Leichte Aufhängungslenker über Metal AM: Revolutionierung der Automobilleistung
Inhaltsübersicht
Einführung - Die Entwicklung der Automobilaufhängung und die Rolle des 3D-Metalldrucks
Die Automobilindustrie steht seit jeher an der Spitze der technischen Innovation und strebt ständig nach höherer Leistung, besserer Effizienz und geringerem Gewicht. Zu den kritischen Komponenten, die diese Faktoren beeinflussen, gehören die Radaufhängungen, die eine entscheidende Rolle für das Fahrverhalten, die Stabilität und den allgemeinen Fahrkomfort eines Fahrzeugs spielen. Diese Komponenten, die traditionell durch Verfahren wie Schmieden oder Gießen hergestellt wurden, durchlaufen nun dank des Aufkommens der additiven Fertigung von Metallen (AM), auch bekannt als Metallguss, eine transformative Entwicklung 3D-Druck. Diese Spitzentechnologie bietet eine noch nie dagewesene Designfreiheit und die Möglichkeit, leichte und dennoch robuste Teile mit optimierten Geometrien herzustellen. Für Ingenieure und Beschaffungsverantwortliche im Automobilsektor ist das Verständnis des Potenzials von Metal AM für die Herstellung von Radaufhängungen kein futuristisches Konzept mehr, sondern eine greifbare Möglichkeit, einen Wettbewerbsvorteil zu erlangen. Unternehmen wie Metall3DPdas Unternehmen mit Hauptsitz in Qingdao, China, steht an der Spitze dieser Revolution und bietet fortschrittliche Metall-3D-Druckgeräte und Hochleistungsmetallpulver an, um Innovationen in der Automobilherstellung voranzutreiben. Ihr Engagement für ein branchenweit führendes Druckvolumen, Genauigkeit und Zuverlässigkeit macht sie zu einem zuverlässigen Partner für die Herstellung unternehmenskritischer Automobilkomponenten.
Wozu dienen leichte Fahrwerkslenker? - Verbesserung der Fahrzeugdynamik und Effizienz
Leichte Radaufhängungen, die mit Hilfe von 3D-Metalldruckverfahren hergestellt werden, dienen demselben grundlegenden Zweck wie ihre traditionell hergestellten Gegenstücke: Sie verbinden verschiedene Teile des Aufhängungssystems des Fahrzeugs, um die Bewegung der Räder zu kontrollieren und einen optimalen Kontakt mit der Straßenoberfläche zu gewährleisten. Die einzigartigen Fähigkeiten der Metall-AM-Technik eröffnen jedoch neue Möglichkeiten für ihr Design und ihre Anwendung.
Wichtige Anwendungsfälle und Funktionen:
- Verringerung der ungefederten Masse: Durch den Einsatz von Leichtbaumaterialien und optimierten Designs reduzieren 3D-gedruckte Aufhängungsglieder die ungefederten Massen - das Gewicht der Komponenten, die nicht von den Aufhängungsfedern getragen werden (z. B. Räder, Reifen, Bremsen und ein Teil des Aufhängungssystems selbst) - erheblich. Geringere ungefederte Masse führt zu:
- Verbesserte Handhabung und Reaktionsfähigkeit
- Verbesserter Fahrkomfort
- Bessere Kraftstoffeffizienz
- Geringerer Reifenverschleiß
- Optimierung von Kinematik und Compliance: Metall-AM ermöglicht die Herstellung komplexer Geometrien, mit denen das kinematische Verhalten (wie sich die Räder im Verhältnis zum Fahrgestell bewegen) und die Nachgiebigkeit (die Flexibilität und Elastizität der Aufhängungskomponenten) der Aufhängung fein abgestimmt werden können. Dies ermöglicht es Ingenieuren,:
- Präzisere Radkontrolle über den gesamten Federweg
- Minimierung von unerwünschten Vibrationen und Lärm
- Verbesserte Kurvenstabilität und Haftung
- Integration der Funktionalität: Die additive Fertigung öffnet Türen für die Funktionsintegration, bei der mehrere Teile zu einer einzigen, optimierten Komponente kombiniert werden können. Für Radaufhängungen könnte dies bedeuten:
- Integrierte Kühlkanäle für Bremssysteme
- Einbau von Sensoren zur Echtzeitüberwachung der Federungsleistung
- Entwurf interner Gitterstrukturen für ein besseres Verhältnis zwischen Festigkeit und Gewicht
- Ermöglichung einer bedarfsgerechten und maßgeschneiderten Produktion: Der 3D-Metalldruck ermöglicht die Herstellung von Kleinserien oder sogar maßgeschneiderten Aufhängungen, die auf bestimmte Fahrzeugmodelle oder Leistungsanforderungen zugeschnitten sind. Dies ist besonders wertvoll für:
- Hochleistungsfahrzeuge und Motorsport
- Entwicklung und Prüfung von Prototypen
- Aftermarket und Ersatzteilherstellung
Die Möglichkeit, das Design und das Material von Aufhängungsgliedern mit Hilfe von Metall-AM maßgeschneidert zu gestalten, ermöglicht es Automobilherstellern und -zulieferern, ein Leistungs- und Effizienzniveau zu erreichen, das mit herkömmlichen Methoden bisher unerreichbar war.
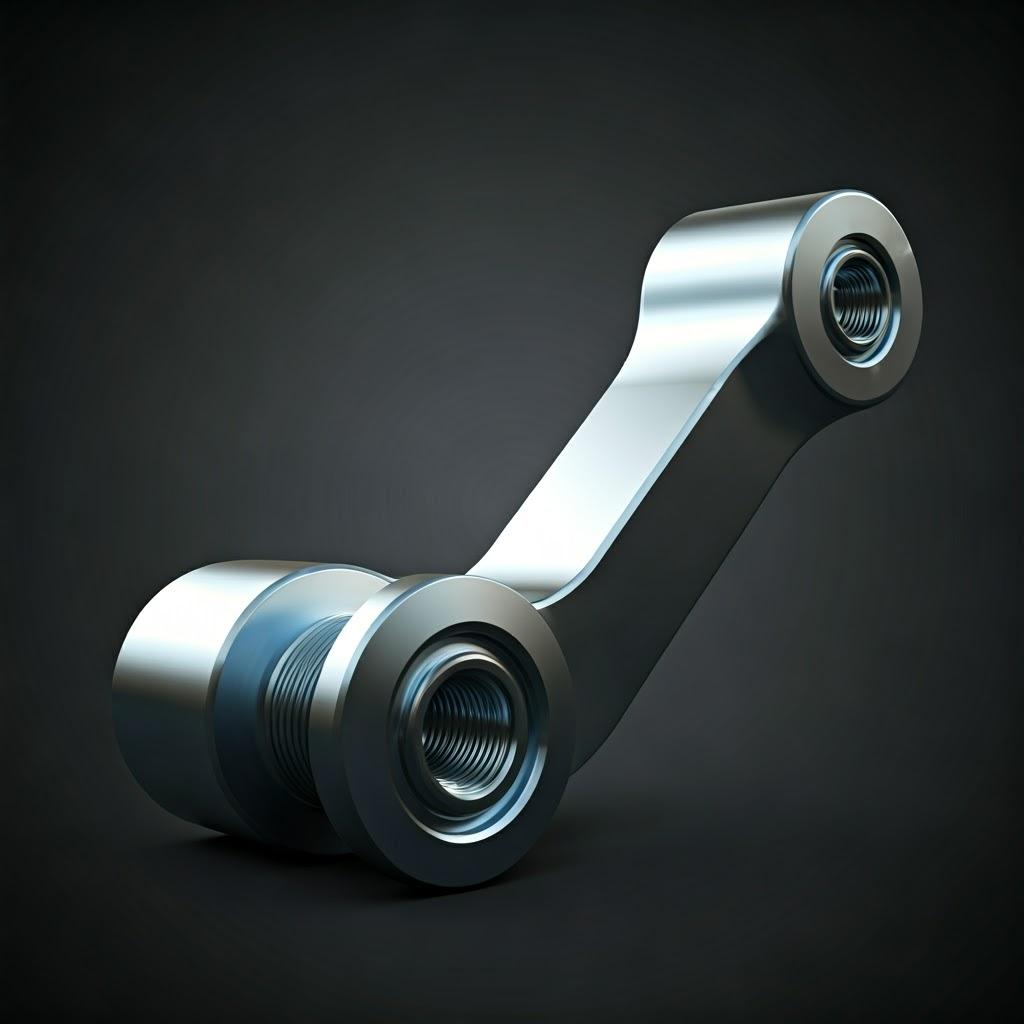
Warum 3D-Metalldruck für leichte Aufhängungsglieder? - Vorteile gegenüber traditioneller Fertigung
Der 3D-Metalldruck für die Herstellung von Leichtbaulenkern bietet eine Reihe von Vorteilen im Vergleich zu herkömmlichen Fertigungsverfahren:
Merkmal | 3D-Druck von Metall | Traditionelle Fertigung (Schmieden, Gießen) |
---|---|---|
Gestaltungsfreiheit | Ermöglicht komplexe Geometrien, komplizierte interne Strukturen (z. B. Gitter) und Funktionsintegration, was zu optimierten Designs für Gewichtsreduzierung und Leistung führt. | Konstruktionsbeschränkungen aufgrund von Werkzeugbeschränkungen; komplexe Formen erfordern oft mehrere Teile und Montage. |
Potenzial zur Gewichtsreduzierung | Ermöglicht den Einsatz von Topologieoptimierung und Leichtbauwerkstoffen wie AlSi10Mg und A7075, um das Gewicht von Bauteilen ohne Beeinträchtigung der Festigkeit deutlich zu reduzieren. | Zur Gewichtsreduzierung sind oft Materialabtragsverfahren erforderlich, die weniger effizient sind und möglicherweise nicht den gleichen Optimierungsgrad erreichen. |
Materialeffizienz | Herstellung von Teilen mit minimalem Materialabfall, da das Material nur dort aufgetragen wird, wo es benötigt wird. Überschüssiges Pulver kann oft recycelt werden. | Es kann erheblicher Materialabfall in Form von Verschnitt und Bearbeitungsspänen entstehen. |
Anpassung und Flexibilität | Ermöglicht schnelles Prototyping, Kleinserienproduktion und individuelle Anpassung von Designs ohne teure Werkzeugänderungen. Ideal für Hochleistungsfahrzeuge und Nischenmärkte. | Hohe Werkzeugkosten und lange Vorlaufzeiten machen die Anpassung an Kundenwünsche und die Produktion von Kleinserien zu einer wirtschaftlichen Herausforderung. |
Reduzierung der Vorlaufzeit | Kann die Durchlaufzeiten erheblich verkürzen, insbesondere bei komplexen Teilen, die bei herkömmlichen Verfahren komplizierte Werkzeuge und mehrere Fertigungsschritte erfordern würden. | Die Herstellung von Werkzeugen kann zeitaufwändig sein, was zu einer längeren Gesamtvorlaufzeit führt. |
Funktionale Integration | Ermöglicht die Integration mehrerer Funktionen in ein einziges Teil, wodurch die Anzahl der Komponenten, der Montageschritte und der potenziellen Fehlerpunkte reduziert wird. | Die Integration mehrerer Funktionen erfordert oft komplexe mehrteilige Konstruktionen und Montageverfahren. |
Lieferkettenoptimierung | Potenzial für On-Demand-Fertigung und lokalisierte Produktion, wodurch die Abhängigkeit von komplexen globalen Lieferketten verringert und die Lagerkosten minimiert werden. | Ist oft auf globale Lieferketten angewiesen, die anfällig für Störungen und längere Lieferzeiten sein können. Erfordert die Vorhaltung größerer Bestände. |
Leistungssteigerung | Optimierte Konstruktionen und Materialauswahl können zu einem besseren Verhältnis von Steifigkeit zu Gewicht, verbesserten NVH-Eigenschaften (Noise, Vibration, Harshness) und einer besseren Gesamtfahrzeugdynamik führen. | Leistungsverbesserungen erfordern oft umfangreiche Design-Iterationen und Materialänderungen, was kostspielig und zeitaufwändig sein kann. |
In Blätter exportieren
Als ein führender Anbieter von Metall-AM-Lösungen, Metall3DP ermöglicht es Automobilherstellern, diese Vorteile durch ihre fortschrittliche Drucktechnologie und hochwertigen Metallpulver zu nutzen.
Empfohlene Materialien und warum sie wichtig sind - AlSi10Mg und A7075 für optimale Leistung
Die Wahl des Materials ist entscheidend für die Leistungsmerkmale von 3D-gedruckten Lenkern für Kraftfahrzeuge. Metall3DP bietet ein umfassendes Portfolio an Hochleistungsmetallpulvern, darunter AlSi10Mg und A7075, die sich aufgrund ihrer hervorragenden Eigenschaften besonders gut für diese Anwendung eignen:
1. AlSi10Mg (Aluminium-Silizium-Magnesium-Legierung):
Eigentum | Wert | Bedeutung für Suspensionsverbindungen |
---|---|---|
Niedrige Dichte | ~2,67 g/cm³ | Trägt erheblich zur Gewichtsreduzierung bei, was zu verbesserter Kraftstoffeffizienz, besserem Handling und geringeren ungefederten Massen führt. |
Hohes Festigkeits-Gewichts-Verhältnis | Zugfestigkeit bis zu 450 MPa, Streckgrenze bis zu 310 MPa (je nach Nachbearbeitung) | Gewährleistet die strukturelle Integrität und Haltbarkeit der Aufhängungsglieder unter anspruchsvollen Betriebsbedingungen. Die hohe Festigkeit ermöglicht dünnere Profile und weitere Gewichtseinsparungen. |
Gute Duktilität | Bruchdehnung bis zu 10% (je nach Nachbearbeitung) | Bietet ein gewisses Maß an Flexibilität und Energieabsorption, was für die Bewältigung von Stoßbelastungen und die Verbesserung des Fahrkomforts von Vorteil ist. |
Ausgezeichnete Wärmeleitfähigkeit | ~160 W/m-K | Erleichtert die Wärmeableitung, was von Vorteil sein kann, wenn sich die Aufhängungsglieder in der Nähe von wärmeerzeugenden Bauteilen wie Bremsen befinden. |
Gute Korrosionsbeständigkeit | Zeigt eine gute Beständigkeit gegen atmosphärische Korrosion, was für die langfristige Zuverlässigkeit in Automobilanwendungen entscheidend ist. | Gewährleistet die Langlebigkeit und strukturelle Integrität der Aufhängungsglieder unter verschiedenen Umweltbedingungen. |
Verarbeitbarkeit mit L-PBF | Gut geeignet für Laser Powder Bed Fusion (L-PBF), ein gängiges 3D-Druckverfahren für Metall, das hohe Präzision und die Möglichkeit zur Erstellung komplexer Geometrien bietet. Metall3DP nutzt die fortschrittliche L-PBF-Technologie für optimale Ergebnisse mit AlSi10Mg. | Ermöglicht die Herstellung komplizierter und optimierter Aufhängeglieder mit hoher Maßgenauigkeit. |
In Blätter exportieren
2. A7075 (Aluminium-Zink-Magnesium-Kupfer-Legierung):
Eigentum | Wert | Bedeutung für Suspensionsverbindungen |
---|---|---|
Ultra-Hochfest | Zugfestigkeit bis zu 570 MPa, Streckgrenze bis zu 500 MPa (je nach Wärmebehandlung) | Bietet eine außergewöhnliche Festigkeit und eignet sich daher ideal für Anwendungen, bei denen hohe Lasten und Spannungen auftreten. Dies kann eine weitere Gewichtsoptimierung durch den Einsatz von weniger Material ermöglichen. |
Gute Ermüdungsbeständigkeit | Zeigt eine gute Beständigkeit gegen Ermüdungsbruch, was für Aufhängungskomponenten, die während des Fahrzeugbetriebs wiederholten Belastungszyklen ausgesetzt sind, entscheidend ist. | Gewährleistet die langfristige Haltbarkeit und Zuverlässigkeit der Aufhängungsglieder unter zyklischen Belastungsbedingungen. |
Leichtgewicht | Ähnliche Dichte wie AlSi10Mg (~2,81 g/cm³) | Trägt zur allgemeinen Gewichtsreduzierung bei, wenn auch etwas weniger als AlSi10Mg. Die höhere Festigkeit kann kompensiert werden, indem dünnere Abschnitte möglich sind. |
Bearbeitbarkeit | Weist im Allgemeinen eine gute Bearbeitbarkeit bei bestimmten Temperaturen auf, was für Nachbearbeitungsschritte, die eine hohe Präzision erfordern, von Vorteil sein kann. | Ermöglicht die präzise Bearbeitung kritischer Oberflächen unter Einhaltung enger Toleranzen. |
Verarbeitbarkeit mit L-PBF | Kann mit L-PBF verarbeitet werden, obwohl es möglicherweise optimierte Parameter und Nachbearbeitung erfordert, um Probleme wie Heißrissbildung zu vermeiden. [Die Erfahrung von Metal3DP in der Metallpulververarbeitung gewährleistet qualitativ hochwertige A7075-Teile. | Ermöglicht die Herstellung von hochfesten, leichten Aufhängungsgliedern mit komplexen Geometrien. |
In Blätter exportieren
Die Wahl zwischen AlSi10Mg und A7075 hängt von den spezifischen Leistungsanforderungen des Fahrzeugaufhängungsglieds ab. AlSi10Mg bietet ein gutes Gleichgewicht zwischen Festigkeit, Duktilität und Verarbeitbarkeit für den allgemeinen Leichtbau, während A7075 eine überlegene Festigkeit für anspruchsvollere Anwendungen bietet, bei denen die maximale Belastbarkeit entscheidend ist. Metall3DP kann eine fachkundige Beratung bei der Materialauswahl auf der Grundlage der spezifischen Anforderungen der jeweiligen Anwendung bieten.
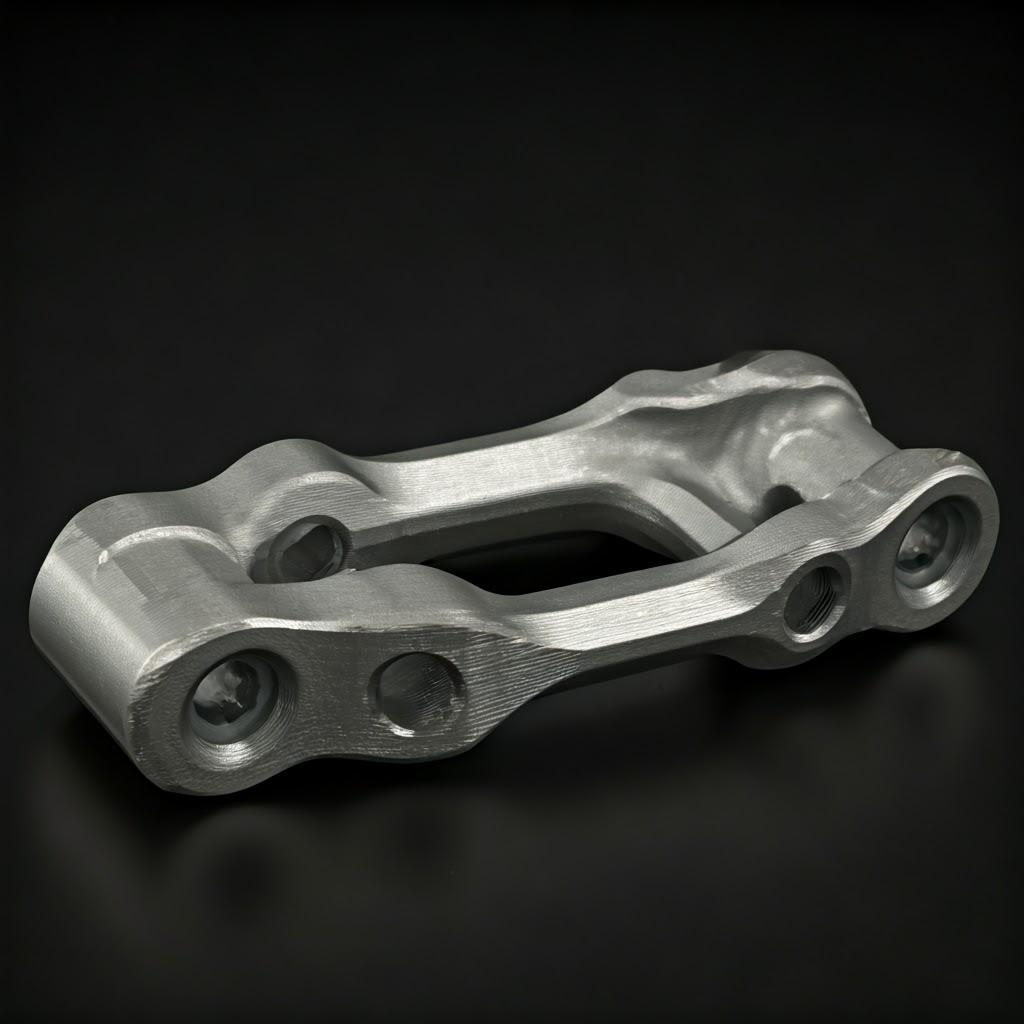
Designüberlegungen für die additive Fertigung - Optimierung der Geometrie für Leistung und Druckbarkeit
Die Entwicklung von Radaufhängungen für den 3D-Druck aus Metall erfordert eine andere Denkweise als die traditionelle Fertigung. Um die Möglichkeiten der additiven Fertigung voll auszuschöpfen und eine optimale Leistung und Druckbarkeit zu erreichen, müssen mehrere wichtige Designüberlegungen berücksichtigt werden:
- Topologie-Optimierung: Diese Berechnungsmethode ermöglicht es Ingenieuren, den Konstruktionsraum, die Belastungsbedingungen und die Leistungsziele zu definieren und dann automatisch eine optimierte Geometrie zu erstellen, indem Material aus Bereichen mit geringer Beanspruchung entfernt wird. Das Ergebnis sind leichte Teile mit maximaler Steifigkeit und einem optimalen Verhältnis zwischen Festigkeit und Gewicht. Metall-AM erleichtert die Herstellung dieser komplexen, organisch anmutenden Strukturen.
- Gitterförmige Strukturen: Der Einbau interner Gitterstrukturen in die Aufhängung kann das Gewicht erheblich reduzieren und gleichzeitig die Steifigkeit und Energieabsorption beibehalten oder sogar erhöhen. Verschiedene Gitterstrukturen (z. B. gyroid, kubisch, diamantförmig) bieten unterschiedliche mechanische Eigenschaften und können auf spezifische Belastungsanforderungen zugeschnitten werden. Der 3D-Metalldruck eignet sich hervorragend für die Herstellung dieser komplizierten Innengeometrien.
- Wandstärke und Riffelung: Die sorgfältige Auswahl der Wandstärke ist sowohl für die strukturelle Integrität als auch für die Druckbarkeit entscheidend. Dünne Wände können das Gewicht reduzieren, sind aber anfällig für Verformungen während des Drucks. Strategisch platzierte Rippen und Versteifungen können zusätzlichen Halt bieten und Verformungen verhindern, ohne das Gewicht zu erhöhen.
- Unterstützende Strukturen: Metall-Pulverbettschmelzverfahren (PBF) erfordern in der Regel Stützstrukturen, um das Teil auf der Bauplatte zu verankern, Verformungen zu verhindern und überhängende Merkmale zu stützen. Die Konstruktion von Teilen mit selbsttragenden Winkeln und die Minimierung von Überhängen kann den Bedarf an umfangreichen Stützstrukturen verringern, was zu weniger Nachbearbeitung und einer besseren Oberflächenqualität führt.
- Orientierung und Platzierung: Die Ausrichtung des Teils auf der Bauplatte kann sich erheblich auf die Oberflächengüte, die Maßgenauigkeit und den Bedarf an Stützstrukturen auswirken. Die Optimierung der Bauausrichtung kann den Stufeneffekt minimieren, der bei der schichtweisen Fertigung auftritt, und die Gesamtqualität des gedruckten Teils verbessern.
- Feature-Konsolidierung: Metall-AM ermöglicht die Konsolidierung mehrerer Komponenten in einem einzigen, integrierten Teil. Bei Aufhängungsgliedern könnte dies die Integration von Buchsen, Befestigungselementen oder sogar Sensorgehäusen direkt in das Design bedeuten, was die Montagezeit und potenzielle Fehlerpunkte reduziert.
- Überlegungen zur Oberflächenbeschaffenheit: Die Oberflächenbeschaffenheit der gedruckten Oberfläche bei der Metall-AM kann je nach Material, Druckparametern und Bauausrichtung variieren. Die Gestaltung kritischer Oberflächen unter Berücksichtigung nachfolgender Bearbeitungs- oder Polierprozesse ist wichtig, um die erforderlichen Toleranzen und die Oberflächenqualität zu erreichen.
Durch die Berücksichtigung dieser Konstruktionsprinzipien können Ingenieure das volle Potenzial des 3D-Metalldrucks ausschöpfen, um leichte, leistungsstarke Aufhängungsglieder für Kraftfahrzeuge zu entwickeln, die die Fähigkeiten herkömmlich hergestellter Teile übertreffen. Metall3DP bietet Fachwissen im Bereich Design für additive Fertigung (DfAM), um Kunden bei der Optimierung ihrer Designs für den erfolgreichen 3D-Druck von Metall zu unterstützen.
Toleranz, Oberflächengüte und Maßgenauigkeit - Präzision bei Metall-AM erreichen
Das Erreichen der erforderlichen Toleranzen, Oberflächengüte und Maßgenauigkeit ist für Aufhängungslenker in der Automobilindustrie von größter Bedeutung, da sich diese Faktoren direkt auf ihre Passform, Funktion und Gesamtleistung auswirken. Die 3D-Drucktechnologien für Metall haben in diesem Bereich große Fortschritte gemacht und bieten Möglichkeiten, die den strengen Anforderungen der Automobilindustrie gerecht werden können.
Faktoren, die die Präzision bei der Metall-AM beeinflussen:
- Druckergenauigkeit und Kalibrierung: Die inhärente Genauigkeit des Metall-3D-Druckers ist ein wichtiger Faktor. Hochwertige Industriedrucker, wie sie beispielsweise von Metall3DPsind so konzipiert und kalibriert, dass sie konsistente und präzise Ergebnisse liefern.
- Materialeigenschaften und Schrumpfung: Verschiedene Metallpulver weisen während des Erstarrungsprozesses unterschiedliche Schrumpfungsgrade auf. Das Verständnis und die Kompensation dieser materialspezifischen Schrumpfungsraten in den Konstruktions- und Druckparametern ist entscheidend für das Erreichen der Maßhaltigkeit.
- Prozessparameter: Druckparameter wie Laserleistung, Scangeschwindigkeit, Schichtdicke und Pulverbetttemperatur haben einen erheblichen Einfluss auf die endgültigen Abmessungen und die Oberflächengüte des Teils. Optimierte Parametersätze, die oft durch umfangreiche Forschung und Erfahrung entwickelt wurden, sind für das Erreichen der gewünschten Präzision unerlässlich.
- Orientierung aufbauen: Wie bereits erwähnt, kann sich die Ausrichtung des Teils auf der Bauplatte auf die Maßgenauigkeit auswirken, insbesondere bei Merkmalen, die in Baurichtung ausgerichtet sind. Abgestufte Oberflächen können eine Nachbearbeitung erfordern, um glatte Oberflächen und genaue Abmessungen zu erzielen.
- Unterstützende Strukturen: Obwohl sie für viele Geometrien notwendig sind, können Stützstrukturen beim Entfernen Oberflächenmängel zurücklassen. Durch eine sorgfältige Konstruktion und optimierte Stützstrategien können diese Auswirkungen minimiert werden.
- Nachbearbeiten: In vielen Fällen werden Nachbearbeitungsschritte wie CNC-Bearbeitung, Schleifen oder Polieren eingesetzt, um engere Toleranzen und glattere Oberflächen zu erreichen, als dies mit dem Druckverfahren allein möglich ist.
Typische erreichbare Toleranzen und Oberflächengüte:
Die genauen Werte hängen zwar von der spezifischen Teilegeometrie, dem Material und dem Druckverfahren ab, aber mit dem 3D-Metalldruck lassen sich in der Regel Maßgenauigkeiten im Bereich von ±0,1 bis ±0,5 mm erzielen. Mit optimierten Parametern und Nachbearbeitung können bei kritischen Merkmalen Toleranzen bis zu ±0,05 mm oder noch enger erreicht werden.
Die Oberflächengüte von frisch gedruckten Metallteilen liegt in der Regel zwischen 5 und 20 µm Ra (durchschnittlicher Rauhigkeitswert). Nachbearbeitungstechniken können dies erheblich verbessern und bei Bedarf Oberflächengüten von bis zu 0,8 µm Ra oder besser erreichen.
[Das Engagement von Metal3DP für branchenführende Genauigkeit stellt sicher, dass die Metall-3D-Druckdienste die anspruchsvollen Toleranz- und Oberflächenanforderungen bei der Herstellung von Aufhängungsgliedern für die Automobilindustrie erfüllen können.
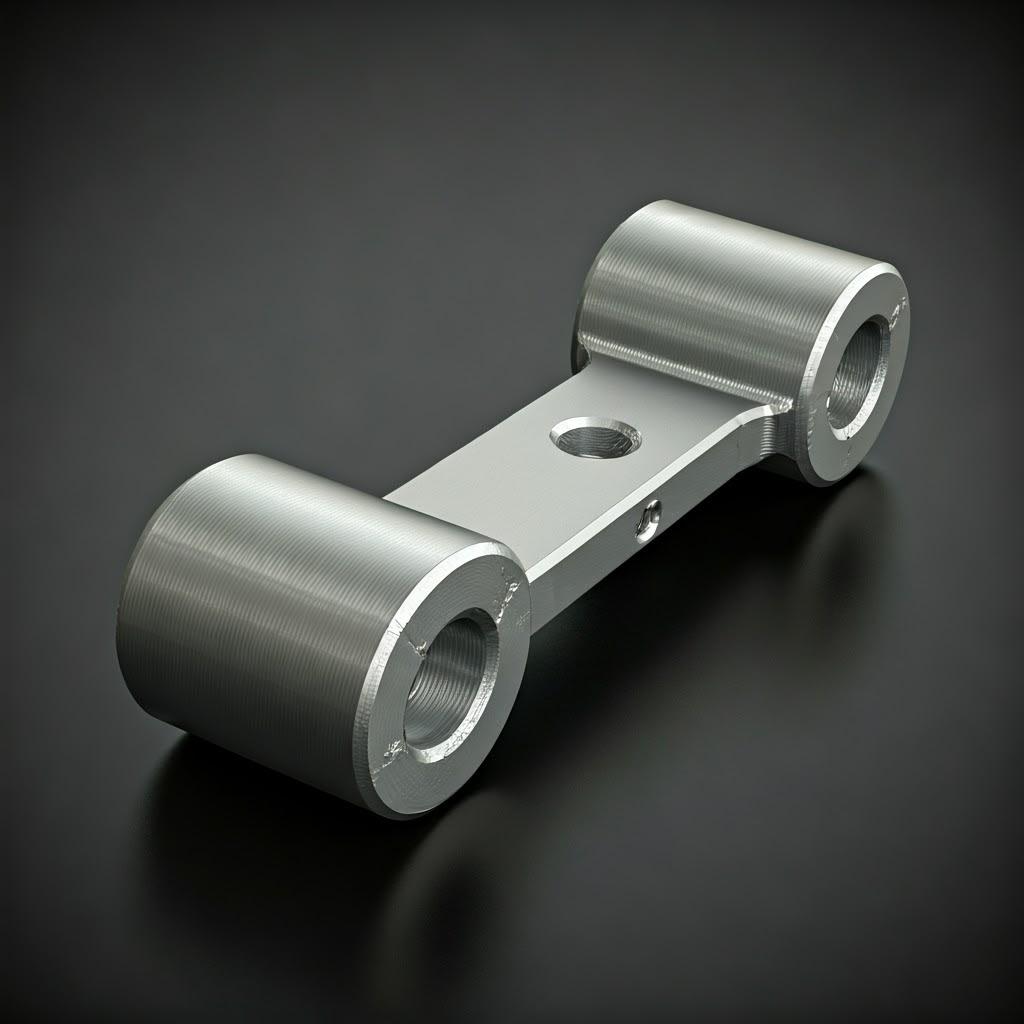
Nachbearbeitungsanforderungen - Verbesserung von Funktionalität und Oberflächenqualität
Der 3D-Metalldruck bietet zwar erhebliche Vorteile bei der Erstellung komplexer Geometrien, doch ist häufig eine Nachbearbeitung erforderlich, um die gewünschten endgültigen Eigenschaften, die Oberflächenbeschaffenheit und die Maßgenauigkeit von Lenkern für Kraftfahrzeuge zu erreichen. Zu den üblichen Nachbearbeitungsschritten gehören:
- Unterstützung bei der Entfernung: Stützstrukturen, die für viele PBF-Verfahren unerlässlich sind, müssen nach dem Druck sorgfältig entfernt werden. Dies kann manuell mit Werkzeugen oder durch automatisierte Verfahren wie das Drahterodieren (Electrical Discharge Machining) erfolgen. Das Design der Stützen und die Teilegeometrie können die Leichtigkeit und Qualität der Entfernung beeinflussen.
- Stressabbau Wärmebehandlung: 3D-gedruckte Metallteile können aufgrund der schnellen Erwärmungs- und Abkühlungszyklen während des Druckvorgangs manchmal Eigenspannungen aufweisen. Durch eine Wärmebehandlung zum Spannungsabbau werden diese Eigenspannungen reduziert, wodurch eine mögliche Verformung oder Rissbildung verhindert und die mechanischen Eigenschaften insgesamt verbessert werden.
- Heiß-Isostatisches Pressen (HIP): HIP ist ein Verfahren, bei dem hoher Druck und hohe Temperaturen auf das gedruckte Teil einwirken, wodurch die innere Porosität verringert und die Dichte erhöht wird. Dadurch können die mechanischen Eigenschaften erheblich verbessert werden, insbesondere die Ermüdungsfestigkeit, die für Radaufhängungen von entscheidender Bedeutung ist.
- CNC-Bearbeitung: Für kritische Oberflächen, die sehr enge Toleranzen oder spezifische Oberflächengüten erfordern, kann die CNC-Bearbeitung als sekundärer Arbeitsgang eingesetzt werden. Dies ermöglicht die präzise Endbearbeitung von Befestigungspunkten, Lagerflächen oder Gewindebohrungen.
- Oberflächenveredelung (Polieren, Schleifen, Strahlen): Je nach den Anforderungen der Anwendung können verschiedene Oberflächenbearbeitungsverfahren eingesetzt werden, um das ästhetische Erscheinungsbild zu verbessern, die Oberflächenrauhigkeit zu verringern oder das Teil für weitere Beschichtungen vorzubereiten. Zu den Techniken gehören Strahlen, Schleifen und Polieren.
- Beschichtungen und Oberflächenbehandlungen: Beschichtungen, wie z. B. Eloxal für Aluminiumlegierungen oder Schutzlacke, können aufgebracht werden, um die Korrosionsbeständigkeit, die Verschleißfestigkeit oder andere funktionelle Eigenschaften der Aufhängeglieder zu verbessern.
Die spezifischen Anforderungen an die Nachbearbeitung von 3D-gedruckten Lenkern für Kraftfahrzeuge hängen vom Material, der geplanten Anwendung und den gewünschten Endeigenschaften und der Oberflächenqualität ab. Metall3DP bietet umfassende Nachbearbeitungsdienste an, um sicherzustellen, dass die fertigen Teile die anspruchsvollsten Automobilstandards erfüllen.
Häufige Herausforderungen und wie man sie vermeidet - Erfolgreiche Metall-AM-Produktion sicherstellen
Der 3D-Metalldruck bietet zwar zahlreiche Vorteile, doch bei der Herstellung von Lenkern für die Automobilaufhängung können bestimmte Herausforderungen auftreten. Das Verständnis dieser potenziellen Probleme und die Umsetzung geeigneter Strategien zu ihrer Vermeidung sind entscheidend für eine erfolgreiche und effiziente Fertigung:
- Verformung und Verzerrung: Eigenspannungen und thermische Gradienten während des Druckvorgangs können insbesondere bei großen oder komplexen Geometrien zu Verwerfungen oder Verzerrungen des Teils führen.
- Milderung: Optimieren Sie die Teileausrichtung, verwenden Sie geeignete Stützstrukturen, setzen Sie eine Wärmebehandlung zum Spannungsabbau ein und kontrollieren Sie die Druckparameter sorgfältig.
- Probleme bei der Entfernung von Stützstrukturen: Schlecht konzipierte oder übermäßige Stützstrukturen können schwer zu entfernen sein und Oberflächenschäden hinterlassen.
- Milderung: Entwerfen Sie Teile mit selbsttragenden Winkeln, optimieren Sie die Platzierung und Geometrie der Stützstruktur und verwenden Sie geeignete Techniken zum Entfernen von Stützen.
- Probleme mit Porosität und Dichte: Ein unzureichendes Schmelzen oder Erstarren des Metallpulvers kann zu Porosität im gedruckten Teil führen, was seine mechanischen Eigenschaften beeinträchtigen kann.
- Milderung: Optimieren Sie die Druckparameter (Laserleistung, Scangeschwindigkeit), sorgen Sie für ein hochwertiges Metallpulver mit guter Fließfähigkeit (wie es das fortschrittliche Pulverherstellungssystem von [Metal3DP] bietet), und ziehen Sie Nachbearbeitungstechniken wie HIP in Betracht.
- Einschränkungen der Oberflächenbeschaffenheit: Die Oberflächenbeschaffenheit im Druckzustand entspricht möglicherweise nicht den Anforderungen für bestimmte Anwendungen, was die Ermüdungseigenschaften beeinträchtigen kann oder eine zusätzliche Nachbearbeitung erforderlich macht.
- Milderung: Optimieren Sie die Bauausrichtung, verwenden Sie feinere Pulverpartikelgrößen und setzen Sie geeignete Nachbearbeitungstechniken wie Bearbeitung oder Polieren ein.
- Maßliche Ungenauigkeiten: Schrumpfung, thermische Ausdehnung oder Kalibrierungsprobleme können zu Abweichungen von den vorgesehenen Abmessungen führen.
- Milderung: Kalibrieren Sie den Drucker regelmäßig, kompensieren Sie die materialspezifische Schrumpfung im Design und ziehen Sie die Verwendung von Opferstrukturen oder Nachbearbeitung für kritische Abmessungen in Betracht.
- Variabilität der Materialeigenschaften: Uneinheitliche Pulverqualität oder suboptimale Druckparameter können zu Schwankungen in den mechanischen Eigenschaften der gedruckten Teile führen.
- Milderung: Beziehen Sie hochwertige Metallpulver von seriösen Anbietern wie [Metal3DP], die strenge Qualitätskontrollen durchführen und robuste und gut kontrollierte Druckverfahren entwickeln.
Indem sie diese potenziellen Herausforderungen durch eine sorgfältige Konstruktion, optimierte Prozessparameter und eine angemessene Nachbearbeitung proaktiv angehen, können Automobilhersteller das volle Potenzial des 3D-Metalldrucks für die Herstellung hochwertiger, leichter Radaufhängungen ausschöpfen.
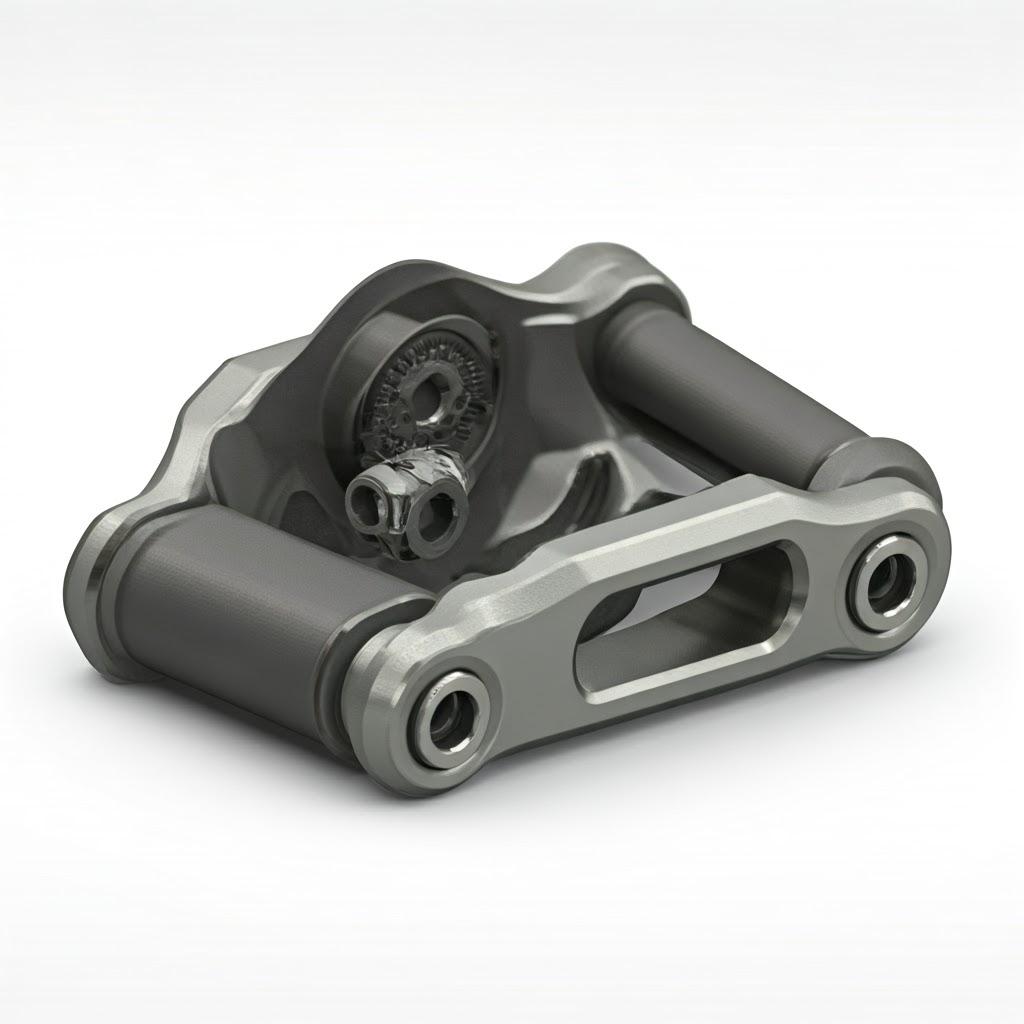
Wie man den richtigen 3D-Druckdienstleister für Metall auswählt - Wichtige Überlegungen für Automobil-OEMs und Zulieferer
Die Auswahl des richtigen 3D-Druckdienstleisters für Metall ist eine wichtige Entscheidung für Automobilhersteller und -zulieferer, die die additive Fertigung für leichte Aufhängungsverbindungen nutzen möchten. Ein zuverlässiger Partner kann qualitativ hochwertige Teile, pünktliche Lieferung und fachkundige Unterstützung während des gesamten Prozesses gewährleisten. Hier sind die wichtigsten Faktoren, die Sie bei der Bewertung potenzieller Anbieter berücksichtigen sollten:
- Materielle Fähigkeiten: Vergewissern Sie sich, dass der Dienstleister die spezifischen Metallpulver anbietet, die Sie für Ihre Anwendung benötigen, z. B. AlSi10Mg und A7075. Prüfen Sie die Erfahrung und das Fachwissen des Anbieters bei der Verarbeitung dieser Materialien und seine Fähigkeit, die Druckparameter für optimale mechanische Eigenschaften anzupassen. Metall3DP verfügt über eine breite Palette an hochwertigen Metallpulvern, die für verschiedene Anwendungen optimiert sind.
- Drucktechnik und Ausrüstung: Informieren Sie sich über die Arten von Metall-3D-Drucktechnologien, die der Anbieter einsetzt (z. B. Laser Powder Bed Fusion (L-PBF), Electron Beam Melting (EBM)). Vergewissern Sie sich, dass die Geräte auf dem neuesten Stand der Technik sind und das für Ihre Teilegröße und -komplexität erforderliche Bauvolumen, die Genauigkeit und die Zuverlässigkeit bieten. [Die Drucker von Metal3DP bieten ein branchenführendes Druckvolumen, Genauigkeit und Zuverlässigkeit.
- Qualitätsmanagement und Zertifizierungen: Überprüfen Sie, ob der Anbieter über ein solides Qualitätsmanagementsystem und entsprechende Zertifizierungen (z. B. ISO 9001, AS9100 für die Luft- und Raumfahrt) verfügt. Dies zeigt, dass er sich der Qualitätskontrolle und der Prozesskonsistenz verpflichtet fühlt.
- Fachwissen im Bereich Design für additive Fertigung (DfAM): Ein sachkundiger Dienstleister sollte DfAM-Unterstützung anbieten, um Ihre Aufhängungslenkerentwürfe für den 3D-Metalldruck zu optimieren und so Herstellbarkeit, Leichtbau und Leistung zu gewährleisten. [Metal3DP] bietet umfassende Lösungen, die fortschrittliche Metallpulver und Anwendungsentwicklungsdienste umfassen.
- Nachbearbeitungsmöglichkeiten: Stellen Sie fest, ob der Anbieter die erforderlichen Nachbearbeitungsdienste anbietet, wie z. B. das Entfernen von Halterungen, Wärmebehandlung, CNC-Bearbeitung und Oberflächenbehandlung, um Ihre Anforderungen an das Endprodukt zu erfüllen. Ein umfassendes Serviceangebot kann den Produktionsprozess rationalisieren.
- Metrologie und Inspektion: Erkundigen Sie sich nach den Mess- und Prüfmöglichkeiten des Anbieters, um sicherzustellen, dass die gedruckten Teile die geforderten Maßhaltigkeits- und Qualitätsstandards erfüllen. Moderne Prüfgeräte und -verfahren sind für kritische Automobilkomponenten unerlässlich.
- Vorlaufzeiten und Produktionskapazität: Besprechen Sie die Vorlaufzeiten für die Prototypen- und Serienproduktion sowie die Fähigkeit des Anbieters, die von Ihnen erwarteten Mengen zu bewältigen. Stellen Sie sicher, dass die Zeitpläne mit Ihren Projektplänen übereinstimmen.
- Kostenstruktur und Transparenz: Verstehen Sie das Preismodell des Anbieters und sorgen Sie für Transparenz bei der Kostenaufschlüsselung. Vergleichen Sie Angebote mehrerer Anbieter und berücksichtigen Sie dabei nicht nur die Druckkosten, sondern auch die Kosten für Designoptimierung, Nachbearbeitung und Qualitätssicherung.
- Kommunikation und Unterstützung: Bewerten Sie die Reaktionsfähigkeit des Anbieters, die Klarheit der Kommunikation und die technische Unterstützung. Eine starke Partnerschaft erfordert effektive Kommunikation und einen kooperativen Ansatz.
- Erfahrung in der Industrie: Suchen Sie nach einem Anbieter, der nachweislich in der Automobilindustrie tätig ist und Erfahrung in der Herstellung ähnlicher Komponenten hat. Ihr Verständnis der Normen und Anforderungen der Automobilindustrie ist von unschätzbarem Wert.
Durch die sorgfältige Berücksichtigung dieser Faktoren können Automobilhersteller und -zulieferer einen 3D-Druckdienstleister für Metall auswählen, der ihren spezifischen Anforderungen entspricht und ihnen hilft, die additive Fertigung erfolgreich in ihre Produktionsprozesse zu integrieren.
Kostenfaktoren und Vorlaufzeit - Verständnis für die Wirtschaftlichkeit von Metall-AM für Aufhängeglieder
Die Kosten und die Vorlaufzeit im Zusammenhang mit dem 3D-Metalldruck von Radaufhängungen für Kraftfahrzeuge werden von mehreren Faktoren beeinflusst. Das Verständnis dieser Elemente ist entscheidend für die Budgetierung und Projektplanung:
Kostenfaktoren:
- Materialkosten: Die Kosten für das Metallpulver sind ein wichtiger Faktor. Legierungen wie A7075 können teurer sein als AlSi10Mg. Auch die Menge des pro Teil verwendeten Materials und das Gesamtbauvolumen wirken sich auf die Materialkosten aus. [Metal3DP stellt eine breite Palette an hochwertigen Metallpulvern her.
- Druckzeit: Die Dauer des Druckprozesses hängt von Faktoren wie Teilegröße, Komplexität, Auslastung des Bauvolumens und Schichtdicke ab. Längere Druckzeiten führen zu höheren Maschinenbetriebskosten.
- Betriebskosten der Maschine: Dazu gehören der Energieverbrauch, die Wartung und die Abschreibung der 3D-Druckausrüstung.
- Kosten für Design und Technik: Die Komplexität des Designs und der für die Optimierung und Druckvorbereitung erforderliche technische Aufwand können die Gesamtkosten beeinflussen. Die Nutzung des DfAM-Fachwissens kann dazu beitragen, diese Kosten auf lange Sicht zu minimieren.
- Nachbearbeitungskosten: Das Ausmaß und die Art der erforderlichen Nachbearbeitung (z. B. Entfernen von Trägern, Wärmebehandlung, maschinelle Bearbeitung, Endbearbeitung) wirken sich erheblich auf die Endkosten aus.
- Kosten für Qualitätssicherung und Inspektion: Gründliche Inspektions- und Qualitätskontrollverfahren erhöhen die Gesamtkosten, sind aber für kritische Automobilkomponenten unerlässlich.
- Werkzeugkosten (indirekt): Obwohl Metall-AM den Bedarf an herkömmlichen harten Werkzeugen eliminiert, fallen immer noch Kosten für die Vorbereitung der Bauplatte, Software und spezielle Vorrichtungen für die Nachbearbeitung an.
- Skalenvorteile: Mit steigendem Produktionsvolumen sinken die Kosten pro Teil in der Regel aufgrund von Faktoren wie einer besseren Auslastung des Produktionsvolumens und der Amortisation der Rüstkosten.
Faktoren für die Vorlaufzeit:
- Entwurf und Optimierung: Die Zeit, die für den Entwurf, die Simulation und die Optimierung des Aufhängungsglieds für Metall-AM benötigt wird.
- Druckvorbereitung: Einrichten des Druckauftrags, einschließlich der Anordnung der Druckplatten, der Erzeugung der Auflage und der Auswahl der Parameter.
- Druckzeit: Die tatsächliche Dauer des 3D-Druckvorgangs.
- Nachbearbeiten: Die Zeit, die für die Entfernung der Halterung, die Wärmebehandlung, die Bearbeitung, die Oberflächenveredelung und andere sekundäre Arbeitsgänge benötigt wird.
- Qualitätsinspektion: Die Zeit, die für Maßkontrollen, Materialprüfungen und andere Qualitätssicherungsverfahren benötigt wird.
- Versand und Logistik: Die Zeit für die Verpackung und den Transport der fertigen Teile.
Der 3D-Metalldruck kann bei komplexen Geometrien und kleinen bis mittleren Produktionsmengen kürzere Vorlaufzeiten bieten als die herkömmliche Fertigung, insbesondere wenn die Werkzeugherstellung ein wichtiger Faktor ist. Bei sehr hohen Stückzahlen einfacherer Teile können konventionelle Verfahren jedoch immer noch kostengünstiger sein. Wenn Sie die spezifischen Anforderungen Ihrer Anwendung verstehen und mit erfahrenen Dienstleistern wie [Metal3DP] zusammenarbeiten, können Sie sowohl Kosten als auch Vorlaufzeiten optimieren.
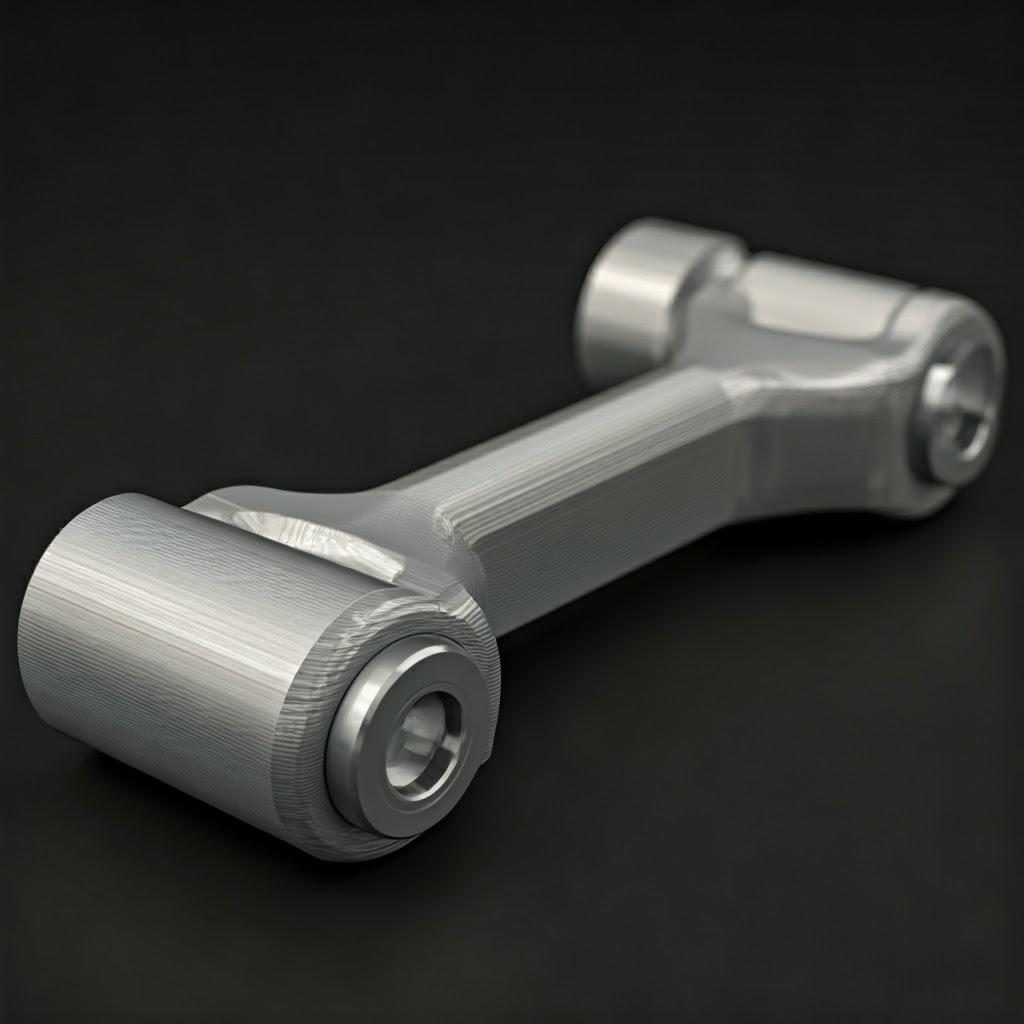
Häufig gestellte Fragen (FAQ)
- Können 3D-gedruckte Aufhängungslenker aus Metall die Sicherheitsstandards für Kraftfahrzeuge erfüllen? Ja, wenn die Teile unter Verwendung geeigneter Materialien und Qualitätskontrollverfahren korrekt entworfen, hergestellt und nachbearbeitet werden, können 3D-gedruckte Aufhängungsglieder aus Metall die strengen Sicherheitsstandards für Kraftfahrzeuge erfüllen. Es ist entscheidend, mit erfahrenen Anbietern wie [Metal3DP] zusammenzuarbeiten, die diese Anforderungen verstehen und über das nötige Fachwissen und die Zertifizierungen verfügen.
- Wie hoch ist die typische Lebensdauer eines 3D-gedruckten Aufhängungsglieds aus Metall in einer Automobilanwendung? Die Lebensdauer hängt von Faktoren wie dem verwendeten Material, der Konstruktion, den Betriebsbedingungen und etwaigen Nachbehandlungen ab. Bei richtiger Materialauswahl (z. B. AlSi10Mg oder A7075), optimiertem Design für Ermüdungsbeständigkeit und geeigneter Nachbearbeitung (z. B. HIP) können 3D-gedruckte Aufhängungslenker aus Metall eine vergleichbare oder sogar höhere Lebensdauer als herkömmlich hergestellte Teile erreichen.
- Ist der 3D-Metalldruck für die Massenproduktion von Autoaufhängungen kostengünstig? Die Kosteneffizienz für die Massenproduktion hängt von der Komplexität des Teils, dem Material und dem Produktionsvolumen ab. Bei komplexen Geometrien und geringen bis mittleren Stückzahlen kann der 3D-Druck von Metallteilen wettbewerbsfähig oder sogar kostengünstiger sein als herkömmliche Verfahren, da keine Werkzeugkosten anfallen und die Teile konsolidiert werden können. Wenn die Stückzahlen für einfachere Konstruktionen steigen, können konventionelle Fertigungsverfahren für hohe Stückzahlen immer noch wirtschaftlicher sein. Die Fortschritte in der 3D-Drucktechnologie und bei den Materialien verbessern jedoch kontinuierlich die Kosteneffizienz für größere Produktionsserien.
Fazit - Die Zukunft der Automobilaufhängung mit 3D-Metalldruck
Der 3D-Metalldruck ist nicht länger eine Nischentechnologie, sondern ein praktikables und zunehmend wichtiges Fertigungsverfahren für die Automobilindustrie, insbesondere für die Herstellung von Leichtbaulenkern. Die Möglichkeit, komplexe, optimierte Geometrien mit Materialien wie AlSi10Mg und A7075 zu erstellen, bietet erhebliche Vorteile in Bezug auf Leistung, Effizienz und Designflexibilität. Unternehmen wie Metal3DP Technology Co. LTD stehen an der Spitze dieser Revolution und bieten die fortschrittlichen Anlagen, hochwertigen Metallpulver und das Anwendungs-Know-how, das für die Innovation in der Automobilherstellung erforderlich ist. Durch das Verständnis der Konstruktionsüberlegungen, der Materialeigenschaften, der Nachbearbeitungsanforderungen und der Auswahl des richtigen Dienstleisters können Automobilingenieure und Beschaffungsmanager Metall-AM getrost in Anspruch nehmen, um die nächste Generation leistungsstarker und leichter Aufhängungssysteme zu entwickeln. Kontakt Metall3DP um herauszufinden, wie ihre Fähigkeiten die Ziele Ihres Unternehmens im Bereich der additiven Fertigung unterstützen und den Wandel zur digitalen Fertigung beschleunigen können.
Teilen auf
MET3DP Technology Co., LTD ist ein führender Anbieter von additiven Fertigungslösungen mit Hauptsitz in Qingdao, China. Unser Unternehmen ist spezialisiert auf 3D-Druckgeräte und Hochleistungsmetallpulver für industrielle Anwendungen.
Fragen Sie an, um den besten Preis und eine maßgeschneiderte Lösung für Ihr Unternehmen zu erhalten!
Verwandte Artikel
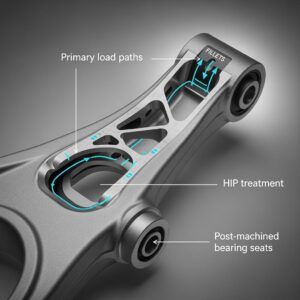
Metal 3D Printing for U.S. Automotive Lightweight Structural Brackets and Suspension Components
Mehr lesen "Über Met3DP
Aktuelles Update
Unser Produkt
KONTAKT US
Haben Sie Fragen? Senden Sie uns jetzt eine Nachricht! Wir werden Ihre Anfrage mit einem ganzen Team nach Erhalt Ihrer Nachricht bearbeiten.
Holen Sie sich Metal3DP's
Produkt-Broschüre
Erhalten Sie die neuesten Produkte und Preislisten