Schutzabdeckungen für Raketensensoren über Metal AM
Inhaltsübersicht
Fortschritt in der Raketentechnik: Additive Fertigung von Metall für Sensor-Schutzhüllen
Das unermüdliche Streben nach Weltraumforschung und Satelliteneinsatz erfordert kontinuierliche Innovationen in der Raketentechnik. Jede Komponente, von den größten Triebwerksstrukturen bis hin zu den kleinsten Sensorgehäusen, spielt eine entscheidende Rolle für den Erfolg der Mission. Zu diesen wichtigen Elementen gehören raketensensorabdeckungen - Schutzgehäuse, die empfindliche Messinstrumente vor den extremen Bedingungen beim Start und im Betrieb schützen. Bei diesen Abdeckungen handelt es sich nicht um bloße Abdeckungen, sondern um präzise konstruierte Komponenten, die die Integrität und Genauigkeit von Daten gewährleisten, die für Navigation, Telemetrie, Systemüberwachung und wissenschaftliche Messungen entscheidend sind. Ein unzureichender Schutz dieser Sensoren kann zu einer Beeinträchtigung der Mission oder zu einem katastrophalen Versagen führen, so dass die Konstruktion und Herstellung der Abdeckungen für Ingenieure und Beschaffungsmanager in der Luft- und Raumfahrt von größter Bedeutung sind.
Traditionell wurden diese speziellen Abdeckungen mit subtraktiven Methoden wie CNC-Bearbeitung von Knüppeln oder komplexen Gussverfahren hergestellt. Diese Verfahren sind zwar effektiv, haben aber oft erhebliche Einschränkungen, insbesondere in Bezug auf die Komplexität des Designs, den Materialabfall, die langen Vorlaufzeiten und die Kosten, vor allem bei den für die Luft- und Raumfahrtindustrie typischen geringen Stückzahlen und hohen Anforderungen an die Individualisierung. Hier kommt Additive Fertigung von Metall (AM), besser bekannt als Metall 3D-Druck. Diese transformative Technologie revolutioniert die Art und Weise, wie Hochleistungskomponenten wie Sensorabdeckungen entworfen und hergestellt werden. Durch den schichtweisen Aufbau von Teilen direkt aus digitalen Modellen unter Verwendung von Hochleistungsmetallpulvern bietet AM eine noch nie dagewesene Designfreiheit, ermöglicht eine erhebliche Gewichtsreduzierung durch optimierte Geometrien, verkürzt die Entwicklungszyklen drastisch und ermöglicht die Verwendung fortschrittlicher Materialien, die speziell für die rauen Umgebungen im Weltraum geeignet sind.
Die Anwendung von Metall-AM für Raketensensorabdeckungen ist eine Antwort auf mehrere zentrale Herausforderungen in der Luft- und Raumfahrtindustrie. Sie ermöglicht es Ingenieuren,:
- Integrieren Sie komplexe Funktionen: Erstellen Sie komplizierte interne Kanäle für Kühlung oder Verkabelung, Befestigungspunkte und aerodynamische Profile, die mit herkömmlichen Methoden nur schwer oder gar nicht zu erreichen sind.
- Optimieren Sie für das Gewicht: Topologieoptimierung und Gitterstrukturen zur Minimierung der Masse ohne Beeinträchtigung der strukturellen Integrität - ein kritischer Faktor, bei dem jedes eingesparte Gramm zu einer erheblichen Senkung der Startkosten oder einer Erhöhung der Nutzlastkapazität führt.
- Teile konsolidieren: Umgestaltung von Baugruppen, die bisher aus mehreren Komponenten bestanden, in ein einziges, einheitliches gedrucktes Teil, wodurch die Komplexität, mögliche Fehlerquellen und die Montagezeit reduziert werden.
- Beschleunigung von Prototyping und Produktion: Sie können Entwürfe schnell iterieren und funktionale Prototypen oder endgültige Teile innerhalb von Tagen statt Wochen oder Monaten herstellen und so die Entwicklungszeiten verkürzen.
- Fortschrittliche Materialien verwenden: Nutzen Sie Materialien wie Titanlegierungen (z. B. Ti-6Al-4V) und hochwertige Edelstähle (z.B. 316L)sie sind bekannt für ihr hervorragendes Verhältnis von Festigkeit zu Gewicht, ihre Korrosionsbeständigkeit und ihre Leistung bei extremen Temperaturen - Eigenschaften, die sich mit AM-Verfahren wie Selective Electron Beam Melting (SEBM) und Laser Powder Bed Fusion (LPBF) leicht erreichen lassen.
Unternehmen, die auf die Herstellung von Luft- und Raumfahrtkomponenten und den Großhandel spezialisiert sind, wenden sich zunehmend an Metall-AM-Dienstleister, um diese Vorteile zu nutzen. Die Suche nach einem zuverlässigen anbieter von Metall-AM für die Luft- und Raumfahrt die in der Lage sind, gleichbleibende Qualität, Materialkenntnisse und zertifizierte Prozesse zu liefern, ist von entscheidender Bedeutung. Met3dp, mit Hauptsitz in Qingdao, China, steht an der Spitze dieses technologischen Wandels. Mit jahrzehntelanger kollektiver Erfahrung in Metall-Additiv-Fertigungmet3dp bietet umfassende Lösungen, einschließlich branchenführender SEBM-Drucker, die für ihr großes Bauvolumen, ihre außergewöhnliche Genauigkeit und Zuverlässigkeit bekannt sind, sowie ein Portfolio von Hochleistungsmetallpulvern, die für anspruchsvolle Anwendungen optimiert sind. Unsere fortschrittlichen Pulverherstellungssysteme, die die Technologien der Gaszerstäubung und des Plasma-Rotations-Elektroden-Verfahrens (PREP) nutzen, gewährleisten die Produktion von hochsphärischen, fließfähigen Metallpulvern - die Grundlage für dichte, hochwertige gedruckte Teile mit überlegenen mechanischen Eigenschaften, die für missionskritische Komponenten wie Raketensensorabdeckungen unerlässlich sind.
Dieser Artikel befasst sich mit den Besonderheiten der Verwendung von Metall-AM zur Herstellung von Schutzabdeckungen für Raketensensoren. Wir untersuchen die Anwendungen, die eindeutigen Vorteile gegenüber der herkömmlichen Fertigung, empfohlene Materialien wie Ti-6Al-4V und 316L, kritische Designüberlegungen (DFAM), erreichbare Präzision, Nachbearbeitungsanforderungen, potenzielle Herausforderungen sowie Hinweise für Beschaffungsmanager und Ingenieure zur Auswahl des richtigen AM-Partners und zum Verständnis der Kostenfaktoren. Ob Sie nun ein Luft- und Raumfahrtingenieur sind, der Trägerraketen der nächsten Generation entwirft, ein Beschaffungsspezialist, der zuverlässige großhandel mit Raketenkomponentenoder ein Händler, der nach innovativen Fertigungslösungen sucht, ist das Verständnis der Möglichkeiten der Metall-AM für Sensorabdeckungen der Schlüssel, um wettbewerbsfähig zu bleiben und den Erfolg der Mission zu gewährleisten.
Kritische Anwendungen: Wofür werden Raketensensorabdeckungen verwendet?
Raketensensorabdeckungen sind unverzichtbare Wächter empfindlicher Instrumente, die ihre Funktionsfähigkeit inmitten des Chaos eines Raketenstarts und der unnachgiebigen Umgebung eines Weltraum- oder Höhenflugs sicherstellen. Ihr Hauptzweck besteht darin, die Sensoren physisch vor einer Flut von schädlichen Faktoren zu schützen und ihnen gleichzeitig zu ermöglichen, die vorgesehenen Messungen präzise durchzuführen. Das Verständnis der spezifischen Anwendungen und der Umgebungen, denen diese Abdeckungen ausgesetzt sind, unterstreicht den entscheidenden Bedarf an robustem Design und fortschrittlichen Fertigungstechniken wie Metall-AM.
Geschützte Sensortypen:
Raketensensorabdeckungen sind so konzipiert, dass sie eine Vielzahl von Sensoren aufnehmen können, von denen jeder für verschiedene Aspekte der Flugsteuerung, Systemüberwachung und Datenerfassung entscheidend ist. Gängige Beispiele sind:
- Druckmessumformer: Messen Sie den atmosphärischen Umgebungsdruck, den Kammerdruck in Motoren oder den Druck in Treibstofftanks. Abdeckungen schützen die empfindlichen Membranen und die Elektronik vor Stößen, extremen Temperaturen und korrosiven Treibgasen.
- Temperatursensoren (Thermoelemente, RTDs): Überwachen Sie die Temperaturen auf der Raketenhaut, in den Triebwerkskomponenten, den Elektronikbuchten oder den Treibstoffleitungen. Abdeckungen bieten thermische Isolierung oder kontrollierte Wärmeleitfähigkeit und schützen gleichzeitig vor Vibrationen und physischen Schäden.
- Instrumente zur Messung von Magnetfeldern, Plasmaeigenschaften, Strahlungswerten oder der atmosphärischen Zusammensetzung erfordern oft eine spezifische Positionierung und Isolierung. 3D-gedruckte Halterungen ermöglichen kundenspezifische Designs, die auf die Bedürfnisse des Sensors zugeschnitten sind und potenziell Abschirmungen oder spezifische thermische Eigenschaften integrieren. Sie enthalten Beschleunigungsmesser und Gyroskope, die für die Navigation und Lageregelung wichtig sind. Abdeckungen schützen diese hochempfindlichen Instrumente vor Stößen, Vibrationen und thermischen Schwankungen, die die Messwerte verfälschen könnten.
- GPS/GNSS-Empfänger: Bereitstellung von Positionsdaten. Abdeckungen, die oft spezielle RF-transparente Materialien oder Designs erfordern, schützen die Antennen und die Elektronik vor der Startumgebung und gewährleisten gleichzeitig den Signalempfang.
- Dehnungsmessstreifen: Messung von Spannung und Dehnung an Bauteilen. Ummantelungen schützen die Messgeräte und ihre empfindliche Verkabelung vor Abrieb, Stößen und extremen Temperaturen.
- Optische Sensoren/Kameras: Sie werden für die Navigation, Beobachtung oder Bestätigung der Stufentrennung verwendet. Die Abdeckungen schützen Linsen und Sensoren vor Trümmern, aerodynamischer Erwärmung und Verschmutzung.
- Akustische Sensoren: Überwachung von Motorgeräuschen oder Strukturvibrationen. Abdeckungen schützen Mikrofone und zugehörige Elektronik vor hohen Schalldruckpegeln und physischen Schäden.
- Annäherungssensoren: Erkennung der relativen Position von Komponenten, die für die Stufentrennung oder Andockmanöver entscheidend ist. Die Abdeckungen schützen vor Stößen und Umwelteinflüssen.
Feindliche Betriebsumgebungen:
Die Umgebungsbedingungen, denen Raketensensorabdeckungen ausgesetzt sind, gehören zu den extremsten, denen technische Systeme ausgesetzt sind:
- Extreme Vibrationen und Stöße: Beim Start entstehen starke, vielfrequente Vibrationen und hohe G-Schocks, die ungeschützte Sensoren leicht beschädigen oder Bauteile aus ihrer Position bringen können. Die Abdeckungen müssen eine sichere Befestigung und Dämpfung gewährleisten.
- Akustische Belastungen: Der Schalldruckpegel beim Start kann 150 dB überschreiten, was zu erheblicher struktureller Ermüdung und zur Beschädigung empfindlicher Elektronik führen kann.
- Thermische Extreme: Die Komponenten sind raschen Temperaturschwankungen ausgesetzt, von kryogenen Treibstofftemperaturen über extreme aerodynamische Erwärmung während des atmosphärischen Aufstiegs bis hin zur intensiven Hitze des Triebwerksbetriebs. Die Abdeckungen müssen die Betriebstemperaturbereiche der Sensoren einhalten.
- Hohe G-Kräfte: Die Beschleunigung während des Starts führt zu erheblichen strukturellen Belastungen für alle Komponenten.
- Druckunterschiede: Der schnelle Wechsel vom Druck auf Meereshöhe zum Vakuum im Weltraum erfordert robuste Dichtungen und strukturelle Integrität.
- Trümmer & Lager; Kontamination: Mikrometeoroiden, Orbitaltrümmer, Eisabwurf und Triebwerksabgase stellen ein Aufprallrisiko dar. Abdeckungen wirken wie eine physische Barriere.
- Korrosive Atmosphären: Die Exposition gegenüber Treibstoffen (wie RP-1, Hydrazin, NTO), Abgasen und möglicherweise Salznebel in der Umgebung des Startplatzes erfordert korrosionsbeständige Materialien.
- Strahlung (Weltraumanwendungen): Bei Missionen außerhalb der Erdatmosphäre müssen die Hüllen möglicherweise einen gewissen Schutz gegen kosmische Strahlung und Sonneneinstrahlung bieten, was die Materialauswahl beeinflussen könnte.
Branchen und breitere Anwendungen:
Der Schwerpunkt liegt hier zwar auf der Raketentechnik (Trägerraketen, Raketen, Raumfahrzeuge), aber die Prinzipien, die bei der Entwicklung und Herstellung von Schutzabdeckungen mit Metall-AM zur Anwendung kommen, gelten auch für andere Branchen mit rauen Umgebungsbedingungen:
- Luft- und Raumfahrt (Flugzeuge): Schutz von Sensoren an Triebwerken, Fahrwerken und Steuerflächen vor Vibrationen, Temperatur und Trümmern.
- Verteidigung: Abschirmung empfindlicher Elektronik und Sensoren in Militärfahrzeugen, Flugzeugen und Munition.
- Automobilindustrie (Motorsport & Prüfung): Schutz von Sensoren in Hochleistungsmotoren, Auspuffanlagen und Fahrgestellen bei Rennen oder unter strengen Testbedingungen.
- Öl- & Gasexploration: Gehäuse für Bohrlochsensoren, die hohem Druck, hohen Temperaturen und korrosiven Flüssigkeiten ausgesetzt sind.
- Industrielle Fertigung: Schutz von Sensoren in schweren Maschinen, Hochtemperaturöfen oder chemisch aggressiven Verarbeitungslinien.
- Marine: Abschirmung von Sensoren auf Tauchbooten oder Überwasserschiffen gegen Druck, Salzwasserkorrosion und Biofouling.
Für Beschaffungsmanager und Distributoren für diese verschiedenen Sektoren ist das Verständnis der Vielseitigkeit von Metall-AM bei der Herstellung von kundenspezifischen Schutzgehäusen entscheidend. Die Möglichkeit, in kürzester Zeit Prototypen zu erstellen und hochoptimierte Abdeckungen aus Materialien wie Ti-6Al-4V oder 316L zu produzieren, macht es zu einer attraktiven Lösung für Lieferanten, die hochmoderne Komponenten anbieten wollen. Die Partnerschaft mit einem erfahrenen Metall-AM-Dienstleister wie Met3dp gewährleistet den Zugang zu den erforderlichen Technologien, Materialien und Fachkenntnissen, um die strengen Anforderungen dieser kritischen Anwendungen zu erfüllen. Met3dp’s Fokus auf hochwertige Metallpulver und zuverlässigen Druckverfahren schlägt sich direkt in robusten, zuverlässigen Sensorabdeckungen nieder, die auch unter schwierigsten Bedingungen einwandfrei funktionieren.
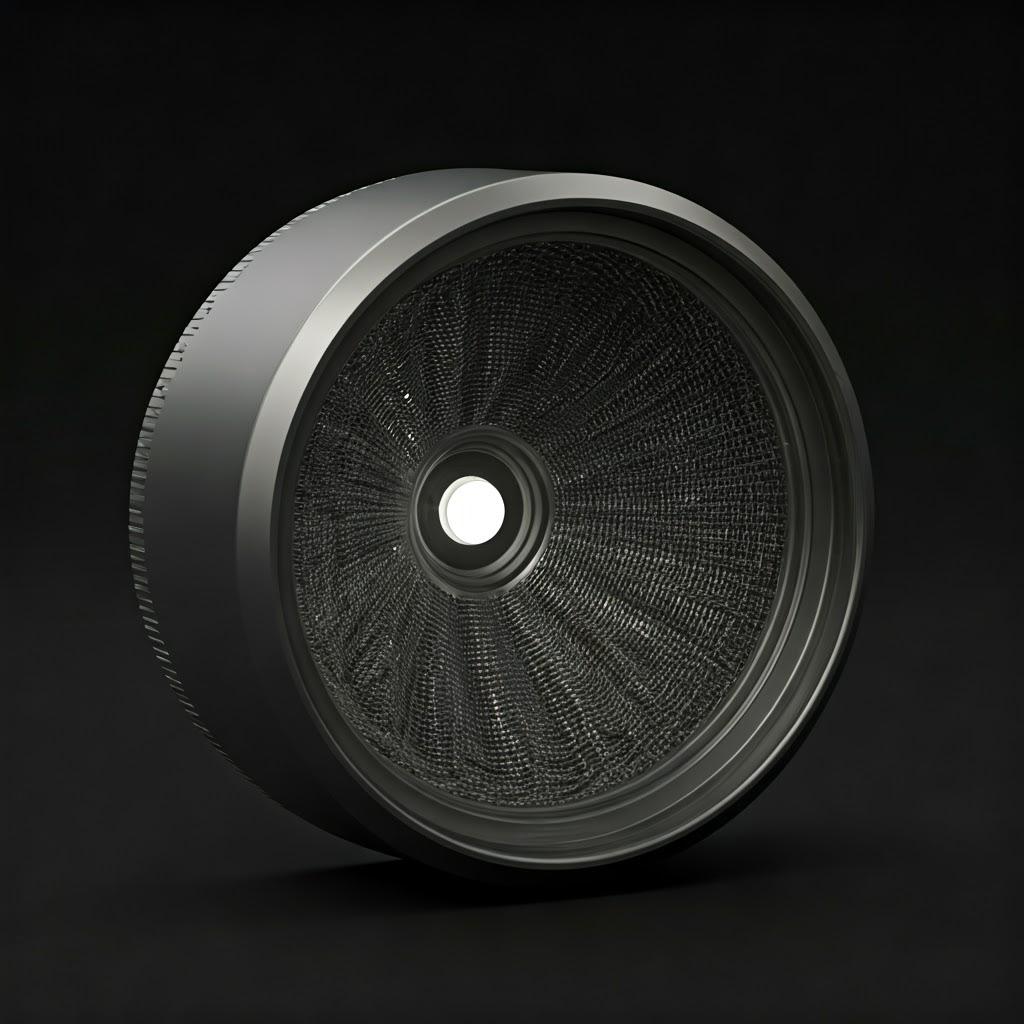
Der additive Vorteil: Warum Metall-3D-Druck für Raketensensorabdeckungen? Einblicke für Zulieferer der Luft- und Raumfahrt
Bei der Entscheidung für die additive Fertigung von kritischen Komponenten wie Raketensensorabdeckungen geht es nicht nur um die Einführung einer neuen Technologie, sondern um eine strategische Entscheidung, die durch greifbare technische und geschäftliche Vorteile getrieben wird, die insbesondere für Luft- und Raumfahrtzulieferer und Hersteller. Im Vergleich zur traditionellen subtraktiven Fertigung (wie CNC-Bearbeitung) oder zu formgebenden Verfahren (wie Gießen oder Schmieden) bietet Metall-AM eine einzigartige Kombination von Vorteilen, die perfekt auf die anspruchsvollen Anforderungen der Luft- und Raumfahrtindustrie abgestimmt sind.
1. Unerreichte Gestaltungsfreiheit und Komplexität:
- Traditionell: Die CNC-Bearbeitung ist durch den Zugang zu den Werkzeugen begrenzt, so dass komplexe innere Merkmale, Hinterschneidungen oder dünnwandige, gekrümmte Geometrien schwierig, zeitaufwändig oder unmöglich in einem einzigen Stück zu fertigen sind. Das Gießen bietet mehr Freiheit bei der Formgebung, erfordert aber oft teure Werkzeuge und hat Probleme mit sehr feinen Details oder dünnen Wänden.
- Metall-AM: Baut Teile schichtweise auf und befreit die Konstrukteure von vielen traditionellen Fertigungsbeschränkungen. Dies ermöglicht:
- Topologie-Optimierung: Algorithmen bestimmen die effizienteste Materialverteilung für die Anforderungen an die Tragfähigkeit, was zu leichten, organisch anmutenden Formen führt, die unmöglich zu bearbeiten sind.
- Gitterförmige Strukturen: Interne Gitter können das Gewicht erheblich reduzieren und gleichzeitig die strukturelle Integrität aufrechterhalten oder spezifische Dämpfungseigenschaften bieten.
- Teil Konsolidierung: Mehrere Komponenten einer Sensorabdeckungsbaugruppe (z. B. Gehäuse, Halterung, Befestigungselemente) können neu entworfen und als eine einzige, integrierte Einheit gedruckt werden. Dies reduziert die Anzahl der Teile, die Montagezeit, das Gewicht und potenzielle Fehlerpunkte (wie Verbindungen oder Schweißnähte).
- Konforme Kanäle: Interne Kanäle für Kühlung, Heizung oder Verkabelung können so gestaltet werden, dass sie den Konturen des Gehäuses folgen, was das Wärmemanagement verbessert oder die Integration vereinfacht.
2. Signifikante Gewichtsreduzierung:
- Traditionell: Eine Gewichtsreduzierung ist oft mit einer umfangreichen Bearbeitung verbunden, die zu Materialabfall und erhöhter Bearbeitungszeit führt. Eine optimale Gewichtsreduzierung wird durch fertigungstechnische Einschränkungen behindert.
- Metall-AM: Ermöglicht Gewichtsreduzierung durch Topologieoptimierung und den Einsatz von Gitterstrukturen, was sich direkt in geringeren Startkosten oder einer höheren Nutzlastkapazität niederschlägt. Für Luft- und Raumfahrtanwendungen ist jedes eingesparte Kilogramm entscheidend. Dies ist ein wichtiger Antrieb für einführung von Metall-AM in der Luft- und Raumfahrt.
3. Rapid Prototyping & Beschleunigte Entwicklungszyklen:
- Traditionell: Die Herstellung von Prototypen erfordert oft spezielle Werkzeuge (Guss) oder erhebliche Zeit für die Einrichtung und Programmierung von Maschinen (CNC). Designiterationen können Wochen oder Monate dauern.
- Metall-AM: Ermöglicht es Ingenieuren, innerhalb weniger Tage direkt von einem CAD-Modell zu einem physischen Metallteil zu gelangen. Das erleichtert die Arbeit:
- Schnellere Iteration: Mehrere Designvarianten können schnell gedruckt und getestet werden, was schneller zu optimierten Lösungen führt.
- Reduzierte Vorlaufzeiten: Bei der Produktion von Kleinserien oder Einzelteilen kann AM die fertigen Komponenten oft viel schneller liefern als herkömmliche Verfahren, die komplexe Lieferketten und lange Vorlaufzeiten für die Werkzeugherstellung mit sich bringen können. Diese Geschwindigkeit ist entscheidend für Zulieferer der Luft- und Raumfahrtindustrie mit engen Projektfristen.
4. Effiziente Materialverwendung & Weniger Abfall:
- Traditionell: Bei der subtraktiven Fertigung, insbesondere bei der CNC-Bearbeitung, wird zunächst ein massiver Materialblock bearbeitet und dann eine große Menge abgetragen, um die endgültige Form zu erhalten. Dies kann zu erheblichem Materialabfall führen, insbesondere bei teuren Luft- und Raumfahrtlegierungen wie Titan.
- Metall-AM: Ein additives Verfahren, bei dem nur das Material verwendet wird, das für die Herstellung des Teils benötigt wird (plus Stützstrukturen, die häufig recycelbar sind). Dies führt zu einem wesentlich günstigeren Verhältnis zwischen Anschaffung und Produktion und senkt die Rohstoffkosten und die Umweltbelastung - ein wichtiger Aspekt für Initiativen zur nachhaltigen Fertigung.
5. Eignung für die Produktion kleiner Mengen mit hohem Mischungsverhältnis:
- Traditionell: Die Einrichtung für die maschinelle Bearbeitung oder die Herstellung von Gussformen ist mit erheblichen Vorlaufkosten verbunden, so dass die Produktion von Kleinserien oder stark individualisierten Teilen eine wirtschaftliche Herausforderung darstellt.
- Metall-AM: Erfordert keine teilespezifische Werkzeugausstattung. Die Hauptkostenfaktoren sind Materialmenge, Maschinenzeit und Nachbearbeitung. Dies macht es äußerst kosteneffizient für:
- Prototypen: Herstellung von funktionalen Metallprototypen ohne Investitionen in Werkzeuge.
- Kundenspezifische Teile: Herstellung einzigartiger Abdeckungen, die auf spezifische Sensoren oder Missionsanforderungen zugeschnitten sind.
- Produktion von Kleinserien: Wirtschaftliche Produktion von kleinen Mengen, die oft für spezielle Luft- und Raumfahrtprojekte benötigt werden. Diese Flexibilität kommt folgenden Aspekten zugute großhändler für Raketenkomponenten die unterschiedliche Kundenbedürfnisse befriedigen müssen.
6. Zugang zu fortgeschrittenen Materialien:
- Traditionell: Einige hochentwickelte Legierungen können schwierig oder kostspielig zu bearbeiten oder zu gießen sein.
- Metall-AM: Verfahren wie SEBM und LPBF eignen sich gut für die Verarbeitung von Hochleistungswerkstoffen, die für die Luft- und Raumfahrt wichtig sind:
- Titanlegierungen (Ti-6Al-4V): Ausgezeichnetes Verhältnis von Festigkeit zu Gewicht, Korrosionsbeständigkeit und Hochtemperaturleistung.
- Rostfreie Stähle (316L): Gute Korrosionsbeständigkeit, Festigkeit und Kosteneffizienz für weniger anspruchsvolle thermische Umgebungen.
- Superlegierungen (Inconel): Wird für extrem hohe Temperaturen in der Nähe von Motoren verwendet.
- Aluminium-Legierungen (AlSi10Mg): Leichte Option, bei der eine hohe Festigkeit weniger wichtig ist. Met3dp ist auf die Herstellung hochwertiger Pulver aus diesen Materialien und die Optimierung der Druckverfahren für diese Materialien spezialisiert, um zuverlässige Materialeigenschaften in der endgültigen Hülle zu gewährleisten. Unser Fachwissen in verschiedenen 3D-Druckverfahren ermöglicht es uns, den besten Ansatz für spezifische Material- und Anwendungsanforderungen zu wählen.
Vergleichende Übersicht:
Merkmal | Additive Fertigung von Metall (AM) | Traditionelle CNC-Bearbeitung | Traditioneller Guss |
---|---|---|---|
Entwurfskomplexität | Sehr hoch (interne Kanäle, Gitter, organische Formen) | Mittel bis hoch (begrenzt durch Werkzeugzugang) | Hoch (Erfordert Werkzeug) |
Optimierung des Gewichts | Ausgezeichnet (Topologie-Opt., Gitter) | Mäßig (subtraktive Entfernung) | Mäßig bis gut |
Teil Konsolidierung | Ausgezeichnet | Begrenzt | Begrenzt |
Vorlaufzeit (Proto) | Fasten (Tage) | Mäßig (Wochen) | Langsam (Wochen/Monate – Werkzeugbau) |
Vorlaufzeit (Low Vol) | Schnell bis mäßig | Mäßig bis langsam | Langsam (Werkzeuge erforderlich) |
Materialabfälle | Niedrig (Additiv) | Hoch (subtraktiv) | Moderat (Gießäste, Angüsse) |
Werkzeugkosten | Keiner | Gering (Vorrichtung) | Hoch (Schablonen/Muster) |
Kosten (geringes Volumen) | Potenziell niedriger | Potenziell höher | Hoch |
Material-Optionen | Wachsende Auswahl an schweißbaren Legierungen | Breite Palette | Gießbare Legierungen |
In Blätter exportieren
Für Luft- und Raumfahrtzulieferer und Beschaffungsmanagerdie Botschaft ist klar: Metall-AM ist nicht nur eine Alternative, sondern oft eine überlegene Methode für die Herstellung komplexer, leichter und leistungsstarker Komponenten wie Raketensensorabdeckungen. Es bietet einen Weg zu Innovation, Effizienz und Wettbewerbsfähigkeit in einer anspruchsvollen Branche. Die Zusammenarbeit mit einem kompetenten Anbieter wie Met3dp gewährleistet den Zugang zu modernsten Anlagen, optimierten Materialien und der technischen Unterstützung, die erforderlich ist, um die Vorteile der additiven Fertigung voll auszuschöpfen. Erforschen Sie die Möglichkeiten weiter, indem Sie mehr erfahren über uns.
Materialfragen: Empfohlene Pulver (Ti-6Al-4V & 316L) für anspruchsvolle Startumgebungen
Die Wahl des richtigen Werkstoffs ist für die Leistung und Zuverlässigkeit eines jeden Bauteils in der Luft- und Raumfahrt von grundlegender Bedeutung, insbesondere wenn es den extremen Bedingungen ausgesetzt ist, denen die Sensorabdeckungen von Raketen ausgesetzt sind. Die additive Fertigung von Metallen bietet die Flexibilität, mit einer Reihe von Hochleistungslegierungen zu arbeiten, aber für diese Anwendung stechen zwei Materialien aufgrund ihrer außergewöhnlichen Eigenschaften und ihrer bewährten Erfolgsbilanz in der Luft- und Raumfahrt hervor: Titanlegierung Ti-6Al-4V (Grad 5) und Austenitischer rostfreier Stahl 316L. Die Kenntnis ihrer Eigenschaften ist für Ingenieure, die die Abdeckungen entwerfen, und für Beschaffungsspezialisten, die die AM-Dienstleistungen für Metalle oder hochreine Metallpulver.
Warum die Materialauswahl für Sensorabdeckungen so wichtig ist:
Das gewählte Material muss widerstandsfähig sein:
- Mechanische Belastungen: Vibrationen, Stöße, Schallenergie und G-Kräfte beim Start.
- Thermische Spannungen: Extreme Temperaturen, von kryogenen Kraftstoffen bis zu aerodynamischer Heizung und Motornähe.
- Korrosion: Exposition gegenüber Treibgasen, Abgasen und atmosphärischen Bedingungen.
- Vakuum (Weltraum): Ausgasungsprobleme und Materialstabilität im Vakuum des Weltraums.
- Gewichtsbeschränkungen: Das ständige Bestreben, die Masse von Bauteilen in der Luft- und Raumfahrt zu minimieren.
Ti-6Al-4V (Titan Grad 5): Das Arbeitspferd der Luft- und Raumfahrt
Ti-6Al-4V, oft einfach Ti64 genannt, ist die am häufigsten verwendete Titanlegierung und macht mehr als 50 % der weltweiten Titantonnage aus. Seine Beliebtheit in der Luft- und Raumfahrt ist aufgrund seiner hervorragenden Eigenschaftskombination wohlverdient und macht es zu einem idealen Kandidaten für anspruchsvolle Sensorabdeckungen, insbesondere wenn das Gewicht eine wichtige Rolle spielt.
- Wichtigste Eigenschaften & Vorteile:
- Hohes Verhältnis von Festigkeit zu Gewicht: Ti64 bietet eine vergleichbare Festigkeit wie viele andere Stähle, jedoch mit etwa 56 % der Dichte. Dies ist sein wichtigster Vorteil in der Luft- und Raumfahrt, der erhebliche Gewichtseinsparungen ermöglicht.
- Ausgezeichnete Korrosionsbeständigkeit: Bildet eine stabile, schützende Oxidschicht, die eine außergewöhnliche Beständigkeit gegen atmosphärische Korrosion, Salzwasser und viele chemische Umgebungen, einschließlich oxidierender Säuren und Chloride, bietet. Entscheidend für die Exposition gegenüber verschiedenen Treibstoffen und Bedingungen am Startplatz.
- Gute Hochtemperaturleistung: Behält bis zu einer Temperatur von ca. 315°C (600°F) eine beträchtliche Festigkeit und kann auch bei höheren Temperaturen zeitweise eingesetzt werden. Geeignet für viele Stellen in einer Trägerrakete, obwohl Superlegierungen möglicherweise näher an den heißen Bereichen des Motors benötigt werden.
- Geringe thermische Ausdehnung: Weist im Vergleich zu Stählen und Aluminiumlegierungen eine geringere Wärmeausdehnung auf, wodurch Probleme mit thermischen Spannungen in Baugruppen mit Temperaturgradienten verringert werden.
- Biokompatibilität: Es ist zwar nicht typisch für Abdeckungen, aber seine Biokompatibilität macht es zu einem Standard für medizinische Implantate.
- Gute AM-Verarbeitbarkeit: Ti-6Al-4V ist gut charakterisiert und lässt sich sowohl mit Laser Powder Bed Fusion (LPBF) als auch mit Selective Electron Beam Melting (SEBM) gut verarbeiten. Dabei werden eine nahezu vollständige Dichte und hervorragende mechanische Eigenschaften erreicht, die nach einer geeigneten Nachbearbeitung (z. B. Heiß-Isostatisches Pressen – HIP) die Spezifikationen von Knetwerkstoffen erfüllen oder übertreffen können.
- Erwägungen:
- Höhere Kosten: Titanlegierungen sind sowohl im Hinblick auf das Rohmaterial als auch auf die Verarbeitung wesentlich teurer als rostfreie Stähle oder Aluminiumlegierungen.
- Reaktivität: Titan kann bei hohen Temperaturen reaktiv sein, insbesondere mit Sauerstoff und Stickstoff, so dass bei der AM-Bearbeitung und der Wärmebehandlung eine kontrollierte Atmosphäre oder eine Vakuumumgebung erforderlich ist.
- Geringere Wärmeleitfähigkeit: Im Vergleich zu Aluminium oder Stahl, was ein Faktor für das Wärmemanagement sein kann.
316L-Edelstahl: Die robuste & vielseitige Option
316L ist ein austenitischer Chrom-Nickel-Edelstahl, der Molybdän enthält, das seine Korrosionsbeständigkeit, insbesondere gegenüber Chloriden und nicht oxidierenden Säuren, erhöht. Es ist ein weithin verfügbares, kostengünstiges und gut bekanntes Material, das häufig in anspruchsvollen Anwendungen in der Industrie und der Luft- und Raumfahrt eingesetzt wird, wo extreme Gewichtseinsparungen weniger wichtig sind als Haltbarkeit und Kosteneffizienz.
- Wichtigste Eigenschaften & Vorteile:
- Ausgezeichnete Korrosionsbeständigkeit: Überlegener als Standard-Edelstahl 304, insbesondere in Meeresumgebungen und gegen Lochfraß/Spaltkorrosion aufgrund seines Molybdängehalts. Die Bezeichnung "L" steht für einen niedrigen Kohlenstoffgehalt (≤0,03 %), der die Karbidausscheidung beim Schweißen oder bei thermischen Zyklen minimiert und die Korrosionsbeständigkeit erhält.
- Gute Festigkeit und Duktilität: Bietet ein gutes Gleichgewicht zwischen Zugfestigkeit, Zähigkeit und Duktilität über einen weiten Temperaturbereich, von kryogenen Temperaturen bis hin zu mäßig erhöhten Temperaturen (typischerweise bis zu ~500-600°C, obwohl die Festigkeit über 425°C deutlich abnimmt).
- Einfache Herstellung & Schweißeignung: Leicht bearbeitbar mit verschiedenen AM-Techniken (insbesondere LPBF) und leicht schweißbar für mögliche Montage- oder Reparaturarbeiten.
- Kosten-Nutzen-Verhältnis: Erheblich preiswerter als Titanlegierungen, was es für Abdeckungen attraktiv macht, bei denen die extremen Gewichtseinsparungen von Ti64 nicht unbedingt erforderlich oder wirtschaftlich vertretbar sind.
- Verfügbarkeit: Weithin verfügbar als hochwertiges, für AM geeignetes Pulver.
- Erwägungen:
- Höhere Dichte: Ungefähr 7,99 g/cm³, deutlich dichter als Ti-6Al-4V (ca. 4,43 g/cm³). Dies macht es weniger geeignet für Anwendungen, bei denen die Gewichtsminimierung oberste Priorität hat.
- Geringeres Verhältnis von Stärke zu Gewicht: Im Vergleich zu Ti64 ist seine Festigkeit gut, aber die höhere Dichte führt zu einem ungünstigeren Verhältnis zwischen Festigkeit und Gewicht.
- Magnetische Permeabilität: Während sie im geglühten Zustand im Allgemeinen nicht magnetisch sind, können die Kaltverformung oder einige Phasen, die sich während der AM bilden, einen leichten Magnetismus hervorrufen, was in der Nähe von empfindlichen magnetischen Sensoren ein Problem darstellen kann.
Materialauswahl-Zusammenfassungstabelle:
Merkmal | Ti-6Al-4V (Klasse 5) | 316L-Edelstahl | Empfehlungskontext für Sensorabdeckungen |
---|---|---|---|
Primärer Vorteil | Hohes Festigkeits-Gewichts-Verhältnis | Korrosionsbeständigkeit & Kosten-Wirksamkeit | Wählen Sie Ti64 für maximale Gewichtseinsparung. Wählen Sie 316L für kostenempfindliche oder weniger gewichtskritische Teile. |
Dichte | ~4,43 g/cm³ | ~7,99 g/cm³ | Signifikanter Gewichtsunterschied. |
Korrosionsbeständigkeit | Ausgezeichnet (oxidierend, Chloride, maritim) | Ausgezeichnet (Allgemein, Lochfraß, Spalt) | Beide sind ausgezeichnet; 316L ist in einigen spezifischen chemischen Umgebungen etwas besser. |
Nutzbarer Temp. Bereich | Gut bis zu ~315°C (600°F) | Gut bis ~425°C (800°F) (Festigkeitsabfall) | Berücksichtigen Sie den Standort im Verhältnis zu den Wärmequellen. |
Relative Kosten | Hoch | Mäßig | Ein wichtiger Faktor bei Beschaffungsentscheidungen. |
AM Verarbeitbarkeit | Ausgezeichnet (LPBF, SEBM) | Ausgezeichnet (hauptsächlich LPBF) | Beide eignen sich gut für AM. |
In Blätter exportieren
Die Rolle von Met3dp bei der Materialexzellenz:
Die ultimative Leistung eines AM-Sensorgehäuses hängt stark von der Qualität des verwendeten Metallpulvers ab. Met3dp nutzt branchenführende Gaszerstäubung und PREP-Technologien zur Herstellung von Metallpulvern, einschließlich Ti-6Al-4V und 316L, gekennzeichnet durch:
- Hohe Sphärizität: Gewährleistet eine gute Fließfähigkeit des Pulvers und eine gleichmäßige Verteilung während des AM-Prozesses.
- Kontrollierte Partikelgrößenverteilung (PSD): Optimiert für bestimmte AM-Prozesse (LPBF, SEBM), um eine hohe Packungsdichte zu erreichen und die Porosität zu minimieren.
- Hohe Reinheit: Geringe Verunreinigungen (wie Sauerstoff und Stickstoff, besonders kritisch für Titan) gewährleisten optimale Materialeigenschaften und Leistung.
- Konsistenz der Chargen: Strenge Qualitätskontrollen garantieren zuverlässige und reproduzierbare Ergebnisse von Bau zu Bau.
Durch die Kontrolle des Pulverherstellungsprozesses bietet Met3dp Luft- und Raumfahrtunternehmen und Komponentenlieferanten mit der Gewissheit, dass die für ihre kritischen Sensorabdeckungen verwendeten Materialien den höchsten Standards entsprechen. Unsere umfassenden Lösungen umfassen nicht nur fortschrittliche Metallpulver, sondern auch hochmoderne SEBM-Drucker und Anwendungsentwicklungsdienste. Das macht Met3dp zu einem wertvollen Partner für Unternehmen, die Metall-AM für anspruchsvolle Anwendungen wie Raketensensorabdeckungen einsetzen. Erkunden Sie unser Angebot an hochwertige Metallpulver geeignet für Ihre Bedürfnisse in der Luft- und Raumfahrt.
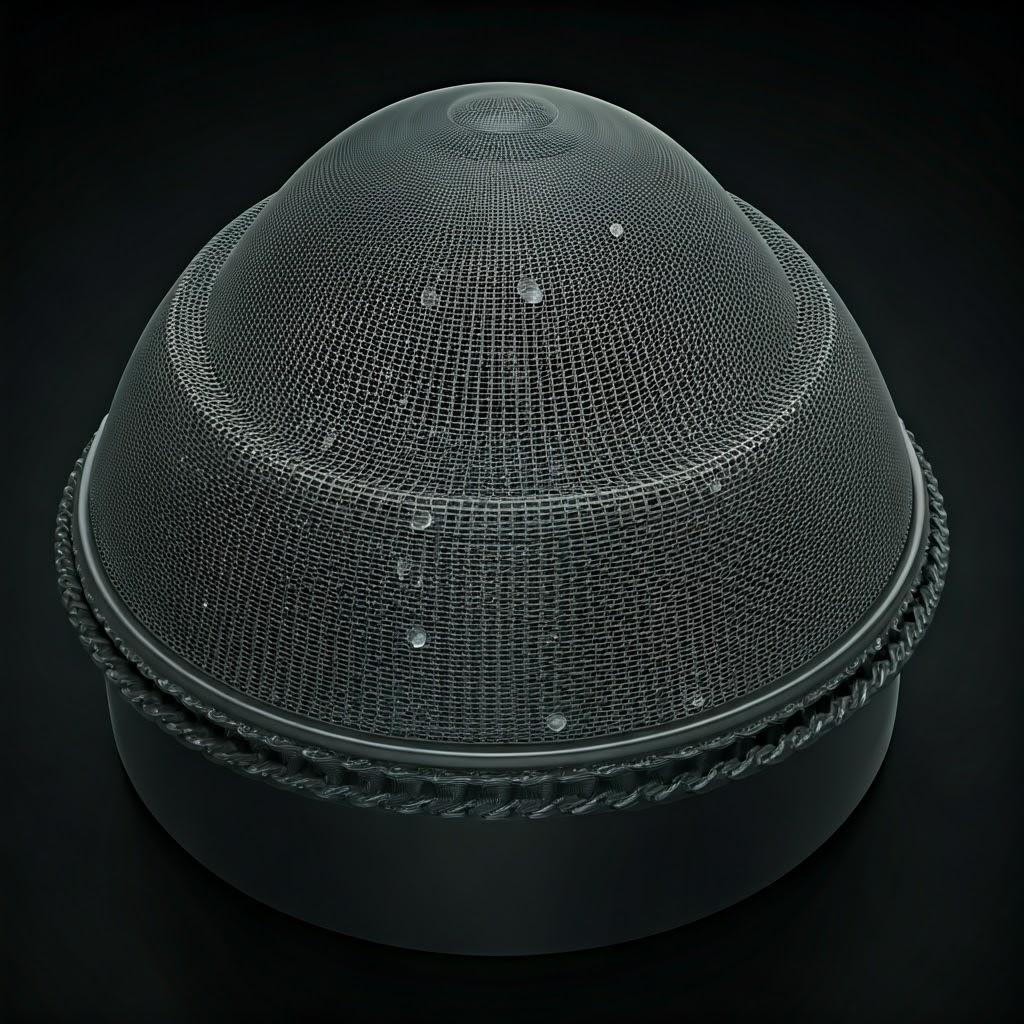
Entwickeln für Additive: Entwicklung überlegener Sensorabdeckungen mit DFAM
Die einfache Nachbildung eines Designs, das für die maschinelle Bearbeitung oder den Guss vorgesehen ist, mit Hilfe der additiven Fertigung von Metallen schöpft nur selten das volle Potenzial dieser Technologie aus. Um die Vorteile der additiven Fertigung - insbesondere Gewichtsreduzierung, Leistungssteigerung und Kosteneffizienz - wirklich nutzen zu können, müssen Ingenieure die folgenden Aspekte berücksichtigen Entwurf für additive Fertigung (DFAM) grundsätze. Bei DFAM wird die Konstruktion von Komponenten von Grund auf neu überdacht, wobei die einzigartigen Fähigkeiten und Einschränkungen der schichtweisen Fertigung berücksichtigt werden. Bei Raketensensorabdeckungen kann die Anwendung von DFAM zu deutlich besseren Komponenten führen als bei traditionell hergestellten Gegenstücken.
Warum DFAM für Sensorabdeckungen von entscheidender Bedeutung ist:
- Optimierung des Gewichts: In der Luft- und Raumfahrt ist die Masse ein kritischer Parameter. DFAM ermöglicht radikale Gewichtseinsparungen durch Topologieoptimierung und Gitterstrukturen, was sich direkt auf die Startkosten und die Fahrzeugleistung auswirkt.
- Funktionale Integration: AM ermöglicht es, komplexe Merkmale wie konforme Kühlkanäle, integrierte Halterungen oder eine optimierte interne Kabelführung direkt in das Gehäuse zu integrieren, wodurch die Anzahl der Teile und die Komplexität der Montage reduziert werden.
- Leistungsverbesserung: Konstruktionen können für bestimmte Lastfälle, Schwingungsdämpfung oder Wärmemanagement in einer Weise optimiert werden, die mit subtraktiven Methoden nicht möglich ist.
- Effizienz in der Produktion: Das Design unter Berücksichtigung der Grenzen des AM-Prozesses (z. B. Minimierung der Stützen, Optimierung der Ausrichtung) reduziert die Druckzeit, den Materialverbrauch und den Nachbearbeitungsaufwand, was zu geringeren Kosten und einer schnelleren Durchlaufzeit führt.
DFAM-Schlüsseltechniken für Sensorwolken:
- Topologie-Optimierung:
- Was es ist: Software-Algorithmen, die die Materialverteilung innerhalb eines definierten Konstruktionsraums auf der Grundlage der angewandten Lasten, Einschränkungen und Leistungsziele (z. B. Minimierung der Masse, Maximierung der Steifigkeit) optimieren.
- Anwendung: Ideal für tragende Elemente der Abschirmung oder der Halterungen. Es entfernt Material aus unkritischen Bereichen, was zu effizienten, oft organisch wirkenden Strukturen führt, die leicht und dennoch stabil sind.
- Nutzen: Erhebliche Gewichtsreduzierung (oft 20-50 % oder mehr) bei gleichzeitiger Erfüllung oder Übererfüllung der strukturellen Anforderungen. Entscheidend für Zulieferer der Luft- und Raumfahrtindustrie anstreben der Leistungsführerschaft.
- Gitterstrukturen & Zellulare Materialien:
- Was sie sind: Technische poröse Strukturen (z. B. Streben-, Skelett-TPMS-, Platten-TPMS-Strukturen), die zum Ausfüllen von Volumina oder zur Herstellung von Leichtbaukomponenten verwendet werden.
- Anwendung: Sie können massive Abschnitte in den Gehäusewänden ersetzen, um Gewicht zu sparen, maßgeschneiderte Schwingungsdämpfungseigenschaften zu bieten, die Wärmedämmung oder Wärmeableitung zu verbessern (je nach Konstruktion) oder die Stoßdämpfung zu erhöhen.
- Nutzen: Weitere Gewichtseinsparungen, die über die reine Topologieoptimierung hinausgehen, multifunktionale Fähigkeiten (strukturell + thermisch/dämpfend), Potenzial für verbesserte Stoßfestigkeit. Das Design erfordert spezielle Softwaremodule.
- Teil Konsolidierung:
- Was es ist: Umgestaltung einer Baugruppe aus mehreren Teilen in ein einziges, monolithisches Bauteil, das durch AM hergestellt wird.
- Anwendung: Eine Sensorabdeckungsbaugruppe könnte ursprünglich aus einem Gehäuse, einer separaten Halterung, Befestigungselementen und vielleicht einer Abdeckplatte bestehen. DFAM ermöglicht es den Ingenieuren, diese Teile in einem einzigen gedruckten Teil zu kombinieren.
- Nutzen: Reduziert die Anzahl der Teile, eliminiert Verbindungselemente (potenzielle Fehlerquellen), vereinfacht die Montage, verkürzt die Lieferkette und reduziert möglicherweise das Gesamtgewicht und die Herstellungskosten. Eine Schlüsselstrategie für großhändler für Raketenkomponenten die optimierte Lösungen anbieten wollen.
- Feature Design für Druckbarkeit & Leistung:
- Selbsttragende Winkel: Entwerfen Sie Überhänge, die in der Regel weniger als 45 Grad von der Horizontalen abweichen, um den Bedarf an Stützstrukturen zu minimieren, die zusätzliche Druckzeit, Materialkosten und Nachbearbeitungsaufwand verursachen.
- Mindestwanddicke: Beachten Sie die minimale druckbare Wandstärke für das gewählte Material und das AM-Verfahren (z. B. typischerweise 0,3-0,5 mm für LPBF, möglicherweise dicker für SEBM).
- Design der Löcher: Richten Sie Löcher nach Möglichkeit vertikal aus, um Rundheit zu gewährleisten und interne Stützen zu vermeiden. Entwerfen Sie horizontale Löcher als Tränen oder Rauten, wenn Stützen vermieden werden müssen. Ziehen Sie das Hinzufügen von Opfermaterial für die spätere Bearbeitung in Betracht, wenn präzise Abmessungen wichtig sind.
- Filets und Radien: Großzügige Verrundungen an scharfen Ecken zur Verringerung von Spannungskonzentrationen und zur Verbesserung der Ermüdungslebensdauer - eine gängige Praxis in der Luft- und Raumfahrt, die mit AM jedoch leicht zu erreichen ist.
- Entwerfen für die Nachbearbeitung: Sicherstellen, dass kritische Merkmale, die hohe Präzision oder eine glatte Oberfläche erfordern, für die Bearbeitung oder das Polieren zugänglich sind. Entwerfen Sie Stützstrukturen, die sich leicht entfernen lassen, ohne die Oberfläche des Teils zu beschädigen.
- Orientierungsstrategie aufbauen:
- Was es ist: Entscheiden Sie, wie das Teil auf der Bauplatte positioniert werden soll.
- Auswirkungen: Die Orientierung wirkt sich erheblich aus:
- Anforderungen an die Unterstützung: Steilere Überhänge erfordern mehr Stützen.
- Oberfläche: Nach unten weisende Flächen und Seitenwände haben in der Regel eine rauere Oberfläche als nach oben weisende Flächen.
- Maßgenauigkeit: Thermische Spannungen können je nach Ausrichtung unterschiedliche Verformungen verursachen.
- Mechanische Eigenschaften: Anisotropie (richtungsabhängige Eigenschaften) kann auftreten, wird aber oft durch geeignete Parameter und Nachbearbeitung wie HIP minimiert.
- Bauzeit und Kosten: Höhere Bauwerke brauchen in der Regel länger. Das effiziente Verschachteln mehrerer Teile hängt von ihrer Ausrichtung ab.
- Kollaboration: Die Bestimmung der optimalen Ausrichtung erfordert oft die Zusammenarbeit zwischen dem Designer und dem AM-Dienstleister, wie Met3dp. Unsere Ingenieure nutzen Simulationstools und umfangreiche Prozesserfahrung, um die beste Ausrichtung zu finden, die Druckbarkeit, Leistung und Kosten in Einklang bringt. Erkunden Sie unser umfassendes 3D-Metalldruckdienste um zu sehen, wie wir DFAM integrieren.
Durch die durchdachte Anwendung dieser DFAM-Prinzipien können Ingenieure eine standardmäßige Raketensensorabdeckung in ein hoch optimiertes, leichtes und integriertes Bauteil verwandeln, das die einzigartigen Vorteile der additiven Fertigung von Metallen voll ausschöpft. Dieser konstruktionsorientierte Ansatz ist unerlässlich, um die Grenzen von Leistung und Effizienz in der Luft- und Raumfahrt zu verschieben.
Präzisionsarbeit: Toleranz, Oberflächengüte und Maßgenauigkeit bei AM-Abdeckungen
Während Metall-AM eine unglaubliche Designfreiheit bietet, ist das Verständnis der erreichbaren Präzisionsniveaus für Ingenieure und Beschaffungsmanager, die Raketensensorabdeckungen spezifizieren, entscheidend. Toleranz, Oberflächengüte und Maßgenauigkeit sind Schlüsselparameter, die die Qualität und Funktionalität des endgültigen Teils bestimmen, insbesondere bei Komponenten, die präzise Passungen, Dichtungen oder spezifische Oberflächeneigenschaften erfordern. Diese Aspekte werden durch das gewählte AM-Verfahren (SEBM vs. LPBF), das Material, die Teilegeometrie, die Fertigungsparameter und die Nachbearbeitungsschritte beeinflusst.
Definieren der Begriffe:
- Verträglichkeit: Die zulässige Abweichung von einem bestimmten Nennmaß. Legt fest, wie viel Abweichung für ein Teilemerkmal (z. B. Durchmesser, Länge, Ebenheit) zulässig ist. Häufig nach Normen wie ISO 2768 (Allgemeintoleranzen) festgelegt.
- Oberflächengüte (Oberflächenrauhigkeit): Misst die feinen Unregelmäßigkeiten auf der Oberfläche eines Teils. Wird üblicherweise durch Ra (durchschnittliche Rauheit) quantifiziert. Beeinflusst Reibung, Verschleiß, Ermüdungslebensdauer, Abdichtung und Ästhetik.
- Maßgenauigkeit: Wie genau das gedruckte Teil insgesamt mit den Abmessungen des ursprünglichen CAD-Modells übereinstimmt. Beeinflusst durch Schrumpfung, Verformung und Prozessschwankungen.
Erreichbare Präzision bei der Metall-AM:
- Allgemeine Toleranzen:
- As-built-Toleranzen für Metall-AM-Verfahren wie LPBF und SEBM liegen typischerweise im Bereich von ±0,1 mm bis ±0,3 mm für kleinere Merkmale, plus einen Prozentsatz der Dimension für größere Merkmale (z. B. ±0,1 % bis ±0,2 %).
- Ein gemeinsamer Bezugspunkt könnte sein ISO 2768-m (mittel) oder manchmal ISO 2768-f (fein) für allgemeine Abmessungen, aber engere Toleranzen erfordern oft eine Nachbearbeitung.
- Zu den Faktoren, die sich auf die Toleranz auswirken, gehören die Maschinenkalibrierung, die thermische Stabilität während der Fertigung, die Materialeigenschaften (Schrumpfung), die Teilegröße und die Komplexität der Geometrie sowie die Unterstützungsstrategie. Das SEBM-Verfahren, das bei höheren Temperaturen arbeitet, kann manchmal weniger Eigenspannungen aufweisen, hat aber möglicherweise etwas geringere Fertigungstoleranzen als das optimierte LPBF-Verfahren für feine Merkmale.
- Oberflächengüte (Ra):
- As-Built Ra: Variiert erheblich je nach Ausrichtung, Verfahren und Material:
- Nach oben gerichtete Oberflächen: Im Allgemeinen die glattesten, potenziell 5-15 µm Ra für LPBF, etwas höher für SEBM.
- Seitenwände (vertikal): Durch Schichtlinien beeinflusste Rauhigkeit, typischerweise 10-25 µm Ra.
- Nach unten gerichtete Oberflächen (Support Interface): In der Regel die gröbsten aufgrund von Stützkontaktpunkten, oft >20-30 µm Ra.
- Eigenschaften des Pulvers: Feinere Pulverpartikel führen im Allgemeinen zu glatteren Oberflächen, können aber die Fließfähigkeit beeinträchtigen und erfordern andere Prozessparameter. Die hochwertigen, kugelförmigen Pulver von Met3dp’ mit kontrolliertem PSD tragen dazu bei, konsistente und optimale Oberflächengüten für den gewählten Prozess zu erzielen.
- Nachbearbeiten: Für kritische Anwendungen in der Luft- und Raumfahrt sind die Oberflächenbeschaffenheiten im Ist-Zustand oft unzureichend. Nachbearbeitungsschritte wie Perlstrahlen, Trommeln, Polieren oder CNC-Bearbeitung werden eingesetzt, um die gewünschten Ra-Werte zu erreichen (bis zu <1 µm Ra beim Polieren).
- As-Built Ra: Variiert erheblich je nach Ausrichtung, Verfahren und Material:
- Maßgenauigkeit:
- Die Gesamtgenauigkeit hängt von einer sorgfältigen Prozesssteuerung ab, die auch das Wärmemanagement einschließt, um Verformungen und Verzerrungen durch Eigenspannungen zu minimieren.
- Simulationswerkzeuge werden zunehmend eingesetzt, um mögliche Verformungen vor dem Druck vorherzusagen und auszugleichen.
- Die Verifizierung ist entscheidend. Koordinatenmessmaschinen (CMM) und 3D-Scannen werden verwendet, um die endgültigen Abmessungen des Teils mit den ursprünglichen CAD-Daten zu vergleichen und sicherzustellen, dass kritische Merkmale innerhalb der Toleranz liegen. Dies ist ein Standard-Qualitätssicherungsschritt für zulieferer für Metall-AM in der Luft- und Raumfahrt.
Strengere Spezifikationen erreichen:
Für Sensorabdeckungen, die eine hohe Präzision erfordern (z. B. Gegenflansche, Schnittstellen zur Sensorbefestigung, Dichtungsflächen), ist ein hybrider Ansatz üblich, der AM mit traditioneller Bearbeitung kombiniert:
- Near-Net-Shape drucken: Verwenden Sie AM, um die komplexe Gesamtgeometrie des Gehäuses zu erstellen und nutzen Sie DFAM zur Gewichtsreduzierung und Teilekonsolidierung. Lassen Sie zusätzliches Material (Bearbeitungszugabe, typischerweise 0,5-2 mm) auf kritischen Oberflächen.
- Nachbearbeiten: Nutzen Sie die CNC-Bearbeitung, um endgültige Toleranzen (möglicherweise bis zu ±0,01 mm oder enger) und spezifische Anforderungen an die Oberflächengüte dieser kritischen Merkmale zu erreichen.
Das Engagement von Met3dp für Präzision:
Wir von Met3dp kennen die strengen Anforderungen der Luft- und Raumfahrtindustrie.
- Unser branchenführende SEBM-Drucker sind auf Genauigkeit und Zuverlässigkeit ausgelegt und gewährleisten gleichbleibende Produktionsbedingungen.
- Wir nutzen hochwertige, optimierte Metallpulver sie werden im eigenen Haus hergestellt und tragen zu einer vorhersehbaren Schrumpfung und einer guten Oberflächenqualität bei.
- Unser Ingenieurteam arbeitet eng mit den Kunden zusammen, um die Entwürfe zu optimieren und die Ausrichtungen für die Dimensionsstabilität zu verbessern.
- Wir führen strenge Qualitätskontrollprotokolledazu gehören die Überwachung während des Fertigungsprozesses und die Inspektion nach der Fertigung mit Hilfe von CMM und anderen Messinstrumenten, um sicherzustellen, dass die endgültigen Sensorabdeckungen die vorgegebenen Toleranzen und Genauigkeitsanforderungen erfüllen.
Zusammenfassende Tabelle: Genauigkeitserwartungen:
Parameter | As-Built Metall AM (typischer Bereich) | Erreichbar mit Post-Processing | Wichtige Einflussfaktoren |
---|---|---|---|
Toleranz | ±0,1 bis ±0,3 mm + % der Abmessung | Bis zu ±0,01 mm (Bearbeitung) | Maschine, Material, Geometrie, Halterungen, thermische Kontrolle |
Oberflächengüte (Ra) | 5 – 30+ µm | <1 µm (Polieren/Bearbeiten) | Orientierung, Verfahren (LPBF/SEBM), Pulvergröße, Parameter |
Maßgenauigkeit | Gut (prozessabhängig) | Sehr hoch (durch CMM verifiziert) | Verzugskontrolle, Simulation, Maschinenkalibrierung, QC |
In Blätter exportieren
Ingenieure und Beschaffungsmanager sollten die geforderten Toleranzen und Oberflächenbeschaffenheiten auf Zeichnungen klar definieren und kritische Merkmale, die eine Nachbearbeitung erforderlich machen könnten, identifizieren. Eine offene Kommunikation mit dem AM-Anbieter ist unerlässlich, um sicherzustellen, dass die Erwartungen übereinstimmen und im Rahmen des Projektumfangs und des Budgets erreichbar sind.
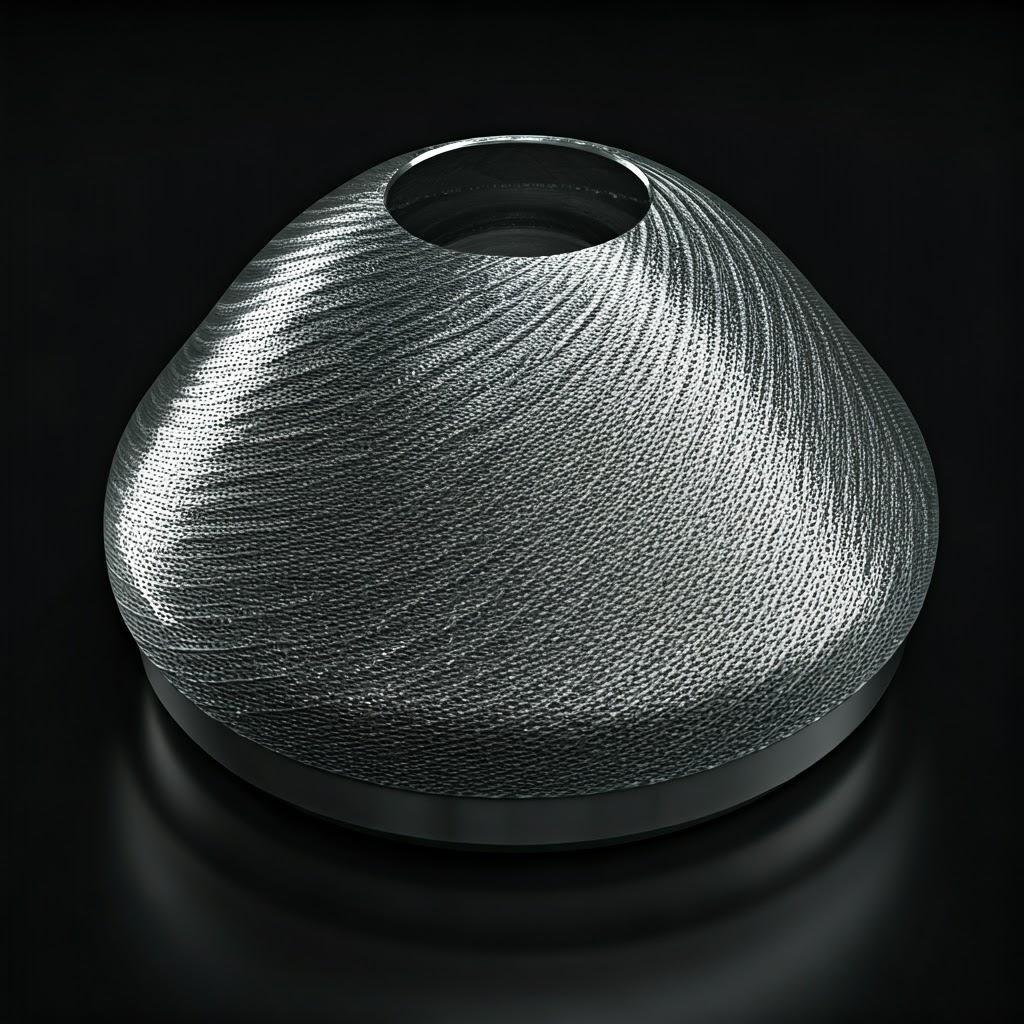
Einsatzbereites Finish: Wichtige Nachbearbeitungsschritte für AM-Sensorabdeckungen aus Metall
Die Herstellung eines Raketensensorgehäuses mittels additiver Fertigung aus Metall endet nicht, wenn der Drucker anhält. Das "grüne" Teil, frisch von der Bauplatte, erfordert eine Reihe von Nachbearbeitungsschritte um es in ein funktionsfähiges, zuverlässiges und einsatzbereites Bauteil zu verwandeln. Diese Schritte sind entscheidend, um innere Spannungen abzubauen, Stützstrukturen zu entfernen, Maßtoleranzen und Oberflächenanforderungen zu erfüllen, die Materialintegrität zu gewährleisten und die Qualität zu überprüfen. Bei kritischen Komponenten für die Luft- und Raumfahrt, wie z. B. Sensorabdeckungen, ist die Nachbearbeitung keine Option, sondern ein integraler Bestandteil des Fertigungsablaufs.
Warum Nachbearbeitung unverzichtbar ist:
- Eigenspannungen: Die schnellen Erwärmungs- und Abkühlungszyklen, die bei AM auftreten, führen zu inneren Spannungen, die zu Verformungen oder Rissen führen können, wenn sie nicht abgebaut werden.
- Unterstützende Strukturen: Überhängende Elemente erfordern während des Baus Stützkonstruktionen, die entfernt werden müssen.
- Oberfläche: Die bestehenden Oberflächen sind oft zu rau für Dichtungen, ermüdungskritische Bereiche oder aerodynamische Anforderungen.
- Porosität: Auch wenn sie mit optimierten Parametern minimiert wird, kann eine gewisse Mikroporosität verbleiben, die die Ermüdungslebensdauer beeinträchtigen kann. Die HIP-Behandlung kann dies beseitigen.
- Toleranzen: Die Teile im Rohzustand entsprechen möglicherweise nicht den engen Toleranzen, die für Schnittstellen und Passungen erforderlich sind.
- Sauberkeit: Pulverreste müssen gründlich entfernt werden.
Gemeinsamer Nachbearbeitungsablauf für AM-Sensorabdeckungen (Ti-6Al-4V / 316L):
- Stressabbau Wärmebehandlung:
- Zweck: Zur Verringerung der inneren Spannungen, die während des Druckvorgangs in das Teil eingeklemmt werden, wodurch das Risiko von Verformungen bei nachfolgenden Schritten (z. B. beim Entfernen von der Bauplatte) minimiert und die Dimensionsstabilität verbessert wird.
- Prozess: Durchgeführt, während das Teil noch an der Bauplatte befestigt ist, typischerweise in einem Vakuum- oder Inertgasofen. Die Zyklen variieren je nach Material und Geometrie (z. B. für Ti-6Al-4V typischerweise 595-840 °C, gefolgt von kontrollierter Abkühlung; für 316L oft höhere Temperaturen ~850-1150 °C für das Lösungsglühen, falls erforderlich, obwohl der einfache Spannungsabbau niedriger sein kann).
- Wichtigkeit: Ein absolut kritischer erster Schritt für die meisten AM-Teile aus Metall, insbesondere bei komplexen Geometrien oder Titanlegierungen.
- Entnahme von der Bauplatte:
- Zweck: Um die gedruckte(n) Abdeckung(en) von der Metallplatte zu trennen, auf der sie gebaut wurden.
- Methoden: Üblicherweise erfolgt dies durch Drahterodieren (Wire EDM) oder mit einer Bandsäge. Dabei muss darauf geachtet werden, dass die Teile nicht beschädigt werden.
- Entfernung der Stützstruktur:
- Zweck: Entfernung der temporären Strukturen, die während der Bauarbeiten Überhänge und komplexe Elemente stützten.
- Methoden: Dies kann vom manuellen Brechen (bei leicht zugänglichen, zerbrechlichen Stützen) bis hin zur maschinellen Bearbeitung, zum Schleifen oder zum Einsatz spezieller Handwerkzeuge reichen. Dies kann arbeitsintensiv sein und erfordert eine sorgfältige Ausführung, um eine Beschädigung der Teileoberfläche zu vermeiden. DFAM spielt eine Schlüsselrolle bei der Konstruktion von Halterungen, die sich leichter entfernen lassen.
- Heiß-Isostatisches Pressen (HIP):
- Zweck: Zur Beseitigung der internen Mikroporosität, zur Verdichtung des Materials auf nahezu 100 % und zur Verbesserung der mechanischen Eigenschaften, insbesondere der Ermüdungsfestigkeit, Duktilität und Bruchzähigkeit. Für kritische Komponenten in der Luft- und Raumfahrt oft vorgeschrieben.
- Prozess: Die Teile werden in einem speziellen HIP-Behälter gleichzeitig einer hohen Temperatur (unter dem Schmelzpunkt) und einem hohen isostatischen Druck (unter Verwendung eines Inertgases wie Argon) ausgesetzt. Typische HIP-Zyklen für Ti-6Al-4V liegen bei 900-950°C und 100-150 MPa.
- Nutzen: Führt zu Materialeigenschaften, die denen von Knet- oder Gussäquivalenten entsprechen oder sie sogar übertreffen können. Unverzichtbar für die Gewährleistung der Zuverlässigkeit von Abdeckungen bei zyklischer Belastung (Vibration).
- Spanende Bearbeitung (CNC):
- Zweck: Zur Erzielung enger Maßtoleranzen, spezifischer Oberflächengüten und Merkmale, die mit AM allein nur schwer herzustellen sind (z. B. präzise Passflächen, O-Ring-Nuten, Gewindebohrungen).
- Prozess: Herkömmliche CNC-Fräs- oder Drehbearbeitungen am AM-Teil. Erfordert ein sorgfältiges Vorrichtungsdesign, um die potenziell komplexe AM-Geometrie zu halten. Materialzugabe muss in der AM-Designphase berücksichtigt werden.
- Oberflächenveredelung und Reinigung:
- Zweck: Um die erforderliche Oberflächenrauheit (Ra) zu erreichen, Verunreinigungen zu entfernen und für nachfolgende Beschichtungen oder Prüfungen vorzubereiten.
- Methoden:
- Abrasive Methoden: Perlstrahlen, Sandstrahlen oder Trommeln können eine gleichmäßige matte Oberfläche erzeugen und lose Partikel (Ra typischerweise 3-10 µm) entfernen.
- Polieren: Manuelles oder automatisiertes Polieren für sehr glatte, spiegelglatte Oberflächen (Ra < 0,8 µm) auf bestimmten Flächen.
- Elektropolieren: Elektrochemisches Verfahren zum Glätten von Oberflächen, besonders wirksam bei nichtrostenden Stählen wie 316L.
- Abrasive Fließbearbeitung (AFM): Schieben von abrasiven Medien durch interne Kanäle, um diese zu glätten.
- Reinigung: Ultraschallreinigung oder Waschen mit Lösungsmitteln, um alle Rückstände von Pulver und Bearbeitungsflüssigkeiten zu entfernen.
- Inspektion und zerstörungsfreie Prüfung (NDT):
- Zweck: Zur Überprüfung der Abmessungen, zur Erkennung von Oberflächen- oder Innenfehlern und um sicherzustellen, dass das Teil vor dem Einsatz alle Spezifikationen erfüllt.
- Methoden:
- Dimensional: CMM, 3D-Scannen.
- Oberfläche: Sichtprüfung, Farbeindringprüfung (DPT), mikroskopische Untersuchung.
- Intern: Computertomographie (CT) (hervorragend geeignet für die Erkennung von inneren Porositäten oder Defekten in komplexen AM-Teilen), Röntgenstrahlen.
- Material: Härteprüfung, eventuell Prüfung der Zugfestigkeit von Prüfstücken.
Integration der Nachbearbeitung in die Gestaltung:
Eine erfolgreiche und kosteneffiziente Nachbearbeitung beginnt bereits in der Entwurfsphase. Ingenieure müssen berücksichtigen:
- Wie werden die Stützen entfernt? Ist ein Zugang vorhanden?
- Welche Flächen müssen bearbeitet werden? Gibt es eine ausreichende Materialzugabe und kann das Teil leicht aufgespannt werden?
- Sind die internen Kanäle für Reinigung und Inspektion ausgelegt?
- Sind die Anforderungen an die Nachbearbeitung den Mitarbeitern klar mitgeteilt worden? Metall-AM-Dienstleister?
Met3dp bietet End-to-End-Lösungen, einschließlich Beratung zu DFAM, die auch die Nachbearbeitung berücksichtigt. Unser Netzwerk und unser Fachwissen stellen sicher, dass Ihre Sensorabdeckungen die notwendigen Nachbearbeitungs- und Qualitätsprüfungsschritte durchlaufen, um wirklich einsatzbereit zu sein. Das Verständnis für die Notwendigkeit und Komplexität dieser Schritte ist entscheidend für Beschaffungsmanager budgetierung und Terminierung von Luft- und Raumfahrtprojekten mit Metall-AM.
Hürden überwinden: Gemeinsame Herausforderungen & Abhilfestrategien beim 3D-Druck von Sensorabdeckungen
Die additive Fertigung von Metallen ist eine leistungsstarke Technologie, aber sie ist nicht ohne ihre Komplexität. Die Herstellung hochwertiger, zuverlässiger Raketensensorabdeckungen erfordert eine sorgfältige Kontrolle des gesamten Prozesses, vom Entwurf und der Simulation bis zum Druck und der Nachbearbeitung. Der Schlüssel zur erfolgreichen Umsetzung und zur Vermeidung von kostspieligen Verzögerungen oder Bauteilausfällen liegt in der Vorwegnahme und Entschärfung allgemeiner Herausforderungen. Luft- und Raumfahrtingenieure und Zulieferer müssen sich dieser potenziellen Hürden bewusst sein.
1. Verformung und Verzerrung:
- Herausforderung: Die erheblichen Temperaturgradienten während des Druckvorgangs erzeugen Restspannungen im Teil. Wenn diese Spannungen nachlassen, können sie dazu führen, dass sich das Teil verzieht oder verformt und von der beabsichtigten Geometrie abweicht, insbesondere bei dünnwandigen oder großen, flachen Abschnitten, wie sie bei Abdeckungen üblich sind.
- Strategien zur Schadensbegrenzung:
- Thermische Simulation: Einsatz von Finite-Elemente-Analyse-Werkzeugen (FEA) zur Vorhersage von Spannungsakkumulation und Verformung auf der Grundlage von Geometrie und Prozessparametern.
- Optimierte Gebäudeausrichtung: Positionierung des Teils, um große flache Bereiche parallel zur Bauplatte zu minimieren und die Wärmeverteilung zu steuern.
- Intelligente Unterstützungsstrukturen: Konstruktion von Stützen nicht nur für die Schwerkraft, sondern auch, um das Teil fest zu verankern und Schrumpf-/Verzugskräften entgegenzuwirken. Die Simulation ist oft die Grundlage für die optimale Platzierung und Art der Stützen.
- Optimierung der Prozessparameter: Feinabstimmung von Laser-/Elektronenstrahlleistung, Scangeschwindigkeit und Schichtdicke zur Steuerung des Wärmeprofils.
- Build Plate Heating: Die Aufrechterhaltung einer hohen Temperatur in der Baukammer (insbesondere beim SEBM) reduziert thermische Gradienten und minimiert die Belastung.
- Unmittelbarer Stressabbau: Durchführung eines Spannungsabbau-Wärmebehandlungszyklus unmittelbar nach dem Druck, häufig vor der Entnahme des Teils von der Bauplatte.
2. Eigenspannung:
- Herausforderung: Selbst wenn erhebliche Verformungen vermieden werden, können hohe Eigenspannungen in der gedruckten Ummantelung verbleiben. Dies kann zu vorzeitiger Rissbildung, verringerter Ermüdungslebensdauer oder Verformung während der Nachbearbeitung führen, wenn Materialschichten entfernt werden.
- Strategien zur Schadensbegrenzung:
- Alle Strategien zur Verringerung des Verzugs tragen auch zur Reduzierung der Eigenspannung bei.
- Sorgfältige Nachbearbeitung: Die Durchführung von Spannungsarmglühungen ist von entscheidender Bedeutung. Bei Werkstoffen wie Ti-6Al-4V können je nach den gewünschten Endeigenschaften mehrere Wärmebehandlungen (Spannungsarmglühen, möglicherweise Lösungsglühen und Altern, HIP) erforderlich sein.
- Überlegungen zum Design: Vermeiden Sie scharfe Innenecken, in denen sich Spannungen konzentrieren können; die Verwendung von Hohlkehlen hilft dabei.
3. Schwierigkeit der Entfernung der Stütze und Oberflächenbeschädigung:
- Herausforderung: Die Stützen müssen stark genug sein, um während des Baus zu funktionieren, aber auch leicht genug, um sie danach zu entfernen, ohne die Oberfläche der Abdeckung zu beschädigen, insbesondere bei komplexen oder empfindlichen Geometrien. Eine unvollständige oder aggressive Entfernung kann Flecken oder Kratzer hinterlassen, die die Lebensdauer oder die Ästhetik beeinträchtigen.
- Strategien zur Schadensbegrenzung:
- DFAM: Die Konstruktion von Teilen mit selbsttragenden Winkeln (typischerweise >45°) minimiert den Bedarf an Stützen. Ausrichtung des Teils, um Überhänge zu reduzieren.
- Optimiertes Support-Design: Verwendung spezieller Stützstrukturen (z. B. Baumstützen, dünnwandige Stützen, Stützen mit speziellen Kontaktpunkten), die eine ausreichende Verankerung bieten, aber leichter brechen. Software-Tools bieten verschiedene Unterstützungsstrategien.
- Abstimmung der Prozessparameter: Anpassung der Parameter für die Verbindung der Stützen mit dem Teil, um eine schwächere Schnittstelle zu schaffen.
- Geeignete Entfernungstechniken: Einsatz der richtigen Werkzeuge (Zangen, Fräser, Schleifer, eventuell Funkenerosion oder maschinelle Bearbeitung bei hartnäckigen Stützen) und sorgfältige Handarbeit. Planung des Zugangs in der Entwurfsphase.
4. Porosität (Gas und fehlende Verschmelzung):
- Herausforderung: Im gedruckten Material können sich kleine Hohlräume bilden, die durch eingeschlossenes Gas (Gasporosität) oder unvollständiges Aufschmelzen/Verschmelzen zwischen Schichten oder Scannerspuren (Lack-of-Fusion-Porosität) entstehen. Porosität wirkt wie ein Spannungskonzentrator, der die Ermüdungslebensdauer und die mechanischen Eigenschaften erheblich verringert.
- Strategien zur Schadensbegrenzung:
- Hochwertiges Pulver: Verwendung von Pulver mit kontrollierter Sphärizität, geringem internen Gasgehalt und geeigneter Partikelgrößenverteilung. Die fortschrittlichen Zerstäubungsprozesse von Met3dp’ (Gaszerstäubung, PREP) sind darauf ausgelegt, solche hochwertigen Pulver herzustellen.
- Optimierte Prozessparameter: Sicherstellung der richtigen Energiedichte (Leistung, Geschwindigkeit, Lukenabstand), um die Pulverschichten vollständig zu schmelzen und eingeschlossene Gase entweichen zu lassen. Dies erfordert eine umfassende Prozessentwicklung und -charakterisierung für jede Material-/Maschinenkombination.
- Kontrollierte Atmosphäre: Aufrechterhaltung einer hochreinen Inertgasatmosphäre (Argon oder Stickstoff) oder eines Vakuums (SEBM) zur Vermeidung von Oxidation und Kontamination.
- Heiß-Isostatisches Pressen (HIP): Die effektivste Methode, um verbleibende innere Porosität nach der Herstellung zu beseitigen, das Teil zu verdichten und Defekte zu heilen. Oft obligatorisch für kritische luft- und Raumfahrtmetall AM Teile.
5. Oberflächenrauheit:
- Herausforderung: Vorhandene Oberflächen, insbesondere an Überhängen und vertikalen Wänden, können rauer sein, als es für funktionale Anforderungen wie Abdichtung oder Ermüdungsfestigkeit erforderlich ist.
- Strategien zur Schadensbegrenzung:
- Optimierung der Parameter: Feinabstimmung der Schichtdicke und der Konturscan-Parameter.
- Orientierung aufbauen: Kritische Oberflächen sollten nach Möglichkeit nach oben gerichtet sein.
- Nachbearbeiten: Anwendung geeigneter Endbearbeitungstechniken (Strahlen, Polieren, Bearbeiten usw.) wie im vorherigen Abschnitt beschrieben.
6. Feine Merkmale und dünne Wände erreichen:
- Herausforderung: Aufgrund der Größe des Schmelzbads, der Größe der Pulverpartikel und der Wärmediffusion gibt es eine Grenze für die Mindestgröße der Merkmale und die Wandstärke, die zuverlässig hergestellt werden können. Sensorabdeckungen können aus Gewichtsgründen dünne Wände oder kleine, komplizierte Details für die Montage von Sensoren erfordern.
- Strategien zur Schadensbegrenzung:
- Einhaltung der Designregeln: Befolgung der vom Hersteller empfohlenen Mindestmerkmalsgrößen für das gewählte Verfahren (LPBF bietet im Allgemeinen eine feinere Auflösung als SEBM).
- Prozessauswahl: Auswahl des für die erforderliche Auflösung am besten geeigneten AM-Verfahrens.
- Sorgfältige Parameterabstimmung: Für feine Merkmale können spezifische Parameter entwickelt werden, manchmal auf Kosten der Baugeschwindigkeit.
Partnerschaften für den Erfolg:
Die Bewältigung dieser Herausforderungen erfordert fundierte Kenntnisse in den Bereichen Materialwissenschaft, Prozessphysik, Simulation und Qualitätskontrolle. Eine Partnerschaft mit einem erfahrenen anbieter von Metall-AM-Lösungen wie Met3dp ist entscheidend. Wir bringen:
- Prozess-Know-how: Jahrzehntelange Erfahrung in der Optimierung von SEBM und anderen AM-Prozessen für Materialien wie Ti-6Al-4V und 316L.
- Erweiterte Ausrüstung: Verwendung von zuverlässigen, branchenführenden Druckern, die für gleichbleibende Ergebnisse sorgen.
- Materialkontrolle: Eigene Herstellung von hochwertigen Pulvern, die für AM zugeschnitten sind.
- Technische Unterstützung: Unterstützung bei DFAM, Simulation und Fehlersuche während des gesamten Projektlebenszyklus.
Durch das Erkennen potenzieller Hürden und die Nutzung von Expertenpartnerschaften können Luft- und Raumfahrtunternehmen Metall-AM zur Herstellung robuster, leistungsstarker Raketensensorabdeckungen einsetzen.
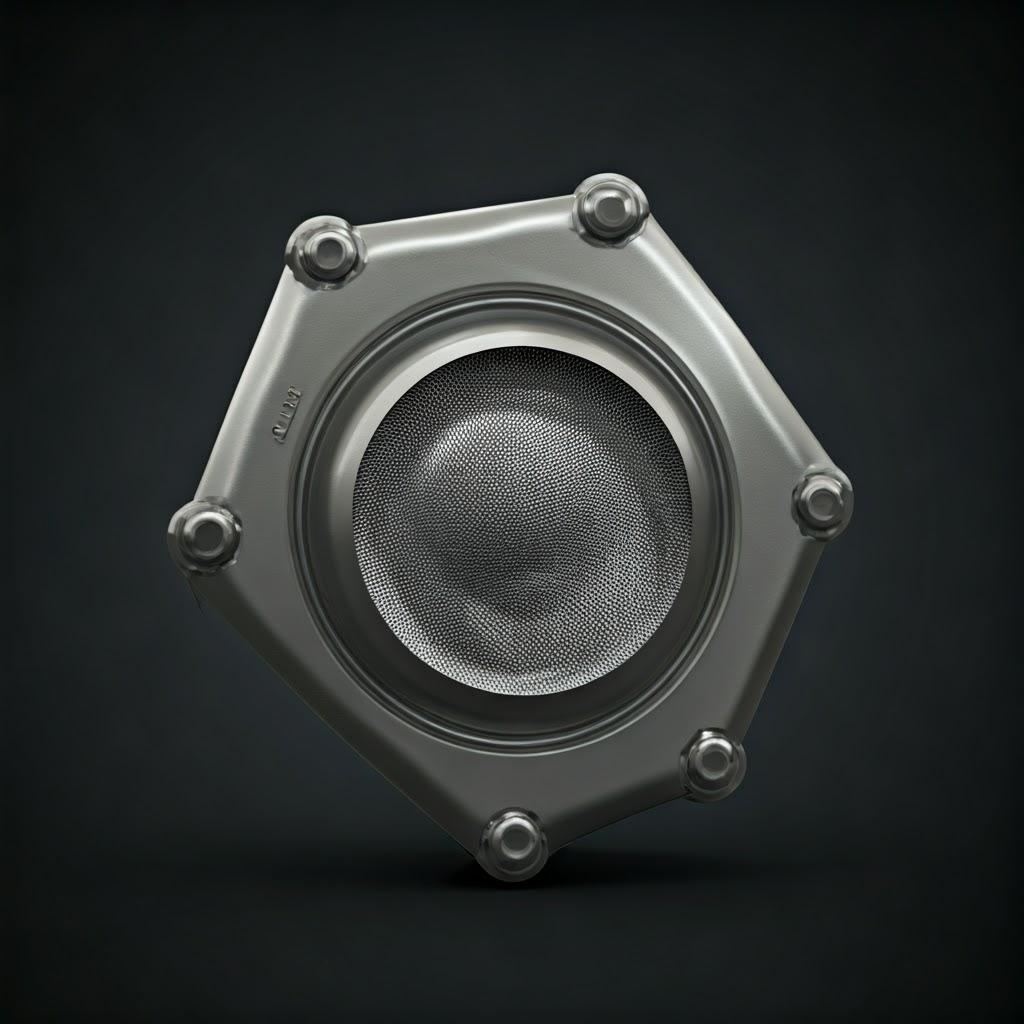
Strategische Beschaffung: Die Wahl des richtigen Metall-AM-Partners für die Lieferung von Raketenkomponenten
Die Auswahl eines Fertigungspartners für kritische Luft- und Raumfahrtkomponenten wie Raketensensorabdeckungen ist eine Entscheidung von erheblichem Gewicht. Die Qualität, Zuverlässigkeit und Leistung dieser Teile hängt in hohem Maße von den Fähigkeiten und dem Fachwissen des gewählten Lieferanten ab. Sich einfach für den günstigsten Bieter oder den Anbieter mit der schnellsten Vorlaufzeit zu entscheiden, kann im anspruchsvollen Luft- und Raumfahrtsektor inakzeptable Risiken mit sich bringen. Strategische Beschaffung erfordert einen gründlichen Evaluierungsprozess zur Identifizierung eines partner für die additive Fertigung von Metallen - nicht nur ein Anbieter - der durchgängig einsatzbereite Komponenten liefern und als Erweiterung Ihres technischen Teams fungieren kann.
Schlüsselkriterien für die Bewertung von Metall-AM-Lieferanten für die Luft- und Raumfahrt:
- Erfahrung in der Luft- und Raumfahrt & Zertifizierungen:
- Erfolgsbilanz: Hat der Lieferant nachweislich Erfahrung in der Herstellung von Teilen für die Luft- und Raumfahrt oder für Verteidigungsanwendungen? Kann er relevante Fallstudien oder Referenzen vorlegen?
- Zertifizierungen: AS9100-Zertifizierung ist von größter Bedeutung. Diese Norm baut auf der ISO 9001 auf und fügt spezifische Anforderungen für das Qualitätsmanagement in der Luft-, Raumfahrt- und Verteidigungsindustrie hinzu. Die Einhaltung dieser Norm weist auf ein robustes, auf die Anforderungen der Luft- und Raumfahrt zugeschnittenes QMS hin. Andere Zertifizierungen (NADCAP für spezielle Prozesse wie Wärmebehandlung oder ZfP) können je nach dem erforderlichen Umfang ebenfalls relevant sein.
- Technisches Fachwissen & Technische Unterstützung:
- Werkstoffkunde: Tiefes Verständnis der spezifizierten Materialien (Ti-6Al-4V, 316L) in ihrem AM-verarbeiteten Zustand, einschließlich Mikrostruktur, mechanische Eigenschaften und geeignete Nachbearbeitung.
- Prozesswissen: Fachwissen über die spezifischen AM-Technologien (SEBM, LPBF), einschließlich der Optimierung der Parameter für Dichte, Genauigkeit und Oberflächengüte.
- DFAM-Fähigkeit: Fähigkeit, konstruktives Feedback zu Entwürfen zu geben, Optimierungen für die additive Fertigung vorzuschlagen und an der Erreichung von Gewichtsreduzierungs- oder Leistungszielen mitzuarbeiten.
- Simulationsfähigkeiten: Einsatz von Wärme- und Prozesssimulationswerkzeugen zur Vorhersage und Minderung von Verformungen und Spannungen sowie zur Optimierung von Stützstrategien.
- Ausrüstungskapazitäten & Kapazität:
- Technologische Übereinstimmung: Verwenden sie die entsprechenden AM-Systeme (z. B. SEBM für bestimmte Ti64-Leistungen, LPBF für feine Merkmale) mit gut gewarteten, kalibrierten Maschinen?
- Bauvolumen: Können ihre Maschinen die Größe der erforderlichen Sensorabdeckungen aufnehmen?
- Materielle Widmung: Gibt es für empfindliche Materialien wie Titan spezielle Maschinen für bestimmte Legierungen, um Kreuzkontaminationen zu vermeiden?
- Kapazität & Redundanz: Verfügen sie über ausreichende Maschinenkapazitäten, um Fristen einzuhalten und möglicherweise die Produktion zu erhöhen? Gibt es eine Redundanz für den Fall eines Maschinenausfalls?
- Kontrolle der Materialqualität:
- Pulverbeschaffung und -handhabung: Strenge Kontrollen bei Beschaffung, Prüfung, Lagerung, Handhabung und Recycling von Metallpulvern, um Reinheit, Konsistenz und Rückverfolgbarkeit zu gewährleisten. Die Kontrolle der Kontamination ist entscheidend.
- Rückverfolgbarkeit: Rückverfolgbarkeit der für bestimmte Teile verwendeten Pulverchargen bis zu ihrem Ursprung und ihren Prüfzertifikaten.
- Robustes Qualitätsmanagementsystem (QMS):
- Dokumentation: Klare, dokumentierte Verfahren für alle Phasen: Auftragsprüfung, Bauvorbereitung, Maschinenbetrieb, Nachbearbeitung, Inspektion und Versand.
- Prozesskontrolle: Prozessbegleitende Überwachung und Datenprotokollierung, um sicherzustellen, dass die Bauprozesse gemäß den validierten Parametern ablaufen.
- Inspektion und Prüfung: Kalibrierung von Messgeräten (CMM, Scanner) und Einführung von NDT-Verfahren (visuell, DPT, CT).
- Umgang mit Abweichungen: Ein definierter Prozess zur Identifizierung, Dokumentation und Behebung von Teilen oder Prozessen, die nicht den Spezifikationen entsprechen.
- Umfassendes Post-Processing:
- In-House vs. Partner: Beherrscht der Lieferant alle erforderlichen Nachbearbeitungsschritte (Spannungsabbau, HIP, Bearbeitung, Endbearbeitung, zerstörungsfreie Prüfung) entweder intern oder über qualifizierte, geprüfte Partner? Sorgen Sie für eine nahtlose Integration und eine durchgängige Qualitätskontrolle.
- Kommunikation & Projektleitung:
- Transparenz: Klare Kommunikation in Bezug auf Fähigkeiten, Zeitpläne, Kosten und potenzielle Herausforderungen.
- Reaktionsfähigkeit: Engagierte Ansprechpartner und zeitnahe Antworten auf Anfragen und technische Fragen.
Warum eine Partnerschaft mit Met3dp?
Met3dp verkörpert die Qualitäten eines strategischen partner für additive Fertigung in der Luft- und Raumfahrt. Wir haben unseren Hauptsitz in Qingdao, China, und bieten an:
- Jahrzehntelanges kollektives Fachwissen: Unser Team verfügt über fundierte Kenntnisse in den Bereichen Metall-AM, Materialwissenschaft und Luft- und Raumfahrtanwendungen.
- Branchenführende Ausrüstung: Wir verwenden fortschrittliche SEBM-Drucker, die für große Produktionsvolumina, Genauigkeit und Zuverlässigkeit bekannt sind und sich ideal für robuste Luft- und Raumfahrtkomponenten eignen.
- Fortschrittliche Pulvertechnologie: Unser einzigartiger Vorteil liegt in unserem eigene Herstellung von hochwertigen Metallpulvern unter Verwendung von Gaszerstäubung und PREP-Technologien. Dies gewährleistet optimale Pulvereigenschaften (Sphärizität, Reinheit, Fließfähigkeit) und eine lückenlose Rückverfolgbarkeit des Materials und bildet die Grundlage für hochwertige gedruckte Teile.
- Umfassende Lösungen: Wir bieten eine durchgängige Unterstützung, von der DFAM-Beratung und dem Druck bis hin zum Nachbearbeitungsmanagement und der Qualitätssicherung.
- Engagement für Qualität: Wir arbeiten mit strengen Qualitätskontrollprotokollen, die auf anspruchsvolle Branchen zugeschnitten sind.
Die Wahl des richtigen Partners mindert das Risiko und maximiert die Vorteile von AM. Setzen Sie sich frühzeitig mit potenziellen Lieferanten in Verbindung, führen Sie bei Bedarf gründliche Audits durch und geben Sie nachgewiesenem Fachwissen und Qualitätssystemen den Vorrang vor reinen Kosten oder Geschwindigkeit. Besuchen Sie https://met3dp.com/ um mehr über unsere Möglichkeiten zu erfahren.
Einblicke in die Beschaffung: Kostenfaktoren & Schätzung der Vorlaufzeit für AM-Sensorabdeckungen
Für Beschaffungsmanager und Ingenieure, die ein Budget für Projekte in der Luft- und Raumfahrt planen, ist es wichtig, die Kostenstruktur und die typischen Vorlaufzeiten im Zusammenhang mit der additiven Fertigung von Metallen zu verstehen. Anders als bei der traditionellen Fertigung, bei der die Werkzeugkosten häufig die Anfangskosten dominieren, wird die Preisgestaltung bei AM von anderen Faktoren bestimmt. Transparenz seitens des AM-Dienstleisters ist der Schlüssel zu einer genauen Budgetierung und Terminplanung.
Die wichtigsten Kostentreiber für AM-Sensorabdeckungen aus Metall:
- Materialkosten:
- Lautstärke: Berechnet auf der Grundlage des endgültigen Teilevolumens plus das Volumen der benötigten Stützstrukturen. Ein effizientes Design (DFAM) mit möglichst wenigen Stützen trägt zur Kostensenkung bei.
- Materialtyp: Es besteht ein erheblicher Kostenunterschied zwischen Metallpulvern in Luft- und Raumfahrtqualität. Ti-6Al-4V-Pulver ist erheblich teurer als 316L-Pulver aus rostfreiem Stahl. Exotische Superlegierungen würden sogar noch höher sein.
- Qualität des Pulvers: Hochreine, hochsphärische Pulver, die für AM optimiert sind, kosten in der Regel einen Aufpreis, sind aber für konsistente, hochwertige Ergebnisse erforderlich.
- AM Machine Time:
- Bauhöhe: Dies ist oft der Hauptfaktor für die Druckzeit. Höhere Teile brauchen länger, unabhängig davon, wie viele auf der Platte verschachtelt sind.
- Teilvolumen und Dichte: Größere oder dichtere Teile erfordern mehr Materialauftrag und möglicherweise längere Scanzeiten.
- Komplexität: Bei komplizierten Merkmalen kann eine geringere Scangeschwindigkeit für die Genauigkeit erforderlich sein.
- Maschinentarif: Ein Stundensatz für die Nutzung der industriellen AM-Maschine, der je nach Maschinentyp, Größe und Anbieter variiert.
- Einrichtung & Arbeit:
- Vorbereitung des Baus: Zeit, die benötigt wird, um das CAD-Modell zu zerschneiden, Stützstrukturen zu generieren, das Baulayout (Verschachtelung) zu planen und die Maschine vorzubereiten. Diese Kosten werden häufig über die Anzahl der Teile in einer Fertigung amortisiert.
- Betrieb der Maschine: Überwachung des Build-Prozesses.
- Nachbearbeitungsarbeiten: Das Herausbrechen von Teilen, das Entfernen von Halterungen, die grundlegende Endbearbeitung und die Inspektion können mit erheblichem Arbeitsaufwand verbunden sein. Die Entfernung komplexer Halterungen ist ein wichtiger Faktor für die Arbeitskosten.
- Nachbearbeitungskosten:
- Wärmebehandlung (Spannungsarmglühen, Glühen): Erfordert Ofenzeit und kontrollierte Atmosphären (Vakuum/Inertgas).
- Heiß-Isostatisches Pressen (HIP): Ein spezielles Verfahren, das häufig ausgelagert wird und erhebliche Kosten pro Zyklus verursacht (die Kosten pro Teil sind niedriger, wenn eine vollständige HIP-Charge ausgeführt werden kann).
- Bearbeitungen: Die Kosten hängen von der Komplexität der zu bearbeitenden Merkmale, der Anzahl der erforderlichen Aufspannungen und der geforderten Toleranz/Fertigkeit ab.
- Oberflächenveredelung: Perlstrahlen, Trommeln, Polieren - die Kosten variieren je nach Methode und gewünschtem Ergebnis.
- ZfP und Inspektion: Kosten im Zusammenhang mit CMM-Zeit, CT-Scanning (kann teuer sein), DPT, usw.
- Nicht wiederkehrendes Engineering (NRE):
- Wenn für ein neues Teil umfangreiche Konstruktionsunterstützung, Simulationsarbeit oder eine spezielle Prozessentwicklung erforderlich ist, können diese Vorlaufkosten für die Konstruktion separat angegeben werden.
Schätzung der Vorlaufzeiten:
Die Vorlaufzeit ist die Gesamtzeit von der Auftragserteilung bis zur Auslieferung der Teile. Sie wird von mehreren Faktoren beeinflusst:
- Druckzeit: Die Dauer kann von Stunden bis zu mehreren Tagen reichen und hängt in erster Linie von der Körpergröße ab.
- Zeit in der Warteschlange: Der aktuelle Maschinenbestand des Lieferanten. Zeiten hoher Nachfrage können die Vorlaufzeiten verlängern.
- Nachbearbeiten: Jeder Schritt kostet Zeit:
- Wärmebehandlung: In der Regel 1-2 Tage (einschließlich Ofenzeit und Abkühlung).
- HIP: Kann sich um 3-7 Tage verlängern (einschließlich des Versands zum/vom HIP-Anbieter, wenn er ausgelagert wurde, plus Zykluszeit).
- Bearbeitungen: Sehr variabel, je nach Komplexität zwischen 1 Tag und mehreren Wochen.
- Entfernung der Stütze/Fertigstellung: Kann je nach Komplexität zwischen Stunden und Tagen dauern.
- Inspektion: in der Regel 1-3 Tage.
- Versand: Zeit für den Transport zum Standort des Kunden.
Typische Vorlaufzeitspannen (Schätzungen):
- Prototypen (1-5 Einheiten): Häufig 1 bis 4 Wochender Preis hängt stark von der Komplexität, dem Material und der erforderlichen Nachbearbeitung ab (insbesondere wenn HIP oder eine umfangreiche Bearbeitung erforderlich ist). Eilige Optionen können gegen einen Aufpreis verfügbar sein.
- Kleinserienproduktion (5-50 Einheiten): Typischerweise 3 bis 8 Wochen oder mehrdie von der Dosiereffizienz, der Maschinenverfügbarkeit und dem gesamten Nachbearbeitungsprozess beeinflusst wird.
Tipps für die Beschaffung:
- Detaillierte Kostenvoranschläge anfordern: Bitten Sie um Angebote, in denen die Kosten aufgeschlüsselt sind (Material, Maschinenzeit, Nachbearbeitungsschritte), um mehr Transparenz zu schaffen.
- Vorlaufzeiten klären: Besprechen Sie die Erwartungen an die Durchlaufzeit im Vorfeld und machen Sie sich die Auswirkungen der verschiedenen Nachbearbeitungsmöglichkeiten bewusst.
- Optimieren Sie das Design: Arbeiten Sie mit den Ingenieuren und dem AM-Anbieter zusammen, um das Design der Abdeckung für die Fertigung zu optimieren (z. B. Minimierung der Stützen, Verringerung der Bauhöhe, falls möglich), um die Kosten zu senken und die Produktion zu beschleunigen.
- Bandpausen: Erkundigen Sie sich nach möglichen Preisnachlässen für größere Losgrößen, da sich die Rüstkosten amortisieren und die Maschinen/Nachbearbeitung effizienter genutzt werden können.
Die Kenntnis dieser Kosten- und Zeitfaktoren ermöglicht eine genauere Projektplanung und Budgetierung bei der Einbeziehung von metallabdeckungen für AM-Sensoren in Luft- und Raumfahrtprogramme.
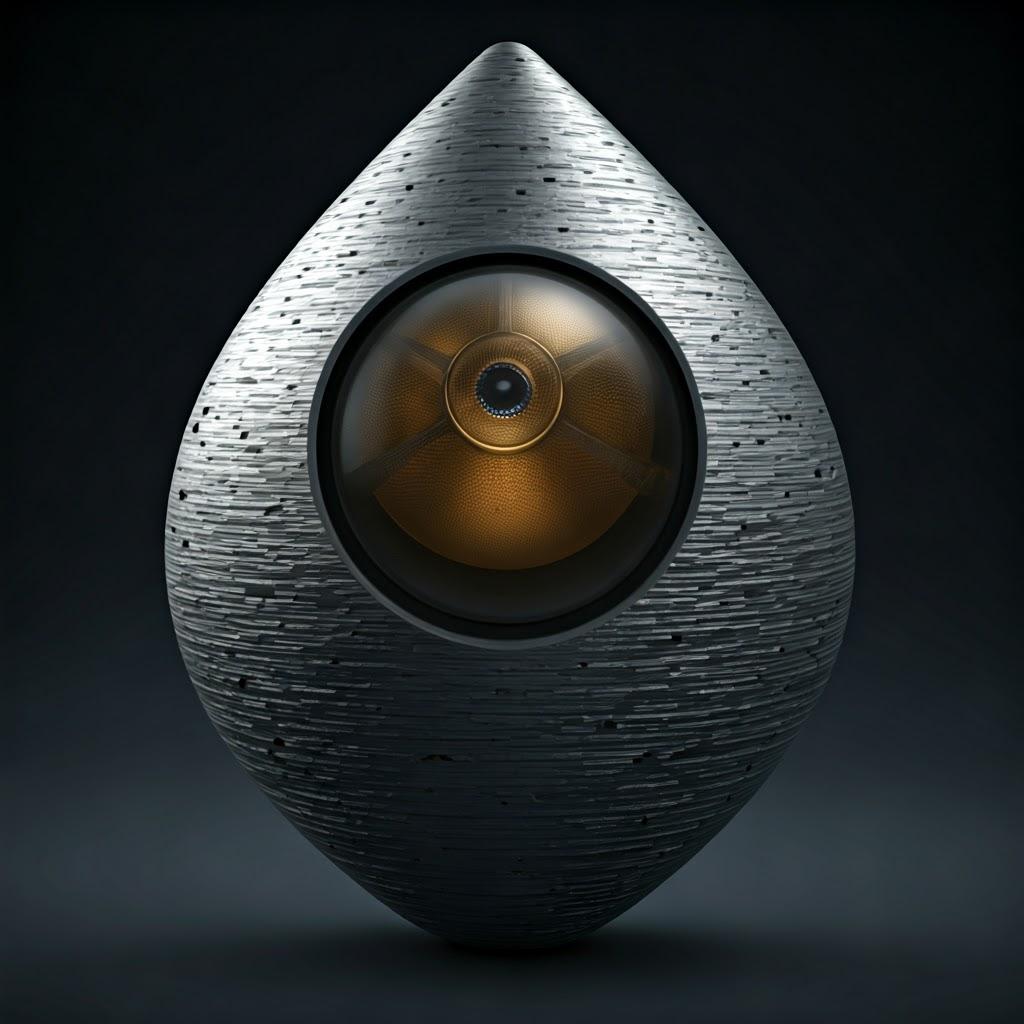
Häufig gestellte Fragen (FAQ) zu AM-Raketensensorabdeckungen aus Metall
Hier finden Sie Antworten auf einige häufig gestellte Fragen von Ingenieuren und Beschaffungsexperten, die eine additive Fertigung von Raketensensorabdeckungen in Betracht ziehen:
F1: Wie lange ist die typische Vorlaufzeit für einen Prototyp im Vergleich zu einer Produktionsserie von AM-Sensorabdeckungen?
A1: Die Vorlaufzeiten variieren je nach Komplexität, Größe, Material, erforderlicher Nachbearbeitung und Warteschlange der Lieferanten erheblich.
- Prototypen (1-5 Einheiten): Erwarten Sie etwa 1 bis 4 Wochen. Dies ermöglicht das Bedrucken, die Entfernung grundlegender Stützen, den Spannungsabbau und die erste Prüfung. Die Vorlaufzeiten verlängern sich erheblich, wenn eine HIP-Behandlung oder eine komplexe mehrachsige CNC-Bearbeitung für den Prototyp erforderlich ist.
- Kleinserienproduktion (5-50 Einheiten): Typischerweise reicht die Bandbreite von 3 bis 8 Wochen oder mehr. Dies berücksichtigt eine mögliche Chargenbildung aus Effizienzgründen, die gesamte Palette der Nachbearbeitungsschritte (einschließlich potenziell längerer Prozesse wie HIP und umfangreicher Bearbeitung, falls für alle Teile erforderlich) sowie eine umfassende Qualitätssicherung für die gesamte Charge. Bestätigen Sie immer die spezifischen Vorlaufzeiten mit dem von Ihnen gewählten Lieferanten auf der Grundlage des endgültigen Teiledesigns und der Anforderungen.
F2: Können Metall-AM-Abdeckungen die strengen Qualitäts- und Rückverfolgbarkeitsanforderungen der Luft- und Raumfahrtindustrie erfüllen?
A2: Ja, absolutdies erfordert jedoch die Zusammenarbeit mit einem fähigen und zertifizierten Lieferanten. Die Einhaltung von Luft- und Raumfahrtstandards erfordert:
- Robustes Qualitätsmanagementsystem: Lieferanten zertifiziert nach AS9100 haben QMS-Prozesse speziell für die Luft- und Raumfahrt demonstriert.
- Prozesskontrolle: Strenge Kontrolle und Validierung der Druckparameter für gleichbleibende Materialeigenschaften.
- Rückverfolgbarkeit von Materialien: Dokumentierte Verfolgung von Metallpulverchargen von der Beschaffung bis zur Produktion. Die eigene Pulverproduktion von Met3dp’ bietet hier eine hervorragende Kontrolle.
- Umfassende ZfP: Einsatz von Methoden wie CT-Scanning, CMM und DPT zur Überprüfung der internen Integrität und Maßhaltigkeit.
- Dokumentation: Bereitstellung von Materialzertifizierungen, Prüfberichten und Konformitätsbescheinigungen. Wenn diese Elemente vorhanden sind, können Metall-AM-Teile die Qualitätsanforderungen für viele anspruchsvolle Luft- und Raumfahrtanwendungen erfüllen und sogar übertreffen.
F3: Wie hoch sind die Kosten für eine AM-Sensorabdeckung aus Metall im Vergleich zu einer durch CNC-Bearbeitung hergestellten Abschirmung?
A3: Darauf gibt es keine einfache Antwort, da sie stark von mehreren Faktoren abhängt:
- Komplexität: Für hochkomplexe Geometrien mit inneren Merkmalen, Hinterschneidungen oder topologieoptimierten Konstruktionen, AM ist oft kostengünstigerdie Bearbeitung von Werkstücken, insbesondere bei kleinen Stückzahlen, ist sehr einfach, da keine komplexen Bearbeitungsvorrichtungen oder Werkzeuge benötigt werden.
- Lautstärke: Für sehr einfache Abdeckungen, die in größeren Mengen hergestellt werden, CNC-Bearbeitung von Knüppeln oder Gussteilen kann billiger sein aufgrund der schnelleren Zykluszeiten pro Teil nach dem Einrichten. Allerdings entfallen bei AM die mit dem Gießen verbundenen Werkzeugkosten.
- Material: Die Materialkosten pro Volumeneinheit sind ähnlich, aber das bessere Verhältnis zwischen Einkauf und Fertigung (weniger Abfall) kann bei teuren Materialien wie Ti-6Al-4V von Vorteil sein, obwohl die Pulverkosten höher sein können als bei Stangenmaterial.
- Gewichtseinsparung: Wenn AM eine erhebliche Gewichtsreduzierung (durch Topologieoptimierung/Gitter) ermöglicht, könnten die höheren Herstellungskosten pro Teil durch niedrigere Startkosten oder eine verbesserte Fahrzeugleistung ausgeglichen werden - ein entscheidender Faktor bei den Gesamtbetriebskosten in der Luft- und Raumfahrt.
- Vorlaufzeit: Die Fähigkeit von AM’s, Teile schnell und ohne Werkzeuge herzustellen, kann zu erheblichen Kosteneinsparungen in Bezug auf die Projektlaufzeiten und die Beschleunigung der Entwicklung führen. Schlussfolgerung: Holen Sie Angebote für beide Verfahren auf der Grundlage Ihres spezifischen Designs, Volumens und Materials ein, um eine fundierte Entscheidung zu treffen. AM ist oft die bessere Wahl, wenn es um Komplexität, individuelle Anpassung und kleine bis mittlere Stückzahlen geht, bei denen die einzigartigen Fähigkeiten des Verfahrens von Vorteil sind.
F4: Welche Informationen werden benötigt, um ein genaues Angebot für den Druck einer Sensorabdeckung zu erhalten?
A4: Um einen genauen Kostenvoranschlag zu erstellen, benötigt ein Metall-AM-Dienstleister wie Met3dp in der Regel:
- 3D-CAD-Modell: Ein hochwertiges Modell in einem Standardformat (z. B. STEP, Parasolid).
- Spezifikation des Materials: Eindeutig definierter Werkstoff (z. B. Ti-6Al-4V Grade 5, Edelstahl 316L) und spezifische Norm, die er erfüllen muss (z. B. ASTM, AMS).
- Menge: Anzahl der benötigten Teile (für Prototypen und potenzielle Produktionsläufe).
- Technische Zeichnung (empfohlen): Eine 2D-Zeichnung, in der kritische Abmessungen, Toleranzen (unter Verwendung von GD&T), erforderliche Oberflächengüten für bestimmte Merkmale und alle Gewinde oder Schnittstellen definiert sind.
- Nachbearbeitungsanforderungen: Geben Sie die erforderlichen Schritte an, wie Wärmebehandlung (Spannungsarmglühen, HIP, Glühen), Bearbeitungsanforderungen, Zielvorgaben für die Oberflächengüte (Ra-Werte) und eventuell erforderliche Beschichtungen.
- Prüfung und Zertifizierung: Geben Sie alle erforderlichen zerstörungsfreien Prüfungen (CT, DPT), Maßprüfungsberichte (CMM), Materialprüfungen oder Zertifizierungsunterlagen (z. B. Konformitätsbescheinigung) an. Die Bereitstellung umfassender Informationen im Vorfeld ermöglicht es dem Lieferanten, ein präzises Angebot und eine realistische Schätzung der Vorlaufzeit zu erstellen.
Schlussfolgerung: Die Zukunft des Sensorschutzes mit metalladditiver Fertigung einleiten
Die Reise einer Rakete von der Startrampe in die Umlaufbahn oder in den Weltraum ist ein Zeugnis für Präzisionsmechanik, die unter extremen Bedingungen arbeitet. Der Schutz der empfindlichen Instrumente, die während dieser Reise Daten leiten, überwachen und sammeln, ist von größter Bedeutung raketensensorabdeckungen sind die unbesungenen Helden, die diese wichtige Aufgabe erfüllen. Wie wir erforscht haben, Additive Fertigung von Metall (AM) hat sich zu einer transformativen Technologie für die Herstellung dieser wesentlichen Komponenten entwickelt und bietet überzeugende Vorteile gegenüber herkömmlichen Verfahren.
Durch den Einsatz von AM erhalten Luft- und Raumfahrtingenieure eine noch nie dagewesene Gestaltungsfreiheit um Abdeckungen zu schaffen, die nicht nur schützend, sondern auch hoch optimiert sind. Techniken wie Topologieoptimierung und Gitterstrukturen ermöglichen erhebliche Gewichtsreduzierung - ein wichtiger Faktor in der Luft- und Raumfahrt - ohne Beeinträchtigung der strukturellen Integrität. Die Möglichkeit, mehrere Teile in einer einzigen gedruckten Komponente zusammenzufassen, verringert die Komplexität, die Montagezeit und potenzielle Fehlerquellen. Außerdem beschleunigt AM die Entwicklungszyklen durch schneller Prototypenbau und erleichtert die Verwendung fortschrittlicher, leistungsstarker Materialien wie Ti-6Al-4V und Edelstahl 316Lsie eignen sich perfekt für die rauen thermischen, mechanischen und korrosiven Bedingungen in der Raketentechnik.
Die Verwirklichung dieser Vorteile erfordert jedoch einen ganzheitlichen Ansatz. Der Erfolg hängt ab von der Umsetzung Entwurf für additive Fertigung (DFAM) grundsätze, Verständnis und Planung für wesentliche Nachbearbeitungsschritte (wie z. B. Wärmebehandlung, HIP, Bearbeitung und NDT) und die Vorwegnahme potenzieller Herstellungsverfahren Herausforderungen. Am wichtigsten ist, dass sie fordert strategisches Sourcing - die Auswahl eines Metall-AM-Partners mit nachgewiesener Erfahrung in der Luft- und Raumfahrt, robusten Qualitätssystemen (AS9100), fortschrittlichen Anlagen, überlegener Materialkontrolle und der technischen Fähigkeit, einsatzbereite Teile zu liefern.
Met3dp ist bereit, dieser Partner zu sein. Mit unserer hochmodernen SEBM-Drucktechnologie, der hauseigenen Produktion von hochreinen Metallpulvern und unserer jahrzehntelangen Erfahrung bieten wir umfassende Lösungen, die auf die anspruchsvollen Anforderungen der Luft- und Raumfahrtindustrie zugeschnitten sind. Wir arbeiten vom Entwurf bis zur Endkontrolle mit unseren Kunden zusammen und stellen sicher, dass die von uns produzierten AM-Sensorabdeckungen aus Metall den höchsten Anforderungen an Qualität, Zuverlässigkeit und Leistung entsprechen.
Die additive Fertigung von Metallen ist nicht mehr nur ein Werkzeug für den Prototypenbau, sondern eine praktikable, leistungsstarke Produktionsmethode, die die nächste Generation von Innovationen in der Luft- und Raumfahrt ermöglicht. Für Sensorabdeckungen und zahllose andere kritische Komponenten bietet die additive Fertigung einen Weg zu leichteren, stärkeren, komplexeren und schneller entwickelten Teilen, die die Zukunft des Sensorschutzes und der Weltraumforschung einläuten.
Möchten Sie herausfinden, wie Metall-AM Ihre Raketensensorabdeckungen oder andere kritische Luft- und Raumfahrtkomponenten optimieren kann? Kontaktieren Sie Met3dp noch heute, um Ihre Projektanforderungen mit unserem Expertenteam zu besprechen.
Teilen auf
MET3DP Technology Co., LTD ist ein führender Anbieter von additiven Fertigungslösungen mit Hauptsitz in Qingdao, China. Unser Unternehmen ist spezialisiert auf 3D-Druckgeräte und Hochleistungsmetallpulver für industrielle Anwendungen.
Fragen Sie an, um den besten Preis und eine maßgeschneiderte Lösung für Ihr Unternehmen zu erhalten!
Verwandte Artikel
Über Met3DP
Aktuelles Update
Unser Produkt
KONTAKT US
Haben Sie Fragen? Senden Sie uns jetzt eine Nachricht! Wir werden Ihre Anfrage mit einem ganzen Team nach Erhalt Ihrer Nachricht bearbeiten.
Holen Sie sich Metal3DP's
Produkt-Broschüre
Erhalten Sie die neuesten Produkte und Preislisten
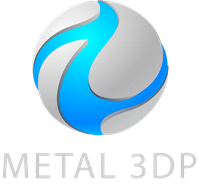
Metallpulver für 3D-Druck und additive Fertigung