Kraftstoffverteiler für die Optimierung des Additivflusses
Inhaltsübersicht
Einführung: Revolutionierung der Kraftstoffzufuhr mit kundenspezifischen 3D-gedruckten Verteilern aus Metall
Der komplizierte Tanz der Technik, der unsere moderne Welt antreibt, beruht oft auf der präzisen Steuerung und Verteilung von Flüssigkeiten. Vom Dröhnen eines Düsentriebwerks, das die Stratosphäre durchstößt, über das feine Brummen eines Hochleistungs-Automotors, der sich durch die Kurven einer Rennstrecke schlängelt, bis hin zum unermüdlichen Betrieb von Turbinen in der industriellen Energieerzeugung ist die effiziente Zufuhr von Kraftstoff von größter Bedeutung. Das Herzstück dieser komplexen Systeme ist eine entscheidende, aber oft unterschätzte Komponente: der Kraftstoffverteiler. Im Wesentlichen dient ein Kraftstoffverteiler als ausgeklügelte Anschlussdose für Flüssigkeiten, die den Kraftstoff von einer Quelle erhält und ihn sorgfältig an mehrere nachgeschaltete Punkte wie Einspritzdüsen, Düsen oder Brennkammern verteilt. Seine Funktion ist von grundlegender Bedeutung: Er sorgt dafür, dass die richtige Kraftstoffmenge zur richtigen Zeit, mit dem richtigen Druck und mit minimalen Verlusten oder Schwankungen an die richtige Stelle gelangt. Ein Ausfall oder eine Ineffizienz des Verteilers kann zu suboptimaler Leistung, erhöhten Emissionen, geringerem Kraftstoffverbrauch und in kritischen Anwendungen wie der Luft- und Raumfahrt zu potenziell katastrophalen Folgen führen. Die Anforderungen an diese Komponenten sind hoch: Sie müssen oft komplexe interne Wege zurücklegen, hohen Drücken und Temperaturen standhalten, mit aggressiven Kraftstoffen kompatibel sein und strenge Anforderungen an Gewicht und Platz erfüllen, insbesondere in der Luft- und Raumfahrt und im Automobilsektor.
In der Vergangenheit stützte sich die Herstellung von Kraftstoffverteilern in hohem Maße auf traditionelle Techniken, vor allem auf Guss, subtraktive Bearbeitung (Fräsen und Bohren) und Montageverfahren wie Löten oder Schweißen. Diese Methoden haben sich in der Industrie zwar seit Jahrzehnten bewährt, sind jedoch mit erheblichen Einschränkungen verbunden, insbesondere wenn Ingenieure nach Spitzenleistung und Effizienz streben.
- Gießen: Während sich das Gießen für die Herstellung komplexer Außenformen eignet, ist es schwierig, komplizierte, optimierte interne Kanalgeometrien zu erzeugen. Interne Kerne können komplex und zerbrechlich sein, was die Designfreiheit einschränkt. Es kann schwierig sein, zuverlässig dünne Wände zu erreichen, und Porosität kann ein Problem darstellen, das zu Lecks oder Schwachstellen führen kann. Die Oberflächenbeschaffenheit interner Gusskanäle ist oft rau, was einen reibungslosen Flüssigkeitsstrom behindert und den Druckabfall erhöht. Darüber hinaus ist die Herstellung und Änderung von Gusswerkzeugen teuer und zeitaufwändig, so dass Konstruktionsänderungen langsam und kostspielig sind.
- Bearbeitungen: Die subtraktive Bearbeitung, bei der in der Regel von einem massiven Metallblock ausgegangen wird, zeichnet sich durch hohe Präzision und hervorragende Oberflächengüte bei extern oberflächen und zugänglich innere Merkmale. Die Herstellung komplexer, sanft gekrümmter interner Durchgänge oder interner Merkmale mit scharfen Hinterschneidungen ist jedoch oft unmöglich oder erfordert die Bearbeitung des Verteilers in mehreren Teilen. Tiefbohrungen für lange, gerade Kanäle sind möglich, aber die Schaffung optimierter, nicht linearer Strömungswege ist stark eingeschränkt. Diese Einschränkung zwingt zu Konstruktionen, die einen Kompromiss zwischen Herstellbarkeit und idealer Strömungsdynamik darstellen. Bei subtraktiven Verfahren fällt außerdem ein erheblicher Materialabfall an.
- Montage (Löten/Schweißen): Um die Grenzen des monolithischen Gießens oder der maschinellen Bearbeitung zu überwinden, werden komplexe Verteiler oft aus mehreren, einfacheren Teilen konstruiert, die durch Löten oder Schweißen miteinander verbunden werden. Dies ermöglicht zwar komplexere interne Netzwerke, aber jede Verbindung führt zu potenziellen Leckagepfaden, erhöht das Gewicht, die Montagezeit und -komplexität und schafft potenzielle Fehlerstellen bei Belastung oder Temperaturwechsel. Um die Unversehrtheit der zahlreichen Verbindungen zu gewährleisten, sind strenge Inspektionen und Qualitätskontrollen erforderlich, was die Gesamtkosten und die Herstellungszeit erhöht.
Diese traditionellen Fertigungsbeschränkungen zwingen die Ingenieure oft dazu, Kompromisse bei idealen Designs einzugehen. Die Strömungswege können suboptimal sein, was zu unnötigen Druckverlusten und einer ungleichmäßigen Kraftstoffverteilung führt. Die Anzahl der Teile steigt, um die gewünschte Komplexität zu erreichen, was zu mehr Gewicht und potenziellen Fehlerquellen führt. Die Vorlaufzeiten für neue Konstruktionen oder Änderungen können sich über Monate erstrecken, da neue Werkzeuge oder komplexe Bearbeitungsvorrichtungen erforderlich sind. In Branchen, in denen Leistung, Gewicht und schnelle Markteinführung entscheidende Unterscheidungsmerkmale sind, stellen diese Einschränkungen erhebliche Hürden dar.
Betreten Sie das Reich der Additive Fertigung von Metall (AM), besser bekannt als 3D-Druck von Metall. Diese transformative Technologie verändert grundlegend die Art und Weise, wie komplexe Komponenten wie Kraftstoffverteiler entworfen und hergestellt werden. Anstatt Material aus einem massiven Block abzutragen oder geschmolzenes Metall in eine Form zu gießen, werden bei der AM Teile Schicht für Schicht direkt aus einem digitalen (CAD-)Modell aufgebaut, indem feine Metallpulverpartikel mit Hilfe einer fokussierten Energiequelle, z. B. einem Laser- oder Elektronenstrahl, miteinander verschmolzen werden. Dieser schichtweise Ansatz befreit die Designer von vielen der Einschränkungen, die durch traditionelle Methoden entstehen.
Die Auswirkungen auf die Konstruktion und Herstellung von Kraftstoffverteilern sind tiefgreifend:
- Beispiellose Designfreiheit: Mit AM lassen sich hochkomplexe Innengeometrien erstellen, die bisher nicht herstellbar waren. Sanft gekrümmte Kanäle, die präzise optimierten Strömungspfaden folgen, interne Reservoirs, integrierte Filter und variable Querschnitte können entworfen und direkt in ein monolithisches Teil eingebaut werden. Diese Fähigkeit ermöglicht es den Ingenieuren, die Funktion in den Vordergrund zu stellen und die Strömungsdynamik zu optimieren, anstatt Kompromisse bei der Herstellbarkeit einzugehen.
- Fluss-Optimierung: Durch die Möglichkeit, komplizierte interne Kanäle zu schaffen, können Konstrukteure scharfe Biegungen minimieren, Turbulenzen reduzieren und eine gleichmäßigere Strömungsverteilung an jedem Auslasspunkt sicherstellen. Dies führt zu einem geringeren Druckabfall über den Verteiler, einer verbesserten Verbrennungseffizienz und einer potenziell höheren Motor- oder Systemleistung. Mithilfe von CFD-Simulationen (Computational Fluid Dynamics) lassen sich hoch optimierte interne Strömungswege entwerfen, und AM kann diese komplexen digitalen Designs direkt in physische Hardware umsetzen.
- Signifikante Gewichtsreduzierung: AM ermöglicht den Einsatz von Algorithmen zur Topologieoptimierung. Diese Software-Tools analysieren die Spannungsverteilung innerhalb eines Teils unter Betriebslasten und entfernen auf intelligente Weise Material aus unkritischen Bereichen, wodurch leichte, aber dennoch starke, organisch aussehende Strukturen entstehen. Bei Kraftstoffverteilern kann dies zu erheblichen Gewichtseinsparungen führen - ein entscheidender Faktor in der Luft- und Raumfahrt, wo sich jedes eingesparte Gramm in Treibstoffeffizienz oder erhöhter Nutzlast niederschlägt, und in der Hochleistungsautomobilbranche, wo eine geringere Masse das Handling und die Beschleunigung verbessert.
- Teil Konsolidierung: Komplexe Baugruppen, die bisher aus mehreren maschinell bearbeiteten und gelöteten Komponenten bestanden, können oft neu entworfen und als ein einziges, monolithisches Teil gedruckt werden. Dies reduziert die Anzahl der Teile drastisch, eliminiert potenzielle Leckagepfade im Zusammenhang mit Verbindungen, vereinfacht die Montageprozesse, reduziert die Lagerhaltung und erhöht die Zuverlässigkeit der Komponente von Natur aus.
Metall 3D-Druck ist nicht nur ein Werkzeug für das Prototyping, sondern eine produktionsreife Technologie, die in der Lage ist, Endverbrauchsteile für die anspruchsvollsten Anwendungen herzustellen. Unternehmen wie Met3dp stehen an vorderster Front und bieten fortschrittliche AM-Lösungen an, darunter hochentwickelte Drucker und Hochleistungsmetallpulver, die speziell auf Branchen wie Luft- und Raumfahrt, Automobilbau und Medizintechnik zugeschnitten sind. Ihr Fachwissen in den Bereichen Materialwissenschaft und Prozesssteuerung gewährleistet die Herstellung von dichten, hochwertigen Metallteilen mit hervorragenden mechanischen Eigenschaften, wodurch die additive Fertigung kritischer Komponenten wie kundenspezifischer Kraftstoffverteiler zu einer zuverlässigen und vorteilhaften Realität wird. Dieser technologische Wandel ermöglicht die Entwicklung und den Bau von Kraftstoffverteilungssystemen, die leichter, effizienter, zuverlässiger und schneller zu entwickeln sind als je zuvor - eine echte Revolution für die Kraftstoffversorgung in zahlreichen High-Tech-Branchen. Beschaffungsmanager und Ingenieure, die Wettbewerbsvorteile durch eine optimierte Leistung von Kraftstoffsystemen anstreben, wenden sich zunehmend an spezialisierte Metall-AM-Anbieter, die diese Komponenten der nächsten Generation liefern können.
Hauptanwendungen: Wo werden kundenspezifische AM-Kraftstoffverteiler eingesetzt?
Die einzigartigen Vorteile der additiven Fertigung von Metallen - insbesondere die Designfreiheit bei der Optimierung des Durchflusses, die Gewichtsreduzierung und die Konsolidierung von Bauteilen - machen sie zu einer außerordentlich gut geeigneten Technologie für die Herstellung von kundenspezifischen Kraftstoffverteilern in einem Spektrum anspruchsvoller Branchen. Während die grundlegende Funktion (Verteilung von Kraftstoff) gleich bleibt, variieren die spezifischen Anforderungen und Vorteile, die durch AM realisiert werden, je nach Anwendungskontext erheblich. Vorausschauende Ingenieurteams und Fertigungsstrategen setzen AM-Kraftstoffverteiler aktiv in Bereichen ein, in denen Leistung, Effizienz und Zuverlässigkeit nicht verhandelbar sind. Lassen Sie uns die Schlüsselindustrien und spezifischen Funktionen erkunden, in denen diese fortschrittlichen Komponenten einen bedeutenden Einfluss haben:
1. Luft- und Raumfahrt und Verteidigung: Dieser Sektor ist wohl der prominenteste frühe Anwender und Nutznießer von AM-Kraftstoffverteilern. Die extremen Betriebsbedingungen (hohe Temperaturen, Drücke, Vibrationen) in Verbindung mit dem unermüdlichen Streben nach Gewichtsreduzierung machen AM zu einer idealen Lösung.
- Gasturbinentriebwerke (Strahltriebwerke): Kraftstoffverteiler und zugehörige Komponenten wie Kraftstoffdüsen sind entscheidend für die Leistung und Effizienz von Motoren. AM ermöglicht:
- Optimierte interne Geometrien: Schaffung komplexer interner Passagen, die eine gleichmäßige Kraftstoffzufuhr zur Brennkammer gewährleisten, die Verbrennungsstabilität und -effizienz verbessern und gleichzeitig die Emissionen reduzieren. Drallelemente oder Mischelemente können direkt integriert werden.
- Gewichtsreduzierung: Durch die Optimierung der Topologie kann das Gewicht des Krümmers im Vergleich zu traditionell bearbeiteten oder gegossenen Versionen erheblich reduziert werden. Dies trägt direkt zu einer verbesserten Treibstoffersparnis des Flugzeugs oder einer erhöhten Reichweite/Nutzlast bei. Wenn beispielsweise eine mehrteilige gelötete Baugruppe durch einen einzigen, topologieoptimierten gedruckten Verteiler ersetzt wird, kann dies zu einer Gewichtseinsparung von 30-50 % oder mehr für diese spezifische Komponente führen.
- Teil Konsolidierung: Die Kombination von Verteilergehäuse, Halterungen und möglicherweise sogar Teilen der Kraftstoffdüsen in einem einzigen gedruckten Bauteil verringert die Komplexität der Montage, eliminiert Leckagepfade an den Verbindungsstellen (ein großes Problem der Zuverlässigkeit) und vereinfacht die Lieferkette. Führende Hersteller von Triebwerken für die Luft- und Raumfahrt setzen bereits 3D-gedruckte Kraftstoffdüsen und Verteilerkomponenten in ihren neuesten Triebwerkskonstruktionen ein.
- Auswahl der Materialien: Die Verwendung von Hochtemperatur-Superlegierungen wie Inconel 625 (IN625) oder speziellen Titanlegierungen, die sich leicht mittels AM verarbeiten lassen, gewährleisten Leistung und Haltbarkeit in der rauen Motorumgebung. Met3dp’s Fachwissen bei der Verarbeitung dieser fortschrittlichen Legierungen mit Techniken wie Selective Electron Beam Melting (SEBM) und Laser Powder Bed Fusion (L-PBF), gekoppelt mit ihren hochwertigen gasverdüsten Pulvern, macht sie zu einem wertvollen Partner für Luftfahrtkrümmerlieferanten.
- Raketenantriebsysteme: Die Anforderungen sind hier noch extremer: kryogene Brennstoffe, hohe Drücke und kurze Betriebszeiten, bei denen es auf maximale Leistung ankommt.
- Komplexe Kühlkanäle: AM ermöglicht die Integration komplizierter Kühlkanäle direkt in die Krümmerwände, was für die Bewältigung der bei der Verbrennung entstehenden starken Hitze, insbesondere in der Nähe der Einspritzdüsen, unerlässlich ist.
- Einspritzdüsenverkleidungen/Verteilerrohre: Die Kombination von Kraftstoff- und Oxidationsmittelverteilern zu komplexen Einspritzdüsenbaugruppen mit präzise gesteuerten Strömungswegen verbessert die Vermischung und die Verbrennungseffizienz, was für die Maximierung des Schubs entscheidend ist.
- Schnelle Iteration: Dank der Geschwindigkeit von AM können Anbieter von Trägerraketen während der Entwicklung schnell auf Krümmer- und Einspritzdüsendesigns zurückgreifen und die Leistung schneller optimieren, als dies mit herkömmlichen Methoden möglich wäre.
- Satelliten und Raumfahrzeuge: Das Gewicht ist hier aufgrund der Startkosten wohl der kritischste Faktor.
- Miniaturisierte, leichtgewichtige Systeme: AM ermöglicht die Herstellung hochkompakter und leichter Kraftstoffverteiler für Lageregelungstriebwerke und Antriebssysteme unter Verwendung von Materialien wie Titan oder Aluminiumlegierungen (z. B. AlSi10Mg für Anwendungen bei niedrigeren Temperaturen).
- Integrierte Funktionen: Sensoranschlüsse, Befestigungspunkte und Flüssigkeitsanschlüsse lassen sich nahtlos in die Verteilerkonstruktion integrieren, was die Komplexität des Gesamtsystems reduziert.
2. Hochleistungs-Automobiltechnik: Die Kostensensibilität ist zwar höher als in der Luft- und Raumfahrt, aber die Leistungsvorteile, die AM-Kraftstoffverteiler bieten, werden immer attraktiver, insbesondere im Rennsport, bei Luxus-/Leistungsfahrzeugen und im fortgeschrittenen Prototypenbau.
- Motorsport (F1, Langstreckenrennen, usw.): Die Teams arbeiten auf dem neuesten Stand der Technik und suchen jeden Leistungsvorteil.
- Optimierter Durchfluss für maximale Leistung: Kundenspezifisch entwickelte Krümmer mit CFD-optimierten internen Kanälen sorgen für eine ausgewogene Kraftstoffzufuhr zu jedem Zylinder und maximieren so den Verbrennungswirkungsgrad und die Leistungsabgabe. Durch die Möglichkeit, schnell Prototypen zu entwickeln und verschiedene Krümmerdesigns zu testen, können Teams die Motorleistung für bestimmte Strecken oder Bedingungen feinabstimmen.
- Gewichtsreduzierung: Selbst kleine Gewichtseinsparungen sind entscheidend für die Verbesserung von Handling, Beschleunigung und Bremsen. Topologieoptimierte AM-Krümmer tragen zur Reduzierung der Gesamtmasse des Fahrzeugs bei.
- Kompakte Verpackung: Die Motorräume von Rennwagen sind sehr eng gepackt. Mit AM können Krümmer so konstruiert werden, dass sie genau in den verfügbaren Raum passen und komplexe Kurven und Formen enthalten.
- Performance Road Cars & Luxusfahrzeuge: Funktionen, die ursprünglich für den Rennsport entwickelt wurden, werden oft nach unten weitergegeben.
- Verbesserte Motoreffizienz & Ansprechverhalten: Eine optimierte Kraftstoffverteilung kann zur Verbesserung des Kraftstoffverbrauchs und der Gasannahme beitragen.
- Design-Differenzierung: Einzigartige Motorkomponenten können ein Verkaufsargument auf dem Luxusmarkt sein.
- Prototyping & Motorentwicklung: AM beschleunigt den Entwicklungszyklus von Motoren erheblich. Ingenieure können neue Krümmerkonzepte innerhalb von Tagen oder Wochen entwerfen, drucken und testen - im Vergleich zu Monaten für den traditionellen Werkzeugbau und die Fertigung - und so Innovationen und Optimierungen beschleunigen.
3. Industrielle Anwendungen: Die Vorteile von AM-Ventilblöcken erstrecken sich auf verschiedene industrielle Bereiche, insbesondere auf solche, in denen Turbinen, schwere Maschinen und Spezialflüssigkeiten zum Einsatz kommen.
- Stromerzeugungsturbinen (Gas und Dampf): Ähnlich wie bei Düsentriebwerken ist bei großen Industrieturbinen eine präzise Kraftstoffzufuhr erforderlich, um Effizienz und Emissionskontrolle zu gewährleisten.
- Langlebigkeit & Leistung bei hohen Temperaturen: AM ermöglicht den Einsatz von robusten Superlegierungen (wie IN625), die den anspruchsvollen Betriebsbedingungen über längere Zeiträume standhalten können.
- Verbesserter Wirkungsgrad & Emissionen: Die optimierte Kraftstoff-Luft-Mischung durch fortschrittliche Düsen- und Verteilerkonstruktionen trägt zu einem höheren thermischen Wirkungsgrad und geringeren NOx-Emissionen bei.
- Reparatur & Ersatz: AM kann zur Herstellung von Ersatzverteilern für ältere Turbinen verwendet werden, für die keine Originalteile oder -werkzeuge mehr verfügbar sind, wobei auch konstruktive Verbesserungen möglich sind. Beschaffungsmanager in der Industrie, die nach zuverlässigen industrielle Flüssigkeitssysteme komponenten können AM sowohl für Neubauten als auch für MRO (Maintenance, Repair, Overhaul) nutzen.
- Schwermaschinen & Geländewagen: Motoren in Bau-, Bergbau- und Landwirtschaftsmaschinen profitieren von robusten und effizienten Kraftstoffsystemen. Die Kosten sind zwar ein wichtiger Faktor, aber das Potenzial für eine verbesserte Kraftstoffeinsparung und Zuverlässigkeit durch optimierte AM-Krümmer gewinnt zunehmend an Aufmerksamkeit.
- Spezialisierte Prüfstände & Forschungsausrüstung: In F&E-Umgebungen ist es von unschätzbarem Wert, schnell kundenspezifische Verteiler für spezielle Experimente zur Handhabung von Flüssigkeiten oder Testaufbauten zu erstellen. AM bietet die Flexibilität, Einzelstücke oder Kleinserien von Komponenten zu fertigen, die auf spezielle experimentelle Anforderungen zugeschnitten sind.
In all diesen Sektoren besteht die Gemeinsamkeit im Streben nach höherer Leistung, verbesserter Effizienz, größerer Zuverlässigkeit und oft auch nach geringerem Gewicht oder geringerer Größe. Kundenspezifische Kraftstoffverteiler, die mit AM-Metall hergestellt werden, sind ein leistungsfähiges Werkzeug, um diese Ziele zu erreichen, und verschieben die Grenzen des Möglichen bei der Konstruktion von Fluidsystemen. Es wird erwartet, dass sich der Einsatz von AM-Kraftstoffverteilern mit zunehmender Reife der Technologie und sinkenden Kosten weiter ausbreitet und zu einer Standardlösung für anspruchsvolle Anwendungen wird, die einen optimierten Durchfluss und komplexe Geometrien erfordern. Unternehmen, die großhandel mit Kraftstoffverteilern Produktion oder spezialisiert hersteller von Kraftstoffverteilern für Kraftfahrzeuge sondieren zunehmend Partnerschaften mit erfahrenen AM-Anbietern wie Met3dp, um diese fortschrittlichen Fähigkeiten zu nutzen.
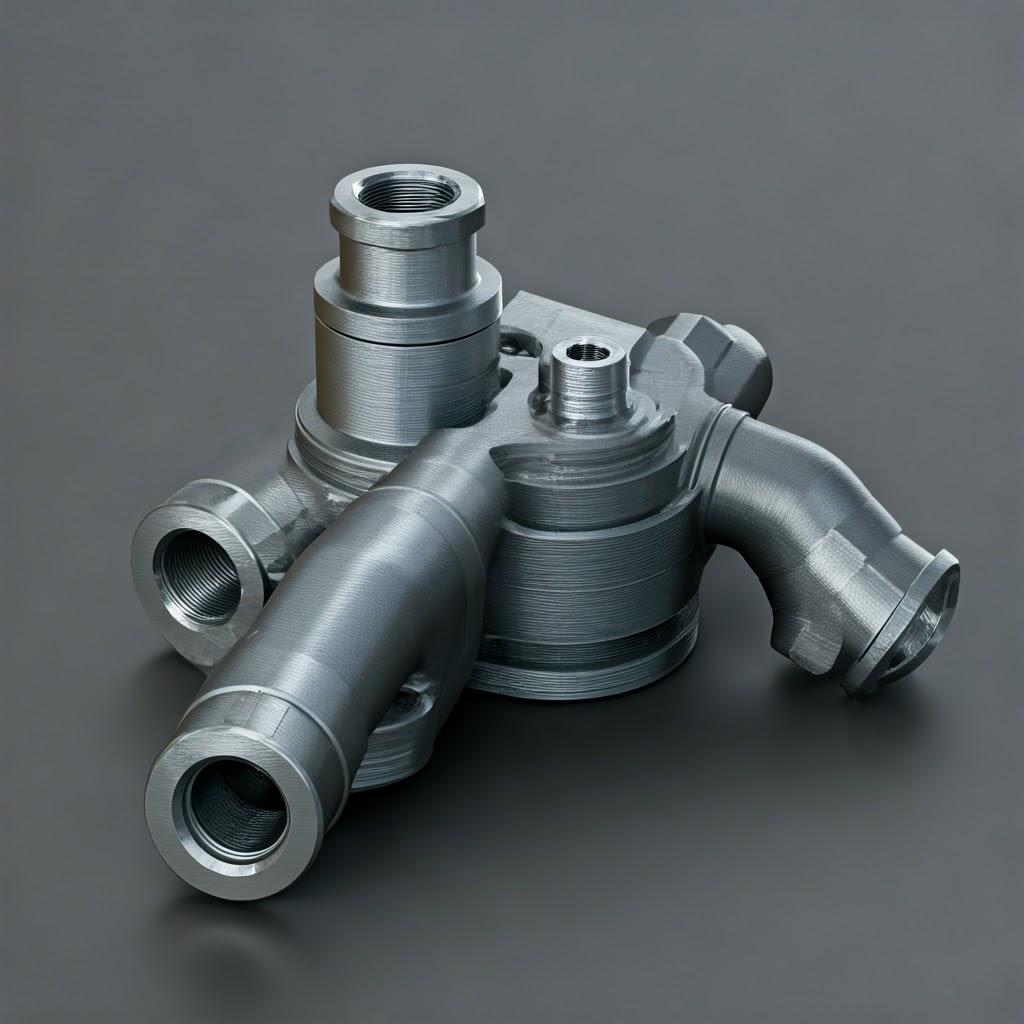
Der Additiv-Vorteil: Warum 3D-Metalldruck für Kraftstoffverteiler wählen?
Die Entscheidung, bei einem kritischen Bauteil wie einem Kraftstoffverteiler von jahrzehntealten traditionellen Fertigungsmethoden auf eine relativ neue Technologie wie die metalladditive Fertigung umzusteigen, wird nicht leichtfertig getroffen. Sie wird von einer Reihe überzeugender Vorteile angetrieben, die die inhärenten Grenzen von Gießen, Bearbeiten und Löten direkt angehen und letztendlich die Herstellung überlegener Komponenten ermöglichen. Für Ingenieure und Beschaffungsmanager, die Produktionsmethoden evaluieren, ist das Verständnis dieser spezifischen Vorteile entscheidend, um fundierte Entscheidungen zu treffen und erhebliche Leistungs- und Logistikgewinne zu erzielen. Der “additive Vorteil” für Kraftstoffverteiler ergibt sich aus einer Synergie von Designfreiheit, Leistungssteigerung, Verbesserung der physikalischen Eigenschaften und Fertigungseffizienz. Lassen Sie uns näher darauf eingehen, warum Metall-AM schnell zur bevorzugten Wahl für hochmoderne Kraftstoffverteilersysteme wird:
1. Unerreichte Gestaltungsfreiheit: Dies ist wohl der größte Vorteil von AM. Die schichtweise Konstruktion befreit die Designer von den Einschränkungen herkömmlicher Methoden, die auf die Herstellbarkeit abzielen (Design for Manufacturability”). * Komplexe innere Geometrien: AM eignet sich hervorragend zur Herstellung komplizierter innerer Kanäle, die durch Bohren oder Gießen einfach nicht zu erreichen sind. Designer können das umsetzen: * Glatte, gekrümmte Fließwege: Durch die Beseitigung scharfer 90-Grad-Bögen, die bei gebohrten Verteilern üblich sind, werden Strömungsablösung und Turbulenzen reduziert, was zu geringeren Druckverlusten und effizienterem Flüssigkeitstransport führt. * Variable Querschnitte: Die Kanäle können ihre Form und Größe entlang ihrer Länge fließend verändern, um die Strömungsgeschwindigkeit und den Druck präzise zu steuern. * Interne Luftleitbleche und Mischelemente: Strukturen zur Verbesserung der Kraftstoffmischung oder zur Steuerung der Strömungsverteilung können ohne Montage direkt in den Verteilerkörper integriert werden. * Optimierte Kreuzungen: An Stellen, an denen mehrere Kanäle zusammenlaufen oder sich aufteilen, kann die Geometrie mithilfe von CFD-Analysen sorgfältig entworfen werden, um sanfte Übergänge und eine ausgewogene Strömung zu gewährleisten. * Topologie-Optimierung: Mit dieser rechnergestützten Konstruktionstechnik, die sich perfekt für AM eignet, können Ingenieure die Belastungsbedingungen und Leistungsanforderungen (z. B. Steifigkeit) festlegen und die Software die optimale Materialverteilung gestalten. Das Ergebnis sind oft organische, gitterartige Strukturen, die Festigkeit und Steifigkeit beibehalten und gleichzeitig den Materialverbrauch und das Gewicht drastisch reduzieren, weit über das hinaus, was mit konventioneller Bearbeitung erreicht werden kann. Für einen Kraftstoffverteiler bedeutet dies, seine Masse zu verringern und gleichzeitig sicherzustellen, dass er den Betriebsdrücken und Vibrationen standhält. * Integrierte Funktionen: Befestigungspunkte, Sensoranschlüsse, Kühlkörper oder Flüssigkeitsanschlüsse, die normalerweise separate Teile sind, die zusammengebaut werden müssen, können als integrale Merkmale des Verteilerkörpers entworfen und gedruckt werden, was das Gesamtsystem vereinfacht.
2. Direkte Leistungsverbesserung: Die durch AM ermöglichte Designfreiheit schlägt sich direkt in messbaren Verbesserungen der Leistung von Kraftstoffverteilern nieder. * Optimierte Fluiddynamik: Wie bereits erwähnt, minimieren glatte, gekrümmte Innenkanäle, die mithilfe von CFD-Simulationen entwickelt wurden, die Druckverluste. Das bedeutet, dass die Kraftstoffpumpe weniger hart arbeitet, was Energie spart, und dass der an die Einspritzdüsen gelieferte Druck gleichmäßiger und berechenbarer ist, was zu einer besseren Zerstäubung und Verbrennung führt. * Gleichmäßige Strömungsverteilung: Komplexe interne Geometrien können sorgfältig abgestimmt werden, um sicherzustellen, dass jede Auslassöffnung eine identische Menge an Kraftstoffdurchfluss und Druck erhält, was für eine ausgewogene Motorleistung entscheidend ist, insbesondere bei Mehrzylindermotoren oder Brennkammern mit mehreren Düsen. Bei herkömmlichen Verteilern ist eine perfekte Verteilung aufgrund von Fertigungsbeschränkungen oft nicht möglich. * Verbessertes Wärmemanagement: Bei Hochtemperaturanwendungen (z. B. in Triebwerken für die Luft- und Raumfahrt) ermöglicht AM die Integration hochentwickelter interner Kühlkanäle direkt in die Krümmerwände, wobei der Kraftstoff selbst oder ein separater Kühlmittelkreislauf verwendet wird. Dies trägt dazu bei, die strukturelle Integrität des Krümmermaterials zu erhalten und verhindert eine Überhitzung oder Verkokung des Kraftstoffs.
3. Deutliche Gewichtsreduzierung: Die Optimierung der Masse ist ein Hauptgrund für die Einführung von AM, insbesondere in der Transportindustrie. * Topologie-Optimierung: Wie bereits erwähnt, trägt dies wesentlich dazu bei, unnötiges Material zu entfernen. * Wahl des Materials: AM ermöglicht den effektiven Einsatz von leichten, hochfesten Werkstoffen wie Aluminiumlegierungen (AlSi10Mg) und Titanlegierungen (Ti6Al4V), die auf herkömmliche Weise nur schwer oder mit hohem Aufwand in komplexe Formen gebracht werden können. * Teil Konsolidierung: Durch die Verringerung der Anzahl der Einzelteile wird das Gesamtgewicht von Flanschen, Verbindungselementen und Dichtungen reduziert. * Auswirkungen: Gewichtseinsparungen von 20 % bis 60 % oder sogar mehr werden häufig für Bauteile in der Luft- und Raumfahrt und in der Automobilindustrie berichtet, die für AM neu konstruiert wurden, verglichen mit ihren konventionellen Gegenstücken. Dies schlägt sich direkt in Kraftstoffeinsparungen, höherer Nutzlast oder verbesserter Fahrzeugdynamik nieder.
4. Konsolidierung der Teile und Vereinfachung des Systems: Dies bietet zahlreiche logistische und zuverlässige Vorteile. * Reduzierte Montagezeit und -kosten: Durch das Drucken eines einzigen integrierten Verteilers entfällt der Zeit- und Arbeitsaufwand für den Zusammenbau mehrerer Komponenten, das Auftragen von Dichtmitteln und das Anziehen von Befestigungselementen. * Beseitigung von Leckagepfaden: Hartgelötete oder geschweißte Verbindungen und mechanische Fittings sind potenzielle Leckagequellen, insbesondere bei hohem Druck, Vibrationen oder Temperaturschwankungen. Ein monolithisches AM-Teil hat drastisch weniger potenzielle Leckstellen, was die Zuverlässigkeit und Sicherheit des Systems erheblich verbessert - ein entscheidender Faktor für Kraftstoffsysteme. * Vereinfachte Lieferkette & Bestandsaufnahme: Die Verwaltung einer einzigen Teilenummer anstelle mehrerer Komponenten vereinfacht die Beschaffung, Logistik, Bestandsverwaltung und Wartung. Dies spricht direkt die Beschaffungsmanager an, die einen rationalisierten Betrieb und geringere Gemeinkosten anstreben. * Erhöhte Verlässlichkeit: Weniger Teile und Verbindungen bedeuten weniger potenzielle Fehlermöglichkeiten, was zu einem robusteren und zuverlässigeren Endprodukt führt.
5. Rapid Prototyping, Iteration und Anpassung: AM beschleunigt den Lebenszyklus der Produktentwicklung und ermöglicht maßgeschneiderte Lösungen. * Geschwindigkeit: Funktionale Metallprototypen können innerhalb von Tagen oder Wochen direkt aus CAD-Daten hergestellt werden, ohne dass teure und zeitaufwändige Werkzeuge (wie Gussformen oder Gesenke) benötigt werden. Auf diese Weise können Entwicklungsteams Entwürfe schnell testen und validieren, Fehler erkennen und viel schneller iterieren, als dies mit herkömmlichen Methoden möglich ist. * Kosteneffiziente Iteration: Bei Konstruktionsänderungen wird die CAD-Datei geändert und eine neue Version gedruckt. Dies ist wesentlich billiger und schneller als die Änderung oder Neuanfertigung herkömmlicher Werkzeuge. * Kundenspezifische Anpassung & Produktion von Kleinserien: AM ist für die Herstellung hochgradig individueller Verteiler oder kleiner Serien wirtschaftlich, da keine Werkzeugkosten anfallen, die sich amortisieren. Dies ist ideal für Spezialanwendungen, den Motorsport oder als Ersatzteil für ältere Systeme. Unternehmen, die rapid Prototyping von Kraftstoffsystemen finden AM von unschätzbarem Wert.
6. Materialeffizienz und Nachhaltigkeit: * Weniger Abfall: Bei der additiven Fertigung wird in der Regel nur das Material verwendet, das für die Herstellung des Teils und seiner Halterungen benötigt wird, was im Vergleich zur subtraktiven Bearbeitung, bei der zunächst ein größerer Block abgetragen wird, zu deutlich weniger Materialabfall führt. Die Wiederverwendung und das Recycling von Pulver sind zwar wichtige Aspekte, aber das Verhältnis von eingekauftem Rohmaterial zum Gewicht des fertigen Teils ist bei AM oft viel besser. * Ermöglichung leichtgewichtiger Designs: Ein geringeres Gewicht der Komponenten trägt zu einer besseren Treibstoffeffizienz in der Endanwendung (Flugzeug, Fahrzeug) bei, was zu geringeren Emissionen während der Lebensdauer des Produkts führt.
Die Wahl des 3D-Metalldrucks für Kraftstoffverteiler ist daher eine strategische Entscheidung, die durch das Potenzial für bessere Leistung, geringeres Gewicht, höhere Zuverlässigkeit und schnellere Entwicklungszyklen bestimmt wird. Auch wenn die anfänglichen Kosten für ein Teil manchmal höher sind als die eines einfachen, maschinell gefertigten Teils, zeigt eine Analyse der Gesamtbetriebskosten oft erhebliche Einsparungen, wenn man die Reduzierung der Montage, die verbesserte Leistung, die Gewichtseinsparungen und die vereinfachte Logistik berücksichtigt. Die Zusammenarbeit mit einem erfahrenen Metall-AM-Anbieter wie Met3dp, die über fundierte Kenntnisse von Werkstoffen, Verfahren wie L-PBF und SEBM sowie DfAM-Prinzipien verfügt, ist der Schlüssel zur vollständigen Nutzung dieser additiven Vorteile für Ihre kritischen Kraftstoffverteilungsanwendungen. Erkundung verschiedener Druckverfahren und Materialoptionen ist entscheidend für die Optimierung des Ergebnisses.
Materialauswahl im Blickpunkt: AlSi10Mg und IN625 für optimale Leistung
Die Auswahl des geeigneten Werkstoffs ist wohl eine der wichtigsten Entscheidungen bei der Konstruktion und Fertigung eines jeden Bauteils, doch bei Kraftstoffverteilern kommt ihr aufgrund der hohen Betriebsanforderungen, denen sie häufig ausgesetzt sind, eine noch größere Bedeutung zu. Das Material muss nicht nur die strukturelle Integrität unter Druck und Vibration gewährleisten, sondern auch möglichen Temperaturextremen standhalten, der Korrosion durch verschiedene Kraftstoffarten widerstehen und idealerweise zur Gewichtsoptimierung beitragen. Die additive Fertigung erweitert die Palette der verfügbaren Materialien und Verarbeitungskombinationen, aber eine sorgfältige Abwägung ist von größter Bedeutung, um sicherzustellen, dass das endgültige Teil alle Anforderungen an Leistung, Sicherheit und Langlebigkeit erfüllt.
Bei kundenspezifischen 3D-gedruckten Kraftstoffverteilern stehen zwei Materialien aufgrund ihrer hervorragenden Eigenschaften und ihrer Verarbeitbarkeit mit gängigen AM-Verfahren wie Laser Powder Bed Fusion (L-PBF) häufig ganz oben auf der Liste: Aluminium-Silizium-Magnesium-Legierung (AlSi10Mg) und Nickel-Chrom-Superlegierung Inconel 625 (IN625). Für Ingenieure und Beschaffungsspezialisten, die AM effektiv nutzen wollen, ist es von entscheidender Bedeutung, die unterschiedlichen Merkmale und idealen Anwendungen der einzelnen Produkte zu verstehen.
1. Aluminium-Silizium-Magnesium (AlSi10Mg): Das leichtgewichtige Arbeitspferd
AlSi10Mg ist eine in der additiven Fertigung weit verbreitete Aluminiumlegierung, die den Eigenschaften herkömmlicher Aluminiumgusslegierungen wie A360 sehr ähnlich ist. Seine Beliebtheit beruht auf einer Kombination wünschenswerter Eigenschaften, die es für eine breite Palette von Anwendungen, einschließlich vieler Kraftstoffsysteme, geeignet machen.
- Wichtige Eigenschaften:
- Geringe Dichte/Leichtgewicht: Mit einer Dichte von ca. 2,67 g/cm3 ist es deutlich leichter als Stähle oder Nickellegierungen und eignet sich daher ideal für Anwendungen, bei denen die Gewichtsreduzierung eine wichtige Rolle spielt (Luft- und Raumfahrt, Automobilbau, Drohnen).
- Gutes Verhältnis von Stärke zu Gewicht: Es ist zwar nicht so fest wie Stahl oder Titan, bietet aber eine beachtliche mechanische Festigkeit, insbesondere nach einer entsprechenden Wärmebehandlung, so dass es sich für moderate Druck- und Strukturanforderungen eignet. Die typische Zugfestigkeit (UTS) für wärmebehandeltes L-PBF AlSi10Mg kann 300 MPa überschreiten.
- Ausgezeichnete Wärmeleitfähigkeit: Aluminiumlegierungen leiten Wärme sehr gut, was bei einigen Konstruktionen von Vorteil sein kann, wenn es darum geht, die Wärme vom Kraftstoff wegzuleiten oder den Verteiler selbst als Kühlkörper zu verwenden.
- Gute Korrosionsbeständigkeit: Weist eine gute Beständigkeit gegen atmosphärische Korrosion und verschiedene Flüssigkeiten auf, wobei die spezifische Kraftstoffverträglichkeit stets überprüft werden sollte.
- Verarbeitbarkeit: Es ist mit L-PBF-Systemen relativ einfach zu bearbeiten und ermöglicht feine Strukturen und gute Oberflächengüten (im Vergleich zu AM).
- Ideale Kraftstoffverteiler-Anwendungen:
- Automobilindustrie: Weit verbreitet für Prototyp- und Serienkrümmer in Hochleistungsfahrzeugen, Standard-Pkw (wo zutreffend) und im Motorsport aufgrund seines geringen Gewichts und seiner angemessenen Leistung für typische Kraftstoffdrücke und -temperaturen in Kraftfahrzeugen.
- Unbemannte Luftfahrzeuge (UAVs / Drohnen): Das Gewicht ist entscheidend, und die Betriebsbedingungen sind im Allgemeinen weniger extrem als bei bemannten Flugzeugtriebwerken.
- Luft- und Raumfahrt (weniger anspruchsvolle Aufgaben): Geeignet für sekundäre Kraftstoffleitungen, hydraulische Verteiler oder Komponenten in Umweltkontrollsystemen, wo Temperaturen und Drücke moderat sind.
- Industrielle Ausrüstung: Anwendungen, bei denen die Betriebstemperaturen relativ niedrig sind und aggressive chemische Korrosion kein großes Problem darstellt.
- Überlegungen zur Verarbeitung (L-PBF):
- Erfordert eine sorgfältige Steuerung der Parameter (Laserleistung, Scangeschwindigkeit, Schichtdicke), um die Porosität zu minimieren und dichte Teile zu erhalten.
- Erfordert in der Regel eine Spannungsarmglühung nach dem Druck, um die während der schnellen Erwärmungs- und Abkühlungszyklen aufgebauten inneren Spannungen zu reduzieren. Eine T6-Wärmebehandlung (Lösungsglühen und künstliche Alterung) wird häufig angewandt, um die Festigkeit und Härte zu maximieren.
- Stützkonstruktionen sind in der Regel für Überhänge erforderlich und werden in der Regel manuell oder durch CNC-Bearbeitung entfernt.
- Met3dp's Fähigkeit: Unternehmen wie Met3dp nutzen fortschrittliche Verfahren zur Pulverherstellung, wie z. B Gaszerstäubungum hochwertiges AlSi10Mg-Pulver herzustellen. Dies gewährleistet eine hohe Sphärizität, eine gute Fließfähigkeit, eine kontrollierte Partikelgrößenverteilung und einen geringen Sauerstoffgehalt - alles kritische Faktoren für das Erreichen konsistenter, hochdichter und zuverlässiger Teile während des L-PBF-Prozesses. Die Beschaffung von Pulver von einem renommierten Anbieter mit einer soliden Qualitätskontrolle wie Met3dp ist für die Gewährleistung der Materialintegrität des fertigen Verteilers von entscheidender Bedeutung. Ihr Angebot an Produkte umfasst verschiedene Hochleistungspulver, die für AM optimiert sind.
2. Inconel 625 (IN625): Der hochtemperatur- und korrosionsbeständige Champion
IN625 ist eine Nickel-Chrom-Molybdän-Niob-Superlegierung, die für ihre außergewöhnliche Leistungsfähigkeit in rauen Umgebungen bekannt ist. Wenn Kraftstoffverteiler mit extremen Temperaturen, hohem Druck und korrosiven Medien konfrontiert sind, ist IN625 oft das Material der Wahl.
- Wichtige Eigenschaften:
- Ausgezeichnete Hochtemperaturfestigkeit: Behält seine hohe Festigkeit und Kriechfestigkeit bei hohen Temperaturen (je nach Bedingungen bis zu 800-900 °C oder höher) bei und eignet sich daher ideal für Bauteile in der Nähe von Verbrennungsräumen oder Abgasanlagen.
- Hervorragende Korrosionsbeständigkeit: Zeigt eine außergewöhnliche Beständigkeit gegen eine Vielzahl von korrosiven Umgebungen, einschließlich oxidierender und reduzierender Säuren, Lochfraß, Spaltkorrosion und Chlorid-Spannungsrisskorrosion. Dies ist von entscheidender Bedeutung beim Umgang mit aggressiven oder alternativen Kraftstoffarten.
- Hohe Ermüdungsfestigkeit: Hält zyklischen Belastungen und Vibrationen stand, was in Motorumgebungen entscheidend ist.
- Ausgezeichnete Schweißbarkeit/Verarbeitbarkeit (in AM): Obwohl es sich bei IN625 um eine komplexe Legierung handelt, lässt sie sich sowohl mit L-PBF als auch mit Elektronenstrahlschmelzen (EBM) leicht verarbeiten und ermöglicht die Herstellung von dichten, rissfreien Teilen mit entsprechender Parametersteuerung.
- Kryogenische Zähigkeit: Behält auch bei sehr niedrigen Temperaturen eine gute Zähigkeit, was für bestimmte Kraftstoffanwendungen in der Luft- und Raumfahrt von Bedeutung ist.
- Ideale Kraftstoffverteiler-Anwendungen:
- Gasturbinentriebwerke für die Luft- und Raumfahrt: Kraftstoffverteiler, Kraftstoffdüsen und Brennerkomponenten, die in den heißen Bereichen des Motors arbeiten.
- Raketenantriebsysteme: Injektorkomponenten, Kraftstoff- und Oxidationsmittelverteiler für extreme Temperaturen und Drücke.
- Industrielle Hochtemperatursysteme: Brennstoffzufuhr in Industrieöfen, chemische Verarbeitungsreaktoren oder Turbinen zur Stromerzeugung, die unter schwierigen Bedingungen arbeiten.
- Anwendungen in der Schifffahrt: Dank seiner Beständigkeit gegen Salzwasserkorrosion eignet es sich für Kraftstoffsysteme in Schiffsdieselmotoren.
- Anwendungen mit korrosiven Brennstoffen: Systeme, die Biokraftstoffe, synthetische Kraftstoffe oder andere Alternativen verwenden, die korrosiver sein können als herkömmliche Erdölprodukte.
- Überlegungen zur Verarbeitung (L-PBF/EBM):
- Erfordert im Vergleich zu Aluminiumlegierungen einen höheren Energieaufwand.
- Anfällig für den Aufbau von Eigenspannungen aufgrund großer thermischer Gradienten; sorgfältige Kontrolle der Erwärmung, der Abtaststrategie und oft auch der Aufbauplattenerwärmung (üblich bei EBM) ist erforderlich.
- Ein Spannungsarmglühen nach dem Druck ist fast immer erforderlich, um Eigenspannungen zu reduzieren und Verformungen oder Risse zu vermeiden. Zur Optimierung der mechanischen Eigenschaften können weitere Wärmebehandlungen (Lösungsglühen, Alterung) erforderlich sein.
- Stützstrukturen sind in der Regel dichter und können schwieriger zu entfernen sein als bei Aluminiumlegierungen, was oft eine maschinelle Bearbeitung oder Drahterosion erfordert.
- Expertise von Met3dp: Met3dp verfügt über beträchtliche Erfahrung in der Herstellung und Verarbeitung von Superlegierungen wie IN625. Ihre fortschrittlichen Pulverherstellungssysteme gewährleisten die Produktion von Pulvern mit den spezifischen Eigenschaften, die für eine erfolgreiche AM-Bearbeitung dieser anspruchsvollen Materialien erforderlich sind. Dank ihrer Erfahrung mit verschiedenen AM-Systemen, einschließlich des selektiven Elektronenstrahlschmelzens (SEBM), das für das Spannungsmanagement in Nickellegierungen von Vorteil sein kann, können sie ihre Kunden über die optimale Material- und Prozesskombination für anspruchsvolle Anwendungen beraten IN625 Luft- und Raumfahrt-Krümmer anwendungen. Das Portfolio geht über diese beiden Werkstoffe hinaus und umfasst innovative Legierungen wie TiNi, TiTa, TiAl, TiNbZr, CoCrMo, rostfreie Stähle und mehr, die umfassende Werkstofflösungen bieten.
Die Wahl zwischen AlSi10Mg und IN625:
Die Auswahl hängt in erster Linie von der Betriebsumgebung ab:
Merkmal | AlSi10Mg | IN625 |
---|---|---|
Primärer Vorteil | Leichtes Gewicht, gute Wärmeleitfähigkeit | Hochtemperaturfestigkeit, Korrosionsbeständigkeit |
Dichte | Niedrig (~2,67g/cm3) | Hoch (~8,44g/cm3) |
Maximale Einsatztemperatur | Mäßig (~150-200∘C) | Sehr hoch (~800-1000∘C) |
Korrosionsbeständigkeit | Gut (Allgemein) | Ausgezeichnet (Aggressive Umgebungen) |
Kosten | Unter | Höher |
Gewicht | Feuerzeug | Schwerer |
Typische Anwendungen | Automotive, Drohnen, Niedertemperatur-Luftfahrt | Triebwerke für die Luft- und Raumfahrt, Raketen, industrielle Hochtemperaturen |
AM Verarbeitung | L-PBF (allgemein) | L-PBF, EBM (gemeinsam) |
In Blätter exportieren
Andere mögliche Materialien:
Während AlSi10Mg und IN625 viele Anwendungen abdecken, können auch andere Werkstoffe in Betracht gezogen werden:
- Titan-Legierungen (z. B. Ti6Al4V): Bieten ein ausgezeichnetes Verhältnis von Festigkeit zu Gewicht, besser als AlSi10Mg, und eine gute Korrosionsbeständigkeit mit mäßiger Hochtemperaturfähigkeit (bis zu ~400∘C). Wird häufig in der Luft- und Raumfahrt verwendet, wo das Gewicht kritisch ist, die Temperaturen aber kein IN625 erfordern.
- Rostfreie Stähle (z. B. 316L, 17-4PH): Bietet gute Korrosionsbeständigkeit und mäßige Festigkeit zu geringeren Kosten als IN625 und eignet sich für verschiedene Industrie- und Automobilanwendungen, bei denen hohe Temperaturen keine Rolle spielen und das Gewicht nicht das Hauptanliegen ist.
Letztendlich erfordert der Prozess der Materialauswahl eine gründliche Analyse der Betriebsbedingungen des Verteilers, der Leistungsanforderungen, der Gewichtsziele und der Budgetbeschränkungen. Die Beratung mit Materialspezialisten und erfahrenen AM-Anbietern wie Met3dp, die die Feinheiten der verschiedenen Metallpulver und ihre Verarbeitung sind entscheidend für die optimale Wahl eines zuverlässigen und leistungsstarken 3D-gedruckten Kraftstoffverteilers. Ihr Hintergrund als Lieferanten von Metallpulver durch den Einsatz branchenführender Technologien erhalten sie einzigartige Einblicke in die Leistungsfähigkeit von Materialien.
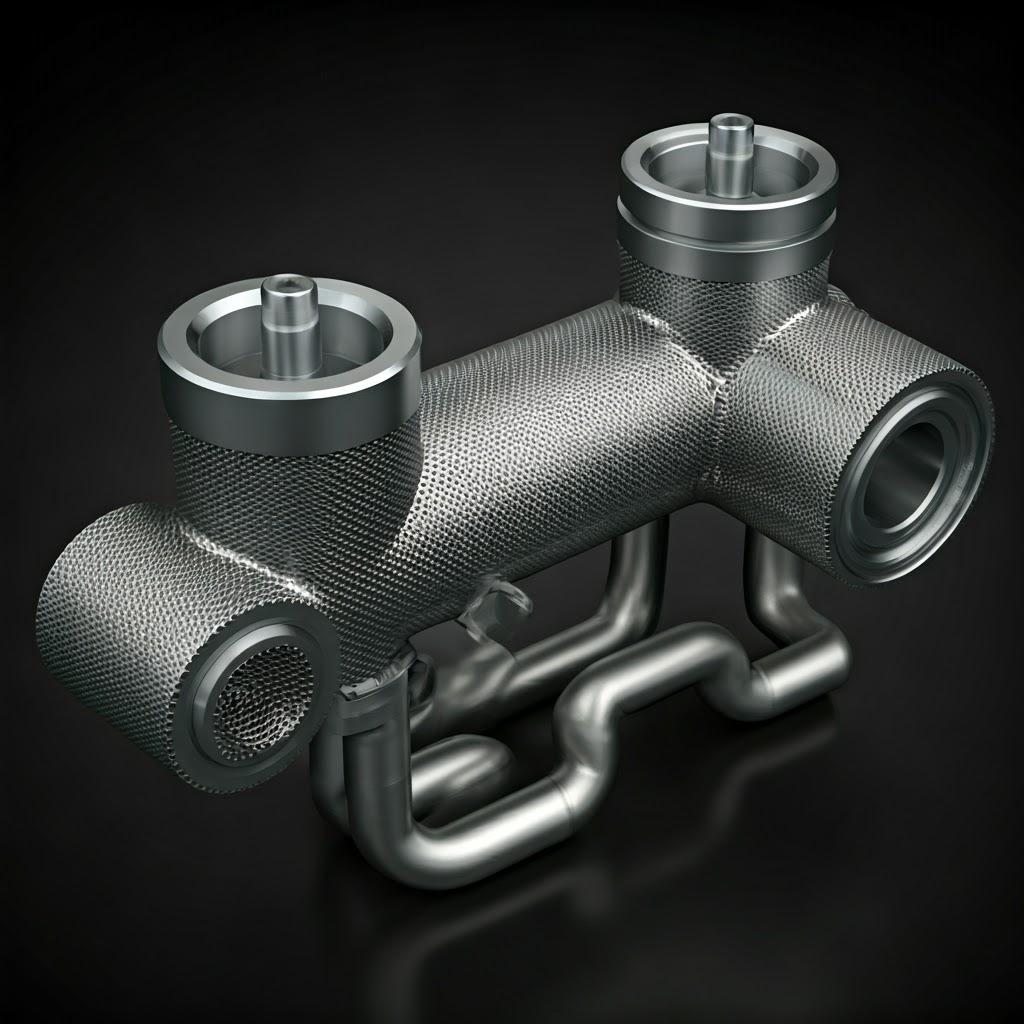
Entwurf für additive Fertigung (DfAM): Optimierung von Kraftstoffverteilern für den Druck
Wenn man einen Entwurf für einen Kraftstoffverteiler, der für die herkömmliche Fertigung vorgesehen ist, einfach an einen 3D-Metalldrucker sendet, werden selten optimale Ergebnisse erzielt. In der Tat kann dies oft zu Druckfehlern, schlechter Teilequalität, übermäßigen Nachbearbeitungsanforderungen und unnötig hohen Kosten führen. Um das transformative Potenzial der additiven Fertigung - die bereits erwähnte Strömungsoptimierung, Gewichtsreduzierung und Bauteilkonsolidierung - wirklich zu erschließen, müssen die Ingenieure folgende Punkte berücksichtigen Design für additive Fertigung (DfAM). DfAM ist nicht nur ein Vorschlag, sondern ein grundlegender Wandel im Designdenken, der die einzigartigen Fähigkeiten und Einschränkungen des schichtweisen Bauprozesses bereits in der Konzeptionsphase berücksichtigt. Bei komplexen Fluidikkomponenten wie Kraftstoffverteilern ist die Anwendung der DfAM-Prinzipien entscheidend für den Erfolg.
DfAM beinhaltet einen ganzheitlichen Ansatz, der Überlegungen zu Materialeigenschaften, Druckerkapazitäten, Anforderungen an die Stützstruktur, Nachbearbeitungsschritte und die gewünschte Funktionalität des Teils einbezieht. Es erfordert oft eine enge Zusammenarbeit zwischen den Konstrukteuren und dem AM-Dienstleister, wobei die praktische Erfahrung und das Prozesswissen des Anbieters genutzt werden. Lassen Sie uns die wichtigsten DfAM-Prinzipien aufschlüsseln, die speziell für die Entwicklung optimierter Kraftstoffverteiler für Metall-AM relevant sind:
1. Interne Kanalgestaltung: Hier bietet AM die größten Vorteile gegenüber den traditionellen Methoden für Verteilerrohre. * Selbsttragende Winkel: Die meisten Pulverbettschmelzverfahren (wie L-PBF und EBM) können überhängende Merkmale ohne Stützstrukturen bis zu einem bestimmten Winkel drucken, in der Regel etwa 45 Grad von der horizontalen Ebene (relativ zur Bauplatte). Durch die Gestaltung interner Kanäle mit sanften Neigungen und die Vermeidung flacher horizontaler Decken wird der Bedarf an internen Stützen minimiert, die aus geschlossenen Passagen nur sehr schwer oder gar nicht entfernt werden können. Wo horizontale Abschnitte unvermeidlich sind, können sie durch einen tropfen- oder rautenförmigen Querschnitt selbsttragend sein. * Glatte Kurven und Filets: Scharfe Innenecken konzentrieren Spannungen und können den Flüssigkeitsstrom stören, was zu Turbulenzen und Druckabfall führt. DfAM fördert die Verwendung von glatten, großzügigen Radien und Verrundungen an Kanalübergängen und Biegungen. AM-Prozesse können diese komplexen Kurven leicht erstellen, was zu einer verbesserten Fluiddynamik und einer besseren strukturellen Integrität führt. * Dünne, tiefe Schlitze meiden: Sehr schmale oder tiefe innere Merkmale können schwierig genau zu drucken und schwierig von Pulverrückständen zu reinigen sein. Bei der Konstruktion sollte darauf geachtet werden, dass die Kanäle groß genug sind, um das Pulver effektiv zu entfernen und gegebenenfalls eine Nachbearbeitung, wie z. B. eine abrasive Fließbearbeitung, durchzuführen. * Optimierung der Strömungswege (CFD-gesteuerter Entwurf): Mit DfAM können Konstrukteure mithilfe von CFD-Simulationswerkzeugen (Computational Fluid Dynamics) die Flüssigkeitsströmung durch vorgeschlagene Verteilerkonstruktionen modellieren. Die Ergebnisse können zur Optimierung von Kanalformen, -größen und -anordnungen führen, um bestimmte Ziele zu erreichen, wie z. B. die Minimierung des Druckabfalls, die Gewährleistung einer gleichmäßigen Strömungsverteilung an allen Auslässen oder die Förderung bestimmter Mischeigenschaften. AM kann dann diese hoch optimierten, oft nicht intuitiven Geometrien direkt herstellen.
2. Überlegungen zur Wanddicke: * Bedruckbare Mindestdicke: AM-Prozesse haben Grenzen für die minimale Wanddicke, die sie zuverlässig herstellen können. Diese liegen in der Regel zwischen 0,3 mm und 1,0 mm, je nach Material, Maschine und Feature-Geometrie. Die Konstruktionen müssen diese Grenzen einhalten, um sicherzustellen, dass die Merkmale vollständig geformt werden. * Strukturelle Integrität & Druckeindämmung: Die Wände müssen dick genug sein, um den Betriebsdrücken des Kraftstoffsystems standzuhalten, ohne nachzugeben oder zu bersten. Die Finite-Elemente-Analyse (FEA) sollte eingesetzt werden, um die Spannungsverteilung unter Druck zu simulieren und eine angemessene Wandstärke zu gewährleisten, insbesondere in Hochdruckzonen oder in Bereichen, die durch Topologieoptimierung als hochbelastet identifiziert wurden. Bei DfAM gilt es, einen Ausgleich zwischen dem Wunsch nach Leichtbau und dem Bedarf an struktureller Robustheit zu schaffen. * Gleichmäßigkeit (Wo immer möglich): Eine variable Wanddicke ist zwar möglich und oft wünschenswert (z. B. durch Topologieoptimierung), doch können große, abrupte Dickenänderungen manchmal zu unterschiedlichen Abkühlungsraten während des Drucks führen, was die Restspannung oder den Verzug erhöhen kann. Allmähliche Übergänge sind daher vorzuziehen.
3. Strategie der Unterstützungsstruktur: Stützstrukturen sind bei der Metall-AM häufig erforderlich, um das Teil auf der Bauplatte zu verankern, überhängende Merkmale (die steiler sind als der selbsttragende Winkel) zu stützen und die Wärme während des Drucks vom Teil wegzuleiten, um Verformungen zu reduzieren. * Minimierung der internen Stützen: Wie bereits erwähnt, sind interne Stützen in geschlossenen Kanälen höchst unerwünscht. DfAM konzentriert sich auf die Ausrichtung des Teils auf der Bauplatte und die Gestaltung der Kanalgeometrien (unter Verwendung von selbsttragenden Winkeln und Formen), um die Notwendigkeit von Stützen zu eliminieren oder drastisch zu reduzieren. * Design für einfache Entfernung: Wenn externe Stützen erforderlich sind (z. B. unter Flanschen oder externen Merkmalen), sollten sie so konstruiert sein, dass sie zugänglich sind und sich mit manuellen Werkzeugen oder durch maschinelle Bearbeitung leicht entfernen lassen, ohne die Oberfläche des Teils zu beschädigen. Dies kann die Verwendung spezieller Halterungstypen (z. B. Gitter- oder Kegelhalterungen) mit minimalen Kontaktpunkten oder die Konstruktion von Zeugenlinien beinhalten, an denen die Halterungen sauber abgearbeitet werden können. * Unterstützungsfunktionalität: Auch beim Wärmemanagement spielen Halterungen eine entscheidende Rolle. In Bereichen, die zu Überhitzung oder Verformung neigen, können dichte Stützen erforderlich sein. Simulationswerkzeuge können helfen, das thermische Verhalten vorherzusagen und die optimale Platzierung und Art der Stützen zu bestimmen.
4. Integration von Funktionen: Mit AM können mehrere Funktionen in einem einzigen Teil kombiniert werden. * Konsolidierung von Komponenten: Suchen Sie nach Möglichkeiten, Halterungen, Montagevorsprünge, Sensoranschlüsse, Gehäuse oder sogar Wärmetauscherelemente direkt in das Verteilergehäuse zu integrieren. Dies reduziert die Anzahl der Teile, den Montageaufwand und potenzielle Leckagepfade. * Integrierte Funktionen für AM entwerfen: Stellen Sie sicher, dass integrierte Features den DfAM-Prinzipien entsprechen (z. B. selbsttragende Winkel für Montagebohrungen, ausreichende Wandstärke um Anschlüsse). Überlegen Sie, wie Nachbearbeitungsschritte wie das Gewindeschneiden oder die Bearbeitung von Dichtflächen an den integrierten Features durchgeführt werden sollen.
5. Topologie-Optimierung & Gewichtsreduzierung: * Anwendung von Lasten und Beschränkungen: Definieren Sie die Betriebslasten (Druck, Vibration, Montagekräfte) und Einschränkungen (Sperrzonen, Anschlusspunkte) für den Verteiler. * Laufende Optimierungsalgorithmen: Verwenden Sie FEA-basierte Topologie-Optimierungssoftware, um iterativ Material aus unkritischen Bereichen zu entfernen und gleichzeitig sicherzustellen, dass das Design weiterhin die Leistungsanforderungen (Steifigkeit, Festigkeit, Eigenfrequenz) erfüllt. * Interpretation und Verfeinerung der Ergebnisse: Das Rohergebnis der Topologieoptimierung muss oft geglättet und interpretiert werden, um ein fertigungsgerechtes Design zu erstellen. Dies kann die Umwandlung komplexer Gitterstrukturen in besser handhabbare Geometrien oder die Einhaltung von Mindestmerkmalgrößen beinhalten. Gitterstrukturen bieten zwar maximale Gewichtseinsparungen, können aber schwierig zu reinigen und intern zu prüfen sein, so dass bei Kraftstoffverteilern ein Gleichgewicht gefunden werden muss. Generative Designtools bieten ähnliche Möglichkeiten und untersuchen oft mehrere Designoptionen auf der Grundlage definierter Einschränkungen.
Zusammenarbeit ist der Schlüssel: Die erfolgreiche Implementierung von DfAM, insbesondere bei kritischen Bauteilen wie Kraftstoffverteilern, profitiert oft immens von einer frühen Zusammenarbeit mit einem erfahrenen AM-Dienstleister wie Met3dp. Deren Ingenieure verfügen über fundierte praktische Kenntnisse der spezifischen Maschinenfähigkeiten, des Materialverhaltens, der Unterstützungsstrategien und der Auswirkungen der Nachbearbeitung. Sie können entscheidendes Feedback zur Machbarkeit des Designs geben, Änderungen vorschlagen, um die Druckbarkeit zu verbessern oder die Kosten zu senken, und dazu beitragen, dass das endgültige Design wirklich für den additiven Prozess optimiert ist. Die Nutzung der Lösungen für die additive Fertigung die von kompetenten Partnern angeboten werden, rationalisieren den Weg vom Konzept zum funktionalen, leistungsstarken Teil. Dieser kooperative Ansatz stellt sicher, dass die Entwürfe nicht nur theoretisch optimal, sondern auch praktisch herstellbar, zuverlässig und kosteneffizient sind. Das Ignorieren der DfAM-Prinzipien ist eine häufige Falle, die zu kostspieligen Fehlern und verpassten Chancen bei der Einführung von Metall-AM führt.
Erreichen von Präzision: Toleranz, Oberflächengüte und Maßgenauigkeit bei AM-Verteilern
Während die additive Fertigung von Metallen eine beispiellose Designfreiheit bietet, ist es für Ingenieure und Beschaffungsmanager von entscheidender Bedeutung, realistische Erwartungen in Bezug auf die erreichbare Präzision, Oberflächengüte und Maßhaltigkeit von 3D-gedruckten Teilen zu haben, insbesondere bei funktionalen Komponenten wie Kraftstoffverteilern, bei denen enge Toleranzen und spezifische Oberflächeneigenschaften entscheidend sein können. Im Gegensatz zur hochpräzisen CNC-Bearbeitung, bei der eine Genauigkeit im Mikrometerbereich erreicht werden kann, sind AM-Prozesse von Natur aus mit thermischen Schwankungen, schichtweisem Aufbau und Pulverpartikeleigenschaften verbunden, die das endgültige Maßergebnis und die Oberflächenbeschaffenheit beeinflussen. Das Verständnis dieser Aspekte ist der Schlüssel für eine effektive Konstruktion und die Festlegung der notwendigen Nachbearbeitungsschritte.
1. Abmessungstoleranzen: * Typische erreichbare Toleranzen: Als allgemeine Richtlinie gilt, dass Metallpulverbettschmelzverfahren (L-PBF und EBM) in der Regel Maßtoleranzen im Bereich von ±0,1 mm bis ±0,2 mm für kleinere Merkmale (z. B. bis zu 100 mm) und einen Prozentsatz der Gesamtabmessung (z. B. ±0,1 % bis ±0,2 %) für größere Teile erreichen. Dies kann jedoch je nach den verschiedenen Faktoren erheblich variieren: * Kalibrierung und Zustand der Maschine: Gut gewartete und präzise kalibrierte Maschinen bieten eine höhere Genauigkeit. * Material: Verschiedene Materialien weisen während der Verarbeitung unterschiedliche Schwindungs- und Wärmeausdehnungsgrade auf (z. B. schrumpfen Aluminiumlegierungen stärker als Nickellegierungen). * Geometrie und Größe des Teils: Komplexe Geometrien, große ebene Flächen und hohe, dünne Merkmale sind anfälliger für Verformungen und Abweichungen. Thermische Spannungen akkumulieren sich je nach Form des Teils unterschiedlich. * Orientierung aufbauen: Die Ausrichtung des Teils auf der Bauplatte wirkt sich auf die Wärmeverteilung, die Anforderungen an die Abstützung und das Potenzial für Verformungen aus, was wiederum die endgültigen Abmessungen beeinflusst. * Thermische Spannungen: Eigenspannungen, die während des Drucks aufgebaut werden, können nach der Entnahme des Teils von der Bauplatte oder während der Wärmebehandlung nach dem Druck zu Verformungen oder Verzerrungen führen. * Design für Toleranz: Kritische Abmessungen, die engere Toleranzen erfordern, als es der Standard-AM-Prozess vermag (z. B. Dichtungsflächen, Lagerschnittstellen, Anschlussdurchmesser), müssen in der Regel durch Nachbearbeitung, in der Regel durch CNC-Bearbeitung, behandelt werden. Bei DfAM werden diese kritischen Merkmale identifiziert und das Teil mit ausreichend zusätzlichem Material (Bearbeitungszugabe oder Rohmaterial) in diesen Bereichen entworfen, um eine präzise Nachbearbeitung zu ermöglichen. * Konsistenz: Zwar ist es eine Herausforderung, Toleranzen von weniger als 0,1 mm direkt aus dem Drucker zu erreichen, doch die Prozesssteuerung und die Konsistenz werden immer besser. Erfahrene Anbieter konzentrieren sich auf die Aufrechterhaltung stabiler Prozesse, um von Teil zu Teil und von Charge zu Charge wiederholbare Dimensionsergebnisse zu gewährleisten.
2. Oberflächengüte (Oberflächenrauheit): * Oberflächenrauhigkeit (Ra) im Ist-Zustand: Die Oberflächenbeschaffenheit von Teilen, die direkt aus der AM-Maschine kommen, ist von Natur aus rauer als bearbeitete Oberflächen. Dies ist auf die teilweise geschmolzenen Pulverpartikel zurückzuführen, die an der Oberfläche haften, sowie auf den schichtweisen "Treppeneffekt" auf gekrümmten oder abgewinkelten Oberflächen. Typische Werte für die Oberflächenrauhigkeit (Ra) bei L-PBF liegen oft zwischen 6μm und 25μm (240μin bis 1000μin), je nach Material, Parametern, Ausrichtung und ob die Oberfläche während der Herstellung nach oben oder unten zeigt. EBM-Teile haben in der Regel eine rauere Oberflächenbeschaffenheit. * Interne vs. externe Oberflächen: Innenkanäle und nach unten weisende Flächen (Auflageflächen) weisen im Allgemeinen rauere Oberflächen auf als nach oben weisende oder vertikale Außenwände, was auf Faktoren wie Auflagekontaktpunkte und Pulverhaftungseigenschaften zurückzuführen ist. Dies ist ein entscheidender Aspekt bei Kraftstoffverteilern, bei denen die Glätte der inneren Kanäle den Flüssigkeitsstrom beeinflusst. * Auswirkungen der Rauheit: Raue Innenflächen können die Reibung erhöhen, was zu höheren Druckverlusten führt und möglicherweise zu Turbulenzen beiträgt. Außerdem können sie Verunreinigungen einschließen oder in hochbelasteten Anwendungen als Ausgangspunkt für Ermüdungsrisse dienen. * Verbesserung der Oberflächengüte: Zur Verbesserung der Oberflächengüte werden verschiedene Nachbearbeitungstechniken eingesetzt (auf die im nächsten Abschnitt näher eingegangen wird), darunter Perlstrahlen, Trommeln, CNC-Bearbeitung, Polieren, Elektropolieren und Fließschleifen (AFM). Die Wahl hängt von der erforderlichen Oberflächengüte, der Zugänglichkeit (intern vs. extern), dem Material und den Kosten ab.
3. Überprüfung der Maßgenauigkeit: Um sicherzustellen, dass der fertige Verteiler den Spezifikationen entspricht, sind robuste Qualitätskontroll- und Prüfverfahren erforderlich. * Koordinatenmessmaschinen (KMG): Ermöglicht hochpräzise Punktmessungen zur Überprüfung kritischer Abmessungen, Bohrungspositionen und geometrischer Bemaßung und Tolerierung (GD&T)-Merkmale. Erfordert physische Abtastung. * 3D-Scannen (strukturiertes Licht/Laser): Erfasst schnell die vollständige 3D-Geometrie des Teils und ermöglicht den Vergleich mit dem ursprünglichen CAD-Modell, um Farbkarten zu erstellen, die Abweichungen auf der gesamten Oberfläche zeigen. Hervorragend geeignet für die Überprüfung der Gesamtform, kann aber bei bestimmten kritischen Abmessungen weniger genau sein als ein KMG. * CT-Scan (Computertomographie): Verwendet Röntgenstrahlen, um ein 3D-Modell des Teils zu erstellen, einschließlich der inneren Merkmale. Dies ist von unschätzbarem Wert für die Prüfung der Abmessungen und der Integrität komplexer interner Kanäle in Verteilern, die Überprüfung von Wandstärken und die Erkennung interner Defekte wie Porosität, ohne das Teil zu zerstören. * Traditionelle Messtechnik: Für spezifische Messungen werden auch Messschieber, Mikrometer, Höhenmessgeräte und Funktionsprüfungen (z. B. das Einpassen von Gegenstücken) verwendet.
Das Engagement von Met3dp für Präzision: Um die erforderliche Präzision für anspruchsvolle Anwendungen wie Luft- und Raumfahrt oder medizinische Komponenten zu erreichen, bedarf es mehr als nur moderner Maschinen. Es erfordert eine strenge Prozesskontrolle, eine sorgfältige Maschinenkalibrierung, hochwertige Ausgangsmaterialien (Pulver) und ein tiefes Verständnis der thermischen und physikalischen Phänomene, die während der Herstellung auftreten. Unternehmen wie Met3dp betonen ihre Fähigkeit, Folgendes zu liefern branchenführendes Druckvolumen, Genauigkeit und Zuverlässigkeit für unternehmenskritische Teile. Dieses Engagement setzt robuste Qualitätsmanagementsysteme (QMS), Investitionen in präzise Messgeräte (wie CMM und möglicherweise 3D-Scanner) und Fachwissen bei der Verwaltung des gesamten Arbeitsablaufs - von der DfAM-Beratung über den Druck und die Nachbearbeitung bis hin zur Endkontrolle - voraus, um die anspruchsvollen Anforderungen an Toleranzen und Oberflächengüte von kritischen Komponenten wie Kraftstoffverteilern zu erfüllen. Ingenieure und Beschaffungsmanager sollten sich bei der Bewertung von Partnern für hochpräzise AM-Projekte nach den spezifischen Messfähigkeiten und Qualitätssicherungsverfahren eines potenziellen Lieferanten erkundigen.
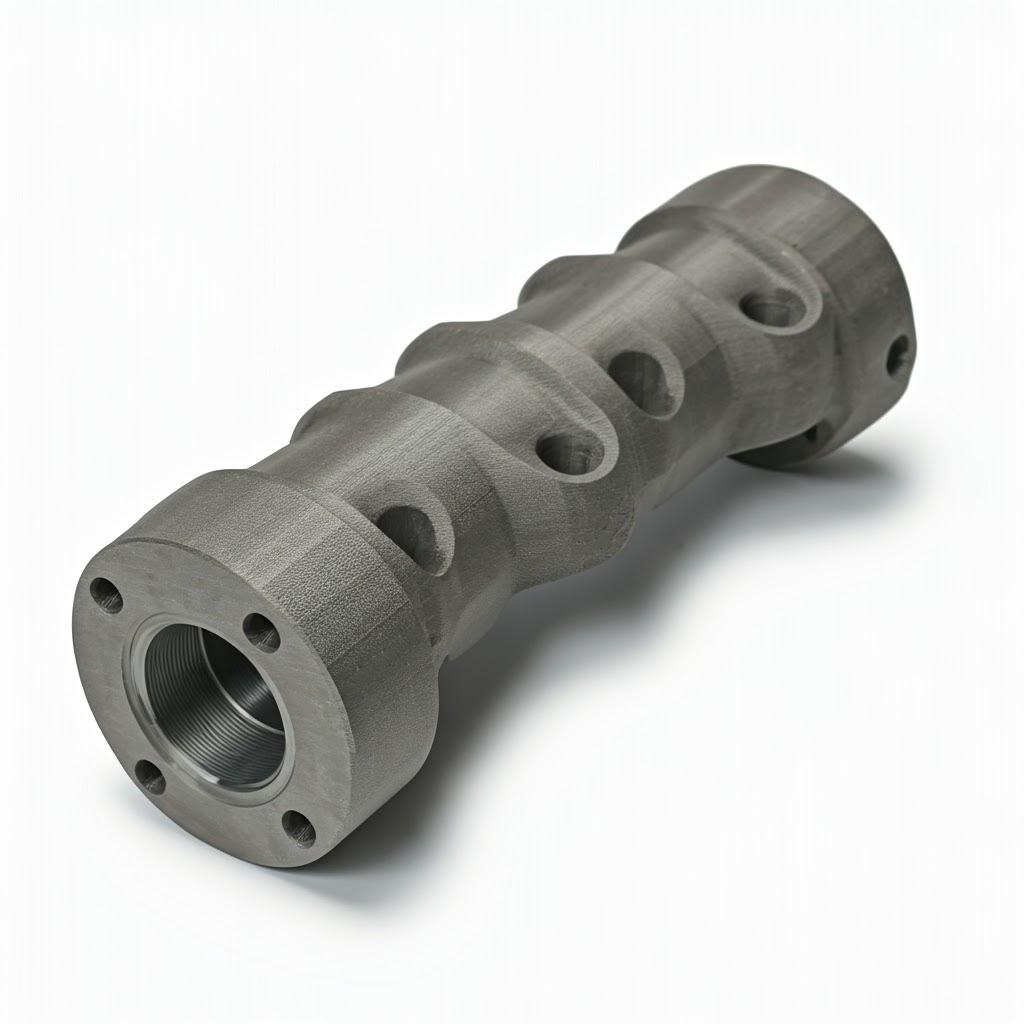
Über das Drucken hinaus: Wichtige Nachbearbeitungsschritte für Kraftstoffverteiler
Ein weit verbreiteter Irrglaube über den 3D-Druck von Metall ist, dass die Teile sofort einsatzbereit aus der Maschine kommen. Während AM die Erstellung komplexer Geometrien erheblich rationalisiert, ist die Realität, insbesondere bei anspruchsvollen Anwendungen wie Kraftstoffverteilern, dass die Druckphase oft nur ein Schritt in einem mehrstufigen Fertigungsprozess ist. Fast immer ist eine Nachbearbeitung erforderlich, um das fertige Teil in ein funktionelles, zuverlässiges Bauteil zu verwandeln, das alle technischen Spezifikationen in Bezug auf Materialeigenschaften, Maßhaltigkeit, Oberflächengüte und Sauberkeit erfüllt. Das Verständnis dieser notwendigen Schritte ist entscheidend für die genaue Abschätzung der gesamten Fertigungszeit und -kosten.
Hier finden Sie einen Überblick über die wichtigsten Nachbearbeitungsschritte, die bei AM-Kraftstoffverteilern aus Metall üblich sind:
1. Stressabbau / Wärmebehandlung: * Zweck: Die schnellen Erwärmungs- und Abkühlungszyklen, die dem Pulverbettschmelzverfahren eigen sind, erzeugen erhebliche innere Spannungen im fertigen Teil. Diese Spannungen können nach der Entnahme des Teils aus der Bauplatte zu Verformungen oder Verwerfungen führen, die Ermüdungslebensdauer des Materials verringern und möglicherweise zu einem vorzeitigen Ausfall führen. Die Spannungsarmglühung wird durchgeführt vor entfernen des Teils von der Bauplatte (wann immer möglich), um diese inneren Spannungen abzubauen. * Prozess: Das Teil, das noch auf der Bauplatte befestigt ist, wird in einem Ofen mit kontrollierter Atmosphäre auf eine bestimmte Temperatur (unterhalb der kritischen Umwandlungspunkte des Materials) erhitzt, eine Zeit lang gehalten und dann langsam abgekühlt. Der genaue Zyklus (Temperatur, Zeit, Atmosphäre) hängt stark vom Material (z. B. unterscheiden sich AlSi10Mg-Zyklen erheblich von IN625-Zyklen) und der Teilegeometrie ab. * Weitere Wärmebehandlungen: Über den Spannungsabbau hinaus können zusätzliche Wärmebehandlungen wie Lösungsglühen und Auslagern (z. B. T6-Behandlung für AlSi10Mg oder spezifische Auslagerungszyklen für IN625) erforderlich sein, um die gewünschten endgültigen mechanischen Eigenschaften (Härte, Festigkeit, Duktilität) für die Anwendung zu erreichen. Diese Behandlungen verändern das Gefüge des Werkstoffs.
2. Entfernen des Teils von der Bauplatte: * Methode: Sobald der Spannungsabbau abgeschlossen ist (sofern er auf der Platte durchgeführt wurde), muss das Teil von der Metallbauplatte getrennt werden, auf der es gedruckt wurde. Dies geschieht in der Regel durch Drahterodieren (Electrical Discharge Machining) oder mit einer Bandsäge. Dabei muss darauf geachtet werden, dass das Teil nicht beschädigt wird.
3. Entfernung der Stützstruktur: * Zweck: Entfernen der temporären Stützstrukturen, die während des Bauprozesses verwendet wurden. * Methoden: Dies kann von einfachem manuellem Ausbrechen für leicht zugängliche, leicht verschweißte Halterungen bis hin zu aufwändigeren Methoden wie Schleifen, Fräsen oder Drahterodieren für dichtere oder schwerer zugängliche Halterungen reichen. Besonders schwierig kann der Zugang zu Halterungen in internen Verteilerkanälen sein, wenn die DfAM-Prinzipien nicht konsequent angewendet wurden, um diese zu vermeiden. Möglicherweise sind spezielle Werkzeuge oder Techniken erforderlich. Dieser Schritt kann arbeitsintensiv sein und erfordert erfahrene Techniker, um eine Beschädigung kritischer Oberflächen zu vermeiden.
4. CNC-Bearbeitung: * Zweck: Zur Erzielung engerer Toleranzen, spezifischer Oberflächengüten und Merkmale, die mit dem AM-Prozess selbst nicht genau hergestellt werden können. * Anwendungen auf Mannigfaltigkeiten: * Kritische Schnittstellen: Bearbeitung von Dichtflächen (z. B. O-Ring-Nuten, ebene Flächen für Dichtungen), um dichte Verbindungen zu gewährleisten. * Hafen-Bearbeitung: Präzise Dimensionierung und Fertigstellung der Anschlussöffnungen. * Gewindeschneiden/Fräsen: Erstellen von Gewindelöchern für Befestigungselemente oder Sensoren. * Enge Toleranzen Merkmale: Erzielung einer Maßgenauigkeit, die über die standardmäßigen AM-Fähigkeiten hinausgeht, bei bestimmten, im Entwurf festgelegten Merkmalen. * Verbesserung der Oberflächengüte: Fräsen oder Drehen bestimmter Außenflächen, um eine sehr glatte Oberfläche (Ra<1μm) zu erzielen. * Erwägungen: Erfordert sorgfältiges Einrichten und Vorspannen des AM-Teils. In der DfAM-Phase muss eine ausreichende Menge an Bearbeitungsmaterial eingeplant worden sein.
5. Oberflächenbehandlung & Endbearbeitung: * Zweck: Verbesserung der Oberflächenrauheit, Verbesserung der Ästhetik, Verbesserung der Ermüdungsfestigkeit, Erhöhung der Verschleißfestigkeit oder Verbesserung der Korrosionsbeständigkeit. * Gemeinsame Techniken für Verteiler: * Perlenstrahlen / Sandstrahlen: Sorgt für eine gleichmäßige matte Oberfläche, entfernt teilweise gesinterte Partikel und kann Druckspannungen erzeugen, die die Ermüdungslebensdauer verbessern. Verschiedene Medien (Glasperlen, Aluminiumoxid) erzeugen unterschiedliche Oberflächen. * Taumeln / Vibrationsgleitschleifen: Verwendet Schleifmittel in einer rotierenden oder vibrierenden Trommel zum Entgraten von Kanten und Glätten von Oberflächen, insbesondere bei Chargen von kleineren Teilen. * Polieren: Manuelles oder maschinelles Polieren mit immer feineren Schleifmitteln, um eine glatte, spiegelglatte Oberfläche zu erzielen. * Elektropolieren: Ein elektrochemisches Verfahren, bei dem eine dünne Materialschicht abgetragen wird, wodurch die Oberflächen geglättet und die Korrosionsbeständigkeit verbessert wird; besonders wirksam bei rostfreien Stählen und einigen Nickellegierungen. Je nach Geometrie können manchmal auch innere Bereiche erreicht werden. * Abrasive Fließbearbeitung (AFM) / Strangpresshonen: Speziell für das Glätten und Polieren der inneren Kanäle verwendet. Ein mit Schleifmitteln beladener Polymerkitt wird unter hohem Druck durch die inneren Kanäle des Verteilers hin- und hergepresst, wobei die Spitzen allmählich abgetragen und die Oberflächen geglättet werden. Unverzichtbar für die Optimierung des Durchflusses in kritischen internen Kanälen, die mit anderen Methoden nicht erreicht werden können. * Beschichtung: Aufbringen spezieller Beschichtungen (z. B. Wärmedämmschichten, Verschleißschutzschichten, korrosionshemmende Schichten) je nach Anwendungsanforderungen.
6. Reinigung und Inspektion: * Zweck: Um alle Rückstände von Pulver, Bearbeitungsflüssigkeiten, Ablagerungen und anderen Verunreinigungen zu entfernen und um zu überprüfen, ob das Teil vor der endgültigen Verwendung alle Spezifikationen erfüllt. * Methoden: * Entfernung von Puder: Druckluftabblasen, Ultraschallreinigungsbäder und spezielle Spülvorrichtungen kommen zum Einsatz, was besonders für die komplexen internen Kanäle von Verteilern wichtig ist. Die vollständige Entfernung des Pulvers ist von entscheidender Bedeutung, um eine Verunreinigung oder Verstopfung der nachgeschalteten Anlagen zu verhindern. * Überprüfung der Sauberkeit: Endoskopische Inspektion der internen Kanäle, Probenahme der letzten Spülflüssigkeit. * Dichtheitsprüfung: Unverzichtbar bei Kraftstoffverteilern. Zu den Methoden gehören die Druckabfallprüfung (Druckbeaufschlagung des Verteilers und Überwachung des Druckabfalls) oder die Helium-Leckprüfung (Verwendung von Helium als Prüfgas, das von einem Massenspektrometer erfasst wird) für eine höhere Empfindlichkeit. Die Farbeindringprüfung kann manchmal Risse an der Oberfläche aufdecken. * Dimensional & NDT-Inspektion: Abschließende CMM-Prüfungen, visuelle Inspektionen und möglicherweise NDT-Methoden wie CT-Scans, um die innere Integrität und den Kanalabstand sicherzustellen.
Die Integration dieser AM-Nachbearbeitung schritte in den Gesamtfertigungsplan zu integrieren, ist entscheidend. Sie haben einen erheblichen Einfluss auf die Endkosten des Teils und die Gesamtdurchlaufzeit. Ein erfahrener AM-Partner wie Met3dp kennt den gesamten Arbeitsablauf und kann auf der Grundlage der spezifischen Anforderungen des Kraftstoffverteilers die effektivsten und effizientesten Nachbearbeitungsstrategien vorschlagen, um sicherzustellen, dass das gelieferte Endteil wirklich für den Zweck geeignet ist. Die Nichtberücksichtigung dieser Schritte kann zu unerwarteten Verzögerungen und Budgetüberschreitungen führen.
Herausforderungen meistern: Potenzielle Probleme bei der AM-Manifold-Produktion und Lösungen
Die additive Fertigung von Metallen bietet zwar bemerkenswerte Möglichkeiten für die Herstellung komplexer Kraftstoffverteiler, aber die Technologie ist nicht ohne Herausforderungen. Um konsistente, qualitativ hochwertige Ergebnisse zu erzielen, sind ein tiefes Verständnis der Prozessphysik, eine sorgfältige Kontrolle der Parameter, hochwertige Materialien und oft auch ausgeklügelte Minderungsstrategien erforderlich. Ingenieure und Beschaffungsmanager sollten sich potenzieller Probleme bewusst sein, um besser mit AM-Anbietern zusammenzuarbeiten und robuste Produktionsprozesse zu gewährleisten. Im Folgenden finden Sie einige häufige Herausforderungen, die bei der Herstellung von AM-Verteilern auftreten, und wie erfahrene Anbieter wie Met3dp diese meistern:
1. Verformung und Verzerrung: * Ausgabe: Ungleichmäßige Erwärmung und Abkühlung während des schichtweisen Schmelzvorgangs führen zu thermischen Spannungen. Wenn sich diese Spannungen akkumulieren, können sie dazu führen, dass sich das Teil verzieht oder verformt und von der vorgesehenen Geometrie abweicht, insbesondere bei großen flachen Abschnitten oder dünnen Merkmalen. * Milderung: * Optimierte Gebäudeausrichtung: Positionierung des Teils auf der Bauplatte, um große flache Bereiche parallel zur Platte zu minimieren und thermische Gradienten zu reduzieren. * Robuste Stützstrukturen: Strategisch platzierte Stützen verankern das Teil fest auf der Bauplatte und wirken als Wärmesenken, die die Wärme gleichmäßiger ableiten. Das Design der Stützen ist entscheidend. * Thermische Simulation: Einsatz von Software zur Vorhersage von Temperaturverteilungen und Spannungsakkumulationen während des Baus, wodurch proaktive Anpassungen der Ausrichtung oder der Stützen ermöglicht werden. * Optimierung der Prozessparameter: Anpassung der Laser-/Strahlleistung, der Scan-Geschwindigkeit und der Scan-Strategie (z. B. Insel-Scanning), um den Wärmeeintrag zu steuern und den Stressaufbau zu reduzieren. * Build Plate Heating: Das Vorheizen der Bauplatte (üblich beim EBM, auch bei einigen L-PBF-Systemen, insbesondere bei rissanfälligen Legierungen) reduziert den Temperaturunterschied und minimiert die Spannungen. * Stressabbau Wärmebehandlung: Die Durchführung dieses Schritts vor der Entnahme des Teils von der Bauplatte ist entscheidend für den Abbau der angesammelten Spannungen.
2. Reststress-Management: * Ausgabe: Selbst wenn ein erheblicher Verzug vermieden wird, können hohe Eigenspannungen im fertigen Teil eingeschlossen bleiben. Dies kann sich im Laufe der Zeit negativ auf die Ermüdungslebensdauer, die Bruchzähigkeit und die Dimensionsstabilität auswirken oder bei der nachfolgenden Bearbeitung Verformungen verursachen. * Milderung: * Strategien, die unter Warping/Verzerrung aufgeführt sind (Ausrichtung, Stützen, Simulation, Parameter, Plattenerwärmung) sind die wichtigsten Methoden zur Schadensbegrenzung. * Wirksame Stressabbau-Zyklen: Sicherstellen, dass der Wärmebehandlungszyklus nach der Herstellung für das Material und die Geometrie geeignet ist, um Spannungen maximal abzubauen, ohne das Gefüge negativ zu beeinflussen. * Prozessüberwachung: In-situ-Überwachungstechniken (experimentell) zielen darauf ab, den Spannungsaufbau während des Drucks zu verfolgen. * Messung & Validierung: Mit Verfahren wie der Röntgenbeugung (XRD) können Eigenspannungen in fertigen Teilen gemessen werden, um die Wirksamkeit von Minderungsstrategien zu überprüfen.
3. Knacken: * Ausgabe: Einige Legierungen, insbesondere bestimmte hochfeste Aluminiumlegierungen, Nickelsuperlegierungen (wie IN625 unter suboptimalen Bedingungen) und Titanlegierungen, können während des Drucks (Erstarrungsrisse) oder während der Abkühlung oder Wärmebehandlung nach der Herstellung (Reckalterungsrisse) zu Rissen neigen. * Milderung: * Materialauswahl und -qualität: Die Verwendung von qualitativ hochwertigem Pulver mit kontrollierter Chemie, die speziell für die AM-Verarbeitung entwickelt wurde, ist entscheidend. Met3dp’s Fokus auf fortschrittliche Pulverproduktion (Gaszerstäubung, PREP) gewährleistet optimale Pulvereigenschaften und reduziert die Anfälligkeit. * Optimierung der Parameter: Eine Feinabstimmung des Energieeintrags, der Scan-Strategien und möglicherweise die Verwendung spezieller Parameter (z. B. gepulste Laser) können die Rissbildungstendenz minimieren. * Build Plate Heating / Steuerung der Kammerumgebung: Durch die Aufrechterhaltung erhöhter Temperaturen werden thermische Gradienten reduziert. * Optimierte Wärmebehandlungen: Sorgfältig konzipierte Entspannungs- und Glühzyklen sind entscheidend. * Heiß-Isostatisches Pressen (HIP): Siehe unten - kann innere Hohlräume schließen und möglicherweise Mikrorisse heilen.
4. Schwierigkeiten bei der Beseitigung von Stützstrukturen: * Ausgabe: Halterungen, insbesondere dichte Halterungen oder solche, die sich in komplexen internen Verteilerkanälen befinden, können sehr schwierig und zeitaufwändig vollständig zu entfernen sein, ohne das Teil zu beschädigen. Eine unvollständige Entfernung kann den Durchfluss behindern oder als Verunreinigung wirken. * Milderung: * DfAM Fokus: Die beste Strategie ist es, Konstruktionsentscheidungen (selbsttragende Winkel, optimale Ausrichtung) zu bevorzugen, die den Bedarf an internen Stützen minimieren oder eliminieren. * Optimiertes Support-Design: Verwendung von Halterungstypen (z. B. konisch, gitterförmig), die leichter zu entfernen sind und möglichst wenige Kontaktpunkte haben. * Spezialisierte Entfernungstechniken: Einsatz von Drahterodieren, Spezialwerkzeugen oder möglicherweise chemischem Ätzen (materialabhängig) für schwierige Träger. Abrasive Fließbearbeitung kann manchmal dazu beitragen, interne Halterungsreste zu entfernen und gleichzeitig den Kanal zu glätten. * Planung der Zugänglichkeit: Planung von Zugangsöffnungen (die später wieder verschlossen werden können), wenn die Entfernung der internen Stütze unvermeidlich ist.
5. Erreichen der Anforderungen an die interne Oberflächengüte: * Ausgabe: Interne Oberflächen sind im Auslieferungszustand naturgemäß rau. Bei Kraftstoffverteilern kann diese Rauheit den Durchfluss behindern, den Druckabfall erhöhen und möglicherweise Verunreinigungen oder Pulverrückstände einschließen. Das Erreichen einer glatten Innenoberfläche, insbesondere in komplexen, nicht sichtbaren Kanälen, ist eine Herausforderung. * Milderung: * Orientierung & Parametereffekte: Die Bauausrichtung wirkt sich auf die innere Oberflächenrauheit aus (‘up-skin’ vs ‘down-skin’). Optimierte Parameter können die Oberfläche leicht verbessern. * Abrasive Fließbearbeitung (AFM) / Strangpresshonen: Die effektivste Methode zur Verbesserung der inneren Kanaloberfläche in komplexen Verteilern. Erfordert eine sorgfältige Prozesskontrolle, um die gewünschte Glätte ohne übermäßigen Materialabtrag zu erreichen. * Elektropolieren: Kann wirksam sein, wenn der Elektrolyt durch alle inneren Kanäle ausreichend fließen kann. * Überlegungen zum Design: Es ist wichtig, die Kanäle groß genug zu gestalten, um eine effektive AFM oder Spülung zu ermöglichen.
6. Kontrolle der Porosität: * Ausgabe: Im gedruckten Material können sich kleine Hohlräume oder Poren bilden, die durch eingeschlossenes Gas (Gasporosität) oder unvollständiges Aufschmelzen/Verschmelzen zwischen Schichten oder Scannerspuren (Lack-of-Fusion-Porosität) entstehen. Porosität verringert die Materialdichte, verschlechtert die mechanischen Eigenschaften (insbesondere die Ermüdungsfestigkeit) und kann potenzielle Leckagepfade schaffen. * Milderung: * Hochwertiges Pulver: Die Verwendung von Pulvern mit einem geringen Gehalt an eingeschlossenen Gasen, einer kontrollierten Partikelgrößenverteilung und einer guten Morphologie (wie bei den Pulvern von Met3dp’) minimiert die Gasporosität. Eine ordnungsgemäße Handhabung des Pulvers (Lagerung, Trocknung) ist entscheidend. * Optimierte Prozessparameter: Die Sicherstellung einer ausreichenden Energiedichte (Laser-/Strahlleistung, Geschwindigkeit) und einer angemessenen Überlappung zwischen den Scannerspuren fördert das vollständige Schmelzen und Verschmelzen und reduziert Schmelzdefekte. * Stabile Prozessumgebung: Die Aufrechterhaltung einer kontrollierten Inertgasatmosphäre (z. B. Argon, Stickstoff) verhindert Oxidation und verringert die Kontamination. * Heiß-Isostatisches Pressen (HIP): Bei diesem Nachbearbeitungsschritt wird das Teil einer hohen Temperatur und einem hohen isostatischen Druck (in der Regel unter Verwendung von Argongas) ausgesetzt. Dadurch werden die inneren Hohlräume und Poren wirksam geschlossen, was die Dichte erheblich erhöht und die mechanischen Eigenschaften verbessert. Dies wird häufig für kritische Bauteile in der Luft- und Raumfahrt oder in der Medizintechnik eingesetzt. * NDT-Inspektion: CT-Scans werden in der Regel zum Nachweis und zur Quantifizierung der inneren Porosität eingesetzt.
7. Pulverentfernung aus komplizierten Passagen: * Ausgabe: Die Sicherstellung, dass das gesamte lose oder teilweise gesinterte Pulver aus dem komplexen internen Netzwerk eines Verteilers entfernt wird, ist entscheidend, aber eine Herausforderung. Eingeschlossenes Pulver kann zu Verunreinigungen führen oder den Durchfluss behindern. * Milderung: * Design für die Reinigung: Vermeidung von Sacklöchern oder Merkmalen, die Pulver einschließen. Gestaltung von Kanälen für eine effektive Spülung. * Gründliche Reinigungsverfahren: Einsatz von Druckluft, Vibration, Ultraschallbädern und möglicherweise speziellen Spülvorrichtungen mit geeigneten Lösungsmitteln oder Flüssigkeiten. * Inspektion: Verwendung von Endoskopen oder CT-Scans zur Überprüfung der vollständigen Entfernung des Pulvers aus den internen Kanälen.
Die Navigation in diesen metall-AM-Herausforderungen erfordert eine Kombination aus robusten DfAM-Praktiken, hochwertigen Materialien, optimierten und streng kontrollierten Druckprozessen, geeigneten Nachbearbeitungstechniken und strenger Qualitätssicherung. Die Zusammenarbeit mit einem erfahrenen AM-Anbieter wie Met3dp, der über das erforderliche Fachwissen, fortschrittliche Ausrüstung (einschließlich potenziell vorteilhafter SEBM-Drucker für bestimmte Legierungen) und Qualitätssysteme verfügt, erhöht die Wahrscheinlichkeit der erfolgreichen Herstellung zuverlässiger, leistungsstarker Produkte erheblich 3D-Druck von Metall und gleichzeitig diese potenziellen Fallstricke zu entschärfen. Ihr umfassender Ansatz, von der Pulverproduktion bis zur Validierung der fertigen Teile, trägt dazu bei, dass die Komplexität von AM effektiv gehandhabt wird.
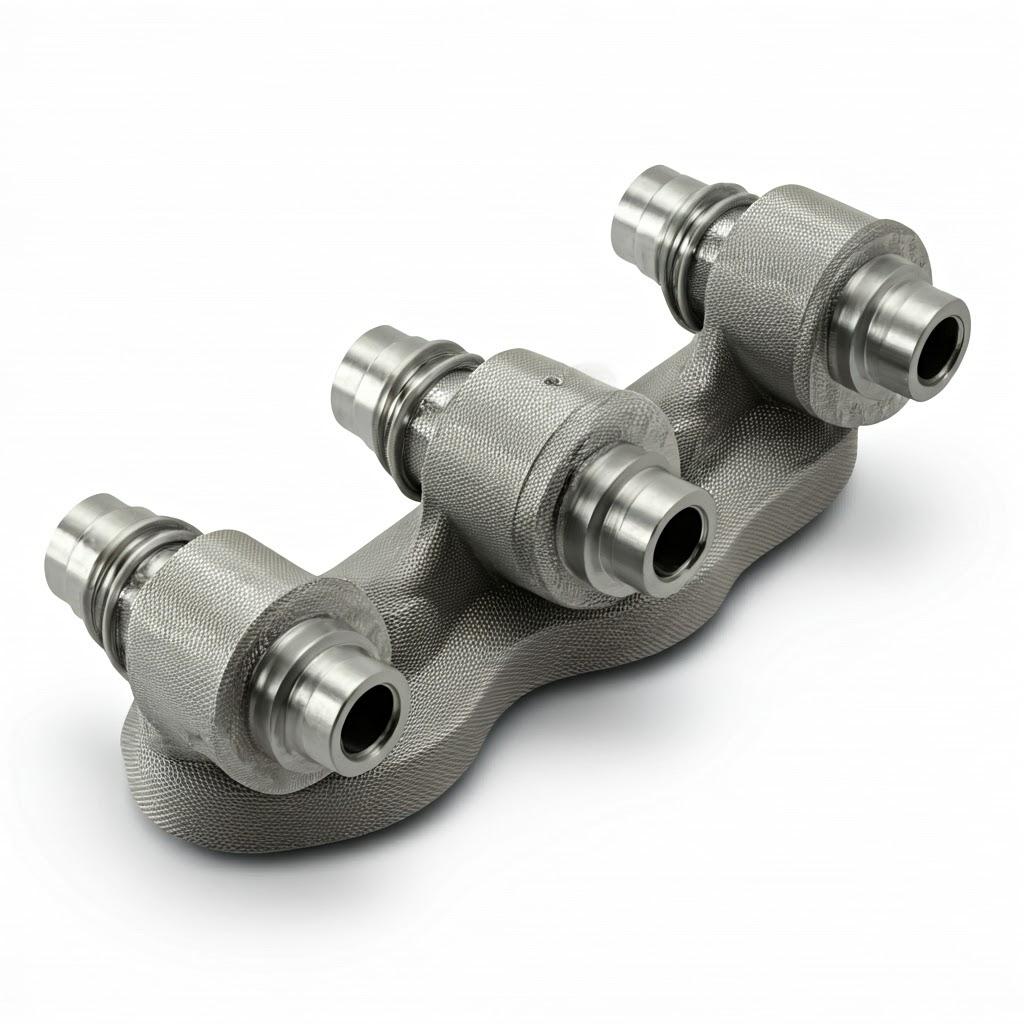
Auswahl des Lieferanten: Die Wahl des richtigen Partners für den 3D-Druck von Kraftstoffverteilern aus Metall
Der Erfolg der Herstellung einer komplexen Hochleistungskomponente wie eines kundenspezifischen Kraftstoffverteilers mittels additiver Fertigung hängt nicht nur von einem guten Design und der Wahl des richtigen Materials ab, sondern auch von der Auswahl des richtigen Fertigungspartners. In der Metall-AM-Landschaft gibt es eine Vielzahl von Dienstleistern, von kleinen Job-Shops bis hin zu großen, spezialisierten Industrieunternehmen. Für kritische Komponenten, die in anspruchsvollen Umgebungen wie der Luft- und Raumfahrt oder der Hochleistungsautomobilbranche eingesetzt werden, ist die Zusammenarbeit mit einem Anbieter, der über die richtige Mischung aus technischem Fachwissen, robusten Prozessen, fortschrittlicher Technologie und strenger Qualitätskontrolle verfügt, von entscheidender Bedeutung. Die falsche Wahl kann zu Projektverzögerungen, Kostenüberschreitungen, minderwertiger Teilequalität oder sogar zu katastrophalen Ausfällen im Feld führen.
Auf welche Kriterien sollten Ingenieure und Beschaffungsmanager also bei der Bewertung potenzieller Metall-AM-Dienstleister partner für die Herstellung von Kraftstoffverteilern? Hier finden Sie eine detaillierte Checkliste:
1. Technisches Fachwissen und nachgewiesene Erfahrung: * Erfolgsbilanz: Hat der Anbieter nachweislich Erfahrung im Druck von Teilen, die in Bezug auf Komplexität und Material mit Ihrem Kraftstoffverteiler vergleichbar sind? Fragen Sie nach Fallstudien oder Beispielen, die sich speziell auf die Handhabung von Flüssigkeiten, Hochtemperaturanwendungen oder relevante Industriezweige (Luft- und Raumfahrt, Automobilindustrie) beziehen. * Material-Spezialisierung: Sind sie auf die von Ihnen benötigten Materialien spezialisiert (z. B. IN625, AlSi10Mg, Ti6Al4V)? Fundierte Kenntnisse der Materialmetallurgie und ihrer Wechselwirkung mit dem AM-Prozess sind entscheidend, insbesondere bei anspruchsvollen Legierungen. Anbieter, die ihre eigenen Pulver herstellen, wie Met3dp, verfügen oft über tiefere materialwissenschaftliche Kenntnisse. * Technischer Scharfsinn: Beurteilen Sie die Qualifikation und Erfahrung des Ingenieurteams. Können sie sich auf sinnvolle DfAM-Diskussionen einlassen und wertvolles Feedback zur Designoptimierung geben? Verstehen sie die physikalischen Grundlagen der Strömung und der Strukturmechanik, die für Verteiler relevant sind? * Industrie-Zertifizierungen: Für Anwendungen in der Luft- und Raumfahrt ist die AS9100-Zertifizierung oft nicht verhandelbar. Für die Automobilindustrie ist die Kenntnis der IATF 16949-Normen von Vorteil. Diese Zertifizierungen weisen auf die Verpflichtung zu strengen Qualitätsprozessen hin, die in diesen Sektoren erforderlich sind. Met3dp unterstreicht seinen Fokus auf “unternehmenskritische Teile in der Luft- und Raumfahrt, der Medizintechnik, der Automobilindustrie und anderen Bereichen,” was darauf hindeutet, dass das Unternehmen Erfahrung mit den strengen Anforderungen der Branche hat.
2. Ausrüstung, Technologie & Fähigkeiten: * Druckerflotte: Mit welchen Arten von Metall-AM-Maschinen arbeiten sie (L-PBF, EBM)? Welches sind die Marken, Modelle und Produktionsmengen? Ein vielfältiger und moderner Maschinenpark deutet auf Investitionen und Fähigkeiten hin. Met3dp zum Beispiel bietet umfassende Lösungen an, darunter SEBM-Druckerdies kann bei bestimmten Werkstoffen wie Nickellegierungen aufgrund der inhärenten Spannungsreduzierung durch die erhitzte Bauumgebung Vorteile bieten. * Prozesssteuerung und -überwachung: Welche Maßnahmen gibt es zur Überwachung und Kontrolle des Herstellungsprozesses (z. B. Sauerstoffgehalt, Schmelzbadüberwachung, Wärmebildtechnik)? Eine konsequente Prozesskontrolle ist der Schlüssel zu wiederholbarer Qualität. * Hausinterne Nachbearbeitung: Bietet der Anbieter kritische Nachbearbeitungsschritte im eigenen Haus an (Spannungsarmglüh-/Wärmebehandlungsöfen, CNC-Bearbeitungszentren, Möglichkeiten zum Entfernen von Halterungen, grundlegende Endbearbeitung)? Inhouse-Kapazitäten führen im Allgemeinen zu einer besseren Integration, Qualitätskontrolle und potenziell kürzeren Vorlaufzeiten im Vergleich zur Auslagerung mehrerer Schritte. * Metrologie-Labor: Über welche Prüfgeräte verfügen sie (CMM, 3D-Scanner, Oberflächenprofilometer, möglicherweise CT-Scanner)? Die Fähigkeit zur genauen Messung und Validierung der Teilegeometrie und der inneren Merkmale ist entscheidend.
3. Materialqualität, Portfolio & Handhabung: * Materialbeschaffung & Qualifizierung: Woher beziehen sie ihre Metallpulver? Stellen sie ihre eigenen her, wie Met3dp mit seinem fortschrittlichen Gaszerstäubung und PREP-Technologienoder von qualifizierten externen Lieferanten beziehen? Wie qualifizieren sie neue Materialien oder Chargen? * Material-Portfolio: Bietet das Unternehmen eine breite Palette relevanter Werkstoffe an, die über Ihren unmittelbaren Bedarf hinausgehen, was auf ein breiteres Fachwissen schließen lässt? Met3dp zum Beispiel führt innovative Legierungen wie TiNi, TiTa, TiAl, TiNbZr, CoCrMo, rostfreie Stähle und Superlegierungen unter ihren hochwertige Metallpulver. * Qualitätskontrolle des Pulvers: Nach welchen Verfahren wird das eingehende Pulver geprüft (Chemie, Partikelgrößenverteilung, Fließfähigkeit, Morphologie, Dichte)? Wie wird das Pulver gelagert, gehandhabt, nachverfolgt (Rückverfolgbarkeit der Chargen) und recycelt, um Verunreinigungen zu vermeiden und Konsistenz zu gewährleisten? Ein konsistentes, hochwertiges Pulver ist die Grundlage für ein gutes AM-Teil. * Materialzertifizierungen: Können sie Materialzertifikate vorlegen, die bestätigen, dass das Pulver bestimmte Industrienormen (z. B. ASTM, AMS) erfüllt?
4. Qualitätsmanagementsystem (QMS): * Zertifizierungen: Sind sie nach einschlägigen Qualitätsnormen wie ISO 9001 zertifiziert? Wie bereits erwähnt, ist AS9100 für die Luft- und Raumfahrt von entscheidender Bedeutung. Diese Zertifizierungen schreiben dokumentierte Verfahren, Prozesskontrolle, Rückverfolgbarkeit, Risikomanagement und kontinuierliche Verbesserung vor. * Dokumentation und Rückverfolgbarkeit: Können sie eine vollständige Rückverfolgbarkeit von der Rohpulvercharge bis zum fertigen Teil gewährleisten, einschließlich Herstellungsprotokollen, Nachbearbeitungsprotokollen und Prüfberichten? Dies ist für kritische Bauteile unerlässlich. * Inspektionsprotokolle: Was sind ihre Standardprüfverfahren? Wie werden kritische Merkmale identifiziert und überprüft? Welche Methoden der statistischen Prozesskontrolle (SPC) werden ggf. eingesetzt? * Umgang mit Abweichungen: Wie sieht ihr Verfahren zur Identifizierung, Dokumentation und Behandlung von nicht konformen Teilen oder Prozessabweichungen aus?
5. Engineering & Unterstützung bei der Anwendungsentwicklung: * DfAM-Konsultation: Bieten sie Dienstleistungen zur Optimierung Ihres Designs für die additive Fertigung an, indem sie potenzielle Probleme identifizieren und Verbesserungen für Druckbarkeit, Leistung und Kosteneffizienz vorschlagen? * Simulationsfähigkeiten: Können sie Simulationsergebnisse (FEA für Spannungs-/Temperaturanalysen, CFD für Strömungsanalysen) zur Unterstützung der Designvalidierung bereitstellen oder nutzen? * Anwendungsentwicklung: Sind sie bereit, bei der Entwicklung neuartiger Anwendungen oder bei der Durchführung besonders anspruchsvoller Projekte zusammenzuarbeiten? Unternehmen wie Met3dp positionieren sich als Anbieter von umfassende Lösungen, die SEBM-Drucker, moderne Metallpulver und Anwendungsentwicklungsdienste umfassendie auf einen partnerschaftlichen Ansatz hinweisen. Untersuchen, wie Met3dp bietet umfassende Lösungen können ihre Tiefe als potenzieller Partner offenbaren.
6. Kapazität, Vorlaufzeit & Kommunikation: * Produktionskapazität: Können sie das von Ihnen gewünschte Volumen bewältigen, egal ob es sich um Prototypen, Kleinserien oder potenziell größere Produktionsläufe handelt? Verfügen sie über ausreichende Maschinenkapazitäten und qualifizierte Arbeitskräfte? * Transparenz der Vorlaufzeiten: Liefern sie realistische und zuverlässige Vorlaufzeitschätzungen? Wie kommunizieren sie den Projektstatus und mögliche Verzögerungen? * Reaktionsfähigkeit: Wie schnell reagieren sie auf Anfragen und Angebotsanfragen? Eine gute Kommunikation ist während des gesamten Projektlebenszyklus von entscheidender Bedeutung. Suchen Sie nach Partnern, die als zuverlässige AM-Produktion quellen.
7. Kostenstruktur & Nutzenversprechen: * Transparenz zitieren: Ist der Kostenvoranschlag klar und detailliert und schlüsselt er die Kosten für Material, Druck, Support, Nachbearbeitung und Prüfung auf? Seien Sie vorsichtig bei Angeboten, die zu niedrig erscheinen, da sie möglicherweise notwendige Schritte auslassen oder Kompromisse bei der Qualität eingehen. * Total Cost of Ownership: Bewerten Sie den Wert, der über den Preis pro Teil hinausgeht. Bietet die Zusammenarbeit mit diesem Anbieter Vorteile wie schnellere Markteinführung, verbesserte Teileleistung, geringere nachgelagerte Montagekosten oder höhere Zuverlässigkeit, die die Investition rechtfertigen?
Die Auswahl des richtigen Lieferant für 3D-Metalldruck ist eine strategische Entscheidung. Sie erfordert eine gründliche Due-Diligence-Prüfung, das Stellen detaillierter Fragen und möglicherweise den Besuch von Anlagen oder die Durchführung von Pilotprojekten. Bei anspruchsvollen Kraftstoffverteileranwendungen kann die Zusammenarbeit mit einem etablierten, technisch versierten und qualitätsorientierten Anbieter wie Met3dp, der die wichtigsten Aspekte von der Pulverherstellung bis zu fortschrittlichen Drucksystemen beherrscht und umfassende technische Unterstützung bietet, den Prozess erheblich entschärfen und die potenziellen Vorteile der additiven Fertigung maximieren.
Die Investition verstehen: Kostenfaktoren und Vorlaufzeiten für AM-Kraftstoffverteiler
Der Übergang zur additiven Fertigung von Kraftstoffverteilern erfordert ein Verständnis der damit verbundenen Kosten und typischen Zeitpläne. Obwohl AM erhebliche Leistungs- und Designvorteile bietet, ist es wichtig, ein klares Bild von den erforderlichen wirtschaftlichen und zeitlichen Investitionen zu haben. Sowohl die Kosten als auch die Vorlaufzeit werden durch ein komplexes Zusammenspiel von Faktoren beeinflusst, die mit dem Teiledesign, der Materialauswahl, den Prozessspezifika und dem erforderlichen Qualitätsniveau zusammenhängen. Beschaffungsmanager und Ingenieure müssen diese Faktoren verstehen, um effektiv zu budgetieren, Projektzeitpläne zu verwalten und genaue Vergleiche mit traditionellen Fertigungsmethoden anzustellen.
Die wichtigsten Kostentreiber für Metall-AM-Kraftstoffverteiler:
- Teilegestaltung & Geometrie:
- Komplexität: Hochkomplexe Designs mit zahlreichen internen Merkmalen, dünnen Wänden oder Merkmalen, die umfangreiche Stützstrukturen erfordern, benötigen im Allgemeinen mehr Zeit für den Druck und die Nachbearbeitung, was die Kosten erhöht. Konstruktionen, die nach DfAM-Prinzipien optimiert wurden, um Stützstrukturen zu minimieren und die Nachbearbeitung zu erleichtern, können kostengünstiger sein.
- Teilvolumen & Bounding Box: Die Gesamtgröße des Verteilers wirkt sich direkt auf die Menge des verbrauchten Materials und die auf der AM-Maschine benötigte Zeit aus. Größere Teile nehmen mehr Platz auf der Bauplatte ein und brauchen länger, um Schicht für Schicht zu drucken. Die Höhe des Teils in der Bauausrichtung ist oft ein Hauptfaktor für die Druckzeit.
- Unterstützungsstruktur Volumen: Stützen verbrauchen Material und erfordern einen erheblichen Arbeits-/Maschinenaufwand für die Entfernung. Konstruktionen, die umfangreiche oder schwer zu entfernende Stützen benötigen, verursachen höhere Kosten.
- Wahl des Materials:
- Pulverkosten: Die Rohstoffkosten variieren erheblich. Hochleistungssuperlegierungen wie IN625 sind pro Kilogramm erheblich teurer als Aluminiumlegierungen wie AlSi10Mg oder nichtrostende Stähle. Titanlegierungen liegen irgendwo dazwischen.
- Materialdichte: Dichtere Materialien (wie IN625) führen bei gleichem Volumen zu schwereren Teilen, was die gewichtsbezogene Materialkostenkomponente direkt erhöht.
- Druckbarkeit: Bei einigen Materialien ist es schwieriger, sie zuverlässig zu bedrucken, so dass möglicherweise langsamere Druckgeschwindigkeiten oder komplexere Parametersätze erforderlich sind, was sich indirekt auf die Maschinenzeitkosten auswirkt.
- Additiver Fertigungsprozess:
- Maschinenzeit: Dies ist oft ein Hauptkostentreiber. Er wird beeinflusst durch:
- Bauzeit: Bestimmt durch die Teilehöhe, die verwendete Schichtdicke (dünnere Schichten = bessere Auflösung, aber längere Bauzeiten), die Scangeschwindigkeit und die Anzahl der Teile, die auf einer einzelnen Bauplatte verschachtelt werden.
- Maschine Stundensatz: Variiert je nach Typ, Größe und Ausgereiftheit der AM-Maschine. Bei High-End-Maschinen mit fortschrittlicher Überwachung sind die Preise höher.
- Nesting-Effizienz: Das gleichzeitige Drucken mehrerer Teile auf einer einzigen Bauplatte (Nesting) trägt dazu bei, die Rüstzeit zu amortisieren und die Maschinenauslastung zu maximieren, wodurch die Kosten pro Teil gesenkt werden, insbesondere bei kleineren Komponenten.
- Bauvorbereitung & Einrichtung: Erforderliche Zeit für die Vorbereitung der Build-Datei (Ausrichtung, Stützen), das Laden des Pulvers und das Einrichten der Maschine.
- Maschinenzeit: Dies ist oft ein Hauptkostentreiber. Er wird beeinflusst durch:
- Nachbearbeitungsanforderungen: Dies kann einen erheblichen Teil (oft 30-70 % oder mehr) der Gesamtkosten ausmachen.
- Wärmebehandlung: Ofenzeit, Energieverbrauch und Arbeitsaufwand für Spannungsabbau und andere erforderliche Zyklen. Öfen mit kontrollierter Atmosphäre verursachen zusätzliche Kosten.
- Unterstützung bei der Entfernung: Die Arbeitsintensität hängt stark von der Komplexität und Zugänglichkeit des Trägers ab. Manuelle Entfernung, maschinelle Bearbeitung oder spezielle Techniken wie EDM sind mit Kosten verbunden.
- CNC-Bearbeitung: Maschinenzeit und qualifizierte Arbeitskräfte für die Herstellung kritischer Merkmale, Dichtungsflächen, Gewinde usw. Die Anzahl und Komplexität der bearbeiteten Merkmale wirken sich direkt auf die Kosten aus.
- Oberflächenveredelung: Die Kosten variieren stark in Abhängigkeit von der Methode (einfaches Perlstrahlen vs. mehrstufiges Polieren oder komplexes AFM für interne Kanäle) und der erforderlichen Oberflächenrauhigkeit (Ra).
- Reinigung: Zeit und Ressourcen für die Entfernung von Pulver (insbesondere intern) und die Endreinigung.
- Qualitätssicherung und Inspektion:
- Ebene der Inspektion: Grundlegende Sicht- und Maßprüfungen sind Standard. Strengere Inspektionen (CMM, 3D-Scannen, Dichtheitsprüfungen, NDT wie CT-Scannen) verursachen erhebliche Mehrkosten, können aber für kritische Anwendungen erforderlich sein.
- Dokumentation: Die Erstellung detaillierter Prüfberichte und Rückverfolgbarkeitsdokumente erfordert Zeit und Ressourcen.
- Bestellmenge:
- Prototypen vs. Produktion: Bei einmaligen Prototypen fallen die vollen Einrichtungskosten an. Die Produktion kleiner bis mittlerer Serien ermöglicht eine bessere Maschinenauslastung (Verschachtelung) und die Amortisation von Einrichtungs- und Programmierkosten, was zu niedrigeren Preisen pro Teil führt. Erhebliche Preisunterschiede sind typisch, wenn die Stückzahlen steigen. Bewertung von Massenproduktion mit AM kosten erfordert spezifische Angebote auf der Grundlage des Volumens.
Faktoren, die die Durchlaufzeiten beeinflussen:
Die Durchlaufzeit ist die Gesamtdauer von der Auftragserteilung (oder der Fertigstellung des Entwurfs) bis zur Lieferung des endgültigen Teils. Sie wird von mehreren sequentiellen und parallelen Aktivitäten beeinflusst:
- Fertigstellung des Entwurfs & Technische Überprüfung: Zeit für DfAM-Prüfungen, Optimierung und Build-Vorbereitung.
- Warteschlangenzeit der Maschine: Warten, bis eine geeignete Maschine zur Verfügung steht. Dies kann je nach Rückstand des Dienstanbieters erheblich variieren.
- Druckzeit: Bestimmt durch die Höhe, Komplexität und Verschachtelung der Teile. Kann von Stunden für kleine Teile bis zu mehreren Tagen für große, komplexe Teile reichen.
- Abkühlungszeit: Lassen Sie die Baukammer und das Bauteil vor der Entnahme ausreichend abkühlen.
- Nachbearbeiten: Dies ist oft der variabelste und potenziell längste Teil der Durchlaufzeit, der aufeinanderfolgende Schritte wie Wärmebehandlung, Entfernen von Halterungen, Bearbeitung, Endbearbeitung und Reinigung umfasst. Engpässe können auftreten, wenn bestimmte Anlagen (z. B. große Öfen, spezielle Endbearbeitungsmaschinen) eine begrenzte Kapazität haben.
- Qualitätsinspektion: Zeitbedarf für Messung und Validierung.
- Versand: Die Logistikzeit hängt vom Standort und der Versandart ab.
Typische Vorlaufzeitspannen:
- Prototypen: Sie liegen oft zwischen 1 und 4 Wochen und hängen stark von der Komplexität, dem Material, der Maschinenverfügbarkeit und dem Umfang der Nachbearbeitung ab.
- Kleinserienproduktion: Je nach Menge und den oben genannten Faktoren kann der Zeitraum zwischen 3 und 8 Wochen oder länger betragen.
Genaue Kostenvoranschläge und Zeitpläne einholen: Um zuverlässige Kosten- und Zeitvoranschläge für Ihr spezifisches Kraftstoffverteilerprojekt zu erhalten, müssen Sie potenziellen Lieferanten detaillierte Informationen zur Verfügung stellen:
- Endgültiges 3D-CAD-Modell (vorzugsweise im STEP-Format).
- Werkstoffspezifikation (z. B. AlSi10Mg, IN625) und alle erforderlichen Normen.
- Detaillierte Zeichnungen mit Angaben zu kritischen Abmessungen, Toleranzen (GD&T), erforderlichen Oberflächengüten (innen und außen) und besonderen Merkmalen wie Gewinden.
- Benötigte Menge (Prototyp, Schätzung der Kleinserienproduktion).
- Spezifische Prüf- oder Inspektionsanforderungen (z. B. Parameter für Dichtheitsprüfungen, NDT-Bedarf).
- Gewünschtes Lieferdatum (falls zutreffend).
Die enge Zusammenarbeit mit einem transparenten und erfahrenen AM-Anbieter wie Met3dp kann bei der Optimierung der Entwürfe im Hinblick auf die Kosteneffizienz helfen und realistische Schätzungen sowohl für Kosten für den 3D-Druck von Metall und AM-Vorlaufzeitund stellt sicher, dass die Erwartungen mit der Projektrealität in Einklang gebracht werden.
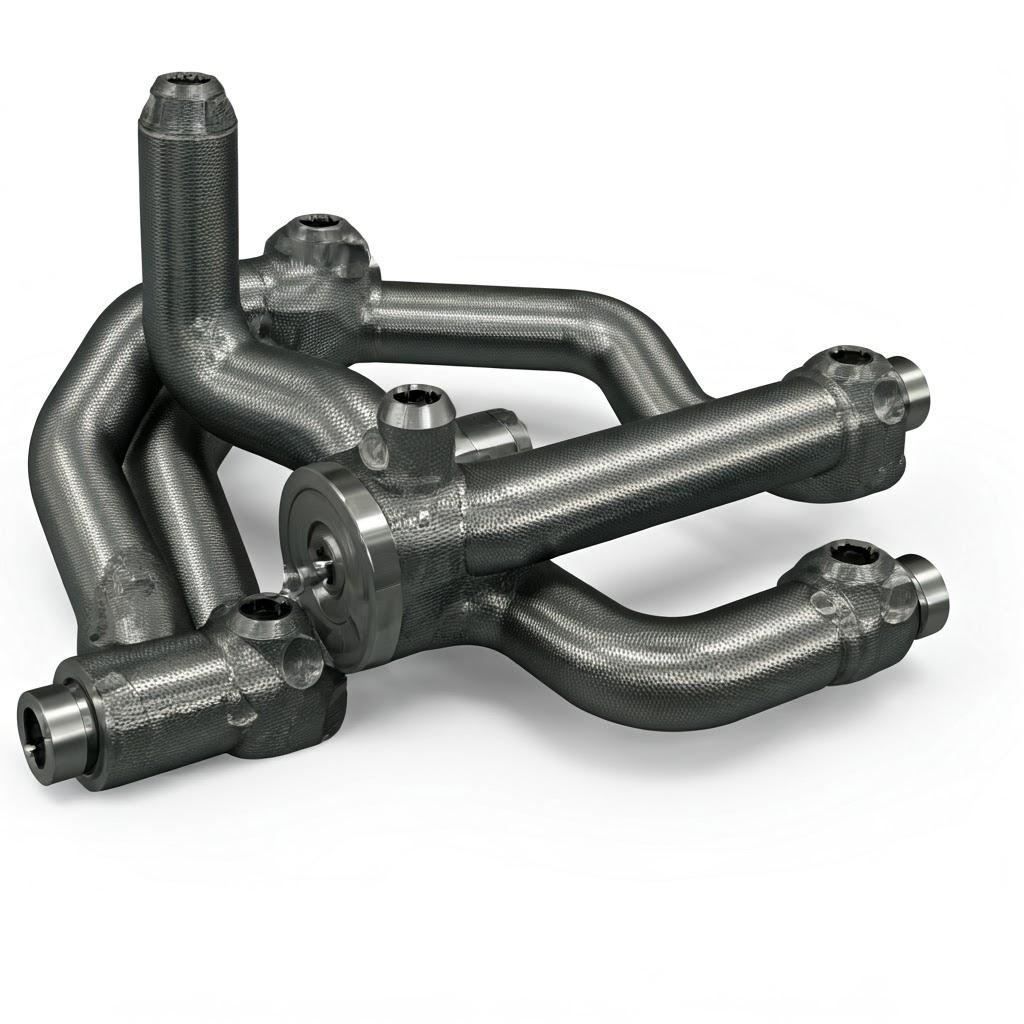
Häufig gestellte Fragen (FAQ) zu 3D-gedruckten Kraftstoffverteilern
Hier finden Sie Antworten auf einige häufig gestellte Fragen von Ingenieuren und Beschaffungsmanagern, wenn sie die additive Fertigung von Metall für Kraftstoffverteilerrohre in Betracht ziehen:
F1: Was sind die Hauptvorteile eines 3D-gedruckten Kraftstoffverteilers gegenüber einem traditionell hergestellten?
- A1: Die wichtigsten Vorteile sind:
- Gestaltungsfreiheit: Die Fähigkeit, hochkomplexe interne Kanäle zu schaffen, die für den Flüssigkeitsfluss optimiert sind (Verringerung des Druckabfalls, Verbesserung der Gleichmäßigkeit der Verteilung) und Merkmale zu integrieren, was beim Gießen oder bei der maschinellen Bearbeitung oft unmöglich ist.
- Gewichtsreduzierung: Erhebliche Masseneinsparungen durch Topologieoptimierung und Teilekonsolidierung, die für die Luft- und Raumfahrt und die Hochleistungsautomobilbranche von entscheidender Bedeutung sind.
- Leistungsverbesserung: Optimierte Strömungswege führen zu einem verbesserten Motor-/Systemwirkungsgrad, einer potenziell höheren Leistungsabgabe und besseren Emissionen.
- Teil Konsolidierung: Die Kombination mehrerer Komponenten in einem einzigen gedruckten Teil verkürzt die Montagezeit, eliminiert potenzielle Leckagepfade an Verbindungsstellen, vereinfacht die Lagerhaltung und erhöht die Zuverlässigkeit.
- Rapid Prototyping und Iteration: Kürzere Entwicklungszyklen im Vergleich zu werkzeugbasierten traditionellen Methoden ermöglichen eine schnellere Designvalidierung und -optimierung.
F2: Können 3D-gedruckte Verteilerrohre den Druck und die Temperaturen in Luft- und Raumfahrtmotoren aushalten?
- A2: Auf jeden Fall. Durch die Auswahl geeigneter Hochleistungswerkstoffe, wie z. B. der Nickelsuperlegierung Inconel 625 (IN625), können 3D-gedruckte Verteilerrohre den extremen Temperaturen (bis zu 800-1000∘C) und hohen Drücken in Gasturbinentriebwerken und Raketenantriebssystemen zuverlässig standhalten. Eine ordnungsgemäße Designvalidierung (FEA), die Einhaltung der DfAM-Grundsätze, optimierte Druckparameter, die erforderlichen Wärmebehandlungen (Spannungsabbau, Alterung) und eine strenge Qualitätskontrolle (einschließlich zerstörungsfreier Prüfungen wie CT-Scans und Lecktests) sind unerlässlich, um die strukturelle Integrität und Leistung in diesen anspruchsvollen Umgebungen sicherzustellen.
F3: Wie glatt können die inneren Kanäle eines 3D-gedruckten Kraftstoffverteilers sein?
- A3: Die interne Oberflächenrauhigkeit (Ra) von AM-Metallteilen liegt in der Regel zwischen 6μm und 25μm oder höher und ist damit rauer als maschinell bearbeitete Oberflächen. Obwohl dies für einige Anwendungen akzeptabel ist, sind glattere Oberflächen für einen optimalen Flüssigkeitsdurchfluss oft erwünscht. Nachbearbeitungsmethoden wie Abrasive Strömungsbearbeitung (AFM) oder Extrude Hone sind speziell dafür ausgelegt, die Oberflächengüte von Innenkanälen, auch von komplexen, erheblich zu verbessern und je nach Ausgangsrauheit, Material und Bearbeitungszeit Ra-Werte von unter 1-5μm zu erreichen. Auch das Elektropolieren kann bei bestimmten Werkstoffen und Geometrien wirksam sein. Die erreichbare Glätte hängt von der gewählten Nachbearbeitungsmethode und der Teilekonstruktion (Kanalgröße/Zugänglichkeit) ab.
F4: Welche Informationen muss ich angeben, um ein Angebot für einen kundenspezifischen 3D-gedruckten Kraftstoffverteiler zu erhalten?
- A4: Um einen genauen Kostenvoranschlag und eine Vorlaufzeitschätzung zu erhalten, sollten Sie Ihrem potenziellen AM-Lieferanten folgende Angaben machen:
- Ein 3D-CAD-Modell der Verteilerkonstruktion (STEP-Format wird allgemein bevorzugt).
- Der spezifizierte Werkstoff (z. B. AlSi10Mg, IN625, Ti6Al4V) und alle relevanten Werkstoffnormen (ASTM, AMS).
- 2D-Zeichnungen mit eindeutigen Angaben zu kritischen Abmessungen, geometrischer Bemaßung und Tolerierung (GD&T), erforderlichen Oberflächenbehandlungen (für Innen- und Außenflächen) und der Lage von Merkmalen wie Gewinden oder Dichtflächen.
- Die Menge der benötigten Teile (unterscheiden Sie zwischen Prototyp und Produktionsvolumen).
- Besondere Anforderungen an die Nachbearbeitung (z. B. ein bestimmter Wärmebehandlungszyklus, eine bestimmte Oberflächenbeschichtung).
- Vorgeschriebene Prüf- und Inspektionsanforderungen (z. B. Druck und Dauer der Dichtheitsprüfung, Anforderungen an die zerstörungsfreie Prüfung, erforderliche Dokumentation/Zertifizierungspaket).
- Die beabsichtigte Anwendung (hilft dem Anbieter, den Kontext und die Kritikalität zu verstehen).
F5: Bietet Met3dp Unterstützung bei der Optimierung meines Verteilers für die additive Fertigung?
- A5: Ja, Met3dp legt Wert darauf, umfassende Lösungen anzubieten, die über das reine Drucken hinausgehen. Ihre Dienstleistungen umfassen Anwendungsentwicklungsdienste und die Nutzung ihrer jahrzehntelanges kollektives Fachwissen in der additiven Fertigung von Metall. Dies bedeutet, dass wir eine Beratung zum Thema Design for Additive Manufacturing (DfAM) anbieten, um Kunden bei der Optimierung ihrer bestehenden Designs oder bei der Entwicklung neuer vielfältiger Konzepte zu unterstützen, die die Vorteile von AM voll ausschöpfen. Dieser kooperative Ansatz trägt dazu bei, dass die Teile für einen erfolgreichen Druck, optimale Leistung, Zuverlässigkeit und Kosteneffizienz ausgelegt sind. Es ist sehr empfehlenswert, bereits in einem frühen Stadium des Entwurfsprozesses mit dem Ingenieurteam des Kunden zusammenzuarbeiten.
Schlussfolgerung: Die Zukunft des Fluidflusses ist additiv – Partnerschaften für optimierte Verteiler
Die Reise durch die Feinheiten der Entwicklung, Herstellung und Qualifizierung von kundenspezifischen Kraftstoffverteilern mit Hilfe der additiven Fertigung von Metall zeigt ein klares Bild: AM ist nicht nur eine Alternative, sondern eine transformative Kraft, die die Zukunft der Fluidströmungssysteme neu gestaltet. Die Fähigkeit, sich von den Fesseln traditioneller Fertigungszwänge zu befreien, eröffnet beispiellose Innovationsmöglichkeiten und ermöglicht die Entwicklung von Verteilern, die leichter sind, bessere Leistungen erbringen, mehr Funktionen integrieren und schneller als je zuvor auf den Markt kommen.
Von den anspruchsvollen Umgebungen der Luft- und Raumfahrt motoren und Raketenantriebe in die wettbewerbsorientierte Welt der hochleistungsautomobil und die robusten Bedürfnisse der Industrie turbinen bietet der 3D-Metalldruck greifbare Vorteile. Optimierte interne Kanäle, die aus CFD-Analysen hervorgehen und durch AM realisiert werden, minimieren Druckverluste und sorgen für eine gleichmäßige Kraftstoffzufuhr, wodurch Effizienz und Leistung gesteigert werden. Durch die Optimierung der Topologie wird kritisches Gewicht eingespart, was den Kraftstoffverbrauch und die Nutzlastkapazität erhöht. Durch die Konsolidierung von Bauteilen wird die Komplexität drastisch reduziert, Leckstellen werden beseitigt und die Lieferketten gestrafft. Materialien wie das leichte AlSi10Mg und die robuste, hochtemperaturbeständige IN625 bieten maßgeschneiderte Lösungen für unterschiedliche Einsatzbedingungen.
Um diese Vorteile nutzen zu können, muss man sich jedoch mit den Feinheiten des Design for Additive Manufacturing (DfAM) auseinandersetzen, die erreichbare Präzision verstehen, die notwendige Nachbearbeitung implementieren und potenzielle Produktionsherausforderungen entschärfen. Der Erfolg hängt von einer sorgfältigen Planung, einer strengen Prozesskontrolle und vor allem von der Wahl des richtigen Fertigungspartners ab.
Ein Partner wie Met3dp zeichnet sich durch einen integrierten Ansatz aus. Mit branchenführenden Fähigkeiten sowohl in fortschrittlicher Pulverherstellung (Gaszerstäubung, PREP), die die Qualität des Materials sicherstellen, und hochentwickelte 3D-Druck-Ausrüstung (einschließlich SEBM-Technologie) beherrschen sie kritische Elemente der Wertschöpfungskette. Ihre umfassenden Lösungen umfassen DfAM-Beratung, Anwendungsentwicklung, verschiedene Materialoptionen und ein Engagement für die Genauigkeit und Zuverlässigkeit, die für unternehmenskritische Komponenten erforderlich sind. Durch die Zusammenarbeit mit einem kompetenten Anbieter können Unternehmen Metall-AM vertrauensvoll nutzen, um sich durch überlegene Kraftstoffverteilertechnologie einen Wettbewerbsvorteil zu verschaffen.
Die Zukunft der effizienten, leistungsstarken Flüssigkeitsverteilung ist unbestreitbar additiv. Wenn Sie Kraftstoffsysteme der nächsten Generation entwickeln oder bestehende Systeme verbessern wollen, ist die Erkundung des Potenzials des 3D-Metalldrucks nicht mehr optional, sondern unerlässlich.
Sind Sie bereit, Ihre Kraftstoffverteiler zu revolutionieren? Machen Sie sich die Möglichkeiten der additiven Fertigung zunutze. Kontakt zu Met3dp um Ihre Projektanforderungen zu besprechen und zu erfahren, wie unser Fachwissen in den Bereichen Metall-AM-Anlagen, fortschrittliche Werkstoffe und Anwendungsentwicklung Sie bei der Entwicklung und Herstellung von Kraftstoffverteilern unterstützen kann, die hinsichtlich Durchfluss, Gewicht und Leistung optimiert sind, und so Ihren Weg zur digitalen Transformation der Fertigung beschleunigen.
Teilen auf
MET3DP Technology Co., LTD ist ein führender Anbieter von additiven Fertigungslösungen mit Hauptsitz in Qingdao, China. Unser Unternehmen ist spezialisiert auf 3D-Druckgeräte und Hochleistungsmetallpulver für industrielle Anwendungen.
Fragen Sie an, um den besten Preis und eine maßgeschneiderte Lösung für Ihr Unternehmen zu erhalten!
Verwandte Artikel
Über Met3DP
Aktuelles Update
Unser Produkt
KONTAKT US
Haben Sie Fragen? Senden Sie uns jetzt eine Nachricht! Wir werden Ihre Anfrage mit einem ganzen Team nach Erhalt Ihrer Nachricht bearbeiten.
Holen Sie sich Metal3DP's
Produkt-Broschüre
Erhalten Sie die neuesten Produkte und Preislisten
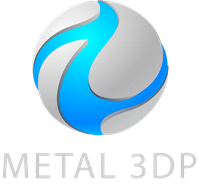
Metallpulver für 3D-Druck und additive Fertigung