3D-gedruckte Turboladergehäuse für Hochleistungsfahrzeuge
Inhaltsübersicht
Revolutionierung der Leistung mit 3D-gedruckten Turboladergehäusen
In ihrem unermüdlichen Streben nach mehr Leistung stoßen die Ingenieure immer wieder an die Grenzen der Motorentechnik. Der Turbolader ist ein zentrales Bauteil von Zwangsansaugsystemen, und sein Gehäuse spielt eine weitaus wichtigere Rolle als nur die Aufnahme der Verdichter- und Turbinenräder. Die turboladergehäuse-bestehend aus dem kälteseitigen Verdichtergehäuse und dem heißseitigen Turbinengehäuse- muss extremen Temperaturen, hohen Drücken, starken Vibrationen und korrosiven Abgasen standhalten und gleichzeitig den Luftstrom präzise lenken, um den Wirkungsgrad und die Motorleistung zu maximieren. Traditionell wurden diese komplexen Komponenten durch Gießen oder umfangreiche maschinelle Bearbeitung hergestellt, was insbesondere bei Spezialanwendungen oft zu Kompromissen in Bezug auf Design, Materialeigenschaften oder Vorlaufzeiten führte.
Eintritt in die Ära der Additive Fertigung (AM), allgemein bekannt als 3D-Druck. Konkret, 3D-Druck von Metall entwickelt sich rasch zu einer transformativen Kraft in der Produktion von Hochleistungs-Automobilkomponenten, einschließlich Turboladergehäusen. Diese Technologie ermöglicht den schichtweisen Aufbau komplizierter Metallteile direkt aus digitalen Entwürfen, was eine noch nie dagewesene Designfreiheit eröffnet, den Einsatz fortschrittlicher Materialien ermöglicht und die Entwicklungszyklen erheblich beschleunigt. Für Ingenieure, die nach optimaler aerodynamischer Effizienz, Leichtbau und Wärmemanagement streben, und für Beschaffungsmanager, die flexible, hochwertige Fertigungslösungen für kundenspezifische Turbolader-Komponentenbietet Metall-AM eine überzeugende Alternative zu herkömmlichen Methoden.
Dieser Wandel ist besonders in anspruchsvollen Sektoren wie dem Motorsport, dem High-Performance-Tuning auf dem Ersatzteilmarkt und dem Nischenfahrzeugbau von Bedeutung, wo Komponenten von der Stange oft nicht ausreichen. Die Fähigkeit zur Erstellung maßgeschneiderter hochleistungs-Turbolader mit optimierten Geometrien, die auf die spezifischen Anforderungen von Motoren zugeschnitten sind, bietet einen spürbaren Wettbewerbsvorteil. Unternehmen wie Met3dp stehen an der Spitze dieser Revolution. Sie bieten nicht nur branchenführende Metall-AM-Drucker an, die für ihre Genauigkeit und Zuverlässigkeit bekannt sind, sondern auch Hochleistungsmetallpulver, die für die anspruchsvollen Bedingungen im metall 3D-Druck Antriebsstrang anwendungen. Im weiteren Verlauf werden wir genau untersuchen, wie diese Technologie die Konstruktion und Fertigung von Turboladern verändert und den Unternehmen, die in der Hochleistungsautomobilbranche tätig sind, erhebliche Vorteile bietet.
Kernanwendungen: Wo sind 3D-gedruckte Turboladergehäuse von Bedeutung?
Die einzigartigen Möglichkeiten der additiven Fertigung von Metallen fördern den Einsatz von 3D-gedruckten Turboladergehäusen in verschiedenen Schlüsselsegmenten der Automobilindustrie. Zwar ist die additive Fertigung noch nicht der Mainstream für die Massenproduktion von Nahverkehrsfahrzeugen (wo die Effizienz des traditionellen Gießens immer noch bei hohen Stückzahlen dominiert), aber sie glänzt dort, wo Individualisierung, Spitzenleistung und schnelle Entwicklung von größter Bedeutung sind. Beschaffungsspezialisten und Ingenieure beschaffen herstellung von Motorsportkomponenten lösungen oder die Suche nach Lieferanten für upgrades für leistungsstarke Fahrzeuge wenden sich zunehmend dem AM zu.
Hier ist eine Aufschlüsselung der wichtigsten Anwendungen:
- Motorsport und Rennen:
- Wettbewerbsvorteil: In der Formel 1, bei Langstreckenrennen (wie der WEC), Rallye-Meisterschaften und anderen hochkarätigen Serien zählt jedes Gramm Gewicht und jeder Bruchteil an aerodynamischer Effizienz. AM ermöglicht es den Teams, hochgradig optimierte, leichte Gehäuse mit komplexen internen Spiralen und Kanälen zu entwickeln, die genau auf die Betriebseigenschaften des Motors und die Anforderungen an das Packaging zugeschnitten sind.
- Schnelle Iteration: Konstruktionsänderungen können innerhalb von Tagen oder Wochen umgesetzt und getestet werden, anstatt Monate für die Herstellung neuer Gusswerkzeuge zu benötigen. Diese Flexibilität ist entscheidend, um während einer Rennsaison wettbewerbsfähig zu bleiben.
- Materielle Überlegenheit: In Rennsportumgebungen werden Werkstoffe bis an ihre absoluten Grenzen gefordert. AM ermöglicht den Einsatz von Hochtemperatur-Superlegierungen wie Inconel 625 oder 718, die eine Haltbarkeit unter extremen thermischen Belastungen gewährleisten, die für herkömmliche Werkstoffe oder Fertigungsmethoden für komplexe Formen eine Herausforderung darstellen könnten.
- Geringes Volumen, hoher Wert: Rennteams benötigen in der Regel nur eine kleine Anzahl hochspezialisierter Bauteile, was den werkzeuglosen Einsatz von AM wirtschaftlich sinnvoll und strategisch vorteilhaft macht.
- High-Performance Aftermarket:
- Verbesserte Leistung: Anbieter von Turboladern für den Ersatzteilmarkt und Tuningfirmen richten sich an Enthusiasten, die eine deutliche Leistungssteigerung anstreben. der 3D-Druck ermöglicht es ihnen, Gehäuse mit besseren Luftstromeigenschaften, verbesserten Wastegate-Designs und potenziell integrierten Funktionen, die in OEM-Teilen nicht zu finden sind, zu entwerfen und anzubieten.
- Einzigartige Geometrien: AM ermöglicht die Herstellung von Gehäusen mit komplexen Formen, wie z. B. Doppelrollenturbinengehäusen mit hoch optimierten, getrennten Kanälen oder Verdichterabdeckungen mit fortschrittlichen Anti-Surge-Eigenschaften, die mit Guss nur schwer oder gar nicht effizient zu realisieren sind.
- Anpassungen: Für spezielle Motortauschaktionen oder einzigartige Konstruktionen ermöglicht AM die Herstellung von maßgeschneiderten Gehäusen, die perfekt in den verfügbaren Raum passen und korrekt mit anderen Motorkomponenten verbunden sind.
- Markendifferenzierung: Das Angebot fortschrittlicher, 3D-gedruckter Komponenten kann ein wichtiges Unterscheidungsmerkmal auf dem wettbewerbsintensiven Ersatzteilmarkt darstellen.
- OEM-Prototyping und Nischenfahrzeuge:
- Beschleunigte Entwicklung: Während der OEM-Turbolader-Entwicklung in der Phase der Entwicklung neuer Motoren ermöglicht AM den Ingenieuren die schnelle Erstellung von Prototypen und die Funktionsprüfung mehrerer Gehäusedesigns. Dies verkürzt die mit herkömmlichen Prototyping-Methoden verbundenen Forschungs- und Entwicklungszeiten und -kosten drastisch. Konstruktionsfehler können schnell identifiziert und korrigiert werden, bevor teure Werkzeuge für die Massenproduktion angeschafft werden müssen.
- Produktion von Nischenfahrzeugen: Für Hypercars, Supercars und andere Spezialfahrzeuge, die in begrenzten Stückzahlen hergestellt werden (kleinserienfertigung in der Automobilindustrie), sind die hohen Kosten für Gusswerkzeuge oft unerschwinglich. Metal AM bietet eine kosteneffiziente Fertigungslösung für die Herstellung der endgültigen, funktionalen Turboladergehäuse für diese exklusiven Fahrzeuge, ohne dass in spezielle Formen investiert werden muss.
- Teil Konsolidierung: AM ermöglicht es den Konstrukteuren, Merkmale wie Halterungen, Sensorbuckel oder Hitzeschilde direkt in das Gehäusedesign zu integrieren, wodurch die Anzahl der Teile, die Montagezeit und die Fehlerquellen reduziert werden können.
Funktionale Vorteile, die durch AM realisiert werden:
Bei all diesen Anwendungen schlagen sich die funktionalen Vorteile direkt in messbaren Leistungssteigerungen nieder:
- Optimierte Aerodynamik: Präzise gesteuerte Innengeometrien (Spiralgehäuse, Diffusoren) führen zu einem höheren Verdichter- und Turbinenwirkungsgrad und damit zu mehr Leistung und schnellerer Gasannahme (geringeres Turboloch).
- Verbessertes Wärmemanagement: Die Integration ausgeklügelter interner Kühlkanäle, insbesondere im Turbinengehäuse, trägt zur Bewältigung extremer Temperaturen bei, verbessert die Materialbeständigkeit und sorgt für eine gleichbleibende Leistung unter Last.
- Gewichtsreduzierung: Algorithmen zur Optimierung der Topologie, die durch AM erleichtert werden, entfernen Material aus unkritischen Bereichen, was zu leichteren Komponenten führt. Dies ist im Motorsport von entscheidender Bedeutung und trägt zur Gesamteffizienz des Fahrzeugs bei.
- Verbesserte Verpackung: Dank der Designfreiheit können die Gehäuse so geformt werden, dass sie auch in enge Motorräume passen, was bei modernen, mit Technik vollgestopften Fahrzeugen von entscheidender Bedeutung ist.
Für B2B-Einkäufer bedeutet die Beschaffung von 3D-gedruckten Turboladergehäusen den Zugang zu einer Spitzentechnologie, die greifbare Leistungsvorteile, schnellere Entwicklungszyklen für kundenspezifische Projekte und eine flexible Fertigungslösung für spezielle, hochwertige Komponenten bietet.
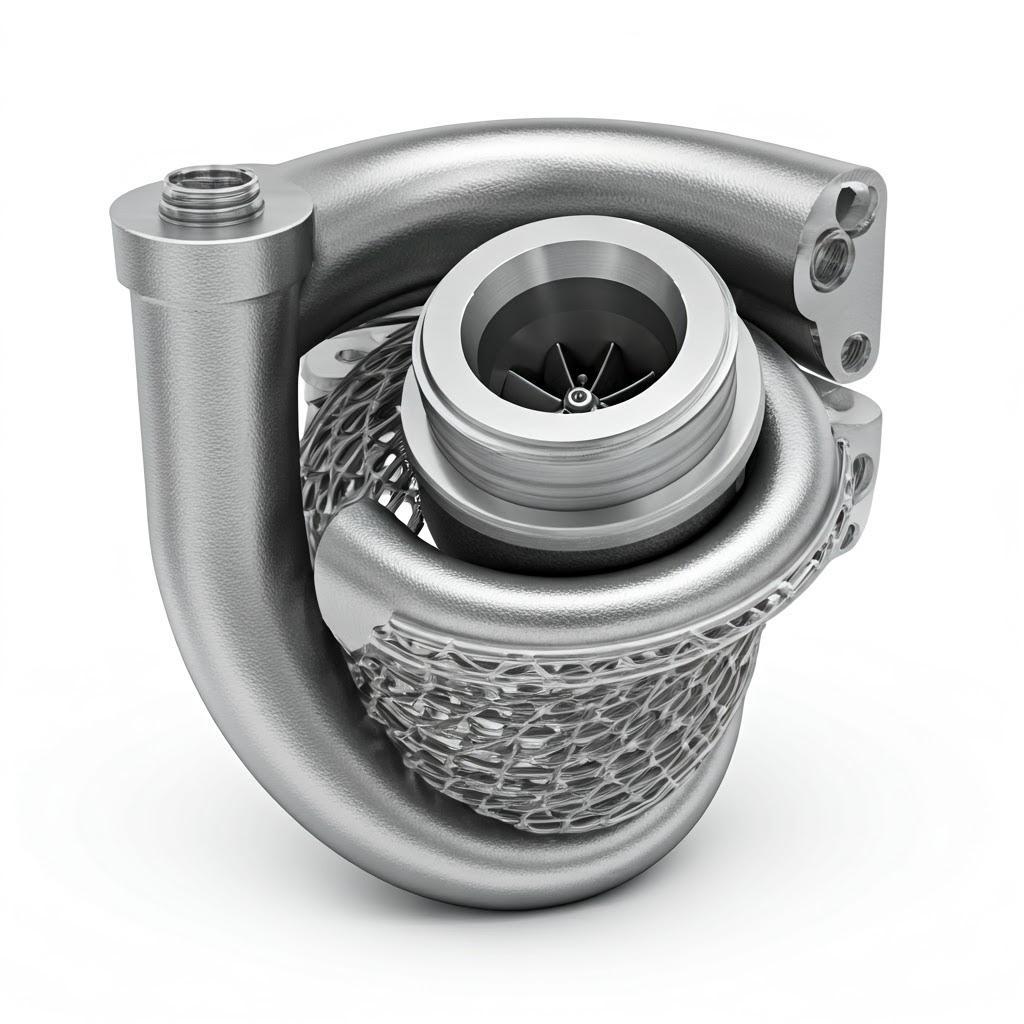
Der Additiv-Vorteil: Warum sollten Sie sich für den 3D-Druck von Turboladergehäusen aus Metall entscheiden?
Während herkömmliche Fertigungsverfahren wie Gießen und Zerspanen der Automobilindustrie seit Jahrzehnten gute Dienste geleistet haben, stellt die additive Fertigung von Metallen einen Paradigmenwechsel dar und bietet deutliche Vorteile, insbesondere für komplexe, leistungsrelevante Komponenten wie Turboladergehäuse. Diese Vorteile zu verstehen, ist für Ingenieure und Beschaffungsmanager, die Produktionsmethoden für Antriebsstrangkomponenten der nächsten Generation evaluieren, entscheidend. Vergleichen wir AM mit konventionellen Techniken und heben wir die vorteile Metall AM Automotive anwendungen bringen.
AM vs. traditionelle Methoden:
- Feinguss:
- Vorteile: Hervorragende Oberflächengüte, gute Maßgenauigkeit, geeignet für komplexe Formen, kostengünstig bei hohen Stückzahlen.
- Nachteile: Erfordert teure und zeitaufwändige Werkzeuge (Wachsmodelle, Keramikschalen), erhebliche Designbeschränkungen (z. B. Entformungswinkel, einheitliche Wandstärke), begrenzte innere Komplexität (Kerne können zerbrechlich sein), lange Vorlaufzeiten für erste Teile. Es ist schwierig, Designs schnell zu iterieren.
- Sandguss:
- Vorteile: Geringere Werkzeugkosten als beim Feinguss, geeignet für größere Teile.
- Nachteile: Schlechtere Oberflächengüte und Maßgenauigkeit, erfordert Nachbearbeitung, erhebliche konstruktive Einschränkungen, weniger geeignet für sehr dünne Wände oder sehr komplizierte Details.
- Bearbeitung aus Billet:
- Vorteile: Hohe Präzision, hervorragende Materialeigenschaften (Knetmaterial), keine Werkzeugkosten.
- Nachteile: Extrem hoher Materialabfall (Einkaufs-zu-Flug-Verhältnis), sehr schwierige oder unmögliche Herstellung komplexer innerer Merkmale (wie Spiralen), lange Bearbeitungszeiten für komplexe äußere Formen, potenziell hohe Kosten pro Teil aufgrund von Abfall und Maschinenzeit.
- Additive Fertigung von Metallen (LPBF/SEBM):
- Vorteile: Werkzeuglose Produktionermöglicht rapid-Prototyping-Turboteile und Kleinserienfertigung kosteneffizient. Unübertroffen herstellung komplexer Geometrien für die Automobilindustrie fähigkeiten, einschließlich komplizierter interner Kanäle und organischer Formen. Erleichtert leichtbauweise des Turboladers durch Topologieoptimierung. Ermöglicht die Konsolidierung von Teilen. Große Auswahl an Materialien, einschließlich Hochleistungs-Superlegierungen. Signifikant reduzierung der Durchlaufzeiten im Automobilbereich entwicklungszyklen.
- Nachteile: Höhere Kosten pro Teil im Vergleich zum Gießen bei sehr hohen Lautstärken. Erfordert in der Regel eine Nachbearbeitung (Wärmebehandlung, Entfernen von Stützen, Oberflächenbearbeitung, Endbearbeitung). Die Baugröße ist je nach Maschine begrenzt. Erfordert Fachkenntnisse in Design for Additive Manufacturing (DfAM).
Die wichtigsten Vorteile von AM für Turboladergehäuse:
- Beispiellose Designfreiheit: Dies ist wohl der wichtigste Vorteil. AM befreit die Designer von den Zwängen der traditionellen Methoden.
- Beispiel: Ingenieure können Verdichter- und Turbinenspiralen mit kontinuierlich variierenden Querschnitten entwerfen, die rein strömungstechnisch optimiert sind, um den Wirkungsgrad über den gesamten Betriebsbereich zu maximieren. Interne Kühlkanäle können auf komplexen Pfaden direkt neben den heißesten Bereichen des Turbinengehäuses verlaufen, was bei Gussteilen praktisch unmöglich ist. Wastegate-Kanäle können nahtlos in die optimalen Strömungswege integriert werden.
- Gewichtsreduzierung durch Topologie-Optimierung: AM arbeitet synergetisch mit computergestützten Designwerkzeugen. Die Software kann Spannungsverteilungen analysieren und Material aus Bereichen entfernen, in denen es strukturell nicht benötigt wird, und so starke und dennoch leichte organische Formen schaffen.
- Beispiel: Ein 3D-gedrucktes Turbinengehäuse könnte außen eine komplizierte Gitterstruktur aufweisen, die die Steifigkeit beibehält und gleichzeitig die Masse im Vergleich zu einem massiven Gussteil erheblich reduziert. Dadurch wird das Gesamtgewicht des Fahrzeugs reduziert und das Einschwingverhalten kann möglicherweise verbessert werden.
- Verbessertes Wärmemanagement: Die Möglichkeit, komplexe interne Kühlkanäle direkt in die Gehäusewände einzubauen, ist ein entscheidender Vorteil, insbesondere für die Turbinenseite, die extremen Abgastemperaturen ausgesetzt ist.
- Beispiel: Flüssigkeits- oder Luftkühlungskanäle können nur wenige Millimeter von den heißesten Gaskanälen entfernt gedruckt werden, was die Materialtemperaturen drastisch senkt, die Haltbarkeit verbessert, ein Durchhitzen verhindert und eine aggressivere Motorabstimmung ermöglicht.
- Rapid Prototyping und Iteration: Der werkzeuglose Charakter von AM bedeutet, dass Designänderungen innerhalb weniger Tage implementiert und getestet werden können.
- Beispiel: Ein Ingenieurteam kann innerhalb einer Woche drei verschiedene Spiralentwürfe hintereinander auf einem Prüfstand testen und empirische Daten sammeln, um die optimale Konfiguration auszuwählen. Beim Gießen könnte dieser Prozess viele Monate dauern und für jede Iteration erhebliche Werkzeugkosten verursachen.
- Fortschrittliche Materialverwendung: AM-Verfahren wie Selective Electron Beam Melting (SEBM) und Laser Powder Bed Fusion (LPBF) eignen sich hervorragend für die Verarbeitung von Hochleistungsmaterialien, die für Turbolader unerlässlich sind.
- Beispiel: Superlegierungen auf Nickelbasis wie IN718 und IN625, die für ihre Hochtemperaturfestigkeit und Korrosionsbeständigkeit bekannt sind, lassen sich durch AM leicht zu dichten, nahezu endkonturierten Teilen verarbeiten. Diese Werkstoffe sind mit herkömmlichen Methoden oft schwierig oder teuer zu bearbeiten, insbesondere bei komplexen Geometrien.
- Teil Konsolidierung: Komponenten, die bisher getrennt waren und zusammengebaut werden mussten (z. B. Gehäuse, Montagehalterungen, Hitzeschilde), können in ein einziges gedrucktes Teil integriert werden.
- Beispiel: Ein Turboladergehäuse könnte mit integrierten Befestigungspunkten und strukturellen Verstärkungen gedruckt werden, was die Anzahl der Teile, den Montageaufwand, das Gewicht und potenzielle Leckagepfade oder Fehlerstellen reduziert.
Für B2B-Kunden bedeuten diese Vorteile einen greifbaren Wert: schnellere Markteinführung innovativer Produkte, überlegene Komponentenleistung, die zu einem Wettbewerbsvorteil führt, vereinfachte Logistik für Teile in kleinen Stückzahlen und die Möglichkeit, Lösungen zu schaffen, die zuvor als unmöglich galten. Die Zusammenarbeit mit einem erfahrenen AM-Anbieter stellt sicher, dass diese Vorteile durch optimiertes Design, Materialauswahl und Prozesskontrolle voll ausgeschöpft werden.
Materialschwerpunkt: IN718 & IN625 für anspruchsvolle Turboladerumgebungen
Die Wahl des richtigen Werkstoffs ist bei Turboladergehäusen angesichts der unglaublich harten Betriebsbedingungen, denen sie ausgesetzt sind, von entscheidender Bedeutung: Temperaturen von bis zu über 1000 °C auf der Turbinenseite, hohe Drücke, zyklische thermische Belastung, Vibrationen und die Einwirkung korrosiver Abgasnebenprodukte. Während in serienmäßig hergestellten Turboladern verschiedene Werkstoffe (wie Gusseisen oder Edelstahl) verwendet werden, erfordern leistungsstarke und anspruchsvolle Anwendungen den Einsatz von Superlegierungen auf Nickelbasis. Inconel 718 (IN718) und Inconel 625 (IN625) eignen sich besonders gut für die additive Fertigung von Metallen, da sie eine außergewöhnliche Kombination von Eigenschaften aufweisen, die sich mit Hilfe von AM leicht verarbeiten lassen. Das Verständnis ihrer Eigenschaften hilft bei der Auswahl des optimalen Werkstoffs für spezifische Gehäuseanforderungen.
Warum Superlegierungen?
Superlegierungen auf Nickelbasis sind so konstruiert, dass sie bei extrem hohen Temperaturen, bei denen herkömmliche Stähle versagen würden, eine hervorragende mechanische Festigkeit, Oberflächenstabilität und Korrosions-/Oxidationsbeständigkeit aufweisen. Dadurch sind sie ideal für die rauen Umgebungsbedingungen in einem Turbolader geeignet, insbesondere für das Turbinengehäuse, das direkt den heißen Abgasen ausgesetzt ist.
Inconel 718 (IN718 / Legierung 718)
- Zusammensetzung: Nickel-Chrom-Legierung mit erheblichen Anteilen an Eisen, Niob und Molybdän sowie Zusätzen von Aluminium und Titan.
- Wichtige Eigenschaften:
- Hochfest & Kriechbeständigkeit: Behält eine ausgezeichnete Zug-, Ermüdungs- und Zeitstandfestigkeit bis zu einer Temperatur von ca. 700°C (1300°F) bei.
- Aushärtbar: Seine Festigkeit beruht in erster Linie auf der Ausscheidungshärtung (Alterungswärmebehandlung) mit Ni3(Nb, Ti, Al)-Phasen. Dies ermöglicht eine sehr hohe Festigkeit.
- Gute Korrosionsbeständigkeit: Bietet eine gute Beständigkeit gegen Oxidation und Korrosion in typischen Motorumgebungen.
- Ausgezeichnete Bedruckbarkeit/Schweißbarkeit: Im Vergleich zu anderen ausscheidungsgehärteten Superlegierungen weist IN718 eine sehr gute Verarbeitbarkeit sowohl beim Schweißen als auch bei der additiven Fertigung auf, was es zu einer beliebten Wahl für komplexe AM-Komponenten macht.
- Turbolader Relevanz: Wird häufig für Verdichtergehäuse (wo die Temperaturen niedriger sind) und möglicherweise für Turbinengehäuse in Anwendungen mit mäßig hohen Abgasspitzentemperaturen verwendet. Sein ausgezeichnetes Verhältnis von Festigkeit zu Gewicht nach der Wärmebehandlung ist sehr vorteilhaft. Es ist im Allgemeinen etwas preiswerter als IN625.
Inconel 625 (IN625 / Legierung 625)
- Zusammensetzung: Nickel-Chrom-Molybdän-Niob-Legierung.
- Wichtige Eigenschaften:
- Hervorragende Festigkeit bei hohen Temperaturen: Basiert auf einer Mischkristallverfestigung aus Molybdän und Niob und bietet eine hervorragende Festigkeit und Zähigkeit bei Temperaturen bis zu 815 °C (1500 °F) und bei kurzen Ausschlägen sogar noch höher. Er behält seine Festigkeit bei den höchsten Temperaturen, die bei aggressiven Turboanwendungen auftreten, besser bei als IN718.
- Hervorragende Korrosionsbeständigkeit: Der hohe Chrom- und Molybdängehalt verleiht ihm eine hervorragende Beständigkeit gegen eine Vielzahl von korrosiven Umgebungen, einschließlich Lochfraß, Spaltkorrosion und saure Kondensate in Abgasen. Seine Korrosionsbeständigkeit übertrifft im Allgemeinen die von IN718.
- Ausgezeichnete Verarbeitbarkeit und Bedruckbarkeit: Es ist bekannt für seine einfache Herstellung und hervorragende Schweiß-/Druckbarkeit, wodurch es sich hervorragend für komplexe AM-Geometrien eignet.
- Zähigkeit: Weist eine hohe Zähigkeit und Dauerfestigkeit über einen breiten Temperaturbereich auf.
- Turbolader Relevanz: Die bevorzugte Wahl für Hochleistungsturbinengehäuse, insbesondere für solche, die den extremsten Temperaturen und potenziell korrosiven Kraftstoffgemischen (z. B. hohem Ethanolgehalt) ausgesetzt sind. Seine überragende Hitze- und Korrosionsbeständigkeit sorgt für mehr Sicherheit und Langlebigkeit in anspruchsvollen Motorsport- oder hochgetunten Aftermarket-Anwendungen.
IN718 vs. IN625 bei 3D-gedruckten Turbogehäusen:
Merkmal | Inconel 718 (IN718) | Inconel 625 (IN625) | Relevanz für Turbogehäuse |
---|---|---|---|
Max. Betriebstemperatur | ~700°C (1300°F) | ~815°C+ (1500°F+) | IN625 besser geeignet für extreme Abgastemperaturen (Turbinenseite) |
Mechanismus der Stärke | Ausscheidungshärtung (Alterung erforderlich) | Solid-Solution-Verstärkung | IN718 potenziell höhere Festigkeit <700°C, erfordert Wärmebehandlung |
Festigkeit bei >700°C | Nimmt schneller ab | Behält die Stärke besser bei | IN625 überlegen für die heißesten Teile des Turbinengehäuses |
Korrosionsbeständigkeit | Gut | Ausgezeichnet | IN625 bietet mehr Robustheit gegen aggressive Abgase |
Druckbarkeit/Schweißbarkeit | Sehr gut | Ausgezeichnet | Beide sind bewährte Materialien für Metall-AM |
Kosten | Im Allgemeinen niedriger | Im Allgemeinen höher | Die Kosten müssen gegen die Anforderungen an die Leistung/Haltbarkeit abgewogen werden |
Typische Anwendung | Verdichtergehäuse, mäßige Turbinenseite | Turbinengehäuse, hochanspruchsvolle Anwendungen | Anpassung der Materialauswahl an das jeweilige Betriebsumfeld |
In Blätter exportieren
Die Rolle von Met3dp bei der Materialexzellenz:
Der erfolgreiche 3D-Druck von Turboladergehäusen aus anspruchsvollen Materialien wie IN718 und IN625 erfordert nicht nur eine fortschrittliche Druckausrüstung, sondern auch ein besonders hochwertiges Metallpulver. Dies ist der Grund Met3dp übertrifft. Durch den Einsatz von branchenführenden Pulverherstellungsverfahren wie der Vakuumgaszerstäubung (VIGA) und dem Plasma-Rotations-Elektroden-Verfahren (PREP) produziert Met3dp Metallpulver mit Eigenschaften, die für eine erfolgreiche additive Fertigung entscheidend sind:
- Hohe Sphärizität: Sorgt für eine hervorragende Fließfähigkeit des Pulvers und eine hohe Packungsdichte im Pulverbett, was zu dichteren und festeren Endteilen führt.
- Niedriger Satellitengehalt: Minimiert feine Partikel, die an größeren Kugeln haften, was die Fließfähigkeit weiter verbessert und mögliche Defekte reduziert.
- Kontrollierte Partikelgrößenverteilung (PSD): Ein optimiertes PSD für bestimmte AM-Prozesse (wie LPBF oder SEBM) gewährleistet eine gleichmäßige Schmelz- und Schichtbildung.
- Hohe Reinheit: Verunreinigungen, die die Materialeigenschaften beeinträchtigen könnten, werden minimiert.
Met3dp stellt eine breite Palette von hochwertigen Metallpulvern her, darunter innovative Legierungen und Standardsuperlegierungen wie IN718 und IN625, die für Laser- und Elektronenstrahl-Pulverbettschmelzverfahren optimiert sind. Das umfassende Fachwissen sowohl in der Pulverherstellung als auch bei AM-Drucksystemen stellt sicher, dass die Kunden Materialien erhalten, die sich perfekt für die Herstellung unternehmenskritischer Komponenten wie Hochleistungs-Turboladergehäuse eignen. Die Wahl eines Anbieters wie Met3dp, der sowohl die Materialwissenschaft als auch den Druckprozess kontrolliert, bietet die Sicherheit, die gewünschten Materialeigenschaften und die Zuverlässigkeit der Komponenten zu erreichen.
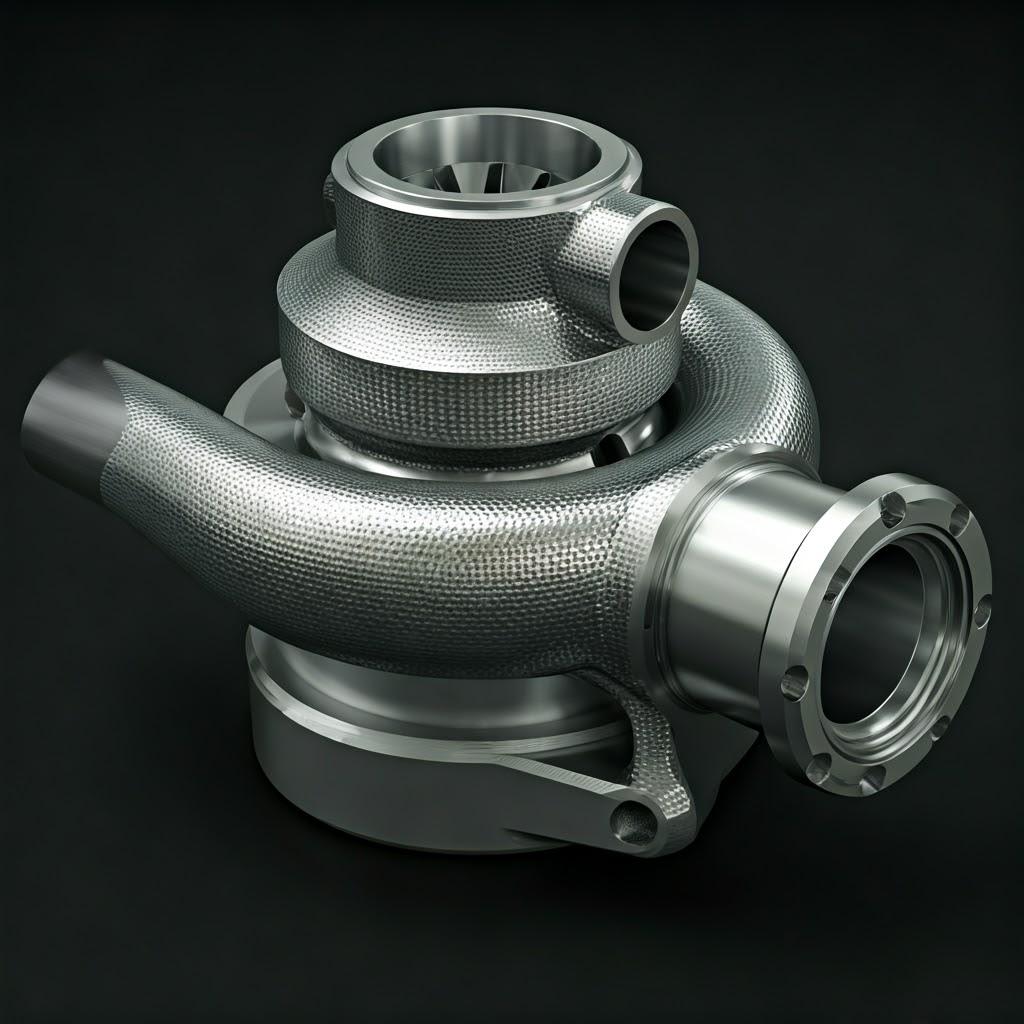
Design für additive Fertigung (DfAM): Optimierung von Turboladergehäusen für den 3D-Druck
Ein weit verbreiteter Irrglaube bei der Einführung der additiven Fertigung von Metallen ist, dass bestehende Entwürfe, die ursprünglich für das Gießen oder die maschinelle Bearbeitung vorgesehen waren, einfach an den Drucker geschickt werden können. Dieser Ansatz ist zwar technisch möglich, nutzt aber nicht die einzigartigen Stärken der additiven Fertigung und führt häufig zu suboptimalen Ergebnissen, höheren Kosten oder sogar zu Druckfehlern. Um das Potenzial von 3D-gedruckten Turboladergehäusen wirklich auszuschöpfen, Design für additive Fertigung (DfAM) ist nicht nur empfehlenswert, sondern unerlässlich. DfAM bedeutet, den Entwurfsprozess von Grund auf zu überdenken und dabei sowohl die Freiheiten als auch die Zwänge des schichtweisen Aufbaus zu berücksichtigen. Ingenieure und Designer, die sich mit DfAM-Autoteile der Schwerpunkt der Entwicklung liegt auf der Maximierung der Leistung bei gleichzeitiger Gewährleistung der Herstellbarkeit.
Die wichtigsten DfAM-Prinzipien für Turboladergehäuse:
- Optimierung der Fließwege: Dies ist der Punkt, an dem AM bei Turboladern wirklich glänzt. Vergessen Sie die Einschränkungen von Gusskernen. Entwerfen Sie glatte, sich kontinuierlich verändernde Spiralen und Kanäle, die genau den aerodynamischen Anforderungen der Verdichter- und Turbinenräder entsprechen. Setzen Sie in der Konstruktionsphase die numerische Strömungsmechanik (CFD) umfassend ein, um die Luftströmungswege zu iterieren und zu perfektionieren, Druckverluste zu minimieren und den Wastegate-Durchfluss für eine bessere Ladedruckregelung zu optimieren. Erwägen Sie die Integration von Merkmalen wie Einlassöffnungen oder optimierte Diffusoren direkt in das Gehäuse.
- Integrierte Komplexe Merkmale: Nutzen Sie AM’s Fähigkeit, komplizierte interne Strukturen zu schaffen.
- Interne Kühlungskanäle: Entwerfen Sie konforme Kühlkanäle, die den Konturen der heißesten Stellen des Turbinengehäuses folgen (z. B. in der Nähe der Spiralfeder oder des Turbineneinlasses). Diese Kanäle, die mit herkömmlichen Methoden nicht hergestellt werden können, ermöglichen eine gezielte Kühlung (Flüssigkeit oder Luft) und verbessern das Wärmemanagement, die Materialbeständigkeit und die Leistungskonstanz unter Last drastisch. Stellen Sie sicher, dass die Kanäle so gestaltet sind, dass sie druckbar sind (möglichst mit selbsttragenden Winkeln) und das Pulver vollständig entfernt wird.
- Integration von Sensoren: Stutzen und Anschlüsse für Druck-, Temperatur- oder Drehzahlsensoren können nahtlos in das Design integriert werden, möglicherweise an optimierten Stellen, die vorher nicht zugänglich waren.
- Minimierung und Optimierung der Stützstruktur: Stützstrukturen sind bei der Metall-AM (insbesondere LPBF) oft notwendig, um das Teil zu verankern, thermische Spannungen zu bewältigen und überhängende Merkmale zu stützen. Sie verbrauchen jedoch zusätzliches Material, verlängern die Druckzeit und müssen in der Nachbearbeitung entfernt werden.
- Strategische Ausrichtung: Die Art und Weise, wie ein Teil auf der Bauplatte ausgerichtet wird, hat einen erheblichen Einfluss auf den Unterstützungsbedarf, die Oberflächengüte und mögliche Verformungen. Analysieren Sie verschiedene Ausrichtungen, um das beste Gleichgewicht zu finden.
- Selbsttragende Winkel: Entwerfen Sie Überhänge so, dass sie möglichst selbsttragend sind. Winkel, die mehr als 45 Grad von der horizontalen Ebene abweichen, werden oft erfolgreich ohne Stützen gedruckt (dies hängt jedoch von dem jeweiligen Verfahren und Material ab). Verwenden Sie Fasen oder Verrundungen anstelle von scharfen horizontalen Überhängen.
- DfAM für den Umzug der Unterstützung: Stellen Sie sicher, dass die Stützen, insbesondere die internen, zum Entfernen zugänglich sind. Entwerfen Sie bei Bedarf Zugangsöffnungen oder ziehen Sie Verfahren wie SEBM in Betracht, die aufgrund der höheren Temperaturen in der Baukammer weniger Stützen erfordern können.
- Wanddicke und Gewichtsreduzierung:
- Topologie-Optimierung: Mithilfe spezieller Software kann Material in Bereichen mit geringer Belastung identifiziert und entfernt werden, so dass organische, für den Lastpfad optimierte Strukturen entstehen. Dies ist der Schlüssel für topologieoptimierung Turbolader konstruktionen, die auf Motorsport oder Höchstleistung ausgerichtet sind und die Rotationsträgheit (bei rotierenden Bauteilen) und das Gesamtgewicht des Fahrzeugs verringern.
- Mindestwanddicke: AM erlaubt relativ dünne Wände (z.B. 0,4mm – 1,0mm je nach Prozess und freitragender Spannweite), aber stellen Sie sicher, dass die Wände dick genug sind für strukturelle Integrität, Handhabung und Druckbarkeit. Vermeiden Sie große, freitragende dünne horizontale Abschnitte.
- Vermeiden Sie dicke Abschnitte: Sehr dicke, massive Profile können übermäßige Wärmespannungen aufbauen, was das Risiko von Rissen oder Verformungen erhöht. Ziehen Sie gegebenenfalls interne Gitterstrukturen oder Hohlprofile anstelle von Massivteilen in Betracht.
- Wärmemanagement beim Drucken: Die hohe Energiezufuhr bei der Metall-AM erzeugt erhebliche Wärmegradienten. Konstruktionsmerkmale zur Abschwächung dieses Phänomens: Hinzufügen von Opferrippen oder Kühlkörpern in kritischen Bereichen, um die Wärme abzuleiten; Gewährleistung sanfter Übergänge zwischen dicken und dünnen Abschnitten; Ausrichtung des Teils, um große, flache Oberflächen parallel zur Bauplatte zu minimieren. Bausimulationssoftware ist hier von unschätzbarem Wert.
- Teil Konsolidierung: Untersuchen Sie die Turboladerbaugruppe und suchen Sie nach Möglichkeiten, angrenzende Komponenten (Halterungen, Befestigungen, Hitzeschilder) direkt in das Gehäusedesign zu integrieren. Dies reduziert die Anzahl der Teile, die Montagezeit, das Gewicht und potenzielle Fehlerpunkte (wie Schraubverbindungen oder Schweißnähte).
- Design der Löcher: Vertikale Löcher werden in der Regel mit besserer Rundheit gedruckt. Horizontale oder abgewinkelte Löcher werden aufgrund des schichtweisen Aufbaus oft leicht unrund (elliptisch oder tropfenförmig) gedruckt. Wenn eine enge Toleranz erforderlich ist, sollten Sie die Löcher für eine spätere Bearbeitung unterdimensioniert entwerfen oder spezielle Formen (z. B. tropfenförmig) einbauen, um die Genauigkeit bei der Herstellung zu verbessern.
Die Zusammenarbeit mit einem erfahrenen additive Fertigung die frühzeitige Einbindung eines Anbieters wie Met3dp in den Entwurfsprozess kann von großem Nutzen sein. Ihre Ingenieure verfügen über fundierte Kenntnisse der DfAM-Prinzipien und können wertvolles Feedback zur Optimierung Ihres Turboladergehäusedesigns für einen erfolgreichen Druck, optimale Leistung und Kosteneffizienz liefern, indem sie die fortschrittlichen CAD für AM automotive Arbeitsabläufe.
Erreichen von Präzision: Toleranz, Oberflächengüte und Maßgenauigkeit bei AM-Gehäusen
Während die additive Fertigung von Metallteilen eine beispiellose Designfreiheit bietet, ist es für Ingenieure und Beschaffungsmanager entscheidend, realistische Erwartungen hinsichtlich der erreichbaren Präzision direkt aus dem Drucker zu haben. Fertige AM-Teile weisen im Allgemeinen nicht die gleichen engen Toleranzen und feinen Oberflächengüten in allen Bereichen auf wie Komponenten, die mit mehrachsigen CNC-Zentren vollständig aus einem Knüppel gefertigt werden. Durch eine sorgfältige Prozesssteuerung, eine angemessene Nachbearbeitung und eine fortschrittliche Qualitätssicherung lassen sich jedoch auch diese Eigenschaften erreichen, 3D-Druck von Präzisionsmetall für die Automobilindustrie komponenten wie Turboladergehäuse können anspruchsvolle Spezifikationen erfüllen.
Toleranzen:
- As-Built-Toleranzen: Die typische Maßgenauigkeit, die direkt mit Laser Powder Bed Fusion (LPBF) oder Selective Electron Beam Melting (SEBM) Verfahren erreicht werden kann, liegt oft im Bereich von ±0,1mm bis ±0,3mm oder ±0,1% bis 0,2% des Nennmaßes, je nachdem, welcher Wert größer ist. Diese Werte sind allgemeine Richtlinien und können je nach Maschine, Material, Teilegeometrie, Größe, Ausrichtung und Prozessparametern erheblich variieren. Bei großen, komplexen Teilen ist es aufgrund von thermischen Effekten schwieriger, die engen Toleranzen einzuhalten.
- Erzielung engerer Toleranzen: Für kritische Schnittstellen - wie z. B. Flansche am Turbinen- und Verdichtergehäuse, Passflächen für die zentrale Gehäusedrehvorrichtung (CHRA), V-Band-Verbindungen oder Montagepunkte - sind die bauartbedingten Toleranzen oft nicht ausreichend. Diese Merkmale erfordern in der Regel ist eine Nachbearbeitung durch CNC-Bearbeitung um die erforderliche Präzision (z. B. ±0,025 mm bis ±0,05 mm) für eine ordnungsgemäße Abdichtung, Ausrichtung und Montage zu erreichen. Das DfAM spielt hier eine Rolle, indem es nur für diese kritischen Merkmale ausreichend Bearbeitungsmaterial vorsieht.
Oberflächengüte (Rauhigkeit Durchschnitt – Ra):
- As-Built Oberflächenbeschaffenheit: Die Textur der Oberfläche eines AM-Teils wird von mehreren Faktoren beeinflusst:
- Pulver Partikelgröße: Feinere Pulver ergeben im Allgemeinen glattere Oberflächen.
- Schichtdicke: Dünnere Schichten führen in der Regel zu glatteren Oberflächen, insbesondere bei geneigten Flächen.
- Orientierung: Vertikale Wände sind in der Regel glatter als nach oben oder unten weisende Flächen. Nach unten gerichtete Oberflächen, die auf Stützen oder dem Pulverbett selbst beruhen, sind in der Regel am rauesten, da das Pulver teilweise geschmolzen ist.
- Prozess: LPBF erzeugt im Allgemeinen glattere Oberflächen (z. B. Ra 6-20 µm) im Vergleich zu SEBM (die Ra 20-35 µm oder höher sein können), was auf Unterschiede in der Strahlenergie und der Pulvergröße zurückzuführen ist.
- Nachbearbeitetes Oberflächenfinish: Die fertige Oberfläche ist oft zu rau für Dichtungsflächen oder eine optimale Luftströmung in kritischen Bereichen. Die Nachbearbeitung dient der Verbesserung der Oberfläche:
- Media Blasting: (z. B. Perlen, Sand, Körner) sorgt für ein gleichmäßiges, mattes Finish und entfernt losen Puder (Ra kann sich leicht verbessern oder die Textur verändern).
- Taumeln/Gleitschleifen: Kann äußere Oberflächen glätten, ist aber für innere Kanäle weniger wirksam.
- Bearbeitungen: Bietet die beste Oberflächengüte bei bestimmten Merkmalen (Ra < 1,6 µm oder besser ist erreichbar).
- Polieren: Es können sehr glatte, spiegelähnliche Oberflächen erzielt werden, wenn dies aus speziellen aerodynamischen oder ästhetischen Gründen erforderlich ist, aber es ist arbeitsintensiv.
Maßgenauigkeit und Qualitätskontrolle:
- Faktoren, die die Genauigkeit beeinflussen: Erreichen einer konsistenten maßgenauigkeit Turbolader komponenten erfordert die Kontrolle des gesamten Arbeitsablaufs: Maschinenkalibrierung, optimierte und validierte Prozessparameter, Wärmemanagementstrategien (Ausrichtung, Stützen), Minimierung von Eigenspannungen und Berücksichtigung kleinerer Verformungen bei der Wärmebehandlung nach dem Druck.
- Die Bedeutung der Qualitätskontrolle (QC): Rigoros qualitätskontrolle bei der additiven Fertigung von Metallen ist unerlässlich. Dies beinhaltet:
- Prozessbegleitende Überwachung: Einige fortschrittliche AM-Systeme bieten eine Echtzeitüberwachung des Schmelzepools und der Schichtkonsistenz.
- Inspektion nach der Fertigstellung: Hochauflösend 3D-Scannen wird häufig verwendet, um die endgültige Teilegeometrie mit dem ursprünglichen CAD-Modell zu vergleichen und detaillierte Abweichungskarten zu erstellen.
- Prüfung mit Koordinatenmessgeräten (CMM): Zur präzisen Messung kritischer Maße, Toleranzen und geometrischer Bemaßung und Tolerierung (GD&T), insbesondere nach der Endbearbeitung.
- Überprüfung der Materialeigenschaften: Prüfung von Zugstäben, die neben dem Hauptteil gedruckt werden, um zu bestätigen, dass die Materialeigenschaften nach der Wärmebehandlung den Spezifikationen entsprechen.
Met3dp’s Beitrag zur Präzision: Met3dp weiß, wie wichtig Präzision für anspruchsvolle Automobilanwendungen ist. Ihre Drucker sind entwickelt für branchenführendes Druckvolumen, Genauigkeit und Zuverlässigkeit. Durch die Kombination von robuster Maschinenkonstruktion, fortschrittlicher Prozesssteuerungssoftware, hochwertigen sphärischen Metallpulvern und strengen Qualitätsmanagementsystemen ermöglicht Met3dp seinen Kunden die zuverlässige Herstellung von dichten, präzisen Turboladergehäusen, die die anspruchsvollen Standards für einsatzkritische Teile in Hochleistungsfahrzeugen erfüllen.
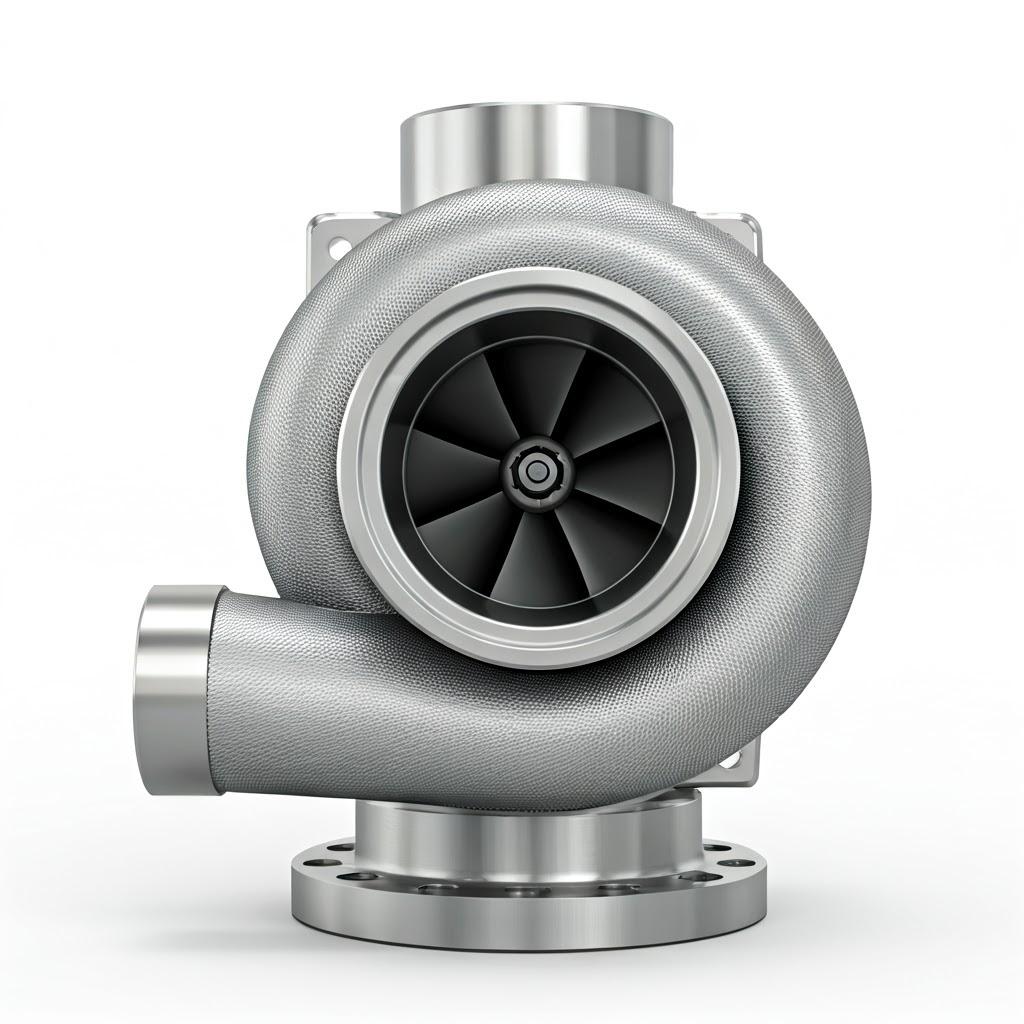
Mehr als der Druck: Wesentliche Nachbearbeitung von Turboladergehäusen
Ein häufiges Versäumnis bei der Planung der additiven Fertigung von Metallen besteht darin, die Bedeutung und den Umfang der Nachbearbeitung zu unterschätzen. Der Erhalt des Turboladergehäuses aus dem 3D-Drucker ist ein wichtiger Meilenstein, aber noch lange nicht der letzte Schritt. Eine Reihe wichtiger Nachbearbeitungsschritte ist erforderlich, um das gedruckte Rohteil in ein funktionales, zuverlässiges Bauteil zu verwandeln, das für die baugruppe Turboladergehäuse. Diese Schritte sind entscheidend für das Erreichen der gewünschten Materialeigenschaften, Maßgenauigkeit, Oberflächengüte und Gesamtintegrität.
Typischer Nachbearbeitungsablauf für AM-Turbo-Gehäuse (IN718/IN625):
- Stressabbau Wärmebehandlung:
- Warum? Die schnellen Erwärmungs- und Abkühlungszyklen beim AM führen zu erheblichen Restspannungen innerhalb des gedruckten Teils. Diese Spannungen können zu Verformungen oder Rissen bei nachfolgenden Schritten wie dem Entfernen von Stützen oder der Bearbeitung oder sogar später im Betrieb führen. Der Spannungsabbau ist in der Regel der allererste Schritt nach Abschluss des Bauprozesses und Abkühlung des Teils.
- Wie? Das Teil (oft noch auf der Bauplatte befestigt) wird in einem Ofen mit kontrollierter Atmosphäre (Vakuum oder Inertgas wie Argon) auf eine bestimmte Temperatur unterhalb der Alterungs- oder Glühtemperatur erhitzt, eine Zeit lang gehalten und dann langsam abgekühlt. Auf diese Weise können innere Spannungen abgebaut werden, ohne dass sich das Gefüge wesentlich verändert.
- Entfernen des Teils von der Bauplatte:
- Warum? Das Teil wird während des Drucks mit einer dicken Metallplatte verschmolzen.
- Wie? Dies geschieht in der Regel durch Drahterodieren (EDM) oder mit einer Bandsäge. Eine sorgfältige Planung der Verbindung des Teils mit der Platte (z. B. mit minimalen Kontaktpunkten oder Stützen) kann diesen Schritt vereinfachen.
- Entfernung der Stützstruktur:
- Warum? Die Stützen werden während des Baus benötigt, müssen aber danach wieder entfernt werden.
- Wie? Dies kann von einfachem manuellem Brechen/Klemmen für zugängliche Stützen bis hin zu aufwändigeren Maßnahmen reichen Abstützung Metall AM techniken wie Schleifen, Fräsen oder Erodieren für hartnäckige oder interne Halterungen. Die Schwierigkeit hängt stark vom Material (Inconel-Träger sind stark) und der Wirksamkeit von DfAM bei der Minimierung und Optimierung der Trägerplatzierung ab. Interne Durchgänge erfordern eine sorgfältige Inspektion, um sicherzustellen, dass alles Stützmaterial und loses Pulver entfernt wird.
- Abschließende Wärmebehandlung (Lösungsglühen/Alterung):
- Warum? In diesem Schritt werden die endgültigen, gewünschten mechanischen Eigenschaften der Superlegierung entwickelt. Die erforderliche Behandlung hängt von der jeweiligen Legierung ab:
- Wärmebehandlung IN718 Teile: IN718 wird normalerweise durch Ausscheidung gehärtet. Dazu gehört das Lösungsglühen (Erhitzen auf eine hohe Temperatur, um Ausscheidungen aufzulösen), gefolgt von einer kontrollierten Abkühlung und einem oder zwei Alterungsschritten bei niedrigeren Temperaturen, um die Verfestigungsphasen (Gamma-Prime und Gamma-Double-Prime) auszufällen. Um die angestrebte Härte und Festigkeit zu erreichen, werden bestimmte Zyklen (z. B. nach AMS 5662/5663) eingehalten.
- IN625: Wird in der Regel im lösungsgeglühten Zustand verwendet, um ein optimales Gleichgewicht der Eigenschaften in korrosiven Hochtemperaturumgebungen zu erreichen. Dies beinhaltet das Erhitzen auf eine hohe Temperatur (z.B. ~1150°C) und das schnelle Abkühlen, um die verstärkenden Elemente (Mo, Nb) in fester Lösung zu halten. Obwohl es nicht wie IN718 gealtert wird, ist dieser Glühschritt (oft in Verbindung mit Spannungsabbau) von entscheidender Bedeutung.
- Wie? Durchgeführt in kalibrierten, atmosphärisch kontrollierten Öfen nach präzisen Zeit-Temperatur-Profilen, die durch Materialspezifikationen oder Luft- und Raumfahrt-/Automobilnormen festgelegt sind.
- Warum? In diesem Schritt werden die endgültigen, gewünschten mechanischen Eigenschaften der Superlegierung entwickelt. Die erforderliche Behandlung hängt von der jeweiligen Legierung ab:
- CNC-Bearbeitung:
- Warum? Um die engen Toleranzen, spezifischen Oberflächengüten und präzisen geometrischen Merkmale zu erreichen, die für Dichtungs- und Montageschnittstellen erforderlich sind.
- Wie? Verwendung von Mehrachsen CNC-Bearbeitung von 3D-gedruckten Komponenten erfordert eine sorgfältige Konstruktion und Programmierung der Vorrichtungen. Zu den wichtigsten bearbeiteten Bereichen gehören:
- Turbinenein- und -auslassflansche (Ebenheit, Ra-Oberfläche für Dichtungen/V-Bänder).
- Einlass- und Auslassanschlüsse des Verdichters.
- Anschlussfläche für die zentrale Gehäusedrehvorrichtung (CHRA).
- Wastegate-Ventilsitz oder Aktuator-Schnittstelle.
- Befestigungspunkte und Gewindelöcher.
- Alle kritischen inneren Bohrungsdurchmesser.
- In der DfAM-Phase hätten speziell für diese Merkmale Bearbeitungsvorräte hinzugefügt werden müssen.
- Oberflächenveredelung:
- Warum? Zur Erzielung eines gleichmäßigen Aussehens, zur Entfernung von Verunreinigungen, zur Verbesserung der Ermüdungsfestigkeit (Shotpeening) oder zur Erreichung bestimmter Rauheitsziele auf unbearbeiteten Oberflächen.
- Wie? Zu den gängigen Methoden gehören:
- Media Blasting: Perlstrahlen oder Sandstrahlen für eine saubere, matte Oberfläche (oberflächenveredelung AM automotive standardverfahren).
- Taumeln/Gleitschleifen: Kann Außenkanten und Oberflächen glätten.
- Manuelles Schleifen/Polieren: Für spezifische Anforderungen an örtlich begrenzte Gebiete.
- Reinigung und Inspektion:
- Warum? Vergewissern Sie sich vor der Montage, dass das Teil frei von Verunreinigungen und Schneidflüssigkeiten ist und alle Spezifikationen erfüllt.
- Wie? Gründliche Reinigungsprozesse. Abschließende Maßprüfung (CMM/Scanning), Sichtprüfung und möglicherweise zerstörungsfreie Prüfung (NDT) wie Fluoreszenzeindringprüfung (FPI) zur Prüfung auf Oberflächenrisse oder Computertomographie (CT) zur Überprüfung der inneren Unversehrtheit und Prüfung auf eingeschlossenes Pulver, insbesondere bei kritischen Anwendungen.
Jeder dieser Nachbearbeitungsschritte ist zeit- und kostenintensiv, aber unverzichtbar, um sicherzustellen, dass das 3D-gedruckte Turboladergehäuse zuverlässig funktioniert und die strengen Anforderungen des Hochleistungs-Automobilsektors erfüllt. Die Zusammenarbeit mit einem Dienstleister, der integrierte Nachbearbeitungsmöglichkeiten bietet, ist oft von Vorteil.
Herausforderungen meistern: Häufige Probleme beim 3D-Druck von Turbogehäusen und Lösungen
Die additive Fertigung von Metallen eröffnet zwar unglaubliche Möglichkeiten für Turboladergehäuse, ist aber auch ein fortschrittliches Verfahren, das eine Reihe potenzieller Herausforderungen mit sich bringt. Das Bewusstsein für diese allgemeinen Probleme in Verbindung mit robusten Strategien zur Abschwächung ist der Schlüssel zur erfolgreichen Herstellung hochwertiger, zuverlässiger Komponenten. Erfahrung und Prozesskenntnisse, wie sie Met3dp anbietet, sind von unschätzbarem Wert, um diese Komplexität zu meistern.
Gemeinsame Herausforderungen und Abhilfestrategien:
- Verformung und Verzerrung:
- Ausgabe: Erhebliche thermische Gradienten während des Drucks erzeugen innere Spannungen (eigenspannungsmanagement AM). Wenn die Schichten abkühlen und sich zusammenziehen, können diese Spannungen dazu führen, dass sich das Teil verzieht, von der Bauplatte abhebt oder von der vorgesehenen Geometrie abweicht. Dies ist besonders häufig der Fall bei verformung von AM-Metallteilen mit großen flachen Bereichen oder deutlicher Asymmetrie.
- Lösungen:
- Simulation aufbauen: Verwendung von Prozesssimulationssoftware zur Vorhersage von Spannungsakkumulation und Verformungsmustern vor drucken. Passen Sie die Ausrichtung oder die Stützstrukturen anhand der Ergebnisse an.
- Optimierte Ausrichtung: Richten Sie das Teil so aus, dass große Querschnitte parallel zur Bauplatte minimiert werden und die thermische Massenverteilung ausgeglichen wird.
- Robuste Unterstützungsstrategie: Verwenden Sie strategisch platzierte Stützen (thermisch und mechanisch), um das Teil fest zu verankern und die Wärme effektiv abzuleiten.
- Kontrolle der Prozessparameter: Optimieren Sie die Scan-Strategien (z. B. Insel-Scanning, wechselnde Schraffurrichtungen), um die Wärme gleichmäßiger zu verteilen.
- Unmittelbarer Stressabbau: Führen Sie die Spannungsarmglühung unmittelbar nach der Fertigung durch, oft bevor Sie das Teil von der Bauplatte nehmen.
- Eigenspannung und Rissbildung:
- Ausgabe: Hohe Eigenspannungen können, wenn sie nicht richtig gehandhabt werden, die Festigkeit des Materials überschreiten und zu Rissen während des Drucks, beim Abkühlen, beim Entfernen der Halterung oder sogar später während der Nutzungsdauer führen. Superlegierungen auf Nickelbasis, insbesondere ausscheidungshärtbare Legierungen wie IN718 (rissbildung beim Inconel-Druck), können anfällig sein, wenn die Prozessparameter und Wärmebehandlungen nicht sorgfältig kontrolliert werden. Dicke Profile und scharfe Innenecken verschärfen dieses Risiko noch.
- Lösungen:
- Wärmemanagement: Die oben genannten Strategien für das Verziehen helfen auch beim Umgang mit Eigenspannungen.
- Optimierte Wärmebehandlungen: Implementieren Sie wissenschaftlich validierte Spannungsabbau- und abschließende Wärmebehandlungszyklen, die speziell auf die Legierung und den AM-Prozess abgestimmt sind.
- DfAM: Konstruieren Sie mit großzügigen Ausrundungsradien anstelle von scharfen Ecken. Vermeiden Sie abrupte Änderungen der Querschnittsdicke.
- Optimierung der Prozessparameter: Gewährleistung einer stabilen Dynamik des Schmelzepools und Vermeidung eines übermäßigen Energieeintrags in bestimmten Gebieten.
- Unterstützung bei der Beseitigung von Schwierigkeiten:
- Ausgabe: Halterungen aus hochfesten Superlegierungen können sehr schwierig und zeitaufwändig zu entfernen sein, insbesondere von komplexen inneren Kanälen oder komplizierten äußeren Merkmalen. Aggressives Entfernen kann die Oberfläche des Teils beschädigen. Unzugängliche innere Stützen können unter Umständen nicht vollständig entfernt werden (schwierigkeiten beim Entfernen der Stütze).
- Lösungen:
- DfAM: Die effektivste Lösung! Entwerfen Sie für selbsttragende Winkel (>45°). Richten Sie das Teil so aus, dass möglichst wenig Stützen in kritischen oder unzugänglichen Bereichen erforderlich sind. Konstruieren Sie Stützen für eine leichtere Entnahme (z. B. mit speziellen Kontaktpunkten oder Strukturen).
- Spezialisierte Unterstützungsstrukturen: Nutzen Sie die Softwarefunktionen für leicht entfernbare Stützen (z. B. Baumstützen, Blockstützen mit Perforation).
- Auswahl des Prozesses: SEBM benötigt oft weniger Stützen als LPBF, da die Teile durch die höhere Prozesstemperatur länger über der Relaxationstemperatur gehalten werden.
- Nachbearbeitungsplanung: Berücksichtigen Sie die Methoden zur Entfernung von Halterungen (manuell, maschinell, EDM) im gesamten Produktionsplan.
- Kontrolle der Porosität:
- Ausgabe: Kleine Hohlräume oder Poren (porositätskontrolle 3D-Druck) können sich im gedruckten Material aufgrund von eingeschlossenem Gas (z. B. Argon in LPBF-Kammern), unvollständiger Verschmelzung zwischen den Schichten oder Keyholing (Dampfdruckkollaps) aufgrund einer zu hohen Energiedichte bilden. Porosität kann die mechanischen Eigenschaften, insbesondere die Ermüdungsfestigkeit, beeinträchtigen.
- Lösungen:
- Qualität des Pulvers: Verwenden Sie hochwertige, trockene, kugelförmige Pulver mit optimiertem PSD (wie Met3dp’s Pulver), um eine gute Fließfähigkeit und Packungsdichte zu gewährleisten.
- Optimierung der Parameter: Entwicklung und Validierung robuster Prozessparameter (Laser-/Strahlleistung, Geschwindigkeit, Schraffurabstand, Schichtdicke) zur Gewährleistung eines vollständigen Schmelzens und Verschmelzens.
- Atmosphärenkontrolle: Sorgen Sie für eine hochreine Inertgasatmosphäre (LPBF) oder ein Hochvakuum (SEBM), um Gaseinschlüsse zu minimieren.
- Heiß-Isostatisches Pressen (HIP): Ein optionaler Nachbearbeitungsschritt, bei dem die Teile einer hohen Temperatur und isostatischem Druck ausgesetzt werden. Dadurch können die inneren Poren wirksam geschlossen werden, was die Dichte und die Ermüdungseigenschaften deutlich verbessert, aber einen zusätzlichen Kosten- und Zeitaufwand bedeutet.
- Oberflächengüte Rauheit:
- Ausgabe: Vorhandene Oberflächen, insbesondere nach unten gerichtete Hänge und Oberflächen, die direkt von Pulver unterstützt werden, können rauer sein als für die Abdichtung oder eine optimale Strömungsdynamik gewünscht.
- Lösungen:
- Orientierung: Bevorzugen Sie kritische Oberflächen, die nach oben oder vertikal ausgerichtet sind, wo dies möglich ist.
- Einstellung der Parameter: Feinere Pulver und dünnere Schichten können das Finish verbessern, aber auch die Druckzeit verlängern.
- Nachbearbeiten: Planen Sie geeignete Schritte für die Oberflächenbearbeitung (Strahlen, Bearbeiten, Polieren) wie im vorherigen Abschnitt beschrieben.
Die erfolgreiche Bewältigung dieser Herausforderungen erfordert eine Kombination aus robusten DfAM-Verfahren, optimierten und validierten Prozessparametern, hochwertigen Materialien, sorgfältiger Nachbearbeitung und strenger Qualitätskontrolle. Die Zusammenarbeit mit einem erfahrenen AM-Dienstleister mit umfassender Erfahrung in der Verarbeitung von Superlegierungen für anspruchsvolle Anwendungen ist entscheidend, um zuverlässige, leistungsstarke 3D-gedruckte Turboladergehäuse zu erhalten.
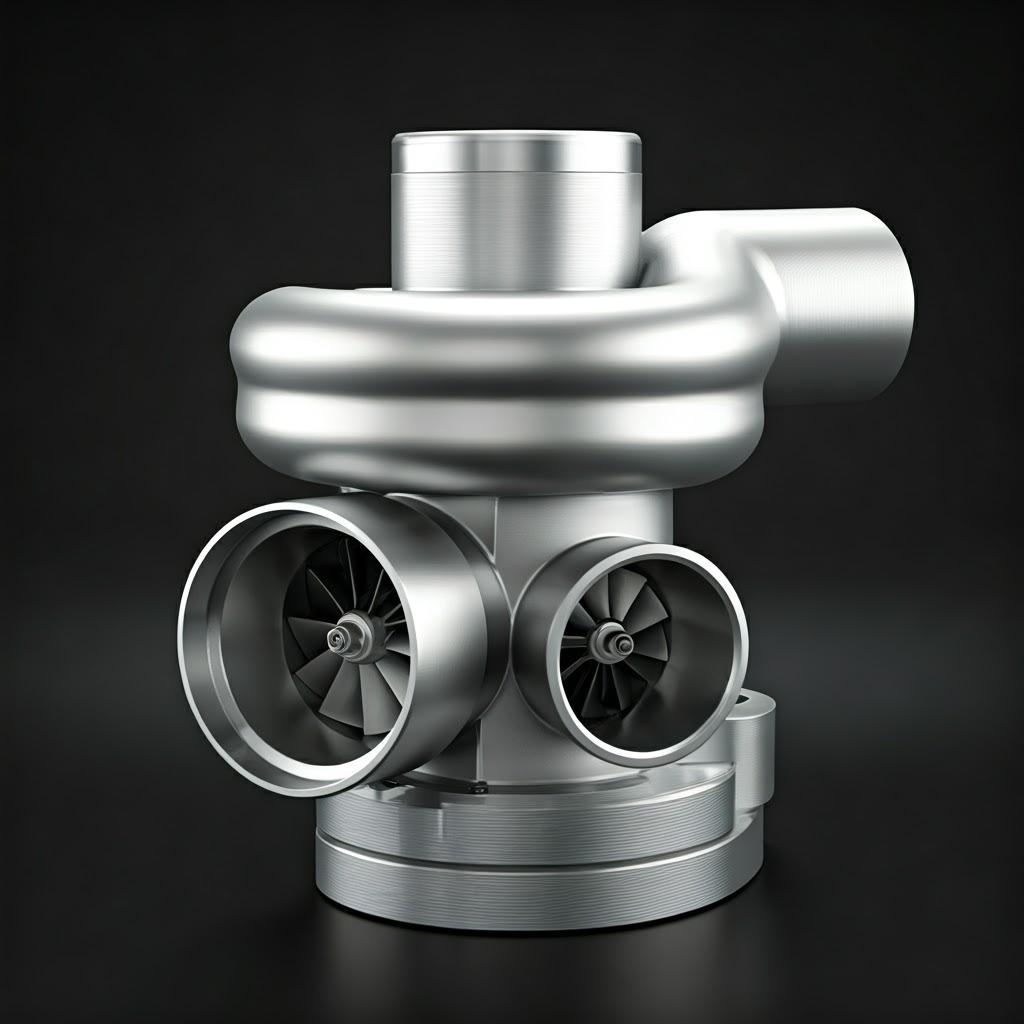
Auswahl der Lieferanten: Die Wahl des richtigen Metall-AM-Partners für Automobilkomponenten
Die Auswahl eines Fertigungspartners ist immer eine kritische Entscheidung, aber wenn es um fortschrittliche Verfahren wie die additive Fertigung von Metall für Hochleistungskomponenten in der Automobilindustrie geht, erfordert die Wahl besondere Sorgfalt. Die Qualität, Zuverlässigkeit und Leistung Ihres 3D-gedruckten Turboladergehäuses sind direkt mit den Fähigkeiten und dem Fachwissen des von Ihnen gewählten Lieferanten verbunden. Für Ingenieure und Beschaffungsmanager bei der Beschaffung metall-AM-Dienstleister Automotive lösungen ist die Bewertung potenzieller Partner auf der Grundlage einer umfassenden Reihe von Kriterien von entscheidender Bedeutung für die Risikominderung und den Projekterfolg.
Schlüsselkriterien für die Bewertung von Metall-AM-Anbietern:
- Nachgewiesene Branchen- & Anwendungserfahrung: Hat der Lieferant nachweislich Erfahrung im Automobilsektor, insbesondere mit Komponenten des Antriebsstrangs oder Teilen, die ähnlich rauen Umgebungen ausgesetzt sind (hohe Temperaturen, hohe Belastung)? Fragen Sie nach Fallstudien, Beispielen für frühere Projekte oder Referenzen in Bezug auf hochleistungs-Turbolader oder ähnlich anspruchsvolle Anwendungen. Allgemeine AM-Erfahrung ist möglicherweise nicht ausreichend.
- Werkstoffkompetenz (IN718/IN625): Fundierte Kenntnisse über die Verarbeitung von Superlegierungen auf Nickelbasis mittels AM sind nicht verhandelbar. Erkundigen Sie sich nach der Erfahrung mit IN718 und IN625, den Prozessparametern, der Art und Weise, wie die Materialeigenschaften überprüft werden (z. B. durch Zugversuche an Prüfstücken), und den Verfahren zur Handhabung des Pulvers. Zulieferer mit werkstoffkompetenz Additive Fertigung sind entscheidend. Es ist auch wichtig, die Beschaffung des Pulvers zu verstehen - stellt das Unternehmen das Pulver selbst her und gewährleistet so eine Qualitätskontrolle, oder verlässt es sich ausschließlich auf externe Lieferanten?
- Technologische Fähigkeiten & Kapazität: Beurteilen Sie den Maschinenpark des Unternehmens. Verfügen sie über gut gewartete, industrietaugliche LPBF- oder SEBM-Maschinen, die für Inconel-Legierungen geeignet sind? Wie groß sind die Bauräume? Können sie die erforderliche Genauigkeit und Wiederholbarkeit erreichen? Investieren sie, um ihre Technologie auf dem neuesten Stand zu halten? Ebenso wichtig ist ihre Kapazität - können sie Ihre Anforderungen erfüllen? Vorlaufzeit Metall-AM-Teile für Prototypen und mögliche Kleinserien?
- Qualitätsmanagementsystem und Zertifizierungen: Dies ist in der Automobilindustrie von größter Bedeutung. Achten Sie auf robuste Qualitätsmanagementsysteme (QMS).
- ISO 9001: Eine Grundvoraussetzung für den Nachweis von Qualitätsprozessen.
- AS9100: Obwohl es sich um eine Luft- und Raumfahrtnorm handelt, ist ihr strenger Fokus auf Prozesskontrolle, Rückverfolgbarkeit und Risikomanagement von großer Bedeutung und wird häufig von Zulieferern für den Hochleistungs-Automobil-/Motorsport übernommen.
- IATF 16949: Der weltweite Automobilstandard. Auch wenn die vollständige Zertifizierung bei spezialisierten AM-Anbietern noch in den Kinderschuhen steckt, ist der Nachweis der Einhaltung ihrer Grundsätze (z. B. Prozesskontrolle, APQP, PPAP-Elemente, wo anwendbar) ein wesentlicher Vorteil. Fragen Sie potenzielle Lieferanten nach ihren qualitätszertifikate AM.
- Integrierte Post-Processing-Funktionen: Ein Turboladergehäuse erfordert eine umfangreiche Nachbearbeitung. Kann der Zulieferer diesen gesamten Arbeitsablauf (Spannungsabbau, Wärmebehandlung nach Spezifikation, CNC-Präzisionsbearbeitung, Oberflächenveredelung, zerstörungsfreie Prüfung) entweder intern oder über ein engmaschiges Netz qualifizierter Partner verwalten? Ein einziger Ansprechpartner, der die gesamte Prozesskette verwaltet, vereinfacht Logistik und Verantwortlichkeit.
- Technik & DfAM-Unterstützung: Die besten Ergebnisse werden durch Zusammenarbeit erzielt. Bietet der Anbieter eine fachkundige DfAM-Beratung an? Kann er Ihnen helfen, Ihr Design hinsichtlich Druckbarkeit, Leistung und Kosteneffizienz zu optimieren? Dieser partnerschaftliche Ansatz ist oft wertvoller als eine rein transaktionale Beziehung.
- Transparenz und Kommunikation: Bewerten Sie den Prozess der Angebotserstellung - ist er klar und detailliert? Wie werden Projektkommunikation und Aktualisierungen gehandhabt? Reagieren sie auf technische Fragen? Mit einem transparenten und kommunikativen Partner lässt sich leichter zusammenarbeiten.
Warum sollte man Met3dp in Betracht ziehen?
Wenn bewertung von 3D-Druck-Anbieternwird Met3dp zu einem überzeugenden Partner für anspruchsvolle Automobilanwendungen. Met3dp hat seinen Hauptsitz in Qingdao, China, und bietet eine einzigartige Kombination von Stärken:
- Anbieter integrierter Lösungen: Met3dp ist nicht nur ein Dienstleistungsunternehmen, sondern entwirft und produziert seine eigenen branchenführenden Druckern bekannt für Genauigkeit, Zuverlässigkeit und Eignung für unternehmenskritische Teile. Entscheidend ist, dass sie auch über fortschrittliche interne Kapazitäten zur Herstellung hochwertiger sphärischer Metallpulver (einschließlich IN718, IN625 und innovativer Legierungen) unter Verwendung von Gaszerstäubung und PREP-Technologien verfügen. Diese vertikale Integration bietet eine außergewöhnliche Kontrolle über die Kernelemente, die die Qualität des Endprodukts beeinflussen.
- Umfassendes Fachwissen: Met3dp verfügt über jahrzehntelange Erfahrung in der additiven Fertigung von Metallen und kennt die Feinheiten der Verarbeitung anspruchsvoller Materialien und komplexer Geometrien.
- Umfassende Partnerschaft: Über die Druckdienstleistungen hinaus bietet Met3dp umfassende Lösungen, darunter Anwendungsentwicklungsdienstesie unterstützen Unternehmen bei der effektiven Implementierung von AM und beschleunigen die Umstellung der Fertigung. Sie arbeiten mit ihren Kunden zusammen, um spezifische technische Ziele zu erreichen.
- Nachgewiesene Erfolgsbilanz: Met3dp konzentriert sich auf die Lieferung modernster Systeme und Pulver für anspruchsvolle Bereiche wie Luft- und Raumfahrt, Medizintechnik und Automobilbau und beweist damit seine Fähigkeit, missionskritische Komponenten zu handhaben.
Auswahl eines Anbieters mit bewährten Met3dp-Fähigkeiten bedeutet, mit einem Unternehmen zusammenzuarbeiten, das in das gesamte AM-Ökosystem investiert, von der Materialwissenschaft bis zur Realisierung des fertigen Teils.
Die Investition verstehen: Kostenfaktoren und Vorlaufzeiten für AM-Turbolader-Gehäuse
Für Beschaffungsmanager und Ingenieure, die Projekte mit 3D-gedruckten Turboladergehäusen planen, ist das Verständnis der Faktoren, die die Kosten und die Vorlaufzeit bestimmen, entscheidend für die Budgetierung, die Planung und den effektiven Vergleich von Angeboten. AM bietet zwar erhebliche Vorteile, hat aber auch andere Kostenstrukturen als die herkömmliche Fertigung. Die Bereitstellung von klaren Informationen für B2B AM-Notierung ist unerlässlich.
Die wichtigsten Kostentreiber für AM-Turboladergehäuse:
- Materialverbrauch:
- Teilband: Das Nettovolumen des endgültigen Gehäuseentwurfs.
- Unterstützungsstruktur Volumen: Stützen verbrauchen Material und müssen einkalkuliert werden. Effizientes DfAM minimiert dies.
- Pulverkosten: Hochleistungssuperlegierungen wie IN718 und IN625 sind von Natur aus teure Rohstoffe im Vergleich zu herkömmlichen Stählen oder Aluminiumlegierungen. Auch die Qualität des Pulvers und das Herstellungsverfahren beeinflussen die Kosten.
- Pulverauffrischung/Recycling: Während unbenutztes Pulver oft recycelt werden kann, können sich seine Eigenschaften durch mehrfache Verwendung leicht verändern, was spezifische Auffrischungsstrategien erfordert, die sich auf die Gesamtmaterialkosten auswirken.
- Maschinenzeit: Dies ist oft der wichtigste Kostenfaktor.
- Bauhöhe: Die Druckzeit wird in erster Linie durch die Anzahl der Schichten (Z-Höhe) bestimmt, nicht nur durch das Volumen des Teils oder die Komplexität der einzelnen Schichten. Höhere Teile brauchen länger.
- Scan-Zeit: Die Zeit, die der Laser- oder Elektronenstrahl zum Abtasten jeder Schicht benötigt. Bei sehr komplexen Geometrien kann sich diese Zeit pro Schicht leicht erhöhen.
- Maschinentarif: Die stündlichen Betriebskosten des industriellen Metall-AM-Systems (einschließlich Energie, Inertgasverbrauch, Wartung, Abschreibung).
- Ausnutzung der Bauplatte (Dichte): Durch das gleichzeitige Drucken mehrerer Teile auf einer einzigen Bauplatte amortisieren sich die festen Zeiten für das Einrichten, Aufheizen, Kühlen und Entfernen der Teile auf mehrere Einheiten, wodurch die Kosten pro Teil gesenkt werden. Dies ist der Schlüssel zur Optimierung von Kleinserien.
- Komplexität der Unterstützungsstruktur: Komplizierte oder dichte Halterungen verbrauchen nicht nur mehr Material, sondern erfordern auch erheblich mehr Zeit und Mühe für die Entfernung während der Nachbearbeitung, was zusätzliche Arbeitskosten verursacht.
- Nachbearbeitungsintensität: Dies ist ein wichtiger Faktor für die endgültige metall 3D-Druck Kosten Automobil komponenten. Jeder Schritt verursacht zusätzliche Kosten:
- Spannungsabbau und abschließende Wärmebehandlungen (Ofenzeit, Kontrolle der Atmosphäre).
- Arbeits-/Bearbeitungszeit für das Entfernen der Stütze.
- CNC-Bearbeitung (Einrichtungszeit, Programmierung, Maschinenzeit, Werkzeuge - möglicherweise komplexe 5-Achsen-Bearbeitung).
- Oberflächenbearbeitung (Strahlen, Trommeln, manuelles Polieren).
- ZfP und detaillierte Inspektionen.
- Qualitätssicherungsanforderungen: Der Umfang der Inspektion (z. B. Standard-Maßkontrolle oder vollständiger CMM-Bericht, Oberflächen-FPI, internes CT-Scannen) wirkt sich direkt auf die Kosten aus.
- Auftragsvolumen: Bei AM entfallen zwar die Werkzeugkosten, aber bei größeren Stückzahlen gibt es immer noch Effizienzgewinne bei der Einrichtung und Programmierung. Der Preis pro Teil sinkt im Allgemeinen bei Stückzahlen, die von einzelnen Prototypen auf Dutzende oder niedrige Hunderte von Einheiten steigen, obwohl die Kurve viel flacher ist als beim Gießen.
- Technik/DfAM-Unterstützung: Wenn der Lieferant das Design optimieren oder beratend tätig werden muss, kann diese Entwicklungszeit in die anfänglichen Projektkosten eingerechnet werden.
Überlegungen zur Vorlaufzeit:
Die vorlaufzeit additiv gefertigter Teile umfasst mehr als nur die Druckzeit:
- Vorverarbeitung: CAD-Dateivorbereitung, Bausimulation, Slicing, Einrichtung des Bauauftrags (kann Stunden bis Tage dauern).
- Drucken: Sehr variabel je nach Höhe und Dichte der Teile (kann bei komplexen Gehäusen zwischen 12 Stunden und mehreren Tagen liegen).
- Kühlung: Die Teile müssen vor der Entnahme in der Maschine ausreichend abkühlen (mehrere Stunden).
- Maschinenwarteschlange: Verfügbarkeit des entsprechenden AM-Systems beim Lieferanten.
- Nachbearbeiten: Oft der längste Teil der Vorlaufzeit. Wärmebehandlungen nehmen Stunden/Tage pro Zyklus in Anspruch; die Bearbeitung kann je nach Komplexität und Werkstattplanung Tage dauern; Endbearbeitung und Inspektion nehmen noch mehr Zeit in Anspruch (kann insgesamt 1-4+ Wochen dauern).
- Versand: Transitzeit zu Ihrer Einrichtung.
Typische Vorlaufzeitspannen:
- Prototypen: Oft 1-4 Wochen, je nach Komplexität und Nachbearbeitungsbedarf.
- Produktion von Kleinserien (z. B. 10-50 Stück): In der Regel 4-8+ Wochen, stark beeinflusst durch die Anforderungen an die Nachbearbeitung und die Effizienz der Dosierung.
Optimierung der Kosten und der Vorlaufzeit:
- Setzen Sie DfAM konsequent ein, um den Materialeinsatz zu reduzieren und die Stützstrukturen zu minimieren.
- Legen Sie die erforderlichen Toleranzen und Oberflächengüten nur dort fest, wo sie kritisch sind, um unnötiges Bearbeiten oder Polieren zu vermeiden.
- Konsolidieren Sie Aufträge, wo dies möglich ist, um die Dichte der Bauplatten zu verbessern.
- Legen Sie im Vorfeld klare und vollständige technische Spezifikationen vor, um Verzögerungen zu vermeiden.
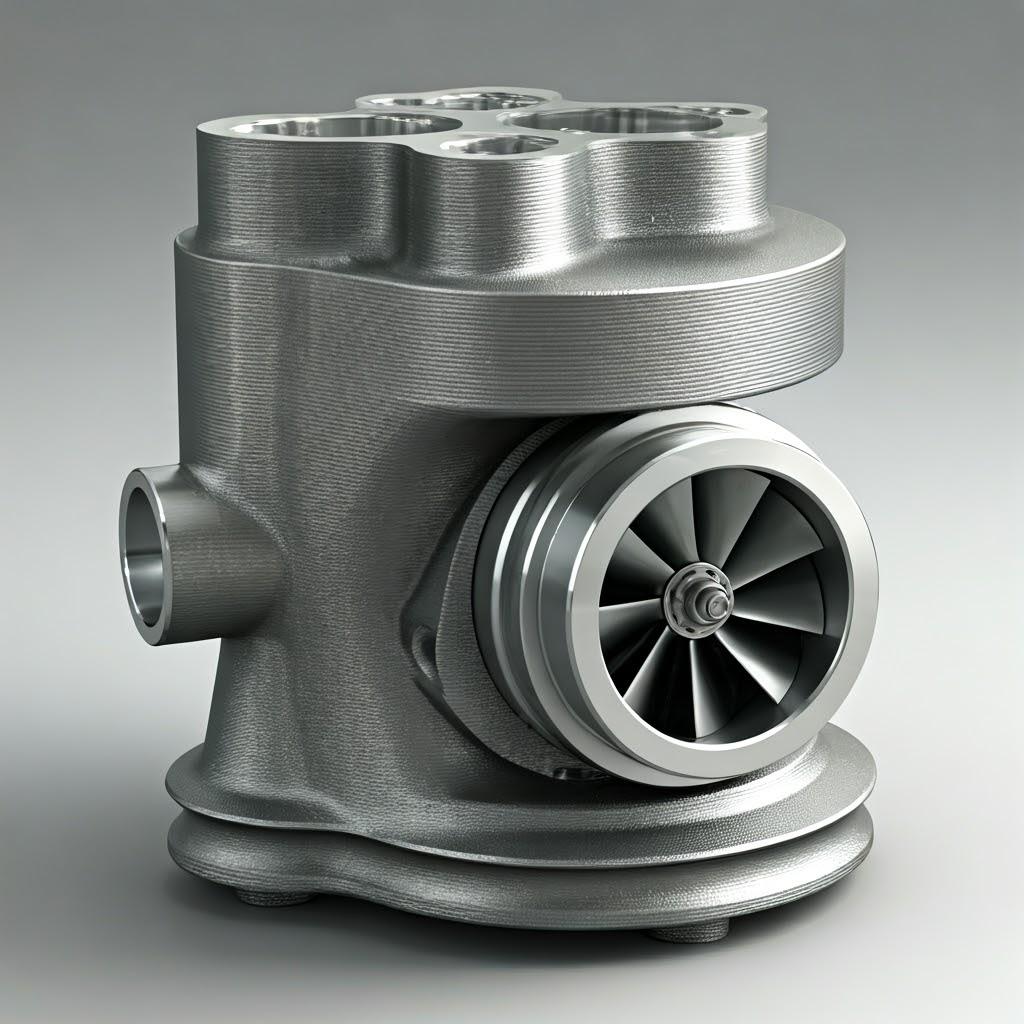
Häufig gestellte Fragen (FAQ) zu 3D-gedruckten Turboladergehäusen
Da die additive Fertigung von Metallen in der Automobilindustrie immer mehr an Bedeutung gewinnt, haben Ingenieure und Beschaffungsmanager häufig einschlägige Fragen zu ihrer Anwendung bei Komponenten wie Turboladergehäusen. Hier finden Sie Antworten auf einige häufig gestellte Fragen:
F1: Sind 3D-gedruckte Turboladergehäuse genauso zuverlässig wie herkömmlich hergestellte?
A: Ja, absolut, vorausgesetzt, sie werden richtig konstruiert und hergestellt. Wenn sie nach robusten DfAM-Prinzipien speziell für die additive Fertigung entworfen, mit validierten Verfahren auf industrietauglichen Maschinen mit hochwertigen Superlegierungen wie IN718 oder IN625 gedruckt und einer angemessenen Nachbearbeitung (insbesondere Wärmebehandlung und Bearbeitung kritischer Merkmale) sowie einer strengen Qualitätskontrolle unterzogen werden, weisen 3D-gedruckte Gehäuse hervorragende zuverlässigkeit eines 3D-gedruckten Turboladers. In vielen Fällen können AM-Teile aufgrund optimierter Geometrien (z. B. integrierte Kühlung, überlegene Strömungswege) und der Verwendung fortschrittlicher Werkstoffe im Vergleich zu ihren konventionellen Pendants eine bessere Leistung und Haltbarkeit bieten, insbesondere unter extremen Betriebsbedingungen. Die Zuverlässigkeit hängt von der Kompetenz in der gesamten Entwicklungs-, Herstellungs- und Validierungskette ab.
F2: Wie hoch sind die Kosten eines 3D-gedruckten Gehäuses im Vergleich zu einem Gussteil bei geringen Stückzahlen?
A: Dies ist eine entscheidende kostenvergleich AM-Autoteile frage. Für Prototypen, einmalige kundenspezifische Teile und Kleinserien (in der Regel von einem Stück bis vielleicht 50-100 Stück, wobei der genaue Grenzwert stark von der Komplexität des Teils und der Gussmethode abhängt) ist die Metall-AM im Allgemeinen kostengünstiger als der traditionelle Feinguss. Dies liegt vor allem daran, dass bei AM die erheblichen Vorabinvestitionen und langen Vorlaufzeiten entfallen, die mit der Erstellung von Gussmodellen und Formen (Werkzeugen) verbunden sind. Wenn das Produktionsvolumen in die Hunderte oder Tausende geht, sinken die Kosten pro Teil beim Gießen aufgrund der Amortisation der Werkzeuge erheblich, so dass es schließlich billiger wird als AM. Es ist jedoch von entscheidender Bedeutung, den Gesamtwertbeitrag zu berücksichtigen: AM ermöglicht oft ein Leistungsniveau, ein geringeres Gewicht oder Designmerkmale, die mit Guss unerreichbar sind, was bei leistungsorientierten Anwendungen höhere Kosten pro Teil rechtfertigen kann. Darüber hinaus beschleunigt AM’s Geschwindigkeit bei der Lieferung der ersten Teile die Entwicklungszyklen.
F3: Welche Art von Leistungsverbesserung kann von einem optimierten AM-Turbogehäuse erwartet werden?
A: Optimierte AM-Gehäuse können zu spürbaren Leistungssteigerungen führen:
- Verbesserte aerodynamische Effizienz: Präzise gestaltete Spiralgehäuse und Strömungswege, die mithilfe von CFD entwickelt wurden und nicht durch Gussbeschränkungen eingeschränkt sind, können die Effizienz von Verdichter und Turbine verbessern. Dies führt zu einem potenziell schnelleren Hochlauf (geringere Verzögerung), höherem Ladedruck und mehr Motorleistung/Drehmoment über den gesamten Betriebsbereich.
- Verbessertes Wärmemanagement: Durch integrierte Kühlkanäle in den Wänden des Turbinengehäuses können die Materialtemperaturen erheblich gesenkt werden, was die Haltbarkeit verbessert, ein Durchsickern der Wärme verhindert, die Notwendigkeit einer übermäßigen Abgasabschirmung verringert und eine gleichmäßigere Leistung bei längerem Hochlastbetrieb (z. B. auf der Rennstrecke) ermöglicht.
- Gewichtsreduzierung: Durch die Optimierung der Topologie kann die Gehäusemasse im Vergleich zu sperrigen Gusskonstruktionen erheblich reduziert werden, was zur Verringerung des Gesamtgewichts des Fahrzeugs beiträgt - ein entscheidender Faktor im Motorsport und bei Hochleistungsfahrzeugen.
- Optimierte Verpackung: Dank der Designfreiheit können die Gehäuse so geformt werden, dass sie in enge Motorräume passen, was kompaktere oder effizientere Motorlayouts ermöglicht.
F4: Können bestehende Turboladergehäuse direkt in 3D gedruckt werden?
A: Während Sie dürfen eine CAD-Datei eines Gussgehäuseentwurfs an einen 3D-Drucker zu senden, wird dringend abgeraten und führt in der Regel zu schlechten Ergebnissen. Für das Gießen optimierte Entwürfe weisen oft einheitliche Wandstärken, Entformungswinkel und große Radien auf, die für die Formfüllung und den Teileauswurf geeignet sind - Merkmale, die bei AM unnötig oder sogar nachteilig sind. Das direkte Drucken eines solchen Entwurfs führt in der Regel zu folgenden Ergebnissen:
- Übermäßig schwere und sperrige Teile (fehlende Möglichkeiten zur Gewichtsreduzierung).
- Erfordernis umfangreicher interner und externer Unterstützungsstrukturen, die die Druckzeit, die Materialkosten und die Nachbearbeitungsschwierigkeiten erhöhen.
- Potenziell höhere Eigenspannungen und Verzug aufgrund einer nicht optimierten Geometrie.
- Nichtausnutzung der wichtigsten Vorteile von AM (z. B. interne Kanäle, komplexe Fließwege). Um die erörterten Vorteile zu erzielen, ist eine Neugestaltung des Gehäuses nach DfAM-Grundsätzen unerlässlich. Vergleich von AM vs. Guss-Turbogehäuse erfordert die Berücksichtigung der Stärken der einzelnen Verfahren.
Schlussfolgerung: Innovation in der Automobilindustrie durch additive Fertigung
Die Landschaft der Hochleistungsautomobiltechnik entwickelt sich ständig weiter, und die additive Fertigung von Metallen erweist sich als leistungsstarker Katalysator für Innovationen, insbesondere im Bereich der Zwangsansaugung. Wie wir erforscht haben, bieten 3D-gedruckte Turboladergehäuse, die aus fortschrittlichen Superlegierungen wie IN718 und IN625 hergestellt werden, ein überzeugendes Paket von Vorteilen, die direkt auf die extremen Anforderungen des Motorsports, des Aftermarket-Tunings und von Spezialfahrzeuganwendungen abgestimmt sind.
Die unvergleichliche Gestaltungsfreiheit aM ermöglicht die Herstellung von Gehäusen mit optimierter Aerodynamik und integriertem Wärmemanagement, die zuvor unmöglich zu realisieren waren. Dies führt zu spürbaren Leistungssteigerungen - schnelleres Ansprechverhalten, höherer Wirkungsgrad und verbesserte Haltbarkeit unter Last. Die Fähigkeit zur Nutzung von Topologieoptimierung führt zu deutlich leichteren Bauteilen, was für den Wettbewerbsvorteil entscheidend ist. Außerdem erleichtert AM schneller Prototypenbau und werkzeuglos Kleinserienfertigungsie beschleunigen die Entwicklungszyklen und bieten einen flexiblen Herstellungsweg für kundenspezifische oder Nischenkomponenten.
Um dieses Potenzial zu erschließen, ist jedoch mehr erforderlich als nur der Zugang zu einem 3D-Drucker. Der Erfolg hängt von einem ganzheitlichen Ansatz ab, der folgende Elemente umfasst Design für additive Fertigung (DfAM), akribische Prozesskontrolle, umfassend Nachbearbeitungrigoros qualitätssicherungund vor allem die Zusammenarbeit mit den richtigen Partnern anbieter von Metall-AM-Lösungen. Die Bewältigung der Herausforderungen durch Eigenspannungen, Stützstrukturen und das Erreichen präziser Toleranzen erfordert ein hohes Maß an Fachwissen und Erfahrung.
Die zukunft der Turboladerherstellung für Hochleistungsanwendungen wird die additive Fertigung zweifelsohne immer mehr Verbreitung finden. Für Ingenieure, die die Leistungsgrenzen erweitern wollen, und für Beschaffungsmanager, die nach innovativen, flexiblen Fertigungslösungen für fortschrittliche Automobilkomponentenstellt Metal AM eine strategische Notwendigkeit dar.
Wenn Ihr Unternehmen bereit ist, das transformative Potenzial des 3D-Metalldrucks für Turboladergehäuse oder andere anspruchsvolle Automobilkomponenten zu erkunden, sollten Sie eine Partnerschaft mit einem führenden Unternehmen in diesem Bereich in Betracht ziehen. Wir laden Sie ein zu Kontakt zu Met3dp um Ihre spezifischen Anforderungen zu besprechen. Nutzen Sie die umfassenden Lösungen des Unternehmens - von branchenführenden SEBM-Druckern über fortschrittliche gasverdüste und PREP-Metallpulver bis hin zu fachkundigen Dienstleistungen für die Anwendungsentwicklung -, um die Ziele Ihres Unternehmens im Bereich der additiven Fertigung zu erreichen und Ihren Weg zur nächsten Generation von Automobilinnovationen zu beschleunigen.
Teilen auf
MET3DP Technology Co., LTD ist ein führender Anbieter von additiven Fertigungslösungen mit Hauptsitz in Qingdao, China. Unser Unternehmen ist spezialisiert auf 3D-Druckgeräte und Hochleistungsmetallpulver für industrielle Anwendungen.
Fragen Sie an, um den besten Preis und eine maßgeschneiderte Lösung für Ihr Unternehmen zu erhalten!
Verwandte Artikel
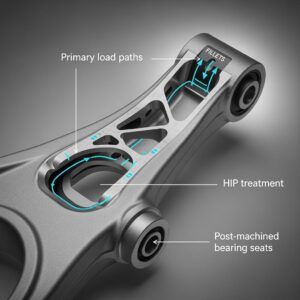
Metal 3D Printing for U.S. Automotive Lightweight Structural Brackets and Suspension Components
Mehr lesen "Über Met3DP
Aktuelles Update
Unser Produkt
KONTAKT US
Haben Sie Fragen? Senden Sie uns jetzt eine Nachricht! Wir werden Ihre Anfrage mit einem ganzen Team nach Erhalt Ihrer Nachricht bearbeiten.
Holen Sie sich Metal3DP's
Produkt-Broschüre
Erhalten Sie die neuesten Produkte und Preislisten