Verständnis der MIM-Technologie
Inhaltsübersicht
Überblick über MIM-Technologie
Das Metall-Spritzgießen (MIM), auch bekannt als Pulverspritzgießen (PIM), ist ein fortschrittliches Fertigungsverfahren, mit dem kleine, komplexe Metallteile in großen Mengen hergestellt werden können.
MIM kombiniert die Designflexibilität und Präzision des Kunststoffspritzgießens mit der Festigkeit und Leistung von maschinell bearbeiteten Metallteilen. Es ermöglicht die kostengünstige Herstellung komplizierter Bauteile mit guten mechanischen Eigenschaften aus modernen Metalllegierungen.
Das MIM-Verfahren beginnt mit einem Ausgangsmaterial aus feinem Metallpulver, das mit einem Bindemittel vermischt wird. Dieses Ausgangsmaterial wird dann mit Hilfe von Kunststoffspritzgießmaschinen in eine Form gespritzt. Das Bindemittel hält das Metallpulver zusammen und sorgt für die Fließfähigkeit beim Formen.
Nach dem Gießen wird das Bindemittel durch einen Entbinderungsprozess aus dem geformten grünen Teil entfernt. Das entbinderte Teil, das so genannte braune Teil, wird dann bei hohen Temperaturen gesintert, wodurch die Metallpartikel zu einem massiven Metallteil verschmelzen, dessen Materialeigenschaften denen eines Schmiedeteils nahe kommen.
MIM eignet sich für die Herstellung kleiner, komplexer Teile aus verschiedenen Metallen wie rostfreiem Stahl, niedrig legierten Stählen, Werkzeugstählen, magnetischen Legierungen, Superlegierungen, Titanlegierungen und Wolframschwermetalllegierungen. Es kombiniert die Vielseitigkeit des Kunststoffspritzgusses mit der Materialflexibilität der Pulvermetallurgie.
Zu den wichtigsten Vorteilen der MIM-Technologie gehören:
- Großserienfertigung für komplexe, detaillierte Metallkomponenten
- Near-Net-Shape-Fertigung reduziert Abfall und minimiert die Bearbeitung
- Gute mechanische Eigenschaften, die denen von Knetwerkstoffen nahe kommen
- Große Auswahl an Metallen, einschließlich rostfreiem Stahl, Werkzeugstahl und Superlegierungen
- Ermöglicht die Konsolidierung von Teilen in einzelne Komponenten
- Niedrige Stückkosten durch hohe Stückzahlen
- Konsistenz und Wiederholbarkeit durch automatisierte Prozesse
Die MIM-Technologie ist ideal für kleine, komplexe Teile wie medizinische Geräte, Waffenteile, Uhrenteile und Automobilteile, die Präzision, Festigkeit, Wirtschaftlichkeit und Massenproduktion erfordern.
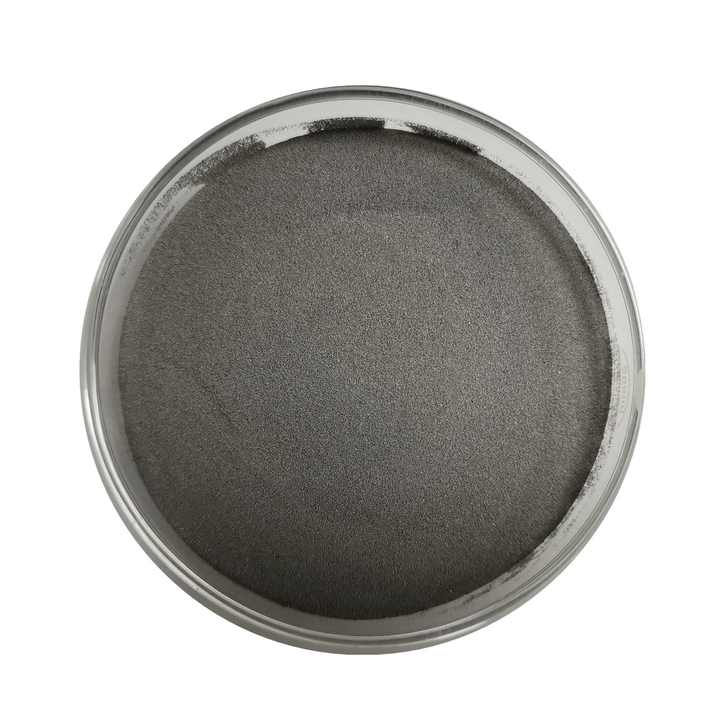
Anwendungen und Einsatzmöglichkeiten der MIM-Technologie
Die MIM-Technologie wird in verschiedenen Branchen eingesetzt, um kleine, hochpräzise Metallteile effizient und in großen Mengen herzustellen. Hier sind einige der wichtigsten Anwendungsbereiche und Einsatzmöglichkeiten der MIM-Technologie:
Industrie | Anwendungen und Einsatzmöglichkeiten |
---|---|
Medizin und Zahnmedizin | Chirurgische Instrumente, Zahnimplantate, orthopädische Implantate, Katheterkomponenten, Nadelkanülen, Skalpellgriffe, Zangen, Klemmen, chirurgische Befestigungselemente, wiederverwendbare chirurgische Instrumente |
Schusswaffen und Verteidigung | Abzüge, Hämmer, Sicherungen, Auswerfer, Magazine, verbrauchte Hülsen, Geschosse, Gefechtskopfkomponenten |
Automobilindustrie | Kraftstoffsystemkomponenten, Ölpumpenzahnräder, Laufräder, Ventile, Turboladerteile, Elektronikteile, Lenkungs-/Getriebeteile |
Luft- und Raumfahrt | Turbinenschaufeln, Laufräder, Getriebezähne, Buchsen, Pumpenkomponenten, Motorteile |
Konsumgüter | Uhrenteile, Schmuckteile, Besteck, Scheren, Rasiermesser, Handwerkzeuge, Teile von Reißverschlüssen |
Industrielle Hardware | Knöpfe, Beschläge, Verschlüsse, Steckdosen, Verbinder, Sprinkler, Düsen |
Elektronik | Steckverbinder, Schalter, Mikromotoren, Mikrozahnräder, Abschirmungsmasken, Induktoren, Magnetrotoren |
** Vorteile von MIM für spezifische Anwendungen**
- Präzision: Ideal für Miniaturteile wie medizinische Geräte oder Uhrenteile mit komplizierter Geometrie.
- Festigkeit: Geeignet für Bauteile, die eine hohe Festigkeit erfordern, wie z. B. Turbolader für Kraftfahrzeuge und Abzüge für Schusswaffen.
- Verschleißbeständigkeit: MIM-Teile aus Werkzeugstahllegierungen haben eine ausgezeichnete Verschleißfestigkeit für eine lange Lebensdauer.
- Korrosionsbeständigkeit: MIM-Teile aus rostfreiem Stahl sind korrosionsbeständig für wiederverwendbare chirurgische Werkzeuge, Implantate usw.
- Hohe Härte: MIM kann Teile mit einer Härte von über 40 HRC herstellen, z. B. Schneidwaren, Werkzeuge, Matrizen usw.
- Elektrische Eigenschaften: MIM wird zur Herstellung von weichmagnetischen Komponenten wie Induktoren, Motorrotoren usw. verwendet.
- Kosteneffektiv: Hohe Stückzahlen reduzieren die Teilekosten im Vergleich zur maschinellen Bearbeitung erheblich.
Leitfäden für MIM-Ausrüstung und -Werkzeuge
Zu den wichtigsten Ausrüstungen für den MIM-Prozess gehören Spritzgießmaschinen, Entbinderungs- und Sinteröfen. Hier ist ein Überblick:
Ausrüstung | Zweck | Überlegungen |
---|---|---|
Spritzgießmaschine | Einspritzen des MIM-Rohmaterials in die Formhohlräume unter Hitze und Druck | Schließkraft, Einspritzgeschwindigkeit und Druckkapazität, Präzision und Wiederholbarkeit, Steuerung und Automatisierungsfunktionen. |
Ofen zur Bindemittelentfernung | Thermisches oder chemisches Entfernen des Binders von Formteilen | Temperaturbereich, Atmosphärensteuerung, Ladekapazität, Gleichmäßigkeit der Entbinderung. |
Sinterofen | Verdichten der entbundenen braunen Teile durch Erhitzen bis nahe an den Schmelzpunkt | Temperaturbereich, Atmosphärensteuerung, Gleichmäßigkeit der Erwärmung, Chargenkapazität, bevorzugt vollautomatisch. |
Formen und Werkzeugbau | Geformte Kavitäten, um das MIM-Rohmaterial in die gewünschte Geometrie zu bringen | Sie halten dem Druck und den Temperaturen beim Formen stand, sind präzisionsgefertigt, haben eine gute Oberflächengüte und ermöglichen eine schnelle Erwärmung/Abkühlung. |
Futtermittel-Ausrüstung | Mischen des Metallpulvers und des Bindemittels zu einem homogenen MIM-Feedstock | Mischer, Temperaturregler, Granulatoren. |
Sekundäre Verarbeitung | Zusätzliche Schritte wie Bearbeitung, Fügen, Oberflächenbehandlung | Je nach Bedarf des Teils, wie CNC-Bearbeitung, Schweißen, Erodieren, Beschichtung. |
Qualitätskontrolle | Prüfung der Eigenschaften des Ausgangsmaterials und der gesinterten Teile | Pulvermorphologie, Dichte, Fließgeschwindigkeit, Viskositätsanalysegeräte, mechanische Prüfgeräte. |
Sicherheitsausrüstung | Sichere Handhabung feiner Pulver | Handschuhe, Atemschutzmasken, Staubabsaugsysteme. |
Design- und Leistungsstandards
- ISO 21227 - Pulver für das Metall-Spritzgießen
- ASTM F2885 - Metall-Spritzgießverfahren
- MPIF 35 - Normen für MIM-Rohstoffe
- ASTM E2781 - Konstruktion von MIM-Zugprüfkörpern
- ISO 2740 - Sintermetall-Spritzgussteile
Kostenaufschlüsselung
Die typische Kostenverteilung in der MIM-Produktion ist:
- Rohstoffe (Pulver + Bindemittel): 50-60%
- Herstellung (Gießen + Entbindern + Sintern): 25-35%
- Sekundäre Verarbeitung: 5-10%
- Qualitätskontrolle: 2-5%
- Technik (F&E, Konstruktion): 2-5%
Lieferanten und Preisgestaltung
Hier finden Sie einige weltweit führende Anbieter von MIM-Ausrüstung und deren Preisklassen:
Anbieter | Produktkategorie | Preisspanne |
---|---|---|
ARBURG | Spritzgießmaschinen | $100,000 – $500,000 |
Indisch-US-MIM | MIM-Rohstoffe und Dienstleistungen | $5 - $50 pro Kg |
Elnik | Entbinderungs- und Sinterungsöfen | $50,000 – $1,000,000 |
FineMIM | End-to-End-MIM-Produktion | $0.5 - $5 pro Teil |
Parmatech | Metallpulver Zerstäubung | $250,000 – $1,000,000 |
Meridian-Technologien | Werkzeug- und Formenbau | $5,000 – $100,000 |
Installation, Betrieb und Wartung
MIM ist ein automatisiertes Verfahren, das jedoch für eine optimale Leistung eine sorgfältige Installation, Bedienung und Wartung erfordert:
Tätigkeit | Einzelheiten |
---|---|
Einrichtung | Präzises Ausrichten von Spritzgießmaschinen und -formen. Kalibrieren von Temperaturreglern. Probelauf mit Versuchschargen. |
Operation | Sicherstellung der Qualitätskontrolle des Ausgangsmaterials gemäß den Normen. Erreichen von Prozessparametern wie Einspritzdruck, Temperatur und Geschwindigkeit. |
Wartung | Planung der vorbeugenden Wartung von Zylindern, Schnecken und Formen für Formmaschinen. Aufrechterhaltung der Atmosphäre des Entbinderungsofens. Kalibrieren von Instrumenten. |
Reinigung | Befolgen Sie die SOPs für die Reinigung der Maschinentrommel nach den Läufen. Sicherstellen, dass sich kein Pulver im Ofen oder in den Kanälen ansammelt. Formenreinigung mit den vorgesehenen Medien. |
Sicherheit | Beim Umgang mit feinen Pulvern ist persönliche Schutzausrüstung zu tragen. Ordnungsgemäße Entsorgung von chemischen Bindemitteln. Den Ofen vor der Wartung abkühlen lassen. |
Ausbildung | Schulung des Bedienpersonals von Maschinen und Öfen in den Verfahren. Durchführung von Auffrischungskursen zu Sicherheit und Wartung. |
Optimierung | Passen Sie die Prozessparameter an, bis sich die Teilequalität innerhalb der Spezifikationen stabilisiert. Führen Sie detaillierte Prozessaufzeichnungen. |
Typische Wartungsaktivitäten und Häufigkeit
Tätigkeit | Frequenz |
---|---|
Reinigung der Düsen von Spritzgießmaschinen | Nach jeder Charge |
Polieren von Formen | Wöchentlich |
Maschinelle Laufreinigung | Monatlich |
Kontrolle der Ofenatmosphäre bei der Bindemittelentfernung | Monatlich |
Kalibrierung des Thermoelementes des Sinterofens | 6 Monate |
Studien zum Formfluss | Jährlich |
Wie man einen MIM-Lieferanten auswählt
Die Wahl eines kompetenten MIM-Lieferanten ist entscheidend für die rechtzeitige Lieferung qualitativ hochwertiger Teile zu angemessenen Kosten. Hier sind wichtige Faktoren zu berücksichtigen:
Faktor | Kriterien |
---|---|
Technisches Leistungsvermögen | Moderne Ausrüstung, langjährige Erfahrung, technisches Know-how |
Material-Optionen | Verschiedene Materialien wie rostfreier Stahl, Werkzeugstahl, Wolframlegierungen |
Sekundäre Verarbeitung | Eigene Bearbeitungs-, Füge- und Beschichtungsanlagen |
Qualitätssysteme | ISO 9001-Zertifizierung, Qualitätskontrolle und Prüfverfahren |
Produktionskapazität | Hohe Produktionskapazität für Stabilität |
Vorlaufzeit | Schnelle Durchlaufzeit vom Entwurf bis zur Lieferung |
Standort | Geografische Nähe für eine effiziente Logistik |
Kosten | Preismodell - Preisgestaltung pro Teil bevorzugt |
Kundenbetreuung | Reaktionsfähigkeit bei Anfragen, technische Unterstützung, Projektmanagement |
Fragen an potenzielle MIM-Lieferanten
- Mit welchen Materialien und Teilegrößen haben Sie Erfahrung?
- Bieten Sie Sekundärverarbeitung wie Bearbeitung oder Beschichtung an?
- Welche Qualitätszertifizierungen und Prüfverfahren werden angewandt?
- Wie wird mit empfindlichen Materialien wie Titanlegierungen oder Wolframkarbiden umgegangen?
- Welche Produktionsmengen können Sie monatlich zuverlässig liefern?
- Wie wird der Ausschuss minimiert und die Ausbeute maximiert?
- Wie groß ist die Variabilität von Teil zu Teil in Bezug auf Abmessungen und Eigenschaften?
- Wie wird die Designoptimierung für das MIM-Verfahren durchgeführt?
- Welche Qualitätsberichte und Kontrollkarten werden zur Verfügung gestellt?
Vergleich von MIM mit anderen Prozessen
Vergleich zwischen MIM und anderen Metallherstellungsverfahren:
Prozess | Vorteile | Benachteiligungen |
---|---|---|
MIM | Komplexe Geometrien, Massenproduktion, endkonturnahe Form, große Auswahl an Materialien | Vorabinvestitionen in Werkzeuge, Größenbeschränkungen |
CNC-Bearbeitung | Materialflexibilität, schnelle Herstellung von Prototypen | Begrenzte Komplexität, geringere Mengen |
Metallgießen | Niedrige Teilekosten, hohe Stückzahlen | Formale Einschränkungen, geringere Festigkeit |
Stanzen von Metall | Hohe Geschwindigkeit, hohe Stückzahlen, niedrige Kosten | Nur für 2D-Geometrien geeignet |
3D-Druck | Gestaltungsfreiheit, schnelles Prototyping | Geringere Festigkeit, höhere Kosten, begrenzte Größen und Materialien |
Vorteile von MIM gegenüber der maschinellen Bearbeitung
- Höhere Materialausnutzung bei annähernder Nettoform
- Keine teure Bearbeitung für komplexe Formen
- Hervorragende mechanische Eigenschaften
- Geringere Werkzeugkosten im Vergleich zur Bearbeitung von Werkzeugen
- Automatisierter Prozess ermöglicht Massenproduktion
- Bessere Oberflächenqualität möglich
Vorteile von MIM gegenüber Metallguss
- Bessere Maßhaltigkeit und Oberflächengüte
- Weniger Defekte wie Porosität im Vergleich zu Gussteilen
- Isotrope Eigenschaften im Gegensatz zum gerichteten Gießen
- Geringe bis keine Grate oder Öffnungen im Gegensatz zu Gussteilen
- Keine schmelzbedingten Reaktionen oder Veränderungen in der Zusammensetzung
- Kerne und Hinterschneidungen im Gegensatz zum Guss möglich
- Vielfältige Materialoptionen über Gusslegierungen hinaus
- Konsistenz der Eigenschaften mit Pulvermetallurgie
Grenzen von MIM gegenüber CNC-Bearbeitung
- Größe begrenzt durch die Kapazität der Spritzgießmaschine
- Mehr Vorlaufzeit und Kosten für die Werkzeugherstellung
- Enge Toleranzen +/- 0,5% gegenüber +/- 0,1% bei CNC-Bearbeitung
- Geometriebeschränkungen vs. uneingeschränkte Bearbeitung
- Geringere maximal erreichbare Härte im Vergleich zur maschinellen Bearbeitung
- Sekundäre Bearbeitung oft noch erforderlich, um Toleranzen zu erreichen
Wann man MIM nicht verwenden sollte
- Sehr große Teile, die die Kapazität der MIM-Anlage übersteigen
- Teile, die extrem enge Toleranzen unter 0,5% erfordern
- Anwendungen, die eine Oberflächenhärte von über 50 HRC erfordern
- Produkte mit sehr geringem Volumenbedarf
- Bauteile mit extremen Seitenverhältnissen, die für das Gießen ungeeignet sind
- Wenn keine Zeit für die Designoptimierung für den MIM-Prozess bleibt
- Kostensensitive Anwendungen mit billigeren Herstellungsoptionen
Überlegungen zur MIM-Konstruktion und -Modellierung
Die richtige Konstruktion von Bauteilen und Rohstoffen ist für MIM entscheidend, um die gewünschten Eigenschaften und Leistungen zu erzielen. Hier sind die wichtigsten Überlegungen zum Design:
Teil Entwurfsphase
- Optimierung der Wandstärken für eine gleichmäßige Formfüllung beim Einspritzen
- Großzügige Innenradien und Ausrundungen erleichtern das Befüllen
- Vermeiden Sie starke Querschnittsveränderungen entlang des Fließweges
- Entwerfen Sie geeignete Formangüsse und Angüsse für geeignete Fließmuster
- Hinzufügen von Verstärkungsrippen und Zwickeln zur Vermeidung von Durchbiegung oder Verformung
- Berücksichtigung der Schrumpfung des Teils während des Sinterns in den ursprünglichen Abmessungen
- Entwicklung von Prototypformen zur Designvalidierung vor der vollständigen Produktion
Entwicklung von Rohstoffen
- Anpassung der Viskosität des Ausgangsmaterials an die Komplexität der Form bei den Formgebungstemperaturen
- Sicherstellen einer ausreichenden Pulverladung für die gewünschte Sinterdichte
- Auswahl geeigneter Bindemittelkomponenten und des Pulververhältnisses für die Mischbarkeit
- Optimierung der Partikelgrößenverteilung für die Packungsdichte des Pulvers
- Anpassung der Rohstoffrezepturen für eine fehlerfreie Bindemittelentfernung
- Validierung der Eigenschaften des Rohmaterials durch Formfließsimulationen
- Testen Sie mehrere Iterationen von Rohstoffen, um eine vollständige Formbarkeit zu erreichen.
Simulation und Modellierung
- Modellierung des Formflusses zur Optimierung von Anschnittstellen und Angusskanälen
- Strukturelle FEA zur Vorhersage von Verzug und zur Optimierung der Teilegeometrie
- CFD-Simulationen für gleichmäßige Bindemittelentfernung und Sinterung
- Thermische Modellierung zur Minimierung von Eigenspannungen
- Mechanische Modellierung zur Maximierung von Stärke und Leistung
- Prozessmodellierungssoftware zur Untersuchung von Wechselwirkungen zwischen Parametern
- Experimentelle Validierung von Software-Vorhersagen durch Prototyp-Formen
Wichtige Ergebnisse der Modellierung
- Formfüllzeit, Viskosität des Ausgangsmaterials, Fließfronttemperatur
- Vorhersage von Schweißnähten, Lufteinschlüssen und anderen Formteilfehlern
- Räumliche Bindemittelgehalts-, Temperatur- und Auflösungsgradienten
- Sintergeschwindigkeit, Dichtegradienten, Schrumpfung, Verzugsentwicklung
- Eigenspannungsverteilung, Heißriss und Rissabschätzung
- Mechanische Festigkeit, Ermüdungslebensdauer, Schadenstoleranzanalyse
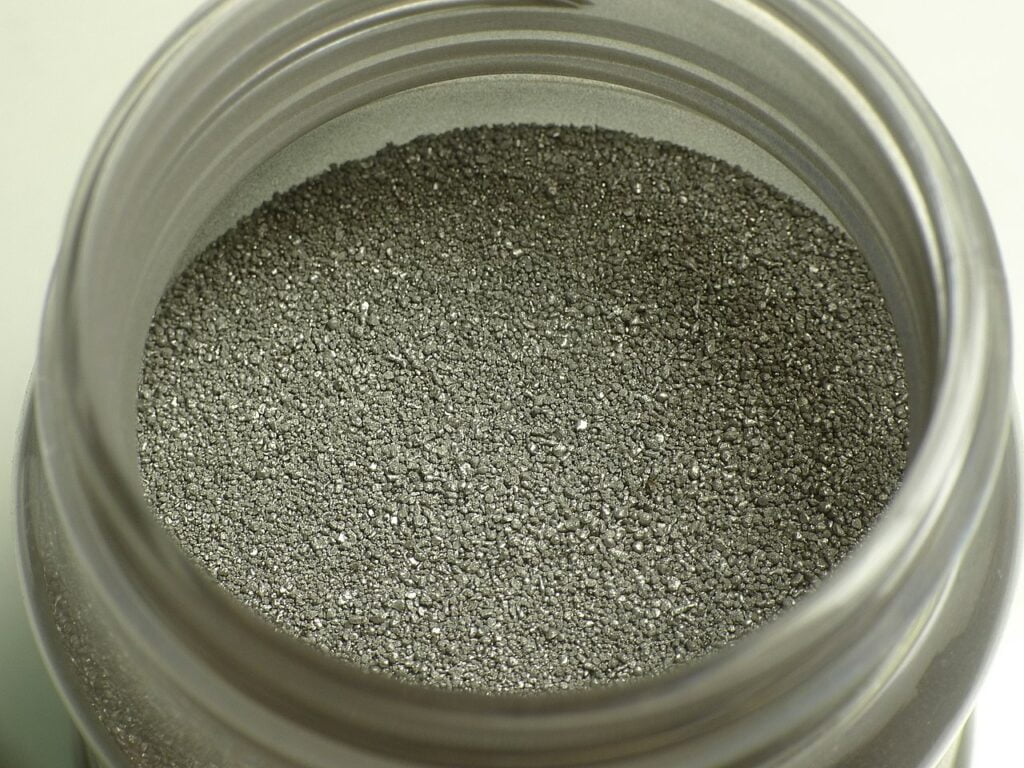
MIM-Fehler und Methoden zur Schadensbegrenzung
Defekte können bei MIM-Bauteilen aufgrund von nicht optimierten Ausgangsmaterialien, Formparametern oder Ofenbedingungen auftreten. Hier sind häufige MIM-Defekte und Methoden zur Abhilfe:
Defekt | Grundlegende Ursachen | Methoden zur Schadensbegrenzung |
---|---|---|
Oberflächenfehler | Niedrige Werkzeugtemperatur, hohe Reibung, Bindemittelkomponenten | Polieren der Form optimieren, Formtrennmittel verwenden, Formtemperatur schrittweise senken |
Schweißlinien | Unerwünschte Rohstoffflussfronten | Optimierung der Anschnitt- und Angusskonstruktion durch Modellierung zur Vermeidung von Schweißnähten |
Verzug | Ungleichmäßige Erwärmung im Ofen, Eigenspannungen | Strukturelle Optimierung, Spannungsabbau vor dem Sintern, optimierte Ofeneinstellungen |
Risse | Schnelle Sinterung, hoher Bindemittelgehalt, steiler Temperaturgradient | Niedrigere Heizrate, Optimierung des Bindemittelsystems, strukturelle Umgestaltung |
Porosität | Geringe Pulvermenge im Ausgangsmaterial, schlechte Durchmischung | Erhöhung des Pulveranteils im Ausgangsmaterial, Verbesserung des Mischprozesses |
Abweichung der Abmessungen | Ungleichmäßige Schrumpfung, Formenverschleiß, Dichtegradienten | Statistische Prozesskontrolle, Formenwartung, Optimierung von Entbinderung und Sinterung |
Verunreinigung | Schlechte Handhabung, Kontrolle der Ofenatmosphäre | Angemessene PSA, Verbesserung der Luftfilter, Vermeidung von Kreuzkontaminationen in Ofenchargen |
Unvollständige Befüllung | Hohe Formtemperatur, hohe Viskosität | Erhöhen Sie die Temperatur der Form und des Rohmaterials, verwenden Sie Bindemittel mit niedrigerer Viskosität. |
Daten und Trends der MIM-Industrie
MIM Globale Marktgröße
Der globale MIM-Markt wurde im Jahr 2022 auf 1,5 Milliarden USD geschätzt und wird bis 2030 voraussichtlich 3,1 Milliarden USD erreichen, mit einer CAGR von 8,7%, angetrieben durch die Nachfrage aus dem Gesundheitswesen, der Automobil- und der Luftfahrtindustrie.
Wachstumstreiber der Branche
- Leichtbautrends in den Sektoren Automobil, Luft- und Raumfahrt, Elektronik
- Nachfrage nach kleinen, komplexen Metallteilen in medizinischen Geräten
- Mit einer breiteren Palette von MIM-fähigen Materialien praktikabler
- Automatisierung senkt Produktionskosten
- Wachstum bei der Herstellung von Präzisionskomponenten
- Zunehmende Verbreitung in neuen Anwendungen wie der Uhrmacherei
Prognostizierte CAGR nach Regionen
- Asien-Pazifik: 9,3% CAGR
- Europa: 10,2% CAGR
- Nordamerika: 7,6% CAGR
- Rest der Welt: 7,9% CAGR
Anteil der MIM-Teile nach Industriezweigen
- Verbraucherprodukte: 22%
- Kraftfahrzeug: 21%
- Schusswaffen: 15%
- Medizinisch: 14%
- Industriell: 13%
- Luft- und Raumfahrt: 8%
- Andere: 7%
Entwicklungstrends der MIM-Technologie
- Neue Bindemittelsysteme zur Verringerung von Fehlern und für komplexe Geometrien
- Neuartige Rohstoffformulierungen für bessere Pulverladung und Sinterung
- Multimaterial-MIM, bei dem verschiedene Pulver in einem Bauteil kombiniert werden
- Automatisierung der Nachbearbeitung wie Bearbeitung, Fügen, Gewindeschneiden usw.
- Hybride MIM + Additive Fertigungstechniken
- Neue Erhitzungsmethoden wie Mikrowellensintern für eine schnellere Verarbeitung
- Integrierte Simulationen, die mehrere physikalische und fertigungstechnische Schritte kombinieren
- Verstärkte Einführung von Qualitätsmanagementsystemen
Zusammenfassung
Die wichtigsten Erkenntnisse:
- MIM ermöglicht die Großserienproduktion komplizierter Metallteile durch die Kombination von Spritzguss und Pulvermetallurgie.
- Geeignet für kleine, komplexe Hochpräzisionsteile in der Medizin-, Waffen-, Automobil-, Luft- und Raumfahrt- und Konsumgüterindustrie.
- Zu den Vorteilen gehören eine nahezu perfekte Form, eine große Auswahl an Materialien und gute mechanische Eigenschaften, die denen von Knetwerkstoffen nahe kommen.
- Beinhaltet das Formen des Ausgangsmaterials, das Entbindern und die Sinterung mit Hilfe spezieller Geräte.
- Erfordert Fachwissen in den Bereichen Teilekonstruktion, Entwicklung von Rohstoffen, Prozessmodellierung, Fehlerkontrolle und Qualitätsmanagement.
- Prognostiziertes globales Wachstum von 8,7% CAGR aufgrund der Nachfrage in allen Branchen.
- Laufende technologische Entwicklungen für schnellere Verarbeitung, mehr Materialien, stärkere Automatisierung und verbesserte Teilequalität.
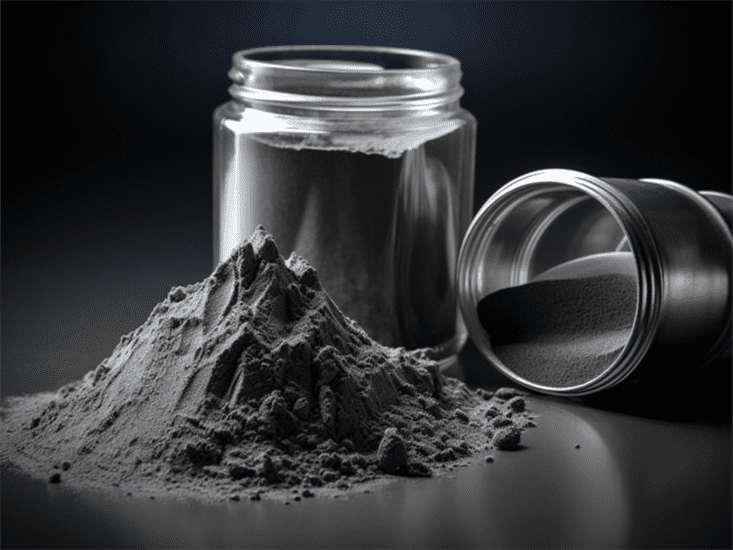
FAQs
F: Was sind die wichtigsten Vorteile der MIM-Technologie?
A: Die wichtigsten Vorteile von MIM sind:
- Fähigkeit zur Herstellung kleiner, komplexer Geometrien, die durch Bearbeitung oder Gießen nicht möglich sind
- Herstellung von endkonturnahen Formen, die zu
F: Was ist die typische Toleranzfähigkeit von MIM?
A: Mit MIM können im Allgemeinen Toleranzen von +/- 0,5% erreicht werden, obwohl für einige Geometrien +/- 0,3% möglich sind und für engere Toleranzen eine maschinelle Bearbeitung erforderlich sein kann.
F: Welche Größe von Teilen kann mit MIM hergestellt werden?
A: MIM kann Teile von 0,1 Gramm bis zu einer Masse von etwa 250 Gramm herstellen. Größere Teile sind möglich, aber aufgrund der begrenzten Größe der Formmaschine eine Herausforderung.
F: Was ist der Unterschied zwischen MIM und Kunststoffspritzgießen?
A: Für beide Verfahren werden zwar Spritzgießmaschinen verwendet, aber mit MIM können Metallteile hergestellt werden, während Kunststoffe eine viel geringere Festigkeit aufweisen. MIM hat jedoch niedrigere Produktionsraten und höhere Kosten als das Kunststoffspritzgießen.
F: Welche Wärmebehandlung wird bei MIM angewendet?
A: Der Sinterprozess bei MIM umfasst das Erhitzen des Metallpulvers bis fast zum Schmelzpunkt, so dass normalerweise keine weitere Wärmebehandlung erforderlich ist. Zusätzliche Wärmebehandlungen können je nach Bedarf durchgeführt werden, um die Eigenschaften zu verändern.
F: Welche Materialien können bei MIM verwendet werden?
A: Eine breite Palette von Werkstoffen ist für das MIM geeignet, darunter rostfreie Stähle, Werkzeugstähle, Superlegierungen, Titan, schwere Wolframlegierungen und magnetische Legierungen. Die Entwicklung neuer Materialien ist ein wichtiger Forschungsbereich beim MIM.
F: Was ist der Unterschied zwischen MIM und 3D-Druck von Metall?
A: MIM kann höhere Stückzahlen mit besserer Oberflächengüte und besseren mechanischen Eigenschaften herstellen. Der 3D-Druck bietet jedoch eine größere Designfreiheit und eine kürzere Markteinführungszeit für Prototypen oder kundenspezifische Teile.
Teilen auf
MET3DP Technology Co., LTD ist ein führender Anbieter von additiven Fertigungslösungen mit Hauptsitz in Qingdao, China. Unser Unternehmen ist spezialisiert auf 3D-Druckgeräte und Hochleistungsmetallpulver für industrielle Anwendungen.
Fragen Sie an, um den besten Preis und eine maßgeschneiderte Lösung für Ihr Unternehmen zu erhalten!
Verwandte Artikel
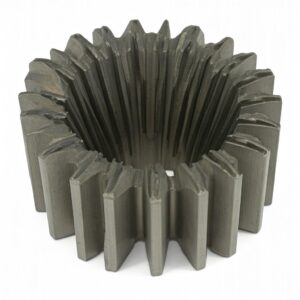
Hochleistungs-Düsenschaufelsegmente: Revolutionierung der Turbineneffizienz mit 3D-Metalldruck
Mehr lesen "Über Met3DP
Aktuelles Update
Unser Produkt
KONTAKT US
Haben Sie Fragen? Senden Sie uns jetzt eine Nachricht! Wir werden Ihre Anfrage mit einem ganzen Team nach Erhalt Ihrer Nachricht bearbeiten.
Holen Sie sich Metal3DP's
Produkt-Broschüre
Erhalten Sie die neuesten Produkte und Preislisten