3D-Drucken von Raketensteuerflossen aus Metall: Verbesserung von Leistung und Effizienz
Inhaltsübersicht
Einführung - Die entscheidende Rolle von Raketenleitwerken und 3D-Metalldruck
Die Steuerflossen von Flugkörpern sind wesentliche Komponenten, die während des Fluges für Stabilität und Manövrierfähigkeit sorgen. Diese scheinbar kleinen Teile entscheiden über die Genauigkeit und Effektivität eines Raketensystems, weshalb ihre Konstruktion und Herstellung von größter Bedeutung sind. Traditionell werden diese Flossen mit konventionellen Methoden wie maschineller Bearbeitung oder Gießen hergestellt, was zeitaufwändig und materialintensiv sein kann und die Komplexität des Designs einschränkt. Das Aufkommen des 3D-Metalldrucks, auch bekannt als additive Fertigung (AM), stellt jedoch einen Paradigmenwechsel in der Art und Weise dar, wie diese kritischen Komponenten für die Luft- und Raumfahrt konzipiert und hergestellt werden. Durch den schichtweisen Aufbau von Teilen aus Metallpulvern können Metall 3D-Druck bietet eine noch nie dagewesene Designfreiheit, die Möglichkeit, Gewicht und Leistung zu optimieren, und das Potenzial für eine erhebliche Reduzierung der Vorlaufzeiten und des Materialabfalls. Dieser Blogbeitrag untersucht die transformativen Auswirkungen des 3D-Metalldrucks auf die Produktion von Raketensteuerungsflossen und beleuchtet die Vorteile, Materialüberlegungen, Designaspekte und wie die Zusammenarbeit mit einem vertrauenswürdigen Lieferanten wie Metall3DP kann Ihre Fertigungsprozesse revolutionieren. Metal3DP, ein führender Anbieter von additiven Fertigungslösungen mit Hauptsitz in Qingdao, China, ist auf Hochleistungsmetallpulver und modernste 3D-Druckanlagen spezialisiert und bietet branchenführende Genauigkeit und Zuverlässigkeit für unternehmenskritische Teile in der Luft- und Raumfahrt sowie im Verteidigungsbereich.
Wofür werden Raketensteuerungsflossen verwendet? - Anwendungen in verschiedenen Verteidigungssystemen
Raketensteuerungsflossen haben eine wichtige aerodynamische Funktion bei der Lenkung von Raketen zu ihren Zielen. Sie werden hauptsächlich für folgende Zwecke verwendet:
- Stabilisierung: Sicherstellen, dass der Flugkörper während seiner Flugbahn eine stabile Flugbahn beibehält und unerwünschte Gier-, Nick- oder Rollbewegungen verhindert werden.
- Manövrieren: Ermöglicht präzise Richtungsanpassungen des Flugkörpers und damit Kurskorrekturen und Zielerfassung.
- Aerodynamische Kontrolle: Erzeugung der notwendigen Auftriebs- und Widerstandskräfte, um die Bewegung des Flugkörpers durch die Atmosphäre zu steuern.
Diese Flossen sind integraler Bestandteil verschiedener Arten von Raketensystemen für unterschiedliche Verteidigungsanwendungen, darunter:
- Luft-Luft-Raketen: Wird von Flugzeugen verwendet, um andere Ziele in der Luft zu bekämpfen.
- Boden-Luft-Raketen: Wird von Boden- oder Seeplattformen aus gestartet, um Bedrohungen aus der Luft abzufangen.
- Luft-Boden-Raketen: Wird von Flugzeugen aus eingesetzt, um Ziele am Boden oder auf See zu treffen.
- Boden-Boden-Raketen: Wird vom Land oder von der See aus gestartet, um Ziele auf dem Boden oder im Wasser zu bekämpfen.
Die spezifischen Konstruktions- und Materialanforderungen an die Steuerflossen können je nach Geschwindigkeit, Reichweite, Einsatzumgebung und beabsichtigtem Ziel des Flugkörpers erheblich variieren. Faktoren wie aerodynamische Belastungen, Temperaturschwankungen, Korrosions- und Schlagfestigkeit sind entscheidende Faktoren. Der 3D-Druck von Metall bietet die Flexibilität, das Design und die Materialauswahl genau auf diese anspruchsvollen Anforderungen abzustimmen.
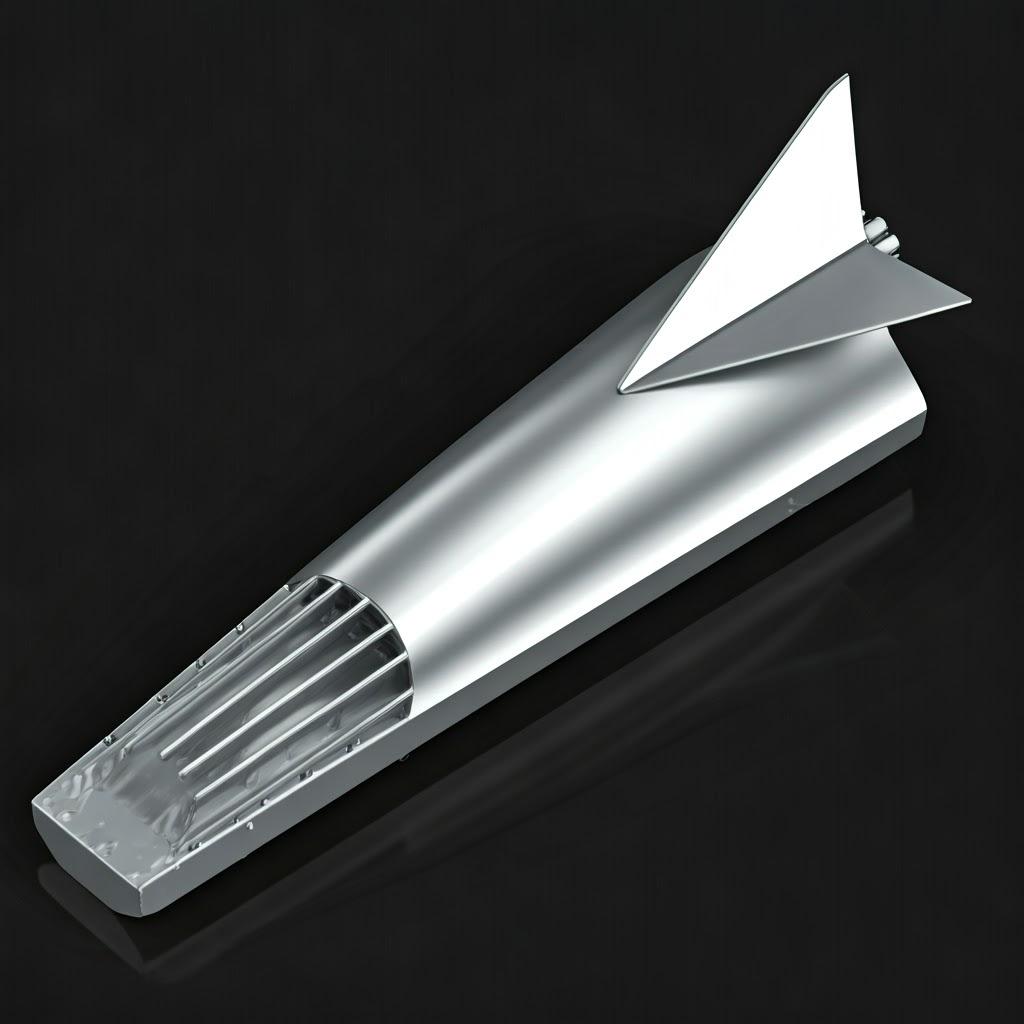
Warum 3D-Metalldruck für Raketensteuerungsflossen? - Vorteile gegenüber traditioneller Fertigung
Der 3D-Metalldruck für die Herstellung von Raketenleitwerken bietet eine Reihe von Vorteilen im Vergleich zu herkömmlichen Fertigungsmethoden:
- Verbesserte Gestaltungsfreiheit: Metall-AM ermöglicht die Herstellung komplexer Geometrien, die mit herkömmlichen Techniken nur schwer oder gar nicht zu erreichen sind. Dazu gehören komplizierte innere Strukturen, optimierte Gitterkonstruktionen zur Gewichtsreduzierung und aerodynamisch bessere Formen, die die Leistung von Flugkörpern verbessern können.
- Optimierung des Gewichts: Die Möglichkeit, interne Gitter und hohle Strukturen zu entwerfen, ermöglicht eine erhebliche Gewichtsreduzierung ohne Beeinträchtigung der strukturellen Integrität. Leichtere Steuerflossen tragen zur Gesamteffizienz des Flugkörpers bei und erhöhen Reichweite, Geschwindigkeit und Nutzlastkapazität.
- Materialeffizienz: Additive Fertigungsverfahren minimieren den Materialabfall, da die Teile Schicht für Schicht aufgebaut werden und nur das notwendige Material verwendet wird. Dies ist besonders vorteilhaft bei der Arbeit mit teuren Hochleistungslegierungen, die häufig in der Luft- und Raumfahrt verwendet werden.
- Reduzierte Vorlaufzeiten: Der 3D-Druck von Metall kann den Produktionszyklus für Steuerrippen erheblich verkürzen. Durch den Wegfall von Werkzeugen, Formen und komplexen Vorrichtungen, die bei herkömmlichen Verfahren erforderlich sind, wird der Fertigungsprozess vom Entwurf bis zum fertigen Teil beschleunigt.
- Teil Konsolidierung: AM ermöglicht die Integration mehrerer Komponenten in ein einziges, 3D-gedrucktes Teil. Dies verringert die Anzahl der Montageschritte, senkt das Risiko von Fehlerstellen und verbessert die allgemeine Zuverlässigkeit. Beispielsweise können Merkmale wie Versteifungsrippen oder Befestigungsschnittstellen direkt in das Flossendesign integriert werden.
- Personalisierung und Rapid Prototyping: Der 3D-Metalldruck eignet sich ideal für die Herstellung kundenspezifischer Steuerflossen für spezielle Einsatzanforderungen oder für das schnelle Prototyping und Testen neuer Designs. Diese Flexibilität in den Entwicklungszyklen ist in der schnelllebigen Luft- und Raumfahrt- und Verteidigungsindustrie entscheidend.
- Verbesserte Leistung: Durch die Optimierung des Designs und der Materialauswahl mittels Metall-AM können die Steuerflossen so konstruiert werden, dass sie extremen aerodynamischen Belastungen, Temperaturschwankungen und korrosiven Umgebungen standhalten, was letztlich die Leistung und Zuverlässigkeit des Flugkörpers verbessert.
Metall3DPdie fortschrittliche 3D-Metalldrucktechnologie und die hochwertigen Metallpulver eignen sich ideal für die Herstellung von Hochleistungs-Raketenleitwerken, die den strengen Anforderungen der Luft- und Raumfahrt sowie des Verteidigungssektors gerecht werden. Unser branchenweit führendes Druckvolumen, unsere Genauigkeit und Zuverlässigkeit gewährleisten die Produktion von unternehmenskritischen Teilen in außergewöhnlicher Qualität.
Empfohlene Materialien und warum sie wichtig sind - Hochleistungsmetallpulver von Metal3DP
Die Auswahl des geeigneten Metallpulvers ist entscheidend für die Erreichung der gewünschten Leistungsmerkmale von 3D-gedruckten Raketensteuerungsflossen. Metall3DP bietet eine Reihe von Hochleistungsmetallpulvern an, die für anspruchsvolle Anwendungen in der Luft- und Raumfahrt optimiert sind, darunter:
- Ti-6Al-4V (Titan Grad 5): Diese Titanlegierung ist bekannt für ihr außergewöhnliches Verhältnis von Festigkeit zu Gewicht, ihre hervorragende Korrosionsbeständigkeit und ihre Hochtemperaturfähigkeit. Seine Biokompatibilität macht es auch für bestimmte Spezialanwendungen geeignet. Die hohe Festigkeit und geringe Dichte von Ti-6Al-4V sind entscheidend für die Gewichtsreduzierung von Steuerflossen bei gleichzeitiger Aufrechterhaltung der strukturellen Integrität unter extremen aerodynamischen Belastungen. Weitere Informationen über unsere hochwertigen Produkte finden Sie unter Ti-6Al-4V-Pulver hier. ————————————- | Eigenschaft | Wert | Bedeutung für Raketensteuerungsflossen | | :—————- | :—————————————– | :——————————————————————————————————————————————————————— | | Zugfestigkeit | 895-930 MPa | Eine hohe Festigkeit ist unerlässlich, um den erheblichen aerodynamischen Kräften während eines Hochgeschwindigkeitsfluges standzuhalten. | Streckgrenze | 825-869 MPa | Zeigt die Widerstandsfähigkeit des Materials gegen dauerhafte Verformung unter Belastung an, die für die Beibehaltung der Form und Funktionalität der Flosse entscheidend ist. | | Dichte | 4,43 g/cm³ | Die geringe Dichte trägt zu einem hohen Verhältnis von Festigkeit zu Gewicht bei, wodurch die Gesamtmasse des Flugkörpers reduziert und die Effizienz verbessert wird. | | Korrosionsbeständigkeit | Hervorragend | Gewährleistet, dass die Lamellen rauen Umgebungsbedingungen und längerer Exposition ohne Beeinträchtigung standhalten können. | | Maximale Betriebstemperatur | ~400°C | Geeignet für Hochgeschwindigkeitsflüge, bei denen aerodynamische Erwärmung auftreten kann. |
- Scalmalloy® (Al-Mg-Sc-Legierung): Diese Hochleistungsaluminiumlegierung, die in Zusammenarbeit mit der Airbus APWORKS GmbH entwickelt wurde, bietet eine einzigartige Kombination aus hoher Festigkeit, geringem Gewicht und guter Schweißbarkeit. Durch den Zusatz von Scandium (Sc) wird die Festigkeit im Vergleich zu herkömmlichen Aluminiumlegierungen deutlich erhöht. Die geringe Dichte und die hohe spezifische Festigkeit machen Scalmalloy®’s zu einer hervorragenden Alternative zu Titan in bestimmten Raketenanwendungen, bei denen das Gewicht ein kritischer Faktor ist. | Eigenschaft | Wert | Bedeutung für Raketenleitwerke | | :——————————- | :————————————— | :—————————————————————————————————| | Zugfestigkeit | >500 MPa | Bietet die notwendige Festigkeit, um aerodynamischen Belastungen standzuhalten. | | Streckgrenze | >470 MPa | Sorgt dafür, dass das Seitenleitwerk seine Form unter Belastung beibehält. | | Dichte | 2,7 g/cm³ | Deutlich geringer als Titan, dadurch erhebliche Gewichtseinsparung. | | Korrosionsbeständigkeit | Gut (besonders nach dem Eloxieren) | Schützt die Rippen vor Umwelteinflüssen. | | Thermische Ausdehnung | ~1,8 E-05 K-1 (bei 100°C) | Geringe thermische Ausdehnung gewährleistet Dimensionsstabilität über einen weiten Betriebstemperaturbereich. |
Metall3DPdas fortschrittliche Pulverherstellungssystem, das auf branchenführenden Gaszerstäubungs- und PREP-Technologien basiert, gewährleistet die Herstellung hochwertiger, kugelförmiger Metallpulver mit hervorragender Fließfähigkeit, die für konsistente und zuverlässige 3D-Druckverfahren unerlässlich sind. Unser umfangreiches Portfolio umfasst auch andere innovative Legierungen, die für spezielle Anwendungen von Raketensteuerungsflossen geeignet sein können. Kontakt Metall3DP um Ihre spezifischen Materialanforderungen zu besprechen und zu erfahren, wie unsere fortschrittlichen Metallpulver die Leistung Ihrer Raketensysteme verbessern können. Quellen und zugehörige Inhalte
Konstruktionsüberlegungen zur additiven Fertigung von Raketensteuerungsflossen
Die Entwicklung von Raketenleitwerken für den 3D-Druck aus Metall erfordert eine andere Denkweise als die herkömmliche Fertigung. Um die Möglichkeiten der additiven Fertigung voll ausschöpfen zu können, müssen Ingenieure mehrere wichtige Designaspekte berücksichtigen:
- Topologie-Optimierung: Metall-AM ermöglicht die Schaffung organischer, frei geformter Geometrien, die hinsichtlich Gewicht und Steifigkeit auf der Grundlage der spezifischen Belastungsanforderungen optimiert werden können. Mithilfe der Finite-Elemente-Analyse (FEA) können Bereiche mit hoher Belastung identifiziert und Material strategisch hinzugefügt werden, während unnötiges Material entfernt werden kann. Das Ergebnis sind leichtere und effizientere Rippenkonstruktionen.
- Gitterförmige Strukturen: Interne Gitterstrukturen können in das Flossendesign integriert werden, um das Gewicht zu reduzieren, ohne die strukturelle Integrität zu beeinträchtigen. Verschiedene Gittermuster, wie z. B. Kreisel, Würfel oder Diamanten, bieten unterschiedliche Steifigkeits- und Dichtegrade und ermöglichen maßgeschneiderte mechanische Eigenschaften.
- Optimierung der Wanddicke: Die minimal erreichbare Wandstärke im Metall-3D-Druck hängt vom gewählten Material und Druckverfahren ab. Das Design mit optimierten Wandstärken kann den Materialverbrauch und die Druckzeit erheblich reduzieren. Die sorgfältige Berücksichtigung der Spannungsverteilung ist entscheidend, um die strukturelle Integrität bei dünneren Wänden zu gewährleisten.
- Unterstützende Strukturen: Überhängende Merkmale und komplexe Geometrien erfordern häufig Stützstrukturen während des Druckprozesses, um ein Zusammenbrechen oder Verziehen zu verhindern. Die Konstruktion von Teilen mit selbsttragenden Winkeln oder die strategische Planung der Platzierung von Stützen ist entscheidend für die Minimierung von Materialabfall und Nachbearbeitungsaufwand. Software-Tools können bei der Optimierung der Stützkonstruktion helfen.
- Merkmal Integration: Metall-AM ermöglicht die Integration mehrerer Merkmale direkt in das Design der Steuerflosse. Dazu können Befestigungslöcher, Versteifungsrippen, Kühlkanäle oder sogar interne Sensoren gehören. Die Konsolidierung von Teilen reduziert die Montagezeit und potenzielle Fehlerquellen. Anstatt separate Montagehalterungen zu bearbeiten, können diese Merkmale beispielsweise direkt als Teil der Rippe gedruckt werden.
- Überlegungen zur Oberflächenbeschaffenheit: Die Oberflächenbeschaffenheit beim 3D-Druck von Metall kann je nach Material und Druckverfahren variieren. Wenn eine glatte Oberfläche für die aerodynamische Leistung erforderlich ist, muss dies während der Designphase berücksichtigt werden, was möglicherweise Nachbearbeitungsschritte wie Bearbeitung oder Polieren erforderlich macht.
- Optimierung der Orientierung: Die Ausrichtung des Bauteils auf der Bauplattform kann die Oberflächengüte, die Anforderungen an die Unterstützung und die mechanischen Eigenschaften erheblich beeinflussen. Eine sorgfältige Berücksichtigung der vorherrschenden Belastungsrichtungen und der gewünschten Oberflächenqualität kann die optimale Bauausrichtung bestimmen.
Metall3DPunsere Expertise in der additiven Fertigung von Metallen umfasst nicht nur fortschrittliche Drucktechnologie, sondern auch Designoptimierung für AM. Unsere Anwendungsentwicklungsdienste können Sie dabei unterstützen, die Vorteile des 3D-Metalldrucks bei der Konstruktion von Lenkflugkörpern voll auszuschöpfen und eine optimale Leistung und Herstellbarkeit zu gewährleisten. Wir können Ihnen helfen, komplexe Geometrien und Leichtbaustrategien zu erforschen, um Ihre Raketensysteme zu verbessern.
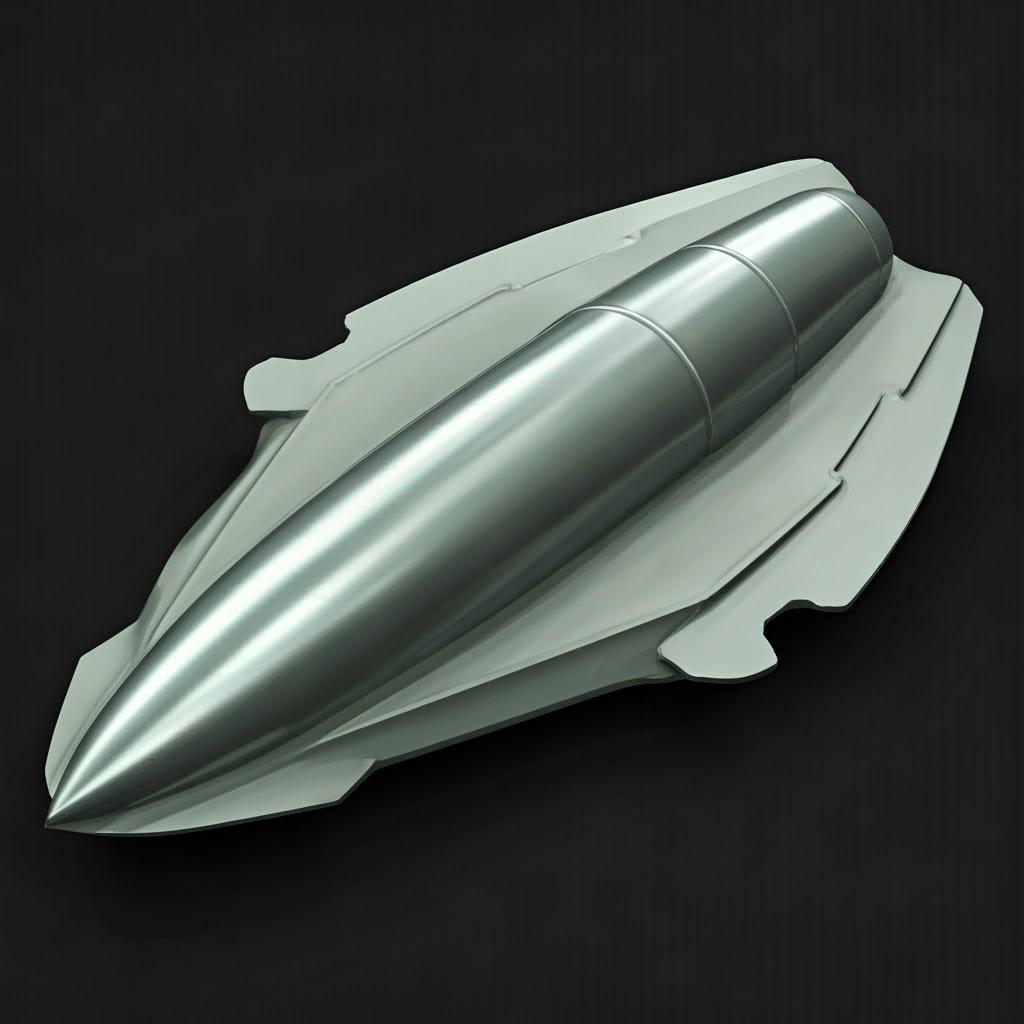
Toleranz, Oberflächenbeschaffenheit und Maßgenauigkeit von 3D-gedruckten Metall-Leitschaufeln
Das Erreichen der geforderten Toleranzen, Oberflächengüte und Maßgenauigkeit ist für die Funktionsfähigkeit und Austauschbarkeit von Raketensteuerungsflossen von größter Bedeutung. 3D-Drucktechnologien für Metall, insbesondere Pulverbettschmelzverfahren (PBF) wie Selective Laser Melting (SLM) und Electron Beam Melting (EBM), bieten ein beeindruckendes Maß an Präzision:
- Maßgenauigkeit: Je nach Material, Teilegeometrie und Druckparametern können Maßgenauigkeiten von ±0,1 mm oder noch feiner erreicht werden. Allerdings müssen Faktoren wie Wärmeausdehnung und Schrumpfung während des Druckvorgangs berücksichtigt werden. Eine genaue Kalibrierung des 3D-Druckers und optimierte Prozessparameter sind für das Erreichen einer hohen Maßgenauigkeit unerlässlich.
- Verträglichkeit: Die mit dem 3D-Druck von Metall erreichbaren Toleranzen liegen in der Regel zwischen ±0,1 mm und ±0,2 mm. Engere Toleranzen können eine Nachbearbeitung, z. B. eine CNC-Bearbeitung, erfordern. Das Design mit Blick auf die erreichbaren Toleranzen ist entscheidend für die Minimierung von Herstellungskosten und Vorlaufzeiten.
- Oberfläche: Die Oberflächenbeschaffenheit nach dem Druck liegt bei PBF-Verfahren in der Regel zwischen Ra 5-20 µm. Dies kann durch die Größe der Pulverpartikel, die Schichtdicke und die Ausrichtung des Aufbaus beeinflusst werden. Für aerodynamische Anwendungen, bei denen eine glattere Oberfläche erforderlich ist, können Nachbearbeitungsverfahren wie Polieren, Sandstrahlen oder chemisches Ätzen eingesetzt werden, um die gewünschte Oberfläche zu erzielen.
Metall3DPdie hochmodernen SEBM-Drucker sind für ihre branchenführende Genauigkeit und Zuverlässigkeit bekannt und gewährleisten die Herstellung von Metallteilen mit außergewöhnlicher Maßkontrolle. Dank unseres Fachwissens in den Bereichen Prozessoptimierung und Materialwissenschaft können wir enge Toleranzen und eine gleichbleibende Teilequalität erzielen. Wir wissen, wie wichtig Präzision bei Bauteilen für die Luft- und Raumfahrt ist, und sind bestrebt, Teile zu liefern, die den anspruchsvollsten Spezifikationen entsprechen. Wenn Sie mehr über unsere Druckverfahren und Fähigkeiten erfahren möchten, besuchen Sie bitte unsere Metal 3D Printing page.
Nachbearbeitungsanforderungen für 3D-gedruckte Raketenleitwerke aus Metall
Der 3D-Metalldruck bietet zwar erhebliche Vorteile, doch sind häufig Nachbearbeitungsschritte erforderlich, um die endgültigen gewünschten Eigenschaften und die Oberflächenbeschaffenheit von Raketensteuerungsflossen zu erreichen:
- Unterstützung bei der Entfernung: Stützstrukturen, die für den Druck komplexer Geometrien unverzichtbar sind, müssen nach Abschluss der Herstellung sorgfältig entfernt werden. Dies kann je nach Trägermaterial und Teilegeometrie manuell mit Werkzeugen oder durch automatisierte Verfahren wie maschinelle Bearbeitung oder chemisches Auflösen erfolgen.
- Wärmebehandlung: Um die während des Druckvorgangs entstandenen inneren Spannungen abzubauen und die gewünschten mechanischen Eigenschaften (z. B. Härte, Zugfestigkeit) zu erreichen, ist häufig eine Wärmebehandlung erforderlich. Spezifische Wärmebehandlungszyklen werden auf das Material und die Anwendungsanforderungen zugeschnitten.
- Oberflächenveredelung: Wie bereits erwähnt, können Nachbearbeitungsverfahren wie CNC-Bearbeitung, Polieren, Schleifen oder Sandstrahlen eingesetzt werden, um die Oberflächengüte zu verbessern und so die aerodynamische Leistung oder die ästhetischen Anforderungen zu erhöhen. Die Wahl der Methode hängt von der gewünschten Oberflächenrauhigkeit und der Komplexität der Teilegeometrie ab.
- Inspektion und Qualitätskontrolle: Strenge Prüfverfahren, einschließlich Dimensionsmessungen, zerstörungsfreie Prüfungen (NDT) wie Farbeindringprüfung oder Ultraschallprüfung und Materialanalyse, sind entscheidend, um die Qualität und Integrität der 3D-gedruckten Steuerrippen zu gewährleisten, insbesondere für kritische Anwendungen in der Luft- und Raumfahrt.
- Beschichtung: Je nach Betriebsumgebung können Beschichtungen aufgebracht werden, um die Korrosionsbeständigkeit, die Verschleißfestigkeit oder andere spezifische Eigenschaften zu verbessern. Beispiele sind die Eloxierung von Aluminiumlegierungen oder Keramikbeschichtungen für Hochtemperaturanwendungen.
Metall3DP bietet umfassende Nachbearbeitungsdienste an, um sicherzustellen, dass Ihre 3D-gedruckten Raketensteuerungsflossen den höchsten Qualitäts- und Leistungsstandards entsprechen. Unser erfahrenes Team ist in der Lage, die Entformung, Wärmebehandlung, Oberflächenveredelung und die strengen Qualitätskontrollverfahren zu übernehmen und bietet Ihnen eine komplette Fertigungslösung.
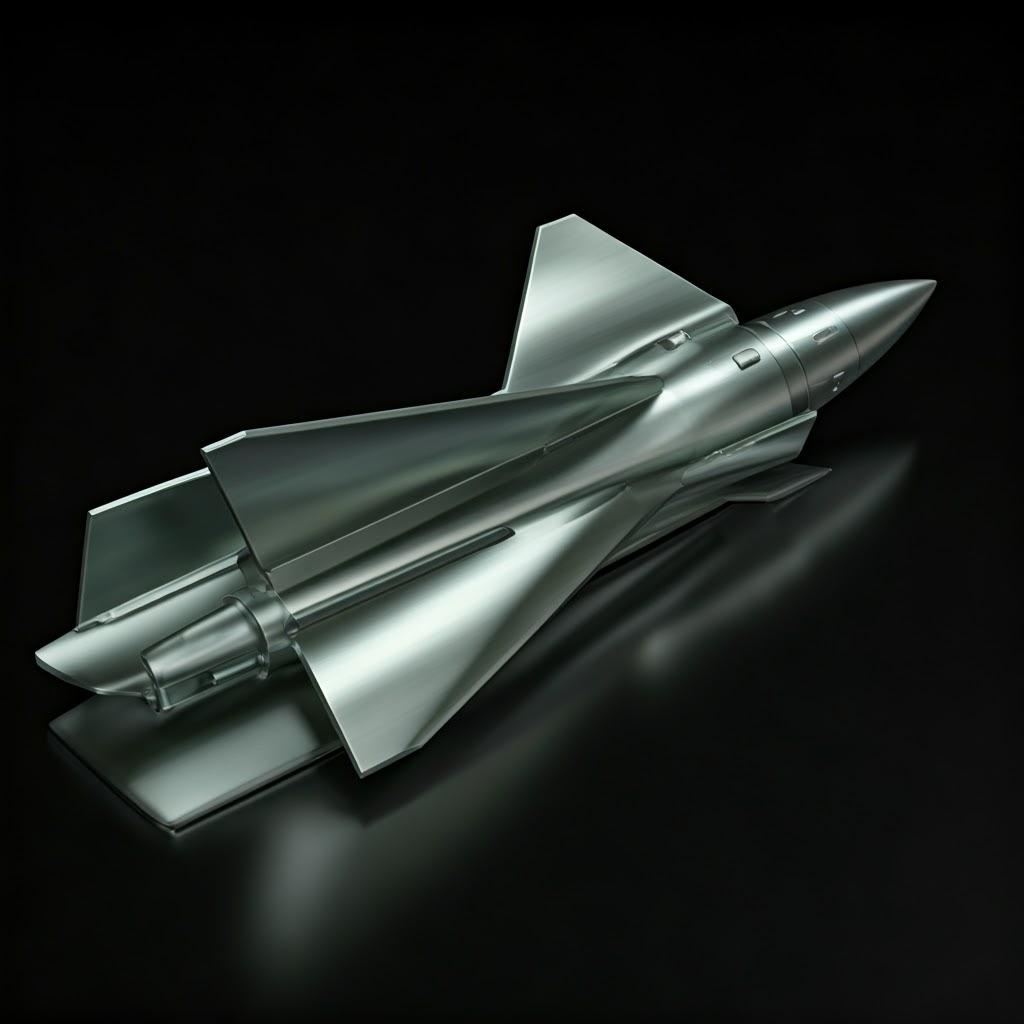
Häufige Herausforderungen und deren Vermeidung beim 3D-Metalldruck von Steuerflossen
Der 3D-Metalldruck bietet zwar zahlreiche Vorteile, doch können während des Prozesses auch verschiedene Probleme auftreten. Das Verständnis dieser potenziellen Probleme und die Umsetzung von Präventivmaßnahmen sind entscheidend für die erfolgreiche Herstellung von Raketensteuerungsflossen:
- Verformung und Verzerrung: Thermische Spannungen während des Druckvorgangs können zu einer Verformung oder Verzerrung des Teils führen, insbesondere bei großen oder komplexen Geometrien. Die Optimierung der Teileausrichtung, die Verwendung geeigneter Stützstrukturen und die sorgfältige Kontrolle der Baukammertemperatur können diese Probleme mindern.
- Porosität: Interne Hohlräume oder Porosität können die mechanischen Eigenschaften des gedruckten Teils beeinträchtigen. Die Verwendung hochwertiger Metallpulver, die Optimierung der Laser- oder Elektronenstrahlparameter und die Aufrechterhaltung einer kontrollierten Atmosphäre in der Baukammer sind entscheidend für die Minimierung der Porosität. Metall3DP‘s hochwertige Metallpulver sind speziell darauf ausgelegt, die Porosität zu minimieren.
- Unterstützung bei der Beseitigung von Schwierigkeiten: Unzureichend konstruierte oder zu komplexe Stützstrukturen können schwierig und zeitaufwändig zu entfernen sein und die Oberfläche des Teils beschädigen. Die Entwicklung selbsttragender Geometrien, wo immer dies möglich ist, und die Optimierung der Platzierung und des Typs der Stützen können dieses Problem lindern.
- Unstimmigkeiten bei der Oberflächenbeschaffenheit: Die Erzielung einer gleichmäßigen Oberflächengüte über das gesamte Bauteil hinweg kann aufgrund von Schwankungen bei der Bauausrichtung und den Auflagepunkten eine Herausforderung darstellen. Die Optimierung der Bauausrichtung und die Anwendung geeigneter Nachbearbeitungstechniken sind der Schlüssel zum Erreichen der gewünschten Oberflächenqualität.
- Variabilität der Materialeigenschaften: Uneinheitliche Materialeigenschaften können auf Schwankungen der Pulverqualität oder der Druckparameter zurückzuführen sein. Die Verwendung von zertifizierten, hochwertigen Pulvern von renommierten Anbietern wie Metall3DP und eine sorgfältige Kontrolle des Druckprozesses sind entscheidend, um gleichbleibende und zuverlässige Materialeigenschaften zu gewährleisten.
- Kostenmanagement: Der 3D-Druck von Metall kann zwar für bestimmte Anwendungen kosteneffizient sein, aber Faktoren wie Materialkosten, Herstellungszeit und Nachbearbeitung können die Gesamtkosten beeinflussen. Die Optimierung des Designs im Hinblick auf die Materialeffizienz und die Minimierung der Nachbearbeitungsschritte sind wichtig für das Kostenmanagement.
Metall3DPdank unserer umfassenden Erfahrung in der additiven Fertigung von Metallen sind wir in der Lage, diese häufigen Herausforderungen vorherzusehen und zu entschärfen. Unser Fachwissen in den Bereichen Materialwissenschaft, Prozessoptimierung und Design für AM stellt sicher, dass Sie hochwertige, fehlerfreie Raketensteuerungsflossen erhalten. Wir arbeiten eng mit unseren Kunden zusammen, um ihre Entwürfe und Herstellungsverfahren sowohl hinsichtlich der Leistung als auch der Kosteneffizienz zu optimieren.
Wie man den richtigen 3D-Druckdienstleister für Raketenleitwerke aus Metall auswählt
Die Auswahl des richtigen 3D-Druckdienstleisters für Metall ist eine wichtige Entscheidung, die sich erheblich auf die Qualität, die Kosten und die Vorlaufzeit Ihrer Raketensteuerungsflossen auswirken kann. Berücksichtigen Sie bei der Bewertung potenzieller Lieferanten die folgenden Faktoren:
- Materielle Fähigkeiten: Vergewissern Sie sich, dass der Anbieter Erfahrung mit den für Ihre Anwendung erforderlichen Metalllegierungen hat, z. B. Ti-6Al-4V oder Scalmalloy®. Er sollte auch über ein solides Verständnis der Materialeigenschaften und Verarbeitungsparameter verfügen. Metall3DP bietet eine breite Palette von Hochleistungsmetallpulvern an, die für Luft- und Raumfahrtanwendungen optimiert sind.
- Technologie und Ausrüstung: Erkundigen Sie sich nach den Arten von 3D-Drucktechnologien für Metall (z. B. SLM, EBM, DED), die eingesetzt werden. Die Wahl der Technologie kann die erreichbare Genauigkeit, Oberflächengüte und das Bauvolumen beeinflussen. Metall3DP setzt fortschrittliche SEBM-Drucker ein, die für ihre Genauigkeit und Zuverlässigkeit bekannt sind. Sie können mehr über unsere druckmethoden hier.
- Qualitätssicherung und Zertifizierungen: Prüfen Sie, ob der Anbieter über solide Qualitätsmanagementsysteme und einschlägige Zertifizierungen verfügt, z. B. AS9100 für Anwendungen in der Luft- und Raumfahrt. Dies gewährleistet die Einhaltung strenger Qualitätsstandards und die Rückverfolgbarkeit.
- Unterstützung bei Design und Technik: Ein guter Dienstleister sollte Dienstleistungen zur Designoptimierung für die additive Fertigung anbieten und Ihnen dabei helfen, die einzigartigen Möglichkeiten des 3D-Metalldrucks zu nutzen und mögliche Fallstricke zu vermeiden. Metall3DP bietet umfassende Anwendungsentwicklungsdienste zur Unterstützung bei Design und Optimierung.
- Nachbearbeitungsmöglichkeiten: Stellen Sie fest, ob der Anbieter die erforderlichen Nachbearbeitungsdienste anbietet, z. B. Entfernen von Halterungen, Wärmebehandlung, Oberflächenbearbeitung und Prüfung, um готовые Teile zu liefern, die Ihren Spezifikationen entsprechen. Metall3DP bietet eine umfassende Palette von Nachbearbeitungsdiensten.
- Erfahrung und Fachwissen: Suchen Sie nach einem Anbieter mit einer nachgewiesenen Erfolgsbilanz bei der Herstellung von Metallteilen für anspruchsvolle Branchen wie Luft- und Raumfahrt oder Verteidigung. Ihre Erfahrung wird sich in einer besseren Prozesskontrolle und einer höheren Qualität der Teile niederschlagen. Metall3DP verfügt über jahrzehntelange Erfahrung in der additiven Fertigung von Metallen. Um mehr über unser Unternehmen zu erfahren, besuchen Sie bitte unsere Über uns-Seite.
- Vorlaufzeiten und Preisgestaltung: Holen Sie klare Informationen über die Vorlaufzeiten für die Herstellung und alle damit verbundenen Kosten ein. Vergleichen Sie die Angebote verschiedener Anbieter und achten Sie dabei auf den Gesamtwertbeitrag, einschließlich Qualität und technisches Know-how.
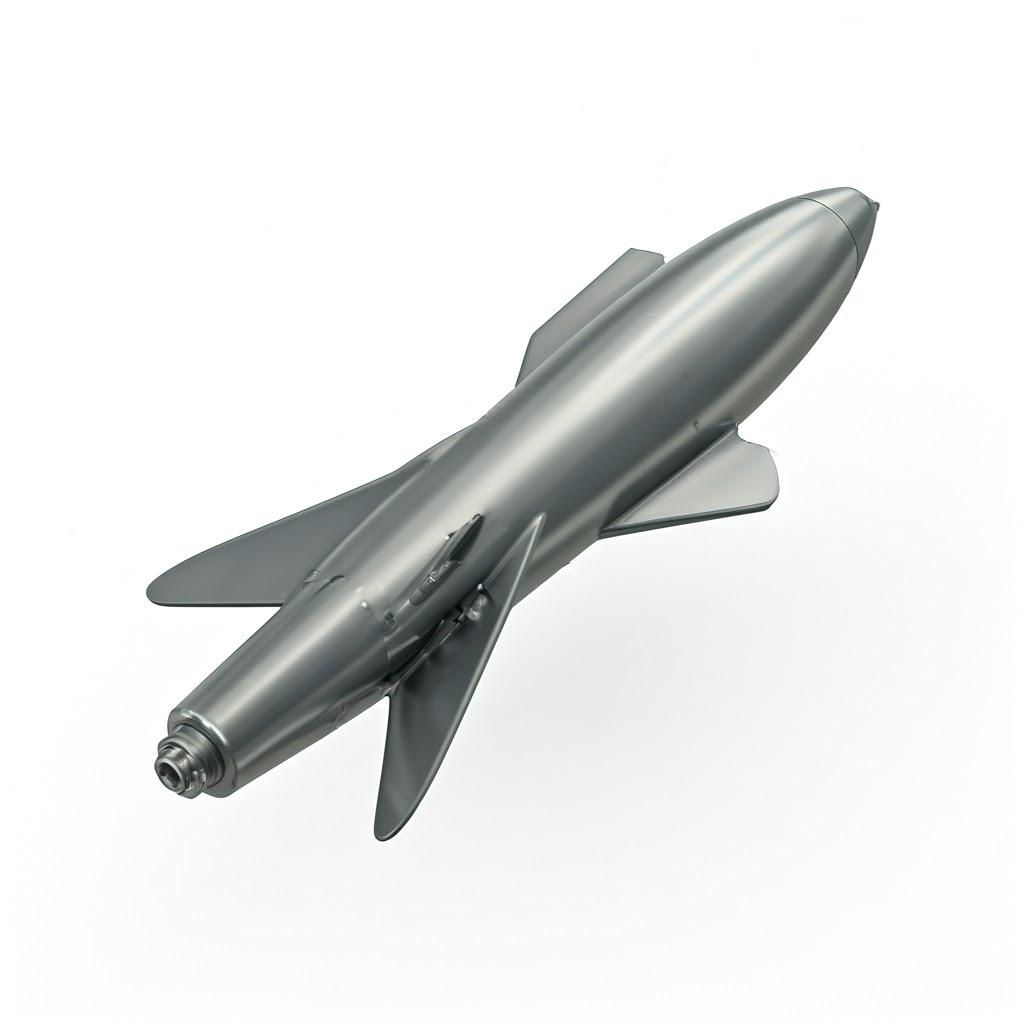
Kostenfaktoren und Vorlaufzeit für 3D-gedruckte Raketenleitwerke aus Metall
Die Kosten und die Vorlaufzeit für die Herstellung von Raketensteuerungsflossen im 3D-Metalldruck werden von mehreren Faktoren beeinflusst:
- Materialkosten: Die Kosten für das Metallpulver sind ein wichtiger Faktor. Hochleistungslegierungen wie Ti-6Al-4V und Scalmalloy® können teuer sein. Auch der Materialverbrauch, der durch Designoptimierung minimiert werden kann, wirkt sich auf die Gesamtkosten aus.
- Bauzeit: Die Zeit, die für den Druck eines Teils benötigt wird, hängt von dessen Größe, Komplexität und den gewählten Druckparametern (z. B. Schichtdicke, Scan-Geschwindigkeit) ab. Längere Bauzeiten führen zu höheren Betriebskosten der Maschine.
- Nachbearbeitungskosten: Der Umfang der erforderlichen Nachbearbeitung (z. B. Entfernen von Trägern, Wärmebehandlung, Bearbeitung, Beschichtung) erhöht die Gesamtkosten und die Vorlaufzeit.
- Arbeitskosten: Entwurf, Druck und Nachbearbeitung erfordern qualifizierte Arbeitskräfte, die in die Endkosten einkalkuliert werden.
- Maschinen- und Gemeinkosten: Die Kosten für den Betrieb und die Wartung der 3D-Drucker sowie die allgemeinen Gemeinkosten des Dienstleisters sind ebenfalls in den Preisen enthalten.
- Auftragsvolumen: Ähnlich wie bei der traditionellen Fertigung können auch beim 3D-Druck Skaleneffekte erzielt werden, wobei größere Produktionsläufe zu niedrigeren Kosten pro Teil führen können.
Die Vorlaufzeiten können je nach Komplexität des Teils, der Verfügbarkeit von Materialien, der Arbeitsbelastung des Dienstleisters und den erforderlichen Nachbearbeitungsschritten variieren. Der 3D-Metalldruck kann im Vergleich zu herkömmlichen Verfahren kürzere Vorlaufzeiten bieten, insbesondere bei komplexen Geometrien und geringen bis mittleren Produktionsmengen, da keine Werkzeuge benötigt werden.
Metall3DP ist bestrebt, transparente und wettbewerbsfähige Preise für unsere 3D-Metalldruckdienste anzubieten. Wir arbeiten eng mit unseren Kunden zusammen, um Entwürfe im Hinblick auf Kosteneffizienz zu optimieren und realistische Vorlaufzeiten auf der Grundlage der spezifischen Anforderungen ihrer Projekte zu bieten. Wenden Sie sich an uns, um ein detailliertes Angebot für die Herstellung Ihrer Raketenkontrollflossen zu erhalten.
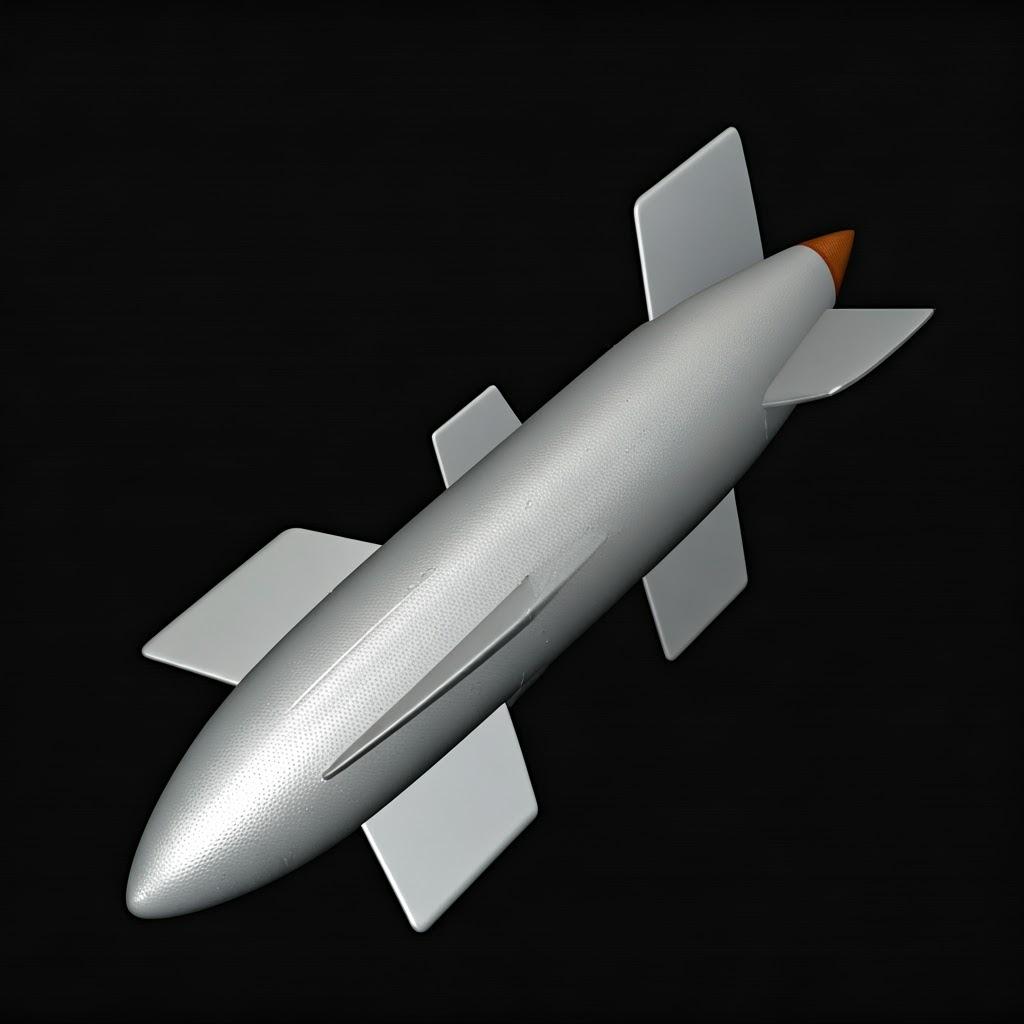
Häufig gestellte Fragen (FAQ)
- Können 3D-gedruckte Steuerflossen aus Metall die Anforderungen an die Festigkeit in der Luft- und Raumfahrt erfüllen? Ja, bei Verwendung geeigneter Hochleistungsmetallpulver wie Ti-6Al-4V oder Scalmalloy® und optimierten Druckparametern können 3D-gedruckte Steuerrippen aus Metall mechanische Eigenschaften aufweisen, die die Normen der Luft- und Raumfahrt erfüllen oder übertreffen. Strenge Tests und Qualitätskontrollen sind unerlässlich, um diese Eigenschaften zu verifizieren. Metall3DP hält sich an strenge Qualitätsstandards, um die strukturelle Integrität unserer 3D-gedruckten Teile zu gewährleisten.
- Wie lang ist die typische Vorlaufzeit für die Herstellung einer kleinen Charge von 3D-gedruckten Raketensteuerflossen aus Metall? Die Vorlaufzeiten können je nach Komplexität des Entwurfs, dem gewählten Material und der erforderlichen Nachbearbeitung variieren. Bei kleinen bis mittleren Serien bietet der 3D-Metalldruck jedoch in der Regel schnellere Durchlaufzeiten als herkömmliche Fertigungsverfahren, die von einigen Tagen bis zu einigen Wochen reichen können. Kontakt Metall3DP für einen konkreten Zeitplan für Ihr Projekt.
- Ist der 3D-Druck von Metall für die Herstellung von Raketensteuerungsflossen kosteneffizient? Der 3D-Druck von Metall kann kosteneffizient sein, insbesondere bei komplexen Konstruktionen, geringen bis mittleren Produktionsmengen und unter Berücksichtigung von Faktoren wie geringerem Materialabfall, Designfreiheit und kürzeren Vorlaufzeiten. Die Gesamtwirtschaftlichkeit hängt von der jeweiligen Anwendung und den Produktionsanforderungen ab. Metall3DP arbeitet mit den Kunden zusammen, um Entwürfe und Produktionsprozesse im Hinblick auf Kosteneffizienz zu optimieren.
Fazit - Mit Metall-3D-Druck und Metal3DP in die Zukunft der Herstellung von Raketenleitwerken
Der 3D-Metalldruck revolutioniert die Herstellung von Raketensteuerungsrippen und bietet eine beispiellose Designfreiheit, Gewichtsoptimierung, Materialeffizienz und kürzere Vorlaufzeiten. Durch den Einsatz fortschrittlicher Materialien wie Ti-6Al-4V und Scalmalloy® und innovativer Drucktechnologien können Ingenieure leistungsstarke, einsatzkritische Komponenten mit verbesserter Funktionalität und Zuverlässigkeit herstellen.
Metall3DP steht an der Spitze dieses technologischen Fortschritts und bietet branchenführende 3D-Druckanlagen für Metall, hochwertige Metallpulver und umfassende Dienstleistungen für die Anwendungsentwicklung. Unser Engagement für Genauigkeit, Zuverlässigkeit und Kundenzufriedenheit macht uns zum idealen Partner für Unternehmen, die sich die Zukunft der Herstellung von Raketensteuerungsflossen erschließen wollen. Kontakt Metall3DP heute, um zu erfahren, wie unsere Fähigkeiten die Ziele Ihres Unternehmens im Bereich der additiven Fertigung unterstützen und die Leistung Ihrer Raketensysteme steigern können
Teilen auf
MET3DP Technology Co., LTD ist ein führender Anbieter von additiven Fertigungslösungen mit Hauptsitz in Qingdao, China. Unser Unternehmen ist spezialisiert auf 3D-Druckgeräte und Hochleistungsmetallpulver für industrielle Anwendungen.
Fragen Sie an, um den besten Preis und eine maßgeschneiderte Lösung für Ihr Unternehmen zu erhalten!
Verwandte Artikel
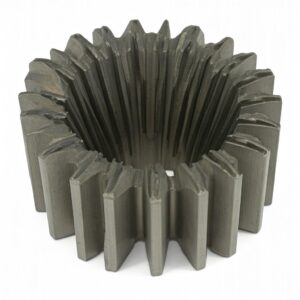
Hochleistungs-Düsenschaufelsegmente: Revolutionierung der Turbineneffizienz mit 3D-Metalldruck
Mehr lesen "Über Met3DP
Aktuelles Update
Unser Produkt
KONTAKT US
Haben Sie Fragen? Senden Sie uns jetzt eine Nachricht! Wir werden Ihre Anfrage mit einem ganzen Team nach Erhalt Ihrer Nachricht bearbeiten.
Holen Sie sich Metal3DP's
Produkt-Broschüre
Erhalten Sie die neuesten Produkte und Preislisten