Kundenspezifische Steckergehäuse für Luft- und Raumfahrtsysteme
Inhaltsübersicht
Einführung: Definition von Steckverbindergehäusen für die Luft- und Raumfahrt und deren Funktion
In der komplexen und anspruchsvollen Welt der Luft- und Raumfahrttechnik spielt jedes noch so kleine Bauteil eine entscheidende Rolle bei der Gewährleistung von Sicherheit, Zuverlässigkeit und Leistung. Zu diesen wesentlichen Elementen gehören steckergehäuse für die Luft- und Raumfahrt. Diese Komponenten stehen vielleicht nicht immer so im Rampenlicht wie Triebwerke oder Tragflächen, aber sie sind von grundlegender Bedeutung für das komplizierte Netzwerk von elektrischen und Datensystemen, die das einwandfreie Funktionieren moderner Flugzeuge, Raumfahrzeuge und Verteidigungsplattformen ermöglichen.
Ein Steckverbindergehäuse für die Luft- und Raumfahrt dient im Wesentlichen als Schutzgehäuse für elektrische oder optische Steckverbinder. Zu seinen Hauptfunktionen gehören:
- Physischer Schutz: Abschirmung der empfindlichen Steckerschnittstellen (Stifte, Buchsen, Glasfaserendstücke) vor physischen Schäden durch Stöße, Vibrationen, Erschütterungen und Abrieb. Dies ist besonders wichtig in Umgebungen, in denen die mechanischen Belastungen konstant und intensiv sind.
- Umweltfreundliche Versiegelung: Verhinderung des Eindringens von Verunreinigungen wie Staub, Feuchtigkeit, Enteisungsflüssigkeiten, Flugzeugtreibstoff, Hydraulikflüssigkeiten und anderen potenziell korrosiven Substanzen, die elektrische Verbindungen beeinträchtigen und zu Systemausfällen führen können. Eine wirksame Abdichtung ist entscheidend für die Aufrechterhaltung der Signalintegrität und die Vermeidung von Kurzschlüssen.
- Elektrische Abschirmung (EMI/RFI): Bei vielen Anwendungen in der Luft- und Raumfahrt, insbesondere bei empfindlichen Avionik- oder Kommunikationssystemen, dienen Steckverbindergehäuse der Abschirmung von elektromagnetischen Störungen (EMI) und Hochfrequenzstörungen (RFI). Dies verhindert, dass externe elektromagnetische Felder die Signalübertragung stören, und schützt andere Systeme in der Nähe vor Störungen, die durch den Steckverbinder selbst erzeugt werden.
- Erleichterung der Belastung: Mechanische Unterstützung für die in den Steckverbinder eintretenden Kabel, um zu verhindern, dass die Belastung direkt auf die Anschlusspunkte übertragen wird. Dies erhöht die Haltbarkeit und Lebensdauer der gesamten Kabelbaugruppe.
- Ausrichten und Zusammenfügen: Sicherstellung der korrekten Ausrichtung und sicheren Verriegelung von Gegensteckern, um eine zuverlässige Verbindung herzustellen und aufrechtzuerhalten, auch unter schwierigen Betriebsbedingungen.
Bei diesen Gehäusen handelt es sich nicht nur um einfache Kästen, sondern um präzise konstruierte Komponenten, die die Integrität lebenswichtiger Daten- und Stromverbindungen in einem Luft- oder Raumfahrzeug gewährleisten sollen. Der Ausfall eines einzigen Steckverbinders, der häufig auf einen unzureichenden Schutz des Gehäuses zurückzuführen ist, kann kaskadenartige Auswirkungen haben und zu einem Ausfall des unternehmenskritischen Systems führen. Aus diesem Grund werden die Konstruktion, die Materialauswahl und das Herstellungsverfahren für diese Gehäuse in der Luft- und Raumfahrtindustrie genauestens geprüft. Da die Systeme immer komplexer und integrierter werden, steigen die Anforderungen an diese scheinbar einfachen Komponenten immer weiter an, was den Bedarf an innovativen Lösungen erhöht.
Die unnachgiebige Luft- und Raumfahrtumgebung: Warum robuste Gehäuse unverzichtbar sind
Die Einsatzbedingungen für Komponenten in der Luft- und Raumfahrt gehören wohl zu den anspruchsvollsten in allen technischen Bereichen. Steckverbindergehäuse müssen einer unerbittlichen Flut von extremen Bedingungen standhalten, wodurch Robustheit und Zuverlässigkeit zu unverzichtbaren Anforderungen werden. Betrachten Sie das Spektrum der Herausforderungen:
- Extreme Temperaturen: Bauteile sind enormen Temperaturschwankungen ausgesetzt, von Minusgraden in großen Höhen oder im Weltraum (-55 °C oder weniger) bis hin zu hohen Temperaturen in der Nähe von Triebwerken oder in Ausrüstungsschächten (+125 °C, +175 °C oder in bestimmten Bereichen sogar noch höher). Die Materialien müssen ihre strukturelle Integrität, ihre Dichtungseigenschaften und ihre Dimensionsstabilität über diese Temperaturbereiche hinweg beibehalten, ohne zu reißen, sich zu verformen oder zu verschlechtern.
- Vibration und Schock: Flugzeuge und Trägerraketen erzeugen während des Starts, des Flugs und der Landung erhebliche Vibrationen. Steckergehäuse müssen diesen konstanten Vibrationsbelastungen sowie plötzlichen Hoch-G-Stößen standhalten, ohne sich zu lockern, zu ermüden oder intermittierende elektrische Kontaktprobleme (Fretting) zu verursachen. Sichere Verriegelungsmechanismen und eine robuste Konstruktion sind unerlässlich.
- Druckunterschiede: Die Komponenten müssen vom Druck auf Meereshöhe bis zu den niedrigen Drücken in großen Höhen oder dem Vakuum im Weltraum zuverlässig funktionieren. Die Dichtungsintegrität ist entscheidend, um Druckverluste in Druckkabinen oder -modulen zu verhindern und die internen Komponenten vor der äußeren Umgebung zu schützen.
- Korrosion und Verschmutzung: Feuchtigkeit, Salzsprühnebel (in Meeresumgebungen oder auf Flugplätzen in Küstennähe), Hydraulikflüssigkeiten, Kraftstoffe, Reinigungs- und Enteisungsmittel erfordern Materialien mit ausgezeichneter Korrosionsbeständigkeit. Auch die Verunreinigung durch Staub, Sand und andere Partikel stellt eine Gefahr für die Schnittstellen der Steckverbinder dar.
- Strahlung: Bei Weltraumanwendungen stellt die ionisierende Strahlung eine Herausforderung dar, da sie bestimmte Materialien mit der Zeit zersetzen kann, was die langfristige Zuverlässigkeit von Steckverbindergehäusen in Satelliten und Weltraumsonden beeinträchtigen kann.
- Ausgasen (Weltraum): Im Vakuum des Weltraums können Materialien eingeschlossene Gase freisetzen (Ausgasung), die empfindliche optische Oberflächen oder Elektronik verunreinigen können. Für weltraumtaugliche Komponenten werden oft Materialien mit geringer Ausgasung benötigt.
- Gewichtsbeschränkungen: In der Luft- und Raumfahrt zählt jedes Gramm. Gehäuse müssen ein Maximum an Schutz und Leistung bieten und gleichzeitig möglichst wenig zum Gesamtgewicht des Systems beitragen. Dieses ständige Streben nach Gewichtsreduzierung treibt die Suche nach fortschrittlichen Materialien und Fertigungsverfahren voran.
Wenn diese strengen Umweltanforderungen nicht erfüllt werden, kann dies zu katastrophalen Systemausfällen führen. Aus diesem Grund legen Luft- und Raumfahrtingenieure und Beschaffungsmanager besonderen Wert auf Steckverbindergehäuse, die aus Hochleistungsmaterialien in Verfahren hergestellt werden, die Konsistenz, Zuverlässigkeit und die Einhaltung strenger Industrienormen (wie AS9100) garantieren.
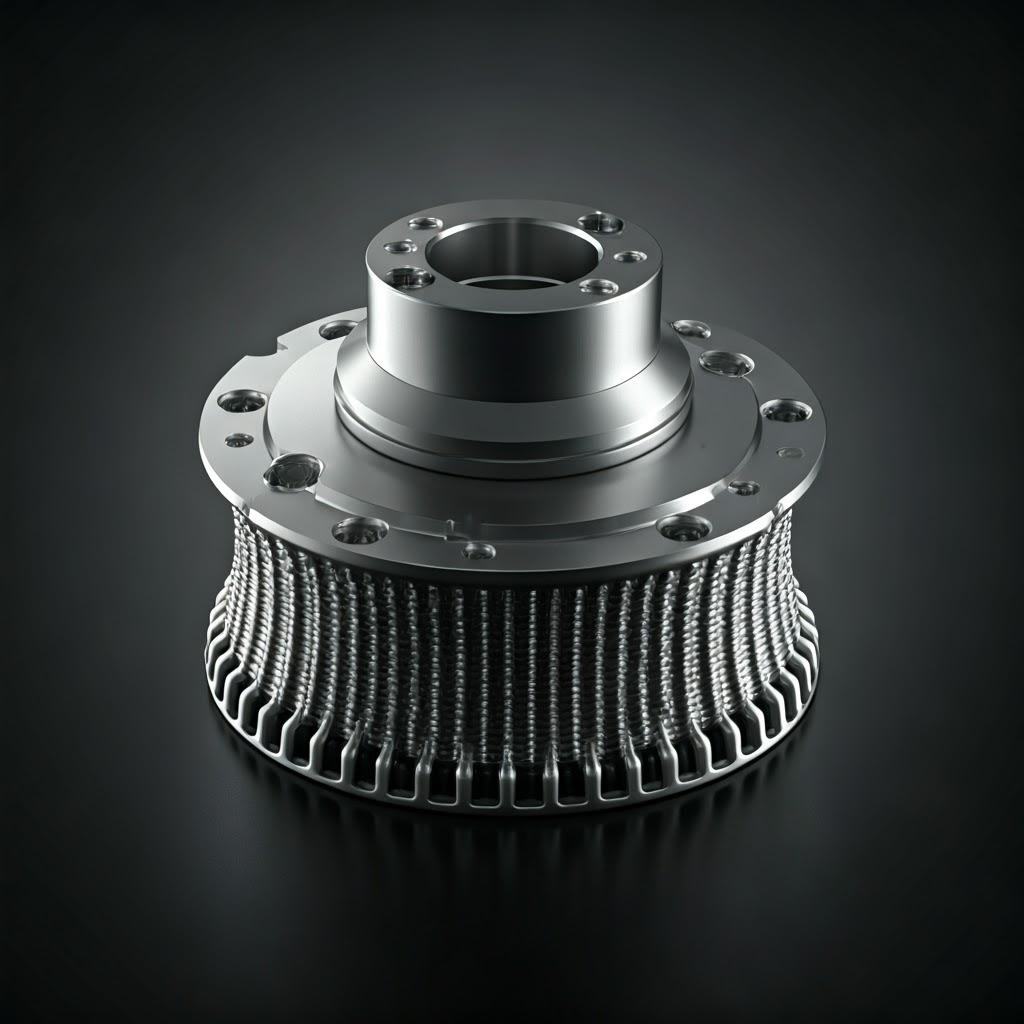
Das Gebot der Individualisierung im modernen Luft- und Raumfahrtdesign
Es gibt zwar standardisierte, handelsübliche Steckverbinder und Gehäuse, doch die zunehmende Komplexität, Miniaturisierung und die spezifischen funktionalen Anforderungen moderner Luft- und Raumfahrtsysteme machen es häufig erforderlich kundenspezifische Steckergehäuse. Dieser Bedarf ist auf mehrere Faktoren zurückzuführen:
- Platzbeschränkungen: Da in Flugzeugen und Raumfahrzeugen immer mehr Elektronik auf engstem Raum untergebracht wird (z. B. in Avionikbuchten, Tragflächenwurzeln, Nutzlasten von UAVs), müssen Steckverbindergehäuse oft besondere Formen, Profile oder Montagemerkmale aufweisen, um genau in die zugewiesenen Bereiche zu passen. Standardmäßige rechteckige oder runde Gehäuse sind unter Umständen nicht machbar.
- Spezifische Paarungsanforderungen: Sonderanfertigungen können erforderlich sein, um Schnittstellen zu speziellen oder nicht genormten Geräten zu schaffen, bestimmte Kabelabgangswinkel zu berücksichtigen oder mehrere Steckertypen in ein einziges, konsolidiertes Gehäuse zu integrieren.
- Integrierte Funktionalitäten: Es gibt einen zunehmenden Trend zur Integration von Merkmalen direkt in das Gehäuse, wie z. B. integrierte Abschirmungen, Kühlkanäle, Montagehalterungen oder Sensorhalterungen. Dies reduziert die Anzahl der Teile, die Montagezeit und mögliche Fehlerquellen.
- Optimierung des Gewichts: Die kundenspezifische Anpassung ermöglicht es den Ingenieuren, die Geometrie des Gehäuses speziell auf die Belastungsanforderungen zuzuschneiden, unnötiges Material durch Topologieoptimierung zu entfernen und maximale Gewichtseinsparungen zu erzielen, die über das hinausgehen, was Standardkomponenten bieten.
- Einzigartige Umweltbedürfnisse: Spezifische Anwendungen können spezielle Dichtungskonfigurationen, einzigartige EMI/RFI-Abschirmungslösungen oder die Kompatibilität mit nicht standardmäßigen Flüssigkeiten oder Temperaturen erfordern, was die Notwendigkeit von kundenspezifischen Konstruktionen und Materialauswahlen mit sich bringt.
- Integration von Altsystemen: Die Nachrüstung neuer Systeme in älteren Flugzeugen erfordert oft kundenspezifische Steckverbinderlösungen, um moderne Elektronik mit vorhandenen Kabelbäumen und Befestigungspunkten zu verbinden.
Herkömmliche Fertigungsmethoden wie die CNC-Bearbeitung von Knüppeln oder das Spritzgießen (für hohe Stückzahlen) können diese kundenspezifischen Anforderungen nur schwer effizient oder kostengünstig erfüllen, vor allem bei den geringen bis mittleren Stückzahlen, die bei Projekten in der Luft- und Raumfahrt häufig erforderlich sind. Die maschinelle Bearbeitung komplexer, organisch geformter oder innen kanalisierter kundenspezifischer Gehäuse kann unglaublich zeitaufwändig sein und zu erheblichem Materialabfall führen. Die Herstellung von Formen oder Werkzeugen für das Gießen oder Spritzgießen ist für kleine Produktionsserien oder Prototypen oft unerschwinglich. Hier kommen die einzigartigen Möglichkeiten der additiven Fertigung von Metall zum Tragen.
Additive Fertigung aus Metall: Ein Paradigmenwechsel für die Produktion von Steckergehäusen
Additive Fertigung von Metallen (AM), allgemein bekannt als Metall 3D-Druckbietet eine leistungsstarke Alternative für die Herstellung von hochleistungsfähigen, kundenspezifischen Steckverbindergehäusen für die Luft- und Raumfahrt. Technologien wie das Pulverbettschmelzen (Powder Bed Fusion, PBF) - zu denen das Selektive Laserschmelzen (SLM), das Direkte Metall-Lasersintern (DMLS) und das Elektronenstrahlschmelzen (EBM) gehören - bauen Teile Schicht für Schicht direkt aus einem digitalen Modell mit feinen Metallpulvern auf. Dieser Ansatz verändert die Produktionslandschaft für Komponenten wie Steckergehäuse grundlegend:
- Beispiellose Designfreiheit: AM beseitigt viele traditionelle Fertigungsbeschränkungen. Ingenieure können hochkomplexe Geometrien, interne Gitterstrukturen zur Gewichtsreduzierung, konforme Kühlkanäle und organisch geformte Gehäuse entwerfen, die für bestimmte Platzverhältnisse optimiert sind - Merkmale, die bei der maschinellen Fertigung oder beim Gießen oft unmöglich oder unpraktisch sind.
- Rapid Prototyping und Iteration: Kundenspezifische Gehäusedesigns können innerhalb weniger Tage gedruckt, getestet und verfeinert werden, was den Entwicklungszyklus im Vergleich zu den Wochen oder Monaten, die für herkömmliche Werkzeug- und Bearbeitungsvorrichtungen erforderlich sind, drastisch beschleunigt. Diese Flexibilität ist in schnelllebigen Luft- und Raumfahrtprogrammen von entscheidender Bedeutung.
- Kosteneffiziente Anpassung: Da es sich bei AM um ein werkzeugloses Verfahren handelt, ist der Kostenunterschied zwischen dem Druck eines kundenspezifischen Designs und zehn geringfügig abweichenden Varianten minimal im Vergleich zu den hohen Werkzeugkosten, die bei herkömmlichen Verfahren anfallen. Dies macht AM ideal für kleine bis mittlere Produktionsserien von Spezialgehäusen.
- Teil Konsolidierung: Mehrere Komponenten einer Steckverbinderbaugruppe (z. B. Gehäuse, Halterung, Zugentlastung) können potenziell in ein einziges, komplexes 3D-gedrucktes Teil integriert werden. Dies verringert die Montagezeit, eliminiert potenzielle Leckagepfade oder Fehlerstellen an Verbindungen und kann das Gewicht weiter reduzieren.
- Materialeffizienz: Bei AM-Prozessen wird in der Regel nur das Material verwendet, das für die Herstellung des Teils und seiner Halterungen benötigt wird, was im Vergleich zu subtraktiven Verfahren wie der CNC-Bearbeitung, bei der bis zu 80-90 % des ursprünglichen Materialblocks für komplexe Teile abgetragen werden können, zu deutlich weniger Materialabfall führt. Dies ist besonders vorteilhaft, wenn teure Legierungen für die Luft- und Raumfahrt wie Titan verwendet werden.
- Fertigung auf Abruf: Digitale Entwürfe können gespeichert und bei Bedarf gedruckt werden, was verteilte Fertigungsmodelle ermöglicht und den Bedarf an großen physischen Beständen verringert. Ersatzteile oder aktualisierte Entwürfe können schnell hergestellt werden, ohne dass vorhandene Werkzeuge benötigt werden.
Für Luft- und Raumfahrtingenieure und Beschaffungsmanager sucht Zulieferer der Luft- und Raumfahrtindustrie metall-AM ist in der Lage, hochgradig kundenspezifische, hochleistungsfähige Steckergehäuse effizient zu liefern, und bietet ein überzeugendes Wertversprechen. Es ermöglicht Innovationen, beschleunigt Zeitpläne und bietet einen kosteneffizienten Weg für komplexe Teile mit geringen Stückzahlen, die in der Industrie immer häufiger vorkommen.
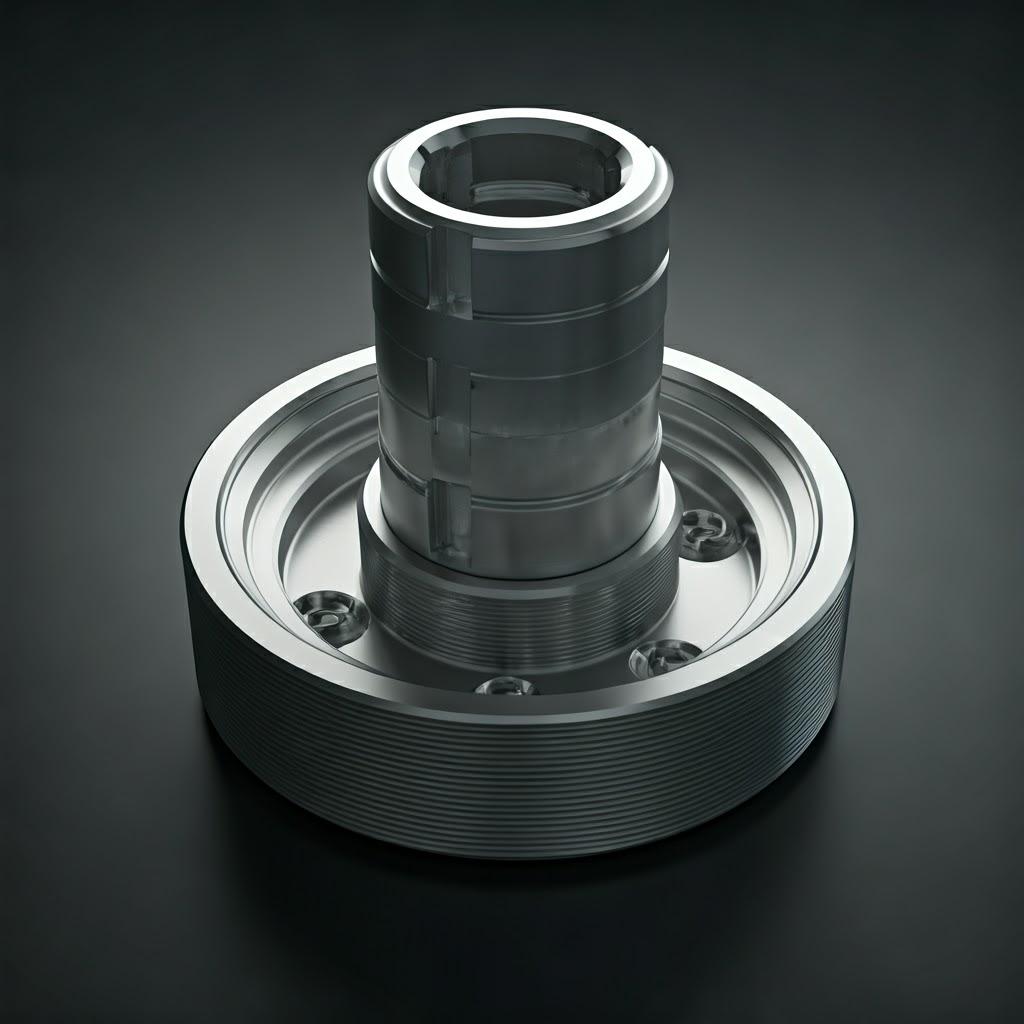
Partnerschaften mit erfahrenen Metall-AM-Anbietern wie Met3dp
Die erfolgreiche Nutzung von Metall-AM für kritische Komponenten wie Steckverbindergehäuse in der Luft- und Raumfahrt erfordert die Zusammenarbeit mit einem sachkundigen und fähigen 3D-Druck-Dienstleister für Metall. Die Feinheiten der Optimierung von Prozessparametern, der Materialkunde, der Qualitätskontrolle und der Nachbearbeitung erfordern spezielles Fachwissen.
Met3dpmit Hauptsitz in Qingdao, China, ist ein führender Anbieter umfassender additiver Fertigungslösungen für anspruchsvolle industrielle Anwendungen, einschließlich der Luft- und Raumfahrt. Unser Know-how erstreckt sich über das gesamte AM-Ökosystem:
- Fortschrittliche Metallpulver: Met3dp stellt eine breite Palette hochwertiger sphärischer Metallpulver her, die speziell für PBF-Verfahren optimiert sind. Durch den Einsatz modernster Gaszerstäubungs- und Plasma-Rotations-Elektroden-Verfahren (PREP) stellen wir sicher, dass unsere Pulver, einschließlich Luft- und Raumfahrtqualitäten wie Ti-6Al-4V und rostfreie Stähle wie 316L, eine hohe Sphärizität, eine hervorragende Fließfähigkeit, eine kontrollierte Partikelgrößenverteilung und eine hohe Reinheit aufweisen - entscheidende Faktoren für die Herstellung dichter, zuverlässiger und leistungsstarker gedruckter Teile.
- Hochmoderne Druckausrüstung: Unser Portfolio umfasst Selective Electron Beam Melting (SEBM)-Drucker, die für ihre Fähigkeit bekannt sind, rissanfällige Hochtemperaturwerkstoffe effizient zu verarbeiten und Teile mit geringen Eigenspannungen zu produzieren, wodurch sich häufig eine umfangreiche Wärmebehandlung erübrigt. Unsere Systeme bieten ein branchenführendes Fertigungsvolumen, Genauigkeit und Zuverlässigkeit, die für unternehmenskritische Luft- und Raumfahrtkomponenten geeignet sind.
- Jahrzehntelanges kollektives Fachwissen: Unser Team verfügt über fundierte Kenntnisse in den Bereichen Metall-AM, Werkstoffkunde und Anwendungstechnik. Wir arbeiten eng mit unseren Kunden zusammen und bieten Unterstützung beim Design für die additive Fertigung (DfAM), Prozessoptimierung und umfassende Lösungen, um Unternehmen bei der erfolgreichen Implementierung des 3D-Drucks zu unterstützen und ihre digitale Fertigungstransformation zu beschleunigen.
Die Wahl eines Anbieters wie Met3dp sichert nicht nur den Zugang zu fortschrittlicher Technologie, sondern auch zu dem entscheidenden Fachwissen, das zur Bewältigung der Komplexität der Herstellung flugtauglicher Luft- und Raumfahrtkomponenten erforderlich ist. Wir kennen die strengen Qualitäts- und Leistungsanforderungen der Branche und sind in der Lage, kundenspezifische Steckergehäuse zu liefern, die den höchsten Standards entsprechen.
Kartierung des Himmels: Wo werden kundenspezifische Steckergehäuse für die Luft- und Raumfahrt überwiegend eingesetzt?
Der Bedarf an robusten, zuverlässigen und oft kundenspezifischen Steckverbindergehäusen zieht sich durch praktisch alle Bereiche der Luft- und Raumfahrtindustrie. Diese Komponenten sind allgegenwärtig und bilden das unsichtbare Rückgrat von elektrischen und Datennetzen in einer Vielzahl von Anwendungen. Wenn man versteht, wo sie am häufigsten eingesetzt werden, werden die verschiedenen Herausforderungen deutlich, die sie bewältigen müssen. Beschaffungsmanager, die von großhändler für Luft- und Raumfahrtkomponenten oder direkt von hersteller von kundenspezifischen Steckverbindern müssen diese unterschiedlichen Anwendungsumgebungen verstehen.
Kommerzielle Luftfahrt: Verbesserung der Sicherheit und Effizienz von Flugsystemen
In Verkehrsflugzeugen verlassen sich täglich Millionen von Passagieren und zahllose Tonnen an Fracht auf das einwandfreie Funktionieren komplexer elektronischer Systeme. Kundenspezifische Steckverbindergehäuse sind in zahlreichen Bereichen unverzichtbar:
- Avionikbuchten: Diese dicht gepackten Bereiche beherbergen das "Gehirn" des Flugzeugs - Flugsteuerungscomputer, Navigationssysteme (GPS, INS), Kommunikationsfunkgeräte (VHF, HF, SATCOM), Wetterradar und Cockpitanzeigen. Steckverbindergehäuse müssen eine außergewöhnliche EMI/RFI-Abschirmung bieten, um Interferenzen zwischen Systemen zu verhindern, Vibrationen standhalten und in extrem enge Platzverhältnisse passen. Kundenspezifische Formen und integrierte Montagefunktionen sind üblich.
- Triebwerksgondeln und Pylone: Die Umgebung in der Nähe von Motoren ist besonders rau und zeichnet sich durch hohe Temperaturen (die Materialien wie Ti-6Al-4V oder Hochtemperatur-Nickellegierungen erfordern), starke Vibrationen und die mögliche Einwirkung von Kraftstoff und Hydraulikflüssigkeiten aus. Steckverbinder für Motorsensoren (Temperatur, Druck, Vibration), FADEC-Systeme (Full Authority Digital Engine Control) und Aktuatoren erfordern besonders robuste und hitzebeständige Gehäuse.
- Fly-by-Wire (FBW) Systeme: Moderne Flugzeuge sind in hohem Maße auf FBW-Systeme angewiesen, bei denen die Eingaben des Piloten elektronisch an die Flugsteuerungsflächen übertragen werden. Die Integrität dieser Datenverbindungen ist von größter Bedeutung. Die Steckergehäuse innerhalb des FBW-Netzes müssen unter allen Flugbedingungen absolute Verbindungszuverlässigkeit gewährleisten und eine hohe Widerstandsfähigkeit gegenüber Vibrationen, Stößen und Umweltfaktoren aufweisen.
- In-Flight Entertainment (IFE) und Kabinensysteme: Das umfangreiche Netzwerk von Anschlüssen für IFE-Bildschirme, Kabinenbeleuchtung, Passagierserviceeinheiten und Bordküchengeräte ist zwar weniger kritisch für die Flugsicherheit, erfordert aber dennoch zuverlässige Gehäuse, die häufig bestimmte Vorschriften zur Entflammbarkeit und Rauchgiftigkeit erfüllen müssen (z. B. FAR 25.853). Für eine ästhetische Integration oder spezielle Einbauszenarien kann eine kundenspezifische Anpassung erforderlich sein.
- Fahrwerksysteme: Steckverbinder in Verbindung mit Fahrwerkspositionssensoren, Bremssystemen (Brake-by-Wire) und Lenkungssteuerungen sind starken Erschütterungen, Vibrationen und der Einwirkung von Rollbahnabfällen, Wasser und Enteisungsflüssigkeiten ausgesetzt. Die Gehäuse müssen außergewöhnlich dicht (IP-Schutz) und mechanisch robust sein.
Verteidigung und militärische Luft- und Raumfahrt: Sicherstellung der Zuverlässigkeit in missionskritischen Anwendungen
Militärflugzeuge, Hubschrauber und Raketensysteme arbeiten unter noch extremeren Bedingungen und erfordern ein Höchstmaß an Zuverlässigkeit und Überlebensfähigkeit. Kundenspezifische Steckergehäuse sind entscheidend für:
- Elektronische Kampfführung (EW) Systeme: Pods und interne Systeme für Radarstörung, Signalaufklärung (SIGINT) und Gegenmaßnahmen enthalten empfindliche Hochfrequenzelektronik. Steckergehäuse müssen eine hervorragende EMI/RFI-Abschirmung bieten (>80dB oder höher) und erfordern oft spezielle Oberflächen oder Materialien.
- Sichere Kommunikation: Verschlüsselte Datenverbindungen und sichere Sprachkommunikationssysteme sind auf Steckverbinder angewiesen, die durch manipulationssichere oder speziell verschlüsselte Gehäuse geschützt sind, um die Signalsicherheit zu gewährleisten.
- Integration von Waffensystemen: Steckverbinder, die Flugzeugpylone mit Raketen, Bomben oder Zielkapseln verbinden, erfordern robuste Schnellverschlussgehäuse, die extremen G-Kräften bei Manövern und Waffenauslösung standhalten. Die Zuverlässigkeit ist absolut entscheidend.
- Radar- und Sensorsysteme: Moderne Active Electronically Scanned Array (AESA)-Radare und verschiedene optische/infrarote Sensoren verwenden zahlreiche Anschlüsse. Die Gehäuse müssen Vibrationen standhalten, die Wärmeableitung bewältigen (was manchmal integrierte Kühlfunktionen erfordert) und die Leistung über einen großen Temperaturbereich hinweg aufrechterhalten. Für konforme Installationen sind oft kundenspezifische Formfaktoren erforderlich.
- Rugged Computing und Vetronics: In militärischen Land- und Luftfahrzeugen werden robuste Computer und Displays eingesetzt, die den harten Bedingungen auf dem Schlachtfeld standhalten sollen. Die externen Anschlüsse sind die wichtigsten Schwachstellen und erfordern extrem robuste, umweltverträgliche und oft speziell entwickelte Gehäuse.
B2B-Lieferanten für Luft- und Raumfahrtteile die den Verteidigungssektor beliefern, müssen strenge militärische Spezifikationen (MIL-STD, DEF STAN) in Bezug auf Materialien, Leistung und Tests für alle Komponenten, einschließlich der Steckergehäuse, einhalten.
Erforschung des Weltraums: Erfüllung extremer Anforderungen jenseits der Erdatmosphäre’
Raumfahrzeuge, Satelliten und Trägerraketen stellen den Gipfel der ökologischen Herausforderungen dar und stoßen an die Grenzen der Materialwissenschaft und -technik. Steckverbindergehäuse für Weltraumanwendungen sind mit besonderen Hürden konfrontiert:
- Vakuum Umgebung: Die Materialien müssen geringe Ausgasungseigenschaften aufweisen, um eine Verunreinigung der empfindlichen Optik oder Elektronik zu verhindern. Die Abdichtung muss Leckagen im Vakuum verhindern.
- Extreme Temperaturzyklen: Satelliten in der Erdumlaufbahn unterliegen schnellen und extremen Temperaturschwankungen, wenn sie zwischen direktem Sonnenlicht und Schatten wechseln. Die Gehäuse müssen den Temperaturschwankungen standhalten, ohne dass sie beschädigt werden oder die Anschlüsse belastet werden.
- Strahlenhärtung: Die Exposition gegenüber kosmischer Strahlung und geladenen Teilchen im Weltraum erfordert Werkstoffe und Konstruktionen, die über lange Einsatzdauern (Jahre oder Jahrzehnte) strahlungsbeständig sind. Bestimmte Materialien können spröde werden oder ihre elektrischen Eigenschaften verändern, wenn sie bestrahlt werden.
- Startbelastungen: Die Gehäuse müssen den starken Vibrationen, dem akustischen Lärm und den hohen G-Kräften beim Raketenstart standhalten.
- Minimierung des Gewichts: Die Startkosten sind direkt proportional zur Masse. Jedes eingesparte Gramm ist entscheidend. Leichte Werkstoffe wie Ti-6Al-4V in Verbindung mit der durch AM ermöglichten Topologieoptimierung sind für Gehäuse von Raumfahrtanschlüssen äußerst vorteilhaft. Zu den Anwendungen gehören die Elektronik von Satellitenbussen, Nutzlastinstrumente, Kommunikationsantennen und Sensoren für das Antriebssystem.
Beschaffung materialien für die Luft- und Raumfahrt und Komponenten für die Raumfahrt erfordern Zulieferer mit spezifischem Fachwissen und die Einhaltung von Standards der Raumfahrtbehörden (z. B. NASA, ESA).
Unbemannte Luftfahrzeuge (UAVs): Ermöglichung kompakter und leichter Konstruktionen
Der schnell wachsende Bereich der UAVs (Drohnen), von kleinen Aufklärungsflugzeugen bis hin zu großen HALE-Plattformen (High-Altitude Long-Endurance), stellt hohe Anforderungen an Größe, Gewicht und Leistung (SWaP). Maßgeschneiderte Steckergehäuse sind der Schlüssel dazu:
- Miniaturisierung: UAVs haben extrem wenig Platz für Elektronik. Kundenspezifische Gehäuse ermöglichen die Integration von Steckverbindern auf engstem Raum, oft mit nicht standardisierten Formen und Befestigungen.
- Gewichtsreduzierung: Die Verwendung leichter Materialien wie Ti-6Al-4V und topologieoptimierter Designs, die durch AM erreicht werden, ist entscheidend für die Maximierung der Flugdauer und der Nutzlastkapazität.
- Integration der Nutzlast: Gehäuse für Steckverbinder, die austauschbare Nutzlasten (Kameras, Sensoren, Kommunikationsrelais) miteinander verbinden, müssen robust und zuverlässig sein und häufig über Mechanismen zum schnellen Einstecken/Demontieren verfügen.
- Umweltexposition: Je nach Einsatzprofil können UAVs erheblichen Vibrationen, Temperaturschwankungen und Regen- oder Staubeinwirkung ausgesetzt sein, was entsprechend abgedichtete und robuste Gehäuse erfordert.
Suche nach Großhändlern und Herstellern von Luft- und Raumfahrtkomponenten
Ingenieure und Beschaffungsexperten, die Lieferanten für diese kritischen Komponenten suchen, sind oft auf der Suche nach “großhandel mit Steckverbindern für die Luft- und Raumfahrt,” “hersteller von kundenspezifischen Luft- und Raumfahrtgehäusen,” oder “B2B-Händler für Luft- und Raumfahrtteileum den richtigen Partner zu finden, muss man nicht nur sein Produktangebot, sondern auch seine Fertigungskapazitäten, seine Qualitätszertifizierungen (AS9100), seine Materialkenntnisse und sein Verständnis der spezifischen Anwendungsumgebung bewerten. Spezialisten für die additive Fertigung wie Met3dp, die sowohl die hochwertige Pulverproduktion als auch die fortschrittlichen Druckverfahren beherrschen, bieten eine vertikal integrierte Lösung, die für die Herstellung von kundenspezifischen, leistungsstarken Steckverbindergehäusen für die Luft- und Raumfahrt, die auf diese vielfältigen und anspruchsvollen Anwendungen zugeschnitten sind, immer attraktiver wird.
Der Additiv-Vorteil: Warum der 3D-Druck von Metall die Produktion von Steckverbindergehäusen in der Luft- und Raumfahrt revolutioniert
Jahrzehntelang beruhte die Produktion von Steckverbindergehäusen für die Luft- und Raumfahrt in erster Linie auf traditionellen Fertigungsverfahren wie der CNC-Bearbeitung von Knüppeln (für Metalle) oder dem Spritzguss (für hochvolumige Polymere). Diese Methoden sind zwar effektiv, stoßen aber an ihre Grenzen, insbesondere wenn es um die zunehmenden Anforderungen an Individualisierung, Komplexität und schnelle Entwicklungszyklen in der modernen Luft- und Raumfahrt geht. Die additive Fertigung von Metallen (AM) bietet eine Reihe von überzeugenden Vorteilen, die die Art und Weise, wie diese kritischen Komponenten entworfen und hergestellt werden, grundlegend verändern. Luft- und Raumfahrtingenieure und Beschaffungsmanager wenden sich zunehmend an Metall-AM-Dienstleister um diese Vorteile zu nutzen.
Entfesselte Gestaltungsfreiheit: Komplexe Geometrien und integrierte Funktionen
Der vielleicht bedeutendste Vorteil der Metall-AM, insbesondere der Pulverbettschmelzverfahren (PBF) wie SLM und SEBM, ist die Befreiung von den traditionellen Design-for-Manufacturability (DfM)-Einschränkungen.
- Komplexe äußere Formen: AM ermöglicht die Herstellung hochorganischer und komplexer Außengehäusegeometrien, die perfekt in begrenzte Räume passen oder die aerodynamischen Profile verbessern, ohne die Komplexität der Einrichtung oder die Beschränkungen der Werkzeugwege bei der CNC-Bearbeitung.
- Aufwändige Innenausstattung: Interne Kanäle für eine konforme Kühlung (zur Wärmeableitung von Hochleistungssteckern), integrierte EMI/RFI-Abschirmungen oder komplexe Pfade für Glasfasern können direkt in die Gehäusestruktur eingearbeitet werden. Die maschinelle Bearbeitung solcher internen Merkmale ist oft unmöglich oder erfordert den Zusammenbau mehrerer Teile.
- Gitterförmige Strukturen: Interne Gitter- oder Kreiselstrukturen können eingebaut werden, um das Gewicht erheblich zu reduzieren und gleichzeitig die strukturelle Integrität aufrechtzuerhalten - eine einzigartige Fähigkeit von AM.
- Merkmal Integration: Montageflansche, Ausrichtungsschlüssel, Kabelmanagementfunktionen und sogar Federelemente können direkt in das einzelne gedruckte Teil integriert werden, wodurch sich die Notwendigkeit einer nachgelagerten Montage verringert.
Diese Designfreiheit ermöglicht es den Ingenieuren, Steckverbindergehäuse zu entwickeln, die wirklich für die Funktion und die Anwendungsumgebung optimiert sind und nicht durch die Beschränkungen bei der maschinellen Bearbeitung oder beim Gießen eingeschränkt werden.
Leichtbaustrategien: Topologie-Optimierung und Material-Effizienz
Das Gewicht ist ein ständiges Problem in der Luft- und Raumfahrtentwicklung. Metall-AM bietet leistungsstarke Werkzeuge für die Herstellung von leichten und dennoch stabilen Steckverbindergehäusen:
- Topologie-Optimierung: Software-Tools können die Spannungsverteilung innerhalb eines Gehäuses unter den zu erwartenden Belastungen analysieren und automatisch Material aus unkritischen Bereichen entfernen, was zu hochgradig optimierten, oft organisch anmutenden Formen führt, bei denen nur ein Minimum an Material benötigt wird. AM ist in einzigartiger Weise in der Lage, diese komplexen, optimierten Geometrien direkt herzustellen.
- Wahl des Materials: AM ermöglicht den effizienteren Einsatz von Materialien mit hohem Festigkeits-Gewichts-Verhältnis wie Ti-6Al-4V. Während Titan dürfen die maschinelle Bearbeitung von Titan ist schwierig und verursacht viel teuren Ausschuss. Bei AM wird nur das notwendige Pulver verwendet, was Titan zu einer wirtschaftlicheren Option für komplexe, gewichtskritische Gehäuse macht.
- Hohle Strukturen und Gitternetze: Wie bereits erwähnt, lässt sich durch die Herstellung von Hohlprofilen oder die Einbindung interner Gitterstrukturen das Gewicht der Teile im Vergleich zu massiv gefertigten Komponenten drastisch reduzieren, wobei die erforderliche Steifigkeit und Festigkeit erhalten bleibt.
Diese Strategien können bei Steckverbindergehäusen zu Gewichtseinsparungen von 30-50 % oder sogar mehr im Vergleich zu traditionell hergestellten Äquivalenten führen, was sich direkt in einer verbesserten Kraftstoffeffizienz, einer höheren Nutzlastkapazität oder einer verbesserten Leistung niederschlägt.
Konsolidierung von Teilen: Verringerung der Montagekomplexität und potenzieller Fehlerquellen
Herkömmliche Steckverbinderbaugruppen bestehen oft aus mehreren Komponenten: dem Hauptgehäuse, den Hinterschalen, den Zugentlastungen, den Befestigungsklammern, den EMI-Dichtungen usw. Jedes Teil erfordert separate Schritte bei der Herstellung, Bestandsverwaltung und Montage. Jede Schnittstelle zwischen den Teilen stellt einen potenziellen Fehlerpunkt dar (z. B. Lockerung bei Vibrationen, beeinträchtigte Umweltabdichtung).
Metall-AM ermöglicht Teilkonsolidierungbei denen mehrere Funktionen in ein einziges, monolithisch gedrucktes Bauteil integriert sind. Zum Beispiel:
- Ein Gehäuse und seine Halterung können in einem Stück gedruckt werden.
- Die Zugentlastung kann direkt in die Rückseite des Gehäuses integriert werden.
- Interne Abschirmwände können bei einigen Konstruktionen separate EMI-Dichtungen oder Einsätze überflüssig machen.
Die Konsolidierung von Teilen bietet erhebliche Vorteile:
- Reduzierte Montagezeit und Arbeitskosten: Weniger Teile bedeuten eine einfachere und schnellere Montage.
- Verbesserte Verlässlichkeit: Durch die Beseitigung von Verbindungen und Schnittstellen werden potenzielle Fehlerquellen reduziert.
- Geringere Teilezahl und geringere Lagerbestände: Vereinfacht Logistik und Lieferkettenmanagement.
- Verbesserte strukturelle Integrität: Monolithische Teile können von Natur aus stärker und steifer sein.
Beschleunigte Zeitpläne: Schnelles Prototyping und verkürzte Vorlaufzeiten für die Produktion
In der Luft- und Raumfahrtindustrie ist Flexibilität gefragt. Metall-AM verkürzt die Zeitspanne vom Designkonzept bis zum funktionsfähigen Teil drastisch:
- Rapid Prototyping: Design-Iterationen für kundenspezifische Gehäuse können innerhalb von Tagen gedruckt und physisch getestet werden, im Vergleich zu Wochen oder Monaten für herkömmliche Prototypen, die Werkzeuge oder komplexe Bearbeitungsvorrichtungen erfordern. Dies ermöglicht eine schnellere Designvalidierung und -optimierung.
- Werkzeuglose Produktion: Mit AM entfällt die teure und zeitaufwändige Herstellung von Formen oder Gesenken (beim Gießen/Gießen) oder die komplexe Konstruktion von Vorrichtungen (bei CNC). Die Produktion kann fast sofort nach Genehmigung des endgültigen Entwurfs beginnen.
- Reduzierte Vorlaufzeiten: Bei kleinen bis mittleren Produktionsserien, wie sie für viele kundenspezifische Bauteile in der Luft- und Raumfahrt typisch sind, ist die Gesamtvorlaufzeit für AM (einschließlich Druck und Nachbearbeitung) oft deutlich kürzer als bei herkömmlichen Verfahren, insbesondere bei komplexen Geometrien. Dies ist entscheidend für die Einhaltung enger Zeitpläne.
- Fertigung auf Abruf: Digitale Teiledateien ermöglichen eine bedarfsgerechtere Fertigung oder die schnelle Herstellung von Ersatzteilen, ohne auf alte Werkzeuge zurückgreifen zu müssen.
Materialvielfalt und Leistungsverbesserung durch Metall-AM
Metall-AM-Verfahren können mit einer breiten Palette von für die Luft- und Raumfahrt relevanten Legierungen arbeiten, darunter rostfreie Stähle (wie 316L), Titanlegierungen (wie Ti-6Al-4V), Aluminiumlegierungen, Nickelsuperlegierungen (wie Inconel 625 oder 718) und Kupferlegierungen. Dies ermöglicht es den Ingenieuren, das optimale Material für die spezifischen Leistungsanforderungen des Steckverbindergehäuses auszuwählen (z. B. Temperaturbeständigkeit, Korrosionsbeständigkeit, Verhältnis von Festigkeit zu Gewicht).
Darüber hinaus kann das Schicht-für-Schicht-Verfahren manchmal zu feinkörnigen Mikrostrukturen mit hervorragenden mechanischen Eigenschaften führen. Unternehmen wie Met3dp konzentrieren sich stark auf die Optimierung der Verbindung zwischen ihren hochwertigen Metallpulver und ihre Druckverfahren (wie SEBM), um sicherzustellen, dass die resultierenden Teile die Eigenschaften von Knet- oder Gusswerkstoffen erfüllen oder übertreffen, und um konsistente, leistungsstarke Komponenten zu liefern, die für anspruchsvolle Luft- und Raumfahrtanwendungen geeignet sind.
Vergleich zwischen Metall-AM (PBF) und traditioneller Fertigung (CNC, Guss)
Um den Vorteil der additiven Fertigung voll zu würdigen, ist es hilfreich, die PBF-Metall-AM mit herkömmlichen Methoden zur Herstellung kundenspezifischer Steckergehäuse zu vergleichen:
Merkmal | Metall-AM (PBF: SLM/SEBM) | CNC-Bearbeitung | Feinguss |
---|---|---|---|
Entwurfskomplexität | Sehr hoch (Interne Kanäle, Gitter) | Mittel bis hoch (begrenzt durch Werkzeugzugang) | Mäßig (begrenzt durch die Komplexität der Form) |
Kosten der Anpassung | Niedrig (werkzeuglos) | Hoch (Programmierung, Einrichtung, Vorrichtungen) | Sehr hoch (Werkzeug-/Formkosten) |
Vorlaufzeit (Proto) | Fasten (Tage) | Mäßig (Tage bis Wochen) | Langsam (Wochen bis Monate) |
Vorlaufzeit (Low Vol) | Mäßig | Mäßig bis hoch | Langsam (Werkzeuge erforderlich) |
Materialabfälle | Niedrig (Pulverrecycling) | Hoch (subtraktives Verfahren) | Moderat (Gießäste, Angüsse) |
Gewichtsreduzierung | Ausgezeichnet (Topologie-Opt., Gitter) | Begrenzt (vor allem Materialauswahl) | Mäßig (Fast-Netzform) |
Teil Konsolidierung | Ausgezeichnet | Begrenzt | Begrenzt |
Oberflächenbeschaffenheit (As-Built) | Mäßig bis rau | Gut bis Ausgezeichnet | Gut |
Erreichbare Toleranz | Gut (Nachbearbeitung oft erforderlich) | Ausgezeichnet | Gut |
Ideales Volumen | Prototypen, niedrig bis mittel | Prototypen, Niedrig-zu-Hoch | Mittel bis hoch |
In Blätter exportieren
Diese Tabelle verdeutlicht, dass die CNC-Bearbeitung zwar bessere Toleranzen und Oberflächengüten bietet, das Gießen jedoch bei hohen Stückzahlen wirtschaftlich ist, metall-AM zeichnet sich durch Designfreiheit, Individualisierung, Schnelligkeit für komplexe Prototypen und Gewichtsreduzierungspotenzial ausdamit ist es für die Herausforderungen der modernen kundenspezifischen Fertigung von Steckverbindergehäusen in der Luft- und Raumfahrt bestens geeignet.
Die Rolle moderner 3D-Drucktechnologien für Metall
Die Effektivität der Metall-AM hängt stark von der Raffinesse der Drucktechnologie und der Qualität der verwendeten Materialien ab. Met3dp nutzt fortschrittliche Verfahren wie Selektives Elektronenstrahlschmelzen (SEBM). Beim SEBM wird anstelle eines Lasers ein Elektronenstrahl verwendet, der in der Regel im Vakuum und bei höheren Baukammertemperaturen arbeitet. Dies bietet besondere Vorteile für bestimmte Anwendungen in der Luft- und Raumfahrt:
- Reduzierte Eigenspannung: Die höheren Verarbeitungstemperaturen führen zu einem Spannungsabbau der Teile während der Fertigung, wodurch sich umfangreiche Wärmebehandlungen nach der Fertigung oft erübrigen, was Zeit und Kosten spart.
- Verarbeitung rissgefährdeter Materialien: SEBM eignet sich besonders gut für die Bearbeitung von Materialien wie Ti-6Al-4V und anderen Hochtemperaturlegierungen, die in laserbasierten Systemen anfällig für Risse sind.
- Hohe Produktivität: Elektronenstrahlen können oft schneller scannen als Laser, was bei bestimmten Geometrien zu höheren Fertigungsraten führen kann.
Die Kopplung fortschrittlicher Drucksysteme wie SEBM mit sorgfältig hergestellten, hochsphärischen Metallpulvern aus Verfahren wie Gasverdüsung oder PREP, wie es Met3dp tut, gewährleistet höchste Qualität und Konsistenz für anspruchsvolle Luft- und Raumfahrtkomponenten wie Steckergehäuse.
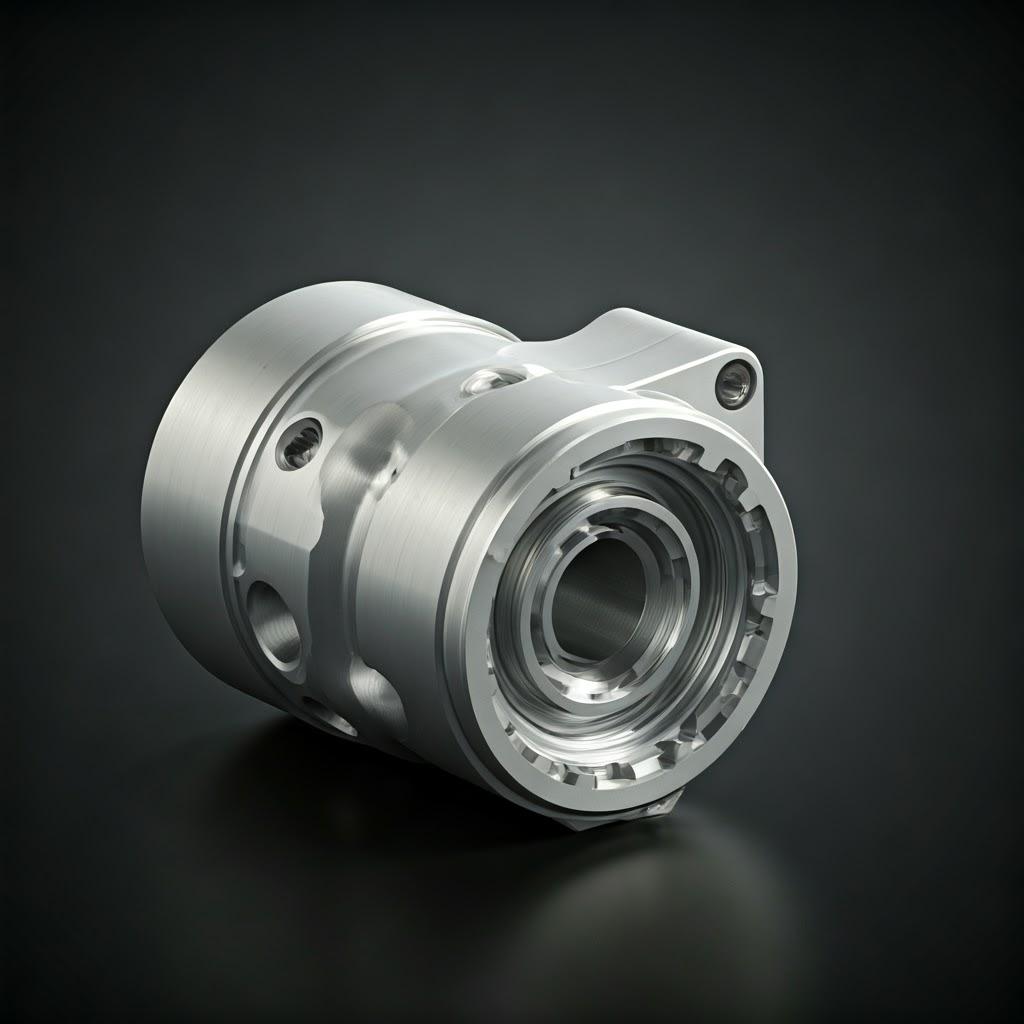
Der Werkstoff ist entscheidend: Die Auswahl des optimalen Metallpulvers (316L & Ti-6Al-4V) für Steckverbinder in der Luft- und Raumfahrt
Die Wahl des richtigen Materials ist von grundlegender Bedeutung für die Leistung und Zuverlässigkeit jeder Komponente in der Luft- und Raumfahrt, und Steckverbindergehäuse bilden hier keine Ausnahme. Das Material bestimmt die Fähigkeit des Gehäuses, rauen Umgebungen zu widerstehen, die empfindlichen Steckerschnittstellen zu schützen, die Gewichtsvorgaben zu erfüllen und die Anforderungen an die elektromagnetische Verträglichkeit (EMV) zu erfüllen. Während Metall-AM die Möglichkeit bietet, verschiedene Legierungen zu verwenden, sind zwei Materialien für 3D-gedruckte Steckergehäuse in der Luft- und Raumfahrt besonders gut geeignet und werden häufig verwendet: 316L-Edelstahl und Ti-6Al-4V Titan-Legierung. Das Verständnis ihrer Eigenschaften und die Bedeutung der Pulverqualität von zuverlässigen Lieferanten von Metallpulver ist entscheidend für den Erfolg.
Die Anforderungen verstehen: Wichtige Materialeigenschaften für Steckergehäuse
Bevor wir uns mit den einzelnen Materialien beschäftigen, wollen wir die wichtigsten Eigenschaften erläutern, die Ingenieure bei der Auswahl eines Materials für ein Steckverbindergehäuse für die Luft- und Raumfahrt bewerten:
- Korrosionsbeständigkeit: Unverzichtbar für die Beständigkeit gegen Feuchtigkeit, Salzsprühnebel, Kraftstoffe, Hydraulikflüssigkeiten und Reinigungsmittel, die in der Luft- und Raumfahrt üblich sind.
- Stärke und Langlebigkeit: Die Fähigkeit, mechanischen Belastungen, Stößen, Vibrationen und Erschütterungen standzuhalten, ohne sich zu verformen oder zu brechen. Streckgrenze, Zugfestigkeit und Ermüdungsfestigkeit sind entscheidende Parameter.
- Temperaturstabilität: Beibehaltung der mechanischen Eigenschaften und der Dimensionsstabilität über einen weiten Betriebstemperaturbereich (-55°C bis +175°C oder höher).
- Gewicht (Dichte): Ein hohes Verhältnis von Festigkeit zu Gewicht ist äußerst wünschenswert, um die Gesamtmasse von Flugzeugen oder Raumfahrzeugen zu minimieren.
- EMI/RFI-Abschirmung wirksam: Die dem Material innewohnende Fähigkeit (oft durch Geometrie und Beschichtungen verbessert), elektromagnetische Störungen zu blockieren. Eine gute elektrische Leitfähigkeit korreliert im Allgemeinen mit einer besseren Abschirmung.
- Herstellbarkeit (Druckbarkeit): Wie leicht und zuverlässig kann das Material mit der gewählten Metall-AM-Technologie (z. B. SLM, SEBM) verarbeitet werden, um dichte, fehlerfreie Teile zu erhalten.
- Kosten: Die Kosten für das Rohmaterial und die Kosten für den Druck und die Nachbearbeitung des Materials.
- Umweltverträglichkeit: Faktoren wie Ausgasung (für den Raum), Entflammbarkeit und Toxizität können je nach spezifischer Anwendung von Bedeutung sein.
316L-Edelstahl: Das robuste und verlässliche Arbeitspferd
316L ist eine austenitische Edelstahllegierung mit Chrom, Nickel und Molybdän. Er wird in vielen Branchen, einschließlich der Luft- und Raumfahrt, aufgrund seiner hervorragenden Kombination aus Eigenschaften und Verarbeitbarkeit durch AM weit verbreitet eingesetzt.
- Wichtige Eigenschaften von 316L:
- Ausgezeichnete Korrosionsbeständigkeit: Der Zusatz von Molybdän sorgt für eine hervorragende Beständigkeit gegen allgemeine Korrosion, Lochfraß und Spaltkorrosion, insbesondere in chloridhaltigen Umgebungen (wie in Küstengebieten oder bei Einwirkung von Tausalzen). Es widersteht auch dem Angriff vieler Industriechemikalien und Luftfahrtflüssigkeiten.
- Gute Festigkeit und Duktilität: 316L bietet ein ausgewogenes Verhältnis zwischen Zugfestigkeit (typischerweise >500 MPa nach dem Druck und Spannungsabbau) und Duktilität (Dehnung >40%), was es zäh und bruchfest macht.
- Gute Hochtemperaturleistung: Obwohl 316L keine Hochtemperatursuperlegierung ist, behält es seine nützliche Festigkeit bis zu moderaten Temperaturen, wie sie in vielen Anwendungen der Luft- und Raumfahrt vorkommen (weit über 200 °C).
- Nicht-magnetisch: Im geglühten Zustand ist 316L in der Regel nicht magnetisch, was für Anwendungen, die auf Magnetfelder reagieren, wichtig sein kann.
- Schweißbarkeit/Fügbarkeit: Sie können leicht geschweißt werden, wenn dies für die Montage oder Änderung erforderlich ist (obwohl die Konsolidierung der Teile durch AM darauf abzielt, dies zu minimieren).
- Ausgezeichnete Druckbarkeit: 316L ist eine der leichteren und etablierteren Metalllegierungen, die sich mit dem Laser Powder Bed Fusion (L-PBF/SLM)-Verfahren zuverlässig verarbeiten lassen und hohe Dichten (>99,5 %) erreichen.
- Kosten-Nutzen-Verhältnis: Im Vergleich zu Titanlegierungen oder Nickelsuperlegierungen ist 316L-Pulver deutlich preiswerter, was es zu einer attraktiven Option macht, wenn nicht das absolut beste Verhältnis von Festigkeit zu Gewicht oder extreme Temperaturbeständigkeit erforderlich ist.
- Luft- und Raumfahrtanwendungen für 316L-Gehäuse:
- Allgemeine Steckverbinder für Avionik- und Kabinensysteme, bei denen ein robuster Schutz vor Umwelteinflüssen und eine hohe Festigkeit erforderlich sind, bei denen das Gewicht jedoch nicht der wichtigste Faktor ist.
- Anschlüsse für die Bodenausrüstung (GSE).
- Anwendungen, die eine ausgezeichnete Korrosionsbeständigkeit unter rauen atmosphärischen Bedingungen erfordern.
- Prototypen, bei denen das Kosten-Nutzen-Verhältnis in den ersten Entwurfsphasen wichtig ist.
- Steckverbinder in weniger temperaturkritischen Bereichen des Flugzeugs.
Beschaffungsmanager auf der Suche nach edelstahl Großhandel Lieferanten für AM-Pulver sollten überprüfen, ob die Pulverqualität den Anforderungen der Luft- und Raumfahrt an Reinheit und Konsistenz entspricht.
Ti-6Al-4V (Grad 5) Titanlegierung: Der Hochleistungs-Leichtbau-Champion
Ti-6Al-4V (oft als Ti64 abgekürzt) ist die am häufigsten verwendete Titanlegierung, auf die mehr als 50 % der gesamten Titantonnage weltweit entfallen. Es handelt sich um eine Alpha-Beta-Legierung, die für ihre außergewöhnliche Kombination aus hoher Festigkeit, geringer Dichte und hervorragender Korrosionsbeständigkeit bekannt ist, was sie zu einem bevorzugten Material für anspruchsvolle Luft- und Raumfahrtanwendungen macht.
- Wichtige Eigenschaften von Ti-6Al-4V:
- Sehr hohes Festigkeits-Gewichts-Verhältnis: Dies ist die entscheidende Eigenschaft von Ti64. Es bietet eine Festigkeit, die mit der vieler Stähle vergleichbar ist, jedoch bei einer etwa 40-45 % geringeren Dichte. Dies macht es ideal für gewichtskritische Komponenten in der Luft- und Raumfahrt. Die typische Zugfestigkeit nach dem Druck und der Wärmebehandlung kann 1000 MPa übersteigen.
- Ausgezeichnete Korrosionsbeständigkeit: Ti64 bildet eine stabile, schützende Oxidschicht, die in den meisten natürlichen Umgebungen, einschließlich Meerwasser, sowie in vielen Industriechemikalien und Flüssigkeiten in der Luft- und Raumfahrt hervorragende Korrosionsbeständigkeit bietet.
- Hochtemperaturfähigkeit: Es behält auch bei hohen Temperaturen eine gute Festigkeit und eignet sich für Anwendungen bis zu 350-400 °C, was es für heißere Bereiche in der Nähe von Motoren oder in Hochgeschwindigkeitsflugzeugen geeignet macht.
- Geringe thermische Ausdehnung: Im Vergleich zu Stählen und Aluminiumlegierungen hat Titan einen geringeren Wärmeausdehnungskoeffizienten, wodurch die thermische Belastung in Baugruppen, die Temperaturschwankungen ausgesetzt sind, verringert wird.
- Biokompatibilität: Während es für Steckergehäuse weniger relevant ist, eignet es sich aufgrund seiner hervorragenden Biokompatibilität für medizinische Implantate (was seine Trägheit beweist).
- Gute Druckbarkeit (insbesondere mit SEBM): Ti64 kann zwar mit L-PBF verarbeitet werden, ist aber etwas reaktiv und profitiert von der Vakuumumgebung und den höheren Verarbeitungstemperaturen der SEBM-Technologie (wie sie von Met3dp verwendet wird), die das Management von Eigenspannungen unterstützt und optimale Materialeigenschaften gewährleistet. Es können hohe Dichten (>99,7 %) erreicht werden.
- Luft- und Raumfahrtanwendungen für Ti-6Al-4V-Gehäuse:
- Gewichtskritische Anwendungen: überall dort, wo die Minimierung der Masse von größter Bedeutung ist (Satelliten, UAVs, Hochleistungsflugzeuge).
- Anwendungen, die eine hohe Festigkeit und Haltbarkeit in anspruchsvollen mechanischen Umgebungen erfordern (z. B. Fahrwerke, Flugsteuerungssysteme).
- Gehäuse, die sich in Hochtemperaturbereichen befinden (Triebwerksgondeln, Pylone, Umweltkontrollsysteme).
- Raumfahrtanwendungen, bei denen geringe Ausgasung und ein gutes Verhältnis zwischen Gewicht und Festigkeit entscheidend sind.
- Bauteile, die eine außergewöhnliche Korrosionsbeständigkeit in Kombination mit hoher Festigkeit erfordern.
Zuverlässig finden verteiler für Titanlegierungen die Spezialisierung auf hochwertige Pulver, die für AM-Prozesse in der Luft- und Raumfahrt zertifiziert sind, ist bei der Spezifikation von Ti-6Al-4V von entscheidender Bedeutung.
Vergleich zwischen 316L und Ti-6Al-4V für Steckergehäuse (Tabellenformat)
Eigentum | 316L-Edelstahl | Ti-6Al-4V (Grad 5) Titanlegierung | Überlegungen zu Steckergehäusen |
---|---|---|---|
Dichte | ~7,9-8,0 g/cm³ | ~4,43 g/cm³ | Erhebliche Gewichtseinsparungen mit Ti-6Al-4V (ca. 45% leichter). |
Typische Zugfestigkeit (AM) | ~500-600 MPa | ~950-1100 MPa (wärmebehandelt) | Ti-6Al-4V bietet viel höhere Festigkeit. |
Verhältnis Stärke/Gewicht | Mäßig | Ausgezeichnet | Wichtiger Vorteil für Ti-6Al-4V in der Luft- und Raumfahrt. |
Korrosionsbeständigkeit | Ausgezeichnet (allgemein, Lochfraß) | Ausgezeichnet (insbesondere in oxidierenden Umgebungen) | Beide sind ausgezeichnet, wobei Ti-6Al-4V in einigen spezifischen Medien einen Vorteil haben kann. |
Maximale Betriebstemperatur | Mäßig (~300°C Dauereinsatzgrenze) | Höher (~350-400°C) | Ti-6Al-4V wird bevorzugt für anwendungen bei höheren Temperaturen. |
Wärmeleitfähigkeit | Niedriger (~16 W/m-K) | Sehr niedrig (~7 W/m-K) | Kann sich auf die Wärmeableitung von Anschlüssen auswirken; kann Konstruktionsmerkmale erfordern. |
Elektrische Leitfähigkeit | Geringer (im Vergleich zu Al, Cu) | Sehr niedrig | Beeinträchtigt die Wirksamkeit der EMI-Abschirmung (Geometrie/Beschichtungen gleichen dies oft aus). |
Druckbarkeit (AM) | Ausgezeichnet (insbesondere L-PBF) | Gut (v.a. SEBM); eher reaktiv | Beides sind bewährte AM-Materialien. |
Pulverkosten | Unter | Erheblich höher | Wichtiger Faktor in den Gesamtkosten des Teils. |
Nachbearbeitung | Standard (Stressabbau, Veredelung) | Erfordert oft spezielle Wärmebehandlungen | Die Verarbeitung von Ti-6Al-4V erfordert mehr Sorgfalt. |
In Blätter exportieren
Schlussfolgerung: Wählen Sie 316L wenn die Kosten eine wichtige Rolle spielen, das Gewicht weniger kritisch ist und die Betriebstemperaturen moderat sind, aber dennoch eine gute Korrosionsbeständigkeit und Haltbarkeit erforderlich sind. Wählen Sie Ti-6Al-4V wenn maximale Gewichtseinsparungen, hohe Festigkeit und/oder höhere Temperaturbeständigkeit primäre Anforderungen sind und die höheren Kosten durch Leistungsgewinne gerechtfertigt sind.
Die Bedeutung von qualitativ hochwertigem Metallpulver von vertrauenswürdigen Lieferanten
Die endgültige Leistung eines 3D-gedruckten Metallverbindergehäuses ist untrennbar mit der Qualität des verwendeten Metallpulvers verbunden. Die einfache Angabe von 316L oder Ti-6Al-4V reicht nicht aus. Für anspruchsvolle Luft- und Raumfahrtanwendungen ist die Zusammenarbeit mit einem anbieter von Metall-AM-Pulver die eine gleichbleibend hohe Materialqualität garantiert, ist von größter Bedeutung. Zu den wichtigsten Pulvereigenschaften, die die Qualität der Teile beeinflussen, gehören:
- Sphärizität: Hochkugelförmige Pulverpartikel fließen gleichmäßig und verdichten sich im Pulverbett, was zu einem gleichmäßigeren Aufschmelzen und einer höheren Dichte des fertigen Teils (weniger Hohlräume) führt.
- Partikelgrößenverteilung (PSD): Ein kontrollierter PSD-Wert gewährleistet eine gute Fließfähigkeit und Auflösung, was sich auf die Oberflächengüte und die Definition der Merkmale auswirkt. In den Normen der Luft- und Raumfahrt sind häufig zulässige PSD-Bereiche festgelegt.
- Fließfähigkeit: Gemessen an der Hall-Durchflussrate sorgt eine gute Fließfähigkeit für einen gleichmäßigen Pulverauftrag auf der Bauplatte Schicht für Schicht und verhindert so Defekte.
- Chemische Reinheit: Verunreinigungen (wie Sauerstoff, Stickstoff, Kohlenstoff in Titan; Einschlüsse in Stahl) können die mechanischen Eigenschaften (insbesondere Ermüdungsfestigkeit und Duktilität) drastisch verschlechtern. Um Verunreinigungen zu minimieren, ist eine strenge Kontrolle des Pulverherstellungsprozesses erforderlich.
- Abwesenheit von Satelliten: Kleine, unregelmäßige Partikel, die sich an größere kugelförmige Partikel anlagern (Satelliten), können die Fließfähigkeit und Packungsdichte beeinträchtigen.
- Konsistenz von Charge zu Charge: Zuverlässige Lieferanten führen strenge Qualitätskontrollen durch, um sicherzustellen, dass die Pulvereigenschaften von einer Charge zur nächsten gleich bleiben, was eine wiederholbare Leistung der Teile garantiert.
Eine minderwertige Pulverqualität kann zu Porosität, schlechten mechanischen Eigenschaften, Maßungenauigkeiten und uneinheitlichen Ergebnissen führen - alles inakzeptabel für flugkritische Bauteile.
Met3dp’s Engagement für Premium-Pulverproduktion (Gaszerstäubung, PREP)
Met3dp hat den kritischen Zusammenhang zwischen der Qualität des Pulvers und der Leistungsfähigkeit der Teile erkannt und in modernste Pulverproduktionstechnologien investiert. Unser Engagement gewährleistet, dass die von uns gelieferten Pulver aus 316L, Ti-6Al-4V und anderen hochentwickelten Legierungen die strengen Anforderungen der Luft- und Raumfahrtindustrie erfüllen.
- Fortgeschrittene Zerstäubungstechnologien: Wir verwenden branchenführende Gaszerstäubung (GA) und Plasma-Rotations-Elektroden-Verfahren (PREP) Techniken.
- Gaszerstäubung: Verwendet Hochdruck-Inertgasdüsen, um einen Strom geschmolzenen Metalls in feine Tröpfchen aufzubrechen, die sich zu kugelförmigem Pulver verfestigen. Unsere firmeneigenen Düsen- und Gasströmungsdesigns optimieren diesen Prozess für hohe Sphärizität und kontrollierte Partikelgrößen.
- VORBEREITEN: Rotiert einen verbrauchbaren Elektrodenstab mit hoher Geschwindigkeit und schmilzt dabei dessen Spitze mit einem Plasmabrenner. Die Zentrifugalkraft schleudert geschmolzene Tröpfchen ab, die sich in einer inerten Atmosphäre verfestigen. Das Ergebnis sind außergewöhnlich saubere und kugelförmige Pulver mit minimalen Satelliten, ideal für die anspruchsvollsten Anwendungen wie Luft- und Raumfahrt und Medizintechnik.
- Strenge Qualitätskontrolle: Jede Charge von Met3dp-Pulver wird umfangreichen Tests auf chemische Zusammensetzung, Partikelgrößenverteilung, Morphologie (Sphärizität), Fließfähigkeit und Dichte unterzogen, um sicherzustellen, dass es die Industriestandards erfüllt oder übertrifft.
- Optimiert für AM-Prozesse: Unsere Pulver werden speziell für optimale Leistung in Pulverbettfusionssystemen, einschließlich unserer eigenen SEBM-Drucker, entwickelt und charakterisiert, um Kompatibilität und vorhersehbare Ergebnisse zu gewährleisten.
Durch die Kontrolle des Pulverherstellungsprozesses mit Hilfe fortschrittlicher Techniken und strenger Qualitätskontrolle bietet Met3dp Luft- und Raumfahrtunternehmen und B2B-Käufer mit der Gewissheit, dass das Ausgangsmaterial für ihre 3D-gedruckten Steckergehäuse von höchstmöglicher Qualität ist, was die Herstellung von dichten, zuverlässigen und leistungsstarken Komponenten ermöglicht. Erfahren Sie mehr über unser umfassendes 3D-Druck von Metall Lösungen.
Design für additive Fertigung (DfAM): Optimierung der Gehäusegeometrie von Steckverbindern für erfolgreichen 3D-Druck aus Metall
Um die Möglichkeiten der additiven Fertigung aus Metall für Komponenten wie Steckverbindergehäuse in der Luft- und Raumfahrt erfolgreich zu nutzen, reicht es nicht aus, eine vorhandene CAD-Datei an den Drucker zu senden. Es erfordert ein grundlegendes Umdenken in der Konstruktion, weg von den Zwängen traditioneller subtraktiver oder formgebender Verfahren, hin zu den Möglichkeiten und dem Respekt vor den Nuancen der schichtweisen Fertigung. Dieser Ansatz ist bekannt als Design für additive Fertigung (DfAM). Die Umsetzung der DfAM-Prinzipien von Anfang an ist entscheidend für die Maximierung der Vorteile von AM - Leichtbau, Teilekonsolidierung, optimale Leistung und Kosteneffizienz. Die Zusammenarbeit mit erfahrenen DfAM-Dienstleister oder metall-AM-Lieferanten wie Met3dp, die über ein umfassendes DfAM-Fachwissen verfügen, können diesen Prozess erheblich rationalisieren und das volle Potenzial der Technologie ausschöpfen.
Additiv denken: Schlüsselprinzipien des DfAM für Gehäuse
DfAM ist nicht nur eine Reihe von Regeln, sondern eine Methodik, die die Fähigkeiten des Fertigungsprozesses in die Konstruktionsphase integriert. Für Metallgehäuse von Luft- und Raumfahrtanschlüssen, die im Pulverbettverfahren (Powder Bed Fusion, PBF) hergestellt werden, gehören zu den wichtigsten DfAM-Prinzipien:
- Komplexität annehmen (wo sie von Vorteil ist): Im Gegensatz zur maschinellen Bearbeitung, bei der die Komplexität zusätzliche Kosten und Zeit verursacht, lassen sich mit AM komplizierte Geometrien relativ einfach herstellen. DfAM ermutigt Ingenieure, dies zu nutzen, indem sie Merkmale wie interne Kanäle, konforme Formen und integrierte Funktionen entwerfen, die zuvor unpraktisch waren.
- Orientierungshilfe gestalten: Wie ein Teil auf der Bauplatte ausgerichtet wird, hat erhebliche Auswirkungen auf die Druckzeit, die Anforderungen an die Stützstruktur, die Oberflächenbeschaffenheit der verschiedenen Seiten und sogar auf die mechanischen Eigenschaften (aufgrund des anisotropen Verhaltens einiger AM-Prozesse/Materialien). DfAM beinhaltet die Berücksichtigung der optimalen Ausrichtung bereits in einem frühen Stadium des Designprozesses.
- Minimierung der Stützstrukturen: Stützstrukturen sind bei PBF oft notwendig, um das Teil auf der Bauplatte zu verankern und überhängende Merkmale zu stützen. Sie verbrauchen jedoch zusätzliches Material, verlängern die Druckzeit und müssen in der Nachbearbeitung entfernt werden, was zusätzliche Arbeitskosten verursacht und die Oberflächengüte beeinträchtigen kann. Ein zentrales Ziel von DfAM ist es, Teile zu entwerfen, die so wenig wie möglich gestützt werden müssen, oft durch die Verwendung selbsttragender Winkel.
- Berücksichtigung der Pulverentfernung: Bei Gehäusen mit inneren Hohlräumen oder Kanälen muss DfAM Entweichungslöcher oder -wege vorsehen, damit das nicht verschmolzene Pulver nach dem Druck entfernt werden kann. Eingeschlossenes Pulver erhöht das Gewicht und kann ein Risiko darstellen, wenn es sich später löst.
- Optimieren für die Nachbearbeitung: DfAM antizipiert nachgelagerte Prozesse. Die Gestaltung von Merkmalen, die für die Entfernung von Halterungen, die Bearbeitung kritischer Schnittstellen oder die Oberflächenbearbeitung leicht zugänglich sind, kann die Nachbearbeitungszeit und -kosten erheblich reduzieren.
- Nutzung der Teilekonsolidierung: DfAM sucht aktiv nach Möglichkeiten, mehrere Komponenten einer Baugruppe (z. B. Gehäuse, Halterung, Backshell) in einem einzigen, integrierten AM-Teil zu kombinieren, um die Komplexität der Baugruppe zu reduzieren und die Zuverlässigkeit zu verbessern.
- Verstehen von Material & Prozessbeschränkungen: DfAM berücksichtigt die spezifischen Fähigkeiten und Grenzen des gewählten AM-Prozesses (z.B. SLM, SEBM) und des Materials (z.B. 316L, Ti-6Al-4V), wie z.B. die minimale Featuregröße, die erreichbaren Toleranzen und das thermische Verhalten.
Der DfAM-Gedanke stellt sicher, dass das endgültige Design nicht nur funktional ist, sondern auch effizient mit dem 3D-Metalldruck hergestellt werden kann, um die Vorteile der Technologie für die Kunden zu maximieren entwurf von Luft- und Raumfahrtkomponenten.
Überlegungen zur Wanddicke und Mindestgröße der Elemente
Bei Metall-AM-Verfahren gibt es Grenzen für die Mindestgröße von Merkmalen und Wänden, die sie zuverlässig herstellen können. Ein Design unterhalb dieser Grenzen kann zu unvollständiger Formgebung, schlechter Auflösung oder strukturellen Schwächen führen.
- Mindestwanddicke: Dies hängt von der jeweiligen AM-Maschine (Strahlfleckgröße, Schichtdicke), dem zu druckenden Material und der Ausrichtung der Wand ab.
- Für PBF-Verfahren wie SLM und SEBM liegt ein allgemeiner Richtwert für robuste Wände oft im Bereich von 0.4 mm bis 1,0 mm. Dünnere Wände sind zwar möglich, erfordern aber eine sorgfältige Validierung und sind möglicherweise anfälliger für Verformungen oder Beschädigungen bei der Handhabung und Nachbearbeitung.
- Vertikale Wände drucken im Allgemeinen zuverlässiger bei minimaler Dicke als horizontale oder niedrig geneigte Wände (die im Wesentlichen zu Überhängen werden).
- Minimale Featuregröße: Dies bezieht sich auf kleine Details wie Stifte, Vorsprünge oder geprägte Texte.
- Positive Merkmale (Vorsprünge) sind im Allgemeinen leichter klein zu drucken als negative Merkmale (Löcher, Schlitze).
- Die minimale, zuverlässig druckbare Strukturgröße ist oft etwas größer als die minimale Wandstärke, typischerweise ab etwa 0.5 mm bis 1,0 mm. Sehr feine Details können aufgrund der Dynamik des Schmelzbades und der Größe der Pulverpartikel an Schärfe verlieren.
- Bildseitenverhältnis: Hohe, dünne Wände können sich während des Baus verziehen oder instabil werden. Das DfAM erwägt, übermäßige Seitenverhältnisse zu begrenzen oder Verstärkungselemente (Rippen) hinzuzufügen.
Ingenieure, die Gehäuse für Steckverbinder entwerfen, müssen sicherstellen, dass alle kritischen Strukturelemente, Dichtungsflächen und Funktionsmerkmale diese Mindestanforderungen erfüllen. Der Versuch, Designs zu replizieren, die für die Mikrobearbeitung vorgesehen sind, ohne die Einschränkungen von AM zu berücksichtigen, wird wahrscheinlich zu Druckfehlern oder nicht funktionierenden Teilen führen.
Strategie für Unterstützungsstrukturen: Minimierung von Abfall und Nachbearbeitung
Stützstrukturen sind eine wichtige, aber oft unerwünschte Notwendigkeit beim PBF-Metalldruck. Sie erfüllen mehrere Funktionen:
- Verankerung: Sichern Sie das Teil auf der Bauplatte, damit es sich während des Bauprozesses nicht verzieht oder verschiebt.
- Stützende Überhänge: Stellen Sie ein Fundament für Elemente bereit, die im Verhältnis zur Bauplatte einen bestimmten Winkel unterschreiten (typischerweise 45 Grad). Ohne Stützen würden sich diese Überhänge verformen oder in das Pulverbett stürzen.
- Wärmeleitung: Sie tragen dazu bei, die Wärme von der Schmelzzone wegzuleiten, wodurch die thermische Belastung verringert und eine Überhitzung empfindlicher Teile verhindert wird.
Die Unterstützung stellt jedoch eine Herausforderung dar:
- Materialabfälle: Stützen sind ein Opfer und stellen eine Verschwendung von teurem Metallpulver dar.
- Verlängerte Bauzeit: Das Drucken von Hilfsmitteln erhöht die Gesamtzeit der Maschine.
- Schwierige Entfernung: Das Entfernen von Metallstützen kann arbeitsintensiv sein (manuelles Brechen, Schneiden, Bearbeiten) und möglicherweise die Oberfläche des Teils beschädigen.
- Auswirkung auf die Oberflächenbeschaffenheit: Die Bereiche, in denen die Stützen am Teil befestigt sind, weisen in der Regel eine raue Oberfläche auf, die verfeinert werden muss.
Zu den wirksamen DfAM-Strategien für Unterstützungsstrukturen gehören:
- Selbsttragende Winkel entwerfen: Entwerfen Sie Überhänge und Elemente nach Möglichkeit so, dass sie oberhalb des kritischen selbsttragenden Winkels liegen (oft ~45 Grad, aber abhängig von Maschine und Material). Die Verwendung von Fasen anstelle von scharfen horizontalen Überhängen ist eine gängige Technik.
- Optimierung der Teileausrichtung: Wählen Sie eine Bauausrichtung, die die Gesamtfläche, die unterstützt werden muss, minimiert. Dies ist oft ein Kompromiss mit anderen Faktoren wie Oberflächenanforderungen oder Bauzeit.
- Optimierte Unterstützungsarten verwenden: Moderne AM-Software ermöglicht verschiedene Stützstrukturen (z. B. Block-, Linien-, Kegel-, Baum- und Gitterstützen). Die Auswahl des Typs, der eine angemessene Unterstützung bei minimalem Materialverbrauch und einfacher Entfernung bietet, ist entscheidend. Gitterstützen können beispielsweise stark sein, aber weniger Material verbrauchen und leichter zu entfernen sein als massive Blöcke.
- Design für Barrierefreiheit: Stellen Sie sicher, dass die Stützstrukturen so angebracht sind, dass sie für die Demontagewerkzeuge leicht erreichbar sind. Vermeiden Sie es, Stützen in tiefen inneren Hohlräumen zu platzieren, es sei denn, sie sind absolut notwendig und zugänglich.
- Minimierung der Kontaktpunkte: Konstruieren Sie die Halterungen so, dass sie möglichst an minimalen Kontaktpunkten oder an unkritischen Oberflächen mit dem Teil verbunden sind, damit die Entfernungsnarben weniger auffällig sind.
Interne Kanäle zur Kühlung oder Abschirmung einbeziehen
Eine der Stärken von AM ist die Möglichkeit, komplexe innere Kanäle in einem Teil zu erzeugen - etwas, das mit herkömmlichen Methoden extrem schwierig oder unmöglich ist. Bei Steckverbindergehäusen für die Luft- und Raumfahrt kann dies genutzt werden, um:
- Konforme Kühlung: Hochleistungssteckverbinder erzeugen Wärme. Interne Kanäle, die sich eng an die Wärmequelle anpassen, können so gestaltet werden, dass ein Luftstrom oder sogar eine Flüssigkeitszirkulation möglich ist, was das Wärmemanagement verbessert und eine Überhitzung verhindert.
- Integrierte Abschirmung: Innerhalb des Gehäuses können Innenwände oder Kammern vorgesehen werden, um eine EMI/RFI-Abschirmung zwischen verschiedenen Steckverbinderabschnitten oder Kabelbündeln innerhalb desselben Gehäuses zu gewährleisten und so die Signalintegrität zu verbessern.
- Kabelverlegung: Komplexe interne Bahnen können möglicherweise Drähte oder Glasfasern innerhalb der Gehäusestruktur selbst führen.
Die Gestaltung wirksamer interner Kanäle erfordert jedoch ein sorgfältiges DfAM:
- Entfernung von Puder: Dies ist die größte Herausforderung. Die Kanäle müssen einen ausreichenden Durchmesser (in der Regel >1-2 mm, je nach Länge und Komplexität) und zugängliche Öffnungen (Fluchtlöcher) haben, damit das nicht verschmolzene Pulver nach dem Bau vollständig entfernt werden kann. Eingeschlossenes Pulver ist inakzeptabel. Bei komplexen Netzwerken sind möglicherweise mehrere Zugangspunkte erforderlich.
- Selbsttragendes Design: Innenliegende Rinnen haben oft Dächer, die als horizontale Überhänge fungieren. Die Gestaltung von Rinnenquerschnitten mit selbsttragenden Formen (z. B. Rauten, Tropfen) kann die Notwendigkeit interner Stützen beseitigen, die extrem schwierig oder unmöglich zu entfernen sind.
- Oberfläche: Die innere Oberfläche von AM-Kanälen ist relativ rau (wie im Bauzustand). Wenn eine glatte Innenoberfläche erforderlich ist (z. B. für den Flüssigkeitsstrom), können sekundäre Bearbeitungsschritte wie abrasive Strömungsbearbeitung oder chemisches Polieren erforderlich sein, was zusätzliche Komplexität und Kosten verursacht.
Design für Orientierung und Platzierung der Bauplatte
Wie bereits erwähnt, ist die Ausrichtung des Steckergehäuses auf der Bauplatte eine kritische DfAM-Entscheidung mit vielfältigen Auswirkungen:
- Unterstützende Strukturen: Die Ausrichtung des Teils, um steile Überhänge zu minimieren, reduziert den Bedarf an Stützen.
- Oberfläche: Nach oben oder vertikal ausgerichtete Flächen haben im Allgemeinen eine bessere Oberflächengüte als nach unten gerichtete Flächen (die durch Auflagepunkte beeinträchtigt werden) oder Flächen mit geringem Winkel (die Treppenstufen aufweisen). Kritische Oberflächen sollten idealerweise so ausgerichtet sein, dass sie optimal bearbeitet werden können, oder so positioniert werden, dass sie leicht nachbearbeitet werden können.
- Bauzeit: Höhere Konstruktionen dauern im Allgemeinen länger. Die Ausrichtung des Teils, um seine Höhe (Z-Dimension) zu minimieren, kann manchmal die Druckzeit verkürzen, obwohl dies oft mit der Minimierung von Stützen kollidiert.
- Mechanische Eigenschaften: Aufgrund des schichtweisen Aufbaus können AM-Teile anisotrope mechanische Eigenschaften aufweisen (die Festigkeit kann je nach Belastungsrichtung relativ zu den aufgebauten Schichten variieren). Kritische Belastungsrichtungen sollten bei der Wahl der Ausrichtung berücksichtigt werden, obwohl dieser Effekt bei optimierten Parametern und Materialien wie Ti-6Al-4V, die mittels SEBM verarbeitet werden, oft weniger ausgeprägt ist.
- Wärmemanagement: Die Ausrichtung kann die Wärmeentwicklung und -ableitung während des Aufbaus beeinflussen, was sich möglicherweise auf die Eigenspannung und den Verzug auswirkt.
- Build Plate Packing: Wenn mehrere Gehäuse gedruckt werden, wirkt sich ihre Ausrichtung und Platzierung darauf aus, wie viele Teile auf eine einzige Bauplatte passen, was sich auf den Gesamtdurchsatz und die Kosten pro Teil auswirkt.
Bei DfAM werden Simulationswerkzeuge und Prozesswissen eingesetzt, um die optimale Ausrichtung zu finden, die diese konkurrierenden Faktoren für das spezifische Gehäusedesign und die Anwendungsanforderungen ausbalanciert.
Nutzung von Simulationswerkzeugen für die Entwurfsvalidierung
Moderne technische Arbeitsabläufe beziehen zunehmend Simulationswerkzeuge in die frühen Phasen des Entwurfsprozesses ein, was für DfAM besonders wertvoll ist:
- Topologie-Optimierung: Wie bereits erwähnt, erzeugen diese Werkzeuge automatisch leichte, belastungsoptimierte Geometrien, die sich ideal für die AM-Produktion eignen.
- Prozess-Simulation: Spezialisierte AM-Simulationssoftware kann potenzielle Probleme vorhersagen vor drucken, wie zum Beispiel:
- Thermische Verformung und Verwerfung: Durch die Simulation des Wärmeaufbaus und der Abkühlung während des schichtweisen Prozesses lassen sich verzugsanfällige Bereiche ermitteln. Auf diese Weise können die Konstrukteure die Ausrichtung anpassen, Stützen hinzufügen oder verstärken oder das Design ändern, um diese Risiken zu mindern.
- Eigenspannung: Die Vorhersage des Aufbaus von Eigenspannungen hilft bei der Optimierung von Wärmebehandlungsstrategien.
- Effektivität der Unterstützungsstruktur: Simulation, ob die geplanten Stützen ausreichen, um ein Versagen des Bauwerks zu verhindern.
- Leistungssimulation: Mit Hilfe von Standard-FEA-Werkzeugen (Finite-Elemente-Analyse) können die strukturelle Integrität, die thermische Leistung (z. B. die Wirksamkeit der Kühlkanäle) und das Schwingungsverhalten des AM-Gehäuses unter Betriebsbelastung überprüft werden.
Der proaktive Einsatz von Simulationen ermöglicht es den Konstrukteuren, das Gehäusedesign digital zu überarbeiten und zu verfeinern, wodurch das Risiko kostspieliger Konstruktionsfehler erheblich verringert und sichergestellt wird, dass das endgültige Teil die Leistungsanforderungen erfüllt. Unternehmen wie Met3dp nutzen solche Werkzeuge häufig als Teil ihrer technische Unterstützungsdienste um Kunden bei der Optimierung von Designs für eine erfolgreiche additive Fertigung zu unterstützen.
Präzision in Perfektion: Erzielung enger Toleranzen, hervorragender Oberflächengüte und Maßgenauigkeit bei 3D-gedruckten Gehäusen
Metall-AM eignet sich zwar hervorragend für die Herstellung komplexer Geometrien, doch das Erreichen des hohen Präzisionsniveaus, das häufig für Bauteile in der Luft- und Raumfahrt erforderlich ist, insbesondere für Verbindungsschnittstellen und Dichtungsflächen an Steckergehäusen, erfordert eine sorgfältige Prozesssteuerung und erfordert häufig sekundäre Nachbearbeitungsschritte. Das Verständnis der erreichbaren Grenzen von Toleranzen beim 3D-Druck von Metalldie Natur der oberflächengüte in Metall AMund die Faktoren, die das Gesamtbild beeinflussen Abmessungsgenauigkeit ist von entscheidender Bedeutung für Ingenieure und Beschaffungsmanager bei der Bewertung lieferanten für Präzisionsfertigung.
Erreichbare Toleranzen beim Metallpulverbettschmelzen verstehen
Unter Toleranz versteht man die zulässige Schwankungsbreite einer Abmessung eines Teils. Bei der Metall-AM werden die erreichbaren Toleranzen von zahlreichen Faktoren beeinflusst, darunter die Maschine, das Material, die Teilegröße und -geometrie sowie die Nachbearbeitung.
- Allgemeine Toleranzen (As-Built): Für typische PBF-Prozesse (SLM, SEBM) werden bei gut beherrschten Prozessen oft allgemeine erreichbare Toleranzen im Bereich von:
- ± 0,1 mm bis ± 0,2 mm für kleinere Abmessungen (z. B. bis zu 50-100 mm).
- ± 0,1 % bis ± 0,2 % des Nennmaßes für größere Merkmale.
- Maschinenspezifität: Höherwertige Maschinen mit besserer Kalibrierung, thermischer Kontrolle und feineren Strahlflecken können oft engere Toleranzen in diesem Bereich erreichen. Met3dp’s Fokus auf branchenführende Ausrüstung trägt zum Erreichen hoher Präzision bei.
- Abhängigkeit von der Geometrie: Komplexe Geometrien, dünne Wände und große ebene Flächen können anfälliger für leichte Abweichungen oder Verformungen sein als einfachere, klobigere Teile.
- Notwendigkeit der Nachbearbeitung: Vor allem bei Merkmalen, die sehr enge Toleranzen erfordern - wie Steckverbinderschnittstellen, O-Ring-Nuten, Gewindebohrungen oder Präzisionsbefestigungsflächen - ist die die AM-Toleranzen sind oft unzureichend, wenn es sich um den Ist-Zustand handelt. Diese kritischen Merkmale werden in der Regel mit zusätzlichem Rohmaterial (Bearbeitungszugabe) entworfen und mit CNC-Bearbeitung nach der Druck- und Spannungsentlastungsphase. Dieser hybride Ansatz nutzt die geometrische Freiheit von AM und die Präzision von CNC, wo sie benötigt wird. Die mit der Nachbearbeitung erreichbaren Toleranzen sind typischerweise ± 0,01 mm bis ± 0,05 mm oder sogar noch enger, was den Standardanforderungen der Luft- und Raumfahrt entspricht.
Es ist wichtig, kritische Maße und Toleranzen auf technischen Zeichnungen klar zu definieren und anzugeben, welche Oberflächen nachbearbeitet werden müssen, um die endgültigen Spezifikationen zu erreichen.
Faktoren, die die Maßgenauigkeit beeinflussen
Das Erreichen einer gleichbleibenden Maßgenauigkeit bei der Metall-AM hängt von der sorgfältigen Kontrolle zahlreicher Faktoren ab:
- Drucker-Kalibrierung: Eine regelmäßige Kalibrierung des Scannersystems, des Strahlenfokus und der Nivellierung der Bauplattform ist unerlässlich.
- Prozessparameter: Laser-/Elektronenstrahlleistung, Scangeschwindigkeit, Schichtdicke, Schraffurabstand und Scanstrategie beeinflussen die Größe und Stabilität des Schmelzbades und damit die Maßgenauigkeit. Optimierte Parametersätze, die von erfahrenen Anbietern wie Met3dp entwickelt wurden, sind entscheidend.
- Materialeigenschaften: Schwankungen in den Pulvereigenschaften (PSD, Fließfähigkeit, Morphologie) können die Packungsdichte und das Schmelzverhalten beeinflussen. Die Verwendung eines gleichbleibend hochwertigen Pulvers ist entscheidend. Auch der Wärmeausdehnungskoeffizient des Materials spielt eine Rolle.
- Thermische Effekte: Ungleichmäßige Erwärmung und Abkühlung während des Bauprozesses führen zu thermischen Spannungen, die Verformungen und Verzerrungen verursachen können, die sich auf die endgültigen Abmessungen auswirken. Faktoren wie die Teileausrichtung, die Unterstützungsstrategie und das Wärmemanagement der Maschine (z. B. beheizte Bauplatte/Kammer wie beim SEBM) beeinflussen dies.
- Größe und Geometrie der Teile: Größere Teile sind einer stärkeren kumulativen thermischen Belastung ausgesetzt. Komplexe Geometrien können örtlich begrenzte Wärmefallen oder Spannungskonzentrationen erzeugen.
- Orientierung aufbauen: Wie unter DfAM erläutert, wirkt sich die Orientierung auf das thermische Verhalten und den Unterstützungsbedarf aus, beides beeinflusst die Genauigkeit.
- Nachbearbeiten: Wärmebehandlungen zum Spannungsabbau sind für die Dimensionsstabilität unerlässlich, können aber leichte, vorhersehbare Dimensionsänderungen verursachen, die berücksichtigt werden müssen. Auch eine unsachgemäße Entfernung von Stützen kann Teile verformen.
Um eine hohe Genauigkeit zu erreichen, ist ein ganzheitlicher Ansatz erforderlich, der robuste Maschinentechnologie, hochwertige Materialien, optimierte Prozessparameter, solide DfAM-Prinzipien und eine kontrollierte Nachbearbeitung kombiniert.
Merkmale der Oberflächenbeschaffenheit: As-Built vs. Post-Processing
Die Oberflächenbeschaffenheit, die in der Regel durch die durchschnittliche Rauheit (Ra) quantifiziert wird, ist ein weiteres kritisches Merkmal für Steckverbindergehäuse, das sich auf die Abdichtung, die Ästhetik und manchmal auch auf den elektrischen Kontakt oder die Reibung auswirkt.
- As-Built Oberflächenbeschaffenheit: Die Oberflächenbeschaffenheit von Teilen direkt nach dem PBF-Druck ist von Natur aus rauer als bearbeitete Oberflächen. Typische Ra-Werte reichen von 5 µm bis 20 µm, abhängig von:
- Orientierung: Die nach oben gerichteten Oberflächen sind im Allgemeinen am glattesten. Vertikale Wände weisen Schichtlinien auf. Nach unten gerichtete Oberflächen, die von Strukturen getragen werden, sind aufgrund der Kontaktpunkte mit den Trägern in der Regel am rauesten. Abgewinkelte Oberflächen weisen eine dem schichtweisen Prozess innewohnende Treppentreppe auf, wobei geringere Winkel zu raueren Oberflächen führen.
- Prozessparameter: Die Schichtdicke (dünnere Schichten = glatter), der Energieeintrag des Strahls und die Scanstrategie beeinflussen die Stabilität des Schmelzbads und die daraus resultierende Oberflächentextur.
- Pulver Partikelgröße: Feinere Pulver können zu einem glatteren Finish beitragen, haben aber möglicherweise Nachteile bei der Fließfähigkeit.
- Maschinentyp: Unterschiedliche Maschinenoptiken und Steuerungssysteme können zu leicht unterschiedlichen Oberflächeneigenschaften führen.
- Nachbearbeitetes Oberflächenfinish: Bei vielen Anwendungen von Steckverbindergehäusen ist die Oberflächenbeschaffenheit der unkritischen Außenflächen im Ist-Zustand akzeptabel. Dichtungsflächen, Gegenstücke oder ästhetisch wichtige Bereiche müssen jedoch oft durch Nachbearbeitung verbessert werden. Zu den gängigen Methoden gehören:
- Perlenstrahlen / Sandstrahlen: Sorgt für ein gleichmäßiges, mattes Finish, entfernt einige lose Partikel und reduziert Ra leicht (z. B. bis auf 5-10 µm Ra).
- Taumeln / Vibrationsgleitschleifen: Glätten von Oberflächen und Abrunden von Kanten mit Hilfe von Schleifkörpern in einer Trommel oder einem Vibrationsbehälter. Kann glattere Oberflächen erzielen (z. B. 1-5 µm Ra), ist aber im Allgemeinen auf Außenflächen und eine weniger präzise Kontrolle der Merkmale beschränkt.
- CNC-Bearbeitung: Wird für kritische Oberflächen verwendet, die glatte Oberflächen (Ra < 1 µm oft erreichbar) und enge Toleranzen erfordern.
- Polieren: Durch manuelles oder automatisiertes Polieren können sehr glatte, spiegelähnliche Oberflächen (Ra << 1 µm) für spezifische Anforderungen erzielt werden.
- Elektropolieren: Ein elektrochemisches Verfahren, bei dem eine mikroskopisch kleine Materialschicht entfernt wird, wodurch die Oberflächen geglättet und die Korrosionsbeständigkeit verbessert wird; besonders wirksam bei rostfreien Stählen wie 316L.
Techniken zur Verbesserung der Oberflächenrauhigkeit (Ra)
Neben der sekundären Verarbeitung können einige Strategien während des Drucks dazu beitragen, die fertige Oberfläche zu optimieren:
- Orientierung: Richten Sie kritische Flächen vorrangig senkrecht oder nach oben aus, wenn möglich.
- Optimierung der Parameter: Die Feinabstimmung von Parametern wie Konturscans (Laserdurchläufe um die Kante jeder Schicht) kann die Seitenwandqualität verbessern.
- Dünnere Schichten: Die Verwendung geringerer Schichtdicken führt zu einer feineren Abstufung auf abgewinkelten Oberflächen, was die gefühlte Glätte erhöht, aber auch die Bauzeit verlängert.
- Kompensation des Strahlversatzes: Die Software kann den Strahlengang geringfügig anpassen, um die Eigenschaften des Schmelzbades zu kompensieren und die Maßgenauigkeit zu verbessern, was sich indirekt auf die effektive Oberflächenglätte der Merkmale auswirkt.
Um jedoch eine mit der maschinellen Bearbeitung vergleichbare Oberflächengüte zu erreichen, sind in der Regel spezielle Nachbearbeitungsschritte erforderlich. Erkunden Sie Met3dp’s Druckverfahren und Fähigkeiten zur Erreichung der gewünschten Teileigenschaften.
Metrologie und Qualitätskontrolle für Luft- und Raumfahrtkomponenten
Insbesondere in der Luft- und Raumfahrt ist es von entscheidender Bedeutung, dass das endgültige 3D-gedruckte und nachbearbeitete Steckverbindergehäuse die spezifizierten Anforderungen an die Abmessungen und die Oberflächengüte erfüllt. Zu den gängigen Messtechniken gehören:
- Koordinatenmessgeräte (CMMs): Hochpräzise Messtaster messen diskrete Punkte, um kritische Maße und geometrische Toleranzen (GD&T) zu überprüfen. Unverzichtbar für die Endabnahme von bearbeiteten Merkmalen.
- 3D-Laserscanning / Structured Light Scanning: Berührungslose Methoden, die Millionen von Punkten erfassen, um ein 3D-Modell des gedruckten Teils zu erstellen. Dieses kann mit dem ursprünglichen CAD-Modell verglichen werden, um Abweichungen auf der gesamten Oberfläche zu visualisieren, was bei komplexen Geometrien und zur Überprüfung der Gesamtform nützlich ist.
- Oberflächenrauhigkeitsprüfgeräte (Profilometer): Tastschnittgeräte messen das Oberflächenprofil, um Ra und andere Rauheitsparameter zu bestimmen.
- Visuelle Inspektion: Vergrößerte Sichtprüfung auf Oberflächenfehler, unvollständige Merkmale oder Reste von Trägermaterial.
- Computertomographie (CT) Scannen: Industrielle Röntgentechnik, die für die zerstörungsfreie Prüfung von inneren Merkmalen verwendet wird, um Pulvereinschlüsse, innere Hohlräume oder Defekte innerhalb des Bauteilvolumens festzustellen. Zunehmend wichtig für die Qualifizierung kritischer AM-Teile für die Luft- und Raumfahrt.
Ein robustes Qualitätsmanagementsystem (QMS), das idealerweise nach Luft- und Raumfahrtnormen wie AS9100 zertifiziert ist, stellt sicher, dass diese Kontrollen konsequent durchgeführt und sorgfältig dokumentiert werden. Hersteller der Luft- und Raumfahrt von ihren Kunden dieses Niveau der Qualitätssicherung verlangen Komponentenlieferanten.
Die Rolle von hochauflösenden Drucksystemen
Die Präzisionsfähigkeiten des Metall-AM-Systems selbst bilden die Grundlage für die Herstellung präziser Teile. Hochauflösende Systeme, gekennzeichnet durch:
- Feinstrahl Spotgröße: Ermöglicht die Erstellung kleinerer Merkmale und schärferer Details.
- Präzise Scanner-Steuerung: Die genaue und schnelle Positionierung des Laser- oder Elektronenstrahls gewährleistet Geometrietreue.
- Fortgeschrittene Software-Algorithmen: Die ausgefeilte Steuerung von Parametern und Scanstrategien optimiert das Schmelzen und minimiert Abweichungen.
- Stabiles Wärmemanagement: Konstante Temperaturen in der Baukammer verringern den Verzug und verbessern die Vorhersagbarkeit.
Met3dp’s Investitionen in branchenführende Druckanlagen bieten eine solide Grundlage für die Herstellung von Steckverbindergehäusen mit hoher Bestandsgenauigkeit und feiner Merkmalsauflösung, wodurch der Umfang der erforderlichen kompensierenden Nachbearbeitung minimiert wird.
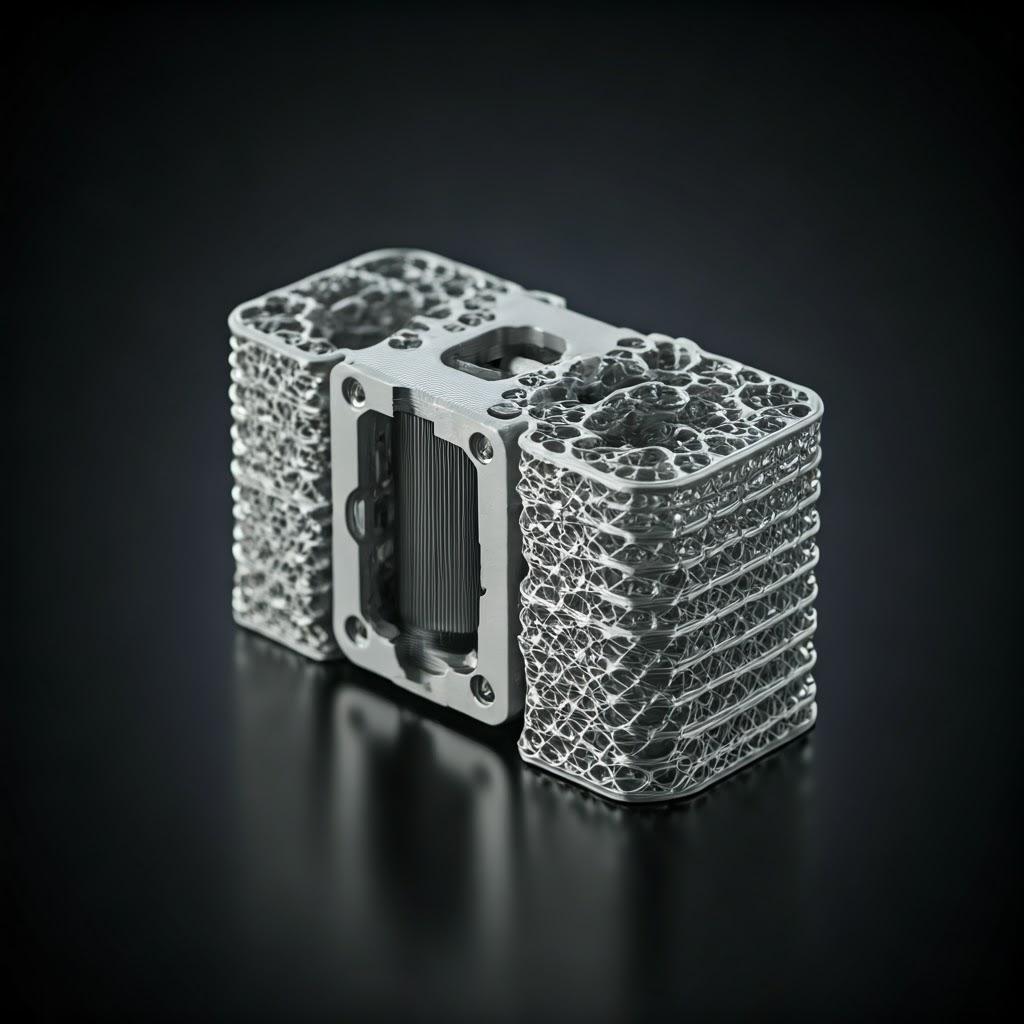
Über den Bau hinaus: Wichtige Nachbearbeitungsschritte für Steckverbindergehäuse in der Luft- und Raumfahrt
Ein weit verbreiteter Irrglaube über den 3D-Druck von Metall ist, dass die Teile fertig aus der Maschine kommen. In Wirklichkeit ist der Druckprozess, insbesondere bei anspruchsvollen Anwendungen wie Steckverbindergehäusen für die Luft- und Raumfahrt, nur der erste Schritt. Eine Reihe von entscheidenden nachbearbeitung von 3D-Metalldruck sind fast immer Schritte erforderlich, um aus dem fertigen Teil ein funktionelles, zuverlässiges Bauteil zu machen, das die strengen Spezifikationen der Luft- und Raumfahrt erfüllt. Diese Schritte betreffen Eigenspannungen, Pulverentfernung, Stützstrukturen, Oberflächengüte, Maßtoleranzen und Materialeigenschaften. Das Verständnis dieser Anforderungen ist entscheidend für die Bewertung von Metall-AM-Dienstleister und die Berechnung der Gesamtkosten und der Durchlaufzeit der Teile.
Spannungsarmglühen und Wärmebehandlung: Sicherstellung von Materialstabilität und Leistung
Die schnellen Erwärmungs- und Abkühlungszyklen, die PBF-Prozessen eigen sind, erzeugen erhebliche innere Spannungen im fertigen Teil. Diese Spannungen können zu Verformungen (insbesondere nach der Entnahme aus der Bauplatte), verminderter mechanischer Leistung und potenzieller Rissbildung im Laufe der Zeit führen.
- Stressabbau: Dies ist in der Regel der allererste Schritt, nachdem der Bauprozess abgeschlossen und das überschüssige Pulver entfernt wurde. Das Teil wird, oft noch auf der Bauplatte befestigt, in einem Ofen auf eine bestimmte Temperatur unterhalb des Umwandlungspunkts erhitzt, eine Zeit lang gehalten und dann langsam abgekühlt. Dadurch kann sich das Kristallgitter des Materials entspannen, was die inneren Spannungen erheblich reduziert.
- Die Notwendigkeit: Dies ist bei Teilen, die mit L-PBF (SLM/DMLS) hergestellt werden, aufgrund der höheren Temperaturgradienten absolut kritisch. Beim SEBM, das bei höheren Temperaturen arbeitet, kann die Notwendigkeit eines umfangreichen Spannungsabbaus manchmal reduziert oder eliminiert werden, was ein Vorteil der SEBM-Technologie von Met3dp’ ist.
- Typische Zyklen: Bei 316L kann der Spannungsabbau durch Erhitzen auf 600-800 °C erfolgen. Bei Ti-6Al-4V wird dies häufig bei 650-800°C in einem Vakuum- oder Schutzgasofen durchgeführt, um eine Oxidation zu verhindern.
- Weitere Wärmebehandlungen (Lösungsglühen, Alterung): Über den Spannungsabbau hinaus können weitere Wärmebehandlungen erforderlich sein, um das gewünschte endgültige Gefüge und die mechanischen Eigenschaften zu erreichen (z. B. Optimierung von Festigkeit, Duktilität, Härte, Ermüdungsfestigkeit).
- Ti-6Al-4V: Wird häufig einer Lösungsbehandlung mit anschließender Alterung (STA) oder Glühzyklen unterzogen, um bestimmte Festigkeits- und Duktilitätskombinationen zu erreichen, die von Luft- und Raumfahrtnormen gefordert werden (z. B. AMS-Spezifikationen für Ti-6Al-4V). Diese erfordern in der Regel höhere Temperaturen (z. B. 900-950 °C für die Lösungsbehandlung) in einem Vakuumofen.
- 316L: Kann bei Bedarf geglüht werden (z. B. bei ~1050 °C), um die Duktilität und Korrosionsbeständigkeit zu erhöhen.
Richtig wärmebehandlung für Legierungen der Luft- und Raumfahrt ist von entscheidender Bedeutung und muss mit kalibrierten Öfen und genau kontrollierten Zyklen durchgeführt werden, gefolgt von geeigneten Tests (z. B. Härte- und Zugtests) zur Überprüfung der Ergebnisse.
Entfernung von Stützstrukturen: Techniken und Überlegungen
Nach dem Spannungsabbau muss das Teil von seinen Stützstrukturen getrennt werden. Dies kann einer der arbeitsintensivsten und potenziell schädlichsten Nachbearbeitungsschritte sein, wenn er während der DfAM nicht sorgfältig geplant wird.
- Entfernen des Teils von der Bauplatte: Dies geschieht in der Regel durch Drahterodieren (Electrical Discharge Machining), Bandsägen oder manchmal auch durch manuelles Brechen für kleinere Teile/Träger. Das Drahterodieren sorgt für einen sauberen Schnitt mit minimaler Krafteinwirkung auf das Teil.
- Unterstützung von Entfernungstechniken:
- Manuelles Brechen/Schneiden: Stützen sind oft mit geschwächten Schnittstellen oder Perforationspunkten versehen, die es ermöglichen, sie mit einer Zange oder einem Handwerkzeug manuell abzubrechen. Das geht schnell, hinterlässt aber grobe Spuren.
- Bearbeitung (Fräsen/Schleifen): Durch CNC-Bearbeitung oder manuelles Schleifen können Stützstrukturen entfernt werden, insbesondere sperrige Strukturen oder solche auf kritischen Oberflächen. Dies bietet mehr Kontrolle über die endgültige Oberfläche, ist aber zeit- und kostenaufwendig.
- Drahterodieren / Senkerodieren: Kann zum präzisen Abtrennen von Stützen in schwer zugänglichen Bereichen verwendet werden, ist aber langsamer.
- Erwägungen:
- Zugänglichkeit: Stützen, die in tiefen Taschen oder internen Kanälen versteckt sind, lassen sich nur schwer entfernen. DfAM ist der Schlüssel, um dies zu vermeiden.
- Material: Titanlegierungen wie Ti-6Al-4V sind schwieriger zu schneiden oder zu bearbeiten als Edelstahl, was die Entfernung von Halterungen aufwändiger macht.
- Risiko der Beschädigung: Wird bei der manuellen Entfernung zu viel Kraft aufgewendet, können empfindliche Teile verformt oder zerstört werden.
Die effiziente und sorgfältige Entfernung von Stützen ist entscheidend für das Erreichen der endgültigen Teilegeometrie ohne Beeinträchtigung der Integrität des Teils.
Operationen zur Oberflächenbearbeitung: Zerspanen, Polieren, Strahlen
Wie bereits erwähnt, muss die Oberflächenbeschaffenheit von AM-Bauteilen oft noch verfeinert werden. Steckergehäuse können je nach funktionalen und ästhetischen Anforderungen verschiedene Nachbearbeitungsschritte erfordern:
- Abrasives Strahlen (Perlen-/Sandstrahlen): Üblich zum Erzielen eines gleichmäßigen matten Finishs, zum Reinigen von Oberflächen und zum Entfernen von halbgesinterten Partikeln. Verschiedene Medien (Glasperlen, Aluminiumoxid) erzeugen unterschiedliche Oberflächen.
- Taumeln/Gleitschleifen: Effektiv zum Glätten von Außenflächen und Entgraten von Kanten an Chargen von Teilen, wodurch die Ra-Werte erheblich reduziert werden.
- CNC-Bearbeitung: Unverzichtbar für das Erreichen enger Toleranzen und glatter Oberflächen an kritischen Schnittstellen (Passflächen, Dichtungsnuten, Montagebohrungen).
- Schleifen/Polieren: Zur Erzielung sehr glatter Oberflächen (niedrige Ra), wo erforderlich, oft manuell oder mit Roboterunterstützung für komplexe Formen.
- Elektropolieren: Besonders effektiv für 316L, da eine sehr glatte, saubere und korrosionsbeständige Oberfläche durch elektrochemischen Materialabtrag erzielt wird.
Die spezifische Kombination von Bearbeitungsschritten hängt ganz von den in der Teilespezifikation und der Zeichnung definierten Anforderungen ab.
Beschichtungen und Verkleidungen für verbesserte Leistung
Während Basismaterialien wie 316L und Ti-6Al-4V gute intrinsische Eigenschaften aufweisen, werden manchmal Beschichtungen oder Plattierungen auf 3D-gedruckte Steckergehäuse aufgebracht, um bestimmte Eigenschaften weiter zu verbessern:
- EMI/RFI-Abschirmung: Während das Metallgehäuse selbst für Abschirmung sorgt, ist die Beschichtung mit hochleitenden Metallen wie kupfer, Nickel oder Silber kann die Wirksamkeit der Abschirmung, insbesondere bei höheren Frequenzen, erheblich verbessern. Die stromlose Vernickelung ist eine gängige Wahl.
- Korrosionsschutz: Obwohl 316L und Ti64 sehr korrosionsbeständig sind, können spezielle Beschichtungen (z. B. chemische Konversionsbeschichtungen wie Chromat- oder Phosphatbeschichtungen, Lacke, PVD-Beschichtungen) für extreme Umgebungsbedingungen oder eine besondere Flüssigkeitsverträglichkeit verwendet werden.
- Abnutzungswiderstand: Harte Beschichtungen (z. B. TiN, CrN durch PVD) können verwendet werden, wenn das Gehäuse starkem Verschleiß ausgesetzt ist, was bei Standard-Steckverbindern jedoch seltener der Fall ist.
- Elektrische Leitfähigkeit: Die Beschichtung kann die Oberflächenleitfähigkeit für Erdungs- oder Kontaktzwecke verbessern.
- Kosmetische Veredelungen: Durch Eloxieren (bei Titan), Lackieren oder Pulverbeschichten können bestimmte Farben oder ästhetische Oberflächen erzielt werden.
Das Auftragen von Beschichtungen erfordert eine ordnungsgemäße Vorbereitung der Oberfläche des AM-Teils, um eine gute Haftung zu gewährleisten. Die Arbeit mit qualifizierten Endbearbeitung von Luft- und Raumfahrtkomponenten lieferanten, die Erfahrung mit AM-Teilen haben, werden empfohlen.
Reinigungs- und Endkontrollprotokolle
Während der gesamten Nachbearbeitungskette sind Reinigungsschritte erforderlich, um Rückstände von Kühlmitteln, Strahlmitteln, Poliermitteln oder Galvanochemikalien zu entfernen.
- Endreinigung: Ein abschließender, gründlicher Reinigungsprozess (oft mit Ultraschallreinigung in speziellen Lösungs- oder Reinigungsmitteln) stellt sicher, dass das Steckergehäuse vor der Endkontrolle und Verpackung frei von Verunreinigungen ist.
- Endkontrolle: Dazu gehören die Überprüfung der Abmessungen (CMM, Scannen), die Kontrolle der Oberflächenbeschaffenheit, die visuelle Inspektion auf Defekte und möglicherweise NDT (wie CT-Scannen bei kritischen Teilen), um sicherzustellen, dass das fertige Gehäuse alle in der Zeichnung und im Qualitätsplan festgelegten Spezifikationen erfüllt. Materialzertifizierungen und die Rückverfolgbarkeit der Prozessdokumentation sind wichtige Leistungen für Komponenten der Luft- und Raumfahrt.
Zusammenarbeit mit qualifizierten Post-Processing-Partnern
Die Vielzahl der erforderlichen Nachbearbeitungsschritte erfordert oft spezielle Geräte und Fachkenntnisse, die nicht alle in einem einzigen AM-Dienstleistungsunternehmen vorhanden sind. Viele Anbieter von 3D-Metalldruckdiensten haben Beziehungen zu qualifizierten Partnern für Dienstleistungen wie Wärmebehandlung, Präzisionsbearbeitung, Beschichtung und NDT aufgebaut. Bei der Auswahl eines Zulieferers ist es wichtig, dessen interne Fähigkeiten im Vergleich zu seinem Netzwerk von Unterauftragnehmern zu verstehen und sicherzustellen, dass die gesamte Lieferkette die Qualitätsstandards der Luft- und Raumfahrt erfüllt (z. B. AS9100-Zertifizierung, Nadcap-Akkreditierung für spezielle Prozesse). Met3dp, das sich auf umfassende Lösungen konzentriert, unterstützt seine Kunden bei der Bewältigung dieser Nachbearbeitungsanforderungen, um eine durchgängige Qualität zu gewährleisten.
Herausforderungen meistern: Überwindung potenzieller Hürden beim 3D-Druck von Luft- und Raumfahrtsteckern aus Metall
Die additive Fertigung von Metallen bietet zwar ein revolutionäres Potenzial für die Herstellung von kundenspezifischen Steckverbindergehäusen für die Luft- und Raumfahrt, ist aber nicht ohne technische Herausforderungen. Um die erforderliche Qualität, Zuverlässigkeit und Konsistenz zu erreichen, ist ein tiefes Verständnis der Prozessphysik, der Werkstoffkunde und der potenziellen Fehlermöglichkeiten erforderlich. Anerkennen dieser probleme beim 3D-Druck von Metall und die Umsetzung robuster Strategien zur Risikominderung sind der Schlüssel zum erfolgreichen Einsatz von AM für kritische Luft- und Raumfahrtkomponenten. Die Partnerschaft mit einem erfahrenen und technologisch fortschrittlichen zuverlässiger AM-Lieferant ein Unternehmen wie Met3dp, das sich diesen Herausforderungen proaktiv stellt, ist für die Risikominderung von entscheidender Bedeutung.
Verringerung von Verformungen und Eigenspannungen
Die vielleicht größte Herausforderung bei PBF aus Metall ist die Bewältigung der thermischen Spannungen, die während der schnellen Heiz- und Kühlzyklen entstehen. Diese Spannungen können Folgendes verursachen:
- Verkrümmen: Verformung des Teils während der Herstellung, was dazu führen kann, dass sich das Teil von den Halterungen abhebt oder mit dem Messer des Pulverbeschichters kollidiert, was zu einem Herstellungsfehler führt.
- Eigenspannung: Eigenspannungen, die nach dem Abkühlen im Teil verbleiben und die Maßhaltigkeit beeinträchtigen, die Ermüdungslebensdauer verringern und möglicherweise zu Rissen führen können.
Strategien zur Schadensbegrenzung:
- Optimierte Unterstützungsstrukturen: Robuste Stützen sind unerlässlich, um das Teil fest auf der Bauplatte zu verankern und den Verformungskräften zu widerstehen. DfAM spielt hier eine Schlüsselrolle.
- Orientierung aufbauen: Die Ausrichtung des Teils, um große ebene Flächen parallel zur Bauplatte zu minimieren und den Gesamtgradienten der thermischen Masse zu reduzieren, kann helfen.
- Optimierung der Scan-Strategie: Die Verwendung spezifischer Muster (z. B. Inselabtastung, Schachbrettmuster) unterbricht lange, durchgehende Schmelzspuren, verteilt die Wärme gleichmäßiger und reduziert den Spannungsaufbau. Parameter wie Strahlleistung und Geschwindigkeit sind ebenfalls entscheidend.
- Prozess-Simulation: Die Vorhersage der Spannungsakkumulation während der Entwurfsphase ermöglicht proaktive Anpassungen der Geometrie oder der Stützen.
- Stressabbau Wärmebehandlung: Wesentlicher Nachbearbeitungsschritt zur Entspannung der inneren Spannungen (wie zuvor beschrieben).
- Verarbeitung bei erhöhter Temperatur (SEBM): Technologien wie das Elektronenstrahlschmelzen (SEBM), das von Met3dp eingesetzt wird, arbeiten mit deutlich höheren Baukammertemperaturen. Dadurch bleibt das Teil während des gesamten Bauprozesses heiß, was wie ein In-situ-Spannungsabbauverfahren wirkt und zu Teilen mit viel geringerer Eigenspannung im Vergleich zu typischem L-PBF führt, was das Verzugsrisiko deutlich reduziert.
Sicherstellen der Teiledichte und Vermeiden von Porosität
Das Erreichen einer nahezu vollständigen Dichte (in der Luft- und Raumfahrt typischerweise >99,5 % oder höher) ist entscheidend für die mechanische Integrität. Porosität (innere Hohlräume) können als Spannungskonzentratoren wirken und die Ermüdungslebensdauer und Gesamtfestigkeit drastisch verringern.
Ursachen der Porosität:
- Fehlende Fusion: Bei unzureichender Energiezufuhr (geringe Leistung, hohe Geschwindigkeit) werden die Pulverpartikel nicht vollständig aufgeschmolzen, so dass Lücken zwischen den Schichten oder Scan-Spuren entstehen.
- Keyholing: Ein übermäßiger Energieeintrag führt zu tiefen, instabilen Schmelztümpeln, die zusammenbrechen können, wodurch Gas eingeschlossen wird und Poren entstehen.
- Gas Porosität: Im geschmolzenen Metall gelöste oder in hohlen Pulverteilchen eingeschlossene Gase können beim Erstarren Poren bilden.
- Schlechte Qualität des Pulvers: Unregelmäßig geformtes Pulver oder Pulver mit inneren Hohlräumen packt weniger effizient und kann Gas einschließen.
Strategien zur Schadensbegrenzung:
- Optimierte Prozessparameter: Umfangreiche Prozessentwicklung ist erforderlich, um das optimale Fenster für Laser-/Strahlleistung, Scangeschwindigkeit, Schichtdicke und Schraffurabstand für jedes Material zu finden, um ein konsistentes, vollständiges Schmelzen ohne Keyholing zu erreichen. Met3dp investiert viel in die Entwicklung robuster Parameter für seine Materialien und SEBM-Systeme.
- Hochwertiges Pulver: Die Verwendung hochkugelförmiger Pulver mit geringem internen Gasgehalt und kontrolliertem PSD, wie sie von Met3dp mit GA und PREP hergestellt werden, ist von grundlegender Bedeutung. Eine gute Fließfähigkeit des Pulvers gewährleistet eine gleichmäßige Schichtabscheidung.
- Kontrolle der inerten Atmosphäre: Die Aufrechterhaltung einer hochreinen Inertgasatmosphäre (Argon oder Stickstoff für L-PBF) oder eines Vakuums (SEBM) minimiert Verunreinigungen und Reaktionen, die zu Porosität führen könnten.
- Heiß-Isostatisches Pressen (HIP): Ein Nachbearbeitungsschritt mit hoher Temperatur und hohem Druck in einer inerten Atmosphäre. HIP kann die inneren Poren (außer denen, die zur Oberfläche hin offen sind) effektiv schließen und eine Dichte von nahezu 100 % erreichen. Es verursacht jedoch erhebliche zusätzliche Kosten und Vorlaufzeiten und kann sich auf die Abmessungen auswirken, weshalb es in der Regel den kritischsten Anwendungen vorbehalten ist, bei denen die Toleranz für interne Poren nahezu null ist. Häufig können gut kontrollierte AM-Prozesse eine ausreichende Dichte ohne HIP erreichen.
Herausforderungen beim Entfernen interner Stützen aus komplexen Geometrien
Wie in den Abschnitten DfAM und Nachbearbeitung hervorgehoben wurde, ist das Entfernen von Stützstrukturen aus komplizierten internen Kanälen oder Hohlräumen in einem Steckergehäuse eine große Herausforderung.
Strategien zur Schadensbegrenzung:
- DfAM ist überragend: Die beste Lösung ist Design die Notwendigkeit interner Stützen, wo immer dies möglich ist, durch selbsttragende Rinnengeometrien (z. B. Tropfen- oder Rautenform).
- Zugang gewähren: Wenn interne Abstützungen unvermeidbar sind, müssen angemessene Zugangsöffnungen für Werkzeuge oder Spülungen vorgesehen werden.
- Spezialisierte Unterstützungsstrukturen: Die Verwendung leicht zerkleinerbarer oder löslicher Trägermaterialien (im Metalldirektdruck weniger üblich, aber erforscht) oder optimierter Gitterträger kann helfen.
- Erweiterte Entfernungstechniken: Abrasive Fließbearbeitung oder chemisches Ätzen könnten in bestimmten Fällen in Betracht gezogen werden, aber diese Verfahren sind komplex, kostspielig und erfordern eine sorgfältige Validierung, um sicherzustellen, dass sie das Teil nicht beschädigen oder kritische Abmessungen verändern. Häufig werden Konstruktionen, die umfangreiche, unzugängliche interne Stützen erfordern, als ungeeignet für die aktuelle AM-Technologie angesehen.
Protokolle über Materialkontamination und Pulverhandhabung
Metallpulver, insbesondere reaktive Pulver wie Ti-6Al-4V, sind empfindlich gegenüber Verunreinigungen durch Sauerstoff, Stickstoff, Feuchtigkeit und Kreuzkontaminationen mit anderen Metallpulvern. Verunreinigungen verschlechtern die mechanischen Eigenschaften erheblich.
Strategien zur Schadensbegrenzung:
- Strenge Handhabung des Pulvers: Durch den Einsatz kontrollierter Umgebungen (Handschuhboxen, versiegelte Behälter), Inertgasspülung und spezieller Geräte (Siebe, Trichter, Baumodule) für jeden Materialtyp werden Kreuzkontaminationen und die Exposition gegenüber der Atmosphäre verhindert.
- Lebenszyklusmanagement für Pulver: Die Nachverfolgung des Pulververbrauchs, das Recycling (Sieben zur Entfernung übergroßer Partikel oder Spritzer) und die regelmäßige Prüfung der Chemie des recycelten Pulvers sind für die Aufrechterhaltung der Materialintegrität unerlässlich. Met3dp hält sich an strenge Pulverhandhabungs- und Qualitätskontrollprotokolle.
- Inertgasqualität: Die Reinheit des Argons oder Stickstoffs, der in der Baukammer (für L-PBF) verwendet wird, muss sichergestellt werden.
Sicherstellung der Konsistenz über alle Produktionschargen hinweg
Für die Luft- und Raumfahrt ist es von entscheidender Bedeutung, bei jedem Teil die gleiche hohe Qualität zu erreichen, unabhängig davon, ob ein oder hundert Steckergehäuse gedruckt werden. Herausforderungen in der Luft- und Raumfahrtindustrie drehen sich oft um die Wiederholbarkeit.
Strategien zur Schadensbegrenzung:
- Robustes Qualitätsmanagementsystem (QMS): Die Einführung eines zertifizierten QMS (wie AS9100) bietet den Rahmen für Prozesskontrolle, Dokumentation, Rückverfolgbarkeit und kontinuierliche Verbesserung.
- Kalibrierung und Wartung von Maschinen: Regelmäßige vorbeugende Wartung und Kalibrierung gewährleisten eine gleichbleibende Leistung des AM-Systems.
- Prozessüberwachung: In-situ-Überwachungsinstrumente (z. B. Schmelzepool-Überwachung, Wärmebildtechnik) können Echtzeitdaten über die Stabilität des Bauwerks liefern und möglicherweise Defekte erkennen, sobald sie sich bilden (obwohl sich diese Technologie für eine endgültige Qualitätsbewertung noch in der Entwicklung befindet).
- Konsistenter Ausgangsstoff: Die Verwendung von Pulver eines vertrauenswürdigen Lieferanten wie Met3dp mit zertifizierter Konsistenz von Charge zu Charge ist von grundlegender Bedeutung.
- Standardisierte Verfahren: Dokumentierte und streng befolgte Verfahren für die Einrichtung, den Betrieb, die Handhabung des Pulvers und die Nachbearbeitung minimieren menschliche Fehler und Schwankungen.
- Statistische Prozesskontrolle (SPC): Die Analyse von Prozessdaten und Teilemessungen im Laufe der Zeit hilft, Trends zu erkennen und die Prozessstabilität zu erhalten.
Durch das Verständnis dieser potenziellen Herausforderungen und die Zusammenarbeit mit einem sachkundigen Anbieter wie Met3dp, der fortschrittliche Technologien (SEBM), hochwertige Materialien, strenge Prozesskontrollen und umfassenden DfAM-Support einsetzt, können Luft- und Raumfahrtingenieure und Beschaffungsmanager Metall-AM vertrauensvoll nutzen, um zuverlässige, leistungsstarke kundenspezifische Steckverbindergehäuse herzustellen.
Lieferantenauswahl: Wie man den richtigen Metall-3D-Druck-Dienstleister für Luft- und Raumfahrtkomponenten auswählt
Die Entscheidung für die additive Fertigung von kritischen Komponenten wie Steckverbindergehäusen für die Luft- und Raumfahrt ist eine wichtige Entscheidung. Die Ausschöpfung des vollen Potenzials dieser Technologie - flugtaugliche Teile, die strenge Leistungs-, Qualitäts- und Zuverlässigkeitsstandards erfüllen - hängt jedoch entscheidend von der Auswahl des richtigen Fertigungspartners ab. Nicht alle Anbieter von 3D-Metalldruckdiensten sind alle gleich, vor allem wenn sie für die anspruchsvolle Luft- und Raumfahrtindustrie bestimmt sind. Ingenieure und Beschaffungsmanager müssen eine gründliche Due-Diligence-Prüfung durchführen und potenzielle Lieferanten anhand einer Reihe strenger Kriterien bewerten, um sicherzustellen, dass sie über das erforderliche Know-how, die Technologie und die Qualitätskontrollen verfügen. Die Zusammenarbeit mit einem fähigen und zertifizierten Lieferanten ist für die Risikominimierung und den Projekterfolg von größter Bedeutung.
Bewertung der technischen Fähigkeiten: Ausrüstung, Materialien, Fachwissen
Die Grundlage eines jeden leistungsfähigen AM-Anbieters liegt in seinen technischen Fähigkeiten. Zu den zu bewertenden Schlüsselbereichen gehören:
- Ausrüstungsportfolio:
- Technologische Übereinstimmung: Verfügen sie über die geeignete PBF-Technologie (SLM, DMLS, SEBM), die für das Material (316L, Ti-6Al-4V) und die Komplexität Ihres Gehäuses am besten geeignet ist? Die SEBM-Technologie, die von Met3dp angeboten wird, eignet sich beispielsweise hervorragend für Ti-6Al-4V, da sie geringere Eigenspannungen aufweist und reaktive Materialien im Vakuum verarbeiten kann.
- Maschinenqualität & Merkmale: Sind ihre Maschinen industrietauglich, gut gewartet und mit den erforderlichen Prozessüberwachungs- oder Steuerungsfunktionen ausgestattet?
- Bauvolumen: Können ihre Maschinen die Größe des Gehäuses Ihres Steckers aufnehmen?
- Auflösung & Genauigkeit: Wie hoch sind die angegebene Genauigkeit und die Mindestgröße des Merkmals bei den jeweiligen Systemen?
- Fachwissen über Werkstoffe:
- Qualifizierte Materialien: Verfügen sie über nachgewiesene Erfahrung und validierte Prozessparameter speziell für 316L und Ti-6Al-4V in Luft- und Raumfahrtqualität? Können sie Materialdatenblätter auf der Grundlage der gedruckten Eigenschaften bereitstellen?
- Breiteres Portfolio: Bieten sie auch andere relevante Legierungen für die Luft- und Raumfahrt an (z. B. Aluminiumlegierungen, Inconel), falls sich Ihre Anforderungen ändern?
- Pulverbeschaffung & Qualität: Woher beziehen sie ihr Pulver? Gibt es strenge Qualitätskontrollen beim Eingang? Ein Anbieter wie Met3dp, der seine eigenen hochwertigen Pulver mit fortschrittlichen GA- und PREP-Methoden herstellt, bietet einen erheblichen Vorteil bei der Kontrolle dieser kritischen Eingangsgröße.
- Prozess-Know-how:
- Entwicklung der Parameter: Verfügen sie über das Know-how, um die Druckparameter für bestimmte Geometrien und Leistungsanforderungen zu optimieren, oder verlassen sie sich ausschließlich auf die Standardeinstellungen der Maschinenhersteller?
- Metallurgisches Verständnis: Gehören zu ihrem Team auch Werkstoffwissenschaftler oder Metallurgen, die die Feinheiten des Legierungsverhaltens bei AM und der anschließenden Wärmebehandlung kennen?
Qualitätsmanagementsysteme und Zertifizierungen (z. B. AS9100)
Für die Luft- und Raumfahrtindustrie ist Qualität nicht nur wünschenswert, sondern zwingend erforderlich. Das Engagement eines Lieferanten für Qualität lässt sich am besten durch sein QMS und die entsprechenden Zertifizierungen nachweisen:
- AS9100-Zertifizierung: Dies ist die international anerkannte QMS-Norm speziell für die Luft-, Raumfahrt- und Verteidigungsindustrie. Sie enthält die Anforderungen der ISO 9001, fügt jedoch strenge Kontrollen für Sicherheit, Zuverlässigkeit, Lufttüchtigkeit, Rückverfolgbarkeit, Konfigurationsmanagement und Risikomanagement hinzu. AS9100-zertifizierte additive Fertigung anbieter sich verpflichten, die höchsten Industriestandards zu erfüllen. Dies sollte bei der Auswahl eines Zulieferers für Flugkomponenten als Hauptanforderung gelten.
- Zertifizierung nach ISO 9001: Ein grundlegender QMS-Standard, der dokumentierte Prozesse für Qualitätskontrolle, Konsistenz und kontinuierliche Verbesserung angibt. Sie ist eine gute Grundlage, reicht aber für Hauptauftragnehmer in der Luft- und Raumfahrt oft allein nicht aus.
- Nadcap-Akkreditierung: Während AS9100 das Gesamtsystem abdeckt, bietet Nadcap eine spezifische Akkreditierung für spezielle Prozesse wie Wärmebehandlung, zerstörungsfreie Prüfung (NDT), Schweißen und Beschichtungen. Wenn Ihr Zulieferer diese kritischen Schritte intern durchführt oder auslagert, bietet die Überprüfung der Nadcap-Akkreditierung des Zulieferers oder seines Partners eine weitere Sicherheitsebene.
Verlangen Sie Nachweise für diese Zertifizierungen und informieren Sie sich über den Umfang der Umsetzung ihres QMS.
Standards für die Rückverfolgbarkeit von Materialien und die Prozesskontrolle
Komponenten für die Luft- und Raumfahrt erfordern eine akribische Rückverfolgbarkeit - die Fähigkeit, die Geschichte eines Teils von der Rohmaterialcharge bis zu jedem Herstellungs- und Prüfschritt zu verfolgen.
- Rückverfolgbarkeit von Pulverchargen: Der Lieferant muss eindeutig nachweisen, welche spezifische Pulvercharge (mit der dazugehörigen Chemie und den PSD-Zertifizierungen) für jeden Bauauftrag verwendet wurde. Dies ist entscheidend für die Untersuchung, falls später Probleme auftreten. Zulieferer wie Met3dp, die die Pulverproduktion kontrollieren, bieten von Haus aus eine solide Rückverfolgbarkeit.
- Prozessparameter-Protokollierung: Industrielle AM-Systeme protokollieren kritische Prozessparameter während der Herstellung (z. B. Strahlleistung, Sauerstoffgehalt der Kammer, Temperatur). Der Lieferant sollte diese Aufzeichnungen als Teil der Bauunterlagen aufbewahren.
- Konfigurationsmanagement: Es müssen strenge Kontrollen durchgeführt werden, um sicherzustellen, dass die richtige Entwurfsversion (CAD-Datei, Zeichnung) für die Fertigung verwendet wird.
- Dokumentation: Umfassende Dokumentationspakete mit Materialzertifikaten, Fertigungsprotokollen, Nachbearbeitungsprotokollen (Wärmebehandlungsdiagrammen), Prüfberichten (CMM, NDT) und Konformitätszertifikaten sind Standardlieferungen für Luft- und Raumfahrtteile.
Überprüfen Sie die Verfahren des Lieferanten zur Aufrechterhaltung dieses Niveaus der Rückverfolgbarkeit und Kontrolle.
Bewertung der technischen Unterstützung und des DfAM-Fachwissens
Wie bereits erwähnt, ist DfAM entscheidend für die Optimierung von Steckverbindergehäusen für die additive Fertigung. Ein wertvoller Lieferant fungiert als Partner und bietet technische Unterstützung:
- DfAM-Konsultation: Können deren Ingenieure Ihren Entwurf überprüfen und konstruktives Feedback zur Optimierung der Geometrie, zur Minimierung der Stützen, zur Gewährleistung der Pulverentfernung und zur Auswahl der besten Ausrichtung geben?
- Simulationsfähigkeiten: Bieten sie Prozesssimulationen an, um Verformungen oder Spannungen vorherzusagen, oder Topologieoptimierungsdienste, um Leichtbauziele zu erreichen?
- Problemlösung: Verfügen sie über das Fachwissen, um potenzielle Probleme bei der Erstellung komplexer Geometrien oder spezifischer Leistungsanforderungen zu beheben?
Dieser kooperative Ansatz gewährleistet, dass das Design effizient und effektiv hergestellt werden kann.
Kapazität, Vorlaufzeiten und Skalierbarkeit für Produktionsvolumina
Berücksichtigen Sie sowohl Ihren unmittelbaren Bedarf an Prototypen als auch potenzielle künftige Produktionsanforderungen:
- Kapazität der Maschine: Verfügen sie über eine ausreichende Maschinenverfügbarkeit, um die von Ihnen geforderten Vorlaufzeiten für Prototypen und mögliche Folgeaufträge einzuhalten? Wie hoch ist ihr typischer Auftragsbestand?
- Skalierbarkeit: Wenn Ihr Projekt von einem Prototyp zu einer kleinen oder mittleren Produktionsmenge übergeht, verfügt der Lieferant dann über die Kapazitäten (mehrere Maschinen, effizienter Arbeitsablauf, robuste Nachbearbeitung), um die Produktion entsprechend zu steigern?
- Transparenz der Vorlaufzeiten: Liefern sie realistische und zuverlässige Vorlaufzeitschätzungen auf der Grundlage der aktuellen Kapazitäten und der Komplexität Ihres Teils und seiner Nachbearbeitungsanforderungen?
Verständnis des Wertangebots: Warum eine Partnerschaft mit Met3dp?
Bei der Auswahl eines Lieferanten geht es nicht nur darum, bestimmte Kriterien zu erfüllen, sondern einen Partner zu finden, der sich für Ihren Erfolg einsetzt. Met3dp bietet Kunden aus der Luft- und Raumfahrt, die nach kundenspezifischen Steckverbindergehäusen suchen, ein überzeugendes Wertangebot:
- Integrierte Lösung: Als Hersteller von hochwertigen Metallpulvern für die Luft- und Raumfahrt (316L, Ti-6Al-4V, kundenspezifische Legierungen), der fortschrittliche GA- und PREP-Technologien einsetzt, und als Anbieter von fortschrittlichen SEBM-Druckdienstleistungen bietet Met3dp eine beispiellose Kontrolle über die gesamte AM-Prozesskette, die Materialqualität und Prozesssynergie gewährleistet.
- Technologie-Vorteil: Unser Fachwissen im SEBM bietet deutliche Vorteile für Werkstoffe wie Ti-6Al-4V und liefert Teile mit geringen Eigenspannungen und hervorragenden Materialeigenschaften, wodurch sich der Nachbearbeitungsbedarf oft verringert.
- Fachwissen: Unser Team besteht aus Fachleuten mit jahrzehntelanger Erfahrung in den Bereichen Metall-AM, Materialwissenschaft und Luft- und Raumfahrtanwendungen und bietet kompetente Unterstützung bei DfAM und Anwendungsentwicklung.
- Schwerpunkt Qualität: Wir arbeiten nach strengen Qualitätskontrollprotokollen, die die Rückverfolgbarkeit der Materialien und eine gleichbleibende Qualität der Teile für anspruchsvolle Branchen gewährleisten. (Mehr erfahren Über uns).
- Zusammenarbeit mit Kunden: Wir arbeiten eng mit unseren Kunden zusammen, um ihre einzigartigen Herausforderungen zu verstehen und maßgeschneiderte Lösungen zu liefern, die das gesamte Potenzial der additiven Fertigung ausschöpfen.
Zuverlässige B2B Metall AM Lieferanten und Hersteller finden
Neben der direkten Suche sollten Sie auch Branchenverzeichnisse, Messen (wie Formnext) und Empfehlungen aus vertrauenswürdigen Quellen berücksichtigen. Bei der Kontaktaufnahme mit potenziellen B2B-Partner im Metalldruckwir erstellen eine detaillierte Angebotsanfrage (RFQ) mit CAD-Modellen, Zeichnungen mit kritischen Abmessungen und Toleranzen, Materialspezifikationen, erforderlichen Zertifizierungen, Mengen und gewünschten Lieferzeiten. Dies ermöglicht genaue Angebote und aussagekräftige Vergleiche zwischen potenziellen Lieferanten.
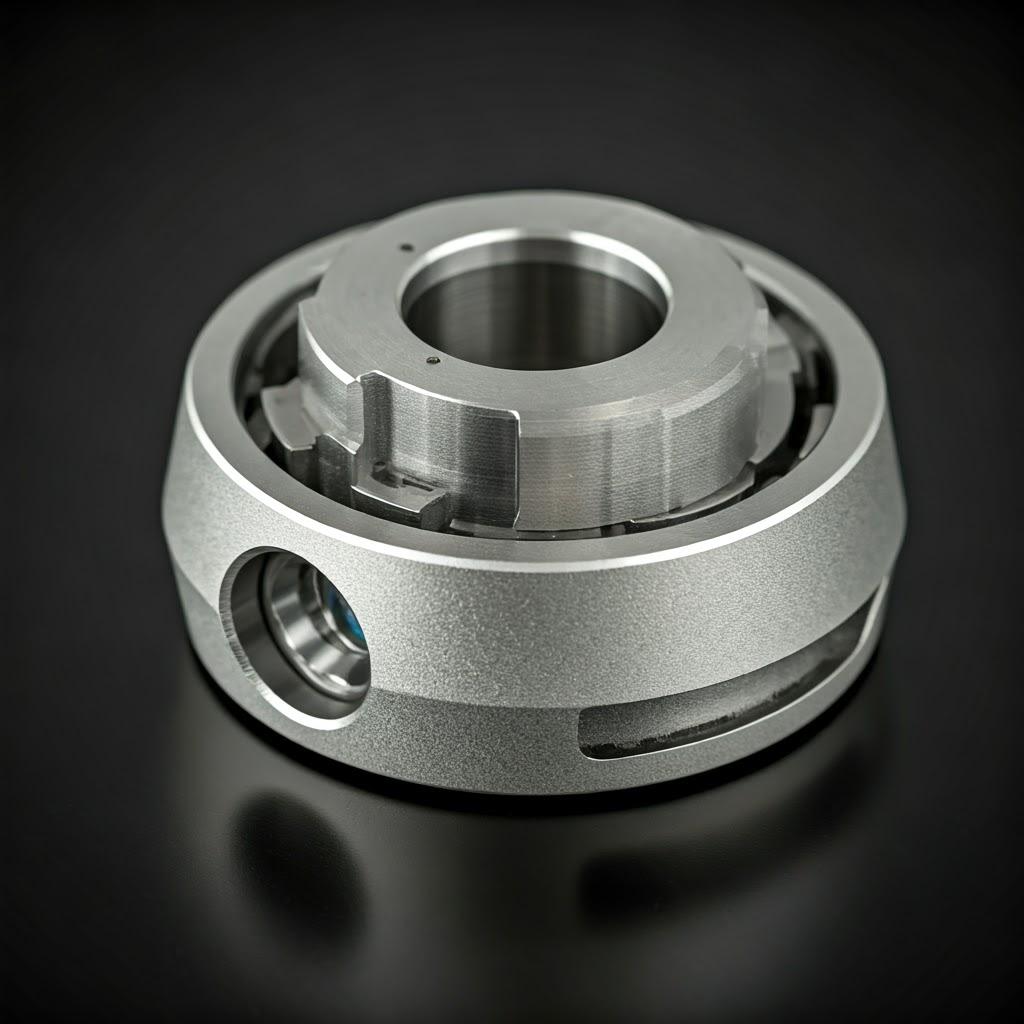
Die Investition verstehen: Wichtige Kostenfaktoren und Vorlaufzeiten für 3D-gedruckte Steckergehäuse
Eine der wichtigsten Überlegungen bei der Einführung einer Fertigungstechnologie ist die Kosteneffizienz und die Zeit, die für die Lieferung der Teile benötigt wird. Metall-AM bietet zwar überzeugende Vorteile für kundenspezifische Steckergehäuse in der Luft- und Raumfahrt, aber es ist wichtig, die Faktoren zu verstehen, die die Kosten für den 3D-Druck von Metall und Einfluss vorlaufzeiten für Luft- und Raumfahrtkomponenten. Dieses Wissen hilft den Ingenieuren, die Wahl der Technologie zu rechtfertigen, und ermöglicht den Beschaffungsverantwortlichen eine effiziente Budgetierung und Planung. Einholung detaillierter Angebote von potenziellen verteiler für 3D-Druck aus Metall oder Dienstleistungsbüros ist von entscheidender Bedeutung, aber das Verständnis der zugrunde liegenden Kostenstruktur bietet einen wertvollen Kontext.
Materialkosten: Pulverpreis und Verbrauch
Material ist ein wesentlicher Kostenfaktor, insbesondere bei teuren Legierungen für die Luft- und Raumfahrt:
- Pulver Preis: Zwischen den gängigen Legierungen gibt es erhebliche Unterschiede bei den Kosten pro Kilogramm.
- 316L-Edelstahl: Relativ wirtschaftlich.
- Ti-6Al-4V Titan-Legierung: Erheblich teurer (oft das 5-10-fache des Preises von 316L oder mehr) aufgrund der Rohstoffkosten und der komplexen Verfahren zur Pulverherstellung.
- Andere Legierungen: Nickel-Superlegierungen (Inconel) sind ebenfalls hochpreisig. Aluminiumlegierungen sind im Allgemeinen preiswerter als nichtrostender Stahl.
- Verbrauchtes Material: Die Kosten bestehen nicht nur aus dem Pulver im Endprodukt, sondern auch aus dem Preis:
- Teilband: Das tatsächliche Volumen des Steckergehäuses.
- Unterstützende Strukturen: Das Volumen des Pulvers, das für Opferträger verwendet wird. Effizientes DfAM minimiert dies.
- Prozessverluste: Ein Teil des Pulvers geht bei der Handhabung, beim Sieben und beim Drucken zwangsläufig verloren (obwohl effiziente Lieferanten den Abfall durch Recycling minimieren).
- Dichte der Bebauung: Dicht gepackte Drucke (mehrere gleichzeitig gedruckte Teile) nutzen das Pulver effizienter als der Druck einzelner Teile in einem großen Bauvolumen.
Mitnehmen: Die Materialauswahl (insbesondere Ti-6Al-4V gegenüber 316L) ist ein wichtiger Kostentreiber. Konstruktionen, die für minimales Volumen und Stützstrukturen (DfAM) optimiert sind, senken direkt die Materialkosten.
Bauzeit: Maschinenstunden und Komplexität
Die Zeit, die die AM-Maschine mit dem Drucken des Teils verbringt, ist ein weiterer wichtiger Kostenfaktor, der in der Regel zu einem Stundensatz in Rechnung gestellt wird, der die Abschreibung der Maschine, die Wartung, Energie, Inertgas/Vakuum und die Gemeinkosten der Einrichtung abdeckt.
- Teil Volumen & Höhe: Der Druck von Teilen mit größerem Volumen dauert natürlich länger. Die Bauzeit korreliert oft stark mit der Höhe des Teils (Z-Dimension), da jede Schicht eine gewisse Zeit zum Ablegen und Verschmelzen benötigt.
- Anzahl der Teile pro Build: Durch das gleichzeitige Drucken mehrerer Teile (Nesting) werden die Rüst- und Abkühlzeiten der Maschine auf mehr Teile verteilt, wodurch die Kosten pro Teil gesenkt werden.
- Komplexität und Scanstrategie: Sehr komplizierte Geometrien oder Anforderungen an spezifische Scan-Strategien (z. B. für feine Merkmale oder Stressreduzierung) können die Gesamtzeit pro Schicht beeinflussen.
- Maschinentechnologie: Verschiedene AM-Technologien und spezifische Maschinenmodelle haben unterschiedliche Fertigungsraten. SEBM kann für bestimmte Materialien/Geometrien aufgrund der schnelleren Strahlabtastung manchmal schnellere Volumenbaugeschwindigkeiten als L-PBF bieten.
Mitnehmen: Optimieren Sie Konstruktionen für eine möglichst geringe Bauhöhe (unter Abwägung des Stützbedarfs) und nutzen Sie die Verschachtelung von Bauplatten für mehrere Teile, um die Maschinenzeitkosten pro Teil zu senken.
Arbeitskosten: Design-Optimierung, Einrichtung, Nachbearbeitung
Während des gesamten AM-Workflows ist menschlicher Einsatz gefragt:
- Technik/DfAM-Unterstützung: Zeit, die die Ingenieure für die Optimierung des Entwurfs, die Simulation des Prozesses und die Vorbereitung der Build-Datei aufwenden.
- Einrichtung und Betrieb der Maschine: Arbeitsaufwand für das Laden von Pulver, das Einrichten des Druckauftrags, die Überwachung des Drucks und das Entladen des fertigen Drucks.
- Pulverbehandlung und Recycling: Zeitaufwand für das Sieben, die Handhabung und die sichere und effiziente Verwaltung des Pulverinventars.
- Teile- & Stützenentfernung: Das vorsichtige Entfernen von Teilen von der Bauplatte und das sorgfältige Entfernen von Stützstrukturen, insbesondere von komplexen oder internen Strukturen, kann mit erheblichem Arbeitsaufwand verbunden sein. Dies ist oft ein großer Engpass und Kostentreiber in der Nachbearbeitung.
- Endbearbeitung und Inspektion: Manuelle Arbeiten zur Oberflächenbearbeitung (Polieren, Entgraten), Reinigung, Sichtprüfung und Messtechnik.
Mitnehmen: Designs, die Stützstrukturen und manuelle Nachbearbeitungsanforderungen minimieren, senken direkt die Arbeitskosten. Die Automatisierung der Nachbearbeitung (wo anwendbar) kann helfen, aber viele Schritte bleiben arbeitsintensiv.
Nachbearbeitungsanforderungen und Komplexität
Wie bereits erwähnt, verursachen die Nachbearbeitungsschritte erhebliche Kosten und Zeitaufwand:
- Wärmebehandlung: Ofenzeit, Energieverbrauch, Kosten für Inertgas/Vakuum. Komplexe Zyklen (wie STA für Ti-6Al-4V) dauern länger und kosten mehr als ein einfacher Spannungsabbau.
- Bearbeitungen: CNC-Maschinenzeit (Fräsen, Drehen, Erodieren), Werkzeugkosten, Programmierzeit. Die Anzahl und die Komplexität der bearbeiteten Merkmale wirken sich direkt auf die Kosten aus.
- Oberflächenveredelung: Kosten im Zusammenhang mit Strahlmitteln, dem Betrieb von Taumelanlagen, Polierverbrauchsmaterialien und Arbeitskräften oder speziellen Verfahren wie Elektropolieren.
- Beschichtungen/Beschichtungen: Kosten, die von spezialisierten Galvanikbetrieben berechnet werden, abhängig von Beschichtungsmaterial, Dicke und Maskierungsanforderungen.
Mitnehmen: Legen Sie nur die notwendigen Nachbearbeitungen fest. Übertriebene Toleranzen oder die Forderung nach unnötig feinen Nachbearbeitungen erhöhen die Kosten drastisch. DfAM sollte darauf abzielen, die Abhängigkeit von umfangreichen Nachbearbeitungen zu minimieren, wo immer dies möglich ist.
Kosten für Qualitätskontrolle und Inspektion
Der Umfang der erforderlichen Inspektion wirkt sich erheblich auf die Kosten aus:
- Standard-Inspektion: Sichtkontrollen, grundlegende Messungen der Abmessungen.
- Fortgeschrittene Metrologie: CMM-Programmierung und Messzeit, 3D-Scannen und Analysezeit.
- Zerstörungsfreie Prüfung (NDT): Kosten für CT-Scans, Durchstrahlungsprüfungen oder Eindringprüfungen, falls diese für die Erkennung von inneren Fehlern oder die Rissprüfung erforderlich sind - insbesondere CT-Scans können teuer sein.
- Dokumentation: Zeitaufwand für die Zusammenstellung umfassender Qualitätsdokumentationspakete.
Mitnehmen: Legen Sie die angemessene Inspektionsstufe auf der Grundlage der Kritikalität fest. Eine umfangreiche ZfP für unkritische Komponenten verursacht unnötige Kosten.
Faktoren, die die Durchlaufzeiten beeinflussen
Die Durchlaufzeit - die Gesamtzeit von der Auftragserteilung bis zum Erhalt der fertigen Teile - wird von vielen der gleichen Faktoren beeinflusst wie die Kosten:
- Design & Vorbereitung: Zeit für DfAM-Prüfung, Simulation (falls erforderlich) und Vorbereitung der Build-Datei (normalerweise 1-3 Tage).
- Druckzeit: Je nach Größe, Komplexität und Menge der Teile sehr unterschiedlich (kann von Stunden für kleine Teile bis zu mehreren Tagen für große, komplexe Teile oder große Chargen reichen).
- Maschinenwarteschlange: Die aktuelle Auslastung der Zulieferer und die Verfügbarkeit der Maschinen wirken sich erheblich darauf aus, wann ein Bauvorhaben beginnen kann. Es ist ratsam, Kapazitäten für Produktionsläufe im Voraus zu buchen.
- Nachbearbeitungszeit: Dies macht oft einen großen Teil der gesamten Vorlaufzeit aus.
- Wärmebehandlung: In der Regel 1-3 Tage (einschließlich Ofenzyklen und Abkühlung).
- Unterstützung/Teilentfernung: Kann je nach Komplexität zwischen Stunden und Tagen dauern.
- Bearbeitungen: Je nach Merkmalen sehr unterschiedlich (kann bei komplexen Teilen Tage oder Wochen dauern).
- Endbearbeitung/Beschichtung: Je nach Verfahren und Vorlaufzeiten der Zulieferer kann dies Tage oder Wochen in Anspruch nehmen.
- Inspektion und Versand: Abschließende QC-Kontrollen und Transitzeit.
Realistische Erwartungen:
- Prototypen: Bei relativ einfachen Steckverbindergehäusen, die eine Standard-Nachbearbeitung erfordern, betragen die Lieferzeiten 1 bis 3 Wochen sind oft realisierbar.
- Produktionsläufe: Bei größeren Mengen oder Teilen, die eine umfangreiche Nachbearbeitung und strenge Qualitätskontrolle erfordern, können sich die Lieferzeiten von mehrere Wochen bis mehrere Monate.
Mitnehmen: Setzen Sie sich frühzeitig mit den Lieferanten in Verbindung, stellen Sie vollständige RFQ-Informationen zur Verfügung und besprechen Sie die Erwartungen an die Vorlaufzeit im Voraus. Ein gut geplantes DfAM und klar definierte Anforderungen können zur Rationalisierung des Prozesses beitragen. Kontakt Met3dp um Ihren spezifischen Projektzeitplan zu besprechen und ein detailliertes Angebot zu erhalten.
Aufwertung von Luft- und Raumfahrtsystemen: Der bleibende Wert von 3D-gedruckten Steckverbindergehäusen aus Metall
Im Laufe dieser Untersuchung haben wir uns mit der kritischen Rolle von Steckverbindergehäusen in der Luft- und Raumfahrt befasst, mit den einzigartigen Herausforderungen, denen sie sich stellen müssen, und damit, wie die additive Fertigung von Metallen, insbesondere unter Verwendung von robusten Materialien wie Edelstahl 316L und der Hochleistungs-Titanlegierung Ti-6Al-4V, einen transformativen Ansatz für ihre Produktion bietet. Die Vorteile, die Metall-AM bietet, sind nicht nur inkrementelle Verbesserungen; sie stellen einen grundlegenden Wandel hin zu größerer Designfreiheit, optimierter Leistung und erhöhter Flexibilität in der Fertigung dar und tragen letztendlich zu sichereren, effizienteren und leistungsfähigeren Luft- und Raumfahrtsystemen bei.
Rekapitulation: Die wichtigsten Vorteile für Luft- und Raumfahrtanwendungen
Der 3D-Metalldruck bietet eine leistungsstarke Kombination von Vorteilen, die sich direkt auf die Anforderungen von Steckverbindergehäusen für die Luft- und Raumfahrt übertragen lassen:
- Unerreichte Designfreiheit: Ermöglichung komplexer Geometrien, interner Merkmale (Kühlung, Abschirmung) und Topologieoptimierung für Leichtbau, die mit herkömmlichen Methoden unmöglich oder unpraktisch sind.
- Schnelle Anpassung & Prototyping: Beschleunigung der Entwicklungszyklen durch rasche Iteration und Produktion von maßgeschneiderten Gehäusedesigns, die auf bestimmte Platz-, Gewichts- oder Funktionsbeschränkungen zugeschnitten sind.
- Gewichtsreduzierung: Erhebliche Reduzierung des Bauteilgewichts durch Optimierung der Topologie und die effiziente Verwendung von Materialien mit hohem Festigkeits-Gewichts-Verhältnis wie Ti-6Al-4V, was zu Treibstoffeinsparungen und erhöhter Nutzlastkapazität beiträgt.
- Teil Konsolidierung: Verringerung der Komplexität der Montage, möglicher Fehlerquellen und des logistischen Aufwands durch Integration mehrerer Funktionen in ein einziges gedrucktes Teil.
- Leistungsverbesserung: Dies ermöglicht den Einsatz optimaler Materialien wie Ti-6Al-4V für hochfeste, hochtemperaturbeständige oder korrosive Umgebungen und ermöglicht Konstruktionen mit integriertem Wärmemanagement oder verbesserter EMI-Abschirmung.
- Effiziente Kleinserienproduktion: Eine kosteneffiziente Methode zur Herstellung kundenspezifischer Chargen in kleinen bis mittleren Stückzahlen, wie sie in der Luft- und Raumfahrt häufig benötigt werden, ohne dass hohe Werkzeugkosten anfallen.
Zukünftige Trends: Fortschritte bei Materialien und Prozessen
Der Bereich der additiven Fertigung von Metallen entwickelt sich ständig weiter und verspricht für die Zukunft noch größere Möglichkeiten für Luft- und Raumfahrtkomponenten:
- Neue Materialien: Entwicklung neuartiger Legierungen, die speziell für AM konzipiert sind und verbesserte Eigenschaften bieten (höhere Temperaturbeständigkeit, größere Festigkeit, bessere Druckbarkeit). Forschung zum Druck von Keramik oder Metallmatrix-Verbundwerkstoffen für spezielle Gehäuseanwendungen.
- Schnellere Druckvorgänge: Innovationen, die darauf abzielen, die Fertigungsgeschwindigkeit zu erhöhen, ohne die Qualität zu beeinträchtigen, und die Wirtschaftlichkeit bei größeren Produktionsmengen weiter zu verbessern.
- Verbesserte In-Situ-Überwachung & Kontrolle: Ausgefeiltere Echtzeit-Überwachung des Schmelzepools und des Herstellungsprozesses, gekoppelt mit KI-gesteuerten Feedbackschleifen zur automatischen Anpassung von Parametern, was zu einer verbesserten Qualitätssicherung und einem geringeren Bedarf an Inspektionen nach dem Herstellungsprozess führt.
- Verstärkte Automatisierung: Stärkere Automatisierung von Nachbearbeitungsschritten wie Pulver- und Stützentfernung zur Senkung von Arbeitskosten und Durchlaufzeiten.
- Hybride Fertigung: Engere Integration von additiven und subtraktiven Verfahren innerhalb einer einzigen Maschinenplattform zur Steigerung der Effizienz.
Die Rolle von Metal AM in der nachhaltigen Luft- und Raumfahrtproduktion
Die additive Fertigung passt auch gut zu der wachsenden Bedeutung der Nachhaltigkeit in der Luft- und Raumfahrtindustrie:
- Geringerer Materialabfall: Im Vergleich zur subtraktiven Bearbeitung fällt bei AM deutlich weniger Materialausschuss an, was vor allem bei der Verwendung teurer Legierungen wie Titan von Vorteil ist. Das Pulverrecycling verbessert die Materialausnutzung weiter.
- Gewichtsreduzierung: Das geringere Gewicht der Komponenten führt direkt zu einem geringeren Kraftstoffverbrauch während des Flugbetriebs und damit zu geringeren Emissionen.
- Produktion auf Abruf & Verteilte Fertigung: Das Drucken von Teilen, wann und wo sie benötigt werden, reduziert die Lagerhaltung und die mit komplexen globalen Lieferketten verbundenen Transportemissionen.
Abschließende Überlegungen: Additive Fertigung als Wettbewerbsvorteil nutzen
Maßgefertigte 3D-gedruckte Metallgehäuse für Steckverbinder sind mehr als nur Komponenten; sie sind die Grundlage für Innovationen. Durch die Befreiung der Konstrukteure von traditionellen Beschränkungen und die Ermöglichung optimierter, integrierter und leichtgewichtiger Lösungen ermöglicht Metall-AM den Luft- und Raumfahrtunternehmen den Bau von Flugzeugen, Raumfahrzeugen und Verteidigungssystemen der nächsten Generation. Es gibt zwar Herausforderungen, aber die Zusammenarbeit mit sachkundigen und technologisch fortschrittlichen Anbietern wie Met3dp, die End-to-End-Lösungen von der hochwertigen Pulverproduktion bis hin zu fortschrittlichem Druck und technischer Unterstützung anbieten, ermöglicht es Unternehmen, die Möglichkeiten der additiven Fertigung zu nutzen. Die Nutzung dieser Technologie wird zunehmend nicht nur zu einer Option, sondern zu einer Notwendigkeit, um in der dynamischen Luft- und Raumfahrtindustrie einen Wettbewerbsvorteil zu erzielen. Entdecken Sie, wie Met3dp’s umfassende Metall-3D-Drucklösungen kann Ihr nächstes Projekt aufwerten.
Häufig gestellte Fragen (FAQ): Ihre wichtigsten Fragen zu 3D-gedruckten Steckverbindergehäusen für die Luft- und Raumfahrt werden beantwortet
F1: Welche typischen Toleranzen sind bei 3D-gedruckten Metallgehäusen von Steckverbindern erzielbar?
A1: Die Fertigungstoleranzen beim Pulverbettschmelzen (SLM, SEBM) liegen in der Regel im Bereich von ±0,1 mm bis ±0,2 mm für kleinere Merkmale bzw. ±0,1 % bis ±0,2 % für größere Abmessungen. Kritische Schnittstellen, Passflächen oder Dichtungsnuten, die engere Toleranzen erfordern (z. B. ±0,01 mm bis ±0,05 mm), müssen jedoch in der Regel nachbearbeitet werden. DfAM beinhaltet die Konstruktion dieser Merkmale mit Bearbeitungszugabe.
F2: Wie hoch sind die Kosten des 3D-Drucks im Vergleich zur CNC-Bearbeitung von kundenspezifischen Steckergehäusen?
A2: Der Kostenvergleich hängt stark von der Komplexität und dem Volumen der Teile ab.
- Für hochkomplexe Geometrien oder geringe Stückzahlen (Prototypen, 1-100 Teile): Der 3D-Druck von Metall ist oft kostengünstiger, da er hohe Werkzeug- und Vorrichtungskosten sowie umfangreiche Programmier- und Einrichtungszeiten vermeidet, die mit der Bearbeitung komplexer Formen aus Knüppeln verbunden sind.
- Für einfachere Geometrien oder größere Mengen: Die CNC-Bearbeitung kann wirtschaftlicher werden, da sich die Rüstkosten über mehr Teile amortisieren, und die Bearbeitungszyklen für einfache Formen können schneller sein als die AM-Bauzeiten. Auch die Materialwahl spielt eine große Rolle: AM reduziert den Abfall bei teuren Materialien wie Ti-6Al-4V und ist damit möglicherweise wettbewerbsfähiger, auch wenn die Bearbeitung schneller erscheint. Ein detaillierter Angebotsvergleich ist immer empfehlenswert.
F3: Auf welche Zertifizierungen sollte ich bei einem Metall-AM-Lieferanten für Luft- und Raumfahrtteile achten?
A3: Die wichtigste Zertifizierung ist AS9100, der Norm für Qualitätsmanagementsysteme speziell für die Luft- und Raumfahrt- und Verteidigungsindustrie. Dies zeigt, dass der Lieferant sich den strengen Qualitäts-, Rückverfolgbarkeits- und Risikomanagementprozessen verpflichtet, die für Flugkomponenten erforderlich sind. ISO 9001 ist eine gute Ausgangsbasis, reicht aber im Allgemeinen allein nicht aus. Je nach erforderlicher Nachbearbeitung ist eine Nadcap-Akkreditierung für spezielle Verfahren wie Wärmebehandlung oder zerstörungsfreie Prüfung ebenfalls von großem Wert.
F4: Können interne Merkmale wie Abschirmungen oder Kühlkanäle effektiv gedruckt werden?
A4: Ja, einer der Hauptvorteile der Metall-AM ist die Möglichkeit, komplexe innere Merkmale zu erzeugen. Eine erfolgreiche Umsetzung erfordert jedoch ein sorgfältiges Design for Additive Manufacturing (DfAM). Zu den wichtigsten Überlegungen gehören:
- Entfernung von Puder: Die Rinnen müssen einen ausreichenden Durchmesser und zugängliche Austrittslöcher aufweisen, damit das ungeschmolzene Pulver vollständig entfernt werden kann.
- Selbsttragende Geometrien: Innenliegende Rinnendächer sollten idealerweise mit selbsttragenden Winkeln (z. B. tropfen- oder rautenförmig) ausgeführt werden, um die Notwendigkeit interner Stützen zu vermeiden, die nur sehr schwer zu entfernen sind.
- Oberfläche: Interne Oberflächen haben eine Rauheit wie im Werk, es sei denn, es werden spezielle sekundäre Verfahren (z. B. abrasive Fließbearbeitung) eingesetzt.
F5: Wie lang ist die typische Vorlaufzeit für die Lieferung von Prototyp- oder Produktionsgehäusen für Luft- und Raumfahrtstecker?
A5: Die Vorlaufzeiten sind sehr unterschiedlich. Zu den Faktoren gehören Komplexität, Größe, Menge, Material, Maschinenverfügbarkeit und der Umfang der erforderlichen Nachbearbeitung (Wärmebehandlung, Bearbeitung, Endbearbeitung, Prüfung).
- Prototypen: Sie reichen oft von 1 bis 3 Wochen.
- Produktionsläufe: Kann variieren von mehrere Wochen bis mehrere Monateund hängt stark von Volumen und Komplexität ab. Die frühzeitige Einbindung von Lieferanten und die Bereitstellung klarer Anforderungen ermöglichen genauere Schätzungen der Vorlaufzeiten.
Teilen auf
MET3DP Technology Co., LTD ist ein führender Anbieter von additiven Fertigungslösungen mit Hauptsitz in Qingdao, China. Unser Unternehmen ist spezialisiert auf 3D-Druckgeräte und Hochleistungsmetallpulver für industrielle Anwendungen.
Fragen Sie an, um den besten Preis und eine maßgeschneiderte Lösung für Ihr Unternehmen zu erhalten!
Verwandte Artikel
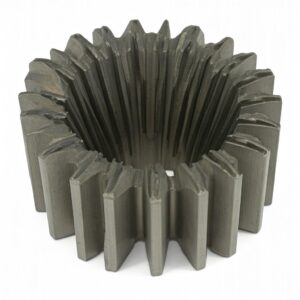
Hochleistungs-Düsenschaufelsegmente: Revolutionierung der Turbineneffizienz mit 3D-Metalldruck
Mehr lesen "Über Met3DP
Aktuelles Update
Unser Produkt
KONTAKT US
Haben Sie Fragen? Senden Sie uns jetzt eine Nachricht! Wir werden Ihre Anfrage mit einem ganzen Team nach Erhalt Ihrer Nachricht bearbeiten.
Holen Sie sich Metal3DP's
Produkt-Broschüre
Erhalten Sie die neuesten Produkte und Preislisten
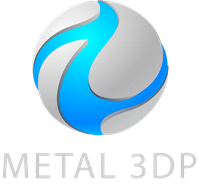
Metallpulver für 3D-Druck und additive Fertigung