Hocheffiziente Kühlrippen durch Metall-3D-Druck
Inhaltsübersicht
Einführung: Verbesserung des Wärmemanagements mit 3D-gedruckten Kühlrippen
In unzähligen industriellen Anwendungen ist ein effektives Wärmemanagement nicht nur ein wünschenswertes Merkmal – es ist eine entscheidende Notwendigkeit. Von Hochleistungs-Computing und Leistungselektronik bis hin zu Automotoren und Luft- und Raumfahrtsystemen ist die Fähigkeit, Wärme effizient abzuleiten, von größter Bedeutung für Zuverlässigkeit, Leistung und Langlebigkeit. Im Herzen vieler Wärmemanagementsysteme befinden sich Kühlrippen, Komponenten, die speziell dafür entwickelt wurden, die Oberfläche zu vergrößern, die für den Wärmeaustausch mit einer umgebenden Flüssigkeit, typischerweise Luft oder einem Flüssigkeitskühlmittel, zur Verfügung steht.
Traditionell wurden Kühlrippen und Kühlkörper mit Methoden wie Extrusion, Gießen, Stanzen oder Bearbeiten hergestellt. Obwohl sie für einfachere Geometrien effektiv sind, stoßen diese herkömmlichen Techniken oft an ihre Grenzen, wenn Ingenieure versuchen, eine wirklich optimierte thermische Leistung zu erzielen. Komplexe Formen, komplizierte interne Kanäle, dünne Wände und ungleichmäßige Rippendichten – Merkmale, die die Wärmeableitung erheblich verbessern können – sind mit traditionellen Fertigungsmethoden oft schwierig, teuer oder sogar unmöglich herzustellen.
Hier ist Additive Fertigung von Metall (AM)gemeinhin als Metall bekannt 3D-Druck, erweist sich als transformative Technologie. Durch den schichtweisen Aufbau von Komponenten direkt aus digitalen Modellen eröffnet das Metall-AM eine beispiellose Designfreiheit. Dies ermöglicht es Ingenieuren und Designern, Kühlrippen mit hochkomplexen Geometrien zu erstellen, die speziell für die thermische Leistung optimiert sind, anstatt durch die Einschränkungen traditioneller Fertigungsprozesse eingeschränkt zu werden. Stellen Sie sich Kühlrippen mit internen Gitterstrukturen vor, die die Oberfläche bei gleichzeitiger Gewichtsreduzierung maximieren, oder Rippen, die sich perfekt an die Form der Wärmequelle anpassen, um einen optimalen thermischen Kontakt zu gewährleisten. Dies sind die Möglichkeiten, die der Metall-3D-Druck ermöglicht.
Die Vorteile gehen über die bloße geometrische Komplexität hinaus. Metall-AM ermöglicht die Verwendung fortschrittlicher Materialien, einschließlich hochleitfähiger Kupferlegierungen wie Kupfer-Chrom-Zirkonium (CuCrZr) und leichter, starker Aluminiumlegierungen wie Aluminium-Silizium-Magnesium (AlSi10Mg), die auf die spezifischen Anforderungen der Anwendung zugeschnitten sind. Darüber hinaus erleichtert AM das Rapid Prototyping und iterative Designverbesserungen, wodurch die Entwicklungszyklen erheblich verkürzt werden. Für Beschaffungsmanager und B2B-Käufer, die nach Großhandelsanbietern von Kühlrippen oder Vertriebspartner für kundenspezifische Thermallösungenbietet das Metall-AM einen Weg zur Beschaffung von Komponenten mit überlegenen Leistungseigenschaften, was potenziell zu effizienteren und kompakteren Endprodukten führt.
Met3dp, ein führendes Unternehmen für additive Fertigungslösungen, nutzt modernste 3D-Druck von Metall Technologien und Hochleistungs-Metallpulver, um Komponenten herzustellen, die die Grenzen des Wärmemanagements verschieben. Unser Fachwissen in Verfahren wie dem selektiven Elektronenstrahlschmelzen (SEBM) und unsere fortschrittlichen Pulverherstellungskapazitäten gewährleisten höchste Qualität und Leistung für anspruchsvolle industrielle Anwendungen. Dieser Beitrag untersucht die erheblichen Vorteile des Einsatzes von Metall-AM für die Herstellung von hocheffizienten Industriekühlrippen und befasst sich mit Anwendungen, Materialauswahl, Designaspekten und der Frage, wie man mit dem richtigen AM-Dienstleister zusammenarbeitet.
Anwendungen von Industriekühlrippen: Wo Leistung zählt
Industriekühlrippen sind unbesungene Helden, die im Hintergrund in einer Vielzahl von Anwendungen unermüdlich arbeiten, bei denen die Wärmeableitung entscheidend ist. Ihre Hauptfunktion ist immer die gleiche – die Wärmeübertragung von einer kritischen Komponente zu verbessern – aber der spezifische Kontext und die Leistungsanforderungen können stark variieren. Das Verständnis dieser vielfältigen Anwendungen unterstreicht die Notwendigkeit optimierter, oft kundenspezifischer Kühllösungen, die das Metall-AM in einzigartiger Weise bieten kann.
Wichtigste Anwendungsbereiche:
- Leistungselektronik und Halbleiter:
- Anwendungsfall: Kühlung von Insulated Gate Bipolar Transistors (IGBTs), Leistungsdioden, Thyristoren, CPUs, GPUs und anderen Hochleistungs-Halbleiterbauelementen.
- Herausforderung: Diese Komponenten erzeugen einen erheblichen, lokalisierten Wärmefluss. Ineffiziente Kühlung führt zu reduzierter Leistung, kürzerer Lebensdauer und potenziellen Ausfällen.
- AM Vorteil: Fähigkeit, kompakte, hochkomplexe Kühlkörper mit optimierten Rippengeometrien (z. B. Stiftrippen, Plattenrippen mit variabler Dichte) direkt in die elektronischen Komponenten zu integrieren oder an diesen zu befestigen, oft unter Verwendung von hochleitfähigen Kupferlegierungen. B2B-Lieferanten können kundenspezifische Lösungen für spezifische Leistungsmodule anbieten.
- Automobilindustrie:
- Anwendungsfall: Motorkühlung (Kühler, Ölkühler), Getriebekühlung, Batteriewärmemanagement in Elektrofahrzeugen (EVs), Kühlung für Turbolader und Abgasrückführungssysteme (AGR), LED-Scheinwerferkühlung.
- Herausforderung: Platz- und Gewichtsbeschränkungen sind entscheidend, ebenso wie Anforderungen an hohe thermische Effizienz und Haltbarkeit unter rauen Betriebsbedingungen (Vibrationen, Temperaturschwankungen).
- AM Vorteil: Leichte Aluminiumlegierungen (wie AlSi10Mg) in Kombination mit Topologieoptimierung können hocheffiziente, gewichtsreduzierte Kühlkomponenten schaffen. Komplexe interne Kanäle für Flüssigkeitskühlsysteme sind leicht zu integrieren. Beschaffungsmanager in der Automobilindustrie suchen nach zuverlässigen Herstellern von Kühlkörpern für die Automobilindustrie , die in der Lage sind, in großen Mengen zu produzieren und kundenspezifisch anzupassen.
- Luft- und Raumfahrt und Verteidigung:
- Anwendungsfall: Kühlung für Avionik, Radarsysteme, Motoren, Umweltkontrollsysteme (ECS) und Directed Energy Weapons (DEW).
- Herausforderung: Extreme Betriebsumgebungen (Temperatur, Druck, Vibrationen), strenge Gewichtsbeschränkungen (jedes Gramm zählt) und die Notwendigkeit außergewöhnlicher Zuverlässigkeit. Materialien müssen oft bestimmte Luft- und Raumfahrtzertifizierungen erfüllen.
- AM Vorteil: Fähigkeit, komplexe, leichte Strukturen aus Materialien in Luft- und Raumfahrtqualität (einschließlich spezieller Aluminium- und Titanlegierungen) herzustellen. Konforme Kühlkanäle und optimierte Rippenstrukturen verbessern die Leistung innerhalb enger räumlicher Hüllen. Vertriebspartner für Luft- und Raumfahrtkomponenten suchen zunehmend nach AM für Wärmelösungen der nächsten Generation.
- Industriemaschinen und -fertigung:
- Anwendungsfall: Kühlung für Hochleistungslaser, Schweißgeräte, Hydrauliksysteme, Motorgehäuse, Spritzgusswerkzeuge (konforme Kühlkanäle) und Prozessausrüstung.
- Herausforderung: Sicherstellung konstanter Betriebstemperaturen für Prozessstabilität und Geräte-Langlebigkeit, oft in anspruchsvollen Fabrikumgebungen. Kühllösungen müssen möglicherweise in bestehende Maschinen integriert werden.
- AM Vorteil: Kundenspezifisch gestaltete Kühlrippen und Wärmetauscher, die auf spezifische Maschinengeometrien zugeschnitten sind. Die additive Fertigung ermöglicht die Herstellung von Ersatzteilen oder verbesserten Kühllösungen für Altanlagen. Lieferanten von Industrieanlagen können AM für spezielle Kühlanforderungen nutzen.
- Medizinische Geräte:
- Anwendungsfall: Kühlung für diagnostische Bildgebungsgeräte (MRT, CT-Scanner), chirurgische Laser und andere medizinische Elektronik, die stabile Betriebstemperaturen erfordert.
- Herausforderung: Hohe Zuverlässigkeit, Biokompatibilität (bei Kontakt mit Körper/Flüssigkeiten) und oft kompakte Abmessungen.
- AM Vorteil: Präzise Herstellung komplexer, kleinformatiger Kühlkomponenten. Fähigkeit, bei Bedarf biokompatible Materialien zu verwenden (obwohl die Kühlung oft extern erfolgt).
- Telekommunikation:
- Anwendungsfall: Wärmemanagement für Basisstationen, Serverracks und Netzwerkausrüstung.
- Herausforderung: Zunehmende Leistungsdichten auf kleinerer Grundfläche erfordern hocheffiziente, oft passive Kühllösungen. Zuverlässigkeit ist der Schlüssel für einen unterbrechungsfreien Betrieb.
- AM Vorteil: Optimierte luftgekühlte Kühlkörper mit komplexen Rippenarrays, die mit Simulationswerkzeugen entworfen wurden, um die natürliche oder erzwungene Konvektion zu maximieren.
Die Breite dieser Anwendungen unterstreicht, dass ein Einheitsansatz für das Design von Kühlrippen oft unzureichend ist. Beschaffungsmanager und Ingenieure, die nach B2B-Kühllösungen suchen, benötigen Partner, die die Nuancen ihrer spezifischen Branche verstehen und optimierte Komponenten liefern können. Der 3D-Metalldruck bietet die Designflexibilität und die Materialoptionen, um diese vielfältigen und anspruchsvollen Anforderungen effektiv zu erfüllen.
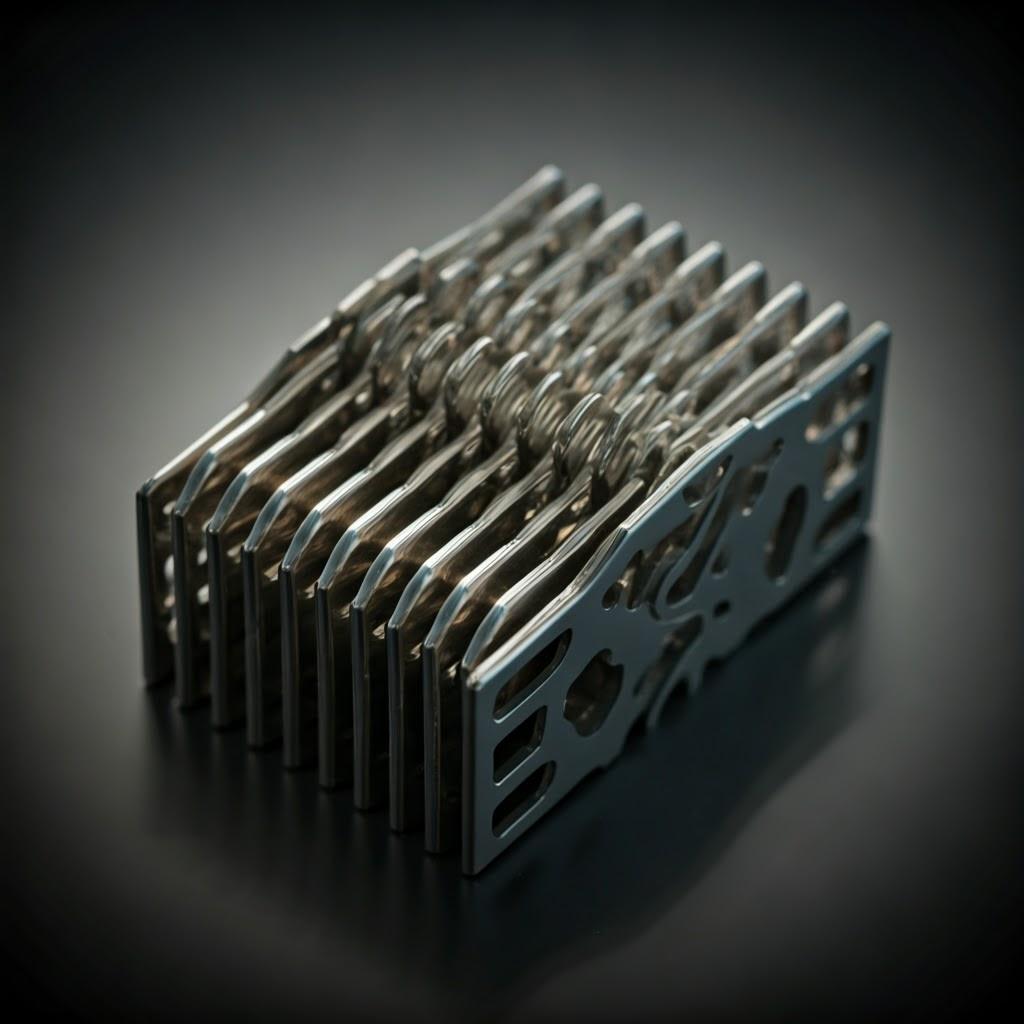
Warum Metall-3D-Druck für die Herstellung von Kühlrippen wählen?
Während herkömmliche Methoden der Industrie seit Jahrzehnten gute Dienste leisten, bietet die additive Metallfertigung überzeugende Vorteile für die Herstellung von Industriekühlrippen, insbesondere wenn eine verbesserte Leistung, Anpassung oder Designinnovation angestrebt wird. Der Vergleich von AM mit herkömmlichen Verfahren wie Extrusion, Gießen und Zerspanung zeigt, warum es für Ingenieure und Beschaffung von Wärmekomponenten spezialisten.
zunehmend eine attraktive Option wird:
Merkmal | Additive Fertigung von Metall (AM) | Herkömmliche Fertigung (Extrusion, Gießen, Zerspanung) | Vorteil für Kühlrippen |
---|---|---|---|
Geometrische Komplexität | Nahezu unbegrenzt; ermöglicht komplexe interne Kanäle, Gitter, variable Rippendichten, konforme Formen. | Begrenzt durch Werkzeuge, Formen, Schneidwege; komplexe Merkmale erfordern oft eine Montage oder sind unmöglich. | Maximiert das Verhältnis von Oberfläche zu Volumen, verbessert den Luftstrom/Flüssigkeitsstrom, erhöht die Wärmeübertragungseffizienz. |
Design-Optimierung | Erleichtert die Topologieoptimierung und das generative Design für leistungsgesteuerte Formen (z. B. Minimierung des Gewichts bei gleichzeitiger Maximierung der Steifigkeit und der thermischen Leistung). | Das Design wird oft durch die Herstellbarkeit eingeschränkt („Design for Manufacturing“). | Führt zu leichteren, effizienteren Kühllösungen, die perfekt auf die Anwendung zugeschnitten sind. |
Teil Konsolidierung | Fähigkeit, mehrere Komponenten als ein einziges, integriertes Teil zu drucken (z. B. Kühlkörperbasis und -rippen). | Erfordert oft die Montage mehrerer Teile (Löten, Schweißen, Befestigen). | Reduziert Montagezeit/-kosten, eliminiert potenziellen Wärmewiderstand an den Verbindungen, verbessert die Zuverlässigkeit. |
Material-Optionen | Große Auswahl an Metallen, einschließlich hochleitfähiger Kupferlegierungen (CuCrZr), leichtem Aluminium (AlSi10Mg), Titan und Edelstählen. | Die Materialauswahl ist oft durch den spezifischen Prozess begrenzt (z. B. extrudierbare Legierungen, gießbare Legierungen). | Ermöglicht die Auswahl des optimalen Materials für Wärmeleitfähigkeit, Gewicht, Festigkeit und Kosten. |
Anpassung & Prototyping | Ideal für Klein- bis Mittelserienfertigung, maßgeschneiderte Designs und Rapid Prototyping. Designänderungen werden schnell über CAD implementiert. | Hohe Werkzeugkosten machen die Anpassung teuer und das Prototyping langsam, insbesondere beim Gießen/Extrudieren. | Schnellere Entwicklungszyklen, kostengünstige Herstellung von kundenspezifischen oder Kleinserien für spezielle Anforderungen. |
Vorlaufzeiten (Prototyping) | Deutlich schneller für erste Prototypen und Designiterationen (Tage/Wochen). | Kann aufgrund der Werkzeugherstellung viel länger dauern (Wochen/Monate). | Beschleunigt die Produktentwicklungs- und Testphasen. |
Abfallreduzierung | Das additive Verfahren verwendet Material hauptsächlich dort, wo es benötigt wird, wodurch der Rohmaterialabfall potenziell reduziert wird (insbesondere im Vergleich zur subtraktiven Zerspanung). | Subtraktive Verfahren (Zerspanung) erzeugen erhebliche Ausschussmengen; Gießen/Extrusion können Prozessabfall haben. | Nachhaltigerer Fertigungsansatz, potenziell niedrigere Materialkosten für komplexe Teile. |
Konforme Kühlung | Erstellt leicht Kühlkanäle oder -rippen, die genau den Konturen der Wärmequelle folgen. | Mit herkömmlichen Methoden schwierig oder unmöglich zu erreichen. | Verbessert den thermischen Kontakt und die Wärmeextraktionseffizienz, was zu kompakteren Designs führt. |
In Blätter exportieren
Spezifische Einschränkungen herkömmlicher Methoden beheben:
- Extrusion: Beschränkt auf Profile mit konstantem Querschnitt. Kann nicht ohne weiteres variable Rippenhöhen, -dichten oder komplexe 3D-Formen erzeugen.
- Gießen: Ermöglicht zwar eine gewisse Komplexität, aber es gibt Einschränkungen hinsichtlich Wandstärke, Merkmalsauflösung, Innenhohlräumen und Oberflächenbeschaffenheit. Werkzeuge sind teuer.
- Bearbeitungen: Kann eine hohe Präzision erreichen, ist aber subtraktiv, was zu Materialabfall führt. Komplexe Geometrien wie komplizierte Rippenarrays können zeitaufwändig und teuer in der Bearbeitung sein. Der Zugang für Schneidwerkzeuge schränkt die Erstellung interner Merkmale ein.
- Gestanzte/gefaltete Rippen: Im Allgemeinen auf einfachere Geometrien und dünnere Materialien beschränkt, was oft eine Montage erfordert (z. B. Löten an einer Grundplatte), was einen Wärmewiderstand mit sich bringt.
Für B2B-Kunden, einschließlich Großhandelskäufer und Vertriebspartner von Wärmekomponenten, bedeutet der Übergang zu AM den Zugang zu Kühllösungen der nächsten Generation. Während herkömmliche Methoden für die Großserienfertigung einfacher Designs geeignet bleiben, zeichnet sich der Metall-3D-Druck dort aus, wo Leistungsoptimierung, komplexe Geometrien, Anpassung und schnelle Innovation die wichtigsten Treiber sind. Unternehmen wie Met3dp, die mit fortschrittlichen Drucktechnologien und Materialexpertise ausgestattet sind, ermöglichen diesen Übergang und bieten Lösungen, die zuvor unerreichbar waren.
Optimale Materialien für 3D-gedruckte Kühlrippen: CuCrZr und AlSi10Mg im Vergleich
Die Wirksamkeit einer Kühlrippe ist grundlegend mit den thermischen Eigenschaften des Materials verbunden, aus dem sie hergestellt wird. Der Metall-3D-Druck bietet ein wachsendes Portfolio an Materialien, aber für hocheffiziente Wärmemanagementanwendungen stechen zwei Legierungen hervor: Kupfer-Chrom-Zirkonium (CuCrZr) und Aluminium-Silizium-Magnesium (AlSi10Mg). Die Wahl des richtigen Materials beinhaltet das Abwägen von Wärmeleitfähigkeit, Gewicht, mechanischer Festigkeit, Korrosionsbeständigkeit und Kosten, basierend auf den spezifischen Anwendungsanforderungen.
1. Kupfer-Chrom-Zirkonium (CuCrZr): Der Champion der hohen Leitfähigkeit
- Überblick: CuCrZr ist eine aushärtbare Kupferlegierung, die für ihre hervorragende Kombination aus hoher Wärme- und elektrischer Leitfähigkeit, guter mechanischer Festigkeit (insbesondere bei erhöhten Temperaturen im Vergleich zu reinem Kupfer) und guter Korrosionsbeständigkeit bekannt ist.
- Wichtige Eigenschaften:
- Wärmeleitfähigkeit: Sehr hoch (typischerweise >300 W/m·K nach entsprechender Wärmebehandlung), was sich reinem Kupfer annähert, aber eine deutlich bessere Festigkeit aufweist. Dies ist entscheidend für die schnelle Ableitung von Wärme von der Quelle.
- Elektrische Leitfähigkeit: Ebenfalls sehr hoch, wodurch es sich für Anwendungen eignet, bei denen elektrischer Strom gleichzeitig mit Wärme auftritt (z. B. Stromschienen mit integrierter Kühlung).
- Mechanische Festigkeit: Gute Zugfestigkeit und Härte, die bei höheren Temperaturen besser erhalten bleiben als bei reinem Kupfer. Dies ermöglicht dünnere und empfindlichere Rippenstrukturen.
- Verarbeitbarkeit: Kann effektiv mittels Laser Powder Bed Fusion (LPBF) und potenziell SEBM verarbeitet werden, obwohl die hohe Reflektivität und Leitfähigkeit von Kupfer Herausforderungen darstellen, die optimierte Prozessparameter erfordern.
- Warum CuCrZr für Kühlrippen verwenden?
- Maximale Wärmeableitung: Sein Hauptvorteil ist die Maximierung der Wärmeübertragungsrate aufgrund seiner außergewöhnlichen Wärmeleitfähigkeit. Ideal für Anwendungen mit hohem Wärmestrom.
- Leistung in kompakten Designs: Ermöglicht eine hocheffiziente Kühlung in räumlich begrenzten Umgebungen, in denen die Maximierung der Wärmeabfuhr pro Volumeneinheit entscheidend ist.
- Anwendungen bei erhöhten Temperaturen: Behält die Festigkeit bei höheren Betriebstemperaturen besser als reines Kupfer oder Aluminiumlegierungen.
- Erwägungen:
- Kosten: Kupferlegierungen sind im Allgemeinen teurer als Aluminiumlegierungen.
- Gewicht: Kupfer ist deutlich dichter als Aluminium (~8,9 g/cm³ vs. ~2,7 g/cm³).
- Druckbarkeit: Erfordert eine sorgfältige Parameterkontrolle während der AM aufgrund der hohen Reflektivität und Wärmeleitfähigkeit. Das Erreichen der vollen Dichte kann eine Herausforderung sein.
- Am besten geeignet für: Hochleistungs-Computing, Leistungselektronik-Kühlung, Wärmetauscher, die maximale Effizienz erfordern, Formen mit konformer Kühlung, Anwendungen, bei denen auch elektrische Leitfähigkeit benötigt wird.
2. Aluminium-Silizium-Magnesium (AlSi10Mg): Der leichte Allrounder
- Überblick: AlSi10Mg ist eine weit verbreitete Aluminiumgusslegierung, die sich aufgrund ihrer hervorragenden Verarbeitbarkeit, ihres guten Festigkeits-Gewichts-Verhältnisses und ihrer vernünftigen thermischen Eigenschaften zu einem festen Bestandteil in der Metall-AM entwickelt hat.
- Wichtige Eigenschaften:
- Wärmeleitfähigkeit: Gut (typischerweise 120-150 W/m·K im hergestellten oder spannungsarmen Zustand, kann durch spezifische Wärmebehandlungen erhöht werden), deutlich besser als Stähle oder Titan, jedoch niedriger als Kupferlegierungen.
- Mechanische Festigkeit: Gute Festigkeit, Härte und dynamische Belastbarkeit, insbesondere nach der Wärmebehandlung.
- Gewicht: Sehr geringe Dichte (~2,68 g/cm³), ideal für gewichtsempfindliche Anwendungen (Luft- und Raumfahrt, Automobil).
- Verarbeitbarkeit: Eine der am einfachsten zu verarbeitenden Metalllegierungen mit LPBF, die feine Merkmale und komplexe Geometrien mit hoher Zuverlässigkeit ermöglicht.
- Korrosionsbeständigkeit: Gute Korrosionsbeständigkeit in verschiedenen Umgebungen.
- Warum AlSi10Mg für Kühlrippen verwenden?
- Gewichtsreduzierung: Deutliche Gewichtseinsparungen im Vergleich zu Kupfer, entscheidend für Automobil-, Luft- und Raumfahrt- sowie tragbare Anwendungen.
- Kosten-Nutzen-Verhältnis: Aluminiumpulver ist im Allgemeinen günstiger als Kupferlegierungspulver, und die Verarbeitung ist in der Regel schneller und etablierter.
- Ausgezeichnete Druckbarkeit: Ermöglicht hochkomplexe und fein detaillierte Rippendesigns mit größerer Leichtigkeit und Zuverlässigkeit im Vergleich zu Kupferlegierungen.
- Gutes Gleichgewicht der Eigenschaften: Bietet eine sehr effektive Kombination aus thermischer Leistung, mechanischer Festigkeit und geringem Gewicht für eine Vielzahl von Anwendungen.
- Erwägungen:
- Geringere Wärmeleitfähigkeit: Nicht so effizient bei der Wärmeübertragung wie Kupferlegierungen, was in Szenarien mit sehr hohem Wärmestrom eine Einschränkung darstellen könnte.
- Geringere Hochtemperaturfestigkeit: Verliert im Vergleich zu CuCrZr oder Stählen bei erhöhten Temperaturen schneller an Festigkeit.
- Am besten geeignet für: Automobilradiatoren und -kühler, thermische Managementkomponenten für die Luft- und Raumfahrt, Elektronikgehäuse mit integrierten Kühlkörpern, leichte Wärmetauscher, allgemeine industrielle Kühlanwendungen, bei denen das Gewicht eine Rolle spielt.
Zusammenfassung der Materialauswahl:
Eigentum | CuCrZr | AlSi10Mg | Wichtigste Erkenntnis für Kühlrippen |
---|---|---|---|
Wärmeleitfähigkeit | ★★★★★ (>300 W/m·K) | ★★★☆☆ (120-150 W/m·K) | CuCrZr für maximalen Wärmestrom; AlSi10Mg für gute Allround-Leistung. |
Dichte | ★☆☆☆☆ (~8,9 g/cm³) | ★★★★★ (~2,7 g/cm³) | AlSi10Mg für Leichtbauanwendungen. |
Mechanische Festigkeit | ★★★★☆ (Gut, besonders bei Temp.) | ★★★☆☆ (Gut, besonders nach Wärmebehandlung) | Beide bieten eine gute strukturelle Integrität; CuCrZr besser bei hohen Temperaturen. |
Druckbarkeit (LPBF) | ★★★☆☆ (Herausfordernd, aber machbar) | ★★★★★ (Hervorragend, gut etabliert) | AlSi10Mg ermöglicht das einfachere Drucken komplexer Designs. |
Kosten | ★★☆☆☆ (Höher) | ★★★★☆ (Niedriger) | AlSi10Mg ist im Allgemeinen kostengünstiger. |
In Blätter exportieren
Materialexpertise von Met3dp:
Bei Met3dp verstehen wir die entscheidende Rolle, die Materialien für die Bauteilleistung spielen. Unsere fortschrittliche Systeme zur Pulverherstellungunter Verwendung von Gasverdüsung und Plasma Rotating Electrode Process (PREP)-Technologien, produzieren Metallpulver mit hoher Sphärizität und hoher Fließfähigkeit, einschließlich Aluminium und potenziell spezialisierter Kupferlegierungen, die für die additive Fertigung optimiert sind. Wir arbeiten eng mit unseren B2B-Kunden zusammen, einschließlich komponentenverteiler und Beschaffungsmanager, um das optimale Material auszuwählen – sei es das Standard-AlSi10Mg für Leichtbau-Effizienz oder die Erforschung fortschrittlicher Optionen wie CuCrZr für maximalen thermischen Durchsatz – und sicherzustellen, dass die endgültigen Kühlrippen strenge Leistungsziele erfüllen. Unsere umfassenden Lösungen umfassen hochwertige Pulver und branchenführende Druckausrüstung und bieten eine zuverlässige Quelle für anspruchsvolle Wärmemanagementkomponenten.
Die Wahl zwischen CuCrZr und AlSi10Mg beinhaltet oft eine Kompromissanalyse, die auf die Einschränkungen und Leistungsziele der Anwendung zugeschnitten ist. Durch die Partnerschaft mit einem erfahrenen AM-Anbieter wie Met3dp können Unternehmen diese Materialauswahl effektiv navigieren, um das volle Potenzial von 3D-gedruckten Kühlrippen auszuschöpfen.
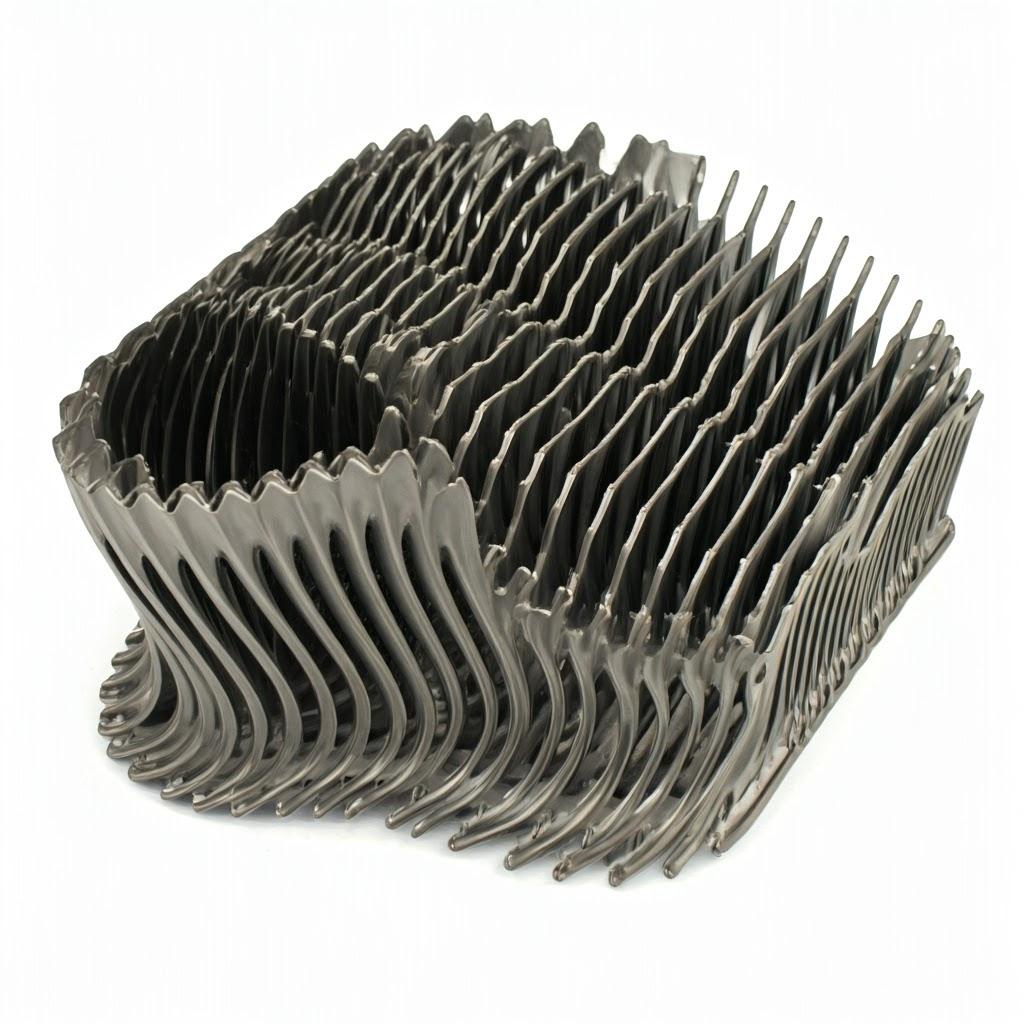
Design for Additive Manufacturing (DfAM) für überlegene Kühlleistung
Das bloße Replizieren einer traditionell gestalteten Kühlrippe mit Metall-3D-Druck verfehlt oft das wahre Potenzial der Technologie. Um eine überlegene thermische Leistung zu erzielen, müssen Ingenieure Design für additive Fertigung (DfAM) Prinzipien anwenden. DfAM beinhaltet ein Umdenken des Bauteildesigns, um die einzigartigen Fähigkeiten der Schicht-für-Schicht-Fertigung zu nutzen, was zu Geometrien führt, die nicht nur über AM herstellbar sind, sondern auch hochgradig für ihre beabsichtigte Funktion – in diesem Fall maximale Wärmeableitung – optimiert sind. Für B2B-Käufer , die nach modernsten thermischen Lösungen suchen, ist das Verständnis der DfAM-Möglichkeiten der Schlüssel zur Spezifizierung wirklich innovativer Komponenten.
Wichtige DfAM-Strategien für Kühlrippen:
- Komplexe Geometrien & dünne Merkmale:
- Fähigkeit: AM zeichnet sich durch die Erstellung dünner Wände (bis zu Bruchteilen eines Millimeters, abhängig vom Verfahren und Material), Rippen mit hohem Seitenverhältnis und komplexen Kurven aus, die mit herkömmlichen Methoden schwierig oder unmöglich sind.
- Thermischer Vorteil: Ermöglicht eine deutlich vergrößerte Oberfläche innerhalb eines bestimmten Volumens. Rippen können höher und dünner gemacht werden, und ihre Formen können gebogen oder profiliert werden, um den Luftstrom oder die Fluiddynamik zu optimieren, die Grenzschichtstagnation zu minimieren und die konvektive Wärmeübertragung zu verbessern. Variable Rippendichten können eingesetzt werden, wobei mehr Oberfläche dort platziert wird, wo der Wärmestrom am höchsten ist.
- Gitterstrukturen & TPMS:
- Fähigkeit: AM ermöglicht die Integration von internen Gitterstrukturen oder Triply Periodic Minimal Surfaces (TPMS) innerhalb der Rippe oder der Kühlkörperbasis. Dies sind komplexe, miteinander verbundene Netzwerke (z. B. Gyroide, Schwarz P) mit sehr hohen Oberflächen-Volumen-Verhältnissen.
- Thermischer Vorteil: Erhöht die effektive Wärmeübertragungsfläche drastisch, besonders vorteilhaft für Flüssigkeitskühlung oder erzwungene Konvektion, bei der das Kühlmittel durch das Gitter fließen kann. Sie bieten auch ein erhebliches Potenzial zur Gewichtsreduzierung im Vergleich zu festen Strukturen. Die Gestaltung effektiver Gitterstrukturen erfordert spezielle Software- und Simulationsfähigkeiten.
- Topologie-Optimierung & Generatives Design:
- Fähigkeit: Software-Tools können algorithmisch Materiallayouts generieren, die für bestimmte Leistungskriterien optimiert sind (z. B. Steifigkeit maximieren, Gewicht minimieren, Fluidströmungspfade optimieren) unter definierten Lasten und Einschränkungen.
- Thermischer Vorteil: Kann zu hochgradig organisch aussehenden, leichten Designs führen, die strategisch Material nur dort platzieren, wo es für die strukturelle Unterstützung und die Wärme- und Konvektionsleitung benötigt wird. Dies führt zu hocheffizienten, gewichtsoptimierten Kühlrippen, die präzise auf die thermische Belastung und die Strömungsbedingungen zugeschnitten sind. Es bewegt das Design über die menschliche Intuition hinaus in die datengesteuerte Optimierung.
- Konforme Kühlung:
- Fähigkeit: AM kann problemlos Kühlrippen oder Kanäle herstellen, die den genauen Konturen der wärmeerzeugenden Komponente folgen.
- Thermischer Vorteil: Minimiert den thermischen Übergangswiderstand zwischen der Wärmequelle und der Kühlstruktur und gewährleistet eine effizientere Wärmeextraktion im Vergleich zu flachen Kühlkörpern, die an gekrümmten Oberflächen befestigt sind. Dies ermöglicht kompaktere und effektivere Wärmemanagementlösungen.
- Teil Konsolidierung:
- Fähigkeit: Mehrere Komponenten (z. B. eine Kühlkörperbasis, Rippen, Halterungen, Flüssigkeitsanschlüsse) können oft als ein einziges, monolithisches Teil neu gestaltet und gedruckt werden.
- Thermischer Vorteil: Eliminiert den thermischen Widerstand, der mit Verbindungen (z. B. Lot, Wärmeleitpaste, Befestigungselemente) zwischen montierten Teilen verbunden ist. Vereinfacht die Montage, reduziert die Teileanzahl und verbessert potenziell die Gesamtzuverlässigkeit.
- Optimierung der Stützstruktur:
- Fähigkeit: Während die Metall-AM oft Stützstrukturen für überhängende Merkmale erfordert, beinhaltet DfAM das Design von Teilen, um den Bedarf an Stützen zu minimieren oder deren Entfernung zu erleichtern. Dies beinhaltet die strategische Ausrichtung des Teils auf der Bauplatte und die Verwendung selbsttragender Winkel (typischerweise >45 Grad zur Horizontalen).
- Thermischer Vorteil: Stützen können nur schwer aus komplizierten Rippenarrays entfernt werden und sich negativ auf die Oberflächenbeschaffenheit auswirken. Die Minimierung reduziert die Nachbearbeitungszeit und -kosten und vermeidet potenzielle Schäden an empfindlichen Rippen während der Entfernung. Die Gestaltung interner Kanäle, die selbsttragend sind, ist für Flüssigkeitskühlanwendungen von entscheidender Bedeutung.
- Fluidströmungsoptimierung:
- Fähigkeit: AM ermöglicht die Erstellung glatter, gekrümmter interner Kanäle, integrierter Strömungsführungen oder optimierter Rippenformen (z. B. Tragflächenprofile), um den Fluidstrom effektiv zu steuern.
- Thermischer Vorteil: Reduziert den Druckabfall in Flüssigkeits- oder Luftkühlsystemen, verbessert die Strömungsverteilung über die Rippenoberflächen, unterbricht thermische Grenzschichten und verbessert den gesamten konvektiven Wärmeübergangskoeffizienten. Die Berechnung der Fluiddynamik (CFD) wird oft in Verbindung mit DfAM verwendet, um diese Designs zu validieren.
DfAM-Überlegungen Zusammenfassungstabelle:
DfAM-Prinzip | AM-Fähigkeit genutzt | Hauptvorteil für Kühlrippen |
---|---|---|
Komplexe Geometrien | Schichtweises Bauen, Auflösung feiner Merkmale | Vergrößerte Oberfläche, optimierte Rippenformen |
Gitter / TPMS | Herstellung komplizierter interner Strukturen | Massive Oberflächenvergrößerung, Gewichtsreduzierung |
Topologieoptimierung | Algorithmische Designerstellung | Leistungsgesteuerte Formen, maximale Effizienz, Gewichtsreduzierung |
Konforme Kühlung | Erstellung von Freiformgeometrien | Verbesserter thermischer Kontakt, reduzierter Übergangswiderstand |
Teil Konsolidierung | Bauen von integrierten Baugruppen | Reduzierte Montage, eliminierter Verbindungs widerstand, verbesserte Zuverlässigkeit |
Minimierung der Unterstützung | Designausrichtung, selbsttragende Winkel | Reduzierte Nachbearbeitung, Kosteneinsparungen, Erhaltung der Oberflächenintegrität |
Fluidströmungspfade | Glatte interne Kanäle, optimierte Profile | Reduzierter Druckabfall, verbesserte Konvektion, bessere Strömungsverteilung |
In Blätter exportieren
Die Implementierung von DfAM erfordert ein Umdenken für Designer, die an traditionelle Fertigungseinschränkungen gewöhnt sind. Die Partnerschaft mit einem erfahrenen Metall-AM-Dienstleister wie Met3dp, der über Fachwissen in beiden Bereichen verfügt Druckverfahren und Wärmemanagementprinzipien, ist von unschätzbarem Wert. Wir können industrielle Beschaffung Teams und Ingenieure bei der Nutzung von DfAM unterstützen, um Kühlrippen zu erstellen, die eine beispiellose Leistung und Effizienz liefern.
Erzielung von Präzision: Toleranz, Oberflächenbeschaffenheit und Maßgenauigkeit bei AM-Kühlrippen
Während die Metall-AM unglaubliche Designfreiheit bietet, ist das Verständnis der erreichbaren Präzisionsniveaus entscheidend, um sicherzustellen, dass die endgültigen Kühlrippen die funktionalen Anforderungen erfüllen. Toleranz, Oberflächenbeschaffenheit und Maßgenauigkeit werden durch das spezifische AM-Verfahren (z. B. LPBF, SEBM), das verwendete Material, die Teilegeometrie, die Ausrichtung während des Drucks und die Nachbearbeitungsschritte beeinflusst. Die Verwaltung der Erwartungen und das Verständnis dieser Faktoren sind für Ingenieure, die die Teile entwerfen, und für Einkaufsleiter , die Anforderungen an ihre AM Anbieter.
stellen, von entscheidender Bedeutung.
- Maßgenauigkeit:
- Typische Präzisionsfähigkeiten: Allgemeine Erwartung:
- Beeinflussende Faktoren: Thermisches Schrumpfen während des Abkühlens, Eigenspannungen, Stützstrukturstrategie, Maschinenkalibrierung und Teilegeometrie spielen alle eine Rolle. Größere oder komplexere Teile können größere Abweichungen aufweisen.
- SEBM: Selektives Elektronenstrahlschmelzen, das oft für Materialien wie Titanlegierungen verwendet wird, aber potenziell auf andere anwendbar ist, arbeitet typischerweise bei höheren Temperaturen, was sich auf die Eigenspannung und die endgültige Genauigkeit auswirken kann, was manchmal zu etwas lockeren Toleranzen als LPBF führt, aber möglicherweise weniger Spannungsabbau erfordert.
- Verträglichkeit:
- Erreichbare Toleranzen: Erreichbare Standardtoleranzen liegen oft im Bereich von ISO 2768-m (mittel) oder manchmal -f (fein) für gefertigte Teile. Engere Toleranzen (die sich denjenigen der spanenden Bearbeitung annähern) an bestimmten Merkmalen erfordern in der Regel eine Nachbearbeitung.
- Entwurfsüberlegungen: Kritische Schnittstellenabmessungen, Montagepunkte oder Merkmale, die enge Passungen erfordern, sollten frühzeitig in der Konstruktionsphase identifiziert werden, wobei potenziell zusätzliches Material (‘Bearbeitungszugabe’) für die CNC-Nachbearbeitung nach dem Druckvorgang berücksichtigt werden sollte.
- Oberflächengüte (Rauhigkeit):
- As-built-Oberflächen: Die Oberflächenbeschaffenheit von Metall-AM-Teilen ist aufgrund des schichtweisen Verfahrens und der an der Oberfläche haftenden, teilweise aufgeschmolzenen Pulverpartikel von Natur aus rauer als bei spanend bearbeiteten Oberflächen.
- Obere Oberflächen: Im Allgemeinen am glattesten.
- Vertikale Mauern: Weisen typischerweise Ra-Werte (durchschnittliche Rauheit) von 6 µm bis 15 µm auf, abhängig von den Prozessparametern und dem Material (z. B. liefert AlSi10Mg oft bessere Oberflächen als CuCrZr).
- Daunenbelag/gestützte Oberflächen: In der Regel am rauesten (Ra > 15 µm), da sie mit den Stützstrukturen interagieren. Auch das Entfernen von Stützen wirkt sich auf die Oberflächenbeschaffenheit aus.
- Thermische Auswirkungen: Die Oberflächenrauheit kann die thermische Leistung beeinflussen:
- Vergrößerte Oberfläche: Die Rauheit vergrößert technisch die mikroskopische Oberfläche, was den Wärmeübergang leicht verbessern könnte.
- Grenzschichteffekte: Übermäßige Rauheit kann jedoch den Flüssigkeitsfluss nahe der Oberfläche stören, wodurch sich die Grenzschicht möglicherweise verdickt und den konvektiven Wärmeübergang leicht behindert oder den Druckabfall in Kanalströmungen erhöht.
- Kontaktwiderstand: Raue Oberflächen können den thermischen Kontaktwiderstand erhöhen, wenn die Basis der Kühlrippe präzise mit einem anderen Bauteil verbunden werden muss.
- Verbesserung: Die Oberflächenbeschaffenheit kann durch verschiedene Nachbearbeitungsverfahren erheblich verbessert werden (siehe nächster Abschnitt).
- As-built-Oberflächen: Die Oberflächenbeschaffenheit von Metall-AM-Teilen ist aufgrund des schichtweisen Verfahrens und der an der Oberfläche haftenden, teilweise aufgeschmolzenen Pulverpartikel von Natur aus rauer als bei spanend bearbeiteten Oberflächen.
Faktoren, die die Präzision beeinflussen:
Faktor | Auswirkungen auf Genauigkeit/Toleranz/Oberfläche | Risikominderung/Kontrollstrategie |
---|---|---|
AM-Prozess | Verschiedene Verfahren (LPBF, SEBM, DED) haben inhärente Genauigkeitsniveaus. | Wählen Sie das Verfahren basierend auf der erforderlichen Präzision und Materialverträglichkeit aus. |
Material | Materialeigenschaften (Leitfähigkeit, Schrumpfung) beeinflussen Verzug/Genauigkeit. | Verwenden Sie optimierte Parameter; erfordern möglicherweise materialspezifische Wärmebehandlungen. |
Teil-Geometrie | Dünne Wände, große flache Bereiche, Überhänge sind anfälliger für Verzug. | Wenden Sie DfAM-Prinzipien an, optimieren Sie die Ausrichtung, verwenden Sie geeignete Stützen. |
Orientierung aufbauen | Beeinflusst den Bedarf an Stützen, die Oberflächenbeschaffenheit (‘Treppenbildung’ an Kurven). | Strategische Ausrichtung zur Ausbalancierung von Stütze, Oberfläche und Bauzeit. |
Unterstützende Strukturen | Kann bei falscher Konstruktion zu Verzug führen; Entfernung beeinflusst die Oberfläche. | Optimiertes Stützdesign, sorgfältige Entfernungsverfahren. |
Thermische Spannungen | Inhärent in PBF-Verfahren; kann Verziehen verursachen und die Genauigkeit beeinträchtigen. | Spannungsarmglühen, optimierte Scanstrategien, Heizung der Bauplatte. |
Nachbearbeitung | Zerspanung verbessert Toleranz/Oberfläche; Wärmebehandlung kann geringfügigen Verzug verursachen. | Planen Sie Nachbearbeitungsschritte ein; berücksichtigen Sie potenzielle Maßänderungen. |
In Blätter exportieren
Qualitätskontrolle:
Renommierte AM-Dienstleister wie Met3dp setzen strenge Qualitätskontrollmaßnahmen ein, darunter:
- Pulveranalyse und -kontrolle.
- In-Prozess-Überwachung (Schmelzbadüberwachung, Schichtinspektion, wo verfügbar).
- Maßprüfung mit CMMs (Koordinatenmessmaschinen), 3D-Scannern oder herkömmlichen Messtechniken.
- Materialdichtekontrollen.
- Validierung der mechanischen und thermischen Eigenschaften (falls erforderlich).
Für B2B-Transaktionen Bei kritischen Komponenten wie Hochleistungskühlrippen ist eine klare Kommunikation bezüglich der erforderlichen Toleranzen, kritischen Abmessungen und Erwartungen an die Oberflächenbeschaffenheit zwischen dem Kunden und dem AM-Anbieter unerlässlich. Met3dp ist stolz darauf, mit Kunden zusammenzuarbeiten, um sicherzustellen, dass die fertigen Teile den Spezifikationen entsprechen, und nutzt dabei unser fundiertes Verständnis der Prozessfähigkeiten und Qualitätssicherungsprotokolle.
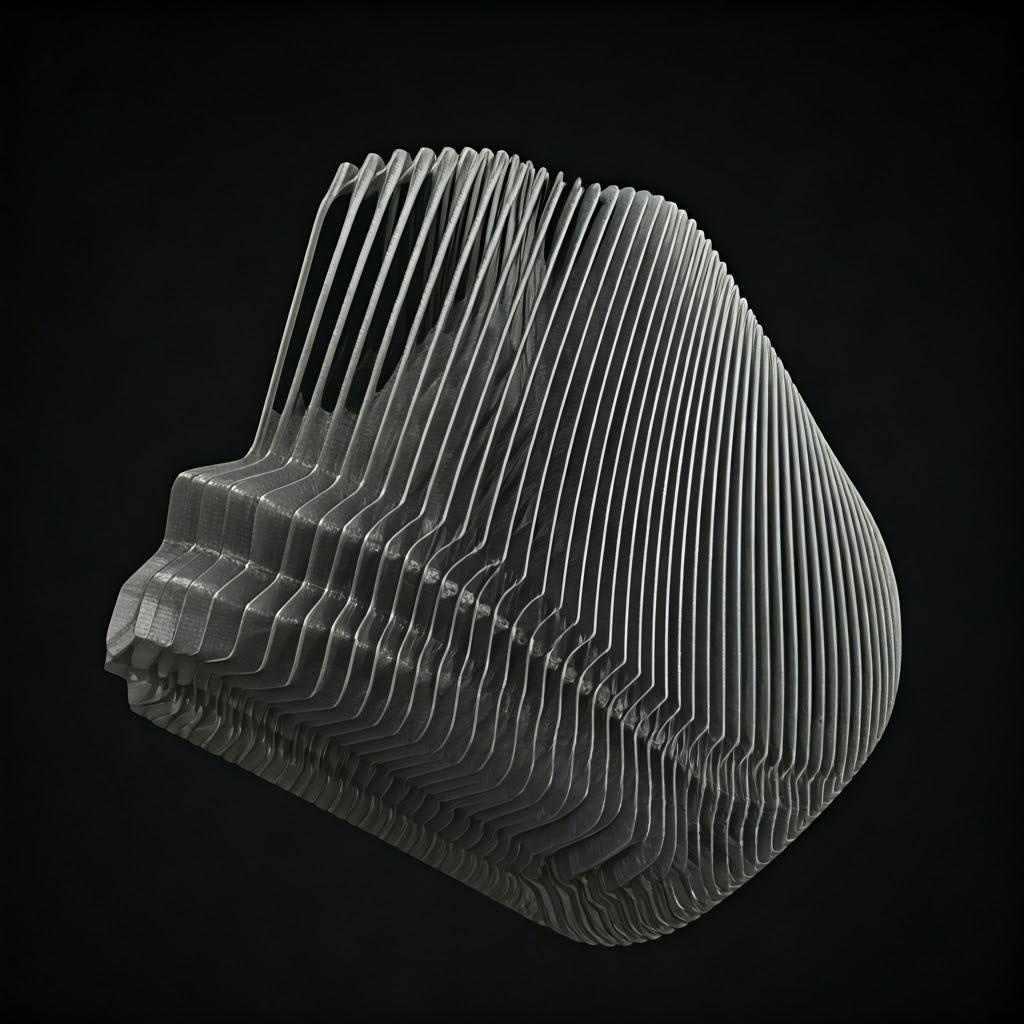
Nachbearbeitungspfade für 3D-gedruckte Kühlrippen
Ein metallisches 3D-gedrucktes Teil ist nach der Entnahme aus dem Drucker selten für seine endgültige Anwendung bereit. Dies gilt insbesondere für anspruchsvolle Komponenten wie industrielle Kühlrippen. Verschiedene Nachbearbeitungsschritte sind in der Regel erforderlich, um die gewünschten Materialeigenschaften, die Maßgenauigkeit, die Oberflächenbeschaffenheit und die Gesamtfunktionalität zu erreichen. Das Verständnis dieser gängigen Pfade ist entscheidend für die Planung von Produktionszeitplänen und -kosten, wenn man sich mit einem AM-Fertigungsdienstleister.
Gemeinsame Nachbearbeitungsschritte:
- Stressabbau / Wärmebehandlung:
- Zweck: Pulverbett-Fusionsverfahren (LPBF, SEBM) beinhalten schnelles Erhitzen und Abkühlen, wodurch erhebliche Eigenspannungen im Teil induziert werden. Diese Spannungen können nach der Entnahme aus der Bauplatte zu Verzug (Verwerfung) führen und die mechanischen Eigenschaften negativ beeinflussen. Eine Wärmebehandlung ist unerlässlich, um diese Spannungen abzubauen und das Gefüge des Materials zu homogenisieren. Spezifische Wärmebehandlungen (z. B. Lösungsglühen, Auslagern für aushärtbare Legierungen wie CuCrZr oder AlSi10Mg) sind ebenfalls erforderlich, um die Zielmechanik, Härte und optimale Wärmeleitfähigkeit zu erreichen.
- Prozess: Die Teile werden in einem Ofen mit kontrollierter Atmosphäre nach spezifischen Temperaturprofilen (Aufheizrate, Haltezeit, Abkühlrate) erhitzt, die auf die Legierung zugeschnitten sind. Für AlSi10Mg kann ein einfaches Spannungsarmglühen ausreichen, oder ein T6-Temper (Lösungsglühen + künstliches Auslagern) kann für maximale Festigkeit verwendet werden. CuCrZr erfordert spezifische Auslagerungsbehandlungen, um seine hohe Leitfähigkeit und Festigkeit zu erreichen.
- Das Ergebnis: Verbesserte Dimensionsstabilität, verbesserte mechanische Eigenschaften (Festigkeit, Duktilität), optimierte Wärmeleitfähigkeit.
- Entfernen und Reinigen von Teilen:
- Zweck: Trennen der gedruckten Teile von der Bauplatte (oftmals unter Verwendung von Drahterosion oder Sägen) und Entfernen von überschüssigem Metallpulver, insbesondere aus internen Kanälen oder komplexen Kühlrippenanordnungen.
- Prozess: Manuelles Bürsten, Druckluftausblasen, Ultraschallreinigungsbäder, Abrasivstrahlbearbeitung (für interne Kanäle). Eine gründliche Pulverentfernung ist entscheidend, um Kontaminationen zu vermeiden und eine ordnungsgemäße Funktion sicherzustellen.
- Das Ergebnis: Saubere Teile ohne loses Pulver, bereit für die nachfolgenden Schritte.
- Entfernung der Stützstruktur:
- Zweck: Entfernen der temporären Strukturen, die während des Druckens zur Unterstützung von Überhängen und komplexen Geometrien erforderlich sind.
- Prozess: Stützen sind in der Regel so konzipiert, dass sie schwächer sind als das Hauptteil. Die Entfernung kann manuelles Brechen/Schneiden (Zangen, Meißel), CNC-Bearbeitung oder manchmal Drahterosion für schwer zugängliche Bereiche umfassen. Es ist darauf zu achten, das Teil selbst, insbesondere empfindliche Kühlrippen, nicht zu beschädigen.
- Das Ergebnis: Die endgültige Teilegeometrie wird sichtbar, aber Oberflächen, an denen Stützen befestigt waren, sind rau und erfordern möglicherweise eine weitere Endbearbeitung.
- Oberflächenveredelung:
- Zweck: Verbesserung der Oberflächenrauheit im gedruckten Zustand für ästhetische, funktionale (z. B. Flüssigkeitsströmung) oder Anforderungen an die Kontaktfläche.
- Prozess: Verschiedene Methoden sind verfügbar, die in Bezug auf Aggressivität und erreichbare Oberfläche variieren:
- Perlstrahlen/Sandstrahlen: Erzeugt eine gleichmäßige matte Oberfläche, entfernt kleinere Unvollkommenheiten. Gut für die allgemeine Oberflächenverbesserung (Ra typischerweise 5-10 µm).
- Taumeln/Gleitschleifen: Teile werden mit Schleifmedien getrommelt, um Oberflächen und Kanten zu glätten. Gut für Chargen kleinerer Teile.
- Abrasive Fließbearbeitung (AFM): Zwingt eine Schleifmasse durch interne Kanäle oder über Oberflächen, effektiv zum Glätten schwer zugänglicher Bereiche.
- Elektropolieren/Chemisches Polieren: Elektrochemische oder chemische Verfahren entfernen Material und führen zu sehr glatten, glänzenden Oberflächen. Besonders effektiv bei bestimmten Legierungen.
- Manuelles Polieren/Schleifen: Für das Erreichen von Spiegeloberflächen oder spezifischer lokaler Glätte, oft arbeitsintensiv.
- Das Ergebnis: Verbesserte Oberflächenästhetik, potenziell reduzierter Reibungs-/Druckabfall, bessere Oberfläche für nachfolgende Beschichtungen.
- CNC-Bearbeitung:
- Zweck: Um enge Toleranzen für bestimmte Merkmale (z. B. Kontaktflächen, Befestigungslöcher, Gewindebohren) zu erreichen, die durch das AM-Verfahren allein nicht zuverlässig eingehalten werden können. Wird auch verwendet, um Merkmale zu erzeugen, die mit AM nicht möglich sind, oder um die Oberflächenbeschaffenheit in kritischen Bereichen zu verbessern.
- Prozess: Standard-Fräs-, Dreh-, Bohr-, Gewindebohroperationen, die auf das AM-Teil angewendet werden. Erfordert oft eine sorgfältige Vorrichtungsgestaltung, um die komplexe AM-Geometrie zu halten.
- Das Ergebnis: Hohe Präzision bei kritischen Abmessungen, flache/glatte Kontaktflächen, Gewindelöcher.
- Beschichtung/Galvanisierung:
- Zweck: Auftragen einer Oberflächenschicht zur Verbesserung der Korrosionsbeständigkeit, Verschleißfestigkeit, elektrischen Isolierung oder zur Modifizierung der thermischen Eigenschaften (z. B. Erhöhung des Emissionsgrades für eine verbesserte Strahlungskühlung).
- Prozess: Eloxieren (für Aluminium), Vernickeln, Lackieren, Pulverbeschichten, spezielle Keramikbeschichtungen.
- Das Ergebnis: Erhöhte Haltbarkeit, spezifische Oberflächeneigenschaften, die auf die Betriebsumgebung zugeschnitten sind.
Beispiel für einen Nachbearbeitungs-Workflow (AlSi10Mg-Kühlrippe):
Bauplatte -> Spannungsarmglühen -> Drahterosion-Schnitt von der Platte -> Pulverentfernung -> Stützenentfernung -> Kugelstrahlen -> CNC-Bearbeitung (Kontaktfläche) -> Endkontrolle
Die spezifische Reihenfolge und Kombination dieser Schritte hängt stark von den Anwendungsanforderungen, der Materialauswahl und der Teilekomplexität ab. Beschaffungsteams sollten die Nachbearbeitungsanforderungen im Vorfeld mit ihrem AM-Anbieter besprechen, da diese Schritte die endgültigen Kosten und die Vorlaufzeit erheblich beeinflussen. Met3dp bietet Beratung an und kann die gesamte Nachbearbeitungskette verwalten, um fertige Kühlrippen zu liefern, die für die Integration bereit sind.
Überwindung häufiger Herausforderungen in der Metall-AM für thermische Komponenten
Obwohl der 3D-Metalldruck erhebliche Vorteile für die Herstellung von Hochleistungskühlrippen bietet, ist er nicht ohne Herausforderungen. Die erfolgreiche Herstellung komplexer thermischer Komponenten erfordert Fachwissen, Prozesskontrolle und ein Verständnis der potenziellen Fallstricke. Das Bewusstsein für diese Herausforderungen hilft sowohl Designern als auch B2B-Käufer die Nuancen zu verstehen, die mit der Beschaffung zuverlässiger AM-Teile verbunden sind.
Zentrale Herausforderungen und Strategien zur Abhilfe:
- Verformung und Verzerrung:
- Ausgabe: Die schnellen Erhitzungs-/Abkühlzyklen, die den PBF-Verfahren innewohnen, erzeugen erhebliche Temperaturgradienten und Eigenspannungen. Diese Spannungen können dazu führen, dass sich Teile, insbesondere solche mit großen flachen Bereichen oder dünnen Kühlrippen mit hohem Seitenverhältnis, während des Druckens oder nach der Entnahme aus der Bauplatte verziehen oder verformen.
- Milderung:
- Optimierte Scan-Strategien: Die Verwendung spezifischer Laser-/Elektronenstrahl-Scanmuster (z. B. Insel-Scannen, Sektorisierung) hilft, die Wärme gleichmäßiger zu verteilen.
- Unterstützende Strukturen: Gut konzipierte Stützen verankern das Teil fest an der Bauplatte und widerstehen so Verformungen während des Baus.
- Thermische Simulation: Die Simulation des Bauprozesses im Voraus kann Bereiche vorhersagen, die anfällig für hohe Spannungen und Verformungen sind, und so Design- oder Stützkorrekturen ermöglichen.
- Build Plate Heating: Die Aufrechterhaltung einer erhöhten Bauplattentemperatur (üblich bei SEBM, manchmal bei LPBF verwendet) reduziert Temperaturgradienten.
- Stressabbau: Die Wärmebehandlung nach dem Bau ist entscheidend für den Abbau von aufgebauten Spannungen.
- Entfernung der Stützstruktur:
- Ausgabe: Komplexe Kühlrippenanordnungen, insbesondere solche mit internen Kanälen oder eng beieinander liegenden Kühlrippen, können Stützstrukturen extrem schwierig, zeitaufwändig oder sogar unmöglich machen, ohne das Teil zu beschädigen. Restliches Stützmaterial kann den Flüssigkeitsfluss behindern und die Leistung negativ beeinflussen.
- Milderung:
- DfAM zur Stützreduzierung: Konstruktion von Teilen mit selbsttragenden Winkeln (>45°), wo immer möglich, Optimierung der Teileausrichtung auf der Bauplatte.
- Spezielle Stützkonstruktionen: Verwendung von leicht zerbrechlichen oder auflösbaren Stützstrukturen, wo dies möglich ist (weniger üblich in der Metall-AM).
- Überlegungen zum Zugang: Konstruktion unter Berücksichtigung des Werkzeugzugangs für die manuelle oder maschinelle Stützenentfernung.
- Prozessauswahl: Einige AM-Verfahren erfordern möglicherweise weniger Stützen als andere für bestimmte Geometrien.
- Porosität:
- Ausgabe: Unvollständige Verschmelzung zwischen Pulverpartikeln oder eingeschlossenes Gas können zu Hohlräumen (Porosität) im gedruckten Material führen. Porosität reduziert die effektive Wärmeleitfähigkeit des Materials (Luft/Gas in Poren wirkt isolierend) und beeinträchtigt die mechanische Festigkeit und die Lebensdauer.
- Milderung:
- Optimierte Prozessparameter: Verwendung sorgfältig entwickelter und validierter Parameter (Laser-/Strahlleistung, Scangeschwindigkeit, Schichtdicke, Schlupfabstand), die für das Material und die Maschine spezifisch sind.
- Hochwertiges Pulver: Sicherstellung der Verwendung von kugelförmigem, fließfähigem Pulver mit geringer innerer Porosität und kontrollierter Partikelgrößenverteilung, wie die von Met3dp.
- Kontrollierte Bauatmosphäre: Aufrechterhaltung einer hochreinen Inertgasatmosphäre (Argon oder Stickstoff), um Oxidation und Kontamination zu verhindern.
- Heiß-Isostatisches Pressen (HIP): Ein Nachbearbeitungsschritt, der hohe Temperatur und Druck beinhaltet, wodurch innere Poren geschlossen und nahezu 100 % Dichte erreicht werden können (erhöht Kosten und Zeit).
- Reststress-Management:
- Ausgabe: Neben der Verformung können hohe Eigenspannungen zu vorzeitigem Reißen oder einer verringerten Lebensdauer des fertigen Bauteils führen.
- Milderung: Dies wird in erster Linie durch optimierte Druckstrategien (Scanmuster, Erwärmung) und obligatorische Wärmebehandlungen zur Spannungsarmglühung gesteuert, die auf die jeweilige Legierung zugeschnitten sind.
- Einschränkungen der Oberflächenbeschaffenheit:
- Ausgabe: Wie bereits erwähnt, ist die Oberflächenbeschaffenheit von AM-Teilen im Urzustand rauer als die von bearbeiteten Oberflächen. Bei Kühlrippen kann sich dies auf die Fluiddynamik und den Wärmeübergangswiderstand auswirken.
- Milderung: Implementierung geeigneter Nachbearbeitungsverfahren (Strahlen, Polieren, AFM) basierend auf den Anwendungsanforderungen. Berücksichtigung dieser Schritte im gesamten Produktionsplan.
- Erzielung einer hohen Wärmeleitfähigkeit (insbesondere CuCrZr):
- Ausgabe: Kupferlegierungen wie CuCrZr sind aufgrund ihres hohen Reflexionsvermögens und ihrer Wärmeleitfähigkeit schwer zu drucken, wodurch es schwieriger wird, eine volle Dichte und eine optimale Mikrostruktur ohne spezielle Ausrüstung und Parameter zu erreichen. Die endgültige Leitfähigkeit ist auch stark von der ordnungsgemäßen Wärmebehandlung nach dem Druck abhängig.
- Milderung: Verwendung von AM-Systemen, die speziell für den Kupferdruck entwickelt oder angepasst wurden, unter Verwendung optimierter Prozessparameter (z. B. leistungsstärkere grüne oder blaue Laser für LPBF) und unter strikter Einhaltung validierter Wärmebehandlungszyklen. Die Zusammenarbeit mit Anbietern, die Erfahrung im Drucken von Kupferlegierungen haben, ist von entscheidender Bedeutung.
- Konsistenz und Qualitätssicherung:
- Ausgabe: Die Gewährleistung einer gleichbleibenden Qualität (Dichte, Maßhaltigkeit, Materialeigenschaften) von Teil zu Teil und von Charge zu Charge ist für die industrielle Produktion und zuverlässige B2B-Lieferketten.
- Milderung: Robuste Qualitätsmanagementsysteme (z. B. ISO 9001), strenge Prozesskontrollen, regelmäßige Maschinenkalibrierung, Pulverqualitätsmanagement, prozessbegleitende Überwachung und gründliche Nachbearbeitungsinspektion und -tests.
Um diese Herausforderungen erfolgreich zu meistern, sind fundierte Prozesskenntnisse, fortschrittliche Ausrüstung und eine strenge Qualitätskontrolle erforderlich. Met3dp kombiniert jahrzehntelange gemeinsame Erfahrung in der additiven Fertigung von Metallen, branchenführende Druckausrüstung (einschließlich SEBM-Fähigkeiten) und fortschrittliche Metallpulverherstellung um diese Hürden zu überwinden. Wir arbeiten eng mit unseren Kunden zusammen, um ihre spezifischen Herausforderungen zu verstehen und hochwertige, zuverlässige Kühlrippen zu liefern, die die Leistungserwartungen erfüllen oder übertreffen, was uns zu einem vertrauenswürdigen Partner für Großhandel und kundenspezifische AM-Komponenten macht.
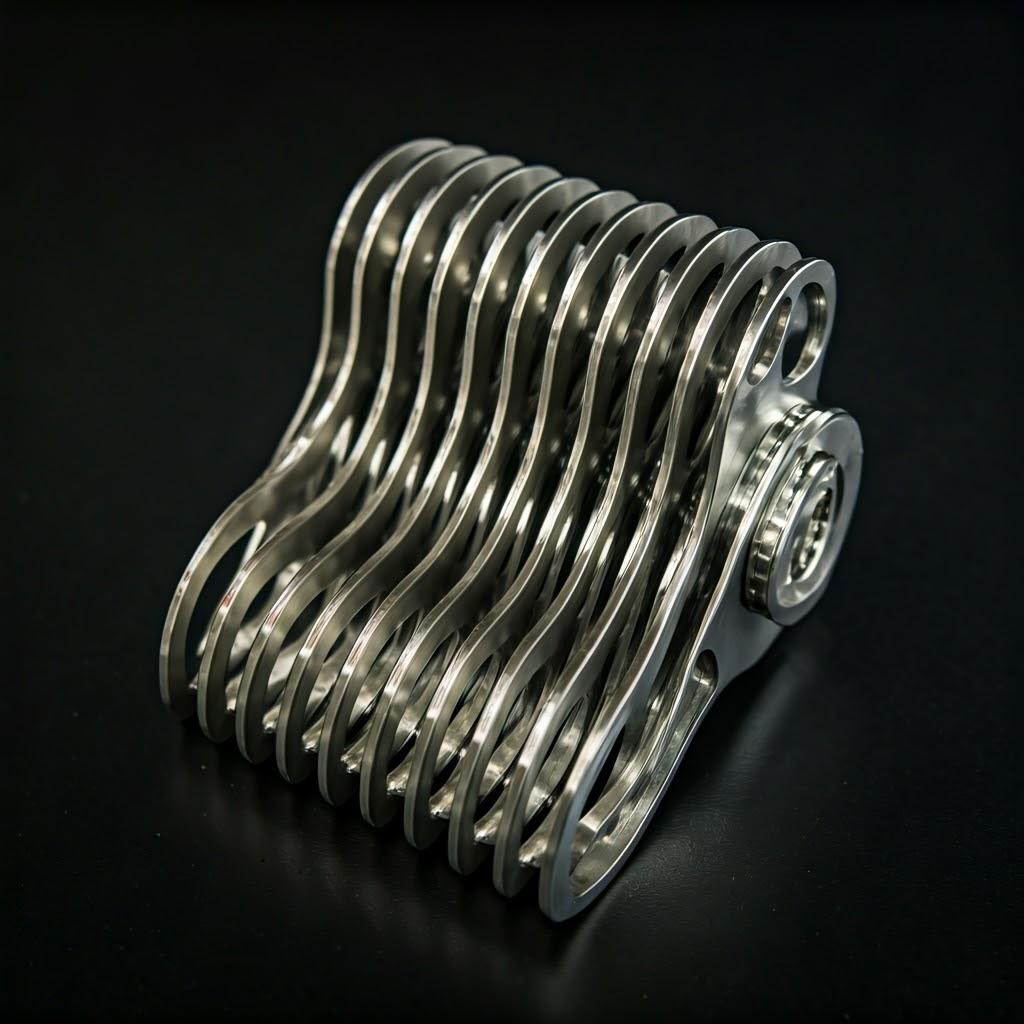
Auswahl Ihres Metall-3D-Druckpartners: Ein Leitfaden für Käufer zur Beschaffung von Kühlrippen
Die Wahl des richtigen Partners für die additive Fertigung ist ebenso wichtig wie die Konstruktion und Materialauswahl, um hochleistungsfähige, zuverlässige Kühlrippen zu erhalten. Die Fähigkeiten, das Fachwissen und die Qualitätsstandards Ihres gewählten AM-Dienstleister wirken sich direkt auf den Erfolg Ihres Projekts aus. Für Ingenieure und Beschaffungsmanager navigieren in der B2B-Umfeld des Metall-3D-Drucks sind hier die wichtigsten Kriterien zur Bewertung potenzieller Lieferanten:
Bewertungskriterien für AM-Partner:
- Technisches Fachwissen und Anwendungskenntnisse:
- Erfordernis: Suchen Sie nach Anbietern mit nachgewiesener Erfahrung nicht nur in der Metall-AM, sondern speziell in Anwendungen des Wärmemanagements. Verstehen sie die Prinzipien der Wärmeübertragung, der Fluiddynamik und die Nuancen der Entwicklung effektiver Kühllösungen? Können sie DfAM-Leitlinien anbieten, die für die thermische Leistung relevant sind?
- Warum das wichtig ist: Ein Partner mit thermischem Fachwissen kann wertvolle Beiträge während der Konstruktionsphase leisten, Optimierungen vorschlagen und die entscheidenden Parameter für den Erfolg verstehen, also über das bloße Drucken einer Datei hinausgehen.
- Materialeigenschaften und Pulverqualität:
- Erfordernis: Stellen Sie sicher, dass der Anbieter die für Ihre Anwendung erforderlichen Legierungen (z. B. AlSi10Mg, CuCrZr) anbietet und über nachgewiesene Erfahrung in deren effektiver Verarbeitung verfügt. Erkundigen Sie sich nach ihren Pulverbeschaffungs- und Qualitätskontrollverfahren. Stellen sie eine hohe Sphärizität, Fließfähigkeit und Reinheit sicher?
- Warum das wichtig ist: Materialeigenschaften sind grundlegend für die Leistung von Kühlrippen. Gleichmäßiges, hochwertiges Pulver, wie es mit den fortschrittlichen Gaszerstäubungs- und PREP-Technologien von Met3dp hergestellt wird, ist unerlässlich, um die gewünschte Dichte, Wärmeleitfähigkeit und mechanische Festigkeit zu erreichen.
- Technologie & Ausrüstung:
- Erfordernis: Beurteilen Sie die Bandbreite der AM-Technologien des Anbieters (LPBF, SEBM usw.) und die spezifischen Maschinen, die er betreibt. Berücksichtigen Sie die Bauvolumenkapazitäten, die Wartungspläne der Maschinen und die Redundanz (Ersatzmaschinen). Ist ihre Technologie für die Komplexität und das Material Ihres Teils geeignet?
- Warum das wichtig ist: Verschiedene Maschinen und Technologien haben unterschiedliche Stärken. Der Zugang zu geeigneter, gut gewarteter Ausrüstung gewährleistet Prozessstabilität, berücksichtigt die Teilegröße und unterstützt die Anforderungen an die Produktionskapazität. Die Investition von Met3dp in branchenführende Drucker garantiert Genauigkeit und Zuverlässigkeit für einsatzkritische Teile.
- Qualitätsmanagementsysteme und Zertifizierungen:
- Erfordernis: Überprüfen Sie, ob der Anbieter relevante Qualitätszertifizierungen besitzt, wie z. B. ISO 9001 (allgemeines Qualitätsmanagement). Je nach Branche können Zertifizierungen wie AS9100 (Luft- und Raumfahrt), IATF 16949 (Automobil) oder ISO 13485 (Medizin) erforderlich sein. Fragen Sie nach ihren Qualitätskontrollprozessen, Inspektionsfähigkeiten (CMM, Scannen) und der Materialrückverfolgbarkeit.
- Warum das wichtig ist: Zertifizierungen weisen auf ein Bekenntnis zu standardisierten Prozessen und Qualitätssicherung hin, was für die Gewährleistung der Teilekonsistenz, Zuverlässigkeit und Konformität, insbesondere in regulierten Branchen, von entscheidender Bedeutung ist. Dies gibt Vertrauen für B2B-Käufer die Beschaffung kritischer Komponenten.
- Nachbearbeitungsmöglichkeiten:
- Erfordernis: Bietet der Anbieter interne oder verwaltet er ein zuverlässiges Netzwerk für erforderliche Nachbearbeitungsschritte wie Wärmebehandlung, Stützentfernung, CNC-Bearbeitung und Oberflächenveredelung? Können sie eine vollständig fertige Komponente liefern?
- Warum das wichtig ist: Ein Anbieter, der umfassende End-to-End-Dienstleistungen anbietet, vereinfacht die Lieferkette, verkürzt die Vorlaufzeiten und gewährleistet eine bessere Kontrolle über den gesamten Herstellungsprozess, vom Pulver bis zum fertigen Teil.
- Kommunikation, Support und Zusammenarbeit:
- Erfordernis: Bewerten Sie die Reaktionsfähigkeit, Transparenz und Bereitschaft des Anbieters zur Zusammenarbeit. Stellen sie klare Angebote bereit, kommunizieren sie proaktiv über den Projektstatus und bieten sie technischen Support an?
- Warum das wichtig ist: Eine starke Arbeitsbeziehung, die auf klarer Kommunikation basiert, ist unerlässlich, um technische Herausforderungen zu lösen, Erwartungen zu managen und den Projekterfolg zu gewährleisten, insbesondere bei kundenspezifischen oder komplexen Komponenten.
- Erfolgsbilanz und Fallstudien:
- Erfordernis: Bitten Sie um Beispiele für ähnliche Projekte oder Fallstudien, insbesondere solche, die thermische Komponenten oder die spezifischen Materialien und Komplexitäten betreffen, die für Ihr Projekt relevant sind. Referenzen können ebenfalls wertvoll sein.
- Warum das wichtig ist: Die bisherige Leistung ist ein guter Indikator für den zukünftigen Erfolg. Der Nachweis erfolgreich abgeschlossener Projekte stärkt das Vertrauen in die Fähigkeiten des Anbieters.
Warum eine Partnerschaft mit Met3dp?
Met3dp verkörpert diese wesentlichen Eigenschaften. Als führender Anbieter mit Hauptsitz in Qingdao, China, sind wir auf fortschrittliche Metall-3D-Druckausrüstung (einschließlich SEBM) und die Herstellung von Hochleistungs-Metallpulvern spezialisiert. Unser fundiertes Fachwissen in der Metall-AM, gepaart mit unserem Fokus auf Materialwissenschaft und Anwendungsentwicklung, macht uns zu einem idealen Partner für anspruchsvolle Wärmemanagementprojekte. Wir bieten:
- Branchenführendes Druckvolumen, Genauigkeit und Zuverlässigkeit.
- Ein Portfolio hochwertiger Metallpulver, einschließlich Legierungen, die für thermische Anwendungen geeignet sind.
- Umfassende Lösungen, die Drucker, Pulver und Anwendungsunterstützung umfassen.
- Ein Bekenntnis zu Qualität und kollaborativen Partnerschaften.
Erfahren Sie, wie die Fähigkeiten von Met3dp die Ziele Ihres Unternehmens in der additiven Fertigung vorantreiben können, indem Sie unsere Website besuchen: https://met3dp.com/. Wir sind in der Lage, als zuverlässiger AM-Lieferant für Unternehmen zu dienen, die hocheffiziente Kühlrippen und andere komplexe Metallkomponenten suchen.
Verständnis der Kostenfaktoren und Vorlaufzeiten für additiv gefertigte Kühlrippen
Während die Metall-AM eine überlegene Leistung ermöglicht, ist das Verständnis der damit verbundenen Kosten und Produktionszeitpläne für die Projektplanung und -budgetierung von entscheidender Bedeutung, insbesondere für B2B-Beschaffung. Die Preisgestaltung für AM-Teile ist vielfältig und unterscheidet sich erheblich von den Kostenstrukturen der traditionellen Fertigung.
Die wichtigsten Kostentreiber:
- Materialtyp & Volumen:
- Auswirkungen: Die Kosten für das Metallpulver sind ein Hauptfaktor. Hochleistungslegierungen wie CuCrZr sind deutlich teurer als Standard-AlSi10Mg oder Stähle. Das gesamte verwendete Materialvolumen (einschließlich der Stützen) wirkt sich direkt auf die Kosten aus.
- Erwägung: Die Materialauswahl beinhaltet das Abwägen von Leistungsanforderungen mit Budgetbeschränkungen. Die Optimierung von Designs zur Minimierung des Volumens (z. B. mithilfe von Topologieoptimierung, Gittern) kann dazu beitragen, die Materialkosten zu senken.
- Druckzeit und Maschinenauslastung:
- Auswirkungen: Je länger ein Teil zum Drucken benötigt, desto höher sind die Kosten, die mit dem Maschinenbetrieb verbunden sind (Energie, Verbrauch von Inertgas, Abschreibung, Arbeitsaufwand). Die Druckzeit wird durch das Teilvolumen, die Höhe (Anzahl der Schichten), die Komplexität und die erforderliche Auflösung/Parameter beeinflusst.
- Erwägung: Das Konstruieren für effizientes Drucken (z. B. Optimierung der Ausrichtung zur Minimierung der Höhe, Verschachtelung mehrerer Teile in einem Build) kann die Kosten für die Maschinenzeit pro Teil senken.
- Teil Komplexität & Design:
- Auswirkungen: Hochkomplexe Geometrien mit komplizierten Merkmalen, dünnen Wänden oder ausgedehnten Überhängen erfordern häufig anspruchsvollere Druckstrategien und mehr Stützstrukturen, was sowohl die Druckzeit als auch den Nachbearbeitungsaufwand erhöht.
- Erwägung: Während Komplexität ein Vorteil der AM ist, können übermäßig komplexe Designs, bei denen einfachere Formen ausreichen, die Kosten unnötig in die Höhe treiben. DfAM sollte Leistungsgewinne mit Herstellbarkeit und Kosten in Einklang bringen.
- Unterstützende Strukturen:
- Auswirkungen: Das Volumen des für die Stützen verwendeten Materials erhöht die Materialkosten. Noch wichtiger ist, dass das Entfernen von Stützen erhebliche Arbeits- und Zeitaufwände in der Nachbearbeitung verursacht, insbesondere bei komplexen internen Merkmalen oder empfindlichen Rippenarrays.
- Erwägung: Die Minimierung der Stützanforderungen durch cleveres Design (DfAM) ist eine wichtige Kostensparstrategie.
- Nachbearbeitungsanforderungen:
- Auswirkungen: Jeder Nachbearbeitungsschritt (Wärmebehandlung, Bearbeitung, Oberflächenveredelung, Beschichtung) erhöht die Kosten und die Zeit. Hochpräzise Bearbeitung oder aufwändiges manuelles Polieren können erhebliche Kostenfaktoren sein.
- Erwägung: Definieren Sie die erforderliche Nachbearbeitung klar auf der Grundlage der funktionalen Anforderungen. Vermeiden Sie die Angabe engerer Toleranzen oder feinerer Oberflächen, als tatsächlich benötigt werden.
- Qualitätssicherung und Inspektion:
- Auswirkungen: Der Grad der erforderlichen Qualitätskontrolle (Dimensionsprüfung, Materialprüfung, zerstörungsfreie Prüfung) wirkt sich auf die Kosten aus. Strengere Inspektionsprotokolle benötigen naturgemäß mehr Zeit und Ressourcen.
- Erwägung: Legen Sie geeignete, aber nicht übermäßige Qualitätssicherungsmaßnahmen fest, die auf der Kritikalität der Komponente basieren.
- Auftragsvolumen:
- Auswirkungen: Wie bei den meisten Herstellungsprozessen gelten auch für die AM Skaleneffekte, wenn auch vielleicht weniger dramatisch als bei traditionellen werkzeuglastigen Verfahren. Die Einrichtungskosten werden auf größere Chargen verteilt, und volle Baukammern sind effizienter. Die Stückkosten sinken typischerweise mit höheren Volumina.
- Erwägung: Besprechen Sie die Volumenprognosen mit Ihrem AM-Anbieter um potenzielle Preisnachlässe für Produktionsmengen im Vergleich zu Prototypen zu verstehen.
Vorlaufzeiten:
Die Vorlaufzeiten für Metall-AM-Kühlrippen können je nach den oben genannten Faktoren sowie der aktuellen Kapazität des Anbieters erheblich variieren.
- Prototyping: Typischerweise schneller als herkömmliche Methoden, von wenigen Tagen bis zu einigen Wochen, je nach Komplexität, Materialverfügbarkeit und Nachbearbeitungsanforderungen. Schnelle Iteration ist ein wichtiger AM-Vorteil.
- Produktionschargen: Die Vorlaufzeiten für die Produktion von kleinen bis mittleren Volumina können zwischen mehreren Wochen und einigen Monaten liegen. Dies beinhaltet Zeit für detaillierte Planung, Druck, vollständige Nachbearbeitung und Qualitätssicherung für die gesamte Charge.
- Faktoren, die die Vorlaufzeit verlängern: Komplexe Nachbearbeitung (insbesondere manuelle Schritte oder mehrstufige Wärmebehandlungen), umfangreiche QS-Anforderungen, Beschaffung von Nicht-Standard-Materialien und hohe Nachfrage/Rückstände beim Dienstleister.
Empfehlung: Fordern Sie immer ein detailliertes Angebot von Ihrem gewählten AM-Partner auf der Grundlage Ihres endgültigen CAD-Modells und klar definierter Spezifikationen (Material, Toleranzen, Ausführung, QS) an. Besprechen Sie die Erwartungen an die Vorlaufzeit frühzeitig im Prozess. Ein zuverlässiger industriezulieferer wie Met3dp bietet transparente Angebote und realistische Zeitpläne.
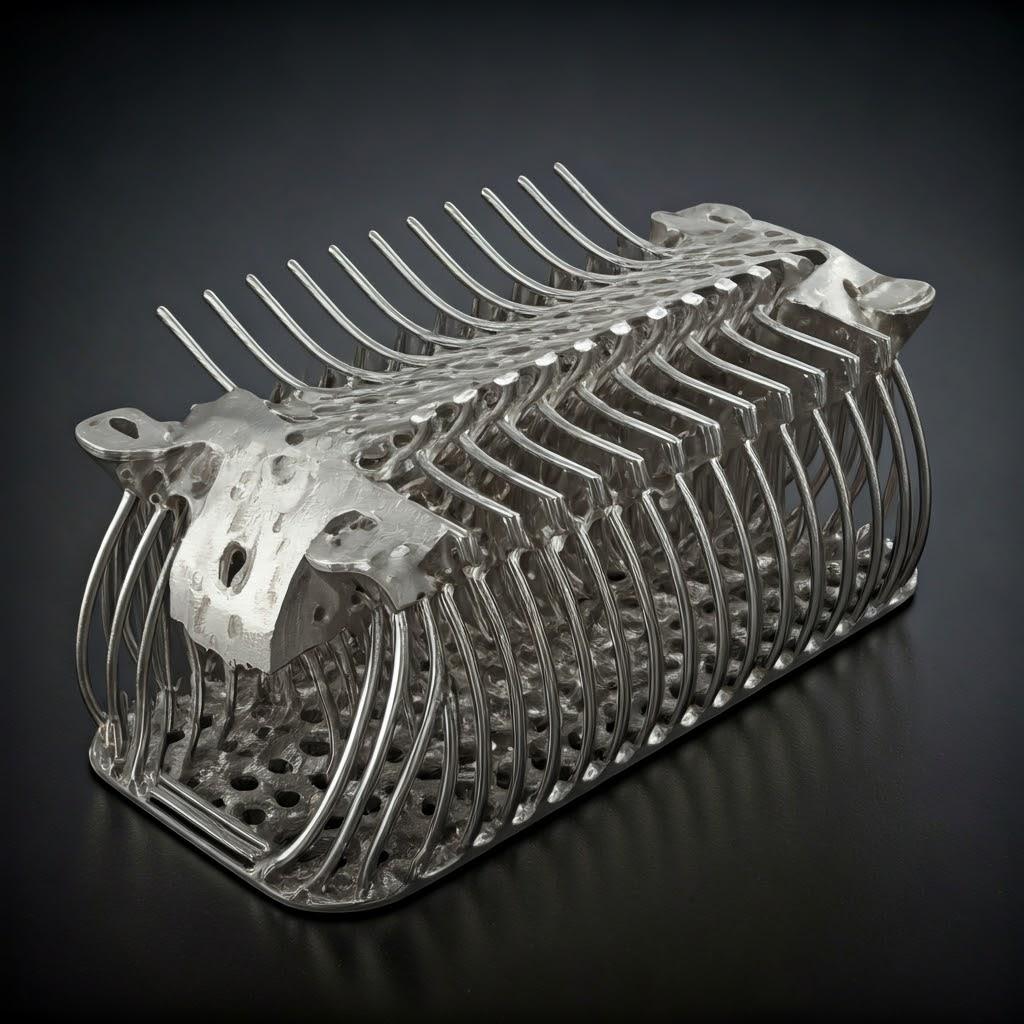
FAQ: Metall-3D-gedruckte Kühlrippen
Hier sind Antworten auf einige häufig gestellte Fragen zur Verwendung der additiven Fertigung von Metallen für industrielle Kühlrippen:
- F1: Wie vergleicht sich die Leistung von 3D-gedruckten Kühlrippen mit der von traditionell hergestellten Kühlrippen (z. B. extrudiert oder bearbeitet)?
- A: Metall-AM ermöglicht oft eine überlegen thermische Leistung im Vergleich zu herkömmlichen Methoden. Dies ist in erster Linie auf die Designfreiheit zurückzuführen, die AM bietet, was Folgendes ermöglicht:
- Optimierte Geometrien: Komplexe Formen (dünnere Rippen, variable Dichten, TPMS/Gitter, konforme Designs), die die Oberfläche maximieren und die Fluiddynamik verbessern.
- Teil Konsolidierung: Beseitigung des Wärmewiderstands von Verbindungen in montierten Kühlkörpern.
- Fortgeschrittene Materialien: Erleichterung der Verwendung von hochleitfähigen Materialien wie CuCrZr in komplexen Formen, die traditionell nur schwer oder gar nicht zu bearbeiten oder zu gießen sind. Während eine einfache extrudierte Rippe für einfache Anwendungen möglicherweise günstiger ist, zeichnet sich AM aus, wenn Leistungsgrenzen überschritten, das Gewicht optimiert oder mit komplexen Integrationsherausforderungen umgegangen werden muss. Leistungsgewinne hängen stark davon ab, dass DfAM-Prinzipien genutzt werden.
- A: Metall-AM ermöglicht oft eine überlegen thermische Leistung im Vergleich zu herkömmlichen Methoden. Dies ist in erster Linie auf die Designfreiheit zurückzuführen, die AM bietet, was Folgendes ermöglicht:
- F2: Ist der Metall-3D-Druck eine kostengünstige Lösung für die Herstellung von Kühlrippen, insbesondere für den Großhandel oder größere Volumina?
- A: Die Wirtschaftlichkeit hängt von der jeweiligen Anwendung und dem Volumen ab.
- Prototyping & Anpassung: AM ist für Prototypen, Designiterationen und die Kleinserienfertigung von kundenspezifischen oder hochkomplexen Kühlkörpern sehr kosteneffektiv, da Werkzeugkosten vermieden werden.
- Leistungsabhängige Anwendungen: Wenn die verbesserte Leistung (was zu kleineren, leichteren oder effizienteren Systemen führt) einen erheblichen Wert darstellt, können die höheren Kosten pro Teil von AM gerechtfertigt sein.
- Mittlere Volumina: Für mittlere Volumina muss die Kostenberechnung im Vergleich zu herkömmlichen Methoden (unter Berücksichtigung der Werkzeugamortisation für Gießen/Extrusion) sorgfältig geprüft werden. Die durch AM ermöglichte Teilekonsolidierung kann manchmal höhere Druckkosten durch die Reduzierung des Montageaufwands ausgleichen.
- Hohe Volumina (einfache Designs): Für sehr hohe Volumina einfacher Kühlkörperdesigns sind herkömmliche Methoden wie Extrusion oder Stanzen im Allgemeinen immer noch kostengünstiger. AM ist am kosteneffektivsten, wenn seine einzigartigen Vorteile (Komplexität, Anpassung, Leistung) voll ausgeschöpft werden. Die Besprechung Ihrer spezifischen Anforderungen mit einem AM-Hersteller wie Met3dp kann helfen, den besten Ansatz zu ermitteln.
- A: Die Wirtschaftlichkeit hängt von der jeweiligen Anwendung und dem Volumen ab.
- F3: Welche Informationen muss ich einem Metall-AM-Dienstleister wie Met3dp zur Verfügung stellen, um ein genaues Angebot für Kühlkörper zu erhalten?
- A: Um das genaueste Angebot und die geschätzte Vorlaufzeit zu erhalten, sollten Sie idealerweise Folgendes angeben:
- 3D-CAD-Modell: Ein hochwertiges Modell in einem Standardformat (z. B. STEP, STL). Stellen Sie sicher, dass das Modell die vorgesehene Endgeometrie widerspiegelt.
- Spezifikation des Materials: Geben Sie die gewünschte Metalllegierung eindeutig an (z. B. AlSi10Mg, CuCrZr).
- Kritische Toleranzen: Geben Sie alle spezifischen Abmessungen oder Merkmale an, die enge Toleranzen erfordern, die über die Standard-AM-Fähigkeiten hinausgehen (was potenzielle Bearbeitungsanforderungen impliziert).
- Anforderungen an die Oberflächenbeschaffenheit: Geben Sie die gewünschte Oberflächenausführung für verschiedene Oberflächen an, falls diese von der Standardausführung abweicht.
- Post-Processing-Bedarf: Detaillieren Sie alle erforderlichen Wärmebehandlungen, Beschichtungen oder andere Veredelungsschritte.
- Menge: Geben Sie die Anzahl der benötigten Teile an (für Prototypen oder Produktionschargen).
- Anwendungskontext (fakultativ, aber hilfreich): Eine kurze Beschreibung der Anwendung kann dem Anbieter helfen, DfAM-Vorschläge zu unterbreiten oder potenzielle Herausforderungen zu identifizieren.
- Qualitäts-/Inspektionsanforderungen: Alle spezifischen Test- oder Zertifizierungsanforderungen. Je detaillierter die Informationen sind, desto genauer wird das Angebot sein.
- A: Um das genaueste Angebot und die geschätzte Vorlaufzeit zu erhalten, sollten Sie idealerweise Folgendes angeben:
Fazit: Die Zukunft der Hochleistungskühlung ist additiv
Ein effektives Wärmemanagement bleibt ein Eckpfeiler für Leistung und Zuverlässigkeit in unzähligen Branchen. Da Geräte immer leistungsfähiger und kompakter werden, wächst die Nachfrage nach effizienteren, leichteren und kundenspezifischen Kühllösungen weiter. Die additive Metallfertigung hat sich definitiv von einer Prototyping-Technologie zu einer leistungsstarken Fertigungslösung entwickelt, die in der Lage ist, diese fortschrittlichen thermischen Herausforderungen direkt anzugehen.
Indem sie Konstrukteure von den Einschränkungen der traditionellen Fertigung befreit, ermöglicht der 3D-Metalldruck die Herstellung von industriellen Kühlrippen mit beispielloser geometrischer Komplexität. Die Nutzung von DfAM-Prinzipien ermöglicht die Konstruktion von Komponenten, die für maximale Wärmeableitung optimiert sind, durch Merkmale wie komplizierte Rippenarrays, interne Gitterstrukturen und konforme Oberflächen – was oft zu erheblichen Verbesserungen der thermischen Effizienz und zu einer Reduzierung von Gewicht und Volumen im Vergleich zu herkömmlichen Gegenstücken führt. Die Möglichkeit, Hochleistungsmaterialien wie leitfähiges CuCrZr und leichtes AlSi10Mg zu verwenden, erhöht das Potenzial für maßgeschneiderte Lösungen zusätzlich.
Obwohl Herausforderungen in Bezug auf Kosten, Präzision und Nachbearbeitung bestehen, mildert die Zusammenarbeit mit einem erfahrenen und gut ausgestatteten Metall-AM-Anbieter wie Met3dp diese Bedenken. Unser Fachwissen in der fortschrittlichen Pulverherstellung, modernsten Drucktechnologien (einschließlich SEBM), robusten Qualitätssystemen und umfassenden Nachbearbeitungsmöglichkeiten stellt sicher, dass unsere Kunden hochwertige, zuverlässige Kühlrippen erhalten, die für ihre spezifischen Anforderungen optimiert sind. Wir ermöglichen es Branchen von der Luft- und Raumfahrt über die Automobilindustrie bis hin zur Elektronik und industriellen Fertigung, Wärmemanagementlösungen der nächsten Generation zu integrieren.
Für Ingenieure, die nach Leistungsdurchbrüchen suchen, und Beschaffungsfachleute die nach zuverlässigen B2B-Lieferanten innovativen thermischen Komponenten suchen, bietet die additive Metallfertigung ein überzeugendes Wertversprechen. Sie stellt nicht nur eine neue Art der Herstellung von Teilen dar, sondern auch eine neue Art, über thermisches Design nachzudenken.
Sind Sie bereit, zu erkunden, wie der 3D-Metalldruck Ihre Wärmemanagementstrategie revolutionieren kann? Kontaktieren Sie Met3dp noch heute, um Ihre Kühlrippenanwendung zu besprechen und die Vorteile der additiven Fertigung zu entdecken.
Teilen auf
MET3DP Technology Co., LTD ist ein führender Anbieter von additiven Fertigungslösungen mit Hauptsitz in Qingdao, China. Unser Unternehmen ist spezialisiert auf 3D-Druckgeräte und Hochleistungsmetallpulver für industrielle Anwendungen.
Fragen Sie an, um den besten Preis und eine maßgeschneiderte Lösung für Ihr Unternehmen zu erhalten!
Verwandte Artikel
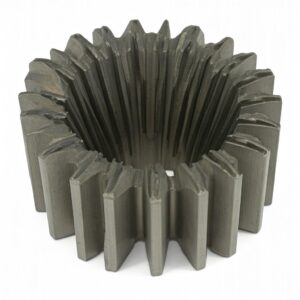
Hochleistungs-Düsenschaufelsegmente: Revolutionierung der Turbineneffizienz mit 3D-Metalldruck
Mehr lesen "Über Met3DP
Aktuelles Update
Unser Produkt
KONTAKT US
Haben Sie Fragen? Senden Sie uns jetzt eine Nachricht! Wir werden Ihre Anfrage mit einem ganzen Team nach Erhalt Ihrer Nachricht bearbeiten.
Holen Sie sich Metal3DP's
Produkt-Broschüre
Erhalten Sie die neuesten Produkte und Preislisten
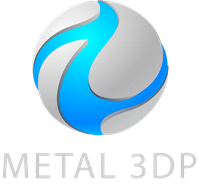
Metallpulver für 3D-Druck und additive Fertigung