3D-gedruckte chirurgische Werkzeuge aus Edelstahl und Titan
Inhaltsübersicht
Revolutionierung der Chirurgie: Der Aufstieg der 3D-gedruckten chirurgischen Werkzeuge aus Edelstahl und Titan
Der Operationssaal ist ein Ort der Präzision, an dem das Können des Chirurgen an erster Stelle steht, aber auch die Qualität und das Design der Instrumente sind entscheidend. Seit Jahrhunderten werden chirurgische Instrumente mit traditionellen Methoden wie Schmieden, Gießen und maschineller Bearbeitung hergestellt. Diese Techniken sind zwar effektiv, stoßen aber oft an ihre Grenzen, wenn es darum geht, hochkomplexe Geometrien und patientenindividuelle Designs herzustellen oder schnelle Iterationen während der Entwicklung zu ermöglichen. Hier kommt die additive Fertigung von Metall (AM) ins Spiel, besser bekannt als 3D-Metalldruck - eine transformative Technologie, die das Design und die Herstellung von chirurgischen Instrumenten und letztlich auch die Ergebnisse für die Patienten neu definieren wird.
Metall 3D-Druck baut Teile Schicht für Schicht direkt aus einem digitalen Modell mit Hochleistungsmetallpulvern auf. Dieser Ansatz eröffnet eine noch nie dagewesene Designfreiheit und ermöglicht die Herstellung von chirurgischen Werkzeugen mit komplizierten Merkmalen, internen Kanälen, Gitterstrukturen zur Gewichtsreduzierung und ergonomischen Formen, deren Herstellung bisher unmöglich oder unerschwinglich war. Stellen Sie sich Pinzetten vor, die perfekt an die Hand des Chirurgen angepasst sind, Führungen, die anhand von CT-Scans genau auf die einzigartige Anatomie des Patienten abgestimmt sind, oder komplexe Retraktoren, die mehrere Funktionen in einem einzigen, optimierten Instrument vereinen. Dies ist keine Science-Fiction, sondern die Realität, die durch Metal AM möglich wird.
Diese Technologie ist besonders in anspruchsvollen Bereichen wie Orthopädie, Neurochirurgie, Herz- und Gefäßchirurgie und minimalinvasiven Verfahren von Bedeutung, wo Standardinstrumente nicht immer ausreichen. Die Möglichkeit, in kürzester Zeit Prototypen zu erstellen und kundenspezifische, kleinvolumige oder hochkomplexe Instrumente zu produzieren, bietet erhebliche Vorteile gegenüber der konventionellen Fertigung, die oft teure Werkzeuge und lange Vorlaufzeiten erfordert, vor allem bei speziellen Designs.
Außerdem werden bei der Metall-AM Materialien verwendet, die für ihre Eignung für medizinische Anwendungen bekannt sind. Zwei herausragende Werkstoffe sind Edelstahl 316L und die Titanlegierung Ti-6Al-4V (Grade 5). Beide bieten eine hervorragende Biokompatibilität, Korrosionsbeständigkeit und die mechanische Festigkeit, die erforderlich ist, um den Strapazen der Chirurgie und wiederholten Sterilisationszyklen standzuhalten. Durch den Einsatz fortschrittlicher Pulverzerstäubungstechniken stellen Anbieter wie Met3dp sicher, dass diese Materialien in Pulverform die hohe Sphärizität und Fließfähigkeit aufweisen, die für die Herstellung dichter, hochwertiger gedruckter Teile mit hervorragenden mechanischen Eigenschaften erforderlich sind, die für kritische chirurgische Anwendungen entscheidend sind. Die Integration von 3D-Druck von Metall in die Lieferkette für chirurgische Instrumente ist nicht nur eine Alternative, sondern ein Upgrade, das mehr Leistung, Personalisierung und potenziell schnellere Innovationszyklen für lebensrettende Geräte verspricht.
Anwendungen von additiv gefertigten chirurgischen Instrumenten: Präzision in allen medizinischen Fachbereichen
Die Vielseitigkeit des 3D-Drucks von Metall ermöglicht seine Anwendung in einem breiten Spektrum chirurgischer Disziplinen. Seine Fähigkeit, komplexe, maßgeschneiderte und leichtgewichtige Instrumente zu erstellen, ist von unschätzbarem Wert, wenn Präzision und spezifische Funktionalität entscheidend sind. Beschaffungsmanager und Lieferanten von chirurgischen Instrumenten erkennen zunehmend das Potenzial von AM, um ungedeckte Bedürfnisse zu erfüllen und die Effizienz von Verfahren zu verbessern.
- Orthopädie: In diesem Bereich wurde AM schon früh für patientenindividuelle chirurgische Führungen (PSI) für Knie- und Hüftprothesen eingesetzt, die eine präzise Implantatplatzierung gewährleisten. Komplexe Bohrschablonen, Osteotome und maßgeschneiderte Instrumente für die Wirbelsäulenfusion oder Traumachirurgie sind ebenfalls gängige Anwendungen. Die Möglichkeit, poröse oder gitterartige Strukturen zu integrieren, kann die Handhabung und Visualisierung der Instrumente erleichtern.
- Neurochirurgie: Die heikle Natur der Neurochirurgie erfordert außergewöhnlich präzise und oft miniaturisierte Instrumente. AM ermöglicht die Entwicklung maßgeschneiderter Führungen für die Elektrodenplatzierung bei der Tiefenhirnstimulation sowie spezieller Mikropinzetten, Dissektoren und Retraktoren, die für die Navigation in komplexen neuralen und vaskulären Strukturen maßgeschneidert sind.
- Herz- und Gefäßchirurgie: Instrumente wie kundenspezifische Ventilgrößen, komplexe Klemmen oder spezielle Komponenten von Einführsystemen für minimalinvasive Verfahren profitieren von der Designfreiheit der AM. Die Möglichkeit, Werkzeuge mit integrierten Funktionen zu erstellen, kann die Anzahl der benötigten Instrumente reduzieren und die Verfahrensdauer potenziell verkürzen.
- Minimal-invasive Chirurgie (MIS): Laparoskopische und endoskopische Verfahren erfordern lange, dünne Instrumente mit komplexen Endeffektoren. AM ermöglicht die Entwicklung ergonomischer Griffe, gelenkiger Werkzeugspitzen und Instrumente mit internen Kanälen für Spülung, Absaugung oder Glasfaseroptik, was die Kontrolle des Chirurgen und die Möglichkeiten des Verfahrens verbessert.
- Kraniomaxillofaziale Chirurgie (CMF): Für die rekonstruktive Chirurgie werden patientenspezifische Schneideschablonen, Repositionierungsschablonen und maßgeschneiderte Instrumente auf der Grundlage von CT/MRI-Daten verwendet, um die Genauigkeit der Knochenschnitte und der Repositionierung zu gewährleisten.
- Zahn- und Oralchirurgie: Maßgeschneiderte Bohrschablonen für das Einsetzen von Implantaten, spezielle Extraktionswerkzeuge und kieferorthopädische Instrumente können mit Metall-AM präzise hergestellt werden.
- Allgemeine Chirurgie: Während viele Standardinstrumente ausreichen, findet AM Anwendung bei der Herstellung spezieller Retraktoren, Klemmen oder Pinzetten für schwierige Fälle oder neuartige chirurgische Ansätze.
- Rapid Prototyping und Werkzeugentwicklung: Neben den Instrumenten für den Endgebrauch ist AM von unschätzbarem Wert für die schnelle Iteration von Designs in der Entwicklungsphase. Chirurgen können verschiedene ergonomische Formen oder funktionale Merkmale schnell und kostengünstig testen, bevor sie sich für die endgültige Produktion entscheiden.
Tabelle: Beispiele für 3D-gedruckte chirurgische Werkzeuge nach Fachgebiet
Medizinisches Fachgebiet | Beispiel für AM-Anwendungen | Angesprochene Hauptvorteile |
---|---|---|
Orthopädie | Patientenspezifische Instrumente (PSI), individuelle Bohrschablonen, Wirbelsäuleninstrumentarium | Genauigkeit, reduzierte OP-Zeit, komplexe Geometrie |
Neurochirurgie | Mikro-Instrumente, kundenspezifische Elektrodenführungen, spezialisierte Retraktoren | Miniaturisierung, Präzision, patientenindividuelle Anpassung |
Herz-Kreislauf | Ventilmessgeräte, komplexe Klemmen, Komponenten für MIS-Zuführungssysteme | Individuelle Anpassung, integrierte Funktionen, komplexe Geometrien |
Minimalinvasiv | Gelenkige Endeffektoren, ergonomische Griffe, Instrumente mit internen Kanälen | Funktionalität, Ergonomie, Miniaturisierung |
Kraniomaxillofazial | Patientenspezifische Schnitt-/Repositionierungshilfen, individuelle Fixierungswerkzeuge | Genauigkeit, Vorhersagbarkeit, verkürzte Operationszeit |
Zahn-/Oralchirurgie | Implantat-Bohrschablonen, Spezialisierte Extraktionswerkzeuge | Präzision, Passgenauigkeit, Effizienz |
Allgemeine Chirurgie | Spezialisierte Retraktoren, individuelle Klammern für einzigartige Fälle | Nischenanwendungen für spezifische anatomische Bedürfnisse |
Entwicklung von Tools | Funktionale Prototypen, Ergonomische Modelle | Geschwindigkeit, Kosteneffizienz, Design-Iteration |
In Blätter exportieren
Die Möglichkeit, Instrumente nicht nur auf das Verfahren, sondern möglicherweise auch auf die Anatomie des einzelnen Patienten oder die Präferenzen des Chirurgen zuzuschneiden, markiert einen bedeutenden Wandel hin zu einer personalisierten chirurgischen Versorgung, der durch Fortschritte in der additiven Fertigungstechnologie vorangetrieben wird.
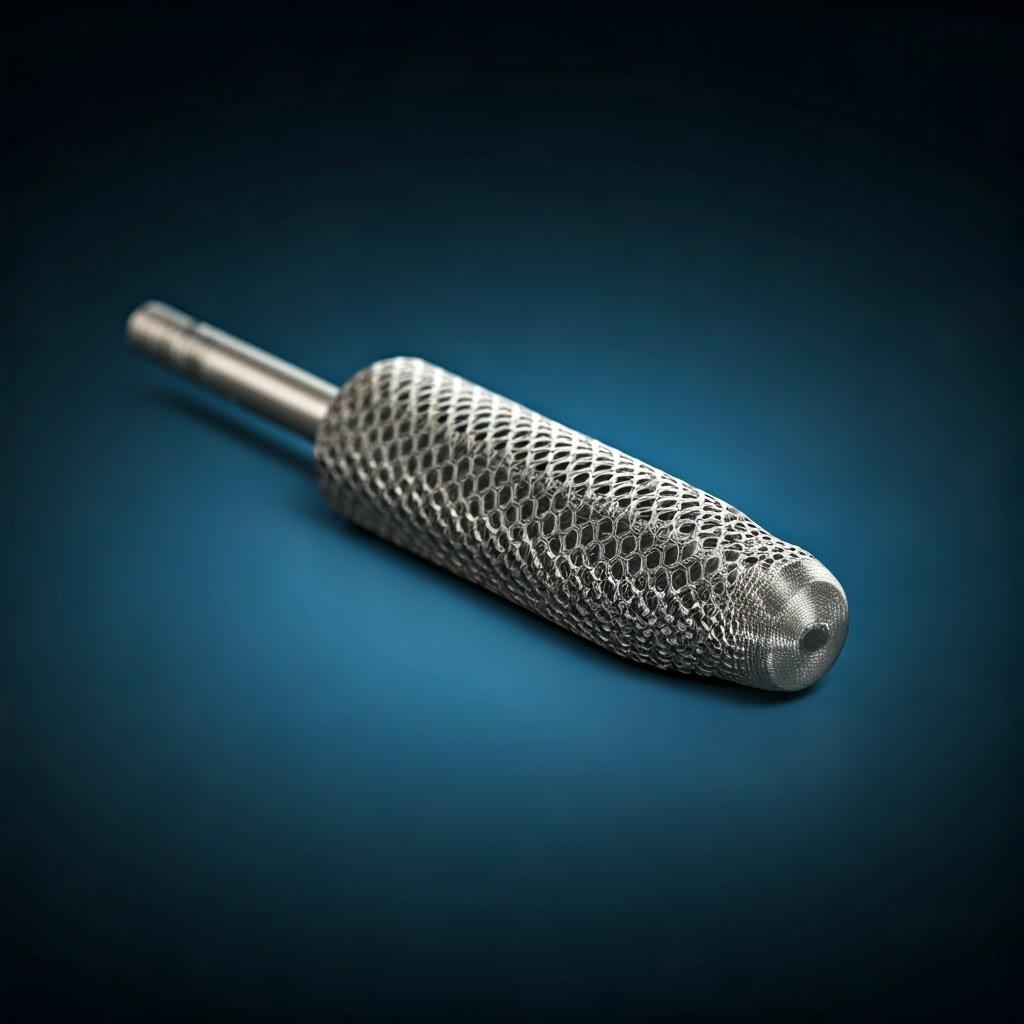
Warum der 3D-Druck von Metall die Herstellung chirurgischer Instrumente verändert
Die herkömmliche Herstellung chirurgischer Instrumente beruht auf subtraktiven (zerspanende Bearbeitung von Material) oder formgebenden Verfahren (Gießen, Schmieden). Obwohl diese Verfahren für Standardinstrumente ausgereift und zuverlässig sind, stellen sie Hürden dar, die durch die additive Fertigung von Metall effektiv überwunden werden können, insbesondere bei speziellen, kundenspezifischen oder komplexen Instrumenten. Für Großeinkäufer und Unternehmen der Medizintechnik, die nach innovativen Lösungen und zuverlässigen Lieferanten für kundenspezifische chirurgische Instrumente suchen, ist es entscheidend, diese Vorteile zu verstehen.
Die wichtigsten Vorteile von Metal AM für chirurgische Werkzeuge:
- Unerreichte Designfreiheit: AM baut Teile Schicht für Schicht auf und ermöglicht so die Herstellung von Geometrien, die mit herkömmlichen Methoden nicht möglich sind. Dies beinhaltet:
- Interne Kanäle: Für die Bewässerung, Absaugung oder die Unterbringung von Lichtleitern.
- Gitterförmige Strukturen: Gewichtsreduzierung ohne Einbußen bei der Festigkeit, Verbesserung der Ergonomie und Verringerung der Ermüdung des Chirurgen.
- Komplexe Kurven und Konturen: Für eine patientenindividuelle Anpassung oder verbesserte Handhabung.
- Teil Konsolidierung: Kombination mehrerer Komponenten einer herkömmlichen Baugruppe in einem einzigen gedruckten Teil, wodurch die Komplexität, potenzielle Fehlerquellen und die Montagezeit reduziert werden.
- Mass Customization und patientenspezifische Instrumente (PSI): AM eignet sich hervorragend für die Herstellung einzigartiger Teile direkt aus digitalen Modellen (z. B. CT/MRI-Scans). Dies ermöglicht es:
- Auf den Patienten abgestimmte Leitfäden: Verbesserung der chirurgischen Genauigkeit in der Orthopädie, CMF und Neurochirurgie.
- Chirurgenspezifische Ergonomie: Werkzeuge, die für optimalen Komfort und Kontrolle für den einzelnen Chirurgen entwickelt wurden.
- Produktion auf Abruf: Herstellung von Spezialwerkzeugen nach Bedarf, wodurch der Lagerbedarf für selten verwendete Artikel reduziert wird.
- Rapid Prototyping und beschleunigte Innovation: Neue Entwürfe für chirurgische Werkzeuge können viel schneller und kostengünstiger als mit herkömmlichen Methoden, die spezielle Werkzeuge erfordern, als Prototypen hergestellt, getestet und wiederholt werden. Dadurch wird der Entwicklungszyklus für neue chirurgische Ansätze und Geräte beschleunigt.
- Materialeffizienz: Bei AM wird in der Regel nur das Material verwendet, das für die Herstellung des Teils und seiner Halterungen benötigt wird, was zu weniger Materialabfall im Vergleich zur subtraktiven Fertigung führt, insbesondere bei komplexen Konstruktionen (Buy-to-Fly-Ratio).
- Optimierung der Lieferkette: Die digitale Fertigung ermöglicht eine dezentralisierte Produktion. Werkzeugentwürfe können digital an zertifizierte Druckereien geschickt werden, die näher am Einsatzort liegen, wodurch sich die Vorlaufzeiten und der logistische Aufwand verringern lassen, auch wenn eine strenge Qualitätskontrolle im medizinischen Bereich nach wie vor von größter Bedeutung ist.
- Potenzial für erweiterte Funktionalität: Die Designfreiheit ermöglicht die Integration von leistungssteigernden Merkmalen, wie z. B. strukturierte Oberflächen für bessere Griffigkeit, optimierte Schneidkanten oder integrierte Sensorfunktionen (in Entwicklung).
Vergleich: Metall-AM vs. traditionelle Fertigung für chirurgische Werkzeuge
Merkmal | Additive Fertigung von Metall (AM) | Traditionelle Fertigung (Schmieden, Zerspanen, Gießen) |
---|---|---|
Komplexität | Hohe Komplexität bei minimalem Kostenanstieg realisierbar | Komplexität erhöht Kosten und Schwierigkeit erheblich |
Personalisierung | Ideal für patientenspezifische und kundenspezifische Teile in kleinen Stückzahlen | Teuer und langsam bei Einzelstücken/Sonderanfertigungen |
Vorlaufzeit (Proto) | Fasten (Tage) | Mäßig bis langsam (Wochen/Monate für die Werkzeugherstellung) |
Vorlaufzeit (Prod) | Mäßig (abhängig vom Volumen, Nachbearbeitung) | Schnell für hochvolumige Standardteile |
Werkzeugkosten | Keine (werkzeuglose Fertigung) | Hohe Anschaffungskosten für Werkzeuge |
Materialabfälle | Im Allgemeinen niedriger (besseres Verhältnis zwischen Anschaffungskosten und Flugkosten) | Kann erheblich sein, insbesondere bei der Bearbeitung |
Gestaltungsfreiheit | Sehr hoch (interne Kanäle, Gitter, organische Formen) | Begrenzt durch Bearbeitungs-/Gussformbeschränkungen |
Teil Konsolidierung | Ausgezeichnete Fähigkeit | Begrenzt, erfordert oft Montage |
Ideales Volumen | Geringes bis mittleres Volumen, Prototypen, Sonderanfertigungen | Hohe Stückzahlen, Standardausführungen |
In Blätter exportieren
AM wird zwar nicht bei allen chirurgischen Instrumenten die herkömmliche Fertigung ersetzen (insbesondere bei einfachen Instrumenten mit hohen Stückzahlen, bei denen die Kosten pro Teil mit herkömmlichen Methoden am niedrigsten sind), aber es bietet einen leistungsstarken, ergänzenden Weg für Innovation, individuelle Anpassung und die Lösung komplexer chirurgischer Herausforderungen. Unternehmen wie Met3dp, die über umfassendes Fachwissen sowohl im Bereich der fortschrittlichen Pulverherstellung als auch der Präzisionsdruckverfahren verfügen, sind wichtige Wegbereiter für diesen Wandel.
Biokompatible Materialien im Blickpunkt: 316L-Edelstahl vs. Ti-6Al-4V-Titan für chirurgische Werkzeuge
Die Wahl des Materials ist für die Entwicklung chirurgischer Instrumente von grundlegender Bedeutung. Die Instrumente müssen stabil, langlebig, korrosionsbeständig gegenüber Körperflüssigkeiten und rauen Sterilisationsverfahren und vor allem biokompatibel sein, d. h. sie dürfen bei der Interaktion mit biologischem Gewebe keine schädlichen Reaktionen hervorrufen. Beim 3D-Druck von chirurgischen Instrumenten aus Metall dominieren zwei Materialien: Edelstahl 316L und die Titanlegierung Ti-6Al-4V (Grade 5). Für Ingenieure und Beschaffungsmanager, die Materialien für die additive Fertigung von Medizinprodukten spezifizieren, ist es wichtig, ihre Eigenschaften zu kennen.
316L-Edelstahl:
- Zusammensetzung: Eine austenitische rostfreie Stahllegierung mit Chrom, Nickel und Molybdän. Das "L" steht für einen niedrigen Kohlenstoffgehalt (<0,03%), der die Korrosionsbeständigkeit verbessert, insbesondere nach dem Schweißen oder Spannungsarmglühen - wichtige Überlegungen nach den thermischen Zyklen beim 3D-Druck.
- Wichtige Eigenschaften:
- Ausgezeichnete Korrosionsbeständigkeit: Sehr widerstandsfähig gegen allgemeine Korrosion, Lochfraß und Spaltkorrosion, entscheidend für die Einwirkung von Körperflüssigkeiten und Sterilisationsmitteln (z. B. Autoklavieren).
- Gute Biokompatibilität: Weithin akzeptiert für temporäre und einige permanente Kontaktanwendungen innerhalb des menschlichen Körpers (gemäß Normen wie ISO 10993).
- Hohe Duktilität und Umformbarkeit: Obwohl sie bei AM weniger relevant ist als bei traditionellen Methoden, deutet sie auf eine gute Zähigkeit hin.
- Gute Festigkeit und Härte: Ausreichend für viele chirurgische Anwendungen wie Retraktoren, Griffe und allgemeine Instrumente.
- Nicht-magnetisch: Im Allgemeinen gelten sie im geglühten Zustand als unmagnetisch, was für die MRT-Kompatibilität wichtig sein kann, obwohl ein gewisser Restmagnetismus durch Kaltverformung oder möglicherweise während der AM-Bearbeitung induziert werden kann.
- Kostengünstig: Im Allgemeinen preiswerter als Titanlegierungen.
- Gut etabliert: Langjährige Verwendung in medizinischen Geräten, die umfangreiche Daten und Vertrautheit liefert.
Ti-6Al-4V (Grad 5) Titanlegierung:
- Zusammensetzung: Eine Alpha-Beta-Titanlegierung mit 6% Aluminium und 4% Vanadium. Sie wird häufig als Ti-6Al-4V ELI (Extra Low Interstitials, Grad 23) für kritische chirurgische Implantate spezifiziert, da sie eine bessere Duktilität und Bruchzähigkeit aufweist, obwohl Grad 5 für Instrumente üblich ist.
- Wichtige Eigenschaften:
- Außergewöhnliche Biokompatibilität: Gilt als eines der am besten biokompatiblen Metalle und wird häufig für Langzeitimplantate (Gelenke, Zahnersatz) und Instrumente verwendet. Bildet eine stabile, passive Oxidschicht.
- Ausgezeichnete Korrosionsbeständigkeit: Hervorragende Beständigkeit gegen Körperflüssigkeiten und verschiedene chemische Umgebungen.
- Hohes Verhältnis von Festigkeit zu Gewicht: Erheblich leichter als Stahl (ca. 40-45% geringere Dichte), aber mit vergleichbarer oder höherer Festigkeit. Dies ist entscheidend für die Verringerung der Ermüdung des Chirurgen bei handgehaltenen Instrumenten und für Instrumente, die in gewichtssensiblen Anwendungen eingesetzt werden.
- Gute Ermüdungsfestigkeit: Wichtig für Instrumente, die wiederholten Belastungszyklen ausgesetzt sind.
- Nicht-magnetisch/MRI-kompatibel: Inhärent nicht magnetisch, daher ideal für Instrumente, die bei MRT-Verfahren verwendet werden.
- Osseointegrationspotenzial: Auch wenn dies eher für Implantate relevant ist, kann die Oberfläche behandelt werden, um das Knochenwachstum zu fördern, falls dies für bestimmte Spezialgeräte erforderlich ist.
- Höhere Kosten: Teureres Rohmaterial und potenziell schwieriger zu verarbeiten als 316L.
Tabelle: Vergleich von 316L und Ti-6Al-4V für 3D-gedruckte chirurgische Werkzeuge
Eigentum | 316L-Edelstahl | Ti-6Al-4V Titan-Legierung | Bedeutung für chirurgische Werkzeuge |
---|---|---|---|
Biokompatibilität | Gut (ISO 10993) | Ausgezeichnet (ISO 10993) | Wesentlich für die Patientensicherheit, Ti-6Al-4V wird oft für Implantate bevorzugt |
Korrosionsbeständigkeit | Ausgezeichnet | Ausgezeichnet / Überragend | Entscheidend für Langlebigkeit und Sterilisationsbeständigkeit |
Dichte | ~8,0 g/cm³ | ~4,4 g/cm³ | Ti-6Al-4V bietet erhebliche Gewichtseinsparungen (Ergonomie) |
Zugfestigkeit (typisch) | Mäßig-hoch (~550-700 MPa, gedruckt) | Sehr hoch (~900-1100 MPa, gedruckt) | Höhere Festigkeit ermöglicht filigranere/robustere Designs mit Ti |
Steifigkeit (Young's Modulus) | Hoch (~193 GPa) | Mäßig (~114 GPa) | 316L ist steifer; Ti-6Al-4V ist flexibler |
Härte | Gut | Gut | Wichtig für Verschleißfestigkeit, Erhaltung scharfer Kanten |
MRI-Kompatibilität | Im Allgemeinen nicht magnetisch (prozessabhängig) | Völlig unmagnetisch | Entscheidend für den Einsatz in MRI-Umgebungen |
Kosten | Unter | Höher | Wesentlicher Faktor bei der Materialauswahl |
Typische AM-Anwendungen | Allgemeine Instrumente, Griffe, Retraktoren | Implantate, hochfeste Werkzeuge, leichte Werkzeuge, MRI-Werkzeuge | Passt die Materialeigenschaften an die Anforderungen der Anwendung an |
In Blätter exportieren
Die Qualität des Materials ist entscheidend: Unabhängig von der gewählten Legierung ist die Qualität des im AM-Verfahren verwendeten Metallpulvers entscheidend. Faktoren wie Partikelgrößenverteilung, Sphärizität, Fließfähigkeit und Reinheit wirken sich direkt auf die Dichte, die mechanischen Eigenschaften und die Oberflächenbeschaffenheit des gedruckten Endprodukts aus. Met3dp nutzt branchenführende Gaszerstäubungs- und Plasma-Rotations-Elektroden-Verfahren (PREP) zur Herstellung hochwertiger sphärischer Metallpulver, einschließlich 316L und Ti-6Al-4V in medizinischer Qualität, um optimale Leistung und Konsistenz für anspruchsvolle chirurgische Anwendungen zu gewährleisten. Die Wahl eines Lieferanten mit robusten Pulverproduktions- und Qualitätskontrollkapazitäten ist für die zuverlässige Herstellung medizinischer Geräte von entscheidender Bedeutung.
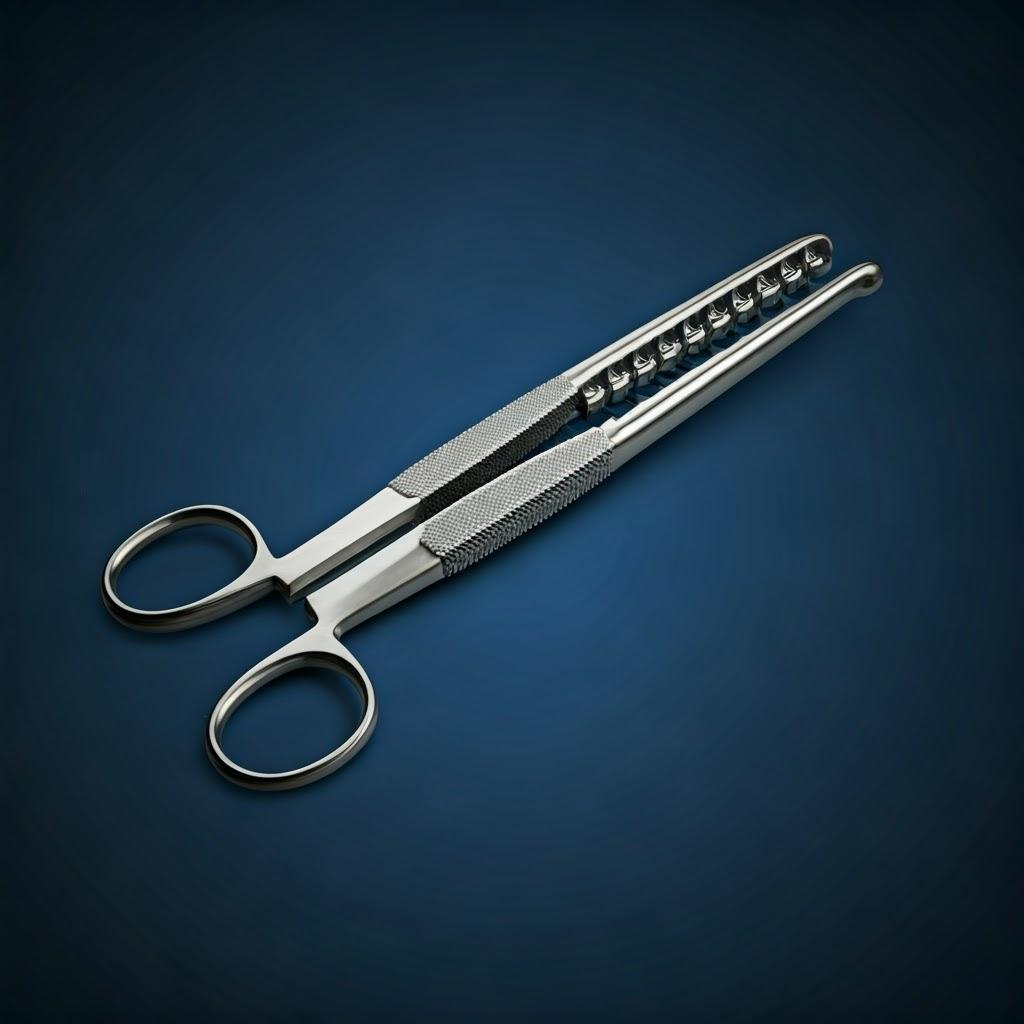
Design for Additive Manufacturing (DfAM)-Prinzipien für hochleistungsfähige chirurgische Werkzeuge
Die einfache Nachbildung eines herkömmlich konstruierten chirurgischen Werkzeugs mit Hilfe des 3D-Drucks schöpft selten das gesamte Potenzial der additiven Fertigung aus. Um die Vorteile der Komplexität, Anpassung und Leistungssteigerung wirklich zu nutzen, müssen Ingenieure das Design for Additive Manufacturing (DfAM) anwenden. DfAM beinhaltet die Konstruktion von Teilen unter Berücksichtigung der spezifischen Fähigkeiten und Einschränkungen des AM-Prozesses. Für chirurgische Instrumente bedeutet dies, dass Funktionalität, Ergonomie, Sterilisierbarkeit und Fertigungseffizienz optimiert werden müssen.
Die Anwendung der DfAM-Prinzipien ist entscheidend für die Herstellung von Werkzeugen, die nicht nur druckbar sind, sondern auch in Bezug auf Leistung und Handhabung überlegen sind. Die Zusammenarbeit mit einem erfahrenen AM-Anbieter wie Met3dp, der die Feinheiten der verschiedenen Druckverfahren und Materialien, können bei der Optimierung von Konstruktionen erheblich helfen.
Wichtige DfAM-Überlegungen für chirurgische Werkzeuge:
- Optimierung der Stützstruktur: Bei AM-Prozessen sind häufig Stützstrukturen erforderlich, um das Teil auf der Bauplatte zu verankern und überhängende Merkmale während des Drucks abzustützen.
- Überhänge minimieren: Richten Sie das Teil auf der Bauplatte so aus, dass steile oder horizontale Überhänge vermieden werden (>45° erfordert oft eine Unterstützung).
- Selbsttragende Winkel entwerfen: Verwenden Sie nach Möglichkeit Fasen oder sanftere Winkel.
- Zugänglichkeit für den Umzug: Stellen Sie sicher, dass die Stützen physisch erreicht und entfernt werden können, ohne empfindliche Teile zu beschädigen. Erwägen Sie gegebenenfalls die Konstruktion von Zugangsöffnungen.
- Auswirkungen auf die Oberflächenbeschaffenheit: Abgestützte Oberflächen haben in der Regel eine rauere Oberfläche und können eine intensivere Nachbearbeitung erfordern. Gestalten Sie kritische Oberflächen nach Möglichkeit selbsttragend.
- Wanddicke und Größe der Merkmale: Bei AM-Prozessen gibt es Mindestwandstärken und Mindestgrößen für druckbare Teile.
- Mindestwanddicke: Je nach Technologie (z. B. LPBF vs. SEBM) und Material liegt die Dicke in der Regel zwischen 0,3 mm und 0,8 mm. Stellen Sie sicher, dass die Wände dick genug für die strukturelle Integrität und die Handhabung sind.
- Kleines Feature Auflösung: Berücksichtigen Sie die Größe des Laserspots oder den Durchmesser des Elektronenstrahls, wenn Sie sehr feine Merkmale wie Zacken oder Stifte entwerfen.
- Bohrungsdurchmesser: Kleine Löcher (<1mm) können schwierig genau zu drucken sein und erfordern möglicherweise ein Nachbohren. Entwerfen Sie entsprechend oder planen Sie eine Bearbeitung ein.
- Interne Kanäle und Hohlräume: AM eignet sich hervorragend zur Erstellung komplexer interner Geometrien für Funktionen wie Flüssigkeitszufuhr, Absaugung oder Kabelführung.
- Selbsttragende Formen: Entwerfen Sie Innenkanäle in Tropfen- oder Rautenform, um die Notwendigkeit von Innenstützen zu vermeiden, die nur sehr schwer oder gar nicht zu entfernen sind.
- Entfernung von Puder: Enthalten Sie Abflusslöcher oder Zugangsstellen, um sicherzustellen, dass das gesamte nicht verschmolzene Pulver nach dem Druck aus den inneren Hohlräumen entfernt werden kann - dies ist entscheidend für die Biokompatibilität.
- Reibungslose Übergänge: Vermeiden Sie scharfe Ecken im Inneren, die Schmutz einschließen oder den Durchfluss behindern könnten.
- Gitterstrukturen und Leichtbau: Durch den Einbau interner Gitter- oder Topologie-optimierter Strukturen kann das Gewicht der Instrumente erheblich reduziert werden, was die Ergonomie verbessert und die Ermüdung des Chirurgen verringert, während gleichzeitig die erforderliche Steifigkeit und Festigkeit erhalten bleibt. Dies ist besonders vorteilhaft für Instrumente aus Titan.
- Teil Konsolidierung: Identifizieren Sie Möglichkeiten, mehrere Komponenten einer herkömmlichen Instrumentenbaugruppe in einem einzigen, monolithisch gedruckten Teil zu kombinieren. Dies reduziert die Montagezeit, die Kosten, mögliche Fehlerquellen und vereinfacht die Lieferkette.
- Oberflächentextur: Entwerfen Sie funktionale Texturen direkt in das Teil, wie z. B. Griffe oder spezifische Rauheit an den Arbeitsenden, wodurch sich Nachbearbeitungsschritte reduzieren lassen.
- Überlegungen zur Sterilisation und Reinigung: Entwerfen Sie Instrumente mit glatten Oberflächen, abgerundeten Kanten und minimalen Spalten, in denen sich biologische Ablagerungen festsetzen könnten. Vermeiden Sie Merkmale, die eine gründliche Reinigung und Sterilisation erschweren. Stellen Sie sicher, dass die Entfernung von Pulver aus den internen Kanälen möglich und nachprüfbar ist.
- Integration der Materialauswahl: Die Wahl der Konstruktion kann durch die Materialeigenschaften beeinflusst werden. So kann beispielsweise die geringere Steifigkeit von Titan für dieselbe Anwendung andere strukturelle Überlegungen erfordern als die von Edelstahl.
Tabelle: Zusammenfassung der DfAM-Leitlinien für chirurgische Werkzeuge
DfAM-Prinzip | Leitfaden | Begründung für chirurgische Werkzeuge |
---|---|---|
Orientierung | Optimierung für minimale Stützen, beste Oberflächengüte an kritischen Stellen | Reduziert Nachbearbeitung, sichert kritische Oberflächenqualität |
Unterstützt | Minimierung von Überhängen (>45°), Sicherstellung des Zugangs zum Ausbau | Kosten, Vorlaufzeit, Oberflächengüte, Vermeidung von Schäden |
Wanddicke | Einhaltung der Prozessminima (z. B. >0,4 mm), Gewährleistung der strukturellen Integrität | Bedruckbarkeit, Festigkeit, Handhabung |
Interne Kanäle | Verwendung von selbsttragenden Formen, Design für Pulverentfernung | Funktionalität, verhindert eingeschlossenes Pulver (Biokompatibilitätsrisiko) |
Gewichtsreduzierung | Gitter/Topologie-Optimierung, wo es angebracht ist | Verbesserte Ergonomie, geringere Ermüdung des Chirurgen |
Teil Konsolidierung | Kombinieren Sie mehrere Komponenten zu einem gedruckten Teil | Weniger Montageaufwand, weniger Fehlerquellen, einfachere Lieferkette |
Reinigbarkeit | Glatte Oberflächen gestalten, tiefe Risse vermeiden, den Weg des Pulvers sicherstellen | Wirksame Sterilisation, verhindert die Ansammlung von Keimen |
In Blätter exportieren
Indem sie von Anfang an additiv denken, können die Hersteller chirurgische Werkzeuge der nächsten Generation herstellen, die überragende Leistung, Ergonomie und Anpassungsfähigkeit bieten und die Grenzen herkömmlicher Fertigungsparadigmen überwinden.
Erreichen kritischer Toleranzen, Oberflächengüte und Genauigkeit bei 3D-gedruckten chirurgischen Instrumenten
Während die Gestaltungsfreiheit ein großer Vorteil ist, erfordern chirurgische Instrumente Präzision. Kritische Abmessungen, Schnittstellenmerkmale und geeignete Oberflächeneigenschaften sind für Funktionalität und Sicherheit nicht verhandelbar. Für Ingenieure und Beschaffungsmanager, die die Technologie für die Herstellung medizinischer Geräte evaluieren, ist es wichtig, die mit Metall-AM erreichbaren Toleranzniveaus, Oberflächengüte und Maßgenauigkeit zu verstehen.
Toleranzen:
- Allgemeine Toleranzen: Bei gedruckten AM-Metallteilen werden in der Regel Toleranzen im Bereich der ISO 2768 mittel (m) oder manchmal fein (f) erreicht. Dies entspricht etwa ±0,1 mm bis ±0,3 mm für kleinere Abmessungen, wobei sich die Toleranzbereiche bei größeren Teilen aufgrund thermischer Effekte während der Herstellung erhöhen.
- Kritische Toleranzen: Für Merkmale, die engere Toleranzen erfordern (z. B. Passflächen, Verriegelungsmechanismen, präzise Durchmesser), ist häufig eine Nachbearbeitung (CNC-Fräsen, Drehen, Schleifen) erforderlich. Mit diesen Nachbearbeitungen können bei bestimmten Merkmalen Toleranzen erreicht werden, die mit der konventionellen Bearbeitung vergleichbar sind (z. B. ±0,01 mm bis ±0,05 mm).
- Prozess-Abhängigkeit: Toleranzen können zwischen verschiedenen AM-Prozessen (z.B. Laser Powder Bed Fusion - LPBF vs. Selective Electron Beam Melting - SEBM) und Maschinen leicht variieren. Hochwertige industrielle Systeme, wie die von Met3dp verwendeten, bieten eine bessere Prozesskontrolle und -konsistenz, was zu einer verbesserten Genauigkeit beim Druck führt.
Oberflächengüte (Rauhigkeit):
- Wie gedruckt: Die Oberflächenbeschaffenheit von AM-Teilen ist von Natur aus rauer als bei maschinell bearbeiteten Oberflächen, was auf den schichtweisen Prozess und die teilweise geschmolzenen Pulverpartikel zurückzuführen ist, die an der Oberfläche haften.
- Typische Ra-Werte (durchschnittliche Rauheit) liegen zwischen 5 µm und 20 µm, je nach Material, Prozessparametern, Partikelgrößenverteilung und Oberflächenausrichtung (nach oben gerichtete Oberflächen sind im Allgemeinen glatter als nach unten gerichtete oder gestützte Oberflächen).
- Post-Processing für Verbesserungen: Für die meisten chirurgischen Anwendungen ist die Oberfläche im gedruckten Zustand zu rau. Es werden verschiedene Nachbearbeitungstechniken eingesetzt:
- Abrasives Strahlen (Perlen-/Sandstrahlen): Sorgt für ein gleichmäßiges, mattes Finish und entfernt lose Partikel (Ra typischerweise 3-6 µm).
- Taumeln/Gleitschleifen: Verwendet Medien zum Glätten von Oberflächen und Kanten, effektiv für Chargen von Teilen (Ra kann 1-3 µm erreichen).
- Elektropolieren: Ein elektrochemisches Verfahren, bei dem eine dünne Materialschicht abgetragen wird, so dass eine sehr glatte, glänzende, saubere und äußerst korrosionsbeständige Oberfläche entsteht. Häufig bevorzugt für chirurgische Werkzeuge aus Edelstahl (Ra < 0,8 µm, manchmal < 0,4 µm).
- Manuelles Polieren: Zur Erzielung von Hochglanzoberflächen auf bestimmten Flächen, die jedoch arbeitsintensiv sind.
- Bearbeitungen: Erzeugt glatte, präzise Oberflächen an kritischen Merkmalen.
- Bedeutung für chirurgische Werkzeuge: Glatte Oberflächen sind entscheidend für die Reinigungsfähigkeit, die Verringerung der Reibung, die Minimierung des Gewebetraumas und die Verhinderung der Adhäsion von Bioburden. Je nach Funktion und Kontaktart des Instruments sind oft spezifische Ra-Ziele erforderlich.
Maßgenauigkeit und Validierung:
- Prozesskontrolle: Um eine gleichbleibende Maßgenauigkeit zu erreichen, ist eine strenge Kontrolle des gesamten AM-Prozesses erforderlich, einschließlich Maschinenkalibrierung, gleichbleibende Pulverqualität (wie die hochkugelförmigen Pulver von Met3dp), optimierte Prozessparameter und kontrolliertes Wärmemanagement.
- Validierung: Die Maßhaltigkeit muss mit geeigneten Messgeräten überprüft werden.
- Messschieber/Mikrometer: Für grundlegende Maßkontrollen.
- Koordinatenmessmaschinen (KMG): Für hochpräzise Messungen komplexer Geometrien und GD&T (Geometric Dimensioning and Tolerancing) Überprüfung.
- 3D-Scannen: Zum Vergleich der endgültigen Teilegeometrie mit dem ursprünglichen CAD-Modell.
- Qualitätsmanagementsystem (QMS): Ein robustes QMS (idealerweise mit ISO 13485-Zertifizierung für Medizinprodukte) stellt sicher, dass die Prozesse dokumentiert, kontrolliert und validiert werden, um Teile zu produzieren, die den Abmessungsspezifikationen entsprechen.
Tabelle: Typische Präzisionsniveaus bei Metall-AM für chirurgische Werkzeuge
Parameter | As-Printed Bereich | Nachbearbeitetes Potenzial | Bedeutung |
---|---|---|---|
Toleranz | ±0,1 bis ±0,3 mm (ISO 2768-m/f) | ±0,01 bis ±0,05 mm (durch maschinelle Bearbeitung) | Passform, Funktion, Gegenstücke |
Oberflächengüte (Ra) | 5 µm - 20 µm | < 0,8 µm (Elektropolieren/Polieren) | Reinigungsfähigkeit, Biokompatibilität, Reibung, Verschleiß |
Merkmal Auflösung | ~0,3 - 0,8 mm Mindestwandstärke/Merkmal | Definiert durch den AM-Prozess | Fähigkeit zur Erstellung feiner Details |
Validierungsmethode | CMM, 3D-Scannen, Messschieber | CMM, Oberflächenprofilometrie | Sicherstellen, dass Teile den Konstruktionsspezifikationen und -standards entsprechen |
In Blätter exportieren
Während AM eine unglaubliche Designflexibilität bietet, erfordert das Erreichen der erforderlichen Präzision für chirurgische Werkzeuge oft eine Kombination aus kontrolliertem Druck und gezielter Nachbearbeitung, die von strengen Qualitätskontrollverfahren geleitet wird.
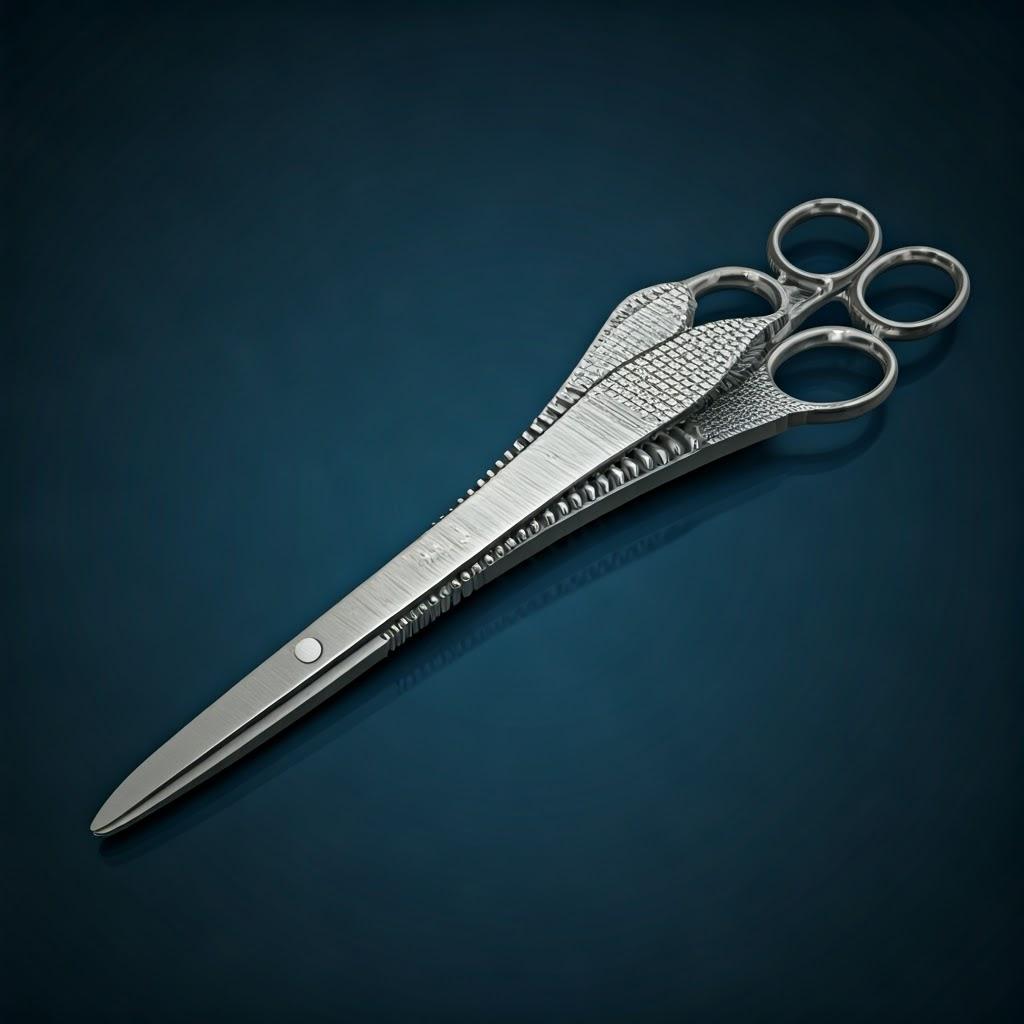
Wichtige Nachbearbeitungsschritte für funktionale und sichere 3D-gedruckte chirurgische Werkzeuge
Ein 3D-gedrucktes Metallteil ist selten direkt nach dem Druck einsatzbereit, insbesondere nicht bei kritischen Anwendungen wie chirurgischen Instrumenten. Es sind eine Reihe wichtiger Nachbearbeitungsschritte erforderlich, um das rohe gedruckte Teil in ein funktionales, sicheres und steriles medizinisches Gerät zu verwandeln. In diesen Schritten werden Eigenspannungen beseitigt, temporäre Strukturen entfernt, die erforderliche Oberflächengüte und Toleranzen erreicht und die Sauberkeit sichergestellt. Der spezifische Arbeitsablauf kann je nach Material, Designkomplexität und Anwendungsanforderungen variieren.
Typischer Post-Processing-Workflow:
- Stressabbau / Wärmebehandlung:
- Warum? Die schnellen Erwärmungs- und Abkühlungszyklen beim AM führen zu inneren Spannungen im Bauteil. Eine Wärmebehandlung (Glühen, Spannungsarmglühen) bei bestimmten Temperaturen homogenisiert das Gefüge, baut diese Spannungen ab (und verhindert so mögliche Verformungen oder Risse) und kann die mechanischen Eigenschaften wie Duktilität und Festigkeit entsprechend den Werkstoffnormen (z. B. ASTM-Normen für 316L oder Ti-6Al-4V) optimieren.
- Wie? Durchgeführt in einem Ofen mit kontrollierter Atmosphäre (Vakuum oder Inertgas) nach validierten, legierungsspezifischen Protokollen.
- Entfernen des Teils von der Bauplatte:
- Wie? Die Teile werden in der Regel durch Drahterodieren (Electrical Discharge Machining) oder mit einer Bandsäge aus der Bauplatte geschnitten.
- Entfernung der Stützstruktur:
- Warum? Die Stützen werden während des Baus benötigt, müssen aber danach wieder entfernt werden.
- Wie? Dies kann manuell (Brechen oder Schneiden), durch CNC-Bearbeitung oder manchmal auch durch Drahterodieren geschehen. Dabei muss darauf geachtet werden, dass das Teil selbst nicht beschädigt wird. Bei komplexen internen Halterungen kann der Zugang schwierig sein.
- Reinigung und Puderentfernung:
- Warum? Alle Reste von Metallpulver, insbesondere aus internen Kanälen oder komplexen Strukturen, müssen sorgfältig entfernt werden. Eingeschlossenes Pulver stellt ein erhebliches Biokompatibilitätsrisiko dar.
- Wie? Zu den Methoden gehören Druckluftblasen, Ultraschallreinigungsbäder und möglicherweise Mikrostrahlen. Konstruktionsmerkmale (Abflusslöcher) unterstützen diesen Prozess.
- Oberflächenveredelung:
- Warum? Um die erforderliche Glätte für Reinigungsfähigkeit, geringere Reibung und Biokompatibilität zu erreichen.
- Wie? Wie bereits erwähnt, umfasst dies Schritte wie:
- Strahlen (z. B. Perlstrahlen) für eine gleichmäßige matte Oberfläche.
- Taumeln/Gleitschleifen zum Glätten von Kanten und Oberflächen.
- Elektropolieren (insbesondere für 316L) für eine sehr glatte, saubere, passive Oberfläche.
- Manuelles Polieren für spezielle Hochglanzanforderungen.
- Bearbeitungen (falls erforderlich):
- Warum? Zur Erzielung kritischer Toleranzen, präziser Lochdurchmesser, flacher Passflächen oder scharfer Schneidkanten, die mit AM allein nicht zuverlässig hergestellt werden können.
- Wie? CNC-Fräsen, Drehen, Schleifen oder Bohren von spezifischen Merkmalen.
- Endreinigung und Passivierung:
- Warum? Zur Entfernung von Rückständen aus der Bearbeitung oder Handhabung und, insbesondere bei Edelstahl und Titan, zur Bildung einer stabilen, passiven Oxidschicht, die die Korrosionsbeständigkeit und Biokompatibilität verbessert.
- Wie? Es handelt sich um validierte mehrstufige Reinigungsprozesse mit Reinigungsmitteln, Lösungsmitteln und gereinigtem Wasser, möglicherweise gefolgt von einer speziellen Passivierungsbehandlung (z. B. Salpetersäure- oder Zitronensäurebad für nichtrostende Stähle).
- Inspektion und Qualitätskontrolle:
- Warum? Überprüfung der Maßhaltigkeit, Oberflächenbeschaffenheit, Materialeigenschaften und Sauberkeit entsprechend den Spezifikationen.
- Wie? CMM, visuelle Inspektion, Oberflächenprofilometrie, eventuell Materialprüfung an Mustern, die neben den Teilen gedruckt werden.
- Sterilisationsvalidierung (vom Medizinproduktehersteller durchgeführt):
- Warum? Obwohl dies in der Regel nicht vom AM-Dienstleister durchgeführt wird, muss das Instrument mit Standard-Sterilisationsverfahren (z. B. Autoklavieren, Gammastrahlung, EtO) kompatibel sein. Der Herstellungsprozess, einschließlich der Reinigung, muss sicherstellen, dass das Gerät effektiv sterilisiert werden kann. Validierungsprotokolle bestätigen, dass die gewählte Sterilisationsmethode durchgängig das erforderliche Sterilitätssicherungsniveau (SAL) erreicht.
Vereinfachtes Flussdiagramm für die Nachbearbeitung (Beispiel):
Code-Schnipsel
Grafik TD
A[3D-Druck abgeschlossen] --> B{Spannungsentlastung / Wärmebehandlung};
B --> C{Entnahme des Teils aus der Platte};
C --> D{Entfernen des Trägers};
D --> E{Erstreinigung/Pulverentfernung};
E --> F{Oberflächenveredelung (Strahlen/Trommeln usw.)};
F --> G{Bearbeitung (falls erforderlich)};
G --> H{Endreinigung & Passivierung};
H --> I[Inspektion (Abmessungen, Oberfläche)];
I --> J(Bereit zum Verpacken/Sterilisieren);
%% Optionale Pfade
F --> H; %% Bearbeitung überspringen
E --> G; %% Bearbeitung vor allgemeiner Oberflächenbehandlung
Jeder Schritt erfordert eine sorgfältige Kontrolle und Validierung, insbesondere im Rahmen eines Qualitätsmanagementsystems für Medizinprodukte wie ISO 13485, um sicherzustellen, dass das endgültige chirurgische Instrument sicher und wirksam ist.
Überwindung von Herausforderungen bei der additiven Fertigung von Metall für chirurgische Anwendungen
Metall-AM bietet zwar erhebliche Vorteile für die Herstellung von chirurgischen Werkzeugen, ist aber auch nicht ohne Herausforderungen. Die erfolgreiche Herstellung hochwertiger, zuverlässiger medizinischer Geräte erfordert die Vorwegnahme und Abschwächung potenzieller Probleme während der gesamten Design-, Druck- und Nachbearbeitungsphase. Das Verständnis dieser Herausforderungen hilft bei der Auswahl kompetenter Fertigungspartner und bei der Festlegung realistischer Erwartungen.
Gemeinsame Herausforderungen und Abhilfestrategien:
- Eigenspannung und Verzug:
- Herausforderung: Schnelle Heiz-/Abkühlzyklen erzeugen innere Spannungen, die dazu führen können, dass sich die Teile während oder nach dem Druck verziehen oder sogar reißen.
- Milderung:
- Simulation: Einsatz von thermischer Simulationssoftware zur Vorhersage des Spannungsaufbaus und zur Optimierung der Teileausrichtung und der Stützstrategien.
- Prozessparameter: Optimierung von Laser-/Strahlleistung, Scangeschwindigkeit und Schichtdicke.
- Plattform Heizung: Das Vorheizen der Bauplattform (üblich bei SEBM, möglich bei einigen LPBF) reduziert thermische Gradienten.
- Strategie unterstützen: Robuste Stützstrukturen tragen zur Verankerung des Teils und zur Wärmeableitung bei.
- Stressabbau: Die Wärmebehandlung nach dem Druck ist entscheidend für den Abbau von Restspannungen.
- Entfernung der Stützstruktur:
- Herausforderung: Das Entfernen von Halterungen, insbesondere von komplexen Innengeometrien oder empfindlichen Merkmalen, kann schwierig und zeitaufwändig sein und das Risiko einer Beschädigung des Teils bergen. Die unterstützten Oberflächen sind in der Regel rau.
- Milderung:
- DfAM: Gestaltung für minimalen Support-Einsatz und einfachen Zugang (siehe Abschnitt DfAM).
- Optimierte Stützen: Verwendung von Stützkonstruktionen, die während der Bauphase stabil genug sind, aber leichter brechen können.
- Erweiterte Entfernungstechniken: Einsatz von Drahterosion oder Präzisionsbearbeitung für schwierige Halterungen.
- Prozessauswahl: Bei einigen Verfahren können für bestimmte Geometrien weniger Stützen erforderlich sein.
- Erreichen der erforderlichen Oberflächengüte und Sauberkeit:
- Herausforderung: Ungedruckte Oberflächen sind rau und für die meisten chirurgischen Anwendungen ungeeignet. Das Erreichen einer gleichmäßigen Glätte (<0,8 µm Ra oft erwünscht) und die Sicherstellung der Entfernung aller Pulver/Rückstände, insbesondere aus den inneren Kanälen, ist entscheidend, aber eine Herausforderung.
- Milderung:
- Optimierte Parameter: Die Feinabstimmung der Druckparameter kann das Druckergebnis leicht verbessern.
- Effektive Nachbearbeitung: Anwendung geeigneter Techniken wie Elektropolieren, Trommeln oder Strahlen, die auf das Material und die Geometrie abgestimmt sind.
- DfAM für Reinigungsfähigkeit: Konstruktion von Teilen ohne Merkmale, die Pulver oder Verunreinigungen einschließen.
- Validierte Reinigungsprotokolle: Einführung strenger, mehrstufiger Reinigungsverfahren mit Überprüfungsschritten.
- Kontrolle der Porosität:
- Herausforderung: Im gedruckten Material können sich manchmal kleine Hohlräume oder Poren aufgrund von unvollständigem Schmelzen, Gaseinschlüssen oder Keyholing-Effekten bilden. Poren können die mechanischen Eigenschaften (insbesondere die Ermüdungsfestigkeit) beeinträchtigen und möglicherweise Bakterien beherbergen.
- Milderung:
- Hochwertiges Pulver: Verwendung von Pulvern mit gleichmäßiger Sphärizität, Größenverteilung und geringem Gasgehalt, wie sie mit der fortschrittlichen Zerstäubung von Met3dp hergestellt werden. Beispiele finden Sie auf unserer Produktseite.
- Optimierte Prozessparameter: Entwicklung und Validierung von Parametersätzen, die vollständiges Schmelzen und volle Dichte gewährleisten (>99,5% ist üblich, >99,9% oft erreichbar).
- Prozessüberwachung: Einsatz von In-situ-Überwachungssystemen (z. B. Schmelzbadüberwachung) zur Erkennung potenzieller Probleme während der Bauphase.
- Heiß-Isostatisches Pressen (HIP): Ein Nachbearbeitungsschritt mit hoher Temperatur und hohem Druck, um die inneren Poren zu schließen (wird häufig bei kritischen, durch Ermüdung belasteten Teilen verwendet, verursacht zusätzliche Kosten).
- Prozesskonsistenz und Reproduzierbarkeit:
- Herausforderung: Um sicherzustellen, dass jedes produzierte Teil den gleichen Spezifikationen entspricht, ist eine strenge Kontrolle zahlreicher Variablen (Maschine, Material, Parameter, Umgebung) erforderlich.
- Milderung:
- Robustes QMS: Umsetzung von ISO 13485 oder eines vergleichbaren Qualitätssystems.
- Kalibrierung und Wartung von Maschinen: Regelmäßige, dokumentierte Kalibrierung und vorbeugende Wartung.
- Pulvermanagement: Strenge Kontrolle über Beschaffung, Handhabung, Lagerung und Recycling-/Aufbereitungsprotokolle für Pulver.
- Prozessvalidierung (IQ/OQ/PQ): Strenge Installationsqualifizierung (IQ), Betriebsqualifizierung (OQ) und Leistungsqualifizierung (PQ) für Maschinen und Prozesse.
- Statistische Prozesskontrolle (SPC): Überwachung wichtiger Prozessindikatoren zur Gewährleistung der Stabilität.
- Einhaltung gesetzlicher Vorschriften und Validierung:
- Herausforderung: Medizinische Geräte sind stark reguliert. Der Nachweis, dass AM-Prozesse und die daraus entstehenden Teile die strengen Anforderungen (Biokompatibilität, mechanische Eigenschaften, Sterilität) erfüllen, erfordert umfangreiche Tests und Dokumentation.
- Milderung:
- Partnerschaften mit erfahrenen Lieferanten: Auswahl von Lieferanten wie Met3dp mit Erfahrung in der Herstellung von Medizinprodukten und entsprechenden Zertifizierungen (z. B. ISO 13485).
- Materialzertifizierung: Verwendung zertifizierter medizinischer Materialien mit vollständiger Rückverfolgbarkeit.
- Gründliche Validierung: Durchführung umfassender Prüfungen (mechanisch, chemisch, Biokompatibilität) gemäß den einschlägigen Normen (ISO, ASTM).
- Dokumentation: Führen detaillierter Aufzeichnungen über alle Schritte der Herstellung und Qualitätskontrolle.
Die Bewältigung dieser Herausforderungen erfordert eine Kombination aus fortschrittlicher Technologie, materialwissenschaftlichem Fachwissen, strenger Prozesskontrolle und einem umfassenden Verständnis der Anforderungen an medizinische Geräte. Die Wahl eines Fertigungspartners mit nachgewiesenen Fähigkeiten in diesen Bereichen ist entscheidend für die erfolgreiche Markteinführung von 3D-gedruckten chirurgischen Werkzeugen.
Auswahl des richtigen Partners für den 3D-Druck von Metall für die Herstellung medizinischer Geräte
Die Wahl des richtigen Fertigungspartners ist bei der Entwicklung von 3D-gedruckten chirurgischen Werkzeugen wohl ebenso entscheidend wie das Design und die Materialauswahl. Die besonderen Anforderungen der Medizintechnikbranche - strenge Vorschriften, hohe Präzision, Biokompatibilität und absolute Zuverlässigkeit - erfordern die Zusammenarbeit mit einem Anbieter von additiver Metallfertigung, der über spezifisches Fachwissen und robuste Qualitätssysteme verfügt. Beschaffungsmanager und Ingenieurteams sollten potenzielle Lieferanten auf der Grundlage einer umfassenden Reihe von Kriterien bewerten.
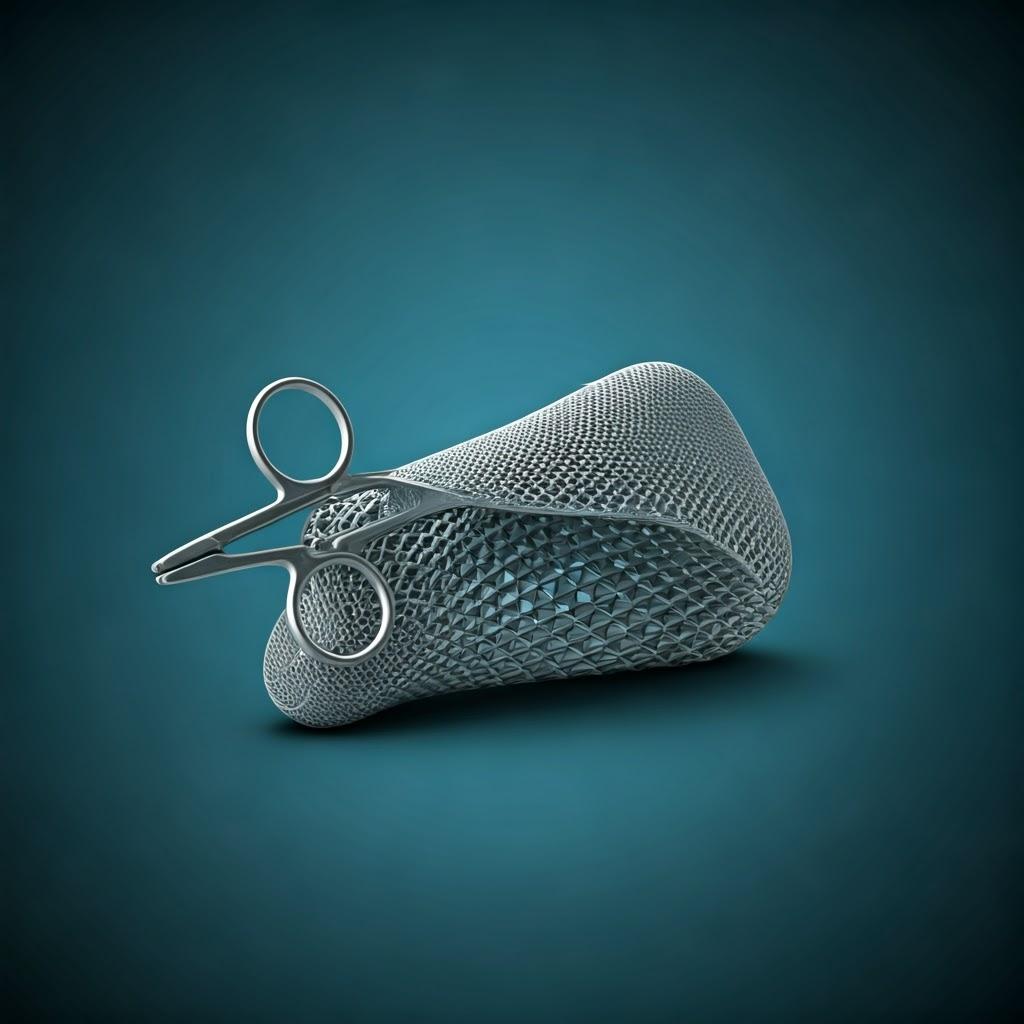
Schlüsselkriterien für die Bewertung von Anbietern von Metall-AM für chirurgische Werkzeuge:
- Qualitätsmanagementsystem (QMS) und Zertifizierungen:
- ISO 13485-Zertifizierung: Dies ist die internationale Norm für Qualitätsmanagementsysteme für Medizinprodukte. Die Zertifizierung zeigt, dass der Lieferant Prozesse für Designkontrollen, Risikomanagement, Rückverfolgbarkeit, Prozessvalidierung und Korrektur-/Vorbeugungsmaßnahmen eingeführt hat, die auf die medizinische Industrie zugeschnitten sind. Dies sollte eine Hauptanforderung sein.
- Zertifizierung nach ISO 9001: Eine allgemeine QMS-Norm, die oft neben der ISO 13485 gilt und auf eine umfassendere Kontrolle der Qualitätsprozesse hinweist.
- Erfahrung mit medizinischen Geräten:
- Nachgewiesene Erfolgsbilanz: Hat der Anbieter nachweislich Erfahrung in der Herstellung medizinischer Komponenten, insbesondere chirurgischer Instrumente oder Implantate? Fragen Sie nach Fallstudien, Beispielen (ggf. unter NDA) und Referenzen.
- Verständnis der Vorschriften: Vertrautheit mit den FDA-Vorschriften (z. B. 21 CFR Part 820), der EU-MDR und anderen einschlägigen Vorschriften ist von entscheidender Bedeutung.
- Materialkenntnis und Handhabung:
- Zertifizierte Materialien: Beziehen und verwenden sie zertifizierte Metallpulver in medizinischer Qualität (z. B. 316L, Ti-6Al-4V ELI) mit vollständiger Rückverfolgbarkeit?
- Qualitätskontrolle des Pulvers: Wie sehen ihre Verfahren für die Eingangskontrolle, Lagerung, Handhabung und Wiederverwertung/Regenerierung von Pulvern aus, um Verunreinigungen zu vermeiden und Konsistenz zu gewährleisten? Unternehmen wie Met3dp, die ihre eigenen hochwertigen Pulver mit fortschrittlichen Zerstäubungstechniken herstellen, bieten erhebliche Vorteile bei der Materialkontrolle und Rückverfolgbarkeit. Mehr über unser Engagement für Qualität erfahren Sie auf unserer Über uns-Seite.
- Auswahl an Materialien: Die Fähigkeit, mit den erforderlichen spezifischen Legierungen (316L, Ti-6Al-4V) zu arbeiten, ist unerlässlich.
- Technologie und Ausrüstung:
- Geeignete AM-Technologie: Betreiben sie gut gewartete, industrietaugliche Metall-AM-Systeme (z. B. LPBF, SEBM), die für die geforderte Präzision und das Material geeignet sind?
- Volumen und Kapazität aufbauen: Können sie die Größe und Menge der benötigten Teile aufnehmen?
- Prozessüberwachung: Verfügen die Maschinen über In-situ-Überwachungsfunktionen für eine verbesserte Qualitätskontrolle?
- Nachbearbeitungsmöglichkeiten:
- In-House vs. Outsourced: Bieten sie die erforderlichen Nachbearbeitungsschritte (Wärmebehandlung, Entfernen von Halterungen, Bearbeitung, Polieren, Reinigung, Passivierung) intern oder über qualifizierte Partner an? Inhouse-Kapazitäten bieten oft eine bessere Kontrolle und potenziell kürzere Vorlaufzeiten.
- Validierte Prozesse: Sind ihre Nachbearbeitungsschritte, insbesondere Reinigung und Passivierung, für medizinische Anwendungen validiert?
- Technisches Fachwissen und Unterstützung:
- DfAM-Unterstützung: Können sie fachkundige Beratung bei der Optimierung von Designs für die additive Fertigung bieten?
- Technische Zusammenarbeit: Sind die Ingenieure während des gesamten Projektlebenszyklus erreichbar und kooperativ?
- Problemlösung: Verfügen sie über das Fachwissen, um potenzielle Probleme bei der Herstellung zu beheben?
- Inspektion und Metrologie:
- Ausrüstung: Verfügen sie über kalibrierte KMGs, Profilometer, Scanner und andere notwendige Messgeräte?
- Berichterstattung: Können sie umfassende Inspektionsberichte vorlegen, die die Maßgenauigkeit, die Oberflächengüte und die Einhaltung der Spezifikationen dokumentieren?
- Vertraulichkeit und Schutz des geistigen Eigentums:
- NDAs: Sind sie bereit und daran gewöhnt, im Rahmen von Vertraulichkeitsvereinbarungen zu arbeiten, um sensibles geistiges Eigentum zu schützen?
Tabelle: Checkliste zur Lieferantenbewertung
Kriterien | Wichtige Fragen | Warum es für chirurgische Werkzeuge wichtig ist |
---|---|---|
ISO 13485 Zertifizierung | Ist der Lieferant zertifiziert? Kann er das Zertifikat vorlegen? | Nachweis der Einhaltung des QMS für Medizinprodukte |
Medizinische Erfahrung | Welche spezifischen medizinischen Teile haben Sie hergestellt? Können Sie Fallstudien/Beispiele nennen? | Gewährleistet das Verständnis der medizinischen Anforderungen |
Materialkontrolle | Wie beschaffen, prüfen, handhaben und verfolgen Sie Pulver in medizinischer Qualität (316L, Ti-6Al-4V)? | Garantiert die Biokompatibilität und die Eigenschaften des Materials |
Technologie und Kapazität | Welche AM-Maschinen verwenden Sie? Wie hoch ist das Bauvolumen/die Genauigkeit? Haben Sie Kapazitäten für mein Projekt? | Gewährleistet technische Fähigkeiten und rechtzeitige Lieferung |
Nachbearbeitung | Welche Schritte werden intern durchgeführt? Sind die Reinigungs-/Passivierungsverfahren validiert? | Entscheidend für die Eigenschaften des Endprodukts, die Sicherheit und das Finish |
Technische Unterstützung | Bieten Sie eine DfAM-Überprüfung an? Wie gehen Sie mit technischen Herausforderungen um? | Optimiert das Design und sorgt für eine reibungslose Produktion |
Inspektion und Qualitätskontrolle | Über welche Messgeräte verfügen Sie? Welches Niveau der Inspektionsberichte ist Standard/verfügbar? | Überprüft, ob die Teile den kritischen Spezifikationen entsprechen |
Vertraulichkeit | Welche Verfahren gibt es zum Schutz des geistigen Eigentums? | Schützt sensible Designinformationen |
In Blätter exportieren
Die Wahl eines Partners wie Met3dp mit jahrzehntelanger kollektiver Erfahrung in den Bereichen fortschrittliche Metallpulverproduktion, Präzisions-SEBM-Drucktechnologie und umfassende Anwendungsentwicklungsdienste bietet eine solide Grundlage für die Entwicklung und Herstellung hochwertiger, zuverlässiger 3D-gedruckter chirurgischer Werkzeuge.
Verständnis der Kostenstrukturen und Vorlaufzeiten für 3D-gedruckte chirurgische Instrumente
Während Metall-AM Innovationen ermöglicht, ist das Verständnis der damit verbundenen Kosten und Produktionszeiträume für die Projektplanung, Budgetierung und Beschaffung von entscheidender Bedeutung. Im Gegensatz zur traditionellen Massenproduktion, bei der die Amortisation der Werkzeuge dominiert, werden die AM-Kosten von anderen Faktoren bestimmt.
Die wichtigsten Kostentreiber für 3D-gedruckte chirurgische Werkzeuge:
- Materialart und Verbrauch:
- Wahl des Materials: Titanlegierungen (Ti-6Al-4V) sind erheblich teurer als nichtrostende Stähle (316L), sowohl was die Kosten für das Rohpulver als auch die häufig erforderliche Verarbeitung betrifft.
- Teilband: Das tatsächliche Volumen des im Teil selbst verwendeten Materials. Größere/dichtere Teile kosten mehr.
- Unterstützende Strukturen: Das für die Stützen verwendete Material erhöht den Verbrauch und erfordert Zeit und Kosten für die Entfernung. Durch eine optimierte Ausrichtung und DfAM kann dies minimiert werden.
- Pulverabfall/Recycling: Ineffiziente Pulverhandhabung oder übermäßiger Abfall erhöhen die Kosten.
- Maschinenzeit (Bauzeit):
- Teilhöhe (Z-Höhe): Die Bauzeit wird in erster Linie durch die Anzahl der Schichten bestimmt, was bedeutet, dass größere Teile länger brauchen, unabhängig davon, wie viele auf die Platte passen. Die effiziente Verschachtelung mehrerer Teile auf der Bauplatte ist der Schlüssel zur Reduzierung der Maschinenzeitkosten pro Teil.
- Teil Komplexität: Sehr komplizierte Merkmale erfordern möglicherweise langsamere Druckparameter.
- Maschine Stundensatz: Variiert je nach Maschinentechnologie, Größe und Bedienerkosten.
- Komplexität des Designs:
- DfAM-Optimierung: Gut optimierte Designs minimieren den Bedarf an Stützen und möglicherweise die Druckzeit. Schlecht konstruierte Teile können übermäßige Stützen oder komplexe Ausrichtungen erfordern, was die Kosten erhöht.
- Interne Merkmale: Komplexe interne Kanäle, die eine schwierige Pulverentfernung erfordern, können die Nachbearbeitungszeit und -kosten erhöhen.
- Nachbearbeitungsanforderungen:
- Intensität: Die Anzahl und Komplexität der Arbeitsschritte wirken sich erheblich auf die Kosten aus. Grundlegendes Abtragen und Strahlen sind kostengünstiger als mehrachsige CNC-Bearbeitung, Elektropolieren und umfangreiche manuelle Nachbearbeitung.
- Toleranz/Oberflächenbehandlung: Engere Toleranzen und feinere Oberflächengüten erfordern eine intensivere (und kostspieligere) Nachbearbeitung.
- Qualitätssicherung und Inspektion:
- Ebene der Inspektion: Grundlegende Maßprüfungen sind weniger kostspielig als vollständige CMM-Berichte, Materialprüfungen (falls pro Charge erforderlich) und detaillierte Oberflächenanalysen.
- Dokumentation: Die umfangreiche Dokumentation, die für die Einhaltung von Vorschriften erforderlich ist, verursacht zusätzlichen Aufwand.
- Bestellmenge:
- Einrichtungskosten: Es gibt zwar keine Werkzeuge, aber es fallen Einrichtungskosten für die Erstellung der Build-Datei, die Einrichtung der Maschine und die Nachbearbeitungsabläufe an. Diese Kosten werden über größere Mengen amortisiert, wodurch der Preis pro Teil sinkt.
- Build Plate Efficiency: Höhere Stückzahlen ermöglichen eine effizientere Verschachtelung der Teile auf der Bauplatte, was die Maschinenzeit pro Teil reduziert.
Tabelle: Zusammenfassung der Kostenfaktoren
Kostentreiber | Primäreinflussnahme | Wie man optimiert |
---|---|---|
Material | Legierungstyp (Ti vs. Stahl), Teilvolumen, Stützvolumen | Geeignetes Material wählen, DfAM für Leichtbau |
Maschinenzeit | Höhe des Teils (Z), Effizienz der Verschachtelung der Bauplatten | Optimierung der Ausrichtung, Maximierung der Nutzung der Bauplatte |
Entwurfskomplexität | Unterstützungsbedarf, interne Merkmale | Anwendung der DfAM-Grundsätze, Vereinfachung wo möglich |
Nachbearbeitung | Anzahl/Art der Stufen, Toleranz-/Fertigstellungsanforderungen | Nur die notwendigen Schritte angeben, Design für einfachere Verarbeitung |
Qualitätssicherung | Inspektionsniveau, Dokumentationsbedarf | Definieren Sie klare, angemessene QC-Anforderungen |
Menge | Amortisation von Einrichtungskosten, Nesting-Effizienz | Bestellen Sie, wenn möglich, in Chargen |
In Blätter exportieren
Vorlaufzeiten:
- Prototyping: Für Einzelstücke oder sehr kleine Chargen mit Standard-Nachbearbeitung können die Vorlaufzeiten relativ kurz sein und liegen oft zwischen 5 bis 15 Arbeitstageje nach Komplexität und Lieferantenrückstand.
- Produktion (geringes bis mittleres Volumen): Für validierte Produktionsteile, die eine vollständige Nachbearbeitung und Qualitätssicherung erfordern, sind die Vorlaufzeiten in der Regel länger und reichen von 3 bis 8 Wochen. Dies berücksichtigt die Terminplanung, die Herstellungszeit (die für eine vollständige Platte mehrere Tage betragen kann), die Wärmebehandlungszyklen, die mehrstufige Nachbearbeitung und die gründliche Prüfung.
- Faktoren, die die Vorlaufzeit beeinflussen: Komplexität, Menge, Nachbearbeitungsintensität, Materialverfügbarkeit, Lieferantenkapazität und erforderliche Validierung/Dokumentation wirken sich alle auf den endgültigen Lieferplan aus.
Eine klare Kommunikation mit dem AM-Anbieter in Bezug auf Anforderungen und Erwartungen ist der Schlüssel zu genauen Kostenvoranschlägen und realistischen Vorlaufzeitprognosen.
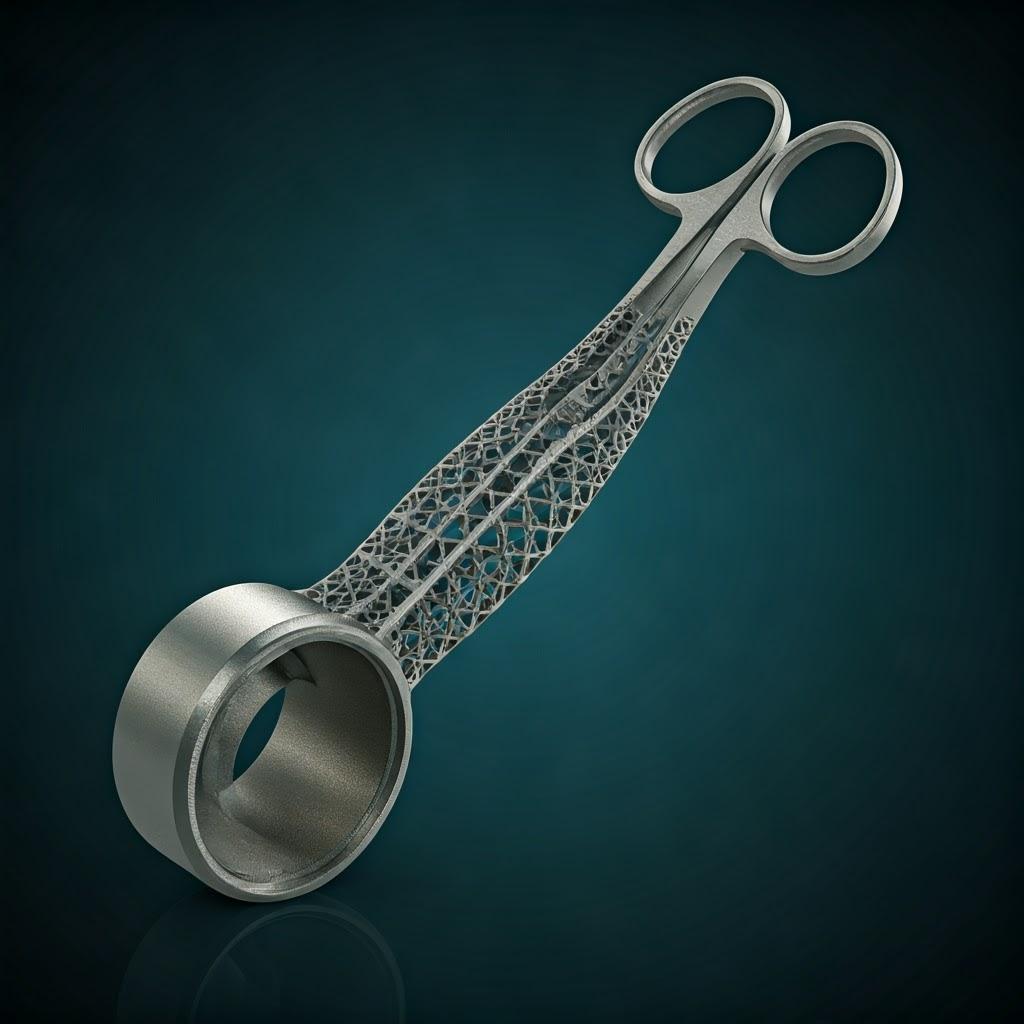
Häufig gestellte Fragen (FAQ) zu 3D-gedruckten chirurgischen Instrumenten
Hier finden Sie Antworten auf einige häufig gestellte Fragen zur Verwendung von 316L-Edelstahl und Ti-6Al-4V-Titan für 3D-gedruckte chirurgische Instrumente:
- Sind 3D-gedruckte chirurgische Werkzeuge aus 316L und Ti-6Al-4V wirklich biokompatibel? Ja, vorausgesetzt, sie werden korrekt hergestellt. Sowohl der rostfreie Stahl 316L als auch Ti-6Al-4V (insbesondere die Sorte ELI) sind weithin anerkannte und verwendete biokompatible Materialien, die Normen wie ISO 10993 entsprechen. Die Biokompatibilität hängt jedoch nicht nur vom Rohmaterial ab, sondern vor allem vom gesamten Prozess: Verwendung von zertifiziertem Pulver in medizinischer Qualität, Erreichen einer hohen Dichte (>99,5%), Sicherstellung der vollständigen Entfernung des Pulvers, Anwendung einer angemessenen Nachbearbeitung (z. B. Passivierung) und Umsetzung validierter Reinigungsprotokolle. Die Zusammenarbeit mit einem nach ISO 13485 zertifizierten Anbieter, der Erfahrung in der medizinischen Fertigung hat, ist unerlässlich, um sicherzustellen, dass die Biokompatibilitätsanforderungen erfüllt werden.
- Wie sieht es mit der Festigkeit und Haltbarkeit von 3D-gedruckten chirurgischen Werkzeugen im Vergleich zu traditionell hergestellten Werkzeugen aus? Die mechanischen Eigenschaften (Festigkeit, Härte, Ermüdungsbeständigkeit) von AM-Metallteilen aus 316L und Ti-6Al-4V können mit denen von herkömmlichen Verfahren wie Schmieden oder Gießen vergleichbar und manchmal sogar besser sein, insbesondere wenn man den Knet- oder Glühzustand berücksichtigt. Eine ordnungsgemäße Wärmebehandlung nach dem Druck ist entscheidend für die Erzielung optimaler Eigenschaften gemäß den ASTM- oder ISO-Normen. Darüber hinaus ermöglicht die Designfreiheit von AM die Optimierung von Geometrien (z. B. durch Topologieoptimierung), um die Steifigkeit oder Festigkeit bei Bedarf zu erhöhen, wodurch möglicherweise stärkere oder leichtere Werkzeuge als bei herkömmlichen Verfahren entstehen.
- Können 3D-gedruckte chirurgische Instrumente aus Edelstahl und Titan mit den üblichen Krankenhausmethoden sterilisiert werden? Unbedingt. Sowohl 316L als auch Ti-6Al-4V weisen eine ausgezeichnete Beständigkeit gegen die in Gesundheitseinrichtungen üblichen Sterilisationsverfahren auf:
- Autoklavieren (Dampfsterilisation): Die gängigste Methode; diese Materialien halten den hohen Temperaturen und Drücken stand.
- Sterilisation mit Ethylenoxid (EtO): Kompatibel.
- Gammastrahlung: Kompatibel.
- Niedertemperatur-Wasserstoffperoxid-Gasplasma: Kompatibel. Die wichtigsten Überlegungen sind, dass das Design des Instruments das Eindringen des Sterilisiermittels und den Kontakt mit allen Oberflächen ermöglichen muss (DfAM für Reinigungsfähigkeit) und dass die Teile vor der Sterilisation gründlich gereinigt werden müssen, um jegliche biologische Verschmutzung oder Herstellungsrückstände zu entfernen.
- Welche Informationen muss ich angeben, um ein Angebot für ein 3D-gedrucktes chirurgisches Instrument zu erhalten? Um ein genaues Angebot zu erhalten, müssen Sie in der Regel folgende Angaben machen:
- 3D-CAD-Modell: Ein hochwertiges Modell in einem Standardformat (z. B. STEP, IGES).
- Spezifikation des Materials: Geben Sie eindeutig den gewünschten Werkstoff an (z. B. Edelstahl 316L oder Ti-6Al-4V).
- Menge: Anzahl der benötigten identischen Teile.
- Kritische Toleranzen: Geben Sie alle spezifischen Abmessungen an, die engere Toleranzen als die Standard-AM-Möglichkeiten erfordern.
- Anforderungen an die Oberflächenbeschaffenheit: Geben Sie die gewünschte Oberflächenrauheit (Ra) oder die Art der Ausführung (z. B. matt gestrahlt, elektropoliert) an.
- Post-Processing-Bedarf: Geben Sie alle erforderlichen Wärmebehandlungs-, Bearbeitungs- oder spezifischen Endbearbeitungsschritte an.
- Anwendungskontext: Beschreiben Sie kurz den Verwendungszweck (hilft dem Anbieter, die funktionalen Anforderungen zu verstehen).
- Erforderliche Bescheinigungen/Dokumente: Geben Sie alle erforderlichen Materialzertifikate oder Prüfberichte an.
Schlussfolgerung: Die Zukunft der Chirurgie ist personalisiert und präzise mit Metal AM
Die additive Fertigung von Metallen entwickelt sich rasch von einer Prototyping-Technologie zu einer praktikablen und oft überlegenen Produktionsmethode für komplexe, hochwertige Komponenten, insbesondere im anspruchsvollen Bereich der Chirurgie. Die Möglichkeit, bewährte biokompatible Materialien wie 316L-Edelstahl und Ti-6Al-4V-Titan zu verwenden, in Kombination mit der beispiellosen Designfreiheit, die AM bietet, ermöglicht es Medizintechnikern und Chirurgen, Instrumente zu entwickeln, die zuvor als unmöglich galten.
Von patientenspezifischen chirurgischen Führungen, die die Genauigkeit des Verfahrens verbessern, über leichte, ergonomische Werkzeuge, die die Ermüdung des Chirurgen verringern, bis hin zu konsolidierten Instrumenten, die komplexe Verfahren vereinfachen, bietet der 3D-Druck von Metall greifbare Vorteile. Er ermöglicht schnellere Innovationszyklen, erleichtert die Massenanpassung und eröffnet neue Wege zur Verbesserung von Operationstechniken und Patientenergebnissen.
Um diese Vorteile zu nutzen, müssen jedoch die Grundsätze des Design for Additive Manufacturing, eine strenge Prozesskontrolle, validierte Nachbearbeitungstechniken und eine strenge Qualitätssicherung beachtet werden. Die Auswahl hochwertiger Metallpulver und eines sachkundigen, erfahrenen Fertigungspartners mit entsprechenden medizinischen Zertifizierungen (z. B. ISO 13485) ist von entscheidender Bedeutung für den Erfolg.
Da die Technologie immer ausgereifter wird und die Kosten möglicherweise sinken, wird sich der Einsatz von 3D-gedruckten chirurgischen Instrumenten beschleunigen, die Chirurgie weiter personalisieren und Fortschritte in allen medizinischen Fachbereichen vorantreiben.
Sind Sie bereit herauszufinden, wie die additive Fertigung von Metallen die Entwicklung Ihrer chirurgischen Instrumente revolutionieren kann? Nutzen Sie das Fachwissen und die hochmodernen Fähigkeiten von Met3dp. Als führendes Unternehmen im Bereich der fortschrittlichen Metallpulverproduktion und der Präzisions Metall-3D-DrucklösungenWir bieten umfassende Unterstützung von der Designoptimierung bis zur Produktion der fertigen Teile. Setzen Sie sich noch heute mit Met3dp in Verbindung, um Ihre Projektanforderungen zu besprechen und zu erfahren, wie unsere Fähigkeiten die Ziele Ihres Unternehmens im Bereich der additiven Fertigung unterstützen können.
Teilen auf
MET3DP Technology Co., LTD ist ein führender Anbieter von additiven Fertigungslösungen mit Hauptsitz in Qingdao, China. Unser Unternehmen ist spezialisiert auf 3D-Druckgeräte und Hochleistungsmetallpulver für industrielle Anwendungen.
Fragen Sie an, um den besten Preis und eine maßgeschneiderte Lösung für Ihr Unternehmen zu erhalten!
Verwandte Artikel
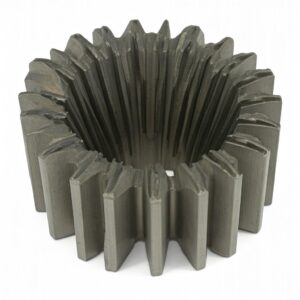
Hochleistungs-Düsenschaufelsegmente: Revolutionierung der Turbineneffizienz mit 3D-Metalldruck
Mehr lesen "Über Met3DP
Aktuelles Update
Unser Produkt
KONTAKT US
Haben Sie Fragen? Senden Sie uns jetzt eine Nachricht! Wir werden Ihre Anfrage mit einem ganzen Team nach Erhalt Ihrer Nachricht bearbeiten.
Holen Sie sich Metal3DP's
Produkt-Broschüre
Erhalten Sie die neuesten Produkte und Preislisten
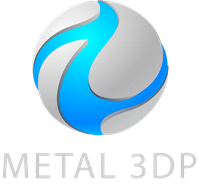
Metallpulver für 3D-Druck und additive Fertigung