Hochpräzise Instrumentenhalterung durch 3D-Metalldruck
Inhaltsübersicht
In der komplizierten Welt der Spitzentechnologie, in der Messungen die Grenzen der Physik ausreizen und Geräte unter anspruchsvollen Bedingungen arbeiten, spielt die einfache Halterung eine überraschend wichtige Rolle. Präzisionsinstrumente - ob sie nun Laser ausrichten, Sensoren in Satelliten stabilisieren, empfindliche Proben in medizinischen Scannern halten oder die Genauigkeit in Messlabors sicherstellen - sind in Bezug auf Stabilität, Ausrichtung und Betriebsintegrität vollständig auf ihre Befestigungssysteme angewiesen. Die kleinste Vibration, thermische Ausdehnung oder Fehlausrichtung kann Daten beeinträchtigen, zu Systemausfällen führen oder Ergebnisse ungültig machen. Die Herstellung dieser hochpräzisen Instrumentenhalterungen erforderte bisher eine komplexe mehrachsige CNC-Bearbeitung, oft aus massiven Knüppeln spezieller Materialien. Dieser Ansatz ist zwar effektiv, stößt aber an seine Grenzen, was die geometrische Komplexität, den Materialabfall, die Vorlaufzeiten und die Möglichkeit angeht, fortschrittliche Merkmale wie interne Kühlkanäle oder optimierte Leichtbaustrukturen zu integrieren. Der Einstieg in die additive Fertigung von Metallen (AM), allgemein bekannt als Metall 3D-Druck. Diese transformative Technologie bietet eine leistungsstarke Alternative, die die Herstellung von Instrumentenhalterungen mit beispielloser Designfreiheit, optimierten Leistungsmerkmalen und dem Potenzial für erhebliche Kosten- und Vorlaufzeiteinsparungen ermöglicht, insbesondere bei komplexen oder kleinen Produktionsserien. Dieser Beitrag taucht in die Welt der hochpräzisen Instrumentenhalterungen ein und untersucht, warum Metall-AM für Ingenieure und Beschaffungsmanager in der Luft- und Raumfahrt, im Automobilsektor, in der Medizin und in der Industrie immer mehr zur bevorzugten Lösung wird, wobei der Schwerpunkt auf Materialien wie Edelstahl 316L und der bemerkenswerten Legierung Invar mit geringer Ausdehnung liegt.
Einleitung: Die entscheidende Rolle von Präzisionsinstrumentenhalterungen in der High-Tech-Industrie
Präzisionsinstrumentenhalterungen sind weit mehr als einfache Halterungen oder Befestigungen; sie sind technische Komponenten, die für die Funktion und Zuverlässigkeit anspruchsvoller Systeme unerlässlich sind. Ihr Hauptzweck besteht darin, empfindliche Instrumente sicher zu halten, zu positionieren und ihre Ausrichtung relativ zu einem Referenzrahmen oder anderen Komponenten beizubehalten, und das oft unter schwierigen Umgebungsbedingungen. Denken Sie an das Lasersystem in einem Halbleiterfertigungswerkzeug, die optischen Komponenten in einem Satellitenteleskop, die Sensoren in einem LiDAR-System eines autonomen Fahrzeugs oder die Taster in einer Koordinatenmessmaschine (KMG). In jedem Fall muss die Halterung eine stabile, vorhersehbare und oft isolierte Plattform bieten.
Warum Stabilität und Präzision wichtig sind:
- Aufrechterhaltung der Angleichung: Optische Systeme erfordern eine Ausrichtung der Komponenten innerhalb von Mikrometern oder sogar Nanometern. Jede Abweichung oder Fehlausrichtung in den Halterungen aufgrund von Vibrationen, Stößen oder thermischen Veränderungen kann das System unbrauchbar machen. Laserpfade, Sensorausrichtungen und Probenpositionen müssen exakt bleiben.
- Schwingungsdämpfung: Viele Instrumente sind empfindlich gegenüber externen Vibrationen (von Maschinen, Akustik oder Transport). Die Halterungen müssen oft über Dämpfungseigenschaften verfügen oder aus Materialien bestehen, die die Übertragung von Schwingungen auf das Instrument von Natur aus reduzieren. Ungedämpfte Schwingungen können zu Rauschen bei den Messungen oder zu Ermüdungsbrüchen führen.
- Thermische Stabilität: Temperaturschwankungen können dazu führen, dass sich Materialien ausdehnen oder zusammenziehen. Bei Präzisionsanwendungen kann selbst eine winzige thermische Ausdehnung zu einer erheblichen Fehlausrichtung oder Belastung führen. Halterungen, insbesondere solche, die in der Optik, Messtechnik oder in der Raumfahrt eingesetzt werden, müssen oft minimale Maßänderungen über einen großen Betriebstemperaturbereich aufweisen. Dies erfordert die Verwendung spezieller Materialien mit niedrigem Wärmeausdehnungskoeffizienten (CTE).
- Strukturelle Integrität: Die Halterungen müssen stark und steif genug sein, um das Gewicht des Geräts zu tragen und allen Betriebsbelastungen (z. B. Beschleunigung in der Luft- und Raumfahrt oder in der Automobilindustrie) standzuhalten, ohne sich zu verformen. Eine Durchbiegung unter Last kann zu einer Fehlausrichtung führen.
- Umweltresistenz: Je nach Anwendung müssen die Halterungen korrosionsbeständig sein (z. B. in medizinischen oder maritimen Umgebungen), ausgasen (in Vakuum- oder Weltraumanwendungen) oder extremen Temperaturen standhalten.
Die Grenzen der traditionellen Fertigung:
Seit Jahrzehnten ist die CNC-Bearbeitung der Standard für die Herstellung hochwertiger Halterungen. Sie ist jedoch mit gewissen Herausforderungen verbunden, insbesondere wenn die Instrumente komplexer werden und die Leistungsanforderungen steigen:
- Geometrische Zwänge: Die Bearbeitung komplexer interner Merkmale, organischer Formen, die für ein optimales Verhältnis von Steifigkeit zu Gewicht optimiert sind (Topologieoptimierung), oder integrierter Funktionen wie konforme Kühlkanäle kann extrem schwierig, zeitaufwändig oder unmöglich sein. Dies führt oft zu Designs, die eher Kompromisse als optimale Lösungen darstellen.
- Materialabfälle: Die subtraktive Fertigung beginnt mit einem größeren Materialblock und entfernt das, was nicht benötigt wird. Bei teuren oder speziellen Materialien wie Invar kann dies zu erheblichem und kostspieligem Abfall führen.
- Komplexität der Montage: Die Herstellung komplexer Geometrien erfordert häufig die Bearbeitung mehrerer Einzelteile und deren anschließenden Zusammenbau. Jede Schnittstelle in einer Baugruppe führt zu potenziellen Toleranzüberschneidungen, Ausrichtungsfehlern und Fehlerpunkten. Die Konsolidierung von Teilen, bei der mehrere Funktionen in ein einziges Bauteil integriert werden, ist höchst wünschenswert, aber bei der Bearbeitung oft schwierig.
- Vorlaufzeiten: Die Einrichtung von Werkzeugen, die Programmierung, die Bearbeitungszeit und die Montage können zu langen Vorlaufzeiten führen, insbesondere bei komplizierten Designs oder kleinen Produktionsmengen. Iterationen beim Prototyping können langsam und teuer sein.
Die Nachfrage nach höherer Leistung, größerer Designkomplexität, geringerem Gewicht und schnelleren Entwicklungszyklen in Branchen, die empfindliche Messgeräte verwenden, hat eine große Chance für alternative Fertigungsverfahren geschaffen. Die additive Fertigung von Metallen geht direkt auf viele der Einschränkungen traditioneller Methoden ein und bietet einen überzeugenden Weg zur Entwicklung der nächsten Generation stabiler Befestigungslösungen für kritische High-Tech-Anwendungen. Unternehmen, die einen Wettbewerbsvorteil bei der Herstellung oder Nutzung von Hochpräzisionsgeräten suchen, wenden sich zunehmend an Metall-AM-Dienstleister, die über das Fachwissen und die fortschrittlichen Fähigkeiten verfügen, wie sie bei Met3dp zu finden sind, um diese fortschrittlichen Designs zu realisieren.
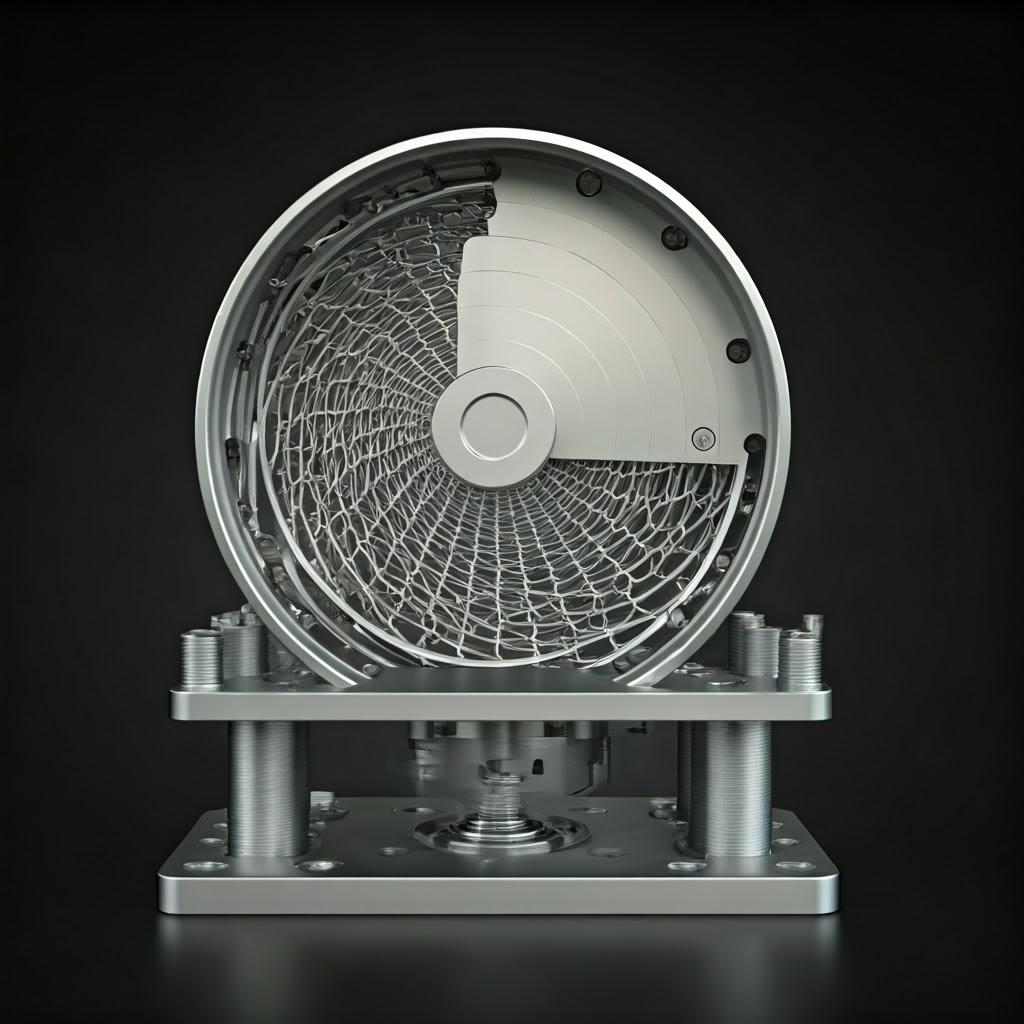
Anwendungen & Anwendungsfälle: Wo sich die Präzisionsmontage auszeichnet
Der Bedarf an hochpräzisen, stabilen Montagelösungen zieht sich durch praktisch alle Bereiche der Hochtechnologie. Die Fähigkeit, Komponenten stabil zu halten, auszurichten und von Umwelteinflüssen zu isolieren, ist von grundlegender Bedeutung. Die additive Fertigung von Metallen setzt sich in diesen Anwendungen immer mehr durch, da sie Konstruktionen und Materialkombinationen ermöglicht, die bisher unerreichbar waren. Hier ein Blick auf die wichtigsten Branchen und spezifischen Anwendungsfälle, in denen 3D-gedruckte Präzisionsinstrumentenhalterungen einen Mehrwert bieten:
1. Luft- und Raumfahrt und Verteidigung:
- Satellitengestützte Instrumente: Halterungen für optische Nutzlasten (Teleskope, Kameras), Sensoren, Antennen und Elektronik müssen den Vibrationen beim Start und den Temperaturschwankungen im Weltraum (-150°C bis +150°C oder darüber hinaus) standhalten und über Jahre hinweg eine extreme Ausrichtungsgenauigkeit aufweisen. Materialien mit geringem WAK wie Invar, oft in Kombination mit einer Topologieoptimierung für minimales Gewicht (entscheidend für die Startkosten), sind ideale Kandidaten für AM.
- Luftfahrzeugsensoren und Avionik: Halterungen für Gyroskope, Beschleunigungsmesser, Navigationssysteme und Zielgeräte erfordern hohe Steifigkeit, Vibrationsdämpfung und Zuverlässigkeit bei hohen G-Kräften und wechselnden Temperaturen. AM ermöglicht komplexe, leichte Halterungen, die direkt in die Flugzeugstruktur integriert werden.
- Optische Bänke und Zielsysteme: Optische Systeme am Boden oder in der Luft benötigen außergewöhnlich stabile Halterungen für Laser, Spiegel und Detektoren. AM ermöglicht die Herstellung monolithischer optischer Bänke mit integrierten Halterungen, was die Komplexität der Montage reduziert und die Stabilität verbessert.
2. Medizinische Geräte:
- Ausrüstung für diagnostische Bildgebung (MRI, CT, PET): Empfindliche Detektoren und Patientenpositionierungssysteme erfordern Halterungen, die nicht magnetisch (oft sind spezielle Legierungen erforderlich), vibrationsbeständig und formstabil sind. AM kann kundenspezifische Halterungen herstellen, die auf bestimmte Maschinengeometrien und Patientenschnittstellen zugeschnitten sind. Üblicherweise werden Materialien wie Edelstahl 316L oder Titanlegierungen verwendet.
- Chirurgische Robotik und Werkzeuge: Halterungen für Roboterarme, Kameras und chirurgische Instrumente erfordern hohe Präzision, Steifigkeit und die Möglichkeit der Sterilisation. AM ermöglicht komplexe, ergonomische Designs, oft mit internen Kanälen zur Kühlung oder Flüssigkeitszufuhr, unter Verwendung biokompatibler Materialien wie 316L oder Ti6Al4V.
- Laborautomatisierung und -analyse: Screening-Systeme, Mikroskope und Probenhandhabungsgeräte mit hohem Durchsatz sind auf eine präzise, wiederholbare Positionierung angewiesen. Kundenspezifische 3D-gedruckte Halterungen können den Arbeitsablauf optimieren, den Platzbedarf verringern und die Integration verschiedener Komponenten verbessern.
3. Metrologie und wissenschaftliche Instrumentierung:
- Koordinatenmessgeräte (CMMs): Tastköpfe, Sensorhalterungen und strukturelle Komponenten erfordern extreme Dimensionsstabilität und Steifigkeit, um die Messgenauigkeit bis in den Submikrometerbereich zu gewährleisten. Materialien mit niedrigem WAK wie Invar sind unverzichtbar, und AM ermöglicht optimierte Rahmendesigns und Sondenhalterungen.
- Mikroskopie (Elektronen-, Atomkraftmikroskopie): Halterungen müssen eine außergewöhnliche Schwingungsisolierung und thermische Stabilität bieten, um eine Auflösung im atomaren Maßstab zu erreichen. AM ermöglicht die Herstellung komplizierter, gedämpfter Halterungsstrukturen, die auf bestimmte Mikroskoptische und Umgebungskammern zugeschnitten sind.
- Synchrotrons und Teilchenbeschleuniger: Beamline-Instrumente, Detektorhalterungen und Probenmanipulatoren arbeiten in anspruchsvollen Umgebungen (Vakuum, Strahlung) und erfordern eine präzise Ausrichtung. AM ermöglicht die Herstellung von komplexen Halterungen aus speziellen Materialien, die diesen Bedingungen standhalten.
- Optische Prüfung und Interferometrie: Halterungen für Laser, Spiegel, Strahlteiler und Detektoren, die in optischen Testaufbauten verwendet werden, erfordern hohe Stabilität und Feinjustierungsmöglichkeiten. AM kann Halterungen mit integrierten Biegungen oder Justiermechanismen herstellen, häufig unter Verwendung von Invar mit niedrigem WAK.
4. Industrielle Automatisierung und Fertigung:
- Roboter-End-Effektoren: Halterungen für Greifer, Sensoren und Werkzeuge an Industrierobotern müssen leicht (zur Maximierung von Nutzlast und Geschwindigkeit) und dennoch stabil sein. AM ermöglicht Topologie-optimierte Designs, die auf spezifische Aufgaben zugeschnitten sind.
- Bildverarbeitungssysteme: Kamera- und Beleuchtungshalterungen erfordern eine stabile Positionierung für eine zuverlässige Prüfung und Führung. Kundenspezifische AM-Halterungen können in enge Bereiche von Produktionslinien passen und Kühl- oder Schutzfunktionen integrieren.
- Ausrüstung für die Halbleiterherstellung: Wafer-Handling-Systeme, Lithographie-Werkzeuge und Prüfstationen erfordern höchste Präzision und Stabilität, oft in Reinraum- oder Vakuumumgebungen. Materialien mit geringer Ausgasung und Legierungen mit niedrigem WAK wie Invar sind entscheidend, und AM bietet Designflexibilität für komplexe Gerätegeometrien. Anbieter von Präzisionskomponenten für den Großhandel setzen zunehmend auf AM, um die individuellen Anforderungen dieses Sektors zu erfüllen.
5. Automobilindustrie:
- Montage von Sensoren (LiDAR, Radar, Kameras): Autonomes Fahren und ADAS-Systeme sind auf eine präzise Sensorausrichtung angewiesen. Die Halterungen müssen Straßenvibrationen, Temperaturschwankungen und Stößen standhalten und gleichzeitig die Sensorkalibrierung beibehalten. AM ermöglicht integrierte, langlebige Montagelösungen speziell für Fahrzeugplattformen.
- Motorprüfstände: Die Montage von Sensoren für Temperatur-, Druck- und Schwingungsmessungen in Motorprüfständen erfordert Robustheit und thermische Stabilität. Kundenspezifische AM-Halterungen können Sensoren in rauen Prüfumgebungen optimal positionieren.
- Fertigungsvorrichtungen: Auch wenn es sich nicht direkt um Instrumentenhalterungen handelt, erfordern die Vorrichtungen, die zum Halten von Teilen während der Herstellung oder Prüfung verwendet werden, hohe Präzision und Stabilität. AM wird häufig eingesetzt, um schnell kundenspezifische, leichte und ergonomische Halterungen herzustellen.
In all diesen unterschiedlichen Bereichen sind die Kernanforderungen oft identisch: Präzision, Stabilität (mechanisch und thermisch), Zuverlässigkeit und oft auch kundenspezifische Anpassung oder komplexe Geometrie. Die additive Fertigung von Metallen, insbesondere mit fortschrittlichen Pulverbettschmelzverfahren wie dem selektiven Elektronenstrahlschmelzen (SEBM) oder dem selektiven Laserschmelzen (SLM), bietet die Werkzeuge, um diese anspruchsvollen Anforderungen zu erfüllen. Dienstleister, die sich spezialisiert haben auf 3D-Druck von Metall sind wichtige Partner für Unternehmen, die diese Hochleistungskomponenten benötigen. Sie bieten Fachwissen in den Bereichen Materialauswahl, Designoptimierung und Prozesskontrolle, um sicherzustellen, dass die endgültige Halterung die Spezifikationen erfüllt oder übertrifft. Die Möglichkeit, Hersteller von kundenspezifischen Instrumentenhalterungen zu finden, die die AM-Technologie nutzen, wird zu einem wichtigen Wettbewerbsvorteil.
Warum Metall-Additive Fertigung für Instrumentenhalterungen? Leistung und Designfreiheit freisetzen
Die Entscheidung für die additive Fertigung (AM) von Metall für die Herstellung hochpräziser Instrumentenhalterungen ergibt sich aus den inhärenten Vorteilen gegenüber traditionellen subtraktiven Verfahren wie der CNC-Bearbeitung, insbesondere bei komplexen Designs, speziellen Materialien oder der Notwendigkeit einer optimierten Leistung. Während die maschinelle Bearbeitung nach wie vor für einfachere Geometrien oder die Großserienproduktion standardisierter Teile geeignet ist, eröffnet die AM Möglichkeiten, die zuvor als undurchführbar oder kostspielig galten. Ingenieure und Beschaffungsmanager erkennen diese Vorteile zunehmend:
1. Unerreichte Gestaltungsfreiheit und Komplexität:
- Komplexe Geometrien: AM baut Teile Schicht für Schicht auf und ermöglicht komplizierte interne Kanäle (für Kühlung, Flüssigkeitsströmung oder Kabelführung), komplexe äußere Formen, negative Entformungswinkel und hohle Strukturen ohne die Einschränkungen, die durch Schneidewerkzeuge oder Formvorschriften entstehen. Diese Freiheit ermöglicht Designs, die wirklich für die Funktion optimiert sind, nicht nur für die Herstellbarkeit mit herkömmlichen Mitteln.
- Topologie-Optimierung: Ingenieure können mit Hilfe von Software-Tools Belastungspfade, Einschränkungen und Leistungsziele definieren (z. B. Maximierung der Steifigkeit, Minimierung des Gewichts), und die Software erzeugt eine organische, oft gitterartige Struktur, die diese Anforderungen mit einem Minimum an Material erfüllt. Die maschinelle Bearbeitung solch komplexer Formen ist oft nicht möglich oder wirtschaftlich unrentabel. Für Instrumentenhalterungen bedeutet dies, dass Strukturen geschaffen werden müssen, die genau dort, wo sie benötigt werden, außergewöhnlich steif und stabil sind, während die Gesamtmasse drastisch reduziert wird - ein entscheidender Faktor für die Luft- und Raumfahrt, die Robotik und tragbare Geräte.
- Teil Konsolidierung: Mehrere Komponenten, die traditionell separat hergestellt und dann zusammengebaut werden (z. B. eine Halterung, ein Kühlkörper, ein Schwingungsdämpfer), können oft neu entworfen und als ein einziges, monolithisches Teil gedruckt werden. Dies spart Montagezeit und -kosten, beseitigt potenzielle Fehlerstellen oder Ausrichtungsfehler an den Schnittstellen, verbessert die strukturelle Gesamtintegrität und verringert Toleranzprobleme.
2. Gewichtsreduzierung:
- Reduzierte Masse: Durch die Optimierung der Topologie und die Möglichkeit, interne Gitterstrukturen oder Hohlprofile zu erzeugen, kann AM das Gewicht von Instrumentenhalterungen im Vergleich zu massiven, maschinell gefertigten Bauteilen erheblich reduzieren und gleichzeitig die Steifigkeit und Festigkeit beibehalten oder sogar erhöhen.
- Vorteile: Lightweighting ist entscheidend für Anwendungen wie:
- Luft- und Raumfahrt: Niedrigere Startkosten, verbesserte Treibstoffeffizienz, höhere Nutzlastkapazität.
- Automobilindustrie: Bessere Fahrdynamik, geringerer Kraftstoffverbrauch.
- Robotik: Schnellere Bewegungen, geringere Trägheit, höhere Nutzlast für den Roboterarm.
- Medizinische Geräte: Verbesserte Tragbarkeit, einfachere Handhabung für tragbare oder am Körper getragene Geräte.
3. Verbesserte Leistungsmerkmale:
- Integrierte Funktionalitäten: Die Designfreiheit ermöglicht die direkte Integration von leistungssteigernden Merkmalen. Beispiele hierfür sind:
- Konforme Kühlkanäle: Interne Kanäle, die genau der Kontur von wärmeerzeugenden Komponenten oder kritischen Bereichen der Halterung folgen, bieten ein weitaus effizienteres Wärmemanagement als gebohrte Kanäle oder angebrachte Kühlkörper.
- Schwingungsdämpfende Konstruktionen: Der Einbau spezieller Gittergeometrien oder die Konstruktion von Biegeelementen direkt in die Halterung kann dazu beitragen, das Instrument von externen Vibrationen zu isolieren.
- Optimierte Flusspfade: Für Halterungen, die auch als Verteiler oder Leitungen für Flüssigkeiten oder Gase dienen.
- Materialeigenschaften: AM-Prozesse führen häufig zu feinkörnigen Mikrostrukturen, die zu hervorragenden mechanischen Eigenschaften (Festigkeit, Ermüdungsbeständigkeit) führen können, die denen von Guss- oder Knetwerkstoffen entsprechen oder diese sogar übertreffen, insbesondere nach einer geeigneten Nachbearbeitung wie dem heißisostatischen Pressen (HIP).
4. Materielle Möglichkeiten:
- Spezialisierte Legierungen: AM eignet sich hervorragend für die Bearbeitung von Materialien, die schwierig oder teuer zu bearbeiten sind, wie Hochtemperatur-Superlegierungen, bestimmte Titanlegierungen und Legierungen mit geringer Ausdehnung wie Invar (FeNi36). Die zerspanende Bearbeitung von Invar beispielsweise ist aufgrund seiner gummiartigen Beschaffenheit und Kaltverfestigung bekanntermaßen schwierig. AM bietet einen effizienteren Weg zur Herstellung komplexer Invar-Komponenten, die für thermisch stabile Halterungen unerlässlich sind.
- Neuartige Materialien: Der schichtweise Aufbau von AM öffnet die Tür zu funktional abgestuften Materialien (unterschiedliche Zusammensetzung des Bauteils) oder Metallmatrix-Verbundwerkstoffen, obwohl diese Bereiche noch im Entstehen sind.
- Geringerer Materialabfall: Da es sich um ein additives Verfahren handelt, wird bei der AM nur das Material verwendet, das für die Herstellung des Teils und seiner Halterungen benötigt wird, was im Vergleich zur subtraktiven Bearbeitung zu deutlich weniger Abfall führt, insbesondere bei komplexen Teilen oder teuren Materialien wie Invar oder Titan in Luft- und Raumfahrtqualität. Dieses Verhältnis zwischen Anschaffung und Fertigung ist viel günstiger.
5. Rapid Prototyping und Iteration:
- Geschwindigkeit: AM ermöglicht die schnelle Herstellung von Prototypen direkt aus CAD-Daten, oft innerhalb weniger Tage, ohne dass Werkzeuge benötigt werden. Dies beschleunigt die Designzyklen und ermöglicht es den Ingenieuren, mehrere Iterationen schnell zu testen und sich viel schneller als bei herkömmlichen Methoden auf ein optimales Design zu einigen.
- Kosteneffiziente Iteration: Die Kosten für die Herstellung eines einzelnen Prototyps oder einer Kleinserie mittels AM sind oft deutlich niedriger als die Kosten für die maschinelle Bearbeitung, was die Erforschung des Designs leichter macht.
6. Personalisierung und Kleinserienproduktion:
- Fertigung auf Abruf: AM ist ideal für die Herstellung kundenspezifischer Einzelteile oder Kleinserien ohne die hohen Einrichtungskosten, die bei der herkömmlichen Fertigung anfallen. Dies ist perfekt für spezielle wissenschaftliche Instrumente, kundenspezifische Vorrichtungen für medizinische Geräte oder Ersatzteile für ältere Systeme.
- Maßgeschneiderte Lösungen: Instrumentenhalterungen können perfekt auf die spezifischen Geometrie-, Gewichts- und Leistungsanforderungen des Instruments und seiner Betriebsumgebung zugeschnitten werden.
Warum AM statt CNC-Bearbeitung für Halterungen wählen? Ein vergleichender Blick:
Merkmal | Additive Fertigung von Metall (AM) | CNC-Bearbeitung | Vorteil für Präzisionshalterungen |
---|---|---|---|
Entwurfskomplexität | Hoch (Interne Kanäle, Gitter, organische Formen) | Mäßig bis hoch (begrenzt durch Werkzeugzugang, Einrichtung) | AM ermöglicht optimierte, leichte und konsolidierte Konstruktionen, die mit maschineller Bearbeitung nicht möglich sind. |
Teil Konsolidierung | Ausgezeichnet | Begrenzt | AM reduziert Montagefehler, Gewicht und potenzielle Fehlerquellen. |
Gewichtsreduzierung | Ausgezeichnet (Topologie-Optimierung, interne Hohlräume) | Begrenzt (Einschränkungen bei der Materialentnahme) | AM reduziert die Masse erheblich und erhält gleichzeitig die Steifigkeit, was für dynamische/bewegliche Anwendungen entscheidend ist. |
Materialabfälle | Niedrig (Additivverfahren) | Hoch (Subtraktives Verfahren, insbesondere komplexe Teile) | AM ist kostengünstiger und nachhaltiger für teure Materialien wie Invar. |
Vorlaufzeit (Proto) | Fasten (Tage) | Mäßig bis langsam (Wochen, je nach Komplexität) | AM beschleunigt die Design-Iteration und -Validierung. |
Vorlaufzeit (Prod.) | Moderat (Bearbeitungszeit + Nachbearbeitung) | Potenziell schneller für große Mengen (wenn einfach) | AM kann bei komplexen Teilen mit geringen Stückzahlen schneller sein. |
Wahl des Materials | Breites Spektrum, hervorragend geeignet für schwer zu bearbeitende Legierungen | Große Auswahl, Standardmaterialien leicht verfügbar | AM verarbeitet effizient kritische Materialien wie Invar, die für die thermische Stabilität benötigt werden. |
Kosten der Einrichtung | Niedrig (keine Werkzeuge) | Hoch (Werkzeuge, Programmierung, Vorrichtungen) | AM ist kosteneffizient für kundenspezifische Teile und geringe Stückzahlen. |
Oberfläche | Mäßig (Nachbearbeitung für eine glatte Oberfläche erforderlich) | Ausgezeichnet (direkt erreichbar) | Bearbeitung bevorzugt für kritische Oberflächen, die eine hohe Oberflächengüte ohne Nachbearbeitung erfordern. |
Toleranzen | Gut (Erfordert Nachbearbeitung für höchste Präzision) | Ausgezeichnet (direkt erreichbar) | Bevorzugte Bearbeitung für Merkmale, die eine Genauigkeit von weniger als 100 Mikrometern erfordern, ohne Nachbearbeitung. |
In Blätter exportieren
Zusammenfassend lässt sich sagen, dass die additive Fertigung von Metallen eine ganze Reihe von Vorteilen für die Herstellung hochpräziser Instrumentenhalterungen bietet, insbesondere wenn Komplexität, Gewicht, Leistungsoptimierung oder die Verwendung spezieller Werkstoffe wie Invar die entscheidenden Faktoren sind. Sie ermöglicht es den Ingenieuren, sich von traditionellen Fertigungsbeschränkungen zu lösen und wirklich innovative Befestigungslösungen zu entwickeln. Die Partnerschaft mit einem erfahrenen AM-Anbieter wie Met3dp, der Fachwissen in fortschrittlichen Druckverfahren mit einer hochwertigen Materialproduktion, stellt sicher, dass das Potenzial von AM für Ihre kritischen Anwendungen voll ausgeschöpft wird.
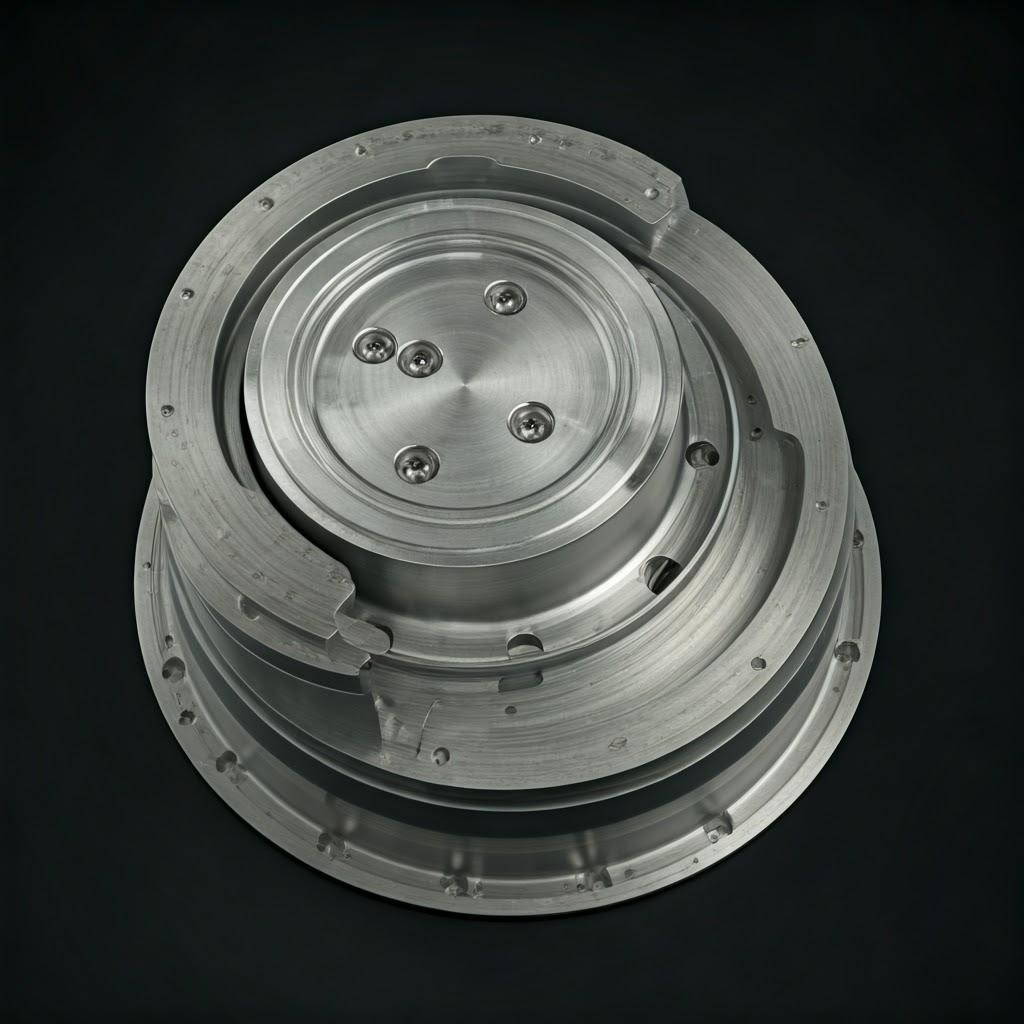
Materialschwerpunkt: 316L-Edelstahl & Invar für optimale Leistung
Die Leistung einer Präzisionsinstrumentenhalterung hängt im Wesentlichen von dem Material ab, aus dem sie hergestellt wird. Während bei der additiven Fertigung von Metallen eine breite Palette von Legierungen verarbeitet werden kann, stechen zwei Werkstoffe aufgrund ihrer spezifischen und oft komplementären Eigenschaften durch ihre häufige Verwendung in hochpräzisen Befestigungsanwendungen hervor: 316L-Edelstahl und Invar (FeNi36). Die Kenntnis ihrer Eigenschaften ist entscheidend für die Auswahl des richtigen Materials für Ihre spezifischen Anforderungen.
1. 316L-Edelstahl (Austenitischer Edelstahl)
316L ist eine der am häufigsten verwendeten Edelstahllegierungen in der additiven Fertigung und bekannt für seine hervorragende Kombination aus Korrosionsbeständigkeit, mechanischen Eigenschaften, Biokompatibilität und Verarbeitbarkeit.
- Wichtige Eigenschaften & Vorteile für Halterungen:
- Ausgezeichnete Korrosionsbeständigkeit: Der hohe Chrom- und Molybdängehalt verleiht 316L eine außergewöhnliche Korrosionsbeständigkeit in einer Vielzahl von Umgebungen, einschließlich Chloriden, Säuren und Körperflüssigkeiten. Dies macht es ideal für Halterungen, die in medizinischen Geräten, in der Schifffahrt, in der chemischen Verarbeitung und in der Lebensmittelindustrie eingesetzt werden.
- Gute mechanische Festigkeit und Duktilität: 316L bietet ein ausgewogenes Verhältnis von Zugfestigkeit, Streckgrenze und Dehnung, so dass die Halterungen robust und bruchfest sind. Seine Eigenschaften sind im Allgemeinen mit denen von 316L in Knetausführung vergleichbar.
- Biokompatibilität: 316L ist für medizinische Implantate und Geräte weithin anerkannt (ISO 10993) und eignet sich daher für chirurgische Werkzeughalterungen oder interne Gerätebefestigungen.
- Schweißbarkeit und Polierbarkeit: Teile aus 316L lassen sich leicht schweißen (falls eine Montage erforderlich ist, obwohl AM darauf abzielt, diese zu konsolidieren) und auf eine hohe Oberflächengüte polieren, was für Reinraum- oder optische Anwendungen wichtig ist.
- Kosten-Nutzen-Verhältnis und Verfügbarkeit: Im Vergleich zu exotischeren Legierungen wie Invar oder Titan ist 316L-Pulver relativ kostengünstig und bei Qualitätslieferanten leicht erhältlich.
- Gute AM-Verarbeitbarkeit: 316L ist gut charakterisiert und lässt sich mit Laser Powder Bed Fusion (LPBF/SLM) und anderen AM-Verfahren zuverlässig verarbeiten, was zu dichten, hochwertigen Teilen führt.
- Beschränkungen:
- Mäßige thermische Ausdehnung: 316L hat einen für austenitische nichtrostende Stähle typischen Wärmeausdehnungskoeffizienten (ca. 16-17×10-6/K). Dieser Ausdehnungskoeffizient ist zwar für viele Anwendungen akzeptabel, kann aber bei Systemen, die sehr empfindlich auf Temperaturschwankungen reagieren, wie z. B. Präzisionsoptiken oder Messgeräte, zu erheblichen Maßänderungen und Ausrichtungsfehlern führen.
- Die Dichte: Es ist dichter als Aluminium- oder Titanlegierungen, was sich bei gewichtskritischen Anwendungen als Nachteil erweisen kann (obwohl die Leichtbaumöglichkeiten von AM dieses Problem abmildern können).
- Typische Anwendungen für 316L-Halterungen:
- Komponenten für medizinische Geräte (Operationsroboter, Diagnosegeräte)
- Marine-Hardware und Sensorhalterungen
- Armaturen für chemische Verarbeitungsgeräte
- Lebensmittelgerechte Maschinenkomponenten
- Allgemeine industrielle Sensor- und Gerätehalterungen, bei denen die extreme thermische Stabilität nicht im Vordergrund steht.
2. Invar (FeNi36 / Legierung 36)
Invar ist eine Eisen-Nickel-Legierung, die speziell für ihren bemerkenswert niedrigen Wärmeausdehnungskoeffizienten (CTE) bei Raumtemperatur und mäßig erhöhten Temperaturen entwickelt wurde. Sein Name kommt von dem Wort “invariable,” und bezieht sich auf seine fehlende thermische Ausdehnung.
- Wichtige Eigenschaften & Vorteile für Halterungen:
- Äußerst niedriger CTE: Dies ist die entscheidende Eigenschaft von Invar. Sein WAK liegt bei Raumtemperatur typischerweise bei etwa 1,2×10-6/K, etwa 10-15 mal niedriger als bei Edelstahl oder Aluminium und deutlich niedriger als bei Titan. Diese außergewöhnliche Dimensionsstabilität macht es zum Material der Wahl für Anwendungen, bei denen selbst geringste thermische Ausdehnungen oder Kontraktionen nicht toleriert werden können.
- Gute Stärke und Zähigkeit: Invar bietet eine ausreichende Festigkeit und Zähigkeit für Montageanwendungen, insbesondere wenn die Dimensionsstabilität eine vorrangige Anforderung ist.
- AM Verarbeitbarkeit: Obwohl Invar-Pulver auf herkömmliche Weise schwierig zu bearbeiten ist, kann es mit LPBF/SLM erfolgreich verarbeitet werden, was die Herstellung komplexer Geometrien unter Ausnutzung des niedrigen WAK ermöglicht. Eine sorgfältige Steuerung der Parameter und eine Wärmebehandlung nach dem Prozess sind entscheidend.
- Beschränkungen:
- Höhere Kosten: Invar-Pulver ist aufgrund seines hohen Nickelgehalts und des speziellen Herstellungsverfahrens wesentlich teurer als Edelstahl 316L.
- Geringere Korrosionsbeständigkeit: Invar besitzt nicht die inhärente Korrosionsbeständigkeit von nichtrostenden Stählen. Es kann in feuchten Umgebungen rostanfällig sein, wenn es nicht durch Beschichtungen (z. B. Vernickelung) geschützt wird.
- Schwierigkeitsgrad der Bearbeitung: Obwohl AM einen Großteil der Schwierigkeiten umgeht, kann die Nachbearbeitung von kritischen Merkmalen im Vergleich zu Stahl immer noch eine Herausforderung darstellen.
- Empfindlichkeit gegenüber Wärmebehandlung: Um den optimalen niedrigen WAK-Zustand von Invar zu erreichen, sind spezielle Wärmebehandlungsprotokolle nach dem Druck erforderlich, um Spannungen abzubauen und das Gefüge zu stabilisieren. Eine unsachgemäße Wärmebehandlung kann die niedrigen Ausdehnungseigenschaften beeinträchtigen.
- Die Dichte: Ähnlich wie Stahl hat es eine relativ hohe Dichte.
- Typische Anwendungen für Invar-Halterungen:
- Optische Halterungen (Spiegel, Linsen, Laser) in Teleskopen, Interferometern und Präzisionsausrichtungssystemen.
- Gestelle und Vorrichtungen für Messgeräte (CMMs, Lehren).
- Strukturen für die Luft- und Raumfahrt, die Maßhaltigkeit erfordern (optische Bänke für Satelliten, Formen für Verbundwerkstoffe).
- Komponenten von Halbleiterfertigungsanlagen (Lithografiestufen, Wafer-Handling).
- Wissenschaftliche Instrumente, die eine hohe Stabilität erfordern (physikalische Experimente, Messgeräte).
Vergleich der Materialeigenschaften:
Eigentum | 316L-Edelstahl | Invar (FeNi36 / Legierung 36) | Bedeutung für Halterungen |
---|---|---|---|
Hauptnutzen | Korrosionsbeständigkeit, Kosten, Verfügbarkeit | Extrem niedrige thermische Ausdehnung (CTE) | Wählen Sie je nach Umwelteinflüssen und dem Bedarf an ultimativer Dimensionsstabilität. |
CTE (approx. @ 20°C) | ~16-17×10-6/K | ~1.2×10-6/K | Invar ist bei temperaturempfindlichen Anwendungen weit überlegen. |
Dichte (ca.) | ~8,0g/cm3 | ~8,1g/cm3 | Ähnliche Dichten; Leichtbau durch AM-Design ist der Schlüssel für beide. |
Streckgrenze (typisch AM) | ~450-550 MPa | ~250-350 MPa (geglüht) | 316L ist im Allgemeinen stärker, aber Invar ist für die meisten statischen Befestigungslasten ausreichend. |
Korrosionsbeständigkeit | Ausgezeichnet | Schlecht (Beschichtung zum Schutz erforderlich) | 316L ist für raue Umgebungen geeignet; Invar benötigt kontrollierte Umgebungen oder eine Beschichtung. |
Relative Kosten | Unter | Erheblich höher | Budgetbeschränkungen begünstigen oft 316L, es sei denn, der niedrige WAK von Invar ist nicht verhandelbar. |
AM Verarbeitbarkeit | Gut etabliert, zuverlässig | Erfordert sorgfältige Kontrolle & Wärmebehandlung | Beides ist machbar, aber Invar erfordert mehr Prozesswissen. |
Bearbeitbarkeit | Gut | Schwierig | AM verringert die Abhängigkeit von der maschinellen Bearbeitung, was der Herstellung von Invar-Teilen zugute kommt. |
In Blätter exportieren
Auswahl des richtigen Materials & Lieferanten:
Die Wahl zwischen 316L und Invar (oder möglicherweise anderen Legierungen wie Titan für ein hohes Festigkeits-Gewichts-Verhältnis) hängt entscheidend von den spezifischen Leistungsanforderungen, der Betriebsumgebung und den Budgetbeschränkungen der Anwendung ab.
- Wenn Korrosionsbeständigkeit oder Kosten sind die wichtigsten Faktoren, und eine moderate Wärmeausdehnung ist akzeptabel: 316L ist oft die beste Wahl.
- Wenn höchste Formstabilität über Temperaturschwankungen hinweg ist von entscheidender Bedeutung (z. B. Optik, Messtechnik, Raumfahrt): Invar ist in der Regel erforderlich, trotz der höheren Kosten und der Notwendigkeit des Umweltschutzes.
Die Qualität des fertigen Teils hängt nicht nur von der Wahl des Materials ab, sondern auch von der Qualität des Metallpulvers und dem Fachwissen des Dienstleisters für die additive Fertigung. Unternehmen wie Met3dp sind auf die Herstellung von hochwertigen, sphärischen Metallpulvern spezialisiert, die für AM-Verfahren wie SEBM und LPBF optimiert sind. Der Einsatz fortschrittlicher Gaszerstäubungs- und PREP-Technologien gewährleistet Pulver mit hoher Sphärizität und guter Fließfähigkeit, was zu dichteren, zuverlässigeren gedruckten Teilen führt. Met3dp stellt eine breite Palette von Pulvern her, darunter auch rostfreie Stähle und potenziell spezielle Legierungen, die für anspruchsvolle Anwendungen benötigt werden, und bietet seinen Kunden sowohl die Materialien als auch die Fachwissen die erforderlich sind, um Metall-AM für hochpräzise Instrumentenhalterungen erfolgreich umzusetzen. Bei der Auswahl eines Anbieters für den 3D-Druck von Invar oder 316L-Edelstahl ist es wichtig, die Verfahren zur Qualitätskontrolle des Pulvers und die Erfahrung mit diesen speziellen Materialien zu überprüfen.
Entwurf für additive Fertigung (DfAM): Optimierung der Halterungen für Druckbarkeit & Funktionalität
Design for Additive Manufacturing (DfAM) stellt einen grundlegenden Wandel in der Denkweise im Vergleich zu den traditionellen Design for Manufacturing (DFM)-Prinzipien dar, die auf subtraktive Verfahren wie CNC-Bearbeitung zugeschnitten sind. Anstatt in erster Linie den Werkzeugzugang, den Entformungswinkel und die Materialabtragungsstrategien zu berücksichtigen, konzentriert sich DfAM auf die Nutzung der einzigartigen Fähigkeiten und die Berücksichtigung der spezifischen Einschränkungen der schichtweisen Fertigung. Die Anwendung von DfAM-Prinzipien ist nicht nur für Präzisionsinstrumentenhalterungen empfehlenswert, sondern auch unerlässlich, um das volle Potenzial von AM in Bezug auf Leistung, Kosteneffizienz und Zuverlässigkeit zu erschließen. Wird der AM-Prozess bei der Konstruktion nicht berücksichtigt, kann dies zu Druckfehlern, suboptimaler Leistung, übermäßigen Nachbearbeitungsanforderungen und höheren Kosten führen.
Grundlegende DfAM-Prinzipien für Präzisionsinstrumentenhalterungen:
- Nutzen Sie die geometrische Freiheit für einen funktionalen Zugewinn:
- Topologie-Optimierung: Dies ist vielleicht die wirkungsvollste DfAM-Technik für Halterungen. Durch die Definition von Lastfällen (Gewicht des Instruments, Schwingungseinflüsse, Betriebskräfte), Randbedingungen (Befestigungspunkte) und Zielen (Minimierung der Masse, Maximierung der Steifigkeit, spezifische Eigenfrequenz) können Software-Algorithmen hocheffiziente, oft organisch anmutende Strukturen erzeugen. Das Ergebnis ist eine Halterung, die genau dort steif und stabil ist, wo sie benötigt wird, und das bei minimalem Materialeinsatz, was zu erheblichen Gewichtseinsparungen führt, ohne die Leistung zu beeinträchtigen. Dies ist von unschätzbarem Wert für Luft- und Raumfahrt, Robotik und tragbare Systeme.
- Gitterförmige Strukturen: Der Einbau interner Gitterstrukturen (z. B. Kreisel, Oktett-Fachwerk) ermöglicht eine weitere Gewichtsreduzierung bei gleichzeitiger Wahrung der strukturellen Integrität. Gitter können auch so konstruiert werden, dass sie bestimmte Schwingungsdämpfungseigenschaften aufweisen oder die Wärmeableitung erleichtern, was für Instrumentenhalterungen sehr wichtig ist.
- Teil Konsolidierung: Suchen Sie aktiv nach Möglichkeiten, mehrere Komponenten einer Montageeinheit in einem einzigen gedruckten Teil zu kombinieren. Können eine Halterung, ein Kühlkörper und ein Schwingungsdämpfer integriert werden? Können Ausrichtungsmerkmale direkt in die Halterung integriert werden? Dies vereinfacht die Montage, reduziert die Toleranzüberlagerung, erhöht die Steifigkeit und senkt die Gesamtkosten des Systems.
- Konforme Kanäle: Entwerfen Sie interne Kanäle, die genau den Konturen von Wärmequellen oder Bereichen folgen, die ein Wärmemanagement benötigen. Bei Instrumenten, die Wärme erzeugen oder bei wechselnden Temperaturen arbeiten, bieten in die Halterung integrierte konforme Kühl-/Heizkanäle im Vergleich zu herkömmlichen Methoden eine bessere Wärmekontrolle. Kabelführungskanäle können ebenfalls integriert werden, um Baugruppen sauberer zu gestalten.
- Optimierung der Gebäudeausrichtung:
- Auswirkungen: Die Ausrichtung, in der die Halterung auf die Bauplatte gedruckt wird, hat erhebliche Auswirkungen auf die Anforderungen an die Stützstruktur, die Oberflächenbeschaffenheit auf den verschiedenen Seiten, die Verteilung der Eigenspannungen, die Bauzeit und möglicherweise die mechanischen Eigenschaften (Anisotropie).
- Erwägungen:
- Stützen minimieren: Richten Sie das Teil so aus, dass das Volumen und die Komplexität der erforderlichen Stützstrukturen reduziert werden, insbesondere bei kritischen Funktionsflächen oder schwer zugänglichen Innenbereichen. Selbsttragende Winkel (typischerweise >45 Grad zur Horizontalen) sollten nach Möglichkeit verwendet werden.
- Oberfläche: Nach unten gerichtete Oberflächen oder Oberflächen, die eine umfangreiche Unterstützung erfordern, weisen im Allgemeinen eine rauere Oberfläche auf. Richten Sie das Teil so aus, dass kritische Oberflächen (z. B. Schnittstellen, optische Ausrichtungspunkte) nach Möglichkeit nach oben oder vertikal ausgerichtet sind oder für die Nachbearbeitung leicht zugänglich sind.
- Mechanische Eigenschaften: Die Eigenschaften können je nach Baurichtung im Verhältnis zur Belastungsrichtung in der endgültigen Anwendung leicht variieren. Richten Sie das Teil so aus, dass die stärkste Bauachse mit dem primären Belastungspfad übereinstimmt, falls dies kritisch ist.
- Wärmemanagement: Die Ausrichtung wirkt sich auf die Wärmeableitung während der Herstellung aus und beeinflusst die Eigenspannung.
- Kollaboration: Bei der Wahl der optimalen Ausrichtung müssen oft Kompromisse eingegangen werden. Die Zusammenarbeit mit einem erfahrenen AM-Dienstleister wie Met3dp während der Entwurfsphase ist von entscheidender Bedeutung, da dieser verschiedene Ausrichtungen simulieren und die beste Strategie auf der Grundlage der spezifischen Anforderungen des Kunden empfehlen kann Produkt fähigkeiten und Prozesswissen.
- Effektive Unterstützungsstrukturen entwerfen:
- Die Notwendigkeit: Stützen sind erforderlich, um das Teil auf der Bauplatte zu verankern, Verformungen durch thermische Spannungen zu verhindern und überhängende Merkmale und nach unten gerichtete Oberflächen während des schichtweisen Aufbaus zu stützen.
- Optimierung: Stützen sind zwar notwendig, verbrauchen aber Material, verlängern die Bauzeit, erfordern einen hohen Aufwand beim Entfernen und können die Oberfläche des Teils beschädigen. DfAM zielt darauf ab, die Abhängigkeit von Stützen durch intelligente Konstruktionsentscheidungen zu minimieren (z. B. Verwendung von Fasen anstelle von scharfen Überhängen, Ausrichtung von Features, die selbsttragend sind) und Stützen zu entwerfen, die effektiv und dennoch leicht zu entfernen sind.
- Typen: Je nach Standort und Funktion können verschiedene Arten von Halterungen (z. B. massiv, gitterförmig, konisch) verwendet werden. Berücksichtigen Sie die leichte Zugänglichkeit für Entnahmewerkzeuge (Zangen, EDM-Drähte, CNC-Werkzeuge).
- Integration: Manchmal können funktionale Merkmale des Teils selbst so gestaltet werden, dass sie während der Herstellung auch als Stützen dienen, wodurch sich der Bedarf an speziellen Opferstrukturen verringern kann.
- Berücksichtigung von Prozesseinschränkungen:
- Mindestwanddicke/Merkmalgröße: Bei AM-Prozessen gibt es Grenzen für die Mindestdicke der Wände und die kleinsten Merkmale (Stifte, Löcher), die zuverlässig hergestellt werden können. Diese hängen von der jeweiligen Maschine, der Größe des Laser-/Elektronenstrahlflecks und den Pulvereigenschaften ab. Entwerfen Sie Wände und Merkmale oberhalb dieser Mindeststärken (z. B. typischerweise >0,4-0,5 mm für feine Merkmale in LPBF).
- Ausrichtung und Form der Löcher: Kleine Löcher werden oft genauer gedruckt, wenn sie vertikal ausgerichtet sind. Horizontal ausgerichtete kleine Löcher können leicht elliptisch gedruckt werden und benötigen möglicherweise Unterstützung; wenn sie als Tropfenform gestaltet werden, können sie selbsttragend sein.
- Entfernung von Puder: Bei Hohlprofilen oder inneren Kanälen ist darauf zu achten, dass ausreichende Austrittslöcher (mindestens 2-3 mm Durchmesser, vorzugsweise größer, und an strategisch günstigen Stellen) vorhanden sind, damit das nicht geschmolzene Pulver nach dem Bau entfernt werden kann. Eingeschlossenes Pulver erhöht das Gewicht und kann ein Kontaminationsproblem darstellen.
- Filets und Radien: An scharfen Innenecken sollten Verrundungen angebracht werden, um Spannungskonzentrationen zu verringern, die Schwachstellen oder Rissbildung darstellen können, insbesondere bei Vibrationen oder Belastung. Glatte Übergänge verbessern im Allgemeinen die Druckbarkeit und die Festigkeit des Teils.
- Design für die Nachbearbeitung:
- Zulagen für die Bearbeitung: Wenn bestimmte Oberflächen enge Toleranzen oder eine sehr glatte Oberfläche erfordern, die nicht direkt durch AM erreicht werden können, fügen Sie zusätzliches Material (Bearbeitungsmaterial, z. B. 0,5-1,0 mm) zu diesen spezifischen Bereichen im CAD-Modell hinzu, um eine Nachbearbeitung zu ermöglichen.
- Zugänglichkeit: Stellen Sie sicher, dass Bereiche, die entfernt, bearbeitet, poliert oder geprüft werden müssen, nach dem Druck des Teils zugänglich sind. Tiefe, schmale innere Kanäle, die eine Oberflächenbearbeitung erfordern, können problematisch sein.
- Befestigen: Überlegen Sie, wie das Teil für verschiedene Nachbearbeitungsschritte wie Bearbeitung oder Messung gehalten werden soll. Die Integration einfacher Vorrichtungen in den Entwurf kann später viel Zeit beim Einrichten sparen.
Die iterative Natur des DfAM:
DfAM ist nicht immer ein linearer Prozess. Er erfordert häufig die Zusammenarbeit zwischen dem Teilekonstrukteur und dem AM-Dienstleister. Tools wie Fertigungssimulationssoftware können potenzielle Probleme wie Verformung oder Überhitzung vorhersagen und ermöglichen es den Konstrukteuren, die Geometrie oder den Fertigungsaufbau proaktiv zu ändern. Prototyping und Tests sind nach wie vor wichtige Schritte, um Designentscheidungen zu validieren und sicherzustellen, dass die endgültige Instrumentenhalterung alle funktionalen Anforderungen erfüllt. Die Berücksichtigung der DfAM-Prinzipien von Anfang an ist der Schlüssel zur Maximierung der Vorteile der Metall-AM bei der Herstellung leichterer, stabilerer, funktionellerer und oft auch kostengünstigerer Präzisionsinstrumentenhalterungen im Vergleich zu denen, die durch traditionelle Fertigungsparadigmen eingeschränkt sind.
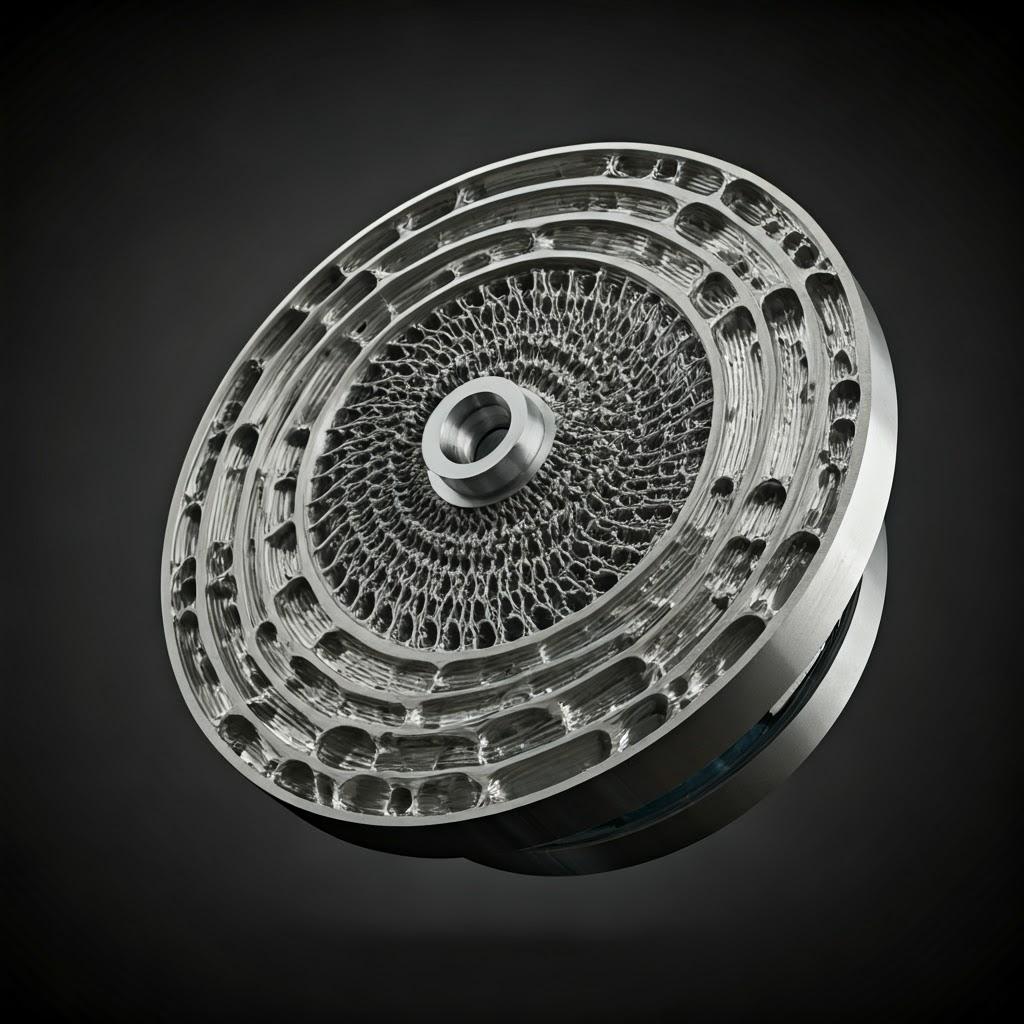
Erreichen von Präzision: Toleranz, Oberflächengüte und Maßgenauigkeit bei 3D-gedruckten Halterungen
Bei Komponenten, die empfindliche Instrumente halten sollen, ist Präzision das A und O. Für Ingenieure, die Halterungen entwerfen, und für Beschaffungsmanager, die Spezifikationen festlegen und Lieferanten bewerten, ist es entscheidend, die mit der additiven Fertigung von Metallen erreichbaren Toleranzniveaus, Oberflächengüten und Maßgenauigkeiten zu verstehen. Metall-AM bietet zwar eine unglaubliche Designfreiheit, hat aber auch inhärente Eigenschaften hinsichtlich der Präzision, die sich von der konventionellen Bearbeitung unterscheiden. Oft ist eine Kombination aus AM und Nachbearbeitung erforderlich, um die strengsten Anforderungen zu erfüllen.
As-Printed-Fähigkeiten:
Metall-AM-Verfahren wie Laser Powder Bed Fusion (LPBF/SLM) und Selective Electron Beam Melting (SEBM) bauen Teile Schicht für Schicht auf, in der Regel mit einer Dicke von 20-100 Mikrometern (mum). Dieses Verfahren beeinflusst naturgemäß die erreichbare Präzision:
- Maßgenauigkeit:
- Allgemeine Toleranzen: Als allgemeine Richtlinie gilt, dass bei gut kontrollierten Prozessen und ordnungsgemäß kalibrierten Maschinen die typischen Maßtoleranzen für gedruckte AM-Metallteile oft im Bereich von pm0,1 mm bis pm0,2 mm für kleinere Merkmale (bis zu ~50-100 mm) oder pm0,1 bis pm0,2 der Gesamtabmessung für größere Teile liegen. Ein 200 mm langes Merkmal könnte beispielsweise eine Toleranz von pm0,2 mm bis pm0,4 mm aufweisen.
- Beeinflussende Faktoren: Die tatsächlich erreichbare Genauigkeit hängt stark von der Teilegeometrie (Komplexität, Größe, Volumen), dem Material (thermische Eigenschaften), der Bauausrichtung, der Stützstrategie, der Maschinenkalibrierung, der Pulverqualität (Partikelgrößenverteilung, Fließfähigkeit) und dem Wärmemanagement während des Baus ab. Eigenspannungen, die sich während des Drucks aufbauen, können Verformungen oder Verzerrungen verursachen, die sich auf die endgültigen Abmessungen auswirken, insbesondere nach dem Entfernen von der Bauplatte.
- Der Ansatz von Met3dp: Das Erreichen einer gleichbleibenden Genauigkeit erfordert eine robuste Prozesssteuerung. Unternehmen wie Met3dp legen großen Wert auf die Zuverlässigkeit und Genauigkeit ihrer Drucksysteme und die Qualität ihrer Metallpulver, die mit fortschrittlichen Zerstäubungstechniken hergestellt werden, um eine gleichbleibende sphärische Morphologie und Fließfähigkeit zu gewährleisten - Faktoren, die für ein vorhersehbares Schmelzen und Erstarren und damit für eine bessere Maßkontrolle entscheidend sind.
- Oberflächengüte (Rauhigkeit):
- Wie-gedruckt Ra: Die Oberflächenbeschaffenheit von as-printed Metallteilen ist aufgrund der teilweise geschmolzenen Pulverpartikel, die an der Oberfläche haften, und des schichtweisen Aufbaus von Natur aus rauer als bearbeitete Oberflächen. Typische Werte für die Oberflächenrauhigkeit (Ra – Arithmetic Average Roughness) hängen von der Ausrichtung und dem Verfahren ab:
- Vertikale Mauern: Oft wird das beste Ergebnis erzielt, möglicherweise Ra 8-15mum.
- Nach oben gerichtete Flächen: Etwas rauher, Ra 10-20mum.
- Nach unten gerichtete Oberflächen (unterstützt): Erheblich rauer an den Stellen, an denen die Stützen befestigt sind, möglicherweise Ra 20-50mum oder mehr, was eine erhebliche Nachbearbeitung erfordert.
- Abgestufte Oberflächen: Auch die Schichtstufen auf schrägen Oberflächen tragen zur Rauheit bei.
- SEBM vs. LPBF: SEBM arbeitet in der Regel bei höheren Temperaturen und verwendet größere Pulverpartikel, was im Vergleich zu LPBF oft zu einer raueren Oberflächenbeschaffenheit (z. B. Ra 25-45mum), aber potenziell zu geringeren Eigenspannungen führt.
- Auswirkungen auf Montagen: Für allgemeine Strukturteile kann die gedruckte Oberfläche ausreichend sein. Für Präzisionsinstrumentenhalterungen, Passflächen, Dichtungsflächen, Schnittstellen von optischen Komponenten oder kinematische Positionierungsmerkmale ist diese Rauheit jedoch in der Regel inakzeptabel und muss durch Nachbearbeitung verbessert werden.
- Wie-gedruckt Ra: Die Oberflächenbeschaffenheit von as-printed Metallteilen ist aufgrund der teilweise geschmolzenen Pulverpartikel, die an der Oberfläche haften, und des schichtweisen Aufbaus von Natur aus rauer als bearbeitete Oberflächen. Typische Werte für die Oberflächenrauhigkeit (Ra – Arithmetic Average Roughness) hängen von der Ausrichtung und dem Verfahren ab:
Höhere Präzision durch Nachbearbeitung:
Bei den meisten hochpräzisen Instrumentenhalterungen müssen kritische Merkmale nachbearbeitet werden, vor allem durch CNC-Bearbeitung, Schleifen oder Läppen, um die erforderlichen Toleranzen und Oberflächengüten zu erreichen.
- Toleranzen: Bei der Nachbearbeitung können Toleranzen im Bereich von pm0,01 mm bis pm0,05 mm (10-50mum) und noch engere Toleranzen bis hinunter zu einzelnen Mikrometern (mum) mit speziellen Schleif- oder Läppverfahren an kritischen Punkten oder Schnittstellen erreicht werden. Auf diese Weise können Designer die geometrische Freiheit von AM für die Gesamtform nutzen und gleichzeitig die Präzision nur dort sicherstellen, wo sie funktional erforderlich ist.
- Oberfläche: Durch maschinelle Bearbeitung kann die Oberflächengüte drastisch verbessert werden, wobei in der Regel Ra 0,8-3,2mum erreicht wird. Durch Schleifen und Läppen lassen sich optisch hochwertige Oberflächen mit einem Ra von deutlich unter 0,1 mm erzielen. Poliertechniken können Oberflächen aus ästhetischen oder funktionalen Gründen (z. B. Reinigungsfähigkeit) ebenfalls deutlich glätten.
Vergleich: Präzision im Originalzustand vs. Nachbearbeitung:
Merkmal | Metall AM wie gedruckt (typisch LPBF) | Nachbearbeitet (Bearbeiten/Schleifen) | Bedeutung für Präzisionshalterungen |
---|---|---|---|
Toleranz | pm0,1-0,2 mm oder pm0,1-0,2 | pm0,01-0,05 mm (Zerspanung)<br> pm0,001-0,01 mm (Schleifen) | AM geeignet für allgemeine Formen; Nachbearbeitung unerlässlich für kritische Schnittstellen & Ausrichtungen. |
Oberflächengüte (Ra) | 8-25mum (variiert je nach Ausrichtung) | 0.8-3,2mum (Bearbeitung)<br> $\< 0,1 \\mu m$ (Läppen/Polieren) | Nachbearbeitung erforderlich für glatte Passflächen, Dichtungen oder optische Schnittstellen. |
Fähigkeit | Komplexe Gesamtgeometrie | Hohe Präzision bei bestimmten Merkmalen | Kombinieren Sie die Komplexität von AM’ mit der Präzision der maschinellen Bearbeitung für optimale Ergebnisse. |
In Blätter exportieren
Qualitätskontrolle und -überprüfung:
Um sicherzustellen, dass die endgültige Fassung die vorgegebenen Präzisionsanforderungen erfüllt, ist eine strenge Qualitätskontrolle erforderlich:
- Prozessbegleitende Überwachung: Moderne AM-Systeme verfügen über Sensoren zur Überwachung des Schmelzbades, der Temperaturgradienten und der Schichtkonsistenz während des Bauprozesses und tragen so zur Prozessstabilität bei.
- Post-Build Metrology: Koordinatenmessgeräte (CMMs), 3D-Laserscanner und optische Profilometer werden eingesetzt, um die Maßgenauigkeit und die Oberflächengüte nach dem Druck und nach allen Nachbearbeitungsschritten zu überprüfen.
- Zerstörungsfreie Prüfung (NDT): Techniken wie das CT-Scannen können zur Inspektion interner Merkmale, zur Überprüfung auf Porosität und zur Überprüfung komplexer Geometrien eingesetzt werden, die sonst nicht zugänglich sind.
Das Wichtigste zum Mitnehmen:
Die additive Fertigung von Metallen bietet eine gute grundlegende Maßgenauigkeit und eine charakteristische Oberflächenbeschaffenheit direkt aus der Maschine. Für die anspruchsvollen Anforderungen von hochpräzisen Instrumentenhalterungen müssen die Konstrukteure jedoch die Notwendigkeit einer gezielten Nachbearbeitung, in erster Linie Zerspanung oder Schleifen, für kritische Merkmale und Oberflächen einkalkulieren. Durch die strategische Kombination der Designfreiheit von AM mit der Präzision subtraktiver Nachbearbeitungstechniken und durch die Zusammenarbeit mit einem qualitätsorientierten AM-Anbieter können Ingenieure Halterungslösungen entwickeln, die sowohl geometrische Komplexität als auch hohe Genauigkeit bieten. Beschaffungsmanager sollten die Toleranz- und Oberflächenanforderungen auf den Zeichnungen klar definieren und angeben, welche Merkmale nachbearbeitet werden müssen, um eine genaue Angebotserstellung und eine erfolgreiche Realisierung der Teile zu gewährleisten.
Wesentliche Nachbearbeitungsschritte für funktionale Instrumentenhalterungen
Ein 3D-gedrucktes Metallteil ist nach der Entnahme aus dem Drucker nur selten bereit für seine endgültige Anwendung, insbesondere im Zusammenhang mit hochpräzisen Instrumentenhalterungen. In der Regel ist eine Reihe von Nachbearbeitungsschritten erforderlich, um das gedruckte Rohteil in ein funktionales, zuverlässiges und fertiges Produkt zu verwandeln. Diese Schritte sind entscheidend, um innere Spannungen abzubauen, temporäre Strukturen zu entfernen, die gewünschten Materialeigenschaften zu erzielen, die Maßhaltigkeit zu gewährleisten, die gewünschte Oberflächenbeschaffenheit zu erreichen und manchmal Schutzschichten hinzuzufügen. Das Verständnis dieses Arbeitsablaufs ist entscheidend für die Planung von Produktionszeiten und -kosten.
Typischer Post-Processing-Workflow für AM-Metallhalterungen:
- Stressabbau Wärmebehandlung:
- Zweck: Die schnellen Erwärmungs- und Abkühlungszyklen beim Pulverbettschmelzen führen zu erheblichen inneren Spannungen innerhalb des gedruckten Teils. Diese Spannungen können zu Verformungen oder Rissen führen, insbesondere nachdem das Teil aus der Verankerung der Bauplatte entfernt wurde. Der Spannungsabbau ist ein kritischer erster Schritt für die meisten Metall-AM-Teile, insbesondere für größere Komponenten oder solche aus Materialien, die zu Spannungsaufbau neigen, wie Titanlegierungen oder Invar.
- Prozess: Das Teil wird, oft noch auf der Bauplatte befestigt, in einem Ofen auf eine bestimmte Temperatur (unter der Umwandlungstemperatur des Materials) erhitzt, für eine bestimmte Zeit gehalten und dann langsam abgekühlt. Dadurch kann sich das Gefüge entspannen, was die Eigenspannungen erheblich reduziert. Die spezifischen Zyklen hängen stark vom Material (z. B. erfordert Invar sorgfältig kontrollierte Zyklen, um seine niedrigen WAK-Eigenschaften zu erhalten) und der Teilegeometrie ab.
- Bedeutung für Halterungen: Gewährleistet Dimensionsstabilität im Laufe der Zeit und verhindert unerwartete Verformungen, die die Ausrichtung der Instrumente beeinträchtigen könnten.
- Entnahme von der Bauplatte:
- Prozess: Nach dem Spannungsabbau (falls auf der Platte durchgeführt) muss das Teil von der Bauplatte getrennt werden, auf der es gedruckt wurde. Dies geschieht in der Regel durch Drahterodieren (EDM), Sägen oder manchmal auch durch CNC-Bearbeitung.
- Erwägungen: Es muss darauf geachtet werden, dass das Teil beim Entfernen nicht beschädigt wird. Die Zwischenschicht zwischen dem Teil/den Stützen und der Platte ist oft so gestaltet, dass sie sich leichter entfernen lässt.
- Pulverentfernung (Depowdering):
- Zweck: Ungeschmolzenes Metallpulver verbleibt in inneren Kanälen und Hohlräumen und haftet nach dem Druck an der Oberfläche des Teils. Dieses lose Pulver muss gründlich entfernt werden.
- Prozess: Dazu gehören in der Regel manuelles Bürsten, Abklopfen und der Einsatz von Druckluft- oder Inertgasdüsen in einer kontrollierten Umgebung (Entpuderungsstation) zur Rückgewinnung des nicht verwendeten Pulvers (das oft gesiebt und wiederverwendet werden kann). Auch Ultraschallreinigungsbäder oder spezielle Vibrationssysteme können eingesetzt werden.
- Herausforderungen: Die Entfernung von Pulver aus komplexen inneren Geometrien oder Gitterstrukturen kann schwierig sein. Die DfAM-Grundsätze (z. B. ausreichende Fluchtlöcher) sind hier entscheidend. Eingeschlossenes Pulver ist inakzeptabel, da es das Gewicht erhöht und eine Quelle für Verunreinigungen sein oder die Funktion beeinträchtigen kann.
- Entfernung der Stützstruktur:
- Zweck: Behelfsmäßige Stützstrukturen, die während des Baus zur Verankerung des Teils und zur Unterstützung von Überhängen verwendet wurden, müssen entfernt werden.
- Prozess: Dies kann vom einfachen manuellen Brechen (bei leicht gesinterten Stützen) bis hin zu aufwändigeren Methoden wie Schneiden mit Handwerkzeugen, Drahterodieren (insbesondere bei komplexen internen Stützen) oder CNC-Bearbeitung reichen. Die Methode hängt von der Konstruktion, dem Material und der Zugänglichkeit des Trägers ab.
- Erwägungen: Die Entfernung der Halterung kann Spuren oder raue Bereiche auf der Oberfläche des Teils (Narben) hinterlassen, die eine weitere Nachbearbeitung erfordern können. Es muss darauf geachtet werden, dass das eigentliche Teil beim Entfernen nicht beschädigt wird. Die Gestaltung von Halterungen für eine einfache Entnahme ist ein wichtiger Aspekt des DfAM.
- Heiß-Isostatisches Pressen (HIP) – Optional, aber oft empfohlen:
- Zweck: HIP ist ein Verfahren, bei dem hohe Temperaturen und hoher Inertgasdruck (in der Regel Argon) kombiniert werden, um die interne Mikroporosität zu beseitigen, die manchmal nach dem AM-Prozess verbleiben kann. Dadurch wird das Material verdichtet, was die Ermüdungslebensdauer, die Bruchzähigkeit und die allgemeine mechanische Integrität erheblich verbessert.
- Prozess: Die Teile werden in einem speziellen HIP-Behälter unter hohem isostatischem Druck für eine bestimmte Dauer erhitzt.
- Wann verwendet: Häufig erforderlich für kritische Komponenten in der Luft- und Raumfahrt, medizinische Implantate und hochbelastete Industrieteile, bei denen die Materialintegrität von größter Bedeutung ist. Für Präzisionsbefestigungen, die Vibrationen oder Ermüdungsbelastungen ausgesetzt sind, kann HIP eine zusätzliche Sicherheitsspanne bieten und langfristige Zuverlässigkeit gewährleisten. Außerdem kann es die Konsistenz der Materialeigenschaften verbessern.
- Bearbeitung / Endbearbeitung kritischer Merkmale:
- Zweck: Wie bereits erwähnt, müssen enge Toleranzen (pm0,01-0,05 mm oder besser) und glatte Oberflächen (Ra $\< 3,2 \\mu m$) auf bestimmten Funktionsflächen (Passflächen, Ausrichtungsbezüge, Lagerbohrungen, optische Schnittstellen) erreicht werden.
- Prozess: Verwendet standardmäßige CNC-Fräs-, Dreh-, Schleif- oder Läpparbeiten. Erfordert ein sorgfältiges Vorrichtungsdesign, um das oft komplexe AM-Teil genau zu halten. Bearbeitungszugaben müssen in der DfAM-Phase berücksichtigt werden.
- Die Notwendigkeit: Fast immer erforderlich für hochpräzise Instrumentenhalterungen, um eine genaue Positionierung und Montage zu gewährleisten.
- Oberflächenbehandlung und Veredelung:
- Zweck: Zur Verbesserung der allgemeinen Oberflächenbeschaffenheit, zur Reinigung des Teils, zur Verbesserung der Ästhetik oder zur Vorbereitung der Beschichtung.
- Vorgänge:
- Perlstrahlen/Shot Peening: Erzeugt eine gleichmäßige matte Oberfläche, entfernt lose Partikel und kann Druckeigenspannungen erzeugen (Shotpeening), um die Ermüdungsfestigkeit zu verbessern.
- Taumeln/Gleitschleifen: Glättet Oberflächen und Kanten mit Hilfe von Schleifkörpern in einer Trommel oder einem Rütteltopf. Gut geeignet für die Stapelverarbeitung kleinerer Teile.
- Elektropolieren: Elektrochemisches Verfahren, bei dem eine dünne Materialschicht entfernt wird, was zu einer sehr glatten, sauberen und glänzenden Oberfläche führt. Wird häufig für medizinische (316L) oder Vakuumanwendungen verwendet.
- Manuelles Polieren/Lackieren: Zum Erzielen spezifischer Hochglanzoberflächen oder zum Glätten lokaler Bereiche.
- Beschichtung oder Plattierung:
- Zweck: Um Korrosionsschutz zu bieten (wichtig für Materialien wie Invar in feuchten Umgebungen), die Verschleißfestigkeit zu erhöhen, die elektrischen oder thermischen Eigenschaften der Oberfläche zu verändern oder die Ästhetik zu verbessern.
- Vorgänge: Vernickeln (üblich bei Invar), Pulverbeschichten, Lackieren, Eloxieren (bei Titan), PVD-Beschichtungen (Physical Vapor Deposition) usw.
- Erwägungen: Die Dicke der Beschichtung muss berücksichtigt werden, wenn sie auf maßhaltige Oberflächen aufgetragen wird. Die Oberflächenvorbereitung ist der Schlüssel für eine gute Haftung.
- Reinigung und Inspektion:
- Zweck: Endreinigung zur Entfernung von Rückständen von Bearbeitungsflüssigkeiten, Poliermitteln oder Verunreinigungen. Bei der Endkontrolle werden die Abmessungen und die Oberflächenbeschaffenheit überprüft und vor dem Versand auf eventuelle Mängel kontrolliert.
- Vorgänge: Ultraschallreinigung, Sichtprüfung, CMM-Messungen, Oberflächenprofilometrie, NDT, falls erforderlich.
Die spezifische Abfolge und Notwendigkeit dieser Schritte hängt stark vom Material (z.B. Invar’s Notwendigkeit einer spezifischen Wärmebehandlung und Beschichtung), der Komplexität des Teils und den strengen Anforderungen der endgültigen Anwendung ab. Die Planung der Nachbearbeitung ist kein nachträglicher Gedanke, sondern ein integraler Bestandteil des Fertigungsablaufs für Metall-AM-Teile, der sich auf die Durchlaufzeiten und Gesamtkosten auswirkt. Die Zusammenarbeit mit einem Full-Service-Anbieter, der umfassende Nachbearbeitungsmöglichkeiten bietet oder Partnerschaften für diese Dienstleistungen aufgebaut hat, ist entscheidend, um funktionale, anwendungsbereite Präzisionsinstrumentenhalterungen zu erhalten.
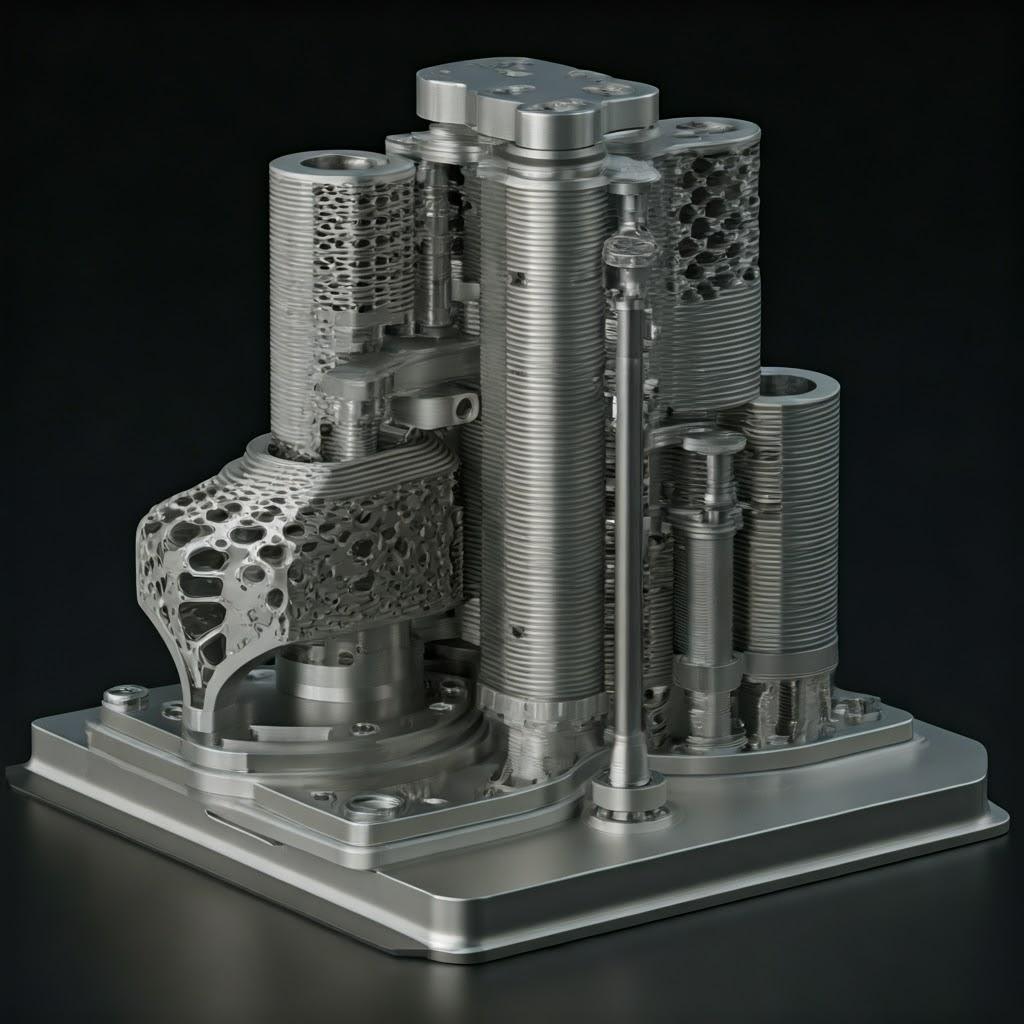
Überwindung von Herausforderungen beim 3D-Druck von Präzisionshalterungen aus Metall
Die additive Fertigung von Metallen bietet zwar erhebliche Vorteile für die Herstellung komplexer und leistungsstarker Instrumentenhalterungen, doch die Technologie ist nicht ohne Herausforderungen. Um die erforderliche Präzision, Materialintegrität und Zuverlässigkeit zu erreichen, sind eine sorgfältige Prozesskontrolle, ein Verständnis der Materialwissenschaft und häufig eine iterative Verfeinerung erforderlich. Das Bewusstsein für diese potenziellen Hürden ermöglicht es Ingenieuren und Herstellern, proaktiv Strategien zur Abschwächung zu implementieren.
Gemeinsame Herausforderungen und Abhilfestrategien:
- Eigenspannung, Verzug und Verwerfung:
- Herausforderung: Die intensive, örtlich begrenzte Erwärmung durch den Laser- oder Elektronenstrahl und die anschließende schnelle Abkühlung erzeugen steile Wärmegradienten, die beim schichtweisen Aufbau zu inneren Spannungen im Bauteil führen. Diese Spannungen können dazu führen, dass sich das Teil verzieht, verformt oder sogar reißt, insbesondere nach der Entnahme von der Bauplatte oder während der Nachbearbeitung. Dies ist ein großes Problem für die Einhaltung der für Präzisionshalterungen erforderlichen Maßgenauigkeit.
- Milderung:
- Prozess-Simulation: Software-Tools können den Bauprozess simulieren, um Bereiche mit hoher Belastung und potenzieller Verformung vorherzusagen, so dass vor dem Druck Anpassungen der Ausrichtung oder der Stützstrategien möglich sind.
- Optimierte Build-Parameter: Die Feinabstimmung von Laser-/Strahlleistung, Scangeschwindigkeit, Schichtdicke und Scanstrategie hilft, den Wärmeeintrag zu steuern und thermische Gradienten zu reduzieren.
- Build Plate Heating: Das Vorheizen der Bauplatte (bei LPBF üblich, bei SEBM im Vakuum) reduziert den Temperaturunterschied zwischen dem erstarrten Material und dem umgebenden Pulverbett und verringert so den Spannungsaufbau.
- Intelligente Stützstrategien: Robuste Stützstrukturen verankern das Teil während des Baus fest und widerstehen den Verformungskräften. Die Stützen dienen auch als Wärmesenken.
- Stressabbau Wärmebehandlung: Wie bereits erwähnt, ist dies ein entscheidender Nachbearbeitungsschritt, um die inneren Spannungen vor dem Entfernen der Halterung oder einer umfangreichen Bearbeitung zu reduzieren. Insbesondere für empfindliche Materialien wie Invar sind spezielle Protokolle erforderlich.
- Entfernung der Stützstruktur:
- Herausforderung: Halterungen sind notwendig, müssen aber sauber entfernt werden, ohne das Teil zu beschädigen. Der Zugang zu Halterungen in komplexen Innengeometrien oder empfindlichen Gitterstrukturen kann äußerst schwierig sein. Eine unvollständige Entfernung hinterlässt unerwünschtes Material, während eine aggressive Entfernung funktionale Oberflächen beschädigen kann.
- Milderung:
- DfAM für die Minimierung der Unterstützung: Durch die Ausrichtung des Teils und die Verwendung von selbsttragenden Winkeln (>45°) wird der Bedarf an Stützen drastisch reduziert. Die Gestaltung von Merkmalen wie Fasen anstelle von scharfen Überhängen ist hilfreich.
- Optimiertes Support-Design: Verwendung von leicht zu entfernenden Halterungen (z. B. dünne Schnittstellen, perforierte Strukturen), Gewährleistung eines angemessenen Abstands für die Werkzeuge und Berücksichtigung der Entfernungsmethode (manuell, Erodieren, maschinelle Bearbeitung) während der Entwurfsphase.
- Erweiterte Entfernungstechniken: Der Einsatz des Drahterodierens bei komplizierten oder schwer zugänglichen Halterungen ermöglicht eine präzise Entfernung bei minimaler Krafteinwirkung auf das Teil.
- Wahl des Materials: Einige Materialien lassen sich leichter von Stützen befreien als andere.
- Porosität (Gas und Lack-of-Fusion):
- Herausforderung: Im gedruckten Material können sich manchmal kleine Hohlräume oder Poren bilden. Gasporosität entsteht durch Gas, das im Pulver eingeschlossen oder im Schmelzbad gelöst ist. Lack-of-Fusion-Porosität tritt auf, wenn die Laser-/Strahlenergie nicht ausreicht, um benachbarte Schmelzspuren oder Schichten vollständig zu schmelzen und zu verschmelzen. Porosität verschlechtert die mechanischen Eigenschaften (insbesondere die Ermüdungsfestigkeit) und kann die Integrität einer Präzisionshalterung beeinträchtigen.
- Milderung:
- Hochwertiges Pulver: Die Verwendung hochwertiger, gaszerstäubter sphärischer Pulver mit geringer innerer Porosität und kontrollierter Partikelgrößenverteilung ist von grundlegender Bedeutung. Der Schwerpunkt von Met3dp’ auf der fortschrittlichen Pulverproduktion mittels Gaszerstäubung und PREP-Technologien zielt direkt darauf ab, Pulver mit hoher Sphärizität, guter Fließfähigkeit und geringem Satellitengehalt zu erzeugen, was eine dichte Packung und ein gleichmäßiges Schmelzen fördert.
- Optimierte Prozessparameter: Die Entwicklung und strenge Kontrolle von material- und maschinenspezifischen Parametern (Leistung, Geschwindigkeit, Schraffurabstand, Schichtdicke) gewährleistet ein vollständiges Schmelzen und Verschmelzen.
- Kontrollierte Atmosphäre: Die Aufrechterhaltung einer hochreinen Inertgasatmosphäre (Argon oder Stickstoff) in der Baukammer minimiert die Oxidation und Gasaufnahme während des Drucks.
- Heiß-Isostatisches Pressen (HIP): Die effektivste Methode, um verbleibende innere Porosität zu beseitigen und das Teil auf nahezu 100 % theoretische Dichte zu verdichten. Für kritische Anwendungen oft zwingend erforderlich.
- Einschränkungen der Oberflächenbeschaffenheit:
- Herausforderung: Wie bereits erwähnt, ist die gedruckte Oberfläche von Natur aus rauer als maschinell bearbeitete Oberflächen. Obwohl sie für einige Anwendungen akzeptabel ist, ist sie oft unzureichend für Passflächen, Dichtungsschnittstellen oder Halterungen für optische Komponenten, die eine glatte Oberfläche zur Ausrichtung oder geringe Reibung erfordern.
- Milderung:
- Orientierungsstrategie: Optimale Positionierung der kritischen Flächen bei der Bauplanung (nach oben gerichtet, vertikal).
- Optimierung der Parameter: Mit feineren Pulvern und dünneren Schichten lassen sich manchmal etwas bessere Oberflächen erzielen, oft auf Kosten der Fertigungsgeschwindigkeit. Strategien zur Konturabtastung können auch die Seitenwandbeschaffenheit verbessern.
- Gezielte Nachbearbeitung: Akzeptieren Sie, wo immer möglich, die Oberfläche, wie sie gedruckt wurde, und planen Sie spezielle Nachbearbeitungsschritte (Bearbeitung, Polieren, Perlstrahlen, Elektropolieren) nur für die Oberflächen, bei denen eine verbesserte Oberfläche funktionell erforderlich ist.
- Anisotropie (richtungsabhängige Eigenschaften):
- Herausforderung: Aufgrund des schichtweisen Aufbaus und des säulenförmigen Kornwachstums, das häufig entlang der Aufbaurichtung (Z-Achse) zu beobachten ist, können sich die mechanischen Eigenschaften (z. B. Festigkeit, Duktilität) von AM-Bauteilen manchmal unterscheiden, je nachdem, ob sie parallel oder senkrecht zur Aufbaurichtung gemessen werden. Diese Anisotropie muss berücksichtigt werden, insbesondere bei Bauteilen, die bestimmten Belastungsrichtungen ausgesetzt sind.
- Milderung:
- Berücksichtigung der Gebäudeausrichtung: Ausrichtung des kritischen Belastungspfads in der Anwendung mit der günstigsten Bauausrichtung (oft XY-Ebene oder 45 Grad), wenn Anisotropie für das gewählte Material/Verfahren von Bedeutung ist.
- Wärmebehandlung: Bestimmte Wärmebehandlungen können dazu beitragen, das Gefüge zu homogenisieren und den Grad der Anisotropie zu verringern.
- Prozessauswahl: Einige Verfahren (wie SEBM mit seiner hohen Bildungstemperatur) können im Vergleich zu anderen zu einer weniger ausgeprägten Anisotropie führen.
- Materialcharakterisierung: Verlassen auf Daten von Zulieferern oder Durchführung von Tests, um das anisotrope Verhalten des spezifischen Materials bei der Verarbeitung mit dem gewählten AM-Verfahren zu verstehen.
- Verwaltung und Handhabung von Pulver:
- Herausforderung: Metallpulver können reaktiv und gefährlich sein (Einatmungsrisiko) und erfordern eine sorgfältige Handhabung, Lagerung und Rückverfolgbarkeit, insbesondere in regulierten Branchen wie der Luft- und Raumfahrt und der Medizintechnik. Die Sicherstellung der Pulverqualität und die Vermeidung von Kreuzkontaminationen zwischen verschiedenen Materialien ist von entscheidender Bedeutung.
- Milderung:
- Strenge Protokolle: Einführung strenger Verfahren für die Handhabung, das Sieben, das Mischen, die Lagerung (z. B. unter Schutzatmosphäre) und die Rückverfolgbarkeit (Chargenverfolgung) von Pulver.
- Dedizierte Ausrüstung: Verwendung separater Geräte (z. B. Siebe, Baumodule) für verschiedene Materialarten, um Kreuzkontaminationen zu vermeiden.
- Qualitätskontrolle der Lieferanten: Die Zusammenarbeit mit seriösen Pulverlieferanten wie Met3dp, die zertifizierte Materialien mit dokumentierter Qualitätskontrolle liefern, bietet einen zuverlässigen Ausgangspunkt.
Die erfolgreiche Bewältigung dieser Herausforderungen erfordert eine Kombination aus robusten DfAM-Praktiken, fundierten Kenntnissen der Materialwissenschaft, sorgfältiger Prozesskontrolle während des Drucks, geeigneten Nachbearbeitungstechniken und strenger Qualitätssicherung. Die Zusammenarbeit mit einem erfahrenen Metall-AM-Dienstleister, der nachweislich über Fachwissen bei der Herstellung von Hochpräzisionskomponenten verfügt, moderne Anlagen besitzt und strenge Qualitätsmanagementsysteme anwendet, ist oft der effektivste Weg, um Risiken zu mindern und die erfolgreiche Produktion von zuverlässigen, leistungsstarken Instrumentenhalterungen sicherzustellen.
Auswahl Ihres Metall-AM-Partners: Die Wahl des richtigen Lieferanten für Präzisionsinstrumentenhalterungen
Der Erfolg Ihres Projekts zur Montage von Präzisionsinstrumenten hängt in hohem Maße von den Fähigkeiten, dem Fachwissen und den Qualitätsstandards des von Ihnen gewählten Dienstleisters für die additive Fertigung von Metallteilen ab. Nicht alle AM-Büros sind gleich, insbesondere wenn es um die strengen Anforderungen von Hochpräzisionskomponenten und speziellen Materialien wie Invar geht. Um eine fundierte Entscheidung zu treffen, müssen potenzielle Partner anhand mehrerer Schlüsselkriterien bewertet werden. Beschaffungsmanager und Ingenieurteams sollten während dieses B2B-Lieferantenauswahlprozesses eng zusammenarbeiten.
Schlüsselkriterien für die Bewertung von Anbietern von Metall-AM-Dienstleistungen:
- Technisches Fachwissen und Beratung:
- Anwendung Verstehen: Versteht der Anbieter die besonderen Herausforderungen und Anforderungen von Präzisionsinstrumentenhalterungen (z. B. Stabilität, Ausrichtung, Wärmemanagement, Vibration)?
- DfAM-Unterstützung: Bieten sie Konstruktionsberatungsdienste an, um Ihre Halterungskonstruktion für die additive Fertigung zu optimieren? Können sie fachkundigen Rat zur Topologieoptimierung, zu Halterungsstrategien, zur Auflösung von Merkmalen und zur Pulverentfernung bei komplexen Geometrien geben?
- Materialwissenschaftliche Kenntnisse: Verfügen sie über fundierte Kenntnisse der erforderlichen Werkstoffe, insbesondere von Speziallegierungen wie Invar (FeNi36)? Verstehen sie die Feinheiten der Verarbeitung dieser Werkstoffe und die erforderlichen Wärmebehandlungen, um die gewünschten Eigenschaften zu erzielen (z. B. niedriger WAK)?
- Problemlösung: Haben sie eine Erfolgsbilanz bei der Lösung komplexer Fertigungsaufgaben im Zusammenhang mit AM-Präzisionsteilen?
- Technologie, Ausrüstung und Fähigkeiten:
- Relevante AM-Prozesse: Verfügen sie über die geeignete Metall-AM-Technologie für Ihre Bedürfnisse? Laser Powder Bed Fusion (LPBF/SLM) ist für eine hohe Auflösung üblich, während Selective Electron Beam Melting (SEBM) Vorteile wie geringere Eigenspannungen und die Eignung für bestimmte reaktive Materialien bietet, die häufig für Anwendungen in der Medizin und der Luft- und Raumfahrt bevorzugt werden. Met3dp zum Beispiel hat sich neben der fortschrittlichen Pulverproduktion auf SEBM-Drucker spezialisiert.
- Maschinenpark: Wie groß, alt und in welchem Zustand ist der Maschinenpark? Verfügen sie über ausreichende Kapazitäten? Sind die Maschinen ordnungsgemäß kalibriert und gewartet, um konsistente Ergebnisse zu erzielen?
- Qualitätskontrolle des Pulvers: Wie verwalten und qualifizieren sie ihre Metallpulver? Verwenden sie qualitativ hochwertige Pulver aus angesehenen Quellen oder stellen sie ihre eigenen Pulver mit strengen Qualitätskontrollen her? Fragen Sie nach der Beschaffung des Pulvers, der Prüfung (z. B. Chemie, Partikelgrößenverteilung, Morphologie, Fließfähigkeit), Handhabung, Lagerung und Rückverfolgbarkeit. Der Schwerpunkt von Met3dp’ auf der hauseigenen Pulverproduktion mit fortschrittlichen Gaszerstäubungs- und PREP-Technologien ist hier ein bedeutender Vorteil, der die Kontrolle über dieses kritische Ausgangsmaterial gewährleistet.
- Hausinterne Nachbearbeitung: Welche Nachbearbeitungsmöglichkeiten gibt es im Unternehmen (z. B. Wärmebehandlungsöfen, CNC-Bearbeitungszentren, Oberflächenbearbeitungsgeräte, Messlabors)? Wenn kritische Schritte von Subunternehmern ausgeführt werden, kann es zu Verzögerungen oder Problemen bei der Qualitätskontrolle kommen. Ein Anbieter mit integrierten Fähigkeiten bietet oft eine bessere Kontrolle und potenziell schnellere Durchlaufzeiten.
- Materialportfolio und Fachwissen:
- Erforderliche Materialien: Verarbeiten sie routinemäßig die spezifischen Materialien, die für Ihre Halterung benötigt werden (z. B. 316L-Edelstahl, Invar)?
- Erfahrung: Wie viele erfolgreiche Projekte haben sie mit diesen spezifischen Materialien durchgeführt? Können sie Materialdatenblätter vorlegen, die auf ihren aktuellen Prozessparametern und Tests basieren?
- Entwicklung neuer Materialien: Sind sie in der Lage, mit Parametern für weniger gebräuchliche oder kundenspezifische Legierungen zu arbeiten oder diese zu entwickeln, falls erforderlich?
- Qualitätsmanagementsystem (QMS) und Zertifizierungen:
- ISO 9001: Dies ist die Basiszertifizierung für ein Qualitätsmanagementsystem, die auf dokumentierte Prozesse und die Verpflichtung zur Qualität hinweist.
- Branchenspezifische Zertifizierungen: Achten Sie je nach Einsatzgebiet auf entsprechende Zertifizierungen:
- AS9100: Qualitätsmanagementnorm für die Luft- und Raumfahrt.
- ISO 13485: Norm für das Qualitätsmanagement von Medizinprodukten.
- Prozesssteuerung und -überwachung: Welche Maßnahmen ergreifen sie, um den Druckprozess in Echtzeit zu überwachen und zu steuern? Wie gewährleisten sie die Konsistenz von Bau zu Bau und von Maschine zu Maschine?
- Inspektion und Prüfung: Welche Messgeräte (CMM, Scanner) und zerstörungsfreien Prüfverfahren (z. B. CT-Scanning, Farbeindringverfahren) werden eingesetzt? Entsprechen ihre Prüfmöglichkeiten den Präzisionsanforderungen Ihrer Halterung?
- Rückverfolgbarkeit: Können sie eine vollständige Rückverfolgbarkeit von Materialien, Prozessparametern und Qualitätsprüfungen während des gesamten Fertigungsablaufs gewährleisten?
- Erfolgsbilanz, Fallstudien und Referenzen:
- Nachgewiesene Erfahrung: Fragen Sie nach Beispielen für frühere Projekte mit ähnlicher Präzision, Komplexität oder Materialien. Fallstudien, die erfolgreiche Ergebnisse zeigen, sind wertvolle Indikatoren.
- Kundenreferenzen: Gespräche mit bestehenden Kunden, insbesondere mit solchen aus ähnlichen Branchen oder mit vergleichbaren Anwendungen, können einen ehrlichen Einblick in die Leistung, Zuverlässigkeit und Kommunikation des Anbieters geben.
- Kapazität, Vorlaufzeit und Skalierbarkeit:
- Projektvolumen: Können sie das von Ihnen benötigte Produktionsvolumen bewältigen, egal ob es sich um Prototypen, Kleinserien oder möglicherweise um eine größere Serienproduktion handelt?
- Zitierte Vorlaufzeiten: Sind die angegebenen Lieferzeiten realistisch und wettbewerbsfähig? Wie handhaben sie die Produktionsplanung und mögliche Engpässe (insbesondere bei der Nachbearbeitung)?
- Skalierbarkeit: Wenn Ihr Bedarf wächst, können sie die Produktion entsprechend skalieren?
- Kommunikation, Zusammenarbeit und Unterstützung:
- Reaktionsfähigkeit: Wie schnell und effektiv reagieren sie auf Anfragen und Angebotsanfragen?
- Transparenz: Sind sie offen über ihre Prozesse, Fähigkeiten und potenziellen Herausforderungen?
- Kollaboration: Fördern sie einen kollaborativen Ansatz und arbeiten mit Ihrem technischen Team zusammen, um das bestmögliche Ergebnis zu erzielen?
- Kundenbetreuung: Welchen Grad an technischer Unterstützung bieten sie vor, während und nach dem Projekt?
Zusammenfassung der Checkliste für die Lieferantenauswahl:
Kriterien | Zentrale Fragen |
---|---|
Technisches Fachwissen | Verstehen sie etwas von Präzisionsmontagen? Bieten sie DfAM-Unterstützung? Kennen sie die Feinheiten von Invar/316L? |
Technologie & Ausstattung | Geeigneter AM-Prozess (LPBF/SEBM)? Qualität/Kapazität der Maschine? Robuste Pulver-QC (wie bei Met3dp’s)? Interne Nachbearbeitung? |
Materialeigenschaften | Bieten Sie die gewünschten Legierungen an? Nachgewiesene Erfahrung mit ihnen? Verlässliche Werkstoffdaten liefern? |
Qualitätssystem & Zertifizierungen | ISO 9001 zertifiziert? AS9100/ISO 13485, falls erforderlich? Starke Prozesskontrolle? Erweiterte Inspektions-/NDT-Fähigkeiten? Vollständige Rückverfolgbarkeit? |
Erfolgsbilanz & Referenzen | Sind relevante Fallstudien verfügbar? Positive Kundenreferenzen? |
Kapazität, Vorlaufzeit, Umfang | Können Sie das erforderliche Volumen bewältigen? Realistische Vorlaufzeiten? Fähigkeit zur Skalierung? |
Kommunikation & Unterstützung | Reaktionsschnell? Transparent? Kooperativ? Gute technische Unterstützung? |
In Blätter exportieren
Die Wahl des richtigen Metall-AM-Partners ist eine strategische Entscheidung. Wenn Sie potenzielle Lieferanten anhand dieser Kriterien gründlich prüfen, erhöht sich die Wahrscheinlichkeit, dass Sie qualitativ hochwertige und zuverlässige Präzisionsgerätehalterungen erhalten, die Ihren Spezifikationen entsprechen und pünktlich und innerhalb des Budgets geliefert werden. Suchen Sie nach Partnern wie Met3dp die einen ganzheitlichen Ansatz verfolgen, indem sie fortschrittliche Drucktechnologie, überlegene Materialqualität und umfassendes Anwendungswissen kombinieren.
Kostenüberlegungen & Vorlaufzeiten für 3D-gedruckte Instrumentenhalterungen
Das Verständnis der Faktoren, die die Kosten und die Vorlaufzeit der additiven Fertigung von Metallen bestimmen, ist entscheidend für die Projektplanung, die Budgetierung und den Vergleich von AM mit traditionellen Fertigungsmethoden. Obwohl AM einzigartige Vorteile bietet, unterscheiden sich die Kostenstruktur und die Produktionszeiten erheblich von der CNC-Bearbeitung oder dem Gießen.
Faktoren, die die Kosten für Metall-AM beeinflussen:
Der Endpreis einer 3D-gedruckten Präzisionsinstrumentenhalterung wird durch ein komplexes Zusammenspiel von Faktoren beeinflusst:
- Materialart und Kosten:
- Die Kosten für das Rohmaterial Pulver sind ein wichtiger Faktor. Speziallegierungen wie Invar sind pro Kilogramm deutlich teurer als herkömmliche Materialien wie Edelstahl 316L. Auch für Titanlegierungen und Superlegierungen werden höhere Preise verlangt.
- Die Qualität des Pulvers (Sphärizität, Reinheit, Partikelgrößenverteilung) wirkt sich ebenfalls auf die Kosten aus, aber eine höhere Qualität führt oft zu besseren Druckergebnissen und möglicherweise zu weniger Ausschuss oder Fehlern.
- Teil Volumen und Masse:
- Sie bestimmt direkt die Menge des verbrauchten teuren Metallpulvers. Größere, dichtere Teile kosten natürlich mehr.
- DfAM-Techniken wie Topologieoptimierung und Gitterstrukturen sind der Schlüssel zur Minimierung des Volumens bei gleichzeitiger Erfüllung der Leistungsanforderungen und damit zur direkten Reduzierung der Materialkosten.
- Teil Komplexität und Geometrie:
- Während AM die Komplexität gut bewältigen kann, erfordern hochkomplexe Entwürfe unter Umständen kompliziertere Stützstrukturen oder längere Druckzeiten aufgrund komplizierter Scanpfade.
- Auch die einfache Entfernung des Pulvers aus den internen Kanälen spielt eine Rolle; Konstruktionen, die eine umfangreiche manuelle Entleerung erfordern, erhöhen die Arbeitskosten.
- Größe und Ausrichtung der Bounding Box eines Teils:
- Die Gesamtabmessungen (Länge x Breite x Höhe) bestimmen, wie viel Platz das Teil in der Baukammer einnimmt. Größere Teile beanspruchen mehr Maschinenkapazität und erfordern möglicherweise längere Bauzeiten, was die Kosten pro Teil erhöht.
- Die Aufbauhöhe (Z-Dimension) ist oft der wichtigste Faktor für die Druckzeit, da die Maschine jede Schicht nacheinander verarbeiten muss. Die Optimierung der Ausrichtung zur Minimierung der Höhe kann manchmal die Kosten senken.
- Umfang und Komplexität der Unterstützungsstruktur:
- Stützen verbrauchen Material (was die Kosten erhöht) und erfordern Zeit und Arbeit für die Entfernung (was die Nachbearbeitungskosten erhöht). Konstruktionen, die möglichst wenig Stützen benötigen, sind kostengünstiger.
- Maschinenzeit (Bauzeit):
- Berechnet auf der Grundlage der Anzahl der Schichten, der zu scannenden Fläche pro Schicht, der gewählten Scanstrategie und der Betriebsparameter der Maschine. Längere Bauzeiten bedeuten höhere Maschinennutzungskosten.
- Faktoren wie Schichtdicke (dünnere Schichten = bessere Auflösung, aber längere Zeit), Laser-/Strahlleistung und Scangeschwindigkeit beeinflussen dies.
- Nachbearbeitungsanforderungen:
- Dies kann ein sehr bedeutend anteil an den Gesamtkosten, der manchmal die Druckkosten selbst übersteigt. Jeder Schritt bedeutet zusätzlichen Arbeitsaufwand, Maschinenzeit und möglicherweise spezielle Werkzeugkosten:
- Spannungsarmglühen / Wärmebehandlung (Ofenzeit, Energie, spezielle Zyklen für Invar).
- Unterstützung Entfernung (Arbeit, Werkzeuge, möglicherweise Drahterodierzeit).
- HIP (teure Spezialausrüstung und lange Zykluszeiten).
- CNC-Bearbeitung (Programmierung, Einrichtung, Maschinenzeit, Werkzeuge - insbesondere für harte Materialien oder enge Toleranzen).
- Oberflächenbearbeitung (Strahlen, Trowalisieren, Polieren - Arbeitskräfte/Medien/Ausrüstung).
- Beschichtung/Vergoldung (Materialien, Bearbeitungszeit).
- Dies kann ein sehr bedeutend anteil an den Gesamtkosten, der manchmal die Druckkosten selbst übersteigt. Jeder Schritt bedeutet zusätzlichen Arbeitsaufwand, Maschinenzeit und möglicherweise spezielle Werkzeugkosten:
- Menge (Chargengröße):
- AM hat relativ niedrige Einrichtungskosten im Vergleich zu Werkzeugen für den Guss oder das Spritzgießen. Es fallen jedoch immer noch Einrichtungsaufgaben an (Bauvorbereitung, Maschineneinrichtung). Die Kosten pro Teil sinken in der Regel mit größeren Losgrößen, da sich die Rüstkosten amortisieren und die Baukammern potenziell mit mehreren Teilen verschachtelt werden können. Die Skaleneffekte sind jedoch in der Regel weniger dramatisch als bei Massenproduktionsverfahren.
- Qualitätssicherung und Inspektion:
- Grundlegende Maßkontrollen sind Standard. Wenn jedoch umfangreiche KMG-Berichte, zerstörungsfreie Prüfungen (z. B. CT-Scans), Materialzertifizierungsprüfungen oder eine detaillierte Dokumentation erforderlich sind, entstehen zusätzliche Arbeits- und Ausrüstungskosten.
Überlegungen zur Vorlaufzeit:
Die Vorlaufzeit ist die Gesamtzeit von der Auftragserteilung bis zur Lieferung des Teils. Bei Metall-AM umfasst sie mehrere Phasen:
- Vorverarbeitung (1-3 Tage):
- Auftragsprüfung, CAD-Dateivorbereitung, Fertigungssimulation (optional), Erstellung von Fertigungsdateien, Produktionsplanung.
- Druck (Bauzeit) (1-7+ Tage):
- Sehr variabel, je nach Teilegröße (insbesondere Höhe), Komplexität, Anzahl (Verschachtelung) und gewählten Parametern. Eine kleine Halterung kann über Nacht gedruckt werden; ein großes, komplexes Teil oder eine komplette Bauplatte kann mehrere Tage bis eine Woche dauern.
- Nachbearbeitung (3 Tage – 2+ Wochen):
- Dies ist oft der längste und variabelste Teil der Vorlaufzeit. Jeder Schritt kostet Zeit:
- Abkühlung und Entpuffung: ~0,5-1 Tag.
- Stressabbau: ~1-2 Tage (einschließlich Ofenzeit und kontrollierter Abkühlung).
- Entfernung von Build-Plates/Support: ~0,5-2 Tage (je nach Komplexität und Methode).
- HIP: ~2-4 Tage (einschließlich des Transports zur/von der HIP-Einrichtung, falls nicht im Haus).
- Bearbeitung: ~2-10+ Tage (je nach Komplexität, Anzahl der Merkmale, Auslastung der Werkstatt).
- Endbearbeitung/Beschichtung: ~1-5 Tage.
- Inspektion: ~0,5-1 Tag.
- Dies ist oft der längste und variabelste Teil der Vorlaufzeit. Jeder Schritt kostet Zeit:
- Versand (1-5 Tage):
- Abhängig von Standort und Versandart.
Geschätzte Gesamtvorlaufzeit:
- Prototypen (einfache, minimale Nachbearbeitung): ~5-10 Arbeitstage.
- Prototypen/Kleinserien (komplex, Bearbeitung/Wärmebehandlung erforderlich): ~2-4 Wochen.
- Produktionschargen: ~3-6+ Wochen (hängt stark von der Menge und der Komplexität der Nachbearbeitung ab).
Vergleich der Durchlaufzeiten von AM und maschineller Bearbeitung:
- Komplex, geringes Volumen: AM ist oft wesentlich schneller als die Bearbeitung von Knüppeln, da komplexe Programmierung, mehrfache Einstellungen und möglicherweise kundenspezifische Werkzeuge vermieden werden können.
- Einfach, hohe Lautstärke: Die CNC-Bearbeitung kann schneller sein, wenn sie einmal eingerichtet ist, insbesondere wenn mehrere Teile gleichzeitig auf effizienten Maschinen bearbeitet werden können.
- Schlüsselfaktor: Der Umfang der Nachbearbeitung, die für das AM-Teil erforderlich ist, wirkt sich erheblich auf den Vergleich der Gesamtvorlaufzeit aus. Wenn ein AM-Teil eine umfangreiche Bearbeitung erfordert, kann sich der Vorteil der Vorlaufzeit verringern.
Die wichtigsten Erkenntnisse für Beschaffung und Technik:
Um genaue Angebote zu erhalten, müssen Sie detaillierte CAD-Modelle, klare Spezifikationen (Material, Toleranzen, Oberflächenbeschaffenheit, erforderliche Zertifizierungen) und die gewünschten Mengen angeben. Sprechen Sie frühzeitig mit potenziellen Lieferanten über DfAM-Möglichkeiten, die sowohl Kosten als auch Lieferzeiten reduzieren können. Seien Sie sich bewusst, dass die Nachbearbeitung bei hochpräzisen Metall-AM-Komponenten oft ein wichtiger Faktor für Kosten und Lieferzeiten ist.
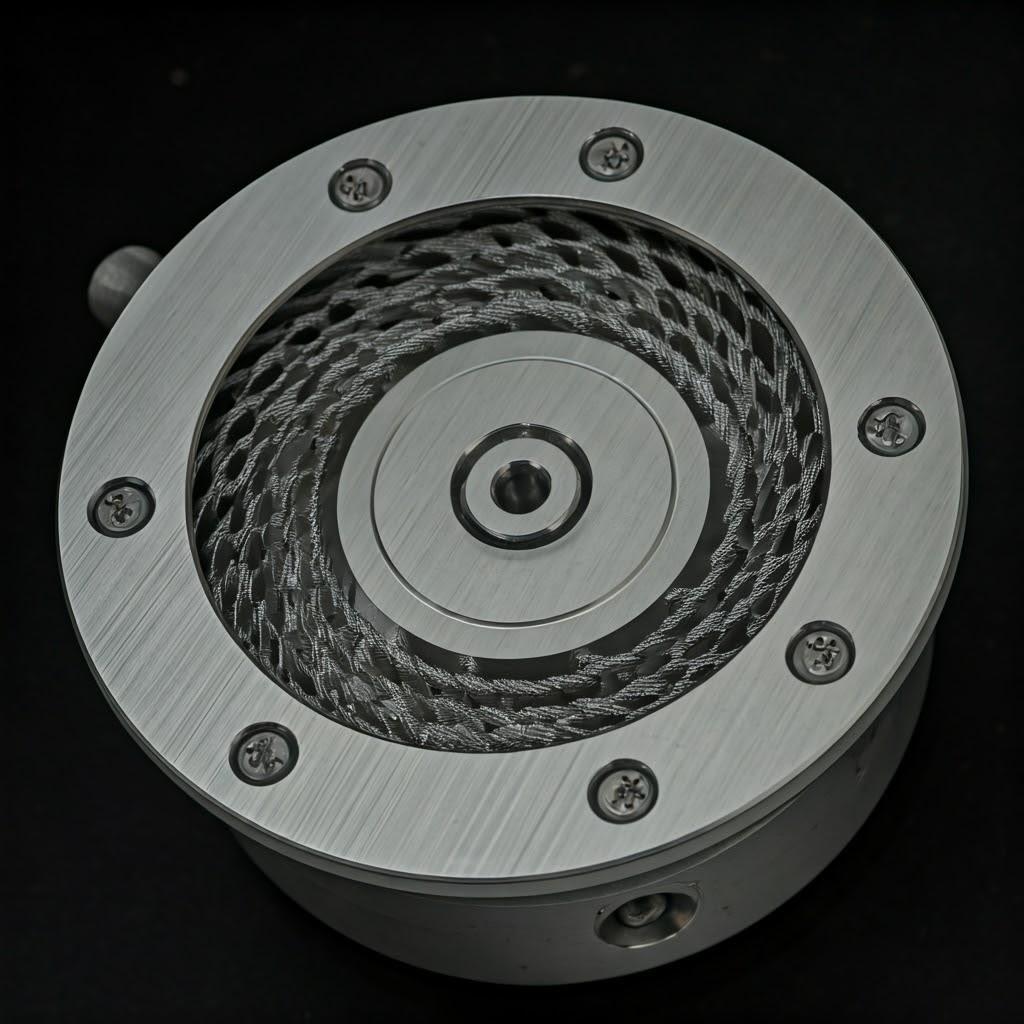
Häufig gestellte Fragen (FAQ) zu 3D-gedruckten Instrumentenhalterungen
Hier finden Sie Antworten auf einige häufig gestellte Fragen von Ingenieuren und Beschaffungsmanagern, wenn sie die additive Fertigung von Metallteilen für Präzisionsgerätehalterungen in Betracht ziehen:
F1: Wie hoch sind die Kosten für eine 3D-gedruckte Instrumentenhalterung aus Metall im Vergleich zu einer CNC-gefrästen Halterung?
A: Darauf gibt es keine einheitliche Antwort, da dies stark von mehreren Faktoren abhängt:
- Komplexität: Bei hochkomplexen Geometrien (interne Kanäle, Topologieoptimierung, Gitterstrukturen), die sich nur schwer oder gar nicht bearbeiten lassen, ist AM oft kostengünstiger, selbst bei geringen Stückzahlen. Die maschinelle Bearbeitung solcher Teile kann mehrere komplexe Aufbauten oder die Herstellung und Montage mehrerer Teile erfordern, was die Kosten erhöht.
- Lautstärke: Bei einfachen Geometrien, die in großen Mengen hergestellt werden, ist die CNC-Bearbeitung aufgrund der etablierten Automatisierung und der schnelleren Zykluszeiten nach dem Einrichten in der Regel kostengünstiger. AM hat geringere Einrichtungskosten, was es für Prototypen und Kleinserien (typischerweise 1-100 Teile) wettbewerbsfähig macht.
- Material: Bei teuren Werkstoffen wie Invar, die schwer zu bearbeiten sind (was zu hohem Werkzeugverschleiß und langsamen Geschwindigkeiten führt) und bei subtraktiven Verfahren erheblichen Abfall erzeugen, kann AM aufgrund der besseren Materialausnutzung (niedrigeres Einkaufs-zu-Flug-Verhältnis) wettbewerbsfähiger sein, selbst wenn die Rohpulverkosten hoch sind.
- Teil Konsolidierung: Wenn AM es ermöglicht, mehrere maschinell gefertigte Teile in einer einzigen gedruckten Komponente zusammenzufassen, kann das AM-Teil unter Berücksichtigung der Gesamtkosten (Teilekosten + Montageaufwand + verringertes Risiko von Montagefehlern) billiger sein.
- Nachbearbeiten: Wenn das AM-Teil eine umfangreiche Nachbearbeitung erfordert, um die Toleranzen einzuhalten, erhöht dies die Kosten erheblich, so dass eine CNC-Bearbeitung von Anfang an rentabler ist, sofern die Geometrie dies zulässt.
- Empfehlung: Holen Sie Angebote für beide Methoden auf der Grundlage Ihrer spezifischen Design-, Material-, Mengen- und Toleranzanforderungen ein, um eine fundierte Entscheidung treffen zu können. Berücksichtigen Sie die gesamten Lebenszykluskosten, einschließlich der Designflexibilität und der potenziellen Leistungssteigerung durch AM.
F2: Welchen Grad an Präzision und thermischer Stabilität kann ich realistischerweise von einer 3D-gedruckten Invar-Fassung erwarten?
A:
- Präzision: Die Maßtoleranzen für Invar im Druckzustand liegen in der Regel im Bereich von ±0,1 mm bis ±0,2 mm oder ±0,1-0,2 %. Die Oberflächengüte (Ra) kann etwa 10-25μm betragen (LPBF). Um die Toleranzen im Mikrometerbereich ($ \pm 0,01 – 0,05$ mm oder besser) und die glatten Oberflächen (Ra <1,6μm) zu erreichen, die normalerweise für kritische Ausrichtungsmerkmale auf optischen oder messtechnischen Präzisionshalterungen erforderlich sind, die Nachbearbeitung dieser spezifischen Merkmale ist unerlässlich.
- Thermische Stabilität: Dies ist der Hauptvorteil von Invar’. Bei korrekter Verarbeitung (einschließlich geeigneter Spannungsabbau- und Stabilisierungswärmebehandlungen nach dem Druck) behält 3D-gedrucktes Invar seinen extrem niedrigen Wärmeausdehnungskoeffizienten (WAK) bei, der bei Raumtemperatur typischerweise bei 1,2×10-6/K liegt. Dies gewährleistet eine minimale Änderung der Abmessungen bei Temperaturschwankungen, was für die Aufrechterhaltung der Ausrichtung in empfindlichen Systemen entscheidend ist. Es ist wichtig, mit einem Anbieter zusammenzuarbeiten, der in der Invar-Verarbeitung und Wärmebehandlung erfahren ist, um diese Eigenschaft zu gewährleisten.
F3: Sind 3D-gedruckte Metallteile genauso stabil und zuverlässig wie Komponenten aus herkömmlichen Knet- oder Gusswerkstoffen?
A: Ja, potenziell. Bei ausgereifter Prozesssteuerung und geeigneter Nachbearbeitung können AM-Metallteile hervorragende mechanische Eigenschaften aufweisen:
- Die Dichte: Verfahren wie LPBF und SEBM können, wenn sie optimiert werden, eine Teiledichte von mehr als 99,5 % erreichen, manchmal sogar eine relative Dichte von mehr als 99,9 %, vergleichbar mit gegossenen oder gekneteten Materialien.
- Festigkeit & Duktilität: Die Eigenschaften von gedruckten Produkten können manchmal denen von gegossenen Pendants entsprechen oder diese sogar übertreffen. Mit Nachbearbeitungsverfahren wie dem Heiß-Isostatischen Pressen (HIP) - das interne Porosität beseitigt - und geeigneten Wärmebehandlungen können die mechanischen Eigenschaften (Streckgrenze, Zugfestigkeit, Dehnung, Ermüdungsfestigkeit) von AM-Teilen oft die Standardspezifikationen für Knetwerkstoffe erreichen oder sogar übertreffen, insbesondere bei bestimmten Legierungen wie Titan.
- Verlässlichkeit: Der Schlüssel ist Beständigkeit. Die Zusammenarbeit mit einem seriösen AM-Anbieter, der hochwertige Pulver verwendet, eine strenge Prozesskontrolle durchführt, die erforderlichen zerstörungsfreien Prüfungen durchführt und Materialzertifizierungen und Testdaten bereitstellen kann, ist entscheidend für die Gewährleistung der Zuverlässigkeit, die für kritische Anwendungen wie Instrumentenhalterungen erforderlich ist. Bei anspruchsvollen Anwendungen sollten die Eigenschaften immer durch Tests überprüft werden, die die Betriebsbedingungen widerspiegeln.
F4: Wie kann ich die Qualität und Konsistenz von 3D-gedruckten Halterungen sicherstellen, insbesondere bei kritischen Anwendungen, die eine Zertifizierung erfordern?
A: Die Sicherung der Qualität erfordert einen vielschichtigen Ansatz in der gesamten Lieferkette:
- Auswahl der Lieferanten: Wählen Sie einen Anbieter mit einem soliden Qualitätsmanagementsystem (QMS), das idealerweise nach ISO 9001 und ggf. AS9100 (Luft- und Raumfahrt) oder ISO 13485 (Medizin) zertifiziert ist. Überprüfen Sie die Erfahrung des Anbieters mit Ihrem spezifischen Material und Anwendungstyp.
- Materialkontrolle: Bestehen Sie auf der Verwendung von Pulver aus seriösen Quellen mit Chargenrückverfolgung und Materialzertifizierungen gemäß den einschlägigen Normen (ASTM, ISO, AMS). Informieren Sie sich über die Verfahren des Lieferanten zur Handhabung und zum Recycling des Pulvers.
- Prozesskontrolle: Stellen Sie sicher, dass der Anbieter Maschinen mit prozessbegleitender Überwachung einsetzt und die kritischen Prozessparameter streng kontrolliert und für jede Produktion dokumentiert.
- Klar Spezifikationen: Legen Sie detaillierte Zeichnungen mit eindeutigen Toleranzen, Anforderungen an die Oberflächenbeschaffenheit (mit Angabe der zu bearbeitenden Oberflächen), erforderlichen Nachbearbeitungen (Wärmebehandlungen, HIP) und etwaigen NDT-Anforderungen vor.
- Nachbearbeitungsprüfung: Sicherstellen, dass alle erforderlichen Nachbearbeitungsschritte korrekt durchgeführt werden (z. B. Überprüfung der Wärmebehandlungszyklen).
- Inspektion und Prüfung: Legen Sie das erforderliche Maß an Inspektion (z. B. CMM-Berichte für kritische Abmessungen, Messungen der Oberflächenrauheit) und zerstörungsfreier Prüfung (z. B. CT-Scannen für innere Unversehrtheit, Farbeindringverfahren für Oberflächenfehler) fest. Fordern Sie Berichte über die Endkontrolle an.
- Dokumentation: Verlangen Sie ein umfassendes Dokumentationspaket mit Materialzertifikaten, Fertigungsprotokollen (falls vorhanden/vereinbart), Wärmebehandlungsprotokollen, Inspektionsberichten und Konformitätsbescheinigungen.
Schlussfolgerung: Verbessern Sie Ihre Instrumentierung mit fortschrittlicher additiver Fertigung von Metall
In den anspruchsvollen Bereichen der Luft- und Raumfahrt, der Medizintechnik, der Messtechnik und der fortschrittlichen industriellen Automatisierung ist das Streben nach höherer Präzision, verbesserter Leistung und größerer Designflexibilität unerbittlich. Präzisionsgerätehalterungen werden zwar oft übersehen, sind aber ein wesentlicher Faktor für den Fortschritt in diesen Bereichen. Wie wir erforscht haben, bietet die additive Fertigung von Metallen einen Paradigmenwechsel in der Art und Weise, wie diese kritischen Komponenten entworfen und hergestellt werden können.
Durch die Überwindung der Beschränkungen der traditionellen Bearbeitung ermöglicht Metall-AM den Ingenieuren die Herstellung von Instrumentenhalterungen, die einzigartig sind:
- Geometrisch optimiert: Topologieoptimierung und generatives Design für ein unvergleichliches Verhältnis von Steifigkeit zu Gewicht.
- Funktional integriert: Merkmale wie konforme Kühlung, schwingungsdämpfende Strukturen und konsolidierte Baugruppen werden direkt in die Halterung integriert.
- Leichtes Gewicht: Drastische Verringerung der Masse für Anwendungen, bei denen das Gewicht entscheidend ist, ohne dabei die Stabilität zu beeinträchtigen.
- Materiell fortgeschritten: Dies ermöglicht den effizienten Einsatz von Speziallegierungen wie Invar mit geringer Ausdehnung für ultimative thermische Stabilität oder korrosionsbeständiges 316L für raue Umgebungen.
- Schnell prototypisiert und angepasst: Beschleunigung der Entwicklungszyklen und Ermöglichung maßgeschneiderter Lösungen für spezifische Instrumentierungsanforderungen.
Die erfolgreiche Nutzung dieser Vorteile erfordert einen ganzheitlichen Ansatz, der strenge Design for Additive Manufacturing (DfAM)-Grundsätze, ein klares Verständnis der erreichbaren Präzision und der erforderlichen Nachbearbeitungsschritte sowie die sorgfältige Beachtung potenzieller Herausforderungen wie Eigenspannungen und Porosität umfasst. Von entscheidender Bedeutung ist die Zusammenarbeit mit einem sachkundigen und fähigen Metall-AM-Dienstleister.
Die Wahl eines Lieferanten wie Met3dpmet3dp kombiniert jahrzehntelange Erfahrung mit modernster Technologie - von fortschrittlichen SEBM-Drucksystemen, die für ihre Genauigkeit und Zuverlässigkeit bekannt sind, bis hin zur hauseigenen Produktion von hochwertigen, sphärischen Metallpulvern - und gewährleistet so eine Grundlage für Qualität und Leistungsfähigkeit. Met3dp bietet umfassende metall-3D-Druck lösungen, die Ausrüstung, Materialien und Anwendungsentwicklungsdienste umfassen, und arbeitet mit Unternehmen zusammen, um deren Einführung der additiven Fertigung zu beschleunigen.
Durch den Einsatz von Metall-AM können Unternehmen nicht nur die Leistung und Zuverlässigkeit ihrer aktuellen Instrumente verbessern, sondern auch völlig neue Möglichkeiten für das Design und die Leistungsfähigkeit von Geräten erschließen. Ganz gleich, ob Sie die außergewöhnliche thermische Stabilität von Invar für optische Systeme, die Biokompatibilität und Korrosionsbeständigkeit von 316L für medizinische Geräte oder topologieoptimierte Leichtbaustrukturen für Sensoren in der Luft- und Raumfahrt benötigen - die additive Fertigung von Metallen bietet die Werkzeuge, um Ihre Instrumente auf die nächste Stufe zu heben.
Möchten Sie erfahren, wie die additive Fertigung von Metallen Ihre Lösungen für die Montage von Präzisionsinstrumenten revolutionieren kann? Setzen Sie sich noch heute mit Met3dp in Verbindung, um Ihre Anwendungsanforderungen mit unserem Expertenteam zu besprechen und herauszufinden, wie unsere fortschrittlichen Fähigkeiten die Innovation in Ihrem Unternehmen vorantreiben können.
Teilen auf
MET3DP Technology Co., LTD ist ein führender Anbieter von additiven Fertigungslösungen mit Hauptsitz in Qingdao, China. Unser Unternehmen ist spezialisiert auf 3D-Druckgeräte und Hochleistungsmetallpulver für industrielle Anwendungen.
Fragen Sie an, um den besten Preis und eine maßgeschneiderte Lösung für Ihr Unternehmen zu erhalten!
Verwandte Artikel
Über Met3DP
Aktuelles Update
Unser Produkt
KONTAKT US
Haben Sie Fragen? Senden Sie uns jetzt eine Nachricht! Wir werden Ihre Anfrage mit einem ganzen Team nach Erhalt Ihrer Nachricht bearbeiten.
Holen Sie sich Metal3DP's
Produkt-Broschüre
Erhalten Sie die neuesten Produkte und Preislisten
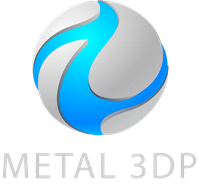
Metallpulver für 3D-Druck und additive Fertigung