Leichtes EV-Batteriegehäuse durch 3D-Druck von Metall
Inhaltsübersicht
Einleitung: Die kritische Rolle von leichten EV-Batteriegehäusen
Die Revolution der Elektrofahrzeuge (EV) verändert die Automobillandschaft, angetrieben durch das Streben nach Nachhaltigkeit, Effizienz und verbesserter Leistung. Das Herzstück eines jeden Elektrofahrzeugs ist der Akku - das Kraftpaket, das die Reichweite, die Beschleunigung und die Gesamtlebensfähigkeit bestimmt. Der Schutz dieser kritischen Komponente ist das EV-Batteriegehäuseein Gehäuse, das mehrere wichtige Funktionen erfüllt, die über die einfache Eindämmung hinausgehen. Sie muss eine robuste strukturelle Integrität bieten, empfindliche Zellen vor Umweltgefahren und potenziellen Stößen schützen, die beim Laden und Entladen entstehenden erheblichen thermischen Belastungen bewältigen und zur allgemeinen Sicherheitsarchitektur des Fahrzeugs beitragen. Herkömmliche Fertigungsmethoden führen jedoch häufig zu Batteriegehäusen, die ein beträchtliches zusätzliches Gewicht aufweisen, was sich direkt auf die Reichweite und die Effizienz des Fahrzeugs auswirkt - zwei Schlüsselkriterien für die Einführung von Elektrofahrzeugen.
Ingenieure und Beschaffungsmanager in der Automobilbranche stehen immer wieder vor der Herausforderung, Batteriegehäuse zu entwickeln und zu beschaffen, die den strengen Anforderungen entsprechen:
- Gewichtsreduzierung: Jedes eingesparte Kilogramm bedeutet eine größere Reichweite oder eine verbesserte Leistungsdynamik. Leichtbau ist das A und O bei der Entwicklung von Elektrofahrzeugen.
- Strukturelle Integrität und Sicherheit: Das Gehäuse muss Vibrationen und Stößen standhalten und, was besonders wichtig ist, die Batteriezellen bei einem Aufprall schützen und ein thermisches Durchgehen verhindern. Die Einhaltung der strengen Sicherheitsnormen für Kraftfahrzeuge (z. B. FMVSS, ECE-Vorschriften) ist nicht verhandelbar.
- Wärmemanagement: Eine effiziente Wärmeableitung ist für die Langlebigkeit, Leistung und Sicherheit von Batterien unerlässlich. Gehäuse erfordern oft integrierte Kühlsysteme oder Merkmale, die den Wärmeaustausch erleichtern.
- Optimierung von Verpackung und Platzbedarf: Der Einbau großer Batteriepakete in Fahrzeugplattformen erfordert kompakte und effizient gestaltete Gehäuse.
- Kosten-Nutzen-Verhältnis: Die Leistung ist zwar entscheidend, aber die Lösungen müssen auch skalierbar und wirtschaftlich tragfähig sein, insbesondere wenn die Produktionsmengen von Elektrofahrzeugen steigen.
Die Bewältigung dieser miteinander verknüpften Herausforderungen erfordert innovative Ansätze. Dies ist der Punkt Additive Fertigung von Metall (AM)gemeinhin als Metall bekannt 3D-Druck, entwickelt sich zu einer transformativen Technologie. Durch den schichtweisen Aufbau von Komponenten direkt aus digitalen Entwürfen unter Verwendung von Hochleistungsmetallpulvern eröffnet AM Designmöglichkeiten und Leistungsmerkmale, die zuvor unerreichbar waren. Für EV-Batteriegehäuse bietet Metall-AM einen überzeugenden Weg zur Schaffung von leichteren, stärkeren und thermisch effizienteren Gehäusen, was die Innovation in der Elektromobilität beschleunigt. Unternehmen sind zunehmend auf der Suche nach zuverlässigen Lösungen für die additive Fertigung um einen Wettbewerbsvorteil in der sich schnell entwickelnden Fahrzeugleichtbau Ethnie.
Wofür werden EV-Batteriegehäuse verwendet?
Die Batteriegehäuse für Elektrofahrzeuge ist weit mehr als nur ein Kasten. Es ist ein multifunktionales, hoch technisiertes System, das für den sicheren und effizienten Betrieb des Fahrzeugs entscheidend ist. Das Verständnis seiner vielfältigen Funktionen verdeutlicht die Komplexität, die mit seiner Konstruktion und Herstellung verbunden ist:
- Schutz der Batteriezellen: Die Hauptfunktion besteht darin, die empfindlichen Batteriezellen (häufig Lithium-Ionen) vor äußeren Einflüssen wie Feuchtigkeit, Staub, Schmutz und Stößen zu schützen. Dies gewährleistet die Langlebigkeit und den zuverlässigen Betrieb des Akkupacks.
- Strukturelle Unterstützung: Das Gehäuse trägt in erheblichem Maße zur strukturellen Gesamtsteifigkeit des Fahrgestells des Elektrofahrzeugs bei, insbesondere bei skateboardartigen Plattformen, bei denen das Batteriepaket Teil der Bodenstruktur des Fahrzeugs ist. Es muss während der Fahrt erheblichen statischen und dynamischen Belastungen standhalten.
- Thermische Regulierung: Die Leistung und die Lebensdauer von Batterien sind sehr temperaturabhängig. Das Gehäuse spielt eine entscheidende Rolle für die EV-Wärmemanagement System. Dabei kann es sich um passive Kühlrippen, Schnittstellen für Flüssigkeitskühlplatten oder sogar um integrierte Kühlkanäle direkt in den Gehäusewänden handeln, ein Merkmal, das durch die additive Fertigung erst möglich wird.
- Umweltfreundliche Versiegelung: Eine robuste Dichtung ist notwendig, um das Eindringen von Wasser, Salz und anderen Verunreinigungen zu verhindern, die Kurzschlüsse oder Korrosion verursachen und die Sicherheit und Leistung beeinträchtigen könnten. IP-Schutzarten (Ingress Protection) wie IP67 oder höher sind gängige Anforderungen.
- Crash-Sicherheit: Im Falle eines Aufpralls muss das Batteriegehäuse die Zellen vor Bruch oder Durchdringung schützen, was zu gefährlichen thermischen Durchschlägen führen könnte. Es muss die Aufprallenergie absorbieren und die strukturelle Integrität unter extremen Bedingungen aufrechterhalten. Dies erfordert eine sorgfältige Materialauswahl und strukturelle Gestaltung.
- Elektrische Isolierung und EMI-Abschirmung: Das Gehäuse muss dazu beitragen, die hohen Spannungen innerhalb des Pakets einzudämmen und möglicherweise elektromagnetische Störungen (EMI) abzuschirmen, um die empfindliche Elektronik im Fahrzeug zu schützen.
Schlüsselindustrien und Anwendungen:
Die wichtigsten Verbraucher sind EV-Hersteller (OEMs) und ihre Tier-1-Lieferanten die für die Montage von Batteriepacks verantwortlich sind. Die Technologie ist aber auch relevant für:
- Leistungsstarke und luxuriöse E-Fahrzeuge: Die Maximierung der Leistung und die Minimierung des Gewichts sind entscheidende Designziele.
- Elektrischer Motorsport: Hier sind maßgeschneiderte, hoch optimierte und leichte Komponenten unerlässlich.
- Spezialisierte Elektrofahrzeuge: Dazu gehören Busse, Lastkraftwagen, Geländewagen und sogar Elektroflugzeuge (eVTOL), die alle maßgeschneiderte Lösungen zum Schutz der Batterien benötigen.
- Entwicklung von Prototypen: AM ermöglicht eine schnelle Iteration und Funktionsprüfung neuer Gehäusedesigns, ohne dass teure Werkzeuge benötigt werden.
- Kleinserienproduktion: Für Nischenfahrzeuge oder erste Produktionsläufe kann AM kostengünstiger sein als Investitionen in herkömmliche Werkzeuge.
Da die Nachfrage nach anspruchsvollen EV-Komponenten-Lieferanten wächst, ist das Verständnis der vielschichtigen Rolle des Batteriegehäuses für die Bereitstellung effektiver und sicherer Lösungen unerlässlich.
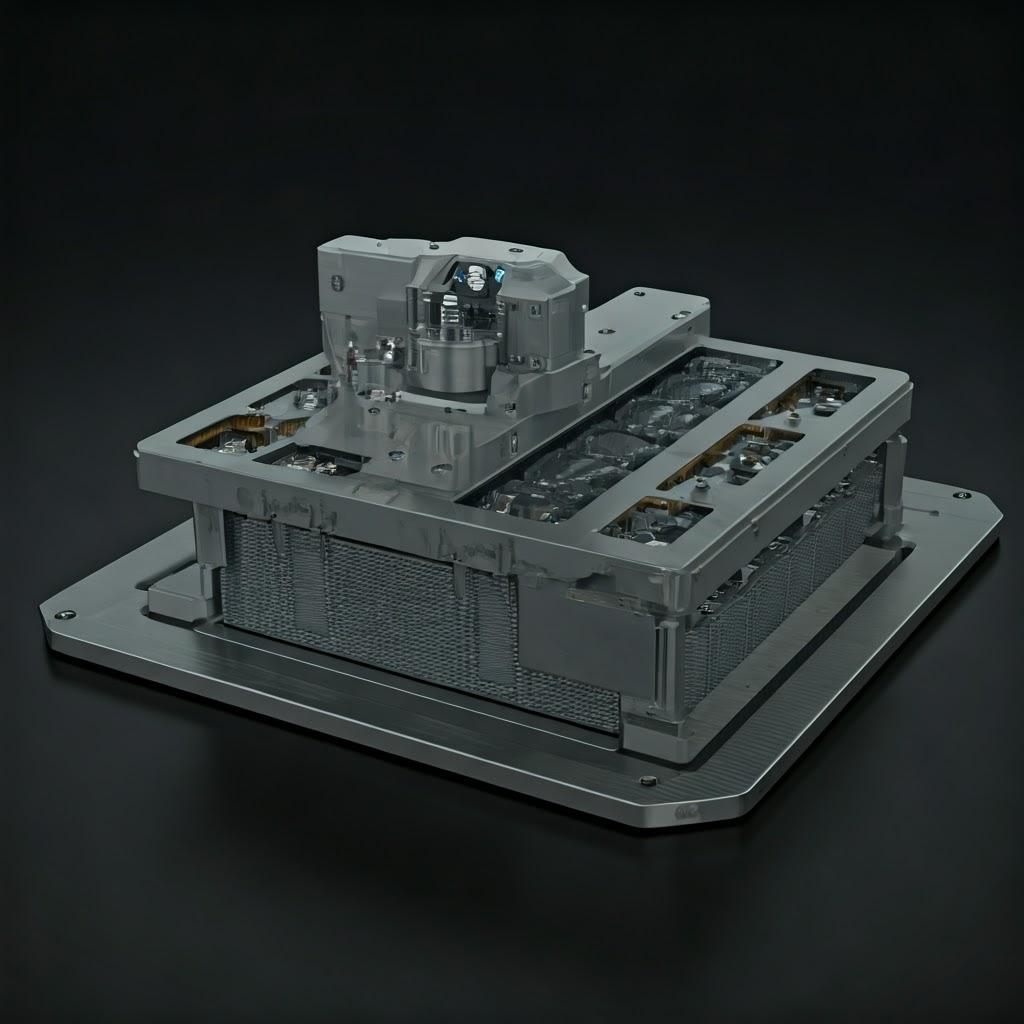
Warum 3D-Druck von Metall für EV-Batteriegehäuse?
Herkömmliche Verfahren wie Druckguss (HPDC), Blechstanzen und CNC-Bearbeitung haben sich zwar bei der Herstellung von Automobilkomponenten bewährt, stoßen aber bei der Entwicklung moderner Batteriegehäuse für Elektrofahrzeuge an ihre Grenzen, insbesondere was das Gewicht und die Komplexität des Wärmemanagements betrifft. Die additive Fertigung von Metallen bietet erhebliche Vorteile, die sie zu einer zunehmend attraktiven Option für Automobil-Strukturbauteile wie Batteriegehäuse:
Vorteile gegenüber traditionellen Methoden:
- Unerreichte Designfreiheit: AM befreit die Designer von den Zwängen der traditionellen Fertigung. Komplexe interne Merkmale, wie komplizierte Kühlkanäle, die den genauen Konturen der Batteriemodule folgen, können direkt in die Gehäusestruktur integriert werden. Dieses Maß an geometrischer Komplexität lässt sich mit Guss oder maschineller Bearbeitung oft nicht oder nur zu hohen Kosten erreichen.
- Beispiel: Entwicklung von konformen Kühlkanälen, die genau auf die wärmeerzeugenden Zonen im Akkupack abgestimmt sind.
- Topologie-Optimierung für Lightweighting: Mithilfe hochentwickelter Software-Algorithmen können die Konstrukteure die Gehäusestruktur optimieren, indem sie das Material nur dort platzieren, wo es benötigt wird, um bestimmten Belastungen standzuhalten. Das Ergebnis sind organisch anmutende, hocheffiziente Strukturen, die das Gewicht im Vergleich zu konventionell konstruierten Teilen deutlich reduzieren und direkt auf die Leichtbauweise EV Herausforderung.
- Teil Konsolidierung: Mehrere Komponenten, die traditionell separat hergestellt und dann zusammengebaut werden (z. B. Gehäusesockel, Kühlplatten, Halterungen, Schnittstellen), können möglicherweise neu entworfen und als eine einzige, integrierte Einheit gedruckt werden. Dies verkürzt die Montagezeit, eliminiert potenzielle Leckagepfade, vereinfacht die Lieferkette und verbessert häufig die strukturelle Integrität.
- Rapid Prototyping und Iteration: Die Erstellung von Prototypen mithilfe von AM ist wesentlich schneller und kostengünstiger als die Herstellung von Formen oder Gesenken für den Guss oder die Einrichtung komplexer Bearbeitungsvorgänge. Dies ermöglicht es den Ingenieuren, verschiedene Designs schnell zu testen, die thermische Leistung zu validieren und eine optimale Lösung zu finden, was die Entwicklungszyklen für Rapid Prototyping von EV-Teilen.
- Materialeffizienz: AM ist ein additives Verfahren, d. h. das Material wird schichtweise hinzugefügt, was zu weniger Materialabfall führt als bei subtraktiven Verfahren wie der CNC-Bearbeitung, bei der von einem festen Block ausgegangen und Material abgetragen wird. Die Wiederverwendung von Pulver ist zwar wichtig, aber das Verhältnis zwischen Anschaffung und Produktion kann deutlich besser sein.
- Fertigung auf Abruf: Digitale Entwürfe können weltweit an jedes fähige Metall-AM-System gesendet werden, was eine dezentralisierte Produktion ermöglicht und die Abhängigkeit von komplexen Lieferketten und Werkzeugbeständen verringert. Dies ist besonders wertvoll für die Produktion kleiner bis mittlerer Stückzahlen oder für Ersatzteile.
Die Vorteile zusammengefasst:
Merkmal | Nutzen für EV-Batteriegehäuse | Beschränkung der traditionellen Methode |
---|---|---|
Gestaltungsfreiheit | Integrierte komplexe Kühlung, optimierte Formen, konforme Merkmale | Beschränkungen bei Form und Werkzeug, Zugangsbeschränkungen bei der Bearbeitung |
Topologieoptimierung | Signifikante Gewichtsreduzierung (verbesserte Reichweite/Leistung) | Es ist schwierig, extremes Lightweighting effizient zu erreichen |
Teil Konsolidierung | Weniger Montageaufwand, weniger potenzielle Leckstellen, verbesserte Steifigkeit | Mehrere Teile müssen verbunden werden (Schweißen, Verbindungselemente, Dichtungen) |
Schnelles Prototyping | Schnellere Designvalidierung, geringere Entwicklungszeit und -kosten | Hohe Werkzeugkosten und lange Vorlaufzeiten für Prototypen |
Potenzial für Kosteneinsparungen | Geringere Kosten für komplexe Teile in kleinen Stückzahlen (kein Werkzeugbau) | Die Amortisation von Werkzeugen erfordert hohe Stückzahlen |
Verbessertes Wärmemanagement. | Effizientere Kühlsysteme direkt im Bauwerk | Häufig sind separate, weniger integrierte Kühlkomponenten erforderlich |
In Blätter exportieren
Erkundung von Vorteile von Metal AM für die Automobilindustrie Anwendungen zeigt ein deutliches Potenzial für die Überwindung der Grenzen konventioneller Verfahren auf, insbesondere wenn Komplexität, Gewicht und thermische Leistung von entscheidender Bedeutung sind, wie es bei EV-Batteriegehäusen der Fall ist. Unternehmen, die nach innovativen Lösungen suchen, vergleichen oft Additive Fertigung vs. Gießen oder Bearbeitung, um die beste Lösung für ihren spezifischen Bedarf an Volumen und Komplexität zu finden.
Empfohlene Aluminiumlegierungen und warum sie wichtig sind
Die Auswahl des richtigen Materials ist entscheidend für den Erfolg jeder technischen Anwendung, und 3D-gedruckte EV-Batteriegehäuse bilden da keine Ausnahme. Aluminiumlegierungen sind aufgrund ihrer ausgezeichneten Ausgewogenheit von geringer Dichte (geringes Gewicht), guter Wärmeleitfähigkeit, ausreichender Festigkeit und Korrosionsbeständigkeit die Spitzenreiter. Für die additive Fertigung von Metallen haben sich bestimmte Aluminiumlegierungen als besonders effektiv erwiesen. Met3dp nutzt seine fortschrittlichen Pulverproduktionskapazitäten, einschließlich der branchenführenden Technologien der Gaszerstäubung und des Plasma-Rotations-Elektroden-Prozesses (PREP), um die Lieferung von hochwertigen, kugelförmigen Aluminium-3D-Druck-Pulver optimiert für anspruchsvolle Anwendungen wie EV-Batteriegehäuse. Unser Fokus auf Pulvereigenschaften wie hohe Sphärizität und gute Fließfähigkeit führt direkt zu dichteren, zuverlässigeren gedruckten Teilen.
Hier sind die besten Empfehlungen für diese Anwendung:
1. AlSi10Mg:
- Beschreibung: Eine silizium- und magnesiumhaltige Aluminiumlegierung, die traditionell beim Gießen verwendet wird. Sie lässt sich gut in Pulverbettschmelzverfahren verarbeiten.
- Wichtige Eigenschaften:
- Hervorragende Bedruckbarkeit und Verarbeitbarkeit im Laser Powder Bed Fusion (LPBF).
- Gute Festigkeit und Härte, geeignet für Strukturteile.
- Gute Wärmeleitfähigkeit.
- Kann wärmebehandelt werden (z. B. im Zustand T6), um die Festigkeit und Härte deutlich zu verbessern.
- Warum dies für Batteriegehäuse wichtig ist: Bietet eine robuste Kombination aus mechanischen Eigenschaften, guter Wärmeleistung und zuverlässigen Druckeigenschaften. Durch seine gussähnliche Beschaffenheit ist es den Ingenieuren vertraut. Durch die Möglichkeit der Wärmebehandlung können die Eigenschaften nach dem Druck angepasst werden. Siehe unser komplettes Angebot an Metallpulver.
- Erwägungen: Die Festigkeit ist im Allgemeinen geringer als bei den hochfesten Legierungen der Serie 7xxx.
2. A6061 (erfordert oft spezielle Parameter oder Nachbearbeitung):
- Beschreibung: Eine weit verbreitete Aluminium-Knetlegierung, die für ihre Vielseitigkeit, Festigkeit, Schweißbarkeit und Korrosionsbeständigkeit bekannt ist. Das Bedrucken von 6061 kann aufgrund seiner Erstarrungseigenschaften schwieriger sein als das von AlSi10Mg, ist aber mit optimierten Parametern und möglicherweise speziellen Maschinen möglich.
- Wichtige Eigenschaften:
- Gute mechanische Festigkeit und Zähigkeit.
- Ausgezeichnete Korrosionsbeständigkeit.
- Gute Wärmeleitfähigkeit.
- Kann für eine deutlich höhere Festigkeit wärmebehandelt werden (z. B. T6).
- Gute Schweißbarkeit (wichtig, wenn nach der Herstellung Verbindungen erforderlich sind).
- Warum dies für Batteriegehäuse wichtig ist: Seine Allround-Eigenschaften, insbesondere die Korrosionsbeständigkeit und die Schweißbarkeit nach der Bearbeitung, machen es attraktiv. Wenn T6-Eigenschaften erforderlich sind, bietet es eine höhere Festigkeit als AlSi10Mg T6 typischerweise in AM erreicht.
- Erwägungen: Kann während des Drucks zu Heißrissen neigen; erfordert eine sorgfältige Kontrolle der Parameter und oft spezifische Wärmebehandlungen, um die gewünschten Eigenschaften zu erreichen. Erfordert oft die Zusammenarbeit mit erfahrenen AM-Anbietern wie Met3dp.
3. A7075 (Hochfeste Anwendungen):
- Beschreibung: Eine hochfeste Aluminium-Zink-Legierung, die typischerweise in der Luft- und Raumfahrt und bei Hochleistungsanwendungen verwendet wird, bei denen das Verhältnis von Festigkeit zu Gewicht von größter Bedeutung ist. Das Drucken von 7075 stellt eine Herausforderung dar, bietet aber erstklassige mechanische Eigenschaften.
- Wichtige Eigenschaften:
- Sehr hohes Festigkeits-Gewichts-Verhältnis, eines der höchsten bei Aluminiumlegierungen.
- Gute Ermüdungsfestigkeit.
- Kann zur Erzielung der höchsten Festigkeit wärmebehandelt werden (z. B. T6, T73).
- Warum dies für Batteriegehäuse wichtig ist: Ideal für Anwendungen, bei denen maximales Leichtgewicht ohne Kompromisse bei der Festigkeit gefragt ist, wie z. B. bei Hochleistungs-EVs oder Motorsport-Batteriegehäusen. Ermöglicht dünnere Wände und eine aggressivere Topologieoptimierung.
- Erwägungen: Aufgrund der Anfälligkeit für Erstarrungsrisse und Eigenspannungen ist es schwieriger, zuverlässig zu drucken als AlSi10Mg. Die Korrosionsbeständigkeit ist im Allgemeinen geringer als bei 6061, was möglicherweise Schutzbeschichtungen erforderlich macht. Erfordert erhebliche Fachkenntnisse bei der Entwicklung von Prozessparametern und der Wärmebehandlung nach dem Prozess.
Vergleich der Materialeigenschaften (typische Werte für AM - können je nach Parametern/Nachbearbeitung erheblich variieren):
Eigentum | AlSi10Mg (Wie-Bau / T6) | A6061 (T6) | A7075 (T6 / T73) | Einheit | Wichtigkeit für das Batteriegehäuse |
---|---|---|---|---|---|
Dichte | ~2.67 | ~2.70 | ~2.81 | g/cm³ | Weniger ist mehr (Lightweighting) |
Zugfestigkeit | ~290 / ~330+ MPa | ~270 - 310+ MPa | ~500 - 570+ MPa | MPa | Strukturelle Integrität, Crash-Sicherheit |
Streckgrenze | ~180 / ~230+ MPa | ~240 - 275+ MPa | ~450 - 500+ MPa | MPa | Widerstandsfähigkeit gegen dauerhafte Verformung |
Dehnung beim Bruch | ~6-10% / ~3-6% | ~8-12% | ~5-10% | % | Duktilität, Schlagzähigkeit |
Wärmeleitfähigkeit | ~130-150 | ~150-170 | ~130-150 | W/(m-K) | Wärmeableitung (Thermal Mgmt.) |
Druckbarkeit | Ausgezeichnet | Mäßig (Bedarf an Kontrolle) | Herausfordernd | – | Herstellbarkeit, Verlässlichkeit |
Korrosionsbeständigkeit | Gut | Ausgezeichnet | Angemessen (Schutzbedürftig) | – | Langlebigkeit, Umweltverträglichkeit |
In Blätter exportieren
Warum Met3dp-Pulver wichtig sind:
Die theoretischen Eigenschaften einer Legierung können nur erreicht werden, wenn das Ausgangsmaterial - das Metallpulver - von außergewöhnlicher Qualität ist. Met3dp nutzt fortschrittliche Gaszerstäubung und PREP (Plasma-Rotations-Elektroden-Verfahren) Technologien. Unsere einzigartigen Düsen- und Gasflussdesigns bei der Gaszerstäubung erzeugen Pulver mit:
- Hohe Sphärizität: Gewährleistet eine gute Fließfähigkeit des Pulvers und eine dichte Packung im Pulverbett, wodurch Hohlräume und Porosität im fertigen Teil minimiert werden.
- Niedriger Satellitengehalt: Verringert Unregelmäßigkeiten, was zu einem gleichmäßigeren Schmelzen und Erstarren führt.
- Kontrollierte Partikelgrößenverteilung (PSD): Optimiert für bestimmte AM-Prozesse (LPBF, EBM), um ein konsistentes Schichtabscheidungs- und Schmelzverhalten zu gewährleisten.
- Hohe Reinheit: Minimierung von Verunreinigungen, die die mechanischen Eigenschaften beeinträchtigen können.
Durch die Kontrolle dieser Pulvereigenschaften bietet Met3dp Hochleistungs-Aluminiumlegierungen die es unseren Kunden ermöglichen, zuverlässig dichte, hochwertige EV-Batteriegehäuse mit überlegenen mechanischen Eigenschaften und Leistungen zu drucken, indem sie die Vorteile von 3D-Druck von Metall. Die Wahl des richtigen Pulvers ist die Grundlage für eine erfolgreiche additive Fertigung.
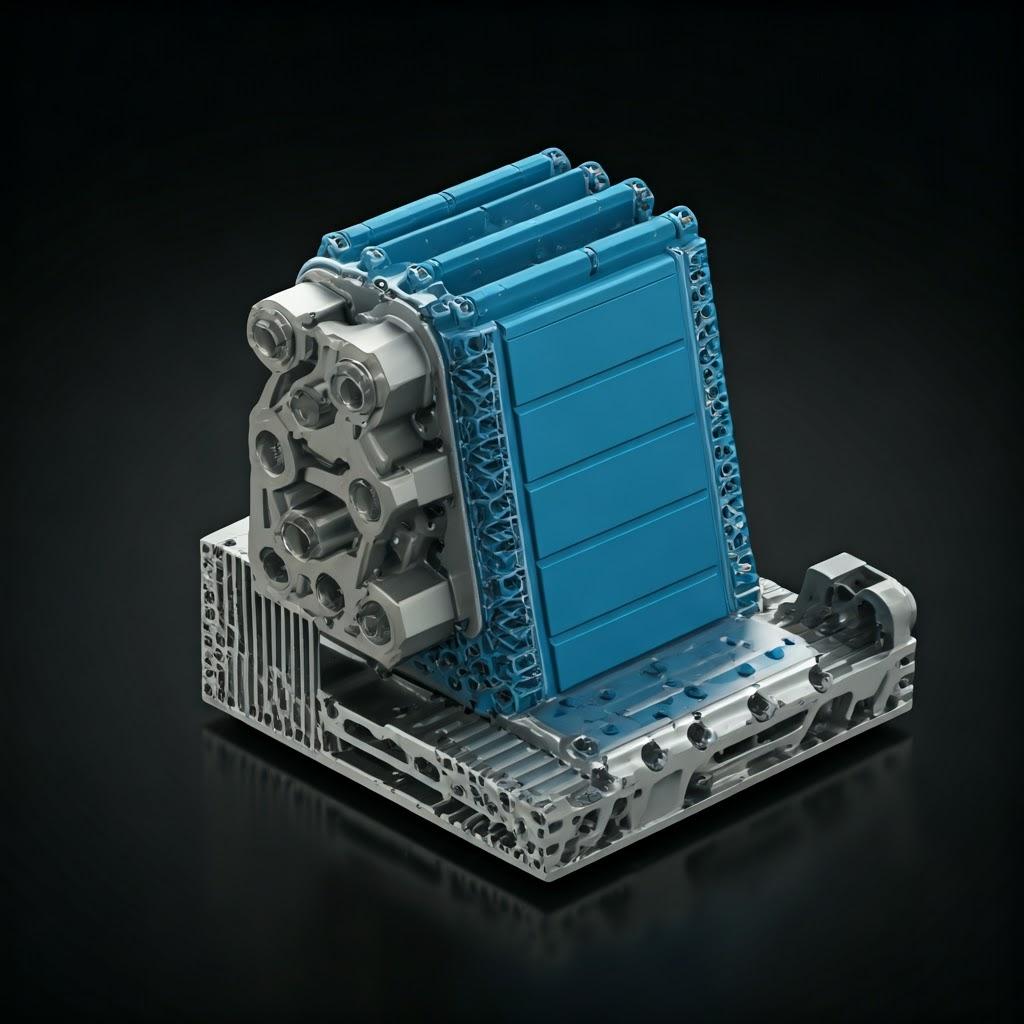
Designüberlegungen zur additiven Fertigung (DfAM) von Batteriegehäusen
Die einfache Nachbildung eines Designs, das für das Gießen oder die maschinelle Bearbeitung vorgesehen ist, scheitert oft daran, das wahre Potenzial der additiven Fertigung von Metall zu nutzen. Um signifikante Vorteile bei der Gewichtsreduzierung, der thermischen Leistung und der funktionalen Integration von EV-Batteriegehäusen zu erzielen, müssen die Konstrukteure folgende Punkte berücksichtigen Design für additive Fertigung (DfAM) Prinzipien. Dabei wird die Geometrie des Teils von Grund auf neu überdacht, wobei der schichtweise Aufbau berücksichtigt wird.
Die wichtigsten DfAM-Prinzipien für EV-Batteriegehäuse:
- Topologie-Optimierung: Dies ist wohl die wirkungsvollste DfAM-Technik für das Lightweighting.
- Prozess: Mithilfe einer speziellen Software definieren die Ingenieure die funktionalen Anforderungen des Teils (Lastfälle, Montagepunkte, Sperrzonen, Leistungsziele wie Steifigkeit). Die Software entfernt dann iterativ Material aus Bereichen, in denen es nicht wesentlich zur Leistung beiträgt, und hinterlässt eine optimierte, oft organisch anmutende Struktur.
- Nutzen: Erzielt eine größtmögliche Gewichtsreduzierung bei gleichzeitiger Erfüllung oder Übererfüllung der strukturellen Leistungsanforderungen. Ideal für DfAM automotive Komponenten, bei denen das Gewicht entscheidend ist.
- Beispiel: Verwandlung einer massiven, blockigen Gehäuseklammer in eine Skelettstruktur, die Lasten effizient überträgt.
- Gitterstrukturen und Ausfachung: Anstelle von festem Material können die Innenräume mit technischen Gitterstrukturen gefüllt werden.
- Typen: Auf Streben basierende Gitter, TPMS (Triply Periodic Minimal Surfaces) Kreisel, usw.
- Vorteile: Drastische Gewichtsreduzierung, maßgeschneiderte Energieabsorptionseigenschaften (entscheidend für die Crashsicherheit), vergrößerte Oberfläche (vorteilhaft für passive Kühlung oder Integration mit aktiven Kühlsystemen), Potenzial für Schwingungsdämpfung.
- Anwendung: Ausfüllen von unkritischen Bauvolumen oder Schaffung leichter Kernstrukturen innerhalb der Gehäusewände. Erkunden Sie Metallgitterstrukturen bietet neue Möglichkeiten für multifunktionales Design.
- Integrierte und konforme Kühlkanäle: AM ermöglicht die Schaffung komplexer interner Kühlkanäle, die den Konturen der wärmeerzeugenden Komponenten (Batteriemodule) genau folgen.
- Vorteil: Weitaus effektivere Wärmeübertragung im Vergleich zu herkömmlichen Kühlplatten oder einfachen gebohrten Kanälen. Verbessert die Leistung, Langlebigkeit und Sicherheit der Batterie.
- Entwurf: Erfordert eine sorgfältige Berücksichtigung der Flüssigkeitsströmung (CFD-Analyse), des Kanaldurchmessers, der Oberflächenrauhigkeit (wie gedruckt oder nachbearbeitet) und der Sicherstellung, dass die Kanäle selbsttragend sind oder so konstruiert sind, dass eine Entfernung der Stützen möglich ist. 3D-Druck mit konformaler Kühlung ist ein großer Vorteil für das Wärmemanagement.
- Integration von Funktionen und Konsolidierung von Teilen: AM ermöglicht es, mehrere Teile zu einem einzigen, komplexen Bauteil zu verschmelzen.
- Beispiele: Integration von Halterungen, Montagevorsprüngen, Flüssigkeitsanschlüssen, Dichtungsnuten oder Kühlkörpern direkt in die Hauptgehäusestruktur.
- Vorteile: Reduziert die Anzahl der Teile, eliminiert Montageschritte und die damit verbundenen Toleranzen/Kosten, beseitigt potenzielle Leckagepfade (z. B. Dichtungen zwischen montierten Teilen), vereinfacht die Lieferkette und erhöht häufig die Gesamtsteifigkeit und Robustheit.
- Design für Selbstunterstützung und Minimierung der Unterstützung: Stützstrukturen sind bei Metall-PBF-Prozessen oft notwendig, um das Teil auf der Bauplatte zu verankern und überhängende Merkmale zu stützen. Sie erhöhen jedoch die Materialkosten und die Druckzeit und erfordern einen hohen Aufwand bei der Entfernung, was die Oberflächengüte beeinträchtigen kann.
- Strategie: Konstruieren Sie Features mit selbsttragenden Winkeln (typischerweise >45 Grad von der horizontalen Ebene für LPBF). Richten Sie das Teil strategisch auf der Bauplatte aus, um den Bedarf an Stützen zu minimieren, insbesondere in schwer zugänglichen internen Bereichen wie Kühlkanälen. Ziehen Sie Opfer-Features in Betracht, die kritische Bereiche unterstützen, aber später leicht weggearbeitet werden können. Minimierung der Unterstützung AM ist der Schlüssel zum kostengünstigen Drucken.
- Wanddicke und Größe der Merkmale: Bei AM-Prozessen gibt es Beschränkungen hinsichtlich der minimalen druckbaren Wandstärke und der Auflösung der Merkmale (abhängig von Maschine, Material und Parametern).
- Erwägung: Stellen Sie sicher, dass die Konstruktionen diese Grenzen einhalten. Dünne Wände sind der Schlüssel zum Leichtbau, müssen aber die strukturelle Integrität erhalten und zuverlässig gedruckt werden. Integrieren Sie Verrundungen und glatte Übergänge, um Spannungskonzentrationen zu reduzieren.
DfAM Workflow Zusammenfassung:
- Definieren Sie Anforderungen: Lasten, thermische Zielvorgaben, Schnittstellen, Zwänge.
- Konzeptioneller Entwurf (AM-fokussiert): Erforschen Sie Topologieoptimierung, Gitter, Merkmalsintegration.
- Detaillierter Entwurf und Simulation: Verfeinerung der Geometrie, Durchführung von FEA- (Struktur-) und CFD-Analysen (Wärme-/Flüssigkeitsanalyse). Simulation des Bauprozesses zur Vorhersage möglicher Probleme (Spannung, Verformung).
- Optimieren für den Druck: Endgültige Anpassungen für Ausrichtung, Unterstützungsstrategie, Mindestmerkmale.
Mit einer DfAM-Mentalität können Ingenieure das EV-Batteriegehäuse von einem einfachen Behälter in eine hoch optimierte, multifunktionale Systemkomponente umwandeln, die die Möglichkeiten fortschrittlicher Technologien voll ausschöpft. Druckverfahren wie sie von Met3dp verwendet werden.
Erreichbare Toleranzen, Oberflächengüte und Maßgenauigkeit
Metall-AM bietet zwar eine unglaubliche Designfreiheit, aber es ist wichtig, die erreichbaren Präzisionsniveaus zu kennen. Ingenieure und Beschaffungsmanager müssen realistische Erwartungen in Bezug auf Toleranzen, Oberflächengüte und allgemeine Maßgenauigkeit für 3D-gedruckte EV-Batteriegehäuse haben. Diese Faktoren sind entscheidend für die ordnungsgemäße Montage, Abdichtung und Funktionalität.
Toleranzen:
- Typische Reichweiten: Bei Metall-Powder-Bed-Fusion-Verfahren (PBF) wie Laser-PBF (LPBF/SLM) und Elektronenstrahl-PBF (EB-PBF) liegen die typischen Maßtoleranzen bei der Herstellung oft im Bereich von ±0,1 mm bis ±0,3 mm oder ±0,1% bis ±0,2% der Abmessung, je nachdem, welcher Wert größer ist. Dies kann jedoch erheblich variieren.
- Faktoren, die die Toleranzen beeinflussen:
- Kalibrierung und Zustand der Maschine: Regelmäßige Kalibrierung und Wartung sind von entscheidender Bedeutung. Met3dp unterstreicht die Genauigkeit und Zuverlässigkeit seiner Drucksysteme für unternehmenskritische Teile.
- Prozessparameter: Schichtdicke, Laser-/Strahlleistung, Scangeschwindigkeit und Schraffurstrategie spielen alle eine Rolle.
- Materialeigenschaften: Die verschiedenen Legierungen weisen ein unterschiedliches Schrumpfungs- und Wärmeverhalten beim Schmelzen und Erstarren auf.
- Geometrie und Größe des Teils: Größere Teile und komplexe Geometrien sind anfälliger für thermische Verformung und Abweichung. Durch den Aufbau von Eigenspannungen können sich Teile verziehen.
- Orientierung und Unterstützung aufbauen: Wie das Teil positioniert und unterstützt wird, beeinflusst die Genauigkeit.
- Nachbearbeiten: Wärmebehandlungen zum Spannungsabbau können geringfügige Maßänderungen bewirken. Durch die maschinelle Bearbeitung werden wesentlich engere Toleranzen für bestimmte Merkmale erreicht.
- Erzielung engerer Toleranzen: Bei kritischen Merkmalen (z. B. Passflächen, Lagerschnittstellen, Dichtungsnuten) können durch CNC-Nachbearbeitung Toleranzen von ±0,01 mm bis ±0,05 mm erreicht werden. Oft ist es am kosteneffizientesten, eine endkonturnahe Form zu drucken und nur die kritischen Schnittstellen zu bearbeiten.
Oberflächengüte (Rauhigkeit):
- Oberflächenrauhigkeit (Ra) im Ist-Zustand: Die Oberflächenbeschaffenheit von gedruckten AM-Metallteilen ist von Natur aus rauer als maschinell bearbeitete Oberflächen.
- Typische Werte: Die Ra-Werte liegen oft zwischen 6 µm und 25 µm, je nach Verfahren (LPBF ist im Allgemeinen glatter als EB-PBF), Material, Ausrichtung (nach oben gerichtete vs. nach unten gerichtete/gestützte Oberflächen) und Parametern.
- Auswirkungen: Beeinflusst die Wirksamkeit der Abdichtung, den Flüssigkeitsstrom in den Kanälen, die Ermüdungslebensdauer und die Ästhetik.
- Verbesserung der Oberflächengüte: In der Regel ist eine Nachbearbeitung erforderlich, um glattere Oberflächen zu erzielen.
- Strahlen (Sand, Perlen): Sorgt für ein gleichmäßiges, mattes Finish und entfernt losen Puder (Ra oft 5-15µm).
- Taumeln/Gleitschleifen: Glättet Oberflächen und Kanten (Ra kann 1-5µm erreichen).
- Bearbeitungen/Schleifen: Erzielt sehr glatte Oberflächen, vergleichbar mit der traditionellen Fertigung (Ra < 1µm möglich).
- Polieren: Für spiegelähnliche Oberflächen, die oft für bestimmte Anwendungen benötigt werden.
- Abrasive Fließbearbeitung (AFM): Kann zum Glätten interner Kanäle verwendet werden.
- Entwurfsüberlegungen: Geben Sie die erforderlichen Oberflächenbehandlungen nur dort an, wo sie funktionell notwendig sind (z. B. Dichtungsflächen, Schnittstellen), um die Kosten zu kontrollieren, da eine umfangreiche Oberflächenbehandlung erhebliche Kosten verursacht.
Verwaltung der Maßgenauigkeit:
- Simulation: Die Simulation des Bauprozesses kann Verzerrungen vorhersagen und eine Kompensation in der ursprünglichen Entwurfsdatei ermöglichen.
- Qualitätskontrolle: Die Prüfung nach dem Druck mittels CMM (Coordinate Measuring Machines) oder 3D-Scanning ist unerlässlich, um die Maßgenauigkeit gegenüber dem CAD-Modell und den Spezifikationen zu überprüfen.
- Kollaboration: Die enge Zusammenarbeit mit einem erfahrenen AM-Anbieter wie Met3dp, der die Prozessmöglichkeiten und das Materialverhalten kennt, ist entscheidend für das Erreichen der gewünschten Maßhaltigkeit EV-Teile.
Zusammenfassende Tabelle: Erwartungen an die Präzision
Parameter | As-Built Typischer Bereich | Erreichbar mit Post-Processing | Wichtige Überlegungen |
---|---|---|---|
Toleranz | ±0,1 bis ±0,3 mm / ±0,1-0,2% | Bis zu ±0,01 - 0,05 mm (maschinelle Bearbeitung) | Teilegröße, Komplexität, Material, kritische Merkmale |
Oberflächengüte (Ra) | 6µm - 25µm+ | < 1µm - 15µm (verschiedene Methoden) | Abdichtung, Ermüdung, Durchfluss, Ästhetik, Kosten |
In Blätter exportieren
Das Verständnis dieser Parameter ermöglicht realistische Design-Spezifikationen und informiert über die notwendigen Nachbearbeitungsschritte, um sicherzustellen, dass das endgültige EV-Batteriegehäuse alle funktionalen Anforderungen erfüllt für Additive Präzisionsfertigung.
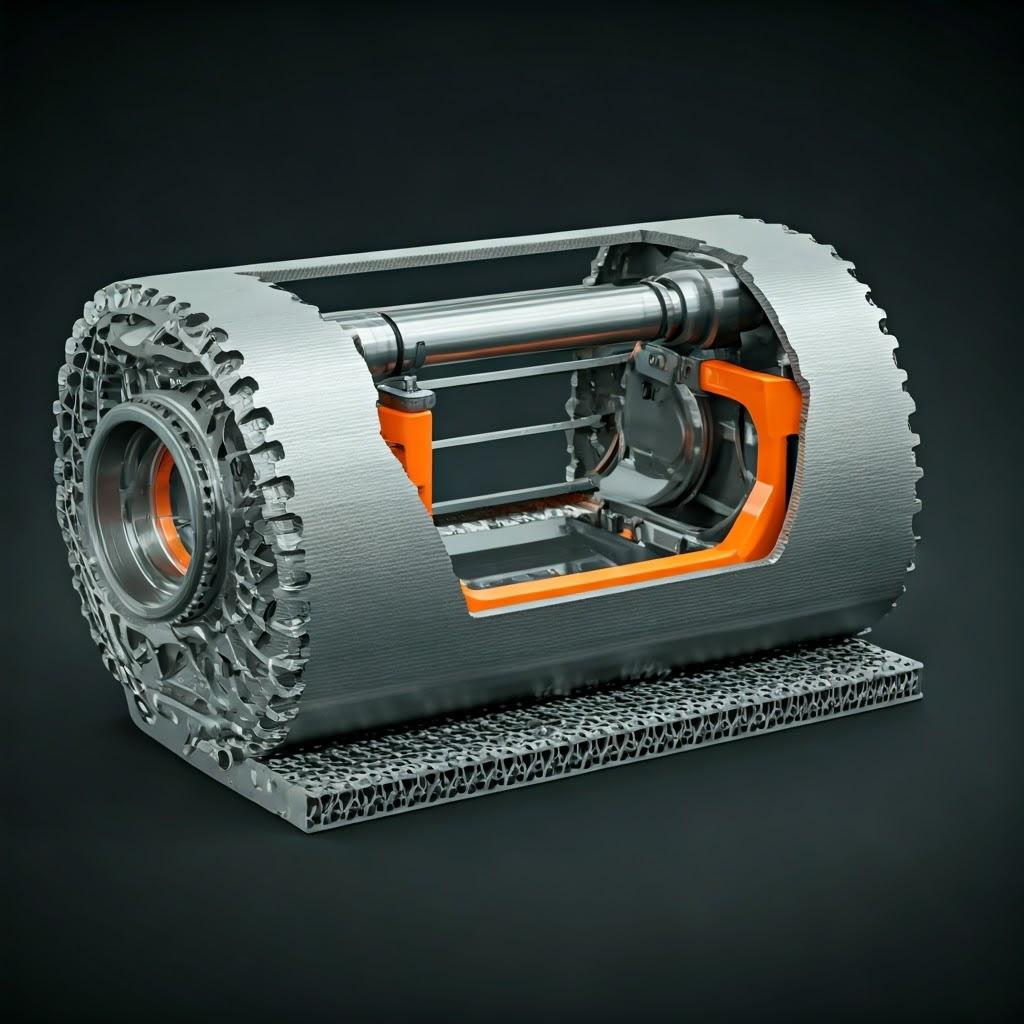
Nachbearbeitungsanforderungen für AM-Batteriegehäuse aus Metall
Ein 3D-gedrucktes Metallteil ist nach der Entnahme aus der Baukammer selten bereit für seine endgültige Anwendung. Dies gilt insbesondere für anspruchsvolle Komponenten wie EV-Batteriegehäuse. Eine Reihe von Nachbearbeitung von Metall-3D-Druck In der Regel sind mehrere Schritte erforderlich, um die erforderlichen Materialeigenschaften, die Maßgenauigkeit, die Oberflächeneigenschaften und die Gesamtqualität zu erreichen.
Gemeinsame Nachbearbeitungsschritte:
- Stressabbau / Wärmebehandlung:
- Zweck: Entlastung von inneren Spannungen, die sich während der schnellen Erwärmungs- und Abkühlungszyklen des Druckprozesses aufbauen, um Verformungen oder Risse zu vermeiden und die gewünschte endgültige Materialmikrostruktur und mechanischen Eigenschaften (z. B. Festigkeit, Härte, Duktilität) zu erreichen.
- Methode: Die Teile werden (oft noch auf der Bauplatte) in einem Ofen mit kontrollierter Atmosphäre nach bestimmten, auf die Legierung zugeschnittenen Temperaturprofilen (Zeit, Temperatur, Abkühlgeschwindigkeit) erhitzt (z. B. T6-Alterung für Aluminium Wärmebehandlung T6 AM). Dies ist entscheidend für Legierungen wie AlSi10Mg, A6061 und A7075.
- Wichtigkeit: Absolut unerlässlich für die strukturelle Integrität und die vorhersehbare Leistung.
- Entfernen des Teils von der Bauplatte:
- Methode: Dies geschieht in der Regel durch Drahterodieren (Electrical Discharge Machining), Sägen oder Zerspanen.
- Erwägung: Um das Teil nicht zu beschädigen, muss es vorsichtig entfernt werden.
- Entfernung der Stützstruktur:
- Zweck: So entfernen Sie die temporären Strukturen, die während des Bauprozesses verwendet wurden.
- Methoden: Dies kann durch manuelles Brechen (bei leicht zugänglichen Stützen), Schneidwerkzeuge, CNC-Bearbeitung oder manchmal auch durch Drahterodieren geschehen. Unterstützung beim 3D-Druck von Metall kann arbeitsintensiv sein, insbesondere bei komplexen Innengeometrien.
- Herausforderungen: Der Zugang zu internen Stützen (z. B. innerhalb von Kühlkanälen) kann schwierig sein und erfordert möglicherweise spezielle Techniken oder DfAM-Überlegungen (Entwurf für die Entfernung). Verbleibende Markierungen ("Zeugenmarkierungen") müssen möglicherweise nachbearbeitet werden.
- CNC-Bearbeitung:
- Zweck: Zur Erzielung enger Toleranzen bei kritischen Merkmalen, zur Schaffung ebener Dichtungsflächen, zum Bohren/Gewindeschneiden präziser Löcher und zur Verbesserung der Oberflächengüte in bestimmten Bereichen.
- Anwendung: Unverzichtbar für Passflächen, Montagepunkte, Dichtungsnuten, Lagersitze und alle Maße, die eine höhere Präzision erfordern als im eingebauten Zustand. CNC-Bearbeitung von AM-Teilen ist ein Standardverfahren für funktionale Komponenten.
- Oberflächenveredelung und Reinigung:
- Zweck: Zur Entfernung von losem Pulver, zur Verbesserung der Oberflächenrauhigkeit, zur Verbesserung der Ästhetik oder zur Vorbereitung der Oberfläche für die Beschichtung.
- Methoden:
- Strahlen (Sand/Perlen): Erzeugt ein gleichmäßiges, mattes Finish.
- Taumeln/Gleitschleifen: Glättet Oberflächen und Kanten.
- Polieren: Für sehr glatte oder reflektierende Oberflächen.
- Abrasive Fließbearbeitung (AFM) / Strangpresshonen: Zum Glätten von inneren Kanälen, indem abrasive Medien durch sie hindurchgeleitet werden.
- Reinigung: Ultraschallreinigung oder chemisches Waschen, um eingeschlossene Pulverrückstände zu entfernen.
- Wichtigkeit: Entscheidend für die Abdichtung, den Flüssigkeitsfluss, die Lebensdauer und die Vermeidung von Pulververschmutzung.
- Beschichtung / Oberflächenbehandlung:
- Zweck: Zur Erhöhung der Korrosionsbeständigkeit (insbesondere bei Legierungen wie A7075), zur Verbesserung der Verschleißfestigkeit, zur elektrischen Isolierung oder zur Veränderung der thermischen Eigenschaften.
- Methoden: Eloxieren (für Aluminium), Lackieren, Pulverbeschichten, chemische Umwandlungsbeschichtungen (z. B. Chromatierung), Galvanisieren. Oberflächenbehandlung 3D-gedrucktes Metall fügt Schutzschichten hinzu.
- Inspektion und Qualitätskontrolle (QC):
- Zweck: Überprüfung, ob das fertige Teil alle Spezifikationen erfüllt.
- Methoden:
- Prüfung der Abmessungen: CMM, 3D-Scannen.
- Prüfung der Materialeigenschaften: Zugversuche an repräsentativen Proben.
- Zerstörungsfreie Prüfung (NDT): CT-Scannen (zur Untersuchung der inneren Merkmale und zur Feststellung von Porosität), Farbeindringprüfung, Ultraschallprüfung.
- Dichtheitsprüfung: Entscheidend für Batteriegehäuse zur Gewährleistung der Dichtheit (Druckabfall, Helium-Lecktest).
- Wichtigkeit: Gewährleistet Sicherheit, Zuverlässigkeit und Leistung. Robust Qualitätskontrolle additive Fertigung Protokolle sind für Kfz-Anwendungen unerlässlich.
Der Umfang und die Art der Nachbearbeitung hängen stark von den spezifischen Anwendungsanforderungen, der Materialauswahl und der Komplexität des Designs ab. Es ist wichtig, diese Schritte in die Gesamtkosten- und Vorlaufzeitberechnung einzubeziehen, wenn man Metall-AM für EV-Batteriegehäuse in Betracht zieht. Die Zusammenarbeit mit einem Anbieter wie Met3dp, der umfassende Lösungen, möglicherweise einschließlich Nachbearbeitung, anbietet oder ein Netzwerk qualifizierter Partner verwaltet, rationalisiert diesen Arbeitsablauf. Mehr erfahren über uns und unsere Fähigkeiten.
Allgemeine Herausforderungen beim 3D-Druck von EV-Batteriegehäusen und Lösungen
Obwohl Metall-AM enorme Vorteile bietet, ist der Druck großer, komplexer Komponenten wie EV-Batteriegehäuse nicht ohne Herausforderungen. Das Bewusstsein für diese potenziellen Probleme und die Umsetzung geeigneter Abhilfestrategien sind der Schlüssel zu erfolgreichen Ergebnissen.
1. Verformung und Eigenspannung:
- Herausforderung: Die hohen thermischen Gradienten, die den PBF-Prozessen eigen sind, können dazu führen, dass sich innerhalb des Teils und an der Schnittstelle zur Bauplatte erhebliche innere Spannungen aufbauen. Dies kann zu Verformungen während des Aufbaus, Verzug nach der Entnahme aus der Platte oder sogar zu Rissen führen. Eigenspannungsminderung AM ist ein wichtiger Schwerpunkt.
- Lösungen:
- Prozess-Simulation: Vorhersage von Spannungsakkumulation und Verformung, die eine Kompensation des Designs oder optimierte Ausrichtungs- und Stützstrategien ermöglicht.
- Optimierte Build-Strategie: Sorgfältige Auswahl der Bauausrichtung, robuste Stützstrukturen zur Verankerung des Teils und zum Wärmemanagement.
- Optimierung der Parameter: Feinabstimmung von Laser-/Strahlleistung, Scangeschwindigkeit und Schichtdicke.
- Build Plate Heating: Die Aufrechterhaltung einer erhöhten Temperatur kann thermische Gradienten reduzieren.
- Obligatorischer Stressabbau: Die Wärmebehandlung nach der Fertigung ist von entscheidender Bedeutung und wird häufig vor der Entnahme des Teils aus der Bauplatte durchgeführt.
2. Entfernen von Stützen aus komplexen internen Geometrien:
- Herausforderung: Integrierte Merkmale wie komplexe Kühlkanäle sind zwar ein entscheidender Vorteil von AM, machen aber die Entfernung von Trägern extrem schwierig oder unmöglich, wenn sie nicht korrekt gestaltet sind. Eingeschlossenes Pulver oder Reste von Trägern beeinträchtigen die Funktionalität (Durchfluss, Wärmeübertragung) und bergen das Risiko einer Kontamination. Entfernung der internen Stütze AM erfordert eine sorgfältige Planung.
- Lösungen:
- DfAM für Barrierefreiheit: Entwerfen Sie Rinnen mit Zugangspunkten für Werkzeuge oder Spülmittel. Optimieren Sie Rinnenverläufe und Querschnitte so, dass sie möglichst selbsttragend sind.
- Spezialisierte Entfernungstechniken: Abrasive Fließbearbeitung (AFM), chemisches Ätzen (bei Aluminiumträgern weniger üblich), Hochdruckspülung.
- Post-Print-Bearbeitung: Konstruieren Sie die Teile so, dass die inneren Merkmale zugänglich sind und bei Bedarf maschinell bearbeitet werden können.
- Sorgfältige Inspektion: Verwenden Sie Methoden wie Endoskopie oder CT-Scans, um die Sauberkeit der Kanäle zu überprüfen.
3. Porosität:
- Herausforderung: Im gedruckten Material können sich kleine Hohlräume oder Poren aufgrund von eingeschlossenem Gas oder unvollständiger Verschmelzung zwischen den Schichten bilden. Poren können die mechanischen Eigenschaften (insbesondere die Ermüdungsfestigkeit) erheblich verschlechtern und potenziell Leckagepfade schaffen.
- Lösungen:
- Hochwertiges Pulver: Die Verwendung von Pulver mit hoher Sphärizität, geringer interner Gasporosität und kontrollierter Partikelgrößenverteilung, wie das hochwertige Metallpulver das von Met3dp mit fortschrittlicher Zerstäubung hergestellt wird, ist von grundlegender Bedeutung. Pulver minderer Qualität ist eine der Hauptursachen für Porosität.
- Optimierte Prozessparameter: Gewährleistung einer ausreichenden Energiedichte für ein vollständiges Schmelzen und eines angemessenen Schutzgasstroms (in LPBF), um Prozessnebenprodukte zu entfernen.
- Heiß-Isostatisches Pressen (HIP): Ein Nachbearbeitungsschritt mit hoher Temperatur und hohem Druck, der die inneren Poren wirksam schließen kann und so die Dichte und die mechanischen Eigenschaften deutlich verbessert. Wird häufig für kritische Anwendungen verwendet. Porositätsreduzierung im Metalldruck ist der Schlüssel für Strukturteile.
4. Erreichen der Dichtheit:
- Herausforderung: Batteriegehäuse erfordern eine hervorragende Abdichtung (z. B. IP67 oder höher), um die Zellen vor Umwelteinflüssen zu schützen. Um dies mit AM zu erreichen, müssen Design, Oberflächenbeschaffenheit und mögliche Porosität sorgfältig berücksichtigt werden.
- Lösungen:
- DfAM für die Versiegelung: Gut definierte Dichtungsnuten für Standard-O-Ringe oder -Dichtungen vorsehen. Achten Sie auf eine ausreichende Wandstärke.
- Kontrolle der Oberflächengüte: Bearbeitung der Dichtungsflächen, um die erforderliche Glätte und Ebenheit zu erreichen.
- Kontrolle der Porosität: Minimierung der Porosität durch Optimierung der Pulverqualität und der Parameter, möglicherweise unter Verwendung von HIP.
- Imprägnierung/Versiegelung: In einigen Fällen kann eine Vakuumimprägnierung mit Dichtungsharzen verbleibende Mikroporen schließen (die Verwendung hängt von der Kompatibilität der Anwendung ab).
- Strenge Dichtheitsprüfungen: Implementierung robuster Lecktestprotokolle (z. B. Druckabfall, Tracergas) als Teil des QC-Prozesses. Sicherstellung lecksicherer 3D-Druck ist entscheidend.
5. Verwaltung großer Gebäudegrößen:
- Herausforderung: Bei Batteriegehäusen kann es sich um große Bauteile handeln, die das Bauvolumen herkömmlicher Metall-AM-Maschinen übersteigen können.
- Lösungen:
- Großformatdrucker: Nutzen Sie Maschinen mit größeren Bauumfängen, die speziell für große Bauteile entwickelt wurden. Met3dp bietet Drucker mit branchenführendes Druckvolumen.
- Segmentierung: Entwerfen Sie das Gehäuse in mehreren Abschnitten, die separat gedruckt und dann zusammengefügt werden können (z. B. durch Schweißen - dies erfordert die Verwendung einer schweißbaren Legierung wie A6061 und ein sorgfältiges Verbindungsdesign).
- Hybride Fertigung: Kombinieren Sie AM für komplexe Teile mit traditioneller Fertigung für einfachere, größere Elemente.
6. Kosten-Wirksamkeit im Vergleich zu traditionellen Methoden:
- Herausforderung: Zwar entfallen bei AM die Werkzeugkosten, doch können die Kosten pro Teil (bedingt durch Material, Maschinenzeit und Nachbearbeitung) höher sein als bei traditionellen Verfahren wie dem Gießen, insbesondere bei hohen Produktionsmengen.
- Lösungen:
- Komplexität ausnutzen: Konzentrieren Sie sich bei AM auf Konstruktionen, bei denen der Mehrwert (geringes Gewicht, integrierte Funktionen, Leistung) die Kosten rechtfertigt, insbesondere bei komplexen Teilen, bei denen der herkömmliche Werkzeugbau extrem teuer wäre.
- Entwurf optimieren (DfAM): Minimieren Sie den Materialverbrauch durch Topologieoptimierung, reduzieren Sie die Bauzeit durch eine Orientierungs- und Stützstrategie und entwerfen Sie ein effizientes Post-Processing.
- Zielanwendungen: Ideal für Prototypen, kleine bis mittlere Serien, hochgradig kundenspezifische Teile oder wenn schnelle Entwicklungszyklen entscheidend sind. Analysieren Sie die Gesamtbetriebskosten (TCO) unter Berücksichtigung von Faktoren, die über den reinen Teilepreis hinausgehen (Vereinfachung der Montage, verbesserte Fahrzeugleistung). Bewerten Sie Großformat Metall AM Kosten Dynamik.
Durch das Verständnis dieser Herausforderungen und die proaktive Umsetzung von Lösungen, oft in Zusammenarbeit mit einem erfahrenen AM-Anbieter, können Hersteller die Möglichkeiten des 3D-Metalldrucks erfolgreich für die Herstellung moderner, leichter EV-Batteriegehäuse nutzen.
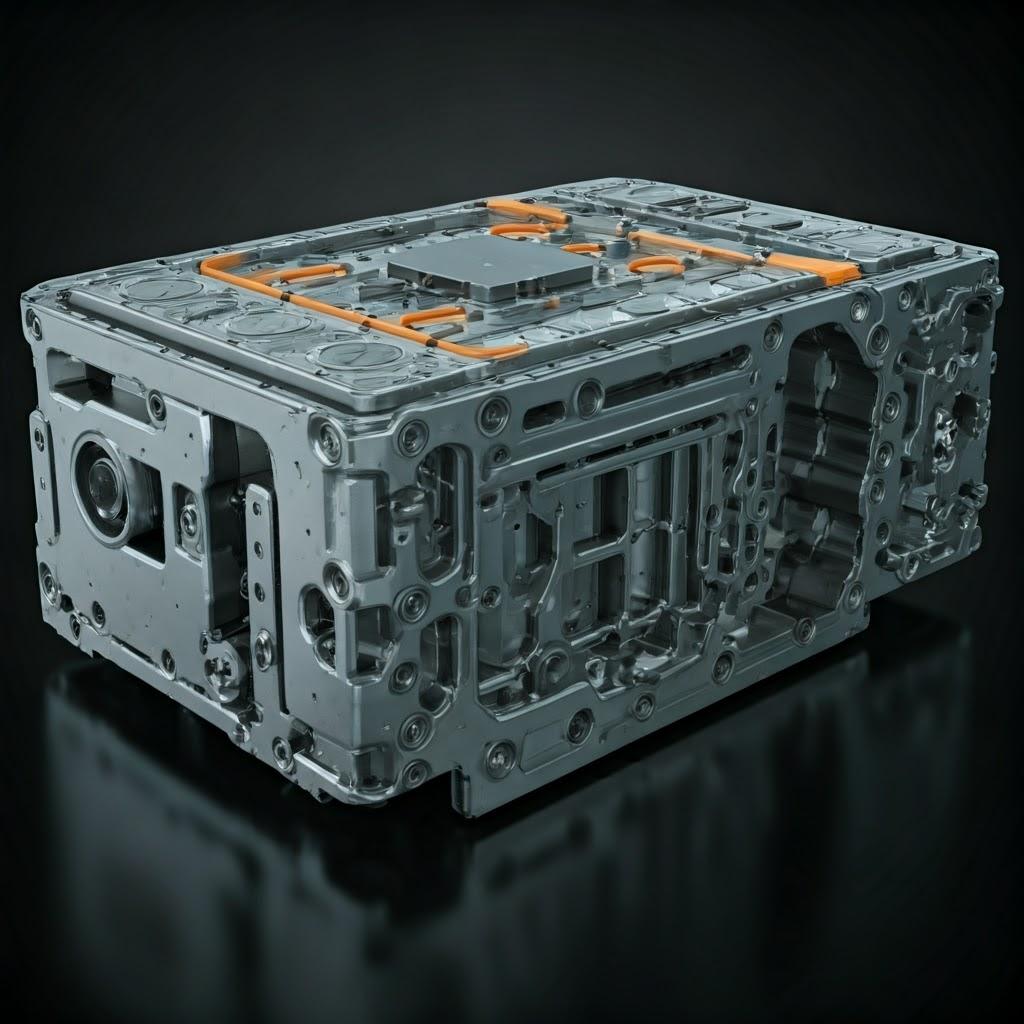
Wie Sie den richtigen 3D-Druckdienstleister für Metall auswählen
Die Auswahl des richtigen Fertigungspartners ist bei der Implementierung der additiven Fertigung von Metall für anspruchsvolle Anwendungen wie EV-Batteriegehäuse ebenso entscheidend wie die Wahl des Designs und der Materialien. Die Fähigkeiten, die Erfahrung und die Qualitätssysteme des von Ihnen gewählten Anbieters werden sich direkt auf den Erfolg Ihres Projekts auswirken. Für Ingenieure und Beschaffungsmanager, die sich in der Landschaft der Metall-3D-Druck-Dienstleister AutomotiveHier sind die wichtigsten Kriterien zur Bewertung:
- Automobil- und Anwendungs-Know-how:
- Verfügt der Anbieter über nachweisliche Erfahrung mit Automobilkomponenten, insbesondere mit Strukturteilen oder Wärmemanagementsystemen?
- Kennen sie die besonderen Herausforderungen und Anforderungen an EV-Batteriegehäuse (Leichtbau, thermische Belastung, Sicherheitsstandards, Abdichtung)?
- Suchen Sie nach Fallstudien oder Beispielen für ähnliche Projekte.
- Werkstoffkompetenz (Aluminiumlegierungen):
- Ist der Anbieter auf den Druck der von Ihnen benötigten Aluminiumlegierungen (AlSi10Mg, A6061, A7075) spezialisiert oder verfügt er über umfangreiche Erfahrungen damit?
- Verfügen sie über validierte Prozessparameter und kennen sie die erforderlichen Wärmebehandlungsprotokolle (z. B. T6-Bedingungen), um die gewünschten mechanischen Eigenschaften zu erzielen?
- Erkundigen Sie sich nach der Materialbeschaffung und der Qualitätskontrolle. Ein Anbieter wie Met3dp, der seine Materialien selbst herstellt hochwertige Metallpulver mit fortschrittliche Systeme zur Pulverherstellung wie die Gaszerstäubung und PREP, bietet eine bessere Kontrolle über Materialkonsistenz und Qualität.
- Maschinenfähigkeiten und Technologie:
- Welche Arten der Metall-AM-Technologie bieten sie an (z. B. Laser Powder Bed Fusion - LPBF, Electron Beam Powder Bed Fusion - EB-PBF)?
- Bieten ihre Maschinen genügend Bauvolumen für die Abmessungen Ihres Batteriegehäuses? Met3dp ist stolz auf Drucker mit branchenführendes Druckvolumen, Genauigkeit und Zuverlässigkeit.
- Wie alt und in welchem Zustand sind die Geräte? Ist sie gut gewartet und kalibriert?
- Integrierte Nachbearbeitungsdienste:
- Kann der Anbieter die erforderlichen Nachbearbeitungsschritte selbst durchführen (Wärmebehandlung, CNC-Bearbeitung, Oberflächenveredelung, Inspektion)? Oder verfügt er über ein stabiles, verwaltetes Netz qualifizierter Partner?
- Ein integriertes Dienstleistungsangebot vereinfacht das Projektmanagement und gewährleistet die Verantwortlichkeit während des gesamten Herstellungsprozesses.
- Qualitätsmanagementsysteme und Zertifizierungen:
- Ist der Anbieter nach ISO 9001 (allgemeines Qualitätsmanagement) zertifiziert?
- Für Lieferketten in der Automobilindustrie ist die IATF 16949-Zertifizierung sehr wünschenswert, da sie die Einhaltung der strengen Qualitätsstandards in der Automobilindustrie belegt.
- Erkundigen Sie sich nach den Qualitätskontrollverfahren, der Materialrückverfolgbarkeit und den Prüfmöglichkeiten (CMM, 3D-Scanning, NDT).
- Technische Unterstützung und Zusammenarbeit:
- Bietet der Anbieter Unterstützung oder Beratung im Bereich Design for Additive Manufacturing (DfAM) an?
- Können sie bei der Simulation des Bauprozesses oder der Topologieoptimierung helfen?
- Effektive Kommunikation und ein kollaborativer Ansatz sind entscheidend, insbesondere bei komplexen Projekten. Met3dp nutzt jahrzehntelange Erfahrung in der additiven Fertigung von Metallen um umfassende Lösungen anzubieten und mit den Kunden zusammenzuarbeiten.
- Vorlaufzeit und Kapazität:
- Können sie die von Ihnen geforderten Fristen für Prototypen und eine mögliche Kleinserienproduktion einhalten?
- Verfügen sie über ausreichende Kapazitäten, um Ihr Projekt ohne größere Verzögerungen durchzuführen?
- Standort und Logistik:
- Berücksichtigen Sie den Standort des Anbieters im Verhältnis zu Ihren Einrichtungen im Hinblick auf Transportzeit und -kosten, insbesondere bei größeren Komponenten.
Checkliste zur Bewertung:
Kriterien | Schlüsselfrage | Bedeutung |
---|---|---|
Erfahrung im Automobilbereich | Nachgewiesene Erfolgsbilanz bei ähnlichen Automobilteilen? | Sehr hoch |
Fachwissen über Aluminiumlegierungen | Fundierte Kenntnisse in der Verarbeitung und Wärmebehandlung von AlSi10Mg, A6061, A7075? | Sehr hoch |
Maschinenkapazität/Volumen | Die richtige Technologie (LPBF/EBPBF) und ein ausreichend großer Bauraum? | Hoch |
Kontrolle der Materialqualität | Robuste Verfahren? Eigene Pulverproduktion (wie Met3dp)? | Sehr hoch |
Post-Processing-Fähigkeit | Integrierte Dienstleistungen für Wärmebehandlung, Bearbeitung, Endbearbeitung, Inspektion? | Hoch |
Qualitätszertifizierungen | ISO 9001 unerlässlich, IATF 16949 für die Automobilindustrie wünschenswert? | Sehr hoch |
Technische Unterstützung / DfAM | Können sie bei der Designoptimierung und Prozesssimulation helfen? | Hoch |
Vorlaufzeit/Kapazität | Können sie die Projektfristen einhalten? | Hoch |
Kommunikation & Projektleitung | Klare Kommunikationskanäle und reaktionsschnelles Projektmanagement? | Hoch |
In Blätter exportieren
Die Auswahl eines Partner für additive Fertigung EV erfordert eine Due-Diligence-Prüfung, die über den bloßen Vergleich von Kostenvoranschlägen hinausgeht. Suchen Sie nach einem Anbieter wie Met3dp, der einen ganzheitlichen Ansatz bietet, der fortschrittliche Technologie, materialwissenschaftliches Fachwissen und eine Verpflichtung zur Qualität kombiniert und sich so als echter Partner für Innovationen positioniert.
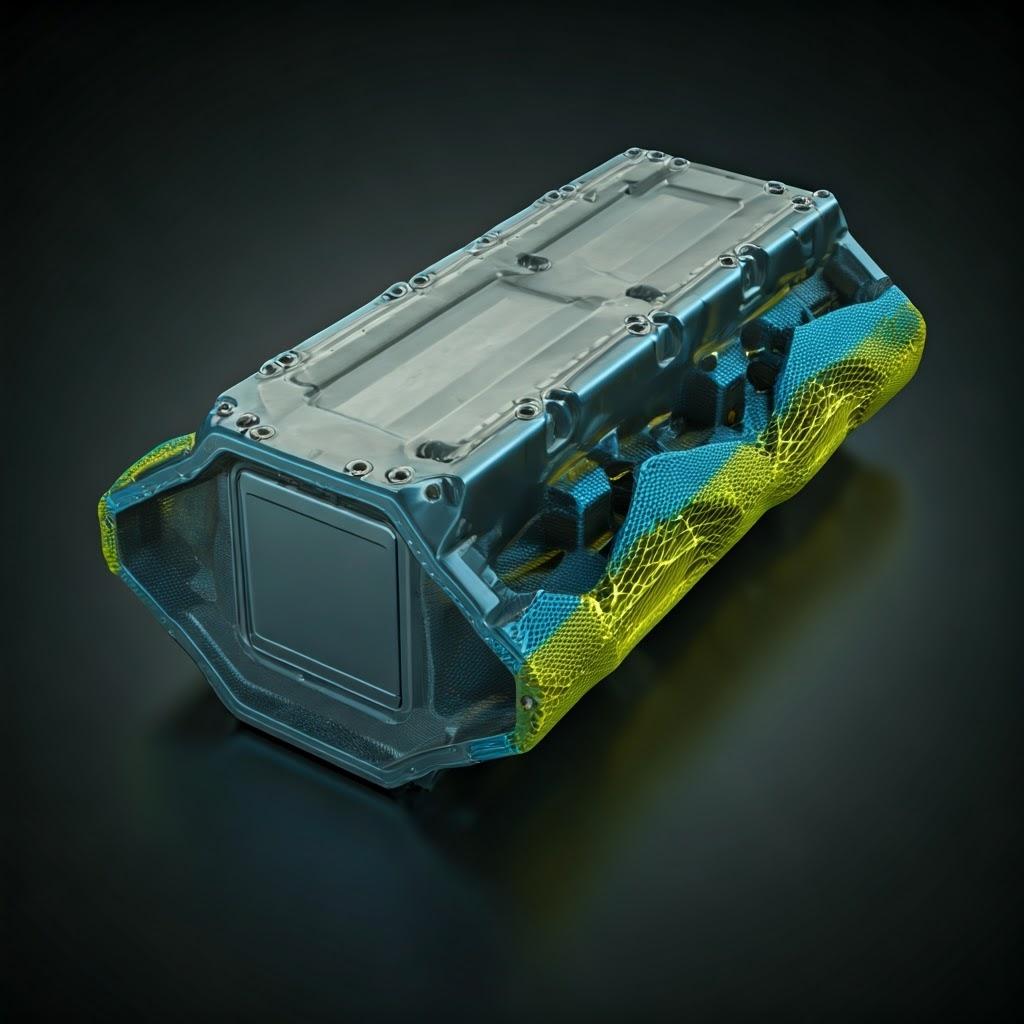
Kostenfaktoren und Vorlaufzeit bei AM-Batteriegehäusen
Das Verständnis der wirtschaftlichen und zeitlichen Aspekte der Herstellung von EV-Batteriegehäusen mittels Metall-AM ist entscheidend für die Projektplanung und Budgetierung. Sowohl die Kosten als auch die Vorlaufzeit werden von mehreren miteinander verknüpften Faktoren beeinflusst.
Faktoren, die die Kosten beeinflussen:
- Teilegestaltung und Komplexität:
- Volumen des Materials: Wirkt sich direkt auf Materialkosten und Druckzeit aus. Die Topologieoptimierung reduziert dies erheblich.
- Gesamtgröße: Größere Teile sind länger in der Baukammer.
- Komplexität: Komplizierte Merkmale können komplexere Stützstrukturen oder längere Druckzeiten pro Schicht erfordern, aber gerade hier bietet AM oft einen Mehrwert gegenüber herkömmlichen Methoden, die an Komplexitätsgrenzen stoßen.
- Materialtyp:
- Die Kosten für spezielle Metallpulver (z. B. hochfeste Aluminiumlegierungen) variieren. Auch die Qualität des Pulvers und die Produktionsmethode beeinflussen den Preis.
- Maschinenzeit:
- Ein primärer Kostentreiber. Wird auf der Grundlage der Gesamtzeit berechnet, die das Teil in der AM-Maschine verweilt. Beeinflusst von der Teilehöhe (Anzahl der Schichten), den Belichtungsparametern und der Verschachtelungseffizienz (gleichzeitiges Drucken mehrerer Teile).
- Unterstützende Strukturen:
- Volumen des für Stützen verwendeten Materials.
- Arbeits- und Zeitaufwand für den Ausbau von Stützen, insbesondere bei komplexen Innenstützen.
- Nachbearbeitungsanforderungen:
- Wärmebehandlung (Ofenzeit, Energie).
- CNC-Bearbeitung (Maschinenzeit, Programmierung, Einrichtung).
- Oberflächenbearbeitung (Arbeit, Verbrauchsmaterial, Spezialausrüstung wie AFM).
- Inspektion (Grad der Strenge, verwendete Geräte - CMM, CT-Scanning).
- Arbeit:
- Einrichten der Maschine, Handhabung des Pulvers, Entfernen der Teile, Entfernen der Halterung, Endbearbeitung, Prüfung.
- Auftragsvolumen:
- Der Preis pro Teil sinkt im Allgemeinen mit höheren Stückzahlen aufgrund der Amortisierung der Einrichtungskosten und des Potenzials für die Optimierung der Verschachtelung von Bauteilen, obwohl das Verhältnis weniger steil ist als bei der traditionellen Amortisierung von Werkzeugen. AM ist in der Regel am wettbewerbsfähigsten für Kosten für das Prototyping von EV-Komponenten und Serien mit geringem bis mittlerem Volumen.
- Unterstützung bei Technik/Entwicklung:
- Kosten im Zusammenhang mit DfAM-Beratung, Simulationsdiensten oder Prozessentwicklung, falls erforderlich.
Faktoren, die die Vorlaufzeit beeinflussen:
- Entwurf & Dateivorbereitung: Erforderliche Zeit für die Fertigstellung des Entwurfs, die DfAM-Optimierung, die Simulation der Konstruktion und die Vorbereitung der Dateien.
- Angebotserstellung und Auftragsabwicklung: Verwaltungsaufwand.
- Maschinenwarteschlange: Verfügbarkeit von geeigneten Maschinen beim Dienstleister.
- Druckzeit: Je nach Höhe, Volumen und Verschachtelung der Teile kann dies von Stunden bis zu mehreren Tagen oder sogar Wochen dauern.
- Abklingzeit: Die Teile müssen vor der Entnahme in der Maschine oder der Baukammer abkühlen.
- Nachbearbeiten: Kann einen beträchtlichen Teil der Gesamtdurchlaufzeit ausmachen und mehrere Schritte umfassen (Wärmebehandlungszyklen, Einrichten/Laufzeit der Bearbeitung, Endbearbeitung, Prüfung).
- Versand: Transitzeit zu Ihrer Einrichtung.
Vorläufige Vorlaufzeiten:
- Prototypen: Typischerweise reichen sie von 1 bis 4 WochenDies hängt stark von der Komplexität, dem Umfang, den Nachbearbeitungsanforderungen und der Kapazität des Anbieters ab.
- Produktion von Kleinserien: Je nach Menge, Komplexität der Teile und erforderlicher Prozessvalidierung/-qualifizierung kann dies zwischen mehreren Wochen und einigen Monaten dauern.
Es ist wichtig, detaillierte Kostenvoranschläge einzuholen, die Folgendes aufschlüsseln Preisfaktoren der additiven Fertigung und bieten realistische Vorlaufzeit Metall-AM-Teile Kostenvoranschläge auf der Grundlage Ihres spezifischen Designs und Ihrer Anforderungen.
Häufig gestellte Fragen (FAQ)
F1: Ist 3D-gedrucktes Aluminium stabil genug für ein strukturelles EV-Batteriegehäuse?
A: Auf jeden Fall. Metall-AM-Verfahren wie LPBF können in Kombination mit geeigneten Aluminiumlegierungen (wie AlSi10Mg, A6061, A7075) und den richtigen Wärmebehandlungen nach dem Prozess (z. B. T6-Zustand) Teile mit mechanischen Eigenschaften (Zugfestigkeit, Streckgrenze) herstellen, die mit denen herkömmlicher Aluminiumgussteile vergleichbar oder ihnen sogar überlegen sind. Durch sorgfältiges Design (DfAM, Topologieoptimierung) und Prozesskontrolle können 3D-gedruckte Gehäuse die anspruchsvollen strukturellen und Crash-Sicherheitsanforderungen für Elektrofahrzeuge erfüllen. Die Zusammenarbeit mit Experten gewährleistet die richtige Materialauswahl und Verarbeitung für optimale Festigkeit.
F2: Wie hoch sind die Kosten für ein 3D-gedrucktes Batteriegehäuse im Vergleich zu einem gegossenen oder gefertigten Gehäuse?
A: Der Kostenvergleich hängt stark von Volumen und Komplexität ab.
- Prototypen und Kleinserien (z. B. < 100-500 Einheiten): Metall-AM ist oft kostengünstiger und deutlich schneller, da die extrem hohen Vorlaufkosten und die lange Vorlaufzeit für die Herstellung von Formen oder Gesenken, die für das Gießen erforderlich sind, entfallen.
- Großes Volumen (z. B. Tausende von Einheiten): Der traditionelle Druckguss bietet in der Regel niedrigere Kosten pro Teil wenn die Werkzeuge amortisiert sind.
- Faktor "Komplexität": Bei hochkomplexen Konstruktionen mit integrierten Merkmalen (z. B. konforme Kühlkanäle), die sich auf herkömmliche Weise nur schwer oder gar nicht gießen oder bearbeiten lassen, kann AM selbst bei moderaten Stückzahlen wettbewerbsfähig bleiben oder Leistungsvorteile bieten, die einen potenziellen Kostenaufschlag rechtfertigen. Der Wert liegt in der Designfreiheit und der möglichen Konsolidierung von Teilen, wodurch die Montagekosten gesenkt werden.
F3: Können komplexe interne Kühlkanäle nach dem Druck effektiv gereinigt und überprüft werden?
A: Ja, aber es erfordert eine sorgfältige Planung. Die DfAM spielt eine entscheidende Rolle - sie entwirft Kanäle für die Zugänglichkeit, möglicherweise mit speziellen Einlass-/Auslassöffnungen für die Spülung, und minimiert den Bedarf an internen Halterungen. Nachbearbeitungstechniken wie Hochdruckspülung, Ultraschallreinigung und Abrasive Flow Machining (AFM) werden eingesetzt, um eingeschlossenes Pulver zu entfernen und die inneren Oberflächen zu glätten. Die Überprüfung ist von entscheidender Bedeutung, wobei häufig Methoden wie Luftströmungstests, Drucktests, boreskopische Inspektion (visuelle Inspektion mit kleinen Kameras) oder bei kritischen Anwendungen sogar CT-Scans eingesetzt werden, um sicherzustellen, dass die Kanäle frei von Verstopfungen oder Stützresten sind.
F4: Wie lange ist die typische Vorlaufzeit für einen Prototyp eines EV-Batteriegehäuses mit Metall-AM?
A: Eine typische Vorlaufzeit für einen funktionalen Prototyp eines EV-Batteriegehäuses, der mittels Metall-AM hergestellt wird, liegt im Allgemeinen bei 1 bis 4 Wochen. Dieser Zeitrahmen hängt in hohem Maße von Faktoren wie der Größe und Komplexität des Teils, der gewählten Legierung, den erforderlichen Nachbearbeitungsschritten (insbesondere Wärmebehandlung und maschinelle Bearbeitung), der aktuellen Maschinenauslastung des Anbieters und dem Umfang der erforderlichen Prüfung ab. Dies ist wesentlich schneller als die Monate, die oft erforderlich sind, um erste Teile aus herkömmlichen Gusswerkzeugen zu erhalten.
Schlussfolgerung: Beschleunigung der EV-Innovation mit Metall-AM-Batteriegehäusen
Das unaufhaltsame Streben nach leichteren, sichereren und effizienteren Elektrofahrzeugen erfordert kontinuierliche Innovationen bei der Konstruktion und Herstellung von Komponenten. Das Batteriegehäuse eines Elektrofahrzeugs, eine entscheidende Komponente, die Reichweite, Leistung und Sicherheit beeinflusst, kann von den Möglichkeiten der additiven Fertigung von Metallen immens profitieren. Wie wir erforscht haben, ist die Verwendung von 3D-Druck von Metall mit fortschrittlichen Aluminiumlegierungen wie AlSi10Mg, A6061 und A7075 ermöglicht die Herstellung von Batteriegehäusen, die:
- Erheblich leichter: Durch Topologieoptimierung und Gitterstrukturen wird das Gesamtgewicht des Fahrzeugs reduziert und die Reichweite erhöht.
- Thermisch überlegen: Komplexe, konforme Kühlkanäle, die direkt in die Struktur integriert sind, sorgen für eine optimale Temperaturkontrolle der Batterie.
- Hochgradig integriert: Konsolidierung mehrerer Funktionen und Teile in einem einzigen Bauteil, wodurch die Montage vereinfacht und die Robustheit erhöht wird.
- Schnell entwickelt: Dies ermöglicht ein schnelleres Prototyping und schnellere Design-Iterationszyklen im Vergleich zu herkömmlichen werkzeugbasierten Methoden.
Auch wenn es Herausforderungen gibt, können diese durch die Zusammenarbeit mit dem richtigen Experten überwunden werden. Met3dp steht an der Spitze dieses technologischen Wandels und bietet ein umfassendes Ökosystem für Automobilkunden. Zu unseren Stärken gehören:
- Fortgeschrittene AM-Systeme: Bereitstellung von branchenführendes Druckvolumen, Genauigkeit und Zuverlässigkeit für unternehmenskritische Teile.
- Hochwertige Metallpulver: Unter Verwendung proprietärer fortschrittliche Systeme zur Pulverherstellung (Gaszerstäubung & PREP) zur Herstellung von hochwertige Metallpulver optimiert für Dichte und Leistung.
- Integriertes Fachwissen: Nutzung von jahrzehntelanges kollektives Fachwissen in den Bereichen Ausrüstung, Werkstoffkunde und Anwendungsentwicklung, um Ihr Projekt vom Konzept bis zur Produktion zu unterstützen.
Metall-AM ist nicht mehr nur ein Werkzeug für das Prototyping; es ist eine praktikable Fertigungslösung, die die Welt umgestalten wird. Zukunft der EV-Herstellung. Durch Umarmung Additive Fertigung in der Automobilindustrie können führende Unternehmen neue Leistungsniveaus erschließen und ihren Weg zur Marktreife beschleunigen.
Sind Sie bereit zu erfahren, wie die additive Fertigung von Metall das Design Ihres EV-Batteriegehäuses revolutionieren kann?
Kontaktieren Sie Met3dp noch heute um Ihre Projektanforderungen zu besprechen und herauszufinden, wie unsere hochmodernen Systeme, fortschrittlichen Materialien und unser fachkundiger Support die Ziele Ihres Unternehmens im Bereich der additiven Fertigung unterstützen und die EV-Innovation in Leichtbauweise. Besuchen Sie unsere Website unter https://met3dp.com/ um mehr zu erfahren.
Teilen auf
MET3DP Technology Co., LTD ist ein führender Anbieter von additiven Fertigungslösungen mit Hauptsitz in Qingdao, China. Unser Unternehmen ist spezialisiert auf 3D-Druckgeräte und Hochleistungsmetallpulver für industrielle Anwendungen.
Fragen Sie an, um den besten Preis und eine maßgeschneiderte Lösung für Ihr Unternehmen zu erhalten!
Verwandte Artikel
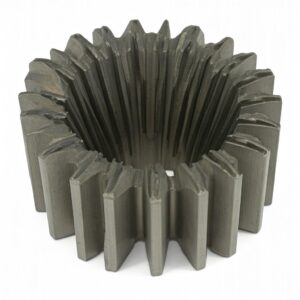
Hochleistungs-Düsenschaufelsegmente: Revolutionierung der Turbineneffizienz mit 3D-Metalldruck
Mehr lesen "Über Met3DP
Aktuelles Update
Unser Produkt
KONTAKT US
Haben Sie Fragen? Senden Sie uns jetzt eine Nachricht! Wir werden Ihre Anfrage mit einem ganzen Team nach Erhalt Ihrer Nachricht bearbeiten.
Holen Sie sich Metal3DP's
Produkt-Broschüre
Erhalten Sie die neuesten Produkte und Preislisten
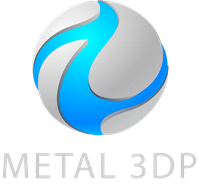
Metallpulver für 3D-Druck und additive Fertigung