Strukturelle Stützbalken aus 3D-gedruckten Aluminiumlegierungen
Inhaltsübersicht
Einführung: Revolutionierung von Luft- und Raumfahrtstrukturen durch additive Fertigung
Die Luft- und Raumfahrtindustrie befindet sich auf dem Zenit ihrer technischen Ambitionen und verschiebt ständig die Grenzen von Leistung, Effizienz und Sicherheit. Von zentraler Bedeutung für das Erreichen dieser Ziele sind die Strukturkomponenten, die das Skelett jedes Flugzeugs, jedes Satelliten und jeder Trägerrakete bilden. Dazu gehören, träger für die Luft- und Raumfahrt spielen eine entscheidende, wenn auch oft unsichtbare Rolle. Diese Komponenten sind von grundlegender Bedeutung für die Verteilung von Lasten, die Aufrechterhaltung der strukturellen Integrität unter extremen Bedingungen und die Gewährleistung der allgemeinen Widerstandsfähigkeit der Flugzeugzelle. Traditionell wurden diese wichtigen Teile mit subtraktiven Methoden wie der CNC-Bearbeitung von großen Materialblöcken oder komplexen Guss- und Schmiedeverfahren hergestellt. Diese Methoden sind zwar effektiv, stoßen aber oft an ihre Grenzen, was die Komplexität der Konstruktion, den Materialabfall und die Vorlaufzeiten angeht.
Eintritt in die Ära der Additive Fertigung (AM), besser bekannt als Metall 3D-Druck. Diese transformative Technologie verändert die Landschaft des Designs und der Produktion in der Luft- und Raumfahrt grundlegend. Anstatt Material abzutragen, baut AM Teile Schicht für Schicht direkt aus digitalen Modellen auf, wobei Hochenergiequellen wie Laser oder Elektronenstrahlen zum Verschmelzen feiner Metallpulver eingesetzt werden. Dieser Ansatz eröffnet eine nie dagewesene Designfreiheit und ermöglicht die Herstellung hochkomplexer Teile, Leichtbaustrukturen die bisher nicht oder nur zu hohen Kosten hergestellt werden konnten.
Für Träger in der Luft- und Raumfahrt sind die Implikationen tiefgreifend. Ingenieure können nun hochentwickelte Konstruktionswerkzeuge wie die Topologieoptimierung nutzen, um Träger zu entwickeln, die deutlich leichter sind und dennoch die erforderlichen Festigkeits- und Steifigkeitseigenschaften beibehalten oder sogar übertreffen. Diese Gewichtsreduzierung führt direkt zu Treibstoffeinsparungen, erhöhter Nutzlastkapazität und verbesserter Gesamtleistung des Flugzeugs - wichtige Messgrößen in der Luft- und Raumfahrt. Darüber hinaus erleichtert AM die Konsolidierung von Teilen, da mehrere Komponenten einer herkömmlichen Baugruppe neu entworfen und als eine einzige, integrierte Einheit gedruckt werden können, wodurch sich die Anzahl der Teile, die Montagezeit und potenzielle Fehlerquellen verringern.
Die Materialien, die diese Revolution in der Luft- und Raumfahrt vorantreiben, sind fortschrittliche Metalllegierungen, insbesondere Hochleistungsaluminiumlegierungen wie AlSi10Mg und das Fachmaterial Scalmalloy®. Diese Materialien bieten ein außergewöhnliches Gleichgewicht aus geringer Dichte, guten mechanischen Eigenschaften und Verarbeitbarkeit durch AM-Techniken wie Laser Powder Bed Fusion (L-PBF). Ihr Einsatz ermöglicht den Herstellern die Herstellung komplizierter Strukturkomponenten für bestimmte Lastfälle und räumliche Beschränkungen optimiert.
Met3dp, mit Hauptsitz in Qingdao, China, steht an der Spitze dieser Entwicklung. Spezialisiert auf industrielle 3D-Druck von Metall lösungen, einschließlich fortschrittlicher Druckanlagen und Hochleistungsmetallpulver, versetzen wir Luft- und Raumfahrtunternehmen in die Lage, das volle Potenzial der additiven Fertigung auszuschöpfen. Unser Engagement für branchenführende Genauigkeit, Zuverlässigkeit und Materialqualität stellt sicher, dass die mit unseren Technologien hergestellten Komponenten die strengen Anforderungen unternehmenskritischer Luft- und Raumfahrtanwendungen erfüllen. Dieser Blog-Beitrag befasst sich mit den Besonderheiten der Verwendung von 3D-gedruckten Aluminiumlegierungen, insbesondere AlSi10Mg und Scalmalloy®, für die Herstellung von robusten, leichten Stützbalken für die Luft- und Raumfahrt, wobei Anwendungen, Vorteile, Materialien und wichtige Überlegungen für die Umsetzung untersucht werden.
Anwendungen: Wo 3D-gedruckte Aluminiumträger in die Luft gehen
Die Vielseitigkeit und die Vorteile der additiven Fertigung von Metallen in Verbindung mit den vorteilhaften Eigenschaften von Aluminiumlegierungen haben eine breite Palette von Anwendungen für 3D-gedruckte Träger in der Luft- und Raumfahrt und verwandten Hochtechnologiesektoren eröffnet. Beschaffungsmanager und Ingenieure, die innovative Lösungen für die Luft- und Raumfahrtfertigung wenden sich zunehmend an AM für Komponenten, bei denen Gewichtseinsparungen, komplexe Geometrien oder konsolidierte Designs erhebliche Vorteile bieten.
Hier sind einige wichtige Anwendungsbereiche:
- Strukturelle Komponenten von Flugzeugen:
- Rumpfspanten & Stringer: Optimierte Balkenstrukturen, die zur Gesamtintegrität des Flugzeugrumpfes beitragen und mittels Topologieoptimierung auf maximale Tragfähigkeit bei minimalem Gewicht ausgelegt sind.
- Flügelrippen & Sparrenelemente: Komplexe interne Balkenstrukturen in Flügeln, die erheblichen aerodynamischen Belastungen standhalten und gleichzeitig die Masse minimieren müssen. AM ermöglicht komplizierte interne Gitterstrukturen.
- Halterungen & Halterungen: Hochgradig individualisierte Halterungen für die Montage von Motoren, Systemen oder Innenraumkomponenten. AM ermöglicht die Herstellung von nicht standardisierten, organisch geformten Halterungen, die perfekt auf ihre spezifische Position und Belastungsanforderungen zugeschnitten sind und oft mehrere Teile zu einem einzigen zusammenfassen.
- Rahmen für Türen und Luken: Strukturelle Träger, die die Öffnungen im Rumpf umgeben und eine hohe Festigkeit und präzise Geometrie erfordern.
- Fahrwerkskomponenten: Bestimmte Strukturelemente in Fahrwerken können vom Leichtbaupotenzial optimierter Aluminium-AM-Teile profitieren, sofern die Anforderungen an Ermüdung und Stoßfestigkeit erfüllt sind.
- Satellitenkomponenten:
- Bus-Strukturen: Die Primärstruktur eines Satelliten, oft ein komplexes Gerüst aus Trägern und Platten. Die Verringerung der Masse dieser Träger ist entscheidend für die Senkung der Startkosten. AM ermöglicht hochgradig optimierte, komplexe trussartige Strukturen.
- Antennenhalterungen & Ausleger: Leichte und dennoch steife Träger werden für die Aufstellung und Abstützung von großen Antennen oder wissenschaftlichen Instrumenten benötigt. Die durch AM ermöglichte Designkomplexität ist hier ein großer Vorteil.
- Optische Bänke: Strukturen, die eine hohe Stabilität und eine geringe thermische Ausdehnung erfordern und bei denen optimierte Trägerkonstruktionen zur Erreichung der Leistungsziele beitragen können.
- Unbemannte Luftfahrzeuge (UAVs) & Drohnen:
- Strukturen der Flugzeugzelle: Die gesamte Flugzeugzelle kleinerer UAVs kann mit 3D-gedruckten Trägern versehen werden, um eine maximale Leichtbauund erhöht damit die Flugdauer und die Nutzlastkapazität.
- Interne Unterstützungsstrukturen: Träger mit Batterien, Sensoren und anderer interner Hardware, optimiert für Platz- und Gewichtsbeschränkungen.
- Anwendungen im Verteidigungsbereich:
- Raketenkomponenten: Strukturelemente in Flugkörpern, bei denen Gewichtsreduzierung und Leistung im Vordergrund stehen.
- Militärische Flugzeuge: Kundenspezifische Träger für Spezialausrüstungen oder Modifikationen in Militärflugzeugen, die von der Fähigkeit von AM’ profitieren, maßgeschneiderte Komponenten schnell herzustellen.
- Hochleistungs-Automobil- und Motorsport:
- Fahrwerkskomponenten: Strukturträger und Knotenpunkte im Fahrgestell von Hochleistungsfahrzeugen, bei denen eine Gewichtsreduzierung die Beschleunigung, das Fahrverhalten und die Kraftstoffeffizienz verbessert.
- Komponenten der Aufhängung: Optimierte Tragarme und Gestänge, bei denen das Verhältnis von Steifigkeit zu Gewicht entscheidend ist.
Die Nachfrage nach diesen Komponenten kommt von großen OEMs (Original Equipment Manufacturers) der Luft- und Raumfahrt, Tier-1- und Tier-2-Zulieferern, Satellitenherstellern, Verteidigungsunternehmen und spezialisierten Ingenieurbüros. Als ein erfahrenes lieferant für Aluminiumlegierungsteile durch den Einsatz fortschrittlicher additiver Fertigung arbeitet Met3dp eng mit diesen Branchenakteuren zusammen, um kundenspezifische Träger zu entwickeln und zu produzieren, die den anspruchsvollen Leistungsspezifikationen entsprechen. Unsere Fähigkeiten reichen von der Prototypenherstellung einzelner komplexer Träger bis hin zur Abwicklung von Serienproduktionsanforderungen, um eine zuverlässige Lieferkette für diese kritischen Teile zu gewährleisten. Die Fähigkeit zu produzieren herstellung von Komponenten nach Maß macht AM besonders attraktiv für spezielle Plattformen oder Aufrüstungsprogramme, bei denen die Kosten für herkömmliche Werkzeuge unerschwinglich wären.
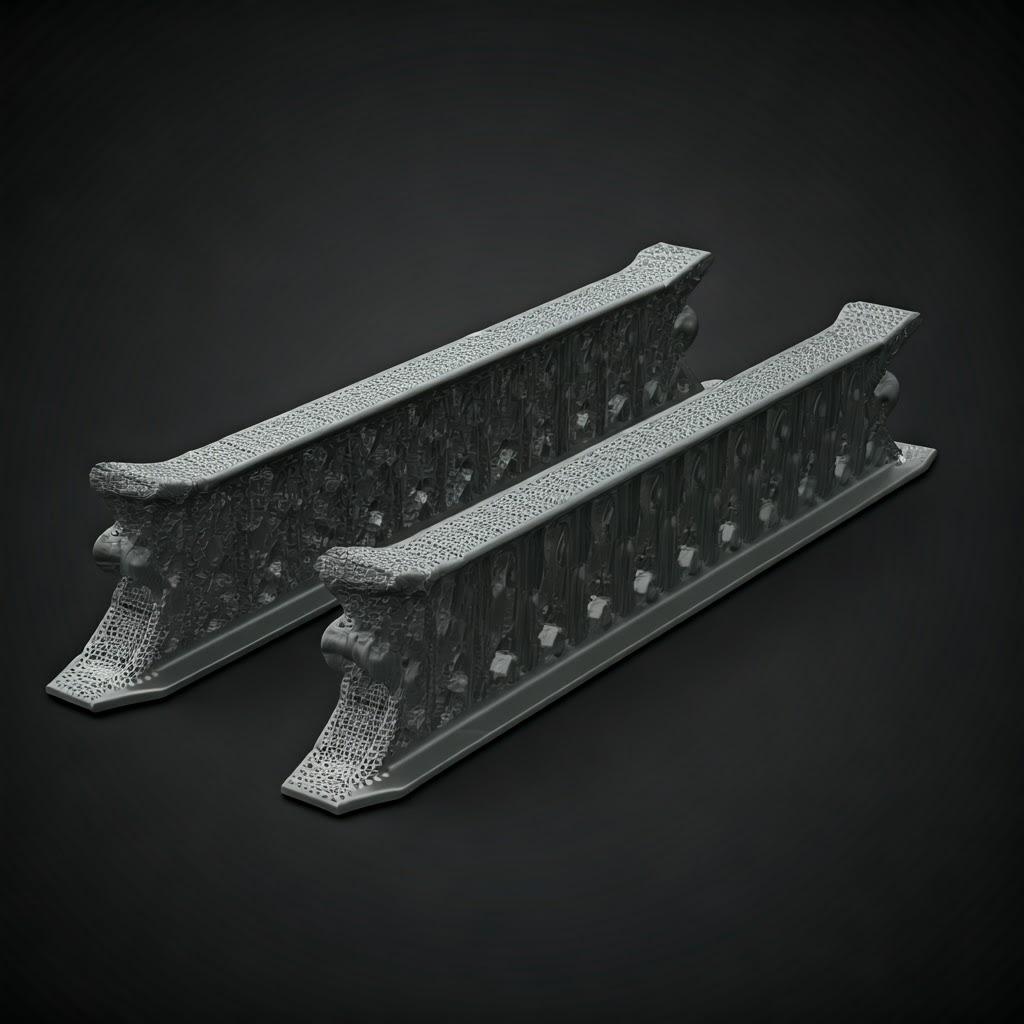
Vorteile: Warum Metall-3D-Druck für Träger in der Luft- und Raumfahrt?
Während herkömmliche Herstellungsverfahren der Luft- und Raumfahrtindustrie seit Jahrzehnten gute Dienste geleistet haben, 3D-Druck von Metall bietet eine Reihe von überzeugenden Vorteilen, insbesondere bei Komponenten wie Strukturträgern, bei denen sich eine Optimierung deutlich auszahlt. Ingenieure und Beschaffungsspezialisten, die Fertigungsrouten evaluieren, sollten die einzigartigen Vorteile der additiven Fertigung im Vergleich zu konventionellen Bearbeitungs-, Guss- oder Fertigungsverfahren in Betracht ziehen.
Hauptvorteile von AM für Träger der Luft- und Raumfahrt:
- Unerreichte Gestaltungsfreiheit und Komplexität:
- Topologie-Optimierung: AM lässt sich nahtlos mit Software zur Topologieoptimierung integrieren. Dies ermöglicht es Ingenieuren, Lastfälle und Konstruktionsbeschränkungen zu definieren, so dass Algorithmen hocheffiziente, oft organisch anmutende Balkenstrukturen erzeugen können, die Material nur dort platzieren, wo es strukturell notwendig ist. Dies führt zu maximaler Leistung bei minimalem Gewicht.
- Komplexe Geometrien: Interne Kanäle zur Kühlung oder Verdrahtung, komplizierte Gitterstrukturen für ein besseres Verhältnis von Steifigkeit zu Gewicht und sanft überblendete variable Querschnitte sind mit AM möglich. Solche Merkmale lassen sich mit herkömmlichen Methoden oft nicht oder nur mit extrem hohen Kosten herstellen.
- Generatives Design: Ähnlich wie bei der Topologieoptimierung können generative Entwurfswerkzeuge Hunderte oder Tausende von Entwurfsvarianten auf der Grundlage von Leistungskriterien untersuchen, was zu innovativen und leistungsstarken Strahldesigns führt.
- Signifikante Gewichtsreduzierung (Lightweighting):
- Dies ist wohl der wichtigste Vorteil für die Luft- und Raumfahrt. Durch den Einsatz von Topologieoptimierung und komplexen Geometrien kann AM Träger herstellen, die 20-50 % leichter (oder manchmal mehr) sind als ihre traditionell hergestellten Gegenstücke und dabei die Anforderungen an Festigkeit und Steifigkeit erfüllen oder übertreffen.
- Jedes Kilogramm, das bei einem Flugzeug eingespart wird, schlägt sich direkt in einem geringeren Treibstoffverbrauch, geringeren Emissionen, einer höheren Nutzlastkapazität oder einer größeren Reichweite über die gesamte Lebensdauer des Flugzeugs nieder.
- Teil Konsolidierung:
- Komplexe Baugruppen, die aus mehreren einzelnen Trägern, Halterungen und Befestigungselementen bestehen, können oft als ein einziges, monolithisches 3D-gedrucktes Bauteil neu entworfen und hergestellt werden.
- Vorteile: Eine geringere Anzahl von Teilen vereinfacht die Lagerhaltung und Logistik, spart Arbeit und Zeit bei der Montage, reduziert potenzielle Fehlerquellen (z. B. Verbindungselemente) und führt häufig zu einer leichteren, steiferen Endstruktur.
- Geringere Vorlaufzeiten (insbesondere für Prototypen & geringe Stückzahlen):
- AM macht teure und zeitaufwändige Werkzeuge (z. B. Formen, Gesenke, Vorrichtungen) überflüssig, die für das Gießen, Schmieden oder komplexe Bearbeitungsvorrichtungen benötigt werden.
- Digitale Designdateien können direkt an den Drucker gesendet werden, was ein schnelles Prototyping und Design-Iterationszyklen ermöglicht. Dies beschleunigt die Produktentwicklung erheblich.
- Für herstellung von Komponenten nach Maß oder Kleinserien, wie sie in der Luft- und Raumfahrt oder bei spezialisierten Plattformen üblich sind, ist AM oft schneller und kostengünstiger als die Einrichtung herkömmlicher Fertigungsstraßen.
- Materialeffizienz & Abfallreduzierung:
- Bei der subtraktiven Fertigung, wie bei der CNC-Bearbeitung, wird zunächst ein großer Materialblock entfernt, von dem möglicherweise 80-90 % abgetragen werden, um die endgültige Form zu erhalten, wobei erhebliche Abfälle (Späne) entstehen.
- Die additive Fertigung ist zwar nicht völlig abfallfrei (Stützstrukturen, ein gewisser Pulververlust), aber sie nutzt das Material viel effizienter und fügt es nur bei Bedarf hinzu. Dies ist besonders vorteilhaft, wenn man mit teuren, für die Luft- und Raumfahrt geeigneten Legierungen arbeitet.
- Optimierung der Lieferkette:
- Die digitale Fertigung ermöglicht eine dezentrale Produktion. Entwürfe können digital übertragen und näher am Ort des Bedarfs gedruckt werden, wodurch sich die Versandkosten und Vorlaufzeiten verringern können.
- Die Möglichkeit der Produktion auf Abruf verringert den Bedarf an großen Lagerbeständen für Ersatzteile.
- Verbesserte Leistung:
- Optimierte Konstruktionen können zu Bauteilen mit einem hervorragenden Verhältnis zwischen Steifigkeit und Gewicht führen.
- Merkmale wie konforme Kühlkanäle (falls für bestimmte Strahlanwendungen in der Nähe von Wärmequellen erforderlich) können direkt in das Design integriert werden.
Obwohl AM diese wesentlichen Vorteile bietet, ist es entscheidend, mit einem erfahrenen Anbieter wie Met3dp zusammenzuarbeiten. Unser tiefes Verständnis von Lösungen für die Luft- und Raumfahrtfertigung stellt sicher, dass diese Vorteile effektiv genutzt werden. Wir setzen unsere fortschrittlichen Drucker und Prozesssteuerungen ein, um das Potenzial von AM für die Herstellung hochwertiger, zuverlässiger Träger für die Luft- und Raumfahrt zu maximieren.
Werkstoff-Fokus: AlSi10Mg und Scalmalloy® für anspruchsvolle Anforderungen der Luft- und Raumfahrt
Die Wahl des Materials ist in der Luft- und Raumfahrttechnik von entscheidender Bedeutung, da sie sich direkt auf das Gewicht, die Festigkeit, die Haltbarkeit und die Widerstandsfähigkeit der Komponenten gegenüber Umwelteinflüssen auswirkt. Für 3D-gedruckte Träger für die Luft- und Raumfahrt werden häufig Aluminiumlegierungen bevorzugt, da sie eine geringe Dichte mit guten mechanischen Eigenschaften verbinden. Zu den für die additive Fertigung geeigneten Aluminiumlegierungen gehören, AlSi10Mg und Scalmalloy® zeichnen sich als Spitzenkandidaten aus, die jeweils unterschiedliche Vorteile bieten.
AlSi10Mg: Die Aluminiumlegierung für alle Fälle
AlSi10Mg ist eine bewährte Aluminiumlegierung, die Silizium und Magnesium enthält und traditionell für Gussstücke verwendet wird. Durch die Anpassung für das Laser Powder Bed Fusion (L-PBF) wurde es zu einem der am häufigsten verwendeten Materialien in der Metall-AM.
- Wichtige Eigenschaften & Vorteile:
- Gutes Verhältnis von Stärke zu Gewicht: Bietet beachtliche mechanische Eigenschaften, die für viele strukturelle Anwendungen geeignet sind, insbesondere nach einer geeigneten Wärmebehandlung (in der Regel T6).
- Ausgezeichnete Verarbeitbarkeit: Die Verarbeitung mit L-PBF ist relativ einfach, und die gut verstandenen Parametersätze führen zu dichten, zuverlässigen Teilen.
- Gute thermische Eigenschaften: Geeignet für Anwendungen, die eine gute Wärmeleitfähigkeit erfordern.
- Korrosionsbeständigkeit: Weist eine gute Korrosionsbeständigkeit auf.
- Kosten-Nutzen-Verhältnis: Im Allgemeinen preiswerter als leistungsfähigere oder spezialisierte Legierungen wie Scalmalloy®.
- Verfügbarkeit: Reaktionsfähigkeit? Technisches Verständnis? Projektaktualisierungen? Dedizierter Kontakt? Lieferanten von Metallpulver.
- Erwägungen:
- Geringere absolute Festigkeit und Ermüdungsleistung im Vergleich zu hochfesten Aluminiumlegierungen oder Scalmalloy®.
- Erfordert eine Wärmebehandlung (in der Regel Lösungsbehandlung und künstliche Alterung – T6) nach dem Druck, um optimale mechanische Eigenschaften zu erreichen. Dies ist ein zusätzlicher Nachbearbeitungsschritt, der bei unvorsichtiger Handhabung zu Verformungen führen kann.
Scalmalloy®: Hochleistungsaluminium für AM
Scalmalloy® ist eine patentierte Hochleistungs-Aluminium-Magnesium-Scandium-Legierung, die speziell für die additive Fertigung von APWORKS entwickelt wurde. Sie verschiebt die Grenzen dessen, was mit 3D-gedrucktem Aluminium erreicht werden kann.
- Wichtige Eigenschaften & Vorteile:
- Außergewöhnliche Stärke: Bietet deutlich höhere mechanische Eigenschaften (Streckgrenze, Zugfestigkeit) als AlSi10Mg und erreicht oder übertrifft sogar die Eigenschaften einiger traditioneller hochfester Aluminiumlegierungen der Serie 7xxx.
- Ausgezeichnete Duktilität & Ermüdungsfestigkeit: Behält trotz seiner hohen Festigkeit eine gute Duktilität bei, was zu hervorragenden Ermüdungseigenschaften führt, die für zyklisch belastete Bauteile in der Luft- und Raumfahrt entscheidend sind.
- Hohe spezifische Festigkeit: Die hervorragende Festigkeit in Verbindung mit der geringen Dichte führt zu einer außergewöhnlichen spezifischen Festigkeit (Verhältnis von Festigkeit zu Gewicht), ideal für Gewichtsreduzierung in der Luft- und Raumfahrt strukturen.
- Gute Schweißbarkeit & Verarbeitbarkeit: Entwickelt für eine gute Leistung während des L-PBF-Verfahrens.
- Stabil bei erhöhter Temperatur: Behält im Vergleich zu AlSi10Mg seine Eigenschaften bei mäßig erhöhten Temperaturen besser bei.
- Erwägungen:
- Höhere Kosten: Scalmalloy®-Pulver ist aufgrund seiner Zusammensetzung (einschließlich Scandium) und seiner Lizenzierung deutlich teurer als AlSi10Mg.
- Spezialisierte Verarbeitung: Kann im Vergleich zu AlSi10Mg feiner abgestimmte L-PBF-Prozessparameter erfordern.
- Verfügbarkeit: Hauptsächlich über lizenzierte Anbieter erhältlich.
Vergleich der Materialeigenschaften (typische Werte nach entsprechender Wärmebehandlung):
Eigentum | Einheit | AlSi10Mg (Zustand T6) | Scalmalloy® (wärmebehandelt) | Anmerkungen |
---|---|---|---|---|
Dichte | g/cm3 | ~2.67 | ~2.68 | Sehr ähnlich, beide leicht |
Streckgrenze (Rp0,2) | MPa | ~230 – 280 | ~450 – 520 | Scalmalloy® deutlich stärker |
Endgültige Zugfestigkeit | MPa | ~330 – 430 | ~500 – 580 | Scalmalloy® deutlich stärker |
Dehnung beim Bruch | % | ~6 – 10 | ~10 – 18 | Scalmalloy® ist im Allgemeinen duktiler |
Elastizitätsmodul | GPa | ~70 – 75 | ~70 – 75 | Ähnliche Steifigkeit |
Härte | HBW | ~100 – 120 | ~140 – 160 | Scalmalloy® härter |
Maximale Betriebstemperatur | °C | ~100 – 150 | ~200 – 250 | Scalmalloy® besser bei höheren Temperaturen |
In Blätter exportieren
Hinweis: Die Eigenschaften können je nach Druckparametern, Bauausrichtung, Wärmebehandlung und spezifischer Pulvercharge variieren.
Met3dp’s Materialfähigkeiten:
Als führendes Unternehmen im Bereich der additiven Fertigung von Metallen weiß Met3dp um die entscheidende Rolle der Pulverqualität. Unser Unternehmen setzt branchenführende Gaszerstäubung techniken zur Herstellung hochwertiger sphärischer Metallpulver, einschließlich für L-PBF optimierter Aluminiumlegierungen. Unser fortschrittliches Pulverherstellungssystem gewährleistet eine hohe Sphärizität, gute Fließfähigkeit und eine kontrollierte Partikelgrößenverteilung - Faktoren, die für den Druck von dichten, hochwertigen Teilen mit überlegenen und gleichbleibenden mechanischen Eigenschaften unerlässlich sind. Ganz gleich, ob Ihre Anwendung die zuverlässige Leistung von AlSi10Mg oder die außergewöhnliche Festigkeit von Scalmalloy® erfordert, Met3dp verfügt über das Know-how und die hochwertige Metallpulver um Ihre Anforderungen zu erfüllen. Wir arbeiten mit Kunden aus der Luft- und Raumfahrt zusammen, um das optimale Material auf der Grundlage von Leistungsanforderungen, Budgetbeschränkungen und Anwendungsspezifika auszuwählen, damit der endgültige 3D-gedruckte Träger kompromisslose Leistung und Zuverlässigkeit bietet.
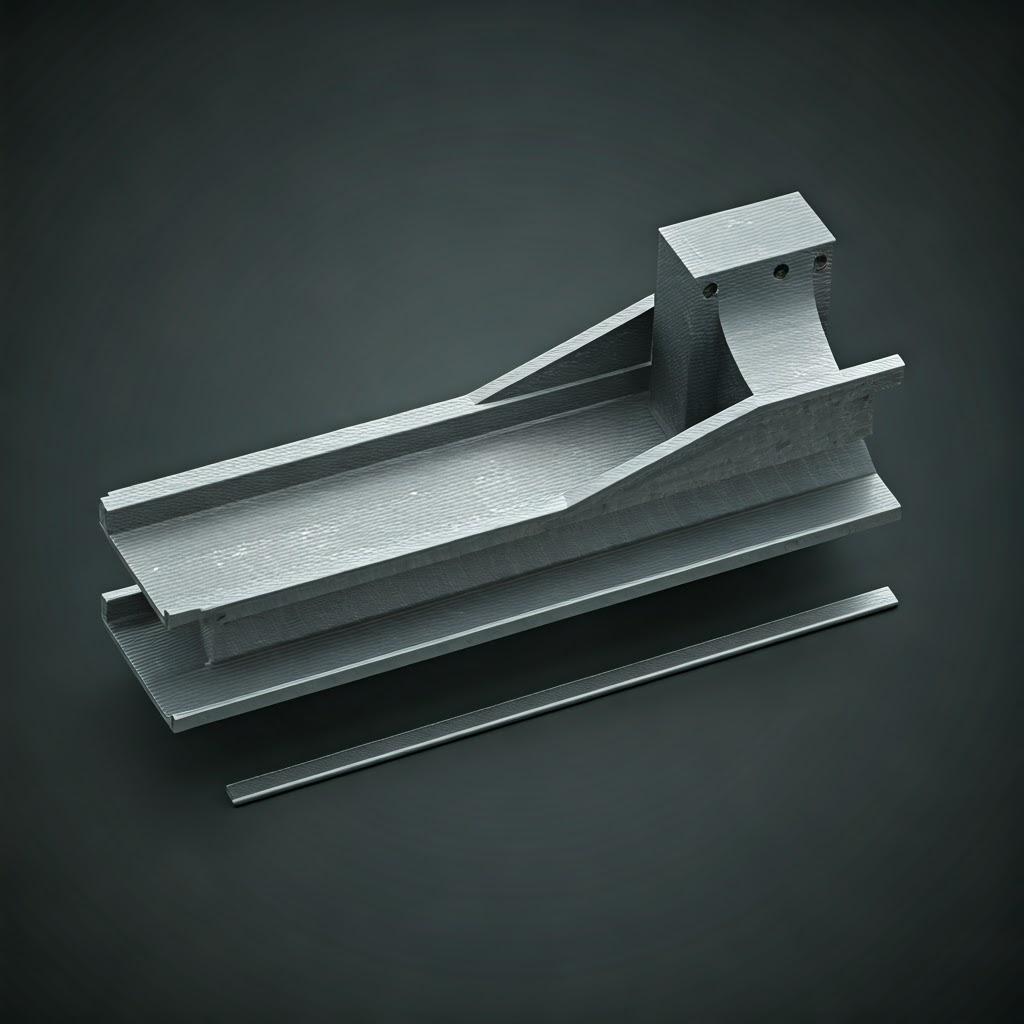
Entwurf für additive Fertigung (DfAM): Optimierung von Trägern für die Druckbarkeit
Die einfache Nachbildung eines Designs, das für die herkömmliche Fertigung vorgesehen ist, mit Hilfe der additiven Fertigung schöpft selten das volle Potenzial der Technologie aus. Um die Vorteile des 3D-Drucks für Träger in der Luft- und Raumfahrt wirklich zu nutzen - insbesondere um erhebliche Gewichtseinsparungen und Leistungssteigerungen zu erzielen - müssen die Ingenieure folgende Punkte berücksichtigen Design für additive Fertigung (DfAM) grundsätze. DfAM ist eine Konstruktionsmethodik, die die Möglichkeiten und Einschränkungen des AM-Prozesses von Anfang an berücksichtigt und zu Teilen führt, die nicht nur funktional sind, sondern auch für einen erfolgreichen, effizienten Druck optimiert sind. Die Anwendung von DfAM ist bei der Arbeit mit Aluminiumlegierungen wie AlSi10Mg und Scalmalloy® unter Verwendung des Laser Powder Bed Fusion (L-PBF) entscheidend.
Wichtige DfAM-Überlegungen für Aluminiumträger in der Luft- und Raumfahrt:
- Topologie-Optimierung & Generatives Design nutzen:
- Diese Berechnungswerkzeuge sind für den Leichtbau von Bauteilen wie Balken unerlässlich. Beginnen Sie mit dem Entwurfsraum, den Lastbedingungen, den Randbedingungen und den Leistungszielen (z. B. Steifigkeit, Spannungsgrenzen).
- Erlauben Sie Software zur Topologieoptimierung um Material aus wenig beanspruchten Bereichen zu entfernen, was zu effizienten, oft organisch anmutenden Strukturen führt, die von Natur aus das Gewicht minimieren und gleichzeitig die strukturellen Anforderungen erfüllen.
- Nutzen Sie generative Gestaltung werkzeuge zur Erkundung eines breiteren Spektrums an herstellbaren Designmöglichkeiten auf der Grundlage definierter Ziele und Einschränkungen.
- Optimierung der Gebäudeausrichtung:
- Die Ausrichtung des Trägers auf der Bauplatte hat erhebliche Auswirkungen auf die Druckzeit, die Anforderungen an die Stützstruktur, die Oberflächenbeschaffenheit, die Akkumulation von Eigenspannungen und potenziell anisotrope mechanische Eigenschaften.
- Versuchen Sie, das Teil so auszurichten, dass möglichst wenig Stützstrukturen erforderlich sind, insbesondere an kritischen Funktionsflächen oder schwer zugänglichen inneren Bereichen.
- Berücksichtigen Sie die primären Belastungsrichtungen; die Ausrichtung kritischer Zugbelastungspfade senkrecht zu den Aufbauschichten wird manchmal bevorzugt, obwohl die Eigenschaften von Aluminium-AM im Vergleich zu einigen anderen Materialien oder Verfahren relativ isotrop sind. Arbeiten Sie mit Ihrem AM-Dienstleister, wie Met3dp, zusammen, um die optimale Ausrichtungsstrategie zu bestimmen.
- Entwurf für Tragwerke:
- L-PBF erfordert Stützstrukturen für überhängende Merkmale (typischerweise Winkel von weniger als 45 Grad zur horizontalen Ebene) und zur Verankerung des Teils auf der Bauplatte, um thermische Spannungen zu bewältigen.
- Überhänge minimieren: Entwerfen Sie, wo immer möglich, mit selbsttragenden Winkeln (idealerweise >45 Grad). Verwenden Sie Abschrägungen oder Verrundungen anstelle von scharfen horizontalen Überhängen.
- Zugänglichkeit für den Umzug: Stellen Sie sicher, dass die Halterungen an Stellen angebracht sind, an denen sie leicht zugänglich sind und bei der Nachbearbeitung entfernt werden können, ohne das Teil zu beschädigen. Vermeiden Sie nach Möglichkeit komplexe interne Stützen.
- Optimierung der Unterstützung: Verwenden Sie spezialisierte Software-Tools, um optimierte Stützstrukturen (z. B. Block-, Kegel- und Baumstützen) zu erstellen, die nur wenig Material verbrauchen, leicht zu entfernen sind und die Wärmeableitung und Verformung effektiv steuern.
- Gitterstrukturen einbeziehen:
- Bei Trägern, die eine hohe Steifigkeit bei minimalem Gewicht erfordern, sollte man in Erwägung ziehen, die Vollprofile durch interne Gitterstrukturen.
- Verschiedene Gittertypen (z. B. kubisch, octet-truss, gyroid) bieten unterschiedliche strukturelle und thermische Eigenschaften. Wählen Sie je nach Lastfall und gewünschter Leistung den entsprechenden Typ und die Dichte aus.
- Stellen Sie sicher, dass die Gitterzellengröße groß genug ist, um das Pulver bei der Nachbearbeitung effektiv zu entfernen.
- Wanddicke und Größe der Merkmale:
- Beachten Sie die minimalen druckbaren Wandstärken (typischerweise 0,4-0,8 mm für L-PBF-Aluminium, je nach Maschine und Geometrie), um sicherzustellen, dass die Features korrekt aufgelöst werden.
- Vermeiden Sie nach Möglichkeit zu dicke Abschnitte, da diese mehr Eigenspannung aufbauen und die Druckzeit und den Materialverbrauch erhöhen können. Die Topologieoptimierung hilft natürlich, unnötig dicke Bereiche zu vermeiden.
- Bewältigen Sie den Reststress:
- Die schnelle Erwärmung und Abkühlung bei L-PBF kann zu Eigenspannungen führen, die Verformungen oder Risse verursachen können, insbesondere bei großen oder komplexen Trägern.
- Design-Strategien: Verwenden Sie abgerundete Ecken anstelle von scharfen Kanten, halten Sie nach Möglichkeit gleichmäßige Wandstärken ein und bauen Sie bei Bedarf spannungsentlastende Elemente ein. Die richtige Bauausrichtung und Stützstrategie sind ebenfalls entscheidend.
- Nachbearbeiten: Eine obligatorische Spannungsarmglühung ist in der Regel unmittelbar nach dem Druck von Aluminiumteilen erforderlich.
- Berücksichtigen Sie die Nachbearbeitungsanforderungen:
- Kennzeichnen Sie kritische Flächen oder Merkmale, die enge Toleranzen oder bestimmte Oberflächengüten erfordern. Fügen Sie diesen Bereichen zusätzliches Material (Bearbeitungsmaterial) zu, wenn eine anschließende CNC-Bearbeitung geplant ist.
- Konstruieren Sie Merkmale wie Löcher oder Kanäle leicht unterdimensioniert, wenn sie durch Bearbeitung oder Reiben fertiggestellt werden, um die endgültigen Toleranzen zu erreichen.
Durch die Integration dieser gestaltungsrichtlinien für Metall-AM in einem frühen Stadium des Entwicklungsprozesses können Ingenieure Stützbalken für die Luft- und Raumfahrt entwickeln, die leichter, stabiler und effizienter hergestellt sind. Die Partnerschaft mit einem AM-Spezialisten wie Met3dp bietet Zugang zu Fachwissen im Bereich DfAM und stellt sicher, dass Ihre Entwürfe für unser fortschrittliches Verfahren optimiert sind Druckverfahren und Materialien nutzt.
Erreichbare Präzision: Toleranz, Oberflächengüte und Maßgenauigkeit
Bei Komponenten für die Luft- und Raumfahrt ist Präzision nicht verhandelbar. Die Träger müssen korrekt in die Baugruppen passen und unter Belastung zuverlässig funktionieren, was eine strikte Einhaltung der Maßtoleranzen und der Anforderungen an die Oberflächengüte erfordert. Obwohl die additive Fertigung von Metallen eine unglaubliche Designfreiheit bietet, ist es für Ingenieure und Beschaffungsmanager wichtig zu verstehen, welche Präzisionsniveaus direkt mit dem L-PBF-Verfahren erreicht werden können und was durch Nachbearbeitung erreicht werden kann.
Maßgenauigkeit und Toleranzen:
- As-Built-Toleranz: Die direkt nach dem Druck mit L-PBF erreichbare Maßgenauigkeit für Aluminiumlegierungen wie AlSi10Mg und Scalmalloy® liegt typischerweise im Bereich von ±0,1 mm bis ±0,3 mm für kleinere Merkmale (z. B. bis zu 50-100 mm) oder ±0,1 % bis ±0,2 % der Gesamtabmessung für größere Teile.
- Zu den Faktoren, die dies beeinflussen, gehören die Maschinenkalibrierung, die Größe des Laserspots, die Schichtdicke, die thermische Stabilität während des Aufbaus, die Pulvereigenschaften und die Teilegeometrie/-ausrichtung.
- Auswirkungen der Wärmebehandlung: Die Wärmebehandlung nach dem Druck (insbesondere der Spannungsabbau und die T6-Alterung bei AlSi10Mg) ist für das Erreichen der gewünschten mechanischen Eigenschaften von entscheidender Bedeutung, kann jedoch zu leichten Maßänderungen (Schrumpfung oder Wachstum) und potenziellem Verzug führen. Diese Auswirkungen müssen entweder bei der ursprünglichen Konstruktion oder bei der anschließenden Bearbeitung berücksichtigt und kompensiert werden.
- Erzielung engerer Toleranzen: Für kritische Schnittstellen, Befestigungspunkte oder Lageroberflächen, die engere Toleranzen als die bauüblichen erfordern (z. B. ±0,025 mm bis ±0,05 mm), Postprozess-CNC-Bearbeitung wird in der Regel verwendet. Für diese Merkmale muss in der AM-Konstruktion ein ausreichendes Bearbeitungsmaterial vorgesehen werden.
Oberflächengüte (Rauhigkeit):
- Oberflächenrauhigkeit (Ra) im Ist-Zustand: Die Oberflächenbeschaffenheit von L-PBF-Teilen ist von Natur aus rauer als die von maschinell bearbeiteten Oberflächen, was auf den schichtweisen Prozess und die teilweise aufgeschmolzenen Pulverpartikel zurückzuführen ist, die an der Oberfläche haften.
- Obere Oberflächen: Sie weisen im Allgemeinen die glatteste Oberfläche auf, oft im Bereich von Ra 5-10 µm.
- Vertikale Mauern: Sie haben in der Regel Ra-Werte zwischen 8-15 µm.
- Nach oben/unten gerichtete Oberflächen: Die Oberflächen, die im Verhältnis zur Bauplatte abgewinkelt sind, variieren, wobei die nach unten weisenden (unterstützten) Oberflächen aufgrund der Kontaktpunkte mit der Unterlage in der Regel rauer sind (Ra 15-25 µm oder mehr).
- Interne Kanäle: Kann schwierig zu bearbeiten sein und eine raue Oberfläche behalten, es sei denn, sie wird durch Fließschleifen oder ähnliche Techniken gezielt bearbeitet.
- Verbesserung der Oberflächengüte: Verschiedene Nachbearbeitungstechniken können die Oberflächengüte erheblich verbessern:
- Perlstrahlen / Shot Peening: Üblicherweise wird damit eine gleichmäßige matte Oberfläche (Ra 3-6 µm) erzielt und es können günstige Druckspannungen erzeugt werden.
- Taumeln / Vibrationsgleitschleifen: Wirksam zum Entgraten und Glätten von Außenflächen kleinerer Teile (Ra 1-3 µm möglich).
- Polieren: Manuelles oder automatisiertes Polieren kann sehr glatte, spiegelähnliche Oberflächen (Ra < 0,5 µm) erzielen, ist jedoch arbeitsintensiv und in der Regel nur für bestimmte Bereiche geeignet.
- Elektrochemisches Polieren / Chemisches Ätzen: Kann Oberflächen glätten, auch komplexe Geometrien, erfordert aber eine sorgfältige Prozesskontrolle.
- Bearbeitungen: Bietet die beste Kontrolle sowohl über die Oberflächengüte (Ra < 1 µm leicht erreichbar) als auch über die Maßgenauigkeit bei spezifischen Merkmalen.
Qualitätskontrolle und Inspektion:
- Erfüllung strenger Qualitätskontrolle in der Luft- und Raumfahrt standards ist unerlässlich. Dies beinhaltet strenge Kontrollen während des gesamten Prozesses.
- Analyse des Pulvers: Sicherstellen, dass das eingehende Metallpulver den Spezifikationen entspricht (Chemie, Partikelgrößenverteilung, Fließfähigkeit).
- Prozessbegleitende Überwachung: Einsatz von Schmelzbadüberwachungs- oder Wärmebildsystemen während der Herstellung, um mögliche Anomalien zu erkennen. Met3dp nutzt eine fortschrittliche Prozessüberwachung, um die Konsistenz der Herstellung zu gewährleisten.
- Prüfung der Abmessungen: Einsatz von Koordinatenmessmaschinen (CMM), 3D-Scannern oder herkömmlichen Messinstrumenten zur Überprüfung der Maßhaltigkeit anhand der Konstruktionsspezifikationen.
- Zerstörungsfreie Prüfung (NDT): Einsatz von Methoden wie der Röntgen-Computertomographie (CT) zur Erkennung innerer Defekte (Porosität, Einschlüsse) und zur Überprüfung der inneren Geometrie, insbesondere bei komplexen Trägern mit inneren Merkmalen.
- Materialprüfung: Durchführung von Zugversuchen, Härtetests und Mikrostrukturanalysen an Musterteilen, die zusammen mit den Teilen gedruckt werden, um zu überprüfen, ob die Materialeigenschaften den Anforderungen entsprechen.
Das Verständnis dieser Präzisionsaspekte ermöglicht realistische Designspezifikationen und informiert über die notwendigen Nachbearbeitungsschritte, um sicherzustellen, dass der endgültige 3D-gedruckte Aluminiumträger alle funktionalen und Endbearbeitung von Luft- und Raumfahrtkomponenten Anforderungen.
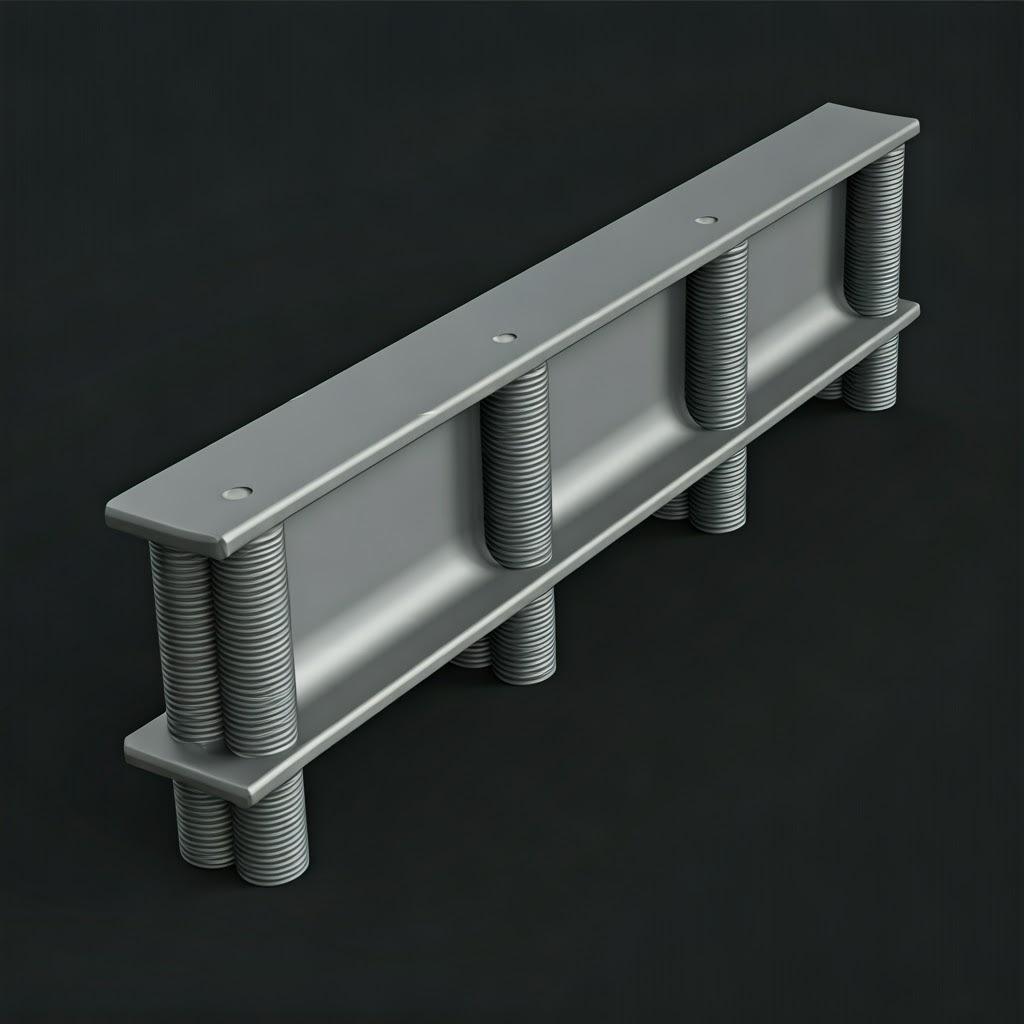
Post-Processing: Verfeinerung von 3D-gedruckten Aluminiumträgern
Mit dem Laser-Pulverbett-Verfahren hergestellte Teile, insbesondere kritische Bauteile für die Luft- und Raumfahrt, wie z. B. Träger aus AlSi10Mg oder Scalmalloy®, sind selten sofort nach dem Verlassen des Druckers einsatzbereit. Eine Reihe von wesentlichen Nachbearbeitung schritte sind erforderlich, um das fertige Teil in ein funktionsfähiges, zuverlässiges Bauteil zu verwandeln, das die strengen Normen der Luft- und Raumfahrt erfüllt. In diesen Schritten werden Eigenspannungen beseitigt, die gewünschten Materialeigenschaften erreicht, Stützstrukturen entfernt, die Oberflächenbeschaffenheit verfeinert und die Maßhaltigkeit sichergestellt.
Gemeinsamer Nachbearbeitungsablauf für Aluminium-AM-Träger:
- Entstaubung / Entpuderung:
- Vorsichtiges Entfernen des Bauteils von der Bauplatte, die oft loses und halbgesintertes Pulver enthält.
- Gründliche Reinigung des Teils, um Pulverrückstände zu entfernen, insbesondere aus internen Kanälen oder komplexen Merkmalen, mit Druckluft, Bürsten oder Ultraschallreinigung. Eine wirksame Entpuderung ist entscheidend für nachfolgende Schritte wie Wärmebehandlung und HIP (falls erforderlich).
- Stressabbau Wärmebehandlung:
- Entscheidender Schritt: Dies ist in der Regel die erste wärmebehandlung, oft während das Teil noch auf der Bauplatte befestigt ist (manchmal aber auch nach vorsichtigem Entfernen).
- Zweck: Um innere Spannungen abzubauen, die während der schnellen Erwärmungs- und Abkühlungszyklen des L-PBF-Verfahrens entstehen, wird das Risiko einer Verformung oder Rissbildung bei der anschließenden Handhabung oder Entfernung der Halterung minimiert.
- Prozess: Erhitzen des Teils auf eine bestimmte Temperatur unterhalb der Alterungstemperatur der Legierung (z.B. ~300°C für AlSi10Mg), Halten des Teils für einen bestimmten Zeitraum (z.B. 1-2 Stunden) und dann langsames Abkühlen.
- Entnahme von der Bauplatte:
- Wenn dies nicht vor dem Spannungsabbau geschieht, wird das Teil sorgfältig von der Bauplatte getrennt, in der Regel durch Drahterodieren (Electrical Discharge Machining), Sägen oder Zerspanen.
- Entfernung der Stützstruktur:
- Entfernen der während des Bauprozesses erzeugten Stützstrukturen.
- Methoden: Dies kann manuelles Brechen und Schneiden (bei leicht zugänglichen Stützen), CNC-Bearbeitung, Schleifen oder manchmal Drahterodieren für empfindliche oder schwer zugängliche Stützen beinhalten. Dabei muss darauf geachtet werden, dass die Oberfläche des Teils nicht beschädigt wird. Wirksam Abstützung Metall AM erfordert eine Planung während der DfAM-Phase.
- Lösungsbehandlung und Alterung (Ausscheidungshärtung – z. B. T6 für AlSi10Mg):
- Zweck: Um die gewünschten mechanischen Eigenschaften (Festigkeit, Härte, Duktilität) zu erreichen. Dies ist besonders wichtig für AlSi10Mg. Scalmalloy® profitiert auch von spezifischen Alterungsbehandlungen.
- Verfahren (Beispiel AlSi10Mg T6):
- Lösung Behandlung: Erhitzen auf eine hohe Temperatur (~500-540°C), um die Legierungselemente in der Aluminiummatrix aufzulösen.
- Abschrecken: Schnelles Abkühlen (z. B. in Wasser oder Polymer), um die Elemente in Lösung zu halten.
- Künstliche Alterung: Wiedererwärmung auf eine niedrigere Temperatur (~150-180°C) für mehrere Stunden, um eine kontrollierte Ausscheidung von Verfestigungsphasen zu ermöglichen.
- Kontrolle: Die genaue Kontrolle der Temperaturen und Zeiten ist von entscheidender Bedeutung. Dieser Schritt kann potenziell zu Verformungen führen, die kontrolliert werden müssen.
- Heiß-Isostatisches Pressen (HIP) – (Optional, aber üblich für kritische Teile):
- Zweck: Zur Schließung interner Mikroporosität, wodurch Ermüdungsfestigkeit, Duktilität und Bruchzähigkeit verbessert werden. Häufig erforderlich für anspruchsvolle Anwendungen in der Luft- und Raumfahrt.
- Prozess: Das Teil wird gleichzeitig einer hohen Temperatur (unter dem Schmelzpunkt) und einem hohen Inertgasdruck (z. B. Argon) ausgesetzt. Durch den Druck kollabieren die inneren Hohlräume.
- Erwägung: HIP kann leichte Maßänderungen verursachen und die Oberflächengüte beeinträchtigen.
- Oberflächenveredelung:
- Angemessene Anwendung oberflächenveredelungstechniken um Anforderungen an die Rauheit, Ästhetik oder Vorbereitung für Beschichtungen zu erfüllen.
- Gängige Methoden: Perlstrahlen (gleichmäßige matte Oberfläche), Kugelstrahlen (Druckspannung), Trommel-/Gleitschleifen (Glätten, Entgraten), Polieren (bestimmte Bereiche) oder spezielle Behandlungen wie elektrochemisches Polieren.
- Endbearbeitung (CNC):
- Durchführung von Hochpräzisions CNC-Bearbeitung von 3D-Drucken bei kritischen Merkmalen, Schnittstellen, Befestigungslöchern oder Oberflächen, die engere Toleranzen oder glattere Oberflächen erfordern, als sie durch AM und andere Nachbearbeitungsschritte erreicht werden können.
- Stellt sicher, dass das fertige Teil alle in der technischen Zeichnung angegebenen Maße einhält.
- Endreinigung und Inspektion:
- Gründliche Reinigung des Teils, um alle Bearbeitungsflüssigkeiten, Ablagerungen oder Rückstände zu entfernen.
- Durchführung der abschließenden Maßprüfung (CMM, Scannen), NDT (CT-Scannen, falls erforderlich) und Überprüfung der Oberflächenbeschaffenheit, um eine vollständige qualitätssicherung AM-Teile.
Die Komplexität und Abfolge dieser Schritte hängt stark von der jeweiligen Legierung, der Teilegeometrie und den Anwendungsanforderungen ab. Met3dp bietet umfassende Lösungen an und verwaltet die gesamte Nachbearbeitungskette, um Träger für die Luft- und Raumfahrt zu liefern, die den höchsten Qualitäts- und Leistungsstandards entsprechen.
Überwindung von Herausforderungen beim Drucken von Trägern für die Luft- und Raumfahrt
Die additive Fertigung von Metallen bietet zwar ein transformatives Potenzial für Luft- und Raumfahrtkomponenten wie z. B. Stützträger, doch das Verfahren ist nicht ohne Herausforderungen. Das erfolgreiche Drucken großer, komplexer oder unternehmenskritischer Aluminiumteile erfordert eine sorgfältige Prozesssteuerung, Materialkenntnis und robuste Qualitätsmanagementsysteme. Das Wissen um diese potenziellen Hürden ermöglicht es Ingenieuren und Herstellern, proaktiv Strategien zur Schadensbegrenzung zu implementieren.
Allgemeine Metall-AM-Herausforderungen und Lösungen für Aluminiumträger:
- Eigenspannung, Verformung und Verwerfung:
- Herausforderung: Die hohen thermischen Gradienten, die bei L-PBF auftreten, führen zu inneren Spannungen, da sich die Schichten schnell erhitzen und abkühlen. Diese Spannungen können dazu führen, dass sich Teile während des Aufbaus verziehen, sich von Halterungen lösen oder sich nach dem Entfernen von der Bauplatte verziehen, insbesondere bei großen flachen Abschnitten oder asymmetrischen Geometrien, wie sie bei Trägern üblich sind. Verziehen von Aluminium ist ein bekanntes Problem.
- Lösungen:
- DfAM: Konstruktionsmerkmale zur Minimierung von Spannungskonzentrationen (Ausrundungen, gleichmäßige Dicke).
- Optimierte Orientierung und Stützen: Richten Sie das Teil strategisch aus und entwerfen Sie robuste Stützstrukturen, um das Teil effektiv zu verankern und die Wärme abzuleiten.
- Optimierung der Prozessparameter: Feinabstimmung von Laserleistung, Scan-Geschwindigkeit und Scan-Strategie (z. B. Insel-Scanning) zur Minimierung von Wärmegradienten.
- Wärmemanagement: Verwendung beheizter Bauplatten und kontrollierter Kammeratmosphären.
- Obligatorischer Stressabbau: Durchführung einer Spannungsarmglühung unmittelbar nach dem Drucken.
- Kontrolle der Porosität:
- Herausforderung: Während des Druckvorgangs können sich kleine innere Hohlräume (Poren) bilden, die durch Gaseinschlüsse (aus Pulver oder Schutzgas) oder unvollständiges Schmelzen (Schmelzlücken) entstehen. Poren können die mechanischen Eigenschaften erheblich verschlechtern, insbesondere die Ermüdungsfestigkeit, die für Strukturträger entscheidend ist.
- Lösungen:
- Hochwertiges Pulver: Die Verwendung von Pulver mit niedriger interner Gasporosität, kontrollierter Partikelgrößenverteilung und guter Fließfähigkeit (Met3dp’s Fokus auf fortschrittliche sicherheit beim Umgang mit Pulver und Produktion ist hier der Schlüssel).
- Optimierte Prozessparameter: Gewährleistung einer ausreichenden Energiedichte für ein vollständiges Schmelzen ohne Keyholing (Dampfdruckinstabilität).
- Kontrolle der inerten Atmosphäre: Aufrechterhaltung einer hochreinen Inertgasumgebung (Argon) in der Baukammer, um die Oxidation und die Gasaufnahme zu minimieren.
- Heiß-Isostatisches Pressen (HIP): Ein effektiver Nachbearbeitungsschritt zum Schließen von Restporosität.
- NDT-Inspektion: Einsatz von CT-Scans zur Feststellung und Quantifizierung von Porosität.
- Unterstützung bei der Beseitigung von Schwierigkeiten:
- Herausforderung: Stützen, die zwar notwendig sind, müssen entfernt werden. Komplexe interne Kanäle oder dicht gepackte Gitterstrukturen in Trägern können die probleme beim Entfernen der Stütze besonders schwierig, zeitaufwändig und potenziell schädlich für das Teil.
- Lösungen:
- DfAM: Entwerfen Sie so, dass die Stützen so gering wie möglich gehalten werden und die Zugänglichkeit gewährleistet ist. Verwenden Sie nach Möglichkeit selbsttragende Winkel (>45°). Entwerfen Sie interne Kanäle, die groß genug für den Zugang und die Entfernung von Pulver und Stützen sind.
- Optimierte Unterstützungsstrukturen: Verwenden Sie Auflagentypen (z. B. Baum, Kegel), die leichter zu entfernen sind und die Kontaktpunkte mit der Werkstückoberfläche minimieren.
- Spezialisierte Entfernungstechniken: Einsatz geeigneter Werkzeuge und Methoden (manuell, maschinell, EDM) je nach Standort und Komplexität des Trägers.
- Einschränkungen der Oberflächenbeschaffenheit:
- Herausforderung: Die Oberflächenrauheit von L-PBF-Bauteilen entspricht möglicherweise nicht den Anforderungen der Luft- und Raumfahrt an die Ermüdungseigenschaften oder die aerodynamische Glätte der Außenflächen.
- Lösungen:
- Orientierung: Ausrichtung der kritischen Flächen nach oben oder vertikal für eine bessere Ausführung im eingebauten Zustand.
- Nachbearbeiten: Durchführung geeigneter Nachbearbeitungsschritte (Perlstrahlen, Bearbeiten, Polieren) wie in der DfAM-Phase geplant.
- Prozesswiederholbarkeit und -konsistenz:
- Herausforderung: Um sicherzustellen, dass jeder produzierte Strahl die gleichen Abmessungen, das gleiche Mikrogefüge und die gleichen mechanischen Eigenschaften aufweist, ist eine strenge Kontrolle der gesamten Prozesskette erforderlich, von der Pulvercharge bis zur Endkontrolle.
- Lösungen:
- Robustes Qualitätsmanagementsystem (QMS): Implementierung strenger Verfahren für Maschinenkalibrierung, Wartung, Pulverhandhabung, Kontrolle der Prozessparameter und Bedienerschulung (unerlässlich für Zertifizierungen in der Luft- und Raumfahrt wie AS9100).
- AM Prozessüberwachung: Einsatz von Sensoren und Überwachungssystemen (z. B. Schmelzbadüberwachung) zur Verfolgung der Baukonsistenz in Echtzeit.
- Umfassende Tests: Einheitliche Materialprüfung (Zugproben) bei jedem Bau.
Met3dp begegnet diesen Herausforderungen mit jahrzehntelanger Erfahrung in der additiven Fertigung von Metallen. Unser umfassender Ansatz, der fortschrittliche SEBM- (Anmerkung: L-PBF wird für Aluminium verwendet) und L-PBF-Drucker, hochwertige Pulverproduktion mittels Gaszerstäubung und PREP-Technologien sowie spezielle Anwendungsentwicklungsdienste umfasst, stellt sicher, dass wir zuverlässig komplexe Träger für die Luft- und Raumfahrt herstellen können, die den anspruchsvollen Standards der Branche entsprechen. Unser Fokus auf Prozesskontrolle und Qualitätssicherung minimiert die Risiken und liefert zuverlässige Komponenten. Erkunden Sie Über uns um mehr über Met3dp’s Engagement zur Förderung der additiven Fertigung zu erfahren.
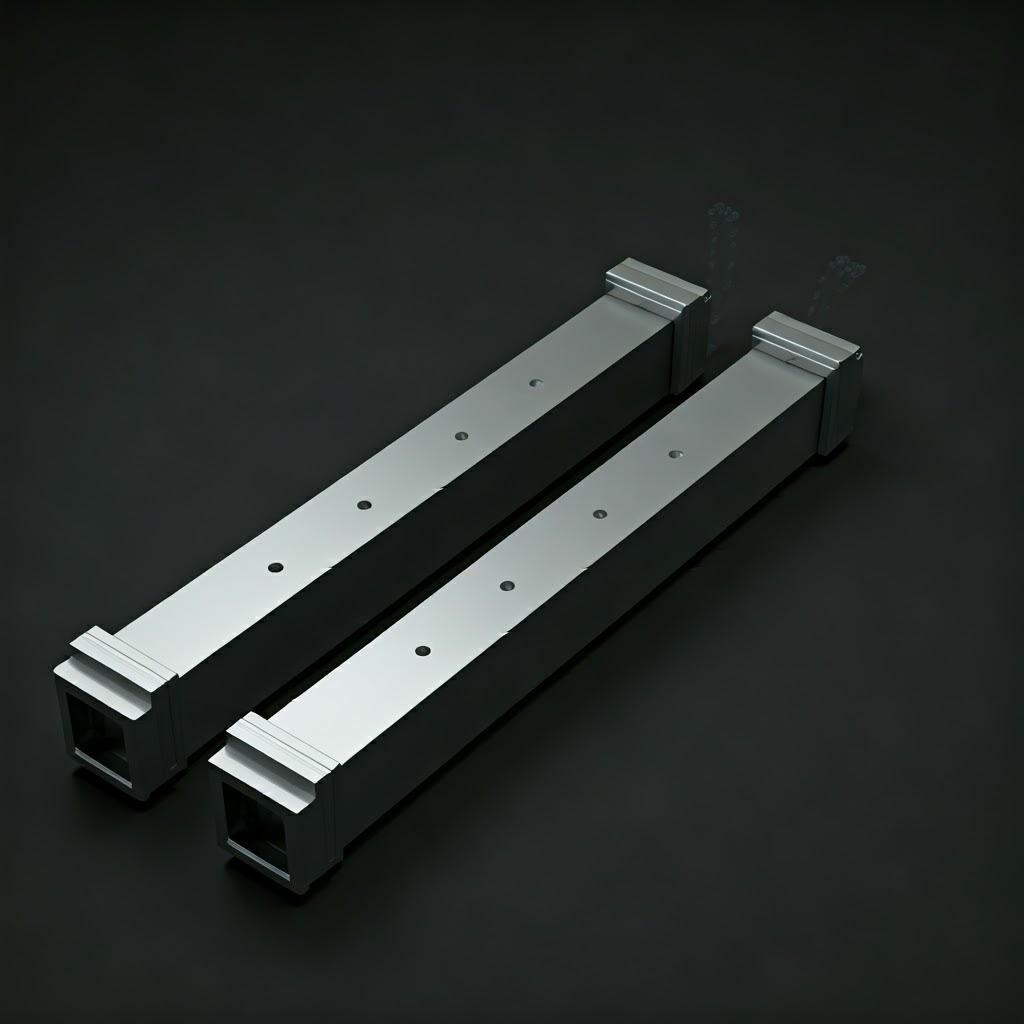
Die Auswahl Ihres Partners: Die Wahl des richtigen 3D-Druckdienstleisters für Metall
Der Erfolg der Integration von 3D-gedruckten Aluminiumträgern in Ihre Luft- und Raumfahrtprojekte hängt wesentlich von den Fähigkeiten und der Zuverlässigkeit Ihres Fertigungspartners ab. Die Wahl des richtigen 3D-Druck-Servicebüro für Metall oder Lieferant für additive Fertigung in der Luft- und Raumfahrt ist eine wichtige Entscheidung für Ingenieure und Beschaffungsmanager. Die einzigartigen Anforderungen der Luft- und Raumfahrtindustrie - strenge Qualitätsanforderungen, komplexe Geometrien, fortschrittliche Materialien und strenge Zertifizierungsanforderungen - erfordern einen Anbieter mit spezialisiertem Fachwissen und bewährter Leistung.
Schlüsselkriterien für die Bewertung von AM-Anbietern für Träger der Luft- und Raumfahrt:
- Zertifizierungen für die Luft- und Raumfahrt & Qualitätsmanagement:
- AS9100-Zertifizierung: Dies ist der Goldstandard für Qualitätsmanagementsysteme (QMS) in der Luft-, Raumfahrt- und Verteidigungsindustrie. Vergewissern Sie sich, dass der Anbieter über eine aktuelle AS9100-Zertifizierung (oder eine gleichwertige Zertifizierung wie EN 9100) verfügt, die robuste, auf die Anforderungen der Luft- und Raumfahrt zugeschnittene Prozesse für Rückverfolgbarkeit, Risikomanagement, Prozesskontrolle und Qualitätssicherung nachweist.
- Dokumentiertes QMS: Auch über die Zertifizierung hinaus sollten Sie die gesamte QMS-Dokumentation überprüfen, einschließlich der Verfahren für Materialhandhabung, Maschinenkalibrierung, Bedienerschulung, Prozessvalidierung und Abweichungsmanagement.
- Materialkenntnis & Fähigkeit:
- Nachgewiesene Erfahrung mit AlSi10Mg & Scalmalloy®: Vergewissern Sie sich, dass der Lieferant über umfangreiche, dokumentierte Erfahrungen mit dem Drucken der für Ihren Träger benötigten Aluminiumlegierung verfügt. Fragen Sie nach Fallstudien, Daten zur Parameterentwicklung oder Testergebnissen zu den Materialeigenschaften dieser Legierungen, die auf ihren Maschinen verarbeitet wurden.
- Qualitätskontrolle des Pulvers: Erkundigen Sie sich nach den Verfahren zur Beschaffung, Prüfung, Handhabung, Lagerung und zum Recycling von Metallpulvern, um Verunreinigungen zu vermeiden und die Konsistenz von Charge zu Charge zu gewährleisten. Anbieter wie Met3dp, die ihre eigenen hochwertigen Pulver mit fortschrittlichen Methoden wie der Gasverdüsung herstellen, bieten erhebliche Vorteile bei der Materialkontrolle und Rückverfolgbarkeit.
- Ausrüstung & Technologie:
- Maschinenplattform: Informieren Sie sich über die spezifischen L-PBF-Maschinen, die sie betreiben. Handelt es sich um industrietaugliche Maschinen, die für ihre Zuverlässigkeit und Konsistenz bekannt sind? (Met3dp setzt branchenführende Drucker ein, die für anspruchsvolle Anwendungen optimiert sind).
- Bauvolumen: Vergewissern Sie sich, dass die Maschinen einen ausreichend großen Bauraum haben, um die Größe Ihres Trägers aufnehmen zu können.
- Prozessüberwachung: Verfügen ihre Maschinen über In-situ-Prozessüberwachungsfunktionen (z. B. Schmelzbadüberwachung, Wärmebildtechnik), um die Qualitätskontrolle während der Herstellung zu verbessern?
- Technisches Fachwissen & Technische Unterstützung:
- DfAM-Unterstützung: Bietet der Anbieter eine Beratung zum Design for Additive Manufacturing (DfAM) an, um Ihr Strahldesign hinsichtlich Druckbarkeit, Gewichtsreduzierung und Leistung zu optimieren?
- Anwendungstechnik: Kann ihr Team Einblicke in die Materialauswahl, die Ausrichtungsstrategien, die Erstellung von Unterlagen und die Nachbearbeitungsplanung geben?
- Problemlösung: Verfügen sie über erfahrene Ingenieure, die in der Lage sind, mögliche Probleme während der Produktion zu beheben?
- Nachbearbeitungsmöglichkeiten:
- In-House vs. Outsourced: Ermitteln Sie, welche Nachbearbeitungsschritte (Spannungsarmglühen, Wärmebehandlung, HIP, Entfernen von Stützen, Bearbeitung, Endbearbeitung, Prüfung) intern und welche extern durchgeführt werden. Eigene Kapazitäten bieten im Allgemeinen eine bessere Kontrolle über Qualität, Vorlaufzeit und Kommunikation.
- Ausrüstung und Fachwissen: Überprüfen Sie, ob sie über die notwendige Ausrüstung (Öfen, CNC-Maschinen, CMMs, NDT-Ausrüstung) und geschultes Personal für die erforderlichen Nachbearbeitungsschritte verfügen.
- Kapazität & Vorlaufzeit:
- Produktionskapazität: Können sie das von Ihnen benötigte Volumen bewältigen, sei es für Prototypen oder für die Serienproduktion?
- Zitierte Vorlaufzeiten: Sind ihre Vorlaufzeiten wettbewerbsfähig und realistisch? Informieren Sie sich über die Verfahren zur Planung und Verwaltung der Produktionsabläufe.
- Angebotsanfrage (RFQ) Prozess & Kommunikation:
- Bewerten Sie ihre Reaktionsfähigkeit und Klarheit während des anfrage für ein Angebot (RFQ) AM verfahren. Wird ein detaillierter Kostenvoranschlag erstellt, in dem alle Kosten und Schritte aufgeführt sind?
- Beurteilen Sie ihre Kommunikationsprotokolle und ihre Bereitschaft zur Zusammenarbeit während des gesamten Projekts.
Met3dp, mit Hauptsitz in Qingdao, China, verkörpert diese Kriterien und positioniert sich als führender Partner für die additive Fertigung in der Luft- und Raumfahrt. Mit jahrzehntelanger kollektiver Erfahrung, branchenführender Drucktechnologie, fortschrittlichen Metallpulver produktionssystemen (Gaszerstäubung und PREP) und einem umfassenden Dienstleistungsangebot, das von der DfAM-Unterstützung bis zur Endkontrolle reicht, bietet Met3dp End-to-End-Lösungen. Unser Engagement für Qualität und Innovation ermöglicht es uns, mit führenden Luft- und Raumfahrtunternehmen auf der ganzen Welt zusammenzuarbeiten und ihnen dabei zu helfen, die Einführung von Metall-AM für kritische Komponenten wie strukturelle Träger zu beschleunigen.
Kostentreiber und erwartete Vorlaufzeiten für 3D-gedruckte Träger
Wenn man 3D-gedruckte Aluminiumträger in Betracht zieht, ist es für die Projektplanung und Budgetierung wichtig, die Faktoren zu verstehen, die die Kosten und den Produktionszeitraum beeinflussen. Während AM langfristige Einsparungen durch Gewichtsreduzierung und Teilekonsolidierung bieten kann, müssen die anfänglichen Komponentenkosten sorgfältig bewertet werden.
Die wichtigsten Kostenfaktoren beim 3D-Druck von Metall:
- Materialverbrauch:
- Teilband: Die Menge an AlSi10Mg- oder Scalmalloy®-Pulver, die für den Druck des Strahls selbst benötigt wird. Scalmalloy® ist pro Kilogramm deutlich teurer als AlSi10Mg.
- Unterstützungsstruktur Volumen: Das für Stützstrukturen benötigte Material, das später entfernt wird, aber dennoch während des Drucks verbraucht wird. Optimiertes Design (DfAM) minimiert den Bedarf an Stützstrukturen.
- Pulverabfall/Recycling: Ein Teil des Pulvers kann nicht vollständig recycelt werden oder geht bei der Handhabung verloren, was die Kosten leicht erhöht.
- Maschinenzeit (Bauzeit):
- Teilhöhe & Volumen: Höhere Teile und Teile mit größeren Querschnittsflächen brauchen länger, um Schicht für Schicht gedruckt zu werden.
- Komplexität: Komplizierte Merkmale oder umfangreiche Gitterstrukturen können die Scanzeit pro Schicht erhöhen.
- Verschachtelung: Das gleichzeitige Drucken mehrerer Teile in einem Bauvorgang (Nesting) kann die Maschinenauslastung verbessern und die Kosten pro Teil senken, was insbesondere für folgende Bereiche relevant ist Großhandelskäufer oder größere Produktionsläufe.
- Maschine Stundensatz: Basierend auf den Kapitalkosten, der Wartung, dem Betrieb und der Abschreibung der industriellen L-PBF-Maschine.
- Nachbearbeiten:
- Arbeit & Ausrüstung: Die Zeit und die Ressourcen, die für die Pulverentfernung, den Spannungsabbau, die Wärmebehandlung, die Entfernung von Stützen, HIP (falls erforderlich), die Oberflächenbearbeitung und die CNC-Bearbeitung erforderlich sind, erhöhen die Endkosten erheblich.
- Komplexität: Die schwierige Entfernung von Trägern oder umfangreiche Bearbeitungsanforderungen erhöhen die Nachbearbeitungskosten.
- Qualitätskontrolle & Inspektion:
- Ebene der Inspektion: Grundlegende Maßprüfungen sind Standard, aber strenge Anforderungen der Luft- und Raumfahrt wie CT-Scans, detaillierte CMM-Berichte oder umfangreiche Materialprüfungen verursachen zusätzliche Kosten.
- Engineering & Einrichtung:
- Vorbereitung der Datei: Zeit, die für die Vorbereitung der CAD-Datei, die Ausrichtung des Teils, die Erzeugung von Stützen und das Schneiden des Modells für den Druck benötigt wird.
- DfAM-Unterstützung: Ist eine umfassende Designberatung erforderlich, so kann diese in Rechnung gestellt werden.
- Auftragsvolumen:
- Prototypen vs. Produktion: Bei einmaligen Prototypen sind die Kosten pro Teil in der Regel höher als bei Serienproduktionen, da sich die Rüstkosten über mehrere Einheiten amortisieren.
- Mengenrabatte: Die Anbieter bieten oft Mengenrabatte für größere Bestellmengen, was den Beschaffungsverantwortlichen bei der Beschaffung von Teilen in großem Umfang zugute kommt.
Typische Erwartungen an die Vorlaufzeit:
Die Vorlaufzeit ist die Dauer von der Auftragsbestätigung bis zur Auslieferung des endgültigen Teils. Sie hängt von der Komplexität des Teils, der Größe, der Menge, der aktuellen Maschinenverfügbarkeit und dem Umfang der erforderlichen Nachbearbeitung ab.
- Prototyping (1-10 Teile): Typischerweise reicht die Bandbreite von 1 bis 4 Wochen. Dies umfasst den Druck, die grundlegende Nachbearbeitung (Spannungsentlastung, Entfernen von Stützen, Perlstrahlen) und die Standardprüfung. Eilige Optionen können zu einem höheren Preis erhältlich sein.
- Kleinserienfertigung (10-100 Teile): Kann von 3 bis 8 Wochenabhängig von den oben genannten Faktoren und der Kapazität des Lieferanten. Die Terminplanung wird kritischer.
- Serienproduktion (100+ Teile): Die Vorlaufzeiten hängen in hohem Maße vom jeweiligen Teil, dem erforderlichen Durchsatz und den vertraglichen Vereinbarungen ab. Es ist eine gezielte Produktionsplanung erforderlich, die häufig gestaffelte Lieferungen über mehrere Wochen oder Monate umfasst.
Hinweis: Ab Ende April 2025 sind dies allgemeine Schätzungen. Holen Sie immer spezifische Angebote und Vorlaufzeiten von Ihrem gewählten Lieferanten ein, die auf Ihrer genauen Teilegeometrie, Ihrem Material und Ihren Anforderungen basieren.
Es ist wichtig, sich frühzeitig mit potenziellen Lieferanten wie Met3dp in Verbindung zu setzen, um genaue Informationen zu erhalten Preisgestaltung bei der additiven Fertigung und Vorlaufzeitschätzungen auf der Grundlage Ihrer spezifischen Luft- und Raumfahrt-Stützbalkenkonstruktion und Projektanforderungen.

Häufig gestellte Fragen (FAQ) zu 3D-gedruckten Aluminiumträgern
Hier finden Sie Antworten auf einige häufig gestellte Fragen von Ingenieuren und Beschaffungsmanagern zum Einsatz der additiven Fertigung für Aluminiumträger in der Luftfahrt:
1. Wie ist die Festigkeit von 3D-gedrucktem AlSi10Mg/Scalmalloy® im Vergleich zu gekneteten Aluminiumlegierungen?
- AlSi10Mg (T6): Die Festigkeit ist im Allgemeinen vergleichbar mit der mittlerer Aluminiumgusslegierungen oder einiger Knetlegierungen der Serie 6xxx. Die hohe Festigkeit von Knetlegierungen für die Luft- und Raumfahrt wie 7075-T6 oder 2024-T3 wird in der Regel nicht direkt erreicht. Sein Vorteil liegt jedoch in der Möglichkeit, optimierte, leichte Konstruktionen (über DfAM) zu erstellen, die die erforderliche strukturelle Leistung mit weniger Material erreichen.
- Scalmalloy® (wärmebehandelt): Diese Legierung wurde speziell für AM entwickelt und bietet eine deutlich höhere Festigkeit als AlSi10Mg. Ihre Streck- und Zugfestigkeit kann an die einiger hochfester Knetlegierungen der Serie 7xxx heranreichen oder diese sogar übertreffen, kombiniert mit ausgezeichneter Duktilität und Ermüdungseigenschaften. Dies macht ihn zu einer sehr wettbewerbsfähigen Option für anspruchsvolle strukturelle Anwendungen, bei denen Gewichtseinsparungen entscheidend sind.
- Das Wichtigste zum Mitnehmen: Die direkte Substitution von Materialien auf der Grundlage der im Datenblatt angegebenen Festigkeit ist nicht das Ziel. Der Wert von AM’ liegt in der Optimierung des Designs in Kombination mit einer geeigneten Materialauswahl (wie Scalmalloy®), um eine überlegene strukturelle Effizienz zu erreichen.
2. Was sind die typischen Vorlaufzeiten für einen Prototyp eines Luft- und Raumfahrtbalkens?
- Wie bereits erwähnt, liegen die typischen Vorlaufzeiten für eine einzelne oder kleine Charge von Prototyp-Aluminiumträgern (einschließlich Druck, Standard-Wärmebehandlung, Entfernen der Träger und grundlegende Endbearbeitung/Inspektion) normalerweise bei 1 bis 4 Wochen. Dies kann je nach Teilegröße, Komplexität, spezifischer Legierung (Scalmalloy® hat möglicherweise leicht abweichende Wärmebehandlungszyklen), aktueller Auslastung des Zulieferers und der Frage, ob optionale Verfahren wie HIP oder umfangreiche Bearbeitung erforderlich sind, variieren. Erkundigen Sie sich immer bei Ihrem Lieferanten.
3. Sind 3D-gedruckte Aluminiumträger flugtauglich?
- Die luft- und Raumfahrtzertifizierung AM-Teile prozess ist komplex und gilt für die gesamten herstellungsprozess, nicht nur das Teil selbst. Ein 3D-gedruckter Balken ist nicht per se flugtauglich, nur weil er gedruckt ist.
- Zertifizierungsweg: Die Erlangung der Flugzulassung beinhaltet:
- Verwendung eines qualifizierten Herstellungsprozesses (Maschinen, Parameter, Nachbearbeitung), der in hohem Maße kontrolliert und reproduzierbar ist.
- Herstellung in einer AS9100-zertifizierten Einrichtung.
- Verwendung von qualifiziertem Material (Pulver, das den Spezifikationen für die Luft- und Raumfahrt wie den AMS-Normen entspricht).
- Strenge Prozessdokumentation, Rückverfolgbarkeit und Qualitätskontrolle.
- Umfassende Bauteilprüfungen (statisch, Ermüdung, Umwelteinflüsse) und Analysen zum Nachweis der Erfüllung der Lufttüchtigkeitsanforderungen, die häufig von den Aufsichtsbehörden (FAA, EASA) und den OEM der Luft- und Raumfahrtindustrie festgelegt werden.
- Viele Unternehmen fliegen bereits erfolgreich mit 3D-gedruckten Strukturbauteilen, darunter Träger und Halterungen aus Aluminium- und Titanlegierungen. Dies erfordert jedoch einen speziellen Qualifizierungs- und Zertifizierungsaufwand, an dem der Bauteildesigner, der Hersteller (wie Met3dp) und der Flugzeug-/Systemintegrator beteiligt sind.
4. Kann Met3dp großvolumige Produktionsaufträge für Träger für die Luft- und Raumfahrt abwickeln?
- Ja, Met3dp ist in der Lage, Anforderungen zu erfüllen, die vom schnellen Prototyping bis hin zur Großserienproduktion reichen. Unsere Einrichtung verfügt über mehrere branchenführende L-PBF-Drucker, die eine skalierbare Produktionskapazität ermöglichen. Wir arbeiten mit Kunden aus der Luft- und Raumfahrtindustrie zusammen, um robuste Produktionsabläufe, Qualitätspläne und Lieferpläne zu erstellen, die auf die Deckung der hohen Nachfrage nach kritischen Komponenten wie z. B. Strukturträgern zugeschnitten sind und eine zuverlässige Lieferkette für Großhandelskäufer und OEMs. Unsere umfassenden Fähigkeiten in der Pulverproduktion, im Druck, in der Nachbearbeitung und in der Qualitätssicherung unterstützen den nahtlosen Übergang vom Prototyp zur Fertigung in Serie.
Schlussfolgerung: Die Zukunft der Luft- und Raumfahrtstrukturen ist additiv
Die Reise durch die Feinheiten der Herstellung träger für die Luft- und Raumfahrt mit 3D-gedruckte Aluminiumlegierungen wie AlSi10Mg und Scalmalloy® zeigt einen klaren Weg auf: Die additive Fertigung ist nicht länger ein Nischenwerkzeug für den Prototypenbau, sondern ein leistungsfähiger Wegbereiter für die Entwicklung und Produktion der nächsten Generation in der Luft- und Raumfahrt. Die Fähigkeit, hochoptimierte, Leichtbaustrukturen durch Topologieoptimierung, die Konsolidierung komplexer Baugruppen zu Einzelteilen und die Verwendung von Hochleistungswerkstoffen wie Scalmalloy® bieten greifbare Vorteile bei Treibstoffeffizienz, Nutzlastkapazität und Gesamtleistung des Flugzeugs.
Von den ersten Designüberlegungen, die sich an den DfAM-Prinzipien orientieren, bis hin zu den entscheidenden Schritten der Nachbearbeitung und der Bewältigung der inhärenten Fertigungsherausforderungen erfordert die erfolgreiche Implementierung von AM Fachwissen, Präzision und eine strenge Qualitätskontrolle. Werkstoffe wie AlSi10Mg bieten eine zuverlässige und kosteneffiziente Lösung für viele Anwendungen, während Scalmalloy® den Leistungsrahmen für die anspruchsvollsten strukturellen Anforderungen sprengt.
Die Wahl des richtigen Fertigungspartners ist von entscheidender Bedeutung. Ein Zulieferer wie Met3dp mit umfassender Erfahrung in der Luft- und Raumfahrt, fortschrittlichen Materialkapazitäten, einschließlich eigener Pulverproduktion, modernster L-PBF-Technologie, umfassender Nachbearbeitung und einem Bekenntnis zu AS9100-Qualität ist unerlässlich, um das Potenzial von AM in flugtaugliche Realität zu verwandeln.
Da die Luft- und Raumfahrtindustrie weiterhin nach innovativen Wegen sucht, um leichtere, schnellere und effizientere Flugzeuge und Raumfahrzeuge zu bauen, wird die additive Fertigung von Metallen zweifellos eine immer wichtigere Rolle spielen. Die Website Zukunft der Luft- und Raumfahrtindustrie beinhaltet die Nutzung dieser fortschrittlichen Techniken zur Herstellung von Komponenten, die bisher als unmöglich galten.
Met3dp ist bereit, Ihr Partner für additive Fertigung an dieser Entwicklung teilhaben. Wir laden Ingenieure, Konstrukteure und Beschaffungsmanager aus der Luft- und Raumfahrt, der Automobilindustrie, der Medizintechnik und der Industrie dazu ein, herauszufinden, wie unsere Fähigkeiten die Ziele Ihres Unternehmens unterstützen können. Besuchen Sie unsere Website unter https://met3dp.com/ oder kontaktieren Sie uns noch heute, um Ihre spezifischen Projektanforderungen zu besprechen und herauszufinden, wie 3D-gedruckte Aluminiumträger Ihre Designs aufwerten können.
Teilen auf
MET3DP Technology Co., LTD ist ein führender Anbieter von additiven Fertigungslösungen mit Hauptsitz in Qingdao, China. Unser Unternehmen ist spezialisiert auf 3D-Druckgeräte und Hochleistungsmetallpulver für industrielle Anwendungen.
Fragen Sie an, um den besten Preis und eine maßgeschneiderte Lösung für Ihr Unternehmen zu erhalten!
Verwandte Artikel
Über Met3DP
Aktuelles Update
Unser Produkt
KONTAKT US
Haben Sie Fragen? Senden Sie uns jetzt eine Nachricht! Wir werden Ihre Anfrage mit einem ganzen Team nach Erhalt Ihrer Nachricht bearbeiten.
Holen Sie sich Metal3DP's
Produkt-Broschüre
Erhalten Sie die neuesten Produkte und Preislisten
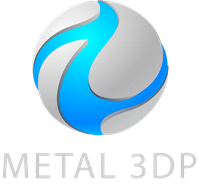
Metallpulver für 3D-Druck und additive Fertigung