3D-Drucken von mechanischen Kupplungen mit Edelstahl: Ein Leitfaden für industrielle Anwendungen
Inhaltsübersicht
Einführung: Revolutionierung mechanischer Kupplungen durch additive Fertigung von Metall
Mechanische Kupplungen sind die unbesungenen Helden der rotierenden Maschinen. Diese unverzichtbaren Komponenten überbrücken die Lücke zwischen Antriebswellen (z. B. Motoren) und angetriebenen Wellen (z. B. Pumpen, Getriebe oder Aktuatoren), übertragen Leistung, gleichen Ausrichtungsfehler aus und dämpfen manchmal Stöße oder Vibrationen. Kupplungen sorgen für einen reibungslosen, zuverlässigen Betrieb - von der komplizierten Robotertechnik in Hochgeschwindigkeits-Fertigungsstraßen bis hin zu den kritischen Kraftübertragungssystemen in Luft- und Raumfahrzeugen und den robusten Antriebssträngen in der Automobilindustrie. Ihr Versagen kann zu kostspieligen Ausfallzeiten, Anlagenschäden und sogar zu Sicherheitsrisiken führen. Bei der Herstellung dieser wichtigen Teile wurde bisher auf bewährte Methoden wie die spanende Bearbeitung von Stangenmaterial oder das Gießen zurückgegriffen, Verfahren, die zwar zuverlässig sind, aber oft mit Einschränkungen hinsichtlich der Komplexität der Konstruktion, des Materialabfalls und der Vorlaufzeiten für kundenspezifische Lösungen einhergehen.
Eintritt in die Ära der Additive Fertigung von Metall (AM), besser bekannt als Metall 3D-Druck. Diese transformative Technologie verändert die Art und Weise, wie komplexe Metallteile entworfen und hergestellt werden, grundlegend. Anstatt Material abzutragen (subtraktive Fertigung) oder geschmolzenes Metall in Formen zu gießen (Gießen), baut AM Teile Schicht für Schicht direkt aus digitalen Entwürfen mit Hochleistungsmetallpulvern auf. Dieser Ansatz eröffnet ungeahnte Möglichkeiten für die Herstellung mechanischer Verbindungen mit verbesserter Leistung, optimiertem Design und größerer Funktionsintegration.
Konkret bedeutet das die Verwendung von rostfreier Stahl in Metall-AM-Verfahren wie Selective Laser Melting (SLM) oder Electron Beam Melting (EBM) bietet eine überzeugende Kombination aus Festigkeit, Korrosionsbeständigkeit und Fertigungsflexibilität, die sich perfekt für anspruchsvolle Kupplungsanwendungen eignet. Branchen wie Luft- und Raumfahrt, Automobilindustrie, Herstellung medizinischer Geräte und allgemeine industrielle Automatisierung wenden sich zunehmend 3D-gedruckten Edelstahlkupplungen zu, um die Grenzen herkömmlicher Methoden zu überwinden. Warum? Weil AM es ermöglicht:
- Komplexe Geometrien: Schaffung komplizierter interner Strukturen oder flexibler Elemente, die sich nicht bearbeiten lassen.
- Massenanpassung: Herstellung von maßgeschneiderten Kupplungskonstruktionen, die auf einzigartige betriebliche Anforderungen zugeschnitten sind, ohne die unerschwinglichen Kosten der traditionellen Werkzeugherstellung.
- Beschleunigte Entwicklung: Rasche Iteration von Prototypen und schnellerer Übergang zur Produktion als je zuvor.
- Optimierung der Leistung: Entwicklung leichterer, stabilerer Kupplungen durch Topologieoptimierung und Teilekonsolidierung.
Dieser Leitfaden befasst sich mit den Besonderheiten des 3D-Metalldrucks, insbesondere mit 316L- und 17-4PH-Edelstahlpulvern, für die Herstellung mechanischer Hochleistungs-Kupplungen. Wir werden die Anwendungen, Vorteile, Materialüberlegungen, Konstruktionsprinzipien, Nachbearbeitungsanforderungen und die Zusammenarbeit mit dem richtigen AM-Dienstleister untersuchen, um den Erfolg sicherzustellen. Ganz gleich, ob Sie ein Ingenieur sind, der Maschinen der nächsten Generation entwirft, oder ein Beschaffungsmanager, der zuverlässige Komponenten beschaffen muss, das Verständnis des Potenzials von 3D-gedruckten Edelstahlkupplungen ist entscheidend, um wettbewerbsfähig zu bleiben.
Wozu werden mechanische Kupplungen verwendet? Anwendungen in verschiedenen Branchen
Eine mechanische Kupplung dient in erster Linie einem Zweck: Sie verbindet zwei rotierende Wellen zur Kraftübertragung. Ihre Aufgaben gehen jedoch weit über eine einfache Verbindung hinaus und beinhalten oft ausgeklügelte Funktionen, um die Komplexität von Maschinen in der Praxis zu bewältigen.
Kernfunktionen von mechanischen Kupplungen:
- Kraftübertragung: Übertragung des Drehmoments und der Drehbewegung von der Antriebswelle auf die angetriebene Welle mit minimalen Verlusten.
- Ausgleich von Fluchtungsfehlern: Ausgleich von leichten Abweichungen zwischen den verbundenen Wellen. Fluchtungsfehler können sein:
- Parallel: Die Achsen der Wellen sind parallel, aber versetzt.
- Winklig: Die Achsen der Wellen schneiden sich in einem Winkel.
- Axial: Die Wellen bewegen sich während des Betriebs näher zueinander oder weiter auseinander (end-float).
- Schwingungsdämpfung: Absorption oder Isolierung von Drehschwingungen, Vermeidung von Resonanz und Lärm und Schutz empfindlicher Geräte.
- Absorption von Schockbelastungen: Abfederung von plötzlichen Drehmomentänderungen oder Stößen im Antriebsstrang.
- Elektrische Isolierung: Verhinderung des Stromflusses zwischen Wellen in bestimmten Anwendungen.
- Überlastungsschutz: Einige Kupplungen sind so konstruiert, dass sie bei einem bestimmten Drehmoment versagen oder durchrutschen und so als mechanische Sicherung zum Schutz teurer Maschinen dienen.
Gängige Arten von Kupplungen:
Die spezifischen Funktionen, die erforderlich sind, bestimmen die Art der verwendeten Kupplung. Während AM potenziell viele Typen herstellen kann, zeigen sich seine Vorteile oft am deutlichsten bei komplexeren Designs:
- Starre Kupplungen: Bieten eine präzise Ausrichtung und hohe Drehmomentkapazität, können aber keine Ausrichtungsfehler ausgleichen. Wird oft verwendet, wenn die Wellen bereits perfekt ausgerichtet sind. AM kann zur Gewichtsreduzierung oder zur Integration von Kühlelementen verwendet werden.
- Flexible Kupplungen (Materialflexion): Verwenden Sie Biegeelemente (wie Scheiben, Membranen oder Balken), um Ausrichtungsfehler auszugleichen. Beispiele hierfür sind:
- Beam Couplings: AM ermöglicht komplexe Balkenmuster und Materialien, die auf eine bestimmte Steifigkeit oder Ermüdungslebensdauer zugeschnitten sind, und wird oft aus einem einzigen Stück mit spiralförmigen Schnitten gefertigt.
- Membrankupplungen: Verwenden Sie dünne Metallplatten; AM könnte möglicherweise Membranfunktionen in eine Nabe integrieren und so Teile konsolidieren.
- Scheibenkupplungen: Verwenden Sie flexible Metallscheiben; AM ermöglicht die Optimierung der Form von Scheibenpaketen.
- Elastische Kupplungen (Elastomer): Sie enthalten Gummi- oder Polymerelemente zur Dämpfung von Vibrationen und Stößen und zum Ausgleich von Ausrichtungsfehlern. Beispiele hierfür sind:
- Backenkupplungen: Verwenden Sie einen Elastomer-"Spider" zwischen den Metallnaben. Für die Metallnaben wird in der Regel AM verwendet, um vielleicht ihre Form oder ihr Gewicht zu optimieren.
- Reifenkupplungen: Verwenden Sie ein flexibles Gummireifenelement. Auch hier konzentriert sich AM auf die Naben.
- Faltenbalg-Kupplungen: Verwenden Sie dünnwandige Metallbälge für hohe Torsionssteifigkeit und Verlagerungsfähigkeit, wie sie häufig in Präzisionsinstrumenten zu finden sind. AM ermöglicht komplexe Balgformen und die Integration in Naben.
- Fluid-Kupplungen: Sie verwenden Hydraulikflüssigkeit zur Übertragung des Drehmoments und bieten einen sanften Anlauf und Überlastschutz. AM kann für komplexe Laufrad- oder Gehäusekonstruktionen verwendet werden.
Anwendungen treiben die Nachfrage nach modernen Kupplungen an:
Der Bedarf an zuverlässigen, leistungsstarken Kupplungen erstreckt sich auf nahezu alle Industriezweige. Effizient Beschaffung von Industriekupplungen erfordert das Verständnis dieser unterschiedlichen Bedürfnisse:
- Luft- und Raumfahrt: Kritische Anwendungen erfordern ein hohes Verhältnis von Festigkeit zu Gewicht, Zuverlässigkeit bei extremen Temperaturen und Vibrationen sowie Ermüdungsbeständigkeit.
- Beispiele: Betätigungssysteme für Steuerflächen, Kraftstoffpumpenantriebe, Hilfstriebwerke (APU), Satellitenmechanismen. 17-4PH wird hier aufgrund seiner Festigkeit oft bevorzugt.
- Automobilindustrie: Der Schwerpunkt liegt auf Langlebigkeit, Kosteneffizienz für die Massenproduktion (obwohl AM bei Hochleistungs-/Nischenfahrzeugen und im Prototypenbau zunimmt), Schwingungsdämpfung und Ausgleich von Fluchtungsfehlern im Antriebsstrang.
- Beispiele: Antriebswellen, Lenksäulenverbindungen, Komponenten für den Antriebsstrang von Elektrofahrzeugen (EV), Differentialverbindungen. Sowohl 316L (für Korrosionsbeständigkeit) als auch potenziell optimierte 17-4PH-Ausführungen finden Verwendung.
- Industrielle Maschinen: Eine große Kategorie mit unterschiedlichen Anforderungen, von hohem Drehmoment in schweren Maschinen bis hin zu Präzision in der Robotik. Zuverlässigkeit, Wartungszugang und Kosten sind Schlüsselfaktoren.
- Beispiele: Pumpen-Motor-Verbindungen, Förderbandantriebe, Gelenke von Roboterarmen, Verpackungsmaschinen, Werkzeugmaschinen, Mischanlagen. 316L ist für die allgemeine Korrosionsbeständigkeit gebräuchlich, während 17-4PH für Hochlastszenarien verwendet wird. AM ermöglicht kundenspezifische Lösungen für einzigartige Maschinenlayouts oder Nachrüstungen.
- Medizinische Geräte: Sie erfordern Biokompatibilität, die Möglichkeit der Miniaturisierung, einen reibungslosen Betrieb und häufig auch Sterilisationsverträglichkeit. Präzision ist das A und O.
- Beispiele: Chirurgische Robotersysteme, diagnostische Bildgebungsgeräte (MRI/CT-Scanner-Antriebe), medizinische Pumpen, Laborautomatisierung. Biokompatible Werkstoffe wie 316L sind unerlässlich. AM ermöglicht komplizierte, patienten- oder anwendungsspezifische Konstruktionen.
- Energiesektor: Anwendungen in der Energieerzeugung (Turbinen, Generatoren) sowie in der Öl- und Gasindustrie (Pumpen, Kompressoren) erfordern eine hohe Drehmomentkapazität, Zuverlässigkeit in rauen Umgebungen und häufig die Einhaltung von Industrienormen (z. B. API).
Die Kenntnis dieser spezifischen Anwendungsanforderungen - Drehmomentkapazität, Betriebsdrehzahl, Verlagerungstoleranz, Torsionssteifigkeit, Umgebungsbedingungen und erforderliche Lebensdauer - ist der erste Schritt bei der Entscheidung, ob eine 3D-gedruckte Edelstahlkupplung die optimale Lösung ist.
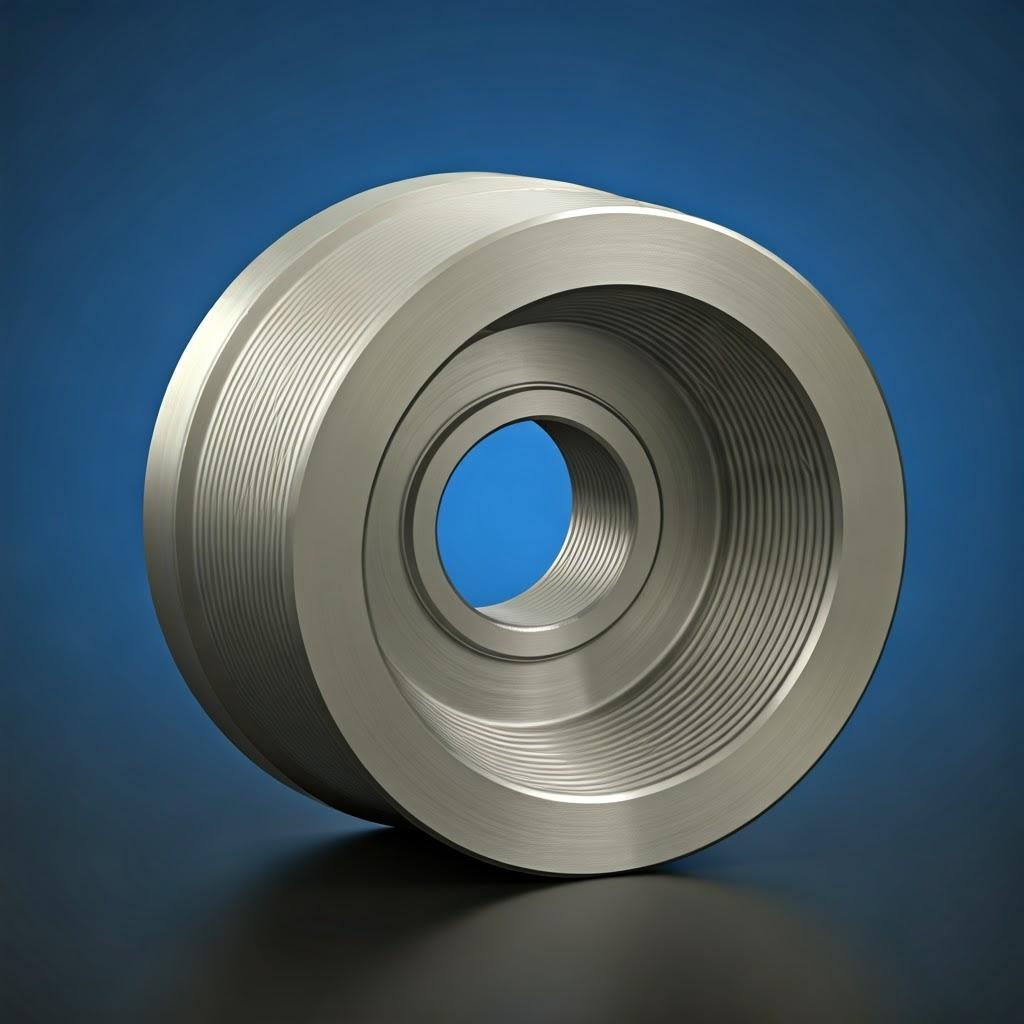
Warum 3D-Metalldruck für Kupplungen aus Edelstahl? Die wichtigsten Vorteile
Während herkömmliche Fertigungsmethoden der Industrie seit Jahrzehnten gute Dienste geleistet haben, stellt die additive Fertigung von Metallen einen Paradigmenwechsel dar, der insbesondere für komplexe oder kundenspezifische Edelstahlkupplungen überzeugende Vorteile bietet. Vergleichen wir AM mit konventionellen Verfahren:
Vergleich: Additive Fertigung vs. traditionelle Methoden für Kupplungen
Merkmal | Additive Fertigung (z. B. SLM/EBM) | Traditionelle Bearbeitung (vom Stangenmaterial) | Traditioneller Guss |
---|---|---|---|
Gestaltungsfreiheit | Sehr hoch (komplexe interne Merkmale, Topologie-Optimierung, Gitternetze) | Mäßig (begrenzt durch Zugang zu Werkzeugen und Verfahren) | Mäßig (begrenzt durch die Komplexität der Form) |
Komplexität Kosten | Weniger empfindlich gegenüber Komplexität; hauptsächlich durch Volumen/Höhe bestimmt | Hoch; Komplexität erhöht Bearbeitungszeit/Schritte | Hoch; Komplexität erhöht die Werkzeugkosten |
Personalisierung | Hoch; einfaches Herstellen einzigartiger Designs pro Los/Einheit | Mäßig; erfordert kundenspezifische Vorrichtungen/Programmierung | Gering; erfordert teure Sonderformen |
Vorlaufzeit (Proto) | Schnell; direkt vom CAD, keine Werkzeuge erforderlich | Mäßig bis langsam; abhängig von der Komplexität/Einrichtung | Langsam; erfordert Entwurf und Herstellung von Formen |
Vorlaufzeit (Prod) | Geeignet für niedriges bis mittleres Volumen; potenziell langsamer für hohes Volumen | Schnell für hohes Volumen, sobald es eingerichtet ist | Schnell für hohe Stückzahlen, sobald die Werkzeuge fertig sind |
Materialabfälle | Gering; verwendet Pulver vor allem dort, wo es benötigt wird (bei den Trägern entsteht etwas Abfall) | Hoch; erheblicher Materialabtrag als Späne | Mäßig; Läufer, Tore, Blinken |
Teil Konsolidierung | Hohes Potenzial; Kombination mehrerer Teile in einem Druck | Geringes Potenzial | Geringes Potenzial |
Typische Materialien | Große Auswahl an schweißbaren Legierungen (einschließlich 316L, 17-4PH) | Zerspanbare Legierungen | Gießbare Legierungen |
Kosten für die Erstausstattung mit Werkzeugen | Minimal/Keine | Gering bis mäßig (Vorrichtungen) | Hoch (Schimmelpilze) |
In Blätter exportieren
Anhand dieses Vergleichs werden die spezifischen Vorteile des Einsatzes von Metall-AM für Edelstahlkupplungen deutlich:
- Unerreichte Designfreiheit: Dies ist wohl der größte Vorteil von AM. Ingenieure sind nicht mehr an die Zwänge des "Design for Manufacturability" gebunden, die mit der maschinellen Bearbeitung oder dem Gießen verbunden sind.
- Beispiel: Entwerfen Sie ein flexibles Kupplungselement mit internen Gitterstrukturen, die für bestimmte Torsionssteifigkeits- und Dämpfungseigenschaften optimiert sind - etwas, das sich nicht maschinell bearbeiten lässt. Oder integrieren Sie Kühlkanäle direkt in eine Kupplungsnabe für hohe Drehmomente, die in einer heißen Umgebung arbeitet. Mithilfe von Topologieoptimierungssoftware kann Material aus unkritischen Bereichen entfernt werden, wodurch das Gewicht drastisch reduziert und gleichzeitig die Festigkeit und Steifigkeit beibehalten oder sogar erhöht wird - ideal für Luft- und Raumfahrt oder Hochgeschwindigkeitsanwendungen.
- Mühelose Anpassung: Benötigen Sie eine Kupplung mit nicht standardisierten Bohrungsgrößen, speziellen Keilnutenabmessungen, einer einzigartigen Länge oder einer optimierten Leistung für eine Nischenanwendung? AM ermöglicht die wirtschaftliche Herstellung von Herstellung von Spezialkupplungen selbst für Einzelstücke oder Kleinserien, ohne hohe Werkzeugkosten zu verursachen. Dies ist von unschätzbarem Wert für das Prototyping, maßgeschneiderte Maschinen oder den Ersatz veralteter Teile.
- Beschleunigtes Prototyping und Iteration: Schneller Übergang von einem CAD-Entwurf zu einem funktionalen Metallprototyp. Testen Sie die Verbindung, ermitteln Sie Verbesserungen, ändern Sie das Design digital und drucken Sie eine neue Iteration innerhalb von Tagen statt Wochen oder Monaten. Diese Geschwindigkeit verkürzt die Entwicklungszyklen drastisch und ermöglicht eine gründlichere Designvalidierung. Dies ist der Schlüssel für Unternehmen, die Rapid-Prototyping-Kupplungen.
- Materialeffizienz und Nachhaltigkeit: Bei der subtraktiven Fertigung können oft 50-90% des ursprünglichen Materialblocks zu Abfallspänen werden. Bei der additiven Fertigung wird das Material viel effizienter genutzt. Zwar wird ein Teil des Pulvers für Stützstrukturen verwendet, und ein Teil kann nicht unbegrenzt recycelt werden, doch ist der Materialverbrauch insgesamt deutlich geringer, was Kosten und Umweltauswirkungen reduziert, insbesondere bei teuren Legierungen.
- Produktion auf Abruf und digitale Bestandsaufnahme: AM ermöglicht den Ansatz eines "digitalen Lagers". Anstatt zahlreiche Kupplungsvarianten auf Lager zu haben, können die Entwürfe digital gespeichert und nach Bedarf gedruckt werden. Dies reduziert die Lagerkosten und den Abfall durch Veralterung und ist ideal für die Herstellung von Ersatzteilen für ältere Systeme oder die Bewältigung einer schwankenden Nachfrage nach Großhandel mit 3D-gedruckten Teilen.
- Verbesserte Leistung durch Optimierung:
- Gewichtsreduzierung: Wie bereits erwähnt, können durch die Topologieoptimierung Kupplungen geschaffen werden, die deutlich leichter sind als ihre herkömmlichen Gegenstücke, was für die Verringerung der Trägheit in Hochgeschwindigkeitssystemen oder für Gewichtseinsparungen in der Luft- und Raumfahrt sowie in der Automobilindustrie von entscheidender Bedeutung ist.
- Verbesserte Funktionalität: Entwerfen Sie flexible Elemente mit genau zugeschnittenen Steifigkeitsprofilen oder integrieren Sie Sensorhalterungen direkt in den Kupplungskörper.
- Teil Konsolidierung: Eine mehrteilige Kupplungsbaugruppe (z. B. Naben, Abstandshalter, flexible Elemente) kann neu entworfen und als ein einziges, komplexes Bauteil gedruckt werden. Dies reduziert die Montagezeit, mögliche Fehlerquellen und oft auch das Gewicht.
Die Wahl von rostfreiem Stahl für diese AM-Prozesse nutzt die inhärenten Vorteile des Materials - Korrosionsbeständigkeit, Festigkeit und Haltbarkeit - die durch die Design- und Fertigungsflexibilität des 3D-Drucks noch verstärkt werden.
Empfohlene Edelstahlpulver (316L & 17-4PH) und warum sie wichtig sind
Der Erfolg einer 3D-gedruckten Metallkupplung hängt wesentlich von der Auswahl des richtigen Materials ab. Metallpulver, die in AM-Verfahren wie Laser Powder Bed Fusion (LPBF - dazu gehören SLM und DMLS) oder Electron Beam Melting (EBM) verwendet werden, müssen strenge Kriterien hinsichtlich Größenverteilung, Sphärizität, Fließfähigkeit und chemischer Reinheit erfüllen, um dichte, zuverlässige Endteile zu gewährleisten.
Bei Kupplungen aus rostfreiem Stahl zeichnen sich zwei Legierungen durch ein hervorragendes Gleichgewicht von Eigenschaften, Bedruckbarkeit und Industrieakzeptanz aus: 316L und 17-4PH.
Wir sind ein führender Anbieter von Lösungen für die additive Fertigung, Met3dp weiß um die entscheidende Rolle der Pulverqualität. Auf der Grundlage jahrzehntelanger Erfahrung setzt Met3dp branchenführende Technologien zur Gaszerstäubung und zum Plasma-Rotations-Elektroden-Prozess (PREP) ein. Unsere fortschrittlichen Pulverherstellungssysteme mit einzigartigen Düsen- und Gasströmungsdesigns bei der Gaszerstäubung erzeugen hochsphärische Metallpulver mit ausgezeichneter Fließfähigkeit und Reinheit. Dieses Engagement stellt sicher, dass Kunden, die Met3dp-Pulver, einschließlich unserer optimierten 316L- und 17-4PH-Sorten, verwenden, zuverlässig dichte, hochwertige Metallteile mit überlegenen mechanischen Eigenschaften drucken können, die die Grundlage für Hochleistungs-Kupplungen bilden. Unser Portfolio umfasst nicht nur rostfreie Stähle, sondern auch innovative Legierungen wie TiNi, TiTa, TiAl, TiNbZr, CoCrMo und verschiedene Superlegierungen, die den unterschiedlichsten industriellen Anforderungen gerecht werden.
Untersuchen wir die Eigenschaften von 316L- und 17-4PH-Edelstahlpulvern für Kupplungsanwendungen:
Austenitischer rostfreier Stahl: 316L
- Überblick: 316L ist ein weit verbreiteter austenitischer Chrom-Nickel-Stahl mit Molybdänzusatz, der vor allem für seine außergewöhnliche Korrosionsbeständigkeit bekannt ist, insbesondere gegenüber Chloriden und nicht oxidierenden Säuren. Das "L" steht für einen niedrigen Kohlenstoffgehalt, der die Schweißbarkeit verbessert und die Sensibilisierung (Karbidausscheidung) bei thermischen Prozessen verringert.
- Wichtige Eigenschaften für Kupplungen:
- Ausgezeichnete Korrosionsbeständigkeit: Ideal für Kupplungen, die in nassen, chemischen, maritimen, lebensmittelverarbeitenden oder medizinischen Umgebungen eingesetzt werden. Beständig gegen Lochfraß und Spaltkorrosion.
- Gute Duktilität und Verformbarkeit: Das Ergebnis sind zähe, nicht spröde Teile.
- Biokompatibilität: Geeignet für viele Anwendungen in der Medizintechnik (ordnungsgemäße Reinigung und Passivierung erforderlich).
- Nicht-magnetisch: Wichtig für bestimmte Messgeräte oder empfindliche Anwendungen.
- Gut schweißbar: Relevant für mögliche hybride Fertigungskonzepte oder die Montage nach dem Druck.
- Leicht ausdruckbar: Für das Erreichen von dichten Teilen mittels LPBF gibt es wohlverstandene Parameter.
- Ideale Kupplungsanwendungen:
- Pumpen und Mischer für die chemische Verarbeitung.
- Ausrüstung für die Verarbeitung von Lebensmitteln und Getränken.
- Schiffsantriebsanlagen oder Decksmaschinen.
- Medizinische Robotik, Pumpen und Instrumentierung.
- Allgemeine industrielle Anwendungen, bei denen Korrosion wichtiger ist als extrem hohe Festigkeit.
- Beschränkungen:
- Geringere Streckgrenze und Härte im Vergleich zu ausscheidungshärtenden Stählen wie 17-4PH. In der Regel nicht die erste Wahl für Anwendungen mit sehr hohem Drehmoment oder hohem Verschleiß, es sei denn, die Korrosionsbeständigkeit steht im Vordergrund.
- Die Festigkeit kann durch Wärmebehandlung nicht wesentlich erhöht werden (nur durch Glühen zum Spannungsabbau/zur Erweichung).
Ausscheidungshärtung (PH) Edelstahl: 17-4PH
- Überblick: 17-4PH ist ein martensitischer, ausscheidungshärtender rostfreier Stahl, der Chrom, Nickel und Kupfer enthält. Sein Hauptmerkmal ist die Fähigkeit, nach einer relativ einfachen Wärmebehandlung bei niedriger Temperatur (Aushärtung) eine sehr hohe Festigkeit und Härte zu erreichen.
- Wichtige Eigenschaften für Kupplungen:
- Hohe Festigkeit und Härte: Nach einer angemessenen Wärmebehandlung (z. B. Bedingung H900) kann es eine Zugfestigkeit von über 1300 MPa erreichen und eignet sich damit für anspruchsvolle Anwendungen mit hohem Drehmoment.
- Gute Korrosionsbeständigkeit: In der Regel besser als die nichtrostenden Stähle der Serie 400, jedoch in der Regel nicht so beständig wie 316L, insbesondere in chloridhaltiger Umgebung. Geeignet für die meisten Industrie- und Raumfahrtatmosphären.
- Gute Zähigkeit: Behält auch bei hoher Festigkeit eine angemessene Zähigkeit bei.
- Mäßige Abnutzungsbeständigkeit: Aufgrund seiner Härte.
- Ausgezeichnete Druckbarkeit: Weit verbreitet in der Metall-AM mit gut etablierten Parametern.
- Ideale Kupplungsanwendungen:
- Antriebssysteme für die Luft- und Raumfahrt und Triebwerkskomponenten, die ein hohes Verhältnis von Festigkeit zu Gewicht erfordern.
- Industriegetriebe, Pumpen und Stellantriebe für hohe Drehmomente.
- Leistungsstarke Komponenten für den Antriebsstrang von Kraftfahrzeugen.
- Robotersysteme mit hohen Lastanforderungen.
- Anwendungen, bei denen eine hohe Dauerfestigkeit entscheidend ist.
- Erwägungen:
- Erfordert eine Wärmebehandlung nach dem Druck: Wesentlich, um die gewünschten hochfesten Eigenschaften zu erreichen. Dies bedeutet einen zusätzlichen Arbeitsschritt und zusätzliche Kosten für den Prozess. Der spezifische Wärmebehandlungszustand (z. B. H900, H1025, H1075, H1150) muss so gewählt werden, dass ein Gleichgewicht zwischen Festigkeit, Zähigkeit und Korrosionsbeständigkeit besteht.
- Etwas geringere allgemeine Korrosionsbeständigkeit als 316L.
- Magnetisch.
Vergleichstabelle: 316L vs. 17-4PH für AM-Kupplungen
Merkmal | 316L-Edelstahl | 17-4PH Edelstahl (wärmebehandelt, z. B. H900) | Wichtige Überlegung für Kupplungen |
---|---|---|---|
Primärer Vorteil | Hervorragende Korrosionsbeständigkeit, Duktilität | Sehr hohe Festigkeit und Härte | Anpassung des Materials an die primäre operative Herausforderung |
Typische Streckgrenze | ~200-250 MPa (wie gedruckt/geglüht) | ~1170 MPa (Zustand H900) | Drehmomentkapazität, Belastbarkeit |
Typische Zugfestigkeit | ~500-600 MPa (wie gedruckt/geglüht) | ~1310 MPa (Zustand H900) | Grenzbruchstelle, Ermüdungsfestigkeit |
Härte | Niedriger (z. B. ~70 HRB) | Hoch (z. B. ~40 HRC) | Verschleißfestigkeit, Beständigkeit gegen Oberflächeneindrücke |
Korrosionsbeständigkeit | Ausgezeichnet (insbesondere Chloride) | Gut (allgemein atmosphärisch/schwache Chemikalien) | Betriebsumgebung |
Wärmebehandlung | Nicht zum Verfestigen (optionales Glühen) | Erforderlich für optimale Eigenschaften | Prozesskomplexität, Kosten, Abstimmung der Endeigenschaften |
Duktilität/Zähigkeit | Höher | Niedriger (aber gut für seine Stärke) | Fähigkeit, Stöße und Schläge zu absorbieren |
Biokompatibilität | Generell als biokompatibel eingestuft | Nicht typischerweise biokompatibel | Medizinische Anwendungen |
Magnetismus | Nichtmagnetisch | Magnetisch | Sensorstörungen, spezifische Anwendungsanforderungen |
Relative Kosten | Generell niedrigere Pulverkosten | Generell höhere Pulver- und Verarbeitungskosten (aufgrund von HT) | Gesamtbudget des Projekts |
In Blätter exportieren
Die Wahl zwischen 316L und 17-4PH erfordert ein klares Verständnis der Betriebsumgebung der Kupplung, der mechanischen Belastungen (Drehmoment, Geschwindigkeit, Stöße) und der spezifischen Anforderungen wie Biokompatibilität oder magnetische Eigenschaften. Die Zusammenarbeit mit einem erfahrenen Metall-AM-Anbieter wie Met3dp, die nicht nur hochwertige Pulver liefern, sondern auch Dienstleistungen zur Anwendungsentwicklung anbieten, können bei diesen Entscheidungen zur Materialauswahl effektiv helfen. Ihr Fachwissen stellt sicher, dass das gewählte Material perfekt mit der Designabsicht und den Leistungszielen für Ihre 3D-gedruckte Edelstahlkupplung übereinstimmt.
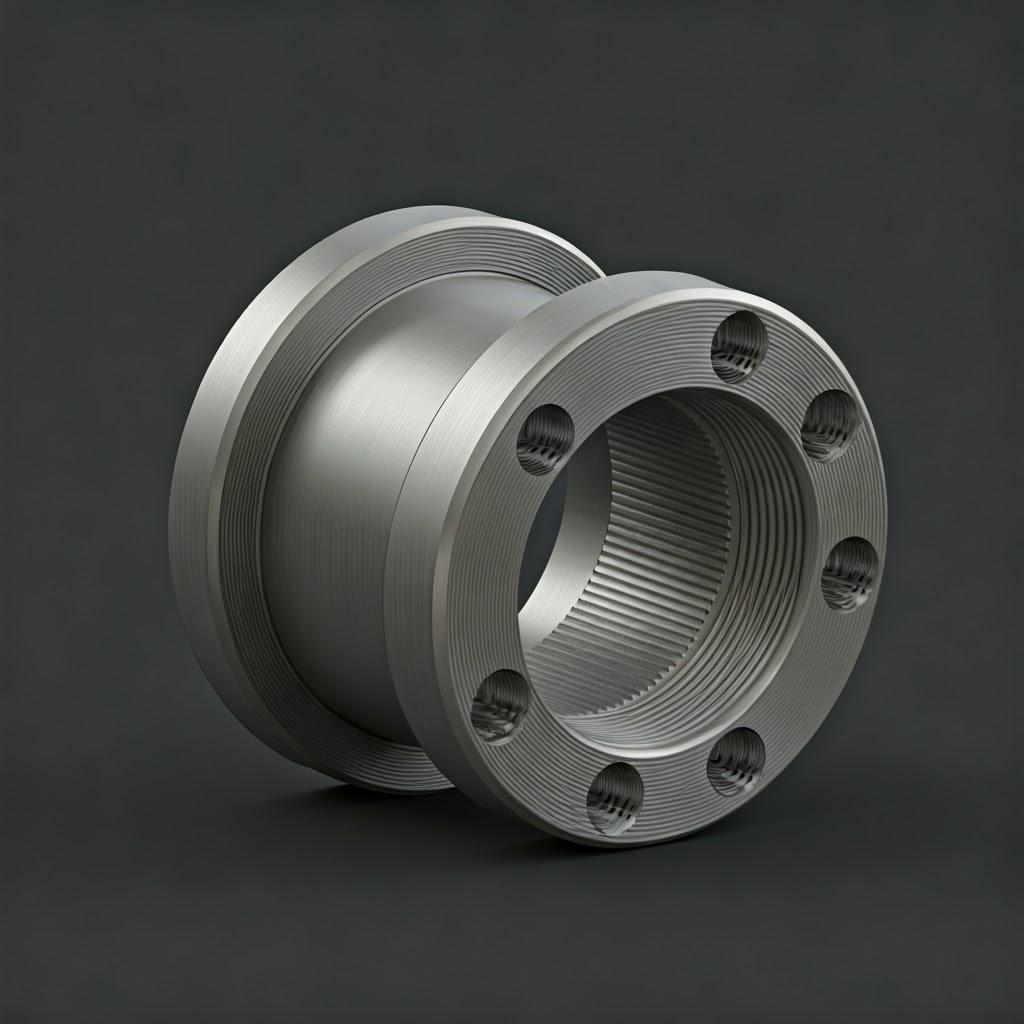
Konstruktionsüberlegungen zur additiven Fertigung von Kupplungen
Einer der überzeugendsten Gründe für die Einführung der additiven Fertigung von mechanischen Kupplungen aus Metall ist die außergewöhnliche Designfreiheit, die sie bietet. Wenn man jedoch ein Design, das für die spanende Bearbeitung vorgesehen ist, einfach an einen 3D-Drucker schickt, werden selten optimale Ergebnisse erzielt. Um die Vorteile von AM wirklich nutzen zu können, müssen Ingenieure Design für additive Fertigung (DfAM) Grundsätze. DfAM bedeutet, den Konstruktionsprozess zu überdenken, um die Stärken von AM zu nutzen und seine einzigartigen Eigenschaften zu berücksichtigen. Zu den wichtigsten DfAM-Überlegungen für mechanische Kupplungen gehören:
- Topologie-Optimierung: Diese Rechentechnik ist revolutionär für die Konstruktion von Kupplungen, insbesondere dort, wo das Gewicht entscheidend ist (Luft- und Raumfahrt, Hochgeschwindigkeitsmaschinen).
- Prozess: Die Software analysiert die Belastungspfade und Spannungen innerhalb eines Kupplungsentwurfs (oder einer Entwurfsraumhülle) und entfernt Material aus Bereichen, die nicht wesentlich zur strukturellen Integrität oder Leistung beitragen.
- Nutzen: Das Ergebnis sind organische, oft komplex aussehende Formen, die deutlich leichter sind (was die Trägheit und den Energieverbrauch verringert) und gleichzeitig die Steifigkeit und Festigkeit im Vergleich zu traditionell konstruierten massiven Teilen beibehalten oder sogar erhöhen. Naben und Abstandshalter sind erstklassige Kandidaten für die Topologieoptimierung bei Kupplungsbaugruppen.
- Beispiel: Eine Standard-Flanschnabenkupplung könnte topologisch so optimiert werden, dass sie 30-50% ihrer Masse einbüßt und dennoch die erforderliche Drehmomentkapazität und Steifigkeit aufweist.
- Gitterförmige Strukturen: AM ermöglicht es, komplizierte innere Gitter- oder Netzstrukturen in den festen Körper einer Kupplung einzubauen.
- Nutzen: Diese Strukturen können ingenieurmäßig bearbeitet werden:
- Gewichtsreduzierung: Ähnlich wie die Topologieoptimierung, aber mit regelmäßigeren, kontrollierbaren internen Geometrien.
- Schwingungsdämpfung: Spezielle Gitterzellenkonstruktionen können Schwingungsenergie absorbieren oder ableiten und so die Systemdynamik verbessern.
- Maßgeschneiderte Flexibilität: Gestaltung bestimmter Abschnitte einer Kupplung (z. B. eines flexiblen Elements) mit Gitterstrukturen, um präzise Steifigkeitseigenschaften in verschiedenen Richtungen (axial, winklig, parallel) zu erreichen.
- Beispiel: Entwurf einer Balkenkupplung, bei der die flexiblen Balken durch eine präzise konstruierte Gitterstruktur ersetzt oder ergänzt werden, um die Eigenschaften des Versatzausgleichs und der Torsionssteifigkeit fein abzustimmen.
- Nutzen: Diese Strukturen können ingenieurmäßig bearbeitet werden:
- Teil Konsolidierung: Herkömmliche Kupplungsbaugruppen bestehen oft aus mehreren Komponenten, die miteinander verschraubt oder verbunden sind (z. B. zwei Naben, ein Zwischenstück, flexible Elemente, Befestigungselemente). Mit AM können Konstrukteure diese mehreren Teile zu einer einzigen, integrierten Komponente zusammenfassen.
- Nutzen: Reduziert den Zeit- und Arbeitsaufwand für die Montage, eliminiert potenzielle Fehlerstellen an den Verbindungsstellen, minimiert die Anzahl der Teile (vereinfacht die Beschaffung und den Lagerbestand) und reduziert häufig das Gesamtgewicht und die Größe des Gehäuses.
- Beispiel: Entwurf einer Klauenkupplung, bei der die Naben und die Grundstruktur, die den (separat eingefügten) Elastomerzahnkranz hält, als ein monolithisches Teil gedruckt werden, oder Entwurf einer komplexen Balgkupplung, bei der das Balgelement nahtlos in die Endnaben integriert ist.
- Merkmal Integration: Die additive Fertigung ermöglicht die nahtlose Integration zusätzlicher Funktionsmerkmale direkt in das Kupplungsdesign.
- Nutzen: Erhöht die Funktionalität, ohne dass weitere Montage- oder Änderungsschritte erforderlich sind.
- Beispiele:
- Integration von Befestigungspunkten für Sensoren (Geschwindigkeit, Vibration, Temperatur).
- Entwurf interner Kanäle für Kühlflüssigkeit oder Schmierung bei Anwendungen mit hoher Hitze oder hohem Verschleiß.
- Merkmale für eine leichtere Montage oder Demontage.
- Hinzufügen spezifischer Geometrien für das Auswuchten bei hohen Geschwindigkeiten.
- Wanddicke und Mindestgröße der Elemente: AM-Prozesse haben Grenzen, wenn es darum geht, dünne Wände oder feine Merkmale zuverlässig herzustellen.
- Erwägung: Die Konstrukteure müssen sich an die spezifischen Richtlinien des gewählten AM-Verfahrens (z. B. LPBF, EBM) und der Maschine halten. Typische Mindestwandstärken liegen bei etwa 0,4-0,8 mm, aber dickere Wände sind in der Regel robuster und leichter zuverlässig zu drucken. Scharfe Innenecken sollten vermieden werden (verwenden Sie Verrundungen), um Spannungskonzentrationen zu verringern.
- Konsultation der Anbieter: Eine frühzeitige Beratung mit Ihrem AM-Dienstleister, wie Met3dp, in der Entwurfsphase ist entscheidend, um die spezifischen Maschinenfähigkeiten und Empfehlungen zu verstehen.
- Unterstützende Strukturen: Die meisten Metall-AM-Prozesse erfordern Stützstrukturen, um das Teil auf der Bauplatte zu verankern, Verformungen zu verhindern und überhängende Merkmale oder Oberflächen zu stützen, die in einem geringen Winkel zur Bauplatte gedruckt werden.
- Ziel der Gestaltung: Minimieren Sie den Bedarf an Stützen, wo immer dies möglich ist, und konstruieren Sie Stützen, die leicht und sauber zu entfernen sind, ohne kritische Oberflächen zu beschädigen.
- Strategien:
- Orientierung: Durch eine sorgfältige Auswahl der Ausrichtung des Teils auf der Bauplatte können Überhänge erheblich reduziert werden.
- Selbsttragende Winkel: Durch die Gestaltung von Auskragungen über einem bestimmten Winkel (in der Regel >45 Grad zur Horizontalen) entfällt häufig die Notwendigkeit einer direkten Abstützung darunter.
- Zugängliche Unterstützungen: Sicherstellen, dass die Stützstrukturen für die manuelle oder maschinelle Entfernung leicht erreichbar sind. Vermeiden Sie nach Möglichkeit Stützen auf kritischen Funktionsflächen oder planen Sie eine Nachbearbeitung ein.
- Fasen/Flanken: Durch das Ersetzen von scharfen horizontalen Überhängen durch abgeschrägte oder abgerundete Kanten können diese selbsttragend werden.
- Orientierung aufbauen: Wie eine Kupplung während des Druckvorgangs ausgerichtet wird, beeinflusst mehrere Faktoren:
- Oberfläche: Oberflächen, die nach oben gerichtet sind, haben im Allgemeinen eine bessere Oberfläche als solche, die nach unten gerichtet sind oder gestützt werden müssen. Seitenwände weisen oft Schichtlinien auf.
- Mechanische Eigenschaften: Aufgrund des schichtweisen Aufbaus können AM-Teile eine leichte Anisotropie aufweisen (Eigenschaften, die je nach Richtung leicht variieren). Bei der Ausrichtung sollten die primären Belastungsrichtungen berücksichtigt werden.
- Anforderungen an die Unterstützung: Wie bereits erwähnt, bestimmt die Orientierung, wo Stützen benötigt werden.
- Bauzeit und Kosten: Größere Bauteile brauchen in der Regel länger. Das effiziente Packen mehrerer Teile auf der Bauplatte ist der Schlüssel zur Kostensenkung, insbesondere bei Großhandel mit 3D-gedruckten Teilen.
Effektives DfAM erfordert ein Umdenken, erschließt aber das volle Potenzial von 3D-gedruckten Edelstahlkupplungen und führt zu Komponenten, die leichter, stabiler, funktioneller und potenziell kostengünstiger sind als ihre traditionell hergestellten Gegenstücke, wenn es um Komplexität oder individuelle Anpassung geht.
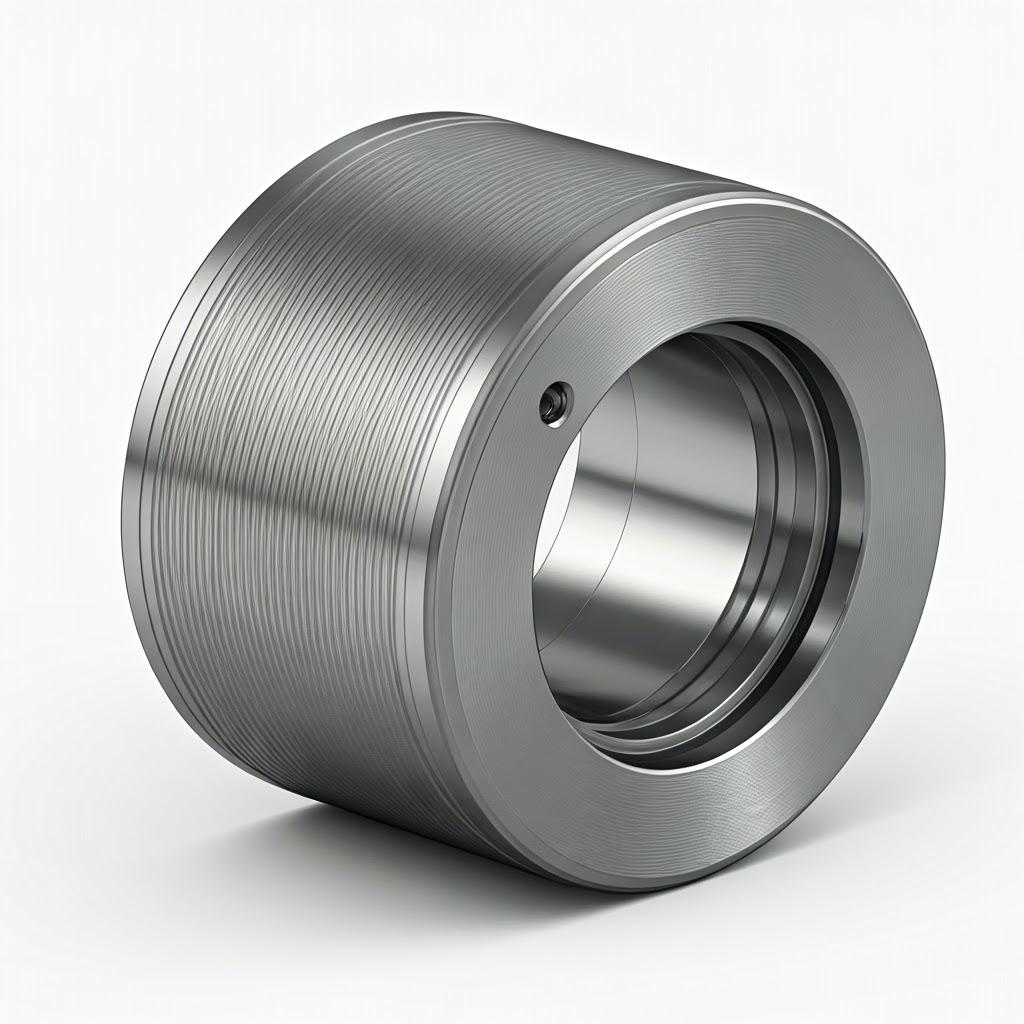
Erreichbare Toleranzen, Oberflächengüte und Maßgenauigkeit bei AM-Kupplungen
Ingenieure und Beschaffungsmanager, die an die engen Toleranzen gewöhnt sind, die mit Präzisionsbearbeitung erreicht werden können, müssen die Möglichkeiten und Grenzen der 3D-Druck von Metall in Bezug auf Maßgenauigkeit und Oberflächengüte. Während sich die AM-Technologie kontinuierlich verbessert, ist es wichtig, realistische Erwartungen an die gefertigten Teile zu stellen.
Maßgenauigkeit und Toleranzen:
- Typische As-Built-Toleranzen: Bei Verfahren wie LPBF (SLM/DMLS) liegen die typischen erreichbaren Toleranzen oft im Bereich von:
- ±0,1 mm bis ±0,2 mm für kleinere Merkmale (z. B. bis zu 20-50 mm).
- ±0,1% bis ±0,2% des Nennmaßes für größere Merkmale.
- EBM weist aufgrund höherer Prozesstemperaturen und Pulvereigenschaften im Allgemeinen etwas geringere Toleranzen auf als LPBF.
- Faktoren, die die Genauigkeit beeinflussen: Das Erreichen dieser Toleranzen hängt stark davon ab:
- Maschinenkalibrierung und Qualität: Hochwertige, gut gewartete Drucker, wie sie möglicherweise von Experten wie Met3dp eingesetzt werden, die dafür bekannt sind, dass sie folgende Punkte priorisieren Genauigkeit und Zuverlässigkeitsind entscheidend.
- Materialeigenschaften: Wärmeausdehnung und Leitfähigkeit des jeweiligen Edelstahlpulvers (316L vs. 17-4PH).
- Thermische Spannungen: Heiz- und Kühlzyklen während der Herstellung können innere Spannungen verursachen, die zu geringfügigen Verformungen oder Verwerfungen führen.
- Geometrie und Größe des Teils: Größere, komplexe Teile sind anfälliger für Abweichungen.
- Strategie unterstützen: Die Art und Weise, wie das Teil gestützt wird, wirkt sich auf die Stabilität während der Fertigung aus.
- Nachbearbeiten: Spannungsabbauzyklen können geringfügige Maßänderungen verursachen.
- Kritische Dimensionen: Bei mechanischen Kupplungen erfordern Merkmale wie Bohrungsdurchmesser, Nutbreiten/-tiefen und Ebenheit der Gegenflächen oft viel engere Toleranzen als die typischen AM-Möglichkeiten (z. B. H7-Passungen für Bohrungen).
- Lösung: Die gängige Praxis in der Industrie besteht darin, diese kritischen Merkmale mit zusätzlichem Material zu konstruieren (Bearbeitungszugabe, z. B. 0,5-1,0 mm) und nach dem Druck eine CNC-Bearbeitung vorzunehmen, um die erforderliche Präzision zu erreichen. Dieser hybride Ansatz (AM + Bearbeitung) nutzt die Designfreiheit der AM und die Präzision der subtraktiven Methoden.
Oberflächengüte (Rauhigkeit):
- As-Built Oberflächenbeschaffenheit: Die Oberflächenbeschaffenheit von as-printed Metallteilen ist aufgrund der teilweise geschmolzenen Pulverpartikel, die an der Oberfläche haften, und der sichtbaren Schichtlinien von Natur aus rauer als bearbeitete Oberflächen.
- Typische Ra-Werte:
- LPBF: Sie liegt oft zwischen 6 µm und 15 µm Ra (240 µin bis 600 µin Ra), je nach Ausrichtung, Parametern und Material. Nach oben gerichtete Oberflächen sind im Allgemeinen glatter als nach unten gerichtete oder vertikale Wände.
- EBM: Typischerweise rauer als LPBF, möglicherweise 20 µm bis 35 µm Ra oder mehr.
- Typische Ra-Werte:
- Faktoren, die das As-Built Finish beeinflussen:
- Druckparameter (Schichtdicke, Laserleistung/Geschwindigkeit).
- Partikelgrößenverteilung des Pulvers.
- Ausrichtung der Oberfläche in Bezug auf die Baurichtung.
- Unterstützen Sie die Kontaktstellen (hinterlassen Sie Markierungen).
- Verbesserung der Oberflächengüte: Wenn die fertige Oberfläche den funktionalen Anforderungen nicht genügt (z. B. Dichtungsflächen, stark beanspruchte Bereiche, Ästhetik), werden verschiedene Nachbearbeitungsschritte durchgeführt:
- Perlenstrahlen / Sandstrahlen: Sorgt für ein gleichmäßiges, mattes Finish und entfernt loses Pulver. Verbessert Ra geringfügig (z. B. bis zu 5-10 µm Ra).
- Taumeln / Vibrationsgleitschleifen: Glättet Oberflächen und Kanten, insbesondere bei kleineren Teilen. Kann Ra-Werte um 1-5 µm erreichen.
- CNC-Bearbeitung: Bietet die beste Oberflächengüte und Genauigkeit bei bestimmten Merkmalen.
- Polieren / Elektropolieren: Ermöglicht sehr glatte, spiegelähnliche Oberflächen (Ra < 0,8 µm oder noch niedriger), die häufig für medizinische oder lebensmitteltechnische Anwendungen erforderlich sind.
Erwartungen setzen:
Bei der Spezifikation einer 3D-gedruckten Edelstahlkupplung ist es wichtig, diese zu kennen:
- Definieren Sie die kritischen Dimensionen klar und deutlich: Identifizieren Sie Merkmale, die enge Toleranzen erfordern, und geben Sie diese auf der Zeichnung an, mit dem Hinweis, dass sie nachbearbeitet werden sollen.
- Legen Sie die Anforderungen an die Oberflächenbeschaffenheit fest: Definieren Sie die erforderlichen Ra-Werte für verschiedene Oberflächen auf der Grundlage ihrer Funktion (z. B. Bohrung, Gegenflächen, externe nicht funktionale Oberflächen).
- Wenden Sie sich an den AM-Anbieter: Diskutieren Sie bereits in einem frühen Stadium des Entwurfsprozesses über die erreichbaren Toleranzen und Oberflächenbehandlungen. Ein erfahrener Anbieter wie Met3dp kann Sie dabei unterstützen, optimale Ergebnisse zu erzielen und die notwendigen Nachbearbeitungsschritte durchzuführen.
Die Erkenntnis, dass Metall-AM häufig als endkonturnaher Prozess dient, insbesondere bei hochpräzisen Bauteilen wie Kupplungen, ermöglicht eine realistische Projektplanung und Kostenkalkulation unter Einbeziehung der erforderlichen Nachbearbeitungsschritte.
Nachbearbeitungsanforderungen für 3D-gedruckte Edelstahlkupplungen
Die Reise einer 3D-gedruckten Metallkupplung endet nicht, wenn der Drucker anhält. Es sind eine Reihe wichtiger Nachbearbeitungsschritte erforderlich, um das gedruckte Rohteil in eine funktionale, zuverlässige und einbaufertige Komponente zu verwandeln. Die einzelnen Schritte hängen vom Material (316L vs. 17-4PH), den Anwendungsanforderungen und der Komplexität des Designs ab.
Gemeinsame Nachbearbeitungsschritte:
- Entfernung von Puder:
- Prozess: Sobald die Baukammer abgekühlt ist, wird die Bauplattform mit dem/den angebrachten Teil(en) entfernt. Überschüssiges Metallpulver, das das Teil umgibt, muss sorgfältig entfernt werden, in der Regel durch Absaugen, Bürsten und Druckluft in einer kontrollierten Umgebung, um die Rückgewinnung und das Recycling des Pulvers zu ermöglichen. Interne Kanäle oder komplexe Geometrien erfordern eine gründliche Reinigung, um sicherzustellen, dass kein loses Pulver eingeschlossen bleibt.
- Wichtigkeit: Sorgt für saubere Teile und ermöglicht eine effiziente Wiederverwendung des Pulvers.
- Stressabbau:
- Prozess: Dies ist häufig der erste thermische Schritt, der durchgeführt wird vor Entfernen des Teils von der Bauplatte. Das (noch befestigte) Teil wird in einem Ofen auf eine bestimmte Temperatur (unterhalb der Umwandlungstemperatur) erhitzt und eine Zeit lang gehalten, gefolgt von einer langsamen Abkühlung. Typische Temperaturen liegen bei ~300 °C für 17-4PH (vor dem Lösungsglühen) oder ~650 °C für 316L, hängen aber von den genauen Verfahren ab.
- Wichtigkeit: Entscheidend für den Abbau der hohen Eigenspannungen, die durch die schnellen Heiz- und Kühlzyklen während des AM-Prozesses entstehen. Der Abbau von Spannungen verhindert Verformungen oder Risse bei der Entfernung des Trägers oder der anschließenden Bearbeitung und verbessert die Maßhaltigkeit.
- Entfernen des Teils von der Bauplatte:
- Prozess: Das spannungsfreie Teil wird in der Regel mit Methoden wie Drahterodieren (Electrical Discharge Machining), Sägen oder Zerspanen von der Metallbauplatte entfernt.
- Wichtigkeit: Trennt das/die fertige(n) Teil(e) für die weitere Bearbeitung ab. Die gewählte Methode sollte die Spannungsinduktion minimieren.
- Entfernung der Stützstruktur:
- Prozess: Die Trägerstrukturen, die ebenfalls aus rostfreiem Stahl bestehen, müssen entfernt werden. Dies kann manuell (mit Zangen, Schleifern, Schneidwerkzeugen) für zugängliche Stützen oder durch CNC-Bearbeitung für integrierte oder schwer zugängliche Stützen erfolgen.
- Wichtigkeit: Gibt die endgültige Teilegeometrie frei. Eine unzureichende Stützentfernung kann die Oberfläche des Teils beschädigen, was eine weitere Nachbearbeitung erforderlich macht. Die Konstruktion für zugängliche Halterungen (wie in DfAM besprochen) vereinfacht diese Phase erheblich.
- Wärmebehandlung (kritisch für 17-4PH):
- Prozess: Durch diesen Schritt werden die Mikrostruktur und die mechanischen Eigenschaften des Materials grundlegend verändert.
- Für 17-4PH: In der Regel ist ein zweistufiges Verfahren erforderlich:
- Lösungsglühen (Bedingung A): Erhitzen auf eine hohe Temperatur (~1040°C / 1900°F), Halten, um Ausscheidungen aufzulösen, dann schnelles Abkühlen (Abschrecken). Dadurch entsteht ein gleichmäßiges martensitisches Gefüge.
- Ausscheidungshärtung (Alterung): Wiedererwärmung auf eine niedrigere Temperatur (z.B. 480°C/900°F für H900, 550°C/1025°F für H1025, bis zu 620°C/1150°F für H1150) und Halten für eine bestimmte Zeit (1-4 Stunden). Dies ermöglicht die Bildung feiner Ausscheidungen (kupferreiche Phasen) innerhalb der martensitischen Matrix, wodurch sich Festigkeit und Härte erheblich erhöhen.
- Für 316L: Verfestigende Wärmebehandlungen sind nicht wirksam. Glühen (~1050°C mit anschließender schneller Abkühlung) kann für maximale Korrosionsbeständigkeit und Duktilität durchgeführt werden, oder Spannungsarmglühen bei niedrigeren Temperaturen (~650°C) kann ausreichend sein, wenn eine hohe Festigkeit nicht das primäre Ziel ist.
- Für 17-4PH: In der Regel ist ein zweistufiges Verfahren erforderlich:
- Wichtigkeit: Unbedingt erforderlich, damit 17-4PH sein hohes Festigkeitspotenzial erreicht. Die gewählte Alterungstemperatur entscheidet über das endgültige Gleichgewicht von Festigkeit, Härte, Zähigkeit und Korrosionsbeständigkeit (siehe Tabelle unten). Bei 316L dient sie in erster Linie dem Spannungsabbau oder der Optimierung der Korrosionsleistung.
- Prozess: Durch diesen Schritt werden die Mikrostruktur und die mechanischen Eigenschaften des Materials grundlegend verändert.
- Oberflächenveredelung:
- Prozess: Wie bereits erwähnt, umfasst dies Behandlungen wie Perlstrahlen (gleichmäßige matte Oberfläche), Trommel-/Gleitschleifen (Glätten von Kanten und Oberflächen), Schleifen oder Polieren, um die erforderlichen Spezifikationen für die Oberflächenrauheit (Ra) aus ästhetischen oder funktionalen Gründen (z. B. Abdichtung, Ermüdungsfestigkeit) zu erfüllen.
- Wichtigkeit: Erzielt die gewünschte Oberflächentextur und beseitigt kleinere Unebenheiten.
- CNC-Bearbeitung:
- Prozess: Einsatz von Präzisionsfräs- oder Drehzentren zur Bearbeitung kritischer Merkmale (Bohrungen, Nuten, Gegenflächen, Gewinde) mit den erforderlichen Endmaßen und engen Toleranzen (z. B. H7-Passungen).
- Wichtigkeit: Garantiert Maßgenauigkeit für Schnittstellen, Konzentrizität und Rechtwinkligkeit, wo AM allein nicht ausreicht. Unverzichtbar für die meisten funktionalen Verbindungen.
- Inspektion und Qualitätskontrolle (QC):
- Prozess: Überprüfung, ob die Kupplung alle Spezifikationen erfüllt. Die Techniken umfassen:
- Prüfung der Abmessungen: Verwendung von Messschiebern, Mikrometern und Koordinatenmessmaschinen (CMM) zur Überprüfung von Toleranzen.
- Prüfung der Materialeigenschaften: Potenzielle Prüfung von neben dem Teil gedruckten Mustercoupons auf Zugfestigkeit, Härte und Dichte.
- Zerstörungsfreie Prüfung (NDT): Methoden wie Röntgen- oder CT-Scans zur Erkennung interner Defekte wie Porosität oder fehlende Verschmelzung, insbesondere bei kritischen Anwendungen.
- Messung der Oberflächengüte: Verwendung von Profilometern.
- Wichtigkeit: Stellt sicher, dass das endgültige Teil für den Zweck geeignet ist und den Qualitätsstandards entspricht, die von den Beschaffung von Industriekupplungen Prozess.
- Prozess: Überprüfung, ob die Kupplung alle Spezifikationen erfüllt. Die Techniken umfassen:
Die Zusammenarbeit mit einem Full-Service-Anbieter für Metall-AM, der diese komplizierten Nachbearbeitungsschritte intern oder über qualifizierte Partner abwickelt, ist entscheidend, um funktionale, hochwertige Edelstahlkupplungen zu erhalten.
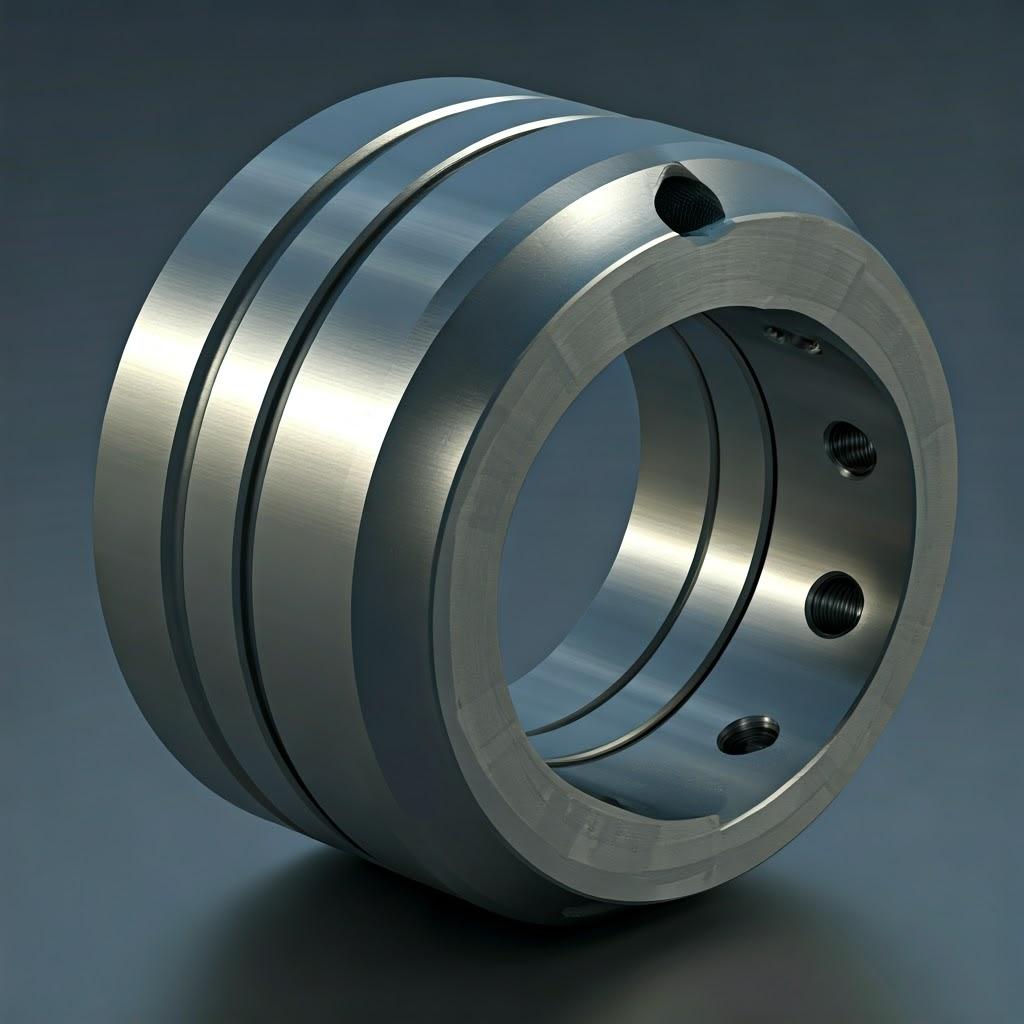
Häufige Herausforderungen beim 3D-Druck von Kupplungen und wie man sie entschärft
Die additive Fertigung von Metallen bietet zwar beträchtliche Vorteile, ist aber auch nicht ohne Herausforderungen. Das Bewusstsein für potenzielle Probleme ermöglicht es Ingenieuren und Beschaffungsspezialisten, proaktiv mit ihren AM Anbieter um Risiken zu minimieren und erfolgreiche Ergebnisse für 3D-gedruckte Edelstahlkupplungen zu gewährleisten.
- Verformung und Verzerrung:
- Die Ursache: Ungleichmäßige Erwärmung und Abkühlung während des schichtweisen Prozesses führen zu inneren Spannungen (Eigenspannungen). Wenn sich diese Spannungen ansammeln, können sie dazu führen, dass sich das Teil verzieht, verformt oder sogar von der Bauplatte ablöst. Größere Teile oder Teile mit erheblichen Querschnittsabweichungen sind dafür besonders anfällig.
- Milderung:
- Optimierte Ausrichtung: Ausrichtung des Teils, um große ebene Flächen parallel zur Bauplatte zu minimieren und thermische Gradienten zu reduzieren.
- Wirksame Unterstützungsstrategie: Robuste Stützen verankern das Teil fest und tragen zur Wärmeableitung bei.
- Prozess-Simulation: Eine fortschrittliche Simulationssoftware kann Bereiche vorhersagen, die für hohe Spannungen und Verformungen anfällig sind, so dass vor dem Druck Design- oder Stützanpassungen vorgenommen werden können.
- Stressabbau-Zyklen: Die Durchführung von Stressabbau nach der Erstellung (oder bei manchen Prozessen auch zwischen den einzelnen Phasen) ist von entscheidender Bedeutung.
- Optimierte Druckparameter: Erfahrene Anbieter nehmen die Feinabstimmung von Laser-/Strahlleistung, Scangeschwindigkeit und Schichtdicke vor.
- Eigenspannung:
- Die Ursache: Ähnlich wie bei der Verformung sind Eigenspannungen durch das örtlich begrenzte Schmelzen und die schnelle Erstarrung bedingt. Selbst wenn sich das Teil nicht sichtbar verzieht, können sich hohe Eigenspannungen negativ auf die Ermüdungslebensdauer, die Dimensionsstabilität und die Anfälligkeit für Risse auswirken.
- Milderung:
- Wärmemanagement: Die Verwendung von beheizten Bauplattformen/Kammern trägt zur Verringerung von Wärmegradienten bei.
- Wärmebehandlung nach der Fertigstellung: Spannungsabbau und Glühzyklen sind unerlässlich, um innere Spannungen auf ein akzeptables Niveau zu reduzieren. Das Lösungsglühen und die Alterung von 17-4PH haben ebenfalls einen erheblichen Einfluss auf den endgültigen Spannungszustand.
- Änderungen am Design: Die Vermeidung von abrupten Dickenänderungen und das Hinzufügen von großzügigen Hohlkehlen kann dazu beitragen, die Belastung gleichmäßiger zu verteilen.
- Porosität:
- Die Ursache: Kleine Hohlräume oder Poren im gedruckten Material können dessen Dichte, Festigkeit und Ermüdungsbeständigkeit beeinträchtigen. Zu den Ursachen gehören eingeschlossene Gase (aus dem Pulver oder der Atmosphäre), unzureichende Energiedichte, die zu unvollständigem Schmelzen (Lack of Fusion - LoF) führt, oder Keyholing (Dampfdruckkollaps) aufgrund zu hoher Energiedichte. Schlechte Qualität oder verunreinigtes Pulver können ebenfalls dazu beitragen.
- Milderung:
- Optimierte Druckparameter: Die präzise Steuerung von Laser-/Strahlleistung, Geschwindigkeit, Fokus und Schraffurmuster ist der Schlüssel zum Erreichen der vollen Dichte (>99,5% ist üblich, >99,9% oft erreichbar).
- Hochwertiges Pulver: Die Verwendung von Pulvern mit gleichmäßiger Sphärizität, Größenverteilung und geringem Gasgehalt, wie die mit den fortschrittlichen Zerstäubungstechniken von Met3dp hergestellten Pulver, ist entscheidend. Auch die richtige Handhabung und Lagerung des Pulvers ist entscheidend.
- Kontrollierte Atmosphäre: Die Aufrechterhaltung einer hochreinen Inertgasatmosphäre (Argon oder Stickstoff für LPBF) oder eines Vakuums (EBM) verhindert Oxidation und Kontamination.
- Heiß-Isostatisches Pressen (HIP): Für kritische Anwendungen, die eine Dichte von nahezu 100% erfordern, kann HIP (Anwendung von hoher Temperatur und isostatischem Gasdruck) als Nachbearbeitungsschritt verwendet werden, um die inneren Poren zu schließen.
- Unterstützung bei der Beseitigung von Schwierigkeiten:
- Die Ursache: Die Entfernung von Halterungen in schwer zugänglichen Innenbereichen oder auf komplex gekrümmten Oberflächen kann schwierig und zeitaufwändig sein. Außerdem kann das Entfernen Spuren oder Unreinheiten auf der Oberfläche des Teils hinterlassen.
- Milderung:
- DfAM für Unterstützungen: Konstruktion von Teilen mit selbsttragenden Winkeln, wo immer möglich. Ausrichtung des Teils, um Stützen auf kritischen oder kosmetischen Oberflächen zu minimieren. Konstruktion von Stützen mit spezifischen Strukturen (z. B. konische Spitzen, Perforation), die sich leichter lösen.
- Erweiterte Software: Verwendung von Software, die die Erzeugung von Stützen für minimalen Kontakt und einfache Entfernung optimiert.
- Nachbearbeitungsplan: Ausreichend Zeit und Ressourcen für die Entfernung von Halterungen und die anschließende Oberflächenbearbeitung einplanen, falls erforderlich. Mit Hilfe der maschinellen Bearbeitung können Halterungen an bestimmten Stellen sauber entfernt werden.
- Erzielung enger Toleranzen und Oberflächengüte:
- Die Ursache: Wie bereits erwähnt, führt die Natur von AM zu engeren Toleranzen und raueren Oberflächen als bei der Präzisionsbearbeitung.
- Milderung:
- Hybrid-Ansatz: Akzeptanz von AM als endkonturnahes Verfahren und Einbeziehung von Toleranzen für die Endbearbeitung kritischer Merkmale in der Entwurfsphase.
- Nachbearbeiten: Anwendung geeigneter Endbearbeitungstechniken (Strahlen, Trowalisieren, Polieren, Bearbeiten) zur Erfüllung der vorgegebenen Anforderungen.
- Realistische Spezifikationen: Vermeidung einer Überspezifizierung von Toleranzen und Oberflächen auf unkritischen Oberflächen.
- Konsistenz der Materialeigenschaften:
- Die Ursache: Schwankungen bei den Druckparametern, der Maschinenkalibrierung, den Pulverchargen oder der thermischen Entwicklung eines großen Teils können zu geringfügigen Abweichungen bei den mechanischen Eigenschaften führen.
- Milderung:
- Robuste Prozesskontrolle: Zusammenarbeit mit Lieferanten, die über strenge Qualitätsmanagementsysteme (z. B. ISO 9001, AS9100), gut gewartete Anlagen und dokumentierte Verfahren verfügen.
- Pulvermanagement: Strenge Kontrolle der Pulverqualität, Rückverfolgbarkeit, Lagerung und Recyclingverfahren.
- Konsistente Nachbearbeitung: Sicherstellen, dass die Wärmebehandlungszyklen genau kontrolliert und gleichmäßig durchgeführt werden.
- Prüfung und Validierung: Verwendung von Zeugencoupons, die zusammen mit den Teilen für die zerstörende Prüfung gedruckt werden, um die Eigenschaften für jeden Bau oder jedes Los zu überprüfen.
Die Bewältigung dieser Herausforderungen erfordert eine Kombination aus guten Designpraktiken (DfAM), sorgfältiger Materialauswahl, präziser Prozesssteuerung während des Drucks, sorgfältiger Nachbearbeitung und robuster Qualitätssicherung. Die Wahl eines erfahrenen Metall-AM-Dienstleisters wie Met3dpDurch das Angebot umfassender Lösungen, die Drucker, hochwertige Pulver und Dienstleistungen für die Anwendungsentwicklung umfassen, werden diese Risiken erheblich gemindert, so dass die erfolgreiche Produktion von 3D-gedruckten Hochleistungs-Edelstahlkupplungen gewährleistet ist.
Wie man den richtigen 3D-Druckdienstleister für Kupplungen aus Metall auswählt
Die Auswahl des richtigen Fertigungspartners ist für die erfolgreiche Nutzung der additiven Fertigung für Ihre Edelstahlkupplungen von entscheidender Bedeutung. Die Qualität, Leistung und Zuverlässigkeit der endgültigen Komponente hängt in hohem Maße von der Erfahrung, den Fähigkeiten und den Qualitätskontrollen des von Ihnen gewählten Anbieters ab. Für Ingenieure und Beschaffungsmanager, die sich mit der Beschaffung von Industriekupplungen Prozesses müssen bei der Bewertung potenzieller Metall-AM-Lieferanten mehrere Faktoren sorgfältig berücksichtigt werden:
- Fachwissen und Erfahrung:
- Spezifität des Materials: Hat der Anbieter nachweislich Erfahrung mit dem Druck von 316L und 17-4PH-Edelstählen? Fragen Sie nach Fallstudien oder Beispielen für ähnliche Projekte.
- Anwendungswissen: Verstehen sie die funktionellen Anforderungen an mechanische Kupplungen (Drehmoment, Ausrichtungsfehler, Ermüdung usw.)? Erfahrung in Ihrer spezifischen Branche (Luft- und Raumfahrt, Medizintechnik, Industrie) ist von großem Vorteil.
- Technische Tiefe: Suchen Sie nach Anbietern mit einem starken metallurgischen und technischen Hintergrund, die mehr als nur Druckdienstleistungen anbieten können. Über Met3dpzum Beispiel nutzt jahrzehntelanges kollektives Know-how in der additiven Fertigung von Metallen.
- Technologische Fähigkeiten:
- Drucktechnik: Bieten sie die geeignete Technologie an (z. B. LPBF/SLM für feine Merkmale und Oberflächengüte, möglicherweise EBM für bestimmte Materialien/Anwendungen)?
- Qualität und Wartung der Maschinen: Welche Art von Maschinen verwenden sie? Sind sie industrietauglich, gut gewartet und kalibriert? Anbieter, die in branchenführende Ausrüstung investieren, bieten oft eine höhere Konsistenz. Met3dp mit Hauptsitz in Qingdao, China, ist auf hochmoderne 3D-Drucker spezialisiert und bekannt für branchenführendes Druckvolumen, Genauigkeit und Zuverlässigkeit.
- Bauvolumen: Können die Maschinen die Größe Ihrer Kupplung aufnehmen?
- Materialqualität und -auswahl:
- Pulverbeschaffung und Qualitätskontrolle: Woher beziehen sie ihre Pulver? Gibt es dort eine strenge Qualitätskontrolle für das eingehende Pulver (Chemie, Größenverteilung, Morphologie, Fließfähigkeit)? Dies ist entscheidend für die Qualität des Endprodukts. Met3dp stellt sein eigenes Pulver her hochwertige Metallpulver unter Verwendung fortschrittlicher Gaszerstäubungs- und PREP-Technologien, die eine hohe Sphärizität und Fließfähigkeit gewährleisten und für AM-Prozesse optimiert sind.
- Zertifizierung: Können sie Materialzertifikate vorlegen, mit denen sich die Pulverchargen zurückverfolgen lassen, um die Einhaltung von Industrienormen zu gewährleisten (z. B. ASTM, ISO, spezielle Luft- und Raumfahrt- oder Medizinprodukte)?
- Nachbearbeitungsmöglichkeiten:
- In-House vs. Partner: Führt der Anbieter kritische Nachbearbeitungsschritte wie Spannungsabbau, Wärmebehandlung (insbesondere komplexe Zyklen für 17-4PH), CNC-Bearbeitung und Oberflächenveredelung selbst durch oder lagert er sie aus? Inhouse-Kapazitäten führen oft zu einer besseren Prozesskontrolle, Verantwortlichkeit und potenziell kürzeren Vorlaufzeiten.
- Angebot an Dienstleistungen: Vergewissern Sie sich, dass sie die spezifischen Endbearbeitungs- und Bearbeitungsprozesse anbieten, die Ihre Kupplung benötigt, um die Spezifikationen für Toleranzen und Oberflächengüte zu erfüllen.
- Qualitätsmanagementsystem (QMS):
- Zertifizierungen: Verfügt der Anbieter über einschlägige Qualitätszertifizierungen, wie z. B. ISO 9001 (allgemeines Qualitätsmanagement) oder AS9100 (Luft- und Raumfahrt)? Diese Zertifizierungen weisen auf eine Verpflichtung zu standardisierten Prozessen, Rückverfolgbarkeit und kontinuierlicher Verbesserung hin.
- Inspektionskapazitäten: Welche Qualitätskontroll- und Prüfverfahren werden eingesetzt (CMM, NDT, Materialprüfung)?
- Technische Unterstützung:
- DfAM-Fachwissen: Können sie wertvolles Feedback zum Design for Additive Manufacturing geben, um Ihr Kupplungsdesign hinsichtlich Druckbarkeit, Leistung und Kosteneffizienz zu optimieren?
- Konsultation: Sind sie bereit, als Partner zu agieren und die Materialauswahl, die Prozessoptimierung und mögliche Herausforderungen zu diskutieren? Met3dp bietet umfassende Lösungen das Drucker, Pulver und Anwendungsentwicklungsdienste umfasst, und arbeitet mit Unternehmen zusammen, um deren AM-Einführung zu beschleunigen.
- Kapazität, Vorlaufzeiten und Skalierbarkeit:
- Durchlaufzeit: Können sie Ihre Projektfristen für Prototypen und Produktionsläufe einhalten? Holen Sie realistische Schätzungen der Vorlaufzeit auf der Grundlage Ihres spezifischen Teils und der Menge ein.
- Kapazität: Verfügen sie über ausreichende Maschinenkapazitäten, um Ihr Auftragsvolumen zu bewältigen, einschließlich potenzieller Großhandel mit 3D-gedruckten Teilen oder Großbestellungen?
- Skalierbarkeit: Können sie Ihre Anforderungen erfüllen, wenn Ihr Volumen wächst?
- Standort und Logistik:
- Berücksichtigen Sie die Versandkosten und -zeiten, insbesondere bei internationalen Lieferanten. Bewerten Sie die Reaktionsfähigkeit der Kommunikation über Zeitzonen hinweg.
- Reputation und Referenzen:
- Prüfen Sie Online-Bewertungen, fragen Sie nach Kundenreferenzen und bewerten Sie die allgemeine Professionalität und Kommunikation des Unternehmens.
Die Wahl der billigsten Option ist in der Metall-AM selten die beste Strategie. Bevorzugen Sie Anbieter, die technische Spitzenleistungen, robuste Qualitätssysteme, umfassende Fähigkeiten und einen kooperativen Ansatz vorweisen können. Eine starke Partner für additive Fertigung ist eine Investition in den Erfolg Ihres Projekts.
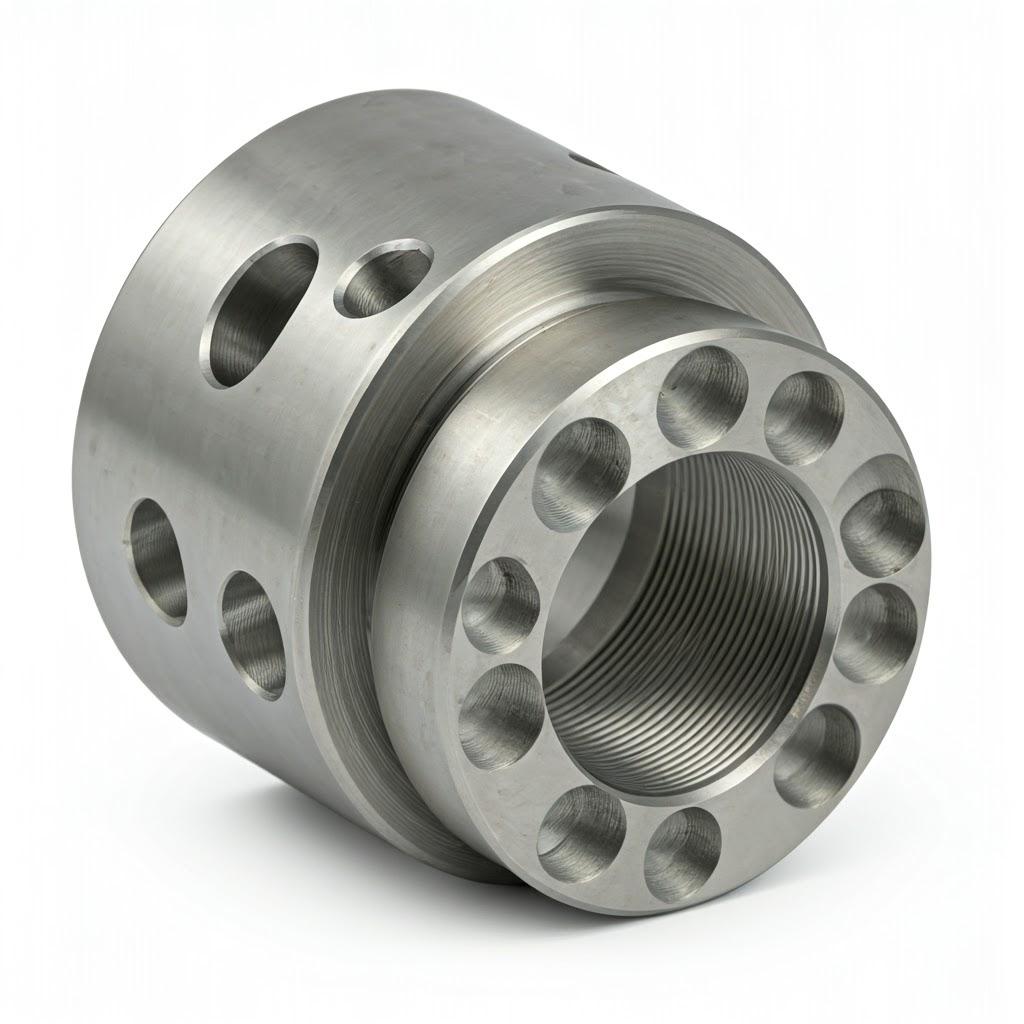
Kostenfaktoren und Vorlaufzeit für 3D-gedruckte Kupplungen aus Edelstahl
Das Verständnis der Kostentreiber und der typischen Vorlaufzeiten im Zusammenhang mit 3D-gedruckten Edelstahlkupplungen ist entscheidend für die Projektplanung, die Budgetierung und den Vergleich von AM mit traditionellen Fertigungsmethoden. Im Gegensatz zu traditionellen Methoden, bei denen die Werkzeugkosten oft die Anfangskosten dominieren, sind die Kosten bei AM enger mit dem Materialverbrauch und der Maschinenzeit verbunden.
Wichtige Kostenfaktoren:
- Materialkosten:
- Pulvertyp: Der Preis pro Kilogramm Pulver aus nichtrostendem Stahl der Klasse AM variiert. Im Allgemeinen kann 17-4PH etwas teurer sein als 316L. Speziallegierungen kosten mehr.
- Teilband: Das tatsächliche Volumen des fertigen Teils hat einen direkten Einfluss auf die Menge des verbrauchten Pulvers.
- Unterstützungsstruktur Volumen: Das für Stützstrukturen verwendete Pulver trägt ebenfalls zu den Kosten bei. Optimierte Konstruktionen minimieren den Stützbedarf.
- Pulver-Recycling: Eine effiziente Wiederverwendung des Pulvers durch den Anbieter trägt zur Kostenkontrolle bei, aber im Laufe der Zyklen kommt es zu einer gewissen Verschlechterung.
- Maschinenzeit:
- Bauhöhe: Dies ist oft der Hauptfaktor für die Druckzeit, da die Maschinen Schicht für Schicht aufbauen. Größere Teile brauchen länger.
- Teilvolumen und Dichte: Größere Volumina erfordern eine längere Scanzeit pro Schicht.
- Anzahl der Teile pro Build: Die effiziente Verschachtelung mehrerer Teile auf einer einzigen Bauplatte senkt die Kosten pro Teil erheblich, da die Maschinenauslastung maximiert wird. Dies ist der Schlüssel zur Reduzierung Kosten für 3D-Druck in großen Mengen.
- Komplexität: Während AM die Komplexität gut handhabt, können sehr komplizierte Merkmale oder umfangreiche Unterstützungsanforderungen die Druckzeit leicht erhöhen.
- Maschine Stundensatz: Dies hängt von den Investitionskosten der AM-Maschine, den Wartungs- und Betriebskosten sowie der Preisstruktur des Anbieters ab.
- Arbeitskosten:
- Vorbereitung und Einrichtung von Dateien: Die Zeit, die für die Vorbereitung der CAD-Datei, die Planung des Baulayouts, die Erstellung von Halterungen und die Einrichtung der Maschine aufgewendet wird.
- Nachbearbeitungsarbeiten: Manueller Aufwand bei der Pulverentfernung, der Entfernung von Halterungen, der Oberflächenbearbeitung (Strahlen, Polieren), der Inspektion und der Verpackung.
- Unterstützung/Beratung durch das DfAM: Wenn eine umfassende Unterstützung bei der Designoptimierung erforderlich ist.
- Nachbearbeitungskosten:
- Stressabbau / Wärmebehandlung: Ofenzeit, Energieverbrauch und Arbeitsaufwand im Zusammenhang mit Wärmebehandlungen. Die Wärmebehandlung von 17-4PH verursacht zusätzliche Kosten im Vergleich zu 316L, bei dem nur ein Spannungsabbau erforderlich sein kann.
- Bearbeitungen: Die Kosten für die CNC-Bearbeitung kritischer Merkmale hängen stark von der Komplexität, der Anzahl der Merkmale, den erforderlichen Toleranzen und der Rüstzeit ab.
- Oberflächenveredelung: Kosten im Zusammenhang mit speziellen Behandlungen wie Trowalisieren, Polieren oder Elektropolieren.
- Inspektion und Prüfung: Kosten für CMM-Inspektion, zerstörungsfreie Prüfung oder Materialprüfung, falls erforderlich.
- Auftragsvolumen:
- Skalenvorteile: Während AM nicht die dramatische Kostenreduzierung pro Teil der Großserienguss- oder -bearbeitung aufweist, sobald die Werkzeugkosten amortisiert sind, gibt es dennoch Skaleneffekte. Das gleichzeitige Drucken mehrerer Teile reduziert die Einrichtungs- und Maschinenzeitkosten, die auf jedes einzelne Teil entfallen. Dies macht AM für Klein- bis Mittelserienproduktionen und Großhandel Bestellungen im Vergleich zu Einzelprototypen zunehmend wettbewerbsfähig.
Einblick in den Kostenvergleich: Für hochkomplexe oder kundenspezifische Kupplungen oder für die Kleinserienfertigung (Prototypen bis zu potenziell Hunderten oder Tausenden, je nach Teil) kann AM aufgrund der Vermeidung von Werkzeugkosten und der Möglichkeit zur Optimierung des Materialverbrauchs kostengünstig oder sogar günstiger sein als herkömmliche Methoden. Für sehr einfache Designs, die in sehr großen Mengen (Zehntausende oder Millionen) hergestellt werden, bleiben herkömmliche Methoden in der Regel wirtschaftlicher wenn das Design für diese Methoden geeignet ist.
Faktoren für die Vorlaufzeit:
Die Vorlaufzeit ist die Gesamtzeit von der Auftragserteilung bis zur Teilelieferung. Für 3D-gedruckte Kupplungen umfasst sie typischerweise:
- Angebotserstellung und Auftragsabwicklung: 1-3 Tage.
- Dateivorbereitung & Planung: 1-2 Tage.
- Druckzeit: Sehr variabel, von Stunden für kleine Teile bis zu mehreren Tagen für große, komplexe Teile oder volle Bauplatten. Hängt stark von der Teilehöhe ab.
- Abkühlung und Entfettung: Mehrere Stunden bis zu einem Tag.
- Stressabbau / Wärmebehandlung: 1-3 Tage (einschließlich Ofenzyklen und Handhabung).
- Stützenentfernung & Grundbearbeitung (z. B. Strahlen): 1-2 Tage.
- CNC-Bearbeitung (falls erforderlich): 2-5 Tage (stark abhängig von der Komplexität und der Terminplanung der Werkstatt).
- Endbearbeitung & Inspektion: 1-2 Tage.
- Versand: Variabel.
Typische Vorlaufzeiten:
- Prototypen (mit minimaler Nachbearbeitung): Oft 5-10 Werktage.
- Produktionsteile (die Wärmebehandlung & Bearbeitung erfordern): Typischerweise 2-4 Wochen, kann aber je nach Komplexität, Menge und Arbeitsauslastung des Lieferanten erheblich variieren.
Fordern Sie immer spezifische Vorlaufzeitschätzungen von Ihrem gewählten Metall-AM-Anbieter basierend auf Ihrem endgültigen Design und Ihren Anforderungen an. Das Verständnis der verschiedenen Druckverfahren und ihre zugehörigen Nachbearbeitungsanforderungen helfen bei der Planung realistischer Projektzeitpläne.
Häufig gestellte Fragen (FAQ) zu 3D-gedruckten Edelstahlkupplungen
Hier sind Antworten auf einige häufige Fragen, die Ingenieure und Beschaffungsspezialisten haben, wenn sie die additive Fertigung für Edelstahlkupplungen in Betracht ziehen:
- F1: Sind 3D-gedruckte Edelstahlkupplungen so stark wie maschinell bearbeitete?
- A: Ja, potenziell. Metall-AM-Verfahren wie LPBF können Teile herstellen, die zu >99,5 % dicht sind, und mechanische Eigenschaften (Zugfestigkeit, Streckgrenze, Härte) erzielen, die mit geschmiedeten oder gegossenen Gegenstücken vergleichbar und manchmal sogar überlegen sind (aufgrund der feinen Kornstruktur) nach geeignete Nachbearbeitung. Für 17-4PH hängt das Erreichen hoher Festigkeit von der richtigen Lösungsglüh- und Ausscheidungshärtungs-Wärmebehandlungszyklus ab. Für 316L sind die Eigenschaften denen von geglühtem geschmiedetem 316L ähnlich. Der Schlüssel ist die Zusammenarbeit mit einem Anbieter, der hochwertiges Pulver, optimierte Druckparameter und geeignete Wärmebehandlungsprotokolle verwendet. In einigen Fällen können DfAM-Techniken wie die Topologieoptimierung zu Designs führen, die Festigkeitsanforderungen bei geringerem Gewicht als ein herkömmlich bearbeitetes Festteil erfüllen.
- F2: Wie groß ist der typische Kostenunterschied zwischen AM und der traditionellen Fertigung für Kupplungen?
- A: Dies hängt stark von mehreren Faktoren ab.
- AM ist oft kostengünstiger für:
- Prototypen und sehr geringe Mengen (wo Werkzeugkosten für das Gießen oder komplexe Bearbeitungseinrichtungen prohibitiv sind).
- Hochkomplexe Geometrien, die schwer oder unmöglich zu bearbeiten oder zu gießen sind.
- Kundenspezifische Designs, die für jede Charge einzigartige Merkmale oder Abmessungen erfordern.
- Anwendungen, bei denen die Teilekonsolidierung oder eine erhebliche Gewichtsreduzierung (über Topologieoptimierung) einen Wert schafft, der einen potenziell höheren Stückpreis ausgleicht.
- Herkömmliche Methoden sind oft kostengünstiger für:
- Einfache Kupplungsdesigns, die in sehr großen Mengen (Zehntausende oder mehr) hergestellt werden.
- Designs, bei denen die Materialkosten der dominierende Faktor sind und AM-Pulver deutlich teurer ist als Stangenmaterial oder Gussrohstoff.
- Holen Sie sich immer Angebote für beide Methoden ein, wenn dies für Ihre spezifische Teilegeometrie und -menge machbar ist, um eine fundierte Entscheidung zu treffen.
- AM ist oft kostengünstiger für:
- A: Dies hängt stark von mehreren Faktoren ab.
- F3: Kann ich zertifizierte Materialien für Luft- und Raumfahrt- oder medizinische Anwendungen erhalten?
- A: Absolut. Renommierte Metall-AM-Dienstleister, insbesondere solche, die kritische Industrien bedienen, arbeiten mit Pulverlieferanten zusammen, die zertifizierte Materialien liefern, die relevanten Standards entsprechen (z. B. ASTM F3184 für AM 316L, ASTM F3301 für AM 17-4PH, spezifische AMS-Spezifikationen für die Luft- und Raumfahrt). Stellen Sie sicher, dass Ihr gewählter Anbieter Teile liefern kann, die mit zertifizierten Pulverchargen gedruckt wurden, und die erforderliche Dokumentation und Rückverfolgbarkeit als Teil seines Qualitätsmanagementsystems bereitstellt. Met3dpzum Beispiel, betont hochwertige Pulver, die für anspruchsvolle Bereiche wie Luft- und Raumfahrt und Medizin geeignet sind.
- F4: Welchen Oberflächengütegrad kann man bei einer 3D-gedruckten Kupplung erwarten?
- A: Die als gedruckt vorliegende Oberflächengüte ist typischerweise rauer als maschinell bearbeitete Oberflächen, oft im Bereich von 6-15 µm Ra für LPBF. Dies kann für einige Außenflächen akzeptabel sein. Funktionale Oberflächen wie Bohrungen, Keilnuten, Dichtflächen oder Bereiche, die eine hohe Ermüdungslebensdauer erfordern, müssen jedoch in der Regel verbessert werden. Nachbearbeitungsschritte wie das Kugelstrahlen liefern eine gleichmäßige matte Oberfläche (z. B. 5-10 µm Ra), während das Trommeln
Fazit: Die Zukunft hochleistungsfähiger Kupplungen ist additiv
Wie wir im Laufe dieses Leitfadens (Stand: 15. April 2025) festgestellt haben, stellt die additive Fertigung von Metallen einen bedeutenden Fortschritt in der Konstruktion und Herstellung von hochleistungsfähigen mechanischen Kupplungen dar. Durch die Nutzung der einzigartigen Fähigkeiten des 3D-Drucks mit robusten Materialien wie 316L und 17-4PH Edelstahlkönnen Ingenieure die Einschränkungen der traditionellen Fertigung überwinden und Lösungen schaffen, die Folgendes sind:
- Optimiert: Erzielung einer beispiellosen Designkomplexität durch Topologieoptimierung und Gitterstrukturen zur Gewichtsreduzierung, maßgeschneiderten Steifigkeit und verbesserten Schwingungsdämpfung.
- Kundenspezifisch: Ermöglichen von Rapid Prototyping und kostengünstiger Produktion von maßgeschneiderten Kupplungen, die auf spezifische Anwendungsanforderungen zugeschnitten sind, ohne die Belastung durch Werkzeugkosten.
- Konsolidiert: Integration mehrerer Komponenten in ein einziges gedrucktes Teil, wodurch Montagezeit, Gewicht und potenzielle Fehlerquellen reduziert werden.
- Beschleunigt: Verkürzung der Entwicklungszyklen von Wochen oder Monaten auf Tage, was schnellere Innovationen und den Markteintritt ermöglicht.
Die Wahl zwischen der hervorragenden Korrosionsbeständigkeit von 316L und der hohen Festigkeit von wärmebehandeltem 17-4PH ermöglicht die Materialauswahl, die genau auf die Betriebsanforderungen von Luft- und Raumfahrt, Automobilindustrie, Industrie und Medizin abgestimmt ist.
Um diese Vorteile zu realisieren, ist jedoch mehr als nur der Zugang zu einem 3D-Drucker erforderlich. Es erfordert die Anwendung von Design for Additive Manufacturing (DfAM)-Prinzipien, das Verständnis der Nuancen der Nachbearbeitung (insbesondere kritische Wärmebehandlungen für 17-4PH) und die sorgfältige Verwaltung von Toleranzen und Oberflächengüten, oft durch einen hybriden AM-Bearbeitungsansatz.
Entscheidend ist, dass der Erfolg von der Auswahl des richtigen Fertigungspartners abhängt. Suchen Sie nach einem Anbieter mit nachgewiesener Expertise in der Edelstahl-AM, robusten Qualitätssystemen, umfassenden internen Fähigkeiten vom Pulver bis zum fertigen Teil und einem kollaborativen Engineering-Ansatz.
Als führendes Unternehmen für Metall-AM-Ausrüstung und -Materialien Met3dp bietet hochmoderne Systeme und hochwertige sphärische Metallpulver, um die Fertigung der nächsten Generation zu ermöglichen. Unsere umfassenden Lösungen und unser fundiertes Fachwissen befähigen Unternehmen, den 3D-Druck effektiv einzusetzen und ihre Produktionskapazitäten zu transformieren.
Die Zukunft hochleistungsfähiger Kupplungen ist zunehmend mit der additiven Fertigung verbunden. Wenn Sie bereit sind, zu erkunden, wie 3D-gedruckte Edelstahlkupplungen Ihre Maschinen oder Produkte revolutionieren können, empfehlen wir Ihnen, sich an uns zu wenden.
Kontakt zu Metal3DP noch heute, um zu erfahren, wie unsere Fähigkeiten die Ziele Ihres Unternehmens im Bereich der additiven Fertigung unterstützen können, und um Ihr nächstes Kupplungsprojekt zu besprechen.
Teilen auf
MET3DP Technology Co., LTD ist ein führender Anbieter von additiven Fertigungslösungen mit Hauptsitz in Qingdao, China. Unser Unternehmen ist spezialisiert auf 3D-Druckgeräte und Hochleistungsmetallpulver für industrielle Anwendungen.
Fragen Sie an, um den besten Preis und eine maßgeschneiderte Lösung für Ihr Unternehmen zu erhalten!
Verwandte Artikel
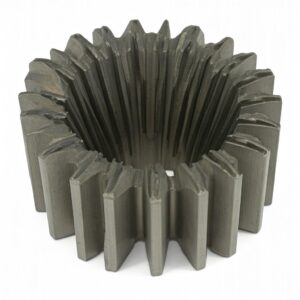
Hochleistungs-Düsenschaufelsegmente: Revolutionierung der Turbineneffizienz mit 3D-Metalldruck
Mehr lesen "Über Met3DP
Aktuelles Update
Unser Produkt
KONTAKT US
Haben Sie Fragen? Senden Sie uns jetzt eine Nachricht! Wir werden Ihre Anfrage mit einem ganzen Team nach Erhalt Ihrer Nachricht bearbeiten.
Holen Sie sich Metal3DP's
Produkt-Broschüre
Erhalten Sie die neuesten Produkte und Preislisten
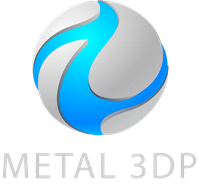
Metallpulver für 3D-Druck und additive Fertigung