3D-gedruckte Stromversorgungsgehäuse für UAV-Elektronik
Inhaltsübersicht
Einführung: Revolutionierung des UAV-Designs mit 3D-gedruckten Energiegehäusen
Die Branche der unbemannten Luftfahrzeuge (UAV) oder Drohnen erlebt ein exponentielles Wachstum und verändert Sektoren wie Verteidigung und Überwachung, Landwirtschaft, Logistik und Infrastrukturinspektion. Das Herzstück eines jeden UAVs ist ein komplexes System aus Elektronik, Batterien und Energiemanagementkomponenten. Der Schutz dieser lebenswichtigen Systeme vor rauen Umgebungsbedingungen, elektromagnetischen Störungen (EMI) und physischen Einwirkungen ist für den Erfolg der Mission und die Betriebszuverlässigkeit von größter Bedeutung. Traditionell wurden Gehäuse für diese empfindliche Elektronik mit Methoden wie CNC-Bearbeitung aus Knüppelmaterial oder Spritzguss für Großserienanwendungen hergestellt. Die einzigartigen Anforderungen des UAV-Sektors - insbesondere das unerbittliche Streben nach geringeres Gewicht, erhöhte Nutzlastkapazitätund verbesserte Leistung - ebnen den Weg für innovative Fertigungslösungen.
Eingeben Additive Fertigung von Metall (AM)gemeinhin als Metall bekannt 3D-Druck. Diese transformative Technologie bewegt sich schnell über die Prototypenherstellung hinaus in die Produktion von Endverbrauchsteilen und Gehäuse für UAV-Stromversorgung sind ein wichtiger Anwendungsbereich. Ein Stromversorgungsgehäuse ist mehr als nur ein Kasten; es ist eine kritische Subsystemkomponente, die es braucht:
- Schützen Sie empfindliche Elektronik: Abschirmung der internen Komponenten (Stromverteilungsplatinen, Batteriemanagementsysteme, Umrichter) vor Feuchtigkeit, Staub, Vibrationen, Stößen und Temperaturschwankungen während des Fluges.
- Sicherstellung der strukturellen Integrität: Sie bieten robuste Halterungen und Befestigungspunkte für interne Komponenten und die gesamte UAV-Zelle und tragen oft zur strukturellen Integrität des Fahrzeugs bei.
- Thermische Belastungen bewältigen: Leiten die von der Leistungselektronik erzeugte Wärme effektiv ab, um Überhitzung zu vermeiden und optimale Leistung und Langlebigkeit zu gewährleisten.
- Minimieren Sie das Gewicht: So wenig Gewicht wie möglich, um Flugzeit, Manövrierbarkeit und Nutzlastkapazität zu maximieren - ein entscheidender Faktor bei der Entwicklung von UAVs.
- Bieten möglicherweise EMI-Abschirmung: Schützen Sie die empfindliche Elektronik vor externen elektromagnetischen Störungen und verhindern Sie, dass das Stromversorgungssystem andere Sensoren oder Kommunikationssysteme an Bord beeinträchtigt.
Der 3D-Metalldruck bietet die einzigartige Möglichkeit, diese vielfältigen Anforderungen auf eine Weise zu erfüllen, wie es die traditionelle Fertigung oft nicht kann. Durch den schichtweisen Aufbau von Teilen direkt aus digitalen Modellen ermöglicht AM die Herstellung von hochkomplexen, leichten und individuellen gehäuse für Drohnenelektronik die für bestimmte Einsatzprofile und Umweltanforderungen optimiert sind. Unternehmen, die spezialisiert sind auf additive Fertigung für die Luft- und Raumfahrt nutzen Materialien wie Aluminiumlegierungen und rostfreie Stähle, um langlebige und leistungsstarke Produkte herzustellen benutzerdefinierte UAV-Teileeinschließlich Stromversorgungsgehäusen, die den strengen Anforderungen dieser dynamischen Branche gerecht werden. In dieser Einführung wird untersucht, wie Metall-AM nicht nur eine Alternative, sondern oft eine überlegene Methode für die Herstellung der nächsten Generation von UAV-Stromversorgungsgehäusen ist, die Innovation und Leistung in diesem Sektor vorantreibt. Verstehen der Fähigkeiten fortschrittlicher Einführung in den 3D-Metalldruck technologien wird für Ingenieure und Beschaffungsmanager, die wettbewerbsfähig bleiben wollen, immer wichtiger.
Anwendungen: Wo werden 3D-gedruckte UAV-Energiegehäuse eingesetzt?
Die Vielseitigkeit der additiven Fertigung von Metallen ermöglicht die Herstellung von Stromversorgungsgehäusen, die auf ein breites Spektrum von UAV-Plattformen und Betriebsumgebungen zugeschnitten sind. Die Möglichkeit, Konstruktionen schnell und kostengünstig an spezifische Anforderungen anzupassen, macht den 3D-Druck für verschiedene Bereiche besonders attraktiv UAV-Anwendungen. Beschaffungsmanager, die zuverlässige anbieter von kommerziellen Drohnen und Ingenieure, die hochmoderne Systeme entwerfen, wenden sich zunehmend an AM für diese kritischen Komponenten.
Hier sind einige Schlüsselbereiche, in denen 3D-gedruckte Metallgehäuse einen bedeutenden Einfluss haben:
- Verteidigung und Überwachung:
- Anwendungen: Taktische Aufklärungsdrohnen, Streumunition, Drohnen für den Grenzschutz, Plattformen für die Nachrichtengewinnung.
- Anforderungen an Gehäuse: Extreme Haltbarkeit, hohe Zuverlässigkeit in rauen Umgebungen (extreme Temperaturen, hohe G-Kräfte), potenzielle EMI-Abschirmung, geringe Beobachtbarkeit (spezielle Beschichtungen/Beschichtungen), geringes Gewicht für längere Einsatzdauer.
- AM Vorteil: Herstellung robuster, komplexer Gehäuse mit integrierten Funktionen, häufig unter Verwendung von für die Luft- und Raumfahrt geeigneten Materialien wie speziellen Aluminium- oder Titanlegierungen (AlSi10Mg und 316L sind jedoch gängige Ausgangspunkte). Die Fähigkeit, kundenspezifische Designs für spezifische Nutzlasten und Missionsanforderungen in kürzerer Zeit als bei herkömmlichen Werkzeugen zu erstellen. Wesentlich für verteidigung UAV Teile.
- Luft- und Raumfahrt und Exploration:
- Anwendungen: HALE-Drohnen (High-Altitude Long-Endurance), Forschungsdrohnen, Plattformen für atmosphärische Probenahmen.
- Anforderungen an Gehäuse: Entscheidend sind ein extrem geringes Gewicht, eine hohe thermische Stabilität für unterschiedliche Höhenlagen, Beständigkeit gegen UV-Strahlung und potenzielle atmosphärische Verunreinigungen sowie eine strenge Qualitätskontrolle und Rückverfolgbarkeit der Materialien.
- AM Vorteil: Topologieoptimierung und generative Designwerkzeuge, die durch AM ermöglicht werden, ermöglichen eine erhebliche Gewichtsreduzierung ohne Beeinträchtigung der strukturellen Integrität. 3D-Druck in der Luft- und Raumfahrt techniken ermöglichen komplexe interne Kühlkanäle und die Konsolidierung mehrerer Teile in einem einzigen gedruckten Bauteil, was die Komplexität der Montage und potenzielle Fehlerquellen reduziert.
- Gewerbliche und industrielle Inspektion:
- Anwendungen: Inspektion von Infrastrukturen (Brücken, Stromleitungen, Windturbinen), Präzisionslandwirtschaft (Ernteüberwachung), Kartierung und Vermessung, Umweltüberwachung.
- Anforderungen an Gehäuse: Gute Abdichtung gegen Umwelteinflüsse (IP-Klassifizierung), Widerstandsfähigkeit gegen Staub und Feuchtigkeit, Langlebigkeit für häufige Einsätze und Rückholaktionen, Kosteneffizienz für den Flottenbetrieb. Das Wärmemanagement ist wichtig für Drohnen, die in der Nähe von Gebäuden oder in direktem Sonnenlicht betrieben werden.
- AM Vorteil: Möglichkeit zur Herstellung langlebiger Gehäuse mit integrierten Dichtungen oder Befestigungselementen. Schnellere Iteration für Designverbesserungen auf der Grundlage von Feedback aus der Praxis. Kostengünstige Produktion für kleine bis mittlere Stückzahlen, wie sie für spezialisierte industrielle Drohnenfertigung. Werkstoffe wie 316L bieten eine hervorragende Korrosionsbeständigkeit für Küstengebiete oder industrielle Umgebungen.
- Logistik und Lieferung:
- Anwendungen: Paketzustelldrohnen, Drohnen für den Transport medizinischer Güter.
- Anforderungen an Gehäuse: Leichtes Gewicht zur Maximierung der Nutzlast, robuste Konstruktion, um möglichen Stößen bei der Landung/Auslieferung standzuhalten, zuverlässiges Wärmemanagement für potenziell leistungsstarke Systeme, leichter Zugang für die Wartung.
- AM Vorteil: Optimierung von Gewicht und Festigkeit. Möglichkeit der Integration von Funktionen wie Batteriesperrmechanismen oder Statusanzeigen. Die schnelle Herstellung ermöglicht eine schnellere Entwicklung neuer Drohnen oder Anpassungen an verschiedene Frachtarten.
- Spezialisierte Anwendungen:
- Anwendungen: Such- und Rettungsdrohnen, UAVs für Filmaufnahmen, wissenschaftliche Forschungsplattformen.
- Anforderungen an Gehäuse: Hochgradig kundenspezifische Konstruktionen auf der Grundlage einzigartiger Sensornutzlasten oder Betriebsbedingungen, die möglicherweise spezielle Schwingungsdämpfungs- oder Wärmeisolierungseigenschaften erfordern.
- AM Vorteil: Unerreichte Designfreiheit, um maßgeschneiderte Gehäuse zu entwickeln, die perfekt auf die spezifische Ausrüstung und das Einsatzprofil abgestimmt sind, was Innovationen in Nischen ermöglicht anwendungsfälle für Drohnenkomponenten.
Bei all diesen Anwendungen ist die Funktion des 3D-gedruckten Leistungsgehäuses nach wie vor entscheidend: Schutz der Leistungselektronik, Wärmemanagement, Beitrag zur strukturellen Integrität, und das bei möglichst geringem Gewicht. Metall-AM bietet die Werkzeuge, um dieses Gleichgewicht effektiv zu erreichen.
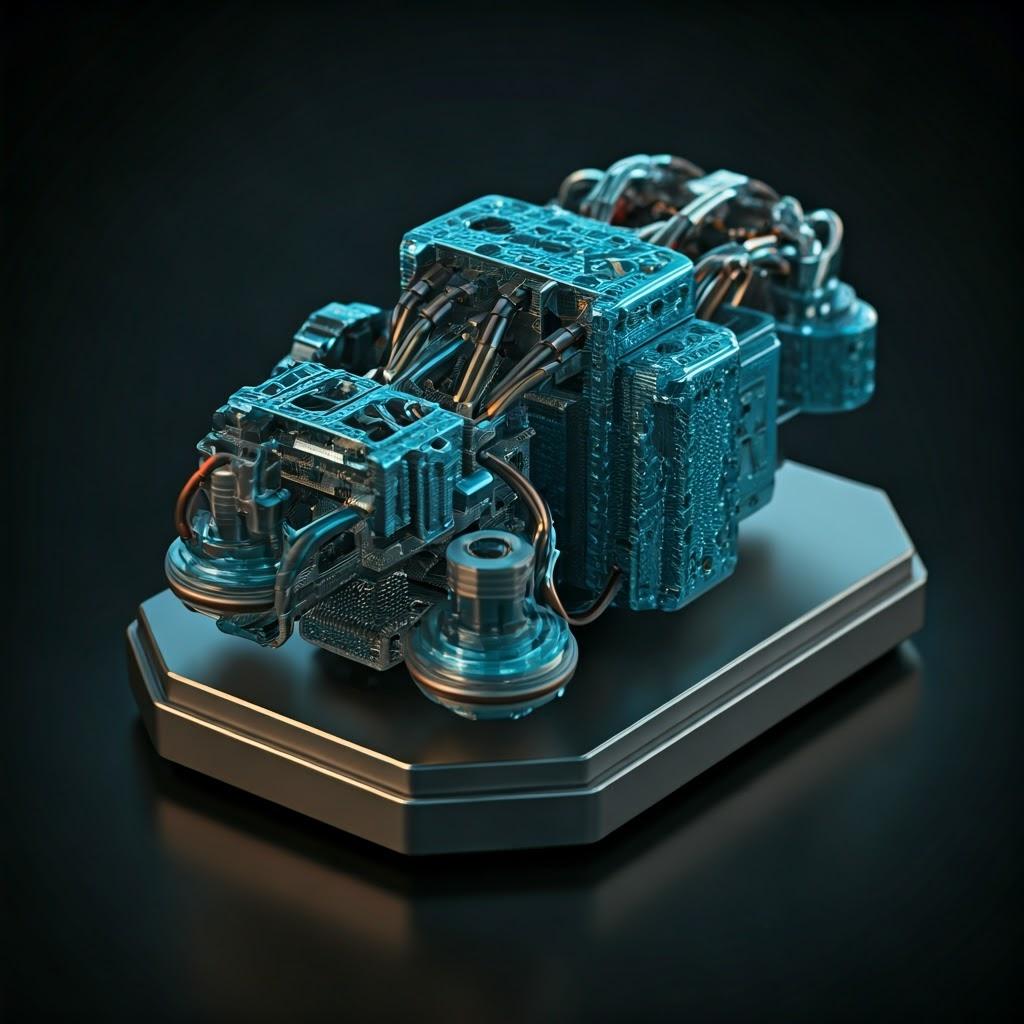
Der Additiv-Vorteil: Warum 3D-Metalldruck für UAV-Gehäuse?
Während herkömmliche Fertigungsmethoden wie CNC-Bearbeitung und Gießen der Branche gute Dienste geleistet haben, bietet die additive Fertigung von Metallen überzeugende Vorteile, die speziell auf die Herausforderungen bei der Herstellung von Hochleistungs-UAV-Netzteilgehäusen zugeschnitten sind. Vergleich traditionelle vs. additive Fertigung verrät, warum Ingenieure und Beschaffungsmanager sich zunehmend für Metal AM entscheiden.
Die wichtigsten Vorteile von Metal AM für UAV-Energiegehäuse:
- Unerreichte Gestaltungsfreiheit und Komplexität:
- Herausforderung: Stromversorgungsgehäuse erfordern oft komplizierte interne Merkmale für die Montage von Komponenten, die Kabelführung, das Luftstrommanagement und die Wärmeableitung. Herkömmliche Methoden haben Schwierigkeiten mit komplexen Innengeometrien oder erfordern mehrteilige Baugruppen.
- AM-Lösung: AM baut Teile Schicht für Schicht auf und ermöglicht so die Herstellung hochkomplexer, monolithischer Strukturen. Dies ermöglicht:
- Konforme Kühlkanäle: Integrierte Kühlkanäle, die den Konturen der wärmeerzeugenden Komponenten genau folgen, sorgen für ein deutlich verbessertes Wärmemanagement.
- Interne Gitternetze: Durch die Verwendung komplexer Gitterstrukturen wird das Gewicht erheblich reduziert, während die strukturelle Steifigkeit erhalten bleibt.
- Integrierte Funktionen: Die Konstruktion von Montagevorsprüngen, Schnappverschlüssen, Kabelkanälen und anderen Merkmalen direkt im Gehäuse reduziert die Anzahl der Teile und die Montagezeit.
- Diese Fähigkeit ist entscheidend für die Herstellung von komplexe Drohnenteile.
- Signifikante Gewichtsreduzierung (Lightweighting):
- Herausforderung: Jedes Gramm, das bei einer Drohne eingespart wird, bedeutet längere Flugzeiten oder eine höhere Nutzlastkapazität. Bei der maschinellen Bearbeitung bleibt oft überschüssiges Material übrig, und bei der Konstruktion von Gussteilen sind Entformungswinkel und einheitliche Wandstärken erforderlich, die möglicherweise nicht gewichtsoptimal sind.
- AM-Lösung: AM zeichnet sich durch die Schaffung leichter Strukturen aus:
- Topologie-Optimierung: Software-Algorithmen ermitteln die effizienteste Materialverteilung, um bestimmten Belastungen standzuhalten, und entfernen unnötiges Material.
- Generatives Design: KI-gesteuerte Designprozesse schaffen organische, hoch optimierte Formen, die auf herkömmliche Weise oft nicht herstellbar sind.
- Dünne Wände & Komplexe Geometrien: Druck von dünneren, aber strukturell soliden Wänden und komplizierten inneren Stützen.
- Diese Konzentration auf die Schaffung leichte UAV-Komponenten ist eine der wichtigsten Triebfedern für die Einführung von AM.
- Teil Konsolidierung:
- Herausforderung: Herkömmliche Gehäuse können aus mehreren maschinell bearbeiteten oder aus Blech gefertigten Teilen bestehen, die miteinander verbunden sind, was das Gewicht, die Montagezeit und potenzielle Fehlerquellen (z. B. Dichtungen zwischen den Teilen) erhöht.
- AM-Lösung: Komplexe Baugruppen können oft neu entworfen und als eine einzige, monolithische Komponente gedruckt werden. Das reduziert den Aufwand:
- Arbeitsaufwand und Zeit für die Montage.
- Bedarf an Verschlüssen und Dichtungen.
- Gesamtgewicht.
- Potenzielle Leckagepfade oder Fehlerstellen.
- Rapid Prototyping und Iteration:
- Herausforderung: Die Entwicklung und Erprobung neuer UAV-Designs erfordert kurze Durchlaufzeiten für Komponenten. Herkömmliche Werkzeuge (Formen, Vorrichtungen) können zeitaufwändig und teuer in der Herstellung und Änderung sein.
- AM-Lösung: AM erfordert keine speziellen Werkzeuge. Designänderungen können digital umgesetzt und ein neues Teil relativ schnell (oft innerhalb von Tagen) gedruckt werden. Dies beschleunigt den Design-Build-Test-Zyklus und ermöglicht eine schnellere Innovation und Produktentwicklung - ein wesentlicher Vorteil für rapid Prototyping Luft- und Raumfahrt Bedürfnisse.
- Personalisierung und Kleinserienproduktion:
- Herausforderung: UAVs werden oft in geringeren Stückzahlen produziert als Konsumgüter für den Massenmarkt, und die Anpassung an bestimmte Aufgaben oder Nutzlasten ist üblich. Die Einrichtung traditioneller Fertigungsstraßen für geringe Stückzahlen kann kostspielig sein.
- AM-Lösung: AM ist wirtschaftlich rentabel für die Herstellung von Einzelstücken oder von Teilen in kleinen bis mittleren Stückzahlen. Es ermöglicht eine Massenanpassung, bei der jedes Gehäuse potenziell maßgeschneidert werden kann, ohne dass erhebliche Kosten für den Wechsel der Werkzeuge anfallen. Dies unterstützt teilefertigung auf Abruf.
- Materialvielfalt:
- Herausforderung: Verschiedene Anwendungen erfordern unterschiedliche Materialeigenschaften (z. B. Wärmeleitfähigkeit, Korrosionsbeständigkeit, Verhältnis von Festigkeit zu Gewicht).
- AM-Lösung: Für AM-Prozesse steht eine wachsende Auswahl an Metallpulvern zur Verfügung, darunter Hochleistungsaluminiumlegierungen, rostfreie Stähle, Titan und Superlegierungen, die die Auswahl des optimalen Materials für die spezifischen Gehäuseanforderungen ermöglichen.
Auch wenn AM im Vergleich zu den traditionellen Verfahren mit hohen Stückzahlen gewisse Nachteile in Bezug auf die Oberflächenbeschaffenheit oder die anfänglichen Teilekosten mit sich bringt, überwiegen bei kritischen Bauteilen wie UAV-Stromversorgungsgehäusen oft die strategischen Vorteile in Bezug auf Designfreiheit, Gewichtsreduzierung und Markteinführungszeit diese Faktoren.
Materialauswahl: Die Wahl des richtigen Metallpulvers für optimale Leistung
Die Wahl des richtigen Materials ist für den Erfolg eines jeden 3D-gedruckten Bauteils von grundlegender Bedeutung, insbesondere bei anspruchsvollen Anwendungen wie UAV-Stromversorgungsgehäusen. Die Wahl wirkt sich direkt auf Gewicht, thermische Leistung, Haltbarkeit, Umweltbeständigkeit und Kosten aus. Für UAV-Gehäuse gibt es zwei allgemein empfohlene und sehr effektive Metallpulver AlSi10Mg und 316L-Edelstahl. Die Kenntnis ihrer Eigenschaften ist für Ingenieure, die Konstruktionsentscheidungen treffen, und für Beschaffungsmanager, die Materialien oder Dienstleistungen einkaufen, von entscheidender Bedeutung.
Führende Anbieter wie Met3dpdurch den Einsatz fortschrittlicher Pulverherstellungsverfahren wie Vakuum-Induktionsschmelz-Gaszerstäubung (VIGA) und Plasma-Rotations-Elektroden-Verfahren (PREP) wird die Verfügbarkeit hochwertiger, kugelförmiger Metallpulver sichergestellt, die für dichte, zuverlässige Drucke mit hervorragenden mechanischen Eigenschaften entscheidend sind.
1. Aluminium-Legierung (AlSi10Mg): Der Leichtbau-Champion
- Beschreibung: AlSi10Mg ist eine weit verbreitete Aluminiumlegierung, die für ihre hervorragende Kombination aus geringer Dichte, guten mechanischen Eigenschaften (Festigkeit und Härte) und Gießbarkeit/Druckbarkeit bekannt ist. Es handelt sich im Wesentlichen um eine Gusslegierung, die für additive Fertigungsverfahren wie Selective Laser Melting (SLM) und Direct Metal Laser Sintering (DMLS) geeignet ist.
- Wichtige Eigenschaften & Vorteile für UAV-Gehäuse:
- Geringe Dichte (~2,67 g/cm³): Dies ist der Hauptvorteil. Erheblich leichter als Stahl oder Titan, was direkt zur Gewichtsreduzierung der Drohne, zu längeren Flugzeiten und einer höheren Nutzlastkapazität beiträgt.
- Gute Wärmeleitfähigkeit (~130-150 W/m-K): Leitet effektiv die von der Leistungselektronik erzeugte Wärme ab, was entscheidend ist, um Überhitzung zu vermeiden und die Zuverlässigkeit der Komponenten zu gewährleisten. Ermöglicht Designs mit integrierten Kühlkörpern oder Kühlrippen.
- Gutes Verhältnis von Stärke zu Gewicht: Bietet nach entsprechender Wärmebehandlung (z. B. T6) ausreichende Festigkeit und Steifigkeit für Gehäuseanwendungen.
- Ausgezeichnete Druckbarkeit: Fließt gut und verfestigt sich vorhersehbar während des Drucks, wodurch komplexe Geometrien und feine Merkmale möglich sind.
- Korrosionsbeständigkeit: Bietet eine gute Korrosionsbeständigkeit, die durch Oberflächenbehandlungen wie Eloxieren oder Lackieren noch verbessert werden kann.
- Erwägungen:
- Geringere absolute Festigkeit und Ermüdungsfestigkeit im Vergleich zu Stahl oder Titan.
- Erfordert eine Wärmebehandlung nach dem Druck, um optimale mechanische Eigenschaften zu erzielen.
- Kann im Vergleich zu einigen anderen Legierungen schwieriger zu schweißen oder nach dem Druck zu bearbeiten sein.
- Ideale Anwendungen: Bei den meisten UAV-Stromversorgungsgehäusen steht das Gewicht im Vordergrund, und die Betriebsumgebung ist nicht extrem korrosiv. Verteidigungs-, Handels-, Logistik- und Inspektionsdrohnen profitieren oft stark von AlSi10Mg Eigenschaften.
Tabelle: AlSi10Mg Schlüsseleigenschaften (typische Werte nach der Wärmebehandlung)
Eigentum | Typischer Wert | Einheit | Bedeutung für UAV-Gehäuse |
---|---|---|---|
Dichte | ~2.67 | g/cm³ | Kritisch für Lightweighting |
Zugfestigkeit (UTS) | 270 – 350+ | MPa | Strukturelle Integrität |
Streckgrenze (0.2%) | 190 – 250+ | MPa | Widerstandsfähigkeit gegen dauerhafte Verformung |
Dehnung beim Bruch | 3 – 10+ | % | Duktilität, Bruchfestigkeit |
Härte | 90 – 120+ | HBW | Verschleiß- und Kratzfestigkeit |
Wärmeleitfähigkeit | ~130 – 150 | W/(m-K) | Hervorragend zur Wärmeableitung geeignet |
Max. Betriebstemp. | ~150 (abhängig von Last/Zeit) | °C | Geeignet für typische elektronische Wärmelasten |
In Blätter exportieren
2. 316L-Edelstahl: Das langlebige Arbeitspferd
- Beschreibung: 316L ist eine austenitische, rostfreie Stahllegierung mit Chrom, Nickel und Molybdän. Das "L" steht für einen niedrigen Kohlenstoffgehalt, der die Schweißbarkeit verbessert und die Sensibilisierung (Chromkarbidausfällung) bei thermischen Zyklen wie dem Drucken verringert. Es ist bekannt für seine hervorragende Korrosionsbeständigkeit und seine guten mechanischen Eigenschaften.
- Wichtige Eigenschaften & Vorteile für UAV-Gehäuse:
- Ausgezeichnete Korrosionsbeständigkeit: Dank seines Chrom- und Molybdängehalts ist es selbst in Meeres- und Industrieumgebungen äußerst rost- und korrosionsbeständig. Ideal für UAVs, die in der Nähe von Salzwasser oder in verschmutzten Gebieten eingesetzt werden oder häufig gereinigt/sterilisiert werden müssen (z. B. bei der medizinischen Versorgung).
- Gute Festigkeit und Duktilität: Bietet im Vergleich zu AlSi10Mg eine höhere Festigkeit und eine deutlich bessere Duktilität (Zähigkeit), wodurch es widerstandsfähiger gegen Stöße und Ermüdung ist.
- Gute Schweißbarkeit & Bearbeitbarkeit: Im Allgemeinen leichter nachzubearbeiten (schweißen, bearbeiten, polieren) als Aluminiumlegierungen.
- Biokompatibilität (für bestimmte Sorten/Verarbeitungen): 316L ist zwar für Stromversorgungsgehäuse weniger relevant, wird aber häufig für medizinische Implantate verwendet, was auf seine Inertheit hinweist.
- Erwägungen:
- Erheblich höhere Dichte (~7,99 g/cm³): Fast dreimal dichter als AlSi10Mg, was bei gleichen Abmessungen zu einem wesentlich schwereren Gehäuse führt. Eine Optimierung des Designs (dünne Wände, Gitter) ist entscheidend, um den Gewichtsnachteil zu mildern.
- Geringere Wärmeleitfähigkeit (~16 W/m-K): Im Vergleich zu Aluminium sehr viel weniger effektiv bei der Wärmeableitung. Konstruktionen können aggressivere Kühlstrategien erfordern (z. B. größere Rippen, forcierte Luftströmung), wenn das Wärmemanagement kritisch ist.
- Ideale Anwendungen: UAVs, die in rauen, korrosiven Umgebungen eingesetzt werden (Seefahrt, Küstengebiete, Industrie). Anwendungen, bei denen extreme Haltbarkeit, Stoßfestigkeit oder leichte Sterilisierbarkeit von größter Bedeutung sind und bei denen der Gewichtsnachteil toleriert oder durch geschicktes Design ausgeglichen werden kann. Unverzichtbar für langlebige uAV aus Edelstahl 316L Komponenten.
Tabelle: schlüsseleigenschaften von 316L (typische Werte – geglüht/im Druckzustand)
Eigentum | Typischer Wert | Einheit | Bedeutung für UAV-Gehäuse |
---|---|---|---|
Dichte | ~7.99 | g/cm³ | Berücksichtigung des Gewichts (Erfordert Design-Offset) |
Zugfestigkeit (UTS) | 500 – 650+ | MPa | Hohe strukturelle Integrität |
Streckgrenze (0.2%) | 200 – 300+ | MPa | Gute Beständigkeit gegen Verformung |
Dehnung beim Bruch | 40 – 60+ | % | Hohe Zähigkeit und Schlagzähigkeit |
Härte | ~150 – 200 | HBW | Gute Dauerhaftigkeit |
Wärmeleitfähigkeit | ~16 | W/(m-K) | Schlechte Wärmeableitung (Erfordert Design Focus) |
Max. Betriebstemp. | ~425 – 870 | °C | Hochtemperaturfähigkeit (selten begrenzender Faktor) |
In Blätter exportieren
Die Wahl zwischen AlSi10Mg und 316L:
Die Entscheidung hängt von den Hauptanforderungen ab:
- Gewicht sparen & Wärmeableitung priorisieren? Wählen Sie AlSi10Mg.
- Vorrang für Korrosionsbeständigkeit & Langlebigkeit? Wählen Sie 316Laber seien Sie darauf vorbereitet, aktiv auf Gewichtsreduzierung zu achten und die thermische Leistung zu steuern.
Beratung durch einen erfahrenen Metall-AM-Dienstleisterein Unternehmen wie Met3dp, das sich sowohl mit den Materialien als auch mit den Feinheiten von UAV-Anwendungen auskennt, ist von entscheidender Bedeutung. Ihr Fachwissen in leitfaden zur Auswahl von Metallpulver prinzipien und der Zugang zu hochreinen Pulvern gewährleisten, dass das gewählte Material im endgültigen gedruckten Gehäuse optimal funktioniert. Die Partnerschaft mit einem Anbieter, der sich auskennt mit materialien für die Luft- und Raumfahrt und ihre spezifischen Anwendungsnuancen sind der Schlüssel zum Erfolg.
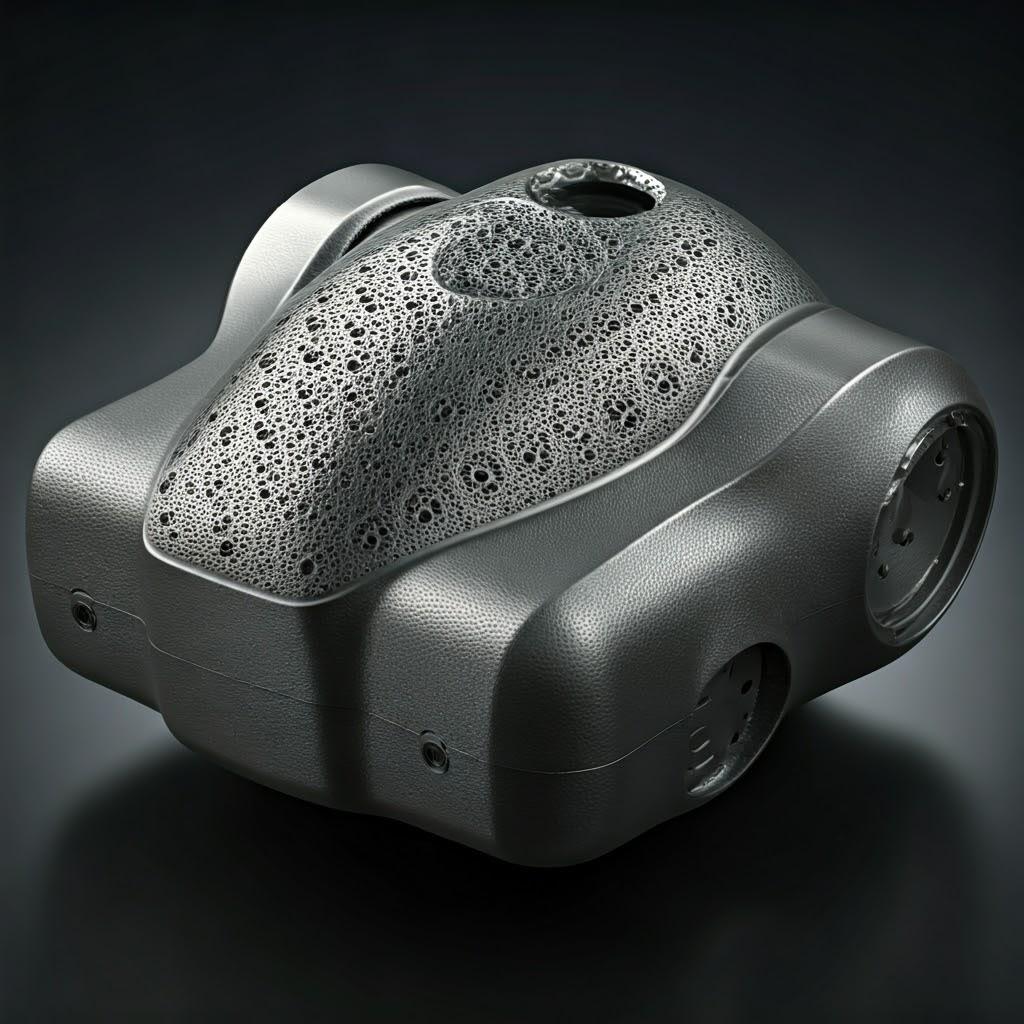
Design für additive Fertigung (DfAM): Optimierung von Gehäusen für Druckbarkeit und Funktion
Die einfache Nachbildung eines Designs, das für die CNC-Bearbeitung oder den Guss vorgesehen ist, in ein 3D-druckbares Format schöpft selten das volle Potenzial der additiven Fertigung aus. Um die Vorteile der Metall-AM für UAV-Stromversorgungsgehäuse - insbesondere Gewichtsreduzierung und verbessertes Wärmemanagement - wirklich zu nutzen, müssen Ingenieure die folgenden Punkte berücksichtigen Design für additive Fertigung (DfAM) grundsätze. DfAM beinhaltet die Konstruktion von Teilen unter Berücksichtigung der spezifischen Fähigkeiten und Beschränkungen des gewählten AM-Verfahrens (wie SLM, DMLS oder SEBM), und zwar bereits in der Konzeptionsphase. Die Anwendung effektiver DfAM-Grundsätze ist entscheidend für die Optimierung der Leistung, die Gewährleistung der Bedruckbarkeit, die Minimierung des Nachbearbeitungsaufwands und letztlich die Senkung der Kosten.
Hier sind die wichtigsten DfAM-Überlegungen für UAV-Stromversorgungsgehäuse:
- Nutzen Sie Topologieoptimierung und generatives Design:
- Konzept: Diese Berechnungswerkzeuge helfen dabei, hocheffiziente, oft organisch anmutende Strukturen zu schaffen, indem das Material nur dort verteilt wird, wo es benötigt wird, um definierte Lasten und Einschränkungen zu unterstützen.
- Anwendung: Definieren Sie Lastfälle (Vibrationen, Befestigungspunkte, Gewicht der internen Komponenten) und funktionale Anforderungen (Wärmeabgabebereiche, Zugangsöffnungen). Lassen Sie die Software leichte und dennoch stabile Konstruktionen erstellen, die sich nicht oder nur schwer bearbeiten lassen. Dies ist von entscheidender Bedeutung für topologieoptimierung UAV Komponenten.
- Nutzen: Erhebliche Gewichtseinsparungen (oft 20-50 % oder mehr im Vergleich zu herkömmlichen Konstruktionen) ohne Beeinträchtigung der strukturellen Integrität.
- Integrieren Sie funktionale Merkmale:
- Konzept: Konsolidieren Sie mehrere Funktionen oder Komponenten in einem einzigen gedruckten Teil.
- Anwendung: Entwerfen Sie integrierte Montagevorsprünge für Leiterplatten, Kanäle für die Kabelführung, Halterungen für Anschlüsse und sogar Elemente von Kühlkörpern oder Kühlplatten direkt in die Gehäusestruktur. Ziehen Sie Schnappverschlüsse oder integrierte Verschlüsse in Betracht, um den Bedarf an separaten Befestigungselementen zu reduzieren.
- Nutzen: Geringere Teilezahl, vereinfachte Montage, geringeres Gewicht und potenziell höhere Zuverlässigkeit durch den Wegfall von Verbindungen und Schnittstellen.
- Optimieren Sie das Wärmemanagement:
- Konzept: Nutzen Sie die geometrische Freiheit von AM’, um überlegene Kühllösungen zu schaffen.
- Anwendung:
- Konforme Kühlkanäle: Entwerfen Sie interne Kanäle, die genau der Form der wärmeerzeugenden Komponenten (z. B. Prozessoren, Leistungsregler) folgen, um eine direkte und effiziente Wärmeabfuhr zu ermöglichen, möglicherweise unter Verwendung von Flüssigkeitskühlung oder Luftstrom.
- Optimierte Kühlkörperlamellen: Erstellung komplexer Rippengeometrien (Stiftrippen, Gitter) mit hohem Verhältnis von Oberfläche zu Volumen für eine verbesserte passive Luftkühlung.
- Integration der Materialauswahl: Kombinieren Sie DfAM mit der Materialauswahl (z. B. mit hoch leitfähigem AlSi10Mg), um eine maximale thermische Leistung zu erzielen.
- Nutzen: Verbesserte Zuverlässigkeit und Leistung der elektronischen Komponenten, Potenzial für eine höhere Leistungsdichte im UAV. Integration von Kühlkanälen ist ein großer Vorteil von AM.
- Design für Druckbarkeit (Minimierung von Stützen und Belastung):
- Konzept: Orientieren Sie das Teil und die Designmerkmale, um den Bedarf an Stützstrukturen zu reduzieren, die zusätzliche Druckzeit, Materialkosten und Nachbearbeitungsaufwand verursachen. Minimieren Sie thermische Spannungen, die zu Verformungen führen können.
- Anwendung:
- Selbsttragende Winkel: Entwerfen Sie Überhänge und Innenkanäle mit Winkeln, die in der Regel größer als 45 Grad zur horizontalen Ebene sind, um Stützen zu vermeiden.
- Teil Orientierung: Wählen Sie eine Bauausrichtung, die das Volumen der erforderlichen Stützen minimiert, insbesondere bei kritischen oder schwer zugänglichen Oberflächen. Berücksichtigen Sie, wie sich die Ausrichtung auf die Eigenspannungsakkumulation auswirkt.
- Merkmale zur Stressreduzierung: Verwenden Sie abgerundete Ecken anstelle von scharfen Kanten und sorgen Sie für eine gleichmäßige Wärmeverteilung, wo dies möglich ist. Einige AM-Prozesse, wie das Elektronenstrahlschmelzen (EBM/SEBM), das von Anbietern wie Met3dp angeboten wird, arbeiten mit höheren Temperaturen, was Eigenspannungen reduzieren kann, aber Auswirkungen auf die Oberflächengüte und die Auflösung der Merkmale haben kann, verglichen mit laserbasierten Systemen, die auf ihre Seite mit Druckmethoden.
- Nutzen: Schnellere Druckzeiten, geringerer Materialverbrauch, einfachere und kostengünstigere Nachbearbeitung (Minimierung der Stützstrukturen), verbesserte Maßhaltigkeit aufgrund geringerer Spannungen.
- Berücksichtigen Sie die Wanddicke und die Größe der Elemente:
- Konzept: Bei AM-Prozessen gibt es Einschränkungen hinsichtlich der minimalen druckbaren Wandstärke und der Auflösung der Merkmale.
- Anwendung: Stellen Sie sicher, dass die Wände dick genug sind, um zuverlässig gedruckt zu werden und den erwarteten Belastungen standzuhalten (typischerweise >0,4-0,5 mm für Metall-PBF). Entwerfen Sie kleine Merkmale (Löcher, Stifte) innerhalb der Auflösungsmöglichkeiten der gewählten Maschine und des Prozesses. Berücksichtigen Sie eine mögliche Schrumpfung oder Verformung.
- Nutzen: Gewährleistet die Bedruckbarkeit und strukturelle Solidität der Teile. Einhalten der Richtlinien für wandstärke Metall AM verhindert Druckausfälle.
- Planen Sie die Nachbearbeitung:
- Konzept: Design mit Blick auf nachgelagerte Prozesse.
- Anwendung: Berücksichtigen Sie zusätzliches Material (Bearbeitungsmaterial) für kritische Oberflächen, die enge Toleranzen oder besondere Oberflächengüten erfordern. Sorgen Sie für die Zugänglichkeit von Abstützwerkzeugen und CNC-Bearbeitungsköpfen. Konstruieren Sie Merkmale, die die Handhabung und Inspektion erleichtern.
- Nutzen: Reibungslosere Arbeitsabläufe, geringere Nachbearbeitungszeit und -kosten gewährleisten, dass die Anforderungen an das Endprodukt erfüllt werden können.
Durch die Einbeziehung dieser DfAM-Strategien können Ingenieure UAV-Stromversorgungsgehäuse entwerfen, die nicht nur leichter sind und eine bessere thermische Leistung aufweisen, sondern auch effizienter und kostengünstiger durch additive Fertigung hergestellt werden können. Die Zusammenarbeit mit erfahrenen AM-Dienstleistern während der Konstruktionsphase kann wertvolle Erkenntnisse liefern und optimale Ergebnisse gewährleisten.
Auf die Präzision kommt es an: Toleranzen, Oberflächengüte und Genauigkeit bei gedruckten Gehäusen
Obwohl Metall-AM eine unglaubliche Designfreiheit bietet, ist es für Ingenieure und Beschaffungsmanager wichtig zu verstehen, welches Maß an Präzision direkt aus dem Drucker erreicht werden kann und wie sich dies auf das endgültige UAV-Stromversorgungsgehäuse auswirkt. Faktoren wie Toleranzen beim 3D-Druck von Metall, oberflächengüte (Ra)und insgesamt maßhaltigkeit AM sind von entscheidender Bedeutung für die Gewährleistung der richtigen Passform, Montage, Abdichtung und Funktion.
Toleranzen:
- Toleranzen wie gedruckt: Bei typischen Metall-Powder Bed Fusion (PBF)-Verfahren wie SLM und DMLS liegen die standardmäßig erreichbaren Toleranzen oft im Bereich von:
- ± 0,1 mm bis ± 0,2 mm für kleinere Merkmale (z. B. bis zu 20-50 mm).
- ± 0,1% bis ± 0,2% des Nennmaßes für größere Merkmale.
- Faktoren, die die Toleranzen beeinflussen: Maschinenkalibrierung, Größe des Laserspots, Schichtdicke, Materialeigenschaften, thermische Spannungen während des Aufbaus, Teilegeometrie und Unterstützungsstrategie spielen alle eine Rolle.
- Auswirkungen auf Gehäuse: Die aufgedruckten Toleranzen sind oft ausreichend für allgemeine Gehäuseabmessungen, unkritische Montagepunkte und interne Spielräume. Schnittstellen, die präzise Passungen erfordern (z. B. Lagersitze, Gegenflächen für die Abdichtung, präzise Steckverbinderpositionen), können jedoch eine engere Kontrolle erfordern.
Oberflächengüte (Rauhigkeit - Ra):
- Wie gedruckt Oberflächenbehandlung: Die Oberflächenbeschaffenheit von AM-Metallteilen ist aufgrund des schichtweisen Verfahrens und der teilweise geschmolzenen Pulverpartikel, die an der Oberfläche haften, naturgemäß rauer als maschinell bearbeitete Oberflächen.
- Vertikale/Seitenwände: Je nach Verfahren, Material und Parametern liegen sie in der Regel zwischen Ra 6 µm und Ra 15 µm (oder höher).
- Obere Oberflächen: Im Allgemeinen glatter.
- Daunenbelag/gestützte Oberflächen: Oft die gröbsten, die Spuren von Stützstrukturen aufweisen.
- Faktoren, die die Rauhigkeit beeinflussen: Schichtdicke, Partikelgrößenverteilung des Pulvers, Laser-/Strahlenergieeintrag und Bauausrichtung.
- Auswirkungen auf Gehäuse:
- Versiegeln: Unbedruckte Oberflächen sind unter Umständen nicht geeignet, um wirksame Umweltabdichtungen (z. B. IP-Einstufungen) ohne geeignete Dichtungskonstruktion oder Nachbearbeitung herzustellen.
- Thermischer Kontakt: Die Oberflächenrauhigkeit kann den Wärmewiderstand an Schnittstellen (z. B. zwischen dem Gehäuse und einem wärmeerzeugenden Bauteil) erhöhen.
- Ästhetik: Bei kritischem Erscheinungsbild kann eine Glättung erforderlich sein.
- Durchflusswiderstand: Raue Innenkanäle können den Luft- oder Kühlmittelfluss im Vergleich zu glatten Kanälen leicht behindern.
Maßgenauigkeit:
- Definition: Bezieht sich darauf, wie genau das endgültige Teil mit den im CAD-Modell angegebenen Abmessungen übereinstimmt. Sie wird durch Toleranzen, aber auch durch mögliche Verformungen oder Verzerrungen beeinflusst.
- Ursachen für Ungenauigkeit: Thermische Eigenspannungen, die während der Aufheiz- und Abkühlzyklen des Drucks entstehen, können dazu führen, dass sich die Teile verziehen oder verzerren, insbesondere bei großen, flachen oder asymmetrischen Designs. Unzureichende Stützstrukturen können dies noch verschlimmern.
- Milderung: Die richtige Simulation des Aufbaus, eine optimierte Ausrichtung, wirksame Unterstützungsstrategien, Wärmebehandlungen zum Spannungsabbau und die Prozesskontrolle sind entscheidend für erreichen enger Toleranzen und Minimierung von Verzerrungen.
Höhere Präzision erreichen:
Wenn die gedruckten Toleranzen oder die Oberflächenbeschaffenheit für bestimmte Merkmale des UAV-Gehäuses nicht ausreichen, ist eine Nachbearbeitung erforderlich:
- Nachbearbeiten: Kritische Merkmale, die engere Toleranzen (z. B. ±0,01 mm bis ±0,05 mm) oder glattere Oberflächen (z. B. Ra < 1,6 µm) erfordern, werden in der Regel erreicht durch 3D-Teile nachbearbeiten durch CNC-Fräsen oder Drehen. Dies ist häufig bei Schnittstellen, Dichtungsnuten, Lagerbohrungen und präzisen Ausrichtungsmerkmalen der Fall. Die DfAM sollte die Hinzufügung von Bearbeitungsmaterial in diesen Bereichen berücksichtigen.
- Oberflächenbehandlungen: Verfahren wie Perlstrahlen, Trommeln, Polieren oder Elektropolieren können die gesamte Oberflächenbeschaffenheit verbessern, lose Partikel entfernen und die Ästhetik verbessern oder Oberflächen für Beschichtungen vorbereiten.
Verständnis für die inhärente Präzision von Metal AM und Planung für die notwendigen qualitätskontrolle Luft- und Raumfahrtteile prüf- und Nachbearbeitungsschritte sind für den erfolgreichen Einsatz von 3D-gedruckten Stromversorgungsgehäusen in anspruchsvollen UAV-Anwendungen unerlässlich. Eine klare Kommunikation der kritischen Abmessungen und Toleranzen mit dem AM-Dienstleister ist unerlässlich.
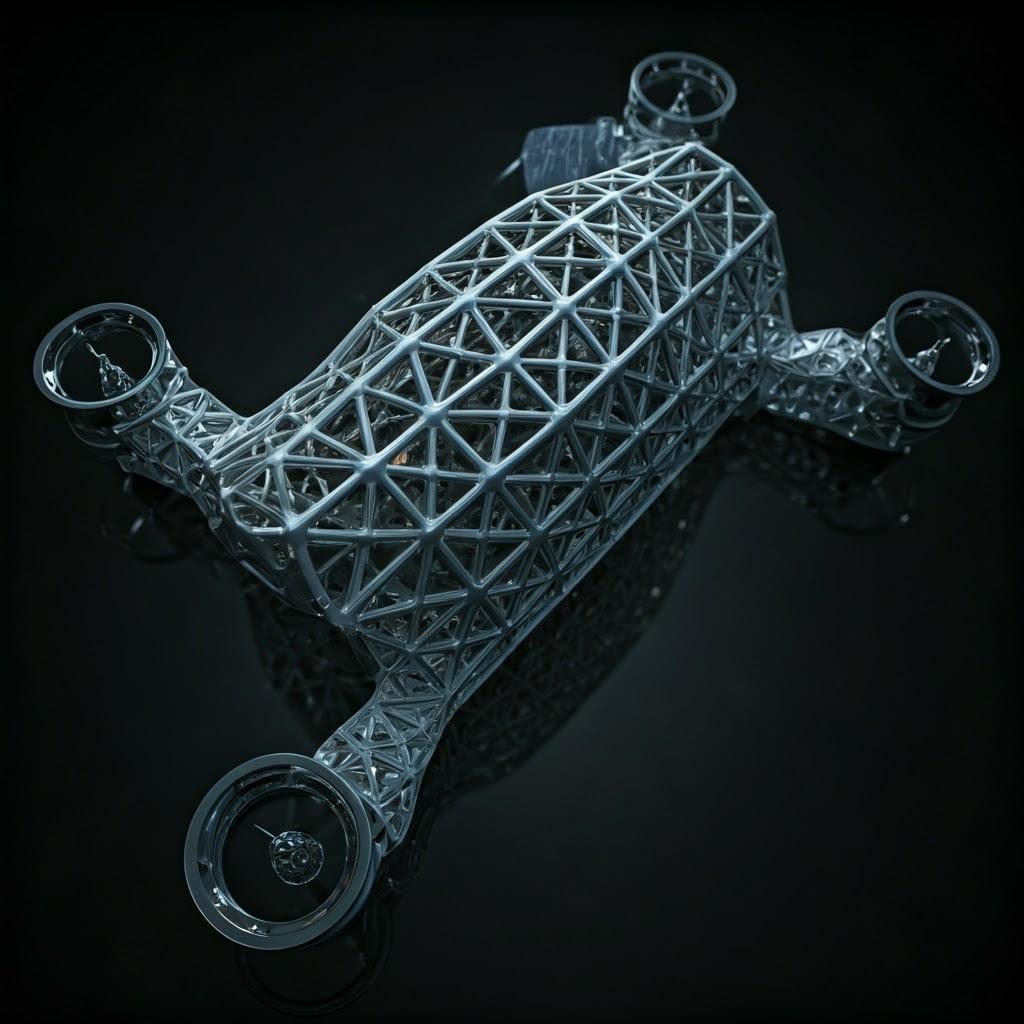
Mehr als der Druck: Wichtige Nachbearbeitungsschritte für UAV-Gehäuse
Die Reise eines 3D-gedruckten UAV-Stromversorgungsgehäuses aus Metall endet nicht, wenn der Drucker anhält. In der Regel sind mehrere entscheidende Nachbearbeitungsschritte erforderlich, um das gedruckte Rohteil in eine funktionale, zuverlässige und montagefertige Komponente zu verwandeln. Das Verständnis dieser Schritte ist für Beschaffungsmanager, die Angebote auswerten, und Ingenieure, die den gesamten Arbeitsablauf planen, von entscheidender Bedeutung. Allgemein Oberflächenbearbeitungsoptionen und Behandlungen gewährleisten, dass das Teil die Anforderungen an Leistung und Haltbarkeit erfüllt.
Wichtige Nachbearbeitungsschritte:
- Stressabbau / Wärmebehandlung:
- Zweck: Um innere Spannungen abzubauen, die während der schnellen Erhitzungs- und Abkühlungszyklen des Druckvorgangs entstehen. Diese Spannungen können zu Verformung, Rissbildung oder vorzeitigem Versagen führen, wenn sie nicht beseitigt werden. Die Wärmebehandlung trägt auch dazu bei, die Mikrostruktur des Materials zu homogenisieren und die gewünschten endgültigen mechanischen Eigenschaften (Festigkeit, Härte, Duktilität) zu erreichen.
- Prozess: Die Teile werden in einem Ofen mit kontrollierter Atmosphäre auf bestimmte Temperaturen und Zeiträume erhitzt und anschließend kontrolliert abgekühlt. Der genaue Zyklus (wärmebehandlung Metall AM) hängt stark vom Werkstoff (z. B. Lösungsbehandlung und Alterung bei AlSi10Mg, Glühen oder Spannungsarmglühen bei 316L) und den Anwendungsanforderungen ab.
- Die Notwendigkeit: Bei kritischen Bauteilen wie UAV-Gehäusen fast immer obligatorisch, um Maßhaltigkeit und mechanische Leistung zu gewährleisten.
- Entfernen des Teils von der Bauplatte:
- Zweck: Um die gedruckten Teile von der Metallgrundplatte zu lösen, auf der sie aufgebaut wurden.
- Prozess: Dies geschieht in der Regel durch Drahterodieren (Electrical Discharge Machining) oder mit einer Bandsäge. Dabei muss darauf geachtet werden, dass die Teile nicht beschädigt werden.
- Entfernung der Stützstruktur:
- Zweck: Um die temporären Stützstrukturen zu entfernen, die während des Drucks für Überhänge und komplexe Merkmale erforderlich sind.
- Prozess: Kann vom einfachen manuellen Abbruch für zugängliche Stützen bis zu komplexeren unterstützung beim 3D-Druck methoden mit Handwerkzeugen, maschineller Bearbeitung oder Spezialwerkzeugen, vor allem bei Innenkanälen oder komplizierten Geometrien. DfAM spielt eine große Rolle bei der Minimierung der Schwierigkeiten und Kosten dieses Schritts.
- Erwägungen: Kann arbeitsintensiv und zeitaufwendig sein. Kann Spuren auf der Oberfläche hinterlassen, die eine weitere Nachbearbeitung erfordern.
- CNC-Bearbeitung:
- Zweck: Zur Erzielung engerer Toleranzen, kritischer Abmessungen, flacher Dichtungsflächen, Gewindebohrungen oder glatterer Oberflächengüten bei bestimmten Merkmalen, die bei dem gedruckten Teil nicht erfüllt werden können.
- Prozess: Verwendung herkömmlicher CNC-Fräs- oder Drehzentren zur präzisen Bearbeitung bestimmter Bereiche des 3D-Druckteils. Erfordert ein sorgfältiges Vorrichtungsdesign, um die komplexe Geometrie sicher zu halten. Wird oft als Teil von CNC-Bearbeitungsdienstleistungen durch umfassende AM-Anbieter.
- Die Notwendigkeit: Wird häufig für Schnittstellen, Befestigungspunkte und Dichtungsflächen an UAV-Triebwerksgehäusen benötigt.
- Oberflächenveredelung und Reinigung:
- Zweck: Zur Verbesserung der Oberflächenrauhigkeit, zur Entfernung loser Pulverpartikel, zur Verbesserung der Ästhetik oder zur Vorbereitung der Oberfläche für die Beschichtung.
- Vorgänge:
- Perlstrahlen/Sandstrahlen: Treibt die Medien gegen die Oberfläche, um eine gleichmäßige, matte Oberfläche zu erzeugen, lose anhaftendes Pulver zu entfernen und möglicherweise die Ermüdungslebensdauer zu verbessern (Shot Peening).
- Taumeln/Gleitschleifen: Verwendet Schleifmittel in einer rotierenden oder vibrierenden Trommel, um Oberflächen zu glätten und Kanten zu entgraten, besonders effektiv für Chargen kleinerer Teile.
- Polieren: Manuelles oder automatisiertes Polieren zur Erzielung sehr glatter, reflektierender Oberflächen (bei Innengehäusen weniger üblich, es sei denn, dies ist aus speziellen Dichtungs- oder thermischen Gründen erforderlich).
- Reinigung: Gründliche Reinigung zur Entfernung von Pulverrückständen, Bearbeitungsflüssigkeiten oder Verunreinigungen vor der Montage oder Beschichtung.
- Beschichtung / Oberflächenbehandlung (optional, aber üblich):
- Zweck: Zur Verbesserung bestimmter Eigenschaften wie Korrosionsbeständigkeit, Verschleißfestigkeit, elektrische Isolierung oder EMI-Abschirmung.
- Verfahren für AlSi10Mg: Eloxieren (verbessert die Korrosions-/Verschleißbeständigkeit, bietet Farboptionen), Chromatieren (Korrosionsbeständigkeit, Grundierung für Farbe), Lackieren/Pulverbeschichten.
- Verfahren für 316L: Passivierung (verbessert die natürliche Korrosionsbeständigkeit durch Entfernung von freiem Eisen), Elektropolieren (glättet und verbessert die Korrosionsbeständigkeit), spezielle Beschichtungen (z. B. PVD/CVD für Verschleiß). Passivierung Edelstahl ist ein gemeinsamer Schritt.
- Die Notwendigkeit: Abhängig von der Betriebsumgebung und den spezifischen funktionalen Anforderungen des beschichtung von 3D-gedruckten Teilen.
- Inspektion und Qualitätskontrolle:
- Zweck: Überprüfung, ob das endgültige Teil alle Maß-, Material- und Funktionsspezifikationen erfüllt.
- Prozess: Maßprüfung (CMM, 3D-Scannen), Materialprüfung (falls erforderlich), Sichtprüfung, NDT (zerstörungsfreie Prüfung wie CT-Scannen für interne Defekte, falls kritisch).
Jeder Nachbearbeitungsschritt erhöht den Zeit- und Kostenaufwand für den gesamten Produktionszyklus. Ein effektives DfAM und eine klare Kommunikation mit dem AM-Dienstleister über die erforderlichen endgültigen Spezifikationen sind für die Optimierung dieses Arbeitsablaufs unerlässlich.
Herausforderungen meistern: Überwindung von Hürden bei der Metall-AM für Gehäuse
Die additive Fertigung von Metallen bietet zwar ein transformatives Potenzial für die Herstellung von UAV-Gehäusen, ist aber nicht frei von Herausforderungen. Das Wissen um diese potenziellen Hürden ermöglicht es Ingenieuren und Beschaffungsmanagern, proaktiv mit ihren AM-Partnern zusammenzuarbeiten, um Risiken zu minimieren und erfolgreiche Ergebnisse zu gewährleisten. Robust qualitätssicherung metall AM protokolle sind während des gesamten Prozesses unerlässlich.
Häufige Herausforderungen und wie man sie vermeidet:
- Verformung und Verzerrung (Eigenspannung):
- Herausforderung: Die intensive, örtlich begrenzte Erwärmung und die schnelle Abkühlung, die den PBF-Verfahren eigen sind, erzeugen innere Spannungen. Diese Spannungen können dazu führen, dass sich Teile, insbesondere große oder asymmetrische Teile, während des Drucks oder nach der Entnahme aus der Bauplatte verziehen, was zu Maßungenauigkeiten führt.
- Strategien zur Schadensbegrenzung:
- Thermische Simulation: Nutzen Sie Simulationssoftware während der Konstruktionsphase, um die Spannungsakkumulation vorherzusagen und die Ausrichtung der Teile und die Stützstrategien zu optimieren.
- Optimierte Build-Parameter: AM-Anbieter nehmen eine Feinabstimmung der Parameter (Laserleistung, Scangeschwindigkeit) vor, um thermische Gradienten zu minimieren.
- Wirksame Unterstützungsstrukturen: Strategisch platzierte Stützen verankern das Teil und tragen zur Wärmeableitung bei.
- Geeignete Wärmebehandlung: Spannungsabbauzyklen nach dem Druck sind entscheidend für den Abbau von Eigenspannungen (Restspannungsmanagement).
- Auswahl des Prozesses: Verfahren wie EBM/SEBM, die bei erhöhten Temperaturen arbeiten, können bei einigen Geometrien und Werkstoffen das Spannungsniveau von Natur aus reduzieren.
- Porosität:
- Herausforderung: Im gedruckten Material können sich kleine Hohlräume oder Poren bilden, die durch eingeschlossenes Gas oder unvollständige Verschmelzung der Pulverpartikel entstehen. Übermäßige Porosität kann die mechanische Festigkeit, die Ermüdungsfestigkeit und die Fähigkeit des Gehäuses, hermetisch abzudichten, beeinträchtigen.
- Strategien zur Schadensbegrenzung:
- Hochwertiges Pulver: Die Verwendung von Pulvern mit kontrollierter Partikelgrößenverteilung, hoher Sphärizität und geringem internen Gasgehalt (wie sie von Met3dp’s fortschrittlicher Zerstäubung produziert werden) ist von grundlegender Bedeutung.
- Optimierte Druckparameter: Eine sorgfältige Kontrolle der Energiedichte (Laser-/Strahlleistung, Geschwindigkeit, Schraffurabstand, Schichtdicke) ist für ein vollständiges Aufschmelzen und Verfestigen entscheidend.
- Kontrollierte Atmosphäre: Durch die Aufrechterhaltung einer hochreinen Inertgasatmosphäre (Argon oder Stickstoff) in der Baukammer werden Oxidation und Gasaufnahme minimiert.
- Heiß-Isostatisches Pressen (HIP): Durch einen Nachbearbeitungsschritt mit hoher Temperatur und hohem Druck können die inneren Poren geschlossen werden (was mit erheblichen Kosten verbunden ist, in der Regel nur bei sehr kritischen Anwendungen).
- NDT-Inspektion: Mit einem CT-Scan kann die innere Porosität erkannt werden, wenn dies für kritische Fehler beim 3D-Druck von Metall analyse.
- Unterstützung Entfernung Schwierigkeitsgrad:
- Herausforderung: Halterungen sind zwar notwendig, machen die Sache aber komplizierter. Ihre Entfernung, insbesondere aus internen Kanälen oder komplizierten Merkmalen innerhalb eines Gehäuses, kann schwierig und zeitaufwändig sein und das Risiko bergen, das Teil zu beschädigen. Eine unvollständige Entfernung kann den Flüssigkeitsdurchfluss behindern oder Verunreinigungen einschließen.
- Strategien zur Schadensbegrenzung:
- DfAM: Entwerfen Sie, wo immer möglich, selbsttragende Winkel (>45°). Verwenden Sie eine optimierte Topologie oder Gitterstrukturen, die den Bedarf an Stützen von Natur aus minimieren. Konstruieren Sie Merkmale für die Zugänglichkeit, wenn Stützen unvermeidbar sind.
- Optimierte Unterstützungsstrukturen: Verwenden Sie gegebenenfalls leicht entfernbare Stützen (z. B. dünnwandige oder perforierte Stützen).
- Prozessauswahl: Einige Prozesse können unterschiedliche Unterstützungsstrategien zulassen.
- Spezialisierte Entfernungstechniken: Verwendung geeigneter Werkzeuge, maschinelle Bearbeitung oder manchmal chemisches Ätzen (bei diesen Materialien weniger üblich).
- Einschränkungen der Oberflächenbeschaffenheit:
- Herausforderung: Wie bereits erwähnt, kann die Oberfläche nach dem Druck rau sein, was sich auf die Abdichtung, den Wärmekontakt oder die Ästhetik auswirken kann. Um eine sehr glatte Oberfläche zu erreichen, sind zusätzliche Schritte erforderlich.
- Strategien zur Schadensbegrenzung:
- Optimierung der Orientierung: Drucken Sie kritische Oberflächen in Ausrichtungen, die von Natur aus bessere Oberflächen erzeugen (z. B. vertikale Wände).
- Parametereinstellung: Feinere Schichtdicken können manchmal das Ergebnis verbessern, verlängern aber die Druckzeit.
- Nachbearbeiten: Planen Sie die erforderlichen Bearbeitungs-, Strahl-, Trowalisierungs- oder Polierschritte entsprechend den Anforderungen.
- Erzielung konsistenter Materialeigenschaften:
- Herausforderung: Die Sicherstellung einer gleichbleibenden Mikrostruktur und gleichbleibender mechanischer Eigenschaften im gesamten Bauteil und zwischen verschiedenen Fertigungen erfordert eine strenge Prozesskontrolle.
- Strategien zur Schadensbegrenzung:
- Strenge Prozesskontrolle: AM-Anbieter müssen die Maschinenkalibrierung, die Parameter, die Pulverqualität und die Atmosphäre streng kontrollieren.
- Standardisierte Verfahren: Einhaltung der festgelegten Verfahren für Druck und Wärmebehandlung.
- Materialprüfung: Durchführung regelmäßiger Zugtests oder anderer Charakterisierungen an Testcoupons, die neben den Teilen gedruckt werden.
- Seriöse Lieferanten: Die Zusammenarbeit mit erfahrenen Anbietern wie Met3dp, die über fundierte materialwissenschaftliche Kenntnisse und robuste Qualitätsmanagementsysteme verfügen, ist entscheidend, um viele dieser Probleme zu entschärfen herausforderungen beim 3D-Druck von Metall.
Durch das Verständnis dieser potenziellen Herausforderungen und die Implementierung geeigneter DfAM-Strategien, Prozesskontrollen und Nachbearbeitungsschritte können hochwertige und zuverlässige 3D-gedruckte Metallgehäuse für die Stromversorgung von UAVs hergestellt werden.
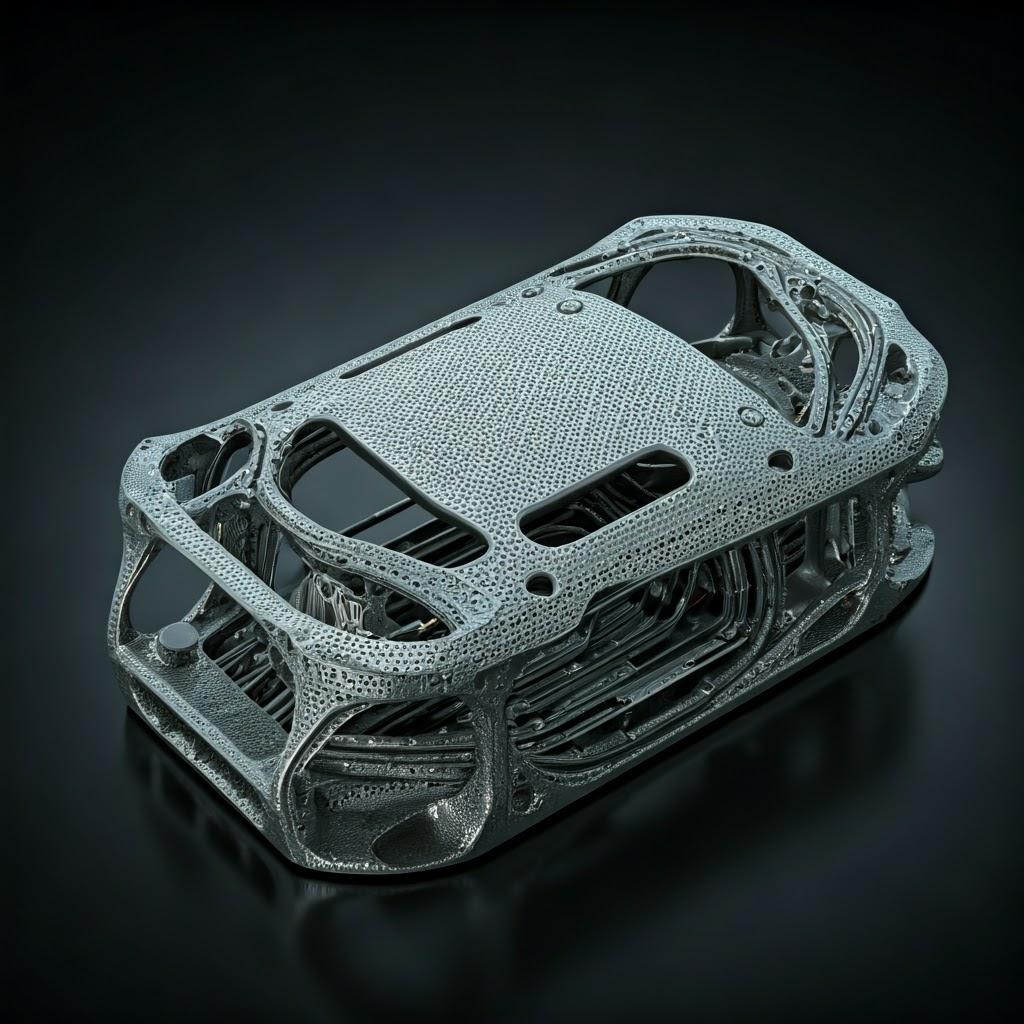
Auswahl der Lieferanten: So finden Sie Ihren idealen 3D-Druckpartner für UAV-Komponenten aus Metall
Die Wahl des richtigen Fertigungspartners ist bei der Herstellung von anspruchsvollen Komponenten wie UAV-Stromversorgungsgehäusen ebenso entscheidend wie das Design und die Materialauswahl. Qualität, Zuverlässigkeit und Leistung des Endprodukts hängen in hohem Maße vom Fachwissen, der Ausrüstung und den Prozessen des von Ihnen gewählten Partners ab Metall-AM-Dienstleister. Für Beschaffungsmanager und Ingenieurteams, die den Einstieg in die additive Fertigung wagen, auswahl eines 3D-Druckbüros erfordert eine sorgfältige Bewertung anhand mehrerer Schlüsselkriterien, insbesondere wenn es sich um Bauteile für die Luft- und Raumfahrt oder anspruchsvolle industrielle Anwendungen handelt.
Schlüsselkriterien für die Bewertung von Metall-AM-Anbietern:
- Branchenerfahrung & Fachwissen:
- Erfordernis: Suchen Sie nach Anbietern mit nachgewiesener Erfahrung in Ihrer spezifischen Branche (z. B. Luft- und Raumfahrt, Verteidigung, Automobilbau, Medizintechnik) und idealerweise mit ähnlichen Komponenten (Gehäuse, Schränke, Wärmemanagementteile). Sie sollten die besonderen Anforderungen und Qualitätserwartungen verstehen.
- Bewertung: Fragen Sie nach Fallstudien, Referenzen und Beispielen für frühere Projekte, die für UAV-Komponenten relevant sind. Beurteilen Sie die technische Tiefe und die DfAM-Unterstützungsfähigkeiten des Teams. Verstehen sie die Herausforderungen von Lieferanten für den 3D-Druck in der Luft- und Raumfahrt anforderungen?
- Zertifizierungen und Qualitätsmanagement:
- Erfordernis: Robuste Qualitätsmanagementsysteme sind für kritische Teile nicht verhandelbar.
- ISO 9001: Eine grundlegende Zertifizierung, die auf einen strukturierten Ansatz im Qualitätsmanagement hinweist.
- AS9100: Diese für die Luft- und Raumfahrt wichtige Norm baut auf der ISO 9001 auf und enthält zusätzliche Anforderungen, die speziell für die Luft- und Raumfahrt- und Verteidigungsindustrie gelten (Rückverfolgbarkeit, Risikomanagement, Prozesskontrolle). Eine AS9100-zertifizierter Lieferant zeugt von einer Verpflichtung zu höchsten Qualitätsstandards.
- Bewertung: Überprüfen Sie die aktuellen Zertifizierungen. Erkundigen Sie sich nach den Qualitätskontrollverfahren, den Protokollen zur Materialrückverfolgbarkeit, den Inspektionsmöglichkeiten (CMM, NDT) und den Verfahren zur Gewährleistung der Prozesswiederholbarkeit.
- Erfordernis: Robuste Qualitätsmanagementsysteme sind für kritische Teile nicht verhandelbar.
- Materialeigenschaften und Pulverqualität:
- Erfordernis: Der Anbieter muss die von Ihnen benötigten Werkstoffe anbieten (z. B. AlSi10Mg, 316L oder potenziell fortschrittlichere Legierungen) und nachweislich Erfahrung mit dem Druck dieser Werkstoffe haben. Entscheidend ist, dass er hochwertige Metallpulver verwendet.
- Bewertung: Bestätigen Sie die Materialverfügbarkeit und die Erfahrung des Unternehmens mit diesen spezifischen Legierungen. Erkundigen Sie sich nach der Beschaffung des Pulvers und den Maßnahmen zur Qualitätskontrolle. Unternehmen wie Met3dp, die ihre eigenen hochreinen sphärischen Pulver mit Hilfe fortschrittlicher Gaszerstäubungs- und PREP-Technologien herstellen, bieten einen Vorteil in Bezug auf Materialkonsistenz und Qualitätskontrolle von der Quelle an. Erkunden Sie ihr Angebot an Met3dp-Lösungen für die additive Fertigung.
- Ausrüstung & Technologie:
- Erfordernis: Der Anbieter sollte über eine gut gewartete, industrietaugliche AM-Ausrüstung verfügen, die für die Größe, die Komplexität und das Material Ihres Teils geeignet ist. Dazu gehören nicht nur Drucker, sondern auch die notwendigen Nachbearbeitungsgeräte (Wärmebehandlungsöfen, CNC-Maschinen, Endbearbeitungswerkzeuge).
- Bewertung: Erkundigen Sie sich nach den spezifischen Druckermodellen (z. B. SLM, DMLS, SEBM), dem Produktionsvolumen und den Wartungsplänen. Informieren Sie sich über die internen Nachbearbeitungsmöglichkeiten im Vergleich zu den ausgelagerten Leistungen. Unternehmen mit integrierten Fähigkeiten, wie Met3dp’s Angebot von Druckern (einschließlich SEBM mit seinen einzigartigen Vorteilen für bestimmte Anwendungen) und Pulvern, bieten oft einen rationalisierten Arbeitsablauf.
- Technik & DfAM-Unterstützung:
- Erfordernis: Ein idealer Partner ist mehr als nur ein Druckdienstleister. Er sollte technische Unterstützung bieten, um Ihr Design für die additive Fertigung (DfAM) zu optimieren, Verbesserungen für die Druckbarkeit oder Leistung vorzuschlagen und mögliche Probleme zu beheben.
- Bewertung: Erörtern Sie den DfAM-Supportprozess. Sind die Ingenieure erreichbar? Können sie Feedback zu Ihren Konstruktionsdateien geben? Bieten sie Simulationsdienste an (thermisch, Stress)?
- Kapazität & Vorlaufzeiten:
- Erfordernis: Vergewissern Sie sich, dass der Lieferant in der Lage ist, Ihre Mengenanforderungen innerhalb akzeptabler Vorlaufzeiten zu erfüllen, sowohl für Prototypen als auch für potenzielle Produktionsläufe.
- Bewertung: Erörtern Sie die derzeitigen Kapazitäten des Unternehmens, die typischen Vorlaufzeiten für ähnliche Projekte und seine Fähigkeit, die Produktion bei Bedarf zu erweitern. Anfrage realistisch Vorlaufzeit der additiven Fertigung schätzungen für Ihr spezifisches Projekt.
- Kommunikation & Projektleitung:
- Erfordernis: Eine klare, konsistente Kommunikation und ein effektives Projektmanagement sind für eine reibungslose Partnerschaft unerlässlich.
- Bewertung: Beurteilen Sie die Reaktionsfähigkeit des Unternehmens während des Angebotsprozesses. Machen Sie sich klar, wer Ihr Hauptansprechpartner sein wird und wie der Fortschritt gemeldet wird.
Bewertung von AM-Anbietern die gründliche Anwendung dieser Kriterien hilft Ihnen bei der Auswahl eines Partners wie Met3dp, der nicht nur über die technischen Fähigkeiten verfügt, sondern auch Ihren Qualitätsstandards und Projektzielen entspricht, um letztendlich die erfolgreiche Produktion von zuverlässigen UAV-Stromversorgungsgehäusen sicherzustellen.
Kosten und Fristen verstehen: Faktoren, die die Produktion beeinflussen
Eine der wichtigsten Überlegungen bei der Einführung von Fertigungstechnologien ist deren Wirtschaftlichkeit und Produktionsgeschwindigkeit. Das Verständnis der wichtigsten Faktoren für Metall-3D-Druck-Kostenfaktoren und typische Lieferzeiten sind entscheidend für die Budgetierung, die Projektplanung und den Vergleich von AM mit herkömmlichen Methoden für UAV-Stromversorgungsgehäuse.
Hauptkostentreiber:
- Teilegestaltung und Komplexität:
- Band & Größe: Größere Teile verbrauchen mehr Material und erfordern eine längere Bearbeitungszeit, was die Kosten direkt erhöht. Die Gesamtgröße des Begrenzungsrahmens beeinflusst, wie viele Teile auf eine Bauplatte passen.
- Komplexität: Während AM die Komplexität gut handhaben kann, erfordern hochkomplexe Designs möglicherweise umfangreichere Stützstrukturen, längere Druckzeiten aufgrund detaillierter Scanpfade und potenziell komplexere Nachbearbeitungen (insbesondere das Entfernen von Stützen), was sich auf die kosten pro Teil AM.
- Wanddicke: Sehr dünne Wände können die Druckgeschwindigkeit aus Stabilitätsgründen verlangsamen, während zu dicke Abschnitte den Materialverbrauch und den Zeitaufwand erhöhen.
- Wahl des Materials:
- Pulverkosten: Die Rohstoffkosten variieren erheblich zwischen den verschiedenen Metallpulvern. Standardlegierungen wie 316L oder AlSi10Mg sind im Allgemeinen billiger als Titanlegierungen oder spezielle Superlegierungen. Materialkosten 3D-Druck ist eine direkte Eingabe.
- Verwendung des Materials: Faktoren wie das Teilevolumen und die Menge des benötigten Trägermaterials wirken sich direkt auf den Gesamtmaterialverbrauch aus.
- Maschinenzeit:
- Bauzeit: Dies ist oft die größte Kostenkomponente. Sie hängt von der Teilehöhe (Anzahl der Schichten), der zu scannenden Fläche pro Schicht, der gewählten Schichtdicke und der Scangeschwindigkeit der Maschine ab. Die Optimierung der Bauplattenauslastung durch Verschachtelung mehrerer Teile kann die Kosten für die Maschinenzeit pro Teil senken.
- Maschinenabschreibung & Betriebskosten: Die hohen Kapitalkosten von industriellen Metall-AM-Systemen und ihre Betriebskosten (Energie, Inertgas, Wartung) sind in den Maschinenstundensätzen enthalten.
- Labor & Nachbearbeitung:
- Einrichten & Abrüsten: Arbeitsaufwand für die Vorbereitung der Druckdatei, das Einrichten der Maschine, das Laden des Pulvers und das Entfernen der Teile nach dem Druck.
- Nachbearbeiten: Dies kann einen erheblichen Kostenfaktor darstellen. Die Kosten umfassen:
- Wärmebehandlungszyklen.
- Arbeitsaufwand für die Entfernung der Halterung (kann bei komplexen Teilen erheblich sein).
- CNC-Bearbeitung für kritische Merkmale (nachbearbeitungskosten).
- Oberflächenbearbeitung (Strahlen, Polieren).
- Qualitätskontrolle und Zertifizierung.
- Menge & Chargengröße:
- Skalenvorteile: AM eignet sich zwar gut für niedrige Stückzahlen, aber bei größeren Chargen lassen sich dennoch Effizienzgewinne erzielen. Die Rüstkosten amortisieren sich über mehr Teile, und die Bauplatten können effizienter genutzt werden. Allerdings ist die Kostenreduzierung pro Teil in der Regel weniger dramatisch als bei Großserienverfahren wie dem Spritzgießen. Mindestbestellmenge 3D-Druck gelten, oder die Kosten pro Teil können bei einzelnen Prototypen erheblich höher sein.
Typische Vorlaufzeiten:
Die Vorlaufzeit ist die Dauer von der Auftragsbestätigung bis zum Versand des Teils. Bei AM-UAV-Gehäusen aus Metall umfasst sie in der Regel mehrere Stufen:
- Vorverarbeitung (1-3 Tage): Überprüfung von Aufträgen, Vorbereitung von Bauakten, Terminplanung.
- Druck (1-5+ Tage): Hängt stark von der Höhe, dem Volumen und der Anzahl der Teile pro Bau ab. Komplexe oder hohe Gehäuse können mehrere Tage kontinuierlichen Drucks erfordern.
- Abkühlen & Entpulvern (0,5-1 Tag): Sicheres Abkühlen der Baukammer und der Teile, Entfernen der Teile und Rückgewinnung des nicht verwendeten Pulvers.
- Nachbearbeitung (2-10+ Tage): In dieser Phase ist die Variabilität oft am größten.
- Wärmebehandlung: In der Regel 1-2 Tage (einschließlich Ofenzeit und Abkühlung).
- Entfernen/Bearbeiten der Stütze: Kann je nach Komplexität von Stunden bis zu mehreren Tagen dauern.
- Oberflächenveredelung/Beschichtung: Erhöht den Zeitaufwand je nach Verfahren.
- Inspektion: Abhängig von den Anforderungen.
- Versand (variabel): Hängt vom Standort und der gewählten Methode ab.
Gesamtvorlaufzeit: Ein typischer Bereich für einen Prototyp eines AM-UAV-Gehäuses aus Metall könnte sein 1 bis 3 Wochen. Die Produktion von Losen kann je nach Menge und erforderlichen Ressourcen länger dauern. Es ist wichtig, genaue Angaben zu erhalten Vorlaufzeit der additiven Fertigung schätzungen Ihres Lieferanten auf der Grundlage Ihres endgültigen Designs und Ihrer Anforderungen. Auch wenn es möglicherweise länger dauert als eine einfache CNC-Bearbeitung für ein einzelnes Teil, kann AM schneller sein, wenn komplexe Geometrien berücksichtigt werden, die bei herkömmlichen Methoden mehrere Aufspannungen oder Werkzeuge erfordern würden, insbesondere während der iterativen Designphase. Verstehen Sie diese Preise für UAV-Komponenten treibern und Zeitplänen hilft, realistische Erwartungen für Projekte festzulegen.
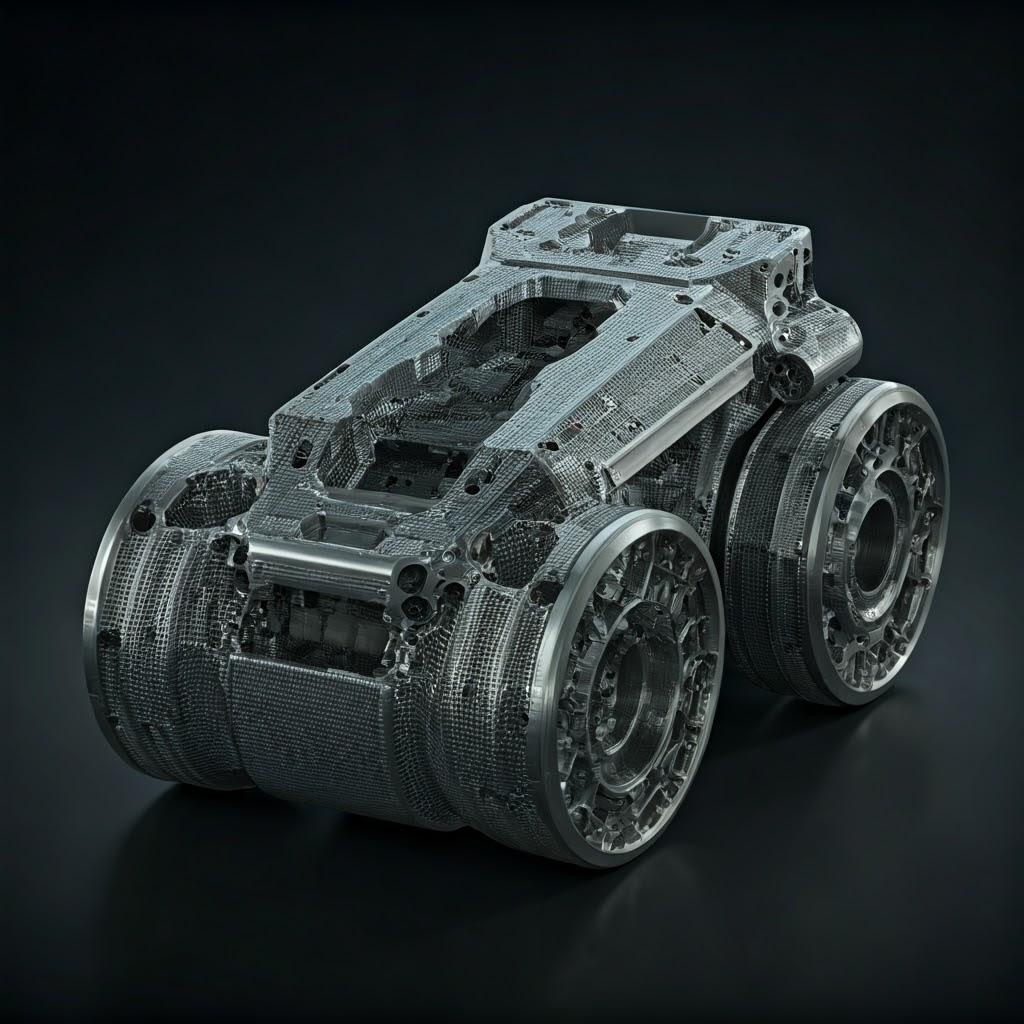
Häufig gestellte Fragen (FAQ)
Hier finden Sie Antworten auf einige häufig gestellte Fragen von Ingenieuren und Beschaffungsmanagern zur Verwendung von 3D-Metalldruck für UAV-Netzteilgehäuse:
- F1: Wie sieht es mit der Festigkeit und Haltbarkeit von 3D-gedruckten Metallgehäusen im Vergleich zu maschinell gefertigten Gehäusen aus?
- A: Bei Verwendung geeigneter Werkstoffe (wie AlSi10Mg oder 316L) und einer angemessenen Nachbearbeitung (insbesondere Wärmebehandlung) können 3D-gedruckte Metallteile mechanische Eigenschaften (Zugfestigkeit, Streckgrenze) erreichen, die mit denen von Knet- oder Gusswerkstoffen, die üblicherweise für die maschinelle Bearbeitung verwendet werden, vergleichbar und in bestimmten Aspekten (z. B. Ermüdungsfestigkeit aufgrund der feinen Mikrostruktur) sogar überlegen sind. Die Eigenschaften können jedoch anisotrop (richtungsabhängig) sein, abhängig von der Herstellungsrichtung. Es ist von entscheidender Bedeutung, das Teil richtig zu konstruieren und zu bearbeiten, um die geforderten Eigenschaften zu erfüllen haltbarkeit des 3D-Drucks. Die hochwertigen Pulver und kontrollierten Druckverfahren von Met3dp’ zielen beispielsweise darauf ab, dichte Teile mit ausgezeichneten mechanischen Eigenschaften für anspruchsvolle Anwendungen herzustellen.
- F2: Wie lang sind die typischen Vorlaufzeiten für Prototypen und Produktionschargen von UAV-Gehäusen?
- A: Wie bereits erwähnt, liegen die Vorlaufzeiten für Prototypen in der Regel zwischen 1 und 3 Wochen, je nach Komplexität und Nachbearbeitungsbedarf. Bei Produktionschargen hängen die Vorlaufzeiten stark von der Menge, der verfügbaren Maschinenkapazität und dem Umfang der erforderlichen Nachbearbeitung und Qualitätssicherung ab. Sie können von mehreren Wochen bis zu einigen Monaten reichen. Am besten besprechen Sie spezifische Vorlaufzeit der additiven Fertigung anforderungen mit dem von Ihnen gewählten Anbieter frühzeitig zu besprechen.
- F3: Können komplexe interne Merkmale zur Kühlung oder Kabelführung effektiv gedruckt werden?
- A: Ja, dies ist eine der Hauptstärken der Metall-AM. Komplexe Innenkanäle, konforme Kühlkanäle, integrierte Kabelkanäle und komplizierte Gitterstrukturen, die mit herkömmlichen Methoden nicht oder nur sehr schwer hergestellt werden können, lassen sich ohne weiteres herstellen. Allerdings müssen die DfAM-Prinzipien angewandt werden, um sicherzustellen, dass die Kanäle, wo immer möglich, selbsttragend sind oder für eine wirksame Stützentfernung und Pulverabsaugung ausgelegt sind.
- F4: Welche Informationen werden benötigt, um ein genaues Angebot für ein 3D-gedrucktes Gehäuse zu erhalten?
- A: Um einen genauen Kostenvoranschlag zu erstellen, benötigen die Anbieter in der Regel:
- Ein 3D-CAD-Modell (vorzugsweise im STEP- oder STL-Format).
- Werkstoffspezifikation (z. B. AlSi10Mg, 316L).
- Benötigte Menge (Prototyp vs. Produktion).
- Kritische Abmessungen, Toleranzen und Anforderungen an die Oberflächenbeschaffenheit sind deutlich gekennzeichnet (idealerweise auf einer 2D-Zeichnung, die dem 3D-Modell beigefügt ist).
- Anforderungen an die Nachbearbeitung (Wärmebehandlung, spezifische Bearbeitung, Endbearbeitung, Beschichtung).
- Erforderliche Zertifizierungen oder spezifische Qualitätsprüfungsverfahren.
- Gewünschte Vorlaufzeit.
- A: Um einen genauen Kostenvoranschlag zu erstellen, benötigen die Anbieter in der Regel:
- F5: Ist der 3D-Druck von Metall teurer als die CNC-Bearbeitung von UAV-Gehäusen?
- A: Das kommt darauf an. Für einfache, blockige Entwürfe, die sich leicht aus Standardmaterial bearbeiten lassen, kann die CNC-Bearbeitung günstiger sein, insbesondere bei höheren Stückzahlen. Bei hochkomplexen Geometrien, Teilen, die eine erhebliche Gewichtsreduzierung durch Topologieoptimierung erfordern, konsolidierten Baugruppen oder kundenspezifischen Teilen in kleinen Stückzahlen ist die Metall-AM jedoch oft kostengünstiger. Die wahre kostenvergleich AM vs. CNC sollten die Gesamtbetriebskosten berücksichtigen, einschließlich möglicher Einsparungen durch geringeres Gewicht, vereinfachte Montage und verbesserte Leistung, die durch die Designfreiheit von AM’ ermöglicht wird.
Schlussfolgerung: Höhere Leistung von UAVs mit fortschrittlicher additiver Fertigung von Metallen
Die Anforderungen, die an moderne UAVs gestellt werden - längere Flugzeiten, schwerere Nutzlasten, höhere Zuverlässigkeit und Betrieb in unterschiedlichen Umgebungen - erfordern Innovationen bei allen Komponenten, einschließlich des kritischen Stromversorgungsgehäuses. Wie wir erforscht haben, bietet die additive Fertigung von Metallen eine leistungsstarke Reihe von Werkzeugen, um diese Herausforderungen zu meistern.
Durch die Nutzung der vorteile von Metal AM recapkönnen Ingenieure und Beschaffungsmanager erhebliche Vorteile erschließen:
- Beispiellose Designfreiheit: Erstellen Sie komplexe, optimierte Geometrien, die mit herkömmlichen Methoden nicht möglich sind.
- Signifikante Gewichtsreduzierung: Nutzen Sie Topologieoptimierung und leichte Materialien wie AlSi10Mg, um die Flugleistung zu maximieren.
- Verbessertes Wärmemanagement: Integrieren Sie konforme Kühlkanäle und optimierte Kühlkörper direkt in das Gehäuse.
- Teil Konsolidierung: Reduzieren Sie die Komplexität der Montage, das Gewicht und mögliche Fehlerquellen.
- Schnelle Iteration & Anpassung: Beschleunigung der Entwicklungszyklen und effiziente Herstellung missionsspezifischer Komponenten.
Die Wahl des richtigen Materials, die Anwendung solider DfAM-Prinzipien, das Verständnis der Nachbearbeitungsanforderungen und die Auswahl eines erfahrenen Fertigungspartners sind der Schlüssel zur Nutzung dieser Vorteile. Unternehmen wie Met3dp mit ihrem umfassenden Fachwissen auf dem Gebiet fortschrittlicher Metallpulvermodernste Druckanlagen (einschließlich SLM- und SEBM-Systeme) und umfassende Lösungen für die additive Fertigungsind bereit, dies zu unterstützen digitale Fertigungstransformation. Sie schließen die Lücke zwischen innovativem Design und zuverlässiger Produktion und liefern die hochwertigen Materialien und das Fertigungs-Know-how, das für kritische UAV-Komponenten benötigt wird.
Bei der Einführung der additiven Fertigung von Metallgehäusen für die Stromversorgung von UAVs geht es nicht nur um die Einführung einer neuen Produktionstechnik, sondern auch darum, die nächste Generation von unbemannten Hochleistungssystemen zu ermöglichen. Kontaktieren Sie die Met3dp-Experten um Ihre spezifischen Anforderungen zu besprechen und herauszufinden, wie die Fähigkeiten des Unternehmens Ihre UAV-Designs verbessern können. Erkunden Sie die Möglichkeiten auf der Website des Unternehmens weiter: https://met3dp.com/.
Teilen auf
MET3DP Technology Co., LTD ist ein führender Anbieter von additiven Fertigungslösungen mit Hauptsitz in Qingdao, China. Unser Unternehmen ist spezialisiert auf 3D-Druckgeräte und Hochleistungsmetallpulver für industrielle Anwendungen.
Fragen Sie an, um den besten Preis und eine maßgeschneiderte Lösung für Ihr Unternehmen zu erhalten!
Verwandte Artikel
Über Met3DP
Aktuelles Update
Unser Produkt
KONTAKT US
Haben Sie Fragen? Senden Sie uns jetzt eine Nachricht! Wir werden Ihre Anfrage mit einem ganzen Team nach Erhalt Ihrer Nachricht bearbeiten.
Holen Sie sich Metal3DP's
Produkt-Broschüre
Erhalten Sie die neuesten Produkte und Preislisten
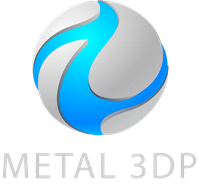
Metallpulver für 3D-Druck und additive Fertigung