3D-gedruckte Verbindungsbügel für Flugzeug-Winglets
Inhaltsübersicht
Einleitung: Die kritische Rolle der Winglet-Verbindungshalterungen in der modernen Luftfahrt
Schauen Sie sich die Flügelspitze fast aller modernen Verkehrsflugzeuge oder Geschäftsreiseflugzeuge genau an, und Sie werden wahrscheinlich eine markante, nach oben (oder manchmal auch nach unten und oben) abgewinkelte Verlängerung sehen: das Winglet. Obwohl sie im Verhältnis zum gesamten Flugzeug klein erscheinen, spielen Winglets eine entscheidende Rolle bei der Verbesserung der aerodynamischen Effizienz, indem sie den durch den Auftrieb verursachten Widerstand verringern. Dies führt direkt zu erheblichen Treibstoffeinsparungen, einer größeren Reichweite und geringeren Emissionen - entscheidende Ziele in der heutigen Luftfahrtindustrie. Doch wie werden diese wichtigen aerodynamischen Flächen sicher an der Haupttragflächenstruktur befestigt und halten so den immensen aerodynamischen Kräften, Vibrationen und Temperaturschwankungen in jedem Flug stand? Die Antwort liegt in der Winglet-Verbindungshalterung.
Diese Halterungen sind die unbesungenen Helden der Luft- und Raumfahrttechnik - kritische Strukturbauteile, die komplexe Lasten zuverlässig zwischen dem Winglet und dem Flügelkasten übertragen sollen. Sie müssen außergewöhnlich stark, steif, ermüdungsbeständig und vor allem leicht sein. Jedes Kilogramm, das bei einem Flugzeugbauteil eingespart wird, trägt zu einer verbesserten Leistung und Betriebswirtschaftlichkeit bei. In der Vergangenheit wurden diese komplizierten, tragenden Komponenten mit traditionellen Methoden wie der maschinellen Bearbeitung aus massiven Metallblöcken (häufig Titan oder hochfestes Aluminium) oder durch Gießen hergestellt. Diese Methoden stoßen jedoch bei der geometrischen Komplexität an ihre Grenzen, können zu erheblicher Materialverschwendung führen (schlechtes Verhältnis zwischen Anschaffung und Nutzung) und sind oft mit langen Vorlaufzeiten für Design-Iterationen und Produktion verbunden.
Hier ist der Paradigmenwechsel hin zu einer fortschrittlichen Fertigung, insbesondere Additive Fertigung von Metall (AM), oder 3D-Druckhat einen tiefgreifenden Einfluss. Metall-AM ermöglicht die Produktion hochkomplexer, topologieoptimierter Leichtbaustrukturen, deren Herstellung bisher unmöglich oder unerschwinglich war. Bei Bauteilen wie Winglet-Verbindungsbügeln ermöglicht diese Technologie ein neues Maß an Leistung und Effizienz. Unternehmen wie Met3dpspezialisiert auf industrielle 3D-Drucklösungen aus Metall, einschließlich fortschrittlicher 3D-Druck von Metall systeme und Hochleistungspulver stehen bei diesem Wandel an vorderster Front und liefern die Werkzeuge und Materialien, die für die Realisierung von Luft- und Raumfahrtdesigns der nächsten Generation benötigt werden. Dieser Beitrag befasst sich mit den Besonderheiten der Verwendung von Metall-AM für die Herstellung von Winglet-Verbindungshaltern in der Luft- und Raumfahrt und untersucht die Anwendungen, Vorteile, Materialien, Designüberlegungen und Lieferkettenaspekte, die für Ingenieure und Beschaffungsmanager im Luftfahrtsektor relevant sind.
Die Funktionalität von Winglet-Brackets verstehen: Anwendungsfälle und Nachfrage der Industrie
Winglet-Verbindungshalterungen sind weit mehr als nur einfache Verbindungselemente; sie sind hochentwickelte Strukturelemente, die für den Einsatz in einem anspruchsvollen Umfeld entwickelt wurden. Ihre primäre Funktion ist es, eine sichere und robuste Schnittstelle zwischen dem Winglet und der primären Flügelstruktur zu bilden, um sicherzustellen, dass die vom Winglet erzeugten aerodynamischen Lasten effizient in den Flügelkasten übertragen und verteilt werden, ohne die strukturelle Integrität zu beeinträchtigen.
Wichtige funktionale Anforderungen:
- Lastübertragung: Die Halterungen müssen erhebliche aerodynamische Belastungen (Biegemomente, Scherkräfte) aufnehmen, die durch das Winglet erzeugt werden, insbesondere bei Flugmanövern, Turbulenzen und in verschiedenen Flugphasen.
- Ermüdungswiderstand: Aufgrund der zyklischen Natur der aerodynamischen Belastungen und der Flugzeugvibrationen müssen Halterungen eine außergewöhnliche Ermüdungsfestigkeit aufweisen, um die strengen Sicherheits- und Langlebigkeitsanforderungen der Luft- und Raumfahrt zu erfüllen (oft Zehntausende von Flugzyklen).
- Steifigkeit und Stabilität: Sie müssen formstabil sein und eine ausreichende Steifigkeit aufweisen, um sicherzustellen, dass das Winglet für eine optimale aerodynamische Leistung korrekt im Verhältnis zum Flügel positioniert bleibt.
- Umweltresistenz: Die Halterungen sind Temperaturschwankungen (vom Boden bis in große Höhen), Feuchtigkeit, Enteisungsflüssigkeiten und möglichen Stößen ausgesetzt, was Materialien mit hervorragender Korrosions- und Umweltbeständigkeit erfordert.
- Minimierung des Gewichts: Wie bei allen Bauteilen in der Luft- und Raumfahrt ist die Minimierung des Gewichts für die Maximierung der Treibstoffeffizienz und der Nutzlastkapazität von größter Bedeutung.
Anwendungen für verschiedene Luftfahrzeugtypen:
Die Nachfrage nach effizienten Winglet-Verbindungshaltern erstreckt sich auf verschiedene Segmente der Luftfahrtindustrie:
- Kommerzielle Verkehrsflugzeuge: Große Passagierflugzeuge (z. B. Boeing 737 MAX, Airbus A320neo-Familie, A350, 787) sind in hohem Maße auf moderne Winglets angewiesen, um den Treibstoffverbrauch auf Mittel- und Langstrecken zu senken. Die Halterungen müssen hier über Jahrzehnte hinweg zuverlässig große Lasten bewältigen. Die Beschaffung dieser Komponenten erfordert strenge Qualifizierungsprozesse, so dass zuverlässige Zulieferer der Luft- und Raumfahrtindustrie entscheidend.
- Geschäftsreiseflugzeuge: Leistung und Reichweite sind die wichtigsten Verkaufsargumente für Geschäftsflugzeuge. Optimierte Winglets tragen wesentlich dazu bei, und ihre Verbindungshalterungen müssen hohe Leistungsstandards erfüllen und gleichzeitig strenge Gewichtsvorgaben einhalten. Die Hersteller suchen oft nach Partnern, die in der Lage sind, maßgeschneiderte Hochleistungshalterungen zu produzieren.
- Unbemannte Luftfahrzeuge (UAVs): Insbesondere für größere UAVs mit langer Lebensdauer, die zur Überwachung oder zum Transport von Fracht eingesetzt werden, ist die aerodynamische Effizienz entscheidend. Leichte, maßgeschneiderte Halterungen, die durch AM ermöglicht werden, können von Vorteil sein.
- Wartung, Reparatur und Überholung (MRO): Der MRO-Sektor stellt eine große Chance dar. AM kann für die Herstellung von Ersatzhalterungen verwendet werden, die möglicherweise auch konstruktive Verbesserungen enthalten, und das manchmal mit kürzeren Vorlaufzeiten als bei der Beschaffung von traditionell hergestellten Ersatzteilen, insbesondere für ältere Flugzeugmodelle. MRO-Lösungen für die Luftfahrt die Anbieter erforschen zunehmend AM für Ersatzteile.
Das unablässige Streben nach verbesserter Treibstoffeffizienz, das sowohl durch wirtschaftlichen Druck (Treibstoffkosten) als auch durch Umweltvorschriften (Emissionsreduzierung) angetrieben wird, sorgt für eine anhaltend hohe Nachfrage nach fortschrittlicher Winglet-Technologie und folglich auch nach den Hochleistungshalterungen, mit denen sie befestigt werden. Beschaffung in der Luft- und Raumfahrt teams sind ständig auf der Suche nach innovativen Fertigungstechniken und zuverlässigen hersteller von Flugzeughalterungen die Komponenten liefern können, die diesen sich entwickelnden Anforderungen entsprechen.
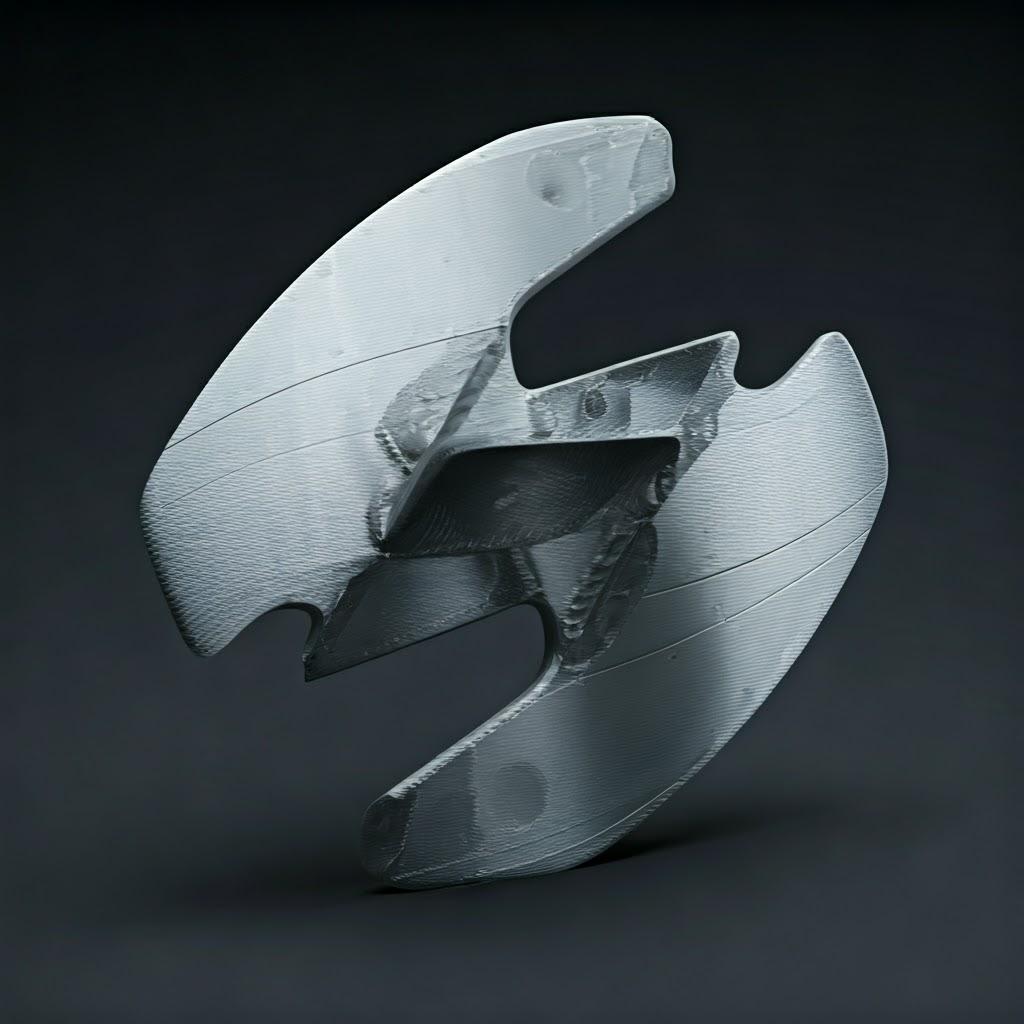
Warum 3D-Metalldruck für Winglet-Verbindungsbügel?
Während traditionelle Fertigungsverfahren wie CNC-Bearbeitung und Feinguss der Luft- und Raumfahrtindustrie jahrzehntelang gute Dienste geleistet haben, bietet die additive Fertigung von Metallen überzeugende Vorteile, insbesondere für komplexe Strukturbauteile wie Winglet-Verbindungshalterungen. Die Grenzen der subtraktiven (maschinellen) und formgebenden (Guss) Verfahren führen oft zu Kompromissen bei Design, Gewicht und Vorlaufzeit, die durch AM überwunden werden können.
Die Grenzen der traditionellen Methoden:
- CNC-Bearbeitung:
- Hoher Materialabfall: Er beginnt mit einem massiven Knüppel aus teurem Material (z. B. Titan) und entnimmt große Mengen, was zu einem schlechten Verhältnis zwischen Einkauf und Fertigung führt (das Verhältnis zwischen dem Gewicht des eingekauften Rohmaterials und dem Gewicht des fertigen Teils). Verhältnisse von 10:1 oder sogar 20:1 sind keine Seltenheit.
- Geometrische Zwänge: Es ist schwierig und zeitaufwändig, komplexe innere Merkmale, dünne Wände oder sehr organische Formen zu erstellen. Der begrenzte Zugang zu den Werkzeugen schränkt die Gestaltungsmöglichkeiten ein.
- Lange Bearbeitungszeiten: Komplexe Teile erfordern mehrere Aufspannungen und umfangreiche Bearbeitungen, was die Durchlaufzeiten und Kosten erhöht.
- Feinguss:
- Werkzeugkosten und Vorlaufzeit: Erfordert beträchtliche Vorabinvestitionen und viel Zeit für die Herstellung von Gussformen, was es für die Kleinserienproduktion oder das Rapid Prototyping weniger geeignet macht.
- Potenzielle Defekte: Anfällig für interne Porosität oder Unregelmäßigkeiten, die umfangreiche Inspektionen und Nacharbeiten erfordern können.
- Beschränkungen des Designs: Obwohl das Gießen bei einigen komplexen Formen besser ist als die maschinelle Bearbeitung, gibt es bei komplizierten inneren Strukturen oder sehr dünnen Merkmalen immer noch Einschränkungen.
Vorteile der additiven Fertigung von Metallen (Powder Bed Fusion – PBF):
Bei der Metall-AM, insbesondere bei Verfahren wie Laser Powder Bed Fusion (L-PBF) und Electron Beam Melting (EBM), werden die Teile Schicht für Schicht direkt aus Metallpulver aufgebaut, was für Winglet-Halterungen entscheidende Vorteile bietet:
- Noch nie dagewesene Gewichtsreduzierung:
- Topologie-Optimierung: AM ermöglicht den Einsatz fortschrittlicher Softwaretools zur Optimierung der Teilegeometrie auf der Grundlage von Belastungspfaden. Das Material wird nur dort platziert, wo es strukturell benötigt wird, wodurch unnötige Masse vermieden wird, während Festigkeit und Steifigkeit erhalten bleiben oder sogar erhöht werden. Dadurch wird das Verhältnis zwischen Anschaffung und Nutzung drastisch verbessert.
- Gitterförmige Strukturen: Durch den Einbau interner Gitter- oder Zellstrukturen kann das Gewicht noch weiter reduziert werden, ohne dass die strukturelle Integrität beeinträchtigt wird - ein Kunststück, das mit herkömmlichen Methoden unmöglich ist.
- Teil Konsolidierung:
- Eine komplexe Halterungsbaugruppe, die traditionell aus mehreren maschinell bearbeiteten oder gegossenen Teilen besteht, die miteinander verschraubt oder verschweißt werden, kann oft als eine einzige, monolithische Komponente neu entworfen und gedruckt werden. Dies reduziert die Anzahl der Teile, eliminiert Verbindungselemente (potenzielle Fehlerpunkte), vereinfacht die Montage, reduziert das Gewicht und verbessert die strukturelle Integrität.
- Verbesserte Gestaltungsfreiheit:
- AM beseitigt viele der geometrischen Beschränkungen, die bei der herkömmlichen Fertigung gelten. Ingenieure können hochkomplexe, organische Formen mit internen Kanälen (z. B. zur Kühlung oder Verdrahtung), glatten Konturen und perfekt auf die jeweilige Anwendung zugeschnittenen Merkmalen entwerfen, ohne sich Gedanken über den Zugang zum Werkzeug oder die Entformungswinkel machen zu müssen. Diese Freiheit ermöglicht ein höheres Leistungsniveau.
- Reduzierte Vorlaufzeiten (Prototyping & Low Volume):
- Für erste Prototypen, Design-Iterationen und Kleinserien kann AM deutlich schneller sein als herkömmliche Methoden, die Werkzeuge oder umfangreiche Bearbeitungsvorgänge erfordern. Designänderungen können schnell umgesetzt und getestet werden.
- Materialeffizienz:
- AM ist ein additives Verfahren, bei dem in erster Linie nur das für das Teil und die Stützstrukturen benötigte Material verwendet wird. Ungeschmolzenes Pulver kann oft recycelt werden, was zu einer viel besseren Materialausnutzung im Vergleich zur subtraktiven Bearbeitung führt.
Um diese Vorteile zu nutzen, sind Fachwissen und die richtige Ausrüstung erforderlich. Met3dp bietet branchenführendes Druckvolumen, Genauigkeit und Zuverlässigkeit mit seinen fortschrittlichen PBF-Systemen, die die Produktion von einsatzkritischen Luft- und Raumfahrtkomponenten wie Winglet-Halterungen machbar und effizient machen. Die Erforschung der Möglichkeiten von vorteile von Metal AM für die Luft- und Raumfahrt kann zu erheblichen Wettbewerbsvorteilen bei der Konstruktion und Herstellung von Flugzeugen führen.
Werkstoff-Fokus: Ti-6Al-4V und Scalmalloy® für leistungsstarke Halterungen
Bei Bauteilen für die Luft- und Raumfahrt ist die Wahl des Werkstoffs von entscheidender Bedeutung, insbesondere bei tragenden Strukturen wie Winglet-Verbindungsbügeln, die unter anspruchsvollen Bedingungen arbeiten. Additive Fertigungsverfahren erfordern spezielle Metallpulver, und für diese Anwendung sind zwei Materialien besonders geeignet: Die Titanlegierung Ti-6Al-4V und die Hochleistungsaluminiumlegierung Scalmalloy®. Die Qualität und Konsistenz des Pulvers wirken sich direkt auf die mechanischen Eigenschaften und die Zuverlässigkeit des Endprodukts aus.
Bedeutung von qualitativ hochwertigen Metallpulvern:
Erfolgreiches Metall-AM hängt in hohem Maße von den Eigenschaften des Ausgangsmaterials Metallpulver ab. Zu den wichtigsten Eigenschaften gehören:
- Sphärizität: Hochkugelförmige Partikel gewährleisten eine gute Fließfähigkeit des Pulvers und eine hohe Packungsdichte im Pulverbett, was zu einem gleichmäßigeren Aufschmelzen und dichteren Endteilen mit weniger Hohlräumen führt.
- Partikelgrößenverteilung (PSD): Eine kontrollierte PSD ist entscheidend für ein gleichmäßiges Schmelzverhalten und das Erreichen der gewünschten Oberflächengüte und Auflösung.
- Reinheit: Ein geringer Gehalt an Verunreinigungen und Schadstoffen (wie Sauerstoff und Stickstoff, insbesondere bei Titan) ist für die Erzielung optimaler mechanischer Eigenschaften und die Vermeidung von Defekten unerlässlich.
- Fließfähigkeit: Ein gleichmäßiger Pulverfluss sorgt dafür, dass gleichmäßige Schichten über die Bauplattform verteilt werden, was für die Prozessstabilität und die Qualität der Teile entscheidend ist.
Met3dp nutzt branchenführende Technologien zur Gaszerstäubung und zum Plasma-Rotations-Elektroden-Verfahren (PREP) zur Herstellung von Metallpulvern, die diesen strengen Anforderungen entsprechen. Ihr fortschrittliches Pulverherstellungssystemmit einzigartigen Düsen- und Gasströmungsdesigns liefert Pulver mit hoher Sphärizität, kontrolliertem PSD und hervorragender Fließfähigkeit, was sie ideal für anspruchsvolle Luft- und Raumfahrtanwendungen macht. Der Zugang zu einer zuverlässigen anbieter von Metallpulver für die Luft- und Raumfahrt wie Met3dp ist entscheidend für gleichbleibend hochwertige Ergebnisse. Sie können das Angebot an innovativen Legierungen und Standardwerkstoffen auf der Website Produktseite.
1. Titanlegierung Ti-6Al-4V (Grad 5):
Ti-6Al-4V ist wohl die in der Luft- und Raumfahrt am häufigsten verwendete Titanlegierung, und das aus gutem Grund. Sie bietet eine hervorragende Kombination von Eigenschaften, die für Strukturbauteile sehr wünschenswert sind:
- Hohes Verhältnis von Festigkeit zu Gewicht: Bietet eine Festigkeit, die mit der vieler Stähle vergleichbar ist, jedoch bei deutlich geringerer Dichte, was für die Gewichtsreduzierung entscheidend ist.
- Ausgezeichnete Korrosionsbeständigkeit: Bildet eine stabile passive Oxidschicht und bietet eine hervorragende Korrosionsbeständigkeit in verschiedenen Umgebungen der Luft- und Raumfahrt, einschließlich der Einwirkung von Flugzeugtreibstoff und Enteisungsflüssigkeiten.
- Gute Ermüdungsfestigkeit: Gute Leistung unter zyklischen Belastungsbedingungen, wie sie für Flugzeugstrukturen typisch sind.
- Eignung für hohe Temperaturen: Behält eine gute Festigkeit bei mäßig erhöhten Temperaturen (bis zu etwa 315°C oder 600°F).
- Biokompatibilität: Obwohl es für Winglets nicht relevant ist, eignet es sich aufgrund seiner Biokompatibilität auch für medizinische Implantate.
- Etablierte Datenbank: Die jahrzehntelange Verwendung bedeutet, dass seine Eigenschaften und sein Verhalten (auch in AM) gut bekannt und dokumentiert sind, was die Zertifizierungsprozesse vereinfacht.
Für Winglet-Halterungen bietet Ti-6Al-4V die erforderliche Festigkeit, Ermüdungsbeständigkeit und Umweltstabilität in einem relativ leichten Paket. Es ist eine gängige Wahl für Halterungen, die sowohl durch traditionelle Bearbeitung als auch durch additive Fertigung hergestellt werden.
2. Scalmalloy®:
Scalmalloy® ist eine Hochleistungslegierung aus Aluminium, Magnesium und Scandium, die speziell für die additive Fertigung entwickelt wurde. Sie verschiebt die Grenzen dessen, was mit Aluminiumlegierungen möglich ist:
- Außergewöhnliche Stärke: Bietet im Vergleich zu herkömmlichen Aluminiumlegierungen für die Luft- und Raumfahrt (z. B. AlSi10Mg) eine deutlich höhere Zug- und Streckgrenze und erreicht bei geringerer Dichte annähernd die Festigkeit einiger Titanlegierungen.
- Ausgezeichnete Duktilität & Ermüdungsfestigkeit: Im Gegensatz zu einigen hochfesten Aluminiumlegierungen behält Scalmalloy® eine gute Duktilität und weist hervorragende Ermüdungseigenschaften auf, wodurch es sich für dynamisch belastete Bauteile eignet.
- Optimiert für AM: Seine Zusammensetzung ist auf eine gute Verarbeitbarkeit mit dem Laser Powder Bed Fusion (L-PBF) zugeschnitten und ermöglicht die Herstellung komplexer, rissfreier Bauteile.
- Schweißeignung: Kann geschweißt werden, was für die Nachbearbeitung oder die Integration in größere Baugruppen von Vorteil sein kann.
- Leichtes Gewicht: Da es sich um eine Aluminiumlegierung handelt, bietet sie im Vergleich zu Komponenten aus Titan oder Stahl ein erhebliches Gewichtseinsparungspotenzial.
Für Winglet-Halterungen, bei denen die Gewichtsminimierung oberste Priorität hat, aber dennoch eine sehr hohe Festigkeit und Ermüdungsbeständigkeit erforderlich ist, stellt Scalmalloy® eine überzeugende Alternative zu Ti-6Al-4V dar. Seine Entwicklung verdeutlicht das Potenzial von Werkstoffen, die speziell für die Nutzung der einzigartigen Möglichkeiten der additiven Fertigung entwickelt wurden.
Vergleich der Materialeigenschaften (typische Werte für AM):
Eigentum | Ti-6Al-4V (Spannungsarmglühen & HIPed) | Scalmalloy® (wärmebehandelt) | Einheit | Anmerkungen |
---|---|---|---|---|
Dichte | ~4.43 | ~2.67 | g/cm³ | Scalmalloy® ist wesentlich leichter. |
Endgültige Zugfestigkeit | > 930 | > 520 | MPa | Ti-6Al-4V ist insgesamt stärker. |
Streckgrenze (0.2%) | > 860 | > 480 | MPa | Ti-6Al-4V hat eine höhere Streckgrenze. |
Dehnung beim Bruch | > 10 | > 13 | % | Scalmalloy® weist eine etwas bessere Duktilität auf. |
Elastizitätsmodul | ~114 | ~70 | GPa | Ti-6Al-4V ist steifer. |
Ermüdungsfestigkeit (R=-1) | ~500 (@ 10⁷ cycles) | ~250 (@ 10⁷ cycles) | MPa | Ti-6Al-4V ist in der Regel höher, variiert aber. |
Max. Betriebstemp. | ~315 | ~150 | °C | Ti-6Al-4V ist besser für höhere Temperaturen geeignet. |
In Blätter exportieren
Hinweis: Die Eigenschaften sind Näherungswerte und hängen stark von den spezifischen AM-Prozessparametern, der Bauausrichtung und der Nachbearbeitung (Wärmebehandlung, HIP) ab. Spezifische Werte finden Sie immer in den Datenblättern der Lieferanten.
Die Wahl zwischen Ti-6Al-4V und Scalmalloy®:
Die Auswahl hängt von den spezifischen Konstruktionsanforderungen ab:
- Wählen Sie Ti-6Al-4V wenn: Maximale Festigkeit, höhere Temperaturbeständigkeit und die Nutzung vorhandener Qualifikationsdaten aus der Luft- und Raumfahrt sind von größter Bedeutung.
- Wählen Sie Scalmalloy® wenn: Absolutes Mindestgewicht ist der wichtigste Faktor, und das außergewöhnliche Verhältnis von Festigkeit zu Gewicht (in dieser Hinsicht besser als Ti-6Al-4V) und die gute Ermüdungsfestigkeit erfüllen die betrieblichen Anforderungen.
Beide Werkstoffe ermöglichen, wenn sie mit hochwertigen Pulvern von Experten wie Met3dp verarbeitet und auf zuverlässigen AM-Systemen hergestellt werden, die Entwicklung überlegener Winglet-Anschlussträger, die die Grenzen der Leistungsfähigkeit und Effizienz von Flugzeugen erweitern.
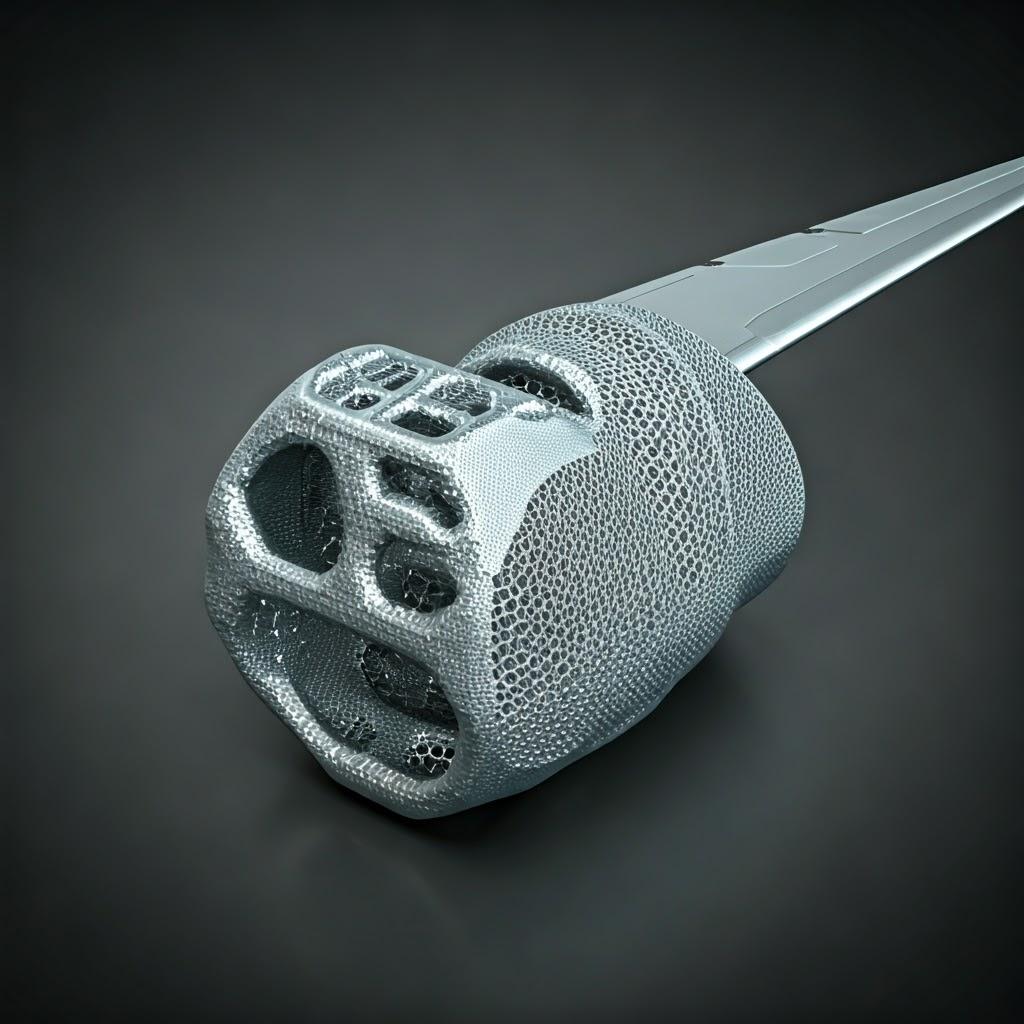
Design for Additive Manufacturing (DfAM)-Prinzipien für eine optimale Leistung der Halterung
Eine der wichtigsten Veränderungen, die bei der Einführung der additiven Fertigung von Metallen erforderlich sind, ist die Umstellung auf Design für additive Fertigung (DfAM). Ein Design, das ursprünglich für die CNC-Bearbeitung oder den Guss vorgesehen war, einfach auf einen 3D-Drucker zu übertragen, wird wahrscheinlich zu einem suboptimalen Teil führen, das die Hauptvorteile von AM nicht nutzen kann. DfAM ist eine Methodik, eine Änderung der Denkweise, die die Fähigkeiten und Einschränkungen des Fertigungsprozesses direkt in die Designphase integriert, um das Potenzial der AM-Technologie für Komponenten wie Winglet-Verbindungsbügel zu maximieren. Die Anwendung der DfAM-Prinzipien ist entscheidend, um eine gezielte Gewichtsreduzierung, Leistungssteigerung und Kosteneffizienz zu erreichen.
Wichtige DfAM-Strategien für Winglet-Halterungen:
- Topologie-Optimierung: Dies ist vielleicht die wirkungsvollste DfAM-Technik für Strukturkomponenten. Mithilfe spezieller Software (z. B. FEA-basierte Optimierungstools) definieren die Ingenieure den Konstruktionsraum, die Lastfälle (aerodynamische Kräfte, Vibrationen), die Einschränkungen (Befestigungspunkte, Sperrzonen) und die Leistungsziele (Minimierung des Gewichts, Maximierung der Steifigkeit). Die Software entfernt dann iterativ Material aus Bereichen mit geringer Belastung, was zu hocheffizienten, oft organisch anmutenden Strukturen führt, die das Material genau dort platzieren, wo es für die Lastaufnahme benötigt wird. Dies kann zu dramatischen Gewichtseinsparungen (30-60 % oder mehr) im Vergleich zu herkömmlich konstruierten Halterungen führen.
- Generatives Design: Generative Designalgorithmen gehen bei der Optimierung noch einen Schritt weiter und untersuchen mehrere Designmöglichkeiten gleichzeitig auf der Grundlage eines definierten Satzes von Regeln, Beschränkungen und Zielen. Dadurch können neuartige, leistungsstarke Designlösungen aufgedeckt werden, an die ein menschlicher Designer vielleicht nicht gedacht hätte, und die Grenzen von Leichtbau und Leistung werden verschoben.
- Teil Konsolidierung: Analysieren Sie bestehende Halterungsbaugruppen. Können mehrere Komponenten (z. B. ein Hauptkörper, separate Flansche, Befestigungselemente) neu entworfen und als ein einziges, integriertes Teil gedruckt werden? Diese DfAM-Strategie reduziert die Anzahl der Teile, eliminiert Verbindungen und Befestigungselemente (potenzielle Fehlerpunkte), vereinfacht die nachgelagerten Montageprozesse und reduziert das Gewicht.
- Minimierung der Stützstruktur: Metall-PBF-Prozesse erfordern in der Regel Stützstrukturen für überhängende Features (in der Regel mit einem Winkel von weniger als 45° zur horizontalen Bauebene), um ein Zusammenbrechen zu verhindern und das Teil auf der Bauplatte zu verankern. Diese Stützen verbrauchen zusätzliches Material, verlängern die Druckzeit und müssen in der Nachbearbeitung manuell oder maschinell entfernt werden, was zusätzliche Kosten und Komplexität verursacht. DfAM konzentriert sich auf:
- Selbsttragende Winkel entwerfen: Ausrichtung von Oberflächen und Merkmalen, um den kritischen Überhangwinkel zu überschreiten, wann immer dies möglich ist.
- Optimierung der Gebäudeausrichtung: Auswahl der Druckausrichtung, die den Bedarf an Stützen auf natürliche Weise minimiert, unter Berücksichtigung anderer Faktoren wie Oberflächengüte und mechanische Eigenschaften (die anisotrop sein können).
- Verwendung von opferbereiten Merkmalen: Konstruktion von Merkmalen, die später weggearbeitet werden sollen und gleichzeitig als Stützen während des Drucks dienen.
- Interne Gitterstrukturen: Anstelle von Vollprofilen können interne Gitter- oder Zellstrukturen (z. B. Kreisel, Waben) in das Design der Halterung integriert werden. Diese reduzieren das Gewicht und den Materialverbrauch erheblich und bieten gleichzeitig maßgeschneiderte strukturelle Unterstützung, Energieabsorption oder schwingungsdämpfende Eigenschaften. Dieses Maß an interner Komplexität ist einzigartig bei AM.
- Konstruktionsregeln für Merkmale: Beachten Sie die spezifischen Einschränkungen des AM-Prozesses:
- Mindestwanddicke: Das Entwerfen von Wänden unterhalb eines bestimmten Schwellenwerts (prozess- und materialabhängig, oft etwa 0,4-0,8 mm) kann zu Druckfehlern oder schlechter Feature-Definition führen.
- Ausrichtung der Löcher: Horizontale Löcher erfordern oft Stützstrukturen oder können im Vergleich zu vertikalen Löchern mit leichten Abweichungen von der perfekten Kreisform gedruckt werden. Die Gestaltung von Rauten- oder Tropfenformen für horizontale Löcher kann dafür sorgen, dass sie selbsttragend sind.
- Wärmemanagement: Berücksichtigung der Wärmeableitung während des Bauprozesses zur Minimierung von Eigenspannungen und möglichem Verzug, insbesondere bei großen oder dichten Abschnitten.
Die Rolle der Simulation: DfAM ist in hohem Maße auf Simulationswerkzeuge angewiesen. Die Finite-Elemente-Analyse (FEA) validiert die strukturelle Leistung von topologieoptimierten Designs unter den zu erwartenden Belastungsbedingungen. Thermische Simulationen helfen bei der Vorhersage und Minderung von Verformungen und Restspannungen während des Druckprozesses. Simulationswerkzeuge für den Druckprozess helfen bei der Optimierung der Bauausrichtung und der Stützstrategien, bevor teures Material und Maschinenzeit eingesetzt werden. Effektive Implementierung DfAM Luft- und Raumfahrt strategien erfordert Fachwissen sowohl über die Konstruktionsprinzipien als auch über die Feinheiten des gewählten AM-Verfahrens.
Erreichen von Präzision: Toleranz, Oberflächengüte und Maßgenauigkeit
Ingenieure und Beschaffungsmanager, die von der traditionellen Fertigung umsteigen, müssen realistische Erwartungen an die Präzision haben, die mit der additiven Fertigung von Metallen erreicht werden kann. Während AM eine unglaubliche Designfreiheit bietet, unterscheidet es sich von Natur aus von der Präzision im Mikrometerbereich, die oft mit der mehrachsigen CNC-Bearbeitung im "as-built"-Zustand verbunden ist. Wenn man jedoch die Möglichkeiten versteht und die notwendigen Nachbearbeitungen einbezieht, können AM-Komponenten wie Winglet-Halterungen die strengen Anforderungen der Luft- und Raumfahrt erfüllen.
Typische Toleranzen:
Die erreichbare Maßtoleranz hängt wesentlich vom spezifischen AM-Prozess (L-PBF vs. EBM), dem zu druckenden Material, der Größe und Komplexität des Teils, seiner Ausrichtung auf der Bauplatte und der Kalibrierung der Maschine ab.
- Laser Powder Bed Fusion (L-PBF): Bietet im Allgemeinen eine höhere Präzision und eine feinere Auflösung der Merkmale aufgrund der geringeren Größe des Schmelzbads. Typische Toleranzen liegen zwischen ±0,1 mm und ±0,2 mm bei kleineren Merkmalen und können sich bei größeren Abmessungen auf ±0,1-0,2 % erhöhen.
- Elektronenstrahlschmelzen (EBM): Das EBM-Verfahren arbeitet häufig bei höheren Temperaturen und verwendet einen größeren Strahlfleck, was im Vergleich zum L-PBF-Verfahren zu einer etwas geringeren Fertigungsgenauigkeit führen kann, etwa im Bereich von ±0,2 mm bis ±0,4 mm oder ±0,2-0,5 % bei größeren Abmessungen. EBM eignet sich jedoch hervorragend für bestimmte Werkstoffe (z. B. Ti-6Al-4V) und erfordert aufgrund der heißen Pulverbettumgebung oft weniger Stützstrukturen. Erforschen Sie verschiedene Druckverfahren um ihre spezifischen Fähigkeiten zu verstehen.
Es ist von entscheidender Bedeutung, dass kritische Merkmale, die engere Toleranzen erfordern (z. B. Passflächen, Lagerschnittstellen, Befestigungslöcher), bei einer Winglet-Halterung in der Regel durch Nachbearbeitungsvorgänge erreicht werden, anstatt sich ausschließlich auf die AM-Toleranz im Ist-Zustand zu verlassen.
Oberflächengüte (Rauhigkeit):
Die Oberflächenbeschaffenheit von AM-Metallteilen ist im Allgemeinen rauer als die von maschinell bearbeiteten Oberflächen, was auf den schichtweisen Prozess und die teilweise geschmolzenen Pulverpartikel zurückzuführen ist, die an den Oberflächen haften.
- As-Built Ra: Die Werte für die Oberflächenrauheit (Ra) liegen in der Regel zwischen 6 µm und 25 µm (240 µin bis 1000 µin), je nach Prozess, Material, Ausrichtung (nach oben oder nach unten weisende Flächen oder Seitenwände) und verwendeten Parametern. EBM-Teile sind oft rauher als L-PBF-Teile.
- Nachbearbeitetes Ra: Verschiedene Nachbearbeitungsschritte wie Perlstrahlen, Trommeln, chemisches Ätzen, Elektropolieren oder CNC-Bearbeitung können die Oberflächengüte erheblich verbessern. Durch maschinelle Bearbeitung können bei Bedarf Ra-Werte unter 1 µm (40 µin) erreicht werden.
Faktoren, die die Maßgenauigkeit beeinflussen:
- Kalibrierung der Maschine: Eine regelmäßige, präzise Kalibrierung des AM-Systems ist unerlässlich.
- Materialeigenschaften: Wärmeausdehnung und Wärmeleitfähigkeit beeinflussen Schrumpfung und Spannung.
- Prozessparameter: Laser-/Strahlleistung, Scangeschwindigkeit, Schichtdicke und Schraffurabstände beeinflussen die Dynamik des Schmelzbades und die daraus resultierende Genauigkeit.
- Thermische Spannungen: Ungleichmäßige Erwärmung und Abkühlung verursachen innere Spannungen, die zu Verwerfungen und Verformungen führen können.
- Teilegeometrie und -ausrichtung: Große ebene Flächen oder freitragende Überhänge sind anfälliger für Abweichungen.
- Strategie unterstützen: Richtig konstruierte Stützen sind entscheidend für die Verankerung des Teils und die Bewältigung der thermischen Belastung.
Qualitätsmanagementsysteme (QMS): Erreichen einer gleichbleibenden Maßgenauigkeit und Einhaltung anforderungen an die Oberflächengüte in der Luft- und Raumfahrt ist in hohem Maße auf eine solide Qualitätskontrolle während des gesamten Arbeitsablaufs angewiesen - vom Pulvermanagement und der Maschineneinrichtung bis hin zur Prozessüberwachung und Nachbearbeitungsprüfung. Seriöse AM-Dienstleister wie Met3dp arbeiten nach strengen QMS-Protokollen (die oft mit Standards wie AS9100 für die Luft- und Raumfahrt abgestimmt sind), um Wiederholbarkeit und Konformität zu gewährleisten. Verlassen Sie sich auf Anbieter mit branchenführendes Druckvolumen, Genauigkeit und Zuverlässigkeit ist der Schlüssel für kritische Komponenten.
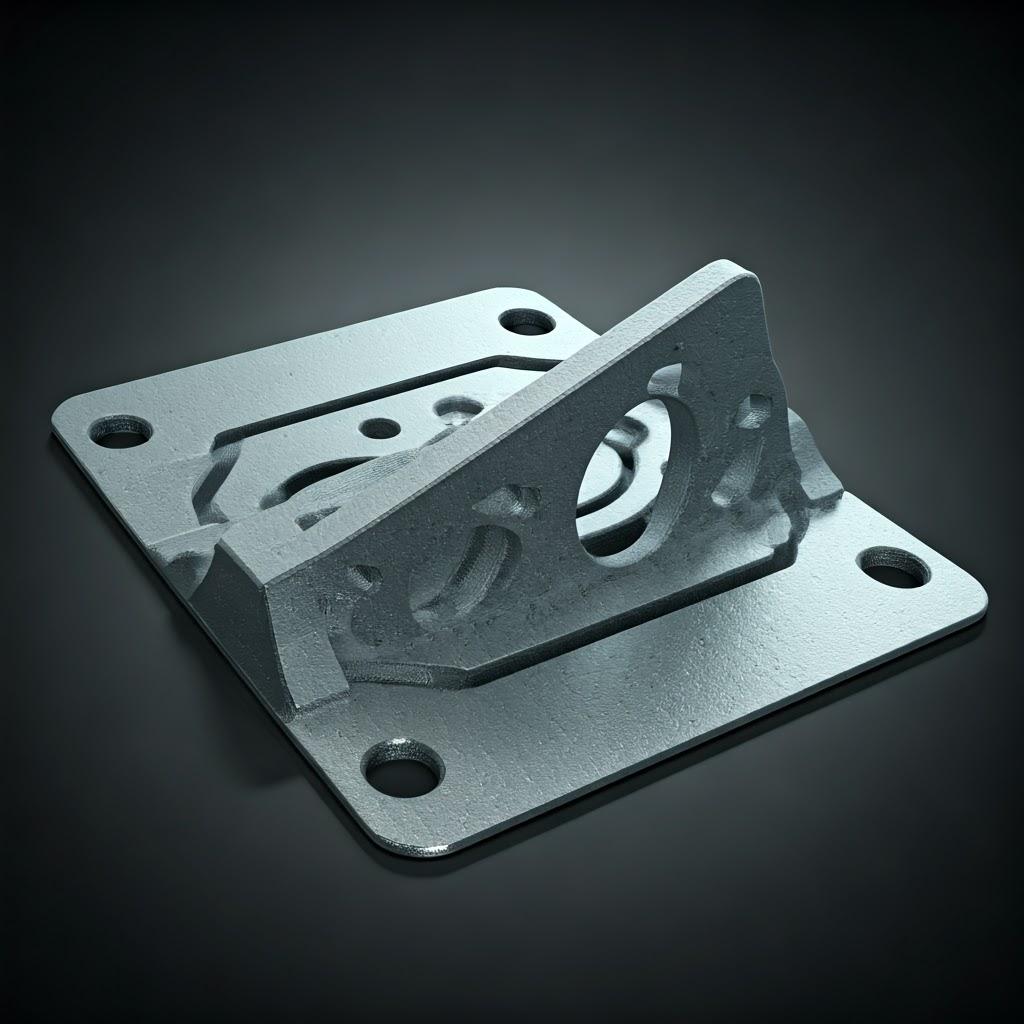
Wesentliche Nachbearbeitungsschritte für Halterungen aus der Luft- und Raumfahrt
Eine 3D-gedruckte Winglet-Halterung aus Metall ist noch nicht flugtauglich, wenn sie von der Bauplatte kommt. Es sind eine Reihe entscheidender Nachbearbeitungsschritte erforderlich, um innere Spannungen abzubauen, Stützstrukturen zu entfernen, die erforderlichen Maßtoleranzen und Oberflächengüte zu erreichen und sicherzustellen, dass das Bauteil die anspruchsvollen mechanischen Eigenschaften und Sicherheitsstandards der Luft- und Raumfahrtindustrie erfüllt. Diese Schritte sind integraler Bestandteil des Fertigungsablaufs und müssen bei der Bewertung von Durchlaufzeiten und Kosten berücksichtigt werden.
Gemeinsamer Nachbearbeitungs-Workflow:
- Entfernung von Puder: Zunächst muss überschüssiges Metallpulver sorgfältig von der fertigen Konstruktion entfernt werden, insbesondere von internen Kanälen oder komplexen Merkmalen. Dies geschieht häufig durch Bürsten, Absaugen oder sanftes Perlstrahlen in einer kontrollierten Umgebung, um das Pulverrecycling zu ermöglichen.
- Stressabbau: Dies ist in der Regel die erste thermische Behandlung, die durchgeführt wird, oft während das Teil noch auf der Bauplatte befestigt ist. Der Aufbau von Wärmegradienten während des schichtweisen Druckprozesses erzeugt erhebliche innere Spannungen. Ein Wärmebehandlungszyklus zum Spannungsabbau (spezifische Temperatur und Dauer hängen vom Material ab) reduziert diese Spannungen und minimiert das Risiko von Verformungen oder Rissen, wenn das Teil von der Bauplatte entfernt wird.
- Entnahme von der Bauplatte: Die Teile werden in der Regel mit Methoden wie Drahterodieren (Electrical Discharge Machining), Bandsägen oder maschineller Bearbeitung von der Bauplatte abgetrennt oder abgelöst.
- Entfernung der Stützstruktur: Dies kann einer der arbeitsintensiveren Schritte sein, je nach Komplexität und Lage der Stützen. Zu den Methoden gehören:
- Manuelle Entfernung: Brechen oder Wegschneiden von leicht zugänglichen Stützen.
- Bearbeitungen: CNC-Fräsen oder -Schleifen zur Entfernung von Halterungen, insbesondere in der Nähe kritischer Oberflächen.
- EDM: Für Unterstützung in schwer zugänglichen Gebieten. Ein sorgfältiges DfAM im Vorfeld kann die Komplexität dieses Schrittes erheblich reduzieren.
- Wärmebehandlung (Lösungsglühen, Alterung usw.): Neben dem Spannungsabbau sind häufig weitere Wärmebehandlungen erforderlich, um die gewünschte endgültige Mikrostruktur und die für die Luft- und Raumfahrtanwendung spezifizierten mechanischen Eigenschaften (z. B. Festigkeit, Duktilität, Härte) zu erreichen. Die genauen Zyklen hängen von der Legierung ab (für Ti-6Al-4V und Scalmalloy® sind spezifische Behandlungen vorgeschrieben).
- Heiß-Isostatisches Pressen (HIP): Dieser Prozess ist häufig obligatorisch für kritische für die Luft- und Raumfahrt geeignet aM-Komponenten aus Metall, insbesondere aus Titan. Beim HIP wird das Teil gleichzeitig einer hohen Temperatur (unterhalb des Schmelzpunkts) und einem hohen Inertgasdruck (in der Regel Argon) ausgesetzt. Durch diese Kombination wird die interne Mikroporosität (Gasporen oder schmelzbedingte Hohlräume), die nach dem Druck vorhanden sein kann, wirksam geschlossen, was die Ermüdungslebensdauer, Duktilität und Bruchzähigkeit erheblich verbessert - Eigenschaften, die für die Sicherheit und Zuverlässigkeit in der Luft- und Raumfahrt entscheidend sind.
- CNC-Bearbeitung: Um enge Toleranzen an kritischen Schnittstellen (z. B. Flächen, die an die Flügelstruktur oder den Winglet-Holm angrenzen), Befestigungslöchern und Lagerstellen zu erreichen, sind Präzisions CNC-Bearbeitung der 3D-gedruckten Teile ist unerlässlich. Dies gewährleistet die korrekte Passform und Funktion innerhalb der größeren Flugzeugbaugruppe.
- Oberflächenveredelung: Je nach Bedarf können weitere Veredelungsschritte hinzukommen:
- Perlstrahlen/Shot Peening: Erzeugt eine gleichmäßige matte Oberfläche, kann lose anhaftende Partikel entfernen, und das Kugelstrahlen kann Druckeigenspannungen induzieren, um die Ermüdungslebensdauer zu verbessern.
- Taumeln/Gleitschleifen: Glättet Oberflächen und entgratet Kanten, insbesondere bei kleineren Teilen.
- Polieren: Zur Erzielung sehr glatter Oberflächen, wo dies erforderlich ist, jedoch weniger häufig für rein strukturelle Halterungen, es sei denn, sie werden für Inspektionen benötigt.
- Zerstörungsfreie Prüfung (NDT): Bei flugkritischen Teilen ist eine strenge Inspektion nicht verhandelbar. NDT für die additive Fertigung stellt sicher, dass das Teil frei von kritischen Fehlern ist und den Maßangaben entspricht. Zu den gängigen Methoden gehören:
- Computertomographie (CT) Scannen: Bietet eine 3D-Ansicht der inneren Struktur, um Porosität, Einschlüsse oder innere geometrische Abweichungen zu erkennen.
- Fluoreszierende Eindringprüfung (FPI): Erkennt Risse, die die Oberfläche durchbrechen.
- Ultraschallprüfung (UT): Kann Fehler unter der Oberfläche erkennen.
- Prüfung der Abmessungen: Einsatz von CMMs (Coordinate Measuring Machines) oder 3D-Scannern zur Überprüfung kritischer Abmessungen anhand der Konstruktionsspezifikationen.
Eine Partnerschaft mit einem AM-Dienstleister, der diese umfassenden metall AM Nachbearbeitung Luft- und Raumfahrt fähigkeiten im eigenen Haus oder durch zertifizierte Partner ist entscheidend für die Rationalisierung der Lieferkette und die Gewährleistung der Qualität der Teile und der Einhaltung der Vorschriften.
Herausforderungen beim 3D-Druck von Winglet-Halterungen und Strategien zur Abhilfe
Die additive Fertigung von Metallen bietet zwar erhebliche Vorteile für die Herstellung von Bauteilen wie Winglet-Verbindungshalterungen für die Luft- und Raumfahrt, ist aber auch nicht ohne Herausforderungen. Das Verständnis dieser potenziellen Hürden und der von erfahrenen AM-Anbietern angewandten Strategien zu ihrer Überwindung ist entscheidend für eine erfolgreiche Einführung, insbesondere wenn man bedenkt großaufträge für Luft- und Raumfahrtkonsolen oder unternehmenskritische Anwendungen.
Gemeinsame Herausforderungen & Abhilfetechniken:
- Eigenspannung und Verformung:
- Herausforderung: Die schnellen Erwärmungs- und Abkühlungszyklen bei PBF-Prozessen erzeugen thermische Gradienten, die zu inneren Spannungen führen. Diese Spannungen können dazu führen, dass sich Teile während des Drucks oder nach der Entnahme aus der Bauplatte verziehen oder verzerren, was die Maßhaltigkeit beeinträchtigt.
- Milderung:
- Simulation: Einsatz von thermischer Simulationssoftware zur Vorhersage der Spannungsakkumulation und zur Optimierung der Bauausrichtung und der Stützstrukturen.
- Optimierte Scan-Strategien: Einsatz spezifischer Laser-/Strahlabtastmuster (z. B. Inselabtastung, Sektorabtastung) zur gleichmäßigeren Verteilung der Wärme.
- Robuste Stützstrukturen: Konstruktion von Stützen nicht nur für Überhänge, sondern auch zur effektiven Verankerung des Teils und als Wärmesenke.
- Plattformheizung (EBM/einige L-PBF): Durch die Aufrechterhaltung einer hohen Temperatur in der Baukammer werden thermische Gradienten reduziert.
- Obligatorischer Stressabbau nach der Drucklegung: Anwendung des entsprechenden thermischen Zyklus unmittelbar nach der Erstellung.
- Porosität:
- Herausforderung: Kleine innere Hohlräume können sich durch eingeschlossenes Gas (Gasporosität) oder unvollständiges Aufschmelzen zwischen den Schichten/Abtastspuren (Lack-of-Fusion-Porosität) bilden. Porosität kann die mechanischen Eigenschaften, insbesondere die Ermüdungsfestigkeit, erheblich beeinträchtigen.
- Milderung:
- Optimierte Prozessparameter: Präzise Steuerung von Laser-/Strahlleistung, Scangeschwindigkeit, Schichtdicke und Gasfluss (bei L-PBF), abgestimmt auf das jeweilige Material.
- Hochwertiges Pulver: Verwendung von Pulver mit geringem Gehalt an eingeschlossenen Gasen, kontrollierter PSD und guter Fließfähigkeit (eine Stärke von Met3dp’s fortschrittlicher Pulverproduktion).
- Kontrolle der inerten Atmosphäre: Aufrechterhaltung einer hochreinen Inertgasumgebung (Argon oder Stickstoff) in der Baukammer, um Oxidation und Kontamination zu verhindern.
- Heiß-Isostatisches Pressen (HIP): Die effektivste Methode zum Schließen der inneren Poren nach dem Druck, die oft für kritische Teile in der Luft- und Raumfahrt erforderlich ist.
- Schwierigkeiten bei der Beseitigung von Stützstrukturen:
- Herausforderung: Halterungen in komplexen inneren Kanälen oder komplizierten Geometrien können extrem schwierig oder unmöglich vollständig zu entfernen sein, ohne das Teil zu beschädigen.
- Milderung:
- DfAM: Vorrang für selbsttragende Konstruktionen und Optimierung der Ausrichtung, um die Abhängigkeit von Stützen in unzugänglichen Bereichen zu minimieren.
- Spezialwerkzeuge/Techniken zum Entfernen: Mittels EDM, chemischem Ätzen (bei einigen Materialien) oder sorgfältiger manueller/bearbeiteter Entfernung.
- Design für den Zugang: Sicherstellung der Berücksichtigung von Umzugswegen in der Entwurfsphase.
- Pulverkontamination und Management:
- Herausforderung: Die Verunreinigung von Metallpulvern (z. B. Kreuzkontamination zwischen Legierungen, übermäßige Sauerstoffaufnahme) kann die Materialeigenschaften und die Druckqualität beeinträchtigen. Die Handhabung und das Recycling von Pulver erfordern sorgfältige Verfahren.
- Milderung:
- Strenge Protokolle für die Handhabung von Pulver: Spezielle Geräte für verschiedene Materialien, Handhabung unter kontrollierter Atmosphäre, ordnungsgemäße Lagerung.
- Pulverkonditionierung/Siebung: Regelmäßiges Sieben des Pulvers, um übergroße Partikel oder Verunreinigungen zu entfernen und eine einheitliche PSD vor der Wiederverwendung sicherzustellen.
- Prüfung der Qualitätskontrolle: Regelmäßige Prüfung der Pulvereigenschaften (Chemie, PSD, Fließfähigkeit).
- Konsistenz und Reproduzierbarkeit (Massenproduktion):
- Herausforderung: Sicherstellung, dass jedes produzierte Teil, insbesondere bei größeren Chargen (anbieter von 3D-Druck in großen Mengen aus Metall kontext), erfüllt genau die gleichen Spezifikationen und Qualitätsstandards.
- Milderung:
- Robuste Qualitätsmanagementsysteme (QMS): Umsetzung und Einhaltung von Luft- und Raumfahrtnormen wie AS9100.
- Prozessüberwachung: In-situ-Überwachung wichtiger Prozessparameter (z. B. Schmelzbadeigenschaften, Temperatur) während der Herstellung.
- Kalibrierung und Wartung von Maschinen: Regelmäßige vorbeugende Wartung und Kalibrierung von AM-Systemen.
- Standardisierte Verfahren: Dokumentierte Arbeitsabläufe für jeden Schritt vom Entwurf bis zur Nachbearbeitung und Prüfung.
- Statistische Prozesskontrolle (SPC): Analyse von Prozessdaten, um die Stabilität zu gewährleisten und mögliche Abweichungen zu ermitteln.
Um diese Herausforderungen erfolgreich zu meistern, ist umfassendes Fachwissen in den Bereichen Materialwissenschaft, Verfahrenstechnik, DfAM und Qualitätskontrolle erforderlich. Dies ist der Punkt, an dem eine Partnerschaft mit einem etablierten und sachkundigen AM-Anbieter wie Met3dp von unschätzbarem Wert ist. Mit jahrzehntelanger kollektiver Erfahrung und einem vertikal integrierten Ansatz, der fortschrittliche SEBM-Drucker, hochwertige Metallpulver aus eigener Herstellung und umfassende Anwendungsentwicklungsdienste umfasst, ist Met3dp gut gerüstet, um die Komplexität der Herstellung anspruchsvoller Luft- und Raumfahrtkomponenten zu bewältigen. Ihr Fokus auf Genauigkeit und Zuverlässigkeit trägt zur Risikominderung bei und gewährleistet die Lieferung hochwertiger, flugtauglicher Winglet-Verbindungsbügel. Mehr über ihren engagierten Ansatz erfahren Sie auf ihrer Über uns Seite.
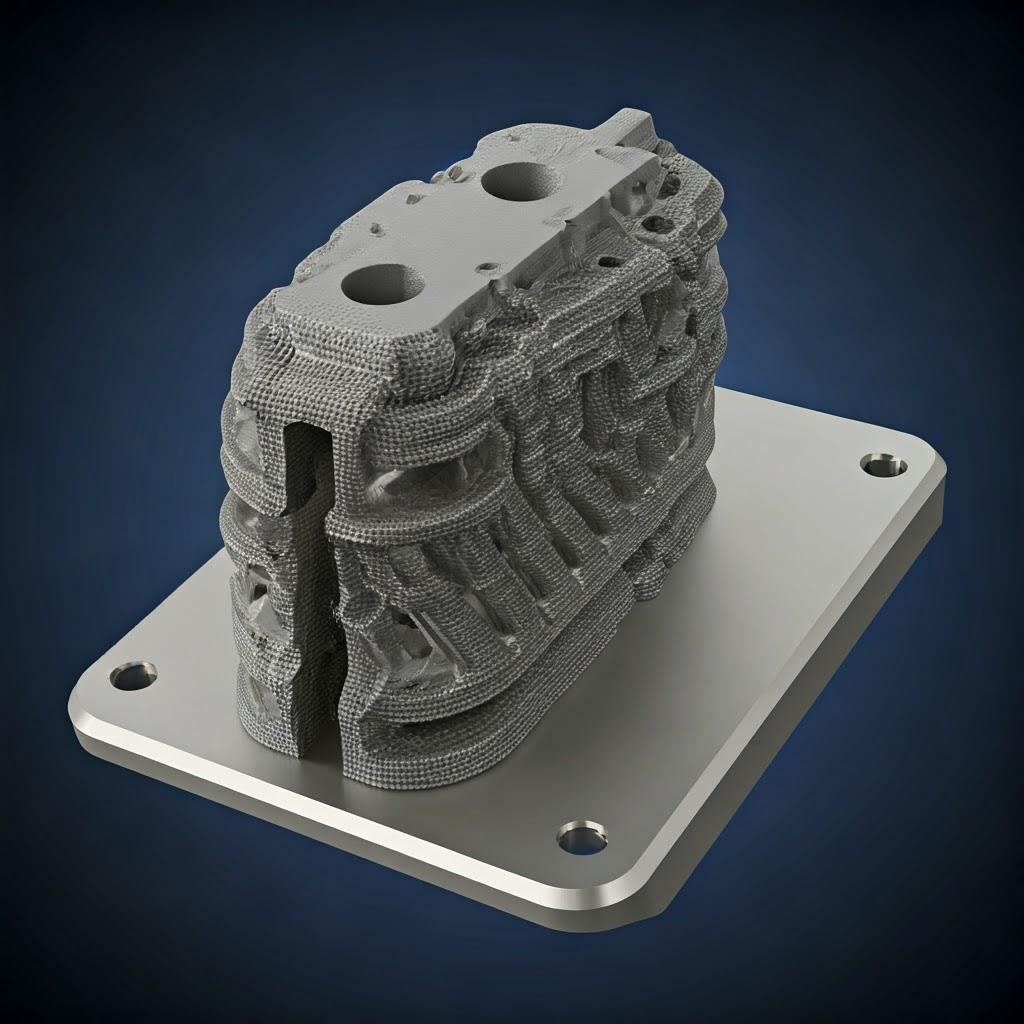
Auswahl des richtigen 3D-Druckdienstleisters für Luft- und Raumfahrtkomponenten aus Metall
Die Wahl des richtigen Fertigungspartners ist wohl eine der kritischsten Entscheidungen bei der Beschaffung von 3D-gedruckten Metallkomponenten für Luft- und Raumfahrtanwendungen wie Winglet-Verbindungshalterungen. Die einzigartigen Anforderungen der Luft- und Raumfahrtindustrie - strenge Sicherheitsvorschriften, komplexe Qualifikationsprozesse und die Notwendigkeit absoluter Zuverlässigkeit - bedeuten, dass nicht alle AM-Dienstleister gleich sind. Ingenieure und Beschaffungsmanager müssen eine gründliche aM-Lieferantenbewertung für die Luft- und Raumfahrt auf der Grundlage einer Reihe von festgelegten Kriterien.
Schlüsselkriterien für die Bewertung von Zulieferern:
- Zertifizierungen für die Luft- und Raumfahrt: Dies ist nicht verhandelbar. Achten Sie vor allem auf Anbieter mit einschlägigen Zertifizierungen:
- AS9100: Die international anerkannte Norm für Qualitätsmanagementsysteme in der Luft-, Raumfahrt- und Verteidigungsindustrie. Die Einhaltung dieser Norm zeigt das Engagement für Qualität, Rückverfolgbarkeit, Risikomanagement und kontinuierliche Verbesserung speziell für die Anforderungen der Luft- und Raumfahrt.
- ISO 9001: Eine grundlegende QMS-Zertifizierung.
- Nadcap-Akkreditierung: Spezifische Akkreditierung für spezielle Verfahren wie Wärmebehandlung, zerstörungsfreie Prüfung (NDT), Schweißen und Materialprüfung, um sicherzustellen, dass diese kritischen Schritte den Industrienormen entsprechen.
- Materialexpertise & Rückverfolgbarkeit: Der Anbieter muss nachweislich Erfahrung in der Verarbeitung der gewünschten Legierungen haben (z. B. Ti-6Al-4V, Scalmalloy®). Fragen Sie nach:
- Pulverbeschaffung: Haben sie zuverlässige Lieferanten oder stellen sie das Pulver selbst her?
- Qualitätskontrolle von Pulvern: Welche Verfahren gibt es für die Prüfung, Handhabung, Lagerung und Wiederverwertung von Pulvern, um Verunreinigungen zu vermeiden und die Konsistenz zu gewährleisten?
- Vollständige Rückverfolgbarkeit der Materialien: Können sie die für jedes einzelne Teil verwendete Pulvercharge bis zu ihrem Ursprung zurückverfolgen? Met3dp’s Fähigkeit zur Herstellung seiner eigenen hochwertige Metallpulver bietet einen deutlichen Vorteil bei der Rückverfolgbarkeit und Qualitätskontrolle.
- Bewährte Erfolgsbilanz in der Luft- und Raumfahrt: Achten Sie auf Nachweise, dass der Lieferant erfolgreich Komponenten (idealerweise strukturelle oder flugkritische) für andere Kunden aus der Luft- und Raumfahrt (OEMs, Tier-1-Lieferanten) hergestellt hat. Fallstudien, Projektbeispiele (innerhalb der NDA-Grenzen) und Referenzen können die Erfahrung und die Fähigkeit, Qualifizierungswege in der Luft- und Raumfahrt zu bewältigen, bestätigen.
- Ausrüstungskapazitäten & Kapazität:
- Verfügen sie über die geeignete AM-Technologie (L-PBF, EBM), die für das Material und das Design Ihrer Halterung geeignet ist?
- Sind die Maschinen gut gewartet und kalibriert?
- Verfügen sie über ein ausreichendes Fertigungsvolumen für Ihre Teilegröße und eine angemessene Maschinenkapazität, um die potenzielle Produktion zu erfüllen (großaufträge für Luft- und Raumfahrtkonsolen) Anforderungen und Vorlaufzeiten?
- Technische und konstruktive Unterstützung: Ein wertvoller Partner ist mehr als nur ein Druckdienstleister. Suchen Sie nach Anbietern, die Folgendes bieten:
- DfAM-Fachwissen: Fähigkeit zur Beratung bei der Designoptimierung für die additive Fertigung.
- Simulationsmöglichkeiten: Unterstützung bei der Validierung von Designs und der Vorhersage von Druckergebnissen.
- Prozessentwicklung: Bereitschaft zur Zusammenarbeit bei der Optimierung von Parametern für spezifische Anwendungen.
- Integriertes Post-Processing: Bietet der Anbieter ein komplettes Paket an erforderlichen Nachbearbeitungsschritten (Spannungsabbau, HIP, Bearbeitung, NDT, Endbearbeitung) entweder intern oder über ein Netz zertifizierter und eng geführter Partner an? Der Umgang mit mehreren Anbietern erhöht die Komplexität und das Risiko.
- Robustes Qualitätsmanagementsystem (QMS): Über die Zertifizierungen hinaus sollten Sie sich über die spezifischen Qualitätsverfahren des Unternehmens informieren:
- Prozessbegleitende Überwachung und Kontrolle.
- Strenge Inspektionsprotokolle (Dimensionen, NDT).
- Kontrolle der Dokumentation und Führung von Aufzeichnungen.
- Konfigurationsmanagement.
- Zuverlässigkeit der Lieferkette und Kommunikation: Bewerten Sie die Reaktionsfähigkeit, die Klarheit der Kommunikation, die Projektmanagementfähigkeiten und die Fähigkeit, zuverlässige Vorlaufzeit der additiven Fertigung kostenvoranschläge und die Einhaltung von Lieferterminen.
Die Wahl eines Anbieters wie Met3dpder die jahrzehntelange Erfahrung in der additiven Fertigung von Metallen mit vertikal integrierten Lösungen, die SEBM-Drucker, moderne Metallpulver und Anwendungsentwicklungsdienstekönnen den Auswahlprozess erheblich rationalisieren. Ihr Fokus auf die Lieferung von branchenführendes Druckvolumen, Genauigkeit und Zuverlässigkeit zielt speziell auf unternehmenskritische Teile in anspruchsvollen Bereichen wie der Luft- und Raumfahrt ab.
Kostenanalyse und Schätzung der Vorlaufzeit für 3D-gedruckte Winglet-Halterungen
Das Verständnis der Kostentreiber und der typischen Vorlaufzeiten im Zusammenhang mit 3D-gedruckten Winglet-Halterungen aus Metall ist für die Projektplanung, die Budgetierung und den Vergleich von AM mit herkömmlichen Fertigungsmethoden unter dem Gesichtspunkt der Gesamtbetriebskosten von wesentlicher Bedeutung. Detaillierte Informationen anfordern großhandel mit 3D-Druck-Angeboten oder projektspezifischen Angeboten ist notwendig, aber die Kenntnis der Einflussfaktoren hilft bei deren Bewertung.
Primäre Kostenfaktoren:
- Materialkosten: Für die Luft- und Raumfahrt geeignete Metallpulver wie Ti-6Al-4V und Scalmalloy® sind im Vergleich zu herkömmlichen technischen Legierungen von Natur aus teure Rohstoffe. Die Gesamtmasse des endgültigen Bauteils sowie das für Stützstrukturen verwendete Material wirken sich direkt auf die Kosten aus.
- Part Volume & Build Height: Größere oder höhere Teile verbrauchen mehr Maschinenzeit. AM-Maschinen stellen erhebliche Investitionen dar, und ihre Betriebszeit (Maschinenstundensatz) ist eine wichtige Kostenkomponente. Eine effiziente Verschachtelung mehrerer Teile auf einer einzigen Bauplatte kann dazu beitragen, die Kosten für die Maschinenzeit pro Teil bei größeren Chargen zu senken.
- Bauzeit: Bestimmt durch die Anzahl der Schichten (Teilehöhe/Schichtdicke) und die für das Scannen jeder Schicht erforderliche Zeit (Komplexität, Querschnittsfläche). Schnellere Maschinen oder Verfahren wie EBM (für einige Anwendungen) können Zeitvorteile bieten.
- Teil Komplexität: Hochkomplexe Designs können komplexere Stützstrukturen oder längere Scanzeiten pro Schicht erfordern. Die Komplexität ist jedoch genau der Punkt, an dem AM oft glänzt. Sie ermöglicht eine Konsolidierung der Teile, die die höheren Druckkosten durch Einsparungen bei der Montage ausgleichen kann.
- Unterstützende Strukturen: Das Volumen des für die Stützen verwendeten Materials und, was noch wichtiger ist, die für ihre Entfernung erforderliche Arbeits- und/oder Bearbeitungszeit tragen zu den Gesamtkosten bei. Die Bemühungen des DfAM zur Minimierung von Stützen zahlen sich hier aus.
- Nachbearbeitungsanforderungen: Dies kann einen erheblichen Teil der Endkosten ausmachen.
- Thermische Behandlungen (Spannungsarmglühen, Wärmebehandlung, HIP): Erfordert spezielle Ofenausrüstung und Zeit; HIP ist besonders energieintensiv und verursacht erhebliche Kosten, ist aber für ermüdungskritische Teile oft unerlässlich.
- Bearbeitungen: Die Präzisions-CNC-Bearbeitung von kritischen Merkmalen verursacht zusätzliche Kosten aufgrund von Komplexität und Zeitaufwand.
- ZfP und Inspektion: Erforderliche Inspektionen (CT-Scanning, FPI, CMM) verursachen zusätzliche Kosten für Ausrüstung, Zeit und Fachwissen.
- Fertigstellung: Die Kosten hängen von der verwendeten Methode und der gewünschten Oberflächenqualität ab.
- Menge: Wie bei den meisten Fertigungsverfahren kommen Größenvorteile zum Tragen. Die Einrichtungskosten (Bauvorbereitung, Maschineneinrichtung, Nachbearbeitungseinrichtung) amortisieren sich über größere Mengen. Mengenrabatte auf Pulver und eine optimierte Nutzung der Bauplatte können die Kosten pro Teil senken für großaufträge für Luft- und Raumfahrtkonsolen.
- Qualifizierung & Zertifizierung: Die Kosten, die mit der Entwicklung eines zertifizierten Prozesses und der Qualifizierung des spezifischen Teils für den Flug verbunden sind, können beträchtlich sein, insbesondere bei der ersten Einführung.
Schätzung der Vorlaufzeit:
Die Gesamt Vorlaufzeit der additiven Fertigung von der endgültigen Konstruktionsgenehmigung bis zur Auslieferung einer flugfähigen Winglet-Halterung sind mehrere Schritte erforderlich:
- Vorbereitung des Baus: Dateivorbereitung, Planung des Baulayouts, Einrichten der Maschine (Stunden bis zu einem Tag).
- Drucken: Das kann von Stunden für kleine Halterungen bis zu mehreren Tagen für große, komplexe Teile oder ganze Bauplatten reichen (je nach Höhe und Volumen).
- Cool Down & Pulverentfernung: Stunden.
- Stressabbau: In der Regel mehrere Stunden bis zu einem Tag (einschließlich Ofenzeit).
- Teil/Träger entfernen: Stunden bis Tage, je nach Komplexität und Methode.
- Wärmebehandlung/HIP: Dies kann mehrere Tage dauern, einschließlich der Ofenzyklen und der Abkühlung.
- Bearbeitungen: Sehr variabel, je nach Bedarf (Stunden bis Tage).
- Fertigstellung: Stunden bis Tage.
- ZfP und Inspektion: Stunden bis Tage, je nach Methode und Berichterstattung.
- Versand: Variabel.
Typische Vorlaufzeiten:
- Prototypen (Form/Passform): Einige Tage bis 1-2 Wochen (wobei häufig einige Nachbearbeitungen wie HIP oder umfangreiche NDT ausgelassen werden).
- Funktional getestete Prototypen: 2-4 Wochen (einschließlich der erforderlichen Wärmebehandlungen und einiger Bearbeitungen/NDT).
- Qualifizierte Produktionsteile: 4-10+ Wochen, stark abhängig vom Umfang der Nachbearbeitung, der strengen zerstörungsfreien Prüfung, den Dokumentationsanforderungen und der Losgröße.
Es ist von entscheidender Bedeutung, eng mit dem von Ihnen gewählten AM-Anbieter zusammenzuarbeiten, um genaue, maßgeschneiderte Kosten- und Vorlaufzeitschätzungen zu erhalten, die auf Ihren spezifischen Design-, Material-, Mengen- und Qualifikationsanforderungen basieren.
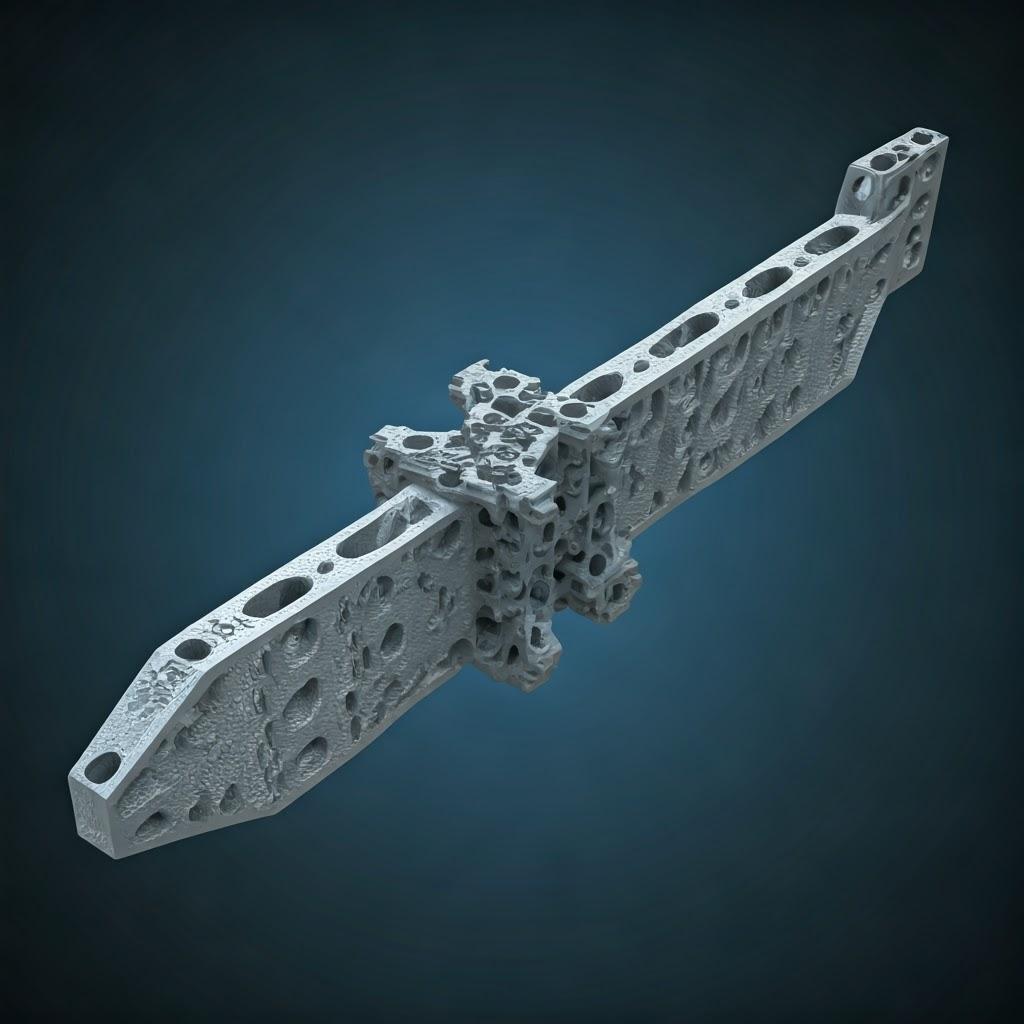
Häufig gestellte Fragen (FAQ) zu 3D-gedruckten Winglet-Halterungen
Hier finden Sie Antworten auf einige häufig gestellte Fragen zum Einsatz der additiven Fertigung von Metallteilen für Winglet-Verbindungshalterungen in der Luftfahrt:
F1: Sind 3D-gedruckte Metallhalterungen für den Flugverkehr zugelassen?
- A: Ja, absolut. Die Flugzulassung wird nicht für die 3D-Drucktechnologie selbst erteilt, sondern für eine bestimmte, streng kontrollierte Herstellungsverfahren. Dazu gehören das spezifische AM-Maschinenmodell, die qualifizierte Materialcharge (z. B. Ti-6Al-4V-Pulver, das den Spezifikationen für die Luft- und Raumfahrt entspricht), validierte Maschinenparameter, definierte Nachbearbeitungsschritte (einschließlich Spannungsabbau, HIP, Wärmebehandlung, Bearbeitung) und die Einhaltung eines zertifizierten Qualitätsmanagementsystems (wie AS9100). Teile, die in diesem streng kontrollierten und zertifizierten Prozess hergestellt und durch umfangreiche zerstörungsfreie Prüfungen und Maßkontrollen verifiziert wurden, können für Fluganwendungen zertifiziert werden. Mehrere Flugzeuge, die heute fliegen, enthalten 3D-gedruckte Strukturkomponenten.
F2: Wie ist die Ermüdungslebensdauer von AM-Klammern im Vergleich zu maschinell gefertigten Klammern?
- A: Bei der Herstellung mit optimierten Parametern, hochwertigen Pulvern und geeigneter Nachbearbeitung (insbesondere HIP zum Schließen der Porosität) kann die Ermüdungslebensdauer von AM-Komponenten aus Ti-6Al-4V die von Gusskomponenten erreichen oder übertreffen und sich den Eigenschaften von Knet-/Bearbeitungskomponenten annähern. Für Scalmalloy® kann die AM-Bearbeitung Ermüdungseigenschaften liefern, die denen vieler konventioneller hochfester Aluminiumlegierungen überlegen sind. Darüber hinaus ermöglicht DfAM Konstruktionen, die Spannungskonzentrationen gezielt minimieren, was zu einer verbesserten Ermüdungsleistung im Vergleich zu traditionell eingeschränkten Konstruktionen führen kann. Die Leistung muss immer durch strenge, anwendungsspezifische Tests validiert werden.
F3: Wie hoch ist die typische Verbesserung des Kauf-zu-Flug-Verhältnisses bei AM-Brackets?
- A: Dies ist einer der wichtigsten Vorteile von AM’s. Bei der herkömmlichen Bearbeitung von Luft- und Raumfahrthalterungen aus Knüppeln, insbesondere aus Titan, kann das Verhältnis zwischen Einkauf und Fertigung 10:1, 15:1 oder sogar noch höher sein (d. h. für jedes Kilogramm im fertigen Teil werden 10-15+ kg Rohmaterial gekauft). Bei der additiven Fertigung (AM), bei der das Material additiv verwendet wird und die Topologie optimiert werden kann, lässt sich das Verhältnis zwischen Einkauf und Fertigung oft drastisch auf Werte wie 2:1 oder 3:1 reduzieren, was erhebliche Einsparungen bei teuren Rohstoffen und geringere Umweltauswirkungen bedeutet.
F4: Können bestehende Halterungsdesigns direkt in 3D gedruckt werden?
- A: Das ist zwar technisch möglich, wird aber im Allgemeinen nicht empfohlen. Das direkte Drucken eines Designs, das für die maschinelle Bearbeitung oder das Gießen optimiert wurde, bietet in der Regel nicht die wichtigsten Vorteile von AM (z. B. Gewichtsreduzierung durch Topologieoptimierung oder Teilekonsolidierung). Außerdem kann es aufgrund von Merkmalen, die sich nicht für AM eignen (z. B. große Überhänge), schwierig sein, effizient zu drucken. Um das volle Potenzial von AM auszuschöpfen, wird dringend empfohlen, die Halterung nach DfAM-Prinzipien neu zu gestalten.
F5: Welche ZfP-Methoden werden zur Qualifizierung von AM-Luftfahrtteilen verwendet?
- A: Um die Integrität kritischer AM-Komponenten für die Luft- und Raumfahrt zu gewährleisten, wird in der Regel eine Kombination von ZfP-Methoden eingesetzt. Die Computertomografie (CT) ist von unschätzbarem Wert für die Erkennung interner Defekte wie Porosität oder Einschlüsse und die Überprüfung der internen Geometrie. Die fluoreszierende Eindringprüfung (FPI) wird häufig eingesetzt, um Risse in der Oberfläche aufzuspüren. Mit der Ultraschallprüfung (UT) lassen sich Fehler unter der Oberfläche aufspüren. Darüber hinaus wird mit Hilfe von Koordinatenmessmaschinen (KMG) oder 3D-Laserscannern eine strenge Maßprüfung durchgeführt, um die Übereinstimmung mit den Konstruktionsspezifikationen zu überprüfen. Der spezifische ZfP-Plan ist auf die Kritikalität und das Design des Teils zugeschnitten.
Schlussfolgerung: Additive Fertigung für die nächste Generation von Tragflächenhalterungen für Flugzeuge
Das unablässige Streben der Luft- und Raumfahrtindustrie nach verbesserter Leistung, höherer Treibstoffeffizienz und geringerer Umweltbelastung erfordert kontinuierliche Innovationen in Design und Fertigung. Die additive Fertigung von Metallen hat sich eindeutig als leistungsfähiger Weg zur Erreichung dieser Ziele erwiesen, insbesondere bei komplexen Strukturkomponenten wie Winglet-Verbindungshalterungen.
Durch die Nutzung der Möglichkeiten von AM-Prozessen wie L-PBF und EBM in Kombination mit fortschrittlichen Werkstoffen wie Ti-6Al-4V, einem Standardwerkstoff für die Luft- und Raumfahrt, und dem Hochleistungswerkstoff Scalmalloy® können Ingenieure nun Halterungen entwerfen und produzieren, die deutlich leichter und potenziell stabiler sind und deren Geometrie für die Funktion optimiert ist, anstatt durch die traditionellen Fertigungsbeschränkungen eingeschränkt zu werden. Die Möglichkeit, Teile zu konsolidieren, den Materialabfall zu reduzieren (und damit das Verhältnis zwischen Anschaffung und Fertigung zu verbessern) und die Design-Iterationszyklen zu beschleunigen, ist ein weiteres Argument für die Einführung von AM.
Zwar gibt es Herausforderungen im Zusammenhang mit der Prozesssteuerung, der Komplexität der Nachbearbeitung und den Qualifizierungswegen, doch werden diese durch Fortschritte in der Technologie, der Materialwissenschaft, den Simulationswerkzeugen und der Einführung robuster Qualitätsmanagementsysteme und Industriestandards erfolgreich angegangen. Der Schlüssel liegt in der Zusammenarbeit mit erfahrenen und fähigen Anbieter von 3D-Metalldruckdiensten die über die erforderlichen Zertifizierungen, Materialkenntnisse, technologischen Fähigkeiten und den strengen Qualitätsanspruch der Luft- und Raumfahrtbranche verfügen.
Die Zukunft der Luft- und Raumfahrtindustrie wird zweifellos eine zunehmende Einführung der additiven Fertigung für strukturelle Anwendungen sehen, die über Prototypen und unkritische Teile hinausgehen und in die Serienproduktion von flugkritischen Komponenten münden. Winglet-Verbindungshalterungen sind eine ideale Anwendung, bei der die Vorteile von AM - Gewichtsreduzierung, Leistungssteigerung und Designfreiheit - einen greifbaren Wert darstellen.
Für Luft- und Raumfahrtingenieure und Beschaffungsmanager, die das Potenzial der Metall-AM für Winglet-Halterungen oder andere anspruchsvolle Anwendungen ausloten möchten, ist es jetzt an der Zeit, aktiv zu werden. Die Zusammenarbeit mit einem sachkundigen Partner kann helfen, die Komplexität zu bewältigen und das transformative Potenzial dieser Technologie zu erschließen.
Sind Sie bereit, Ihre Luft- und Raumfahrtkomponenten zu revolutionieren? Entdecken Sie die neuesten Lösungen für die additive Fertigung von Metallen mit Met3dp. Besuchen Sie https://met3dp.com/ um mehr über unsere fortschrittlichen SEBM-Drucker, Hochleistungsmetallpulver und umfassenden, auf die Luft- und Raumfahrtindustrie zugeschnittenen Anwendungsentwicklungsdienste zu erfahren. Kontaktieren Sie uns noch heute, um zu besprechen, wie Met3dp Lösungen für die Luft- und Raumfahrt kann die Ziele Ihres Unternehmens im Bereich der additiven Fertigung unterstützen und Ihnen helfen, die Zukunft des Fliegens zu gestalten.
Teilen auf
MET3DP Technology Co., LTD ist ein führender Anbieter von additiven Fertigungslösungen mit Hauptsitz in Qingdao, China. Unser Unternehmen ist spezialisiert auf 3D-Druckgeräte und Hochleistungsmetallpulver für industrielle Anwendungen.
Fragen Sie an, um den besten Preis und eine maßgeschneiderte Lösung für Ihr Unternehmen zu erhalten!
Verwandte Artikel
Über Met3DP
Aktuelles Update
Unser Produkt
KONTAKT US
Haben Sie Fragen? Senden Sie uns jetzt eine Nachricht! Wir werden Ihre Anfrage mit einem ganzen Team nach Erhalt Ihrer Nachricht bearbeiten.
Holen Sie sich Metal3DP's
Produkt-Broschüre
Erhalten Sie die neuesten Produkte und Preislisten
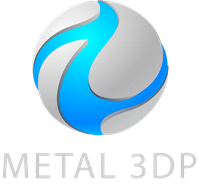
Metallpulver für 3D-Druck und additive Fertigung