Wärmeableitungspaneele für Satelliten mittels Metall-AM
Inhaltsübersicht
Einführung: Die entscheidende Rolle des Wärmemanagements in Satellitensystemen
Die letzte Grenze, der Weltraum, präsentiert eine Umgebung extremer Gegensätze. Satelliten, die unseren Planeten umkreisen oder sich weiter in den Kosmos wagen, sind auf der einen Seite intensiver Sonnenstrahlung ausgesetzt, während sie auf der anderen Seite dem eisigen Vakuum des Weltraums ausgesetzt sind. Intern erzeugen die hochentwickelte Elektronik, leistungsstarke Kommunikationssysteme, empfindliche optische Nutzlasten und Antriebseinheiten erhebliche Mengen an Abwärme. Die Bewältigung dieser thermischen Belastungen ist nicht nur eine betriebliche Annehmlichkeit, sondern absolut entscheidend für den Missionserfolg, die Langlebigkeit der Komponenten und die Gesamtzuverlässigkeit dieser Millionen- oder sogar Milliarden-Dollar-Vermögenswerte. Unzureichendes Wärmemanagement kann zu Überhitzung von Komponenten, Leistungsverschlechterung, Signalverzerrung, verkürzter Lebensdauer und in katastrophalen Fällen zum vollständigen Ausfall der Mission führen. Das Gebiet der thermischen Steuerung von Satelliten widmet sich der Aufrechterhaltung aller Satellitenkomponenten innerhalb ihrer spezifischen, oft engen zulässigen Temperaturbereiche während aller Missionsphasen – von Start und Aussetzung bis hin zu Orbitaloperationen und potenziellen Manövern am Ende der Lebensdauer. Dies beinhaltet ein komplexes Zusammenspiel von passiven Methoden (wie Isolationsdecken und Oberflächenbeschichtungen) und aktiven Methoden (wie Heizungen und mechanisch gepumpten Flüssigkeitsschleifen). Zentral für viele passive thermische Steuerungsstrategien sind Wärmeableitungstafeln, oft als Radiatoren bezeichnet, die so konzipiert sind, dass sie Abwärme von internen Quellen effizient sammeln und in die kalte Weite des Weltraums abstrahlen.
Traditionell wurden diese entscheidenden Komponenten mit Methoden wie der CNC-Bearbeitung von festen Metallblöcken (oft Aluminium- oder Kupferlegierungen), der Montage komplexer Strukturen durch Löten oder Kleben mehrerer Teile oder dem Einbetten von Wärmerohren in Tafeln hergestellt. Obwohl diese konventionellen Ansätze effektiv sind, stoßen sie auf inhärente Einschränkungen, insbesondere wenn Satellitenkonstruktionen kompakter und energiehungriger werden und eine höhere Leistung innerhalb strenger Massenbudgets erfordern. Die Bearbeitung komplexer interner Kanalgeometrien für einen verbesserten Flüssigkeitsfluss oder komplizierter externer Rippenstrukturen für eine maximale Strahlungsoberfläche kann schwierig, zeitaufwändig sein und erhebliche Materialverschwendung verursachen. Die Montage mehrerer Teile führt zu potenziellen Fehlerstellen an Verbindungen und erhöht die Komplexität der Fertigungs- und Qualitätssicherungsprozesse. Darüber hinaus ist die Gestaltungsfreiheit, die diese Methoden bieten, oft eingeschränkt, was das Potenzial für eine wirklich optimierte thermische Leistung und Gewichtsreduzierung einschränkt – ein entscheidender Faktor, da jedes Kilogramm, das in die Umlaufbahn gebracht wird, erhebliche Kosten verursacht.
Eingeben Additive Fertigung von Metall (AM)auch bekannt als Metall 3D-Druck. Diese disruptive Technologie verändert rasant die Landschaft der Luft- und Raumfahrttechnik und bietet beispiellose Möglichkeiten zur Herstellung hochkomplexer, leichter und leistungsoptimierter Komponenten. Im Gegensatz zu subtraktiven Verfahren, bei denen Material entfernt wird, baut AM Teile Schicht für Schicht direkt aus einem digitalen Modell auf, typischerweise unter Verwendung eines Hochenergielasers oder Elektronenstrahls, um feine Metallpulver zu verschmelzen. Dieser schichtweise Ansatz eröffnet eine neue Dimension der Gestaltungsfreiheit und ermöglicht die Herstellung von Geometrien, die zuvor unmöglich oder unerschwinglich teuer herzustellen waren. Für Satelliten-Wärmeableitungstafeln bedeutet dies die Fähigkeit, Komponenten mit folgenden Merkmalen zu entwerfen und herzustellen:
- Optimierte Topologien: Interne Strukturen können algorithmisch so konzipiert werden, dass sie den thermischen Lastpfaden präzise folgen und Material nur dort platzieren, wo es für die Wärmeübertragung und die strukturelle Unterstützung benötigt wird, wodurch die Masse drastisch reduziert wird.
- Komplexe Binnenkanäle: Konforme Kühlkanäle, die den Konturen wärmeerzeugender Komponenten genau folgen, oder komplizierte Netzwerke, die biologische Gefäßsysteme nachahmen, können direkt gedruckt werden, wodurch die Wärmeabsorptionseffizienz maximiert wird.
- Integrierte Funktionen: Befestigungspunkte, Halterungen, Flüssigkeitsanschlüsse und sogar eingebaute Sensorgehäuse können in einem einzigen monolithischen Teil integriert werden, wodurch die Montagekomplexität und potenzielle Leckpfade reduziert werden.
- Erhöhte Oberfläche: Gitterstrukturen, Rippen und komplexe Oberflächenstrukturen können integriert werden, um die effektive Strahlungsoberfläche ohne proportionalen Massezuwachs deutlich zu erhöhen.
- Werkstoff-Innovation: AM ermöglicht die Verarbeitung fortschrittlicher Legierungen, die speziell für ihre thermischen Eigenschaften und Weltraumtauglichkeit ausgewählt wurden, und eröffnet sogar die Tür zu funktional abgestuften Materialien, bei denen die Eigenschaften innerhalb einer einzigen Komponente variieren.
Unternehmen wie Met3dp, ein führender Anbieter von additiven Fertigungslösungen, der sich auf Hochleistungs-Metallpulver und industrielle 3D-Druckausrüstung spezialisiert hat, steht an vorderster Front dieses technologischen Wandels. Durch die Nutzung fortschrittlicher Pulverherstellungstechniken wie Gasverdüsung und Plasma Rotating Electrode Process (PREP) produziert Met3dp hochwertige kugelförmige Metallpulver, einschließlich Legierungen, die sich ideal für thermische Anwendungen in der Luft- und Raumfahrt eignen, und gewährleistet so die Konsistenz und Reinheit, die für missionskritische Komponenten erforderlich sind. Ihr Fachwissen in Verfahren wie dem selektiven Elektronenstrahlschmelzen (SEBM) ermöglicht zudem die Herstellung dichter, zuverlässiger Metallteile mit überlegenen mechanischen Eigenschaften. Da die Luft- und Raumfahrtindustrie weiterhin die Grenzen von Leistung und Effizienz verschiebt, ist Metall-AM bereit, das Design und die Herstellung von thermischen Managementsystemen für Satelliten zu revolutionieren und Weltraummissionen leistungsfähiger, zuverlässiger und kostengünstiger zu machen. Beschaffungsmanager und Luft- und Raumfahrtingenieure, die nach B2B-Lösungen und zuverlässigen Lieferanten für fortschrittliche Satellitenhardware suchen, sollten das transformative Potenzial der Metall-AM-Anbieter in Betracht ziehen.
Wofür werden Satelliten-Wärmeableitungstafeln verwendet?
Satelliten-Wärmeableitungstafeln dienen in ihren verschiedenen Formen (Radiatoren, Kühlkörper, Thermostraps) einem einzigen, entscheidenden Zweck: der Aufrechterhaltung des thermischen Gleichgewichts des Raumschiffs. Sie fungieren als primäre Schnittstelle für die Ableitung von Abwärme, die von Bord-Systemen erzeugt wird, in die umgebende Weltraumumgebung. Ohne eine effiziente Wärmeableitung könnten die Innentemperaturen eines Satelliten schnell über die Betriebsgrenzen empfindlicher Elektronik, wissenschaftlicher Instrumente, Batterien und anderer kritischer Hardware ansteigen.
Kernfunktion: Das Grundprinzip ist die Wärmeabstrahlung. Wärme, die von internen Komponenten erzeugt wird, wird (über Wärmerohre oder Flüssigkeitsschleifen) an die Radiatorplatte geleitet oder konvektiert. Die äußere Oberfläche dieser Platte, die oft mit spezifischen Beschichtungen behandelt wird, um den thermischen Emissionsgrad zu maximieren und die Solarabsorption zu minimieren, strahlt diese Wärmeenergie dann als Infrarotstrahlung in das nahezu perfekte Vakuum des Weltraums ab, das als effektiver Kühlkörper fungiert. Die Effizienz dieses Prozesses hängt stark von der Oberfläche der Platte, ihren Oberflächeneigenschaften (Emissionsgrad), ihrer Temperatur und ihrem Sichtfaktor zum kalten Weltraum (Vermeidung von Sonnen-, Erd- oder anderen Raumschiffteilen) ab.
Schlüsselindustrien & Interessengruppen:
- Raumschiffhersteller: Hauptauftragnehmer (z. B. Boeing, Airbus Defence and Space, Lockheed Martin, Thales Alenia Space, Maxar Technologies) und spezialisierte Satellitenbauer, die komplette Satellitensysteme entwerfen, montieren, integrieren und testen, sind stark auf effiziente thermische Steuerungsteilsysteme angewiesen. Sie sind Großverbraucher und Großhandelskäufer von Satellitenkomponenten, einschließlich Wärmeableitungstafeln.
- Satelliten-Betreiber: Unternehmen und Regierungsbehörden (z. B. Intelsat, SES, Eutelsat, NASA, ESA, nationale Weltraumagenturen), die Satellitenkonstellationen für Kommunikations-, Erdbeobachtungs-, Navigations- oder wissenschaftliche Zwecke besitzen und betreiben, sind auf die langfristige Zuverlässigkeit angewiesen, die durch ein robustes Wärmemanagement gewährleistet wird.
- Luft- und Raumfahrt- & Verteidigungsunternehmen: Unternehmen, die Teilsysteme und Komponenten an Haupthersteller liefern, sind oft auf Bereiche wie thermische Steuerungshardware spezialisiert. Diese B2B-Lieferanten benötigen Zugang zu fortschrittlichen Fertigungstechnologien wie Metall-AM, um anspruchsvolle Spezifikationen zu erfüllen.
- Komponentenlieferanten & -distributoren: Unternehmen, die sich auf die Bereitstellung spezifischer Komponenten in Luft- und Raumfahrtqualität konzentrieren, einschließlich Wärmemanagement-Hardware, fungieren oft als Vermittler oder spezialisierte Hersteller und suchen nach zuverlässigen Quellen für Masse Bestellungen oder kundenspezifische Teile.
Spezifische Anwendungen innerhalb von Satelliten:
- Primäre Radiatorplatten: Dies sind oft große, extern montierte Tafeln, manchmal ausfahrbar, die dazu bestimmt sind, den Großteil der Abwärme des Raumschiffs abzuleiten. Ihre Größe und Platzierung werden sorgfältig auf der Grundlage der gesamten Wärmelast und der orbitalen Umgebung berechnet. Metall-AM ermöglicht leichte Konstruktionen mit integrierten Wärmerohren oder komplexen Rippengeometrien, um das Verhältnis von Fläche zu Masse zu maximieren.
- Komponentenspezifische Kühlkörper: Hochleistungs-Elektronikkomponenten wie Solid State Power Amplifiers (SSPAs), Traveling Wave Tube Amplifiers (TWTAs), Prozessoren und FPGAs erzeugen konzentrierte Wärmelasten. Kleinere, dedizierte Kühlkörper, oft aufwendig geformt, um der Stellfläche der Komponente zu entsprechen und die Kontaktfläche zu maximieren, werden verwendet, um Wärme effektiv abzuleiten. AM ermöglicht hochkomplexe Formen, potenziell mit internen Mikrokanalstrukturen für die Flüssigkeitskühlungsintegration oder optimierten Rippendesigns, die weit über die Bearbeitungsmöglichkeiten hinausgehen.
- Integrierte Struktur-/Wärmetafeln: Im modernen Satellitendesign gibt es einen Trend zu multifunktionalen Strukturen. Tafeln, die sowohl als tragende Strukturelemente als auch als Wärmestrahler dienen, sind immer häufiger anzutreffen. Metall-AM ist ideal für die Herstellung solcher Komponenten und optimiert sowohl die mechanische Steifigkeit als auch die Wärmeableitungspfade innerhalb eines einzigen, leichten Teils. Topologieoptimierungsalgorithmen können komplexe, organisch aussehende Strukturen erzeugen, die sowohl mechanische Belastungen als auch den Wärmefluss effizient verwalten.
- Thermostraps und Doubler: Flexible Thermostraps werden manchmal verwendet, um Wärme über Verbindungen oder bewegliche Teile zu leiten, während Thermodoubler (dünne Platten aus hochleitfähigem Material) dazu beitragen, konzentrierte Wärmelasten über einen größeren Bereich einer Radiatorplatte zu verteilen. Während Straps oft aus verschiedenen Materialien bestehen, kann AM verwendet werden, um hochoptimierte Thermodoubler oder starre Thermoverbindungen mit komplexen Formen und minimaler Masse herzustellen und sie potenziell direkt in die Plattenstruktur zu integrieren.
- Wärmerohranordnungen: Wärmerohre sind hocheffiziente passive Wärmeübertragungsgeräte. AM kann verwendet werden, um komplexe Verdampfer- und Kondensatorabschnitte für Wärmerohre herzustellen oder sogar die Wärmerohrstruktur direkt in die Wände einer Strukturplatte oder eines elektronischen Gehäuses einzubetten, was zu hochintegrierten und effizienten thermischen Lösungen führt. Dies erfordert spezielle AM-Techniken und -Materialien, oft unter Verwendung von Kupferlegierungen wie CuCrZr für den Docht und das Gehäuse aufgrund ihrer hohen Wärmeleitfähigkeit.
Die Nachfrage nach immer ausgefeilteren Satellitenfähigkeiten, gepaart mit dem Drang nach kleineren, leichteren und kostengünstigeren Plattformen (wie CubeSats und SmallSats), übt immensen Druck auf die thermischen Managementsysteme aus. Beschaffungsmanager und Ingenieure in der Satellitenindustrie suchen ständig nach innovativen Lösungen und zuverlässigen Zulieferer der Luft- und Raumfahrtindustrie in der Lage, Leistung der nächsten Generation zu liefern. Die additive Metallfertigung, die von erfahrenen Anbietern angeboten wird, stellt einen überzeugenden Weg dar, um diese sich entwickelnden Anforderungen an Satelliten-Wärmeableitungstafeln und zugehörige thermische Hardware zu erfüllen und beispiellose Gestaltungsfreiheit und Leistungspotenzial zu bieten.
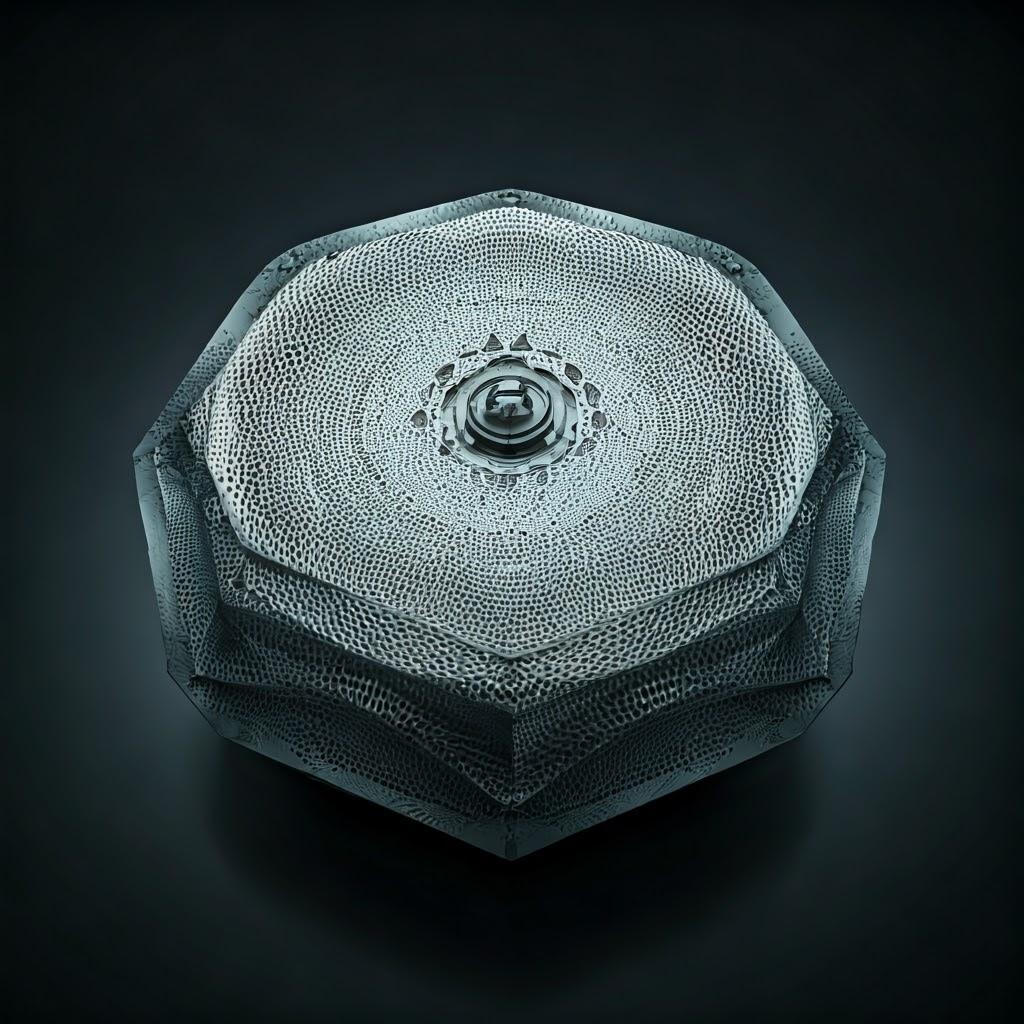
Warum Metall-3D-Druck für Satelliten-Wärmeableitungstafeln verwenden?
Die Entscheidung, die additive Metallfertigung für kritische Komponenten wie Satelliten-Wärmeableitungstafeln einzusetzen, ergibt sich aus einem Zusammenfluss überzeugender Vorteile, die die Einschränkungen herkömmlicher Methoden direkt angehen und perfekt mit den anspruchsvollen Anforderungen der Luft- und Raumfahrtindustrie übereinstimmen. Während konventionelle Fertigungstechniken wie CNC-Bearbeitung, Blechumformung und Löt-/Schweißbaugruppen der Industrie gute Dienste geleistet haben, bietet Metall-AM einen Paradigmenwechsel, der eine verbesserte Leistung, kürzere Vorlaufzeiten und neue Gestaltungsmöglichkeiten ermöglicht. Für B2B-Beschaffung Spezialisten und Konstrukteure, die sich auf die Optimierung von Satellitensystemen konzentrieren, ist das Verständnis dieser Vorteile von entscheidender Bedeutung.
Hauptvorteile von Metall-AM für Wärmeableitungstafeln:
- Unübertroffene geometrische Komplexität: Dies ist wohl der wichtigste Vorteil. AM baut Teile schichtweise auf und befreit Designer von den Einschränkungen, die durch subtraktive Bearbeitungs- oder Montageprozesse auferlegt werden.
- Optimierte interne Kanäle: Entwerfen Sie komplizierte, sanft geschwungene interne Kanäle, die sich präzise an die Wärmequellen anpassen und den thermischen Widerstand minimieren. Erstellen Sie komplexe Verteilerkonstruktionen für flüssigkeitsgekühlte Tafeln, die nicht maschinell bearbeitet werden können.
- Gitterförmige Strukturen: Integrieren Sie periodische oder stochastische Gitterstrukturen in die Tafel. Diese zellularen Materialien bieten extrem hohe Oberfläche-zu-Volumen-Verhältnisse, ideal zur Verbesserung der konvektiven Wärmeübertragung (bei interner Kühlung) oder der Strahlungsoberfläche, während sie gleichzeitig strukturelle Unterstützung bei sehr geringen Dichten bieten. Dies führt zu deutlich leichteren Tafeln im Vergleich zu festen Strukturen.
- Biomimikry: Natürliche Kühlstrukturen nachahmen, wie Gefäßnetzwerke oder Lungenalveolen, um hocheffiziente Wärmeaustauschpfade zu schaffen.
- Integrierte Funktionen: Drucken Sie Befestigungsbuchsen, Ausrichtungsmerkmale, Anschlussanschlüsse und komplexe Rippengeometrien als integrale Bestandteile der Tafel, wodurch Montageschritte entfallen, die Teileanzahl reduziert und die Zuverlässigkeit verbessert wird.
- Deutliche Gewichtsreduzierung (Massenoptimierung): Die Startkosten sind ein Haupttreiber im Satellitendesign und kosten oft Zehntausende von Dollar pro Kilogramm, das in die Umlaufbahn geschickt wird. AM zeichnet sich durch die Herstellung leichter Strukturen aus.
- Topologie-Optimierung: Verwenden Sie Berechnungswerkzeuge, um Material nur dort zu verteilen, wo es für die thermische Leistung und die strukturelle Integrität benötigt wird, und unnötige Masse zu entfernen. Dies führt zu hocheffizienten, oft organisch aussehenden Designs, die deutlich leichter sind als herkömmlich hergestellte Gegenstücke.
- Dünne Wände & komplexe Kerne: Drucken Sie Tafeln mit dünnen, strukturell soliden Wänden und komplexen internen Wellungen oder Gitterkernen, um eine hohe Steifigkeit und thermische Leistung bei minimalem Materialverbrauch zu erzielen.
- Teil Konsolidierung: Gestalten Sie Baugruppen, die zuvor aus mehreren verbundenen Teilen hergestellt wurden, in eine einzige, monolithische AM-Komponente um. Dies reduziert das Gewicht inhärent, indem Befestigungselemente, Flansche und redundantes Material an den Schnittstellen eliminiert werden.
- Teilekonsolidierung und reduzierte Montage: Wie bereits erwähnt, vereinfacht die Fähigkeit, mehrere Funktionen und Merkmale in einem einzigen gedruckten Teil zu integrieren, die Lieferkette und den Herstellungsprozess dramatisch.
- Weniger Komponenten: Reduziert die Bestands
- Vereinfachte Montage: Weniger Zeit- und Arbeitsaufwand für die abschließende Satellitenintegration.
- Verbesserte Verlässlichkeit: Monolithische Teile weisen im Allgemeinen eine höhere strukturelle Integrität und weniger potenzielle Leckpfade im Vergleich zu komplexen Baugruppen auf.
- Rapid Prototyping und beschleunigte Designiteration: AM ermöglicht es Ingenieuren, sich schnell von der digitalen Konstruktion zum physischen Prototypen zu bewegen.
- Schnellere Testzyklen: Herstellung von Funktionsprototypen von Wärmeableitungspanels in Tagen oder Wochen statt in Monaten, was schnelle Tests, Validierung und Verfeinerung von Designs ermöglicht.
- Flexibilität bei der Gestaltung: Einfache Modifizierung von Designs basierend auf Testergebnissen und schnelles Drucken neuer Iterationen ohne die Notwendigkeit teurer Werkzeugumrüstungen, die mit herkömmlichen Methoden verbunden sind. Dieser iterative Prozess führt zu stärker optimierten Endteilen.
- Anpassungen: Effiziente Herstellung einzigartiger oder kundenspezifischer Designs in geringen Stückzahlen, die auf spezifische Missionsanforderungen oder Komponentenschnittstellen zugeschnitten sind, ohne hohe Einrichtungskosten zu verursachen.
- Materialoptimierung und fortschrittliche Legierungen: AM-Verfahren können mit einer wachsenden Palette fortschrittlicher Metalllegierungen arbeiten, einschließlich solcher, die speziell für das Wärmemanagement und die Weltraumumgebung optimiert wurden.
- Optimierte Materialauswahl: Wählen Sie Materialien wie AlSi10Mg für seine Ausgewogenheit aus geringer Dichte und guter Wärmeleitfähigkeit oder CuCrZr für Anwendungen, die maximale Wärmeübertragung erfordern, und nutzen Sie die spezifischen Stärken jeder Legierung.
- Funktionell abgestufte Materialien (Forschungsbereich): Es besteht zukünftiges Potenzial, die Materialzusammensetzung über ein einzelnes Teil mithilfe von AM zu variieren, wodurch möglicherweise Panels mit maßgeschneiderten Wärmeleitfähigkeitsgradienten oder integrierten Zonen mit hoher Festigkeit und hoher Leitfähigkeit entstehen.
- Geringerer Materialabfall: AM ist ein additives Verfahren, das typischerweise nur das für das Teil und die erforderlichen Stützen benötigte Material verwendet, was zu deutlich weniger Abfall führt als subtraktive Bearbeitung, bei der bis zu 80-90 % des Ausgangsmaterials abgetragen werden können. Dies ist besonders wichtig für teure Luft- und Raumfahrtlegierungen. Beschaffung Metallpulver im Großhandel wird effizienter.
- Reduzierte Vorlaufzeiten für komplexe und kundenspezifische Teile: Während die Einrichtung eines AM-Aufbaus Vorbereitung erfordert, kann die tatsächliche Druck- und Nachbearbeitungszeit für hochkomplexe oder kundenspezifische Teile in geringen Stückzahlen deutlich kürzer sein als die kombinierte Zeit, die für Werkzeugbau, Bearbeitungseinrichtung, Mehrachsenfräsen und Montage mit herkömmlichen Methoden benötigt wird. Dies ist ein entscheidender Vorteil für Luft- und Raumfahrtzulieferer die Einhaltung enger Programmzeitpläne.
Die Auswahl einer 3D-Druck-Dienstleister für Metall wie Met3dp, mit fundiertem Fachwissen in Luft- und Raumfahrtanwendungen, fortschrittlichen Materialien wie AlSi10Mg und CuCrZr und einer robusten Prozesskontrolle, ermöglicht es Satellitenherstellern und ihren B2B-Partnern diese Vorteile voll auszuschöpfen. Der Fokus von Met3dp auf die Herstellung hochwertiger, sphärischer Pulver gewährleistet eine optimale Verarbeitung und Endteilqualität, während ihre Erfahrung mit industriellen Druckern die Genauigkeit und Zuverlässigkeit garantiert, die für missionskritische Weltraumhardware erforderlich sind. Der Übergang zu AM für Komponenten wie Wärmeableitungspanels stellt einen strategischen Schritt hin zum Bau leistungsfähigerer, leichterer und kostengünstigerer Satelliten dar.
Empfohlene Materialien (AlSi10Mg & CuCrZr) und warum sie wichtig sind
Die Auswahl des richtigen Materials ist grundlegend für den Erfolg jeder technischen Komponente, und dies gilt insbesondere für Satelliten-Wärmeableitungspanels, bei denen Leistung, Gewicht und Zuverlässigkeit entscheidend sind. Die additive Metallfertigung eröffnet Möglichkeiten, erfordert aber auch eine sorgfältige Berücksichtigung des Verhaltens von Materialien während des Druckprozesses und wie ihre endgültigen Eigenschaften mit den Anwendungsanforderungen übereinstimmen. Für das Wärmemanagement im Weltraum stechen in der AM-Landschaft häufig zwei Materialien hervor: Aluminiumlegierung AlSi10Mg und Kupferlegierung CuCrZr. Das Verständnis ihrer jeweiligen Eigenschaften, Verarbeitungsnuancen und idealen Anwendungsfälle ist für Ingenieure und Beschaffungsmanager die Beschaffung von AM-Komponenten oder Metallpulver im Großhandel.
Aluminiumlegierung: AlSi10Mg
AlSi10Mg ist eine der gebräuchlichsten und gut charakterisierten Aluminiumlegierungen, die in der Metall-AM verwendet werden, insbesondere über Laser Powder Bed Fusion (LPBF). Es ist im Wesentlichen eine Gusslegierung, die für additive Verfahren angepasst wurde und für ihre hervorragende Kombination von Eigenschaften bekannt ist, die sie für eine Vielzahl von Luft- und Raumfahrtanwendungen, einschließlich thermischer Komponenten, sehr gut geeignet macht.
- Wichtige Eigenschaften:
- Geringe Dichte: Ungefähr 2,67 g/cm3. Dies ist ein großer Vorteil für die Luft- und Raumfahrt und trägt im Vergleich zu Kupfer-, Stahl- oder Titanlegierungen erheblich zur Gewichtsreduzierung bei.
- Gute Wärmeleitfähigkeit: Typischerweise im Bereich von 120−180 W/(m⋅K) nach entsprechender Wärmebehandlung. Obwohl es nicht so hoch ist wie reines Aluminium oder Kupfer, reicht es für viele Anwendungen in Kühlkörpern und Kühlkörpern aus, insbesondere wenn AM Designs mit stark vergrößerter Oberfläche ermöglicht.
- Gutes Verhältnis von Stärke zu Gewicht: Bietet eine gute mechanische Festigkeit und Steifigkeit, insbesondere nach der Wärmebehandlung (z. B. T6), wodurch Panels auch strukturelle Rollen übernehmen können.
- Ausgezeichnete Verarbeitbarkeit in AM: Schmilzt und erstarrt gut unter Laserbestrahlung, was im Allgemeinen zu dichten Teilen mit guter Maßgenauigkeit führt. Es ist weit verbreitet von verschiedenen Lieferanten von Metallpulver.
- Korrosionsbeständigkeit: Weist eine gute Korrosionsbeständigkeit auf.
- Eignung für Wärmeableitungspanels:
- Ideal für größere Kühlkörperplatten, bei denen die Gesamtmasse im Vordergrund steht.
- Geeignet für integrierte Struktur-/Wärmekomponenten, bei denen sowohl mechanische Unterstützung als auch Wärmeableitung erforderlich sind.
- Effektiv für Kühlkörper, die mit moderaten Wärmelasten umgehen, bei denen die Designfreiheit von AM die moderate Wärmeleitfähigkeit durch eine größere Oberfläche (Rippen, Gitter) kompensieren kann.
- Kostengünstig im Vergleich zu Kupferlegierungen oder spezialisierten Hochtemperaturmaterialien.
- Überlegungen zur Verarbeitung:
- Wird typischerweise mit LPBF-Systemen verarbeitet.
- Erfordert eine Nachbearbeitungswärmebehandlung (z. B. Spannungsarmglühen, gefolgt von Lösungsglühen und künstlichem Altern – T6-Zyklus), um die mechanischen Eigenschaften und die Wärmeleitfähigkeit zu optimieren und die Dimensionsstabilität sicherzustellen.
- Kann anfällig für Porosität sein, wenn die Prozessparameter oder die Pulverqualität nicht sorgfältig kontrolliert werden.
- Stützstrukturen sind im Allgemeinen für überhängende Merkmale erforderlich und müssen sorgfältig entfernt werden.
- Beschaffung: Hochwertiges AlSi10Mg-Pulver, das sich durch eine kontrollierte Partikelgrößenverteilung, hohe Sphärizität, geringen Satellitengehalt und niedrige Sauerstoffgehalte auszeichnet, ist entscheidend für das Erreichen gleichmäßiger Teile mit hoher Dichte. Renommierte B2B-Pulverhändler und Hersteller wie Met3dp, die fortschrittliche Zerstäubungstechniken (wie Gaszerstäubung) einsetzen, stellen sicher, dass diese kritischen Pulvereigenschaften erfüllt werden, und liefern Pulver, die für anspruchsvolle LPBF-Anwendungen optimiert sind. Das Sortiment an Metallpulvern von Met3dp umfasst hochwertiges AlSi10Mg, das für die Anforderungen der Luft- und Raumfahrt geeignet ist.
Kupferlegierung: CuCrZr (Kupfer-Chrom-Zirkonium)
Wenn maximale Wärme- und elektrische Leitfähigkeit die primäre Anforderung ist, sind Kupferlegierungen die erste Wahl. CuCrZr ist eine ausscheidungsgehärtete Legierung, die eine außergewöhnliche Kombination aus hoher Leitfähigkeit und relativ guter mechanischer Festigkeit bietet, insbesondere bei mäßig erhöhten Temperaturen, was sie in Bezug auf Verarbeitbarkeit und strukturelle Integrität in AM reinem Kupfer überlegen macht.
- Wichtige Eigenschaften:
- Ausgezeichnete Wärmeleitfähigkeit: Typischerweise über 300 W/(m⋅K), mehr als das Doppelte von AlSi10Mg. Dies ist entscheidend für die effiziente Übertragung hoher Wärmeströme.
- Ausgezeichnete elektrische Leitfähigkeit: Besitzt auch eine hohe elektrische Leitfähigkeit, wodurch es sich für Anwendungen eignet, die ein kombiniertes Wärme-/Elektromanagement umfassen (z. B. Stromschienen mit integrierter Kühlung).
- Gute Hochtemperaturfestigkeit: Behält seine Festigkeit bei erhöhten Temperaturen besser bei als reines Kupfer oder viele Aluminiumlegierungen.
- Gute Korrosionsbeständigkeit: Ähnlich wie Kupfer bietet es eine gute Beständigkeit in vielen Umgebungen.
- Höhere Dichte: Deutlich dichter als Aluminiumlegierungen (ca. 8,9 g/cm3), wodurch das Gewicht zu einer kritischeren Designüberlegung wird.
- Eignung für Wärmeableitungspanels:
- Ideal für kompakte Hochleistungskühlkörper, die mit sehr konzentrierten Wärmelasten umgehen (z. B. Kühlung von Hochleistungselektronik, Laserdioden).
- Wird in Wärmetauschern und Wärmerohrkomponenten verwendet, bei denen die Maximierung des Wärmeübertragungswirkungsgrads von größter Bedeutung ist.
- Anwendungen, die neben der Wärmeableitung eine hohe elektrische Leitfähigkeit erfordern.
- Situationen, in denen die höhere Dichte toleriert oder durch hochoptimierte AM-Designs ausgeglichen werden kann.
- Überlegungen zur Verarbeitung:
- Herausfordernd in der Verarbeitung über AM aufgrund der hohen Reflexionsfähigkeit und hohen Wärmeleitfähigkeit von Kupfer, was die Energieabsorption von Lasern oder Elektronenstrahlen beeinflusst.
- Erfordert Hochleistungslaser (oft grüne Laser in LPBF) oder Elektronenstrahlen (SEBM) mit sorgfältig optimierten Parametern, um dichte, fehlerfreie Teile zu erzielen.
- Anfällig für Oxidation; die Verarbeitung unter einer hochreinen Inertgasatmosphäre oder im Vakuum (wie bei SEBM) ist unerlässlich.
- Erfordert eine Nachbearbeitungswärmebehandlung (Lösungsbehandlung und Alterung), um die gewünschte Kombination aus Festigkeit und Leitfähigkeit zu erreichen.
- Die Pulverqualität (Sphärizität, Reinheit, Fließfähigkeit) ist für eine erfolgreiche Verarbeitung von entscheidender Bedeutung.
- Beschaffung: Suche nach einem zuverlässigen CuCrZr-Pulverlieferant mit Erfahrung in der Herstellung von Pulvern speziell für AM ist aufgrund der Verarbeitungsprobleme von entscheidender Bedeutung. Das Pulver muss eine ausgezeichnete Fließfähigkeit und hohe Reinheit aufweisen. Unternehmen wie Met3dp, die ihr Fachwissen in fortschrittlichen Pulverherstellungsverfahren wie PREP (Plasma Rotating Electrode Process) für reaktive und hochwertige sphärische Pulver nutzen, sind gut aufgestellt, um anspruchsvolle Materialien wie CuCrZr zu liefern und die für erfolgreiche Hochleistungs-AM-Aufbauten erforderlichen Eigenschaften sicherzustellen. Beschaffungsmanager sollten sich bei der Bewertung von Großhandelsanbietern von AM-Materialien.
Vergleichstabelle: AlSi10Mg vs. CuCrZr für AM-Wärmeanwendungen
Merkmal | AlSi10Mg | CuCrZr | Wichtige Überlegung für Satellitenplatten |
---|---|---|---|
Primärer Vorteil | Leichtgewicht, gute Verarbeitbarkeit | Ausgezeichnete Wärme-/elektrische Leitfähigkeit | Anwendung bestimmt Priorität (Gewicht vs. Leistung) |
Dichte | Niedrig (~2,67g/cm3) | Hoch (~8,9g/cm3) | Entscheidend für die Startkosten; bevorzugt AlSi10Mg |
Wärmeleitfähigkeit | Gut (120−180 W/(m⋅K)) | Ausgezeichnet (>300 W/(m⋅K)) | Entscheidend für hohen Wärmestrom; bevorzugt CuCrZr |
Mechanische Festigkeit | Gut (insbesondere nach T6-Behandlung) | Mäßig bis gut (ausscheidungsgehärtet) | Wichtig für strukturelle/thermische Rollen |
AM Verarbeitbarkeit | Im Allgemeinen einfacher (LPBF üblich) | Herausfordernder (Hochleistung/Reflexionsvermögen) | Wirkt sich auf Kosten, Vorlaufzeit, Auswahl des AM-Anbieters aus |
Kosten | Unter | Höher | Wesentlicher Faktor bei Budgetbeschränkungen |
Typische Anwendung | Große Kühlkörper, Strukturplatten, moderate Kühlkörper | Hochleistungskühlkörper, Wärmetauscher, Leiter | Material auf spezifische Wärmelast & Funktion abstimmen |
In Blätter exportieren
Die Rolle von Met3dp bei der Materialexzellenz:
Ein erfolgreiches AM-Ergebnis für anspruchsvolle Anwendungen wie Satelliten-Wärmeableitungspanels beginnt mit der Qualität des Rohmaterials. Das Engagement von Met3dp für Exzellenz in der Metallpulverherstellung ist ein wichtiger Enabler für Luft- und Raumfahrthersteller.
- Fortschrittliche Zerstäubung: Die Verwendung von branchenführender Gaszerstäubung für Legierungen wie AlSi10Mg gewährleistet hohe Sphärizität, gute Fließfähigkeit, eine kontrollierte Partikelgrößenverteilung (PSD) und einen geringen Sauerstoffgehalt – alles entscheidend für das Erreichen dichter, zuverlässiger Teile in LPBF.
- PREP-Technologie: Für anspruchsvolle oder reaktive Materialien, die möglicherweise spezielle Kupferlegierungen oder hochschmelzende Metalle umfassen, die manchmal für Anwendungen bei extremen Temperaturen in Betracht gezogen werden, verwendet Met3dp die PREP-Technologie. Diese elektrodenbasierte Zerstäubungsmethode erzeugt außergewöhnlich sphärische Pulver mit sehr hoher Reinheit und minimalen Satellitenpartikeln, ideal für anspruchsvolle Prozesse und kritische Anwendungen.
- Qualitätskontrolle: Strenge Tests und Charakterisierung von Pulverchargen gewährleisten Konsistenz, Rückverfolgbarkeit und die Einhaltung strenger Spezifikationen für Luft- und Raumfahrtmaterialien.
- Material-Portfolio: Met3dp stellt eine breite Palette von Pulvern her, darunter AlSi10Mg und möglicherweise CuCrZr oder andere relevante Legierungen (wie Ti-Legierungen, Superlegierungen, die ebenfalls in der Luft- und Raumfahrt verwendet werden), und bietet eine zuverlässige Quelle für Großhandelsbeschaffung von Metallpulvern.
Zusammenfassend lässt sich sagen, dass sowohl AlSi10Mg als auch CuCrZr einzigartige Vorteile für additiv gefertigte Satelliten-Wärmeableitungspanels bieten. AlSi10Mg bietet eine leichte, kostengünstige Lösung, die für viele Anwendungen geeignet ist, während CuCrZr eine überlegene thermische Leistung für Hochwärmestromszenarien liefert, wenn auch mit höherer Dichte und Verarbeitungskomplexität. Die Wahl hängt entscheidend von den spezifischen thermischen Anforderungen, dem Massenbudget und den strukturellen Anforderungen der Anwendung ab. Die Zusammenarbeit mit einem sachkundigen AM-Anbieter wie Met3dp, der nicht nur die Nuancen der Verarbeitung dieser Materialien versteht, sondern auch die hochwertigen Pulver liefert, die für den Erfolg unerlässlich sind, ist der Schlüssel zur Erschließung des vollen Potenzials von Metall-AM für fortschrittliches Satelliten-Wärmemanagement.
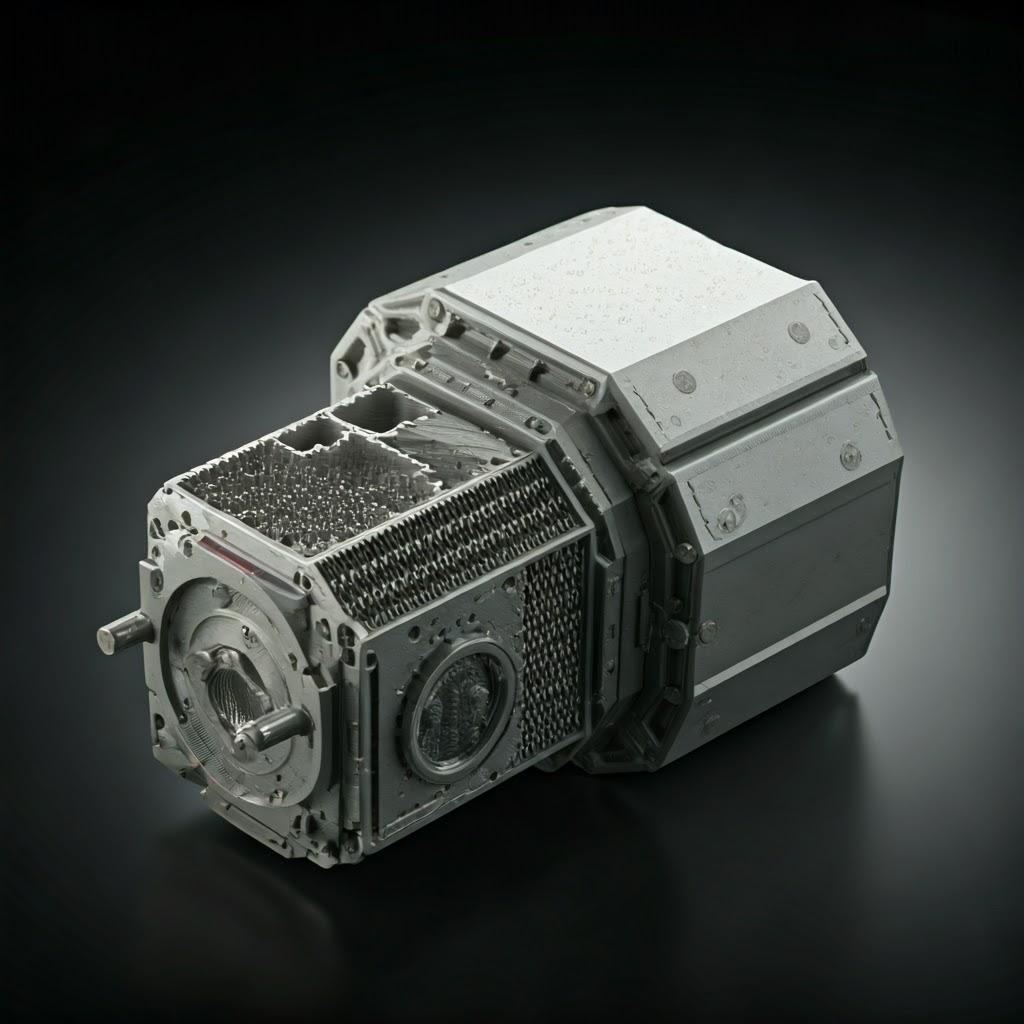
Designüberlegungen für additiv gefertigte Wärmeableitungstafeln
Die wahre Stärke der additiven Fertigung von Metallen liegt nicht nur in der Fähigkeit, Teile zu bauen, sondern auch in der Fähigkeit, Komponenten auf bisher unvorstellbare Weise zu optimieren. Für Wärmeableitungstafeln von Satelliten ist die Nutzung der Design for Additive Manufacturing (DfAM)-Prinzipien nicht nur von Vorteil, sondern unerlässlich, um das volle Potenzial der Technologie in Bezug auf thermische Leistung, Gewichtsreduzierung und Gesamtsystemeffizienz auszuschöpfen. DfAM ist eine Denkweise, die über das bloße Replizieren von traditionell konstruierten Teilen mit AM hinausgeht und sich auf die Konstruktion konzentriert, die für die einzigartigen Fähigkeiten und Einschränkungen des Schicht-für-Schicht-Verfahrens berücksichtigt. Ingenieure und Konstrukteure, die mit arbeiten, AM-Lieferanten müssen diese Prinzipien frühzeitig im Konstruktionszyklus anwenden.
Nutzung von DfAM für thermische Überlegenheit:
- Topologieoptimierung (TopOpt): Diese Berechnungstechnik ist revolutionär für die Konstruktion von leichten Hochleistungsstrukturen.
- Prozess: Finite-Elemente-Analyse (FEA)-Simulationssoftware analysiert die thermischen Belastungen und strukturellen Anforderungen der Tafel. Algorithmen entfernen dann iterativ Material aus Bereichen mit geringer Belastung oder geringem Wärmefluss und hinterlassen eine optimierte Lastpfadstruktur, die Wärme effizient überträgt und mechanischen Belastungen mit minimaler Masse standhält.
- Das Ergebnis: Führt oft zu organischen, von der Natur inspirierten Formen, die hocheffizient, aber konventionell nicht herstellbar sind. Für Wärmeableitungstafeln bedeutet dies die Schaffung von Strukturen, die Wärme direkt zu Strahlungsoberflächen oder Fluidkanälen leiten und gleichzeitig die notwendige Steifigkeit bieten, wodurch das Gewicht im Vergleich zu massiven oder konventionell bearbeiteten Tafeln drastisch reduziert wird.
- Erwägungen: Erfordert spezielle Software und Fachwissen. Die resultierende komplexe Geometrie muss sorgfältig auf die Herstellbarkeit innerhalb der AM-Einschränkungen (z. B. minimale Feature-Größe, Stützstrukturanforderungen) hin untersucht werden. Die Zusammenarbeit mit einem, aM-Lieferant für die Luft- und Raumfahrt der DfAM-Expertise anbietet, ist von hohem Wert.
- Gitterstrukturen und zelluläre Materialien: AM ermöglicht die direkte Herstellung von komplizierten internen Gitterstrukturen.
- Typen: Gängige Typen sind strutbasierte Gitter (wie kubisch, Oktaeder-Truss) und oberflächenbasierte Gitter (wie Triply Periodic Minimal Surfaces – TPMS, z. B. Gyroid, Schwarz).
- Vorteile für thermische Tafeln:
- Massive Vergrößerung der Oberfläche: Gitter bieten außergewöhnlich hohe Oberfläche-zu-Volumen-Verhältnisse. Bei Verwendung in Fluidkanälen verbessert dies die Konvektionswärmeübertragung. Bei Verwendung als Teil der äußeren Strahlungsstruktur (obwohl Beschichtungen immer noch wichtig sind), können sie den effektiven Emissionsgrad über einen bestimmten projizierten Bereich mit minimaler Masse erhöhen.
- Gewichtsreduzierung: Gitter haben eine inhärent geringe Dichte und ersetzen festes Material durch miteinander verbundene Streben oder Schalen, was zu erheblichen Gewichtseinsparungen bei gleichzeitiger Beibehaltung der maßgeschneiderten strukturellen Steifigkeit führt.
- Multifunktionalität: Kann so konzipiert werden, dass sie den Flüssigkeitsstrom steuern, strukturelle Unterstützung bieten und möglicherweise sogar Vibrationen oder Stoßenergie absorbieren.
- Designauswahl: Die Wahl des Einheitszellentyps, der Zellgröße, der Streben-/Wandstärke (relative Dichte) ermöglicht es Ingenieuren, die mechanischen Eigenschaften (Steifigkeit, Festigkeit) und thermischen Eigenschaften (effektive Leitfähigkeit, Oberfläche) der Tafel anzupassen. TPMS-Gitter bieten oft glattere Oberflächen und eine bessere Spannungsverteilung im Vergleich zu strutbasierten Gittern.
- Komplexes internes Kanaldesign:
- Konforme Kühlung/Heizung: Kanäle entwerfen, die genau den Konturen der an der Tafel montierten wärmeerzeugenden Komponenten folgen, um einen engen thermischen Kontakt und eine effiziente Wärmeabfuhr zu gewährleisten. Dies ist einem Bohren von geraden Löchern in einen bearbeiteten Block weit überlegen.
- Optimierte Flusspfade: Erstellen Sie glatte, gekrümmte Kanäle mit optimierten Querschnitten, um den Druckabfall zu minimieren und die Wärmeübertragung für flüssigkeitsgekühlte Tafeln oder die Integration von Wärmerohren zu maximieren. Vermeiden Sie scharfe Ecken, die Pulver einschließen oder den Fluss behindern können.
- Manifold-Integration: Komplexe Einlass-/Auslassverteiler für die Flüssigkeitsverteilung können nahtlos in das Tafellayout integriert werden, wodurch die Notwendigkeit externer Rohrleitungen und potenzieller Leckstellen reduziert wird.
- Entwerfen für AM-Prozessbeschränkungen: Obwohl AM Freiheit bietet, hat es seine eigenen Regeln. Werden diese ignoriert, führt dies zu Baufehlern, Defekten oder übermäßigen Nachbearbeitungskosten.
- Minimum Feature Size & Wandstärke: Jede AM-Maschinen- und Materialkombination hat Grenzen für die kleinsten Merkmale und dünnsten Wände, die sie zuverlässig herstellen kann (oft um 0,3-0,5 mm, variiert aber). Designs müssen diese Grenzen berücksichtigen. Dünne Wände sind für das Gewicht wünschenswert, müssen aber strukturell solide und herstellbar sein.
- Überhänge und Stützstrukturen: Merkmale, die in einem bestimmten Winkel relativ zur Bauplatte liegen (typischerweise <45 Grad für viele Metall-LPBF-Verfahren), erfordern Stützstrukturen, um ein Zusammenbrechen während des Druckens zu verhindern. Stützen verbrauchen zusätzliches Material, erhöhen die Druckzeit, erfordern Aufwand für die Entfernung (ein wesentlicher Kostentreiber) und können die Oberfläche beschädigen. DfAM beinhaltet:
- Selbsttragende Winkel entwerfen: Ausrichten von Merkmalen oder Verwenden von Fasen/Hohlkehlen, um den kritischen Überhangwinkel wann immer möglich zu überschreiten.
- Optimierung der Teileausrichtung: Wählen einer Bauausrichtung, die das Volumen der erforderlichen Stützen minimiert, selbst wenn dies die Bauzeit oder die Oberflächenbeschaffenheit auf bestimmten Flächen geringfügig beeinträchtigt.
- Konstruktion für die Stützenentfernung: Sicherstellen, dass die Stützen für die manuelle oder maschinelle Entfernung zugänglich sind. Interne Stützen in komplexen Kanälen können besonders schwierig oder unmöglich zu entfernen sein, was Designänderungen (z. B. rauten- oder tropfenförmige Kanäle, die selbsttragend sind) erforderlich macht.
- Entfernung von Puder: Für Teile mit internen Kanälen oder Hohlräumen ist die vollständige Entfernung von ungeschmolzenem Pulver nach dem Drucken von entscheidender Bedeutung. Designs sollten strategisch platzierte Ablass-/Zugangslöcher enthalten und Geometrien vermeiden, die Pulver einschließen. Glatte Innenflächen erleichtern die Entfernung.
- Reststress-Management: AM beinhaltet schnelles Erhitzen und Abkühlen, was zu inneren Spannungen führt. Während Prozessparameter und Nachbehandlungswärmebehandlungen dies angehen, können Designentscheidungen (z. B. Vermeidung großer Massen, die durch dünne Abschnitte verbunden sind, Verwendung großzügiger Hohlkehlen) dazu beitragen, die Spannungskonzentration und potenzielles Verziehen oder Reißen zu mildern. Simulationstools können den Spannungsaufbau vorhersagen und Designanpassungen informieren.
- Merkmal Integration: Konsolidieren Sie Teile, indem Sie Merkmale direkt in das AM-Design integrieren.
- Befestigungspunkte: Drucken Sie Ansätze, Gewindelöcher (können Nachbearbeitung/Einsätze erfordern) und Ausrichtungsmerkmale direkt.
- Anschlüsse: Integrieren Sie Anschlüsse für Flüssigkeits- oder elektrische Anschlüsse.
- Versteifungsrippen: Fügen Sie strategisch platzierte Rippen für die strukturelle Integrität hinzu, ohne übermäßiges Gewicht hinzuzufügen.
Die frühzeitige Zusammenarbeit mit einem erfahrenen AM-Partner wie Met3dp in der Designphase ist von entscheidender Bedeutung. Ihr Verständnis der spezifischen Metall-3D-Druckverfahren wie SEBM und LPBF, Materialverhalten (AlSi10Mg, CuCrZr) und die Nuancen von DfAM können helfen, B2B-Kunden ihre Wärmeableitungstafeln für Satelliten hinsichtlich Herstellbarkeit, Leistung und Wirtschaftlichkeit zu optimieren. Dieser kollaborative Ansatz stellt sicher, dass das endgültige Design die AM-Fähigkeiten voll ausschöpft und gleichzeitig seine Einschränkungen berücksichtigt.
Toleranz, Oberflächenbeschaffenheit und Maßgenauigkeit in der Metall-AM
Die Erzielung der erforderlichen Präzision ist für Luft- und Raumfahrtkomponenten nicht verhandelbar. Während die Metall-AM eine unglaubliche geometrische Freiheit bietet, ist das Verständnis der erreichbaren Toleranz-, Oberflächenbeschaffenheits- und Gesamtmaßgenauigkeitsniveaus entscheidend, um die Erwartungen zu steuern und sicherzustellen, dass Teile die strengen Anforderungen der Satellitenintegration erfüllen. Diese Faktoren werden durch das gewählte AM-Verfahren, das Material, die Teilegeometrie, die Maschinenkalibrierung und die Nachbearbeitungsschritte beeinflusst. Beschaffung in der Luft- und Raumfahrt Teams müssen diese Anforderungen klar angeben und mit fähigen zusammenarbeiten Präzisionsmetallkomponentenlieferanten.
Maßgenauigkeit und Toleranzen:
- Typische erreichbare Toleranzen: Metall-AM-Verfahren wie Laser Powder Bed Fusion (LPBF) und Selective Electron Beam Melting (SEBM) können typischerweise Maßgenauigkeiten im Bereich von:
- ±0,1 bis ±0,2 mm für kleinere Abmessungen (z. B. < 100 mm).
- ±0,1 % bis ±0,2 % für größere Abmessungen.
- Dies sind allgemeine Richtlinien; engere Toleranzen können manchmal auf bestimmten Merkmalen mit sorgfältiger Prozesskontrolle und -optimierung erreicht werden, während komplexe Geometrien oder große Teile geringfügig größere Abweichungen aufweisen können. Der Fokus von Met3dp auf branchenführende Geräte und Prozesskontrolle zielt darauf ab, hohe Genauigkeit und Zuverlässigkeit zu liefern.
- Faktoren, die die Genauigkeit beeinflussen:
- Kalibrierung der Maschine: Eine regelmäßige und präzise Kalibrierung der Laser/Elektronenstrahlen, des Scansystems und der Z-Achsen-Bewegung des Druckers ist von grundlegender Bedeutung.
- Thermische Effekte: Das schnelle Erhitzen und Abkühlen, das der AM innewohnt, verursacht Ausdehnung und Kontraktion. Restspannungen können sich aufbauen, was möglicherweise zu Verziehen oder Verformungen führt, insbesondere bei großen oder geometrisch komplexen Teilen. Dies ist eine Hauptursache für Maßabweichungen. SEBM, das oft bei erhöhten Kammertemperaturen durchgeführt wird (wie von Met3dp für relevante Materialien verwendet), kann dazu beitragen, Restspannungen im Vergleich zu einigen LPBF-Verfahren zu reduzieren.
- Materialeigenschaften: Verschiedene Legierungen haben unterschiedliche Schrumpfungsraten und Wärmeleitfähigkeiten, die das Erstarrungsverhalten und die endgültigen Abmessungen beeinflussen.
- Geometrie und Größe des Teils: Große, sperrige Teile oder solche mit signifikanten Querschnittsvariationen sind anfälliger für thermische Verformungen. Innere Spannungen können sich je nach Form unterschiedlich akkumulieren.
- Scan-Strategie: Das Muster, das der Laser/Elektronenstrahl zum Schmelzen der Pulverschichten verwendet, beeinflusst die thermische Historie und die resultierende Mikrostruktur und die Spannungen.
- Unterstützende Strukturen: Stützen helfen, das Teil zu verankern und Wärme abzuleiten, was sich auf die Genauigkeit auswirkt, aber ihre Entfernung kann auch die endgültigen Abmessungen geringfügig beeinflussen.
- Enge Toleranzen einhalten: Für kritische Schnittstellen, Befestigungspunkte oder Passflächen, die engere Toleranzen als die Standard-AM-Fähigkeiten erfordern, wird typischerweise die CNC-Nachbearbeitung eingesetzt. Dies kombiniert die geometrische Freiheit der AM mit der hohen Präzision der subtraktiven Bearbeitung.
Oberflächengüte (Rauhigkeit):
- Oberflächenrauhigkeit (Ra) im Ist-Zustand: Die Oberflächenbeschaffenheit von Teilen direkt aus der AM-Maschine ist naturgemäß rauer als bearbeitete Oberflächen. Typische Ra-Werte hängen stark ab von:
- Prozess: LPBF erzeugt im Allgemeinen etwas glattere Oberflächen als SEBM aufgrund feinerer Pulvergrößen.
- Material: Pulvereigenschaften beeinflussen das Schmelzbadverhalten und die Oberflächenstruktur.
- Orientierung: Oberflächen parallel zur Bauplatte (nach oben gerichtet) sind tendenziell glatter als vertikale Wände, die glatter sind als nach unten gerichtete Oberflächen oder solche, die Stützstrukturen erfordern. Nach unten gerichtete Oberflächen weisen aufgrund der daran haftenden, teilweise geschmolzenen Pulverpartikel oft die höchste Rauheit auf.
- Parameter: Schichtdicke, Strahlleistung, Scangeschwindigkeit spielen alle eine Rolle.
- Typische Ra-Werte: As-built Ra für Metall-AM liegt oft im Bereich von 5 μm bis 25 μm (200 μin bis 1000 μin), dies kann jedoch erheblich variieren.
- Einfluss der Oberflächenbeschaffenheit:
- Thermische Strahlung: Die Oberflächenbeschaffenheit, insbesondere nach dem Beschichten, wirkt sich erheblich auf den Emissionsgrad und das Absorptionsvermögen von Radiatorplatten aus. Während die intrinsische Materialrauheit den Beschichtungseigenschaften nachgeordnet sein kann, ist eine kontrollierte Oberfläche für eine gleichmäßige Beschichtungshaftung und -leistung erforderlich.
- Fluid Flow: Für interne Kanäle in flüssigkeitsgekühlten Tafeln oder Wärmerohren können raue Oberflächen den Druckabfall erhöhen und möglicherweise die Wärmeübergangskoeffizienten beeinflussen.
- Montage: Raue Oberflächen an Passflächen können die Passung und den Wärmekontaktwiderstand beeinflussen.
- Erreichen der gewünschten Oberflächengüte: Wenn die As-built-Rauheit unzureichend ist, werden verschiedene Nachbearbeitungstechniken eingesetzt:
- Abrasives Strahlen (Perlen-/Sandstrahlen): Bietet eine gleichmäßige matte Oberfläche, die effektiv zum Entfernen von teilweise gesinterten Partikeln und zur Verbesserung des kosmetischen Aussehens ist. Ra-Werte verbessern sich typischerweise auf den Bereich von 3−10 μm.
- Taumeln/Gleitschleifen: Verwendet Schleifmittel in einer Trommel oder Vibrationsschale, um Oberflächen zu glätten und Kanten zu entgraten, besonders effektiv für Chargen kleinerer Teile.
- Polieren (manuell oder automatisiert): Kann sehr glatte, spiegelähnliche Oberflächen erzielen (Ra < 0,8 μm oder besser), ist aber oft arbeitsintensiv oder erfordert komplexe Roboteraufbauten, insbesondere für komplexe Formen.
- Chemisches Ätzen/Elektropolieren: Kann Oberflächen glätten, insbesondere komplexe interne Kanäle, erfordert aber sorgfältige Kontrolle und Materialverträglichkeit.
- CNC-Bearbeitung: Wird für bestimmte Oberflächen verwendet, die eine hohe Glätte und enge Toleranzen erfordern.
Das Engagement von Met3dp für Präzision:
Die Erzielung einer gleichmäßigen Maßgenauigkeit und vorhersehbaren Oberflächenbeschaffenheit erfordert eine strenge Prozesskontrolle und fortschrittliche Ausrüstung. Met3dp verwendet branchenführende Drucksysteme, möglicherweise einschließlich der hochpräzisen SEBM-Technologie, die für die Herstellung von Teilen mit geringen Restspannungen und guter Genauigkeit in geeigneten Materialien bekannt ist. Gepaart mit ihrem Fachwissen in der Pulverqualitätskontrolle und optimierten Bauparametern ist Met3dp bestrebt, Teile zu liefern, die den anspruchsvollen Spezifikationen der Luft- und Raumfahrtindustrie entsprechen. Sie verstehen, wie wichtig es ist, eng mit zusammenzuarbeiten B2B-Kunden zur Definition erreichbarer Toleranzen und Oberflächengüten, unter Einbeziehung der notwendigen Nachbearbeitungsschritte, um die Konformität für missionskritische Satellitenkomponenten zu gewährleisten. Bei der Bewertung AM-Dienstleister, die für Beschaffungsteams unerlässlich ist, um sich nach ihren Qualitätsmanagementsystemen, Maschinenfähigkeiten und der Erfolgsbilanz bei Präzisionsbauteilen für die Luft- und Raumfahrt zu erkundigen.
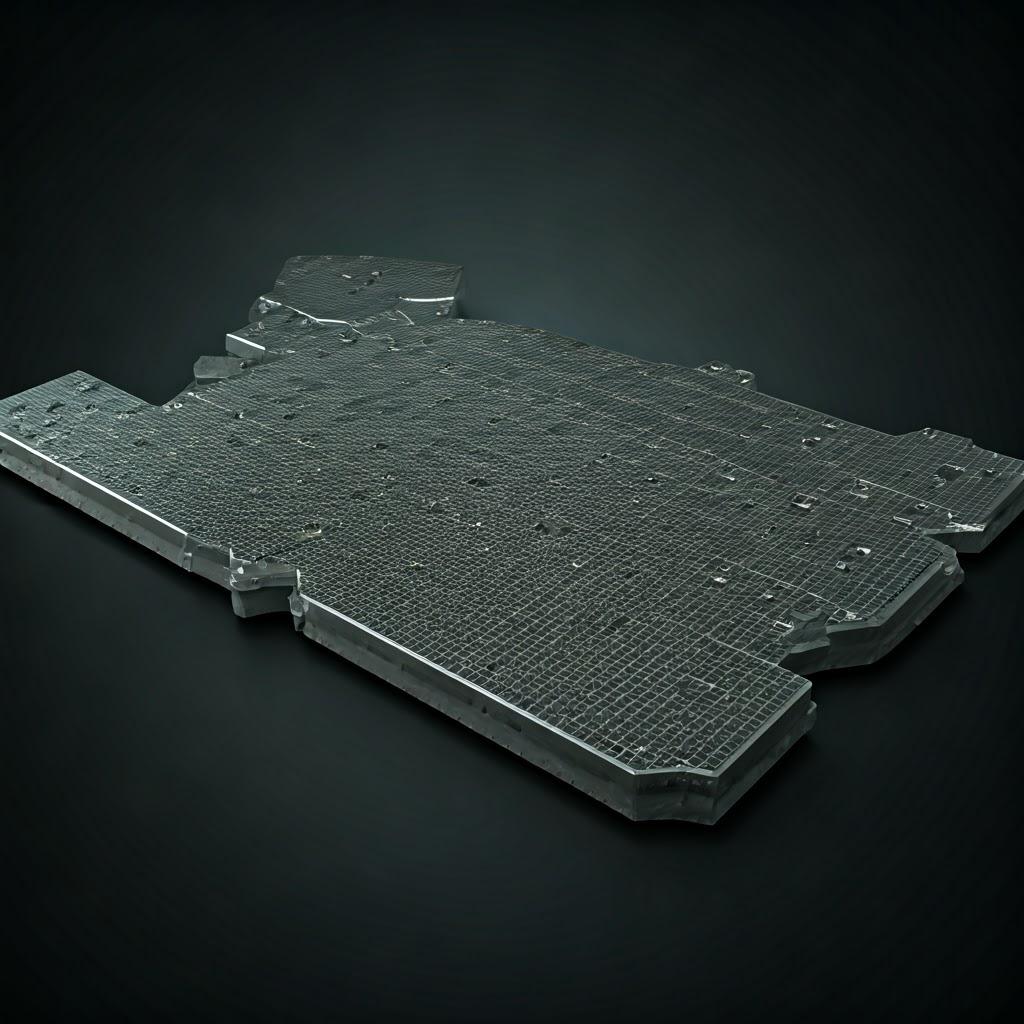
Nachbearbeitungsanforderungen für AM-Satellitenplatten
Ein weit verbreitetes Missverständnis über die additive Fertigung von Metallen ist, dass Teile aus der Maschine einsatzbereit herauskommen. In Wirklichkeit ist der Druckprozess insbesondere bei anspruchsvollen Anwendungen wie der Luft- und Raumfahrt oft nur der erste wichtige Schritt. Eine Reihe entscheidender Nachbearbeitungsschritte sind in der Regel erforderlich, um das gebaute Teil in eine funktionale, zuverlässige Wärmeableitungsplatte für Satelliten zu verwandeln, die alle Leistungs-, Qualitäts- und Integrationsspezifikationen erfüllt. Diese Schritte erhöhen die Kosten und den Zeitaufwand, sind aber unerlässlich, um die Integrität und Funktionalität der Komponente in der rauen Umgebung des Weltraums zu gewährleisten. Großserienproduktion von AM Die Planung muss diese wesentlichen Phasen berücksichtigen.
Wesentliche Nachbearbeitungsschritte:
- Entpudern: Sorgfältiges Entfernen des gesamten ungeschmolzenen Metallpulvers aus der Baukammer und, was entscheidend ist, aus dem Teil selbst. Dies umfasst loses Pulver auf Oberflächen und eingeschlossenes Pulver in internen Kanälen oder komplexen Gitterstrukturen. Zu den Methoden gehören Bürsten, Absaugen, Strahlreinigen, sowie spezielle Vibrations- oder Spülsysteme für interne Geometrien. Eine unvollständige Pulverentfernung kann die Leistung beeinträchtigen, das Gewicht erhöhen und Risiken bergen, wenn sich Partikel während des Betriebs lösen. Design für die Pulverentfernung (Zugangsöffnungen, glatte Kanäle) ist unerlässlich.
- Stressabbau: Gebaute Metall-AM-Teile enthalten erhebliche Eigenspannungen aufgrund der schnellen Heiz- und Kühlzyklen. Eine spannungsarme Wärmebehandlung, die durchgeführt wird, während das Teil möglicherweise noch an der Bauplatte befestigt ist, ist oft der erste thermische Schritt. Dies beinhaltet das Erhitzen des Teils auf eine bestimmte Temperatur (unterhalb kritischer Transformationspunkte), das Halten für einen bestimmten Zeitraum und anschließendes langsames Abkühlen. Dies reduziert die inneren Spannungen, minimiert das Verformungsrisiko während der anschließenden Entfernung von der Bauplatte oder während der Bearbeitung und verhindert vorzeitiges Versagen unter Last. Spezifische Zyklen hängen von der Legierung ab (z. B. AlSi10Mg vs. CuCrZr).
- Entnahme von der Bauplatte: Trennen des/der gedruckten Teils/Teile von der Metallbauplatte, an die es/sie verschmolzen wurde/n. Dies geschieht typischerweise mit Draht-Funkenerosion (EDM) oder einer Bandsäge. Es ist darauf zu achten, das Teil nicht zu beschädigen.
- Entfernung der Stützstruktur: Entfernen der während des Bauprozesses erforderlichen Stützstrukturen. Dies kann ein arbeitsintensiver Schritt sein, abhängig von der Komplexität und Zugänglichkeit der Stützen.
- Manuelle Entfernung: Abbrechen oder Abschneiden von Stützen mit Handwerkzeugen. Geeignet für leicht zugängliche Strukturen.
- Bearbeitungen: Verwendung von CNC-Fräsen oder -Schleifen zum Entfernen von Stützen, besonders nützlich, um eine saubere Oberflächengüte an den Stützpunkten zu erzielen.
- Drahterodieren: Kann manchmal für eine präzise Entfernung in engen Bereichen verwendet werden.
- Designauswirkungen: Die Minimierung des Bedarfs an Stützen durch DfAM reduziert diesen Aufwand und diese Kosten erheblich.
- Lösungsglühen und Auslagern (Wärmebehandlung): Über die Spannungsarmglühung hinaus sind oft weitere Wärmebehandlungen erforderlich, um die gewünschten endgültigen Materialeigenschaften (Festigkeit, Duktilität, Härte, Wärmeleitfähigkeit) zu erzielen.
- AlSi10Mg: Unterliegt typischerweise einem T6-Zyklus, der eine Lösungsbehandlung (Erhitzen zum Auflösen von Ausscheidungen), Abschrecken (schnelles Abkühlen) und künstliches Auslagern (Wiedererhitzen auf eine niedrigere Temperatur, um Festigungsphasen auszuscheiden) beinhaltet. Dies verbessert die mechanische Festigkeit erheblich.
- CuCrZr: Erfordert eine Lösungsbehandlung, gefolgt von einer Auslagerung, um die Chrom- und Zirkoniumausscheidungen zu entwickeln, die ihre Festigkeit verleihen und gleichzeitig die hohe Leitfähigkeit weitgehend erhalten.
- Prozesskontrolle: Eine genaue Ofensteuerung, geeignete Atmosphären (inert oder Vakuum zur Verhinderung von Oxidation) und ein präzises Timing sind entscheidend für eine erfolgreiche Wärmebehandlung. Dies erfordert spezielle Ausrüstung und Fachwissen, das oft bei erfahrenen Zulieferer der Luft- und Raumfahrtindustrie oder dedizierten B2B-Wärmebehandlungsdienstleistern zu finden ist..
- Oberflächenveredelung: Wie bereits erwähnt, erfordert das Erreichen der erforderlichen Oberflächenglätte (Ra) oft zusätzliche Schritte über die grundlegende Pulverentfernung hinaus.
- Abrasivstrahlen: Gemeinsam für ein einheitliches, mattes Finish.
- Taumeln/Gleitschleifen: Für glattere Oberflächen und zum Entgraten, geeignet für die Chargenverarbeitung.
- Polieren: Für sehr niedrige Ra-Anforderungen auf bestimmten Oberflächen.
- Chemisches/Elektropolieren: Zum Glätten komplexer interner oder externer Oberflächen.
- CNC-Bearbeitung: Für kritische Abmessungen, Toleranzen und Oberflächengüten, die durch AM allein nicht erreicht werden können. Dies beinhaltet:
- Steckverbindungen: Sicherstellung flacher, glatter Oberflächen für die Montage von Elektronik oder die Integration mit anderen Strukturen, wodurch der thermische Kontaktwiderstand minimiert wird.
- Gewindebohrungen: Erstellen präziser Gewinde für Befestigungselemente (oft unter Verwendung von Gewindeeinsätzen wie Helicoils für weichere Legierungen wie Aluminium).
- Versiegeln von Oberflächen: Erreichen der erforderlichen Glätte und Ebenheit für Flüssigkeits- oder Vakuumdichtungen.
- Präzise Durchmesser/Bohrungen: Bearbeiten von Löchern oder Merkmalen gemäß engen Toleranzanforderungen.
- Thermisch kontrollierte Beschichtungen: Satellitenradiatoroberflächen werden fast immer beschichtet, um ihre thermooptischen Eigenschaften anzupassen.
- Zweck: Erzielen einer hohen thermischen Emissionsfähigkeit (effiziente Wärmeabstrahlung, typischerweise > 0,85) und einer geringen Sonnenabsorption (Minimierung des Wärmegewinns durch die Sonne, typischerweise < 0,2).
- Gemeinsame Beschichtungen: Spezialisierte weiße Farben (z. B. Polyurethan- oder Silikonbasis mit Pigmenten wie AZ-93), versilbertes Teflon (Optical Solar Reflectors – OSRs) oder möglicherweise neuere Technologien wie nanostrukturierte Oberflächen.
- Anwendung: Erfordert spezielle Reinigungs- und Beschichtungsverfahren, die in kontrollierten Umgebungen durchgeführt werden, um die Haftung und die Lebensdauer im Weltraum zu gewährleisten. Erfordert die Zusammenarbeit mit qualifizierten Lieferanten von thermischen Satellitenbeschichtungen.
- Reinigung: Endgültige Reinigungsverfahren, um sicherzustellen, dass das Teil vor der Integration frei von Verunreinigungen (Öle, Rückstände von Handhabung oder Bearbeitung, lose Partikel) ist.
- Zerstörungsfreie Prüfung (NDT) und Inspektion: Eine strenge Inspektion ist für Luft- und Raumfahrtkomponenten obligatorisch, um die Integrität und Qualität zu gewährleisten.
- Prüfung der Abmessungen: Verwendung von Koordinatenmessmaschinen (CMM), 3D-Scannen oder herkömmlichen Messtechniken zur Überprüfung von Abmessungen und Toleranzen.
- Inspektion der inneren Struktur: Die Röntgen-Computertomographie (CT-Scannen) ist für AM-Teile von unschätzbarem Wert und ermöglicht die Visualisierung interner Geometrien (Kanäle, Gitter), die Erkennung interner Defekte (Porosität, Einschlüsse) und die Überprüfung der Pulverentfernung.
- Inspektion von Oberflächendefekten: Sichtprüfung, Farbstoff-Eindringprüfung (DPI) oder Magnetpulverprüfung (MPI, für ferromagnetische Materialien) zur Erkennung von Oberflächenrissen oder -fehlern.
- Dichtheitsprüfung: Für Platten mit Flüssigkeitskanälen oder Wärmerohren gewährleistet eine Druckprüfung oder Heliumleckprüfung die Integrität.
- Materialverifizierung: Möglicherweise ist eine positive Materialidentifizierung (PMI) oder eine andere Materialprüfung erforderlich.
Integrierte Lösungen:
Die Verwaltung dieser komplexen Kette von Nachbearbeitungsschritten erfordert erhebliche logistische Koordination und technisches Fachwissen. Einige B2B-Dienstleister für additive Fertigungwie möglicherweise Met3dp oder deren enge Partner, bieten möglicherweise vertikal integrierte Lösungen an, die viele dieser Schritte intern oder über ein Netzwerk qualifizierter Großhandelspartner für die Nachbearbeitungverwalten. Dies vereinfacht die Lieferkette für den Kunden und gewährleistet Rechenschaftspflicht und einen optimierten Arbeitsablauf von der ersten Designberatung bis zur endgültigen, inspizierten und beschichteten Teilelieferung. Bei der Auswahl eines AM-Partners ist das Verständnis seiner Nachbearbeitungsmöglichkeiten und seines Qualitätsmanagementsystems genauso wichtig wie seine Drucktechnologie.
Häufige Herausforderungen bei AM für Wärmeableitungsplatten und wie man sie vermeidet
Während die additive Fertigung von Metallen ein transformatives Potenzial für Satellitenkomponenten bietet, ist sie nicht ohne ihre Herausforderungen. Das Bewusstsein für potenzielle Probleme und die Umsetzung von Minderungsstrategien während des Designs, der Simulation, des Drucks und der Nachbearbeitung ist entscheidend für erfolgreiche Ergebnisse, insbesondere angesichts der hohen Einsätze von Luft- und Raumfahrtanwendungen. Die Zusammenarbeit mit einem erfahrenen AM-Lieferant wie Met3dp, der diese Herausforderungen versteht und über die Technologie und das Fachwissen verfügt, um sie zu meistern, ist von entscheidender Bedeutung.
Zentrale Herausforderungen und Strategien zur Abhilfe:
- Verformung und Verzerrung (Eigenspannung):
- Herausforderung: Das schnelle, lokalisierte Erhitzen und Abkühlen während der AM erzeugt erhebliche Temperaturgradienten, die zu inneren Spannungen innerhalb des Teils führen. Wenn sich diese Spannungen Schicht für Schicht aufbauen, können sie dazu führen, dass sich das Teil verzieht, verformt oder sich sogar von der Bauplatte löst, wodurch die Maßgenauigkeit beeinträchtigt wird. Dies ist besonders bei großen Teilen oder Designs mit unterschiedlichen Querschnitten verbreitet.
- Milderung:
- Simulation: Verwenden Sie Prozesssimulationssoftware, um Temperaturgradienten und Spannungsansammlungen basierend auf der Teilegeometrie und der Scanstrategie vorherzusagen. Ändern Sie das Design, die Ausrichtung oder die Stützstrukturen proaktiv.
- Optimierte Unterstützungsstrukturen: Entwerfen Sie robuste Stützen, um das Teil sicher an der Bauplatte zu verankern und die Wärme abzuleiten, wodurch Verformungen minimiert werden.
- Build Plate Heating: Das Vorheizen der Bauplatte (in vielen LPBF-Maschinen üblich und bei höheren Temperaturen in SEBM Standard) reduziert Temperaturgradienten zwischen dem verfestigten Material und der neuen Schicht, wodurch die Eigenspannung deutlich reduziert wird. Met3dps potenzieller Einsatz von SEBM nutzt diesen Vorteil.
- Optimierte Scan-Strategien: Verwenden Sie bestimmte Scanmuster (z. B. Inselscannen, abwechselnde Schrägstrichrichtungen), um die Wärmezufuhr gleichmäßiger zu verteilen und den Spannungsaufbau zu reduzieren.
- Stressabbau Wärmebehandlung: Die Durchführung eines Spannungsarmzyklus unmittelbar nach dem Drucken (oft bevor das Teil von der Bauplatte entfernt wird) ist entscheidend, um innere Spannungen abzubauen.
- Unvollständige Entfernung des Pulvers:
- Herausforderung: Ungeschmolzenes Pulver kann in komplizierten internen Kanälen, komplexen Gitterstrukturen oder kleinen Hohlräumen eingeschlossen werden. Wenn es nicht vollständig entfernt wird, erhöht dies die unerwünschte Masse, kann den Flüssigkeitsfluss oder die Wärmeübertragung behindern und sich möglicherweise während des Betriebs lösen, wodurch eine Kontamination oder Beschädigung verursacht wird.
- Milderung:
- DfAM für die Pulverentfernung: Entwerfen Sie interne Kanäle mit glatten Pfaden, ausreichenden Durchmessern und strategisch platzierten Ablass-/Zugangsöffnungen. Vermeiden Sie Sackgassenhohlräume. Tropfen- oder Diamantkanalquerschnitte können selbsttragend sein und leichter zu reinigen als einfache kreisförmige.
- Optimierte Ausrichtung: Richten Sie das Teil auf der Bauplatte so aus, dass die Pulverableitung nach dem Bau erleichtert wird.
- Gründliche Nachbearbeitung: Verwenden Sie strenge Entpulverungstechniken (Vibration, Druckluft/Inertgasblasen, möglicherweise Ultraschallreinigung oder Spülen für bestimmte Designs).
- Inspektion: Verwenden Sie CT-Scannen oder Boreskope, um die vollständige Pulverentfernung aus kritischen inneren Durchgängen zu überprüfen.
- Porosität:
- Herausforderung: Kleine Hohlräume oder Poren innerhalb des gedruckten Materials können als Spannungskonzentratoren wirken, wodurch die mechanische Festigkeit und die Ermüdungslebensdauer verringert und möglicherweise die Dichtheit beeinträchtigt wird. Porosität kann durch Gas entstehen, das im Pulver oder Schmelzbad eingeschlossen ist (Gasporosität), oder durch unvollständiges Schmelzen zwischen Schichten oder Scanpfaden (Mangel an Fusionsporosität).
- Milderung:
- Hochwertiges Pulver: Verwenden Sie Pulver mit hoher Sphärizität, geringem inneren Gasgehalt, kontrollierter Partikelgrößenverteilung und geringer Satellitenpräsenz. Met3dps Fokus auf die fortschrittliche Pulverherstellung unter Verwendung von Gaszerstäubung und PREP geht dies direkt an und gewährleistet optimale Pulvereigenschaften. Die Beschaffung von einem zuverlässigen B2B-Metallpulververtrieb mit strenger Qualitätskontrolle ist unerlässlich.
- Optimierte Prozessparameter: Die Feinabstimmung der Laser-/Elektronenstrahlleistung, der Scangeschwindigkeit, der Schichtdicke und des Schrägabstands ist entscheidend, um ein vollständiges Schmelzen und Verschmelzen zu gewährleisten. Die Parameterentwicklung ist der Schlüssel für jede spezifische Legierung und Maschine.
- Kontrollierte Atmosphäre: Die Verarbeitung in einer hochreinen Inertgasumgebung (LPBF) oder Vakuum (SEBM, wie von Met3dp verwendet) minimiert die Sauerstoffaufnahme und reduziert die Gasporosität.
- Heiß-Isostatisches Pressen (HIP): Für Anwendungen, die maximale Dichte und Ermüdungslebensdauer erfordern (obwohl dies möglicherweise Kosten und Komplexität erhöht), kann HIP als Nachbearbeitungsschritt verwendet werden, um innere Poren durch hohen Druck und hohe Temperatur zu schließen.
- ZFP: Verwenden Sie CT-Scannen, um die innere Porosität zu erkennen und zu quantifizieren.
- Knacken:
- Herausforderung: Einige Legierungen, insbesondere bestimmte Aluminium- oder Nickel-Superlegierungen, können während der schnellen Heiz-/Kühlzyklen von AM anfällig für Erstarrungsrisse oder Verflüssigungsrisse sein, insbesondere unter hohen Eigenspannungsbedingungen.
- Milderung:
- Auswahl der Legierung: Wählen Sie Legierungen, von denen bekannt ist, dass sie gut schweißbar/bedruckbar sind (AlSi10Mg ist im Allgemeinen gut; einige andere Al-Legierungen können schwieriger sein).
- Optimierung der Parameter: Durch Anpassen der Parameter (z. B. Vorheizen, Scanstrategie) kann die thermische Historie geändert werden, um die Rissneigung zu verringern.
- Spannungsmanagement: Die Umsetzung wirksamer Spannungsreduzierungstechniken (Bauplattenheizung, Stützen, Spannungsarmglühen) ist entscheidend.
- Entwurf: Vermeiden Sie scharfe Ecken oder abrupte Geometrieänderungen, die als Spannungskonzentratoren wirken.
- Erreichen von Dichtheit:
- Herausforderung: Bei Wärmeableitungsplatten mit Flüssigkeitskanälen oder Heatpipes ist die Gewährleistung der vollständigen Dichtheit
- Milderung:
- Robuste Prozesskontrolle: Sicherstellung eines dichten, fehlerfreien Drucks durch Pulverqualität, optimierte Parameter und kontrollierte Atmosphäre.
- Angemessenes Design: Sicherstellung einer ausreichenden Wandstärke für Kanäle.
- Nachbearbeiten: HIP kann helfen, potenzielle Leckpfade zu schließen. Eine sorgfältige Bearbeitung der Dichtflächen ist erforderlich.
- Strenge Tests: Durchführung gründlicher Lecktests (z. B. Druckabfalltest, Helium-Massenspektrometrie) als Teil des Qualitätssicherungsprotokolls.
- Kontrolle der Oberflächengüte:
- Herausforderung: Die Erzielung der spezifischen Oberflächengüte, die für thermische Strahlung, Fluiddynamik oder Baugruppenschnittstellen erforderlich ist, kann aufgrund der inhärenten Rauheit direkt aus dem AM-Prozess schwierig sein.
- Milderung:
- Verstehen der As-Built-Grenzen: Erkennen Sie den typischen Ra-Wert, der für den Prozess und das Material erreichbar ist, und planen Sie entsprechend.
- Gezielte Nachbearbeitung: Planen Sie notwendige Oberflächenbearbeitungsschritte (Strahlen, Polieren, Bearbeiten) auf kritischen Oberflächen als Teil des Fertigungs-Workflows. Budgetieren und planen Sie entsprechend.
Die erfolgreiche Bewältigung dieser Herausforderungen erfordert eine Kombination aus sorgfältigem Design, Verständnis der Materialwissenschaften, präziser Prozesskontrolle, gründlicher Nachbearbeitung und strenger Qualitätssicherung. Die Zusammenarbeit mit einem erfahrenen Partner für additive Fertigung (B2B) wie Met3dp, das Fachwissen in Materialien (hochwertige Pulver), Prozessen (fortschrittliche SEBM/LPBF-Drucker) und potenziell integrierter Nachbearbeitung und Qualitätskontrolle kombiniert, bietet die beste Grundlage zur Minderung dieser Risiken und zur zuverlässigen Herstellung von Hochleistungs-Satelliten-Wärmeableitungspaneelen.
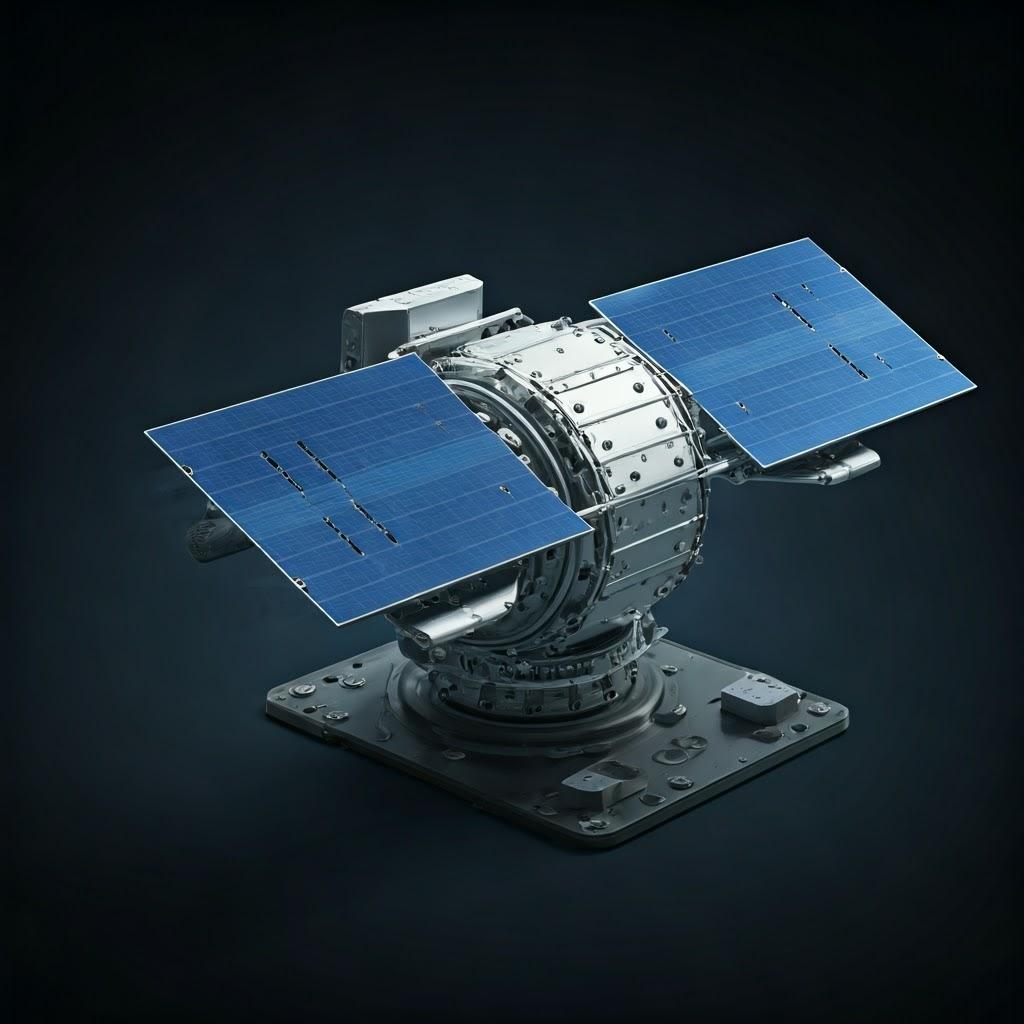
Wie man den richtigen 3D-Druckdienstleister für Luft- und Raumfahrtkomponenten aus Metall auswählt
Die Auswahl des richtigen Fertigungspartners ist immer entscheidend, aber die Einsätze sind außergewöhnlich hoch, wenn es um Luft- und Raumfahrtkomponenten geht, die mit fortschrittlichen Technologien wie der additiven Metallfertigung hergestellt werden. Die Leistungs- und Zuverlässigkeitsanforderungen von Satellitensystemen lassen keinen Raum für Fehler. Für Ingenieure und Beschaffungsmanager mit der Beschaffung von AM-Wärmeableitungspaneelen beauftragt sind, erfordert die Auswahl eines Dienstanbieters eine strenge Bewertung, die über den Preis hinausgeht. Es ist notwendig, einen echten B2B-Partner mit nachgewiesenem Fachwissen, robusten Prozessen und einem tiefen Verständnis der Anforderungen der Luft- und Raumfahrt zu finden.
Hier ist eine umfassende Checkliste, die Sie bei der Auswahl unterstützen soll, wenn Sie potenzielle metall-AM-Lieferanten für missionskritische Satellitenhardware bewerten:
1. Zertifizierungen für die Luft- und Raumfahrt und Qualitätsmanagementsystem (QMS): * AS9100-Zertifizierung: Dies ist der Goldstandard für QMS für die Luftfahrt-, Raumfahrt- und Verteidigungsindustrie. Die Zertifizierung nach AS9100 (oder gleichwertig) zeigt das Engagement eines Anbieters für Qualität, Rückverfolgbarkeit, Risikomanagement und kontinuierliche Verbesserungsprozesse, die speziell auf die Luft- und Raumfahrt zugeschnitten sind. Unverzichtbar für kritische Fluggeräte. * Robustes QMS: Bewerten Sie über das Zertifikat hinaus die Reife und Umsetzung ihres QMS. Fragen Sie nach ihrer Dokumentenkontrolle, ihren Prozesskontrollverfahren, Korrekturmaßnahmen und wie sie die Konsistenz von Charge zu Charge gewährleisten. * NADCAP-Akkreditierung: Obwohl nicht immer für die Herstellung von einfachen AM-Teilen erforderlich, kann die NADCAP-Akkreditierung (National Aerospace and Defense Contractors Accreditation Program) relevant sein, wenn der Lieferant kritische interne Spezialprozesse wie Wärmebehandlung, ZfP oder chemische Verarbeitung/Beschichtung durchführt.
2. Nachgewiesene Erfahrung und Sachkenntnis: * Erfolgsbilanz in der Luft- und Raumfahrt: Haben sie bereits erfolgreich Teile für frühere Weltraummissionen oder anspruchsvolle Luft- und Raumfahrtanwendungen hergestellt? Können sie (nicht vertrauliche) Fallstudien oder Referenzen vorlegen? Erfahrung ist von entscheidender Bedeutung, um die einzigartigen Herausforderungen der Weltraumhardware zu meistern. * Fachwissen über Werkstoffe: Verfügen sie über umfassende, nachgewiesene Erfahrung in der Verarbeitung der erforderlichen spezifischen Legierungen (z. B. AlSi10Mg, CuCrZr)? Verstehen Sie ihre Erfahrung mit der Parameterentwicklung, dem Erreichen der gewünschten Materialeigenschaften und der Behandlung potenzieller Probleme mit diesen Materialien. Fragen Sie nach ihrem Metallpulverbeschaffung – verwenden sie hochwertiges Pulver von renommierten Distributoren oder Herstellern wie Met3dp oder stellen sie sogar ihr eigenes her? * DfAM-Unterstützung: Bietet der Anbieter eine Design-for-Additive-Manufacturing-Beratung an? Können ihre Ingenieure mit Ihrem Team zusammenarbeiten, um das Design für Leistung, Herstellbarkeit und Wirtschaftlichkeit zu optimieren und die einzigartigen Vorteile von AM zu nutzen?
3. Technologische Leistungsfähigkeit und Kapazität: * Geeignete AM-Technologie: Betreiben sie die richtige Art von AM-Maschinen für Ihre Material- und Anwendungsanforderungen (z. B. LPBF für allgemeines AlSi10Mg, potenziell Hochleistungs-LPBF oder SEBM für CuCrZr)? Das potenzielle Fachwissen von Met3dp in SEBM könnte beispielsweise für bestimmte Materialien von Vorteil sein, die eine Hochtemperaturverarbeitung und geringe Restspannungen erfordern. * Maschinenpark: Wie groß und wie alt ist ihre Maschinenflotte? Verfügen sie über ausreichende Kapazität, um Ihre Projektzeitpläne zu bewältigen, einschließlich potenzieller Großaufträge oder Großserienproduktion Läufe? Wie groß ist das Bauvolumen ihrer Maschinen – können sie die Größe Ihrer Wärmeableitungspaneele aufnehmen? * Kalibrierung und Wartung von Maschinen: Wie sind ihre Verfahren zur Gewährleistung der Maschinenpräzision und -konsistenz? Regelmäßige Kalibrierung und vorbeugende Wartung sind für einen zuverlässigen Output unerlässlich.
4. Interne vs. ausgelagerte Nachbearbeitung: * Umfassende Fähigkeiten: Bietet der Anbieter die notwendigen Nachbearbeitungsschritte intern an (Spannungsarmglühen, Wärmebehandlung, Stützentfernung, grundlegende Oberflächenbearbeitung, potenziell CNC-Bearbeitung, ZfP)? Ein integrierter Workflow führt oft zu besserer Kontrolle, Verantwortlichkeit und potenziell kürzeren Vorlaufzeiten. * Verwaltetes Partnernetzwerk: Wenn sie bestimmte Schritte auslagern (z. B. Spezialbeschichtungen, erweiterte ZfP, komplexe Bearbeitung), verfügen sie über ein gut geprüftes Netzwerk qualifizierter Großhandelspartner für die Nachbearbeitung? Wie verwalten sie Qualität und Rückverfolgbarkeit in dieser Lieferkette? Verstehen Sie ihr Verfahren zur Verwaltung externer Anbieter.
5. Materialrückverfolgbarkeit und -prüfung: * Pulverkontrolle: Wie verwalten und verfolgen sie Metallpulverchargen von der Beschaffung bis zur Produktion? Vollständige Rückverfolgbarkeit ist in der Luft- und Raumfahrt unerlässlich. Fragen Sie nach ihren Pulverprüfungs- und Recyclingverfahren. Die Verwendung hochwertiger Pulver, wie sie von Met3dp unter Verwendung fortschrittlicher Zerstäubung hergestellt werden, bietet einen guten Ausgangspunkt. * Überprüfung der Materialeigenschaften: Verfügen sie über Möglichkeiten, Materialproben zu testen, die parallel zu den Teilen gedruckt werden, um zu überprüfen, ob die mechanischen Eigenschaften, die Mikrostruktur und die Dichte den Spezifikationen entsprechen?
6. Projektmanagement und Kommunikation: * Klare Kommunikation: Ist ihr Team reaktionsschnell, sachkundig und leicht zu kommunizieren? Der Aufbau einer guten Arbeitsbeziehung ist für komplexe Projekte von entscheidender Bedeutung. * Projektleitung: Verfügen sie über klare Prozesse für die Projektannahme, Statusaktualisierungen und die Verwaltung von Lieferungen?
7. Kosten und Vorlaufzeit (siehe nächster Abschnitt): * Transparente Angebote: Stellen sie detaillierte, transparente B2B-Angebote bereit, die die Kosten aufschlüsseln? * Realistische Vorlaufzeiten: Können sie zuverlässige Vorlaufzeitschätzungen auf der Grundlage der aktuellen Kapazität und Projektkomplexität liefern?
Met3dp als Ihr potenzieller Partner: Unternehmen wie Met3dp, die sich auf fortschrittliche 3D-Druck von Metall Geräte und Hochleistungs-Metallpulver spezialisiert haben, sind einzigartig positioniert. Ihre potenzielle vertikale Integration – das Verständnis der Pulverherstellung (Gaszerstäubung, PREP), des Maschinenbetriebs (potenziell SEBM und LPBF) und der Anwendungsentwicklung – bietet ein tiefes, fundamentales Verständnis der gesamten AM-Prozesskette. Berücksichtigen Sie bei der Bewertung von Partnern Lieferanten wie Met3dp, die dieses umfassende Fachwissen einbringen und sich auf die Qualitätskontrolle vom Rohmaterial bis zum fertigen Teil konzentrieren, was sie zu einem starken Kandidaten für die Herstellung von missionskritischen Satellitenkomponenten macht. Die gründliche Prüfung potenzieller Lieferanten anhand dieser Kriterien hilft sicherzustellen, dass Sie einen Partner auswählen, der in der Lage ist, die hochwertigen, zuverlässigen AM-Wärmeableitungspaneele zu liefern, die Ihre Satellitenmission erfordert.
Kostenfaktoren und Vorlaufzeit für AM-Satelliten-Wärmeableitungspaneele
Während die Leistungsvorteile von additiv gefertigten Satellitenkomponenten überzeugend sind, ist das Verständnis der damit verbundenen Kosten und typischen Vorlaufzeiten für die Projektplanung, Budgetierung und effektive B2B-Beschaffungunerlässlich. Metall-AM beinhaltet andere Kostentreiber als die traditionelle Fertigung, und die Vorlaufzeiten können je nach Komplexität und Workflow erheblich variieren. Um genaue AM-Angebote zu erhalten, ist es erforderlich, potenziellen Lieferanten.
Die wichtigsten Kostentreiber:
- Materialkosten:
- Pulver Preis: Die Kosten pro Kilogramm Metallpulver in Luft- und Raumfahrtqualität variieren erheblich je nach Legierung. Gängige Legierungen wie AlSi10Mg sind im Allgemeinen günstiger als hochleitfähige Kupferlegierungen wie CuCrZr oder spezielle Superlegierungen. Der Preis wird von den Rohstoffkosten, der Herstellungskomplexität (z. B. Zerstäubungsverfahren) und den Qualitätsspezifikationen beeinflusst. Beschaffung Metallpulver im Großhandel kann Kostenvorteile für größere Volumina bieten.
- Teilvolumen und Dichte: Das schiere Volumen des für das Teil benötigten Materials wirkt sich direkt auf die Kosten aus. Dichtere Materialien wie CuCrZr (8,9 g/cm3) kosten für das gleiche Volumen naturgemäß mehr als AlSi10Mg (2,67 g/cm3).
- Unterstützungsstruktur Volumen: Material, das für Stützstrukturen verwendet wird, erhöht ebenfalls die Kosten. Die Minimierung von Stützen durch DfAM ist der Schlüssel.
- Buy-to-Fly-Verhältnis: AM hat im Allgemeinen ein viel besseres Buy-to-Fly-Verhältnis (Verhältnis von gekauftem Rohmaterial zum Gewicht des fertigen Teils) als subtraktive Bearbeitung, wodurch Abfall reduziert wird, insbesondere bei komplexen Teilen und teuren Materialien.
- Maschinenzeit:
- Vorbereitung des Baus: Zeit, die Ingenieure mit der Einrichtung der Bauakte verbringen (Ausrichtung, Stützen, Schneiden, Parameterzuweisung) unter Verwendung spezieller Software.
- Druckzeit: Der Kernkostenfaktor, der durch das Gesamtvolumen des zu verschmelzenden Materials (Teil + Stützen) und direkter durch die Anzahl der Schichten (Teilhöhe in der Bauausrichtung) bestimmt wird. Höhere Teile dauern länger. Die Maschinenstundensätze variieren je nach Technologie (LPBF, SEBM), Größe und Ausgereiftheit des Druckers.
- Auslastung der Maschine: Die Kosten werden oft auf der Grundlage der Buchungszeit auf teuren Anlagegütern berechnet. Das effiziente Verschachteln mehrerer Teile in einem einzigen Bau kann die Maschinenzeitkosten pro Teil für Großaufträge.
- Arbeitskosten:
- Einrichten & Abrüsten: Arbeitsaufwand für die Vorbereitung der Maschine, das Laden von Pulver, die Überwachung des Baus und das Entfernen der fertigen Bauplatte und der Teile.
- Nachbearbeitungsarbeiten: Dies kann ein sehr bedeutend Kostenkomponente. Die manuelle Stützentfernung, das Entpulvern komplexer Teile, die Oberflächenbearbeitung (insbesondere manuelles Polieren), die Inspektion und die Montage (falls erforderlich) erfordern alle Arbeitsstunden von Fachkräften. Die Komplexität des Teils hat einen großen Einfluss darauf.
- Komplexität der Unterstützungsstruktur:
- Lautstärke: Mehr Stützen bedeuten mehr Materialkosten und potenziell längere Druckzeiten.
- Entfernungsschwierigkeit: Stützen in schwer zugänglichen Bereichen oder an empfindlichen Merkmalen erfordern mehr Zeit und Geschick, um sie sauber zu entfernen, ohne das Teil zu beschädigen, was die Arbeitskosten in die Höhe treibt.
- Nachbearbeitungsintensität:
- Wärmebehandlung: Kosten im Zusammenhang mit Ofenzeit, Energieverbrauch und potenziell speziellen Atmosphären (Vakuum, Inertgas). Komplexe mehrstufige Zyklen dauern länger und kosten mehr.
- CNC-Bearbeitung: Die Kosten hängen von der Anzahl der zu bearbeitenden Merkmale, den erforderlichen Toleranzen, der Oberflächengüte, der Einrichtungszeit und der Maschinenzeit ab.
- Oberflächenveredelung: Die Kosten variieren stark je nach Methode (Strahlen ist relativ kostengünstig; umfangreiches Polieren ist teuer) und dem erforderlichen endgültigen Ra-Wert.
- Beschichtung: Spezielle Wärmeschutzbeschichtungen erfordern spezifisches Fachwissen und Einrichtungen, was erhebliche Kosten verursacht.
- Qualitätssicherung und Inspektion:
- ZFP: Die Kosten für CT-Scannen, DPI, Lecktests usw. hängen von der Höhe der Inspektion ab, die von den Luft- und Raumfahrtstandards und den Projektspezifikationen gefordert wird. 100 % Inspektion ist für kritische Teile üblich.
- Prüfung der Abmessungen: CMM- oder 3D-Scannzeit und -analyse.
- Dokumentation: Zeitaufwand für die Erstellung der erforderlichen Qualitätsdokumentation und Zertifizierungen.
- Auftragsvolumen:
- Prototypen: Haben typischerweise höhere Kosten pro Teil aufgrund von Einrichtungsaufwendungen, die auf eine kleine Menge verteilt werden.
- Produktionsläufe: Größere Großaufträge ermöglichen die Abschreibung der Einrichtkosten, die potenzielle Optimierung von Bau-Layouts (Verschachtelung) und können manchmal Großhandelspreisgestaltung Strukturen, was zu geringeren Kosten pro Teil führt.
Typische Vorlaufzeiten:
Die Vorlaufzeiten für AM-Teile können stark variieren, von Tagen für einfache Prototypen bis zu vielen Wochen oder Monaten für komplexe Produktionsteile, die eine umfangreiche Nachbearbeitung und Qualifizierung erfordern.
- Prototyping: Einfache AlSi10Mg-Teile können je nach Maschinenverfügbarkeit und grundlegenden Nachbearbeitungsanforderungen in 1-3 Wochen hergestellt werden. Komplexere Prototypen oder solche, die anspruchsvolle Materialien wie CuCrZr verwenden, könnten länger dauern.
- Produktionsteile: Für qualifizierte Luft- und Raumfahrtkomponenten sind Vorlaufzeiten von 6-12 Wochen oder mehr üblich, wobei Folgendes berücksichtigt wird:
- Detaillierte Planung und potenzielle DfAM-Iteration.
- Druckzeit (kann mehrere Tage für große/komplexe Bauten dauern).
- Vollständige Nachbearbeitungskette (Wärmebehandlungen, Bearbeitung, Endbearbeitung, Beschichtung können jeweils Tage oder Wochen hinzufügen).
- Strenge ZfP- und Inspektionsverfahren.
- Wartezeiten bei der AM-Lieferant und alle externen Nachbearbeitungspartner.
- Faktoren, die die Geschwindigkeit beeinflussen: Die Teilekomplexität, die Größe, die Materialauswahl, die erforderlichen Nach
Erhalten gen
Um eine aussagekräftige additive Fertigungsangebot von einem Lieferanten wie Met3dp zu erhalten, geben Sie bitte so viele Informationen wie möglich an:
- CAD-Modell: 3D-Modell in einem Standardformat (z. B. STEP).
- 2D-Zeichnungen: Wenn spezifische Toleranzen, Oberflächenausführungen oder kritische Abmessungen über die Standard-AM-Fähigkeiten hinaus erforderlich sind.
- Spezifikation des Materials: Geben Sie eindeutig die Legierung (z. B. AlSi10Mg, CuCrZr) und alle erforderlichen Standards (z. B. AMS-Spezifikationen) an.
- Menge: Anzahl der benötigten Teile (geben Sie an, ob Prototyp oder Produktionsvolumen).
- Toleranzanforderungen: Definieren Sie kritische Maßtoleranzen.
- Anforderungen an die Oberflächenbeschaffenheit: Geben Sie die erforderlichen Ra-Werte für bestimmte Oberflächen an.
- Post-Processing-Bedarf: Detaillieren Sie alle erforderlichen Schritte (Wärmebehandlungszyklus, Bearbeitungsvorgänge, spezifische Oberflächenausführung, Beschichtungsart).
- Prüfung und Zertifizierung: Listen Sie alle erforderlichen zerstörungsfreien Prüfungen, Inspektionen und Zertifizierungsanforderungen auf (z. B. CMM-Bericht, Materialzertifikate, AS9100-Konformität).
- Gewünschtes Lieferdatum: Geben Sie Ihren gewünschten Zeitplan an.
Die Bereitstellung umfassender Informationen ermöglicht es potenziellen B2B-Lieferanten die Arbeitsumfang genau zu beurteilen und eine realistische Kosten- und Vorlaufzeitschätzung abzugeben.
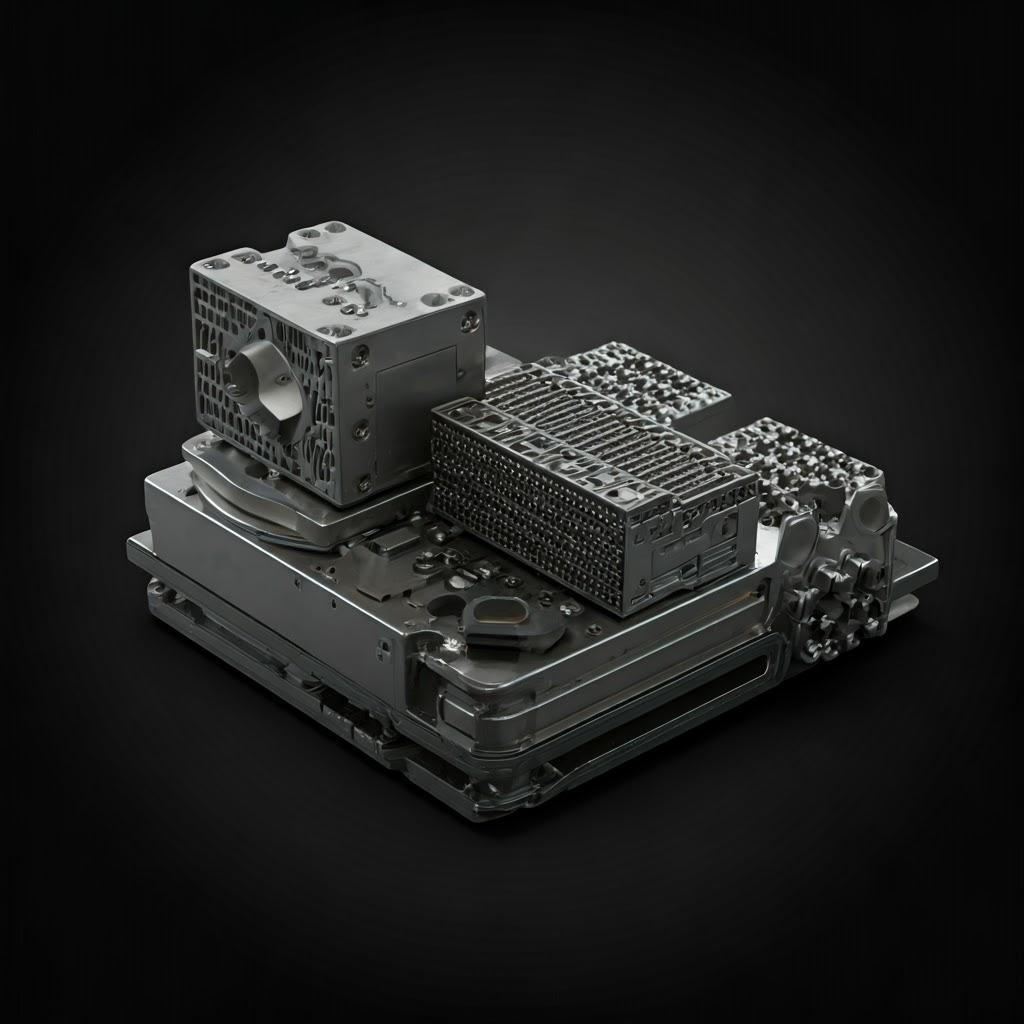
Häufig gestellte Fragen (FAQ)
Hier sind Antworten auf einige häufige Fragen, die Ingenieure und Beschaffungsmanager zur Verwendung von Metall-AM für Wärmeableitungstafeln von Satelliten haben:
F1: Was sind die primären Vorteile der Verwendung von AM für Satellitenradiatoren im Vergleich zu herkömmlichen Methoden?
- A1: Die wichtigsten Vorteile ergeben sich aus der Designfreiheit von AM:
- Verbesserte thermische Leistung: Die Fähigkeit, komplexe Geometrien wie interne Gitter oder konforme Kanäle zu erstellen, erhöht die Oberfläche für die Wärmeübertragung erheblich, was oft zu einer effizienteren Kühlung innerhalb der gleichen Volumen- oder Massenbeschränkungen im Vergleich zu einfacheren bearbeiteten oder montierten Konstruktionen führt.
- Signifikante Gewichtsreduzierung: Topologieoptimierung und Gitterstrukturen ermöglichen es, Material nur dort zu platzieren, wo es für thermische und strukturelle Anforderungen benötigt wird, wodurch die Bauteilmasse drastisch reduziert wird, was für die Senkung der Startkosten entscheidend ist.
- Teil Konsolidierung: Mehrere Komponenten (z. B. Platte, Halterungen, Verteiler) können oft zu einem einzigen, monolithischen AM-Teil kombiniert werden, wodurch die Montagekomplexität und potenzielle Fehlerpunkte (Verbindungen, Schweißnähte) reduziert und die Lieferkette vereinfacht wird.
- Schnelle Prototypenerstellung und Anpassung: AM ermöglicht schnellere Iterationen während der Designphase und eine effiziente Produktion von kundenspezifischen oder Kleinserienteilen, die auf spezifische Missionsanforderungen zugeschnitten sind, ohne die hohen Werkzeugkosten herkömmlicher Methoden.
F2: Wie vergleicht sich die thermische Leistung von AM AlSi10Mg oder CuCrZr mit herkömmlich hergestellten Teilen?
- A2: Bei korrekter Verarbeitung und geeigneten Nachbehandlungen können die Masseneigenschaften (einschließlich der Wärmeleitfähigkeit) von AM AlSi10Mg und CuCrZr sehr nahe an ihren Guss- oder Knetgegenstücken liegen. Für AlSi10Mg ist eine T6-Wärmebehandlung entscheidend für die Optimierung der Leitfähigkeit. Für CuCrZr wird durch geeignetes Lösungsglühen und Auslagern eine hohe Leitfähigkeit erreicht. Während AM-Teile im Urzustand zunächst leicht unterschiedliche Mikrostrukturen aufweisen können, zielt die Nachbearbeitung darauf ab, die Eigenschaften zu homogenisieren. Entscheidend ist, dass die Systemebene thermische Leistung einer AM-Wärmeableitungstafel oft übersteigt die von herkömmlichen Designs aufgrund der Fähigkeit, hochoptimierte Geometrien (erhöhte Oberfläche, optimierte Strömungswege) zu erstellen, die einfach nicht anders hergestellt werden können. Die durch AM ermöglichte Designfreiheit ist der wichtigste Leistungsunterschied.
F3: Nach welchen Qualitätszertifizierungen sollte ich bei einem B2B-Lieferanten von AM-Satellitenkomponenten suchen?
- A3: Die wichtigste Zertifizierung ist AS9100. Dies bedeutet, dass der Lieferant ein Qualitätsmanagementsystem betreibt, das speziell für die strengen Anforderungen der Luft-, Raumfahrt- und Verteidigungsindustrie entwickelt wurde und Aspekte wie Rückverfolgbarkeit, Risikomanagement, Prozesskontrolle und Konfigurationsmanagement abdeckt. Abhängig vom Arbeitsumfang kann eine NADCAP-Akkreditierung für spezielle Prozesse (wie Wärmebehandlung, zerstörungsfreie Prüfung, Schweißen/Hartlöten, falls zutreffend für die Montage, Beschichtungen), die im eigenen Haus durchgeführt werden, ebenfalls relevant oder vom Hauptauftragnehmer gefordert sein. ISO 9001 ist ein allgemeiner QMS-Standard, wird aber in der Regel für kritische Luft- und Raumfahrt-Hardware allein als unzureichend angesehen. Überprüfen Sie immer den Umfang und die Gültigkeit der Zertifizierungen.
F4: Kann Met3dp Großaufträge für Wärmeableitungstafeln von Satelliten abwickeln?
- A4: Met3dp positioniert sich als Anbieter sowohl von industriellen AM-Geräten als auch von hochwertigen Metallpulvern, was auf einen Fokus auf die Ermöglichung der industriellen additiven Fertigung hindeutet. Während spezifische Produktionskapazitätsdetails direkt besprochen werden müssten, sind Unternehmen wie Met3dp mit ihrer Grundlage in der AM-Technologie und den Materialien typischerweise so strukturiert, dass sie Großhandel und Großbestellung Anforderungen für B2B-Kundenunterstützen können. Es wird empfohlen, sich direkt mit Met3dp in Verbindung zu setzen, um spezifische Volumenanforderungen, Produktionsplanung und Fähigkeiten zur Skalierung von Prototypen bis zur Serienproduktion zu besprechen.
F5: Welche Informationen werden benötigt, um ein genaues Angebot für ein AM-Wärmeableitungstafelprojekt von einem Händler oder Lieferanten zu erhalten?
- A5: Um das genaueste B2B-Angebotzu erhalten, geben Sie Folgendes an:
- 3D-CAD-Modell (bevorzugt STEP-Format).
- 2D-Zeichnungen, die kritische Abmessungen, Toleranzen und Oberflächenausführungen angeben.
- Spezifiziertes Material (z. B. AlSi10Mg, CuCrZr) und alle relevanten Materialstandards.
- Erforderliche Menge (und ob es sich um Prototyping oder Produktion handelt).
- Detaillierte Nachbearbeitungsanforderungen (Wärmebehandlungszyklus, zu bearbeitende Oberflächen, erforderliche Ra-Werte, Beschichtungsspezifikationen).
- Alle erforderlichen Test-, Inspektions- (z. B. CT-Scannen, Dichtheitsprüfung) und Zertifizierungsunterlagen.
- Gewünschter Lieferzeitplan. Je mehr Details im Voraus bereitgestellt werden, desto schneller und genauer kann der Lieferant das Projekt beurteilen und ein zuverlässiges Angebot erstellen.
Fazit: Steigerung der Satellitenleistung mit fortschrittlicher Metall-AM-Wärmeableitung
Die thermischen Herausforderungen, mit denen moderne Satelliten konfrontiert sind, erfordern innovative Lösungen. Da Raumfahrzeuge immer leistungsfähiger, kompakter werden und in zunehmend anspruchsvollen Umgebungen arbeiten, ist eine effiziente und zuverlässige Wärmeableitung wichtiger denn je. Herkömmliche Fertigungsmethoden, obwohl ausgereift, haben oft Schwierigkeiten, die komplexen Geometrien und optimierten Strukturen zu liefern, die erforderlich sind, um diese eskalierenden Anforderungen innerhalb strenger Massenbudgets zu erfüllen.
Die additive Metallfertigung stellt eine grundlegende Veränderung dar und bietet beispiellose Designfreiheit, um Wärmeableitungstafeln für Satelliten zu erstellen, die leichter, effizienter und hochintegriert sind. Durch die Nutzung von Techniken wie Topologieoptimierung und Gitterstrukturen ermöglicht AM es Ingenieuren, Wärmemanagementkomponenten zu entwerfen, die zuvor auf den Bereich der Theorie beschränkt waren. Materialien wie das leichte, vielseitige AlSi10Mg und das hochleitfähige CuCrZr bieten bei der Verarbeitung mit kontrollierten AM-Techniken und geeigneter Nachbearbeitung die Materialeigenschaften, die für anspruchsvolle Weltraumanwendungen benötigt werden.
Die Nutzung des vollen Potenzials von AM erfordert jedoch mehr als nur den Zugang zu einem Drucker. Es erfordert Fachwissen in Design for Additive Manufacturing, ein tiefes Verständnis der Materialwissenschaft, präzise Prozesskontrolle, strenge Nachbearbeitungsfähigkeiten und ein unerschütterliches Engagement für die Qualitätssicherung – alles im Rahmen der Standards der Luft- und Raumfahrtindustrie. Die Wahl des richtigen Fertigungspartners, eines mit nachgewiesener Erfahrung in der Luft- und Raumfahrt, den richtigen Zertifizierungen (wie AS9100), fortschrittlichen technologischen Fähigkeiten und umfassender Unterstützung, ist von entscheidender Bedeutung für den Erfolg.
Met3dp verkörpert mit seiner Grundlage sowohl in fortschrittlichen AM-Systemen als auch in der Herstellung hochwertiger Metallpulver unter Verwendung branchenführender Techniken wie Gasverdüsung und PREP das für solche kritischen Anwendungen erforderliche Fachwissen. Ihr Fokus auf die Ermöglichung der Fertigung der nächsten Generation positioniert sie als wertvollen Partner für Luft- und Raumfahrtunternehmen, die die Grenzen der Satellitenleistung erweitern möchten.
Der Weg zur Implementierung von AM für kritische Fluggeräte beinhaltet eine sorgfältige Berücksichtigung von Design, Materialien, Toleranzen, Kosten und Lieferantenfähigkeiten. Durch die Nutzung von Metall-AM und die Zusammenarbeit mit sachkundigen Experten kann die Luft- und Raumfahrtindustrie weiterhin leistungsfähigere, zuverlässigere und kostengünstigere Satelliten entwickeln und die Leistung in der letzten Grenze wirklich steigern.
Sind Sie bereit, zu erkunden, wie die additive Metallfertigung Ihre Satelliten-Wärmemanagementsysteme revolutionieren kann? Kontaktieren Sie Met3dp noch heute, um Ihre spezifischen Anforderungen zu besprechen und zu erfahren, wie unsere umfassenden Lösungen die additiven Fertigungsziele Ihres Unternehmens unterstützen können.
Teilen auf
MET3DP Technology Co., LTD ist ein führender Anbieter von additiven Fertigungslösungen mit Hauptsitz in Qingdao, China. Unser Unternehmen ist spezialisiert auf 3D-Druckgeräte und Hochleistungsmetallpulver für industrielle Anwendungen.
Fragen Sie an, um den besten Preis und eine maßgeschneiderte Lösung für Ihr Unternehmen zu erhalten!
Verwandte Artikel
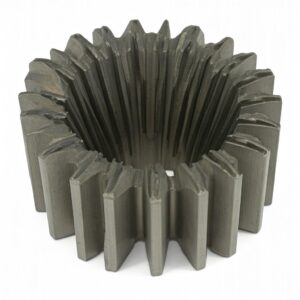
Hochleistungs-Düsenschaufelsegmente: Revolutionierung der Turbineneffizienz mit 3D-Metalldruck
Mehr lesen "Über Met3DP
Aktuelles Update
Unser Produkt
KONTAKT US
Haben Sie Fragen? Senden Sie uns jetzt eine Nachricht! Wir werden Ihre Anfrage mit einem ganzen Team nach Erhalt Ihrer Nachricht bearbeiten.
Holen Sie sich Metal3DP's
Produkt-Broschüre
Erhalten Sie die neuesten Produkte und Preislisten
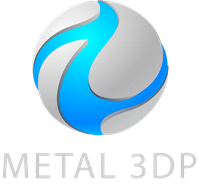
Metallpulver für 3D-Druck und additive Fertigung