Korrosionsbeständige Rohrverschraubungen aus rostfreiem Stahl 316L
Inhaltsübersicht
Einleitung: Die entscheidende Rolle korrosionsbeständiger Rohrleitungsarmaturen in der modernen Industrie
Rohrverschraubungen sind die unbesungenen Helden unzähliger industrieller Systeme. Diese wesentlichen Komponenten verbinden Rohre, leiten den Durchfluss um, ändern die Rohrgröße und steuern die Flüssigkeitsbewegung in komplexen Netzwerken. Von riesigen chemischen Verarbeitungsanlagen und Offshore-Ölplattformen bis hin zu sterilen pharmazeutischen Produktionslinien und lebensmittelverarbeitenden Anlagen hängt die Zuverlässigkeit von Rohrleitungssystemen direkt von der Integrität ihrer Fittings ab. In vielen anspruchsvollen Umgebungen sind Standardmaterialien jedoch unzureichend. Die allgegenwärtige Bedrohung durch Korrosion - die allmähliche Zersetzung von Materialien durch chemische Reaktionen mit der Umgebung - kann zu Leckagen, Systemausfällen, kostspieligen Ausfallzeiten, Verunreinigungen und erheblichen Sicherheitsrisiken führen. An dieser Stelle wird die Spezifikation korrosionsbeständiger Materialien nicht nur vorteilhaft, sondern absolut entscheidend für den betrieblichen Erfolg, die Sicherheit und die Langlebigkeit.
Jahrzehntelang waren Werkstoffe wie rostfreie Stähle die bevorzugte Lösung. Unter ihnen, 316L rostfreier Stahl zeichnet sich durch seine hervorragende Beständigkeit gegen eine Vielzahl von korrosiven Medien, insbesondere Chloride, aus und ist daher ideal für Anwendungen in der Schifffahrt, der Chemie und der Lebensmittelindustrie. Der niedrige Kohlenstoffgehalt ("L") verbessert die Schweißbarkeit und die Beständigkeit gegen Sensibilisierung, eine Form der interkristallinen Korrosion, zusätzlich. Wenn Standard 316L nicht ausreicht, können fortschrittliche Legierungen wie 254SMO bieten eine noch größere Widerstandsfähigkeit in sehr aggressiven Umgebungen.
Traditionell wurden diese Armaturen mit Verfahren wie Gießen, Schmieden und Zerspanen hergestellt. Diese Methoden sind zwar effektiv, haben aber oft ihre Grenzen, z. B. lange Vorlaufzeiten für die Werkzeugherstellung, Konstruktionsbeschränkungen, Materialabfall und Schwierigkeiten bei der effizienten Herstellung komplexer oder kundenspezifischer Geometrien, insbesondere bei kleinen bis mittleren Stückzahlen oder Ersatzteilen. Hier vollzieht sich ein Paradigmenwechsel, der durch Fortschritte in den folgenden Bereichen vorangetrieben wird Additive Fertigung von Metall (AM)die gemeinhin als 3D-Metalldruck bekannt ist.
Metal AM ermöglicht die direkte Herstellung von dichten, funktionalen Metallteilen, einschließlich komplizierter Rohrverbindungen, Schicht für Schicht aus einer digitalen Konstruktionsdatei unter Verwendung von speziellen Metallpulvern. Diese Technologie ermöglicht eine noch nie dagewesene Designfreiheit, erleichtert das Rapid Prototyping und die Produktion auf Abruf, minimiert den Materialabfall und ermöglicht die Herstellung optimierter, leistungsstarker Komponenten, die bisher nur schwer oder gar nicht zu fertigen waren. Für Ingenieure, die Fluidsysteme der nächsten Generation entwerfen, und für Beschaffungsmanager, die nach robusten, zuverlässigen und effizient beschafften Komponenten suchen, wird es immer wichtiger, das Zusammenspiel von korrosionsbeständigen Materialien wie 316L und den Möglichkeiten der Metall-AM zu verstehen. Unternehmen wie Met3dpDie auf hochentwickelte Metallpulver und industrielle 3D-Drucksysteme spezialisierten Unternehmen stehen bei der Bereitstellung dieser innovativen Lösungen an vorderster Front und bieten Wege zu verbesserter Leistung und optimierten Lieferketten. Dieser Artikel befasst sich mit den Besonderheiten des Metall-3D-Drucks, insbesondere mit 316L und verwandten Legierungen, zur Herstellung von hochleistungsfähigen, korrosionsbeständigen Rohrfittings für anspruchsvolle industrielle Anwendungen.
Anwendungen enthüllt: Wo sind korrosionsbeständige 316L-Rohrverschraubungen unverzichtbar?
Die Nachfrage nach korrosionsbeständigen Rohrverschraubungen, insbesondere nach solchen aus Edelstahl 316L, erstreckt sich über ein breites Spektrum von Branchen, in denen die Handhabung von Flüssigkeiten unter schwierigen Bedingungen von größter Bedeutung ist. Die inhärenten Eigenschaften von 316L - seine Widerstandsfähigkeit gegen Lochfraß und Spaltkorrosion durch Chloride, seine Langlebigkeit und seine hygienischen Qualitäten - machen es in Anwendungen unverzichtbar, in denen andere Materialien schnell versagen würden. Lassen Sie uns einige Schlüsselsektoren und spezifische Anwendungsfälle untersuchen:
1. Chemisch verarbeitende Industrie (CPI):
- Umwelt: Exposition gegenüber einer breiten Palette von Säuren, Laugen, Lösungsmitteln und chemischen Zwischenprodukten, häufig bei hohen Temperaturen und Drücken.
- Anwendungen: Verbindung von Reaktoren, Destillationskolonnen, Wärmetauschern, Lagertanks und Transferleitungen. Armaturen wie Bögen, T-Stücke, Reduzierstücke und Flansche müssen potenziell gefährliche Stoffe zuverlässig und ohne Beeinträchtigung aufnehmen.
- Warum 316L/254SMO? 316L bietet eine breite Beständigkeit, die für viele gängige Chemikalien geeignet ist. Bei hochkonzentrierten Chloriden, Schwefelsäure oder anderen aggressiven Medien kann die überlegene Beständigkeit superaustenitischer nichtrostender Stähle wie 254SMO von Verfahrenstechnikern gefordert werden. Die Vermeidung von Verunreinigungen und die Gewährleistung einer langen Lebensdauer sind entscheidend für die Sicherheit und Wirtschaftlichkeit der Anlage. Beschaffungsmanager in der CPI suchen nach zuverlässigen Lieferanten, die Optionen für Massenlieferungen und dokumentierte Materialrückverfolgbarkeit bieten.
2. Marine und Offshore:
- Umwelt: Ständiger Kontakt mit Salzwasser (hohe Chloridkonzentration), Salzsprühnebel und feuchte, korrosive Umgebungen. Auch Biofouling kann die Korrosion verschlimmern.
- Anwendungen: Seewasserkühlsysteme, Ballastwassermanagementsysteme, Hydraulikleitungen, Entsalzungsanlagen (insbesondere Speisewasser- und Solebehandlung) und allgemeine Sanitärinstallationen auf Schiffen und Offshore-Plattformen.
- Warum 316L/254SMO? 316L bietet eine gute Leistung in Meeresatmosphären und allgemeinen Meerwasseranwendungen. In stagnierendem Meerwasser, bei geringer Strömung oder in Spalten (z. B. unter Flanschdichtungen) können jedoch Lochfraß und Spaltkorrosion ein Problem darstellen. 254SMO bietet mit seinem höheren Molybdän- und Stickstoffgehalt eine deutlich bessere Beständigkeit gegen diese lokal begrenzten Korrosionsformen und ist daher ideal für kritische Meerwassersysteme und Entsalzungskomponenten. Die Beschaffung von Industriearmaturen für die Schifffahrt erfordert die Einhaltung bestimmter maritimer Normen und Zertifizierungen.
3. Öl und Gas (Upstream, Midstream, Downstream):
- Umwelt: Exposition gegenüber korrosiven Elementen wie Schwefelwasserstoff (H2S - Sauergas), Kohlendioxid (CO2), Chloriden (im Produktionswasser) und verschiedenen Kohlenwasserstoffen, häufig unter hohem Druck und bei hohen Temperaturen.
- Anwendungen: Fließleitungen, Rohrleitungen für Verarbeitungsanlagen, Einspritzleitungen (Wasser, Chemikalien), Versorgungssysteme auf Plattformen und in Raffinerien.
- Warum 316L/254SMO? 316L wird unter weniger strengen Einsatzbedingungen verwendet, insbesondere in Versorgungssystemen oder dort, wo der Chlorid- und H2S-Gehalt kontrolliert wird. Für den Umgang mit Sauergas oder hochchloridhaltigem Produktionswasser sind jedoch häufig widerstandsfähigere Legierungen erforderlich. Während nichtrostende Duplexstähle weit verbreitet sind, kann 254SMO bei bestimmten Anwendungen mit hohem Chloridgehalt und moderaten Temperaturen, bei denen eine höhere Lochfraßbeständigkeit erforderlich ist, eine brauchbare Alternative darstellen. Die Zuverlässigkeit jeder einzelnen Armatur ist aufgrund der extremen Drücke und der gefährlichen Natur der Flüssigkeiten von größter Bedeutung.
4. Pharmazeutische und Biotechnologie:
- Umwelt: Strenge Anforderungen an Reinheit, Reinigungsfähigkeit, Sterilisierbarkeit und Korrosionsbeständigkeit gegenüber Prozessflüssigkeiten und Reinigungsmitteln (z. B. Clean-in-Place/Sterilize-in-Place-Systeme mit Laugen, Säuren, Dampf).
- Anwendungen: Prozessrohrleitungen für Bioreaktoren, Gärtanks, Reinigungssysteme (Chromatographie, Filtration), WFI (Water For Injection)-Verteilerkreisläufe, Transferpanels.
- Warum 316L? 316L ist das vorherrschende Material aufgrund seiner ausgezeichneten Reinigungsfähigkeit, seiner guten Korrosionsbeständigkeit gegenüber typischen pharmazeutischen Prozessflüssigkeiten und Reinigungschemikalien, seiner relativ niedrigen Kosten und seiner etablierten Akzeptanz (ASME BPE-Normen). Seine glatte Oberflächenbeschaffenheit minimiert potenzielle Bereiche für Bakterienwachstum. Die Verhinderung von Produktkontaminationen hat absolute Priorität. Die Beschaffung umfasst häufig die Beschaffung von hygienischen Fittings (Sanitärklemmen, Tri-Clamp®) mit spezifischen Anforderungen an die Oberflächenbeschaffenheit (elektropoliert).
5. Essen und Trinken:
- Umwelt: Ähnlich wie in der Pharmazie werden hohe Anforderungen an Hygiene, Reinigungsfähigkeit und Beständigkeit gegen Lebensmittelsäuren (Zitronensäure, Essigsäure), Reinigungslösungen und Prozessbedingungen (Temperaturschwankungen, Dampf) gestellt.
- Anwendungen: Molkereilinien, Brauerei-Rohrleitungen, Saft- und Saucenproduktion, Wasserabfüllanlagen, Zutatentransferlinien.
- Warum 316L? Wie in der Pharmazie wird 316L wegen seiner hygienischen Eigenschaften, seiner Korrosionsbeständigkeit gegenüber Lebensmitteln und der Einhaltung der Vorschriften für den Kontakt mit Lebensmitteln häufig verwendet. Fittings müssen leicht zu reinigen sein und ein Auslaugen in das Produkt verhindern. Die Fähigkeit, lebensmitteltaugliche Fittings schnell zu beschaffen, manchmal in kundenspezifischen Konfigurationen für bestimmte Verarbeitungslinien, ist für die Hersteller entscheidend.
6. Zellstoff und Papier:
- Umwelt: Stark ätzende Bleichchemikalien (Chlordioxid, Peroxide), saure Prozessflüssigkeiten und hohe Chloridkonzentrationen in Wildwassersystemen.
- Anwendungen: Rohrleitungen der Bleichanlage, Fermenterumlaufleitungen, Stoffaufbereitungssysteme, Rückgewinnungskesselbereiche.
- Warum 316L/254SMO? Während 316L in weniger aggressiven Bereichen eingesetzt wird, erfordern die extrem korrosiven Bedingungen in Bleichanlagen oft höhere Legierungen. 254SMO wird häufig wegen seiner hervorragenden Beständigkeit gegen Chlorid-Spannungsrisskorrosion und Lochfraß/Spaltkorrosion in diesen anspruchsvollen Umgebungen spezifiziert.
7. Wasser- und Abwasserbehandlung:
- Umwelt: Exposition gegenüber behandeltem und unbehandeltem Wasser (unterschiedliche chemische Zusammensetzung, Potenzial für Chloride, Sulfate), Desinfektionschemikalien (Chlor, Ozon) und Schlamm.
- Anwendungen: Chemikaliendosierleitungen, Filtersysteme, Belüftungsrohre, Schlammbehandlung, Entsalzung (wie in Marine erwähnt).
- Warum 316L/254SMO? 316L ist für viele kommunale Wasseranwendungen geeignet. Bei Brackwasser, Industrieabwässern mit hohem Chloridgehalt oder bestimmten chemischen Behandlungsstufen kann jedoch die erhöhte Beständigkeit von 254SMO oder anderen superaustenitischen/Duplex-Stählen für langfristige Zuverlässigkeit erforderlich sein.
Allen diesen Sektoren gemeinsam ist der Bedarf an zuverlässigen, langlebigen Rohrverschraubungen, die den spezifischen korrosiven Herausforderungen standhalten können. Ingenieure müssen die Werkstoffe auf der Grundlage der genauen Betriebsbedingungen sorgfältig auswählen, während Beschaffungsmanager Zugang zu Lieferanten benötigen, die qualitativ hochwertige, zertifizierte Fittings liefern können und dabei möglicherweise fortschrittliche Fertigungsmethoden nutzen wie 3D-Druck von Metall zur Erfüllung spezifischer Designanforderungen oder anspruchsvoller Vorlaufzeiten.
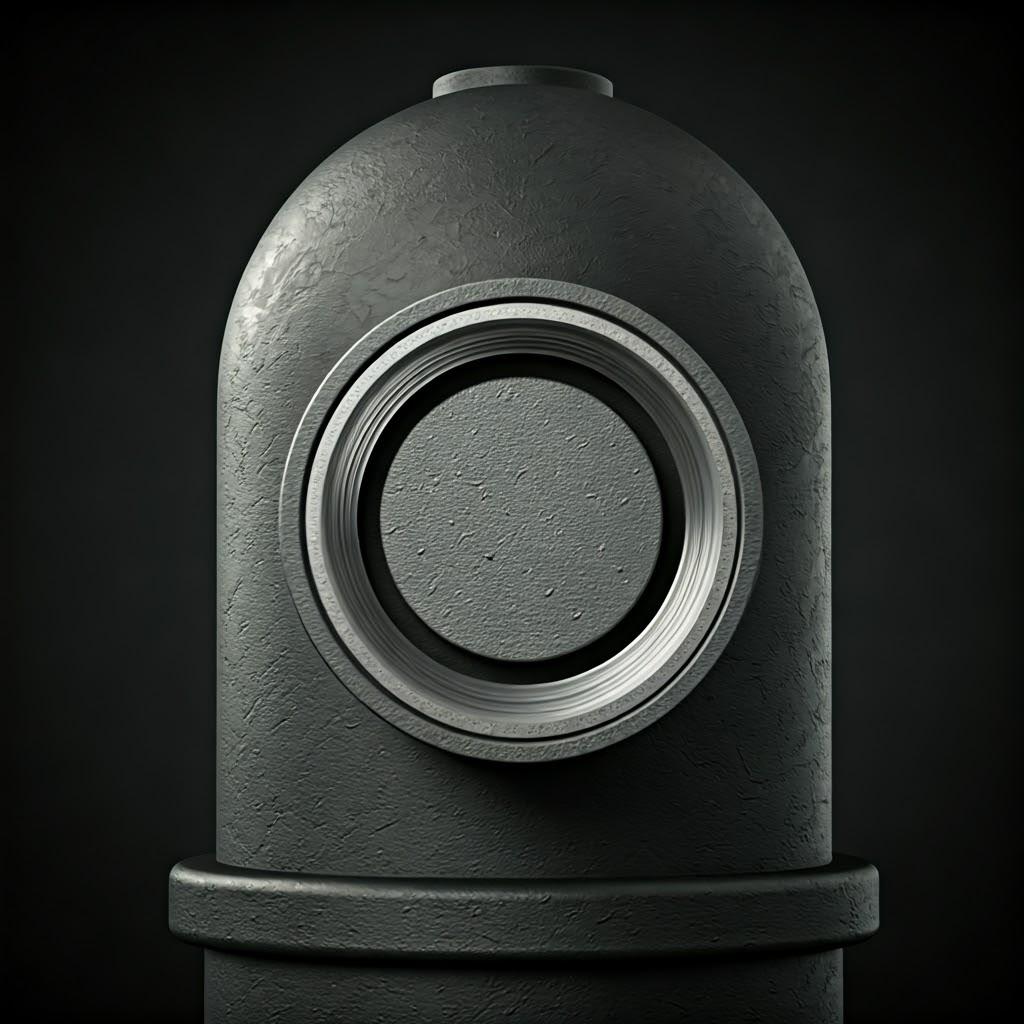
Der Vorteil der additiven Fertigung: Warum Metall-3D-Druck für Rohrverbindungen?
Während herkömmliche Herstellungsverfahren wie Gießen, Schmieden und maschinelle Bearbeitung der Industrie seit langem bei der Herstellung von Rohrformstücken dienen, bietet die additive Fertigung von Metallen (AM) eine Reihe überzeugender Vorteile, insbesondere für korrosionsbeständige Formstücke wie solche aus 316L oder 254SMO. Diese Vorteile kommen bei Ingenieuren, die eine optimale Leistung anstreben, und bei Beschaffungsmanagern, die sich auf Effizienz, Kosteneffizienz und Stabilität der Lieferkette konzentrieren, gut an.
1. Unerreichte Gestaltungsfreiheit und Komplexität:
- Herausforderung mit traditionellen Methoden: Das Gießen erfordert Formen, was die interne Komplexität einschränkt und oft zu sperrigen Designs führt. Die spanabhebende Bearbeitung beginnt mit massivem Material, was zu erheblichem Abfall führt und Probleme mit komplizierten inneren Kanälen oder gemischten Oberflächen mit sich bringt. Schmieden bietet Festigkeit, ist aber auf relativ einfache Formen beschränkt.
- AM Vorteil: Metal AM baut Teile Schicht für Schicht direkt aus einem CAD-Modell auf. Dies ermöglicht:
- Optimierte interne Geometrien: Entwicklung von Armaturen mit glatteren internen Strömungswegen, die Druckverluste und Turbulenzen reduzieren. Interne Merkmale wie Strömungsteiler oder Mischer können direkt integriert werden.
- Teil Konsolidierung: Kombination mehrerer Komponenten einer Armaturenbaugruppe in einem einzigen gedruckten Teil, wodurch potenzielle Leckstellen, die Montagezeit und die Komplexität der Lagerhaltung reduziert werden.
- Komplexe äußere Formen: Herstellung von Armaturen, die in enge Räume passen oder sich nahtlos in die umgebende Ausrüstung einfügen, ohne die Einschränkungen durch Formschrägen oder den Zugang zu Bearbeitungswerkzeugen.
- Gewichtsreduzierung: Einbeziehung von Gitterstrukturen oder Topologieoptimierung (wo anwendbar und strukturell sinnvoll), um das Gewicht zu reduzieren, ohne die Festigkeit zu beeinträchtigen - besonders wichtig in der Luft- und Raumfahrt oder bei mobilen Anwendungen.
2. Schnelligkeit, Agilität und kürzere Vorlaufzeiten:
- Herausforderung mit traditionellen Methoden: Die Erstellung von Modellen und Formen für das Gießen oder die Einrichtung komplexer mehrachsiger Bearbeitungsroutinen kann Wochen oder Monate dauern, insbesondere bei Sonderanfertigungen oder geringen Stückzahlen. Mindestbestellmengen (MOQs) für Guss-/Schmiedeteile können für die Herstellung von Prototypen oder die Beschaffung von nur wenigen Ersatzteilen prohibitiv sein.
- AM Vorteil:
- Rapid Prototyping: Die Herstellung von Funktionsprototypen aus dem Zielmaterial (z. B. 316L) innerhalb weniger Tage ermöglicht eine schnelle Design-Iteration und -Überprüfung, bevor größere Produktionsläufe in Angriff genommen werden.
- Beseitigung von Werkzeugen: AM ist ein werkzeugloser Prozess, bei dem der erhebliche Zeit- und Kostenaufwand für die Herstellung, Wartung und Lagerung von Formen oder speziellen Vorrichtungen entfällt.
- Produktion auf Abruf: Die Herstellung von Armaturen nach Bedarf reduziert die Kosten für die Lagerhaltung und den mit Überbeständen verbundenen Abfall. Dies ist ideal für Ersatzteile, insbesondere für ältere Systeme, bei denen die ursprünglichen Lieferanten möglicherweise nicht mehr existieren.
- Schnelleres Time-to-Market: Bei neuen Produktentwicklungen oder System-Upgrades beschleunigt AM die Zeitspanne von der Konzeption bis zur Bereitstellung funktionaler Teile erheblich. Diese Agilität ist ein wichtiger Wettbewerbsvorteil.
3. Materialeffizienz und Nachhaltigkeit:
- Herausforderung mit traditionellen Methoden: Bei der subtraktiven Fertigung (spanabhebende Bearbeitung) können erhebliche Materialabfälle (Späne) anfallen, die manchmal das Gewicht des fertigen Teils übersteigen. Beim Gießen kann auch erhebliches Material in Anschnitten und Speisern anfallen, das entfernt werden muss.
- AM Vorteil: AM, insbesondere Pulverbettschmelzverfahren, ist von Natur aus ressourcenschonender.
- Fast-Netzform: Die Teile werden nahe an ihren endgültigen Abmessungen gefertigt, wodurch der Materialbedarf minimiert wird und weniger Nachbearbeitung erforderlich ist.
- Wiederverwendbarkeit des Pulvers: Ungeschmolzenes Metallpulver in der Baukammer kann oft zurückgewonnen, gesiebt und in nachfolgenden Bauvorgängen wiederverwendet werden (unter Einhaltung strenger Qualitätskontrollverfahren), was die Materialausnutzung weiter verbessert. Auch wenn das 100%-Verfahren nicht abfallfrei ist, stellt es doch eine erhebliche Verbesserung gegenüber herkömmlichen subtraktiven Verfahren dar.
4. Personalisierung und Kleinserienproduktion:
- Herausforderung mit traditionellen Methoden: Hohe Rüstkosten machen die Herstellung von Kleinserien oder einmaligen Sonderanfertigungen durch Gießen oder Schmieden wirtschaftlich schwierig.
- AM Vorteil: Da AM keine teilespezifischen Werkzeuge erfordert, sind die Kosten pro Teil weniger von der Losgröße abhängig. Das macht es äußerst kosteneffizient für:
- Kundenspezifische Beschläge: Anpassung von Abmessungen, Anschlusstypen oder internen Merkmalen an spezifische Anwendungsanforderungen ohne hohe Werkzeugkosten.
- Produktion von Kleinserien: Effiziente Herstellung von Nischenbeschlägen oder Ersatzteilen in kleinen Mengen.
- Brückenproduktion: Herstellung erster Chargen eines neuen Armaturendesigns mittels AM, während die traditionellen Werkzeuge für die Massenproduktion vorbereitet werden.
5. Potenzial für verbesserte Leistung:
- AM Vorteil: Die schnelle Erstarrung, die vielen Metall-AM-Verfahren eigen ist, kann zu feinkörnigen Mikrostrukturen führen, die im Vergleich zu konventionell gegossenen Teilen bessere mechanische Eigenschaften (Festigkeit, Ermüdungsbeständigkeit) bieten können, obwohl Nachbearbeitungen wie Wärmebehandlung zur Optimierung dieser Eigenschaften entscheidend sind. Darüber hinaus ermöglicht die Designfreiheit eine Leistungsoptimierung (z. B. Fließeffizienz), die mit anderen Mitteln nicht zu erreichen ist. Unternehmen mit fundiertem materialwissenschaftlichem Fachwissen, wie Met3dp, die ihre fortschrittlichen Pulverherstellungssysteme nutzen, können sicherstellen, dass die entstehenden Teile strenge Leistungsanforderungen erfüllen.
Auswirkungen auf B2B-Einkäufer und das Beschaffungswesen:
- Widerstandsfähigkeit der Lieferkette: AM bietet einen digitalen Herstellungsweg, der die Abhängigkeit von geografisch konzentrierten traditionellen Lieferanten und komplexen Werkzeuglieferketten verringert. Teile können potenziell näher am Ort des Bedarfs gedruckt werden.
- Geringere Lagerkosten: Durch die Möglichkeit, nach Bedarf zu drucken, wird der Bedarf an großen Ersatzteilbeständen minimiert, wodurch Kapital und Lagerfläche frei werden.
- Total Cost of Ownership: Auch wenn die Kosten pro Teil bei AM manchmal höher sind als bei der Massenproduktion herkömmlicher Teile, können die Vorteile in Form von kürzeren Durchlaufzeiten, minimiertem Abfall, geringeren Werkzeugkosten, reduziertem Lagerbestand und potenziell verbesserter Leistung zu niedrigeren Gesamtbetriebskosten führen, insbesondere bei komplexen, kundenspezifischen oder in kleinen Stückzahlen gefertigten Fittings.
- Rationalisierte RFQs: Digitale Konstruktionsdateien (CAD-Modelle) bilden die Grundlage für die AM-Produktion und können den Prozess der Angebotsanfrage (RFQ) bei qualifizierten AM-Dienstleistern vereinfachen.
Zusammenfassend lässt sich sagen, dass der 3D-Metalldruck eine leistungsstarke Alternative oder Ergänzung zu herkömmlichen Methoden zur Herstellung korrosionsbeständiger Rohrformstücke darstellt. Seine Fähigkeit, Komplexität zu bewältigen, die Lieferung zu beschleunigen, Anpassungen zu ermöglichen und potenziell die Leistung zu verbessern, macht ihn zu einer zunehmend attraktiven Option für Ingenieure und Beschaffungsexperten in anspruchsvollen Branchen.
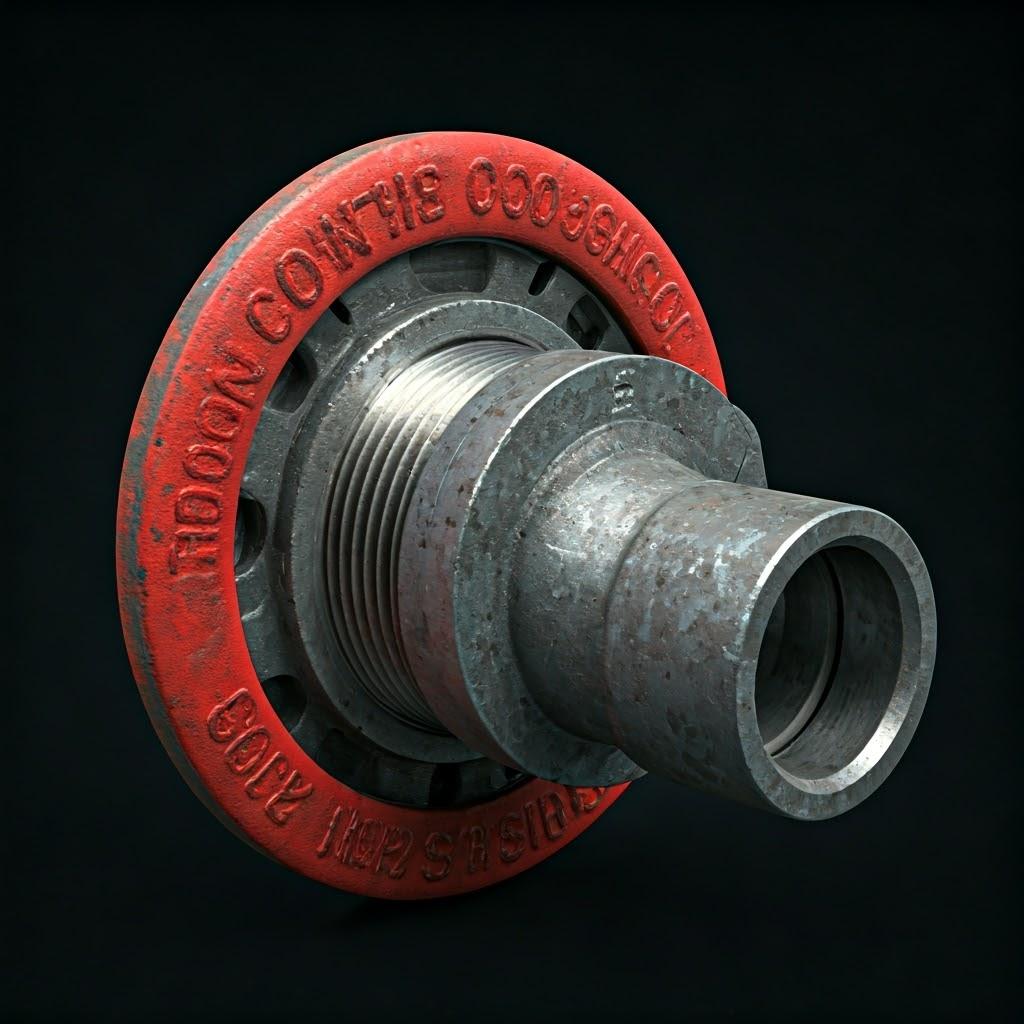
Materialfragen: Tiefe Einblicke in 316L und 254SMO für die additive Fertigung
Der Erfolg eines jeden additiv gefertigten Bauteils hängt entscheidend von der Qualität und Eignung des verwendeten Materials ab. Für korrosionsbeständige Rohrformstücke kommen in erster Linie Edelstahl 316L und die superaustenitische Sorte 254SMO in Frage, die je nach der Schwere der Anwendungsumgebung unterschiedliche Vorteile bieten. Das Verständnis ihrer Eigenschaften, ihres Verhaltens während der AM-Verarbeitung und der Bedeutung der Pulverqualität ist für Ingenieure und Beschaffungsspezialisten von entscheidender Bedeutung.
316L-Edelstahl (UNS S31603): Das vielseitige Arbeitspferd
- Zusammensetzung: Eine austenitische rostfreie Stahllegierung, die hauptsächlich Eisen (Fe), Chrom (Cr: ~16-18%), Nickel (Ni: ~10-14%) und Molybdän (Mo: ~2-3%) enthält. Die Bezeichnung "L" steht für einen niedrigen Kohlenstoffgehalt (<0,03%), der entscheidend für die Minimierung der Sensibilisierung (Chromkarbidausscheidung an den Korngrenzen) während des Schweißens oder der thermischen Zyklen bei AM ist, wodurch eine maximale Korrosionsbeständigkeit erhalten bleibt, insbesondere im eingebauten oder spannungsfreien Zustand.
- Wichtige Eigenschaften:
- Ausgezeichnete allgemeine Korrosionsbeständigkeit: Widersteht einer Vielzahl von atmosphärischen, chemischen und maritimen Bedingungen.
- Gute Lochfraß- und Spaltkorrosionsbeständigkeit: Der Molybdängehalt bietet im Vergleich zu Edelstahl 304/304L eine deutlich bessere Beständigkeit gegen chloridinduzierte lokale Korrosion.
- Gute Umformbarkeit und Schweißbarkeit: Obwohl dies für die Herstellung von AM-Teilen weniger relevant ist, ist eine gute Schweißbarkeit wichtig, wenn nach dem Druck geschweißt werden muss.
- Hygienische Qualitäten: Erzielt glatte Oberflächen und eignet sich daher für Anwendungen in der Lebensmittel-, Getränke- und Pharmaindustrie.
- Biokompatibilität: Weit verbreitet für medizinische Implantate (für die Verwendung als Implantat sind jedoch spezielle Zertifizierungen erforderlich).
- Gute Festigkeit und Duktilität: Bietet ein gutes Gleichgewicht der mechanischen Eigenschaften bei Raumtemperatur und mäßig erhöhten Temperaturen.
- Eignung für die additive Fertigung: 316L ist einer der gebräuchlichsten und am besten charakterisierten nichtrostenden Stähle, die in der Metall-AM verwendet werden, insbesondere im Laser Powder Bed Fusion (L-PBF) und Electron Beam Powder Bed Fusion (EB-PBF/SEBM). Die Druckparameter sind relativ gut etabliert und ermöglichen die Herstellung von Teilen mit hoher Dichte (>99,5%), deren Eigenschaften mit denen von Knetteilen vergleichbar sind oder diese nach entsprechender Nachbearbeitung (wie Spannungsabbau oder Lösungsglühen) sogar übertreffen.
- Beständigkeit gegen Korrosionsmechanismen: Widersteht in erster Linie gleichmäßiger Korrosion und bietet aufgrund der schützenden passiven Chromoxidschicht, die durch Molybdän verstärkt wird, einen guten Schutz gegen Chlorid-Lochfraß und Spaltkorrosion in gemäßigten Umgebungen.
- Anwendungen in AM-Armaturen: Ideal für die allgemeine chemische Verarbeitung, Lebensmittel-/Getränkeleitungen, pharmazeutische Systeme, Beschläge für die Schifffahrt (oberhalb der Wasserlinie oder bei mäßiger Exposition), architektonische Elemente und Wasseraufbereitungskomponenten, bei denen eine gute Korrosionsbeständigkeit und Reinigungsfähigkeit erforderlich ist.
254SMO® (UNS S31254): Überlegene Beständigkeit für extreme Bedingungen
- Zusammensetzung: Ein hochlegierter "superaustenitischer" rostfreier Stahl. Im Vergleich zu 316L enthält er wesentlich mehr Chrom (~20%), Nickel (~18%) und Molybdän (~6%) sowie einen bedeutenden Anteil an Stickstoff (~0,2%). (Hinweis: 254SMO ist eine Marke von Outokumpu).
- Wichtige Eigenschaften:
- Außergewöhnliche Lochfraß- und Spaltkorrosionsbeständigkeit: Der hohe Cr-, Mo- und N-Gehalt führt zu einer sehr hohen Pitting Resistance Equivalent Number (PREN = Cr% + 3,3 * Mo% + 16 * N%), typischerweise >42, was auf eine hervorragende Beständigkeit in Umgebungen mit hohem Chloridgehalt wie Meerwasser, Brackwasser und Bleichlösungen hinweist. Erheblich besser als 316L (PREN ~24).
- Hohe Beständigkeit gegen Chlorid-Spannungsrisskorrosion (SCC): Bietet eine bessere Beständigkeit gegen SCC als die Standard-Edelstähle der 300er-Reihe, ist jedoch nicht immun dagegen.
- Hohe Festigkeit: Hat eine höhere Streck- und Zugfestigkeit als 316L.
- Gut schweißbar: Kann geschweißt werden, erfordert jedoch geeignete Verfahren und Zusatzwerkstoffe.
- Gute Duktilität und Zähigkeit: Behält seine gute Zähigkeit auch bei niedrigen Temperaturen bei.
- Eignung für die additive Fertigung: 254SMO-Pulver ist zwar weniger verbreitet als 316L, aber es ist verfügbar und kann mit AM-Techniken wie L-PBF verarbeitet werden. Das Erreichen optimaler Eigenschaften und Korrosionsbeständigkeit erfordert eine sorgfältige Entwicklung der Parameter und häufig spezifische Wärmebehandlungen nach der Verarbeitung (in der Regel Lösungsglühen bei hohen Temperaturen, gefolgt von schnellem Abschrecken), um sicherzustellen, dass die Legierungselemente ordnungsgemäß gelöst und schädliche Phasen vermieden werden. Die Verarbeitung kann aufgrund des höheren Legierungsgehalts schwieriger sein als bei 316L.
- Beständigkeit gegen Korrosionsmechanismen: Speziell entwickelt zur Bekämpfung von schwerem Lochfraß, Spaltkorrosion und SCC in aggressiven chloridhaltigen Medien, wo 316L unzureichend wäre. Der hohe Legierungsanteil erzeugt einen sehr stabilen und schnell reparierenden Passivfilm.
- Anwendungen in AM-Armaturen: Sie eignen sich für sehr anspruchsvolle Anwendungen wie Komponenten von Entsalzungsanlagen (Soleerhitzer, Rohrleitungen), Bleichanlagen für die Zellstoff- und Papierindustrie, Meerwasseraufbereitungssysteme für Offshore-Plattformen, chemische Verarbeitungsanlagen für konzentrierte Chloride oder Säuren und Rauchgasentschwefelungsanlagen.
Warum die Qualität von Materialpulvern bei AM wichtig ist
Unabhängig von der gewählten Legierung ist die Qualität des im AM-Verfahren verwendeten Metallpulvers von entscheidender Bedeutung für die Herstellung zuverlässiger, leistungsstarker Rohrformstücke. Hier spielen spezialisierte Pulverhersteller wie Met3dp eine entscheidende Rolle. Zu den wichtigsten Pulvereigenschaften gehören:
- Sphärizität: Hochkugelförmige Pulverpartikel sorgen für eine gute Fließfähigkeit im Wiederbeschichtungssystem der AM-Maschine und führen zu einer dichteren, gleichmäßigeren Packung im Pulverbett. Dies trägt wesentlich dazu bei, eine hohe Teiledichte zu erreichen und die Porosität zu minimieren. Met3dp nutzt fortschrittliche Gaszerstäubung und Plasma-Rotations-Elektroden-Verfahren (PREP) zur Herstellung von Pulvern mit hoher Sphärizität.
- Partikelgrößenverteilung (PSD): Eine kontrollierte PSD, die für das jeweilige AM-Verfahren (z. B. L-PBF, SEBM) optimiert ist, ist entscheidend für ein gleichmäßiges Schmelzen, eine gute Oberflächengüte und vorhersehbare Teileigenschaften. Zu viele feine Partikel können die Fließfähigkeit behindern und ein Sicherheitsrisiko darstellen, während zu viele große Partikel zu unvollständigem Schmelzen und Porosität führen können.
- Chemische Zusammensetzung: Die Pulverchemie muss sich streng an die angegebene Legierungsnorm halten (z. B. ASTM-Normen für 316L oder S31254). Verunreinigungen oder Abweichungen können die Korrosionsbeständigkeit und die mechanischen Eigenschaften beeinträchtigen. Eine strenge Qualitätskontrolle bei der Herstellung und Handhabung des Pulvers ist daher unerlässlich.
- Fließfähigkeit: Wie bereits erwähnt, sorgt eine gute Fließfähigkeit für eine gleichmäßige Pulverschichtabscheidung, was für ein gleichmäßiges Schmelzen und fehlerfreie Teile von grundlegender Bedeutung ist.
- Abwesenheit von Satelliten und Porosität: Qualitativ hochwertige Pulver sollten nur minimale Satelliten (kleinere Partikel, die an größeren Partikeln haften) und eine geringe innere Porosität aufweisen, die sich beide negativ auf die Packungsdichte und die Qualität des Endprodukts auswirken können.
Die Rolle von Met3dp bei der Materialexzellenz:
Das Engagement von Met3dp für den Einsatz branchenführender Zerstäubungstechnologien und eine strenge Qualitätskontrolle gewährleistet, dass die hochwertige Metallpulvereinschließlich rostfreier Stähle wie 316L und potenziell fortschrittlicher Legierungen, erfüllen die anspruchsvollen Anforderungen für kritische Anwendungen wie korrosionsbeständige Rohrverbindungen. Ihr Fachwissen in der Pulverherstellung schlägt sich direkt in der Herstellung von dichten, zuverlässigen und leistungsstarken AM-Komponenten mit hervorragenden mechanischen Eigenschaften und Korrosionsbeständigkeit nieder. Bei der Beschaffung von AM-Fittings ist es ebenso wichtig, die Pulverquelle und die Verpflichtung des Lieferanten zur Materialqualität zu kennen wie den Druckprozess selbst.
Vergleichende Übersichtstabelle:
Merkmal | 316L-Edelstahl (UNS S31603) | 254SMO® (UNS S31254) |
---|---|---|
Primäre Anwendung | Allgemeine Korrosionsbeständigkeit, mäßige Chloride | Starke Chloridbelastungen, hohe Lochfraßbeständigkeit |
Wichtige Legierungselemente | Cr (~17%), Ni (~12%), Mo (~2,5%), niedriges C (<0,03%) | Cr (~20%), Ni (~18%), Mo (~6%), N (~0,2%) |
PREN (typisch) | ~24 | >42 |
Lochfraß-/Spaltresistent. | Gut | Ausgezeichnet |
Chlorid SCC-Beständigkeit | Mäßig | Gut |
Stärke | Gut | Hoch |
AM Verarbeitbarkeit | Gut etabliert, relativ einfach | Anspruchsvoller, erfordert sorgfältige Kontrolle der Parameter |
Gemeinsamer AM-Nachbearbeitungsprozess | Stressabbau / Lösungsglühen | Lösungsglühen & Abschrecken |
Relative Kosten | Unter | Höher |
Geeignete Branchen | CPI (allgemein), Lebensmittel/Bev, Pharma, Marine (mod.) | Entsalzung, Zellstoff/Papier (Bleiche), Offshore (schwer) |
In Blätter exportieren
Die Wahl zwischen 316L und 254SMO für eine additiv gefertigte Rohrverschraubung erfordert eine gründliche Analyse der Einsatzumgebung, der Leistungsanforderungen und des Budgets, wobei stets die Verwendung eines hochwertigen, prozessoptimierten Metallpulvers sichergestellt werden muss.
Design für Langlebigkeit: Wichtige Überlegungen für AM-Rohrfittings
Die Umstellung der Konstruktion eines Rohrfittings von herkömmlichen Fertigungsmethoden auf die additive Fertigung ist nicht nur eine Frage der Konvertierung eines Dateiformats. Um die Vorteile der additiven Fertigung voll auszuschöpfen und die Produktion robuster, zuverlässiger und kostengünstiger korrosionsbeständiger Fittings (z. B. aus 316L oder 254SMO) zu gewährleisten, müssen die Ingenieure folgende Punkte berücksichtigen Design für additive Fertigung (DfAM) Grundsätze. DfAM geht über die einfache Nachbildung von Geometrien hinaus und umfasst die Optimierung des Designs für den schichtweisen Aufbau, die Minimierung potenzieller Probleme und die Maximierung der Leistung. Bei kritischen Komponenten wie Rohrverschraubungen sind Haltbarkeit unter Druck, Durchflussleistung und einfache Integration von größter Bedeutung.
Hier sind die wichtigsten Überlegungen zur Konstruktion von AM-Rohrformstücken:
1. Optimieren Sie die Durchflusseffizienz:
- Herausforderung: Abrupte Richtungsänderungen (scharfe Krümmungen), plötzliche Kontraktionen/Expansionen oder interne Hindernisse können Turbulenzen erzeugen, den Druckabfall erhöhen und möglicherweise Erosion oder lokale Korrosion beschleunigen. Die herkömmliche Herstellung schränkt die Schaffung glatter, optimierter interner Pfade oft ein.
- DfAM-Lösung: AM ermöglicht die Herstellung von Armaturen mit:
- Schwungvolle Kurven: Ersetzen Sie scharfe 90-Grad-Kurven durch sanftere Kurven mit größerem Radius, um Strömungsablösung und Druckverlust zu minimieren.
- Allmähliche Übergänge: Entwerfen Sie Reduzier- oder Aufweitungsstücke mit sanfteren Konuswinkeln für eine effizientere Durchflussanpassung.
- Integrierte Strömungslenker: Interne Leitschaufeln oder Merkmale zur gleichmäßigen Strömungslenkung, insbesondere in komplexen Abzweigungen wie T-Stücken oder Verteilern, wodurch sich der Bedarf an separaten Strömungskonditionierungselementen in der Folgezeit verringern kann.
- Computergestützte Strömungsmechanik (CFD): Frühzeitige CFD-Analyse in der Entwurfsphase, um die Flüssigkeitsströmung durch die von AM entworfene Armatur zu simulieren, Bereiche mit hohen Turbulenzen oder niedrigem Druck zu identifizieren und die Geometrie iterativ für eine optimale hydraulische Leistung zu verfeinern vor Drucken.
2. Verwalten Sie die Wandstärke:
- Herausforderung: Zu dünne Wände lassen sich möglicherweise nicht genau bedrucken, können zerbrechlich sein oder erfüllen nicht die Anforderungen an die Drucksicherheit gemäß den einschlägigen Rohrleitungsvorschriften (z. B. ASME B31.3). Zu dicke Wände erhöhen den Materialverbrauch, die Druckzeit, die Kosten und möglicherweise auch die Restspannung.
- DfAM-Lösung:
- Bedruckbare Mindestdicke: Machen Sie sich mit der minimalen Wandstärke vertraut, die mit dem gewählten AM-Verfahren (L-PBF, SEBM) und dem Material erreicht werden kann (z. B. typischerweise 0,4-1,0 mm, kann aber variieren). Entwerfen Sie Wände oberhalb dieses Grenzwertes.
- Druckberechnungen: Führen Sie die erforderlichen technischen Berechnungen durch (auf der Grundlage von Auslegungsdruck, Temperatur, zulässiger Materialspannung und Armaturengeometrie), um die erforderliche Mindestwandstärke für den Druckbehälter zu bestimmen. Berücksichtigen Sie ggf. entsprechende Sicherheitsmargen und Korrosionszuschläge.
- Einheitlichkeit (soweit möglich): Achten Sie auf relativ gleichmäßige Wandstärken im gesamten Fitting, um eine gleichmäßige Abkühlung während des Drucks zu fördern und das Risiko des Verziehens und des Aufbaus von Eigenspannungen zu verringern. Wenn Dickenänderungen erforderlich sind, sollten Sie schrittweise Übergänge einführen.
- Topologie-Optimierung: Bei drucklosen Strukturelementen oder Anwendungen, bei denen das Gewicht eine wichtige Rolle spielt (z. B. in der Luft- und Raumfahrt), kann Topologieoptimierungssoftware dabei helfen, Material aus Bereichen mit geringer Belastung zu entfernen und gleichzeitig die strukturelle Integrität zu erhalten.
3. Strategie für Unterstützungsstrukturen:
- Herausforderung: Pulverbettschmelzverfahren erfordern in der Regel Stützstrukturen für überhängende Merkmale (in der Regel Winkel unter 45 Grad zur Horizontalen) und zur Verankerung des Teils auf der Bauplatte, um ein Verziehen zu verhindern. Interne Stützen in komplexen Passgeometrien können nach dem Druck extrem schwierig oder unmöglich zu entfernen sein.
- DfAM-Lösung:
- Selbsttragende Winkel: Entwerfen Sie Überhänge mit Winkeln von mehr als 45 Grad, wo immer dies möglich ist, um den Bedarf an Stützen zu minimieren. Verwenden Sie Abschrägungen oder Tropfenformen für Löcher auf horizontalen Flächen.
- Orientierung aufbauen: Überlegen Sie sich sorgfältig die optimale Ausrichtung der Konstruktion. Wenn Sie die Armatur so ausrichten, dass nach unten weisende Flächen und interne Überhänge minimiert werden, können Sie den Unterstützungsbedarf erheblich reduzieren. Wird beispielsweise ein Standardkrümmer auf der Seite gedruckt, ist möglicherweise weniger interne Unterstützung erforderlich als beim Druck im Hochformat. Dies ist ein wichtiger Aspekt, bei dem die Zusammenarbeit mit einem erfahrenen AM-Anbieter wie Met3dp, der sich mit verschiedenen Druckverfahren und ihre Zwänge, ist von unschätzbarem Wert.
- Zugängliche interne Stützen: Wenn interne Stützen unvermeidbar sind, sollten sie so konstruiert werden, dass sie zugänglich sind. Dazu kann es gehören, Zugangsöffnungen einzubauen (die später verschlossen oder verschweißt werden können) oder Stützen zu konstruieren, die zerbrechlich sind oder chemisch aufgelöst werden können (weniger üblich bei 316L/254SMO). Manchmal muss eine Konstruktion in mehrere Teile geteilt werden, um das Entfernen der inneren Stützen zu ermöglichen, und dann nach dem Druck zusammengefügt werden (z. B. durch Schweißen).
- Unterstützung von Optimierungssoftware: Nutzen Sie fortschrittliche AM-Vorbereitungssoftware, um effiziente Stützstrukturen zu erzeugen, die nur wenig Material verbrauchen, leicht zu entfernen sind und eine angemessene Wärmeleitung und Verankerung bieten.
4. Funktionale Merkmale einbeziehen:
- Herausforderung: Herkömmliche Armaturen erfordern unter Umständen separate Komponenten oder eine Nachbearbeitung für Merkmale wie Schlüsselflächen, Montagehalterungen oder Sensoranschlüsse.
- DfAM-Lösung: Mit AM können diese Merkmale direkt in das gedruckte Armaturendesign integriert werden:
- Schraubenschlüssel-Flats: Entwerfen Sie sechseckige oder abgeflachte Abschnitte, um sie beim Ein- und Ausbau leicht greifen zu können.
- Montagefüße/Halterungen: Integrieren Sie die Befestigungspunkte direkt in den Armaturenkörper, um die Anzahl der Teile und die Komplexität der Montage zu reduzieren.
- Sensoranschlüsse: Entwerfen Sie Gewinde- oder Flanschanschlüsse für Manometer, Temperatursensoren oder Probenahmestellen direkt in der Armaturenwand (achten Sie auf eine ausreichende Wandstärke um die Anschlüsse).
- Markierungen: Betten Sie Teilenummern, Materialbezeichnungen, Durchflussindikatoren oder Logos während des Druckvorgangs direkt auf der Oberfläche ein.
5. Minimieren Sie Stresskonzentrationen:
- Herausforderung: Scharfe Innenecken, abrupte Querschnittsänderungen und Bereiche um Verbindungen (Gewinde, Flansche) können als Spannungserhöhungen wirken, die bei Druckwechsel oder Vibrationen zu Ermüdungsversagen oder Rissbildung führen können.
- DfAM-Lösung:
- Filetieren und Radizieren: Bringen Sie an allen Innen- und Außenecken großzügige Rundungen und Radien an, um die Belastung gleichmäßiger zu verteilen.
- Reibungslose Übergänge: Sorgen Sie für eine allmähliche Veränderung der Geometrie und der Wandstärke.
- Verstärkung: Erwägen Sie die Zugabe von zusätzlichem Material (lokale Verdickung) in Bereichen mit hoher Belastung, die durch die Finite-Elemente-Analyse (FEA) ermittelt wurden. FEA sollte für kritische Armaturen in Betracht gezogen werden, insbesondere für solche mit komplexer Geometrie oder für solche, die unter hohem Druck/Temperatur oder zyklischer Belastung arbeiten.
DfAM-Überlegungen Zusammenfassungstabelle:
DfAM-Prinzip | Zielsetzung | Wichtige Aktionen | Nutzen Sie |
---|---|---|---|
Fluss-Optimierung | Druckabfall und Turbulenzen minimieren | Verwendung von geschwungenen Kurven, allmählichen Übergängen, integrierten Führungen; CFD-Analyse | Verbesserte Systemeffizienz, weniger Erosion/Korrosion |
Steuerung der Wanddicke | Sicherstellung von Druckintegrität, Druckbarkeit, Kosten | Mindestdicke einhalten, Druckberechnungen durchführen, Gleichmäßigkeit anstreben, Übergänge nutzen | Strukturelle Integrität, zuverlässiger Druck, optimierter Materialeinsatz |
Unterstützungsstrategie | Stützen minimieren, Abnehmbarkeit sicherstellen | Selbsttragende Winkel entwerfen, Ausrichtung optimieren, begehbare Stützen entwerfen | Geringere Nachbearbeitungszeit/-kosten, verbesserte interne Oberflächenqualität |
Integration von Merkmalen | Reduzieren Sie die Anzahl der Teile, vereinfachen Sie die Montage | Schlüsselflächen, Halterungen, Anschlüsse und Markierungen direkt in das Design einbetten | Geringerer Montageaufwand, verbesserte Funktionalität, bessere Rückverfolgbarkeit |
Stressabbau | Erhöhte Lebensdauer, Vermeidung von Ausfällen | Verwendung von Verrundungen/Radien, glatten Übergängen, Verstärkungen; FEA-Analyse | Erhöhte Haltbarkeit, höherer Sicherheitsfaktor, längere Nutzungsdauer |
In Blätter exportieren
Durch die durchdachte Anwendung dieser DfAM-Prinzipien können Ingenieure korrosionsbeständige Rohrfittings aus 316L oder 254SMO entwerfen, die nicht nur mittels AM hergestellt werden können, sondern auch hinsichtlich Leistung, Haltbarkeit und Kosteneffizienz optimiert sind und die strengen Anforderungen industrieller B2B-Anwendungen erfüllen.
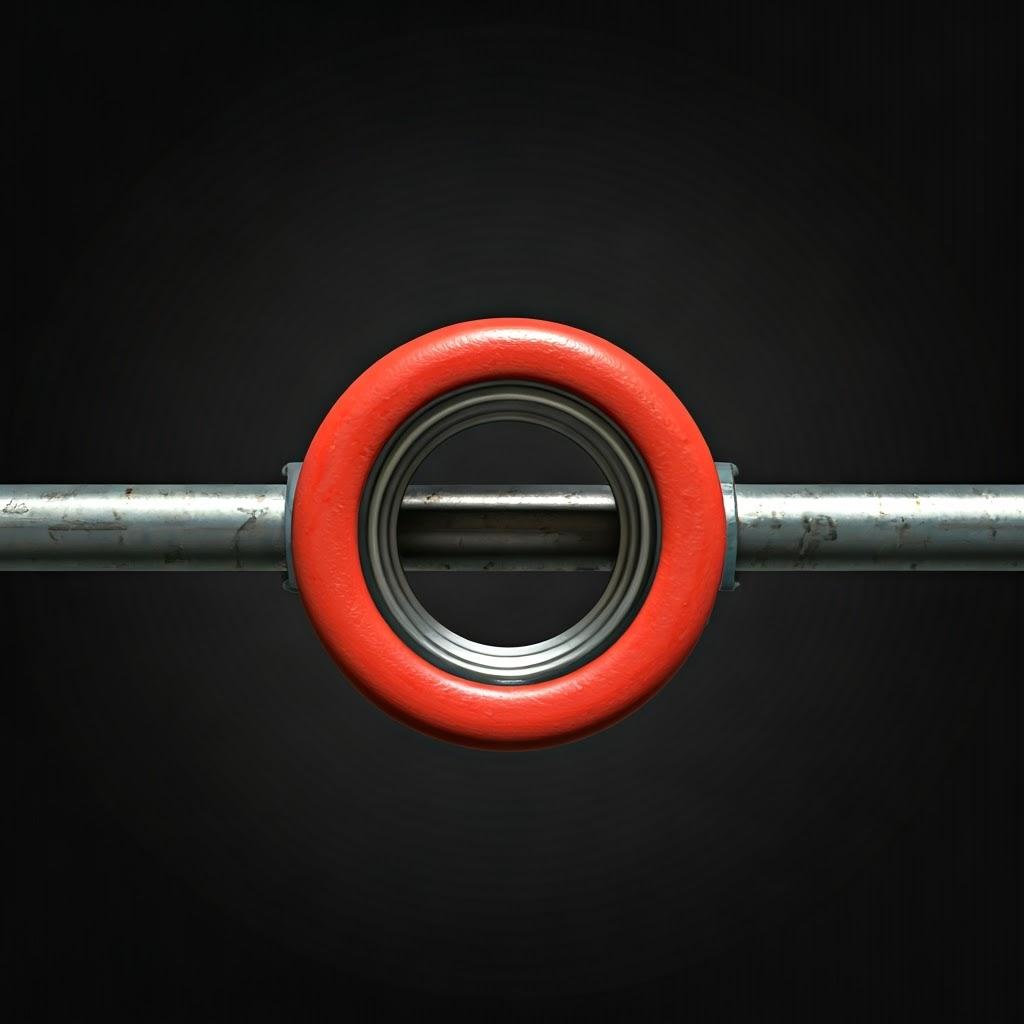
Präzisionsleistung: Erzielung enger Toleranzen und Oberflächengüte
Während die additive Fertigung von Metallen eine bemerkenswerte geometrische Freiheit bietet, erfordert das Erreichen der erforderlichen Präzision für funktionale Rohrverbindungen - insbesondere an Verbindungspunkten und Dichtungsflächen - eine sorgfältige Berücksichtigung von Toleranzen und Oberflächengüte. Ingenieure und Beschaffungsverantwortliche müssen die typischen Fähigkeiten von AM-Verfahren wie L-PBF und SEBM für Materialien wie 316L und 254SMO verstehen und erkennen, wo eine Nachbearbeitung erforderlich ist, um die Spezifikationen zu erfüllen.
Maßgenauigkeit und Toleranzen:
- As-Built-Genauigkeit: Die Maßgenauigkeit eines Teils direkt aus der AM-Maschine hängt von mehreren Faktoren ab, u. a. von der jeweiligen Maschine, den Prozessparametern, dem Material (316L und 254SMO verhalten sich im Allgemeinen gut), der Größe und Geometrie des Teils und der Bauausrichtung. Typische erreichbare Toleranzen für mittelgroße Teile (z. B. bis zu 150-200 mm) liegen oft im Bereich von:
- L-PBF: ±0,1 mm bis ±0,2 mm oder ±0,1-0,2% des Nennmaßes, je nachdem, welcher Wert größer ist.
- SEBM: Oft etwas ungenauer als L-PBF im eingebauten Zustand, vielleicht ±0,2 mm bis ±0,4 mm oder ±0,5-1,0%. SEBM erzeugt jedoch Teile mit geringerer Eigenspannung, was den Verzug bei der Nachbearbeitung verringern kann.
- Faktoren, die die Genauigkeit beeinflussen:
- Thermische Effekte: Eigenspannungen, die sich während des Drucks und der anschließenden Entspannungswärmebehandlung aufbauen, können zu geringfügigen Verformungen oder Schrumpfungen führen, die in der Entwurfs- oder Fertigungsvorbereitungsphase berücksichtigt und möglicherweise kompensiert werden müssen.
- Unterstützende Strukturen: Die Lage und Entfernung von Stützstrukturen kann die Abmessungen und die Oberflächenqualität der gestützten Flächen leicht beeinflussen.
- Teil Komplexität & Größe: Größere und komplexere Teile sind im Allgemeinen anfälliger für Abweichungen.
- Enge Toleranzen einhalten: Für kritische Dimensionen, wie z. B.:
- Flansch-Schraubenlöcher: Präzise Position und Durchmesser für die richtige Ausrichtung und das Einsetzen der Schrauben.
- Flansch-Dichtflächen: Ebenheit und Parallelität sind entscheidend für eine wirksame Abdichtung der Dichtung.
- Gewindeverbindungen (innen/außen): Die Einhaltung von Gewindenormen (z. B. NPT, BSP, ISO) ist für leckdichte Verbindungen unerlässlich.
- Rohrplan Abmessungen: Außendurchmesser (OD) und Innendurchmesser (ID) müssen mit den Standard-Rohrgrößen übereinstimmen, damit eine ordnungsgemäße Verbindung möglich ist (z. B. Schweißen, Klemmverschraubung).
- Gesamtlänge/Ausrichtung: Entscheidend für den Einbau in bestehende Rohrleitungen. In der Regel ist es notwendig, Nachbearbeitungsschritte einzubeziehen für diese Merkmale. Mit AM können zwar endkonturnahe Formen hergestellt werden, aber um engere Toleranzen als ~±0,1 mm oder bestimmte geometrische Abmessungen und Toleranzen (wie Ebenheit, Rechtwinkligkeit, Rundlauf) zu erreichen, ist in der Regel eine CNC-Bearbeitung nach dem Druck und der Wärmebehandlung erforderlich. Die Entwürfe sollten eine angemessene Bearbeitungszugabe (z. B. 0,5-2,0 mm) für Oberflächen mit engen Toleranzen vorsehen.
Oberflächengüte (Rauhigkeit):
- Oberflächenrauhigkeit (Ra) im Ist-Zustand: Die Oberflächenbeschaffenheit von AM-Teilen ist aufgrund des schichtweisen Aufbaus und der teilweise aufgeschmolzenen Pulverpartikel, die an der Oberfläche haften, von Natur aus rauer als maschinell bearbeitete Oberflächen. Typische "as-built" Ra-Werte:
- Obere Oberflächen: Im Allgemeinen glatter, vielleicht Ra 5-15 µm.
- Vertikale Mauern: Mäßige Rauhigkeit, Ra 8-20 µm.
- Überhängende/gestützte Flächen: Typischerweise die gröbsten, potenziell Ra 15-30 µm oder höher, je nach Trägertyp und Abtragsmethode.
- Interne Kanäle: Kann schwierig zu kontrollieren und zu messen sein; oft rauer als Außenflächen.
- Einfluss der Oberflächenbeschaffenheit:
- Versiegeln: Raue Oberflächen an Flanschflächen oder Gewindeverbindungen können zu Leckagen führen.
- Durchflusswiderstand: Raue Innenflächen erhöhen die Reibung und den Druckabfall.
- Korrosion: Raue Oberflächen können potenziell Verunreinigungen einschließen oder Ansatzpunkte für Spaltkorrosion schaffen, obwohl die inhärente Passivität von 316L/254SMO dies im Vergleich zu weniger widerstandsfähigen Legierungen deutlich abschwächt.
- Reinigungsfähigkeit: Entscheidend für hygienische Anwendungen (Pharma, Lebensmittel); glattere Oberflächen sind leichter zu reinigen und weniger anfällig für die Anhaftung von Bakterien.
- Erreichen der gewünschten Oberflächengüte: Für die meisten industriellen Rohrfittinganwendungen ist die Oberflächenbeschaffenheit im Ist-Zustand für unkritische Außenflächen oft akzeptabel. Allerdings:
- Versiegeln von Oberflächen: Fast immer ist eine Nachbearbeitung (Drehen, Fräsen, Schleifen) erforderlich, um glatte, ebene Oberflächen zu erzielen (z. B. Ra 1,6 µm, 0,8 µm oder noch glatter, je nach Dichtungstyp und Druck). Spezielle Schnittmuster (z. B. phonographische/gezackte Oberflächen für Flansche) können erforderlich sein.
- Hygienische Anwendungen: Kann mechanisches Polieren und/oder Elektropolieren erfordern, um sehr niedrige Ra-Werte (z. B. <0,8 µm oder <0,4 µm) für optimale Reinigungsfähigkeit und Korrosionsbeständigkeit zu erreichen.
- Verbesserter Fluss: Für Hochleistungsanwendungen kann eine Innenpolitur oder eine abrasive Fließbearbeitung in Betracht gezogen werden, obwohl dies bei komplizierten Fittings sehr aufwändig und kostspielig sein kann.
- Allgemeine Verbesserung: Oberflächenbehandlungen wie Perlstrahlen oder Trowalisieren können für eine gleichmäßigere, matte Oberfläche sorgen und lose Pulverpartikel entfernen, wodurch sich der Ra-Wert im Vergleich zum Rohzustand leicht verbessert.
Qualitätskontrolle und Metrologie:
Um sicherzustellen, dass die Beschläge die geforderte Präzision erfüllen, ist eine strenge Qualitätskontrolle erforderlich:
- Prüfung der Abmessungen: Verwendung von kalibrierten Werkzeugen wie Messschiebern, Mikrometern, Höhenmessgeräten und Koordinatenmessmaschinen (KMG) zur Überprüfung kritischer Abmessungen anhand von Zeichnungen und Spezifikationen. Das 3D-Scannen kann auch zum Vergleich des fertigen Teils mit dem ursprünglichen CAD-Modell verwendet werden.
- Messung der Oberflächenrauhigkeit: Verwendung von Profilometern zur Quantifizierung des Ra-Wertes auf kritischen Oberflächen.
- GD&T-Prüfungen: Überprüfung der geometrischen Toleranzen wie Ebenheit, Parallelität, Konzentrizität usw. mit Hilfe geeigneter Messgeräte.
Fähigkeit der Lieferanten: Bei der Beschaffung von AM-Rohrfittings ist es entscheidend, mit einem Anbieter wie Met3dp zusammenzuarbeiten, dessen Industriedrucker bekannt sind für branchenführendes Druckvolumen, Genauigkeit und Zuverlässigkeit. Ein fähiger Lieferant kennt die erreichbaren Toleranzen seiner Maschinen, gibt Hinweise zur notwendigen Nachbearbeitung und verfügt über robuste Qualitätsmanagementsysteme (z. B. ISO 9001-Zertifizierung) und Messmöglichkeiten, um zu überprüfen, ob die fertigen Teile alle technischen Spezifikationen erfüllen. Eine klare Kommunikation der Toleranz- und Oberflächenanforderungen auf technischen Zeichnungen ist für eine erfolgreiche Beschaffung unerlässlich.
Über den Druck hinaus: Unverzichtbare Nachbearbeitung für 3D-gedruckte Rohrfittings
Die Erstellung eines maßgenauen Rohrformstücks mit der gewünschten Geometrie auf einem Metall-3D-Drucker ist nur der erste Schritt. Bei Werkstoffen wie 316L und 254SMO, insbesondere wenn sie in anspruchsvollen industriellen Anwendungen eingesetzt werden, ist in der Regel eine Reihe von entscheidenden Nachbearbeitungsschritten erforderlich, um das fertige Teil in ein funktionales, zuverlässiges und sicheres Bauteil zu verwandeln. Diese Schritte sind unerlässlich, um die erforderlichen mechanischen Eigenschaften, Maßtoleranzen, Oberflächenmerkmale und die allgemeine Integrität zu erreichen. Beschaffungsmanager und Ingenieure müssen diese Prozesse in den Zeitplan und die Kostenkalkulation des Projekts einbeziehen.
Gemeinsame Nachbearbeitungsschritte für AM-Rohrfittings (316L/254SMO):
- Stressabbau Wärmebehandlung:
- Zweck: Die schnellen Erwärmungs- und Abkühlungszyklen bei Pulverbettschmelzverfahren (insbesondere L-PBF) erzeugen erhebliche Eigenspannungen innerhalb des gedruckten Teils. Diese Spannungen können nach der Entnahme aus der Bauplatte zu Verformungen oder Verwerfungen führen, die mechanische Leistung (insbesondere die Ermüdungslebensdauer) verringern und die Anfälligkeit für Spannungsrisskorrosion in bestimmten Umgebungen erhöhen. Die Spannungsentlastung zielt darauf ab, diese Eigenspannungen zu reduzieren, ohne das Mikrogefüge oder die Härte wesentlich zu verändern.
- Prozess: In der Regel wird das Teil (oft noch an der Bauplatte befestigt) in einem Ofen mit kontrollierter Atmosphäre (z. B. Argon oder Vakuum, um Oxidation zu verhindern) auf eine bestimmte Temperatur unterhalb der Glühtemperatur der Legierung erhitzt (z. B. liegen die üblichen Spannungsarmglühzyklen für 316L bei etwa 650 °C, aber die optimalen Zyklen hängen von den spezifischen Anforderungen ab und können höher liegen; für 254SMO sind möglicherweise andere Zyklen erforderlich). Das Teil wird für einen bestimmten Zeitraum auf Temperatur gehalten, gefolgt von einer langsamen, kontrollierten Abkühlung.
- Wichtigkeit: Dies ist wohl die am kritischsten erster Nachbearbeitungsschritt für maßhaltige Teile und zur Gewährleistung einer optimalen Leistung. Er sollte in der Regel vor der Entnahme des Teils von der Bauplatte durchgeführt werden.
- Entfernen und Reinigen von Teilen:
- Zweck: Trennen der gedruckten Armatur(en) von der Bauplatte und Entfernen von losem oder halbgesintertem Pulver.
- Prozess: Die Teile werden in der Regel durch Drahterodieren (Electrical Discharge Machining) oder mit einer Bandsäge aus der Bauplatte geschnitten. Überschüssiges Pulver wird mit Bürsten, Vakuumsystemen und Druckluftstrahlern in einer kontrollierten Umgebung entfernt (die Handhabung des Pulvers erfordert Sicherheitsvorkehrungen).
- Entfernung der Stützstruktur:
- Zweck: Entfernen der temporären Strukturen, die zur Unterstützung von Überhängen und zur Verankerung des Teils während des Drucks verwendet werden.
- Prozess: Dies kann ein arbeitsintensiver Schritt sein, der oft manuelles Brechen oder Schneiden (mit Zangen, Schleifern, Handwerkzeugen) oder maschinelle Bearbeitung (Fräsen) erfordert. Die Leichtigkeit des Entfernens hängt stark von den angewandten DfAM-Prinzipien ab (siehe Zwischenüberschrift 5). Um eine Beschädigung der Werkstückoberfläche zu vermeiden, ist eine sorgfältige Entfernung erforderlich. Bereiche, in denen Stützen angebracht waren, weisen in der Regel eine raue Oberflächenbeschaffenheit auf, die unter Umständen eine weitere Nachbearbeitung erfordert.
- Heißisostatisches Pressen (HIP) - (optional, aber empfohlen für kritische Anwendungen):
- Zweck: Beseitigung der internen Mikroporosität, die nach dem AM-Prozess verbleiben könnte. Porosität kann als Spannungskonzentrator wirken, die Ermüdungslebensdauer verkürzen und potenziell Leckagepfade in druckhaltenden Komponenten schaffen. HIP verbessert die Materialdichte, Duktilität, Ermüdungsfestigkeit und Schlagzähigkeit erheblich.
- Prozess: Dabei wird das Teil in einen speziellen Hochdruckbehälter gelegt, auf eine hohe Temperatur erhitzt (unterhalb des Schmelzpunkts, oft ähnlich den Temperaturen beim Lösungsglühen) und gleichzeitig aus allen Richtungen gleichmäßig mit hohem Inertgasdruck (z. B. Argon) beaufschlagt (in der Regel 100 MPa oder mehr). Dieser Druck lässt die inneren Hohlräume kollabieren.
- Erwägung: HIP erhöht zwar die Kosten und die Vorlaufzeit, bietet aber eine erhebliche Verbesserung der Materialintegrität, so dass die Eigenschaften des AM-Teils oft denen von Knetmaterial entsprechen oder sogar besser sind. Es wird dringend für Armaturen empfohlen, die unter hohem Druck, bei Ermüdung oder bei extremen Temperaturen eingesetzt werden.
- Lösungsglühen (speziell für 254SMO oder nach HIP/Schweißen):
- Zweck: Zur Auflösung schädlicher Sekundärphasen (wie der Sigma-Phase), die sich während des Drucks oder früherer thermischer Zyklen gebildet haben, zur Homogenisierung des Gefüges und zur Wiederherstellung der maximalen Korrosionsbeständigkeit und Duktilität. Dies ist besonders wichtig bei hochlegierten Werkstoffen wie 254SMO oder wenn umfangreiche Schweißarbeiten durchgeführt wurden. Bei 316L kann es nach dem HIP-Verfahren durchgeführt werden oder wenn bestimmte Eigenschaften erforderlich sind, aber ein einfacher Spannungsabbau ist oft ausreichend.
- Prozess: Das Teil wird für eine bestimmte Dauer auf eine höhere Temperatur als die des Spannungsabbaus erhitzt (z. B. ~1050-1150 °C für 316L, möglicherweise höher für 254SMO), gefolgt von einer schnellen Abkühlung (Abschrecken, normalerweise in Wasser), um die erneute Ausscheidung unerwünschter Phasen zu verhindern. Das Verfahren muss in einer kontrollierten Atmosphäre oder im Vakuum durchgeführt werden.
- CNC-Bearbeitung:
- Zweck: Erzielung enger Maßtoleranzen, spezifischer geometrischer Merkmale (GD&T) und geforderter Oberflächengüten in kritischen Bereichen, die mit dem AM-Prozess im Ist-Zustand nicht erreicht werden können.
- Prozess: Durch Fräsen, Drehen, Bohren, Gewindeschneiden oder Schleifen. Wie bereits erwähnt, ist dies wesentlich für:
- Flanschflächen (Ebenheit, Glattheit, Verzahnung)
- Gewindeverbindungen (richtiges Profil und richtige Größe)
- Dichtungsflächen (O-Ring-Nuten, Dichtungssitze)
- Präzise Gesamtlängen oder Ausrichtungsmerkmale
- Vorbereitung der Rohrenden zum Schweißen (Anschrägen)
- Erfordernis: Die Entwürfe müssen ein ausreichendes Bearbeitungsmaterial für die betreffenden Flächen enthalten.
- Oberflächenveredelung:
- Zweck: Zur Verbesserung der Oberflächenrauhigkeit, der Reinigungsfähigkeit, der Ästhetik oder zur Vorbereitung der Beschichtung.
- Prozess: Zu den Optionen gehören:
- Perlstrahlen/Sandstrahlen: Erzeugt eine gleichmäßige matte Oberfläche, beseitigt kleinere Oberflächenfehler und Verfärbungen durch Wärmebehandlung.
- Taumeln/Gleitschleifen: Verwendet Schleifmittel in einer rotierenden oder vibrierenden Trommel, um Kanten zu entgraten und eine glattere, gleichmäßigere Oberfläche zu erzielen, insbesondere bei Chargen von kleineren Teilen.
- Manuelles Schleifen/Polieren: Gezielte Entfernung von Stützzeugen oder Erzielung bestimmter Oberflächen auf zugänglichen Flächen.
- Elektropolieren: Ein elektrochemisches Verfahren, bei dem eine mikroskopisch kleine Materialschicht entfernt wird, so dass eine sehr glatte, saubere, passive und oft glänzende Oberfläche entsteht. Weit verbreitet für hygienische Anwendungen (Pharma, Lebensmittel) zur Verbesserung der Reinigungsfähigkeit und Korrosionsbeständigkeit.
- Passivierung:
- Zweck: Verbesserung der natürlichen Korrosionsbeständigkeit von nichtrostenden Stählen (einschließlich 316L und 254SMO) durch Entfernung von freiem Eisen oder anderen Verunreinigungen von der Oberfläche und Verdickung der passiven Chromoxidschicht. Obwohl nichtrostende Stähle von Natur aus passiv sind, können durch Prozesse wie Bearbeitung, Handhabung oder sogar durch die Luft in der Werkstatt Verunreinigungen eingebracht werden.
- Prozess: In der Regel wird der Fitting in eine milde Oxidationsmittellösung wie Salpetersäure oder Zitronensäure getaucht (spezifische Konzentration, Temperatur und Zeit hängen von der Norm ab, z. B. ASTM A967).
- Wichtigkeit: Oftmals eine Standardanforderung, insbesondere für chemische, pharmazeutische und lebensmitteltechnische Anwendungen, um von Anfang an eine maximale Korrosionsleistung zu gewährleisten.
- Inspektion und Prüfung:
- Zweck: Um zu überprüfen, ob die fertige Armatur alle spezifizierten Anforderungen vor dem Versand oder der Installation erfüllt.
- Prozess: Enthält:
- Endabnahme der Abmessungen: Verifizierung aller kritischen Maße und GD&T-Angaben nach allen Bearbeitungs- und Endbearbeitungsschritten.
- Visuelle Inspektion: Prüfung auf Oberflächenfehler, ordnungsgemäße Verarbeitung und Markierungen.
- Dichtheitsprüfung (Druckprüfung): Unerlässlich für druckhaltende Komponenten. Die hydrostatische Prüfung (mit Wasser) oder die pneumatische Prüfung (mit Luft oder Stickstoff) wird bei einem bestimmten Druck (in der Regel dem 1,5-fachen Auslegungsdruck) durchgeführt, um sicherzustellen, dass keine Lecks vorhanden sind.
- Zerstörungsfreie Prüfung (NDT): Für hochkritische Anwendungen können Methoden wie die Farbeindringprüfung (PT) zum Aufspüren von Oberflächenrissen, die Magnetpulverprüfung (MT - bei austenitischen Stählen weniger üblich), die Durchstrahlungsprüfung (RT - Röntgen) zum Aufspüren von inneren Hohlräumen oder Einschlüssen oder die Ultraschallprüfung (UT) vorgeschrieben werden.
- Überprüfung der Materialzertifizierung: Sicherstellung der Rückverfolgbarkeit und Konformität des verwendeten Pulvers und Überprüfung von Nachbearbeitungsschritten wie der Wärmebehandlung.
Die spezifische Reihenfolge und die Notwendigkeit dieser Schritte hängen stark von der Komplexität der Konstruktion, dem Material, der Kritikalität der Anwendung und den geltenden Industrienormen ab. Die Zusammenarbeit mit einem erfahrenen AM-Dienstleister, der umfassende Nachbearbeitungsmöglichkeiten bietet, ist entscheidend, um sicherzustellen, dass der endgültige korrosionsbeständige Rohrfitting alle Leistungs- und Qualitätserwartungen erfüllt.
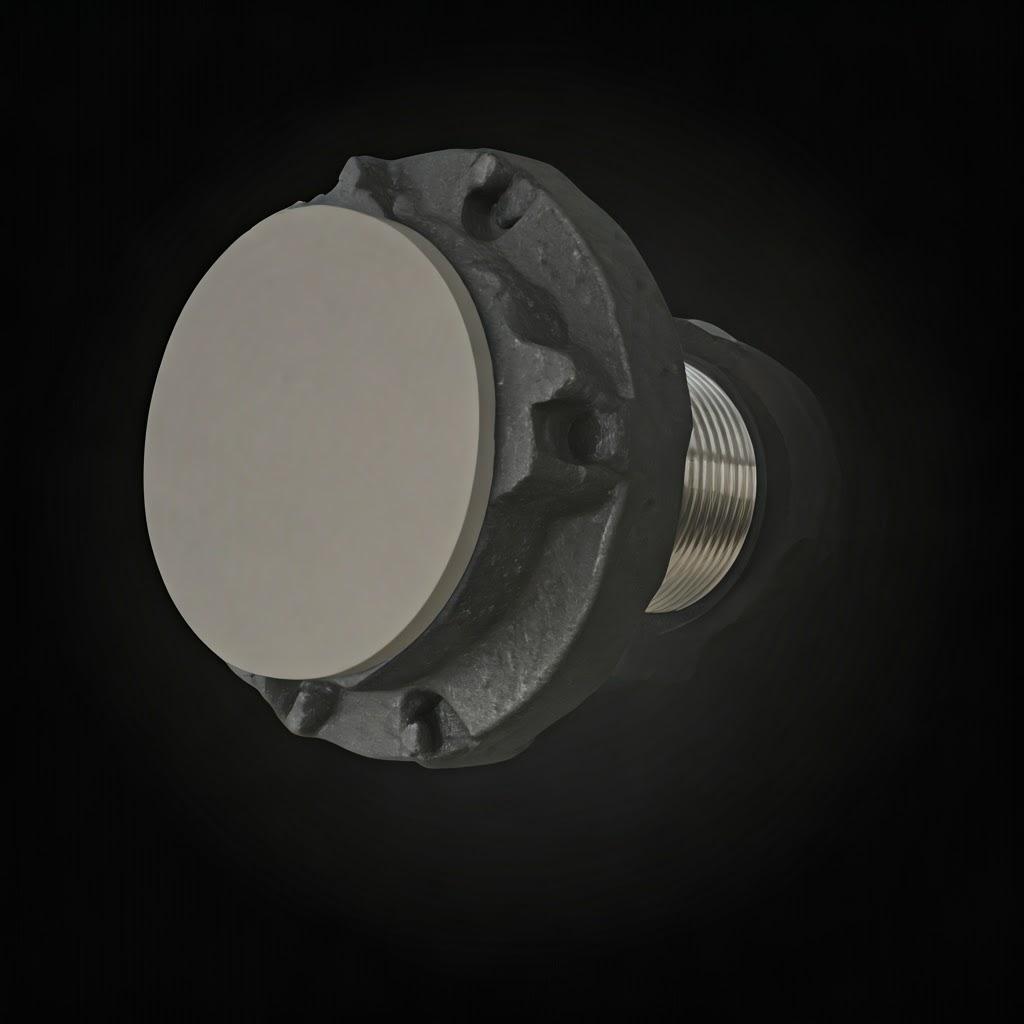
Herausforderungen meistern: Überwindung von Hürden bei Metall-AM für Beschläge
Die additive Fertigung von Metallen bietet zwar erhebliche Vorteile für die Herstellung korrosionsbeständiger Rohrformstücke, doch wie jedes fortschrittliche Fertigungsverfahren birgt sie auch eine Reihe potenzieller Herausforderungen. Das Erkennen dieser Hürden und die Implementierung geeigneter Abhilfestrategien - oft durch eine Kombination aus intelligentem Design (DfAM), optimierten Prozessparametern, sorgfältiger Nachbearbeitung und robuster Qualitätskontrolle - ist der Schlüssel zur erfolgreichen Nutzung von AM für anspruchsvolle industrielle Anwendungen. Die Zusammenarbeit mit einem erfahrenen Anbieter wie Met3dpmit seiner jahrzehntelangen Erfahrung in der additiven Fertigung von Metallen kann uns bei der Bewältigung dieser komplexen Aufgaben erheblich helfen.
Im Folgenden finden Sie einige häufige Herausforderungen und wie Sie sie bewältigen können:
1. Verformung und Verzerrung (Eigenspannung):
- Herausforderung: Durch die intensive örtliche Erwärmung und die schnelle Abkühlung beim Schmelzen im Pulverbett entstehen innere Spannungen. Beim Entfernen von der Bauplatte oder bei der anschließenden Wärmebehandlung können diese Spannungen dazu führen, dass sich das Teil verzieht, verformt oder sogar reißt, was die Maßgenauigkeit beeinträchtigt.
- Strategien zur Schadensbegrenzung:
- DfAM: Konstruieren Sie Teile mit allmählichen Dickenübergängen und minimieren Sie große, flache, freitragende Abschnitte.
- Orientierungs- und Unterstützungsstrategie aufbauen: Richten Sie das Teil so aus, dass sich möglichst wenig Spannungen ansammeln, und verwenden Sie robuste Stützstrukturen, um das Teil während des Drucks fest auf der Bauplatte zu verankern. Gut konzipierte Stützen helfen auch, die Wärme abzuleiten.
- Optimierte Prozessparameter: Erfahrene AM-Anbieter nehmen eine Feinabstimmung von Laser-/Elektronenstrahlleistung, Scangeschwindigkeit, Schichtdicke und Scan-Strategien vor, um den Spannungsaufbau für bestimmte Materialien wie 316L und 254SMO zu minimieren. Met3dp konzentriert sich auf die Zuverlässigkeit des Druckers und bietet eine stabile Prozesskontrolle.
- Geeignete Wärmebehandlung: Durchführung einer Spannungsarmglühung vor Die Entnahme des Teils von der Bauplatte ist entscheidend. Das anschließende Lösungsglühen (falls erforderlich) muss ebenfalls sorgfältig kontrolliert werden.
- Simulation: Thermische Simulationssoftware kann die Spannungsverteilung und mögliche Verformungen vorhersagen und ermöglicht so Design- oder Prozessanpassungen vor der Fertigung.
2. Porosität:
- Herausforderung: Im gedruckten Material können kleine Hohlräume oder Poren verbleiben, die durch unvollständiges Schmelzen, Gaseinschlüsse (von Pulver oder Schutzgas) oder Keyholing (Zusammenbruch durch Dampfdruck) entstehen. Porosität verringert die Dichte, verschlechtert die mechanischen Eigenschaften (insbesondere die Ermüdungsfestigkeit) und kann zu Undichtigkeiten in Druckanschlüssen führen.
- Strategien zur Schadensbegrenzung:
- Hochwertiges Pulver: Die Verwendung von Pulvern mit hoher Sphärizität, kontrollierter PSD, geringer interner Gasporosität und guter Fließfähigkeit (wie die gaszerstäubten Pulver von Met3dp) ist von grundlegender Bedeutung. Die Handhabung und Lagerung des Pulvers ist ebenfalls von entscheidender Bedeutung, um Feuchtigkeitsaufnahme oder Verunreinigungen zu vermeiden.
- Optimierte Druckparameter: Eine sorgfältige Kontrolle der Energiedichte (Laser-/Strahlleistung, Geschwindigkeit, Schraffurabstand) ist unerlässlich, um ein vollständiges Schmelzen und Verschmelzen der Schichten ohne übermäßige Verdampfung zu gewährleisten.
- Richtige Maschinenkalibrierung und -wartung: Sicherstellen, dass das AM-System korrekt kalibriert und gewartet wird, einschließlich Optik und Gasflusssysteme.
- Heiß-Isostatisches Pressen (HIP): Wie bereits in der Nachbearbeitung erwähnt, schließt HIP die inneren Poren sehr effektiv, wodurch die Dichte und mechanische Integrität kritischer Teile erheblich verbessert wird.
- NDT-Inspektion: Einsatz von Methoden wie Röntgen-Computertomographie (CT) oder Radiographie (RT) zur Erkennung und Quantifizierung der inneren Porosität, falls dies von den Spezifikationen gefordert wird.
3. Entfernen der internen Stütze:
- Herausforderung: Das Entfernen von Stützstrukturen aus komplexen internen Kanälen oder Hohlräumen innerhalb einer Armatur kann extrem schwierig, zeitaufwändig oder manchmal sogar unmöglich sein, ohne das Teil zu beschädigen. Verbleibendes Stützmaterial kann den Durchfluss behindern oder als Ausgangspunkt für Korrosion dienen.
- Strategien zur Schadensbegrenzung:
- DfAM ist der Schlüssel: Die wichtigste Lösung besteht darin, die inneren Merkmale so zu gestalten, dass sie selbsttragend sind (z. B. Verwendung von Winkeln >45°, tropfen- oder rautenförmigen Kanälen anstelle von kreisförmigen horizontalen Kanälen).
- Orientierung: Wählen Sie eine Bauausrichtung, die interne Überhänge, die abgestützt werden müssen, minimiert.
- Zugängliche Unterstützungen: Wenn interne Stützen unvermeidbar sind, sollten sie durch Öffnungen erreichbar sein oder der Beschlag sollte in Abschnitten konstruiert werden, die einen Zugang vor der endgültigen Verbindung ermöglichen.
- Alternative AM-Verfahren: Für einige komplexe Innenkanaldesigns, bei denen die Entfernung von Trägern nicht möglich ist, kann das Aufspritzen von Bindemitteln mit anschließender Sinterung in Betracht gezogen werden (obwohl die Eigenschaften von der Pulverbettschmelze abweichen können).
- Abrasive Fließbearbeitung/Chemisches Polieren: Kann manchmal die inneren Oberflächen glätten, entfernt aber möglicherweise nicht vollständig die Reste von robusten Stützen.
4. Erreichen von lecksicheren Dichtungen:
- Herausforderung: Um zuverlässige, leckdichte Dichtungen an Verbindungsstellen (Flansche, Gewinde, Klemmringverschraubungen) zu gewährleisten, sind präzise Abmessungen und geeignete Oberflächenbeschaffenheiten der Dichtflächen erforderlich. Die AM-Oberflächen sind in der Regel zu rau für eine direkte Abdichtung.
- Strategien zur Schadensbegrenzung:
- Design for Sealing: Standardmäßige Dichtungsmerkmale (z. B. hochgezogene Flansche, O-Ring-Nuten) gemäß den Industrienormen.
- Nachbearbeiten: Es ist von entscheidender Bedeutung, dass die Dichtungsflächen (Flanschflächen, Gewindeprofile) mit den erforderlichen Maßtoleranzen und Oberflächengüten (z. B. spezifischer Ra-Wert, Ebenheit, geriffelte Oberfläche) bearbeitet werden. Stellen Sie sicher, dass in der AM-Konstruktion ein angemessenes Bearbeitungsmaterial vorgesehen ist.
- Geeignete Dichtungen/Dichtmittel: Wählen Sie kompatible Dichtungen oder Gewindedichtmittel je nach Flüssigkeit, Temperatur, Druck und Oberflächenbeschaffenheit.
- Strenge Dichtheitsprüfungen: Führen Sie hydrostatische oder pneumatische Dichtheitsprüfungen bei bestimmten Drücken nach der Endmontage oder Bearbeitung durch, um die Integrität der Dichtungen zu überprüfen.
5. Sicherstellung gleichbleibender Materialeigenschaften und Mikrostruktur:
- Herausforderung: Das Erreichen gleichmäßiger mechanischer Eigenschaften und der gewünschten Mikrostruktur in einem komplexen AM-Teil erfordert konsistente Verarbeitungsbedingungen und eine angemessene thermische Nachbearbeitung. Abweichungen können die Festigkeit, Duktilität und Korrosionsbeständigkeit beeinträchtigen.
- Strategien zur Schadensbegrenzung:
- Prozesssteuerung und -überwachung: Verwendung von AM-Systemen mit robusten Überwachungs- und Steuerungsfunktionen, um eine gleichmäßige Energiezufuhr, Pulverabscheidung und atmosphärische Bedingungen zu gewährleisten.
- Standardisierte Parameter: Entwicklung und Einhaltung von qualifizierten, material- (316L, 254SMO) und maschinenspezifischen Druckparametern.
- Geeignete Wärmebehandlung: Gleichmäßige Anwendung der erforderlichen Spannungsarmglüh- und/oder Lösungsglühzyklen auf das gesamte Teil, um die Mikrostruktur zu homogenisieren und die Eigenschaften zu optimieren. Auch HIP trägt zur Gleichmäßigkeit bei.
- Materialprüfung: Durchführung von Zugversuchen, Härtetests und ggf. Gefügeanalysen (Metallografie) an repräsentativen Proben oder an neben den Teilen gedruckten Prüfmustern, um zu überprüfen, ob die Materialeigenschaften den Spezifikationen entsprechen.
Herausforderungen überwinden - Übersichtstabelle:
Herausforderung | Hauptursache(n) | Wichtige Strategien zur Schadensbegrenzung |
---|---|---|
Verwerfung/Verzerrung | Eigenspannung | DfAM, Stützen, Optimierte Parameter, Spannungsentlastung (Vorabbau), Simulation |
Porosität | Unvollständiges Schmelzen, Gaseinschluss | Qualitätspulver, optimierte Parameter, Maschinenkalibrierung, HIP, NDT |
Entfernen der internen Stütze | Komplexe innere Überhänge | DfAM (selbsttragend), Orientierung, barrierefreie Hilfen, Design-Segmentierung |
Lecksichere Dichtungen | Maßliche Ungenauigkeit, raue Oberflächenbeschaffenheit | Konstruktion für die Abdichtung, Nachbearbeitung (kritisch), richtige Dichtungen/Dichtmittel, Dichtheitsprüfung |
Inkonsistente Eigenschaften | Prozessschwankungen, unzureichende Wärmebehandlung | Prozesskontrolle, standardisierte Parameter, korrekte Wärmebehandlung, Materialprüfung |
In Blätter exportieren
Wenn diese potenziellen Herausforderungen durch sorgfältiges Design, Prozessoptimierung, gründliche Nachbearbeitung und strenge Qualitätskontrolle proaktiv angegangen werden, können Hersteller und Endanwender die additive Fertigung von Metall zur Herstellung hochwertiger, zuverlässiger und korrosionsbeständiger Rohrfittings aus 316L und 254SMO selbst für die anspruchsvollsten industriellen Umgebungen nutzen.
Strategie der Lieferantenauswahl: Die Wahl Ihres Partners für den 3D-Druck von Metall
Die Auswahl des richtigen Dienstleisters für die additive Fertigung ist ebenso wichtig wie die Perfektionierung des Designs oder die Wahl des richtigen Materials (wie 316L oder 254SMO) für Ihre korrosionsbeständigen Rohrfittings. Qualität, Zuverlässigkeit und Leistung der endgültigen Komponente hängen in hohem Maße von den Fähigkeiten, dem Fachwissen und den Qualitätssystemen des von Ihnen gewählten Partners ab. Für Ingenieure und Beschaffungsmanager, die sich in der AM-Landschaft zurechtfinden müssen, insbesondere bei der Beschaffung kritischer Industriekomponenten, ist ein strukturierter Bewertungsprozess unerlässlich.
Hier sind die wichtigsten Kriterien, die Sie bei der Auswahl eines Anbieters für den 3D-Druck von Rohrformstücken aus Metall berücksichtigen sollten:
1. Technisches Fachwissen und Unterstützung durch das DfAM:
- Worauf Sie achten sollten: Verfügt der Lieferant über Metallurgen und Ingenieure, die speziell mit 316L, 254SMO und anderen relevanten Legierungen im Zusammenhang mit AM Erfahrung haben? Kann er aussagekräftiges Feedback zum Design for Additive Manufacturing (DfAM) geben, um Ihr Fittingdesign im Hinblick auf Druckbarkeit, Leistung, Kosteneffizienz und minimale Nachbearbeitung zu optimieren? Verstehen sie die Feinheiten der Fluiddynamik, die für Rohrfittings relevant sind?
- Warum das wichtig ist: Das Fachwissen gewährleistet die korrekte Auswahl der Parameter, geeignete Empfehlungen für die Nachbearbeitung und mögliche Designverbesserungen, die Sie möglicherweise nicht in Betracht gezogen haben, was zu einem besseren Endprodukt führt.
2. Fähigkeit und Kapazität der Ausrüstung:
- Worauf Sie achten sollten: Betreibt der Anbieter gut gewartete, industrietaugliche AM-Systeme (z. B. L-PBF, SEBM), die für die Herstellung dichter Metallteile geeignet sind? Wie groß ist der Bauraum (kann er Ihre Passmaße aufnehmen)? Verfügt das Unternehmen über ausreichende Maschinenkapazitäten, um die von Ihnen geforderten Vorlaufzeiten einzuhalten, einschließlich des Potenzials für Massenfertigung oder wiederkehrende Aufträge? Wie sieht es mit der Zuverlässigkeit und Betriebszeit aus?
- Warum das wichtig ist: Die Qualität und Kalibrierung der AM-Maschine wirkt sich direkt auf die Qualität der Teile aus. Ausreichende Kapazitäten gewährleisten eine pünktliche Lieferung und Skalierbarkeit für zukünftige Anforderungen. Anbieter wie Met3dp, die branchenführendes Druckvolumen, Genauigkeit und Zuverlässigkeit, ein Engagement für robuste Produktionskapazitäten zeigen.
3. Materialqualität, Handhabung und Rückverfolgbarkeit:
- Worauf Sie achten sollten: Woher bezieht der Anbieter seine Metallpulver (z. B. 316L, 254SMO)? Verwendet er Pulver von namhaften Herstellern mit zertifizierter Chemie (z. B. gemäß ASTM-Normen)? Welche Verfahren gibt es für die Handhabung, Lagerung, Prüfung (z. B. Chemie, PSD, Fließfähigkeit) und das Recycling des Pulvers (falls zutreffend)? Kann das Unternehmen eine vollständige Rückverfolgbarkeit des Materials (z. B. Wärme-/Losnummer) gewährleisten, die eine Verbindung zwischen der Pulvercharge und Ihrem spezifischen Teil herstellt, was häufig durch Materialzertifizierungen nach EN 10204 3.1 dokumentiert wird?
- Warum das wichtig ist: Die Qualität des Pulvers ist für die Integrität der Teile von grundlegender Bedeutung. Eine strenge Handhabung verhindert Verunreinigungen und Beeinträchtigungen. Eine vollständige Rückverfolgbarkeit ist oft eine Voraussetzung für kritische Anwendungen in Branchen wie Luft- und Raumfahrt, Medizin sowie Öl und Gas, um die Verantwortlichkeit und Qualitätssicherung zu gewährleisten. Unternehmen wie Met3dp, die ihre eigenen hochwertige Metallpulver die fortschrittliche Zerstäubungstechniken verwenden, haben oft eine bessere Kontrolle über die Materialkonsistenz. Erkunden Sie ihr Angebot an Drucker und Puder um ihren vertikal integrierten Ansatz zu sehen.
4. Umfassende Post-Processing-Fähigkeiten:
- Worauf Sie achten sollten: Bietet der Lieferant die erforderlichen Nachbearbeitungsschritte intern oder über qualifizierte Partner an? Dazu gehören Spannungsabbau, HIP (falls erforderlich), Entfernen von Stützen, CNC-Bearbeitung (für kritische Toleranzen und Merkmale), Oberflächenbehandlung (Strahlen, Polieren, Passivieren) und relevante Wärmebehandlungen (wie Lösungsglühen).
- Warum das wichtig ist: Inhouse-Kapazitäten rationalisieren oft den Arbeitsablauf, verkürzen die Vorlaufzeiten und gewährleisten eine bessere Prozesskontrolle und Verantwortlichkeit als die Verwaltung mehrerer Subunternehmer. Überprüfen Sie deren Fachwissen und Ausrüstung für jeden erforderlichen Schritt.
5. Qualitätsmanagementsystem (QMS) und Zertifizierungen:
- Worauf Sie achten sollten: Arbeitet der Lieferant mit einem soliden QMS, das idealerweise nach Normen wie ISO 9001 zertifiziert ist? Für bestimmte Branchen können Zertifizierungen wie AS9100 (Luft- und Raumfahrt) oder ISO 13485 (Medizin) relevant oder erforderlich sein. Verfügt er über dokumentierte Verfahren für Prozesskontrolle, Inspektion, Kalibrierung und Abweichungsmanagement?
- Warum das wichtig ist: Ein zertifiziertes QMS demonstriert das Engagement für gleichbleibende Qualität, Prozesskontrolle, kontinuierliche Verbesserung und Kundenzufriedenheit - unerlässlich für das Vertrauen der industriellen Beschaffung.
6. Inspektions- und Prüfkapazitäten:
- Worauf Sie achten sollten: Über welche messtechnische Ausrüstung verfügt der Lieferant (KMG, Profilometer, Scanner)? Kann er die erforderlichen zerstörungsfreien Prüfungen (PT, RT, UT) und Druck-/Dichtheitsprüfungen durchführen? Verfügt er über Verfahren zur Endkontrolle und Dokumentation?
- Warum das wichtig ist: Verifizierung ist der Schlüssel. Der Lieferant muss in der Lage sein, mit objektiven Beweisen nachzuweisen, dass die hergestellten Armaturen alle Zeichnungsspezifikationen und Leistungsanforderungen erfüllen.
7. Kommunikation, Zusammenarbeit und Unterstützung:
- Worauf Sie achten sollten: Ist der Lieferant während des gesamten Ausschreibungs-, Bestell- und Produktionsprozesses ansprechbar und transparent? Bietet er eine klare technische Kommunikation und eine effektive Zusammenarbeit bei Design- oder Fertigungsproblemen? Welchen Grad an Unterstützung bietet der Lieferant nach der Lieferung?
- Warum das wichtig ist: Eine starke Arbeitsbeziehung, die auf einer klaren Kommunikation beruht, ist entscheidend, um die Komplexität von AM zu bewältigen und den Projekterfolg sicherzustellen.
Zusammenfassung der Checkliste zur Lieferantenbewertung:
Kriterien | Zentrale Fragen | Wichtigkeitsstufe |
---|---|---|
Technisches Fachwissen / DfAM | Erfahrung mit Legierungen/AM? DfAM-Unterstützung angeboten? Verständnis für Anwendungen? | Hoch |
Ausstattung/Kapazität | Industrielle Maschinen? Ist die Baugröße angemessen? Kapazität für Volumen/Durchlaufzeit? | Hoch |
Materialqualität/Rückverfolgbarkeit | Seriöse Pulverquelle? Handhabungsverfahren? Vollständige Rückverfolgbarkeit gewährleistet? | Hoch |
Post-Processing-Fähigkeit | Sind die erforderlichen Schritte verfügbar (bevorzugt intern)? Kompetenz in jedem Schritt? | Hoch |
QMS / Zertifizierungen | ISO 9001 oder relevante Branchenzertifikate? Dokumentierte Verfahren? | Hoch |
Inspektion / Prüfung | Messtechnische Ausrüstung? ZfP-Fähigkeit? Dichtheitsprüfung? Endprüfungsprotokoll? | Hoch |
Kommunikation / Unterstützung | Reaktionsschnell? Transparent? Kooperativ? Unterstützung nach der Auslieferung? | Mittel-Hoch |
Kosten / Vorlaufzeit | Wettbewerbsfähige Preise? Verlässliche Schätzungen der Vorlaufzeit? | Mittel-Hoch |
In Blätter exportieren
Durch die systematische Bewertung potenzieller Lieferanten anhand dieser Kriterien können Unternehmen einen Partner für den 3D-Metalldruck finden, der in der Lage ist, qualitativ hochwertige, zuverlässige und korrosionsbeständige Rohrfittings zu liefern, die den hohen Anforderungen ihrer spezifischen Anwendung entsprechen.
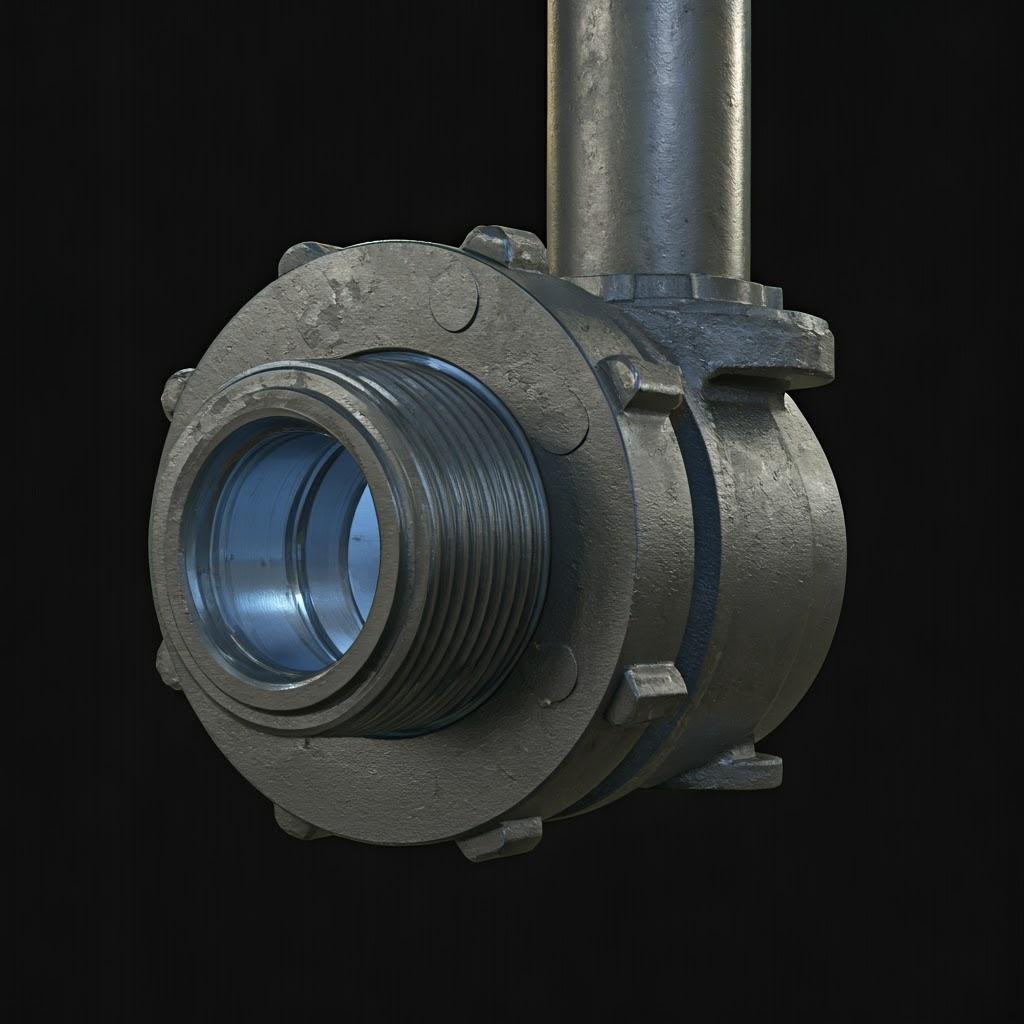
Die Investition verstehen: Kostenfaktoren und Vorlaufzeiten für AM-Rohrfittings
Die technischen Vorteile der additiven Fertigung von korrosionsbeständigen Rohrformstücken sind zwar überzeugend, doch Beschaffungsmanager und Projektingenieure müssen sich auch über die damit verbundenen Kosten und Vorlaufzeiten im Klaren sein. Im Gegensatz zur traditionellen Massenproduktion, bei der die Amortisation der Werkzeuge dominiert, werden die AM-Kosten von anderen Faktoren bestimmt. Das Verständnis dieser Faktoren hilft bei der genauen Budgetierung, der Bewertung der Gesamtbetriebskosten (TCO) und der Verwaltung von Projektzeitplänen.
Die wichtigsten Kostentreiber für AM-Rohrfittings (316L/254SMO):
- Teilvolumen und Bounding Box:
- Auswirkungen: Größere Teile verbrauchen mehr Material und brauchen länger zum Drucken. Die Gesamtgröße (Bounding Box) bestimmt auch, wie viele Teile auf eine einzige Bauplatte passen (Verschachtelungsdichte), was die Effizienz der Maschinenzeit beeinflusst.
- Erwägung: Optimieren Sie Ihre Entwürfe, um unnötige Masse zu minimieren und gleichzeitig die strukturellen Anforderungen zu erfüllen. Effizientes Nesting durch den AM-Anbieter ist entscheidend für die Reduzierung der Maschinenzeitkosten pro Teil.
- Teil Komplexität:
- Auswirkungen: Sehr komplizierte Designs mit komplexen internen Kanälen oder Merkmalen, die umfangreiche Stützstrukturen erfordern, erhöhen die Vorbereitungszeit für den Bau, die Druckzeit (aufgrund von mehr Scanner-Bewegungen) und den Aufwand für die Nachbearbeitung (Entfernen von Stützstrukturen) erheblich.
- Erwägung: Nutzen Sie DfAM, um Konstruktionen so weit wie möglich zu vereinfachen und schwer zu entfernende Halterungen zu minimieren. Die Stärke von AM liegt jedoch in der Bewältigung von Komplexität, die auf andere Weise nicht möglich ist, sodass der Wert des komplexen Merkmals gegen seine Kosten abgewogen werden muss.
- Materialtyp:
- Auswirkungen: Die Kosten für Metallpulver sind sehr unterschiedlich. Hochleistungslegierungen wie 254SMO sind aufgrund höherer Kosten für Legierungselemente und potenziell geringerer Produktionsmengen pro Kilogramm erheblich teurer als rostfreier Standardstahl 316L.
- Erwägung: Wählen Sie das kostengünstigste Material, das die Korrosionsbeständigkeit und die mechanischen Anforderungen der Anwendung erfüllt. Überspezifizieren Sie nicht, wenn 316L ausreichend ist.
- Maschinenzeit:
- Auswirkungen: Dies ist oft ein primärer Kostentreiber, der auf der Grundlage der Stunden berechnet wird, die die AM-Maschine mit dem Druck des Teils/der Teile beschäftigt ist. Sie hängen von der Teilehöhe (Anzahl der Schichten), dem Teilevolumen und der Baurate der jeweiligen Maschine ab.
- Erwägung: Optimieren Sie die Bauausrichtung und Verschachtelung, um die Anzahl der Teile pro Bau zu maximieren und die Bauhöhe zu minimieren, wo dies möglich ist.
- Nachbearbeitungsintensität:
- Auswirkungen: Dies kann erheblich zu den Endkosten beitragen. Jeder Schritt - Spannungsabbau, Entfernen von Stützen, HIP, Lösungsglühen, umfangreiche CNC-Bearbeitung, Hochglanzpolieren, Passivierung, zerstörungsfreie Prüfung - verursacht zusätzliche Kosten für Arbeit, Maschinenzeit und möglicherweise Spezialausrüstung.
- Erwägung: Definieren Sie klar und deutlich die erforderlich Nachbearbeitung auf der Grundlage der Anwendungsanforderungen. Vermeiden Sie die Angabe unnötiger Schritte. Zum Beispiel ist HIP vorteilhaft, verursacht aber erhebliche Kosten; rechtfertigen Sie seine Verwendung auf der Grundlage der Kritikalität. Besprechen Sie die Optionen mit dem Lieferanten, um die kostengünstigste Nachbearbeitung zu finden.
- Bestellte Menge:
- Auswirkungen: Obwohl bei AM keine Werkzeugkosten anfallen, gibt es dennoch Größenvorteile. Die Rüstkosten (Bauvorbereitung) amortisieren sich bei größeren Chargen über mehr Teile. Die Materialkosten können durch den Kauf von Massenpulver leicht sinken. Dedizierte Maschinenläufe werden effizienter.
- Erwägung: Während sie für Prototypen und kleine Mengen ideal sind, sinken die Kosten pro Teil im Allgemeinen bei mittleren Auflagen im Vergleich zu einmaligen Drucken. Erörtern Sie mögliche Preisnachlässe für höhere Stückzahlen während des RFQ-Prozesses.
- Qualitätssicherungsanforderungen:
- Auswirkungen: Umfassende zerstörungsfreie Prüfungen (z. B. CT-Scans), detaillierte CMM-Berichte für jedes Teil oder zusätzliche Materialtests bedeuten einen erheblichen Kosten- und Zeitaufwand.
- Erwägung: Legen Sie die Anforderungen an die Qualitätssicherung entsprechend der Kritikalität des Teils fest. Standard-Materialzertifizierungen und Maßprüfungen können für unkritische Fittings ausreichen, während Anwendungen in der Luft- und Raumfahrt oder im Nuklearbereich weitaus strengere (und kostspieligere) Validierungen erfordern.
Vorlaufzeit Komponenten:
Die Gesamtvorlaufzeit bis zum Erhalt der fertigen AM-Rohrformstücke umfasst mehrere Stufen:
- Angebots- und Auftragsabwicklung: (1-5 Tage) Überprüfung der Entwurfsdateien, DfAM-Feedback, Angebotserstellung, Auftragsbestätigung.
- Vorbereitung des Baus: (1-2 Tage) Dateivorbereitung, Planung des Baulayouts (Verschachtelung), Generierung des Supports, Einrichtung der Maschine.
- Warteschlangenzeit der Maschine: (Variabel: Tage bis Wochen) Warten auf einen freien Maschinenplatz, je nach Auslastung des Lieferanten.
- Druckzeit: (Stunden bis Tage) Hängt von der Teilehöhe, dem Volumen, der Verschachtelungsdichte und der Maschinengeschwindigkeit ab. Kann von ~12 Stunden für einen kleinen Bau bis zu mehreren Tagen für einen hohen oder dicht gepackten großen Bau reichen.
- Abkühlung und Entfettung: (Stunden bis 1 Tag) Abkühlung der Baukammer, Entfernen der Bauplatte und erste Pulverentfernung.
- Nachbearbeiten: (Variabel: Tage bis Wochen) Dies ist häufig die zeitaufwändigste Phase, die Folgendes umfasst:
- Wärmebehandlung (Spannungsabbau/Glühen/HIP): 1-3 Tage pro Zyklus (einschließlich Ofenzeit).
- Entfernen von Teilen und Stützen: Je nach Komplexität sehr unterschiedlich (Stunden bis Tage).
- Bearbeitungen: Abhängig von der Komplexität und der Anzahl der Merkmale (Stunden bis Tage).
- Endbearbeitung/Passivierung: 1-2 Tage.
- Inspektion und Qualitätskontrolle: (1-3 Tage) Maßprüfungen, NDT, Überprüfung der Dokumentation.
- Verpackung und Versand: (1-5 Tage je nach Standort/Methode).
Typische Gesamtvorlaufzeiten: Erwarten Sie Vorlaufzeiten von 1-2 Wochen für einfache, schnell bearbeitete Prototypen zu 4-8 Wochen oder länger für komplexe Fittings, die eine umfangreiche Nachbearbeitung (insbesondere HIP und Bearbeitung) und eine strenge Qualitätskontrolle erfordern, oder für größere Serienaufträge. Eine klare Kommunikation mit dem Lieferanten ist der Schlüssel zu realistischen Kostenvoranschlägen.
Rentabilitätsperspektive (ROI):
Auch wenn die Stückkosten eines AM-Beschlags manchmal höher erscheinen mögen als die eines in Massenproduktion hergestellten herkömmlichen Beschlags, sollte bei der ROI-Kalkulation berücksichtigt werden:
- Wegfall der Werkzeugkosten: Erhebliche Einsparungen bei Prototypen, Kleinserien oder Sonderanfertigungen.
- Reduzierte Vorlaufzeiten: Kürzere Markteinführungszeiten für neue Produkte oder schnellerer Austausch wichtiger Ersatzteile, wodurch kostspielige Ausfallzeiten minimiert werden.
- Optimierung des Designs: Potenzial für verbesserte Leistung (Strömungseffizienz, Gewichtsreduzierung), die zu einer besseren Systemleistung führt.
- Teil Konsolidierung: Verringerung der Montagezeit und möglicher Leckstellen.
- Reduzierung der Bestände: Die Produktion auf Abruf minimiert die Kosten für die Lagerhaltung von Ersatzteilen.
Für die richtigen Anwendungen - komplexe Geometrien, dringender Bedarf, kundenspezifische Anpassungen, geringe bis mittlere Stückzahlen, Ersatz von Altteilen - bietet Metall-AM trotz potenziell höherer anfänglicher Kosten pro Teil ein überzeugendes Wertversprechen und einen hohen ROI.
Häufig gestellte Fragen (FAQ) zu 3D-gedruckten 316L-Rohrverschraubungen
Hier sind Antworten auf einige häufige Fragen, die sich Ingenieure und Beschaffungsspezialisten zur Verwendung der additiven Metallfertigung für korrosionsbeständige 316L-Rohrverbindungen stellen:
1. Können 3D-gedruckte 316L-Rohrverbindungen den Standarddruckwerten (z. B. ASME B16.9, B16.5) entsprechen?
- Antwort: Ja, es ist möglich, dass AM 316L-Fittings die Anforderungen der Standarddruckrohrleitungscodes erfüllen oder sogar übertreffen, aber es ist nicht automatisch. Der Erfolg hängt ab von:
- Richtige Konstruktion: Sicherstellen, dass Wandstärken und Gesamtgeometrie den Codeberechnungen für den vorgesehenen Druck und die Temperatur entsprechen, unter Berücksichtigung der mechanischen Eigenschaften von AM 316L (die sich geringfügig von gewalztem Material unterscheiden können).
- Hochwertige AM-Verarbeitung: Erreichen von vollständig dichten Teilen (>99,5 %) mit minimalen Defekten durch optimierte Druckparameter und hochwertiges Pulver.
- Geeignete Nachbearbeitung: Durchführung notwendiger Wärmebehandlungen (Spannungsarmglühen, potenziell Lösungsglühen) zur Optimierung der Mikrostruktur und der mechanischen Eigenschaften. Für kritische Hochdruckanwendungen wird häufig das Heißisostatische Pressen (HIP) empfohlen oder erforderlich, um maximale Dichte zu gewährleisten und potenzielle Leckpfade zu eliminieren.
- Verifizierungstests: Durchführung von Bersttests an Prototypen oder rigorosen ZfP- und Drucktests (hydrostatisch) an Produktionsteilen, wie vom Code oder der Anwendungsspezifikation gefordert. Die Zusammenarbeit mit einem erfahrenen AM-Anbieter mit Kenntnissen über die Anforderungen an Druckkomponenten ist von entscheidender Bedeutung.
2. Welche Materialzertifizierungen und Qualitätsdokumentation kann ich bei AM 316L-Fittings erwarten?
- Antwort: Renommierte AM-Dienstleister sollten in der Lage sein, eine umfassende Dokumentation bereitzustellen. Zu den gängigen Lieferungen gehören:
- Materialzertifizierung: Typischerweise ein EN 10204 Typ 3.1-Zertifikat für die spezifische Charge des verwendeten 316L-Pulvers, das bestätigt, dass seine chemische Zusammensetzung den Standards entspricht (z. B. ASTM A276/A479 chemische Anforderungen).
- Konformitätszertifikat (CoC): Eine Erklärung des AM-Anbieters, die bestätigt, dass die Teile gemäß den angegebenen Prozessen, Zeichnungen und Qualitätsverfahren hergestellt wurden.
- Wärmebehandlungsberichte: Aufzeichnungen mit Angaben zu den Parametern (Temperatur, Zeit, Atmosphäre), die für Spannungsarmglühen, Glühen oder HIP-Zyklen verwendet wurden.
- Bericht zur Maßprüfung: Messdaten, die bestätigen, dass kritische Abmessungen innerhalb der Toleranz liegen (z. B. CMM-Bericht).
- ZfP-Berichte: Ergebnisse von allen angegebenen zerstörungsfreien Prüfungen (PT, RT, UT usw.).
- Druckprüfzertifikat: Dokumentation, die den erfolgreichen Abschluss der erforderlichen Leck- oder Druckprüfungen bestätigt.
- QMS-Zertifizierung: Nachweis der Zertifizierung des Qualitätssystems des Anbieters (z. B. ISO 9001).
3. Wie vergleicht sich die Korrosionsbeständigkeit von additiv gefertigtem 316L mit herkömmlichem gewalztem oder gegossenem 316L?
- Antwort: Bei korrekter Herstellung (hohe Dichte, richtige Chemie) und entsprechender Nachbearbeitung (spannungsarm/geglüht, passiviert) wird die Korrosionsbeständigkeit von AM 316L im Allgemeinen als vergleichbar oder potenziell sogar etwas besser als herkömmliches 316L in vielen Umgebungen.
- Die Dichte: Das Erreichen einer nahezu vollen Dichte (>99,5 %) ist entscheidend; Restporosität kann als Ausgangspunkt für lokale Korrosion dienen. HIP kann dies effektiv beseitigen.
- Mikrostruktur: Die feinkörnige Mikrostruktur, die in AM oft erreicht wird, dürfen verbessert manchmal die Passivität, obwohl dies stark von der thermischen Geschichte abhängt. Eine ordnungsgemäße Wärmebehandlung ist der Schlüssel, um Homogenität zu gewährleisten und schädliche Phasenausscheidungen zu verhindern.
- Oberfläche: As-built AM-Oberflächen sind rauer als bearbeitete Oberflächen. Während die Passivierung hilft, können sehr raue Oberflächen anfangs etwas anfälliger für Spalteffekte oder Biofilmbefall sein. Für kritische Anwendungen verbessert die Nachbearbeitung oder das Polieren von Schlüsselflächen die Korrosionsbeständigkeit und gewährleistet gleichzeitig die Abdichtbarkeit.
- Chemie: Sicherzustellen, dass das Pulver der chemischen Spezifikation 316L entspricht, ist von grundlegender Bedeutung.
4. Gibt es Mindestbestellmengen (MOQs) für 3D-gedruckte Rohrverbindungen?
- Antwort: Einer der wesentlichen Vorteile von AM ist seine Flexibilität in Bezug auf die Losgröße. Im Allgemeinen gibt es keine strengen MOQs. AM ist sehr gut geeignet für:
- Prototypen: Herstellung von Einzelstücken oder sehr kleinen Stückzahlen für Tests und Designvalidierung.
- Produktion von Kleinserien: Herstellung von Nischen- oder kundenspezifischen Fittings in kleinen Mengen (z. B. 1-100 Stück), bei denen die Werkzeugkosten für herkömmliche Methoden zu hoch wären.
- Ersatzteile: Drucken von Einzelersatzteilen für veraltete oder schwer zu beschaffende Komponenten.
- Obwohl es keinen technischen MOQ gibt, ist der Preis pro Teil sinkt tendenziell mit größeren Mengen aufgrund der Amortisation der Einrichtungskosten und einer effizienteren Maschinenauslastung. Besprechen Sie die Mengenstaffelpreise mit Ihrem Lieferanten.
5. Können Sie kundenspezifische Gewindetypen oder Flanschnormen direkt drucken?
- Antwort: AM dürfen drucken die Form von Gewinden und Flanschmerkmalen direkt. Das Erreichen der erforderlichen Präzision, Oberflächengüte und die strikte Einhaltung von Normen (z. B. NPT-Konizitätsgenauigkeit, ASME B16.5-Flächenfinish und -Abmessungen) direkt durch Drucken ist jedoch sehr anspruchsvoll und oft nicht zuverlässig für eine leckdichte Abdichtung.
- Bewährte Praxis: Der Standardansatz ist, das Fitting mit Bearbeitungszugabe an den Gewinde- oder Flanschbereichen. Diese kritischen Merkmale werden dann CNC-bearbeitet nach dem Drucken und der Wärmebehandlung, um die genauen Spezifikationen und die erforderliche Oberflächengüte zu erfüllen. Dies gewährleistet die Maßhaltigkeit, die richtige Abdichtung und die Austauschbarkeit mit Standardkomponenten. Während also die Gesamtgeometrie durch AM ermöglicht wird, basieren Präzisionsgewinde und -flansche auf der Nachbearbeitung.
Fazit: Zukunftsfähige Fluidsysteme mit additiv gefertigten korrosionsbeständigen Fittings
Die Landschaft der industriellen Flüssigkeitshandhabung entwickelt sich ständig weiter und erfordert Komponenten, die eine höhere Leistung, eine größere Zuverlässigkeit und agilere Lieferketten bieten. Die additive Fertigung von Metallen hat sich als transformative Technologie herauskristallisiert, die in der Lage ist, diese Anforderungen zu erfüllen, insbesondere für kritische Komponenten wie korrosionsbeständige Rohrverbindungen aus bewährten Materialien wie 316L und fortschrittlichen Legierungen wie 254SMO.
Wie wir festgestellt haben, sind die Vorteile klar:
- Beispiellose Designfreiheit: Ermöglichen komplexer Geometrien für optimierten Durchfluss, Teilekonsolidierung und maßgeschneiderte Lösungen.
- Beschleunigte Zeitpläne: Erleichterung von Rapid Prototyping und deutliche Reduzierung der Vorlaufzeiten für kundenspezifische oder Kleinserienproduktionen im Vergleich zu werkzeugbasierten Methoden.
- Verbesserte Effizienz: Minimierung des Materialabfalls durch nahezu endkonturnahe Produktion und Ermöglichung der On-Demand-Fertigung zur Reduzierung der Lagerkosten.
- Vielseitigkeit der Materialien: Effektive Verarbeitung robuster, korrosionsbeständiger Legierungen, die für anspruchsvolle Anwendungen in der Chemie, der Schifffahrt, der Energie und der Pharmazie unerlässlich sind.
Die erfolgreiche Implementierung von AM für Fittings erfordert jedoch einen ganzheitlichen Ansatz. Es erfordert die Anwendung von Design for Additive Manufacturing (DfAM)-Prinzipien, das Verständnis der entscheidenden Rolle einer sorgfältigen Nachbearbeitung (einschließlich Wärmebehandlung, Bearbeitung und Endbearbeitung) und die Bewältigung potenzieller Herausforderungen wie Eigenspannungen und Porosität durch sorgfältige Prozesskontrolle.
Entscheidend ist, dass die Partnerschaft mit dem richtigen AM-Lieferanten – einem mit fundiertem technischem Fachwissen, robuster Ausrüstung, strenger Materialqualitätskontrolle, umfassenden Nachbearbeitungsmöglichkeiten und zertifizierten Qualitätssystemen – von größter Bedeutung ist, um das volle Potenzial dieser Technologie auszuschöpfen.
Met3dp ist bereit, dieser Partner zu sein. Mit unserer Grundlage in fortschrittlicher Pulverherstellungunter Verwendung branchenführender Gaszerstäubungs- und PREP-Technologien zur Herstellung hochkugelförmiger, hochwertiger Metallpulver und unserem Portfolio an industriellen SEBM-Druckern , die außergewöhnliche Genauigkeit und Zuverlässigkeit liefern, bieten wir eine umfassende Lösung. Unsere jahrzehntelanges kollektives Fachwissen in der additiven Metallfertigung ermöglichen es uns, effektiv mit Ingenieuren und Beschaffungsleitern zusammenzuarbeiten und DfAM-Unterstützung, Prozessoptimierung und End-to-End-Fertigungsdienstleistungen anzubieten.
Ganz gleich, ob Sie Systeme der nächsten Generation entwickeln, die komplexe kundenspezifische Fittings erfordern, nach schnellen Prototypen zur Validierung suchen oder eine zuverlässige On-Demand-Produktion von kritischen Ersatzteilen in 316L, 254SMO oder anderen Hochleistungslegierungen benötigen, die Metall-AM bietet einen leistungsstarken Weg.
Sind Sie bereit, zu erkunden, wie die additive Fertigung Ihre Fluidsysteme verbessern kann? Kontaktieren Sie die Experten von Met3dp noch heute, um Ihre Anwendungsanforderungen zu besprechen und zu erfahren, wie unsere hochmoderne Ausrüstung, unsere hochwertigen Metallpulver und unser umfassendes Know-how Ihnen helfen können, stärkere, effizientere und zuverlässigere korrosionsbeständige Rohrverbindungen herzustellen.
Teilen auf
MET3DP Technology Co., LTD ist ein führender Anbieter von additiven Fertigungslösungen mit Hauptsitz in Qingdao, China. Unser Unternehmen ist spezialisiert auf 3D-Druckgeräte und Hochleistungsmetallpulver für industrielle Anwendungen.
Fragen Sie an, um den besten Preis und eine maßgeschneiderte Lösung für Ihr Unternehmen zu erhalten!
Verwandte Artikel
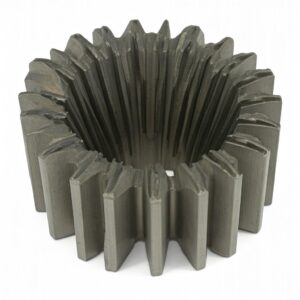
Hochleistungs-Düsenschaufelsegmente: Revolutionierung der Turbineneffizienz mit 3D-Metalldruck
Mehr lesen "Über Met3DP
Aktuelles Update
Unser Produkt
KONTAKT US
Haben Sie Fragen? Senden Sie uns jetzt eine Nachricht! Wir werden Ihre Anfrage mit einem ganzen Team nach Erhalt Ihrer Nachricht bearbeiten.
Holen Sie sich Metal3DP's
Produkt-Broschüre
Erhalten Sie die neuesten Produkte und Preislisten
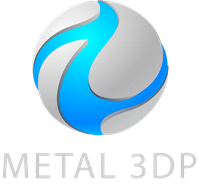
Metallpulver für 3D-Druck und additive Fertigung