3D-gedruckte Antriebsdüsen für Schiffssysteme
Inhaltsübersicht
Einleitung: Die Entwicklung von Schiffsantriebsdüsen mit Metall-AM
Das Streben nach Effizienz, Leistung und Zuverlässigkeit stand in der Schifffahrtsindustrie schon immer an erster Stelle. Von riesigen Containerschiffen, die die globalen Handelsrouten durchqueren, über wendige Marineschiffe, die die Küsten schützen, bis hin zu hochentwickelten Unterwasserfahrzeugen, die die Tiefsee erforschen, ist das Antriebssystem das Herzstück der betrieblichen Leistungsfähigkeit. Im Mittelpunkt vieler dieser Systeme steht die Antriebsdüse - ein Bauteil, das vom Konzept her einfach erscheint, in seiner hydrodynamischen Funktion jedoch unglaublich komplex ist. Ob es sich um eine Kort-Düse zur Maximierung des Schubs für einen Schlepper, einen präzisionsgefertigten Kanal für einen Wasserstrahl oder eine spezielle Schubdüsenkomponente für die dynamische Positionierung handelt, die Konstruktion der Düse wirkt sich direkt auf den Kraftstoffverbrauch, die Geschwindigkeit, die Manövrierfähigkeit und die akustische Signatur aus.
Für die Herstellung dieser kritischen Komponenten werden traditionell bewährte Verfahren wie Gießen, Schmieden und umfangreiche mechanische Bearbeitung eingesetzt. Diese Verfahren sind zwar zuverlässig, setzen aber oft Grenzen hinsichtlich der Komplexität des Designs, der Materialauswahl, der Vorlaufzeiten und der Möglichkeit, hochgradig individuelle oder optimierte Geometrien zu erstellen. Hier kommt die transformative Kraft von Additive Fertigung von Metall (AM), besser bekannt als Metall 3D-Druck. Diese Technologie führt in allen Branchen zu einem raschen Paradigmenwechsel, und ihr Potenzial für die Schiffstechnik, insbesondere für Antriebskomponenten, ist immens.
Metall-AM ermöglicht es Ingenieuren und Schiffsarchitekten, sich von den Beschränkungen der traditionellen Fertigung zu befreien. Es ermöglicht die Herstellung von Antriebsdüsen mit komplizierten inneren Strukturen, optimierten hydrodynamischen Profilen und konsolidierten Designs, deren Herstellung bisher unmöglich oder unerschwinglich war. Durch den schichtweisen Aufbau von Teilen direkt aus digitalen Modellen unter Verwendung von Hochleistungsmetallpulvern bietet AM eine noch nie dagewesene Designfreiheit, beschleunigt das Prototyping und die Produktionszyklen und öffnet die Tür zur Verwendung fortschrittlicher Materialien, die auf die raue Meeresumgebung zugeschnitten sind.
Für Ingenieure, die eine verbesserte Schiffsleistung anstreben, und für Beschaffungsmanager, die zuverlässige und innovative schiffbauzuliefererund Unternehmen, die modernste Technologien nutzen wollen maritime Ausstattungdas Verständnis der Fähigkeiten von metall AM für Schiffskomponenten ist nicht länger optional - es ist unerlässlich, um wettbewerbsfähig zu bleiben. Dieser Beitrag befasst sich mit den Besonderheiten des Metall-3D-Drucks für Schiffsantriebsdüsen, erforscht Anwendungen, Vorteile, Schlüsselmaterialien wie CuNi30Mn1Fe und IN625, Designüberlegungen und wie man mit Experten wie Met3dp zusammenarbeitet, um diese leistungsstarke Technologie zu nutzen. Met3dp, spezialisiert auf fortschrittliche Metall-AM-Systeme und die Herstellung hochwertiger sphärischer Metallpulver durch branchenführende Gaszerstäubung und PREP-Technologien, ist bereit, die Entwicklung der maritimen Industrie zu unterstützen.
Kernanwendungen: Wo machen 3D-gedruckte Antriebsdüsen Furore?
Die Anwendbarkeit des 3D-Drucks von Metallen ist nicht auf Nischen- oder Versuchsanwendungen beschränkt, sondern findet praktische, hochwertige Verwendung bei der Herstellung verschiedener Arten von Antriebsdüsen in verschiedenen Bereichen der Schifffahrt. Die Fähigkeit, komplexe Geometrien zu erstellen und spezielle Materialien zu verwenden, macht AM besonders geeignet für Komponenten, bei denen eine Leistungsoptimierung zu erheblichen betrieblichen Vorteilen führt.
Hier sind einige Schlüsselbereiche, in denen 3D-gedruckte Antriebsdüsen ihren Wert unter Beweis stellen:
- Kort-Düsen:
- Funktion: Diese Kanalpropeller sind so konstruiert, dass sie den Schub von Propellern deutlich erhöhen, insbesondere bei niedrigen Geschwindigkeiten, wie sie auf Schleppern, Trawlern und einigen großen Schiffen üblich sind.
- AM Vorteil: Metall-AM ermöglicht die Erstellung von hochoptimierten Kanalprofilen, die auf spezifische Propellerdesigns und Rumpfinteraktionen zugeschnitten sind, wodurch die Schubverstärkung maximiert und die Kavitationsleistung potenziell verbessert wird. Komplexe interne Versteifungsstrukturen können ohne Schweißen integriert werden, was die strukturelle Integrität und Ermüdungslebensdauer verbessert. Die Anpassung an die Hydrodynamik eines bestimmten Schiffes wird leichter möglich.
- Komponenten für Wasserstrahlantriebe:
- Funktion: Wasserstrahlen verwenden einen Impeller, um Wasser anzusaugen und es mit hoher Geschwindigkeit durch eine Düse auszustoßen und so für Vortrieb und Lenkung zu sorgen. Zu den wichtigsten Komponenten gehören Ansaugrohre, Statoren, Laufräder (bei AM-Düsen weniger üblich) und die endgültige Auslassdüse.
- AM Vorteil: Die komplexen Innengeometrien von Wasserstrahlstatoren und -düsen, die für eine effiziente Strömungslenkung entscheidend sind, eignen sich ideal für AM. Glatte, optimierte interne Durchgänge minimieren die hydraulischen Verluste. Die Konsolidierung von Teilen ist ein großer Vorteil, da mehrere traditionell gefertigte Teile in einer einzigen gedruckten Komponente kombiniert werden können, was die Montagezeit und potenzielle Leckagepfade reduziert. Hochfeste, korrosionsbeständige Materialien wie IN625 lassen sich für anspruchsvolle Durchflussbedingungen mit hohen Geschwindigkeiten problemlos mit AM verarbeiten.
- Triebwerksdüsen (Azimut, Tunnel, dynamische Positionierung):
- Funktion: Triebwerke sorgen für die Manövrierfähigkeit und die Fähigkeit, die Position zu halten. Ihre Düsen lenken den vom Propeller erzeugten Schub, was oft eine präzise Steuerung und Haltbarkeit erfordert.
- AM Vorteil: AM ermöglicht die Herstellung von Düsen mit optimierten hydrodynamischen Formen für maximale Schubeffizienz und reduzierte Geräuschsignatur. Bei dynamischen Positionierungssystemen, die schnelle Änderungen des Schubvektors erfordern, können leichte Konstruktionen, die durch Topologieoptimierung (möglich mit AM) erreicht werden, die Trägheit verringern. Die Möglichkeit, robuste Materialien wie IN625 zu drucken, gewährleistet Langlebigkeit in anspruchsvollen Betriebszyklen. Für Triebwerke mit hoher Leistungsdichte könnten interne Kühlkanäle integriert werden.
- Spezialisierte Unterwasserfahrzeugantriebe (AUVs, ROVs):
- Funktion: Autonome Unterwasserfahrzeuge (AUVs) und ferngesteuerte Fahrzeuge (ROVs) benötigen oft kompakte, hocheffiziente und manchmal auch akustisch leise Antriebssysteme.
- AM Vorteil: AM eignet sich perfekt für die Herstellung maßgeschneiderter Hochleistungsdüsen in kleinen Stückzahlen, die auf die besonderen Anforderungen und Größenbeschränkungen dieser Fahrzeuge zugeschnitten sind. Komplexe, biologisch inspirierte Designs für verbesserte Effizienz oder Stealth können realisiert werden. Gewichtsreduzierung durch AM ist entscheidend für die Maximierung der Nutzlastkapazität und Ausdauer von batteriebetriebenen AUVs. Werkstoffe mit hervorragender Korrosionsbeständigkeit, wie CuNi-Legierungen oder spezielle Titansorten, die ebenfalls von Met3dp angeboten werden, sind für einen längeren Unterwasserbetrieb unerlässlich.
- Propeller-Boss-Cap-Fins (PBCFs) & Effizienzgeräte:
- Funktion: Vorrichtungen wie PBCFs sind zwar keine Düsen im eigentlichen Sinne, werden aber an Propellern angebracht, um Nabenwirbel zu brechen und Rotationsenergie zurückzugewinnen, was die Effizienz verbessert. Ähnliche effizienzsteigernde Anbauteile können manchmal düsenähnliche Merkmale aufweisen.
- AM Vorteil: Die komplexen, oft nicht achsensymmetrischen Formen dieser Geräte können auf herkömmliche Weise schwer herzustellen sein. AM ermöglicht die präzise Erstellung dieser Geometrien, die möglicherweise direkt in andere Propellerkomponenten integriert werden können, oder die schnelle Herstellung von Prototypen und die Erprobung neuer Konzepte zur Verbesserung der Effizienz.
Begünstigte Branchen:
- Kommerzieller Versand: Verbesserung der Kraftstoffeffizienz, geringere Wartung (Antifouling-Materialien) und zuverlässige Komponenten.
- Naval & Verteidigung: Sie erfordern eine hohe Leistung, Langlebigkeit, potenziell geringere akustische Signaturen und eine schnelle Bereitstellung von kundenspezifischen Lösungen.
- Offshore Öl & Gas / Erneuerbare Energien: Einsatz von DP-Systemen, ROVs der Arbeitsklasse und Bedarf an robusten Komponenten für raue Umgebungen.
- Meeresforschung & Exploration: Einsatz von AUVs und ROVs, die spezielle, leichte und korrosionsbeständige Antriebe benötigen.
- Segeln: Auf der Suche nach Hochleistungs-Wasserstrahlkomponenten oder maßgeschneiderten Strahlruderlösungen.
Der gemeinsame Nenner dieser Anwendungen ist der Bedarf an verbesserter Leistung, kundenspezifischer Anpassung und Zuverlässigkeit unter schwierigen Betriebsbedingungen - genau dort, wo die einzigartigen Fähigkeiten von Metal AM zum Tragen kommen. Beschaffungsmanager auf der Suche nach lieferanten von maritimer Ausrüstung die in der Lage sind, diese fortschrittlichen Komponenten zu liefern, wenden sich zunehmend an Metall-AM-Spezialisten.
Warum 3D-Metalldruck für Antriebsdüsen? Vorteile gegenüber traditionellen Methoden
Herkömmliche Fertigungsverfahren wie Gießen und Zerspanen haben sich in der Schifffahrtsindustrie zwar seit Jahrzehnten bewährt, sind jedoch von Natur aus mit Einschränkungen verbunden, insbesondere angesichts der Nachfrage nach immer komplexeren und optimierten Antriebsdüsenkonstruktionen. Die additive Fertigung von Metallen bietet eine Reihe überzeugender Vorteile, die diese Einschränkungen direkt angehen und Ingenieuren, Konstrukteuren und Schiffsbetreibern einen erheblichen Mehrwert bieten.
Vergleichen wir Metall-AM (speziell Powder Bed Fusion – PBF-Verfahren wie Selective Laser Melting/Melting (SLM/SLM) und Electron Beam Melting (EBM)) mit traditionellen Ansätzen für die Düsenproduktion:
Vergleich: Metall-AM vs. traditionelle Fertigung für Schiffsdüsen
Merkmal | Metallbasierte additive Fertigung (PBF) | Traditionelle Fertigung (Gießen/Schmieden + Bearbeitung) | Auswirkungen auf die Meeresindustrie |
---|---|---|---|
Entwurfskomplexität | Sehr hoch: Ermöglicht komplizierte interne Kanäle, komplexe Kurven, Topologieoptimierung, Gitterstrukturen. Die Kosten hängen weniger von der Komplexität ab. | Begrenzt: Begrenzt durch die Möglichkeiten der Form und den Zugang zu den Werkzeugen für die Bearbeitung. Komplexe Merkmale erhöhen die Kosten erheblich. | AM ermöglicht hydrodynamisch überlegene Designs, integrierte Funktionen und einen potenziell leiseren Betrieb. |
Teil Konsolidierung | Ausgezeichnet: Mehrere Komponenten können oft neu gestaltet und als ein einziges Teil gedruckt werden. | Schlecht: Komplexe Baugruppen erfordern oft mehrere Teile, Schweißarbeiten und Verbindungselemente. | Geringere Montagezeit, weniger potenzielle Fehlerstellen (Schweißnähte, Dichtungen), verbesserte strukturelle Integrität. |
Materialnutzung | Hoch: Es wird nur das Material verwendet, das für das Teil und die Halterungen benötigt wird (recycelbar). Minimaler Abfall. | Tiefer: Das Gießen kann eine vernünftige Ausbeute haben, aber die Bearbeitung ist subtraktiv und erzeugt erheblichen Ausschuss (Späne). | Nachhaltigere Herstellung, Kosteneinsparungen bei teuren Legierungen wie IN625. |
Vorlaufzeit (Prototypen) | Schnell: Tage bis Wochen von der CAD-Datei bis zum physischen Teil. Ermöglicht schnelle Design-Iterationen. | Langsam: Wochen bis Monate, insbesondere wenn Werkzeuge (Formen, Matrizen) erforderlich sind. | Kürzere Entwicklungszyklen, schnellere Prüfung und Validierung neuer Düsenkonzepte. |
Vorlaufzeit (Produktion) | Mäßig bis schnell: Abhängig von Teilegröße, Menge und Nachbearbeitung. Gut für kleine bis mittlere Mengen & auf Anfrage. | Variiert: Kann schnell sein für etablierte Teile mit hohen Stückzahlen, aber die Vorlaufzeit für die Werkzeuge ist im Voraus. Langsam bei geringen Stückzahlen. | AM bietet Flexibilität, Ersatzteile auf Abruf und einen geringeren Lagerbedarf für bestimmte Teile. |
Werkzeugkosten | Keine: Direkte digitale Fertigung, keine teilespezifischen Werkzeuge erforderlich. | Hoch: Formen, Gesenke oder komplexe Vorrichtungen können erhebliche Vorabinvestitionen bedeuten. | AM ist kostengünstig für kundenspezifische Teile, Prototypen und Kleinserien. |
Gewichtsreduzierung | Erhebliches Potenzial: Topologieoptimierung und interne Gitter können das Gewicht bei gleichbleibender Festigkeit drastisch reduzieren. | Begrenzt: Die Gewichtsreduzierung beruht oft nur auf der Wahl der Materialien oder der grundlegenden Konstruktionsweise. | Geringeres Schiffsgewicht, verbesserte Treibstoffeffizienz, geringere Trägheit der Strahlruder. |
Material-Optionen | Wuchsbereich: Große Auswahl an schweißbaren Legierungen, einschließlich Hochleistungs-Ni-Legierungen, Ti-Legierungen, Cu-Legierungen und rostfreie Stähle. | Gut etabliert: Sehr große Auswahl, aber bestimmte Kombinationen oder Geometrien können durch das Verfahren eingeschränkt sein. | AM ermöglicht die Verwendung fortschrittlicher Werkstoffe wie IN625 oder spezielle CuNi-Legierungen für optimale Leistung. |
Personalisierung | Einfach: Jeder Druck kann ein Unikat sein, ohne dass dadurch erhebliche Kosten entstehen. Ideal für maßgefertigte Designs. | Schwierig/teuer: Erfordert Werkzeugwechsel oder umfangreiche Neuprogrammierung für Variationen. | Maßgeschneiderte Düsen für die Hydrodynamik von Schiffen oder für bestimmte betriebliche Anforderungen werden möglich. |
In Blätter exportieren
Die wichtigsten Vorteile werden herausgearbeitet:
- Unerreichte Gestaltungsfreiheit: Dies ist wohl der bedeutendste Vorteil. AM ermöglicht es den Ingenieuren, interne Strömungswege zu entwerfen, die ausschließlich für die hydrodynamische Effizienz optimiert sind und nicht durch die Notwendigkeit von Entformungswinkeln (Gießen) oder Werkzeugzugang (Bearbeitung) eingeschränkt werden. Komplexe Kühlkanäle, geräuschdämpfende Merkmale oder integrierte Sensorgehäuse können direkt in die Düsenstruktur integriert werden.
- Beschleunigte Innovation: Die Möglichkeit, innerhalb weniger Tage von einem digitalen Entwurf zu einem physischen Metallprototyp zu gelangen, verändert den Entwicklungszyklus grundlegend. Mehrere Design-Iterationen für ein neues Düsenkonzept können in der Zeit gedruckt und getestet werden, die ein einziger Prototyp im herkömmlichen Gießverfahren benötigen würde, was viel schneller zu leistungsfähigeren Endprodukten führt. Erforschen Sie die Möglichkeiten mit Met3dp’s Metall 3D-Druck Lösungen.
- On-Demand-Produktion und reduzierter Lagerbestand: Für bestimmte kritische Ersatzteile oder kundenspezifische Düsen in kleinen Stückzahlen ermöglicht AM eine Fertigung auf Abruf. Dies reduziert den Bedarf an umfangreichen physischen Beständen und setzt Kapital und Lagerplatz frei. Eine digitale Datei ist alles, was benötigt wird.
- Gewichtsreduzierung: Besonders wichtig für AUVs, Hochgeschwindigkeitsfahrzeuge oder Komponenten, die sich hoch über dem Schwerpunkt des Schiffes befinden, kann AM in Kombination mit einer Topologieoptimierungssoftware Düsen herstellen, die deutlich leichter sind als ihre traditionell hergestellten Gegenstücke und gleichzeitig die Festigkeitsanforderungen erfüllen oder übertreffen.
- Verbesserte Materialleistung: AM-Prozesse führen häufig zu feinkörnigen Mikrostrukturen, die in einigen Fällen und bei entsprechender Nachbearbeitung bessere mechanische Eigenschaften als gegossene Äquivalente aufweisen können. Außerdem ermöglicht AM die Verwendung von Werkstoffen, die sich nur schwer oder gar nicht in komplexe Düsenformen gießen oder schmieden lassen.
Für die Produktion von Standarddüsen in hohen Stückzahlen sind herkömmliche Verfahren zwar nach wie vor praktikabel, Metall-Additiv-Fertigung ist eine leistungsstarke Alternative für Anwendungen, die eine höhere Leistung, individuelle Anpassung, schnellere Entwicklung oder komplexe Geometrien erfordern. Es befähigt Schiffsingenieure und schiffbauhersteller um die Grenzen der Konstruktion von Antriebssystemen zu erweitern.
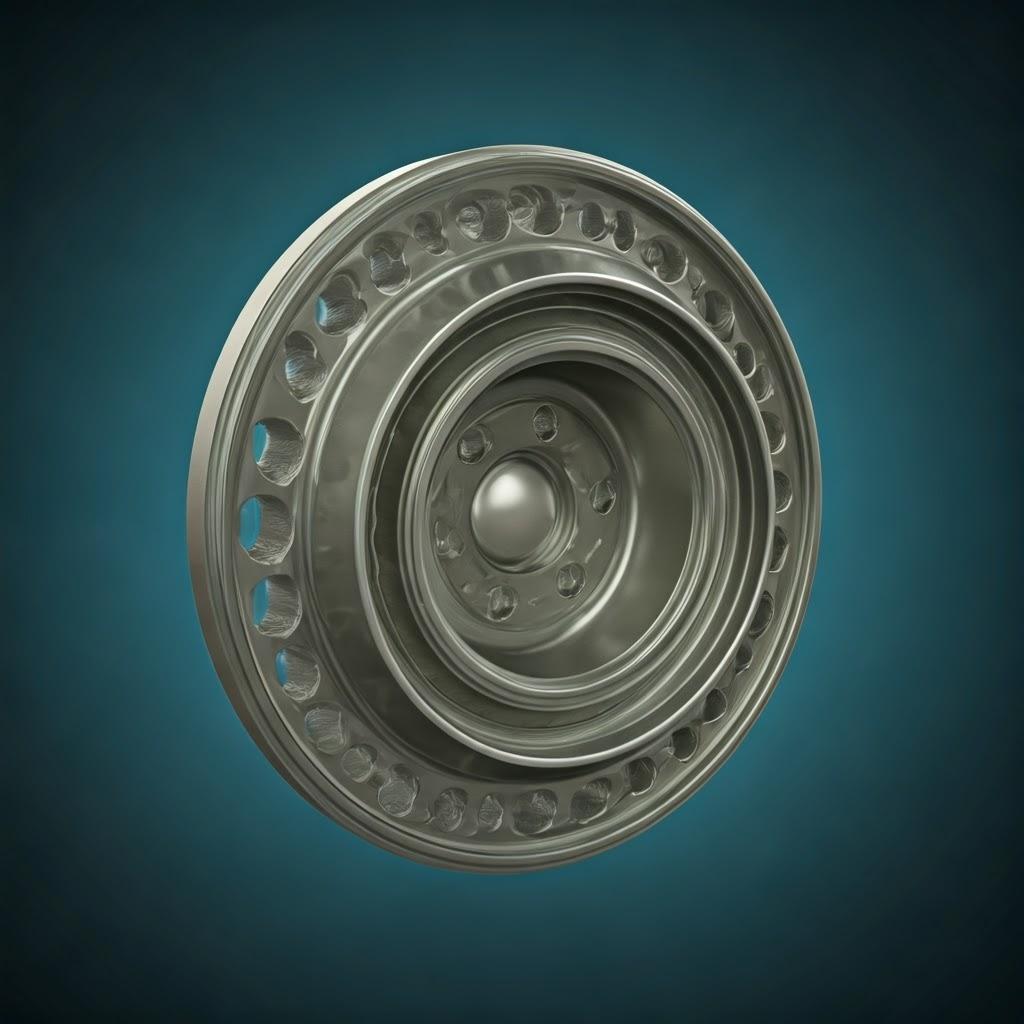
Werkstoff-Fokus: CuNi30Mn1Fe und IN625 für überragende maritime Leistung
Die Wahl des Werkstoffs ist für alle Schiffskomponenten entscheidend, insbesondere für Antriebsdüsen, die ständig korrosivem Meerwasser, hohen Strömungsgeschwindigkeiten, potenzieller Kavitation und mechanischen Belastungen ausgesetzt sind. Die additive Fertigung von Metallen ermöglicht nicht nur komplexe Formen, sondern auch die Verwendung fortschrittlicher Legierungen, die speziell für diese anspruchsvollen Bedingungen geeignet sind. Zwei herausragende Materialien für 3D-gedruckte Schiffsdüsen sind CuNi30Mn1Fe (eine Kupfer-Nickel-Legierung) und IN625 (eine Nickel-Chrom-Superlegierung). Die Qualität des ursprünglichen Metallpulvers ist für einen erfolgreichen Druck von entscheidender Bedeutung, und Met3dp nutzt seine fortschrittliche Gaszerstäubung und PREP-Technologien zur Herstellung von hochsphärischen, fließfähigen Pulvern, die für die Herstellung dichter, hochwertiger Teile unerlässlich sind.
CuNi30Mn1Fe: Der Korrosionsschutz & Anti-Fouling Champion
Kupfer-Nickel-Legierungen, die oft als Kupfernickellegierungen bezeichnet werden, haben aufgrund ihrer außergewöhnlichen Korrosionsbeständigkeit gegenüber Meerwasser und ihrer inhärenten Resistenz gegen Biofouling eine lange und erfolgreiche Geschichte in maritimen Anwendungen. CuNi30Mn1Fe (ähnlich wie C71500) ist eine spezielle Zusammensetzung, die für ein ausgewogenes Verhältnis von Festigkeit, Haltbarkeit und maritimer Leistung optimiert ist.
Wichtige Eigenschaften und Vorteile für Schiffsdüsen:
- Hervorragende Seewasser-Korrosionsbeständigkeit: Kupfernickellegierungen bilden eine stabile, fest haftende Oxidschutzschicht, wenn sie Meerwasser ausgesetzt werden. Diese Schicht bietet eine hervorragende Beständigkeit gegen allgemeine Korrosion, Lochfraß und Spaltkorrosion in salzhaltigen Umgebungen, selbst in verschmutzten Gewässern oder bei höheren Durchflussraten, wie sie in Düsen vorkommen.
- Inhärente Anti-Fouling-Eigenschaften: Kupferionen verhindern auf natürliche Weise die Ansiedlung und das Wachstum von Meeresorganismen wie Seepocken, Muscheln und Algen. Für eine Antriebsdüse ist dies ein bedeutender Vorteil. Biofouling erhöht die Oberflächenrauhigkeit, was die hydrodynamische Effizienz drastisch verringert, den Kraftstoffverbrauch erhöht und möglicherweise zu Leistungseinbußen oder Ungleichgewicht führt. Die Verwendung von CuNi30Mn1Fe minimiert den Bedarf an häufigen Reinigungen oder Antifouling-Beschichtungen und reduziert so Betriebskosten und Ausfallzeiten.
- Gute Festigkeit und Duktilität: CuNi30Mn1Fe ist zwar nicht so fest wie Superlegierungen, bietet aber eine ausreichende mechanische Festigkeit und Zähigkeit für viele Düsenanwendungen, insbesondere dort, wo extreme Belastungen oder Temperaturen nicht das Hauptanliegen sind. Seine Duktilität lässt eine gewisse plastische Verformung vor dem Bruch zu und trägt so zur allgemeinen Haltbarkeit bei.
- Schweißbarkeit & Verarbeitbarkeit (traditioneller Kontext): Obwohl wir uns auf AM konzentrieren, lässt sich seine traditionell gute Schweißbarkeit gut auf das schichtweise Fusionsverfahren bei AM übertragen und trägt zu fehlerfreien Drucken bei.
- Mäßige Kosten: Im Vergleich zu Nickelsuperlegierungen oder Titan ist Kupfernickel im Allgemeinen eine kostengünstigere Option, was es für Anwendungen attraktiv macht, bei denen seine spezifischen Vorteile hoch geschätzt werden.
Warum die Qualität des Pulvers wichtig ist: Um die gewünschte Korrosionsbeständigkeit und die mechanischen Eigenschaften zu erreichen, muss beim AM ein dichtes, homogenes Teil gedruckt werden. Dies erfordert Metallpulver mit: * Hohe Sphärizität: Gewährleistet eine gute Packungsdichte des Pulverbettes und ein gleichmäßiges Schmelzen. * Gute Fließfähigkeit: Ermöglicht eine gleichmäßige Verteilung des Pulvers während des Druckvorgangs. * Kontrollierte Partikelgrößenverteilung (PSD): Beeinflusst die Verpackung, das Schmelzen und die endgültige Oberflächenbeschaffenheit. * Niedrige Verunreinigungswerte (insbesondere Sauerstoff): Sauerstoffverunreinigungen können die mechanischen Eigenschaften und die Korrosionsbeständigkeit beeinträchtigen. Die fortschrittlichen Zerstäubungstechniken von Met3dp’ sind darauf ausgelegt, diese Eigenschaften für anspruchsvolle Anwendungen zu optimieren.
CuNi30Mn1Fe Eigenschaftsübersicht (Typische Werte für Kneten/Gießen – AM-Eigenschaften hängen von Prozess/Nachbearbeitung ab):
Eigentum | Typischer Wertebereich | Bedeutung für Schiffsdüsen |
---|---|---|
Dichte | ~ 8,94 g/cm³ | Standarddichte, Berücksichtigung des Gewichts bei der Konstruktion. |
Zugfestigkeit | 380 - 550 MPa | Ausreichend für viele Düsenanwendungen mit mittlerer Belastung. |
Streckgrenze | 140 – 415 MPa | Widerstand gegen bleibende Verformung unter Last. |
Dehnung | 15 – 40% | Zeigt eine gute Duktilität und Zähigkeit an. |
Korrosionsbeständigkeit | Ausgezeichnet in Meerwasser | Hauptvorteil: lange Lebensdauer, Beständigkeit gegen Lochfraß/Spaltenbildung. |
Resistenz gegen Biofouling | Ausgezeichnet | Reduziert den Luftwiderstand, erhält die Effizienz und senkt die Wartungskosten. |
In Blätter exportieren
Ideale Anwendungen: Kortdüsen für Arbeitsboote, Strahlruderdüsen unter mäßigen Bedingungen, Komponenten, bei denen Bewuchsschutz eine wichtige Rolle spielt, Teile, die lange Tauchzeiten erfordern.
IN625 (Inconel 625): Das hochfeste, hochbeständige Kraftpaket
IN625 ist eine Nickel-Chrom-Molybdän-Niob-Superlegierung, die für ihre außergewöhnliche Kombination aus hoher Festigkeit, hervorragender Korrosionsbeständigkeit (insbesondere gegen Lochfraß und Spaltkorrosion in aggressiven Umgebungen) und Hochtemperaturstabilität bekannt ist. Sie ist ein bevorzugtes Material für einige der anspruchsvollsten Schiffsanwendungen.
Wichtige Eigenschaften und Vorteile für Schiffsdüsen:
- Hervorragende Korrosionsbeständigkeit: IN625 zeichnet sich durch eine bemerkenswerte Beständigkeit in einer Vielzahl von korrosiven Medien aus, darunter Meerwasser mit hohem Chloridgehalt, saure Bedingungen und stehende oder verschmutzte Gewässer. Der hohe Nickel- und Chromgehalt sorgt für allgemeine Korrosionsbeständigkeit, während Molybdän die Beständigkeit gegen Lochfraß und Spaltkorrosion - kritische Fehlerarten in Meeresumgebungen - deutlich erhöht.
- Hohe Festigkeit und Zähigkeit: IN625 weist eine hohe Zug-, Streck- und Kriechbruchfestigkeit bei kryogenen Temperaturen bis zu ~815°C (1500°F) auf. Dadurch eignet es sich für Hochleistungsdüsen, die erheblichen hydrodynamischen Kräften, Druckschwankungen oder erhöhten Temperaturen ausgesetzt sind (z. B. in der Nähe von Motorabgasen oder in Systemen mit hoher Leistungsdichte).
- Ausgezeichnete Ermüdungsfestigkeit: Aufgrund der zyklischen Belastung, der Antriebskomponenten ausgesetzt sind, ist die Ermüdungsfestigkeit von entscheidender Bedeutung. IN625 zeigt unter Ermüdungsbedingungen eine außergewöhnlich gute Leistung und trägt so zu einer langen Lebensdauer bei.
- Beständigkeit gegen Spannungsrisskorrosion (SCC): Besonders wichtig in chloridreichen Meeresumgebungen ist IN625 sehr widerstandsfähig gegen SCC.
- Gute Verarbeitbarkeit (AM-Kontext): IN625 ist eine der leichter bedruckbaren Nickel-Superlegierungen, die mit PBF-Verfahren hergestellt werden können, obwohl eine sorgfältige Kontrolle der Parameter und Nachbearbeitung (z. B. Spannungsabbau) unerlässlich ist.
Warum die Qualität des Pulvers wichtig ist: Wie bei CuNi hängt die Leistung eines AM IN625-Bauteils von der Pulverqualität ab. Angesichts der höheren Leistungsanforderungen, die häufig an IN625-Bauteile gestellt werden, sind Faktoren wie: * Geringe Porosität: Wesentlich für Ermüdungsfestigkeit und Korrosionsbeständigkeit. Erfordert optimierte Pulvereigenschaften (Sphärizität, Fließfähigkeit, PSD) und Druckparameter. * Minimale Satellitenteilchen: Feine Partikel, die an größeren Kugeln haften, können die Fließfähigkeit und Packungsdichte beeinträchtigen. Kontrollierte Zerstäubungsprozesse minimieren diese. * Präzise chemische Zusammensetzung: Um die erwarteten mechanischen und korrosiven Eigenschaften zu erreichen, muss sichergestellt werden, dass das Pulver die genaue IN625-Spezifikation erfüllt. Seriös Lieferanten von Metallpulver wie Met3dp bieten zertifizierte Pulver mit streng kontrollierten chemischen Eigenschaften.
IN625 Eigenschaftsübersicht (Typische Werte – AM-Eigenschaften hängen von Prozess/Nachbearbeitung ab):
Eigentum | Typischer Wertebereich (geglüht) | Bedeutung für Schiffsdüsen |
---|---|---|
Dichte | ~ 8,44 g/cm³ | Etwas leichter als Stahl oder Kupfernickel. |
Zugfestigkeit | 830 – 1030 MPa | Sehr hohe Festigkeit für anspruchsvolle Belastungen und Hochdruckumgebungen. |
Streckgrenze | 415 – 760 MPa | Hohe Beständigkeit gegen dauerhafte Verformung. |
Dehnung | 30 – 50% | Ausgezeichnete Duktilität und Zähigkeit, auch bei hoher Festigkeit. |
Korrosionsbeständigkeit | Hervorragend, insbesondere Pitting & Crevice | Geeignet für die aggressivsten maritimen Bedingungen, lange Lebenserwartung. |
Hochtemperaturfestigkeit | Ausgezeichnet bis zu ~815°C | Relevant, wenn die Düse in der Nähe von Wärmequellen oder in Hochenergiesystemen betrieben wird. |
In Blätter exportieren
Ideale Anwendungen: Hochleistungs-Wasserstrahldüsen und -statoren, Komponenten für Schiffsschrauben, Düsen für Tiefsee-ROVs/AUVs, die in korrosiven oder Hochdruckgebieten arbeiten, Komponenten, die eine maximale Haltbarkeit und Beständigkeit gegen Kavitationserosion erfordern.
Die Wahl zwischen CuNi30Mn1Fe und IN625 hängt von den spezifischen betrieblichen Anforderungen, dem Budget und den Leistungszielen für die Antriebsdüse ab. Beide Werkstoffe bieten erhebliche Vorteile, wenn sie mit hochwertigen Pulvern und optimierten Metall-Additiv-Fertigungsverfahren verarbeitet werden, was die Herstellung von Schiffsantriebskomponenten der nächsten Generation ermöglicht.
Design für additive Fertigung (DfAM): Optimierung von Düsen für den 3D-Druck
Die erfolgreiche Nutzung der additiven Fertigung von Metall für Schiffsantriebsdüsen geht über die einfache Konvertierung eines vorhandenen CAD-Modells hinaus, das für den Guss oder die maschinelle Bearbeitung entwickelt wurde. Um die Vorteile der additiven Fertigung - Komplexität, Konsolidierung, Leichtbau und Effizienz - wirklich nutzen zu können, müssen die Ingenieure die folgenden Aspekte berücksichtigen Design für additive Fertigung (DfAM) grundsätze. DfAM umfasst die Gestaltung von Teilen speziell für den schichtweisen Aufbauprozess, wobei dessen einzigartige Fähigkeiten und Einschränkungen von Anfang an berücksichtigt werden. Die Anwendung von DfAM auf Schiffsdüsen kann die Druckbarkeit erheblich verbessern, die Kosten senken, die Nachbearbeitung minimieren und die Leistung des fertigen Teils verbessern.
Hier sind die wichtigsten DfAM-Überlegungen für optimierung der Düsengeometrie für AM:
- Optimieren Sie die internen Strömungswege:
- Reibungslose Übergänge: Vermeiden Sie scharfe Ecken und abrupte Richtungsänderungen in internen Kanälen. Diese führen zu Spannungskonzentrationen, können schwierig genau zu drucken sein und erfordern möglicherweise umfangreiche interne Stützstrukturen. Entscheiden Sie sich für allmähliche Kurven und Verrundungen, um die Fließdynamik und Druckbarkeit zu verbessern.
- Hydrodynamischer Wirkungsgrad: Nutzen Sie CFD-Analysen (Computational Fluid Dynamics) bereits in der Entwurfsphase, um die Strömung durch die Düse zu simulieren. AM ermöglicht die direkte Erstellung komplexer, optimierter interner Geometrien, die mit CFD ermittelt werden und mit herkömmlichen Methoden nur schwer oder gar nicht zu erreichen wären.
- Überhänge und Stützkonstruktionen minimieren:
- Selbsttragende Winkel: Metallpulverschmelzverfahren (PBF) können in der Regel Überhänge im Verhältnis zur Bauplatte bis zu einem bestimmten Winkel (oft etwa 45 Grad) drucken, ohne dass Stützstrukturen darunter erforderlich sind. Das Design von Merkmalen wie konvergierenden/ divergierenden Abschnitten oder internen Kanälen mit Winkeln, die größer als diese kritische Grenze sind, reduziert den Bedarf an Stützen erheblich.
- Unterstützung der Strategieintegration: Wo Stützen unvermeidbar sind (z. B. bei horizontalen Flächen oder niedrigen Winkeln), sollten Sie bei der Konstruktion des Teils die Entfernung der Stützen berücksichtigen. Sorgen Sie für einen angemessenen Zugang für Werkzeuge, um Stützstrukturen zu entfernen oder zu bearbeiten, insbesondere in inneren Hohlräumen. Berücksichtigen Sie kleine Konstruktionsmerkmale (z. B. spezielle Fasen) an den Stellen, an denen die Stützen auf das Teil treffen, um das Entfernen zu erleichtern und die Oberflächenvernarbung zu minimieren.
- Alternative Orientierungen: Prüfen Sie frühzeitig verschiedene Bauausrichtungen. Manchmal kann das Drehen des Teils auf der Bauplatte das Volumen der benötigten Stützen drastisch reduzieren und so Material, Druckzeit und Nachbearbeitungsaufwand sparen.
- Wanddicke und Größe der Merkmale:
- Mindestwanddicke: Informieren Sie sich über die minimale druckbare Wandstärke für das gewählte Material und den AM-Prozess (oft im Bereich von 0,4-1,0 mm für PBF). Stellen Sie sicher, dass alle Strukturwände diese Mindestanforderung erfüllen. Dünne Wände können sich verziehen oder lassen sich möglicherweise nicht genau auflösen.
- Einheitlichkeit: AM erlaubt zwar unterschiedliche Wandstärken, doch können plötzliche große Änderungen zu unterschiedlichen Abkühlungsraten und erhöhter thermischer Belastung führen. Streben Sie nach Möglichkeit allmähliche Übergänge in der Dicke an.
- Kleine Merkmale: Achten Sie auf die Mindestgröße der auflösbaren Merkmale (Löcher, Stifte, Schlitze). Sehr feine Merkmale werden möglicherweise nicht genau gedruckt oder könnten bei der Nachbearbeitung leicht beschädigt werden.
- Teil Konsolidierung:
- Baugruppen umgestalten: Suchen Sie aktiv nach Möglichkeiten, mehrteilige Düsenbaugruppen (z. B. Düsenkörper, interne Strömungsgleichrichter, Montageflansche) zu einer einzigen, integrierten Komponente umzugestalten. Dadurch entfallen Schweiß-/Löt-/Befestigungsschritte, das Gewicht wird reduziert, die strukturelle Integrität verbessert und die Lieferkette vereinfacht.
- Topologie-Optimierung und Gewichtsreduzierung:
- Lastpfad-Optimierung: Nutzen Sie Software zur Topologieoptimierung, um zu ermitteln, wo Material strukturell notwendig ist, und es dort zu entfernen, wo es nicht notwendig ist, basierend auf den erwarteten Betriebslasten. Dies kann zu erheblichen Gewichtseinsparungen führen - entscheidend für leistungsrelevante Anwendungen wie AUVs oder Hochgeschwindigkeitsfahrzeuge - bei gleichzeitiger Beibehaltung der erforderlichen Festigkeit. AM ist in einzigartiger Weise in der Lage, die organischen, oft komplexen Geometrien herzustellen, die sich aus der Topologieoptimierung ergeben.
- Gitterförmige Strukturen: Interne Gitterstrukturen in weniger kritischen Bereichen, um das Gewicht und den Materialverbrauch weiter zu reduzieren und gleichzeitig die Struktur zu unterstützen.
- Überlegungen zum Wärmemanagement:
- Vermeiden Sie große massive Blöcke: Sehr große, dichte Abschnitte können während des Drucks eine erhebliche thermische Belastung darstellen. Ziehen Sie die Aushöhlung von Abschnitten in Betracht (wenn dies strukturell möglich ist) oder bauen Sie interne Merkmale ein, um die Wärmeverteilung zu steuern.
- Allmähliche Querschnittsveränderungen: Wie bereits bei der Wandstärke erwähnt, sollten Sie auf glatte Übergänge im Gesamtquerschnitt des Teils achten, um einen lokalen Wärmestau zu minimieren und die Gefahr von Verformungen oder Rissen zu verringern.
Die Anwendung dieser DfAM-Grundsätze erfordert zwar ein Umdenken, zahlt sich aber in hohem Maße aus. Die Zusammenarbeit mit erfahrenen AM-Dienstleistern, wie dem Team, das Über Met3dpkann in der Konstruktionsphase wertvolle Einblicke und Hilfestellungen geben, um sicherzustellen, dass Ihr Schiffsdüsendesign für eine erfolgreiche additive Fertigung optimiert ist. Ihr Fachwissen umfasst die Bereiche Materialwissenschaft, Prozessoptimierung und Anwendungsentwicklung und hilft Kunden bei der Bewältigung der komplizierten DfAM-Problematik für anspruchsvolle Komponenten.
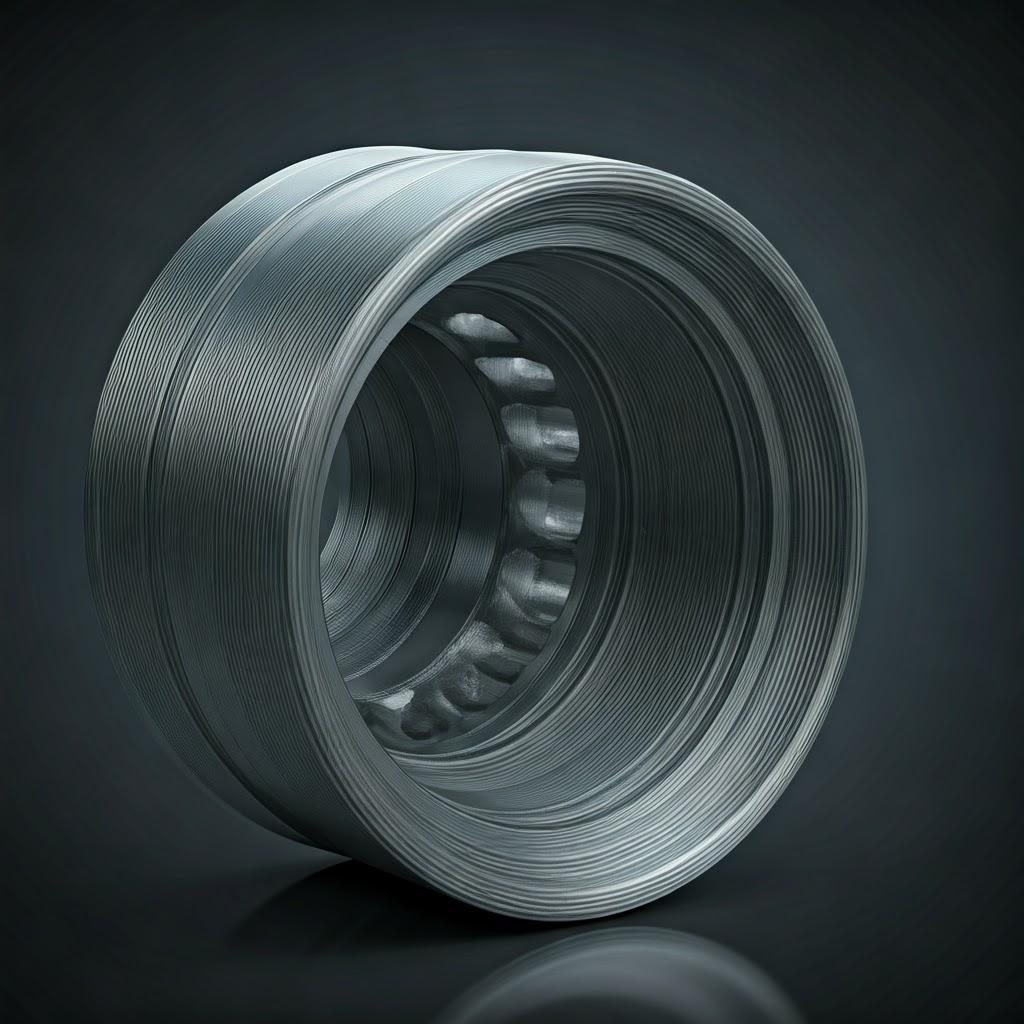
Erreichbare Präzision: Toleranz, Oberflächengüte und Maßgenauigkeit bei AM-Düsen
Ingenieure und Beschaffungsmanager, die an die engen Toleranzen gewöhnt sind, die mit der Präzisionsbearbeitung erreicht werden können, müssen die inhärenten Eigenschaften der additiven Fertigung von Metallen in Bezug auf Maßgenauigkeit und Oberflächengüte verstehen. AM bietet zwar eine unglaubliche Designfreiheit, produziert aber Teile mit einer anderen Präzision als subtraktive Verfahren. Die Festlegung realistischer Erwartungen und die Planung der erforderlichen Nachbearbeitungsschritte sind von entscheidender Bedeutung.
Abmessungstoleranzen:
- Typische PBF-Toleranzen: Metallpulverbettschmelzverfahren (wie SLM/DMLS und EBM) erreichen in der Regel Maßtoleranzen im Bereich von ±0,1 mm bis ±0,2 mm für kleinere Merkmale (z. B. bis zu 50-100 mm) oder ±0,1 % bis ±0,2 % für größere Abmessungen. Diese Werte können variieren je nach:
- Die spezifische AM-Maschine und ihre Kalibrierung.
- Das zu bedruckende Material (verschiedene Metalle weisen unterschiedliche Schrumpfungseigenschaften auf).
- Teilegeometrie und -größe (bei größeren, komplexen Teilen kann es zu größeren Abweichungen kommen).
- Aufbau einer Orientierungs- und Unterstützungsstrategie.
- Wärmemanagement während des Baus.
- Vergleich zur maschinellen Bearbeitung: Diese Toleranzen sind in der Regel enger als bei der Standard-CNC-Bearbeitung (bei der oft ±0,01 mm bis ±0,05 mm oder enger eingehalten werden können).
- Auswirkung: Bei Merkmalen, die eine sehr hohe Präzision erfordern (z. B. kritische Gegenflansche, Lagerschnittstellen, präzise Innendurchmesser, die den Durchfluss bestimmen), kann es sein, dass das fertige AM-Teil nicht den Spezifikationen entspricht. Diese Merkmale erfordern in der Regel eine Nachbearbeitung nach dem Druck. Es ist wichtig, diese kritischen Merkmale während der Designphase zu identifizieren und Bearbeitungszugaben (zusätzliches Material) in das AM-Design einzubauen.
Oberflächengüte (Rauhigkeit):
- Oberflächenrauhigkeit (Ra) im Ist-Zustand: Die Oberflächenbeschaffenheit von gedruckten AM-Metallteilen ist aufgrund des schichtweisen Prozesses und der teilweise geschmolzenen Pulverpartikel, die an der Oberfläche haften, von Natur aus rauer als bearbeitete Oberflächen. Typische Ra-Werte für PBF-Prozesse reichen von 5 µm bis 25 µm (Mikrometer). Zu den Faktoren, die Ra beeinflussen, gehören:
- Schichtdicke: Dünnere Schichten führen in der Regel zu glatteren Oberflächen, verlängern aber die Druckzeit.
- Pulver Partikelgröße: Feinere Pulver können zu glatteren Oberflächen führen, können aber auch Probleme bei der Handhabung und Fließfähigkeit mit sich bringen. Die Qualität und Sphärizität von Pulvern, wie denen von Met3dp, spielen hier eine Rolle.
- Orientierung aufbauen: Oberflächen, die relativ zur Baurichtung abgewinkelt sind, weisen oft bessere Oberflächen auf als rein horizontale, nach oben oder unten gerichtete Flächen. Vertikale Wände neigen zu einer mäßigen Rauheit.
- Laser-/Strahlparameter: Energiezufuhr und Scanning-Strategie beeinflussen die Dynamik des Schmelzbads und die Oberflächenbeschaffenheit.
- Material: Verschiedene Materialien können leicht unterschiedliche Oberflächeneigenschaften aufweisen.
- Hydrodynamische Auswirkungen: Bei Antriebsdüsen ist die Oberflächenrauhigkeit von entscheidender Bedeutung. Raue Innenflächen erhöhen die Reibung und Turbulenzen, was die hydrodynamische Effizienz verringert und möglicherweise die Geräuschentwicklung oder Kavitationsbildung erhöht. Raue Außenflächen erhöhen den Luftwiderstand.
- Verbesserung: Die Prozessoptimierung kann zwar eine Feinabstimmung der fertigen Oberfläche bewirken, doch um glatte Oberflächen zu erzielen, die mit polierten oder fein bearbeiteten Teilen vergleichbar sind (Ra < 1 µm), sind in der Regel Nachbearbeitungsschritte wie Perlstrahlen, Trommeln, Fließschleifen (AFM), Elektropolieren oder manuelles Polieren erforderlich.
Maßgenauigkeit und Qualitätskontrolle:
- Ursachen der Ungenauigkeit: Mögliche Ursachen sind Materialschrumpfung beim Abkühlen, Verformung durch thermische Eigenspannungen, leichte Ungenauigkeiten bei der Maschinenkalibrierung und geringfügige Abweichungen beim Pulverauftrag oder beim Schmelzvorgang.
- Milderung: Eine sorgfältige Prozesssimulation (Vorhersage der Verformung), optimierte Fertigungsparameter, robuste Stützstrukturen, kontrollierte Fertigungsumgebungen und Spannungsabbau nach der Fertigung tragen alle zur Maximierung der Maßgenauigkeit bei. Das Verstehen der spezifischen Druckverfahren und ihre Nuancen sind entscheidend.
- Qualitätssicherung: Seriöse AM-Dienstleister wenden strenge Qualitätskontrollmaßnahmen an. Dazu gehören häufig:
- Analyse des Pulvers: Sicherstellen, dass das eingehende Metallpulver den Spezifikationen entspricht.
- Prozessbegleitende Überwachung: Einige fortschrittliche Systeme überwachen die Eigenschaften des Schmelzbades oder die Schichtkonsistenz während der Herstellung.
- Inspektion nach der Fertigstellung: Visuelle Inspektion, Maßkontrolle mit kalibrierten Werkzeugen (Messschieber, Mikrometer), 3D-Scannen im Vergleich zum ursprünglichen CAD-Modell und Überprüfung der kritischen Maße mit Koordinatenmessgeräten (CMM).
- Zerstörungsfreie Prüfung (NDT): Bei kritischen Anwendungen können ZfP-Methoden wie die Farbeindringprüfung (PT) oder die Computertomographie (CT) eingesetzt werden, um Oberflächenrisse oder innere Porosität zu erkennen.
Die Kenntnis dieser erreichbaren Präzisionsniveaus ermöglicht es den Ingenieuren, effektiv zu konstruieren, bei Bedarf Bearbeitungsmaterial einzubeziehen und geeignete Anforderungen an die Oberflächenbeschaffenheit festzulegen, um sicherzustellen, dass die endgültige 3D-gedruckte Düse alle Funktions- und Leistungskriterien erfüllt.
Jenseits des Druckens: Wichtige Nachbearbeitung für Schiffsdüsen
Ein weit verbreiteter Irrglaube über den 3D-Druck von Metall ist, dass das Teil sofort nach dem Verlassen der Maschine einsatzbereit ist. In Wirklichkeit ist die Druckphase bei anspruchsvollen Anwendungen wie Schiffsantriebsdüsen nur ein Teil des gesamten Fertigungsablaufs. Eine Reihe von entscheidenden Nachbearbeitung fast immer sind Schritte erforderlich, um das Bauteil im Ist-Zustand in ein funktionsfähiges, zuverlässiges Bauteil mit den gewünschten Materialeigenschaften, der Maßgenauigkeit und der Oberflächenbeschaffenheit umzuwandeln.
Zu den wichtigsten Nachbearbeitungsschritten für 3D-gedruckte Schiffsdüsen aus Metall gehören:
- Stressabbau / Wärmebehandlung:
- Hier ist eine Aufschlüsselung des typischen Nachbearbeitungs-Workflows für 3D-gedruckte Aluminium-Drohnenhüllen: Die schnellen Erwärmungs- und Abkühlungszyklen bei PBF-Verfahren führen zu erheblichen inneren Spannungen im gedruckten Teil. Diese Eigenspannungen können zu Verformungen (insbesondere nach der Entnahme aus der Bauplatte), verringerter Ermüdungslebensdauer und möglicherweise zu Rissen führen. Eine Wärmebehandlung ist unerlässlich, um diese Spannungen abzubauen und das Gefüge zu homogenisieren.
- Prozess: Die Teile werden in der Regel in einem Ofen mit kontrollierter Atmosphäre auf eine bestimmte Temperatur erhitzt (unterhalb des Schmelzpunkts, aber hoch genug, um die Atomdiffusion zu ermöglichen), eine Zeit lang gehalten und dann langsam abgekühlt. Der genaue Zyklus (Temperatur, Zeit, Abkühlgeschwindigkeit) hängt stark vom Material (z. B. unterscheiden sich die Zyklen für IN625 von denen für CuNi-Legierungen oder nichtrostende Stähle) und den gewünschten endgültigen Materialeigenschaften (z. B. Glühen für maximale Duktilität vs. Altern für Spitzenfestigkeit) ab.
- Optimierung der Eigenschaften: Die Wärmebehandlung wird auch eingesetzt, um die für die Anwendung spezifizierte Mikrostruktur und mechanischen Eigenschaften (Festigkeit, Härte, Duktilität, Korrosionsbeständigkeit) zu erreichen. Für Legierungen wie IN625 sind häufig spezielle Lösungsglüh- und/oder Alterungsbehandlungen erforderlich, um die Spezifikationen des Datenblatts zu erfüllen.
- Entnahme von der Bauplatte:
- Prozess: Die Teile werden in der Regel auf eine dicke Metallplatte gedruckt. Sie müssen getrennt werden, in der Regel durch Drahterodieren (Electrical Discharge Machining), Sägen oder Zerspanen. Dies muss sorgfältig geschehen, um das Teil nicht zu beschädigen. Häufig wird ein Spannungsabbau durchgeführt vor von der Platte entfernt werden, um die Verformung zu minimieren.
- Entfernung der Stützstruktur:
- Die Notwendigkeit: Stützen werden während des Drucks für Überhänge und komplexe Merkmale benötigt, müssen aber danach wieder entfernt werden.
- Methoden: Die Entfernung kann durch manuelles Abbrechen (bei leicht zugänglichen, leicht verbundenen Stützen), Schneiden/Schleifen oder maschinelle Bearbeitung erfolgen. Der Zugang zu und das Entfernen von internen Halterungen in komplexen Düsenkanälen kann eine besondere Herausforderung darstellen und erfordert eine sorgfältige Planung während der DfAM-Phase. An den Verbindungspunkten der Stützen verbleibende Markierungen oder Fehlstellen müssen oft geglättet werden.
- Bearbeitungen:
- Zweck: Zur Erzielung enger Toleranzen bei kritischen Abmessungen, zur Schaffung spezifischer Dichtungsflächen oder zur Verbesserung der Oberflächengüte in Funktionsbereichen.
- Gemeinsame Bereiche: Flanschflächen, die mit anderen Bauteilen zusammenpassen, Innenbohrungen, die präzise Durchmesser für Lager oder Dichtungen erfordern, Gewindebohrungen und kritische hydrodynamische Oberflächen erfordern oft eine CNC-Bearbeitung nach dem Druck. Konstrukteure müssen dies berücksichtigen, indem sie im ursprünglichen AM-CAD-Modell zusätzliches Material (Bearbeitungsmaterial) zu diesen Merkmalen hinzufügen.
- Oberflächenveredelung:
- Das Ziel: Verringerung der Oberflächenrauhigkeit im eingebauten Zustand zur Verbesserung der hydrodynamischen Leistung, der Ästhetik oder der Reinigungsfähigkeit.
- Techniken:
- Perlstrahlen/Shot Peening: Treibt Medien (Glasperlen, Keramikkugeln) an die Oberfläche. Glättet mäßig, erzeugt eine gleichmäßige matte Oberfläche und kann vorteilhafte Druckspannungen hervorrufen (Peening).
- Taumeln/Gleitschleifen: Legt die Teile in eine Wanne mit Schleifmittel, das durch Trommeln oder Vibrationen allmählich Oberflächen und Kanten glättet. Gut geeignet für die Massenbearbeitung.
- Abrasive Fließbearbeitung (AFM): Drückt eine mit Schleifmittel beladene Spachtelmasse durch die inneren Kanäle und glättet so die komplexen inneren Durchgänge, die in Düsen üblich sind.
- Elektropolieren: Ein elektrochemisches Verfahren, bei dem eine dünne Materialschicht abgetragen wird, was zu einer sehr glatten, glänzenden Oberfläche führt. Besonders effektiv bei bestimmten Legierungen wie rostfreien Stählen.
- Manuelles Schleifen/Polieren: Es ist arbeitsintensiv, ermöglicht aber ein gezieltes Glätten und ein sehr feines Finishing an bestimmten Stellen.
- Reinigung und Inspektion:
- Reinigung: Gründliches Entfernen von Pulverresten (insbesondere aus den inneren Kanälen), Bearbeitungsflüssigkeiten oder Polierpasten.
- Endkontrolle: Umfassende Prüfung mit Sichtkontrolle, abschließender Überprüfung der Abmessungen (CMM, Scannen), Bestätigung der Materialeigenschaften (falls Testcoupons mitgedruckt wurden) und ggf. ZfP (z. B. Dichtheitsprüfung, Farbeindringprüfung), um sicherzustellen, dass die Düse vor dem Einsatz alle Qualitätsstandards erfüllt.
Der Umfang und die Art der Nachbearbeitung wirken sich erheblich auf die Endkosten und die Vorlaufzeit der 3D-gedruckten Düse aus. Die sorgfältige Planung dieser Schritte und ihre Integration in die Gesamtstrategie für die Herstellung ist für die erfolgreiche Umsetzung von AM für Schiffskomponenten von entscheidender Bedeutung.
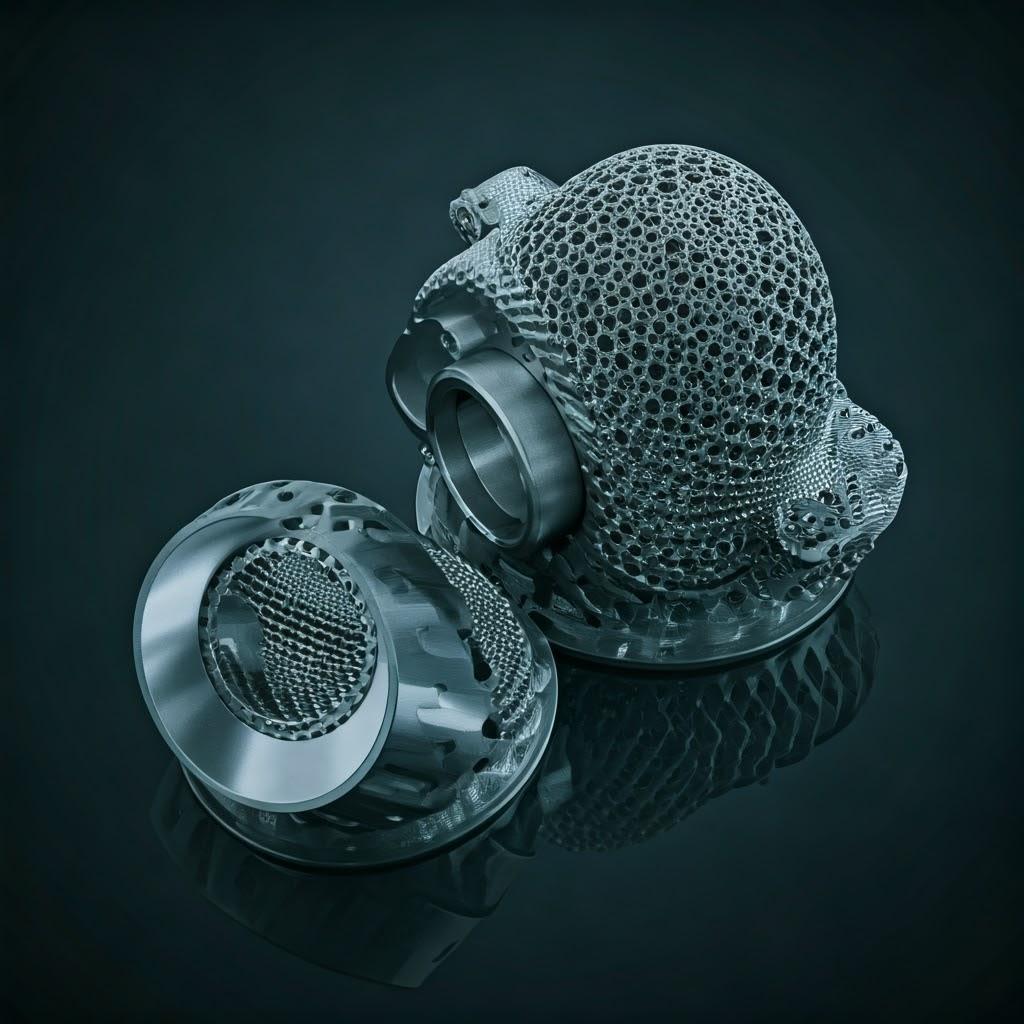
Herausforderungen meistern: Häufige Probleme beim 3D-Druck von Schiffsdüsen und Lösungen
Die additive Fertigung von Metallen bietet zwar enorme Vorteile, ist aber auch ein komplexer Prozess mit potenziellen Herausforderungen, die verstanden und bewältigt werden müssen, insbesondere bei der Herstellung kritischer Komponenten wie Schiffsantriebsdüsen. Das Bewusstsein für diese potenziellen Probleme ermöglicht eine proaktive Entschärfung durch sorgfältiges Design, Prozesskontrolle und Zusammenarbeit mit erfahrenen AM-Anbietern.
Hier sind einige häufige Herausforderungen und ihre Lösungen:
Gemeinsame Herausforderungen bei der Metall-AM für Schiffsdüsen & Abhilfestrategien
Herausforderung | Beschreibung / Mögliche Ursache | Minderungsstrategien |
---|---|---|
Verziehen/Verzerrung | Durch ungleichmäßige Erwärmung/Abkühlung und Aufbau von Eigenspannungen verbogene oder von der vorgesehenen Geometrie abweichende Teile. | DfAM: Optimieren Sie die Ausrichtung der Teile, entwerfen Sie sie so, dass sie thermisch stabil sind (vermeiden Sie abrupte große Massenänderungen). <br> Unterstützt: Verwenden Sie robuste, strategisch platzierte Stützstrukturen, um das Teil zu verankern. <br> Prozess: Optimieren Sie die Scan-Strategie, verwenden Sie möglicherweise die Heizung der Bauplatte. <br> Nachbearbeiten: Führen Sie eine Spannungsarmglühung durch, häufig vor der Entnahme aus der Bauplatte. |
Porosität (Fehlen von Fusion/Gas) | Kleine innere Hohlräume im gedruckten Material, die Dichte, Festigkeit, Ermüdungslebensdauer und Korrosionsbeständigkeit verringern. Verursacht durch falsche Parameter, Gaseinschlüsse im Pulver/Schmelzbad oder schlechte Pulverqualität. | Qualität des Pulvers: Verwenden Sie hochwertiges, trockenes, kugelförmiges Pulver mit kontrolliertem PSD (z. B. von Met3dp’s advanced atomization). <br> Prozess-Optimierung: Feinabstimmung von Laser-/Strahlleistung, Scangeschwindigkeit und Schichtdicke für vollständiges Schmelzen. Optimieren Sie den Schutzgasfluss. <br> Nachbearbeiten: Heißisostatisches Pressen (HIP) kann innere Poren schließen (zusätzliche Kosten/Zeit). |
Schwierigkeit beim Entfernen der Stütze | Stützen sind schwer zugänglich oder brechen sauber ab und können das Teil beschädigen oder erhebliche Oberflächenfehler hinterlassen. Interne Stützen sind besonders schwierig. | DfAM: Minimierung des Bedarfs an Stützen durch selbsttragende Winkel. Entwurf für zugang (z. B. temporäre Zugangslöcher). Verwenden Sie optimierte Trägerarten (z. B. dünnere Verbindungspunkte). <br> Prozess: Wählen Sie in der Software die geeigneten Parameter für die Erzeugung der Unterstützung; Nachbearbeiten: Einsatz von Spezialwerkzeugen, eventuell Drahterodieren oder maschinelle Bearbeitung zur Entfernung. |
Eigenspannung / Rissbildung | Hohe innere Spannungen können zu Mikrorissen oder sogar zu großen Brüchen während des Drucks oder der Nachbearbeitung führen, insbesondere bei rissempfindlichen Legierungen oder komplexen Geometrien. | DfAM: Scharfe Innenecken sind zu vermeiden, das Design ist für allmähliche Dickenänderungen ausgelegt. <br> Prozess: Simulation des thermischen Verlaufs, Optimierung der Scan-Strategie (z. B. sektorbasiertes Scannen) zur Beherrschung des Wärmestaus. <br> Auswahl der Materialien: Berücksichtigen Sie die Materialanfälligkeit. <br> Nachbearbeiten: Führen Sie sofort nach dem Druck sorgfältig geplante Entlastungszyklen durch. |
Probleme mit der Oberflächenrauhigkeit | Die fertige Oberfläche ist zu rau für die hydrodynamischen Anforderungen, was zu Ineffizienz oder Kavitation führt. | DfAM: Richten Sie kritische Oberflächen optimal für das Finish aus. <br> Prozess: Optimieren Sie die Parameter (Schichtdicke, Energieaufwand), verwenden Sie feineres Pulver, wenn möglich. <br> Nachbearbeiten: Anwendung geeigneter Techniken zur Oberflächenbearbeitung (Strahlen, Polieren, AFM usw.), wie es die Anwendung erfordert. |
Maßliche Ungenauigkeit | Die endgültigen Abmessungen der Teile liegen außerhalb der vorgegebenen Toleranzen. | DfAM: Konstruieren Sie kritische Merkmale mit Bearbeitungszugabe. <br> Prozess: Stellen Sie die Maschinenkalibrierung sicher, verwenden Sie die Prozesssimulation zur Vorhersage von Schrumpfung/Verzug und kompensieren Sie diese im CAD. <br> Nachbearbeiten: Spannungsentlastung richtig umsetzen. Verwenden Sie CNC-Bearbeitung für kritische Toleranzen. <br> QA: Durchführung einer strengen Maßkontrolle (Scannen, CMM). |
Inkonsistente Materialeigenschaften | Die mechanischen oder korrosiven Eigenschaften variieren innerhalb des Teils oder zwischen den einzelnen Fertigungsstufen. | Pulverkontrolle: Sicherstellung einer gleichbleibenden Pulverqualität, Handhabung und Wiederverwendungsprotokolle; Prozesskontrolle: Strenge Kontrolle über alle Druckparameter (Leistung, Geschwindigkeit, Gasfluss, Temperatur). <br> Nachbearbeiten: Gewährleistet gleichbleibende, optimierte Wärmebehandlungszyklen. <br> Prüfung: Drucken und testen Sie Materialcoupons zusammen mit Teilen. |
In Blätter exportieren
Fehlersuche beim 3D-Druck von Metall erfordert ein tiefes Verständnis des Zusammenspiels von Konstruktion, Werkstoffen, Prozessparametern und Nachbearbeitung. Die Zusammenarbeit mit einem sachkundigen Dienstleister, der über robuste Prozesskontrollen, Qualitätsmanagementsysteme und Fachwissen über Werkstoffe wie CuNi30Mn1Fe und IN625 verfügt, ist der Schlüssel zur Bewältigung dieser Herausforderungen und zur zuverlässigen Herstellung hochwertiger, einsatzkritischer Schiffsantriebsdüsen.
Die Auswahl Ihres Partners: Wie Sie den richtigen Metall-AM-Dienstleister für Schiffskomponenten auswählen
Die Wahl des richtigen Fertigungspartners ist immer von entscheidender Bedeutung, aber bei fortschrittlichen Technologien wie der additiven Fertigung von Metallen für anspruchsvolle Schiffsanwendungen gewinnt sie noch mehr an Bedeutung. Die Qualität, Zuverlässigkeit und Leistung Ihrer 3D-gedruckten Antriebsdüse hängt in hohem Maße vom Fachwissen, den Prozessen und den Fähigkeiten des von Ihnen gewählten Partners ab Metall-AM-Servicebüro. Für Ingenieure und Beschaffungsmanager, die sich in dieser Landschaft zurechtfinden müssen, bedeutet die Bewertung potenzieller Lieferanten, dass sie nicht nur auf den Preis schauen, sondern sich auf eine Reihe von technischen und betrieblichen Faktoren konzentrieren müssen.
Hier sind die wichtigsten Kriterien, die bei der Auswahl eines Lieferant für 3D-Metalldruck für Schiffskomponenten:
- Technisches Fachwissen & Beratung:
- Werkstoffkunde: Verfügen sie über umfassende Kenntnisse der vorgeschlagenen Werkstoffe (z. B. CuNi30Mn1Fe, IN625)? Können sie Sie bei der Materialauswahl auf der Grundlage Ihrer spezifischen Betriebsumgebung und Leistungsanforderungen beraten? Verstehen sie die Feinheiten der Verarbeitung dieser Materialien durch AM?
- DfAM-Unterstützung: Kann er Sie bei der Optimierung Ihres Düsendesigns für die additive Fertigung fachkundig beraten? Ein guter Partner arbeitet mit Ihnen zusammen, um sicherzustellen, dass das Design druckbar und kosteneffizient ist und die funktionalen Anforderungen erfüllt.
- Prozesswissen: Verstehen sie die Feinheiten des jeweiligen AM-Prozesses (z. B. SLM, EBM), einschließlich der Parameteroptimierung für Dichte, Genauigkeit und Oberflächengüte?
- Maschinenkapazität & Technologie:
- Angemessene Technologie: Betreiben sie die richtige Art von Metall-AM-System (typischerweise Laser- oder Elektronenstrahl-Pulverbettfusion für Düsen) für Ihr Material und Ihre Anwendung?
- Bauvolumen: Ist der Bauraum der Maschine groß genug, um Ihr Düsendesign unterzubringen?
- Genauigkeit und Auflösung: Können ihre Maschinen die für Ihr Bauteil erforderliche Detailgenauigkeit und Toleranz erreichen (unter Berücksichtigung möglicher Nachbearbeitungen)?
- Maschinenwartung & Kalibrierung: Verfügen sie über strenge Protokolle für die Maschinenwartung, um gleichbleibende Ergebnisse zu gewährleisten?
- Materialqualität & Handhabung:
- Pulverbeschaffung & Zertifizierung: Woher beziehen sie ihre Metallpulver? Bieten sie Materialzertifikate an, die die chemische Zusammensetzung und die Eigenschaften des Pulvers bestätigen? Unternehmen wie Met3dp, die ihre eigenen hochwertigen Pulver mit fortschrittlichen Methoden wie Gasverdüsung und PREP herstellen, bieten eine bessere Kontrolle und Rückverfolgbarkeit. Erkunden Sie ihr Angebot an hochleistungsmetallpulver und -systeme.
- Handhabung des Pulvers: Gibt es strenge Verfahren für die Lagerung, Handhabung, Siebung und Rückverfolgbarkeit des Pulvers, um Verunreinigungen zu vermeiden und die Konsistenz von Charge zu Charge zu gewährleisten? Die Aufnahme von Sauerstoff kann zum Beispiel die Eigenschaften von Meereslegierungen beeinträchtigen.
- Qualitätsmanagementsystem (QMS) & Zertifizierungen:
- ISO 9001: Dies ist eine Basiszertifizierung, die anzeigt, dass ein dokumentiertes QMS vorhanden ist.
- Branchenspezifische Zertifizierungen: Je nach Anwendung (z. B. Marine, klassifiziert) können Zertifizierungen wie AS9100 (Luft- und Raumfahrt, oft für anspruchsvolle Industrien übernommen) oder spezielle Zulassungen der Schifffahrtsklassifikationsgesellschaften (z. B. DNV, ABS, Lloyd’s Register oder Zulassungen für bestimmte Materialien/Prozesse) erforderlich oder wünschenswert sein. Erkundigen Sie sich nach den aktuellen Zertifizierungen und dem Fahrplan des Unternehmens.
- Erfahrung & Fallstudien:
- Nachgewiesene Erfolgsbilanz: Haben sie erfolgreich ähnliche Komponenten in Bezug auf Komplexität, Größe oder Material hergestellt?
- Erfahrung in der Industrie: Verfügen sie über Erfahrung in der Schifffahrtsindustrie oder in anderen Sektoren mit ähnlich hohen Anforderungen (z. B. Luft- und Raumfahrt, Energie)? Fordern Sie Fallstudien oder Referenzen an, die für Ihre Anwendung relevant sind.
- Nachbearbeitungsmöglichkeiten:
- Integrierte Dienstleistungen: Können sie die erforderlichen Nachbearbeitungsschritte (Wärmebehandlung, maschinelle Bearbeitung, Oberflächenveredelung, zerstörungsfreie Prüfung) entweder selbst oder durch qualifizierte Partner durchführen? Ein integrierter Arbeitsablauf vereinfacht die Projektabwicklung.
- Kommunikation & Unterstützung:
- Reaktionsfähigkeit: Reagieren sie auf Anfragen und Bitten um technische Informationen?
- Transparenz: Sind sie offen über ihre Prozesse, Fähigkeiten und potenziellen Herausforderungen?
- Technische Konsultation: Ist das Team während des gesamten Projektlebenszyklus für technische Diskussionen erreichbar?
- Kosten und Vorlaufzeit:
- Klare Zitate: Werden detaillierte Kostenvoranschläge vorgelegt, in denen alle Kosten (Druck, Material, Träger, Nachbearbeitung, Qualitätssicherung) aufgeführt sind?
- Realistische Zeitpläne: Bieten sie erreichbare Vorlaufzeiten auf der Grundlage der aktuellen Kapazitäten und der Komplexität Ihres Projekts?
Die Wahl eines Partners wie Met3dp, der jahrzehntelange kollektive Erfahrung in der Metall-AM, branchenführende Ausrüstung, fortschrittliche Pulverherstellungsfähigkeiten und umfassende Anwendungsentwicklungsdienste kombiniert, bietet eine starke Grundlage für die erfolgreiche Implementierung metall-AM für kritische Schiffskomponenten. Wenn Sie potenzielle Lieferanten anhand dieser Kriterien gründlich prüfen, können Sie sicherstellen, dass Sie mit einem Anbieter zusammenarbeiten, der in der Lage ist, hochwertige und zuverlässige Antriebsdüsen zu liefern, die Ihren Spezifikationen entsprechen.
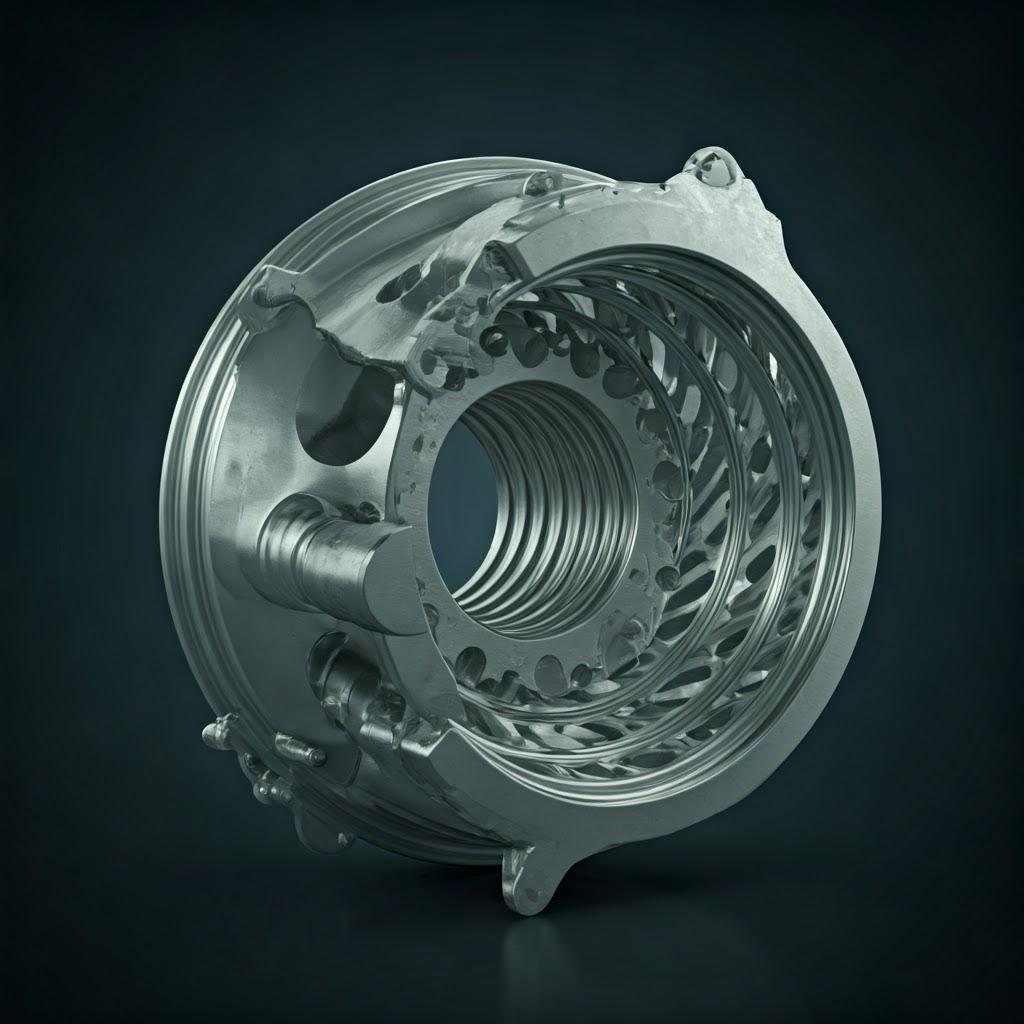
Die Investition verstehen: Kostenfaktoren und Vorlaufzeiten für AM-Antriebsdüsen
Eine der wichtigsten Fragen von Beschaffungsmanagern und Ingenieuren, die Metall-AM in Betracht ziehen, ist die nach den erforderlichen Kosten und dem Zeitaufwand. AM bietet zwar erhebliche Vorteile, aber das Verständnis der Treiber hinter Kostenvoranschlag für den 3D-Druck von Metall und typische vorlaufzeiten der additiven Fertigung ist entscheidend für die Projektplanung und Budgetierung. Die Kosten pro Stück sind in der Regel höher als bei herkömmlichen Methoden für einfache, großvolumige Teile, können aber bei komplexen, klein- bis mittelvolumigen oder kundenspezifischen Komponenten wie Antriebsdüsen sehr wettbewerbsfähig sein.
Die wichtigsten Kostentreiber für 3D-gedruckte Schiffsdüsen:
- Materialart und -verbrauch:
- Pulverkosten: Die Rohstoffkosten sind sehr unterschiedlich. Nickel-Superlegierungen wie IN625 sind erheblich teurer als CuNi-Legierungen oder nichtrostende Stähle.
- Teil Volumen/Masse: Die Menge an Material, die direkt für das Teil und seine Stützstrukturen verbraucht wird, ist ein wichtiger Kostenfaktor. Größere, dichtere Teile kosten mehr. DfAM-Techniken wie die Topologieoptimierung können helfen, den Materialverbrauch zu senken.
- Druckzeit:
- Bauhöhe: Die Druckzeit in PBF-Systemen wird in erster Linie durch die Anzahl der Schichten bestimmt, d. h. größere Teile brauchen länger, unabhängig davon, wie viele Teile sich auf der Bauplatte befinden (bis zum Limit der Platte).
- Teilmenge & Komplexität: Die Höhe ist zwar ausschlaggebend, aber auch das Gesamtvolumen und die Komplexität der Scanpfade innerhalb jeder Ebene tragen zur Zeit bei.
- Maschinentarif: Die Dienstleister kalkulieren einen Stundensatz für den Maschinenbetrieb ein, der Energie, Abschreibung, Wartung und Inertgasverbrauch umfasst.
- Teil Komplexität & Design:
- Unterstützende Strukturen: Komplexe Geometrien mit vielen Auskragungen erfordern umfangreiche Stützstrukturen. Dadurch wird mehr Material verbraucht, die Druckzeit verlängert und der Nachbearbeitungsaufwand für die Entfernung deutlich erhöht. Die Konzentration von DfAM auf selbsttragende Designs ist der Schlüssel zur Kostensenkung.
- Gute Eigenschaften: Sehr komplizierte Details erfordern unter Umständen langsamere Druckparameter oder spezielle Maschinenfähigkeiten, was den Zeit- und Kostenaufwand erhöhen kann.
- Nachbearbeitungsanforderungen:
- Wärmebehandlung: Die Ofenzeit und die Komplexität des erforderlichen Zyklus (insbesondere bei Legierungen, die eine spezielle Alterungsbehandlung erfordern) verursachen zusätzliche Kosten.
- Bearbeitungen: Der Umfang der erforderlichen CNC-Bearbeitung (Anzahl der Merkmale, enge Toleranzen) ist aufgrund der Arbeits- und Maschinenzeit ein wesentlicher Kostenfaktor.
- Oberflächenveredelung: Techniken wie manuelles Polieren oder AFM für interne Kanäle sind arbeitsintensiv und verursachen im Vergleich zu einfacheren Methoden wie Perlstrahlen erhebliche Kosten.
- Qualitätssicherung und Inspektion:
- Grundlegende QA: Standardmäßige Maßkontrollen und Sichtprüfungen sind in der Regel inbegriffen.
- Fortgeschrittene ZfP: Anforderungen für Farbeindringprüfungen, CT-Scans oder spezifische Materialeigenschaftstests verursachen zusätzliche Kosten aufgrund spezieller Ausrüstung und Fachkenntnisse.
- Zertifizierung: Dokumentationspakete für die Materialrückverfolgbarkeit und die Prozesszertifizierung erfordern einen hohen Verwaltungsaufwand.
- Auftragsvolumen:
- Einrichtungskosten: Mit der Einrichtung eines jeden Builds (Dateivorbereitung, Maschineneinrichtung) sind feste Kosten verbunden. Diese Kosten werden über die Anzahl der Teile in einem Build amortisiert.
- Reduzierung der Stückkosten: Der Druck mehrerer Kopien einer Düse in einem einzigen Bauvorgang senkt im Allgemeinen die Kosten pro Einheit im Vergleich zum Druck einer einzigen Düse. Diskutieren Sie kosten für 3D-Druck im Großhandel oder Batch-Preise bei Ihrem Anbieter für mögliche Mengenrabatte.
Typische Vorlaufzeiten:
Die Vorlaufzeit bezieht sich auf die Gesamtzeit von der Auftragserteilung (und der endgültigen Übermittlung der CAD-Datei) bis zum Erhalt des fertigen Teils. Sie wird von mehreren Faktoren beeinflusst:
- Dateivorbereitung & Warteschlangenzeit: Die erste technische Überprüfung, die Vorbereitung des Aufbaus und der aktuelle Maschinenrückstand des Dienstleisters (kann von Tagen bis Wochen reichen).
- Druckzeit: Wie bereits erwähnt, hängt dies in erster Linie von der Höhe der Teile ab (kann von Stunden für kleine Teile bis zu mehreren Tagen für große/hohe Komponenten reichen).
- Nachbearbeitungszeit: Je nach den beteiligten Schritten kann dies oft der längste Teil der Vorlaufzeit sein. Wärmebehandlungszyklen nehmen Zeit in Anspruch, komplexe Bearbeitungsvorgänge dauern Tage, und komplizierte Oberflächenbehandlungen sind arbeitsintensiv (sie können zwischen Tagen und mehreren Wochen dauern).
- QA & Versand: Endkontrolle und Durchlaufzeit.
Insgesamt: Für eine mäßig komplexe Metallschiffsdüse liegen die typischen Vorlaufzeiten bei 2 bis 6 Wochendies kann jedoch stark variieren. Sehr große oder komplexe Teile, die eine umfangreiche Nachbearbeitung erfordern, können länger dauern. Fordern Sie immer einen konkreten Kostenvoranschlag für die Vorlaufzeit an, der auf Ihrem endgültigen Entwurf und Ihren Anforderungen basiert.
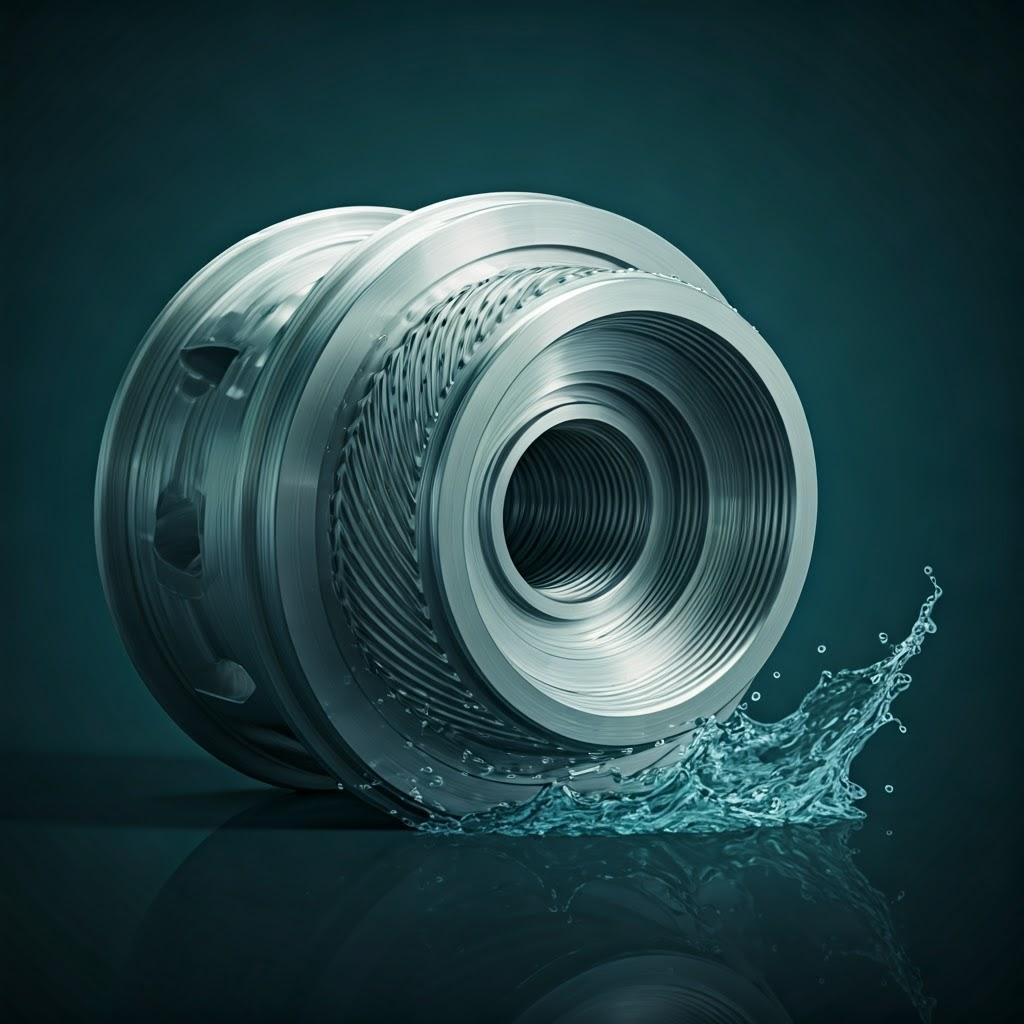
Häufig gestellte Fragen (FAQ) zu 3D-gedruckten Schiffsdüsen
Da sich die additive Fertigung von Metallen in der Schifffahrtsindustrie immer mehr durchsetzt, haben Ingenieure, Konstrukteure und Beschaffungsspezialisten häufig wiederkehrende Fragen. Hier finden Sie Antworten auf einige häufig gestellte Fragen:
- Wie ist die Haltbarkeit/Lebensdauer einer 3D-gedruckten Düse im Vergleich zu einer traditionell hergestellten Düse (z. B. aus Guss)?
- Bei der Herstellung mit optimierten Parametern, hochwertigen Pulvern und geeigneter Nachbearbeitung (insbesondere Wärmebehandlung) können AM-Metallteile mechanische Eigenschaften (Festigkeit, Ermüdungsbeständigkeit, Zähigkeit) erreichen, die mit denen von gleichwertigen Gussbauteilen vergleichbar sind oder diese sogar übertreffen. Das feinkörnige Gefüge, das bei PBF-Prozessen häufig erreicht wird, kann dabei von Vorteil sein. Zu den Schlüsselfaktoren, die eine lange Lebensdauer gewährleisten, gehören:
- Erreichen der vollen Dichte: Die Minimierung der Porosität durch Prozesskontrolle oder HIP ist entscheidend für die Lebensdauer und Korrosionsbeständigkeit.
- Korrekte Wärmebehandlung: Wesentlich für den Spannungsabbau und die Entwicklung der gewünschten endgültigen Materialeigenschaften.
- Geeignete Materialauswahl: Verwendung von Werkstoffen wie IN625 oder CuNi30Mn1Fe, die für ihre Langlebigkeit auf See bekannt sind.
- Qualitätskontrolle: Strenge zerstörungsfreie Prüfungen und Inspektionen stellen sicher, dass das Teil vor dem Einsatz die Integritätsstandards erfüllt.
- Zusammenfassend lässt sich sagen, dass von einer gut konzipierten und ordnungsgemäß hergestellten AM-Düse eine ausgezeichnete Haltbarkeit und Lebensdauer zu erwarten ist, die möglicherweise die Leistung herkömmlicher Teile übertrifft, wenn AM bessere Designs oder Materialkombinationen ermöglicht.
- Bei der Herstellung mit optimierten Parametern, hochwertigen Pulvern und geeigneter Nachbearbeitung (insbesondere Wärmebehandlung) können AM-Metallteile mechanische Eigenschaften (Festigkeit, Ermüdungsbeständigkeit, Zähigkeit) erreichen, die mit denen von gleichwertigen Gussbauteilen vergleichbar sind oder diese sogar übertreffen. Das feinkörnige Gefüge, das bei PBF-Prozessen häufig erreicht wird, kann dabei von Vorteil sein. Zu den Schlüsselfaktoren, die eine lange Lebensdauer gewährleisten, gehören:
- Welche Zertifizierungen sind für 3D-gedruckte Schiffskomponenten erforderlich oder verfügbar?
- Basislinie: Die ISO 9001-Zertifizierung des Produktionspartners belegt ein solides Qualitätsmanagementsystem.
- Materialzertifizierungen: Verlangen Sie immer Materialzertifikate, die bestätigen, dass die Pulverchemie den einschlägigen Normen entspricht (z. B. ASTM, UNS-Spezifikationen für IN625 oder CuNi-Legierungen).
- Marine-Klassifikationen: Die großen Schifffahrtsklassifikationsgesellschaften (wie DNV, ABS, Lloyd’s Register, Bureau Veritas) arbeiten aktiv an der Entwicklung von Normen und Richtlinien für die additive Fertigung. Während weit verbreitete teilespezifische Zertifizierungen noch in der Entwicklung sind, haben diese Gesellschaften Rahmenwerke und Leitfäden veröffentlicht. Einige Dienstleister haben möglicherweise spezielle Zulassungen für bestimmte Materialien, Maschinen oder Verfahren erhalten. Bei kritischen Bauteilen kann eine frühzeitige Kontaktaufnahme mit Klassifikationsgesellschaften notwendig sein, um die Anforderungen für die Qualifizierung oder Abnahme zu verstehen.
- Anwendungsspezifisch: Für Marine- oder Verteidigungsanwendungen können zusätzliche spezifische militärische Normen (MIL-STD) oder Qualifikationsanforderungen gelten.
- Ist der 3D-Druck für die Serienproduktion von Düsen kosteneffizient oder nur für Prototypen?
- Das Kosten-Nutzen-Verhältnis hängt in hohem Maße von mehreren Faktoren ab, so dass es einen Übergangspunkt gibt, an dem AM wirtschaftlicher wird als herkömmliche Methoden:
- Komplexität: Je komplexer das Düsendesign ist (z. B. komplizierte interne Kanäle, Topologieoptimierung), desto kosteneffektiver wird AM, da die herkömmlichen Herstellungskosten mit der Komplexität rapide ansteigen.
- Lautstärke: AM ist äußerst kosteneffizient für Prototypen und Kleinserien (z. B. 1-100 Stück), da hohe Werkzeugkosten (Gussformen, Schmiedegesenke) entfallen. Bei sehr hohen Stückzahlen (Tausende) sind herkömmliche Methoden oft billiger wenn die Konstruktion ist einfach genug für die Herstellung von Werkzeugen.
- Werkzeugkosten: Wenn die herkömmliche Fertigung teure und komplexe Werkzeuge erfordert, verschiebt sich der Break-even-Punkt, wodurch AM bei höheren Stückzahlen wettbewerbsfähig wird.
- Wert der Vorlaufzeit: Wenn eine schnelle Markteinführung oder eine rasche Verfügbarkeit von Ersatzteilen von entscheidender Bedeutung ist, können die kürzeren Vorlaufzeiten von AM (insbesondere die Vermeidung von Verzögerungen bei der Werkzeugherstellung) einen erheblichen Wert darstellen, der die potenziell höheren Stückkosten rechtfertigt.
- Leistungssteigerungen: Wenn AM ein Design ermöglicht, das die Treibstoffeffizienz erheblich verbessert oder die Wartung reduziert (z. B. durch bewuchshemmende Materialien), könnten die Gesamtbetriebskosten über die Lebensdauer des Schiffes zugunsten der AM-Komponente ausfallen, selbst wenn die Anschaffungskosten höher sind.
- Daher eignet sich Metall-AM zunehmend nicht nur für Prototypen, sondern auch für serienproduktion von speziellen, komplexen oder kundenspezifischen Schiffsdüseninsbesondere dort, wo Leistung und Vorlaufzeit eine wichtige Rolle spielen.
- Das Kosten-Nutzen-Verhältnis hängt in hohem Maße von mehreren Faktoren ab, so dass es einen Übergangspunkt gibt, an dem AM wirtschaftlicher wird als herkömmliche Methoden:
Schlussfolgerung: Die Zukunft des Schiffsantriebs mit additiver Fertigung gestalten
Die maritime Welt befindet sich in einer Phase bedeutender technologischer Fortschritte, die durch den Bedarf an höherer Effizienz, verbesserter Leistung, geringerer Umweltbelastung und flexibleren Fertigungslösungen angetrieben werden. Die additive Fertigung von Metallen steht an der Spitze dieses Wandels und bietet nie dagewesene Möglichkeiten für kritische Komponenten wie Schiffsantriebsdüsen.
Wie wir erforscht haben, ermöglicht die Nutzung von Metall-AM Ingenieuren und Herstellern,:
- Designfreiheit freischalten: Erstellung hydrodynamisch optimierter Düsen mit komplexen Innengeometrien, die bisher unerreichbar waren.
- Die Leistung verbessern: Verbesserung des Schubs, des Wirkungsgrads, der Kavitationsresistenz und potenzielle Verringerung der akustischen Signaturen durch maßgeschneiderte Konstruktionen.
- Verwendung fortschrittlicher Materialien: Verwendung von Hochleistungslegierungen wie korrosionsbeständige, bewuchshemmende CuNi30Mn1Fe oder hochfeste, umweltbeständige IN625 genau dort, wo sie gebraucht werden.
- Innovation beschleunigen: Schnelle Prototypentwicklung und Iteration neuer Designs, um bessere Produkte schneller auf den Markt zu bringen.
- Aktivieren Sie die Anpassung und Konsolidierung: Stellen Sie maßgeschneiderte Düsen effizient her und reduzieren Sie die Anzahl der Teile, was die Montage vereinfacht und die Zuverlässigkeit erhöht.
Die erfolgreiche Integration dieser Technologie erfordert die Bewältigung von Herausforderungen im Zusammenhang mit der Designoptimierung (DfAM), der Prozesssteuerung, der Materialkunde und der Nachbearbeitung. Die Zusammenarbeit mit einem sachkundigen und fähigen anbieter von Metall-AM-Lösungen ist von entscheidender Bedeutung.
Met3dp ist einzigartig positioniert, um die Einführung der additiven Fertigung in der Schifffahrtsindustrie zu fördern. Mit modernster Technik SEBM-Drucker branchenführender Genauigkeit und Zuverlässigkeit, fortschrittlicher Metallpulverherstellung durch den Einsatz von Gaszerstäubungs- und PREP-Technologien für höchste Pulverqualität und jahrzehntelange Erfahrung bietet Met3dp umfassende Lösungen. Von der Lieferung zertifizierter Hochleistungspulver wie speziellem CuNi, IN625, Ti-Legierungen und rostfreiem Stahl bis hin zur Bereitstellung von Anwendungsentwicklungsdiensten und hochmodernen Druckanlagen unterstützt Met3dp Unternehmen bei der Beschleunigung ihrer digitalen Fertigungstransformation.
Der Weg zu optimierten Schiffsantrieben ist zunehmend mit den Möglichkeiten der additiven Fertigung verknüpft. Durch den Einsatz von AM können Schiffsbauer, Schiffsingenieure und Ausrüstungslieferanten die nächste Generation von Antriebssystemen entwickeln, die effizienter und zuverlässiger sind und auf die anspruchsvollen Bedingungen der Meeresumwelt zugeschnitten sind.
Sind Sie bereit zu erfahren, wie die additive Fertigung von Metallteilen Ihre Schiffsantriebskomponenten revolutionieren kann? Besuchen Sie Met3dp und erfahren Sie mehr über unsere modernen Metallpulver, Drucksysteme und umfassenden AM-Lösungen.
Teilen auf
MET3DP Technology Co., LTD ist ein führender Anbieter von additiven Fertigungslösungen mit Hauptsitz in Qingdao, China. Unser Unternehmen ist spezialisiert auf 3D-Druckgeräte und Hochleistungsmetallpulver für industrielle Anwendungen.
Fragen Sie an, um den besten Preis und eine maßgeschneiderte Lösung für Ihr Unternehmen zu erhalten!
Verwandte Artikel
Über Met3DP
Aktuelles Update
Unser Produkt
KONTAKT US
Haben Sie Fragen? Senden Sie uns jetzt eine Nachricht! Wir werden Ihre Anfrage mit einem ganzen Team nach Erhalt Ihrer Nachricht bearbeiten.
Holen Sie sich Metal3DP's
Produkt-Broschüre
Erhalten Sie die neuesten Produkte und Preislisten
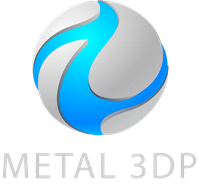
Metallpulver für 3D-Druck und additive Fertigung