Ummantelung von Elektromotoren durch 3D-Metalldruck für mehr thermische Effizienz
Inhaltsübersicht
Das unablässige Streben nach höherer Leistung, größerer Reichweite und schnellerer Aufladung auf dem Markt für Elektrofahrzeuge (EV) setzt die Konstruktion von Komponenten, insbesondere von Wärmemanagementsystemen, unter immensen Druck. Der Elektromotor, das Herzstück des EV-Antriebsstrangs, erzeugt während des Betriebs erhebliche Wärme. Die effiziente Ableitung dieser Wärme ist nicht nur für die Leistung und Zuverlässigkeit, sondern auch für die Langlebigkeit des Motors und der zugehörigen Komponenten von größter Bedeutung. Herkömmliche Kühllösungen stoßen oft an ihre Grenzen hinsichtlich Komplexität, Gewicht und thermischer Effizienz. Hier kommt die additive Fertigung von Metall (AM), oder 3D-Druckist eine bahnbrechende Technologie, die die Herstellung von hoch optimierten Kühlmänteln für Elektromotoren mit noch nie dagewesener Designfreiheit und thermischer Leistung ermöglicht. Unternehmen, die sich auf fortschrittliche Metallpulver und 3D-Druck von Metall lösungen wie Met3dp stehen an der Spitze dieser Revolution und ermöglichen es Automobilingenieuren und Beschaffungsmanagern, das Wärmemanagement-Design neu zu überdenken.
Einführung: Revolutionierung des EV-Wärmemanagements mit 3D-gedruckten Motorkühlmänteln
Der Kühlmantel eines Elektromotors (EV), auch Motorgehäuse oder Statorgehäuse mit integrierten Kühlkanälen genannt, ist eine wichtige Komponente, die für die Regulierung der Betriebstemperatur des Elektromotors verantwortlich ist. Bei der Umwandlung von elektrischer Energie in mechanische Bewegung entsteht durch die Widerstandsverluste in den Wicklungen und im Kern erhebliche Wärme. Wenn diese Hitze nicht wirksam bekämpft wird, kann sie zu einer Überhitzung führen:
- Geringerer Wirkungsgrad des Motors: Höhere Temperaturen erhöhen den elektrischen Widerstand, was zu einem größeren Energieverlust führt.
- Degradierung der Komponenten: Wenn der Motor über längere Zeit übermäßiger Hitze ausgesetzt ist, können Isoliermaterialien, Lager und Magnete beschädigt werden, was die Lebensdauer des Motors erheblich verkürzt.
- Leistungsdrosselung: Um eine Überhitzung zu vermeiden, kann das Steuersystem des Fahrzeugs die Motorleistung begrenzen, was sich negativ auf die Fahrleistung auswirkt, insbesondere unter anspruchsvollen Bedingungen wie bei hoher Geschwindigkeit oder beim Abschleppen.
- Sicherheitsaspekte: In extremen Fällen kann eine Überhitzung ein Sicherheitsrisiko darstellen.
Der Hauptzweck des Kühlmantels besteht darin, Wege für ein Kühlmittel (in der Regel ein Wasser-Glykol-Gemisch) zu schaffen, das um die wärmeerzeugenden Teile des Motors, vor allem den Stator, zirkuliert, die Wärme aufnimmt und an einen Kühler abgibt. Die Effektivität dieser Wärmeübertragung steht in direktem Zusammenhang mit der Gestaltung der Kühlkanäle innerhalb des Mantels - ihrem Verlauf, ihrer Form, ihrer Oberfläche und ihrer Nähe zu Wärmequellen.
Warum Wärmemanagement bei E-Fahrzeugen wichtiger denn je ist:
Die Anforderungen an die Wärmemanagementsysteme für Elektrofahrzeuge steigen aufgrund verschiedener Branchentrends:
- Erhöhte Leistungsdichte: Die Motoren werden immer kleiner und leistungsfähiger, um die Leistungserwartungen und die Anforderungen an die Bauweise zu erfüllen, wodurch die Wärmeerzeugung auf ein kleineres Volumen konzentriert wird.
- Schnelleres Aufladen: Das Hochgeschwindigkeitsladen erzeugt nicht nur in der Batterie erhebliche Wärme, sondern beeinflusst auch die thermische Belastung des gesamten Antriebssystems während des späteren Betriebs.
- Ziele mit erweiterter Reichweite: Die Optimierung aller Aspekte der Fahrzeugeffizienz, einschließlich der Minimierung von Energieverlusten durch Wärme, ist entscheidend für die Maximierung der Fahrreichweite.
- Anforderungen an die Leistung: Die Verbraucher erwarten von E-Fahrzeugen eine Beschleunigung und eine anhaltende Leistung, die mit der von Fahrzeugen mit Verbrennungsmotor vergleichbar oder sogar besser ist, was ein robustes Wärmemanagement erfordert.
Traditionelle Fertigungsbeschränkungen:
Herkömmlichen Herstellungsverfahren für Motorkühlmäntel wie dem Gießen (Sandguss, Druckguss) und der maschinellen Bearbeitung von Knüppeln sind inhärente Grenzen gesetzt:
- Geometrische Zwänge: Mit Gussverfahren lassen sich nur schwer hochkomplexe innere Kanalgeometrien mit dünnen Wänden oder komplizierten Bahnen herstellen, die für einen optimalen Kühlmittelfluss und Wärmeaustausch erforderlich sind. Entformungswinkel, Kernplatzierungsbeschränkungen und Mindestwandstärken schränken die Designfreiheit ein.
- Gewicht: Gegossene Komponenten sind oft dicker als strukturell notwendig, einfach aufgrund von Einschränkungen im Herstellungsprozess, was zu unnötigem Gewicht führt - ein kritischer Nachteil bei Elektrofahrzeugen, bei denen die Reichweite von entscheidender Bedeutung ist.
- Werkzeugkosten und Vorlaufzeiten: Die Herstellung von Formen und Gesenken für das Gießen ist teuer und zeitaufwändig und daher weniger geeignet für kleine bis mittlere Produktionsserien oder schnelle Prototyping-Wiederholungen.
- Komplexität der Montage: Manchmal müssen bei komplexen Kühlkreisläufen mehrere gegossene oder maschinell bearbeitete Teile zusammengebaut und abgedichtet werden, was potenzielle Leckagepfade und zusätzliche Fertigungsschritte mit sich bringt.
Die Transformation der additiven Fertigung:
Der 3D-Metalldruck überwindet diese Einschränkungen grundlegend. Durch den schichtweisen Aufbau des Kühlmantels direkt aus Metallpulver (z. B. aus Speziallegierungen wie CuCrZr oder AlSi10Mg) ermöglicht AM:
- Unerreichte Gestaltungsfreiheit: Ingenieure können hochkomplexe, topologieoptimierte interne Kühlkanäle entwerfen, die genau den Konturen der Wärmequellen folgen und die Oberfläche und die turbulente Strömung für eine hervorragende Wärmeübertragung maximieren. Merkmale wie dünne Wände, komplizierte Gitterstrukturen und konforme Kanäle, die mit herkömmlichen Methoden unmöglich oder unerschwinglich sind, werden möglich.
- Teil Konsolidierung: Mehrere Komponenten einer herkömmlichen Kühlungsbaugruppe können in ein einziges 3D-gedrucktes Teil integriert werden, was die Montagezeit, das Gewicht und mögliche Fehlerquellen reduziert.
- Gewichtsreduzierung: Das Material kann genau dort platziert werden, wo es für die strukturelle Integrität und die thermische Funktion benötigt wird, was eine erhebliche Gewichtsreduzierung im Vergleich zu gegossenen Gegenstücken ermöglicht.
- Rapid Prototyping und Iteration: Entwürfe können schnell geändert und neu gedruckt werden, ohne dass teure Werkzeugänderungen erforderlich sind, was die Entwicklungszyklen beschleunigt und eine Leistungsoptimierung ermöglicht.
- Materialanpassung: AM ermöglicht die Verwendung fortschrittlicher Metalllegierungen, die speziell für ihre Wärmeleitfähigkeit, ihr Verhältnis von Festigkeit zu Gewicht und ihre Korrosionsbeständigkeit ausgewählt werden und auf die anspruchsvollen Umgebungsbedingungen von Elektrofahrzeugen zugeschnitten sind.
Führende Anbieter wie Met3dp, die fortschrittliche Pulverherstellungsverfahren wie die Gaszerstäubung und das Plasma-Rotations-Elektroden-Verfahren (PREP) zusammen mit hochmodernen Selective Electron Beam Melting (SEBM)- und Laser Powder Bed Fusion (L-PBF)-Druckern einsetzen, bieten die hochwertigen Materialien und die Fertigungspräzision, die für diese kritischen Komponenten erforderlich sind. Ihr Fachwissen erstreckt sich über die gesamte Prozesskette, von der Pulverproduktion bis zum fertigen Teil, und gewährleistet Zuverlässigkeit und Leistung für anspruchsvolle Automobilanwendungen. Angesichts der rasanten Expansion der Elektrofahrzeugindustrie wird Metall-AM zu einem unverzichtbaren Werkzeug für die Entwicklung und Herstellung der nächsten Generation von Hochleistungskühlmänteln für Motoren werden.
Kernanwendungen: Wo sind 3D-gedruckte Kühlmäntel für Elektrofahrzeuge von Bedeutung?
Das Potenzial von 3D-gedruckten Kühlmänteln erstreckt sich über verschiedene Elektromotoranwendungen. Am stärksten verbreitet sind sie derzeit in Sektoren, in denen Leistung, Gewicht und Designoptimierung entscheidende Unterscheidungsmerkmale sind. Automobilhersteller (OEMs) und ihre Tier-1-Zulieferer sind die ersten Entdecker und Anwender, angetrieben durch die einzigartigen Anforderungen des Elektromarktes. Beschaffungsmanager und Ingenieurteams in diesen Unternehmen evaluieren zunehmend Anbieter von Metall-AM-Lösungen, sowohl für Prototypen als auch für die Serienproduktion.
Wichtigste Anwendungsbereiche:
- Leistungsstarke Elektrofahrzeuge (Hypercars & Sport-EVs):
- Herausforderung: Diese Fahrzeuge stoßen an die Grenzen von Leistungsdichte und dauerhafter Leistung. Die Motoren arbeiten unter extremen Belastungen und erzeugen eine enorme Hitze, die herkömmliche Kühlsysteme nur schwer in den Griff bekommen. Auch für das Fahrverhalten und die Beschleunigung ist eine Gewichtsreduzierung von größter Bedeutung.
- AM-Lösung: Der 3D-Metalldruck ermöglicht topologieoptimierte Kühlmäntel mit hochkomplexen internen Kanälen, die mithilfe von CFD-Simulationen (Computational Fluid Dynamics) entwickelt wurden. Diese Ummantelungen maximieren die Wärmeabfuhr aus kritischen Bereichen wie Statorwicklungen und Endwindungen und ermöglichen eine höhere Dauerleistung ohne Überhitzung. Materialien wie Kupferlegierungen (z. B. CuCrZr), die eine hervorragende Wärmeleitfähigkeit aufweisen, werden oft bevorzugt, trotz der Herausforderungen bei der Herstellung, die durch AM überwunden werden können. Leichtbau durch optimiertes Design verbessert die Fahrzeugdynamik weiter. Spezialisierte Hersteller und Leistungsabteilungen sind die wichtigsten Großabnehmer in dieser Nische.
- Premium & Mainstream-Elektrofahrzeuge:
- Herausforderung: Auch wenn sie vielleicht nicht so extrem sind wie Hypercars, benötigen herkömmliche Elektrofahrzeuge dennoch ein effizientes Wärmemanagement für Reichweite, Zuverlässigkeit und Schnellladefähigkeit. OEMs suchen nach kosteneffizienten Lösungen, die Verbesserungen gegenüber dem herkömmlichen Guss bieten, insbesondere da die Leistungsdichte der Motoren in allen Segmenten steigt. Die Reduzierung von NVH (Noise, Vibration, Harshness) durch ein optimiertes Gehäusedesign ist ebenfalls ein Faktor.
- AM-Lösung: Die additive Fertigung, insbesondere unter Verwendung kostengünstiger und gut erprobter Aluminiumlegierungen wie AlSi10Mg, bietet einen Weg zu einer verbesserten thermischen Leistung im Vergleich zu einfachen Gusskonstruktionen. AM ermöglicht konforme Kühlkanäle, die den Stator enger umschließen und so den Wärmewiderstand verringern. Die Konsolidierung von Teilen kann Montagelinien vereinfachen. Auch wenn die Kostenkonkurrenz zum Druckguss in großen Stückzahlen nach wie vor eine Überlegung ist, bietet AM in der Entwicklungsphase einen erheblichen Wert für schnelle Iterationen und Leistungsvalidierung. In dem Maße, wie die AM-Technologie reift und die Kosten sinken, wird sie zunehmend in der Serienproduktion für Premiumsegmente eingesetzt, wobei die Händler eine Rolle bei der Verwaltung der Lieferkette für diese Komponenten spielen.
- Elektro-Motorsport (Formel E, Elektro-GT, etc.):
- Herausforderung: Der Motorsport ist der Gipfel der Leistungsoptimierung unter strengen Vorschriften. Die Teams benötigen maximale Leistung, minimales Gewicht und extreme Zuverlässigkeit unter Rennbedingungen. Die Entwicklungszyklen sind kurz und erfordern eine schnelle Prototypenerstellung und die Fertigung maßgeschneiderter Komponenten.
- AM-Lösung: Der 3D-Metalldruck wird im Motorsport häufig eingesetzt, da er die Möglichkeit bietet, in kürzester Zeit hochgradig individuelle, leichte Komponenten mit optimierten Leistungsmerkmalen herzustellen. Kühlmäntel sind erstklassige Kandidaten, die es den Teams ermöglichen, das Wärmemanagement genau auf ihre einzigartigen Motorkonstruktionen und Rennstrategien abzustimmen. Die Möglichkeit, Designs zwischen den Rennen auf der Grundlage von Leistungsdaten zu iterieren, ist von unschätzbarem Wert. Die Wahl des Materials (oft hochfestes Aluminium oder spezielle Legierungen) und komplizierte Innengeometrien sind wichtige Vorteile, die von Rennteams genutzt werden, die oft direkt mit AM-Dienstleistern zusammenarbeiten.
- Elektrische Nutzfahrzeuge (Busse, Lastwagen):
- Herausforderung: In schweren Elektrofahrzeugen werden große, leistungsstarke Motoren eingesetzt, die unter konstanten Lastzyklen arbeiten. Zuverlässigkeit, Langlebigkeit und Effizienz sind entscheidend für die Minimierung der Betriebskosten. Das Wärmemanagement muss robust sein, um anhaltend hohe Drehmomentanforderungen und unterschiedliche Umgebungsbedingungen zu bewältigen.
- AM-Lösung: Während die Kostensensibilität hoch ist, kann das Potenzial für verbesserte Effizienz und Zuverlässigkeit durch optimierte Kühlung einen langfristigen Wert bieten. AM kann zur Herstellung von Kühlmänteln mit verbesserter Verteilung des Kühlmittelflusses verwendet werden, wodurch heiße Stellen vermieden und die Lebensdauer des Motors verlängert werden. Für spezielle Nutzfahrzeuge oder bei der Entwicklung neuer Antriebsstrangplattformen bietet AM eine flexible Fertigungslösung. Beschaffungsabteilungen im Nutzfahrzeugbau suchen nach zuverlässigen Lieferanten für den industriellen Metalldruck, die in der Lage sind, die Haltbarkeitsstandards zu erfüllen.
- Elektrischer Antrieb für die Luft- und Raumfahrt (urbane Luftmobilität, Drohnen):
- Herausforderung: Obwohl erst im Entstehen begriffen, erfordert der elektrische Antrieb in der Luft- und Raumfahrt eine extreme Gewichtsreduzierung und eine außergewöhnlich hohe Zuverlässigkeit. Das Wärmemanagement ist aufgrund der veränderten Luftdichte und der schwerwiegenden Folgen eines Komponentenausfalls von entscheidender Bedeutung.
- AM-Lösung: Der 3D-Metalldruck ist in der Luft- und Raumfahrt bereits ein fester Bestandteil, da er die Herstellung leichter, komplexer Teile ermöglicht. Für die Kühlung von Elektromotoren in Drohnen oder zukünftigen UAM-Fahrzeugen ermöglicht AM hochintegrierte und optimierte Wärmemanagementsysteme, die oft Strukturelemente mit Kühlkanälen in einem einzigen Bauteil kombinieren und Materialien wie hochfeste Aluminium- oder Titanlegierungen verwenden. Strenge Qualitätskontrollen und Zertifizierungen, die von erfahrenen Anbietern wie Met3dp angeboten werden, sind dabei unerlässlich.
Verbesserte Funktionen durch 3D-Druck:
Bei all diesen Anwendungen verbessert der 3D-Metalldruck speziell die Funktion des Kühlmantels:
- Verbesserte Wärmeübertragung: Eine optimierte Kanalgeometrie (komplexe Pfade, Turbulatoren, vergrößerte Oberfläche) verbessert den Wärmeübergangskoeffizienten zwischen den Motorkomponenten und dem Kühlmittel.
- Gezielte Kühlung: Der Kühlmittelfluss kann genau auf die identifizierten Hotspots im Motor gerichtet werden.
- Reduzierte thermische Gradienten: Durch die gleichmäßigere Kühlung werden Temperaturschwankungen im Motor minimiert, was zu einer geringeren Belastung und einer längeren Lebensdauer führt.
- Verbesserter Kühlmittelfluss: Das optimierte Kanaldesign minimiert den Druckabfall und ermöglicht so kleinere, effizientere Kühlmittelpumpen.
- Integrationspotenzial: Die Kühlkanäle können direkt in die Motorkomponenten integriert werden, was die Anzahl der Teile und die Komplexität der Montage reduziert.
Die Möglichkeit, diese funktionalen Verbesserungen zu nutzen, macht 3D-gedruckte Kühlmäntel zu einem überzeugenden Angebot für Ingenieure, die eine Leistungssteigerung anstreben, und für Beschaffungsmanager, die nach innovativen Lösungen von fortschrittlichen Fertigungslieferanten suchen.
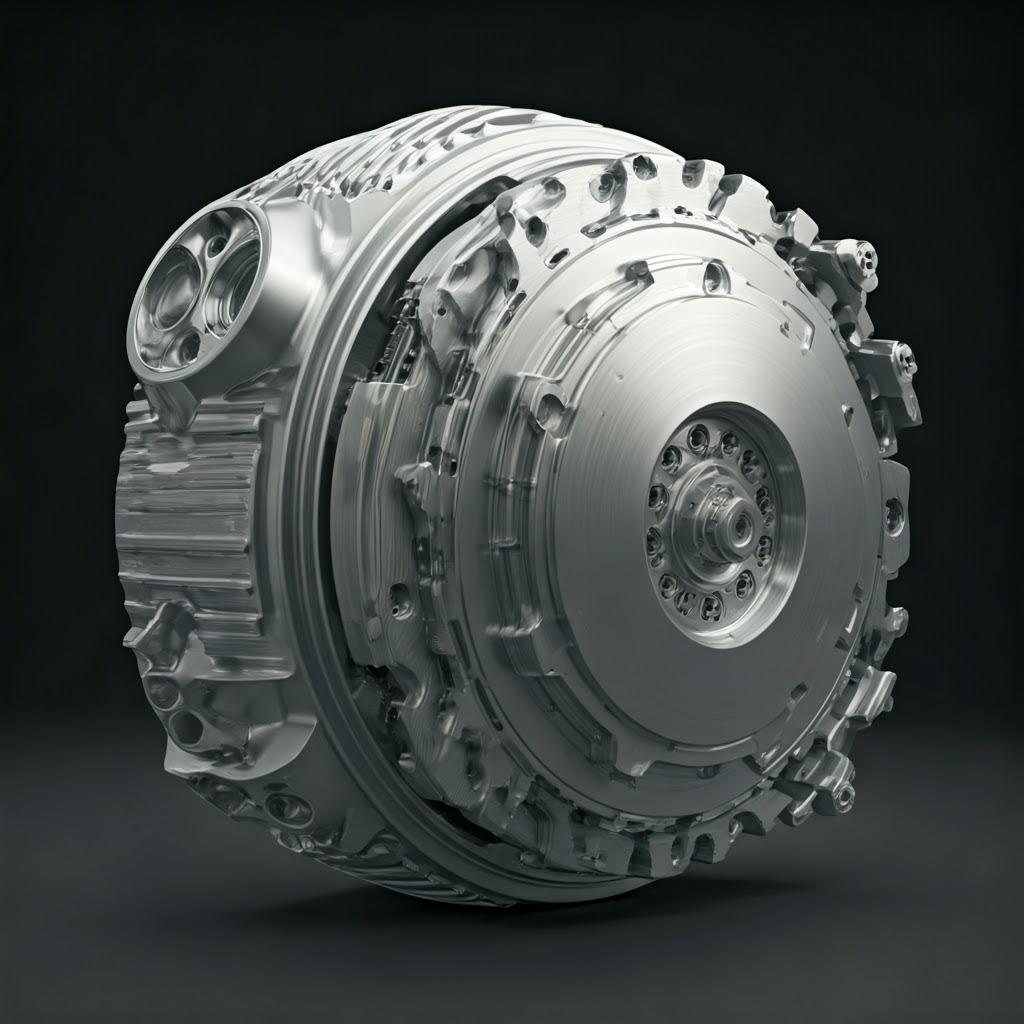
Der Additiv-Vorteil: Warum sollten Sie den 3D-Druck von Metall für EV-Kühlmäntel herkömmlichen Methoden vorziehen?
Die Entscheidung von Automobilherstellern, Tier-1-Zulieferern und Herstellern von Hochleistungsfahrzeugen für die additive Fertigung von Kühlmänteln für Elektromotoren beruht auf einer Reihe von überzeugenden Vorteilen, die die Unzulänglichkeiten herkömmlicher Verfahren wie Gießen und Zerspanen direkt ausgleichen. Während herkömmliche Verfahren für bestimmte Anwendungen nach wie vor geeignet sind, bietet die Metall-AM ein transformatives Potenzial, insbesondere wenn es darum geht, die Grenzen von Leistung, Effizienz und Designintegration zu verschieben. Die Bewertung dieser Vorteile ist für technische Leiter und Beschaffungsspezialisten bei der Beschaffung moderner Automobilkomponenten von entscheidender Bedeutung.
1. Unerreichte geometrische Komplexität & Gestaltungsfreiheit:
- Traditionelle Einschränkung: Gießverfahren sind durch die Notwendigkeit von Formen und Kernen eingeschränkt. Die Gestaltung komplizierter innerer Durchgänge mit Hinterschneidungen, scharfen Kurven oder variablen Querschnitten ist schwierig, kostspielig oder unmöglich. Es sind Entformungswinkel erforderlich, und die Mindestwandstärken übersteigen oft die strukturellen Notwendigkeiten. Die maschinelle Bearbeitung von Innenkanälen in einem massiven Block ist ebenfalls sehr restriktiv.
- AM Vorteil: Durch den schichtweisen Aufbau werden die meisten geometrischen Beschränkungen aufgehoben. Metall-AM ermöglicht:
- Topologieoptimierte Kanäle: Algorithmen ermitteln die effizientesten Belastungspfade und Materialverteilungen. Bei Kühlmänteln bedeutet dies, dass die Kanäle genau den Wärmequellen folgen, wodurch die Kontaktfläche maximiert und der Materialverbrauch und das Gewicht minimiert werden.
- Konforme Kühlung: Die Kanäle können sich genau an die Form des Stators oder Rotors anpassen, wobei ein gleichmäßiger, minimaler Abstand für eine hocheffiziente Wärmeübertragung eingehalten wird, im Gegensatz zu den oft kompromittierten Pfaden in Gusskonstruktionen.
- Interne Gitterstrukturen: Leichte, komplizierte Gitterstrukturen können in die Kanalwände oder den Mantelkörper eingebaut werden, um die strukturelle Steifigkeit zu erhöhen und gleichzeitig die Masse zu minimieren, oder sogar in die Kanäle selbst, um eine turbulente Strömung zu fördern und die Wärmeübertragungsfläche zu vergrößern.
- Dünne, gleichmäßige Wände: Die Wände können sehr viel dünner (bis in den Submillimeterbereich, sofern der Prozess dies zulässt) und gleichmäßiger gestaltet werden als beim Gießen, wodurch Gewicht und Wärmewiderstand reduziert werden.
- Integrierte Funktionen: Funktionale Merkmale wie Befestigungspunkte, Sensorgehäuse oder Flüssigkeitsanschlüsse können nahtlos in das einzelne gedruckte Teil integriert werden.
2. Hervorragende thermische Leistung:
- Traditionelle Einschränkung: Die geometrischen Beschränkungen des Gießens führen häufig zu suboptimalen Strömungswegen für das Kühlmittel, zu potenziellen Totzonen, in denen das Kühlmittel stagniert, und zu größeren Abständen zwischen dem Kühlmittel und der Wärmequelle, was zu einem höheren Wärmewiderstand und einer weniger effizienten Wärmeableitung führt.
- AM Vorteil: Die durch AM ermöglichte Designfreiheit führt direkt zu einer überlegenen thermischen Leistung:
- Maximierte Oberfläche: Komplexe Innengeometrien, einschließlich Rippen oder Gitterstrukturen in den Kanälen, vergrößern die für den Wärmeaustausch verfügbare Oberfläche drastisch.
- Optimierte Flusspfade: Mithilfe von CFD-Simulationen lassen sich Kanäle entwerfen, die eine gleichmäßige Kühlmittelgeschwindigkeit gewährleisten, den Druckabfall minimieren und bei Bedarf Turbulenzen erzeugen, um den Wärmeübergangskoeffizienten zu maximieren.
- Reduzierte thermische Engpässe: Konforme Kanäle minimieren den Weg, den die Wärme von der Quelle (Statorwicklungen) bis zum Kühlmittel zurücklegen muss, und verringern so den Wärmewiderstand erheblich.
- Gezielte Kühlung: Das Kühlmittel kann bevorzugt zu bekannten Hotspots innerhalb der Motorkonstruktion geleitet werden.
3. Erhebliches Potenzial zur Gewichtsreduzierung:
- Traditionelle Einschränkung: Beim Gießen sind oft dickere Abschnitte erforderlich, um die Form zu füllen und die strukturelle Integrität zu gewährleisten, was zu schwereren Komponenten führt. Die maschinelle Bearbeitung von Knüppeln beginnt mit überschüssigem Material.
- AM Vorteil: Material wird nur dort hinzugefügt, wo es benötigt wird. Topologieoptimierung und Gitterstrukturen ermöglichen eine drastische Reduzierung des Materialverbrauchs bei gleichbleibender oder sogar höherer struktureller Leistung und Steifigkeit im Verhältnis zum Gewicht. Gewichtsreduzierung ist bei Elektrofahrzeugen entscheidend, um die Reichweite, das Handling und die Gesamteffizienz zu verbessern. Schon ein paar eingesparte Kilogramm sind ein bedeutender Beitrag.
4. Teil Konsolidierung:
- Traditionelle Einschränkung: Komplexe Kühlsysteme erfordern möglicherweise mehrere gegossene oder bearbeitete Komponenten (z. B. separate Mantelhälften, Verteiler, Anschlüsse), die zusammengebaut, verschraubt, geschweißt oder gelötet werden müssen, was zu potenziellen Leckstellen, Montageaufwand und Toleranzproblemen führt.
- AM Vorteil: Metall-AM ermöglicht die Konsolidierung mehrerer Funktionselemente in einem einzigen, monolithisch gedruckten Teil. Dies vereinfacht die Lieferkette, verringert die Montagezeit und -kosten, verbessert die Zuverlässigkeit durch den Wegfall von Verbindungen und Dichtungen und trägt häufig zu einer weiteren Gewichtsreduzierung bei. Dies ist ein bedeutender Vorteil für Großeinkäufer und Beschaffungsteams, die komplexe Baugruppen verwalten.
5. Beschleunigte Entwicklung & Prototyping:
- Traditionelle Einschränkung: Die Herstellung von Werkzeugen (Gussformen, Matrizen) für den Guss ist eine große Investition in Zeit (Wochen oder Monate) und Kosten. Iterationen des Designs erfordern teure Werkzeugänderungen oder komplette Neuanfertigungen. Die maschinelle Bearbeitung von Prototypen kann schneller sein, aber möglicherweise nicht die Eigenschaften oder die Geometrie des endgültigen Gussteils genau wiedergeben.
- AM Vorteil: AM ist ein werkzeugloses Verfahren. Die Entwürfe können direkt vom CAD an den Drucker gesendet werden. Prototypen können innerhalb von Tagen hergestellt werden, so dass Ingenieure ihre Entwürfe auf der Grundlage von thermischen und strukturellen Simulationen oder physikalischen Tests schnell testen und überarbeiten können. Dadurch wird der Entwicklungszyklus drastisch verkürzt, das Risiko verringert und die endgültigen Entwürfe können besser optimiert werden, bevor sie in die Massenproduktion gehen. Unternehmen wie Met3dp, die sowohl fortschrittliche Drucker als auch Materialien anbieten, können diesen schnellen Iterationsprozess erleichtern.
6. Materialflexibilität & Moderne Legierungen:
- Traditionelle Einschränkung: Das Gießen ist oft auf bestimmte, gut etablierte Legierungen beschränkt (hauptsächlich Aluminiumlegierungen für Kühlmäntel). Die Einführung neuer oder schwierig zu gießender Legierungen kann eine Herausforderung sein.
- AM Vorteil: Metall-AM-Prozesse wie L-PBF und SEBM sind mit einer breiteren Palette an modernen Metallpulvern kompatibel, darunter:
- Kupferlegierungen mit hoher Wärmeleitfähigkeit (z. B. CuCrZr): Bieten eine deutlich bessere Wärmeübertragung als Aluminium, sind aber bekanntermaßen schwierig, komplexe Formen ohne Defekte zu gießen. AM macht komplizierte Ummantelungen aus Kupferlegierungen machbar.
- Hochfeste Aluminium-Legierungen: Spezielle Al-Legierungen, die für AM optimiert sind, bieten ein hervorragendes Verhältnis von Festigkeit zu Gewicht.
- Titan-Legierungen: Für Anwendungen, die ein extrem geringes Gewicht und eine hohe Korrosionsbeständigkeit erfordern (aufgrund der geringeren Wärmeleitfähigkeit und der höheren Kosten weniger verbreitet für Primärkühlmäntel).
- Kundenspezifische Legierungen: AM-Anbieter wie Met3dp, die über eine eigene Pulverproduktion mit Techniken wie der Gasverdüsung verfügen, können sogar die Entwicklung und Verwendung kundenspezifischer Legierungen unterstützen, die auf spezifische thermische und mechanische Anforderungen zugeschnitten sind.
B2B Supply Chain & Fertigung Vorteile:
- Reduzierte Werkzeuginvestition: Die hohen Vorlaufkosten für Gussformen entfallen.
- Produktion auf Abruf: Ermöglicht die Herstellung näher am Ort des Bedarfs, was die Logistik vereinfachen kann.
- Flexible Chargengrößen: Wirtschaftlich rentabel für kleine bis mittlere Produktionsserien, ideal für Nischenfahrzeuge, Motorsport oder erste Produktionsanläufe, bevor die Herstellung von Großserienwerkzeugen gerechtfertigt ist.
- Digitales Inventar: Die Entwürfe liegen als digitale Dateien vor, so dass die Teile je nach Bedarf gedruckt werden können, was den Bedarf an physischen Beständen reduziert.
Vergleichstabelle: AM vs. traditionelle Methoden für EV-Kühlmäntel
Merkmal | Additive Fertigung von Metall (AM) | Traditioneller Guss | Traditionelle Bearbeitung |
---|---|---|---|
Geometrische Komplexität | Sehr hoch (interne Kanäle, Gitter, konform) | Mäßig bis gering (Abzugswinkel, Kerngrenzen) | Niedrig (begrenzte interne Funktionen) |
Thermische Leistung | Potenziell sehr hoch (optimierter Fluss, max SA) | Mäßig (Beeinträchtigte Fließwege) | Mäßig bis hoch (wenn es das Design erlaubt) |
Gewichtsreduzierung | Hervorragend (Topologieoptimierung, Netze) | Angemessen (Mindestwanddickengrenzen) | Angemessen (Grenzwerte für den Materialabtrag) |
Teil Konsolidierung | Hohes Potenzial | Geringes Potenzial | Sehr geringes Potenzial |
Prototyping-Geschwindigkeit | Sehr schnell (Tage) | Langsam (Wochen/Monate für Werkzeuge) | Moderat (Tage/Wochen) |
Werkzeugkosten | Keine / Sehr gering | Hoch | Gering (Vorrichtung) |
Material-Optionen | Breit (Al, Cu, Ti, Stahl, Sonderlegierungen) | Begrenzt (Hauptsächlich Al, einige Fe-Legierungen) | Breit (abhängig von der Verfügbarkeit von Knüppeln) |
Ideales Volumen | Niedrig bis mittel, Prototyping | Hoch | Niedrig, Prototyping |
Kosten pro Teil (Low Vol) | Mäßig bis hoch | Sehr hoch (aufgrund der Werkzeugamortisation) | Hoch |
Kosten pro Teil (hohes Volumen) | Hoch (Prozesszeit) | Niedrig | Mäßig bis hoch |
Lieferkette | Potenziell einfacher (On-demand, digital) | Komplexe (Werkzeuglieferanten, Gießereien) | Einfacher (Materiallieferanten, Maschinenwerkstätten) |
In Blätter exportieren
Während die Kosten pro Teil bei sehr hohen Stückzahlen immer noch zugunsten des traditionellen Gießens ausfallen können, machen die überzeugenden technischen Vorteile, insbesondere in Bezug auf Leistung, Gewicht und Entwicklungsgeschwindigkeit, den 3D-Metalldruck zu einem zunehmend attraktiven und strategisch wichtigen Herstellungsverfahren für Kühlmäntel von Elektromotoren, insbesondere für leistungsorientierte Anwendungen und Unternehmen, die einen Wettbewerbsvorteil suchen. Die Wahl eines erfahrenen Partners für die additive Fertigung ist der Schlüssel zur Nutzung dieser Vorteile.
Das Material ist entscheidend: Auswahl von Hochleistungspulvern wie CuCrZr und AlSi10Mg
Die Wahl des Materials ist von grundlegender Bedeutung für die Leistung und Zuverlässigkeit eines jeden technischen Bauteils, und 3D-gedruckte Kühlmäntel für Elektromotoren bilden hier keine Ausnahme. Die Wahl des Metallpulvers bestimmt die Wärmeleitfähigkeit, die mechanische Festigkeit, das Gewicht, die Korrosionsbeständigkeit und letztlich die Fähigkeit, die hohen Anforderungen von Elektrofahrzeugantrieben zu erfüllen. Die additive Fertigung ermöglicht den Einsatz von Materialien, die sich mit herkömmlichen Methoden nur schwer oder gar nicht formen lassen, was den Ingenieuren mehr Flexibilität bietet, aber auch sorgfältige Überlegungen erfordert. Bei Kühlmänteln für Elektrofahrzeuge stechen zwei Materialfamilien hervor: Aluminiumlegierungen und Kupferlegierungen.
Warum die Materialauswahl so wichtig ist:
- Wärmeleitfähigkeit: Dies ist wohl die wichtigste Eigenschaft. Eine höhere Wärmeleitfähigkeit ermöglicht eine leichtere Wärmeübertragung von den Wärmequellen des Motors (Stator) durch das Mantelmaterial zum Kühlmittel, wodurch der Wärmewiderstand minimiert und der Motor kühler gehalten wird.
- Mechanische Festigkeit & Langlebigkeit: Der Kühlmantel ist häufig ein struktureller Teil der Motorbaugruppe. Er muss während der gesamten Lebensdauer des Fahrzeugs Vibrationen, mechanischen Belastungen und dem inneren Kühlmitteldruck standhalten. Auch Temperaturschwankungen führen zu thermischen Spannungen.
- Gewicht: Die Minimierung des Gewichts der Komponenten ist entscheidend für die Maximierung der Reichweite und Leistung von Elektrofahrzeugen. Leichtere Materialien tragen direkt zu diesem Ziel bei.
- Korrosionsbeständigkeit: Das Material muss mit handelsüblichen Kfz-Kühlmitteln (z. B. Wasser-Glykol-Gemischen) verträglich und über viele Jahre hinweg korrosionsbeständig sein und unterschiedlichen Umweltbedingungen ausgesetzt werden.
- Herstellbarkeit (Druckbarkeit): Nicht alle Legierungen lassen sich mit Metall-AM-Technologien wie L-PBF oder SEBM gleich gut verarbeiten. Faktoren wie die Absorption des Laser-/Elektronenstrahls, die Fließfähigkeit des Pulvers, die Schweißbarkeit und die Anfälligkeit für Rissbildung oder Eigenspannungen während des Drucks müssen berücksichtigt werden.
- Kosten: Die Materialkosten sind ein bedeutender Faktor für den Gesamtpreis der Komponenten, insbesondere bei der Produktion größerer Stückzahlen. Die Beschaffungsteams müssen die Leistungsanforderungen mit den Budgetbeschränkungen in Einklang bringen.
Empfohlene Puder für EV-Kühljacken:
1. Aluminium-Legierungen (insbesondere AlSi10Mg):
- Überblick: AlSi10Mg ist eine der gängigsten und am besten charakterisierten Aluminiumlegierungen, die in der additiven Fertigung von Metallen verwendet werden. Es handelt sich im Wesentlichen um eine Aluminium-Silizium-Magnesium-Gusslegierung, die in Pulverform hergestellt wird.
- Wichtige Eigenschaften:
- Gute Wärmeleitfähigkeit: AlSi10Mg bietet eine gute Wärmeleitfähigkeit (etwa 150-180 W/m-K nach der Wärmebehandlung), die zwar nicht so hoch ist wie die von Kupfer, aber deutlich besser als die von Stählen oder Titanlegierungen.
- Ausgezeichnetes Verhältnis von Stärke zu Gewicht: Aluminiumlegierungen sind von Natur aus leicht (Dichte ~2,68 g/cm³). AlSi10Mg bietet eine gute mechanische Festigkeit und Steifigkeit, insbesondere nach einer geeigneten Wärmebehandlung (T6), wodurch es sich für Strukturbauteile eignet.
- Gute Druckfähigkeit: Es lässt sich im Allgemeinen gut mit L-PBF-Systemen verarbeiten und weist im Vergleich zu einigen anderen Legierungen eine gute Schweißbarkeit und relativ geringe Eigenspannungen auf. Dies macht ihn zu einer zuverlässigen Wahl für komplexe Geometrien.
- Korrosionsbeständigkeit: Zeigt eine gute Korrosionsbeständigkeit, geeignet für typische Kühlmittelumgebungen in Kraftfahrzeugen.
- Kosten-Nutzen-Verhältnis: Aluminiumpulver sind in der Regel preiswerter als Kupfer- oder Titanlegierungen, was AlSi10Mg zu einem guten Kandidaten für kostensensitive Anwendungen und die Skalierung zur Serienproduktion macht.
- Warum das für Kühljacken wichtig ist: AlSi10Mg bietet eine ausgewogene Kombination aus thermischer Leistung, geringem Gewicht, angemessener Festigkeit, guter Herstellbarkeit und angemessenen Kosten. Es ist häufig der Standard-Ausgangspunkt für viele AM-Anwendungen in der Automobilindustrie, einschließlich Komponenten für das Wärmemanagement. Die weit verbreitete Verwendung bedeutet, dass die Verarbeitungsparameter von erfahrenen AM-Dienstleistern gut verstanden werden.
2. Kupferlegierungen (insbesondere CuCrZr – Kupfer-Chrom-Zirkonium):
- Überblick: Kupferlegierungen sind aufgrund ihrer außergewöhnlichen Wärmeleitfähigkeit für das Wärmemanagement sehr attraktiv. CuCrZr ist eine ausscheidungsgehärtete Kupferlegierung, die ein gutes Gleichgewicht zwischen Leitfähigkeit und mechanischer Festigkeit bei hohen Temperaturen bietet.
- Wichtige Eigenschaften:
- Ausgezeichnete Wärmeleitfähigkeit: Dies ist der Hauptvorteil. CuCrZr verfügt über eine sehr hohe Wärmeleitfähigkeit (typischerweise >300 W/m-K), die etwa doppelt so hoch ist wie die von AlSi10Mg. Dies ermöglicht eine wesentlich effizientere Wärmeabfuhr aus dem Motor.
- Gute mechanische Festigkeit (bei Temperatur): Während reines Kupfer weich ist, ermöglichen die Zusätze von Chrom und Zirkonium eine Aushärtung, wodurch die Festigkeit deutlich erhöht wird und das Material selbst bei den hohen Betriebstemperaturen in Elektromotoren gute mechanische Eigenschaften behält.
- Gute Korrosionsbeständigkeit: Im Allgemeinen kompatibel mit Kühlmitteln für Kraftfahrzeuge.
- Höhere Dichte: Kupferlegierungen sind wesentlich dichter (~8,9 g/cm³) als Aluminiumlegierungen, was bedeutet, dass ein Kupfermantel schwerer ist als ein Aluminiummantel mit identischer Geometrie. Die verbesserte thermische Leistung könnte jedoch kleinere oder dünnere Konstruktionen ermöglichen, was den Gewichtsnachteil teilweise ausgleichen könnte.
- Herausforderungen:
- Druckbarkeit: Kupferlegierungen sind bekanntermaßen schwierig mit L-PBF zu drucken, vor allem wegen der hohen Reflexionsfähigkeit und Wärmeleitfähigkeit von Kupfer. Es reflektiert einen Großteil der Laserenergie (was Laser mit höherer Leistung, häufig grüne Laser, erfordert) und leitet die Wärme schnell ab, was die Bildung eines stabilen Schmelzbades erschwert. Dies kann zu Defekten wie Porosität oder fehlender Verschmelzung führen, wenn nicht sorgfältig vorgegangen wird. Die Verarbeitung erfordert eine spezielle Ausrüstung und fein abgestimmte Parameter. SEBM kann aufgrund der besseren Energieabsorption von Vorteil sein.
- Kosten: Kupferlegierungspulver sind wesentlich teurer als Aluminiumpulver.
- Warum das für Kühljacken wichtig ist: Für Anwendungen, die ein absolutes Höchstmaß an thermischer Leistung erfordern (z. B. Hochleistungs-Rennmotoren, Anwendungen mit extrem hoher Leistungsdichte), kann die überlegene Wärmeleitfähigkeit von CuCrZr genutzt werden. Sie ermöglicht es den Ingenieuren, die thermischen Grenzen weiter zu verschieben als dies mit Aluminium möglich ist, was zu einer höheren Dauerleistung oder kompakteren Motorkonstruktionen führen kann. Die Herausforderungen bei der Herstellung bedeuten, dass eine Partnerschaft mit einem sehr erfahrenen AM-Anbieter mit bewährten Kupferdruckfähigkeiten unerlässlich ist. Großabnehmer auf den Leistungsmärkten suchen gezielt nach Lieferanten, die mit diesen fortschrittlichen Materialien umgehen können.
Die Rolle von Met3dp bei der Materialexzellenz:
Die Wahl des richtigen Pulvers ist nur ein Teil der Gleichung; die Qualität des Pulvers ist ebenso entscheidend für die Herstellung zuverlässiger, leistungsstarker Teile. Hier bietet ein vertikal integrierter Partner wie Met3dp einen erheblichen Mehrwert:
- Fortschrittliche Pulverproduktion: Met3dp verwendet branchenführende Technologien zur Herstellung von Pulvern:
- Gaszerstäubung (GA): Bei diesem Verfahren werden Hochdruck-Inertgasstrahlen verwendet, um einen Strom geschmolzenen Metalls in feine Tröpfchen aufzubrechen, die sich zu kugelförmigen Pulverpartikeln verfestigen. Die Anlagen von Met3dp’ verwenden einzigartige Düsen- und Gasflussdesigns, um eine hohe Sphärizität und gute Fließfähigkeit zu erreichen - entscheidend für eine gleichmäßige Pulverbettschichtung in AM-Maschinen.
- Plasma-Rotations-Elektroden-Verfahren (PREP): Bei PREP wird eine schnell rotierende Elektrode aus dem Zielmetall durch einen Plasmabrenner geschmolzen. Die Zentrifugalkraft schleudert geschmolzene Tröpfchen ab, die in einer inerten Atmosphäre zu hochgradig kugelförmigen Pulvern mit sehr wenigen Satelliten (kleineren anhaftenden Teilchen) und geringer innerer Porosität erstarren. Dies führt häufig zu einer hervorragenden Pulverqualität, die sich ideal für anspruchsvolle Anwendungen eignet.
- Qualitätskontrolle: Eine strenge Kontrolle der Partikelgrößenverteilung (PSD), Morphologie (Sphärizität), Fließfähigkeit, chemischen Zusammensetzung und Reinheit ist unerlässlich. Eine gleichbleibende Pulverqualität gewährleistet ein vorhersehbares Druckverhalten und die Eigenschaften des Endprodukts.
- Breites Materialportfolio: Während AlSi10Mg und CuCrZr für Kühlmäntel von zentraler Bedeutung sind, stellt Met3dp ein breites Spektrum an hochwertigen Metallpulvern her, darunter verschiedene Titanlegierungen (TiNi, TiTa, TiAl, TiNbZr), Kobalt-Chrom (CoCrMo), rostfreie Stähle und Superlegierungen. Diese Bandbreite an Fachwissen gewährleistet ein tiefes Verständnis der Eigenschaften und der Verarbeitung von Metallpulvern. Weitere Informationen über das Angebot finden Sie auf der Website Produktseite.
- Material & Prozesswissen: Met3dp kombiniert sein Pulver-Know-how mit fundierten Kenntnissen der AM-Druckverfahren (einschließlich SEBM und L-PBF) und stellt so sicher, dass das ausgewählte Pulver optimal verarbeitet wird, um die gewünschten Materialeigenschaften im endgültigen Kühlmantel zu erzielen.
Vergleichstabelle: Wichtige Materialeigenschaften
Eigentum | AlSi10Mg (typisch, wärmebehandelt) | CuCrZr (typisch, wärmebehandelt) | Einheiten | Bedeutung für die Kühlung der Jacke |
---|---|---|---|---|
Wärmeleitfähigkeit | ~150 – 180 | >300 | W/m-K | Sehr hoch |
Dichte | ~2.68 | ~8.9 | g/cm³ | Hoch (niedriger ist besser) |
Streckgrenze | ~250 – 300 | ~400 – 500 | MPa | Hoch |
Endgültige Zugfestigkeit | ~400 – 450 | ~500 – 600 | MPa | Hoch |
Druckbarkeit (L-PBF) | Gut | Herausfordernd | – | Hoch |
Relative Kosten | Unter | Höher | – | Hoch |
Korrosionsbeständigkeit | Gut | Gut | – | Hoch |
In Blätter exportieren
Schlussfolgerung zu den Materialien:
Die Wahl zwischen AlSi10Mg und CuCrZr (oder anderen potenziellen Legierungen) hängt stark von den Leistungsanforderungen der jeweiligen Anwendung und den Kosten- und Gewichtsbeschränkungen ab. AlSi10Mg bietet eine robuste, kostengünstige Lösung mit guten Allround-Eigenschaften, die für viele EV-Anwendungen geeignet ist. CuCrZr bietet eine überlegene thermische Leistung für die anspruchsvollsten Szenarien, wenn auch mit höheren Kosten und höherer Fertigungskomplexität. Die Zusammenarbeit mit einem sachkundigen Materiallieferanten und AM-Dienstleister wie Met3dp, der die Pulverqualität von der Zerstäubung bis zum endgültigen Druck kontrolliert, gewährleistet den Zugang zu hochwertigen Materialien und das Fachwissen, das erforderlich ist, um sie für eine optimale Kühlmantelleistung des EV-Motors effektiv zu nutzen.
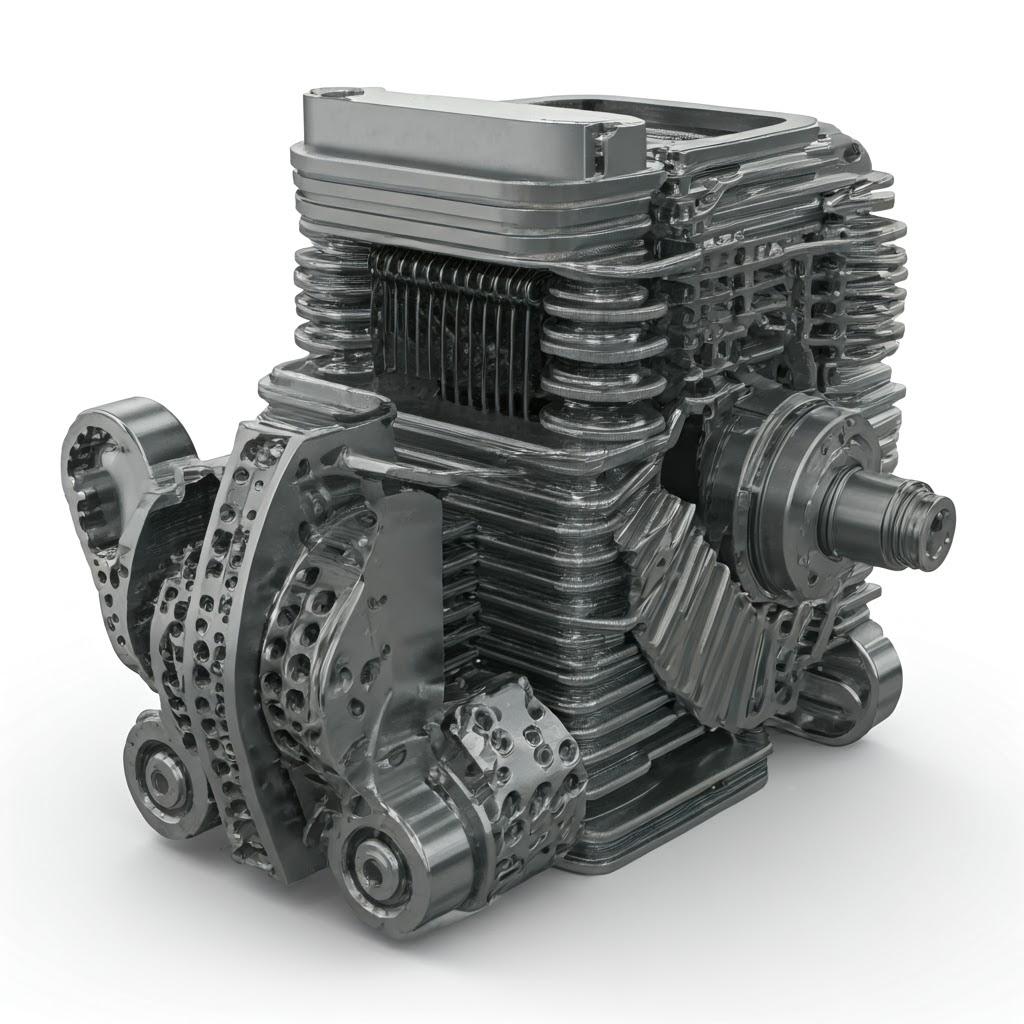
Design für additive Fertigung (DfAM): Optimierung der Kühlmantelgeometrie für höchste Leistung
Die einfache Nachbildung eines Designs, das für den Guss oder die maschinelle Bearbeitung mit Hilfe der additiven Fertigung von Metall vorgesehen ist, schöpft selten das volle Potenzial der Technologie aus. Um die Vorteile des 3D-Drucks für Kühlmäntel von Elektromotoren - verbesserte thermische Leistung, geringeres Gewicht und Konsolidierung der Teile - wirklich zu nutzen, müssen die Ingenieure das Design for Additive Manufacturing (DfAM) anwenden. DfAM ist nicht nur ein Regelwerk, sondern ein Umdenken, das die Konstrukteure dazu ermutigt, in Schichten zu denken, für das jeweilige AM-Verfahren zu optimieren (z. B. Laser Powder Bed Fusion – L-PBF oder Selective Electron Beam Melting – SEBM) und die gebotene geometrische Freiheit zu nutzen. Für Beschaffungsmanager, die mit AM-Lieferanten zusammenarbeiten, hilft das Verständnis der DfAM-Prinzipien bei der Bewertung der Machbarkeit und des Optimierungsgrads der vorgeschlagenen Designs.
Zentrale DfAM-Prinzipien für EV-Kühlmäntel:
- Umfassen Sie die Komplexität für die Funktion:
- Konventionelles Denken in Frage stellen: Vergessen Sie die Beschränkungen durch Entformungswinkel, Kernzüge und den Zugang zur Bearbeitung mit Sichtkontakt. AM gedeiht durch Komplexität wenn es einem Zweck dient.
- Optimierung der internen Kanäle: Hier glänzt AM bei Kühlmänteln. Anstelle von einfachen runden oder rechteckigen Kanälen, Design:
- Konforme Kanäle: Pfade, die genau den Konturen des Stators oder anderer Wärmequellen folgen und einen minimalen, gleichmäßigen Abstand für eine optimale Wärmeübertragung einhalten.
- Variable Querschnitte: Kanäle, die sich verengen oder verbreitern, um die Geschwindigkeit des Kühlmittels zu steuern, die Turbulenz in bestimmten Bereichen zu erhöhen oder um Verpackungseinschränkungen zu berücksichtigen.
- Komplexe Pfade: Sie können Kanäle auf komplizierte Weise teilen, zusammenführen und verlegen, um sicherzustellen, dass das Kühlmittel alle kritischen Bereiche und Hotspots erreicht, die durch thermische Simulationen (CFD) ermittelt wurden.
- Interne Merkmale: Durch den Einbau von Turbulatoren (Rippen, Grübchen, Kreiselstrukturen) direkt in die Kanalwände wird die Grenzschicht ausgelöst, die turbulente Strömung verstärkt und der Wärmeübergangskoeffizient deutlich erhöht, ohne dass es bei richtiger Auslegung zu erheblichen Druckverlusten kommt.
- Integrieren Sie die Funktionalität: Kombinieren Sie Montagevorsprünge, Sensoranschlüsse, Flüssigkeitsein- und -auslässe und sogar Strukturelemente direkt in einem einzigen gedruckten Mantel, wodurch Montageschritte und potenzielle Leckstellen entfallen.
- Topologie-Optimierung und Gewichtsreduzierung:
- Lassen Sie Software Guide: Nutzen Sie Topologie-Optimierungssoftware in einem frühen Stadium des Entwurfsprozesses. Definieren Sie Lastfälle (mechanisch, thermisch), Sperrzonen und Leistungsziele (z. B. Maximierung der Steifigkeit, Minimierung der Masse, Optimierung des Wärmestroms). Die Software erzeugt organische, oft nicht intuitive Formen, die das Material nur dort effizient verteilen, wo es benötigt wird.
- Gitterförmige Strukturen: Interne Gitterstrukturen (z. B. Bienenwaben, Gyroide, stochastischer Schaum) in die festen Wände der Ummantelung einbauen. Diese können das Gewicht erheblich reduzieren und gleichzeitig eine hohe Steifigkeit und Festigkeit gewährleisten. Verschiedene Gittertypen bieten unterschiedliche Eigenschaften (isotrop vs. anisotrop), die für unterschiedliche Belastungsbedingungen geeignet sind. Stellen Sie sicher, dass die gewählte Gitterzellengröße mit dem gewählten AM-Prozess und der gewählten Auflösung druckbar ist.
- Dünne, gerippte Wände: Ersetzen Sie dicke, massive Profile durch dünnere, mit optimierten Rippenmustern verstärkte Wände, um eine ähnliche strukturelle Leistung mit weniger Material und Gewicht zu erreichen.
- Minimieren und Optimieren von Stützstrukturen:
- Selbsttragende Winkel: Konstruktionsmerkmale mit Auskragungswinkeln, die größer sind als der kritische selbsttragende Winkel für das gewählte Material und den Prozess (typischerweise etwa 45° für L-PBF, möglicherweise höher für SEBM). Dies minimiert den Bedarf an opferbereiten Stützstrukturen.
- Interne Kanalgestaltung: Entwerfen Sie interne horizontale oder leicht geneigte Kanäle mit nicht kreisförmigem Querschnitt (z. B. Teardrop, Diamant), die von Natur aus selbsttragend sind und den Bedarf an internen Stützen, die nur schwer oder gar nicht entfernt werden können, reduzieren oder eliminieren. Vermeiden Sie lange, flache Innendecken.
- Zugängliche Unterstützungen: Wo Stützen unvermeidlich sind (z. B. an Ein- und Auslässen, komplexen äußeren Merkmalen), sollten sie so gestaltet sein, dass sie bei der Nachbearbeitung leicht entfernt werden können, ohne die Funktionsflächen zu beschädigen. Berücksichtigen Sie Ausbruchsstellen oder Strukturen, die den Zugang zum Werkzeug ermöglichen. Pulverbasierte Halterungen (üblich beim SEBM) sind leichter zu entfernen als Schmelzbadhalterungen (L-PBF), können aber die Oberflächengüte beeinträchtigen.
- Support Strategy Matters: Besprechen Sie die Support-Strategie frühzeitig mit dem von Ihnen gewählten AM-Dienstleister, wie Met3dp. Ihre Erfahrung mit bestimmten Maschinen und Materialien kann bei der Auswahl des Designs helfen, um die Supportanforderungen und die damit verbundenen Kosten/Risiken zu minimieren.
- Berücksichtigen Sie die Wanddicke und die Auflösung der Merkmale:
- Mindestwanddicke: Erkennen Sie die minimale druckbare Wandstärke für das Verfahren und das Material (oft 0,3-0,5 mm für L-PBF, etwas dicker für SEBM). Entwerfen Sie die Wände dick genug für die strukturellen und thermischen Anforderungen, aber vermeiden Sie unnötige Masse. Sehr dünne Wände sind anfällig für Verformungen oder Beschädigungen.
- Merkmal Auflösung: Kleine Merkmale, scharfe Ecken und komplizierte Details haben Grenzen, die auf der Größe des Strahlflecks, der Größe der Pulverpartikel und der Schichtdicke beruhen. Stellen Sie sicher, dass kritische Merkmale wie Dichtungsflächen oder kleine Kanaldetails innerhalb der erreichbaren Auflösung liegen. Vermeiden Sie Messerkanten; verwenden Sie kleine Radien oder Fasen.
- Planen Sie die Nachbearbeitung:
- Zulagen für die Bearbeitung: Identifizieren Sie kritische Schnittstellen, Dichtungsflächen oder Merkmale, die enge Toleranzen erfordern und nach dem Druck CNC-bearbeitet werden müssen. Fügen Sie in diesen Bereichen während der Entwurfsphase ausreichend Opfermaterial (z. B. 0,5-2 mm) hinzu.
- Entfernung von Puder: Entwerfen Sie Innenkanäle mit ausreichendem Durchmesser und glatten Übergängen, um das Entfernen von ungeschmolzenem Pulver nach dem Bau zu erleichtern. Sehen Sie bei komplexen internen Netzwerken gegebenenfalls Zugangsöffnungen vor, die später verschlossen oder verschweißt werden können. Eingeschlossenes Pulver stellt ein erhebliches Qualitätsrisiko dar.
- Überlegungen zur Wärmebehandlung: Verstehen, wie eine Wärmebehandlung (die für optimale Eigenschaften von Legierungen wie AlSi10Mg und CuCrZr erforderlich ist) zu geringfügigem Verzug führen kann. Konstruieren Sie robuste Merkmale oder planen Sie eine Endbearbeitung nach der Wärmebehandlung.
- Einsatz von Simulationen (CFD & FEA):
- Iterative Entwurfsschleife: DfAM ist am effektivsten, wenn es eng mit der Simulation verbunden ist. Verwenden Sie Computational Fluid Dynamics (CFD), um den Kühlmittelfluss und die Wärmeübertragung in den vorgeschlagenen Kanaldesigns zu modellieren. Verwenden Sie die Finite-Elemente-Analyse (FEA), um die strukturelle Integrität unter mechanischen und thermischen Belastungen zu bewerten.
- Validieren Sie die Optimierung: Nutzen Sie die Simulationsergebnisse, um die Kanalwege zu verfeinern, die Wandstärken zu optimieren, die Ergebnisse der Topologieoptimierung zu validieren und potenzielle Problembereiche (z. B. Hotspots, hohe Spannungskonzentrationen) vorherzusagen, bevor Sie einen Druckauftrag erteilen. Dieser iterative Kreislauf aus Entwurf, Simulation und Verfeinerung ist der Schlüssel zur Maximierung der Leistung.
DfAM-Richtlinien Zusammenfassungstabelle:
DfAM-Prinzip | Wichtige Überlegungen für EV-Kühlmäntel | Nutzen Sie |
---|---|---|
Umfassen Sie die Komplexität | Konforme Kanäle, variable Querschnitte, interne Turbulatoren, Integration | Hervorragende thermische Leistung, reduzierter Wärmewiderstand, geringere Teilezahl |
Topologieoptimierung | Frühzeitig bewerben, Lasten/Einschränkungen definieren, Software effektiv nutzen | Maximaler Leichtbau, optimaler Materialeinsatz, hohe Steifigkeit im Verhältnis zum Gewicht |
Gitterförmige Strukturen | Interne Einbindung für Gewicht/Steifigkeit, Prüfung der Druckbarkeit | Signifikante Gewichtsreduzierung, maßgeschneiderte mechanische Eigenschaften |
Minimierung der Unterstützung | Selbsttragende Winkel (>45°) entwerfen, innere Kanalformen optimieren | Geringere Nachbearbeitungszeit/-kosten, geringeres Risiko von Oberflächenschäden |
Zugängliche Unterstützungen | Planen Sie den Zugang zum Umzug, berücksichtigen Sie Ausbruchsstellen | Leichtere und sauberere Entnahme der Stützen, Erhaltung der Funktionsflächen |
Wanddicke | Minimal-/Maximalgrenzen einhalten, dünne Wände + Rippen verwenden | Geringeres Gewicht, schnellere Druckzeiten, Materialeinsparungen |
Merkmal Auflösung | Prozessgrenzen bei kleinen Merkmalen, Löchern und scharfen Kanten einhalten | Gewährleistet die Herstellbarkeit, verhindert das Versagen oder die Ungenauigkeit von Merkmalen |
Plan für die Nachbearbeitung | Bearbeitungsmaterial hinzufügen, für Pulverabtrag konstruieren, Wärmebehandlungseffekte berücksichtigen | Erzielt Endtoleranzen, gewährleistet Sauberkeit, verhindert Verzugsprobleme |
Simulation der Hebelwirkung | CFD für thermische/strömungstechnische Untersuchungen, FEA für strukturelle Untersuchungen, Iteration des Entwurfs | Leistungsvorhersage & Optimierung, reduzierte physische Prototypen |
In Blätter exportieren
Durch die Anwendung dieser DfAM-Prinzipien können Ingenieurteams den 3D-Druck nicht nur als Ersatz für eine andere Fertigungsmethode nutzen, sondern seine Leistungsfähigkeit wirklich ausschöpfen, um Kühlmäntel für Elektrofahrzeuge der nächsten Generation zu entwickeln, die ihre herkömmlichen Gegenstücke deutlich übertreffen. Die Zusammenarbeit mit erfahrenen AM-Anbietern, die die Feinheiten der verschiedenen Druckverfahren und Materialien, ist entscheidend für eine erfolgreiche Umsetzung von DfAM.
Entfesselte Präzision: Erzielung enger Toleranzen und hervorragender Oberflächengüte bei 3D-gedruckten Kühlmänteln
Die additive Fertigung von Metallen eignet sich hervorragend für die Herstellung komplexer Geometrien. Eine häufige Frage von Ingenieuren und Beschaffungsmanagern, insbesondere von solchen, die an die Präzisionsbearbeitung gewöhnt sind, dreht sich um die erreichbare Maßgenauigkeit, die Toleranzen und die Oberflächenbeschaffenheit von 3D-gedruckten Teilen. Bei funktionalen Komponenten wie Kühlmänteln für Elektromotoren sind diese Aspekte entscheidend für die ordnungsgemäße Montage, Abdichtung, Fluiddynamik und Gesamtleistung. Die Fähigkeiten und Grenzen der Metall-AM in dieser Hinsicht zu verstehen, ist wichtig, um realistische Erwartungen zu setzen und die notwendigen Nachbearbeitungsschritte zu planen.
Verständnis von Toleranzen in der Metall-AM:
- Allgemeine Toleranzen: Als Ausgangspunkt können Metall-AM-Verfahren wie L-PBF und SEBM in der Regel allgemeine Maßtoleranzen erreichen, die mit denen des Feingusses vergleichbar sind. Eine gängige Norm, auf die verwiesen wird, ist ISO 2768, wobei die Teile oft in die mittleren (m) oder groben (c) Toleranzklassen fallen Ist-Zustand.
- ISO 2768-m (Mittel): Oftmals für viele Merkmale direkt aus dem Drucker erreichbar. Bei einer Featuregröße von 100 mm könnte die Toleranz beispielsweise ±0,3 mm betragen.
- ISO 2768-c (Grob): Eine sicherere Annahme für weniger kritische Abmessungen oder komplexere Geometrien. Für 100 mm könnte dies ±0,5 mm sein.
- Engere Toleranzen: Das Erreichen engerer Toleranzen als ISO 2768-m erfordert in der Regel eine Nachbearbeitung bestimmter Merkmale. Toleranzen, die für die CNC-Bearbeitung typisch sind (z. B. ±0,05 mm oder besser), sind im Allgemeinen nicht direkt mit dem AM-Verfahren für das gesamte Teil erreichbar.
- Faktoren, die die Verträglichkeit beeinflussen:
- Maschinenkalibrierung und Qualität: Hochwertige Industriedrucker, wie die von Met3dp verwendeten, mit präziser Bewegungssteuerung, Strahlenkalibrierung und Wärmemanagementsystemen, produzieren von Natur aus genauere Teile. Regelmäßige Wartung und Kalibrierung sind entscheidend.
- Materialeigenschaften: Verschiedene Metallpulver weisen unterschiedliche Schrumpfungsraten, Wärmeausdehnungskoeffizienten und Spannungsverhalten während des Drucks auf, was sich auf die endgültigen Abmessungen auswirkt. Erfahrene Anbieter entwickeln spezifische Parametersätze, um das Materialverhalten zu kompensieren.
- Geometrie und Größe des Teils: Große, komplexe Teile oder solche mit erheblichen Querschnittsabweichungen sind anfälliger für thermischen Verzug und Abweichungen von der vorgesehenen Geometrie. Innere Spannungen, die während des schichtweisen Verfahrens aufgebaut werden, können zu Verformungen führen.
- Orientierung und Unterstützung aufbauen: Die Ausrichtung eines Teils auf der Bauplattform wirkt sich auf die Maßgenauigkeit aus, z. B. durch Schichtabstufungen auf gekrümmten Oberflächen und den Einfluss von Stützstrukturen. Stützstrukturen können die Oberflächen beim Entfernen leicht beschädigen und die Geometrie lokal beeinflussen.
- Wärmemanagement: Die Heiz- und Kühlzyklen während des Bauprozesses wirken sich erheblich auf die Eigenspannung und den möglichen Verzug aus. Verfahren wie SEBM, die mit erhöhten Baukammertemperaturen arbeiten, führen im Vergleich zu L-PBF oft zu geringeren Eigenspannungen und können die Dimensionsstabilität für bestimmte Geometrien und Materialien verbessern.
- Nachbearbeiten: Wärmebehandlungen zum Spannungsabbau können geringfügige Änderungen der Abmessungen verursachen. Die Entfernung von Stützen kann die lokale Genauigkeit beeinträchtigen. Die maschinelle Bearbeitung dient dazu, die endgültigen, präzisen Toleranzen bei kritischen Merkmalen zu erreichen.
Oberflächengüte (Rauhigkeit):
- Oberflächenrauhigkeit (Ra) im Ist-Zustand: Die Oberflächenbeschaffenheit von AM-Metallteilen ist von Natur aus rauer als die von bearbeiteten Oberflächen. Sie wird durch die Größe der Pulverpartikel, die Schichtdicke, die Strahlparameter und die Oberflächenausrichtung beeinflusst.
- Typische Ra-Werte (L-PBF): Sie reichen oft von 6 µm bis 20 µm (Mikrometer) Ra, abhängig von den oben genannten Faktoren. Nach oben gerichtete Oberflächen sind in der Regel glatter als nach unten gerichtete Oberflächen (die eine Abstützung erfordern) oder vertikale Wände (die Schichtlinien aufweisen).
- Typische Ra-Werte (SEBM): Im Allgemeinen rauer als L-PBF aufgrund größerer Pulverpartikel und partieller Sinterung, oft im Ra-Bereich von 20 µm bis 35 µm oder höher.
- Einfluss der Oberflächenbeschaffenheit:
- Versiegeln: Die Oberflächen im eingebauten Zustand sind in der Regel zu rau für eine wirksame O-Ring- oder Dichtungsabdichtung. Diese Oberflächen müssen normalerweise bearbeitet oder poliert werden.
- Fluiddynamik: Raue innere Kanaloberflächen können den Druckabfall erhöhen und möglicherweise die Wärmeübertragungseigenschaften im Vergleich zu glatten Kanälen verändern. Auch wenn es manchmal von Vorteil ist, Turbulenzen zu erzeugen, ist eine übermäßige Rauheit in der Regel unerwünscht.
- Müdigkeit Leben: Oberflächenrauhigkeit kann als Ausgangspunkt für Ermüdungsrisse dienen, obwohl dies bei Kühlmänteln oft weniger kritisch ist als bei hochbelasteten Strukturkomponenten.
- Verbesserung der Oberflächengüte: Verschiedene Nachbearbeitungstechniken können die Oberflächengüte erheblich verbessern:
- CNC-Bearbeitung: Bietet die glatteste, präziseste Oberfläche, ist aber in der Regel auf zugängliche Flächen beschränkt.
- Abrasive Fließbearbeitung (AFM): Lässt abrasive Medien durch interne Kanäle fließen, um sie zu glätten.
- Elektrochemisches Polieren: Entfernt Material auf elektrochemischem Weg und sorgt so für eine glänzende, glatte Oberfläche.
- Massenveredelung (Taumeln, Gleitschleifen): Verwendet Medien zum Glätten von Außenflächen.
- Mikro-Bearbeitung / Polieren: Manuelles oder automatisiertes Polieren für bestimmte Bereiche.
Das Engagement von Met3dp für Präzision:
Das Erreichen gleichmäßiger Toleranzen und gewünschter Oberflächengüten erfordert nicht nur fortschrittliche Anlagen, sondern auch ein tiefes Prozessverständnis. Met3dp legt Wert darauf:
- Branchenführende Ausrüstung: Die Verwendung von Druckern, die für ihre Genauigkeit und Zuverlässigkeit bekannt sind, bildet die Grundlage.
- Optimierte Parameter: Umfassende Erfahrung in der Entwicklung und Verfeinerung von Bauparametern für bestimmte Legierungen wie AlSi10Mg und CuCrZr, um Abweichungen zu minimieren und konsistente Ergebnisse zu erzielen.
- Strenge Qualitätskontrolle: Durchführung von messtechnischen Kontrollen (z. B. CMM-Scanning, 3D-Scanning) während und nach der Produktion zur Überprüfung der Maßhaltigkeit anhand der Spezifikationen.
- Integriertes Post-Processing: Angebot oder Leitung der erforderlichen Nachbearbeitungsschritte, einschließlich Präzisionsbearbeitung und Oberflächenveredelung, um die Anforderungen der endgültigen Zeichnung zu erfüllen.
Toleranzen & Erwartungen an die Oberflächengüte Zusammenfassung:
Parameter | As-Built (typischer Bereich) | Erreichbar mit Post-Processing | Bedeutung für die Kühlung der Jacke |
---|---|---|---|
Allgemeine Toleranz | ISO 2768-m / -c (±0.3 to ±0.5mm @100mm) | Bearbeitungstoleranzen (±0,05mm+) | Mäßig (Gesamtpassform), Hoch (Schnittstellen) |
Oberflächenrauhigkeit (Ra) | 6-35 µm (L-PBF/SEBM) | <1 µm möglich (bearbeitet/poliert) | Hoch (Dichtungsflächen), Mäßig (Interne Kanäle) |
Wiederholbarkeit | Gut (mit Prozesskontrolle) | Ausgezeichnet (Bearbeitung) | Hoch (für Serienproduktion) |
In Blätter exportieren
Fazit zur Präzision:
AM-Metallteile kommen zwar nicht mit der Hochglanzoberfläche und der Genauigkeit im Mikrometerbereich der CNC-Bearbeitung auf allen Oberflächen aus dem Drucker, aber sie bieten eine bemerkenswerte Komplexität in Kombination mit einer respektablen Präzision im eingebauten Zustand. Bei EV-Kühlmänteln erfordern kritische Schnittstellen, die enge Toleranzen oder glatte Dichtungsflächen erfordern, in der Regel eine Nachbearbeitung. Der Großteil der komplexen Geometrie, einschließlich der internen Kanäle, kann jedoch oft mit den vorhandenen Toleranzen und Oberflächenbehandlungen oder, falls erforderlich, mit speziellen internen Nachbearbeitungsverfahren verwendet werden. Die Festlegung klarer Spezifikationen in den Zeichnungen, das Verständnis der Prozessmöglichkeiten und die Zusammenarbeit mit einem kompetenten AM-Partner wie Met3dp sind der Schlüssel zur erfolgreichen Nutzung des 3D-Metalldrucks für präzisionssensible Anwendungen.
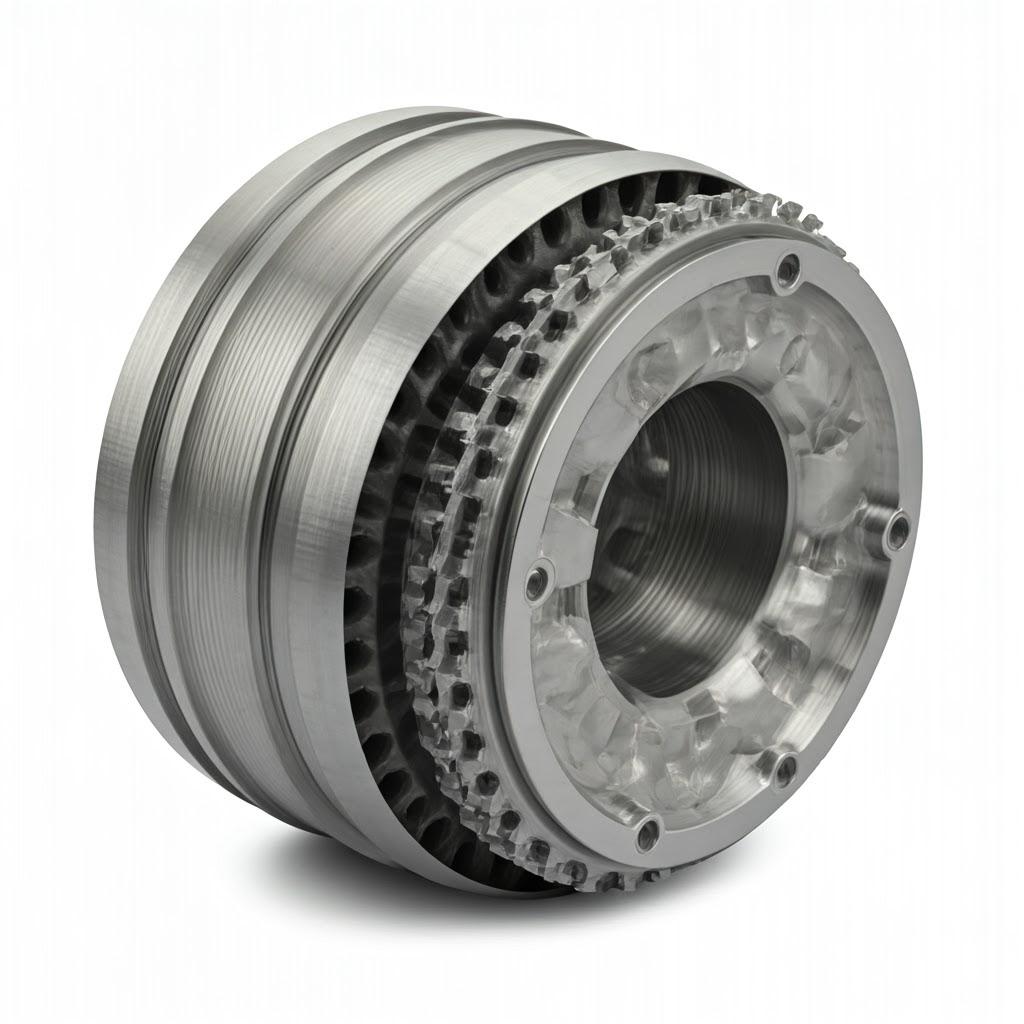
Über den Bau hinaus: Wichtige Nachbearbeitungsschritte für funktionale EV-Kühlmäntel
Die Reise eines 3D-gedruckten Metallteils endet nicht, wenn der Drucker anhält. Damit ein Kühlmantel für einen Elektromotor von einem rohen, gedruckten Teil zu einem funktionalen, zuverlässigen Bauteil wird, das für die Fahrzeugintegration bereit ist, muss er eine Reihe von entscheidenden Nachbearbeitungsschritten durchlaufen. Diese Schritte sind keine optionalen Extras, sondern ein wesentlicher Bestandteil, um die von der Automobilindustrie geforderten mechanischen Eigenschaften, die Maßgenauigkeit, die Oberflächenmerkmale und die Gesamtqualität zu erreichen. Das Verständnis dieses Arbeitsablaufs ist für die Ingenieure, die die Teile entwerfen, und für die Beschaffungsteams, die einen AM-Lieferanten auswählen, von entscheidender Bedeutung, da die integrierten Nachbearbeitungsfunktionen einen erheblichen Einfluss auf die Vorlaufzeit, die Kosten und die Qualität des fertigen Teils haben.
Gemeinsamer Post-Processing-Workflow für AM-Kühlmäntel:
- Entpudern / Reinigen:
- Zweck: Um alle Reste von ungeschmolzenem Metallpulver zu entfernen, die im Bauteil eingeschlossen sind, insbesondere aus komplizierten internen Kühlkanälen.
- Methoden: Dazu gehören in der Regel manuelles Bürsten, Abblasen mit Druckluft, Perlstrahlen oder spezielle Pulverhandhabungsstationen, manchmal kombiniert mit Vibration. Bei komplexen internen Netzwerken können spezielle Spül- oder Durchflusssysteme erforderlich sein. Eine sorgfältige Konstruktion (DfAM) mit Zugangsöffnungen und zur Vermeidung von Pulverfallen ist hier entscheidend.
- Wichtigkeit: Eingeschlossenes Pulver kann den Kühlmittelfluss behindern, sich später ablösen und das System verunreinigen, das Gewicht erhöhen und nachfolgende Schritte wie Wärmebehandlung oder Schweißen beeinträchtigen. Gründliche Reinigung ist von größter Bedeutung.
- Stressabbau:
- Zweck: Die schnellen Erwärmungs- und Abkühlungszyklen bei L-PBF und, in geringerem Maße, bei SEBM erzeugen erhebliche innere Spannungen im gedruckten Teil. Spannungsabbau ist eine Wärmebehandlung, die vor entfernen des Teils von der Bauplatte (oder unmittelbar danach), um diese inneren Spannungen zu verringern.
- Methode: Erhitzen der gesamten Bauplatte mit den daran befestigten Teilen in einem Ofen mit Schutzgasatmosphäre auf eine bestimmte Temperatur (unterhalb der Alterungs- oder Lösungstemperatur), Halten der Platte und anschließendes langsames Abkühlen. Temperaturen und Zeiten sind materialspezifisch (z. B. ~300-350 °C für AlSi10Mg).
- Wichtigkeit: Verringert das Risiko von Verformungen oder Rissen beim Ausschneiden des Teils aus der Bauplatte und bei der anschließenden Bearbeitung oder thermischen Zyklen im Betrieb.
- Entfernen des Teils von der Bauplatte:
- Zweck: Um die gedruckte(n) Kühlhülle(n) von der Metallbauplatte zu trennen, mit der sie während des Druckvorgangs verschmolzen wurden.
- Methoden: Dies geschieht in der Regel durch Drahterodieren (EDM) oder mit einer Bandsäge. Das Drahterodieren liefert im Allgemeinen einen saubereren Schnitt mit weniger mechanischer Belastung, ist aber langsamer.
- Wichtigkeit: Dies muss sorgfältig geschehen, damit das Teil nicht beschädigt wird.
- Entfernung der Stützstruktur:
- Zweck: Entfernung der während des Drucks erzeugten Stützstrukturen zur Verankerung von Überhängen und komplexen Merkmalen.
- Methoden: Dies kann manuelles Brechen und Schleifen (für zugängliche Halterungen), CNC-Bearbeitung oder Erodieren beinhalten. Die Entfernung von Stützen aus internen Kanälen ist besonders schwierig und unterstreicht die Bedeutung von DfAM, um interne Stützen zu minimieren oder sie so zu gestalten, dass sie entfernt werden können (z. B. durch chemisches Ätzen für einige Materialien/Stützentypen, obwohl dies für Al/Cu weniger üblich ist).
- Wichtigkeit: Stützen sind nicht funktionsfähig und verursachen zusätzliches Gewicht. Ihre Entfernung kann Spuren oder etwas rauere Oberflächen (Narben) hinterlassen, die je nach Standort eine weitere Bearbeitung erfordern. Eine unvollständige Entfernung ist inakzeptabel.
- Wärmebehandlung (Solutionizing, Aging, Annealing):
- Zweck: Um die gewünschten mechanischen Eigenschaften (Festigkeit, Härte, Duktilität) zu erreichen und die Stabilität des Gefüges zu gewährleisten. Die meisten AM-Metalle erfordern eine Wärmebehandlung, um die Leistung zu optimieren, da die fertige Mikrostruktur oft nicht im Gleichgewicht und anisotrop ist.
- AlSi10Mg: Wird in der Regel einem T6-Anlassverfahren (Lösungsglühen mit anschließender künstlicher Alterung) unterzogen, um Festigkeit und Härte deutlich zu erhöhen.
- CuCrZr: Erfordert eine Lösungsbehandlung mit anschließender Alterung, um eine Ausscheidungshärtung zu erreichen, die die Festigkeit erhöht und gleichzeitig eine gute Leitfähigkeit beibehält.
- Methode: Kontrollierte Erwärmungs- und Abkühlungszyklen in kalibrierten Öfen, oft unter Vakuum oder inerter Atmosphäre, um Oxidation zu verhindern. Spezifische Temperaturprofile und -dauern sind kritisch und legierungsabhängig.
- Wichtigkeit: Unerlässlich für die Erfüllung der im Entwurf festgelegten mechanischen Leistungsanforderungen. Beeinflusst die endgültigen Abmessungen geringfügig, daher wird es oft vor der endgültigen Bearbeitung durchgeführt.
- Zweck: Um die gewünschten mechanischen Eigenschaften (Festigkeit, Härte, Duktilität) zu erreichen und die Stabilität des Gefüges zu gewährleisten. Die meisten AM-Metalle erfordern eine Wärmebehandlung, um die Leistung zu optimieren, da die fertige Mikrostruktur oft nicht im Gleichgewicht und anisotrop ist.
- CNC-Bearbeitung:
- Zweck: Zur Erzielung enger Toleranzen, spezifischer Oberflächengüten und präziser geometrischer Merkmale an kritischen Schnittstellen, die nicht direkt durch das AM-Verfahren erreicht werden können.
- Gemeinsame Bereiche: Dichtungsflächen (O-Ring-Nuten, flache Dichtungsflächen), Montagelöcher/Bohrungen, Verbindungsschnittstellen, alle Flächen, die eine hohe Rechtwinkligkeit, Ebenheit oder Parallelität erfordern.
- Methode: Verwendung von Standard-CNC-Fräsmaschinen, Drehbänken oder Schleifmaschinen. Erfordert ein sorgfältiges Vorrichtungsdesign, um das komplexe AM-Teil sicher und ohne Verformung zu halten. Erfordert den DfAM-Schritt des Hinzufügens von Bearbeitungsmaterial.
- Wichtigkeit: Garantiert den korrekten Zusammenbau, die Unversehrtheit der Dichtungen und das Zusammenspiel mit den Gegenstücken in der Motorbaugruppe.
- Oberflächenveredelung:
- Zweck: Zur Verbesserung der Oberflächenglätte (Reduzierung von Ra), zur Verbesserung des Aussehens oder zur Vorbereitung von Oberflächen für Beschichtungen.
- Methoden (je nach Bedarf):
- Externe Oberflächen: Perlstrahlen (für eine gleichmäßige matte Oberfläche), Trommel-/Gleitschleifen (für allgemeines Glätten/Entgraten), manuelles oder robotergestütztes Polieren (für bestimmte glatte Bereiche).
- Interne Kanäle: Abrasive Fließbearbeitung (AFM), chemisches Polieren/Ätzen (werkstoffabhängig), oder möglicherweise Belassen im Ist-Zustand, wenn die CFD-Analyse zeigt, dass die Rauheit akzeptabel oder vorteilhaft ist.
- Wichtigkeit: Entscheidend für die Abdichtung von Oberflächen, kann die Flüssigkeitsdynamik in Kanälen verbessern und beeinflusst das ästhetische Erscheinungsbild.
- Reinigung und Inspektion:
- Zweck: Endreinigung zur Entfernung von Bearbeitungsflüssigkeiten, Ablagerungen oder Verunreinigungen. Umfassende Inspektion zur Überprüfung der Übereinstimmung mit allen Spezifikationen.
- Methoden: Wässrige oder lösungsmittelhaltige Reinigung, Ultraschallreinigung. Die Inspektion umfasst:
- Dimensional: Koordinatenmessmaschine (CMM), 3D-Scannen.
- Integrität: Die Dichtheitsprüfung (Druckabfall- oder Immersionstest) ist wesentlich für einen Kühlmantel, um sicherzustellen, dass keine Porosität oder Risse ein Austreten von Kühlmittel ermöglichen. Zerstörungsfreie Prüfungen (NDT) wie Röntgen- oder CT-Scans können eingesetzt werden, um interne Defekte aufzuspüren oder die Pulverentfernung in hochkritischen Anwendungen zu überprüfen.
- Material: Härteprüfung, eventuell Gefügeanalyse an Prüfstücken.
- Visuell: Gründliche Sichtprüfung auf Oberflächenfehler.
- Wichtigkeit: Die abschließende Qualitätsprüfung stellt sicher, dass das Teil für den Zweck geeignet ist und alle Zeichnungsanforderungen erfüllt, bevor es an den Kunden oder die Montagelinie geliefert wird.
Die Bedeutung der integrierten Dienste:
Die Verwaltung dieser mehrstufigen Nachbearbeitungskette kann sehr komplex sein. Die Zusammenarbeit mit einem AM-Dienstleister wie Met3dp, der diese Prozesse in einem integrierten Arbeitsablauf anbietet oder verwaltet, bietet mehrere Vorteile für Beschaffungsteams und Ingenieure:
- Rationalisierte Logistik: Eine einzige Anlaufstelle reduziert die Komplexität.
- Prozesskontrolle: Sorgt für Konsistenz und Qualitätskontrolle in allen Phasen.
- Optimierter Arbeitsablauf: Verkürzung der Gesamtdurchlaufzeit im Vergleich zum Versand von Teilen zwischen mehreren spezialisierten Anbietern.
- Rechenschaftspflicht: Klare Verantwortung für die Qualität des Endprodukts.
Übersichtstabelle Nachbearbeitung:
Schritt | Zweck | Gemeinsame Methoden | Wichtige Überlegungen |
---|---|---|---|
Entpulvern | Pulverreste entfernen | Bürsten, Luftstrahl, Strahlen, Spülen | Interne Kanäle, Pulverfalle, Vollständigkeit |
Entspannung | Eigenspannungen vor dem Ausbau des Teils reduzieren | Wärmebehandlung im Ofen (auf der Bauplatte) | Verhindert Verzug/Rissbildung, materialspezifischer Zyklus |
Entfernen von Teilen | Teil von der Bauplatte abtrennen | Drahterodieren, Bandsäge | Teilebeschädigung vermeiden, Schnittqualität |
Entfernen der Stütze | Opferstützen entfernen | Manuelles Brechen, Zerspanung, Schleifen, EDM | Zugänglichkeit (intern), Oberflächenmarkierungen, Vollständigkeit |
Wärmebehandlung | Erreichen der endgültigen mechanischen Eigenschaften (Festigkeit, Härte) | Ofenzyklen (Lösungsglühen, Alterung), Vakuum/Schutzgas | Werkstoffspezifisch (T6 für Al, Aging für CuCrZr), beeinflusst die Abmessungen |
CNC-Bearbeitung | Erzielen enger Toleranzen & feines Finish bei kritischen Merkmalen | Fräsen, Drehen, Schleifen | Bearbeitung von Rohmaterial (DfAM), Konstruktion von Spannvorrichtungen, Toleranzen |
Oberflächenveredelung | Verbesserung von Ra, Ästhetik, Vorbereitung für Beschichtung | Strahlen, Polieren, AFM (intern), Trommeln | Dichtungsflächen, interne Kanäle, spezifische Anforderungen |
Reinigung und Inspektion | Endgültige Sauberkeit, Überprüfung der Konformität mit den Spezifikationen | Reinigungsmethoden, CMM, 3D-Scan, Dichtheitsprüfung, NDT, Visuell | LEAK TESTING IS CRITICAL, Maßkontrollen |
In Blätter exportieren
Die erfolgreiche Navigation durch das Labyrinth der Nachbearbeitung ist entscheidend für die Herstellung hochwertiger, funktionaler Kühlmäntel für Elektromotoren mittels Metall-AM. Dies erfordert eine sorgfältige Planung während der Designphase und eine enge Zusammenarbeit mit einem erfahrenen Fertigungspartner, der die Feinheiten der einzelnen Schritte versteht.
Herausforderungen meistern: Häufige Fallstricke beim 3D-Druck von Kühlmänteln und Strategien zur Abhilfe
Die additive Fertigung von Metallen bietet zwar erhebliche Vorteile für die Herstellung komplexer Komponenten wie Kühlmäntel für Elektromotoren, doch die Technologie ist nicht ohne Herausforderungen. Für Ingenieure, die diese Teile entwerfen, und für Beschaffungsmanager, die zuverlässige Lieferanten auswählen, ist es entscheidend zu verstehen, welche potenziellen Fallstricke es gibt und wie erfahrene Hersteller diese entschärfen. Die proaktive Bewältigung dieser Herausforderungen gewährleistet eine höhere Qualität, bessere Konsistenz und ein geringeres Risiko bei der Einführung von AM für kritische Automobilanwendungen.
Gemeinsame Herausforderungen und Abhilfestrategien:
- Eigenspannung, Verformung und Verzerrung:
- Herausforderung: Die schnelle, örtlich begrenzte Erwärmung und Abkühlung bei Schicht-für-Schicht-Fusionsverfahren (insbesondere L-PBF) erzeugt erhebliche Wärmegradienten, die zu inneren Spannungen führen. Diese Spannungen können dazu führen, dass sich Teile während des Aufbaus verziehen, sich verformen, wenn sie von der Bauplatte entfernt werden, oder sogar brechen. Große, flache Abschnitte oder asymmetrische Designs sind besonders anfällig.
- Strategien zur Schadensbegrenzung:
- Optimierte Gebäudeausrichtung: Ausrichtung des Teils, um große ebene Flächen parallel zur Bauplatte zu minimieren und thermische Gradienten zwischen den Schichten zu reduzieren.
- Wärmetechnik: Verwendung optimierter Scan-Strategien (z. B. Insel-Scanning, Schachbrettmuster), um die Wärme gleichmäßiger zu verteilen und lokale Spannungsspitzen zu reduzieren.
- Geeignete Stützstrukturen: Gut konzipierte Stützen verankern das Teil sicher auf der Bauplatte und widerstehen den Verformungskräften während des Bauprozesses.
- Prozessauswahl: SEBM mit seiner Hochtemperatur-Bauumgebung führt im Allgemeinen zu geringeren Eigenspannungen im Vergleich zu L-PBF, was bei großen oder komplexen Teilen, die zum Verzug neigen, von Vorteil sein kann.
- Stressabbau Wärmebehandlung: Durchführen eines Stressabbauzyklus vor das Entfernen des Teils von der Bauplatte ist entscheidend, um innere Spannungen abzubauen.
- Simulation: Einsatz von Simulationssoftware zur Vorhersage von Spannungsakkumulation und Verformung, um Designänderungen oder optimierte Stützstrategien vor dem Druck zu ermöglichen.
- DfAM: Konstruktion von Teilen mit Merkmalen, die von Natur aus die Spannungskonzentration verringern (z. B. Vermeidung scharfer Innenecken, Verwendung von Verrundungen).
- Porosität:
- Herausforderung: Im gedruckten Material können sich kleine Hohlräume oder Poren bilden, die durch eine unvollständige Verschmelzung zwischen den Schichten, durch Gaseinschlüsse aus dem Pulver oder der Atmosphäre oder durch Keyholing-Defekte (Dampfeinbrüche) infolge eines übermäßigen Energieeintrags entstehen. Poren können die mechanischen Eigenschaften (insbesondere die Ermüdungsfestigkeit) verschlechtern und, was für einen Kühlmantel kritisch ist, potenzielle Leckagepfade schaffen.
- Strategien zur Schadensbegrenzung:
- Hochwertiges Pulver: Die Verwendung von Pulver mit hoher Sphärizität, guter Fließfähigkeit, geringer interner Gasporosität und kontrollierter Partikelgrößenverteilung ist von grundlegender Bedeutung. Der Einsatz von GA- und PREP-Technologien bei Met3dp’ zielt auf diese Eigenschaften ab.
- Optimierte Prozessparameter: Sorgfältige Abstimmung von Laser-/Strahlleistung, Scangeschwindigkeit, Schichtdicke, Schraffurabstand und Gasfluss (bei L-PBF) auf das jeweilige Material, um vollständiges Schmelzen und Verschmelzen ohne Überhitzung zu gewährleisten. Umfangreiche Parameterentwicklung ist der Schlüssel.
- Kontrolle der inerten Atmosphäre: Aufrechterhaltung einer hochreinen Inertgasatmosphäre (Argon oder Stickstoff für L-PBF, Vakuum für SEBM) zur Minimierung von Oxidation und Gasaufnahme während des Schmelzens.
- Qualitätskontrolle (NDT): Einsatz von zerstörungsfreien Prüfverfahren wie Röntgenradiographie oder Computertomographie (CT) zur Erkennung interner Porosität, insbesondere in kritischen Bereichen oder im Rahmen der Prozessqualifizierung. Dichtemessungen (z. B. Archimedes-Methode) können einen allgemeinen Hinweis auf Porosität geben.
- Dichtheitsprüfung: Obligatorische Druckprüfung jedes Kühlmantels zur Bestätigung seiner Unversehrtheit und des Fehlens von Durchlässigkeit.
- Unterstützung bei der Beseitigung von Schwierigkeiten (insbesondere intern):
- Herausforderung: Obwohl Halterungen notwendig sind, kann es schwierig, zeitaufwändig und kostspielig sein, sie sauber zu entfernen, ohne das Teil zu beschädigen. Halterungen in komplexen internen Kühlkanälen sind besonders schwierig, da der Zugang beschränkt ist. Eine unvollständige Entfernung kann den Durchfluss behindern oder sich später ablösen.
- Strategien zur Schadensbegrenzung:
- DfAM Fokus: Die Hauptstrategie besteht darin, so zu konstruieren, dass möglichst wenig Stützen verwendet werden, insbesondere im Inneren (selbsttragende Winkel, optimierte Kanalformen).
- Barrierefreies Support-Design: Gestaltung von Außenstützen für einen einfachen Zugang mit Entnahmewerkzeugen und Einbau von Abreißvorrichtungen.
- Auswahl des Prozesses: Beim SEBM werden häufig pulverförmige Träger verwendet, die sich im Allgemeinen leichter durch Strahlen entfernen lassen als die bei L-PBF üblichen vollständig geschmolzenen Träger.
- Spezialisierte Entfernungstechniken: Einsatz von Verfahren wie Abrasive Flow Machining (AFM) oder chemisches Ätzen (sofern die Materialkompatibilität dies zulässt) für interne Kanalstützreste oder Oberflächenglättung.
- Inspektion: Verwendung von Boreskopen oder CT-Scans zur Überprüfung der vollständigen Abstützung und Pulverentfernung aus den inneren Kanälen.
- Puderentfernung & Kreuzkontamination:
- Herausforderung: Es kann schwierig sein, sicherzustellen, dass das gesamte ungeschmolzene Pulver aus den internen Kanälen entfernt wird. Wenn ein Hersteller mehrere Materialtypen verarbeitet, ist es außerdem von entscheidender Bedeutung, eine Kreuzkontamination zwischen den Pulvern zu verhindern (z. B. die Vermischung von Stahlpulver mit Aluminium), da selbst Spuren von Pulver die Materialeigenschaften drastisch beeinflussen können.
- Strategien zur Schadensbegrenzung:
- DfAM für die Pulverentfernung: Entwurf von Kanälen mit ausreichendem Durchmesser, sanften Biegungen und Zugangsöffnungen.
- Strenge Reinigungsprotokolle: Durchführung von mehrstufigen Reinigungsverfahren (Abblasen, Vibration, Spülen) und Überprüfung der Sauberkeit.
- Dedizierte Ausrüstung: Idealerweise sollten spezielle Drucker, Baumodule und Pulverhandhabungsgeräte für verschiedene Materialfamilien (z. B. reaktiv vs. nicht reaktiv, Stahl vs. Aluminium vs. Kupfer) verwendet werden, um Kreuzkontaminationen zu vermeiden.
- Strenge Verfahren zur Handhabung des Pulvers: Umsetzung sorgfältiger Verfahren für das Laden, Entladen, Sieben und Lagern von Pulver. Die Rückverfolgbarkeit der Chargen ist unerlässlich.
- Oberflächengüte & Rauheitskontrolle:
- Herausforderung: Die Oberflächenbeschaffenheit von AM-Teilen ist im Vergleich zur maschinellen Fertigung relativ rau. Während einige Oberflächen akzeptabel sind, müssen kritische Bereiche wie Dichtungsflächen verbessert werden, und die Rauheit interner Kanäle kann sich auf unvorhersehbare Weise auf die Strömung und Wärmeübertragung auswirken, wenn sie nicht gehandhabt wird.
- Strategien zur Schadensbegrenzung:
- Optimierung der Parameter: Die Feinabstimmung von Parametern (z. B. Konturscans, geringere Schichthöhen) kann die Oberflächengüte bei bestimmten Oberflächen verbessern, geht aber oft auf Kosten der Bauzeit.
- Orientierung aufbauen: Optimale Ausrichtung der kritischen Flächen in Bezug auf die Baurichtung (z. B. sind nach oben gerichtete Flächen oft glatter).
- Nachbearbeiten: Einsatz geeigneter Oberflächenbearbeitungsverfahren (Bearbeitung, Polieren, AFM usw.) für die Oberflächen, die glatt sein müssen.
- CFD-Analyse: Einsatz von CFD, um die Auswirkungen der zu erwartenden internen Kanalrauhigkeit auf den Druckabfall und die Wärmeübertragung zu verstehen und so Informationen für Konstruktionsentscheidungen oder Nachbearbeitungsanforderungen zu erhalten.
- Erreichen einer lecksicheren Integrität:
- Herausforderung: Die Dichtheit eines Kühlmantels ist ein unverzichtbares Kriterium. Porosität, Mikrorisse (durch Eigenspannung) oder Defekte an Schnittstellen können zu Kühlmittellecks führen.
- Strategien zur Schadensbegrenzung:
- Robuste Prozesskontrolle: Alle Strategien zur Verringerung von Porosität und Eigenspannung tragen dazu bei.
- Sorgfältige Nachbearbeitung: Sicherstellen, dass durch die Bearbeitung oder das Entfernen von Stützen keine Fehler entstehen.
- 100%ige Dichtheitsprüfung: Durchführung obligatorischer, strenger Dichtheitsprüfungen (z. B. Druckabfalltests) an jedem einzelnen Teil gemäß den festgelegten Automobilstandards. Dies ist eine entscheidende letzte Qualitätskontrolle.
- Potenzielle Imprägnierung: In einigen Fällen (wenn auch weniger wünschenswert) kann die Mikroporosität mit speziellen Imprägnierharzen versiegelt werden, aber dies ist in der Regel eher eine Wiederherstellungsmaßnahme als eine primäre Strategie.
Die Bewältigung von Herausforderungen erfordert Fachwissen:
Um diese potenziellen Fallstricke zu überwinden, sind umfangreiche Fachkenntnisse in den Bereichen Materialwissenschaft, Physik des AM-Prozesses, DfAM und strenge Qualitätskontrolle erforderlich. Aus diesem Grund ist die Wahl eines erfahrenen Fertigungspartners wie Met3dp entscheidend. Das tiefgreifende Verständnis der Pulvereigenschaften (aus der eigenen fortschrittlichen Produktion), der Druckerkapazitäten, der Optimierung der Prozessparameter und der integrierten Nachbearbeitung, unterstützt durch robuste Qualitätsmanagementsysteme, bietet die Gewissheit, dass diese Herausforderungen proaktiv gemeistert werden, um zuverlässige, leistungsstarke EV-Kühlmäntel zu liefern. Die frühzeitige Einbindung von Zulieferern in der Designphase ermöglicht es den Ingenieuren, dieses Know-how zu nutzen und potenzielle Probleme zu entschärfen, bevor sie entstehen.
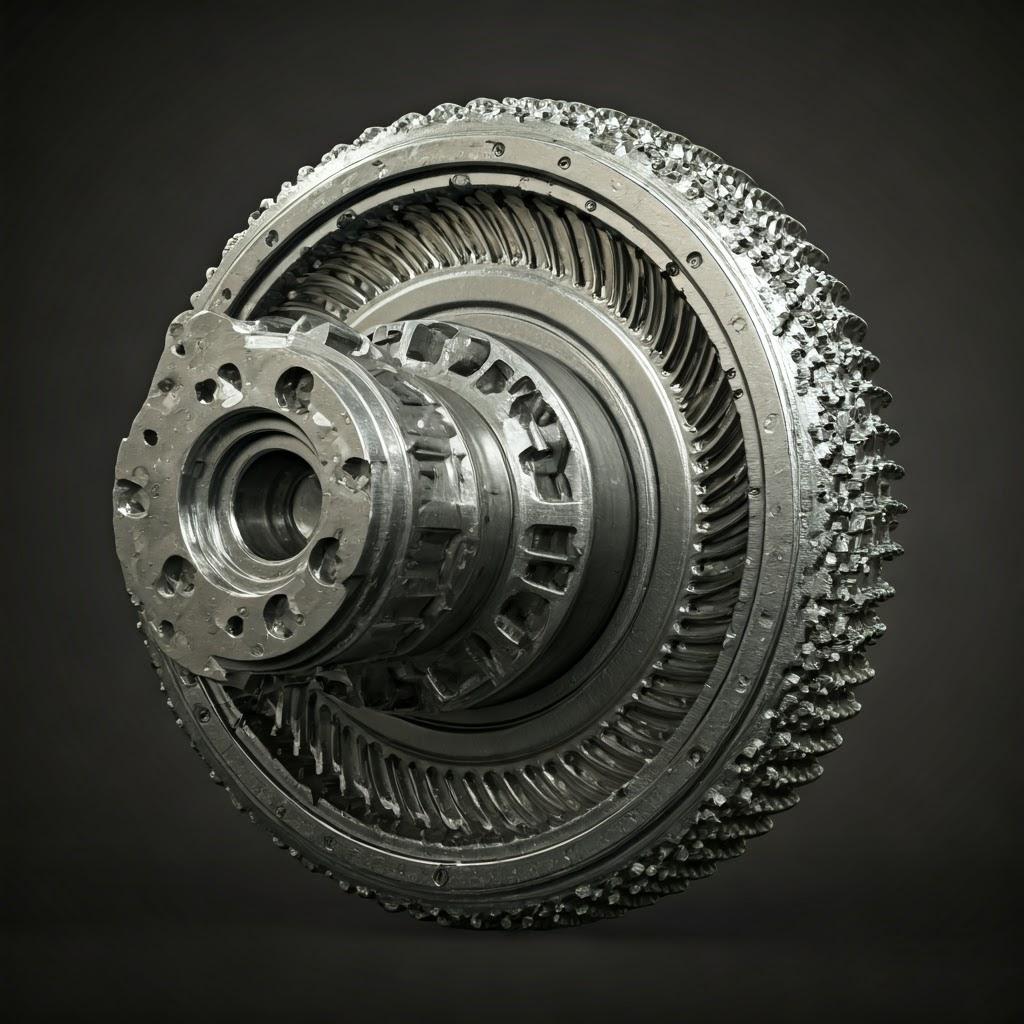
Auswahl der Partner: Die Wahl des richtigen 3D-Druckdienstleisters für Automobilkomponenten aus Metall
Der Erfolg der Implementierung der additiven Fertigung von Metall für kritische Komponenten wie Kühlmäntel für Elektromotoren hängt nicht nur von einem robusten Design und der Materialauswahl ab, sondern auch von den Fähigkeiten und der Zuverlässigkeit des gewählten Fertigungspartners. Die Auswahl des richtigen AM-Dienstleisters ist eine strategische Entscheidung für Entwicklungsteams und Beschaffungsmanager, die sich auf Qualität, Kosten, Vorlaufzeit und den Gesamterfolg des Projekts auswirkt. Angesichts der hohen Anforderungen in der Automobilindustrie gehen die Bewertungskriterien über die bloßen Druckfähigkeiten hinaus.
Schlüsselkriterien für die Bewertung von Metall-AM-Lieferanten für Automobilanwendungen:
- Qualitätsmanagementsysteme und Zertifizierungen:
- Erfordernis: Die Automobilindustrie verlangt eine strenge Qualitätskontrolle. Achten Sie auf Lieferanten mit einem robusten Qualitätsmanagementsystem (QMS), das nach ISO 9001 zertifiziert ist. Die IATF 16949-Zertifizierung (der globale Automobilstandard) ist bei reinen AM-Dienstleistern zwar derzeit noch selten, aber der Nachweis eines Bewusstseins für diese Norm, die Ausrichtung an ihren Grundsätzen (z. B. Prozesskontrolle, Rückverfolgbarkeit, Risikomanagement) und ein klarer Fahrplan zur Erreichung dieser Norm sind ein großer Vorteil.
- Warum das wichtig ist: Zertifizierungen zeigen, dass man sich zu dokumentierten Prozessen, kontinuierlicher Verbesserung, Rückverfolgbarkeit und gleichbleibender Qualität verpflichtet hat - eine wesentliche Voraussetzung für die zuverlässige Lieferung von Automobilkomponenten.
- Bewertung: Fragen Sie nach aktuellen Zertifizierungen, Auditberichten (wenn möglich), Einzelheiten zu ihrem QMS, Rückverfolgbarkeitsverfahren (von der Pulvercharge bis zum fertigen Teil) und Kalibrierungsunterlagen.
- Materialexpertise & Qualitätskontrolle bei Pulver:
- Erfordernis: Ein tiefes Verständnis der zu verarbeitenden Werkstoffe (z. B. AlSi10Mg, CuCrZr) ist entscheidend. Dazu gehört auch die Kenntnis ihres metallurgischen Verhaltens beim Druck und bei der Wärmebehandlung. Entscheidend ist, dass der Lieferant strenge Kontrollen der eingehenden Pulverqualität und der Handhabungsverfahren durchführt, um Verunreinigungen zu vermeiden und die Konsistenz zu gewährleisten.
- Warum das wichtig ist: Die Materialeigenschaften bestimmen direkt die Leistung des Teils. Uneinheitliche Pulverqualität oder schlechte Handhabung führen zu unvorhersehbaren Druckergebnissen und möglichen Bauteilausfällen. Fachwissen stellt sicher, dass die richtigen Parametereinstellungen und Wärmebehandlungen angewendet werden.
- Bewertung: Erkundigen Sie sich nach der Beschaffungsstrategie für das Pulver (interne Produktion wie Met3dp oder externe Lieferanten), den Verfahren zur Prüfung des Pulvers (PSD, Morphologie, Chemie, Fließfähigkeit), der Chargenverfolgung, den Lagerbedingungen und den Handhabungsprotokollen (insbesondere für reaktive Metalle oder zur Vermeidung von Kreuzkontaminationen). Erörtern Sie deren Erfahrung mit den erforderlichen spezifischen Legierungen. Ein Anbieter wie Met3dp, der seine eigenen hochwertigen Pulver mit fortschrittlichen Methoden wie PREP und Gaszerstäubung herstellt, bietet einen deutlichen Vorteil bei der Kontrolle dieses kritischen Inputs. Sie können mehr erfahren über uns und unseren integrierten Ansatz.
- Technologische Fähigkeiten & Kapazität:
- Erfordernis: Der Lieferant sollte über modernste AM-Anlagen (L-PBF, SEBM oder andere für die Anwendung relevante) verfügen, die für die gewählten Materialien und die erforderliche Präzision geeignet sind. Ebenso wichtig sind umfassende interne oder straff geführte externe Kapazitäten für alle erforderlichen Nachbearbeitungsschritte (Spannungsabbau, Wärmebehandlung, Bearbeitung, Endbearbeitung, Prüfung). Ausreichende Kapazitäten für die Herstellung von Prototypen und die Skalierung auf kleine bis mittlere Serien sind ebenfalls entscheidend.
- Warum das wichtig ist: Die Technologie diktiert die Leistungsfähigkeit (Genauigkeit, Geschwindigkeit, Materialkompatibilität). Die integrierte Nachbearbeitung rationalisiert den Arbeitsablauf, verkürzt die Vorlaufzeiten und gewährleistet die Verantwortlichkeit. Angemessene Kapazitäten verhindern Engpässe und gewährleisten eine termingerechte Lieferung, was für die Zeitplanung in der Automobilindustrie entscheidend ist.
- Bewertung: Beurteilen Sie den Maschinenpark (Typ, Alter, Anzahl der Maschinen, Bauvolumen), die verfügbaren Nachbearbeitungsgeräte, die messtechnischen Möglichkeiten (CMM, Scanner), die Softwaretools (Bauvorbereitung, Simulation) und die angegebenen Kapazitäten. Erkundigen Sie sich, ob das Unternehmen in der Lage ist, die Produktion bei Bedarf zu skalieren. Met3dp’s Fokus auf branchenführendes Druckvolumen, Genauigkeit und Zuverlässigkeit spricht diese Anforderungen direkt an.
- Technisches Fachwissen & Technische Unterstützung:
- Erfordernis: Der ideale Partner ist mehr als nur ein Druckbüro; er sollte DfAM-Anleitung, Machbarkeitsbewertungen, Erkenntnisse aus der Fertigungssimulation und gemeinsame Problemlösungen anbieten. Zu seinem Team sollten erfahrene Ingenieure und Metallurgen gehören, die sowohl AM als auch die Anforderungen der Zielanwendung verstehen.
- Warum das wichtig ist: Durch die Zusammenarbeit wird sichergestellt, dass die Entwürfe im Hinblick auf Herstellbarkeit, Leistung und Kosteneffizienz optimiert werden. Die Unterstützung durch Experten kann helfen, Designherausforderungen zu überwinden und die Entwicklung zu beschleunigen.
- Bewertung: Prüfen Sie Fallstudien oder Beispiele für ähnliche Projekte. Beurteilen Sie bei den ersten Gesprächen die technische Tiefe des Teams. Erkundigen Sie sich nach dem DfAM-Unterstützungsprozess und den Simulationsmöglichkeiten. Suchen Sie nach Partnern, die bereit sind, Zeit zu investieren, um Ihre spezifischen Anforderungen zu verstehen.
- Erfolgsbilanz & Branchenerfahrung:
- Erfordernis: Nachgewiesene Erfahrung in der Herstellung von Teilen für anspruchsvolle Industrien, idealerweise für die Automobilindustrie oder die Luft- und Raumfahrt, ist von großem Wert. Referenzen oder Fallstudien, die die erfolgreiche Durchführung von Projekten, insbesondere mit ähnlichen Werkstoffen oder Bauteiltypen, belegen, schaffen Vertrauen.
- Warum das wichtig ist: Erfahrung bedeutet, dass man mit den Erwartungen der Branche, den üblichen Herausforderungen und den Qualitätsanforderungen vertraut ist. Eine nachweisliche Erfolgsbilanz verringert das Risiko, das mit der Einführung einer relativ neuen Fertigungstechnologie verbunden ist.
- Bewertung: Fragen Sie nach relevanten Fallstudien, Kundenberichten oder Referenzen (unter Wahrung der Vertraulichkeit). Erkundigen Sie sich nach ihrer Erfahrung mit Teilen, die Dichtheitsprüfungen, enge Toleranzen oder spezielle Materialzertifizierungen erfordern.
- Projektmanagement und Kommunikation:
- Erfordernis: Klare Kommunikationskanäle, definierte Projektzeitpläne, regelmäßige Aktualisierungen und ein reaktionsschneller Kundendienst sind von entscheidender Bedeutung, insbesondere während der Prototypenerstellung und des Produktionsanlaufs. Ein professionelles Projektmanagement sorgt für einen reibungslosen Ablauf.
- Warum das wichtig ist: Hält Projekte auf Kurs, erleichtert die schnelle Lösung von Problemen und baut eine starke Arbeitsbeziehung auf. Entscheidend für die Einhaltung enger Zeitpläne in der Automobilentwicklung.
- Bewertung: Beurteilen Sie die Reaktionsfähigkeit während der Angebots- und der ersten Gesprächsphase. Erkundigen Sie sich nach dem Projektmanagementprozess und den vorgesehenen Ansprechpartnern.
- Kosten & Kampf; Wettbewerbsfähigkeit bei den Vorlaufzeiten:
- Erfordernis: Obwohl die Kosten nicht der nur die Preisstruktur des Anbieters muss transparent und wettbewerbsfähig im Verhältnis zum angebotenen Wert und zur Qualität sein. Die Lieferzeiten müssen mit den Projektfristen übereinstimmen.
- Warum das wichtig ist: Die Einhaltung des Budgets und die pünktliche Lieferung sind grundlegende Geschäftsanforderungen.
- Bewertung: Holen Sie detaillierte Angebote ein, in denen die Kosten aufgeschlüsselt sind (Material, Maschinenzeit, Nachbearbeitung, NRE). Vergleichen Sie Angebote von mehreren qualifizierten Anbietern. Diskutieren Sie realistische Vorlaufzeitschätzungen unter Berücksichtigung von Komplexität und Nachbearbeitungsbedarf.
Zusammenfassung der Checkliste zur Lieferantenbewertung:
Kriterien | Wichtige Fragen | Warum es für Automotive AM von entscheidender Bedeutung ist |
---|---|---|
Qualitätssystem/Zertifikate | ISO 9001? IATF-Bewusstsein/Pläne? Prozess der Rückverfolgbarkeit? Audit-Ergebnisse? | Gewährleistet gleichbleibende Qualität, Zuverlässigkeit und Prozesskontrolle |
Werkstoffkompetenz | Erfahrung mit den erforderlichen Legierungen? Pulverbeschaffung/QC? Handhabungsprotokolle? | Garantiert korrekte Materialeigenschaften, verhindert Defekte und Verunreinigungen |
Technologie und Kapazität | Maschinenpark (Art/Anzahl/Volumen)? Nachbearbeitungsmöglichkeiten (intern)? Metrologie? Skalierbarkeit? | Ermittlung der technischen Machbarkeit, der Effizienz der Arbeitsabläufe und der fristgerechten Lieferung |
Technische Unterstützung | DfAM-Anleitung angeboten? Simulationsmöglichkeiten? Fachwissen des Ingenieurteams? Kollaborativer Ansatz? | Optimiert das Design für AM, beschleunigt die Entwicklung, löst Probleme |
Erfolgsbilanz | Erfahrung in der Automobilindustrie/einschlägigen Branchen? Fallstudien/Referenzen? Ähnliche Teile hergestellt? | Reduziert das Risiko und zeigt, dass er die Anforderungen der Branche versteht |
Projektleitung | Kommunikationsprozess? Projektaktualisierungen? Reaktionsfähigkeit? Engagierte Ansprechpartner? | Sorgt für einen reibungslosen Ablauf, hält Fristen ein, schafft Vertrauen |
Kosten und Vorlaufzeit | Transparente Preisgestaltung? Konkurrenzfähiges Angebot? Realistische Vorlaufzeiten? Abstimmung auf die Projektanforderungen? | Einhaltung von Budget- und Terminvorgaben |
In Blätter exportieren
Die Auswahl des richtigen Metall-AM-Partners ist ein entscheidender Schritt für jedes Unternehmen, das diese Technologie für anspruchsvolle Anwendungen wie Kühlmäntel von Elektromotoren nutzen möchte. Eine gründliche Bewertung auf der Grundlage dieser Kriterien hilft bei der Identifizierung von Lieferanten wie Met3dp, die über die notwendige Kombination von Qualitätssystemen, Materialkontrolle, technologischem Können, Fachwissen und Kundenorientierung verfügen, um zuverlässige, leistungsstarke Komponenten für die Zukunft der Elektromobilität zu liefern.
Die Investition verstehen: Kostenfaktoren und typische Vorlaufzeiten für 3D-gedruckte Kühlmäntel
Während die technischen Vorteile des 3D-Drucks von Metall für EV-Kühlmäntel überzeugend sind, ist das Verständnis der damit verbundenen Kosten und Vorlaufzeiten für die Projektplanung, die Budgetierung und das Treffen fundierter Entscheidungen unerlässlich, insbesondere für Beschaffungsabteilungen, die AM mit traditionellen Fertigungsverfahren vergleichen. Die Kostenstruktur von AM unterscheidet sich erheblich von der des Gießens oder der maschinellen Bearbeitung, insbesondere in Bezug auf die Volumenabhängigkeit und den Werkzeugbau.
Die wichtigsten Kostentreiber in der additiven Metallfertigung:
- Materialkosten & Verbrauch:
- Pulver Preis: Die Grundkosten pro Kilogramm des Metallpulvers sind ein wichtiger Faktor. Hochwertige Legierungen wie CuCrZr sind deutlich teurer als gewöhnliches AlSi10Mg. Qualitativ hochwertiges Pulver mit spezifischen Eigenschaften (Sphärizität, PSD) hat ebenfalls einen höheren Preis.
- Teilvolumen und Dichte: Das tatsächliche Volumen des fertigen Teils bestimmt die Menge des geschmolzenen Pulvers. DfAM-Techniken wie Topologieoptimierung und Gitterstrukturen senken direkt den Materialverbrauch und die Kosten.
- Unterstützende Strukturen: Das für die Stützstrukturen verwendete Material trägt ebenfalls zum Gesamtverbrauch bei, obwohl dieses Pulver (bei sorgfältiger Qualitätskontrolle) häufig wiederverwertbar ist. Die Minimierung der Stützstrukturen durch DfAM senkt diese Kosten.
- Abfall/Recycling: Ein Teil des Pulvers geht während der Handhabung und des Drucks unweigerlich verloren oder wird abgebaut. Effiziente Pulverrecyclingverfahren, die vom Lieferanten eingesetzt werden, können dazu beitragen, diese Kosten zu verringern, erfordern aber strenge Tests, um die Qualität des recycelten Pulvers sicherzustellen.
- Maschinenzeit (Bauzeit):
- Haupttreiber: Dies ist oft die größte Kostenkomponente, da sie die Zeit darstellt, die die teure AM-Maschine für den Druck des Teils benötigt.
- Beeinflussende Faktoren:
- Teilhöhe (Z-Achse): Die Bauzeit ist direkt proportional zur Anzahl der Schichten, daher ist die Höhe des Teils in der Bauausrichtung entscheidend.
- Teilvolumen/Fläche pro Schicht: Die Menge des zu schmelzenden Materials in jeder Schicht beeinflusst die für das Scannen benötigte Zeit.
- Komplexität: Hochkomplexe Geometrien können langsamere Scan-Geschwindigkeiten oder kompliziertere Scan-Strategien erfordern.
- Schichtdicke: Dünnere Schichten verbessern die Auflösung und die Oberflächengüte, erhöhen aber die Anzahl der Schichten und damit die Bauzeit erheblich.
- Maschinentyp & Leistung: Schnellere Maschinen mit leistungsstärkeren Lasern/Strahlen oder mehreren Strahlen können die Bauzeiten verkürzen, haben aber höhere Betriebsstundenzahlen.
- Verschachtelung/Verpackungsdichte: Das gleichzeitige Drucken mehrerer Teile in einem Bauvorgang verbessert die Maschinenauslastung erheblich und reduziert die Kosten pro Teil. Erfahrene Lieferanten optimieren Build-Layouts.
- Arbeitskosten:
- Vorverarbeitung: Für die Bauvorbereitung (Verarbeitung von CAD-Dateien, Ausrichtung, Erzeugung von Stützen, Slicing) sind qualifizierte Techniker/Ingenieure erforderlich.
- Betrieb der Maschine: Überwachung des Build-Prozesses.
- Nachbearbeiten: Dies kann sehr arbeitsintensiv sein und umfasst das Entpulvern, die Entfernung des Teils, die Entfernung der Halterung, die Einrichtung der Wärmebehandlung, die Einrichtung/Bearbeitung, die Endbearbeitung, die Reinigung und die Prüfung. Die Komplexität des Teils und der Grad der erforderlichen Nachbearbeitung beeinflussen den Arbeitsaufwand für die Nachbearbeitung erheblich.
- Nachbearbeitungskosten:
- Verbrauchsgüter & Energie: Wärmebehandlung (Ofenzeit, Schutzgas/Vakuum), Bearbeitung (Werkzeugverschleiß, Kühlmittel), Endbearbeitungsmedien (Strahlen, Polieren).
- Spezialisierte Prozesse: Kosten im Zusammenhang mit bestimmten Schritten wie Drahterodieren, AFM, CT-Scannen oder speziellen Beschichtungsanwendungen.
- Qualitätskontrolle & Inspektion:
- Arbeit & Ausrüstung: Zeitaufwand für Dimensionsprüfung (CMM, Scannen), Dichtheitsprüfung, zerstörungsfreie Prüfung, Materialprüfung (falls erforderlich) und Dokumentation. Der Umfang der erforderlichen Qualitätskontrolle wirkt sich auf die Kosten aus.
- Nicht wiederkehrendes Engineering (NRE):
- Ersteinrichtung: Kosten im Zusammenhang mit der anfänglichen Konstruktionsberatung, der DfAM-Optimierung, der Konstruktion spezifischer Vorrichtungen (für die Bearbeitung/Inspektion) oder der Entwicklung von Prozessparametern für spezielle Anwendungen. Werden in der Regel über die erste Charge von Teilen amortisiert.
- Menge (Chargengröße):
- Amortisation: Die NRE-Kosten und der Rüstaufwand werden auf die Anzahl der produzierten Teile verteilt.
- Auslastung der Maschine: Größere Lose ermöglichen eine bessere Verschachtelung der Bauplatten, was die Effizienz der Maschinenzeit erheblich verbessert und die Kosten pro Teil senkt.
- Lernkurve: Die Effizienz der Nachbearbeitung kann oft durch größere Chargen gesteigert werden.
- Bandpausen: Die Lieferanten bieten oft mengenabhängige Preise an.
Vorbehalte beim Kostenvergleich:
Ein direkter Vergleich der AM-Kosten mit traditionellen Methoden erfordert eine sorgfältige Berücksichtigung des Volumens.
- Prototyping & Kleinserien (<100s): AM ist oft sehr wettbewerbsfähig oder sogar billiger, da keine Werkzeugkosten (Formen für das Gießen) anfallen.
- Mittleres Volumen (100er – niedrige 1000er): Der Vergleich wird komplex. Optimierte AM-Teile (leicht, konsolidiert) können funktionale Vorteile bieten, die einen möglichen Kostenaufschlag rechtfertigen, oder die Kosten können je nach Komplexität und Nachbearbeitung vergleichbar sein.
- Großes Volumen (10.000+): Herkömmliche Verfahren wie das Druckgießen bieten aufgrund von Skaleneffekten in der Regel niedrigere Kosten pro Teil, vorausgesetzt, das Design ist für das Gießen geeignet. Allerdings sollten die Gesamtbetriebskosten (unter Berücksichtigung von Leistungssteigerungen, Gewichtseinsparungen, vereinfachter Montage durch AM) bewertet werden.
Typische Vorlaufzeiten:
Die Vorlaufzeit ist die Dauer von der Auftragserteilung (und der endgültigen Bestätigung des Entwurfs) bis zur Auslieferung des Teils. Sie ist sehr unterschiedlich, folgt aber einem allgemeinen Muster:
- Prototyping (1-10 Einheiten):
- Typischer Bereich: 1 bis 4 Wochen.
- Beeinflussende Faktoren: Aktuelle Maschinenverfügbarkeit, Bauzeit (oft 1-3 Tage für einen Kühlmantel, je nach Größe/Komplexität), erforderliche Nachbearbeitungskomplexität (einfacher Spannungsabbau und Entfernung von Unterstützungen im Vergleich zu vollständiger Wärmebehandlung, umfangreicher Bearbeitung und Endbearbeitung). Eilige Optionen sind oft gegen einen Aufpreis erhältlich.
- Produktion kleiner Mengen (10er – niedrige 100er):
- Typischer Bereich: 4 bis 8 Wochen.
- Beeinflussende Faktoren: Es besteht Bedarf an optimierten Fertigungslayouts, an der Planung von Maschinenzeiten für mehrere Fertigungsschritte, an der Entwicklung spezifischer Vorrichtungen für die Bearbeitung oder Prüfung und an der effizienten Steuerung des Flusses durch verschiedene Nachbearbeitungsschritte. Auch die Materialverfügbarkeit für größere Mengen kann eine Rolle spielen.
- Mittlere Produktionsmengen (hohe 100er – 1000er):
- Typischer Bereich: 8 bis 16+ Wochen (oft mit gestaffelten Lieferungen).
- Beeinflussende Faktoren: Erfordert eine umfangreiche Planung der Maschinenkapazitäten, möglicherweise dedizierte Maschinenzeit, eine robuste Lieferkette für Pulver, möglicherweise eine Aufstockung der Nachbearbeitungsmöglichkeiten und eine umfassende Planung der Qualitätskontrolle. Prozessoptimierung und die Festlegung eines stabilen Produktionsrhythmus sind entscheidend.
Faktoren, die die Durchlaufzeiten beschleunigen/verzögern:
- Beschleunigen: Klare Konstruktionsspezifikationen, DfAM-optimierte Teile (weniger Halterungen, weniger Nachbearbeitung), leicht verfügbares Pulver, gute Lieferantenbeziehungen/Kommunikation, Auswahl eines Lieferanten mit integrierten Fähigkeiten.
- Verlangsamen: Konstruktionsänderungen während des Prozesses, komplexe Geometrien, die umfangreiche Halterungen oder komplizierte Nachbearbeitungen erfordern, nicht standardisierte Materialanforderungen, Kapazitätsengpässe bei Zulieferern, Verzögerungen bei Versand/Logistik.
Vorlaufzeit & Kostenübersichtstabelle:
Faktor | Auswirkungen auf die Kosten | Auswirkungen auf die Vorlaufzeit | Milderung/Optimierung |
---|---|---|---|
Entwurfskomplexität | Erhöhungen (Bauzeit, Supports, Post-Prozesse) | Erhöhungen (Build, post-proc.) | DfAM zur Vereinfachung, wo immer möglich, optimiert Unterstützungen |
Teilegröße/Volumen | Erhöhungen (Material, Bauzeit) | Erhöhungen (Bauzeit) | DfAM für Leichtbau, Verschachtelung von Teilen im Bau |
Wahl des Materials | Signifikant (CuCrZr >> AlSi10Mg) | Geringfügig (unterschiedliche Parameter), erheblich (bei Beschaffungsverzögerungen) | Auswahl nach tatsächlichem Bedarf, Sicherstellung, dass der Lieferant über Materialkenntnisse verfügt |
Menge | Verminderungen pro Teil (Amortisation, Effizienz) | Erhöhungen insgesamt, Verminderungen pro Teil potenziell (Effizienz) | Optimierung der Losgrößen, Planung des Produktionsplans |
Nachbearbeitung | Wesentliche Treiber (Arbeit, Zeit für Ausrüstung) | Wesentlicher Treiber | DfAM zur Minimierung des Bearbeitungs-/Fertigstellungsbedarfs, integrierter Lieferant |
Anforderungen an die Qualität | Erhöhungen (Inspektionszeit, NDT-Kosten) | Erhöhungen (Inspektionszeit) | Anforderungen im Vorfeld klar definieren |
In Blätter exportieren
Das Verständnis des Zusammenspiels dieser Faktoren ermöglicht eine genauere Budgetierung und Projektplanung, wenn Metall-AM für Kühlmäntel von Elektromotoren in Betracht gezogen wird. Offene Gespräche mit potenziellen Lieferanten wie Met3dp über spezifische Designanforderungen und Volumenerwartungen sind entscheidend, um realistische Kostenschätzungen und Vorlaufzeitprognosen zu erhalten.
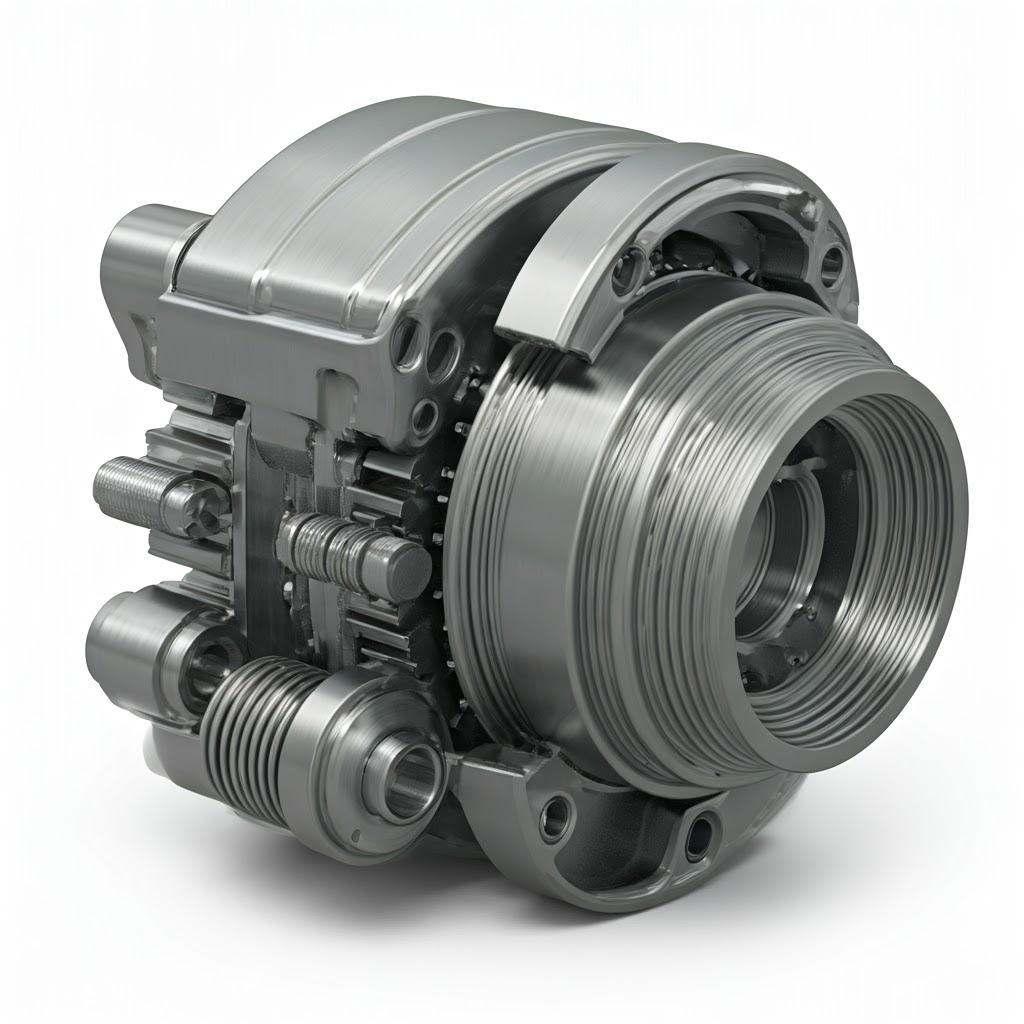
Häufig gestellte Fragen (FAQ) für Beschaffungs- und Ingenieurteams
Hier finden Sie Antworten auf einige häufig gestellte Fragen von Ingenieuren und Beschaffungsmanagern, die den 3D-Druck von Metall für Kühlmäntel von Elektrofahrzeugen in Betracht ziehen:
1. Wie sieht es mit den Kosten eines 3D-gedruckten Kühlmantels im Vergleich zum herkömmlichen Guss aus, insbesondere wenn die Produktionsmenge steigt?
- Antwort: Der Kostenvergleich hängt stark von Volumen und Komplexität ab.
- Prototypen & Kleinserien (< ~100 Einheiten): Der Metall-3D-Druck ist oft kostengünstiger als das Gießen, weil es die extrem hohen Vorlaufkosten und die lange Vorlaufzeit vermeidet, die mit der Herstellung von Gussformen oder Gesenken verbunden sind.
- Mittleres Volumen (~100 – 2.000 Einheiten): Dies ist ein Übergangsbereich. Die Wettbewerbsfähigkeit von AM hängt von Faktoren wie der Komplexität des Designs (AM kann die Komplexität besser bewältigen), dem Potenzial für die Konsolidierung von Teilen (Verringerung der Montagekosten), den Vorteilen des Leichtbaus (Wert des eingesparten Gewichts) und dem spezifischen AM-Prozess/Material im Vergleich zum Gussverfahren (z. B. Sand- oder Druckguss) ab. Optimierte AM-Teile könnten einen durch Leistungssteigerungen gerechtfertigten Aufpreis erzielen.
- Großes Volumen (10.000+ Einheiten): Bei relativ einfachen Entwürfen, die im Druckgussverfahren hergestellt werden können, wird mit herkömmlichen Verfahren in der Regel eine niedrigerer Stückpreis aufgrund von Größenvorteilen. Wenn AM jedoch erhebliche Leistungsverbesserungen (bessere Kühlung, höherer Motorwirkungsgrad) oder Gewichtsreduzierungen (größere Reichweite des Fahrzeugs) ermöglicht, könnte eine Analyse der Gesamtbetriebskosten selbst bei höheren Stückzahlen für bestimmte Anwendungen immer noch für AM sprechen. Es ist entscheidend, nicht nur den Stückpreis, sondern das gesamte Wertangebot zu bewerten.
2. Welche Prüf- und Validierungsverfahren sind typischerweise erforderlich, um einen 3D-gedruckten Kühlmantel aus Metall für den Einsatz in der Automobilindustrie zu qualifizieren?
- Antwort: Die Qualifizierung umfasst strenge Prüfungen, die über die Standardabmessungen hinausgehen und die Anforderungen an traditionell gefertigte Teile widerspiegeln, wobei jedoch zusätzlich AM-spezifische Aspekte berücksichtigt werden. Zu den wichtigsten Verfahren gehören:
- Überprüfung der Materialeigenschaften: Zugprüfung, Härteprüfung und Mikrostrukturanalyse (oft unter Verwendung von neben den Teilen gedruckten Proben), um zu bestätigen, dass das Material nach dem Druck und der Wärmebehandlung den Spezifikationen entspricht. Die Konsistenz wird über alle Produktionen hinweg überwacht.
- Dichtheitsprüfung: Obligatorische 100%ige Druckabfall- oder Helium-Lecktests, um die Integrität des Flüssigkeitsbehälters unter Betriebsdruck sicherzustellen. Die Akzeptanzkriterien sind in der Regel sehr streng.
- Dimensionale Validierung: Vollständige Layout-Inspektion mit CMM oder 3D-Scanning zur Überprüfung der Konformität mit den Zeichnungen, einschließlich kritischer Schnittstellenabmessungen und GD&T Callouts.
- Zerstörungsfreie Prüfung (NDT): Je nach Kritikalität können CT-Scans oder Röntgeninspektionen eingesetzt werden (insbesondere während der Prozessqualifizierung), um interne Defekte wie Porosität oder fehlendes Schmelzen zu erkennen. Farbeindring- oder Magnetpulverprüfungen können bei Oberflächen nach der Bearbeitung eingesetzt werden.
- Berstdruckprüfung: Prüfung von Proben bis zum Versagen unter hydrostatischem Druck, um die Sicherheitsmarge über dem maximalen Betriebsdruck zu bestimmen.
- Thermische Wechselbeanspruchung & Vibrationsprüfung: Simulation von Betriebsbedingungen zur Bewertung der Haltbarkeit und Ermüdungsbeständigkeit unter kombinierten thermischen und mechanischen Belastungen.
- Prüfung der Kühlmittelkompatibilität: Gewährleistung einer langfristigen Korrosions- und Degradationsbeständigkeit, wenn sie bestimmten Kfz-Kühlmitteln ausgesetzt sind.
- Prozessvalidierung (PPAP-Elemente): Die Anpassung an die Elemente des PPAP-Rahmens (Production Part Approval Process), einschließlich Prozessflussdiagrammen, FMEAs (Failure Modes and Effects Analysis), Kontrollplänen und Fähigkeitsstudien, zeigt, dass die Fertigung für die Serienproduktion bereit ist.
3. Können die mit DfAM entworfenen komplexen inneren Kühlkanäle zuverlässig und konsistent hergestellt werden, und wie wird ihre innere Qualität überprüft?
- Antwort: Ja, die zuverlässige Herstellung komplexer interner Kanäle ist eine der Hauptstärken der Metall-AM, aber sie erfordert ein sorgfältiges Design und eine strenge Prozesskontrolle.
- Verlässlichkeit & Konsistenz: Erreicht durch:
- DfAM: Entwicklung von Kanälen mit selbsttragenden Formen (z. B. tropfenförmig, rautenförmig) und glatten Übergängen, um den Bedarf an internen Stützen zu minimieren und die Pulverentfernung zu erleichtern.
- Optimierte Parameter: Verwendung von validierten Druckparametern, die auf das Material und die Kanalgeometrie abgestimmt sind, um eine vollständige Verschmelzung zu gewährleisten und Fehler zu minimieren.
- Qualität des Pulvers: Verwendung von hochwertigem, fließfähigem Pulver.
- Robuste Reinigung: Einführung gründlicher, validierter Entpuderungsverfahren.
- Verifizierung: Die interne Qualität wird überprüft durch:
- Visuelle Inspektion (soweit möglich): Verwendung von Endoskopen zur visuellen Inspektion der zugänglichen Teile der Kanäle auf Verstopfungen, Reste von Stützen oder grobe Mängel.
- Durchflussprüfung: Messung des Druckabfalls in den Kanälen bei definierten Durchflussraten, um sicherzustellen, dass sie klar sind und den CFD-Vorhersagen entsprechen. Verstopfungen oder erhebliche Abweichungen deuten auf Probleme hin.
- CT-Scan: Die Computertomografie liefert eine detaillierte 3D-Ansicht der inneren Struktur und ermöglicht die Überprüfung der Kanalgeometrie, die Erkennung von inneren Porositäten oder Pulverresten und die Bewertung der Wandstärke. Dies wird häufig bei der Prozessentwicklung und -qualifizierung sowie möglicherweise bei Stichproben während der Produktion von hochkritischen Teilen eingesetzt.
- Dichtheitsprüfung: Dies dient als abschließende Funktionskontrolle, die die Gesamtintegrität der Kanalwände bestätigt.
- Verlässlichkeit & Konsistenz: Erreicht durch:
Die Zusammenarbeit mit einem erfahrenen AM-Anbieter wie Met3dp, der über robuste Prozesse für DfAM, Parameteroptimierung, Reinigung und Inspektion (einschließlich potenzieller ZfP) verfügt, ist für das Erreichen zuverlässiger und überprüfbarer komplexer Innengeometrien von entscheidender Bedeutung. Erkunden Sie unser Angebot an metallpulver und -lösungen für diese anspruchsvollen Anwendungen geeignet.
Schlussfolgerung: Die Zukunft der EV-Leistung mit additiv gefertigten Kühlmänteln
Der Übergang zur Elektromobilität erfordert kontinuierliche Innovationen bei allen Fahrzeugsystemen, und das Wärmemanagement erweist sich als entscheidender Faktor für Leistung, Reichweite und Zuverlässigkeit. Wie wir erforscht haben, stellen Kühlmäntel für Elektromotoren eine erstklassige Gelegenheit dar, bei der die Grenzen der traditionellen Fertigung durch die transformativen Fähigkeiten der additiven Fertigung von Metallen überwunden werden können.
Durch den Einsatz des 3D-Drucks von Metallen erhalten Ingenieure eine noch nie dagewesene Designfreiheit. Sie können Kühlmäntel mit komplizierten, konformen internen Kanälen herstellen, die durch fortschrittliche Simulationen optimiert werden und die Wärmeübertragung genau dort maximieren, wo sie benötigt wird. Topologieoptimierung und Gitterstrukturen ermöglichen eine erhebliche Gewichtsreduzierung, was sich direkt auf die Effizienz und Reichweite des Fahrzeugs auswirkt. Darüber hinaus vereinfacht die Möglichkeit, mehrere Komponenten in einem einzigen gedruckten Teil zusammenzufassen, die Montage, verringert potenzielle Fehlerquellen und rationalisiert die Lieferkette.
Der Weg dorthin führt über eine sorgfältige Materialauswahl, bei der man sich für die ausgewogene Leistung von Legierungen wie AlSi10Mg oder die überlegene Wärmeleitfähigkeit von CuCrZr entscheidet, die von hochwertigen Pulvern unterstützt werden. Um erfolgreich zu sein, müssen die Grundsätze des Design for Additive Manufacturing (DfAM) genauestens eingehalten, potenzielle Herausforderungen wie Eigenspannungen und Porosität durch eine fachkundige Prozesssteuerung gemeistert und umfassende Nachbearbeitungs- und Validierungsschritte, einschließlich wichtiger Dichtheitsprüfungen, durchgeführt werden.
Die Wahl des richtigen Fertigungspartners - eines Partners mit bewährtem Fachwissen, robusten Qualitätssystemen, fortschrittlichen technologischen Fähigkeiten und einem tiefgreifenden Verständnis der Materialien - ist von größter Bedeutung. Unternehmen wie Met3dp sind mit ihren vertikal integrierten Fähigkeiten, die von der fortschrittlichen Pulverproduktion bis hin zum Präzisionsdruck und der Unterstützung bei der Anwendungsentwicklung reichen, ideal positioniert, um Automobilherstellern dabei zu helfen, das volle Potenzial von AM auszuschöpfen.
Der 3D-Metalldruck ist nicht mehr nur ein Werkzeug für das Prototyping, sondern eine praktikable, strategische Fertigungslösung mit spürbaren Leistungsvorteilen für anspruchsvolle Elektrofahrzeugkomponenten. Da sich der Markt für Elektrofahrzeuge weiter beschleunigt, wird der Einsatz von additiv gefertigten Motorkühlmänteln zweifellos eine immer wichtigere Rolle dabei spielen, die Grenzen der thermischen Effizienz, der Leistungsdichte und der Gesamtleistung des Fahrzeugs zu verschieben. Durch die Zusammenarbeit mit führenden Experten und die Nutzung dieser fortschrittlichen Technologie können OEMs und Zulieferer dazu beitragen, die Zukunft der Elektromobilität voranzutreiben.
Erfahren Sie auf unserer Website, wie die innovativen Systeme und Pulver von Met3dp’ die Ziele Ihres Unternehmens im Bereich der additiven Fertigung unterstützen können: https://met3dp.com/.
Teilen auf
MET3DP Technology Co., LTD ist ein führender Anbieter von additiven Fertigungslösungen mit Hauptsitz in Qingdao, China. Unser Unternehmen ist spezialisiert auf 3D-Druckgeräte und Hochleistungsmetallpulver für industrielle Anwendungen.
Fragen Sie an, um den besten Preis und eine maßgeschneiderte Lösung für Ihr Unternehmen zu erhalten!
Verwandte Artikel
Über Met3DP
Aktuelles Update
Unser Produkt
KONTAKT US
Haben Sie Fragen? Senden Sie uns jetzt eine Nachricht! Wir werden Ihre Anfrage mit einem ganzen Team nach Erhalt Ihrer Nachricht bearbeiten.
Holen Sie sich Metal3DP's
Produkt-Broschüre
Erhalten Sie die neuesten Produkte und Preislisten
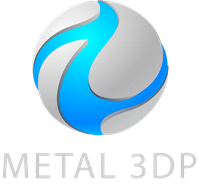
Metallpulver für 3D-Druck und additive Fertigung