Abgaskrümmer für hohe Temperaturen durch 3D-Druck
Inhaltsübersicht
Einleitung: Die entscheidende Rolle der Auspuffkrümmer für die Leistung bei hohen Temperaturen
Auspuffkrümmer sind die unbesungenen Helden im Ökosystem des Antriebsstrangs. Sie sind direkt mit dem Zylinderkopf des Motors verschraubt und haben eine wichtige, aber schwierige Aufgabe: Sie sammeln die heißen Abgase aus mehreren Zylindern und leiten sie in ein einziges Auspuffrohr. Dieser Prozess findet unter extremen Bedingungen statt, bei denen die Abgase Temperaturen ausgesetzt sind, die bei Hochleistungsanwendungen leicht 800 bis 1000 °C überschreiten können, und zwar in Verbindung mit erheblichen Temperaturschwankungen, Vibrationen und korrosiven Verbrennungsnebenprodukten.
Schlüsselfunktionen und Herausforderungen:
- Gassammlung und -weiterleitung: Effiziente Kanalisierung von Gasen mit hoher Geschwindigkeit und hoher Temperatur.
- Wärmemanagement: Sie müssen extremer Hitze standhalten, ohne zu versagen, sich zu verziehen oder Risse zu bekommen. Wiederholte Heiz- und Kühlzyklen führen zu erheblichen thermischen Belastungen.
- Druckeindämmung: Bewältigt schwankende Abgasdrücke.
- Schwingungsdämpfung: Dämpft die über die Befestigungspunkte übertragenen Motorvibrationen.
- Korrosionsbeständigkeit: Widersteht Oxidation und chemischen Angriffen durch Abgase.
- Durchfluss-Effizienz: Die interne Geometrie wirkt sich direkt auf die Motorleistung, den Gegendruck und den Spüleffekt aus.
Auspuffkrümmer werden traditionell durch Gießen (in der Regel aus Gusseisen oder Edelstahl) oder durch Schweißen gebogener Rohre (häufig aus Edelstahl) hergestellt. Diese Methoden sind zwar für die Massenproduktion und Anwendungen mit geringerer Leistung geeignet, stoßen jedoch an ihre Grenzen, wenn es um die Anforderungen moderner Hochleistungsmotoren, des Motorsports oder der Hilfsturbinen (APUs) in der Luftfahrt geht. Die geometrische Komplexität für eine optimale Strömung wird oft durch die Beschränkungen der Gussformen oder die Schwierigkeiten bei der Herstellung komplizierter Rohrbaugruppen eingeschränkt. Außerdem ist es ein ständiger Kampf, leichte Konstruktionen zu erreichen, ohne die Haltbarkeit zu beeinträchtigen.
Hier verschiebt sich die Landschaft. Das Streben nach höherer Effizienz, geringeren Emissionen und verbesserter Leistung, insbesondere in Sektoren, die kundenspezifische Lösungen oder Kleinserien erfordern, erfordert die Erforschung fortschrittlicher Fertigungstechniken. 3D-Druck von MetallDas Verfahren der additiven Fertigung (AM) ist eine leistungsstarke Alternative, die eine noch nie dagewesene Designfreiheit und die Möglichkeit bietet, Hochleistungssuperlegierungen zu verwenden, die speziell für extreme Temperaturbedingungen geeignet sind. Für Ingenieure und Beschaffungsmanager in anspruchsvollen Branchen wird das Verständnis des Potenzials von AM für Komponenten wie Abgaskrümmer immer wichtiger, um einen Wettbewerbsvorteil zu erhalten.
Anwendungen: Wo werden 3D-gedruckte Hochtemperatur-Abgaskrümmer eingesetzt?
Die einzigartigen Möglichkeiten der additiven Fertigung von Metallen eignen sich besonders für die Herstellung von Hochtemperatur-Abgaskrümmern, bei denen Leistung, komplexe Geometrien, geringe Stückzahlen, kundenspezifische Anpassungen oder eine schnelle Entwicklung im Vordergrund stehen. Die Fähigkeit, mit fortschrittlichen Superlegierungen zu arbeiten, verschiebt die Grenzen der Betriebstemperatur und der Langlebigkeit der Komponenten.
Schlüsselindustrien und Anwendungsfälle:
- Motorsport und Hochleistungsautomobile:
- Optimierte Flusspfade: AM ermöglicht komplizierte Innengeometrien, geglättete Krümmungen und präzise berechnete Laufradlängen, die die Abgasspülung maximieren und den Gegendruck minimieren, was sich direkt in mehr Leistung und Drehmoment niederschlägt.
- Gewichtsreduzierung: Durch die Verwendung von Superlegierungen und die Optimierung der Topologie können 3D-gedruckte Krümmer deutlich leichter sein als gegossene oder gefertigte Gegenstücke, was für die Verbesserung der Fahrzeugdynamik und der Kraftstoffeffizienz im Rennsport entscheidend ist.
- Rapid Prototyping und Iteration: Teams können schnell mehrere Iterationen von Krümmern entwerfen, drucken und testen, um die Motorleistung zu optimieren, was die Entwicklungszyklen im Vergleich zu herkömmlichen Methoden drastisch verkürzt.
- Anpassungen: Maßgeschneiderte Krümmer für bestimmte Motorenkonstruktionen, Fahrwerksbeschränkungen oder Turboladerplatzierungen werden machbar und kosteneffektiv, sogar für Einzelfahrzeuge oder begrenzte Produktionsserien. B2B-Zulieferer, die auf Leistungsteile spezialisiert sind, nutzen AM für maßgeschneiderte Kundenlösungen.
- Luft- und Raumfahrt:
- Hilfsturbinen (APUs): APU-Auspuffanlagen arbeiten bei sehr hohen Temperaturen und erfordern außergewöhnliche Zuverlässigkeit und geringes Gewicht. AM ermöglicht komplexe, konsolidierte Konstruktionen mit zertifizierten Superlegierungen für die Luft- und Raumfahrt wie Inconel.
- Unbemannte Luftfahrzeuge (UAVs): Das Gewicht ist bei Drohnen von größter Bedeutung. 3D-gedruckte Krümmer bieten erhebliche Gewichtseinsparungen für Auspuffanlagen von Verbrennungsmotoren, die in größeren Drohnen verwendet werden.
- Komponentenkonsolidierung: Mehrere gefertigte Teile können oft neu entworfen und als ein einziges, robusteres Bauteil gedruckt werden, wodurch potenzielle Fehlerpunkte (wie Schweißnähte) reduziert und die Montage vereinfacht werden.
- Industrielle Stromerzeugung und Schwermaschinenbau:
- Spezialisierte Motoren: Abgaskrümmer für große stationäre Motoren, Generatoren oder spezielle Off-Highway-Geräte erfordern oft robuste Werkstoffe und einzigartige Konstruktionen, die sich nicht für die Massenproduktion von Werkzeugen eignen.
- Raue Umgebungen: Anwendungen, die einen kontinuierlichen Hochtemperaturbetrieb erfordern oder korrosiven Industrieatmosphären ausgesetzt sind, profitieren von den hervorragenden Materialeigenschaften der AM-Superlegierungen.
- Ersatzteile: Die Herstellung von Ersatz für veraltete oder schwer zu beschaffende Verteiler für ältere Geräte wird möglich, ohne dass Originalwerkzeuge benötigt werden. Händler finden AM wertvoll für die Erfüllung von Nischenanforderungen für B2B-Teile.
- Prototyping und Forschung:
- Motorentwicklung: Forscher und Motorenentwickler nutzen 3D-gedruckte Krümmer, um neue Konzepte für die Emissionskontrolle, das Wärmemanagement oder die akustische Abstimmung schnell zu testen.
- Materialprüfung: Bietet eine Plattform für die Bewertung der Leistung neuer Hochtemperaturlegierungen unter realen Motorbedingungen.
Treiber der Marktnachfrage:
Treiber | Hauptsächlich betroffene Branchen | Nutzen von 3D-Druck | Zielpublikum |
---|---|---|---|
Leistungssteigerung | Motorsport, Hochleistungs-Auto | Optimierter Ablauf, Leichtgewichtigkeit, schnelle Iteration | Ingenieure, Rennteams |
Gewichtsreduzierung | Luft- und Raumfahrt, Motorsport | Topologieoptimierung, Materialauswahl, Teilekonsolidierung | Entwicklungsingenieure |
Komplexe Geometrien | Alle (v.a. Motorsport, Luft- und Raumfahrt) | Designfreiheit jenseits von Guss-/Fertigungsbeschränkungen | Entwicklungsingenieure |
Schnelles Prototyping | Alle (insbesondere Automobilindustrie, F&E) | Schnellere Entwicklungszyklen, geringere Werkzeugkosten | F&E-Leiter, Ingenieure |
Anpassung/Kleines Volumen | Motorsport, Industrie, Ersatzteile | Kostengünstige Produktion ohne spezielle Werkzeuge | Beschaffung, MRO |
Hochtemperatur-Legierungen | Luft- und Raumfahrt, Industrie, Performance Auto | Zugang zu Materialien wie IN625, IN718, Hastelloy X | Werkstoff-Ingenieure |
Teil Konsolidierung | Luft- und Raumfahrt, Industrie | Geringere Anzahl von Teilen, höhere Zuverlässigkeit, einfachere Montage | Konstruktions- und Fertigungsingenieure |
In Blätter exportieren
Die Einführung des 3D-Metalldrucks für Abgaskrümmer wird durch den eindeutigen Bedarf an Lösungen vorangetrieben, die über die Grenzen der konventionellen Fertigung hinausgehen, insbesondere dort, wo extreme Temperaturen und Leistung von entscheidender Bedeutung sind.
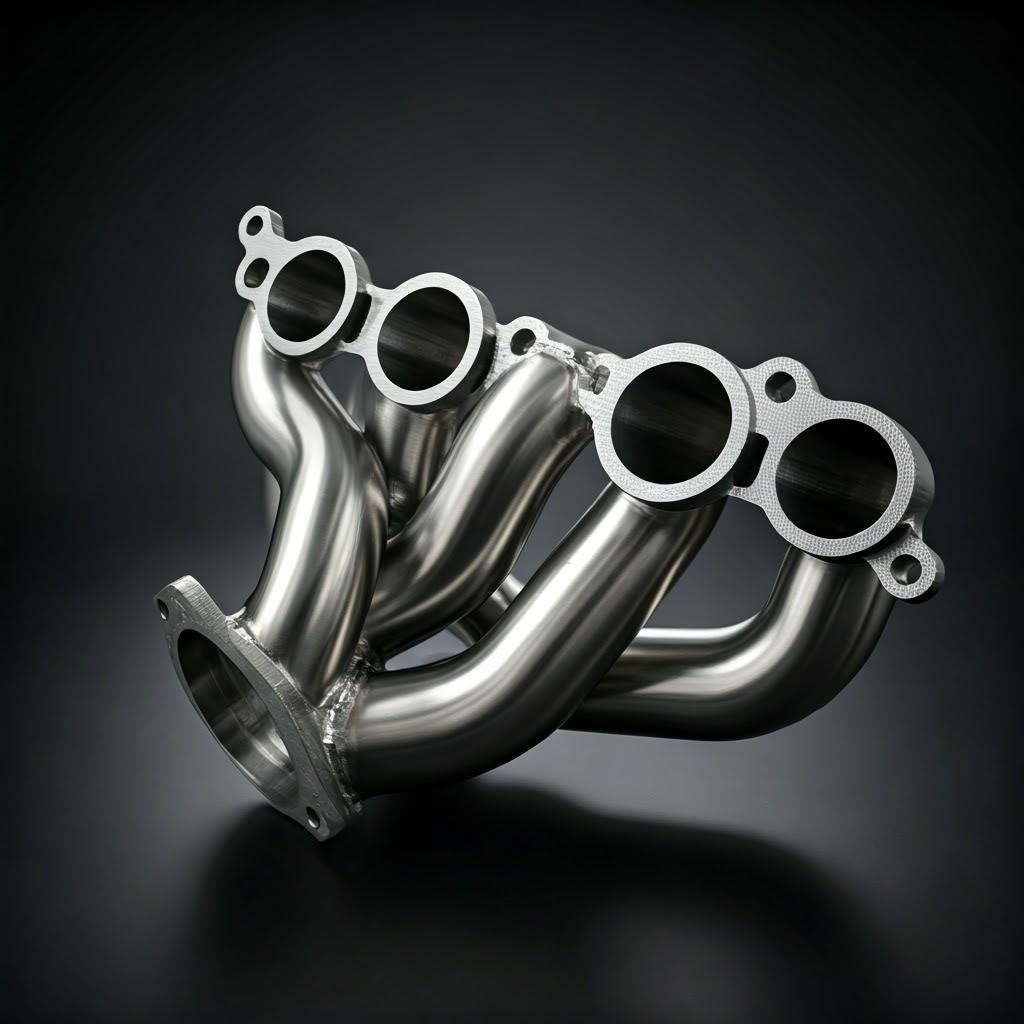
Warum 3D-Metalldruck für Hochtemperatur-Abgaskrümmer? Leistungssteigerungen freisetzen
Während herkömmliche Herstellungsverfahren wie Gießen und Fabrikation der Branche gute Dienste geleistet haben, bietet die additive Fertigung von Metallen eine Reihe von Vorteilen, die speziell für die Konstruktion und Produktion von Hochtemperatur-Abgaskrümmern von Vorteil sind. Diese Vorteile betreffen die inhärenten Herausforderungen extremer Hitze, komplexer Strömungsanforderungen und den Bedarf an leichten, langlebigen Komponenten.
Die wichtigsten Vorteile von Metal AM:
- Unerreichte Gestaltungsfreiheit und Komplexität:
- Herausforderung: Herkömmliche Methoden haben mit komplizierten internen Kanälen, glatten, organischen Übergängen und komplexen Kollektorkonstruktionen zu kämpfen, die für einen optimalen Abgasstrom und Spülung erforderlich sind. Das Gießen erfordert Entformungswinkel und Kernbegrenzungen, während die Herstellung komplexe Rohrbiege- und Schweißarbeiten erfordert.
- AM-Lösung: Der schichtweise Aufbau ermöglicht eine praktisch unbegrenzte geometrische Komplexität. Ingenieure können Verteilerrohre mit entwerfen:
- Optimierte Läuferpfade: Glatte, mathematisch abgeleitete Kurven, die den Durchfluss auf ein Minimum reduzieren.
- Integrierte Funktionen: Turboladerflansche, Wastegate-Anschlüsse, O2-Sensorstutzen und Montagehalterungen können als Teil des Verteilers gedruckt werden, wodurch Schweißarbeiten und potenzielle Leckstellen vermieden werden.
- Interne Kühlkanäle (Erweitert): Für extreme Anwendungen könnten interne Kanäle für Luft- oder Flüssigkeitskühlung integriert werden.
- Variable Wandstärken: Das Material kann genau dort platziert werden, wo es für die Festigkeit benötigt wird, während unkritische Bereiche ausgedünnt werden können, um Gewicht zu sparen.
- Teil Konsolidierung:
- Herausforderung: Gefertigte Verteiler bestehen oft aus mehreren gebogenen Rohren, Flanschen und Sammlern, die miteinander verschweißt sind. Jede Schweißnaht führt zu Eigenspannungen, potenziellen Fehlerpunkten und zusätzlichen Montagezeiten und -kosten.
- AM-Lösung: Mehrere Komponenten können neu entworfen und als ein einziges, monolithisches Teil gedruckt werden. Dies reduziert:
- Anzahl der Teile und Montagearbeiten.
- Mögliche Leckagepfade und Fehlerstellen (Schweißnähte).
- Gesamtgewicht und Toleranzausgleich.
- Gewichtsreduzierung:
- Herausforderung: Hochtemperaturfähigkeit erfordert oft dichte Materialien (wie rostfreie Stähle oder Gusseisen). Eine Gewichtsreduzierung ohne Beeinträchtigung der Festigkeit oder Wärmebeständigkeit ist mit herkömmlichen Methoden schwierig.
- AM-Lösung:
- Topologie-Optimierung: Die Software kann Spannungsbelastungen analysieren und Material aus unkritischen Bereichen entfernen, so dass organisch geformte, leichte Strukturen entstehen, die weder gegossen noch hergestellt werden können.
- Fortgeschrittene Materialien: Superlegierungen sind zwar dicht, aber die Designfreiheit ermöglicht optimierte Strukturen, die bei gleicher Festigkeit insgesamt weniger Material verbrauchen als eine voluminösere traditionelle Konstruktion.
- Zugang zu Hochleistungssuperlegierungen:
- Herausforderung: Während einige Hochleistungslegierungen dürfen Bestimmte Werkstoffe, die sich ideal für extreme Hitze und Korrosion eignen (z. B. bestimmte Inconel- oder Hastelloy-Sorten), lassen sich auf herkömmliche Weise nur schwer oder sehr teuer verarbeiten. Das Schweißen unterschiedlicher Abschnitte oder das Erreichen gleichmäßiger Eigenschaften bei komplexen Gussstücken kann problematisch sein.
- AM-Lösung: Pulverbettschmelzverfahren (PBF) wie selektives Laserschmelzen (SLM) oder Elektronenstrahlschmelzen (EBM) eignen sich hervorragend für die Verarbeitung von Hochleistungssuperlegierungen. Führende Anbieter wie Met3dp sind auf die Entwicklung und den Einsatz fortschrittlicher Metallpulver spezialisiert, die für hochdichte, homogene Teile mit hervorragenden mechanischen Eigenschaften sorgen, die auf anspruchsvolle thermische Umgebungen zugeschnitten sind. Ihr Fachwissen erstreckt sich auf Materialien, die speziell für Anwendungen wie Auspuffkrümmer ausgewählt wurden.
- Rapid Prototyping und Entwicklung:
- Herausforderung: Die Herstellung von Gusswerkzeugen oder Vorrichtungen für die Fertigung ist zeitaufwändig und teuer, insbesondere bei iterativen Designänderungen während der Entwicklung oder beim Prototyping.
- AM-Lösung: Entwürfe können innerhalb von Tagen, nicht Wochen oder Monaten, direkt vom CAD-Modell zum physischen Teil werden. Dies ermöglicht:
- Schnellere Entwurfsvalidierung und Leistungsprüfung.
- Kostengünstige Erkundung mehrerer Designvarianten.
- Verkürzte Markteinführungszeit für neue Motorplattformen oder Leistungsverbesserungen.
- Kosteneffizienz bei geringen Stückzahlen und individuelle Anpassung:
- Herausforderung: Die Werkzeugkosten machen die herkömmliche Fertigung für Einzelteile, Prototypen oder Kleinserien (z. B. Motorsport, Sonderanfertigungen, Ersatzteile) unerschwinglich.
- AM-Lösung: AM ist eine werkzeuglose Fertigung. Die Kosten pro Teil sind weniger volumenabhängig, was es für die Unternehmen wirtschaftlich rentabel macht:
- Maßgeschneiderte Krümmer, die auf spezifische Fahrzeug- oder Motoranforderungen zugeschnitten sind.
- Kleinserienproduktion für Nischenmärkte.
- On-Demand-Fertigung von Ersatzteilen für Vertriebshändler und Servicezentren.
Vergleichstabelle: Traditionelle vs. Metall-AM für Abgaskrümmer
Merkmal | Traditioneller Guss | Traditionelle Fabrikation | Metall-3D-Druck (PBF) |
---|---|---|---|
Entwurfskomplexität | Begrenzt durch Formen, Entformungsschrägen | Begrenzt durch Rohrbiegen/Schweißen | Hoch (komplexe interne Kanäle, organische Formen) |
Teil Konsolidierung | Begrenzt | Niedrig (viele geschweißte Komponenten) | Hoch (kann monolithische Teile drucken) |
Gewichtsreduzierung | Mäßig (begrenzter Materialabtrag) | Mäßig (dünne Röhren möglich) | Hoch (Topologieoptimierung, optimierte Strukturen) |
Material-Optionen | Gut (Gusseisen, Edelstahl) | Gut (Edelstahl, Titan) | Ausgezeichnet (Superlegierungen wie IN625/718, Hastelloy X) |
Prototyping-Geschwindigkeit | Langsam (Werkzeuge erforderlich) | Mäßig bis langsam (Vorrichtungen erforderlich) | Schnell (werkzeuglos) |
Niedrige Volumenkosten | Hoch (aufgrund der Werkzeugausstattung) | Mäßig bis hoch (arbeitsintensiv) | Mäßig (ideal für geringe Mengen) |
Vorlaufzeit (Neuteil) | Wochen/Monate | Wochen | Tage/Wochen |
Optimaler Fluss | Mäßig | Gut | Ausgezeichnet (hochoptimierte Designs möglich) |
In Blätter exportieren
Durch die Nutzung dieser Vorteile ermöglicht der 3D-Metalldruck Ingenieuren und Herstellern die Herstellung von Hochtemperatur-Auspuffkrümmern, die bisher nicht möglich oder nicht praktikabel waren, und eröffnet damit ein neues Niveau an Leistung, Effizienz und Designinnovation.
Empfohlene Materialien für den 3D-Druck von Abgaskrümmern: IN625, IN718, Hastelloy X
Die Auswahl des richtigen Materials ist angesichts der extremen Betriebsbedingungen für den Erfolg eines 3D-gedruckten Abgaskrümmers von entscheidender Bedeutung. Das Material muss eine außergewöhnliche Hochtemperaturfestigkeit, Beständigkeit gegen thermische Ermüdung, hervorragende Korrosions- und Oxidationsbeständigkeit sowie eine gute Verarbeitbarkeit durch additive Fertigungsverfahren wie Powder Bed Fusion (PBF) aufweisen. Superlegierungen auf Nickelbasis sind aufgrund ihrer bewährten Leistung in rauen Umgebungen die wichtigsten Kandidaten. Zu diesen gehören Inconel 625 (IN625), Inconel 718 (IN718) und Hastelloy X, die sich als besonders empfehlenswert erweisen.
Die Wahl eines seriösen Pulverlieferanten ist ebenso wichtig wie die Auswahl der richtigen Legierung. Unternehmen wie Met3dp, die fortschrittliche Pulverherstellungstechniken wie Gaszerstäubung und PREP (Plasma Rotating Electrode Process) einsetzen, gewährleisten die Verfügbarkeit von hochwertigen, sphärischen Metallpulvern, die für die additive Fertigung optimiert sind. Ihre Produktportfolio umfasst eine Reihe von Superlegierungen, die für anspruchsvolle Anwendungen geeignet sind. Hohe Sphärizität und gute Fließfähigkeit, Eigenschaften, die durch den Herstellungsprozess von Met3dp hervorgehoben werden, sind entscheidend für die Erzielung dicht gepackter Pulverbetten und die Herstellung hochwertiger, fehlerfreier gedruckter Teile.
1. Inconel 625 (IN625 / Legierung 625)
- Zusammensetzung: Nickel-Chrom-Molybdän-Niob-Legierung (NiCrMoNb).
- Wichtige Eigenschaften:
- Ausgezeichnete Hochtemperaturfestigkeit: Behält eine gute Zug-, Kriech- und Bruchfestigkeit bei Temperaturen bis zu ~815°C (1500°F) bei, wobei die nützlichen Eigenschaften bei Anwendungen mit kurzer Dauer oder geringerer Belastung sogar noch höher sind.
- Hervorragende Korrosionsbeständigkeit: Hochgradig beständig gegen eine Vielzahl korrosiver Umgebungen, einschließlich Oxidation, Aufkohlung und Angriff durch Abgaskondensate (Säuren). Der hohe Chrom- und Molybdängehalt bietet eine hervorragende Beständigkeit gegen Lochfraß und Spaltkorrosion.
- Hervorragende Verarbeitbarkeit und Schweißbarkeit: Während es für monolithische AM-Teile weniger kritisch ist, führt seine inhärente Schweißbarkeit zu einer guten Verarbeitbarkeit in PBF-Systemen und reduziert die Anfälligkeit für Risse während des Drucks und der Abkühlung.
- Hohe Ermüdungsfestigkeit: Widersteht Versagen bei zyklischer Belastung durch Motorvibrationen und Temperaturwechsel.
- Warum es für Auspuffkrümmer wichtig ist: IN625 bietet ein fantastisches Gleichgewicht zwischen Hochtemperaturfestigkeit, außergewöhnlicher Korrosionsbeständigkeit (entscheidend für den Umgang mit sauren Nebenprodukten und atmosphärischer Belastung) und robuster Leistung bei Temperaturwechseln. Es wird oft als bevorzugtes Material für anspruchsvolle Abgasanwendungen, einschließlich Motorsport- und Raumfahrtkomponenten, angesehen.
2. Inconel 718 (IN718 / Legierung 718)
- Zusammensetzung: Nickel-Chrom-Legierung, ausscheidungshärtbar mit Niob und Molybdän, plus Zusätze von Eisen, Titan und Aluminium (NiCrFeNbMoTiAl).
- Wichtige Eigenschaften:
- Außergewöhnliche mechanische Festigkeit: Bietet im Vergleich zu IN625 eine deutlich höhere Zugfestigkeit und Streckgrenze, insbesondere bei Temperaturen bis zu ~700°C (1300°F), aufgrund seines Ausscheidungshärtungsmechanismus (Gamma-Doppelprimphase).
- Gute Kriechbruchfestigkeit: Behält seine Integrität auch bei anhaltender Belastung und hohen Temperaturen bei.
- Gute Korrosionsbeständigkeit: Obwohl es im Allgemeinen sehr gut ist, kann es in bestimmten hochspezifischen korrosiven Umgebungen etwas weniger beständig sein als IN625. Dennoch eignet es sich hervorragend für die meisten Abgasanwendungen.
- Gute Schweißbarkeit/Verarbeitbarkeit: Leichte Verarbeitung mit AM-Techniken, allerdings sind Wärmebehandlungen nach dem Druck (Lösungsglühen und Alterung) erforderlich um seine optimalen hochfesten Eigenschaften zu erreichen.
- Warum es für Auspuffkrümmer wichtig ist: IN718 wird gewählt, wenn maximale Festigkeit und Kriechbeständigkeit bei sehr hohen Temperaturen (bis zu ~700°C) die wichtigsten Konstruktionsfaktoren sind. Sein besseres Verhältnis von Festigkeit zu Gewicht im Vergleich zu IN625 kann bei gewichtskritischen Anwendungen wie in der Luft- und Raumfahrt und im Spitzensport von Vorteil sein, sofern die erforderliche Wärmebehandlung durchgeführt wird.
3. Hastelloy X (Legierung X)
- Zusammensetzung: Nickel-Chrom-Eisen-Molybdän-Legierung (NiCrFeMo).
- Wichtige Eigenschaften:
- Hervorragende Oxidationsbeständigkeit: Bildet eine hartnäckige, schützende Oxidschicht, die eine ausgezeichnete Oxidationsbeständigkeit bei sehr hohen Temperaturen bietet und IN625 und IN718 in oxidierenden Atmosphären bis zu 1200°C (2200°F) übertreffen kann.
- Sehr gute Hochtemperaturfestigkeit: Behält eine gute Festigkeit bei erhöhten Temperaturen, wenn auch typischerweise nicht so hoch wie aushärtbares IN718 unter ~700°C.
- Hervorragende Verarbeitbarkeit: Bekannt für gute Umform- und Schweißeigenschaften in der traditionellen Fertigung, die sich gut auf die AM-Verarbeitung übertragen lassen.
- Widerstandsfähigkeit gegen Spannungsrisskorrosion: Gute Leistung in Umgebungen, in denen Chlorid-Spannungsrisskorrosion ein Problem darstellen könnte.
- Warum es für Auspuffkrümmer wichtig ist: Hastelloy X wird häufig für Anwendungen gewählt, bei denen die Oxidationsbeständigkeit in Gasturbinen-ähnlichen Umgebungen mit extremen Temperaturen der kritischste Faktor ist und die Inconel-Sorten unter rein oxidierenden Bedingungen möglicherweise übertrifft. Er wird häufig für Komponenten in der Verbrennungszone, Nachbrenner und Teile von Industrieöfen verwendet und eignet sich hervorragend für die heißesten Bereiche einiger Abgassysteme.
Leitfaden zur Materialauswahl:
Merkmal | IN625 | IN718 | Hastelloy X |
---|---|---|---|
Primäre Stärke | Ausgewogene Festigkeit und Korrosionsbeständigkeit | Höchste Festigkeit (bis zu ~700°C) | Beste Oxidationsbeständigkeit (bei höchsten Temperaturen) |
Maximale Einsatztemperatur (Stärke) | ~815°C (1500°F) | ~700°C (1300°F) - Die Festigkeit sinkt schneller über | ~900°C+ (1650°F+), übertrifft Oxidation bei >1000°C |
Korrosionsbeständigkeit | Hervorragend (Breites Spektrum) | Sehr gut | Sehr gut (außergewöhnliche Oxidation) |
Ist eine Wärmebehandlung erforderlich? | Nein (oder einfacher Stressabbau) | Ja (Lösung + Altershärtung unerlässlich) | Nein (oder einfacher Stressabbau) |
Relative Kosten | Hoch | Hoch | Hoch |
Typischer Anwendungsschwerpunkt | Motorsport, Schifffahrt, chemische Verarbeitung | Luft- und Raumfahrt, Gasturbinen, Hochfestigkeitsbedarf | Verbrennungsauskleidungen, Nachbrenner, Öfen |
In Blätter exportieren
Die Wahl des richtigen Pulvers und Verfahrens:
Die Auswahl der geeigneten Superlegierung ist nur ein Teil der Gleichung. Die Qualität des Metallpulvers und die gewählte 3D-Druckverfahren (in der Regel SLM oder DMLS für diese Legierungen) sind entscheidend.
- Qualität des Pulvers: Parameter wie die Partikelgrößenverteilung (PSD), die Sphärizität, die Fließfähigkeit und der geringe Sauerstoff-/Zwischengittergehalt wirken sich direkt auf die Dichte, die Mikrostruktur und die endgültigen mechanischen Eigenschaften des gedruckten Teils aus. Die Verwendung von Pulvern von spezialisierten Anbietern wie Met3dp, die in kontrollierten Verfahren wie VIGA (Vacuum Induction Gas Atomization) oder PREP hergestellt werden, gewährleistet Konsistenz und Qualität.
- Prozessparameter: Optimierte Laserleistung, Scangeschwindigkeit, Schichtdicke und Kontrolle der Baukammeratmosphäre sind entscheidend, um Defekte wie Porosität oder Eigenspannungen zu minimieren und die gewünschten Materialeigenschaften für die gewählte Legierung zu erzielen.
Durch die sorgfältige Berücksichtigung der spezifischen Betriebsbedingungen (Temperatur, Atmosphäre, Belastung) und die Nutzung der einzigartigen Stärken von Werkstoffen wie IN625, IN718 und Hastelloy X in Kombination mit hochwertigen Metallpulvern und optimierten AM-Prozessen können die Ingenieure Abgaskrümmer herstellen, die auch bei den anspruchsvollsten Anwendungen außergewöhnliche Leistung und Haltbarkeit bieten.
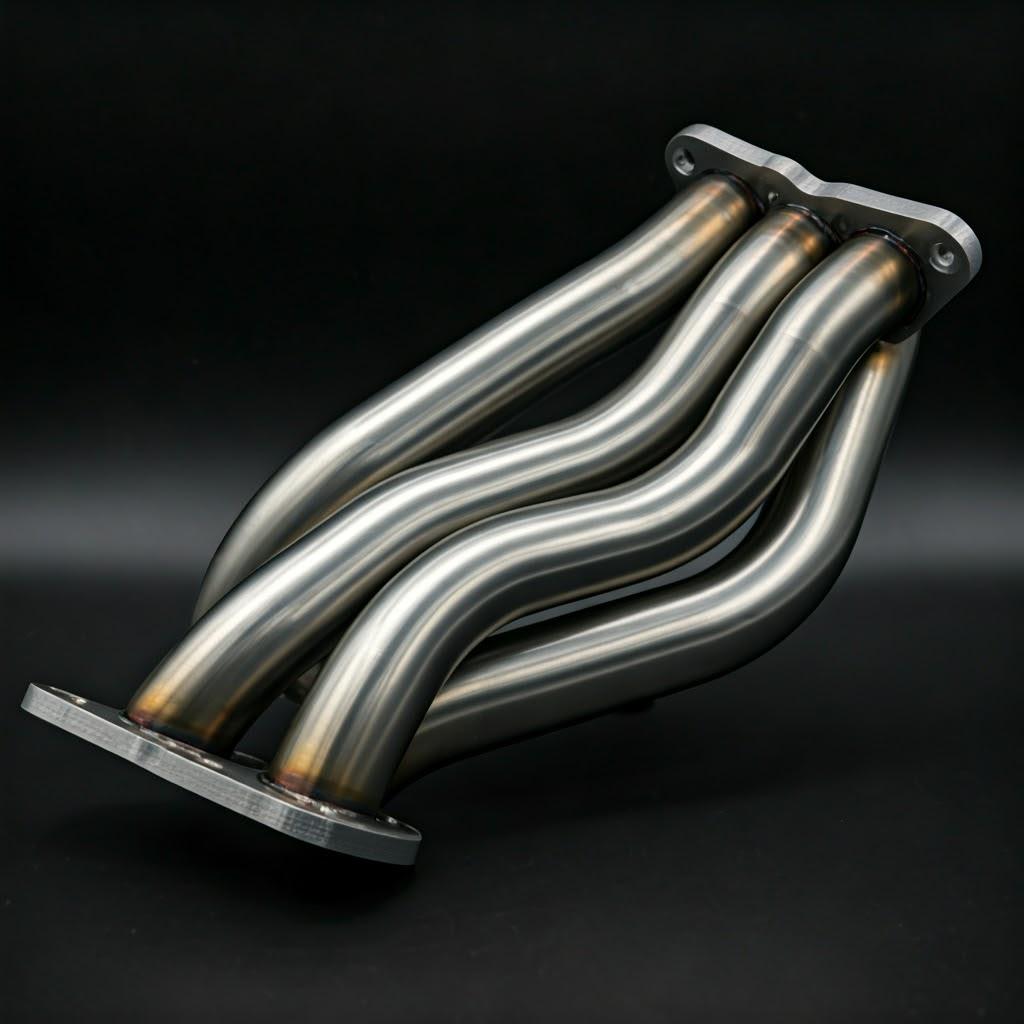
Konstruktionsüberlegungen für die additive Fertigung von Abgaskrümmern
Der Übergang von herkömmlichen Fertigungsmethoden zur additiven Fertigung (AM) von Abgaskrümmern aus Metall erfordert eine Änderung der Designphilosophie. Die einfache Konvertierung eines gegossenen oder gefertigten Designs für den 3D-Druck schöpft selten das volle Potenzial von AM aus und kann sogar neue Herausforderungen mit sich bringen. Entwerfen für Additive Manufacturing (DfAM) ist entscheidend, um die Leistung zu maximieren, die Kosten zu minimieren und einen erfolgreichen Druck zu gewährleisten.
Die wichtigsten DfAM-Prinzipien für Auspuffkrümmer:
- Optimierung der Fließwege:
- Das Ziel: Minimierung des Gegendrucks, Maximierung der Abgasgeschwindigkeit und des Spüleffekts.
- AM Vorteil: Erstellen Sie glatte, geschwungene Kurven und komplexe Kollektorgeometrien, die mit herkömmlichen Methoden nicht möglich sind.
- Erwägungen:
- Nutzen Sie CFD-Simulationen (Computational Fluid Dynamics) bereits in der Entwurfsphase, um die Gasströmung zu modellieren und die Formen, Längen und Konvergenzwinkel der Laufräder zu optimieren.
- Vermeiden Sie scharfe innere Ecken oder abrupte Querschnittsänderungen, die Turbulenzen verursachen können.
- Entwerfen Sie glatte Übergänge zwischen den Kanälen und dem Kollektor/Turboflansch.
- Management der Wanddicke:
- Das Ziel: Gewährleistung der strukturellen Integrität bei thermischer und mechanischer Belastung bei gleichzeitiger Minimierung von Gewicht und Materialeinsatz.
- AM Vorteil: Möglichkeit, die Wandstärke präzise zu variieren und eine Topologieoptimierung durchzuführen.
- Erwägungen:
- Einheitlichkeit: Streben Sie nach Möglichkeit eine relativ gleichmäßige Wandstärke an, um eine gleichmäßige Kühlung zu fördern und die thermische Belastung während des Drucks zu verringern. Die minimale bedruckbare Wandstärke hängt von der Maschine, dem Material und der Ausrichtung ab (in der Regel ~0,4-1,0 mm).
- Topologie-Optimierung: Verwenden Sie die Software, um Material aus wenig beanspruchten Bereichen zu entfernen, so dass organische, tragfähige Strukturen entstehen. Stellen Sie sicher, dass optimierte Konstruktionen die Anforderungen an thermische Ermüdung und Vibrationen erfüllen.
- Wärmeleitfähigkeit: Dickere Abschnitte speichern die Wärme länger; berücksichtigen Sie diese Auswirkung auf die thermischen Gradienten während des Drucks und des Betriebs.
- Strategie der Unterstützungsstruktur:
- Das Ziel: Verankern Sie das Teil auf der Bauplatte, stützen Sie überhängende Merkmale (typischerweise müssen Winkel <45° von der Horizontalen unterstützt werden) und bewältigen Sie thermische Spannungen.
- AM Herausforderung: Halterungen verbrauchen zusätzliches Material, verlängern die Druckzeit, müssen entfernt werden (Nachbearbeitung) und können die Oberflächengüte beeinträchtigen. Interne Stützen in komplexen Verteilerkanälen sind besonders schwierig zu entfernen.
- Erwägungen:
- Selbsttragende Winkel: Entwerfen Sie, wo immer möglich, Überhänge von mehr als ~45°. Richten Sie das Teil auf der Bauplatte strategisch aus, um die Notwendigkeit von Stützen in kritischen oder unzugänglichen Bereichen zu minimieren.
- Interne Kanäle: Entwerfen Sie interne Durchgänge so, dass sie selbsttragend sind (z. B. Verwendung von Rauten- oder Tropfenformen anstelle von kreisförmigen Formen für horizontal ausgerichtete Abschnitte), oder sorgen Sie für freie Zugangswege für Abstützungsentfernungswerkzeuge oder abrasive Fließbearbeitung.
- Art der Unterstützung: Wählen Sie geeignete Stützstrukturen (z. B. Block, Kegel, Linie) auf der Grundlage des zu stützenden Merkmals und der einfachen Entfernung. Ziehen Sie spezielle Softwarefunktionen zur Erzeugung leicht entfernbarer oder optimierter Stützen in Betracht.
- Wärmemanagement: Dichte Stützen können als Wärmesenken wirken und die Abkühlungsrate beeinflussen. Dies muss bei der Konstruktionsstrategie berücksichtigt werden.
- Merkmal Integration:
- Das Ziel: Reduzieren Sie die Anzahl der Teile, eliminieren Sie Schweißnähte und verbessern Sie die allgemeine Robustheit.
- AM Vorteil: Druckflansche, Sensorbuchsen (O2, EGT), Wastegate-Anschlüsse, Hitzeschilder und Montagehalterungen als integrale Bestandteile des Verteilers.
- Erwägungen:
- Achten Sie auf eine ausreichende Materialstärke um die integrierten Merkmale herum, um Festigkeit und Abdichtung zu gewährleisten (falls zutreffend).
- Konstruieren Sie Features unter Berücksichtigung der Einschränkungen des AM-Prozesses (z. B. Mindestlochgrößen, Feature-Auflösung).
- Ziehen Sie den Zugang zur Nachbearbeitung in Betracht, wenn kritische Toleranzen für integrierte Merkmale (z. B. Flanschflächen) erforderlich sind.
- Wärmemanagement beim Drucken:
- Das Ziel: Minimierung von Eigenspannungen, Verzug und möglichen Rissen, die durch die schnellen Aufheiz- und Abkühlzyklen beim Pulverbettschweißen verursacht werden.
- Erwägungen:
- Orientierung: Die Ausrichtung der Teile wirkt sich auf die Wärmeverteilung und den Unterstützungsbedarf aus.
- Scan-Strategie: Der Weg des Laser- oder Elektronenstrahls beeinflusst die lokale Wärmeentwicklung. Erfahrene AM-Dienstleister optimieren Scanstrategien.
- Geometrie des Teils: Große, flache Abschnitte oder abrupte Dickenänderungen können zum Verziehen neigen. Der Einbau von sanften Übergängen oder Versteifungsrippen (wo angebracht) kann helfen.
- Entfernung von Puder:
- Das Ziel: Vergewissern Sie sich, dass das gesamte ungeschmolzene Pulver, insbesondere aus den inneren Kanälen, nach dem Druck entfernt werden kann.
- Erwägungen:
- Entwerfen Sie Innenkanäle mit ausreichendem Durchmesser und glatten Wegen für den Abtransport des Pulvers.
- Bringen Sie strategisch platzierte Abfluss-/Zugangslöcher an (die bei Bedarf später verstopft oder zugeschweißt werden können). Vermeiden Sie komplizierte innere Hohlräume ohne Fluchtweg.
Durch die durchdachte Anwendung dieser DfAM-Prinzipien können Ingenieure 3D-gedruckte Abgaskrümmer erstellen, die nicht nur funktional sind, sondern auch in Bezug auf Leistung, Haltbarkeit, Gewicht und Herstellbarkeit mit additiven Verfahren optimiert wurden. Die Zusammenarbeit mit einem erfahrenen AM-Dienstleister, der mit Hochtemperaturanwendungen vertraut ist, ist in der Entwurfsphase von unschätzbarem Wert.
Erreichbare Toleranzen, Oberflächengüte und Maßgenauigkeit bei 3D-gedruckten Verteilern
Für Ingenieure und Beschaffungsmanager, die 3D-gedruckte Abgaskrümmer spezifizieren, ist es entscheidend, die erreichbare Präzision zu verstehen. Metall-AM bietet zwar eine unglaubliche geometrische Freiheit, hat aber auch inhärente Eigenschaften in Bezug auf Toleranzen, Oberflächengüte und Gesamtgenauigkeit. Diese Aspekte machen häufig Nachbearbeitungsschritte für kritische Merkmale erforderlich.
1. Toleranzen:
- Toleranzen wie gedruckt: Metall-Powder-Bed-Fusion-Verfahren (PBF) wie SLM/DMLS erreichen in der Regel allgemeine Maßtoleranzen, die vergleichbar sind mit ISO 2768-m (mittel) oder manchmal ISO 2768-f (fein) für kleinere, gut unterstützte Funktionen. Dies bedeutet im Allgemeinen:
- +/- 0,1 mm bis +/- 0,3 mm für Merkmale bis zu ~100 mm.
- +/- 0,1% bis +/- 0,2% des Nennmaßes für größere Merkmale.
- Faktoren, die die Verträglichkeit beeinflussen:
- Kalibrierung der Maschine: Regelmäßige Kalibrierung und Wartung sind entscheidend.
- Materialeigenschaften: Verschiedene Legierungen weisen ein unterschiedliches Schrumpfungs- und Wärmeverhalten auf.
- Größe und Geometrie des Teils: Größere Teile und komplexe Geometrien sind anfälliger für thermische Verformungen, die sich auf die Endtoleranzen auswirken.
- Orientierung und Unterstützung: Wie das Teil ausgerichtet und gestützt wird, wirkt sich auf die Spannung und die mögliche Verformung aus.
- Thermische Belastung: Der Aufbau von Eigenspannungen kann zu leichten Verformungen führen.
- Kritische Toleranzen: Merkmale, die hohe Präzision erfordern, wie z. B.:
- Flanschanschlussflächen (Ebenheit, Rechtwinkligkeit)
- Bolzenlochdurchmesser und -positionen
- Schnittstellen zu anderen Komponenten (z. B. Turboladereinlass) Erfordert fast immer eine Nachbearbeitung (CNC-Fräsen/Drehen), um enge Toleranzen zu erreichen. (z. B. innerhalb von +/- 0,025 mm bis +/- 0,05 mm oder besser). Die eindeutige Kennzeichnung dieser kritischen Merkmale in den Zeichnungen ist unerlässlich.
2. Oberflächengüte (Rauhigkeit):
- Wie gedruckt Oberflächenbehandlung: Die Art der schichtweisen Verschmelzung führt zu einer charakteristischen Oberflächenbeschaffenheit.
- Obere Oberflächen: Im Allgemeinen glatter, oft im Bereich von Ra 5-15 µm (Mikrometer).
- Seitenwände (vertikal/abgestuft): Zeigen Sie Schichtlinien, typischerweise Ra 8-20 µm.
- Unterstützte Oberflächen (nach unten gerichtet): Die rauesten Bereiche, an denen Stützstrukturen angebracht waren, haben vor der umfangreichen Nachbearbeitung möglicherweise eine Ra von 15-30 µm oder mehr.
- Interne Kanäle: Das Finish hängt stark von der Ausrichtung ab und davon, ob Stützen erforderlich waren. Es kann schwierig sein, eine sehr glatte innere Oberfläche ohne Nachbearbeitung zu erzielen.
- Verbesserung der Oberflächengüte: Verschiedene Nachbearbeitungstechniken können die Oberflächengüte erheblich verbessern:
- Strahlen (Perlen/Sand): Sorgt für ein gleichmäßiges, mattes Finish, wirksam bei der Entfernung von halbgesinterten Partikeln (Ra 5-10 µm).
- Taumeln/Gleitschleifen: Glättet Oberflächen und Kanten, insbesondere bei kleineren Teilen (kann Ra < 5 µm erreichen).
- Abrasive Fließbearbeitung (AFM): Besonders geeignet zum Glätten von Innenkanälen durch Durchströmen mit abrasiven Medien.
- Manuelles Polieren/Schleifen: Zur Erzielung sehr glatter, spiegelähnlicher Oberflächen auf bestimmten Außenflächen.
- Bearbeitungen: Bietet die beste Oberflächenbeschaffenheit bei spezifischen Merkmalen wie Flanschflächen.
3. Maßgenauigkeit:
- Definition: Wie genau das gedruckte Teil mit den Abmessungen des ursprünglichen CAD-Modells übereinstimmt.
- Faktoren, die die Genauigkeit beeinflussen: Umfasst alle Faktoren, die sich auf die Toleranz auswirken (Maschine, Material, Größe, Geometrie, Spannung) sowie:
- Qualität des CAD-Modells: Sicherstellung einer wasserdichten, fehlerfreien STL- oder 3MF-Datei.
- Vorbereitung der Scheiben: Korrigieren Sie die Einstellungen der Skalierungs- und Slice-Parameter.
- Nachbearbeitungseffekte: Spannungsabbau kann zu geringfügigen Maßänderungen führen; die Bearbeitung bringt ein eigenes Genauigkeitsniveau mit sich.
- Erzielung einer hohen Genauigkeit: Erfordert eine sorgfältige Prozesssteuerung, robuste Stützstrategien, effektives Wärmemanagement (einschließlich Spannungsabbau nach dem Druck) und oft eine gezielte Bearbeitung kritischer Abmessungen. Die Validierung durch 3D-Scannen oder CMM-Prüfung ist bei hochwertigen Teilen gängige Praxis.
Erwartungsmanagement:
Für Designer und Käufer ist es wichtig zu verstehen, dass Metall-AM nicht von Natur aus ein hochpräzises Verfahren für alle Merkmale direkt von der Maschine. Das Erreichen enger Toleranzen und spezifischer Oberflächengüten ist zwar unglaublich komplex, erfordert aber in der Regel die Planung von Nachbearbeitungsschritten, die in den Fertigungsablauf und das Budget einbezogen werden müssen. Es ist wichtig, dem AM-Dienstleister die kritischen Anforderungen an die Abmessungen und die Oberflächenbeschaffenheit klar mitzuteilen.
Merkmal | Wie gedruckt Typischer Bereich | Nachbearbeitetes Potenzial | Kontrollmethode |
---|---|---|---|
Allgemeine Toleranz | ISO 2768-m/f (~ +/- 0,1-0,3mm) | N/A (durch Prozess definiert) | Prozesssteuerung, Maschinenkal. |
Kritische Toleranz | Wie oben | +/- 0,025 mm oder besser | CNC-Bearbeitung |
Oberflächenrauhigkeit (Ra) | 8-20 µm (Seitenwände) | < 1 µm (poliert), 3-8 µm (gestrahlt) | Strahlen, Trommeln, AFM, Polieren |
Flansch Ebenheit | Mäßig | Hoch (<0,05 mm typisch) | CNC-Bearbeitung |
Finish des Innenkanals | Ra 10-30 µm+ | Ra < 10 µm (AFM möglich) | DfAM, AFM, Prozesskontrolle |
In Blätter exportieren
Wesentliche Nachbearbeitungsanforderungen für 3D-gedruckte Auspuffkrümmer
Ein 3D-gedrucktes Metallteil, insbesondere eine Hochleistungskomponente wie ein Abgaskrümmer aus Superlegierungen, ist selten direkt nach der Herstellung einsatzbereit. Die Nachbearbeitung ist eine kritische Phase im Fertigungsablauf, die notwendig ist, um Spannungen abzubauen, Stützstrukturen zu entfernen, die erforderlichen Toleranzen und Oberflächengüten zu erreichen und sicherzustellen, dass das Material die gewünschten mechanischen Eigenschaften besitzt.
Gemeinsame Nachbearbeitungsschritte:
- Stressabbau:
- Warum? Die schnelle Erwärmung und Abkühlung während des PBF-Verfahrens führt zu erheblichen inneren Spannungen im Bauteil. Wenn diese Spannungen nicht abgebaut werden, können sie zu Verformungen, Rissen (möglicherweise sogar noch Tage oder Wochen nach dem Druck) und einer verringerten Ermüdungslebensdauer führen. Dies ist insbesondere kritisch für Superlegierungen auf Nickelbasis wie IN625, IN718 und Hastelloy X.
- Wie? Das Teil wird, oft noch auf der Bauplatte befestigt, in einem Ofen einem kontrollierten Heiz- und Kühlzyklus unterzogen. Die spezifische Temperatur und Dauer hängen stark von der Legierung und der Teilegeometrie ab, umfassen aber in der Regel eine Erwärmung auf mehrere hundert Grad Celsius unterhalb der Glüh- oder Alterungstemperatur.
- Wichtigkeit: Betrachten Sie dies als einen obligatorischen ersten Schritt nach dem Druck, bevor sie in größerem Umfang bearbeitet oder von der Bauplatte entfernt werden.
- Entnahme von der Bauplatte:
- Warum? Das Teil wird während des Drucks mit einer dicken Metallplatte verschmolzen.
- Wie? Dies geschieht in der Regel durch Drahterodieren (Electrical Discharge Machining) oder mit einer Bandsäge. Dabei muss darauf geachtet werden, dass das Teil nicht beschädigt wird.
- Entfernung der Stützstruktur:
- Warum? Die Stützen sind während des Drucks notwendig, müssen aber für das endgültige Teil entfernt werden.
- Wie? Dies kann sehr arbeitsintensiv sein. Zu den Methoden gehören:
- Manuelle Entfernung: Abbrechen oder Wegschneiden von zugänglichen Stützen mit Handwerkzeugen (Zangen, Schneidegeräte, Schleifmaschinen).
- CNC-Bearbeitung: Abfräsen oder Abschleifen von Stützstrukturen, insbesondere in der Nähe kritischer Oberflächen.
- Drahterodieren: Wird manchmal zur Entfernung komplizierter Stützen verwendet.
- Herausforderungen: Das Entfernen von Stützen aus komplexen Innenkanälen ist besonders schwierig und erfordert eine sorgfältige DfAM-Planung (siehe vorheriger Abschnitt). Abdrücke von Halterungen auf der Werkstückoberfläche erfordern oft eine weitere Nachbearbeitung.
- Wärmebehandlung (Lösungsglühen & Alterung - hauptsächlich für IN718):
- Warum? Bestimmte Legierungen, insbesondere ausscheidungshärtbare Legierungen wie IN718, erfordern spezifische Wärmebehandlungszyklen, um ihre vollen mechanischen Eigenschaften (Festigkeit, Härte, Kriechfestigkeit) zu erreichen. IN718 hat im unbedruckten Zustand eine deutlich geringere Festigkeit als im vollständig wärmebehandelten Zustand. IN625 und Hastelloy X sind mischkristallverfestigt und müssen in der Regel nur spannungsarmgeglüht werden, wobei manchmal auch ein Glühen erforderlich ist.
- Wie? Das Teil wird auf eine bestimmte hohe Temperatur erwärmt (Lösungsglühen), um Ausscheidungen aufzulösen, dann abgeschreckt und anschließend bei einer oder mehreren niedrigeren Temperaturen gealtert, um die Verfestigungsphasen auszufällen (Gamma-Grundierung und Gamma-Doppelgrundierung bei IN718). Diese Zyklen müssen in einem kalibrierten Ofen, oft unter Vakuum oder inerter Atmosphäre, genau kontrolliert werden.
- Wichtigkeit: Unbedingt erforderlich für IN718, um die Leistungsspezifikationen zu erfüllen. Weniger kritisch, aber je nach den Anforderungen der Anwendung manchmal für andere Legierungen vorgeschrieben.
- Bearbeitung (kritische Abmessungen und Merkmale):
- Warum? Zur Erzielung enger Toleranzen, spezifischer Oberflächengüten und zur Sicherstellung ordnungsgemäßer Dichtungs-/Passflächen.
- Wie? Die Bearbeitung erfolgt durch CNC-Fräsen, Drehen oder Schleifen:
- Flanschflächen (Motorkopf und Auslass-/Turboanschlüsse) auf Ebenheit und Oberflächengüte.
- Schraubenlöcher mit präzisen Durchmessern und Positionen.
- Alle anderen kritischen Schnittstellenabmessungen.
- Wichtigkeit: Obligatorisch für den ordnungsgemäßen Einbau und die Abdichtung bei den meisten Auspuffkrümmern.
- Oberflächenveredelung:
- Warum? Um die Ästhetik zu verbessern, die Ermüdungslebensdauer zu erhöhen (durch Beseitigung von Oberflächenfehlern), das Teil zu reinigen und die gewünschte Oberflächenstruktur zu erreichen.
- Wie?
- Gedruckte Oberflächen sind typischerweise rau und können teilsinterte Partikel zurückhalten. Verschiedene Techniken werden verwendet, um die gewünschte Oberfläche zu erzielen: Gemeinsam für ein einheitliches, mattes Finish.
- Taumeln/Gleitschleifen: Glättet Oberflächen und Kanten.
- Abrasive Flow Machining (AFM) oder Extrude Hone: Wird zum Glätten von internen Kanälen verwendet.
- Manuelles Schleifen/Polieren: Für besondere ästhetische oder funktionale Anforderungen.
- Reinigung und Inspektion:
- Warum? Sicherstellen, dass sämtliches Stützmaterial, loses Pulver, Bearbeitungsspäne und Verunreinigungen entfernt werden. Überprüfen Sie die Unversehrtheit und Maßhaltigkeit der Teile.
- Wie? Ultraschallreinigung, Lösungsmittelreinigung, Sichtprüfung, Dimensionsprüfung (CMM, 3D-Scannen), zerstörungsfreie Prüfungen (NDT) wie CT-Scannen oder FPI (Fluorescent Penetrant Inspection) können bei kritischen Anwendungen (insbesondere in der Luft- und Raumfahrt) erforderlich sein, um interne Defekte oder Oberflächenrisse zu prüfen.
Der Umfang und die Reihenfolge dieser Nachbearbeitungsschritte hängen vom Material, der Komplexität des Designs und den Anwendungsanforderungen ab. Die Integration dieser Schritte in den Produktionsplan und das Budget ist entscheidend. Die Zusammenarbeit mit einem Full-Service-Anbieter wie Met3dpWer den gesamten Arbeitsablauf vom Pulver bis zum fertigen Teil, einschließlich der erforderlichen Nachbearbeitung für Hochtemperaturlegierungen, kennt, kann den Prozess rationalisieren und optimale Ergebnisse gewährleisten.
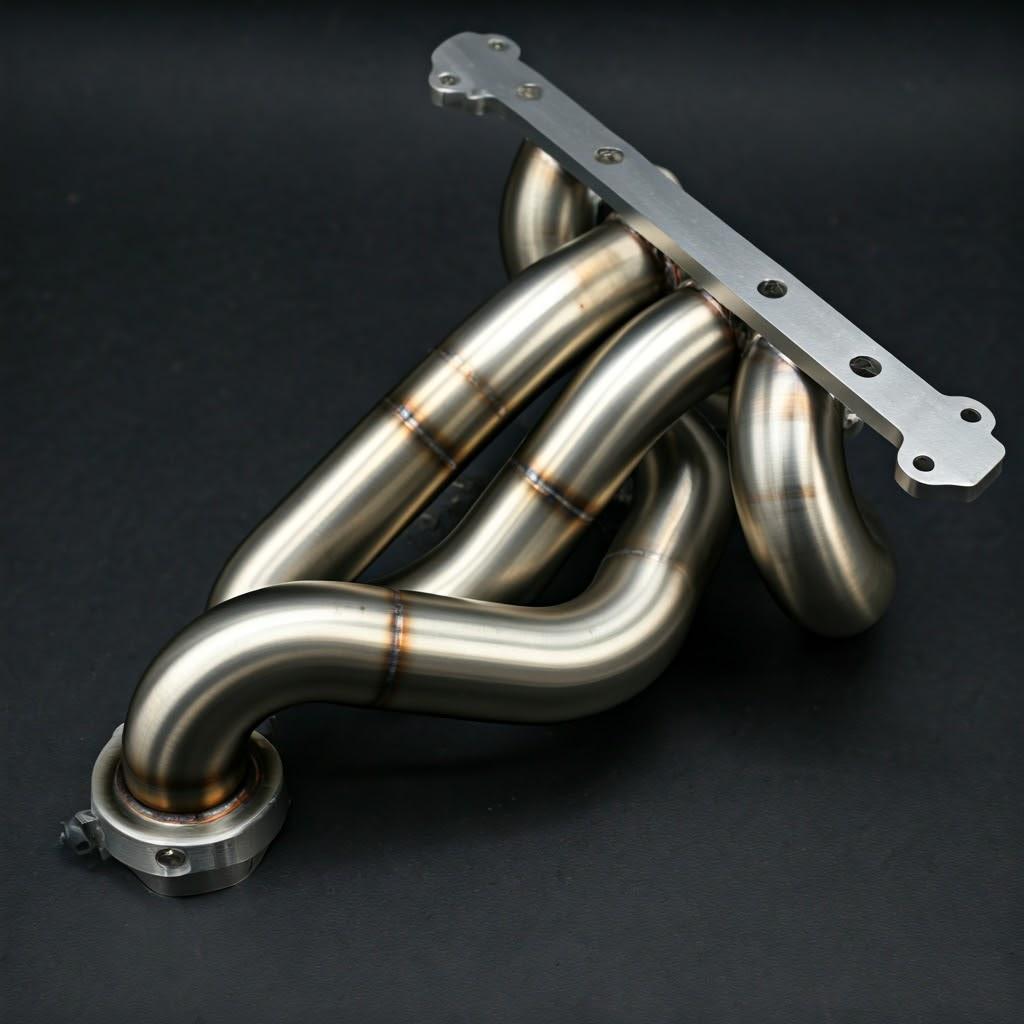
Allgemeine Herausforderungen beim 3D-Druck von Abgaskrümmern und Strategien zur Abhilfe
Metall-AM bietet zwar erhebliche Vorteile für die Herstellung von Hochtemperatur-Abgaskrümmern, ist aber auch nicht ohne Herausforderungen. Das Verständnis dieser potenziellen Probleme und die Umsetzung wirksamer Strategien zur Schadensbegrenzung sind der Schlüssel zur erfolgreichen Herstellung zuverlässiger, leistungsstarker Teile.
1. Verformung und Verzerrung:
- Die Ursache: Ungleichmäßige Erwärmung und Abkühlung während des schichtweisen PBF-Prozesses führen zu erheblichen Wärmegradienten und Eigenspannungen, wodurch sich das Teil verformt oder von der Bauplatte wegzieht. Große flache Bereiche und asymmetrische Designs sind besonders anfällig. Nickelsuperlegierungen haben hohe Wärmeausdehnungskoeffizienten, die dieses Problem noch verschärfen.
- Milderung:
- Optimierte Ausrichtung: Positionieren Sie das Teil auf der Bauplatte so, dass große ebene Flächen parallel zur Platte möglichst gering sind und keine freitragenden Überhänge entstehen.
- Robuste Unterstützungsstrategie: Verwenden Sie gut durchdachte Stützstrukturen, um das Teil fest zu verankern und als Wärmesenke zu fungieren, um die Wärmeenergie gleichmäßiger abzuleiten.
- Optimierung der Prozessparameter: Die Feinabstimmung von Laser-/Strahlleistung, Scan-Geschwindigkeit und Scan-Strategie (z. B. Insel-Scanning) kann die lokale Überhitzung minimieren.
- Build Plate Heating: Durch das Vorheizen der Bauplatte wird der Wärmegradient zwischen dem erstarrten Material und dem umgebenden Pulver bzw. der Platte verringert.
- Stressabbau: Die Durchführung eines Entlastungszyklus unmittelbar nach dem Druck ist von entscheidender Bedeutung, um innere Spannungen abzubauen, bevor es zu erheblichen Verformungen kommt.
- DfAM: Die Gestaltung von Merkmalen wie Rippen oder Riffelungen kann die Steifigkeit erhöhen; eine gleichmäßigere Wandstärke hilft bei der Bewältigung von Temperaturgradienten.
2. Rissbildung (Erstarrung oder Wärmebehandlung):
- Die Ursache:
- Erstarrungsrisse: Tritt während des Drucks auf, wenn lokale Spannungen die Festigkeit des Materials beim Erstarren und Abkühlen überschreiten. Bestimmte Legierungen sind dafür anfälliger.
- Wärmebehandlung Rissbildung: Kann während der Wärmebehandlung nach dem Druck (Spannungsabbau oder Alterung) auftreten, wenn die Erhitzungs-/Abkühlungsgeschwindigkeiten zu schnell sind oder wenn bereits vorhandene Defekte als Spannungskonzentratoren wirken. Superlegierungen können empfindlich sein.
- Milderung:
- Auswahl der Legierung: Wählen Sie Legierungen mit guter AM-Verarbeitbarkeit (IN625 und Hastelloy X haben im Allgemeinen eine bessere Druckbarkeit als IN718, obwohl IN718 sehr häufig erfolgreich gedruckt wird).
- Optimierung der Parameter: Eine sorgfältige Kontrolle des Energieeintrags und der Scanstrategie ist entscheidend.
- Heiß-Isostatisches Pressen (HIP): Obwohl dies mit Kosten verbunden ist, kann HIP innere Hohlräume schließen und möglicherweise Mikrorisse heilen, wodurch die Lebensdauer bei Ermüdung verbessert wird (oft für kritische Luft- und Raumfahrtteile erforderlich).
- Kontrollierte Wärmebehandlungszyklen: Verwenden Sie langsame, kontrollierte Aufheiz- und Abkühlraten während des Spannungsabbaus und der Alterung und befolgen Sie die etablierten Protokolle für die jeweilige Legierung. Stellen Sie die ordnungsgemäße Kalibrierung des Ofens und die Kontrolle der Atmosphäre sicher.
- Robuste Stützen: Eine ausreichende Abstützung hilft, Spannungen während des Aufbaus zu bewältigen.
3. Schwierigkeiten beim Entfernen von Stützen (insbesondere intern):
- Die Ursache: Komplexe innere Geometrien von Verteilerrohren erschweren den Zugang zu und die Entfernung von Stützstrukturen, ohne das Teil zu beschädigen. Verschmolzene Stützen können sehr stark sein.
- Milderung:
- DfAM für den Zugang: Konstruieren Sie interne Kanäle nach Möglichkeit selbsttragend (z. B. tropfenförmige/diamantförmige Querschnitte). Wenn Stützen unvermeidlich sind, stellen Sie sicher, dass es Zugangsöffnungen oder geradlinige Pfade für Werkzeuge oder AFM-Medien gibt.
- Optimiertes Support-Design: Verwenden Sie Stütztypen, die für eine einfachere Entfernung ausgelegt sind (z. B. geringere Dichte, bestimmte Kontaktpunkte). Spezialisierte Software kann bei der Erstellung dieser helfen.
- Nachbearbeitungstechniken: Verwenden Sie Methoden wie CNC-Bearbeitung für externe Stützen in der Nähe kritischer Flächen oder ziehen Sie AFM für Reststücke der internen Kanalstütze und Oberflächenglättung in Betracht. Planen Sie dies während der Konstruktionsphase ein.
4. Entfernung von eingeschlossenem Pulver:
- Die Ursache: Nicht verschmolzenes Pulver kann in komplizierten inneren Durchgängen oder teilweise gesinterten Hohlräumen eingeschlossen werden.
- Milderung:
- DfAM für die Entpulverung: Konstruieren Sie klare Abflusspfade und Zugangslöcher. Vermeiden Sie die Erstellung geschlossener innerer Hohlräume. Stellen Sie sicher, dass die minimalen Kanaldurchmesser den Pulverfluss ermöglichen.
- Optimierte Ausrichtung: Richten Sie das Teil so aus, dass der Pulverabfluss während des Ausbruchprozesses erleichtert wird.
- Gründliche Reinigung: Verwenden Sie Vibrationen, Druckluft und möglicherweise Ultraschallreinigung in Kombination mit speziellen Entpulverungsgeräten, um eingeschlossenes Pulver nach dem Aufbau zu entfernen. CT-Scannen kann die vollständige Pulverentfernung überprüfen, falls erforderlich.
5. Oberflächenbeschaffenheit der Innenseite:
- Die Ursache: Nach unten gerichtete Oberflächen und Bereiche, die interne Stützen erfordern, weisen in PBF-Verfahren naturgemäß eine rauere Oberfläche
- Milderung:
- DfAM & Ausrichtung: Konstruieren Sie selbsttragende interne Kanäle und richten Sie das Bauteil optimal aus.
- Abrasive Fließbearbeitung (AFM): Die effektivste Methode zur deutlichen Verbesserung der Oberflächengüte im Inneren durch das Fließen von Schleifmedien durch die Kanäle.
- Optimierung der Parameter: Bestimmte Prozessparameter können die Oberflächengüte im Inneren geringfügig beeinflussen, aber DfAM und Nachbearbeitung haben einen größeren Einfluss.
6. Qualitätskontrolle und Konsistenz:
- Die Ursache: Um sicherzustellen, dass jedes Teil die Dichtheitsanforderungen erfüllt, frei von kritischen Fehlern (Porosität, Risse) ist und die gewünschten mechanischen Eigenschaften aufweist, sind eine strenge Prozesskontrolle und -prüfung erforderlich.
- Milderung:
- Robustes Qualitätsmanagementsystem (QMS): Arbeiten Sie mit Lieferanten zusammen, die Zertifizierungen wie ISO 9001 oder AS9100 (für die Luft- und Raumfahrt) besitzen.
- Prozessüberwachung: In-situ-Überwachungswerkzeuge (Schmelzbadüberwachung, Wärmebildgebung) können Echtzeit-Qualitätsindikatoren liefern.
- Qualitätskontrolle des Pulvers: Die Sicherstellung einer gleichbleibenden, hochwertigen Pulverausgangsbasis ist unerlässlich.
- Zerstörungsfreie Prüfung (NDT): Verwenden Sie CT-Scannen, FPI oder Ultraschallprüfung, je nach Anwendungskritikalität, um die innere Integrität zu überprüfen.
- Mechanische Prüfung: Führen Sie Zugversuche, Härteprüfungen usw. an repräsentativen Proben oder Teststäben durch, die parallel zu den Teilen hergestellt wurden.
Die Bewältigung dieser Herausforderungen erfordert eine Kombination aus intelligenten Konstruktionspraktiken (DfAM), sorgfältiger Materialauswahl, optimierten Prozessparametern, geeigneter Nachbearbeitung und strenger Qualitätskontrolle. Die Zusammenarbeit mit einem erfahrenen Metall-AM-Anbieter, der die Feinheiten des Druckens von Hochtemperatur-Superlegierungen für Anwendungen wie Auspuffkrümmer versteht, ist oft der Schlüssel zur erfolgreichen Bewältigung dieser Hürden.
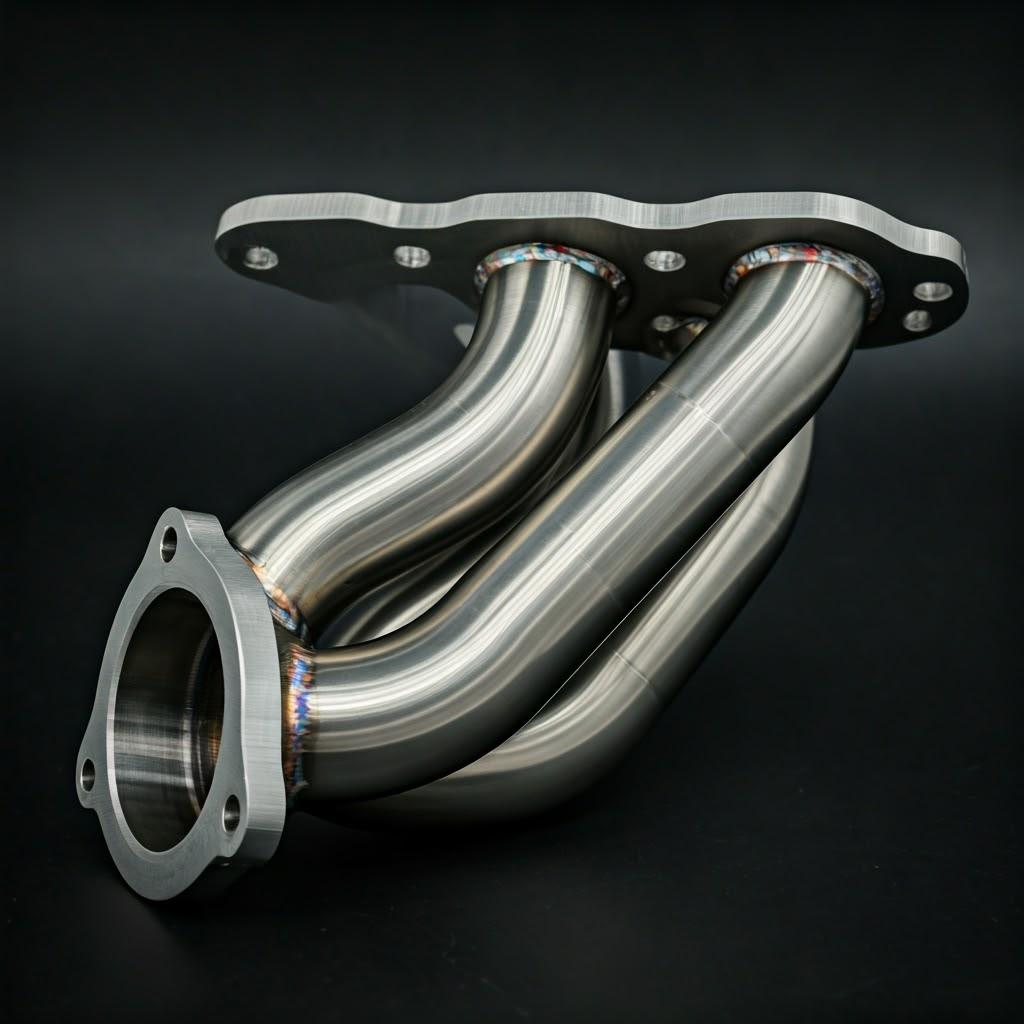
So wählen Sie den richtigen Metall-3D-Druckdienstleister für Auspuffkrümmer aus
Die Auswahl des richtigen Fertigungspartners ist ebenso entscheidend wie die Perfektionierung des Designs und die Auswahl des richtigen Materials, insbesondere für anspruchsvolle Komponenten wie Hochtemperatur-Auspuffkrümmer. Nicht alle Anbieter von metalladditiver Fertigung (AM) verfügen über das spezifische Fachwissen, die Ausrüstung und die Qualitätssysteme, die erforderlich sind, um diese anspruchsvollen Teile unter Verwendung von Superlegierungen erfolgreich herzustellen. Für Ingenieure und Einkaufsmanager ist eine sorgfältige Bewertung potenzieller Lieferanten unerlässlich.
Wichtige Faktoren für die Bewertung:
- Erfahrung mit Hochtemperatursuperlegierungen:
- Erfordernis: Nachgewiesene Erfahrung im Drucken von IN625, IN718, Hastelloy X oder anderen relevanten Hochtemperaturmaterialien. Dies beinhaltet das Verständnis ihrer einzigartigen Verarbeitungsanforderungen, potenzieller Herausforderungen (wie Rissneigung) und erforderlicher Nachbearbeitungswärmebehandlungen.
- Suchen Sie nach: Fallstudien, Beispiele für produzierte ähnliche Teile, Materialdatenblätter basierend auf ihren Druckergebnissen und sachkundige technische Mitarbeiter, die über Materialspezifika sprechen können. Unternehmen wie Met3dp, die nicht nur Druckdienstleistungen anbieten, sondern sich auch auf die Entwicklung und Herstellung spezialisiert haben Hochleistungsmetallpulver, verfügen über fundiertes materialwissenschaftliches Fachwissen.
- Geeignete Technologie und Ausrüstung:
- Erfordernis: Zugang zu geeigneten Pulverbett-Fusions-(PBF)-Technologien (Selektives Laserschmelzen – SLM / Direktes Metall-Lasersintern – DMLS oder potenziell Elektronenstrahlschmelzen – EBM) mit ausreichendem Bauvolumen für die Krümmergröße. Die Maschinen sollten gut gewartet und kalibriert sein.
- Suchen Sie nach: Informationen zu ihren spezifischen Druckermodellen, den Abmessungen des Bauraums, den Laser-/Strahlleistungsfähigkeiten und der Atmosphärenkontrolle (unerlässlich für reaktive Legierungen). Met3dp verwendet branchenführende Geräte, die für Präzision und Zuverlässigkeit bekannt sind und sich für missionskritische Teile eignen.
- Integrierte Post-Processing-Funktionen:
- Erfordernis: Fähigkeit, die erforderlichen Nachbearbeitungsschritte intern oder über qualifizierte Partner durchzuführen. Dies umfasst Spannungsarmglühen, spezielle Wärmebehandlungen (wie Vakuumlösungsglühen und Auslagern für IN718), Stützentfernung, CNC-Bearbeitung für kritische Merkmale, Oberflächenveredelung und Reinigung.
- Suchen Sie nach: Ein umfassendes Serviceangebot, das den gesamten Workflow vom Druck bis zum fertigen Teil abdeckt. Fragen Sie nach ihrer spezifischen Ausrüstung und Erfahrung mit der Bearbeitung von Superlegierungen und der Handhabung komplexer Geometrien. Ein Anbieter, der eine Komplettlösung anbietet, vereinfacht die Lieferkette und gewährleistet die Verantwortlichkeit.
- Qualitätsmanagementsystem und Zertifizierungen:
- Erfordernis: Robuste Qualitätskontrollprozesse sind nicht verhandelbar. Zertifizierungen belegen das Engagement für Qualität und Prozesskontrolle.
- Suchen Sie nach: Die ISO 9001-Zertifizierung ist eine Grundlage. Für die Luft- und Raumfahrt oder sehr anspruchsvolle Anwendungen ist häufig die AS9100-Zertifizierung erforderlich. Erkundigen Sie sich nach ihren Inspektionsfähigkeiten (CMM, 3D-Scannen) und ZfP-Optionen (CT-Scannen, FPI). Met3dp legt Wert auf branchenführende Genauigkeit und Zuverlässigkeit, unterstützt durch strenge Qualitätskontrolle.
- DfAM-Unterstützung und technisches Fachwissen:
- Erfordernis: Die Fähigkeit, bei der Designoptimierung für die additive Fertigung (DfAM) zusammenzuarbeiten. Ein erfahrener Partner kann wertvolles Feedback zur Verbesserung der Druckbarkeit, zur Reduzierung des Stützbedarfs und zur Leistungsoptimierung geben.
- Suchen Sie nach: Anbieter, die technische Supportleistungen, Designberatung oder Feedbackmechanismen während des Angebots-/Onboarding-Prozesses anbieten.
- Nachgewiesene Erfolgsbilanz und Branchenerfahrung:
- Erfordernis: Nachgewiesener Erfolg bei der Herstellung von Teilen für relevante Branchen (Automobil, Motorsport, Luft- und Raumfahrt, Industrie).
- Suchen Sie nach: Fallstudien, Testimonials, Referenzen und Beispiele von Projekten, die in Bezug auf Komplexität und Materialanforderungen ähnlich sind.
- Vorlaufzeit und Kommunikation:
- Erfordernis: Realistische Vorlaufzeitschätzungen und klare, reaktionsschnelle Kommunikation während des gesamten Projektlebenszyklus.
- Suchen Sie nach: Transparenter Angebotsprozess, proaktive Aktualisierungen und zugängliche technische Ansprechpartner.
Checkliste zur Lieferantenbewertung:
Kriterien | Zu stellende Fragen | Idealer Reaktionsindikator |
---|---|---|
Werkstoffkompetenz | Welche Hochtemperatur-Superlegierungen drucken Sie regelmäßig? Können Sie Datenblätter/Fallstudien für IN625/IN718/HastX weitergeben? | Fundierte Kenntnisse, nachgewiesene Ergebnisse, spezifische Erfahrung mit relevanten Legierungen. |
Technologie & Ausstattung | Welche PBF-Maschinen verwenden Sie? Wie lautet das Bauvolumen? Wie stellen Sie die Maschinenkalibrierung sicher? | Moderne, gut gewartete Geräte, die für die Teilegröße und das Material geeignet sind (z. B. SLM/DMLS). |
Nachbearbeitung | Bieten Sie hausinternes Spannungsarmglühen, Wärmebehandlung (Vakuum?), CNC-Bearbeitung, ZfP an? Welche Veredelungsoptionen gibt es? | Umfassende interne Fähigkeiten oder eng geführte, qualifizierte Partner. |
Qualitätssysteme | Sind Sie nach ISO 9001 / AS9100 zertifiziert? Wie lauten Ihre Standardinspektionsmethoden? Können Sie Materialzertifikate vorlegen? | Relevante Zertifizierungen, detaillierte Qualitätsverfahren, rückverfolgbare Materialchargen. |
DfAM / Technische Unterstützung | Überprüfen Sie Designs auf Druckbarkeit? Bieten Sie DfAM-Beratung an? | Proaktives Design-Feedback, kollaborativer Ansatz. |
Erfolgsbilanz | Können Sie Beispiele für ähnliche Projekte oder Referenzen in unserer Branche nennen? | Relevante Branchenerfahrung, positives Kundenfeedback. |
Vorlaufzeit & Kommunikation | Wie lautet Ihre typische Vorlaufzeit für ein solches Teil? Wer ist mein technischer Ansprechpartner? | Realistische Zeitpläne, klare Kommunikationskanäle, Reaktionsfähigkeit. |
Pulverbeschaffung & Qualität | Wo beziehen Sie Ihre Pulver? Wie stellen Sie die Pulverqualität und -konsistenz sicher? | Renommierte Quellen oder Eigenproduktion (wie Met3dp), strenge Pulvermanagementprotokolle. |
In Blätter exportieren
Die Wahl des richtigen Partners ist eine Investition in den Erfolg Ihres Projekts. Ein Anbieter wie Met3dp, der integrierte Lösungen anbietet, die fortschrittliche 3D-Druck von Metall Geräte, hochwertige Metallpulver, die mit modernsten Zerstäubungstechniken hergestellt werden, und umfassende Anwendungsentwicklungsdienste, stellt die Art von fähigem und zuverlässigem Partner dar, der für die Herstellung von Hochleistungs-3D-gedruckten Auspuffkrümmern benötigt wird.
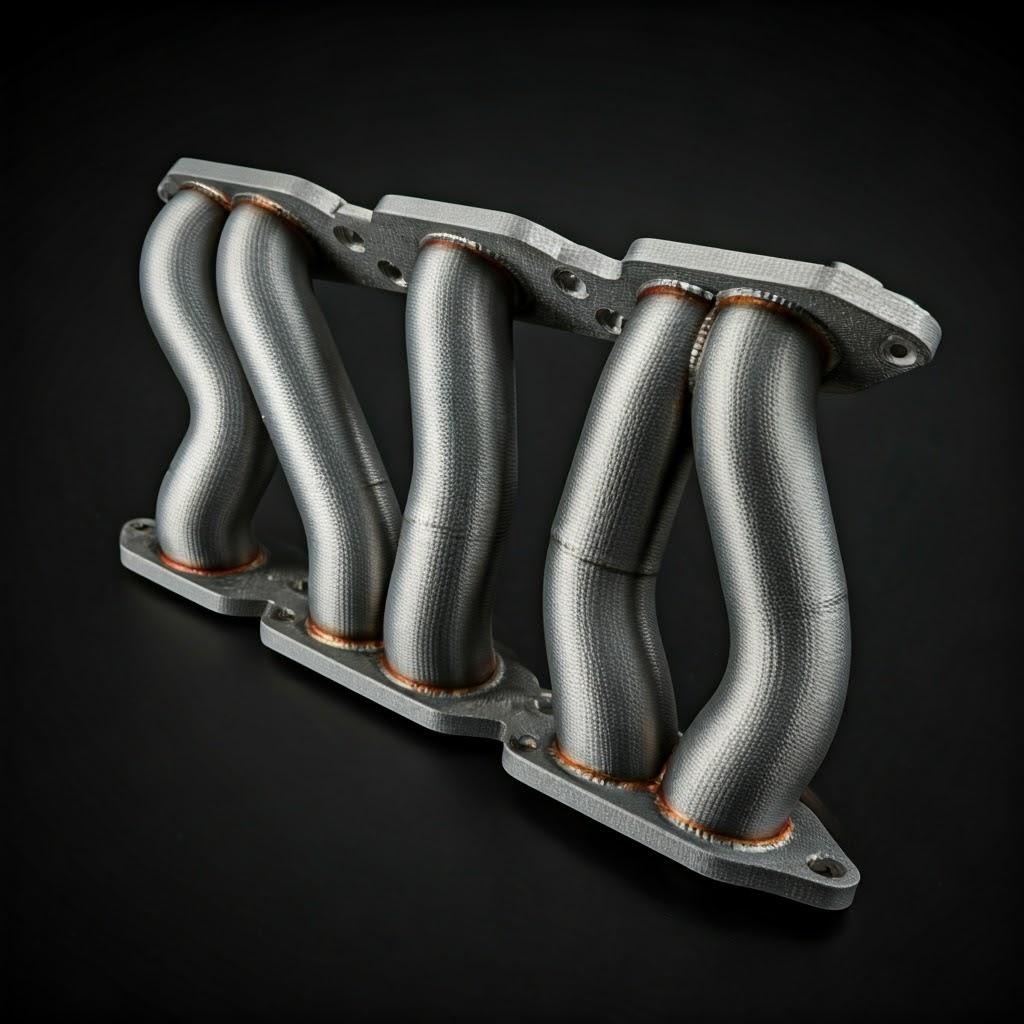
Verstehen der Kostenfaktoren und Vorlaufzeiten für 3D-gedruckte Auspuffkrümmer
Während die Metall-AM erhebliche technische Vorteile bietet, ist das Verständnis der damit verbundenen Kosten und Produktionszeitpläne für die Projektplanung und -budgetierung von entscheidender Bedeutung, insbesondere für B2B-Beschaffungs- und Großhandelsüberlegungen.
Die wichtigsten Kostentreiber:
- Materialkosten:
- Faktor: Nickelbasierte Superlegierungen (IN625, IN718, Hastelloy X) sind im Vergleich zu Standardstählen oder Aluminiumlegierungen von Natur aus teure Rohstoffe. Die Pulverherstellung für AM verursacht zusätzliche Kosten.
- Auswirkungen: Der Materialverbrauch (Teilevolumen + Stützvolumen) ist oft ein primärer Kostentreiber. Die Designoptimierung zur Minimierung des Volumens bei gleichzeitiger Erfüllung der Anforderungen ist der Schlüssel.
- Druckzeit (Maschinenzeit):
- Faktor: Berechnet auf der Grundlage der Gesamtzeit, in der die AM-Maschine belegt ist. Beeinflusst durch die Teilehöhe (Anzahl der Schichten), das Teilevolumen (Fläche, die pro Schicht gescannt werden soll) und die gewählten Schichtdicken/-Scanparameter. Komplexe interne Strukturen können die Druckzeit erhöhen.
- Auswirkungen: Größere oder höhere Teile oder sehr komplexe Geometrien, die aufwendiges Scannen erfordern, erhöhen die Maschinenzeitkosten direkt. Mehrere Teile, die effizient in einem einzigen Aufbau verschachtelt sind, können die Maschinenzeitkosten pro Teil senken.
- Unterstützende Strukturen:
- Faktor: Stützen verbrauchen Material und erhöhen die Druckzeit. Noch wichtiger ist, dass sie einen erheblichen Arbeits- und Zeitaufwand für die Nachbearbeitung zur Entfernung erfordern.
- Auswirkungen: Designs, die umfangreiche oder schwer zugängliche Stützen erfordern, verursachen höhere Kosten sowohl aufgrund des Materialverbrauchs als auch des Entfernungsaufwands. DfAM, das auf die Minimierung von Stützen abzielt, ist sehr vorteilhaft.
- Nachbearbeitungsintensität:
- Faktor: Dies kann einen erheblichen Teil der Gesamtkosten ausmachen. Beinhaltet:
- Spannungsarmglühen (Ofenzeit, Energie).
- Wärmebehandlung (komplexe Zyklen, Vakuumofenzeit, qualifizierte Arbeitskräfte).
- Stützentfernung (manuelle Arbeit, Bearbeitungszeit).
- CNC-Bearbeitung (Einrichtungszeit, Programmierung, Bearbeitungszeit, Werkzeugverschleiß bei harten Superlegierungen).
- Oberflächenbearbeitung (Arbeit, Verbrauchsmaterial, Spezialausrüstung wie AFM).
- Inspektion/ZfP (Gerätezeit, qualifizierte Techniker).
- Auswirkungen: Der Grad der Veredelung, die Toleranzanforderungen und die erforderliche Qualitätssicherung haben einen großen Einfluss auf die Kosten. Teile, die eine umfangreiche Bearbeitung und ZfP benötigen, sind deutlich teurer als Teile, die nur eine einfache Veredelung benötigen.
- Faktor: Dies kann einen erheblichen Teil der Gesamtkosten ausmachen. Beinhaltet:
- Engineering & Einrichtung:
- Faktor: Vorbereitung der ursprünglichen Datei, Bausimulation, Entwicklung der optimalen Ausrichtung und Stützstrategie sowie Maschinen-Einrichtungszeit.
- Auswirkungen: Normalerweise über den Produktionslauf amortisiert; signifikanter als Prozentsatz für einzelne Prototypen im Vergleich zur Kleinserienproduktion.
- Menge:
- Faktor: Während die AM Werkzeugkosten vermeidet, sind Skaleneffekte immer noch vorhanden. Die Einrichtkosten verteilen sich auf mehr Teile, Maschinen können kontinuierlicher betrieben werden, und die Nachbearbeitung kann für Chargen rationalisiert werden.
- Auswirkungen: Die Kosten pro Teil sinken im Allgemeinen mit höheren Volumina, obwohl die Reduzierung typischerweise weniger dramatisch ist als bei herkömmlichen Massenproduktionsmethoden. AM bleibt am wettbewerbsfähigsten für Prototypen, niedrige bis mittlere Volumina und hochkomplexe/kundenspezifische Teile.
Typische Vorlaufzeit Komponenten:
Die Vorlaufzeit für einen 3D-gedruckten Auspuffkrümmer ist die Summe aus mehreren Phasen:
- Angebotserstellung & Design-Finalisierung: (1-5 Tage) Erste Überprüfung, DfAM-Feedback, Angebotserstellung, Auftragsbestätigung.
- Vorbereitung des Baus: (1-3 Tage) Detaillierte Bauplanung, Slicing, Stützgenerierung, Maschinenplanung.
- Drucken: (2-7+ Tage) Sehr abhängig von Teilegröße, Komplexität und Verschachtelung. Große oder komplexe Verteiler können leicht mehrere Tage ununterbrochenes Drucken in Anspruch nehmen.
- Abkühlen & Ausbrechen: (1 Tag) Ermöglichen Sie dem Bauraum und dem Teil ein sicheres Abkühlen, Entfernen des Teils aus der Maschine, erste Pulverentfernung.
- Nachbearbeiten: (3-10+ Tage) Dies ist sehr variabel und oft die längste Phase. Beinhaltet Spannungsarmglühen, Entfernung von der Platte, Stützentfernung, Wärmebehandlung (kann allein 1-2 Tage dauern), Bearbeitung, Veredelung und Inspektion. Jeder Schritt fügt Zeit hinzu.
- Endkontrolle & Versand: (1-3 Tage) Endgültige Qualitätskontrollen, Verpackung und Versand.
Geschätzte Gesamtvorlaufzeit: Für einen komplexen Auspuffkrümmer aus Superlegierung, der eine erhebliche Nachbearbeitung erfordert, rechnen Sie mit Vorlaufzeiten von 3 bis 6 Wochen oder möglicherweise länger, je nach Komplexität, Menge und Kapazität des Dienstleisters. Das Prototyping könnte etwas schneller sein, wenn aufwändige Veredelungen oder Wärmebehandlungen zunächst übersprungen werden.
Es ist unerlässlich, die spezifischen Kostentreibern und Vorlaufzeiterwartungen mit potenziellen Lieferanten auf der Grundlage von finalisierten Designs und klaren Anforderungen an Toleranzen, Veredelung und Qualitätssicherung zu besprechen.
Häufig gestellte Fragen (FAQ) zu 3D-gedruckten Auspuffkrümmern
F1: Was sind die Hauptvorteile des 3D-Drucks eines Auspuffkrümmers im Vergleich zu herkömmlichem Gießen oder der Herstellung?
A: Die Hauptv Geometrische Komplexität: Fähigkeit zur Erstellung hochoptimierter interner Strömungswege und komplexer Formen für verbesserte Motorleistung, was durch Gießen oder Schweißen von Rohren schwierig oder unmöglich zu erreichen ist. * Material-Optionen: Ermöglicht die Verwendung fortschrittlicher Hochtemperatur-Superlegierungen (wie IN625, IN718, Hastelloy X), die für extreme Hitze- und Korrosionsbeständigkeit optimiert sind. * Teil Konsolidierung: Mehrere Komponenten (Läufer, Sammler, Flansche, Halterungen) können als ein einziges Teil gedruckt werden, wodurch Gewicht, potenzielle Fehlerstellen (Schweißnähte) und Montagezeit reduziert werden. * Gewichtsreduzierung: Designfreiheit in Kombination mit Topologieoptimierung ermöglicht eine erhebliche Gewichtsreduzierung im Vergleich zu herkömmlichen Designs, was für Motorsport und Luft- und Raumfahrt entscheidend ist. * Rapid Prototyping & Kleinserienfertigung: Schnellere Iteration während der Entwicklung und kostengünstige Herstellung für kundenspezifische Teile oder Kleinserien ohne teure Werkzeuge.
F2: Was ist die typische maximale Betriebstemperatur für einen 3D-gedruckten Krümmer unter Verwendung von Inconel 625 oder 718?
A: Die maximale Betriebstemperatur hängt von der spezifischen Legierung, den beteiligten Belastungen und der erforderlichen Lebensdauer der Komponente ab. Als allgemeine Richtlinie: * Inconel 625 (IN625): Behält eine ausgezeichnete Festigkeit und Oxidationsbeständigkeit bis zu etwa 815-900 °C (1500-1650 °F) bei, wobei nützliche Eigenschaften potenziell höher reichen können bei geringerer Belastung oder kürzeren Expositionszeiten. * Inconel 718 (IN718): Bietet aufgrund seiner aushärtenden Natur eine höhere Festigkeit bis etwa 700 °C (1300 °F). Seine Festigkeit nimmt oberhalb dieser Temperatur im Vergleich zu IN625 schneller ab, obwohl seine Oxidationsbeständigkeit bei höheren Temperaturen erhalten bleibt. * Hastelloy X: Bekannt für hervorragende Oxidationsbeständigkeit bis zu 1200 °C (2200 °F), wodurch es für die heißesten Anwendungen geeignet ist, obwohl seine Festigkeit bei Zwischentemperaturen (~650 °C) geringer sein kann als die von IN718. Das Design muss Kriechen, Ermüdung und thermische Zyklen innerhalb des Zielbetriebsfensters berücksichtigen.
F3: Wie vergleichen sich die Kosten eines 3D-gedruckten Auspuffkrümmers mit herkömmlichen Methoden?
A: Es ist ein Kompromiss: * Prototypen & Kleinserien (1-50 Teile): Der 3D-Druck ist oft kostengünstiger da es die Notwendigkeit teurer Werkzeuge (Gussformen, Fertigungsvorrichtungen) überflüssig macht. * Großserien (100+ bis 1000+ Teile): Herkömmliches Gießen oder die Großserienfertigung wird typischerweise pro Teil weniger teuer aufgrund amortisierter Werkzeugkosten und schnellerer Zykluszeiten. * Leistungswert: Für Hochleistungsanwendungen können die potenziell höheren Kosten eines 3D-gedruckten Krümmers durch erhebliche Leistungsgewinne (PS, Effizienz), Gewichtseinsparungen oder Haltbarkeitsverbesserungen gerechtfertigt werden, die mit herkömmlichen Methoden nicht erreichbar sind. Die gesamte Wertschöpfung, nicht nur die Teilekosten, sollte berücksichtigt werden.
F4: Können die Innenflächen eines 3D-gedruckten Auspuffkrümmers für einen optimalen Luftstrom glatt gemacht werden?
A: Eine perfekt glatte Innenfläche, die mit mandrellgebogenen Rohren vergleichbar ist, kann direkt aus dem Drucker eine Herausforderung darstellen, insbesondere auf nach unten gerichteten Oberflächen oder dort, wo interne Stützen erforderlich waren (als gedrucktes Ra könnte 10-30 µm+ betragen). Jedoch: * DfAM: Das Design selbsttragender interner Kanäle hilft, die Rauheit zu minimieren. * Orientierung: Eine strategische Ausrichtung kann die Oberfläche kritischer Strömungswege verbessern. * Nachbearbeiten: Techniken wie Abrasive Strömungsbearbeitung (AFM) oder ähnliche Extrusionshonverfahren sind speziell dafür konzipiert, Innenpassagen durch das Fließen von Schleifmedien durch sie zu glätten, wodurch die Rauheit erheblich reduziert (potenziell auf Ra < 5-10 µm) und die Strömungseigenschaften verbessert werden. Dies erhöht die Kosten, ist aber für leistungsentscheidende Anwendungen effektiv.
Fazit: Die Zukunft von Hochleistungs-Auspuffanlagen mit metalladditiver Fertigung vorantreiben
Die Herausforderungen, die extreme Temperaturen, komplexe Strömungsdynamik und das unermüdliche Streben nach Leistung in modernen Motoren mit sich bringen, erfordern innovative Fertigungslösungen. Die metalladditive Fertigung hat sich fest als eine transformative Technologie etabliert, die in der Lage ist, diese Anforderungen für Komponenten wie Hochtemperatur-Auspuffkrümmer direkt zu erfüllen.
Durch die Erschließung beispielloser Designfreiheit, die Ermöglichung der Verwendung fortschrittlicher Nickelbasis-Superlegierungen wie IN625, IN718 und Hastelloy X sowie die Erleichterung von Rapid Prototyping und Teilekonsolidierung bietet der 3D-Metalldruck greifbare Vorteile, die sich direkt in verbesserter Leistung, reduziertem Gewicht und verbesserter Haltbarkeit niederschlagen. Während herkömmliche Methoden für Standardanwendungen weiterhin praktikabel sind, bietet AM einen deutlichen Wettbewerbsvorteil in Sektoren, in denen die Optimierung von entscheidender Bedeutung ist – einschließlich Motorsport, Luft- und Raumfahrt, Hochleistungsautomobil und spezialisierter Industrieausrüstung.
Die erfolgreiche Nutzung dieser Technologie erfordert einen ganzheitlichen Ansatz, der Design for Additive Manufacturing (DfAM), sorgfältige Materialauswahl, kontrollierte Verarbeitung, gründliche Nachbearbeitung und strenge Qualitätssicherung umfasst. Die Bewältigung von Herausforderungen wie dem Wärmespannungsmanagement und der Stützenentfernung erfordert Fachwissen und Zusammenarbeit.
Die Wahl des richtigen Fertigungspartners – mit nachgewiesener Erfahrung in Hochtemperaturlegierungen, robusten Qualitätssystemen und umfassenden Fähigkeiten – ist von entscheidender Bedeutung. Unternehmen wie Met3dpmit ihrem fundierten Fachwissen sowohl in fortschrittlichen Metallpulvern als auch in additiven Fertigungssystemen, veranschaulichen den integrierten Ansatz, der erforderlich ist, um komplexe Designs in zuverlässige, hochleistungsfähige Realitäten umzusetzen.
Da sich die Metall-AM-Technologien weiterentwickeln und die Materialwissenschaften Fortschritte machen, werden sich die Möglichkeiten zur Optimierung von Auspuffanlagen und anderen kritischen Hochtemperaturkomponenten nur noch erweitern. Für Ingenieure und Beschaffungsmanager, die danach streben, die Grenzen von Leistung und Effizienz zu erweitern, ist die Einführung der metalladditiven Fertigung nicht länger nur eine Option; es ist ein strategischer Imperativ, um die Zukunft von Hochleistungssystemen voranzutreiben.
Teilen auf
MET3DP Technology Co., LTD ist ein führender Anbieter von additiven Fertigungslösungen mit Hauptsitz in Qingdao, China. Unser Unternehmen ist spezialisiert auf 3D-Druckgeräte und Hochleistungsmetallpulver für industrielle Anwendungen.
Fragen Sie an, um den besten Preis und eine maßgeschneiderte Lösung für Ihr Unternehmen zu erhalten!
Verwandte Artikel
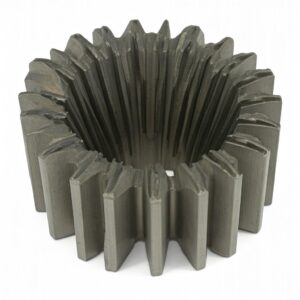
Hochleistungs-Düsenschaufelsegmente: Revolutionierung der Turbineneffizienz mit 3D-Metalldruck
Mehr lesen "Über Met3DP
Aktuelles Update
Unser Produkt
KONTAKT US
Haben Sie Fragen? Senden Sie uns jetzt eine Nachricht! Wir werden Ihre Anfrage mit einem ganzen Team nach Erhalt Ihrer Nachricht bearbeiten.
Holen Sie sich Metal3DP's
Produkt-Broschüre
Erhalten Sie die neuesten Produkte und Preislisten
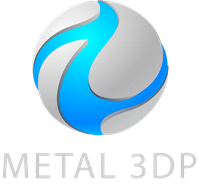
Metallpulver für 3D-Druck und additive Fertigung