Leichte Satellitenhalterungen durch 3D-Druck von Aluminium
Inhaltsübersicht
Einleitung: Die entscheidende Rolle der Leichtbauweise bei Satellitenhalterungen
Satelliten stellen die Spitze der menschlichen Ingenieurskunst dar. Sie arbeiten autonom in der rauen Umgebung des Weltraums und erfüllen wichtige Funktionen, die von globaler Kommunikation und Navigation bis hin zu Erdbeobachtung und wissenschaftlicher Forschung reichen. Jedes Bauteil dieser hochentwickelten Maschinen wird sorgfältig entworfen und streng getestet, um Zuverlässigkeit und Leistung unter extremen Bedingungen zu gewährleisten, einschließlich Startvibrationen, Temperaturschwankungen und Strahlenbelastung. Zu den wesentlichen, aber oft übersehenen Komponenten gehören die Satellitenhalterungen. Diese scheinbar einfachen Strukturelemente erfüllen die lebenswichtige Aufgabe, verschiedene Subsysteme im Satellitenbus oder Nutzlastmodul zu befestigen, zu sichern und auszurichten. Sie sind die unbesungenen Helden, die dafür sorgen, dass empfindliche Avionik, ausfahrbare Anhängsel wie Solarzellen und Antennen, Antriebstanks, wissenschaftliche Instrumente und komplizierte Kabelbäume während der gesamten Lebensdauer des Satelliten präzise positioniert und strukturell stabil bleiben.
Im Bereich der Weltraumforschung und des Einsatzes von Satelliten ist jedoch ein Faktor ausschlaggebend: masse. Jedes einzelne Gramm, das in die Umlaufbahn geschossen wird, ist mit erheblichen Kosten verbunden, die sich je nach Trägerrakete und Zielorbit (niedrige Erdumlaufbahn, geostationäre Umlaufbahn usw.) oft auf Tausende oder sogar Zehntausende von US-Dollar pro Kilogramm belaufen. Diese wirtschaftliche Realität übt einen immensen Druck auf die Konstrukteure und Hersteller von Satelliten aus, die Masse aller Komponenten zu minimieren, ohne die strukturelle Integrität oder Funktionalität zu beeinträchtigen. Dieses unerbittliche Streben nach Massenreduzierung ist bekannt als Leichtbauund ist ein grundlegendes Prinzip für die Konstruktion von Satelliten. Die Verringerung der Masse von Strukturkomponenten wie Halterungen führt direkt zu niedrigeren Startkosten, was möglicherweise eine größere Nutzlastkapazität (z. B. zusätzliche Instrumente oder Treibstoff für längere Missionen) oder den Einsatz kleinerer, kostengünstigerer Trägerraketen ermöglicht. Darüber hinaus kann eine Verringerung der Gesamtmasse des Satelliten die Manövrierfähigkeit verbessern und den Treibstoffbedarf für die Anpassung der Umlaufbahn verringern.
Traditionell verließen sich die Ingenieure bei der Herstellung von Satellitenhalterungen auf Materialien wie Aluminiumlegierungen, die für ihr günstiges Verhältnis von Festigkeit zu Gewicht bekannt sind, und auf Fertigungsverfahren wie die CNC-Bearbeitung (Computer Numerical Control). Die maschinelle Bearbeitung ist zwar effektiv, doch wird dabei von einem massiven Materialblock ausgegangen und überschüssiges Material entfernt (subtraktive Fertigung), was zu erheblichem Materialabfall und Einschränkungen bei der geometrischen Komplexität führen kann, wodurch wirklich optimierte, leichtgewichtige Konstruktionen oft nicht möglich sind. Andere Methoden wie das Gießen können für komplexe Formen verwendet werden, sind aber oft mit Werkzeugkosten, längeren Vorlaufzeiten und potenziell schlechteren Materialeigenschaften im Vergleich zu geschmiedeten oder gekneteten Materialien verbunden.
Eingeben Additive Fertigung von Metall (AM)gemeinhin als Metall bekannt 3D-Druck. Diese transformative Technologie bietet einen Paradigmenwechsel in der Art und Weise, wie Komponenten wie Satellitenhalterungen entworfen und hergestellt werden. Anstatt Material abzutragen, werden bei der additiven Fertigung die Teile Schicht für Schicht direkt aus einem digitalen Modell mit Metallpulvern aufgebaut. Dieser additive Ansatz eröffnet eine nie dagewesene Designfreiheit und ermöglicht die Herstellung hochkomplexer, organisch geformter und topologisch optimierter Strukturen, deren Herstellung bisher unmöglich oder unerschwinglich war. Speziell für Satellitenhalterungen, Aluminium-3D-Druckdie additive Fertigung, insbesondere mit Verfahren wie Laser Powder Bed Fusion (LPBF), ermöglicht es den Ingenieuren, das geringe Gewicht von Aluminium zu nutzen und gleichzeitig die Möglichkeiten der additiven Fertigung auszuschöpfen, um die Masse von Bauteilen drastisch zu reduzieren, weit über das hinaus, was mit herkömmlichen Methoden erreicht werden kann. Diese Synergie zwischen fortschrittlichen Aluminiumlegierungen und additiven Fertigungsverfahren revolutioniert die Konstruktion und Produktion von komponenten der Satellitenstrukturund ebnet damit den Weg für leichtere, leistungsfähigere und kostengünstigere Satelliten. Dieser Artikel befasst sich mit den Besonderheiten des 3D-Drucks von Aluminium für die Herstellung leichter Satellitenhalterungen und untersucht die Anwendungen, Vorteile, Materialien, Konstruktionsüberlegungen und Kriterien für die Auswahl von Lieferanten, die für Luft- und Raumfahrtingenieure und Beschaffungsmanager in diesem anspruchsvollen Sektor entscheidend sind.
Anwendungen: Wo werden 3D-gedruckte Aluminium-Satellitenhalterungen eingesetzt?
Die Vielseitigkeit der additiven Fertigung von Aluminium ermöglicht die Herstellung von maßgeschneiderten Halterungen für eine Vielzahl von Funktionen innerhalb der Architektur eines Satelliten. Die Möglichkeit, mehrere Funktionen in einem einzigen, komplexen Teil zu vereinen und gleichzeitig die Masse zu minimieren, macht 3D-gedruckte Aluminiumhalterungen besonders attraktiv für zahlreiche montage des Satelliten-Teilsystems aufgaben. Im Folgenden werden einige wichtige Anwendungsbereiche näher beleuchtet:
- Avionik und Elektronik Gehäuse/Einbau: Satelliten sind vollgepackt mit empfindlichen elektronischen Komponenten wie Bordcomputern, Kommunikationstranspondern, Stromverteilungseinheiten und Datenverarbeitungssystemen. Diese avionik-Konsolen müssen diese empfindlichen Komponenten sicher halten und sie vor den starken Vibrationen und G-Kräften beim Start schützen. Darüber hinaus erzeugt die Elektronik Wärme, und die Halterungen können mit integrierten Wärmemanagementfunktionen entworfen werden, wie z. B. komplexen internen Kanälen für Wärmerohre oder optimierten Geometrien, die die Wärmeübertragung an die Hauptstruktur des Satelliten oder an Kühler verbessern. der 3D-Druck ermöglicht hochgradig maßgeschneiderte Gehäuse und Halterungen, die sich perfekt an die Elektronikboxen anpassen, Volumen und Masse minimieren und gleichzeitig die strukturelle Unterstützung und thermische Effizienz maximieren.
- Mechanismen für die Aufstellung von Solarzellen und Antennen: Große ausfahrbare Strukturen wie Solarpaneele und Kommunikationsantennen sind für den Betrieb von Satelliten von entscheidender Bedeutung, müssen aber beim Start sicher verstaut und nach dem Einschwenken in die Umlaufbahn zuverlässig ausgefahren werden. Halterungen spielen eine entscheidende Rolle bei den Scharnieren, Verriegelungen und Stützstrukturen dieser mechanismen für den Einsatz von Solaranlagen und Antennenausrichtungssysteme. 3D-gedruckte Aluminiumhalterungen, insbesondere solche aus hochfesten Legierungen wie Scalmalloy®, können die nötige Steifigkeit und Festigkeit bieten, um Einsatzlasten zu bewältigen, und sind gleichzeitig deutlich leichter als herkömmlich bearbeitete Pendants. Die Designfreiheit ermöglicht eine komplexe Kinematik und integrierte Funktionen in der Halterungsstruktur selbst.
- Komponenten des Antriebssystems: Halterungen werden für die Montage von Treibstofftanks, Treibstoffleitungen, Ventilen und Triebwerken benötigt. Diese Komponenten müssen erheblichen Druckschwankungen, thermischen Zyklen und Vibrationen standhalten, insbesondere beim Zünden der Triebwerke. 3D-gedruckte Aluminiumhalterungen können topologisch optimiert werden, um diese spezifischen Lastpfade zu bewältigen und eine sichere Befestigung bei minimaler Masse zu gewährleisten. Die Möglichkeit, komplexe Geometrien zu erstellen, erleichtert auch die effiziente Verlegung von Treibstoffleitungen und die Integration von Sensoren.
- Montage von Instrumenten und Sensoren: Wissenschaftliche Instrumente, Erdbeobachtungssensoren, Kameras und Star Tracker erfordern extrem stabile und präzise Montageplattformen. Jede kleine Verschiebung oder Vibration kann die Datenqualität beeinträchtigen. 3D-gedruckte Halterungen können mit einem hohen Steifigkeits-Gewichts-Verhältnis und maßgeschneiderten Geometrien entworfen werden, um eine präzise Ausrichtung zu gewährleisten und thermisch bedingte Verformungen zu minimieren. Durch die Konsolidierung von Teilen kann auch die Anzahl der Schnittstellen reduziert werden, was die Stabilität weiter erhöht.
- Optische Bankstützen: Bei Satelliten, die Teleskope oder optische Kommunikationssysteme tragen, ist die Ausrichtung von Spiegeln, Linsen und Detektoren von größter Bedeutung. Halterungen, die Teil der optischen Bank sind, müssen außergewöhnliche Stabilität und minimale Wärmeausdehnung bieten. Während für die ultimative Stabilität oft Materialien wie Invar verwendet werden, können leichte Aluminium-AM-Halterungen in tragenden Strukturen eingesetzt werden, die manchmal komplexe Gitterkonstruktionen enthalten, um eine hohe Steifigkeit bei sehr geringer Masse zu erreichen.
- Verlegung von Hohlleitern und Koaxialkabeln: Die effiziente Verlegung von HF-Wellenleitern und elektrischen Kabeln im Satelliten ist von entscheidender Bedeutung. Kundenspezifische 3D-gedruckte Halterungen können für eine sichere Klemmung und präzise Verlegungspfade sorgen, die sich oft an komplexe strukturelle Konturen anpassen. Dadurch werden Schäden durch Vibrationen vermieden und die Montage vereinfacht. Diese Halterungen können mit glatten, abgerundeten Kanten entworfen werden, um ein Scheuern der Kabel zu verhindern.
- Sekundäre strukturelle Stützen: Neben der Montage spezifischer Geräte werden 3D-gedruckte Halterungen als allgemeine sekundäre Strukturelemente verwendet, die Paneele verbinden, Verbindungen verstärken und Lasten innerhalb der Satellitenbusstruktur übertragen. Die Topologieoptimierung wird hier intensiv genutzt, um hocheffiziente, tragende Strukturen mit minimalem Gewicht zu schaffen.
Jenseits von Satelliten: Branchenübergreifende Relevanz
Die Prinzipien und Vorteile, die bei Satellitenanwendungen beobachtet wurden, lassen sich ohne weiteres auf andere Branchen übertragen, in denen Gewicht, Leistung und Komplexität entscheidende Faktoren sind:
- Unbemannte Luftfahrzeuge (UAVs / Drohnen): Leichtbau ist entscheidend für die Verlängerung der Flugzeit und die Erhöhung der Nutzlastkapazität. 3D-gedruckte Aluminiumhalterungen werden für die Montage von Motoren, Sensoren, Batterien und Fahrwerk verwendet.
- Hochleistungsautomobile (Motorsport, Elektrofahrzeuge): Eine Gewichtsreduzierung verbessert die Beschleunigung, das Handling und die Effizienz. AM-Halterungen werden für die Motor-/Antriebsstrangbefestigung, Aufhängungskomponenten und die Montage elektronischer Steuergeräte (ECUs) verwendet.
- Medizinische Geräte: Es werden zwar häufig andere Materialien verwendet (wie Titan), aber das Prinzip der Herstellung komplexer, leichter, patienten- oder gerätespezifischer Brackets für Implantate oder externe Geräte nutzt die Möglichkeiten von AM’.
- Robotik und industrielle Automatisierung: Kundenspezifische Halterungen für die Montage von Greifern, Sensoren und Aktoren an Roboterarmen profitieren von der Designfreiheit und den möglichen Gewichtseinsparungen, die AM bietet.
Überall dort, wo ein Bauteil zum Verbinden, Stützen, Montieren oder Ausrichten anderer Teile benötigt wird und wo die Verringerung der Masse bei gleichzeitiger Beibehaltung oder Verbesserung der Leistung ein wichtiges Ziel ist, stellen 3D-gedruckte Aluminiumhalterungen eine überzeugende Fertigungslösung dar, insbesondere für komplexe Konstruktionen oder kleine bis mittlere Produktionsserien, wie sie in fertigung von Luft- und Raumfahrtkomponenten und verwandten High-Tech-Bereichen.
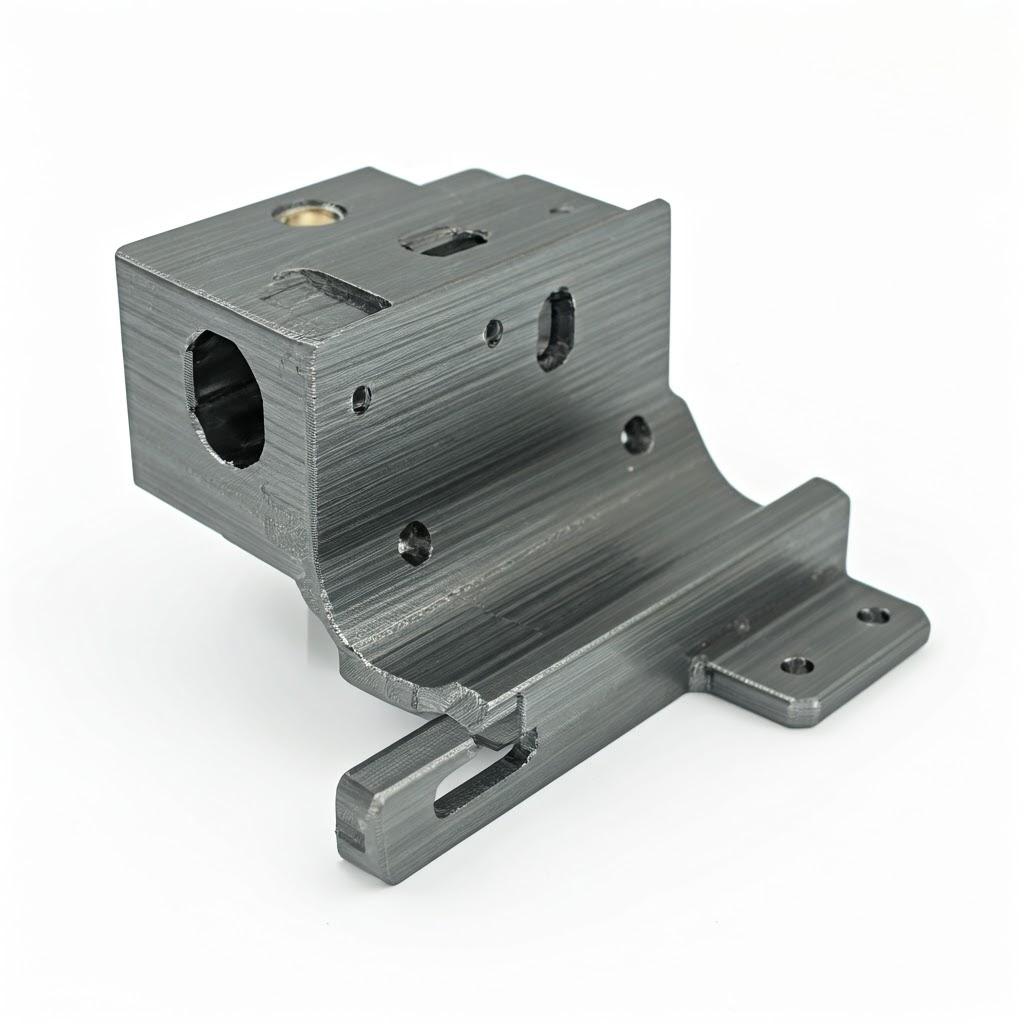
Warum 3D-Druck von Metall für Satellitenhalterungen? Leistungssteigerungen freisetzen
Die Entscheidung für die additive Fertigung von Metallen, insbesondere das Laser Powder Bed Fusion (LPBF), zur Herstellung von Satellitenhalterungen beruht auf einer Reihe von überzeugenden Vorteilen gegenüber herkömmlichen Fertigungsverfahren. Diese Vorteile gehen direkt auf die zentralen Herausforderungen der Luft- und Raumfahrttechnik ein: Maximierung der Leistung bei gleichzeitiger Minimierung von Gewicht und Kosten sowie Beschleunigung der Entwicklungszeiten. Für Beschaffungsmanager und Ingenieure, die Produktionsmethoden bewerten, ist das Verständnis dieser Vorteile der Schlüssel zu fundierten Beschaffungsentscheidungen.
1. Noch nie dagewesene Gestaltungsfreiheit und Komplexität:
- Traditionelle Zwänge durchbrechen: Herkömmliche Fertigungsmethoden wie die CNC-Bearbeitung sind durch den Zugang zu den Werkzeugen und den subtraktiven Charakter des Prozesses von Natur aus begrenzt. Komplexe innere Merkmale, Hinterschneidungen und organische Formen sind oft schwierig, zeitaufwändig oder gar unmöglich zu erstellen. Metall-AM, bei dem die Teile Schicht für Schicht aufgebaut werden, beseitigt diese Einschränkungen.
- Topologie-Optimierung: Dies ist wohl der wichtigste Treiber für AM bei Strukturbauteilen. Spezialisierte Software analysiert die Belastungspfade und Spannungen, denen eine Halterung im Betrieb ausgesetzt ist, und entfernt dann algorithmisch Material aus unkritischen Bereichen. Zurück bleibt eine optimierte, oft organisch anmutende Struktur, die alle Leistungsanforderungen bei möglichst geringer Masse erfüllt. Dieser Ansatz kann zu Gewichtseinsparungen von 30-70 % oder sogar mehr im Vergleich zu konventionell entworfenen und hergestellten Teilen führen, was sich direkt auf die Startkosten und die Leistung des Satelliten auswirkt. Dies ist ein Kerngedanke von topologieoptimierung Luft- und Raumfahrt Anwendungen.
- Gitterförmige Strukturen: AM ermöglicht die Einbindung komplexer interner Gitterstrukturen. Diese technischen Mikroarchitekturen können das Verhältnis von Steifigkeit zu Gewicht erheblich verbessern, Schwingungsdämpfungseigenschaften bieten oder die Wärmeübertragung erleichtern, und das alles innerhalb des Designbereichs der Halterung.
- Generatives Design: Über die Topologieoptimierung hinaus können generative Entwurfswerkzeuge autonom Hunderte oder Tausende von Entwurfsvarianten auf der Grundlage vordefinierter Randbedingungen (Lasten, Material, Fertigungsverfahren, Sperrzonen) erstellen, so dass die Ingenieure einen größeren Entwurfsraum erkunden und neuartige, leistungsstarke Lösungen entdecken können.
2. Teil Konsolidierung:
- Verringerung der Montagekomplexität: Traditionell kann eine komplexe Halterungsbaugruppe aus mehreren Einzelteilen bestehen (bearbeitete Platten, gebogene Bleche, Befestigungselemente). Jedes Teil bedeutet zusätzliches Gewicht, erfordert Zeit für die Montage und birgt potenzielle Fehlerquellen an Verbindungen und Schnittstellen.
- Erhöhter Zuverlässigkeit: Metall-AM ermöglicht es Ingenieuren, diese verschiedenen Komponenten in einem einzigen, monolithischen 3D-gedruckten Teil zu konsolidieren. Dadurch wird die Anzahl der Verbindungselemente (Schrauben, Nieten), Dichtungen und Schnittstellen drastisch reduziert, was zu vorteile der Teilkonsolidierung wie z. B. niedrigere Arbeitskosten bei der Montage, geringere Teilezahl und Bestandsverwaltung, geringeres Gesamtgewicht und deutlich verbesserte strukturelle Integrität und Zuverlässigkeit durch die Beseitigung potenzieller Fehlermöglichkeiten im Zusammenhang mit Verbindungen.
3. Rapid Prototyping und beschleunigte Entwicklung:
- Beschleunigung der Iteration: In der schnelllebigen Welt der Satellitenentwicklung ist es von unschätzbarem Wert, Entwürfe schnell zu iterieren. Die herkömmliche Fertigung erfordert oft lange Vorlaufzeiten für die Werkzeugherstellung (Guss) oder komplexe Bearbeitungsvorgänge. Mit AM kann eine Designänderung in CAD implementiert werden, und ein neuer Prototyp kann oft innerhalb von Tagen oder Wochen gedruckt werden, nicht erst nach Monaten.
- Schnellere Qualifizierung: Diese Rapid-Prototyping-Fähigkeit ermöglicht eine schnellere physische Prüfung und Validierung von Halterungsentwürfen und beschleunigt so erheblich die rapid Prototyping von Raumfahrt-Hardware zyklus und verkürzt die Gesamtzeit bis zum Start neuer Satellitenmissionen oder -komponenten. Funktionsprototypen können aus dem Zielmaterial (AlSi10Mg oder Scalmalloy®) hergestellt werden und liefern bereits in einem frühen Stadium des Entwicklungsprozesses hochrelevante Testdaten.
4. Geringerer Materialabfall:
- Additiv vs. Subtraktiv: Die CNC-Bearbeitung beginnt mit einem massiven Block oder Knüppel aus Material und schneidet den Überschuss weg. Bei komplexen Geometrien kann die Menge des abgetragenen (und als Späne oder Schrott verschwendeten) Materials beträchtlich sein und manchmal 80-90 % des ursprünglichen Blocks übersteigen (das sogenannte "Buy-to-Fly"-Verhältnis).
- Effiziente Materialverwendung: Beim LPBF-Verfahren wird nur das Material verwendet, das für die Herstellung des Teils und seiner Stützstrukturen erforderlich ist. Zwar wird ein Teil des Pulvers für die Stützstrukturen verwendet, und ein Teil kann nicht unbegrenzt recycelt werden, doch ist die Materialausnutzung insgesamt deutlich besser als bei subtraktiven Verfahren, insbesondere bei komplexen, leichtgewichtigen Konstruktionen. Dies wird sowohl aus Kosten- als auch aus Nachhaltigkeitssicht immer wichtiger.
5. Eignung für die Produktion kleiner bis mittlerer Mengen:
- Beseitigung von Werkzeugen: Verfahren wie Gießen oder Spritzgießen erfordern teure Vorabinvestitionen in Formen oder Gesenke und sind daher nur bei hohen Produktionsmengen wirtschaftlich. Metall-AM erfordert keine teilespezifischen Werkzeuge.
- Kosteneffiziente Anpassung: Dies macht LPBF-Aluminium-Druck das System ist äußerst kosteneffizient für die Produktionsmengen, die typischerweise bei Satelliten und anderen Luft- und Raumfahrtanwendungen anfallen, bei denen nur einige wenige oder vielleicht ein paar Dutzend identische Halterungen pro Mission oder Plattform benötigt werden. Es ermöglicht auch die wirtschaftliche Produktion von kundenspezifischen Halterungsvarianten für verschiedene Satellitenkonfigurationen.
Nutzung der Technologie mit Fachwissen:
Die Vorteile liegen auf der Hand, aber die erfolgreiche Umsetzung 3D-Druck von Metall erfordert spezielle Kenntnisse in den Bereichen Design for AM (DfAM), Werkstoffkunde, Prozessparametersteuerung und Nachbearbeitung. Die Zusammenarbeit mit einem erfahrenen Metall-AM-Servicebüro oder Lösungsanbieter ist oft entscheidend. Unternehmen wie Met3dp, die über umfassendes Fachwissen im Bereich der additiven Fertigungstechnologien und Hochleistungswerkstoffe verfügen, bieten nicht nur Druckdienstleistungen an, sondern auch umfassende Lösungen, einschließlich Konstruktionsunterstützung und Materialberatung, um sicherzustellen, dass das volle Potenzial von AM für kritische Komponenten wie Satellitenhalterungen genutzt wird. Ihr Fokus auf branchenführende Ausrüstung und fortschrittliche Pulverherstellung gewährleistet die von der Luft- und Raumfahrtbranche geforderte Zuverlässigkeit und Qualität.
Empfohlene Materialien: AlSi10Mg und Scalmalloy® für Raumfahrtanwendungen
Die Wahl des richtigen Materials ist für die Konstruktion von Satellitenhalterungen, die strenge Anforderungen an Leistung, Gewicht und Umweltverträglichkeit erfüllen, von entscheidender Bedeutung. Aluminiumlegierungen werden aufgrund ihrer geringen Dichte, ihrer guten Wärmeleitfähigkeit und ihrer relativ einfachen Verarbeitung mittels Laser Powder Bed Fusion (LPBF) bevorzugt. Innerhalb der Aluminiumfamilie stechen zwei Legierungen für 3D-gedruckte Satellitenanwendungen hervor: AlSi10Mg und Scalmalloy®. Das Verständnis ihrer unterschiedlichen Eigenschaften und Vorteile ist für die Materialauswahl entscheidend.
AlSi10Mg: Die Aluminiumlegierung für alle Fälle
AlSi10Mg ist eine der gebräuchlichsten und am besten charakterisierten Aluminiumlegierungen, die in der additiven Metallfertigung verwendet werden. Es handelt sich im Wesentlichen um eine für LPBF angepasste Gusslegierung, die etwa 9-11 % Silizium und 0,2-0,45 % Magnesium enthält.
- Wichtigste Eigenschaften & Vorteile:
- Gutes Verhältnis von Stärke zu Gewicht: Obwohl es sich nicht um die höchstfeste Aluminiumlegierung handelt, bietet sie eine beachtliche Festigkeit, insbesondere nach einer geeigneten Wärmebehandlung (in der Regel T6), in Kombination mit einer geringen Dichte (≈2,67 g/cm3). Dadurch eignet sie sich für eine breite Palette von mäßig belasteten strukturellen Anwendungen.
- Ausgezeichnete Wärmeleitfähigkeit: Der hohe Siliziumgehalt trägt zu einer guten Wärmeleitfähigkeit bei (≈100-140W/m⋅K je nach Wärmebehandlung), was für Halterungen, die Wärme von montierter Elektronik oder anderen Bauteilen ableiten müssen, sehr vorteilhaft ist.
- Gute Korrosionsbeständigkeit: AlSi10Mg weist eine gute Beständigkeit gegen atmosphärische Korrosion auf.
- Verarbeitbarkeit & Kosten-Wirksamkeit: Die Verarbeitung mit LPBF ist relativ einfach, und viele handelsübliche Maschinen verfügen über gut etablierte Parameter. Außerdem ist das Pulver im Allgemeinen preiswerter als Hochleistungslegierungen wie Scalmalloy®.
- Schweißeignung: Obwohl es für monolithische AM-Teile weniger relevant ist, besitzt es eine vernünftige Schweißbarkeit, die nützlich sein kann, wenn ein Fügen nach der Herstellung erforderlich ist.
- Nachbearbeiten: Es lässt sich gut mit den üblichen Nachbearbeitungstechniken bearbeiten, einschließlich Spannungsabbau, T6-Wärmebehandlung (Lösungsglühen und künstliche Alterung) zur deutlichen Verbesserung von Festigkeit und Härte, CNC-Bearbeitung und Oberflächenveredelung wie Eloxieren oder chemische Umwandlungsbeschichtung.
- Typische Anwendungen: Ideal für Halterungen mit mäßiger struktureller Belastung, für Komponenten, bei denen das Wärmemanagement eine wichtige Rolle spielt, für komplexe Geometrien, bei denen die Herstellbarkeit mittels AM im Vordergrund steht, und für Anwendungen, bei denen die Kosten einen wichtigen Faktor darstellen. Beispiele sind Avionikgehäuse, Gehäuse, allgemeine Stützstrukturen und in Halterungen integrierte Kühlkörper.
Scalmalloy®: Hochleistungsaluminium für anspruchsvolle Anwendungen
Scalmalloy® ist eine patentierte Hochleistungslegierung aus Aluminium-Magnesium-Scandium (Al-Mg-Sc), die von APWorks (einer Airbus-Tochter) speziell für die additive Fertigung entwickelt wurde. Sie verschiebt die Grenzen dessen, was mit Aluminiumlegierungen erreichbar ist, und bietet Eigenschaften, die in bestimmten Aspekten mit denen einiger Titanlegierungen konkurrieren.
- Wichtigste Eigenschaften & Vorteile:
- Außergewöhnliches Verhältnis von Stärke zu Gewicht: Dies ist das herausragende Merkmal von Scalmalloy®’. Im Vergleich zu AlSi10Mg (Streckgrenze ≈230-300MPa nach T6) weist es eine deutlich höhere Streckgrenze (≈450-520MPa) und Zugfestigkeit (≈500-580MPa) auf, während es eine ähnlich niedrige Dichte (≈2,67g/cm3) aufweist. Dies ermöglicht eine noch größere Gewichtseinsparung bei festigkeitskritischen Anwendungen.
- Ausgezeichnete Duktilität und Dauerfestigkeit: Im Gegensatz zu vielen hochfesten Aluminiumlegierungen behält Scalmalloy® eine gute Duktilität (Dehnung ≈8-15%) und weist eine hervorragende Ermüdungsleistung auf, so dass es sich für Bauteile eignet, die zyklischen Belastungen, Vibrationen und dynamischen Beanspruchungen ausgesetzt sind - übliche Bedingungen für Satellitenkomponenten beim Start und im Betrieb.
- Hohe spezifische Festigkeit: Die Kombination aus hoher Festigkeit und geringer Dichte verleiht ihm eine spezifische Festigkeit (Festigkeit geteilt durch Dichte), die viele andere Aluminium- und sogar einige Titanlegierungen übertrifft, was es ideal für den Leichtbau in der Luftfahrt macht.
- Mikrostrukturstabilität bei erhöhten Temperaturen: Im Vergleich zu Standard-Aluminiumlegierungen behält es seine Eigenschaften bei leicht erhöhten Temperaturen besser bei.
- Gute Schweißbarkeit und Korrosionsbeständigkeit: Ähnlich wie AlSi10Mg weist es im Allgemeinen eine gute Schweißbarkeit und Korrosionsbeständigkeit auf.
- Typische Anwendungen: Bevorzugt für hochbelastete strukturelle Halterungen, Komponenten, bei denen die Ermüdungsfestigkeit entscheidend ist, Anwendungen, bei denen ein absolutes Mindestgewicht für eine bestimmte Festigkeitsanforderung erforderlich ist, und Teile, die schwerere Titankomponenten ersetzen. Beispiele hierfür sind primär tragende Strukturen, Komponenten von Auslösemechanismen, Motorhalterungen und Halterungen, die erheblichen Vibrationen oder dynamischen Belastungen ausgesetzt sind. Die höheren Material- und Lizenzkosten sind durch die erheblichen Leistungssteigerungen gerechtfertigt.
Vergleichstabelle: AlSi10Mg vs. Scalmalloy® für Satellitenhalterungen
Eigentum | AlSi10Mg (typisch T6 wärmebehandelt) | Scalmalloy® (Typisch As-Built/Spannungsentlastet) | Einheit | Anmerkungen |
---|---|---|---|---|
Dichte | ≈2.67 | ≈2.67 | g/cm3 | Beide bieten erhebliche Gewichtseinsparungen gegenüber Stahl oder Titan. |
Streckgrenze (Rp0,2) | ≈230-300 | ≈450-520 | MPa | Scalmalloy® bietet eine deutlich höhere Festigkeit. |
Höchstzugkraft (Rm) | ≈330-430 | ≈500-580 | MPa | Scalmalloy® weist eine hervorragende Endfestigkeit auf. |
Dehnung beim Bruch | ≈3-10 | ≈8-15 | % | Scalmalloy® bietet im Allgemeinen eine bessere Duktilität bei höherer Festigkeit. |
Elastizitätsmodul | ≈70-75 | ≈70-76 | GPa | Ähnliche Steifigkeit für beide Materialien. |
Wärmeleitfähigkeit | ≈100-140 | ≈120-150 | W/(m⋅K) | Beide bieten eine gute Wärmeleitfähigkeit, die bei Scalmalloy® etwas besser ist. |
Ermüdungsfestigkeit (R=-1) | Mäßig | Hoch | Vergleichend | Scalmalloy® eignet sich hervorragend für ermüdungskritische Anwendungen. |
Maximale Betriebstemperatur | ≈100-150 | ≈150-200 | °C | Scalmalloy® behält seine Festigkeit bei leicht erhöhten Temperaturen besser bei. |
Relative Kosten | Unter | Höher | Vergleichend | AlSi10Mg ist für weniger anspruchsvolle Anwendungen kostengünstiger. |
Hauptvorteil | Ausgewogene Eigenschaften, Kosten, Thermik | Maximale Festigkeit gegen Gewicht, Ermüdungslebensdauer | – | Wählen Sie auf der Grundlage der wichtigsten Designfaktoren. |
In Blätter exportieren
(Hinweis: Die Eigenschaften sind Näherungswerte und hängen in hohem Maße von den spezifischen LPBF-Prozessparametern, der Bauausrichtung, der Wärmebehandlung und den Testbedingungen ab. Spezifische Werte finden Sie immer in den Datenblättern der Lieferanten)
Die Bedeutung der Pulverqualität und des Fachwissens des Lieferanten
Unabhängig von der gewählten Legierung sind Qualität und Konsistenz des im LPBF-Verfahren verwendeten Metallpulvers entscheidend für das Erreichen der gewünschten mechanischen Eigenschaften und die Gewährleistung der Zuverlässigkeit der endgültigen Satellitenhalterung. Defekte im Pulver (z. B. unregelmäßige Form, innere Porosität, Satelliten, falsche Partikelgrößenverteilung) können sich in Defekten im gedruckten Teil niederschlagen und dessen strukturelle Integrität beeinträchtigen.
Hier kommt die Partnerschaft mit einem sachkundigen anbieter von Metallpulver für die Luft- und Raumfahrt und AM-Dienstleister wie Met3dp unverzichtbar wird. Met3dp setzt branchenführende Technologien zur Pulverherstellung ein, darunter Gaszerstäubung und Plasma-Rotations-Elektroden-Verfahren (PREP), um hochwertige sphärische Metallpulver herzustellen.
- Gaszerstäubung: Einzigartiges Düsen- und Gasflussdesign zur Herstellung von Metallkugeln mit hoher Sphärizität und hervorragender Fließfähigkeit - entscheidend für eine gleichmäßige Pulverbettdichte in LPBF.
- VORBEREITEN: Erzeugt hochreine und kugelförmige Pulver, die häufig für reaktive Materialien wie Titanlegierungen bevorzugt werden, aber auch für andere Metalle von höchster Qualität geeignet sind.
Das Engagement von Met3dp’ geht über Aluminium hinaus; das Portfolio umfasst innovative Legierungen wie TiNi, TiTa, TiAl, TiNbZr, CoCrMo, rostfreie Stähle und Superlegierungen und beweist damit ein breites Fachwissen in Met3dp Metall-Pulver die für anspruchsvolle Anwendungen in der Luft- und Raumfahrt, der Medizin und der Industrie geeignet sind. Dieses Fachwissen in der Pulverherstellung in Kombination mit dem Betrieb von branchenführenden SEBM- (Selective Electron Beam Melting) und LPBF-Druckern, die für ihre Genauigkeit und Zuverlässigkeit bekannt sind, gewährleistet, dass die Kunden Teile erhalten, die aus gut charakterisiertem, hochwertigem Ausgangsmaterial hergestellt und unter strengen Qualitätskontrollen verarbeitet werden. Die Wahl eines Lieferanten mit nachweisbarer Pulverqualitätskontrolle und fundierten materialwissenschaftlichen Kenntnissen ist ein nicht verhandelbarer Aspekt bei der Beschaffung von unternehmenskritischen 3D-Druck von Aluminium im Vergleich komponenten wie Satellitenhalterungen.
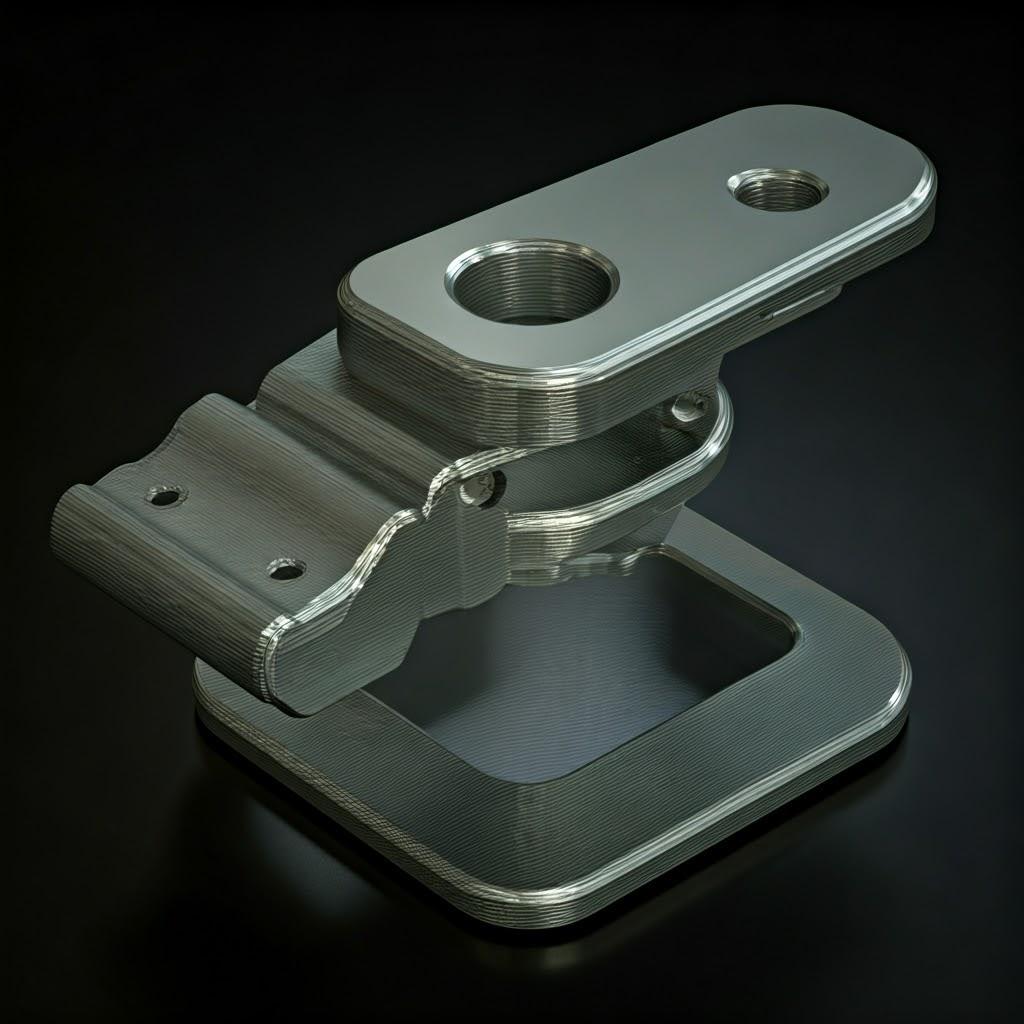
Designüberlegungen zur additiven Fertigung (DfAM) von Satellitenhalterungen
Die erfolgreiche Nutzung des 3D-Drucks von Aluminium für Satellitenhalterungen erfordert mehr als nur die Umwandlung eines bestehenden, traditionell hergestellten Designs in eine druckbare Datei. Es erfordert eine grundlegende Änderung der Designphilosophie, die folgende Aspekte umfasst Design für additive Fertigung (DfAM) grundsätze. Bei DfAM geht es nicht nur um die Sicherstellung eines Teils dürfen es geht darum, die einzigartigen Möglichkeiten additiver Verfahren wie Laser Powder Bed Fusion (LPBF) aktiv zu nutzen, um die Leistung zu maximieren, das Gewicht zu minimieren, die Kosten zu senken und Funktionen auf bisher unerreichte Weise zu integrieren. Für Ingenieure, die kritische Satelliten-Hardware entwickeln, ist die Beherrschung von DfAM der Schlüssel zur Erschließung des vollen Potenzials von Aluminium-AM.
1. Topologie-Optimierung und generatives Design einbeziehen:
- Jenseits konventioneller Formen: Vergessen Sie die Beschränkungen durch Knüppel, Blöcke und den Zugang zu Werkzeugen, die bei der maschinellen Bearbeitung bestehen. AM ermöglicht freie, organische Formen, die von der Physik und den Leistungsanforderungen diktiert werden, nicht von Fertigungsbeschränkungen.
- Arbeitsablauf der Topologie-Optimierung: Diese leistungsstarke Rechentechnik ist das Herzstück der Leichtbauweise von Bauteilen wie Klammern. Der typische Arbeitsablauf umfasst:
- Definition des Gestaltungsraums: Angabe des maximal zulässigen Volumens, das die Halterung einnehmen kann.
- Lasten und Beschränkungen festlegen: Anwendung realistischer Lastfälle (statisch, dynamisch, thermisch), denen die Halterung während des Starts und des Betriebs in der Umlaufbahn ausgesetzt ist. Festlegung von Randbedingungen (wo die Halterung befestigt ist) und Sperrzonen (Bereiche, die für die Montage anderer Komponenten oder den Zugang benötigt werden).
- Ziele setzen: In der Regel besteht das Hauptziel darin, die Masse zu minimieren und gleichzeitig die Beschränkungen hinsichtlich der maximalen Spannung und Durchbiegung zu erfüllen (oder die Steifigkeit bei einer bestimmten Masse zu maximieren).
- Durchführung der Optimierung: Verwendung spezialisierter Software zur Topologieoptimierung (z.B. Altair Inspire, nTopology, ANSYS Discovery, Siemens NX), um iterativ Material aus Bereichen mit geringer Belastung zu entfernen und Material nur dort zu belassen, wo es strukturell notwendig ist, um die Lasten zu tragen.
- Interpretieren und Rekonstruieren: Das Rohergebnis ist oft eine Netzdarstellung, die interpretiert und in eine glatte, herstellbare CAD-Geometrie umgewandelt werden muss (oft mit NURBS-Oberflächen oder impliziten Modellierungstechniken). Dieser Schritt erfordert technisches Urteilsvermögen, um sicherzustellen, dass das Ergebnis praktikabel ist und alle funktionalen Anforderungen erfüllt.
- Generative Design Exploration: Um die Optimierung noch einen Schritt weiter zu treiben, können generative Entwurfswerkzeuge auf der Grundlage der definierten Einschränkungen und Ziele autonom Tausende potenzieller Entwurfslösungen untersuchen und dabei oft nicht intuitive, aber hocheffiziente Strukturkonzepte präsentieren.
- Ergebnis: Halterungen, die sich von ihren maschinell gefertigten Gegenstücken radikal unterscheiden - oft ähneln sie Knochenstrukturen oder komplexen Fachwerken -, aber erhebliche Gewichtseinsparungen (oft 30-70 %) bieten und gleichzeitig die Leistungsanforderungen erfüllen oder übertreffen.
2. Nutzung von Gitterstrukturen:
- Entwickelte Mikroarchitekturen: AM ermöglicht in einzigartiger Weise die Integration komplexer interner gitterstrukturentwurf AM in festen Bauteilen. Diese sich wiederholenden Einheitszellen (z. B. kubisch, diamantförmig, Oktett-Fachwerk, Kreisel, TPMS – Triply Periodic Minimal Surfaces) können strategisch in einer Klammerkonstruktion eingesetzt werden:
- Verbessertes Verhältnis von Steifigkeit zu Gewicht: Die Füllung bestimmter Volumina mit Gittern geringer Dichte anstelle von Vollmaterial kann die Gesamtsteifigkeit bei minimalem Gewichtszuwachs erheblich erhöhen.
- Schwingungsdämpfung: Spezielle Gittergeometrien können so gestaltet werden, dass sie Schwingungsenergie absorbieren oder ableiten, was für den Schutz der auf der Halterung montierten empfindlichen Geräte von entscheidender Bedeutung ist.
- Wärmemanagement: Offenzellige Gitter ermöglichen eine Flüssigkeitsströmung (falls für die aktive Kühlung erforderlich) oder eine größere Oberfläche für die passive Wärmeableitung.
- Überlegungen zum Design: Erfordert eine sorgfältige Auswahl des Gittertyps, der Zellengröße, der Streben-/Wanddicke und weiche Übergänge zu massiven Abschnitten, um Spannungskonzentrationen zu vermeiden und die Druckbarkeit zu gewährleisten. Es werden Analysewerkzeuge benötigt, um die effektiven mechanischen Eigenschaften des Gitterbereichs vorherzusagen.
3. Einhaltung der LPBF-Prozessbeschränkungen (aluminiumspezifisch):
- Minimale Featuregröße: Es gibt eine Grenze, bis zu der kleine Merkmale zuverlässig gedruckt werden können. Die Mindestwanddicke liegt in der Regel bei 0,4-0,8 mm und variiert je nach Maschine und Material. Auch die minimalen Lochdurchmesser sind begrenzt.
- Überhänge und Stützstrukturen: LPBF baut Teile Schicht für Schicht auf. Flächen, die parallel zur Bauplatte verlaufen, lassen sich gut drucken, ebenso wie vertikale Wände. Für schräge Flächen (Überhänge) sind jedoch Stützstrukturen erforderlich, sobald der Winkel im Verhältnis zur Bauplatte einen bestimmten Schwellenwert unterschreitet (bei Aluminium in der Regel unter 45 Grad).
- Selbsttragende Winkel: Konstruieren Sie die Bauteile so, dass sie möglichst selbsttragende Winkel (größer als 45 Grad) aufweisen, um den Bedarf an Stützen zu minimieren.
- Strategie unterstützen: Wo Stützen unvermeidlich sind, müssen sie sorgfältig entworfen werden. Sie verlängern die Druckzeit, verbrauchen Material, erfordern eine Nachbearbeitung zum Entfernen und können die Oberflächenbeschaffenheit des gestützten Bereichs beeinträchtigen. Entwerfen Sie Stützen, die stark genug sind, um Verformungen zu verhindern, aber leicht zu entfernen sind, ohne das Teil zu beschädigen (z. B. durch reduzierte Kontaktpunkte, Perforationen). Vermeiden Sie große, flache, nach unten gerichtete Flächen (die umfangreiche Stützen erfordern) in der Nähe der Bauplatte.
- Reststress-Management: Berücksichtigen Sie Konstruktionsmerkmale, die den Aufbau von Eigenspannungen vermindern, wie z. B. abgerundete Ecken anstelle von scharfen Kanten und die Vermeidung abrupter Querschnittsänderungen. Auch die Bauausrichtung spielt eine entscheidende Rolle.
- Ausrichtung der Löcher: Horizontale Löcher werden aufgrund des schichtweisen Aufbaus oft mit besserer Rundheit gedruckt als vertikale Löcher, obwohl vertikale Löcher glattere Innenflächen haben können. Berücksichtigen Sie die Ausrichtung anhand der funktionalen Anforderungen.
- Teilentfernung: Konstruieren Sie Merkmale oder berücksichtigen Sie die Ausrichtung, um das Teil nach dem Druck leichter von der Bauplatte zu entfernen (was oft Drahterodieren oder Sägen erfordert).
4. Integration der Funktionalität:
- Jenseits der Struktur: Denken Sie nicht nur an das Festhalten von Dingen. Kann die Halterung auch anderen Zwecken dienen?
- Kabel-/Drahtmanagement: Integrieren Sie Kanäle, Clips oder Fräswege direkt in die Halterungsstruktur.
- Wärmemanagement: Entwerfen Sie integrierte Kühlkörper, Kanäle für die Flüssigkeitskühlung oder Merkmale, die die Wärmeübertragung fördern.
- Handhabung von Flüssigkeiten: Für Antriebs- oder Wärmesysteme können interne Kanäle für den Flüssigkeitsstrom eingebaut werden, so dass keine separaten Schläuche und Anschlüsse erforderlich sind.
- Kinematische Merkmale: Integrieren Sie Scharniere, Drehpunkte oder nachgiebige Mechanismen direkt in das Design der Halterung.
5. Simulationsgestützter Entwurf und Validierung:
- Virtuelle Tests: Angesichts der komplexen Geometrien, die sich häufig aus Topologieoptimierung und Gitterstrukturen ergeben, FEA-Simulation AM-Teile ist absolut kritisch. Durchführung von Strukturanalysen (statisch, dynamisch, Knickung) und thermischen Analysen für das vorgeschlagene AM-Design vor sich zum Druck zu verpflichten.
- Berücksichtigung der Anisotropie: LPBF-Teile können einen gewissen Grad an Anisotropie aufweisen (unterschiedliche mechanische Eigenschaften in verschiedenen Richtungen relativ zu den Aufbauschichten). Bei fortgeschrittenen Simulationen muss dies möglicherweise berücksichtigt werden.
- Leistung wie gedruckt: Die Simulation sollte idealerweise die Leistung des endgültigen, nachbearbeiteten Teils vorhersagen, wobei die Auswirkungen der Wärmebehandlung und etwaiger Bearbeitungsvorgänge zu berücksichtigen sind. Der Vergleich von Simulationsergebnissen mit physikalischen Testdaten von gedruckten Coupons ist für die Validierung von Modellen unerlässlich.
Partnerschaften für DfAM-Fachwissen:
Die Beherrschung von DfAM erfordert Erfahrung. Die Zusammenarbeit mit AM-Dienstleistern wie Met3dp, die über ein tiefes Wissen über spezifische Druckverfahren wie LPBF und Materialien wie AlSi10Mg und Scalmalloy®, können von unschätzbarem Wert sein. Sie bieten oft DfAM Dienstleistungen Luft- und Raumfahrt kunden verlassen sich auf unsere Beratung bei der Optimierung von Designs hinsichtlich Druckbarkeit, Leistung und Kosteneffizienz, um sicherzustellen, dass die einzigartigen Vorteile von AM für anspruchsvolle Satellitenanwendungen voll ausgeschöpft werden.
Erreichbare Toleranzen, Oberflächengüte und Maßgenauigkeit bei Aluminium-AM
Während die additive Fertigung von Metallen eine beispiellose Designfreiheit bietet, ist es für Ingenieure und Beschaffungsmanager von entscheidender Bedeutung, realistische Erwartungen hinsichtlich der erreichbaren Präzision im Vergleich zu traditionellen Hochpräzisionsfertigungsmethoden wie der CNC-Bearbeitung zu haben. Das Verständnis der typischen Toleranzen, Oberflächeneigenschaften und Faktoren, die die Maßgenauigkeit beim Laser Powder Bed Fusion (LPBF) von Aluminiumlegierungen beeinflussen, ist für die Konstruktion funktionaler Satellitenhalterungen und die Planung der erforderlichen Nachbearbeitungsschritte unerlässlich.
1. Abmessungstoleranzen:
- Allgemeine Erwartungen: Als allgemeine Richtschnur gilt, dass typische Toleranzen beim 3D-Druck von Metall für mittelgroße Aluminiumteile, die mittels LPBF hergestellt werden, liegen im Bereich von ±0,1 mm bis ±0,2 mm für kleinere Merkmale (bis zu ~50-100 mm) und ±0,1 % bis ±0,2 % des Nennmaßes für größere Merkmale. Ein 200 mm langes Merkmal könnte zum Beispiel eine Toleranz von ±0,2 mm bis ±0,4 mm aufweisen.
- Vergleich zur maschinellen Bearbeitung: Diese Toleranzen sind in der Regel größer als bei der CNC-Präzisionsbearbeitung (bei der oft Toleranzen von ±0,01 mm bis ±0,05 mm oder enger eingehalten werden können). Daher werden AM-Teile oft als "endkonturnah" bezeichnet, insbesondere bei kritischen Schnittstellen.
- Faktoren, die die Verträglichkeit beeinflussen:
- Kalibrierung der Maschine: Die regelmäßige Kalibrierung und Wartung des LPBF-Systems ist von entscheidender Bedeutung.
- Prozessparameter: Laserleistung, Scangeschwindigkeit, Schichtdicke und Schraffurstrategie beeinflussen die Stabilität des Schmelzbades und die Schrumpfung.
- Thermische Effekte: Eigenspannungen, die sich während der schnellen Erwärmungs- und Abkühlungszyklen aufbauen, können zu Verformungen und Verwerfungen führen, die die endgültigen Abmessungen beeinträchtigen, insbesondere bei großen oder geometrisch komplexen Teilen.
- Größe und Geometrie der Teile: Größere Teile und solche mit erheblichen freitragenden Überhängen oder dünnen Wänden sind anfälliger für Abweichungen.
- Orientierung aufbauen: Die Ausrichtung des Teils auf der Bauplatte beeinflusst den thermischen Verlauf und die Anforderungen an die Abstützung und wirkt sich auf die Maßgenauigkeit aus.
- Nachbearbeiten: Wärmebehandlungen zum Spannungsabbau können geringfügige Änderungen der Abmessungen verursachen. Die Entfernung der Halterung und die anschließende Bearbeitung wirken sich natürlich auf die endgültigen Abmessungen aus.
2. Oberflächengüte (Rauhigkeit):
- Rauheit im Ist-Zustand: Die Oberflächenbeschaffenheit von LPBF-Aluminiumteilen ist von Natur aus rauer als bearbeitete Oberflächen. Typische durchschnittliche Rauhigkeitswerte (Ra) liegen zwischen 10 µm und 25 µm. Diese Rauheit entsteht durch:
- Teilweise geschmolzenes Pulver: An die Oberfläche gesinterte Pulverpartikel.
- Layer-Linien: Sichtbare Linien, die den einzelnen Schichten entsprechen (normalerweise 20-60 µm dick).
- Treppeneffekt: Auf gewinkelten oder gekrümmten Oberflächen erzeugt die schichtweise Annäherung eine treppenförmige Textur, die auf Oberflächen mit flachen Winkeln relativ zur Bauplatte stärker ausgeprägt ist. Nach oben weisende Oberflächen (parallel zur Bauplatte) sind tendenziell glatter als Seitenwände oder nach oben/unten weisende abgewinkelte Oberflächen. Nach unten gerichtete Flächen, an denen Stützen angebracht waren, sind nach dem Entfernen der Stützen oft am rauesten.
- Auswirkungen auf die Leistung: Dieser Ist-Zustand LPBF-Oberfläche aus Aluminium kann für einige unkritische Oberflächen akzeptabel sein, kann sich aber negativ auf die Ermüdungslebensdauer auswirken (die Oberflächenrauheit wirkt als Spannungskonzentrator) und ist für Dichtungsoberflächen oder Schnittstellen, die einen glatten Kontakt erfordern, möglicherweise nicht geeignet.
- Verbesserung der Oberflächengüte: Nachbearbeitungsschritte wie Perlstrahlen, Trommeln, chemisches Ätzen oder Polieren sind in der Regel erforderlich, um glattere Oberflächen zu erzielen (z. B. Ra < 5 µm oder sogar < 1 µm beim Polieren).
3. Maßgenauigkeit und Geometriekontrolle:
- Allgemeine Form: Jenseits von Merkmalstoleranzen, Maßhaltigkeit additive Fertigung bezieht sich auch auf die geometrische Gesamttreue des Teils im Vergleich zum ursprünglichen CAD-Modell (z. B. Ebenheit, Parallelität, Kreisform).
- Verformung und Verzerrung: Wie bereits erwähnt, stellen thermische Spannungen eine große Herausforderung dar. Eine sorgfältige Prozesssimulation, eine optimierte Teileausrichtung, robuste Stützstrukturen und kontrollierte Heiz-/Kühlstrategien werden von erfahrenen AM-Anbietern eingesetzt, um die Verformung zu minimieren und sicherzustellen, dass das Teil seine vorgesehene Form beibehält.
- Interne Merkmale: AM ermöglicht komplexe interne Kanäle, aber die Überprüfung ihrer Geometrie und die Sicherstellung, dass sie frei von Hindernissen (wie eingeschlossenem Pulver) sind, erfordert eine spezielle Inspektion.
4. Metrologie und Inspektion für die Qualifizierung in der Luft- und Raumfahrt:
In Anbetracht der kritischen Natur von Satellitenkomponenten sind strenge Inspektionen und Messverfahren nicht verhandelbar. Standardmessverfahren werden für AM-Teile angepasst und erweitert:
- Koordinatenmessmaschinen (KMG): Wird für hochpräzise Messungen von spezifischen Merkmalen, Bezugspunkten und kritischen Abmessungen verwendet, insbesondere nach der Endbearbeitung. CMM-Prüfung Luft- und Raumfahrt Die Protokolle sind gut etabliert.
- 3D-Scannen: Techniken wie strukturiertes Licht oder Laserscanning erfassen Millionen von Punkten auf der Oberfläche des Teils und erstellen ein detailliertes 3D-Modell, das direkt mit den ursprünglichen CAD-Daten verglichen werden kann. Dies eignet sich hervorragend zur Überprüfung der Gesamtform, zur Identifizierung unerwarteter Abweichungen und zur Durchführung qualitätskontrolle beim 3D-Scannen.
- Computertomographie (CT) Scannen: Diese röntgenbasierte Technik ist von unschätzbarem Wert für die zerstörungsfreie Prüfung der inneren Struktur von AM-Teilen. CT-Scannen von AM-Teilen ermöglicht:
- Erkennung von Porosität: Identifizierung der Größe, Lage und Verteilung innerer Hohlräume (Gas- oder Schmelzfehlporosität), die die mechanischen Eigenschaften beeinflussen können.
- Überprüfung der internen Geometrie: Messen der Abmessungen und Bestätigen des Spielraums von internen Kanälen oder komplexen Merkmalen.
- Messung der Gesamtdichte: Bewertung der Konsistenz der Materialkonsolidierung.
- Materialprüfung: Die zerstörende Prüfung von Testkupons, die zusammen mit den tatsächlichen Teilen gedruckt werden, ist entscheidend für die Überprüfung, ob das Material die geforderten mechanischen Eigenschaften (Zugfestigkeit, Streckgrenze, Dehnung, Ermüdungsfestigkeit) erfüllt.
Zusammenfassend lässt sich sagen, dass bei der Aluminium-AM mittels LPBF zwar endkonturnahe Teile mit bemerkenswerter geometrischer Freiheit hergestellt werden, die Ingenieure jedoch die erreichbaren Toleranzen und Oberflächenbeschaffenheiten im Auge behalten müssen. Kritische Abmessungen und Oberflächen werden fast immer eine Nachbearbeitung erfordern. Robuste Mess- und Prüfpläne, die häufig CMM, 3D-Scanning und CT-Scanning umfassen, sind für die Qualifizierung von 3D-gedruckten Aluminiumhalterungen für anspruchsvolle Anwendungen unerlässlich inspektion von Luft- und Raumfahrtteilen Normen.
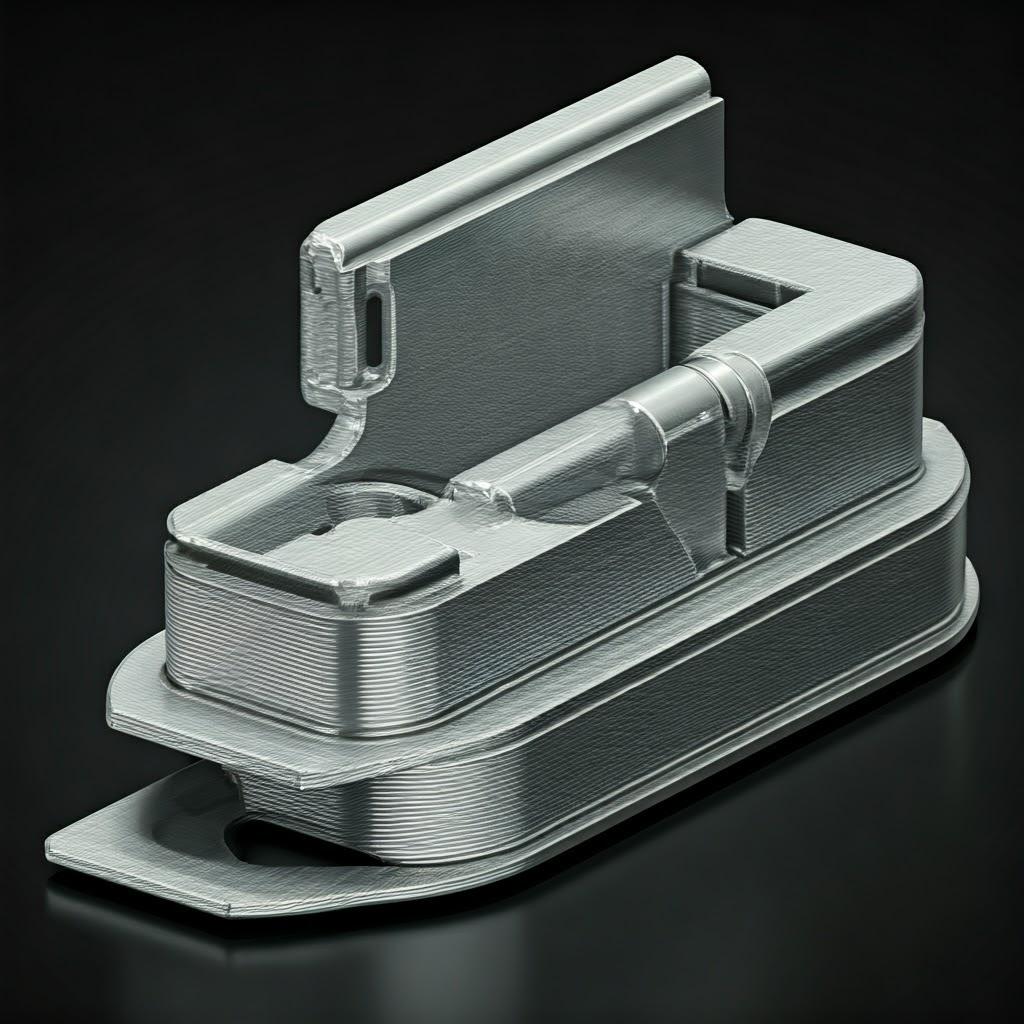
Nachbearbeitungsanforderungen für missionskritische Satellitenhalterungen
Das Drucken einer Satellitenhalterung aus Aluminium mittels Laser Powder Bed Fusion (LPBF) ist oft nur der erste Fertigungsschritt. Um das rohe Bauteil in ein funktionsfähiges, flugtaugliches Bauteil zu verwandeln, sind in der Regel eine Reihe von entscheidenden Nachbearbeitungsschritten erforderlich. Diese Schritte sind unerlässlich, um innere Spannungen abzubauen, die gewünschten mechanischen Eigenschaften zu erzielen, Stützstrukturen zu entfernen, die erforderliche Oberflächenbeschaffenheit und Maßtoleranzen zu erreichen und die von der Weltraumumgebung geforderte Sauberkeit zu gewährleisten. Das Verständnis dieser Anforderungen ist für die Planung der Produktionszeiten und -kosten von entscheidender Bedeutung.
1. Stressabbau und Wärmebehandlung:
- Warum es notwendig ist: Die schnelle Erwärmung und Abkühlung, die dem LPBF-Verfahren innewohnt, führt zu erheblichen Temperaturgradienten innerhalb des Teils, während es Schicht für Schicht aufgebaut wird. Dies führt zum Aufbau von inneren Eigenspannungen. Diese Spannungen können während oder nach dem Druck Verformungen (Verwerfungen) und Risse verursachen und die mechanische Leistung und Lebensdauer des Teils beeinträchtigen.
- Stressabbau: Häufig ist der erste Schritt nach dem Druck (der manchmal durchgeführt wird, während das Teil noch auf der Bauplatte befestigt ist) eine Spannungsarmglühung. Dabei wird das Teil auf eine bestimmte Temperatur erwärmt (unterhalb der Alterungstemperatur für AlSi10Mg) und eine Zeit lang gehalten, gefolgt von einer langsamen Abkühlung. Dadurch werden die inneren Spannungen abgebaut, ohne das Gefüge oder die Härte wesentlich zu verändern.
- Lösungsglühen und Alterung (z. B. T6 für AlSi10Mg): Bei Legierungen wie AlSi10Mg ist eine vollständige Wärmebehandlung AlSi10Mg T6 zyklus wird üblicherweise angewendet, um optimale mechanische Eigenschaften (Festigkeit und Härte) zu erreichen. Dies beinhaltet:
- Lösungsglühen: Erhitzen auf eine hohe Temperatur (z.B. ~530°C), um die Legierungselemente (Si, Mg) in der Aluminiummatrix aufzulösen.
- Abschrecken: Schnelles Abkühlen (in der Regel in Wasser oder Polymer), um diese Elemente in einer übersättigten festen Lösung einzuschließen.
- Künstliche Alterung: Wiedererwärmung auf eine niedrigere Temperatur (z. B. ~160-170 °C) für mehrere Stunden, wodurch sich in der Aluminiummatrix feine Ausscheidungen bilden, die die Festigkeit und Härte erheblich erhöhen.
- Scalmalloy® Wärmebehandlung: Scalmalloy® erreicht seine hohe Festigkeit in der Regel im eingebauten oder entspannten Zustand aufgrund seines einzigartigen Ausscheidungsverhaltens während des Druckprozesses selbst. Je nach den Anforderungen der Anwendung kann der Materiallieferant spezifische Entspannungszyklen empfehlen.
- Atmosphärenkontrolle: Wärmebehandlungen werden in der Regel unter kontrollierter Atmosphäre (Vakuum oder Inertgas) durchgeführt, um Oxidation, insbesondere bei hohen Temperaturen, zu verhindern.
2. Entfernen der Bauplatte und Entfernen der Stützstruktur:
- Abtrennung: Das/die Teil(e) muss/müssen vorsichtig von der Bauplatte entfernt werden. Dies geschieht häufig durch Drahterodieren (EDM), Sägen oder CNC-Fräsen.
- Unterstützung von Entfernungstechniken: Das Entfernen der beim Drucken entstandenen Stützstrukturen erfordert sorgfältige manuelle oder automatisierte Arbeit. Zu den gängigen Methoden gehören:
- Manuelles Brechen/Clipping: Für Halterungen mit schwachen Schnittstellen.
- Schleifen/Feilen von Hand: Um die restlichen Stütznoppen zu entfernen.
- CNC-Bearbeitung: Für die präzise Entfernung oder den Zugang zu schwierigen Stellen.
- Drahterodieren: Kann manchmal zur Entfernung komplizierter Stützen verwendet werden.
- Herausforderungen: Entfernung der AM-Stütze kann arbeitsintensiv sein und birgt die Gefahr, dass die Oberfläche des Teils beschädigt wird, wenn nicht sorgfältig gearbeitet wird. Das Design für die additive Fertigung (DfAM) spielt eine entscheidende Rolle bei der Minimierung des Bedarfs an Halterungen und bei deren Gestaltung für eine leichtere Entfernung. Auf den Oberflächen, an denen die Stützen angebracht wurden, bleiben oft Restspuren zurück, die eine weitere Nachbearbeitung erforderlich machen können.
3. Oberflächenveredelung:
Die Oberfläche von LPBF-Bauteilen ist im Allgemeinen zu rau für viele Anwendungen in der Luft- und Raumfahrt. Es können verschiedene Nachbearbeitungsschritte durchgeführt werden:
- Perlstrahlen / Shot Peening: Schleudern von kleinen Kügelchen (Glas, Keramik) oder Kugeln (Metall) an die Oberfläche. Perlstrahlen von Aluminium erzeugt ein gleichmäßiges, ungerichtetes, mattes Finish, entfernt lose Pulverpartikel und kann vorteilhafte Druckeigenspannungen erzeugen (Shotpeening), um die Ermüdungsfestigkeit zu verbessern.
- Taumeln / Vibro-Finishing: Platzieren von Teilen in einem Tumbler oder einer Rüttelschale mit Schleifmitteln, um Oberflächen zu glätten und scharfe Kanten abzurunden. Effektiv für Chargen von kleineren Teilen.
- Polieren: Durch manuelles oder automatisiertes Polieren lassen sich bei Bedarf sehr glatte, spiegelglatte Oberflächen (Ra < 0,1 µm) auf bestimmten Oberflächen (z. B. Dichtungsflächen, optische Halterungen) erzielen, doch ist dies arbeitsintensiv.
- Eloxieren: Ein elektrochemischer Prozess, der eine harte, dauerhafte Aluminiumoxidschicht auf der Oberfläche erzeugt. Eloxieren von 3D-gedruckten Teilen (AlSi10Mg und Scalmalloy® können beide eloxiert werden) erhöht die Korrosionsbeständigkeit, verbessert die Verschleißfestigkeit, bietet elektrische Isolierung und ermöglicht die Farbgebung (obwohl funktionelle Beschichtungen im Weltraum in der Regel dekorativen vorgezogen werden). Es gibt verschiedene Typen (z. B. Typ II Schwefel, Typ III Hartbeschichtung).
- Chemische Konversionsbeschichtung (z. B. Alodine® / Chromat / Nicht-Chromat): Erzeugt einen dünnen chemischen Film, der die Korrosionsbeständigkeit verbessert und eine hervorragende Haftgrundlage für Farben und Beschichtungen bietet. Unverzichtbar für oberflächenbehandlung für die Luft- und Raumfahrt konformität. Für Weltraumanwendungen sind oft spezielle Typen (z. B. MIL-DTL-5541-konform) erforderlich.
4. Präzisions-CNC-Bearbeitung:
Da die LPBF-Toleranzen möglicherweise nicht für alle Merkmale ausreichen, CNC-Bearbeitung von AM-Komponenten ist ein üblicher und oft notwendiger Nachbearbeitungsschritt. Dieser hybride Fertigungsansatz nutzt die geometrische Freiheit von AM und die Präzision von CNC:
- Kritische Schnittstellen: Bearbeitung von Passflächen, Montagebohrungen, Lagersitzen und anderen Merkmalen, die enge Toleranzen erfordern (in der Regel enger als ±0,1 mm).
- Versiegeln von Oberflächen: Erzielung der für O-Ring-Nuten oder andere Dichtungsanwendungen erforderlichen Ebenheit und Glätte.
- Fäden: Erstellen von präzisen Gewindelöchern oder Merkmalen.
- Verbesserung der Oberflächengüte: Bearbeitung bestimmter Oberflächen, um einen definierten Rauheitswert zu erreichen.
- Arbeitsablauf: Das endkonturnahe Teil wird mittels LPBF gedruckt, wärmebehandelt und dann auf eine CNC-Maschine übertragen, wo die Bezugspunkte festgelegt und die kritischen Merkmale nach den endgültigen Spezifikationen bearbeitet werden.
5. Reinigung und Passivierung:
- Strenge Anforderungen: Reinigung von Satellitenkomponenten die Protokolle sind extrem streng. Alle verbleibenden Verunreinigungen (Pulverpartikel, Bearbeitungsflüssigkeiten, Fingerabdrücke, organische Rückstände) können in der Vakuum- und Wärmeumgebung des Weltraums Probleme verursachen (z. B. Ausgasung, Korrosion, elektrische Probleme).
- Reinigungsverfahren: In der Regel werden mehrstufige Reinigungsverfahren mit Ultraschallbädern, spezifischen Lösungsmitteln, Reinigungsmitteln und Reinstwasserspülungen eingesetzt. Die Verfahren müssen sorgfältig dokumentiert und validiert werden.
- Passivierung: Während sie häufig mit Edelstahl in Verbindung gebracht werden, können bei Aluminiumlegierungen spezielle Passivierungsverfahren angewandt werden, um eine stabile, inerte Oberflächenoxidschicht zu gewährleisten.
Jeder dieser Nachbearbeitungsschritte erhöht den Zeit- und Kostenaufwand bei der Herstellung einer 3D-gedruckten Satellitenhalterung. Es ist von entscheidender Bedeutung, diese Anforderungen bereits in der Entwurfsphase zu berücksichtigen und mit einem AM-Anbieter zusammenzuarbeiten, der über validierte Prozesse und Fachwissen bei der Durchführung dieser Vorgänge nach Luft- und Raumfahrtstandards verfügt.
Allgemeine Herausforderungen beim 3D-Druck von Aluminiumhalterungen und Strategien zur Abhilfe
Aluminium-LPBF bietet zwar ein transformatives Potenzial für Satellitenhalterungen, aber der Prozess ist nicht ohne Herausforderungen. Um die von der Luft- und Raumfahrtindustrie geforderte gleichbleibende Qualität, Zuverlässigkeit und Leistung zu erreichen, sind eine sorgfältige Kontrolle, ein tiefes Prozessverständnis und proaktive Strategien zur Schadensbegrenzung erforderlich. Das Bewusstsein für diese potenziellen Fallstricke ist sowohl für Konstrukteure als auch für Beschaffungsteams bei der Spezifikation und Beschaffung von AM-Komponenten unerlässlich.
1. Eigenspannung, Verformung und Verziehen:
- Die Herausforderung: Die intensive, örtlich begrenzte Erwärmung durch den Laser und die anschließende schnelle Abkühlung erzeugen steile Wärmegradienten innerhalb des Teils und zwischen dem Teil und der Bauplatte. Dies führt zu einer unterschiedlichen Ausdehnung und Kontraktion, was zu erheblichen Eigenspannungen führt. Wenn diese Spannungen die Streckgrenze des Materials bei hohen Temperaturen überschreiten, können sie zu Verformungen (Abweichungen von der beabsichtigten Form), Verwerfungen (insbesondere Abheben von Kanten/Ecken) oder sogar zu Rissen während des Aufbaus oder beim Entfernen von der Bauplatte führen. Metall AM Eigenspannung ist ein Hauptanliegen.
- Strategien zur Schadensbegrenzung:
- Prozess-Simulation: Einsatz von Software zur Simulation des Bauprozesses, zur Vorhersage von Wärmegradienten und Spannungsakkumulation sowie zur Ermittlung potenzieller Problembereiche vor dem Druck.
- Optimierte Gebäudeausrichtung: Ausrichtung des Teils auf der Bauplatte, um große flache Bereiche parallel zur Platte zu minimieren, Überhänge zu reduzieren und die Wärmeverteilung zu steuern.
- Robuste Stützstrukturen: Die Konstruktion von Stützen dient nicht nur dazu, Überstände zu halten, sondern auch dazu, das Teil fest auf der Bauplatte zu verankern, um Verformungskräften zu widerstehen und als Wärmesenke zu dienen.
- Optimierte Scan-Strategie: Verwendung spezifischer Laserscanning-Muster (z. B. Inselabtastung, Schachbrettmuster), um den Wärmeeintrag zu steuern und lokale Spannungsspitzen zu reduzieren.
- Build Plate Heating: Durch das Vorheizen der Bauplatte wird der Wärmegradient zwischen dem gedruckten Teil und der Platte verringert.
- Stressabbau nach der Bauphase: Eine angemessene Wärmebehandlung unmittelbar nach der Herstellung (oft vor dem Entfernen der Stützen) ist entscheidend für den Abbau von Restspannungen.
2. Kontrolle der Porosität:
- Die Herausforderung: Porosität bezieht sich auf kleine Hohlräume innerhalb des bedruckten Materials. Gängige Typen in LPBF sind:
- Gas Porosität: Verursacht durch gelöste Gase (häufig Wasserstoff in Aluminium), die beim Erstarren im Schmelzbad eingeschlossen werden. Kann auch durch Gasblasen innerhalb der zerstäubten Pulverpartikel entstehen.
- Lack-of-Fusion (LoF) Porosität: Unregelmäßig geformte Hohlräume zwischen Schichten oder Scannerspuren, die durch unzureichendes Aufschmelzen/Schmelzen entstehen, oft verursacht durch falsche Prozessparameter (z. B. zu geringe Laserleistung, zu hohe Scangeschwindigkeit).
- Auswirkungen: Porosität wirkt als Spannungskonzentrator und verringert die Duktilität, Ermüdungsfestigkeit und Bruchzähigkeit erheblich - Eigenschaften, die für Bauteile in der Luft- und Raumfahrt entscheidend sind. LPBF-Porositätsfehler muss minimiert werden.
- Strategien zur Schadensbegrenzung:
- Hochwertiges Pulver: Verwendung von Pulver mit hoher Sphärizität, geringer innerer Porosität, kontrollierter Partikelgrößenverteilung und geringem Gehalt an Feuchtigkeit/gelösten Gasen. Dies beginnt mit fortschrittlichen Pulverherstellungstechniken, wie sie Met3dp für seine Metallpulver. Eine ordnungsgemäße Lagerung und Handhabung unter inerten Bedingungen ist unerlässlich.
- Optimierte Prozessparameter: Entwicklung und sorgfältige Kontrolle von Laserleistung, Scangeschwindigkeit, Schichtdicke, Schraffurabstand und Inertgasatmosphäre (hochreiner Argonfluss zur Beseitigung von Dämpfen und zur Vermeidung von Oxidation), um ein vollständiges Schmelzen und Verschmelzen zu gewährleisten. Die Parametersätze sind oft spezifisch für die Maschine und die Materialcharge.
- Wartung der Maschine: Sicherstellen, dass das Lasersystem, die Optik und die Gasflusssysteme sauber sind und ordnungsgemäß funktionieren.
- Zerstörungsfreie Prüfung (NDT): Einsatz von CT-Scans zur Erkennung, Quantifizierung und Charakterisierung der inneren Porosität in fertigen Teilen oder Prüfstücken. Festlegung klarer Akzeptanzkriterien auf der Grundlage des Porositätsniveaus.
3. Schwierigkeiten beim Entfernen der Stützen:
- Die Herausforderung: Obwohl sie unerlässlich sind, kann das Entfernen von Stützstrukturen schwierig und zeitaufwändig sein, insbesondere bei komplexen Innengeometrien oder empfindlichen Merkmalen. Eine unsachgemäße Entfernung kann die Oberfläche des Teils beschädigen oder Eigenspannungen hinterlassen. Bei der Konstruktion von Stützstrukturen muss man einen Kompromiss eingehen: Sie müssen stark genug sein, um während der Herstellung zu funktionieren, aber auch einfach genug, um danach entfernt zu werden.
- Strategien zur Schadensbegrenzung:
- DfAM zur Stützreduzierung: Konstruktion von Teilen mit selbsttragenden Winkeln (>45°), wo immer dies möglich ist, Verwendung von Fasen anstelle von kleinen Überhängen und strategische Ausrichtung des Teils zur Minimierung der unterstützten Bereiche.
- Optimiertes Support-Design: Verwendung spezialisierter optimierung der Tragstruktur techniken (z. B. Baumstützen, Blockstützen mit minimalen Kontaktpunkten oder Perforationen, konische Stützen), die auf die Geometrie und das Material abgestimmt sind.
- Prozessparameter für Unterstützungen: Verwendung unterschiedlicher Laserparameter für Stützstrukturen, um diese weniger dicht oder spröder zu machen, damit sie leichter entfernt werden können.
- Nachbearbeitungsplanung: Auswahl geeigneter Entfernungsmethoden (manuell, CNC, EDM) je nach Art und Lage des Trägers. Ausreichend Zeit und Ressourcen für eine sorgfältige Entfernung einplanen.
4. Pulverhandhabung, Qualitätskontrolle und Rückverfolgbarkeit:
- Die Herausforderung: Die Gewährleistung der Qualität und Konsistenz des Aluminiumpulvers während seines gesamten Lebenszyklus (von der Produktion über Lagerung, Handhabung, Druck und Recycling) ist entscheidend für luft- und Raumfahrt Pulvermanagement. Verunreinigungen (z. B. mit anderen Metallen, Oxiden, organischen Stoffen) oder Veränderungen der Partikelgrößenverteilung können die Qualität und die mechanischen Eigenschaften der Teile beeinträchtigen. Die vollständige Rückverfolgbarkeit der für bestimmte Fluggeräte verwendeten Pulverchargen ist obligatorisch.
- Strategien zur Schadensbegrenzung:
- Lieferantenqualifizierung: Beschaffung von Pulver von renommierten Anbietern wie Met3dp mit zuverlässiger Qualitätskontrolle und Chargenprüfung.
- Strenge Handhabungsprotokolle: Einsatz spezieller Geräte, kontrollierter Umgebungen (Feuchtigkeitskontrolle, inerte Atmosphäre) und dokumentierter Verfahren für das Laden, Entladen, Sieben und Lagern von Pulver.
- Pulver-Recycling-Strategie: Implementierung von validierten Verfahren für das Recycling von unbenutztem Pulver, einschließlich der Verfolgung der Anzahl der Wiederverwendungszyklen und regelmäßiger Tests, um die Qualität zu gewährleisten. Mischen von neuem und recyceltem Pulver gemäß qualifizierten Verhältnissen.
- Rückverfolgbarkeit der Chargen: Führen akribischer Aufzeichnungen, die bestimmte Pulverchargen (und die Geschichte ihrer Wiederverwendung) mit den damit gedruckten Teilen verknüpfen (erforderlich für AM-Qualitätssicherung Luft- und Raumfahrt).
5. Sicherstellung gleichbleibender mechanischer Eigenschaften:
- Die Herausforderung: Das Erreichen wiederholbarer mechanischer Eigenschaften (Festigkeit, Duktilität, Ermüdungslebensdauer) von Bau zu Bau, zwischen verschiedenen Maschinen und sogar innerhalb verschiedener Stellen auf derselben Bauplatte kann aufgrund der Empfindlichkeit des Prozesses gegenüber zahlreichen Variablen eine Herausforderung darstellen. Teile können auch Anisotropie aufweisen (Eigenschaften, die mit der Richtung relativ zu den Fertigungsschichten variieren).
- Strategien zur Schadensbegrenzung:
- Prozessstandardisierung und -kontrolle: Strenge Prozessüberwachung, strenge Kontrolle aller kritischen Parameter und Anwendung standardisierter, validierter Nachbearbeitungsverfahren (insbesondere Wärmebehandlung).
- Kalibrierung und Wartung von Maschinen: Regelmäßige Kalibrierung der Laserleistung, der Scannergenauigkeit und der Umweltkontrollen.
- Prüfung der Materialeigenschaften: Drucken und Testen von Zeugencoupons zusammen mit den tatsächlichen Teilen bei jedem Bau gemäß den Luft- und Raumfahrtnormen (z. B. ASTM, MMPDS), um zu überprüfen, ob die Eigenschaften die Mindestspezifikationen erfüllen. Prüfung von Coupons in verschiedenen Ausrichtungen (X, Y, Z) zur Charakterisierung der Anisotropie.
- Statistische Prozesskontrolle (SPC): Überwachung wichtiger Prozessindikatoren und Materialeigenschaften im Laufe der Zeit, um Stabilität zu gewährleisten und potenzielle Abweichungen zu erkennen.
- Partnerschaft mit erfahrenen Anbietern: Zusammenarbeit mit AM-Dienstleistern wie Met3dp, die über ausgereifte Prozesse, robuste Qualitätsmanagementsysteme (QMS) und eine nachgewiesene Erfolgsbilanz bei der Erbringung von Leistungen verfügen konsistente AM-Teileigenschaften für kritische Anwendungen. Ihre Erfahrung hilft dabei, diese inhärenten Herausforderungen wirksam zu meistern und zu entschärfen.
Die Bewältigung dieser Herausforderungen erfordert eine Kombination aus fortschrittlicher Technologie, sorgfältiger Prozesskontrolle, robusten Qualitätssystemen und fundiertem technischen Fachwissen. Wenn die Luft- und Raumfahrtindustrie diese potenziellen Probleme versteht und mit qualifizierten Partnern zusammenarbeitet, kann sie Aluminium-AM für leichte, leistungsstarke Satellitenhalterungen getrost einsetzen.
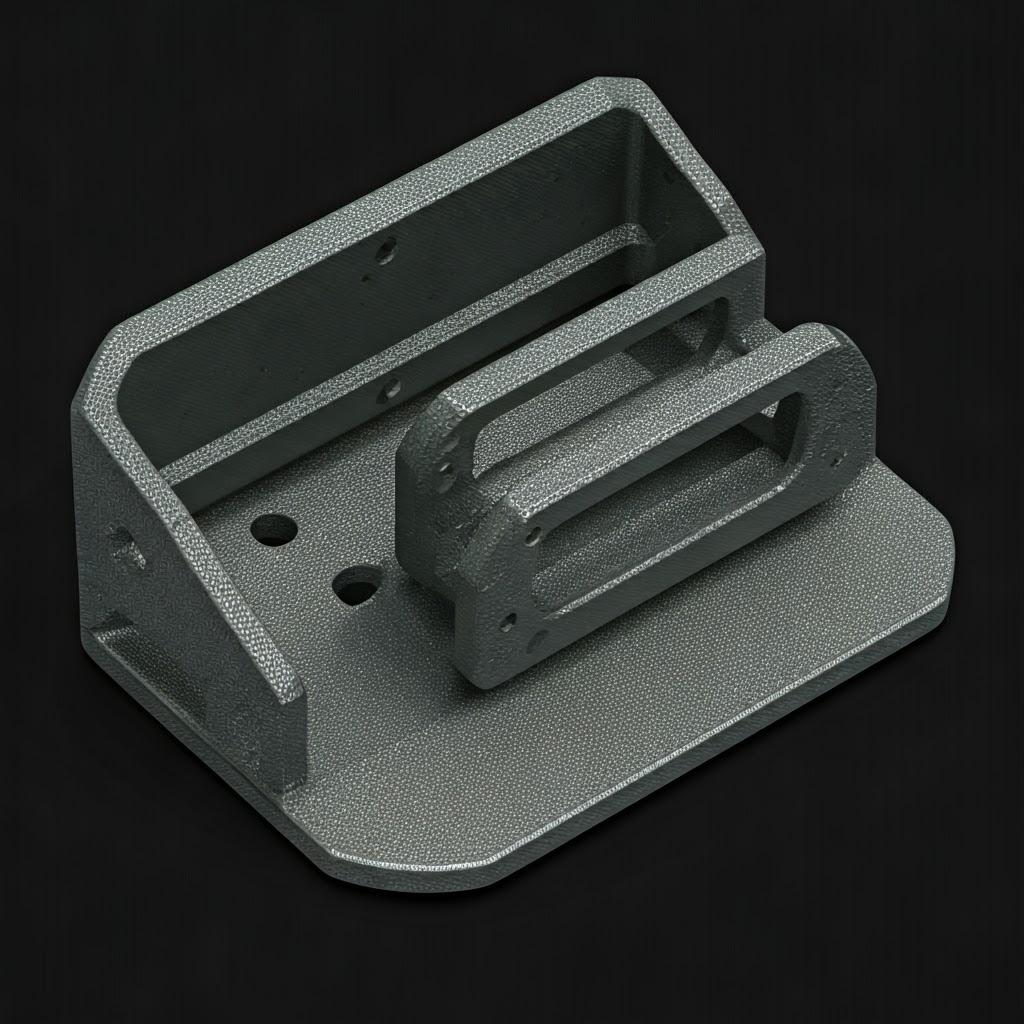
So wählen Sie den richtigen 3D-Druckdienstleister für Satellitenkomponenten aus Metall
Die Auswahl des richtigen Fertigungspartners ist bei der Herstellung von einsatzkritischer Hardware wie Satellitenhalterungen mittels additiver Fertigung ebenso entscheidend wie die Wahl des Designs und des Materials. Die einzigartigen Anforderungen der Luft- und Raumfahrtindustrie - strenge Qualitätsanforderungen, komplexe Geometrien, fortschrittliche Materialien und die Notwendigkeit absoluter Zuverlässigkeit - erfordern die Zusammenarbeit mit einem Metall-AM-Dienstleister, der über spezielles Fachwissen, robuste Prozesse und die richtigen Zertifizierungen verfügt. Eine falsche Wahl kann zu Projektverzögerungen, Kostenüberschreitungen, minderwertiger Teilequalität und potenziell katastrophalen Bauteilausfällen führen. Für Beschaffungsmanager und Ingenieurteams ist ein gründlicher Bewertungsprozess unerlässlich. Hier sind die wichtigsten Kriterien, die bei der Durchführung zu berücksichtigen sind qualifizierung von AM-Lieferanten für die Luft- und Raumfahrt:
1. Wesentliche Zertifizierungen und Qualitätsmanagementsystem (QMS):
- AS9100-Zertifizierung: Dies ist die international anerkannte Norm für Qualitätsmanagementsysteme in der Luft-, Raumfahrt- und Verteidigungsindustrie (ASD). AS9100 umfasst die Anforderungen von ISO 9001, fügt jedoch strenge, speziell auf die Luft- und Raumfahrt ausgerichtete Kontrollen hinzu, die Bereiche wie Konfigurationsmanagement, Risikomanagement, Rückverfolgbarkeit, Lieferantenkontrolle und Schutz vor gefälschten Teilen umfassen. Die Partnerschaft mit einem AS9100-zertifizierter 3D-Druck anbieter (oder ein Anbieter, der aktiv die Einhaltung der Vorschriften nachweist und eine Zertifizierung anstrebt) bietet eine wichtige Gewähr dafür, dass strenge Qualitätsprozesse vorhanden sind.
- Zertifizierung nach ISO 9001: Der grundlegende QMS-Standard, der anzeigt, dass der Anbieter Prozesse für konsistente Qualität, Kundenzufriedenheit und kontinuierliche Verbesserung eingeführt hat und aufrechterhält. AS9100 ist der bevorzugte Standard für Arbeiten in der Luft- und Raumfahrt.
- Robuste QMS-Implementierung: Bewerten Sie über das Zertifikat hinaus die umsetzung ihres QMS. Ist es speziell auf die Besonderheiten der additiven Fertigung ausgerichtet? Zu den wichtigsten Aspekten gehören:
- Prozess-Validierung: Dokumentierte Nachweise, dass ihre LPBF-Verfahren für bestimmte Werkstoffe (AlSi10Mg, Scalmalloy®) durchgängig Teile produzieren, die den vordefinierten Spezifikationen entsprechen (z. B. Dichte, mechanische Eigenschaften).
- Prozessbegleitende Überwachung: Systeme zur Überwachung kritischer Prozessparameter während der Herstellung (z. B. Laserleistung, Sauerstoffgehalt, Eigenschaften des Schmelzbads).
- Zerstörungsfreie Prüfung (NDT): Eigene oder qualifizierte Fremdkapazitäten für CT-Scans, Ultraschallprüfungen oder andere für die Prüfung von AM-Teilen relevante Methoden.
- Metrologie-Fähigkeiten: Kalibrierte CMMs, 3D-Scanner und andere Messgeräte, die für die Überprüfung der Abmessungen und Geometrie von AM-Teilen geeignet sind.
- Kontrolle der Dokumentation: Strenge Verfahren zur Verwaltung von Konstruktionsdaten, Prozessparametern, Prüfergebnissen und Aufzeichnungen zur Materialrückverfolgbarkeit.
- Ausbildung des Personals: Sicherstellen, dass Bediener, Ingenieure und Prüfer für ihre Aufgaben im AM-Workflow angemessen geschult und qualifiziert sind. Eine effektive qMS für die additive Fertigung ist umfassend und tief integriert.
2. Nachgewiesene Erfahrung in der Luft- und Raumfahrt und Materialkenntnisse:
- Erfolgsbilanz: Hat der Anbieter bereits erfolgreich Komponenten für Luft- und Raumfahrt- oder Satellitenanwendungen hergestellt? Kann er einschlägige Fallstudien, Referenzen oder Beispiele vorlegen (unter Wahrung der Vertraulichkeit)? Erfahrungen mit den besonderen Herausforderungen von Raumfahrt-Hardware (z. B. Ausgasungsanforderungen, thermische Zyklen, Strahlungseffekte) sind von unschätzbarem Wert.
- Material-Spezialisierung: Verfügt das Unternehmen über fundierte Kenntnisse in der Verarbeitung der von Ihnen gewünschten Aluminiumlegierungen (AlSi10Mg, Scalmalloy®)? Dazu gehören validierte Parametersätze, Kenntnisse der Beziehungen zwischen Mikrostruktur und Eigenschaften sowie bewährte Nachbearbeitungsprotokolle (insbesondere Wärmebehandlungen). Fragen Sie nach der Erfahrung des Unternehmens bei der Qualifizierung dieser Werkstoffe für anspruchsvolle Anwendungen.
- Kompetenz im Pulvermanagement: Überprüfen Sie ihre Verfahren für luft- und Raumfahrt Pulvermanagement:
- Pulverbeschaffung und Lieferantenqualifizierung.
- Kontrolle und Prüfung des eingehenden Pulvers.
- Kontrollierte Lagerumgebung (Feuchtigkeit, Temperatur).
- Handhabungsverfahren zur Vermeidung von Kontaminationen und zur Gewährleistung der Sicherheit des Bedienpersonals.
- Rückverfolgbarkeit des Pulvers (Chargenverfolgung).
- Validierte Strategie für das Recycling/ die Wiederverwendung von Pulvern und deren Verfolgung. Anbieter wie Met3dp, die auch hochwertige Pulver mit fortschrittlichen Methoden wie der Gaszerstäubung herstellen, haben hier oft einen klaren Vorteil.
3. Ausrüstung, Technologie und Einrichtung:
- Industrietaugliche Maschinen: Verwenden sie seriöse, industrietaugliche Fähigkeiten der LPBF-Ausrüstung bekannt für Stabilität, Zuverlässigkeit und Konsistenz? Erkundigen Sie sich nach ihren spezifischen Maschinenmodellen und -konfigurationen.
- Wartung und Kalibrierung von Maschinen: Verfügen sie über dokumentierte Verfahren und Aufzeichnungen für die regelmäßige Wartung der Maschinen, die Kalibrierung (Laserleistung, Scannergenauigkeit) und die Überwachung des Systemzustands?
- Umweltkontrollen: Wird die Anlage umwelttechnisch kontrolliert (Temperatur, Luftfeuchtigkeit), um Prozessstabilität und Pulverintegrität zu gewährleisten?
- Kapazität und Redundanz: Verfügen sie über ausreichende Maschinenkapazitäten, um die Anforderungen Ihres Projekts in Bezug auf Volumen und Vorlaufzeit zu erfüllen? Gibt es eine Redundanz für den Fall eines Maschinenausfalls?
4. Technische Unterstützung und DfAM-Dienste:
- Fachwissen im Bereich Design für additive Fertigung (DfAM): Bietet der Anbieter DfAM Dienstleistungen Luft- und Raumfahrt kunden benötigen? Können deren Ingenieure Ihre Entwürfe überprüfen und konstruktives Feedback geben, um die Druckbarkeit zu optimieren, Stützstrukturen zu reduzieren, die Leistung zu verbessern oder die Kosten zu senken? Dieser kooperative Ansatz ist oft entscheidend für die Maximierung der Vorteile von AM’s.
- Aufbau von Simulationsfähigkeiten: Können sie Simulationen des Bauprozesses durchführen, um potenzielle Probleme wie Verformung oder Spannungskonzentration vorherzusagen und den Aufbau (Ausrichtung, Stützen) zu optimieren?
- Problemlösung: Verfügen sie über erfahrene Ingenieure, die bei der Behebung von Problemen helfen können, die während des Designs, des Drucks oder der Nachbearbeitung auftreten können?
5. Kommunikation, Vorlaufzeiten und Gesamtkosten:
- Reaktionsfähigkeit und Kommunikation: Wie schnell reagieren sie auf Anfragen und technische Fragen? Gibt es eine klare Kontaktstelle? Eine gute Kommunikation ist während des gesamten Projektlebenszyklus von entscheidender Bedeutung.
- Angebotsprozess: Ist der Prozess der Angebotserstellung transparent? Werden die Kosten für Material, Druck, Nachbearbeitung und Qualitätssicherung klar aufgeschlüsselt?
- Realistische Vorlaufzeit: Können sie auf der Grundlage ihrer derzeitigen Arbeitsbelastung und der Komplexität des Projekts realistische Schätzungen der Vorlaufzeit abgeben? Haben sie eine Erfolgsbilanz bei der Einhaltung von Fristen?
- Gesamtwert-Angebot: Wählen Sie nicht nur nach dem niedrigsten Preis pro Teil. Betrachten Sie die Gesamtkosten, die den Wert des Fachwissens, die Robustheit des Qualitätssystems, das Niveau der technischen Unterstützung und die Minderung der Risiken im Zusammenhang mit der Herstellung kritischer Fluggeräte umfassen. Ein etwas höherer Preis eines hochqualifizierten Anbieters steht oft für einen besseren Gesamtwert und ein geringeres Projektrisiko. Bewerten Sie potenzielle Partner auf der Grundlage ihrer Fähigkeit, eine echte metall-AM-Partnerschaft.
Evaluierung potenzieller Partner wie Met3dp:
Bei der Evaluierung potenzieller Lieferanten sollten Sie Unternehmen wie Met3dp. Met3dp mit Hauptsitz in Qingdao, China, positioniert sich als führender Anbieter umfassender Lösungen für die additive Fertigung. Das Unternehmen ist sowohl auf 3D-Druckanlagen (einschließlich SEBM- und LPBF-Systeme, die für branchenweit führendes Volumen, Genauigkeit und Zuverlässigkeit bekannt sind) als auch auf Hochleistungsmetallpulver spezialisiert, die für industrielle Anwendungen entscheidend sind. Der Einsatz fortschrittlicher Pulverherstellungsverfahren (Gaszerstäubung, PREP) und das Produktportfolio, das nicht nur Aluminiumlegierungen, sondern auch Titanlegierungen (TiNi, TiTa, TiAl, TiNbZr), CoCrMo, rostfreie Stähle und Superlegierungen umfasst, zeugen von tiefgreifender materialwissenschaftlicher Kompetenz. Die Konzentration auf unternehmenskritische Teile für die Luft- und Raumfahrt, die Medizintechnik und die Automobilindustrie lässt auf Erfahrung mit anspruchsvollen Qualitätsanforderungen schließen. Spezifische Zertifizierungen wie AS9100 sollten zwar immer direkt überprüft werden, aber die Positionierung als umfassender Lösungsanbieter, der auch Anwendungsentwicklungsdienste anbietet, deutet auf eine starke technische Unterstützung hin. Eine gründliche Bewertung anhand der oben aufgeführten Kriterien würde die Eignung des Unternehmens für ein bestimmtes Satellitenhalterungsprojekt bestimmen.
Die Wahl des richtigen auswahl des Metall-AM-Servicebüros erfordert eine sorgfältige Prüfung. Bitten Sie um Betriebsbesichtigungen (virtuell oder persönlich), prüfen Sie die QMS-Dokumentation, sehen Sie sich Fallstudien an und führen Sie ausführliche technische Gespräche, um sicherzustellen, dass das Unternehmen über die erforderlichen Fähigkeiten, das Fachwissen und das Qualitätsbewusstsein für Ihre kritischen Satellitenkomponenten verfügt.
Kostenfaktoren und Vorlaufzeit für 3D-gedruckte Aluminium-Satellitenhalterungen
Das Verständnis der finanziellen und zeitlichen Investitionen, die für die Herstellung von Aluminium-Satellitenhalterungen mittels LPBF erforderlich sind, ist entscheidend für die Projektplanung, die Budgetierung und den Vergleich von AM mit alternativen Fertigungsmethoden. Sowohl die Kosten als auch die Vorlaufzeit werden durch ein komplexes Zusammenspiel von Faktoren beeinflusst, die sich auf Design, Material, Verarbeitung und Qualitätsanforderungen beziehen.
Aufschlüsselung der Kostentreiber:
Die Kostenanalyse für den 3D-Druck von Metall für eine Satellitenhalterung umfasst in der Regel mehrere Schlüsselkomponenten:
- 1. Materialkosten:
- Pulvertyp: Die Grundkosten des Metallpulvers. Hochleistungslegierungen wie Scalmalloy® sind aufgrund von Legierungselementen (Scandium) und Lizenz-/Entwicklungskosten deutlich teurer als Standard-AlSi10Mg.
- Teilband: Die Menge des Pulvers, die direkt für die Herstellung der eigentlichen Halterung verbraucht wird. Größere oder dichtere Teile kosten natürlich mehr.
- Unterstützungsstruktur Volumen: Pulver, das zum Bau der erforderlichen Stützstrukturen verwendet wird, später entfernt wird und oft nur teilweise recycelbar ist. Optimierte Konstruktionen minimieren das Stützvolumen.
- Pulverhandling & Abfall: Kosten im Zusammenhang mit der Verwaltung des Pulvers, der Siebung, der Qualitätsprüfung und unvermeidlichen kleineren Verlusten bei der Handhabung.
- 2. Kosten der Maschinenzeit:
- Vorbereitung des Baus: Arbeits- und Zeitaufwand für das Einrichten der Konstruktionsdatei (Ausrichtung, Halterungen, Schneiden, Parameterzuweisung) und die Vorbereitung der Maschine.
- Druckzeit: Die Zeit, in der die LPBF-Maschine aktiv läuft, um das/die Teil(e) zu drucken. Dies wird stark beeinflusst durch:
- Teilhöhe: Sie bestimmt in erster Linie die Druckzeit, da jede Schicht eine bestimmte Zeit zum Aufbringen und Verschmelzen benötigt, unabhängig von der Fläche der Schicht (innerhalb bestimmter Grenzen).
- Teil Volumen/Komplexität: Beeinflusst den Umfang der pro Schicht erforderlichen Laserabtastung.
- Schichtdicke: Dünnere Schichten bieten eine bessere Auflösung, verlängern aber die Druckzeit erheblich.
- Scan-Strategie: Komplexe Schraffurmuster oder spezifische Parameteranforderungen können die Geschwindigkeit beeinflussen.
- Verschachtelung: Das Drucken mehrerer (identischer oder unterschiedlicher) Teile innerhalb eines einzigen Druckauftrags kann die Kosten für die Maschinenzeit pro Teil erheblich senken, indem die Auslastung der Druckplatte optimiert wird.
- Maschinenbetrieb & Abschreibung: In den Stundensätzen sind Maschinenkosten, Wartung, Verbrauchsmaterialien (Filter, Inertgas), Energie und Gemeinkosten der Einrichtung berücksichtigt.
- 3. Nachbearbeitungskosten:
- Arbeitsintensität: Viele Nachbearbeitungsschritte sind arbeitsintensiv (z. B. manuelles Entfernen von Stützen, Polieren, detaillierte Prüfung).
- Wärmebehandlung: Kosten im Zusammenhang mit Ofenzeit, Energie, kontrollierter Atmosphäre und Arbeit für Spannungsabbau und/oder T6-Zyklen.
- Unterstützung bei der Entfernung: Kosten für Arbeitskräfte und möglicherweise spezielle Ausrüstung (EDM, CNC).
- Bearbeitungen: Kosten für CNC-Maschinenzeit, Werkzeuge, Programmierung und qualifizierte Arbeitskräfte, insbesondere wenn komplexe Mehrachsenbearbeitung für kritische Merkmale erforderlich ist.
- Oberflächenveredelung: Die Kosten variieren je nach Methode erheblich (Perlstrahlen ist relativ billig; umfangreiches Polieren oder spezielle Beschichtungen wie Eloxieren in Raumfahrtqualität sind teurer).
- Reinigung: Kosten für Spezialgeräte (Ultraschallreiniger), Verbrauchsmaterialien (Lösungsmittel, Reinigungsmittel) und Arbeitskräfte für mehrstufige Reinigungsprotokolle in der Luft- und Raumfahrt.
- 4. Kosten für Qualitätssicherung und Inspektion:
- Grad der Prüfung: Je kritischer die Klammer ist, desto umfangreicher (und kostspieliger) sind die Anforderungen an die Qualitätssicherung.
- Inspektionsmethoden: Kosten im Zusammenhang mit der Programmierung und dem Betrieb von KMGs, 3D-Scans und -Analysen, CT-Scans (die oft pro Teil oder pro Stunde berechnet werden) und zerstörenden Materialprüfungen (Zugversuche, Ermüdungsversuche an Teststücken).
- Dokumentation: Arbeitsaufwand für die Erstellung umfassender Dokumentationspakete (Konformitätsbescheinigungen, Materialzertifikate, Prüfberichte, Testdaten, Rückverfolgbarkeitsaufzeichnungen).
- 5. Kosten für Technik und Design:
- DfAM und Optimierung: Kosten im Zusammenhang mit der Entwicklungszeit für Topologieoptimierung, generatives Design, DfAM-Prüfungen und Build-Simulation, sofern vom Dienstleister durchgeführt.
Kostenvergleich mit CNC-Bearbeitung:
- Komplexitätsvorteil (AM): Für hochkomplexe, topologieoptimierte Halterungen kann AM erheblich billiger sein als der Versuch, die gleiche Geometrie aus einem massiven Block zu bearbeiten (was unter Umständen unmöglich ist oder umfangreiche mehrachsige Bearbeitungs- und Einrichtungsarbeiten erfordert).
- Lautstärke-Nachteil (AM): Bei einfacheren Halterungskonstruktionen, die in größeren Stückzahlen hergestellt werden, ist die herkömmliche CNC-Bearbeitung aufgrund der schnelleren Zykluszeiten pro Teil nach dem Einrichten oft kostengünstiger.
- Werkzeugbau (AM Advantage): AM vermeidet die hohen Werkzeugkosten, die beim Gießen oder Formen entstehen.
- Buy-to-Fly-Verhältnis (AM-Vorteil): AM nutzt das Material in der Regel effizienter als die subtraktive Bearbeitung und senkt so die Rohmaterialkosten, insbesondere bei komplexen Teilen, die große Rohblöcke für die CNC erfordern.
- Total Cost of Ownership: Bei der Evaluierung preise für additive Fertigung in der Luft- und Raumfahrtbedenken Sie die nachgelagerten Vorteile von AM’s Gewichtseinsparungen (reduzierte Startkosten), die oft die höheren Herstellungskosten pro Teil aufwiegen können.
Faktoren, die die Vorlaufzeit beeinflussen:
Die Schätzung der AM-Vorlaufzeit hängt von zahlreichen sequentiellen und parallelen Aktivitäten ab:
- Vorverarbeitung: Fertigstellung des Entwurfs, DfAM-Prüfung, Simulation (falls erforderlich), Genehmigung des Kostenvoranschlags, Vorbereitung der Build-Datei, Planung/Wartung der Maschinenverfügbarkeit (kann je nach Arbeitsbelastung des Anbieters erheblich sein). (Tage bis Wochen)
- Drucken: Tatsächliche Bauzeit auf der LPBF-Maschine. (Stunden bis mehrere Tage)
- Abkühlung: Die Bauplatte und die Teile müssen vor der Bearbeitung ausreichend abkühlen. (Stunden)
- De-Powdering & Entfernen der Bauplatte: Entfernen des überschüssigen Pulvers und Trennen der Teile von der Platte. (Stunden)
- Nachbearbeiten:
- Spannungsarmglühen / Wärmebehandlung: Zykluszeit im Ofen (Stunden bis Tage) + Abkühlung.
- Support-Entfernung: (Stunden bis Tage, je nach Komplexität und Methode).
- CNC-Bearbeitung: (Stunden bis Tage, je nach Komplexität und Einrichtung).
- Oberflächenveredelung: (Stunden bis Tage, je nach Methode).
- Reinigung: (Stunden).
- Inspektion & Qualitätssicherung: CMM, CT-Scannen, Vorbereitung der Dokumentation. (Tage)
- Versand: Logistik. (Tage)
Typische Zeitpläne & Optimierung:
- Prototypen: Für einfachere Brackets mit minimaler Nachbearbeitung können Prototypen in 1-3 Wochen geliefert werden.
- Produktionsteile: Für flugtaugliche Brackets, die eine vollständige Nachbearbeitung und strenge Qualitätskontrolle erfordern, sind Vorlaufzeiten von 3-8 Wochen oder länger üblich.
- Optimierung: Eine klare Definition der Anforderungen im Vorfeld, die Optimierung des Designs im Hinblick auf die Herstellbarkeit (DfAM für Support-Reduzierung), die effiziente Verschachtelung von Teilen in einem Build und eine klare Kommunikation mit dem Anbieter können dazu beitragen, den Prozess zu straffen und möglicherweise die Vorlaufzeiten zu verkürzen. Fordern Sie einen detaillierten Zeitplan mit Ihrem metall AM Angebotsanfrage ist ratsam.
Letztlich sind sowohl die Kosten als auch die Vorlaufzeit sehr projektspezifisch. Die Einholung detaillierter Angebote von qualifizierten Anbietern auf der Grundlage endgültiger Entwürfe und klar definierter Anforderungen ist für eine genaue Budgetierung und Zeitplanung unerlässlich.
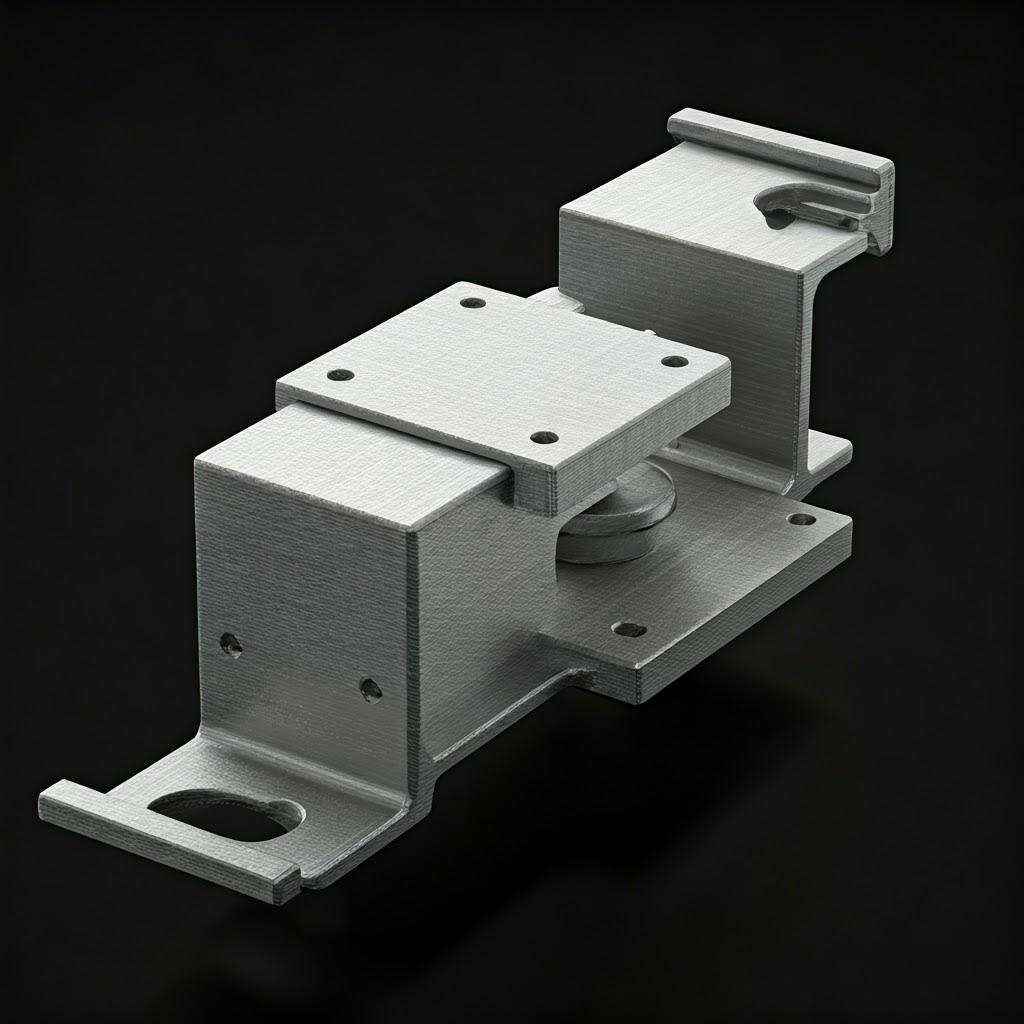
Häufig gestellte Fragen (FAQ) zu 3D-gedruckten Aluminium-Satellitenhalterungen
Hier finden Sie Antworten auf einige häufig gestellte Fragen von Ingenieuren und Beschaffungsmanagern, die eine additive Fertigung von Aluminium für Satellitenhalterungen in Betracht ziehen:
- F1: Welche typischen Festigkeits- und Steifigkeitswerte können mit 3D-gedrucktem AlSi10Mg und Scalmalloy® erreicht werden?
- A1: Die Eigenschaften hängen stark von den Prozessparametern und der Nachbearbeitung ab, aber typische Werte sind:
- AlSi10Mg (T6 wärmebehandelt): Streckgrenze ≈ 230-300 MPa, Höchstzugkraft ≈ 330-430 MPa, Elastizitätsmodul ≈ 70-75 GPa. Bietet eine gute Ausgewogenheit der Eigenschaften, die für mäßig belastete Teile geeignet sind.
- Scalmalloy® (As-Built/Stress Relieved): Streckgrenze ≈ 450-520 MPa, Höchstzugkraft ≈ 500-580 MPa, Elastizitätsmodul ≈ 70-76 GPa. Bietet deutlich höhere 3D-gedrucktes Aluminium Stärkeund nähert sich einigen Titangüten an, ideal für hochbelastete, gewichtskritische Anwendungen. Die Steifigkeit (Modulus) ist ähnlich wie bei AlSi10Mg. Die garantierten Mindestwerte sind stets in den spezifischen Materialdatenblättern des Anbieters zu finden.
- A1: Die Eigenschaften hängen stark von den Prozessparametern und der Nachbearbeitung ab, aber typische Werte sind:
- F2: Wie sieht es mit der Ermüdungsfestigkeit von 3D-gedrucktem Aluminium im Vergleich zu geschmiedetem Aluminium oder herkömmlichen Konstruktionen aus?
- A2: Dies ist komplex. LPBF-Bauteile haben oft eine geringere Ermüdungslebensdauer als Knetbauteile, was auf die Oberflächenrauhigkeit und mögliche innere Mikrofehler (Porosität) zurückzuführen ist. Allerdings:
- Scalmalloy® wurde speziell für hohe Anforderungen ermüdungslebensdauer Scalmalloy und übertrifft im Allgemeinen AlSi10Mg und sogar einige Knetlegierungen in Ermüdungstests, insbesondere nach entsprechender Oberflächenbehandlung (wie Kugelstrahlen oder Polieren).
- AlSi10Mg die Ermüdungsfestigkeit kann durch eine T6-Wärmebehandlung, Heiß-Isostatisches Pressen (HIP – reduziert die Porosität) und eine Oberflächenveredelung erheblich verbessert werden, kann aber immer noch niedriger sein als bei hochfesten Knetlegierungen.
- Design ist wichtig: Topologieoptimierte AM-Konstruktionen reduzieren häufig die Spannungsspitzen im Vergleich zu herkömmlichen blockförmigen Konstruktionen, was die Ermüdungsleistung des gesamten Systems verbessern kann komponenteselbst wenn die Ermüdungsfestigkeit des Grundmaterials etwas geringer ist. Sorgfältige Konstruktion, Materialauswahl, Prozesskontrolle und Nachbearbeitung sind für ermüdungsanfällige Anwendungen entscheidend.
- A2: Dies ist komplex. LPBF-Bauteile haben oft eine geringere Ermüdungslebensdauer als Knetbauteile, was auf die Oberflächenrauhigkeit und mögliche innere Mikrofehler (Porosität) zurückzuführen ist. Allerdings:
- F3: Können komplexe interne Kanäle für Kühlung oder Verkabelung in 3D-gedruckte Halterungen integriert werden?
- A3: Ja, die Integration AM interne Kanäle ist einer der Hauptvorteile der additiven Fertigung. LPBF kann komplizierte, konforme Kühlkanäle oder Pfade für die Verlegung kleiner Kabel direkt in der Halterungsstruktur erzeugen, was mit herkömmlichen Methoden unmöglich oder äußerst schwierig wäre. Allerdings sind konstruktive Überlegungen von entscheidender Bedeutung:
- Kanäle müssen selbsttragend oder so konstruiert sein, dass interne Stützen entfernt werden können (bei sehr komplexen Pfaden oft schwierig/unmöglich).
- Der minimale Kanaldurchmesser wird durch die Prozessauflösung und die Fähigkeit zur Pulverentfernung begrenzt (in der Regel > 1-2 mm).
- Gründliche Reinigungsprotokolle sind unabdingbar, um sicherzustellen, dass alle Pulverrückstände aus den internen Kanälen entfernt werden, was häufig durch CT-Scans oder Durchflussprüfungen überprüft wird.
- A3: Ja, die Integration AM interne Kanäle ist einer der Hauptvorteile der additiven Fertigung. LPBF kann komplizierte, konforme Kühlkanäle oder Pfade für die Verlegung kleiner Kabel direkt in der Halterungsstruktur erzeugen, was mit herkömmlichen Methoden unmöglich oder äußerst schwierig wäre. Allerdings sind konstruktive Überlegungen von entscheidender Bedeutung:
- F4: Welches Maß an Qualitätskontrolle und -dokumentation wird normalerweise für AM-Teile für die Luft- und Raumfahrt bereitgestellt?
- A4: Für Flug-Hardware, umfassende qualitätsdokumentation für die Luft- und Raumfahrt AM ist Standard. Ein typisches Dokumentationspaket umfasst:
- Konformitätszertifikat (CoC): Angabe, dass die Teile den vorgegebenen Zeichnungsanforderungen und Normen entsprechen.
- Materialzertifizierung: Rückverfolgbarkeit bis zur verwendeten Pulvercharge, einschließlich Lieferantenzertifikaten zur Überprüfung der chemischen Zusammensetzung und der Partikelgrößenverteilung.
- Logbuch erstellen: Aufzeichnung des spezifischen Bauauftrags, der verwendeten Maschine und der wichtigsten Prozessparameter, die während des Baus überwacht wurden.
- Nachbearbeitungsaufzeichnungen: Bestätigung und Einzelheiten der durchgeführten Wärmebehandlungszyklen, Bearbeitungsvorgänge und Oberflächenbehandlungen.
- Inspektionsberichte: Ergebnisse der Maßprüfung (CMM-Bericht, 3D-Scan-Vergleich), ZfP-Berichte (z. B. CT-Scan-Zusammenfassung, die die Dichte bzw. das Fehlen kritischer Fehler bestätigt) und Ergebnisse visueller Prüfungen.
- Mechanische Testergebnisse: Daten aus Zugversuchen, Ermüdungstests (falls erforderlich) oder Härtetests, die auf neben den Teilen gedruckten Prüfstücken durchgeführt wurden. Die genauen Anforderungen werden durch die Spezifikationen des Kunden und die Qualitätsnormen (wie AS9100) festgelegt.
- A4: Für Flug-Hardware, umfassende qualitätsdokumentation für die Luft- und Raumfahrt AM ist Standard. Ein typisches Dokumentationspaket umfasst:
- F5: Wie lange dauert es normalerweise, bis ein Prototyp einer Satellitenhalterung aus Aluminium fertig ist?
- A5: Zeit für das Prototyping von Satellitenkomponenten lPBF ist wesentlich schneller als herkömmliche Methoden, die eine Werkzeugherstellung erfordern. Bei einem typischen Prototyp-Bracket, das nur eine minimale Nachbearbeitung erfordert (z. B. Spannungsabbau, Entfernen der Grundhalterung, Perlstrahlen), können die Durchlaufzeiten zwischen 1 bis 3 Wochenabhängig von der Komplexität der Teile, der Auslastung des Anbieters und der Verfügbarkeit der Maschinen. Wenn spezielle Wärmebehandlungen, umfangreiche Bearbeitungen oder komplexe Endbearbeitungen selbst für den Prototyp erforderlich sind, verlängert sich die Vorlaufzeit. Bestätigen Sie die Vorlaufzeiten immer mit dem Anbieter auf der Grundlage Ihrer spezifischen Anforderungen.
Schlussfolgerung: Leichtere und stärkere Satelliten mit AM-Halterungen aus Aluminium starten
Die Reise in die Erdumlaufbahn ist anspruchsvoll, und die wirtschaftlichen Aspekte des Weltraumstarts verlangen unablässig nach einer Minimierung der Masse. Wie wir erforscht haben, bietet die additive Fertigung von Metallen, insbesondere das Laser Powder Bed Fusion von fortschrittlichen Aluminiumlegierungen wie AlSi10Mg und der Hochleistungslegierung Scalmalloy®, eine leistungsstarke Lösung für die Herstellung von leichten, komplexen und hoch optimierten Satellitenhalterungen, die für die nächste Generation von Weltraummissionen benötigt werden.
Die Vorteile sind überzeugend: erhebliche Gewichtsreduzierungen durch Topologieoptimierung und generatives Design, die Möglichkeit, mehrere Komponenten zu einzelnen, komplexen Teilen zusammenzufassen, was die Zuverlässigkeit erhöht, und die Beschleunigung der Entwicklungszyklen durch Rapid Prototyping und werkzeuglose Produktion. Diese Vorteile schlagen sich direkt in niedrigeren Startkosten, höherer Nutzlastkapazität, verbesserter Satellitenleistung und schnellerer Umlaufzeit nieder. Zwar gibt es Herausforderungen in Bezug auf Prozesskontrolle, Nachbearbeitung und Qualitätssicherung, doch werden diese durch technologische Fortschritte, strenge Prozessvalidierung und robuste Qualitätsmanagementsysteme wirksam angegangen.
Die Wahl zwischen dem Arbeitspferd AlSi10Mg, das ein ausgewogenes Verhältnis von guten Eigenschaften und Kosteneffizienz bietet, und dem außergewöhnlichen Verhältnis von Festigkeit zu Gewicht und Ermüdungsleistung von Scalmalloy® ermöglicht es den Ingenieuren, die Materialauswahl genau auf die spezifischen strukturellen Anforderungen und die Kritikalität der jeweiligen Halterungsanwendung abzustimmen.
Um das volle Potenzial der Aluminium-AM für missionskritische Satellitenkomponenten zu nutzen, ist jedoch mehr erforderlich als nur der Zugang zu einem Drucker. Es erfordert einen ganzheitlichen Ansatz, der eine fachkundige DfAM-Anleitung, eine sorgfältige Prozesskontrolle, validierte Nachbearbeitungstechniken, eine strenge Qualitätssicherung und fundierte werkstoffwissenschaftliche Kenntnisse umfasst. Dies unterstreicht die entscheidende Bedeutung der Auswahl des richtigen Fertigungspartners.
Unternehmen wie Met3dp sind ein Beispiel für die Art von Partner, die für den Erfolg in der additiven Fertigung in der Luft- und Raumfahrt benötigt wird. Mit integrierten Fähigkeiten, die die fortschrittliche Pulverproduktion mit Gaszerstäubung und PREP-Technologien, branchenführende Druckanlagen (SEBM und LPBF), ein breites Portfolio an fortschrittliche Werkstoffe für die Luft- und Raumfahrtund umfassende Anwendungsentwicklungsdienste bietet das Unternehmen die für anspruchsvolle Projekte erforderliche Kompetenz und Zuverlässigkeit. Das Unternehmen konzentriert sich darauf, die Herstellung der nächsten Generation durch modernste Systeme und Pulver zu ermöglichen, und ist damit perfekt auf die Bedürfnisse der sich entwickelnden Raumfahrtindustrie abgestimmt. Erfahren Sie mehr über das gesamte Leistungsspektrum und den partnerschaftlichen Ansatz des Unternehmens Über Met3dp.
Die zukunft der Satellitenherstellung wird zweifelsohne eine stärkere Abhängigkeit von der additiven Fertigung mit sich bringen. Mit immer besseren Werkstoffen, höheren Prozessgeschwindigkeiten und ausgefeilteren Konstruktionswerkzeugen wird die Aluminium-AM eine noch größere Rolle bei der Herstellung leichterer, stärkerer und leistungsfähigerer Satellitenstrukturen spielen. Indem wir uns diese Technologie zu eigen machen und mit Experten zusammenarbeiten metall-AM-Partnerschaft anbietern kann die Luft- und Raumfahrtindustrie weiterhin die Grenzen der Forschung und Innovation verschieben.
Sind Sie bereit zu erfahren, wie die additive Fertigung von Aluminium die Konstruktion Ihrer Satellitenhalterungen revolutionieren kann? Setzen Sie sich noch heute mit Met3dp in Verbindung, um Ihre Projektanforderungen zu besprechen und herauszufinden, wie das Unternehmen seine Ziele im Bereich der additiven Fertigung erreichen kann.
Teilen auf
MET3DP Technology Co., LTD ist ein führender Anbieter von additiven Fertigungslösungen mit Hauptsitz in Qingdao, China. Unser Unternehmen ist spezialisiert auf 3D-Druckgeräte und Hochleistungsmetallpulver für industrielle Anwendungen.
Fragen Sie an, um den besten Preis und eine maßgeschneiderte Lösung für Ihr Unternehmen zu erhalten!
Verwandte Artikel
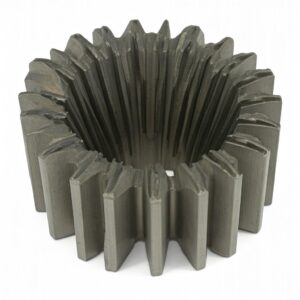
Hochleistungs-Düsenschaufelsegmente: Revolutionierung der Turbineneffizienz mit 3D-Metalldruck
Mehr lesen "Über Met3DP
Aktuelles Update
Unser Produkt
KONTAKT US
Haben Sie Fragen? Senden Sie uns jetzt eine Nachricht! Wir werden Ihre Anfrage mit einem ganzen Team nach Erhalt Ihrer Nachricht bearbeiten.
Holen Sie sich Metal3DP's
Produkt-Broschüre
Erhalten Sie die neuesten Produkte und Preislisten
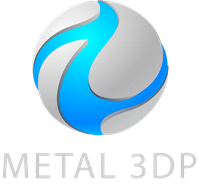
Metallpulver für 3D-Druck und additive Fertigung