Komponenten des Batterierahmens für die Kühlung von EVs durch 3D-Druck von Metall
Inhaltsübersicht
Einführung: Revolutionierung des EV-Wärmemanagements mit 3D-gedruckten Batterie-Kühlrahmen aus Metall
Die Revolution der Elektrofahrzeuge (EV) beschleunigt sich, angetrieben von Fortschritten in der Batterietechnologie, der Effizienz des Antriebsstrangs und einem weltweiten Vorstoß in Richtung nachhaltiger Mobilität. Das Herzstück eines jeden leistungsstarken Elektrofahrzeugs ist die Batterie - ein hochentwickeltes Energiespeichersystem, das eine präzise Kontrolle über seine Betriebsumgebung erfordert. Wirksames Wärmemanagement ist von entscheidender Bedeutung und wirkt sich direkt auf die Lebensdauer, Leistung, Sicherheit und Ladegeschwindigkeit der Batterie aus. Herkömmliche Fertigungsmethoden haben oft Schwierigkeiten, die komplexen, leichten und hocheffizienten Kühlkomponenten herzustellen, die erforderlich sind, um die ständig steigenden Anforderungen moderner Elektrofahrzeuge zu erfüllen. Dies ist der Grund Additive Fertigung von Metall (AM)gemeinhin als Metall bekannt 3D-Druckzu einer transformativen Technologie wird.
Genauer gesagt, die batteriekühlrahmeneine kritische Komponente, die für die Ableitung der während der Lade- und Entladezyklen entstehenden Wärme verantwortlich ist, kann erheblich von AM profitieren. Durch die Verwendung fortschrittlicher Metallpulver wie Aluminium-Silizium-Magnesium-Legierungen (AlSi10Mg) und Kupfer-Chrom-Zirkonium (CuCrZr) können Hersteller jetzt Kühlrahmen mit komplizierten internen Kanaldesigns, optimierten Flüssigkeitsströmungswegen und deutlich reduziertem Gewicht im Vergleich zu konventionell hergestellten Teilen herstellen. Der 3D-Metalldruck ermöglicht die Integration komplexer Merkmale, die Konsolidierung mehrerer Teile in einem einzigen Bauteil und schnelle Design-Iterationen, wodurch die Entwicklungszyklen beschleunigt und neue Leistungsniveaus erschlossen werden. Für Ingenieure und Beschaffungsmanager im wettbewerbsintensiven Automobilsektor ist das Verständnis des Potenzials von Metall-AM für Komponenten wie Batteriekühlrahmen nicht mehr optional, sondern unerlässlich, um die Nase vorn zu haben. Diese Technologie bietet einen Weg zu verbesserten Kühlung von EV-Batterienreichweite des Fahrzeugs und eine höhere Zuverlässigkeit des Gesamtsystems, was einen bedeutenden Sprung nach vorn in der automobile Innovation. Unternehmen, die zuverlässige Metall-Additiv-Fertigung lösungen wenden sich zunehmend an erfahrene Partner, die in der Lage sind, durchgängig hochwertige Komponenten zu liefern.
Als führendes Unternehmen im Bereich Metall-AM bietet Met3dp umfassende Lösungen an, die auf jahrzehntelanger Erfahrung in fortschrittlichen Drucktechnologien und Hochleistungswerkstoffen basieren. Unser Engagement für Qualität, von der Pulverproduktion bis zur Endkontrolle der Teile, stellt sicher, dass unsere Kunden aus der Automobilindustrie Komponenten erhalten, die den strengen Anforderungen der EV-Industrie entsprechen. Entdecken Sie, wie unsere Fähigkeiten Ihre Wärmemanagementsysteme der nächsten Generation unterstützen können.
Die kritische Rolle des Batteriekühlrahmens in Elektrofahrzeugen
Das Akkupaket ist wohl die wichtigste und teuerste Komponente eines Elektrofahrzeugs. Ihr Zustand und ihre Effizienz bestimmen direkt die Reichweite, die Beschleunigung, die Ladezeit und die allgemeine Langlebigkeit des Fahrzeugs. Lithium-Ionen-Batterien, der derzeitige Standard für E-Fahrzeuge, sind empfindlich gegenüber Temperaturschwankungen. Der Betrieb außerhalb ihres optimalen Temperaturfensters (in der Regel 15°C bis 35°C) kann zu beschleunigtem Abbau, verringerter Kapazität, thermischem Durchgehen und Beeinträchtigungen führen Leistung von EV-Batterien. Daher ist ein effektives Wärmemanagementsystem (BTMS) nicht nur von Vorteil, sondern von grundlegender Bedeutung für sicherheit von Elektrofahrzeugen und Zuverlässigkeit.
Die batteriekühlrahmen hat oft eine multifunktionale Rolle innerhalb des BTMS und der gesamten Batteriepackstruktur. Seine Hauptfunktion ist die Wärmeableitung. Sie enthält in der Regel Kanäle oder Platten, durch die eine Kühlflüssigkeit (Flüssigkeit oder manchmal Luft) zirkuliert, die überschüssige Wärme von den Batteriezellen aufnimmt und an einen Kühler oder Wärmetauscher weiterleitet. Das Design dieser Kühlkanäle ist entscheidend, um eine gleichmäßige Temperaturverteilung über alle Zellen zu gewährleisten und lokale Hot Spots zu vermeiden, die zu Degradation oder Ausfall führen können.
Neben der Wärmeregulierung kann der Kühlrahmen auch zur strukturellen Integrität des Akkupacks beitragen. Er kann Teil des Gehäuses sein, die Zellen vor äußeren Stößen und Vibrationen schützen und Befestigungspunkte für andere Komponenten bieten. Dieser Aspekt der strukturellen Integration macht Leichtbau ein entscheidender Faktor für das Design. Die Gewichtsreduzierung des Rahmens trägt direkt zur Verbesserung der Gesamtenergieeffizienz und der Reichweite des Fahrzeugs bei - entscheidende Kriterien auf dem wettbewerbsintensiven Markt für Elektrofahrzeuge.
Die Funktionen eines Batteriekühlrahmens lassen sich wie folgt zusammenfassen:
- Wärmeableitung: Effiziente Ableitung der von den Batteriezellen während des Betriebs und des Ladens erzeugten Wärme.
- Gleichmäßigkeit der Temperatur: Gewährleistung gleichmäßiger Temperaturen im gesamten Batteriemodul, um die Lebensdauer und Leistung zu maximieren.
- Strukturelle Unterstützung: Mechanische Unterstützung und Schutz für die Batteriezellen.
- Integration von Komponenten: Dient als Befestigungspunkt für Sensoren, Kabelbäume und andere Komponenten des Batteriemanagementsystems.
- Versiegelung und Eindämmung: Verhinderung von Kühlmittelleckagen und Schutz der Zellen vor Umwelteinflüssen.
In Anbetracht dieser kritischen Rolle erfordern Entwurf und Herstellung von Batteriekühlrahmen hohe Präzision, spezifische Materialeigenschaften (wie hohe Wärmeleitfähigkeit und gutes Verhältnis von Festigkeit zu Gewicht) und komplexe Geometrien. Herkömmliche Methoden wie Gießen, Strangpressen oder maschinelle Bearbeitung stoßen oft an ihre Grenzen, wenn es darum geht, die komplizierten inneren Kanäle und dünnen Wände herzustellen, die für eine optimale Wärmeleistung und ein geringes Gewicht erforderlich sind. Hier kommen die einzigartigen Fähigkeiten von die Herstellung von Automobilkomponenten über den 3D-Metalldruck bieten einen eindeutigen Vorteil: Sie ermöglichen Konstruktionen, die bisher als unmöglich galten, und verbessern die allgemeine antriebseffizienz. Beschaffungsmanager, die verlässliche Lieferanten für diese kritischen Komponenten suchen, müssen Hersteller mit nachgewiesener Expertise in fortschrittlichen Materialien und Prozessen in Betracht ziehen.
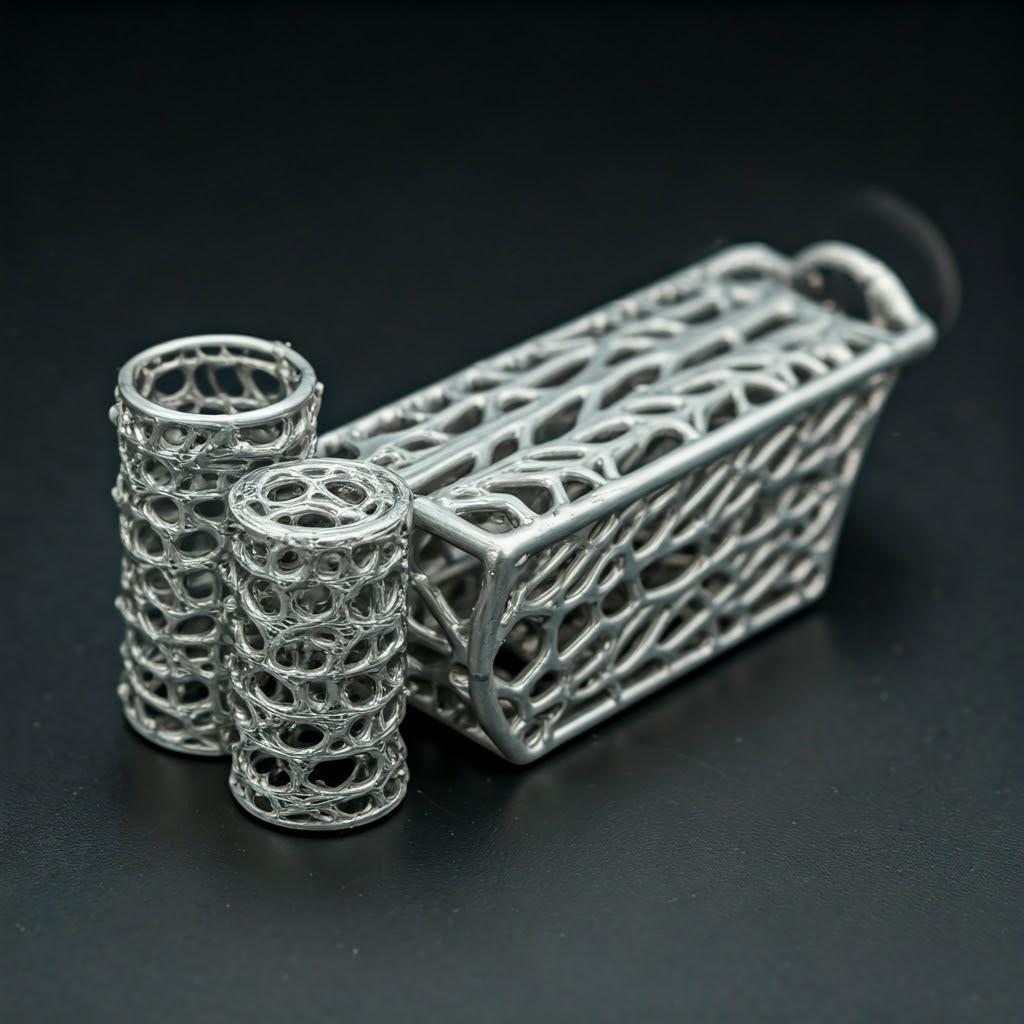
Warum die additive Fertigung von Metall ideal für Kühlkomponenten von EV-Batterien ist
Der Übergang zur Elektrifizierung stellt die Automobilhersteller vor große technische Herausforderungen, insbesondere in den Bereichen Wärmemanagement und Leichtbau. Die additive Fertigung von Metallen bietet überzeugende Lösungen für diese Herausforderungen, was sie zu einer zunehmend attraktiven Option für die Herstellung von Komponenten wie Kühlrahmen für Elektrofahrzeuge macht. Die Vorteile gegenüber herkömmlichen Fertigungsverfahren (Gießen, CNC-Bearbeitung, Stanzen, Löten) sind zahlreich und einschneidend:
- Unerreichte Gestaltungsfreiheit und Komplexität:
- Ausgeklügelte Kühlkanäle: AM ermöglicht die Erstellung hochkomplexer interner Kühlkanalgeometrien, einschließlich konformer Kanäle, die den Konturen der Batteriezellen genau folgen und den Oberflächenkontakt und die Wärmeübertragungseffizienz maximieren. Die Entwürfe können Merkmale wie Turbulatoren oder optimierte Strömungspfade enthalten, die mit herkömmlichen Methoden nicht oder nur mit unverhältnismäßig hohem Aufwand zu realisieren sind. Denken Sie an Mikrokanäle, variable Querschnitte und bio-inspirierte Strukturen für maximale thermische Leistung.
- Topologie-Optimierung: Ingenieure können die Struktur des Rahmens mit Hilfe von Berechnungswerkzeugen optimieren, indem sie Material in Bereichen mit geringer Belastung entfernen und kritische Stellen verstärken. Dies führt zu deutlich leichteren Teilen (**Leichtbaustrukturen**), ohne die strukturelle Integrität zu beeinträchtigen - ein entscheidender Faktor für die Erhöhung der Reichweite von Elektrofahrzeugen.
- Teil Konsolidierung: Mehrere Komponenten (z. B. Durchflussverteiler, Montagehalterungen, Rahmenteile), die traditionell separat hergestellt und dann zusammengebaut werden (was oft Löten oder Schweißen erfordert, was zu Fehlern führen kann), können integriert und als ein einziges, monolithisches Teil gedruckt werden. Dadurch werden Montagezeit, Kosten, Gewicht und potenzielle Leckagepfade reduziert, was zu einer robusteren konsolidierte Teile.
- Beschleunigte Entwicklung & Prototyping:
- Schnelle Iteration: Metall-AM ermöglicht rapid Prototyping Automotive komponenten direkt aus CAD-Daten. Designänderungen für Kühlkanäle oder Strukturelemente können innerhalb von Tagen implementiert und getestet werden, anstatt Wochen oder Monate für Werkzeugänderungen beim Gießen oder Strangpressen zu benötigen. Dies beschleunigt den Entwicklungszyklus für neue Akkupack-Designs dramatisch.
- Werkzeuglose Produktion: Durch AM entfällt der Bedarf an teuren und zeitaufwändigen Werkzeugen (Gussformen, Gesenke). Dies ist besonders vorteilhaft für kleine bis mittlere Produktionsläufe, kundenspezifische Anpassungen oder die Herstellung von Altteilen, für die es keine Originalwerkzeuge mehr gibt.
- Material Vorteile & Optimierung:
- Fortschrittliche Legierungen: Bei AM-Prozessen können Hochleistungslegierungen eingesetzt werden, die speziell aufgrund ihrer Wärmeleitfähigkeit (wie Kupferlegierungen) oder ihres Festigkeits-Gewichts-Verhältnisses (wie Aluminiumlegierungen) ausgewählt und genau auf die Bedürfnisse der Anwendung zugeschnitten werden. Met3dp hat sich auf die Verarbeitung von Materialien wie AlSi10Mg spezialisiert und bietet Fachwissen bei der Entwicklung von Parametern für Legierungen wie CuCrZr.
- Optimierte Materialverwendung: AM ist ein additives Verfahren, d. h. das Material wird nur dort eingesetzt, wo es benötigt wird. Dies führt im Vergleich zu subtraktiven Verfahren wie der CNC-Bearbeitung häufig zu weniger Materialabfall und trägt so zu Kosteneinsparungen und Nachhaltigkeit bei.
- Flexibilität der Lieferkette & On-Demand-Produktion:
- Dezentralisierte Fertigung: Die Teile können möglicherweise näher am Montageort gedruckt werden, wodurch sich die Versandkosten und die Vorlaufzeiten verringern.
- Digitales Inventar: Die Entwürfe werden digital gespeichert, so dass die Teile nach Bedarf gedruckt werden können, was den Bedarf an großen physischen Beständen verringert.
Während sich die herkömmlichen Methoden nach wie vor für die Produktion sehr hoher Stückzahlen bei einfacheren Designs eignen, ist die einzigartige Metall-AM-Vorteile - Komplexität, Konsolidierung, Geschwindigkeit und Optimierung - machen es außerordentlich geeignet für die anspruchsvollen Anforderungen der nächsten Generation von EV-Batteriekühlrahmen. Da die Industrie auf höhere Energiedichten und schnelleres Aufladen drängt, wird die Fähigkeit, hoch optimierte Wärmemanagementkomponenten durch AM zu schaffen, immer wichtiger werden. Die Wahl eines kompetenten 3D-Druck von Metall ein Partner wie Met3dp, der über Fachwissen zu den relevanten Materialien und Prozessen verfügt, ist der Schlüssel zur effektiven Nutzung dieser Vorteile.
Vertiefung der Materialien: AlSi10Mg und CuCrZr für optimale thermische Leistung
Die Wahl des Materials ist von grundlegender Bedeutung für die Leistung eines EV-Batteriekühlrahmens. Das Material muss eine Kombination von Eigenschaften aufweisen: hohe Wärmeleitfähigkeit, um die Wärme effizient von den Zellen abzuleiten, gute mechanische Festigkeit, um strukturelle Lasten und Vibrationen zu bewältigen, geringe Dichte für geringes Gewicht, Korrosionsbeständigkeit gegen Kühlmittel und hervorragende Verarbeitbarkeit durch additive Fertigung. Zwei herausragende Kandidaten, die häufig für diese Anwendung in Betracht gezogen werden, sind AlSi10Mg (eine Aluminiumlegierung) und CuCrZr (eine Kupferlegierung). Das Verständnis ihrer jeweiligen Stärken und Schwächen ist entscheidend für auswahl von Werkstoffen für die Automobilindustrie.
1. AlSi10Mg (Aluminium-Silizium-Magnesium-Legierung): Das leichte Arbeitspferd
AlSi10Mg ist eine der am häufigsten verwendeten Aluminiumlegierungen in der additiven Fertigung von Metallen, insbesondere beim Laser Powder Bed Fusion (LPBF). Seine Beliebtheit beruht auf der hervorragenden Ausgewogenheit seiner Eigenschaften und seiner guten Verarbeitbarkeit.
- Eigenschaften:
- Gute Wärmeleitfähigkeit: AlSi10Mg ist zwar nicht so hoch wie reines Aluminium oder Kupferlegierungen, bietet aber eine respektable Wärmeleitfähigkeit (typischerweise 120-140 W/m-K nach der Wärmebehandlung), die für viele Flüssigkühlungsanwendungen ausreicht.
- Ausgezeichnetes Verhältnis von Stärke zu Gewicht: Dies ist ein großer Vorteil. Aluminiumlegierungen sind wesentlich leichter als Stahl oder Kupfer, was direkt zur Gewichtsreduzierung und zur Verbesserung der Reichweite von Fahrzeugen beiträgt. AlSi10Mg bietet eine gute mechanische Festigkeit und Härte, insbesondere nach einer geeigneten Wärmebehandlung.
- Gute Korrosionsbeständigkeit: Aluminium bildet von Natur aus eine schützende Oxidschicht, die eine gute Beständigkeit gegen gängige Kühlmittel bietet.
- Ausgezeichnete Druckbarkeit: AlSi10Mg ist gut bekannt und lässt sich mit LPBF-Systemen relativ einfach verarbeiten. Es weist eine gute Schmelzbadstabilität auf und führt zu dichten Teilen.
- Kosten-Nutzen-Verhältnis: Im Vergleich zu Kupferlegierungen sind Aluminiumpulver im Allgemeinen kostengünstiger.
- Eignung für Kühlregale: AlSi10Mg ist eine ausgezeichnete Wahl, wenn Leichtbau eine wichtige Rolle spielt und die thermische Belastung überschaubar ist. Seine Verarbeitbarkeit ermöglicht die komplexen Geometrien, die für effiziente Kühlkanäle erforderlich sind. Es ist oft die Standardwahl für Strukturbauteile mit integrierten Kühlfunktionen. Eine Nachbearbeitung, einschließlich Wärmebehandlung (z. B. T6-Alterung), ist in der Regel erforderlich, um optimale mechanische Eigenschaften zu erzielen.
- Angebot von Met3dp: Met3dp verfügt über umfassende Erfahrung in der Verarbeitung von AlSi10Mg-Pulver und nutzt fortschrittliche Gaszerstäubungstechniken, um hochgradig kugelförmige Pulver mit hervorragender Fließfähigkeit herzustellen, die für die Erzielung einer gleichmäßigen Dichte und mechanischer Eigenschaften in gedruckten Teilen entscheidend sind. Unsere strenge Qualitätskontrolle gewährleistet, dass die Pulverchargen den strengen Spezifikationen der Automobilindustrie entsprechen.
Tabelle: AlSi10Mg-Eigenschaften (typische Werte für AM)
Eigentum | Typischer Wert (nach der Wärmebehandlung) | Einheit | Bedeutung für Kühlregale |
---|---|---|---|
Dichte | ~2.67 | g/cm³ | Hervorragend geeignet für Lightweighting |
Wärmeleitfähigkeit | 120 – 140 | W/(m-K) | Gute Wärmeableitungsfähigkeit |
Streckgrenze | 230 – 280 | MPa | Gute strukturelle Integrität |
Endgültige Zugfestigkeit | 330 – 400 | MPa | Robustheit gegen mechanische Belastungen |
Dehnung beim Bruch | 6 – 10 | % | Duktilität, Bruchfestigkeit |
Druckbarkeit | Ausgezeichnet | K.A. | Ermöglicht komplexe Designs, zuverlässige Fertigung |
Relative Kosten | Mäßig | K.A. | Kostengünstige Lösung |
In Blätter exportieren
2. CuCrZr (Kupfer-Chrom-Zirkonium-Legierung): Der Meister der Wärmeleitfähigkeit
Wenn maximale Wärmeableitung absolute Priorität hat, kommen Kupferlegierungen wie CuCrZr ins Spiel. Kupfer verfügt über eine wesentlich höhere Wärmeleitfähigkeit als Aluminium.
- Eigenschaften:
- Außergewöhnliche Wärmeleitfähigkeit: Dies ist der Hauptvorteil von CuCrZr. Seine Wärmeleitfähigkeit (typischerweise >300 W/m-K) ist mehr als doppelt so hoch wie die von AlSi10Mg, was eine äußerst effiziente Wärmeübertragung ermöglicht, die für Hochleistungsakkus oder Schnellladeszenarien entscheidend ist.
- Gute Hochtemperaturfestigkeit: CuCrZr behält im Vergleich zu reinem Kupfer eine angemessene Festigkeit bei erhöhten Temperaturen.
- Gute elektrische Leitfähigkeit: Während es für Kühlrahmen weniger kritisch ist, ist seine hohe elektrische Leitfähigkeit bemerkenswert.
- Höhere Dichte: Kupferlegierungen sind wesentlich dichter (~8,9 g/cm³) als Aluminiumlegierungen, was eine Herausforderung für die Leichtbauziele darstellt. Der Gewichtsnachteil muss durch die überlegene thermische Leistung gerechtfertigt werden.
- Herausforderungen bei der Verarbeitung: Kupferlegierungen sind aufgrund ihrer hohen Reflektivität und Wärmeleitfähigkeit bekanntermaßen schwieriger mit laserbasiertem AM zu bearbeiten, was zu Prozessinstabilitäten und Defekten wie Porosität führen kann, wenn nicht mit Fachwissen und optimierten Anlagen gearbeitet wird. Elektronenstrahlschmelzen (EBM/SEBM), wie die von Met3dp-Partnern potenziell angebotenen oder genutzten Systeme, kann aufgrund der besseren Energieabsorption manchmal Vorteile für die Bearbeitung von Kupfer bieten.
- Höhere Kosten: Pulver aus Kupferlegierungen sind im Allgemeinen teurer als Pulver aus Aluminiumlegierungen.
- Eignung für Kühlregale: CuCrZr ist das bevorzugte Material, wenn die thermische Leistung im Vordergrund steht und die Bedenken hinsichtlich des zusätzlichen Gewichts und der Kosten überwiegen. Es ist ideal für lokale Bereiche mit hohem Wärmefluss oder anspruchsvolle Anwendungen, die eine schnelle Ableitung großer Wärmemengen erfordern. Das Design muss die thermischen Eigenschaften des Materials ausnutzen, um seine Verwendung zu rechtfertigen, was oft hoch optimierte, dünnwandige Strukturen erfordert, die durch AM erreicht werden können.
- Der Ansatz von Met3dp: Kupferlegierungen stellen zwar eine Herausforderung dar, aber Met3dp’s Fokus auf fortschrittliche Pulverproduktion und Prozesskontrolle durch seine SEBM-Drucker und Fachwissen ist es in der Lage, anspruchsvolle Materialien zu verarbeiten. Wir arbeiten eng mit unseren Kunden zusammen, um die Machbarkeit zu bestimmen und die Parameter für Materialien wie CuCrZr zu optimieren, damit die Teile die strengen thermischen und mechanischen Anforderungen erfüllen. Der Zugang zu hochwertigem, gasverdüstem CuCrZr-Pulver mit kontrollierten Eigenschaften ist der Schlüssel, ein Bereich, in dem Met3dp’s fortschrittliches Pulverherstellungssystem übertrifft.
Tabelle: CuCrZr-Eigenschaften (typische Werte für AM)
Eigentum | Typischer Wert (nach der Wärmebehandlung) | Einheit | Bedeutung für Kühlregale |
---|---|---|---|
Dichte | ~8.9 | g/cm³ | Erheblicher Gewichtsnachteil gegenüber Aluminium |
Wärmeleitfähigkeit | >300 | W/(m-K) | Außergewöhnliche Fähigkeit zur Wärmeableitung |
Streckgrenze | 350 – 450 | MPa | Gute mechanische Festigkeit |
Endgültige Zugfestigkeit | 450 – 550 | MPa | Hohe Robustheit |
Dehnung beim Bruch | 10 – 20 | % | Gute Duktilität |
Druckbarkeit | Herausfordernd (Erfordert Fachwissen) | K.A. | Prozesskontrolle ist entscheidend für die Teilequalität |
Relative Kosten | Hoch | K.A. | Kosten durch Leistungsanforderungen gerechtfertigt |
In Blätter exportieren
Schlussfolgerung zu den Materialien:
Die Wahl zwischen AlSi10Mg und CuCrZr hängt in hohem Maße von den spezifischen Anforderungen der EV-Batteriekühlrahmenanwendung ab.
- Wählen Sie AlSi10Mg wenn: Ein geringes Gewicht wichtig ist, die thermische Belastung moderat ist, die Kosten ein wichtiger Faktor sind und eine einfache Verarbeitung gewünscht ist.
- Wählen Sie CuCrZr wenn: Maximale Wärmeableitung das primäre Ziel ist, ein höheres Gewicht akzeptabel ist und das Budget ein hochwertigeres Material und möglicherweise eine komplexere Verarbeitung zulässt.
Häufig werden hybride Ansätze oder die lokale Verwendung von Kupfereinsätzen innerhalb eines Aluminiumrahmens in Betracht gezogen, obwohl AM monolithische Designs in beiden Materialien ermöglicht. Die Arbeit mit einem anbieter von Hochleistungslegierungen und ein AM-Experte wie Met3dp stellt sicher, dass die Materialauswahl im Hinblick auf Leistung, Kosten und Herstellbarkeit optimiert wird, um das volle Potenzial des 3D-Metalldrucks für das fortschrittliche Wärmemanagement von Elektrofahrzeugen auszuschöpfen.
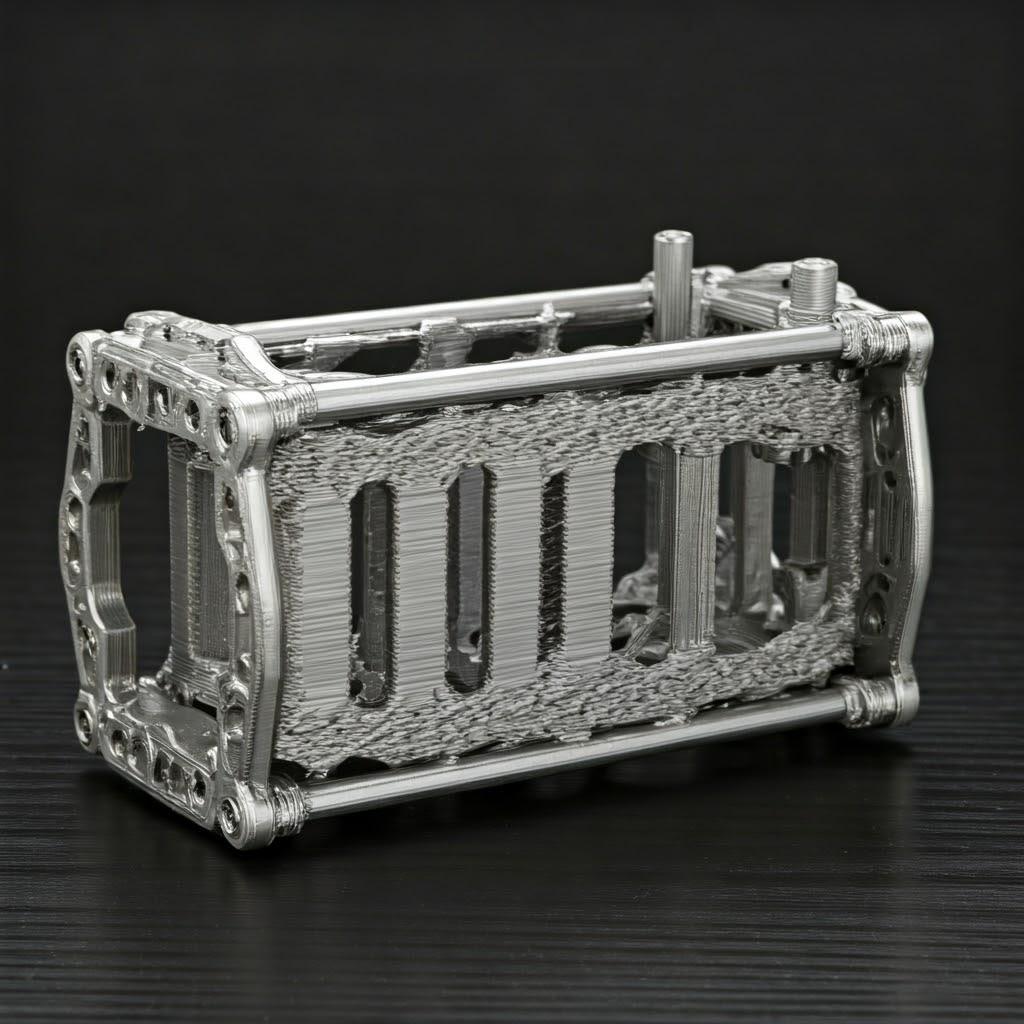
Design for Additive Manufacturing (DfAM)-Grundsätze für Batterie-Kühlrahmen
Die einfache Nachbildung eines Designs, das für die herkömmliche Fertigung mit 3D-Metalldruck vorgesehen ist, schöpft selten das gesamte Potenzial der additiven Technologie aus. Um die Vorteile von AM für Komponenten wie Kühlrahmen für Elektroautos wirklich zu nutzen, müssen Ingenieure die folgenden Aspekte berücksichtigen Design für additive Fertigung (DfAM) grundsätze. DfAM bedeutet, den Konstruktionsprozess zu überdenken, um die Vorteile der schichtweisen Fertigung zu maximieren, wie z. B. geometrische Komplexität, Bauteilkonsolidierung und Leichtbau, und gleichzeitig die Einschränkungen des spezifischen AM-Prozesses zu berücksichtigen (z. B. Laser Powder Bed Fusion – LPBF oder Selective Electron Beam Melting – SEBM). Anwendung von DfAM automotive strategien ist für die Entwicklung leistungsfähiger und kostengünstiger Kühllösungen von entscheidender Bedeutung.
Zu den wichtigsten DfAM-Prinzipien, die für die Kühlung von EV-Batterien relevant sind, gehören:
- Optimierung der internen Kühlkanäle:
- Komplexe Geometrien: Gehen Sie über einfache gerade oder kreisförmige Kanäle hinaus. AM ermöglicht sanft gekrümmte Pfade, variable Querschnitte und konforme Kanäle, die der Form der Batteriezellen oder -module genau folgen. Dies maximiert die Kontaktfläche für die Wärmeübertragung und kann den Druckabfall verringern.
- Merkmale der Flussoptimierung: Integrieren Sie Merkmale wie interne Rippen, Turbulatoren oder optimierte Krümmer direkt in das Design, um die Kühlmittelvermischung und die Wärmeübertragungseffizienz zu verbessern. CFD-Simulationen (Computational Fluid Dynamics) werden zu leistungsstarken Werkzeugen, wenn sie mit der geometrischen Freiheit von AM kombiniert werden, um optimierung der Kühlkanäle.
- Selbsttragende Kanäle: Entwerfen Sie interne Kanäle mit Querschnitten (z. B. tropfenförmig, rautenförmig) und Ausrichtungen, die den Bedarf an internen Stützstrukturen minimieren oder eliminieren, die nach dem Druck nur sehr schwer oder gar nicht entfernt werden können. Winkel von mehr als 45 Grad zur Horizontalen sind im Allgemeinen selbsttragend.
- Strategien zur Gewichtsreduzierung:
- Topologie-Optimierung: Mithilfe von Softwaretools werden die strukturellen Belastungen des Rahmens analysiert und automatisch Material aus unkritischen Bereichen entfernt, was zu organisch wirkenden, hocheffizienten Strukturen führt. Dies ist ein Eckpfeiler von leichtbauweise der Komponenten für EVs.
- Gitterförmige Strukturen: Interne Gitter- oder Zellenstrukturen in dickere Rahmenabschnitte einbauen. Diese Strukturen verringern das Gewicht und den Materialverbrauch erheblich, während die erforderliche Steifigkeit und Festigkeit erhalten bleibt. Außerdem können sie das Aufprallverhalten durch Energieabsorption verbessern.
- Dünne Mauern: AM ermöglicht die Herstellung sehr dünner, aber dennoch strukturell solider Wände (bis zu ca. 0,3-0,5 mm je nach Material und Maschine), was das Gewicht im Vergleich zu den minimalen Wandstärken, die mit Guss erreicht werden können, weiter reduziert.
- Teil Konsolidierung:
- Integrierte Funktionen: Konstruieren Sie Montagehalterungen, Sensorgehäuse, Durchflussanschlüsse und Strukturelemente als integrale Bestandteile des Kühlrahmens. Dadurch entfallen Montageschritte, die Anzahl der Teile wird reduziert, potenzielle Leckstellen (wie Dichtungen oder Lötstellen) werden minimiert und das Gesamtgewicht und die Kosten werden häufig gesenkt.
- Minimierung der Stützstrukturen:
- Orientierung: Berücksichtigen Sie sorgfältig die Ausrichtung des Teils auf der Bauplatte. Wenn Sie Features so ausrichten, dass sie selbsttragend sind (in der Regel mit einem Überhang von mehr als 45°), verringert sich das Volumen der benötigten Stützstrukturen.
- Optimierung der Unterstützung: Wenn Stützen unvermeidlich sind (z. B. große flache Unterseiten), sollten sie so gestaltet sein, dass sie leicht zu entfernen sind und kritische Oberflächen nur minimal beeinträchtigen. Verwenden Sie spezielle Stützentypen (z. B. Baumstützen, Blockstützen), die von der AM-Vorbereitungssoftware angeboten werden.
- Stressabbau: Berücksichtigen Sie, wie Teilegeometrie und -ausrichtung den Aufbau von Eigenspannungen während des Drucks beeinflussen. Große flache Bereiche oder abrupte Übergänge können das Spannungs- und Verformungspotenzial erhöhen.
- Prozessspezifische Überlegungen:
- Minimale Featuregröße: Verstehen Sie die Auflösungsgrenzen des gewählten AM-Verfahrens (LPBF bietet in der Regel feinere Merkmale als SEBM). Stellen Sie sicher, dass kritische Merkmale wie dünne Wände oder kleine Kanaldetails im Rahmen der Möglichkeiten der Maschine liegen.
- Entfernung von Puder: Vergewissern Sie sich, dass die Konstruktion Wege oder Öffnungen aufweist, durch die nicht verschmolzenes Pulver nach dem Druck leicht aus den internen Kanälen und Hohlräumen entfernt werden kann. Eingeschlossenes Pulver kann das Gewicht erhöhen und möglicherweise den Betrieb beeinträchtigen.
Durch die Anwendung dieser DfAM-Prinzipien können Ingenieure über inkrementelle Verbesserungen hinausgehen und schrittweise Veränderungen in der Kühlleistung, Gewichtsreduzierung und Bauteilintegration erreichen. Die Zusammenarbeit mit einem AM-Experten wie Met3dp während der Entwurfsphase kann unschätzbare Einblicke in die Prozessfähigkeiten und -beschränkungen liefern und sicherstellen, dass der Entwurf für die Herstellbarkeit und Leistung optimiert ist. Das Team von Met3dp kann bei DfAM helfen, indem es verschiedene Druckverfahren um den spezifischen Anforderungen Ihres EV-Batteriekühlrahmens am besten gerecht zu werden.
Erreichen von Präzision: Toleranzen, Oberflächengüte und Genauigkeit bei Metall-AM
Während die additive Fertigung von Metallen eine beispiellose Designfreiheit bietet, ist es für Ingenieure und Beschaffungsmanager von entscheidender Bedeutung, den Grad der erreichbaren Präzision in Bezug auf Maßgenauigkeit, Toleranzen und Oberflächengüte zu verstehen. Diese Faktoren wirken sich direkt auf die Funktionalität, den Zusammenbau und die Leistung von EV-Batteriekühlrahmen aus, insbesondere in Bezug auf die Dichtungsflächen, die Schnittstellen zu den Batteriemodulen und die Kühlmittelströmungseigenschaften. Das Erreichen der erforderlichen Toleranzen beim 3D-Druck von Metall und normen für die Oberflächenbeschaffenheit im Automobilbereich anwendungen erfordern eine sorgfältige Kontrolle des gesamten AM-Workflows.
Maßgenauigkeit und Toleranzen:
Die Genauigkeit eines Metall-AM-Teils bezieht sich darauf, wie genau seine endgültigen Abmessungen mit dem ursprünglichen CAD-Modell übereinstimmen. Toleranzen definieren die zulässige Abweichung für bestimmte Abmessungen. Die typischerweise erreichbare Genauigkeit und Toleranzen hängen von mehreren Faktoren ab:
- AM-Prozess: LPBF bietet im Allgemeinen eine höhere Genauigkeit und feinere Details als SEBM, obwohl SEBM bei bestimmten Geometrien und Materialien schneller sein kann.
- Kalibrierung der Maschine: Die Präzision und Kalibrierung des 3D-Druckers sind entscheidend. Gut gewartete, hochwertige Maschinen, wie die von Met3dp verwendeten, sind unerlässlich.
- Material: Verschiedene Werkstoffe verhalten sich beim Schmelzen und Erstarren unterschiedlich, was sich auf die Schrumpfung und mögliche Verformung auswirkt. AlSi10Mg und CuCrZr haben unterschiedliche thermische Eigenschaften, die sich auf die endgültige Genauigkeit auswirken.
- Größe und Geometrie der Teile: Größere Teile oder komplexe Geometrien sind anfälliger für thermische Spannungen und mögliche Abweichungen.
- Orientierung aufbauen: Die Ausrichtung des Teils auf der Bauplatte beeinflusst die Genauigkeit aufgrund der anisotropen Natur des Schicht-für-Schicht-Prozesses.
- Nachbearbeiten: Schritte wie die Wärmebehandlung können zu geringfügigen Maßänderungen führen, während die CNC-Bearbeitung häufig eingesetzt wird, um sehr enge Toleranzen bei kritischen Merkmalen zu erreichen.
Typische Werte:
- Allgemeine Toleranzen (wie gedruckt): Bei gut kontrollierten LPBF-Prozessen liegen die allgemeinen Maßtoleranzen häufig im Bereich von ±0,1 mm bis ±0,2 mm für kleinere Merkmale (z. B. bis zu 50-100 mm) und können sich bei größeren Abmessungen leicht erhöhen (z. B. ±0,2 % des Nennmaßes).
- Engere Toleranzen (mit maschineller Bearbeitung): Für kritische Schnittstellen, Befestigungspunkte oder Dichtungsflächen, die eine engere Kontrolle erfordern, wird in der Regel eine CNC-Nachbearbeitung durchgeführt. Durch die maschinelle Bearbeitung können leicht Toleranzen von ±0,025 mm bis ±0,05 mm oder sogar noch enger erreicht werden, was den herkömmlichen Fertigungsstandards entspricht.
Oberflächengüte (Rauhigkeit):
Die Oberflächengüte, die häufig durch den arithmetischen Mittelwert der Rauheit (Ra) quantifiziert wird, ist ein weiterer wichtiger Aspekt, insbesondere bei internen Kühlkanälen und Dichtungsflächen.
- Oberflächenrauhigkeit im Druckzustand: Die Oberflächenbeschaffenheit von AM-Teilen ist aufgrund des schichtweisen Aufbaus und der teilweise geschmolzenen Pulverpartikel, die an der Oberfläche haften, von Natur aus rauer als bei maschinell bearbeiteten Oberflächen.
- Obere Oberflächen: Im Allgemeinen glatter (Ra 5-10 µm).
- Vertikale Mauern: Mäßige Rauhigkeit (Ra 8-15 µm).
- Nach oben/unten gerichtete Oberflächen: Die Rauheit hängt stark vom Winkel relativ zur Bauplatte ab. Nach unten gerichtete Oberflächen (<45°) erfordern Stützstrukturen, und ihre Entfernung hinterlässt Spuren, die die Rauheit erheblich erhöhen (Ra > 15-20 µm).
- Interne Kanäle: Die Rauheit in engen oder komplexen internen Kanälen ist besonders schwierig zu kontrollieren und zu verbessern. Die aufgedruckte Rauheit kann sich auf die Fluiddynamik auswirken und möglicherweise den Druckabfall erhöhen oder die Wärmeübergangskoeffizienten beeinträchtigen. DfAM-Überlegungen (z. B. Kanalform, Ausrichtung) spielen hier eine Rolle.
- Verbesserung der Oberflächengüte: Nachbearbeitungsmethoden sind unerlässlich, um glattere Oberflächen zu erzielen:
- Abrasive Fließbearbeitung (AFM): Kann zum Glätten interner Kanäle verwendet werden.
- Perlstrahlen/Sandstrahlen: Sorgt für ein gleichmäßiges mattes Finish und entfernt losen Puder, reduziert aber nur mäßig Ra.
- Taumeln/Gleitschleifen: Wirksam zum Glätten der Außenflächen kleinerer Teile.
- Polieren: Manuelles oder automatisiertes Polieren zur Erzielung sehr glatter, spiegelähnlicher Oberflächen (Ra < 0,8 µm) auf bestimmten Flächen.
- Bearbeitungen: Bietet die beste Kontrolle der Oberflächenbeschaffenheit von zugänglichen Merkmalen.
Qualitätskontrolle:
Sicherstellung einer einheitlichen Maßgenauigkeit, die die Metall-AM teile erfordert eine strenge Qualitätskontrolle während des gesamten Prozesses. Dies beinhaltet:
- Überprüfung der Qualität des Pulvers.
- Regelmäßige Maschinenkalibrierung und -wartung.
- Prozessbegleitende Überwachung (z. B. Schmelzbadüberwachung).
- Maßkontrolle nach der Fertigung mit CMM (Coordinate Measuring Machines) oder 3D-Scanning.
- Messungen der Oberflächenrauhigkeit.
Met3dp legt großen Wert auf die Qualitätskontrolle und setzt fortschrittliche Messgeräte und eine strenge Prozessüberwachung ein, um sicherzustellen, dass die Kühlrahmen für Elektrofahrzeuge die von den Kunden der Automobilindustrie geforderten genauen Spezifikationen erfüllen. Das Verständnis für die erreichbare Präzision und die Planung der notwendigen Nachbearbeitungsschritte sind wichtige Bestandteile des Beschaffungsprozesses für 3D-Druck von Metall Komponenten.

Wichtige Nachbearbeitungsschritte für 3D-gedruckte Kühlrahmen
3D-gedruckte Metallteile, wie z. B. Kühlrahmen für Elektroautos aus AlSi10Mg oder CuCrZr, kommen selten fertig aus dem Drucker. Die Nachbearbeitung ist eine kritische Phase im Fertigungsablauf, die notwendig ist, um die erforderlichen Materialeigenschaften, Maßtoleranzen, Oberflächengüte und Gesamtfunktionalität zu erreichen. Das Verständnis dieser Schritte ist für Beschaffungsmanager und Ingenieure bei der Planung von Produktionszeitplänen und Kostenschätzungen von entscheidender Bedeutung.
Zu den üblichen Nachbearbeitungsschritten für AM-Batteriekühlrahmen aus Metall gehören:
- Stressabbau / Wärmebehandlung:
- Zweck: Die schnellen Erwärmungs- und Abkühlungszyklen bei AM-Verfahren (insbesondere LPBF) führen zu inneren Spannungen im gedruckten Teil. Diese Eigenspannungen können zu Verformungen oder Rissen während des Drucks, der Entfernung des Trägers oder später im Lebenszyklus des Teils führen. Durch eine Wärmebehandlung werden diese Spannungen abgebaut und, was besonders wichtig ist, die Mikrostruktur des Materials verändert, um die gewünschten mechanischen Eigenschaften (Festigkeit, Härte, Duktilität) zu erreichen.
- Verfahren:
- Stressabbau: In der Regel wird dies durchgeführt, während das Teil noch auf der Bauplatte befestigt ist. Dabei wird das Teil auf eine bestimmte Temperatur erwärmt (unterhalb der Alterungstemperatur für AlSi10Mg) und für einen bestimmten Zeitraum gehalten, gefolgt von einer langsamen Abkühlung.
- Lösungsglühen & Alterung (z. B. T6 für AlSi10Mg): Bei Legierungen wie AlSi10Mg ist oft eine mehrstufige Wärmebehandlung (Lösungsglühen bei hoher Temperatur, Abschrecken, dann künstliche Alterung bei niedrigerer Temperatur) erforderlich, um Festigkeit und Härte deutlich zu erhöhen. Spezifische Wärmebehandlung AlSi10Mg zyklen hängen von den gewünschten Endeigenschaften ab. CuCrZr profitiert auch von spezifischen Wärmebehandlungen zur Optimierung seiner Festigkeit und Leitfähigkeit.
- Erwägungen: Die Wärmebehandlung muss sorgfältig kontrolliert werden (Atmosphäre, Temperaturrampen, Haltezeiten), um gleichbleibende Ergebnisse zu erzielen. Sie kann zu leichten Maßänderungen führen, die berücksichtigt werden müssen.
- Entfernen des Teils von der Bauplatte:
- Zweck: Trennen der gedruckten Komponente(n) von der Metallbauplatte, mit der sie während des Drucks verschmolzen wurden.
- Verfahren: Dies geschieht in der Regel durch Drahterodieren (Electrical Discharge Machining) oder mit einer Bandsäge. Dabei muss darauf geachtet werden, dass das Teil nicht beschädigt wird.
- Entfernung der Stützstruktur:
- Zweck: Entfernen der temporären Strukturen, die zur Unterstützung von Überhängen und komplexen Elementen während des Bauprozesses gedruckt wurden.
- Verfahren: Dies kann ein schwieriger und arbeitsintensiver Schritt sein, insbesondere bei komplexen Innengeometrien. Methoden umfassen:
- Manuelle Entfernung mit Zangen, Scheren oder Schleifgeräten.
- CNC-Bearbeitung.
- Manchmal elektrochemische Bearbeitung oder andere Verfahren für schwer zugängliche Stellen.
- Erwägungen: Die Entfernung von Halterungen kann Spuren oder Grate auf der Oberfläche hinterlassen, die oft weitere Bearbeitungsschritte erfordern. DfAM spielt eine entscheidende Rolle bei der Minimierung des Bedarfs an Halterungen und bei deren Gestaltung für eine leichtere Entfernung.
- CNC-Bearbeitung:
- Zweck: Zur Erzielung enger Toleranzen bei kritischen Abmessungen, zur Herstellung präziser Passflächen, zur Gewährleistung der Ebenheit von Dichtungen oder zur Verbesserung der Oberflächengüte bestimmter Merkmale.
- Verfahren: Verwendung von Standard-CNC-Fräs- oder Drehbearbeitungen zur Bearbeitung bestimmter Bereiche des AM-Teils.
- Anwendungen: Bearbeitung von Schraubenlöchern mit präzisen Durchmessern und Positionen, Herstellung von O-Ring-Nuten, Abflachung von Dichtungsflächen, Erzielung spezifischer Ra-Werte an Schnittstellen. CNC-Bearbeitung von AM-Metallteilen ist bei funktionalen Komponenten sehr verbreitet.
- Oberflächenveredelung und Reinigung:
- Zweck: Zur Entfernung von losem Pulver, zur Verbesserung der Oberflächenglätte, zur Erzielung eines gewünschten ästhetischen Aussehens oder zur Vorbereitung der Oberfläche für die Beschichtung.
- Verfahren:
- Entfernung von Puder: Entleerung mit Hilfe von Druckluft, Vibration oder Spezialgeräten, besonders wichtig bei internen Kanälen.
- Sprengen: Perlstrahlen oder Sandstrahlen erzeugt eine gleichmäßige matte Oberfläche.
- Taumeln/Gleitschleifen: Glättet Außenflächen und Kanten.
- Polieren: Für sehr niedrige Ra-Werte auf bestimmten Flächen.
- Abrasive Fließbearbeitung (AFM) / Strangpresshonen: Zum Glätten von inneren Kanälen, indem abrasive Medien durch sie hindurchgeleitet werden.
- Dichtheitsprüfung:
- Zweck: Absolut wichtig für alle Komponenten, die Kühlmittel führen. Gewährleistet die Integrität der Kühlkanäle und verhindert Leckagen.
- Verfahren: Dabei werden die Kühlkanäle unter Druck gesetzt (in der Regel mit Luft oder Helium unter Wasser oder mit Druckabfall-Sensoren), um undichte Stellen oder Porositäten, die die Kanalwände durchbrechen, zu erkennen. Dichtheitsprüfung von Kühlsystemen ist ein nicht verhandelbarer Schritt der Qualitätssicherung.
- Inspektion und Qualitätskontrolle:
- Zweck: Überprüfung, ob das Teil alle Maß-, Material- und Funktionsspezifikationen erfüllt.
- Verfahren: Maßkontrolle (CMM, 3D-Scanning), Messung der Oberflächenrauheit, Prüfung der Materialeigenschaften (falls erforderlich), visuelle Endkontrolle.
Das Besondere Post-Processing-Dienstleistungen hängt von der Komplexität des Designs des Kühlrahmens, dem verwendeten Material und den spezifischen Anforderungen der Anwendung ab. Die Zusammenarbeit mit einem Full-Service-Anbieter wie Met3dp, der sich mit den Feinheiten des Drucks und der Nachbearbeitung auskennt, gewährleistet einen optimierten Arbeitsablauf und qualitativ hochwertige Endkomponenten, die in das EV-Batteriepaket integriert werden können.
Überwindung von Herausforderungen beim 3D-Druck von Metall für Automobilanwendungen
Die additive Fertigung von Metallen bietet zwar erhebliche Vorteile für die Herstellung komplexer Komponenten wie Kühlrahmen für Elektroautos, ist aber nicht ohne Herausforderungen. Die erfolgreiche Implementierung von AM für anspruchsvolle Automobilanwendungen erfordert Fachwissen, eine sorgfältige Prozesskontrolle und ein Verständnis für mögliche Fallstricke. Die proaktive Bewältigung dieser Herausforderungen ist der Schlüssel zur Gewährleistung von Qualität, Zuverlässigkeit und Kosteneffizienz der Teile.
Zu den häufigsten Herausforderungen und Strategien zur Abhilfe gehören:
- Eigenspannung und Verformung:
- Herausforderung: Die schnelle, örtlich begrenzte Erwärmung und Abkühlung bei Pulverbettschmelzverfahren führt zu thermischen Gradienten und damit zu inneren Spannungen im Bauteil. Übermäßige eigenspannung Metall AM teile können sich während der Herstellung verziehen, nach der Entnahme aus der Bauplatte verzerren oder sogar Risse bekommen. Große, flache Abschnitte oder scharfe geometrische Übergänge verschlimmern dies noch.
- Milderung:
- DfAM: Konstruktion von Teilen mit spannungsreduzierenden Merkmalen (z. B. Vermeidung von großen massiven Blöcken, Verwendung von Gitterstrukturen, Hinzufügen von Opferrippen).
- Strategie aufbauen: Optimierung der Teileausrichtung, Verwendung geeigneter Stützstrukturen (die auch zur Verankerung des Teils und zur Wärmeableitung beitragen) und Optimierung der Laser-/Elektronenstrahl-Scanstrategien.
- Prozessparameter: Feinabstimmung von Parametern wie Schichtdicke, Energiezufuhr und Plattformheizung (besonders wichtig bei SEBM).
- Nachbearbeiten: Durchführung wirksamer Wärmebehandlungen zum Spannungsabbau unmittelbar nach dem Druck, oft vor der Entnahme des Teils von der Bauplatte.
- Porosität:
- Herausforderung: Im gedruckten Material können sich kleine Hohlräume oder Poren bilden, die durch eingeschlossenes Gas, unvollständige Verschmelzung zwischen den Schichten oder Keyholing-Phänomene (kollabierende Dampfdepressionen) entstehen. Poren können die mechanischen Eigenschaften (insbesondere die Ermüdungsfestigkeit) beeinträchtigen und, was bei Kühlrahmen kritisch ist, zu Leckagen führen, wenn sich Poren verbinden oder eine Oberfläche durchbrechen.
- Milderung:
- Qualität des Pulvers: Verwendung von hochwertigen, kugelförmigen Metallpulvern mit geringer innerer Porosität und kontrollierter Partikelgrößenverteilung, wie sie mit der fortschrittlichen Gaszerstäubung von Met3dp’ hergestellt werden. Gewährleistung einer ordnungsgemäßen Handhabung und Lagerung des Pulvers, um eine Feuchtigkeitsaufnahme zu verhindern.
- Optimierung der Parameter: Entwicklung und Validierung von robusten Prozessparametern (Laserleistung, Scangeschwindigkeit, Schraffurabstand, Schichtdicke), die speziell auf das Material und die Maschine abgestimmt sind, um ein vollständiges Schmelzen und Verschmelzen zu gewährleisten. Met3dp investiert viel in die Entwicklung von Prozessparametern.
- Prozessüberwachung: Einsatz von In-situ-Überwachungssystemen (z. B. Schmelzbadüberwachung) zur Erkennung potenzieller Anomalien während der Bauphase.
- Nachbearbeiten: Heiß-Isostatisches Pressen (HIP) kann in einigen Fällen zum Schließen interner Poren verwendet werden, obwohl es zusätzliche Kosten und Komplexität verursacht. Eine ordnungsgemäße Dichtheitsprüfung ist unerlässlich, um kritische Porosität zu erkennen.
- Entfernung der Stützstruktur:
- Herausforderung: Stützstrukturen sind zwar notwendig, verursachen aber sowohl beim Druck als auch bei der Nachbearbeitung zusätzliche Zeit und Kosten. Ihre Entfernung, insbesondere von komplexen inneren Kanälen oder empfindlichen Merkmalen, kann schwierig und arbeitsintensiv sein und birgt das Risiko, die Oberfläche des Teils zu beschädigen.
- Milderung:
- DfAM: Entwurf von selbsttragenden Winkeln (>45°), wo immer möglich, Optimierung der inneren Kanalformen und strategische Ausrichtung des Teils.
- Design unterstützen: Verwendung spezieller Softwarefunktionen zur Erstellung von Stützen, die wirksam und gleichzeitig leichter zu entfernen sind (z. B. dünnere Kontaktpunkte, perforierte Strukturen).
- Nachbearbeitungstechniken: Anwendung geeigneter Entfernungsmethoden (manuell, CNC, eventuell elektrochemisch) je nach Lage des Trägers und der Teilegeometrie.
- Oberfläche:
- Herausforderung: Die inhärente schichtweise Beschaffenheit und die Haftung des Pulvers führen im Vergleich zur herkömmlichen Bearbeitung zu einer raueren Oberfläche. Dies kann bei Dichtungsflächen oder im Inneren von Kühlkanälen problematisch sein, wo es den Flüssigkeitsstrom beeinträchtigt.
- Milderung:
- Optimierung der Parameter: Die Feinabstimmung der Parameter kann die Oberflächengüte im Ist-Zustand leicht verbessern.
- Orientierung: Optimale Ausrichtung der kritischen Oberflächen auf der Bauplatte.
- Nachbearbeiten: Durchführung der notwendigen Nachbearbeitungsschritte wie Bearbeitung, Polieren, Strahlen oder AFM, wie bereits erwähnt.
- Konsistenz und Skalierbarkeit:
- Herausforderung: Die Sicherstellung einer gleichbleibenden Teilequalität über mehrere Fertigungen und verschiedene Maschinen hinweg und die effiziente Skalierung der Produktion, um den Anforderungen der Automobilindustrie gerecht zu werden, erfordern robuste Prozesssteuerungs- und Qualitätsmanagementsysteme.
- Milderung:
- Standardisierung: Implementierung standardisierter Arbeitsabläufe, strenger Maschinenkalibrierung und konsistenter Pulvermanagementprotokolle.
- Qualitätsmanagement-Systeme: Einhaltung einschlägiger Zertifizierungen (z. B. ISO 9001, möglicherweise IATF 16949 für Automobilzulieferer).
- Prozessüberwachung & Datenanalyse: Kontinuierliche Überwachung der Gebäudedaten, um Konsistenz zu gewährleisten und mögliche Abweichungen zu erkennen.
- Partnerschaften: Zusammenarbeit mit erfahrenen AM-Anbietern wie Met3dp, die über etablierte Qualitätssysteme und Erfahrung mit der Skalierung der Produktion verfügen.
- Kosten:
- Herausforderung: Metall-AM kann im Vergleich zu traditionellen Methoden höhere Vorlaufkosten pro Teil verursachen, insbesondere bei einfachen Designs und hohen Stückzahlen, bedingt durch Maschineninvestitionen, Materialkosten und Prozesszeit.
- Milderung:
- DfAM: Nutzung von Teilekonsolidierung und Leichtbau, um die Kosten durch reduzierte Montagezeit und geringeren Materialverbrauch zu senken.
- Prozess-Optimierung: Minimierung der Bauzeit und der Unterstützungsstrukturen.
- Lautstärke: Die Kosten pro Teil sinken deutlich, wenn das Produktionsvolumen steigt.
- Total Cost of Ownership: Dabei geht es um Einsparungen durch schnellere Entwicklung, verbesserte Leistung und Flexibilität in der Lieferkette, nicht nur um die Kosten einzelner Teile.
Die Bewältigung dieser Herausforderungen erfordert ein tiefes Verständnis der Materialwissenschaft, der Physik des AM-Prozesses, der DfAM-Prinzipien und einer strengen Qualitätskontrolle. Die Zusammenarbeit mit einem erfahrenen 3D-Druck von Metall dienstleistungsanbieter wie Met3dp, der über die notwendige Technologie, das Fachwissen und das Engagement verfügt, um qualitätssicherung automotive AM ist entscheidend für die erfolgreiche Implementierung von Metall-AM für kritische Komponenten wie Kühlrahmen für Elektroautos. Unser Team arbeitet mit den Kunden zusammen, um diese Komplexität zu bewältigen und optimierte, zuverlässige Lösungen zu liefern.
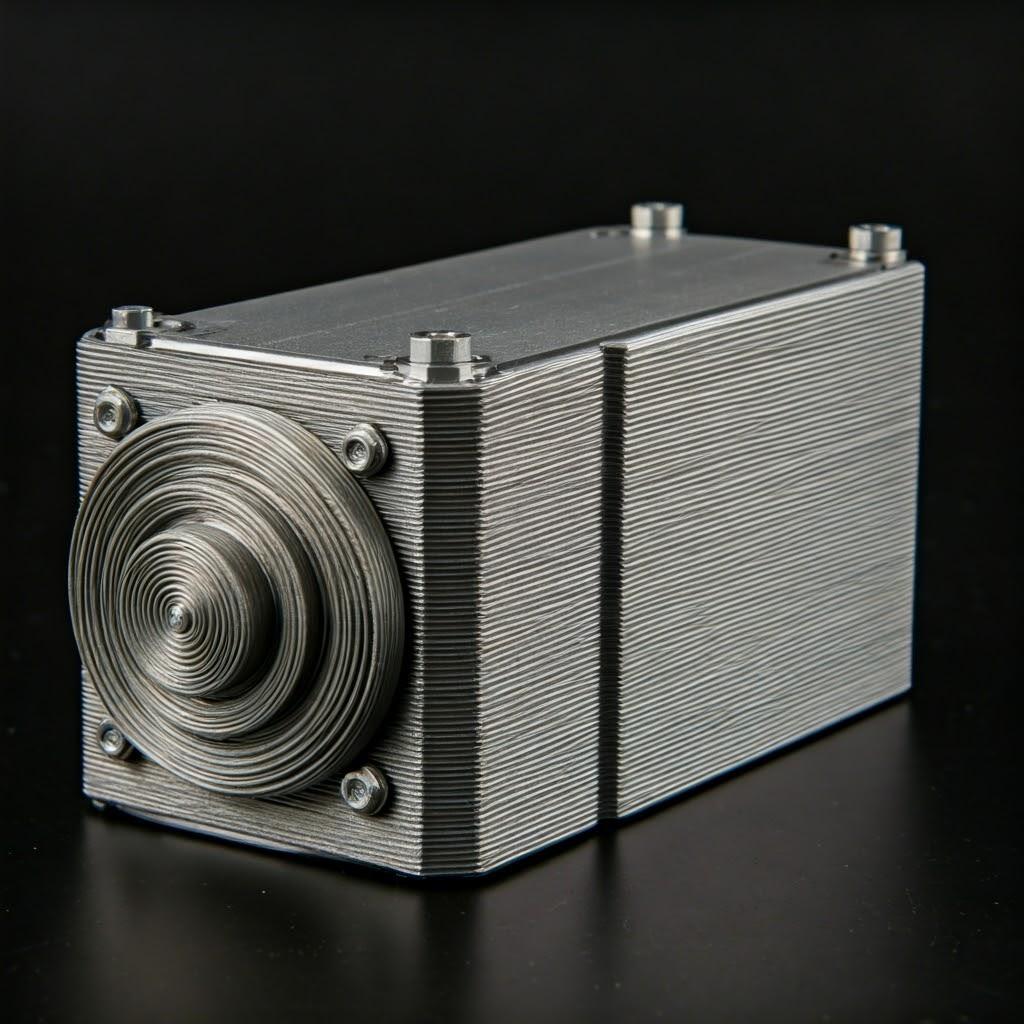
Auswahl eines Partners für die additive Fertigung von Metall: Wichtige Überlegungen für EV-Lieferanten
Die Wahl des richtigen Fertigungspartners ist ebenso entscheidend wie die Technologie selbst, insbesondere bei anspruchsvollen Automobilkomponenten wie Kühlrahmen für Elektroautos. Der Erfolg Ihres Projekts hängt von der Kompetenz, der Zuverlässigkeit und der Fähigkeit des Anbieters ab, strenge Qualitätsstandards zu erfüllen. Für Ingenieure und Beschaffungsmanager, die sich in der 3D-Druck-Dienstleister für Metall landschaft, sollten mehrere Schlüsselfaktoren für die bewertung von AM-Zulieferern für die Automobilindustrie prozess:
- Technische Kompetenz und Erfahrung:
- Material-Spezialisierung: Hat der Anbieter nachweislich Erfahrung mit den von Ihnen gewünschten Legierungen (z. B. AlSi10Mg, CuCrZr)? Fragen Sie nach Fallstudien oder Beispielen für ähnliche Projekte. Tief werkstoffkompetenz AM ist von entscheidender Bedeutung und umfasst die Handhabung von Pulver, die Entwicklung von Parametern und das Verständnis des Materialverhaltens während des Drucks und der Nachbearbeitung.
- Prozesswissen: Beherrschen sie das am besten geeignete AM-Verfahren (LPBF, SEBM) für Ihre Anwendung? Verstehen sie die Feinheiten, um optimale Dichte, Genauigkeit und Materialeigenschaften zu erreichen?
- Erfahrung in der Industrie: Haben sie in der Automobilbranche oder anderen anspruchsvollen Branchen (Luft- und Raumfahrt, Medizintechnik) mit ähnlichen Qualitätsanforderungen gearbeitet? Verständnis für die Herstellung von Automobilkomponenten anforderungen ist der Schlüssel.
- Technologie und Ausrüstung:
- Maschinenqualität & Leistungsfähigkeit: Welche Arten von Druckern werden dort betrieben? Sind sie gut gewartet und kalibriert? Verfügen sie über Maschinen, die in der Lage sind, das erforderliche Bauvolumen zu bewältigen und die erforderliche Präzision zu erreichen? Met3dp arbeitet mit branchenführenden Druckern, die für ihre Genauigkeit und Zuverlässigkeit bekannt sind.
- Qualitätskontrolle des Pulvers: Wie beschaffen und verwalten sie ihre Metallpulver? Verfügen sie über eine solide Qualitätskontrolle der eingehenden Materialien? Der Vorteil von Met3dp’ liegt in der hauseigenen Produktion von hochwertigen, kugelförmigen Metallpulvern unter Verwendung fortschrittlicher Zerstäubungstechniken.
- Software & Simulation: Nutzen sie fortschrittliche Software für die Bauvorbereitung und möglicherweise Simulationswerkzeuge zur Optimierung der Ausrichtung, der Stützen und zur Vorhersage möglicher Probleme wie Verformungen?
- Qualitätsmanagement-Systeme:
- Zertifizierungen: Verfügt der Anbieter über einschlägige Qualitätszertifizierungen, wie z. B ISO 9001? Während die IATF 16949 (die Automobilnorm) für viele AM-Anbieter noch in den Kinderschuhen steckt, ist der Nachweis der Einhaltung strenger Qualitätsprotokolle unerlässlich.
- Prozesskontrolle: Welche Maßnahmen gibt es für die prozessbegleitende Überwachung und Qualitätskontrolle während des gesamten Herstellungsprozesses (Pulverhandling, Druck, Nachbearbeitung, Prüfung)?
- Rückverfolgbarkeit: Können sie eine vollständige Rückverfolgbarkeit der Materialien und Prozessparameter für jedes produzierte Teil gewährleisten?
- Kapazität und Skalierbarkeit:
- Produktionsvolumen: Kann der Anbieter die von Ihnen geforderten Produktionsmengen bewältigen, vom Prototyping bis hin zu einer möglichen Klein- oder Mittelserienproduktion? Verfügt er über ausreichende Maschinenkapazitäten und qualifiziertes Personal?
- Vorlaufzeiten: Können sie Ihre Projektfristen einhalten? Haben sie eine Erfolgsbilanz bei der zuverlässigen Lieferung?
- Technische und unterstützende Dienstleistungen:
- DfAM-Unterstützung: Können sie fachkundige Beratung zum Thema Design für die additive Fertigung anbieten, um Ihr Kühlkörperdesign hinsichtlich Leistung, Kosten und Herstellbarkeit zu optimieren?
- Nachbearbeitungsmöglichkeiten: Bieten sie ein umfassendes Angebot an internen oder eng geführten Nachbearbeitungsdienstleistungen (Wärmebehandlung, Bearbeitung, Endbearbeitung, Prüfung)?
- Kommunikation & Zusammenarbeit: Sind sie reaktionsschnell, transparent und bereit, bei der Lösung von Problemen zusammenzuarbeiten? Wahl des AM-Partners geht es um den Aufbau einer Beziehung, nicht nur um eine Transaktion.
- Gesamtwert-Angebot:
- Kosten-Nutzen-Verhältnis: Die Kosten sind zwar ein Faktor, aber bewerten Sie die insgesamt wert, der nicht nur den Preis pro Teil, sondern auch Qualität, Zuverlässigkeit, Fachwissen, Geschwindigkeit und Support berücksichtigt.
- Standort und Logistik: Berücksichtigen Sie den Standort des Anbieters im Verhältnis zu Ihren Montageeinrichtungen und seine logistischen Möglichkeiten.
Met3dp verkörpert diese Qualitäten und positioniert sich nicht nur als Lieferant, sondern als strategischer Partner. Mit tiefen Wurzeln in beiden additive Fertigungslösungen und fortschrittliche Metallpulverproduktionbieten wir eine einzigartige Mischung aus materialwissenschaftlichem Know-how und der Beherrschung von Druckverfahren. Unser Engagement für Qualität, unsere Investitionen in branchenführende Technologien und unser kooperativer Ansatz machen uns zu einem idealen Partner für Automobilunternehmen, die Metall-AM für kritische EV-Komponenten wie Batteriekühlrahmen nutzen möchten.
Verständnis der Kostentreiber und Vorlaufzeiten für 3D-gedruckte Batterierahmen
Metall-AM ermöglicht zwar erhebliche Leistungssteigerungen und Designmöglichkeiten für Kühlrahmen von Elektroautos, doch ist die Kenntnis der damit verbundenen Kosten und Produktionsfristen für die Projektplanung und Beschaffung von entscheidender Bedeutung. Sowohl Kostenanalyse für den 3D-Druck von Metall und schätzung der Durchlaufzeit von Automobilteilen hängen von einer Vielzahl miteinander verbundener Faktoren ab.
Die wichtigsten Kostentreiber:
- Materialart und Verbrauch:
- Pulverkosten: Die Rohstoffkosten sind je nach Legierung sehr unterschiedlich. Kupferlegierungen wie CuCrZr sind wesentlich teurer als Aluminiumlegierungen wie AlSi10Mg.
- Teil Volumen & Gewicht: Größere, dichtere Teile verbrauchen natürlich mehr Pulver, was sich direkt auf die Materialkosten auswirkt. DfAM-Techniken wie Topologieoptimierung und Gitterstrukturen können den Materialverbrauch erheblich reduzieren.
- Unterstützende Strukturen: Das für die Stützstrukturen verwendete Material trägt zum Gesamtverbrauch bei und muss mit einberechnet werden. Die Minimierung der Stützen durch DfAM reduziert diese Kosten.
- Maschinenzeit:
- Bauzeit: Dies ist oft der wichtigste Kostentreiber. Er hängt vom Volumen des Teils (insbesondere seiner Höhe in der Baukammer), der Komplexität, der verwendeten Schichtdicke und der Effizienz der Laser-/Elektronenstrahl-Abtaststrategie der Maschine ab. Höhere Teile oder Teile, die sehr dünne Schichten erfordern, benötigen mehr Zeit zum Drucken.
- Maschinentarif: Die stündlichen Betriebskosten des industriellen Metall-3D-Druckers unter Berücksichtigung von Abschreibung, Energie, Verbrauchsmaterialien (Filter, Gase) und Wartung.
- Entwurfskomplexität & Build Setup:
- Unterstützt: Komplexe Geometrien, die umfangreiche Stützstrukturen erfordern, verlängern sowohl die Druckzeit (mehr abzulieferndes Material) als auch den Nachbearbeitungsaufwand (Entfernen der Stützstrukturen).
- Nisten & Baudichte: Wie effizient mehrere Teile in einem einzigen Bauvolumen verschachtelt werden können, wirkt sich auf die Maschinenzeitkosten pro Teil aus. Erfahrene Anbieter optimieren Build-Layouts.
- Zubereitungszeit: Zeit, die von den Ingenieuren für die Vorbereitung der Build-Datei benötigt wird (Ausrichtung, Erzeugung von Stützen, Slicing).
- Nachbearbeiten:
- Arbeit & Ausrüstung: Jeder Nachbearbeitungsschritt (Spannungsarmglühen, Wärmebehandlung, Entfernen von Stützen, Bearbeitung, Endbearbeitung, Inspektion) verursacht zusätzliche Zeit- und Arbeitskosten.
- Komplexität: Komplizierte innere Kanäle, die eine spezielle Endbearbeitung (wie AFM) erfordern, oder enge Toleranzen, die eine umfangreiche CNC-Bearbeitung erfordern, erhöhen die Kosten erheblich.
- Qualitätsanforderungen: Höhere Inspektionsstufen (z. B. umfangreiche CMM, CT-Scans) erhöhen die Kosten.
- Auftragsvolumen:
- Skalenvorteile: Wie bei den meisten Fertigungsprozessen führen höhere Stückzahlen in der Regel zu niedrigeren Kosten pro Teil, da sich die Rüstkosten amortisieren, die Verschachtelung der Bauteile optimiert wird und die Arbeitsabläufe effizienter werden. Volumenproduktion AM wird zunehmend rentabel, auch wenn sich die Kostenstrukturen von denen der traditionellen Großserienverfahren unterscheiden.
Faktoren, die die Durchlaufzeiten beeinflussen:
- Designfinalisierung & Vorbereitung: Erforderliche Zeit für die DfAM-Konsultation (falls erforderlich) und die Vorbereitung der Bauunterlagen.
- Warteschlange drucken: Verfügbarkeit geeigneter Maschinen beim Dienstanbieter. Hohe Nachfrage kann zu Warteschlangen führen.
- Druckzeit: Die tatsächliche Zeit, die das Teil beim Druck in der Maschine verbringt (kann je nach Größe und Komplexität von Stunden bis zu mehreren Tagen reichen).
- Nachbearbeiten: Die Gesamtzeit, die für alle notwendigen Schritte nach dem Druck benötigt wird (Wärmebehandlungszyklen, Bearbeitung, Endbearbeitung, Prüfung). Dies kann oft genauso lange oder länger dauern als die Druckzeit selbst.
- Versand & Logistik: Zeit, die für den Transport zum endgültigen Bestimmungsort benötigt wird.
Typische Zeitpläne:
Einfache Prototypen sind zwar stark projektabhängig, können aber in 1-2 Wochen hergestellt werden. Bei komplexeren Bauteilen, die eine umfangreiche Nachbearbeitung erfordern, oder bei Teilen aus anspruchsvollen Werkstoffen kann die Vorlaufzeit 3 bis 8 Wochen oder mehr betragen, insbesondere bei den ersten Produktionsläufen. Der Aufbau einer Beziehung zu einem Anbieter wie Met3dp ermöglicht eine bessere Planung und potenziell kürzere Fristen, sobald die Prozesse validiert sind. Genaue Kostenvoranschläge und Vorlaufzeiten erfordern eine detaillierte Prüfung der CAD-Daten des Endprodukts, der Materialspezifikationen und der Qualitätsanforderungen. Wirksam beschaffung Metall 3D-Druck dazu gehört, dass den potenziellen Lieferanten klare Spezifikationen vorgelegt werden.
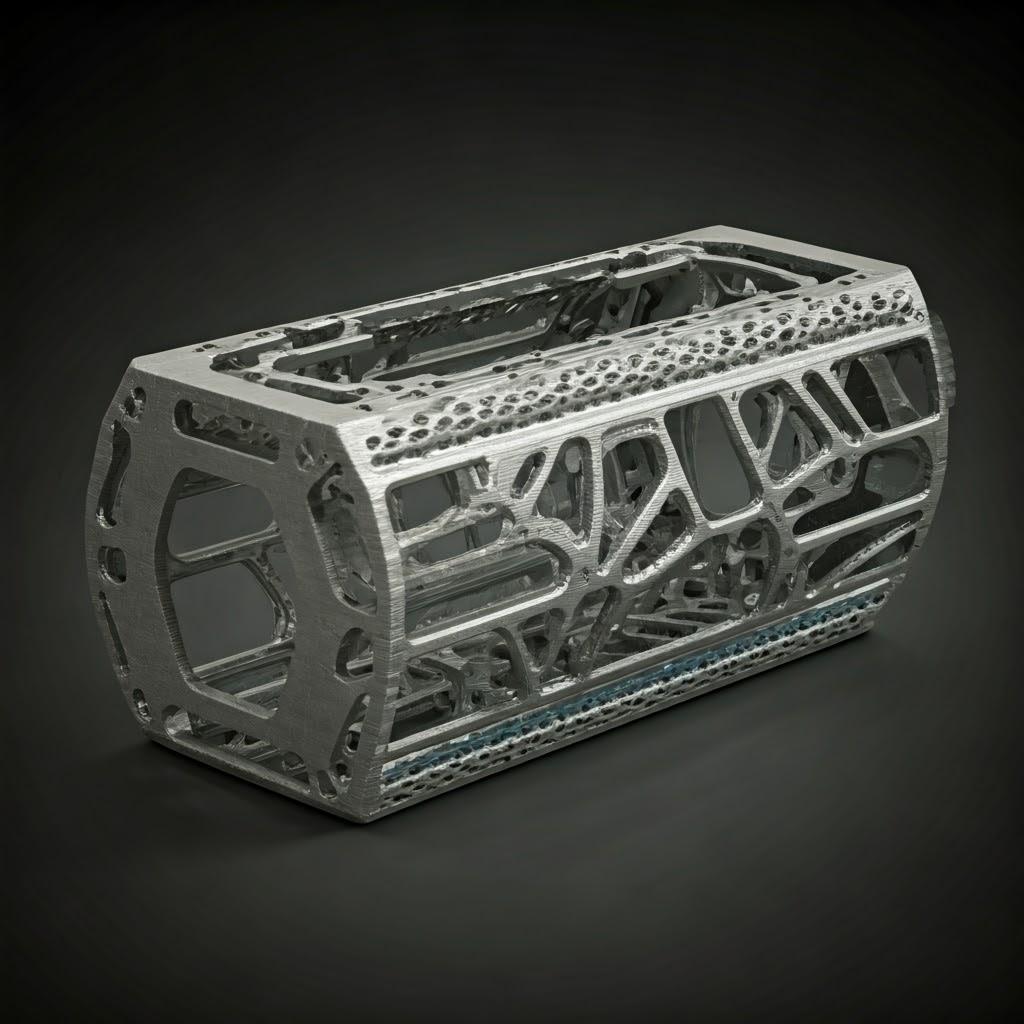
Häufig gestellte Fragen (FAQ) zu 3D-gedruckten EV-Kühlrahmen aus Metall
Hier finden Sie Antworten auf einige häufig gestellte Fragen von Ingenieuren und Beschaffungsmanagern zur Verwendung von Metall-AM für Kühlkomponenten von Elektrofahrzeugen:
1. Was sind die Hauptvorteile der Verwendung von Metall-AM für Kühlrahmen im Vergleich zu traditionellen Methoden wie Gießen oder gelöteten Baugruppen?
Metal AM bietet mehrere entscheidende Vorteile:
- Geometrische Komplexität: Die Möglichkeit, hochkomplexe interne Kühlkanäle (z. B. konforme, optimierte Strömungswege) zu schaffen, die bei Guss oder maschineller Bearbeitung unmöglich oder unpraktisch sind, führt zu einer überlegenen thermischen Leistung.
- Gewichtsreduzierung: Ermöglicht Topologieoptimierung und Gitterstrukturen, wodurch das Gewicht der Komponenten im Vergleich zu massiven Gussteilen erheblich reduziert wird, was die Reichweite der Fahrzeuge erhöht.
- Teil Konsolidierung: Ermöglicht die Integration mehrerer Funktionen (Kühlung, Struktur, Montage) in ein einziges gedrucktes Teil, wodurch die Komplexität der Montage, potenzielle Leckstellen und oft auch Gewicht/Kosten reduziert werden.
- Geschwindigkeit für Prototypen/geringe Stückzahlen: Schnellere Iteration während der Entwicklung und schnellere Produktion bei kleinen bis mittleren Stückzahlen, da keine Werkzeuge erforderlich sind.
- Material-Optionen: Erleichtert die Verwendung von Hochleistungslegierungen wie AlSi10Mg für Leichtbau oder CuCrZr für maximale Wärmeleitfähigkeit.
2. Wie dicht sind die Kühlkanäle in 3D-gedruckten Rahmen?
Das Erreichen einer lecksicheren Integrität ist von größter Wichtigkeit und mit einer angemessenen Prozesskontrolle gut zu erreichen. Zu den Schlüsselfaktoren gehören:
- Optimierung der Parameter: Verwendung von validierten Druckparametern zur Gewährleistung einer vollständigen Verdichtung (>99,5 %, oft höher) und Minimierung der Porosität im Material.
- Qualität des Pulvers: Die Verwendung von hochwertigem Metallpulver mit geringer Porosität ist unerlässlich.
- Entwurf: Vermeidung von Konstruktionsmerkmalen, die anfällig für Defekte sind (z. B. sehr dünne Wände ohne angemessene Unterstützung).
- Nachbearbeiten: HIP kann zwar interne Poren schließen, ist aber oft nicht erforderlich, wenn die Druckparameter gut kontrolliert werden.
- Strenge Tests: Einführung obligatorischer Lecktests (z. B. Druckabfall, Helium-Lecktests) als Standard-Qualitätskontrollschritt für jede produzierte Kühlkomponente. Bei korrekter Herstellung durch einen erfahrenen Anbieter wie Met3dp erfüllen metallische AM-Kühlrahmen strenge Anforderungen an die Dichtheit.
3. Kann Metall-AM die erforderliche Oberflächengüte innerhalb der Kühlkanäle für einen effizienten Flüssigkeitsstrom erzielen?
Die gedruckte Oberflächenbeschaffenheit innerhalb der AM-Kanäle ist von Natur aus rauer (typischerweise Ra 10-20 µm oder höher) als bei konventionell bearbeiteten Kanälen. Dies kann zwar zu einem geringfügig höheren Druckabfall im Vergleich zu einem vollkommen glatten Rohr führen, doch überwiegen die Leistungsgewinne durch eine optimierte Kanalgeometrie häufig den Effekt der Oberflächenrauheit. Für Anwendungen, die glattere Innenoberflächen erfordern:
- Entwurf: Die Ausrichtung von Kanälen und die Verwendung bestimmter Formen (z. B. Teardrop) können die Oberfläche bestimmter Innenflächen verbessern.
- Nachbearbeiten: Techniken wie das Abrasive Flow Machining (AFM) oder das chemische Polieren können eingesetzt werden, um die innere Oberflächengüte deutlich zu verbessern, wenn auch zu zusätzlichen Kosten. Die gewünschte innere Oberfläche sollte spezifiziert und mit dem AM-Anbieter besprochen werden.
4. Welche Informationen benötigt Met3dp normalerweise, um ein Angebot für einen 3D-gedruckten Batteriekühlrahmen zu erstellen?
Um einen genauen Kostenvoranschlag zu erstellen, benötigen wir in der Regel:
- 3D-CAD-Modell: STEP- oder STL-Datei der endgültigen Teilekonstruktion.
- Spezifikation des Materials: Gewünschte Legierung (z. B. AlSi10Mg, CuCrZr) und alle spezifischen Anforderungen an die Materialeigenschaften.
- Technische Zeichnung: Angabe kritischer Abmessungen, Toleranzen, erforderlicher Oberflächengüten (insbesondere bei Dichtungs-/Paarungsflächen) sowie aller zu bearbeitenden Besonderheiten.
- Menge: Anzahl der benötigten Teile (für Prototyp, Kleinserie oder Serienproduktion).
- Nachbearbeitungsanforderungen: Einzelheiten über Wärmebehandlung, spezifische Oberflächenbehandlungen, Prüfanforderungen (z. B. Parameter für die Dichtheitsprüfung).
- Zeitplan für die Lieferung: Erforderliches Lieferdatum.
5. Ist Metall-AM für die Großserienproduktion dieser Rahmen für die Automobilindustrie geeignet?
Metall-AM entwickelt sich rasch weiter, und obwohl es sich hervorragend für die Herstellung von Prototypen, die kundenspezifische Anpassung und die Produktion kleiner bis mittlerer Mengen eignet, ist seine Eignung für traditionell (Hunderttausende oder Millionen pro Jahr) befindet sich im Vergleich zum Gießen oder Stanzen noch in der Entwicklung einfach konstruktionen. Für komplexe Hochleistungskühlrahmen, bei denen AM erhebliche Leistungs- oder Konsolidierungsvorteile bietet, die auf andere Weise nicht zu erreichen sind, wird es jedoch zu einer praktikablen Option, selbst für die Serienproduktion von Tausenden oder Zehntausenden. Die Kosteneffizienz hängt stark von der Komplexität des Designs und dem Wert ab, der sich aus den einzigartigen Fähigkeiten von AM’ ergibt. Met3dp arbeitet mit Kunden zusammen, um den Business Case zu bewerten für serienproduktion mit AM.
Schlussfolgerung: Die Zukunft der EV-Leistung mit Met3dp’s Additive Manufacturing Lösungen
Das unablässige Streben nach höherer Leistung, größerer Reichweite und schnellerem Laden auf dem Markt für Elektrofahrzeuge setzt die Wärmemanagementsysteme für Batterien unter immensen Druck. Die additive Fertigung von Metallen hat sich eindeutig als Schlüsseltechnologie herauskristallisiert und bietet beispiellose Möglichkeiten für die Entwicklung und Herstellung von Kühlrahmen für Elektrofahrzeuge, die leichter, komplexer und thermisch besser sind als die mit herkömmlichen Methoden hergestellten. Durch die Nutzung der Designfreiheit von AM mit fortschrittlichen Materialien wie leichtem AlSi10Mg oder hochleitfähigem CuCrZr können Automobilhersteller die Effizienz, Langlebigkeit und Sicherheit von Batteriepaketen erheblich verbessern - entscheidende Faktoren für den Erfolg im Wettbewerb der Elektrofahrzeuge.
Von der Optimierung komplizierter interner Kühlkanäle über DfAM bis hin zur Gewährleistung von Präzision durch sorgfältige Prozesskontrolle und Nachbearbeitung bietet Metal AM ein leistungsstarkes Toolkit für fortgeschrittene Fertigung Automobilindustrie anwendungen. Um die Komplexität von Materialauswahl, Designoptimierung, Prozessparametern und Qualitätssicherung zu bewältigen, ist jedoch umfassendes Fachwissen erforderlich.
Die Wahl des richtigen Partners ist von entscheidender Bedeutung. Met3dp steht an der Spitze dieser technologischen Welle und kombiniert branchenführende SEBM/LPBF-Drucktechnologie mit unübertroffener Kompetenz in herstellung von Hochleistungsmetallpulvern. Unser integrierter Ansatz, vom zerstäubten Pulver bis zum fertigen und geprüften Bauteil, gewährleistet die von der Automobilindustrie geforderte Qualität, Zuverlässigkeit und Leistung. Wir sind mehr als nur ein Dienstleister; wir sind ein kooperativer Partner, der Ihnen hilft, das volle Potenzial der additiven Fertigung für Ihre wichtigsten EV-Komponenten zu erschließen.
Sind Sie bereit, Ihr EV-Wärmemanagement zu revolutionieren? Kontaktieren Sie Met3dp noch heute um Ihr Batteriekühlrahmenprojekt zu besprechen und herauszufinden, wie unsere hochmodernen Systeme, fortschrittlichen Materialien und Anwendungsentwicklungsdienste Ihre Reise zur nächsten Generation von Elektrofahrzeugen beschleunigen können. Lassen Sie uns die zukünftige EV-Technologie gemeinsam gestalten.
Teilen auf
MET3DP Technology Co., LTD ist ein führender Anbieter von additiven Fertigungslösungen mit Hauptsitz in Qingdao, China. Unser Unternehmen ist spezialisiert auf 3D-Druckgeräte und Hochleistungsmetallpulver für industrielle Anwendungen.
Fragen Sie an, um den besten Preis und eine maßgeschneiderte Lösung für Ihr Unternehmen zu erhalten!
Verwandte Artikel
Über Met3DP
Aktuelles Update
Unser Produkt
KONTAKT US
Haben Sie Fragen? Senden Sie uns jetzt eine Nachricht! Wir werden Ihre Anfrage mit einem ganzen Team nach Erhalt Ihrer Nachricht bearbeiten.
Holen Sie sich Metal3DP's
Produkt-Broschüre
Erhalten Sie die neuesten Produkte und Preislisten
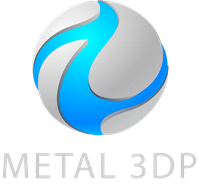
Metallpulver für 3D-Druck und additive Fertigung