Wärmedämmplatten für Raumfahrtsysteme mittels Metal AM
Inhaltsübersicht
Einleitung: Die kritische Rolle der Wärmedämmung in Raumfahrzeugen
Raumfahrzeuge, ob sie die Erde umkreisen, zu fernen Planeten reisen oder an Raumstationen andocken, arbeiten in einer der extremsten Umgebungen, die man sich vorstellen kann. Sie sind einer unerbittlichen Flut von Herausforderungen ausgesetzt: dem Vakuum des Weltraums, intensiver Sonnenstrahlung, Mikrometeoriteneinschlägen und extremen Temperaturschwankungen von Hunderten von Grad Celsius zwischen direktem Sonnenlicht und Schatten. Ein effektives Management dieser thermischen Belastungen ist nicht nur wünschenswert, sondern von grundlegender Bedeutung für den Erfolg der Mission. Jede Komponente, von empfindlicher Elektronik und Antriebssystemen bis hin zu wissenschaftlichen Instrumenten und Strukturelementen, hat bestimmte Betriebstemperaturbereiche. Abweichungen können zu Fehlfunktionen, verminderter Leistung, verkürzter Lebensdauer oder katastrophalen Ausfällen führen. Dies ist der Punkt thermomanagement für Raumfahrzeuge und innerhalb dieser kritischen Disziplin von entscheidender Bedeutung ist, wärmedämmplatten eine unverzichtbare Rolle spielen.
Bislang wurden für die Isolierung von Raumfahrzeugen mehrschichtige Isoliermatten (MLI), spezielle Beschichtungen und passive Wärmeregulierungselemente verwendet. Diese Methoden sind zwar effektiv, stoßen aber häufig an ihre Grenzen, was die geometrischen Einschränkungen, die Komplexität der Integration, den strukturellen Beitrag und die Anfälligkeit für Schäden oder Degradation bei langen Missionen angeht. Da die Entwürfe von Raumfahrzeugen immer komplexer und miniaturisierter werden und die Grenzen der Erforschung immer weiter hinausschieben, ist der Bedarf an integrierten, robusten und geometrisch optimierten thermischen Lösungen erheblich gestiegen.
Eingeben Additive Fertigung von Metallen (Metal AM)auch bekannt als Metall 3D-Druck. Diese transformative Technologie verändert die Art und Weise, wie Ingenieure an die Entwicklung und Produktion komplexer Produkte herangehen, rapide Luft- und Raumfahrtkomponenteneinschließlich Wärmedämmplatten. Im Gegensatz zur traditionellen subtraktiven Fertigung (z. B. CNC-Bearbeitung), bei der Material aus einem massiven Block abgetragen wird, oder zu formgebenden Verfahren (z. B. Gießen oder Schmieden) werden bei der AM Teile Schicht für Schicht direkt aus einem digitalen Modell unter Verwendung von speziellen Metallpulvern aufgebaut. Dieser grundlegende Unterschied eröffnet eine nie dagewesene Designfreiheit und ermöglicht die Erstellung komplizierter Geometrien, interner Merkmale und optimierter Strukturen, deren Herstellung bisher unmöglich oder unerschwinglich war.
Für Wärmedämmplatten bietet Metall-AM eine einzigartige Konvergenz von Vorteilen. Es ermöglicht den Ingenieuren,:
- Integrieren Sie die Funktionalität: Kombinieren Sie strukturelle Unterstützung mit Wärmedämmeigenschaften in einem einzigen Bauteil und reduzieren Sie so die Anzahl der Teile und die Komplexität der Montage.
- Optimieren Sie die Geometrie: Erstellen Sie komplexe Formen, die genau auf das verfügbare Volumen und die thermischen Anforderungen zugeschnitten sind, einschließlich interner Hohlräume, dünner Wände und konformer Designs, die andere Komponenten umschließen.
- Leichte Strukturen: Durch Topologieoptimierung und Gitterstrukturen lässt sich die Masse erheblich reduzieren - ein entscheidender Faktor bei Weltraummissionen, bei denen jedes eingesparte Gramm zu geringeren Startkosten oder einer höheren Nutzlastkapazität führt.
- Verwendung fortschrittlicher Materialien: Nutzung von Hochleistungsmetalllegierungen, die speziell aufgrund ihrer thermischen Eigenschaften, ihres Verhältnisses von Festigkeit zu Gewicht und ihrer Widerstandsfähigkeit gegenüber der rauen Weltraumumgebung ausgewählt wurden.
- Beschleunigen Sie die Entwicklung: Rasche Iteration von Entwürfen und Herstellung von Prototypen oder flugfertigen Teilen in viel kürzerer Zeit als mit herkömmlichen Methoden möglich, was für anspruchsvolle Missionspläne entscheidend ist.
Unternehmen, die sich auf fortschrittliche Fertigungslösungen spezialisiert haben, stehen an der Spitze dieser Revolution. Met3dp, ein führender Anbieter mit Hauptsitz in Qingdao, China, ist ein Beispiel für diesen Wandel. Mit Fachwissen in beiden 3D-Druck von Metall met3dp ermöglicht es der Luft- und Raumfahrtindustrie, das volle Potenzial von AM auszuschöpfen, indem das Unternehmen seine Anlagen, insbesondere das selektive Elektronenstrahlschmelzen (SEBM), und die Herstellung von Hochleistungsmetallpulvern mit fortschrittlichen Techniken wie Gaszerstäubung und Plasma-Rotations-Elektroden-Verfahren (PREP) einsetzt. Der Fokus auf branchenführende Druckvolumina, Genauigkeit und Zuverlässigkeit stellt sicher, dass missionskritische Teile, wie z. B. Wärmedämmplatten, die strengen Anforderungen von Raumfahrtanwendungen erfüllen.
Dieser Artikel befasst sich mit der Anwendung von Metall-AM zur Herstellung fortschrittlicher Wärmedämmplatten für Raumfahrtsysteme. Wir werden die spezifischen Anwendungsfälle, die überzeugenden Vorteile gegenüber herkömmlichen Methoden, die empfohlenen Materialien wie IN625 und AlSi10Mg, entscheidende Designüberlegungen (DfAM), die erreichbare Präzision, Nachbearbeitungsanforderungen, allgemeine Herausforderungen, Kriterien für die Lieferantenauswahl und Kostenfaktoren untersuchen und schließlich einige häufig gestellte Fragen beantworten. Unser Ziel ist es, Ingenieuren, Beschaffungsmanagern und Entscheidungsträgern in der Luft- und Raumfahrtbranche ein umfassendes Verständnis dafür zu vermitteln, wie Metall-AM das Wärmemanagement von Raumfahrzeugen umgestaltet und Lösungen bietet, die leichter und effizienter sind und den Herausforderungen der nächsten Generation der Weltraumforschung gerecht werden. Unabhängig davon, ob Sie an der Herstellung von Satelliten, der Entwicklung von Trägerraketen oder der Konstruktion von Weltraumsonden beteiligt sind, wird das Verständnis der Möglichkeiten der Metall-AM für thermische Komponenten immer wichtiger.
Anwendungen von fortschrittlichen Isolierplatten in Raumfahrtsystemen
Die Notwendigkeit einer präzisen Wärmeregulierung durchdringt nahezu jeden Aspekt der Konstruktion und des Betriebs von Raumfahrzeugen. Wärmedämmplatten, insbesondere solche, die durch die Designfreiheit der additiven Fertigung von Metallen verbessert wurden, finden vielfältige und kritische Anwendungen in verschiedenen Raumfahrtsystemen. Ihre Hauptfunktion besteht darin, den Wärmefluss zu kontrollieren - entweder um zu verhindern, dass empfindliche Komponenten durch interne Verlustleistung oder externe Strahlung überhitzen, oder um kritische Systeme in den kalten Weiten des Weltraums innerhalb ihres Betriebstemperaturbereichs zu halten. Die Möglichkeit, die Geometrie, die Materialeigenschaften und die integrierten Merkmale mit Hilfe von AM anzupassen, erweitert ihren Nutzen im Vergleich zu herkömmlichen flachen Platten oder einfachen Abstandshaltern erheblich.
Hier eine Übersicht über die wichtigsten Anwendungsbereiche:
1. Satelliten (LEO, MEO, GEO, und darüber hinaus):
- Elektronikgehäuse Isolierung: Empfindliche Elektronikgehäuse mit Prozessoren, Kommunikationsgeräten und Sensorschnittstellen erzeugen während des Betriebs Wärme und sind gleichzeitig schwankenden Außentemperaturen ausgesetzt. AM-Isolierplatten aus Metall können diesen Gehäusen angepasst werden, indem sie dünne Wände, interne reflektierende Hohlräume oder sogar integrierte Wärmerohre oder Dampfkammern (die durch die Komplexität von AM ermöglicht werden) enthalten, um thermische Belastungen effizient zu isolieren und zu bewältigen. Sie können als strukturelle Halterungen fungieren und gleichzeitig für thermischen Abstand sorgen.
- Schutz des Batteriemoduls: Batterien haben enge optimale Temperaturbereiche für Leistung und Langlebigkeit. Isolierplatten schirmen die Batteriemodule vor extremen Außentemperaturen ab und tragen dazu bei, die bei den Lade-/Entladezyklen entstehende Wärme zu bewältigen, um Sicherheit und Zuverlässigkeit zu gewährleisten. Leichte AlSi10Mg-Platten werden hier oft bevorzugt.
- Isolierung von Sensoren und Instrumenten: Wissenschaftliche Instrumente, Kameras und Sensoren benötigen oft extrem stabile thermische Umgebungen, um korrekt zu funktionieren und hohe Präzision zu erreichen. Maßgeschneiderte AM-Isolierplatten können thermisch stabile Gehäuse oder Montageschnittstellen schaffen und so die thermische Drift und das Rauschen minimieren. Die niedrige Wärmeleitfähigkeit in Verbindung mit der strukturellen Integrität macht Materialien wie IN625 für spezifische Isolationsanforderungen geeignet.
- Komponenten des Antriebssystems: Triebwerke, Treibstofftanks und die dazugehörigen Rohrleitungen arbeiten bei unterschiedlichen Temperaturen, die manchmal kryogen und manchmal sehr hoch sind. Isolierplatten tragen zur Aufrechterhaltung der Treibstofftemperaturen bei, schützen die angrenzenden Strukturen vor der Hitze der Triebwerksfahne und stellen sicher, dass Ventile und Leitungen korrekt funktionieren. Hochtemperaturbeständige Legierungen wie IN625 sind hier unerlässlich.
- Thermische Brüche an strukturellen Schnittstellen: Wo verschiedene Strukturelemente aufeinandertreffen, können Wärmebrücken entstehen, die eine unerwünschte Wärmeübertragung ermöglichen. AM ermöglicht die Konstruktion komplexer Schnittstellenplatten mit minimaler Kontaktfläche, dünnen Querschnitten oder integrierten Isoliermerkmalen (wie Waben oder Gitter), die als wirksame Wärmebrücken fungieren und gleichzeitig mechanische Lasten tragen.
2. Trägerraketen:
- Schutz von Avionik und Leitsystemen: Während des Aufstiegs sind Trägerraketen starker aerodynamischer Erwärmung und Vibrationen ausgesetzt. Isolierplatten schützen kritische Avionik-, Navigations- und Steuersysteme, die in der Struktur des Fahrzeugs untergebracht sind.
- Abschirmung des Motorraums: Raketentriebwerke erzeugen enorme Wärmemengen. AM-Isolierplatten aus Metall, häufig aus Superlegierungen wie IN625, werden als Hitzeschilde verwendet, um die umliegenden Strukturen, Kraftstoffleitungen und Stellglieder im Triebwerksraum zu schützen. Ihre komplexen Formen können für maximale Abdeckung und minimales Gewicht optimiert werden.
- Isolierung von Kryogenik-Tanks: Während MLI weit verbreitet ist, können strategisch platzierte AM-Struktur-/Isolationsplatten dazu beitragen, das Abdampfen zu kontrollieren und die strukturelle Integrität um kryogene Treibstofftanks herum zu erhalten, insbesondere an Befestigungspunkten oder Schnittstellen.
3. Raumstationen und Lebensräume:
- Gerätegestelle und Module: In den unter Druck stehenden Modulen erzeugen zahlreiche Experimente und Subsysteme Wärme. Integrierte Isolierplatten tragen dazu bei, die Wärmelasten lokal zu steuern, Hotspots zu vermeiden und einen effizienten Betrieb der Kühlsysteme zu gewährleisten.
- Schutz externer Komponenten: Extern an Raumstationen montierte Geräte (wie Antennen, Experimente oder Roboterarme) sind dem gesamten Spektrum der thermischen Bedingungen im Weltraum ausgesetzt. AM-Isolierplatten bieten dauerhaften, zuverlässigen Wärmeschutz und strukturelle Befestigung.
4. Sonden und Rover für den Weltraum:
- Überleben bei extremen Temperaturen: Sonden, die in das äußere Sonnensystem reisen oder auf Planeten wie dem Mars oder Monden wie Europa landen, sind mit extremer Kälte konfrontiert, während Missionen, die sich der Sonne nähern, mit großer Hitze zu kämpfen haben. AM-Isolierplatten, die möglicherweise aus abgestuften Materialien oder komplexen internen Strukturen bestehen, sind überlebenswichtig, da sie die Betriebstemperaturen für Elektronik und wissenschaftliche Nutzlasten über jahrzehntelange Missionen aufrechterhalten.
- Integration von Heizkörpern und Wärmerohren: AM ermöglicht die direkte Integration von Isolationsmerkmalen in Komponenten des Wärmeregelungssystems, wie z. B. Heizkörperverkleidungen oder Befestigungsstrukturen für Wärmerohre, und optimiert so die Wärmeabfuhrwege bei gleichzeitiger Minimierung parasitärer Wärmelecks.
Großhandel für Luft- und Raumfahrtteile und Überlegungen zur Lieferkette:
Für großhandel für Luft- und Raumfahrtteile zulieferern und Herstellern bietet Metal AM ein neues Paradigma. Beschaffungsmanager suchen zunehmend nach Lieferanten, die nicht nur Standardkomponenten, sondern hoch optimierte, anwendungsspezifische Teile liefern können. Die Fähigkeit, komplexe Isolierplatten auf Anfrage zu produzieren und dabei möglicherweise mehrere Funktionen in einem Teil zu vereinen, bietet erhebliche Vorteile:
- Reduzierte Bestände: Es ist weniger notwendig, zahlreiche Variationen von Standardisolierungskomponenten zu lagern.
- Kürzere Vorlaufzeiten: AM ermöglicht eine schnellere Durchlaufzeit von der Fertigstellung des Designs bis zur Auslieferung der Teile im Vergleich zu werkzeugintensiven traditionellen Methoden.
- Anpassungen: Die Fähigkeit, maßgeschneiderte Isolierlösungen zu liefern, die auf die spezifischen Anforderungen des Einsatzes zugeschnitten sind, ohne die mit der traditionellen Herstellung verbundenen erheblichen NRE-Kosten (Non-Recurring Engineering).
- Widerstandsfähigkeit der Lieferkette: Verteilte AM-Kapazitäten können im Vergleich zu geografisch konzentrierten traditionellen Fertigungszentren belastbarere Lieferketten bieten.
Metallische AM-Isolierplatten stellen einen bedeutenden Fortschritt dar, da sie über einfache Barrieren hinausgehen und zu integrierten, multifunktionalen Komponenten werden, die für die anspruchsvollen thermischen und strukturellen Anforderungen der modernen satelliten-Wärmekontrolle, isolierung der Trägerraketeund Missionen im Weltraum. Da die Hersteller in der Luft- und Raumfahrt nach leichteren, leistungsfähigeren und schnell entwickelten Systemen suchen, wird die Nachfrage nach fortschrittlichen AM-Lösungen von kompetenten Anbietern wie Met3dp nur weiter steigen.
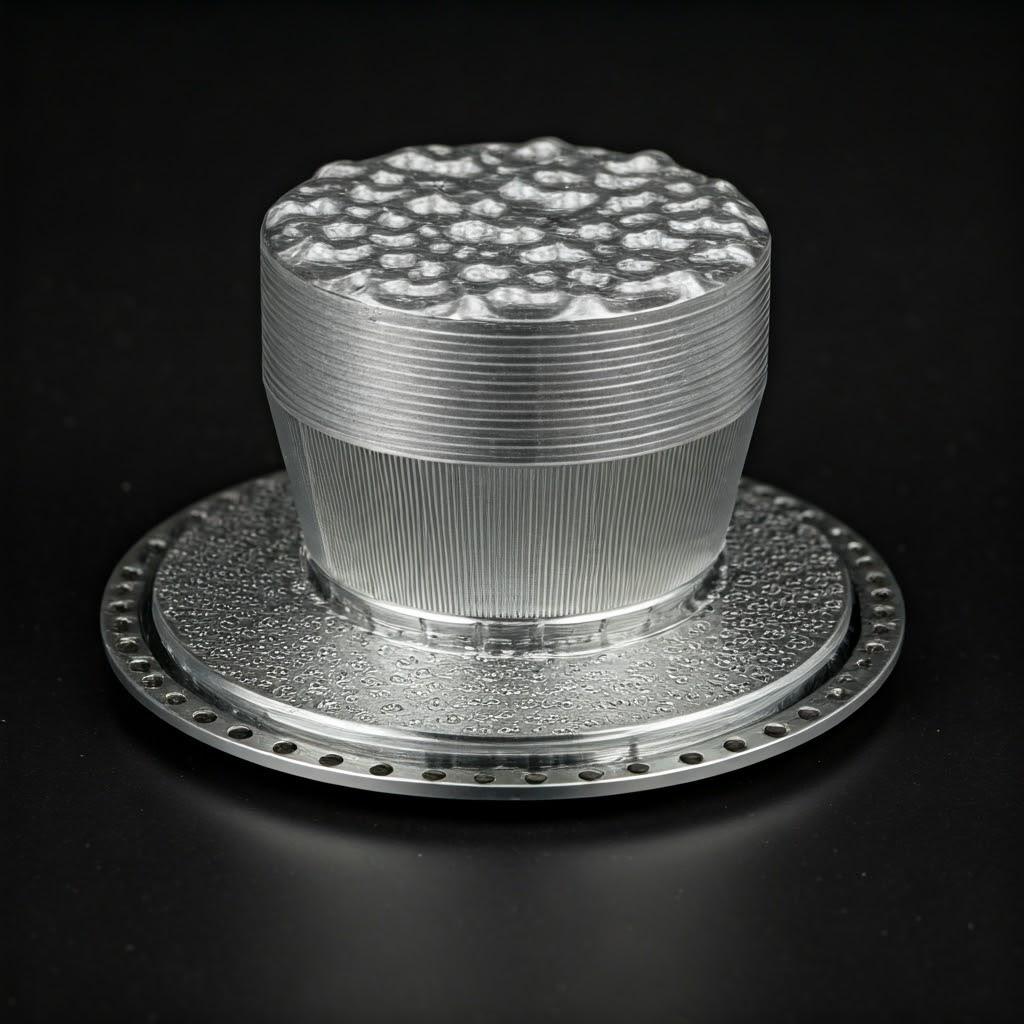
Warum sich die additive Fertigung von Metall für Isolierplatten von Raumfahrzeugen anbietet
Die rauen Bedingungen im Weltraum - extreme Temperaturen, Vakuum, Strahlung - in Verbindung mit dem unablässigen Streben nach geringerer Masse und höherer Leistung stellen außergewöhnliche Anforderungen an die Komponenten von Raumfahrzeugen. Wärmedämmplatten sind da keine Ausnahme. Während traditionelle Fertigungsverfahren wie Zerspanung, Gießen und Blechumformung in der Luft- und Raumfahrtindustrie seit Jahrzehnten zum Einsatz kommen, bietet die additive Fertigung (AM) von Metallen eine Reihe überzeugender Vorteile, insbesondere für komplexe Komponenten wie optimierte Isolierplatten. Diese Vorteile verändern die Design- und Produktionsmöglichkeiten grundlegend und machen AM zu einer zunehmend bevorzugten Wahl für unternehmenskritische Anwendungen.
Lassen Sie uns die wichtigsten Gründe dafür aufschlüsseln Metall AM ist außerordentlich gut geeignet für die Herstellung von isolierplatten für Raumfahrzeuge:
1. Unerreichte Gestaltungsfreiheit und Komplexität:
- Geometrische Raffinesse: Herkömmliche Verfahren sind von Natur aus durch den Zugang zu Werkzeugen, Formzwänge oder die Verformbarkeit von Blechen begrenzt. AM baut Schicht für Schicht auf und gibt den Designern die Freiheit, praktisch jede erdenkliche Form zu schaffen. Für Isolierplatten bedeutet dies:
- Konforme Designs: Die Platten können den Konturen empfindlicher Geräte perfekt angepasst werden, was den Platzbedarf minimiert und die Isolationsabdeckung maximiert.
- Interne Merkmale: Komplexe interne Kanäle, Hohlräume oder Gitterstrukturen können direkt in die Platte eingearbeitet werden. Diese können für minimale Wärmeleitfähigkeit, integrierte Kühlkanäle (falls erforderlich) oder spezifische strukturelle Leistungen optimiert werden. Stellen Sie sich eine Isolierplatte mit einer inneren Wabenstruktur vor, die für Steifigkeit und minimale Wärmeleitpfade sorgt - mit AM leicht zu realisieren.
- Organische Formen: Topologie-Optimierungsalgorithmen können eingesetzt werden, um Material strategisch aus wenig beanspruchten Bereichen zu entfernen, was zu leichten, organisch geformten Platten führt, die sowohl thermische als auch strukturelle Anforderungen effizient erfüllen.
- Traditionelle Zwänge: Die maschinelle Bearbeitung hat mit tiefen Taschen, dünnen Wänden und inneren Merkmalen zu kämpfen. Das Gießen erfordert komplexe Formen und führt oft zu dickeren, schwereren Teilen. Die Blechumformung ist auf relativ einfache Biegungen und Formen beschränkt.
2. Erhebliches Leichtbaupotenzial:
- Die Messe ist König: In der Luft- und Raumfahrt ist die Verringerung der Masse von entscheidender Bedeutung. Jedes eingesparte Kilogramm reduziert die Startkosten erheblich oder ermöglicht mehr Nutzlast (Treibstoff, Instrumente usw.).
- Topologie-Optimierung: Wie bereits erwähnt, ermöglicht AM den Einsatz von Softwaretools zur Optimierung der Struktur der Platte auf der Grundlage der angewandten Lasten und thermischen Einschränkungen, wobei das Material nur dort platziert wird, wo es benötigt wird. Dies führt routinemäßig zu Gewichtseinsparungen von 30-60 % oder mehr im Vergleich zu traditionell konstruierten Teilen.
- Gitterförmige Strukturen: AM ermöglicht den Einbau von internen Gitter- oder Zellstrukturen. Diese Metamaterialien können so konstruiert werden, dass sie ein hervorragendes Verhältnis von Steifigkeit zu Gewicht und maßgeschneiderte Wärmeleitfähigkeitseigenschaften aufweisen, wodurch hocheffiziente strukturelle Isolatoren entstehen.
- Dünne Mauern: Technologien wie das selektive Elektronenstrahlschmelzen (SEBM), die von Anbietern wie Met3dp eingesetzt werden, eignen sich hervorragend für die Herstellung von Bauteilen mit sehr dünnen, aber dennoch strukturell soliden Wänden, wodurch das Gewicht im Vergleich zu den minimalen Dicken, die mit Guss oder maschineller Bearbeitung erreicht werden können, weiter reduziert wird.
3. Konsolidierung von Teilen und integrierte Funktionalität:
- Verringerung der Komplexität: Eine herkömmliche Isolierbaugruppe kann aus einer strukturellen Halterung, einer separaten Isolierplatte, Abstandshaltern und Befestigungselementen bestehen. Metall-AM ermöglicht es den Konstrukteuren, diese verschiedenen Komponenten in einem einzigen, monolithischen Teil zusammenzufassen.
- Vorteile der Konsolidierung:
- Reduzierte Teileanzahl: Vereinfacht Lagerhaltung, Logistik und Montage.
- Geringere Montagezeit & Kosten: Weniger Schritte, weniger Arbeitsaufwand.
- Verbesserte Verlässlichkeit: Eliminiert potenzielle Fehlerquellen im Zusammenhang mit Verbindungen und Befestigungselementen (z. B. Lockerung durch Vibration, Ermüdung durch Temperaturwechsel).
- Verbesserte Leistung: Beseitigt Wärmebrücken, die oft durch Verbindungselemente oder Fugen entstehen, und verbessert so die Wirksamkeit der Isolierung insgesamt.
- Gewichtseinsparung: Oft ist das konsolidierte Teil leichter als die Summe seiner ursprünglichen Bestandteile.
4. Materialeffizienz und Abfallvermeidung:
- Additiv vs. Subtraktiv: Die maschinelle Bearbeitung beginnt mit einem massiven Block und trägt Material ab, wobei häufig ein erheblicher Abfall (Späne) entsteht, insbesondere bei komplexen Teilen für die Luft- und Raumfahrt, bei denen das endgültige Teilevolumen viel kleiner ist als das ursprüngliche Knüppelvolumen (hohes Kauf-zu-Flug-Verhältnis).
- Fast-Netzform: Beim AM werden die Teile schichtweise aufgebaut, wobei in erster Linie nur das Material verwendet wird, das für das endgültige Bauteil und die Stützstrukturen benötigt wird. Ungeschmolzenes Pulver kann in der Regel recycelt und in späteren Bauprojekten wiederverwendet werden.
- Nachhaltigkeit und Kosten: Dieses endkonturnahe Verfahren reduziert den Materialabfall drastisch, was besonders wichtig ist, wenn man mit teuren Luft- und Raumfahrtlegierungen wie Inconel (IN625) oder speziellen Titansorten arbeitet. Dies trägt zu niedrigeren Materialkosten und einem nachhaltigeren Herstellungsprozess bei.
5. Rapid Prototyping und beschleunigte Entwicklungszyklen:
- Geschwindigkeit zum ersten Teil: AM erfordert keine herkömmlichen Werkzeuge (Gussformen, Gesenke, Vorrichtungen), deren Konstruktion und Herstellung Wochen oder Monate dauern kann. Eine Designänderung kann in CAD implementiert und ein neues Teil relativ schnell gedruckt werden (Tage oder Wochen, je nach Komplexität und Größe).
- Iterativer Entwurf: Diese Geschwindigkeit ermöglicht eine schnelle Design-Iteration. Ingenieure können Isolierplattenkonzepte viel schneller entwerfen, drucken, testen und verfeinern als mit herkömmlichen Methoden, was zu optimierten Lösungen innerhalb eines verkürzten Projektzeitrahmens führt.
- Fertigung auf Abruf: AM erleichtert die Produktion von Teilen auf Abruf, was den Bedarf an großen Lagerbeständen verringert und schnellere Reaktionen auf unerwartete Anforderungen oder Konstruktionsänderungen in einem späten Stadium eines Programms ermöglicht.
6. Eignung für Hochleistungswerkstoffe für die Luft- und Raumfahrt:
- Verarbeitung anspruchsvoller Legierungen: Metall-AM-Verfahren, einschließlich SEBM und Laser Powder Bed Fusion (L-PBF), eignen sich gut für die Bearbeitung von Hochleistungs metallpulver für die Luft- und Raumfahrt wie Nickel-Superlegierungen (IN625) und spezielle Aluminium- oder Titanlegierungen (AlSi10Mg, Ti6Al4V). Diese Werkstoffe stellen aufgrund ihrer Härte, Reaktivität oder ihres Schmelzpunkts oft eine Herausforderung für die herkömmliche Bearbeitung oder das Gießen dar.
- Optimierte Mikrostrukturen: Die Parameter des AM-Prozesses können so eingestellt werden, dass bestimmte Mikrostrukturen und Materialeigenschaften erreicht werden, die möglicherweise die Leistungsmerkmale für die thermische Isolierung und die strukturelle Integrität in Weltraumumgebungen verbessern.
Zusammenfassung des Vergleichs: Metall-AM vs. traditionelle Methoden für Isolierplatten
Merkmal | Additive Fertigung von Metall (AM) | Traditionelle Bearbeitung (CNC) | Traditioneller Guss | Blechumformung |
---|---|---|---|---|
Entwurfskomplexität | Sehr hoch (interne Merkmale, Gitter, konform) | Mäßig (Zugang zu Werkzeugen eingeschränkt) | Mäßig (Grenzwerte für Formen) | Niedrig (Biegungen, einfache Formen) |
Gewichtsreduzierung | Ausgezeichnet (Topologie opt., Gitter, dünne Wände) | Mäßig (Materialentfernung) | Angemessen (oft dickere Wände) | Fair (Materialauswahl) |
Teil Konsolidierung | Ausgezeichnet (mehrere Teile in einem) | Schlecht (Montage erforderlich) | Schlecht (Montage erforderlich) | Schlecht (Montage erforderlich) |
Materialabfälle | Gering (Netto-Form, Pulverwiederverwendung) | Hoch (subtraktives Verfahren) | Moderat (Tore, Steigleitungen) | Mäßig (Verschnitt) |
Vorlaufzeit (Proto) | Schnell (keine Werkzeuge erforderlich) | Moderat (Programmierung, Einrichtung) | Langsam (Werkzeuge erforderlich) | Langsam (Werkzeuge erforderlich) |
Werkzeugkosten | Keine / Minimal | Niedrig (Standardwerkzeuge) | Hoch (Formenbau/Fertigung) | Hoch (Entwurf/Fertigung der Matrize) |
Materialeignung | Ausgezeichnet (Superlegierungen, Ti, Al-Legierungen) | Gut (abhängig von der Bearbeitbarkeit) | Gut (abhängig von der Gießbarkeit) | Angemessen (abhängig von der Formbarkeit) |
Ideales Volumen | Geringe bis mittlere, hohe Komplexität | Gering bis hoch, mäßige Komplexität | Mittel bis Hoch | Hohe, niedrige Komplexität |
In Blätter exportieren
Zusammenfassend lässt sich sagen, dass die Vorteile der Metall-AM - beispiellose Designfreiheit, erhebliche Gewichtsreduzierung, Teilekonsolidierung, Materialeffizienz, schnelle Entwicklung und Eignung für fortschrittliche Werkstoffe - sie zu einer äußerst überzeugenden Technologie für die Produktion der nächsten Generation machen isolierplatten für Raumfahrzeuge. Herkömmliche Methoden haben zwar nach wie vor ihre Berechtigung, insbesondere bei einfacheren Designs oder sehr hohen Stückzahlen, aber AM eröffnet Leistungs- und Integrationsmöglichkeiten, die entscheidend sind, um die Grenzen der thermomanagement in der Luft- und Raumfahrt und ermöglicht ehrgeizigere Weltraummissionen. Die Partnerschaft mit einem erfahrenen Metall-AM-Anbieter wie Met3dp, ausgestattet mit der richtigen Technologie (z. B. SEBM) und Materialkenntnis, ist der Schlüssel zur Realisierung dieser Vorteile.
Materialschwerpunkt: IN625 und AlSi10Mg für extreme Umgebungen
Die Auswahl des richtigen Materials ist von grundlegender Bedeutung für den Erfolg einer jeden Raumfahrzeugkomponente, und Wärmeisolationsplatten bilden da keine Ausnahme. Das Material muss nicht nur die gewünschten thermischen Eigenschaften aufweisen (in der Regel eine niedrige Wärmeleitfähigkeit für die Isolierung), sondern auch eine angemessene strukturelle Festigkeit, eine geringe Dichte, Beständigkeit gegenüber der Weltraumumgebung (Strahlung, atomarer Sauerstoff, thermische Zyklen) und Kompatibilität mit dem gewählten Herstellungsverfahren. Die additive Fertigung von Metallen ermöglicht die Verwendung von Hochleistungslegierungen, deren Verarbeitung mit herkömmlichen Methoden schwierig oder kostspielig sein könnte. Für die Isolierplatten von Raumfahrzeugen werden häufig zwei Materialien verwendet, die sich durch eine hervorragende Ausgewogenheit ihrer Eigenschaften auszeichnen: Inconel 625 (IN625)einer Nickel-Chrom-Superlegierung, und Aluminium Silizium Magnesium (AlSi10Mg)eine weit verbreitete Aluminiumgusslegierung, die für AM geeignet ist.
Das Verständnis der Merkmale dieser metallpulver für die Luft- und Raumfahrt und warum sie für AM-produzierte Isolierplatten geeignet sind, ist für Ingenieure und Beschaffungsmanager entscheidend.
1. Inconel 625 (IN625): Das hochtemperaturbeständige, hochfeste Arbeitspferd
- Zusammensetzung: Hauptsächlich Nickel (Ni), mit erheblichen Beimischungen von Chrom (Cr), Molybdän (Mo) und Niob (Nb).
- Wichtige Eigenschaften:
- Ausgezeichnete Hochtemperaturfestigkeit: Behält eine hohe Festigkeit und Kriechbeständigkeit bei hohen Temperaturen (bis zu ~800-900°C oder höher für kurze Zeit), was für Anwendungen in der Nähe von Motoren oder bei direkter Sonneneinstrahlung entscheidend ist.
- Hervorragende Korrosionsbeständigkeit: Hochgradig resistent gegen Oxidation und ein breites Spektrum an korrosiven Umgebungen, einschließlich der Resistenz gegen atomare Sauerstofferosion im erdnahen Orbit (LEO).
- Gute Ermüdungsfestigkeit: Widersteht zyklischer Belastung und thermischer Ermüdung durch extreme Temperaturschwankungen im Weltraum.
- Gute Verarbeitbarkeit (in AM): Generell weist es eine gute Schweißbarkeit auf, was sich in einer guten Verarbeitbarkeit in AM-Verfahren wie SEBM und L-PBF niederschlägt.
- Moderate Wärmeleitfähigkeit: Seine Wärmeleitfähigkeit ist zwar nicht so niedrig wie die einiger Keramiken oder Verbundwerkstoffe, aber deutlich geringer als die von Aluminiumlegierungen, so dass es sich gut für thermische Isolierungsanwendungen eignet, bei denen die strukturelle Integrität auch bei hohen Temperaturen erforderlich ist. (λ≈10-15 W/m-K je nach Temperatur).
- Mäßige Dichte: Relativ hohe Dichte im Vergleich zu Al- oder Ti-Legierungen (ρ≈8,44 g/cm³). Dies ist ein Kompromiss für seine Hochtemperaturleistung.
- Warum es für Isolierplatten wichtig ist:
- Hitzeschutzschilder: Ideal für Isolierplatten, die als Hitzeschild in der Nähe von Raketentriebwerken, Triebwerken oder Bauteilen, die starker Strahlungswärme ausgesetzt sind, dienen.
- Strukturelle thermische Brüche: Durch die Kombination von Festigkeit und mäßiger Wärmeleitfähigkeit eignet es sich für die Herstellung von Strukturbauteilen, die auch als thermische Trennung in Hochtemperaturbaugruppen dienen.
- Langlebigkeit: Seine Robustheit und Widerstandsfähigkeit gegenüber der Weltraumumgebung gewährleisten eine langfristige Leistung für anspruchsvolle Missionen.
- AM Überlegungen: IN625 kann sowohl mit L-PBF als auch mit SEBM effektiv verarbeitet werden. SEBM, das von Anbietern wie Met3dp angeboten wird, erfordert aufgrund der höheren Temperaturen in der Baukammer, die die Eigenspannung reduzieren, oft weniger Stützstrukturen, was bei komplexen Plattengeometrien von Vorteil sein kann. Die Nachbearbeitung umfasst in der Regel eine Spannungsarmglühung.
2. Aluminium-Silizium-Magnesium (AlSi10Mg): Der Leichtbau-Champion
- Zusammensetzung: Aluminium (Al), hauptsächlich legiert mit Silizium (Si) und einer kleinen Menge Magnesium (Mg). Ursprünglich eine Gusslegierung, eignet sie sich aufgrund ihrer Eigenschaften hervorragend für AM.
- Wichtige Eigenschaften:
- Geringe Dichte: Erheblich leichter als Stahl, Titan oder Nickellegierungen (ρ≈2,67 g/cm³). Dies ist sein Hauptvorteil für massekritische Raumfahrtanwendungen.
- Gutes Verhältnis von Stärke zu Gewicht: Bietet eine gute mechanische Festigkeit, insbesondere nach entsprechender Wärmebehandlung (z. B. T6).
- Gute Wärmeleitfähigkeit: Besitzt eine relativ hohe Wärmeleitfähigkeit (λ≈120-150 W/m-K). Dies mag zwar kontra-intuitiv erscheinen für isolierungist es von Vorteil, wenn die Platte’ primärer die thermische Isolierung wird eher durch das geometrische Design (dünne Wände, minimale Kontaktfläche, integrierte Abstandshalter) als durch inhärente Materialeigenschaften erreicht. Es kann auch von Vorteil sein, wenn die Platte Wärme leiten muss weg von einer bestimmten lokalisierten Quelle zu einem Strahler.
- Ausgezeichnete Verarbeitbarkeit in AM: Eine der gebräuchlichsten und bekanntesten Legierungen für L-PBF, die eine gute Oberflächengüte und Auflösung der Merkmale bietet.
- Gute Korrosionsbeständigkeit: Weist eine gute allgemeine Korrosionsbeständigkeit auf.
- Warum es für Isolierplatten wichtig ist:
- Leichte Strukturkomponenten: Ideal, wenn das Hauptziel darin besteht, eine leichte strukturelle Halterung oder ein Gehäuse zu schaffen mit einige thermischer Abstand, der geometrisch erreicht wird. Beispiele hierfür sind Elektronikgehäuse, Batteriehalterungen und Halterungen, bei denen Masseneinsparungen von größter Bedeutung sind.
- Konforme Gehäuse: Die einfache Verarbeitung ermöglicht komplexe, dünnwandige, konforme Gehäuse, die strukturelle Unterstützung und Umweltschutz bei minimalem Gewichtsverlust bieten.
- Kosten-Nutzen-Verhältnis: Im Allgemeinen preiswerter als IN625 oder Titanlegierungen.
- AM Überlegungen: AlSi10Mg wird überwiegend mit L-PBF verarbeitet. Es erfordert in der Regel einen Spannungsabbau und häufig eine T6-Wärmebehandlung (Lösungsglühen und künstliche Alterung), um optimale mechanische Eigenschaften zu erzielen. Im Allgemeinen sind Stützstrukturen erforderlich, die bei der Konstruktion sorgfältig berücksichtigt werden müssen.
Tabelle zum Materialvergleich:
Eigentum | IN625 | AlSi10Mg | Relevanz für Isolierplatten |
---|---|---|---|
Primäre Rolle | Hochtemperaturfestigkeit, Korrosionsbeständigkeit. | Leichtgewichtigkeit, gute Festigkeit/Gewicht | Wählen Sie nach dem primären Bedarf: Wärmedämmung vs. leichte Struktur |
Dichte | Hoch (≈8,44 g/cm³) | Niedrig (≈2,67 g/cm³) | AlSi10Mg wird für massekritische Anwendungen stark bevorzugt. |
Maximale Betriebstemperatur (ca.) | Hoch (≈800-900°C) | Niedrig (≈150-200°C) | IN625 erforderlich für Hochtemperaturbereiche (Motoren usw.). |
Wärmeleitfähigkeit | Mäßig (≈10-15 W/m-K) | Hoch (≈120-150 W/m-K) | IN625 bietet eine bessere inhärente Isolierung. Bei AlSi10Mg kommt es auf die Geometrie an. |
Stärke | Sehr hoch | Gut (vor allem nach T6-Wärmebehandlung) | Beide bieten strukturelle Fähigkeiten, IN625 ist bei der Temperatur überlegen. |
AM Verarbeitbarkeit | Gut (SEBM, L-PBF) | Ausgezeichnet (L-PBF) | Beide sind mit etablierten AM-Methoden leicht zu verarbeiten. |
Relative Kosten | Hoch | Mäßig | Die Kosten sind ein Faktor, der gegen die Leistungsanforderungen abgewogen werden muss. |
In Blätter exportieren
Die Rolle von Met3dp bei der Materialexzellenz:
Die Wahl des richtigen Materials ist nur ein Teil der Gleichung. Die Qualität des Metallpulvers selbst hat erheblichen Einfluss auf die Eigenschaften und die Zuverlässigkeit des fertigen Teils. Hier bieten spezialisierte Anbieter wie Met3dp einen erheblichen Mehrwert. Met3dp beschäftigt branchenführende Pulverherstellungstechnologien:
- Gaszerstäubung (GA): Bei diesem Verfahren werden Hochdruck-Inertgasstrahlen verwendet, um einen Strom geschmolzenen Metalls in feine Tröpfchen aufzubrechen, die zu kugelförmigen Pulvern erstarren. Die einzigartigen Düsen- und Gasströmungsdesigns von Met3dp’ optimieren diesen Prozess, um Pulver mit hoher Sphärizität und guter Fließfähigkeit zu produzieren - kritische Eigenschaften für eine gleichmäßige Schichtverteilung und eine dichte Teilekonsolidierung beim Pulverbettschmelzverfahren AM.
- Plasma-Rotations-Elektroden-Verfahren (PREP): PREP verwendet einen schnell rotierenden Elektrodenstab aus der Ziellegierung, der an der Spitze durch einen Plasmabrenner geschmolzen wird. Die Zentrifugalkraft schleudert geschmolzene Tröpfchen ab, die sich im Flug zu hochkugelförmigen Pulvern mit sehr geringem Satellitengehalt und hoher Reinheit verfestigen, die häufig für kritische Anwendungen bevorzugt werden, die hervorragende Materialeigenschaften erfordern.
Durch die Kontrolle des Pulverherstellungsprozesses gewährleistet Met3dp seine hochwertige Metallpulvereinschließlich Nickelsuperlegierungen wie IN625 und Aluminiumlegierungen wie AlSi10Mg (aber auch Ti-Legierungen, CoCrMo, Stähle und innovative Legierungen wie TiNi, TiTa usw.), erfüllen die strengen Anforderungen der Luft- und Raumfahrtindustrie. Dieses Engagement für die Qualität des Pulvers schlägt sich direkt in 3D-gedruckten Komponenten nieder, wie z. B. Wärmeisolationsplatten, die sich durch eine überragende Dichte, vorhersehbare mechanische Eigenschaften und erhöhte Zuverlässigkeit auszeichnen - eine wesentliche Voraussetzung für den Erfolg von Missionen in der extremen Umgebung des Weltraums. Ihr Fachwissen erstreckt sich nicht nur auf die Pulverproduktion, sondern auch auf die Druckverfahren selbst, um optimale Ergebnisse von Pulver zu Teil zu gewährleisten.
Zusammenfassend lässt sich sagen, dass sowohl IN625 als auch AlSi10Mg einzigartige Vorteile für metallische AM-Isolierplatten für Raumfahrzeuge bieten. IN625 eignet sich hervorragend für strukturell anspruchsvolle Hochtemperaturanwendungen, die eine inhärente thermische Isolierung erfordern, während AlSi10Mg die erste Wahl für leichtgewichtige strukturelle Anwendungen ist, bei denen der thermische Abstand in erster Linie durch die Konstruktionsgeometrie erreicht wird. Die Wahl hängt in hohem Maße von den spezifischen Anwendungsanforderungen, der Betriebsumgebung und den Leistungskonflikten ab. Die Verwendung hochwertiger Pulver von erfahrenen Lieferanten stellt sicher, dass das gewählte Material sein volles Potenzial im endgültigen additiv gefertigten Bauteil entfaltet.
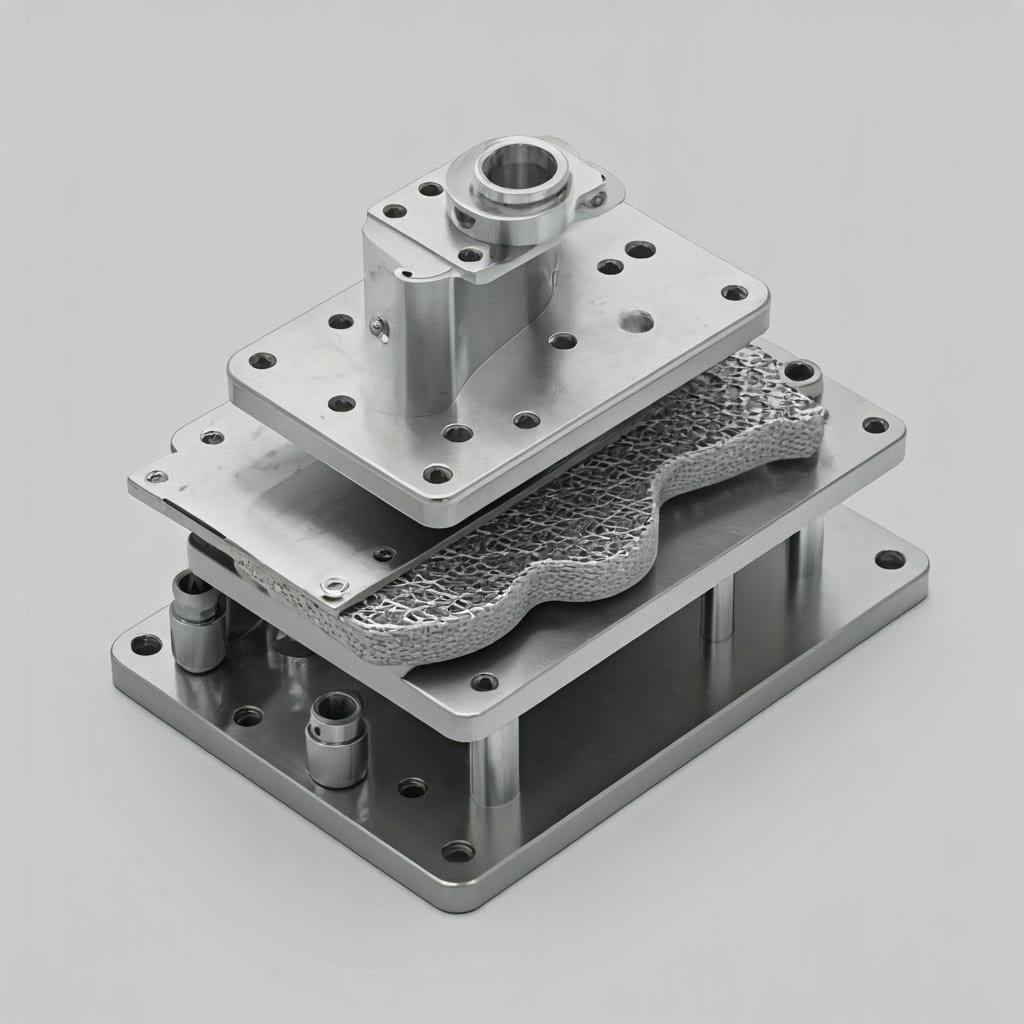
Design for Additive Manufacturing (DfAM) Prinzipien für Thermoplatten
Beim Übergang von der traditionellen Fertigung zur additiven Fertigung von Metallen (AM) geht es nicht nur darum, eine Produktionsmethode gegen eine andere auszutauschen. Um das revolutionäre Potenzial der AM wirklich zu nutzen, insbesondere für komplexe Komponenten wie die Wärmedämmplatten von Raumfahrzeugen, ist ein grundlegender Wandel im Designdenken erforderlich. Die einfache Nachbildung eines Designs, das ursprünglich für die maschinelle Bearbeitung oder den Guss vorgesehen war, kann die einzigartigen Stärken der AM nicht nutzen und kann sogar neue Herausforderungen mit sich bringen. Dies ist der Punkt, an dem Design für additive Fertigung (DfAM) wesentlich wird. DfAM Luft- und Raumfahrt prinzipien helfen Ingenieuren bei der Entwicklung von Teilen, die nicht nur mit AM-Verfahren wie Selective Electron Beam Melting (SEBM) oder Laser Powder Bed Fusion (L-PBF) hergestellt werden können, sondern auch hinsichtlich Leistung, Gewicht, Kosten und Zuverlässigkeit optimiert sind.
Bei Wärmedämmplatten, die für die anspruchsvolle Umgebung des Weltraums bestimmt sind, ist die Anwendung der DfAM-Prinzipien entscheidend, um Ziele wie maximale Wärmeisolierung, minimale Masse, strukturelle Integrität und Missionszuverlässigkeit zu erreichen. Lassen Sie uns die wichtigsten DfAM-Überlegungen untersuchen:
1. Topologie-Optimierung: Material, wo es darauf ankommt
- Konzept: Bei der Topologieoptimierung handelt es sich um eine rechnergestützte Entwurfstechnik, mit der die Materialanordnung innerhalb eines definierten Entwurfsraums unter Berücksichtigung bestimmter Lasten, Randbedingungen und Einschränkungen (z. B. maximale Spannung, minimale Steifigkeit, thermische Leistungsziele) optimiert wird. Die Software schneidet im Wesentlichen unnötiges Material weg und hinterlässt eine oft organisch anmutende, hocheffiziente Tragstruktur.
- Vorteile für Isolierplatten:
- Massenreduzierung: Der wichtigste Treiber. Topologieoptimierung Raumteile können im Vergleich zu herkömmlichen Konstruktionen erhebliche Gewichtseinsparungen (oft 30-60 % und mehr) erzielen, was sich direkt auf die Startkosten und die Nutzlastkapazität auswirkt.
- Erhöhung der Steifigkeit: Optimierte Strukturen weisen oft ein höheres Verhältnis von Steifigkeit zu Gewicht auf.
- Thermische Pfadkontrolle: Kann implizit oder explizit zur Beeinflussung der Wärmestromwege verwendet werden, um die Wärmeleitung durch Strukturelemente zu minimieren.
- Umsetzung: Erfordert spezialisierte Software (z. B. Altair OptiStruct, ANSYS Mechanical, nTopology) und eine klare Definition von Lastfällen (mechanisch, thermisch) und Konstruktionsbeschränkungen. Die daraus resultierende Geometrie ist oft komplex und ideal für AM geeignet.
2. Gitterstrukturen und zelluläre Materialien: Technische Mikrogeometrie
- Konzept: AM ermöglicht die direkte Herstellung komplizierter interner gitterförmige Strukturen thermisch oder zelluläre Materialien (wie Bienenwaben, stochastische Schäume oder dreifach periodische Minimaloberflächen). Dabei handelt es sich nicht einfach um Hohlräume, sondern um technische Strukturen mit maßgeschneiderten Eigenschaften.
- Vorteile für Isolierplatten:
- Weitere Gewichtsreduzierung: Gitter bieten eine extrem hohe Porosität bei gleichzeitiger Wahrung der strukturellen Integrität.
- Abstimmbare Wärmeleitfähigkeit: Die Geometrie, die Dichte und das Material des Gitters können so gestaltet werden, dass die effektive Wärmeleitfähigkeit im Vergleich zu einem massiven Block desselben Materials erheblich reduziert und die Isolierung verbessert wird. Insbesondere TPMS-Strukturen bieten glatte Oberflächen und potenziell hervorragende thermische Eigenschaften.
- Multifunktionalität: Kann neben der thermischen und strukturellen Leistung auch Energieabsorption (Schwingungsdämpfung), Strömungswege für Flüssigkeiten (wenn für integrierte Kühlung/Heizung ausgelegt) und Schalldämmung bieten.
- Überlegungen zum Design: Erfordert spezielle Design-Tools (nTopology, Materialise 3-matic, CAD-Add-Ins). Zu berücksichtigen sind die minimale Streben-/Wanddicke, die mit dem AM-Verfahren hergestellt werden kann, die Pulverentfernung aus internen Zellen und Spannungskonzentrationen an Knotenpunkten.
3. Merkmalsauflösung und Mindestmerkmalsgröße:
- Strategische Auswahl der Ausrichtung der Lasche auf der Bauplatte, um die Gesamtfläche, die eine Stütze benötigt, zu minimieren. Jedes AM-Verfahren hat Grenzen für die Mindestgröße von Merkmalen, die es genau herstellen kann. Dazu gehören die Mindestwandstärke, der Mindestlochdurchmesser, die kleinste erreichbare Stiftgröße und die Schärfe der Ecken.
- Typische Werte: Bei Pulverbettschmelzverfahren (L-PBF, SEBM) liegt die Mindestwandstärke oft im Bereich von 0,3 mm bis 0,8 mm, je nach Material, Maschine und Höhe der Wand. Kleine Löcher können bis zu einer Dicke von 0,5 mm möglich sein, aber die Genauigkeit nimmt ab.
- DfAM-Implikationen: Die Konstrukteure müssen sicherstellen, dass kritische Merkmale wie dünne Isolierwände, kleine Befestigungslöcher oder feine Details auf der Platte innerhalb der erreichbaren Grenzen des gewählten AM-Prozesses und -Materials entworfen werden. Eine Beratung mit dem AM-Dienstleister, wie Met3dp, hinsichtlich seiner spezifischen Ausrüstungsmöglichkeiten (z. B. die mit seinen SEBM-Systemen erreichbare Präzision) ist von entscheidender Bedeutung. Die Konstruktion von Merkmalen unterhalb der Prozessfähigkeit führt zu Druckfehlern oder Teilen, die nicht den Spezifikationen entsprechen.
4. Strategie für Unterstützungsstrukturen: Auf Fundamenten aufbauen
- Zweck: Beim Schmelzen im Pulverbett sind häufig Stützstrukturen erforderlich:
- Stützende Überhänge: Verankerung von Abschnitten des Teils, die unter einem bestimmten Winkel über das Pulverbett hinausragen (typischerweise 45° zur Horizontalen, jedoch abhängig von Verfahren und Material).
- Wärmeübertragung: Ableitung der Wärme aus der Schmelzzone zur Vermeidung von Überhitzung und Verformung, insbesondere bei empfindlichen Merkmalen oder großen Massen.
- Verankerung: Verhinderung von Verformungen und Sicherung des Teils auf der Bauplatte.
- DfAM-Ziel: Minimieren Sie den Bedarf an Stützen oder gestalten Sie sie so, dass sie leicht zu entfernen sind. Stützen verursachen zusätzliche Materialkosten, verlängern die Bauzeit, erfordern Nachbearbeitungsaufwand und können die Oberflächenbeschaffenheit an den Verbindungsstellen beeinträchtigen.
- Strategien:
- Teil Orientierung: Durch eine sorgfältige Auswahl der Ausrichtung des Teils auf der Bauplatte können Überhänge drastisch reduziert werden.
- Selbsttragende Winkel: Planung von Überhängen, die über dem kritischen selbsttragenden Winkel für das jeweilige Material und Verfahren liegen (z. B. 45°).
- Fasen/Flanken: Die Verwendung von Fasen anstelle von scharfen horizontalen Überhängen kann dazu führen, dass die Elemente selbsttragend sind.
- Entwerfen für die Beseitigung: Wenn Stützen unvermeidlich sind, ist es wichtig, sie so zu gestalten, dass sie nur minimale Berührungspunkte aufweisen, dass sie abbrechbar sind und dass der Zugang zu den Entfernungswerkzeugen gewährleistet ist. Dies ist besonders kritisch für interne Kanäle innerhalb von Isolierplatten. SEBM erfordert oft weniger Stützen als L-PBF, da die hohe Temperatur in der Baukammer die Beanspruchung reduziert - ein bemerkenswerter Vorteil.
5. Teil Orientierung: Die Weichen für den Erfolg stellen
- Auswirkungen: Die Ausrichtung der Dämmplatte auf der Bauplattform hat erheblichen Einfluss:
- Oberfläche: Nach oben und nach unten weisende Oberflächen haben aufgrund von Schichtabstufungseffekten und Stützkontaktpunkten andere Rauheitseigenschaften als vertikale Wände.
- Anforderungen an die Unterstützung: Wie bereits erwähnt, bestimmt die Ausrichtung, welche Merkmale Unterstützung benötigen.
- Bauzeit: Höhere Teile brauchen im Allgemeinen länger zum Drucken. Die kürzeste Abmessung vertikal auszurichten, kann den Bau manchmal beschleunigen (obwohl auch die Querschnittsfläche eine Rolle spielt).
- Mechanische Eigenschaften: AM-Teile können aufgrund des schichtweisen Aufbaus und thermischer Gradienten anisotrope Eigenschaften aufweisen (Festigkeit variiert mit der Richtung). Bei der Ausrichtung sollten die primären Belastungsrichtungen berücksichtigt werden.
- Eigenspannung: Die Ausrichtung kann die Entstehung von Wärmespannungen beeinflussen.
- Entscheidungsprozess: Bei der Wahl der optimalen Ausrichtung müssen diese konkurrierenden Faktoren oft gegeneinander abgewogen werden, was manchmal Simulationen oder empirische Tests erfordert.
6. Thermomanagement in der Konstruktion:
- Jenseits der Struktur: Bei DfAM für Thermobleche geht es nicht nur um die Struktur und die Herstellbarkeit, sondern auch darum, die thermische Leistung von Anfang an zu berücksichtigen.
- Techniken:
- Leitende Pfade minimieren: Verwendung von dünnen Wänden, minimalen Kontaktflächen und Materialien mit geringer Wärmeleitfähigkeit (z. B. IN625, wo dies angebracht ist).
- Bauen Sie thermische Pausen ein: Gezielte Gestaltung von Lücken, Schlitzen oder Gitterabschnitten mit niedriger Leitfähigkeit, um den Wärmefluss zu behindern.
- Strahlungskontrolle: Gestaltung der inneren Hohlräume mit speziellen Oberflächen (die möglicherweise nachbearbeitet oder beschichtet werden müssen), um die Strahlungswärmeübertragung zu kontrollieren.
- Integrierte Kühlung/Heizung: Für ein aktives Wärmemanagement müssen interne Kanäle für den Flüssigkeitsstrom oder Integrationspunkte für Heizelemente entworfen werden.
7. Konsolidierungsstrategie: Vereinfachung der Komplexität
- Identifizierung von Chancen: Bevor mit der detaillierten Planung begonnen wird, sollten die Ingenieure die umgebende Baugruppe analysieren, um festzustellen, ob die Isolierplatte die Funktion der angrenzenden Halterungen, Befestigungen oder Strukturelemente übernehmen kann.
- Überprüfung der Leistungen: Überprüfen Sie die Vorteile der Teilekonsolidierung (reduzierte Anzahl, Gewicht, Montagezeit, verbesserte Zuverlässigkeit), um den Konstruktionsaufwand zu rechtfertigen.
- Durchführbarkeitsprüfung: Sicherstellen, dass das konsolidierte Design mittels AM herstellbar ist und alle funktionalen Anforderungen erfüllt.
Expertise von Met3dp: Die wirksame Anwendung dieser DfAM-Prinzipien erfordert nicht nur die richtigen Software-Tools, sondern auch fundierte Kenntnisse der AM-Prozesse und der Werkstoffkunde. Unternehmen wie Met3dp bieten umfassende Lösungen an, die über den reinen Druck hinausgehen. Bei der Anwendungsentwicklung arbeiten sie eng mit ihren Kunden zusammen, um die Designs für ihre spezifischen AM-Prozesse (wie SEBM), Materialien und Anwendungsanforderungen zu optimieren und sicherzustellen, dass die endgültigen Wärmedämmplatten maximale Leistung und Zuverlässigkeit für anspruchsvolle Raumfahrtmissionen bieten. Das Verständnis für die Nuancen verschiedener additive Fertigungsverfahren ist der Schlüssel zur erfolgreichen Umsetzung von DfAM.
Durch den Einsatz von DfAM können Luft- und Raumfahrtingenieure das volle Potenzial von Metall-AM ausschöpfen und Wärmedämmplatten für Raumfahrzeuge herstellen, die leichter, effizienter und besser integriert sind als je zuvor und damit die Grenzen des Designs und der Erforschung von Raumfahrzeugen verschieben.
Erreichen von Präzision: Toleranz, Oberflächengüte und Genauigkeit bei Metall-AM
Während die additive Fertigung von Metallen eine noch nie dagewesene Designfreiheit bietet, dreht sich eine häufige Frage von Ingenieuren und Beschaffungsmanagern, insbesondere von denen, die an die hohe Präzision der CNC-Bearbeitung gewöhnt sind, um die erreichbaren Toleranzniveaus, die Oberflächengüte und die allgemeine Maßgenauigkeit. Bei einsatzkritischen Komponenten wie Isolierplatten für Raumfahrzeuge ist das Verständnis der Präzisionsmöglichkeiten und -grenzen von Metall-AM-Verfahren wie SEBM und L-PBF von entscheidender Bedeutung, um die Erwartungen zu steuern und sicherzustellen, dass die Teile die strengen Anforderungen der Luft- und Raumfahrt erfüllen.
1. Toleranzen bei Metall-AM:
- Definition: Die Toleranz bezieht sich auf die zulässige(n) Grenze(n) der Abweichung von einer physikalischen Dimension eines Teils.
- Allgemeine Fähigkeiten: Metall-AM-Verfahren erreichen in der Regel Toleranzen, die mit denen des Feingusses oder des Metall-Spritzgusses vergleichbar sind. Als allgemeine Richtlinie gilt, dass Teile oft so hergestellt werden können, dass sie Standards wie die folgenden erfüllen ISO 2768-m (mittel) oder manchmal ISO 2768-f (fein) im Ist-Zustand. Um jedoch engere Toleranzen zu erreichen, die mit der maschinellen Bearbeitung vergleichbar sind (z. B. innerhalb von zehn Mikrometern), sind in der Regel sekundäre Bearbeitungsvorgänge an kritischen Merkmalen erforderlich.
- Typische Reichweiten:
- Für kleinere Teile (< 100 mm): Toleranzen von ±0,1 mm bis ±0,3 mm sind oft erreichbar.
- Für größere Teile (> 100 mm): Die Toleranzen können von ±0,2 mm bis ±0,5 mm oder möglicherweise ±0,2 % bis ±0,5 % des Nennmaßes reichen.
- Beeinflussende Faktoren:
- Kalibrierung der Maschine: Die Genauigkeit hängt stark von der jeweiligen AM-Maschine, ihrem Kalibrierungsstatus, der Größe des Laser-/Elektronenstrahls und der verwendeten Schichtdicke ab.
- Materialeigenschaften: Verschiedene Materialien weisen unterschiedliche Grade von Schrumpfung, Ausdehnung und Verformung während der Heiz- und Abkühlzyklen auf, die bei AM auftreten.
- Geometrie und Größe des Teils: Größere Teile und komplexe Geometrien mit dünnen Wänden oder großen Querschnitten sind anfälliger für thermischen Verzug, was sich auf die Endtoleranzen auswirkt.
- Thermische Spannungen: Während des Drucks aufgebaute Eigenspannungen können beim Entfernen von der Bauplatte zu Verformungen führen.
- Strategie unterstützen: Die Art und Weise, wie das Teil gestützt wird, hat Einfluss auf die Stabilität während der Fertigung und auf mögliche Verformungen.
- Nachbearbeiten: Wärmebehandlungen (Spannungsabbau, Glühen) können geringfügige Maßänderungen verursachen.
2. Oberflächengüte (Rauhigkeit):
- Definition: Die Oberflächengüte, die oft mit dem arithmetischen Mittelwert der Rauheit (Ra) angegeben wird, beschreibt die Beschaffenheit der Oberfläche eines Teils. AM-Teile haben aufgrund des schichtweisen Aufbaus und der teilweise geschmolzenen Pulverpartikel, die an der Oberfläche haften, von Natur aus eine rauere Oberfläche als bearbeitete Teile.
- Rauheit im Ist-Zustand:
- Typische Ra-Werte für AM-Teile aus Metall (L-PBF/SEBM) liegen im Bereich von 5 µm bis 25 µm (Mikrometer)oder etwa 200 bis 1000 µin (Mikrozoll).
- Variationen: Die Oberflächenrauhigkeit hängt wesentlich von folgenden Faktoren ab:
- Orientierung: Nach unten weisende Flächen (gestützt) sind im Allgemeinen rauer als nach oben weisende Flächen oder vertikale Wände. Gestufte Merkmale auf gekrümmten Oberflächen (Treppenstufen) tragen ebenfalls zur Rauheit bei.
- Prozessparameter: Schichtdicke, Strahlleistung und Scangeschwindigkeit beeinflussen die Dynamik des Schmelzbades und die endgültige Oberflächentextur.
- Material: Verschiedene Metallpulver können unterschiedliche Oberflächeneigenschaften aufweisen.
- Pulver Partikelgröße: Feinere Pulver können manchmal zu glatteren Oberflächen führen, können aber auch andere verfahrenstechnische Herausforderungen mit sich bringen.
- Erzielung glatterer Oberflächen: Für Anwendungen, die glattere Oberflächen erfordern (z. B. Dichtungsflächen, besondere thermische/optische Eigenschaften, ermüdungskritische Bereiche), ist eine Nachbearbeitung erforderlich. Techniken wie Strahlen, Taumeln, Bearbeiten, Schleifen oder Polieren können die Ra-Werte erheblich verbessern, so dass durch Bearbeiten oder Polieren Oberflächen von unter 1 µm Ra erreicht werden können.
3. Maßgenauigkeit:
- Definition: Die Maßgenauigkeit bezieht sich auf den Grad der Übereinstimmung eines gefertigten Teils mit den im CAD-Modell angegebenen Abmessungen. Sie umfasst sowohl Toleranzen (Abweichungen) als auch systematische Abweichungen (z. B. Schrumpfung).
- Faktoren, die die Genauigkeit beeinflussen:
- Schrumpfungsausgleich: AM-Software enthält in der Regel Algorithmen, um die Materialschrumpfung während der Erstarrung und Abkühlung zu kompensieren, aber eine perfekte Vorhersage ist schwierig.
- Verformung und Verzerrung: Ungleichmäßige Erwärmung und Abkühlung führen zu Eigenspannungen, die das Teil verziehen können, insbesondere nach der Entnahme aus der Bauplatte. Dies ist bei L-PBF aufgrund der hohen Baukammertemperatur stärker ausgeprägt als bei SEBM.
- Prozessstabilität: Die Aufrechterhaltung einer gleichbleibenden Strahlleistung, Punktgröße, Pulverauftragung und Kammerbedingungen während des gesamten Bauprozesses ist von entscheidender Bedeutung.
- Teilentfernung: Das Entfernen des Teils von der Bauplatte (z. B. Drahterodieren, Sägen) muss sorgfältig durchgeführt werden, um Verformungen zu vermeiden.
- Sicherstellung der Genauigkeit: Erreichen einer hohen maßhaltigkeit Luft- und Raumfahrt die Herstellung von Bauteilen erfordert eine sorgfältige Prozesskontrolle, möglicherweise eine Fertigungssimulation zur Vorhersage von Verformungen, optimierte Stützstrategien, geeignete Spannungsentlastungszyklen und häufig eine abschließende Bearbeitung kritischer Schnittstellen und Merkmale.
Das Engagement von Met3dp für Präzision: Das Erreichen einer zuverlässigen Präzision bei der Metall-AM erfordert mehr als nur fortschrittliche Maschinen; es erfordert eine strenge Prozesskontrolle und ein tiefes Verständnis der Materialien. Met3dp betont branchenführendes Druckvolumen, Genauigkeit und Zuverlässigkeit. Dies wird erreicht durch:
- Erweiterte Ausrüstung: Der Einsatz modernster SEBM-Drucker, die für ihre Fähigkeit bekannt sind, thermische Spannungen effektiv zu bewältigen, führt zu niedrigeren Eigenspannungen und potenziell besserer Dimensionsstabilität, insbesondere bei großen oder komplexen Teilen im Vergleich zu L-PBF in einigen Fällen.
- Prozess-Optimierung: Dank jahrzehntelanger Erfahrung in der Metall-AM ist Met3dp in der Lage, die Druckparameter für bestimmte Materialien wie IN625 und AlSi10Mg zu optimieren und eine gleichbleibende Schmelzbaddynamik und Teilequalität zu gewährleisten.
- Qualitätskontrolle: Durchführung solider Qualitätskontrollen während des gesamten Prozesses, von der Eingangsprüfung des Pulvers bis hin zur Validierung der fertigen Teile durch zerstörungsfreie Prüfung und Messtechnik.
Zusammenfassende Präzisionstabelle:
Parameter | Typischer Bereich im Ist-Zustand (L-PBF/SEBM) | Nachbearbeitetes Potenzial | Wichtige Einflussfaktoren |
---|---|---|---|
Toleranz | ISO 2768-m/f (±0,1 bis ±0,5 mm+) | Bearbeitungstoleranzen (<0,05mm) | Maschine, Material, Größe, Geometrie, thermische Belastung, Stützen |
Oberflächengüte (Ra) | 5 µm – 25 µm | < 1 µm (Bearbeitung/Polieren) | Orientierung, Parameter, Material, Stützen, Nachbearbeitung |
Maßgenauigkeit | Gut, aber durch Verzerrung beeinträchtigt | Hoch (mit Nachbearbeitung) | Schrumpfung, Verformung, Prozesskontrolle, Teileentnahme, Wärmebehandlung |
In Blätter exportieren
Fazit zur Präzision: Ingenieure, die entwerfen Toleranzen beim 3D-Druck von Metall in ihre Isolierplatten für Raumfahrzeuge einbauen, müssen sich darüber im Klaren sein, dass AM zwar eine unglaubliche geometrische Freiheit bietet, die Erzielung einer Präzision auf Bearbeitungsniveau jedoch in der Regel Nachbearbeitungsschritte für kritische Merkmale erfordert. Für viele Merkmale, insbesondere interne Strukturen oder unkritische Schnittstellen, ist die Präzision im Ist-Zustand jedoch oft ausreichend. Eine effektive Kommunikation mit dem AM-Dienstleister in Bezug auf kritische Abmessungen, Toleranzen (Qualitätskontrolle Metall-Druck), und die Anforderungen an die Oberflächengüte sind von größter Bedeutung. Durch die Nutzung des Fachwissens und der fortschrittlichen Fähigkeiten von Partnern wie Met3dp wird sichergestellt, dass die endgültigen Komponenten die anspruchsvollen Präzisionsstandards erfüllen, die für einen zuverlässigen Betrieb im Weltraum erforderlich sind.
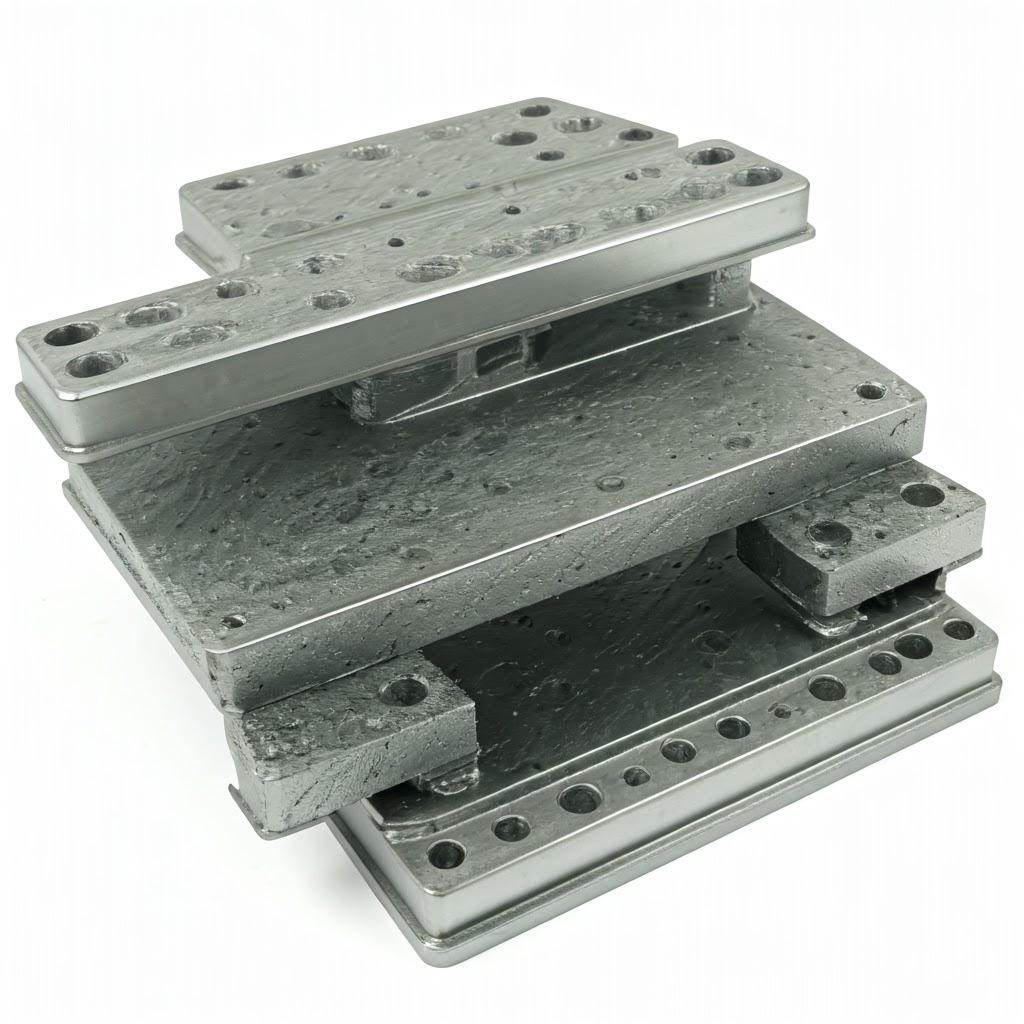
Unverzichtbare Nachbearbeitung für einsatzkritische Isolierplatten
Ein weit verbreiteter Irrglaube über die additive Fertigung von Metallen ist, dass die Teile aus dem Drucker kommen und sofort einsatzbereit sind. AM produziert zwar nahezu endkonturierte Komponenten, aber für anspruchsvolle Anwendungen wie die Isolierplatten von Raumfahrzeugen ist das fertige Teil nur der Ausgangspunkt. Eine Reihe von wesentlichen Nachbearbeitung in der Regel sind mehrere Schritte erforderlich, um das AM-Rohteil in ein flugfertiges Bauteil zu verwandeln, das die strengen Anforderungen der Luft- und Raumfahrt an mechanische Eigenschaften, Maßgenauigkeit, Oberflächengüte und allgemeine Zuverlässigkeit erfüllt.
Die Kenntnis dieser Nachbearbeitungsschritte ist für Konstrukteure, Ingenieure und Beschaffungsmanager von entscheidender Bedeutung, um Zeit und Kosten genau zu kalkulieren und sicherzustellen, dass das endgültige Teil die beabsichtigte Leistung erbringt. Die spezifischen Schritte hängen vom Material (z. B. IN625 vs. AlSi10Mg), dem verwendeten AM-Prozess (SEBM, L-PBF), der Komplexität des Teils und den spezifischen Anwendungsanforderungen ab.
Gemeinsame Nachbearbeitungsschritte für AM-Wärmedämmplatten:
1. Stressabbau / Wärmebehandlung:
- Zweck: Die schnellen Erwärmungs- und Abkühlungszyklen beim Pulverbettschmelzen erzeugen erhebliche Eigenspannungen im Bauteil. Diese Spannungen können bei der Entnahme aus der Bauplatte Verformungen verursachen, zu vorzeitiger Rissbildung führen und die mechanischen Eigenschaften (insbesondere die Ermüdungsfestigkeit) negativ beeinflussen. Eine Wärmebehandlung ist unerlässlich, um diese Spannungen abzubauen und/oder die Mikrostruktur des Materials für die gewünschten Eigenschaften zu optimieren.
- Typische Zyklen:
- Stressabbau: Wird im Allgemeinen durchgeführt, während das Teil noch an der Bauplatte befestigt ist (insbesondere bei L-PBF) oder unmittelbar nach der Entfernung. Hierbei wird das Teil auf eine bestimmte Temperatur unterhalb des kritischen Umwandlungspunkts erwärmt und für eine bestimmte Dauer gehalten, gefolgt von einer kontrollierten Abkühlung. Dadurch werden innere Spannungen abgebaut, ohne dass das Gefüge wesentlich verändert wird. Das SEBM, das bei höheren Temperaturen arbeitet, reduziert von Natur aus den Spannungsaufbau, kann aber dennoch von einem Spannungsabbauzyklus nach dem Bau profitieren.
- Glühen (z. B. für IN625): Eine Behandlung bei höheren Temperaturen, um Spannungen abzubauen, die Duktilität zu verbessern und das Gefüge zu homogenisieren. Die spezifischen Temperaturen und Zeiten hängen von den gewünschten Eigenschaften ab.
- Lösungsglühen und Alterung (z. B. T6 für AlSi10Mg): Eine mehrstufige Wärmebehandlung für ausscheidungshärtende Legierungen wie AlSi10Mg. Bei der Lösungsglühung werden die Legierungselemente in der Matrix gelöst, dann abgeschreckt und anschließend künstlich gealtert (Erwärmung auf eine niedrigere Temperatur), um feine Partikel auszufällen, die die Festigkeit und Härte deutlich erhöhen.
- Wichtigkeit: Wärmebehandlung Metall AM ist wohl der kritischste Nachbearbeitungsschritt zur Gewährleistung der strukturellen Integrität und Maßhaltigkeit von Luft- und Raumfahrtkomponenten.
2. Entfernen des Teils von der Bauplatte:
- Methode: Die Teile werden in der Regel während des Drucks mit einer dicken Metallplatte verschmolzen. Zur Entfernung wird das Teil in der Regel durch Drahterodieren (EDM), Sägen oder Schleifen abgetrennt.
- Erwägungen: Es muss darauf geachtet werden, dass das Teil beim Entfernen nicht beschädigt wird. Die Wahl des Verfahrens hängt von der Teilegeometrie, dem Werkstoff und der erforderlichen Präzision der Grundfläche ab. Das Drahterodieren bietet eine hohe Präzision, ist aber langsamer.
3. Entfernung der Stützstruktur:
- Die Notwendigkeit: Wie in DfAM erörtert, sind häufig Stützstrukturen erforderlich, die jedoch entfernt werden müssen, bevor das Teil verwendet werden kann.
- Methoden:
- Manuelle Entfernung: Stützen sind oft mit geschwächten Verbindungspunkten konstruiert und können manuell abgebrochen oder mit Handwerkzeugen (Zangen, Scheren) entfernt werden.
- Bearbeitungen: Durch CNC-Bearbeitung oder Schleifen können Stützstrukturen entfernt werden, insbesondere in zugänglichen Bereichen oder wenn an den Kontaktpunkten eine bestimmte Oberflächengüte erforderlich ist.
- Drahterodieren: Zum präzisen Abtragen, insbesondere für Stützen in komplizierten Bereichen.
- Herausforderungen: Das Entfernen von Halterungen aus komplexen internen Kanälen oder empfindlichen Gitterstrukturen kann äußerst schwierig und zeitaufwändig sein. DfAM spielt eine entscheidende Rolle bei der Gestaltung von Halterungen, die sich leicht entfernen lassen oder ganz vermieden werden können. Unterstützung von Entfernungstechniken muss bereits in der Entwurfsphase berücksichtigt werden.
Die Entfernung der Stützen kann arbeitsintensiv sein und birgt die Gefahr, die Oberfläche des Teils zu beschädigen, wenn sie nicht sorgfältig durchgeführt wird. Dies unterstreicht die Bedeutung der DfAM-Prinzipien, die darauf abzielen, den Stützbedarf zu minimieren und Stützen für eine einfachere Entfernung zu konstruieren.
- Zweck: Zur Verbesserung der Oberflächenrauheit (Ra) im eingebauten Zustand, zur Entfernung teilweise geschmolzener Pulverpartikel, zur Beseitigung von Schichtlinien und zur Erfüllung spezifischer Oberflächenanforderungen in Bezug auf thermische, optische, dichtende oder ermüdungsbedingte Eigenschaften.
- **Techniken für Oberflächenveredelung in der Luft- und Raumfahrt:
- Abrasives Strahlen (Sandstrahlen, Perlstrahlen): Schleudert Schleifmittel (Sand, Glasperlen, Keramikpartikel) gegen die Oberfläche, um eine gleichmäßige, matte Oberfläche zu erzeugen und loses Pulver zu entfernen. Wirksam für die allgemeine Oberflächenreinigung, aber nur begrenzt geeignet, um Ra deutlich zu verbessern.
- Taumeln/Gleitschleifen: Die Teile werden in eine Wanne mit einem Medium (Keramik, Kunststoff) gelegt, das vibriert oder taumelt, wodurch das Medium an den Teilen reibt und die Kanten und Oberflächen mit der Zeit glättet. Gut für die Stapelverarbeitung, aber weniger kontrolliert.
- Bearbeitungen/Schleifen: Ermöglicht die höchste Präzision und die glattesten Oberflächen an spezifischen Merkmalen (z. B. Passflächen, Schnittstellen, Dichtungsnuten). Häufig erforderlich, um enge Toleranzen zu erreichen.
- Polieren: Erzielt sehr glatte, spiegelähnliche Oberflächen für optische Anwendungen oder dort, wo eine extrem niedrige Ra erforderlich ist. Kann manuell oder automatisch erfolgen.
- Elektropolieren: Ein elektrochemisches Verfahren, das eine dünne Materialschicht abträgt, Oberflächen glättet und Verunreinigungen entfernt. Wirksam bei komplexen Formen.
5. Inspektion und Validierung (NDT):
- Zweck: Um sicherzustellen, dass das Teil frei von kritischen Fehlern (Porosität, Risse, fehlende Verschmelzung) ist und die Maßvorgaben erfüllt. Entscheidend für validierung von AM-Metallteilen in der Luft- und Raumfahrt.
- Methoden:
- Visuelle Inspektion: Grundlegende Prüfung auf offensichtliche Mängel oder Unstimmigkeiten.
- Dimensionelle Metrologie: Verwendung von Koordinatenmessmaschinen (CMMs), 3D-Scannern oder Messschiebern zur Überprüfung der Abmessungen und Toleranzen anhand des CAD-Modells.
- Zerstörungsfreie Prüfung (NDT):
- Computertomographie (CT) Scannen: Auf Röntgenstrahlen basierende Methode, die detaillierte 3D-Bilder der inneren Struktur liefert und hocheffektiv ist, um innere Porosität und Risse zu erkennen und komplexe innere Merkmale (wie Gitterstrukturen oder Kühlkanäle) zu überprüfen. Wird häufig für kritische Teile in der Luft- und Raumfahrt vorgeschrieben.
- Farbeindringprüfung (Dye Penetrant Inspection, DPI): Erkennt Risse, die die Oberfläche durchbrechen.
- Ultraschallprüfung (UT): Kann Fehler unter der Oberfläche erkennen.
- Durchleuchtungsprüfung (RT): Herkömmliches Röntgen zur Erkennung interner Defekte.
- Wichtigkeit: Rigoros NDT-Prüfung Luft- und Raumfahrt protokolle sind unerlässlich, um die Integrität und Zuverlässigkeit der Flughardware zu gewährleisten.
6. Reinigung und Beschichtung:
- Reinigung: Sicherstellen, dass die Teile vor der Montage oder dem Auftragen von Beschichtungen frei von Pulverrückständen, Schneidflüssigkeiten (von der Bearbeitung) und anderen Verunreinigungen sind.
- Thermisch kontrollierte Beschichtungen: Die Isolierplatten von Raumfahrzeugen können spezielle Beschichtungen erfordern, die nach anderen Nachbearbeitungsschritten aufgebracht werden, um bestimmte thermische Eigenschaften (z. B. niedriges Sonnenabsorptionsvermögen α, hohes Wärmeabstrahlvermögen ϵ) für eine wirksame passive Wärmeregulierung zu erreichen. Dazu können spezielle Lacke (weiß, schwarz), aufgedampfte Schichten (Gold, Silber, Aluminium) oder Eloxalbehandlungen gehören.
Integration der Nachbearbeitung in die Gestaltung: Eine erfolgreiche AM-Implementierung setzt voraus, dass die Nachbearbeitung von Anfang an berücksichtigt wird. Konstrukteure sollten dies berücksichtigen:
- Sind Merkmale, die enge Toleranzen oder glatte Oberflächen erfordern, für die Bearbeitung leicht zugänglich?
- Wie werden die internen Stützen entfernt?
- Führt die gewählte Wärmebehandlung zu einem akzeptablen Grad an Verzug?
- Ermöglicht die Konstruktion eine wirksame ZfP-Prüfung kritischer Bereiche?
Die Nachbearbeitung erhöht den Zeit- und Kostenaufwand für den gesamten Fertigungsablauf, ist aber für die Herstellung hochwertiger, zuverlässiger Metall-AM-Komponenten für Raumfahrtanwendungen unerlässlich. Das Verständnis dieser Schritte ermöglicht eine bessere Planung, Kostenkalkulation und Designoptimierung und stellt sicher, dass die endgültige Isolationsplatte alle Missionsanforderungen erfüllt.
Überwindung häufiger Herausforderungen in der Metall-AM für thermische Komponenten
Die additive Fertigung von Metallen birgt zwar ein erhebliches Potenzial für die Herstellung fortschrittlicher Wärmedämmplatten, aber die Technologie ist nicht ohne Herausforderungen. Die Herstellung komplexer, einsatzkritischer Komponenten für die Luft- und Raumfahrt erfordert ein sorgfältiges Prozessmanagement, um mögliche Fehler zu vermeiden und eine gleichbleibende Qualität zu gewährleisten. Das Bewusstsein für diese allgemeinen Herausforderungen und die Strategien zu ihrer Abschwächung sind entscheidend für eine erfolgreiche Umsetzung.
1. Eigenspannung, Verformung und Rissbildung:
- Herausforderung: Die extremen thermischen Gradienten, die beim Schmelzen im Pulverbett auftreten (schnelles Schmelzen und Erstarren), führen unweigerlich zum Aufbau von inneren eigenspannungs-Metalldruck. Wenn diese Spannungen die Streckgrenze des Materials überschreiten, können sie Verformungen (Verzerrungen der Teilegeometrie) oder sogar Risse verursachen, entweder während der Herstellung oder nach dem Ausbau.
- Strategien zur Schadensbegrenzung:
- Prozess-Simulation: Mit Hilfe von Finite-Elemente-Analysen (FEA), die speziell für AM-Simulationen entwickelt wurden, können thermische Gradienten, Spannungsakkumulationen und potenzielle Verformungen vorhergesagt werden, was eine Anpassung des Designs oder der Parameter ermöglicht vor Drucken.
- Optimierte Scan-Strategien: Die Anpassung des Laser- oder Elektronenstrahls (z. B. Inselabtastung, wechselnde Richtungen) kann dazu beitragen, die Wärme gleichmäßiger zu verteilen und lokale Spannungsspitzen zu reduzieren.
- Wirksame Unterstützungsstrukturen: Gut durchdachte Halterungen verankern das Teil fest auf der Bauplatte und dienen als Wärmesenken, um thermische Gradienten auszugleichen und Verformungen während des Bauprozesses zu verhindern.
- Geeignete Wärmebehandlung: Entspannungszyklen nach der Fertigung sind wichtig, um innere Spannungen abzubauen und die Geometrie des Teils zu stabilisieren.
- Prozesswahl (SEBM-Vorteil): Verfahren wie das selektive Elektronenstrahlschmelzen (SEBM), bei dem das Pulverbett bei erhöhten Temperaturen (mehrere hundert °C) gehalten wird, reduzieren die Temperaturgradienten während des Aufbaus im Vergleich zu L-PBF erheblich. Dies führt zu wesentlich geringeren Eigenspannungen und minimiert das Risiko von Verzug und Rissbildung, insbesondere bei großen Teilen oder rissempfindlichen Legierungen wie IN625. Dies ist ein wesentlicher Vorteil der von Anbietern wie Met3dp verwendeten Technologie.
2. Porosität:
- Herausforderung: Porosität bezieht sich auf kleine Hohlräume oder Poren im fertigen Teil. Diese wirken als Spannungskonzentratoren und können die mechanischen Eigenschaften, insbesondere die Ermüdungsfestigkeit und Bruchzähigkeit, erheblich beeinträchtigen - was für kritische Bauteile nicht akzeptabel ist. Porosität kann aus zwei Hauptursachen entstehen:
- Gas Porosität: Eingeschlossenes Gas (z. B. Argon, das als Schutzgas in L-PBF verwendet wird, oder gelöste Gase im Pulver) bildet Blasen, die in das erstarrende Metall eingefroren werden.
- Lack-of-Fusion-Porosität: Unzureichender Energieeintrag oder unsachgemäße Überlappung zwischen den Scanspuren, was zu unvollständigem Schmelzen und Verbinden zwischen Schichten oder benachbarten Schmelzbädern führt.
- Strategien zur Schadensbegrenzung:
- Hochwertiges Pulver: Verwenden Metallpulver mit hoher Sphärizität, kontrollierter Partikelgrößenverteilung, geringer innerer Porosität und niedrigem Gehalt an gelösten Gasen ist entscheidend. Die fortschrittlichen Pulverherstellungsmethoden von Met3dp’ (Gaszerstäubung, PREP) sind darauf ausgelegt, solche hochwertige Metallpulver. Regelmäßiges Sieben des Pulvers und sorgfältige Handhabung/Recycling-Protokolle sind ebenfalls wichtig, um Verunreinigungen und Abbau zu verhindern.
- Optimierte Prozessparameter: Die Wahl der richtigen Strahlleistung, Scangeschwindigkeit, Schichtdicke und Schraffurabstände ist von entscheidender Bedeutung, um ein vollständiges Schmelzen und Verschmelzen ohne übermäßigen Energieeintrag zu gewährleisten, der das Material verdampfen oder die Gasaufnahme erhöhen könnte.
- Heiß-Isostatisches Pressen (HIP): Ein Nachbearbeitungsschritt, bei dem das Teil einer hohen Temperatur und einem hohen Inertgasdruck ausgesetzt wird. Auf diese Weise können innere Hohlräume (sowohl Gas- als auch Fehlschmelzporosität) wirksam geschlossen werden, wodurch sich die Dichte und die mechanischen Eigenschaften deutlich verbessern. Dies ist häufig für ermüdungskritische Teile in der Luft- und Raumfahrt erforderlich.
- NDT-Inspektion: Das CT-Scannen ist besonders effektiv für die Erkennung und Charakterisierung von internen Porositätskontrolle bei der additiven Fertigung.
3. Schwierigkeiten beim Entfernen der Stützen:
- Herausforderung: Während DfAM darauf abzielt, die Anzahl der Stützen zu minimieren, können komplexe interne Geometrien wie Gitterstrukturen oder Kühlkanäle innerhalb einer Isolierplatte die Entfernung von Stützen extrem schwierig oder unmöglich machen, ohne das Teil zu beschädigen.
- Strategien zur Schadensbegrenzung:
- DfAM Fokus: Bevorzugen Sie selbsttragende Konstruktionen, orientieren Sie die Teile strategisch, verwenden Sie lösliche oder leicht zerbrechliche Trägermaterialien/Strukturen, wo dies möglich ist (obwohl dies bei Metall-AM weniger üblich ist).
- Design für den Zugang: Stellen Sie sicher, dass Werkzeuge oder Flüssigkeiten (für chemisches Ätzen, wenn auch seltener) die inneren Träger erreichen können.
- Prozess-Simulation: Erkennen Sie Bereiche, die Unterstützung benötigen, und versuchen Sie, diese neu zu gestalten.
- Akzeptanz: In einigen Fällen kann es notwendig sein, interne Stützen an Ort und Stelle zu belassen, wenn sie die Leistung nicht kritisch beeinträchtigen und nicht entfernt werden können - dies muss sorgfältig geprüft werden.
4. Erzielung enger Toleranzen und Oberflächengüte:
- Herausforderung: Wie bereits erwähnt, entsprechen die Toleranzen und die Oberflächenbeschaffenheit von AM-Bauteilen im Ist-Zustand möglicherweise nicht den Anforderungen für alle Merkmale, insbesondere für kritische Schnittstellen oder Dichtungsflächen.
- Strategien zur Schadensbegrenzung:
- Hybride Fertigung: Entwerfen Sie das Teil für AM und nutzen Sie die geometrische Freiheit, aber planen Sie zusätzliches Material (Bearbeitungszugabe) für kritische Oberflächen ein, die mit konventioneller CNC-Bearbeitung fertiggestellt werden.
- Gezielte Nachbearbeitung: Wenden Sie spezielle Endbearbeitungstechniken (Strahlen, Polieren, Schleifen) nur auf die Bereiche an, die eine verbesserte Oberflächenqualität oder Toleranz erfordern.
- Realistische Erwartungen: Verstehen Sie die inhärenten Fähigkeiten des AM-Prozesses und vermeiden Sie die Festlegung unnötig enger Toleranzen oder Oberflächen, wenn sie funktional nicht erforderlich sind.
5. Materialkontamination und Pulvermanagement:
- Herausforderung: Metallpulver, insbesondere reaktive Pulver wie Aluminium- und Titanlegierungen, können leicht durch Sauerstoff, Stickstoff oder Feuchtigkeit aus der Atmosphäre verunreinigt werden, oder es kommt zu einer Kreuzkontamination, wenn mehrere Materialien ohne sorgfältige Reinigung auf derselben Maschine verarbeitet werden. Verunreinigungen verschlechtern die Qualität des Pulvers und die Eigenschaften des fertigen Teils.
- Strategien zur Schadensbegrenzung:
- Inertatmosphäre: Verarbeitung in einer streng kontrollierten Inertgasumgebung (Argon oder Stickstoff für L-PBF, Vakuum für SEBM).
- Strenge Protokolle für die Handhabung von Pulver: Spezielle Geräte für bestimmte Materialien, angemessene Lagerbedingungen (versiegelte Behälter, kontrollierte Luftfeuchtigkeit), regelmäßiges Sieben zur Entfernung von abgebauten Partikeln und kontrollierte Verfahren für das Pulverrecycling.
6. Anisotropie:
- Herausforderung: Aufgrund des schichtweisen Aufbaus und der gerichteten Erstarrung können AM-Teile anisotrope mechanische Eigenschaften aufweisen (unterschiedliche Festigkeit/Dehnbarkeit in Aufbaurichtung (Z) gegenüber der Aufbaufläche (X-Y)).
- Strategien zur Schadensbegrenzung:
- Orientierung aufbauen: Richten Sie das Teil so aus, dass die primären Lastpfade mit den Richtungen der optimalen Materialeigenschaften übereinstimmen.
- Optimierung der Prozessparameter: Die Feinabstimmung der Parameter kann das Gefüge (z. B. die Kornstruktur) beeinflussen und den Grad der Anisotropie verringern.
- Nachbearbeitende Wärmebehandlungen: Bestimmte Wärmebehandlungen können zur Homogenisierung des Gefüges und zur Verringerung der Anisotropie beitragen.
- Konstruktionszulassungen: Berücksichtigen Sie die potenzielle Anisotropie bei Konstruktionsberechnungen mit Hilfe von richtungsspezifischen Materialeigenschaftsdaten.
Die Überwindung dieser gemeinsame Herausforderungen erfordert eine Kombination aus robusten DfAM-Praktiken, sorgfältiger Prozesskontrolle, hochwertigen Materialien, angemessener Nachbearbeitung und strenger Prüfung. Die Zusammenarbeit mit erfahrenen Metall-AM-Fehlerbehebung die Zusammenarbeit mit Experten und Dienstleistern wie Met3dp, die über fundierte Kenntnisse in den Bereichen Materialien, Prozesse (einschließlich der spezifischen Vorteile von SEBM für das Stressmanagement) und Qualitätskontrolle verfügen, erhöht die Wahrscheinlichkeit der erfolgreichen Herstellung von zuverlässigen, leistungsstarken Wärmedämmplatten für die anspruchsvollen Bedingungen im Weltraum erheblich. Adresse validierung von Luft- und Raumfahrtkomponenten erfordert es, diese Herausforderungen frontal anzugehen.
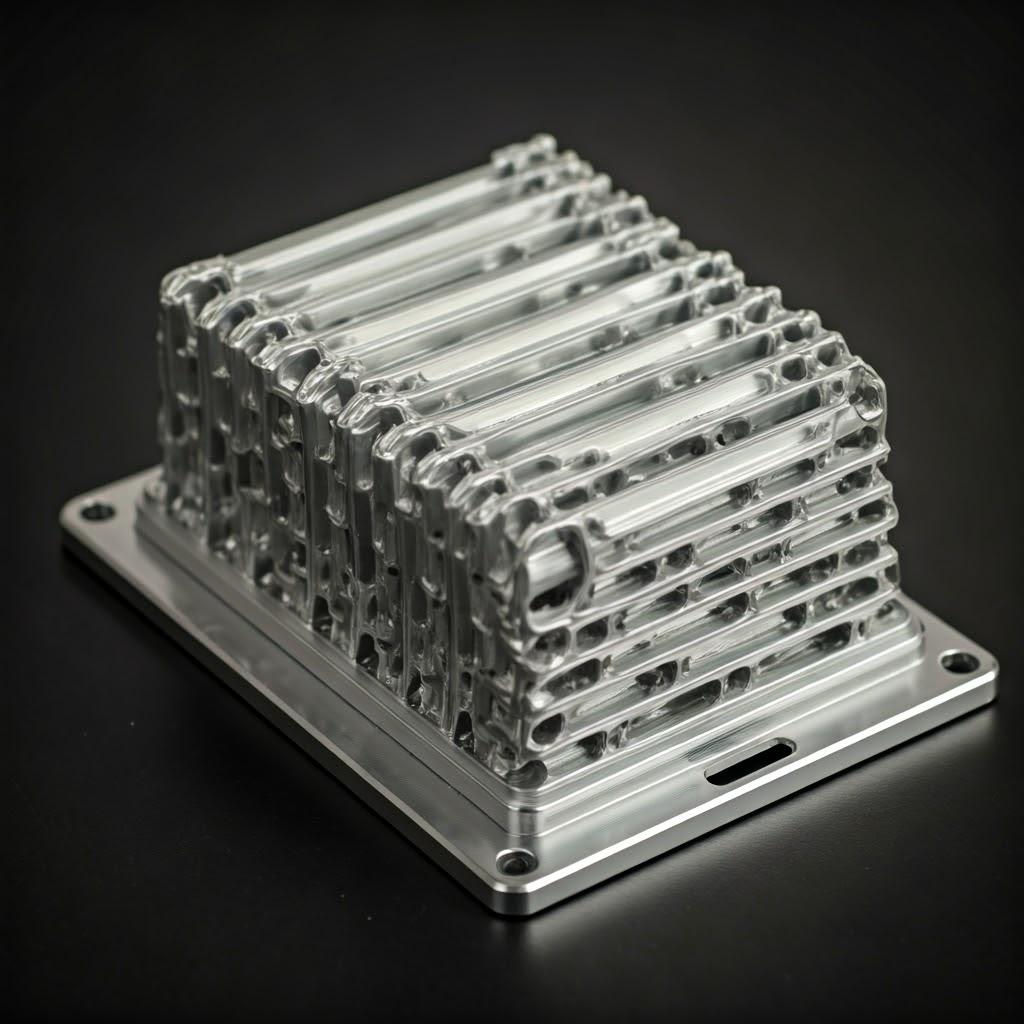
Die Auswahl Ihres strategischen Partners: Die Wahl eines Metall-AM-Dienstleisters
Der Weg von einem Wärmedämmplattenkonzept zu einem flugtauglichen Bauteil hängt nicht nur von der Technologie selbst ab, sondern auch vom Fachwissen und den Fähigkeiten des gewählten Dienstleisters für die additive Fertigung von Metallen. Für Luft- und Raumfahrtanwendungen, bei denen Sicherheit, Zuverlässigkeit und Leistung nicht verhandelbar sind, ist die Auswahl des richtigen Partners eine wichtige strategische Entscheidung. Die Zuliefererlandschaft ist sehr unterschiedlich und reicht von kleinen Lohnfertigern bis hin zu großen, vertikal integrierten Herstellern. Beschaffungsmanager und Ingenieurteams brauchen einen soliden Rahmen für aM-Lieferantenbewertung für die Luft- und Raumfahrt um sicherzustellen, dass der von ihnen gewählte Partner die strengen Anforderungen der Raumfahrtindustrie erfüllen kann.
Hier sind die wichtigsten Kriterien, die zu berücksichtigen sind, wenn bewertung von Anbietern der additiven Fertigung zur Herstellung von Wärmedämmplatten für Raumfahrzeuge:
1. Qualitätsmanagementsystem (QMS) und Zertifizierungen:
- AS9100: Dies ist der international anerkannte QMS-Standard für die Luft- und Raumfahrtindustrie. Die Zertifizierung nach AS9100 zeigt das Engagement eines Anbieters in den Bereichen Qualität, Rückverfolgbarkeit, Risikomanagement und kontinuierliche Verbesserung speziell für die Anforderungen der Luft- und Raumfahrt. Sie ist häufig eine zwingende Voraussetzung für Lieferanten von Flughardware.
- ISO 9001: Ein grundlegender QMS-Standard, der auf robuste allgemeine Qualitätsprozesse hinweist.
- Nadcap-Akkreditierung: Während AS9100 das Gesamtsystem abdeckt, bietet Nadcap die Akkreditierung für bestimmte Spezialprozesse, die für die Luft- und Raumfahrt von entscheidender Bedeutung sind, wie z. B. Wärmebehandlung, zerstörungsfreie Prüfung (ZfP), Schweißen (relevant für AM) und Werkstoffprüfung. Ein Anbieter, der über die entsprechenden Nadcap-Akkreditierungen verfügt, bietet zusätzliche Sicherheit für die Prozesskontrolle in diesen speziellen Bereichen.
- Verifizierung: Überprüfen Sie immer den Status und den Umfang der Zertifizierungen.
2. Materialkenntnis und Handhabung:
- Nachgewiesene Erfahrung: Der Anbieter muss nachweislich Erfahrung im Umgang mit den spezifischen Metallpulvern für die Luft- und Raumfahrt haben (z. B., IN625, AlSi10Mg, Titanlegierungen). Dazu gehört das Verständnis ihrer Verarbeitungsnuancen, erforderlichen Wärmebehandlungen und potenziellen Herausforderungen.
- Qualitätskontrolle des Pulvers: Strenge Verfahren für die Eingangsprüfung des Pulvers (Chemie, Partikelgrößenverteilung, Morphologie, Fließfähigkeit), sichere Lagerung, kontrollierte Handhabung (Vermeidung von Verunreinigungen), Rückverfolgbarkeit der einzelnen Chargen und Protokolle für die Aufbereitung/Recycling des Pulvers sind unerlässlich. Fragen Sie nach der Beschaffung des Pulvers - vertikal integrierte Lieferanten wie Met3dp, die ihre eigenen hochwertige Metallpulver mit fortschrittlichen Methoden wie Gaszerstäubung und PREP, bieten eine bessere Kontrolle und Rückverfolgbarkeit.
- Materialcharakterisierung: Verfügt der Anbieter über Möglichkeiten (intern oder über Partner), die Materialeigenschaften des Pulvers und des Endprodukts zu charakterisieren (Zugfestigkeit, Mikrostruktur, Dichte usw.), um sicherzustellen, dass sie den Spezifikationen entsprechen?
3. Ausrüstung, Technologie und Kapazität:
- Angemessene Technologie: Verfügt der Anbieter über die richtige Art von AM-Maschinen (z. B. L-PBF, SEBM), die für das Material und die Anwendung geeignet sind? Zum Beispiel ist Met3dp’s Fokus auf SEBM-Drucker kann Vorteile bei der Verringerung der Eigenspannung für komplexe IN625-Teile bieten.
- Maschinenbedingung und Kalibrierung: Werden die Maschinen gut gewartet, regelmäßig kalibriert und mit den erforderlichen Prozessüberwachungsfunktionen ausgestattet (z. B. Schmelzbadüberwachung, Sauerstoffsensoren)?
- Bauvolumen: Können ihre Maschinen die Größe der erforderlichen Isolierplatten aufnehmen?
- Kapazität und Redundanz: Verfügen sie über ausreichende Kapazitäten, um die geforderten Vorlaufzeiten einzuhalten, insbesondere wenn sie von der Prototypen- zur Kleinserienfertigung übergehen? Verfügen sie über mehrere Maschinen, um Redundanz zu bieten?
4. Prozesskontrolle und Qualitätssicherung:
- Dokumentierte Verfahren: Robuste, dokumentierte Verfahren für jeden Schritt, von der Bauvorbereitung und den Parametereinstellungen bis zur Nachbearbeitung und Prüfung.
- Rückverfolgbarkeit: Eine durchgängige Rückverfolgbarkeit, die das fertige Teil mit der spezifischen Maschine, den Herstellungsparametern, der Pulvercharge, dem Bediener und den Nachbearbeitungsschritten verknüpft, ist für die Luft- und Raumfahrt entscheidend.
- Prozessbegleitende Überwachung: Nutzung verfügbarer Tools zur Überwachung der Build-Stabilität und zur Erkennung potenzieller Probleme in Echtzeit.
- NDT-Fähigkeiten: Eigene oder von Dritten zertifizierte Kapazitäten für die erforderlichen ZfP-Methoden (CT-Scanning, DPI, UT usw.) sind für die Teilevalidierung unerlässlich.
5. Technische Unterstützung und DfAM-Fachwissen:
- Kollaboration: Ein echter strategischer Partner arbeitet mit Ihrem technischen Team zusammen und nimmt nicht nur Aufträge entgegen. Suchen Sie nach Anbietern, die Anwendungsentwicklungsdienste.
- DfAM-Leitfaden: Können sie fachkundigen Rat zur Optimierung des Isolierplattendesigns für AM geben (Topologieoptimierung, Unterstützungsstrategie, Featureauflösung, Materialauswahl)?
- Simulationsfähigkeiten: Werden Tools zur Simulation der Konstruktion eingesetzt, um potenzielle Probleme wie Verformung oder thermische Belastung vorherzusagen und zu mindern?
- Problemlösung: Verfügen sie über erfahrene Ingenieure, die bei der Fehlersuche und Lösungsfindung helfen können? Met3dp ist stolz auf jahrzehntelanges kollektives Fachwissen in Metall-AM zur Unterstützung von Kundenprojekten. Mehr erfahren über Met3dp’s Fähigkeiten.
6. Erfolgsbilanz in der Luft- und Raumfahrtindustrie:
- Bewährte Leistung: Haben sie erfolgreich Teile für ähnliche Raumfahrt- oder anspruchsvolle Luft- und Raumfahrtanwendungen hergestellt? Können sie (nicht vertrauliche) Fallstudien oder Referenzen vorlegen?
- Verstehen der Anforderungen: Sind sie mit den spezifischen Dokumentations-, Test- und Qualitätsanforderungen vertraut, die für Luft- und Raumfahrtprogramme typisch sind?
7. Vorlaufzeit, Reaktionsfähigkeit und Kommunikation:
- Realistische Zeitpläne: Können sie genaue Vorlaufzeitschätzungen abgeben und Liefertermine konsequent einhalten?
- Kommunikation: Eine klare, proaktive Kommunikation während des gesamten Projektlebenszyklus ist unerlässlich.
- Flexibilität: Fähigkeit, eventuelle Designänderungen oder beschleunigte Anfragen (in angemessenem Rahmen) zu berücksichtigen.
8. Kostentransparenz und Wert:
- Eindeutig zitieren: Detaillierte Kostenvoranschläge, in denen die Kosten aufgeschlüsselt sind (Material, Maschinenzeit, Arbeit, Nachbearbeitung, Qualitätssicherung), ermöglichen eine bessere Bewertung.
- Wert-Angebot: Betrachten Sie den Gesamtwert, nicht nur den niedrigsten Preis. Fachwissen, Qualität, Zuverlässigkeit und technische Unterstützung tragen wesentlich zum Gesamtwert und zur Risikominderung bei.
Den richtigen Sitz finden: Auswahl eines Metall-AM-Dienstleisters für beschaffung von Metall-AM-Dienstleistungen erfordert eine Due-Diligence-Prüfung, die über einen einfachen Preisvergleich hinausgeht. Dazu gehört die Bewertung der technischen Fähigkeiten, der Qualitätssysteme, der Materialkenntnisse, der technischen Unterstützung und der Erfolgsbilanz. Unternehmen wie Met3dp, die umfassende Lösungen von fortschrittliche Metallpulver mit Hilfe modernster Techniken auf dem neuesten Stand der Technik produziert SEBM-Drucker und engagierte Anwendungsunterstützung stellen die Art von vertikal integriertem, fachkundigem Partner dar, der für die erfolgreiche Umsetzung von Metall-AM für missionskritische Raumfahrtkomponenten wie Wärmedämmplatten erforderlich ist. Eine starke Partnerschaft, die auf Vertrauen, Transparenz und technischer Exzellenz aufbaut, ist von grundlegender Bedeutung für die effektive Nutzung von AM für die Herausforderungen der Weltraumforschung.
Verständnis der Kostendynamik und Vorlaufzeiten für AM-Isolierplatten
Eine der wichtigsten Überlegungen bei der Einführung von Fertigungstechnologien ist deren wirtschaftliche Tragfähigkeit und Produktionsgeschwindigkeit. Die additive Fertigung von Metallen bietet zwar überzeugende technische Vorteile für Isolierplatten von Raumfahrzeugen, aber das Verständnis der damit verbundenen Metall-3D-Druck-Kostenfaktoren und typische vorlaufzeiten der additiven Fertigung ist entscheidend für die Projektplanung, die Budgetierung und den Vergleich von AM mit traditionellen Alternativen wie CNC-Bearbeitung. Die Kostenstruktur und der Zeitplan für AM unterscheiden sich erheblich von subtraktiven oder formgebenden Verfahren.
Aufschlüsselung der Kostenfaktoren:
Der Endpreis einer AM-produzierten Wärmedämmplatte wird durch ein komplexes Zusammenspiel von Faktoren beeinflusst:
- Materialkosten:
- Pulver Preis: Die Rohstoffkosten pro Kilogramm sind je nach Legierung sehr unterschiedlich. Hohe Leistung metallpulver für die Luft- und Raumfahrt wie IN625 oder spezielle Titanlegierungen sind erheblich teurer als AlSi10Mg oder nichtrostende Stähle.
- Pulververbrauch: Dies umfasst das Material, aus dem das fertige Teil besteht und die Stützstrukturen. Konstruktionen, die umfangreiche Stützen erfordern, verbrauchen mehr Pulver.
- Recycling-Effizienz: Ungeschmolzenes Pulver kann zwar recycelt werden, aber es gibt Grenzen und damit verbundene Kosten (Sieben, Testen, mögliche Verschlechterung über die Zyklen). Die Effizienz des Anbieters bei der Wiederverwendung des Pulvers wirkt sich auf die gesamten Materialkosten aus.
- Maschinenzeit:
- Bauzeit: Dies ist oft der größte Kostenfaktor. Sie wird in erster Linie durch die höhe des Teils (Anzahl der Schichten) und die Band oder querschnittsfläche pro Schicht (mit Einfluss auf die Scanzeit). Komplexe Geometrien oder dichte Gitterstrukturen erfordern mehr Scans pro Schicht.
- Maschine Stundensatz: Dieser Satz beinhaltet die Abschreibung der Maschine, den Energieverbrauch, die Wartung, den Verbrauch von Inertgas (Argon/Stickstoff für L-PBF, Vakuumsystem für SEBM) und die Gemeinkosten der Anlage. Industrielle Metall-AM-Systeme der Spitzenklasse stellen eine erhebliche Kapitalinvestition dar.
- Arbeitskosten:
- Vorverarbeitung: Für die Vorbereitung der Dateien, die Optimierung des Build-Layouts, die Generierung der Stützstruktur und die Auswahl der Prozessparameter sind qualifizierte Techniker oder Ingenieure erforderlich.
- Betrieb der Maschine: Einrichten, Überwachen des Bauprozesses und Entfernen der ersten Teile.
- Nachbearbeiten: Die Entnahme der Teile von der Platte, die (oft manuelle oder halbautomatische) Entfernung der Halterung, die Einrichtung der Wärmebehandlung, die Oberflächenbearbeitung und die Prüfung sind mit erheblichem Arbeitsaufwand verbunden. Dies kann bei komplexen Teilen manchmal die tatsächlichen Druckzeitkosten übersteigen.
- Nachbearbeitungskosten:
- Spezifische Prozesse: Jeder Nachbearbeitungsschritt (Spannungsarmglühen/Wärmebehandlung, HIP, maschinelle Bearbeitung, Strahlen, Polieren, zerstörungsfreie Prüfung) ist mit entsprechenden Ausrüstungs-, Verbrauchsmaterial- und Arbeitskosten verbunden.
- Komplexität: Bei Teilen, die eine umfangreiche Stützentfernung, eine mehrachsige Bearbeitung für enge Toleranzen oder eine fortschrittliche zerstörungsfreie Prüfung (wie CT-Scannen) erfordern, fallen höhere Nachbearbeitungskosten an.
- Qualitätssicherung und Zertifizierung:
- Inspektion: Der Umfang der erforderlichen Prüfung (Sichtprüfung, Maßprüfung, zerstörungsfreie Prüfung) wirkt sich direkt auf die Kosten aus. Umfassende ZfP wie CT-Scans sind teuer, aber oft notwendig für validierung von Luft- und Raumfahrtkomponenten.
- Dokumentation: Die Erstellung der für die Luft- und Raumfahrt erforderlichen detaillierten Dokumentation, Materialzertifizierungen und Rückverfolgbarkeitsaufzeichnungen erhöht die Gemeinkosten erheblich.
- Entwurfskomplexität und Teilevolumen:
- Komplexität: AM ermöglicht zwar Komplexität, aber Merkmale wie sehr dünne Wände, komplizierte interne Kanäle oder umfangreiche Gitterstrukturen können die Herstellungszeit und die Nachbearbeitungsschwierigkeiten erhöhen und sich somit auf die Kosten auswirken.
- Teilband: Bezieht sich auf die Gesamtgröße des Teils und beeinflusst den Materialverbrauch und die Bearbeitungszeit.
- Dichte der Bebauung: Das Drucken mehrerer Teile in einem einzigen Bauvorgang (Nesting) kann die Einrichtungszeit amortisieren und die Kosten pro Teil im Vergleich zum Drucken einzelner Teile möglicherweise senken, obwohl dies von der Teilegeometrie und der Höhenkonsistenz abhängt.
Überlegungen zur Vorlaufzeit:
Vorlaufzeiten der additiven Fertigung für Metallteile sind in der Regel kürzer als herkömmliche Verfahren mit Werkzeugbau (wie Gießen oder Spritzgießen), insbesondere bei Prototypen und geringen Stückzahlen. Allerdings ist es kein sofortiger Prozess.
- Typische Phasen:
- Angebotserstellung und Auftragsbestätigung: (1-5 Tage) Hängt von der Komplexität und der Reaktionsfähigkeit des Lieferanten ab.
- Designüberprüfung & Vorbereitung: (1-3 Tage) DfAM-Prüfungen, Einrichtung der Build-Datei, Simulation (falls erforderlich).
- Warteschlangen & Zeitplanung: (Variabel) Abhängig von der Verfügbarkeit der Maschinen und der Auslastung der Lieferanten.
- Drucken: (1-7+ Tage) Hängt stark von der Höhe, dem Volumen und der Komplexität der Teile ab. Bei großen/komplexen Teilen kann die Bearbeitung mehrere Tage dauern.
- Cool Down & Entpowern: (0,5-1 Tag)
- Nachbearbeiten: (2-10+ Tage) Wärmebehandlungszyklen, Entfernen von Halterungen, Bearbeitung, Endbearbeitung, zerstörungsfreie Prüfung (NDT) - all das kostet viel Zeit. Dies kann die längste Phase sein.
- Endkontrolle & Versand: (1-3 Tage)
- Beeinflussende Faktoren:
- Teil Komplexität/Größe: Größere, komplexere Teile benötigen mehr Zeit für den Druck und die Nachbearbeitung.
- Verfügbarkeit der Maschine: Eine hohe Nachfrage kann zu längeren Wartezeiten führen.
- Nachbearbeitungsanforderungen: Umfangreiche Bearbeitungen oder spezielle zerstörungsfreie Prüfungen verlängern den Zeitplan erheblich.
- Wahl des Materials: Einige Werkstoffe können längere Wärmebehandlungszyklen erfordern.
- Menge: Das Drucken größerer Chargen dauert zwar länger, kann aber insgesamt effizienter sein als mehrere kleine Druckvorgänge.
- Allgemeiner Vergleich: Für einen einzelnen komplexen Prototyp oder eine Kleinserie (1-10) von Isolierplatten für Raumfahrzeuge können die AM-Vorlaufzeiten zwischen 1 bis 4 Wochenund hängt stark von den oben genannten Faktoren ab. Dies ist oft deutlich schneller als die Monate, die es dauern kann, bis erste Artikel aus Guss- oder werkzeugintensiven Verfahren vorliegen.
Rentabilität der Investition (ROI):
Obwohl die Kosten pro Teil bei der Metall-AM manchmal höher sind als bei traditionellen Methoden (insbesondere im Vergleich zu hochvolumigen Prozessen oder einfach bearbeiteten Teilen), sind die ROI additive Fertigung berechnung für die Luft- und Raumfahrt sieht oft günstig aus, wenn man sie berücksichtigt:
- Geringere Entwicklungszeit: Schnellere Iterationen führen zu einem schnelleren Projektabschluss.
- Gewichtseinsparung: Niedrigere Startkosten oder eine höhere Nutzlastkapazität bringen erhebliche wirtschaftliche Vorteile.
- Leistungsverbesserungen: Ein verbessertes Wärmemanagement kann die Zuverlässigkeit und Lebensdauer des Systems erhöhen.
- Teil Konsolidierung: Geringere Montagezeit, Komplexität und Lagerkosten.
- Beseitigung von Werkzeugen: Keine hohen Vorlaufkosten für die Werkzeugherstellung, so dass die Produktion von Kleinserien wirtschaftlich machbar ist.
Das Verständnis der spezifischen Kostentreiber und realistischen Vorlaufzeiten, die mit Metall-AM für Komponenten wie Wärmedämmplatten verbunden sind, ermöglicht es Luft- und Raumfahrtunternehmen, fundierte Entscheidungen zu treffen, ein genaues Budget zu erstellen und das umfassendere Wertangebot über das Preisschild der Komponente hinaus voll zu schätzen. Die Zusammenarbeit mit sachkundigen Lieferanten, die transparente preise für Luft- und Raumfahrtkomponenten und realistische Zeitvorgaben sind der Schlüssel zur erfolgreichen Projektdurchführung.
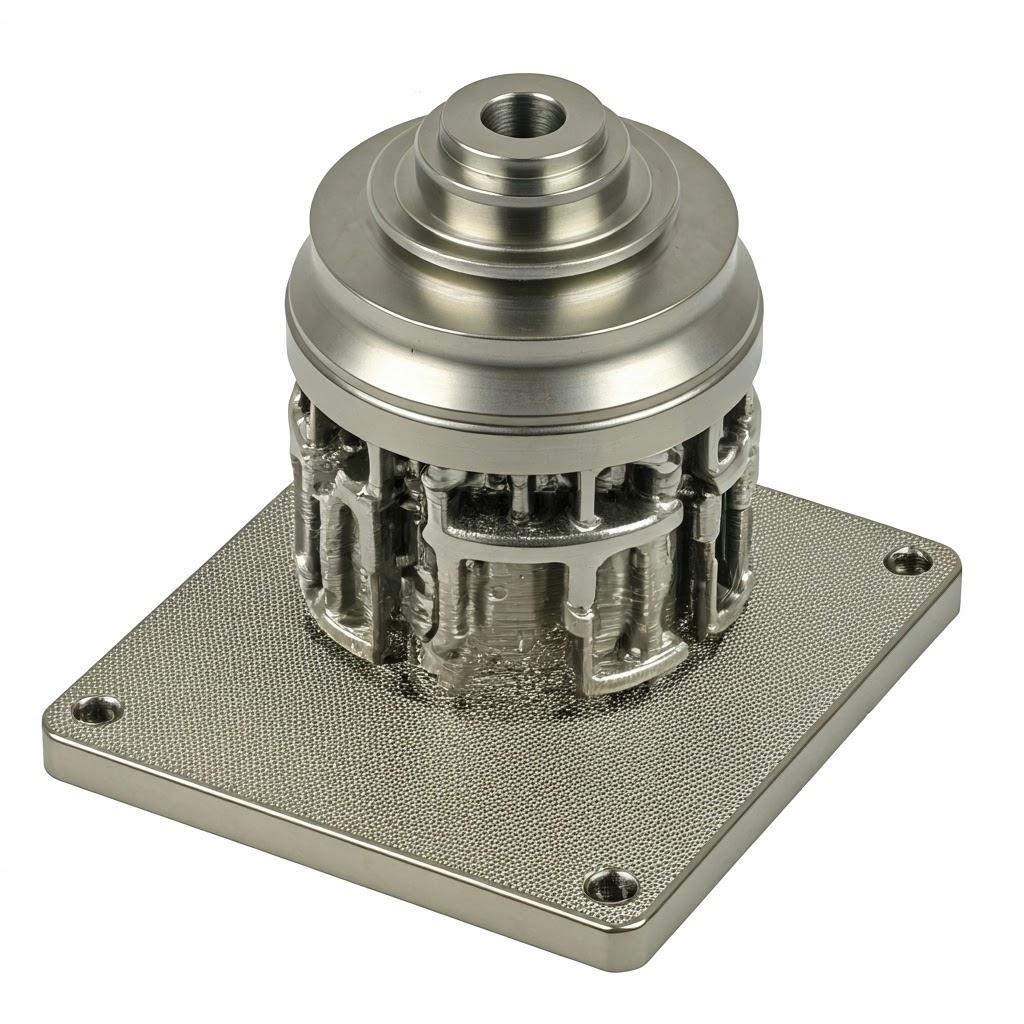
Häufig gestellte Fragen (FAQ) zu Metall AM für die Raumdämmung
Da sich die additive Fertigung von Metallen in der Luft- und Raumfahrtindustrie immer mehr durchsetzt, haben Ingenieure, Konstrukteure und Beschaffungsspezialisten oft spezifische Fragen zu ihrer Anwendung für Komponenten wie Wärmedämmplatten. Hier finden Sie Antworten auf einige häufig gestellte Fragen:
1. Welche typischen Wärmeleitfähigkeitswerte lassen sich mit AM IN625 und AlSi10Mg Isolierplatten erreichen, insbesondere unter Berücksichtigung von Gitterstrukturen?
- Eigenschaften des Grundmaterials: Die inhärente Wärmeleitfähigkeit (λ) des Grundmaterials bleibt der wichtigste Faktor. Wie bereits erwähnt, hat geknetetes IN625 in der Regel λ≈10-15 W/m-K, während AlSi10Mg bei Raumtemperatur λ≈120-150 W/m-K aufweist. AM-Versionen weisen im Allgemeinen eine ähnliche Leitfähigkeit auf, wenngleich aufgrund von Unterschieden im Mikrogefüge geringfügige Abweichungen auftreten können.
- Auswirkungen von Gitterstrukturen: Einbindung von gitterförmige Strukturen thermisch ist eine Schlüsselstrategie, um das Problem der wirksam wärmeleitfähigkeit eines Bauteils aus einem relativ leitfähigen Material wie AlSi10Mg oder zur weiteren Verbesserung der Isoliereigenschaften von IN625. Durch den Ersatz von festem Material durch ein Netz aus dünnen Verstrebungen und Hohlräumen wird der Weg für die Wärmeleitung viel gewundener, und auch die Strahlung/Konvektion innerhalb der Gitterporen spielt eine Rolle.
- Erreichbare Reduktion: Die genaue Reduzierung hängt stark von der Gittertopologie (z. B. Octet, Kelvin Cell, TPMS Gyroid), der relativen Dichte (Prozentsatz des festen Materials), der Strebendicke und dem Material ab. Eine Verringerung der effektiven Wärmeleitfähigkeit um Faktoren von 5, 10 oder sogar mehr im Vergleich zum festen Material ist möglich, wodurch das effektive λ einer AlSi10Mg-Gitterstruktur erheblich gesenkt werden kann, während die nützlichen strukturellen Eigenschaften erhalten bleiben.
- Verifizierung: Die Vorhersage der genauen effektiven Wärmeleitfähigkeit erfordert eine thermische Simulation (FEA) der spezifischen Gittergeometrie oder idealerweise eine experimentelle Prüfung repräsentativer Coupons, die mit demselben AM-Verfahren und denselben Parametern wie das endgültige Teil hergestellt wurden. Zulieferer mit starker technischer Unterstützung können bei dieser Analyse helfen.
2. Können komplexe interne Merkmale, wie Kühlkanäle oder Wärmerohre, zuverlässig in AM-Isolierplatten integriert und verifiziert werden?
- AM-Fähigkeit: Ja, die Integration komplexe Kühlkanäle AM oder die Gestaltung von Hohlräumen für das spätere Einsetzen von Wärmerohrdochten/-hüllen ist eine der größten Stärken der additiven Metallfertigung. AM ermöglicht glatte, organisch geformte Kanäle, die optimalen Pfaden folgen, die mit herkömmlichen Bohrungen oder maschineller Bearbeitung oft unmöglich zu erstellen sind. Dies ermöglicht ein hocheffizientes, lokalisiertes Wärmemanagement, das direkt in die Struktur der Isolierplatte integriert ist.
- Überlegungen zum Design: Zu den wichtigsten Herausforderungen bei der Konstruktion gehören die Gewährleistung selbsttragender Kanalgeometrien (oder die Entwicklung wirksamer interner Stützen) und, was besonders wichtig ist, die Gewährleistung, dass das gesamte ungeschmolzene Pulver nach dem Bau aus diesen Kanälen entfernt werden kann. Zu den Konstruktionsregeln gehören häufig Mindestkanaldurchmesser (z. B. >1-2 mm), glatte Kurven, die Vermeidung scharfer Ecken, in denen sich das Pulver verfangen kann, und die Konstruktion von Zugangsöffnungen für die Pulverentfernung (z. B. mit Druckluft, Vibration).
- Verifizierung: Es ist von größter Bedeutung, dass die Kanäle klar und maßgenau sind. NDT-Prüfung Luft- und Raumfahrt methoden, insbesondere industrielle CT-Abtastungsind hierfür von unschätzbarem Wert. CT-Scans können die inneren Kanäle in 3D sichtbar machen, bestätigen, dass sie frei von Pulver sind, kritische Abmessungen messen und mögliche Defekte wie Risse oder Porosität entlang der Kanalwände erkennen. Je nach Anwendung können auch funktionelle Durchflussprüfungen erforderlich sein.
3. Wie hoch sind die Kosten der Metall-AM im Vergleich zur herkömmlichen CNC-Bearbeitung von komplexen Isolierplatten für Raumfahrzeuge in kleinen Stückzahlen?
- Komplexität ist der Schlüssel: Die kostenvergleich AM vs. CNC-Raumfahrtteile hängt stark von der Komplexität der Teile und dem Produktionsvolumen ab.
- Hohe Komplexität / geringes Volumen (1-50 Teile): Für hochkomplexe Isolierplatten mit Topologieoptimierung, internen Gittern, konformen Formen oder integrierten Merkmalen, metall-AM ist oft kostengünstiger als CNC-Bearbeitung. Der Grund dafür ist, dass durch AM die hohen Kosten und die Vorlaufzeit für spezielle Werkzeuge/Vorrichtungen vermieden werden, der Materialabfall minimiert wird (CNC hat bei komplexen Teilen ein hohes Einkaufs-zu-Flug-Verhältnis) und eine Konsolidierung der Teile möglich ist, was die Montagekosten senkt. Die Bearbeitung solch komplexer Geometrien aus einem massiven Block würde mehrachsige Maschinen und viel Programmierzeit erfordern und zu erheblichem Ausschuss führen.
- Einfache Geometrie / geringes Volumen: Bei relativ einfachen Plattengeometrien, die leicht aus Standardmaterial bearbeitet werden können, kann die CNC-Bearbeitung selbst bei geringen Stückzahlen aufgrund niedrigerer Maschinenstundensätze und potenziell kostengünstigerer Rohmaterialformen (Knüppel im Vergleich zu Pulver) pro Teil günstiger sein.
- Höhere Volumina: Mit steigendem Produktionsvolumen sinken die Kosten pro Teil bei der CNC-Bearbeitung aufgrund von Skaleneffekten und der Amortisation der Programmier- und Einrichtungszeit in der Regel deutlicher als bei AM. Die AM-Kosten sinken mit dem Volumen weniger dramatisch. Der Übergangspunkt hängt ganz von der spezifischen Teilegeometrie und -komplexität ab.
- Andere Faktoren: Berücksichtigen Sie die Gesamtbetriebskosten, einschließlich der Entwicklungszeit (AM ist schneller bei Iterationen), potenzieller Gewichtseinsparungen (Senkung der Startkosten) und Leistungssteigerungen, die durch die Designfreiheit von AM ermöglicht werden. Für viele fortschrittliche Raumfahrtanwendungen, bei denen Komplexität, Gewicht und Leistung von entscheidender Bedeutung sind, bietet AM trotz potenziell vergleichbarer oder sogar höherer anfänglicher Kosten pro Teil in einigen Szenarien einen höheren Wert. Erkundung eines Lieferanten Produkt angebote, einschließlich verschiedener Materialien und Druckoptionen, können helfen, den besten Ansatz zu bestimmen.
Die Beantwortung dieser FAQ über Metall AM für die Raumdämmung hebt die differenzierten Überlegungen hervor, die mit der Anwendung dieser Technologie verbunden sind. Die Beratung durch erfahrene AM-Anbieter ist von entscheidender Bedeutung für die Auswahl von Materialien, die Optimierung des Designs, Verifizierungsstrategien und Kosten-Nutzen-Analysen für Ihre Anwendung.
Schlussfolgerung: Fortschritte in der Weltraumforschung mit thermischen Metall-AM-Lösungen
Die lebensfeindliche Umgebung des Weltraums erfordert unablässige Innovationen bei der Konstruktion von Raumfahrzeugen, insbesondere im kritischen Bereich des Wärmemanagements. Wie wir in dieser Diskussion erörtert haben, hat sich die additive Fertigung von Metallen zu einer leistungsstarken Technologie entwickelt, die die Herangehensweise von Ingenieuren an die Entwicklung und Produktion von wichtigen Komponenten wie wärmedämmplatten für Raumfahrtsysteme. Durch die Überwindung der Beschränkungen der traditionellen Fertigung bietet die Metall-AM eine Reihe überzeugender Vorteile, die perfekt auf die Bedürfnisse der Luft- und Raumfahrtindustrie abgestimmt sind.
Die Fähigkeit, zu nutzen, fortgeschrittene Materialien wie die Hochtemperaturbeständigkeit von IN625 oder die leichte Effizienz von AlSi10Mg ist nur der Ausgangspunkt. Die wahre transformative Kraft von Metal AM liegt in seiner unvergleichliche Designfreiheit. Ingenieure können jetzt hochgradig komplexe Geometrieneinschließlich konformer Formen, interner Hohlräume und anspruchsvoller gitterförmige Strukturen thermischund optimiert die Platten gleichzeitig für die Wärmedämmung und die strukturelle Leistung. Diese Fähigkeit, kombiniert mit Topologieoptimierungerleichtert erhebliche Leichtbau - ein vorrangiges Ziel bei der Senkung der Startkosten und der Maximierung der Einsatzfähigkeit. Darüber hinaus ist das Potenzial für Teilkonsolidierungdurch die Zusammenführung von Halterungen, Abstandshaltern und Isolierung in einzelne, monolithische Komponenten wird die Zuverlässigkeit erhöht und gleichzeitig die Montagezeit und -komplexität reduziert.
Um diese Vorteile zu nutzen, bedarf es jedoch mehr als nur des Zugangs zu einem 3D-Drucker. Es erfordert einen ganzheitlichen Ansatz, der Folgendes umfasst Design für additive Fertigung (DfAM) , die Einhaltung strenger Prozesskontrollegeeignet Nachbearbeitung techniken (einschließlich Wärmebehandlung und Oberflächenveredelung), und strenge qualitätssicherung einbeziehung von NDT-Methoden wie CT-Scanning. Die Bewältigung inhärenter Herausforderungen wie Eigenspannungen, Porosität und das Erreichen enger Toleranzen erfordert fundiertes Fachwissen und fortschrittliche technologische Fähigkeiten.
Dies unterstreicht die entscheidende Bedeutung von strategische Lieferantenauswahl. Die Zusammenarbeit mit einem sachkundigen und erfahrenen Metall-AM-Anbieter, der nicht nur über modernste Ausrüstung verfügt (wie SEBM-Drucker bekannt für die Bewältigung von Wärmestress), sondern auch tiefgreifende Werkstoffkompetenzrobuste Qualitätssysteme (wie AS9100-Zertifizierung) und eine umfassende technische Unterstützung sind für den Erfolg von grundlegender Bedeutung. Unternehmen wie Met3dp, die End-to-End-Lösungen anbieten, die die Produktion von hochwertige Metallpulver, fortschrittliche Drucktechnologien und spezielle Anwendungsentwicklungsdienste sind die wichtigsten Voraussetzungen für Luft- und Raumfahrtunternehmen, die das volle Potenzial der metall AM Innovation Luft- und Raumfahrt.
Die zukunft der Raumfahrtproduktion wird die additive Fertigung zweifelsohne immer mehr Verbreitung finden. Für Wärmedämmplatten und zahlreiche andere Komponenten von Raumfahrzeugen bietet die Metall-AM einen Weg, leichtere, effizientere und zuverlässigere Systeme schneller als je zuvor herzustellen. Sie ermöglicht es den Ingenieuren, ohne die Beschränkungen vieler traditioneller Fertigungsverfahren optimale Funktionen zu entwickeln, was letztlich zu ehrgeizigeren und erfolgreicheren Weltraummissionen beiträgt. Indem die Luft- und Raumfahrtindustrie die Metall-AM nutzt und mit kompetenten Partnern zusammenarbeitet, kann sie die Grenzen des Machbaren weiter verschieben und mit Systemen, die auf der Grundlage der additiven Innovation aufgebaut sind, noch weiter in den Kosmos vordringen. Erfahren Sie, wie Ihr nächstes Luft- und Raumfahrtprojekt von diesen fortschrittlichen Möglichkeiten profitieren kann, kontaktieren Sie Met3dp noch heute.
Teilen auf
MET3DP Technology Co., LTD ist ein führender Anbieter von additiven Fertigungslösungen mit Hauptsitz in Qingdao, China. Unser Unternehmen ist spezialisiert auf 3D-Druckgeräte und Hochleistungsmetallpulver für industrielle Anwendungen.
Fragen Sie an, um den besten Preis und eine maßgeschneiderte Lösung für Ihr Unternehmen zu erhalten!
Verwandte Artikel
Über Met3DP
Aktuelles Update
Unser Produkt
KONTAKT US
Haben Sie Fragen? Senden Sie uns jetzt eine Nachricht! Wir werden Ihre Anfrage mit einem ganzen Team nach Erhalt Ihrer Nachricht bearbeiten.
Holen Sie sich Metal3DP's
Produkt-Broschüre
Erhalten Sie die neuesten Produkte und Preislisten
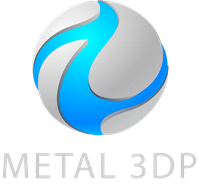
Metallpulver für 3D-Druck und additive Fertigung