Raketentriebwerksklappen durch additiv hergestellte Superlegierungen
Inhaltsübersicht
Einleitung: Die kritische Rolle der Leitbleche im modernen Raketenantrieb
Das unermüdliche Streben nach höherer Leistung, Effizienz und Zuverlässigkeit von Raketenantriebssystemen treibt die Luft- und Raumfahrtindustrie zu ständigen Innovationen an. Von interplanetaren Missionen bis hin zu kommerziellen Satellitenstarts und Verteidigungsanwendungen sind die Anforderungen an Raketentriebwerke immens. Diese komplexen Maschinen arbeiten unter extremen Temperatur-, Druck- und Vibrationsbedingungen und erfordern Komponenten, die so konstruiert und gefertigt sind, dass sie auch den härtesten Bedingungen standhalten. Zu den kritischen Elementen in der Schubkammer eines Raketentriebwerks gehören die Leitbleche - scheinbar einfache Komponenten, die eine äußerst wichtige Rolle für eine stabile und effiziente Verbrennung spielen.
Umlenkbleche für Raketentriebwerke sind strategisch platzierte Strukturen, oft innerhalb der Einspritzfrontplatte oder der Brennkammer, die in erster Linie dazu dienen, Verbrennungsinstabilitäten zu unterdrücken. Diese Instabilitäten, die sich in Form von hochfrequenten Druckschwankungen äußern, können die Triebwerksleistung stark beeinträchtigen, kritische Bauteile beschädigen und sogar zu einem katastrophalen Ausfall führen. Durch die Unterbrechung der Ausbreitungswege akustischer Wellen und die Veränderung der Strömungsdynamik wirken Leitbleche als wichtige Dämpfer, die die gleichmäßige, kontrollierte Freisetzung von Energie für den Antrieb von Raumfahrzeugen gewährleisten. Darüber hinaus können Leitbleche zum Wärmemanagement beitragen, indem sie empfindliche Komponenten wie die Einspritzdüsen vor der starken Verbrennungshitze schützen und das Mischungsverhältnis von Treibstoff und Oxidationsmittel beeinflussen. Da die Hersteller von Trägerraketen und die Raumfahrtagenturen die Grenzen der Leistungsfähigkeit immer weiter hinausschieben, sind die Entwicklung und Herstellung von hochentwickelten, hochbelastbaren Leitblechen von größter Bedeutung. Bisher war die Herstellung dieser Komponenten mit komplexen Bearbeitungs-, Füge- und Montageverfahren verbunden, was die Designmöglichkeiten oft einschränkte und zu erheblichen Vorlaufzeiten und Kosten führte. Doch mit dem Aufkommen der 3D-Druck von Metalloder additive Fertigung (AM), insbesondere unter Verwendung von Hochleistungssuperlegierungen, revolutioniert die Art und Weise, wie Leitbleche für Raketentriebwerke konzipiert, entworfen und hergestellt werden. Diese Technologie eröffnet eine nie dagewesene Designfreiheit und ermöglicht die Herstellung komplizierter interner Kühlkanäle, komplexer Geometrien, die für die akustische Dämpfung optimiert sind, und konsolidierter Bauteildesigns, die zuvor unmöglich oder unpraktisch zu fertigen waren. Unternehmen, die auf der Suche nach zuverlässigen Zulieferern und Herstellern von Luft- und Raumfahrtkomponenten sind, wenden sich zunehmend an AM-Spezialisten, die in der Lage sind, anspruchsvolle Superlegierungen zu verarbeiten und strenge Qualitätsanforderungen zu erfüllen. Dieser Wandel bedeutet einen großen Sprung nach vorn in der Antriebstechnologie und verspricht leichtere, effizientere und zuverlässigere Raketentriebwerke für die Zukunft der Weltraumforschung und -nutzung. Dieser Artikel befasst sich mit den Besonderheiten der additiven Fertigung, insbesondere mit fortschrittlichen Superlegierungen wie IN718 und Haynes 282, für die Herstellung von Hochleistungs-Raketentriebwerksbehältern und untersucht die damit verbundenen Anwendungen, Vorteile, Materialüberlegungen und Fertigungsnuancen.
Das Problem der Verbrennungsinstabilität hat die Entwicklung von Raketentriebwerken seit ihren Anfängen belastet. Bei den frühen Flüssigkeitsraketentriebwerken, insbesondere bei den größeren, traten häufig zerstörerische Schwingungen auf, die die Ingenieure verblüfften. Das Verständnis und die Abschwächung dieser Instabilitäten wurden zu einem der Hauptschwerpunkte der Forschung und Entwicklung. Leitbleche erwiesen sich als eine der wirksamsten passiven Kontrollvorrichtungen. Ihre Wirksamkeit liegt in ihrer Fähigkeit, in die Rückkopplungsschleife einzugreifen, die die Verbrennungsinstabilitäten aufrechterhält. Diese Schleife beinhaltet in der Regel eine Kopplung zwischen dem Verbrennungsprozess (Schwankungen der Wärmefreisetzung) und der Kammerakustik (Druckwellen). Die durch die Verbrennung erzeugten Druckwellen können sich durch die Kammer ausbreiten, von den Oberflächen reflektiert werden und in die Verbrennungszone zurückkehren, was die weitere Wärmefreisetzung auf eine Weise beeinflusst, die die Schwingungen verstärkt. Schallwände sorgen für akustische Impedanzfehlanpassungen und Dämpfung, wodurch diese Resonanzkopplung effektiv unterbrochen wird. Sie erreichen dies durch mehrere Mechanismen:
- Akustische Dämpfung: Schallwände dienen als physische Barrieren, die akustische Energie absorbieren, streuen und ableiten. Ihre Geometrie, Platzierung und innere Struktur (falls vorhanden) werden sorgfältig entworfen, um bestimmte Instabilitätsmodi (Frequenzen und Formen) zu erreichen, die durch Computational Fluid Dynamics (CFD) und akustische Modellierung vorhergesagt werden.
- Flussunterbrechung: Indem sie in die Brennkammer hineinragen oder die Einspritzfläche segmentieren, verändern Leitbleche die Strömungsmuster von Treibstoffen und Verbrennungsgasen. Dadurch können die organisierten Strukturen von Wirbeln oder Rezirkulationszonen unterbrochen werden, die ansonsten zur Instabilitätskopplung beitragen könnten.
- Kompartimentierung: Bei einigen Konstruktionen, insbesondere auf der Einspritzseite, bilden Leitbleche Kammern, die verschiedene Verbrennungsbereiche isolieren. Dadurch wird verhindert, dass sich Instabilitäten, die in einer Zone entstehen, leicht ausbreiten und in der gesamten Kammer verstärken.
Abgesehen von der Stabilitätskontrolle erfüllen Schalldämpfer oft sekundäre, aber wichtige Aufgaben:
- Thermischer Schutz: Die Frontplatten von Injektoren sind einem starken Wärmestrom ausgesetzt. Schikanen können Teile der Frontplatte abschirmen oder interne Kühlkanäle (die durch AM ermöglicht werden) einbauen, um die Temperaturen zu steuern und Überhitzung oder Erosion zu verhindern.
- Mixing Enhancement/Control: Die Anordnung und Form der Leitbleche kann die Vermischung von Brennstoff- und Oxidationsmittelströmen in der Nähe der Einspritzdüse beeinflussen, was sich möglicherweise auf die Verbrennungseffizienz und -leistung auswirkt, obwohl die Stabilität ihre Hauptfunktion bleibt.
Die traditionellen Fertigungsverfahren für Schallwände, wie die Bearbeitung aus einem Block oder das Gießen mit anschließender Bearbeitung und Schweißen/Löten, stoßen an erhebliche Grenzen, insbesondere da die Schallwandkonstruktionen immer komplexer werden, um höhere Motorleistungen zu erzielen:
- Geometrische Zwänge: Die Bearbeitung komplizierter interner Merkmale wie gekrümmter Kühlkanäle oder feiner akustischer Dämpfungsstrukturen ist extrem schwierig, kostspielig und manchmal sogar unmöglich. Komplexe Hinterschneidungen und innere Hohlräume sind oft nicht herstellbar.
- Materialabfälle: Subtraktive Verfahren wie die spanabhebende Bearbeitung können zu erheblichem Materialabfall führen, vor allem wenn man mit großen Knüppeln aus teuren Superlegierungen beginnt.
- Fügeprozesse: Der Zusammenbau von Ablenkblechen aus mehreren maschinell bearbeiteten oder gegossenen Teilen führt zu potenziellen Schwachstellen an den Verbindungsstellen (Schweißnähte oder Lötstellen), die extremen Belastungen und Temperaturgradienten standhalten müssen. Diese Verbindungen erfordern eine strenge Inspektion und können das Wärmemanagement erschweren.
- Vorlaufzeiten: Der mehrstufige Charakter der traditionellen Fertigung mit Werkzeugbau, Gießen, Bearbeitung, Fügen und Prüfung führt zu langen Vorlaufzeiten, die schnelle Design-Iterationen und Entwicklungszyklen behindern, die in der Luft- und Raumfahrtindustrie entscheidend sind.
Die additive Fertigung geht direkt auf diese Einschränkungen ein. Durch den schichtweisen Aufbau von Leitblechen aus Metallpulver bietet AM:
- Unerreichte Gestaltungsfreiheit: Sie ermöglichen komplexe interne Kanäle, optimierte Topologien, Gitterstrukturen zur Gewichtsreduzierung und verbesserten Dämpfung sowie konforme Kühlkanäle, die den Oberflächen der Schallwand eng folgen.
- Teil Konsolidierung: So können mehrere Komponenten einer Schallwand als ein einziges, monolithisches Teil gedruckt werden, wodurch Verbindungen entfallen, das Gewicht reduziert und die Montage vereinfacht wird.
- Geringerer Materialabfall: Die Verwendung von Material nur dort, wo es benötigt wird, macht AM zu einer nachhaltigeren Option, insbesondere bei teuren Superlegierungen.
- Beschleunigte Entwicklung: Erleichterung des Rapid Prototyping und der Konstruktionswiederholungen, wodurch der Entwicklungszyklus für neue Motorkomponenten erheblich verkürzt wird.
Die Integration der additiven Fertigung in die Produktion kritischer Komponenten wie Raketentriebwerksklappen stellt einen Paradigmenwechsel dar und ermöglicht es den Ingenieuren der Luft- und Raumfahrt, Antriebssysteme zu entwerfen und zu bauen, die robuster, effizienter und leistungsfähiger sind als je zuvor. In dem Maße, in dem spezialisierte AM-Anbieter wie Met3dp die Prozesse für Superlegierungen verfeinern und eine gleichbleibende Qualität und Zuverlässigkeit nachweisen, wird der Einsatz von AM für solch anspruchsvolle Anwendungen weiter zunehmen und die Grenzen der Raumfahrttechnologie verschieben. Met3dp, mit Hauptsitz in Qingdao, China, nutzt sein Fachwissen im Bereich der fortschrittlichen Pulverherstellung und der Metallverarbeitung 3D-Druck systeme, um genau diese Art von anspruchsvollen Luft- und Raumfahrtanwendungen zu unterstützen, und bietet hochwertige Superlegierungspulver und Druckdienstleistungen an.
Wozu dienen die Schallwände von Raketentriebwerken? Definition von Funktion und Bedeutung
Leitbleche für Raketentriebwerke sind integrale Bestandteile der Brennkammer oder der Einspritzdüsenbaugruppe, deren Hauptaufgabe darin besteht, die Stabilität und Effizienz des Verbrennungsprozesses zu gewährleisten. Ihre Funktion ist entscheidend, da eine unkontrollierte Verbrennung zum Scheitern der Mission führen kann. Um ihre spezifische Rolle zu verstehen, muss man sich mit der Physik des Raketenantriebs und den Herausforderungen befassen, die mit der Verbrennung großer Treibstoffmengen unter extremen Bedingungen verbunden sind.
Primäre Funktion: Unterdrückung von Verbrennungsinstabilitäten
Der Hauptzweck fast aller Leitbleche für Raketentriebwerke besteht darin, Verbrennungsinstabilitäten zu verhindern oder zu unterdrücken. Dabei handelt es sich um selbsterhaltende Schwankungen des Kammerdrucks, die oft mit Schwankungen der Wärmeabgabe der verbrennenden Treibstoffe einhergehen. Sie können von relativ niederfrequentem Tuckern bis hin zu schädlichem hochfrequentem Kreischen oder Schreien reichen;
- Mechanismus der Instabilität: Stellen Sie sich vereinfacht gesagt einen kleinen, zufälligen Druckanstieg in der Kammer vor. Diese Druckwelle breitet sich aus, wird reflektiert und kehrt möglicherweise in die Verbrennungszone zurück. Wenn sie zu einem Zeitpunkt eintrifft, an dem sie die mehr treibstoff zu verbrennen (z. B. durch Erhöhung der Mischungs- oder Reaktionsraten), erzeugt dies einen noch stärkeren Druckimpuls. Wenn das Timing (die Phase) stimmt, verstärkt sich diese Rückkopplungsschleife und führt zu großflächigen, potenziell zerstörerischen Schwingungen. Die Kammergeometrie, die Treibstoffarten, die Einspritzmethode und die Betriebsbedingungen beeinflussen, welche Frequenzen am anfälligsten für Instabilität sind.
- Wie Baffles eingreifen: Luftleitbleche wirken als Schalldämpfer und Strömungsstörer, um diesen Rückkopplungskreislauf zu unterbrechen.
- Akustische Dämpfung: Sie stellen physikalische Barrieren dar, die die akustischen Verluste innerhalb der Kammer erhöhen. Schallwellen, die von Baffelstrukturen reflektiert werden oder diese passieren, verlieren aufgrund von viskosen Effekten, Wärmeleitung an Oberflächen und geometrischer Streuung Energie. Komplexe interne Strukturen in Schallwänden, die mittels AM hergestellt werden können, lassen sich speziell auf die Dämpfung problematischer Frequenzen abstimmen. Man kann sie sich wie akustische Kacheln in einem Aufnahmestudio vorstellen, die jedoch für eine höllisch energetische Umgebung konzipiert sind.
- Änderung des Strömungsfeldes: Indem sie die Einspritzfläche physisch unterteilen oder in die Kammer hineinragen, verändern Leitbleche die Wege der Treibstoffströme und Verbrennungsgase. Dies kann die Bildung großer, kohärenter Strukturen (wie z. B. Wirbel) verhindern, die sich andernfalls stark mit akustischen Moden verbinden könnten. Sie schotten den Verbrennungsprozess effektiv ab und erschweren es, dass sich lokale Störungen zu kammerweiten Instabilitäten ausweiten.
Arten von Luftleitblechen und ihre Platzierung:
Das spezifische Design und die Position der Leitbleche hängen stark vom Triebwerkstyp (z. B. Zweistoff-Flüssigkeitstriebwerk, Feststoffraketenmotor), den erwarteten spezifischen Instabilitätsmodi und der Gesamtarchitektur des Triebwerks ab. Übliche Typen sind:
- Einspritzdüsen-Stirnwände: Sie sind vielleicht der häufigste Typ in Zweistofftriebwerken für Flüssigkeiten. Sie bestehen häufig aus radialen Speichen oder einem Naben- und Speichenmuster, das direkt auf der Einspritzplatte angebracht ist. Diese Anordnung unterteilt den Einspritzbereich in kleinere Segmente (kuchenförmig oder ringförmig), wodurch die kammerübergreifende Übertragung von Schallwellen eingeschränkt und transversale Instabilitätsmoden unterbrochen werden. Sie können direkt in das Injektordesign integriert oder als separate Komponenten angebracht werden. AM ermöglicht die Einbettung komplizierter Kühlkanäle in diese Leitbleche, um sie und die darunter liegende Injektorfläche zu schützen.
- Akustische Hohlräume/Resonatoren: Manchmal bauen die Konstrukteure anstelle von massiven Leitblechen Hohlräume oder Helmholtz-Resonatoren in die Kammerwände oder die Stirnfläche des Injektors ein. Diese wirken wie abgestimmte Absorber, die bestimmte Resonanzfrequenzen dämpfen. AM ermöglicht die präzise Herstellung dieser komplexen Resonanzgeometrien.
- Kammer-Schallwände: Bei Flüssigkeitsmotoren weniger üblich, aber manchmal verwendet, können dies ringförmige Ringe oder andere Strukturen sein, die weiter unten in der Verbrennungskammer selbst angebracht sind, um Längs- oder Schüttgutinstabilitäten zu stören.
- Schallwände für Feststoffraketenmotoren (SRM): Auch bei SRM kann es zu Instabilitäten kommen, die oft durch Wechselwirkungen zwischen der Gasströmung und der Oberfläche des brennenden Treibstoffs (Treibstoffkorn) verursacht werden. Lamellen oder andere schalldämpferähnliche Strukturen können in das Korndesign oder die Kammerisolierung integriert werden, um akustische Modi zu unterbrechen, obwohl sich die Mechanismen etwas von denen der Flüssigtriebwerke unterscheiden.
Sekundäre Funktionen:
Auch wenn die Stabilität von größter Bedeutung ist, tragen Schalldämpfer zu anderen Aspekten des Motorbetriebs bei:
- Wärmemanagement: Die Stirnflächen der Einspritzdüsen, insbesondere in der Mitte, sind extremen Wärmebelastungen ausgesetzt. Umlenkbleche können Teile der Einspritzdüse physisch abschirmen oder, was bei AM noch effektiver ist, ausgeklügelte interne Kühlkanäle mit Hilfe des Treibstoffflusses (regenerative Kühlung) oder eines separaten Kühlmittelkreislaufs einbauen. Dies verhindert Materialverschleiß und gewährleistet die strukturelle Integrität und die funktionelle Langlebigkeit des Injektors. Die Entwicklung von konformen Kühlkanälen, die den Konturen der Prallplatte genau folgen, was durch AM ermöglicht wird, maximiert die Kühleffizienz.
- Mischungssteuerung: Das Vorhandensein von Leitblechen beeinflusst unweigerlich das lokale Strömungsfeld in der Nähe der Injektoren. Obwohl dies normalerweise nicht ihr primäres Konstruktionsziel ist, kann diese Interaktion die Effizienz der Treibstoffmischung subtil beeinflussen. Die Konstrukteure müssen dies berücksichtigen, um sicherzustellen, dass die Leistungsziele neben den Stabilitätsanforderungen erfüllt werden. Schlecht konstruierte Umlenkbleche können die effiziente Vermischung behindern und zu Leistungseinbußen führen.
- Strukturelle Unterstützung: Bei einigen integrierten Konstruktionen können Umlenkbleche zur strukturellen Verstärkung der Einspritzdüsenfrontplatte selbst dienen.
Bedeutung im Kontext der Luft- und Raumfahrt:
Aufgrund der hohen Anforderungen an die Zuverlässigkeit von Raketentriebwerken, insbesondere für die bemannte Raumfahrt und hochwertige Nutzlasten, ist ein effektives Schalldämpferdesign unverzichtbar.
- Mission Erfolg: Verbrennungsinstabilitäten können zu geringerem Schub, ineffizientem Treibstoffverbrauch, starken Vibrationen, die das Triebwerk oder das Raumfahrzeug beschädigen, und im schlimmsten Fall zur schnellen Zerstörung des Triebwerks führen. Leitbleche sind die wichtigste Schutzmaßnahme gegen diese Fehlfunktionen.
- Förderung der Leistung: In dem Maße, in dem Ingenieure höhere Kammerdrücke und energiereichere Treibstoffe anstreben, um die Triebwerksleistung (Schub und spezifischer Impuls) zu steigern, nimmt die Tendenz zur Instabilität häufig zu. Fortschrittliche Umlenkblechkonstruktionen, die durch AM ermöglicht werden, sind entscheidend, um diese höheren Leistungsniveaus zuverlässig zu erreichen.
- Kosten und Zeitplan: Triebwerksausfälle während der Erprobung oder im Flug sind unglaublich teuer. Robuste Stabilitätsspannen, die durch wirksame Leitbleche gewährleistet werden, verringern das Risiko kostspieliger Rückschläge während der Entwicklung und des Betriebs. Auch wenn die Herstellung der Leitbleche selbst Kosten verursacht, so sind diese im Vergleich zu den Kosten eines Triebwerksausfalls verblasst. Der Einsatz von AM kann die Entwicklungszyklen durch schnellere Iterationen bei der Gestaltung von Leitblechen im Vergleich zu herkömmlichen Methoden verkürzen.
Beschaffungsmanager und -ingenieure, die Komponenten für Luft- und Raumfahrtprojekte beschaffen, müssen sich der kritischen Bedeutung von Leitblechen bewusst sein. Es handelt sich dabei nicht nur um passive Metallteile, sondern um sorgfältig konstruierte Vorrichtungen, die für den sicheren und effektiven Betrieb des gesamten Antriebssystems unerlässlich sind. Die Zusammenarbeit mit Zulieferern, die über fundierte Kenntnisse sowohl in der Werkstoffkunde (insbesondere Superlegierungen) als auch in fortschrittlichen Fertigungstechniken wie AM verfügen, ist von entscheidender Bedeutung. Met3dp mit seinem Schwerpunkt auf Hochleistungsmetallpulvern und industriellen 3D-Drucklösungen passt perfekt zu den Anforderungen von Luft- und Raumfahrtherstellern, die modernste Produktionsmöglichkeiten für Leitbleche suchen. Ihr Verständnis der Materialeigenschaften und der Prozesssteuerung ist entscheidend für die Herstellung von Leitblechen, die den strengen Anforderungen des Raketenantriebs entsprechen.
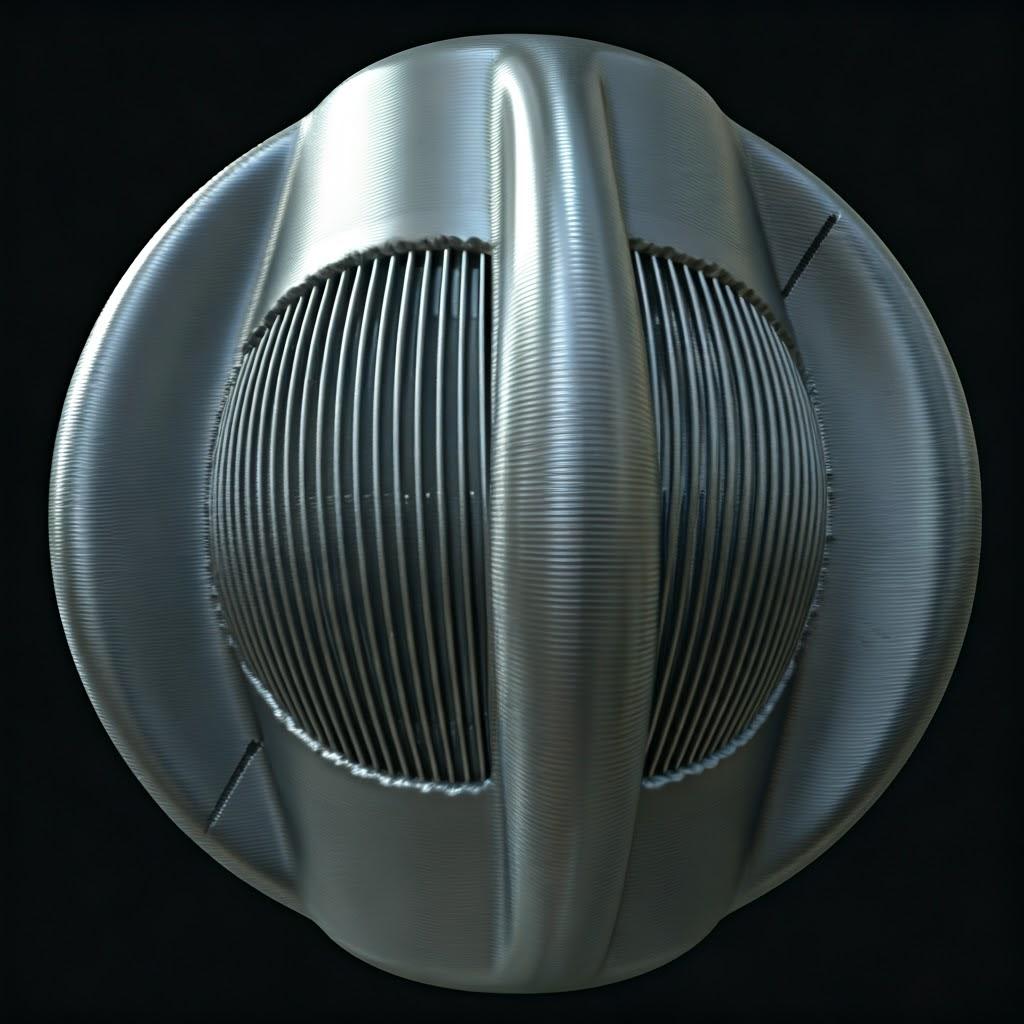
Warum 3D-Metalldruck für Raketentriebwerksschallwände? Vorteile gegenüber konventionellen Methoden
Bei der Entscheidung für die additive Fertigung von Metallen (AM) für kritische Komponenten wie Raketentriebwerksklappen geht es nicht nur darum, Neues zu entdecken, sondern auch um greifbare technische und wirtschaftliche Vorteile, die die Unzulänglichkeiten herkömmlicher Fertigungstechniken (Gießen, Schmieden, Zerspanen, Löten/Schweißen) direkt ausgleichen. Für Luft- und Raumfahrtingenieure und Beschaffungsmanager, die Produktionsmethoden evaluieren, ist das Verständnis dieser Vorteile der Schlüssel zur Nutzung des vollen Potenzials von AM’, insbesondere bei komplexen Geometrien und Hochleistungssuperlegierungen wie IN718 und Haynes 282.
1. Noch nie dagewesene Designfreiheit und geometrische Komplexität:
- Traditionelle Einschränkungen: Die maschinelle Bearbeitung hat mit inneren Merkmalen, Hinterschneidungen und komplexen Kurven zu kämpfen. Stellen Sie sich vor, Sie versuchen, komplizierte, gleichmäßig gekrümmte Kühlkanäle tief im Inneren eines massiven Metallblocks zu bearbeiten. Durch Gießen kann eine gewisse Komplexität erreicht werden, aber oft mangelt es an Präzision und eine Nachbearbeitung ist erforderlich. Das Verbinden mehrerer einfacher Teile führt zu Schwachstellen und erhöht die Komplexität der Montage.
- AM Vorteil: AM baut Teile Schicht für Schicht direkt aus einem 3D-CAD-Modell auf. Dieser grundlegende Unterschied befreit Konstrukteure von vielen traditionellen Fertigungsbeschränkungen.
- Interne Kanäle: AM zeichnet sich durch die Schaffung komplexer interner Kühlkanäle aus, die sich genau an die Form des Ablenkblechs anpassen (konforme Kühlung). Dies ermöglicht ein hocheffizientes Wärmemanagement, das für den Schutz von Leitblechen und Einspritzdüsenflächen vor extremen Temperaturen entscheidend ist. Die Kanäle können gekrümmt verlaufen, einen unterschiedlichen Querschnitt aufweisen und Bereiche erreichen, die mit Bohrern oder Fräsen nicht erreichbar sind.
- Optimierte Topologien: Konstrukteure können Topologieoptimierungssoftware verwenden, um Material aus Bereichen mit geringer Belastung zu entfernen und so leichte, aber dennoch stabile Schallwandstrukturen zu schaffen. Dies führt oft zu organischen, gitterähnlichen Geometrien, die auf herkömmliche Weise nicht bearbeitet werden können, sich aber für AM problemlos eignen. Leichtbau ist in der Luft- und Raumfahrt von entscheidender Bedeutung für die Maximierung der Nutzlastkapazität.
- Akustische Stimmung: Die Geometrie von Schallwänden beeinflusst ihre akustischen Dämpfungseigenschaften erheblich. AM ermöglicht die Schaffung komplizierter innerer Merkmale, Resonanzkammern oder spezifischer Oberflächentexturen, die darauf ausgelegt sind, akustische Energie bei bestimmten Instabilitätsfrequenzen effektiver zu absorbieren oder zu streuen als einfache massive Formen.
- Integrierte Funktionen: Merkmale wie Befestigungspunkte, Sensoranschlüsse oder Strömungsführungen können direkt während des Druckvorgangs in das Leitblech integriert werden, wodurch sich die Anzahl der Teile und die Montageschritte verringern.
2. Teil Konsolidierung:
- Traditioneller Ansatz: Komplexe Schallwandbaugruppen können aus mehreren maschinell bearbeiteten oder gegossenen Teilen bestehen, die präzise eingepasst und verbunden werden müssen (z. B. geschweißt oder gelötet). Jede Verbindung stellt einen potenziellen Fehlerpunkt dar, erfordert eine Inspektion und erhöht das Gewicht und die Montagezeit.
- AM Vorteil: AM ermöglicht den Druck einer gesamten komplexen Schallwandanordnung als einzelnes, monolithisches Bauteil.
- Eliminierung der Gelenke: Dies beseitigt die Risiken, die mit Schweiß- oder Lötarbeiten in Umgebungen mit hoher Belastung und hohen Temperaturen verbunden sind. Monolithische Teile sind strukturell oft überlegen.
- Reduzierte Teileanzahl: Vereinfacht das Bestandsmanagement, die Lieferkettenlogistik und die Motorendmontage.
- Gewichtsreduzierung: Der Wegfall von Verbindungselementen, Flanschen und überlappendem Material, das für die Verbindung benötigt wird, trägt zur Gewichtseinsparung bei.
3. Beschleunigte Entwicklung und Rapid Prototyping:
- Traditionelle Zeitpläne: Die Erstellung von Werkzeugen für Gussstücke oder komplexe Bearbeitungsvorrichtungen erfordert viel Zeit und Investitionen. Bei der Überarbeitung eines Entwurfs werden diese langwierigen Prozesse üblicherweise wiederholt.
- AM Vorteil: AM ist ein werkzeugloser Prozess. Der Weg von einem überarbeiteten CAD-Modell zu einem physischen Prototyp kann oft innerhalb von Tagen oder Wochen statt Monaten zurückgelegt werden.
- Schnellere Iteration: Ingenieure können schnell verschiedene Leitblechgeometrien testen (z. B. unterschiedliche Speichenanzahl, Kanaldesigns, Dämpfungsmerkmale), um die optimale Konfiguration für Stabilität und thermische Leistung zu finden. Diese schnelle Feedbackschleife verkürzt den Motorentwicklungszyklus erheblich.
- Geringere Entwicklungskosten: Einzelne AM-Teile mögen zwar zunächst teuer erscheinen, aber die Möglichkeit, schnell zu iterieren und Werkzeugkosten zu vermeiden, kann die Gesamtkosten des Entwicklungsprogramms drastisch senken.
4. Materialeffizienz und Abfallvermeidung:
- Traditioneller Abfall: Bei der subtraktiven Fertigung, insbesondere bei der Bearbeitung von Knüppeln, können beträchtliche Mengen an Materialabfall (Späne) anfallen. Bei teuren Superlegierungen wie IN718 oder Haynes 282 stellt dieser Abfall einen erheblichen Kostenfaktor dar.
- AM Vorteil: AM ist ein additives Verfahren, bei dem nur das für die Herstellung des Teils benötigte Material sowie einige Stützstrukturen verwendet werden. Zwar sind ein gewisses Pulvermanagement und die Entfernung von Stützstrukturen erforderlich, doch ist die Gesamtmaterialnutzung in der Regel viel höher als bei subtraktiven Verfahren.
- Einsparmaßnahmen: Ein geringerer Rohstoffverbrauch führt direkt zu niedrigeren Komponentenkosten, insbesondere bei den in der Luft- und Raumfahrt üblichen Buy-to-Fly-Verhältnissen.
- Nachhaltigkeit: Weniger Abfallerzeugung trägt zu umweltbewussteren Herstellungspraktiken bei.
5. Eignung für hochleistungsfähige Materialien:
- Herausforderungen bei der Bearbeitung: Superlegierungen wie IN718 und Haynes 282 sind aufgrund ihrer hohen Festigkeit, Zähigkeit und Kaltverfestigungseigenschaften bekanntermaßen schwer zu bearbeiten. Dies führt zu langsamen Bearbeitungsgeschwindigkeiten, schnellem Werkzeugverschleiß und erhöhten Herstellungskosten.
- AM Vorteil: Während das Drucken von Superlegierungen eine Reihe von Herausforderungen mit sich bringt (die eine sorgfältige Prozesskontrolle erfordern), sind AM-Verfahren wie Laser Powder Bed Fusion (L-PBF) und Electron Beam Melting (EBM) gut geeignet, um diese Hochtemperaturmaterialien Schicht für Schicht zu schmelzen und zu verschmelzen.
- Anpassungsfähigkeit der Prozesse: Die AM-Parameter (Laserleistung, Scangeschwindigkeit, Strahlfokus, Schichtdicke, Kammertemperatur) können für bestimmte Superlegierungen genau gesteuert und optimiert werden, um dichte, hochwertige Teile mit den gewünschten Mikrostrukturen und mechanischen Eigenschaften zu erhalten. Unternehmen wie Met3dp sind darauf spezialisiert, diese Parameter mit ihren fortschrittlichen Drucksystemen und hochwertigen Metallpulvern zu optimieren.
Zusammenfassende Vergleichstabelle:
Merkmal | Traditionelle Fertigung (Zerspanung/Gießen/Verbinden) | Additive Fertigung von Metall (AM) | Vorteil von AM für Baffles |
---|---|---|---|
Geometrische Komplexität | Begrenzte, insbesondere interne Funktionen | Hoch, ermöglicht komplexe interne Kanäle, Gitter | Optimierte Kühlung, akustische Dämpfung, Gewichtsreduzierung möglich |
Teil Konsolidierung | Erfordert das Zusammenfügen mehrerer Teile | Ermöglicht monolithische einteilige Konstruktion | Eliminiert Verbindungen (Schwachstellen), reduziert die Anzahl der Teile, vereinfacht die Montage |
Geschwindigkeit der Entwicklung | Langsam (Werkzeugbau, mehrstufiger Prozess) | Schnell (werkzeuglos, direkt vom CAD) | Schnelles Prototyping und Design-Iteration, kürzere Entwicklungszyklen |
Materialabfälle | Hoch (subtraktive Verfahren) | Niedrig (additives Verfahren) | Kosteneinsparungen bei teuren Superlegierungen, mehr Nachhaltigkeit |
Vorlaufzeit | Lang (Werkzeuge, mehrere Arbeitsgänge) | Potenziell kürzer (insbesondere bei komplexen Teilen) | Schnellere Lieferung für Prototypen und potenzielle Kleinserienproduktion |
Handhabung von Superlegierungen | Schwierig und kostspielig zu bearbeiten | Gut geeignet (L-PBF, EBM), erfordert jedoch Fachwissen | Ermöglicht die Verwendung von idealen Hochtemperaturmaterialien ohne extreme Bearbeitungskosten |
Anfängliche Kosten (einfach) | Kann bei sehr einfachen Formen/hohem Volumen niedriger sein | Kann bei einfachen Teilen höher sein, bei komplexen wettbewerbsfähig | Kostengünstig für komplexe Geometrien, Vorteile der Teilekonsolidierung |
Werkzeugkosten | Hoch (Formen, Gesenke, Vorrichtungen) | Keiner | Keine großen Vorabinvestitionen, flexible Produktion |
In Blätter exportieren
Schlussfolgerung für Beschaffung und Technik:
Bei Leitblechen für Raketentriebwerke, wo zunehmend komplexe Geometrien für das Wärmemanagement und die akustische Dämpfung erforderlich sind und wo Hochtemperatur-Superlegierungen unverzichtbar sind, sind die Vorteile der Metall-AM zwingend. Es ermöglicht die Herstellung von Bauteilen, die potenziell leichter, effizienter, zuverlässiger (aufgrund der Konsolidierung der Teile) und schneller zu entwickeln sind als konventionell hergestellte. Während Fachwissen in den Bereichen Prozesskontrolle, Materialwissenschaft und Nachbearbeitung entscheidend ist, ist die Zusammenarbeit mit einem kompetenten AM-Anbieter wie Met3dp, der sowohl fortschrittliche Druckanlagen als auch optimierte hochwertige Metallpulverermöglicht es Luft- und Raumfahrtunternehmen, diese Vorteile voll auszuschöpfen. Der Übergang zu AM für solche kritischen Teile ist nicht nur ein Trend, sondern ein strategischer Schritt zur Verbesserung der Leistungsfähigkeit von Antriebssystemen und der Wettbewerbsfähigkeit im anspruchsvollen Luft- und Raumfahrtsektor.
Materialschwerpunkt: IN718 und Haynes 282 Superlegierungen für extreme Umgebungen
Die Auswahl der Werkstoffe für Raketentriebwerkskomponenten wird durch die außerordentlich raue Betriebsumgebung bestimmt: extreme Temperaturen (oft über 1000°C, im Verbrennungskern möglicherweise bis zu 3000°C), hohe Drücke, starke thermische Wechselbeanspruchung, starke Vibrationen und die Belastung durch korrosive Verbrennungsprodukte. Die Leitbleche von Raketentriebwerken, die sich direkt in oder in der Nähe dieser feindlichen Zone befinden, erfordern Werkstoffe, die unter diesen Bedingungen außergewöhnliche mechanische Eigenschaften und Umweltbeständigkeit aufweisen. Superlegierungen auf Nickelbasis sind die Arbeitspferde für solche Anwendungen, und unter ihnen ragen Inconel 718 (IN718) und Haynes 282 als erstklassige Kandidaten heraus, die sich besonders gut für die additive Fertigung eignen. Die Kenntnis ihrer Eigenschaften ist für Ingenieure, die Ablenkbleche entwerfen, und für Beschaffungsmanager, die Materialien und Fertigungsdienstleistungen beschaffen, von entscheidender Bedeutung.
Was sind Superlegierungen?
Superlegierungen sind metallische Legierungen, in der Regel auf Nickel-, Kobalt- oder Eisenbasis, die sich durch hervorragende mechanische Festigkeit, Kriechbeständigkeit (Verformung unter langfristiger Belastung bei hohen Temperaturen), gute Oberflächenstabilität und außergewöhnliche Korrosions- und Oxidationsbeständigkeit bei hohen Temperaturen (im Allgemeinen über 540 °C oder 1000 °F) auszeichnen. Ihre Leistungsfähigkeit beruht auf einer komplexen Mikrostruktur, die häufig eine kubisch-flächenzentrierte (FCC) Austenitmatrix aufweist, die durch Ausscheidungen (wie Gamma prime γ’ und Gamma double-prime γ”) und festigkeitssteigernde Elemente in fester Lösung verstärkt wird.
Inconel 718 (IN718 / Legierung 718): Das bewährte Arbeitspferd
IN718 ist wohl die am weitesten verbreitete Superlegierung auf Nickelbasis, da sie eine hervorragende Kombination von Eigenschaften, eine gute Verarbeitbarkeit (einschließlich Schweißbarkeit und Druckbarkeit) und relativ niedrigere Kosten im Vergleich zu einigen anderen Hochleistungssuperlegierungen aufweist.
- Zusammensetzung: Vor allem Nickel (Ni), Chrom (Cr), Eisen (Fe), Niob+Tantal (Nb+Ta), Molybdän (Mo), Titan (Ti), Aluminium (Al). Die wesentliche Verstärkung ergibt sich aus der Ausscheidung von γ” (Ni3Nb) und γ’ (Ni3(Al,Ti)) Phasen innerhalb der FCC-Matrix.
- Wichtige Eigenschaften:
- Hohe Festigkeit: Hervorragende Zug-, Streck-, Kriech- und Bruchfestigkeit bis zu etwa 700°C (1300°F). Seine Festigkeit ergibt sich größtenteils aus der Ausscheidung der γ” Phase, die einen speziellen Wärmebehandlungszyklus erfordert.
- Gute Korrosionsbeständigkeit: Der hohe Chromgehalt sorgt für eine gute Oxidations- und Korrosionsbeständigkeit in verschiedenen Umgebungen, einschließlich Verbrennungsatmosphären.
- Ausgezeichnete Schweißbarkeit/Bedruckbarkeit: Im Vergleich zu vielen anderen ausscheidungsgehärteten Superlegierungen weist IN718 eine überragende Beständigkeit gegen Dehnungsrissbildung beim Schweißen oder bei den schichtweisen thermischen Zyklen von AM auf. Dadurch lässt es sich relativ einfach mit L-PBF und EBM verarbeiten, wodurch dichte, rissfreie Teile entstehen.
- Good Fatigue Life: Wichtig für Bauteile, die Schwingungsbelastungen ausgesetzt sind.
- Breite Verfügbarkeit und Datenbank: Über seine Eigenschaften und Verarbeitung liegen umfangreiche Daten vor, die Konstrukteuren und Herstellern Sicherheit geben.
- Überlegungen zur additiven Fertigung:
- IN718 ist eines der ausgereiftesten Materialien für Metall-AM. Optimierte Parameter für L-PBF und EBM sind gut etabliert.
- Erfordert nachgelagerte Wärmebehandlungen (Lösungsglühen und Auslagern), um die gewünschte Mikrostruktur zu entwickeln und optimale mechanische Eigenschaften zu erzielen. Heißisostatisches Pressen (HIP) wird häufig eingesetzt, um verbleibende innere Porosität zu schließen und die Ermüdungseigenschaften weiter zu verbessern.
- Met3dp stellt hochwertiges, gaszerstäubtes IN718-Pulver her, das speziell für AM-Prozesse optimiert ist und eine hohe Sphärizität, eine gute Fließfähigkeit und eine kontrollierte Partikelgrößenverteilung gewährleistet, die für das Erzielen konsistenter, hochdichter Drucke entscheidend sind.
- Beschränkungen: Seine Festigkeit ist zwar ausgezeichnet, nimmt aber oberhalb von 700 °C im Vergleich zu einigen fortschrittlicheren Superlegierungen deutlich ab. Für Bauteile, die noch höheren Dauertemperaturen ausgesetzt sind, könnten Alternativen erforderlich sein.
Haynes 282: Der fortschrittliche Kandidat für höhere Temperaturen
Haynes 282 ist eine Gamma-Prime (γ’) verfestigte Superlegierung der neuesten Generation, die speziell für eine verbesserte Kriechfestigkeit, thermische Stabilität, Verarbeitbarkeit und Schweißbarkeit im Vergleich zu anderen hochfesten Legierungen wie Waspaloy oder R-41 entwickelt wurde und für Anwendungen im Bereich von 650-930°C (1200-1700°F) vorgesehen ist.
- Zusammensetzung: Hauptsächlich Nickel (Ni), Chrom (Cr), Kobalt (Co), Molybdän (Mo), Titan (Ti), Aluminium (Al), mit Zusätzen wie Bor (B) für erhöhte Kriechfestigkeit. Seine Verfestigung hängt stark von der Ausscheidung der γ’ Phase ab.
- Wichtige Eigenschaften:
- Hervorragende Kriechfestigkeit: Bietet eine deutlich bessere Kriechbeständigkeit als IN718 und Waspaloy, insbesondere im Bereich von 750°C – 900°C. Dies ist entscheidend für Bauteile, die bei sehr hohen Temperaturen dauerhaft belastet werden.
- Ausgezeichnete thermische Stabilität: Widersteht der mikrostrukturellen Verschlechterung bei langer Exposition gegenüber hohen Temperaturen.
- Gute Oxidationsbeständigkeit: Vergleichbar oder besser als andere Hochleistungs-Superlegierungen.
- Gute Verarbeitbarkeit: Entwickelt für verbesserte Schweißbarkeit und Widerstandsfähigkeit gegen Dehnungsrissbildung im Vergleich zu ähnlich starken Legierungen wie Waspaloy, wodurch es sich für AM eignet.
- Good Fatigue Life: Behält seine Festigkeit auch bei zyklischer Belastung bei hohen Temperaturen.
- Überlegungen zur additiven Fertigung:
- Die Prozessentwicklung für Haynes 282 ist zwar noch nicht so weit fortgeschritten wie die für IN718 im AM-Bereich, aber sie reift schnell. Das Erreichen optimaler Eigenschaften erfordert eine sorgfältige Kontrolle der AM-Parameter und der Wärmebehandlungen nach der Verarbeitung (Lösungsglühen und mehrstufige Alterung).
- Seine gute Schweißbarkeit führt zu einer relativ guten Bedruckbarkeit, auch wenn möglicherweise eine strengere Prozesskontrolle als bei IN718 erforderlich ist, um Eigenspannungen zu bewältigen und Fehler zu vermeiden.
- Die Verfügbarkeit von hochwertigem Haynes 282-Pulver, das für AM geeignet ist, ist entscheidend. Anbieter, die sich auf fortschrittliche Pulverproduktion konzentrieren, wie Met3dp, die Gaszerstäubung und PREP-Technologien einsetzen, sind für die Bereitstellung von Pulvern mit der erforderlichen Reinheit, Sphärizität und Partikelgrößenverteilung für anspruchsvolle Anwendungen unerlässlich.
- Anwendung Nische: Ideal für Ablenkbleche oder andere Motorkomponenten, die konstant bei Temperaturen betrieben werden, bei denen die Kriechfestigkeit von IN718’ marginal wird, um die Leistungsgrenzen weiter zu verschieben.
Gründe für die Materialauswahl bei Baffles:
Die Wahl zwischen IN718 und Haynes 282 für ein bestimmtes Raketentriebwerk hängt von einer detaillierten Analyse der Betriebsbedingungen ab:
- Spitzentemperaturen und anhaltende Temperaturen: Wenn die Betriebstemperaturen konstant über ~700-750°C liegen, insbesondere bei erheblicher mechanischer Belastung (Druckunterschiede, Vibrationen), ist die überragende Kriechfestigkeit von Haynes 282’ sehr vorteilhaft.
- Komplexität und Druckbarkeit: IN718 hat derzeit ein etablierteres und potenziell nachsichtigeres Verarbeitungsfenster für AM, das für extrem komplexe Geometrien, bei denen die Minimierung von Druckfehlern von größter Bedeutung ist, bevorzugt werden könnte, vorausgesetzt, die Eigenschaften sind ausreichend.
- Kosten: IN718 ist im Allgemeinen preiswerter als Haynes 282, sowohl bei den Rohstoffkosten als auch möglicherweise bei der Verarbeitungsreife. Wenn IN718 die Leistungsanforderungen erfüllt, kann es die wirtschaftlichere Wahl sein.
- Fähigkeit der Lieferanten: Die Fähigkeit des gewählten AM-Dienstleisters, die gewählte Legierung zuverlässig zu verarbeiten, ist entscheidend. Dazu gehören validierte Prozessparameter, geeignete Nachbearbeitungsmöglichkeiten (Vakuumöfen für die Wärmebehandlung, HIP) und eine strenge Qualitätskontrolle.
Met3dp’s Rolle bei der Materialbereitstellung:
Ein Unternehmen wie Met3dp spielt eine entscheidende Rolle, wenn es darum geht, die Verwendung dieser fortschrittlichen Materialien zu ermöglichen. Ihre Fähigkeiten sind entscheidend für die Grundlage des AM-Prozesses:
- Fortschrittliche Pulverproduktion: Durch den Einsatz von branchenführenden Techniken wie der Vakuum-Induktionsschmelz-Gaszerstäubung (VIGA) und dem Plasma-Rotations-Elektroden-Verfahren (PREP) kann Met3dp Superlegierungspulver (einschließlich IN718 und möglicherweise Haynes 282 oder kundenspezifische Varianten) mit produzieren:
- Hohe Reinheit: Minimierung von Verunreinigungen, die die Materialeigenschaften beeinträchtigen könnten.
- Hohe Sphärizität: Gewährleistung einer guten Fließfähigkeit des Pulvers in AM-Maschinen, was zu einer gleichmäßigen Schichtverteilung und einem konsistenten Schmelzbadverhalten führt.
- Kontrollierte Partikelgrößenverteilung (PSD): Optimierung des PSD für hohe Packungsdichte und vorhersehbare Schmelzeigenschaften.
- Niedriger Satellitengehalt: Verringerung von Problemen im Zusammenhang mit der Ausbreitung von Pulver und möglichen Defekten.
- Sachkenntnis: Dank jahrzehntelanger Erfahrung in der Metall-AM kennt Met3dp die Feinheiten des Drucks von anspruchsvollen Materialien wie Superlegierungen und kann bei der Materialauswahl und Prozessoptimierung helfen.
- Integrierte Lösungen: Durch das Angebot von hochwertigen Pulvern und fortschrittlichen Drucksystemen (wie den SEBM-Druckern, die für die Verarbeitung von Hochtemperaturlegierungen und die Reduzierung von Eigenspannungen bekannt sind) bietet Met3dp eine umfassende Lösung für Hersteller in der Luft- und Raumfahrt, die AM für kritische Komponenten wie Leitbleche einsetzen möchten.
Zusammenfassend lässt sich sagen, dass IN718 und Haynes 282 eine ausgezeichnete Materialwahl für additiv gefertigte Raketentriebwerksleitbleche darstellen, da sie die erforderliche Hochtemperaturfestigkeit und Umweltbeständigkeit bieten. IN718 ist eine bewährte, zuverlässige und kostengünstige Lösung für viele Anwendungen, während Haynes 282 die Temperaturbeständigkeit für anspruchsvollere Szenarien noch weiter erhöht. Der Erfolg der Herstellung von Leitblechen aus diesen Materialien mittels AM hängt in hohem Maße von der Qualität des Eingangspulvers und dem Fachwissen des Fertigungspartners ab, was die Bedeutung spezialisierter Lieferanten in der Lieferkette der Luft- und Raumfahrtindustrie unterstreicht. Quellen und verwandte Inhalte
Design für additive Fertigung (DfAM): Optimierung von Schikanen für den 3D-Druck
Der Übergang von herkömmlichen Fertigungsparadigmen zur additiven Fertigung (AM) erfordert mehr als die einfache Konvertierung einer vorhandenen CAD-Datei. Um die Vorteile des 3D-Metalldrucks für komplexe Komponenten wie die Schallwände von Raketentriebwerken wirklich nutzen zu können, müssen die Ingenieure das Design for Additive Manufacturing (DfAM) anwenden. Bei DfAM handelt es sich um eine Methode, bei der Teile so konstruiert werden, dass sie die einzigartigen Fähigkeiten von AM-Verfahren wie Laser Powder Bed Fusion (L-PBF) und Electron Beam Melting (EBM) nutzen und deren Beschränkungen berücksichtigen. Die Anwendung der DfAM-Prinzipien auf die Leitbleche von Raketentriebwerken kann zu erheblichen Leistungsverbesserungen (Wärmemanagement, akustische Dämpfung), Gewichtsreduzierung und Fertigungseffizienz führen. Die Zusammenarbeit mit einem erfahrenen AM-Dienstleister, der die Feinheiten der verschiedenen Druckverfahrenist oft entscheidend für die erfolgreiche Umsetzung von DfAM.
Die wichtigsten DfAM-Prinzipien für Raketentriebwerksschallwände:
- Nutzung geometrischer Freiheiten zur Funktionsverbesserung:
- Konforme Kühlkanäle: Dies ist eine der leistungsfähigsten Anwendungen von AM für thermisch belastete Bauteile. Anstelle von geraden Bohrungen ermöglicht AM, dass die Kühlkanäle präzise den komplexen Konturen der Umlenkflächen folgen und einen gleichmäßigen Abstand zu den heißen Verbrennungsgasen einhalten.
- Überlegungen zum Design: Der Kanaldurchmesser (typischerweise >0,5-1 mm für die Reinigbarkeit), das Seitenverhältnis, minimale Biegeradien, glatte Übergänge und ein möglichst stützenfreier Druck sind entscheidend. CFD-Analysen werden eingesetzt, um die Kanalwege für eine maximale Wärmeabfuhr dort zu optimieren, wo sie am meisten benötigt wird.
- Nutzen: Erheblich verbesserte Kühleffizienz, die zu niedrigeren Temperaturen auf der Oberfläche der Ablenkbleche und einer längeren Lebensdauer der Komponenten führt und möglicherweise höhere Motorbetriebstemperaturen oder die Verwendung von Materialien mit etwas niedrigeren Temperaturgrenzen ermöglicht.
- Optimierte akustische Dämpfung Merkmale: Einfache massive Schallwände bieten eine gewisse Dämpfung, aber AM ermöglicht weitaus ausgefeiltere Designs.
- Gitterförmige Strukturen: Der Einbau interner Gitter- oder Kreiselstrukturen kann die Oberfläche innerhalb der Schallwand drastisch vergrößern und so die Ableitung von Schallenergie durch viskose Effekte verbessern. Die Dichte und der Zelltyp des Gitters können im gesamten Bauteil abgestuft werden, um bestimmte Frequenzen zu erreichen oder bei Bedarf strukturelle Unterstützung zu bieten.
- Resonanzkammern: Der Entwurf interner Helmholtz-Resonatoren oder komplexer Hohlraumnetzwerke, die auf bestimmte problematische Instabilitätsfrequenzen abgestimmt sind, kann eine sehr gezielte akustische Dämpfung bieten.
- Nutzen: Effektivere Unterdrückung von Verbrennungsinstabilitäten über einen größeren Bereich von Betriebsbedingungen, was zu einer stabileren und zuverlässigeren Motorleistung führt.
- Optimierung der Fließwege: Die Form des Leitblechs beeinflusst die lokale Treibstoffmischung und die Gasströmung. AM ermöglicht aerodynamisch optimierte Formen, die bei Bedarf Merkmale wie Strömungsgleichrichter oder kontrollierte Turbulenzgeneratoren enthalten können, die direkt in die Prallplattenstruktur integriert sind.
- Konforme Kühlkanäle: Dies ist eine der leistungsfähigsten Anwendungen von AM für thermisch belastete Bauteile. Anstelle von geraden Bohrungen ermöglicht AM, dass die Kühlkanäle präzise den komplexen Konturen der Umlenkflächen folgen und einen gleichmäßigen Abstand zu den heißen Verbrennungsgasen einhalten.
- Teil Konsolidierung:
- Strategie: Identifizieren Sie Schallwandbaugruppen, die zuvor aus mehreren gelöteten oder geschweißten Komponenten bestanden. Gestalten Sie sie als ein einziges, monolithisches AM-Teil neu.
- Erwägungen: Sicherstellen, dass das konsolidierte Design mittels AM herstellbar ist (z. B. Zugang zur Pulverentfernung aus internen Hohlräumen). Analysieren Sie Spannungskonzentrationen, um sicherzustellen, dass das monolithische Design robust ist.
- Nutzen: Eliminiert Verbindungsfehler, reduziert das Gewicht, vereinfacht die Montage, verkürzt die Lieferkette und verbessert die strukturelle Integrität.
- Gewichtsreduzierung durch Topologie-Optimierung:
- Strategie: Verwenden Sie die Finite-Elemente-Analyse (FEA), um die Spannungsverteilung innerhalb der Schallwand unter Betriebslasten (Druck, Vibration, thermische Belastung) zu verstehen. Einsatz von Topologie-Optimierungssoftware, um systematisch Material aus spannungsarmen Bereichen zu entfernen und gleichzeitig die strukturelle Integrität und funktionale Oberflächen zu erhalten.
- Ergebnis: Häufig entstehen organische, lastpfadoptimierte Strukturen, die deutlich leichter sind als herkömmliche Konstruktionen. Diese komplexen Formen sind ideal für AM geeignet.
- Nutzen: Ein geringeres Gewicht der Komponenten ist in der Luft- und Raumfahrt von entscheidender Bedeutung, um die Nutzlastkapazität zu erhöhen und die Startkosten zu senken.
- Design für Herstellbarkeit (AM Constraints):
- Minimierung der Stützstruktur: Stützstrukturen sind bei L-PBF und EBM oft notwendig, um das Teil auf der Bauplatte zu verankern, überhängende Merkmale zu stützen und Wärme abzuleiten. Stützstrukturen verbrauchen jedoch zusätzliches Material, verlängern die Druckzeit, müssen entfernt werden (was insbesondere bei internen Kanälen schwierig sein kann) und können die Oberflächenqualität beeinträchtigen.
- Techniken: Richten Sie das Teil strategisch auf der Bauplatte aus, um Überstände zu minimieren. Verwenden Sie selbsttragende Winkel (typischerweise >40-45° von der Horizontalen für viele Prozesse/Materialien, obwohl dies variiert). Entwerfen Sie interne Kanäle mit rautenförmigem oder tropfenförmigem Querschnitt anstelle von kreisförmig, um sie selbsttragend zu machen. Verwendung von Opfermerkmalen oder Strukturen, die für einen leichteren Abbruch ausgelegt sind.
- Mindestgröße und Wanddicke des Elements: AM-Prozesse haben Grenzen bei den kleinsten Merkmalen, die sie zuverlässig herstellen können. Zu dünne Wände können sich verziehen oder nicht richtig aufgelöst werden. Typische Mindestwandstärken liegen oft im Bereich von 0,3-0,5 mm, hängen jedoch stark von der jeweiligen Maschine, dem Material und der Feature-Geometrie ab.
- Entfernung von Puder: Bei Konstruktionen mit inneren Hohlräumen oder komplexen Kanälen ist darauf zu achten, dass geeignete Öffnungen vorhanden sind, um nicht verschmolzenes Pulver nach dem Bau zu entfernen. Eingeschlossenes Pulver erhöht das Gewicht und kann nachteilig sein. Berücksichtigen Sie Vibrations- oder Luftströmungswege für die Pulverabfuhr.
- Wärmemanagement während des Baus: Sehr große oder dichte Teile können erheblichen thermischen Stress verursachen. DfAM kann die Konstruktion von Reliefs oder die Optimierung des Baulayouts beinhalten, um Verformungen und Verzerrungen zu minimieren. EBM mit seiner Hochtemperatur-Bauumgebung reduziert von Natur aus thermische Gradienten und Eigenspannungen im Vergleich zu L-PBF.
- Minimierung der Stützstruktur: Stützstrukturen sind bei L-PBF und EBM oft notwendig, um das Teil auf der Bauplatte zu verankern, überhängende Merkmale zu stützen und Wärme abzuleiten. Stützstrukturen verbrauchen jedoch zusätzliches Material, verlängern die Druckzeit, müssen entfernt werden (was insbesondere bei internen Kanälen schwierig sein kann) und können die Oberflächenqualität beeinträchtigen.
Überlegungen zum DfAM-Workflow:
- Enge Zusammenarbeit: Effektives DfAM erfordert eine enge Zusammenarbeit zwischen Konstrukteuren (die die funktionalen Anforderungen verstehen) und AM-Spezialisten (die die Möglichkeiten und Grenzen des Verfahrens kennen). Anbieter wie Met3dp, die über umfassendes Fachwissen in Bezug auf Materialien und Druckverfahren verfügen, können in der Entwurfsphase einen unschätzbaren Beitrag leisten.
- Simulationsgestützter Entwurf: Der Einsatz von CFD für die Wärme- und Strömungsanalyse, FEA für die Struktur- und Spannungsanalyse und die Simulation des AM-Prozesses zur Vorhersage potenzieller Probleme wie Verformung oder Überhitzung während der Herstellung wird dringend empfohlen.
- Iterativer Ansatz: DfAM ist häufig ein iterativer Prozess. Die ersten Entwürfe werden auf ihre Herstellbarkeit und Leistung geprüft und dann auf der Grundlage von Simulationsergebnissen oder Rückmeldungen des AM-Anbieters verfeinert. Die Rapid-Prototyping-Fähigkeit von AM erleichtert diesen iterativen Kreislauf.
Durch die durchdachte Anwendung der DfAM-Prinzipien können Ingenieure über die einfache Nachbildung herkömmlich konstruierter Leitbleche mit AM hinausgehen und stattdessen Komponenten der nächsten Generation schaffen, die eine bessere Leistung, ein geringeres Gewicht und eine höhere Zuverlässigkeit bieten und so das transformative Potenzial der additiven Fertigung in der Luft- und Raumfahrttechnik voll ausschöpfen.
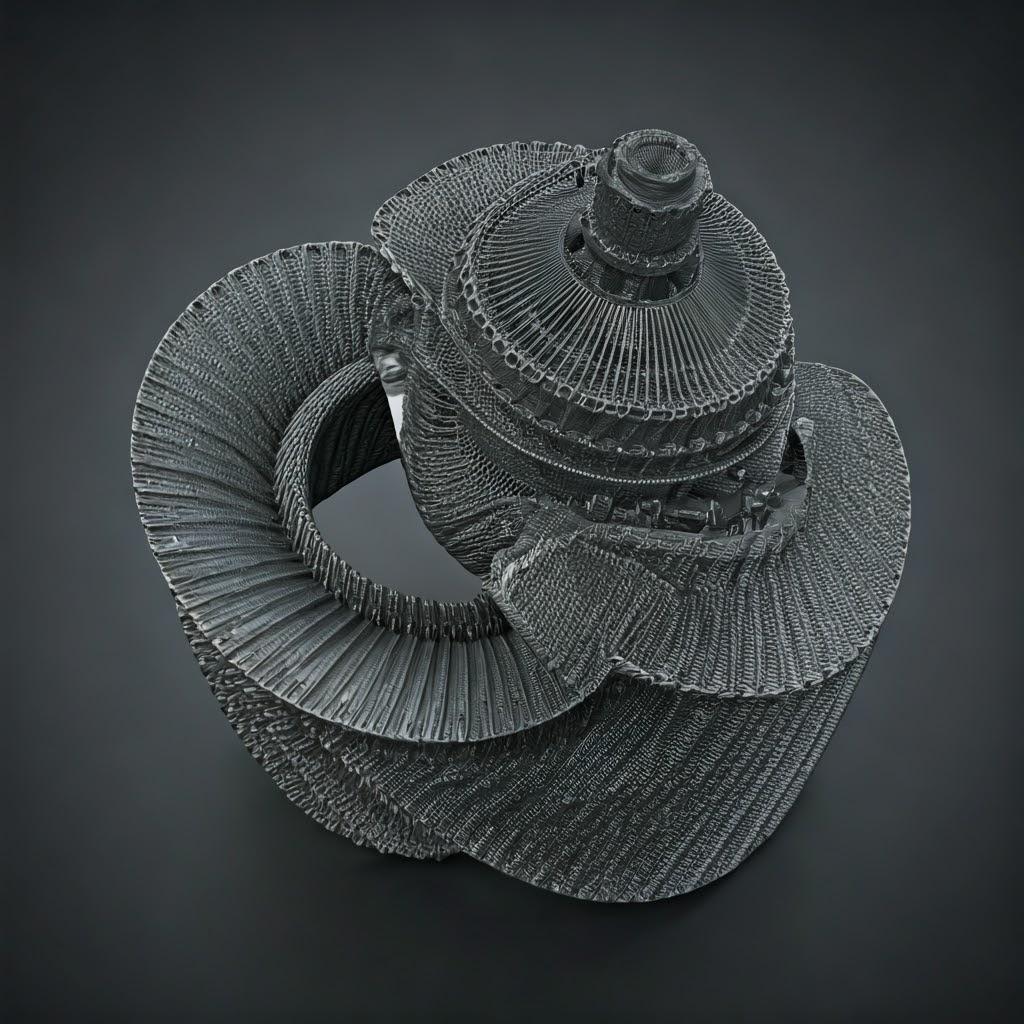
Erreichbare Toleranzen, Oberflächengüte und Maßgenauigkeit bei AM-Baffles
Obwohl die additive Fertigung eine beispiellose Designfreiheit bietet, ist es für Ingenieure und Beschaffungsmanager von entscheidender Bedeutung, realistische Erwartungen in Bezug auf die erreichbaren Toleranzen, die Oberflächenbeschaffenheit und die allgemeine Maßgenauigkeit von AM-produzierten Komponenten zu haben, insbesondere bei kritischen Anwendungen wie Raketentriebwerksleitblechen aus Superlegierungen. Diese Faktoren wirken sich direkt auf die Passform, die Abdichtung, die Strömungsdynamik, die thermische Leistung und die Notwendigkeit nachfolgender Nachbearbeitungsschritte aus. Die spezifischen Ergebnisse hängen stark vom gewählten AM-Prozess (L-PBF vs. EBM), dem Material (IN718, Haynes 282), der Maschinenkalibrierung, der Teilegeometrie und den Nachbearbeitungsschritten ab.
Maßgenauigkeit und Toleranzen:
Die Maßhaltigkeit bezieht sich darauf, wie genau die endgültigen Abmessungen des Teils mit den im CAD-Modell angegebenen Nennmaßen übereinstimmen. Die Toleranz definiert den zulässigen Abweichungsbereich für ein bestimmtes Maß.
- Typische As-Built-Toleranzen:
- L-PBF (Laser Powder Bed Fusion): Im Allgemeinen wird davon ausgegangen, dass eine höhere Genauigkeit und feinere Merkmale als beim EBM möglich sind. Typische erreichbare Toleranzen für gut beherrschte Prozesse liegen oft im Bereich von ±0,1 mm bis ±0,2 mm (±0,004″ bis ±0,008″) für kleinere Abmessungen, möglicherweise etwas höher für größere Teile (z. B. ±0,1 % bis ±0,2 % der Gesamtabmessung). Mit bestimmten Maschinen und optimierten Verfahren können lokal noch engere Toleranzen erreicht werden.
- EBM (Electron Beam Melting): EBM wird bei höheren Temperaturen betrieben, was die Eigenspannung reduziert, aber manchmal zu einer etwas geringeren Maßgenauigkeit im Vergleich zu L-PBF führen kann, was auf Faktoren wie Wärmeausdehnung/Kontraktion und mögliche Sintereffekte des Pulvers zurückzuführen ist. Typische Toleranzen liegen zwischen ±0,2 mm und ±0,4 mm (±0,008″ bis ±0,016″), wobei jedoch ständig Verbesserungen vorgenommen werden.
- Faktoren, die die Genauigkeit beeinflussen:
- Kalibrierung der Maschine: Eine regelmäßige und präzise Kalibrierung des Scannersystems, des Strahlenfokus und der Bauplattform ist unerlässlich.
- Thermische Effekte: Eine ungleichmäßige Erwärmung und Abkühlung während des Bauprozesses kann zu Verformungen und Verzerrungen führen, die sich auf die endgültigen Abmessungen auswirken. Prozessparameter, Scan-Strategien und die Temperaturkontrolle in der Baukammer (insbesondere die erhöhte Temperatur bei EBM) spielen eine Rolle.
- Teilegeometrie und -größe: Große, sperrige Teile oder solche mit erheblichen Querschnittsveränderungen sind anfälliger für thermische Verformung. Innere Spannungen, die sich über viele Schichten aufbauen, können die Genauigkeit beeinträchtigen.
- Materialeigenschaften: Wärmeleitfähigkeit, Ausdehnungskoeffizient und Schmelzbadverhalten der jeweiligen Superlegierung beeinflussen den Prozess.
- Unterstützende Strukturen: Die Art und Weise, wie das Teil gestützt wird, kann die Spannungsakkumulation und mögliche Verformung beim Entfernen beeinflussen.
- Nachbearbeiten: Spannungsabbau und HIP-Zyklen können geringfügige, im Allgemeinen vorhersehbare Dimensionsänderungen verursachen, die berücksichtigt werden müssen.
- Erzielung engerer Toleranzen: Bei kritischen Merkmalen wie Passflächen, Dichtungsdurchmessern oder Schnittstellen, die eine hohe Präzision erfordern, reichen die AM-Toleranzen im Ist-Zustand möglicherweise nicht aus. In diesen Fällen, Nachbearbeitung verwendet wird. Bereiche, die enge Toleranzen erfordern, werden oft mit zusätzlichem Material (Bearbeitungszugabe oder Rohmaterial) versehen, das nach dem AM-Aufbau und der Wärmebehandlung durch CNC-Bearbeitung präzise entfernt wird. Die durch Nachbearbeitung erreichbaren Toleranzen sind mit den Standards der konventionellen Bearbeitung vergleichbar (z. B. ±0,01 mm bis ±0,05 mm oder besser).
Oberflächengüte (Rauhigkeit):
Die Oberflächenbeschaffenheit, die in der Regel durch die durchschnittliche Rauheit (Ra) quantifiziert wird, beschreibt die Beschaffenheit der Oberflächen des Teils. AM-Teile haben aufgrund des schichtweisen Aufbaus und der teilweise geschmolzenen Pulverpartikel, die an der Oberfläche haften, von Natur aus eine rauere Oberfläche als maschinell bearbeitete Oberflächen.
- Typische Oberflächenrauhigkeit (Ra) im Ist-Zustand:
- L-PBF: Erzeugt im Allgemeinen eine bessere Oberflächengüte als EBM. Ra-Werte liegen oft zwischen 6 µm und 15 µm (ca. 240 µin bis 600 µin) an vertikalen oder nahezu vertikalen Wänden, können aber an nach oben und vor allem nach unten gerichteten Oberflächen (gestützte Oberflächen) deutlich rauer sein (z. B. >20 µm).
- EBM: Dies führt in der Regel zu raueren Oberflächen im Vergleich zu L-PBF, oft mit Ra-Werten von 20 µm bis 40 µm (ca. 800 µin bis 1600 µin) oder höher. Dies ist zum Teil auf die größere Strahlfleckgröße und den höheren Energieeintrag zurückzuführen, die zu einer stärkeren Versinterung des Pulvers führen.
- Faktoren, die die Oberflächenbeschaffenheit beeinflussen:
- Schichtdicke: Dünnere Schichten führen im Allgemeinen zu glatteren Oberflächen, insbesondere bei schrägen Merkmalen, verlängern aber die Bauzeit.
- Partikelgrößenverteilung (PSD): Feinere Pulver können zu einem besseren Finish beitragen, können aber Probleme mit der Fließfähigkeit und der Handhabung mit sich bringen.
- Prozessparameter: Die Leistung des Laser-/Elektronenstrahls, die Scangeschwindigkeit und der Abstand zwischen den Luken beeinflussen die Dynamik des Schmelzbads und die Qualität der Oberflächenschmelze.
- Teil Orientierung: Senkrechte Wände sind in der Regel glatter als schräge oder horizontale Flächen. Nach unten gerichtete Oberflächen, die von Strukturen gestützt werden, sind nach der Entfernung der Stützen in der Regel am rauesten.
- Gasfluss (L-PBF): Bei der L-PBF kann der Durchfluss von Inertgas zur Entfernung von Verarbeitungsnebenprodukten die Oberflächenqualität beeinflussen.
- Auswirkungen der Oberflächenrauhigkeit:
- Fluiddynamik: Raue innere Kanaloberflächen können den Druckverlust erhöhen und die Strömungseigenschaften beeinträchtigen.
- Thermische Übertragung: Die Oberflächenrauhigkeit kann die Wärmeübergangskoeffizienten beeinflussen.
- Müdigkeit Leben: Raue Oberflächen können als Ausgangspunkt für Ermüdungsrisse dienen, was die Lebensdauer von Bauteilen bei zyklischer Belastung verringern kann. Die HIP-Bearbeitung ist von entscheidender Bedeutung für die Abschwächung der Auswirkungen der mit der Rauheit verbundenen Oberflächen- und Untergrundporosität.
- Versiegeln: Vorhandene Oberflächen sind im Allgemeinen für dynamische oder Hochdruckdichtungen ungeeignet.
- Verbesserung der Oberflächengüte: Wenn glattere Oberflächen erforderlich sind:
- Nachbearbeiten: Besonders geeignet für Außenflächen oder zugängliche Innenflächen, die eine hohe Glätte und enge Toleranzen erfordern.
- Abrasive Fließbearbeitung (AFM): Zum Polieren interner Kanäle und komplexer Passagen, indem abrasive Medien durch sie hindurchgeleitet werden.
- Massenbearbeitung: Verfahren wie Trowalisieren oder Gleitschleifen können die allgemeine Oberflächenglätte verbessern, eignen sich aber möglicherweise nicht für empfindliche Merkmale oder die Erhaltung scharfer Kanten.
- Elektropolieren: Kann eine sehr glatte Oberfläche erzeugen, erfordert jedoch spezielle Elektrolyte und eine Prozesskontrolle.
Das Engagement von Met3dp:
Das Erreichen einer gleichbleibenden Maßgenauigkeit und die Beherrschung der Oberflächengüte erfordern ein tiefes Prozessverständnis und eine robuste Qualitätskontrolle. Unternehmen wie Met3dp, die sich auf industrielle Anwendungen in Sektoren wie der Luft- und Raumfahrt konzentrieren, setzen hier Prioritäten:
- Hochwertige Pulver: Die Verwendung von Pulvern mit kontrollierter Sphärizität und PSD trägt zu stabileren Schmelzbädern und einer besseren Oberflächenqualität bei.
- Fortschrittliche Drucksysteme: Einsatz von Druckern mit präziser Kalibrierung, stabilem Wärmemanagement (einschließlich SEBM-Funktionen, die für Superlegierungen von Vorteil sind) und optimierten Prozessparametern.
- Prozesssteuerung und -überwachung: Strenge Qualitätskontrollen und möglicherweise eine Vor-Ort-Überwachung, um die Konsistenz von Bau zu Bau zu gewährleisten.
- Nachbearbeitungs-Know-how: Verständnis der Auswirkungen von Wärmebehandlung und HIP auf die Abmessungen und Angebot integrierter Nachbearbeitungslösungen.
Zusammenfassende Tabelle: AM-Schallwandtoleranzen & Ausführung
Parameter | Typischer L-PBF-Bereich | Typischer EBM-Bereich | Wichtige Einflussfaktoren | Methoden zur Verbesserung |
---|---|---|---|---|
Toleranz (As-Built) | ±0,1 bis ±0,2 mm (oder ±0,1-0,2 %) | ±0,2 bis ±0,4 mm (oder ±0,2-0,4%) | Maschinenkalibrierung, thermische Effekte, Geometrie, Material | Prozessoptimierung, Post-Machining (für kritische) |
Oberflächengüte Ra (As-Built) | 6-15 µm (vertikale Wände) >20 µm (nach unten gerichtet) | 20-40+ µm | Schichtdicke, PSD, Parameter, Orientierung, Verfahrenstyp | Nachbearbeitung, AFM, Massenveredelung, Polieren |
In Blätter exportieren
Ingenieure, die AM-Raketenleitbleche entwerfen, müssen die erforderlichen Toleranzen und Oberflächenbeschaffenheiten auf der Grundlage der funktionalen Anforderungen spezifizieren und sich darüber im Klaren sein, dass engere Spezifikationen oft Nachbearbeitungsschritte erforderlich machen, die zusätzliche Kosten und Vorlaufzeiten verursachen. Eine klare Kommunikation mit dem AM-Anbieter in Bezug auf kritische Merkmale und Akzeptanzkriterien ist für eine erfolgreiche Bauteilherstellung unerlässlich.
Wesentliche Nachbearbeitungsschritte für additiv gefertigte Schikanen
Das einfache Entfernen einer 3D-gedruckten Raketentriebwerksklappe aus Metall von der Bauplatte ist noch lange nicht das Ende des Herstellungsprozesses. Für kritische Luft- und Raumfahrtkomponenten, die aus Superlegierungen wie IN718 oder Haynes 282 hergestellt werden, sind eine Reihe wichtiger Nachbearbeitungsschritte erforderlich, um innere Spannungen abzubauen, Stützstrukturen zu entfernen, die gewünschte Materialmikrostruktur und mechanischen Eigenschaften zu erreichen, die Maßgenauigkeit zu gewährleisten, die erforderliche Oberflächengüte zu erzielen und die Integrität des Teils zu überprüfen. Diese Schritte sind unverzichtbar, um die Sicherheit, Zuverlässigkeit und Leistung des fertigen Bauteils in der anspruchsvollen Umgebung eines Raketentriebwerks zu gewährleisten. Wird einer dieser Schritte vernachlässigt oder unsachgemäß ausgeführt, kann das gesamte Bauteil gefährdet sein.
Typischer Post-Processing-Workflow für AM Superalloy Baffles:
- Stressabbau:
- Zweck: Die schnellen Erwärmungs- und Abkühlungszyklen bei L-PBF und, in geringerem Maße, bei EBM führen zu erheblichen Eigenspannungen im gedruckten Teil. Diese Spannungen können zu Verformungen (insbesondere nach dem Entfernen von der Bauplatte), Rissen und verminderter mechanischer Leistung führen. Der Spannungsabbau ist ein thermischer Zyklus, der diese inneren Spannungen abbauen soll, bevor das Teil von der Bauplatte entfernt oder in größerem Umfang gehandhabt/bearbeitet wird.
- Prozess: In der Regel wird das Teil (oft noch auf der Bauplatte) in einem Ofen mit kontrollierter Atmosphäre (Inertgas wie Argon oder Vakuum, um Oxidation zu verhindern) auf eine Temperatur unterhalb der Alterungs- oder Lösungsglühtemperaturen erhitzt, für eine bestimmte Dauer gehalten und dann langsam abgekühlt. Die genauen Parameter hängen von der Legierung und der Teilegeometrie ab. EBM-Teile, die bei höheren Temperaturen hergestellt werden, weisen im Allgemeinen geringere Eigenspannungen auf, können aber dennoch von einem Spannungsabbauzyklus profitieren.
- Wichtigkeit: Dies ist ein wichtiger erster Schritt, um Risse oder Verformungen bei der späteren Handhabung und der Entfernung der Stützen zu verhindern.
- Entfernen des Teils von der Bauplatte:
- Prozess: Dies geschieht in der Regel durch Drahterodieren (Electrical Discharge Machining), Sägen oder manchmal auch durch Fräsen/Schleifen, je nach Teilegeometrie und Material.
- Erwägungen: Dies muss sorgfältig geschehen, damit das Teil nicht beschädigt wird. Die Grenzschicht zwischen dem Teil und der Platte ist oft so gestaltet, dass sie sich leichter trennen lässt.
- Entfernung der Stützstruktur:
- Zweck: Entfernen Sie die temporären Strukturen, die während des Bauprozesses verwendet wurden.
- Prozess: Dies kann vom einfachen manuellen Brechen/Schneiden für zugängliche Stützen bis hin zu komplexeren Bearbeitungen (Fräsen, Schleifen) oder Erodieren für Stützen an komplizierten oder internen Stellen reichen. Dies kann einer der arbeitsintensivsten und anspruchsvollsten Nachbearbeitungsschritte sein, insbesondere bei Schallwänden mit komplexen inneren Kanälen oder Gitterstrukturen.
- Herausforderungen: Gefahr der Beschädigung der Teileoberfläche, schwieriger Zugang zu den inneren Halterungen, Gewährleistung der vollständigen Entfernung. DfAM spielt eine entscheidende Rolle bei der Konstruktion leicht entfernbarer Halterungen.
- Wärmebehandlung (Gefüge- und Eigenschaftsentwicklung):
- Zweck: AM-Superlegierungen weisen in der Regel nicht das optimale Mikrogefüge oder die optimalen mechanischen Eigenschaften (Festigkeit, Duktilität, Kriechfestigkeit) auf, die für anspruchsvolle Anwendungen erforderlich sind. Durch die Wärmebehandlung wird das Gefüge homogenisiert, unerwünschte Phasen, die sich während des Druckens gebildet haben, werden aufgelöst, und die verstärkenden Phasen (γ’ und/oder γ”) werden kontrolliert ausgeschieden.
- Prozess (Beispiel für IN718):
- Lösungsglühen: Erhitzen auf eine hohe Temperatur (z.B. ~980°C – 1065°C je nach gewünschten Eigenschaften), um vorhandene Ausscheidungen aufzulösen und die Matrix zu homogenisieren, gefolgt von einer schnellen Abkühlung.
- Behandlung der Alterung: Ein zweistufiger Alterungsprozess (z.B. ~720°C gefolgt von ~620°C), um die γ’ und γ” Verstärkungsphasen in der optimalen Größe und Verteilung auszufällen.
- Prozess (Beispiel für Haynes 282): Typischerweise wird eine höhere Lösungsglühtemperatur (z. B. ~1135°C – 1177°C) verwendet, gefolgt von einem mehrstufigen Alterungsprozess (z. B. ~1010°C gefolgt von ~790°C).
- Umwelt: Muss im Vakuum oder in einem Ofen mit kontrollierter Schutzgasatmosphäre durchgeführt werden, um Oxidation zu vermeiden, insbesondere bei den hohen Temperaturen. Genaue Temperaturkontrolle und Abschreckraten sind entscheidend.
- Wichtigkeit: Unbedingt erforderlich, um die für die Anwendung geforderten mechanischen Eigenschaften (Zugfestigkeit, Streckgrenze, Kriechfestigkeit, Ermüdungsfestigkeit) zu erreichen. Die Eigenschaften im eingebauten Zustand sind in der Regel minderwertig.
- Heiß-Isostatisches Pressen (HIP):
- Zweck: Schließen der inneren Porosität (Mikrohohlräume), die nach dem AM-Prozess aufgrund von Faktoren wie eingeschlossenem Gas oder unvollständiger Verschmelzung verbleiben kann. Porosität wirkt als Spannungskonzentrator und verschlechtert die mechanischen Eigenschaften erheblich, insbesondere die Ermüdungsfestigkeit und Bruchzähigkeit. HIP verdichtet das Material und verbessert seine Integrität.
- Prozess: Das Teil wird in einem speziellen HIP-Behälter unter Verwendung eines Inertgases (in der Regel Argon) sowohl einer hohen Temperatur (in der Regel knapp unterhalb der Lösungsglühtemperatur) als auch einem hohen Druck (z. B. 100-200 MPa oder 15.000-30.000 psi) ausgesetzt. Die Kombination aus Hitze und Druck bewirkt, dass die inneren Hohlräume kollabieren und sich metallurgisch schließen.
- Wichtigkeit: Weithin als obligatorisch für kritische Komponenten in der Luft- und Raumfahrt angesehen, insbesondere für solche, die einer Ermüdungsbelastung ausgesetzt sind. Sie verbessert die mechanischen Eigenschaften erheblich, verringert die Datenstreuung und verbessert die Prüfbarkeit. Sie wird oft vor dem Lösungsglühen der Wärmebehandlung durchgeführt oder mit diesem integriert.
- Oberflächenveredelung:
- Zweck: Zur Erzielung der erforderlichen Oberflächenrauheit aus funktionalen Gründen (z. B. Flüssigkeitsdurchfluss, Abdichtung) oder zur Beseitigung von Oberflächenfehlern, die als Auslöser für Ermüdung dienen könnten.
- Prozesse (je nach Bedarf):
- CNC-Bearbeitung: Für kritische Abmessungen, Toleranzen und glatte Oberflächen an bestimmten Merkmalen (z. B. Passflächen, Dichtungsnuten). Erfordert sorgfältiges Vorrichtungsdesign für potenziell komplexe AM-Formen.
- Abrasive Fließbearbeitung (AFM), Strangpressen und Honen: Zum Glätten interner Kanäle und Durchgänge.
- Massenfinish (Trommeln, Vibration): Zum allgemeinen Entgraten und Glätten, falls für die Teilegeometrie geeignet.
- Manuelles Schleifen/Polieren: Für örtliche Nachbearbeitung oder komplexe Formen.
- Inspektion und zerstörungsfreie Prüfung (NDT):
- Zweck: Überprüfung der Integrität des Endprodukts und Sicherstellung, dass es alle Spezifikationen und Qualitätsstandards erfüllt, bevor es in Betrieb genommen wird.
- Gemeinsame Techniken für AM-Teile für die Luft- und Raumfahrt:
- Prüfung der Abmessungen: Einsatz von CMM (Coordinate Measuring Machines), Laserscanning oder Structured Light Scanning zur Überprüfung der Abmessungen und Toleranzen anhand des CAD-Modells.
- Computertomographie (CT) Scannen: Röntgenbasierte Methode, die eine 3D-Ansicht der inneren Struktur des Teils liefert und in der Lage ist, innere Hohlräume, Einschlüsse und Risse zu erkennen und die innere Kanalgeometrie zu überprüfen. Zunehmend wichtig für komplexe AM-Teile.
- Farbeindringprüfung (Dye Penetrant Inspection, DPI) oder Fluorescent Penetrant Inspection (FPI): Zum Aufspüren von Oberflächenrissen oder Porosität.
- Ultraschallprüfung (UT): Kann unterirdische Fehler erkennen, obwohl komplexe Geometrien eine Herausforderung darstellen können.
- Visuelle Inspektion: Gründliche Untersuchung unter Vergrößerung.
- Wichtigkeit: Abschließende Qualitätsprüfung, um sicherzustellen, dass die Schallwand frei von kritischen Mängeln ist und alle technischen Anforderungen erfüllt. Strenge zerstörungsfreie Prüfungen sind Standardverfahren für flugkritische Luft- und Raumfahrtteile.
Fähigkeit der Lieferanten:
Die Durchführung dieser komplexen Abfolge von Nachbearbeitungsschritten erfordert beträchtliches Fachwissen, Spezialausrüstung (Vakuumöfen, HIP-Einheiten, NDT-Systeme) und robuste Qualitätsmanagementsysteme (z. B. AS9100-Zertifizierung). Bei der Auswahl eines AM-Dienstleisters für Raketentriebwerksklappen ist es entscheidend, dessen interne Fähigkeiten oder seine Beziehungen zu zertifizierten Partnern für alle erforderlichen Nachbearbeitungsschritte zu überprüfen. Ein Anbieter wie Met3dp, der sich auf die Bereitstellung von End-to-End-Lösungen für industrielle Anwendungen spezialisiert hat, weiß um die Wichtigkeit dieser Schritte und integriert sie in seine Qualitätssicherungsprotokolle. Ihr Wissen geht über den Druck hinaus und umfasst die gesamte Fertigungskette, die für Komponenten in Luft- und Raumfahrtqualität erforderlich ist.
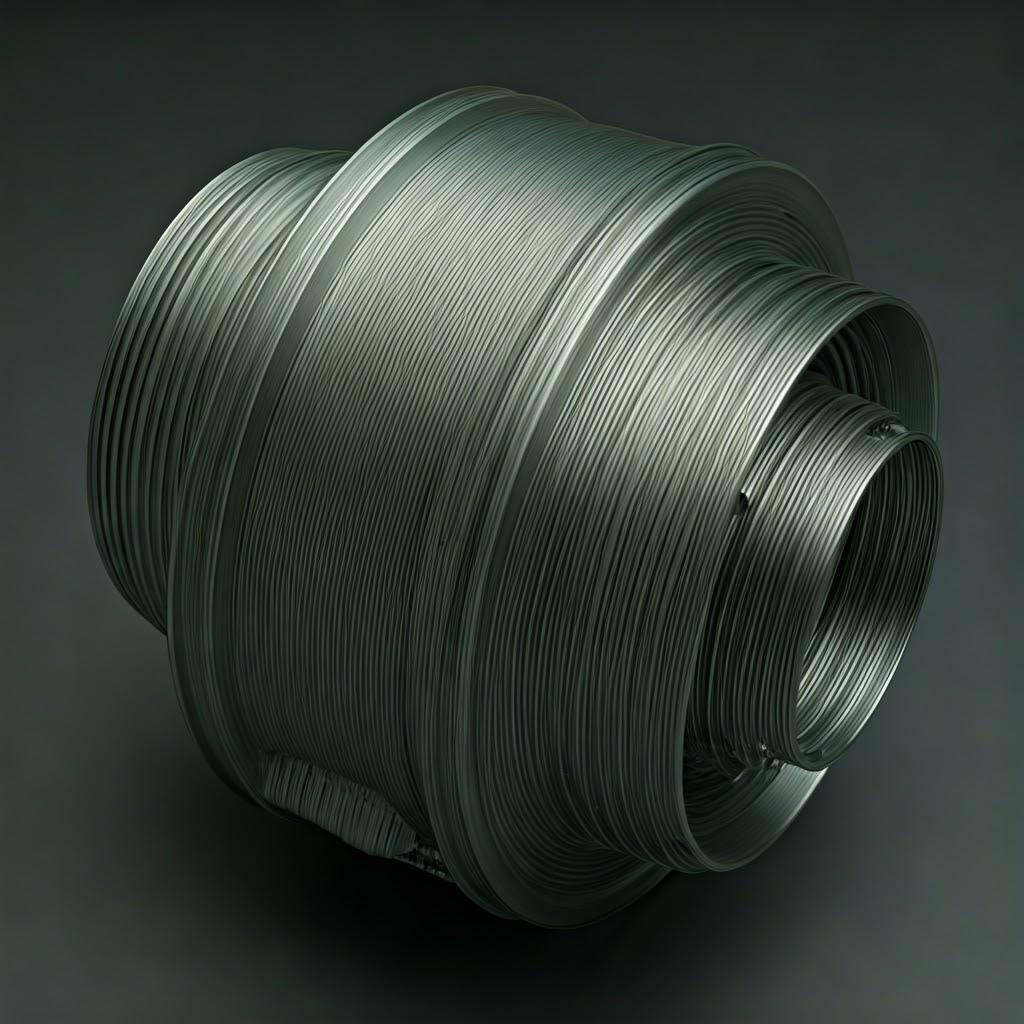
Überwindung allgemeiner Herausforderungen beim 3D-Druck von Raketentriebwerksschallklappen
Die additive Fertigung von Metallen birgt zwar ein erhebliches Potenzial für die Herstellung fortschrittlicher Raketentriebwerksklappen, doch das Verfahren ist nicht ohne Herausforderungen, insbesondere bei komplexen Geometrien und anspruchsvollen Superlegierungen wie IN718 und Haynes 282. Die erfolgreiche Herstellung flugtauglicher Komponenten erfordert die Vorwegnahme, das Verständnis und die Abmilderung dieser potenziellen Probleme durch sorgfältige Konstruktion, strenge Prozesskontrolle und fortschrittliche materialwissenschaftliche Kenntnisse. Hersteller und Zulieferer in der Luft- und Raumfahrt müssen diese Hürden geschickt meistern.
1. Eigenspannung und Verformung:
- Herausforderung: Die schnelle, örtlich begrenzte Erwärmung und Abkühlung bei L-PBF und EBM erzeugt steile thermische Gradienten, die beim Erstarren und Zusammenziehen der Schichten zum Aufbau von inneren Eigenspannungen führen. Übermäßige Spannungen können verursachen:
- Verzerrung/Verwerfung: Das Teil verformt sich während der Herstellung oder nach der Entnahme von der Bauplatte, was zu Maßungenauigkeiten führt.
- Knacken: Spannungen, die die Festigkeit des Materials bei erhöhten Temperaturen überschreiten, können während des Baus zu Erstarrungs- oder Verflüssigungsrissen führen.
- Reduzierte Leistung: Hohe Eigenspannungen können sich negativ auf die Ermüdungslebensdauer und die Bruchzähigkeit auswirken.
- Strategien zur Schadensbegrenzung:
- Optimierte Scan-Strategien: Techniken wie Inselabtastung, Sektorisierung oder die Anpassung der Länge und Ausrichtung von Abtastvektoren helfen, die Wärme gleichmäßiger zu verteilen und lokale Spannungsspitzen zu reduzieren.
- Plattenheizung aufbauen (L-PBF): Durch das Vorheizen der Bauplatte wird der Wärmegradient zwischen dem erstarrten Material und der neuen Schicht verringert, wodurch die Spannungsakkumulation reduziert wird.
- Hochtemperatur-Umgebung (EBM): EBM arbeitet von Natur aus mit erhöhten Temperaturen in der Baukammer (mehrere hundert °C), was die thermischen Gradienten und Eigenspannungen im Vergleich zu den meisten L-PBF-Systemen erheblich reduziert. Dies ist ein entscheidender Vorteil bei der Verarbeitung rissempfindlicher Legierungen oder großer, komplexer Teile.
- Entwurf der Stützstruktur: Stützen wirken als Wärmesenken und mechanische Verankerungen und beeinflussen die Belastung. Ein sorgfältiges Design ist erforderlich, um die Effektivität der Stützen mit einer einfachen Demontage in Einklang zu bringen.
- Thermische Nachbearbeitung: Die obligatorischen Spannungsabbauzyklen (die häufig auf der Bauplatte durchgeführt werden) sind entscheidend für den Abbau der angesammelten Spannungen vor der Entnahme des Teils. HIP trägt auch zur Verringerung von Eigenspannungen bei.
- AM-Prozesssimulation: Software-Tools können die Spannungsakkumulation und Verformung auf der Grundlage der Teilegeometrie und der Prozessparameter vorhersagen und ermöglichen so Design- oder Prozessanpassungen vor dem Druck.
2. Entwurf und Entfernung von Stützstrukturen:
- Herausforderung: Luftleitbleche weisen oft komplexe interne Durchgänge, Überhänge und Gitterstrukturen auf, die während der Herstellung unterstützt werden müssen. Es ist schwierig, Stützen zu entwerfen, die effektiv sind (Einsturzschutz, Wärmeleitung) und dennoch leicht und vollständig entfernt werden können, ohne das Teil zu beschädigen. Interne Stützen können besonders schwierig oder unmöglich mechanisch zu entfernen sein.
- Strategien zur Schadensbegrenzung:
- DfAM zur Stützreduzierung: Der effektivste Ansatz ist die Konstruktion von Features, die selbsttragend sind (mit geeigneten Winkeln, Teardrop-/Diamantkanälen). Die optimale Ausrichtung des Teils auf der Bauplatte ist entscheidend.
- Optimiertes Support-Design: Verwendung von Stützentypen (z. B. Block, Kegel, Baum) und Parametern (z. B. Dichte, Fragmentierung), die ein Gleichgewicht zwischen Festigkeit und Bruchfestigkeit herstellen. Spezialisierte Software hilft bei der Erzeugung effizienter Stützen.
- Wahl des Materials: Einige Trägermaterialien sind so konzipiert, dass sie chemisch aufgelöst werden können, obwohl dies bei Hochtemperatursuperlegierungen weniger üblich ist.
- Zugang zur Entfernung: Entwurf von Zugangsöffnungen oder -wegen zur Entfernung von internen Stützen oder eingeschlossenem Pulver.
- Nachbearbeitungsmethoden: Einsatz von CNC-Bearbeitung, EDM oder AFM zur präzisen Entfernung von Stützen in schwierigen Bereichen. Eine gründliche Inspektion (z. B. Endoskop, CT-Scan) ist erforderlich, um die vollständige Entfernung zu überprüfen.
3. Qualitätsmanagement und Handhabung von Pulvern:
- Herausforderung: Die Qualität und Konsistenz des Metallpulver-Rohstoffs (IN718, Haynes 282) sind von größter Bedeutung. Dazu gehören folgende Punkte:
- Kontamination: Das Einbringen von Fremdpartikeln oder die Kreuzkontamination mit anderen Legierungen kann Defekte verursachen und die Materialeigenschaften beeinträchtigen.
- Abbau des Pulvers: Die wiederholte Wiederverwendung von Pulver kann seine Chemie (z. B. Sauerstoffaufnahme) oder Morphologie (Partikelform/Größenverteilung) verändern, was die Verarbeitbarkeit und die Qualität der Teile beeinträchtigt.
- Fragen der Fließfähigkeit: Ein schlechter Pulverfluss kann zu einer ungleichmäßigen Verteilung der Schichten führen, was wiederum Fehler verursacht.
- Sicherheit: Der Umgang mit feinen Metallpulvern erfordert angemessene Sicherheitsvorkehrungen (inerte Atmosphären, Erdung, persönliche Schutzausrüstung), um Explosions- oder Inhalationsrisiken zu verringern.
- Strategien zur Schadensbegrenzung:
- Hochwertiges Virgin Powder: Beschaffung von Pulver von renommierten Lieferanten wie Met3dp, die fortschrittliche Zerstäubungstechniken (VIGA, PREP) und strenge Qualitätskontrollen anwenden, um hohe Reinheit, Sphärizität, kontrollierte PSD und einen geringen Satellitengehalt zu gewährleisten. Informationen über uns und unser Engagement für Qualitätspulver können Sie auf unserer Website nachlesen.
- Strenge Protokolle für die Handhabung von Pulver: Spezielle Geräte, kontrollierte Umgebungen (z. B. Handschuhkästen), Siebverfahren und sorgfältige Verfolgung von Pulverchargen und Wiederverwendungszyklen.
- Charakterisierung des Pulvers: Regelmäßige Prüfung von neuem und wiederverwendetem Pulver (Chemie, PSD, Fließfähigkeit, Morphologie), um sicherzustellen, dass es innerhalb der Spezifikationen bleibt.
- Atmosphärenkontrolle: Aufrechterhaltung einer hochreinen Inertgasatmosphäre (Argon, Stickstoff) im Drucker und in den Handhabungssystemen, um die Aufnahme von Sauerstoff/Feuchtigkeit zu minimieren.
4. Porosität:
- Herausforderung: Das Vorhandensein kleiner innerer Hohlräume (Poren) innerhalb des gedruckten Materials. Porosität verschlechtert die mechanischen Eigenschaften, insbesondere die Ermüdungsfestigkeit, erheblich. Zu den Ursachen gehören:
- Gas Porosität: Eingeschlossenes Gas in den Pulverpartikeln oder gelöstes Gas im Schmelzbad, das während der Erstarrung aus der Lösung kommt.
- Fehlende Fusionsporosität: Unzureichender Energieeintrag oder unsachgemäße Überlappung des Schmelzbads, was zu unvollständigem Schmelzen zwischen Schichten oder benachbarten Scannerspuren führt.
- Schlüsselloch-Porosität: Übermäßige Energiedichte, die zur Verdampfung des Metalls führt, was zu Instabilität und Gaseinschlüssen führt, wenn der Dampfraum kollabiert.
- Strategien zur Schadensbegrenzung:
- Optimierte Prozessparameter: Die sorgfältige Steuerung von Laser-/Strahlleistung, Scangeschwindigkeit, Schichtdicke, Schraffurabstand und Fokus gewährleistet ein stabiles Schmelzen und eine vollständige Verschmelzung. Die Parameterentwicklung ist legierungsspezifisch.
- Hochwertiges Pulver: Verwendung von Pulver mit geringem internen Gasgehalt. Vakuum-Induktionsschmelzen (VIM) während der Zerstäubung hilft, gelöste Gase zu minimieren.
- Atmosphärenkontrolle: Sicherstellung einer sauberen, hochreinen Inertgasumgebung in der Baukammer.
- Heiß-Isostatisches Pressen (HIP): Die effektivste Methode zum Schließen von Restporosität (Fehlen von Schmelz- und Gasporen) nach dem Druck. Sie gilt als unerlässlich für kritische Bauteile.
5. Knacken:
- Herausforderung: Bildung von Rissen während der Erstarrung (Erstarrungsrissbildung) oder in der Wärmeeinflusszone während der nachfolgenden thermischen Zyklen (Liquorrissbildung). Superlegierungen, insbesondere hochlegierte, können aufgrund ihres breiten Erstarrungsbereichs und ihres Ausscheidungsverhaltens anfällig sein.
- Strategien zur Schadensbegrenzung:
- Auswahl der Legierung: IN718 und Haynes 282 gelten im Allgemeinen als relativ widerstandsfähig gegen Rissbildung während der AM im Vergleich zu einigen anderen Superlegierungen, weshalb sie bevorzugt werden.
- Optimierung der Parameter: Die Steuerung des Energieeintrags und der Abkühlungsraten über die Scanstrategie und die Parameter kann die Rissanfälligkeit minimieren.
- Wärmemanagement: Die Beheizung von Bauplatten (L-PBF) oder der Betrieb bei hohen Temperaturen (EBM) reduziert thermische Gradienten und das Risiko der Rissbildung.
- Geeignete Wärmebehandlung: Wärmebehandlungen nach dem Bau müssen sorgfältig ausgewählt werden, um schädliche Phasenausscheidungen oder Relaxationsmechanismen zu vermeiden, die zu Rissen führen könnten.
Die erfolgreiche Bewältigung dieser Herausforderungen erfordert eine Kombination aus robuster Maschinentechnologie, hochwertigen Werkstoffen, optimierten Prozessparametern, die durch strenge Experimente entwickelt wurden, sorgfältiger Prozesskontrolle, umfassender Nachbearbeitung und fundiertem metallurgischem Fachwissen. Die Zusammenarbeit mit einem erfahrenen AM-Dienstleister, der mit den richtigen Werkzeugen und Kenntnissen ausgestattet ist, ist entscheidend für die Herstellung zuverlässiger, leistungsstarker Raketentriebwerksklappen, die den strengen Anforderungen der Luft- und Raumfahrtindustrie genügen.
Die Wahl Ihres Partners: Die Auswahl des richtigen Metall-AM-Dienstleisters für Luft- und Raumfahrtkomponenten
Die erfolgreiche Einführung der additiven Fertigung für flugkritische Komponenten wie Triebwerksklappen hängt nicht nur von fortschrittlichem Design und Materialien ab, sondern auch von den Fähigkeiten und der Zuverlässigkeit des gewählten Fertigungspartners. Die Auswahl des richtigen Metall-AM-Dienstleisters ist eine wichtige Entscheidung für Luft- und Raumfahrtingenieure und Beschaffungsmanager. Es steht unglaublich viel auf dem Spiel, denn es wird ein Anbieter benötigt, der nicht nur technische Kompetenz, sondern auch ein unermüdliches Engagement für Qualität, Rückverfolgbarkeit und Prozesskontrolle gemäß den Standards der Luft- und Raumfahrtindustrie unter Beweis stellt. Die Bewertung potenzieller Partner erfordert einen vielschichtigen Ansatz, der über die reinen Druckfähigkeiten hinausgeht.
Schlüsselkriterien für die Bewertung von AM-Lieferanten in der Luft- und Raumfahrt:
- Zertifizierungen und Qualitätsmanagementsystem (QMS):
- AS9100-Zertifizierung: Dies ist der international anerkannte QMS-Standard für die Luft-, Raumfahrt- und Verteidigungsindustrie. AS9100 umfasst die Anforderungen von ISO 9001, fügt jedoch strengere Kriterien hinzu, die speziell für die Luft- und Raumfahrt gelten und Aspekte wie Konfigurationsmanagement, Risikomanagement, Rückverfolgbarkeit und Überprüfung von eingekauften Produkten abdecken. Für flugkritische Hardware ist die Zusammenarbeit mit einem AS9100-zertifizierten Lieferanten oft obligatorisch oder sehr wünschenswert. Damit wird das Engagement für strenge Qualitätskontrollprozesse unter Beweis gestellt.
- Zertifizierung nach ISO 9001: Ein grundlegender Qualitätsmanagement-Standard, der robuste Prozesse für Konsistenz und Kundenzufriedenheit angibt.
- Dokumentiertes QMS: Auch über die Zertifizierungen hinaus sollte der Lieferant über ein gut dokumentiertes und konsequent umgesetztes QMS verfügen, das alle Stufen von der Handhabung des Pulvers bis zur Endkontrolle und zum Versand abdeckt.
- Technische Kompetenz und Erfahrung:
- Werkstoffkunde: Fundierte Kenntnisse der Metallurgie, insbesondere von Superlegierungen auf Nickelbasis wie IN718 und Haynes 282. Dazu gehören Kenntnisse über ihr Verhalten bei der AM-Bearbeitung, die erforderlichen Wärmebehandlungen und die erreichbaren Eigenschaften.
- Prozesskompetenz (L-PBF/EBM): Nachgewiesene Fähigkeiten in der Anwendung und Optimierung der spezifischen AM-Technologie (z. B. L-PBF, EBM), die für die Umlenkplatte erforderlich ist. Erfahrung mit der gewählten Superlegierung ist von entscheidender Bedeutung. Verlangen Sie Fallstudien oder Nachweise über erfolgreiche Projekte mit ähnlichen Materialien und ähnlicher Komplexität.
- DfAM-Unterstützung: Der ideale Partner kann am Design für die additive Fertigung mitarbeiten, Feedback zur Machbarkeit des Designs geben und Optimierungen für die Druckbarkeit, die Reduzierung des Aufwands oder die Verbesserung der Leistung vorschlagen.
- Erfahrung mit Luft- und Raumfahrtanwendungen: Nachgewiesene Erfolgsbilanz bei der Herstellung von Komponenten für die Luft- und Raumfahrt oder ähnlich anspruchsvolle Branchen. Ein Verständnis der spezifischen Anforderungen und Herausforderungen von Antriebssystemen ist ein großer Vorteil.
- Ausrüstung, Technologie und Einrichtungen:
- Geeignete AM-Systeme: Gut gewartete, industrietaugliche L-PBF- oder EBM-Maschinen, die für die Bearbeitung reaktiver Superlegierungen geeignet sind. Zu den Faktoren gehören Bauvolumen, Laser-/Strahlleistung, Atmosphärensteuerung, Wärmemanagementfähigkeiten (z. B. hohe Bauplattenheizung für L-PBF, hohe Kammertemperatur für EBM wie die SEBM-Systeme von Met3dp’) und Überwachungsmöglichkeiten.
- Handhabung des Pulvers: Spezielles, kontrolliertes Umfeld und Verfahren für die Handhabung, Lagerung, Siebung und Verwaltung von Superlegierungspulvern, um Verunreinigungen zu vermeiden und Konsistenz zu gewährleisten.
- Nachbearbeitungsgeräte: Eigener oder streng kontrollierter Zugang über zertifizierte Partner für alle erforderlichen Nachbearbeitungsschritte: Spannungsarmglühöfen, Vakuum-Wärmebehandlungsöfen, Heiß-Isostatisches Pressen (HIP), CNC-Bearbeitungszentren, Oberflächenbearbeitungswerkzeuge und umfassende NDT-Ausrüstung.
- Kalibrierung und Wartung: Regelmäßige, dokumentierte Kalibrierungs- und vorbeugende Wartungspläne für alle kritischen Geräte (AM-Maschinen, Öfen, Prüfwerkzeuge).
- Umfassende Nachbearbeitungsmöglichkeiten:
- Wie bereits erwähnt, ist die Nachbearbeitung entscheidend. Überprüfen Sie, ob der Anbieter in der Lage ist, den gesamten Arbeitsablauf zu verwalten, einschließlich:
- Entspannung
- Unterstützung bei der Entfernung von Fachwissen (insbesondere bei komplexen internen Funktionen)
- Präzisionswärmebehandlung (Vakuum/Schutzgasatmosphäre, genaue Temperaturkontrolle)
- HIP-Verarbeitung (Zugang zu zertifizierten Einrichtungen)
- CNC-Bearbeitung (für enge Toleranzen und kritische Merkmale)
- Oberflächenveredelung (einschließlich interner Kanäle, falls erforderlich, z. B. AFM)
- Wie bereits erwähnt, ist die Nachbearbeitung entscheidend. Überprüfen Sie, ob der Anbieter in der Lage ist, den gesamten Arbeitsablauf zu verwalten, einschließlich:
- Strenge Inspektions- und NDT-Fähigkeiten:
- Eigener oder partnerschaftlicher Zugang zu wichtigen ZfP-Methoden wie CT-Scanning, FPI/DPI, UT und Dimensionsprüfgeräten (CMM, Scanner).
- Qualifiziertes ZfP-Personal, das nach den einschlägigen Normen (z. B. NAS 410 / EN 4179) zertifiziert ist.
- Robuste, in den gesamten Fertigungsprozess integrierte Prüfprotokolle.
- Rückverfolgbarkeit von Materialien:
- Vollständige Rückverfolgbarkeit der Materialien von der Wiege bis zur Bahre, die das fertige Teil mit bestimmten Pulverchargen, Verarbeitungsparametern, Wärmebehandlungszyklen und Prüfergebnissen in Verbindung bringt. Dies ist eine grundlegende Anforderung von AS9100.
- Kapazität, Vorlaufzeit und Kommunikation:
- Ausreichende Maschinenkapazität und Arbeitskräfte, um die Projektfristen zuverlässig einzuhalten.
- Transparente Kommunikation über Vorlaufzeiten, mögliche Risiken und den Projektstatus.
- Reaktionsfähigkeit und Bereitschaft zur engen Zusammenarbeit mit dem technischen Team des Kunden.
Warum eine Partnerschaft mit Met3dp?
Obwohl spezifische Zertifizierungen immer auf der Grundlage der aktuellen Projektanforderungen überprüft werden sollten, verkörpert Met3dp viele Qualitäten, die man von einem hochkarätigen AM-Partner für die Luft- und Raumfahrt erwartet:
- Stiftung in Materialien: Als Entwickler und Hersteller von hochwertigen Metallpulvern unter Verwendung der fortschrittlichen VIGA- und PREP-Technologien verfügt Met3dp über ein grundlegendes Verständnis der Materialeigenschaften und ihrer Wechselwirkung mit dem AM-Prozess. Dieses Know-how erstreckt sich auch auf anspruchsvolle Superlegierungen wie IN718.
- Fortgeschrittene AM-Systeme: Wir bieten Industriedrucker an, darunter die SEBM-Technologie (Selective Electron Beam Melting), die für ihre Vorteile bei der Verarbeitung von rissanfälligen Hochtemperaturlegierungen bekannt ist, da die Umgebung, in der sie hergestellt wird, eine hohe Temperatur aufweist und die Restspannung reduziert.
- Integrierte Lösungen: Met3dp positioniert sich selbst als Anbieter umfassender Lösungen, die Drucker, Pulver und Anwendungsentwicklungsdienste umfassen, was darauf hindeutet, dass es in der Lage ist, Kunden vom Entwurf bis zur Produktion zu unterstützen.
- Fokus auf industrielle Anwendungen: Zu ihren Zielbranchen gehören die Luft- und Raumfahrt, die Medizintechnik und die Automobilindustrie, was auf Erfahrungen mit hohen Anforderungen und Qualitätserwartungen schließen lässt.
- Engagement für Qualität: Ihr Schwerpunkt auf branchenführender Genauigkeit und Zuverlässigkeit deutet auf eine Kultur hin, die darauf ausgerichtet ist, die strengen Anforderungen von Branchen wie der Luft- und Raumfahrt zu erfüllen.
Die Wahl des richtigen Lieferanten ist eine Übung in Risikomanagement. Eine gründliche Bewertung auf der Grundlage dieser Kriterien wird dazu beitragen, dass Ihre additiv gefertigten Raketentriebwerksleitbleche nach den höchsten Qualitäts-, Zuverlässigkeits- und Leistungsstandards hergestellt werden und die Möglichkeiten dieser transformativen Technologie voll ausschöpfen.

Verständnis der Kostentreiber und Vorlaufzeiten für AM Rocket Baffles
Die additive Fertigung bietet zwar erhebliche technische Vorteile für die Herstellung komplexer Raketentriebwerksklappen, doch ist es für Beschaffungsmanager und Ingenieure unerlässlich, die Faktoren zu verstehen, die Kosten und Vorlaufzeit beeinflussen. Ein klares Bild dieser Elemente ermöglicht eine bessere Budgetierung, Planung und einen Vergleich mit traditionellen Fertigungsmethoden oder alternativen AM-Lieferanten. Die Kostenstruktur für AM unterscheidet sich von der traditioneller Methoden und beinhaltet oft höhere anfängliche Kosten pro Teil für einfache Artikel, wird aber wettbewerbsfähig oder sogar vorteilhaft für hochkomplexe oder konsolidierte Designs, insbesondere wenn man die gesamten Lebenszyklus- und Entwicklungskosten berücksichtigt.
Die wichtigsten Kostentreiber für AM-Raketenschallwände:
- Materialkosten:
- Pulver Preis: Superlegierungen auf Nickelbasis wie IN718 und Haynes 282 sind von Natur aus teure Rohstoffe im Vergleich zu Standardstählen oder Aluminiumlegierungen. Haynes 282 ist im Allgemeinen teurer als IN718. Auch die Qualität des Pulvers (Reinheit, Sphärizität, PSD) beeinflusst den Preis.
- Verwendetes Volumen: Das tatsächliche Volumen des Ablenkblechs und das Volumen der erforderlichen Stützstrukturen bestimmen die Menge des direkt im Teil verbrauchten Pulvers.
- Pulververlust/Recycling-Effizienz: Ein Teil des Pulvers geht bei der Handhabung, dem Druck und der Rückgewinnung zwangsläufig verloren. Die Effizienz der Pulversiebung und des Recyclingprozesses wirkt sich auf die Gesamtmaterialkosten pro Teil aus. Eine strenge Qualitätskontrolle des wiederverwendeten Pulvers ist notwendig, was einen gewissen Mehraufwand bedeutet.
- Buy-to-Fly-Verhältnis: AM hat im Allgemeinen ein viel besseres Verhältnis zwischen Anschaffungskosten (Gewicht des eingekauften Rohmaterials und Gewicht des fertigen Teils) als die subtraktive Bearbeitung, was bei teuren Materialien ein großer Vorteil ist.
- AM Machine Time:
- Bauzeit: Dies ist oft der wichtigste Kostenfaktor. Er wird bestimmt durch:
- Teil Volumen & Höhe: Größere und höhere Teile benötigen mehr Zeit zum Drucken.
- Komplexität: Komplizierte Merkmale, dünne Wände und Gitterstrukturen können langsamere Scangeschwindigkeiten oder spezielle Strategien erfordern, was den Zeitaufwand erhöht.
- Anzahl der Teile pro Build: Das gleichzeitige Drucken mehrerer Teile (Nesting) kann die effektiven Maschinenzeitkosten pro Teil erheblich senken, indem die Nutzung der Bauplattformfläche und die Einrichtungszeit optimiert werden.
- Schichtdicke: Dünnere Schichten verbessern die Auflösung und die Oberflächengüte an Hängen, erhöhen aber die Anzahl der Schichten und damit die Bauzeit.
- Maschine Stundensatz: In diesem Satz sind die Abschreibung der Maschine, der Energieverbrauch, die Wartung, die Gemeinkosten der Anlage und der Verbrauch von Inertgas enthalten. Industrielle Metall-AM-Systeme stellen eine erhebliche Kapitalinvestition dar.
- Bauzeit: Dies ist oft der wichtigste Kostenfaktor. Er wird bestimmt durch:
- Arbeitskosten:
- Einrichten & Abrüsten: Das Vorbereiten der Maschine, das Laden des Pulvers, das Einrichten der Build-Datei und das anschließende Entfernen des fertigen Builds, das Reinigen der Maschine und die Entnahme der Teile erfordern qualifizierte Arbeitskräfte.
- Nachbearbeitungsarbeiten: Dies kann erheblich sein, insbesondere für:
- Unterstützung bei der Entfernung: Die manuelle oder halbautomatische Entfernung von Halterungen, insbesondere von komplexen internen Halterungen, kann zeitaufwändig sein.
- Basic Finishing: Erste Reinigung oder Glättung der Oberfläche.
- Inspektion und Qualitätssicherung: Arbeit im Zusammenhang mit Maßprüfungen, NDT-Vorbereitung und Dokumentation.
- Nachbearbeitungskosten (extern oder intern):
- Thermische Behandlungen: Spannungsarmglühen, Lösungsglühen, Alterung und HIP-Zyklen erfordern spezielle Öfen und HIP-Anlagen. Diese Prozesse verursachen erhebliche Kosten durch den Betrieb der Anlagen (Energie, Inertgas) und die Zykluszeit. HIP ist besonders kostspielig, aber oft obligatorisch.
- Bearbeitungen: Wenn bei bestimmten Merkmalen enge Toleranzen oder spezielle Oberflächen erforderlich sind, verursacht die CNC-Bearbeitung zusätzliche Kosten aufgrund der Komplexität, der Einrichtungszeit und der Bearbeitungszeit. Die Bearbeitung von Superlegierungen ist von Natur aus langsamer und erfordert eine robustere Werkzeugausstattung.
- Oberflächenveredelung: Die Kosten für AFM, Polieren oder andere Endbearbeitungsmethoden hängen vom erforderlichen Niveau und der Komplexität der zugänglichen Oberflächen (insbesondere im Inneren) ab.
- ZFP: Kosten im Zusammenhang mit der Durchführung von CT-Scans, FPI, UT usw., einschließlich der Gerätezeit und der Arbeit des zertifizierten Bedieners.
- Kosten für Design und Technik:
- DfAM: Wenn erhebliche Umgestaltungen oder Optimierungen für AM erforderlich sind, erhöht die Entwicklungszeit die anfänglichen Projektkosten, obwohl sie sich oft durch geringere Herstellungskosten oder verbesserte Leistung auszahlt.
- Simulation: Kosten im Zusammenhang mit der Durchführung von AM-Prozess-Simulationen oder CFD/FEA zur Designvalidierung.
- Qualitätssicherung und Zertifizierung:
- Die Aufrechterhaltung der AS9100-Zertifizierung und die Einhaltung der strengen Anforderungen an Dokumentation, Rückverfolgbarkeit und Prozesskontrolle verursachen zusätzliche Kosten, die sich im Endpreis der Teile niederschlagen. Diese Investition ist jedoch entscheidend für die Gewährleistung von Qualität und Zuverlässigkeit in der Luft- und Raumfahrt.
Typische Vorlaufzeiten für AM Rocket Baffles:
Die Vorlaufzeit ist die Gesamtzeit von der Auftragserteilung bis zur Lieferung des Teils. Bei komplexen AM-Superlegierungsbauteilen kann sie, abhängig von verschiedenen Faktoren, zwischen einigen Wochen und mehreren Monaten liegen:
- Designfinalisierung & Vorbereitung: Erforderliche Zeit für abschließende DfAM-Prüfungen, Support-Generierung, Vorbereitung der Build-Datei und Simulation (falls durchgeführt). (Tage)
- Maschinenwarteschlange & Zeitplanung: Verfügbarkeit der geeigneten AM-Maschine. Hohe Nachfrage oder Wartungsarbeiten können zu Rückständen führen. (Tage bis Wochen)
- Druckzeit: Tatsächliche Zeit, die das Teil beim Bau in der Maschine verbringt. Sie kann von ~24 Stunden bis zu über einer Woche oder mehr bei großen/komplexen Teilen reichen. (Tage bis Wochen)
- Nachbearbeiten: Dies macht oft einen erheblichen Teil der Vorlaufzeit aus:
- Abkühlen & Spannungsarmglühen: (1-2 Tage)
- Entfernen und Reinigen von Teilen: (1 Tag)
- Wärmebehandlung & HIP: Oft ist eine Chargierung von Teilen und lange Ofen-/HIP-Zyklen erforderlich, plus Transportzeit, wenn die Produktion ausgelagert wird. (1-3 Wochen)
- Entfernen von Stützen & Bearbeitung: Abhängig von der Komplexität. (Tage bis Wochen)
- Finishing & NDT: (Tage bis Woche)
- Versand: (Tage)
Faktoren, die die Vorlaufzeit beeinflussen:
- Teil Komplexität: Komplexere Teile erfordern längere Druckzeiten und eine intensivere Nachbearbeitung.
- Lieferantenkapazität & Rückstand: Aktuelle Arbeitsbelastung des AM-Dienstleisters.
- Nachbearbeitungskette: Effizienz und Planung interner und externer Nachbearbeitungsschritte (HIP-Zyklen, Wärmebehandlungschargen).
- Menge: Das Prototyping einzelner Teile mag anfangs schneller sein, aber die Optimierung von Builds mit mehreren Teilen kann die pro Teil vorlaufzeit in Produktionsszenarien, auch wenn die Gesamtzeit einer Charge länger sein kann.
- Qualitätsanforderungen: Strengere Inspektions- und Dokumentationsanforderungen bedeuten mehr Zeitaufwand.
Zusammenfassung:
Das Verständnis des Zusammenspiels von Materialkosten, Maschinenzeit, Arbeitsaufwand, umfangreicher Nachbearbeitung und Qualitätssicherung ist der Schlüssel für eine genaue Schätzung der Kosten und der Vorlaufzeit für additiv gefertigte Raketentriebwerksschallwände. AM kann zwar den Prozess beschleunigen entwicklung in der Phase des Rapid Prototyping umfasst die Vorlaufzeit für die Herstellung von Teilen in Produktionsqualität zahlreiche Schritte, die über den reinen Druck hinausgehen. Eine klare Kommunikation mit Lieferanten wie Met3dp in Bezug auf Erwartungen, Spezifikationen und Zeitpläne ist für eine erfolgreiche Projektdurchführung unerlässlich.
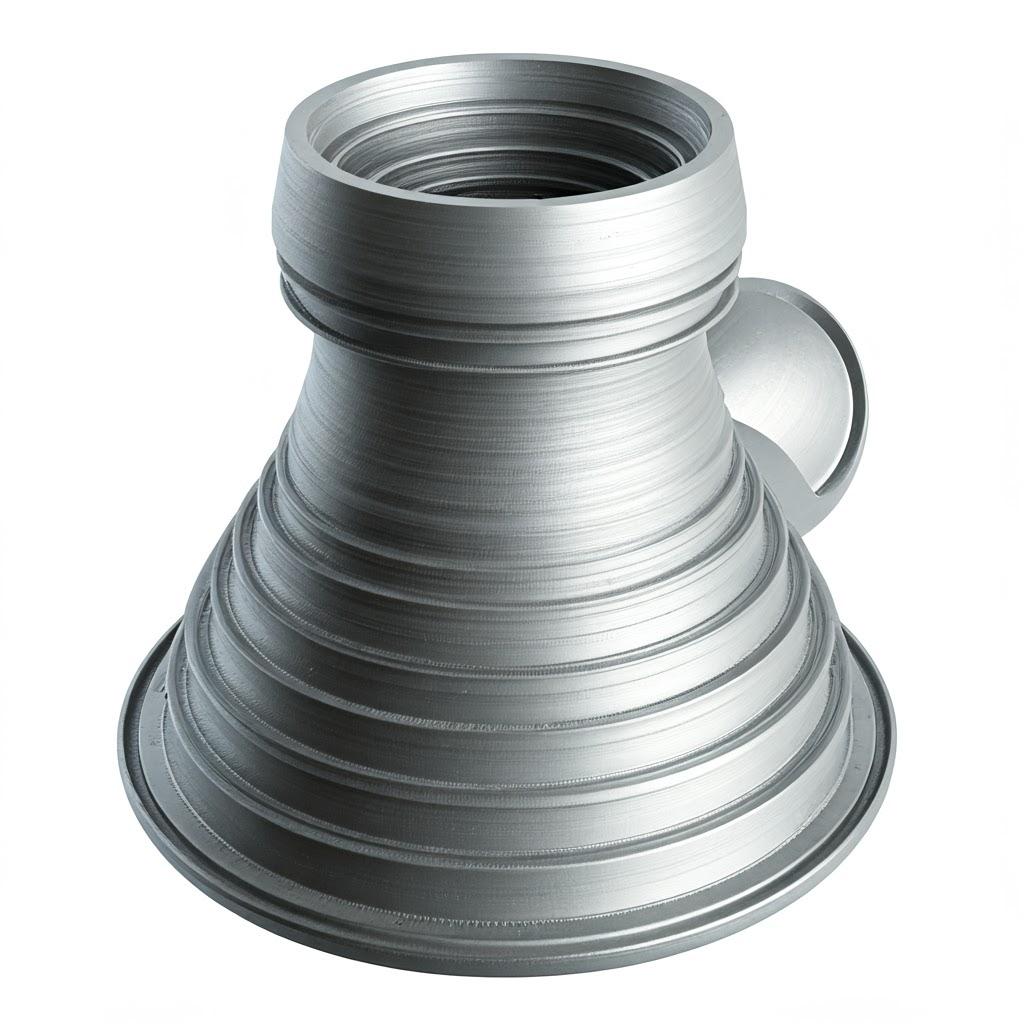
Häufig gestellte Fragen (FAQ) zu AM Rocket Engine Baffles
Wenn Ingenieure und Beschaffungsmanager die additive Fertigung von kritischen Komponenten, wie z. B. Leitblechen für Raketentriebwerke, unter Verwendung von Superlegierungen in Betracht ziehen, haben sie oft spezielle Fragen zu Leistung, Qualität und Prozessspezifika. Hier finden Sie Antworten auf einige häufig gestellte Fragen:
1. Wie sieht es mit der Zuverlässigkeit und Ermüdungslebensdauer von AM-Schalldämpfern (IN718, Haynes 282) im Vergleich zu traditionell hergestellten Schalldämpfern aus?
- Antwort: Bei der Herstellung mit gut kontrollierten und optimierten AM-Prozessen, gefolgt von einer geeigneten Nachbearbeitung, einschließlich Heiß-Isostatisches Pressen (HIP) und einer rigorosen Wärmebehandlung können die mechanischen Eigenschaften (einschließlich Zugfestigkeit, Kriechfestigkeit und Ermüdungslebensdauer) von AM-Superlegierungsschilden erfüllen oder sogar übertreffen die von Bauteilen, die mit traditionellen Verfahren wie Gießen oder Schmieden hergestellt werden.
- Schlüsselfaktoren: Die Erzielung von Eigenschaften, die denen von Knetwerkstoffen gleichwertig oder überlegen sind, hängt in hohem Maße davon ab, dass die volle Materialdichte erreicht wird (HIP ist entscheidend für die Schließung der inneren Porosität), dass durch die Wärmebehandlung die richtige Mikrostruktur erzielt wird und dass Fehler minimiert werden.
- Vorteile von AM: Durch die Bauteilkonsolidierung werden Verbindungen (Schweißnähte/Lötstellen) eliminiert, die bei herkömmlichen Baugruppen häufig Schwachstellen oder Orte der Ermüdungsauslösung sind. DfAM kann optimierte Konstruktionen mit besserer Spannungsverteilung ermöglichen.
- Erfordernis: Strenge Prozessvalidierung, Materialtests (unter Verwendung von Testcoupons, die zusammen mit den Teilen gedruckt werden) und zerstörungsfreie Prüfungen (NDT) sind unerlässlich, um die Zuverlässigkeit von flugkritischer Hardware zu gewährleisten.
2. Welcher Grad an Materialrückverfolgbarkeit ist für AM-Teile für die Luft- und Raumfahrt vorgesehen, und warum ist dies wichtig?
- Antwort: Für Luft- und Raumfahrtkomponenten, die von qualifizierten Lieferanten hergestellt werden (insbesondere von solchen, die nach AS9100 zertifiziert sind), vollständige Rückverfolgbarkeit des Materials ist Standard und obligatorisch. Dies bedeutet:
- Verfolgung von Pulverchargen: Jede Charge Metallpulver (neu oder wiederverwendet) wird mit eindeutigen Identifikatoren nachverfolgt, einschließlich der Herkunft, der chemischen Zertifizierung und der Verarbeitungsgeschichte.
- Verknüpfung herstellen: Jedes gedruckte Teil ist mit der verwendeten AM-Maschine, der Build-Datei mit allen Prozessparametern, den geladenen Pulverchargen und dem Datum und der Uhrzeit des Builds verknüpft.
- Nachbearbeitungsaufzeichnungen: Alle nachfolgenden Schritte (Spannungsabbau, Wärmebehandlung, HIP, Bearbeitung, zerstörungsfreie Prüfung) werden dokumentiert und mit dem Teil oder der Charge verknüpft, einschließlich Ofentabellen, HIP-Protokollen, Bearbeitungsprotokollen und zerstörungsfreien Prüfberichten.
- Wichtigkeit: Die Rückverfolgbarkeit ist für die Qualitätskontrolle von entscheidender Bedeutung, da sie es den Herstellern ermöglicht, potenzielle Probleme bis zu ihrer Quelle zu untersuchen (z. B. eine bestimmte Pulvercharge oder eine Prozessabweichung). Sie gibt dem Endnutzer (dem Hersteller des Raketentriebwerks) die Gewissheit, dass das Teil gemäß den Spezifikationen mit qualifizierten Materialien und Verfahren hergestellt wurde.
3. Können bestehende Schallwanddesigns, die ursprünglich für die herkömmliche Fertigung entwickelt wurden, direkt mit AM gedruckt werden?
- Antwort: Technisch ist es oft möglich, ein bestehendes Design direkt mit AM zu drucken. Allerdings ist dies nutzt selten die wichtigsten Vorteile der additiven Fertigung und können sogar suboptimal oder ineffizient sein.
- Verpasste Gelegenheiten: Der Direktdruck nutzt nicht die Fähigkeit von AM’, komplexe interne Kühlkanäle, optimierte Gitterstrukturen oder konsolidierte Baugruppen zu erstellen. Das Design enthält wahrscheinlich Kompromisse, die speziell für die Beschränkungen der traditionellen Fertigung gemacht wurden (z. B. gerade bohrbare Kühllöcher, mehrere Teile, die zusammengebaut werden müssen).
- Mögliche Probleme: Entwürfe, die für das Gießen oder die maschinelle Bearbeitung vorgesehen sind, können Merkmale aufweisen (z. B. große Überhänge, dünne freitragende Wände), die sich mit AM nur schwer oder ineffizient drucken lassen und umfangreiche Stützstrukturen erfordern.
- Empfehlung: Der Direktdruck kann für erste Bewertungen oder unkritische Prototypen verwendet werden, die Umgestaltung der Schallwand nach DfAM-Prinzipien wird dringend empfohlen um die Möglichkeiten von AM’ in Bezug auf Leistungssteigerung (bessere Kühlung, Dämpfung), Gewichtsreduzierung und potenziell reduzierte Fertigungskomplexität (Teilekonsolidierung) voll zu nutzen.
4. Welches sind die kritischsten Qualitätsprüfungsmethoden, die bei der Qualifizierung von AM-Raketentriebwerksklappen für den Flug eingesetzt werden?
- Antwort: Die Qualifizierung von AM-Baffles umfasst eine umfassende Reihe von Inspektions- und NDT-Methoden, um sowohl die geometrische Konformität als auch die innere Integrität sicherzustellen. Zu den wichtigsten Methoden gehören:
- Prüfung der Abmessungen: Einsatz von Hochpräzisions-KMGs oder 3D-Scans zur Überprüfung aller kritischen Abmessungen und Toleranzen anhand der technischen Zeichnung und des CAD-Modells.
- Computertomographie (CT) Scannen: Gilt als unverzichtbar für komplexe AM-Teile. Bietet eine detaillierte 3D-Röntgenansicht zur zerstörungsfreien Prüfung interner Merkmale (wie Kühlkanäle), zur Erkennung interner Defekte (Porosität, Einschlüsse, Risse) und zur Überprüfung der geometrischen Gesamtintegrität.
- Fluoreszierende Eindringprüfung (FPI): Wird verwendet, um Risse, Poren oder andere Unregelmäßigkeiten in der Oberfläche zu erkennen. Ein Standard-ZfP-Verfahren für kritische metallische Komponenten.
- Materialprüfung: Zerstörende Prüfung von repräsentativen Mustern oder Proben, die neben den eigentlichen Teilen (oft auf derselben Bauplatte) gedruckt werden, um zu überprüfen, ob die Zugeigenschaften, die Mikrostruktur (Metallografie) und möglicherweise die Ermüdungs- oder Kriecheigenschaften nach der Nachbearbeitung den Spezifikationen entsprechen.
- Erprobungsprüfung/Funktionsprüfung: Je nach Kritikalität des Bauteils können Druck- oder Durchflussprüfungen durchgeführt werden, um die Funktionsfähigkeit unter simulierten Betriebsbedingungen zu überprüfen.
Schlussfolgerung: Innovation in der Luft- und Raumfahrt mit additiv gefertigten Baffeln vorantreiben
Die Reise in das Herz eines Raketentriebwerks offenbart Komponenten, die einigen der extremsten Bedingungen ausgesetzt sind, denen technische Systeme ausgesetzt sind. Unter diesen Komponenten ist das Leitblech ein entscheidender Faktor für eine stabile und effiziente Verbrennung. Das Design der Leitbleche, das traditionell durch die Grenzen der subtraktiven Fertigung und Montage eingeschränkt war, tritt nun in eine neue Ära ein, die durch die additive Fertigung von Metall ermöglicht wird.
Wie in diesem Artikel dargelegt, bietet der Einsatz fortschrittlicher AM-Prozesse wie Laser Powder Bed Fusion (L-PBF) und Electron Beam Melting (EBM) in Kombination mit Hochleistungssuperlegierungen wie IN718 und Haynes 282 entscheidende Vorteile für Raketentriebwerksleitbleche:
- Unerreichte Designfreiheit: Sie ermöglichen komplexe interne Kühlkanäle, akustisch optimierte Geometrien und leichte Gitterstrukturen, die bisher unerreichbar waren.
- Verbesserte Leistung: Dies führt zu einem besseren Wärmemanagement, einer effektiveren Unterdrückung von Verbrennungsinstabilitäten und potenziell höheren Motorleistungsgrenzen.
- Teil Konsolidierung: Reduzierung von Komplexität, Gewicht und potenziellen Fehlerquellen durch Integration mehrerer Komponenten in ein einziges, monolithisches Teil.
- Beschleunigte Entwicklung: Erleichterung schneller Design-Iterationen und Prototyping-Zyklen, die für die schnelllebige Luft- und Raumfahrtindustrie entscheidend sind.
Um diese Vorteile zu nutzen, ist jedoch mehr erforderlich als nur der Zugang zu einem 3D-Drucker. Es erfordert einen ganzheitlichen Ansatz, der Folgendes umfasst:
- Design für additive Fertigung (DfAM): Überdenken von Designstrategien, um die Möglichkeiten von AM voll auszuschöpfen.
- Hochwertige Materialien: Verwendung von hochwertigen Superlegierungspulvern mit kontrollierten Eigenschaften.
- Strenge Prozesskontrolle: Optimierung und sorgfältige Verwaltung der AM-Parameter.
- Umfassendes Post-Processing: Durchführung wichtiger Schritte wie Spannungsabbau, Wärmebehandlung, HIP und Präzisionsendbearbeitung.
- Strenge Qualitätssicherungsmaßnahmen: Einsatz gründlicher ZfP- und Inspektionsprotokolle.
Um sich in diesem komplexen Umfeld zurechtzufinden, bedarf es starker Partnerschaften. Die Zusammenarbeit mit einem erfahrenen und fähigen Metall-AM-Dienstleister - einem Anbieter mit tiefem Fachwissen über Materialien, Prozesse, Nachbearbeitung und die strengen Qualitätsanforderungen der Luft- und Raumfahrtbranche - ist von größter Bedeutung. Unternehmen wie Met3dp mit ihrer Grundlage in der fortschrittlichen Pulverherstellung, modernsten Drucktechnologien (einschließlich SEBM) und ihrem Fokus auf umfassende Industrielösungen sind die Art von Partner, die für eine erfolgreiche Implementierung von AM für kritische Anwendungen wie Raketentriebwerksklappen erforderlich ist.
Die additive Fertigung ist nicht nur eine alternative Produktionsmethode, sondern auch ein Katalysator für Innovationen in der Antriebstechnik. Durch die Möglichkeit, anspruchsvollere, zuverlässigere und effizientere Komponenten herzustellen, trägt die Metall-AM dazu bei, die Zukunft der Weltraumforschung und -nutzung zu gestalten. In dem Maße, wie die Technologie weiter ausreift und die Akzeptanz wächst, können wir davon ausgehen, dass additiv gefertigte Teile eine zunehmend wichtige Rolle beim Antrieb der nächsten Generation von Trägerraketen und Raumfahrzeugen spielen werden.
Um herauszufinden, wie Met3dp’s fortschrittliche Fähigkeiten in der additiven Metallfertigung die Luft- und Raumfahrtprojekte Ihres Unternehmens unterstützen können, besuchen Sie unsere Website oder kontaktieren Sie unser Team noch heute. https://met3dp.com/
Teilen auf
MET3DP Technology Co., LTD ist ein führender Anbieter von additiven Fertigungslösungen mit Hauptsitz in Qingdao, China. Unser Unternehmen ist spezialisiert auf 3D-Druckgeräte und Hochleistungsmetallpulver für industrielle Anwendungen.
Fragen Sie an, um den besten Preis und eine maßgeschneiderte Lösung für Ihr Unternehmen zu erhalten!
Verwandte Artikel
Über Met3DP
Aktuelles Update
Unser Produkt
KONTAKT US
Haben Sie Fragen? Senden Sie uns jetzt eine Nachricht! Wir werden Ihre Anfrage mit einem ganzen Team nach Erhalt Ihrer Nachricht bearbeiten.
Holen Sie sich Metal3DP's
Produkt-Broschüre
Erhalten Sie die neuesten Produkte und Preislisten
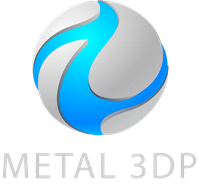
Metallpulver für 3D-Druck und additive Fertigung