Verständnis des Metall-Spritzgießens (MIM)
Inhaltsübersicht
Metall-Spritzgießen (MIM) ist ein Fertigungsverfahren, mit dem kleine, komplexe Metallteile mit engen Toleranzen hergestellt werden können. MIM kombiniert die Vielseitigkeit des Kunststoffspritzgusses mit der Festigkeit und Integrität von bearbeiteten Metallen. Dieser Artikel gibt einen detaillierten Überblick über die MIM-Technologie, Anwendungen, Ausrüstung, Verfahren, Designüberlegungen und mehr.
Überblick über das Metall-Spritzgießen
Das Metall-Spritzgießen ist ein pulvermetallurgisches Verfahren, das die Großserienproduktion von kleinen Präzisionsmetallteilen im Spritzgussverfahren ermöglicht.
Wie MIM funktioniert
Beim MIM-Verfahren wird feines Metallpulver mit einem Bindemittel gemischt, um ein Ausgangsmaterial zu erzeugen, das in Formen gespritzt werden kann. Die geformten Teile, die so genannten Grünteile, werden dann gesintert, um das Bindemittel zu entfernen und das Metallpulver zu einer festen Struktur zu verfestigen. Die grundlegenden Schritte sind:
- Mischen - Feines Metallpulver wird mit Bindemitteln gemischt, um ein homogenes Ausgangsmaterial zu schaffen
- Spritzgießen - Das Ausgangsmaterial wird geschmolzen und in die Form gespritzt, um Grünteile zu formen
- Entbinden - Das Bindemittel wird durch Lösungsmittel, thermische oder katalytische Entbinderung entfernt.
- Sintern - Die entgrateten Teile werden gesintert, um die Metallstruktur zu verdichten und zu verstärken.
- Sekundäre Operationen - Zusätzliche Bearbeitungsschritte wie Zerspanen, Bohren, Gewindeschneiden usw.
Vorteile von MIM
MIM bietet im Vergleich zu anderen Fertigungstechniken mehrere Vorteile:
- Großserienproduktion mit niedrigen Kosten pro Teil
- Komplexe Geometrien mit engen Toleranzen
- Verschiedene Materialien wie rostfreier Stahl, Titan, Wolfram, Kobalt-Chrom usw.
- Minimale Ausschussverluste und Materialabfälle
- Netzformnahe Fertigung reduziert die Bearbeitung
- Kleine Teilegrößen von 0,005 lbs bis 0,5 lbs
- Teilekonsolidierung durch Kombination von Baugruppen
- Glatte Oberflächen und gute Verarbeitung
Beschränkungen von MIM
Einige Einschränkungen des Metall-Spritzgießens sind:
- Hohe Anlauf- und Werkzeugkosten
- Begrenzter Größenbereich für Teile
- Spezialisierte Ausrüstung erforderlich
- Mehrstufiger Prozess mit langsamerer Produktion
- Abmessungsbeschränkungen aufgrund der Pulvereigenschaften
- Beschränkungen der Teilegeometrie aufgrund des Pulverflusses
Anwendungen von MIM
MIM wird häufig zur Herstellung kleiner, komplexer Teile mit engen Toleranzen in verschiedenen Branchen eingesetzt:
- Medizin - orthopädische Implantate, Zahnimplantate, chirurgische Instrumente
- Automobilindustrie - Motorkomponenten, Ventile, Zahnräder
- Luft- und Raumfahrt - Turbinenschaufeln, Laufräder, Düsen
- Elektronik - Steckverbinder, Mikrogetriebe, Abschirmung
- Schusswaffen - Abzüge, Hämmer, Sicherungen
- Uhren - Uhrengehäuse, Armbänder, Krone
- Industrie - Knöpfe, Verschlüsse, Schneidwerkzeuge
MIM konkurriert bei der Herstellung von Metallteilen mit anderen Verfahren wie Feinguss, Zerspanung und Stanzen.
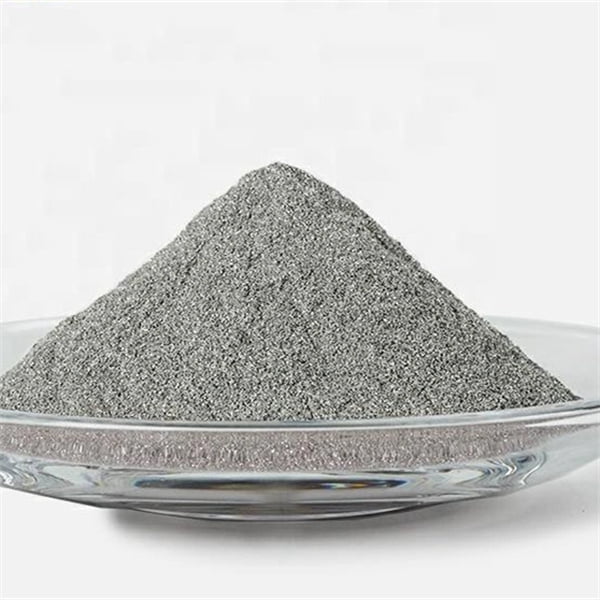
Metall-Spritzgießen Ausrüstungsführer
Für jede Phase des MIM-Prozesses ist eine spezielle Ausrüstung erforderlich. Hier sind die wichtigsten MIM-Ausrüstungstypen:
Ausrüstung | Funktion |
---|---|
Pulverdosierer | Genaue Dosierung von feinen Pulvern |
Mixer | Pulver und Bindemittel homogen mischen |
Granulatoren | Ausgangsmaterial zu Granulat für die Formgebung formen |
Spritzgießmaschinen | Formen des Ausgangsmaterials in die gewünschten Formen |
Entbinderungsöfen | Binder von Formteilen entfernen |
Sinteröfen | Verdichtung und Verstärkung der Metallstruktur |
Schleifmaschinen | Entfernen von Toren, Kufen und glatten Flächen |
Bearbeitungszentren | Bohren, Drehen, Fräsen von Merkmalen in gesinterte Teile |
Moderne Automatisierungs-, Handhabungssysteme und Steuerungen werden eingesetzt, um den Prozess zu integrieren und die Produktivität zu maximieren. Die Ausrüstung muss auf der Grundlage von Faktoren wie Material, Teilegröße, Produktionsvolumen und Qualitätsanforderungen sorgfältig ausgewählt werden.
Metall-Spritzgießen Prozess Schritt für Schritt
Die MIM-Verarbeitung umfasst mehrere Schritte zur Umwandlung von feinem Metallpulver in vollständig dichte Endkomponenten.
Schritt 1 - Mischen
- Das Metallpulver und das Bindemittel werden in einem Mischer gründlich vermischt, um ein homogenes Ausgangsmaterial zu erhalten.
- Größe, Form und Verteilung der Pulverpartikel beeinflussen die Formbarkeit und die Sinterung
- Bindemittel sorgen für Fließfähigkeit und Haftung beim Spritzgießen
- Wachse, Thermoplaste wie PP, PE, PVC und als Bindemittel verwendete Polymere
- Mischen mit Sigma-Messer, Z-Messer, Doppelplanetenmischer
Schritt 2 - Granulierung
- Die Ausgangsstoffmischung wird zu kleinen Pellets für das Spritzgießen granuliert
- Verbessert den Materialfluss und verhindert Entmischung im Fass
- Granulatoren verwenden rotierende Messer, um das Ausgangsmaterial in gleichmäßige Körner zu schneiden.
- Form und Größe des Granulats beeinflussen Packungsdichte und Formbarkeit
Schritt 3 - Spritzgießen
- Das Ausgangsmaterialgranulat wird in die gewünschte Form und Größe des Teils geformt
- Verwendet modifizierte Spritzgießmaschinen mit kontrollierter Temperatur und kontrolliertem Druck
- Wichtig ist die Optimierung der Formparameter zur Minimierung von Fehlern
- Formgegossene Teile, so genannte Grünteile, haben eine bestimmte Form, aber keine Festigkeit.
Schritt 4 - Entbinden
- Das Bindemittel wird durch Lösungsmittel, thermische oder katalytische Verfahren aus den grünen Teilen extrahiert.
- Beim Entbindern mit Lösungsmitteln wird das Bindemittel durch Kapillarwirkung aufgelöst.
- Bei der thermischen Entbinderung wird das Bindemittel in einem Ofen zersetzt.
- Katalytische Entbinderung beschleunigt die Bindemittelentfernung mit einem Katalysator
- Beim Entbindern entstehen braune Teile mit einer porösen Struktur aus Metallpartikeln
Schritt 5 - Sintern
- Braune Teile werden in einem Ofen mit kontrollierter Atmosphäre gesintert.
- Bindungen zwischen Metallteilchen entstehen durch Diffusion und Stofftransport
- Nahezu volle Dichte von bis zu 96-99% während des Sinterns erreicht
- Atmosphäre, Temperatur, Zeit optimiert, um Defekte zu vermeiden
- Berücksichtigung der Sinterschwindung bei der Formgebung
Schritt 6 - Sekundäre Operationen
- Zusätzliche Metallbearbeitungsschritte wie Glühen, Bearbeiten, Bohren, Beschichten
- Glühen baut innere Spannungen aus der Sinterung ab
- CNC-Bearbeitung entfernt Angüsse, glättet Oberflächen, fügt Merkmale hinzu
- Beschichtungen und Anstriche zur Veredelung oder zum Korrosionsschutz
Das MIM-Verfahren ermöglicht komplexe, hochpräzise Metallteile, indem es die Vorteile des Kunststoffspritzgießens und der Pulvermetallurgie kombiniert.
Konstruktionsüberlegungen für MIM-Teile
MIM ermöglicht geometrische Freiheiten, die bei der maschinellen Bearbeitung nicht möglich sind, erfordert aber bestimmte konstruktive Überlegungen:
- Wandstärke - Typischer Bereich von 0,3 - 4,0 mm mit einigen Pulvern, die bis zu 6 mm Wandstärke unterstützen
- Oberflächengüte - Glattere Oberfläche als beim Gießen, aber nicht so fein wie beim Zerspanen; ein Ra-Wert von 1 - 4 μm ist typisch für MIM
- Toleranzen bei den Abmessungen - ±0,1% bis ±0,5% je nach Teilegeometrie mit einer Genauigkeit im Mikrometerbereich möglich
- Dichte - Bei optimierter Sinterung kann eine volle Dichte von bis zu 99% erreicht werden
- Geometrie - Die Vermeidung von Pulvereinschlüssen und das Entweichen des Bindemittels sind von entscheidender Bedeutung.
- Entwurfswinkel - Konische Wände mit einem Entformungswinkel von 1-3° erleichtern das Auswerfen der Teile
- Radien und Filets - Allmähliche Übergänge sind scharfen Ecken vorzuziehen
- Löcher und Hohlräume - Mindestdurchmesser von 0,25 - 0,5 mm für Durchgangslöcher
- Fäden - Kann geformt werden, wird aber oft nach dem Sintern bearbeitet, um eine bessere Genauigkeit zu erzielen.
- Details zur Oberfläche - Begrenzung feiner Details zur Verringerung des Werkzeugverschleißes; Nachbearbeitungsprozesse können die
Bei der MIM-Konstruktion sollte der Schwerpunkt auf einer Geometrie liegen, die die Leistung maximiert, und nicht auf einer einfachen Herstellung. Das Verfahren ermöglicht die Konsolidierung von mehrteiligen Baugruppen zu einem einzigen Teil mit erheblichen Kosten- und Gewichtseinsparungen.
Materialien für das Metall-Spritzgießen
Mit MIM können Teile aus einer Vielzahl von Metallen, Legierungen und Keramiken in verschiedenen Branchen hergestellt werden.
Material | Anwendungen | Eigenschaften |
---|---|---|
Rostfreier Stahl | Medizin, Schusswaffen, Marine | Korrosionsbeständigkeit, Festigkeit |
Niedrig legierter Stahl | Automobilindustrie, Industrie | Magnetische Reaktion, Bearbeitbarkeit |
Weichmagnetische Legierungen | Sensoren, Aktoren | Hohe Durchlässigkeit |
Hartmetall-Legierungen | Schneidewerkzeuge | Abriebfestigkeit, Härte |
Kupferlegierungen | Elektronik, thermisch | Elektrische Leitfähigkeit |
Aluminium-Legierungen | Elektrisch, thermisch | Leichtigkeit, Leitfähigkeit |
Titan-Legierungen | Luft- und Raumfahrt, Automobilindustrie | Festigkeit, Biokompatibilität |
Wolfram-Legierungen | Strahlungsabschirmung | Hohe Dichte |
Cermets | Elektronik, Optik | Oxidationsbeständigkeit |
Faktoren wie Bauteilfunktion, Kosten, Nachbearbeitungsschritte und Legierungskompatibilität bestimmen die ideale Wahl des MIM-Materials.
MIM-Lieferanten und Ausrüstungshersteller
Viele Unternehmen bieten weltweit MIM-Materialien, Dienstleistungen, Produktion und Ausrüstung an. Hier sind einige der wichtigsten MIM-Anbieter entlang der Wertschöpfungskette:
Unternehmen | Produkte/Dienstleistungen |
---|---|
BASF | Ausgangsstoffe, Bindemittel |
Sandvik Fischadler | Metall-Pulver |
Höganäs | Metall-Pulver |
CNPC-Pulver | Metall-Pulver |
Indo-Mim | MIM-Produkte, Dienstleistungen |
MPP | MIM-Produkte, Dienstleistungen |
ARC-Gruppe | MIM-Produkte, Dienstleistungen |
Atlas gepresste Metalle | MIM-Teile-Produktion |
Epson Atmix | MIM-Ausrüstung |
Milacron | Spritzgießmaschinen |
Elnik | Sinteröfen |
TCN | Entbinderungs- und Sinterungsöfen |
Darüber hinaus gibt es viele kleinere regionale Akteure in der MIM-Lieferkette. Endnutzer, die MIM einsetzen wollen, können je nach den erforderlichen Fähigkeiten mit Materiallieferanten und Auftragsfertigern zusammenarbeiten.
Kostenanalyse von MIM-Teilen im Vergleich zu Alternativen
Hier ist ein Vergleich der geschätzten Kosten für die Herstellung von 1000 Teilen mit verschiedenen Herstellungsverfahren:
Prozess | Einrichtungskosten | Kosten der Maschine | Werkzeugkosten | Teil Kosten | Insgesamt (1000 Teile) |
---|---|---|---|---|---|
CNC-Bearbeitung | Niedrig | $100,000 | $2,000 | $50 | $52,000 |
Feinguss | Hoch | $500,000 | $40,000 | $20 | $60,000 |
Metall-Spritzgießen | Hoch | $750,000 | $100,000 | $15 | $115,000 |
Stanzen | Hoch | $1,000,000 | $150,000 | $10 | $160,000 |
- CNC-Bearbeitung hat geringe Stückzahlen, hohe Teilekosten, begrenzte Komplexität
- Feinguss ist besser für Mengen bis zu 10.000 Stück
- MIM hat Vorteile bei mittleren bis hohen Stückzahlen mit komplexer Geometrie
- Stanzen hat sehr hohe Werkzeugkosten, aber den niedrigsten Teilepreis bei hohen Stückzahlen über 100.000 Stück
Der Übergangspunkt, an dem MIM wirtschaftlicher wird als andere Verfahren, hängt von Volumen, Komplexität und Größe ab.
Auswahl eines MIM-Lieferanten oder -Partners
Die Auswahl eines kompetenten MIM-Lieferanten oder -Produktionspartners ist entscheidend für eine kosteneffiziente Teileproduktion. Hier sind die wichtigsten Überlegungen:
- Technisches Fachwissen - Frühere Erfahrungen mit ähnlichen MIM-Teilen, Materialien, Industrie
- Qualitätssysteme - Zertifizierung nach ISO 9001, Qualitätskontrollverfahren
- Produktionskapazität - Fähigkeit, den gegenwärtigen und künftigen Mengenbedarf zu decken
- Sekundäre Prozesse - Bearbeitungs-, Stanz-, Beschichtungs- und Lackiermöglichkeiten
- Teilweise Optimierung - Design für MIM-Unterstützung zur Maximierung der Vorteile
- Prototyping - Rapid-Prototyping-Dienste zur Validierung von Entwürfen
- Werkzeugtechnische Fähigkeiten - Eigene Konstruktion und Fertigung von Werkzeugen bevorzugt
- Zugang zu Rohstoffen - Etablierte Lieferkanäle für Ausgangsstoffe
- F&E-Fähigkeiten - Laufende FuE im Bereich fortschrittlicher Materialien und Fertigungstechniken
- Kundenorientierung - Eingehen auf die Bedürfnisse und Ansatz zur Zusammenarbeit
- Kostenstruktur - Preismodell und Wettbewerbsfähigkeit bei prognostizierten Mengen
- Logistik - Fähigkeit, Teile zuverlässig zu liefern und dabei die Vorlaufzeiten einzuhalten
Die Priorisierung dieser Faktoren hilft dabei, den richtigen strategischen MIM-Partner für eine bestimmte Anwendung zu finden.
Installation der MIM-Ausrüstung
Für Unternehmen, die MIM-Funktionen im eigenen Haus installieren, ist eine ordnungsgemäße Geräteinstallation von entscheidender Bedeutung. Hier sind die wichtigsten Überlegungen:
- Für die MIM-Linie wird eine Fläche von etwa 2000 bis 5000 Quadratmetern benötigt.
- Stabile Stromversorgung mit 200-600 kVA Leistung erforderlich
- Druckluftleitungen für einen Druck von 100 psi
- Entlüftung für Wärme, Emissionen und Staubabscheidung
- Versorgungsleistungen wie Stickstoff-, Brauchwasser- und Gasversorgung
- Temperatur- und Feuchtigkeitskontrolle von ca. 20±3 °C, 50±20%
- Mezzanine, Plattformen für die Installation von Zusatzgeräten
- Materialhandhabungssysteme wie Hebezeuge, Gabelstapler, Lagerbehälter
- Kontrollraum, Computersysteme zur Überwachung
- Schulung des Personals in Bezug auf Prozesssicherheit und Gerätebedienung
- Prozesssimulationen, Testläufe zur Validierung der Installation
- Kalibrierung und vorbeugende Wartungspläne
Ausreichend Platz, Versorgungseinrichtungen und kontrollierte Bedingungen sind für einen reibungslosen Betrieb der MIM-Anlagen unerlässlich. Gründliche Tests und Schulungen bereiten auf die reale Produktion vor.
Wartung der MIM-Ausrüstung
Eine konsequente Wartung verbessert die Betriebszeit und Leistung von MIM-Produktionsanlagen. Wichtige Aspekte:
- Dokumentierter Plan zur vorbeugenden Wartung für jede Maschine
- Tägliche Beseitigung von verschüttetem Material, Leckagen, Staub und Schutt
- Überprüfung von Flüssigkeitsständen, Lecks, ungewöhnlichen Geräuschen und Vibrationen
- Überwachung von Druck, Temperatur und Stromverbrauch
- Prüfung von Heiz-, Kühl- und Regelsystemen
- Austausch von Verschleißteilen wie Siebe, Schnecken, Trommeln
- Inspektionen auf Bauteilermüdung, Beschädigung, Ausrichtung
- Regelmäßige Überholungen und Überholungen auf der Grundlage der Betriebsstunden
- Verfolgung von Wartungsprotokollen zur Analyse
- Lagerung von Ersatzteilbeständen für kritische Komponenten
- Schulungen zur ordnungsgemäßen Bedienung und Sicherheit der Geräte
- Rechtzeitiger Service und Support von Geräteanbietern
Gut geschultes Personal und die Zusammenarbeit mit den Geräteanbietern tragen dazu bei, die Produktivität der MIM-Anlagen zu maximieren und gleichzeitig die Ausfallzeiten zu minimieren.
Metall-Spritzguss-Simulationssoftware
Mithilfe von Simulationssoftware wird der MIM-Prozess vor der eigentlichen Produktion digital modelliert. Die Vorteile umfassen:
- Vorhersage von Formfüllmustern und Optimierung der Anschnittstellen
- Identifizierung von Schweißnähten und Lufteinschlüssen zur Vermeidung von Defekten
- Untersuchung von Wärmegradienten und Erstarrung in komplexen Geometrien
- Simulation der Auswirkungen von Entbinderungs- und Sinterprofilen auf die endgültige Form
- Validierung von Werkzeugentwürfen vor der Fertigung
- Reduzierung der Versuchskosten durch virtuelles Prototyping
- Schulung des Personals durch visuelle Darstellungen
Einige kommerzielle MIM-Simulationspakete umfassen:
- MIMSIM - Integrierte Simulation für die Formgebung durch Sintern
- Sigma Weich - 3D-FEM-Analyse von Formfüllung und Verzug
- Netzsch MIMPre - Modellierung der rheologischen Eigenschaften von MIM-Rohstoffen
- Simufact Zusatzstoff - Multiphysikalische Simulation von AM-Prozessen
- EOS PSW - Simulation mit Schwerpunkt auf Sinterung und Wärmebehandlung
Der Einsatz von MIM-Software verbessert die Prozesskonsistenz, optimiert die Teilequalität und senkt die Kosten für das physische Prototyping. Ein integrierter Workflow von der Simulation bis zur Produktion wird bevorzugt.
Fehlersuche bei häufigen MIM-Fehlern
Einige typische Fehler in MIM-Teilen und mögliche Ursachen sind:
Defekt | Verursacht |
---|---|
Kurze Schüsse | Niedriger Einspritzdruck, vorzeitige Verfestigung |
Blitzlicht | Überpackte Schimmelpilze, Schimmelpilzschäden |
Verzug | Ungleichmäßige Abkühlung, Bindemittelprobleme |
Risse | Schnelle Sinterung, hoher Bindemittelgehalt |
Porosität | Schlechte Homogenisierung, eingeschlossene Gase |
Verunreinigung | Kreuzkontamination, Ofenatmosphäre |
Maßabweichungen | Probleme mit Rohstoffen, Formenverschleiß, Schrumpfung |
Oberflächenfehler | Gasporosität, Versprödung von Flüssigmetall |
Einschlüsse | Verunreinigte Rohstoffe, Düsenverstopfungen |
Eine systematische Fehleranalyse sollte eingesetzt werden, um die fehlerverursachenden Prozessparameter zu isolieren und Korrekturmaßnahmen zu ergreifen, wie z. B. die Anpassung der Rezeptur des Ausgangsmaterials, der Formparameter, des Entbinderungs- und des Sinterungsprofils.
Vorteile der MIM-Technologie
MIM bietet erhebliche Vorteile gegenüber anderen Verfahren zur Herstellung von Metallteilen:
- Komplexität - Komplexe 3D-Geometrien möglich, konsolidiert Baugruppen
- Konsistenz - Hochgradig wiederholbarer Prozess mit geringer Teilevarianz
- Wirkungsgrad - Nettoformnahe Fertigung mit weniger Rohstoffabfall
- Automatisierung - Hochautomatisierter Prozess reduziert Arbeitsaufwand
- Flexibilität - Breites Spektrum an Materialien wie Metalle, Keramik, Verbundwerkstoffe
- Qualität - Gute Oberflächengüte und mechanische Eigenschaften
- Produktivität - Hohe Produktionsmengen bei niedrigen Kosten pro Teil
- Miniaturisierung - Mikrobauteile mit Details bis zu 10 μm
- Nachhaltigkeit - Energieeffizienz im Vergleich zur maschinellen Bearbeitung
- Kosten - Niedrigere Gesamtkosten für mittlere bis hohe Produktionsmengen
Die einzigartigen Fähigkeiten von MIM fördern die Akzeptanz in verschiedenen Branchen wie der Automobilindustrie, der Luft- und Raumfahrt, der Medizintechnik und der Elektronik.
Grenzen des Metall-Spritzgießens
Trotz vieler Vorteile hat die MIM bestimmte Einschränkungen:
- Hohe Anfangsinvestitionen für Werkzeuge
- Begrenzter Größenbereich, in der Regel unter 65 Gramm
- Geringere Genauigkeit als bei der CNC-Bearbeitung
- Porositätsrisiken, die Prozesskontrollen erfordern
- Eingeschränkte Materialauswahl aufgrund von Pulvereigenschaften
- Sicherheitsrisiken von feinen Pulvern
- Beschränkungen der Teilegeometrie in Bezug auf die Formbarkeit
- Potenzielle Variabilität von Los zu Los
- Geringere mechanische Eigenschaften als Knetwerkstoffe
- Begrenzte Produktion von Prototypen in geringer Stückzahl
- Erfordernis der sekundären Bearbeitung bei vielen Anwendungen
- Spezialisierte Ausrüstung und geschultes Personal erforderlich
Für sehr hochpräzise oder größere Metallteile, die in geringen Stückzahlen hergestellt werden, sind andere Verfahren möglicherweise besser geeignet als MIM.
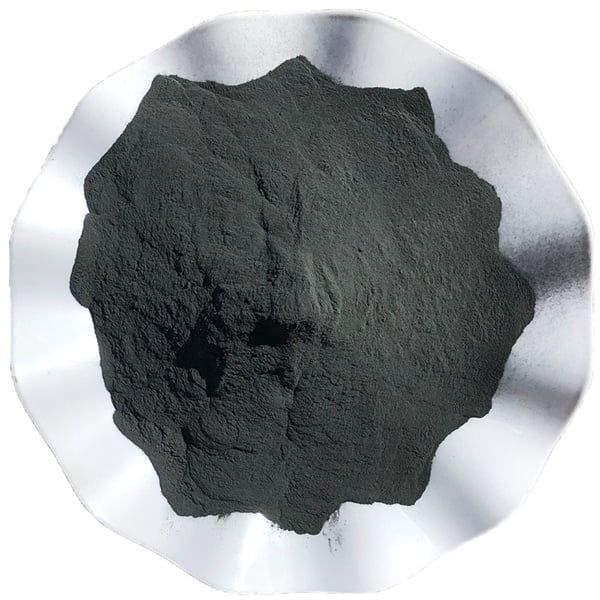
Die Zukunft des Metall-Spritzgießens
Es wird erwartet, dass MIM weiterhin ein starkes Wachstum verzeichnen wird, da sich die Technologie und die Materialien weiter verbessern:
- Neue Bindemittelsysteme zur Verbesserung der Formbarkeit und Grünfestigkeit
- Neuartige Rohstoffformulierungen unter Verwendung von Nanokompositen
- Größere Teile, die die Stromgrenzen überschreiten
- Verstärkter Einsatz von Keramik und Wolframlegierungen
- Starkes Nachfragewachstum in den Bereichen Medizin und Elektronik
- Einsatz der additiven Fertigung zur Herstellung von MIM-Werkzeugen
- Automatisierung durch Robotik und Integration von Industrie 4.0
- Mehr Anwendungen in extremen Umgebungen
- Konvergenz mit dem 3D-Metalldruck durch gebundene Metallabscheidung
Mit zunehmender Forschung und Entwicklung und leichterer Akzeptanz wird der Einsatz von MIM in den kommenden Jahren in verschiedenen Anwendungsbereichen rasch zunehmen.
Teilen auf
MET3DP Technology Co., LTD ist ein führender Anbieter von additiven Fertigungslösungen mit Hauptsitz in Qingdao, China. Unser Unternehmen ist spezialisiert auf 3D-Druckgeräte und Hochleistungsmetallpulver für industrielle Anwendungen.
Fragen Sie an, um den besten Preis und eine maßgeschneiderte Lösung für Ihr Unternehmen zu erhalten!
Verwandte Artikel
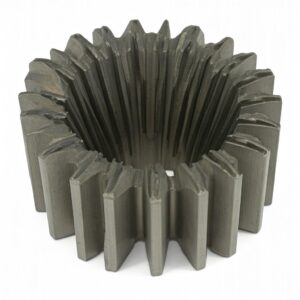
Hochleistungs-Düsenschaufelsegmente: Revolutionierung der Turbineneffizienz mit 3D-Metalldruck
Mehr lesen "Über Met3DP
Aktuelles Update
Unser Produkt
KONTAKT US
Haben Sie Fragen? Senden Sie uns jetzt eine Nachricht! Wir werden Ihre Anfrage mit einem ganzen Team nach Erhalt Ihrer Nachricht bearbeiten.
Holen Sie sich Metal3DP's
Produkt-Broschüre
Erhalten Sie die neuesten Produkte und Preislisten
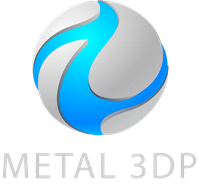
Metallpulver für 3D-Druck und additive Fertigung