige relevante Normen umfassen:
- ASTM International (ASTM): Eine prominente Organisation, die verschiedene Normen im Zusammenhang mit Materialien veröffentlicht, einschließlich solcher für Metallpulver und Hartauftraglegierungen. (z. B. ASTM B214 für Nickel-Chrom-Pulver)
- Internationale Organisation für Normung (ISO): Diese globale Organisation legt Normen für eine Vielzahl von Produkten und Materialien fest, einschließlich metallischer Werkstoffe. (z. B. ISO 4499 für Wolframkarbidpulver)
Die Beratung der relevanten Normen für Ihre spezifische Anwendung stellt sicher, dass die gewählte Hartmetalllegierung aus Chrompulver die erforderlichen Leistungskriterien erfüllt.
Lieferanten und Preisgestaltung:
Eine Vielzahl von globalen und regionalen Lieferanten bietet Hartmetalllegierungen aus Chrompulver in verschiedenen Formen an. Die Preise können je nach Faktoren variieren wie:
- Spezifische Legierung: Komplexere Legierungen mit höheren Leistungseigenschaften erzielen in der Regel einen höheren Preis.
- Menge: Großeinkäufe profitieren oft von Skaleneffekten, was zu niedrigeren Stückkosten führt.
- Form: Pulver sind aufgrund der zusätzlichen Verarbeitung in der Regel günstiger als bearbeitete Teile.
- Standort: Geografische Faktoren und lokale Marktdynamiken können die Preisgestaltung beeinflussen.
Die sorgfältige Recherche potenzieller Lieferanten und der Vergleich ihrer Angebote in Bezug auf Produktqualität, Preisgestaltung und Lieferzeiten ist entscheidend, um die optimale Lösung für Ihre Anforderungen zu finden.
Der nächste Abschnitt befasst sich mit einem direkten Vergleich verschiedener Hartmetalllegierungen aus Chrompulver und hebt ihre Stärken und Schwächen hervor, um Sie in die Lage zu versetzen, fundierte
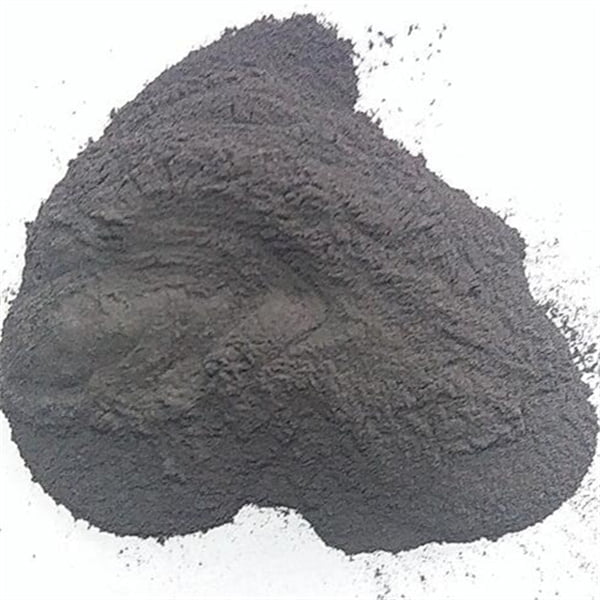
Chrom-Pulver-Hartlegierung Showdown
Bei der großen Auswahl an Chrompulver-Hartlegierungen kann sich die Wahl der richtigen Legierung wie ein Irrgarten anfühlen. In diesem Abschnitt werden einige der gängigsten Legierungen gegeneinander ausgespielt, um ihre Stärken und Schwächen in einem direkten Vergleich zu beleuchten. Machen wir uns bereit für den Kampf!
Herausforderer im Ring:
- WC-Ni (Wolframkarbid-Nickel): Der klassische Krieger, bekannt für seine außergewöhnliche Härte und Verschleißfestigkeit.
- CrC-Ni (Chromkarbid-Nickel): Der Held unter den Hochtemperaturen, der sich durch eine hervorragende Oxidationsbeständigkeit auszeichnet.
- (Fe,Cr)C-Ni ((Eisen, Chrom) Karbid-Nickel): Der Allrounder, der ein ausgewogenes Verhältnis von Härte, Zähigkeit und Korrosionsbeständigkeit bietet.
- Ni-Si (Nickel-Silizium): Der Verschleißkrieger mit Schwerpunkt auf der Hochtemperaturoxidationsbeständigkeit.
Runde 1: Härte und Abriebfestigkeit
Hier glänzt WC-Ni. Sein hoher Anteil an Wolframkarbid macht es zum unangefochtenen Champion in Sachen Härte und Verschleißfestigkeit. Es ist die erste Wahl für Anwendungen wie Schneidewerkzeuge und Verschleißplatten, bei denen es auf die Bekämpfung der Reibung ankommt.
Runde 2: Leistung bei hohen Temperaturen
Hier steht CrC-Ni im Mittelpunkt des Interesses. Sein Chromkarbidgehalt verleiht ihm eine außergewöhnliche Beständigkeit gegen Oxidation bei hohen Temperaturen. Es ist die ideale Wahl für Ofenkomponenten und Heißprägewerkzeuge, die dem feurigen Zorn der industriellen Prozesse standhalten müssen.
Runde 3: Zähigkeit und Korrosionsbeständigkeit
Diese Runde endet mit einem Unentschieden zwischen (Fe,Cr)C-Ni und Ni-Si. Beide bieten ein ausgewogenes Verhältnis von Härte und Zähigkeit und eignen sich daher für Anwendungen wie Zahnräder und Pumpenwellen. Darüber hinaus verfügt Ni-Si über eine beeindruckende Korrosionsbeständigkeit, was es zu einem wertvollen Werkstoff in Umgebungen macht, in denen eine chemische Belastung ein Problem darstellt.
Das Fazit: Eine strategische Wahl, kein Knockout
Es gibt keine einzige “beste” Chrompulver-Hartlegierung. Jeder Kandidat hat seine Stärken und Schwächen, so dass es entscheidend ist, diejenige auszuwählen, die am besten zu Ihren spezifischen Anwendungsanforderungen passt.
Hier ist ein kurzer Spickzettel, der Ihnen bei der Entscheidungsfindung helfen soll:
- Benötigen Sie die ultimative Härte und Verschleißfestigkeit? WC-Ni ist dein Champion.
- Kämpfen Sie mit hohen Temperaturen? CrC-Ni ist Ihr hitzebeständiger Held.
- Sie suchen nach einer ausgewogenen Option mit guter Zähigkeit und Korrosionsbeständigkeit? Ziehen Sie je nach Ihren spezifischen Bedürfnissen (Fe,Cr)C-Ni oder Ni-Si in Betracht.
Denken Sie daran, dass es sehr empfehlenswert ist, einen Materiallieferanten zu konsultieren, der sich mit Chrompulver-Hartlegierungen auskennt. Er kann Ihnen bei der Auswahl der optimalen Legierung für Ihre spezielle Anwendung wertvolle Tipps geben.
FAQs
Auch wenn Sie die Welt der Chrompulver-Hartlegierungen erkundet haben, bleiben vielleicht noch einige Fragen offen. Hier ist eine Aufschlüsselung einiger häufig gestellter Fragen, um mehr Licht ins Dunkel zu bringen:
F: Sind Chrompulver-Hartlegierungen schwer zu bearbeiten?
A: Die Bearbeitbarkeit dieser Legierungen kann je nach der spezifischen Zusammensetzung variieren. Im Allgemeinen können Legierungen mit höherem Karbidgehalt schwieriger zu bearbeiten sein und erfordern möglicherweise spezielle Werkzeuge oder Techniken. Dank der Fortschritte in der Bearbeitungstechnologie ist es jedoch möglich, viele Chrompulver-Hartlegierungen effektiv zu bearbeiten.
F: Können Chrompulver-Hartlegierungen geschweißt werden?
A: Das Schweißen dieser Legierungen kann aufgrund möglicher Rissbildung oder Probleme mit der Wärmeeinflusszone eine Herausforderung darstellen. Spezielle Schweißtechniken wie Laserschweißen oder Reibschweißen können jedoch in bestimmten Situationen eingesetzt werden. Es wird empfohlen, einen Schweißexperten zu Rate zu ziehen, bevor Sie versuchen, Chrompulver-Hartlegierungen zu schweißen.
F: Wie unterscheiden sich Chrompulver-Hartlegierungen von herkömmlichen Materialien wie gehärtetem Stahl?
A: Gehärteter Stahl bietet zwar eine gute Verschleißfestigkeit, aber Chrompulver-Hartlegierungen übertreffen sie im Allgemeinen in Bezug auf die reine Härte, die Beständigkeit gegen abrasiven Verschleiß und die Hochtemperaturleistung. Allerdings muss der Kostenfaktor berücksichtigt werden, da Chrompulver-Hartlegierungen im Vorfeld teurer sein können.
F: Gibt es irgendwelche Umweltaspekte im Zusammenhang mit Chrompulver-Hartlegierungen?
A: Bei der Herstellung einiger Chrompulver-Hartlegierungen kommen möglicherweise Materialien oder Verfahren zum Einsatz, die sich auf die Umwelt auswirken. Verantwortungsbewusste Hersteller legen Wert auf umweltfreundliche Praktiken und halten sich an die einschlägigen Umweltvorschriften.
Teilen auf
MET3DP Technology Co., LTD ist ein führender Anbieter von additiven Fertigungslösungen mit Hauptsitz in Qingdao, China. Unser Unternehmen ist spezialisiert auf 3D-Druckgeräte und Hochleistungsmetallpulver für industrielle Anwendungen.
Fragen Sie an, um den besten Preis und eine maßgeschneiderte Lösung für Ihr Unternehmen zu erhalten!
Verwandte Artikel
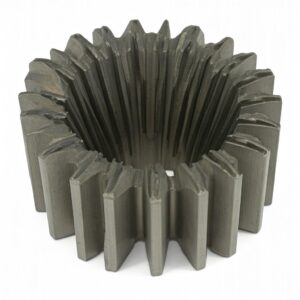
Hochleistungs-Düsenschaufelsegmente: Revolutionierung der Turbineneffizienz mit 3D-Metalldruck
Mehr lesen "Über Met3DP
Aktuelles Update
Unser Produkt
KONTAKT US
Haben Sie Fragen? Senden Sie uns jetzt eine Nachricht! Wir werden Ihre Anfrage mit einem ganzen Team nach Erhalt Ihrer Nachricht bearbeiten.
Holen Sie sich Metal3DP's
Produkt-Broschüre
Erhalten Sie die neuesten Produkte und Preislisten
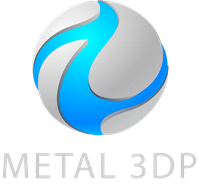
Metallpulver für 3D-Druck und additive Fertigung