Langlebige Ventilkörper über Metall AM für den Einsatz in der Schifffahrt
Inhaltsübersicht
Langlebige Ventilkörper über Metall AM für den Einsatz in der Schifffahrt
Die maritime Industrie arbeitet unter einigen der anspruchsvollsten Bedingungen der Welt. Durch die ständige Einwirkung von korrosivem Salzwasser, extremen Temperaturen, hohem Druck und erheblicher mechanischer Belastung wird jedes Bauteil immens beansprucht. Zu den wichtigsten Elementen, die die Betriebssicherheit und Effizienz gewährleisten, gehören Ventilkörper. Diese unverzichtbaren Komponenten regeln den Flüssigkeitsdurchfluss in lebenswichtigen Systemen, vom Ballastwassermanagement und der Motorkühlung bis hin zu Entsalzungsanlagen und Hydrauliksteuerungen. Bei der Herstellung von Ventilkörpern, die traditionell durch Gießen oder Schmieden hergestellt werden, stellen lange Vorlaufzeiten, Konstruktionszwänge und Materialbeschränkungen eine Herausforderung dar, insbesondere wenn es um komplexe Geometrien oder spezielle Legierungen geht, die für raue Meeresumgebungen erforderlich sind. Mit dem Aufkommen der additiven Fertigung von Metallen (AM), allgemein bekannt als Metall 3D-Druck, revolutioniert die Art und Weise, wie diese kritischen Teile hergestellt werden, und bietet beispiellose Vorteile in Bezug auf Designfreiheit, Materialleistung und Flexibilität in der Lieferkette für maritime technische Lösungen.
Einführung: Verbesserter Schiffsbetrieb mit AM-Ventilkörpern
Ventilgehäuse sind das Grundgerüst von Ventilen und enthalten die inneren Komponenten (wie Schieber, Kugeln oder Kegel), die den Durchfluss von Flüssigkeiten oder Gasen steuern. In der Schifffahrt ist ihre Integrität von größter Bedeutung. Ein Ausfall kann zu Systemabschaltungen, kostspieligen Reparaturen, Umweltschäden oder sogar zu katastrophalen Sicherheitsvorfällen führen. Die verwendeten Materialien müssen der starken Korrosion durch Meerwasser standhalten, die häufig durch Schadstoffe, schwankende Temperaturen und mikrobielle Aktivität noch verstärkt wird. Außerdem erfordern die inneren Drücke und Belastungen eine hohe mechanische Festigkeit und Haltbarkeit.
Traditionelle Herstellungsverfahren wie Sandguss, Feinguss oder Schmieden haben sich in der Industrie seit Jahrzehnten bewährt. Sie eignen sich zwar für die Massenproduktion von Standarddesigns, sind aber oft mit Kosten verbunden:
- Lange Vorlaufzeiten: Die Erstellung von Werkzeugen (Gussformen, Matrizen) kann Wochen oder Monate dauern und die Produktion verzögern, insbesondere bei kundenspezifischen Teilen oder Kleinserien.
- Beschränkungen des Designs: Bestimmte komplexe Innengeometrien, optimierte Fließwege oder integrierte Merkmale lassen sich mit subtraktiven oder formgebenden Verfahren nur schwer oder gar nicht kostengünstig realisieren.
- Materialabfälle: Bei der maschinellen Bearbeitung kann viel Abfallmaterial anfallen, was die Kosten und die Umweltbelastung erhöht.
- Komplexität der Lieferkette: Die Beschaffung spezieller Guss- oder Schmiedeteile, insbesondere für veraltete oder alte Systeme, kann schwierig und teuer sein und sich auf die Wartungs- und Reparaturpläne von Schiffsbetreibern und Schiffsdienstleistern auswirken.
Die additive Fertigung von Metallen bietet eine transformative Alternative. Dabei werden Teile Schicht für Schicht direkt aus digitalen Modellen unter Verwendung von Hochleistungsmetallpulvern hergestellt, 3D-Druck von Metall bietet Lösungen für viele dieser traditionellen Probleme. Diese Technologie ermöglicht die Herstellung von hochkomplexen, optimierten und langlebigen Ventilgehäusen, die speziell auf die unnachgiebigen Bedingungen der Schifffahrt und des Offshore-Bereichs zugeschnitten sind. Unternehmen wie Met3dp, die auf jahrzehntelange Erfahrung in der Metall-AM zurückgreifen können, stehen an der Spitze dieses Wandels und bieten nicht nur fortschrittliche Druckanlagen, sondern auch spezielle Metallpulver, die für Schiffsanwendungen entscheidend sind. Das in Qingdao, China, ansässige Unternehmen Met3dp nutzt branchenführende Technologien, um umfassende AM-Lösungen zu liefern, die es dem maritimen Sektor ermöglichen, die betriebliche Zuverlässigkeit und Effizienz durch die Fertigung der nächsten Generation zu verbessern.
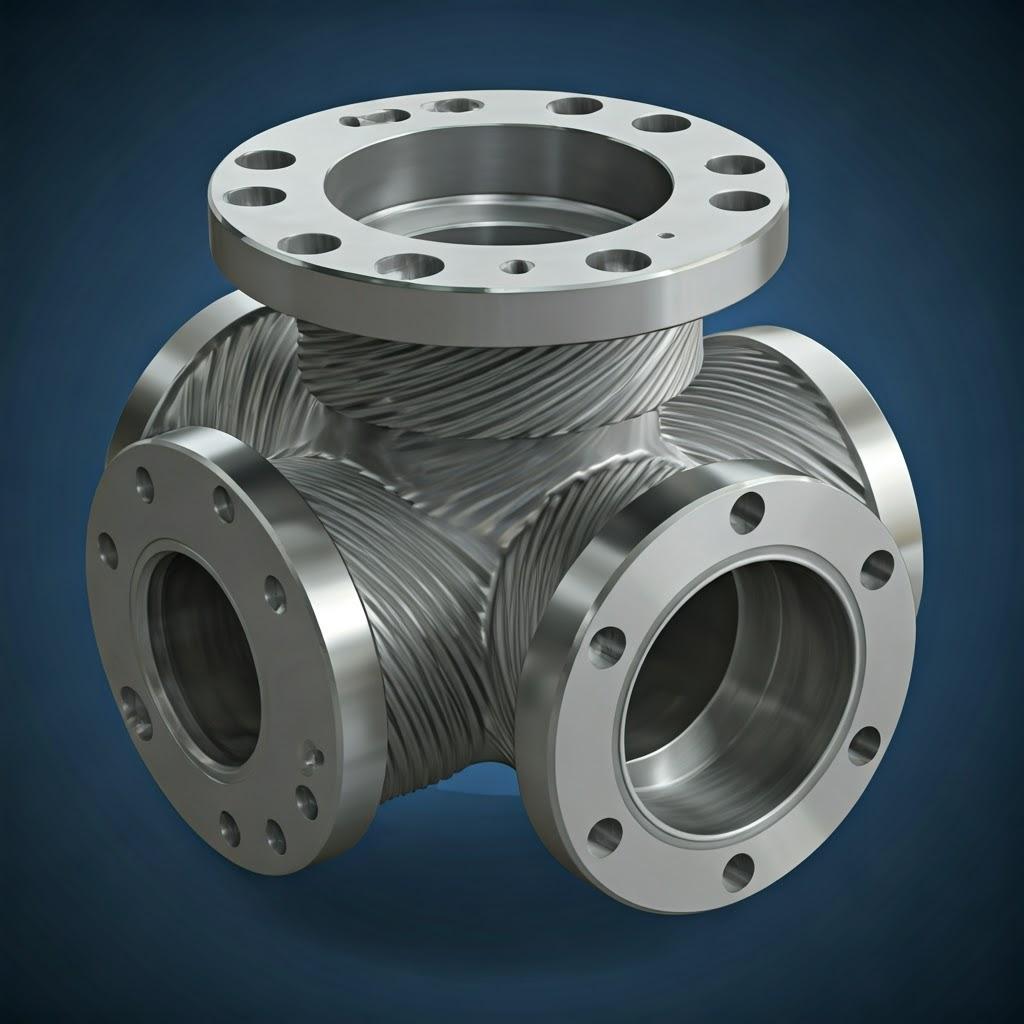
Marine-Ventilgehäuse-Anwendungen: Wo Langlebigkeit auf Nachfrage trifft
Der Anwendungsbereich von Ventilkörpern in der Schifffahrtsindustrie ist groß und spiegelt die Komplexität moderner Schiffe und Offshore-Strukturen wider. Metal AM erweist sich als besonders wertvoll, wenn Leistung, Zuverlässigkeit und maßgeschneiderte Lösungen entscheidend sind. Zu den wichtigsten Anwendungsbereichen gehören:
- Schiffbau und Schiffsbetrieb:
- Ballastwasser-Bewirtschaftungssysteme (BWMS): Sie benötigen Ventile, die gegen unterschiedliche Wasserqualitäten und Behandlungschemikalien (z. B. Chlor, Ozon) beständig sind. AM ermöglicht optimierte Durchflusswege und die Integration von Sensoren in kompakte Konstruktionen. Materialien wie rostfreie Super-Duplex-Stähle (wie 254SMO) oder Nickel-Kupfer-Legierungen bieten eine hervorragende Korrosionsbeständigkeit.
- Seewasser-Kühlsysteme: Unverzichtbar für Motoren und Hilfsmaschinen. Die Ventilgehäuse müssen einem kontinuierlichen Seewasserfluss standhalten und erfordern eine hohe Beständigkeit gegen allgemeine Korrosion, Lochfraß und Spaltkorrosion. CuNi-Legierungen (z. B. CuNi30Mn1Fe) werden häufig wegen ihrer hervorragenden Beständigkeit gegen Biofouling und Seewasserkorrosion bevorzugt.
- Kraftstoff- und Schmierungssysteme: Es werden Ventile benötigt, die mit verschiedenen Kraftstoffarten und Ölen kompatibel sind und oft unter Druck stehen. Rostfreie Stähle wie 316L bieten ein gutes Gleichgewicht zwischen Korrosionsbeständigkeit und Festigkeit.
- Systeme zur Brandbekämpfung: Sie erfordern hohe Zuverlässigkeit und Beständigkeit gegen Korrosion durch stehendes Meerwasser. AM ermöglicht robuste Konstruktionen, in die Überwachungsfunktionen integriert werden können.
- Hydraulische Systeme: Der Betrieb von Kränen, Winden und Lenkanlagen erfordert hohe Drücke. AM kann Ventilkörper aus hochfesten Legierungen mit komplexen internen Kanälen herstellen, die für den Durchfluss von Hydraulikflüssigkeit optimiert sind.
- Offshore-Öl- und Gasplattformen:
- Produktions- und Prozesssysteme: Die Förderung von Erdöl, Erdgas und Produktionswasser erfordert Materialien, die gegen aggressive Chemikalien (H2S, CO2) und hohe Drücke/Temperaturen beständig sind. Mittels AM bedruckbare Speziallegierungen bieten maßgeschneiderte Lösungen.
- Unterwasser-Ausrüstung: Ventile, die tief unter Wasser eingesetzt werden, sind extremen Drücken, niedrigen Temperaturen und galvanischen Korrosionsrisiken ausgesetzt. AM ermöglicht die Herstellung äußerst zuverlässiger, kompakter Ventilkörper aus exotischen Legierungen, die für eine lange Lebensdauer an unzugänglichen Orten ausgelegt sind. Beschaffungsmanager für Offshore-Projekte schätzen die Möglichkeit, robuste, maßgeschneiderte Komponenten zu beziehen.
- Versorgungssysteme: Ähnlich wie die Systeme an Bord von Schiffen (Kühlung, Löschwasser), aber oft in größerem Umfang und unterliegt strengen Offshore-Vorschriften.
- Entsalzungsanlagen (schiffsgestützt und landgestützt in Meeresnähe):
- Umkehrosmose-Systeme (RO): Hochdruck-Seewasser erfordert extrem korrosionsbeständige Werkstoffe, um ein vorzeitiges Versagen zu verhindern. Superaustenitische oder Duplex-Edelstähle (wie 254SMO) sind von entscheidender Bedeutung, und AM erleichtert komplexe Verteiler- und Ventilkörperkonstruktionen, um den Durchfluss zu optimieren und den Druckabfall zu minimieren. Großabnehmer für Entsalzungsprojekte suchen nach zuverlässigen Lieferanten für diese wichtigen Komponenten.
- Anwendungen in der Marine:
- Militärschiffe erfordern hohe Stoßfestigkeit, geringe magnetische Permeabilität (in einigen Fällen) und extreme Zuverlässigkeit. AM bietet Wege zur Herstellung spezieller Ventilkörper, die den strengen Spezifikationen der Marine entsprechen und oft schwer zu bearbeitende Materialien erfordern.
Tabelle: Hauptanwendungsbereiche für AM-Ventilkörper in der Schifffahrt
Anwendungsbereich | Wichtige Systeme, die langlebige Ventile erfordern | Kritische Anforderungen | Potenzielle AM-Vorteile | Überlegungen zum Zielpublikum |
---|---|---|---|---|
Schiffbau/Betrieb | Ballastwasser, Seewasserkühlung, Kraftstoff, Feuer | Korrosionsbeständigkeit (Seewasser, Chemikalien), Verlässlichkeit | Optimierter Durchfluss, kompaktes Design, Materialauswahl | Schiffsbetreiber, Schiffswerften, Schiffszulieferer |
Offshore-Öl und Gas | Produktion, Unterwassersteuerung, Versorgungssysteme | Hoher Druck, chemische Beständigkeit, extreme Temperaturen | Komplexe Geometrien, hochfeste Legierungen, Zuverlässigkeit | Plattformbetreiber, EPC-Auftragnehmer, Unterwassertechniker. |
Entsalzung | Umkehrosmose, Vorbehandlung | Extreme Korrosionsbeständigkeit (Sole), hoher Druck | Optimierte Verteiler, Super Duplex/Austenitische Stähle | Anlagenplaner, Lieferanten für Wasseraufbereitung |
Marineschiffe | Alle kritischen Flüssigkeitssysteme | Schockresistenz, spezifische Signaturen, hohe Verlässlichkeit | Speziallegierungen, Sonderanfertigungen, Ersatzteile auf Abruf | Beschaffung für die Marine, Verteidigungsunternehmen |
In Blätter exportieren
Die Möglichkeit, Metall-3D-Druck zu verwenden, ermöglicht es Ingenieuren und Beschaffungsmanagern, Ventilkörper zu beschaffen, die für spezifische Herausforderungen innerhalb jeder Anwendung optimiert sind und die Grenzen von Standardkomponenten von der Stange überschreiten. Dies ist besonders wichtig für Upgrades, Nachrüstungen oder Situationen, die einzigartige Leistungsmerkmale erfordern.
Warum 3D-Metalldruck für Schiffsventilgehäuse? Vorteile gegenüber traditionellen Methoden
Der Einsatz von Metall-AM für die Herstellung von Schiffsventilgehäusen ist nicht nur ein neuartiger Ansatz, sondern bietet greifbare, überzeugende Vorteile gegenüber konventionellen Fertigungstechniken wie Gießen und Schmieden und erfüllt die wichtigsten Anforderungen der Branche in Bezug auf Leistung, Geschwindigkeit und Anpassung. Diese Vorteile kommen bei Ingenieuren, die nach besseren Designs suchen, und bei Beschaffungsmanagern, die nach zuverlässigen, effizienten Beschaffungslösungen suchen, sehr gut an.
- Unerreichte Gestaltungsfreiheit:
- Komplexe innere Geometrien: AM eignet sich hervorragend für die Herstellung komplizierter interner Kanäle, Strömungswege und Kammern, die beim Gießen (komplexe Kerne erforderlich) oder bei der maschinellen Bearbeitung (aufgrund der eingeschränkten Zugänglichkeit des Werkzeugs) nur schwer oder gar nicht zu realisieren sind. Dies ermöglicht hydrodynamisch optimierte Konstruktionen, die den Druckabfall reduzieren, Turbulenzen minimieren, Kavitation verhindern und den Gesamtwirkungsgrad von Ventilen verbessern.
- Topologie-Optimierung: Ingenieure können mithilfe von Software-Tools die Struktur des Ventilgehäuses optimieren, indem sie nur dort Material einsetzen, wo es benötigt wird, um bestimmten Belastungen und Drücken standzuhalten. Dies führt zu deutlich leichteren Komponenten ohne Einbußen bei der Festigkeit - ein entscheidender Faktor bei gewichtssensiblen Schiffsanwendungen.
- Teil Konsolidierung: Mehrere Komponenten, die zuvor zusammengebaut wurden (z. B. ein Ventilgehäuse und angrenzende Fittings oder Sensorhalterungen), können möglicherweise zu einem einzigen gedruckten Teil zusammengefasst werden. Dies verkürzt die Montagezeit, beseitigt potenzielle Leckstellen an den Verbindungsstellen und vereinfacht die Bestandsverwaltung.
- Integrierte Funktionen: Kühlkanäle, Sensoranschlüsse oder Befestigungselemente können während des Druckprozesses direkt in das Design des Ventilkörpers integriert werden.
- Beschleunigte Vorlaufzeiten und On-Demand-Produktion:
- Keine Werkzeuge erforderlich: Metall-AM umgeht den zeit- und kostenaufwändigen Schritt der Herstellung von Gussformen oder Gesenken. Die Produktion kann fast sofort nach Fertigstellung des digitalen Designs beginnen. Dies verkürzt die Vorlaufzeiten drastisch, insbesondere bei Prototypen, Sonderanfertigungen oder Kleinserien.
- Rapid Prototyping: Ingenieure können Entwürfe schnell wiederholen und Prototypen in einem Bruchteil der Zeit drucken und testen, die für herkömmliche Methoden benötigt wird. Dadurch wird der Entwicklungszyklus für neue Ventiltechnologien beschleunigt.
- Ersatzteile auf Abruf: Für alternde Schiffe oder Anlagen mit veralteten Teilen bietet Metal AM eine leistungsstarke Lösung. Anstatt nach seltenen Originalgussteilen zu suchen oder teure Reverse-Engineering- und Umrüstarbeiten durchzuführen, kann ein digitaler Scan eines vorhandenen Teils verwendet werden, um ein Ersatzteil auf Abruf zu drucken. Dadurch werden Ausfallzeiten minimiert und die Lebensdauer wichtiger Anlagen verlängert. Marinedienstleister und Schiffsbetreiber profitieren in hohem Maße von dieser Möglichkeit.
- Materialeffizienz und Abfallvermeidung:
- Additiv vs. Subtraktiv: AM baut Teile schichtweise auf, wobei nur das für das Bauteil selbst erforderliche Material verwendet wird (plus Stützstrukturen, die häufig wiederverwertbar sind). Dies steht in scharfem Kontrast zur subtraktiven Bearbeitung, bei der ein erheblicher Teil des ursprünglichen Materialblocks zu Abfallspänen wird. Die Handhabung des Pulvers erfordert zwar Sorgfalt, doch ist die Materialausnutzung im Allgemeinen viel höher.
- Optimierter Materialeinsatz: Die Optimierung der Topologie führt zwangsläufig dazu, dass bei gleicher oder besserer Leistung weniger Material verwendet wird, was zu Kosteneinsparungen und Nachhaltigkeit beiträgt.
- Verbesserte Materialeigenschaften und -auswahl:
- Spezialisierte Legierungen: Metall-AM kann eine breite Palette von Hochleistungslegierungen, die für die Schifffahrt von entscheidender Bedeutung sind, effektiv bearbeiten, darunter rostfreie Stähle (316L), Nickelbasislegierungen, Kupfer-Nickel-Legierungen (CuNi30Mn1Fe) und superaustenitische/duplexe rostfreie Stähle (254SMO). Einige Legierungen, die bekanntermaßen schwer zu gießen oder zu bearbeiten sind, lassen sich mit AM leichter verarbeiten. Met3dp beispielsweise stellt ein vielfältiges Portfolio an hochwertigen Metallpulvern her, die speziell für AM-Verfahren wie Selective Electron Beam Melting (SEBM) und Laser Powder Bed Fusion (LPBF) optimiert sind und optimale Materialeigenschaften gewährleisten.
- Feinkörnige Mikrostrukturen: Je nach AM-Verfahren und -Parametern kann die schnelle Erstarrung während des Drucks zu feinkörnigen Mikrostrukturen führen, die im Vergleich zu grobkörnigen Gussteilen möglicherweise bessere mechanische Eigenschaften wie Festigkeit und Ermüdungsbeständigkeit aufweisen.
- Maßgeschneiderte Korrosionsbeständigkeit: Die Möglichkeit, den Herstellungsprozess präzise zu steuern und optimale Legierungen wie 254SMO auszuwählen, ermöglicht die Herstellung von Ventilgehäusen mit außergewöhnlicher Beständigkeit gegen Lochfraß, Spaltkorrosion und allgemeine Korrosion in aggressiven, chloridreichen Umgebungen wie Meerwasser.
- Widerstandsfähigkeit der Lieferkette und digitale Bestandsaufnahme:
- Dezentralisierte Fertigung: Teile können potenziell näher am Ort des Bedarfs gedruckt werden, was die Versandkosten und die Abhängigkeit von langen, komplexen globalen Lieferketten verringert.
- Digitales Lagerhaus: Anstatt zahlreiche Varianten von Ventilgehäusen auf Lager zu haben, können Unternehmen eine digitale Bibliothek von Bauteildesigns führen. Die Komponenten können je nach Bedarf gedruckt werden, was die Lagerkosten und das Risiko der Veralterung reduziert. Beschaffungsmanager gewinnen Flexibilität bei der Beschaffung wichtiger Komponenten.
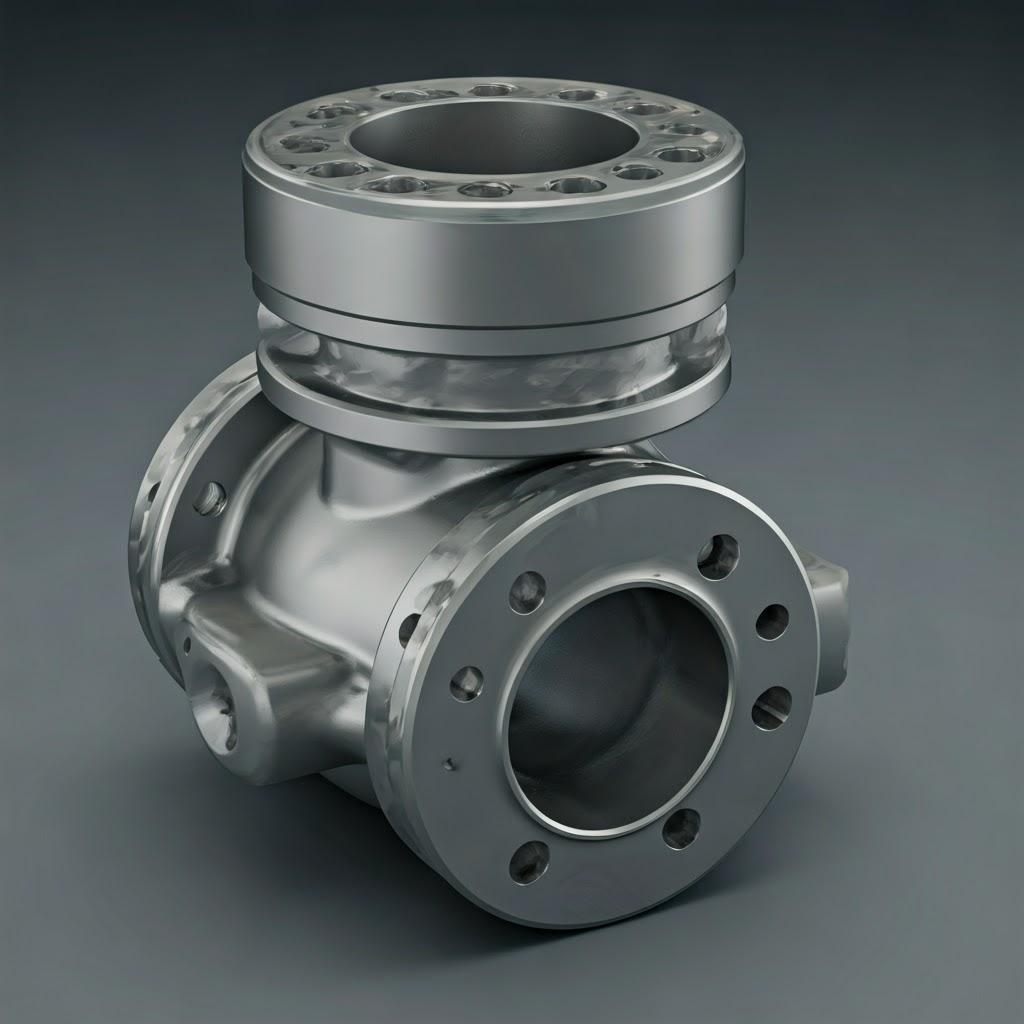
Tabelle: Metall-AM vs. traditionelle Fertigung für Schiffsventilgehäuse
Merkmal | Additive Fertigung von Metall (AM) | Traditionell (Gießen/Schmieden/Bearbeiten) | Vorteil für Marine AM |
---|---|---|---|
Gestaltungsfreiheit | Hoch (Komplexe interne Kanäle, Topologie opt.) | Mäßig bis gering (begrenzt durch Werkzeugbau/Bearbeitung) | Optimierte Leistung, Gewichtsreduzierung |
Vorlaufzeit | Kurz (Tage/Wochen - keine Werkzeuge) | Lang (Wochen/Monate - Werkzeugbau erforderlich) | Schnelleres Prototyping, Ersatzteile auf Abruf |
Werkzeugkosten | Keiner | Hoch (Gussformen, Matrizen) | Kostengünstig für kleine/mittlere Mengen |
Materialabfälle | Gering (Additivverfahren, Pulverrecycling) | Hoch (Zerspanungsschrott, Gusskanäle/Sprenger) | Kosteneinsparungen, Nachhaltigkeit |
Teil Konsolidierung | Hohes Potenzial | Geringes Potenzial | Weniger Montageaufwand, weniger Leckstellen |
Auswahl des Materials | Breite Palette, einschließlich schwer zu bearbeitender Legierungen | Für gängige Legierungen etabliert, einige Einschränkungen | Zugang zu optimalen Hochleistungsmaterialien |
Mindestbestellmenge | Niedrig (kostengünstig für Einzelteile oder kleine Chargen) | Hoch (oft erforderlich, um Werkzeugkosten zu amortisieren) | Flexibilität für kundenspezifische Teile und Ersatzteile |
Bestandsaufnahme | Potenzial des digitalen Lagers | Erfordert physische Lagerhaltung | Geringere Lagerhaltungskosten, weniger Veralterung |
In Blätter exportieren
Während herkömmliche Methoden weiterhin für die Großserienproduktion von Standardteilen geeignet sind, bietet Metall-AM überzeugende technische und logistische Vorteile für Schiffsventilkörper, die komplexe Designs, spezielle Materialien, schnelle Verfügbarkeit oder verbesserte Leistungsmerkmale erfordern. Die Zusammenarbeit mit einem erfahrenen AM-Anbieter wie Met3dp gewährleistet den Zugang zu den erforderlichen Technologien, Materialien und Fachkenntnissen, um diese Vorteile effektiv zu nutzen.
Die Auswahl der richtigen Legierungen: 316L, CuNi30Mn1Fe, 254SMO für Meeresumgebungen
Die Wahl des Werkstoffs ist wohl der wichtigste Faktor für den Erfolg und die Langlebigkeit eines Ventilgehäuses im Schiffsbetrieb. Der unerbittliche korrosive Angriff des Meerwassers in Verbindung mit den Betriebsbelastungen erfordert Werkstoffe mit spezifischen Eigenschaften. Die additive Fertigung von Metallen bietet die Flexibilität, mit fortschrittlichen Legierungen zu arbeiten, die für diese Herausforderungen perfekt geeignet sind. Zu den wichtigsten und empfohlenen Pulvern für Schiffsventilgehäuse gehören 316L-Edelstahl, CuNi30Mn1Fe (Kupfer-Nickel) und 254SMO (superaustenitischer Edelstahl). Für Ingenieure, die Komponenten entwerfen, und für Beschaffungsspezialisten, die zuverlässige Teile beschaffen, ist es wichtig, ihre einzigartigen Eigenschaften zu kennen.
- 316L-Edelstahl (austenitischer Edelstahl):
- Zusammensetzung: Hauptsächlich Eisen, mit viel Chrom (16-18%), Nickel (10-14%), Molybdän (2-3%) und wenig Kohlenstoff (<0,03%).
- Wichtige Eigenschaften:
- Gute allgemeine Korrosionsbeständigkeit: Das Chrom bildet eine passive Oxidschicht, die vor allgemeiner Korrosion schützt. Molybdän erhöht die Beständigkeit gegen Lochfraß und Spaltkorrosion, insbesondere in chloridhaltigen Umgebungen (wie z. B. Meerwasser, allerdings weniger beständig als Speziallegierungen).
- Ausgezeichnete Verformbarkeit und Schweißbarkeit: Relativ einfach zu bearbeiten, sowohl in der traditionellen Fertigung als auch bei AM.
- Gute Festigkeit und Duktilität: Bietet eine solide Kombination mechanischer Eigenschaften, die für Anwendungen mit mittlerem Druck geeignet sind.
- Hygienische Eigenschaften: Wird häufig bei Anwendungen verwendet, bei denen Sauberkeit wichtig ist.
- Kostengünstig: In der Regel preiswerter als spezielle Nickel- oder Kupferlegierungen.
- Anwendungen in der Schifffahrt: Geeignet für weniger kritische Systeme, Frischwasserkreisläufe an Bord, strukturelle Komponenten, Kraftstoff-/Ölsysteme oder Umgebungen mit geringerer Chloridkonzentration oder weniger aggressiven Bedingungen. Wird häufig von Lieferanten von Schiffskomponenten für Standardanwendungen spezifiziert.
- AM Überlegungen: Weithin verfügbar als AM-Pulver, gut charakterisierte Druckparameter. Gute Druckbarkeit, die zu dichten Teilen führt. Nachbearbeitungen wie Wärmebehandlung (Spannungsabbau) können von Vorteil sein.
- CuNi30Mn1Fe (Kupfer-Nickel-Legierung, oft C71500):
- Zusammensetzung: Hauptsächlich Kupfer, mit Nickel (ca. 30%), Mangan (ca. 1%) und Eisen (ca. 1%).
- Wichtige Eigenschaften:
- Hervorragende Seewasser-Korrosionsbeständigkeit: Hochgradig beständig gegen gleichmäßige Korrosion und Spannungsrisskorrosion in Meerwasser. Das Vorhandensein von Eisen und Mangan erhöht die Beständigkeit gegen Erosionskorrosion, die durch hohe Durchflussraten verursacht wird.
- Hervorragender Widerstand gegen Biofouling: Kupferionen, die von der Oberfläche ausgewaschen werden, hemmen auf natürliche Weise die Ansiedlung und das Wachstum von Meeresorganismen (Algen, Seepocken), was ein großer Vorteil für die Reinhaltung und Effizienz von Meerwassersystemen ist.
- Gute Festigkeit und Verformbarkeit: Bietet robuste mechanische Eigenschaften, die für Drucksysteme geeignet sind.
- Gute Wärmeleitfähigkeit: Relevant für Wärmetauscherkomponenten, die manchmal in Ventilsysteme integriert sind.
- Anwendungen in der Schifffahrt: Ideal für Seewasserkühlrohre, Wärmetauscher, Kondensatoren, Löschwassersysteme und Ventilkörper, die direkt mit Seewasser in Berührung kommen, insbesondere wenn Biofouling ein Problem darstellt. Eine bevorzugte Wahl für viele maritime und kommerzielle Rohrleitungssysteme.
- AM Überlegungen: Kann mittels AM verarbeitet werden, erfordert jedoch eine sorgfältige Parameteroptimierung aufgrund der hohen Wärmeleitfähigkeit und des Reflexionsvermögens von Kupfer (insbesondere bei laserbasierten Systemen). Die Qualität des Pulvers ist entscheidend. Die Nachbearbeitung umfasst häufig ein Spannungsarmglühen.
- 254SMO (superaustenitischer rostfreier Stahl, z. B. UNS S31254):
- Zusammensetzung: Hohe Gehalte an Chrom (ca. 20%), Nickel (ca. 18%), Molybdän (ca. 6%), Stickstoff (ca. 0,2%) und wenig Kohlenstoff.
- Wichtige Eigenschaften:
- Außergewöhnliche Lochfraß- und Spaltkorrosionsbeständigkeit: Der hohe Molybdän-, Chrom- und Stickstoffgehalt sorgt für eine hervorragende Beständigkeit in aggressiven Chloridumgebungen wie warmem Meerwasser, Brackwasser und Entsalzungslauge. Seine Pitting Resistance Equivalent Number (PREN) ist in der Regel >42,5 und damit deutlich höher als bei 316L (PREN ≈ 25).
- Hohe Festigkeit: Stärker als austenitische Standardstähle wie 316L.
- Gute Duktilität und Zähigkeit: Behält auch bei niedrigen Temperaturen gute mechanische Eigenschaften.
- Gut schweißbar: Kann mit geeigneten Techniken geschweißt werden.
- Anwendungen in der Schifffahrt: Leistungsstarke Wahl für kritische Anwendungen mit aggressivem Meerwasser, chloriertem Meerwasser (z. B. nach BWMS-Behandlung), Komponenten von Entsalzungsanlagen (Hochdruckseite), Prozesssysteme auf Offshore-Plattformen, die mit korrosiven Flüssigkeiten umgehen, und Unterwasserausrüstung. Spezifiziert, wenn 316L nicht ausreicht. Großhändler haben oft Komponenten aus dieser Güte für anspruchsvolle Projekte auf Lager.
- AM Überlegungen: Eine erfolgreiche AM-Bearbeitung führt zu hochdichten Teilen mit Eigenschaften, die mit denen von Knetmaterial vergleichbar sind. Erfordert optimierte Parameter und möglicherweise spezifische Wärmebehandlungen (Lösungsglühen), um optimale Korrosionsbeständigkeit und mechanische Eigenschaften zu gewährleisten. Pulverhersteller wie Met3dp konzentrieren sich auf die Bereitstellung hochwertiger, gaszerstäubter 254SMO-Pulver mit kontrollierter Chemie und Partikelgrößenverteilung, die für das Erreichen zuverlässiger Druckergebnisse entscheidend sind. Ihr fortschrittliches Pulverherstellungssystem, das Technologien wie die Gaszerstäubung mit einzigartigen Düsenkonstruktionen einsetzt, gewährleistet eine hohe Sphärizität und Fließfähigkeit, die für eine gleichmäßige Schichtabscheidung bei Pulverbettfusionsverfahren entscheidend sind.
Tabelle: Vergleich der empfohlenen Legierungen für Marine-AM-Ventilkörper
Eigentum | 316L-Edelstahl | CuNi30Mn1Fe | 254SMO Super Austenitischer Edelstahl | Bedeutung für Schiffsventile |
---|---|---|---|---|
Primäre Elemente | Fe, Cr, Ni, Mo | Cu, Ni, Mn, Fe | Fe, Cr, Ni, Mo, N | Bestimmt grundlegende Merkmale |
Allgemeine Korrosion (SW) | Gut | Ausgezeichnet | Ausgezeichnet | Widerstandsfähigkeit gegen Gesamtmetallverlust |
Lochfraß/Spaltkorr. (SW) | Mäßig | Gut | Außergewöhnlich | Widerstandsfähigkeit gegen lokale Angriffe im Meerwasser |
Resistenz gegen Biofouling | Niedrig | Ausgezeichnet | Niedrig | Verhindert die Blockierung/Unwirksamkeit des Meereswachstums |
Stärke | Gut | Gut | Hoch | Fähigkeit, Druck/Belastung standzuhalten |
PREN (typisch) | ~25 | N/A (anderer Mechanismus) | >42.5 | Indikator für die Lochfraßbeständigkeit von Chloriden |
Kosten | Unter | Höher | Höchste | Beitrag zum Materialaufwand |
Primärer Anwendungsfall | Allgemeiner Zweck, weniger rau | Handhabung von Seewasser, Biofouling | Aggressives Meerwasser, Entsalzung | Anwendungsspezifische Eignung |
AM-Pulver Verfügbarkeit | Hoch | Mäßig | Mäßig bis hoch | Leichte Beschaffung für den Druck |
In Blätter exportieren
Die Auswahl des optimalen Werkstoffs erfordert eine gründliche Analyse der spezifischen Betriebsumgebung (Temperatur, Druck, Durchflussmenge, Wasserchemie, Vorhandensein von Schadstoffen, Biofouling-Risiko) und der Leistungsanforderungen an das Ventilgehäuse. Die Beratung durch Materialexperten und erfahrene AM-Dienstleister wie Met3dp, die sich sowohl mit den Materialien als auch mit den Druckverfahren bestens auskennen, ist entscheidend, um die richtige Wahl zu treffen und die langfristige Zuverlässigkeit der kritischen Schiffskomponenten zu gewährleisten. Das Engagement von Met3dp bei der Herstellung von hochwertigen Metallpulvern, einschließlich innovativer, auf anspruchsvolle Sektoren zugeschnittener Legierungen, macht das Unternehmen zu einem wertvollen Partner für die Herausforderungen der Schiffstechnik.
Entwurf für additive Fertigung (DfAM): Optimierung von Ventilkörpern für den Druck
Die einfache Nachbildung eines herkömmlich konstruierten Ventilgehäuses mit Hilfe der additiven Fertigung aus Metall schöpft oft nicht das volle Potenzial der Technologie aus und kann sogar neue Herausforderungen mit sich bringen. Um die Vorteile von AM - verbesserte Leistung, geringeres Gewicht, schnellere Produktion - wirklich nutzen zu können, müssen Ingenieure die Grundsätze des Design for Additive Manufacturing (DfAM) anwenden. DfAM bedeutet, die Konstruktion des Bauteils von Grund auf zu überdenken und dabei die einzigartigen Fähigkeiten und Einschränkungen des gewählten AM-Verfahrens (wie Laser Powder Bed Fusion - LPBF oder Selective Electron Beam Melting - SEBM) zu berücksichtigen. Die Optimierung von Ventilkörpern für AM speziell für Schiffsanwendungen erfordert die sorgfältige Beachtung mehrerer Schlüsselbereiche:
- Topologie-Optimierung und Gitter-Strukturen:
- Das Ziel: Reduzieren Sie Gewicht und Materialverbrauch, während Sie die strukturelle Integrität unter Druck- und Betriebsbelastungen beibehalten oder erhöhen.
- Wie? Verwenden Sie spezielle Software, um die Lastpfade zu analysieren und Material aus unkritischen Bereichen zu entfernen. Ersetzen Sie massive Abschnitte durch interne Gitterstrukturen, wo dies sinnvoll ist.
- Nutzen für die Marine: Leichtere Komponenten verringern das Gesamtgewicht des Schiffes, was die Kraftstoffeffizienz verbessert oder eine höhere Nutzlast ermöglicht. Ein geringerer Materialverbrauch senkt die Kosten, insbesondere bei teuren Marine-Legierungen. Effiziente tragende Strukturen gewährleisten Zuverlässigkeit unter anspruchsvollen Seebedingungen.
- Optimierung der internen Kanäle und Fließwege:
- Das Ziel: Verbessern Sie die Fluiddynamik, reduzieren Sie den Druckabfall, minimieren Sie Turbulenzen und verhindern Sie Erosion oder Kavitation.
- Wie? AM ermöglicht glatte, gekrümmte Innenkanäle und komplexe Verteilerkonstruktionen, die durch Bohren oder Gießen nicht möglich sind. Strömungssimulationen können die Gestaltung optimaler Wege leiten. Selbsttragende Kanalformen (z. B. tropfen- oder rautenförmige Querschnitte) können den Bedarf an schwer zu entfernenden internen Stützen minimieren.
- Nutzen für die Marine: Ein verbesserter Wirkungsgrad des Ventils trägt zu einer besseren Systemleistung bei (z. B. Kühlung, Ballastmanagement). Geringere Erosion verlängert die Lebensdauer des Ventilkörpers bei abrasiven oder schnell fließenden Flüssigkeiten.
- Minimierung und Optimierung der Stützstruktur:
- Das Ziel: Reduzieren Sie die Druckzeit, den Materialabfall und den Nachbearbeitungsaufwand, der mit dem Entfernen von Stützstrukturen verbunden ist.
- Wie? Richten Sie das Teil strategisch auf der Bauplatte aus. Konstruieren Sie Merkmale mit selbsttragenden Winkeln (typischerweise >45 Grad zur Horizontalen). Verwenden Sie leicht abnehmbare Stützstrukturen, wo dies unvermeidlich ist, und vermeiden Sie diese insbesondere an kritischen Innen- oder Dichtflächen. Integrieren Sie Features, die als inhärente Stütze dienen.
- Nutzen für die Marine: Schnellere Produktionszyklen, niedrigere Herstellungskosten und geringeres Risiko der Beschädigung des Teils beim Entfernen der Halterung. Stellt sicher, dass die internen Durchgänge ungehindert bleiben.
- Überlegungen zur Wanddicke und zur Größe der Elemente:
- Das Ziel: Sicherstellung der strukturellen Integrität, der Druckbarkeit und der ordnungsgemäßen Wärmeableitung während des Bauprozesses.
- Wie? Halten Sie die für die AM-Maschine und das Material spezifischen Mindestwandstärken und Featuregrößen ein (z. B. typischerweise >0,4-0,5 mm für LPBF). Behalten Sie nach Möglichkeit eine gleichmäßige Wandstärke bei, um thermische Spannungskonzentrationen zu vermeiden. Verdicken Sie Bereiche, die hohen Belastungen oder Druck ausgesetzt sind.
- Nutzen für die Marine: Verhindert Druckfehler, stellt sicher, dass das Ventilgehäuse dem Betriebsdruck standhält, und verbessert die Gesamtqualität und Konsistenz der Teile.
- Konsolidierung von Teilen und Integration von Funktionen:
- Das Ziel: Reduzieren Sie die Komplexität der Montage, potenzielle Leckstellen und die Gesamtzahl der Teile.
- Wie? Umgestaltung angrenzender Komponenten (Flansche, Sensoranschlüsse, Montagehalterungen), um sie als eine einzige, monolithische Ventilkörpereinheit zu drucken. Integrieren Sie interne Merkmale wie Strömungsgleichrichter oder Mischkammern.
- Nutzen für die Marine: Vereinfacht die Beschaffung und die Lagerhaltung für Schiffslieferanten und Endverbraucher. Erhöht die Zuverlässigkeit des Systems durch den Wegfall von Verbindungen und Dichtungen. Reduziert das Gesamtgewicht und die Stellfläche des Systems.
- Entwerfen für die Nachbearbeitung:
- Das Ziel: Stellen Sie sicher, dass kritische Oberflächen für die erforderlichen Nachbearbeitungsschritte leicht zugänglich sind.
- Wie? Fügen Sie zusätzliches Material (Bearbeitungsmaterial) für Oberflächen hinzu, die enge Toleranzen oder besondere Oberflächengüten erfordern (z. B. Dichtflächen, Flanschverbindungen). Stellen Sie sicher, dass die inneren Kanäle für Reinigung, Inspektion und eventuelles Polieren zugänglich sind.
- Nutzen für die Marine: Garantiert, dass der Ventilkörper nach Abschluss aller Fertigungsschritte die funktionalen Anforderungen an Dichtung, Anschluss und Durchfluss erfüllt.
Tabelle: Wichtige DfAM-Überlegungen für Marine-Ventilgehäuse
DfAM-Prinzip | Zielsetzung | AM-gestützte Technik | Vorteil für Marine-Ventilkörper |
---|---|---|---|
Gewichtsreduzierung | Masse minimieren, Material sparen | Topologie-Optimierung, Gitter-Strukturen | Kraftstoffeffizienz, niedrigere Kosten (hochwertige Legierungen) |
Durchfluss-Effizienz | Druckabfall reduzieren, Turbulenzen minimieren | Glatte/gekrümmte Innenkanäle, optimierte Pfade | Bessere Systemleistung, weniger Erosion |
Druckbarkeit | Unterstützung minimieren, Erfolg sichern | Teilausrichtung, selbsttragende Winkel | Schnellerer Druck, niedrigere Kosten, einfachere Nachbearbeitung |
Strukturelle Integrität | Druck und Belastungen standhalten | Regeln für Mindestwandstärken, Größenbestimmung von Merkmalen | Verlässlichkeit, Sicherheit, Langlebigkeit |
Systemvereinfachung | Reduzieren Sie die Anzahl der Teile, die Montage und die Leckstellen | Teilekonsolidierung, integrierte Funktionen | Leichtere Beschaffung, höhere Zuverlässigkeit |
Funktionsweise | Erfüllen Sie die Leistungsspezifikationen nach dem Druckvorgang | Entwerfen für die Nachbearbeitung (Bearbeitung von Rohmaterial) | Garantiert Passform, Dichtheit und Funktion |
In Blätter exportieren
Die wirksame Anwendung von DfAM erfordert nicht nur Fachwissen über Gestaltungsprinzipien, sondern auch über die spezifischen Nuancen der verschiedenen Metall-AM-Druckverfahren. Die Zusammenarbeit mit einem erfahrenen AM-Dienstleister wie Met3dp, der das Zusammenspiel zwischen Design, Werkstoffen (wie den hochwertigen 316L-, CuNi- und superaustenitischen Pulvern) und Maschinenfähigkeiten (einschließlich des branchenführenden Druckvolumens und der Genauigkeit) versteht, ist für die Entwicklung wirklich optimierter Schiffsventilgehäuse von entscheidender Bedeutung. Die Ingenieurteams des Unternehmens können Kunden bei der Anpassung oder Neugestaltung von Komponenten unterstützen, um die Vorteile der additiven Fertigung zu maximieren.
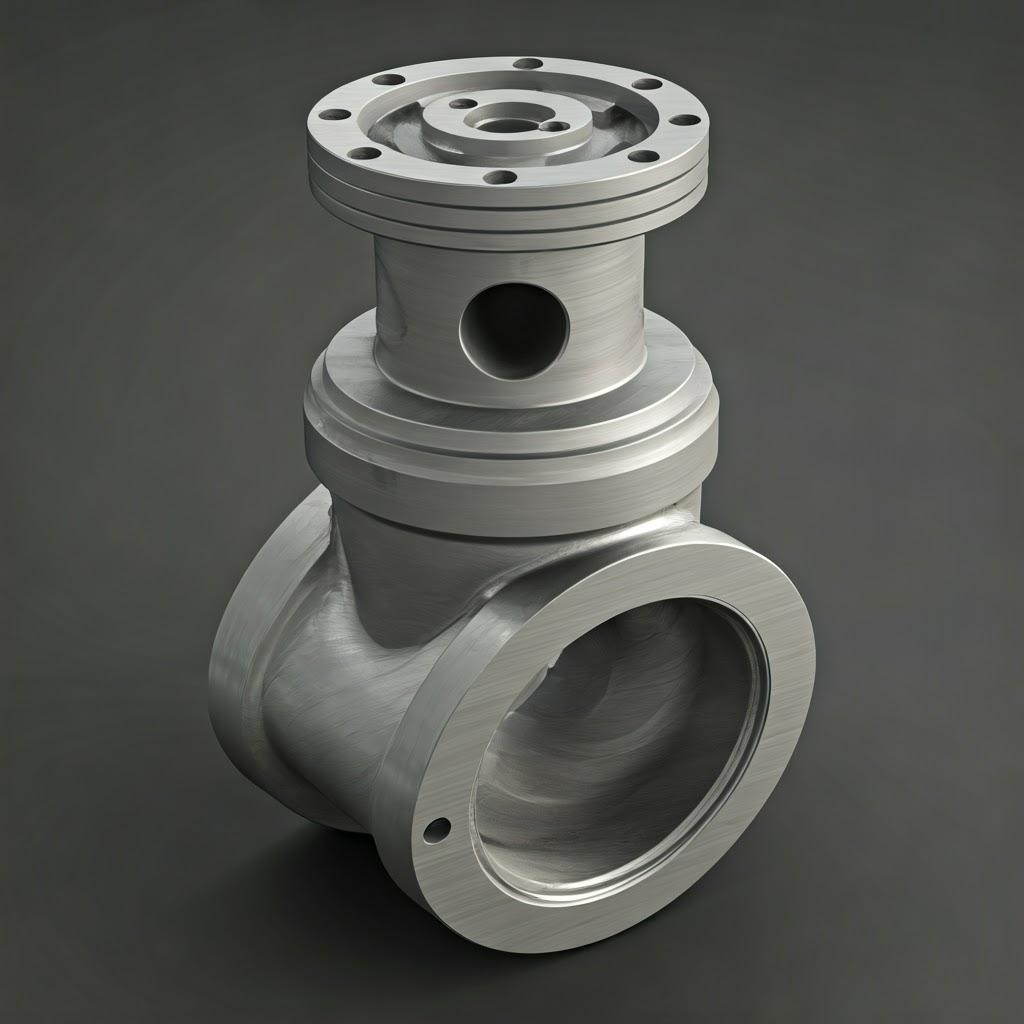
Auf die Präzision kommt es an: Toleranzen, Oberflächengüte und Maßgenauigkeit bei AM-Ventilkörpern
Metall-AM bietet zwar eine große Designfreiheit, aber das Verständnis der erreichbaren Präzisionsniveaus - Toleranzen, Oberflächenbeschaffenheit und Maßgenauigkeit - ist für funktionale Komponenten wie Ventilgehäuse, insbesondere für Dichtungsflächen und Schnittstellen, von entscheidender Bedeutung. Ingenieure und Beschaffungsmanager müssen realistische Erwartungen an den gedruckten Zustand haben und die Nachbearbeitungsanforderungen berücksichtigen.
- Maßgenauigkeit:
- Definition: Wie genau das endgültige gedruckte Teil mit den im CAD-Modell angegebenen Abmessungen übereinstimmt.
- Typische Werte: Bei Pulverbettschmelzverfahren (LPBF, SEBM) liegt die typische Maßgenauigkeit oft im Bereich von ±0,1 mm bis ±0,2 mm oder ±0,1% bis ±0,2% der Abmessung, je nachdem, welcher Wert größer ist. Dies kann jedoch je nach den folgenden Faktoren erheblich variieren:
- Größe und Geometrie des Teils (größere Teile können mehr Verzug aufweisen)
- Materialeigenschaften (Wärmeausdehnung, Schrumpfung)
- Maschinenkalibrierung und -zustand
- Bauparameter (Schichtdicke, Energieaufwand)
- Thermische Spannungen während der Bau- und Abkühlungsphase
- Relevanz für das Meer: Entscheidend für die korrekte Passung mit den entsprechenden Rohren (Flanschen), Antrieben und internen Ventilkomponenten. Während die allgemeinen Gehäuseabmessungen im Druckzustand akzeptabel sein können, erfordern kritische Schnittstellen oft eine strengere Kontrolle.
- Oberflächengüte (Rauhigkeit):
- Definition: Das Maß für die feinen Unregelmäßigkeiten auf einer Oberfläche, oft ausgedrückt als Ra (durchschnittliche Rauheit).
- Typische As-Printed-Werte:
- Obere Oberflächen: Im Allgemeinen glatter, möglicherweise Ra 5-15 µm.
- Vertikale Mauern: Mäßige Rauhigkeit, oft Ra 8-20 µm, beeinflusst durch Schichtlinien.
- Daunenbelag/gestützte Oberflächen: In der Regel die gröbsten, möglicherweise Ra 15-30 µm oder mehr, aufgrund der Kontaktpunkte mit der Unterlage oder der Art der Pulverschmelze an abwärts gerichteten Hängen.
- Interne Kanäle: Die Rauheit hängt stark von der Ausrichtung, dem Durchmesser und davon ab, ob Stützen erforderlich waren. Es kann schwierig sein, ohne Nachbearbeitung glatte Oberflächen zu erzielen.
- Faktoren, die die Rauhigkeit beeinflussen: Korngrößenverteilung des Pulvers (feinere Pulver führen zu glatteren Oberflächen), Schichtdicke (dünnere Schichten verbessern im Allgemeinen die Oberfläche), Laser-/Strahlparameter und Teileausrichtung.
- Relevanz für das Meer: Entscheidend für Dichtungsflächen (Dichtungsflächen, Ventilsitze), bei denen eine glatte Oberfläche (oft Ra < 1,6 µm oder besser) erforderlich ist, um Lecks zu verhindern. Raue Innenflächen können die Reibungsverluste erhöhen, potenziell Verunreinigungen einschließen und in manchen Fällen sogar die Korrosionsbeständigkeit beeinträchtigen.
- Toleranzen:
- Definition: Die zulässige Schwankungsbreite für ein bestimmtes Maß.
- Realisierbarkeit: Während die allgemeine Maßgenauigkeit ±0,1-0,2 mm betragen kann, müssen engere Toleranzen (z. B. ±0,025 mm bis ±0,05 mm) bei bestimmten Merkmalen (wie Dichtungsnuten, Lagerbohrungen, Flanschflächen) in der Regel nachbearbeitet werden.
- DfAM-Betrachtung: Dies muss bei der Konstruktion berücksichtigt werden, indem kritische Oberflächen in der AM-Konstruktionsdatei mit Bearbeitungsmaterial (z. B. 0,5 mm bis 1,5 mm) versehen werden.
- Relevanz für das Meer: Wesentlich für die Austauschbarkeit von Teilen, die richtige Abdichtung unter Druck und den korrekten Zusammenbau mit anderen Systemkomponenten. In den Beschaffungsspezifikationen sind oft bestimmte Toleranzen für kritische Merkmale vorgeschrieben.
Tabelle: Typische Präzisionsparameter bei der Metall-AM (Pulverbettfusion)
Parameter | Typischer Bereich wie gedruckt | Beeinflussende Faktoren | Post-Processing-Potenzial | Relevanz für Schiffsventile |
---|---|---|---|---|
Maßgenauigkeit | ±0,1 bis ±0,2 mm / ±0,1-0,2% | Teilgröße, Material, Maschine, Parameter, thermische Belastung | Bearbeitung für hohe Genauigkeit | Passend zu Rohren, Aktuatoren, internen Komponenten |
Oberflächengüte (Ra) | 5 µm - 30+ µm | Oberflächenausrichtung, Schichthöhe, Pulvergröße, Stützen | Spanende Bearbeitung, Polieren, Strahlen | Dichtungsflächen, Durchflussleistung, Korrosion |
Toleranzen | Limitierte Druckauflage | (Gleiche wie Genauigkeit) | CNC-Bearbeitung für engen Tol erforderlich. | Austauschbarkeit, Abdichtung, Montage |
In Blätter exportieren
Es ist wichtig anzumerken, dass Anbieter wie Met3dp mit ihrem Schwerpunkt auf branchenführender Genauigkeit und Zuverlässigkeit stark in Maschinenkalibrierung, Prozesskontrolle und Qualitätssicherungsmaßnahmen investieren, um die bestmögliche Präzision im gedruckten Zustand zu erreichen. Für die anspruchsvollen Anforderungen vieler Schiffsventilanwendungen ist jedoch eine Kombination aus präzisem AM-Druck und anschließender gezielter Nachbearbeitung oft die effektivste Strategie, um alle Spezifikationen für Abmessungen und Oberflächengüte zu erfüllen. Eine klare Kommunikation zwischen den Konstrukteuren, dem Beschaffungsteam und dem AM-Dienstleister hinsichtlich kritischer Abmessungen und Toleranzen ist unerlässlich.
Wege der Nachbearbeitung: Der letzte Schliff für optimale Leistung
Ein gedrucktes Metall-AM-Teil ist selten sofort einsatzbereit, insbesondere bei kritischen Anwendungen wie Schiffsventilkörpern. Nachbearbeitungsschritte sind fast immer notwendig, um innere Spannungen abzubauen, Stützstrukturen zu entfernen, erforderliche Toleranzen und Oberflächengüten zu erreichen und sicherzustellen, dass das Material die gewünschten mechanischen und korrosiven Eigenschaften besitzt. Das Verständnis dieser gemeinsamen Wege ist entscheidend für die Planung von Produktionszeiten und -kosten.
- Stressabbau / Wärmebehandlung:
- Zweck: Um innere Spannungen abzubauen, die während der schnellen Heiz- und Kühlzyklen des AM-Prozesses entstehen. Dies verhindert spätere Verformungen oder Risse und stabilisiert die Abmessungen des Teils. Wird auch verwendet, um bestimmte metallurgische Phasen und Eigenschaften (z. B. Festigkeit, Duktilität, Korrosionsbeständigkeit) zu erreichen.
- Methoden:
- Stressabbau: Erhitzen des Teils auf eine moderate Temperatur (unterhalb der Umwandlungspunkte) und Halten des Teils, gefolgt von einer langsamen Abkühlung. Üblich für viele Legierungen.
- Glühen/Lösungsglühen: Erhitzen auf höhere Temperaturen, um Ausscheidungen aufzulösen, das Gefüge zu homogenisieren und die Duktilität oder Korrosionsbeständigkeit zu verbessern (z. B. entscheidend für die Optimierung der Korrosionsleistung von 254SMO). Erfordert spezifische Temperaturprofile und Abkühlungsraten (z. B. Wasserabschrecken).
- Alterung/Ausfällung Härtung: Wird für bestimmte Legierungen verwendet (in der Regel nicht für die primären Marinelegierungen, aber für andere relevant), um die Festigkeit zu erhöhen.
- Erwägungen: Muss in Öfen mit kontrollierter Atmosphäre (Vakuum oder Schutzgas) durchgeführt werden, um Oxidation zu verhindern, insbesondere bei reaktiven Legierungen. Die Wärmebehandlungsparameter sind legierungsspezifisch und entscheidend für die Leistung.
- Entfernung der Stützstruktur:
- Zweck: Um die temporären Strukturen zu entfernen, die zur Verankerung des Teils auf der Bauplatte und zur Unterstützung überhängender Features während des Drucks verwendet werden.
- Methoden: Das Spektrum reicht vom manuellen Brechen (für leicht zugängliche, leicht gesinterte Träger) bis zum Schneiden, Schleifen oder zur CNC-Bearbeitung. Drahterodieren wird manchmal für komplizierte oder schwer zugängliche Halterungen verwendet. Der Zugang zu internen Kanalstützen kann besonders schwierig sein.
- Erwägungen: Dies muss sorgfältig geschehen, damit die Oberfläche des Teils nicht beschädigt wird. DfAM spielt eine große Rolle, wenn es darum geht, die Notwendigkeit einer schwierigen Stützentfernung zu minimieren.
- CNC-Bearbeitung:
- Zweck: Zur Erzielung enger Maßtoleranzen, spezifischer geometrischer Merkmale (wie O-Ring-Nuten oder Gewindebohrungen) und glatter Oberflächen an kritischen Stellen.
- Anwendungen für Ventilkörper: Bearbeitung von Flanschflächen auf Ebenheit und Oberflächengüte, Aufbohren von Innendurchmessern für Ventilsitze oder Kolben, Bearbeitung von Dichtflächen, Gewindeschneiden von Anschlussöffnungen.
- Erwägungen: Erfordert eine genaue Fixierung des potenziell komplexen AM-Teils. In der DfAM-Phase muss ein ausreichendes Bearbeitungsmaterial eingeplant werden.
- Oberflächenveredelung:
- Zweck: Zur Verbesserung der Oberflächenglätte (Reduzierung von Ra), zur Beseitigung kleinerer Unebenheiten, zur Verbesserung der Ästhetik oder zur Vorbereitung der Oberfläche für die Beschichtung.
- Methoden:
- Abrasives Strahlen (Sandstrahlen, Perlstrahlen): Sorgt für ein gleichmäßig mattes Finish, entfernt lose Puderpartikel.
- Taumeln/Gleitschleifen: Verwendet Medien zum Glätten von Oberflächen und Kanten, geeignet für Chargen von kleineren Teilen.
- Polieren: Mechanisches oder elektrolytisches Polieren zur Erzielung sehr glatter, spiegelähnlicher Oberflächen, die manchmal für bestimmte Fließwege oder Dichtungsbereiche erforderlich sind.
- Mikro-Bearbeitung/Abrasive Flow Machining (AFM): Kann verwendet werden, um die Oberfläche von Innenkanälen zu verbessern.
- Erwägungen: Die Wahl hängt von dem erforderlichen Ra-Wert, der Zugänglichkeit der Geometrie und den Kosten ab.
- Reinigung und Inspektion:
- Zweck: Entfernen Sie alle Reste von losem Pulver, Bearbeitungsflüssigkeiten oder Verunreinigungen. Prüfen Sie die Maßhaltigkeit und die Unversehrtheit der Oberfläche und kontrollieren Sie auf Fehler.
- Methoden: Ultraschallreinigung, Sichtprüfung, Prüfung mit Koordinatenmessgeräten (CMM), zerstörungsfreie Prüfungen (NDT) wie Röntgen- oder CT-Scans (insbesondere bei kritischen drucktragenden Teilen zur Prüfung auf innere Porosität).
- Erwägungen: Wesentliche Qualitätssicherungsschritte vor der Einführung.
Tabelle: Übliche Nachbearbeitungsschritte für AM-Ventilkörper für die Schifffahrt
Nachbearbeitungsschritt | Zweck | Gemeinsame Methoden | Wichtige Überlegungen |
---|---|---|---|
Wärmebehandlung | Spannungen abbauen, Materialeigenschaften optimieren (Korrosion, Festigkeit) | Spannungsabbau, Glühen, Lösungsglühen | Legierungsspezifische Parameter, kontrollierte Atmosphäre |
Entfernen der Stütze | Teil von der Bauplatte abnehmen, Überhangstützen entfernen | Manuelles Abbrechen, Bearbeitung, Schleifen, Drahterodieren | Zugang (insbesondere intern), Vermeidung von Teilebeschädigungen |
CNC-Bearbeitung | Erzielung enger Toleranzen, kritischer Oberflächengüten, Merkmale | Fräsen, Drehen, Bohren, Gewindeschneiden | Vorrichtungen, Aufmaß für Bearbeitungsmaterial (DfAM) |
Oberflächenveredelung | Verbesserung der Glätte (Ra), Ästhetik, Vorbereitung für die Beschichtung | Strahlen, Trommeln, Polieren, AFM | Erforderliche Ra, Zugänglichkeit, Kosten |
Reinigung und Inspektion | Verunreinigungen entfernen, Maße überprüfen, auf Mängel prüfen | Ultraschallreinigung, CMM, visuelle Prüfung, NDT (Röntgen) | Endgültige QS, die die Gebrauchstauglichkeit sicherstellt |
In Blätter exportieren
Der Umfang und die Reihenfolge der Nachbearbeitung hängen stark von der Komplexität des Ventilkörpers, der Materialwahl und den Anwendungsanforderungen ab. Beschaffungsmanager sollten diese Schritte bei der Beschaffung von AM-Komponenten in die Gesamtvorlaufzeit- und Kostenberechnung einbeziehen. Die Zusammenarbeit mit einem Full-Service-Anbieter wie Met3dp, der diese notwendigen Nachbearbeitungsschritte verwalten oder koordinieren kann, gewährleistet einen optimierten Arbeitsablauf und garantiert, dass das endgültige Teil alle Spezifikationen erfüllt.
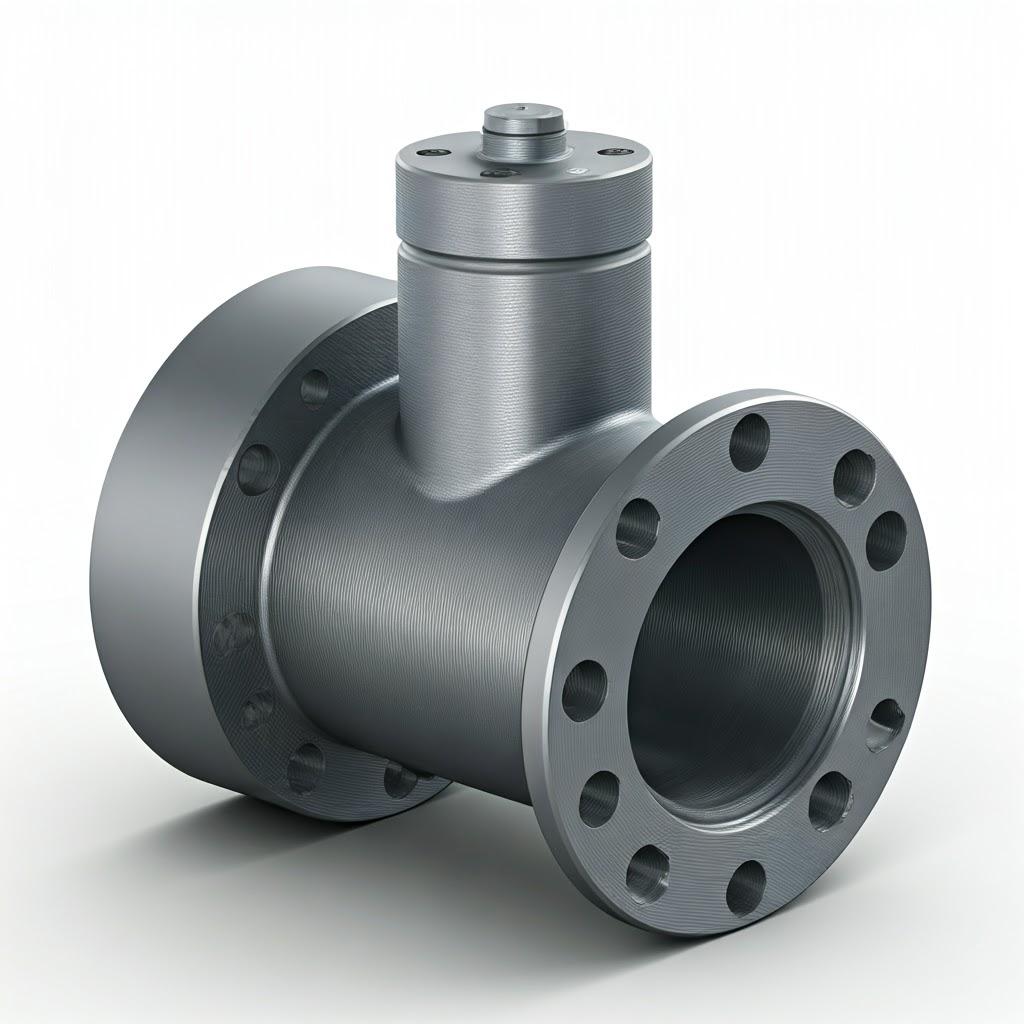
Herausforderungen bei der Produktion von AM-Ventilkörpern meistern: Lösungen und Best Practices
Die additive Fertigung von Metallen bietet zwar erhebliche Vorteile für die Herstellung von Schiffsventilgehäusen, ist aber nicht ohne potenzielle Herausforderungen. Das Erkennen dieser Hürden und die Implementierung von Best Practices ist entscheidend für die Gewährleistung einer gleichbleibenden Qualität, Zuverlässigkeit und Leistung. Erfahrene AM-Anbieter haben Strategien entwickelt, um diese allgemeinen Probleme zu entschärfen.
- Eigenspannung und Verformung:
- Herausforderung: Die schnellen Erwärmungs-/Abkühlungszyklen können innere Spannungen hervorrufen, die dazu führen können, dass sich das Teil während oder nach der Herstellung verzieht oder sogar reißt. Dies ist bei großen Teilen oder komplexen Geometrien besonders ausgeprägt.
- Lösungen:
- Optimierte Build-Strategie: Sorgfältige Auswahl von Scanmustern, Schichtzeiten und Wärmemanagement während des Aufbaus.
- Robuste Stützstrukturen: Gut konzipierte Halterungen helfen, das Teil zu verankern und die Wärmeableitung zu steuern.
- Geeignete Wärmebehandlung: Spannungsabbauzyklen nach der Fertigung sind entscheidend für die Stabilisierung des Teils.
- Simulation: Thermische Simulationswerkzeuge können die Belastungsakkumulation vorhersagen und über Anpassungen der Design-/Baustrategie informieren.
- Porosität:
- Herausforderung: Im gedruckten Material können sich kleine Hohlräume oder Poren bilden, die auf eine unvollständige Verschmelzung der Pulverpartikel, eingeschlossenes Gas oder Keyholing-Phänomene (Dampfdruckinstabilität) zurückzuführen sind. Porosität kann die mechanische Festigkeit, die Ermüdungsfestigkeit und die Druckbeständigkeit beeinträchtigen, was für Ventilgehäuse entscheidend ist.
- Lösungen:
- Optimierte Druckparameter: Feinabstimmung von Laser-/Elektronenstrahlleistung, Scangeschwindigkeit, Schichtdicke und Fokus für das jeweilige Material, um eine Dichte von >99,5% zu erreichen (oft sind auch >99,9% möglich).
- Hochwertiges Pulver: Verwendung von Pulvern mit kontrollierter Partikelgrößenverteilung, Morphologie (hohe Sphärizität) und geringem Gasgehalt, wie sie von Met3dp mit fortschrittlichen Gaszerstäubungs- und PREP-Technologien hergestellt werden. Eine gleichbleibende Pulverqualität ist von größter Bedeutung.
- Prozessüberwachung: In-situ-Überwachungssysteme können potenzielle Anomalien während der Bauphase erkennen.
- Heiß-Isostatisches Pressen (HIP): Ein Nachbearbeitungsschritt, der hohe Temperaturen und Druck erfordert, um innere Hohlräume zu schließen. Dies ist häufig für kritische Komponenten in der Luft- und Raumfahrt oder im Unterwasserbereich erforderlich und verursacht zusätzliche Kosten und Zeitaufwand, garantiert aber eine maximale Dichte.
- Unterstützung bei der Beseitigung von Schwierigkeiten:
- Herausforderung: Abstützungen in komplexen internen Kanälen oder schwer zugänglichen Bereichen lassen sich nur sehr schwer oder gar nicht vollständig entfernen und können den Durchfluss behindern oder als Ausgangspunkt für Korrosion dienen.
- Lösungen:
- DfAM Fokus: Der beste Ansatz ist die Entwicklung selbsttragender interner Kanäle und die Minimierung des Bedarfs an internen Stützen.
- Optimiertes Support-Design: Verwendung von Trägerstrukturen, die für eine leichtere Entfernung ausgelegt sind (z. B. spezielle Geometrien, Träger mit geringerer Dichte).
- Erweiterte Entfernungstechniken: Chemisches Ätzen (für bestimmte Materialkombinationen) oder Abrasive Flow Machining (AFM) für die Endbearbeitung der Innenkanäle in Erwägung ziehen, obwohl dies die Komplexität erhöht.
- Inspektion: Endoskopische Inspektion oder CT-Scan zur Überprüfung der vollständigen Entfernung aus kritischen Passagen.
- Erzielung von Toleranzen und Oberflächengüte:
- Herausforderung: Wie bereits erwähnt, erfüllen as-printed Teile selten die engen Toleranzen und glatten Oberflächen, die für Dichtungsflächen oder dynamische Komponenten ohne Nachbearbeitung erforderlich sind.
- Lösungen:
- Integrierter Arbeitsablauf: Planung der Nachbearbeitung ab der DfAM-Phase durch Einbeziehung des Bearbeitungsmaterials.
- Präzise Nachbearbeitung: Einsatz von Hochpräzisions-CNC-Bearbeitung und geeigneten Oberflächenveredelungstechniken.
- Metrologie: Strenge CMM-Prüfung zur Überprüfung der endgültigen Abmessungen und Toleranzen.
- Validierung und Konsistenz von Materialeigenschaften:
- Herausforderung: Sicherstellung, dass die mechanischen Eigenschaften (Festigkeit, Duktilität, Härte) und die Korrosionsbeständigkeit des AM-Teils durchgängig den Spezifikationen für die gewählte Legierung und den Anwendungsanforderungen entsprechen. Die Eigenschaften können durch Herstellungsparameter, Ausrichtung und Wärmebehandlung beeinflusst werden.
- Lösungen:
- Standardisierte Verfahren: Einhaltung etablierter ASTM- oder ISO-Normen für AM-Prozesse und -Tests.
- Entwicklung der Parameter: Gründliche Validierung der Druckparameter für jede spezifische Legierung.
- Gutscheine bezeugen: Drucken von Testcoupons neben dem Hauptteil für zerstörende Prüfungen (Zugversuche, Härte, Mikrostrukturanalyse).
- Materialzertifizierung: Verwendung von zertifizierten Pulvern und Bereitstellung von Materialprüfberichten (MTRs) mit den gelieferten Teilen. Unternehmen wie Met3dp legen großen Wert auf die Materialqualität und bieten umfassende Lösungen, einschließlich Anwendungsentwicklungsdienste.
- Qualitätssicherung und Zertifizierung:
- Herausforderung: Nachweis einer konsistenten Qualitäts- und Prozesskontrolle, insbesondere für kritische Anwendungen in der Schifffahrt, die häufig die Zulassung durch eine Klassifikationsgesellschaft (z. B. DNV, ABS, Lloyd's Register) erfordern.
- Lösungen:
- Robustes Qualitätsmanagementsystem (QMS): Umsetzung von ISO 9001 oder branchenspezifischen Normen (z. B. AS9100 für die Luft- und Raumfahrt, die eine gewisse Strenge aufweisen).
- Rückverfolgbarkeit: Die vollständige Rückverfolgbarkeit von Pulverchargen, Maschinenparametern und Nachbearbeitungsschritten für jedes Teil.
- Zerstörungsfreie Prüfung (NDT): Einsatz von Methoden wie CT-Scan, Röntgen oder Farbeindringprüfung zur Überprüfung der Integrität.
- Zusammenarbeit mit Klassifikationsgesellschaften: Proaktive Zusammenarbeit mit Schiffsklassifikationsgesellschaften zur Qualifizierung von Materialien, Verfahren und Komponenten für bestimmte Anwendungen.
Die Bewältigung dieser Herausforderungen erfordert eine Kombination aus fortschrittlicher Technologie, materialwissenschaftlichem Fachwissen, strenger Prozesskontrolle und einem starken Fokus auf Qualitätssicherung. Die Zusammenarbeit mit einem sachkundigen und erfahrenen Metall-AM-Anbieter ist der effektivste Weg für Schiffsingenieure und Beschaffungsmanager, um Risiken zu minimieren und AM für anspruchsvolle Ventilkörperanwendungen erfolgreich umzusetzen. Met3dp's Engagement für Zuverlässigkeit, Genauigkeit und umfassende Lösungen, unterstützt durch seine fortschrittlichen Pulverherstellungs- und Druckfähigkeiten, positioniert sie gut, um diese Herausforderungen der Industrie zu bewältigen.
Wählen Sie Ihren Partner: Auswahl eines Metall-AM-Dienstleisters für Schiffskomponenten
Der Erfolg der additiven Fertigung von kritischen Schiffskomponenten wie Ventilgehäusen hängt entscheidend von der Auswahl des richtigen Fertigungspartners ab. Nicht alle AM-Dienstleister verfügen über das spezifische Fachwissen, die Ausrüstung, die Materialkenntnisse und die Qualitätssysteme, die für das anspruchsvolle maritime Umfeld erforderlich sind. Ingenieure und Beschaffungsmanager, die diese Komponenten beschaffen, sollten potenzielle Partner auf der Grundlage einer Reihe strenger Kriterien bewerten:
- Fachwissen über Meereslegierungen:
- Erfordernis: Nachgewiesene Erfahrung und validierte Verfahren für den Druck von maritimen Legierungen wie 316L, Kupfer-Nickel (CuNi30Mn1Fe), superaustenitischen/Duplex-Edelstählen (254SMO, Duplex) und möglicherweise Nickellegierungen oder Titan für spezielle Anwendungen.
- Bewertung: Fragen Sie nach Fallstudien, Materialdatenblättern für AM-Teile und Belegen für erfolgreiche Drucke mit relevanten Materialien. Vergewissern Sie sich, dass sie die besonderen Herausforderungen jeder Legierung während des Drucks und der Nachbearbeitung verstehen (z. B. thermische Eigenschaften von CuNi, Wärmebehandlung für 254SMO).
- Qualitätsmanagementsystem (QMS) und Zertifizierungen:
- Erfordernis: Ein solides QMS, idealerweise zertifiziert nach ISO 9001 oder einer vergleichbaren Norm. Für bestimmte kritische Anwendungen sind Erfahrungen bei der Erarbeitung oder Erlangung von Zertifizierungen, die für die Schifffahrts- oder Offshore-Industrie relevant sind (z. B. Vertrautheit mit den Anforderungen von DNV, ABS, Lloyd's Register), von großem Vorteil.
- Bewertung: Erfragen Sie Einzelheiten zur QMS-Zertifizierung. Erkundigen Sie sich nach der Erfahrung des Unternehmens mit den Anforderungen der Klassifikationsgesellschaften und dem Verfahren zur Qualifizierung von Teilen, falls erforderlich. Achten Sie auf Belege für eine strenge Prozesskontrolle und Dokumentationspraxis.
- Technologische Leistungsfähigkeit und Kapazität:
- Erfordernis: Zugang zu geeigneten AM-Technologien (z. B. LPBF, SEBM), die für die gewählten Materialien und die Komplexität der Teile geeignet sind. Ausreichendes Fertigungsvolumen für die erforderlichen Ventilkörpergrößen und Kapazitäten zur Einhaltung der Projektfristen. Hochmoderne Ausrüstung gewährleistet höhere Genauigkeit und Zuverlässigkeit.
- Bewertung: Verstehen Sie den Maschinenpark, die Baugrößen und die typischen Vorlaufzeiten. Beurteilen Sie deren Wartungs- und Kalibrierungsverfahren. Met3dp zum Beispiel ist stolz auf seine Drucker, die ein branchenweit führendes Druckvolumen, Genauigkeit und Zuverlässigkeit bieten.
- Materialqualität und Rückverfolgbarkeit:
- Erfordernis: Verwendung von hochwertigen, zertifizierten Metallpulvern, die speziell für AM entwickelt wurden und deren Chemie und Partikeleigenschaften kontrolliert werden. Vollständige Rückverfolgbarkeit von der Rohpulvercharge bis zum fertigen Teil ist unerlässlich.
- Bewertung: Erkundigen Sie sich nach den Verfahren zur Pulverbeschaffung und Qualitätskontrolle. Stellen sie ihre eigenen Pulver her, wie Met3dp mit seinen fortschrittlichen Gaszerstäubungs- und PREP-Systemen, die eine strenge Qualitätskontrolle gewährleisten? Fragen Sie nach Materialprüfberichten (MTRs) und Dokumentationsverfahren zur Rückverfolgbarkeit.
- Unterstützung des Designs für additive Fertigung (DfAM):
- Erfordernis: Technisches Fachwissen zur Unterstützung der Kunden bei der Optimierung von Designs für AM, Minimierung von Stützen, Gewichtsreduzierung und Nutzung der einzigartigen Vorteile der Technologie.
- Bewertung: Erläutern Sie ihre DfAM-Fähigkeiten und ihre Bereitschaft zur Zusammenarbeit bei der Designoptimierung. Überprüfen Sie Beispiele, wie sie anderen Kunden geholfen haben, ihre Komponenten durch DfAM zu verbessern.
- Nachbearbeitungsmöglichkeiten:
- Erfordernis: Fähigkeit, die erforderlichen Nachbearbeitungsschritte durchzuführen oder zu leiten, einschließlich Wärmebehandlung (in kontrollierter Atmosphäre), Entfernung von Halterungen, CNC-Präzisionsbearbeitung, Oberflächenbehandlung und Reinigung, um alle Spezifikationen zu erfüllen.
- Bewertung: Beurteilen Sie die internen Fähigkeiten des Unternehmens im Vergleich zu seinem Netz von vertrauenswürdigen Zulieferern. Vergewissern Sie sich, dass diese ein fertiges Teil liefern können, das alle Anforderungen an Abmessungen, Oberflächen und Materialeigenschaften erfüllt.
- Inspektion und Prüfung:
- Erfordernis: Umfassende Prüfmöglichkeiten, einschließlich dimensioneller Messtechnik (CMM), Oberflächenrauheitsprüfung und zerstörungsfreie Prüfverfahren (NDT) wie Röntgen, CT-Scanning oder Farbeindringprüfung, um die Integrität der Teile sicherzustellen, insbesondere bei drucktragenden Komponenten.
- Bewertung: die Standard-QA/QC-Verfahren und die verfügbaren ZfP-Methoden zu verstehen. Bestätigen Sie, dass das Unternehmen in der Lage ist, die erforderlichen Prüfberichte und Zertifizierungen zu erstellen.
- Erfolgsbilanz und Reputation:
- Erfordernis: Nachgewiesene Erfolge bei der Lieferung von hochwertigen AM-Metallteilen für anspruchsvolle Branchen (Schifffahrt, Luft- und Raumfahrt, Medizin, Öl und Gas). Positive Kundenreferenzen und Fallstudien.
- Bewertung: Fragen Sie nach relevanten Projektbeispielen und Referenzen. Prüfen Sie den Ruf des Unternehmens in der Branche und das Feedback seiner Kunden. Erkunden Sie den Hintergrund eines potenziellen Partners, indem Sie mehr über über Met3dpSie können einen Einblick in ihre Erfahrung, ihre Werte und ihr Engagement für Innovation und Qualität geben.
Tabelle: Schlüsselkriterien für die Auswahl eines Marine Metal AM Partners
Kriterien | Warum es für Schiffsventilkörper wichtig ist | Bewertungspunkte |
---|---|---|
Fachwissen über Meereslegierungen | Gewährleistet die korrekte Verarbeitung für Korrosion und mechanische Anforderungen | Erfahrung mit 316L, CuNi, 254SMO; Datenblätter, Fallstudien |
QMS & Zertifizierungen | Garantiert gleichbleibende Qualität und Prozesskontrolle | ISO 9001; Vertrautheit mit DNV/ABS; QA-Verfahren |
Technologie und Kapazität | Bestimmt Machbarkeit, Genauigkeit, Geschwindigkeit und Größenbeschränkungen von Teilen | Maschinentyp (LPBF/SEBM), Bauvolumen, Kalibrierung, Vorlaufzeiten |
Qualität der Materialien | Wirkt sich direkt auf die Eigenschaften und die Zuverlässigkeit des Endprodukts aus | Pulverquelle (intern wie Met3dp?), QC, Rückverfolgbarkeit, MTRs |
DfAM-Unterstützung | Optimiert das Design für Leistung, Kosten und Druckbarkeit | Technische Ressourcen, kollaborativer Ansatz, Optimierungsbeispiele |
Nachbearbeitung | Sicherstellen, dass das fertige Teil alle funktionalen Anforderungen erfüllt | Eigene Dienstleistungen vs. Managed Services (Wärmebehandlung, Bearbeitung, Veredelung) |
Inspektion und Prüfung | Überprüft die Integrität, die Abmessungen und die Abwesenheit von Mängeln | CMM, NDT-Möglichkeiten (Röntgen/CT), Berichterstattung |
Erfolgsbilanz | beweist Zuverlässigkeit und Erfahrung in anspruchsvollen Sektoren | Marine/Offshore-Projekte, Kundenreferenzen, Ansehen in der Branche |
In Blätter exportieren
Bei der Wahl eines Partners geht es nicht nur darum, einen Lieferanten zu finden, sondern auch darum, eine partnerschaftliche Beziehung mit einem Experten aufzubauen, der die einzigartigen Anforderungen der Schifffahrtsindustrie versteht. Ein Anbieter wie Met3dp, der umfassende Lösungen für Drucker, hochentwickelte Metallpulver und Anwendungsentwicklungsdienste anbietet, verkörpert die Art von Partnerschaft, die für die erfolgreiche Nutzung von AM für kritische Komponenten erforderlich ist.
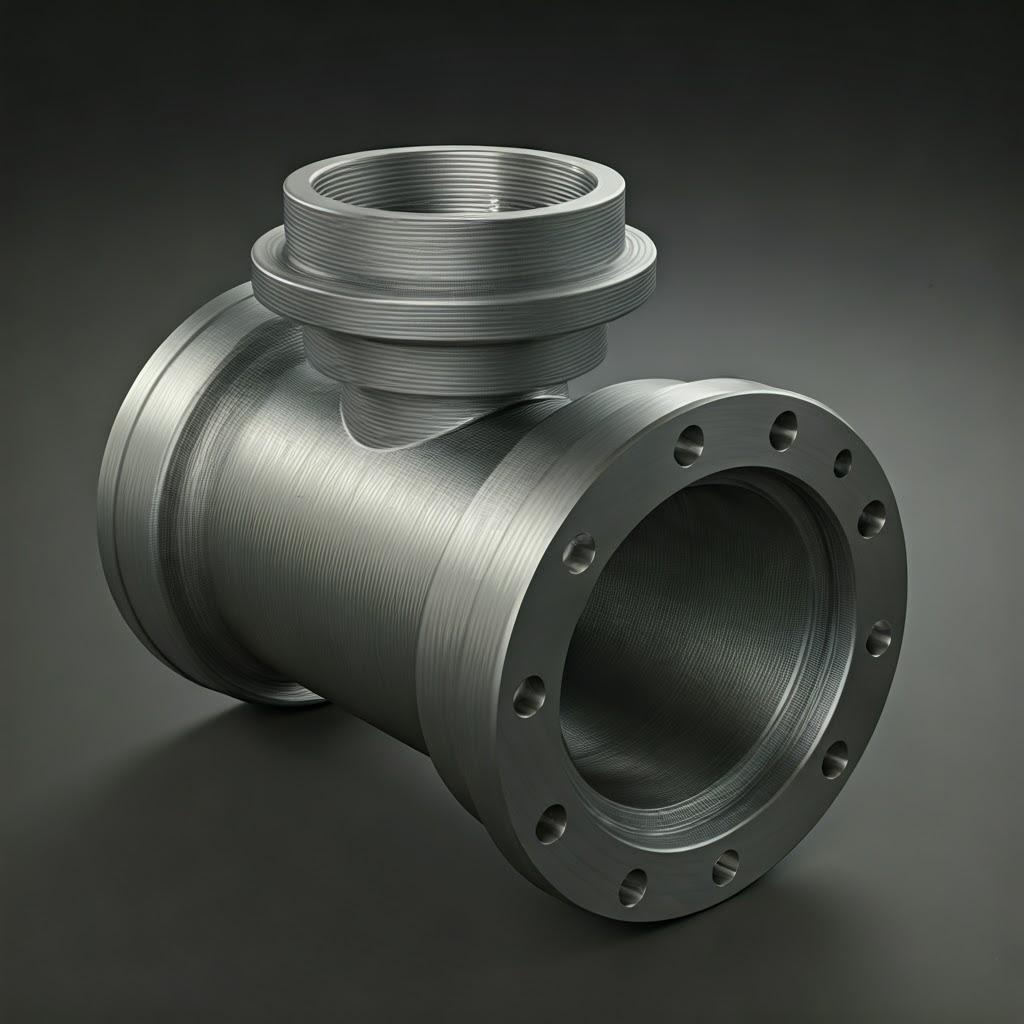
Kosten und Vorlaufzeiten für AM-Ventilgehäuse für die Schifffahrt kennenlernen
Eine der wichtigsten Überlegungen für Beschaffungsmanager und Ingenieure bei der Bewertung von Fertigungsmethoden sind die damit verbundenen Kosten und Vorlaufzeiten. Die additive Fertigung von Metallen stellt im Vergleich zum herkömmlichen Gießen oder Schmieden ein anderes Paradigma dar, das sich insbesondere auf diese beiden Faktoren auswirkt.
Kostenfaktoren bei AM-Ventilkörpern aus Metall:
Die Kosten für die Herstellung eines Ventilkörpers mittels Metall-AM werden von mehreren miteinander verbundenen Variablen beeinflusst:
- Materialtyp und Volumen: Hochleistungs-Marinelegierungen wie 254SMO oder CuNi30Mn1Fe sind von Natur aus teurer als rostfreier Standardstahl 316L. Die schiere Menge des im Teil verwendeten Materials (nach der DfAM-Optimierung) ist ein Hauptkostentreiber. Auch die Qualität des Pulvers und seine Beschaffung spielen eine Rolle.
- Teil Komplexität und Größe: Während AM die Komplexität gut handhaben kann, können sehr komplizierte Designs mehr Stützstrukturen und längere Druckzeiten erfordern. Größere Teile beanspruchen mehr Maschinenzeit und verbrauchen mehr Material, was die Kosten erhöht. Die Gesamtabmessungen wirken sich darauf aus, wie viele Teile in einen einzigen Bauvorgang passen.
- Bauzeit: Bestimmt durch das Teilevolumen, die Schichthöhe und die Scanparameter. Längere Bauzeiten bedeuten höhere Maschinenbetriebskosten, die auf das Teil umgelegt werden.
- Unterstützende Strukturen: Das Volumen des für die Stützen verwendeten Materials und der Zeit- und Arbeitsaufwand für deren Entfernung erhöhen die Kosten. Ein wirksames DfAM zielt darauf ab, dies zu minimieren.
- Nachbearbeitungsanforderungen: Jeder Schritt verursacht zusätzliche Kosten:
- Wärmebehandlung: Ofenzeit, Energie, Verwendung kontrollierter Atmosphäre.
- Bearbeitungen: Einrichtungszeit, Maschinenzeit, Komplexität der Funktionen.
- Oberflächenveredelung: Arbeit, Verbrauchsmaterial, Spezialausrüstung (z. B. Polieren, AFM).
- Zerstörungsfreie Prüfung (NDT): Methoden wie das CT-Scannen verursachen erhebliche Kosten, können aber bei kritischen Komponenten erforderlich sein, um die innere Unversehrtheit sicherzustellen.
- Menge: Obwohl bei AM keine Werkzeugkosten anfallen, gibt es immer noch Einrichtungskosten pro Bau. Die Stückkosten sinken tendenziell leicht mit größeren Losgrößen, aber der Effekt ist weniger dramatisch als bei traditionellen Massenproduktionsverfahren, bei denen die Amortisation der Werkzeuge die Kosten für kleine Stückzahlen dominiert.
- Qualitätssicherung und Dokumentation: Strenge Inspektionen und detaillierte Dokumentationspakete verursachen zusätzlichen Aufwand, sind aber für kritische Anwendungen notwendig.
Vorlaufzeiten für AM im Vergleich zu traditionellen Methoden:
Hier zeigt sich oft ein überzeugender Vorteil von AM, insbesondere bei bestimmten Szenarien:
- Prototyping: AM: Tage bis 1-2 Wochen. Traditionell (Gießen/Schmieden): Wochen bis Monate (vor allem wegen der Werkzeugerstellung).
- Kleinserienfertigung / Kundenspezifische Teile: AM: In der Regel 1-4 Wochen (je nach Komplexität, Nachbearbeitung, Warteschlangenzeiten). Traditionell: Monate (die Vorlaufzeit für die Werkzeuge ist der größte Engpass).
- Ersatzteile (On-Demand): AM: Kann innerhalb von 1-3 Wochen aus einer digitalen Datei hergestellt werden, was für die Minimierung von Ausfallzeiten entscheidend ist (MRO - Maintenance, Repair, Operations). Traditionell: Kann Monate dauern, wenn die Werkzeuge neu erstellt werden müssen oder das Teil veraltet ist; es können Mindestbestellmengen gelten.
- Großserienproduktion: Traditionelles Gießen/Schmieden ist oft kostengünstiger pro Teil und kann schneller erreicht werden. pro Teil Produktionsraten nach die erste Phase der Werkzeugherstellung. AM-Vorlaufzeiten sind weniger volumenabhängig, werden aber durch die Maschinenkapazität begrenzt.
Tabelle: Überlegungen zu Kosten und Vorlaufzeiten - AM vs. Traditionell
Faktor | Additive Fertigung von Metall | Traditionell (Gießen/Schmieden + mechanische Bearbeitung) | Wichtigste Erkenntnisse für Marineventile |
---|---|---|---|
Werkzeugkosten | Keiner | Hoch (Formen, Gesenke) | AM kostengünstig für Kleinserien, Prototypen, Ersatzteile |
Stückkosten (Low Vol) | Möglicherweise niedriger (keine Amortisation der Werkzeuge) | Hoch (vor allem durch Werkzeugkosten) | AM-Vorteil für kundenspezifische/eilige Anforderungen |
Stückkosten (hohe Volumina) | Höher (Maschinenzeit, materieller Schwerpunkt) | Niedriger (Effizienz der Massenproduktion) | Traditionell oft besser für massengefertigte Standardteile |
Materialkosten | Wesentlicher Treiber (Optimierung ist der Schlüssel) | Wesentlicher Treiber | Hochleistungslegierungen bei beiden Methoden kostspielig |
Komplexität Kosten | Mäßige Auswirkung (wird vom Prozess gut bewältigt) | Hohe Belastung (komplexe Werkzeuge, Bearbeitung) | AM ermöglicht komplexe Designs auf wirtschaftliche Weise |
Vorlaufzeit (Proto) | Sehr schnell (Tage/Wochen) | Langsam (Wochen/Monate) | AM ideal für schnelle Iteration |
Vorlaufzeit (Prod) | Fasten für niedriges Volumen (Wochen) | Anfangs langsam (Monate), dann schneller pro Teil | AM überlegen für dringende Ersatzteile in kleinen Stückzahlen |
Abfall | Niedriger (additives Verfahren) | Höher (Bearbeitung, Kufen/Risers) | AM ist im Allgemeinen materialsparender |
In Blätter exportieren
Zusammenfassend lässt sich sagen, dass die Kosten pro Teil für ein einfaches, in großen Stückzahlen gefertigtes Ventilgehäuse bei herkömmlichem Guss zwar niedriger sein mögen, dass Metall-AM jedoch erhebliche Kosten- und Zeitvorteile für komplexe Konstruktionen, spezielle Materialien, Prototypen, kleine bis mittlere Produktionsserien und vor allem für die schnelle Herstellung von Ersatzteilen für Schiffsanlagen bietet. Die Einholung eines konkreten Angebots von einem AM-Anbieter wie Met3dp auf der Grundlage eines detaillierten CAD-Modells und von Spezifikationen ist der beste Weg, um die Kosten und den Zeitrahmen für ein bestimmtes Schiffsventilgehäuseprojekt zu ermitteln.
Häufig gestellte Fragen (FAQ) zu AM-Ventilkörpern aus Metall für die Schifffahrt
Hier finden Sie Antworten auf einige häufig gestellte Fragen von Ingenieuren und Beschaffungsexperten zur Verwendung des 3D-Drucks von Metall für Schiffsventilgehäuse:
- F1: Welche Druckstufen können AM-Ventilgehäuse aus Metall bewältigen?
- A: Die Druckstufe eines AM-Ventilkörpers wird in erster Linie durch seine Konstruktion (Wandstärke, Geometrie), die Festigkeit des gewählten Materials (Streck- und Zugfestigkeit bei Betriebstemperatur) und die Qualität des Herstellungsprozesses (Gewährleistung der vollen Dichte und Abwesenheit kritischer Defekte) bestimmt. Bei korrektem Entwurf, Druck und Nachbearbeitung (bei kritischen Anwendungen möglicherweise einschließlich HIP) können AM-Ventilkörper aus Metall, die aus Legierungen wie 316L, 254SMO oder hochfesten Stählen hergestellt werden, Druckwerte erreichen, die vergleichbar oder sogar besser sind als die ihrer traditionell hergestellten Gegenstücke, die den einschlägigen ASME- oder ISO-Normen entsprechen. Der Schlüssel dazu ist eine ordnungsgemäße technische Validierung, die möglicherweise durch Berstversuche und Finite-Elemente-Analysen (FEA) unterstützt wird, die speziell auf das endgültige Produkt.
- F2: Sind 3D-gedruckte Ventilkörper aus Metall von Schiffsklassifikationsgesellschaften (wie DNV, ABS) zertifiziert oder zugelassen?
- A: Die Zertifizierung ist in der Regel anwendungsspezifisch und umfasst die Qualifizierung des gesamten Prozesses: des Materials, der AM-Maschine, der Druckparameter, der Nachbearbeitungsschritte und des spezifischen Bauteildesigns. Während die Klassifikationsgesellschaften zunehmend Richtlinien und Rahmenwerke für die additive Fertigung entwickeln, erfordert die Erlangung einer Klassenzulassung für einen kritischen Ventilkörper oft ein spezielles Qualifizierungsprogramm, das in Zusammenarbeit zwischen dem Endanwender, dem AM-Dienstleister und der Klassifikationsgesellschaft durchgeführt wird. Erfahrene Anbieter wie Met3dp kennen diese Anforderungen und können ihre Kunden bei den erforderlichen Tests, Dokumentationen und Qualifizierungsprozessen unterstützen, die für die Erlangung der Zertifizierung für spezielle Schiffsanwendungen erforderlich sind. Das geschieht nicht automatisch, sondern erfordert bewusste Anstrengungen.
- F3: Wie hoch sind die Kosten für ein AM-Ventilgehäuse aus Metall im direkten Vergleich zu einem gegossenen oder geschmiedeten Äquivalent?
- A: Das hängt sehr stark von den spezifischen Gegebenheiten ab. Bei einem einfachen Standard-Ventilgehäuse, das in hohen Stückzahlen produziert wird, ist das traditionelle Gießen aufgrund von Skaleneffekten nach Amortisierung der Werkzeugkosten oft billiger pro Teil. Metall-AM wird jedoch äußerst wettbewerbsfähig oder sogar kostengünstiger, wenn:
- Werkzeugkosten sind unerschwinglich (geringe Stückzahlen, Prototypen).
- Der Entwurf ist komplex (schwierig/kostenintensiv zu gießen oder zu bearbeiten).
- Vorlaufzeit ist entscheidend (AM vermeidet Verzögerungen bei der Werkzeugherstellung).
- Spezialisierte Legierungen erforderlich sind, die schwer zu gießen/schmieden sind.
- Ersatzteile auf Abruf benötigt werden (Vermeidung von Lagerbeständen und langen Wartezeiten für veraltete Teile).
- DfAM ermöglicht eine erhebliche Gewichtsreduzierung oder die Konsolidierung von Teilen, was zu Einsparungen auf Systemebene führt. Daher muss ein direkter Kostenvergleich Volumen, Komplexität, Material, Vorlaufzeitempfindlichkeit und die Gesamtbetriebskosten berücksichtigen, einschließlich potenzieller Einsparungen bei Ausfallzeiten durch AM-Ersatzteile.
- A: Das hängt sehr stark von den spezifischen Gegebenheiten ab. Bei einem einfachen Standard-Ventilgehäuse, das in hohen Stückzahlen produziert wird, ist das traditionelle Gießen aufgrund von Skaleneffekten nach Amortisierung der Werkzeugkosten oft billiger pro Teil. Metall-AM wird jedoch äußerst wettbewerbsfähig oder sogar kostengünstiger, wenn:
Schlussfolgerung: Segel setzen mit moderner Ventilkörperfertigung
Die Meeresumwelt erfordert Komponenten, die kompromisslose Zuverlässigkeit, Korrosionsbeständigkeit und Leistung bieten. Ventilkörper sind als kritische Durchflusssteuerungselemente von zentraler Bedeutung für den sicheren und effizienten Betrieb von Schiffen und Offshore-Anlagen. Während herkömmliche Fertigungsmethoden der Branche seit langem gute Dienste leisten, stellt die additive Fertigung von Metallen eine leistungsstarke, moderne Alternative dar, die transformative Vorteile bietet, die auf die Herausforderungen der maritimen Welt zugeschnitten sind.
Von der Ermöglichung hoch optimierter, komplexer Konstruktionen, die die Strömungseffizienz verbessern und das Gewicht reduzieren, bis hin zur Verwendung fortschrittlicher korrosionsbeständiger Legierungen wie 316L, CuNi30Mn1Fe und 254SMO - Metall-AM verschiebt die Grenzen des Machbaren. Die Fähigkeit, schnell Prototypen zu erstellen, kundenspezifische Komponenten auf Anfrage zu produzieren und die Vorlaufzeiten für wichtige Ersatzteile drastisch zu verkürzen, bietet Ingenieuren, Betreibern und Beschaffungsteams in der Schifffahrt eine unvergleichliche Flexibilität. Wenn man sich die DfAM-Prinzipien zu eigen macht und die Feinheiten der Nachbearbeitung und Qualitätssicherung versteht, können die potenziellen Herausforderungen von AM effektiv gemeistert werden, was zu Komponenten führt, die die Leistung herkömmlicher Gegenstücke erreichen oder übertreffen.
Um diese Vorteile nutzen zu können, ist die Wahl des richtigen Partners entscheidend. Suchen Sie nach Anbietern mit nachgewiesenem Fachwissen über Schiffslegierungen, robusten Qualitätssystemen, fortschrittlichen technologischen Fähigkeiten und einem kooperativen Ansatz. Unternehmen wie Met3dp mit Hauptsitz in Qingdao, China, sind ein Beispiel für dieses Engagement. Mit jahrzehntelanger kollektiver Erfahrung, branchenführenden SEBM-Druckern und Gaszerstäubungspulvern, einem breiten Portfolio an Hochleistungsmetallpulvern und umfassenden Lösungen für Ausrüstung, Materialien und Anwendungsentwicklung ermöglicht Met3dp die Fertigung der nächsten Generation in anspruchsvollen Sektoren.
Da sich die maritime Industrie weiter entwickelt, wird die Einführung digitaler Fertigungstechnologien wie Metall-AM der Schlüssel zur Verbesserung von Effizienz, Zuverlässigkeit und Nachhaltigkeit sein. Für Ventilgehäuse und unzählige andere kritische Komponenten ist die additive Fertigung nicht nur eine Möglichkeit für die Zukunft - sie ist eine Lösung für die Gegenwart, die erhebliche Wettbewerbsvorteile bietet. Erfahren Sie, wie diese Fähigkeiten die Ziele Ihres Unternehmens im Bereich der additiven Fertigung unterstützen können, indem Sie uns besuchen Met3dp online.
Teilen auf
MET3DP Technology Co., LTD ist ein führender Anbieter von additiven Fertigungslösungen mit Hauptsitz in Qingdao, China. Unser Unternehmen ist spezialisiert auf 3D-Druckgeräte und Hochleistungsmetallpulver für industrielle Anwendungen.
Fragen Sie an, um den besten Preis und eine maßgeschneiderte Lösung für Ihr Unternehmen zu erhalten!
Verwandte Artikel
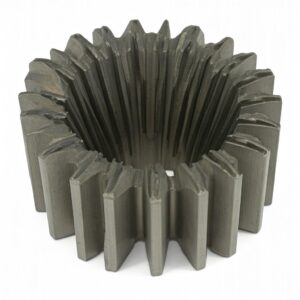
Hochleistungs-Düsenschaufelsegmente: Revolutionierung der Turbineneffizienz mit 3D-Metalldruck
Mehr lesen "Über Met3DP
Aktuelles Update
Unser Produkt
KONTAKT US
Haben Sie Fragen? Senden Sie uns jetzt eine Nachricht! Wir werden Ihre Anfrage mit einem ganzen Team nach Erhalt Ihrer Nachricht bearbeiten.
Holen Sie sich Metal3DP's
Produkt-Broschüre
Erhalten Sie die neuesten Produkte und Preislisten
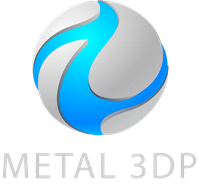
Metallpulver für 3D-Druck und additive Fertigung