Raketentreibstoffdüsenspitzen 3D-gedruckt in Superlegierungen
Inhaltsübersicht
Einführung: Revolutionierung des Raketenantriebs mit 3D-gedruckten Treibstoffdüsenspitzen
Das unermüdliche Streben nach effizienterer, leistungsstärkerer und zuverlässigerer Weltraumforschung hängt von der kontinuierlichen Innovation in der Raketentriebwerkstechnologie ab. Im Herzen dieser hochentwickelten Antriebssysteme befindet sich eine scheinbar kleine, aber grundlegend kritische Komponente: die Treibstoffdüsenspitze. Dieses komplizierte Stück bestimmt das präzise Mischen und Einspritzen von Treibstoffen in die Brennkammer und beeinflusst direkt die Motorleistung, -stabilität und den Gesamterfolg der Mission. Traditionell durch komplexe Guss- und Bearbeitungsverfahren hergestellt, stellen Treibstoffdüsenspitzen erhebliche Herausforderungen dar, da sie komplexe Geometrien, anspruchsvolle Materialanforderungen und die extremen Betriebsbedingungen aufweisen, denen sie ausgesetzt sind – Temperaturen von über tausend Grad Celsius, immense Drücke und die Einwirkung von hochkorrosiven Treibstoffen.
Betreten Sie die additive Metallfertigung (AM) oder 3D-Druck. Diese transformative Technologie verändert rasant die Landschaft der Luft- und Raumfahrtkomponentenproduktion und bietet beispiellose Designfreiheit, beschleunigte Entwicklungszyklen und die Fähigkeit, hochoptimierte Teile zu erstellen, deren Herstellung zuvor unmöglich oder unerschwinglich teuer war. Für Raketentreibstoffdüsenspitzen eröffnet Metall-AM, insbesondere unter Verwendung von Hochleistungs-Nickelbasis-Superlegierungen wie Inconel 718 (IN718) und Inconel 625 (IN625), eine neue Welt der Möglichkeiten. Es ermöglicht die Herstellung von integrierten Kühlkanälen, komplexen internen Merkmalen zur verbesserten Vermischung und konsolidierten Designs, die die Teileanzahl und potenzielle Fehlerpunkte reduzieren.
Die Auswirkungen für Luft- und Raumfahrtingenieure und Beschaffungsmanager sind tiefgreifend. Metall-AM bietet einen Weg zu leichteren, effizienteren Raketentriebwerken, wodurch möglicherweise die Startkosten gesenkt und ehrgeizigere Missionen ermöglicht werden. Darüber hinaus erleichtert die digitale Natur von AM schnellere Designiterationen und die On-Demand-Produktion, wodurch die Lieferketten rationalisiert und die Abhängigkeit von traditionellen Fertigungsengpässen verringert werden. Unternehmen, die nach qualifizierten Zulieferer der Luft- und Raumfahrtindustrie und zuverlässige Metall-AM-Dienstleister suchen, wenden sich zunehmend der additiven Fertigung zu, um sich einen Wettbewerbsvorteil zu verschaffen.
Met3dp mit Hauptsitz in Qingdao, China, steht an der Spitze dieser technologischen Revolution. Als ein führender Anbieter von umfassenden Lösungen zur additiven Metallfertigung, Met3dp ist auf fortschrittliche 3D-Druckgeräte und die Herstellung von Hochleistungs-Metallpulvern spezialisiert, die für anspruchsvolle Anwendungen wie Raketentreibstoffdüsenspitzen unerlässlich sind. Unser fundiertes Fachwissen in der Materialwissenschaft, insbesondere mit Superlegierungen wie IN718 und IN625, gepaart mit unseren hochmodernen Gasverdüsungs- und Plasma Rotating Electrode Process (PREP)-Pulverherstellungstechnologien, stellt sicher, dass Ingenieure und Beschaffungsprofis Komponenten erhalten, die den strengen Anforderungen der Luft- und Raumfahrtindustrie entsprechen. Dieser Blogbeitrag befasst sich mit den Besonderheiten der Verwendung von Metall-3D-Druck für Raketentreibstoffdüsenspitzen, untersucht die kritischen Funktionen, Materialauswahlen, Designüberlegungen und Herstellungsprozesse und hebt hervor, wie Met3dp die nächste Generation des Weltraumantriebs unterstützt. Wir werden untersuchen, warum IN718 und IN625 die Materialien der Wahl sind, die von Experten bezogen werden Superlegierungspulverhersteller wie Met3dp, und wie AM die Einschränkungen herkömmlicher Methoden überwindet.
Die entscheidende Rolle von Treibstoffdüsenspitzen für die Leistung von Raketentriebwerken
Um die Auswirkungen der additiven Fertigung auf Raketentreibstoffdüsenspitzen voll und ganz zu würdigen, muss man zunächst ihre unverzichtbare Funktion innerhalb des komplexen Ökosystems eines Raketentriebwerks verstehen. Diese Komponenten sind weit mehr als nur einfache Leitungen für Treibstoff; sie sind Präzisionsinstrumente, die unter einigen der extremsten Bedingungen arbeiten, die von der Menschheit entwickelt wurden. Zu ihren Hauptaufgaben gehören:
- Treibmittelzerstäubung: Die Düsenspitze muss den ankommenden flüssigen Treibstoff (und manchmal auch das Oxidationsmittel, je nach Injektordesign) in ein feines Sprühm
- Präzise Kraftstoffeinspritzung: Die Düse muss den zerstäubten Treibstoff mit einer bestimmten Durchflussrate, einem bestimmten Sprühmuster (z. B. konisch, fächerförmig) und einem bestimmten Winkel in die Brennkammer abgeben. Diese präzise Abgabe gewährleistet eine optimale Mischungsdynamik mit dem Oxidationsmittel, was zu einer kontrollierten Verbrennung und einer Maximierung der Schubentwicklung führt. Abweichungen können zu lokalen Hot Spots, unvollständiger Verbrennung und Fehlausrichtungen des Schubvektors führen.
- Erzeugung spezifischer Mischmuster: Bei vielen fortschrittlichen Injektordesigns (wie Pintle- oder Koaxialwirbelinjektoren) sind die Kraftstoffdüsenspitzen integrale Bestandteile der Injektoranordnung, die im Zusammenspiel mit Oxidationsmittelkanälen spezifische turbulente Mischmuster erzeugen. Diese Muster erhöhen den Verbrennungswirkungsgrad und die Stabilität, insbesondere bei unterschiedlichen Schubniveaus.
- Beständigkeit in extremen Umgebungen: Dies ist wohl der anspruchsvollste Aspekt. Kraftstoffdüsenspitzen befinden sich an der Schwelle der Brennkammer und sind folgenden Bedingungen ausgesetzt:
- Extreme Temperaturen: Oftmals über 3000 °C (5432 °F) in der Verbrennungszone, obwohl das Düsenmaterial selbst durch Design und regenerative Kühlung kühler gehalten wird. Dennoch ist das Material intensiven Temperaturgradienten und einem hohen Wärmestrom ausgesetzt.
- Hohe Drücke: Brennkammern arbeiten bei Drücken von zehn bis hundert Atmosphären (Bar). Die Düsenspitze muss unter diesen immensen Belastungen ihre strukturelle Integrität bewahren.
- Korrosive Treibstoffe: Raketentreibstoffe (wie RP-1, Methan, Wasserstoff) und Oxidationsmittel (wie flüssiger Sauerstoff) können stark korrosiv sein, insbesondere bei erhöhten Temperaturen.
- Vibrationen und Akustik: Der Verbrennungsprozess erzeugt intensive Vibrationen und akustische Energie, denen die Düsenspitze ohne Ermüdungsbruch standhalten muss.
- Thermisches Zyklieren: Motoren erfahren während des Anfahrens eine rasche Erwärmung und während des Abstellens eine Abkühlung, wodurch thermische Spannungen induziert werden.
Die Leistungsmerkmale, die direkt von der Kraftstoffdüsenspitze beeinflusst werden, umfassen:
- Verbrennungswirkungsgrad (c*): Ein Maß dafür, wie effektiv die chemische Energie der Treibstoffe in Wärmeenergie umgewandelt wird. Eine optimale Zerstäubung und Mischung, die durch das Düsendesign angetrieben wird, sind der Schlüssel.
- Schub: Die vom Motor erzeugte Kraft. Eine effiziente Verbrennung führt direkt zu einem höheren Schub bei einer bestimmten Treibstoffdurchflussrate.
- Spezifischer Impuls (Isp): Ein Maß für den Wirkungsgrad des Motors (Schub pro verbrauchter Treibstoffeinheit pro Sekunde). Ein höherer Verbrennungswirkungsgrad führt im Allgemeinen zu einem höheren Isp.
- Stabilität der Verbrennung: Ein gleichmäßiges, vorhersehbares Brennen ist entscheidend. Eine schlechte Düsenleistung kann zu Instabilitäten wie „Chugging“ oder hochfrequenter „Schrei“-Verbrennung führen, was einen Motor zerstören kann.
- Motorhaltbarkeit und Lebensdauer: Düsendesigns, die thermische Belastungen reduzieren und Erosion/Korrosion widerstehen, tragen zu einer längeren Motorlebensdauer und Wiederverwendbarkeit bei.
Angesichts dieser kritischen Funktionen und rauen Betriebsbedingungen erfordert die Konstruktion und Herstellung von Kraftstoffdüsenspitzen außergewöhnliche Präzision und die Verwendung von Materialien, die in der Lage sind, ihre Festigkeit und Integrität bei extremen Temperaturen zu erhalten. Jeder Kompromiss bei der Qualität oder Leistung kann katastrophale Folgen für den Motor und die Mission haben. Dies unterstreicht die Bedeutung der Auswahl geeigneter Materialien in Luft- und Raumfahrtqualität und Partnerschaften mit erfahrene Hersteller von Luft- und Raumfahrtkomponenten , die die Nuancen der Herstellung dieser missionskritischen Teile verstehen. Das Engagement von Met3dp für die Herstellung hochreiner, kugelförmiger Metallpulver unter Verwendung fortschrittlicher Techniken wie Gasverdüsung gewährleistet die grundlegende Materialqualität, die für solch anspruchsvolle Anwendungen erforderlich ist.
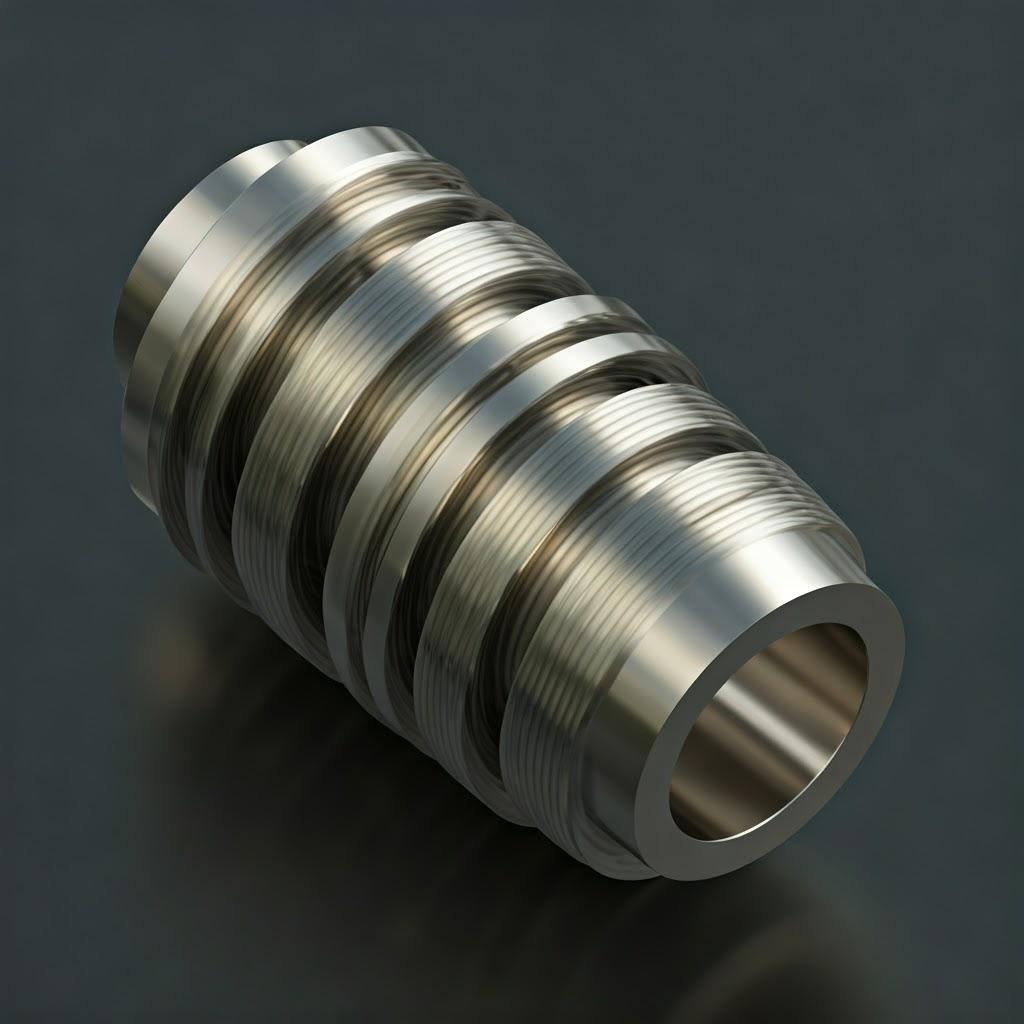
Warum die additive Fertigung von Metallen ideal für komplexe Raketenkraftstoffdüsen ist
Herkömmliche Herstellungsverfahren für Raketenkraftstoffdüsenspitzen, wie z. B. Mehrachsen-CNC-Bearbeitung, Funkenerosion (EDM) und Feinguss, haben der Industrie seit Jahrzehnten gedient. Sie weisen jedoch inhärent Einschränkungen auf, insbesondere wenn Ingenieure nach Designs streben, die Leistung und Effizienz maximieren. Die additive Fertigung überwindet grundlegend viele dieser Einschränkungen und ist damit eine zunehmend bevorzugte Methode zur Herstellung fortschrittlicher Kraftstoffdüsen.
Einschränkungen der traditionellen Fertigung:
- Geometrische Zwänge: Die Bearbeitung hat Schwierigkeiten bei der Erstellung komplexer interner Merkmale wie gekrümmter Kühlkanäle, komplizierter Mischgeometrien oder Hohlstrukturen. Der Feinguss ermöglicht mehr Komplexität, erfordert aber oft mehrteilige Baugruppen und kann Einschränkungen in Bezug auf die Auflösung der Merkmale und die Wandstärke aufweisen.
- Herausforderungen bei der Teilekonsolidierung: Komplexe Düsen müssen oft in mehreren Teilen hergestellt und dann verbunden werden (z. B. Löten, Schweißen). Diese Verbindungen führen zu potenziellen Schwachstellen, erhöhen das Gewicht, fügen Herstellungsschritte hinzu und erschweren die Qualitätskontrolle.
- Materialabfälle: Subtraktive Verfahren wie die Bearbeitung beginnen mit einem größeren Block aus teurem Superlegierungsmaterial und entfernen erhebliche Teile, was zu hohen „Buy-to-Fly“-Verhältnissen und erhöhten Materialkosten führt.
- Lange Vorlaufzeiten und Werkzeugkosten: Die Erstellung von Werkzeugen für den Guss oder komplexen Vorrichtungen für die Bearbeitung kann zeitaufwändig und teuer sein, insbesondere bei Kleinserien oder Prototypen. Designiterationen werden langsam und kostspielig.
- Schwierigkeiten bei der Designiteration: Die Änderung eines Designs erfordert oft erhebliche Änderungen an Werkzeugen oder Bearbeitungsprogrammen, was schnelle Optimierungszyklen behindert.
Vorteile der additiven Fertigung (AM) von Metallen für Kraftstoffdüsen:
Metal AM, insbesondere das Laser Powder Bed Fusion (L-PBF), baut Teile Schicht für Schicht direkt aus einem digitalen Modell mit hochwertigen Metallpulvern auf. Dieser Ansatz bietet überzeugende Vorteile für die Herstellung von Raketenkraftstoffdüsen:
- Beispiellose Designfreiheit:
- Komplexe innere Geometrien: AM zeichnet sich durch die Erstellung komplizierter interner Kühlkanäle aus, die sich präzise an die Außenflächen der Düse anpassen (konforme Kühlung). Dies ermöglicht eine hocheffiziente Wärmeabfuhr, was höhere Verbrennungstemperaturen oder eine längere Düsenlebensdauer ermöglicht.
- Optimierte Mischmerkmale: Ingenieure können ausgeklügelte interne Strukturen entwerfen, um die Zerstäubung und Mischung des Treibstoffs weit über das hinaus zu verbessern, was mit herkömmlichen Methoden erreichbar ist.
- Gewichtsreduzierung: Topologieoptimierung und Gitterstrukturen können in das Design integriert werden, um die Masse zu reduzieren, ohne die strukturelle Integrität zu beeinträchtigen – entscheidend für die Verbesserung der Nutzlastkapazität.
- Teil Konsolidierung: AM ermöglicht das Drucken von zuvor mehrteiligen Baugruppen als einzelne, monolithische Komponente. Dies eliminiert Verbindungen, reduziert das Gewicht, vereinfacht die Montage, verkürzt die Lieferkette und verbessert die Gesamtzuverlässigkeit durch die Beseitigung potenzieller Fehlerquellen. Eine einzelne, integrierte Düsenspitze ist von Natur aus robuster.
- Beschleunigte Entwicklung & Prototyping: Designs können schnell iteriert werden. Ein modifiziertes CAD-Modell kann direkt an den Drucker gesendet werden, sodass Ingenieure mehrere Designvarianten viel schneller und kostengünstiger testen können als bei herkömmlichen Prototypen, wodurch der Motorentwicklungsprozess erheblich beschleunigt wird.
- Materialeffizienz: AM ist ein additives Verfahren, bei dem nur das Material verwendet wird, das zum Bau des Teils erforderlich ist (plus Stützen). Dies reduziert den Materialabfall im Vergleich zu subtraktiven Verfahren drastisch, was besonders wichtig ist, wenn mit teuren Superlegierungen wie IN718 und IN625 gearbeitet wird. Niedrigere Buy-to-Fly-Verhältnisse sind ein erheblicher Kostenvorteil.
- Verbesserte Leistung: Die Fähigkeit, optimierte Kühl- und Mischmerkmale direkt zu implementieren, führt zu spürbaren Leistungsgewinnen: höherer Verbrennungswirkungsgrad, verbessertes Wärmemanagement, größere Stabilität und potenziell längere Lebensdauer der Komponenten.
Vergleichstabelle: AM vs. traditionelle Fertigung für Kraftstoffdüsen
Merkmal | Additive Fertigung von Metall (L-PBF) | Traditionelle Fertigung (Bearbeitung/Gießen) |
---|---|---|
Entwurfskomplexität | Sehr hoch (komplexe interne Kanäle, Gitter, Topologieopt.) | Mäßig bis hoch (begrenzt durch Werkzeuge/Zugang) |
Teil Konsolidierung | Ausgezeichnet (monolithische Teile möglich) | Begrenzt (erfordert oft Montage/Verbindung) |
Materialabfälle | Gering (konturnahe Form) | Hoch (subtraktive Bearbeitung) / Mäßig (Gussläufer) |
Vorlaufzeit (Prototyp) | Fasten (Tage/Wochen) | Langsam (Wochen/Monate, erfordert Werkzeuge/Vorrichtungen) |
Werkzeugkosten | Keiner | Hoch (Gussformen) / Mäßig (Bearbeitungsvorrichtungen) |
Kosten für Kleinserien | Wirtschaftlich | Hoch (aufgrund der Amortisation von Einrichtung/Werkzeugen) |
Kühlungskanäle | Hochoptimierte, konforme Kanäle leicht integriert | Schwierig/unmöglich, komplexe interne Kanäle zu erstellen |
Gewichtsreduzierung | Ausgezeichnetes Potenzial durch Topologieoptimierung & Gitter | Begrenztes Potenzial |
Entwicklungszyklus | Schnelle Iteration möglich | Langsamere Iteration aufgrund von Werkzeug-/Programm-Änderungen |
In Blätter exportieren
Partnerschaft mit einem sachkundigen Metall-AM-Dienstleister wie Met3dp den Zugang nicht nur zur Drucktechnologie, sondern auch zu dem entscheidenden Fachwissen in Prozessoptimierung und Materialwissenschaft sicherstellt, das erforderlich ist, um diese Vorteile voll auszuschöpfen. Die Erfahrung von Met3dp mit Anwendungen in der Luft- und Raumfahrt und der Fokus auf die Herstellung hochwertiger, AM-optimierter Superlegierungspulver machen das Unternehmen zu einem idealen Partner für Unternehmen, die fortschrittliche, 3D-gedruckte Raketenkraftstoffdüsenspitzen beschaffen möchten.
IN718 & IN625 Superlegierungen: Die wichtigsten Materialauswahlen für Raketendüsenspitzen
Die Materialauswahl für eine Raketenkraftstoffdüsenspitze ist unumgänglich; sie muss der brutalen Betriebsumgebung standhalten und gleichzeitig die Dimensionsstabilität und strukturelle Integrität bewahren. Nickelbasierte Superlegierungen haben sich als Goldstandard für diese anspruchsvollen Hochtemperaturanwendungen etabliert, wobei Inconel 718 (IN718) und Inconel 625 (IN625) zu den am weitesten verbreiteten Optionen gehören, insbesondere für die additive Fertigung. Ihre Eignung ergibt sich aus einer außergewöhnlichen Kombination von Eigenschaften:
- Hohe Temperaturbeständigkeit: Sie behalten eine erhebliche Festigkeit und widerstehen Verformungen (Kriechen) bei Temperaturen, bei denen viele andere Metalle erheblich schwächer werden würden. Dies ist entscheidend, um eine Düsenverformung unter thermischer und druckbedingter Belastung zu verhindern.
- Ausgezeichnete Korrosionsbeständigkeit: Sie weisen eine hervorragende Beständigkeit gegen Oxidation und Korrosion durch heiße Verbrennungsgase und aggressive Treibstoffe über einen weiten Temperaturbereich auf.
- Good Fatigue Life: Raketentriebwerke unterliegen zyklischer Belastung (thermisch und mechanisch), wodurch eine hohe Ermüdungsfestigkeit für die Haltbarkeit und Wiederverwendbarkeit unerlässlich ist.
- Schweißbarkeit/Bedruckbarkeit: Sowohl IN718 als auch IN625 weisen im Allgemeinen gute Eigenschaften für additive Fertigungsverfahren wie L-PBF auf, obwohl die Verfahrensparameter sorgfältig kontrolliert werden müssen, um Eigenspannungen zu verwalten und Defekte zu vermeiden.
Lassen Sie uns jede Legierung genauer untersuchen:
Inconel 718 (IN718 / Legierung 718)
- Zusammensetzung: Hauptsächlich Nickel-Chrom, mit signifikanten Zusätzen von Eisen, Niob und Molybdän sowie kleineren Mengen an Aluminium und Titan.
- Verstärkungsmechanismus: Ausscheidungshärtung. Es erhält seine außergewöhnliche Festigkeit durch Wärmebehandlungsverfahren (Lösungsglühen gefolgt von Doppelalterung), die verstärkende Phasen (hauptsächlich Gamma Double Prime – γ′′) innerhalb der Metallmatrix ausfällen.
- Wichtige Eigenschaften:
- Ausgezeichnete mechanische Festigkeit (Zug-, Streckgrenze, Kriechbruch) bis etwa 700 °C (1300 °F).
- Gute Korrosions- und Oxidationsbeständigkeit.
- Relativ gute Schweißbarkeit/Druckbarkeit für eine ausscheidungshärtende Superlegierung aufgrund ihrer langsameren Alterungskinetik.
- Weit verbreitet und gut charakterisiert in der Luft- und Raumfahrtindustrie (oft als Arbeitspferd betrachtet).
- AM Überlegungen: Erfordert eine sorgfältige Kontrolle der L-PBF-Parameter (Laserleistung, Scangeschwindigkeit, Schichtdicke) und Nachbearbeitungswärmebehandlungen (Spannungsarmglühen, Lösungsglühen, Alterung), um eine optimale Mikrostruktur und mechanische Eigenschaften zu erzielen, die mit geschmiedeten Gegenstücken vergleichbar sind. Die Beschaffung von hochwertigem, vorlegiertem IN718-Pulver mit gleichmäßiger kugelförmiger Morphologie und geringem Sauerstoffgehalt, wie es von den fortschrittlichen Gasverdüsungssystemen von Met3dp hergestellt wird, ist für den erfolgreichen Druck entscheidend.
Inconel 625 (IN625 / Legierung 625)
- Zusammensetzung: Hauptsächlich Nickel-Chrom, mit signifikanten Zusätzen von Molybdän und Niob. Geringerer Eisengehalt als IN718.
- Verstärkungsmechanismus: Festlösungsverfestigung. Molybdän- und Niob-Atome lösen sich in der Nickel-Chrom-Matrix auf, verzerren das Kristallgitter und behindern die Bewegung von Versetzungen, was Festigkeit verleiht. Es erfordert keine Ausscheidungshärtungswärmebehandlungen zur Verstärkung, obwohl das Glühen verwendet wird.
- Wichtige Eigenschaften:
- Ausgezeichnete Verarbeitbarkeit und Schweißbarkeit/Druckbarkeit.
- Hervorragende Beständigkeit gegen eine Vielzahl korrosiver Umgebungen, sowohl oxidierend als auch reduzierend, oft IN718 in bestimmten aggressiven Medien (z. B. Lochfraß, Spaltkorrosion) überlegen.
- Sehr gute Festigkeit und Zähigkeit von kryogenen Temperaturen bis etwa 815 °C (1500 °F), wobei die Festigkeit bei etwas höheren Temperaturen als IN718 beibehalten wird, obwohl seine Spitzenfestigkeit bei moderaten Temperaturen geringer sein kann als bei vollständig wärmebehandeltem IN718.
- Ausgezeichnete Ermüdungsfestigkeit.
- AM Überlegungen: Gilt im Allgemeinen als einfacher zu drucken als IN718, da es sich um eine Festlösung handelt, was zu geringeren Eigenspannungen und einer geringeren Rissneigung während Lieferanten von Luft- und Raumfahrtmaterialien und Endanwender erhalten Pulver, das für additive Verfahren optimiert ist.
Materialauswahlvergleich: IN718 vs. IN625 für Kraftstoffdüsen
Eigentum | IN718 (wärmebehandelt) | IN625 (geglüht) | Überlegungen für Kraftstoffdüsen |
---|---|---|---|
Max. Betriebstemp. | Gute Festigkeit bis zu ~ 700 °C (1300 °F) | Gute Festigkeit bis zu ~ 815 °C (1500 °F) | IN625 kann einen leichten Vorteil bieten, wenn die Spitzentemperaturen des Materials höher sind, aber das Kühlungsdesign ist entscheidend. |
Festigkeit (moderate Temperatur) | Im Allgemeinen höher (aufgrund der γ′′-Ausscheidung) | Geringer als der Spitzenwert von IN718 | IN718 wird oft für maximale Festigkeit bevorzugt, wenn die Temperaturen dies zulassen. |
Korrosionsbeständigkeit | Sehr gut | Ausgezeichnet (oft überlegen, insbesondere bei Lochfraß/Spaltkorrosion) | Hängt von der spezifischen Treibstoffchemie ab; IN625 könnte für stark korrosive Gemische besser geeignet sein. |
Druckbarkeit | Gut (erfordert sorgfältige Kontrolle und Wärmebehandlung) | Ausgezeichnet (weniger anfällig für Rissbildung, einfachere Wärmebehandlung) | IN625 kann den AM-Prozess vereinfachen und das Risiko verringern, wodurch möglicherweise Herstellungskosten. |
Wärmebehandlung | Komplex (Spannungsarmglühen + Lösungsglühen + Doppelalterung) | Einfacher (Spannungsarmglühen / Glühen) | IN718 erfordert eine aufwändigere Nachbearbeitung. |
Industriedatenbank | Umfangreich (Allzwecklegierung) | Umfassend | Beide sind gut verstandene Materialien in der Luft- und Raumfahrt. |
Kosten | Im Allgemeinen vergleichbar, kann je nach Markt und Form variieren | Im Allgemeinen vergleichbar, kann je nach Markt und Form variieren | Die Pulverqualität und -konsistenz sind wichtige Faktoren. |
In Blätter exportieren
Der Met3dp-Vorteil bei Superlegierungspulvern:
Die Wahl der richtigen Legierung ist nur ein Teil der Gleichung. Die Qualität des Metallpulvers, das im L-PBF-Verfahren verwendet wird, ist von entscheidender Bedeutung, um die gewünschten Materialeigenschaften und fehlerfreie Komponenten zu erzielen. Hier werden die Fähigkeiten von Met3dp für Beschaffungsmanager und Ingenieure, die Materialien für additive Massenfertigung oder kritische Komponenten beziehen, entscheidend.
- Fortschrittliche Pulverproduktion: Met3dp verwendet branchenführende Gasverdüsungs- (GA) und Plasma-Rotations-Elektroden-Verfahrens- (PREP) Technologien. Unsere GA-Ausrüstung verfügt über einzigartige Düsen- und Gasströmungsdesigns, die für die Herstellung von Pulvern mit folgenden Eigenschaften optimiert sind:
- Hohe Sphärizität: Gewährleistet eine ausgezeichnete Pulverbettdichte und Fließfähigkeit innerhalb der AM-Maschine, was zu gleichmäßigeren Schichten und einem vorhersehbaren Schmelzverhalten führt.
- Geringe Porosität: Minimiert innere Hohlräume in den Pulverpartikeln, wodurch potenzielle Defekte im fertigen Teil reduziert werden.
- Kontrollierte Partikelgrößenverteilung (PSD): Maßgeschneiderte PSD für spezifische AM-Prozesse gewährleisten ein optimales Pack- und Schmelzverhalten.
- Hohe Reinheit: Die Minimierung von Verunreinigungen (wie Sauerstoff und Stickstoff) ist entscheidend, um die gewünschten mechanischen Eigenschaften und die Korrosionsbeständigkeit in Superlegierungen zu erreichen.
- Qualitätskontrolle: Strenge Tests und Charakterisierungen gewährleisten eine Chargen-zu-Chargen-Konsistenz, eine wesentliche Anforderung für Luft- und Raumfahrtanwendungen, bei denen die Prozesswiederholbarkeit von entscheidender Bedeutung ist.
- Material-Portfolio: Neben IN718 und IN625 bietet Met3dp eine breite Palette an Hochleistungspulvern, darunter Titanlegierungen (Ti6Al4V, TiNi, TiTa, TiAl, TiNbZr), CoCrMo, Edelstähle und andere Superlegierungen, was uns zu einem umfassenden Anbieter von Metallpulver für vielfältige industrielle Anforderungen macht. Entdecken Sie die Palette der Hochleistungs-Metallpulver von Met3dp.
Durch die Nutzung von AM mit hochwertigen IN718- oder IN625-Pulvern von einem vertrauenswürdigen Lieferanten wie Met3dp können Luft- und Raumfahrtunternehmen Raketentreibstoffdüsenspitzen mit überlegener Leistung, erhöhter Zuverlässigkeit und potenziell geringeren Gesamtbetriebskosten herstellen und so die Zukunft der Weltraumantriebstechnologie vorantreiben.
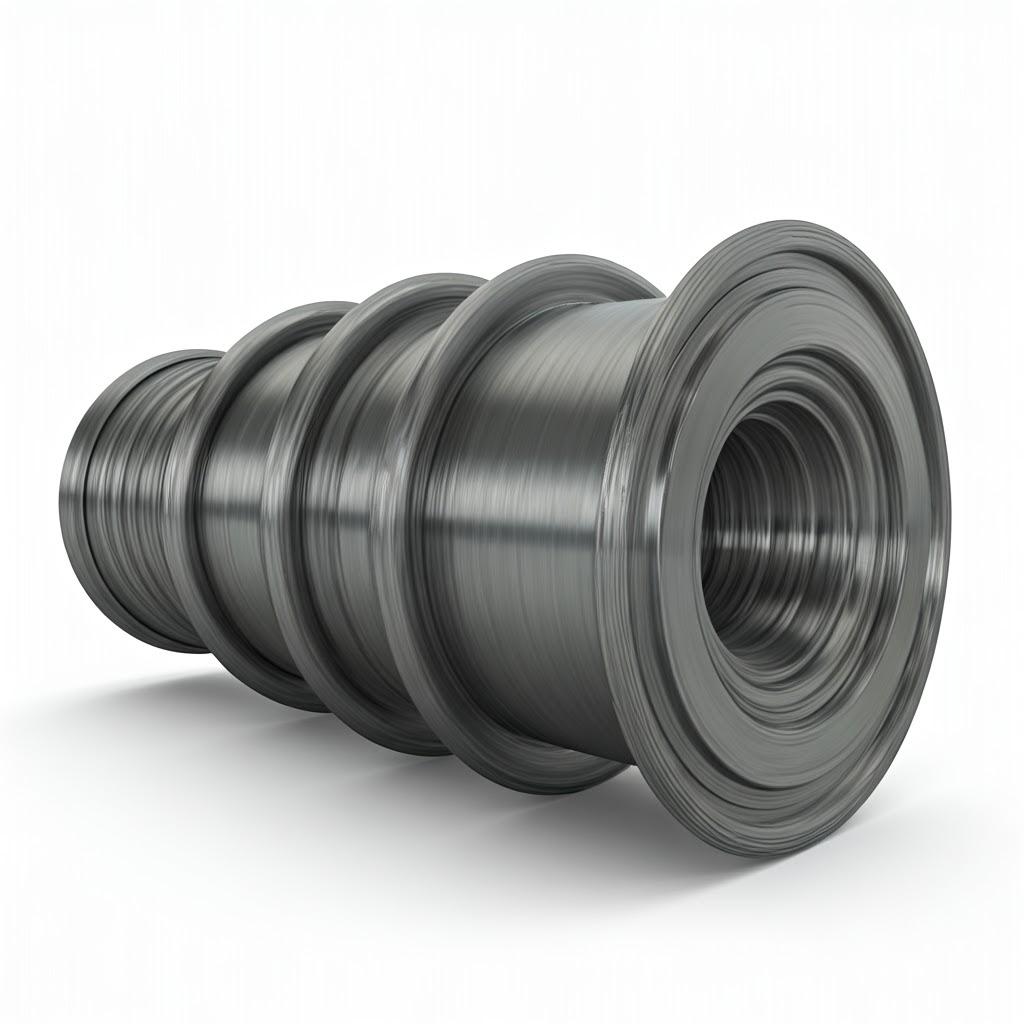
Design for Additive Manufacturing (DfAM)-Strategien für optimierte Kraftstoffdüsenleistung
Das bloße Replizieren eines Designs, das ursprünglich für die traditionelle Fertigung bestimmt war, unter Verwendung additiver Verfahren, erfasst oft nicht das wahre Potenzial des 3D-Drucks. Um die zuvor beschriebenen Vorteile – komplexe Geometrien, Teilekonsolidierung, Leichtbau und verbesserte Leistung – voll auszuschöpfen, müssen Ingenieure Design for Additive Manufacturing (DfAM) anwenden. DfAM ist nicht nur eine Reihe von Richtlinien; es ist ein Paradigmenwechsel im Denken über das Komponentendesign, der von Anfang an die einzigartigen Fähigkeiten und Einschränkungen des schichtweisen AM-Prozesses berücksichtigt. Für eine so komplizierte und kritische Komponente wie eine Raketentreibstoffdüsenspitze ist der Einsatz von DfAM-Strategien unerlässlich, um Leistung, Zuverlässigkeit und Herstellbarkeit zu maximieren.
Effektives DfAM für Kraftstoffdüsen beinhaltet mehrere Schlüsselstrategien:
- Nutzung der geometrischen Freiheit für das Wärmemanagement (konforme Kühlung):
- Konzept: Traditionelle Kühlkanäle sind oft gerade Linien, die in die Komponente gebohrt werden, was zu ungleichmäßiger Kühlung und potenziellen Hotspots führt. AM ermöglicht die Erstellung von Kühlkanälen, die genau den Konturen der beheizten Oberflächen der Düse folgen (konforme Kanäle).
- Vorteile: Dies führt zu einer viel gleichmäßigeren und effizienteren Wärmeabfuhr aus kritischen Bereichen wie dem Düsenauslass oder der Stirnseite. Zu den Vorteilen gehören:
- Reduzierte Spitzentemperaturen des Materials, wodurch die Lebensdauer und die Sicherheitsmargen der Komponente erhöht werden.
- Geringere Temperaturgradienten, wodurch thermische Spannungen und Verformungen minimiert werden.
- Potenzial, die Leistungsgrenzen des Motors zu verschieben (höhere Verbrennungstemperaturen/-drücke).
- Reduzierter Kühlmittelbedarf, wodurch Gewicht an anderer Stelle im System eingespart wird.
- Umsetzung: DfAM beinhaltet die Konstruktion von Kanalwegen, Querschnittsformen (z. B. Optimierung für Wärmeübertragung und Druckabfall) und Einlass-/Auslassverteilern direkt in das CAD-Modell, wobei die Fähigkeiten von L-PBF genutzt werden, um diese komplizierten internen Netzwerke zu erstellen.
- Optimierung der internen Strömungswege und Mischelemente:
- Zerstäubung & Mischen: AM ermöglicht die Konstruktion von hochkomplexen internen Geometrien innerhalb der Düsenöffnung selbst – Merkmale wie optimierte Wirbelgeneratoren, einzigartig geformte Auslässe oder komplizierte Durchgänge, die darauf ausgelegt sind, die Treibstoffzerstäubung und die Mischeffizienz weit über das hinaus zu verbessern, was durch Bearbeitung oder Gießen erreicht werden könnte.
- Glatte Durchgänge & dünne Wände: Designer können glatte, aerodynamisch effiziente interne Durchgänge erstellen, um Druckabfälle zu minimieren und eine präzise Kraftstoffzufuhr zu gewährleisten. AM ermöglicht auch die Erstellung von dünnen, aber strukturell soliden Wänden, wo dies erforderlich ist, was zu Leichtbau und optimaler thermischer Leistung beiträgt. Die Wandstärken müssen unter Berücksichtigung der Druckbelastungen, der Materialeigenschaften und der Auflösung des AM-Prozesses sorgfältig abgewogen werden.
- Nutzung der Teilekonsolidierung:
- Konzept: Wie bereits erwähnt, ermöglicht AM die Integration mehrerer Komponenten in ein einziges, monolithisches Teil. Eine traditionell gefertigte Kraftstoffdüsenbaugruppe könnte aus einem Körper, internen Wirblern, Haltemuttern und Dichtungselementen bestehen, die alle eine komplexe Montage und Verbindung erfordern.
- DfAM-Ansatz: Ingenieure können die gesamte Baugruppe als eine einzige druckbare Einheit neu gestalten. Dies beinhaltet die Integration von Befestigungselementen, internen Strömungselementen und sogar Teilen der Injektorstirnseite in ein einziges Teil.
- Vorteile: Eliminiert Verbindungen (potenzielle Leckpfade und Fehlerstellen), reduziert die Montagezeit und den Arbeitsaufwand erheblich, senkt die Gesamtteilanzahl und vereinfacht Beschaffung und Lieferkettenmanagementund reduziert oft das Gewicht.
- Strategische Konstruktion für Stützstrukturen:
- Die Notwendigkeit: L-PBF erfordert typischerweise Stützstrukturen für überhängende Merkmale (normalerweise unter 45 Grad zur Horizontalen) und zur Verankerung des Teils an der Bauplatte, wodurch thermische Spannungen bewältigt werden.
- DfAM-Überlegungen:
- Minimierung: Ausrichten des Teils auf der Bauplatte, um den Bedarf an Stützen zu minimieren (selbsttragende Winkel). Konstruieren von Merkmalen mit Fasen oder Rundungen anstelle von scharfen Überhängen.
- Zugänglichkeit: Sicherstellen, dass Stützen, insbesondere interne (z. B. in Kühlkanälen), nach dem Drucken zugänglich sind. Dies kann die Konstruktion bestimmter Zugangsöffnungen beinhalten, die später abgedichtet werden, oder die Berücksichtigung der Einschränkungen von Werkzeugen zum Entfernen.
- Art der Unterstützung: Konstruieren von Stützen, die stark genug sind, um Verformungen zu verhindern, aber für eine einfachere Entfernung optimiert sind (z. B. konische Stützen, perforierte Strukturen).
- Auswirkungen: Stützstrukturen erhöhen die Druckzeit, verbrauchen Material und erfordern Nachbearbeitungsschritte zum Entfernen und zur Oberflächenbearbeitung. Effektives DfAM minimiert diese Auswirkungen.
- Implementierung von Topologieoptimierung und Gitterstrukturen:
- Topologie-Optimierung: Verwendung von Softwarealgorithmen, um Material aus Bereichen zu entfernen, in denen es strukturell nicht benötigt wird, basierend auf definierten Lastfällen und Einschränkungen. Dies kann das Gewicht von Montageflanschen oder nicht-kritischen Strukturelementen der Düsenbaugruppe erheblich reduzieren, was entscheidend ist, um das Gesamt-Schub-Gewichts-Verhältnis des Motors zu verbessern.
- Gitterförmige Strukturen: Das Ersetzen von Festkörpervolumina durch interne Gitter- oder Zellstrukturen kann das Gewicht weiter reduzieren, während die erforderliche Steifigkeit erhalten bleibt oder der Flüssigkeitsfluss oder die Wärmeableitung erleichtert wird. Diese komplexen Strukturen sind nur durch AM realisierbar.
- Berücksichtigung der Bauausrichtung:
- Auswirkungen: Die Ausrichtung, in der die Düse gedruckt wird, beeinflusst die Oberflächenbeschaffenheit (Treppeneffekt auf gekrümmten Oberflächen), die Position und Menge der benötigten Stützstrukturen, die Verteilung der Eigenspannungen, die Bauzeit und möglicherweise die mechanischen Eigenschaften aufgrund der anisotropen Natur der AM-Verfahren.
- DfAM-Strategie: Die Auswahl der optimalen Bauausrichtung ist ein kritischer DfAM-Schritt, bei dem Faktoren wie die Anforderungen an die Oberflächenqualität für bestimmte Merkmale (z. B. Dichtflächen), die Minimierung interner Stützen, die Bewältigung thermischer Spannungen und die Ausrichtung kritischer Merkmale auf die besten Auflösungsachsen des Druckers abgewogen werden.
Die erfolgreiche Implementierung von DfAM erfordert eine enge Zusammenarbeit zwischen Konstrukteuren, Materialwissenschaftlern und AM-Prozessspezialisten. Unternehmen wie Met3dp, mit fundierter Expertise in beiden Bereichen fortschrittliche Metallpulver und additive Fertigungsverfahren, können während der Konstruktionsphase unschätzbare Beiträge leisten und sicherstellen, dass das Kraftstoffdüsendesign vollständig auf Druckbarkeit, Leistung und Zuverlässigkeit optimiert ist. Die Einbindung eines erfahrenen aM-Partner für die Luft- und Raumfahrt frühzeitig ist der Schlüssel zur effektiven Nutzung von DfAM.
Erzielung von Präzision in Luft- und Raumfahrtqualität: Toleranz, Oberflächenbeschaffenheit und Maßhaltigkeit bei AM-Düsen
Raketentreibstoffdüsenspitzen sind Präzisionskomponenten, bei denen geringfügige Abweichungen in den Abmessungen oder Oberflächenmerkmalen die Motorleistung und -sicherheit erheblich beeinträchtigen können. Das Erreichen des erforderlichen Präzisionsniveaus mit additiver Fertigung, insbesondere unter Verwendung von Superlegierungen wie IN718 und IN625, erfordert eine sorgfältige Prozesskontrolle, das Verständnis des Materialverhaltens und oft ergänzende Nachbearbeitungsschritte. Ingenieure und Beschaffungsmanager müssen realistische Erwartungen an die Fähigkeiten von L-PBF haben und entsprechend planen.
Maßgenauigkeit und Toleranzen:
- As-Built-Toleranzen: Die Maßhaltigkeit, die direkt aus dem L-PBF-Verfahren (as-built) erreicht werden kann, liegt typischerweise im Bereich von ±0,1 mm bis ±0,3 mm (±0,004" bis ±0,012") für allgemeine Abmessungen auf gut kontrollierten Industriemaschinen. Kleinere Merkmale oder engere Toleranzen können erreicht werden, hängen aber oft stark von der Merkmalgeometrie, der Position, der Ausrichtung und einer rigorosen Prozessoptimierung ab.
- Faktoren, die die Genauigkeit beeinflussen:
- Kalibrierung der Maschine: Die Präzision des Laserscansystems, die Steuerung der Schichtdicke und die allgemeine Maschinenstabilität sind von grundlegender Bedeutung. Met3dp verwendet branchenführende Geräte, die für ihre Genauigkeit und Zuverlässigkeit bekannt sind.
- Prozessparameter: Laserleistung, Scangeschwindigkeit, Hatch-Abstand und Schichtdicke beeinflussen direkt die Schmelzbadgröße und -stabilität und wirken sich auf die Maßkontrolle aus.
- Thermische Effekte: Das schnelle Erhitzen und Abkühlen, das L-PBF innewohnt, induziert thermische Spannungen, die zu Verformungen und Verzerrungen führen können, wenn sie nicht durch Stützstrategien und optimierte Scanmuster richtig gehandhabt werden. Superlegierungen mit hohen Wärmeausdehnungskoeffizienten erfordern eine sorgfältige Handhabung.
- Qualität des Pulvers: Eine gleichmäßige Partikelgrößenverteilung, Morphologie (Kugelförmigkeit) und Fließfähigkeit des Metallpulvers (wie das gasverdüste IN718/IN625 von Met3dp) tragen zu einer gleichmäßigen Pulverbettdichte und einem vorhersehbaren Schmelzverhalten bei, was die Maßhaltigkeit verbessert.
- Größe und Geometrie der Teile: Größere Teile oder Teile mit erheblichen Querschnittsvariationen können anfälliger für thermische Verformungen sein.
- Strategie unterstützen: Stützen spielen eine entscheidende Rolle bei der Verankerung des Teils und der Bewältigung der Wärmeableitung, was die endgültigen Abmessungen beeinflusst.
- Nachbearbeitung für kritische Toleranzen: Für Merkmale, die engere Toleranzen erfordern, als L-PBF zuverlässig as-built erreichen kann (z. B. Dichtflächen, Schnittstellendurchmesser
Oberflächengüte (Rauhigkeit):
- As-Built Oberflächenbeschaffenheit: Die Oberflächenbeschaffenheit, typischerweise gemessen als Rauheitsmittelwert (Ra), von direkt gefertigten L-PBF-Bauteilen wird von mehreren Faktoren beeinflusst:
- Schichtdicke: Dünnere Schichten führen im Allgemeinen zu glatteren Oberflächen.
- Partikelgröße: Feinere Pulver können zu glatteren Oberflächen beitragen, können aber die Fließfähigkeit beeinträchtigen.
- Orientierung:
- Vertikale Mauern: Neigen zu relativ guten Oberflächen, die dadurch beeinflusst werden, dass die Pulverpartikel teilweise an den Seiten anhaften.
- Nach oben gerichtete Oberflächen: Im Allgemeinen die glattesten, direkt durch das Laserschmelzen geformt. Typische Ra-Werte können 5-15 µm betragen.
- Nach unten gerichtete (überhängende) Oberflächen: Neigen aufgrund des notwendigen Kontakts mit Stützstrukturen oder des „Treppeneffekts“ bei flachen Winkeln dazu, am rauesten zu sein. Ra-Werte können 15-20 µm oder mehr überschreiten.
- Prozessparameter: Laserparameter und Scanstrategien beeinflussen die Schmelzbad-Dynamik und die Oberflächenstruktur.
- Auswirkungen auf die Leistung: Die Oberflächenrauheit im Inneren der Düse kann die Fluiddynamik (Druckabfall, Strömungsablösung) und den Wärmeübergang beeinflussen. Raue Außenflächen sind möglicherweise weniger kritisch, es sei denn, es handelt sich um Dichtflächen.
- Verbesserung der Oberflächengüte: Wenn die direkt gefertigte Oberfläche unzureichend ist, werden verschiedene Nachbearbeitungstechniken eingesetzt (detailliert im nächsten Abschnitt), einschließlich Zerspanung, Polieren, Abrasiv-Fließbearbeitung (AFM) oder elektrochemisches Polieren (ECP), insbesondere für Innenkanäle, in denen ein gleichmäßiger Fluss entscheidend ist.
Messtechnik und Qualitätssicherung:
Sicherstellen, dass die endgültige Kraftstoffdüse die strengen Luft- und Raumfahrt-Toleranz Anforderungen erfüllt, erfordert fortschrittliche Messtechnik. Koordinatenmessgeräte (KMG) werden für präzise Dimensionskontrollen verwendet, während optische Scanner und CT-Scans umfassende 3D-Vergleiche mit dem ursprünglichen CAD-Modell ermöglichen, einschließlich der Überprüfung der Innenkanalabmessungen und der Erkennung von Defekten. Die Partnerschaft mit einem AM-Anbieter wie Met3dp, der die Prozesskontrolle in den Vordergrund stellt und hochwertige Materialien und Geräte verwendet, bietet eine solide Grundlage für die Erzielung von Präzision in Luft- und Raumfahrtqualität. Das Verständnis der Nuancen verschiedener Druckverfahren und ihrer erreichbaren Präzision ist für die Festlegung realistischer Erwartungen von entscheidender Bedeutung.
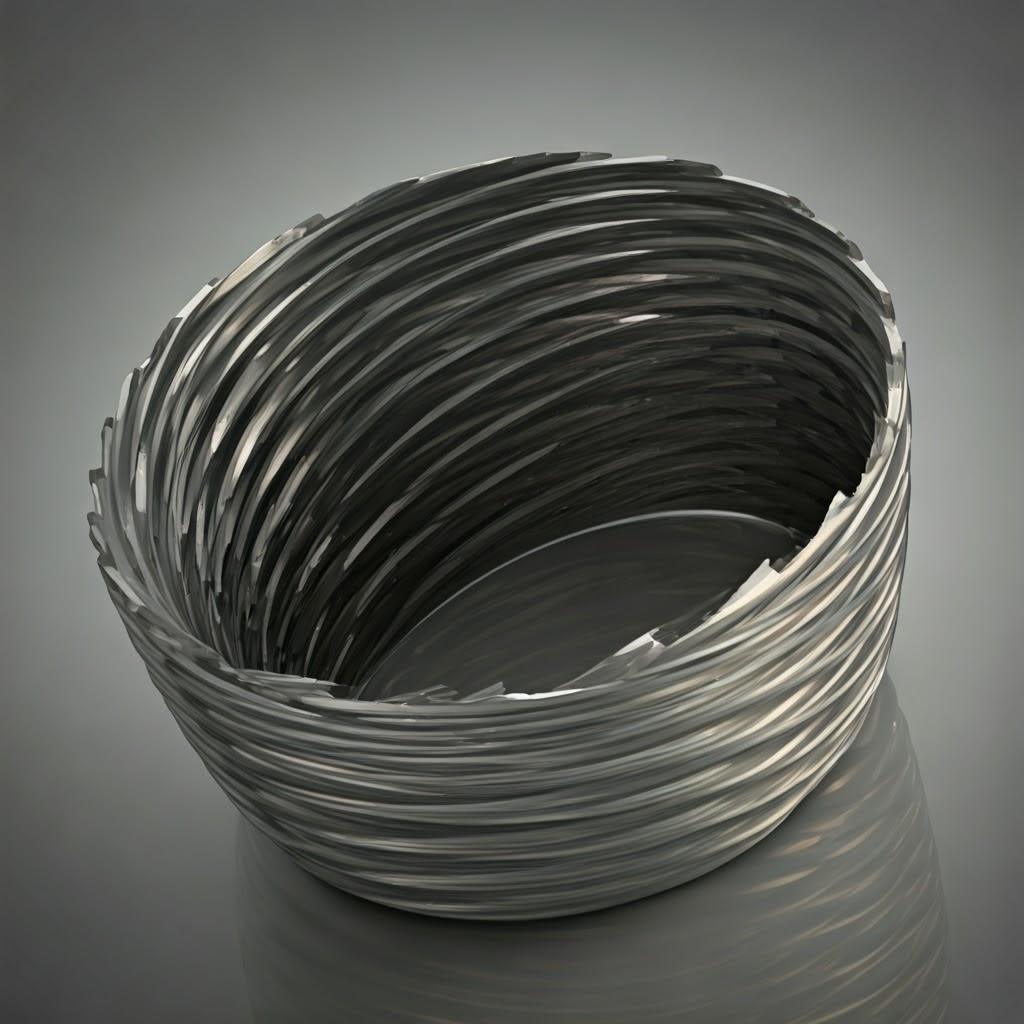
Wesentliche Nachbearbeitungsschritte für 3D-gedruckte Raketen-Kraftstoffdüsenspitzen
Die Herstellung einer Kraftstoffdüsenspitze mittels Laser Powder Bed Fusion ist ein anspruchsvoller Prozess, aber die Reise von der digitalen Datei zur flugfertigen Hardware endet selten, wenn der Drucker anhält. Für missionskritische Komponenten aus Superlegierungen wie IN718 und IN625 ist eine Abfolge sorgfältig kontrollierter Nachbearbeitungsschritte unerlässlich, um Spannungen abzubauen, die erforderlichen Materialeigenschaften zu erzielen, die Maßgenauigkeit sicherzustellen, Stützen zu entfernen, Oberflächen zu verfeinern und die Integrität zu überprüfen. Diese Schritte sind oft komplex, zeitaufwändig und erfordern spezielle Ausrüstung und Fachwissen, was erheblich zu den Gesamtstückkosten und der Vorlaufzeit des fertigen Teils beiträgt. Beschaffungsmanager müssen diese Anforderungen bei der Projektplanung und Lieferantenauswahl berücksichtigen.
Zu den wichtigsten Nachbearbeitungsschritten gehören:
- Stressabbau:
- Zweck: Das schnelle, lokale Erhitzen und Abkühlen während des L-PBF erzeugt erhebliche Eigenspannungen innerhalb des gedruckten Teils. Diese Spannungen können zu Verformungen oder Rissen führen, wenn das Teil von der Bauplatte entfernt wird oder während der anschließenden Verarbeitung. Eine Spannungsarmglühung wird durchgeführt vor Entfernen des Teils von der Bauplatte.
- Prozess: Die gesamte Bauplatte mit dem/den befestigten Teil(en) wird in einem Ofen mit kontrollierter Atmosphäre (Vakuum oder Inertgas wie Argon zur Verhinderung von Oxidation) auf eine bestimmte Temperatur unterhalb der Alterungs- oder Glühtemperatur erhitzt, für eine bestimmte Zeit gehalten und dann langsam abgekühlt. Typische Zyklen für IN718/IN625 können das Erhitzen auf 850−1000∘C (1560−1830∘F) umfassen.
- Wichtigkeit: Dies ist ein obligatorischer erster Schritt für die meisten AM-Teile aus Superlegierungen, um die Dimensionsstabilität zu gewährleisten und ein anschließendes Versagen zu verhindern.
- Entnahme von der Bauplatte:
- Methode: Nach der Spannungsarmglühung muss das Teil von der Bauplatte getrennt werden. Dies geschieht üblicherweise mit Draht-Funkenerosion (Draht-EDM) oder einer Bandsäge. Es ist darauf zu achten, das Teil selbst nicht zu beschädigen.
- Entfernung der Stützstruktur:
- Herausforderung: Stützen, die während des Baus unerlässlich sind, müssen jetzt entfernt werden. Dies kann arbeitsintensiv sein, insbesondere bei komplexen Geometrien oder internen Stützen.
- Methoden: Abhängig von der Konstruktion und Zugänglichkeit können Stützen manuell (Brechen, Schneiden), durch CNC-Bearbeitung oder möglicherweise Schleifer entfernt werden. Interne Stützen innerhalb von Kanälen stellen eine erhebliche Herausforderung dar und erfordern möglicherweise fortschrittliche Techniken wie Abrasiv-Fließbearbeitung (AFM), wenn der Zugang dies zulässt, oder eine sorgfältige DfAM-Planung, um sie zu minimieren. Unvollständiges oder unsachgemäßes Entfernen von Stützen kann unerwünschte Oberflächenartefakte oder Spannungskonzentratoren hinterlassen.
- Wärmebehandlung (Lösungsglühen & Auslagern / Glühen):
- Zweck: Zur Homogenisierung der Mikrostruktur, die während der schnellen Erstarrung von AM entwickelt wurde, und zur Erzielung der für die Legierung spezifizierten Zieleigenschaften (Festigkeit, Duktilität, Härte, Kriechbeständigkeit).
- Verfahren für IN718 (Aushärten durch Ausscheidung): Beinhaltet typischerweise:
- Lösungsglühen: Erhitzen auf eine hohe Temperatur (z. B. 950−1050∘C oder 1740−1920∘F), um vorhandene Ausscheidungen aufzulösen und die Mikrostruktur zu homogenisieren, gefolgt von schnellem Abkühlen.
- Behandlung der Alterung: Eine zweistufige Wärmebehandlung bei niedrigerer Temperatur (z. B. 720∘C/1325∘F gefolgt von 620∘C/1150∘F), um die verstärkenden γ′- und γ′′-Phasen auszuscheiden. Eine präzise Zeit- und Temperaturkontrolle ist entscheidend.
- Verfahren für IN625 (Festlösungsgehärtet): Beinhaltet typischerweise ein Glühen Schritt (z. B. 870−1175∘C oder 1600−2150∘F, die spezifische Temperatur hängt von den gewünschten Eigenschaften ab), um Spannungen abzubauen, die Kornstruktur zu rekristallisieren und sicherzustellen, dass Niob in Lösung ist, gefolgt von kontrolliertem Abkühlen. Für die Verstärkung ist kein Auslagerungsschritt erforderlich.
- Atmosphäre: Alle Hochtemperatur-Wärmebehandlungen für Superlegierungen müssen in einem Vakuum oder einer hochreinen Inertatmosphäre durchgeführt werden, um eine Oxidation zu verhindern, die die Materialeigenschaften beeinträchtigen kann.
- Heiß-Isostatisches Pressen (HIP):
- Zweck: Zur Beseitigung interner Mikroporosität (wie Gasporen oder kleine Fehlstellen) , die nach dem AM-Prozess verbleiben könnten. Dies verbessert die Lebensdauer, die Duktilität, die Bruchzähigkeit und die allgemeine Materialkonsistenz erheblich, was für kritische Luft- und Raumfahrtkomponenten (bruchkritisch oder missionskritisch Teile).
- Prozess: Das Teil wird gleichzeitig in einem speziellen HIP-Behälter einer hohen Temperatur (unterhalb des Schmelzpunkts, aber oft in der Nähe der Lösungsglühtemperaturen) und einem hohen Inertgasdruck (typischerweise Argon, bei 100-200 MPa oder 15.000-30.000 psi) ausgesetzt. Der Druck lässt innere Hohlräume kollabieren und verbindet das Material über die Hohlraumgrenzfläche durch Diffusionsbindung.
- Erwägung: HIP kann geringfügige Dimensionsänderungen verursachen und die Oberflächenbeschaffenheit beeinflussen, was manchmal eine anschließende Bearbeitung erfordert.
- Bearbeitungen:
- Zweck: Um endgültige Toleranzen für kritische Abmessungen zu erreichen, bestimmte Schnittstellenmerkmale (Gewinde, Dichtflächen) zu erstellen oder sehr glatte Oberflächen (z. B. Ra < 1 µm) zu erhalten, die durch AM oder andere Polierverfahren allein nicht erreichbar sind.
- Prozess: Es werden standardmäßige Mehrachsen-CNC-Bearbeitungstechniken verwendet, aber die Bearbeitung von Superlegierungen erfordert aufgrund ihrer hohen Festigkeit und ihres Verfestigungsverhaltens geeignete Werkzeuge, Geschwindigkeiten und Vorschübe.
- Oberflächenveredelung:
- Zweck: Zur Verbesserung der Oberflächenglätte über den direkt gefertigten oder nach-HIP-Zustand hinaus, insbesondere für Innenkanäle oder Außenflächen, die bestimmte aerodynamische oder Dichtungseigenschaften erfordern.
- Methoden:
- Abrasives Strahlen (Sand-/Kugelstrahlen): Sorgt für ein gleichmäßiges, mattes Finish und beseitigt kleinere Unebenheiten.
- Taumeln/Gleitschleifen: Verwendet Medien zum Glätten von Oberflächen und Entgraten von Kanten, geeignet für Chargen von kleineren Teilen.
- Abrasive Fließbearbeitung (AFM): Drückt abrasive Spachtelmasse durch Innenkanäle oder über Außenflächen, um Kanten zu polieren und zu verrunden. Wirksam für unzugängliche Innenpassagen.
- Elektrochemisches Polieren (ECP): Entfernt Material elektrochemisch, was zu einer sehr glatten, glänzenden Oberfläche führt. Kann für Innenkanäle angepasst werden.
- Manuelles Polieren: Zum Erreichen von Spiegeloberflächen auf zugänglichen Oberflächen.
- Zerstörungsfreie Prüfung (NDT) und Inspektion:
- Zweck: Um die Integrität des fertigen Teils zu überprüfen und sicherzustellen, dass es alle Spezifikationen erfüllt, ohne es zu beschädigen. Dies ist ein kritischer Schritt für die Qualitätssicherung in der Luft- und Raumfahrt.
- Methoden:
- Visuelle Inspektion: Grundlegende Prüfung auf offensichtliche Mängel.
- Dimensionelle Metrologie: CMM, 3D-Scannen.
- Röntgen-Computertomographie (CT-Scan): Unerlässlich zur Erkennung interner Defekte (Porosität, Einschlüsse, Risse) und zur Überprüfung der Innengeometrie in komplexen AM-Teilen.
- Fluoreszierende Eindringprüfung (FPI): Erkennt Risse in der Oberfläche oder Porosität.
- Ultraschallprüfung (UT): Kann Fehler unter der Oberfläche erkennen.
- Materialanalyse: Überprüfung der chemischen Zusammensetzung und Mikrostruktur (oft zerstörend an Testproben, die zusammen mit dem Teil gedruckt werden).
Die spezifische Reihenfolge und Kombination dieser Nachbearbeitungsschritte hängt stark von der Designkomplexität der Düse, der gewählten Legierung (IN718 vs. IN625) und den strengen Anforderungen der Luft- und Raumfahrtanwendung ab. Die effektive Verwaltung dieses komplexen Workflows erfordert erhebliches Fachwissen und Investitionen in spezielle Einrichtungen, was den Wert der Partnerschaft mit erfahrenen Metall-AM-Lösungsanbietern.
Überwindung häufiger Herausforderungen beim 3D-Druck von Superlegierungs-Kraftstoffdüsen
Während die additive Fertigung von Metallen enorme Vorteile für die Herstellung von Raketen-Kraftstoffdüsenspitzen bietet, stellt die Arbeit mit Hochleistungs-Superlegierungen wie IN718 und IN625 in einem Prozess, der schnelles Schmelzen und Erstarren beinhaltet, einzigartige Herausforderungen dar. Das Verständnis dieser potenziellen Probleme und die Umsetzung von Minderungsstrategien sind entscheidend für die konsistente Herstellung hochwertiger, zuverlässiger Komponenten. Luft- und Raumfahrtingenieure und Beschaffungsmanager sollten sich dieser Herausforderungen bewusst sein, wenn sie AM-Teile spezifizieren und Lieferanten auswählen.
1. Eigenspannung und Verzug:
- Herausforderung: Der intensive, lokalisierte Wärmeeintrag durch den Laser und die anschließende schnelle Abkühlung erzeugen steile Temperaturgradienten, die zu inneren Spannungen innerhalb des Teils führen. Diese Spannungen können dazu führen, dass sich das Teil während des Baus verzieht, sich von den Stützen löst oder sich nach dem Entfernen von der Bauplatte verformt. Superlegierungen mit ihrer relativ hohen Wärmeausdehnung und Festigkeit bei Temperatur sind besonders anfällig.
- Strategien zur Schadensbegrenzung:
- Optimierte Scan-Strategien: Die Verwendung von Techniken wie der Aufteilung der Schicht in kleinere Segmente (‚Insel‘- oder ‚Schachbrett‘-Scannen) und die Variation des Scanvektors zwischen den Schichten trägt dazu bei, die Wärme gleichmäßiger zu verteilen und die Spannungsansammlung zu reduzieren.
- Robuste Stützstrukturen: Gut gestaltete Stützen verankern das Teil sicher an der Bauplatte und wirken als Kühlkörper, wodurch thermische Spannungen effektiv bewältigt werden. DfAM spielt hier eine Schlüsselrolle.
- Prozess-Simulation: Thermomechanische Simulationssoftware kann die Spannungsverteilung und den Verzug vorhersagen, wodurch die Optimierung der Ausrichtung und der Stützstrategien vor dem Drucken ermöglicht wird.
- Optimierung der Parameter: Die Feinabstimmung von Laserleistung, Scangeschwindigkeit und Schichtdicke kann das thermische Erlebnis beeinflussen.
- Unmittelbarer Stressabbau: Die Durchführung der Spannungsarmglühung unmittelbar nach dem Bau, bevor das Teil von der Platte entfernt wird, ist von entscheidender Bedeutung.
2. Rissbildung (Erstarrung, Verflüssigung, Dehnungsalterung):
- Herausforderung: Superlegierungen, insbesondere aushärtbare Legierungen wie IN718, können während oder nach dem AM-Prozess anfällig für verschiedene Formen der Rissbildung sein. Erstarrungsrisse treten im Schmelzbad auf, Verflüssigungsrisse treten in teilweise geschmolzenen Zonen in der Nähe des Schmelzbads auf, und Dehnungsalterungsrisse können während der Nachbearbeitungswärmebehandlung in IN718 auftreten, wenn die Eigenspannungen zu hoch sind.
- Strategien zur Schadensbegrenzung:
- Qualität des Pulvers: Die Verwendung von hochreinem Pulver mit geringen Mengen an rissanfälligen Elementen (wie Schwefel, Phosphor) ist unerlässlich. Die fortschrittlichen Pulverherstellungsverfahren von Met3dp konzentrieren sich auf das Erreichen hoher Reinheit und kontrollierter Chemie.
- Optimierung der Parameter: Sorgfältige Kontrolle des Energieeintrags (Laserleistung, Scangeschwindigkeit) zur Steuerung der Schmelzbad-Dynamik und der Abkühlraten.
- Heiß-Isostatisches Pressen (HIP): Kann helfen, kleine Risse zu schließen, obwohl es in erster Linie auf Porosität abzielt.
- Geeignete Wärmebehandlung: Richtige Spannungsarmglüh- und Alterungszyklen sind entscheidend, insbesondere für IN718, um Dehnungsalterungsrisse zu vermeiden.
- Auswahl der Legierung: IN625 ist aufgrund seines Festlösungsmechanismus im Allgemeinen weniger anfällig für Rissbildung während des Druckens als IN718.
3. Porosität (Gas und fehlende Verschmelzung):
- Herausforderung: Kleine Hohlräume innerhalb des gedruckten Materials können als Spannungskonzentratoren wirken und die mechanischen Eigenschaften, insbesondere die Lebensdauer, beeinträchtigen.
- Gas Porosität: Verursacht durch Gas (z. B. Argon-Schutzgas, gelöste Gase im Pulver), das im schnell erstarrenden Schmelzbad eingeschlossen wird.
- Lack-of-Fusion (LoF) Porosität: Verursacht durch unzureichenden Energieeintrag, was zu unvollständigem Schmelzen und Verbinden zwischen Pulverpartikeln oder -schichten führt.
- Strategien zur Schadensbegrenzung:
- Hochwertiges Pulver: Die Verwendung von Pulver mit geringem innerem Gasgehalt und guter Kugelform/Fließfähigkeit (wie das von Met3dp) minimiert eingeschlossenes Gas und gewährleistet ein dichtes Pulverbett.
- Optimierte Prozessparameter: Sicherstellen einer ausreichenden Energiedichte (Laserleistung, Scangeschwindigkeit, Schichtdicke), um vollständiges Schmelzen und Verschmelzen zu erreichen, ohne Überhitzung, wodurch die Gasporosität erhöht werden kann.
- Kontrolle der inerten Atmosphäre: Die Aufrechterhaltung einer hochreinen Inertgasatmosphäre (Argon) in der Baukammer minimiert die Kontamination.
- Heiß-Isostatisches Pressen (HIP): Sehr effektiv beim Schließen von Gas- und LoF-Porosität, oft als obligatorisch für kritische Anwendungen angesehen.
4. Stütze entfernen Schwierigkeitsgrad:
- Herausforderung: Das Entfernen von Stützstrukturen, insbesondere aus komplexen internen Kanälen, die in Düsen üblich sind, kann schwierig, zeitaufwendig und riskant sein, da das Teil beschädigt werden kann. Restliches Stützmaterial kann den Fluss behindern oder als Ausgangspunkt für Ausfälle dienen.
- Strategien zur Schadensbegrenzung:
- DfAM: Konstruktion für minimalen Stützmaterialeinsatz (selbsttragende Winkel > 45°), Optimierung der Ausrichtung und Konstruktion des Zugangs für Werkzeuge zum Entfernen.
- Spezialisierte Entfernungstechniken: Verwendung von CNC-Bearbeitung, EDM, AFM oder ECP, wo dies angemessen und machbar ist.
- Wahl des Materials: Stützen aus dem gleichen Material können eine Herausforderung darstellen; die Forschung nach unterschiedlichen, leicht entfernbaren Stützmaterialien ist im Gange, aber für Superlegierungen weniger ausgereift.
5. Anisotropie:
- Herausforderung: Aufgrund des Schicht-für-Schicht-Aufbauprozesses und der gerichteten Erstarrung können AM-Teile anisotrope mechanische Eigenschaften aufweisen, was bedeutet, dass sich die Eigenschaften (wie Festigkeit oder Duktilität) je nach der Testrichtung relativ zur Bauausrichtung (X, Y vs. Z) unterscheiden können. Dies muss bei der Konstruktion und Qualifizierung berücksichtigt werden.
- Strategien zur Schadensbegrenzung:
- Charakterisierung: Gründliche Prüfung der Materialeigenschaften in verschiedenen Ausrichtungen unter Verwendung repräsentativer Coupons, die zusammen mit den Teilen gedruckt werden.
- Entwurfsüberlegungen: Ausrichten des Teils so, dass die kritischsten Spannungen mit der stärksten Bauausrichtung übereinstimmen.
- Wärmebehandlung & HIP: Kann helfen, die Mikrostruktur zu homogenisieren und Anisotropie zu reduzieren, aber nicht immer zu eliminieren.
6. Oberflächenrauheit:
- Herausforderung: As-built-Oberflächen, insbesondere nach unten gerichtete und steil abgewinkelte Oberflächen, können rauer sein als für Fluidströmungs- oder Dichtungsanwendungen erforderlich.
- Strategien zur Schadensbegrenzung:
- Optimierung der Orientierung: Priorisierung glatter Oberflächen auf kritischen Merkmalen während der Ausrichtungsauswahl.
- Optimierte Parameter: Verwendung spezifischer ‘Kontur’- oder ‘Skin’-Parameter für Außenflächen.
- Nachbearbeiten: Einsatz von Bearbeitung oder verschiedenen Poliertechniken (AFM, ECP, Gleitschleifen, manuell).
7. Qualitätskontrolle und Prozesskonsistenz:
- Herausforderung: Um sicherzustellen, dass jedes hergestellte Teil die strengen Luft- und Raumfahrtanforderungen erfüllt, ist eine robuste Qualitätskontrolle während des gesamten Prozesses erforderlich, vom Pulvermanagement bis zur Endprüfung. Die Aufrechterhaltung der Konsistenz von Bau zu Bau ist von größter Bedeutung.
- Strategien zur Schadensbegrenzung:
- Pulverkontrolle: Strenge Prüfung und Handhabung eingehender Pulverchargen. Met3dp bietet zertifizierte Pulverqualität.
- Prozessüberwachung: Verwendung von In-situ-Überwachungswerkzeugen (z. B. Schmelzbadüberwachung, Thermografie) zur Erkennung von Anomalien während des Baus.
- Standardisierte Verfahren: Implementierung qualifizierter Fertigungsverfahren unter einem robusten Qualitätsmanagementsystem (QMS), idealerweise zertifiziert nach Standards wie AS9100 für die Luft- und Raumfahrt.
- Umfassende ZfP: Einsatz geeigneter zerstörungsfreier Prüfverfahren (insbesondere CT-Scannen) zur Fehlererkennung und geometrischen Verifizierung.
- Partnerschaften mit Experten: Zusammenarbeit mit erfahrenen Metall-AM-Dienstleister wie Met3dp, die über fundierte Prozesskenntnisse und ein Engagement für Qualität verfügen, ist entscheidend, um diese Herausforderungen effektiv zu meistern.
Durch proaktives Angehen dieser potenziellen Probleme durch sorgfältige Konstruktion, hochwertige Materialien, optimierte Prozesskontrolle, gründliche Nachbearbeitung und strenge Inspektion können die Herausforderungen des Druckens von Superlegierungs-Düsen erfolgreich gemeistert werden, wodurch das volle Potenzial der additiven Fertigung für die Raketenantriebstechnologie der nächsten Generation freigesetzt wird.
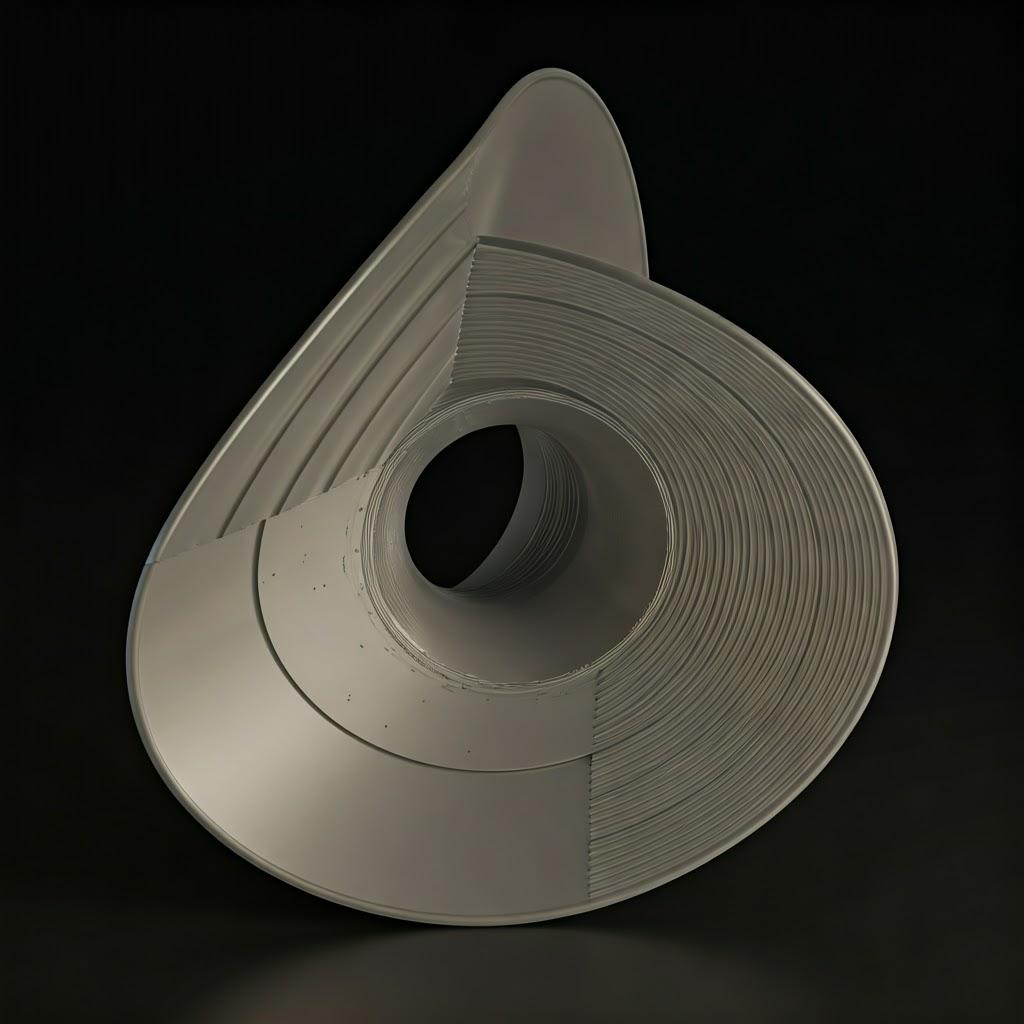
Auswahl des richtigen Metall-AM-Partners: Bewertung von Lieferanten für Luft- und Raumfahrtkomponenten
Die Entscheidung, die additive Fertigung für kritische Luft- und Raumfahrtkomponenten wie Düsenspitzen zu nutzen, ist von Bedeutung. Ebenso wichtig ist jedoch die Auswahl des richtigen Partners für die additive Fertigung. Dies ist nicht nur eine transaktionale Lieferantenbeziehung; es ist eine strategische Partnerschaft, die Vertrauen, technische Ausrichtung und ein gemeinsames Engagement für Qualität und Zuverlässigkeit erfordert. Für Einkaufsmanager und Ingenieure, die sich in der komplexen Landschaft von Metall-AM-Dienstleisterbewegen, ist ein gründlicher Bewertungsprozess von entscheidender Bedeutung, um den Projekterfolg und die Komponentenintegrität sicherzustellen.
Die Wahl eines ungeeigneten Partners kann zu Verzögerungen, Kostenüberschreitungen, minderwertiger Komponentenqualität und potenziell katastrophalen Ausfällen in der Anwendung führen. Hier sind die wichtigsten Kriterien, die bei der Bewertung potenzieller Metall-AM-Lieferanten für Düsen in Luft- und Raumfahrtqualität zu berücksichtigen sind:
1. Fachwissen und nachgewiesene Erfahrung:
- Spezialisierung auf Legierungen: Verfügt der Lieferant über nachweisliche Erfahrung im Drucken mit der erforderlichen spezifischen Superlegierung (IN718 oder IN625)? Fragen Sie nach ihrer Prozessentwicklung für diese Materialien.
- Prozesskompetenz: Überprüfen Sie ihre Expertise im relevanten AM-Verfahren, typischerweise Laser Powder Bed Fusion (L-PBF) für diese Anwendungen. Verstehen Sie ihre Kontrolle über Prozessparameter.
- Anwendungs-Track Record: Haben sie erfolgreich ähnliche Luft- und Raumfahrtkomponenten hergestellt, insbesondere solche mit komplexen internen Merkmalen, hohen Temperaturen oder strengen Qualitätsanforderungen? Fordern Sie nicht-proprietäre Fallstudien oder Beispiele relevanter Arbeiten an. Herstellung von Luft- und Raumfahrtkomponenten erfordert spezifisches Fachwissen.
2. Ausrüstung, Technologie und Einrichtungen:
- Industriemaschinen: Stellen Sie sicher, dass sie moderne, gut gewartete industrielle L-PBF-Systeme verwenden, die für Genauigkeit und Wiederholbarkeit bekannt sind. Verstehen Sie den Maschinenhersteller und das Modell.
- Prozessüberwachung: Erkundigen Sie sich nach der Verwendung von In-situ-Prozessüberwachungsfunktionen (z. B. Schmelzbadüberwachung, Thermografie), die wertvolle Daten für die Qualitätssicherung liefern können.
- Umgebung der Einrichtung: Beurteilen Sie die Sauberkeit, Organisation und Umweltkontrollen (Feuchtigkeit, Temperatur) ihrer Produktionsstätte, insbesondere in Bezug auf Pulverhandhabungsbereiche.
3. Materialqualität, Beschaffung und Kontrolle:
- Pulverbeschaffung: Wo beziehen sie ihr IN718/IN625-Pulver? Stellen sie es selbst her oder kaufen sie es von qualifizierten Lieferanten? Das Verständnis des Ursprungs und der Qualität des Pulvers ist entscheidend.
- Pulvermanagement: Wie handhaben, lagern, testen und recyceln sie Metallpulver, um Reinheit zu gewährleisten, Kontamination zu verhindern und die Chargenrückverfolgbarkeit aufrechtzuerhalten? Unsachgemäße Handhabung kann die Teilequalität beeinträchtigen.
- Materialzertifizierung: Können sie Materialzertifizierungen (z. B. Konformitätszertifikate) vorlegen, die die chemische Zusammensetzung und die Eigenschaften des Pulvers bestätigen? Dies ist oft eine Anforderung für Beschaffung von Luft- und Raumfahrtmaterialien.
- Met3dp Vorteil: Hier glänzt die einzigartige Position von Met3dp. Als Hersteller von Hochleistungs-Metallpulvern unter Verwendung fortschrittlicher Gaszerstäubungs- und PREP-Technologien hat Met3dp die direkte Kontrolle über die Pulverqualität, -konsistenz und -eigenschaften und gewährleistet so einen optimalen Ausgangspunkt für kritische AM-Bauten. Unsere Pulver sind speziell für AM-Prozesse optimiert.
4. Umfassende Post-Processing-Fähigkeiten:
- Integrierter Arbeitsablauf: Bietet der Lieferant die erforderlichen Nachbearbeitungsschritte im eigenen Haus an (Spannungsarmglühen, Wärmebehandlung, Stützmaterialentfernung, Grundbearbeitung)? Oder verwalten sie ein Netzwerk qualifizierter Subunternehmer für spezielle Prozesse wie HIP, fortschrittliche Bearbeitung, zertifizierte zerstörungsfreie Prüfung (CT-Scannen, FPI) und spezifische Oberflächenbehandlungen?
- Fachwissen über alle Schritte hinweg: Stellen Sie sicher, dass sie (oder ihre Partner) über das erforderliche Fachwissen und die erforderlichen Zertifizierungen für jeden kritischen Nachbearbeitungsschritt verfügen, insbesondere für die Wärmebehandlung und die zerstörungsfreie Prüfung für Luft- und Raumfahrtstandards. Das Verständnis der gesamten Herstellungskette ist von entscheidender Bedeutung.
5. Robustes Qualitätsmanagementsystem (QMS):
- Zertifizierungen: Dies ist für die Luft- und Raumfahrt nicht verhandelbar. Suchen Sie nach Lieferanten, die nach AS9100 (dem QMS-Standard der Luft- und Raumfahrtindustrie) oder mindestens nach ISO 9001 mit nachgewiesener Erfahrung in der Luft- und Raumfahrt zertifiziert sind. Die Zertifizierung bietet Gewähr für dokumentierte Prozesse, Rückverfolgbarkeit, Qualitätskontrolle und kontinuierliche Verbesserung.
- Qualitätsverfahren: Erkundigen Sie sich nach ihren spezifischen Verfahren zur Prozessvalidierung, Teileprüfung, Nichtkonformitätsmanagement und Dokumentationspraktiken.
- Rückverfolgbarkeit: Können sie die vollständige Rückverfolgbarkeit von der Rohpulvercharge bis zur fertigen, geprüften Komponente gewährleisten?
6. Engineering, DfAM und Anwendungsunterstützung:
- Kollaborativer Ansatz: Bieten sie Design for Additive Manufacturing (DfAM)-Unterstützung an? Können ihre Ingenieure mit Ihrem Team zusammenarbeiten, um das Düsendesign auf Druckbarkeit, Leistung und Wirtschaftlichkeit zu optimieren?
- Simulationsfähigkeiten: Verwenden sie Prozesssimulationstools, um Risiken wie Verzug oder Eigenspannungen vorherzusagen und zu mindern?
- Lösungsanbieter: Suchen Sie nach einem Partner, der als Lösungsanbieter fungiert und Einblicke und Unterstützung über reine Druckdienstleistungen hinaus bietet. Met3dp ist stolz auf seine jahrzehntelange gemeinsame Erfahrung in der Metall-AM und bietet umfassende Lösungen, die Ausrüstung, Materialien und Anwendungsentwicklungsdienste.
7. Kapazität, Vorlaufzeiten und Skalierbarkeit:
- Die Nachfrage befriedigen: Beurteilen Sie ihre aktuelle Kapazität und Fähigkeit, die Zeitvorgaben Ihres Projekts und die potenziellen zukünftigen Produktionsvolumenanforderungen zu erfüllen.
- Realistische Vorlaufzeiten: Erhalten Sie klare und realistische Schätzungen der Vorlaufzeiten, die den gesamten Arbeitsablauf berücksichtigen, einschließlich aller Nachbearbeitungs- und Inspektionsschritte.
- Skalierbarkeit: Können sie einen Übergang vom Prototyping zur Klein- oder sogar Mittelserienproduktion unterstützen, falls erforderlich?
8. Kommunikation, Standort und Logistik:
- Reaktionsfähigkeit: Bewerten Sie ihre Reaktionsfähigkeit und Klarheit in der Kommunikation.
- Standortfaktoren: Berücksichtigen Sie die Auswirkungen des Standorts des Lieferanten in Bezug auf Versandkosten, Transitzeiten, Kommunikation über Zeitzonen hinweg und alle potenziellen Exportkontrollbestimmungen für sensible Luft- und Raumfahrtkomponenten. Met3dp mit Sitz in Qingdao, China, bedient eine globale Kundschaft und verfügt über Erfahrung in der Navigation durch internationale Logistik.
9. Kosten vs. Wert:
- Detaillierte Angebote: Stellen Sie sicher, dass die Angebote umfassend sind und alle enthaltenen Prozessschritte, Materialien, Qualitätssicherungsmaßnahmen und Zertifizierungen klar umreißen.
- Wert-Angebot: Bewerten Sie die Kosten nicht isoliert, sondern im Kontext des Fachwissens, der Qualität, der Zuverlässigkeit und des Gesamtwerts des Lieferanten, den er in das Projekt einbringt. Für missionskritische Teile ist die Wahl des billigsten Metall-AM-Anbieter oft eine falsche Sparsamkeit.
Zusammenfassung der Checkliste zur Lieferantenbewertung:
Kriterien | Zentrale Fragen | Wichtigkeit (Luft- und Raumfahrt) |
---|---|---|
Technisches Fachwissen | Erfahrung mit Legierung/Prozess/Anwendung? Fallstudien? | Kritisch |
Ausrüstung und Technologie | Maschinentyp/Zustand? Prozessüberwachung? | Hoch |
Materialqualität/Kontrolle | Pulverquelle? Handhabungsverfahren? Zertifizierungen? (Met3dp-Vorteil) | Kritisch |
Nachbearbeitung | Inhouse-/Managed-Fähigkeiten? Fachwissen in Wärmebehandlung, HIP, ZfP? | Kritisch |
Qualitätssystem (QMS) | AS9100 / ISO 9001 zertifiziert? Dokumentierte Verfahren? Rückverfolgbarkeit? | Obligatorisch |
Technik/DfAM-Unterstützung | DfAM-Expertise? Simulation? Kooperativer Ansatz? (Met3dp-Vorteil) | Sehr hoch |
Kapazität und Vorlaufzeit | Erfüllt Projektzeitplan/Volumen? Realistische Zeitpläne? Skalierbarkeit? | Hoch |
Kommunikation/Logistik | Reaktionsschnell? Standortfaktoren? Exportkontrollen? | Mäßig bis hoch |
Kosten vs. Wert | Detailliertes Angebot? Preis durch Qualität/Zuverlässigkeit/Service gerechtfertigt? | Hoch |
In Blätter exportieren
Die Auswahl des richtigen Partners erfordert Due Diligence, aber die Investition von Zeit in diesen Bewertungsprozess erhöht die Wahrscheinlichkeit, hochwertige, zuverlässige 3D-gedruckte Düsenspitzen zu erhalten, die den anspruchsvollen Anforderungen von Luft- und Raumfahrtantriebssystemen entsprechen, erheblich.
Verstehen der Kostentreiber und Vorlaufzeiten für additiv gefertigte Düsen
Während die additive Fertigung erhebliche Vorteile in Bezug auf Designfreiheit und potenzielle Leistungssteigerungen bietet, ist das Verständnis der Faktoren, die die Kosten und die Vorlaufzeit für die Herstellung von Komponenten wie Düsenspitzen beeinflussen, für eine effektive Projektplanung, Budgetierung und Beschaffung unerlässlich. Die AM-Kosten unterscheiden sich erheblich von der traditionellen Fertigung, und die Vorlaufzeiten umfassen oft mehr als nur die Druckdauer.
Wichtige Kostentreiber für AM-Düsen:
- Materialkosten:
- Legierungspreis: Nickelbasierte Superlegierungen wie IN718 und IN625 sind im Vergleich zu Standardstählen oder Aluminiumlegierungen von Natur aus teure Rohstoffe.
- Qualität des Pulvers: Pulver in Luft- und Raumfahrtqualität, das sich durch hohe Reinheit, eine bestimmte Partikelgrößenverteilung und hervorragende Kugelform auszeichnet (wie sie von Met3dp hergestellt werden), erfordert einen Aufpreis, ist aber für die Qualität unerlässlich.
- Materialverbrauch: Beinhaltet das Material im fertigen Teil sowie alle Stützstrukturen und potenziell verschwendetes Pulver (obwohl L-PBF relativ effizient ist). Die Reduzierung des Stützvolumens durch DfAM trägt zur Senkung der Kosten bei.
- Maschinenzeit (Bauzeit):
- Teil Volumen & Höhe: Der Haupttreiber ist die Zeit, die die AM-Maschine belegt ist. Dies hängt vom Gesamtvolumen des/der zu druckenden Teile(s) (Begrenzungsrahmen) und, noch wichtiger, von der gesamten Bauhöhe (Bestimmung der Anzahl der Schichten) ab.
- Komplexität: Hochkomplexe Teile oder Bauten mit dichten Stützstrukturen erhöhen die Druckzeit.
- Maschinentarif: Basierend auf den Investitionskosten des industriellen AM-Systems, der Wartung, der Verbrauchsmaterialien (Filter, Wischer), dem Energieverbrauch und dem Einsatz von Inertgas.
- Arbeitskosten:
- Fachkräfte: Erfordert geschulte Techniker für den Bauaufbau, die Maschinenbedienung, die Überwachung, die Pulverhandhabung, das Ausgraben und die Entfernung von Teilen.
- Nachbearbeitungsarbeiten: Ein erheblicher Arbeitsaufwand ist mit der Entfernung von Stützmaterial (oft manuell), der Teilebearbeitung, dem Einrichten der Inspektion und dem Betrieb von Nachbearbeitungsgeräten verbunden.
- Engineering/Qualität: Zeitaufwand für die Bauvorbereitung, Qualitätskontrollen, Dokumentation und Projektmanagement.
- Designkomplexität & DfAM-Auswirkungen:
- Während AM Komplexität ermöglicht, erhöhen extrem komplizierte Designs dürfen die Druckzeit und die Anforderungen an die Stützstrukturen. Effektives DfAM führt jedoch oft zu Kosteneinsparungen durch Teilekonsolidierung (Reduzierung des Montageaufwands und der Komplexität der Lieferkette) und Leistungsverbesserungen, die einen nachgelagerten Wert bieten und möglicherweise höhere anfängliche Teilekosten ausgleichen.
- Nachbearbeitungskosten:
- Dies ist oft ein Hauptkomponente der endgültigen Teilekosten. Jeder Schritt erhöht die Kosten:
- Stressabbau/Wärmebehandlung: Kosten für Ofenzeit, Energie und kontrollierte Atmosphäre.
- HIP: Spezialausrüstung, lange Zyklen, Kosten für die Chargenverarbeitung.
- Bearbeitungen: CNC-Maschinenzeit, Werkzeuge (Superlegierungen verursachen hohen Werkzeugverschleiß), Programmierung, Einrichtung.
- Unterstützung bei der Entfernung: Arbeitsintensiv, potenziell Spezialwerkzeuge (EDM, AFM).
- Oberflächenveredelung: Ausrüstung, Verbrauchsmaterialien, Arbeitsaufwand je nach Verfahren.
- ZfP/Inspektion: Hohe Kosten für Ausrüstung (insbesondere CT-Scanner), zertifizierte Inspektoren, Zeit pro Teil.
- Dies ist oft ein Hauptkomponente der endgültigen Teilekosten. Jeder Schritt erhöht die Kosten:
- Qualitätssicherung & Zertifizierung:
- Die strengen Tests, die Dokumentation und die Prozesskontrollen, die für Qualitätssicherung in der Luft- und Raumfahrt (z. B. AS9100-Konformität) erforderlich sind, erhöhen den Gemeinaufwand und die Kosten, sind aber für die Zuverlässigkeit unerlässlich.
- Auftragsvolumen:
- Während AM traditionelle Werkzeugkosten vermeidet, gibt es immer noch Einrichtkosten (Bauvorbereitung, Maschineneinrichtung, Pulverbeladung/-entladung). Diese Einrichtkosten werden auf die Anzahl der Teile in einem Bau verteilt. Daher reduziert das gleichzeitige Drucken mehrerer Teile oder die Platzierung von Großaufträge für AM im Allgemeinen die Kosten pro Teil im Vergleich zu Einzelteilaufträgen, obwohl die Skaleneffekte typischerweise weniger dramatisch sind als bei Massenproduktionstechniken wie Gießen oder Spritzgießen.
Typische Aufschlüsselung der Vorlaufzeit:
Die Vorlaufzeit für eine vollständig bearbeitete und geprüfte AM-Düse wird oft mehr durch die Nachbearbeitung und das Anstehen als durch den Druck selbst bestimmt. Ein typischer Arbeitsablauf könnte so aussehen:
- Auftragsbearbeitung & Vorbereitung (1-5 Tage): Dateiprüfung, DfAM-Prüfungen (falls erforderlich), Bausimulation, Stützgenerierung, Erstellung der Baudatei, Terminplanung.
- Maschinenwartezeit (variabel): Hängt von der Maschinenverfügbarkeit des Lieferanten ab (kann von Tagen bis Wochen dauern).
- Druck (1-7+ Tage): Stark abhängig von Teilegröße, Höhe, Komplexität und Anzahl der Teile pro Bau. Düsen können 24 Stunden bis mehrere Tage zum Drucken benötigen.
- Abkühlen & Entpulvern nach dem Druck (0,5-1 Tag): Sicheres Abkühlen der Baukammer und der Teile, sorgfältiges Entfernen von überschüssigem Pulver.
- Spannungsarmglühen (1-2 Tage): Einschließlich Ofenbeladung, Zykluszeit (oft 8-24 Stunden einschließlich Aufheiz-/Abkühlphase), Entladung.
- Teileentfernung & Entfernung der Stützstrukturen (1-3 Tage): Je nach Methode (Säge/EDM) und Komplexität der Stützstrukturen. Kann ein Engpass sein.
- Wärmebehandlung (Lösungsglühen/Aushärten oder Anlassen) (2-4 Tage): Ofenzeit (kann lange Zyklen sein), kontrollierte Abkühlung, potenziell Verzögerungen durch Chargen.
- HIP (3-7 Tage): Beinhaltet oft Chargen und Terminplanung mit spezialisierten HIP-Anbietern; die Zykluszeiten sind lang.
- Bearbeitung (variabel): Hängt von der Komplexität, der Einrichtzeit und der Maschinenverfügbarkeit ab (Tage bis Wochen, wenn umfangreich).
- Endbearbeitung & Inspektion (2-5 Tage): Oberflächenbearbeitung, umfassende ZfP (CT-Scannen kann Zeit für Einrichtung, Scannen und Analyse in Anspruch nehmen), endgültige Maßkontrollen, Vorbereitung des Dokumentationspakets.
- Versand (variabel): Abhängig von Standort und Versandart.
Gesamtvorlaufzeit: Durch das Hinzufügen dieser Schritte können typische Vorlaufzeiten für komplexe AM-Komponenten aus Superlegierungen wie Düsen, die eine vollständige Nachbearbeitung und Qualifizierung für die Luft- und Raumfahrt erfordern, zwischen 3 bis 10 Wochen, manchmal länger, je nach Komplexität und Auftragsrückständen des Lieferanten, betragen.
Das Wichtigste zum Mitnehmen: Stellen Sie bei der Anforderung von Angeboten für AM-Düsen sicher, dass der Lieferant eine detaillierte Aufschlüsselung der enthaltenen Schritte sowie der damit verbundenen Kosten und Vorlaufzeiten liefert. Das Verständnis dieser Faktoren ermöglicht eine bessere Beschaffungsplanung, realistische Terminplanung und fundierte Entscheidungen über die Gesamtbetriebskosten unter Berücksichtigung sowohl der Herstellungskosten als auch der potenziellen Leistungsvorteile, die durch die additive Fertigung ermöglicht werden.
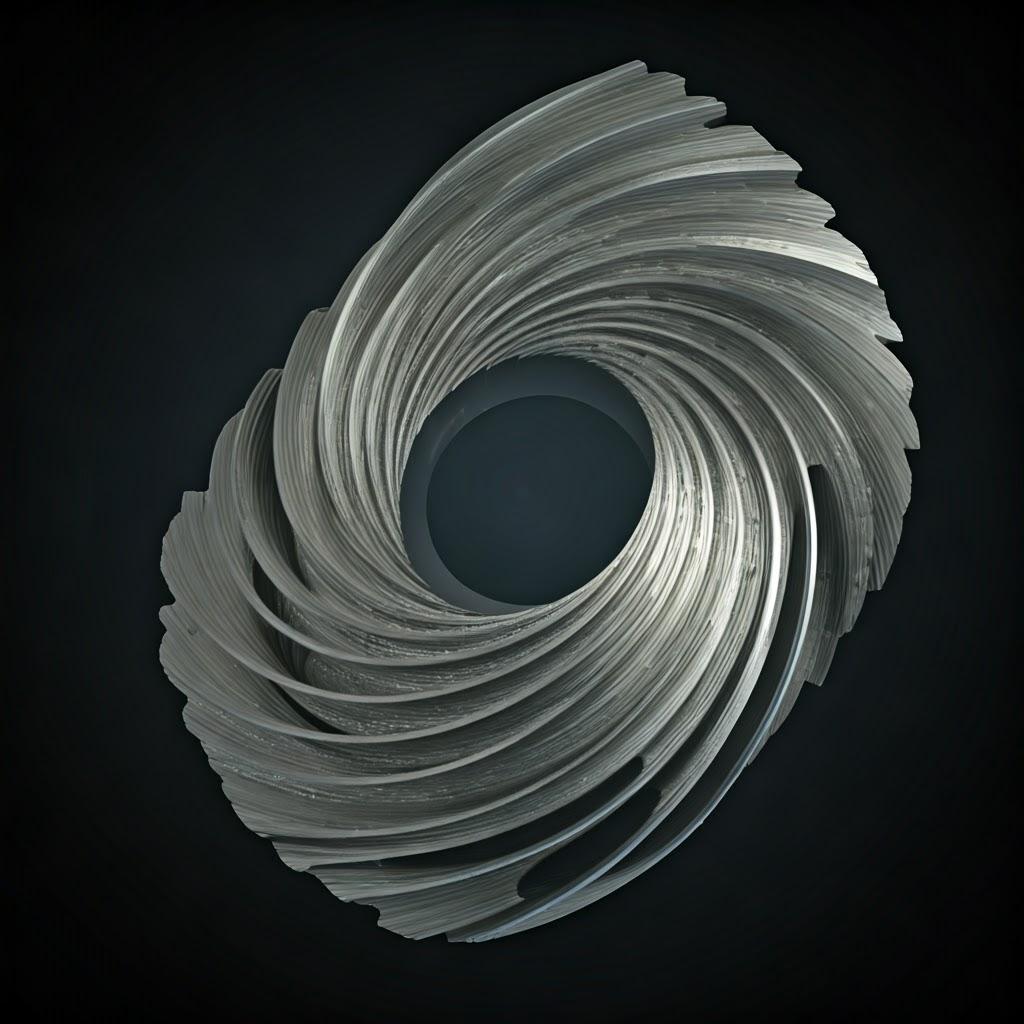
Häufig gestellte Fragen (FAQ) zu 3D-gedruckten Raketentriebwerksdüsenspitzen
Hier sind Antworten auf einige häufige Fragen zur additiven Fertigung von Raketentriebwerksdüsenspitzen unter Verwendung von Superlegierungen:
F1: Sind 3D-gedruckte IN718/IN625-Düsen so stark und zuverlässig wie herkömmlich hergestellte Düsen (z. B. geschmiedet, gegossen)?
A: Ja, wenn sie richtig konstruiert, gedruckt und nachbearbeitet werden, können AM-Düsen aus IN718 oder IN625 mechanische Eigenschaften (wie Zugfestigkeit, Streckgrenze, Duktilität und vor allem die Lebensdauer) aufweisen, die die von herkömmlich hergestellten Teilen erreichen oder sogar übertreffen. Die feinkörnige Mikrostruktur, die in L-PBF oft erreicht wird, kann sich besonders positiv auf die Ermüdungsbeständigkeit auswirken. Zu den Schlüsselfaktoren gehören die Verwendung von hochwertigem Pulver (wie dem von Met3dp), optimierte Druckparameter, geeignete Wärmebehandlungen (Lösungsglühen, Aushärten für IN718; Anlassen für IN625) und Heißisostatisches Pressen (HIP) zur Beseitigung der inneren Porosität. Gründliche Qualifizierungstests gemäß den etablierten Luft- und Raumfahrtstandards sind unerlässlich, um die Leistung und Zuverlässigkeit für jede spezifische Anwendung zu validieren.
F2: Was bestimmt die Lebensdauer oder die Anzahl der Wiederverwendungen für eine 3D-gedruckte Düsenspitze?
A: Die Betriebsdauer und die Wiederverwendbarkeit hängen von einem komplexen Zusammenspiel von Faktoren ab, nicht nur von der Herstellungsmethode. Zu den Schlüsselelementen gehören die spezifische Motorkonstruktion, ihr Betriebszyklus (Schubstufen, Dauer, Anzahl der Starts), die Treibstoffkombination, die Wirksamkeit des Kühlsystems (wobei die konformen Kanäle von AM potenzielle Vorteile bieten), das gewählte Material (Eigenschaften von IN718 vs. IN625) und die etablierten Inspektions- und Überholungsprotokolle. Während AM Designs ermöglicht, die potenziell widerstandsfähiger gegen bestimmte Ausfallmodi sind (z. B. thermische Ermüdung aufgrund besserer Kühlung), wird die tatsächliche Lebensdauer durch umfangreiche Bodentests, Flugdaten und regelmäßige zerstörungsfreie Prüfungen (wie CT-Scannen oder FPI) zwischen den Einsätzen ermittelt, um eine Verschlechterung oder Beschädigung festzustellen.
F3: Kann Met3dp den gesamten Prozess verwalten, von der Lieferung des Pulvers bis zur Lieferung einer vollständig fertigen und geprüften Düse?
A: Met3dp zeichnet sich durch die Herstellung von hochreinen, AM-optimierten Superlegierungspulvern (IN718, IN625 usw.) unter Verwendung unserer fortschrittlichen Zerstäubungstechnologien aus und bietet modernste Metall-3D-Druckausrüstung und -dienstleistungen. Wir bieten umfassende Lösungen für die additive Fertigung und Anwendungsentwicklungsunterstützung und arbeiten eng mit Kunden an DfAM und Druckoptimierung zusammen. Während wir den Kern-AM-Prozess verwalten, umfasst die umfangreiche Nachbearbeitungskette, die für Luft- und Raumfahrtkomponenten erforderlich ist (wie zertifizierte Wärmebehandlung, HIP, spezielle ZfP wie CT-Scannen, Präzisionsbearbeitung mit engen Toleranzen), oft die Nutzung eines Netzwerks von vertrauenswürdigen, akkreditierten Partnern, die sich auf diese Bereiche spezialisiert haben. Met3dp kann diesen Arbeitsablauf koordinieren und verwalten oder qualifizierte Partner empfehlen, um sicherzustellen, dass Kunden eine vollständig geprüfte und zertifizierte Komponente gemäß ihren Spezifikationen erhalten. Unser Fokus liegt darauf, einen nahtlosen Weg zu hochwertigen AM-Teilen zu bieten und dabei das beste Fachwissen in jedem Schritt zu nutzen.
F4: Ist der Metall-3D-Druck eine kostengünstige Lösung für die Herstellung von Düsen, insbesondere im Vergleich zu herkömmlichen Methoden?
A: Die Wirtschaftlichkeit von AM für Düsen hängt stark von der spezifischen Anwendung und dem Produktionsvolumen ab. AM glänzt am meisten, wenn:
- Die Komplexität hoch ist: Designs enthalten komplizierte interne Merkmale (konforme Kühlung, komplexe Mischgeometrien), die traditionell schwer oder unmöglich zu erreichen sind.
- Die Teilekonsolidierung einen Wert bietet: Verringerung der Komplexität der Montage, des Gewichts und möglicher Fehlerquellen.
- Leistungsgewinne signifikant sind: Optimierte Designs führen zu messbaren Verbesserungen der Motoreffizienz, des Schubs oder der Lebensdauer der Komponenten, was potenziell höhere Kosten pro Teil rechtfertigt.
- Die Entwicklungszeit entscheidend ist: Schnelle Prototyping- und Iterationszyklen beschleunigen die Motorentwicklung.
- Die Volumen niedrig bis mittel sind: AM vermeidet hohe anfängliche Werkzeugkosten, die mit dem Gießen verbunden sind, wodurch es für kleinere Produktionsläufe oder kundenspezifische Designs wettbewerbsfähig ist. Für sehr einfache Düsendesigns, die in großen Mengen hergestellt werden, könnten herkömmliche Methoden wie Gießen auf Teilebasis günstiger bleiben. Eine Analyse der „Gesamtbetriebskosten“ unter Berücksichtigung der Entwicklungsgeschwindigkeit, der Montageeinsparungen und der Leistungsvorteile zeigt jedoch oft, dass AM für fortschrittliche Luft- und Raumfahrtkomponenten sehr vorteilhaft ist.
F5: Welche Informationen werden in der Regel benötigt, um ein genaues Angebot für den 3D-Druck einer Düsenspitze von einem Lieferanten wie Met3dp zu erhalten?
A: Um ein genaues Angebot zu erstellen, benötigen Lieferanten in der Regel Folgendes:
- 3D-CAD-Modell: Ein hochwertiges Modell in einem Standardformat (z. B. STEP, IGES).
- Spezifikation des Materials: Geben Sie die erforderliche Legierung (z. B. IN718 oder IN625) und alle spezifischen Materialstandards (z. B. AMS-Spezifikationen) deutlich an.
- Menge: Anzahl der benötigten Teile (für den aktuellen Auftrag und potenziell prognostizierte Mengen).
- Kritische Toleranzen & Abmessungen: Eine 2D-Zeichnung oder ein annotiertes Modell, das kritische Abmessungen, erforderliche Toleranzen und Bezugsmerkmale hervorhebt.
- Anforderungen an die Oberflächenbeschaffenheit: Geben Sie die erforderlichen Ra-Werte für kritische innere und äußere Oberflächen an.
- Erforderliche Nachbearbeitung: Listen Sie alle obligatorischen Schritte auf (z. B. spezifischer Wärmebehandlungszyklus, HIP-Anforderung, Bearbeitungsvorgänge, Oberflächenbehandlungen).
- Qualitäts- und Inspektionsanforderungen: Geben Sie die erforderlichen ZfP-Methoden (FPI, CT-Scan usw.), die erforderlichen Qualitätsstandards (z. B. Einhaltung von AS9100) und alle erforderlichen Unterlagen (Materialzertifikate, Inspektionsberichte, Konformitätszertifikat) an. Die Bereitstellung umfassender Informationen im Voraus ermöglicht es Lieferanten wie Met3dp, genaue Angebote und realistische Vorlaufzeiten zu liefern, die auf Ihre spezifischen Bedürfnisse zugeschnitten sind.
Fazit: Die Förderung der Zukunft der Weltraumforschung mit den Lösungen der additiven Fertigung von Met3dp
Die Raketentriebwerksdüsenspitze, die an der feurigen Schnittstelle zwischen Treibstoffzufuhr und Verbrennung arbeitet, stellt eine der anspruchsvollsten Komponenten innerhalb eines Raketentriebwerks dar. Ihr kompliziertes Design muss eine präzise Treibstoffzerstäubung und -einspritzung unter extremen Temperaturen, Drücken und korrosiven Bedingungen gewährleisten. Herkömmliche Herstellungsmethoden, obwohl etabliert, haben oft Schwierigkeiten, die hochoptimierten Geometrien zu erzeugen, die erforderlich sind, um die Grenzen der Motorleistung und -effizienz zu verschieben.
Die additive Metallfertigung, insbesondere unter Verwendung von Hochleistungs-Superlegierungen wie IN718 und IN625, hat sich als transformative Lösung erwiesen. AM befreit Designer von herkömmlichen Zwängen und ermöglicht die Herstellung von Düsen mit beispielloser geometrischer Komplexität. Merkmale wie integrierte konforme Kühlkanäle, konsolidierte Baugruppen, die die Teileanzahl und die Fehlerpunkte reduzieren, und topologieoptimierte Leichtbaustrukturen sind jetzt erreichbar und führen direkt zu greifbaren Vorteilen: verbesserte Wärmeableitung, verbesserte Verbrennungsstabilität und -effizienz, längere Lebensdauer der Komponenten und reduziertes Gesamtgewicht des Motors.
Um diese Vorteile zu realisieren, ist jedoch mehr als nur der Zugang zu einem 3D-Drucker erforderlich. Es erfordert einen ganzheitlichen Ansatz, der strenge Design-for-Additive-Manufacturing (DfAM)-Prinzipien, die Verwendung von außergewöhnlich hochwertigen, AM-optimierten Metallpulvern, eng kontrollierte Druckprozesse und eine umfassende Reihe spezialisierter Nachbearbeitungsschritte umfasst – einschließlich Spannungsarmglühen, Wärmebehandlung, Heißisostatisches Pressen (HIP), Präzisionsbearbeitung und sorgfältige zerstörungsfreie Prüfung – alle unterliegen strengen Qualitätsstandards für die Luft- und Raumfahrt.
Met3dp ist ein wichtiger Wegbereiter in diesem fortschrittlichen Fertigungsökosystem. Mit unseren tiefen Wurzeln in der Materialwissenschaft, die durch unsere branchenführenden Gaszerstäubungs- und PREP-Pulverproduktionstechnologien demonstriert werden, liefern wir die hochreinen, hochkugelförmigen IN718-, IN625- und anderen kritischen Legierungspulver, die die Grundlage für zuverlässige Luft- und Raumfahrtkomponenten bilden. Unser Fachwissen erstreckt sich auf die Bereitstellung modernster Metall-AM-Systeme und umfassender Anwendungsentwicklungsunterstützung, wobei wir mit Innovatoren der Luft- und Raumfahrt zusammenarbeiten, um ehrgeizige Designs in flugfertige Hardware umzuwandeln. Wir verstehen die Herausforderungen und Feinheiten, die mit der Herstellung von missionskritischen Teilen verbunden sind, und sind bestrebt, Lösungen zu liefern, die den höchsten Qualitäts- und Leistungsstandards entsprechen.
Da die Menschheit immer weiter in den Weltraum vordringt, wird der Bedarf an leistungsfähigeren, effizienteren und zuverlässigeren Antriebssystemen nur noch zunehmen. Die additive Fertigung von Metallen ist nicht nur eine alternative Produktionsmethode, sondern eine entscheidende Schlüsseltechnologie für diese Zukunft. Durch die Nutzung der Leistungsfähigkeit der AM mit kompetenten Partnern wie Met3dp können Luft- und Raumfahrtunternehmen Innovationen beschleunigen, die Leistung optimieren und die Zukunft der Weltraumforschung weiter vorantreiben.
Möchten Sie erfahren, wie die additiven Fertigungsmöglichkeiten von Met3dp Ihre Luft- und Raumfahrtkomponenten revolutionieren können? Kontaktieren Sie uns noch heute , um Ihre spezifischen Anforderungen mit unserem Expertenteam zu besprechen.
Teilen auf
MET3DP Technology Co., LTD ist ein führender Anbieter von additiven Fertigungslösungen mit Hauptsitz in Qingdao, China. Unser Unternehmen ist spezialisiert auf 3D-Druckgeräte und Hochleistungsmetallpulver für industrielle Anwendungen.
Fragen Sie an, um den besten Preis und eine maßgeschneiderte Lösung für Ihr Unternehmen zu erhalten!
Verwandte Artikel
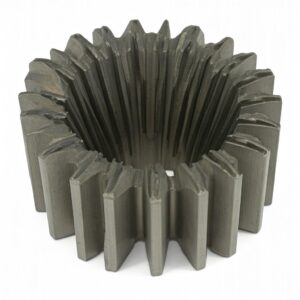
Hochleistungs-Düsenschaufelsegmente: Revolutionierung der Turbineneffizienz mit 3D-Metalldruck
Mehr lesen "Über Met3DP
Aktuelles Update
Unser Produkt
KONTAKT US
Haben Sie Fragen? Senden Sie uns jetzt eine Nachricht! Wir werden Ihre Anfrage mit einem ganzen Team nach Erhalt Ihrer Nachricht bearbeiten.
Holen Sie sich Metal3DP's
Produkt-Broschüre
Erhalten Sie die neuesten Produkte und Preislisten
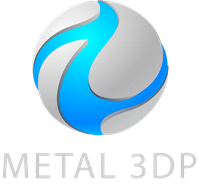
Metallpulver für 3D-Druck und additive Fertigung